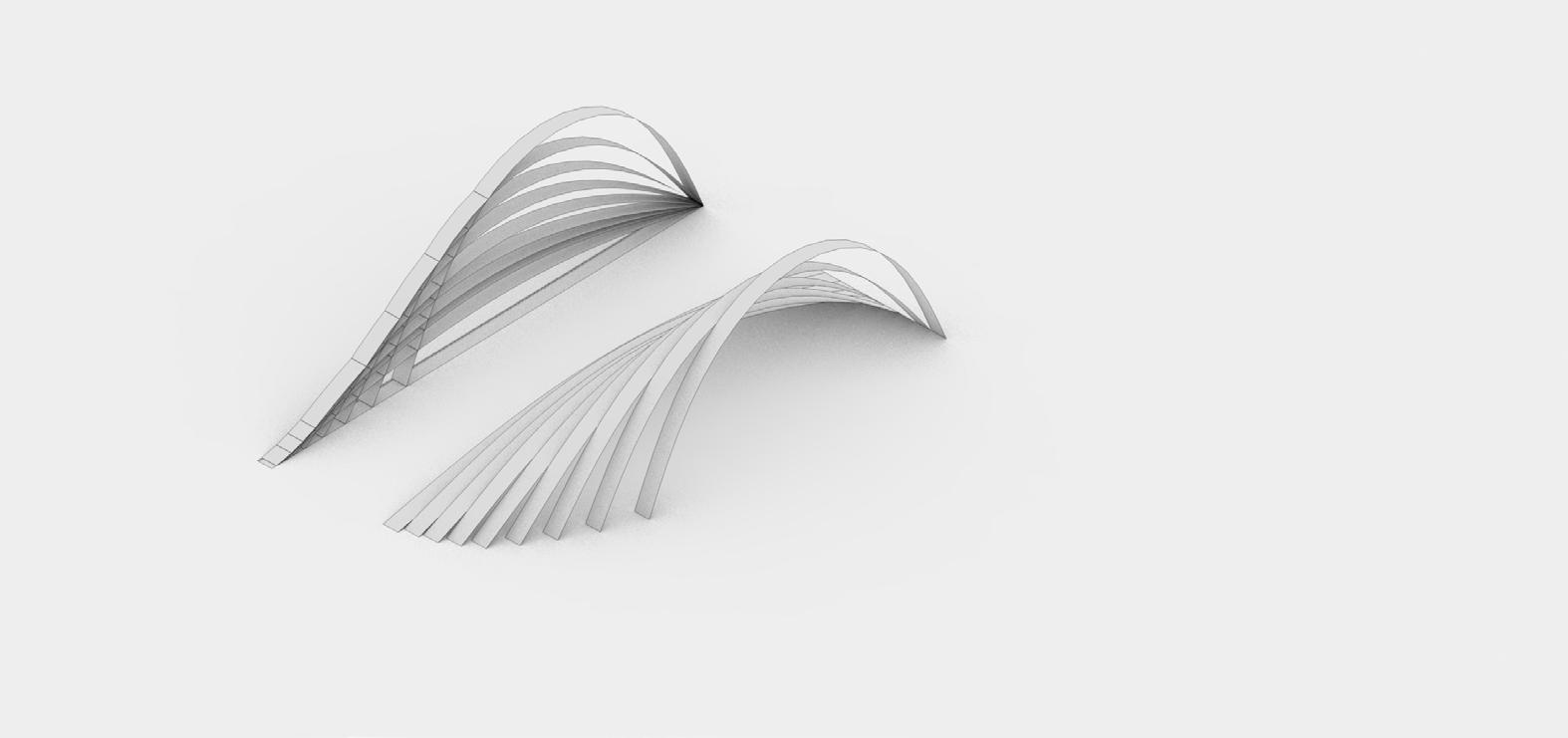
1 minute read
4.2_PHYSICAL TO DIGITAL CALIBRATION
from Towards a Lively Architecture - Exploring Response in Bent Wood Assemblies | Thesis by David Heaton
by David Heaton
Using the gained knowledge of how the wood strips perform at a larger scale, there was a need to calibrate those behaviors into the digital realm. Whereas in the earlier digital simulations explored tendencies and examined system response to forces, these digital simulations had the goal of calibrating on-screen mesh behavior to the real world behaviors of the wooden strips. This was attempted with Kangaroo v2.3, a physics-based engine that uses dynamic relaxation for interactive simulation, formfinding, optimization, and constraint solving. Kangaroo is under development by Daniel Piker as an add-on to the graphical algorithm editor, Grasshopper v0.9.0076. Grasshopper is tightly integrated into the 3D modeling tools of Rhinoceros 5.
At first, a single directional bending force in the strips was calibrated. This was done by adjusting spring forces within Kangaroo and measuring the resulting bending radius of the strip until it came as close as possible to the same measured bending radius in the real world. This allowed for a fine-tuning in the script to be as close as possible to the actual bending behavior. The final results could simulate the bending behavior down to +/- 1/2” of the actual bending radius. This was as close as the simulation needed to be in order to understand how varying aggregates would react to one another. Secondly, multi-directional bending including the rotation of the strips was simulated. This was explored in 5 degree increments from 0 degree rotation to 45 degree rotation. What was gained from these experiments is a concrete understanding of how drastically a subtle rotation of a strip could affect the overall bending radius, but more importantly how it could add a large amount of stiffness in a unit.
Advertisement
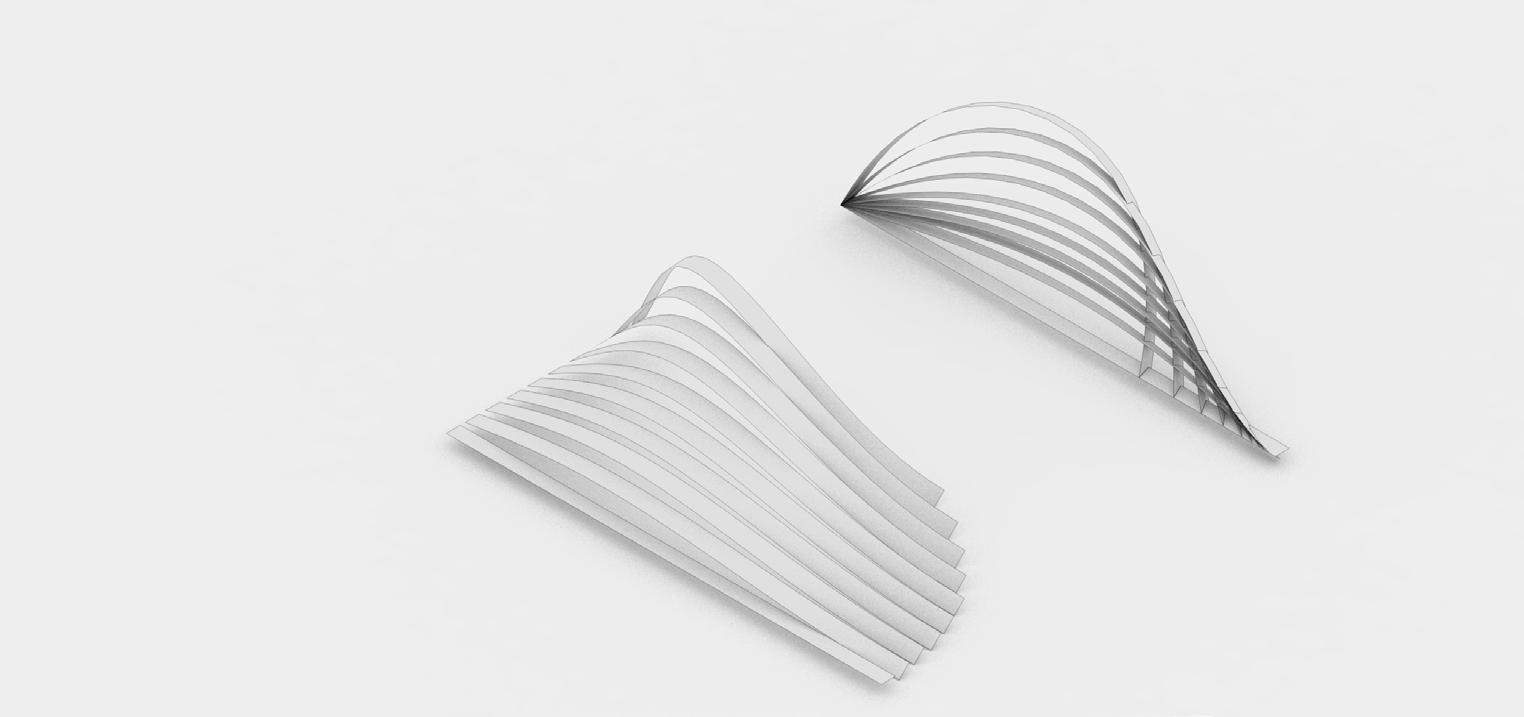