Weaving Octopus
Smart knitted surface
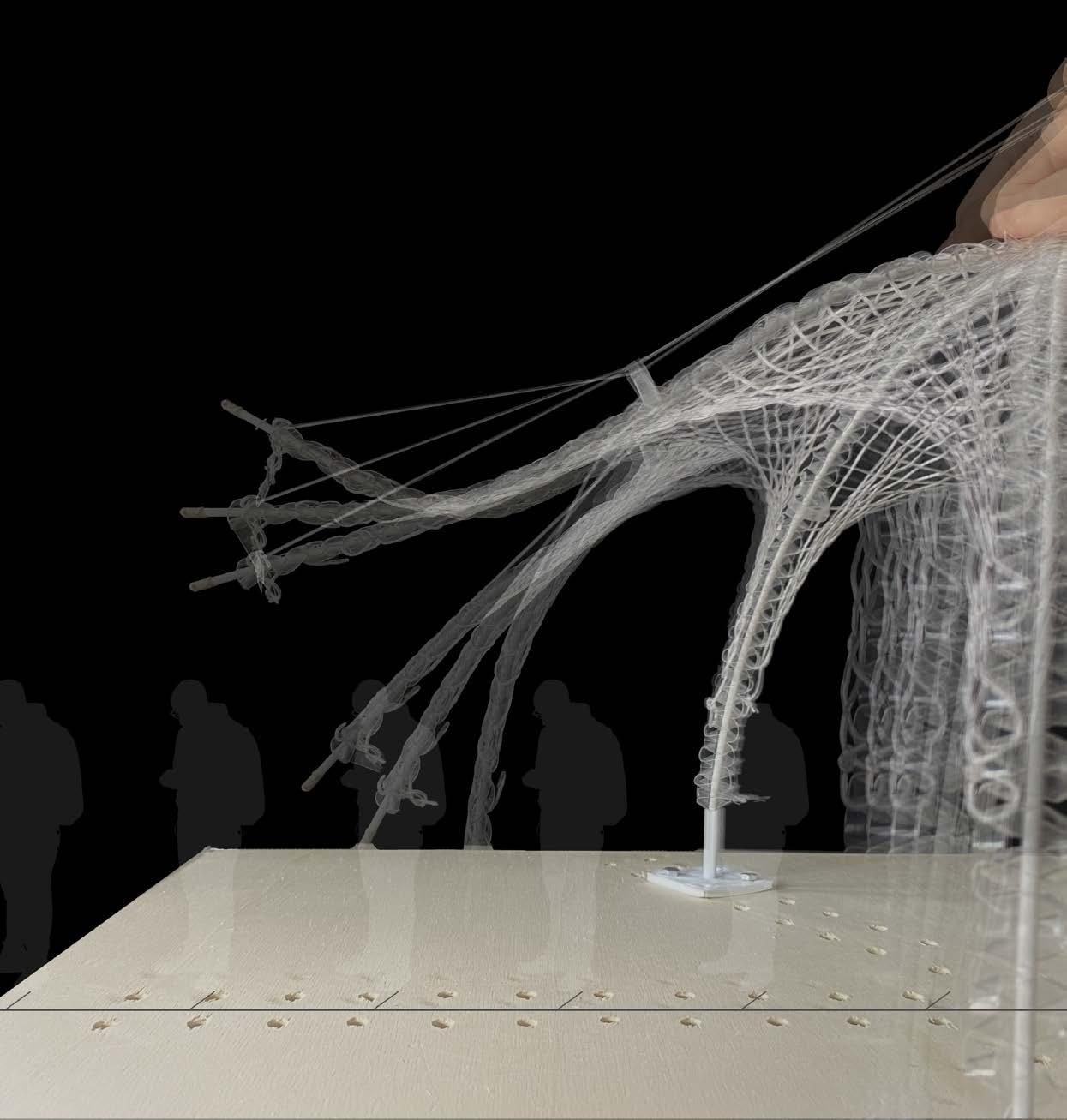
Ziqi Cui: Chapters written: 00, Introduction; 02, Concept; 04,Typology Exploration; 07,Conclusion; 08, Appendix
Siman Zhang: Chapters written: 00, Introduction; 01, Literature Review; 03, Hybrid Textile System; 05, Circular Assessment; 6, Applications; 07,Conclusion; 08, Appendix
0, Introduction
5, Life Circular Assessment
5.1 Product Life Management Overview
5.2 Strat of Life
1, Literature Review
1.1
1.2
1.3
1.4
1.5
2, Concept
2.1
2.2
2.3
2.4
5.3 Middle and End of Life
6, Applications Outlook
6.1 Future Outlook via AI Image
L, M, S
6.2 Scale-up Adaptive Applications
7, Conclusion & Discussion
2.5
2.7
The concept of lightweight architecture has emerged as a responsive approach to meet the diverse needs of individuals in contemporary society. Among the various sustainable and flexible materials, textile architecture has gained significant attention for its potential in facilitating adaptable use. Extensive analysis of the current state of the field has revealed a growing interest within the scientific community in these structures. In light of this, the present project aims to explore the unexplored possibilities offered by PolRe®, a hybrid synthetic fiber material, in the domain of lightweight interactive kinetic structures and decorative surfaces. The research encompasses several interconnected domains, including interactive lightweight construction design, bending-active textile hybrids, form-finding, circular economy, and mass customization. The research methodology unfolds through three primary stages, namely, prototype design, parametric simulation and optimization, and physical-scale testing. The employed methodology encompasses various approaches:
1. Finite Element Analysis (FEA) based mechanical performance simulation, utilizing Kangaroo and Karamba for analysing structural behaviour, as well as the parametric tool GH for simulating weaving surfaces.
2. Adoption of the evolutionary multi-objective optimization tool Wallacei to prioritize objectives, with a focus on minimizing material consumption, reducing force displacement, and maximizing available coverage volume.
3. Integrating the Arduino interactive system into the physical model to govern dynamic behaviour and lighting systems, thereby enhancing user experience.
4. Guiding material usage and practical hand-weaving applications through a customized parametric website, facilitating a thoughtful and efficient approach to construction.
The objective of this research is to develop a user-friendly, assembly-disassembly capable, and customizable prototype of hybrid textile structures. These prototypes will demonstrate heightened interactivity and variability, enabling them to adapt to diverse spatial requirements. By exploring the potential of the "weaving octopus" prototype, this project aims to contribute to advancements in lightweight construction design while promoting sustainable practices within the realm of textile architecture.
Light Weight Construction; Bending-active Textile Hybrids ; Parametric Design;From-finding; Assembly-Disassembly; Kinetic Adaptive Design;
In recent years, there has been a growing interest in the development and implementation of temporary architecture to meet the evolving needs of citizens. Temporary structures are designed to respond to immediate demands for housing, services, and adaptable spaces, providing flexible and modular solutions [1]. These structures are characterized by their ability to change and adapt within contemporary reality, reflecting the dynamic nature of modern society.
The widespread adoption of temporary structures has led to notable advancements in construction technologies and materials. The construction industry has witnessed a surge in the use of flexible, modular, and adaptable technologies, allowing for the rapid assembly and disassembly of temporary structures [2]. These technologies not only fulfill the immediate needs of the community but also offer a level of versatility that is lacking in permanent structures.
The exploration of materials and technologies for temporary construction has become a significant area of research. Researchers and practitioners have been experimenting with various materials and techniques to optimize the performance and functionality of temporary structures. Of particular interest is the use of textiles in temporary architecture, which offers numerous advantages such as lightweight, flexibility, and cost-effectiveness [3]. The integration of fabric/ material, design, mechanical technology, and modeling software plays a crucial role in achieving the desired performance of textile installations.
Furthermore, the intersection of culture, art, and technology has emerged as an area of exploration within temporary architecture. This interdisciplinary approach seeks to understand and analyze the impact of adaptive textile systems in the urban environment, evaluating their design potential and future developments [4]. By incorporating elements of culture, art, and technology, researchers aim to enhance the aesthetic and functional aspects of temporary structures, thereby creating more engaging and sustainable urban environments.
However, despite the progress made in temporary architecture, there are challenges that need to be addressed. One significant challenge is the environmental impact associated with temporary structures. Many temporary constructions generate significant waste and pollution due to their short lifespan and lack of consideration for sustainable practices [5]. Therefore, there is a growing need to develop environmentally friendly approaches in temporary architecture, focusing on the reuse and recycling of materials to minimize waste and promote sustainability.
In the realm of textile construction, textiles have traditionally been used for decorative purposes in interior design or as flat textiles in tensile-stressed lightweight constructions such as roofs and temporary buildings [6]. Textile hybrid construction bodies refer to structures composed of a combination of materials, including textiles, composite materials, and metals, to achieve specific design goals. These structures offer several advantages, such as lightweight, flexibility, cost-effectiveness, and ease of installation, making them suitable for various building applications [7, 8].The development of digital modeling and simulation tools has further enhanced the design and analysis capabilities of architects and engineers, resulting in reduced costs and construction time, as well as improved building performance and sustainability [9].
In the following sections, we will give the state of art on textile hybrid bending—active structure and their adaptive experiments .
The thesis explores a material-based computational design MCD [10] approach, drawing inspiration from nature and employing hybrid textile materials to create a soft and flexible variable structure. Extensive case studies were conducted, leading to the identification of a bending-active system as the fundamental structural framework for the design. Through experiments and computer simulations, the system's various forms under different external forces were validated. After careful selection, these forms were further developed and found applications in architecture, decoration, clothing, and other fields. Additionally, interactive design elements were introduced at the smallest unit level, enhancing the device's versatility and fostering engaging interactions with users.
The iterative workflow is designing-prototyping-testing-scaling up. It is a systematic approach used in the development process and enables continuous improvement and refinement of designs, ensuring they align with desired objectives and perform optimally in real-world scenarios.
In this paper, our research focuses on the exploration of flexible structures and textile materials in order to develop a versatile design prototype. Building upon the findings of our study, we have created an interactive device that allows for free assembly.
The functionality of this installation is diverse and can be applied in various contexts such as wearable clothing, facade decoration, public art, and temporary buildings. It can also be dispersed throughout urban spaces, contributing to the transformation of local environments and enhancing the urban atmosphere. Additionally, as a modular unit, it offers the flexibility to be easily assembled and disassembled, enabling the formation of large temporary public buildings. This feature facilitates convenient transportation, installation, and the ability to adapt the shape according to specific needs.
In the current era, the architecture and engineering industries are facing significant challenges, including increased complexity, cost-effectiveness, and the demand for customization. Traditional building structures and design methods have proven insufficient in addressing these challenges. However, recent advancements in lightweight construction applications, along with developments in fibre-based materials and matrix systems, have introduced innovative solutions [4]. As a result, temporary lightweight construction bodies have emerged to incorporate a wider range of building products and offer efficient solutions for digital modelling and practical construction.
Within the field of textile construction, textiles have traditionally been used either as decorative elements in interior design or as flat textiles in tensile-stressed lightweight constructions such as roofs and temporary buildings [6]. However, the concept of textile hybrid construction bodies has emerged, referring to structures that combine various materials, including textiles, composite materials, and metals, to achieve specific design goals. These structures offer a range of advantages, including being lightweight, flexible, cost-effective, and easy to install, making them an ideal choice for a variety of building applications[7, 8].
Furthermore, the development of digital modelling and simulation tools has enabled architects and engineers to design and analyze these structures more effectively. Utilizing these digital tools can help reduce design and construction costs and time, as well as improve the performance and sustainability of buildings [9]. The interdisciplinary collaboration between architects, engineers, and other relevant disciplines plays a crucial role in achieving successful lightweight design, particularly in the development of lightweight systems [5].
Material
• Hybrid Textile
• Sustainable
• Complexity structure and high costeffectiveness demond
• Mass customization
• Kinetic adaptive
•
• Accessible
• Operable
•
• Predictable simulation
• Degital twins
• Practical construction
• Senser interactive
• ```````
Structure
• Transformation structure
• Light-weight structure
• Adaptive structure
•
The literature review section provides a concise overview of four main topics: bending-active structures, textile hybrid materials, dynamic adaptive systems, and circular design with mass customization. The objective is to gain a comprehensive understanding of the simulation process and computational optimization of form-finding using textile hybrid bending-active structures. It also explores the principles and key points behind lightweight design using flexible textile materials. The application of lightweight dynamic adaptive structural prototypes and the design elements under the requirements of mass production and circular design are also discussed. By examining previous research and relevant case studies, research gaps are identified, which serve as the basis for the methodological approach adopted in subsequent research and design.
Active bending refers to the use of large elastic deformation to transform initially flat or linear elements into curved structures [11] This concept, known as bending active structures, leverages the inherent elastic behavior of flexible elements and is commonly employed in the design of deformable or deployable structures[12]. It has given rise to numerous dynamic architectural concepts. By simplifying the complexity typically associated with rigid mechanisms, variable bending active structures have become a popular choice in dynamic architectural design
The key advantage of these structures lies in the ability to introduce curvature during the assembly process, greatly simplifying the production and transportation of prefabricated planar components. Bending active structures can be applied to various structural types, including plates, and bending bar elements[13, 14]. They represent a structural formation process that offers versatility and flexibility in design.
Pre-bent components
Self-restraining systems
Post-restrained structures
Beam Elements
Plates Elements
Based on how bending is induced and maintained, there are three types of structures: pre-bent components[11, 15], selfrestraining systems [16], and post-restrained structures[11]. Pre-bent components are assembled in the workshop, where the bending is predetermined before installation. Similarly, self-restraining systems can also be pre-assembled, allowing for controlled bending during the assembly process. In contrast, post-restrained structures are assembled on the ground, where the bending is achieved by applying external forces or constraints.
The choice of structure type depends on specific design requirements and constraints, such as available construction space and the desired shape's complexity. Each structure type offers different advantages and considerations in terms of fabrication, transportation, and installation. The selection should be made based on a thorough assessment of the project's needs to ensure optimal performance and efficiency.
Rod Elements
Active bending structures require materials with high elasticity to strength ratios. The load-bearing behaviour of such structures varies with different curved geometries. Form-finding techniques have evolved from empirical experiments to modern methods based on dynamic equilibrium principles. The stiffness of bending-active structures is determined by three components: elastic, initial displacement, and geometric stiffness [17, 18].
The design of curved active building structures involves form-finding strategies and simulations, which can be broadly categorized into five sections [19]:
1. Variables of the Form-Finding Process
2. Form Development
3. Analytical Approximation
4. Computational Form-finding
5. Validation of Finite Element Simulation
Notably, the section on form development suggests that while computational form-finding methods have enabled a fully digital planning process, physical form-finding using structural physical models is still used in conceptual design. Additionally, as there is dimensional scaling in the form-finding experiments of the physical model, it is important to take into account the scaling of material behaviour at this stage[19-21].
Research on structural design cases utilizing bending active components has shown that a prevalent approach involves combining flexible bending elements with textiles to create what is known as a textile hybrid system. The term textile hybrid stands for the mutual exchange of structural action between bending- and form-active systems based on textile material behaviour [22].
Textile hybrid structures acquire both their geometry and structural behaviour from a reciprocal interaction between bending element and membrane.[23] Specifically, the integration of tensile (form-active) surfaces and linear networks of actively bent (bending active) composite beams comprises the lightweight self-stable textile hybrid system. [24] Through this interaction, the tensile membrane restrains the bending elements, which in turn prestress the membrane. This principle, in which the membrane becomes part of the primary structure of the system, can lead to an efficient loadbearing behaviour, as the pre-tensioning improves the stress stiffening effect[19].
Furthermore, the constraint provided by the membrane allows for the creation of fully self-tensioned structures without mesh distortion or incompatibility issues in deployable systems. This enables unconstrained rigid body deployment prior to textile connection. The combination of flexible rods for structural support and textile materials for spatial enclosure enhances the versatility of textile hybrid systems in various applications.
The arrangement of base and functional materials is critical in determining the properties and behavior of active structures. Choi et al. proposed a classification system for 4D printing structures, which can also be applied to evaluate the structure of 4D textiles [26]. By controlling the arrangement and direction of materials, the shape and behavior of the structure can be predicted and controlled. Leveraging advanced technology and manufacturing processes, textile hybrid materials offer significant flexibility and potential for use in industrial and architectural design[27].
different
It is worth noting that by varying the distribution of warp and weft threads and utilizing different weaving techniques, textile materials can form skins with different mechanical states, resulting in diverse morphological shapes under the same structural state. Overall, the use of advanced technologies and manufacturing processes unlocks significant flexibility and dynamic potential for industrial and architectural design through the application of hybrid textile materials.
This design focuses on the use of PolRe @, a flexible strip material made entirely from recycled and recyclable materials . Polre possesses anisotropic properties , with strong axial tensile and shear resistance , as well as moderate bending flexibility. This makes it a promising material for industrial and architectural design applications, which can be further explored through weaving and other fabrication techniques. The use of Polre aligns with the principles of sustainable design and circular economy, as it promotes the use of recycled and reusable materials while offering unique structural and aesthetic possibilities. Further research and experimentation can be conducted to fully harness the potential of Polre in structural and architectural design.
According to the former exploration of the TEXTILES HUB and PolRe Textile Innovation, the learning-by-doing educational experiment successfully explored the versatility and dynamic adaptability potential of different waving approaches to hand-woven structures.
It is possible that the next step in the research of using computer software to customise, simulate, and optimise performance based on the former waving method. Computer simulations can be used to model and predict the behaviour of complex systems, including the behaviour of textile materials and structures. Besides,Mass Customization is another potential area of research that could using digital technologies and computer-aided design tools to accurate design and guiding manufacturing process.
Kinetic structures utilize the inherent elasticity of flexible elements to design transformable and deployable structures, offering versatile kinetic possibilities while simplifying complex mechanisms[28]. The field of active bending is rapidly expanding, with researchers exploring various materials and geometries to optimize structural designs [29, 30].
To meet the increasing demand for customized technical solutions, especially in architectural applications, researchers propose integrating flexible motion principles observed in plant movements into lightweight and simplified bio-inspired mechanical devices[31-33]. This hypothesis was tested through a collaborative effort involving architects, engineers, and biologists [34]. By leveraging interdisciplinary expertise, the aim was to explore the transferability and scalability of these principles in creating innovative and efficient kinetic structures.
Incorporating dynamic behavior into facade components and architectural elements brings numerous advantages, including optimized utilization of daylight and the creation of interactive kinetic facades. Recognizing the importance of various disciplines in kinetic architecture, such as occupants' visual and thermal comfort, biomimicry, and microclimate, researchers aim to conceptualize adaptive facade forms that dynamically respond to variations in daylight [35, 36]. The integration of kinetic movements, release mechanisms, and structural configurations holds great potential for enhancing the functionality of responsive buildings[37].
Studies emphasize the remarkable potential of a biomimetic morphological approach in exploring and identifying relevant analogies that achieve functional convergence. However, the successful implementation of complex kinetic facades inspired by biology requires interdisciplinary collaboration, particularly involving material and structural experts [38]. By fostering collaboration among these experts, the integration of biomimetic design principles with advanced materials and structural considerations can be effectively achieved.
This collaborative effort ultimately leads to the development of efficient and functional kinetic facades in architectural design, further advancing the field of kinetic architecture. The integration of flexible motion principles, interdisciplinary collaboration, and advanced materials offers new possibilities for creating dynamic and visually appealing structures that adapt to their environments and interact with occupants.
The evolution of simulation-based design tools has led to significant advancements in the field of textiles. One notable development is the emergence of textile software capable of working in 3D, enabling a deeper understanding of 3D woven structures. These tools utilize simulations to predict and visualize the geometric structure of woven materials, offering valuable insights into their behavior[39, 40]. By integrating these tools with parametric modelers, designers can engage in iterative workflows involving shaping, simulating, and refining their textile constructions, resulting in impressive textile structures that demonstrate the potential of these integrated design approaches[41].
Smart Textile is the next generation of textiles, sensing and responding to environmental stimuli. It combines textile design, information technology, and material science, creating a unique interdisciplinary field[42]. Technological advancements have led to climate-responsive fabrics that optimize energy efficiency and comfort in confined spaces. By integrating parametric design and modeling software, the performance of shielding fabrics can be enhanced. The combination of textiles with sensors, actuators, processors, and microsystems opens up new possibilities [3, 43]. Architectural robots show potential in generating diverse kinematic behaviors, enhancing user experience. Research explores adaptive, kinematic spaces using textiles and mobile robotic connectors, aiming for energy efficiency and portability [24, 43, 44].
Left: Bally Ribbon Mills engineers and manufactures woven materials for use in a variety of critical applications. This woven reinforcement layer of coated polyester and embedded sensor collects data on stress and strain. Right: Ada, created by Jenny Sabin Studio, celebrates AI through architecture that responds to facial patterns, voice tones and sounds, processing this through AI algorithms that correlate to the sentiment expressed. The suspended structure is made of custom 3D printed nodes, fiberglass rods, integrated LED and fiber optics and is clad in knit photoluminescent yarns.
Of particular interest is the application of these tools in the development of shape-changing woven fabrics. Such fabrics often exhibit dimensional surface behavior through a hybrid architecture that combines weave structures with active yarn [40]. The incorporation of structural "bending-active" elements like GFRP rods and elastic fabric textile in hybrid textile architectures exemplifies the capabilities of these tools in creating shape-changing weaving constructions. These advancements hold great promise for revolutionizing the design and construction processes in the field of textiles.
Smart Textile is a dynamic field that offers significant potential for innovation in the textile industry and lightweight temporary structures. By combining advanced technologies and design principles, intelligent and responsive textile-based systems can be created. This requires interdisciplinary collaboration and the integration of cutting-edge materials and robotics. By pushing the boundaries of traditional textile applications, designers can unlock new possibilities for various industries.
Circular design principles
Life cycle assessment (LCA) has become the predominant means of assessing the environmental impact of a product or system. However, determining the environmental impacts of a building is one of the most complex applications of LCA The use of LCA in the built environment is standardised by European Standard (EN) 15978 (BSI, 2012) and EN 15804 (BSI, 2020b) for assessments at building level and product level, respectively[49].
Figure 15:Applying circular economy design principles at different points of intervention [45].
The international standard BS ISO 20887:2020 relating to sustainability in buildings and civil engineering works contains guidance for assessing and measuring the degree of disassembly and adaptability for a system and shows a summary chart for a mechanical and electrical engineering scenario, in which circularity parameters are marked if present in the mechanical and electrical services design [46].
Design principles for adaptability that shall be considered are
a) versatility;
b) convertibility;
c) expandability
d) Standardization
The level of standardisation within the built asset can be determined at various levels. This could be through a percentage of the overall build (cost, volume or mass), for each of the following categories:
i) dimensions;
ii) components;
iii) connections;
iv) modularity;
v) interoperability.
Circular construction embraces simplicity, standardization, and modularity in design, sustainably sourced materials, transparent mechanical connections, and a manufacturing-style approach. Designing for disassembly enables reversible construction and reusable components, reducing waste. Designing for adaptability allows buildings to be easily reconfigured or repurposed, minimizing demolition due to obsolescence. These principles promote resource efficiency and create more sustainable, adaptable structures [47].
– discussed in 5.2 End-of-life, 5.3 Module D – benefits and loads beyond the system boundary
TEXTILESHUB (TH Lab) at Politecnico di Milano has conducted design consultancies, educational exercises, and scientific campaigns since 2015. Their focus is on assessing the applicability of flexible materials and advancing the use of ultra-lightweight building systems. With a diverse range of skills and an accredited laboratory, TH Lab offers testing services for mechanical and optical behavior, as well as prototyping activities. Adopting a systemic design approach, TH Lab integrates material choice throughout the design process to drive innovation in the building sector[49].
Mass customization requires four key requirements: modularization, flexibility, information technology, and customer involvement. The product design must be modular to enable efficient customization, and the production process must be flexible enough to accommodate customization without significant cost and time increases. Information technology, including CAD, CAM, and PDM systems, is crucial for efficient management of production processes. Finally, customer involvement in the customization process is necessary for understanding their preferences and developing personalized products[50].
The designer used multi-objective optimization to find the best grid configuration for maximum load-bearing capacity. To specify a grid configuration with maximum load-bearing capacity, a parametric model was defined. The models were optimized towards three objectives: minimization of the cost and deflection, and maximization of the buckling factor.The cost was estimated using a custom-made cost function, while the deflection and buckling factor were evaluated with Karamba3D under factorized dead load [51].
https://waconnect.uwaterloo.ca/work/coursework/muscular-architecture-interactive-bending-active-system
The design of a cable bending-active structure has been presented in the current paper, attributing to considerations of adaptability and structural interaction toexternal moving loads.The construction design and manufacturing of the structural members and connections aimed at a high degree of structural modularization and mass customization.The present prototype development as such envisages providing technologically intelligent kinetic structural systems that effectively adapt to external conditions, in interactive and experiential way [29].
Active bending is calling for a paradigm shift in the way structures are designed and built. It is in this context that natural materials can play a significant role in the development of more sustainable and economical material practices in architecture.
The presented project aims to develop a modular bending-active system that relies on an interactive joint mechanism to induce stiffening stresses within the closed system. As seen in the modules, the bending and torsion forces developed in the “skin”, oak veneer, are induced through the pulling forces caused as a result of the bending forces applied on the “tendon”, zip tie, by the sliding joint.
Through modifications to the modules, it is possible to achieve a variety of end shape results. The benefits of this system is that it allows for a quick assembly and disassembly process, and it can be easily transported.
A design modelling pipeline for shaping FAHS using the projection-based methods of the Kangaroo2 library
The development of novel form-active hybrid structures (FAHS) is impeded by a lack of modelling tools that allow for exploratory topology modelling of shaped assemblies. We present a flexible and real-time computational design modelling pipeline developed for the exploratory modelling of FAHS that enables designers and engineers to iteratively construct and manipulate form-active hybrid assembly topology on the fly. The pipeline implements Kangaroo2’s projection-based methods for modelling hybrid structures consisting of slender beams and cable networks. A selection of design modelling sketches is presented in which the developed modelling pipeline has been integrated to explore the design space delineated by FAHS [52, 53].
The realisation of the bending-active membrane hybrid Isoropia was only possible, through an integration of the Structural, Design, Material and Fabrication system. This transdisciplinary and interscalar approach allowed us to design and build a morphing structural membrane system in only 4,5 months, which delivers new spatial experiences and a new level of detailing to the field of small scale membrane structures. Isoropia is until today the largest structure made in preprogrammed CNC-knit, with every single membrane being unique [54, 55].
The approach chosen in Isorpoia opens up opportunities for new design expressions in textile architectures and an integrative approach towards other building elements. Isoropia morphs between two very radically structural systems and spatial expressions: from a more normative outer appearance to the radically textile space in the inner area. A unified impression is created through the use of similar design features - the textile cones - in both systems and the ability to specify gradual shifts in families of elements and materials.
Architectural concept of Isoropia. 1) The southern exterior part (left) welcomes visitors to the Biennale and creates a canopy like structure guiding visitors into the Danish Pavilion. 2) The interior passage (middle) is the only entrance to the Danish Pavilion. The aim was to create a dense textile space, which creates curiosity on side of the visitors, allows them to slow down, study movies and text about the installation and finally redirects them into the further exhibition of the pavilion. 3) The northern exterior part (right) is directed towards the lively cafe zone of the Biennale and creates an shading entrance canopy, which adapts to the rhythm of the colonade of the existing Danish Pavilion.
This project highlights the design potentials of a recently proposed form-driven approach for bending-active tensile structures, in which the geometry of the actively bent elements can be directly defined without the recourse to a formfinding procedure. The approach is applied to the design of a lightweight sun-shading system that can be used to protect glazed building façades, and in which actively bent beams are restrained by pre-stressing strips. Other than structural requirements, the geometry of this hybrid structure is informed by functional and environmental considerations to prevent overheating and glare inside the building [29].
Research idea: Hybridized actuation of KRF: (a) KRF design and (b) Applicability to a curved/free-form building surface [56].
FUNDING: UNIVERSITY OF MICHIGAN, TAUBMAN COLLEGE OF ARCHITECTURE AND URBAN PLANNING, RESEARCH THROUGH MAKING GRANT
DATES: 2014-15
The first architectural pavilion project to incorporate AI, Ada is a lightweight knitted pavilion structure designed with Microsoft Research which embodies performance, material innovation, human-centred adaptive architecture and emerging technologies, including artificial intelligence and affective computing. An external rigid experimental shell structure assembled from a compressive network of 895 unique 3D-printed nylon nodes and fibreglass rods holds Ada’s form in continuous tension. Working with researchers and engineers at Microsoft Research, Ada is driven by individual and collective sentiment data collected and housed within the Microsoft Research Building 99[43].
Tensile meshes simulated in springFORM, a Javabased form-finding software developed by Sean Ahlquist, are translated into data for CNC knitting.
With material computation advancements, design and fabrication integration goes beyond materialization. This article explores incorporating sensing, feedback, and engagement in design exploration. Prototypes, methodologies, and technologies are used to harness textile micro-architecture for structural, spatial, and sensory-responsive qualities. The research instrumentalizes fiber structure, creating form- and bendingactive structures and deepening the understanding of material behavior during fabrication. The architecture aims to address challenges in sensory filtering for children with autism spectrum disorder [24].
A network of sensors and cameras located throughout the building offer multiple opportunities for visitors and participants to engage, interact with, and drive the project. The data include facial patterns, voice tones and sound that are processed by AI algorithms and correlated with sentiment. Three scales of responsive and gradated lighting, including a network of addressable LEDs, a custom fibre optic central tensegrity cone, and five external PAR lights respond in real time to continuous streams of sentiment data. These data are correlated with colours, spatial zones within the project, and responsive materials.
Sewing pattern drawing for inner net surface showing distribution of ‘cones’ and ‘cells’. The tension elements or ‘cones’ connect the inner surface to the outer surface, behaving as springs. Courtesy Jenny Sabin Studio.
It would be a very positive thing if cities were filled with devices that could interact with humans.
When people approach these devices, the movement of the devices can be activated. Human behavior and status can also be responded to at any time. It's fun, but also somewhat of a placebo. In addition, the light emitted by the installation can improve the originally closed and negative environment in some corners of the city, thereby bringing convenience to the surrounding residents.
More broadly, this kind of installation that symbolizes positive may not only exist in the city in the future, but even enter the residents' homes to become decorative components, lighting systems, art displays, etc.
These units are modular units that can be freely spliced. They will have the potential to be flexibly assembled, eventually forming a large public space. Modular units provide a convenient way to transport, build, and rebuild large sites. It also provides a variety of choices for users' flexible and changeable needs.
3 Waving methodology trials for bending element
Octopus, jellyfish have soft body structure. Flowers have flexible petals. This allows them to move flexibly and respond to complex external conditions. This design tries to take inspiration from nature and design a soft and flexible variable structure in a bionic way. So as to better adapt to the environment and meet the different needs of users.
compression ratio=6.4/1
different weaving method
compression ratio=material length before weaving/material length after weaving
2.4 Hybrid Textile System
(a) Kit of components
From the perspectives of both circle economic and environmental sustainability, the original concept behind this project was to use a single material and leverage its various anisotropic properties through weaving and shaping, in order to achieve a bending active structure that would be easy to disassemble and recycle
However, the outcomes of our initial attempts, which focused on the weaving method and relied solely on polre, did not meet our expectations. The following factors help explain why:
(b) Flat deployable grid
1. The weaving method alone does not provide enough axial elasticity for the curved members, making it difficult to generate the necessary mechanical support during bending
2. The bending process of rod-shaped objects formed by weaving can result in unexpected lateral displacements, which hinder the accurate prediction of their shape through software simulations
Therefore, we decided to abandon the original idea of using a single material and instead introduced elastic rod that composed hybraid textile structure which are better suited for bending-active characteristics. The selection and dimensions of these materials will be discussed in greater detail later in this paper.
C B' C'
Bending element Textile element B
C B' C'
B
A A'
Different shapes of the structure in different environments
This research gap seeks to explore the distinctions in dynamic behavior observed in hybrid textiles created through various manual weaving techniques. By conducting experiments and measurements, researchers can compare the dynamic properties of these textiles and visually represent the variations through graphs or charts. Such visual representations provide valuable insights into the relationship between weaving techniques and the dynamic performance of hybrid textiles, aiding textile designers and manufacturers in selecting the most appropriate weaving methods for specific applications.
To address this gap, researchers would utilize mechanical computational software to simulate and optimize bending-active structures. Through simulations, they can visualize the behavior of these structures under different conditions, displaying the relationship between applied forces and resulting deformations. Such visual representations assist in understanding the complex behavior of bending-active structures, facilitating the design and optimization process.
This research aims to explore the integration of computer-aided design (CAD) software with manual weaving processes to enhance customization and design capabilities. Visual representations, such as flowcharts or diagrams, can illustrate the step-by-step process of creating custom designs using CAD software and generating weaving patterns for the manual weaving process. These visuals highlight how CAD software assists users in designing and customizing handwoven textiles, addressing the gap and supporting designers in achieving more intricate and personalized designs.
To bridge this research gap, researchers aim to embed circular economy and sustainable principles throughout the entire textile design and manufacturing workflow. A visual representation, such as a circular economy diagram or lifecycle assessment (LCA) graph, can showcase how sustainable thinking is integrated into raw material sourcing, manufacturing processes, product use, and end-of-life disposal. By visually demonstrating the implementation of circular economy and sustainable principles, this research promotes environmentally conscious textile design and manufacturing practices.
Abstract
Hybrid Textile System
Bending Skeleton System
Tensile Skin System
Kinetic Structural System
Step 1
Material selection
Shape-finding
Waving method
Form-finding
Bending control
Step 2
synthesize and optimize the three subsystems in the GH platform
The figure above illustrates an initial prototype model, which consists of three components, namely, the bending skeleton system, the tensile skin system, and the kinetic structural system. In-depth analysis and investigation have been conducted to optimize material selection, shape-finding, and bending controled simulation
The mechanical proformace of bending element greatly depend on parameters including length, disposition, ratio, etc. In the figure the choice of common building materials is listed and plotted on a graph with the ratio of flexural strength against stiffness on a logarithmic scale, based on the ‘Ashby diagrams’.
Bending Behavior Experient
The digital and physical simulation with the same material of the deformation for a single skeleton under different external force.
Morphologies of Bending-Active Structures under Various Constraints.
The below diagram shows the digital simulation of the bending moment diagram and morphologies of the bending-active structure under 3 constraints.
Physical model
Computation model
In this study, we investigate the deformation of three combinations of bending rods controlled by tensioned wires. The wires are fixed at intersection point O and have free ends A, A', B, B', C, C', D, D'. The deformation of the rods is induced by forces applied in the axial plane of the rods. The deformation is simulated using the following input parameters:
1) the ratio of the contracted length of the bending rods to their original length when under tension;(0~1)
2) the direction of the force in the axial plane of the rods (up or down).
The test results of the above three groups of bending rod deformations are not all listed, and we have only listed several representative deformation states. According to the test results, the more bending rods there are, the more complex the resulting morphological changes.
Considering that the deformation of eight bending rods is too complex, and the deformation of four bending rods is not widely applicable, we will choose the case of six combined rods for further in-depth analysis. In addition, the hexagonal basic geometry composed of six rods has strong geometric expandability and stability, which will be further elaborated and studied in the subsequent unit cell combinations.
Weaving is a widely used art that can serve as an ideal structural element in architectural design, providing both support and elasticity . Originally used for basket weaving, traditional bamboo weaving has gradually been incorporated into furniture design, decorative design, interior facade design, and even fully woven pavilions.
Designers often employ different weaving techniques to achieve pattern and shape variations, as such methods have a decisive impact on the final outcome. For most weaving materials, there are two main categories: rigid weaving and elastic weaving. In this project, we focus on exploring the weaving methods of rigid materials, based on the selected inelastic properties of Polre@
Research Zone
Step 1 Step 2 Step 3
Decision-making criteria: Waving Methodology
Material
Weaving Skeleton Weaving Skin Rigid waving
Waving Test : 2D 3D
1 Durability and stability
2 Material cost
3 Aesthetics
Integration different weaving algorithm in GH platform
This section studies the methods of weaving. Due to the limitations of material elasticity, the weaving method belongs to rigid waving. Secondly, according to the different weaving parts, the research can be divided into the study of the skeleton and the skin
The research steps are as follows: first, design and performance testing of weaving methods in 2D and 3D situations; second, basic selection of weaving methods according to materials, durability, stability and aesthetics; third, integrating rigid weaving methods into bending-active rods and performing comprehensive calculations in conjunction with the gh platform.
Weaving steps and final weaving outcome
Weaving steps and final weaving outcome
1. Provide support points for adding structural ropes.
2. Provide a better integration of skeleton and braided skin.
3. Provide space for braided wires.
Starting design with 2D drawings
Different weaving methodology of the skin
Different length of the used material with different weaving method
Durable and Stable Test
The evaluation of the durable test here is mainly obtained by the deformation of the rod after bending as judged by the naked eye.
After comprehensive consideration of weaving material cost and stability after braiding and bending, we have selected type C for further research.
The surface woven using weaving method A displays the following characteristics during manual bending tests:
1. Differences in shape due to different weaving starting points: The supporting bars of the woven surface exhibit different three-dimensional shapes depending on the starting edge of the weaving method. Since the later woven lines are constrained by the earlier ones, the later woven shape tends to be flatter, while the end of the earlier woven section forms a three-dimensional cavity. This shape difference is more pronounced when the A and B bars are bent.
2. Differences in degree of freedom of movement due to different weaving starting points: The first woven line has only the tension provided by AB bars with no constraint from later woven lines. Therefore, when the A-bar bends inward, the line becomes loose, making it difficult to maintain its shape and also move upward. In contrast, the B-bar has greater freedom of movement when bent upward or inward.
The surface woven using weaving method B displays the following characteristics during manual bending tests:
1. Three-dimensional space of the woven surface: The weaving logic of method B requires a reverse position between the AB bars' shortest connection. During the weaving process, the symmetrical weaving lines of this method cross only once. When the AB bars are bent to the same degree, the weaving lines form a spatial intersection without constraint between the weaving lines. Therefore, after weaving is completed, the woven surface exhibits a three-dimensional state.
2. Limited degree of freedom of the supporting bars after weaving: Bending tests of models indicate that when the bars bend inward, the weaving lines limit the bars' freedom of movement due to the nonelasticity of the woven material. Meanwhile, it is difficult for the bars to bend upwards while under tension from the woven lines, causing the lines to become loose which lose the ability to maintain the bent bars' shape and control the final form.
The surface woven using weaving method C displays the following characteristics during manual bending tests:
1. The knitted surface exhibits a mesh state: The surface generated by the knitting logic of C tends to be in a non-elastic mesh state from a morphological logical perspective. This is because the warp and weft of this knitting method constrain each other, resulting in the highest consumption of materials but the most stable mechanical performance compared method A and B.
2. Larger degree of freedom of the rods after weaving : The model bending tests show that the rods will form a curved surface regardless of whether they bend inward or upward. Although the degree of freedom of the rods after weaving the surface is limited due to the lack of elasticity in the weaving material, the degree of freedom of the rods under the constraint of the C knitting method is larger than that of the A and B weaving method.
2D Exploration
3D Experiment Waving Feature Further Topic
• Material Usage :
• Stability of skin:
• Flexibility of bar:
• Spatial form:
• Material Usage :
• Stability of skin:
• Flexibility of bar:
• Spatial form:
1.Structural Optimization
2.Mass Customization
Weaving Method B and C
• Material Usage :
• Stability of skin:
• Flexibility of bar:
• Spatial form:
1.Kinetic Exploration
Based on the previous research on different weaving methods for skins ranging from 2d to 3d, different weaving method exhibit varying characteristics as follows:
A: More material-efficient, but depending on the starting points of rods a and b, there is a significant difference in the freedom of inward or upward bending of the two rods after the completion of the woven skin.
B: Most material-efficient, producing a more diverse three-dimensional space after weaving, but the flexibility of rods a and b in inward or upward bending is limited after the completion of the woven skin.
C: Most material-consuming, but the resulting mesh surface is the most stable under this weaving method, and the flexibility of rods a and b in inward or upward bending is higher after the completion of the woven skin.
Therefore, based on the characteristics mentioned above, weaving method A introduces significant differences in the flexibility of rods a and b, making it difficult to conduct further research. Subsequent studies will focus on the in-depth investigation of prototypes under weaving methods B and C.
BWeaving type: B
Pons: more stable, can be customized. Co ns: th e sha pe ca nnot be ch anged af ter assembly
CWeaving type: C
Pons: high flexibility and interactive potential
Cons: not stable enough
TypeB method is more stable, and its final shape is more affected by consumables. Therefore, this method is suitable for helping the prototype form finding by controlling the consumables.
This chapter mainly conducts further indepth research on Type B. Try to apply it to the development design of the prototype. And explore what development potential the properties of Type B can bring to the prototype.
Data Collection: Total material usage(m), Height (m), Area(m2), Max displacementce(cm)
Section and Geometry
Material Load
Display of Mechanical Evaluation
Karamba3D Analyze
Height(m): 3.13
Area(m^2): 21.28
Max displacement(cm): 0.76
Maximun curvature(rad/m): 0.45
Material usage(m)
AOC: 58.66
A'OC': 58.66
A'OB: 58.66
AOB': 58.66
BOC: 58.66
B'OC': 58.66
Total material usage(m): 351.97
Using typeB, observing what effect it has on the final shape while reducing the weaving material in each two skeleton evenly at the same time.
Gradually reduce the weaving consumables between each two skeletons.
Using typeB, observing what effect it has on the final shape while reducing the weaving material in each two skeleton unevenly.
Input: material usage for each two skeleton
Out put: form/height/area/curvature/displacement of prototype
Iteration 2
Iteration 17
Height(m):3.1
Area(m^2):18.9
Max displacement(cm):1.35
Material usage(m)
AOC:59.8
A'OC':59.54
A'OB:59.54
AOB':59.8
BOC:59.8
B'OC':59.8
Total material usage(m): 358.46
Maximun curvature(rad/m):0.58
Height(m):3.4
Area(m^2):11.26
Max displacement(cm):1.44
Material usage(m)
AOC:60.8
A'OC':61.0
A'OB:60.8
AOB':61.0
BOC:50.9
B'OC':51.2
Total material usage(m): 345.94
Maximun curvature(rad/m):0.62
Height(m):3.1
Area(m^2):18.9
Max displacement(cm):1.35
Material usage(m)
AOC:59.8
A'OC':59.54
A'OB:59.54
AOB':59.8
BOC:59.8
B'OC':59.8
Total material usage(m): 358.46
Maximun curvature(rad/m):0.58
Height(m):3.4
Area(m^2):11.26
Max displacement(cm):1.44
Material usage(m)
AOC:60.8
A'OC':61.0
A'OB:60.8
AOB':61.0
BOC:50.9
B'OC':51.2
Total material usage(m): 345.94
Maximun curvature(rad/m):0.62
Height(m): 2.9
Area(m^2): 25.2
Max displacement(cm): 1.24
Material usage(m)
AOC: 57.8
A'OC': 57.8
A'OB: 58.8
AOB': 58.8
BOC: 66.2
B'OC': 66.2
Total material usage(m): 365.63
Maximun curvature(rad/m):0.59
Among the many variations above, these results are selected by human beings, and they can usually form a more reasonable space that can be used by people.
Height(m): 3.76
Area(m^2): 2.39
Max displacement(cm): 0.47
Material usage(m)
AOC: 51.96
A'OC': 51.96
A'OB: 51.96
AOB': 51.96
BOC: 51.96
B'OC': 51.96
Total material usage(m): 311.78
Maximun curvature(rad/m): 0.74
In order to go futher explore this prototype. We iterated nearly 24,000 results (see in appendix) using optimized s election t ool(Wallaice) i n g rasshopper. D uring t he generation process, some important factors are considered by us, such as the stability of the structure, the consumables of the structure, and whether it can form a usable space. Through these to determine our optimization direction, it helps us to select relatively better results among the 24,000 possibilities.
Fittness01: Minimize total material usage
The total material usage can be calculated using the following equation:
Total Material usage = Material usage
(AOC+A'OC'+A'OB+AOB'+BOC+B'OC')
Fittness02: Minimize dispacement
The maximum displacement in Kramaba 3d can be calculated using the following equation:
δ_max=5qL4/384EI
δ_max : is the maximum displacement at the center of the beam
q : is the uniform load applied to the beam
L : is the length of the beam
E : is the Young's modulus of the beam material
I : is the moment of inertia of the beam's crosssection
Fittness03: Available space
Generation_id: 199
Individual_id: 11
Total material usage(m): 165.65
Generation_id: 199
Individual_id: 104
Total material usage(m): 291.16
Generation_id: 199
Individual_id: 119
Total material usage(m): 299.20
Generation_id: 199
Individual_id: 26
Total material usage(m): 309.62
Material usage
Generation_id: 199
Individual_id: 4
Max displacement(cm):0.48
Maximun curvature(rad/m):0.90
The ratio of height and area in some range(0.058-2.444) to be sure each iterations can form enough space for human activies.
The available space can be calculated using the following equation:
Available space = H/Area
Height: 2.19197 m
Area: 37.77415 sqm
H/A Ratio: 0.058
Generation_id: 199
Individual_id: 29
Max displacement(cm):0.73
Maximun curvature(rad/m):0.90
Generation_id: 1
Individual_id: 79
Max displacement(cm):0.94
Maximun curvature(rad/m):0.66
Generation_id: 1
Individual_id:110
Max displacement(cm):1.56
Maximun curvature(rad/m):0.70
Dispacement
Height: 2.88 m
Area: 26.02 sqm
H/A Ratio: 0.11
Height: 3.374m
Area: 14.391 sqm
H/A Ratio: 0.234
Height: 3.575 m
Area: 4.923 sqm
H/A Ratio: 0.726
Height: 3.768 m
Area: 1.54 sqm
H/A Ratio: 2.444
Ratio of height and area
The spaces generated by a small number of iterations do not meet the requirements, and they will be removed during further selection.
Fittness03=0 means the H/A ratio in the ideal range, it can form availabe space for peopel use, which is the reslut what we want.
After 24thousands of iterations, the final generated results will gradually meet our ideal results.
Material consumables(fittness01) for optimized results are approximately around 295-304m. Structure displacement(fittness02) for optimized results are approximately around 0.4-0.6cm.
Height/Area ratio of most smaples are near to 0, which means they can meet the requirements for space availability.
Outerlier: height/area not in a reasonable range.
The first few generations: optimization results generated at the beginning.
The last few generations: optimization results generated as the number of iterations increases.
Outerlier: form crashes, unable to generate a valid shape.
By observing the first few generation results, for example, in generation01 results, the shape of the prototype is closer to an exaggerated form. In these cases the value of the material consumables and the structural displacement are relatively large.
All the results(remove duplication) from generation01: 96/120
As the evolutionary direction moves closer to the fitness goal, in the last few generation results(for example generation199). The shape of each prototype is closer together, forming a similar cocoon shape. At same time, the material consumables and structural stability are optimized compared to the original generation results.
All the results(remove duplication) from generation199(last generation): 17/120
Different from the previous selection criteria, this time we select the computer-optimized results according two different fittness. The results show that as the iterations progressed, the computer gradually optimized our prototype into a cocoon-like structure that performed relatively well in terms of consumables and stability But actually all generated results have application potential in the case of controlled H/A ratio, which depends on the specific needs of users. Therefore, our design purpose is not to obtain the only fixed result, but we can give further application opinions by setting fittness.
In the experimental Typology B setup of a physical model, the bending members are subjected to both the elastic force of the bent member itself and the tension exerted by a woven textile covering. These forces work together to achieve a dynamic equilibrium, allowing the structure to maintain its original shape even after removing the anchor point at the bottom of the bent member.
The following images depict the performance of the unit with the ends of bent members in different states: fixed state (left), free state (middle), and a comparison of the two states (right). There is a noticeable deviation in the shape between these two states, primarily due to the lack of control over the weaving precision. Therefore, the next experiment will attempt to achieve more accurate control over the shape by implementing pre-encoded control of the length of the woven textile.
The second experiment in the physical model aims to control the final shape of the model by encoding the length of the textile material. The purpose is to incorporate the pre-simulated segmented lengths obtained through parametric design into the actual construction process, thereby reducing the discrepancy between the physical model and the computer-generated model in terms of shape.
The following images depict the workflow of achieving precise control through the encoding of the material from parametric design to physical construction.By implementing this workflow, the aim is to bridge the gap between the physical model and the computer-generated model, allowing for more precise control over the shape of the physical model by incorporating the encoded material lengths based on parametric design.
Design phase : Parameterization :
Translation :
Construction process:
Coding the Textile Material Assembled Skin after Coding
TypeC method has better flexibility and can f orm a p erfect s urface b etween t he t wo s keletons. It's suitable for developing some kinetic structures.
This chapter mainly conducts further in-depth research on Type C. Try to apply it to the development design of the prototype. And explore what development potential the properties of Type C can bring to the prototype.
Mechanical Evaluation
Height(m): 1.9
Area(m^2): 21.28
Max displacement(cm): 8.11
Maximun curvature(rad/m): 1.09
Material usage(m)
AOC: 48.66
A'OC': 48.66
A'OB: 48.66
AOB': 48.66
BOC: 48.66
B'OC': 48.66
Total material usage(m): 291.98
Bionic inspired kinetic mechanical system
Bionics-Inspired
By imitating the activity of finger joints, a mechanical dynamic mechanism based on bend-active structure was designed. In the preliminary test, we manually simulated bending up and bending down based on rope pulling.
Bending up
Bending down
The next step of the research will focus on how to automate and intelligentize this dynamic behavior through sensors and servos.
The prototype of “Weaving Octopus” combines the dynamic mechanism of traction, and the C method exhibits excellent flexibility in this dynamic mechanism. The next step of research will be based on this dynamic mechanism, combined with senser and engine, to establish a working system that combines intelligent interaction.
In addition to their respective features, both of the above prototypes can be flexibly self-assembled while connecting one or more adjacent prototypes. This makes them potentially become the smallest unit for modular design. This chapter will gradually discuss this feature and its application in depth.
When two independent prototypes can be connected through a foot point, there are two connection methods.l
When two independent prototypes can be connected through two foot points at the same time, there are two ways of connection, and they will form different aggregation forms.
In addition, two independent prototypes can also be connected through three foot points at the same time. With these two connection possibilities, they will form different aggregation forms.
In this chapter, an interactive system will be introduced to the "Weaving Octopus" prototype using electronic components such as the Arduino microcontroller, servo motors, and ultrasonic sensors. The objective is to explore the dynamic adaptability and interactive potential of the prototype.
Weaving Type B
People Behaviors
Weaving Type C
Interactive Lighting
Ultrasonic Sensor Optical Fiber
Arduino Hardware
Interactive Kinetic
Coding Control
Ultrasonic Sensor Steering engine
People Behaviors
4.32 Interactive Lighting System
Auduino Control System
Type B Methodology
Ardunio electronic components
https://clipchamp.com/watch/O3yGP6nQRvz
Auduino Control System
Type C Methodology
Ardunio electronic components
https://clipchamp.com/watch/O3yGP6nQRvz
Bending Inward and Bending Outward
https://clipchamp.com/watch/O3yGP6nQRvz
Bending Outward
Strategies used in "weaving Octupos"
Beginning
•
•
•
•
6.21 Design for Manufacturing and Assembly (DFMA)
User Oriented Design Interface
Closed loop recycling
Material production
Customization design Website(OP1,OP2,···)
Order materials form factory
Materials recyceled by customer
Material use cost and "Weaving Octopus" Guidebook 1
OPT2 Material use cost and "Weaving Octopus" Guidebook
Assembling
Disassembling
Customer Requirement
Assembling according to Guidebook 1
Assembling according to Guidebook 2
Assembling according to Guidebook 3
OPT3 Material use cost and "Weaving Octopus" Guidebook
Assembling
Disassembling
Manufacture OP1
Assembling
Disassembling
Manufacture OP2
Manufacture
• Recycle
• Resuse
• Disposal
AI Exporation and Scale-up Applications
Based on the previous exploration of the “Weaving Octpus” prototype structure and form, this chapter will explore further investigate the prototype through the application of the L-M-S three scales.
S scale: Accessories Rotic Toy
M scale: Furniture Tent
L scale: Installation
Based on the previous exploration of the “Weaving Octpus” prototype structure and form, this chapter will explore further investigate the prototype through the application of the L-M-S three scales.
Use furniture as example:
Customization Product AI Platform Text-To-Image Model
Parameters:
(((People's perspective view)), the streets of Milan,some people walking in the street , some plants, building detials, realistic rendering,8k, Negative prompt: (worst quality), dark,map Steps:
Parameters:
industrial style ,living room ,(((dusk))) dvArchModern, interior, 85mm, f1.8photo realistic, hyperrealistic, super detailed, intricate, dramatic, sunset lighting, shadows, high dynamic range <lora:xsarchit ectural_7Safetensors:0.5>
Negative prompt: signature, soft, blurry, drawing, sketch, poor quality, ugly, text, type, word, logo, pixelated, low resolution, saturated, high contrast, oversharpened
Parameters:
Minimalism:1.6 ,children room playing corner, ((bright color)),(((( big carpet)))), dvArchModern, interior, 85mm, f1.8photo realistic, hyperrealistic, super detailed, intricate, dramatic, sunset lighting, shadows, high dynamic range <lora:xsarchit ectural_7Safetensors:1> Negative prompt: ((((people)))),(((big furnitures))),((sofa)),((chairs)),signature, soft, blurry, drawing, sketch, poor quality, ugly, text, type, word, logo, pixelated, low resolution, saturated, high contrast,
Parameters:
high Fashion Model :1.5 ,ACGN,half-length Portrait,show,(futuristic sense),((cyberpunk)), strong light studio ((highly detailed )), sharp focus, volumetric fog, 8k UHD, DSLR, high quality, film grain, Fujifilm XT3, RAW, analog style <lora:fashionGirl_v53:0.6> Negative prompt: (((((nsfw))))), ((((big hands, un-detailed skin, semi-realistic, cgi, 3d, render, sketch, cartoon, drawing, anime)))), (((ugly mouth, ugly eyes, missing teeth, crooked teeth, close up, cropped, out of frame))), worst quality, low quality, jpeg artifacts, ugly, duplicate, morbid, mutilated, extra fingers, mutated hands, poorly drawn hands, poorly drawn face, mutation, deformed, blurry dehydrated, bad anatomy, bad proportions, extra limbs, cloned face, disfigured, gross proportions, malformed limbs, missing arms, missing legs, extra arms, extra legs, fused fingers, too many fingers, long neck, Easy_neg
Steps: 20, Sampler: Euler a, CFG scale: 8, Seed: 4271478382, Face restoration: CodeFormer, Size: 512x800, Model hash: c0d1994c73, Model: realisticVisionV20_v20, Denoising strength: 0.55, Mask blur: 0, ControlNet-0 Enabled: True, ControlNet-0 Module: canny, ControlNet-0 Model: control_mlsdfp16 [e3705cfa], ControlNet-0 Weight: 1.7, ControlNet-0 Guidance Start: 0, ControlNet-0 Guidance End: 0.54, ControlNet-1 Enabled: True, ControlNet-1 Module: depth_leres,
Parameters:
high Fashion Model :1.7 ,Portrait,((ACGN)),(meta),((cyberpunk)), strong light studio,Dark simple background, future sense ((highly detailed )), sharp focus, volumetric fog, 8k UHD, DSLR, high quality, film grain, Fujifilm XT3, RAW, analog style <lora:fashionGirl_v53:0.8>
Negative prompt: (((((nsfw))))), ((((big hands, un-detailed skin, semi-realistic, cgi, 3d, render, sketch, cartoon, drawing, anime)))), (((ugly mouth, ugly eyes, missing teeth, crooked teeth, close up, cropped, out of frame))), strong makeup, worst quality, low quality, jpeg artifacts, ugly, duplicate, morbid, mutilated, extra fingers, mutated hands, poorly drawn hands, poorly drawn face, mutation, deformed, blurry, dehydrated, bad anatomy, bad proportions, extra limbs, cloned face, disfigured, gross proportions, malformed limbs, missing arms, missing legs, extra arms, extra legs, fused fingers, too many fingers, long neck, Easy_neg,
Kinetic Textile Facade exampled with the case Pedagogy in Secondary Education School Universidad Católica / Alberto Moletto + Sebastián Paredes
Lcase: 0
Axial Stress(KN/cm2)
Lcase: all
This part further verified the feasibility of the prototype in specific scenarios through mechanical simulation of the facade design. In order to simplify the calculation, we cut the simulation range into a building facade of 6m*6m. These 12 connected facade elements are considered as a structural whole for calculation. The focus of the simulation is to compare the stress in the skeleton and weaving system of the WO facade under normal state and wind load, as well as the deformation displacement of the whole structure. In the parametric structural engineering tool, Karamba 3D, we preset that the structure consists of three parts: control rope, GFRP skeleton and weaving system. Detailed material selection and input parameters in karamba3D are as shown in this Table.
Lcase: 0 Lcase: all
Axial Stress(KN/cm2)
The maximum utilization in both states does not exceed 100%. Under the action of wind load, the maximum displacement of the structure is approximately 0.676cm, which is far less than the maximum threshold allowed for structural deformation.
The maximum value of tensile stress in this weaving system is 3.02 kN/ cm2, in control rope is 2.85 kN/ cm2. The yield strength of PET is 5.52 kN/ cm2, which means this weaving system can withstand relatively high wind speeds. The maximum value of the axial stress in skeleton is 3.47 kN/ cm2. The yield strength of GFRP is 45 kN/ cm2. Through the above simulation and calculation, it can be seen that the structure as a whole can distribute high loads without crushing. It is feasible to apply this structure to building facades.
The research on the typology of the "Weaving Octopus" indicates that a hybrid textile system based on a bending-active structural system, created through weaving methodology, is both feasible and beneficial.
1.Different weaving method employed for the skin result in distinct dynamic behavioral characteristics, providing users with the ability to choose suitable methods based on desired states. For instance, when using Method B, the woven skin exhibits more constraints, enabling better control over the final form and maintenance of the bending-active structure, even after being freely anchored. Consequently, precise customization of the final form can be achieved by encoding the weaving material.On the other hand, woven skin with Method C exhibit higher degrees of freedom, making it more suitable for dynamic movementsand accommodating a diverse range of spatial requirements.
2.Furthermore, this research demonstrates significant potential for the adaptive application of hybrid textile prototypes based on bending-active structures formed through weaving. From an individual unit perspective, the "Weaving Octopus" can derive customized forms that align with various spatial requirements. Moreover, these prototype units can be flexibly assembled and connected with one or more adjacent units, making them ideal as the smallest modular elements for adaptive designs at larger scales. This modular design opens up infinite possibilities for diverse application scenarios.
3.From a life cycle perspective, there are several advantages. Firstly, weaving the skin and structural elements effectively reduces the type amd amount of connection joints and materials, facilitating material recycling and subsequent recovery efforts. Secondly, the typology formed through weaving enables users to conveniently assemble and disassemble the product, enhancing its circular disassembly for different needs. Lastly, the utilization of parameterized platform assists in design and production process,enabling precise control over the final effect and required materials, leading to significant savings in material resources waste and time costs. These three aspects collectively address the demands and challenges of the "Weaving Octopus" in terms of circular economy and environmental friendliness.
The development and design of the "Weaving Octopus" typology present innovative approaches for sustainable and environmentally friendly textile temporal construction and decoration. However, there are limitations in the research that require further investigation and consideration.
1.Due to the manual hand weaving involved in this typology, it is challenging to achieve precise control over the weaving accuracy. Additionally, the weaving methodology requires users to invest time in learning the techniques, limiting its universal applicability. Possible solutions could involve combining robotic arms for precise weaving manufacturing or integrating virtual reality (VR), augmented reality (AR), and mixed reality (XR) technologies to assist users in achieving precise manufacturing.
2.While this typology exhibits dynamic and variable potential, it lacks responsiveness to climatic conditions. Future research could focus on developing responses to solar and rain based on the dynamic behavior of the "Weaving Octopus." This would enable the realization of dynamic shading components, solar energy collection, and rainwater harvesting
3.The practical application of the prototype requires further consideration of specific details. For example, the detail design of anchor points for outdoor installations and the ability to withstand wind and rain loads. These factors need to be addressed to ensure the structural integrity and performance of the "Weaving Octopus" in outdoor environments.
In conclusion, the research on the "Weaving Octopus" typology presents a promising solution for sustainable textile construction and decoration. However, addressing limitations such as manual weaving accuracy and environmental responsiveness will require further research and development. Interdisciplinary collaboration and the integration of advanced manufacturing technologies will play crucial roles in overcoming these challenges and advancing the practical application of the "Weaving Octopus" typology.
1. Mankus, M.J.M.L.a.S.F.o.L., Tactics for temporary uses of buildings and spaces in architecture. Typology and sociocultural value. 2015. 7(1): p. 132-140.
2. Rotilio, M., et al., Temporary building construction to make cities more sustainable: An innovative “Square Box” proposal. Journal of Cleaner Production, 2022. 372.
3. Gasparini, K., Digital Hybridisation in Adaptive Textiles for Public Space. Textiles, 2022. 2(3): p. 436-446.
4. Cherif, C.J.T.M.M.P., Textile materials for lightweight constructions. 2016.
5. Lienhard, J. and P. Eversmann, New hybrids – from textile logics towards tailored material behaviour. Architectural Engineering and Design Management, 2021. 17(3-4): p. 169-174.
6. Lüling, C., et al., Advanced 3D Textile Applications for the Building Envelope. Applied Composite Materials, 2021. 29(1): p. 343-356.
7. Ahlquist, S., et al. Exploring material reciprocities for textile-hybrid systems as spatial structures. in Prototyping Architecture: The Conference Papers. 2013.
8. Kamble, Z. and B.K. Behera, Sustainable hybrid composites reinforced with textile waste for construction and building applications. Construction and Building Materials, 2021. 284.
9. Popescu, M., et al., Structural design, digital fabrication and construction of the cable-net and knitted formwork of the KnitCandela concrete shell. Structures, 2021. 31: p. 1287-1299.
10. Yazici, S. and L. Tanacan, Material-based computational design (MCD) in sustainable architecture. Journal of Building Engineering, 2020. 32.
11. Lienhard, J., et al., Active Bending, a Review on Structures where Bending is Used as a Self-Formation Process. International Journal of Space Structures, 2013. 28(3-4): p. 187-196.
12. Lienhard, J., et al., Active Bending, a Review on Structures where Bending is Used as a Self-Formation Process. 2013. 28(3-4): p. 187-196.
13. Laccone, F., et al., Integrated computational framework for the design and fabrication of bending-active structures made from flat sheet material. Structures, 2021. 34: p. 979-994.
14. La Magna, R., Bending-active plates: strategies for the induction of curvature through the means of elastic bending of plate-based structures. 2017: Stuttgart: Institut für Tragkonstruktionen und Konstruktives Entwerfen ….
15. Lienhard, J. and C. Gengnagel, Recent developments in bending-active structures. 2018.
16. Brancart, S., et al., Bending-active reciprocal structures: geometric parameters and their stiffening effect. 2018.
17. <Diss_Bending_Active_Structures_Julian_Lienhard (1).pdf>.
18. Schleicher, S., et al., Form-Finding and Design Potentials of Bending-Active Plate Structures. 2015. p. 53-63.
19. Lienhard, J., Bending-active structures: form-finding strategies using elastic deformation in static and kinetic systems and the structural potentials therein. 2014.
20 Lienhard, J., et al., Form-finding bending-active structures with temporary ultra-elastic contraction elements. 2014. 107: p. 115.
21. Davis-Sikora, D., R. Liu, and L. Ohrn-McDaniel, Form-finding and fabrication of BeTA pavilion: a bending-active biotensegrity textile assembly. SN Applied Sciences, 2020. 2(12).
22. Ahlquist, S., et al. Physical and numerical prototyping for integrated bending and form-active textile hybrid structures. in Rethinking Prototyping: Proceeding of the Design Modelling Symposium, Berlin. 2013.
23. Lienhard, J., et al. Extending the functional and formal vocabulary of tensile membrane structures through the interaction with bending-active elements. 2013.
24. Ahlquist, S., Sensory material architectures: Concepts and methodologies for spatial tectonics and tactile responsivity in knitted textile hybrid structures. International Journal of Architectural Computing, 2016. 14(1): p. 63-82.
25. Millentrup, V., M.R. Thomsen, and P. Nicholas, Actuated Textile Hybrids.
26. Choi, J., et al., 4D Printing Technology: A Review. 3D Printing and Additive Manufacturing, 2015. 2(4): p. 159-167.
27. Koch, H.C., D. Schmelzeisen, and T. Gries, 4D Textiles Made by Additive Manufacturing on Pre-Stressed Textiles—An Overview. Actuators, 2021. 10(2).
28. Brancart, S., L. De Laet, and N. De Temmerman, Deployable Textile Hybrid Structures: Design and Modelling of Kinetic Membrane-restrained Bending-active Structures. Procedia Engineering, 2016. 155: p. 195-204.
29. Boulic, L., et al., Form-driven design of a bending-active tensile façade system. International Journal of Space Structures, 2020. 35(4): p. 174-190.
30. Maierhofer, M., et al., Self-Choreographing Network: Towards cyber-physical design and operation processes of adaptive and interactive bending-active systems. 2019.
31. Schleicher, S., et al., A methodology for transferring principles of plant movements to elastic systems in architecture. Computer-Aided Design, 2015. 60: p. 105-117.
32. Lienhard, J., et al., Flectofin: a hingeless flapping mechanism inspired by nature. Bioinspir Biomim, 2011. 6(4): p. 045001.
33. Schleicher, S., Bio-inspired compliant mechanisms for architectural design: transferring bending and folding principles of plant leaves to flexible kinetic structures. 2015.
34. Liang, H. and L. Mahadevan, Growth, geometry, and mechanics of a blooming lily. Proceedings of the National Academy of Sciences, 2011. 108(14): p. 5516-5521.
35. Hosseini, S.M., et al., A morphological approach for kinetic façade design process to improve visual and thermal comfort: Review. Building and Environment, 2019. 153: p. 186-204.
36. Barozzi, M., et al., The Sustainability of Adaptive Envelopes: Developments of Kinetic Architecture. Procedia Engineering, 2016. 155: p. 275-284.
37. Lurie-Luke, E., Product and technology innovation: what can biomimicry inspire? Biotechnol Adv, 2014. 32(8): p. 1494-505.
38. Hosseini, S.M., F. Fadli, and M. Mohammadi, Biomimetic Kinetic Shading Facade Inspired by Tree Morphology for Improving Occupant’s Daylight Performance. Journal of Daylighting, 2021. 8(1): p. 65-85.
39. Wu, R., et al., Weavecraft: an interactive design and simulation tool for 3D weaving. 2020. 39(6): p. 210:1-210:16.
40. Meiklejohn, E., B. Hagan, and J. Ko, Rapid Sketching of Woven Textile Behavior: The Experimental Use of Parametric Modeling and Interactive Simulation in the Weaving Process. Computer-Aided Design, 2022. 149.
41. Bauer, A.M., et al. Exploring software approaches for the design and simulation of bending active systems. in Proceedings of IASS Annual Symposia. 2018. International Association for Shell and Spatial Structures (IASS).
42. Berglin, L., Interactive Textile Structures : Creating Multifunctional Textiles based on Smart Materials, in Doktorsavhandlingar vid Chalmers tekniska högskola. Ny serie. 2008, Chalmers University of Technology.
43. Ahlquist, S., L. Ketcheson, and C. Colombi, Multisensory Architecture: The Dynamic Interplay of Environment, Movement and Social Function. Architectural Design, 2017. 87(2): p. 90-99.
44. Wyller, M., et al., Adaptive kinematic textile architecture. Construction Robotics, 2020. 4(3-4): p. 227-237.
45. Cheshire, D., The Handbook to Building a Circular Economy. 2021: Routledge.
46. ISO, I.C., 20887: 2020 Sustainability in Buildings and Civil Engineering Works—Design for Disassembly and Adaptability—Principles, Requirements and Guidance.
47. Dams, B., et al., A circular construction evaluation framework to promote designing for disassembly and adaptability. Journal of Cleaner Production, 2021. 316: p. 128122.
48. Roberts, M., et al., Understanding the global warming potential of circular design strategies: Life cycle assessment of a design-for-disassembly building. Sustainable Production and Consumption, 2023. 37: p. 331-343.
49. Zanelli, A., C. Monticelli, and S.J.R.o.t.B.E.f.a.C.E.P. Viscuso, Closing the Loops in Textile Architecture: Innovative Strategies and Limits of Introducing Biopolymers in Membrane Structures. 2020: p. 263-276.
50. Bonev, M., et al., Formal computer-aided product family architecture design for mass customization. Computers in Industry, 2015. 74: p. 58-70.
51. Cichocka, J.M., INFRAME-design and construction of a sequentially erected elastic timber gridshell. 2020, Massachusetts Institute of Technology.
52. Deleuran, A.H., et al., Exploratory Topology Modelling of Form-active Hybrid Structures. Procedia Engineering, 2016. 155: p. 71-80.
53. Thomsen, M.R., et al. Hybrid tower, designing soft structures. in Modelling Behaviour: Design Modelling Symposium 2015. 2015. Springer.
54. La Magna, R., et al. Isoropia: An encompassing approach for the design, analysis and form-finding of bendingactive textile hybrids. in Proceedings of IASS annual symposia. 2018. International Association for Shell and Spatial Structures (IASS).
55. Thomsen, M., et al., Systems for transformative textile structures in CNC knitted fabrics - Isoropia. 2019.
56. Kim, M.-j., et al., Flexural biomimetic responsive building façade using a hybrid soft robot actuator and fabric membrane. Automation in Construction, 2023. 145: p. 104660.
We would like to express our sincere gratitude to Prof. Alessandra Zanelli and Salvatore Viscusor for their invaluable support in terms of theory and technology throughout this project. Their guidance and expertise have been instrumental in our research.
We would also like to extend our appreciation to PhD Candidate Amirhossein Ahmadnia for his valuable assistance in 3D printing, which greatly contributed to the success of our experiments.
Furthermore, we would like to thank PolRe company for their generous material support, which enabled us to carry out our experiments and prototype development.
Lastly, we are grateful to the Textile lab for providing us with the necessary space and equipment support, which has been crucial to the execution of our research.
Our heartfelt thanks go to all individuals and organizations mentioned above for their contributions and support throughout this project.
Only the first three pages are displayed beacuse of huge dataset. https://drive.google.com/ file/d/1wN94mb4gXrKNhTAxh8qM0sBgTQN5XrV/ view?usp=drive_link
https://drive.google.com/ file/d/1wN94mb4gXrKNhTAxh8qM0sBgTQN5XrV/ view?usp=drive_link
https://drive.google.com/ file/d/1wN94mb4gXrKNhTAxh8qM0sBgTQN5XrV/ view?usp=drive_link