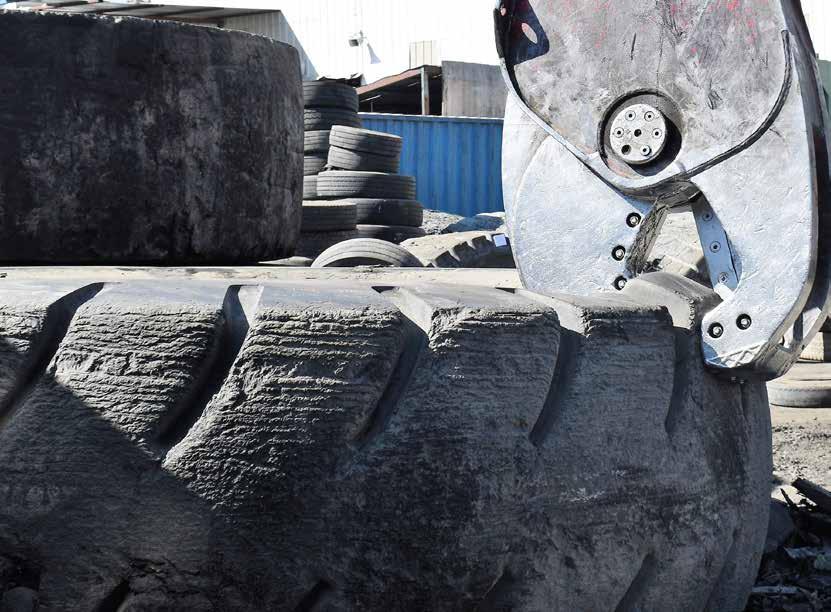
9 minute read
Minería Sustentable, Reciclaje de neumáticos mineros
En enero pasado se publicó el decreto de la ley de Responsabilidad Extendida del Productor (REP), que establece metas de recolección y valorización de neumáticos que serán de cumplimiento obligatorio para los importadores de estos elementos al país. La normativa considera dos clases de neumáticos. Por un lado, los más comunes, denominados categoría A, que incluyen aquellos que tengan un aro inferior a 57 pulgadas, con excepción de los que tengan un aro igual a 45 pulgadas, a 49 pulgadas y a 51 pulgadas. Mientras, la categoría B corresponde a los neumáticos mineros (aro igual a 45 pulgadas, a 49 pulgadas, a 51 pulgadas y aros iguales o mayores a 57 pulgadas). En el caso de estos últimos, se reglamentó que durante el primer año de aplicación de las metas tengan que recolectar y valorizar un 25% del total de neumáticos, hasta llegar a 100% al octavo ejercicio de vigencia de los objetivos, lo que implica una serie de desafíos para el sector minero. En términos generales se producen en el país 140.000 toneladas de residuos neumáticos al año. Existen diferentes estimaciones de cuántas toneladas de estas corresponden a neumáticos mineros, donde esta industria utiliza todo tipo de neumáticos (camionetas, camión, maquinaria pesada para pequeña y mediana minería, neumáticos gigantes en el caso de la gran minería, etc). Para efectos de este análisis, concluimos que la generación anual de la minería es de aproximadamente 56.000 toneladas. Esto es lo que entra anualmente producto de la operación minera, por lo que la acumulación de este residuo al interior de las faenas mineras durante todos los años de operación es de cientos de miles de toneladas”, explica Jorge Rodriguez, gerente general de Morgan Empresas, dedicada al reciclaje de estos productos en Chile.
Aporte a la sustentabilidad
Consultado respecto a las estimaciones de costos que implica para las compañías la gestión de los neumáticos mineros, el ejecutivo explica que el costo depende de diferentes factores, como por ejemplo la cantidad de neumáticos a recolectar y valorizar, el tipo de neumáticos, la distancia de la faena en particular, etc. “El reciclaje de neumáticos mineros es una realidad en Chile hace bastante tiem-
Foto: Gentileza Morgan Empresas.
La norma fija meta metas de recolección y valorización de neumáticos.
Reciclaje de neumáticos mineros: Beneficios de una tarea necesaria
Ante las exigencias que conlleva la Ley REP, las compañías tienen la oportunidad de incrementar el nivel de sostenibilidad de sus procesos, donde se estima que la minería chilena genera anualmente unas 56.000 toneladas.
po. Nuestra empresa está reciclando neumáticos de diferentes mineras y contratistas hace años, como Anglo American Los Bronces, Yamana Gold , Punta del Cobre, Minera Carola, SKC, Finning, Komatsu, etc., por nombrar algunas. Con estas mineras nos adelantamos a la Ley REP con sus prácticas de sustentabilidad. Hoy con la publicación oficial de las metas de recolección y valorización de los neumáticos hay un mayor interés de muchas otras mineras por sumarse al reciclaje de los neumáticos mineros”, asevera Jorge Rodriguez. En relación a los beneficios desde el punto de vista económico, social o ambiental, sostiene que el análisis general de impacto económico y social (AGIES) elaborado por el Ministerio del Medio Ambiente “determinó en 1,25 la relación beneficio-costo de realizar esta actividad con los neumáticos mineros. Los precios utilizados para el cálculo de esta rentabilidad actualmente están más acotados, por lo que estimo que la rentabilidad calculada por el AGIES en realidad debiese ser superior. Por lo tanto es altamente rentable desde una perspectiva social”.
Logística del reciclaje
Para afrontar este tipo de requerimientos, el ejecutivo menciona que “la lejanía de la ubicación de las faenas mineras es un dato con el cual hay que trabajar, es una condición base. Esto junto con los altos estándares en diferentes materias tales como seguridad, encarecen cualquier operación relacionada con la minería. Algunos de los desafíos que se han ido abordando dicen relación con la optimización de los costos de transporte: Esto depende de la ubicación de cada faena en particular, hay algunas muy lejanas a las ciudades o plantas de reciclaje y otras más cercanas”. Por ejemplo, “hemos analizado la posibilidad de disminuir el tamaño de los neumáticos gigantes mineros en la faena misma para tratar de optimizar su traslado, sin embargo el tipo de formato del trozo del neumático junto con las restricciones de carga y transporte por motivos de seguridad condicionan la cantidad de toneladas a cargar y el tipo de camión a utilizar, lo que sumado a los mayores costos operativos de procesar al interior de la faena nos han llevado a concluir, que por el momento, es mejor
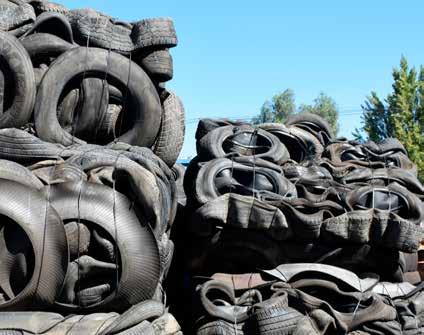

Fotos: Gentileza Morgan Empresas.
Izq.: Jorge Rodríguez, gerente general de Morgan Empresas. Der.: Los neumáticos desechados se pueden someter a un proceso de conversión térmica. trasladarlos sin procesar a nuestra planta de tratamiento”, señala. Otra opción es implementar la planta de reciclaje al interior de la faena evitando trasladar el residuo para su procesamiento. “Sin embargo, los costos operativos de los altos estándares mineros, sumado a que la generación de los subproductos se verían encarecidos en relación a sus competidores, hace que estos subproductos sean menos competitivos. Adicionalmente, no está claro que los subproductos generados por los procesos de reciclaje, como por ejemplo el combustible alternativo (pirooil generado por procesos de pirolisis), puedan ser utilizado por las mismas mineras, ya que los fabricantes de los equipos debiesen certificar estos combustibles como válidos a usar en sus equipos para efectos de garantías y eso lo veo poco probable todavía”, indica. A su juicio, la mejor solución “es trasladar los neumáticos fuera de la faena para su procesamiento, la planta atenderá varios clientes, mayor volumen, menores costos operativos, productos más competitivos y mejores precios finalmente. Por otra parte, el costo de transporte comenzará a disminuir con el tiempo al incorporar mayores oferentes de transporte para esta carga especializada”.
Posibles usos
Jorge Rodriguez comenta que hay diferentes alternativas para darle una segunda vida a los neumáticos: “Lo primero es la posibilidad de extender la vida útil del neumático a través de ocuparse de su mantención, que implica el correcto montaje en las llantas, reparaciones preventivas-correctivas y finalmente el recauchaje. Este ha ido limitándose mucho con la incorporación de la oferta de neumáticos de menor costo principalmente provenientes de China. En la mediana minería y en los neumáticos de carretera (auto-camión) la presencia de neumáticos de menor costo ha mermado sustancialmente las posibilidades de recauchar. En la gran minería todavía hay menor competencia y se puede recauchar, pero el mercado es muy agresivo y aumentará la competencia”, afirma. Y añade: “Lo segundo es transformar el neumático en materia prima a través de su reciclaje material transformándolos por ejemplo en gránulos para canchas deportivas, pisos de goma, polvo asfáltico, muebles, etc”. Otra alternativa es someter a los neumáticos a un proceso de conversión térmica, más conocido como pirolisis, desde el cual se generan tres subproductos: el acero, el negro de humo o carbón black y el piro-oil, un combustible alternativo utilizado en procesos industriales. Este proceso es el más utilizado para el reciclaje de neumáticos mineros. Y, Adicionalmente, se pueden usar como reemplazo del carbón para los hornos cementeros para aprovechar su energía calórica.
MAGOTTEAUX POTENCIA NEGOCIO DE RECICLAJE PARA SU PRODUCCIÓN DE BOLAS FUNDIDAS
En base al concepto de economía circular, la empresa apunta a convertirse en el principal reciclador directo de materiales ferrosos de la zona centro-norte del país.
Ampliar su capacidad de recibir y reprocesar excedentes de residuos industriales de origen ferroso para la fabricación de bolas de molienda, mediante alianzas con empresas mineras e industriales, busca Magotteaux, empresa de origen belga, perteneciente al grupo nacional Sigdo Koppers. La idea es pasar de ser un receptor de materia prima para reciclaje, a ser un socio estratégico de las compañías que generan estos residuos industriales. “Ingresamos estos residuos de origen ferroso a nuestra planta productiva, la fundimos y la reincorporamos al sistema productivo de nuestros clientes, con un producto de alto rendimiento. Para una minera, es la venta de un excedente o residuo; para nosotros, es la obtención de materia prima fundamental”, señala Cristián Abarca, Gerente de Abastecimiento y Logística de Magotteaux. El ejecutivo, quien está a cargo de las plantas de Chile y Perú, indica que la decisión de potenciar esta gestión se tomó a raíz de las complicaciones en la cadena de suministros provocadas por la pandemia de Covid-19, además de seguir los lineamientos corporativos de sustentabilidad, por lo que se comenzó a generar alianzas para la recuperación de chatarra, iniciando con las empresas del grupo, Fepasa y Enaex, que generan estos desechos. Hoy Magotteaux desarrolla un proyecto de retiro de residuos ferrosos con un importante cliente minero que se encuentra en proceso de desmantelamiento estructurales de edificios, analizando también la opción de alianza con otra importante minera en la Región de Antofagasta, y algunas faenas de la Región de Atacama. “Tenemos capacidad logística para ir y recoger la chatarra desde las faenas mineras. Con una capacidad de fundición de 50.000 toneladas en la planta de Til Til, estamos abiertos a más opciones que se generen en esta industria”, sostiene Abarca.
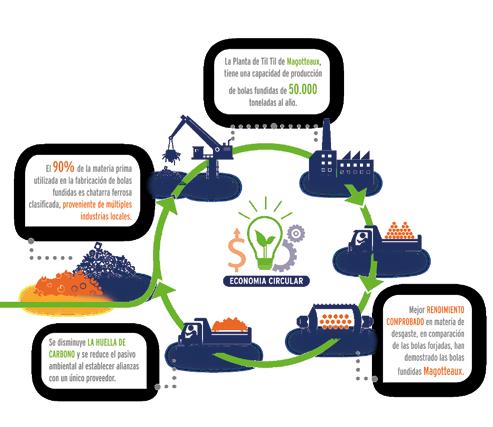
Economía circular
Por su parte, Patricio Moreno, Gerente HSEC de la firma, indica que el objetivo es “ser uno de los principales captadores de la zona central. Vamos a la fuente donde se generan y almacenan estos excedentes. Queremos que todas las mineras puedan procesar sus excedentes ferrosos chatarra con nosotros”. Ello se enmarca en el concepto de economía circular con que la empresa busca apalancar la red de suministro de bolas de molienda. “A los clientes les ofrecemos un producto al que podrán acceder a un mejor precio, en la medida que nos retornen todo el residuo que generen”, afirma el ejecutivo. Asevera que la cercanía de las instalaciones con las principales mineras de la zona centro-norte se ve facilitada por los menores traslados del material, reduciendo la huella de carbono. “Deseamos que los productos que vendemos no se transformen en desechos, sino que vuelvan a ingresar al proceso productivo. Podemos ser un comprador y un vendedor continuo, privilegiando como la economía circular dentro de la industria”, concluye Moreno.
Modelo customizado
El 90% de la materia prima que utiliza Magotteaux en la fabricación de las bolas fundidas es chatarra ferrosa clasificada, ofreciendo a las mineras captar el residuo: • Mediante el reciclaje de bolas que ya cumplieron su vida útil en el proceso de molienda • De desmantelamientos tras cierre de faenas • De renovación de maquinarias ya en desuso • De desmantelamiento de edificios e instalaciones • De desechos ferrosos que llegan como destino final de tratamiento de residuos “Nos adaptamos a las distintas condiciones de las faenas. Podemos trabajar directamente con la minera retirando sus residuos o excedentes ferrosos, o con un tercero que le preste servicios”, afirma Moreno.