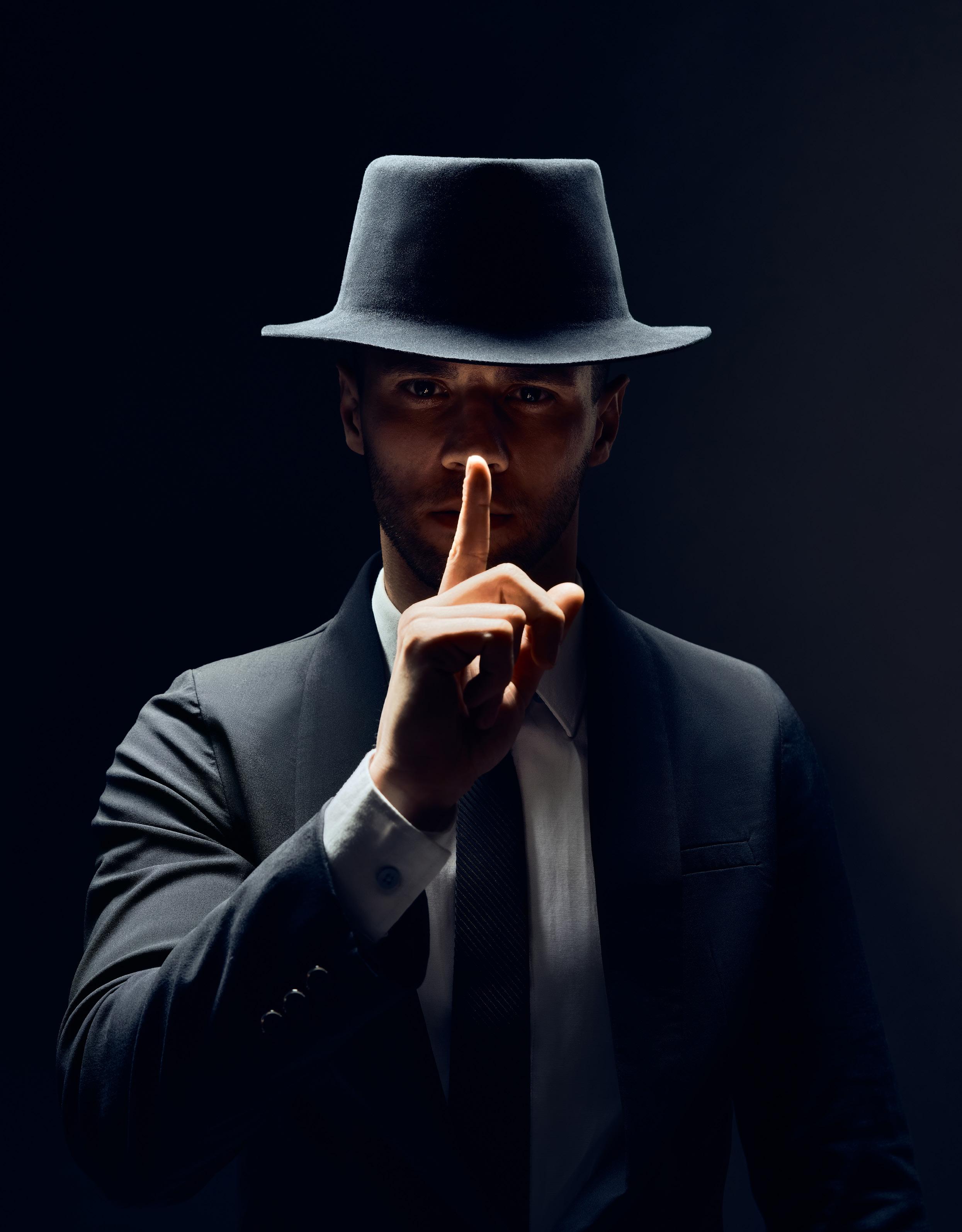
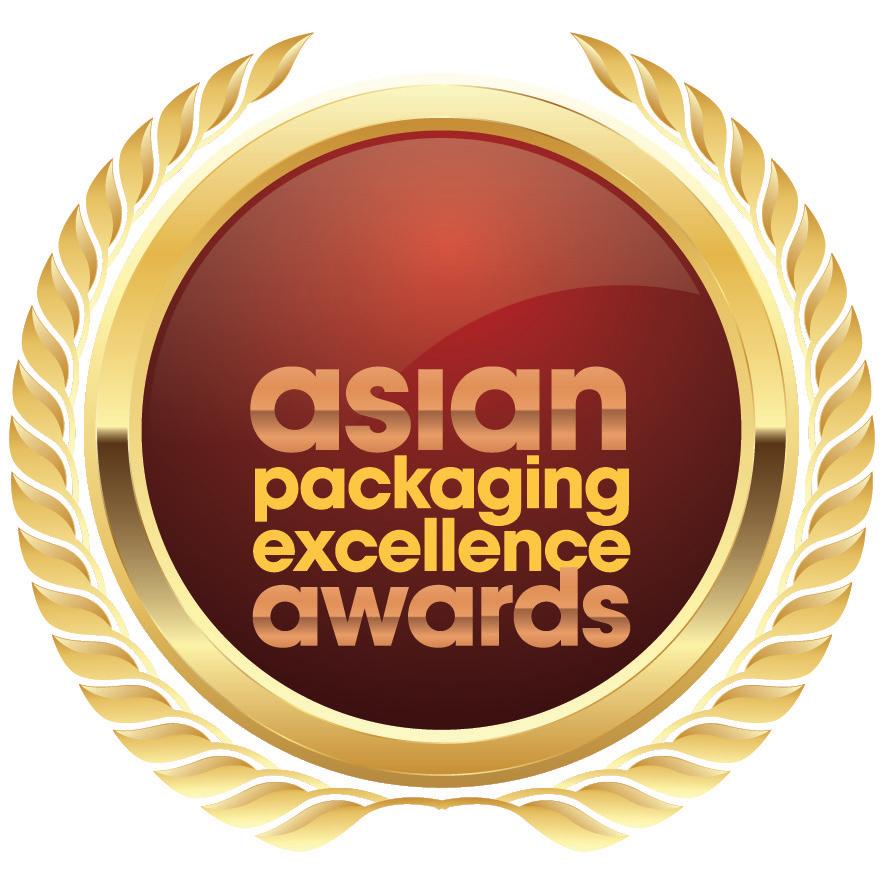
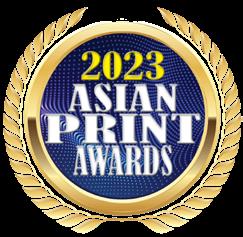
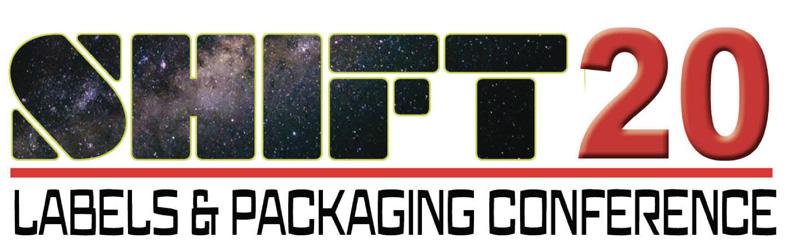
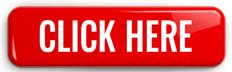
Curious to know who has won the awards? Stay tune to our announcement in November.
Innovation Print Award (IPA) is an annual competition that seek to recognise FUJIFILM Business Innovation’s customers creativity and innovation in print.
Push the creativity and technical boundaries of print with FUIFILM Business Innovation technologies – the only limit is your imagination!
Welcome to the 8th drupa Global trends Report Executive Summary. A lot has happened since the last one was drafted in Spring 2020! Covid pandemic, global supply chain difficulties, regional wars, trade wars, rising inflation, climate change - the list goes on.
But so does life and the print industry is remarkably resilient. So strikingly, printers globally were on average slightly more confident about their companies than they were in 2019 and have strong expectations for 2023.
Globally in 2022 34% of the printer panel stated their company current economic condition to be ‘good’ and 16% described it as ‘poor’, a net positive balance of +18%. It is this net balance, positive or negative that is used in many of the charts. The detailed breakdown of printers and suppliers by market and region is given
in the full report’s Appendix, but the data sets for Australia/Oceania and the Middle East were too small to use separately, though they are included in the global data. The same applies to Functional printers. Where small data sets have been included e.g. North America and Africa, attention is drawn to this limitation in both the text and the charts.
We can see striking variations in optimism e.g. between Europe – cau tious and South/Central America or Asia - optimistic. Looking at the data by market, Packaging printers show increasing confidence, Publishing
printers show a recovery from a poor result in 2019 while Commercial print ers reported a small decline in confi dence this year but have expectations of recovery in 2023.
“Raw materials availability, rising inflation rates and rising product pric es, declining margins, ruinous price wars between competitors [combine to be the biggest threat over the next 12 months].“ Commercial printer, Germany
“Take advantage of economy growth after pandemic times. Communicate our innovation and sell our added
Suppliers were more confident, a global net positive of +34% for 2022 and notably more positive for Europe for 2023. Whilst they were a little more cautious for the Commercial and Publishing markets for 2022 - down 4 or 5% on 2019, they have strong positive forecasts for all market sec tors for 2023 (net positive balances for Publishing +36%, Commercial +38%, Packaging +48%, Functional +51%).
Between 2013 and 2019, more print ers dropped prices than raised them by an average of -12% despite ever increasing paper/substrate prices. Then suddenly in 2022 there is an unprecedented positive net balance of +61%in favour of those raising rather than lowering prices.
Yes, there were heavy paper/sub strate price increases, but those never prompted such price increases to end customers in the past. What is going on? What is more, this pattern is global, applying to most regions and markets. It should be noted that mar gins remain under pressure for almost everybody – so some things stay the same.
It is a similar story for Suppliers with a +60% net increase in pricing – pre viously the highest was +18% in 2018. Clearly emerging from Covid, pricing behaviour has changed radically and this has implications for inflation if repeated across other industries.
Turning to printer operational mea sures, one key metric that has been tracked since 2014 is the volume of print produced by the huge variety of print technology. The Appendix of the main report provides this in full, but Chart C gives the headlines, shown
as net positive or negative net balances in volume of printed material. A large drop in Sheetfed offset in Commercial was almost matched by an increase in Packaging.
It is worth remembering that the first negative net balance in Commercial was only in 2018 and then only very small. The other standout features are the huge growth in Flexo for Packaging and substantial gains in Digital toner cutsheet colour and Digital inkjet rollfed colour.
One trend we would expect to have seen sustained through the pandemic is the growth of digital print as a % of total turnover. Yet this appears to have stalled globally between 2019 and 2022 – except in Commercial print which grew modestly.
Next, we must report a real puzzle. There has been a steady decline in the % of printers reporting they oper ate a Web-to-Print/Digital storefront from a peak of only 27% in 2017 to 23% in 2019 and 20% in 2022. For Commercial printers this has dropped from 38% in 2017 to 26% in 2022, while Publishing grew to 33% this year, but Packaging fell from 15% in 2019 to 7% in 2022. We acknowledge the reduction in sample size, but the numbers are still good globally. We will just have to see if next year shows a recovery.
growth had stalled with no significant growth globally across all markets between 2014 and 2019 (just 17% of the panel with Web-to-Print reporting that more than 25% of turnover came that way in both years). But since then, it has shot up to 26% and the increase is across all markets.
Not surprisingly Capital expenditure has fallen back since 2019 both glob ally and in all markets, but the pros pects for 2023 and beyond are good. Regionally all regions forecast growth next year, except Europe with a flat line forecast. Finishing equipment and print technology were by far the most popular targets.
Regarding print technology, the clear winner in 2023 will be Sheetfed offset (31%), followed by Digital toner cut
sheet colour at 18% and Digital inkjet wide format and Flexo both at 17%. It is very striking that Sheetfed offset remains the favourite target in 2023, despite a clear decline in volume of print by that means in some markets. For some it is to consolidate, reduce labour and wastage, for others it is to grow capacity. What is more the popularity of Sheetfed Offset remains for all three markets - see table 1.
Strikingly when asked about long term (5 year) investment plans, top came Digital Print at 62% then Automation at 52%. Conventional print was still listed as the third most important likely investment 32%, this is not to overlook the fact that the Digital tech nologies are growing fast if we collate the various technologies together.
However, for those with Web-to-Print installations, the Covid period saw a substantial increase in turnover via that channel (Chart D). Pre Covid this
As for suppliers, they reported a net positive balance +15% for Cap Ex in 2022 and a net positive of +31% in 2023. Investment forecasts for 2023 were more muted in Commercial and Publishing but strong in Packaging and Functional.
Looking at the emerging strategic challenges, both printers and suppliers have been struggling with supply chain difficulties (paper/substrates and con sumables for printers and raw materi als for suppliers) and they expect these to continue into 2023.
41% of printers and 33% of suppliers also reported labour shortages. Wage/ salary rises have been and/or will be the result.
Environmental, Social and Governance issues are increasingly important across the globe for both printers, suppliers and their customers.
Considering short term constraints on the Print Market globally, the tradi tional issues dominate: Strong compe tition and Lack of sales/Demand – the former highlighted more by Packaging printers, the latter more by Commercial printers. Looking to the next 5 years, the impact of Digital media is highlighted by both print ers and suppliers followed almost equally by Lack of specialist skills and Overcapacity in the industry.
When we started the Trends Report series, we paid only modest attention to broader socio-economic issues. However, given the increasing impact these were having on the print market, we introduced questions on this in 2019. Given Covid and the other chal lenges that have come fast and furious since, this was a wise move. Globally 52% highlighted the impact of pan demics either directly or on the econ omy and 42% chose Economic reces sion in their country or region. But there were some noticeable regional variations.
For example, 62% of Asian print ers chose pandemic impact versus 52% globally; 58% of South/Central American printers chose Economic recession versus 42% globally; and 32% of European printers chose regional physical wars versus 21% globally. And there was a clear majori ty (59%) that thought socio-economic pressures were either more important than or of equal importance to mar ket pressures.
In conclusion we were encouraged by the broadly positive outlook that printers and suppliers had both of trading in 2022 and the prospects for 2023. Indeed, perhaps the single most striking result of the survey was that globally the Barometer of Economic Confidence was slightly higher in 2022 than in 2019 before Covid struck.
Then again, most regions and markets forecast better trading in 2023. This was not universal and there are strong headwinds to make things more dif ficult – some global, some regional.
Clearly investment fell during the Covid pandemic and companies have taken time to recover. Nevertheless, printers and suppliers report a deter mination to grow their businesses, investing as necessary, starting in 2023. As there are few signs that market and broader economic pressures will less en, this is just as well. For only those companies who invest wisely, bring their costs down by raising productiv ity, diversify and innovate and invest in their team, will prosper. This is well summarised in a quote from a printer in Portugal.
“ Looking for the biggest opportu nity, my company must be alert, be patient and look for new demands... The Covid pandemic, and the Russia/ Ukraine war will bring new disrup tions in market, but equally may cre ate new opportunities. [These] could be found in markets where innovation and rehabilitation [reform] could hap pen. For that, my company will look essentially for digital operations... (labelling, digital printing - wide format and medium format).” Commercial, Packaging and Functional printer, Portugal
The 8th drupa Global Trends Report will be published in September 2022. The first results from a survey conducted this spring are now available. One important conclusion: overall, confidence is on the rise and all regions and markets forecast higher investment in 2023.
FUJIFILM Business Innovation Asia Pacific introduces the Jet Press 1160CF, a high-speed continuous feed colour inkjet printing system for the transactional printing and publishing markets. Equipped with the highest printing speed and printing density in its class*1, the product will be available to the Asia Pacific*2 region in stages starting from November 2022.
Transactional print, such as statements, invoices or personalised direct-mail communication is required to be on time, and short run publishing is driven by time to market, both are produced in a narrow production window. The technology now must be able to complete high-volume, highly versioned printing jobs quickly and intensively.
With greater data availability, the demand to personalise customer
graphic images at high speed with great complexity.
To meet these demands, the new Jet Press 1160CF offers two advance printing modes: the speed priority mode and the image quality priority mode. The speed priority mode*3 prints at top class speed of 160 meters per minute (equivalent to 2,096 pages per minute on precut A4 paper), which is 1.6 times faster than the previous model*4.
The image quality priority mode*5 prints at a high resolution of 1,200 x 1,200 dpi. The newly developed high concentration pigment inks available in both modes, enable the highest printing density in its class*6, producing sharp and vivid printouts especially images with text and numbers.
Equipped with high image quality and speed options
Users get to enjoy vivid print quality of 1200 x 1200 dpi at a print speed of 80 meters per minute.
Dual speed and quality level selection with 1200 x 1200 dpi at 80 meters per minute (image quality priority mode) or 1200 x 600 dpi at 160 meters per minute (speed priority mode).
Utilises newly developed high concentration pigment ink to print high density output.
Adopts Artificial Intelligence (AI) technology to optimise image with newly developed print server.
Speedy turnaround time with new printing speed that is boosted to 1.6 times that of the previous model while retaining the compactness of its predecessor*7 without the need for additional space.
Newly developed print server can handle quick conversion of output data and printing simultaneously. This reduces the time required for pre-printing data generation, which shortens the overall printing time.
Efficient operational support Minimise transition time by seamlessly migrating print jobs and adopt different types of applications through the dedicated FUJIFILM Business Innovation specialists.
Ease of operations include ink replacements with newly designed CMYK four-colour ink packs, each weighing approximately 20 kg, thus reducing operators’ workload. The ink packs can remain in the specialised ink compartment during reloading.
*1 As of September 2022, in continuous feed color inkjet printing systems using water-based pigment inks. Survey by FUJIFILM Business Innovation Corp.
*2 Please check with your local FUJIFILM Business Innovation office on the availability of the machine
*3 The printing resolution in the speed priority mode is 1,200 × 600 dpi
*4 1400 Inkjet Color Continuous Feed Printing System (Model-T2H)
*5 The printing speed in the image quality priority mode is 80 m per minute (equivalent to 1,048 pages per minute on
Printing United Alliance’s State of the Industry report cemented what many of us have known for a long time. The survey found we are edging ever closer to a recession as the economy continues to slow appreciably over the next 12 months. Its view of the market is something that will resonate strongly with Print Service Providers (PSPs) too.
The survey found the top seven challenges identified by commercial printers, graphic and sign producers, packaging printers and converters and apparel decorators were:
Rising substrate costs
Material shortages
Rising labour costs
Rising transportation costs
Labour shortages
Maintaining profitability
Rising energy costs
Four fifths of respondents reported increased sales on a year ago although only half experienced a rise in pretax profitability. And while two thirds signalled interest in investing in capital equipment – hardware and software in 2023 – 28.7% were unsure of their investment plans with uncertainty about the economy cited as the main influencing factor.
The recently released 8th drupa Global Trends Report from Messe Düsseldorf research partners Printfuture (UK), and Wissler & Partner (Switzerland), found that Print Service Providers (PSPs) are quite resilient in the face of many crises.
The headline figures were optimistic. Globally, in 2022, 34% of the printer panel stated their company’s current economic condition to be “good” and 16% described it as “poor,” yielding a net positive balance of +18%.
The expectations for 2023 are even better, with a net balance of 27% of participants expecting good business. However, European printers anticipate their economic condition will worsen in 2023 due to rising paper and energy prices and a general stalling of the economy.
The report also found that, since 2019, capital expenditure had fallen steadily reaching a low in 2022. But, as
a result, a rebound in investments is expected in 2023 and could potentially surpass the capital expenditure in all previous years as operations catch up.
According toWalter Fricke’s How to Survive a Recession and Thrive Afterwards, “Recessions are a high pressure exercise in change management, and to navigate one successfully, a company needs to be flexible and ready to adjust. It’s tempting to think of a recession as a time to batten down the hatches and play it safe. However, downturns …encourage the adoption of new technologies.”
Ranjay Gulati, Nitin Nohria, and Franz Wohlgezogen, take this approach a step further when they say instead of retreating into survival mode and hoping for the best, businesses can prepare to come “roaring out of recession.”
Both point to agile PSPs as those most likely to identify opportunities and ride out a downturn and lay firm foundations for continued success once the downturn ends.
By working through its lean canvas (see example below) PSPs can evaluate and identify relevant opportunities.
They could also consider questions such as: Why now?
Precisely for whom will we create the value/solve the problem? How big is the opportunity? What alternatives are out there? Why are we best suited to pursue this? What’s our differentiator?
The aim is to avoid wasting time and money on poor opportunities while gaining an understanding of what will be required to succeed with good opportunities.
What factors – internal and external — are critical to success?The globalized manufacturer unveiled at K, as a world premiere, its new Onyx GO CI flexo press, designed to print short runs efficiently and economically. Upshot: 3 minutes to get the best print setup, waste close to 0, speed up to 400 mpm, & more. Revolutionized processes and components.
consumption according to the printing characteristics (it use only the drying power needed for each printing unit), assisted by a particularly effective ventilation system. And so, is the inking system, that dispenses only the quantity of ink needed to each printing unit; the optimized positioning of its elements optimizes flows and generates energy savings (up to 60 percent).
Uteco chooses this year-end's most important international trade fair to present Onyx GO, the new compact, productive and economically and managerially convenient CI flexo press designed to print short and very short runs with rationality - the result of suggestions and needs transmitted by customers in an ongoing dialogue that traces the way.
At the “Amazing Reveal”, 4 managers took turns on stage, of course declined by temperament - clear and essential that of CEO Mario Tomasi, ironic and captivating that of Aldo Peretti, Group Executive Chairman and historical memory of the group, passionate and proud that of Alessandro Bicego, Chief Innovation Officer and "dad" of the new machine. To outline the present and the near future of the group's new customer service was Patrizia Pinto, Chief Customer Service Officer.
The features of the Onyx GO seem to fit the definition "less in more" well. The very small dimensions - less than 50 sqm footprint - the compactness of the body composed of only two complementary blocks (very beautiful to see), the essentiality of the layout that facilitates the job of the operator, the optimization of each individual component... everything introduces a dimension of savings.
Hence the performance with a minus sign and the corresponding with a plus sign: less than 3 minutes for printing pressures and register setup translates into +55% faster setup process and up to 240 extra hours of production/ year, with up to 1.8M€ higher revenue.
On the other hand, more robustness reduces wear and vibrations, ensuring print quality even at the highest process speeds (up to 400 mpm) and lowering noise level, which remains below 80 decibels.
During the designing phase, Uteco engineers revisited all the machine's components, creating new patented solutions that increase the automation, precision and rationality of the various process steps. Among them, the system for cliché’s 3D characteristics recognition automatically transmits information to the relevant components – typically the inking and drying systems. Similarly, and with the same objective in mind, the automatic adjustment of printing pressure among the cylinder, cliché and substrate, and the almost instantaneous printing register, with important advantages in terms of maintenance as well.
Significant energy savings - up to 50 percent per year - are due to the new patented smart drying system, the Active Dry® , that optimize energy
The washing system has also been revisited and reduces solvent consumption (up to 40 percent), as has the new Dynamic Doctoring® system: very light (less than 10 kg) with low consumption and blades wear.
The attention to the operator that the designers kept well in mind when developing the Onyx GO translates into greater comfort and easiness of operation, whose operating space is all packed into 50 sqm. Onyx GO processes all types of materials, with water- and solvent-based inks, and is easily configured for different types of work through special predefined kits. Three printing widths: 820, 1020 and 1320 mm.
Again, a sum of factors contributes to the result: the interactive, adaptive cockpit allows monitoring and management of data in real time; the drying boxes are easily removable with a single move and without effort; the access to the central drum for cleaning and maintenance is much easier and direct; the upper part of the machine is accessible by means of a catwalk.
To further simplify work and optimize print quality, there are even small but relevant details such as the creation of fully removable and upgradable drying boxes, with nozzles of different shapes, to be chosen according to the specific needs of the process at hand.
The megatrend of digitalization is one of the main topics at drupa 2024. But do you know the difference between digitization, digitalization and digital transformation? Let us explain the symbiotic relationship between these buzzwords.
organizational processes of the company system are optimized via technological implementation.
Think of technologies as an extension of the human body which has a supportive role during the transformation. To undergo a successful digital transformation, many aspects must be considered, for instance areas with potential for improvement must be analyzed in advance, and professionals with a knowledge of business, IT and technologies are needed in the enterprise to guide the company towards a digital transformation. Furthermore, enterprises must redefine customer value proposition with ongoing changing consumer patterns.
Looking back, the music sector was the first among other industries to have been digitized. In a blink of an eye, we moved away from owning physical cassettes and CDs to owning songs individually and digitally via music streaming services, for instance, iTunes or Spotify. Technologies have boomed at an exponential rate and have grown to us in an unprecedented way. As a result, consumer behaviour has changed drastically and it is up to enterprises to make products and services available anywhere and at any time, and thus digital transformation is inevitable, also in the printing industry.
Nowadays, terms, such as digitization and digitalization, are often used interchangeably. What’s the difference between digitization and digitalization?
If one converts analogue information into digital, then one has digitized the paper-based information, e.g. transforming a handwritten text into digital form. In the case of digitalization, one must implement
technologies into processes that have been done manually so far.
With reference to it, automation of workflow is a common aspect of digitalization whereby the process efficiency is increased. To get a better understanding, one can imagine a print worker using computer-controlled equipment to control the quality of printed products instead of doing it individually and manually. As a result of digitalization, work roles might be shifted. To put it simply, digitization is the first step and digitalization is the second step to getting closer to a digital transformation.
Some businesses believe mistakenly to have already transformed digitally.
The adjective “digital“ seems to be misleading. Under digital transformation, one understands the business transformation process as a whole: more complex than at first glance. In other words, the
To put it in another way, businesses are supposed to be quick to unlock the potential of an underserved market segment in order to succeed in a competitive market. So as to create a new business model, companies must have a customer-centric approach and make the best out of technologies, and hence a digital transformation strategy is essential to meet customer demands in this day and age, especially in the printing industry where large volumes are produced.
Leading IT analyst Jason Bloomberg sums up the phenomenon for Forbes:
“In the final analysis, therefore, we digitize information, we digitalize processes and roles that make up the operations of a business, and we digitally transform the business and its strategy. Each one is necessary but not sufficient for the next, and most importantly, digitization and digitalization are essentially about technology, but digital transformation is not. Digital transformation is about the customer.“
Founded in 2019, Xiamen Songde Printing focuses mainly on product development and design as well as cigarette packaging, paper product packaging, and paper cup manufacturing. Today Xiamen Songde is one of the few printing companies in Xiamen City, Fujian Province, China, that can provide one-stop services to customers
The Lithrone G40 advance eight-color machine with new coater, the first of its kind in the world, is equipped with Full-APC Automatic Plate Changing, ink distributor roller cooling, automatic blanket cleaning, automatic ink and dampening roller cleaning, a new Komorimatic dampening system, and KHS-AI and PDC-SX systems for automatic control of register and color.
"Why did we choose a Komori press for our production equipment? The reason can be traced back to Print China 2019 held in Dongguan," says Wang Huiquan, President of Xiamen, "When I saw the Komori machine at the exhibition, I was very impressed by the press's appearance, printing speed and printing quality. Following the exhibition, I contacted Komori right away, and after we visited several printing plants in Xiamen, I decided to install the first Komori press in our new plant."
The five-color Lithrone G40 with coater was installed and commissioned in October 2019. The Komori engineers demonstrated outstanding skills during the installation, providing excellent installation guidance and after-sales service. This further improved the reputation of Komori products in the view of Xiamen Songde. As a result, when the company made plans in 2020 to expand into cigarette packaging production, it did not hesitate to choose Komori for its next machine.
According to President Wang, "At the time, we wanted to install an eight-
color UV printing press with coater. Our first Komori press had been in operation for more than a year, and its excellent performance had impressed us tremendously.
After seeing the Komori UV presses and printing samples, we decided to order a Komori machine. When we learned that an eight-color press with coater was being exhibited at China Print 2021 in Beijing, we immediately decided to purchase the display machine, the world's first eight-color Lithrone G40 advance press with the latest coater. In early July 2021, after the exhibition, the machine was delivered to our factory. After about 20 days of installation and adjustment, it started up smoothly and went into full operation. To date, there have been no problems of any kind."
According to press chief Shao Fangyong, "The Lithrone G40 advance has a maximum printing speed of 17,200 sph*. We handle a large variety of substrates, such as thin and thick papers, foils, films and specialty substrates. The feeder of the new machine consistently feeds all of them stably.
These systems greatly increase production efficiency and reduce manual operations. Because of the high-quality print capability, the Lithrone G40 advance is now their go to press for jobs such as cigarette, liquor, cosmetics, and luxury goods package printing. An additional advantage is that the press reduces the amount of postpress work. The UV curable inks and inline coating unit produce effects inline that are very close to traditional offline laminating, silk screening, and embossing.
Regarding the future growth of the company, President Wang says, "According to the current forecast, conventional printing is expected to be the mainstream for the next few years, and at this point our printing business is expected to continue to grow healthily, and the prospects for business expansion are very bright. We will continue to expand our business by installing more Komori machines to enhance our production lines."
"In addition, we have been paying attention to the growth of Komori's business in digital printing equipment and are considering purchasing Komori digital products when the time is right," he adds.
Connect to Grow. That is your key to stay ahead in a demanding market. By connecting with MPSConnect, you ensure the best in reliability and productivity from your printing press. You will increase competitive advantages and maximize profits.
To improve productivity and profi tability, it’s critical to increase the understanding of your overall label print operation. With MPSConnect, you get real-time insights in the operator activities. You dive into the printing press and see exactly what’s happening.
mps-printing.com/connect-to-grow
mps-printing.com
Diageo-owned Johnnie Walker has partnered with Air-Ink on a series of limited edition bottle designs for its Black Label collection, illustrated using ink made from air pollution.
Named the Johnnie Walker “Keep Walking City Collection”, the bottles were designed in partnership with Air-Ink, a brand that creates ink by condensing carbon-based gaseous effluents generated by air pollution.
Each limited edition bottle depicts one of six cities rendered by illustrations designed by five artists. The cities are: Mexico City, New Delhi, Warsaw,
Bangkok, Istanbul and Madrid. Only 2,500 bottles are available for purchase. Johnnie Walker global brand director Julie Bramham commented: “Johnnie Walker is built on a legacy of making positive, progressive choices and to bring this collection to life we asked artists to shine a light on what makes their city special and inspires people to come together to ‘keep walking’.
“We are really thrilled by the unique depictions that have come out of this brief and combined with the Air-Ink partnership it demonstrates the power of combining art and innovation, making this limited edition range a true collectible.”
The collection has already proved hugely popular, selling out in Warsaw and Bangkok in just over a week, according to Hypebeast.
The artists who illustrated the bottles are: Alek Morawski for Warsaw; Okuda San Miguel, for Madrid; Paola Delfín, for Mexico City; Shilo Shiv Suleman, for Delhi; Mr Hure for Istanbul; and Gongkan, for Bangkok.
The Johnnie Walker Black Label Blended Scotch Whisky boasts flavours of toffee, fruit and spicy vanilla and comprises 40% ABV.
This was organized by tripartite collaboration between Messe Düsseldorf Asia, The Thai Packaging Association and The Thai Printing Association.
This trade fair presents a leading showcase for technology innovations, machinery, equipment, and solutions for packaging and printing industrial. With the successful participants over 19,000 international visitors from 62 Countries & Regions.
Heidelberg Thailand attended this exhibition in the theme of “Unfold Your Potential” presents the printing press “Speedmaster CX 75-4” with Heidelberg UX , Die-Cutter machine “Promatrix 106 CS”, Prinect Workflow, Lifecycle Solutions and also Gallus to boost your productivity and enhance your offering in the commercial, packaging and label printing productions. Giving you the most cost-effective result and deliver higher quality across the entire production process.
Heidelberg presents 3 rounds per day of LIVE DEMO on machinesMulticolor Printing on Speedmaster CX75-4 and High Productivity for DieCutting process with Promatrix 106CS. Both machines had been sold.
Not only the LIVE DEMO on machine, Heidelberg also presents total solutions for customers into 3 additional zones including Prinect Workflow – to
demonstrate how Prinect makes Smart Printing Production by integrated all printing production steps. Lifecycle Solutions – presents new innovative service offerings such as remote agreement, eCall , VDO support along with genuine parts and Saphira Consumables. Gallus – Narrow web printing for Labels.
Heidelberg Thailand's successfully in the exhibition by several key achievements such as overwhelming participants attended Live Demo, The successfully deals for Sheetfed machine, Postpress machine, CtP machine and Prinect Workflow during the event and
along with many prospects for further follow up.
Mr.Surasit Ruengjaratphiphat, Managing Director of Heidelberg Thailand said “Our objective to join this event is to meet with some new
customers which we could find more than 50 customers which are not in our database and we received many good feedback and enquiry from our existing customers”
Two decades after Zhongke Printing first put a Muller Martini system into operation, the graphic arts company in the Chinese capital Beijing invested in the latest perfect binder technology with an Alegro A7 and a Publica PRO12.
Founded in 1957 by the Chinese Academy of Sciences and employing over 1200 people in two shifts, the fullservice print shop is one of the largest producers of textbooks and scientific works for the Chinese domestic market. The total daily production is between 300,000 to 400,000 copies with an increasing number of jobs below 5,000 copies. In addition, magazines are printed for mainly domestic publishers.
As a result of the expansion of printing capacity, new market challenges, higher quality demands from customers and the desire to reduce waste, Zhongke Printing modernized its softcover
equipment. After the good experience of the past 20 years, the choice again fell on two perfect binding lines from Muller Martini – a Publica PRO12 with a ZU 832 gathering machine, streamfeeder, Orbit three-knife trimmer and CB 18 book stacker, and an Alegro A7 with a ZTM 3694 gathering machine, streamfeeder, Easy Fly PRO front trimmer, double splitting saw, Orbit three-knife trimmer and CB 18 book stacker.
The fact that Zhongke Printing, which is 8 percent digital, opted for two different Muller Martini models is due to its diverse job structure. It uses the
Publica PRO12 primarily for teaching materials that have to be bound in a short time. The Alegro A7, on the other hand – keyword front trimmer – primarily produces more complex books. With the commissioning of the two perfect binders, which the machine operators were able to get to grips with in a short time, Zhongke Printing significantly increased its productivity.
Machine operator Yidong Xin in front of the new Publica PRO12 perfect binder at Zhongke Printing.
A new NOVACUT 106 ER Autoplaten® die-cutter is the latest investment in BOBST technology by Bangkok-based Thung Hua Sinn Group. Installed at the company’s TPN Packaging division, the flatbed machine has helped increase productivity and efficiency in the production of folding cartons for global brand owner customers
A leader in print and packaging innovation, Thung Hua Sinn Group (THSG) in Thailand has won many top industry awards in recognition of its commitment to excellence and sustainability in every aspect of its business. For over 20 years, THSG has relied on BOBST converting technology as part of its setup allowing it to produce high quality paperboard packaging for many of the world’s best known brands.
Focus on equipment, quality, and people Established in Chinatown in Bangkok in 1953, as a small letter-press company, THSG is today one of the largest print and packaging manufacturers in South East Asia, led by Managing Director (and son of the original founder) Perapong Thungkasemvathana.
The Group comprises six business units – Thung Hua Sinn, Thung Hua Sinn Printing Network, TPN Flexpak, TPN
Packaging, TPN Medical Packaging, and TPN Food Packaging – each with its own specialism and expertise in labels, flexible packaging, folding cartons and corrugated boxes. Products are sold to markets in Thailand and beyond, including the food & beverage, textile, electronics, health care, medical, and automotive sectors.
While the packaging industry faces many challenges in regard to material cost and supply chain, THSG has positioned itself firmly at the forefront of developments through strategic investments in innovative solutions, great emphasis on educating its workforce and its dedication to client satisfaction. The company prides itself on keeping its production capabilities in peak condition by replacing individual machines every five years, on average, and is on track to post double-digit growth figures again this year.
“With our state-of-the-art equipment and highly skilled workforce, we are able to guarantee high quality and consistency in every order we produce despite the ongoing problems we are seeing in the market,” said Deputy Managing Director Teeruth Thungkasemvathana. He explained further, “Apart from the effects of the global pandemic, the biggest issue currently is the high cost of raw materials and consumables. After that, comes the need to predict new packaging trends and demands in an ever-changing market.”
Extending folding carton capabilities
Located on the thriving Wellgrow Industrial Estate, in Chachoengsao, east of Bangkok city center, THSG includes Thung Hua Sinn Printing Network, which was established up in 1993 as a one-stop solution for folding carton production.
These capabilities were extended in 2014 with the introduction of TPN Packaging Company Limited. Set up in a separate 15,000 square meters facility, this ultra-modern factory is dedicated to leveraging machine automation and fully integrated workflow processes, increasing the focus on quality, hygiene, food safety, and not least sustainability.
The combined folding carton division offers printing, water-based and UV coating, laminating, die-cutting, window patching, blister coating, box forming and special effects, utilizing amongst others eight offset presses, 16 die-cutters, and nine folder-gluers. Accounting for THB 2 billion (US$ 53.5m) worth of revenue in 2021, it operates two shifts covering 24 hours six days of the week and employs more than 800 qualified and experienced personnel.
Having worked with BOBST converting equipment for over two decades, the latest acquisition from the Swiss manufacturer is a NOVACUT 106 ER Autoplaten® flatbed die-cutter brought in to support growth and increase capacity at TPN Packaging.
The new machine offers cutting, stripping and blanking in one pass, handling paper, carton and solid board, and light corrugated board, in maximum sizes of 1,060 x 760 mm (41.73 x 29.92 in) at a processing speed of up to 7,000 sheets per hour. It features smooth feeding, precise registration and perfect in-line stripping as well as automatic non-stop delivery for greater productivity and reduced waste.
“The positioning of the NOVACUT model perfectly fits our needs in term of job run length, speed, and applications, and we have already seen an increase in productivity and efficiency since adding it to our factory floor,” said Mr Teeruth Thungkasemvathana. “The machine is also very user friendly for both new and experienced operators thanks to the
intuitive HMI and simple step-by-step guides for job setups.”
The key to success of any business is to understand the customers’ specific needs and requirements; a fundamental premise which pervades the company ethos of THSG and TPN Packaging, as well as BOBST. In today’s market, the impact of packaging on the planet is at the forefront of consumers’ minds which means all brands are looking for more eco-friendly solutions from their suppliers.
“Our commitment not only to efficiency, client satisfaction and innovation, but also to people, ethics, social and environmental obligations, differentiates us from our competitors,” said Mr Thungkasemvathana. “Our customers today want sustainability in terms of both processes and the packaging itself, so we strive to lead the way with solutions and production methods that help reduce the impact on the environment.”
Sustainable manufacturing requires reliable machines that increase productivity and efficiency while also cutting waste of material and operator time, such as the BOBST NOVACUT 106 ER. Reliability, however, extends beyond the machine itself to the service and support structure provided by the manufacturer. “We have always been well supported by BOBST. They have a strong local service team, which is crucial for us to avoid unplanned downtime so we can deliver on time for our customers,” said Mr Thungkasemvathana.
He concluded, “We want to continue to provide our customers with innovative and sustainable solutions that meet their packaging needs, and BOBST is a key partner in helping us to achieve this goal. Reliability and productivity are the main reasons why we chose the NOVACUT and why we have worked with BOBST for more than 20 years.”
Products with medium-sized packaging will be hit the hardest by changes to consumer shopping amid rising inflation, says GlobalData, as the leading data and analytics company notes an emerging polarization in the market.
Inflation pressures trigger both trading down and premiumization
Brands will need to find new ways to increase value for money when it comes to packaging, as rising inflation is causing customers to be torn between bulk buying to save money and item quality.
Ramsey Baghdadi, Consumer Analyst at GlobalData, comments: “In response to rising inflation, consumers are either spending less by buying less overall, switching out some products to save money, or buying higher quality produce to get better value for money. This is causing a polarization in the market, with brands either increasing package sizes to appeal to bulk buyers or shrinking packs. Proving value for money will be key, with solutions
such as larger pack sizes and reusable packaging expected to become more common.”
Old Spice refillable antiperspirant an example of refillable solution Refillable packaging is re-emerging, with recent announcements by brands such as Unilever’s Old Spice. In 2022, GlobalData’s Q3 survey of 21,000 respondents revealed that the majority (67%) of consumers globally found refillable or recyclable packaging extremely/quite important in their product search.
Baghdadi continues: “GlobalData expected refillable packaging to take off pre-pandemic. However, because of the spike of hygiene concerns, the demand for refillable packaging dropped. Now safety anxieties are
starting to lessen in Europe and North America, reusable/refillable products are making a comeback. More importantly, packaging companies should quickly make a move while the iron is hot.”
Medium-sized packaging impacted by private label preferences
As a consequence of reduced disposable income and tighter budgets, demand is rising for private label products (supermarket own brand food, for example). According to a survey by GlobalData, a notable proportion (30%) of consumers globally claim that they typically purchase private label dairy products.
Ramsey Baghdadi, Consumer Analyst at GlobalData, comments: “Premiumpriced products are at risk of being left on shelves, as consumers switch to private label/cheaper brand alternatives. This has clear implications for change on packaging design and costs. GlobalData forecasts that larger packs sizes (3,001-5,000 g/ml) will grow in volume at a rate of 4.3% per year to 2025, outpacing that of smaller pack sizes.
However, smaller pack sizes are still expected to continue to dominate the consumer packaging market overall. Longer term, rise of both shrinkflation and larger pack sizes will lead to further polarisation of packaging sizes in many product categories, with the standard medium-sized pack hit hardest.”
Partnerships between converters and brands matter in today’s fast-changing, dynamic packaging industry. Many businesses make such collaborations a big part of their strategy, but few have taken the partnership concept to the level found at Colombian flexible packaging converter Litoplas.
Add in its intricate approach to Expanded Color Gamut (ECG) flexo printing, which, according to the company’s Chief Customer Officer, Luis Mora “has only been possible to implement successfully with FLEXCEL NX Plates,” and you’ve got an award-winning business strategy.
Founded in 1967, food packaging forms the bulk of production at its manufacturing plant in the northern city of Barranquilla (a second plant will open in Guatemala in 2023).
The Litoplas website describes the company’s mission as “delivering unique solutions through the design, development and manufacture of flexible packaging”, and its vision as becoming brands’ “first-choice partner for flexible packaging value.”
The partnership between Litoplas and its customers was one of the things that caught the attention of the judging panel at the Miraclon-sponsored Global Flexo Innovation Awards, where Litoplas won a Silver Award for achievement in two categories: Gravureto-Flexo Conversion and efficiency in Print Production Workflow. The judges noted that Litoplas’s entries — all of which were examples of ECG printing produced with FLEXCEL NX Plates — “highlighted what can be achieved when converter and brand work closely together.”
‘Only FLEXCEL NX Technology makes ECG possible’ Litoplas first added ECG printing to the toolbox in 2015. “We had seen ECG at drupa, and at first sight it appeared magical because of the
The steady return of Manroland Sheetfed into the Indian packaging market in the last several years is bearing fruit as the company has considerably lifted its game in the past year. As the pandemic and the lockdowns ended, the company’s wholly-owned subsidiary in India, Manroland Sheetfed India became bolder and went
to its considerable installed footprint in the India monocarton industry.
This has paid off, as the industry returns to structured capacity building with several converters who have held off investments in the past two or three years purchasing highly automated 7-color plus coater automated B1 presses. The Manroland Evolution series are thus recognized by the Indian packaging converters as one of the modern automated options that have to be evaluated when looking at
Recently, Manroland Sheetfed Evolution 700 presses were purchased by two monocarton companies in the Delhi NCR-Sain Packaging and Galaxy Offset. The presses with full automate loading with interdeck and end-of-press UV cassettes besides the standard IR and hot air dryers. The Sain Packaging press will be installed at its plant north of the city in Sonipat, while Galaxy’s Evolution will come to its new plant built south of Manesar. The two Evolution presses will be shipped in the coming months and installed within the financial year that
The return of Manroland Sheetfed to the ranks of global suppliers selling
new 7-color coater UV presses with automation into the Indian market a welcome and successful renewal of intensity by the third German offset sheetfed press manufacturer. It has been an uphill climb. But the reestablishment of the company with its persistence in the supplying spares,
efficiency and capacity benefits it offered – to both converters and brands – especially as there has been a need for shorter turnaround times as well as an increase in SKUs. However, it also seemed utopian, because at first the all-important statistical process control was missing. Anyone could buy a machine, the inks existed, but without strict process control you couldn’t reap the productivity benefits. For us, that was a critical shortcoming, which wasn’t rectified until FLEXCEL NX Technology came on the scene.”
By the time Litoplas invested in a FLEXCEL NX System in 2017, he recalls, “we understood what we needed to make ECG work, and the flattop dot made all the difference. Our previous technology was plagued by pinholes and voids that produced poor data for process control. The flat-top dots delivered the precise, predictable and consistent color. Without that, excellent ECG printing is impossible.”
There are other ways in which FLEXCEL NX Plates enable ECG to
show its potential, says Luis. “We can print more vivid colors without using excess ink, which adds to the on-shelf impact at a competitive price. And the flat-top dots don’t wear, they stay stable during the run so we stop the press less for adjustments.”
Tightly embedded partnerships
Luis Mora’s title as Litoplas’s Chief Customer Officer testifies to how tightly the company has embedded partnership with customers at the heart of the business. To ensure this, Litoplas has formalized the concept into two models — a ‘Partnership Model’ designed to ‘build trust through collaboration’, and a ‘Packaging for Value Model’ that aims to build value through technology.
The models are the result of much careful thought and analysis, as Luis Mora explains: “We are a very technology-focused company, and the idea of applying technology to create value is very important to us. But we recognize that it is essential that our clients trust us to provide the level of technology and support that is right for them.” He goes on to explain how the Packaging for Value Model achieves this. “The model has four ‘Levels’ — 1 through 4 — to which customers are allocated depending on which of the technologies in our toolbox best fit their requirements. The higher the Level, the more of our technologies the customer can call on.”
A major benefit of this approach, he continues, is “it prevents us overpromising and underdelivering, because if that happens it damages trust. Take ECG as an example: we only offer it to customers on Level 3, because they have the right level of technical expertise.”
The ’Partnership Model’, meanwhile, complements this approach by reimagining how Litoplas’s people work with their customers’ internal staff. “Businesses today are too complex for a one-to-one relationship alone, so now our structure encourages fluent conversations between all our people working on the account and the corresponding contact at the customer. In this way, every conversation between the two companies is high quality, which builds trust.”
Patience, hard work and trust drives ECG adoption
As with any radical new technology, persuading customers to implement ECG printing requires patience, hard work and trust between converter and brand. The reason why Litoplas only provides ECG to Level 3 customers becomes clear when Luis describes the negotiations involved in planning a typical gravure-to-flexo conversion.
“There are times when for FLEXCEL NX Technology and ECG to play to their strengths, the customer might need to change the design slightly. For example, we recommend printing small typefaces in a single color to avoid any possibility of misregister. Or, the pastels enabled by FLEXCEL NX Plates are a big benefit brands can play on. A mature conversation like that doesn’t happen the first time you talk. But if we’re talking after winning the customer’s trust, it’s a different matter.”
The execution of the winning entry, Cordillera Dark Chocolate packaging produced for Compañía Nacional de Chocolates, is a prime example of the Litoplas partnership strategy in action, and of the company’s innovative approach to selling technology. The
commission was a direct result of a ‘Packaging Academy’ Litoplas organized to show the customer what ECG is about — as Luis puts it, “to show the pros and cons, and how best we could reproduce their artwork.
“We asked the design team to give us a really challenging job, and they did. It was a premium-quality chocolate product, currently in cardboard packaging but which they wanted to switch to flexible packaging. The color of the chocolate on the packaging had to exactly match the product itself, and because for a period both forms of packaging would be side by side on the shelves, it was vital there was no difference in color between the cardboard and the flexible packaging. They also wanted to get the product to market as quickly as possible and produce a relatively small quantity.”
Litoplas met the requirements in every way, using green, orange and violet in ECG to render vivid, dense colors that the customer liked, and precisely matching the background color. In a radical approach to color measurement, to match the color of the chocolate Litoplas went so far as to spread real
chocolate on a sheet of Pantone white paper and measure the color using the color measurement system.
As Litoplas prepares to expand into Guatemala next year, ECG printing will continue to be central to the company’s offering — so much so that one of the three new presses in Guatemala will be a custom-built Bobst machine dedicated to 100% ECG production.
“As for how big a share of production ECG can reach,” says Luis, “to migrate customers to ECG we need to build an ECG technology that’s better than conventional technology. We believe we are busy doing that.”
He adds that Miraclon have provided excellent support so far, and he expects this to continue in the future. “We really value their support to enhance print capabilities and press performance. With the in-country technical support here in Colombia, any issues have been solved promptly - one thing Miraclon has is adaptive capacity, backed up by persistence. We could not have been as successful as we have been without our partnership with Miraclon.”
Technical upgrades and new design on W&H’s flagship and fastest press - Windmöller & Hölscher (W&H) has launched the VISTAFLEX II, a wide-web, CI flexographic press with upgrades for enhanced performance, improved print quality, and easy job changeovers.
W&H launched the original VISTAFLEX in 2008 for a small segment of high-end printers in the flexible packaging market who required a workhorse wide-web press that could run jobs 24/7 at speeds of up to 800 m/min (2,620 ft/min) with quick and easy job changeovers. Unique features of the press were the ability to prepare and store four additional jobs while the press was running and to execute fullyautomated changeovers with two highspeed robots by pressing a button.
The VISTAFLEX II, available as of August 2022, provides all these same features along with technical upgrades and a fresh, modern look. “When we started conceptualizing how and what to update on the VISTAFLEX, we realized, what an exceptional press it still is well over a decade after its inception. To make the press even better for our customers, who run these machines extremely hard over prolonged periods of time, we started with improving the bearing system to increase stability and
print quality,” said Hermann Veismann, General Manager for Printing and Finishing at Windmöller and Hölscher.
“Automation and assistance systems are making a dramatic difference in production efficiency, by shortening changeover times, minimizing waste, and making the process more straightforward and easier for press operators. With this top of mind, we integrated W&H systems directly into the VISTAFLEX II,” added Dr. Holger Kreilkamp, Team Leader Product Management.
These include an improved CI drum cleaning system, which is particularly beneficial for paper and non-woven products, EASY-SET and EASY-REG for automated impression and register setting, the W&H VISION for web monitoring and defect detection, and the TURBOCLEAN ADVANCED E, which is W&H’s resource-efficient, award-winning washing and inking system.
Also available is the RUBY IoT platform. Coupled with Connect 4 Flow the system creates a direct link between a customer’s ERP system and the press, which allows jobs data to be sent remotely for automated smart job queueing and optimized workflow. The VISTA-PORT, where prepared cylinders and sleeves are stored, then organizes the integrated cylinder magazine automatically and prepares the necessary robotic changes. This concept is unique on the market and designed to bring the future of autonomous printing closer.
In addition, W&H has developed the FILMATIC II C winder to complement the press. The new non-stop, highperformance winder is available with an integrated slitting module. At maximum speeds, even extremely sensitive substrates that can be difficult to wind, such as breathable films and nonwovens, can be cut into very small ups and wound with straight edges.
Over 100 of the original VISTAFLEX presses are being used by customers in Europe, North America, and Asia to print on paper and film, as well as for special products from the hygiene sector such as non-wovens or back sheet films. While the press is typically used for long runs, especially in largeformat printing applications such as for beverage packaging (up to 1,250mm / 49.2” repeat), it is also extremely efficient for short jobs with many changeovers due to the fast, fullyautomated changeover robots.
HP has unveiled the HP PageWide T700i Press – a new 67 in. (1.7 m), digital web-fed platform that helps converters achieve greater operational efficiency for high-volume production of digital single-face lamination, corrugation, and folding carton applications.
HP is continuing its investment in the packaging market to create new opportunities for packaging converters and brands to benefit from the analog to digital transformation.
The HP PageWide T700i Press, which is expected to be available for installation in late 2023, will be configurable to meet specific customer and market needs and includes a variety of inline options for manual or continuous unwinding, priming, varnishing, and delivery in both roll and sheet format.
Select configurations will be capable of up to 1,000 feet per minute (300 m/min) supported by HP’s single-pass Thermal Inkjet technology with true water-based inks for printing packaging which can be recycled, further
supporting the converter’s circular economy goals.
The new press platform supports increased plant capacity and reduced manufacturing costs for paper-based packaging production and will enable packaging converters to print with significantly accelerated turnaround times and lower minimum order quantity requirements that optimize inventories, while focusing analog print capacity on longer runs1.
For converters facing increasing supply chain pressure, this press represents a substantial opportunity for business growth by enabling improved economics, greater production versatility, and more sustainable packaging solutions.
”We listened to the needs of our customers and the market when designing the T700i Press. Now more than ever, converters need greater flexibility to respond to dynamic market trends and challenges, and digital
packaging continues to fundamentally transform the packaging supply chain for high-volume and mainstream production,” said Annette Friskopp, Global Head and General Manager, HP PageWide Industrial.
“The HP T700i Press enables customers to achieve production cost savings and shorter lead times and enables them to go after higher value print jobs1."
The new press will feature the next generation HP Thermal Inkjet printheads capable of robust industrial production. The proven inkjet technology builds on HP’s previous generations of thermal inkjet to enable customers to achieve consistent and repeatable 6-color offset print quality at high speeds for high-graphics packaging.
T700i Press customers will benefit from HP’s manufacturing scalability and vertical integration across HP’s Industrial Print businesses, creating a distinct advantage for their business. The HP PageWide T700i Press will
The new 67 in. (1.7 m) web-fed press will boost efficiency for high-volume production of corrugated and folding carton
be the second press format built in collaboration with Koenig & Bauer, after first unveiling the 110-inch HP PageWide T1100S Press in 2015, later followed by upgrades including the HP PageWide T1170, T1190, and the latest T1195i Press.
“Koenig & Bauer is one of the world’s leading traditional press manufacturers,
with over 200 years of experience in press engineering and developing innovative solutions that meet customers’ quality expectations,” said Christoph Müller, Koenig & Bauer executive board member.
“Together with HP’s leadership and innovation in the field of thermal inkjet technology, the HP PageWide
T700i Press was developed to once again combine our complementary technological strengths to provide packaging converters with unprecedented flexibility and quality consistency.”
In this day and age, smart packaging is a one-way ticket to combating counterfeiting, strengthening brand protection, winning over consumers and increasing recycling rates. In other words, intelligent packaging solutions will not only boost brand integrity but will also drive the packaging sector forward – towards a digital transformation.
How Digimarc and EVRYTHNG’s New Technologies Work
Digimarc Corporation is a global leader in product digitization known for creating Digimarc watermarks that accelerate next-generation digital identification. The included dual-factor authentication, such as QR codes and digital watermarks, is visible on a single package. Recently merged with EVRYTHNG, Digimarc integrates its identification technologies with the EVRYTHNG Product Cloud: the concept of the digital twin on the web for physical items. To put it simply, the digital twin provides intelligence data in one place, also called the ability to learn about each product’s journey and interactions via its traceability.
Ken Sickles, Chief Product Officer at Digimarc, explains further: “The company has created a uniquely digital solution that leverages the ubiquity of smartphones and other digital devices to make product authentication much more streamlined and less prone to human error”.
accurate than traditional physical authentication measures.
EVRYTHNG’s
The new Digimarc® Brand Integrity digital solution provides brands and their customers an opportunity to verify the authenticity of products in a more flexible manner. By assigning each product a serialized digital identity that can be tracked in the cloud and accessed via scanning, for example the QR code on the product, the authentication process seems more
Mr. Sickles clarifies the impetus for the launch of Digimarc‘s Brand Integrity solution:
“As counterfeiters have become more sophisticated and supply chains more diffuse, companies are recognizing that traditional brand protection approaches that are largely reactive and reliant on trained inspectors and specialized equipment, are both ineffective and inefficient”.
To sum up, Digimarc’s Brand Integrity solution protects and strengthens the reputation of brands, as it assigns every product a digital presence and
connects it to the cloud that records and tracks each product’s journey. As a result, Digimarc’s intelligent packaging solution makes the supply chain more transparent and sustainable, as it can reveal counterfeits or information about recyclability, for instance.
Digitizing products with QR codes and coupling them with the cloud play an active part not only in speeding up the assimilation of technologies into the marketplace but also in embarking towards a digital transformation.
Managed and owned by Ahmed and Aslam Monia, JMB Labels is one of South Africa’s leading and fastest growing label printing specialists. From humble beginnings in 1987, JMB Labels today occupies a 1 500 m² office and factory site in Amalgam, Johannesburg.
JMB Labels’ early success was built on supplying plain and printed selfadhesive labels for the FMCG and retail markets. Due to a surge in demand, the company was compelled to expand the business and invest in additional machinery.
In 2013, JMB Labels became the proud owners of an MPS EC UV flexo multisubstrate press, thanks to Rotocon, a leading supplier of state-of-the-art printing technology and consumables for South Africa’s narrow-web and label printing industries.
The MPS EC UV has multi-substrate capabilities and can handle material thickness from 12 to 450 µm. A 410
mm web width makes it ideal for the production of self-adhesive and shrinksleeve labels at speeds of up to 200 m/ min.
Aslam and Ahmed considered several presses that could potentially meet their needs. However, it was more than just technology that won MPS flexo press the deciding vote. “We were blown away by the press’s state-of-the-art features and by the people who make it all happen.”
One year after the initial installation, Aslam says JMB Labels had entered new markets, attracted new customers, including FMCG companies, and achieved a 30% increase in sales.
“We’re still very much focused on doing business with independent companies, instead of multicorporations. That’s because we’re able to offer them that ‘personal touch.’ It’s a strong component of our operation,” comments Aslam.
“We’ve built strong relationships with our customers over the years. As they’ve grown, so have we.” According to him, market trends have also evolved, and many products traditionally bearing self-adhesive labels are now presented in wraparound or shrink sleeve labels. “As a result, we’ve had to make changes to our business model to keep one step ahead and meet brand owners’ requirements.”
Equipment extraordinaire Impressed with the capabilities of the MPS EC UV, and how it managed to streamline its core business, owners Ahmed and Aslam purchased a second MPS flexo press – the EB 370 – in 2015.
Rotocon’s technicians since installed a Domino K600i one-colour digital print bar into the MPS EB 370 press to transform it into a value-add hybrid press that can print variable data including text, sequential numbers, barcodes and 2D codes at a native resolution of 600dpi and operating speeds of up to 150m/min. ‘Although there hasn’t been a need to transition to a digital print shop yet because our run lengths are typically 10 000 and over, we’ve always referred to the EB as our digital press. This is because our operator can perform job changeovers so quickly that we can average 10 to 12
jobs on it daily with proper planning,’ Aslam enthuses.
JMB Labels bought their third MPS press via WhatsApp in 2019 after Rotocon shared the deal details and price of the EFS 430 model from Labelexpo Europe in Brussels.
“The MPS EFS press has improved our production process at all levels,” says Farhad Evans, production manager at JMB Labels. “Make-ready times are shorter with the use of printing sleeves as compared to conventional printing cylinders. The short web path facilitates cost saving on material and reduces wastage.”
Most importantly for Aslam and his team is the print quality of the MPS is constant throughout the run and it has given them the confidence to target more companies seeking high-end, quality labels and packaging for their products.
The brothers’ admiration for MPS press technology dates back to 2001, when they saw the first press in action at Labelexpo Europe and appreciated how the technology made printing so much easier. ‘The fact that the company was built by a core group of friends and that co-founder Eric Hoendervangers came to visit our facility in Johannesburg when he was in South Africa – although we weren’t ready to buy a press yet – and started building a relationship left a lasting impression,’ Aslam recalls. ‘We are firm believers in dreaming and setting our targets and goals, and so far, we’ve reached all of them, including owning three MPS presses.’
He says the MPS flexo presses feature
predictable, high-quality label printing and user-friendly press operation. “MPS is known for its reliable productivity, and we haven’t looked back since.”
“We’re completely satisfied with the MPS presses. Runs of 10 000 to 1 million labels are done with ease and efficiency. We’re also quite pleased with the level of service received from the entire MPS and Rotocon teams.
The MPS flexo presses are built standard with Crisp.Dot light technology delivering superior print quality, iSet intelligent pressure settings, iStop technology ensuring zero waste at roll change, full-length rail system, quick change die-station and a preregister function.
JMB Labels is continuously growing with its customer base to provide them with top-quality products. It’s been ably supported in this mission by its suppliers who offer the perfect combination of ultra-modern machinery and top-class service.
It’s been nine years since the initial MPS installation at JMB Labels, and Aslam says the machines have been running tip-top without a hitch. “MPS’s reputation for quality and reliability is legendary. Not only are the machines easy to install and operate, but they have worked perfectly from day one.”
• Management system established for information security
• External audit and certification to ISO 27001
In these days of networked industrial systems and increasing digitization, information security and cybersecurity are becoming ever more vital for companies. Even in the printing industry, it is hard to imagine working without automated and digitally networked processes anymore. To offer its customers the greatest possible protection for their data, Heidelberg has established a comprehensive management system for information security. This has now been externally audited by DQS GmbH and certified to the international ISO 27001 standard.
“This management system for information security will enable us to safeguard a high level of cybersecurity at HEIDELBERG in the future, too,” says Dr. Ludwin Monz, CEO of HEIDELBERG. “Ongoing assessment of risks from malware and other threats makes it possible for us to continuously improve the security of our systems and solutions.”
HEIDELBERG offers cutting-edge, networked, and heavily automated machinery, control software, and cloud solutions for print shops.
Control software from HEIDELBERG with in-built artificial intelligence can be used to automate processes, even to the extent of implementing autonomous printing.
Assistance systems with in-built artificial intelligence can be used to automate processes, even to the extent of implementing autonomous printing. B2B platforms for consumables and service parts, software for controlling the entire workflow in the printing process, and Internet-based remote diagnoses for machine maintenance are also included in the service range.
The successful HEIDELBERG “Subscription” contract models would also be impossible without comprehensive cybersecurity. In these cases, customers no longer pay for the press itself, but rather for the number of sheets printed.
As Dr. Monz says, “Over the past decades, HEIDELBERG has developed from a conventional mechanical engineering company that offers the associated services to a technology company with a high proportion of digital processes, products, and services. We see this ISO 27001 certification as both a recognition of our efforts and motivation to keep going. It proves that information security is integrated into the management and organization system of the HEIDELBERG Group, as assessed to recognized principles. This means we can live up to the justified expectations of our customers.”
The Stahlfolder P-Stacker robot arranges ready-cut, folded print products on a pallet for further transport.
and Wisconsin. Around 70 percent of customers can be found in the flexible packaging sector, but the company also serves label (20 percent) and folding carton (10 percent) converters with high-quality solvent flexographic plates. End-use applications are mainly for the food, beverage, pet food and pharmaceutical markets.
Those are the pledges Cyber Graphics makes to its customers. The team, whether based in Memphis, Cleveland, Milwaukee, Nashville or Neenah, stands in unison in saying it “prides itself on delivering precision to an imprecise industry.”
To put it more succinctly, the staff embraces the motto “Perfecting prepress; protecting brands.” The slogan speaks to what the entire organization believes to be a true competitive advantage. It promises “no compromises in quality” and guarantees “packaging done right—right away.” To them, results must be “Predictable. Repeatable. Unbeatable.”
Established in 1994, Cyber Graphics is a prepress trade shop that knows flexographic plates and is familiar with what happens on a pressroom floor. This long-time FTA member, affiliated with the Association since 1996, works with well-known brand owners, large printers and converters, and design agencies, supplying digital photopolymer plates, plate-on-sleeve solutions, seamless in-the-round
(ITR) photopolymer, laser engraving, along with design, prototyping, color management and other prepress creative services.
Walking the Walk Originally the plate making division of film and flexible packaging manufacturer Bryce Corp, Cyber Graphics is today a stand-alone business with more than 120 employees spread over its four locations in Tennessee
“We are an independent packaging prepress trade shop focusing on serving major converters across North America, but we still operate with a printer’s mindset and are very proactive, which goes way back to the days of being Bryce’s in-house plate making department. Most of our employees have hands-on experience of flexographic print production, and they know the difficulties our customers are up against every day and how to address any potential issues head on,” explains Kevin Bourquin, VP operations.
Elaborating on that point, Cyber Graphics’ website explains, “When it comes to printing, we talk the talk and walk the walk. We know that when
No surprises, no excuses.” “No headaches, no fingerpointing.” “No unnecessary rework and no paying for someone else’s mistakes.”
packaging graphics are designed with print production in mind, we can speed time-to-market and reduce costs.”
Print quality management stands at the core of the five-location enterprise. Critical to its success is a commitment to, “Ask the right questions. Gather the right specifications. Build the right workflows and take every measure to ensure accuracy and repeatability.”
Included among specifics are the following:
Take approved and mechanically assembled art and convert it into pressoptimized layouts
Apply various screens to improve and control TVI and ink laydown on plate imaging files
Mask, clone and assemble image parts to create a realistic image Adjust file construction to account for process, substrate and printer variables Benchmark and fingerprint a set of print conditions to accurately predict color
Measure, analyze and report data on printed packaging to a set of tolerances Manage press approval at a printer on behalf of the brand
With all of that accomplished, Cyber Graphics credits its color separation expertise as being responsible for “files that are mechanically sound, print friendly and on brand.” As a result, it says, “Expectations are met upstream. Re-engineering is avoided downstream. Time and money are saved.”
Cyber Graphics operates four automated plate processing lines, which allow for printing plates to be shipped out to customers the next day. “Just-in-time delivery is crucial for our customers, so we rely on a very high level of automation to ensure we have the productivity and the consistency that these converters need to serve their brand owner customers,” says Bourquin.
“Everyone works to a very fastchanging schedule in today’s market, so maximum flexibility and fastest turnaround are top priorities,” he continues. “Having that extra speed really helps offset some of the challenges we are currently facing when it comes to getting the plate delivered to the customer.”
It’s that concern that prompted a recent capital investment—purchase and delivery of a new XSYS ThermoFlexX Catena-WDLS (washer, dryer, lightfinisher and stacker), which arrived in Memphis this past June as the first of its kind in North America.
Crediting the installation with, “more than living up to expectations,” Bourquin explains the rationale behind the move. “Due to the pandemic, we had to go ahead with the decision to buy the Catena-WDLS without seeing it live; instead, we experienced its superior technology through videos and saw it operate via conference calls, where we had the opportunity to drill down into all the features. Now it is here and even better than we anticipated,” he says.
He adds, “What has been most impressive about the installation so far is that we were putting production jobs through the WDLS in a matter of days. Usually, it takes weeks to implement new processing technology and get it working seamlessly, but the machine just slotted in, and we were up and running in no time.”
Taking many variables out of the equation, including operator handling of plates between each of the processes, the ThermoFlexX Catena-WDLS is fully automated. This means that after loading a plate into the system, no further intervention is required until the fully finished plate comes out. “It is so user-friendly and intuitive to use,” says Bourquin about the feedback from the factory floor. Current expectations are that the new plate production line will boost productivity by as much as 15 percent.
He continues, “If you’re serving multiple customers around the country, automation is paramount for controlling costs, quality and waste; it also means your team can focus on value-added tasks instead of minding the machine. With the new line, we don’t need to pull the plate out to inspect it during the process, because we know we’re going to get the result we want.” An added benefit: Sealed operation keeps all solvent fumes contained for a safer working environment. To lower the environmental impact, the company is also able to reclaim in excess of 93 percent of the solvent and distill it into fresh solvent.
Bourquin took pride in delivering another Cyber Graphics’ assurance: “We have been the first with many new developments over the years, such as LED plate exposure, which we introduced back in 2013. Now we are the first to leverage the power of the WDLS.” In a further nod to automation’s benefits, he confides, “We had a major outage in 2019 when a machine broke down and our other sites had to cover for a full 11 days. We just can’t afford for that to happen again. The ThermoFlexX ProServeX cloud-based monitoring service, which features predictive maintenance, will prevent such incidents in the future and that’s incredibly reassuring.”
Loading a plate into the ThermoFlexX Catena WDLSKodak gives the world’s fastest platesetter another speed upgrade
The speed of the high-performance KODAK MAGNUS Q800 Platesetter has been increased once again with T-speed Plus, offering a throughput of up to 84 B1 or 8-up plates per hour (pph). Kodak introduced the T-speed, then the world's fastest 8-up CTP system, about two years ago.
From
tesa announces the launch of their newest product tesa® 60412: a packaging tape made of recycled PET bottles. Composed of recycled materials and bio-based raw materials, tesa‘s recycled PET packaging tape provides a more sustainable alternative to conventional packaging tape.
With its latest recycled PET packaging tape, tesa, the international provider of self-adhesive system solutions and manufacturer of innovative adhesive tapes, offers businesses in food and beverage, pharmaceuticals, e-commerce and logistics a more sustainable alternative to the conventional polyvinyl chloride (PVC) packaging tape, and thus will facilitate the embarkation on a circular journey across the global supply chain.
to PVC tapes when it comes to their elevated tear resistance – yet more sustainable.
Thanks to their wear-resistant backing, the tapes can be adhered to recycled cardboard easily and also guarantee strong adhesion. The production process itself is completely solventfree, as the used PET products, mostly recycled bottles, are utilized as raw material for the backing. To put it simply: Without jeopardizing the paper recycling process, the recycled PET packaging tapes can be disposed together with the packaging in the wastepaper, and therefore will contribute to a circular economy.
In terms of printability, the tesa tapes are compatible with all kinds of ink systems, and hence logos and advertising can be printed onto the tape itself. In addition, the tapes are low-noise, as they are being used.
The MAGNUS Q800 Platesetter can now output a plate every 42.9 seconds. This marks Kodak's third speed upgrade for the MAGNUS Q800 in four years, with more than 40% speed improvement over the former Z-Speed from 2018. The MAGNUS Q800 Platesetter can also image KODAK SONORA XTRA Process Free Plates at its new top speed.
The upgraded CTP device helps sheetfed and web offset printers to further maximize the productivity of their offset workflows. All automation options available for the MAGNUS Q800 Platesetter, including the SinglePallet Loader (SPL), Multi-Pallet Loader (MPL) and Multi-Cassette Unit (MCU), support the new speed.
In view of the new platesetter speed upgrade, it is of great advantage that the Multi-Pallet Loader can hold up to 3,200 plates in up to four different plate sizes – two pallets of 1,500 plates each and two cassettes of 100 plates each. Also helpful for long operating times without manual intervention is the recently implemented 40% increase in the capacity of the slip sheet removal system for the SPL/ MPL.
Circular
The newest tesa® 60412 is made of a waterborne acrylic adhesive system and includes a polyester backing whereby 70% of it comes from postconsumer recycling. Not only reduces tesa the consumption of virgin plastic but it has also developed a green packaging alternative to conventional packaging film tapes like PVC. tesa‘s tape is suitable for light and mediumweight packaging up to 30 kg.
On top of that, recycled PET packaging tapes boast their high performance: They are comparable
with optical systems for UV curing and drying
"We are excited that we have been able to make the world's fastest CTP system even faster. This is further evidence that Kodak continues to bring solutions to market that enable our customers in the printing industry become more competitive and profitable through greater efficiency and productivity," commented Jeff Zellmer, Vice President, Global Sales & Strategy, Kodak.
The MAGNUS Q800 Platesetter with T-Speed Plus is now available worldwide. MAGNUS Q800 Platesetters already installed at customer sites can be upgraded to the new top speed on site.
HP Inc. announces changes to their Digital Corrugated Business
It was recently announced that Nick Price will lead HP’s Digital Corrugated Post Print Business in the Americas and Asia Pacific regions. Nick originates from the UK and after an early start in the print and packaging industry moved to Asia in 1996.
During his 25 year tenure in the region he has lived in Singapore, Japan and
Australia holding various regional senior management positions with Esko, Schawk, Kodak and HP Inc.
Nick has worked for HP for the last 10 years and in 2021 relocated to Dallas, Texas from where he will manage sales of the HP C500 Corrugated Post Print Press
in two of the fastest growing regions.
The HP C500 platform allows for high quality digital print directly onto corrugated boards, replacing the need for expensive tooling and reducing waste.
The HP C500 inks are water-based providing a fully sustainable solution for a wide variety of corrugated packaging.
“We see high demand for digital transformation in the corrugated market and so I am extremely excited to be leading the teams to deliver growth for HP and our customers”.
Please feel free to contact Nick directly to learn more about digital corrugated packaging. nick.price@hp.com
Let’s talk about the state of our Packaging industry post pandemic. What to look out for moving forward. The SHIFT 2022 Packaging Conference.
No doubting it, our industry in under pressure, not from print job volumes, but by the ever-increasing cost of our production supplies, like film, board, plates, inks, freight, wages and other increases that we are being subjected to. Every business today is in the same boat, and this is not just a packaging issue. But we honestly only care about the costs that effect our business post pandemic in our industry.
What can we do to help elevate some of these costs with careful and correct purchases. How willing are supply companies wanting to work with you! By changing suppliers on consumables (for example) due to cheaper prices, is it really going to help long term?. What about workflow, can that help save you costs. Is that cheaper machine purchase going to be the right investment you need at this stage.
We are having the SHIFT 22 conference in Bangkok on December the 8th and will try to address these issues and many others as well. The one-day event will bring back (for our 19th year) industry leaders so you can hear from people and companies who have the answers. Network with other companies who like you need to find these ways forward.
Following the one day “intensive” SHIFT conference we will hold the industries only regional Asian Packaging Excellence Awards dinner, where we showcase the quality packaging companies who have been awarded Gold Silver and Bronze in the 2022 competition, always a highlight of the year. Register and book your seat booked today for the 2022 SHIFT conference and also get your best printed work ready to enter in the Awards Competition. Nothing says it better than being a winning quality packaging printer in Asia. And nothing helps more than you having the right information for your business moving forward.
Details we be sent to you soon on how to register for this event