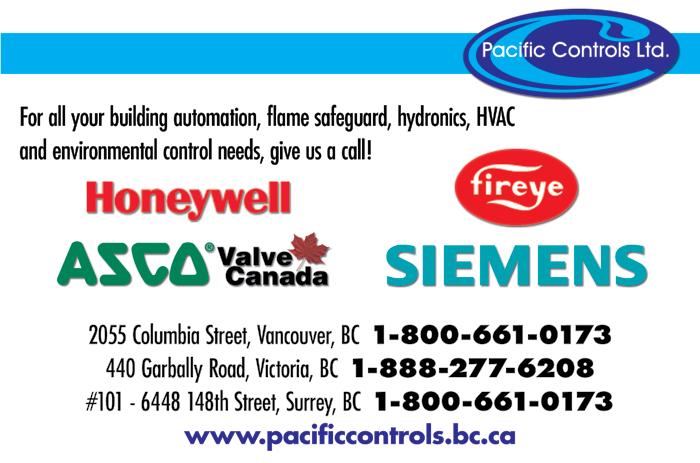
15 minute read
Considerations for overcoming the scheduling dilemma
By Steve Woods, M.Eng., MBA, P.Eng.
Scheduling is a daily activity for all of us. We review our appointments for the day, decide which tasks to complete, prioritize emergent problems, and plan for upcoming events. Scheduling is also a key function of maintenance management. Effective scheduling enhances customer satisfaction and improves workforce productivity while avoiding unnecessary costs. However, “changing a company’s maintenance practices is like turning around a supertanker. Maintenance change is a five-year effort involving progressive action. It takes two years to get the change underway, and another three to see the full impact” (Hora, 2001, p. 74).
This article examines effective scheduling characteristics and approaches. Sources of the scheduling dilemma are described. Next, common scheduling roadblocks are identified. Finally, some techniques for managing the scheduling dilemma are presented.
Characteristics of Effective Scheduling
Given that organizations often view maintenance as controllable overhead and not as a key value-added aspect of strategic planning, scheduling begins with the objectives of minimizing required resources while maximizing the amount of work completed. Facilities maintenance personnel tend to view these objectives from the perspective of mitigating the risk of service disruptions and damage from equipment breakdowns. Building occupants often focus more on predictable work order turn-around times, timely support for educational programs, and avoiding conflicts with school activities.
Cost savings are a key performance indicator of maintenance management systems. Effective work order scheduling can enable cost savings by reducing materials overhead, potentially leading to just-in-time materials management. Further, schedulers can consolidate similar work orders to achieve economies of scale through (a) minimizing set-up time, (b) bulk purchasing, and (c) efficient hiring or contracting processes.
Gray and Larson (2008) present the concept of delaying noncritical work during periods of peak workload as a technique to improve resource utilization without adjusting maintenance capacity. “Because payroll is one of the largest costs in many organizations, a
relatively minor improvement in employee scheduling can provide a significant return on investment” (Studebaker, 1997, p. 16). Creating stable work schedules by deferring noncritical work to periods of low maintenance activity and, conversely, accelerating seasonal or time-sensitive work is a key characteristic of effective scheduling. Additionally, improved employee morale results from (a) not being overwhelmed by too much work; (b) less exposure to layoffs; and (c) more certainty when planning absences or vacations. From the employer’s perspective, the maintenance organization benefits by having greater flexibility to accommodate unforeseen employee absences and reduced employee turnover.
Creating stable work schedules leads to predictable work order turnaround times and supports management of customer expectations. Alfieri (2009) advocates transparent, flexible and easy-to-understand decision support systems. For example, providing customers a “dashboard” of key performance indicators gives customers a sense of a well-managed maintenance system. To accommodate operating environments in which information is hard to quantify, these decision support systems should be adaptable to different scheduling problems and approaches.
Approaches to Scheduling
Scheduling issues are usually approached as either capacity-constrained or time-constrained problems. Capacity-constrained problems begin with the perspective of more work orders than available
SANITARY SPECIALTIES
Mfg. Ltd. PROVIDING THE LATEST IN GREEN CLEANING SUPPLIES AND EQUIPMENT
we want to help you
We have been providing Schools, Building Owners, Property Managers, Contract Cleaners and Hospitals with a complete line of Janitorial Supplies, Floor & Carpet Cleaning Equipment for over 55 years!
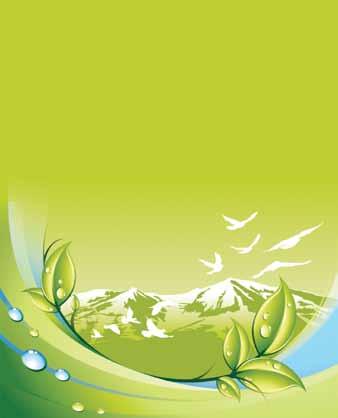
Take a trip to our showroom at 1841 Pandora Street, Vancouver, B.C. V5L 1M4 Tel: 604.255.2220 Fax: 604.255.5655
resources. Time-constrained problems focus on work deadlines. Although these approaches are not mutually exclusive, one approach often dominates the scheduling problem under consideration.
Infinite capacity scheduling is appropriate when, without incurring a cost premium, resources can be quickly expanded, contracted, or reallocated as needed. Examples include the use of casual labourers, well-stocked materials inventories, and Standing Offer Agreement contracts. Since the organization has infinite capacity, completion deadlines are given relatively little consideration. Scheduling on a “first-come, first-serve” basis is typical of infinite capacity scheduling. Customers often link work priorities with scheduling expectations. For example, if a safety-related work order is a higher priority than an office renovation, the safety-related work order is always completed first.
Finite capacity scheduling is appropriate for organizations unable to adjust resources without incurring a cost premium or, despite full utilization of the existing resources, “there is no control valve that adjusts random work requests automatically with the fairly constant available staff hours. Result: too many jobs in progress and too few being completed…” (Westerkamp, 2001, p. 37). Not surprisingly, finite capacity scheduling is typically very complex (Gray & Larson, 2008, p. 240). A simplifying technique, ideal for “shelf” or “shovel-ready” projects, is to only consider the length of time required to complete the work order (Lui, 2008). That is, no deadline exists and the work order is done as resources permit.
Visit us on the web at www.sksanitary.com or email us at info@sksanitary.com
Our Suppliers:
Surrey • Victoria • Kelowna • Edmonton • Lethbridge • Red Deer • Calgary • Regina • Saskatoon • Winnipeg
Studebaker (1997) identifies two methods for time-constrained scheduling. Backward scheduling begins from the work order completion deadline and continues “backward” in time to determine the latest date that a work order can start. Backward scheduling gives priority to meeting the work completion deadline. For example, cartage support for a school assembly in a gymnasium typically requires backward scheduling to reduce risk of event postponement. In contrast to backward scheduling, forward scheduling gives priority to delivering work efficiently and cost effectively. Forward scheduling begins from the first available date when work can begin and continues “forward” in time to determine when the work order will be completed. Schedulers sometimes need to combine backward and forward scheduling. For example, if the gymnasium was in use just prior to previously mentioned school assembly, the pre-defined time constraints on work site availability (start and end times) transform this work order into a capacityconstrained problem.
Sources of the Scheduling Dilemma
The root cause of a scheduling problem is the creation of work orders. Many (if not the majority) of work orders are systemic to asset maintenance and management. That is, customers are relatively unaware of work occurring “behind the scenes.” These maintenance work orders are triggered by either events or on a fixed schedule based on calendar dates.
Preventive maintenance typically triggers a work order based on occurrence of a predictable event (e.g., number of kilometres driven, number of hours in operation, equipment exceeding allowable operating tolerances). Other event sources include the arrival of a new piece of equipment and repairs to correct findings from an inspection. The order-based shop environment described by Liu (2008), in which a customer order is not shipped until all jobs within the order are completed, is analogous to an event created by completion of another work order. Triggering work orders based on calendar dates is less common than using events because calendar dates ignore the actual amount of wear-and-tear on the asset. Nevertheless, calendar dates are used when deterioration is assumed to be at a constant rate (e.g., roof inspections) or when the activity is regulated (e.g., fire extinguisher maintenance).
Vandalism, unforeseen breakdowns and customer requests are sources of work orders that place variable workload demands on maintenance staff. Ideally, Computerized Maintenance Management Systems (CMMS) are used when submitting work requests. This process facilitates effective work scheduling. In some cases, however, customers ask maintenance staff to perform minor tasks while attending the site to do other work orders. In addition to placing staff in the difficult position of circumventing work order discipline, these maintenance “targets of opportunity” stress the CMMS by placing unvetted tasks ahead of planned work and thereby undermining scheduling systems.
Once a work order is created, resource availability is dependent on funding. Contractors, materials (e.g., tools, consumables/building supplies, shop equipment), and staffing all require sufficient funding. When resources cannot satisfy peak workloads, capacity-constrained scheduling is used. Delay of noncritical work orders or extending the length of time to complete a work order are potential consequences of insufficient resources (Gray & Larson, 2008, p. 234).
Carver (2001) argues an organization’s preventive maintenance program determines its minimum manpower requirements. Chase, Jacobs and Aquilano (2005, p. 679) support this position by noting that the ideal staffing plan sustains the minimal workforce levels to accomplish the daily work while reducing the variance between actual and planned output. Given the organizational uncertainty created by unpredictable funding, Gray and Larson (2008, p. 237) note the common assumption of capacity-constrained scheduling that, once work begins, sufficient funding will remain in place to complete the work order (regardless of cost).
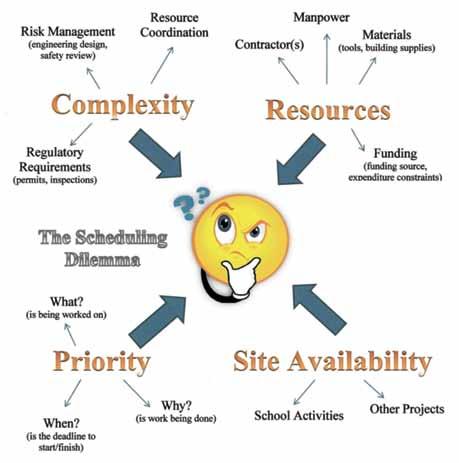
Work complexity and the coordination of multiple resources is another source of the scheduling dilemma. Technically challenging work may require detailed engineering analysis, design, and site supervision. Regulatory requirements may delay the work or impose conditions (e.g., building permits, fire inspections, environmental protection measures). Work order completion may also be delayed by the lead time needed to obtain specialized parts or the maintainability of equipment (e.g., availability of access panels). Achieving economies of scale is relatively difficult when implementing complex work orders. When opportunities for economies of scale are found, however, the benefits to capacity-constrained scheduling are significant.
Bringing together the right number of people, with the right skills, at the right time is an important aspect of work-order coordination. Gray and Larson (2008, p. 236) state “human resources are usually classified by the skills they bring to the project.” In some cases, skills may be interchangeable but may result in some loss of productivity (i.e., extending the amount of time needed to complete the work order). Conversely, some loss of productivity may be acceptable. For example, consistently assigning the toughest assignments to the most skilled tradespersons will undermine employee morale and fail to develop less experienced personnel (Gray & Larson, 2008, p. 252).
Scheduling dilemmas may arise from access to the work site. The previously mentioned example of cartage support for a school assembly in a busy gymnasium shows how work site availability can create a capacity-constrained scheduling problem. Other work in progress, such as a seismic upgrade, can delay projects unless leveraging opportunities are found. Multi-trade work orders can also create scheduling problems. For example, unforeseen delays in completing drywall installation will result in re-scheduling of painting.
Work order prioritization is often the most contentious aspect of scheduling because, as previously mentioned, maintenance staff and building occupants have different perspectives. Customers provide direct input into the prioritization of their work orders. Unfortunately, this input is provided without full knowledge of the organization’s systemic work orders and other scheduling factors. Therefore, in the absence of any other scheduling factors, customers often expect “contention for resources is resolved in favour of [the] job with the higher priority that is ready to run” (Mahesh et al., 2008, p. 17).
Rules are used to determine the relative priority of a work order. For example, a simple prioritization chart may be based on the type of asset under consideration (e.g., classroom, bus garage, school board office) and the nature of work (e.g., health and safety, renovation, restoration of electrical service). Chase et al (2005, p. 668) identify several other common prioritization rules, including (a) required due date; (b) amount of time required to complete a work order; (c) amount of materials required; and (d) availability of underutilized resources.

Effective scheduling requires weighing different factors, including funding (or resource availability), work complexity, worksite availability and work-order prioritization. This evaluation, however, must be in the context of the objectives of work order scheduling, including (a) meeting due dates; (b) minimizing lead time; (c) minimizing setup time; (d) minimizing inventory levels; and (e) maximizing resource utilization (Chase et al., 2005, p. 667). When weighing scheduling factors, the possibility of time-line slippage needs to be recognized. Critical-chain project management techniques may be appropriate in organizations having “a corporate culture which values accurate estimates and refrains from blaming people for not meeting deadlines” (Gray & Larson, 2008, p. 271).
Common Roadblocks to Effective Scheduling
Whether due to an unforeseen customer request or an emergency breakdown (possibly arising from poor maintenance scheduling), emergent work orders “jumping the queue” threaten an organization’s ability to schedule maintenance work effectively. Developing the flexibility to absorb emergent work requires investment in scheduling capabilities. In many organizations, data collection and management is a key issue. “Without documentation of each job, effective scheduling is impossible” (Carver, 1971, p. 44).
Given the complexity of many scheduling problems, computer-based tools are essential in most maintenance organizations. Properly used, these tools should be more than simple migration of a manual system into an electronic format. For example, enterprise data management solutions enable seamless interface with other business functions, including payroll, procurement, and capital asset management. Scheduling software enables maintenance organizations to identify scheduling conflicts and resource shortfalls before they occur and facilitates “what if” analysis to avoid pending issues. Reports should be available in a variety of formats, to suit users’ needs and level of expertise.
Where an organization has the necessary tools (e.g., project management software, Computerized Maintenance Management Systems), poor data integrity may undermine the technology investment. Chase et al. (2005, p. 677) stress the importance of shop discipline and data responsibility by everyone interacting with the work order. As exemplified by the many technologies developed for real-time communication (e.g., bar codes, work order applications for hand-held devices, radio frequency identification tags), data responsibility includes
Interior Turf Equipment • 1-800-994-9990 • www.iteequipment.com
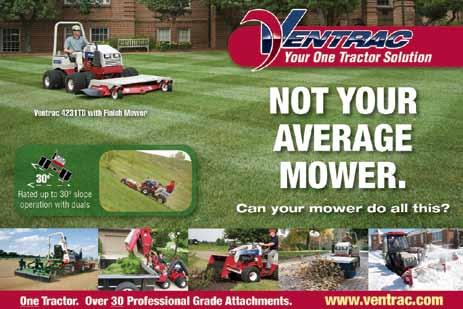
recording information as soon as possible. However, changing an organization’s culture and the training of work receptionists and maintenance supervisors can be difficult and costly. Similarly, hiring schedulers entails benefits that may be difficult measure until the “supertanker begins to turn around.” Westerkamp (2006, p. 41) equates the number of schedulers in an organization with an equivalent number of maintenance personnel. Therefore, in the short term, benefits may be limited to maintenance supervisors and tradespersons spending less time vetting emergent work orders (and more time on repairs).
Monitoring the Schedule
“The key to creating and using a schedule successfully is having the ability to measure the activity and compare actual status against the plan” (Studebaker, 1997, p. 14). In addition to proactive work order management, Gray and Larson (2008, p. 255) note that monitoring the schedule is critical for tracking costs because resource utilization will follow the work order schedule. Chase et al. (2005) distinguish between shortterm (daily) and long-term scheduling.
Short-term scheduling is best controlled within the maintenance shop or production centre, particularly during peak workloads (Carver, 2001). Shops focus on work orders issued for that day. This provides shop supervisors more time to oversee work because their planning horizon is limited to the day’s activities.
Large maintenance organizations often use a work control centre for long-term scheduling. Work control centres are a business function in which resources are organized (Chase et al., 2005, p. 664). In smaller organizations, a single person may be responsible for long-term scheduling or the function may be combined with another position’s duties. Regardless, shortterm and long-term scheduling requires coordination through ongoing communication and frequent scheduling meetings. For example, a common understanding of standard times for maintenance tasks is required. These standard times serve as a good start point for work order scheduling,
but may not reflect local conditions. Incor- a review of how work orders are triggered. porating feedback from maintenance shops Following a discussion of common roadinto long-term scheduling results in greater blocks facing many organizations, a system accuracy of the schedule and facilitates for monitoring and improving work order better management of customer expecta- schedules was provided. tions.
Knowing the current status of the work About the Author orders, schedulers are well-positioned to Steve Woods, M.Eng., MBA, P.Eng., is encollaborate with customers. As exempli- ergy manager and manager of operations at fied by providing customers a choice of School District No. 72 (Campbell River). two options among “fast, cheap, good” (SixSide.com, 2005), “most research in References scheduling either ignores due dates or asAlfieri, A. A. (2009). Workload simulation sumes that due dates are set a-priori and and optimisation in multi-criteria are an input to the problem” (Charnsirisakhybrid flowshop scheduling: a case skul, Griffin, and Keskinocak, 2004, p. 698). With respect to work order due dates, study. International Journal of customer satisfaction declines after their Production Research, 47(18), 5129-5145. preferred due date until reaching the latest doi:10.1080/00207540802010823 allowable due date (after which the work is Carver II, J. O. (1971). Short-interval no longer required). By understanding this, maintenance scheduling for abnormal schedulers can shift the due date paradigm workloads. Management Review, 60(9), and achieve greater lead time flexibility. 41-44. Chase, R., Jacobs, F., Aquilano, N. (2006). Conclusion Operations Management for Competitive
This article has described considerations Advantage, 11th ed. New York: McGrawfor overcoming the scheduling dilemma. Hill. Characteristics of effective scheduling and Charnsirisakskul, K., Griffin, P. M., & two scheduling approaches, capacity-con- Keskinocak, P. (2004). Order Selection strained and time-constrained, were pre- and Scheduling with Leadtime Flexibility. sented. Typical sources of the scheduling IIE Transactions, 36(7), 697-707. dilemma were identified, beginning with ShutterShade_Ad.qxd_ShutterShade_Ad.qxd 12- doi:10.1080/07408170490447366 Gray, C. F., & Larson, E. W. (2008). Project management: The managerial process (4th ed.). New York: McGraw-Hill/Irwin. Hora, M. E. (1987). The Unglamorous Game of Managing Maintenance. Business
Horizons, 30(3), 67-75. Liu, C. H. (2009). Lot streaming for customer order scheduling problem in job shop environments. International
Journal of Computer Integrated
Manufacturing, 22(9), 890-907. doi:10.1080/09511920902866104 Mahesh, V. V., Dulluri, S., Reddy, C., & Rao, C.
P. (2008). Powers of Two-Based Heuristic for Job-Shop Scheduling. ICFAI Journal of
Operations Management, 7(1), 16-31. Prasad, R., & Altaf, M. (2008). Turnaround
Planning. AACE International
Transactions, 1-7. SixSide.com. (2005). The Right Tool for the Right Job. Retrieved December 18, 2011, from http://www.sixside.com/ fast_good_cheap.asp Studebaker, D. (1997). Improving customer satisfaction through advanced scheduling. IIE Solutions, 29(3), 14-17. Westerkamp, T. A. (2006). Maintaining maintenance. Industrial Engineer, 38(7), 37-42. Westerkamp, T. (2001). Plan for maintenance productivity. IIE Solutions, 33(8), 36-41. b
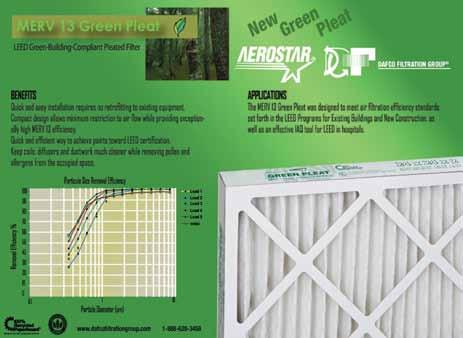
