Since 1989
Since 1989
March-April 2023, Vol 34 No.2
March-April 2023, Vol 34 No.2
Grand Egyptian Museum
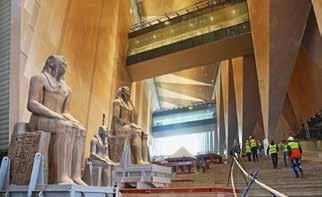
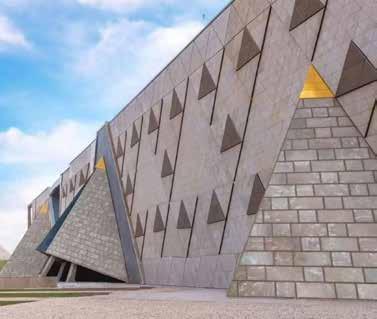
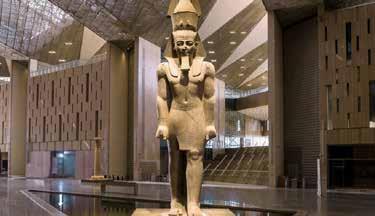
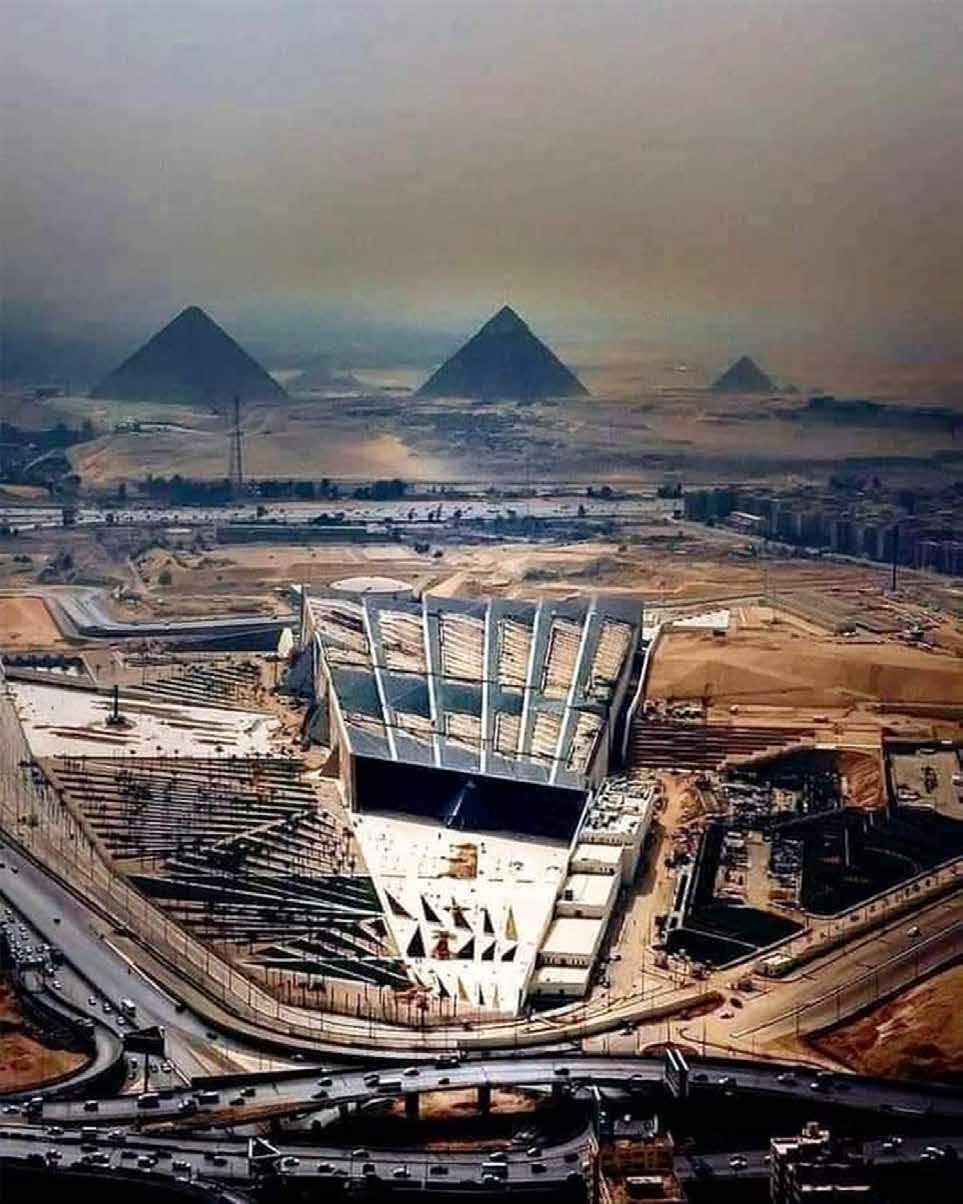
World's largest archeological museum
Concrete Curing
Pre-stressed Slabs
Towable Generators
Home Solar Systems

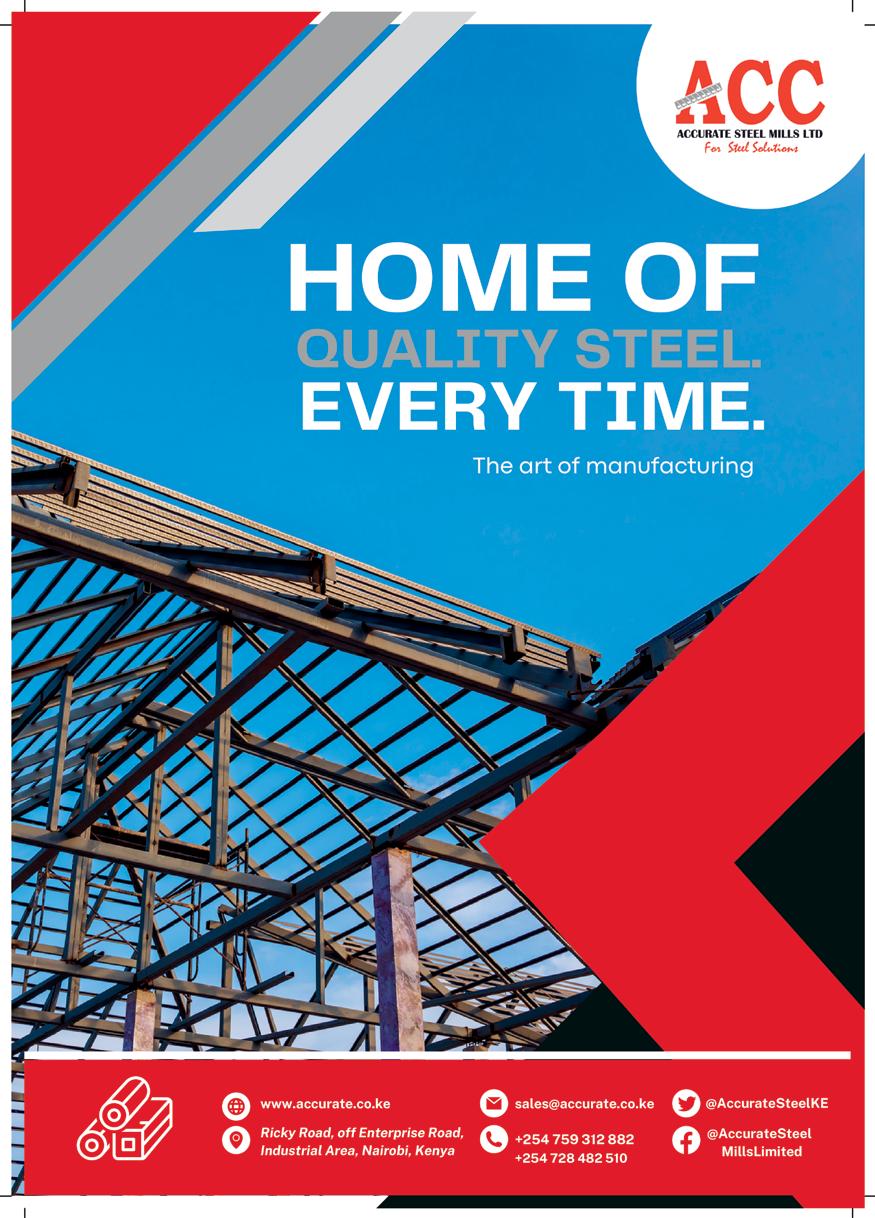
Since 1989
Since 1989
March-April 2023, Vol 34 No.2
March-April 2023, Vol 34 No.2
World's largest archeological museum
Pre-stressed Slabs
Towable Generators
Home Solar Systems
The Building Company (TBCo) hosted its biggest General Building Material (GBM) trade show on 15 February at the Cape Town International Convention Centre (CTICC).
The trade show, hosted by TBCo’s most prominent GBM brands, Buco and Timbercity; brought together suppliers, buyers and store managers from across the country to showcase the latest industry innovations and cemented the company’s role as a trusted and preferred industry partner.
Over 100 suppliers attended TBCo’s most successful trade show to date. The event had to be moved to a larger venue after exhibitor capacity was exceeded at the prior venue. It was an excellent opportunity to showcase new products and technologies with the trade show serving as a merchandise innovation ‘think tank’, where new ways of merchandising were presented. Among the themes covered were creating displays for target customers; why specific signage is now vital, and why sales team knowledge can make or break a brand. This tied in well with the trade show’s theme of ‘Vibrancy’.
Effective display of goods in the hyper-competitive post-Covid landscape has become a critical sales tool where time-pressed consumers need easy and instant access to what they are looking for in a store environment that is both welcoming and easy to navigate.
The event also used technology to its advantage. Suppliers and delegates were given access to an app where live interaction with all delegates was facilitated. They could livestream the event, post pictures and videos and participate in competition polls. This clever use of technology encouraged participants to move through the space using the app, to share details thereby forming relationships and strategic partnerships to enhance the delegates’ networking experience.
“This trade show truly exceeded our expectations. It embodied our business philosophy of building strong, strategic partnerships and symbiotic relationships with our suppliers so that they share in the company’s growth and success,” says company CEO, Steve Du Toit. “Even though the trade show was a full day, we feel as if we wanted much more time to network, brainstorm and share innovative ideas. All in all, I think
participants left feeling energised and excited with a vibrancy that fuels the kind of innovation that the industry needs,” he adds.
Merchandise executive Stuart Jowett opened the trade show stressing the importance of how success in the industry is predicated on creative solutions and nimble thinking. “We know that the majority of customers that buy from us do so to make a living, but we are also building the capability to service our DIY customers. Through effective partnerships and by leveraging new technologies, processes, products, and solutions, we can make our operations more efficient and improve added value to our customers.”
Following the trade show, TBCo hosted a supplier dinner to thank and recognise their suppliers. The suppliers who won awards were PPC Cement, Duram, Academy Brushware, Stevens & Co, IB McIntyre & Co, Vermont Sales, Handyman, Bostik South Africa, PG Bison, Kwikbuild Cement, Swartland, Safe Door, Ryobi and Plascon.
At the supplier dinner, John Stevens of Ryobi delivered an address on behalf of the suppliers: “We would like to extend a big thank you to Buco and Timbercity for hosting a phenomenal event. This has been one of the better Expos we have participated in, in a while. The interaction with the delegates were particularly good. We believe that this is a great business to get behind based on their commitment to growth.”
The following day TBCo hosted another successful event which was their Annual Conference. Attendance was in excess of 250 delegates and included a company update from Steve Du Toit and Pepkor’s COO, Sean Cardinaal, as well as overviews from key operating units within the company.
“The success of these events, which I believe is the best we’ve ever held, truly highlights the ways in which Buco and Timbercity are growing and finding ways to do things bigger and better,” says Steve.
A special thanks to the Platinum Suppliers at the Trade Show: Academy Brushware, Hamilton Brushware, Dulux, Duram, Plascon, IB McIntyre, Steven & Co, Vermont Sales, PG Bison, Safedor, Eco Rubber, Eureka DIY, Eurolux and Matus.
MANAGING EDITOR
Robert Barnes
DEPUTY MANAGING EDITOR
Francis Makari
EDITOR - in - CHIEF
Dennis Ayemba
COUNTRY EDITORS
Uganda - Betty Nabakooza
Nigeria - Boladale Ademiju
South Africa - Jimmy Swira
WRITERS, Pascal Musungu, Anita Anyango, Patrick Mulyungi
WEB & GRAPHIC DESIGN
Gerald Oswald
Sales and Marketing Manager
Faith Mburu
ADVERTISING
Kenya: William Mutama, Lilian Khavosa, Joyce Ndamaiyu, Wendy Kinya
South Africa: Thuli Nkosi, Winnie Sentabire, Angeline Ntobeng,
Uganda: Nobert Turiyo, Selina Salumah Namuli
Botswana: Dickson Manyudza, Gerald Mazikana
Ethiopia: Haimanot Tesfaye, Ruth Girma
Tanzania: Tom Kiage
Malawi: Anderson Fumulani
Ghana: Samuel Hinneh, Caleb Donne Hadjah
Zambia: Susan Kandeke
Zimbabwe: Chiedza Chimombe
Rwanda: Collison Lore
Nigeria: Seni Bello
China:Weng Jie
The editor accepts letters and manuscripts for publication from readers all over the world. Include your name and address as a sign of good faith although you may request your name to be withheld from publication. We reserve the right to edit any material submitted .
Send your letters to: info@constructionreviewonline.com
Construction Review is published eleven times a year and is circulated to members of relevant associations, governmental bodies and other personnel in the building and construction industry as well as suppliers of equipment, materials and services in Africa, the Middle and Far East. The editor welcomes articles and photographs for consideration. Material may not be reproduced without prior permission from the publisher. The publisher does not accept responsibility for the accuracy or authenticity of advertisements or contributions contained in the journal. Views expressed by contributors are not necessarily those of the publisher.
© All rights reserved.
The Grand Egyptian Museum Giza (GEM), also known as the Giza Museum, is a museum of artifacts of ancient Egypt that is nearing completion. Described as the largest archaeological museum in the world.
Published by Group Africa Publishing Ltd
Head Office and for all enquiries: P.O. Box 10109
Nairobi 00100 Kenya, Tel: +254 722525326 +254-208000307
Email: info@groupafricapublishing. com
Uganda Agent Projects Unusual Uganda Ltd.
Jemba Plaza, Luwum St.
Kampala,
Development works are set to resume after approximately two years since the implementation of the Cabo Delgado liquefied natural gas (LNG) project came to a halt after attacks from rebel forces.
The government has revealed plans to construct a 50-kilometer Tanzania mainland-Zanzibar bridge, which will be the first of its kind in Africa
The use of precast concrete brings quite a lot of savings compared to alternative solutions. The savings come from a number of sources. Read about it here.
Ghana Agent
Image Consortium
1st Floor, The Ecobank Building, Tesano. Tel: 233(0)30 223 2728 I 233(0)274807127 I
+233(0)206299159
Fax: 233(0)24 882 8286
Email: ghana@groupafricapublishing.com, Calebhadjah@gmail.com
Kenya Agent
Northwest Ventures Ltd
P.O. Box 16414 - 00100
G.P.O
Nairobi, Kenya
Tel: +254 20 2679808
Email: kenya@constructionreviewonline.com, info@northwest.or.ke
Nigeria Agent Rahma Associates
B23/24, Aishetu Emoewa Plaza, 196, Iju Water Works Road, Ifako Ijaye Lga,Agege, Lagos. Tel: 234-1-7347860
Email: nigeria@constructionreviewonline.com
Rwanda Agent
Kolline & Hemed Inc., B.P. 3328, Kigali, Rwanda
E-mail: rwanda@constructionreviewonline.com
Zambia Agent
Dayflex Limited, Dedan Kimathi Road, Lusaka, Zambia.
Email: zambia@constructionreviewonline.com
Tanzania Agent:
Group Africa Publishing Ltd
tz@constructionreviewonline.com
Dar-es-salaam
Precast concrete structures (PCS) reduce workforce dependency and construction time. However, they are subjected to vibrations and strain during transport from their manufacturing site to the construction site. Effective quality control measures require continuous logging of vibration and strain measurement during the delivery, an essential feature that is missing in current systems. To this end, researchers have now developed a novel portable sensing system that can monitor strain and acceleration to enable efficient PCS delivery.
Dr. Park and his colleagues at Chung-Ang University recently developed a smart sensing system to monitor PCS during transportation in real time. The system integrates IoT sensors that detect vibrations and deformations during movement.
The novel portable wireless sensing system is capable of real-time recording of acceleration and strain measurement during transport. Moreover, the system generates a safety assessment report for PCS that adjusts initial strain offset and calculates the absolute strain. To demonstrate the capabilities of their smart system, the researchers further conducted a field test constituting an 80-minute delivery of a 12-meters long precast concrete beam and evaluated its condition by measuring the acceleration, tilts, and strain of the structure in real time.
In Incheon, South Korea, Riventa has installed a new fixed monitoring system that will, in real-time, analyse the performance of 10 pumps at one of the city’s most important pumping stations.
The data gathered by Riventa will enable the water supply system providers to better plan for capital expenditure and minimise wholelife costs. The fixed monitoring will also help reduce the pumps’ energy consumption, carbon emissions, hydraulic failure and premature wear.
As the pumps in Incheon are part of a key dynamic system, their contribution varies with demand and system characteristics. Riventa’s FREEFLOWi4.0 system will monitor hydraulic performance and pump efficiency. In conjunction with operator interface software, the real-time effectiveness of each pump will be evaluated, and accurate data generated to make optimisation happen.
This latest order for Riventa follows its successful work in the port city of Yeosu in South Korea, where at a tyre manufacturer’s water pumping plant, it identified annual energy savings of 13%.
Lu An Highway Industry’s Lintec CSM4000HRC containerised asphalt batch plant mixed more than 2 million tons of hot mix asphalt with a high percentage of Reclaimed Asphalt Pavement (RAP). After reaching this milestone, it has now finished supporting construction of the S244 regional expressway and other rehabilitation projects in China’s Anhui province.
The installation process began in February 2016 on a site in Lu’An city. The plant began operations the following June, providing hot mix asphalt for the 23.04km Huoqiu Garden to Xuji interchange section of the S244. The plant produced approximately 150,000 tons for the 03 section of the highway, after which the project was completed in 2022.
Having concluded work on the expressway, the asphalt batch plant has since been used to carry out asphalt pavement repair and maintenance projects on other expressways in Anhui province. To date, total production for the plant has now passed the 2 million ton mark. Thanks to the HRC component in the CSM4000HRC asphalt plant, 40% of the hot mix asphalt was from RAP making it a more environment-friendly choice.
The Lintec CSM4000 asphalt mixing plant with a 320 tph capacity paired with the HRC hot recycling system yielded efficient integration of RAP with exceptional productivity. The HRC attachment is able to be retrofitted into any Lintec asphalt plant for the processing of milling waste or material
excavated from road pavement recycling. This will then result in a significant contribution to the conservation of natural resources while massively reducing the transport and production costs of bitumen and aggregates.
It has given us huge cost savings while ensuring mix quality remains at the highest level – all while being extremely simple to operate,” said a spokesperson from Lu An Highway Industry.
The Big 5 Construct Southern Africa, previously African Construction Expo, is a significant contributor to the economic growth, recovery and transformation within Southern Africa’s construction industry and places a special focus on facilitating face-to-face buyer and seller engagements and showcasing the most innovative solutions for the region.
The Big 5 Construct Southern Africa will be co-located with Totally Concrete Expo, African Smart Cities Summit, Deck & Flooring Africa and Woodex for Africa.
Taking place 27 – 29 June 2023 at the Gallagher Convention Centre, this exhibition and conference is an absolute must-attend event for anyone in the construction industry in Southern Africa.
We are pleased to invite you to participate at the Home and Building Expo, co-located with Architecture and Urban Planning Expo, which is taking place from 10-12 October 2023 at the Oman Convention and Exhibition Centre.
The Expos will showcase the most comprehensive range of innovative products, services, solutions and the entire supply chain under one roof by local and international participants to trade visitors, potential buyers, policy makers, government officials, C-Level executives, business leaders, leading industry experts, top-tier public visitors and key decision makers from the region and beyond, making it a definitive power packed networking platform, where new projects and partnerships are initiated and visionary objectives are implemented.
Commercial UAV Expo, September 5-7, 2023 in Las Vegas is the premier event for the commercial drone industry focusing on the integration/operation of commercial UAS.
The event will feature exhibits and demonstrations by UAS solutions providers; keynotes, panel discussions, and presentations with interactive Q&A and chat; AI-powered networking; and more. Industries covered include Construction; Drone Delivery; Energy & Utilities; Forestry & Agriculture; Infrastructure & Transportation; Mining & Aggregates; Public Safety & Emergency Services; Security; and Surveying & Mapping.
It is presented by Commercial UAV News and organized by Diversified Communications. Use code SAVE100 for a $100 discount and/or FREE expo admission. 4,000 attendees from 75 nations. www.expouav.com
Kenya
- Architectural Association of Kenya
- Institute of Quantity Surveyors of Kenya
- Institute of Engineers of Kenya
- Association of Consulting Engineers of - Kenya
- Association of Professional Societies of East Africa APSEA)
- Kenya Property developers Association
- Institution of Surveyors of Kenya
-Town and County Planners Association of Kenya (TCPAK)
South Africa
- ASAQS - SAICE
- South African Council for the Quantity Surveying Profession
- Khuthaza ( Women for Housing)
- Concrete Manufacturers Association
- Green Building council of SA
- South African Property Owners Association
- Master Builders South Africa
Uganda
Institute of Surveyors of Uganda
Uganda Institute of Professional Engineers (UIPE) &
Uganda society of Architects
Botswana
- Institute of Botswana Quantity Surveyors
Ethiopia
- Association of Ethiopian Architects
- Ethiopian Association of Civil Engineers
- Construction Contractors Association of Ethiopia
Zimbabwe
- Zimbabwe Institute of Quantity Surveyors
- Zimbabwe Institute of Engineers
- The Construction Industry Federation of Zimbabwe (Cifoz)
Ghana
- Ghana Institute of Engineers
- Architects Registration Council
- Ghana Institute of Surveyors
- Ghana Green Builders Association
- Ghana Institute of Planners
- Association of Building and Civil Engineering Contractors of Ghana
Namibia
- Institute of Namibian Quantity Surveyors
- Association of Consulting Engineers of Namibia
Tanzania
- Tanzania Institute of Quantity Surveyors
- Construction Regulation Board (CRB)
- Tanzania’s Registration Board of Architects and Quantity Surveyors (AQSRB)
Nigeria
- Association of Consulting Engineers Nigeria
- Association of Professional Women
Engineers Of Nigeria
- Council of Registered Builders of Nigeria
- The Nigerian Institute of Architects
- American Association of Petroleum
Geologists Africa Region
- Nigeria Society of Engineers
- Nigeria Institute of Architects
- Building and Construction Skilled Artisans Association of Nigeria (BACSAAN)
Zambia
- Zambia Institute of Architects (ZIA)
- Association of Building and Civil Engineering Contractors (ABCEC).
works are set to resume after approximately two years since the implementation of the Cabo Delgado liquefied natural gas (LNG) project came to a halt. The project was paused owing to attacks made on civilians by rebels affiliated with ISIL (ISIS) in the northern Mozambican province.
The Mozambique LNG project comprises two developments. The first one is the Golfinho-Atum gas field development in the offshore Area 1 Block of the deep-water Rovuma Basin.
The second one is the construction of a 12.88 million tonnes per annum (Mtpa) onshore liquefied natural gas (LNG) facility on the Cabo Delgado coast of Mozambique. This will be the first onshore LNG facility in Mozambique.
The Golfinho and Atum gas fields are located in 1,600m-deep waters within the Rovuma Basin Area 1, approximately 40km off the coast of Cabo Delgado.
The Offshore Area-1 is estimated to contain 75 trillion cubic feet (tcf) of recoverable natural gas resources. The LNG processing and export facility will be developed in the Afungi peninsula in Cabo Delgado, the northernmost province of Mozambique.
The Area 1 Mozambique LNG facility will consist of two liquefaction trains with a combined nameplate capacity of 12.88Mtpa in the initial phase. It will also house gas pre-treatment facilities and full-containment LNG storage tanks. The LNG production capacity of the facility is proposed to be further expanded up to 50Mtpa in the future.
The plant will receive feed gas supply from the Golfinho-Atum gas field through the pipeline and produce LNG for export to the Asian and European markets, as well as for domestic consumption in Mozambique.
Other support facilities for the LNG plant will include materials offloading facility and an LNG marine terminal capable of accommodating large LNG carriers, which will also be shared with upcoming Area 4 LNG projects.
The government has revealed plans to construct a 50-kilometer Tanzania mainland-Zanzibar bridge, which will be the first of its kind in Africa. The revelation was made in Parliament by the deputy minister of Works and Transport Godfrey Kasekenya on April 2023.
This revelation comes approximately two years since the Revolutionary Government of Zanzibar unveiled another plan to build sea bridges connecting its main islands to its inhabited islets. The main islands in question are Unguja and Pemba while the inhabited islets are Tumbatu, Fundo, Kojani, Kisiwapanza, Kokota, and Makoongwe.
The plan to build sea bridges connecting Zanzibar’s main islands to its inhabited islets is contained in the Revolutionary Government of Zanzibar’s Vision 2050. The bridges are expected to increase human activities such as food, fish production, and trade in the islets.
Development of the plans for the Tanzania mainland-Zanzibar bridge
According to Kasekenya talks on the development and construction of the Tanzania mainland-Zanzibar bridge began on March 11, 2023, and are currently in advanced stages.
The parties involved have also met with the prospective investors of M/S China Overseas Engineering Group Company (COVEC). The latter has reportedly shown interest in building the bridge. The outcome of the meeting is still being worked according to by the deputy minister of Works and Transport.
Kasekenya revealed the status of the project development while answering Mwantum Dau Haji (CCM Special Seats) question. Haji wanted to know when the construction of the bridge, whose main objective is to ease the movement of goods and people, would kick off.
TheGrand Egyptian Museum Giza (GEM), also known as the Giza Museum, is a museum of artifacts of ancient Egypt that is nearing completion. Described as the largest archaeological museum in the world, the museum is under construction and is scheduled to be fully open later this year, exhibiting the full Tutankhamun collection with many pieces to be displayed for the first time. The museum is sited on 50 hectares (120 acres) of land approximately two kilometers from the Giza pyramids and is part of a new master plan for the plateau.
The design of the building was decided by means of an architectural competition. The building is designed by Heneghan Peng Architects, Buro Happold and Arup. The exhibition masterplan, exhibition design and museology is by Metaphor and Cultural Innovations Ltd.
The building is shaped like a chamfered triangle in plan. It sits on a site two kilometers west of the pyramids, near a motorway interchange. The building's north and south walls line up directly with the Great Pyramid of Khufu and the Pyramid of Menkaure. In front of the building is a large plaza, filled with date plants. One of the main features of the museum is the translucent stone wall, made of alabaster, that makes up the front facade of the building. Inside the main entrance is a large atrium, where large statues will be exhibited.
On 2 February 2010, Hill International announced that Egypt's Ministry of Culture had signed a contract with a joint venture of Hill and EHAF Consulting Engineers to provide project management services during the design and construction of the Grand Egyptian Museum. The new museum is designed to include the latest technology, including virtual reality. The museum will also be an international center of communication between museums, to promote direct contact with other local and international museums. The Grand Egyptian Museum will include a children's museum, conference center, training center, and workshops similar to the old Pharaonic places.
The exhibition will cover about one third of the total museum grounds displaying 50,000 artefacts. The main attraction will be the first exhibition of the full tomb collection of King Tutankhamun. The collection includes about 5000 items in total and will be relocated from the Egyptian Museum in Cairo. Other objects will be relocated from storages and museums in Luxor, Minya, Sohag, Assiut, Beni Suef, Fayoum, the Delta, and Alexandria.
TheKenyan construction industry is not for the faint hearted. It is crowded with many companies competing for projects. Building a name can be an uphill task, more so considering the negative perception facing the industry due to persistent incidents of defective buildings. While getting to the top is difficult, maintaining leadership is even harder owing to the fast changing dynamics in the industry.
One company that has defied the status quo in the country’s construction company is Mahesh and Tirth Construction Limited (M&T). In less than a decade, the company has caused significant disruptions by going against the norms of longevity to emerge as the top construction firm. From its humble beginnings in 2013, M&T is today one of Kenya’s premier building construction and civil engineering companies. This was affirmed after M&T was named the Overall Contractor of the Year Award 2023 and the Best Contractor for Building Works during the recent Construction Excellence Awards held by industry regulator, the National Construction Authority (NCA).
“We have only been around for eight years but our reputation in the market is unrivalled,” says Mahesh Jani, M&T Director. Making inroads in the industry and emerging as the best contractor is no mean achievement for the relatively young company. However, it has not come easily. Rather, it has been achieved through years of strategic actions anchored on core values among them integrity, quality work, teamwork and passion for M&T to become a top contractor.
While its core values define M&T, the clear strategy in project implementation that is grounded on quality work, cost effectiveness and delivering projects on time and on cost has made the company the first point of call for developers mainly in the commercial and industrial buildings market segment. Moreover, adequate investments in latest equipment and technology, a young and vibrant team of employees majority of whom are under 40 and the determination to build long lasting partnerships has ensured that jobs are always flowing for M&T.
“We are a versatile company with a reputation for outstanding quality workmanship, which has broadened our focus with new fields of specialization, modern technologies and we have maintained continued success by looking forward in offering best services to our clients,” explains Mahesh, who is one of the two directors of M&T, both of whom boast over 55 years of experience in the construction industry both locally and internationally.
This is evident from the growing number of projects in the company’s fold. Over the past four years alone, M&T has completed a total of 15 projects cutting across industrial, commercial, hospitality and institutional developments. Among them are the Alp North Logistics Park located at Tatu City. M&T was commissioned for the development of the state-of-the-art park, a project that was well crafted and whose scope involved intensive study of production line techniques and incorporation of state-of-the-art packaging facilities and sophisticated fire safety installations. The ability for M&T to execute the project beyond expectations saw it scoop the best Logistics Park Award at the Africa Properties Award Show in South Africa in 2018.
Other projects include the Alp West Tilisi, an ultra-modern Grade A warehouses and godowns facility, Saj Ceramics Showroom located at Ridgeways, Tune/Ibis Style Hotel, Champaign Ridge Holiday Home, extension of Olympic School and St. Andrews School Turi among many others. “One thing that stands out in our projects is that we implement them on time and on budget,” states Mahesh.
While these traits of workmanship are inscribed in nearly all of its projects, they have been immortalized by M&T’s latest project, The Cube office block located on Riverside Drive. A prestigious state-of-the-art office block, The Cube is nothing short of exquisite and breathtaking development that has significantly brought a new dimension of commercial buildings along the high-end Riverside Drive that is already home to the Australian, Netherlands, German and Danish Embassies and also hosts headquarters of major commercial banks such as Prime Bank, Standard Chartered Bank and CFC Stanbic. The location is also popular among multinationals like BBC News, Thales East Africa, Dow Chemicals, Sumitomo Corporation, GIZ, Pioneer Hi-Bred Kenya Limited and Jetro.
James Ng’ang’a, The Cube Project Manager, explains that The Cube is an ultra-modern exclusive prime ‘Grade-A’ office development that comprises six floor office totaling approximately 77,876 square feet of modern environmentally sensitive office space. Constructed at a cost of KSh800 million, the office complex offers high quality office accommodation designed to international standards offering occupiers a secure, highly efficient and flexible working environment.
The building offers a grandiose outdoor breakout terrace on the ground floor, generous onsite parking with an excellent parking capacity of 36o cars, main power connections with 500 KVA and 300 KVA backup generators, three high speed passenger lifts and highest standards in security incorporating access control to each floor, 24-hour security and provision for CCTV surveillance.
Other amenities include fibre-optic connectivity and full trunking for data/power/voice, borehole, electric fence and fire alarm & detection system. More importantly, The Cube has achieved Advanced EDGE green building certification standards with 41 percent reduction in energy consumption, 50 percent reduction in water consumption and 21 percent reduction in energy embodied in materials. It also represents unrivalled commitment to the environment with the key sustainability features like high thermal performance glazing, LED efficient lighting for all lighting, lighting control systems, Solar PV system and high efficiency flush/flow fixtures.
Notably, M&T broke ground on the project in January 2021 and completed it in November 2022 as per the agreed delivery timeline and within budget. “We had a clear program of works that made sure the project was implemented as per the requirements of the client,” says Ng’ang’a. He avers that despite encountering challenges like Covid-19 disruptions, rising costs of materials, bad weather and logistics bottlenecks, M&T did not lose focus of its obligation to the client.
“Our approach and attitude played big roles in delivery of the project,” adds Mahesh. This was critical owing to the fact that being the main contractor, M&T was working with a big team including consultants. Working in harmony while seeking to address challenges amicably was thus essential in delivering a high quality project. “The final project is an iconic building which is eye-catching,” he states.
While success has come in a relatively short span, M&T intends to continue riding on its principles for continuous growth. Part of its sacrosanct principle is integrity. Despite being in an industry where tendencies for shortcuts, using substandard materials, price undercutting when bidding for jobs and shoddy jobs are rampant, the company operates on a resolve on non-compromise on integrity. Being an NCA-1 Contractor, abiding by the rules and regulations is a fundamental trait of the company. “We follow the rules and
regulations to the letter,” explains Mahesh, adding that even when dealing with public officials, being uptight on integrity has greatly enhanced the company’s reputation in the market. He adds that the company’s ultimate goal is to exceed clients’ expectations by maintaining the highest level of professionalism, integrity, honesty and fairness in its relationships with suppliers, subcontractors, partners, professional associates and customers.
Though M&T believes that continuous growth is assured, emerging challenges in the building and construction industry are casting a dark shadow on the entire industry. With Kenya experiencing severe macroeconomic headwinds like a depreciating local currency, high inflation, high costs of doing business coupled by external shocks like the Russia Ukraine war, the local industry is not immune. Luckily for M&T, having many repeat clients means jobs will keep flowing. For the company, which strongly believes in corporate social responsibility and is involved in among others school feeding programs and making donations to drought afflicted areas, the sky is the limit.
TenwekHospital is a 402-bed Teaching and Referral Hospital situated in Bomet Township, Bomet County. It was founded in 1937 by the World Gospel Mission (WGM) of the United States of America in partnership with the Africa Gospel Church (AGC) in Kenya.
As a non-profit making health facility, the hospital is supported by individuals and organizations who partner with it to fulfill its mission.
Since its inception, Tenwek Hospital has had a significant impact on the healthcare space not only in Kenya but also across sub-Saharan Africa. Over the years, the hospital has grown to become a specialty hospital offering a variety of health services.
Tenwek Hospital serves over a million people in the vast Southwest region of Kenya and the country at large. “We also see patients from outside the country, that is, East, Central, and West of Africa”, says Shem Tangus, Chief Executive. The hospital offers a broad range of services that include Inpatient, Outpatient, Diagnostic, Medical Outreach, Training and Research.
The new Cardiothoracic and Emergency Centre Tenwek Hospital is uniquely positioned as a center of excellence in cardiothoracic care for patients with heart diseases in the Sub-Saharan Africa region. According to Mr Tangus, the hospital is currently performing more open-heart surgical procedures than any other hospital in the region at a fraction of the cost it would take
to perform the same procedures in countries outside Africa, says Mr Tangus. “We are caring primarily for patients with rheumatic heart disease and patients with congenital heart disease.”
Tenwek Hospital Board and Management have embarked on expanding and modernizing these services through the construction of an ultra-modern Cardiothoracic Centre.
The Hospital envisions a high-level center where it will offer training to cardiothoracic surgeons, cardiologists, perfusionists, cardiac nurse anesthetists, cardiac critical care nurses, echocardiographers, cardiac rehabilitation therapists, and specially trained chaplains. After the Tenwek Cardiothoracic site is fully established, the hospital anticipates fostering other sites
throughout the region that can use the Tenwek model as a starting point for new cardiothoracic units.
Leading architectural studio Triad Architects in collaboration with HFG Architecture of Kansas USA were commissioned to design the Cardiothoracic Center for Tenwek Hospital.
The 4-storey building with 2 basements is an ultramodern 176-bed self-contained surgical center located 300m west of the main Tenwek Hospital campus. The building is composed of 2 blocks forming 2 wings connected by a central core with 3 hospital lifts and a W-shaped ramp. Each wing has adequate provision of staircases for fire escape within a 30m running
distance.
The hospital comprises:
• an out-patient center on ground level with examination rooms, a pharmacy, a lab, a blood bank, CT and X-ray machines on ground level
• an endoscopy suite on 2nd floor with 4No. theatres, a 16-bed recovery room
• a training center on 2nd floor with classrooms,
• a conference hall, and offices on 2nd floor
• the heart surgery suite on 3rd floor with 6No. cardiothoracic theatres, 1No. hybrid theater, an 8-bed preoperative holding area and a 32-bed post anesthesia care center
• the general wards accommodating 80No. beds distributed in the 4 No. floors.
The patient wards have large floor to ceiling windows to provide adequate views to the undulating green hills beyond Tenwek valley. This also creates a pleasurable light atmosphere which enhances quick healing. Running through all floors is a chapel. It is defined by 2 thick curved concrete walls whose concept mimics a candle flame in the night when interior lights are on. This symbolizes the metaphor of Christ being the light of the world.
To increase resiliency during frequent power interruptions, the hospital features a mechanically assisted natural ventilation system (the surgical ward and many patient areas feature full humidity and temperature control) and supplemental ramps that facilitate the uninterrupted movement of patients. Other sustainable innovations include solar panels positioned on a low-slope standing seam roof, the use of hollow core concrete blocks produced on site, and the collection and reuse of rainwater for on-site laundry.
This project also encompasses housing for visiting fellows. These residential towers are located near the hospital and include 15 three-bedroom and 5 two-bedroom apartments. Improved water infrastructure also ensures that the entire medical campus has access to reliably clean water from a nearby river.
Tenwek Hospital expects the project to have major impact on health delivery as well as multiple associated benefits once completed.
When fully operational, the Hospital will employ over 300 Kenyans.
Advanced training will become available to many Kenyan health professionals and will attract other high-end professionals seeking training from around Africa.
The professionals trained at the Cardiothoracic Centre will go on to provide specialized Cardiothoracic
care and treatment in other service centers across Kenya and Africa, creating a positive ripple effect in the healthcare space.
Medical tourism will bring economic benefits to Kenyans and will mark the country as a leader in cardiovascular health. Within Africa, there are few options for heart surgery and currently, many people go to India for care.
The Cardiothoracic center is a high-end service center that will perform major heart and chest surgeries and will be a solution to the lack of adequate cardiac centers in Africa and a source of hope for people suffering from heart disease and in need of surgery.
The staggering scope of the heart disease challenge means that addressing the disease burden will be necessary to achieve Universal Health Care so that Kenyans will have
increased access to preventive, curative, rehabilitative, and palliative health services at minimum financial burden, thereby eliminating inequalities in access to healthcare.
The cost of heart surgery at Tenwek is a fraction of the cost of the same surgery when done outside the country.
Client: Tenwek Mission Hospital
Project Location: Bomet, Kenya
Gross Area: 30,436 Sq. meters
Project Director: Julius Kibwage
Project Architect: Julius Talaam
The GoDown Arts Centre is a nonprofit public interest organization incorporated in 2002, with a vision of a culturally confident, creative and prosperous Kenya. In 2003, The GoDown established itself in the Industrial Area of Nairobi, in an old warehouse complex at the corner of Dunga and Dundori Roads. The GoDown grew from the need for Kenyan and East African artists to come together in a creative hub to grow the creative economy. The GoDown contributes to social development by promoting community engagement, providing access to culture and the arts, and is also active in policy advocacy for a better working environment for Kenyan artists. The strength of The GoDown as Kenya’s leading platform for cultural exchange lies in its multi-disciplinary and inter-sectoral approach to programming. As a focal point for artistic experimentation, cross-sector partnerships and creative collaborations in East Africa, The GoDown has been recognised as one of Kenya’s leading platforms for cultural exchange.
About The GoDown Property Re-development Initiative
The Property Re-development Initiative is the transformation of The GoDowns 1.6-acre property in Industrial Area from 7,000 Sq.M of adaptive reuse/renovated warehouses, into a 25,000 Sq.M mixed-use public purpose development - a New GoDown Cultural Arts Complex that responds to the latent opportunities culture holds for Nairobi City. It will be the first major public complex for contemporary performing and visual arts to be built since Kenya’s independence.
The New Go Down will boast numerous arts and culture enrichment amenities including 20 visual artist studios, 20 offices for creative businesses, 2 dance studios, 1 music recording studio, 2 band rehearsal spaces, 12 instrument practice rooms, a 500-seater multi-use auditorium, a 200-seater black box, 3 levels of gallery and exhibition space, a mini-museum of the city, media recording and broadcasting spaces and a specific children’s atelier. Other community facilities include a visitor information centre, a public library & digital resource centre, a youth services centre, a number of outdoor open spaces and roof gardens, and public washrooms. Other spaces for that will be leased out include open plan offices, serviced
offices, meeting and conference rooms, as well as spaces for a convenience shop, restaurant, bar and food court.
The design process has drawn on inputs from many stakeholders. Through physical workshops and online initiatives, ideas and wishlists have been generated from The GoDown’s
Project Team:
community which includes artists, creative entrepreneurs, school children, local businesses, city representatives and the general public. This process has been an ongoing dialogue, so the resultant designs are continually energised, refreshed, and reflected upon.
Developer: The Performing and Visual Arts Centre Limited
Design Architects: White Arkitekter
Project Architect: Planning Systems Services Ltd
Quantity Surveyor: CMAS Quantity Surveying Ltd
Structural Engineer: Engplan Consulting Engineers Ltd
Services Engineer: Bosch East Africa
Enabling Works Contractor: Mandip Singh Construction (Kenya) Limited
Gate
P.O.
Tel: (254 020)203 4568
Email: info@cmasltd.com
Website: http://www.cmasltd.com/
PROJECT
PROGRAMME
CONTRACT
QUANTITY
ALTERNATIVE
We are proud to be associated with the Redevelopment of GODOWN
Using3D steel moulds for production at the factory may be applicable to premanufacturing of bathroom and elevator shaft modules. However, it is important to keep in mind that there is a balance of just how heavy and complex precast concrete products are feasible to pre-manufacture.
Architectural freedom may get very limited if buildings are completely built using 3D moulds. Modern precast offers practicality and saves costs Modern, design-focused precast concrete is suitable for all types of buildings, in seismic areas and also in areas prone to tornadoes.
Precast concrete can be used as the main building material or only partly as a structural component. When high-quality, energyefficient buildings have been the target, the modern, design-focused precast concrete has repeatedly been selected as the construction method.
Precast concrete is a proven, industrialised building method. Even if installation still takes place at the construction site, the main part
of the work is transferred from the chaos of a building site to controlled, organised factory conditions. In addition, housing units are still completed within a reasonable time, costefficiently and in a safe manner. The use of precast concrete brings quite a lot of savings compared to alternative solutions. The savings come from a number of sources.
As an example, in residential buildings, the span of pre-stressed precast hollow core slabs can be from 8 meters to 12 meters. The external insulated precast concrete wall panels can work as the only load-bearing walls.
Furthermore, pre-stressed hollow-core slabs save up to 45 percent in concrete compared to reinforced concrete floor casted in a 3D mould, or a plain cast-in-situ reinforced slab. Prestressing steel can also be cut by 30 percent because of the lower self-weight of hollow core slabs. In an average apartment this means savings of about 14 tons of concrete and more than 250 kg of steel.
Moreover, pre-stressed hollow core slabs can be partly recessed which makes it easier to prepare bathroom plumbing. Optimised production
process Modern automated precast concrete production plants optimise entire precast production process, from 3D building design, to the construction site.
The production lines feature advanced software, modern table circulation and state-of the art production machinery. Automated functions cover planning, monitoring and controlling the process of producing building blocks for acceptable buildings.
An acceptable building for a home should, first of all, be affordable and of a decent quality, with sufficient living space, good structural stability and located in a sustainable neighbourhood.
The acceptable home needs to match expectations of future home owners and tenants. “To sum up, good quality and low life-cycle costs of precast concrete buildings make them an attractive choice for home owners.
Add to that short construction time and cost efficiency of the construction process and you get an optimal choice for large housing projects.
Water pumps are essential tools that are used to move water from one location to another. They are widely used in many different applications, including agriculture, construction, and water treatment. There are several types of water pumps available, each designed for specific purposes. By understanding the different types of water pumps and their uses, one can choose the best pump for one’s specific needs.
Centrifugal Pumps
Centrifugal pumps are the most commonly used type of water pump. They work by using a spinning impeller to create a vacuum that pulls water in and then pushes it out through a discharge port. These pumps are efficient and can handle large volumes of water, making them ideal for applications such as irrigation and water circulation.
Submersible Pumps
Submersible pumps are designed to operate while submerged in water. They are commonly used in applications such as groundwater pumping, sewage pumping, and well water pump-
ing. Submersible pumps are efficient and have a long lifespan since they are protected from environmental factors such as debris, dust, and moisture.
Diaphragm Pumps
Diaphragm pumps are positive displacement pumps that use a flexible diaphragm to move water. They are often used in applications that require the transfer of chemicals or hazardous fluids. These pumps are versatile and can handle a wide range of fluids, making them ideal for use in agriculture, chemical processing, and industrial applications.
Jet Pumps
Jet pumps work by using an impeller to create a vacuum that pulls water in, and then a nozzle to increase the water's velocity before discharging it through a pipe. These pumps are often used in applications such as water wells, shallow lakes, and streams.
Gear Pumps
Gear pumps use rotating gears to move water.
They are commonly used in applications that require precise flow control, such as in hydraulic systems and oil drilling operations. Gear pumps are efficient and can handle high-pressure applications.
Hand Pumps
Hand pumps are manually operated and are often used in remote locations where there is no access to electricity. These pumps are ideal for emergency water supply and can be used to pump water from wells or other water sources.
TechnicalTrading Corporation (TTC) is one of the leading suppliers of pumps in Kenya. The Trading, Engineering, Procurement and Commissioning company has been in the market for over 40 years dealing primarily in Energy, Prime Movers, Mechanical Power Transmission and Fluid Handling. It is located along Pemba Street, off Lusaka Road, within Nairobi’s Industrial Area.
The company deals in all types of pumps including:
• Centrifugal - Domestic, Commercial and Industrial
• Vertical and Horizontal Multistage Pumps
• Chemical Pumps
• Dosing Pumps
• Sewage/Drainage Pumps
• Submersible Pumps (Borehole and Shallow Well)
• Gear Pumps
• Screw Pumps
• Vacuum Pumps
• Roots Blowers
TTC’s imports high quality products manufactured to International Standards (ISO) in India, China and Europe. Their brands include LEO Pumps in the domestic pumping range and AB Equipment/Pumps in the industrial and submersible category.
The company sells its products to a host of customers who include service providers in the fluid handling industry such as plumbers, borehole drillers, pump re-sellers, equipment installers, swimming pools
builders and farmers who need pumps for irrigation. Other customers are manufacturing plants and construction companies.
According to TTC’s Sales Executives Bhavesh Bhogaita and Deep Shah, TTC offers premium quality products and steers clear of cheap or substandard quality products. “The company understands to a deeper level than many competitors the intricate details of the product and hence we can offer tailor-made solutions to overcome a specific pumping challenge and provide consultancy on pump selection and maintenance”, they say.
They add that TTC’s products are priced more affordably compared to the competition so that other retailers may afford to comfortably resell them.
They have however noted that some consumers overly focus on price before quality or reliability. “While we agree that pricing and finances are important, a higher awareness is needed on the fact that not all pumps are made equal and the true performance of cheap pumps is not equal to higher end pumps”, they caution.
On trends in the industry, the TTC sales executives have observed that solarization of pumps has become increasingly prevalent. “Hand pumps, for example, are being replaced with solar DC submersible pumps, which are even cheaper than the hand pumps and require no manual input or force to operate”, they note.
Thisyear, Trident Plumbers Limited is celebrating 35 years since inception. Construction Review looks at the company’s journey to becoming one of the top-rated plumbing and mechanical services contractor.
When it comes to the installation, repair and maintenance of plumbing or mechanical services in residential and commercial buildings, one name immediately comes to mind - Trident Plumbers Limited.
For 35 years, this company has endeared itself to the construction industry by offering top-notch mechanical services for the simplest projects to the most complex. Indeed, one cannot discuss the plumbing landscape in Kenya without mentioning Trident Plumbers Ltd as a leader in this field.
The company’s full business scope includes Plumbing, Sanitary ware Installation, Drainage, Firefighting System Installation, Installation of Boilers, Sprinkler Systems, Ventilation Systems, Air conditioning Systems and regular
maintenance of the same.
Established in 1988 and incorporated in 1993, Trident Plumbers Limited has built its name as a formidable force in the industry by cultivating excellent relations with clients, consultants and suppliers as well as being innovative and adaptive to new technology and new ways of doing things. The founders of the company are still guiding the company and providing leadership today.
Trident Plumbers understands that close cooperation with all parties involved in a project is crucial in order for the work to be completed on time, within budget and as expected in terms of quality, the reason quality is a core principle and practice in all projects they undertake.
Registered with the National Construction Authority (NCA) as Category 1 contractor, Trident Plumbers Ltd boasts state-of-the-art equipment as well as highly trained and specialized personnel. As a result, the company has been able to undertake a large number of
projects ranging from multi-storey buildings, residential buildings, hotels, schools and colleges to factories and apartments. Others include hospitals, laboratories, warehouses and social buildings. The company has also carried out external water reticulation, external drainage, and installation of all types of firefighting systems including sprinklers.
From only 30 employees in 1990, Trident Plumbers Limited has seen steady growth and consequently continue to add employment opportunities into the economy, with hundreds of employees on its payroll.
Some of the major projects Trident Plumbers has accomplished include The Aga Khan Hospital, Standard Chartered Bank Headquarters, Fortis Tower, Parliament, Kenya Airways Pride Centre, Jomo Kenyatta International Airport, ICRC Regional Hub, AAR Hospital, Two Rivers Mall and Morningside Office Park among many others.
Trident Plumbers makes every effort to understand the client’s requirements, build interactive rapport and provide quality materials backed by excellent workmanship and timely delivery. These qualities clearly set them apart from their competitors in the industry.
However, like any other business, the company is faced with various challenges that include increased prices of materials, delayed contracts agreement, delayed payments and inadequate skilled labour in the market. The company sometimes also has to contend with local substandard material that compels it to sometimes make overseas sourcing, hence raising operational costs.
Notwithstanding these challenges, Trident Plumbers Limited is focused on delivery and keeping its clients and business associates happy with its quality of service. The company appreciates that this is the only way it can continue having an edge over competition and remaining the natural go-to plumbing and mechanical services contractor.
Different Concrete curing methods apply to different situations and this is important because strength of concrete is affected by a number of factors, one of which is the length of time for which it is kept moist. Curing of concrete entails providing adequate moisture, temperature, and time to allow the concrete to achieve the desired properties for its intended use. The process takes place immediately after concrete placing and finishing. Properly cured concrete has an adequate amount of moisture for continued hydration and development of strength, volume stability, resistance to freezing and thawing, and abrasion and scaling resistance.
The length of adequate curing is dependent on a number of factors among them mixture proportion, specified strength, weather conditions and future exposure conditions.
Concrete curing methods fall into three broad catagories: those that minimise moisture loss from the concrete, for example by covering it with a relatively impermeable membrane, those that prevent moisture loss by continuously wetting the exposed surface of the concrete and those that keep the surface moist and, at the same time, raise the temperature of the concrete, thereby increasing the rate of strength gain.
Formwork. Leaving formwork in place is often an efficient and cost-effective method of curing concrete, particularly during its early stages. In very hot dry weather, it may be desirable to moisten timber formwork, to prevent it drying out during the curing period, thereby increasing the length of time for which it remains effective. It is desirable that any exposed surfaces of the concrete like the tops of beams be covered with plastic sheeting or kept moist by other means. It should be noted that, when vertical formwork is eased from a surface its effectiveness as a curing system is significantly reduced.
Plastic sheeting. Plastic sheets, or other similar material, form an effective barrier against
water loss, provided they are kept securely in place and are protected from damage. Their effectiveness is very much reduced if they are not kept securely in place. The movement of forced draughts under the sheeting must be prevented. They should be placed over the exposed surfaces of the concrete as soon as it is possible to do so without marring the finish. On flat surfaces, such as pavements, they should extend beyond the edges of the slab for some distance, eg or at least twice the thickness of the slab, or be turned down over the edge of the slab and sealed.
For flat work, sheeting should be placed on the surface of the concrete and, as far as practical, all wrinkles smoothed out to minimize the mottling effects (hydration staining), due to uneven curing, which might otherwise occur. Flooding the surface of the slab under the sheet can be a useful way to prevent mottling. Strips of wood, or windrows of sand or earth, should be placed across all edges and joints in the sheeting to prevent wind from lifting it, and also to seal in moisture and minimise drying. For decorative finishes or where colour uniformity of the surface is required sheeting may need to be supported clear of the surface if hydration staining is of concern. This can be achieved with wooden battens or even scaffolding components, provided that a complete seal can be achieved and maintained. For vertical work,
the member should be wrapped with sheeting and taped to limit moisture loss. As with flatwork, where colour of the finished surface is a consideration, the plastic sheeting should be kept clear of the surface to avoid hydration staining. Care must also be taken to prevent the sheeting being torn or otherwise damaged during use. A minimum thickness is required to ensure adequate strength in the sheet; ASTM C 171 Sheet Materials for Curing Concrete specifies 0.01 mm. Plastic sheeting may be clear or coloured. Care must be taken that the colour is appropriate for the ambient conditions. For example, white or lightly coloured sheets reflect the rays of the sun and, hence, help to keep concrete relatively cool during hot weather. Black plastic, on the other hand, absorbs heat to a marked extent and may cause unacceptably high concrete temperatures. Its use should be avoided in hot weather, although in cold weather its use may be beneficial in accelerating the rate at which the concrete gains strength. Clear plastic sheeting tends to be more neutral in its effect on temperature but tends to be less durable than the coloured sheets, thereby reducing its potential for re-use.
Membrane-forming curing compounds Curing compounds are liquids which are usually sprayed directly onto concrete surfaces and which then dry to form a relatively impermeable membrane that retards the loss of moisture
from the concrete. Their properties and use are described in AS 3799 Liquid Membraneforming Curing Compounds for Concrete. They are an efficient and cost-effective means of curing concrete and may be applied to freshly placed concrete or that which has been partially cured by some other means. However, they may affect the bond between concrete and subsequent surface treatments. Special care in the choice of a suitable compound needs to be exercised in such circumstances. The residue from some products may prevent the adhesion of flooring products and tiles onto the concrete surface.
It is extremely important to check the subsequent floor finish. Most curing compounds must be removed before the application of any applied floor finishes such as direct stick carpet and vinyl, epoxy or polyurethane coatings and ceramic tile adhesives. Finally, it should be noted when using curing compounds that are solvent-based adequate ventilation must always be provided in enclosed spaces and other necessary safety precautions taken. Manufacturer’s recommendations should always be followed.
Internal curing compounds These are incorporated into the concrete as an admixture hence known as internal curing compounds. They inhibit moisture loss and thereby improve long term strength and reduce drying shrinkage. Internal curing compounds are relatively new and care should be taken when utilised. They have been used in tunnel linings and underground mines to provide at least partial curing when traditional methods are difficult or even impossible to employ.
General Water curing is carried out by supplying water to the surface of concrete in a way that ensures that it is kept continuously moist. The water used for this purpose should not be more than about 5°C cooler than the concrete surface. Spraying warm concrete with cold water may give rise to ‘thermal shock’ that may cause or contribute to cracking. Alternate wetting and drying of the concrete must also be avoided as this causes volume changes that may also contribute to surface crazing and cracking.
Ponding Flat or near-flat surfaces such as
floors, pavements, flat roofs and the like may be cured by ponding. A ‘dam’ or ‘dike’ is erected around the edge of the slab and water is then added to create a shallow ‘pond’. Care must be taken to ensure the pond does not empty due to evaporation or leaks. Ponding is a quick, inexpensive and effective form of curing when there is a ready supply of good ‘dam’ material, a supply of water, and the ‘pond’ does not interfere with subsequent building operations. It has the added advantage of helping to maintain a uniform temperature on the surface of the slab. There is thus less likelihood of early age thermal cracking in slabs that are cured by water ponding.
Sprinkling or fog curing Using a fine spray or fog of water can be an efficient method of supplying additional moisture for curing and, during hot weather, helps to reduce the temperature of the concrete. As with other methods of moist curing, it is important that the sprinklers keep the concrete permanently wet. However, the sprinklers do not have to be on permanently; they may be on an intermittent timer. Sprinklers require a major water supply, can be wasteful of water and may need a drainage system to handle run-off. The alternative is to have a ‘closed’ system where the water is collected and recycled. Sprinkler systems may be affected by windy conditions and supervision is required to see that all of the concrete is being kept moist and that no part of it is being subjected to alternated wetting and drying. This is not easy to achieve.
Wet coverings Fabrics such as hessian, or materials such as sand, can be used like a ‘mulch’ to maintain water on the surface of the concrete. On flat areas, fabrics may need to be weighed down. Also, it is important to see that the whole area is covered. Wet coverings should be placed as soon as the concrete has hardened sufficiently to prevent surface damage. They should not be allowed to dry out as they can act as a wick and effectively draw water out of the concrete. Fabrics may be particularly useful on vertical surfaces since they help distribute water evenly over the surface and even where not in contact with it, will reduce the rate of surface evaporation. Care should be taken however, that the surface of the concrete is not stained, perhaps by impurities in the water, or by the covering material. New fabrics can leach fabric stains, pre washing should be essential. Prior to
placement of any fabric – pre moisten to avoid wicking of moisture from the concrete that can result in the fabric texture negatively absorbed into the concrete surface.
With several brands flocking the market, a buyer is at the risk of falling for substandard materials. Mr. Andrea Di Iorio, East Africa Sales Manager at CONTROLS GROUP advices clients and suppliers to invest in quality. He say the materials, the equipment used as well as the personnel involved should be of high quality. Mr. Andrea suggests that the industry should be well equipped with the latest technology as opposed to use of obsolete standards and techniques. CONTROLS is the global leader in the production of Testing Equipment for the construction industry with seven branches and more than 4.000 products in three main business areas (Concrete, Soil and Road) , the group has a consolidated presence in Africa for over three decades supplying the main contractors, universities, public and private laboratories.
Tom Schuler, President and CEO of Solidia Technologies, says it is advisable to work with customers on the adoption of new technology and incorporate their feedback and guidance into making the systems easy to adopt as well as making the end-products equal or superior to traditional concrete products. He says customers are pivotal in highlighting the challenges encountered in rising energy and inventory. Solidia Technologies is a cement and concrete technology company that has developed patented processes to ease production and improve performance of cement and concrete, while reducing the carbon footprint of products up to 70% and water consumption 60-80% during manufacturing. Starting with sustainable Solidia Cement™, Solidia Concrete™ is cured with CO₂ instead of water, all using the same raw materials, formulations and equipment with only slight modifications. Saving manufacturers time, energy and money, Solidia Concrete products cure within 24 hours, compared to the 28 days required for traditional concrete to reach full strength. Solidia Technologies has partnered with global industry leader LarfargeHolcim to work on research and development, as well as marketing for their cement and concrete systems.
Towablegenerators are a reliable source of backup power. These generators can be used for a variety of commercial and industrial applications. Towable generators are a common sight at concerts, sports events, outdoor parties, and constriction sites.
If you want to use it for a building you need a wired generator connection panel for manual transfer of power. The towable models are ideal for powering up air conditioners, heaters, security systems, computers, refrigerators, and freezers.
In the past, almost all towable generators ran on diesel. Now users have many choices. You can buy very efficient units that run on propane and natural gas as well. These generators can supply power during emergencies to shops and offices as well. These days, units that run on gasoline, diesel, natural gas or LPG are more desirable. You can have an unlimited supply of gas coming from the kitchen gas lines. LPG cylinders are easy to store and use.
All towable generators are built to withstand harsh weather conditions. Generac, Kohler and Briggs & Stratton build world-class models to meet the need of the demanding market. For industrial use, you can get the larger units mounted on a trailer. These are many types of generators used in commercial applications. You can buy one for permanent installation or buy a towable unit. Size is also important while considering a unit for your place of business or manufacturing.
Gasoline, diesel, propane, natural gas and so forth are just a form of energy that is used by a generator set to produce electric power. When the primary source of
energy is disrupted, the backup generator furnishes the electric power. Seamless continuity of power is possible with an installed unit that is wired to the electric panels well. On the other hand, a portable unit will have to plug into the system as and when required.
In all buildings, the use of permanently installed units is common. There is no need for a mobile generator in these buildings. The only exception is a hospital which may own towable units to power specific parts of the campus. For commercial use, a standby system is more preferable.
For roadside jobs, the towable units are commonly used. They generate less power but it is ample to run lights and the construction tools. The power generation capacity of the mobile generator is less than the permanent ones. When you know you need more power for a specific number of days or months, get the towable type for your factory. Sometimes the surplus of orders results in renting more machines to meet the project timelines. In such a scenario a towable generator will keep these additional machines running and you can produce more to meet the new production targets.
The price of mobile units varies. Generac produces very good models that you may want to look into. Generac Magnum MMG55DF4 Mobile Towable Generator, Generac 6782 Mobile Towable Generator MLG8K/STD, and Generac MDG100DF4 STD Mobile Towable Generator with Trailer (MMG100D) are all good models. The latter comes with various options and you can select the type of trailer you need.
maintain. It has a cabinet that is loaded with user-friendly features. The generator has a Tier 4 engine with long run time. Users are able to select the power output they require. The aluminum enclosure makes the unit rust-proof and attenuates sound. Use it for events or at the construction job site with full peace of mind. The model has a 24-hour run time and has a 3-position selector switch for power output. This sturdy and durable modern has a Power Zone™ controller and display. Use the push buttons for easy operation. Safety wise this is a good model as it has 9 warning and shutdown features. The control box is lockable and so is the lug box.
The model is a bit pricey and if you want something more affordable, take a look at the Generac 6782 Mobile Towable Generator MLG8K/STD. This model features a Kubota diesel engine and is fuel efficient. The high performance of this model makes it a good choice. If you have a small load and have single phase power needs this model will be just right for you. It is portable, efficient, and rugged. It has a full tubular steel frame, lockable enclosure, fade resistant powder coat finish and is very reliable. When the oil level is low or when the unit heats up it will auto shut down so no damage is caused to the Kubota diesel engine. The best thing about the Generac 6782 Mobile Towable Generator is that it is very easy to use. The 3-cylinder engine is self-priming and the generator has the external convenience outlets with individual breakers.
Sometimes in factories, the power can break down at peak hours of operations and at such times it pays to be well prepared for the situation. A backup source of power saves the day and the machines could continue running as usual. When production stops it could mean big financial losses and when orders are not delivered in time the company can also lose buyers.
Manufacturers take into consideration all the needs and requirements of industrial clients and come up with models that are easy for them to use. If you need a new unit for your factory or your construction site, check online for what is on offer. The dealers can take care of all sorts of needs of clients.
Towable generators come with wheels that never go flat. They are easy to store and maintain. You can find all sorts of accessories to enhance functionality. When you buy the right model, read the owner’s manual so you get more familiar with the new asset. Get a cover, weather kits, fuel stabilizer, and other accessories online at good rates.
If you like a unit that is a bit beyond your budget, use the easy financing offered by dealers to make easy monthly installments. After sale service ensures the generator continues to work efficiently for long.
Assolar energy continues to soar in popularity, many homeowners are eager to install solar systems. In fact, the last few years have seen many Americans choosing to power their homes using solar energy. Not only does solar energy offer amazing cost-saving and eco-friendly perks, but it has also become incredibly affordable to install in residential properties.
You can expect solar panels to become more commonplace in everyday life. You don't have to be a solar expert to reap the numerous benefits of solar energy. If you're considering installing a solar system to sustain your home's energy needs, contacting a reputable solar company like Phoenix Valley Solar can help determine whether it's an investment that will work for you. They'll also help you obtain permits, apply for financing, and install the solar system. Here are three major signs that your home may need a solar installation:
One of the main reasons most homeowners choose to go for the solar option is due to the ever-rising electricity bills. If you live in a state with extremely high electricity rates, solar installation is for you. The average solar installation cost is about $12,500, after which you may need to replace components once in thirty years.
However, if you can't afford such an amount, multiple solar financing options could suit you
well. Although the initial investment is substantial, the long-term savings will be worth it. Once installed, you'll be set to supply power to your home's needs for many years. Solar panels can offer significant savings if they are installed and maintained accordingly.
To maximize your home's overall value, you should live in a neighborhood with consistent sunlight. That’s because solar installation is typically best suited for areas with ample sunshine throughout the year. Ensure your home gets adequate exposure to the sun before installing solar to maximize the energy returns.
Additionally, make sure there are no obstacles, such as trees, blocking the sun from reaching your compound. However, solar panels harvest energy from daylight and not necessarily sunlight. The hours of sunlight may not translate to how well your solar installation saves you energy. Be sure to contact a solar company to help you identify the ideal location to install your home solar system.
Typically, roofs are the most strategic position to maximize solar light absorption. You should always inspect your roofing system's condition before investing in solar installation. If your roof has brittle materials or damaged shingles, solar installation may damage the structure even further.
It's best to start by upgrading your roof before moving forward with solar installation. Once you've upgraded the roof, you can safely install the solar panels. Don't worry about your solar panel's angle; let the professionals handle that for you.
Before planning a solar panel installation, research to see if solar panels suit your home's energy needs and if your location is ideal for solar use. If you want to save on your electricity bills while still easing the climate change burden on the planet, then you're ready for the sun's self-replenishing energy. Remember to choose the solar installation option that best suits your home rather than the most popular one.