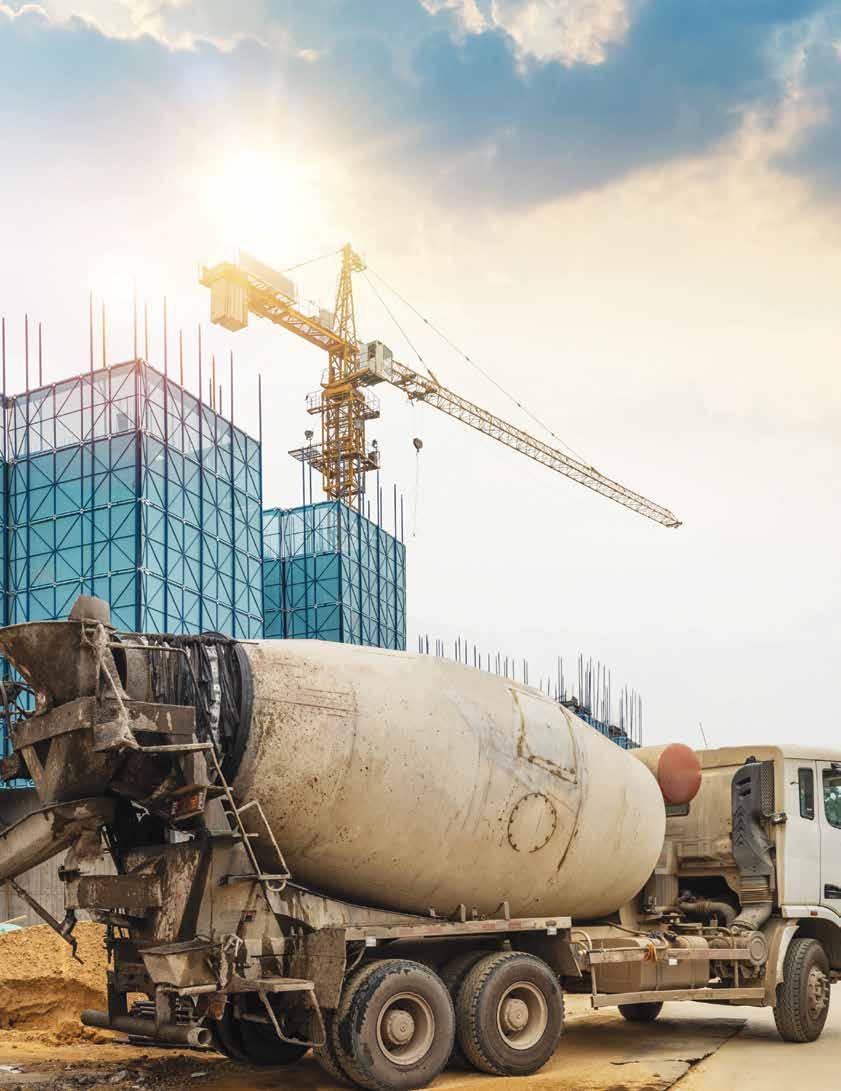
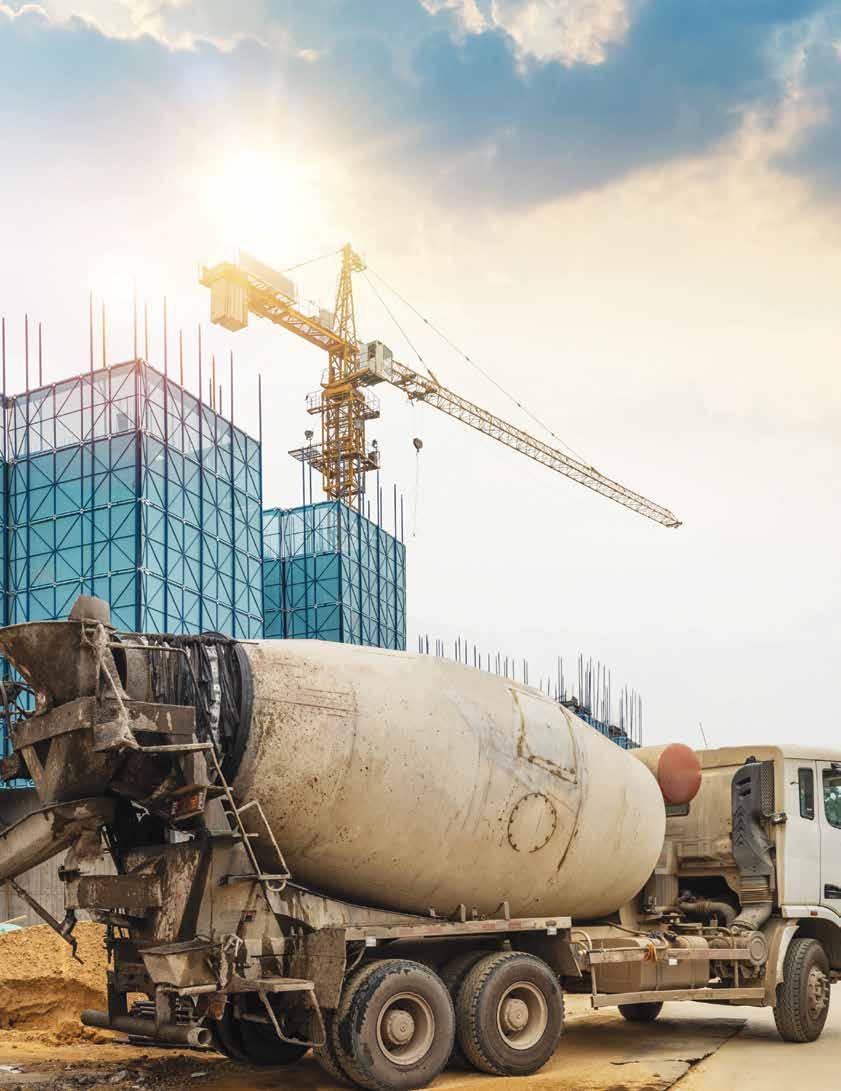
CANADIAN CONCRETE PUMPERS
2025 EDITION
Concrete foundations: Paving the way to a net-zero future
Pumped concrete foundations offer sustainability and quality
The critical role of temperature control in mass concrete durability
CANADIAN concrete pumpers

eC lebrating
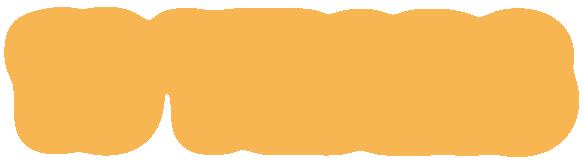
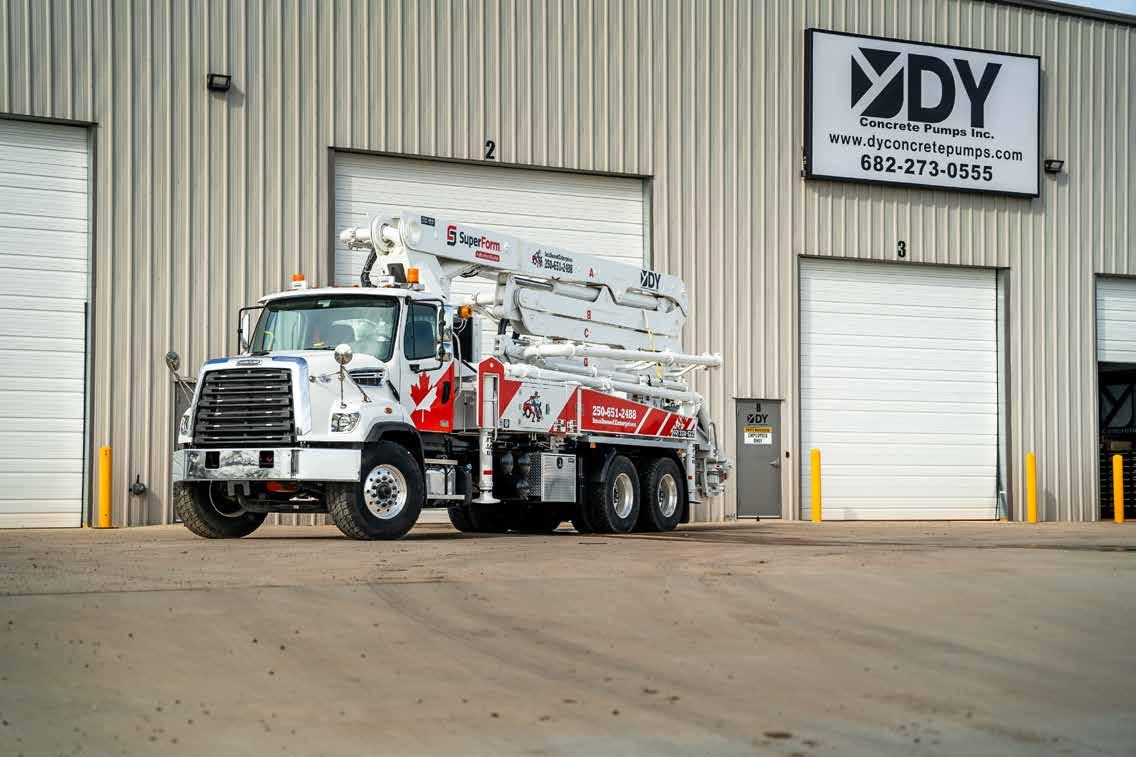
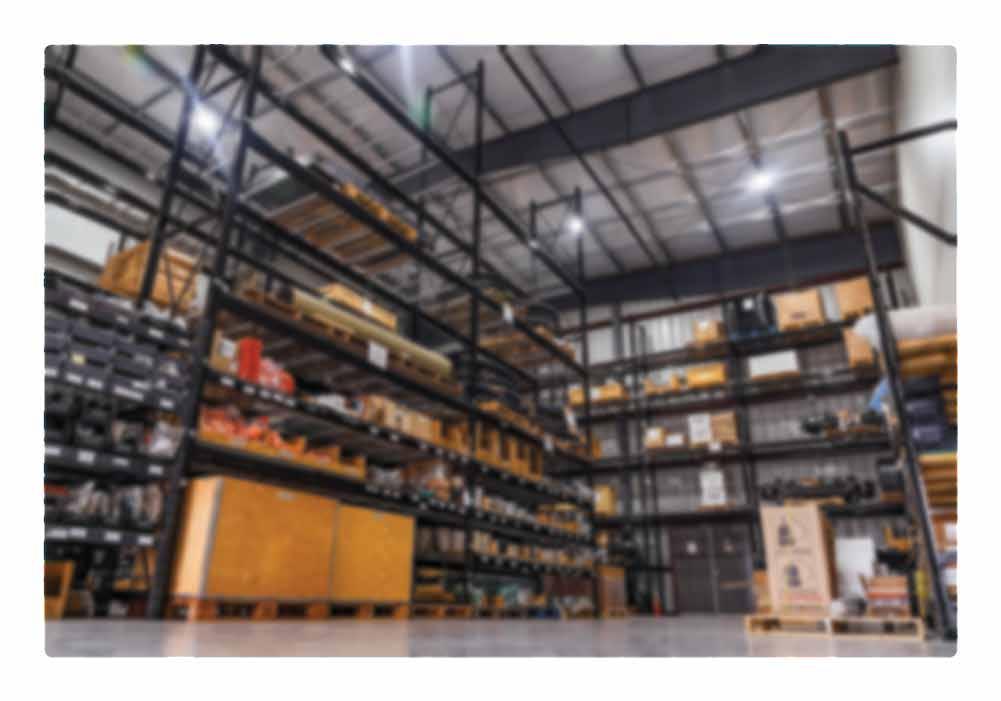
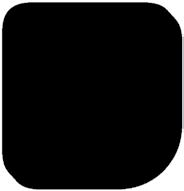

MESSAGE FROM THE EDITOR SHAYNA WIWIERSKI
shayna@delcommunications.com
As we continue to navigate a rapidly evolving construction landscape, the Canadian concrete pumping community remains at the forefront of shaping the future of our industry. Concrete pumping professionals across the nation are playing a pivotal role in transforming the built environment, not only by delivering exceptional service on every job site, but also by driving the adoption of more sustainable practices that will help reduce our collective carbon footprint.
This issue of the Canadian Concrete Pumpers magazine focuses on one of the most urgent and impactful areas of change: achieving embodied carbon reduction in concrete elements for residential structures. Embodied carbon, which refers to the emissions produced during the entire lifecycle of building materials—from raw material extraction to manufacturing and transportation—has become a key consideration in the construction and concrete industries. Residential buildings, which account for a significant portion of new construction across Canada, present a major opportunity to make a difference in reducing the carbon footprint of the built environment.
For many years, concrete has been seen as a major contributor to global carbon emissions. However, the sector has made impressive strides in recent years, developing and implementing solutions to lower its environmental impact. The Canadian cement and concrete industries are leading the way in this transformation, utilizing cutting-edge technologies, innovative mix designs, and the use of alternative materials to produce concrete with significantly reduced embodied carbon.
A critical element of this progress is the “Roadmap to Net-Zero Carbon Concrete by 2050”, a ground-breaking initiative introduced in November 2022 in partnership between Innovation, Science, and Economic Development Canada and the Cement Association of Canada (CAC). This roadmap sets out a clear and ambitious vision for how Canada’s cement and concrete sector can achieve net-zero carbon emissions by mid-century, aligning with the country’s broader climate goals. Through ongoing innovation, collaboration, and a commitment to continuous improvement, the industry is embracing new ways to reduce carbon emissions—from the development of low-carbon cements to advances in carbon capture and storage technologies.
While the road to net-zero may be challenging, it is certainly
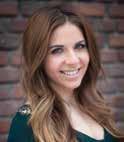
within reach. Achieving this goal will require the concerted efforts of all members of the construction ecosystem—from designers and architects to contractors and concrete pumpers. With innovation as our driving force and strong industry leadership, we are confident that the Canadian concrete sector will meet and exceed these challenges.
In this issue, we explore several key strategies for reducing embodied carbon in concrete. One of the most promising approaches is the use of supplementary cementitious materials (SCMs) such as fly ash, slag, and silica fume. These materials can partially replace traditional Portland cement in concrete, offering a substantial reduction in the carbon footprint of each cubic metre produced. Additionally, we take a closer look at the exciting advancements in low-carbon concrete alternatives, including high-performance concrete (HPC) and ultra-low-carbon cements.
For those working in concrete pumping, these changes are especially relevant. As demand for low-carbon concrete grows, so too does the need for concrete pumpers to stay informed and adapt to new mix designs. The role in ensuring that these innovative materials are efficiently and safely delivered to construction sites is more important than ever. Understanding the properties and performance of these advanced mixes will be essential to our success in supporting sustainable building practices.
Beyond the technical advancements, this issue also highlights the importance of collaboration across the industry. Achieving net-zero carbon concrete will require a collective effort from all stakeholders—governments, suppliers, manufacturers, contractors, and yes, concrete pumpers. By working together, we can ensure the successful adoption of these sustainable solutions and drive positive change across the entire construction sector.
The Canadian concrete industry is setting a global example of how innovation and sustainability can go hand in hand. As concrete pumpers, we are proud to play an integral role in this transformation, contributing to the creation of a more sustainable built environment for future generations.
Thank you for your ongoing commitment to excellence in your craft and your responsibility to the environment. Together, we are not just building structures; we are building a more sustainable future. We hope you enjoy this issue. n
Concrete foundations: Paving the way to a net-zero future

The concrete industry is at a pivotal moment. With cement production responsible for around seven per cent of global greenhouse gas emissions, the call to decarbonize is urgent. But rather than seeing this as a challenge, we should view it as a once-in-a-generation opportunity.
Canada’s cement and concrete sector is leading the charge. Driven by innovation and a strong commitment to progress, our government is proud to stand alongside industry leaders. In November 2022, we introduced the ambitious “Roadmap to Net-Zero Carbon Concrete by 2050”, in partnership with the Cement Association of Canada.
This roadmap isn’t just a vision; it’s a detailed action plan. Together, we are setting the course for net-zero emissions by 2030 and full carbon neutrality by 2050.
The Canadian cement industry is already harnessing cutting-edge technologies—carbon capture, alternative fuels, and optimized production processes. The goal isn’t just to reduce the carbon footprint; it’s to revolutionize the entire industry.
As co-chair of the Cement and Concrete Breakthrough Initiative, Canada is leading on the global stage, shaping the future of cement and concrete production in collaboration with international partners.
These goals are already taking shape. Industry leaders like Lafarge Canada are pioneering low-carbon alternatives such as LC3 cement, reducing CO2 emissions by 30 per cent. Compa-
By the Honourable François-Philippe Champagne, Minister of Innovation, Science and Industry
nies like CarbonCure Technologies are incorporating recycled CO2 into concrete to strengthen the material while lowering emissions. Additionally, low-carbon solutions like green hydrogen and biofuels are being explored to reduce reliance on fossil fuels. The Canadian government’s Roadmap supports these efforts with targeted investments, policies, and advisory services to organizations on federal support through the Clean Growth Hub. These help deploy clean technologies, including carbon capture, essential for achieving a net-zero concrete sector.
To our industry partners: your role is pivotal. As Canada moves towards net-zero, you’ll be at the forefront of adopting new technologies, practices, and sustainable materials. The Government of Canada is committed to supporting this journey with targeted investments, collaborative R&D, and policies that drive progress.
This transition is not just an environmental imperative—it’s an economic opportunity. By leading this global transformation, we aim to safeguard 158,000 jobs, sustain a $76 billion industry, and position Canada at the forefront of a sustainable construction revolution.
The strength of concrete isn’t just in its durability, but in its capacity to evolve. Together, government and industry will build a greener, more resilient future.
The changes we make today will stand as a testament to Canada’s innovation, collaboration, and leadership — for generations to come. n
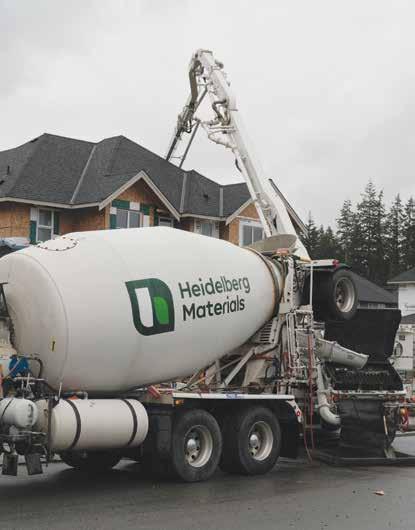
Consumer demand continues to grow for sustainable and eco-friendly housing, and real estate companies are taking steps to meet this demand.
Achieving embodied carbon reduction for the concrete elements in residential structures is an important way to reduce overall carbon emissions associated with a residential building project. For Qualico, an integrated real estate company, Heidelberg Materials is not only supplying, to the extent possible, its EvoBuild™ low carbon concrete, but provides pumping services, using concrete boom pumps to place foundations for Foxridge Homes, which is a single-family home division of Qualico. Typical boom pump sizes on Foxridge Homes projects range from 32 to 39 metres. Currently, Heidelberg Materials North America has a fleet of 10 concrete pumps, affording the flexibility to offer Foxridge Homes exceptional service when called upon.
Pumped concrete foundations offer sustainability and quality
Currently, Heidelberg Materials North America has a fleet of 10 concrete pumps, affording the flexibility to offer Foxridge Homes, a single-family home division of Qualico, exceptional service when called upon.
“At Heidelberg Materials, we use our fleet of 10 pump trucks to provide fast and precise concrete placement. Our reliable pumps ensure accurate placement, reduce material waste, and deliver consistent, high-quality results so projects stay on schedule,” said Leigh Evans, senior transportation manager, Heidelberg Materials. “Furthermore, our pumpers don’t shy away from challenging site conditions. We’ll tackle difficult terrain and go places other pumpers might not, ensuring we can maximize the value offered by pumped, lower-carbon concrete.”
Nicholas Bell, vice-president of Foxridge Homes BC, said that the service and reliability of Heidelberg Materials’ pumped concrete operations has been a key trade relationship for Foxridge Homes for many years. Heidelberg Materials is involved in roughly 80 per cent of their active subdivisions.
By using lower-carbon pumped concrete for their house foundations, Qualico is achieving efficiencies of scale.
“Footings and foundations can make up to one-third of the embodied carbon for a single-family home,” said Shane Mulligan, technical marketing manager, Heidelberg Materials. “So, carbon savings add up across the development of a new community…not to mention the fact that some low-carbon concrete strategies can contribute to fast, efficient placement and benefit the construction schedule.”
With Qualico’s focus on quality, letting buyers know they are using lower carbon concrete is important.
Byron Young, sales manager at Heidelberg Materials added that EvoBuild signs placed at construction sites were an important way to let buyers know that Qualico was making every effort to
By using lower-carbon pumped concrete for their house foundations, Qualico is achieving efficiencies of scale.

build sustainably. Those buyers could talk to sales representatives to find out exactly how much carbon was being saved, in terms of equivalencies, and understand the beneficial impact their home purchase was having.
“By including EvoBuild low-carbon concrete in our construction program we’re able to showcase our continued environmental leadership by effectively reducing the embodied carbon of our homes,” said Bell. “And Heidelberg Materials’ signage effectively translates the embodied carbon savings into relatable statistics like effective passenger vehicles removed from the road and tree seedlings planted.” n
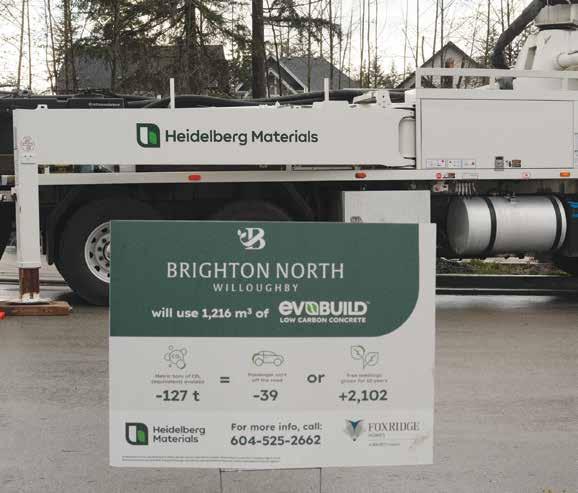
Concrete Pump Operator Safety: A journey towards mandatory certification

In 2004, the booming construction industry in British Columbia highlighted the urgent need for basic training for new concrete pump operators.
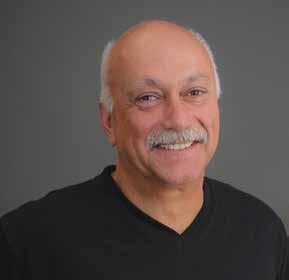
“The lack of any training requirements for operating complex and potentially dangerous equipment posed significant risks on jobsites and, as an industry, we needed to address it,” recalls Frank Antonio from F&F Pumping in Richmond, B.C., who chaired the Concrete Pump Committee for Concrete BC for over a decade. “Untrained employees were more likely to engage in unsafe practices, inadequately respond to emergencies, and unintentionally disregard safety protocols, resulting in a higher risk of accidents, injuries, and potential fatalities on construction sites. The status quo was unacceptable to us.”
To address these safety concerns, a task force of industry leaders was established in 2005. This group included members from Concrete BC, non-mem-
bers, union and non-union companies, regional representatives, and WorkSafeBC. They aimed to develop competency standards for concrete pump operators to improve safety practices and training. The task force identified several critical issues: the inadequacy of a commercial driver’s license as the sole qualification for operating a concrete pump, a lack of awareness among contractors about their responsibilities, and insufficient inspection regimes.
From 2006 to 2008, significant progress was made in developing a comprehensive safety program. An occupational analysis was completed, and a curriculum was developed in partnership with the BC Construction Safety Alliance (BCCSA). WorkSafeBC reviewed the course materials to ensure compliance
WorkSafeBC Office Education On Concrete Pumps.
Frank Antonio from F&F Pumping in Richmond, B.C., chaired the Concrete Pump Committee for Concrete BC for over a decade.
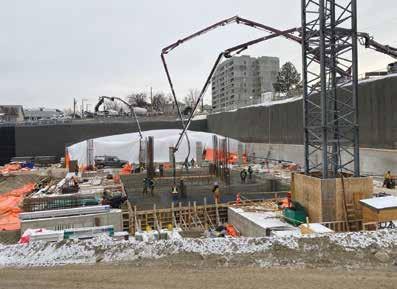
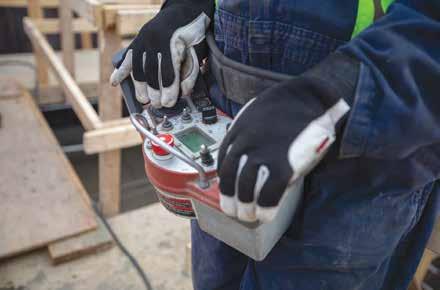
The Certified Concrete Pump Operator (CCPO) Program is administered by the BCCSA and is currently the only WorkSafeBC-approved certification program for concrete pumps.
with the highest safety standards. By 2008, a one-day comprehensive training course was being delivered across the province by subject matter experts from the concrete industry. The course included electrical safety, fundamentals of concrete, personal safety, pre-trip inspection, trip planning and travel, jobsite setup, operator responsibilities, line and boom pumping, daily maintenance and equipment checks, environmental safety, and technical notes. A specific module to calculate and understand Boom Pump Outrigger Cribbing & Soil Type Evaluation was added in 2010.
This initiative received support from WorkSafeBC and various construction associations, including the Council of Construction Associations (COCA) and the Independent Contractors and Businesses Association (ICBA).
Between 2015 and 2019, efforts focused on developing provincial standards and a framework for voluntary competency certification. This culminated in the launch of a voluntary certification program in September 2019. Concurrently, regulations were drafted to make certification mandatory.
In 2021, WorkSafeBC held public hear-
ings regarding mandatory certification for concrete pump operators. This effort led to significant regulatory changes effective January 1, 2024; anyone operating a concrete pump or placing boom at a workplace in British Columbia must now hold a valid concrete pump operator certificate or work under certified supervision. This requirement applies to various types of concrete pumps including tower placing booms, high-pressure and low-pressure line pumps, and truck-mounted boom pumps.
The Certified Concrete Pump Operator (CCPO) Program is administered by the BCCSA and is currently the only WorkSafeBC-approved certification program for concrete pumps. This certification ensures that operators have demonstrated both theoretical knowledge and practical competence in concrete pump operations. With advancements in concrete pump technology, certified operators are required to have a deeper understanding of equipment features and safety measures.
This journey from voluntary standards to mandatory certification marks a significant advancement in workplace safety for the concrete pumping in-
dustry in British Columbia. It reflects a collaborative effort between industry stakeholders and regulatory bodies to address the unique challenges and risks associated with concrete pumping operations.
Reflecting on the journey, Antonio expresses pride in the concrete industry’s unwavering commitment.
“Our dedication has been nothing short of inspiring. We’ve invested not just substantial financial resources, but also poured our brains and hearts into this endeavour. Countless dedicated professionals have volunteered their time, expertise, and passion as subject matter experts and instructors to build this robust training and certification program from the ground up. It’s been a challenging yet rewarding path to ensure every concrete pump operator in British Columbia achieves certification,” he says. “As I look back, I can’t help but feel a profound sense of fulfillment. What greater legacy could we leave than a safer workplace for every single worker in our industry? This achievement will resonate for generations to come, protecting lives and fostering a culture of safety excellence.” n
Pumping in Kamloops in 2022.
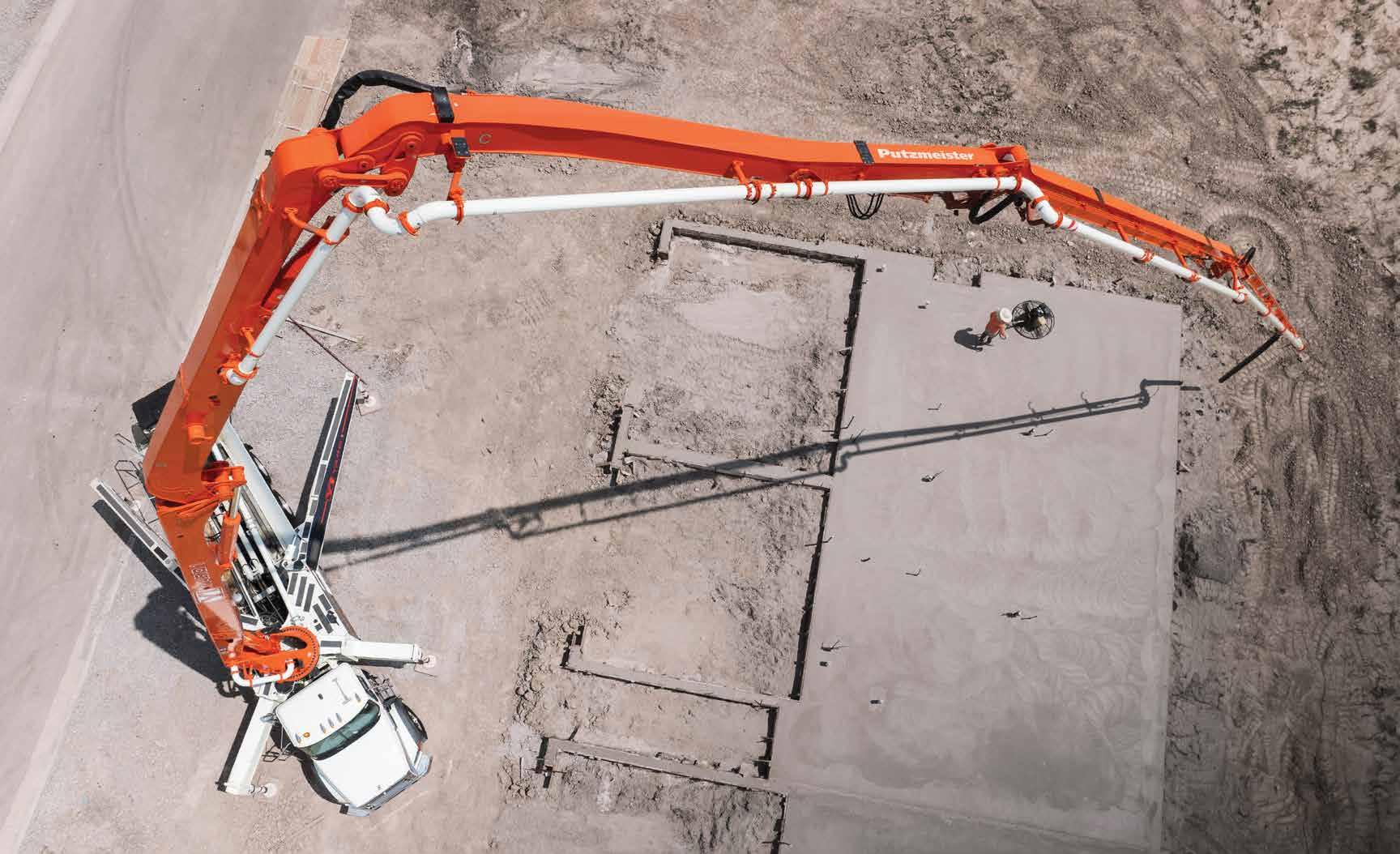
Putzmeister 47Z Full Flex and iSA
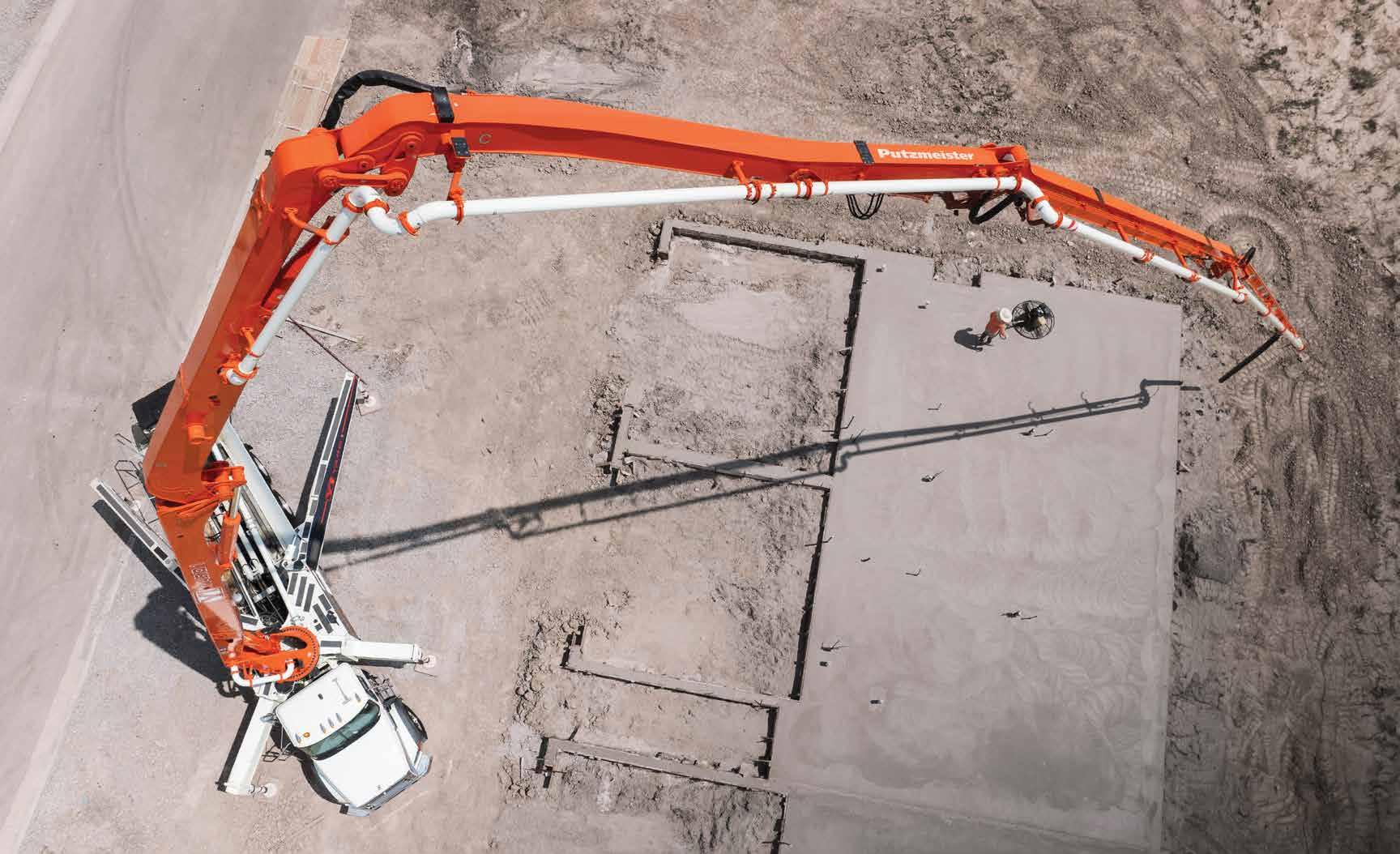
FLEX ON EVERY JOBSITE
Set up the way you want to reach what you need with the industry’s most flexible setup configuration. Full Flex and intelligent Setup Ass istance (iSA).
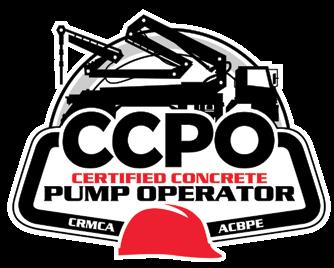
Certified Concrete Pump Operator (CCPO) program: Made in B.C., ready for North America
Unique certification program combines written test with practical exam
It’s undeniable that the Certified Concrete Pump Operator (CCPO) program was developed in response to concrete pump incidents in British Columbia. But it’s just as true that the CCPO program was designed to offer its benefits to jurisdictions outside the province, across Canada and the United States.
Under provincial law, which came into effect January 1, 2024, all concrete pump operators in B.C. must be certified under the CCPO program to continue operating concrete pump equipment. However, the development of the program by the BC Construction Safety Alliance (BCCSA) began long before the regulation was announced.
A series of high-profile incidents and fatalities involving concrete pumps in B.C. underlined the need for the program. These included concrete pump boom failures, workers being struck by equipment, and concrete pump trucks that had toppled at worksites. At the same time, there were no significant barriers preventing inexperienced operators from renting a concrete pump and deploying it at a construction site.
“The situation was considered so serious that the industry itself was calling for both regulation and a certification program,” says Ammar Kavazovic, director, programs and initiatives with the BCCSA. “If the certification program came first, employers were willing to ensure that they would enforce it at an industry level.”
Working with industry representatives and provincial workplace health and safety regulator WorkSafeBC, the BCCSA developed the first program of its kind in North America, combining a written test of theoretical knowledge with a practical exam.
“We were committed to incorporating the practical exam from the start,” Kavazovic says. “The CCPO program is based on industry best practices, so the written portion of the exam should resonate with operators in any jurisdiction. The practical portion of the exam should also confirm the skills of the operator wherever the program is deployed, whether Saskatchewan or Newfoundland.”
Concrete Alberta, which represents more than 90 per cent of concrete producers in the province, was the first jurisdiction outside B.C. to adopt the CCPO program in mid-2024. The BCCSA worked with the organization to ensure that the program could be seamlessly deployed in Alberta. It required only minor adjustments to the curriculum to reflect subtle differences in Alberta regulation and legislation.
Paul Masson, director of technical services and training with Concrete Alberta, notes that the organization selected the CCPO program for two primary reasons.
“CCPO is a nationally-recognized certification program,” he says. “For the benefit of our members, specifically those who operate across provincial borders, a single nationally-recognized certification program makes the most sense for industry. However, the practical exam portion of this program is what separates it from the other options currently offered. It’s what makes the CCPO the highest standard of certification for pump operators and a critical piece of training and certification for our industry.”
As with the B.C. concrete industry, Concrete Alberta proactively adopted the CCPO program as its preferred training solution before regulation required it. However, Masson says that the organization intends to advocate for mandatory certification in Alberta in collaboration with its concrete pump members. Kavazovic notes that support for the CCPO program is also growing in other jurisdictions, including Ontario, where industry advocates have been actively discussing the potential for its implementation.
“The BCCSA is ready to work with groups in any jurisdiction who want to adopt CCPO certification, whether from an industry or regulatory perspective,” he says.
For more information on the CCPO program, visit www.ccpo.ca. n
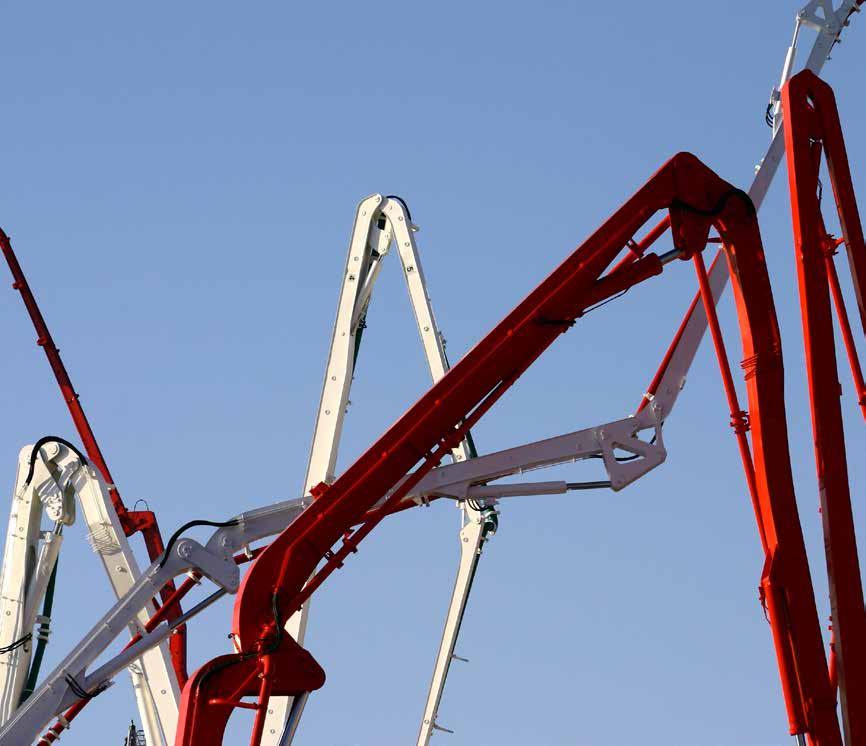
The critical role of temperature control in mass concrete durability
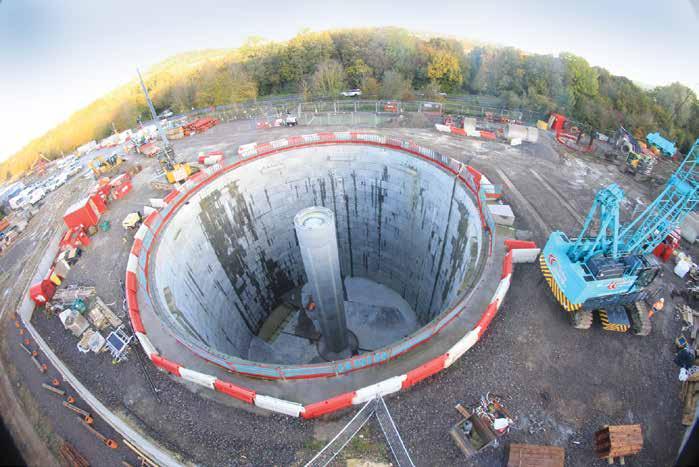
As mass concrete becomes essential in construction, understanding factors that impact its quality and strength gain is critical. Contractors must carefully monitor the maximum temperature, which typically peaks within the first 48 hours after pouring, often at the core of the mass element. This temperature results from both initial placement heat and additional heat rise. Managing these factors is crucial to prevent quality issues and ensure structural integrity. Let’s explore further challenges associated with temperature control in mass concrete.
What is Delayed Ettringite Formation (DEF)?
The ettringite formation is a normal process that occurs during the hydration phases of cement. It is formed as a result of the reaction of the tricalcium aluminate (C3A), sulfate compounds, and gypsum. This reaction takes place during the concrete setting and is a regular product formed during
the hydration process. The purpose of this reaction is to consume most of the sulfate present in the mix and prevent fast stiffening of the concrete. Initially, this is formed in the early ages and can be referred to as “primary ettringite”.
The primary concern with the maximum allowable temperature of concrete is the risk of delayed ettringite formation, or DEF. As ettringite has limited temperature stability, it does not form at high temperatures. When high heat generation occurs, the potential for volumetric expansion at later stages could lead to considerable cracking and reduce the durability of the concrete element.
Dealing with the maximum temperature of concrete and DEF
When the concrete temperature is too high at an early age, the primary ettringite becomes unstable and can lead to
Mass concrete project, Stroud Sewerage. Courtesy of Galliford Try.
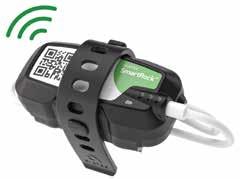

SmartRock mobile app showing temperature readings from the sensor.
Inset: SmartRock wireless concrete sensor.
delayed ettringite formation. The effects appear years later when moisture causes delayed ettringite formation, leading to concrete expansion, cracking, and reduced durability and lifespan. This is the reason why DEF mainly occurs in foundation elements as they go through to a higher temperature. However, DEF can also occur in heat-cured elements, such as precast concrete beams.
Delayed ettringite formation is a concern when the concrete temperature exceeds 158°F (70°C). However, not all concrete mixtures and structures have the same level of susceptibility to DEF. In fact, concrete designed with supplementary cementitious materials (SCM) mixtures tends to perform much better, allowing a higher maximum temperature of concrete.
Using advanced monitoring technology for temperature monitoring
In North America, the maximum allowable temperature of mass concrete varies depending on the project specifications because there is no universal consensus on a specific limit. However, standards and recommendations have been put in place to guide engineers to build more durable structures. For this purpose, the ACI 201.2R Guide to Durable Concrete provides important specifications. If the maximum temperature of concrete is lower than 158°F (70°C), no prevention is need-
ed. Yet, if the temperature is between the ranges of 158°F and 185°F (70°C and 85°C), there are different approaches that must be followed to minimize the risk of expansion. Nevertheless, in no circumstances should the concrete temperature exceed 185°F (85°C).
Luckily, contractors and engineers can take advantage of advanced technology that monitor concrete temperatures like SmartRock®, an easy-to-install wireless concrete sensor with innovative dual-temperature functionality. This award-winning sensor offers precise real-time temperature readings for mass concrete pours at the surface and centre of the element. These readings are sent in real-time to the sensor’s mobile app, allowing users to access their concrete data anytime, anywhere, onsite or off.
In conclusion, managing the maximum temperature in mass concrete is essential for ensuring its long-term durability and structural integrity. High temperatures can lead to delayed ettringite formation (DEF), which poses significant risks of cracking and reduced lifespan due to expansion under later exposure to moisture. Understanding temperature factors and following guidelines enables engineers to design and monitor mass concrete effectively, reducing DEF risks and enhancing durability for safer, more resilient structures. n
Safety tips: How to prevent risks for repetitive strain and overexertion injuries
Musculoskeletal injuries (MSIs) are the most common type
of workplace
injury
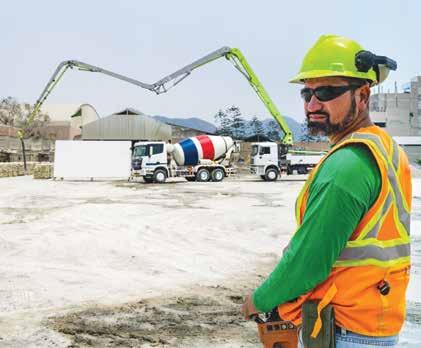
By Alexandra Skinner
The work of concrete pump operators requires the constant handling of heavy equipment, often under challenging conditions. Due to the physical demands and repetitive movements involved, concrete pump operators are at risk for musculoskeletal injuries (MSIs).
This type of injury can affect an operator’s back, shoulders, wrists, and/or hands. While lifting heavy materials can cause acute injuries, the continuous, repetitive nature of tasks — such as lifting, twisting, pulling, and handling of vibrating equipment — is a common cause of MSIs in concrete pump workers.
While MSIs affect thousands of workers each year, they are largely preventable.
What is an MSI?
A musculoskeletal injury involves damage to muscles, tendons, ligaments, joints, nerves, blood vessels, or related soft tissue. It can include sprains, strains, and inflammation, which can be caused or aggravated by work.
MSIs are the most common type of workplace injury. Between 2019 to
MSIs are the most common type of workplace injury. Between 2019 to 2023, WorkSafeBC accepted nearly 11,000 claims from B.C. workers in the construction sector due to MSIs, resulting in an average of 81 days of missed work.
2023, WorkSafeBC accepted nearly 11,000 claims from B.C. workers in the construction sector due to MSIs, resulting in an average of 81 days of missed work.
Although these injuries are common, limited awareness across the industry remains a significant barrier to effectively managing MSI risks.
Employer responsibilities
All employers must conduct risk assessments for MSIs in their workplace and then introduce controls to eliminate or minimize the hazards and risks.
“Addressing musculoskeletal-injury prevention before the work starts is crucial — not only to protect the health and wellbeing of workers, but also to help employers maintain continuity and efficiency by reducing time-loss claims,” says Michael Paine, occupational health and safety manager with WorkSafeBC.
Identify and assess risks
The risk assessment should be done by someone who understands how to identify risks for MSIs, knows the work tasks involved, is familiar with the po-
tential hazards, and understands how to properly conduct the assessment and its limitations.
Key physical risk factors for MSIs at work include:
• Force: The force a worker is required to place on an object during a task.
• Repetition: Using the same muscles repeatedly.
• Duration: The length of time a task is performed.
• Work posture: Holding awkward or static body positions.
• Local contact stress: Contact between hard or sharp objects and the skin.
For each risk area, and before a worker begins a task, it is important to consider the magnitude, frequency, and duration of exposure. The risk of a musculoskeletal injury increases when two or more risk factors are present at the same time.
Involving workers in identifying risk factors is important. They are the ones performing these tasks daily and can provide valuable insights into potential hazards and practical solutions.
Eliminate or mitigate the risks by implementing controls
Once hazards and risks are identified and assessed, employers should follow the hierarchy of controls — a system used to reduce hazards by first attempting to eliminate the hazard.
“In concrete pumping, the variety of tasks and changing job conditions mean that MSI risks are always evolving, making it challenging to rely on onesize-fits-all solutions,” says Paine.
If elimination is not feasible, employers should move to substitution or engineering controls (e.g., redesigning tools or workspaces, or the use of a mechanical aid), administrative controls (e.g., job rotations, team lifts), and finally, personal protective equipment (PPE) as the last line of defense.
Controls to consider during the application phase would include the use of a concrete hose hook to assist with the movements of the rubber end of the concrete delivery system. The use of this hook helps to mitigate awkward postures and heavy lifting associated with MSIs.
Other controls can include administrative measures, such as rotating certified workers between tasks that involve different muscle groups to reduce the time spent on each activity.
In some circumstances, the use of PPE can be used if engineering or administrative controls cannot be applied. This could involve ensuring workers have safety goggles, padded or vibration-limiting gloves, and steel-toe boots.
Protecting workers from harm requires
ongoing effort. Employers need to monitor the effectiveness of controls and improve any that do not measure up. Review risk assessments at least once a year, and whenever new equipment, materials, or work processes are introduced.
WorkSafeBC resources
WorkSafeBC has resources for employers to help evaluate a worker’s exposure to primary physical risk factors and assess the level of risk associated with specific tasks.
For more information, visit www. worksafebc.com/en/health-safety/ hazards-exposures/ergonomics.
Alexandra Skinner is the manager, government, and media relations at WorkSafeBC n
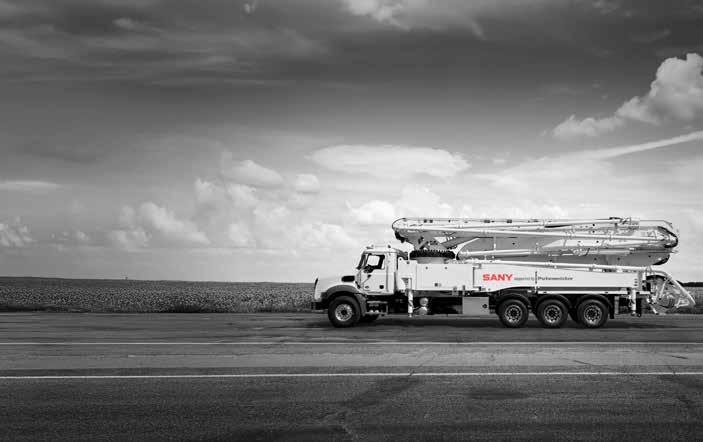
SANY SAFE, SANY STRONG
Safety features to protect your number 1 priority
BOOM WARNING SYSTEM
Ensures proper boom storage every time.
AUTOMATIC ONE SIDE SUPPORT
Prevents over-slewing when short-rigged.
RFID HOPPER SAFETY SWITCH
Eliminates access to moving parts.
A decade of DY Concrete Pumps
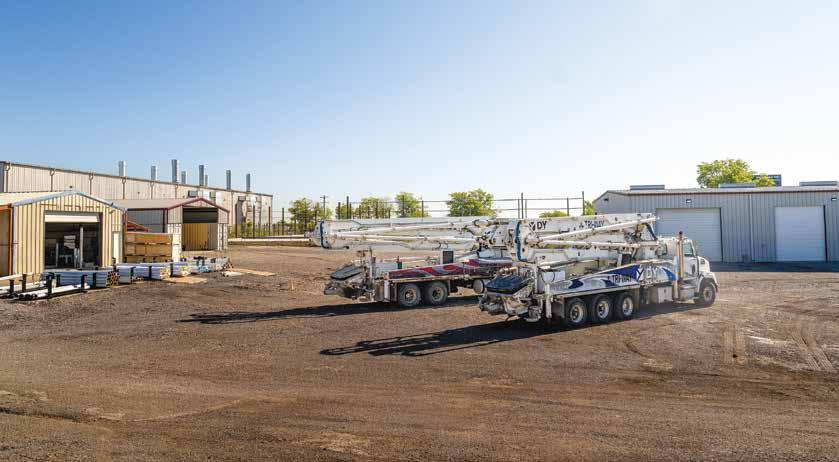
Ten years ago in Calgary, Alta., DY Concrete Pumps recognized a critical issue in the concrete pumping industry: a lack of reliable, customer-centered support. Driven to fill this need, we introduced DY Concrete Pumps to the North American market, combining quality machines with dependable service. Our team, founded by operators and owners, offers a deep understanding of the challenges in the field, ensuring we deliver the support our customers truly deserve.
Our journey led us to Texas, where in 2021, we opened our headquarters, featuring one of the largest paint booths in the south and a 7,000-square-foot parts facility. DY’s current parts department is larger than our original manufacturing facility in Canada, a testament to our growth over the last decade. Today, we have over 300 machines working across North America; an accomplishment made possible by our customers’ trust and our commitment to reliability, simplicity, and service.
Over the past 10 years, DY Concrete Pumps has introduced 17 models, refining our lineup to the top 13 models available today. Our current product range includes nine truck-mounted boom pumps, two truck-mounted concrete line pumps, and two trailer pumps. Our award-winning CTY-100 truck-mounted line pump stands as a true testament to innovation and has become a favourite among operators of all levels. The CTY-100 exemplifies DY’s ability to take a proven concept and elevate it to new heights.
Our pumps have demonstrated resilience, with the first production units of our 43X-5RZ and 37X-4R models still actively pumping today. Tri-Way Concrete’s 43X-5RZ remains in operation after 10 years of continuous pumping, while Economy Concrete’s original 37X-4R was recently serviced at our headquarters before being sold and driven to Utah to keep the concrete flowing. These two early models endure rugged demands across the con-
tinent and continue to perform reliably every day.
The DY Difference is built into every machine. Features like emergency bypass switches and our patented 360-degree continuous swing turret reduce downtime and increase job site efficiency. Combined with our focus on simplicity and reliability, DY pumps are easy to operate, maintain, and depend on.
So, why DY? The answer lies in our commitment to service. DY has always strived to deliver reliable, customer-centered support. Many of our team members come from pumping backgrounds, giving us a firsthand understanding of the challenges operators face and allowing us to provide service that truly makes a difference. We operate the best service centre in Texas, supported by our 24/7 emergency service line. We’re here when you need us most, ensuring your pumps stay running.
By DY Concrete Pumps
Passenger-side rear quarter photo of Economy Concrete’s 2015 DY 37X-4R and Tri-Way Concrete’s 2015 DY 43X-5RZ, pictured on Thursday, April 4, 2024, outside the DY Service Center in Alvarado, Texas. These two machines are among the first three concrete pumps produced by DY for the North American market.
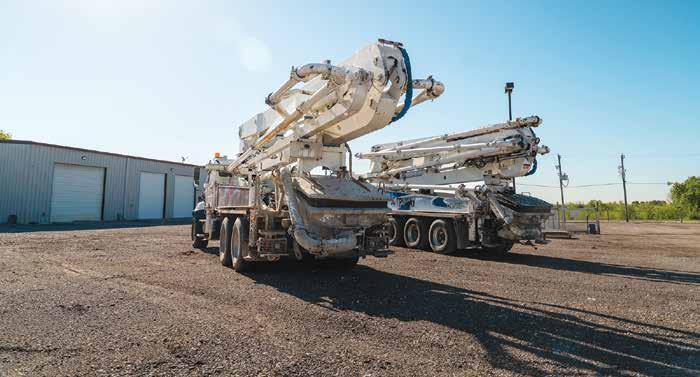
The future is bright for DY Concrete Pumps. We’re introducing two new trailer pump models, along with our HP 3250 high-pressure line pump, bringing enhanced performance and versatility to our lineup. Also, DY is developing an e-commerce platform for online ordering, making our parts department more accessible for our customers.
This journey would not have been possible without the steadfast support of our customers.
“Thank you to all our current and future members of the DY family. Your trust in the DY team’s ability to support your business has been crucial over the past 10 years,” says Jason Delehay, our vice-president. “We look forward to continuing our industry-leading customer support and are excited about what the future brings for DY in North America.”
As we celebrate our 10-year anniversary, we are deeply grateful for your trust and look forward to continuing to support you for decades to come.
Stay connected by following us on Facebook, Instagram, YouTube, and
LinkedIn at @DYConcretePumps. Join us at the World of Concrete 2025, Booth C5715, to experience the DY difference firsthand.
To our customers, partners, and team
members: thank you again for your trust, loyalty, and support over the past decade. Here’s to many more years of raising the bar and setting new standards in the concrete pumping industry. n
BULLET-PROOF CORNERS
Our updated corner tie and bracket mitigates one of the biggest challenges ICF installers face: corner blowouts.
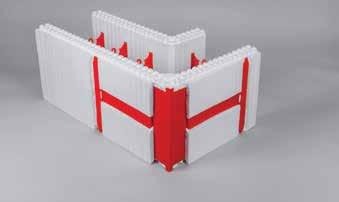
Close up, rear quarter photo of Economy Concrete’s 2015 DY 37X-4R and Tri-Way Concrete’s 2015 DY 43X-5RZ, pictured on Thursday, April 4, 2024, outside the DY Service Center in Alvarado, Texas. These two machines are among the first three concrete pumps produced by DY for the North American market.

SMOOTH

There’s only one place you’ll find the heavy hitters of concrete and masonry this January: Vegas, baby — at World of Concrete 2025, the largest and only annual international event dedicated to your business. Be here to mix with industry giants. Get your hands on the latest technologies revolutionizing safety, performance and speed. And learn what it takes to not only claim a piece of our industry’s massive projected growth but dominate the field. Join the power players of concrete and masonry. OPERATOR Learn


EXHIBITS: JANUARY 21-23, 2025
EDUCATION: JANUARY 20-23
LAS VEGAS CONVENTION CENTER