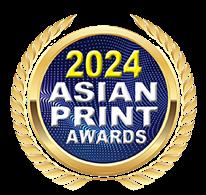


Interview on page 4


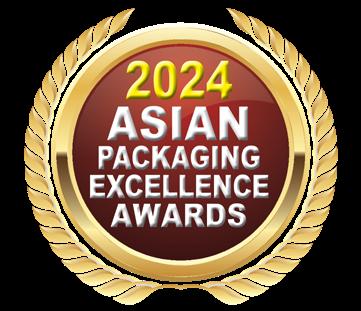
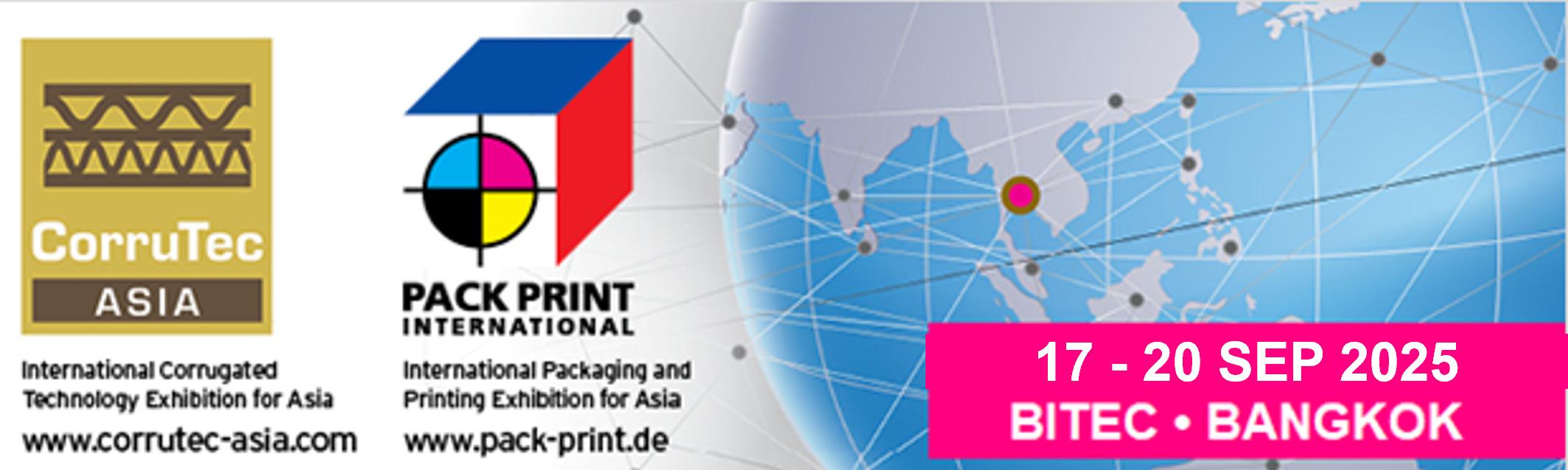
Interview on page 4
During their whirlwind trip visiting customers across Asia and Australia, we caught up with Miraclon Andy Yarrow, Regional Commercial Director for Asia Pacific, and Steve Smith, Principal Consultant discuss the industry and how Miraclon customers are reaping the benefits of modern flexo.
Q Modern flexo is your focus at the moment, tell us a little more about it
Chris Payne (CP) Modern flexo is about going from a traditional, ‘craftbased’ approach, requiring a lot of human intervention, to a standardised, sustainable manufacturing process. So, if you think about how a printing press works, you have to get up to colour quickly and consistently, for short runs and long runs, and you need to do this efficiently and sustainably, in fact more and more sustainably over time; it’s really about printing by numbers rather than printing in a ‘craft’ sense. Miraclon’s differentiated FLEXCEL plate technology and print applications expertise are key enablers of this move to modern flexo.
Our customers who we have been visiting, they are not eyeballing the colour at the end of a press line, tweaking how the ink or the anilox is laying down the ink, they are now printing by numbers, checking the densities and letting the system do the calibration. As a result, they are more efficient and sustainable in their production.
We have been to Japan. India, Sri Lanka and Australia and I would say the customers are really at the forefront and have in some cases ‘leapfrogged’ flexo printing in other parts of the world. They have gone from printing gravure to
printing in modern flexo without going through the stages of ‘traditional’ flexo with all its complexities and workarounds. Working with our Miraclon experts, they have implemented ECG or process colour printing without spot colours and they have made that conversion. Our proprietary FLEXCEL NX technology makes this possible through the ultimate control of ink transfer on which modern flexo is founded, and which is enabled by our multi-form surface patterning. We find this super exciting as this will open up more opportunities for other companies to follow suit in the region.
Q: How do you think this will ultimately be accepted in Asia?
Andy Yarrow (AY) I can tell you that the customers we have been talking to are excited about the possibilities. What we have seen in many cases are companies that have made investment in flexo presses in the past have struggled to get all the parts to work effectively.
What I have learned is that there are so many variable elements, from anilox rollers, tapes, inks and other areas, and it makes for a very complex set-up. What people are really looking for is a way to make it easier so they can shift as many jobs as they can, and experience the efficiency and sustainability benefits of modern flexo.
Some companies have made big investments, and others are about to make investments in flexo and they need help in getting up and running quickly so they can convert jobs to flexo. As Chris said, sustainability is a big factor for all these customers and if they can move to a more sustainable printing process while experience efficiency gains, then that’s a massive motivation for them.
Q – Steve Smith - As you move around the region being a wellknown technical guru for the industry, what is the main question you are getting from your customers and future customers? What are they really looking for?
Steve Smith (SS) When you look at most brands, they’re now looking at how they can improve their sustainability and a common perception is that sustainability comes at a cost, and in most cases brands are just not willing to pay for it.
So when you look at it from the converters perspective, it’s all about how can they be more cost effective? Certainly, printing at 300 line screen or 200 line screen is not cost effective in terms of printability and its value for the consumer, so the most effective way is to print with 133 line screen with process colours or ECG (extended colour gamut).
Miraclon CEO Chris Payne, Consultant from Miraclon, to
With the FLEXCEL NX plate we can have an expanded gamut. Because of the high densities we deliver with FLEXCEL NX they can actually produce more colours within that gamut, which means that the brands don’t have to compromise their result based on the fact that they go flexo or that they’re getting the best value for their money regarding the printability.
Our focus at Miraclon is based on what we call visual parity on a shelf. You should not be able to tell when viewing as a consumer does, on a shelf, or at armslength, if a product is printed gravure, flexo, offset or digital, but in the past, this has not been the case. With traditional flexo there had to be compromises made with minimum dots, leading to dirty colours and a need to use spot colour inks because you couldn’t get the vibrancy on the product. There was a visible difference between gravure and flexo.
Today you should not be able to pick up on this difference and modern flexo is what sets this apart, but more importantly it’s the cost value to the brand. Modern flexo allows you to print at lower line screens than gravure – but get the same
visual result on the shelf. Gravure prints at 175 lpi because this is the only way it can print smooth text.
We don’t need to do that with modern flexo. We can go to lower line screens,
increase printability and reduce production costs. Our biggest challenge –as print experts - is that we need to change our mindset. We tend to look at things through a magnifying glass and assume that things need to look identical at that level. We need to change our thinking. Brands, and importantly, consumers, really don’t care about dots; they care about the quality of the packaging on the shelf.
Q What are your plans to try and inform the gravure industry that flexo is on par and in some cases should be the preferred print process on many jobs that could cross over from gravure?
Chris Payne – We feel that flexo is a great alternative in terms of production method. Flexo is the most efficient printing process and over the last 10 years, driven by our differentiated FLEXCEL NX technology, flexo is now capable of a totally different level of efficiency and has the levels of print quality that is required. The other key driver for flexo is sustainability. By enabling visual parity with gravure, FLEXCEL NX technology
also enables work to be transitioned to the lower environmental footprint of flexo production and delivers excellent results with lighter weight and more sustainable materials.
Here we are talking about less wastage and certainly looking at cost savings, higher speeds, less energy wastage, so our message is that there is a place for gravure however there is a huge growing area for flexo in the packaging industry to meet their customer needs.
Andy Yarrow – The great thing is, this is not just lip-service, what we showcased at Drupa are these modern flexo principles
in action. Real-life examples of products you can buy in the supermarket that have been produced with all of the modern flexo benefits; lower line screens, fewer spot colours, faster set-up times and with greater sustainability.
The team at Miraclon is looking forward to engaging with both flexo and gravure printers and partnering with them on a journey to modern flexo that will put them in a position to address the most important requirements of their brand clients, while optimising their own business model. This is an exciting time for flexo in Asia Pacific.
Simply consistent
Decrease waste and setup with predictable plates
Simply efficient
Increase on-press performance with a robust plate
Simply sustainable
Support sustainable inks and substrates all with the same plate
Simply better
Address your most demanding brand and quality requirements
From prepress to on-press, deliver the efficiencies and productivity needed from your plates to maximize your bottom line.
• Focus on global increase in demand for sustainable, recyclable, compostable packaging
• Boardmaster on show in Print Media Center at HEIDELBERG Wiesloch-Walldorf site
Following the successful market launch of the Boardmaster, Heidelberger Druckmaschinen AG (HEIDELBERG) is planning to extend the range of applications for this new inline flexographic web printing system to flexible paper packaging in the medium term. “The global increase in demand for sustainably produced, budget-friendly, and recyclable or compostable packaging makes flexible paper an attractive growth market for us,” says Christian Steinmassl, who is in charge of the Packaging segment at HEIDELBERG. “Our Boardmaster flexographic web printing system – which can process water-based inks, coatings, and barrier layers at production speeds of up to 600 meters per minute with an availability of up to 90 percent – is ideal for this market,” he adds.
Boardmaster in PMC at HEIDELBERG Wiesloch-Walldorf site
A complete Boardmaster will be available for customer demonstrations in the Print Media Center (PMC) at the
HEIDELBERG Wiesloch-Walldorf site from drupa 2024 onward. Options for a variety of requirements maximize the number of automation and inspection functions this press can demonstrate for the benefit of potential customers. The Boardmaster is available in a total of four printing widths ranging from 850 through to 1,650 mm.
Successful market launch – initial Boardmaster systems in operation When developing the system, the company focused on the key challenges and requirements of its customers –significant cost pressures, quality and operational reliability, sustainability, and high investment security. “Systems are already operating in the USA, the order situation is very encouraging, and we have received inquiries from
Michael Buechel, Region Asia Pacific
Business
Development
Manager,
Web Carton Converting at drupa 24
all over the world,” reveals Steinmassl. Printers currently using large-format offset production for food and beverage packaging are also expressing an interest. The Boardmaster is designed for maximum overall equipment efficiency in non-stop operation with flying job changes. It achieves an availability of up to 90 percent and a printing speed of 600 meters per minute.
This corresponds to double the productivity of previous, comparable systems. Maintenance costs are 50 percent lower than for systems that use other printing processes. A high degree of automation and simple operation support production with low staffing levels. This also counteracts the shortage of operating personnel. Last but by no means least, the AI-supported printing plate and sleeve scanner Intellimatch helps ensure print results meet high quality standards.
of your images. Unlike conventional CMYK printers, this advanced machine brings colours to life with stunning accuracy, making your prints as vivid as they appear on digital monitors.
However, the magic doesn't stop there. Once your designs have been printed
2D and 3D foiling, clients can customise and personalise specific elements to create unique and memorable prints, enhancing both the visual and tactile quality of each piece.
Graphic designers and print businesses
and premiumises print applications and collaterals to the next level. Whether it's raised textures, embossed patterns, or shimmering metallic finishes, your prints will leave a lasting impression.
This combination isn’t just about
efficiency. The AccurioShine 3600 with iFoil One simplifies the process of adding complex embellishments, eliminating the need for screens, plates, or dies. With no cleaning needed between jobs and faster preparation times, you can take on more lucrative short and medium print runs with higher complexity, resulting in lower operational costs and higher profit
Adding these machines to your fleet enhances your print quality and streamlines your workflow. Our technology integrates with a suite of digital software solutions, offering centralised management, automated workflow processing, colour management, and full connectivity across
all Konica Minolta printing systems. This reduces workload and waste, minimises man-hours spent on quality control, and allows for creative freedom with customisable embellishments.
By incorporating the AccurioPress C84hc and the AccurioShine 3600 into your production fleet, you'll have the flexibility to produce designs with radiant and striking colours, gloss effects of varying thicknesses, and metallic foiling in 2D and 3D.
Investing in these machines means investing in the future of your print business. Enhance your print capabilities, boost productivity, and set your business apart as a leader in the industry, providing premium services that clients will appreciate and seek out.
Experience a new level of printing excellence. Reach out to us today to learn more about how the AccurioPress C84hc and the AccurioShine 3600 with iFoil One can transform your business.
This is your sign to explore opportunities in digitally printed signage
As the signage market evolves, it will surprise no-one that printed signage faces increased competition from digital technologies.
This challenging environment and market factors such as post Coronavirus recovery have contributed to the global market for printed signage experiencing contractions, says Smithers’ The Future of Signage in a Digital World to 2028.
However, analyst data goes on to indicate a positive future. Printed signage will see growth between now and 2028, with the market still worth as much as $41.4 billion and representing 10.4 billion square metres. And Europe continues to have a healthy share with 19% of the global value and nearly 15% of printed area.
These are among the reasons many innovative operations can see the fresh opportunities this market presents that could help them successfully expand their service offering.
Among the performance benefits that ensures printed signage remains widely used for indoor and outdoor advertising, as well as Point of Purchase, are its:
• Cost effectiveness and speed – this is particularly when compared to advertising channels such as television and radio advertising.
• Durability – making it ideal for locations where vandalism is more likely to occur. A damaged poster is easier, faster, and cheaper to replace than a digital display.
• Ease of dismantling and disposal – in Europe, cardboard and paper is recycled with wastepaper and there are many ways to recover textile and foil printed signage.
• Enablement of efficient mounting –especially if there are frames already installed on site. Also, there is no requirement for power or internet connections or specialist staff.
• Familiarity – that can be reassuring. People with special needs, such as the visually impaired, or passersby with attention deficit disorders, prefer static content.
• Interactivity – printed QR codes offer easy access to websites.
Among the opportunities continuing to contribute to this positive outlook are: Customisation for printed signage in retail increasing – Today’s competitive retail landscape drives the development of new ways to attract customers and
enhance brand recognition. Printed signage is a powerful marketing tool that engages effectively with target audiences and drives footfall to physical stores. Vibrant and eyecatching, it can create immersive instore experiences to differentiate, convey promotional messages, highlight product features, and guide visitors to specific areas of interest. Digital print enables offers to be cost effectively and quickly updated and adapted in response to customer demand and seasonal promotions. It can integrate with omnichannel campaigns to reinforce storytelling and branding, too.
Post pandemic return to shows and events – Earlier this year UFI, the Global Association of the Exhibition Industry reported in its Global Exhibition Barometer research that in most markets, in 2023, the exhibition industry fully recovered from the pandemic slump and was set to record the highest ever revenue levels in 2024. Smithers concurred.
It said a huge 1,865 million metres squared output of corporate graphics, exhibitions, and trade show materials in 2022 would grow to 1,958 million metres squared by 2028. This buoyant sector is perfectly poised to benefit from the sustainable, customisable, and interactive elements printed signage can deliver.
Embracing embellishments – The pandemic inspired innovation and
many businesses diversified into new technologies and revenue streams. Specialists in display graphics and signage were often at the forefront of this transformation. When attention returned to the retail e-commerce sector, the need for standout signage increased as did interest in the role of digital embellishments in capturing consumer attention.
A study conducted by Taktiful, found digital embellishment technology accelerated in adoption across various sectors while WhattheyThink! reported 90% of users expressed a positive outlook on their digital embellishment business. The addition of 3D varnishes, textured finishes, and metallics, can create multisensory experiences that attract attention and invite physical interaction –especially as much of the work is one-off, bespoke projects.
And new systems are in development as manufacturers continue to expand large format and flatbed products with innovative technologies and applications to support this booming market, as well as other fields such as industrial and CAD, while offering viable alternatives to screen printing.
In addition, versatile software that ensures smooth high quality production includes the modular and scalable workflow solution ColorGATE Productionserver. It manages accurate processing of graphically rich PDF content and reproduction of complex design files. There is also Color-Logic that provides access to 250 accurate metallic colours and simplifies the design and print production process in a fraction of the time and cost compared to traditional print embellishments.
Clicheria DP Studio has upgraded its flexo platemaking capabilities with a ThermoFlexX Catena-E 80 high performance exposure frame from XSYS. Installed to deliver best-in-class quality to its customers, the new equipment has exceeded the expectations of the Brazilian prepress company.
Clicheria DP Studio, founded in 1990, serves customers in the label and flexible packaging sectors with photopolymer plates for flexo printing. Based in Londrina, in the northern region of Paraná, Brazil, the award-winning prepress provider is known for its high level of skill and professionalism. The operations cover the whole country, as well as Bolivia and Paraguay, always maintaining its ethical principles and search for quality in all its products.
To maintain its leading edge, DP Studio continually seeks out the best technologies, installing state-of-the-art equipment for imaging and processing flexo plates. In a new partnership with XSYS, DP Studio has brought in a ThermoFlexX Catena-E 80 exposure frame, which utilizes the latest technology UVA LEDs for both main and back exposure, ensuring accurate image reproduction, stable flattop dots, and guaranteed repeatability. This investment complements the customer's current use of XSYS plates, specifically the nyloflex® NEF. The nyloflex® NEF is a high durometer plate optimized for LED exposure technology like Catena-E, offering excellent flat top dot creation, improved ink lay-down, and high solid ink density.
“The new ThermoFlexX Catena-E 80 has already surprised the whole team due to the robustness and the performance, which exceeded initial expectations,” said Agnaldo Moraes, Technical Commercial Manager at DP Studio. “The first jobs we put through the machine quickly demonstrated the improvements that can be achieved with Catena exposure, particularly in the highlight areas. Furthermore, we’re also saving time and energy.”
High quality and sustainable platemaking With 70 employees, DP Studio prides
itself on the quick supply of plates, created to the exact requirements desired. The large design team works closely with customers, finding a personalized solution that will deliver their packaging vision, as well as cooperating with the machine operators to ensure that the plates will print exceptional quality. The new Catena unit allows DP Studio to expand these capabilities and offer even more advanced solutions while also contributing to sustainability.
The ThermoFlexX Catena-E 80 provides high-performance LED exposure –perfect for imaging the finest surface microstructures such as Woodpecker Nano. Processing plates in sizes up to 1270 x 2032 mm (50 x 80”), it also utilizes LEDs for the back exposure, ensuring consistent and even floors across the entire plate.
Not only does LED technology produce the most consistent and precise flat-top dot plates, it also reduces the carbon footprint of the platemaking process.
LEDs require no warmup, meaning less energy is consumed, and last longer than conventional lamps, thereby minimizing toxic waste. In fact, the LEDs in the Catena system have been fully tested to 10,000 operating hours and beyond.
Future-proofing with Catena and XSYS support
Built as an open system, the Catena-E 80 has easily slotted into DP Studio’s current workflow. It features an intuitive Graphic User Interface (GUI), running the latest Windows OS, with a Full HD touchscreen, making operation extremely fast and simple.
“We chose the Catena-E 80 LED exposure unit because of the many benefits it brings, including guaranteed stable quality, optimized speed, ease of operation, and lower environmental impact. This means we can better meet the many demands of our customers,” stated Marcos Balestra Industrial Manager at DP Studio.
With the steady development of the domestic economy and the recovery of the consumer market in recent years, the packaging printing industry has maintained a rapid growing momentum.
At the same time, it has also increased its requirements for the quality, technology and efficiency of packaging printing. In order to better meet the needs of the packaging printing market and further improve its comprehensive market competitiveness, Dalian Tianli Printing Co., Ltd. has recently partnered with Manroland for the first time with the introduction of a brand new ROLAND 706 Evolution 3B LV. The new press has been successfully installed and officially put into production by now.
According to Mr. Bo Hao, the company’s executive general manager, Tianli Printing, founded in 2012, is a packaging printer specializing in an extensive range of packaging print products with an area of nearly 30,000 square meters. When talking about why Manroland was their first choice, he said, “With the vigorous
growth of the packaging printing market, the number of domestic packaging printers has been rising in recent years with an annual growth rate of about 7%.
Therefore, the market competition is becoming increasingly fierce. If we want to survive in the market competition, we must continuously improve our comprehensive market competitiveness by improving our productivity and product quality and lowering the production costs at the same time.”
“Our company’s newly installed ROLAND 706 Evolution 3B LV, which is equipped with a series of automated technology functions such as the TripleFlow, provides us with unprecedented efficiency, productivity and print quality. It not only ensures highly stable and consistent colors, but
also significantly reduces the production costs.
In addition, Manroland’s century-old packaging printing brand name could not only help us to enhance our own brand images in the market but also largely enhance customers’ confidence and trust in our packaging print products. Our company’s comprehensive market competitiveness has reached a new level,” Mr. Bo continued with a smile.
The following is a brief introduction to how the automated technology functions equipped on Evolution press can help packaging printers to improve their productivity and print quality, and at the same time lower the production costs.
With three different ink distributions at the push of a button, TripleFlow
offers high color consistency during the whole print run and drastic savings in waste, which could further reduce the production costs.
Simultaneous Plate Loading technology, plate loading and blanket cleaning all take place simultaneously, which drastically reduces make-ready times. Plate exchange, blanket cylinder and back cylinder washing can be done simultaneously in all printing units in less
than 4 minutes, resulting in significant cost savings, higher productivity and superior print quality.
InlineInspector 3.0 detects even the smallest hickeys, splashes, scratches, creases, streaks, scumming or smearing just as reliably as it detects color deviations or substrate defects, which could lower the manpower costs.
Dalian Tianli Printing Co., Ltd. with an area of nearly 30,000 square meters.
InlineColorPilot 3.0 measures and controls register and color automatically without the need of a pull sheet, which not only ensures the high color stability, but also at the same time significantly saves time and wasted sheets and increase productivity.
InlineFoiler 2.0 is a groundbreaking enhancement solution that meets market demands for more creative, more eyecatching and more vibrant print. With the InlineFoiler, printers can cold foil and overprint a full spectrum of colours inline on a broad range of substrates in a single pass and it can be combined with delicate embossing and effect or spot coatings or varnishes for maximum impact. It could achieve excellent printing effects, while at the same time the productivity could be increased to a very large extent.
With the outstanding performance of ROLAND 706 Evolution 3B LV and the strong support from Manroland’s professional service team, Tianli Printing will surely be able to soar to the new heights.
Effortlessly convert images to CMYK + Pink without modifying the originals.
• Digital innovations generated enthusiasm among visitors
• Presentation of the world's fastest medium-format sheetfed offset press
• Great interest in end-to-end solutions in packaging production
• Daily demonstrations and panel discussions on packaging workflow, digit lisation, commercial, CI flexo and digital printing
• Extraordinary order intake situation: around 250 million euros marketed since end of May 2024
Koenig & Bauer presented its broad product portfolio and numerous digital innovations in hall 16 at the world's largest and leading trade fair for printing technology. CEO Dr Andreas Pleßke, who is also Chairman of the drupa Committee, explains: “After eight years, both the exhibiting companies and the visitors have come to Düsseldorf with a great deal of commitment and enthusiasm. You can see how profoundly the entire industry has changed in recent years. Topics such as sustainability and digitalisation are key issues that visitors are increasingly demanding to be addressed and solutions found.”
Digital innovations become a crowd-puller
Pioneering digital innovations, presented in exciting live shows, prove to be real crowd-pullers. The digital intelligence Kyana came to life before the visitors' eyes and introduced herself personally to the interested audience as a virtual cohost. The myKyana portal presented itself
as the centrepiece of the digital product world and impressively underlined how digitalisation can increase the efficiency, productivity and sustainability of companies. Kyana Assist caused quite a stir among the drupa visitors. The first AI chatbot in the printing industry enables Koenig & Bauer customers to interact directly with Kyana and receive direct support without waiting times.
In individual live demonstrations, visitors gained a detailed insight into the advantages of the comprehensive myKyana ecosystem directly on the stand. “At drupa, we showed how the combination of traditional printing and state-of-the-art AI and data-based technologies is shaping the future of the printing industry. The countless discussions with customers confirmed that digital productivity tools are becoming the decisive factor for investing in our technologies for printing and finishing,” emphasises Sandra Wagner, Vice President Digitalisation at Koenig & Bauer.
The new connected packaging solution FOLLOW attracted particular interest from brand owners and packaging manufacturers. The innovative platform transforms packaging into end-to-end, multimedia communication channels and takes the entire consumer experience to a new level. With augmented reality features and gamification elements, FOLLOW ensures a breathtaking product experience. In addition, the platform fulfils future regulations such as the Digital Product Passport and thus
contributes to the sustainability and traceability of products.
With a strong order intake, Koenig & Bauer has exceeded its own targets, especially in the sheetfed offset division. The majority of orders have come from China, Spain and Brazil. However, orders were also received from the DACH region, many other countries in Central Europe, Asia and North and South America. The orders relate to all format classes as well as the post-press area, which was on show at the drupa as part of an end-to-end packaging workflow. There was great interest in the innovative rotary die-cutters from the CutPRO X 106 series, flatbed die-cutters and foldergluers.
The seven-colour Rapida 106 X with coater and extended delivery, which was presented on the stand with printing speeds of up to 22,000 sheets per hour, is the world's fastest medium-format sheetfed offset press. It was sold to the printing company I.G.B. - Innovative Graphic Boxes - in northern Italy during drupa. Once installed in Viggiù, the press will primarily produce pharmaceutical packaging.
All the postpress systems on show were also sold directly from the stand. Qualvis Print & Packaging, for example, will receive the Omega Alius 90 folder gluer, which the company from Leicester in the UK ordered in combination with a Rapida 106 with unique functionalities. A further Rapida 106 with seven inking units and double coater is already in production at Qualvis Print & Packaging.
The CutPRO Q 106 flatbed die-cutter will go to AM-PG Group, a commercial and security printer in Yerevan, Armenia. The company has been a Koenig & Bauer customer for more than 15 years and operates a medium-format Rapida press. The CutPRO X 106 rotary die-cutter, which can run at speeds of up to 16,000 sheets per hour, also attracted a lot of interest from international trade visitors. It was sold at the trade fair in various versions, including for die-cutting labels.
Koenig & Bauer Durst impressed with high quality and flexibility in digital printing
The VariJET 106 digital folding carton printing press from the Koenig
& Bauer Durst joint venture was presented at a trade fair for the first time and impressed visitors during the product demonstrations with its high print quality and the flexibility of the entire configuration. In particular, the possibility of adding several coating and conventional printing units generated a great deal of enthusiasm among the trade fair visitors.
Koenig & Bauer Durst, together with Highcon, demonstrated the possibilities of a fully digital production workflow from printing to finishing. The joint venture also confirmed two beta customers for the VariJET 106 and the planned installation of a VariJET at a European customer in July. With water-based digital printing in white for corrugated substrates in primary food packaging, there was also another industry first on show at the stand.
Technological and sustainable innovations from the Digital & Webfed segment
An 18 metre long décor that stretched across the Koenig & Bauer stand immediately caught the eye of drupa visitors. Every centimetre of the AIgenerated décor was unique and underlined the innovation and technology leadership of the Koenig & Bauer RotaJET in the field of digital decor printing. Furthermore, folding carton and top-liner products were at the centre of the RotaJET presentation.
The products which combine highvolume digital packaging printing with the AR solution FOLLOW and the brand
security solution ValiPACK deserved special interest. Koenig & Bauer had printed 15,000 TetraPaks on the RotaJET especially for drupa, which were available to visitors at the stand.
The information areas for corrugated board and CI flexo printing were also very popular. The focus was on printing on bio-based and biodegradable substrates as well as the highly efficient ChromaCUT X Pro and Chroma HighTech 2S machines for printing on both sides of corrugated board.
High order intake at drupa: Confirmation of forecast for current financial year
“The great interest and the remarkable sales successes show that Koenig & Bauer has once again lived up to its claim of developing pioneering technologies for the printing industry for over 200 years,” emphasises CFO Dr Stephen Kimmich. Since the end of May 2024, Koenig & Bauer has marketed new orders worth €250m, including around €200m in legally binding orders.
The order intake relates to all segments. The new orders were placed at and outside of drupa. The company confirms its forecast of achieving an operating EBIT margin and sales development at the previous year's stable level for the current financial year. The path already taken to achieve an EBIT margin of 6 to 7 percent on consolidated sales of € 1.5 billion by the 2026 financial year at the latest is also secured by the ‘Spotlight’ focus programme.
Make the move to digital – and unbox your business with the flexibility to accommodate fast turns, versioning requests, last minute edits, and changing buying decisions.
With the new EFITM Nozomi 14000 LED digital press for corrugated packaging and POS, you can reduce process steps from weeks and days to hours and minutes. And personalize runs from one to infinity at higher margins and with lower costs – all in a single pass.
Let’s build your brilliant future. Together.
Scan to learn how corrugated converters and packaging printers are opening up new ways to say, “Yes!”
Knowing today what will be trendy tomorrow. If we look in the direction of packaging design, packaging production and design, this is not an impossibility. More and more, the trends for the coming years are already becoming apparent. Various market research companies are already publishing their trend studies up to the year 2030.
Various sociological focal themes influence the production and design of packaging.
The Corona crisis and the shaking up of society now awaken in us the desire for security and the familiar. In design, therefore, the past wins for the moment, such as the look of the 90s or 70s.
These familiar designs stand in contrast to the new influences of the environment. McKinsey reports in a study on five gamechangers in the packaging industry: E-commerce continues to grow. This circumstance has an impact on the demand for packaging.
Personalisation is a growing consumer desire that can certainly be implemented well on packaging. However, this implies ever faster turning numbers and smaller production volumes. Consumers are also leaning more and more towards convenience and health. Affordability is a growing desire that is being passed down the value chain to the manufacturing sector.
No new themes, but certainly two overarching themes that will be with us in the next 5 to 10 years are sustainability and digitalisation along the value chain.
If you want to stand out in retail, you have to think of something special. Packaging is an interplay of feel, look and material. But size also plays a decisive role today.
1. illustrations - what's inside quickly becomes visible
Because the eye eats along with the food, the ingredients of food are already included in the design of the packaging. This not only satisfies the need for convenience, but also for safety.
The illustrations rely on a simple, childlike style. This again underlines the purpose and generates positive feelings. When choosing colours, 99-Designs advises
to choose rich and fresh colours, the lines are bold. The product thus appears appealing to amusing.
2. Tactile textures on labels
Exciting cuttings, haptic typography or raised foil embossing make products look exciting and unusual to end consumers. While they are looking for a product that underlines their individuality, they like to reach for these products. It is suggested to them that they are choosing quality. Until now, these techniques were more familiar from the luxury segment. Now we know that digitalisation has opened up these printing and finishing processes to the broad market as well. This makes it easier for smaller, unknown brands to stand out in the crowd and position themselves in the quality segment.
3. Seamless patterns in 360°
Front and back cover design is a timehonoured classic that communicates brand messages and mandatory information in a limited space. The trend is to break down the boundaries. Digital printing allows us to seamlessly design products without a recognisable beginning or visible end to the design. Especially on the shelf, the exciting character of this design technique unfolds.
4. Striking and bright colours
The colour selection follows the neon colours of the 2000s. Those who want to apply the colour selection in a
contemporary way combine the striking colours with each other and clearly interrupt them with rich black. The strong colours communicate self-confidence and cheerfulness.
5. Nostalgia - retro designs from the 50s to the 70s
As already mentioned, "tried and tested" designs provide security. Cute comics with simple line drawings that we know from the 50s or earlier take away the seriousness and suggest ease with the product. Retro design awakens a feeling of security in us. These nostalgic values are equally appealed to by the yellowbeige-brown tones and flowing elements of 70s designs.
But design is not everything when it comes to standing out as a brand. When we talk about packaging trends, we also include materials, material application and manufacturing processes.
In the context of sustainability, packaging design - in terms of appearance without graphic elements - has changed enormously.
Minimalism has become a big buzzword. We want to reduce packaging waste - without reducing the unboxing experience. We want to stand out with foil stamping - without jeopardising the recyclability of the packaging.
Established in the mid-1980s, Imprimerie RGI is a leading commercial print business with a well-deserved reputation for delivering exceptional quality and customer service, with the company’s investment in the Jet Press 750S High Speed Model and Revoria Press PC1120 delivering multiple benefits in terms of quality and productivity
Imprimerie RGI began its partnership with Fujifilm in 2011 with the investment in offset plates, CTP and workflow optimisation,. In early 2022, Imprimerie RGI made a strategic decision to venture into digital printing, evaluating various options available in the market. After careful consideration, the company opted to invest in the Jet Press 750S High-Speed model, marking its first foray into digital printing technology.
“We are thrilled with our ongoing partnership with Fujifilm, which represents a significant milestone in our commitment to innovation and customer satisfaction,” said Serge Coissin, President, Imprimerie RGI. “The Jet Press 750S High Speed model has revolutionised our printing capabilities, enabling us to cater to the diverse needs of our clients with unmatched efficiency and quality.
“In June 2023, we decided to make an additional investment in the Revoria Press PC1120. The added value it gives
our business is exceptional, enabling us to enhance our print capabilities with metallic tones such as gold and silver, and also white, allowing us to expand our offerings to meet the evolving demands of the market.
“Our partnership with Fujifilm has not only enhanced our production quality and flexibility but has also significantly
improved our responsiveness to client needs,” added Serge. “Both the Jet Press and Revoria have minimal downtime, with maximum reliability and ease of use. Our staff are motivated and satisfied with these presses, further underscoring the success of our collaboration.
“The investments in Fujifilm technology have enabled us to expand our product offerings, catering to an increasingly dynamic and evolving market. Clients have expressed high satisfaction with the print quality, with some specifically requesting the Jet Press for their projects.
“We cherish our partnership with Fujifilm and look forward to a long-lasting collaboration that will continue to drive innovation within the printing industry,” concludes Serge.
“Imprimerie RGI’s commitment to excellence and innovation aligns with Fujifilm’s own ethos of delivering cuttingedge solutions to the printing industry,” comments Taro Aoki, Head of Digital Press Solutions, Fujifilm Europe. “We are proud to have been able to add value to Imprimerie RGI’s business and we look forward to continuing this collaborative partnership.”
Based on its foundation in the printing business and the introduction of accumulated experience and cutting-edge technology, the Komatsu Printing Group provides "solution design" to its customers.
Equipped with 24 web presses and 17 sheetfed presses -- all from Komori -- in 2023 the company introduced a 2-color Lithrone G40 advance (40-inch Offset Printing Press) and System 35S (546mmcutoff Sixteen Page Web Offset Press) at the head office factory to further raise production efficiency.
We interviewed President and Representative Director Hidetoshi Komatsu, Executive Officer and General Manager, Manufacturing Division Takeo Makino, Deputy General Manager, Manufacturing Department 1, Manufacturing Division Takahiro Mori, and Deputy Manager, B Format Web Press Section, Manufacturing Department 1, Manufacturing Division Yasuhiro Matsuoka about the background, effects of the introduction, and future prospects.
Solution design by the group's overall strength
Under the corporate slogan "Always challenge the future," the Komatsu Group is committed to enhancing
the value of printed materials and utilizing the latest digital technology and IT solutions to expand the scope of solution design (problem solving) for its customers. The strengths lie in three areas: the organization's comprehensive strength, with 9 factories nationwide and more than 1,230 group employees, the enhancement of product and service offerings through Group companies' collaboration, and having one of the leading facilities in Japan by focusing on labor-saving and manpower-saving as well as integrated production.
President Komatsu stated, "We are increasing overall cooperation to extend individual strengths and straighten out weaknesses within the group. For example, during a typhoon, we have established backup systems so that we can align with the predicted path and switch production from, for example, Shikoku to Osaka. Taking advantage of Komatsu's quality, we respond promptly to production and delivery needs with our national network."
“Komori is an indispensable presence. In the future, we expect support not just as ‘Komori in machinery’ but as ‘Komori in printing.’”
Hidetoshi Komatsu, President and Representative Director
President Komatsu further discussed the focus on equipment: "We emphasize labor-saving and manpower-saving. Since our workplace has many female employees, we focus on reducing physical work. Proposals such as automatic pallet stacking and packaging automation have been implemented, significantly improving operations in the last 3-4 years. Suggestions also come from within the company, such as 'With this machine, work becomes easier' or 'We can be more Komatsu efficient'."
Lithrone G40 advance and the sheetfed team “We only have one machine for the 100th-anniversary commemoration, so we believe we are using a special machine.”
Acting Chief of Manufacturing Department Mori
A relationship with Komori starting in 1988
The recently introduced Lithrone G40 advance is the first machine with Komori's 100th-anniversary emblem. President Komatsu reflected on the longstanding relationship with Komori: "The purchase of a half-size 4-color offset printing press in 1988 marked the start of our relationship with Komori. All our printing presses are from Komori. The introduction of new models with the latest technology always enhances our capabilities. Through regular introduction of new models, we have continued to increase our production capacity."
He also states, "Even machines that are 20 years old continue to produce thanks to Komori's service system. "We have also been taught from scratch about maintenance methods. When service personnel come, it has become a habit for the operator to perform maintenance together. We also replace parts ourselves. To avoid major overhauls, a culture of conducting maintenance ourselves has been thoroughly ingrained."
Effects of Lithrone G40 advance on production line
Deputy General Manager Takahiro Mori discussed the background of introducing the Lithrone G40 advance: "In response to the increasing demand for 2-color and monochrome projects and to ensure quality assurance and make the process streamlined and efficient, we had high expectations for the Lithrone G40 advance, equipped with a quality inspection device." He noted
that previously they occasionally printed monochrome on a 5-color press, but with the new machine, they can cover monochrome with a dedicated machine, allowing the 5-color machine to focus on color printing, contributing to production efficiency.
Regarding the functional aspects he stated: "With the existing machine there were feeder stoppages due to waviness when the paper was printed with a web offset press, but the new machine provides stable paper feeding, improved by structural changes in the front gauge of the feeder. The capability to precisely control air in the delivery fan zone results in excellent alignment of thin paper and an increased operating speed."
Regarding quality assurance, he said, "The PQA-S (Print Quality Assessment System) is essential from a quality assurance perspective. Being able to inspect at the optimal level depending on the paper is reassuring. The PDC-SG (Spectral Print Density Control) has greatly reduced the time required for color matching because it can measure all colors at the same time. It is useful since we have many projects with special colors."
"In terms of color startup, KHS-AI (Advanced Interface) is very useful. It learns job characteristics and speeds up the process from print startup to final printing by means of the pre-inking learning function that forms the optimal ink film through preset data."
Recycling facilities for used paper at the Ayagawa Plant
“To continue as a company, SDG compliance is essential. Some people say, ‘paper affects the environment,’ but I believe there is no business more considerate of the environment than the printing industry. We sort and recycle 12 types of used paper at our company.”
President Komatsu
System 35S for small lots and high-mix work
General Manager Makino explained the background of introducing the System 35S: "As the trend toward small lots and high-mix work progresses even on web presses, we wanted another dedicated machine to consolidate B4 sheet jobs. The new press significantly increased the overall productivity of the plant."
The existing press introduced in 2015 has the Semi-APC Semi-Automatic Plate Changer while the new press is equipped with Full-APC. Deputy Manager Matsuoka, responsible for the press, evaluating productivity and quality, noted: "For small lots and high-mix work with more plate changes, Full-APC is essential. With Semi-APC, it took almost five minutes to change eight plates, but Full-APC completes it in about 1.5 minutes. Since there is a significant number of plate changes, we can feel the effectiveness. Additionally, PQA-W can detect defective paper and automatically reject it, allowing us to work with the confidence that defective products are not mixed in."
President Komatsu shared his thoughts on the future of the Komatsu Printing Group: "Through the experience of the Covid-19 pandemic, I now feel that the printing industry is connected to all industries and sectors. While continuing to be particular about printing on paper, we are strengthening our ability to respond in non-paper fields. Furthermore, we will focus extensively on strengthening collaboration among group companies, collaborating with companies outside the group, implementing mergers and acquisitions, and taking business
5pm September 24th 2024
The annual Asian Print Awards was founded to recognise outstanding achievement in the print and packaging industries across Asia. With more than half the world’s population represented in this fast growing area, communication in the form of printed matter links Asia’s diverse cultures. It is imperative that such print achievements do not go unrecognised, especially among the population base that Asia enjoys.
The Awards are judged on a wholly quality-oriented set of criteria to ensure that fair play is enacted at all times.
The Independent Judging Panel comprises highly qualified personnel from within Asia and around the world. The independent judging panel has no knowledge of the actual entrants details. ALL ENTRIES ARE NUMBER-CODED. Entries must be commercially produced work.
The Asian Print Awards is the only regional print quality competition of its kind in Asia. Supported by leading industry-supply companies, any progressive quality print house should enter and prove that they are the best - by winning the Gold, Silver or Bronze award. Proving pride in quality awareness is what customers love to see. It’s not just empty words, you can prove it.
Categories 22-27 : Specialty Categories
23. Multi–Piece Productions and Campaigns
Any substrate or print process: Multi–piece Production must be 3 or more items such as folder, leaflets, ring binders, inserts, envelopes including their contents. Campaigns must be 3 or more items with a consistent theme produced during the year by the same printer for the same client.
5. Limited Editions & Artwork Reproductions (under
run) 6. Web Offset – Coated stock 70gsm and above
7. Web Offset –LWC (light weight coated) 65gsm or less 8.
- 21 : Digital Printing
24. Embellishment
Any substrate – any combination - for example: embossing – diecutting – foil stamping –laminatingcoating.
25. Innovation / Specialty Printing / New technology
The entry must exhibit any innovative and/ special application of machinery, process, substrate or finishing. A short description must be provided for the judges, detailing reasons for entry into this category.
26. Company Self Promotion
Any item printed to promote a product or company involved in the graphic arts industry. Self promotion cannot be entered into any other Category.
27. Judges Special Award (A job that catches all the Judges’ attention)
28. Design and layout. We look at the impact and visual effect.
29. Security applications
Send your entries by 24th September 2024 - by 5pm to: Asian Print Awards
c/o Print & Media Association of Singapore 627A Aljunied Road, Biztech Centre, #04-07 Singapore, 389842 Tel +61 422 869 728
INNOVATION PRINT AWARDS
Deadline for Entries Submission: 24th September 2024, 5pm
Remember to submit 2 copies of each job! Why? - Just in case one is damaged.
If you win an Award, YOU MUST attend the Award Dinner in Person. This is part of the competition rules!
SECTION A (This will not be shown to judges). Please fill the form in capital letters.
Entered by (company name): ______________________________________________________________________________________
Contact Person: ________________________________________________ Email______________________________________________
Address: ___________________________________________________________________________________________________________
Telephone: __________________________________ Country____________________________________________________
Category entered: ___________________________________________________________ (Example Cat 4 Book printing)
Title of entry (ie: " Paul's Ice Cream" ): ________________________________________________________________________________
Printed by (Printers name): ________________________________________________________________________________________
Client name: _______________________________________________________________________________________________________
Designer Pre Press House: ___________________________________________________________________________________________
Brand of Printing Machine used: _____________________________________________________________________________________
Stock supplied by (Merchant’s name): ______________________________________________________________________________
Ink used to produce the entry : ____________________________________________________________________________
By signing here you accept the rules and conditions of the Asian Print Awards
Signature over printed name_____________________________ Name_____________________________________________________
SECTION B Production information to be shown to judges ( tape this securely to the back of your entries)
Category entered (Same as above): __________ Entry number (Administrative use only]
Title of entry (ie: " Paul's Ice Cream" )__________________________________________Print method: _______________________
Number of ink colours (4-6-8 etc) ________ Any Embellishment (foil stamping etc) __________________________________
Quantity produced (Print run copies): ___________ Other technical details (finishing processes etc) ________________________
The Awards Dinner will be held in October in Jakarta Indonesia Send all entries to - Asian Print Awards
c/o Print & Media Association of Singapore 627A Aljunied Road, Biztech Centre, #04-07 Singapore, 389842
email:Paul@printinnovationasia.com Tel. +61 422 869728 Additional entry forms can be downloaded online at www.printinnovationasia.com All entries are non-returnable unless a prepaid self addressed courier pack can be provided
https://issuu.com/cpublish/docs/2024_asian_print_ awards_flyer
https://issuu.com/cpublish/docs/2024_asian_print_ awards_flyer
https://issuu.com/cpublish/docs/2024_asian_print_ awards_flyer
https://issuu.com/cpublish/docs/2024_asian_print_ awards_flyer
An Intense one day program you must be part of
For the first time, the Asian Print Awards will hold an industry conference that will cover ALL areas of print production. If you put INK on PAPER then come and join us for this 1-day event, followed in the evening by the regional only printing competition, the Asian Print Awards.
The day’s events
Asian Print Awards Industry Conference
Morning ession from 10:00 am till 1:00 pm. (Lunch Break)
Afternoon session from 2:00 pm till 5:00 pm
Coffee and tea in the display area till 6:00 pm
Asian Print Awards 2024 Cocktails from 6:00 pm till 7:00 pm
Awards Gala Dinner 7:00 pm till late
Hear from companies and people who know what is needed to help your business grow. Also hear what technologies at drupa shape our industry. What you should look out for and be aware of as you drive your company forward.
Title Sponsor:
Sponsor:
https://issuu.com/cpublish/docs/2024_asian_print_
https://issuu.com/cpublish/docs/2024_asian_print_
https://issuu.com/cpublish/docs/2024_asian_print_
Click on the logo to download the 2024 Entry Form
The first negotiations with Vivar Printing, one of the largest private printing companies in Malaysia, began in 2004.
Now the company has signed the purchase contract for a Diamant MC 60 bookline at Muller Martini's drupa stand. The company is situated in Rawang, Malaysia and has set itself the goal of developing the perfect book and thus making more and more people fall in love with books and reading. As the company now manufactures 90 per cent of its products for export, the quality aspect of the end products has become increasingly important in recent years.
The aim is to automate and thus better organize the production of hardcover books. "With the Diamant MC 60, the customer saves a lot of time during set-up and changeover," explains Simon Leong, General Manager at Muller Martini Malaysia. "The new bookline offers them many new functions and production options that will enable them to serve
new product segments and business areas in the future."
Vivar Printing is relying on Muller Martini's experience and extensive expertise in hardcover production for the purchase and praises the cooperative course of the negotiations. "It is a great pleasure for Muller Martini to be able to count Vivar Printing among our customers," says Michael Starford, Regional Sales Manager at Muller Martini, who has been accompanying the customer for 20 years.
The Diamant MC for conventionally and digitally printed books produces at up to 60 cycles per minute. The motion control technology ensures shortest set-up times
in combination with highest flexibility, quality and productivity. This enables you to produce a maximum variety of products with the Diamant MC.
The modular platform also allows individual customer solutions and generates synergy effects due to high amount of common parts with the Diamant MC Digital. Therefore the conventional bookline always benefits from the further developments of the digital bookline. This results an enormous investment protection and makes the Diamant MC the most powerful bookline with the highest degree of automation on the market!
The next generation of the family-run printing company Vivar Printing used drupa to find out about the latest developments in the graphic arts industry. They met with the entire sales team and CEO Bruno Müller at the Muller Martini drupa stand to finalise the purchase of the Diamant MC 60.
Elevate your printing possibilities with Extended Colour Gamut (ECG) technology. Our MPS presses enable you to produce 97% of Pantone colours using ECG along with unparalleled image detail.
The graphic arts industry is undergoing a transformation driven by the need for innovative technologies that enhance productivity, reduce costs, and minimize environmental impact.
Among the latest advancements, Freecure, a cutting-edge UV curing technology developed through a collaborative effort between IST Metz UV specialists and the chemical group BASF, stands out. Freecure leverages a novel approach to UV curing by enabling direct crosslinking of C=C double bonds without the need for traditional photoinitiators. This breakthrough addresses several critical challenges associated with conventional UV curing processes and paves the way for more sustainable practices in the industry.
In traditional UV curing processes, photoinitiators play a crucial role. These compounds are mixed into the varnish or ink and, upon exposure to UV radiation, absorb the energy and generate radicals. These radicals initiate UV polymerization, which converts the C=C double bonds in
the varnish or ink, effectively curing the material. Despite their importance, the use of photoinitiators presents several significant challenges:
The availability of photoinitiators has become increasingly constrained due to environmental regulations. China, the primary producer of photoinitiators and their raw materials, has tightened environmental regulations, leading to supply bottlenecks. The REACH regulation (Registration, Evaluation, Authorisation and Restriction of Chemicals) in Europe further complicates the situation. It is conceivable that certain types of photoinitiators could be reclassified, restricting their availability in the future. This regulatory landscape creates uncertainty and challenges for the ink and varnish industry.
Swiss and German Printing Ink Regulations: Focus on Photoinitiators
Overview
Swiss and German regulations for printing inks are designed to ensure consumer safety and environmental protection. Both countries have specific rules governing the use of photoinitiators, which are chemicals used to cure inks through ultraviolet (UV) light exposure.
Swiss Regulations
In Switzerland, the Ordinance on Materials and Articles (SR 817.023.21) outlines the requirements for substances used in printing inks, including photoinitiators.
The Swiss Ordinance aligns closely with the EU regulations but also includes a specific list of substances authorized for use in food contact materials. This ordinance is managed by the Swiss Federal Office of Public Health (FOPH).
Key points:
- Photoinitiators must be included in the positive list of permitted substances.
- Migration limits are set to ensure that photoinitiators do not transfer from packaging to food in quantities that could pose health risks.
- Compliance with Good Manufacturing
Practices (GMP) is mandatory to minimize contamination.
German Regulations
Germany follows the European Union framework for printing inks, particularly under the Framework Regulation (EC) No 1935/2004 and the Plastics Regulation (EU) No 10/2011. The German Federal Institute for Risk Assessment (BfR) provides additional guidance and recommendations for specific substances, including photoinitiators.
Key points:
- Photoinitiators used in food contact materials must comply with EU regulations, ensuring they do not pose a risk to human health.
- BfR publishes recommendations on safe levels of photoinitiators and other additives in printing inks.
- Regular monitoring and testing are conducted to ensure compliance with safety standards.
Common Photoinitiators and Restrictions
Both Swiss and German regulations scrutinize commonly used photoinitiators such as benzophenone, 4-methylbenzophenone, and ITX (isopropyl thioxanthone) due to their
potential health risks. Limits on specific migration levels (SML) are established to control their presence in food packaging.
Compliance and Enforcement
- Documentation and Declarations: Manufacturers must provide detailed documentation proving compliance with the regulations.
- Testing and Certification: Regular testing of inks and printed materials is required to ensure that photoinitiators remain within the prescribed limits.
- Regulatory Updates: Both countries frequently update their regulations and positive lists to incorporate new scientific findings and technological advancements.
Swiss and German regulations on printing inks, particularly regarding photoinitiators, emphasize consumer safety and environmental protection. Compliance with these regulations involves adhering to specified substance lists, migration limits, and manufacturing practices. Continuous monitoring and updates ensure that these regulations remain effective and relevant.
Photoinitiators have the potential to cause odors and migration, which are significant concerns in applications such as food
packaging. The migration of photoinitiator residues into food products can pose health risks and violate safety standards. Consequently, UV curing processes that rely heavily on photoinitiators are often excluded from sensitive applications or require extensive modifications to meet safety standards.
The environmental impact of photoinitiators is another critical concern. The production, use, and disposal of these chemicals contribute to environmental pollution. As industries worldwide strive to reduce their carbon footprint and adopt greener practices, finding alternatives to photoinitiators has become imperative.
Freecure addresses these challenges head-on by eliminating the need for photoinitiators through a novel approach to UV curing. This innovative technology directly crosslinks C=C double bonds using UV light at a specific wavelength, thereby bypassing the need for traditional photoinitiators. The key to this process lies in the precise control and optimization of the UV light spectrum and the materials used in the curing system.
Freecure's success is rooted in several critical innovations that enhance the efficiency and effectiveness of the UV curing process:
The plasma technology within the UV lamp has been meticulously adapted and optimized to facilitate efficient UV curing. This optimization ensures that the plasma generates the necessary light energy to directly crosslink C=C double bonds, thereby eliminating the need for photoinitiators.
The use of specialized materials for lamps, reflectors, and pass filters is another cornerstone of Freecure's innovation. These materials are designed to withstand the high energy levels required for effective curing and to enhance the overall performance and durability of the system.
Freecure incorporates advanced electronic controls to optimize the operation of the UV curing system. These controls ensure precise management of the light spectrum, enhancing the system's efficiency and reliability. By fine-tuning the electronic controls, Freecure achieves a power increase of more than 70% in the UVC spectral range, with a disproportionate increase in wavelengths below 220 nm.
Compatibility and Versatility
One of Freecure's standout features is its versatility. The technology is suitable for both 100% UV systems and water-borne UV systems. When formulating these UV systems, several critical aspects were taken into account:
-Absence of Photoinitiators: By eliminating photoinitiators, Freecure addresses the availability, odor, and migration issues associated with traditional UV curing processes.
-Chemical Composition and Functionality of the Binder: The binders used in Freecure formulations are carefully selected and optimized for their chemical composition and functionality, ensuring effective curing without photoinitiators.
-Amine Modification for Oxygen Inhibition: Oxygen inhibition, a common issue in traditional UV curing, is effectively suppressed through amine modification of the binder. This modification prevents the termination reaction of chain formation via oxygen, ensuring efficient curing.
- Physical Surface Drying of Aqueous UV Dispersions: In water-borne UV systems,
physical surface drying is crucial. Freecure ensures tack-free surfaces after drying, preventing excessive oxygen inhibition and ensuring high-quality finishes.
Enhanced Performance and Environmental Benefits
The innovative approach of Freecure not only addresses the technical challenges of traditional UV curing but also offers significant environmental benefits. By eliminating photoinitiators and optimizing the UV curing process, Freecure aligns with the industry's growing emphasis on sustainability.
Mitigating Oxygen Inhibition
Oxygen inhibition is a major challenge in traditional UV curing processes. It occurs when oxygen molecules interfere with the polymerization process, leading to incomplete curing and compromised surface properties. In traditional systems, this issue is often mitigated through inertization of the irradiation space or excessive addition of photoinitiators. However, these solutions introduce additional complexities and environmental concerns. Freecure's direct crosslinking mechanism effectively mitigates oxygen inhibition without the need for such measures, resulting in a more efficient and environmentally friendly curing process.
Reducing Environmental Impact
Freecure significantly reduces the environmental impact of UV curing systems. By eliminating photoinitiators, the technology minimizes the production and disposal of these chemicals, reducing
pollution and environmental harm. Additionally, the optimized UV curing process of Freecure consumes less energy, contributing to lower carbon emissions and a reduced carbon footprint.
Supporting Sustainable Practices
The development and implementation of Freecure reflect a broader industry trend towards sustainability. As companies worldwide strive to adopt greener practices, Freecure offers a practical and effective solution for UV curing in the graphic arts industry. Its ability to deliver high-performance curing without the environmental drawbacks of traditional systems makes it an attractive choice for businesses committed to sustainability.
Application and Efficacy
Freecure's innovative approach has been rigorously tested and proven effective across various applications in the graphic arts industry. Comprehensive binder screenings and trials have demonstrated its suitability for different UV binders and its ability to deliver high-quality curing results.
Performance
In comprehensive binder screenings, Freecure was found to be suitable for various UV binders, including epoxy (EA), amine-modified polyether acrylates (POA), and highly functional urethane acrylates (UA). Each type showed varying degrees of conversion and resistance:
- Epoxy (EA) and Amine-Modified Polyether Acrylates (POA): These binders demonstrated higher conversion and resistance, making them ideal for
applications requiring robust curing and durability.
- Highly Functional Urethane Acrylates (UA): Urethane acrylates exhibited surface hardening and chemical resistance to alcohol, although their double bond conversion was lower compared to other binders. However, optimized coating compositions (combinations of EA/ UA with POA resins) and increased lamp power and dose achieved double bond conversions comparable to standard curing using photoinitiators.
Extensive trials confirmed Freecure's capability to address the entire curing spectrum, from partial curing of electron beam (EB) ink formulations to fully cured inks involving SIR technology. Key findings from the trials include:
- Effective Pinning of EB Ink
Formulations: Freecure demonstrated substantial double bond conversion in EB ink formulations, ensuring effective curing and high-quality finishes.
- Compliance with Migration Limits: The migration results indicated that typical three- and tetra-functional monomers present in the tested inks stayed below their specific migration limits (SMLs), ensuring compliance with safety standards.
- Reduced Photoinitiator Content: Freecure's ability to reduce the photoinitiator content in formulations is a significant advantage, particularly in light of regulatory requirements and environmental concerns.
- Applicability to Colored Inks: Freecure proved effective for colored inks.
Implications
Freecure's efficacy extends to various practical applications, including food packaging and other sensitive areas. Its ability to reduce photoinitiator content and mitigate oxygen inhibition makes it a sustainable, efficient, and environmentally friendly solution for UV curing in the graphic arts industry.
Freecure represents a significant advancement in UV curing technology, addressing the limitations of traditional processes and paving the way for a more sustainable future in the graphic arts industry. Its innovative approach to direct crosslinking without photoinitiators, coupled with optimized UV systems, offers enhanced performance, environmental benefits, and compliance with stringent regulatory standards. As the industry continues to prioritize ecofriendly solutions, Freecure stands out as a pioneering technology set to redefine UV curing in graphic arts.
With its versatile applications, rigorous performance testing, and alignment with sustainability goals, Freecure is not just a technological innovation but a comprehensive solution that addresses the industry's current challenges while setting a new standard for future developments. As companies adopt this groundbreaking technology, the graphic arts industry will move closer to achieving its sustainability objectives, ensuring high-quality, efficient, and environmentally responsible UV curing processes.
to print MDO-PE
Highest quality with best register
Connected to RUBY to digitize the value chain ... and many more!
Windmöller & Hölscher KG
Lengerich / Germany
Phone + 49 5481 14 - 0 · info@wuh-group.com www.wh.group/int/en/
Best profitability at printing speeds up to 600 m/min. and fast job changes
In a strategic move, Sunrise Paper has partnered with BOBST, installing a VISION M1 automated modular label press to successfully navigate the future with the latest in flexo printing technology.
Since its inception over three decades ago, Sunrise Paper has grown to become one of the leading label converters in the northern part of Malaysia. Located in Seberang Perai, Penang, the company has an enviable reputation for delivering highquality identification products, including full-color, self-adhesive labels, to local and global brand owners. These can be found in various sectors, including consumer goods, food and beverage, electronics and electrical, semiconductors, medical, automotive, and solar.
Under the leadership of Managing Director Mr CC Chong and General Manager Mr KH Ang, Sunrise Paper has expanded its reach to supply markets globally, maintaining a robust operational model through strategic shift patterns to ensure continuous production.
In the face of an increasingly competitive market with numerous new foreign investors, Sunrise recognizes the imperative to stay ahead by constantly innovating and adapting. “Our commitment to sourcing advanced machinery is the reason we reached out to BOBST, as we strive to meet the ever-evolving demands of our industry,” said Mr CC Chong.
Supporting growth with new BOBST flexo press
Recently, as part of its strategic roadmap, Sunrise Paper invested in a BOBST VISION M1 8-color inline flexo press, which runs at up to 180 m/min (590 ft/ min). This decision was driven by the need to support business growth, increase capacity, and streamline operations to meet market demands.
The installation of the VISION M1 has made a significant impact, enabling Sunrise to consistently produce highquality prints at higher speeds. This has not only enhanced productivity but also enabled Sunrise to meet the increasing customer demands for speed and quality. “The VISION M1 is opening more doors for Sunrise. In particular, it is enabling the company to further develop opportunities in FMCG and personal care labeling,” commented Peter Woods, Zone Business Director for Label and Inline Flexo solutions at BOBST.
The VISION M1 comes with features that significantly boost operational efficiency. It has been designed to deliver high press uptime by maximizing machine availability and minimizing downtime. The fully automatic register setup and
control system, Print Tutor, ensures precise and consistent print quality at high speed. A laser-assisted pre-register system for cylinder positioning reduces setup time and improves accuracy. The easyto-operate HMI touch panel simplifies machine operation, making the VISION M1 user-friendly even to novice operators. There is also a great feature for handling and storing magnetic cylinders, making the process easy, effort-free, and safe.
Another important aspect of the new press is the reduction of waste and energy consumption. “Sustainability is at the core of Sunrise’s culture,” Mr KH Ang explained, “and the VISION M1 label press aligns with our sustainability goals, offering advanced features that reduce waste, conserve energy, and enhance overall efficiency. By investing in such technology, we not only improve our productivity but also contribute to a more sustainable future.”
Having observed a notable shift in customer requirements, Sunrise Paper is continually assessing its requirements in terms of technology. “There is a growing emphasis on the need for faster delivery and higher-quality printing solutions,” said Mr. CC Chong. To address these demands, Sunrise is exploring more opportunities with BOBST technology, aiming to leverage BOBST innovative solutions to secure additional jobs and further expand its market presence.
He concluded, “Our relationship with BOBST holds immense potential. We believe that the performance of this new
Mr. CC. Chong, Managing Director of Sunrise Paper (M) Sdn. Bhd.
acquisition will be a crucial factor in our future investments. We are confident the VISION M1 will deliver the anticipated results and we are committed to further investing in BOBST technology to fuel our growth and maintain our competitive edge.”
Sunrise Paper (M) Sdn. Bhd. Production team led by General Manager Mr KH Ang and Peter Woods, BOBST Zone Business Director Label
On behalf of BOBST, Mr Woods commented, “We are very proud to partner with Sunrise Paper, supporting them in their journey to even greater achievements. With the VISION M1, this company has the perfect tool to respond to those urgent demands from brand owners for faster delivery and higher quality. But this is just the beginning; we eagerly anticipate the extension this partnership in the coming years.”
The UV Analyzer is a app-based UV radiation measuering device.
The measuring is quite easy. Put the strip on your substrate, irradiate it with UV and measure the strip with the stick. The app will show you the measured dose in mJ/cm². This dose value can be compared with your reference value to determine aging.
Scope of delivery:
UV Analyzer Stick and reference white, charging cable, lanyard, measuring strips
Did you know that a simple act of writing down your goals significantly increases the likelihood of achieving them?
Research shows that individuals who put their aspirations on paper are more likely to follow through and turn abstract dreams into actionable plans. In this article, we’ll explore the science behind this phenomenon and share practical tips for harnessing the power of paper to manifest your goals.
The Encoding Effect: Why Writing Matters
When you write down your goals, you engage in two critical processes: external storage and encoding. Imagine posting your goal on a piece of paper in your office. This external storage makes the information easily accessible for review. Visual cues serve as reminders, reinforcing your commitment to the goal. Encoding is the biological process by which our brain analyses and decides what information to store in long-term memory. In other words, writing increases the chances of remembering the goal and engraining it to memory.
The Generation Effect
Neuropsychologists have identified the “generation effect.” Here’s how it applies to goal setting- When you create a mental image of your goal, you’re actively generating it in your mind, first instance of the generation effect. The second instance of the generation effect occurs when you put your goal into words on paper. As you write, you reprocess and regenerate the mental image, reinforcing its importance and manifesting it into reality.
Scientific Evidence: Dr. Gail Matthews’ Study
Dr. Gail Matthews, a psychology professor at the Dominican University in California, conducted a study on goal setting. She
gathered participants from various backgrounds, including entrepreneurs, educators, healthcare professionals, artists, lawyers, and bankers. Here’s what she found:
Those who wrote down their goals and dreams regularly achieved them at a significantly higher level than those who didn’t.
By simply writing down their aspirations, participants became 42% more likely to realize their dreams.
Examples
Tony Robbins: Awaken the Giant Within
Tony Robbins, the world’s #1 success coach, emphasizes the power of writing down goals. In his best-selling book, “Awaken the Giant Within,” he shares his personal experience. Robbins wrote his goals on a piece of old Russian map, and the rest is history. His coaching has transformed lives of influential figures worldwide like Bill Clinton, Leonardo DiCaprio, Serena Williams, Nelson Mandela and many more.
Bruce Lee: A Letter to Himself
At Planet Hollywood in New York City, there is a letter hanging on the wall that martial artist and actor Bruce Lee wrote to himself on January 9, 1970—a pact that would shape his destiny. He wrote a letter to himself, describing his aspirations “Starting 1970, I will achieve
world fame, and from then onward till the end of 1980, I will have in my possession $10,000,000. I will live the way I please and achieve inner harmony and happiness.” His clarity and determination fueled his incredible success!
What can you do for personal growth?
In a world filled with distractions, putting pen to paper remains a timeless practice. Whether you’re aiming for personal growth, career milestones, or creative achievements, remember: Make it real. Put it on paper. So here are some practical tips:
Write It Down: Putting your goals in a designated space on paper increases the likelihood of achieving them.
Visualize: Draw pictures related to your goals. Create mental images of success and reinforce them through writing.
Be Specific: Use numbers and be precise. Create a timeline with actual dates for milestones along the way.
Commit: Your ink shapes your future. Declare your intentions with clarity and confidence.
Happy goal setting! Your goals deserve the tangible commitment on paper that only writing can provide. As Sir John Hargrave, author of Mind Hacking, says, “Until it’s on paper, it’s vapor”.
Your one stop for all flexo plate mounting solutions
With our extensive range of flexographic technology solutions, including unique plate mounting technologies, splicing and process tapes, we offer unparalleled expertise. Our dedicated team will help you find the perfect solution, providing onsite training to enhance your operational expertise. Witness the remarkable results: improved print quality, enhanced efficiencies, and a tangible reduction in waste and emissions. Choose tesa as your trusted flexo partner.
New primer technology for non-food packaging applications offers a validated solution for safe, economic deinking of UV-printed selfadhesive labels.
Siegwerk has announced the launch of its first full UV flexo deinking system for the European market: CIRKIT CLEARPRIME UV E02. The new primer technology for non-food packaging applications offers a validated solution for safe and economic deinking of UVprinted self-adhesive labels (PSL). As a result, it improves the recyclability of labeled plastic packaging and enables the recovery of high-quality recyclates that are suitable for reuse in non-food packaging applications.
Although UV inks offer some advantageous properties for printing labels, they also pose a challenge for the subsequent recycling. “Depending on the substrate, UV inks are often very difficult to remove and can therefore lead to contaminations of recyclates, which significantly limits their further reuse,” explains Marc Larvor, head of technology, Narrow EMEA at Siegwerk. “As a result, it is not surprising that UV-printed packaging has so far been considered as problematic in terms of a Circular Economy.”
With CIRKIT CLEARPRIME UV E02, Siegwerk now offers a primer solution that specifically addresses this challenge. By enabling easy and safe deinking of UVprinted self-adhesive labels, it eliminates the need for prior label removal if the used plastics are compatible.
“Such combined mechanical recycling of labels and plastic packaging can not only help to increase recycling rates, but also to save time and costs,” adds Marc Larvor. “Thereby, our new UV flexo deinking primer actively contributes to realize high-quality recyclates for circular waste streams.”
In a first field test with Masterpress, one of Europe’s leading suppliers of highquality labels and printed decorative packaging, Siegwerk’s new deinking primer has proven its effectiveness in all aspects. Masterpress’ research and development (R&D) experts used uncoated transparent or white pressure sensitive labels (PSL) made of PE85 and applied Siegwerk's CIRKIT CLEARPRIME UV E02 followed by bleeding resistant UV flexo inks and an UV flexo OPV.
First, the primer created a perfect adhesion between substrate and inks and later enabled full ink and varnish removal of the printed polyethylene (PE) film at standard deinking conditions based on the QT 507 washing protocol of the European PET Bottle Platform (EPBP).
The primer layer also dissolved residuefree in the hot washing process and thus proved its ability to generate high-quality transparent or white recyclates, while the used non-bleeding ink formulations ensured a clean and reusable washing solution.
In-house laboratory tests at Masterpress and Siegwerk have shown great recyclate results underlining the effectiveness of the new deinking primer.
“Consistently investing in its R&D laboratory, Masterpress brings state-ofthe-art capabilities to test and trial new inks or materials before they enter the market.
We are dedicated to advancing innovation within the shrink sleeve and self-adhesive label industry and are well positioned to help accelerate the commercialization of new, sustainable, recyclable products and materials on the market,” said Katarzyna Wasilewska, research and development manager at Masterpress.
“Our tests confirmed an impressive recyclability of the UV-printed PE labels. Compared to other labels with no deinking technology, we could observe that contaminations of plastic recyclates due to discoloration could be massively reduced by using Siegwerk's UV Deinking Primer.”
Siegwerk says CIRKIT CLEARPRIME UV E02 works perfectly with the company’s Sicura flexo series such as the non-low migration Sicura Flex 39-8 or the dual-curing series Sicura Flex Dual Cure. In addition, the new primer is compliant with different film materials and allows an inline printing of deinkable materials in a 100% UV-Flexo press setup keeping the complexity for users as low as possible.
“With only three minutes, the new UV flexo primer even offers a deinking speed as fast as a water-based deinking primer making it to a great alternative for converters who are using a pure UV flexo press and are not able to process a water-based primer,” adds Katarzyna Wasilewska.
The Asian Packaging Excellence Awards is the only regional Independent Packaging Print competition. Since 2001, awarding Gold Silver and Bronze for packaging printers who have excelled in producing world class quality. The judges are non-supplier but are retired educators or production professionals and come from all over Asia/Europe/Australia.
* We MUST have 2 consecutive samples for each job in ALL catergories you enter (If 1 is damaged)
* ONLY 3 jobs allowed for each catergory that you enter.
1. Narrow Web Flexo (up to 500mm width only)
1.a Paper/Board
1.b Film
2. Mid Web Flexo (501mm to 914mm width only)
2.a Paper/Board
2.b Film
3. Wide Web Flexo (915mm and over)
3.a Paper/Board
3.b Film
4. Carton & Cups
5. Post Print for Corrugated
6. Pre Print for Corrugated
1. Flexo 2. Letterpress
3. Offset Labels
4. Gravure Labels
5. Combination Printing (Many different processes)
6. Non Pressure Sensitive material
7.Digital Labels
7.a Up to 4 colours
7.b 4 to 5 colours
7.c 5 to 6 colours
7.d 7 + Colours
1. Paper/Board
2. Metallised Paper/ Aluminium Foil Surface Print
3. Film
3.a Surface Print
3.b Reversive Print
4.Speciality Gravure (Must provide written explanation)
6. Embellishment
7. Digital Embellishment
8. Mockup/Sample
9. Digital Packaging
10. Hybrid Printing
11. Offset Packaging
THIS IS YOU FREE ENTRY FORM. PLEASE WRITE CLEARLY SO WE CAN READ IT
PLEASE READ: Asian Packaging Excellence Awards are open to all packaging companies across Asia. It is free to enter and winners will be presented Gold Silver Bronze awards live on stage in Vietnam 8th November 2024. If you do not attend, we will not send awards to you. Jobs must have been produced from November 2023 till September 20th 2024.
SECTION A - This is seen by the Judges ONLY 3 JOBS PER CATERGORY
Catergory Entered for this job (See catergories opposite page)
Company Name_____________________________Contact Person________________________
Company Address________________________________________________________________
Country________________Contact Number _______________e-mail ______________________
Name of Entry_____________________________Printing Company_______________________ Your Name ________________________________Signature_____________________________
SECTION B - CUT AND TAPE THIS TO THE BACK OF THE JOB ENRTY - *fill out each process
Catergory Entered_____________Print Method_______________Number of colours__________
*Brand of Machine
*Plate Supplier
*Ink Supplier
*Tape Supplier
*Pre Press by *Printed Quanity
*Paper/Board/Film/Label supplier
*Web Width ___________________Other detials_______________________________________
If you would like to supply more information, please attach this to Section A above
Please send your entries to: Send your best work to: Att: Asian Packaging Excellence Awards c/o PRINT & MEDIA ASSOCIATION OF SINGAPORE 627A Aljunied Road, Biztech Centre, #04-07, Singapore, 389842 Telephone: +65 6336 4227
Current and Valuable
Industry Information Nov 8
The SHIFT 24 conference will cover all industry sectors from:
Flexographic
Gravure
Digital Labels
Corrugated Converting Offset
Embelishment Design
PrePress Ink
Paper/Board/Label stock Plates and much more
Networking and Display Area Nov
Relax - network - connect in the supplier display area over a coffee or tea
Nov 7th - SHIFT - 24 Asian Packaging Excellence Awards VIP winners dinner
Asian Packaging Excellence Awards 2024 - Nov 8th
Join us for the highlight of the 2024 Packaging Indusrty at the dinner awards ceremony
At the dinner we will award the winners of the 2024 competition Gold Silver Bronze live on stage
Come and witness the best packaging compnaies in Asia as see first hand quality of the higest levels
6pm till 10.30pm. All the winners of the Awards will be hosted to a privarte VIP dinner where by they can meet others from around the region and talk shop (each winning company will recieve 3 VIP tickets)
Nov 8th - SHIFT - 24 Conference
10am till 5.00pm. A line up of 12 speakers will share their knowledge with you covering all areas of packaging production - Display area open from 8:30am till 5:30pm
Awards Pre-Dinner Cocktails 6pm till 7pm 2024 Asian Packaging Excellence Awards Gala Dinner 7pm till late
Click Here
SHIFT 24 Conference
Including all coffee tea breaks, lunch and entrance - SHIFT24
US$50pp Industry
US$80pp Supplier
SHIFT 24 Conference
Including all coffee tea breaks, lunch and entrance into SHIFT24 + Awards dinner
US$110pp Industry
US$160pp Supplier
Conference Venue
https://www.hisaigonairport.comawards_entry_form
For Visitors that require Visa - we use and recommend the following companys services
*We advise to book the meet on arrival and fast track services as at peak times the wait can be very long to clear immigration.
*They can also arrange baggabe pick up - to car for fast and efficent hotel transport.
Website for Vietnam visa services, Fasttrack, and Airport Car: Click below https://www.trustvietnamvisa.com
Website for Fasttrack Service for individuals exempted from Vietnam Visa or those with visas in advance, for expedited procedures at the airport: Click below https://vietnamfasttrackservice.com
Use this code IPC2024 at the payment area and receive the SHIFT24 special rate.