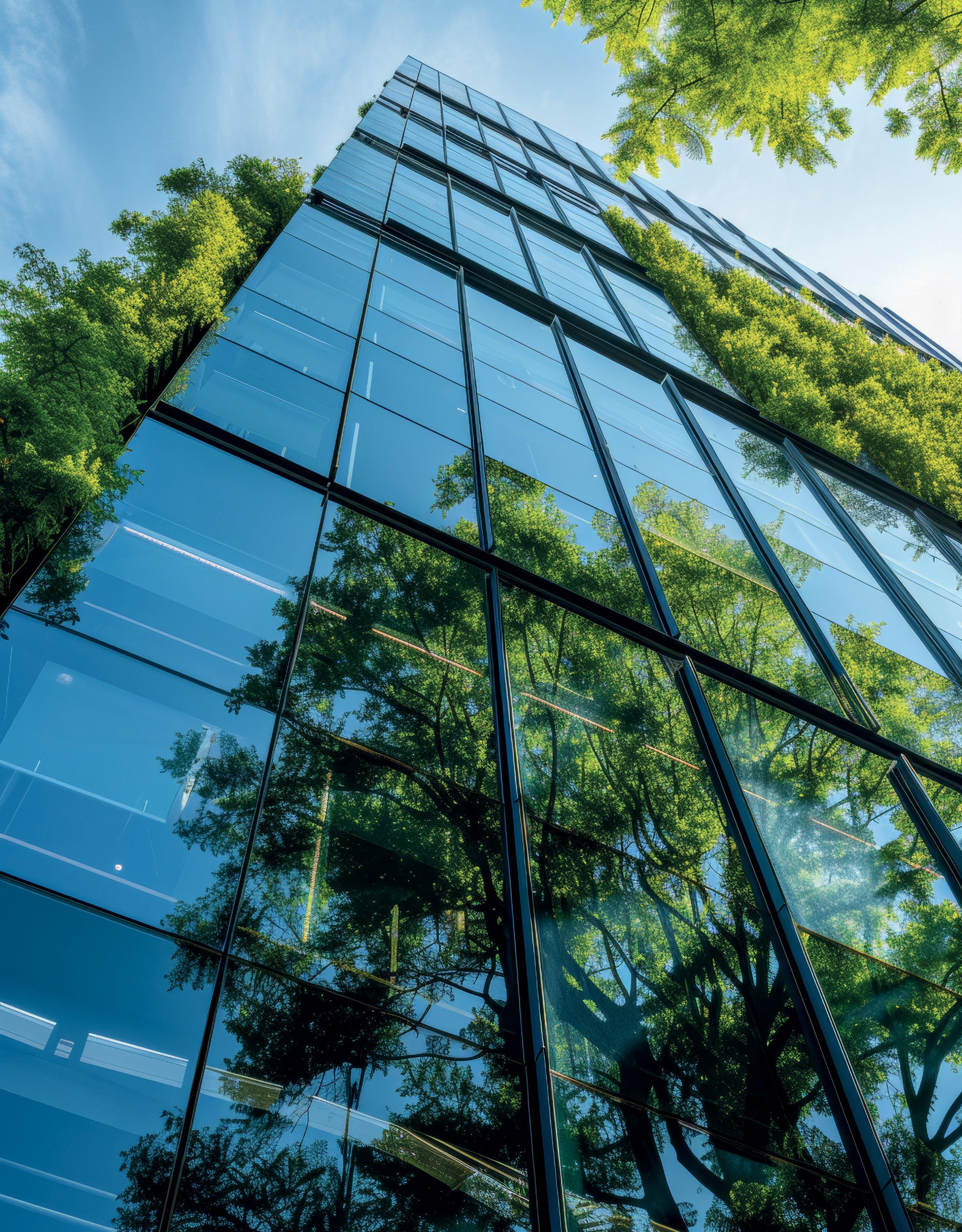
A SPECIAL ISSUE DEDICATED TO MEP WORKS AND ACHIEVING NET ZERO IN THE BUILT ENVIRONMENT
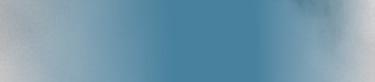
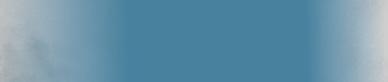

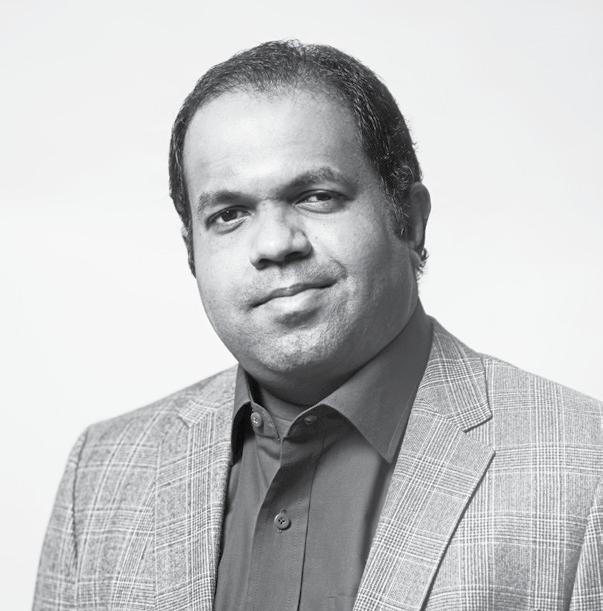
A SPECIAL ISSUE DEDICATED TO MEP WORKS AND ACHIEVING NET ZERO IN THE BUILT ENVIRONMENT
On behalf of Big Project Middle East (BPME) and CPI Trade Media, I wish you all a happy, safe and prosperous New Year 2025! As one of the leading construction-focused B2B titles in the MEA region, BPME has significant plans for the year ahead, both from an editorial standpoint, and in terms of our various events. I’m sure you’re well aware that the latter now includes networking events, roundtables, conferences and, of course, awards programmes.
In fact the forthcoming edition of the BPME Awards is a significant milestone for us – the 2025 BPME Awards will actually be the 15th edition of our annual awards ceremony. That’s an incredible milestone and it represents an unbroken run, as the BPME Awards continued unabated whilst the world was dealing with the outbreak of the COVID-19 pandemic (following all government mandated safety protocols of course).
To mark the occasion, the team and I updated the nomination
process for this edition, with the goal of making it easier to highlight achievements to us at BPME and our independent panel of judges.
I’m also pleased to confirm that the BPME team has been hard at work on designing all new trophies to present to winners – I personally think they look fantastic and look forward to hearing your feedback post event. From a conference standpoint, we’ll be scaling up our flagship events, continuing to develop our newer properties, and launching a couple of all new conferences. The latter tie into recent goingsons in the region and I’m excited to work with the BPME team and all of you on those conferences in due course. See you then!
Jason Saundalkar HEAD OF CONTENT
8 The Briefing
Etihad Rail has launched the region's first-ever CO2 Emission Avoidance and Reduction Certificates
14 The Big Picture
A wrap-up of the biggest international construction news stories for the month
16 Market Report
Lower interest rates, robust project pipeline, and increased transparency are fuelling optimism in KSA's real estate sector says JLL
20 In Profile MEP in the spotlight
AECOM, AESG and Parsons speak to BPME about the importance of high-quality MEP design, engineering and delivery, modular MEP and challenges in the segment
32 Comment
The future of MEP is now
The modular MEP industry is at an inflection point, driven by increasing stakeholder involvement, technological advancements, and the business and sustainability benefits of offsite construction says ALEMCO's Rejil Kumar
48 Comment
Achieving Net Zero is a Middle Eastern imperative for a sustainable future says ACCIONA's Marcos Dorao
56 Comment
By staying ahead of trends and embracing new technologies, the industry can set a global benchmark for sustainable and transformative growth according to Carter Hones Associates senior leaders
60 Final Update
Ellington Properties hands over Berkeley Place to residents
GROUP
MANAGING DIRECTOR Raz Islam
DIRECTOR OF FINANCE & BUSINESS OPERATIONS Shiyas Kareem
PUBLISHING DIRECTOR Andy Pitois
EDITORIAL
HEAD OF CONTENT Jason Saundalkar
ASSOCIATE EDITOR Priyanka Raina
ADVERTISING
SALES DIRECTOR Arif Bari
STUDIO
ART DIRECTOR Simon Cobon
GRAPHIC DESIGNER Percival Manalaysay
PHOTOGRAPHER Maksym Poriechkin
CIRCULATION & PRODUCTION
DIRECTOR OF MARKETING & MEDIA OPERATIONS
Phinson Mathew George
PRODUCTION & IT SPECIALIST Jarris Pedroso
MARKETING
MARKETING & EVENTS EXECUTIVE Lakshmy Manoj
SOCIAL MEDIA EXECUTIVE Franzil Dias
WEB DEVELOPMENT
SENIOR DIGITAL MANAGER Abdul Baeis
WEB DEVELOPER Umair Khan
FOUNDER Dominic De Sousa (1959-2015)
raz.islam@cpitrademedia.com
shiyas.kareem@cpitrademedia.com andy.pitois@cpitrademedia.com
jason.s@cpitrademedia.com priyanka.raina@cpitrademedia.com
arif.bari@cpitrademedia.com
simon.cobon@cpitrademedia.com percival.manalaysay@cpitrademedia.com maksym.poriechkin@cpitrademedia.com
phinson.george@cpitrademedia.com jarris.pedroso@cpitrademedia.com
lakshmy.manoj@cpitrademedia.com franzil.dias@cpitrademedia.com
abdul.baeis@cpitrademedia.com umair.khan@cpitrademedia.com
When you have finished with this magazine, please recycle it
The publisher of this magazine has made every effort to ensure the content is accurate on the date of publication. The opinions and views expressed in the articles do not necessarily reflect the publisher and editor. The published material, adverts, editorials and all other content are published in good faith. No part of this publication or any part of the contents thereof may be
© Copyright 2025. All rights reserved.
MEConstructionNews.com
@meconstructionn
MEConstructionNews
me-construction-news
PROPERTY
Q4 Dubai real estate transactions exceed $31bn
Dubai’s real estate market continues to demonstrate remarkable strength and global appeal, underpinned by strategic planning, visionary developments, and investor confidence
PROPERTY
Ellington Properties hands over Berkeley Place
Eco-conscious features include EV charging stations and bicycle parking, indoor and outdoor fitness studios, yoga deck, and a rooftop infinity pool with views of Dubai’s skyline
SUSTAINABILITY
ABB partners with World Green Building Council buildings across Europe
This collaboration marks another step in ABB’s sustainability journey to provide products and solutions that support its customers’ sustainability needs
INFRASTRUCTURE
Two new bridges to boost Abu Dhabi traffic flow
The strategic infrastructure project will significantly improve traffic flow and reduce average delays at the intersection by up to 80% during peak morning hours
CONSTRUCTION
The Sustainable City – Yiti achieves infrastructure milestone
The Sustainable City – Yiti is committed to 100% water recycling, 100% waste diversion from landfills, and achieving 80% self-sufficiency in food production
The milestone reinforces Etihad Rail’s role as a key contributor to the UAE’s climate change agenda, aligning with the nation’s Net Zero by 2050 Strategy
Etihad Rail has introduced the region’s first-ever ‘CO2 Emission Avoidance and Reduction Certificates’, an innovative initiative that highlights the environmental benefits of rail transport for its customers. This significant milestone reinforces Etihad Rail’s role as a key contributor to the UAE’s climate change agenda, aligning with the nation’s Net Zero by 2050
Strategy through a transparent Environmental, Social, and Governance (ESG) framework linked to the UN Sustainable Development Goals (SDGs), said a statement from the company. The certificates - powered by EcoTransIT, a tool for assessing the environmental impact of transport- quantify and validate the carbon savings businesses achieved
by choosing rail over alternative transport modes, directly contributing to the UAE’s decarbonisation goals.
Using EcoTransIT’s accredited methodology, the certificates calculate CO2 Equivalents (CO2e) by factoring in direct emissions from diesel and indirect emissions from biofuels (where applicable).
The process includes Well-toWheel (WTW) analysis, covering the full lifecycle of fuel use - from extraction to combustion - ensuring an accurate measurement of the environmental impact of each tonne-kilometre transported. It also accounts for cargo weight and distance using shipment-specific data
and geocoordinates. For comparison, rail freight emissions are calculated in comparison to truck emissions, providing a clear basis to highlight rail's environmental advantages.
By launching these certificates, Etihad Rail is empowering its customers by providing credible and tangible data that reflects the positive environmental impact of their shift from road to rail. This initiative not only supports businesses’ ESG objectives and commitments but also presents an opportunity to showcase their leadership in environmental stewardship, said the company.
By adopting rail as a primary mode of transport, companies
By adopting rail as a primary mode of transport, companies can align their operations with the ‘Reduction of Climate Change Effects’, ensuring compliance with national climate regulations while advancing their sustainability goals.
can align their operations with the ‘Reduction of Climate Change Effects’, ensuring compliance with national climate regulations while advancing their sustainability goals. These certificates allow customers to enhance their corporate sustainability reports, improve ESG
In October 2024, the company signed an agreement with Emerge, a JV between Abu Dhabi Future Energy Company PJSC - Masdar and EDF Group to solarise the railway network’s freight terminal in Ghuweifat.
Ratings, attract environmentally conscious stakeholders.
“At Etihad Rail, sustainability is not just a commitment - it is a cornerstone of our identity and operations. The introduction of our CO2 Emission Avoidance and Reduction Certificates underscores our dedication to pioneering climate action and delivering tangible value to our customers. This initiative empowers businesses to take active
roles in reducing their carbon footprint, while leveraging the unparalleled efficiency and reliability of rail transport. By aligning with the UAE’s Net Zero by 2050 Strategy and the UAE Climate Change law, we are driving transformative change in the logistics sector, building a more sustainable future for the UAE and the region,” said Omar Alsebeyi, Executive Director of Commercial & Performance of Etihad Rail.
He added: "The introduction of Etihad Rail's CO2 Emission Avoidance and Reduction Certificates presents a unique value proposition for our customers. As businesses increasingly prioritise environmental responsibility, these certificates not only allow them to align their operations with the UAE’s
decarbonisation goals but also demonstrate their commitment to sustainability. We’re proud to be part of this pioneering initiative that is rapidly becoming a key market differentiator, helping us attract and retain customers focused on reducing their environmental impact while enhancing their logistics operations.”
Etihad Rail aims to transport 60m tonnes of cargo annually by 2030, contributing to the UAE’s economic diversification, enhancing supply chain resilience, and contributing to its climate targets. Etihad Rail’s operations are projected to reduce CO2 emissions from the UAE’s road transport sector by 21% annually by 2050, taking up to 300 trucks off the roads for every train journey and removing 8.2m tonnes of CO2 per year.
The school project’s timeline could not be achieved under a traditional procurement process and required a PPP approach
The new campus will accommodate 3,380 students in Khalifa City and is expected to be operational in 2026.
BESIX-Plenary Group has achieved financial close on the Khalifa City School project in Abu Dhabi. The project was procured using an augmentation procurement framework within the existing Zayed City Schools public-private partnership (PPP) project. Led by Abu Dhabi Investment Office (ADIO), the design and use of this framework for school infrastructure marks another first for the region.
The Abu Dhabi Department of Education and Knowledge (ADEK) requires Khalifa City School to be operational by August 2026, a timeline that could not be achieved via a traditional procurement process, said a statement.
Through planning and implementation, ADIO developed a specific framework that enabled the school’s infrastructure to be procured and awarded within a record time-frame of twelve months, demonstrating ADIO’s commitment to delivering critical infrastructure efficiently and on schedule. This approach aligns with broader efforts to attract and enable investments that support the emirate’s vision for world-class educational infrastructure.
Early works commenced in July, with construction scheduled to begin shortly which comprises the design, build, finance, and 18-year operation and maintenance of a new campus, which will accommodate 3,380 students in Khalifa City. The school is scheduled to be completed in time for the 2026 academic year. Zayed City Schools project delivered three state-of-the-art schools on time earlier this year.
ADIO led the augmentation process in collaboration with the ADEK and
the BESIX-Plenary Group consortium. BESIX-Plenary delivered a valuefor-money solution, subsequently reaching commercial and financial close, the statement explained.
Plenary Group Chief Investment Officer Paul Crowe said, “The augmentation deal underlines the flexibility of the PPP model and the ability to enhance value for money for the procurer. This project, and the underlying Zayed City Schools project, is a great demonstration of the strength and flexibility of the PPP model. The Khalifa City School is a brilliant result for ADEK and its future students and staff, and we are proud to have provided such a meaningful outcome for ADIO.”
Peter Lembrechts, General Manager of BESIX Middle East added, “BESIX’s strength lies in our unique combination of capabilities: equity investment, EPC expertise, and longterm operations and maintenance leadership. This integrated approach allows us to deliver successful projects at every stage, creating lasting value for all stakeholders.”
Elias Sfeir, Head of Concessions & Assets, BESIX Middle East commented, “Leveraging our combined financial strength, technical expertise, and a unified vision to deliver ADEK’s and ADIO’s goals for sustainability and innovation, this strong partnership will once more redefine possibilities and set new benchmarks in infrastructure development.”
Equity financing is provided by Plenary (50%) and BESIX (50%), while debt is being provided by leading domestic and international banks Abu Dhabi Commercial Bank, HSBC, Intesa Sanpaolo and Norinchukin.
California has unveiled a US $310bn plan to develop and construct a connected mass transit rail system over the next 25 years.
Governor Gavin Newsom announced the project, dubbed the State Rail Plan. The high-speed electrified network would stretch across an area of about 900km long from north to south, with multiple lines running east and west into major metros like San Francisco, San Jose and also Las Vegas, in the neighbouring State of Nevada.
Ireland has unveiled ‘Europe’s first’ 3D-printed concrete social housing project.
The 3D concrete printed (3DCP) dwellings are located in Grange Close, Dundalk, County Louth, Ireland. The 330m2 footprint includes three three-bedroom houses.
A public-private housing development consortium in Ireland consisting of Louth County Council, 3D-printing firm Harcourt Technologies, and materials provider Roadstone are said to have built the homes using a BOD2 3D Construction Printer from Cobod.
Hilton signed a partnership deal with Al Sorouh Hospitality Development Real Estate for the launch of its debut Waldorf Astoria property in Bahrain.
Located in the heart of the capital Manama, Waldorf Astoria Bahrain Bay will bring the top Hilton brand’s signature service and sophisticated accommodations to one of the capital’s most exclusive districts, as per a statement from Hilton.
Waldorf Astoria Bahrain Bay will feature 120 rooms and apartments and is scheduled to open in 2028.
DHL Express has opened an all-new facility at Muscat International Airport, Oman.
Over the past two decades, DHL Express has invested more than US $30.81mn in developing this state-of-the-art facility, which spans a total area of 12,621sqm, with a built-up space of 8,074sqm. The facility houses a ground operations hub, an import/ export gateway, and a regional office, with the capacity to process approximately 2,400 shipments per hour, while serving more than 4,200 customers.
AD Ports Group has signed a foundation agreement with SEMURG INVEST (Semurg), the owner and developer of the Sarzha Multifunctional Marine Terminal at Kuryk Port, Kazakhstan. Sarzha Grain Terminal will see a total investment of US $50mn over the two phases, with AD Ports Group contributing around $30mn.
Under the terms of this agreement, AD Ports Group owns a 51% stake and Semurg owns a 49% stake in the Sarzha Grain Terminal.
Abu Dhabi Future Energy Company (Masdar) has announced its entry into the Philippines market, signing agreements with the government to develop one gigawatt (GW) of clean energy projects.
The implementation agreement with the Department of Energy and the Memorandum of Understanding with the Board of Investments of the Republic of the Philippines covers the development of solar, wind and battery energy storage systems (BESS) with a total capacity of up to 1GW by 2030.
Lower
project pipeline, and
transparency
As the global macroeconomic backdrop brightens and headline inflation eases, Saudi Arabia's real estate market is witnessing a surge in investment driven by lower interest rates and proactive government initiatives, revealed a JLL roundtable discussion that took place in Jeddah.
Falling borrowing costs and a robust pipeline of construction projects entering the execution phase are fuelling optimism and driving activity across the Kingdom’s real estate sector, said industry leaders and experts who discussed the dynamic opportunities and emerging trends shaping the Kingdom's real estate landscape.
Saudi Arabia’s risk management strategies for dealing with disruptions have proven effective in mitigating their impact on the nation’s economy, including the real estate sector. This resilience, alongside the prioritisation of economic diversification strategies under the Kingdom's ambitious Vision 2030 reform agenda, underpins growth and instils confidence among investors.
In recent years, Saudi Arabia has taken a targeted government approach
and increased focus on sustainability and technological integration to boost real estate transparency. With 18 new legislations, including updated real estate systems and regulatory frameworks, the Kingdom is now ranked second among the top improved markets in real estate transparency globally.
Alongside the Kingdom's high transparency score, the adoption of innovative construction techniques and technologies will be critical for the continued development and successful execution of some of the world’s largest urban development projects currently underway across cities, including in Jeddah.
Reflecting on the Kingdom’s broader efforts to enhance the real estate landscape, James Allan, CEO of JLL MEA said, “Saudi Arabia’s significant improvement in JLL’s Global Real Estate Transparency Index (GRETI) demonstrates the Kingdom’s progress in establishing strong regulatory frameworks and enhancing market transparency. These advancements are crucial as the Kingdom continues to transform its real estate sector in line with Vision 2030 objectives.”
As Saudi Arabia sharpens its focus on aligning key projects with Vision 2030 goals, the roundtable highlighted several crucial themes impacting the Saudi real estate market, such as a strong affinity for sustainability and Net Zero targets, and a renewed commitment to local sourcing and manufacturing.
Saud Al Sulaimani, Country Head, KSA, outlined the promising prospects for the Saudi real estate market, emphasising the government’s cohesive approach to advancing key areas such as urban development, sustainability, and housing affordability. He said, “The growing appetite for publicprivate partnerships (PPPs) is driving innovation and growth, and we anticipate robust performance across most sectors in Q4, following key approvals and resumption of projects.”
Presenting an overview of KSA’s projects market, Maroun Deeb, Head
of Projects and Development Services, KSA and Bahrain noted, “The total value of projects being awarded may have slowed for now, and the Kingdom expects a significant increase in projected cash flow in the coming years, with spending peaking in 2027. The future projects pipeline encompasses projects worth $826.3bn that are now in the design stage while more than $100bn are in varying stages of the project implementation phase.”
The roundtable also addressed the development potential of high-quality industrial and logistics real estate in KSA. Currently ranked 38th on the Logistics Performance Index (LPI), the Kingdom presents a compelling opportunity for growth in this sector, especially in Jeddah, a primary warehousing hub. The city accounts for only 10% of Grade A warehousing, signalling a prime opportunity for expansion given the rising demand from e-commerce, 3PLs, and cold storage.
Participants at the roundtable explored the impact of global events like the World Cup 2034 and Expo 2030 on Jeddah’s real estate market, recognising the city’s growing global appeal as a prime real estate investment destination. This is evident in the residential sector
BPME ’S JASON SAUNDALKAR SPEAKS TO EXPERTS FROM AECOM, AESG AND PARSONS ABOUT THE IMPORTANCE OF HIGH-QUALITY MEP DESIGN, ENGINEERING AND DELIVERY, DESIGN AND DELIVERY CHALLENGES, AND THE RISE OF MODULAR MEP SYSTEMS IN THE REGION
At its core mechanical, electrical and plumbing (MEP) design and engineering is one of the key elements responsible for providing a comfortable and functional space for a building’s users. In the Middle East, buildings are significant consumers of energy and water due to a number of different factors, which means that well planned and executed MEP works are absolutely crucial to ensuring that a building is as efficient as possible, and complies with current and future sustainability standards and requirements. The latter is particularly important as countries in the region - along with the rest of the world - battle to prevent catastrophic climate change and achieve Net Zero.
With calls for buildings to get smarter and more efficient, MEP works are now more important than ever before, and there has been a lot of innovation in the space in recent times.
“Generally I think we’re seeing increased adoption in the integration of smart building technologies and consideration of digital resilience certifications such as Smart Score or Wired Score. The use of BIM is also continuing to grow and is now the default solution for design practices for drawing production and coordination. But we’re now starting to see wider adoption of Digital Design in which the model is used as the single source of truth for calculation and design via self-developed scripts in python or dynamo or increasing feature sets in 'out of the box' Revit,” says Nicholas Byczynski, Director of Building Services, AESG.
COMPLYING WITH STANDARDS
Compliance with global standards such as LEED are becoming a priority, with MEP systems being optimised for energy consumption, water efficiency, and improved indoor air quality says Marinelli.
“There is also a growing emphasis on energy efficiency through the use of renewable energy sources, such as solar power, and the incorporation of advanced HVAC systems that provide better indoor air quality and lower energy consumption in particular being driven by the PIF entities in Saudi Arabia, who have a strong focus on building performance and sustainability. Finally, we’re seeing a growing understanding of the impact of embodied a carbon associated with MEP systems and there will shortly be an update to the CIBSE TM65
standard localised for the UAE Market which was developed by the UAE CIBSE Technical committee.”
Srinivas Reddy, Technical Director, Building Services, Middle East at AECOM adds, “The MEP industry in the Middle East is embracing digital transformation, with the adoption of computational engineering software such as Integrated Environmental Solutions (IES), CFD and advanced BIM-integrated design platforms such as Magicad/Stabicad for designing systems, to bridge the gap between conventional design and automated design processes. These innovations are driving efficiency and precision in design and implementation.”
“The shift towards Net Zero energy and green initiatives, including alternative passive energy systems and specifying highly efficient systems are at the forefront of design strategies. Advanced engineering solutions tailored to the region's climatic needs, and integration of Intelligent Building Energy Management System through IoT-enabled monitoring systems to enable predictive maintenance assist in driving designs that are optimised and operationally efficient. Additionally, the use of modular and prefabricated MEP components is streamlining project execution by reducing onsite work and improving overall quality control.”
Robert Marinelli, Program Director at Parsons highlights, “The future of any city is to be digital and smart building technologies will continue to have an increasingly prominent role. This manifests in the adoption of IoT based systems, smart HVAC controls, and integrated building
management systems. All of these elements contribute to enhanced operational efficiency. In fact, automation and artificial intelligence will play a larger role for predictive maintenance and energy optimisation moving forward.”
MEP engineers need to take responsibility for delivering the most efficient building possible within the clients budget and the other project constraints – regardless of the certification levels targeted.
“Aligned with governments’ sustainability agendas, the MEP space has a lot to offer to maintain efficiencies by using more energy-efficient systems, including heat recovery and renewable energy integration, such as solar panels. Green building certifications will also go hand-in-hand with sustainability initiatives. Compliance with global standards such as LEED are becoming a priority, with MEP systems being optimised for energy consumption, water efficiency, and improved indoor air quality. At Parsons, we will continue to champion innovation in the projects we deliver and drive the implementation of sustainable and resilient infrastructure.”
With regards to how important MEP works are in terms of ensuring that buildings are as efficient as possible, and are in compliance with current sustainability
requirements and standards, Marinelli responds, “The benefits of well-coordinated MEP systems are manifold. Well-designed MEP systems provide optimum living and working conditions for building residents. By optimising MEP systems, we can maximise energy efficiency, remain compliant with sustainability standards and contribute to a healthier building environment. Augmenting HVAC, lighting and electrical systems will significantly lower operational costs and reduce carbon emissions. These systems are critical in meeting green building standards such as LEED as well as local codes. Effective MEP systems consider key factors such as temperature, air quality, and lighting to ensure healthy living environments.”
Reddy explains, “MEP systems play a critical role in achieving energy and water conservation goals, which
EFFICIENCY ADVOCATE
systems by enabling predictive maintenance, real-time monitoring, and energy optimisation - creating buildings that are intelligent, efficient, and sustainable.”
Reddy comments, “Smart building technologies are seamlessly integrated with MEP systems through the use of IoT and Integrated Building Energy Management Systems (IBEMS), which allow for real-time performance monitoring and effective energy management. Ensuring interoperability through unified communication protocols like BACnet is crucial for harmonious operation. The most effective approach is to integrate these technologies at the conceptual stage, fostering a holistic design that enhances both functionality and sustainability.”
Byczynski adds, “This can be achieved through the use of IoT devices, advanced sensors, and automation systems. These technologies combined can control and monitor MEP systems in real-time, optimising performance and energy consumption. The best way to ensure both systems coexist harmoniously is through comprehensive planning and the use of integrated software platforms that facilitate communication between smart systems and MEP components.”
Aggressive timelines can be quite challenging with the increased focus on fully resolved BIM models as a project deliverable says Byczynski.
Pressed about the main issues affecting MEP design/ deployments in the region, aggressive project timelines are highlighted as one of the main pain points. “MEP design in the region faces challenges such as fast-track project schedules, increasing building complexity, and a shortage of skilled professionals. Poor inter-disciplinary coordination often leads to design clashes, while overdesign or under-design may occur due to potential deviation from regional codes and regulations applicable to the project site and lack of system optimisation through diversity and sensitivity analysis,” Reddy highlights. He continues, “Furthermore, inefficient system commissioning and handover processes compromise the systems from achieving the specified design conditions and often resulting in extensive redesign that have both time and cost implications. These challenges can be addressed through
The future of any city is to be digital and smart building technologies will continue to have an increasingly prominent role.
early design collaboration and continuous engagement with all stakeholders, local authorities and facilities management team and adoption of robust BIM tools like Revitzo for interdisciplinary reviews and clash resolution. Employing stringent commissioning processes early at the design stages ensures system integrity, adherence to operation brief and reduces errors during project handover.”
Byczynski says, “Timelines continue to be very aggressive which can be challenging especially with the increased focus on fully resolved BIM models as a project deliverable. We often see programs that are not properly aligned with, for example, later appointment of ID consultants – while this may have been possible in the past, completion of building services packages now requires full coordination with ceilings and elevations which can’t be done without the ID packages being fixed. Too often the project planning and program is not reflective of modern ways of working, which ultimately reduces the quality and coordination or results in excessive abortive work which is hard to manage commercially.”
Marinelli says that as the region evolves into a globally connected hub, he sees innovation playing a critical role in providing effective solutions to address challenges in the industry.
He points out that space constraints are also a challenge at times, explaining “Space constraints can be a limitation for some buildings; and to counter this, early-stage design collaboration and 3D modelling can help optimise space usage in high-rise buildings. For example, our adoption and utilisation of advanced construction supervision platforms such as OpenSpace, driven by AI, integrates 360° photography, BIM, and diverse data types enabling a holistic and easily accessible view of project site progress. From inception to operation, the life-cycle costing and maintenance stages, this approach advances seamless collaboration, accelerates reporting to near-real time reporting, supports the enhancement of safety measures, and promotes CO2 reduction. This transformative approach is truly setting a new benchmark in the project delivery landscape.”
“Another commonly referenced strain in this part of the world is the availability of a skilled workforce. Training programs and local talent development initiatives are essential to address the demand for skilled MEP professionals. In such an expansive industry, we need to coordinate between disciplines. For example, Integrated Project Delivery (IPD) and BIM tools can enhance coordination among structural and architectural elements. Compliance with evolving regulations may become a pain point for some within the industry. This will give rise to regular training and software tools that track code updates, to ensure that the organisation always remains compliant with evolving standards,” he elaborates. Modern buildings can boast complex designs and - at the same time - offer precious little space for the installation of MEP works. This can be challenging
to design and build around but, in the long term, this issue may also pose challenges relating to maintenance work and potential future requirements.
Commenting on this, Reddy says, “Limited space for MEP installations, often caused by reduced footprints or constrained building designs, requires careful planning and innovative solutions. Compact and modular systems can be utilised to optimise space, while maintaining performance.
Advanced 3D BIM modelling helps create efficient layouts and resolves spatial conflicts early in the design process. Additionally, centralised plant rooms and well-planned access provisions ensure ease of maintenance and future upgrades, making the systems both functional and sustainable.”
“As high-rise buildings are now the norm in the region, MEP systems need to be planned for functionality and comfort. Effective planning and the use of AI design software,
and BIM for 3D modelling can help manage complex MEP design within limited spaces. Vertical distribution methods can also help save floor space. These two techniques, among others, will cater to the unique challenges presented by complex building designs,” Marinelli notes.
For buildings with complex designs and limited space for MEP installations, it’s important to ensure we’re not compromising on space for access and future maintenance, as this will only solve a problem for today but create a new one for the life of the building, warns Byczynski.
ON-GOING CHALLENGE
Constrained project budgets continue to impact the design, engineering and delivery of quality MEP works in the region.
He explains, “Generally coordination has improved hugely in the last five years due to the rapid adoption of BIM, and engineers are now able to better understand spatial constraints early in the design process and also explain to client and architects the critical pinchpoints. From my own career in the built environment, the Natural History Museum and the UAE pavilion by Santiago Calatrava are great examples of how BIM can help delivery complex engineering within exceptional architecture with incredibly complex forms.”
Another challenge that can affect the design, engineering
The MEP industry is embracing digital transformation with the adoption of computational engineering software such as Integrated Environmental Solutions, CFD and advanced BIM-integrated design platforms.
and delivery of quality MEP works are constrained project budgets. Pressed about this particular issue and how it can be addressed, Marinelli comments, “Improving MEP system quality and performance within constrained budgets requires early, strategic decision-making, deep technical expertise, and a focus on life-cycle costing.”
“By considering long-term operational efficiency and maintenance costs during the early design stages, it’s possible to optimise performance, while ensuring cost viability. Techniques such as value engineering, modular systems, and optimised system sizing can drive cost-efficiency without compromising quality. Additionally, integrating automation and smart technologies enhances energy efficiency, reduces operational costs, and supports healthier living conditions— delivering long-term value that aligns with project budgets.”
Byczynski states, “Ultimately it’s the designer’s responsibility to deliver the most energy efficient and cost efficient building regardless of whether it’s intended to be LEED Platinum or simply achieving minimum local code compliance. If digitalisation techniques are
adopted to help allow save time in the back end of design, the resource can be focused on the front end to assess different design options to make sure the proposed solution are the best balance of cost and performance.”
Reddy agrees with Marinelli’s comment in terms of early strategic planning, saying, “Improving the quality and performance of MEP systems within constrained budgets requires strategic planning based on life cycle cost analysis and lessons learned from past projects. Prioritising value engineering for critical components ensures cost efficiency without compromising quality. Modular solutions and digital twin technology can also be leveraged to optimise designs, reduce rework, and minimise installation costs, ultimately delivering value to stakeholders while maintaining budgetary constraints.”
On the deployment side, modular MEP systems - where MEP components are developed or pre-fabricated off-site and then integrated into a structure - have been gaining
Enhancing the efficiency and sustainability of existing buildings through MEP upgrades is a key strategy for compliance with current and future regulations.
significant traction in the region in recent years. Asked about its prevalence and the positives and negatives associated with pre-fabricated MEP works, Byczynski says, “Modular MEP has gained traction in the region due to its numerous advantages. These include reduced construction time, improved quality control, and the ability to perform off-site fabrication, which minimises on-site disruptions. However, challenges such as transportation logistics and the need for precise coordination between modules must be addressed. Overall, in many situations the pros outweigh the cons, making modular MEP a viable solution for many projects.”
“Modular MEP came about as a solution to traditional construction methods that did not always keep pace with rapid urbanisation. Traditionally MEP systems were among the most labor-intensive aspects of construction. Modular MEP offers benefits including faster installation, superior quality control and safety in assembly and installation. While modular MEP often requires higher upfront costs and limited customisation for certain projects, we have seen an uptake in this approach in the region,” Marinelli says.
Reddy continues, “Modular MEP systems have gained significant traction in the region due to their ability to reduce on-site construction time, minimise material wastage, and ensure higher quality through offsite fabrication. These systems are particularly advantageous for fast-track projects where time and precision are critical. While modular systems offer benefits such as faster installation and better quality control, they also present challenges, including higher upfront costs and logistical difficulties in transporting larger modules. Despite these challenges, modular MEP systems remain a highly effective solution for many projects.”
Older structures, which could be classified as low performance in terms of their energy and water efficiency, can sometimes be given a new lease on life and be made more efficient by reworking the MEP systems. While refurbishing old buildings is arguably a more sustainable alternative to knocking down a structure and starting from scratch, a number of elements come into play that muddy the waters on how viable this approach is and how often it is undertaken in the region. Byczynski comments, “This is a big topic, and one that deserves its own article! We have a huge existing building stock with MEP systems that are approaching the end of its service life and focus on these buildings
By considering long-term operational efficiency and maintenance costs during the early design stages, it’s possible to optimise performance, while ensuring cost viability.
can have a massive impact on the carbon footprint of the built environment. Every high performance new build we deliver is still adding to the total consumption of power and water – by focusing on refurbishment, we can make meaningful reductions but there is generally a lack of will from owners to invest the capital needed, particularly when it also results in a loss of revenue in the short or medium term while modifications are made.”
“Enhancing the efficiency and sustainability of existing buildings through MEP upgrades is a key strategy for compliance with current and future regulations. Energyefficient HVAC systems, LED lighting, and water-saving plumbing fixtures are among the primary upgrades that can significantly improve performance. The use of digital twins to assess system efficiency and incorporate improvements further enhances operational sustainability. Integration of Building Management Systems (BMS) ensures centralised energy monitoring and control, creating a more sustainable and efficient environment,” Reddy comments.
Marinelli continues, “As buildings age, they may not be able to support modern efficiency standards or comply with sustainability codes. Refurbishing existing structures requires a deep understanding of the building itself, combined with knowledge of local regulations and codes.”
He concludes, “Refurbishing such structures can include retrofitting outdated MEP systems, conducting energy audits, integrating renewable energy solutions, and ensuring compliance with current regulations, all of which can enhance the efficiency and sustainability of the existing structure. This optimises the lifespan and functionality of a building, while preparing it for the future. Often times placing an emphasis on enhancing the efficiency of whole-life asset management strategy can maximise ROI, as this factors capital works, operations, and maintenance into the planning process.”
The modular MEP industry is at an inflection point, driven by increasing stakeholder involvement, technological advancements, and the clear business and sustainability benefits of offsite construction says ALEMCO’s Rejil Kumar
In an industry besieged by labor productivity and project delays, the acceptance and wide-spread use of prefabricated MEP as a lever to manage projects, has been catching up steadily.
Although the advantages of offsite construction are evident, we see a thrust to integrate offsite construction into their core delivery strategy. Notably, large residential developers have recently driven this shift, recognising the benefits of improved quality and adherence to strict project timelines that off-site MEP solutions offer.
The increased involvement of multiple stakeholders - developers, contractors, suppliers, in recent years is set to further accelerate the adoption of prefabricated MEP systems. This broader engagement across the value chain brings additional benefits, such as capitalising on potential including enhanced efficiency and collaboration, and positioning offsite MEP as a norm rather than an exception.
While the advantages of offsite prefabrication - such as reduced dependencies on workfront availability, controlled environment access, minimised logistics needs, and the ability to inventorise project components - are well recognised, a deeper understanding of manufacturing principles is still emerging within the industry.
One of the most critical aspects still evolving in the industry is the ability to adopt a manufacturing mindset. The propensity to automate, adjust construction sequences, leverage crossskilling, and implement on-the-job training represents a significant departure from traditional construction methods. These practices mark a significant shift from traditional construction methods, requiring project teams to fundamentally
Designing MEP modules with adaptability in mind allows for minor changes to be accommodated without disrupting the fabrication process.
change their approach to project delivery when operating offsite. Embracing these changes is essential for maximising the benefits of offsite construction and adapting to a more streamlined, efficient construction model. The shift may have be gradual, but it is essential for achieving a more modern, productive, and cost-effective construction model.
The construction industry has long lagged in efficiency and cost management in comparison to the likes of the manufacturing industry. Wastage on site is less appreciated and much less controlled as a result of several factors. Unlike a controlled factory set up, construction sites offer limited flexibility to control material waste in a chaotic construction environment. This includes detailed engineering designs used in modular, re-use cut of length, better nesting capabilities on CNC machines used in a factory and a sheer factory mindset which optimises the use of materials. Typically, with these standardised processes, one can expect to save about 15 % of material in second fix items through the use of MEP modules.
Additionally, the industry has gotten used to the issue of not being able to meet tender labour costs due to factors such as rework, chaotic construction environment realities etc. In contrast Modern Methods of Construction (MMC) leverage controlled environments, advance skill sets and machinery to use a fraction of the labour at site. This approach also leads to far superior product quality.
In a controlled environment, workers operate in comfortable conditions, with full visual and physical access to the work front thus eliminating the need for physically strenuous positions like ‘hands above shoulder’ installations commonly required for ceiling services. Coupled with a factory mindset that embraces
specialised machines, tools, methods, and distinct skill sets, MMC produces products of much higher quality compared to traditional construction methods.
The right approach
Scope changes are an unavoidable reality on most construction sites and can present challenges for both MEP modular construction and traditional builds. However, several key factors can help ensure the successful adoption of modular methods:
Early stakeholder involvement:
Engaging all stakeholders - developers, designers, contractors, and suppliers - early in the project initiation stage is critical. This collaborative approach ensures alignment and a shared understanding of the project's larger goals.
Collaboration led by the developer: When the developer takes the lead in fostering collaboration among stakeholders, the process typically yields better results by aligning priorities and mitigating potential conflict from the beginning of the project ensuring involvement of all stakeholder. Communication and alignment tend to be better controlled in such projects.
Design time advantage: A key benefit of MMC is the ability to delay production to align with the project schedule. Unlike traditional builds that require construction to begin weeks in advance, MMC provides additional time for design refinement and scope adjustments, ensuring higher accuracy and fewer disruptions.
Adaptable module design: Designing MEP modules with adaptability in mind allows for minor changes to be accommodated without disrupting the fabrication process. This flexibility can be particularly beneficial in dynamic projects where scope changes are common.
Controlled environments see better adoption of machinery, technology and tools in comparison to a traditional builds. In terms of technology, since there is a compulsion to meet the dimensional challenges when assembling multiple services which have to fit into a specific location at site, the use of highly detailed 3D drawing incorporating multiple design inputs is one of the pre-requisites for modular construction. The ability to coordinate and validate designs
has been accelerated by the maturity in adoption of fabrication content in most software such as REVIT, which has been evolving rapidly in the recent years.
The adoption of tools and machinery is significantly higher in factory settings compared to construction sites, primarily because many machines are unsuitable for onsite use due to space, logistics, and environmental restrictions. More importantly, the factory mindset fosters the implementation of lean production principles, which are ideal for incorporating modern tools and techniques. For example, small fabrication units within a manufacturing facility can leverage tools like winches and benches, enabling better utilization of equipment and resources. This structured environment enhances
Engaging all stakeholders early in the project initiation stage is critical, this approach ensures alignment and a shared understanding of the project's larger goals.
productivity, reduces waste, and ensures optimal use of machinery -capabilities that are difficult to achieve in the chaotic and restricted construction environment.
The modular MEP industry is at an inflection point, driven by increasing stakeholder involvement, technological advancements, and the clear business and sustainability benefits of offsite construction. To unlock its full potential, the adoption of a manufacturing mindset, advanced tools, and collaborative delivery methods will be pivotal. By doing so, the industry can move towards a future of streamlined, efficient, and higher-quality project outcomes.
It’s time to embrace performance-based standards and innovation says AtkinsRéalis’ Johanna Staples and Michael Aghabi
Concrete and steel account for about 70% of construction emissions, with concrete alone being responsible for eight percent of global carbon emissions.
Across the Gulf’s ambitious megaprojects, there are clues to what sustainable construction in the region could look like. Among the cranes that dot the cities, the construction industry is trialling a technology that injects captured CO2 into concrete, effectively removing it from the atmosphere. This innovative approach, albeit still at a trial level, exemplifies how key players within the industry are reimagining their approach to sustainability.
The urgent need for decarbonisation is driving a transformative shift. Buildings and construction account for about 21% of global greenhouse gas emissions. In the GCC, this challenge is intensified by high cooling demands, leading the building sector to consume up to 80% of electricity.
Reducing the gap between this current state and the desired decarbonisation path of the Paris Agreement goals, along with regional Net Zero targets, requires critical action. Thankfully, the evolution of sustainability standards, coupled with emerging technologies and materials, is reshaping how we approach building design and construction in the region.
While established sustainability frameworks like LEED and Estidama have been present in the GCC for over a decade, a new generation of standards are moving beyond traditional checklist-based approaches. These latest iterations also focus on contemporary challenges such as decarbonisation, resilience, equity, and health.
LEED v5, currently in pilot review, exemplifies this evolution with its enhanced focus on carbon reduction and human wellbeing. These performancebased standards offer greater flexibility in achieving sustainability goals, making them particularly suitable for large-scale projects seeking advanced sustainability solutions.
Regional companies are also at the forefront of developing sustainable solutions on a commercial scale.
In the GCC’s arid climate conditions, the benefits of these performance-based approaches are immediately visible, with substantial savings accruing over a building’s lifetime. Recent studies indicate that high-performance buildings in the region can reduce energy consumption by 40-50% compared to conventional buildings. It’s encouraging to see many regional megaprojects, especially in Saudi Arabia, aiming for the highest LEED certifications, including LEED Platinum and Net Zero energy standards.
Building resilience to climate change is also crucial. However, this transition brings both challenges and opportunities, requiring a deeper understanding of building performance simulation, carbon tracking, and innovative design solutions.
Material developments
To achieve Net Zero goals, addressing embodied carbon in construction materials is crucial. Concrete and steel account for about 70% of construction emissions, with concrete alone being responsible for eight percent of global carbon emissions.
Though the industry is historically conservative, innovative solutions are emerging such as zero-carbon cement alternatives using magnesium oxide, or incorporating CO2 in the concrete mix to offset carbon emissions. These new technologies have demonstrated potential carbon reductions of 30-70% compared to traditional cement.
Cement 2 Zero, a UK-based demonstrator project led by the Materials Processing Institute, supported by the University of Cambridge, and in collaboration with AtkinsRéalis and other key players, will help Cambridge Electric Cement (CEC) to produce 20% of the world’s first zero emissions cement on an industrial scale.
Regional companies are also at the forefront of developing sustainable solutions
As innovative materials and techniques prove their value in prestigious projects, they will naturally flow into mainstream construction practices.
on a commercial scale. Partanna has introduced a carbon-negative concrete that actively removes CO2 from the atmosphere, with applications already demonstrated in projects such as the Red Sea. ClimateCrete uses locally sourced sand aggregates and reduces cement content, achieving significant carbon footprint reductions.
The steel industry is also undergoing transformation. Materials like graphene are being tested in projects across the UAE and Saudi Arabia for use in rebar. More importantly, efforts are underway to decarbonise the steel manufacturing process itself, with renewable energy and hydrogen-powered production methods showing promising results. This includes a green steel plant being developed in Oman. Studies indicate that green steel production has the potential to reduce emissions by at least 60% compared to traditional methods.
Paying attention to the whole supply and value chain is also critical to progress. This includes managing Scope 3 emissions, the indirect emissions from the supply chain and raw material use which can represent over 90% of a construction company’s total carbon footprint.
The focus on Scope 3 emissions is particularly important for major projects seeking international investment, as green financing increasingly requires comprehensive emissions reporting and management. With the GCC’s green finance market growing rapidly, this presents both a challenge and an opportunity for the construction sector.
The ‘circular economy’ approach presents another opportunity for reducing environmental impact to meet this demand. A report found that a circular scenario could reduce global carbon emissions from building materials by 38% in 2050, due to a reduced demand for materials.
As general agent for Bahri Line (one of the Business Units of the Saudi Arabian National Shipping Company) in Northern Europe and Scandinavia TO GROUP offers a wide range of cargo opportunities on six state-of-the-art vessels. With two trades from the USA (Global Service) and Europe to Far East (via Mediterranean Sea, Middle East, Asia, India and vice versa) you can reach your growth markets even better and faster from the Continent.
Each Ro/Con vessel is equipped with two heavy lift cranes and is perfectly designed to carry a wide range of products, from cars and commercial vehicles, construction materials, various IMO Classes, mining and agriculture machinery to various breakbulk products and containers.
Take a look at our schedules on our website and don‘t hesitate to make an inquiry!
Modern methods of construction (MMC) are emerging as another crucial element in this transformation. Studies show that offsite construction modular buildings can lead to around 80% reduction of onsite overall construction waste. While the current application might be limited to specific building elements, in the context of the GCC’s large developments, this represents an important first step toward more comprehensive modular construction methods.
Looking ahead, the example of renewable energy – which has seen costs decrease by over 80% in the past decade - suggests a similar path for sustainable construction. As innovative materials and techniques prove their value in projects, they will naturally flow into mainstream construction practices.
AtkinsRéalis is at the forefront of supporting the GCC’s transition to Net Zero, with our Advisory Services helping businesses transform their operations to achieve sustainability goals. Further,
A recent report found that a circular scenario for the built environment could reduce global carbon emissions from building materials by 38% in 2050, due to a reduced demand for materials.
initiatives like Engineering Net Zero and the integration of energy modelling into design processes are part of our commitment. We also guide clients on an educational journey, demonstrating the long-term benefits of sustainable practices and shifting the perception of sustainability from a cost to a value-driven approach.
As we navigate this transformation, the industry must invest in upskilling, developing new tools and frameworks, and integrating sustainability into every aspect of planning, design and construction. By embracing performance-based standards and innovative materials, while managing emissions across the supply chain, the sector can lead the way in sustainable development and help achieve the region’s ambitious Net Zero goals.
Johanna Staples is Regional Head of Advisory Services, Middle East at AtkinsRéalis.
Michael Aghabi is Principal
Sustainability Consultant, Middle East at AtkinsRéalis.
In tackling climate change, the building industry must reimagine its approach, embracing circular design principles that prioritise resource regeneration and waste reduction says Gensler’s Samar Hussein
The building industry accounts for over onethird of all global carbon emissions. As more people move to cities, urban development is expected to grow by the equivalent of the size of Paris, every week, so the impact of our industry has the potential to snowball.
Our industry needs to take drastic steps to reduce its carbon footprint now. This means a holistic view on both sources of its emissions; embodied carbon generated by constructing buildings and sourcing of materials, and operational carbon resulting from the use of buildings and its operational systems. While operational carbon emissions currently account for over 70% of global building emissions, this percentage is estimated to drop to 50% by 2050 as building systems get more efficient and energy sources are cleaner. While the industry has started implementing strong measures to reduce buildings energy consumption, improvement measures related to embodied carbon are still in infancy mode, and remain largely an unchartered territory.
By next year, annual global construction waste is estimated to reach 2.2bn tons. To put this into perspective, this equates to throwing away 4,400 Burj Khalifa’s each year. These statistics may seem dramatic, but they represent a realistic snapshot of where we are with building materials now.
In fact, design and construction waste accounted for almost 40% of the global solid waste stream, and as much as 30% of all building materials delivered to a construction site end up as waste. This poses a critical question: what can we do to change that?
The formula in its basic principle is simple and it has been communicated within sustainable design circles for generations: Reduce, Reuse, Recycle. Yet, we are now using more raw materials than ever, and our construction sites are key contributors to our global waste problem. Some of the most celebrated, innovative and energy efficient
By next year, annual global construction waste is estimated to reach 2.2bn tons. To put this into perspective, this equates to throwing away 4,400 Burj Khalifa’s each year.
buildings have shied away from addressing this issue and more accountability is needed.
Circularity, while not a new concept in construction, remains challenging to adopt fully, primarily due to a common focus on upfront capital costs. However, the hidden value of circular design often far outweighs these initial costs. By creating a sustainable supply chain that isn’t affected by lead times, resource extraction, or material shortages, circularity unlocks a resilient stock of materials already in circulation. These materials, which can be reused for multiple building lifetimes, preserve natural resources and significantly reduce embodied carbon.
Even when evaluated purely for its financial benefits, circularity offers strong economic returns. By 2030, revenue from circular products and services is projected to increase by 30% from 2021 levels, according to Bain research. As part of our commitment to reduce carbon emissions associated with our global portfolio, we at Gensler are now focusing more on materials sustainability criteria, including their circularity potential and reuse.
One example of this is our Upcycle project in Austin, Texas, a repositioning of an existing warehouse into a multi-tenant creative office space. In this project, Gensler reused 100% of the original building’s structure, including the building’s skin, which was turned inside out to expose its natural finish. This reuse strategy resulted in a 40% cost reduction and exemplifies how circular design can minimize waste, preserve resources, and create a sustainable impact.
Despite major advancements in materials science and product knowledge, significant gaps remain in the monitoring of materials used in construction. There is still no consistent or widely accepted platform to track or measure the materials and components integrated into buildings— and as the saying goes, we cannot manage what we cannot measure. Circular design principles
could address this challenge by enabling us to track materials throughout their lifecycle, not just in their completed form, but also down to their basic components and ingredients.
As circular economic principles become more widely adopted in design, the need to locate and store circular materials will increase as well. A robust solution to support this shift would be the creation of a global marketplace where available materials can be exchanged, shipped, and reused over multiple generations. These marketplace hubs could also serve as data resources, providing insights on when, where, and how materials can be repurposed, linking users, materials, and projects seamlessly. While a few regional exchange platforms exist, they are often run by SMEs with limited capacity and a narrow range of materials. A globally connected network of circular economy hubs would unlock substantial potential, supporting the industry’s material needs at local, regional, and international levels on demand.
Adopting circular economic principles in design will require a new collaborative methodology, fostering alignment across all project stakeholders and breaking down the silos that currently define much of the construction industry. This approach will
CONSTRUCTION WASTE
As much as 30% of all building materials delivered to a construction site end up as waste says
Hussein.
bring new voices into the project setup, including stakeholders who were not previously part of the decision-making process, broadening the conversation.
Such operational shifts could even lead to new roles, such as a ‘Chief of Circularity’, who would set circular design goals and procedures from the project's inception through its use and re-use stages. This evolution in methodology not only transforms traditional construction practices but also creates new job opportunities in the industry.
In tackling climate change, the building industry must reimagine its approach, embracing circular design principles that prioritise resource regeneration and waste reduction. By creating a global marketplace for reusable materials and fostering collaborative, interdisciplinary methods, the industry can move beyond conventional practices to achieve meaningful sustainability. As circular practices gain traction, the sector has the opportunity to reshape not only construction but also the roles and responsibilities within it, paving the way for resilient, low-carbon urban growth.
Samar Hussein is Associate and Design Resilience Regional Leader at Gensler ME.
Achieving Net Zero is a Middle Eastern imperative for a sustainable future
By embracing innovative practices, collaborating across sectors, and investing in technology and education, the construction industry can be shifted to be more sustainable says ACCIONA’s Marcos Dorao
The initial costs associated with sustainable practices can deter investment, as many stakeholders perceive green construction as more expensive warns Dorao.
As the Middle East faces the mounting impacts of climate change, the construction industry stands at a pivotal moment. Responsible for a significant share of carbon emissions, this sector must adapt to the realities of a warming planet, and the pathway to a sustainable future is clear: achieving Net Zero. This ambitious goal entails balancing greenhouse gas emissions with equivalent sequestration or offsetting, ensuring a viable future not just for the industry but for society as a whole.
The construction sector in the Middle East is projected to grow substantially, driven by urbanisation and economic diversification efforts. However, it also accounts for a considerable portion of the region’s carbon emissions, with estimates suggesting that construction-related activities contribute around 30% of total emissions in some Gulf Cooperation Council (GCC) countries. As climate-related challenges intensify—ranging from extreme heat to water scarcity - failing to act could have dire consequences for both the environment and economic stability.
The urgency of achieving Net Zero is underscored by regional commitments to climate action. The UAE, for example, has set ambitious targets to reduce its carbon footprint and has committed to reaching Net Zero by 2050. However, these goals require immediate and significant changes in the construction industry.
Innovative approaches to Net Zero
Achieving Net Zero in construction in the Middle East requires a multi-faceted approach that incorporates innovative technologies, sustainable materials, and holistic design strategies. Here are a few examples:
Utilising Sustainable Materials: The Middle East has abundant resources that can be harnessed for sustainable construction. For instance, utilising local materials such as rammed earth and recycled aggregates can lower the carbon footprint associated with transportation. Innovations like carbon-capturing concrete are also vital for reducing embodied carbon.
In line with this, ACCIONA introduced for the first time in one of its project last year the use of renewable biofuels generated from hydrotreated vegetable waste oil to power heavy machinery for civil works, in a pioneering initiative aimed at decarbonizing infrastructure construction. Renewable biofuel generated from hydrotreated vegetable oil (HVO) is a renewable liquid fuel that has similar properties to traditional fossil fuels but produces 90% fewer emissions. The remaining 10% mainly comes from the emissions released by the HVO production process instead from its consumption. The implementation of this pilot project reduced 1,000t of CO2 emissions from the project. It is important to highlight that its continuous use for the project curbed most 40% the projected greenhouse gas emissions of ACCIONA's Construction business in 2023.
Speaking of sustainable materials, it is also worth mentioning the use of low-emissions circular steel in another of our projects achieving two fundamental sustainability objectives: on the one hand, it advances circularity in the use of materials, as the steel that is obtained during demolition in the project will be returned in the form of material to be used. On the other hand, this achieves a reduction of more than 40% of the emissions associated with the product compared to the average of steel mills with similar technology. In addition, using this type of steel avoids the release of over 1,900t of CO2 emissions from the equivalent use of a conventional product.
This measure is aligned with ACCIONA's position as a provider of sustainable infrastructure and renewable energy solutions, in the spirit of the various initiatives it carries out to reduce emissions linked to its supply chain.
Another important measure to achieve Net Zero in construction is the use of electrical machinery. We became the first Spanish construction company to acquire this kind of sustainable machinery, as part of the company’s decarbonisation plan. Specifically, we purchased four telescopic handlers and two rotating dumpers, which will mainly be used in urban construction projects. Thanks to their 100% electrical operation, great improvements are made in reducing pollutant emissions and noise levels on site. Overall, it is estimated that the use of this electrical machinery could reduce up to 100t of CO2 emissions.
In line with the latest studies on climate change, we have undertaken to reduce ACCIONA’s direct emissions and those generated by our energy consumption by 60% between 2017 and 2030, aiming at the most ambitious target of the Paris Climate Agreement to limit global warming to no more than 1.5-degrees Celsius above pre-industrial levels.
Achieving
Zero in construction in the Middle East requires a multi-faceted approach that incorporates innovative technologies, sustainable materials, and holistic design strategies.
Among the measures that we have implemented to achieve this target, the company has launched a ‘decarbonisation fund’ to finance projects with potential for significantly reducing emissions. This purchase of electrical machinery and the use of HVO in heavy machinery (previously explained) are some of the initiatives that will receive support from the company’s decarbonisation fund.
Both are part of ACCIONA's emissions reduction program within its 2025 Sustainability Master Plan and are financed by ACCIONA's Decarbonisation Fund. The purpose of the fund is to support initiatives that promote carbon neutrality in the company’s operations. Last year in 2023, this fund contributed to the financing of 17 decarbonisation initiatives in a variety of global ACCIONA projects.
To drive meaningful change, collaboration among policymakers, industry stakeholders, and the public is essential. Governments in the Middle East must establish clear regulations and incentives that promote sustainable practices. For example, building codes could be updated to mandate energy efficiency standards, while financial incentives could encourage the use of green materials and technologies.
Regarding this, I don’t want to miss this opportunity to mention that we have just now secured a new sustainable financing worth $327mn to fund key projects aimed at reducing carbon emissions and fostering sustainable growth in the Gulf Cooperation Council area (GCC). The sustainable financing is structured as a green loan with local impact, aligned with ACCIONA’s Sustainable Impact Financing Framework. The margin of the financing is linked to a local impact initiative, which aims to boost sustainable construction by supporting local suppliers to develop and produce
lower or zero-carbon building materials, such as cement, steel and concrete.
While the path to Net Zero is filled with opportunities, it is not without challenges, particularly in the Middle East. The initial costs associated with sustainable practices can deter investment, as many stakeholders perceive green construction as more expensive. To overcome this barrier, it’s vital to communicate the longterm economic benefits of sustainability, including reduced operational costs and enhanced property values. Additionally, the industry faces a skills gap in green building practices. As new technologies and methodologies emerge, it's crucial for the workforce to be equipped with the right knowledge and skills. Educational institutions and training programs should prioritise sustainability to prepare future construction professionals.
ACCIONA was the first Spanish construction company to acquire sustainable machinery, an initiative that’s part of the company’s decarbonisation plan.
Achieving Net Zero in construction is not just an industry goal; it is a societal imperative for the Middle East. As the region confronts the realities of climate change, the construction sector must take bold, transformative actions to reduce its carbon footprint. By embracing innovative practices, collaborating across sectors, and investing in technology and education, we can shift the industry toward sustainability. This journey will require commitment and cooperation from all stakeholders, including architects, engineers, builders, and policymakers. Together, we can create a built environment that meets the needs of today while preserving the planet for future generations. The time to act is now, and the construction industry in the Middle East must lead the charge toward a sustainable, Net Zero future.
Hybrid water heaters pose a smart solution to the Middle East’s energy challenges, Rheem MEA’s Samer Bachour explains
Sustainability is at the forefront of every current conversation in the construction industry. And, with initiatives such as the UAE’s Energy Strategy 2050 and Saudi Arabia’s Vision 2030 progressing at pace, our region's rapid development and ambitious growth plans have made energy efficiency not just a ‘nice-tohave’, but a necessity. So, as developers, businesses and homeowners alike seek to reduce their carbon footprint and cut operational costs, the emphasis on integrating energy-efficient technologies into projects has never been greater.
Water heating typically accounts for nearly 20% of a household’s energy consumption, with commercial usage varying depending on the size and type of facility being served.
One innovative solution that aligns seamlessly with these sustainability goals is the hybrid water heater. Combining the advanced efficiency of heat pump technology with the reliability of traditional electric heating, hybrid water heaters offer a compelling alternative to conventional systems. Their ability to significantly reduce energy consumption, while providing consistent performance has led to a surge in popularity across both residential and commercial applications. Water heaters might not be the first appliances that come to mind when
considering how to optimise energy efficiency – especially in the hot climates of the Middle East. However, water heating typically accounts for nearly 20% of a household’s energy consumption, with commercial usage varying depending on the size and type of facility being served. This often makes water heating the second-largest energy expense after air conditioning. That’s why now is the time to make the switch from traditional water heating systems to smarter, more efficient hybrid models, and set a new standard for sustainable development in the region.
But why hybrid? The benefits of these systems extend far beyond basic functionality, offering a range of advantages that make them an ideal choice for modern, sustainable buildings.
At the heart of hybrid water heaters lies an innovative approach to heat sourcing which sets them apart from conventional systems. By leveraging advanced heat pump technology, these heaters draw ambient air to heat water, reducing traditional reliance on electric heating elements and consuming far less energy in the process. Some hybrid models can even be up to five times more efficient than conventional systems, and use less energy than a classic 100W incandescent light bulb.
Many hybrid models are also integrated with smart energy management systems, which enable advanced water heating management. For example, those with WiFi integration allow occupants to monitor and manage their energy expenditure from their phones, for greater control.
However, perhaps the most convenient hybrid water heater technology efficiency is its ability to produce cold air during the heating cycle, which can be used as a secondary cooling source in residential properties. This increases
Hybrid water heaters offer a tangible way to reduce their carbon footprint and contribute to regional sustainability goals.
both overall efficiency and the quality of the customer experience compared to that of a traditional water heater.
The energy efficiencies of hybrid water heaters directly translate into one of the most attractive benefits for residential and commercial users alike: cost savings. While the initial cost of a hybrid water heater may be higher than that of a conventional model, the long-term energy savings - resulting in lower bills - more than justify the expense.
Inefficiencies in older water heating systems equates to significant unnecessary energy expenses annually across the region. In contrast, investing in hybrid water heating technology can save households significantly in energy cost savings.
In commercial properties these savings can be even more substantial, particularly in facilities with high hot water demand such as hotels or healthcare centers.
However, these savings aren’t only beneficial to a building owner’s pocket; they’re also better for the planet. By using significantly less electricity than conventional systems, hybrid water heaters contribute to a substantial reduction in carbon emissions, and every kilowatt-hour of electricity saved translates into a direct reduction in greenhouse gas emissions.
The use of hybrid water heaters also aligns with international green building initiatives, such as LEED (Leadership in Energy and Environmental Design). These certifications prioritise energy efficiency and low environmental impact. So, for developers and property owners committed to sustainability - and who want to future-proof their buildingshybrid water heaters offer a tangible way to reduce their carbon footprint and contribute to regional sustainability goals.
One of the most compelling benefits of hybrid water heaters is their versatility. Their adaptable design allows them to be integrated seamlessly into both new constructions and retrofit projects, providing flexibility for property owners and developers. In residential settings, hybrid water heaters can be installed in spaces similar to those required by traditional models – even tighter spaces such as closets – while in commercial properties, they can be scaled to meet higher hot water demands. This adaptability ensures that hybrid water heaters can meet the specific needs of any project, regardless of its size or complexity.
Durability
A global innovation with regional resonance, hybrid water heaters are designed to withstand the challenging conditions of the Middle East, offering durability and reliability that surpass traditional systems. The robust design of these heaters includes corrosionresistant materials and advanced components that are built to last, even in the region’s harshest climates. This durability translates into lower maintenance requirements and a
Some hybrid models are integrated with smart energy management systems, which enable advanced water heating management over WiFi connection.
longer operational lifespan with most units lasting between 13-15 years, compared to the average 10-year lifespan of traditional units.
For property owners, this means not only fewer disruptions but also lower maintenance costs over time, leading to a lower total cost of ownership and a better ROI than traditional models. In an environment where consistent performance is crucial, hybrid water heaters offer the peace of mind that comes with knowing the system will deliver, year after year.
One of the most compelling benefits of hybrid water heaters is their versatility.
As sustainability drives the construction industry forward, hybrid innovation is undoubtedly the smart solution to current water heating challenges in the region and beyond. Prioritising investment in this technology means that building occupants and owners stand to benefit in the long term from lower energy and operational bills, while industry professionals can support the advancement of regional sustainability initiatives. And this could be a significant step to ensuring a cleaner, greener future for all.
By staying ahead of trends and embracing new technologies, the regional construction industry can set a global benchmark for sustainable and transformative growth
The Middle East continues to be a global hub of innovation and development, with the UAE and Saudi Arabia at the helm. Both nations are embarking on transformative projects that align with UAE Vision 2031 and Saudi Vision 2030. From giga-projects like NEOM and Qiddiya City in Saudi Arabia to smart city initiatives in the UAE, the scale and ambition of these developments are reshaping the region’s construction and real estate industries. However, as we move into 2025, stakeholders must address evolving challenges, while capitalising on emerging opportunities.
Based on our experience at Carter Hones Associates, we’ve identified key trends that will define the year ahead—as well as the strategies needed to overcome common project challenges while maximising success:
1. Integrated Design Management: Coordinating Complexity
Mega-developments in the region are becoming increasingly intricate, involving interconnected disciplines ranging from architecture and interior design to engineering and facility management. This complexity necessitates a more integrated approach to design management. Without clear workflows and alignment among stakeholders, projects risk costly delays and misaligned deliverables.
“Projects today are ecosystems, not isolated efforts,” explains Nathan Hones, Chief Operating Officer and Partner at Carter Hones Associates. “Efficient design management ensures cohesion, minimises duplication, and guarantees timely, cost-effective delivery.”
For example, a recent Deloitte report revealed that poor communication and coordination in construction projects can lead to up to 45% of time being
COORDINATION
A recent Deloitte report said that poor communication and coordination in construction projects can lead to up to 45% of time being spent on non-valueadding activities.
spent on non-value-adding activities. By implementing robust design management protocols, developers can streamline processes, enhance collaboration, and maintain project momentum.
2. Designing to Budget: Balancing Ambition with Practicality
Rising material costs and inflation are prompting developers to place greater emphasis on value engineering and cost consultancy. Pre-construction services, including feasibility studies and cost forecasting, are now indispensable for ensuring financial sustainability.
“Cost alignment is no longer a luxury; it’s a necessity,” says Zane Heasman, Chief Commercial Officer and Partner. “Our role is to keep designs on scope and on schedule, ensuring projects meet their financial objectives without compromising quality.”
Projects today are ecosystems, not isolated efforts. Efficient design management ensures cohesion, minimises duplication, and guarantees timely, costeffective delivery.
According to the International Construction Market Survey 2023 by Turner & Townsend, material costs in the Middle East rose by an average of 9% last year. With no signs of immediate relief, design-to-budget strategies are critical for managing financial risks. By engaging cost consultants early in the process, developers can identify cost-saving opportunities without sacrificing the project’s vision.
3. National Visions Driving Development
The ambitious goals outlined in Saudi Vision 2030 and UAE Vision 2031 are shaping the region’s construction landscape. These frameworks emphasise sustainable urban planning, mixed-use developments, and digital transformation. Projects like the Red Sea Project in Saudi Arabia and Dubai’s Expo City exemplify this shift.
Feasibility studies and strategic planning have taken on a new
dimension, ensuring projects not only align with these visions but also adapt to changing market demands.
Developers are increasingly looking to consultancies like ours for guidance in balancing long-term objectives with short-term market realities.
As construction activity continues to surge, a growing talent shortage has become a pressing issue. The region’s rapid growth has exposed gaps in project management, technical expertise, and skilled labour. The Middle East Construction Outlook 2024 by JLL highlighted that over 60% of developers in the region face difficulties in securing qualified project managers and engineers.
To address this, secondment services are becoming a popular solution. By embedding specialised professionals directly within project teams, developers can bridge immediate workforce gaps, while enabling knowledge transfer to in-house staff.
“Secondment offers a dual advantage,” notes Craig Carter,
Secondment offers a dual advantage. It fills immediate needs while upskilling internal teams for future challenges.
Managing Director and Partner. “It fills immediate needs while upskilling internal teams for future challenges.”
Digital transformation is no longer optional; it is a requirement for staying competitive. From the latest in Building Information Modelling (BIM) to advanced analytics of big data, developers are leveraging data to enhance decision-making, improve efficiency, and mitigate risks.
“Data is transforming how projects are managed,” says Carter. “Real-time insights allow us to address risks proactively and make evidence-based decisions.”
McKinsey’s ‘The Next Normal in Construction’ report predicts that digital tools could boost productivity by up to 15% and reduce project costs by as much as 10%. For developers in the UAE and KSA, the adoption of these technologies is a strategic imperative.
While these trends represent opportunities, they also bring challenges. At Carter Hones Associates, we’ve seen how issues in cost and design management can derail projects if not addressed effectively. Common challenges include:
1. Scope Creep: Unclear objectives and shifting priorities can lead to scope changes that inflate costs and timelines.
2. Poor Coordination: Misalignment among stakeholders often results in inefficiencies and rework.
3. Material and Labor Cost Volatility: Fluctuating prices can disrupt budgets and impact procurement strategies.
1. Early Engagement of Consultants: Involving cost and design management experts during the early stages of a project allows for proactive risk identification and mitigation.
2. Clear Protocols and Communication Channels: Establishing structured workflows and open lines of communication can minimise misunderstandings and ensure alignment among all parties.
3. Flexible Budgeting: Incorporating contingency allowances into budgets provides a buffer against unexpected cost increases. For instance, in a recent mixed-use development we managed, early engagement and robust coordination protocols enabled us to reduce projected
Feasibility studies and strategic planning have taken on a new dimension, ensuring projects not only align with these visions but also adapt to changing market demands.
costs by 12%, while maintaining the project’s ambitious design objectives.
As the UAE and KSA continue to lead global development initiatives, the region’s construction landscape will continue to evolve rapidly. Integrated strategies for design management, cost optimisation, and workforce agility will be key to navigating the challenges and opportunities that lie ahead.
Cost alignment is no longer a luxury; it’s a necessity.
At Carter Hones Associates, we remain committed to helping developers, architects, and contractors achieve success by delivering innovative, cost-effective solutions tailored to the unique demands of the Middle East. By staying ahead of trends and embracing new technologies, the industry can not only meet its ambitious goals but also set a global benchmark for sustainable and transformative growth.
Ellington Properties has announced the handover of Berkeley Place, which is billed as a landmark addition to Mohammed Bin Rashid City (MBR City). The residential development is said to feature innovative design and curated amenities which converge to create an unparalleled lifestyle.
Berkeley Place features 127 apartments, including studios, one-bedroom, and two-bedroom units, and each home is said to maximise space and natural light to enhance everyday living. This development transcends conventional living, with façade, layouts, and resort-inspired amenities, the developer said.
The residential project goes beyond a residence, offering amenities that inspire balance
and connection, with a lobby and lounge that lead to landscaped gardens for serene retreats, an urban basketball court, and an arcade room for recreation. Eco-conscious features include EV charging stations and bicycle parking, indoor and outdoor fitness studios, yoga deck, and a rooftop infinity pool with views of Dubai’s skyline. The adjoining pool spa and terrace provide setting for relaxation and leisure, the developer added.
Elie Naaman, Co-Founder and CEO of Ellington Properties explained, “At Ellington Properties, we believe in creating spaces that inspire and elevate daily life, Berkeley Place exemplifies our commitment to design-led living, combining
innovative architecture with lifestyle-enhancing amenities in MBR City. These aren’t just homes - they represent refined living, offering residents a unique blend of comfort, style, and value. With its completion, we are proud to deliver a community that truly stands apart”.
The completion of Berkeley Place signifies another milestone in Ellington Properties’ journey of redefining living spaces. It is said to reflect the company’s legacy of design excellence and dedication to crafting spaces beyond the ordinary. Berkeley Place is poised to become a defining landmark in Dubai’s real estate landscape, offering residents a lifestyle that is as inspiring as rewarding, the company concluded.
Bring information, teams and workflows together on one easy-to-use platform. Whether you’re an owner, contractor or subcontractor, you can achieve real-time visibility into project status, drive collaboration, and move your business forward with Procore. Connect teams on one intelligent, easyto-use