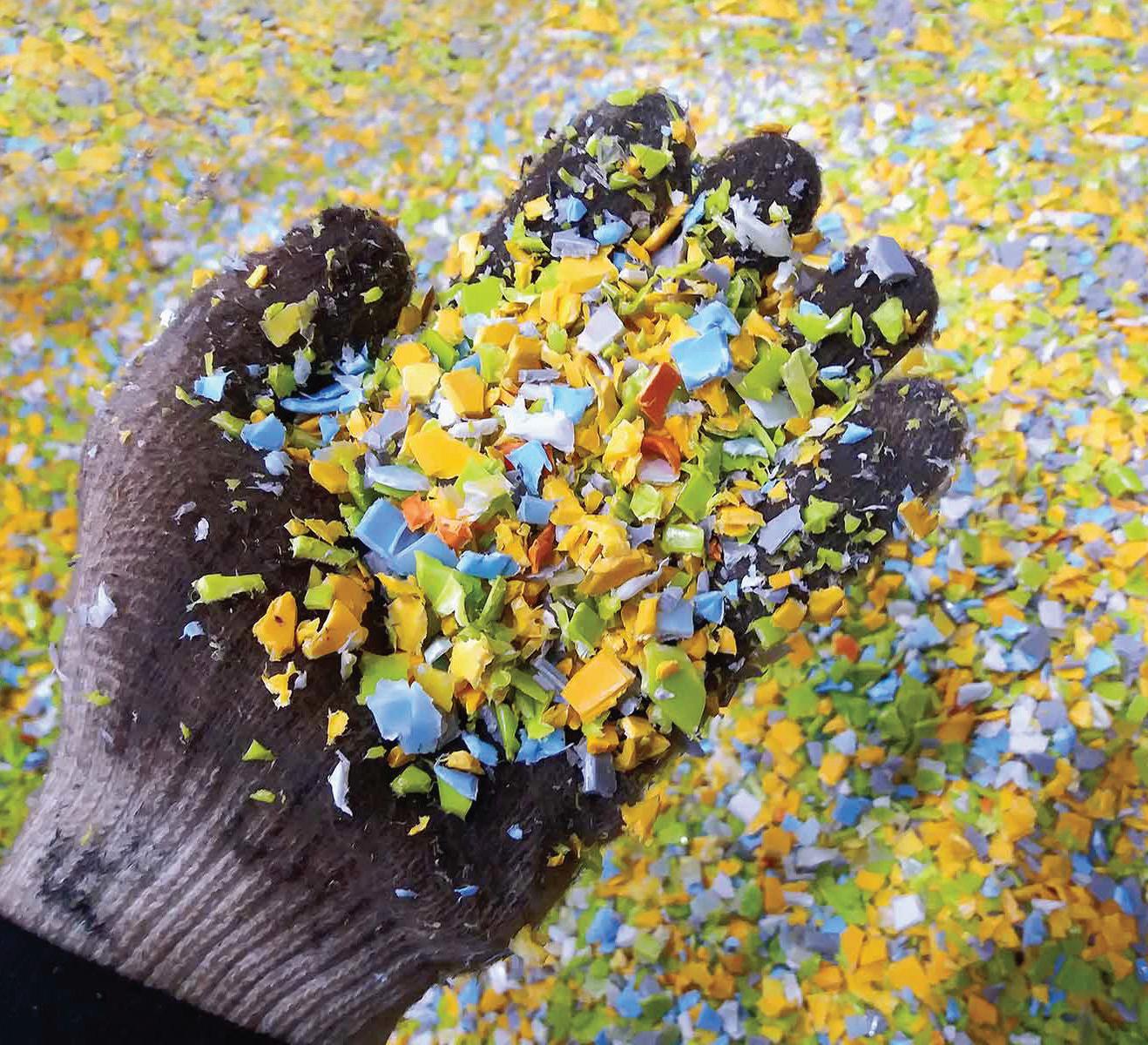
6 minute read
infection | CONTROL
• Polybutylene succinate (PBS) is produced from starch and sugar. This is a more flexible polymer than PLA and less prone to break.
• Polyhyroxyalkanoates (PHAs) are produced from food residues and liquefied plastic wastes using bacteria. By controlling the size of the repeating unit, the resulting polymer can be made rigid and brittle, or soft and flexible.
• Polyvinyl alcohol (PVA) is the only vinyl polymer that is readily biodegradable.
• Polycaprolactone (PCL) is used in sutures and in implantable devices such as scaffolds used for tissue engineering. It undergoes hydrolysis, both within human tissues and within the environment, where it is readily broken down by bacteria and fungi in seawater within several weeks.
• Polyglycolic acid (PGL) can be combined with polylactic acid (PLA) to create a copolymer (PLGA) that has high biocompatibility and degrades faster than PCL. This has attracted interest for use as scaffolds in tissue engineering applications. By altering the properties of the PLGA, its mechanical stiffness and degradation rates can be tuned.
• Cellulose is the most abundant natural polymer and can be processed into a range of materials. It can also be added to existing bioplastics to enhance their strength. While cellulose is degradable, the related compound of cellulose acetate degrades extremely slowly.
Understanding biodegradation
Each polymer which can undergo biodegradation has specific requirements in terms of the processes involved, including the presence of bacteria, the type of bacteria, the temperature range and the presence of moisture, oxygen or ultraviolet light.
The rate of biodegradation varies according to the chemical structure of the polymer and whether any stabilisers were added to it during its production.
When higher temperatures are used, this increases the susceptibility of polymers to chemical, enzymatic and microbial degradation.
Achieving a suitable temperature and maintaining this for a sufficient length of time may be problematic in home-based or practice-based composting facilities.
It is important to ensure that when composting is used, the plastics decompose completely and are not simply fragmented into microplastic particles. When biodegradation is undertaken at industrial scale, it can achieve complete digestion of a biodegradable plastic, while the same time avoiding the formation of microplastics or the generation of other contaminants. Disintegration means that at least 90% of the material is now in particles that are smaller than 2 mm in size after 3 months of being kept at temperatures between
Aerobic composting generates carbon dioxide, whereas anaerobic composting generates methane gas, which can be used for generating electricity by combustion, that will in turn produce carbon dioxide. Biological recycling processes using specific microorganisms can break down polymers into their individual monomers allowing them to be reused. For certain plastics such as polyethylene furanoate (PEF), this provides the optimal means for recycling the plastic back into a form that can be reused.
40-70°C, depending on the particular ISO standard.
The ISO standards for biodegradation of polymers focus on industrial composting facilities and on practical composting process times of up to 8 weeks. Several ISO standards also address degradation that would occur if the plastics are in the ocean.
ISO 13432 specifies biodegradation as meaning that at least 90% of the material is converted into carbon dioxide gas in an inoculum derived from compost at a temperature of 58°C after a period of 6 months.
Staff in dental practices are becoming more aware of life-cycle considerations for plastic items used in their practice. At the consumer level, the removal of disposable plastic shopping bags and plastic straws and their replacements with alternatives are examples of how substitution can be applied. When it comes to biodegradation, the situation is more complex because of the array of different international standards regarding biodegradation of plastics (Table 2). The ISO standards on biodegradation describe the specific conditions required for industrial composting (under EN 13432) and for degradation in ocean water.
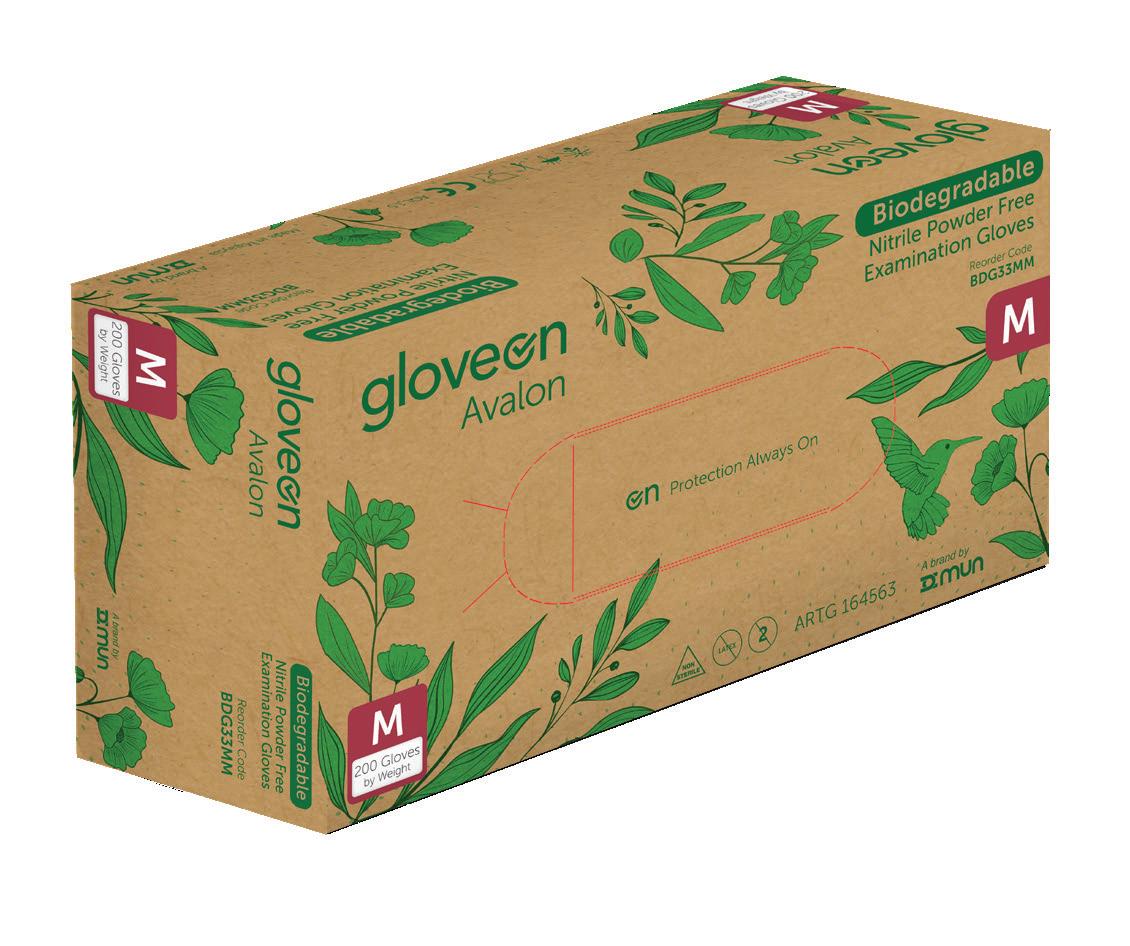
Avoiding the problem of “wishcycling”
Staff in dental practice should have an awareness of what product labels mean on plastic items, including the “triangular chasing arrows” symbol that appears on some products. This does not necessarily mean that the item can be placed in a recycling bin (a problem known as “wishcycling”). It is important to check with your local council regarding their specific requirements for what can be placed in
Conclusions
There are significant moves to greater use of degradable bioplastics at the global scale and this is a very positive development. Having said that, sustainability considerations depend strongly on how the material is made and how it can be recycled, rather than it simply being made from a renewable resource.
Table 2. ISO standards for biodegradation of plastics
Aerobic biodegradation in water (ISO 14851, 14852)
Anaerobic biodegradation in water (ISO 14853)
Aerobic composting (ISO 14855)
Anaerobic high solid decomposition (ISO 15985)
Aerobic soil burial (ISO 17556)
Disintegration at a pilot scale (ISO 16929)
Disintegration at laboratory scale (ISO 20200)
Table 3. Degradation of polymers
Degradable by industrial composting, biologically based: polylactic acid (PLA), polyglycolic acid (PGA)
Degradable by industrial composting, fossil-based: polyvinyl alcohol (PVA), polycaprolactone (PCL), polybutylene succinate (PBS)
Non-degradable, biologically based: Bio-PE, Bio-PET, polyethylene furanoate (PEF)
Non-degradable, fossil-based: Polystyrene, polypropylene, polyvinylchloride, polyethylene, PET council kerbside recycling bins. Staff also need to be aware of facilities that exist for recycling specific containers where a rebate is provided as an incentive for this.
Given the confusion that has existed around the recyclability of various plastics, it is important to be aware that there are changes in the labelling of recyclable plastics and that newer labels may be seen on plastic items that are imported from Europe or the UK. Some labels may indicate that certain products are not suitable for recycling. New labels could be found on items ranging from packaging materials through to PPE. There are moves afoot to try to standardise labelling internationally so that confusion (“greenwashing”) is avoided.
This is why life cycle analysis is so important as it looks at all aspects of environmental impact. Looking to the future, there is growing interest in advanced recycling technologies (involving physical, chemical and biological processes) so that these become more efficient and more cost-effective. Manufacturers are thinking more about how plastic products can be designed to be recyclable, which may mean simplifying their design and using a single material rather than a multilayered material.
Ideally, a complete circular process could be created for many common plastics and the successful deployment of refund schemes for containers have shown that this can be effective when it is easy to do and well accepted at the community level.
Relying just on biodegradation will not solve all the problems of plastic pollution. Complete re-use is the goal for achieving circularity. Various regulatory incentives will no doubt drive progress in this space, as much as will the individual desire of each dental practice to be more environmentally sustainable.
Recommended reading
1. Geyer R, et al. Production, use, and fate of all plastics ever made. Sci. Adv. 2017; 3:25-29.
2. Harmsen PFH, et al. Green building blocks for bio-based plastics. Biofuel. Bioprod. Biorefin. 2014; 8:306-324.
3. Hottle T A, et al. Biopolymer production and end of life comparisons using life cycle assessment. Resour. Conserv. Recycl. 2017; 122:295-306.
4. Hong M, Chen EYX. Chemically recyclable polymers: a circular economy approach to sustainability. Green Chem. 2017; 19: 3692-3706.
5. Spierling S, et al. Bio-based plastics - A review of environmental, social and economic impact
6. assessments. J. Clean. Prod. 2018; 185:476-491.
7. Zheng J, Suh S. Strategies to reduce the global carbon footprint of plastics. Nat. Clim. Change 2019; 9:374-378.
8.Lamberti FM, et al. Recycling of bioplastics: routes and benefits. J. Polym. Environ. 2020; 28:2551–2571.
9.Rosenbloom JG, et al. Bioplastics for a circular economy. Nature Rev. Mater. 2022; 7:117-137.
About the author
Emeritus Professor Laurence J. Walsh AO is a specialist in special needs dentistry who is based in Brisbane, where he served for 36 years on the academic staff of the University of Queensland School of Dentistry, including 21 years as Professor of Dental Science and 10 years as the Head of School. Since retiring in December 2020, Laurie has remained active in hands-on bench research work, as well as in supervising over 15 research students at UQ who work in advanced technologies and biomaterials and in clinical microbiology. Laurie has served as Chief Examiner in Microbiology for the RACDS for 21 years and as the Editor of the ADA Infection Control Guidelines for 12 years. His published research work includes over 390 journal papers, with a citation count of over 18,300 citations in the literature. Laurie holds patents in 8 families of dental technologies. He is currently ranked in the top 0.25% of world scientists. Laurie was made an Officer of the Order of Australia in January 2018 and a life member of ADAQ in 2020 in recognition of his contributions to dentistry.