Print & Packaging INNOVATION Asia
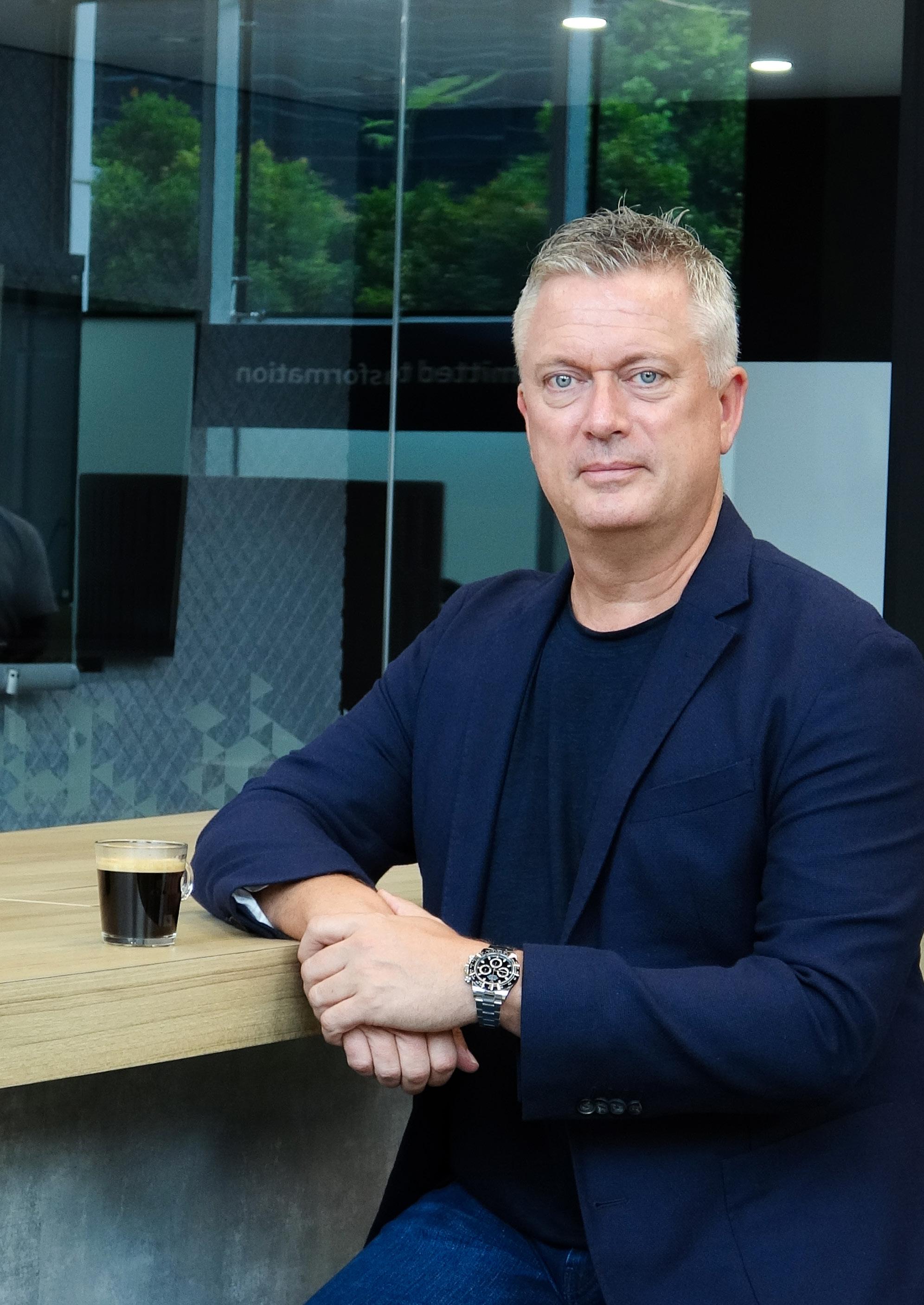
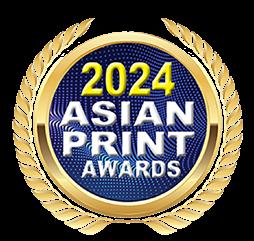
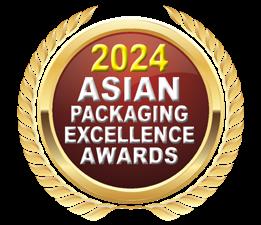
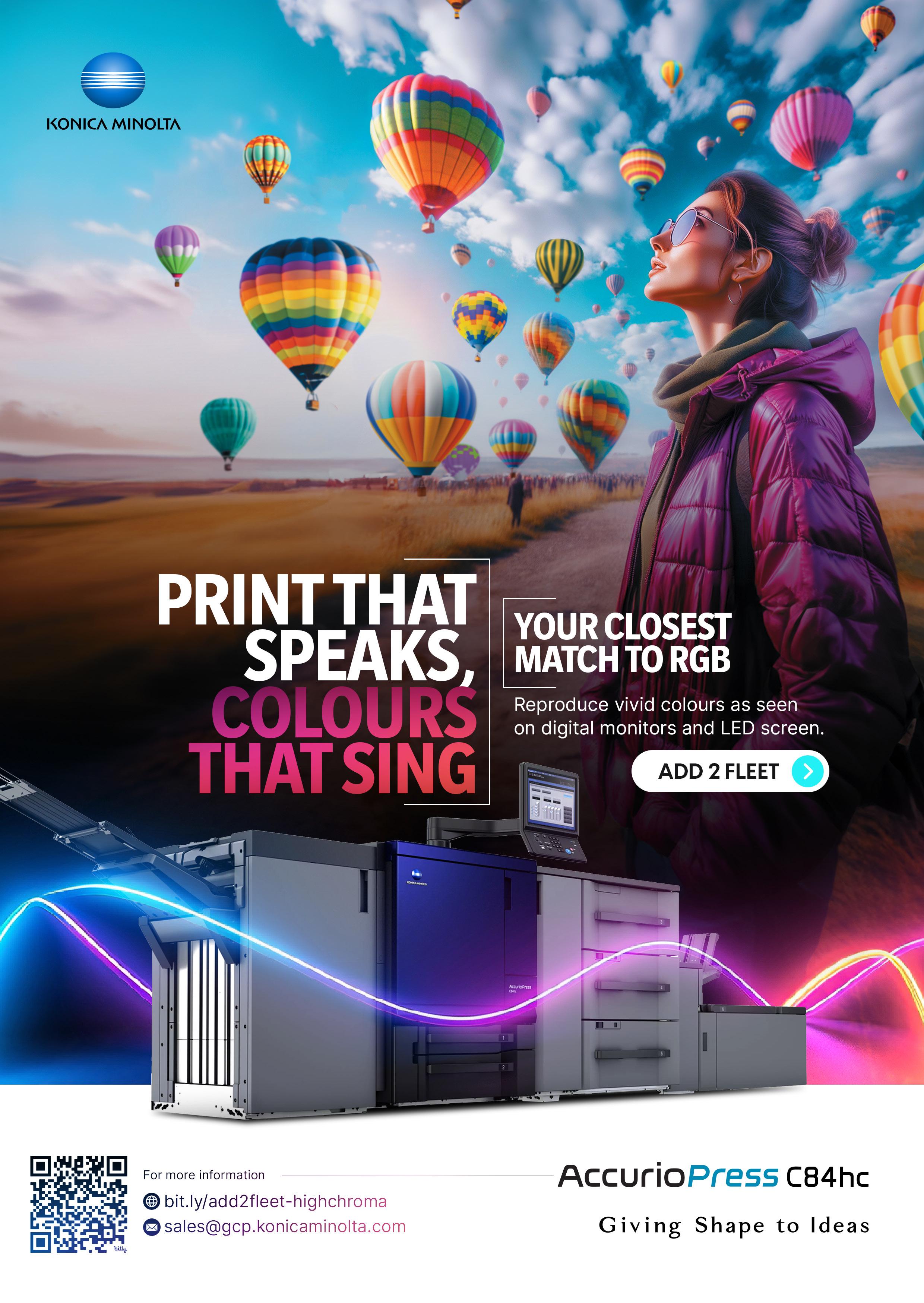
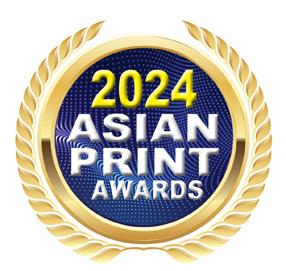

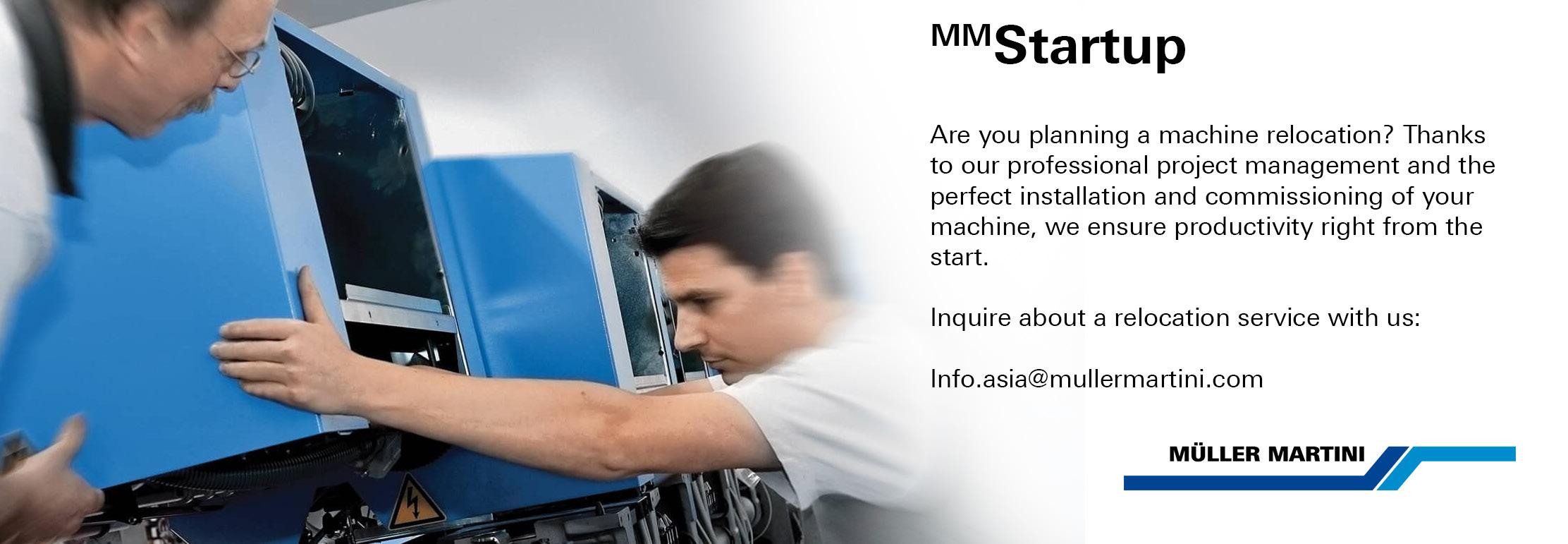
We recently sat down with Scott Mackie - General Manager, Graphic Communications Business - FUJIFILM Business Innovation Asia Pacific and Senior Group Manager International Sales & Marketing to see where things stand with FUJIFILM and whats happening in the industry
Q. It’s been some time since the merging or FUJIFILM (FF) and FUJIFILM Business Innovation (FBI). Where are we today with this and have there been any obstacles/benefits.
SM. We have been going to market as one Fujifilm Graphic Communications team across Asia Pacific for some time now with the aim of maximizing our synergy between our Advanced Industrial and Digital Printing solutions go to market.
Like any operational changes it hasn’t been a straight path for us internally but I believe that externally the market is responding well to the fact that Fujifilm has the ability to cater to such a broad scope of needs, analogue or digital.
We have one of the largest industry offerings across commercial printing, packaging, publishing and transactional as well as print on demand and in-plant capabilities.
Q. How is the digital print market in general, is it hitting highs or lows at the moment and what do you see in the immediate future.
SMThe last 12 months or so have seen a lot of volatility in the markets, across East Asia especially but, we see a return of volumes across all markets and especially in digital colour.
That heralds that re-investments will increase also on current demands which
Scott Mackie - General Manager, Graphic Communications Business - FUJIFILM Business Innovation Asia Pacific and Senior Group Manager International Sales & Marketing
are strong in most market segments, so overall we see a challenging market with growing confidence, despite regional and global headwinds.
Q. What are some of the most common questions you get asked about technology these days.
SM I think firstly, flexibility is one of the key concerns for digital investment, especially from companies which are new to digital production technology. The technology must enable them the broadest scope possible within segment, allowing greater production integration
that in turns accelerates the return on investment.
Secondly, workflow discussions that enable the right technology to fit into existing production environments with the capability to drive new revenues as seamlessly as possible.
Both are key to a successful adoption of analogue and digital hybrid production in the early stages; flexibility and adaptability limit the risks and maximize the upsides.
Q. What’s your view on the general offset market.
SM I visited with peers at key offset vendors during Drupa and the market leaders were extremely busy, far exceeding their expectations which was exciting to
hear. It signals a healthy industry, one which is ready to make strong investments to ensure ongoing growth.
However, I think that the market demands that print production has both analogue and digital capability, for offset producers to have only analogue equipment applies unnecessary limitations on their ability and growth. Offset has a long tail globally, digital has a long growth track.
Q. Drupa highlights from FF and what was your general impression about technology available if you got a chance to walk the halls
SM I think the overwhelming response was, it was great to be back and those who attended had growth mindsets, targeting the latest innovation. We personally
exceeded our own expectations for the show with two new JetPress technologies attracting a lot of attention.
The JetPress inkjet product line showed two new presses, the JetPress FP790 a new flexible packaging press and also the JetPress 1160 CFG a roll fed publishing and transactional printing press.
Both received huge attention, especially the FP790 which brought class leading quality and productivity to the market, our business is expanding rapidly globally in this segment.
The 1160 CFG is an advancement of the 1160 CF which we launched at iGAS a couple of years ago, but with gloss coated substrate inks without the need for any pre-coating it drew huge attention also.
In our Revoria Press range, we showcased two mid to high level production presses with CMYK+ capability which when launched later this year will enable a Revoria Press colour portfolio which is entirely CMYK+.
On that we also demonstrated a couple of technologies to come for CMYK+, new green inks we have in development which enables RGB simulation to great effect and a pressure sensitive ink which enables sealed mailers for non-critical or confidential mailers. There is more but would ask your readers to get in touch to discuss what we are doing and how we can help them.
Q. What will be the focus with your technology as FF moves forward, will we see more emphasis on Packaging, Wide format, the Jet press technology etc.
SM In short, yes but not forsaking dry ink technologies or other markets. Globally the printing industry is still growing, whether that is commercial print, or packaging.
However, packaging has the growth in digital that we witnessed in commercial printing 20 years ago and will remain for some time I believe, the challenges are within each print medium and which one delivers the appropriate output for each application, whatever the market sector may be.
So, for Fujifilm the development track will focus on bringing truly innovative technology to bear where we see the gains in the market in terms of demand generation needs.
Q. At drupa FF had the 1st Global Innovation Awards (how was the response) , combined with a very informative full day seminar. Will we see more of these types of these seminar events in the future?
SM We launched the Print Innovation Awards a couple of years ago and to finally make it a global concern was received well by everyone. Recognition of excellence never grows old, and the industry is filled with creative and technical genius which we need to pause and celebrate, whenever possible.
Going forward we’ll continue to grow the awards globally and hope to develop further initiatives that underpin our customers success through thought leadership and development programs.
Q. looking ahead, do you see any roadblocks that may impact our industry.
SM Human beings can be naturally reluctant to change, we shun the unknown at times, but some do embrace change. Not understanding the changes in the industry is a past, present and future roadblock to any and all industry and printing has been going through a digital transformation before it became a buzz word.
In the early 2010’s we started to define digital transformation along the lines of, “Digital transformation is the process of using digital technologies to create new — or modify existing — business processes, culture, and customer experiences to meet changing business and market requirements.”
Digital print production technology, workflows and services are core to this transformation which is well underway.
However, we are now entering an age of AI and Robotics that we have no impression of the future impact, but one thing is for sure, there will be positive and negative outcomes from the changes that are coming.
Ultimately, how we react to this change, will determine whether the industry and its players thrive, survive or otherwise.
Q In closing what advice can you give companies that are maybe considering getting their foot in the door with digital printing, or just looking at upgrading.
SM My best advice is to, at the very least, invest the time to understand the changes in the market and how it affects you, assess the risks for your business considering this and then determine the opportunity that is ahead of you, either in front or laterally.
In short, change is a constant, keep it in view and you’ll have the best opportunities to not just maintain but grow your business.
We can help with this and if we are not in contact with anyone reading this, I urge them to reach out, that we may share our knowledge and help them understand their options to move into digital.
Effortlessly convert images to CMYK + Pink without modifying the originals.
We recently had the opportunity to talk to industry veteran Sven Olsen, Managing Director, Region Asia Pacific from Muller Martini about the latest happenings in the area of finishing, and where he sees this heading into the future. Below is the full interview, its a must read.
Q. Can you please give our readers a brief outline of who you are and what your related experience is here in Asia Pacific
Sven Olsen (SO): Originally from Denmark, I’ve been in Asia since the early 90’s, and joined Muller Martini in 2015 as Regional Managing Director in connection with that Muller Martini combined the Asia-Pacific region into one unit – previously Greater China had been run separate to the rest of Asia. Prior to that I had been running a FMCG business in Asia, as well as a beverage packaging business for another Swiss company.
But if you go all the way back to the last century, I actually represented Muller Martini in the Taiwan market, as head
of the long gone EACgraphics. I was also heading up the Heidelberg business in Taiwan for a couple of years before I made the move into FMCG. So when I returned to the print finishing business with Muller Martini it was obviously a very different business from what I had dealt with in the past.
Q. Many years ago, it was a fact that the finishing area of a print house was always left to be upgraded last, has that focus shifted at all
(SO): Nothing has changed and that is a real pity! Especially because most printing houses have much more potential for making significant improvements in their finishing area versus their printing operation, where improvements often are small and incremental. On the other
hand, in the finishing areas many print shops can make huge strides in efficiency and automation with a significant impact on their overall competitiveness and profitability.
One problem here is of course that it can feel somewhat counterintuitive to make such investments when overall print volumes are flat and possibly even sliding and run-lengths continue to decrease. But new finishing solutions that can deal with these changing circumstances is exactly what is needed.
Q. Where is the industry moving to in your view, more digital, more offset or is it still the same mix as before. How is Muller Martini dealing with this in terms of equipment for the various market segments
(SO): The digital transformation in the finishing area is coming also in Asia Pacific. And it might be coming quicker than we think. Just a few years back, the ratio of digital finishing equipment Muller Martini sold in the region (vs. conventional finishing equipment) was less than 10%. This year it’s 25%, and in our 2025 equipment backlog it is one third, but with the different markets in the region moving at very different speeds.
The inclusion of the Hunkeler business in the Muller Martini Group has strengthened the array of digital solutions that we are now able to offer our customers and have also brought us into the cut-sheet segment where our offers previously were limited. Not only have we got additional equipment in our digital portfolio, but we also got 300 new colleagues who live and breathe digital finishing.
Q. What are some of the signs that come to a head when people start looking at upgrading to more modern equipment. Is it just the speed or modular systems or other features
and how do they decide what is the best fit for their print house. What are some of the dangers people need to be fully aware of?
(SO): Speed – or rather output - is still important to some of our customer segments. Principally those who still benefit from long-run jobs (they still exist!). However, these customers will typically have new requirements in relation to automation, such as streamfeeders, palletizers etc., thus minimizing the manpower needed for the new lines.
More prevalent though are print/binding factories who spend more time on setting up their older binding equipment, than they do running them, due to the decrease in average run-lengths. Here all the focus is on make-ready time when considering new equipment. Basically it doesn’t matter if the machine top speed is 12.000 or 7.000, if you are making 3.000 books. What matters is how quickly you can get the line ready and produce sellable books.
In the digital sphere the issues are somewhat different. In many cases
customers don’t know exactly what their future incoming order profile will look like in terms of average quantities, sizes and format ranges. Is it book-of-one or is it 1.500 book average runs? While it potentially is a complex decision for digital printers to make when it comes to the digital binding, there are two basic advises:
1) Don’t try to get one line that can do it all (If it exist, it’ll be inefficient and likely too expensive)
2) Invest in something that is scalable. Meaning, stand-alone equipment without any workflow solutions might get you started small-scale, but it will not get you to the next level when the business grows.
Q. What is the future of finishing looking like in the eyes of Muller Martini. Is Asia also at the same level in terms of accepting new technology as say Europe or the USA.
(SO): You’ll find some of the latest, largest and most automated conventional soft- and hardcover binding lines in
China. So yes, talking conventional binding solutions, Asia is definitely at least on par with Europe and the US.
When it comes to digital printing/binding, US and Europe still have an edge on AsiaPacific, but there are large differences across the region on the acceptance of digital solutions with countries such as Australia, Taiwan and Korea leading the way, with China starting to show some progress as well. On the other hand, the level of acceptance of digital book printing in Japan is frustratingly low. But we have a suspicion that this is more an industry issue than a consumer acceptance issue.
Overall, there will be a time where any book printer will be faced with the question of to which extent their business will transform into a digital operation. In Muller Martini we want to be ready to assist our customers to drive this digital transformation.
Q. What is the one question you and your sales force in Asia/Pacific hear more times than others. (like service costs, upgradability etc)
(SO): Can you help me reduce my manpower requirements? Traditionally
Asia built a lot of its competitiveness on low personnel costs. This is changing. Salaries are increasing and so a related cost to social welfare etc. Furthermore, finding qualified operators is a constant struggle for many companies, and in parallel demand for consistent quality has increased. Therefore, equipment lines that require less staff and less human intervention (=more consistent quality) are what many companies are looking for when they upgrade their machine portfolio.
This is also reflected by the fact that we see more and more instances of where customers replace two old finishing lines with just one new line, and still being able to produce the same volume with less than half the staff.
Q. What is your view on the Newspaper industry and its future when you consider how people get their news these days via the web etc.
(SO): Personally I’m a big fan of newspapers (I’m giving away my age). However, the writing is on the wall, the traditional newspaper is disappearing quickly around the region. Possibly with the exception of India where newspapers may be able to survive for a
longer time due to the unique population circumstances.
That being said, we are currently working on a handful of digital newspaper projects in different markets. So there might still be a niche for printed newspapers in the future, but with significantly different circulation figures.
Q. How was the drupa 2024 show for Muller Martini with a focus on Asia Pacific
(SO): We are still walking around with our arms up above our heads! We had a really good event with a lot of visitors from Asia-Pacific experiencing our concepts for Driving the Digital Transformation.
This resonated really well with our customers from Asia, which was also reflected in the number of committed customer orders we received that came in significantly above expectations. An accomplishment we’ll try to replicate during the coming Hunkeler Innovation Days (February 24-27, 2025) and China Print (May 15-19, 2025).
Q. In closing what is the best advice you can give companies when they start the process of looking for finishing equipment to purchase
(SO): If you are in the finishing business for the long term, make sure that this is reflected in the way you set up your operation and the business decisions you make. That’s what we do in Muller Martini, as we aim to practice what we preach.
The Vareo PRO perfect binder is the most ideal perfect binder for print finishing specialists and printing plants that use conventional printing modes or are engaged in digital printing. Whether for medium, short or ultra-short runs, right down to runs of one copy, the Vareo is an all-rounder and stands for outstanding binding quality. The first book produced with the three-clamp perfect binder is already available for sale.
mullermartini.com/vareopro
MPS is excited to introduce the EF Packaging press, a powerful expansion within our portfolio that’s designed to meet the evolving demands of the market.
The MPS EF Packaging press builds on the foundation of the MPS EF narrow web press series that represents the benchmark in label printing known for its high automation level and ease of use in terms of operation. With the introduction of the EF Packaging press, a press that is targeted at flexible packaging and shrink sleeve applications operating at an extended web width of 26” can open new markets and opportunities for label converters that look to venture into different market segments or flexible packaging converters that are looking for a solution for short runs.
Designed to meet diverse market needs
The EF Packaging press is specifically engineered to deliver exceptional results across a broad spectrum of applications, including:
·Wrap-around labels
·Shrink sleeves
·Flexible packaging
·Laminated products
·Filmic labels or products
In today’s competitive landscape, the need for versatile, high-performance printing solutions has never been greater. The EF Packaging press addresses this need by providing unmatched flexibility and precision, ensuring that your business can tackle even the most challenging print jobs with ease.
The EF Packaging press: your competitive edge MPS has long been recognized as a leader in the printing industry, and the EF series is a testament to our commitment to innovation and customer satisfaction. The new EF Packaging press continues this tradition, offering a wider print format that not only boosts production capacity but also offers extremely quick change-over times between jobs, allowing you to maximize uptime and meet tight deadlines.
What sets the EF Packaging press apart is its unparalleled user-friendliness. Designed with operators in mind, this press ensures that even the most complex tasks can be executed with ease, minimizing the learning curve and increasing operational efficiency.
At the heart of the EF Packaging press are several unique features that elevate its performance and make it an essential tool for modern printing operations:
Elevate your printing possibilities with Extended Colour Gamut (ECG) technology. Our MPS presses enable you to produce 97% of Pantone colours using ECG along with unparalleled image detail.
· Crisp.Dot Technology: Achieve the highest level of print quality, and repeatability, no which substrate.
· E-Sleeve Technology: Experience quick and effortless changeovers, reducing downtime and increasing the number of jobs you can complete in a day. MPS patented lightweight aluminum E-Sleeves guarantee an even distribution of print pressure and durability.
· Lightweight, Fast-Change Ink Chamber
Doctor Blade System: This system, which can be used with or without an ink pump, in combination with the MPS slide-out ink drawer, minimizes ink waste, optimizes flexibility, and allows for fast ink changeovers with ergonomic handling for the operator.
These features are designed not just to improve the quality of your prints, but also to enhance the overall efficiency of your production process, ensuring that you can deliver more in less time.
Advanced automation for consistent results
The EF Packaging press is equipped with advanced automation features that make it a reliable and efficient choice for your printing needs:
· Fully Automatic Mark-to-Mark Register
Setting: Ensures perfect alignment, reducing errors and material waste, and delivering consistent results with every run.
· Dynamic and pre-settable impression settings: Allow for faster job setup and consistent print quality throughout the print run, significantly reducing make ready waste.
· MPS Virtual Coach: Provides continuous guidance to operators based on real-time data from MPSConnect, helping you maintain peak efficiency and optimize operator performance.
· MPSConnect enhanced service platform: This platform is designed to improve uptime, productivity, and efficiency, offering valuable insights and support to keep your press running smoothly and profitably.
We understand that every business has unique requirements, which is why the EF Packaging press is fully customizable. You can choose from additional modules to
create the ideal press configuration for your specific needs:
· MPS Rotogravure Printing Unit: Ideal for adding water-based and solvent-based metallic inks, whites, or varnishes to your prints.
· MPS Solvent-Based Printing Unit: Perfect for applying water-based and solvent-based primers, whites, or varnishes, allowing for a wide range of applications.
· Turner bars: Designed for printing on the reverse side of the material.
· Lamination modules: Used for laminating different materials.
Invest in the Future of Your Business
The launch of the EF Packaging Press is more than just an introduction of new equipment - it’s an opportunity to enhance your business’s capabilities and stay ahead in an increasingly competitive market. With its wide print format, advanced automation features, and customizable options, the EF Packaging press is designed to help you achieve greater efficiency, productivity, and profitability.
drupa 2024 was all about what can make printing better now, but also what the next four years could hold. Here are three trends we spotted on the exhibition floor that could define the future of flexography:
In hall 15 at drupa 2024, surrounded by press manufacturers, every stand was talking about new automated features and visitors were looking at automation to find new value today and in the future. That means significant investments are being made to automate press functions.
But any value in print automation can only be realized if the process being automated is consistent and predictable enough to not require frequent human intervention.
It’s clear that automation needs to be paired with standardization. It relies on a consistent print process and consistent, reliable results. By taking a modern flexo approach – that moves away from ‘craft’ processes on press – printers can start automating steps in their production,
harnessing the potential efficiencies on offer.
Striving for sustainability
Sustainable print was a hot topic at drupa. Visitors to our stand were discussing the growing demands to meet what brands, consumers and regulators are asking for.
But what was also clear was the twin pressures printers were focused on: driving efficiency in how they operate while becoming more sustainable. This is a fast-moving trend that we will continue see in the years to come.
It was great to be able to talk about the potential of modern flexo to reduce costs and operate more efficiently while printing in a more sustainable way –two for one. And a chance to explore how we can continue to help customers
By Andy Yarrow, Regional Commercial Director, Asia Pacific Region, Miraclon
benchmark their environmental impact and meet the regulations they’re facing.
Alliances to achieve
Forging success through strategic partnerships and alliances well and truly landed on the exhibition floor at drupa. The flow of partnership announcements was steady, reflecting a key strategy the industry is adopting to solve the complex challenges it’s facing: from the continued skills shortage to sustainability stepchanges.
It’s an approach we’re familiar with, our work with partners across the flexo value chain is critical in the move to modern flexo.
Visitors to drupa saw our plates in action at 12 stands around the exhibition hall: in press (and press-related equipment) demonstrations, and as the plate used for challenging print samples, a strong reflection of the close alliances we’ve been forging.
With so many industry players and visitors in the same place at the same time, drupa was once again a great place to take the temperature of the industry and look at what the flexographic future could hold.
Simply consistent
Decrease waste and setup with predictable plates
Simply efficient
Increase on-press performance with a robust plate
Simply sustainable
Support sustainable inks and substrates all with the same plate
Simply better
Address your most demanding brand and quality requirements
From prepress to on-press, deliver the efficiencies and productivity needed from your plates to maximize your bottom line.
We had the chance to talk to Lars Kraeft Chief Commercial Officer and Roy Schoettle VP Asia Pacific about the market at the approach XSYS are taking *(Note - since the interview XSYS has announced the signing of the acquisition of the MacDermid Graphics Solutions Business. We will do a separate story on this at a latter date)
Q: First Lars could you give our readers a little background on yourself
LK: I joined XSYS a year ago, and my first 12 months have been filled with exciting industry events featuring XSYS's participation. Notably, drupa 2024, the world's largest trade show for our industry, where XSYS made its debut as a stand-alone company. Alongside these events, XSYS launched significant and innovative products across all divisions, including printing plates, equipment, software, sleeves, and adapters.
I bring over two decades of experience in international sales, having had the privilege of working with renowned companies such as VOITH TURBO GmbH, ZF Friedrichshafen AG, and Rolls Royce Power Systems. Since joining XSYS as Chief Commercial Officer last September, I have been closely collaborating with our teams to drive commercial excellence.
Q: Roy can you also refresh our readers about yourself, most know you after your 25 years being the face of Flexo” in the region but a recap would be nice.
RS: Yes Indeed, for the last 25 years I am handling the plate business of XSYS and its predecessors Flint Group and BASF Printing System in the Asia Pacific region. We saw big changes in our approach to the business as well as in the development of our sales. We started here with one technician operating out of Bangkok and servicing the market through a team of distributors in 15 markets.
At that time my responsibility also included the offset and flexo ink business as well as the pigment business for the region. Today, we have a large team of sales, technicians and engineers operating in most of the market we serve. Our customers can enjoy the dual support of an excellent distributor network and the XSYS team they have access to on an almost 24/7 basis.
Q: For both of you, you had several new product launches at the recent Drupa show, give us a overview of these and how was the response and what will be your priorities in rolling these out into both the global markets but here in Asia Pacific
RS: At the recent Drupa show, we had the opportunity to launch several innovative
products that garnered significant attention from the industry. One of the highlights was the introduction of the nyloflex® eco series, a groundbreaking line of flexo plates that incorporate up to 29% renewable raw materials into their formulation.
These plates not only maintain the high print quality that our customers have come to expect but also offer a 20% faster processing time, resulting in energy and time savings. This series marks a significant step forward in our commitment to sustainability, and the response at drupa was overwhelmingly positive, particularly from customers focused on improving their environmental footprint.
Another major launch was the Catena ProServX, a cloud-based tool designed for real-time equipment monitoring,
which elevates the efficiency of our Catena plate processing and ThermoFlexX TFxX Imaging equipment. This tool is a game-changer in terms of proactive maintenance and quality control, providing customers with deep insights into machine performance and consumable usage, thus advancing their operations toward Industry 4.0 standards.
Additionally, we introduced EcoFillX, an innovative software feature for our ThermoFlexX imagers that significantly reduces the amount of solvent used in the plate washing process. This feature targets non-image areas of the plate, reducing solvent consumption by up to 30%, which not only lowers operational costs but also contributes to more sustainable platemaking processes.
Q: Lars, with these new products, how do you determine what direction you needed to drive the company in these developments, is it customer feedback or looking at the competition
LK: The direction we take in developing new products is primarily driven by close collaboration with our customers. We make it a priority to listen to their needs, gather their feedback, and integrate their insights into the product development phase. This customer-centric approach ensures that the solutions we bring to market are not only innovative but also aligned with the practical requirements and challenges faced by our customers.
Our approach goes further. We actively collaborate with leading industry partners, such as press manufacturers, and participate in Flexo associations worldwide. These partnerships enable us to exchange knowledge and expertise, keeping us at the forefront of industry developments and ensuring our innovations remain relevant and forwardthinking.
When it comes to sustainability, we recognize that our industry is undergoing a significant shift towards more sustainable practices. At XSYS, we are
committed to leading this change. We understand that while the impact of one company’s actions might seem small, if the entire industry and value chain moves in this direction, the collective impact could be monumental. This belief drives us to not only innovate in ways that reduce our environmental footprint but also to encourage and support others in the industry to do the same.
Q: How well do you think these new products will be put into practice here in the Asia/Pacific region (where most of our readers are from) and how different is your approach to the market compared to the competition. Do you feel that this is what our industry needs now.
RS: We feel that these products will fit perfectly into the Asia Pacific. As you know, almost every conference and convention is focussing these days on Sustainability, Circular Economy, renewable resources, zero waste, etc. We had that same topic also as the core for last
years SHIFT conference. So, the market is asking for ways and solutions to deliver more sustainable production methods and products. Thus our new plates and software solutions are answering that call.
Of course, there will be differences from market to market and customer. However, the desire for a more sustainable approach in our industry is undeniable. With that we can confirm that also our competition is trying to meet the environmental concern of our industry. However, we believe that with our latest launches we were able to leapfrog our competitors in this area of concern. Thus, it is our intention to assume a leadership role in the area of resource preservation in our industry in the APAC region.
Q: What about sustainability, it’s been the buzz word for so long now, what is XSYS approach to this and are the dynamics of the industry changing.
RS: As Lars mentioned in question 4,
sustainability is not just a buzzword for us at XSYS; it’s a core component of our business strategy and innovation process.
Our commitment to sustainability is also evident in the recognition we’ve received. For example, our Willstaett site was awarded the EcoVadis Silver Medal in 2022, and we were proud to achieve the Gold Medal in 2023. These achievements reflect our continuous efforts to improve our environmental and social practices. Additionally, we joined the UN Global Compact in December 2022, further solidifying our dedication to upholding the highest standards of sustainability and corporate responsibility.
The dynamics of the industry are changing, with more players recognizing the importance of sustainability. At XSYS, we’re not just following this trend—we’re leading it. We are the first plate manufacturer to invest heavily in R&D to develop a new plate formulation based on renewable resources, enabling faster plate processing and energy savings for our customers.
Q: Where are we heading as an industry in packaging. And I would like to break this down into 3 areas (for both of you)
A. Flexo growing, the same or decreasing (global and Asia)
RS: Flexo in Asia overall is growing strongly, also here it depends on the individual market of course. The implementation of flexo printing is accelerating.
LK: This overall growth trend we also see on a global scale however growth rates are different from continent to continent and sometime even from county to country.
B. Digital and its impact on tradition packaging industry and the markets you serve (global and Asia)
RS: As everywhere in the world also in Asia Digital printing is outpacing all the other printing processes. However, we can’t forget that this is still coming from
XSYS Corrugated Pre Print portfolio of nyloflex® plates for printing on coated and uncoated liners in combination with our automated ThermoFlexX Catena plate processing line and rotec® sleeves and adapters will help reduce total cost of ownership while achieving highest quality printing results.
a relatively small base of installation compared to other printing process. Also there continue to be a number of limitations and conditions for digital which prevents them to break into a meaningful way into the strongholds of other processes.
LK: The growing need for shorter print runs and the demand for variable data and customized packaging will undoubtedly drive further development in digital printing. However, for many applications typically handled by Flexo and other mature printing processes, digital printing does not yet provide a complete solution. What Roy mentioned for Asia is equally true for the rest of the world.
C. Gravure, growing, the same or decreasing (global and Asia)
RS: Whilst other printing processes are taking business from Gravure, the installation base in Asia is huge and within the packaging industry Gravure in Asia is dominating and will most probably dominate for the foreseeable future. Even if gravure where not to
grow, it will take many years to replace all the existing gravure presses through other technologies. Nevertheless, as flexo closed the quality gap to gravure for a few years already, we anticipate that more and more gravure jobs will be converted into flexo.
LK: The global print market is evolving rapidly, driven by changing consumer, retailer, and client demands. The growing need for more variation and shorter print runs is accelerating advancements in flexographic technology to improve efficiency in an increasingly digitalized environment. Outside of Asia, Flexo already holds a larger market share than Rotogravure.
Flexo continues to develop both qualitatively and quantitatively, with advancements in automation, new ink chemistries, and innovative printing plates. In contrast, gravure printing faces challenges in achieving competitive advantages, relying on consistent reorientation or upgrades to existing equipment. Its weaknesses—high investment and pre-printing costs, long
delivery times, cumbersome cylinder storage and handling, setup costs, and start-up waste—remain unchanged.
Q: What are the areas that your customers need to be aware of.
LK: Governments worldwide are introducing new directives to support environmental sustainability. Given gravure's larger negative impact on the environment, these regulations may accelerate a shift from gravure to flexo, positively affecting the growth of our customers and markets. Additionally, as average print job lengths decrease and time to market shortens, Flexo is becoming the preferred printing process, especially with its ability to achieve quality comparable to gravure.
We anticipate a growing shift towards FTD (Flat Top Dot) due to its quality advantages, reduced waste, and potential for ink savings. This trend will likely be accompanied by a broader adoption of ECG (Expanded Gamut) printing. With its unique and comprehensive portfolio of equipment, software, and printing plates, combined with exceptional service, XSYS is well-positioned to support customers through this technological shift.
Q: And last, prices going up., staying the same. How will you strategies and manage any change here to benefit your customers.
LK: To address pricing challenges in the market, a key factor is the combination of innovation and cost control, particularly concerning primary raw materials. XSYS is no exception to this approach. Despite significant increases in raw material costs due to macroeconomic issues post-COVID-19, XSYS has expanded its supplier network to secure multiple sources for each material.
However, achieving sustainable growth requires careful selection of reliable vendors, focusing on quality, stability, and service. It's important to note that a dualsource strategy isn't always feasible for unique raw materials used in XSYS flexo plates, as high-performance products often depend on a specific set of suppliers. While the chemical industry still faces price risks, XSYS has worked hard to mitigate cost impacts with our current suppliers. Nevertheless, it is unlikely that prices will return to the levels seen 4-5 years ago.
The new nyloflex® eco series provides a unique and new approach of printing plates which are using renewable raw materials as part of the plate build up. Beside of being more sustainable, this Flexo plates comes with the advantage of a 20% faster plate processing capability, leading to time & energy savings.
The nyloflex® eco plates have been developed to enhance the quality standard in flexographic printing and lifting it to a sustainable future.
Contains renewable raw material
Proven, consistent quality in a more sustainable way
Suitable for bank- & LED exposure
Energy & Time saving
Stable & reliable plate processing
eco ACT for paper & board applications with water based inks
eco FAC for high performance corrugated post print to cope with all requirements
It has 11 colour channels, including a new Green and can match 99% of Pantone swatches. Building on the success of its acclaimed SureColor S-Series signage printer range, the PrecisionCore printhead is user-replaceable for the first time.
Epson's new eco-solvent printer has additional Green channel, making 11 colours and user-changeable printhead At the Printing United expo, Epson announced the next-generation SureColor S9170. The SureColor S9170 made its worldwide debut at Printing United. Ecosolvent printers continue to deliver wider colour gamuts, faster speeds and better abrasion-resistance for critical signage.
The new 64-inch eco-solvent printer leverages an advanced 11-color GS3 ink set, including Red, Orange and an all-new Green, to achieve an expansive color gamut and faithfully reproduce virtually any color, delivering over 99% Pantone coverage. With the first–ever user-replaceable printhead in its class, the SureColor S9170 delivers consistent high–quality output and unparalleled productivity for small to medium sign shops, print franchises and e-commerce printers.
Matt McCausland, group product manager, Industrial Printing, Epson America says: “Consistent, reliable color is crucial for industrial printers and sign shops to capture attention, accurately represent products, uphold brand integrity, and convey messages effectively. The Epson SureColor S-Series printers has built a reputation based on their exceptional colour gamut. With the introduction of the SureColor S9170, we’ve combined this extreme color gamut with the latest imaging technology in a new modern, sleek form factor to redefine expectations in signage printing, delivering compact printers engineered for reliability, superior image quality, and enhanced production capabilities for sign shops.”
Offering the same expansive colour gamut Epson is known for, the SureColor S9170 leverages UltraChrome GS3 ink, including Red, Orange and an all-new Green, as well as opaque White Ink which
can be used on clear or dark substrates to add versatility and enhance color. The fast-drying ink set allows for same day lamination3 and the ability to mix and match ink packs, providing print shops the opportunity to install either 800mL or 1,500mL pouches of any color to best suit workflow needs.
The SureColor S9170 features the firstever user-replaceable PrecisionCore Micro TFP printhead in its class with an integrated temperature sensor control for reliable image quality and consistent color – job to job, panel to panel. Encompassing a new sleek, compact, modern design with a precise and efficient footprint, the SureColor S9170 supports easy upkeep with automatic daily printhead maintenance and integrates with powerful management tools to streamline production, including Epson Edge Print Pro RIP software and Epson Cloud Solution PORT for production monitoring and fleet management.
Tyler Brûlé is a media, design and global affairs expert and the founder of Monocle magazine. He explains why Monocle remains committed to paper.
“If we look back to when Monocle launched in 2007, there was very much this view that there wouldn't be magazines anymore and we'd be in a world where everyone wore Google Glasses. Yet, here we are 16 years later and as a publisher, we're buying more paper than we've ever bought before.
The world moves very fast, but it doesn't necessarily always go in the direction people think it's going to go. There's a post-magazine generation who find magazines exotic now. I'm a child of the 1970s and there were two dailies lying on our doorstep every morning.
Print offers a different rhythm in terms of people's media habits. When everyone has screen fatigue, we realise that value.
Now, I think print takes on a new quality. It offers a different rhythm in terms of people's media habits. When everyone has screen fatigue, we realise that value.
Obviously, I consume a lot of media digitally – more of a shift away from trade papers and some newspapers. They were never printed on the best quality paper anyway. But I never look at digital magazines. Show me a successful monthly magazine online – where they've really done a great job and people say, ‘God, I can't wait to look at the British Vogue digital edition’ each month. That's just not happening.
We use paper and different quality stock to mark different sections, which also signifies different approaches to content.
Print allows you to stand out because our world is so commoditised by screens. Monocle’s standout is our choice of paper – the choice of suppliers that we work with, and in that choice, the quality of what we're printing on and binding.
I'm looking at the July/August issue and I think there are maybe seven different stocks in the magazine. Each of those stocks fulfils a very different role within the line-up of the title. We use paper and different quality stock to mark different sections, which also signifies different approaches to content. It can be more photo-driven or more text-driven or it can be a texture-driven section as well.
There's a lot of considerations that we look at, both for the experience of the reader as well as our advertisers.
Monocle’s standout is our choice of paper – the choice of suppliers that we work with, and in that choice, the quality of what we're printing on and binding.
The world is moving at different speeds. There are some corners of the world which are still very paper-focused – Japan, for example, where there is a healthy book trade, a healthy magazine trade, some of the highest print circulation newspapers in the world – and then there are other parts of the world where there's next to no paper anymore. But as a global magazine we need to have not just the paper but the distribution channels.
There are so many players involved in getting a magazine into somebody’s hands. At Monocle, we are fully committed to paper. And it’s because we see the demand.
We have to be vigilant every single day. It’s a collective thing. It’s not just down to the paper company. It’s down to the paper company, the printer, the media company, the media owner, the retailer. There are so many players involved in getting a magazine into somebody’s hands. At Monocle, we are fully committed to paper. And it’s because we see the demand.”
Make the move to digital – and unbox your business with the flexibility to accommodate fast turns, versioning requests, last minute edits, and changing buying decisions.
With the new EFITM Nozomi 14000 LED digital press for corrugated packaging and POS, you can reduce process steps from weeks and days to hours and minutes. And personalize runs from one to infinity at higher margins and with lower costs – all in a single pass.
Let’s build your brilliant future. Together.
Scan to learn how corrugated converters and packaging printers are opening up new ways to say, “Yes!”
• Fast, cost-effective, and high-quality in-line matte finishing process brings digital inkjet to profitable new market segment
• New MatteJet technology to drive digital adoption across the industry, further empowering converters to embrace inkjet technology for a smart, connected printshop
Gallus is poised to transform the narrowweb print landscape with its latest research breakthrough: Gallus MatteJet technology. Announced at Labelexpo Americas 2024, the landmark innovation represents an important advancement in inkjet printing, unlocking a premium matte finish previously unachievable with digital inkjet, bringing the possibilities of inkjet technology to the wine label market for the very first time.
Exemplifying HEIDELBERG’s position as a total solution provider for all modern printing processes – offering the entire spectrum from toner to inkjet, offset
printing to flexo and all controlled from a common Prinect workflow – MatteJet was developed in-house at Gallus’ innovation hub in St. Gallen, the Gallus Experience Center. At Labelexpo, Gallus exhibited alongside HEIDELBERG, where it showed how this transformative innovation addresses one of the key challenges that has historically restricted the growth of digital inkjet technology. Also how MatteJet will transform the entire market segment for wine and spirit labels and provide converters with the key to a profitable new area of business growth.
The glossy finish inherent to digital inkjet technology has been one of the foremost barriers to its widespread adoption across labels and packaging – specifically in premium segments such as wine and spirit labels where brands traditionally expect a sophisticated matte finish. Until today, this was only achievable through conventional printing, or the addition of post-processing equipment to utilize matt varnishes, adding time, complexity and cost.
Now, in a groundbreaking industry milestone, Gallus MatteJet technology delivers fast, cost-effective, and high-
quality matte finishing capabilities, integrated directly into the digital inkjet process. This will allow converters, for the first time, to achieve a high-end matte finish at the touch of a button, without changing inks or adding overprint varnish, eliminating the need for external finishing processes or separate conventional machines.
By removing one of the key barriers traditionally restricting the expansion of inkjet printing, Gallus’ new innovative process presents an enormous opportunity for converters to now access a highly profitable market segment. Importantly, MatteJet will also enable more converters and brands than ever before to enjoy the benefits of digital printing, such as more profitable short runs, personalization, and on-demand printing – representing a huge leap in the industry’s digital transformation.
“The development of Gallus MatteJet technology marks a pivotal moment in the evolution of inkjet printing, opening up a world of new opportunities and ultimately, completely transforming the very foundation of what’s possible with inkjet technology,” comments Dario Urbinati, CEO, Gallus Group. “By unlocking matte finishing for digital inkjet, we’ll be able to make an entirely new market segment accessible to converters without the sizeable
investment into separate offset solutions – boosting profitability and exemplifying our commitment to building a new era of flexibility that will enable our industry to thrive long-term.”
Developed as part of the company’s ongoing R&D efforts at the Gallus Experience Center – established last year to drive innovation through collaboration for long-term industry-wide success – the new finishing process leverages advanced, cutting-edge technology never-beforeseen in labels and packaging.
“The new MatteJet technology is revolutionary not just in the opportunities it opens up, but also in what its development represents,” continues Urbinati. “We opened the Gallus Experience Center with a vision for a dynamic, collaborative industry hub that would drive significant, meaningful industry change.
Gallus MatteJet exemplifies and is testament to the kinds of transformative developments that can be achieved when you combine this vision with realworld insights as to what the market needs today, and of course the essential resources and expertise of our parent company, HEIDELBERG. MatteJet truly embodies our long-term mission and brings the smart, connected print future within touching distance.”
Designed to integrate with Gallus’ Digital Printing Unit, the new MatteJet technology also represents further expansion of Gallus’ System to Compose concept, which provides unprecedented levels of compatibility across its leading product lines. Under the System to Compose, converters can add, adjust and remove units to their Gallus One as their business needs evolve – now further expanded to comprise workflow and service options as well as equipment, following its overwhelming reception at drupa 2024.
The latest iteration of the Gallus One also makes its global tradeshow debuted at Labelexpo, in the newly-expanded 430mm web width, unlocking more application possibilities than ever before. Visitors to the stand saw firsthand the possibilities achievable with its recently-extended color gamut, with the integration of Orange and Violet Saphira inks developed jointly in-house with HEIDELBERG, and helping converters to achieve shelf standout for brand differentiation.
As a subsidiary, Gallus remains an important pillar in the company’s growth strategy for the packaging and label market and will continue to play a key role in the HEIDELBERG future.
Canon today announces the addition of its FLXflow technology to the Arizona 1300 series, which brings new productivity and performance features to the flatbed printer series.
Previously known as FLOW technology, the new FLXflow offers not only the original ‘Hold’ functionality, which helps to hold media down on the flatbed table, but also the new optional ‘Float’ and ‘Instant Switch’ functionalities to improve media handling. With over 8,000 installations worldwide, Arizona users can now benefit from enhanced productivity, print quality and application versatility thanks to FLXflow, a range of print modes, ease of use, workflow optimisation and UV-LED curing technology.
The Canon Arizona 1300 FXLflow Catering to growing mid-volume operations, the Arizona 1300 FLXflow supports a wide variety of substrates and applications. This enables large format graphics printers and other print service providers (PSPs), to offer customers a wide range of applications for the retail, interior décor, packaging, and industrial market segments more efficiently.
Offering a patented way not only to hold but also to float the media, FLXflow comes with three functionalities – Hold, Float and Instant Switch – allowing users to move heavier and irregular-sized media faster and more easily around the table.
The Hold functionality, a feature of the original FLOW technology, works by keeping the media in place with a patented airflow technique. Using automatic measurement and adjustment of airflow levels to firmly and accurately hold various types of media in place, the functionality results in flexible positioning with far less masking.
The new Float functionality pushes air from the table upwards to create a cushion, enabling the easy positioning of heavy or challenging substrates and reducing the risk of media damage or waste. It also results in the smoother registration of all types of media, with a ‘floating without drifting’ functionality
enabling several pieces of media to be precisely positioned at the same time. The Instant Switch functionality allows the operator to easily change from Hold to Float by using the foot pedal(s) for simple operability of the printer, making it easy to remove media from the table. Enhanced flexibility
Arizona 1300 FLXflow customers can also take advantage of the Advanced Image Layout Controls, which allow lastminute adjustments at the printer, giving additional flexibility when positioning substrates on the table and reducing waste of expensive materials. Productivity is further enhanced by service support tools such as PRISMAservice, which provides predictive maintenance and facilitates authorised remote assistance by qualified service technicians to increase uptime. In-field upgradability
Existing Canon Arizona 1300 FLOW users can upgrade to FLXflow technology Customers of the current Arizona 1300 series with FLOW technology can upgrade their printer to the latest version with FLXflow technology, including
The varioPRINT iX-series revolutionises the commercial printing business experience. It combines stunning image quality and a wide media range with the high productivity and the attractive cost-efficiency of inkjet.
P R O D U C T I V I T Y . Q U A L I T Y .
V E R S A T I L I T Y .
As a global market leader in sheetfed inkjet, Canon offers more experience in this segment than others. Invest with confidence to expand profit and opportunity! Experience iX!
the optional Float and Instant Switch functionalities. Upgrades also include features like the Advanced Image Layout Controls.
They can also add PRISMA XL Suite workflow software to provide a preview function, which allows users to see what the final product will look like before it’s printed while allowing them to make any necessary adjustments. This makes it possible to preview complex, multilayered, textured jobs and to provide cost estimates before printing, thus saving time.
The Canon Arizona 1300 FLXflow offers new ‘Float’ and ‘Instant Switch’ functionalities to improve media handling
Available with the Arizona 1300 FLXflow is PRISMAelevate XL, which enables layered printing up to a height of 4 mm (0.157”) to help customers create stand-out, tactile artwork for elevated print applications that enhance and expand their product offering. It enables customers to explore new applications, such as high-value, textured, permanent signage, product decoration, awards, décor materials and package prototyping, as well as applications for the visually impaired.
PRISMAelevate XL software makes prints durable without additional finishing steps, such as lamination, coating or spray varnishing, and results in less waste and higher production efficiency. Designed with circularity in mind
Offering reduced waste and lower energy consumption than its predecessors, the Arizona 1300 FLXflow has been designed with the circular economy in mind. FLXflow technology requires less masking and underlays to hold media in place, resulting in less waste.
As LED-UV printers, the series also consumes at least 15% less energy compared with its UV-halide predecessors, and offers power-saving features such as first-time-right printing and instant-on functionality. Its inks are UL GREENGUARD Gold certified, which ensures prints are safe for use in sensitive environments such as hospitals, schools and other public places.
Customers can also take advantage of Canon’s remanufacturing programme, where they can trade in their Arizona printers when purchasing a replacement. These older systems are inspected, serviced and prepared for sale as refurbished printers, further extending the lifespan of the Arizona.
The Arizona 1300 FLXflow is available immediately via accredited partners as well as from Canon’s direct sales organisations.
https://issuu.com/cpublish/docs/2024_asian_print_ awards_flyer
https://issuu.com/cpublish/docs/2024_asian_print_ awards_flyer
https://issuu.com/cpublish/docs/2024_asian_print_ awards_flyer
https://issuu.com/cpublish/docs/2024_asian_print_ awards_flyer
An Intense one day program you must be part of
For the first time, the Asian Print Awards will hold an industry conference that will cover ALL areas of print production. If you put INK on PAPER then come and join us for this 1-day event, followed in the evening by the regional only printing competition, the Asian Print Awards.
The day’s events
Asian Print Awards Industry Conference
Morning ession from 10:00 am till 1:00 pm. (Lunch Break)
Afternoon session from 2:00 pm till 5:00 pm
Coffee and tea in the display area till 6:00 pm
Asian Print Awards 2024 Cocktails from 6:00 pm till 7:00 pm Awards Gala Dinner 7:00 pm till late
Hear from companies and people who know what is needed to help your business grow. Also hear what technologies at drupa shape our industry. What you should look out for and be aware of as you drive your company forward.
Title Sponsor Sponsor
Jarkata Indonesia
13th November
https://reg.eventnook.com/event/asianprintawardsindustryconference/home
https://issuu.com/cpublish/docs/2024_asian_print_
https://issuu.com/cpublish/docs/2024_asian_print_
https://issuu.com/cpublish/docs/2024_asian_print_
Click on the logo to download the 2024 Entry Form
Fujika Co., Ltd. was founded in 1970 as a paper wholesaler and currently sells printing paper and paper products and performs print processing.
1987 they have actively invested in equipment, including the introduction of over 10 Komori machines, and in January 2023 they introduced the new Apressia CTX132 Programmable Hydraulic Clamp Cutting System. We interviewed President Yoshiaki Kato, Operating Officer and Production Control Division Manager Kouji Kato, CD Section Leader Toshimitsu Yonezaki, and Production Control Division Printing Team Leader Masayoshi Katayose about the effects of introducing this machine and the Lithrone G37P advance 37-inch Convertible Perfecting Offset Printing Press introduced around the same time.
Automated, easy-to-use cutting machine solves the issues of aging and lack of successors
Engaged in both wholesale paper sales and printing on consignment, Fujika leverages its solid knowledge of paper and extensive knowhow and paper-related experience to propose optimal paper and print processing to its customers. President Kato said, “We are working to enable printing companies to focus on planning and production by taking on part of their print production.”
The company has been actively enhancing their equipment to complement their
customers’ manufacturing. Aging cutting operators and the lack of successors were the background to the introduction of the Apressia CTX132 this time. A high volume of cutting is required for both the paper supplied to customers and the cutting required by the printing process. As a result, the cutting machines are characterized by an extremely high frequency of use.
However, retaining skilled personnel and passing down their expertise has been a long-standing challenge, as the role of a cutter involves a high degree of craftsmanship.”
When Kato saw the announcement of the launch of the Apressia CTX series, he was excited and thought, “This is the first time I’ve come across a paper cutting machine that can be automated and requires no skilled labor. I wanted to try it. If we can automate cutting work with a high degree of precision, it might complement the skills of craftsmen.”
Apressia CTX132 significantly increases cutting production volume The Apressia CTX132 is equipped with unique technologies such as Apressia Front Loading and the Apressia Rotary Gripper. While automatically transporting and cutting the paper, the operator can stack the paper onto the jogger, enabling one-person operation. Division Manager Kato explained,
“Previously, we needed an assistant worker, so for two machines we required a team of four persons, but now we can operate the one existing machine and the Apressia CTX132 with a team of three people. This is possible because the Apressia CTX132 allows for oneman operation without the need for an assistant.
By assigning the freed-up person to the newly installed shrink-wrapping machine, bottlenecks in the processing department after cutting were eliminated, smoothing the production flow. The cutting production volume increased by 130% in the three months after installation compared to the three-month period prior to installation.”
President Kato also said, “In addition to covering the increased printing volume with the Lithrone G37P advance, the flexibility and efficiency of personnel have improved, giving the impression that overall productivity has increased by about 50%.”
Division Manager Kato looked back on the pre-introduction days, stating: “Cutting was completely manual work, and specific skills and experience affected precision.” CD Section Leader Yonezaki evaluated the precision of cutting today, saying, “By using front loading and side pushers, the variability among operators has been eliminated, and uniform precision can be achieved.”
He added, “Automated cutting has eliminated the need to rotate the paper, significantly reducing the physical load. Also, thanks to the AWR (Automatic Waste Removal) function, there’s no need to stop work to dispose of waste, allowing time to be spent on training and taking care of details, so we can always move with the flow of activities in mind for efficiency. Also, the paper alignment
on the unloader is very good, helping to stack neatly. I think it’s a very good machine.”
President Kato also appreciated the support system, saying, “Like the printing presses, it responds quickly, which is reassuring.”
Handling the increase in printing volume with the Lithrone G37P advance
The company introduced the Lithrone G37P advance in December 2022. President Kato said, “The increase in the workload with single-sided presses alone had reached a limit. The Lithrone G37P advance, a one-pass double-sided printing press, contributes with overwhelming productivity that is about 50% higher per hour compared to conventional machines.”
Division Manager Kato also added, “Compared to the existing 40-inch press, the 37-inch press has a smaller
plate size and it uses less electric power, achieving energy-efficient printing. Since we originally used the Lithrone A37, the operation is the same and operators quickly mastered it.” Printing Team Leader Katayose said, “The fans in the delivery can be finely adjusted, making air adjustment easy, and stable production at the highest printing speed of 15,000 sph is possible.
The function that maintains density during printing makes it easy to stabilize the color, so even young workers with less experience can be assigned with confidence. High-quality printing can be maintained, so I think it was very good to introduce it.”
In the future, the company plans to fully pass on cutting technology by utilizing the JDF linkage function of the Apressia CTX132. Division Manager Kato expects, “By utilizing the function that automatically calculates the cutting process from imposition data and guides the order and position of cutting, the burden on instructors will be reduced and the time required for training can be shortened.”
Finally, President Kato said, “We will stick to our role as the ‘stagehand’ that complements our customers’ factory functions. We aim to be trusted by promoting further automation and workforce reduction to improve productivity. We will also work on environmental issues and creating a comfortable work environment for our employees, promoting a company that can contribute more to society. We look forward to continued support from Komori in terms of machine support as well as the best proposals regarding quality, productivity, and competitiveness.”
This prestigious ennoblement of the physical book as object stands out: the coloured edge book or book edge printing as an “old” and new form.
The optics, colour and design alone are also important sales arguments at the point of sale for books as consumer goods and cultural assets. The challenge for many creative people in the print and media industry has long been how to revitalise classic book design with innovative ways of expression.
Needless to say, graphic designers and typographers, media designers and publishing house manufacturers are aware that this basically involves defined geometric shapes such as corners and edges, pages and surfaces. Then again, the many possibilities for " embellishing" print publications seemed to have been largely exhausted in recent years.
The enhancement of hardcovers and softcovers of various genres is nowadays not limited to covers, book covers and back covers. In favour of further visual enhancement, book edgings can be printed as desired after the book block has been trimmed. For over five years now, this
attractive finish has been spreading rapidly - also thanks to digital inkjet printing in the print product world.
Strolls through historical libraries reveal: Indeed, the coloured edge book is not a new invention. Leather-bound Bible editions with gilded edges have always been among the most valuable publications. Even a visit to a modern bookstore today shows: Meanwhile, colour variants of filigree ornamental patterns on editions of novel series are also gaining popularity again.
Be it coloured areas and gradients, typographic elements and lettering, filigree illustrations, subtle patterns, images or photos that visually run from the book cover to the edge of the book: Colourful works can be found in fiction and entertainment, non-fiction and specialist books as well as art books, in corporate publishing editions and in the stationery notebook range. Not only should editors
and publishers of print publications define a coherent design for the cover or book cover and book block, they should also coordinate the workflow in the correct sequence with the commissioned service providers in good time before production begins.
Hardcovers and softcovers with book edge printing can eventually create a positive mood and, in combination with colouring and 3D fascination, inspire both clients and consumers. A number of printing companies, paper processors and bookbinderies use "self-made" machines. More frequently, systems from
Durrer from Immensee, Ochsner from Schmerikon or Schmedt from Hamburg are used based on inkjet printing units.
Intriguing technologies
Book objects are embellished with glossy, shimmering and luminous applications in a particularly striking way. Special colours
as well as day and night fluorescent colours can be used for sprayed and the UV coloured edge book. An inexpensive finishing option is available with the sprayed coloured edge book in accordance with the corresponding colour template or Pantone colour specification.
For foil cutting, foils in various colours are used: in gold or silver, metallic variants such as copper, red or blue, as well as hologram or diffraction foils. Foil cutting can also be finished with hallmark embossing - an attractive decoration for gold cuts. The “eye-catcher” is, for example, the UV book colour cut in combination with rounded book corners in gold. The front-cut underlay, in which an image can be seen when the book is opened, is fascinating - a combination of foil cut and digital printing.
Many different service providers in the print media industry, such as industrial printers and bookbinderies, have dedicated their portfolios to the coloured edge book as a special finishing feature. The bookbindery Richard Mayer from Esslingen am Neckar or the bookbindery Steinbrener in Schärding and Neuhaus am Inn, for example, ensure a high level of attention.
Shanghai Bozhi Graphic Reproduction Co Ltd has installed another ThermoFlexX 60 digital imaging system from XSYS to boost output quality, speed and capacity.
The strategic choice of the high productivity, dual-head TFxX 60D model, with added Woodpecker surface screening technology, is the first of its kind in the country, setting a new benchmark for platemaking in China.
Willstaett, Germany. 02 September 2024 – Shanghai Bozhi Graphic Reproduction Co Ltd specializes in the production of high quality flexographic plates for customers that serve a multitude of global brand owners, such as Procter & Gamble, Johnson & Johnson, Unilever, Disney, Adidas, and Yinlu Foods, as well as fast food restaurant chains KFC and McDonald’s. Applications include wine labels, aseptic packaging, self-adhesive labels, film and soft tubes, and various paper cups, to name a few.
As a member of the Flexographic Printing Branch of China Printing Technology Association, Shanghai Bozhi was among the pioneers in China to embrace ThermoFlexX thermal imaging
technology. In 2020, the company decided to install a ThermoFlexX TFxX 60S Imager which has since elevated its standards in terms of both quality and productivity to higher levels. More recently, the company expanded its ambition with a dual-head TFxX 60D Imager supplemented by Woodpecker surface screening technology.
“With our first ThermoFlexX Imager, we took a real leap of faith because we believed that this technology from XSYS had the potential to revolutionize our platemaking business, and we have certainly not been disappointed,” said Mr. Weining Huang, GM of Shanghai Bozhi. “
That first imager brought us to new heights cementing our reputation for excellent quality and fast, reliable service, so it was an easy decision to implement the new dual-head TFxX 60D machine into our portfolio.”
Second ThermoFlexX Imager with double capacity
ThermoFlexX imaging technology excels through its high speed, excellent quality and remarkable ease of use. Featuring highest levels of automation, it is an open system that can image all digital plates, any brand, whether for solvent, waterwashable or thermal processing.
The ThermoFlexX portfolio includes five sizes of imagers to handle the widest range of plate dimensions. The two 60 model machines at Shanghai Bozhi’s facility can image plates up to 1067 x 1524mm (42 x 60 inches). Minimizing operator intervention, plates are automatically loaded and unloaded with just one touch of a button, while the FlexTray mobile table facilitates easy plate transport and handling to avoid accidental damage. Importantly, the company’s new TFxX 60D Imager is configured with dual 100W lasers effectively doubling productivity by increasing the output from 6 to 12 square meters per hour at the same high quality of 2540dpi.
Shanghai Bozhi also chose to implement ThermoFlexX Woodpecker surface screening technology which boosts solid ink density and delivers a smoother ink laydown with lower volume anilox, to save on costs and gain a further competitive advantage. Applying microstructures to flat-top dots on the plate surface, Woodpecker screening is introduced at the imaging stage without any changes to the workflow and helps maintain print quality at the highest printing speeds.
Bringing in a new era with ThermoFlexX
Partnering with XSYS to enjoy the many outstanding benefits of ThermoFlexX imaging and Woodpecker screening has also supported Shanghai Bozhi in establishing a dedicated technical department to better serve customers. With a team of experts who have more than 10 years of experience in flexo platemaking and printing, the prepress company can now provide customers with all the technical requirements needed to successfully convert print jobs from
offset and gravure to flexo. This not only shortens the lead time for brand owners, but also greatly improves efficiency for the benefits of all stakeholders.
[Mr. Weining Huang] concluded, “The highly innovative ThermoFlexX technology immediately set us on a path of guaranteed growth, giving our company the quality and capacity boost we required. Now with the new dual-head TFxX 60D, Imager we have taken another step up to ensure we stay at the forefront of platemaking innovation in China. We are also grateful for the excellent
partnership with XSYS which ensures that we maximize the full power of our two imagers as we bring in a new era for Shanghai Bozhi.”
Commenting on this second investment, Magenta Zheng, GM of XSYS China, said, “With its high level of automation, impressive speed and exceptional quality, there is no doubt that the new ThermoFlexX TFxX 60D digital imager will significantly enhance Shanghai Bozhi’s competitiveness. We are extremely proud to partner with the company and look forward to growing together with this industry innovator.”
The UV Analyzer is a app-based UV radiation measuering device.
The measuring is quite easy. Put the strip on your substrate, irradiate it with UV and measure the strip with the stick. The app will show you the measured dose in mJ/cm². This dose value can be compared with your reference value to determine aging.
Scope of delivery:
UV Analyzer Stick and reference white, charging cable, lanyard, measuring strips
Sometimes innovation brings incremental benefits. And other times, it can take great leaps forward.
With smartGRAVURE, BOBST has achieved a great, game-changing leap forward for gravure printing. smartGRAVURE totally revolutionizes the gravure printing process from being a highly manual operation to a fully digitalized workflow. The traditional advantages and disadvantages of gravure are well known. While it enables highquality printing and high-speed production with excellent consistency, the setup is timely and expensive, resulting in longer production lead times and making small print runs non-viable.
In addition, gravure printing traditionally has had some challenges around manual and time consuming color adjustment compared to other printing methods like offset or digital printing, and there are also some sustainability challenges around the use of solvent-based inks.
smartGRAVURE changes all that. BOBST has developed smartGRAVURE for its gravure machine platform MASTER
RS 6003. smartGRAVURE offers an endto-end digitalized process, which enables printers to meet and exceed the highest industry standards with ease. It overcomes the set-up time and tuning required with gravure printing, which requires high level operator skills. With offline setup and
automatic selection of the optimal process data for each new job, the machine frees up press time and disengages from the operator skills level.
Therefore, the optimal settings for each print job are automatically determined by smartGRAVURE at the push of a button, while the system continuously ensures that the gravure machines operate with the optimal production parameters during the printing process. Compared to the previous manual setup process, the time required is minimized, input errors are reduced, and waste during setup is significantly lowered.
With ECG printing, digitalized set up and controls, and connectivity with BOBST Connect, smartGRAVURE increases productivity and output consistency, reduces downtime and complexity, and offers considerable sustainability benefits.
Easy as 1-2-3: oneSET, onePRINT, oneECG smartGRAVURE is modular. The complete system includes three components—oneSET, onePRINT, and oneECG (Extended Color Gamut)—each offering various benefits and collectively
revolutionizing the gravure printing process.
oneSET is part of the BOBST Connect recipe management function. It is 100% automated, meaning a fast and accurate machine set-up. After taking over the customer's order data in the form of PDF files, the system suggests the most suitable and efficient machine settings on its own. Importantly, this step no longer needs to be performed on the printing machines but can be moved to the prepress stage. One click is enough to transfer the offlinecreated recipes to the print queue of the machines.
onePRINT is an innovative new inking system with in-line and fully automated process color measurement and adjustment, significantly relieving machine operators. Continuous monitoring and adjustment of the process colors are based on measurements with an inline
spectrophotometer. This provides input for the onePRINT color control, that when combined with oneECG ensures reliable color stability from the first to the last print.
The new system limits the amount of ink in the color circuit to the necessary minimum, reducing ink in the machine by over 50% compared to conventional gravure solutions and reducing ink waste simultaneously.
oneECG is BOBST’s technology for fixed palette printing, now available for gravure printing and an essential element of digitizing this printing process. oneECG works with a fixed set of up to seven printing inks, so gravure printers only need to change the printing cylinders for job changes, while the inks remain in the printing machines. This reduces ink waste. A digitalized version of “color matching” can therefore be performed in
the prepress stage—before the print jobs are transferred to the machine controls.
A smart investment with significant benefits
The benefits for converters and brand owners are immediately clear. Downtime in job changeovers is reduced by up to 70%, enabling significant productivity gains.
The machine provides 100% job repeatability and perfect color consistency. In fact, the MASTER RS 6003 with oneECG technology is officially Pantone validated, providing complete peace of mind.
It has significant sustainability benefits. The innovative technology reduces waste and ink waste drastically by up to 50%, and lowers the energy consumption of this printing process, which also provides an economic advantage.
Excitingly, it opens up gravure printing for medium and short jobs. It enables profitable production of smaller and medium-sized orders from about 5,000 m². Orders can be delivered faster with high profitability, whether they are small, medium or long runs.
For brand owners that require premium quality packaging, gravure has always been the obvious choice. However, until now, it has been a challenge for gravure printers to meet the increasing demands for shorter print runs, faster delivery and more sustainability.
Now, with the leap forward in innovation provided by smartGRAVURE, all of this is possible, setting them on the path for a highly productive and profitable future.
tesa® self-adhesive tape assortment for flexographic label printing
Enhance your label printing processes and boost overall efficiency with our state-of-the-art plate mounting tapes and complementary solutions. Optimize your printing process by utilizing our superior label printing tape solutions or a combination of tape solutions. Find out more about how we can elevate your label printing experience at www.tesa.com.
New water recycling system, combined with CrystalCleanConnect, underscores NABEPROCESS’s dedication to pioneering eco-balanced practices and sets a new benchmark for sustainable manufacturing processes
Asahi Photoproducts, a pioneer in flexographic photopolymer plate development, a subsidiary of Asahi Kasei, today reported that NABEPROCESS Co., Ltd., a major Japanese printing company and one of the first companies in the world to install CrystalCleanConnect, has advanced its sustainability initiatives even further by adding an Asahi AWP-LOOP™ water recycling system to its CrystalCleanConnect configuration. CrystalCleanConnect is an offering jointly developed by Asahi Photoproducts, ESKO, and Kongsberg that automates the flexographic platemaking process, reducing steps from 12 to 1 and dramatically reducing potential for error. The system produces flexographic plates ready for mounting on press.
“The Asahi AWP-LOOP™ system represents a state-of-the-art solution that facilitates the recycling and reuse of water in the plate-making process, drastically reducing environmental impact, said Mr. Yasuo Naka, Flexography Division Manager, NABEPROCESS Co., Ltd. “This strategic move aligns with our commitment to sustainability and operational efficiency. Over several months the system has been operational, we have seen a reduction in water usage of about 50% and an overall reduction in greenhouse gas emissions. We have also seen savings in our waste treatment fees. We are now in a position to phase out solvent-based plate production entirely, reducing our carbon footprint even further.”
In this configuration, NABEPROCESS is using Asahi’s AWP™ water-washable
plates in conjunction with CrystalCleanConnect which automates platemaking and reduces overall time to market. Mr. Naka adds, “We are using the AWP-LOOP™ system once a day on average, working in harmony with CrystalCleanConnect. We engage the LOOP system after a half day of platemaking with CrystalCleanConnect to treat the processing water. By reducing the need for outsourced wastewater treatment, we have achieved significant cost savings.”
“This is a great example of a company that is taking advantage of Asahi’s innovative approach to flexographic platemaking,
increasing efficiency, sustainability, and quality while reducing time to market, all critical elements in today’s highly competitive marketplace,” added Arata Ohnoko, Marketing and Sales Manager at Asahi Kasei.
NABEPROCESS has also been pleased with the installation, calibration, and training that took place upon receiving the AWP-LOOP™ system, as well as previous and ongoing support of its CrystalCleanConnect system, including both remote and on-site support, preventative maintenance, and more.
to print MDO-PE
Highest quality with best register
Connected to RUBY to digitize the value chain ... and many more!
Windmöller & Hölscher KG
Lengerich / Germany
Phone + 49 5481 14 - 0 · info@wuh-group.com www.wh.group/int/en/
Best profitability at printing speeds up to 600 m/min. and fast job changes
FUJIFILM - Scott Mackie
The Rise of the Digital
Gallues Group - Dario Urbinati
Navigating in an Ever-changing Environment
XSYS - Supachai Theravithayangkura
Sustainability in Motion
Bobst (Packaging) - Peter Woods
Latest Trends for Narrow Mid Web Label Production
Bobst (Flexible) Diego Accatino
Topic: TBA
CGS ORIS - Lilly Xiao
Smart Color Solutions for Decor & Packaging!
Miraclon - Andy Yarrow
Introduction to Modern Flexo
MPS - Tham Zee Cheng
Unlocking Printing Success: How to Drive
Productivity and Profit in Uncertain Times
W&H - Niels van Groenendaal
Latest Printing Technology for Sustainable Flexible Packaging
Asian Packaging Excellence
Awards 2024 - Nov 8th
Join us for the highlight of the 2024 Packaging Indusrty at the award dinner ceremony
We will award the winners of the 2024 competition - Gold Silver Bronze live on stage
Come and witness the best packaging companies in Asia and see first hand quality of the highest levels
SOMETHING FOR EVERY COMPANY
The SHIFT 24 conference will cover all industry sectors from:
Heidelberg Asia - Michael Buechel
Unfold your Potential
Tesa Tape - Wong Yi Kai
Mastering the Challenges - Advanced Troubleshooting
Techniques for Flexo Plate Mounting Tape Application
HYBRID Software Bert Van der Perre
Driving Efficiency through Automation and Cloud Integration
COACH - Steve Dawson
Why Audiences Can’t Follow Your Business Presentation
Flexographic
Gravure
Digital Labels
Corrugated
Converting Offset
Embelishment Design
PrePress Ink Paper/Board/Label stock Plates and much more
*We advise to book the meet on arrival and fast track services as at peak times the wait can be very long to clear immigration.
*They can also arrange baggabe pick up - to car for fast and efficent hotel transport.
Website for Vietnam visa services, Fasttrack, and Airport Car: Click below https://www.trustvietnamvisa.com
Website for Fasttrack Service for individuals exempted from Vietnam Visa or those with visas in advance, for expedited procedures at the airport: Click below https://vietnamfasttrackservice.com
Use this code IPC2024 at the payment area and receive the SHIFT24 special rate.