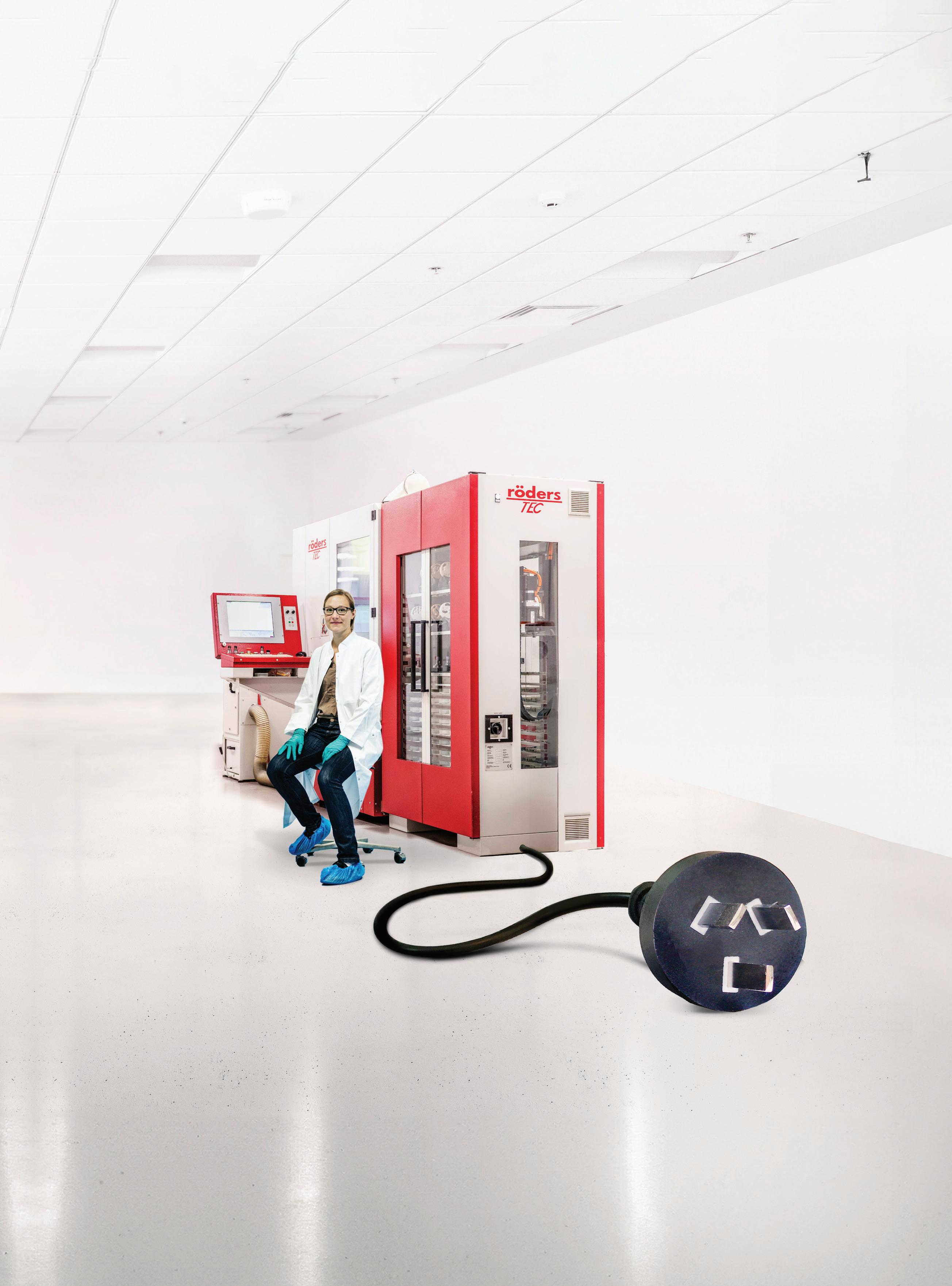
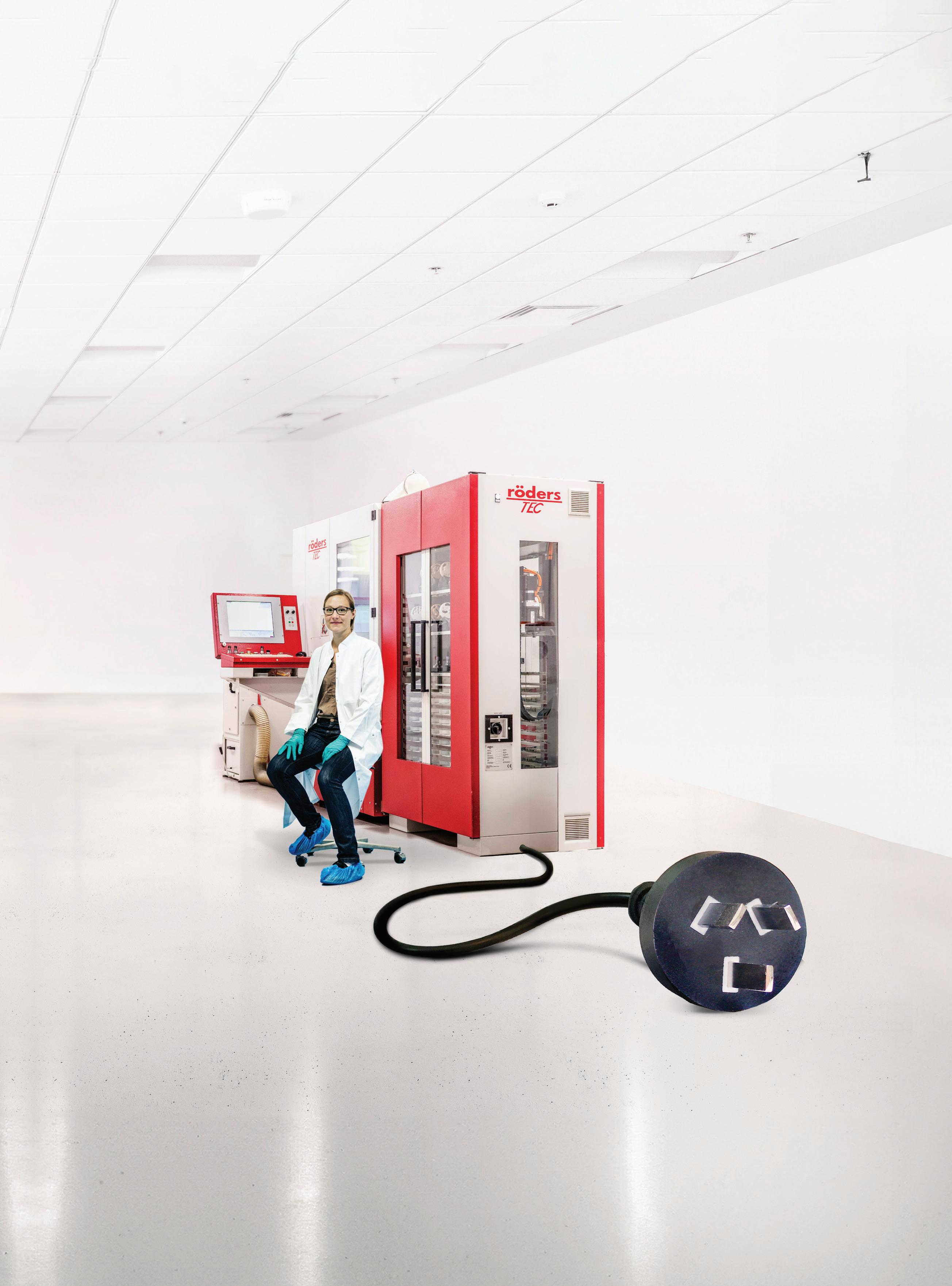
that easily plug into your business. State-of-the-art services
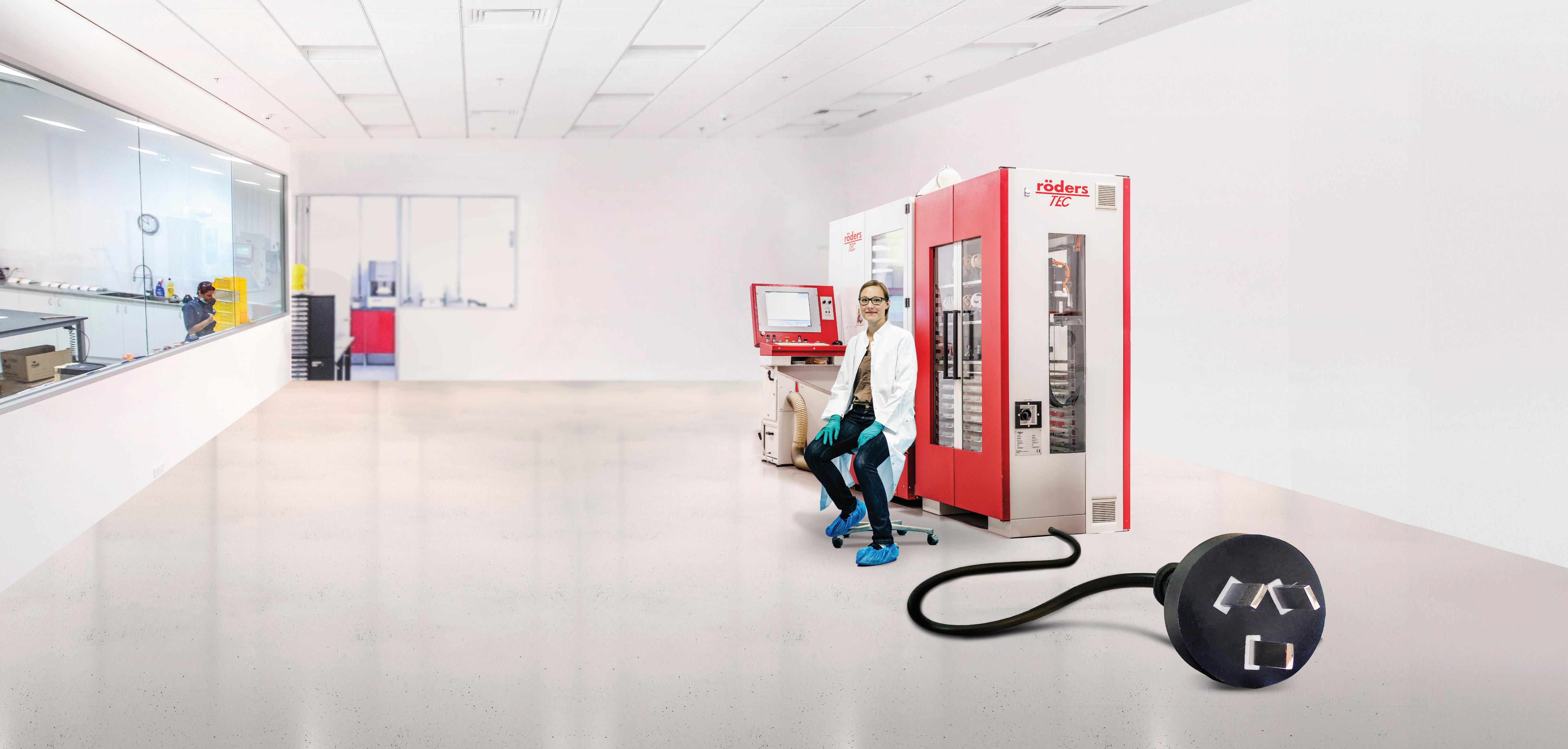
Whether you need assistance with complex cases or during busy periods, our purpose-built milling centre is here to help. Using the latest CAD/CAM technology and Australia’s only Röder’s High-Speed Dental Milling Machines, Dentmill can seamlessly manufacture a variety of top-end quality dental products for your lab.
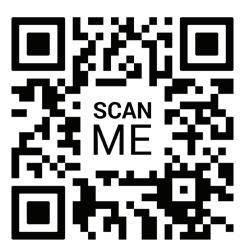
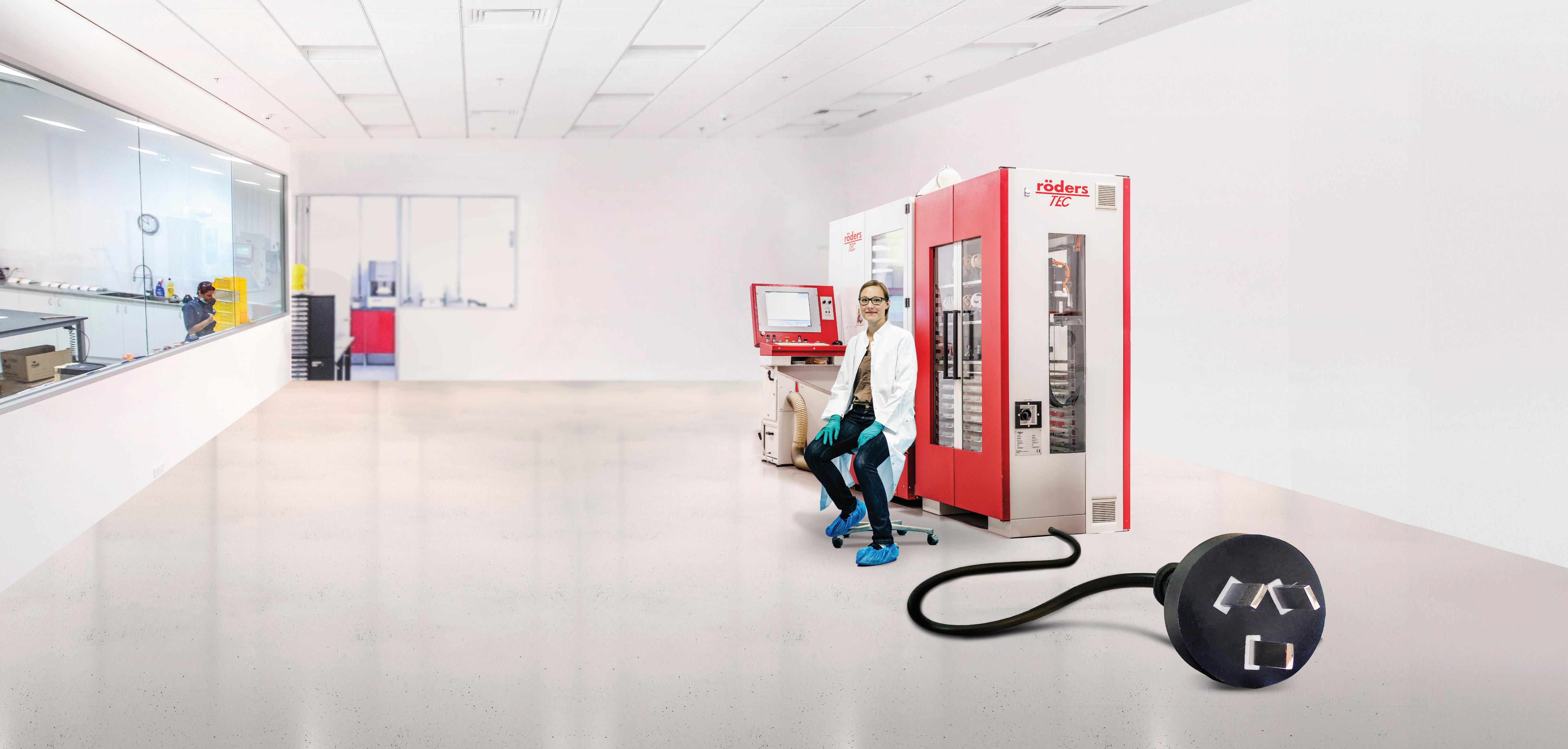
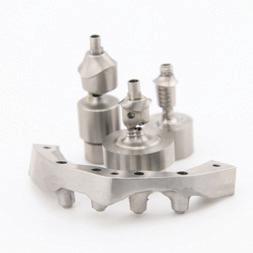
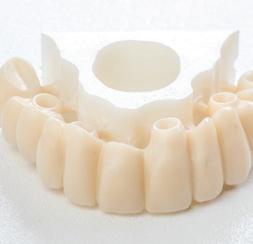
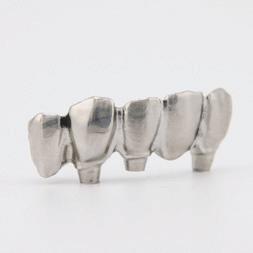

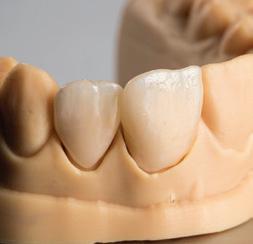
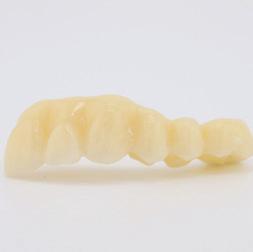
Titanium Zirconia substructures
Cobalt chrome 3D resin printing Glass ceramics
PMMA materials

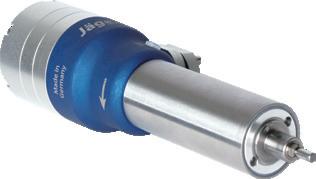
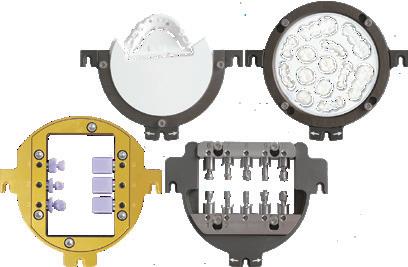
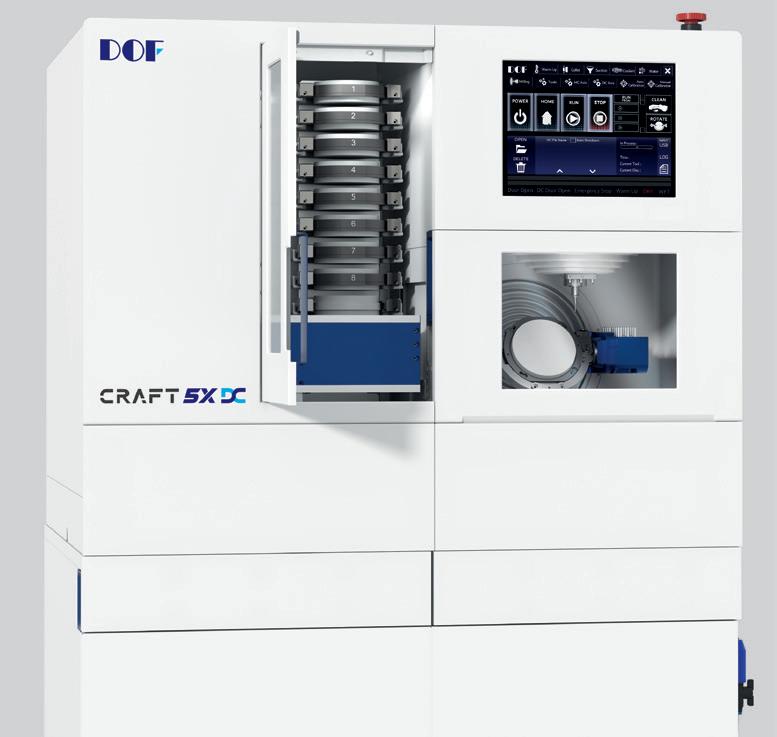

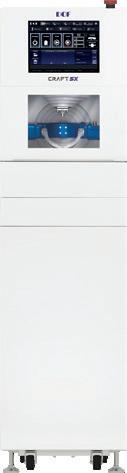
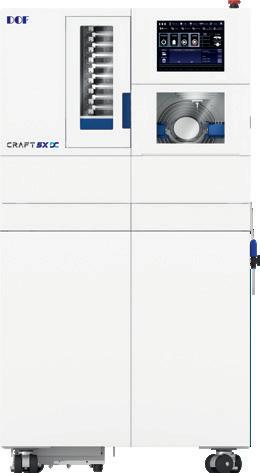


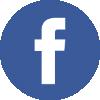
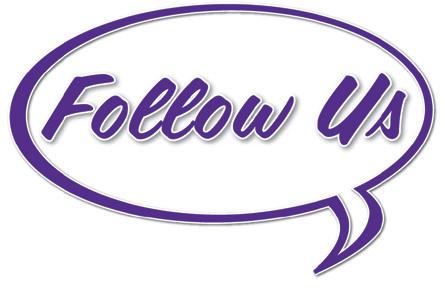


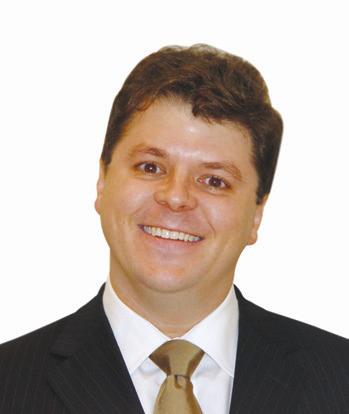
By Joseph Allbeury
Doing it all again...
If you love quality education and you love a bargain, then register immediately for our two major digital dentistry events in 2024 to take advantage of the early bird rates. SUPER HOT discounts currently apply for both 3D Printing in Dentistry 2025 on February 21-22 plus the sixth instalment of Digital Dentistry and Dental Technology 2025 on May 30-31.
Both of these two-day events feature a stellar line-up of expert speakers that are not to be missed.
Planning is well underway for 3D Printing in Dentistry 2025 on February 21-22. This event is a single stream conference with multiple speakers and this year, as well as looking at new tech and new materials, we’ll have a particular focus on the next evolution of printers approaching more autonomous operation and artificial intelligence. There are solutions already available in Australia, some serious, some novel, that are introducing automation at various levels and the use of AI is continually on the increase. We’ll also again be looking at validated workflows to ensure consistency in printed objects. The event at the beginning of 2024 included lively debate in relation to the regulatory side of 3D printing and we hope to also present an update on that. Plus, we will again feature clinical and technical case studies and a range of other topics of interest, all interlaced with plenty of interaction and debate delivered by the best speakers from Australia and New Zealand.
AND... for the first time, we’re introducing stepped pricing with monthly increases, so REGISTER NOW and SAVE! (Remember, the CPD cycle ends in late 2025)
Then, for the sixth time, we’re staging Digital Dentistry & Dental Technology 2025 on May 30-31, 2025. This event attracts some 500 delegates and if you register now, you’ll again save, with 75% off the full price (pay just $220 until November 24). Our signature event brings together dentists, prosthetists and technicians in a multi-stream programme that covers every area of digital technology and its applications in the clinic and the lab. Apart from 3D printing, topics covered include intraoral scanning, 3D facial scanning, milling, CAD and CAM software, materials, smile design, digital dentures, implantology, CBCT, restorative, aligners, orthodontics and more. DDDT25 is two months after IDS, Cologne, so expect the new products to be in Australia and on display.
Digital dentistry continues to define the clinic and the lab and offers tremendous gains in efficiency, time and labour saving that is delivering a revolution in the profession. Both of these events offer clinicians and technicians unprecedented access to expert information to help navigate the transition to digital dentistry and how to take its use to the next level and beyond.
So register now and SAVE!
Enjoy the edition...
Joseph Allbeury, Editor and Publisher
2025 VITA Excellence Award now open
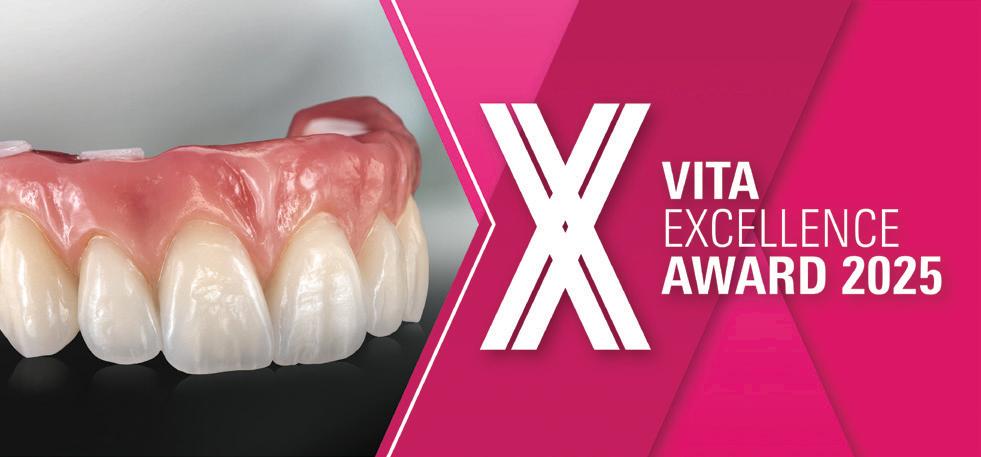
Through the VITA Excellence Award 2025, VITA is honouring outstanding prosthetic restorations among its users worldwide. The goal of the fourth-generation family business based in southern Germany, celebrating its 100 year anniversary in 2024, remains the pursuit of continuously improved solutions for perfect prosthetics in both function and aesthetics - VITA Perfect Match. Here’s how you can take part and win! The VITA Excellence Award 2025 is focused on work involving the leucite-enhanced, glass-ceramic veneering ceramic VITA LUMEX AC. The Next Generation of Veneering: A reliable and highly aesthetic solution for everyone! A jury of five will use the following criteria to evaluate the patient cases that are submitted: Aesthetics, function, documentation and preparation work. The prize is a 12.9 inch Apple iPad Pro and an invitation to IDS 2025 in Cologne to visit the VITA exhibition stand where VITA will cover your travel costs and an onsite overnight hotel stay. You will also have the opportunity to present your patient case to a wider audience. Additional information, along with the eligibility requirements are available online at www.vita-excellence-award.com. Participation consists of sending in all required documents by November 15, 2024 to excellenceaward@vita-zahnfabrik.com.
VITA LUMEX AC – One for All Ceramics and More
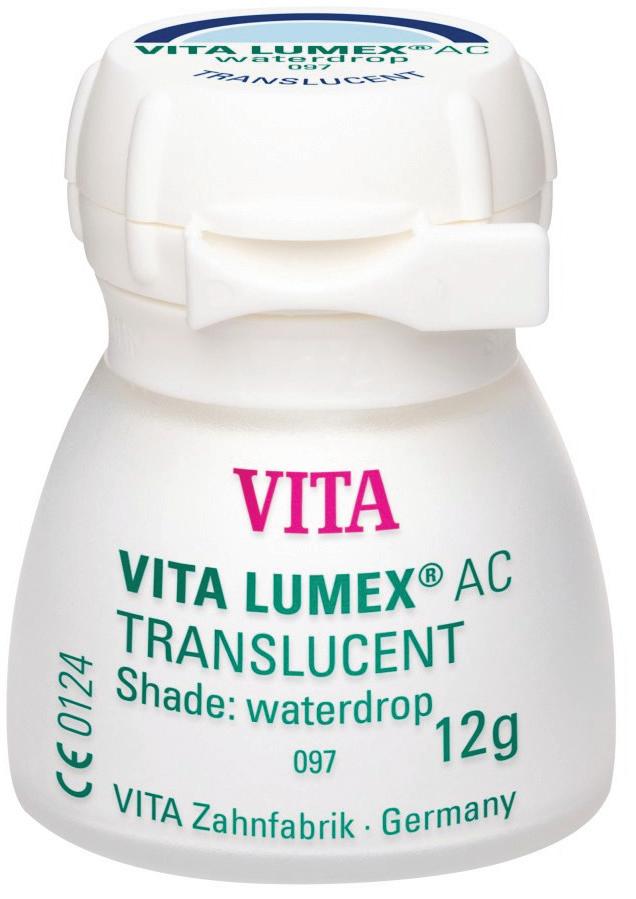
As the next generation of veneering ceramics, VITA LUMEX AC offers easy-to-handle and highly aesthetic veneering on ceramic materials such as lithium disilicate, zirconia and feldspar ceramic as well as on titanium substructures. VITA LUMEX AC can be used for a variety of techniques, including quick and easy micro-veneering, cut-back and full veneering. Reliable reproduction of tooth shades and natural shade and light effects, thanks to ceramic materials with outstanding shade fidelity and excellent light dynamics. VITA LUMEX AC retains its shape even after several firings and also bonds reliably with the substructure. The material is also characterised by minimal material shrinkage - whether using the one-bake technique or a complete dental arch.
Apply now for the second VITA EXCELLENCE AWARD and show off your winning work. Further information can be found at www.vita-excellence-award.com.

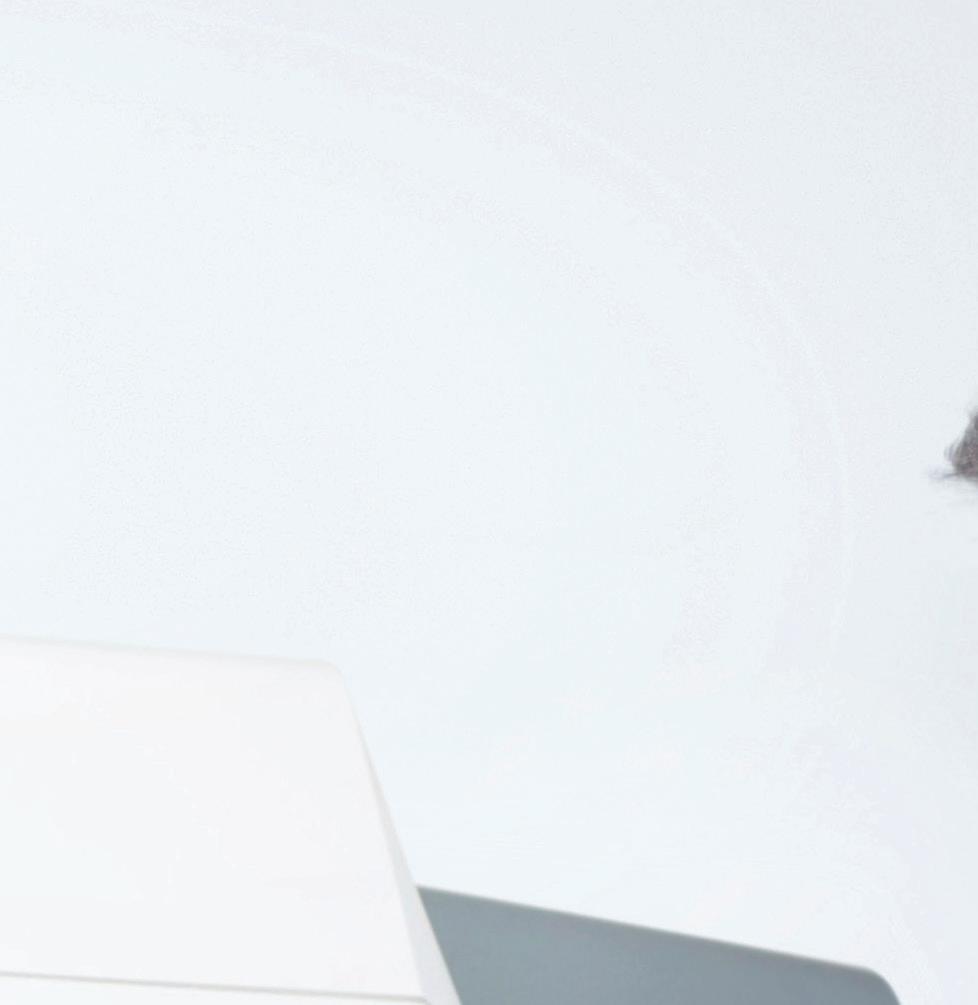
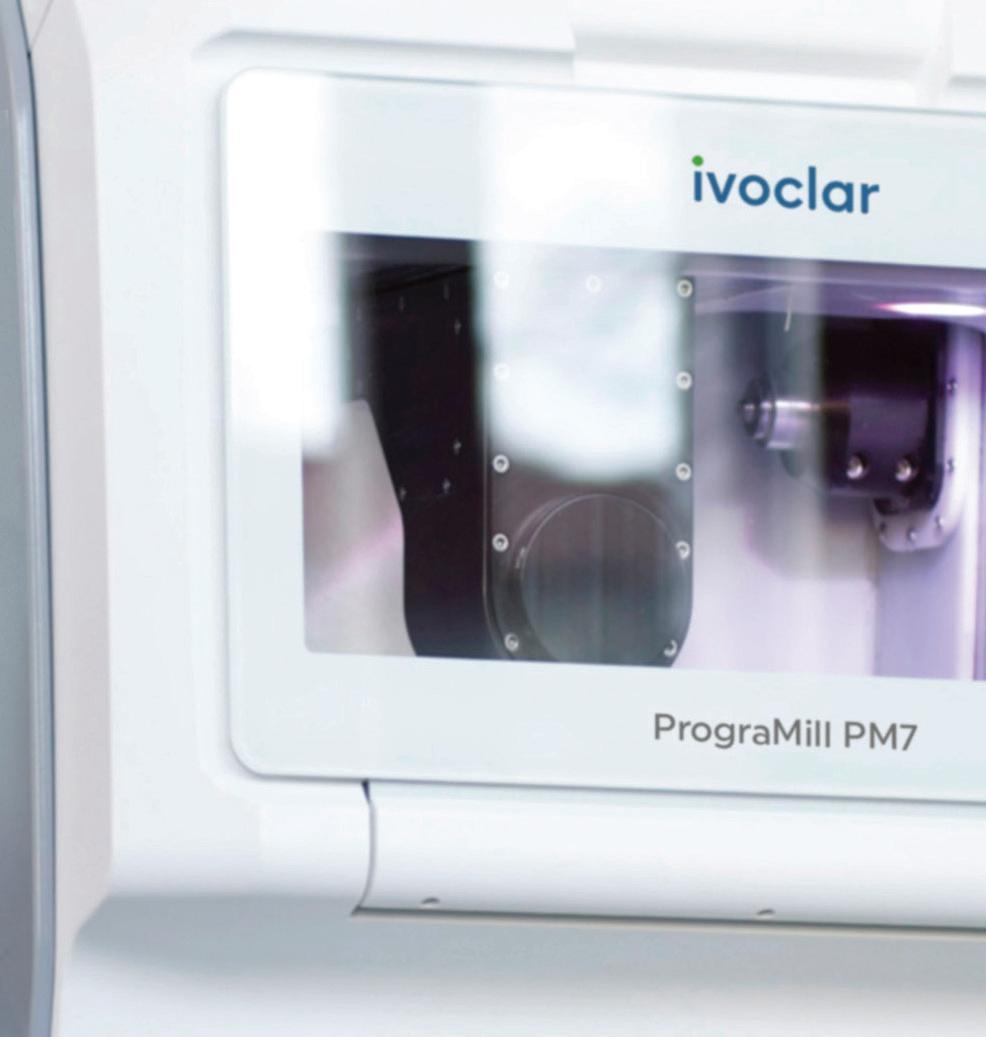
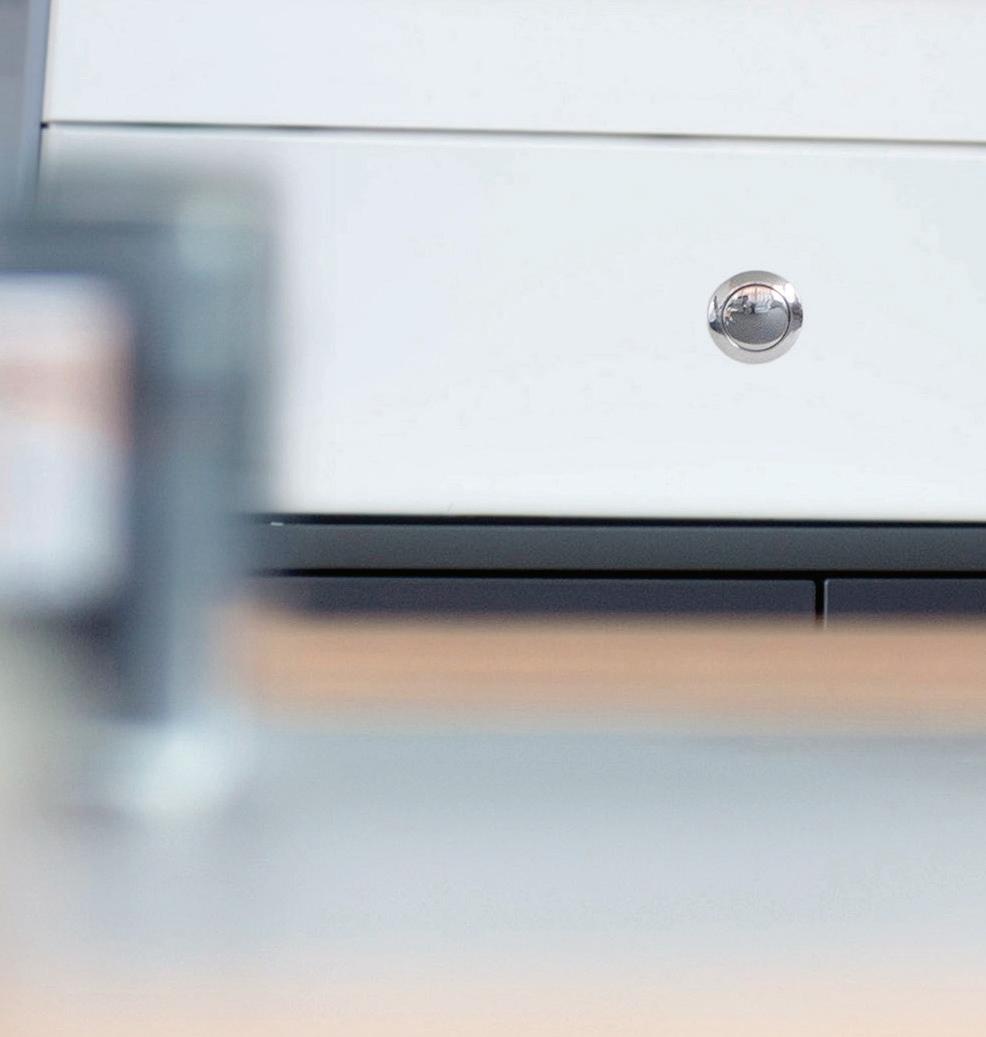


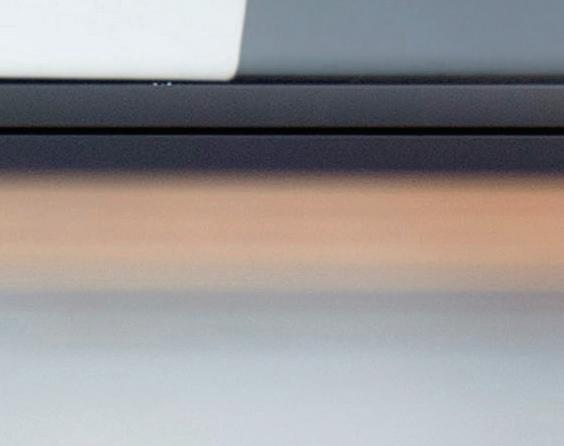

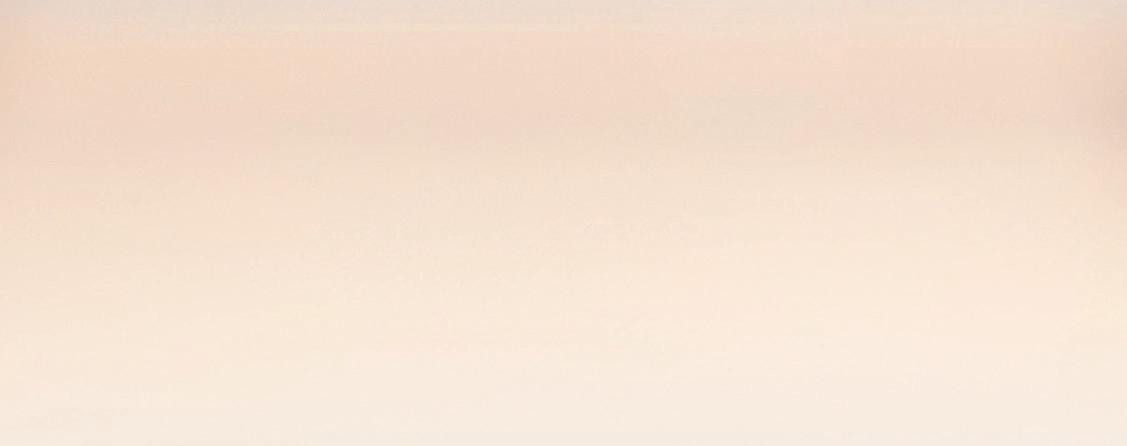
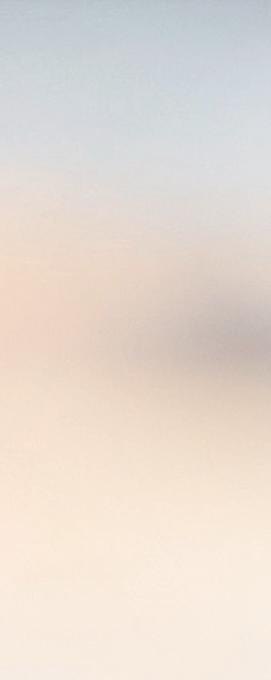
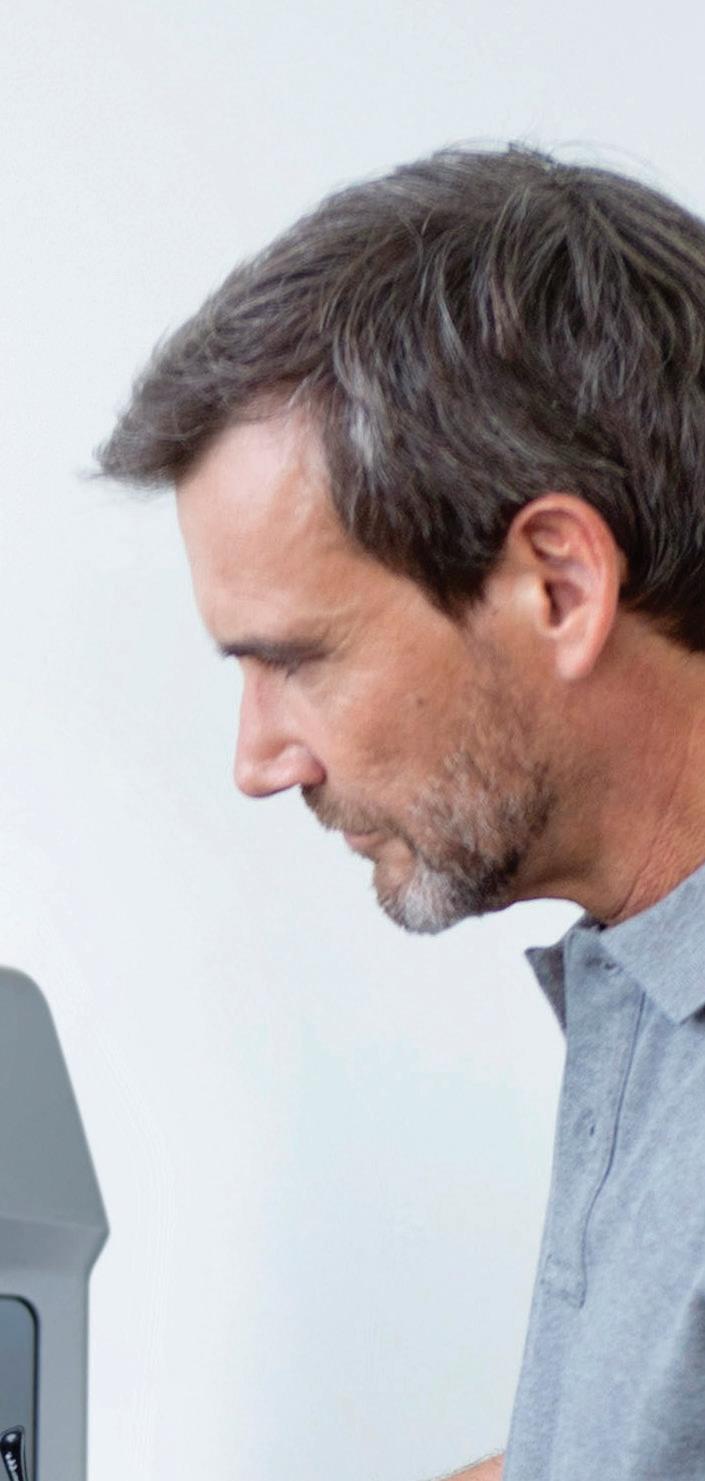
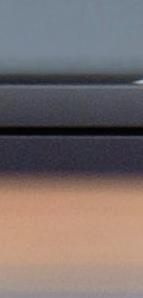
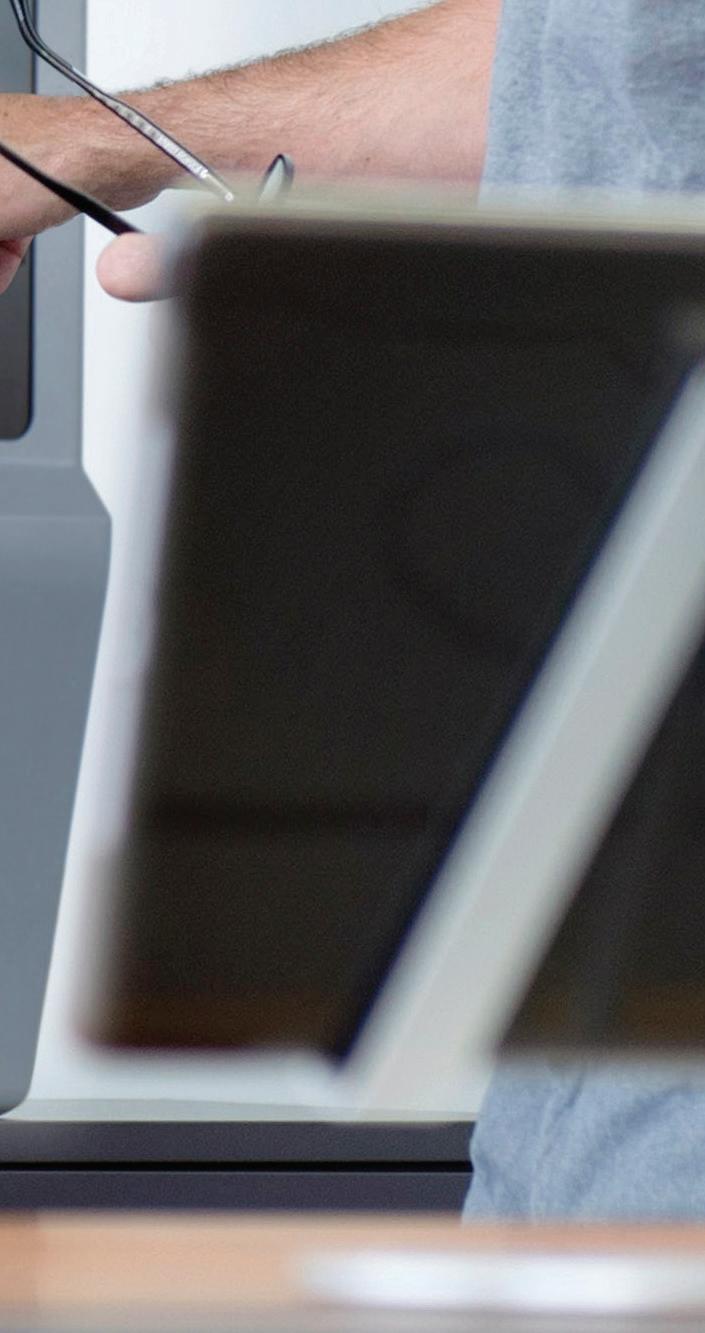
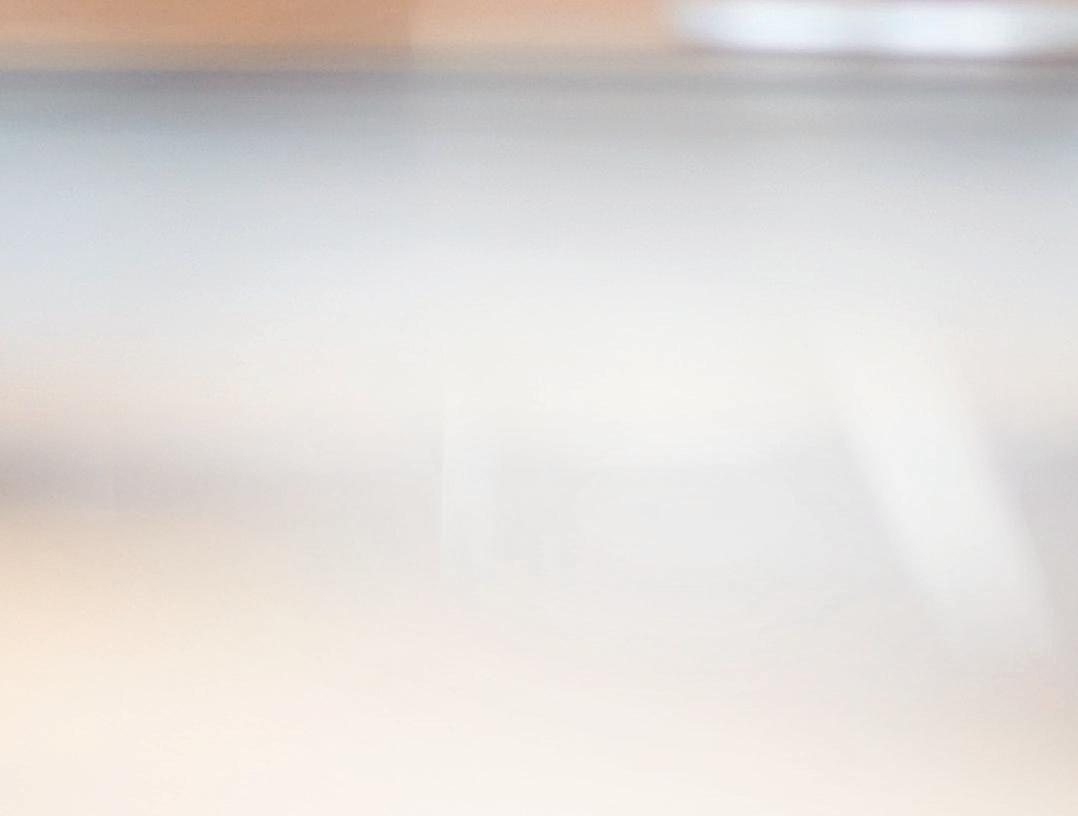
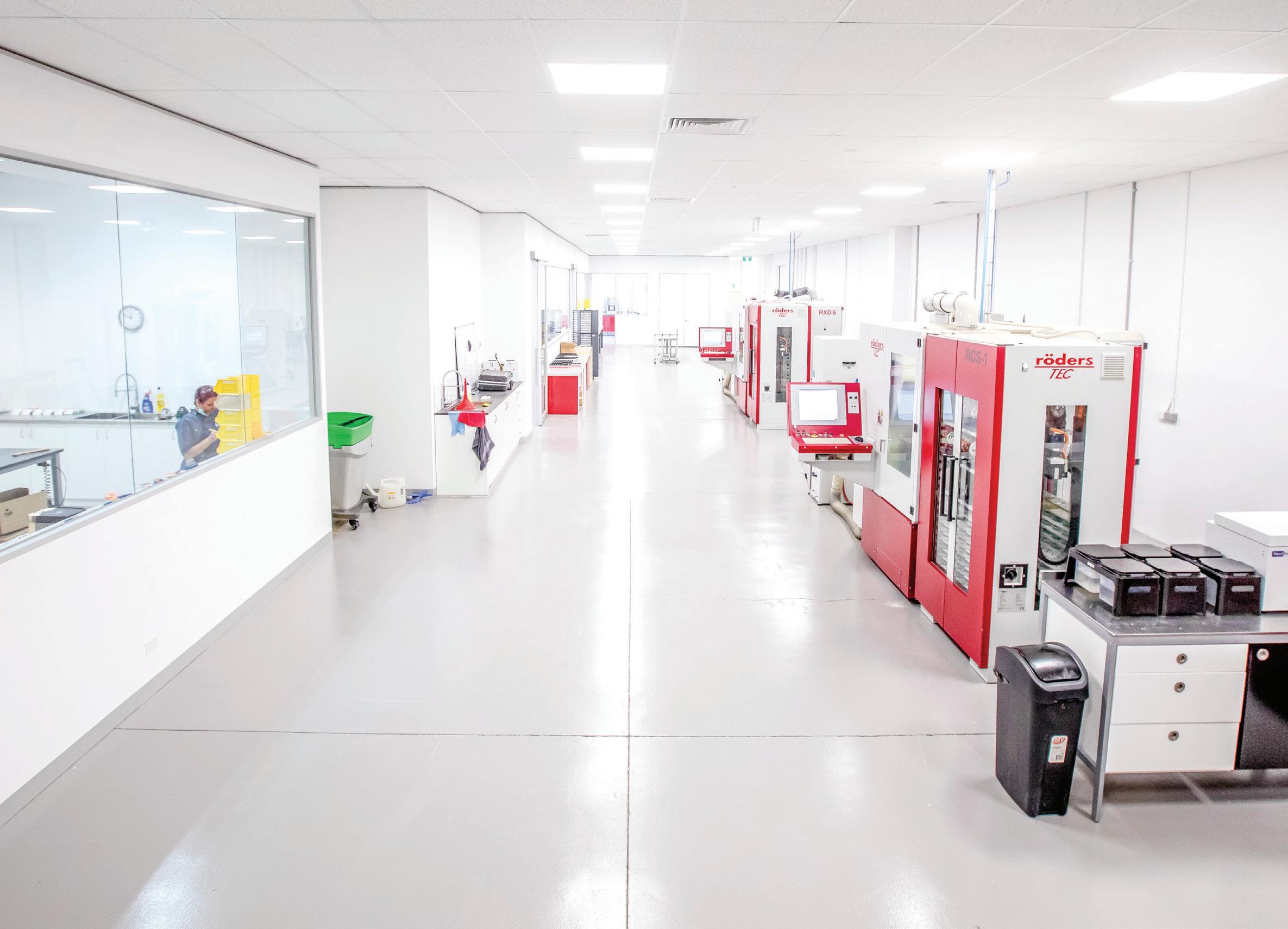
Unlocking the potential of digital dentistry for dental labs
Dentists around the world are increasingly adopting digital dentistry in their clinics. However, not all labs are equipped with the technology to handle the digital design and manufacturing requests from their customers. Often that comes down to whether or not they can afford to invest in expensive new technology - or whether they’re getting enough complex cases to justify the expense.
Enter Dentmill, a state-of-the-art dental manufacturing centre in Melbourne that’s helping labs embrace digital dentistry - no matter what stage they’re at in their digital journey. With a wealth of experience in computer-aided design (CAD) and manufacturing, Dentmill can produce every type of milled and printed dental product - crowns, bridges, bars, models, surgical guides and dentures - with access to a full range of dental materials, including zirconia, titanium, IPS e.max ®, cobaltchrome, PMMA and 3D printed resins.
Dentmill provides labs with the capabilities they need to thrive as digital dentistry becomes more and more commonplace.
“We take that stress and the pressure off labs, so they don’t have to worry about the investment in equipment and training. They can focus on adding their value to the dental restoration – their key business,” says Kevin Bird, General Manager at Dentmill.
Streamlining digital design and manufacturing
Dentmill takes the entire design and production process off a lab’s hands - all they need to do is forward their digital files to Dentmill and they’ll handle the rest. Or, for labs already using a dental CAD system, they can design the restoration in-house and then send it to Dentmill for manufacture.
Equipped with ten milling machines, including the only Röder’s High Speed Dental Milling Machines in Australia and a dozen 3D printers, Dentmill not
only offers unsurpassed quality for its customers, but it can also speed up the manufacturing process for dental laboratories, reducing turnaround times by two weeks or more for those labs using offshore manufacturers.
“We’re not limited to one piece of equipment, which means we don’t have to wait if an urgent case comes in,” says Kevin. “We have that flexibility.”
Taking the headaches out of complex cases
“There’s nothing we’ve seen that we can’t do,” Kevin continues. “We’re here to handle the complex cases that labs might shy away from.”
Dentmill’s advanced manufacturing capabilities, a staff with more than 50 years of combined experience in CAD/ CAM and a product offering that includes custom titanium abutments, cobalt chrome frameworks and genuine implant componentry, means they’re masters at handling complex cases.

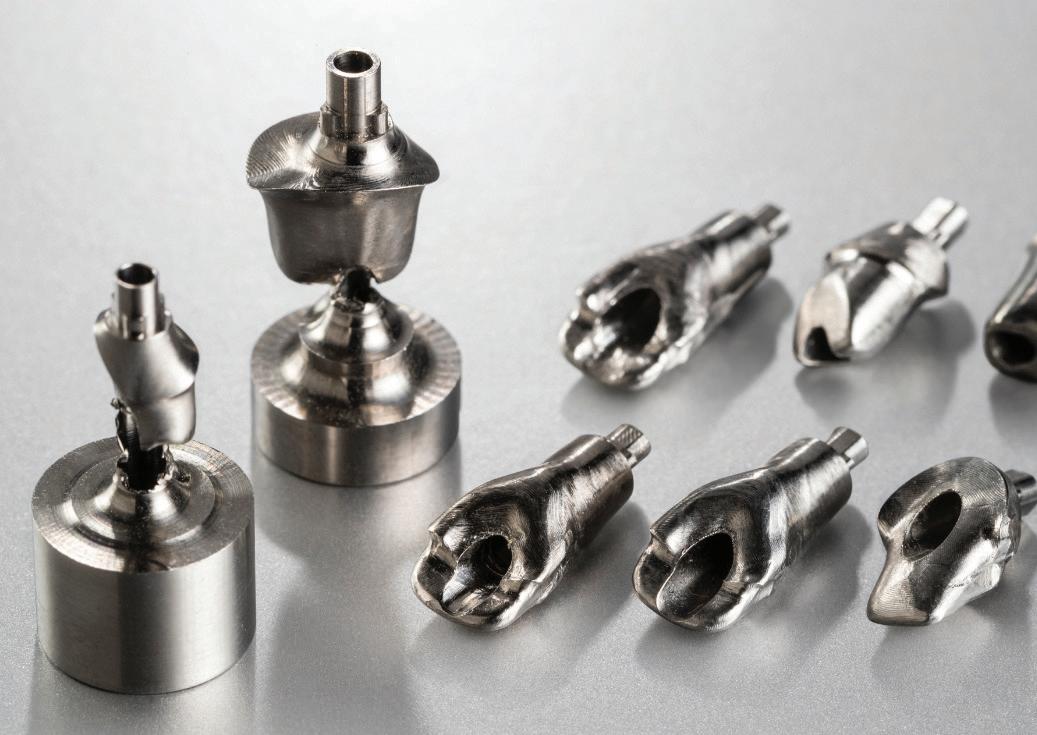
One of the common issues dental labs face is milling implant cases in hard materials, including genuine custom abutments.
“We get a lot of customers who say, ‘I just can’t do this on my equipment – every time I try to cut this material, I break these cutters.’ That’s where we tell them to give it to us, we’ll do it for you,” says Kevin.
Kevin recommends labs focus on their “bread and butter cases” on their own equipment and send their challenging ones to Dentmill. “We’ve seen all the pitfalls and all the headaches and we know where things can go wrong,” he says. “Send those difficult cases to us - even if it’s the most obscure restoration you’ve ever seen, we’ll always get the job done.”
Quality control standards that set a high bar
Quality control is yet another factor that sets Dentmill apart, he noted. He’s worked within a range of industries, including aerospace and automotive, where ensuring a product meets rigorous quality
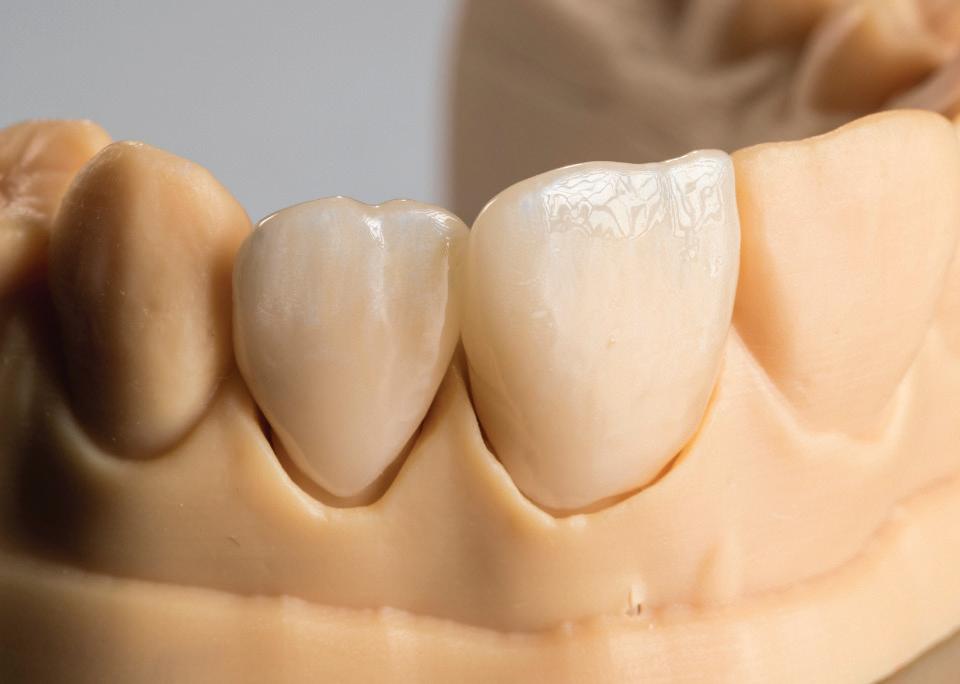
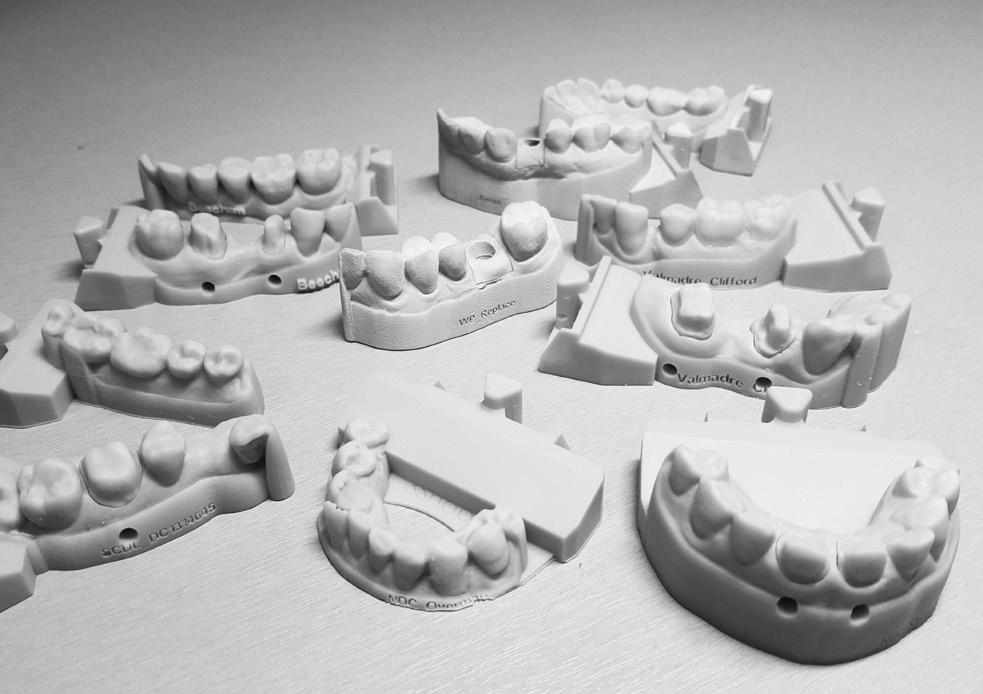
control standards isn’t just important – it’s a matter of life and death. He brings the same approach to his work at Dentmill.
“I never send out anything I’m not happy with,” says Kevin.
And quality matters to labs that don’t want to waste time fixing up substandard work. Kevin gives the example of a new customer, who had been working with another manufacturer, who came to Dentmill with a single case: a cobalt chrome implant abutment. A couple of days after receiving the finished product from Dentmill, he came back with another. And then another. After a couple of weeks and half a dozen cases, the customer called Kevin to say thank you. Kevin was glad to hear it, but couldn’t help asking “What for?”
It transpired that the work the customer had been getting back from the previous manufacturer hadn’t been up to scratch - the finish was poor, the fit wasn’t rightand he was having to spend precious time fixing products before sending them on to the dentists. “He said, ‘You don’t know how much of a relief it is for me to find a
manufacturing centre I can work with that gives me exactly what I want’.”
Bridging the tech gap to future-proof dental labs
Dentmill is empowering dental labs to take on digital dentistry with a partnership that elevates their capabilities, enhances their efficiency and ensures the highest quality for their customers.
With their state-of-the-art technology and extensive CAD/CAM experience, they offer a seamless solution for labs that don’t have the resources or time to invest in and master new technologies.
“Getting a good quality dental restoration is the combination of knowing what the best processes are, knowing what equipment you need and having the skills to bring all those together,” says Kevin. “We have the knowledge to do a good job and the equipment that allows us to do that.”
Start working with Dentmill by calling (03) 9416-2039 or visit dentmill.com.au.
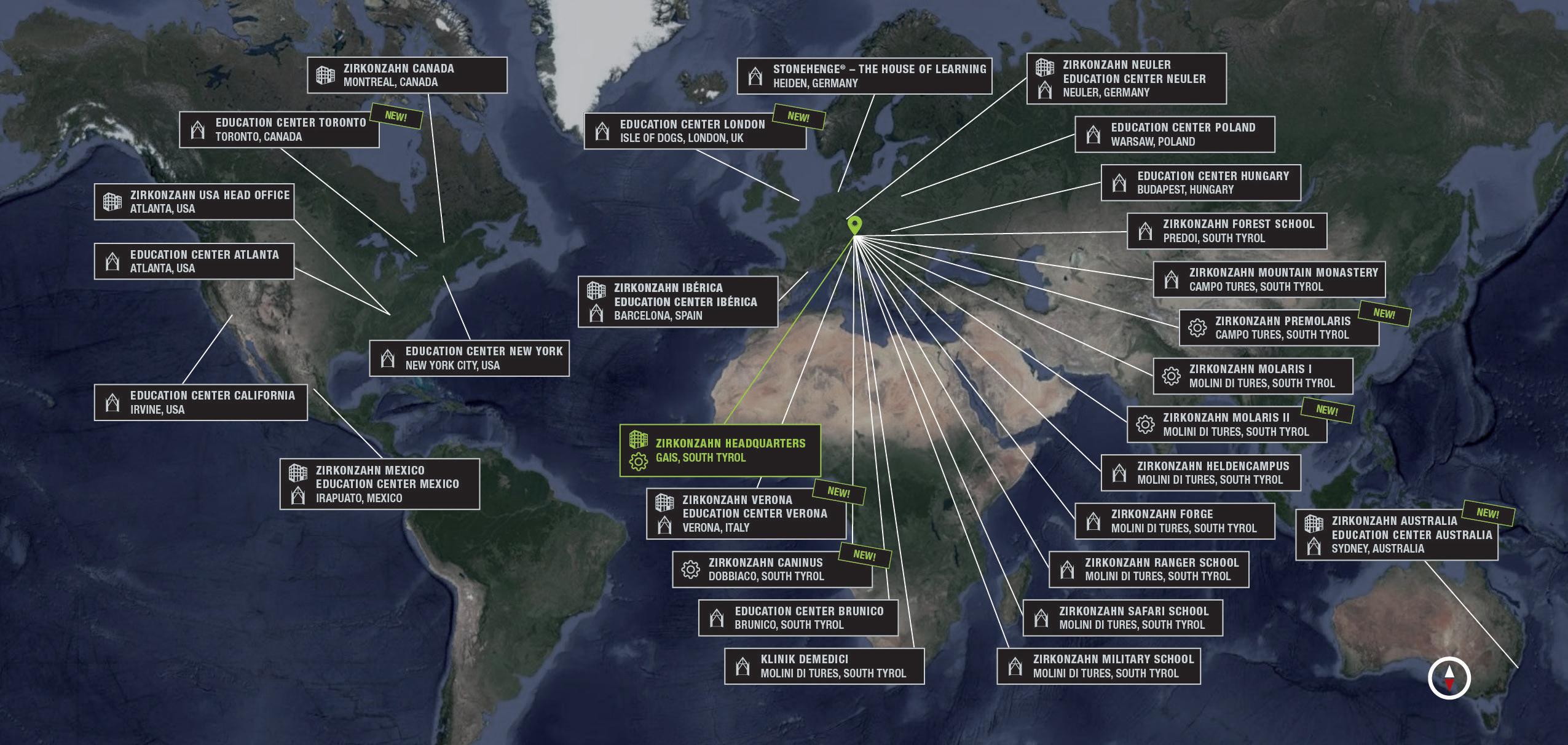
New Zirkonzahn facility in Sydney opens its doors!
After the openings in Toronto and London, the Italian company lands in the southern hemisphere
We’re almost there! In the north of Sydney, Zirkonzahn will open soon a brand-new facility: Zirkonzahn Australia – the company’s 14th location worldwide, following the last openings in Toronto and London. Only a few minutes from the city centre in St Leonards, the facility will host educational training on Zirkonzahn’s products and devices for all dentists and dental technicians who wish to know more about the company’s workflow and work philosophy.
The training courses offered on-site are part of the Zirkonzahn School - the wide, well-structured and targeted educational programme developed by the Italian company with the aim of teaching the use of its equipment and materials with no knowledge gaps.
But that’s not all – Zirkonzahn Australia will also feature a logistics department for supplying materials without delivery delays. Moreover, the on-the-ground experts DT Rian Barnard and Hanna Kukula will support clients and potential customers in the creation of their workflow with Zirkonzahn products, explaining and showing the different components as well as answering to all technical questions.
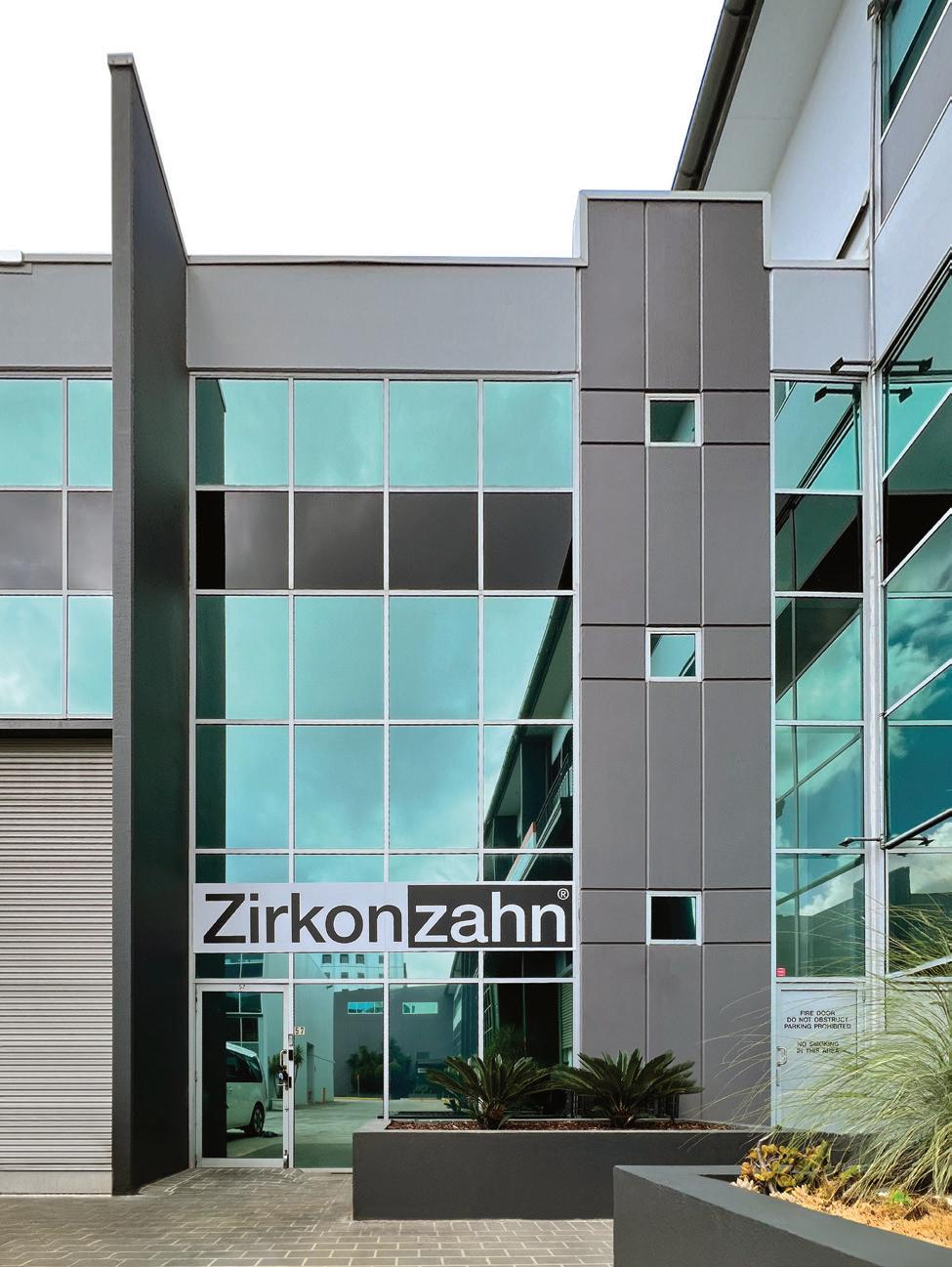
Zirkonzahn Australia is the company’s 14th location worldwide.
From a one-person business to more than 350 employees all over the world, Zirkonzahn is now a global revolution.
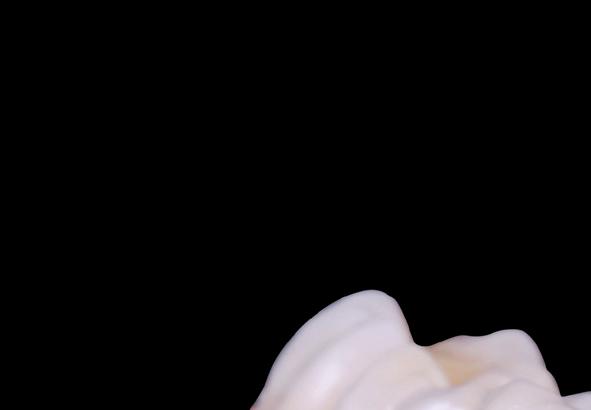
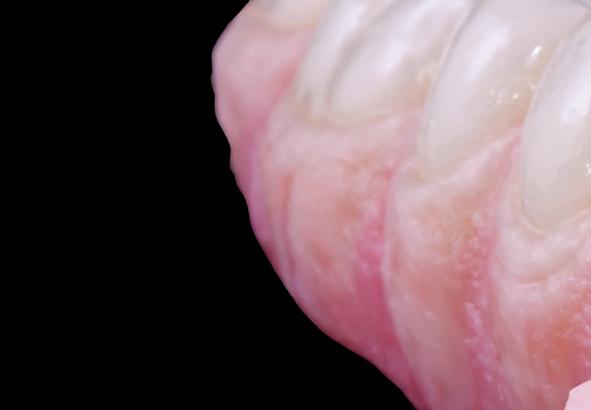
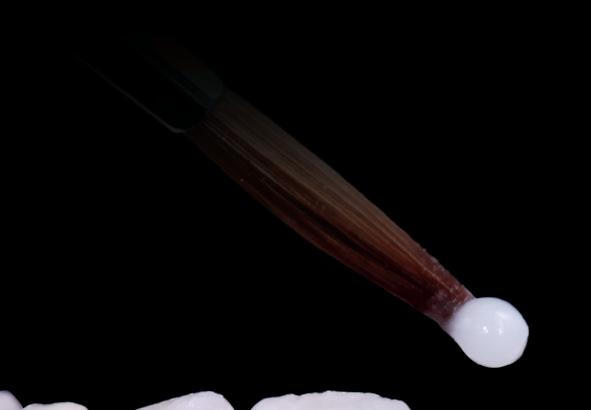
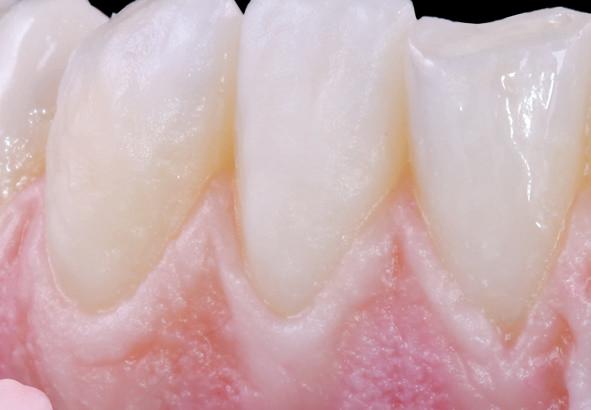
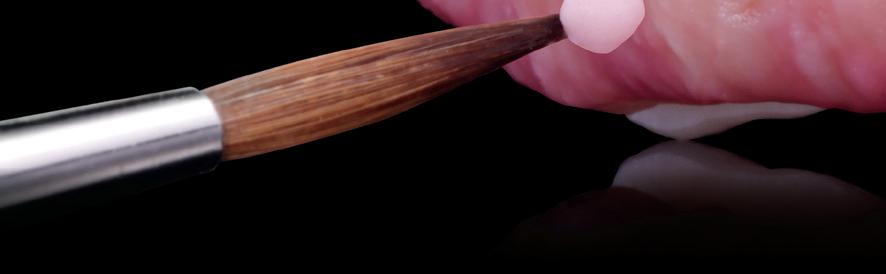
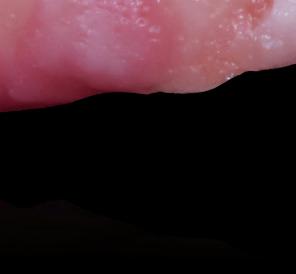


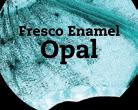
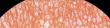

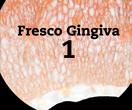
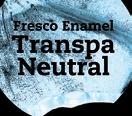
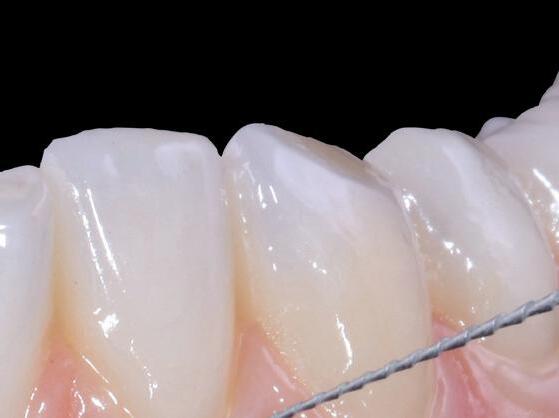



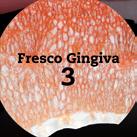
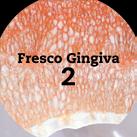
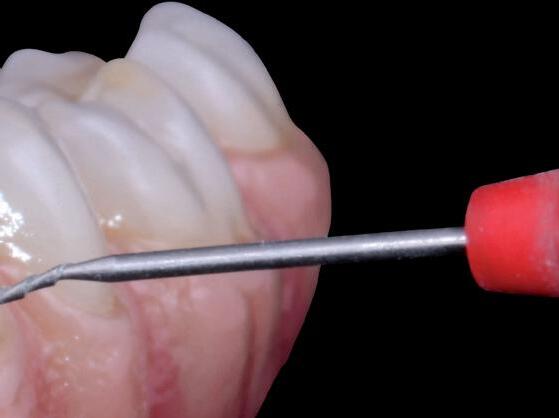
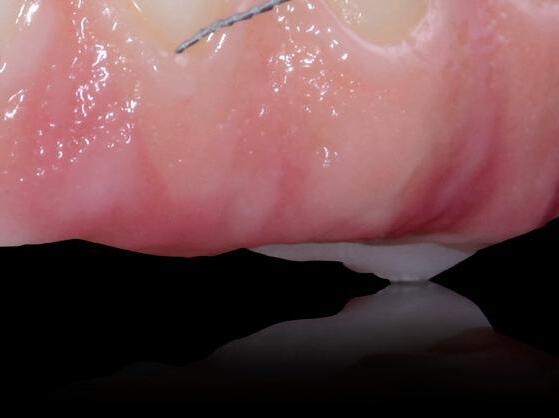

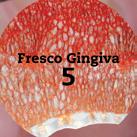
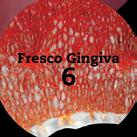
Bar-supported, monolithic restoration in Prettau® 3 Dispersive® zirconia, layered with Fresco Gingiva and Fresco Enamel
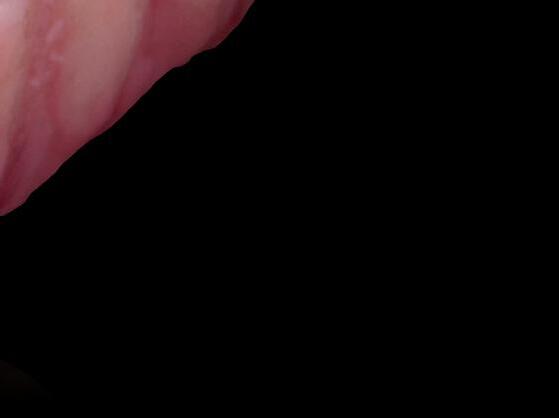
ZIRKONZAHN FRESCO CERAMICS
THE NEW ART OF LAYERING ZIRCONIA
- Ceramic pastes Fresco Gingiva and Fresco Enamel for layering gingival and vestibular tooth areas
- For monolithic as well as slightly reduced zirconia structures
- Natural gingival reproduction by solely applying Fresco Gingiva; characterisation with stains is no more necessary
- Excellent modelling properties due to paste-like consistency, which can be further personalised by adding Fresco Liquid and Fresco Gel
- Low shrinkage due to high primary density and effi cient firing process
- Colour spectrum: Fresco Gingiva 1 to 6 as well as Fresco Enamel Fluo, Opal, Transpa 3, Transpa Neutral, Transpa Orange and Transpa Grey
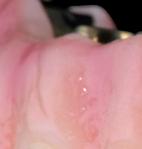
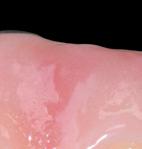

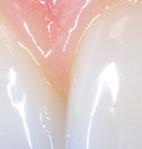
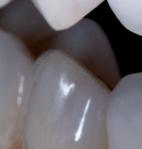
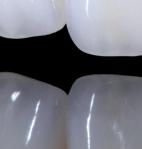
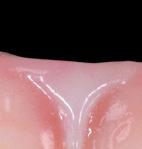
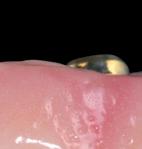
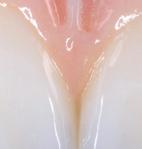
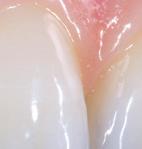
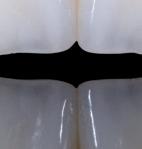
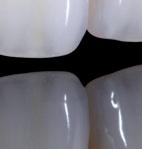
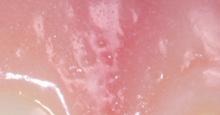
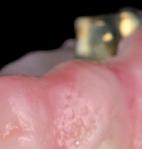
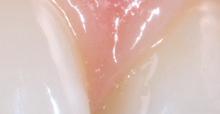
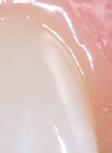
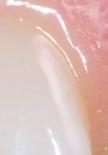
SET FRESCO ESSENTIAL
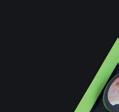
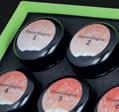
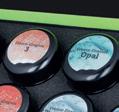
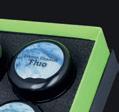
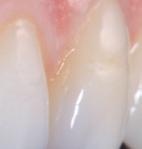
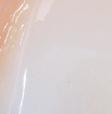
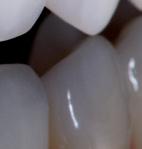
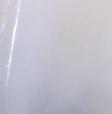
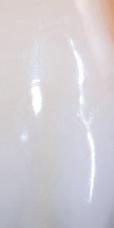
OPTIONAL
FRESCO ENAMEL TRANSPA ORANGE AND FRESCO ENAMEL TRANSPA GREY
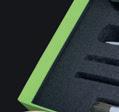


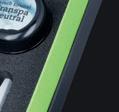
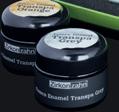

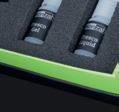
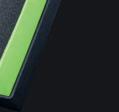
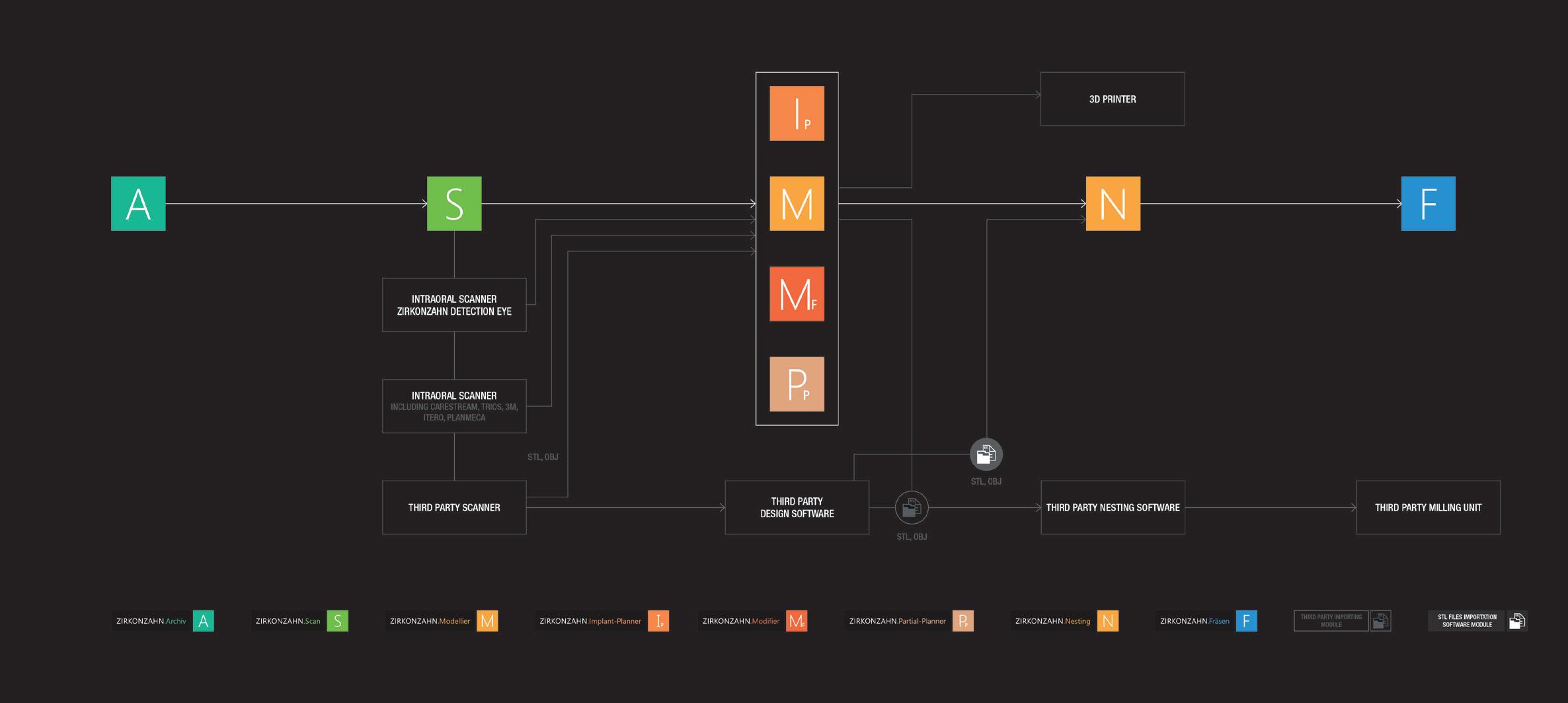
With our products we offer a complete solution to produce high-quality dental restorations.
With the new opening, Zirkonzahn customers and potential clients from Australia can now see first-hand all of the company’s innovations and solutions without flying to Italy, which is, however, always worth a visit: Zirkonzahn doors are always open to dentists and dental technicians wishing to discover where all products are manufactured and enjoy the typical South Tyrolean culture that has shaped Zirkonzahn since the beginning.
Dental technology 100% made in Italy
In the heart of the Italian Alps, with the core values of discipline, innovation, trust and responsibility, the family-run company Zirkonzahn has been providing solutions and approaches for the dental sector since its foundation in 2003. The know-how and skills developed during the years are inherited from father to son, both Master Dental Technicians, ensuring continuity to clients and building with customers last relationships based on mutual trust.
From patient diagnostics to the final restoration, Zirkonzahn’s main goal is to optimise the collaboration and communication between dentists and dental technicians, providing clinics and laboratories with dedicated instruments forming an optimum match in the complete workflow. Under the motto “Everything under one roof”, all milling units, dental materials, hardware equipment, software, tools and implant prosthetic components are conceived and developed in-house to guarantee constant controls over the production process and thereby comply with the highest quality standards. Only in this way, all products can be perfectly coordinated with each other.
From Zirkonzahn, customers don’t just buy “a product”. They buy a whole work philosophy that includes the conception of a seamless and well-coordinated dental workflow - with the possibility of switching from digital to analogue and vice versaa complete package of services and reliable support.
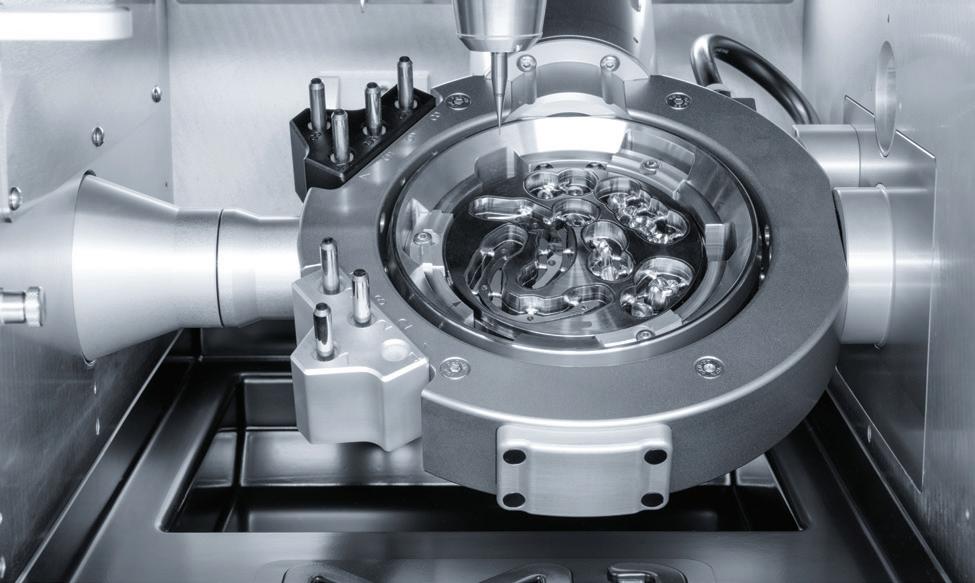
Zirkonzahn is open
Always developing innovative technologies and searching for smart, unconventional solutions, all company’s hardware components and software modules generate open data formats (e.g. STL, OBJ) which are therefore compatible with all open CAD systems, milling units or 3D printers. Of course, also open data (scans or design files) from other manufacturers can be processed with Zirkonzahn wide range of products. In this way, customers can benefit from a complete system which can be personalised und upgraded according to different combination possibilities to meet all one’s requirements. Moreover, the CAD/ CAM system design can be customised on request in all colours and different styles, expressing every attitude.
Zirkonzahn Australia Pty Ltd is located at Unit 57, 6-8 Herbert Street, 2065 St Leonards, NSW 2065. Tel: +61 432446682 Fax: +45 7022 7158 info.australia@zirkonzahn.com For more information, visit www.zirkonzahn.com
TELESKOPER ORBIT Ø 125 mm 1






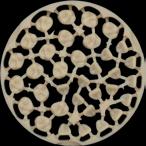
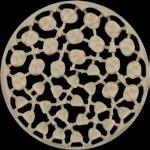




















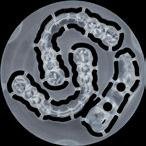
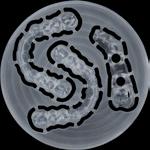









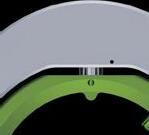
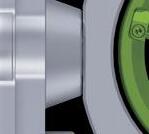
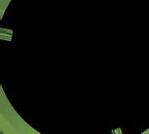


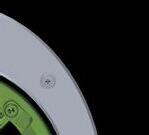
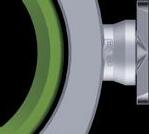
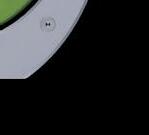












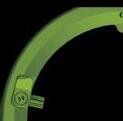
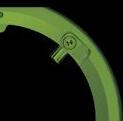
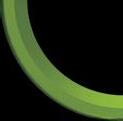
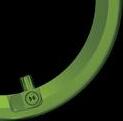




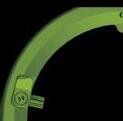
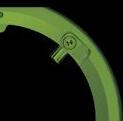
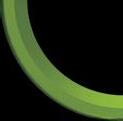
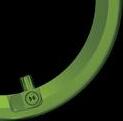
Extra-large Teleskoper Orbit (Ø 125 mm) for milling material blanks with Ø 95 mm, 98 mm, 106 mm or even 125 mm, mini zirconia blanks (size 1) for single crowns as well as glass ceramics and Raw-Abutments ® blanks. Blanks can be removed and reinserted later at exactly the same position with high precision in micron range – particularly useful for adjusting the friction of telescopic jobs and for the two-stage production of immediate restorations in case of implant-supported prostheses (Double Milling technique)
MINI ZIRCONIA BLANKS (SIZE 1)
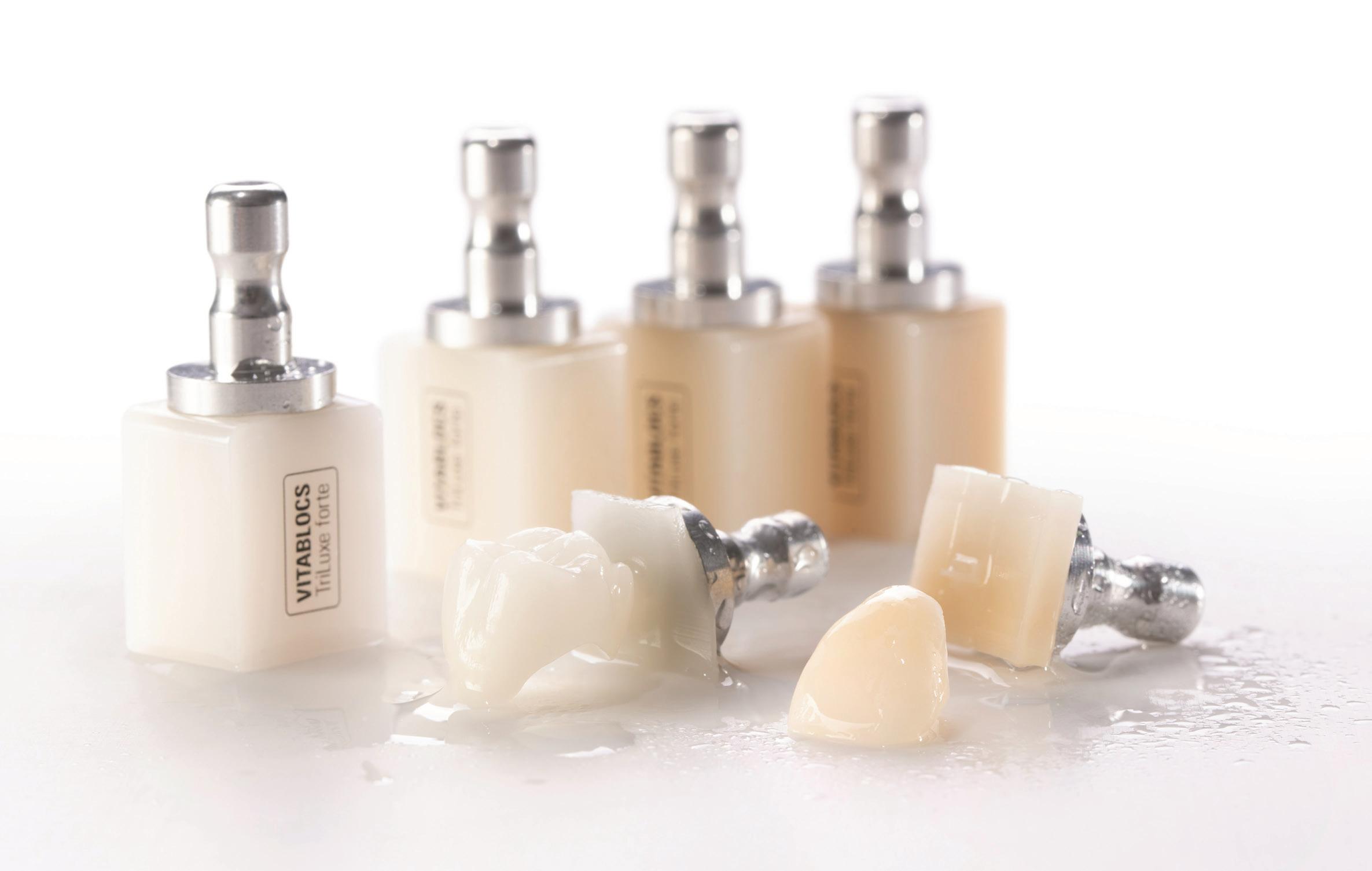
Figure 1. VITABLOCS TriLuxe forte makes efficient CAD/CAM restorations possible with impressive results.
VITABLOCS TriLuxe forte: Premium aesthetics with even more options
VITA Zahnfabrik offers highly aesthetic solutions for prosthetics. The same applies to the proven VITABLOCS TriLuxe forte CAD/CAM blocks. Just in time for the 100th anniversary, the blocks are now available in five new VITA classical A1-D4 shades.
Aesthetics and proven high quality
With its integrated shade gradient, VITABLOCS TriLuxe forte is especially suitable for CAD/CAM fabrication of crowns and veneers in the smile zone. The four intensity layers guarantee
a natural interplay of colour and light –as close to the aesthetics of natural teeth as possible.
Proven feldspar ceramic – for over 35 years
This material has a special fine structure, which is proven to make it exceptionally easy to polish, as well as resistant to abrasion. Numerous clinical studies confirm the long-term durability of restorations using VITABLOCS.
Simple and efficient to use
VITABLOCS TriLuxe forte will also be available in the shades B1, B2,
B3, C2 and C3, in addition to the VITA classical shades A1, A2, A3 and A3.5 that have already been available. This gives users even more options for quickly and easily creating restorations with matching shades.
VITABLOCS TriLuxe forte also saves time and makes the workflow more efficient. A chairside treatment in just one session at a dental practice is easily possible using VITABLOCS.
Patients not only benefit from the fast treatment, but also from the highly aesthetic results.
For More info on VITABLOCS TriLuxe forte see www.vita-zahnfabrik.com/ vitablocs_TP6_Multicolor.html
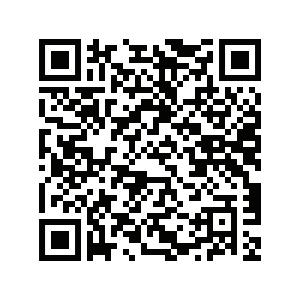

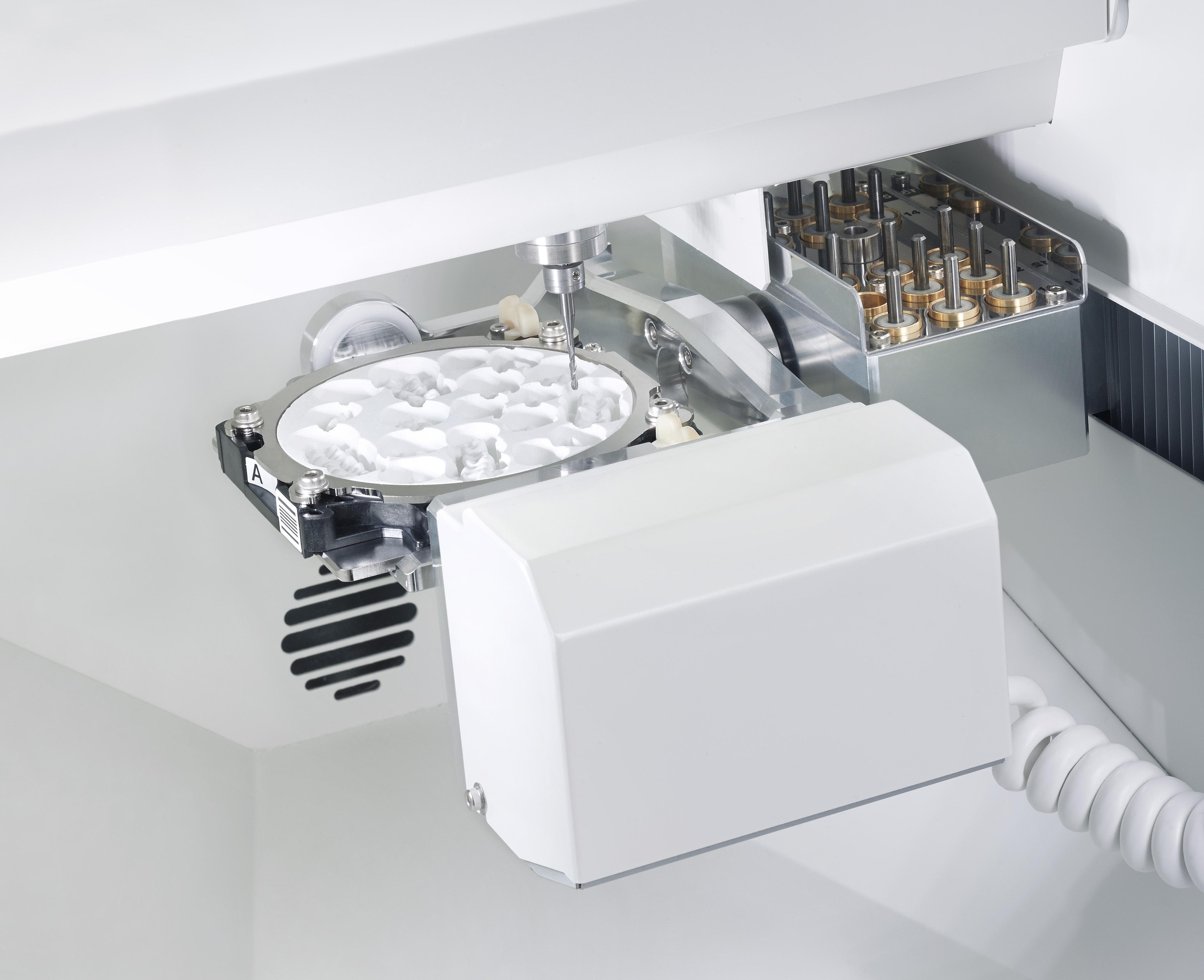
Optimising model positioning and supports for 3D printing
By Charlie Anderson
As 3D printing technology continues to advance, its applications in dental labs have grown exponentially. Among the various techniques, Digital Light Processing (DLP) and Masked Stereolithography (MSLA) stand out for their precision and reliability when working with resin. Despite the progress, there remains a significant knowledge gap regarding the optimal positioning of models on the build plate and the appropriate use of supports.
This article aims to address these issues, offering practical advice to help dental lab technicians achieve the best results.
Challenges of hollowing models in 3D printing
While hollowing models can save material and reduce print times, it also introduces several challenges that can impact print quality and structural integrity. One major issue is the creation of a “suction cup” effect. This occurs due to the forces of pressure when the model lifts out of the resin and then re-enters the vat. As the model lifts, trapped air within the hollowed sections tries to escape, exerting an outward pressure. This can lead to layer splitting and the formation of holes in the model.
To overcome this, it’s recommended to lift the models using supports, which allows the trapped air to escape through the support structure. Some 3D printers have build plates with holes, which can help alleviate this issue by providing additional escape routes for the air. However, using such build plates can introduce another problem: the uneven surface of the build plate will transfer to the back of the model, resulting in unevenness that mirrors the shape of the holes.
“Creating drain holes would also overcome the cupping effect and allow printing flat without supports,” says Jeroen Klijnsma, Director of Dentiq, who provides 3D printing training for dental professionals from beginners to advanced users honing their skills.
Some materials are prone to warping, which can occur if models are not cured for long enough on the printer and the user relies more on the post-cure process. This leaves uncured material within the model, which can cause warping when subsequently cured. If warping after post-curing is present, check the exposure times on the printer if possible. Alternatively, leaving the models on the build plate during the cleaning and curing process can help prevent warping. Some users choose to hollow the models to reduce the amount of material that can cause warping

after curing. However, the supports required to print hollow can cause other problems, such as increased resin consumption and potential dimensional inaccuracies.
Another common issue with using supports is the high likelihood of support material becoming loose and breaking off during the printing process. MSLA technology, which utilises an LCD screen to mask the shape of each layer, is particularly vulnerable to “dead-spots” caused by small pieces of cured resin being pushed against the screen by the build plate as the first layers are printed. Even a tiny fragment of support material breaking away and remaining in the vat can seriously damage the printer’s LCD. Once this type of damage occurs, the screen will need to be replaced. It is advisable to have a spare LCD screen for each printer model you use, as they are relatively simple to replace.
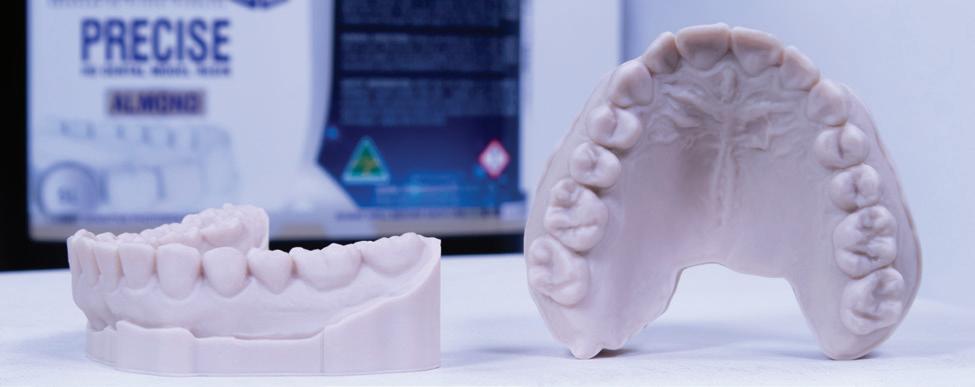
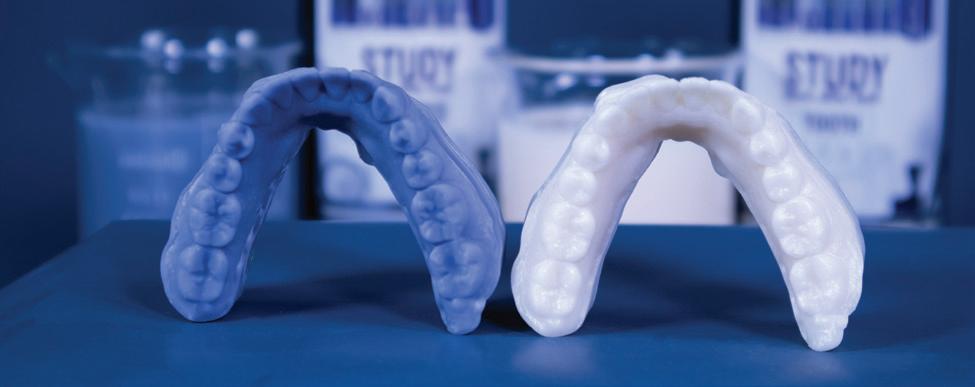
Most companies provide online tutorials or information, as these screens are considered consumables, typically requiring replacement after approximately 2500 hours of use.
There are 3D printers on the market that are equipped with obstruction sensors that automatically detect any hard material floating in the vat. This feature is convenient, but detection is not always successful and can sometimes be overly sensitive, resulting in false negatives. This can be frustrating and timeconsuming to resolve. If an obstruction warning is detected, it is recommended to completely empty the vat and filter the resin back into the original bottle to capture any cured particles. Additionally, it is essential to clean the vat and wipe the build plate with RESINAWAY® or IPA to remove any potential causes.
Some labs prefer hollowing models to create gypsum articulated models, believing that hollowed models with textured bases stick better to the plaster. While this might be true, this approach could be costing you extra time and resin for a problem that could be solved differently. When adopting new processes, such as 3D printing models, it is important to explore all options rather than merely transferring the traditional process to include the 3D printed model. This can be inefficient and not the best way to achieve optimal results.
There are also some 3D printers whose software requires hollow models, giving the user no choice. Such closed systems can be frustrating and restrictive.
Many high-quality printers on the market are considered open-source, not locking the user into using proprietary resins. Before deciding on your next printer purchase, consider the opensource versus closed system debate. The material development for resin-based 3D printers is advancing rapidly, with developers worldwide working to meet industry demands.
You never know where the next resin breakthrough will come from and having a closed system might prevent you from accessing the latest innovations, potentially giving your competitors an advantage. New printers are being launched regularly, so keep an eye out by following social media groups and companies and reading eLABORATE
Head to Head: Solid models vs Hollow models
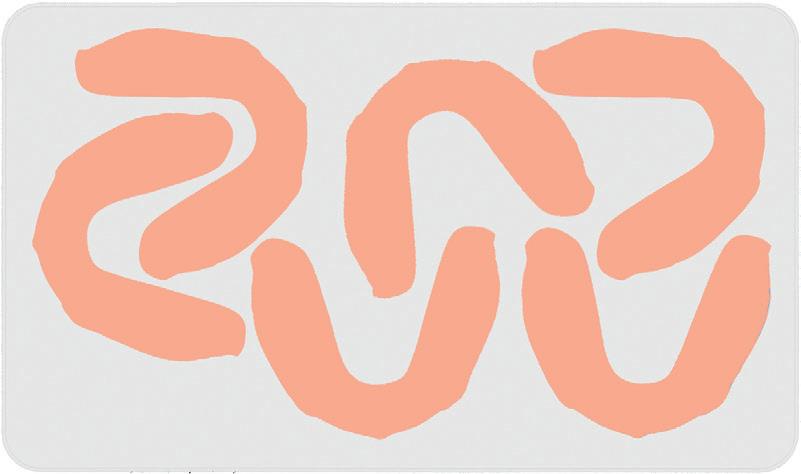
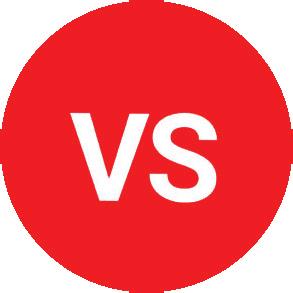
1. Material conservation - Solid models eliminate the need for extensive supports and rafts, making overall material usage more efficient and straightforward.
2. Time saving - Solid models offer a straightforward preparation process, allowing them to be placed flat on the build plate without the need for additional modifications, resulting in faster setup and printing times.
3. Weight reduction - Solid models are heavier, which can provide greater strength and durability but may be heavier resulting in higher shipping costs.
4. Ease of post-processing - Solid models are easier to postprocess since there are no internal supports to remove, simplifying the cleaning and curing steps.
5. Print times - Print times of solid models typically have faster print times as they are placed flat on the build plate without the need for rafts or extensive supports, reducing overall printing duration.
6. Structural integrity - Solid models offer superior structural integrity, reducing the risk of deformation and warping and ensuring higher dimensional accuracy and stability.
7. Potential cracking over time - Solid models have less risk of cracking over time since there is no trapped uncured resin, ensuring a uniformly cured and stable structure.
8. Risk of print failures - Since solid models do not rely on support structures, it eliminates the risk of support material becoming loose and causing print failures or damage to the printer screen.
9. Risk of damage to models - Solid models don’t have supports, eliminating the risk of damaging the finished model with support nibs during removal and pre-serving surface quality.
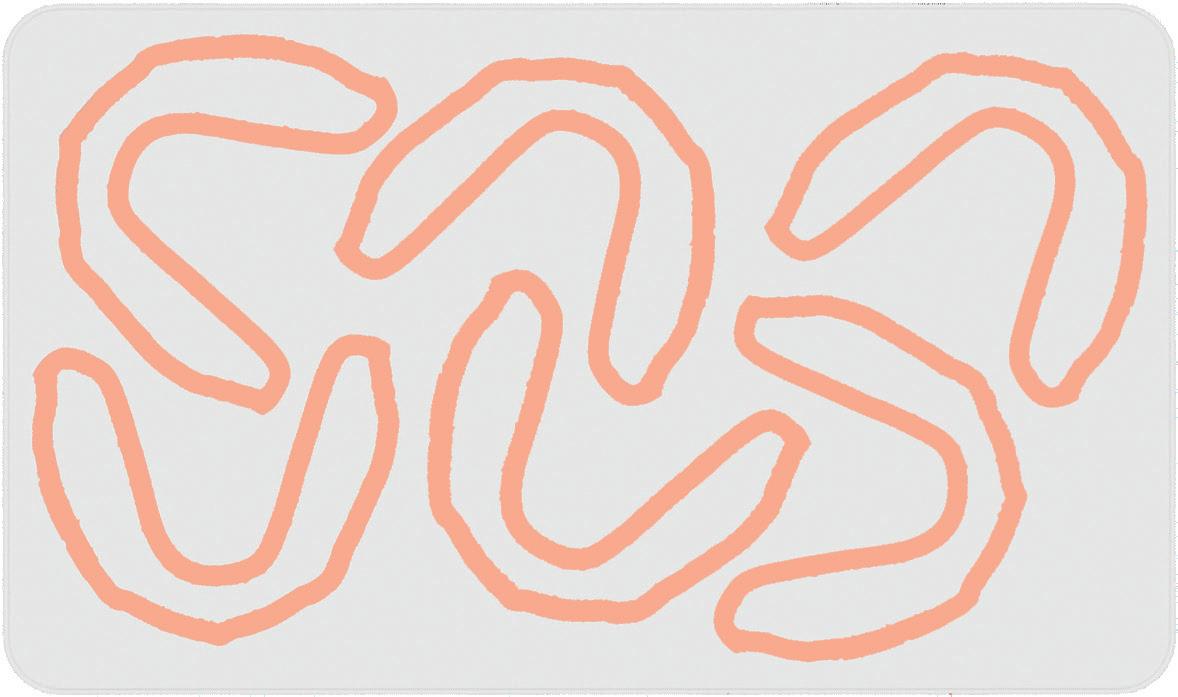
1. Material conservation - While reducing the resin used for the model itself, hollow models require additional supports and rafts that can consume similar or even greater material.
2. Time saving - Hollow models require extra time for preparation, including hollowing, adding supports and creating rafts, which increases both setup and print times, making the overall process more time-consuming.
3. Weight reduction - Can be lighter due to reduced material use, making them easier to handle and transport, though they may compromise on structural integrity and stability.
4. Ease of post-processing - Hollow models require removal of internal supports, which is time-consuming, making postprocessing more complex and labour-intensive.
5. Print times - Hollow models take longer to print due to the additional height from rafts and supports, which increases the total print time and complexity of the printing process.
6. Structural integrity - Hollow models have thinner walls and rely on internal supports, which can compromise structural integrity and increase the likelihood of deformation and warping.
7. Potential cracking over time - Hollow models are more prone to cracking over time due to trapped uncured resin within the model, which can lead to structural weaknesses and long-term durability issues.
8. Risk of print failures - Hollow models require extensive supports, which can become loose during printing, leading to print failures and potential damage to the printer screen from floating debris.
9. Risk of damage to models - Hollow models require more supports, increasing the likelihood of leaving visible support nibs and causing damage to the surface during removal, which can affect the final quality of the model.
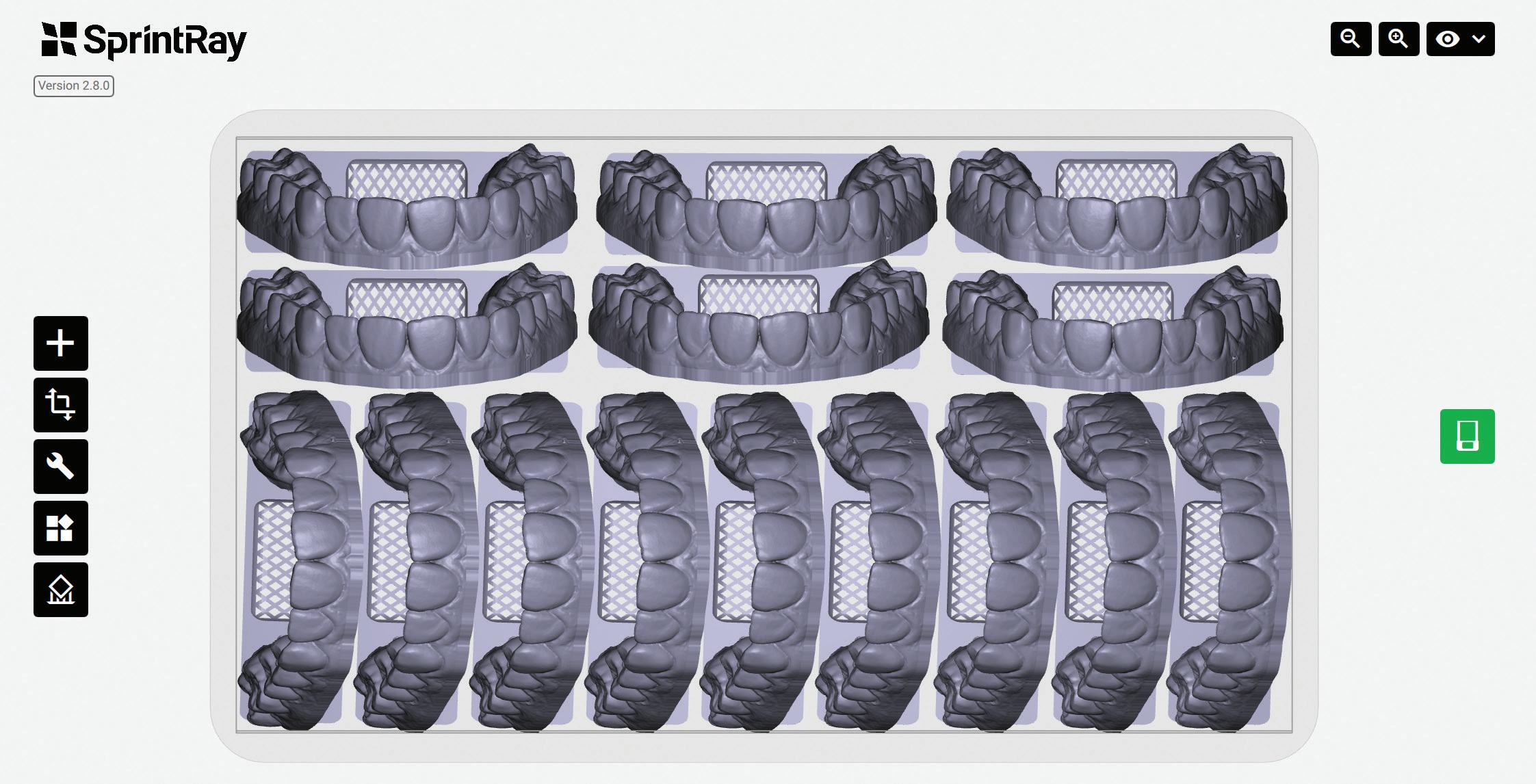
Positioning models on the build plate
One of the most critical aspects of 3D printing with DLP and MSLA technology is the positioning of models on the build plate. Many technicians choose to hollow their models and use extensive supports, primarily to conserve resin. However, this approach can often lead to complications and does not necessarily result in significant resin savings.
For dental applications, where precision and strength are paramount, positioning models flat on the build plate offers several advantages:
• Stability: Flat positioning reduces the need for extensive supports, minimising the risk of deformation during printing.
• Strength: Solid models ensure structural integrity, crucial for dental components that must withstand considerable forces.
• Efficiency: Simplified post-processing and reduced support removal enhance efficiency and reduce the risk of damaging delicate features.
Effective use of supports
Supports do play a crucial role in ensuring the success of 3D printed models, particularly in maintaining the accuracy and quality of intricate dental components such as surgical guides.
To create the best supports with minimal damage, consider the following strategies...
A. Pillar supports
• Key areas: Use thicker pillar supports (3-5mm) in critical areas where the model needs maximum stability. These areas typically include overhangs and large, flat surfaces that are prone to warping or shifting during printing.
• Strength and stability: Pillar supports provide robust support, reducing the likelihood of print failures and ensuring that the model remains firmly in place throughout the printing process.
B. Smaller supports
• Reducing damage: Supplement pillar supports with smaller, more delicate supports to hold finer details and prevent sagging. These supports should be strategically placed to balance the need for stability with the goal of minimising contact points, thereby reducing potential damage during removal.
• Strategic placement: Focus on areas where the model might experience minimal stress but still requires some support. This approach helps maintain the integrity of intricate features while ensuring the model prints successfully.
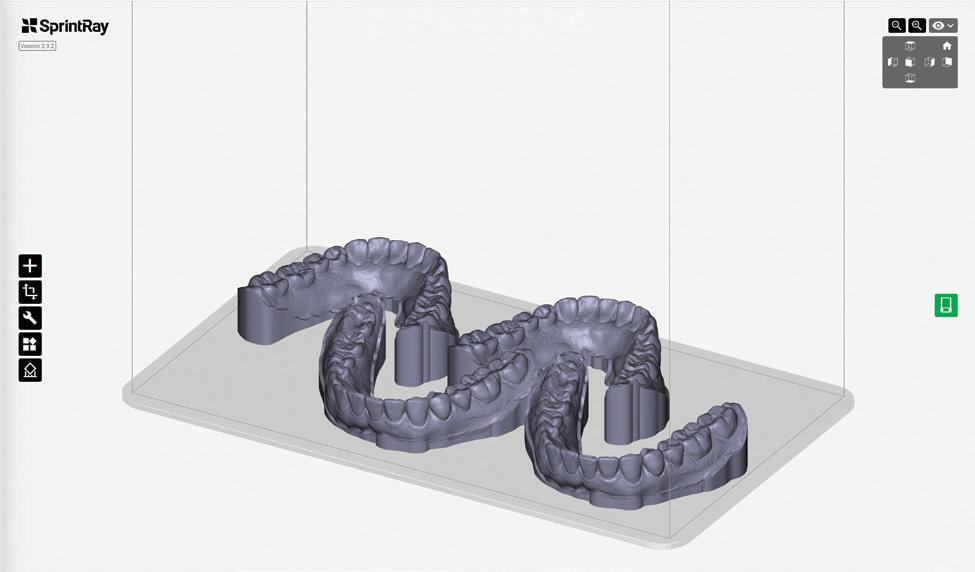
C. Optimising support settings
• Density and size: Adjust the density and size of supports based on the model’s complexity and the specific requirements of the print. Higher density may be necessary for intricate models, while larger supports can be used sparingly to provide additional strength where needed.
• Angled supports: Consider using angled supports to distribute forces more evenly and reduce stress on the model. This technique can be particularly useful for delicate dental components that require precise detail.
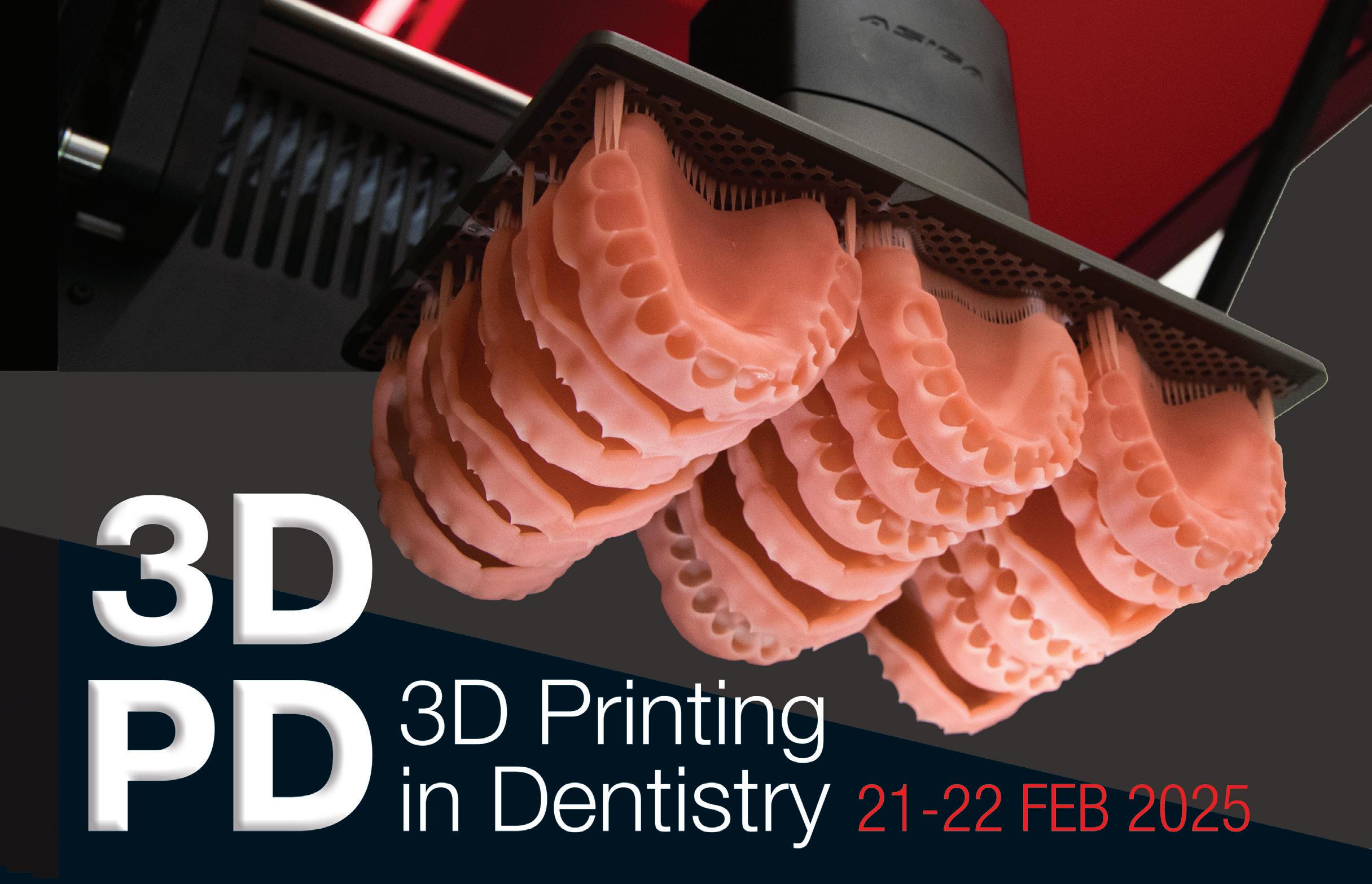
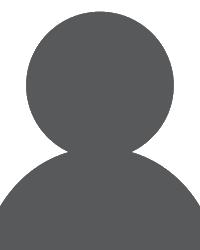
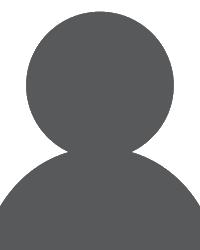
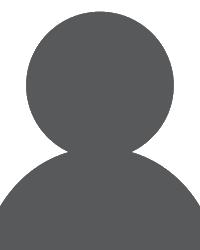
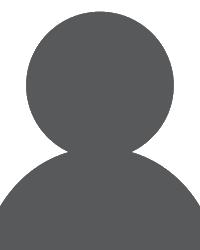
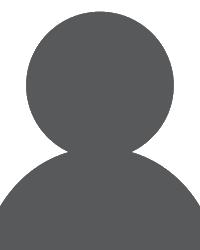
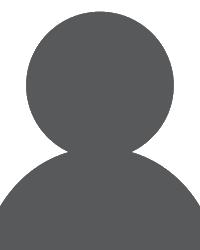
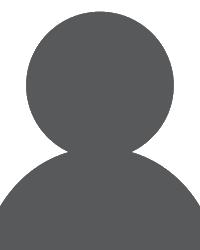
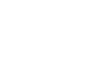
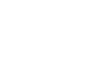
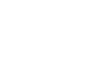
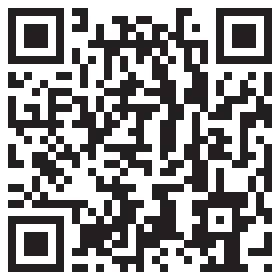
Model orientation
When it comes to 3D printing dental models, the orientation of the models on the build plate plays a crucial role in the efficiency and quality of the print. Here’s a comparison of positioning dental models vertically versus flat:
A. Vertical positioning
Advantages
1. Maximising build plate space: By positioning the models vertically, you can fit more models on the build plate. This is particularly useful when you need to produce multiple models in one print run, optimising the use of available space.
2. Detail preservation: Vertical positioning can help preserve fine details, as the layers are built up along the vertical axis, reducing the likelihood of details being lost or distorted.
“It depends where you want the detail,” says Jeroen Klijnsma, Director of Dentiq. “If placed vertically, ‘islands’ will occur on the labial area of the centrals. However, in the posterior area, you have smoother occlusal surfaces.”
Considerations
1. Print time: Vertical models can increase print time due to the increased height, leading to more layers needing to be printed.
2. Support requirements: Vertically oriented models often require more extensive supports, which can be time-consuming to remove and may leave marks on the model.
B. Flat positioning
Advantages
1. Reduced print time: Printing models flat can significantly reduce print time, as the height of the print is lower, resulting in fewer layers to print.
2. Minimised print failures: By printing models solid and flat on the build plate, the risk of print failures is reduced. This method provides a stable base, reducing the likelihood of models detaching from the build plate during printing.
3. Simplified post-processing: Flat models typically require fewer supports, making post-processing easier and faster with less risk of damaging the model when removing supports.
“When printing vertically, the labial area of the centrals is more detailed and the occlusal area of the posteriors will have little ‘islands’,” says Jeroen Klijnsma, Director of Dentiq.
Considerations
1. Limited model fit: When printing flat, you cannot fit as many models on the build plate, which may require multiple print runs to achieve the desired quantity.
2. Potential for detail loss: Depending on the model’s design, fine details on the side resting on the build plate might be less defined due to compression and potential surface imperfections.
Conclusion
The choice between vertical and flat positioning for dental models depends on the specific requirements of your print job. Vertical positioning is ideal for fitting more models in one go and preserving details, while flat positioning offers reduced print times, lower failure rates and easier post-processing .Understanding the nuances of positioning models and using supports effectively is crucial for maximising the potential of DLP and MSLA 3D printing in dental laboratories.
By prioritising flat positioning on the build plate and employing a combination of pillar and smaller supports, dental technicians can achieve superior results with minimal material waste and post-processing effort.
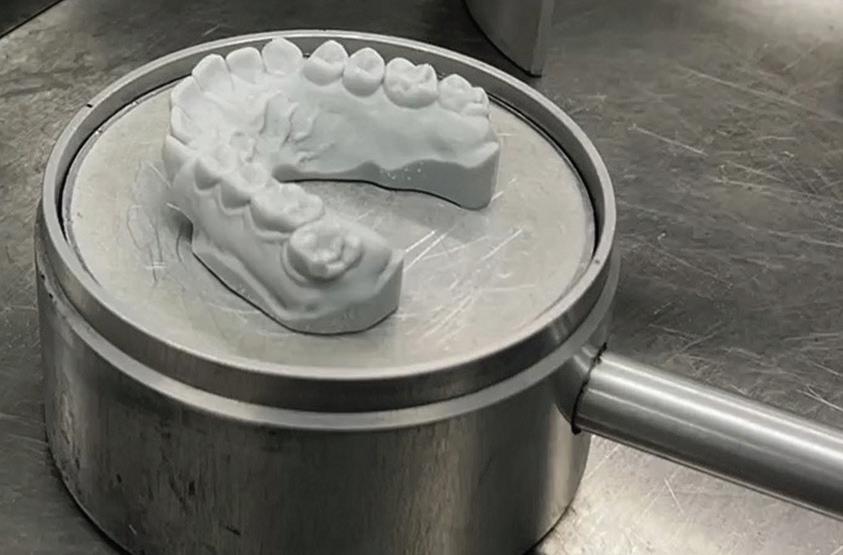
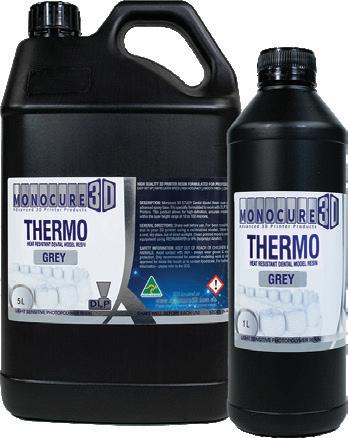
Implementing these strategies will not only enhance the quality and reliability of 3D printed dental components but also streamline the workflow, making the technology more accessible and efficient for everyday use in dental labs.
Special thanks to Jeroen Klijnsma, Director of Dentiq, for his valuable insights and expertise. For those interested in 3D printing training, whether you’re a beginner wanting to learn the basics or an advanced user looking to hone your skills, you can contact Jeroen through his website at https://dentiq.com.au/training
About the author
Charlie Anderson is a director of Australian 3D printing resin manufacturer Monocure 3D. In a previous life, Charlie worked in the TV industry in Australia and abroad for over 20 years. He started working at Monocure in 2014, when his father, Alan, asked him to join his industrial chemical business developing and manufacturing surface coatings for the print, packaging and label industries. While a far cry from the TV director’s chair, he was ready for a new challenge! In 2016, under Charlie’s instruction, the development team created the first Australian made 3D Printer Resin and Monocure 3D was born. Over the next few years, Charlie was the driving force in transforming the company to focus solely on 3D printing consumables and accessories. His involvement and interest in the 3D printing industry are vital as he supports the growing list of customers and resellers locally and overseas.
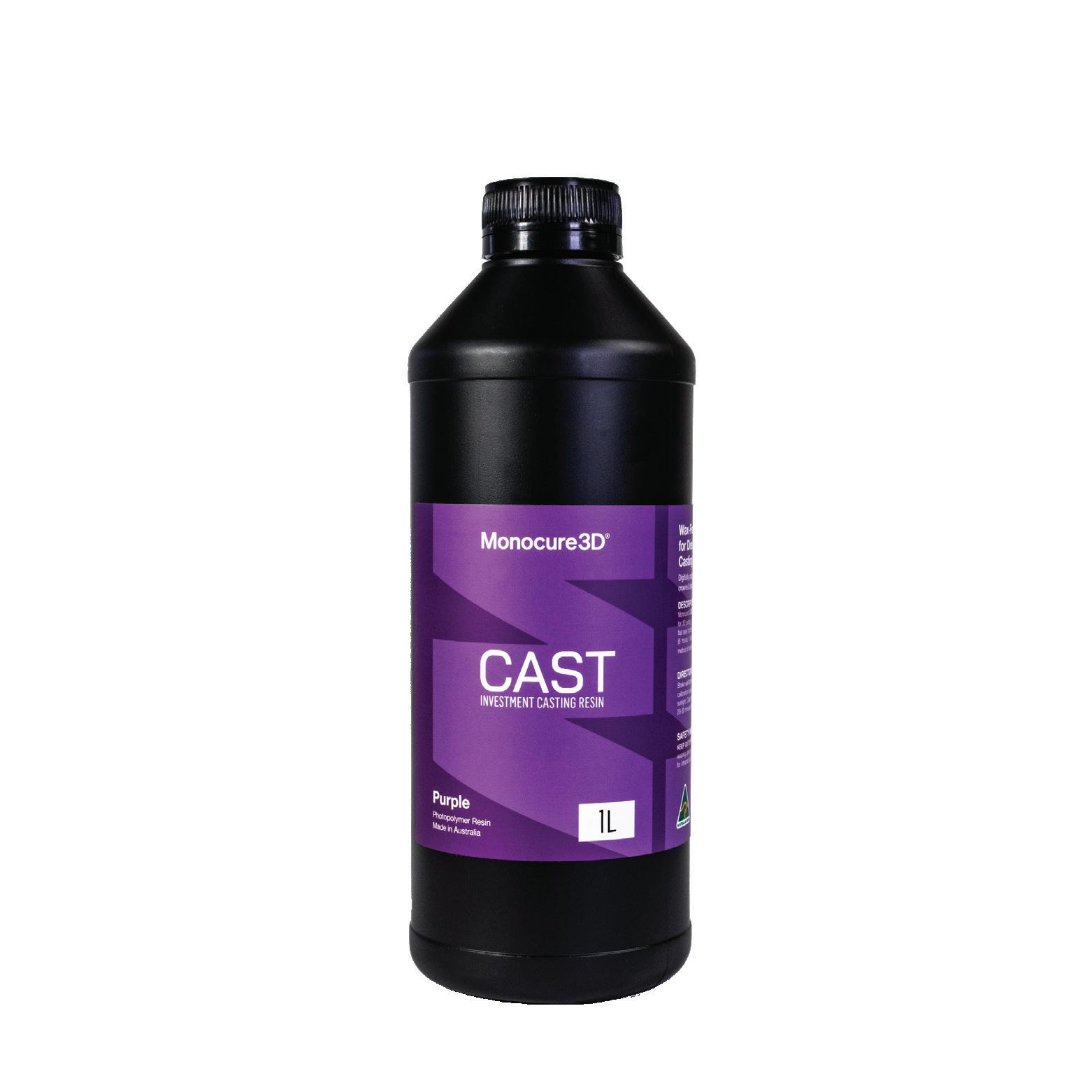
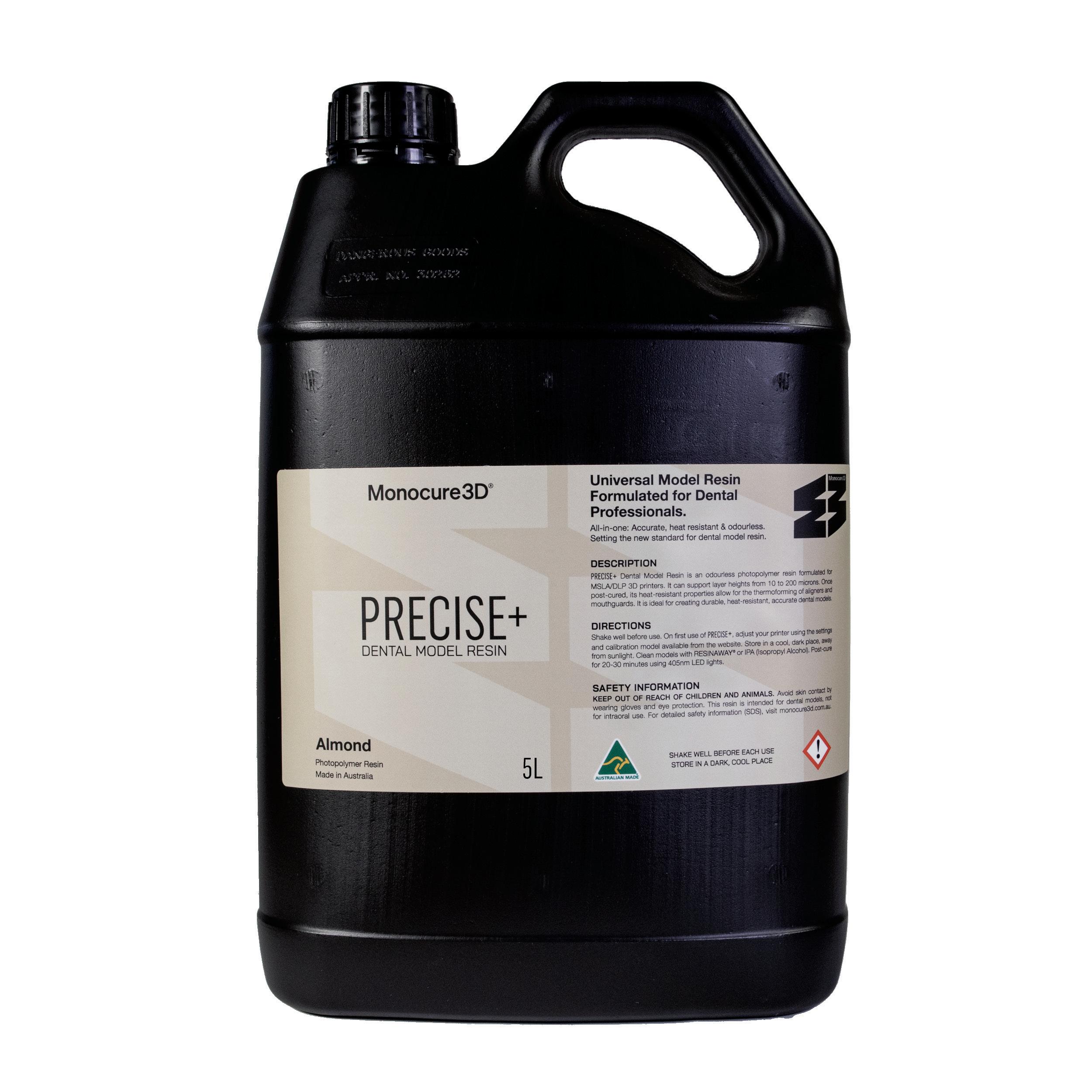
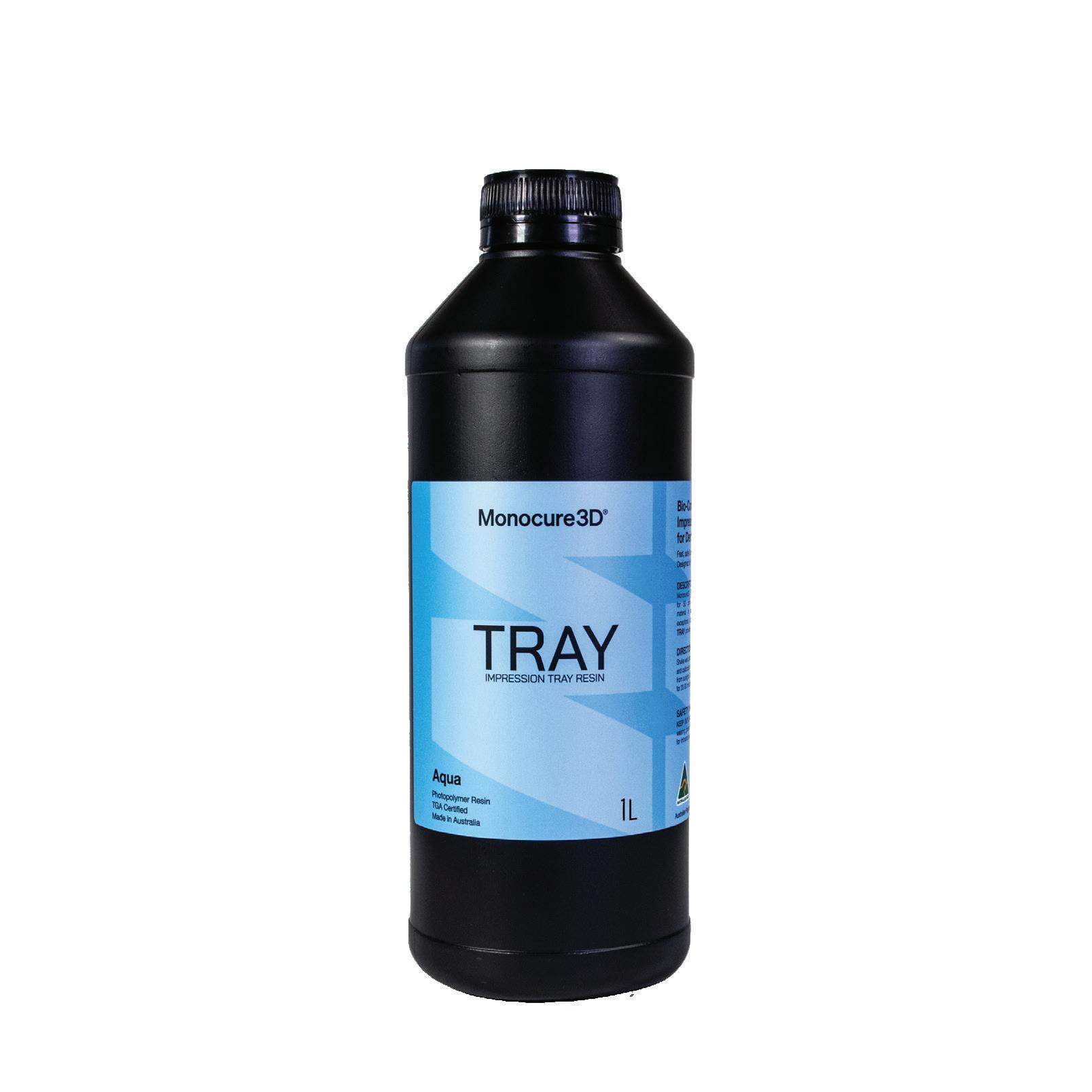
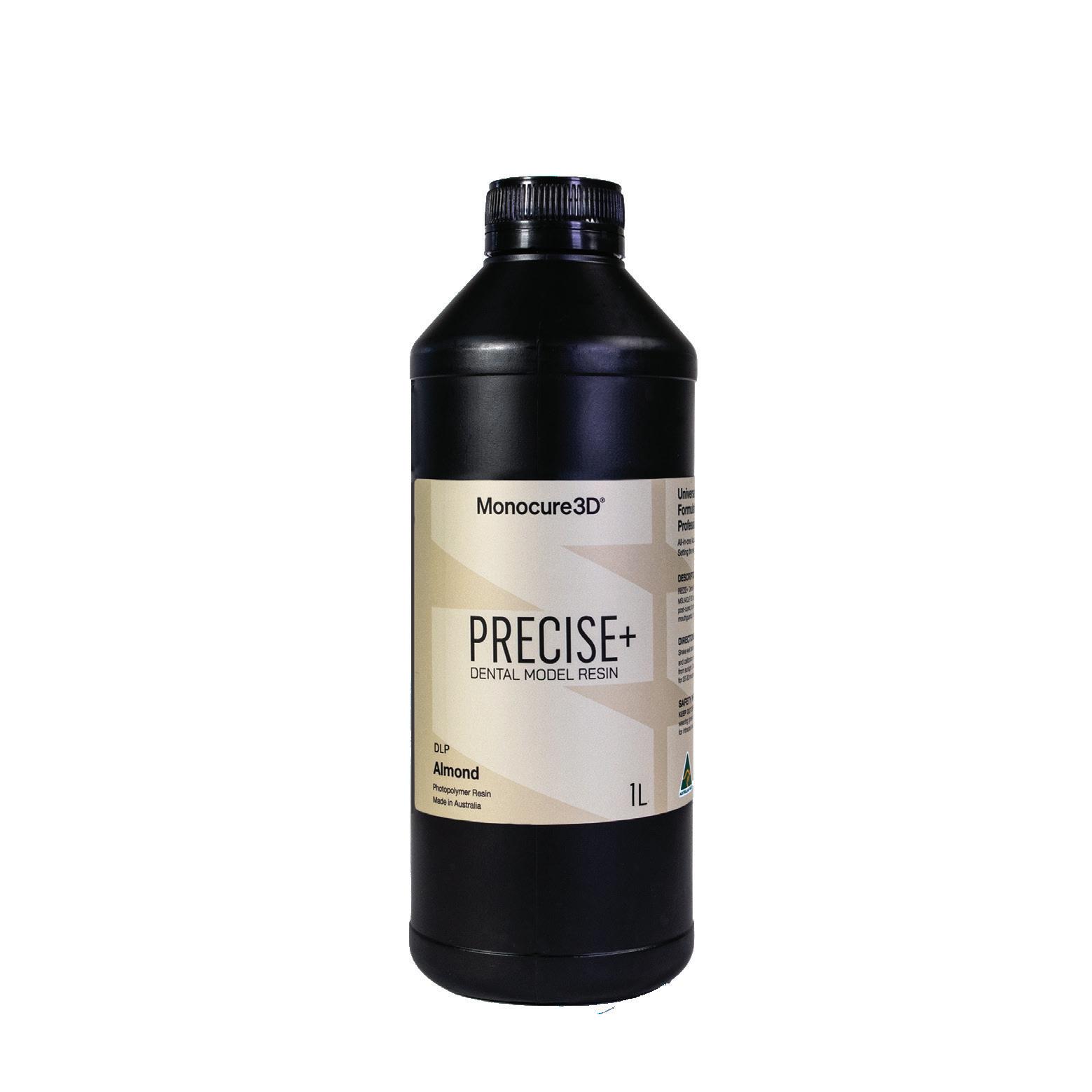
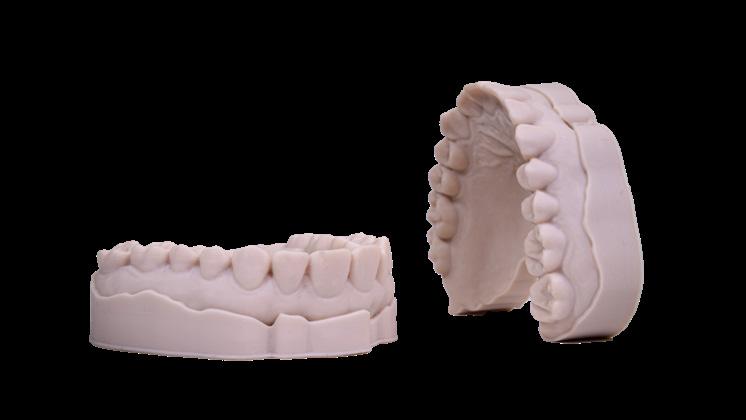


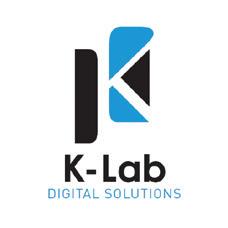
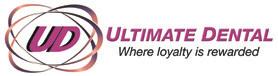
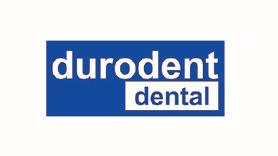
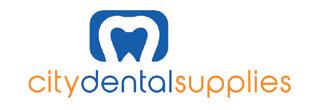

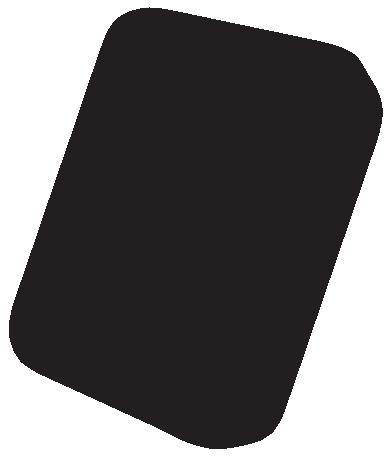
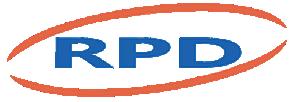
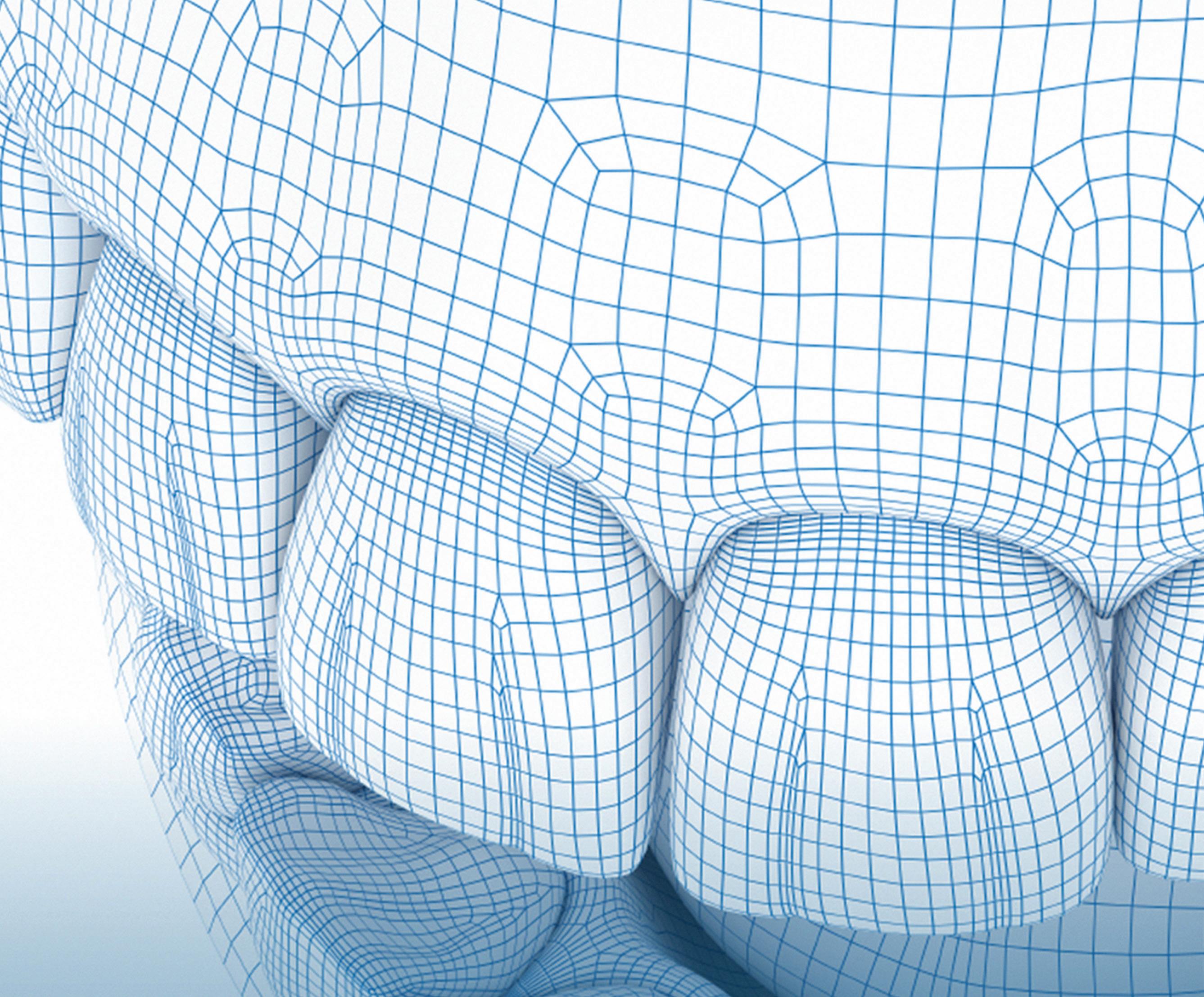
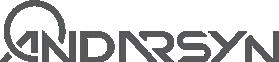
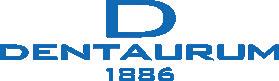
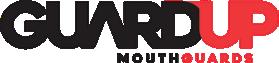
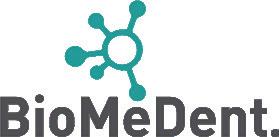



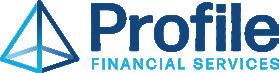
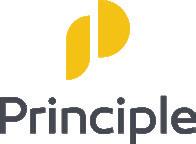

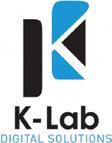

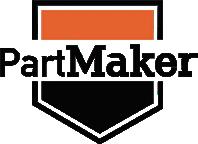

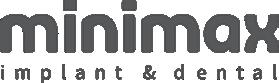
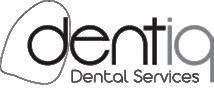
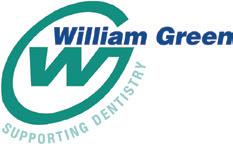
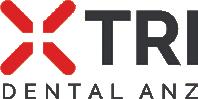
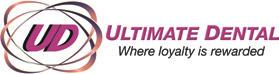
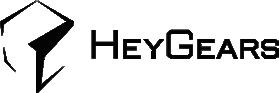
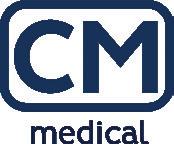
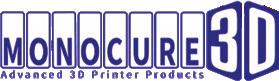
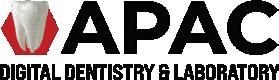
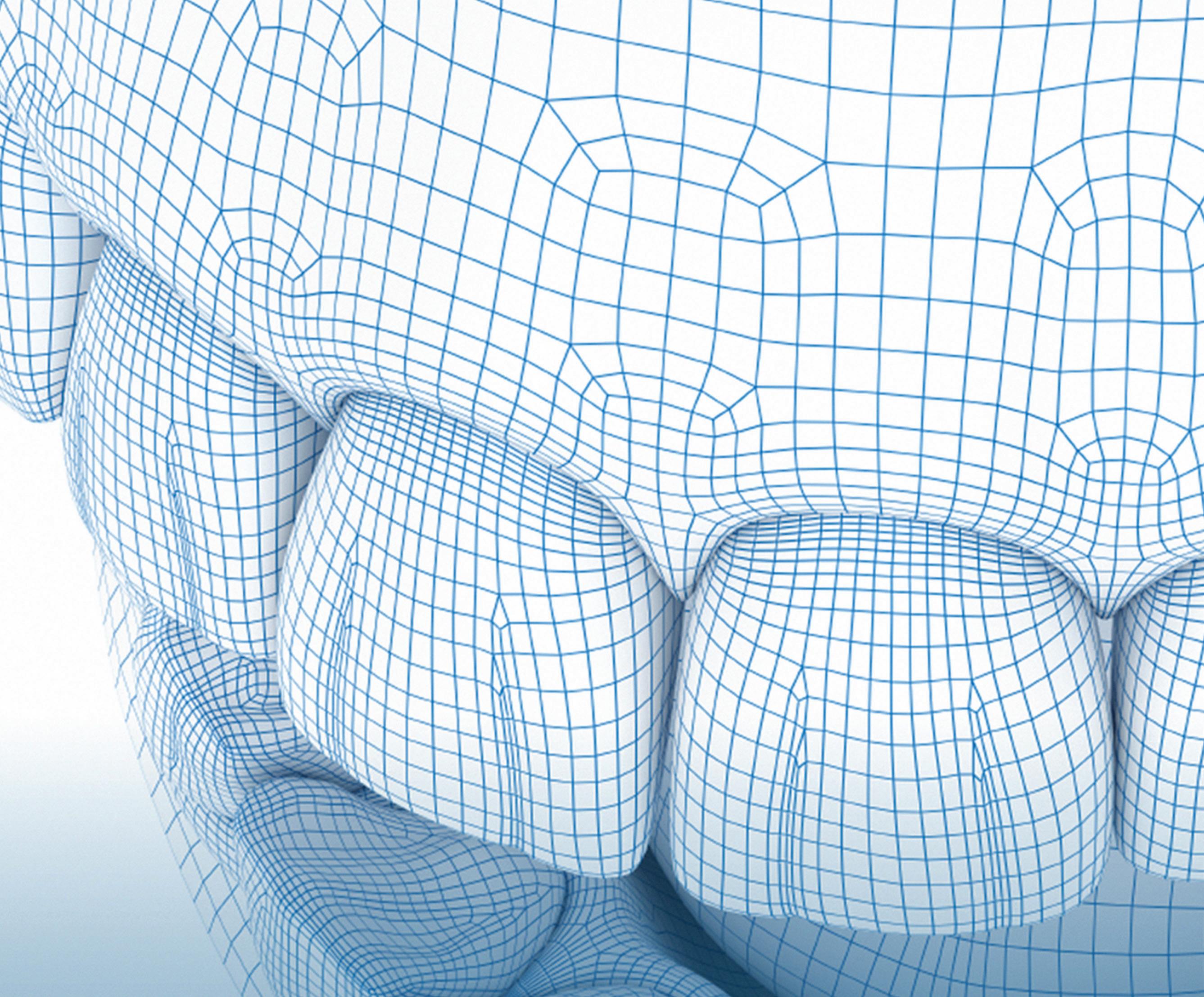
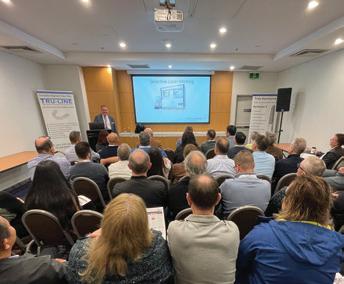
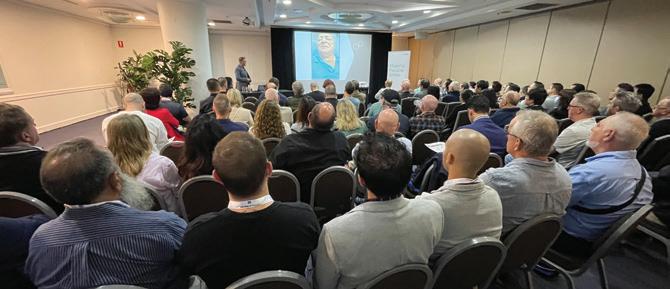
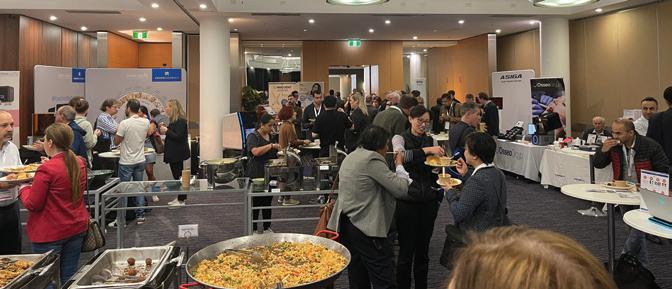
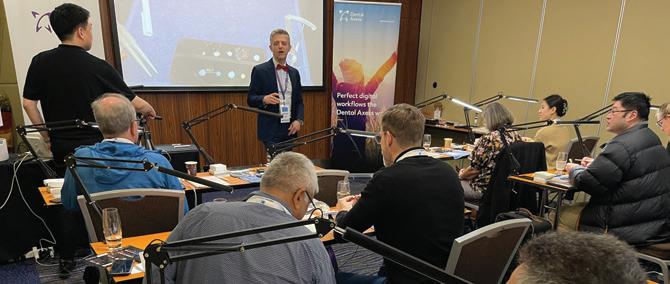
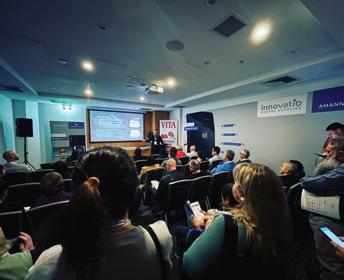
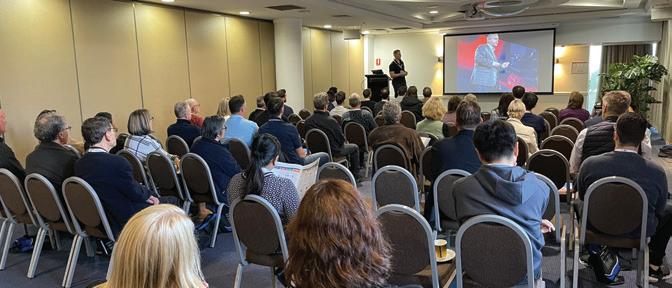

ONLY $440 FOR 2 DAYS OF EDUCATION (12 HOURS OF CPD) IF YOU REGISTER BEFORE 24 JANUARY 2024 (SAVE 50%) Full details of the speakers and presentations online
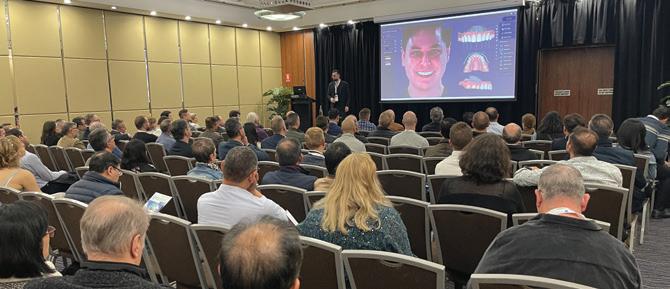
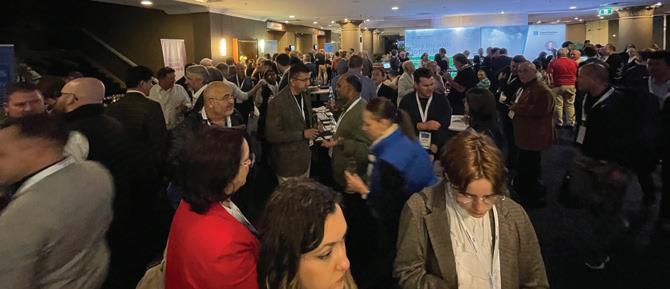
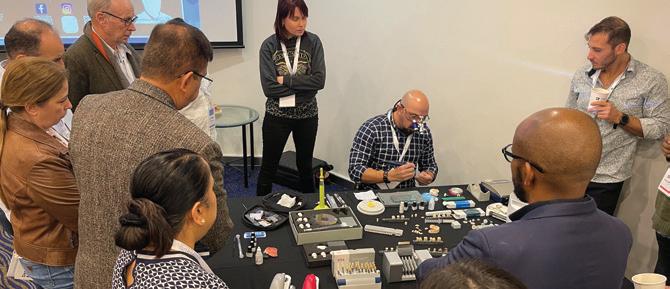
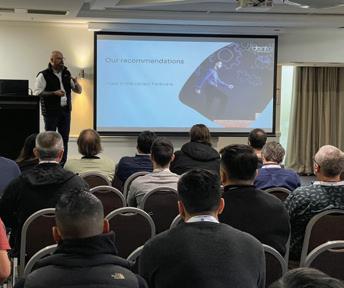
Join us again or for the first time at Digital Dentistry & Dental Technology No 6 for a fun, exciting and fully immersive learning experience with the best of the best in the new age of dentistry. This year’s program will again cover Digital Smile Design • Digital orthodontics • Intraoral scanning • 3D Facial Scanning • Digital implantology • Digital full arch restorations and full mouth rehabilitations • Digital Dentures • 3D Printing • Milling • CBCT • Materials and applications • Software and more with MORE Hands-on Sessions • MORE Advanced Sessions • MORE New Products • NEW Masterclasses... and more!
Join us again or for the first time at Digital Dentistry & Dental Technology No 5 for a fun, exciting and fully immersive learning experience with the best of the best in the new age of dentistry. This year’s program will again cover Digital Smile Design • Digital orthodontics • Intraoral scanning • 3D Facial Scanning • Digital implantology • Digital full arch restorations and full mouth rehabilitations • Digital Dentures • 3D Printing • Milling • CBCT • Materials and applications • Software and more with MORE Hands-on Sessions • MORE Advanced Sessions • MORE New Products • NEW Masterclasses... and more!
REGISTRATION FEES
$880 inc gst
$880 inc gst EARLY BIRD PRICING
EARLY BIRD PRICING
$220 before 30 nov 2024
$440
price increases $110 on the 30th of every month INCLUSIONS
Registration
TWO DAYS OF LECTURES AND WORKSHOPS ON DIGITAL DENTISTRY FOR DENTISTS, SPECIALISTS, DENTAL TECHNICIANS AND PROSTHETISTS The current AHPRA CPD Cycle concludes on 30 Nov 2025
PROGRAMME DETAILS
DETAILS
FRIDAY 30 MAY 2025 9.00am - 5.00pm - education 5.00pm - 7.00pm - happy hour
SATURDAY 31 MAY 2025 9.00am - 5.00pm - education
FRIDAY 24 MAY 2024 9.00am - 5.00pm - education 5.00pm - 7.00pm - happy hour SATURDAY 25 MAY 2024 9.00am - 5.00pm - education 12 HOURS CPD
12 HOURS CPD
ONLINE CPD CENTRE
Answer the questions online at www.dentalcommunity.com.au To retrieve your FREE Dental Community Login, Call (02) 9929 1900 or email joseph@dentist.com.au

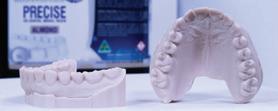

Question 1. Hollowing of models can...
a. Cause no issues.
b. Never be successful.
c. Cause a suction cup effect.
d. None of the above.
Question 2. One advantage of an open source printer is...
a. It cannot use third party resins.
b. The build volume is not big enough.
c. Resin tanks do not use a film.
d. They can use third party resins and resins being developed.
Question 3. One of the most critical aspects of MSLA and DLP printers is...
a. Positioning of models on the build platform.
b. Using cheap resins.
c. Using resin tints.
d. None of the above.
Question 4. Why are supports so important?
a. They reduce resin consumption.
b. They have a direct correlation to dimensional accuracy and ability to print.
c. They assist with curing.
d. They will protect the model.
Question 5. One advantage of flat or horizontal model positioning compared to vertical is...
a. Longer print time.
b. Equal print time.
c. Shorter print time.
d. None of the above.
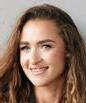
By Nela Zielonka, Dental
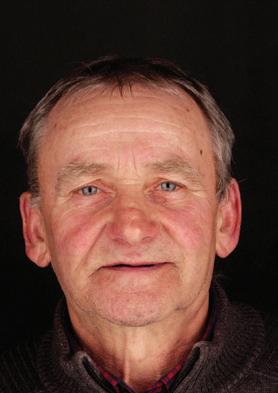
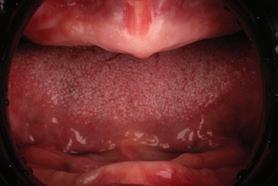
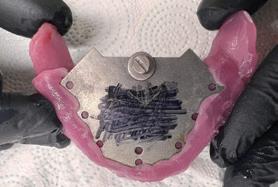
Question 6. With full dentures, it’s sometimes advantageous to consider...
a. Face shape and initial situation from old photographs.
b. Old broken dentures.
c. Anecdotal evidence of allergies to moss.
d. Residual monomer.
Question 7. There was severe Atrophy in the...
a. Upper anterior region.
b. Lower anterior region.
c. Upper posterior region.
d. Lower posterior region.
Question 8. One of the issues of the described case was...
a. Limited vertical dimension.
b. Too much vertical dimension.
c. No vertical dimension.
d. Only vertical dimension on the lower.
Question 9. The teeth selected were...
a. Vitaplane.
b. Vitaplan.
c. Vitapan.
d. Olympic.
Question 10. The posterior teeth were setup with...
a. Automatic Centric Finding.
b. An arbitrary setup.
c. Without the pre-molars.
d. Without the molars.
INSTRUCTIONS:
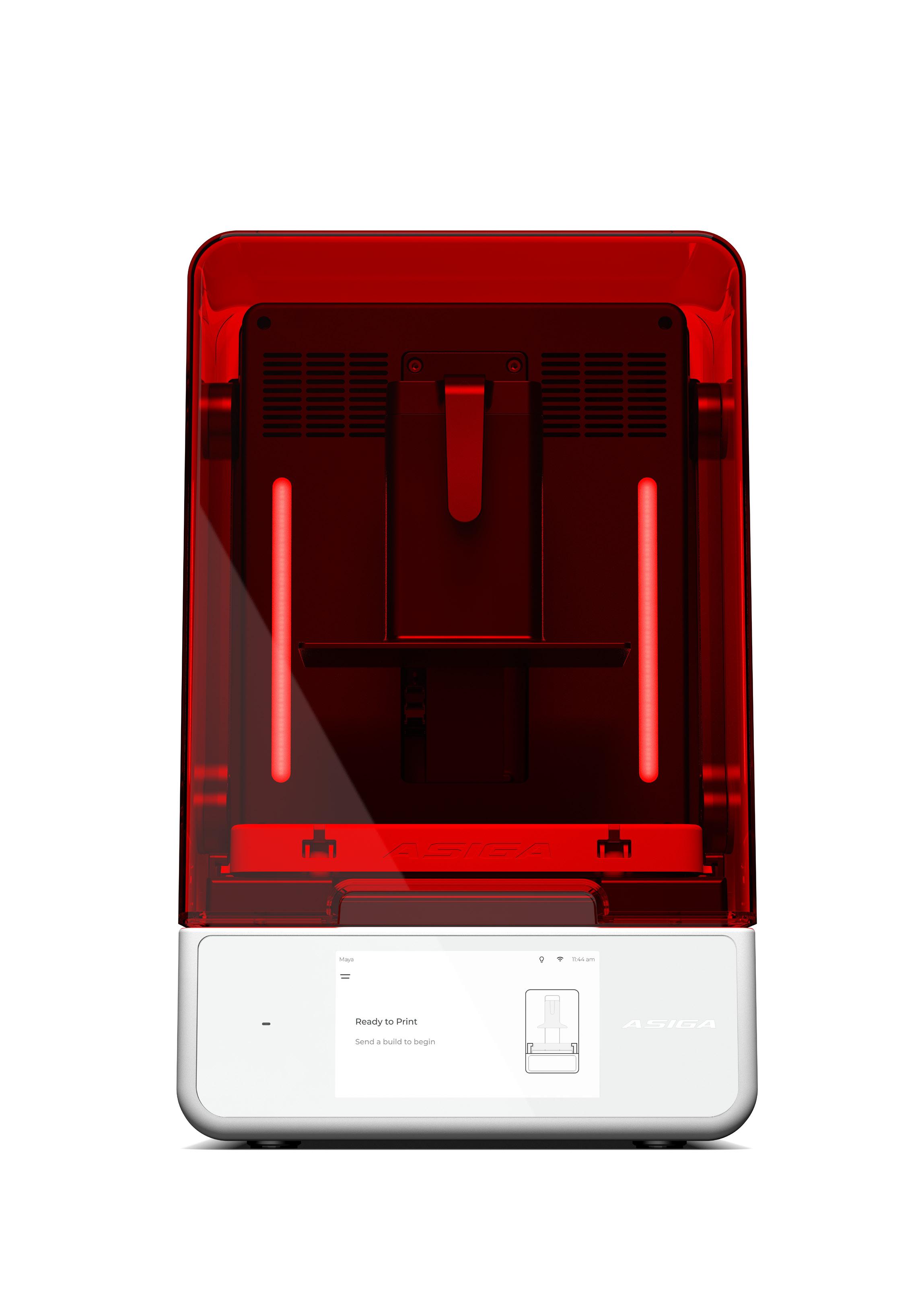
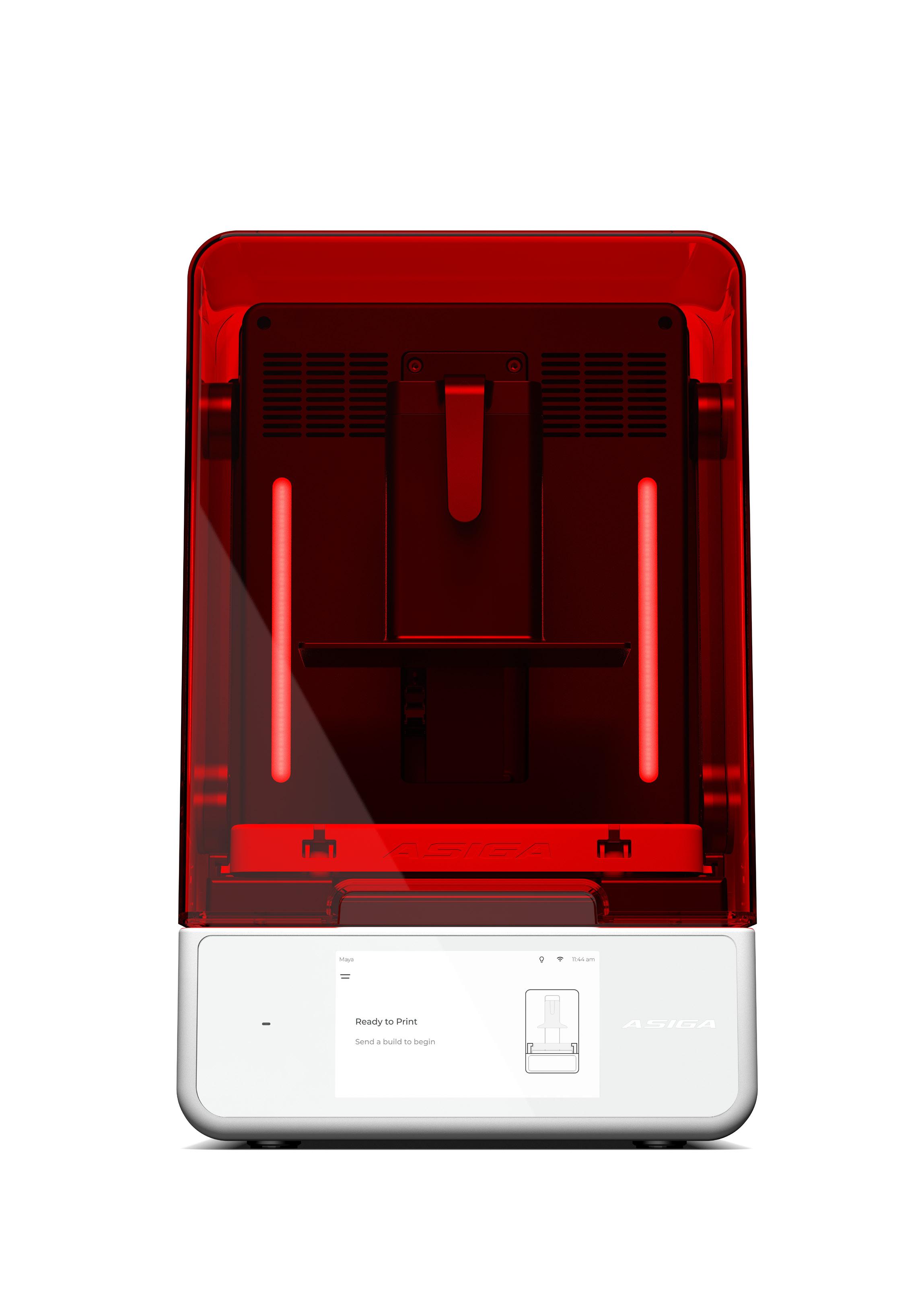
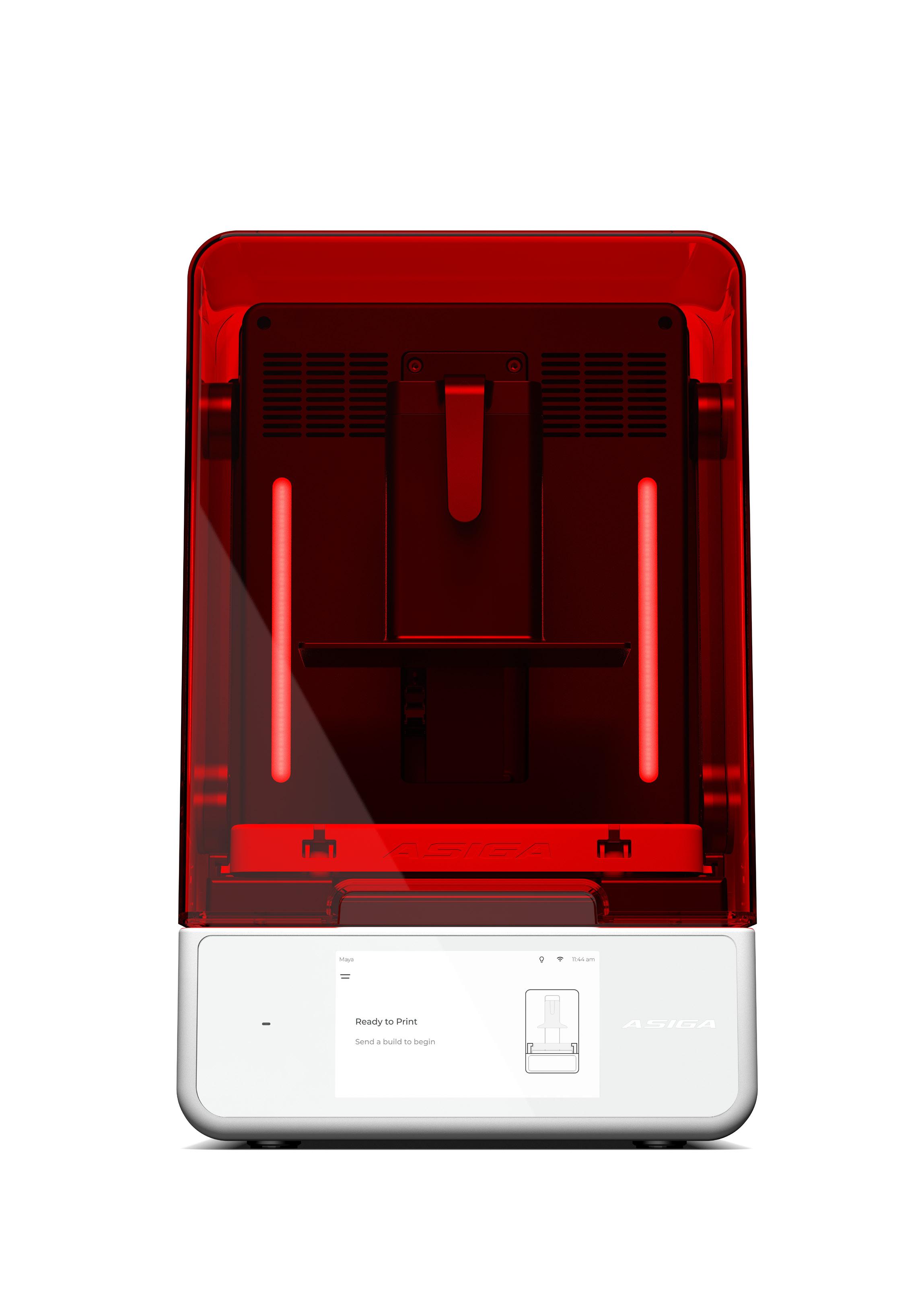
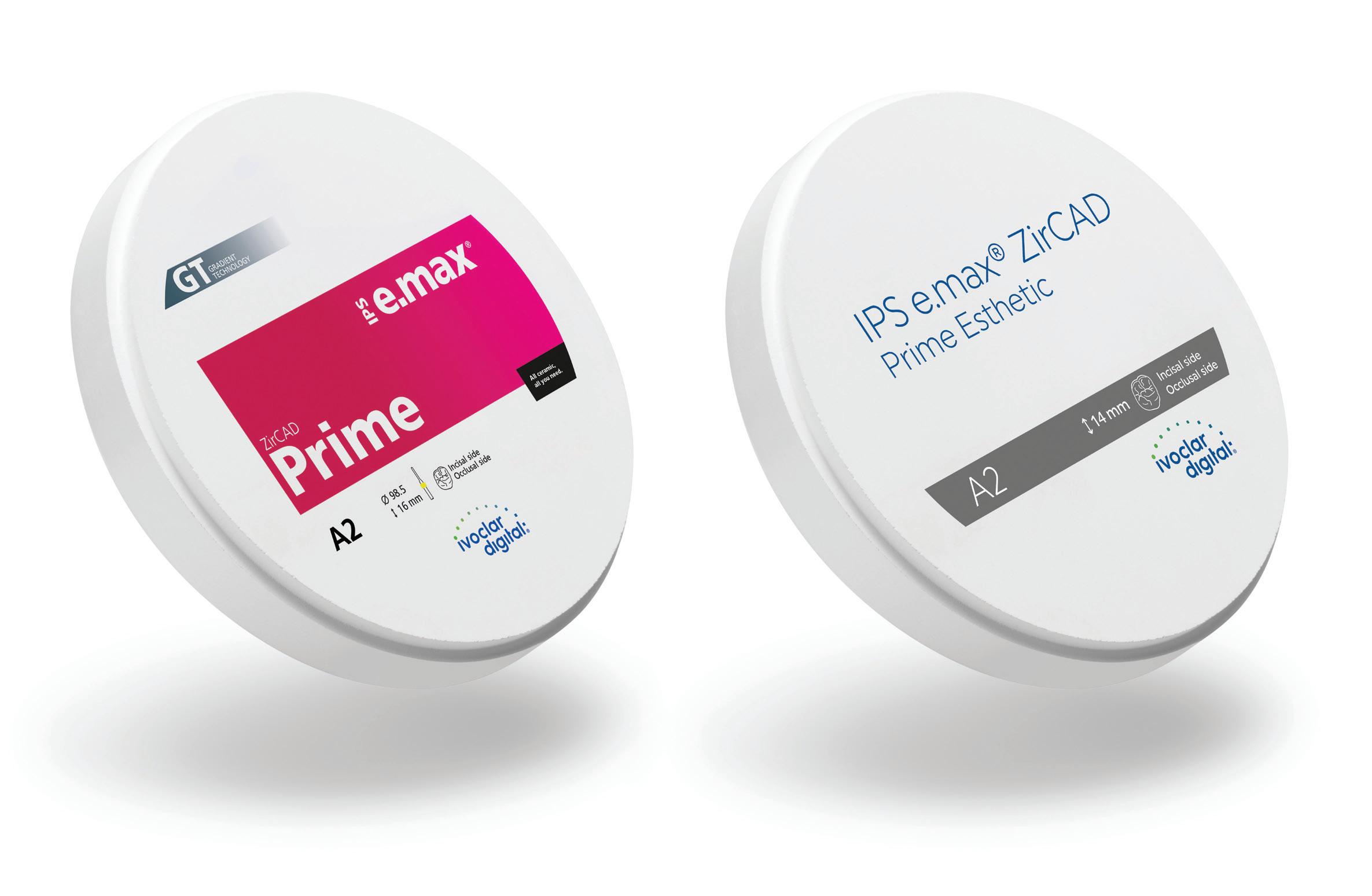
Making ordinary extraordinary - Part 2
By Dr Andrea Kim, DDS and Kyungsik Park, dT
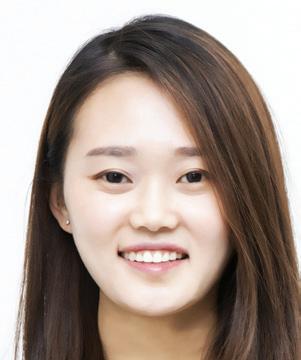

A25-year-old female patient presented with notable dental challenges. Clinically, there was evidence of severe attrition across her dentition, attributed to a history of bruxism as well as a thinned and glossy appearance of the enamel due to erosion.12 Furthermore, the patient reported a consistent sensation of mild xerostomia, raising concerns about its impact on her oral health. A thorough intraoral examination revealed that a number of her resin restorations, likely placed in previous years, were of compromised quality and showed signs of hypomineralisation. The dental literature consistently indicates that the presence of xerostomia not only heightens the susceptibility to carious lesions but also challenges the longevity of existing resin-based restorations.13

In an initial attempt to address the issue, multiple composite resin restorations were revised as per the patient’s specifications. However, she expressed continued dissatisfaction regarding the morphology and shade of the treated teeth. Self-conscious of her smile, the patient sought a solution for a brighter and more natural-looking appearance (Figure 24).
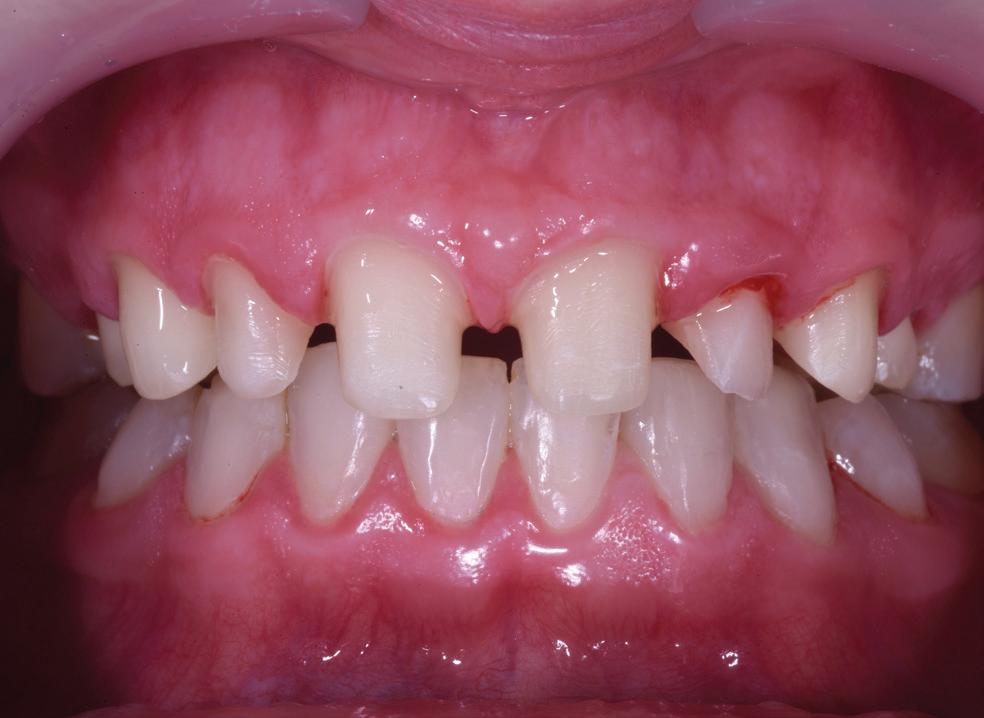
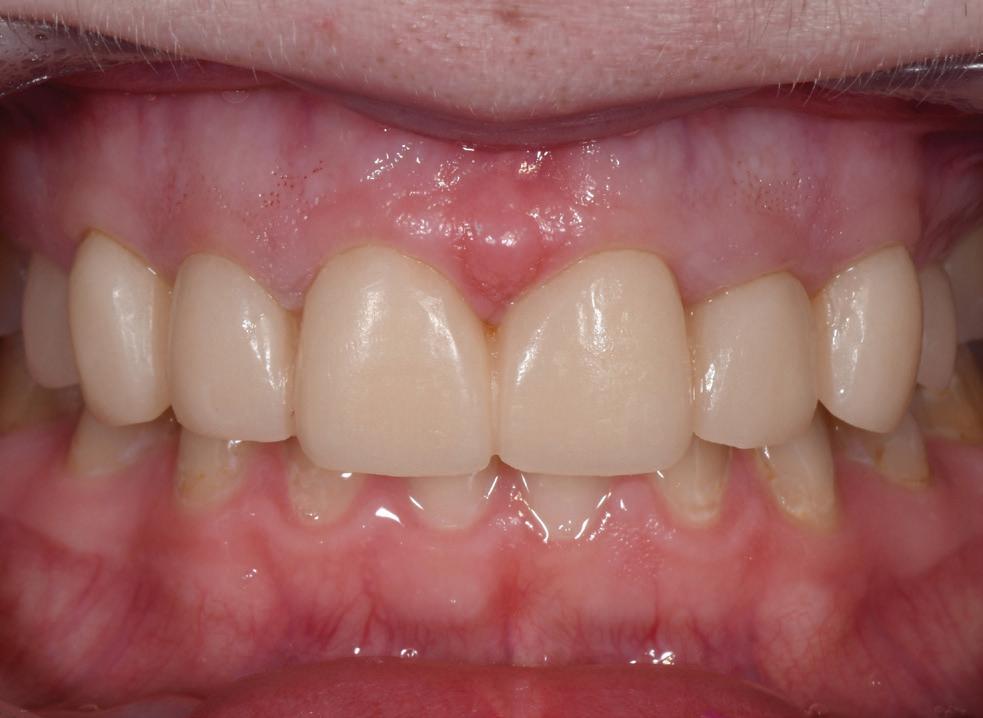
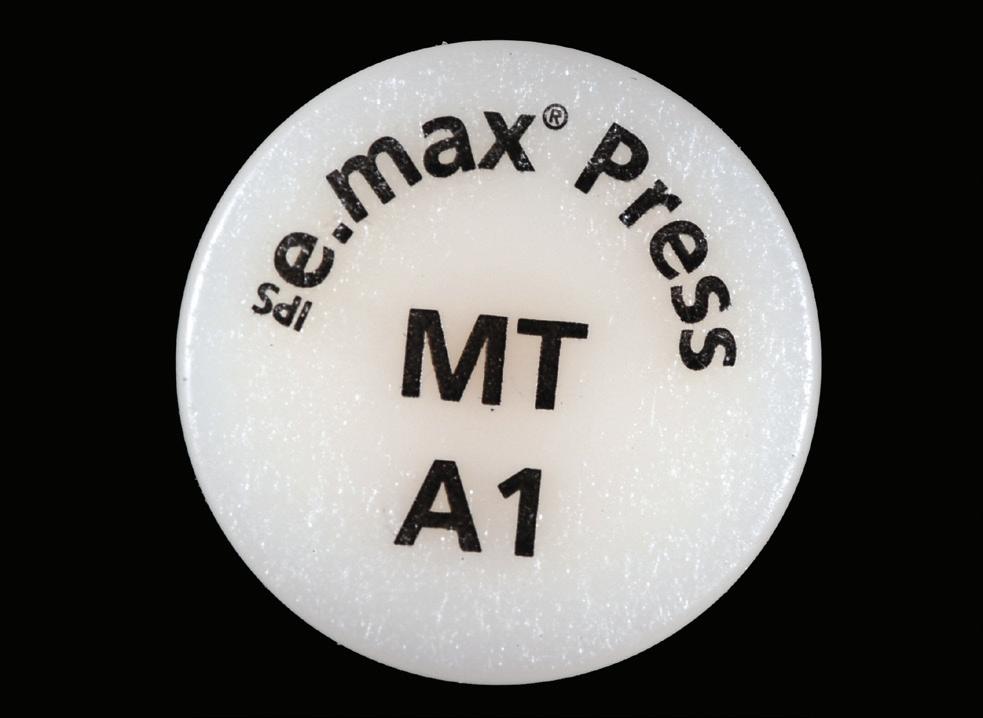

Planning
In developing a treatment strategy for this patient, several factors were at the forefront.
Chiefly, there was the concern of significant attrition attributed to bruxism, the evident erosion and a heightened susceptibility to dental caries. The patient also exhibited a square tooth appearance that did not harmonise with her round facial profile.
Prior to undergoing extensive prosthodontic treatment, a clear aligner orthodontic treatment plan was devised. The primary objective was to align the maxillary and mandibular incisors, minimising the need for excessive tooth reduction. Additionally, it was essential to preserve the vitality of the teeth.
Considering the compromised state of the numerous composite resin restorations and the risks associated – potential fractures and accelerated erosion – the decision was made to opt for full-coverage solutions. The plan involved the placement of crowns on the first premolars as well, as they had multiple failing composite restorations.
TClinical treatment
he patient underwent a three-month clear aligner orthodontic treatment during which the teeth were successfully aligned. Following this, the patient was deemed ready for crown treatment. The four central incisors were initially prepped and temporised, followed by the remaining teeth on the next day. The patient expressed immediate satisfaction with her improved smile, as the temporary crown shape was more in harmony with her facial profile, presenting a more oval appearance (Figures 25-26).
Subsequently, impressions were taken and initially, six IPS e.max® Press (Ivoclar) crowns (lithium disilicate glass ceramic) were placed on the anterior teeth, with full contour monolithic zirconia crowns using IPS e.max® ZirCAD Prime (Ivoclar) being used on premolar teeth (Figures 27-28).
Figure 27. IPS e.max® Press Ingots.
Figure 26. Provisional crowns.
Figure 28. IPS e.max® ZirCAD Prime Disc.
Figure 25. Preparation of eight maxillary abutment teeth.
ceramic | TECHNIQUES

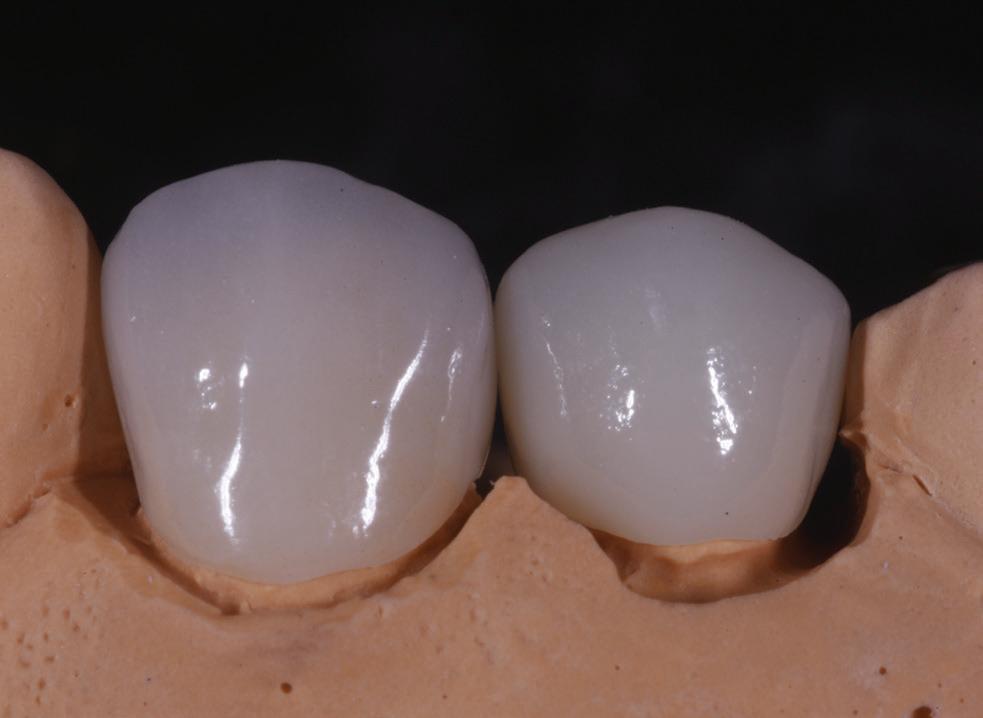
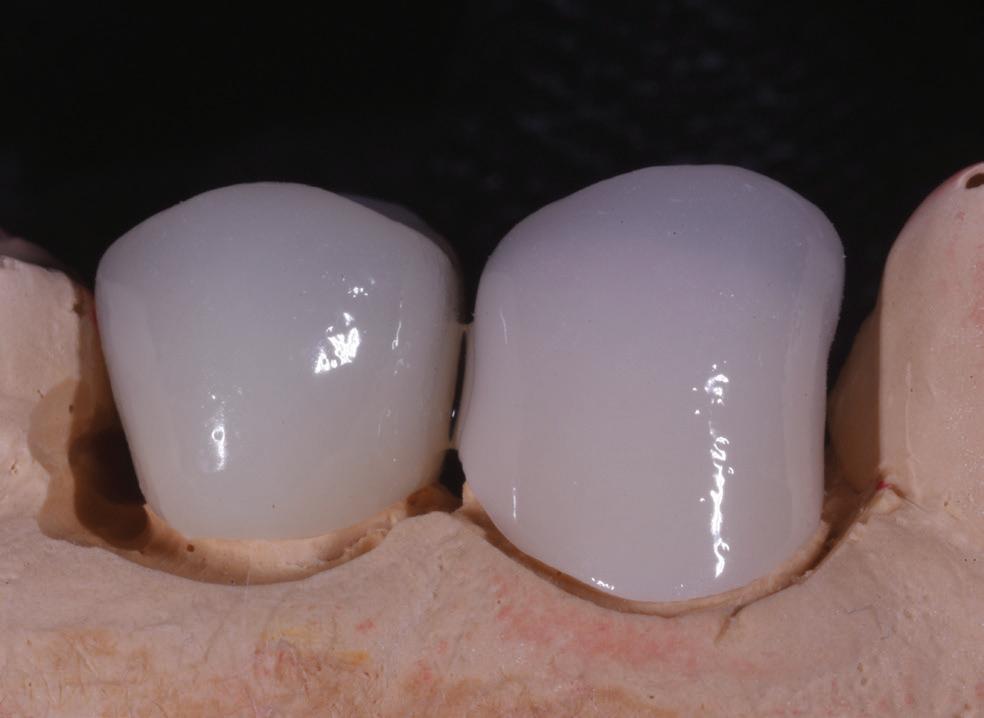
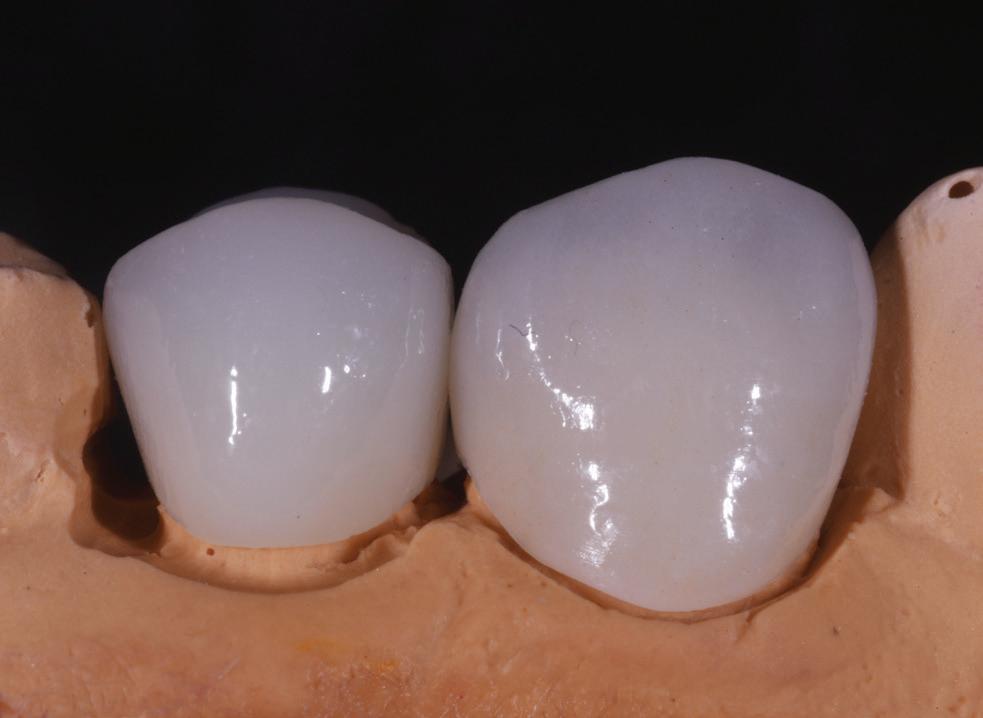
Fabrication of the crowns in the laboratory
While the new crowns were being temporised for two weeks, the patient returned with a fractured IPS e.max® Press crown on one of the canines. It appeared that the lingual reduction was insufficient, as the crown’s lingual thickness measured only about 0.4mm. Considering the significance of the canines as guidance teeth, the decision was made to replace the crowns with zirconia crowns featuring labial facing. No stain was added on the premolar where IPS e.max® ZirCAD Prime full zirconia was used. The lower central incisors were restored using composite resin after tooth whitening (Figures 29-32).
IPS e.max® Press crowns were fabricated for teeth 12-22 using MT ingots (Medium Translucency), shade A1. The crowns for the canines were made of IPS e.max ZirCAD Prime MT, shade A2.
First, a wash firing was conducted for all crowns. Subsequently, the cervical areas were built up with standard A1 dentine and the incisal areas with a 1:1 mixture of dentine and neutral powder. The built-up crown was then subjected to cut back to achieve a more natural mamelon shape.
To express a thick enamel-like appearance on the mesial and distal aspects of the crowns, OE2 or OE4 (Opal Effect) powder was used to create a milky white appearance. Segmental build-up between the mesial and distal areas was achieved using OE1 and TI (Transpa Incisal) powders and OE1 powder was applied to shape the restoration.
The use of opal effect powder naturally enhances opalescence, preventing the crown from reducing the brightness value of the ceramic compared to regular transparent powder (Figures 33-38).
Figure 31. Labial facing of tooth 23 and full zirconia crown of tooth 24.
Figure 30. Completion.
Figure 29. Labial facing of tooth 13 and full zirconia crown of tooth 14.
Figure 32. Completion.

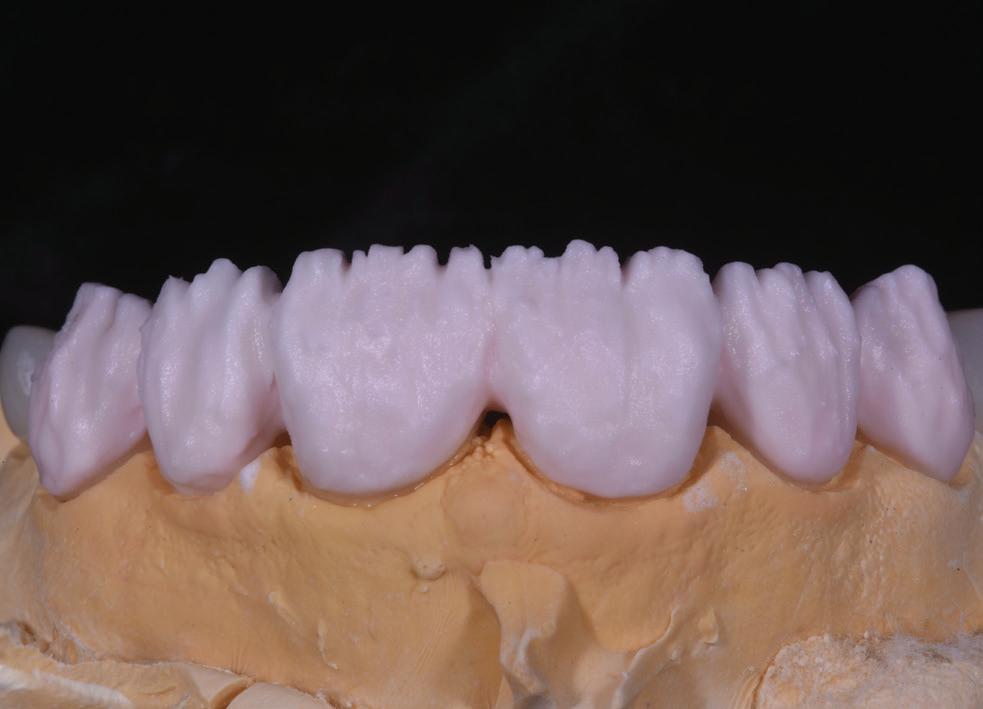
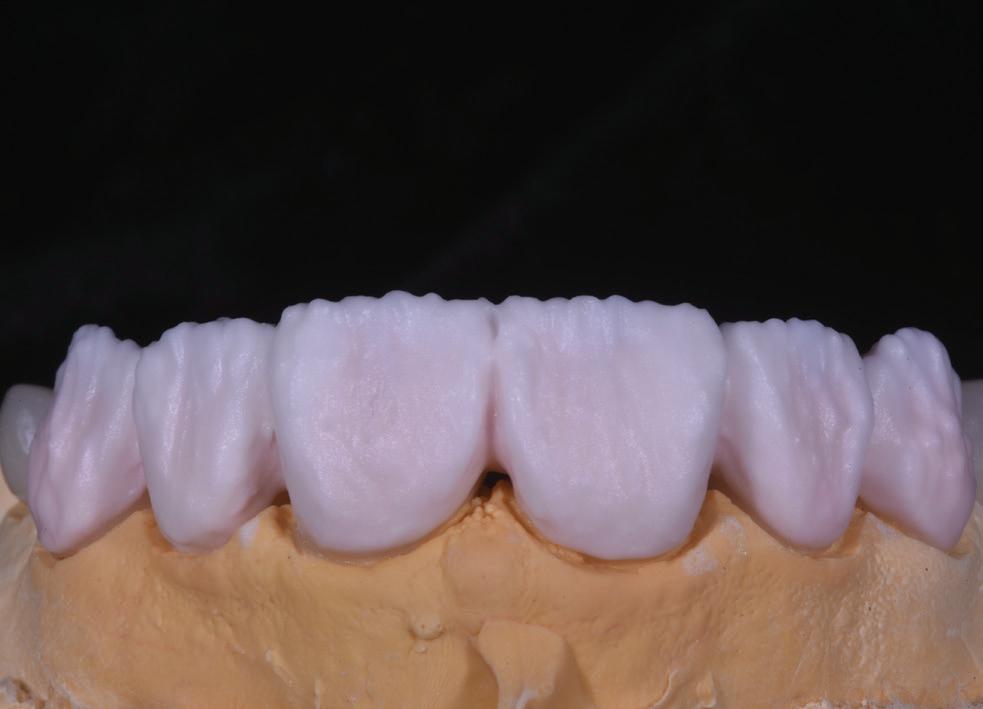
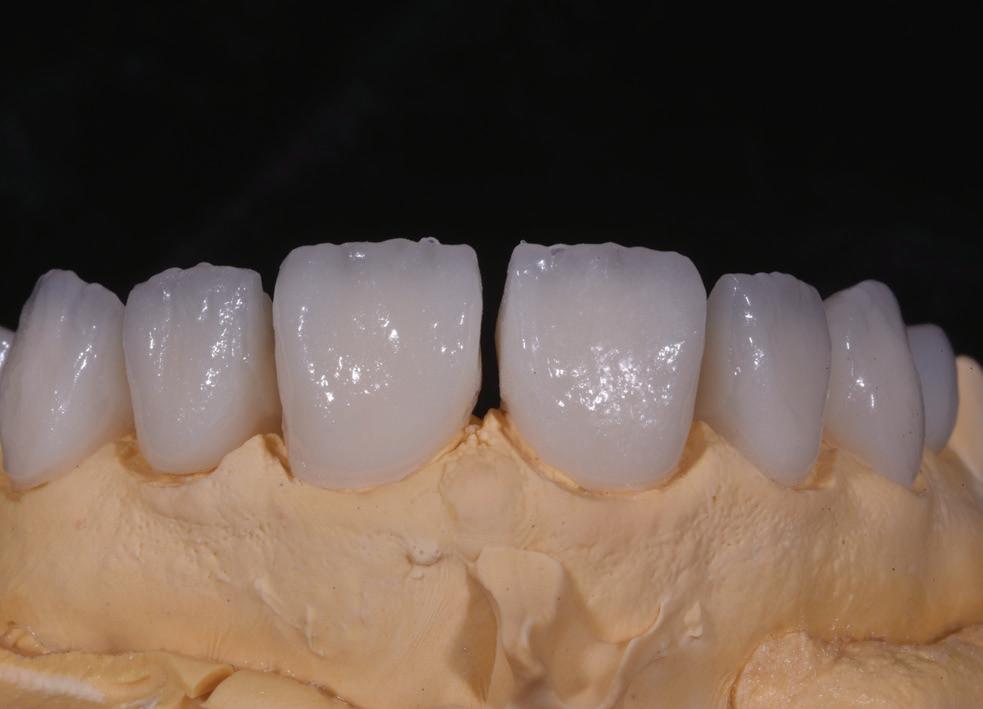
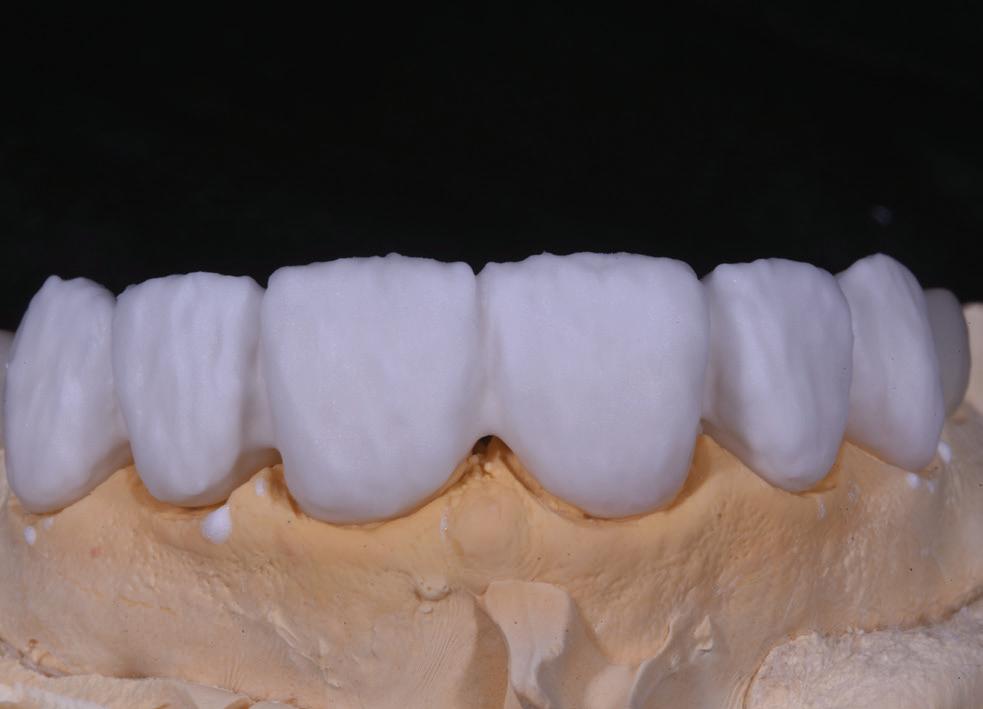
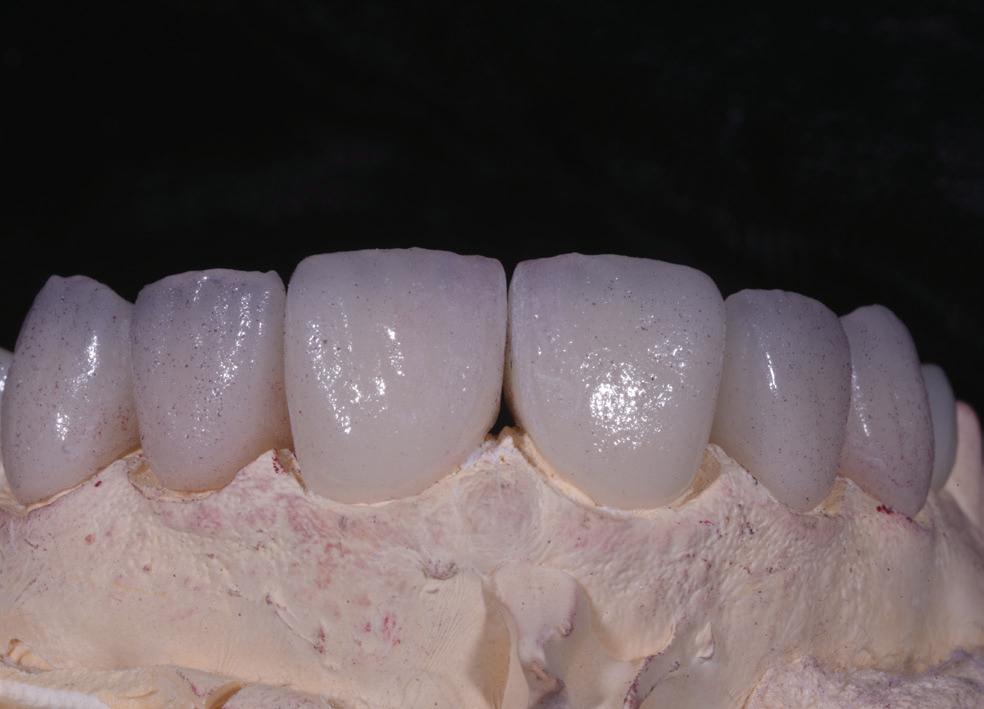
Figure 35. 1st build-up using IPS e.max Ceram OE1, OE2 and TI.
Figure 37. The 2nd build-up using IPS e.max Ceram OE1.
Figure 34. Cut-back performed after the IPS e.max Ceram dentine build-up.
Figure 33. IPS e.max Press is used for the build-up of the four maxillary anterior teeth and IPS e.max ZirCAD Prime for the reconstruction of the canines and 1st molars.
Figure 36. After the 1st bake.
Figure 38. After the 2nd bake.
ceramic | TECHNIQUES

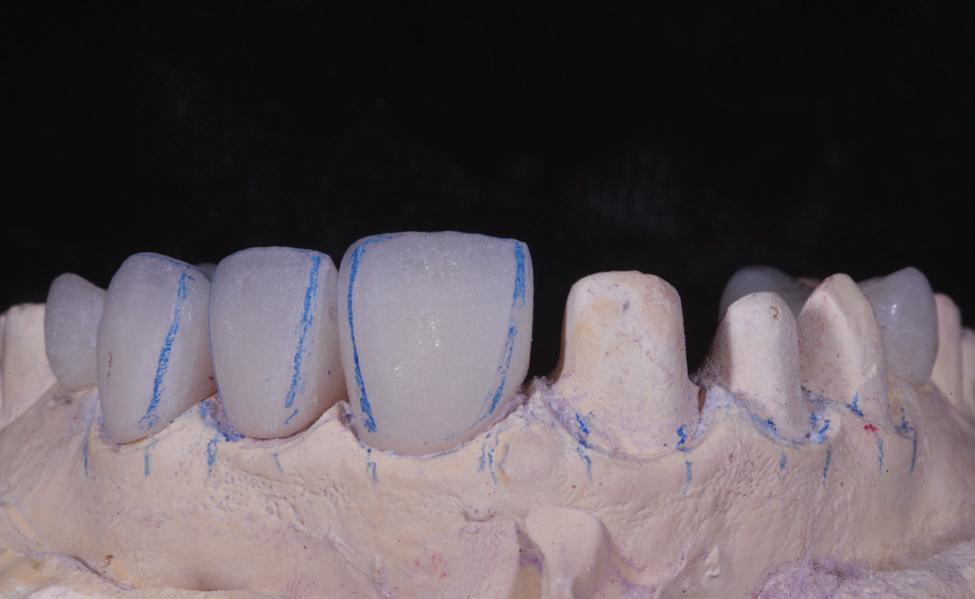


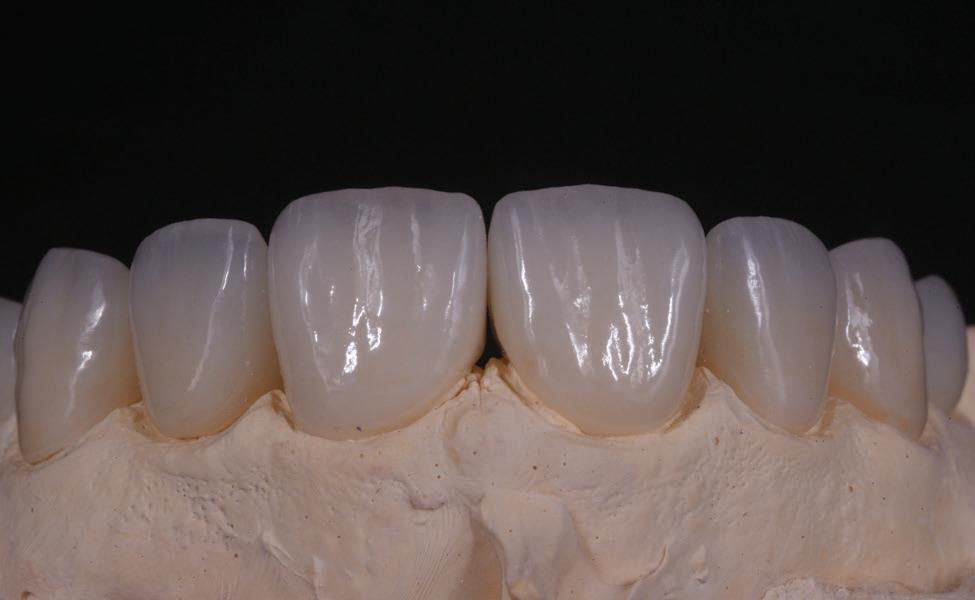
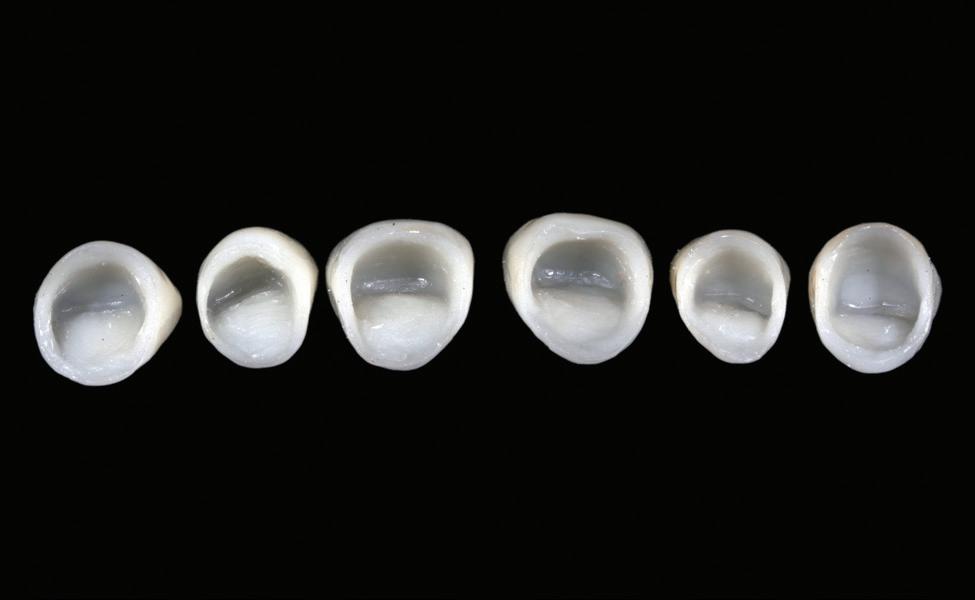
Contouring14
When observing the margin of the prepped tooth, an arbitrary point can be set where it turns towards the direction of the mesial and distal on the labial side. This area becomes the starting point of the line angle of the crown, which determines the width of the crown. Once the width of the crown is determined, the contouring process can be carried out in the following steps:
1. Formation of the three-dimensional shape of the tooth;
2. Formation of the line angle of the mesial and distal;
3. Reproduction and arrangement of the appropriate shape of each tooth;
4. To attain a symmetrical gingival profile, the facial free gingival margin on tooth 22 was adjusted on the model to align the facial gingival zenith with that of tooth 12. A crown was subsequently made based on this revised model. The crown’s contour was designed to produce an aesthetically pleasing soft tissue profile and the reaction of the soft tissue was biologically sound;15
5. After completing labial texture contouring, the crowns are gently polished and glazed; 6. Post firing, a natural surface is obtained by mechanical polishing (Figures 39-44).
Figure 40. Connecting the line angles of the crowns to their roots.
Figure 39. Formation of crowns’ line angles.
Figure 41. Trimming the free gingival margin on 22 on the model to achieve a symmetrical gingival profile in comparison to tooth 12.
Figure 42. Formation of crown textures.
Figure 43. Completed crowns.
Figure 44. The facial cervical of the tooth 22 crown is designed to be pronounced to achieve a symmetrical gingival profile.

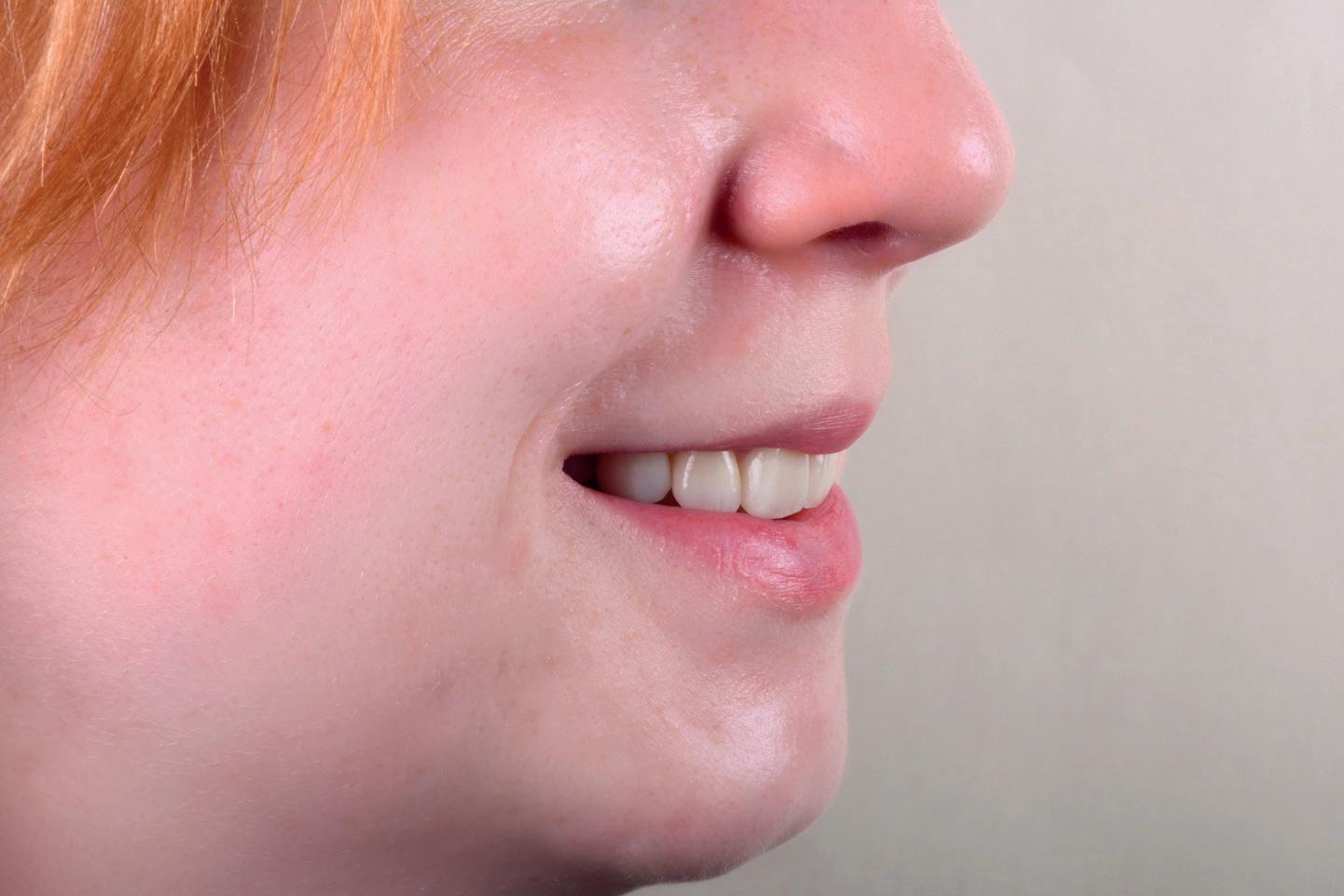
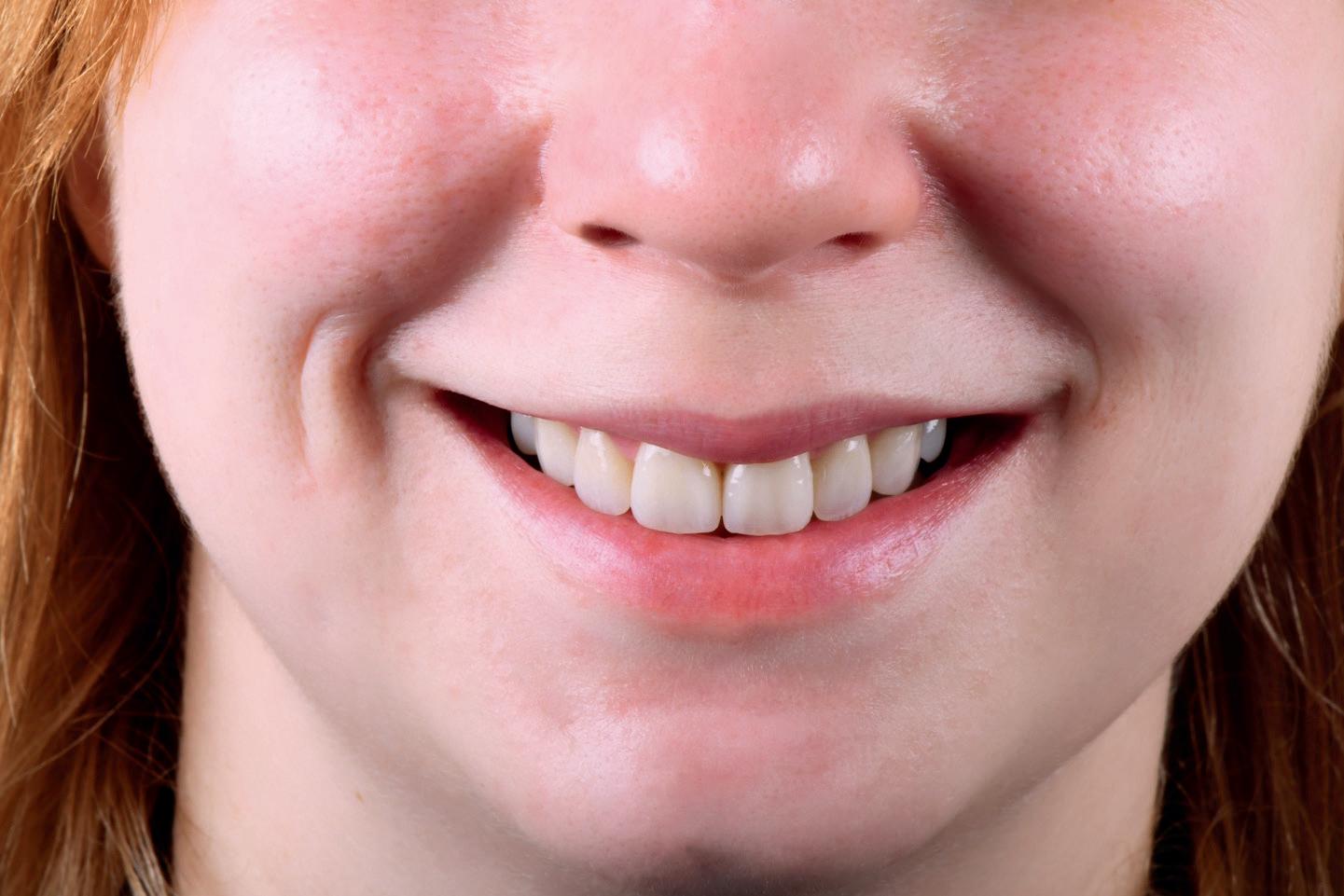
Result
The outcome was natural-looking and well-suited to the patient’s individuality and facial morphology. One important observation is that despite using different materials for the incisors, canines and premolars, they blend together seamlessly, exhibiting no discernible signs of inconsistency. The areas treated with labial facing and those left untouched integrate

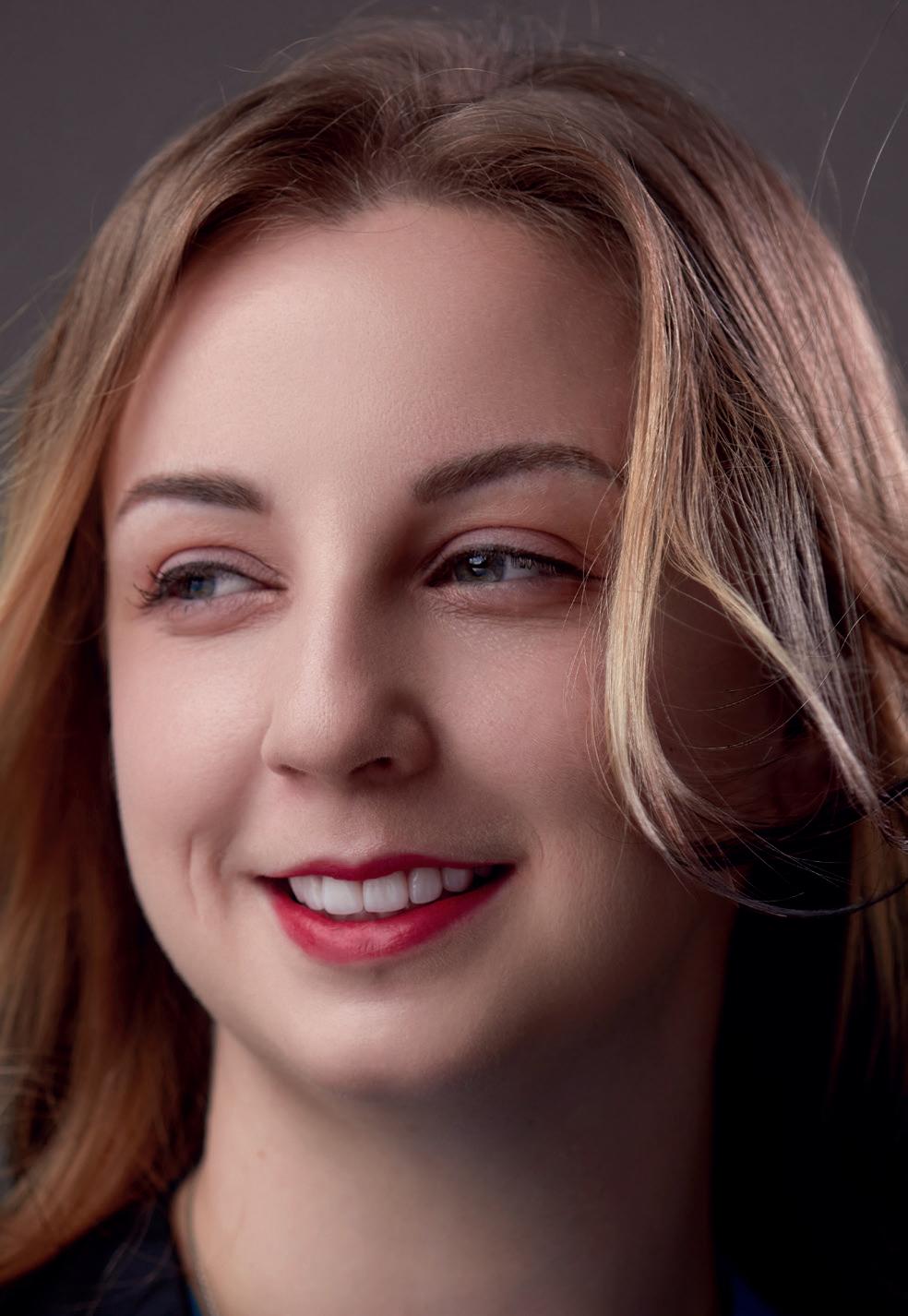
harmoniously, resulting in a cohesive aesthetic outcome without any visible indications of variation.
Following treatment, the patient was strongly advised to wear a custom-made nightguard to safeguard the restorations as well as opposing mandibular incisors from the deleterious effects of bruxism (Figures 45-50).16
Case 3 will appear in Part 3 of this article.
Figure 47. Natural look from the side view.
Figure 46. Cemented Crowns.
Figure 45. Crowns harmoniously positioned in relation to the lip.
Figure 48. A patient with a beautiful smile.
Figure 49. Never seen her smile so much.
ceramic | TECHNIQUES
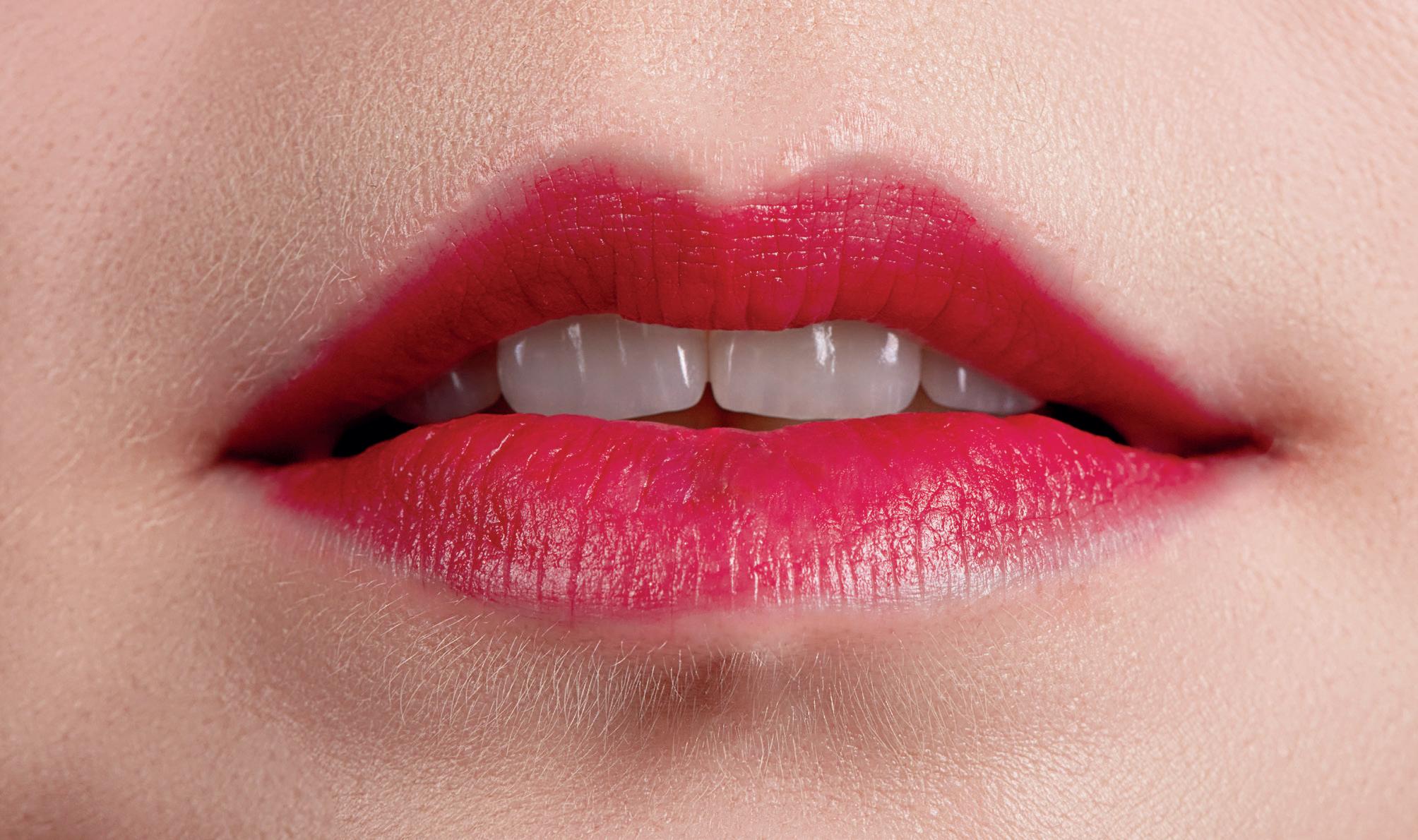
Figure 50. One-year follow-up.
About the authors
Dr Andrea Kim, DDS is a general dentist at Global Dental Clinic in Seoul, South Korea.
Kyung-Sik Park is a dental technician who trained at Daejeon Health Sciences College, Korea and Goldman Dental Laboratory in Germany. He has lectured at the Ivoclar International Meeting in Liechtenstein and has been published internationally in leading dental technology journals including Dental Dialogue and Dental Labor. He is President of Natural Line Dental Laboratory in Seoul, Korea; Director of the Natural Line Clinical Research Centre; and an Ivoclar Korea Instructor.
References
12. Kinsel, R. P., Pope, B. I., & Capoferri, D. (2015). A Review of the Positive Influence of Crown Contours on Soft-Tissue Esthetics. Compendium of Continuing Education in Dentistry, 36(5), 352–357.
13. Leinonen, J., Vähänikkilä, H., Raninen, E., Järvelin, L., Näpänkangas, R., & Anttonen, V. (2021). The survival time of restorations is shortened in patients with dry mouth. Journal of Dentistry, 113, 103794. https://doi.org/10.1016/j.jdent.2021.103794
14. Shigeo Kataoka, Yoshimi Nishimura, & Avishai Sadan. (2002). Nature’s morphology: an atlas of tooth shape and form. Quintessence.
15. Kinsel, R. P., Pope, B. I., & Capoferri, D. (2015). A Review of the Positive Influence of Crown Contours on Soft-Tissue Esthetics. Compendium of Continuing Education in Dentistry, 36(5), 352–357.
16. Oh, W., DeLong, R., & Anusavice, K. J. (2002). Factors affecting enamel and ceramic wear: A literature review. The Journal of Prosthetic Dentistry, 87(4), 451–459. https://doi.org/10.1067/mpr.2002.123851
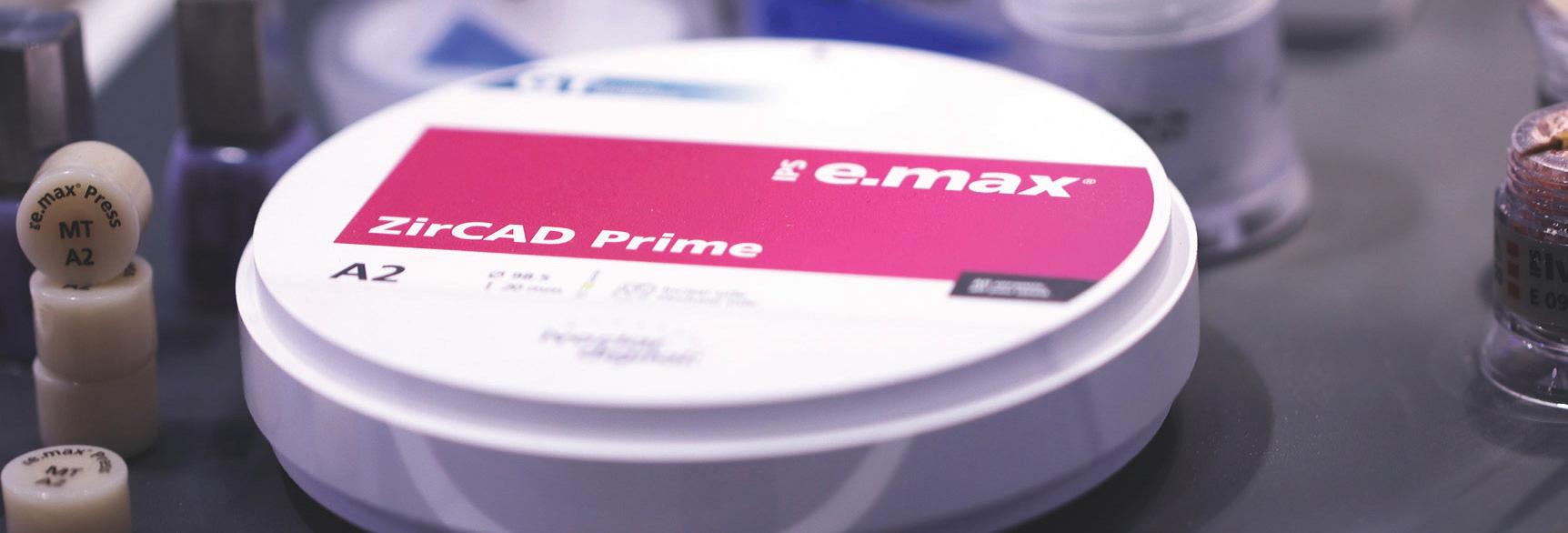

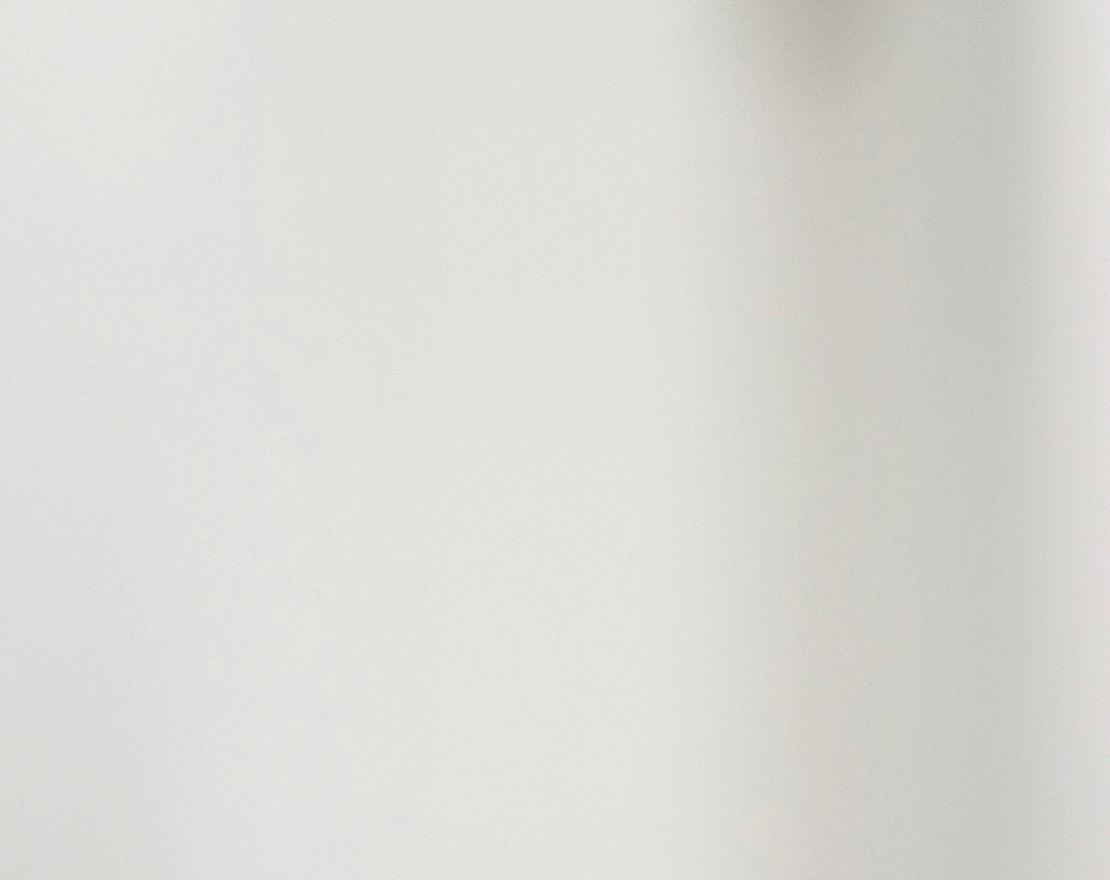
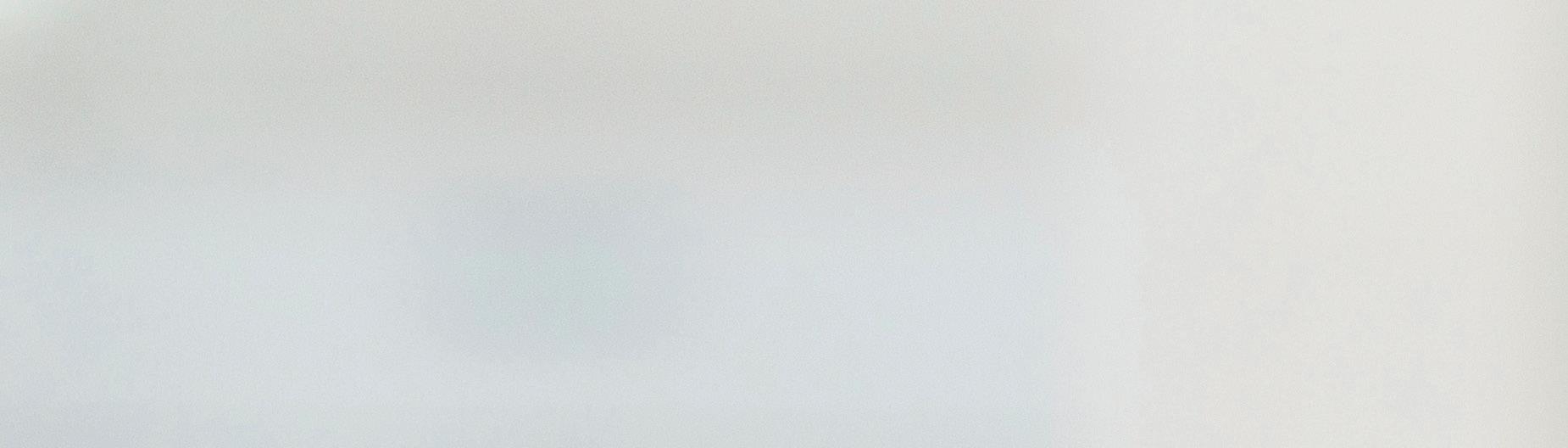

– The all-purpose One-Disc Solution for a wide range of requirements – Maximum flexibility and creative freedom – Extremely high strength teamed with exceptional aesthetics

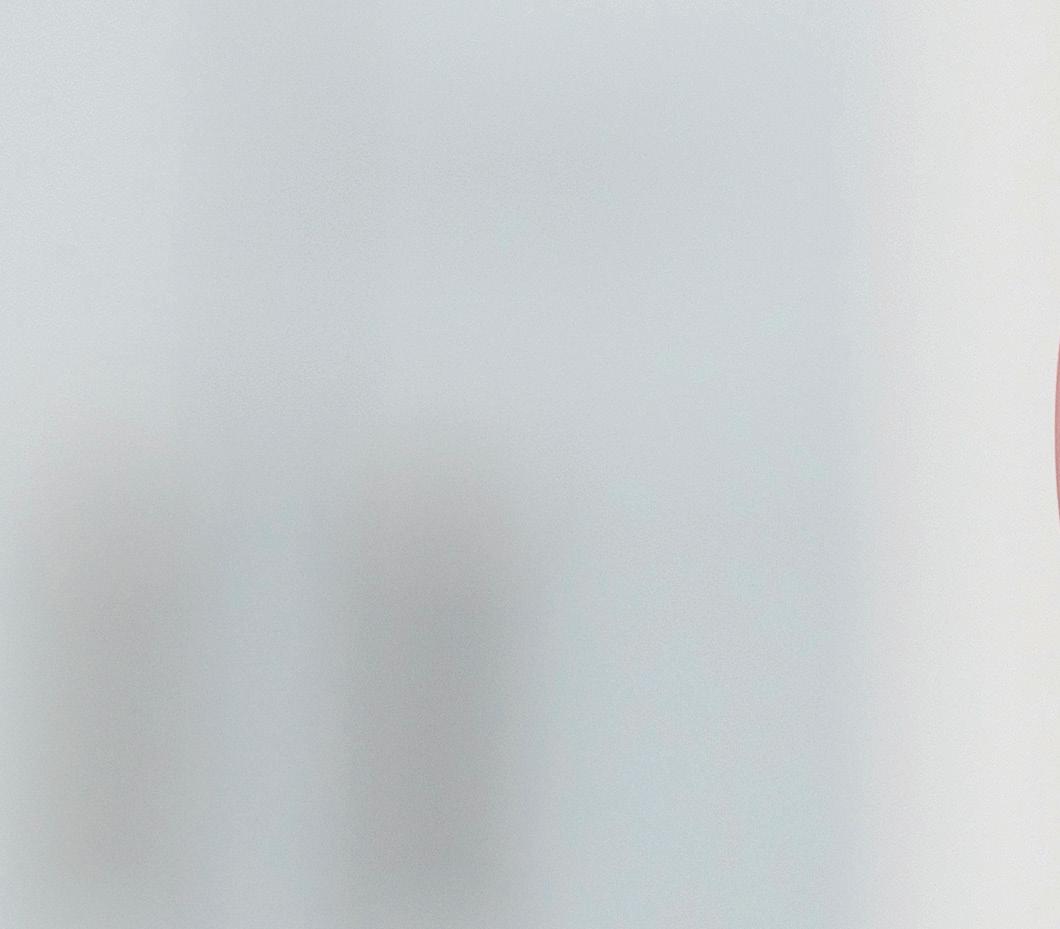
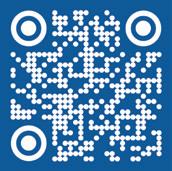
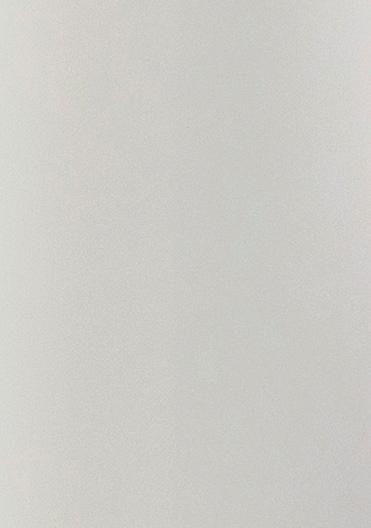

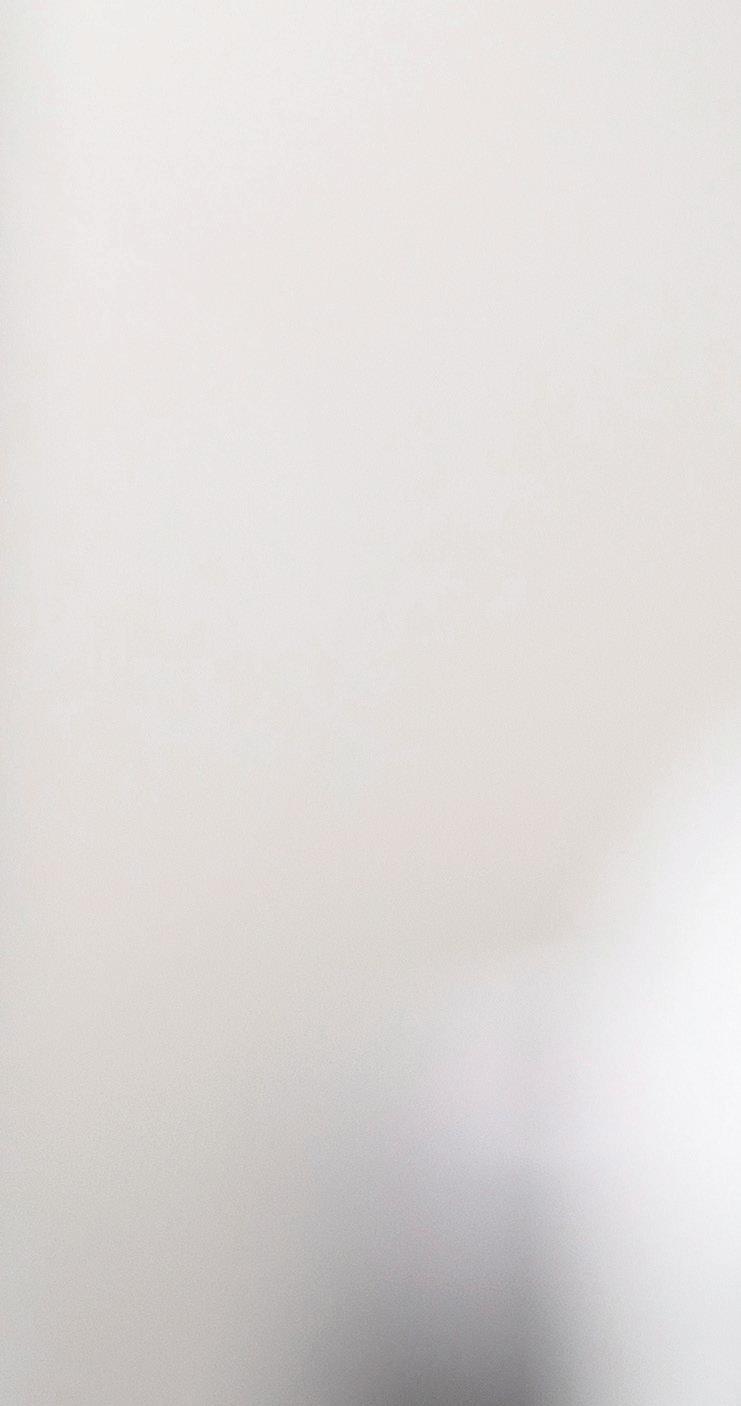

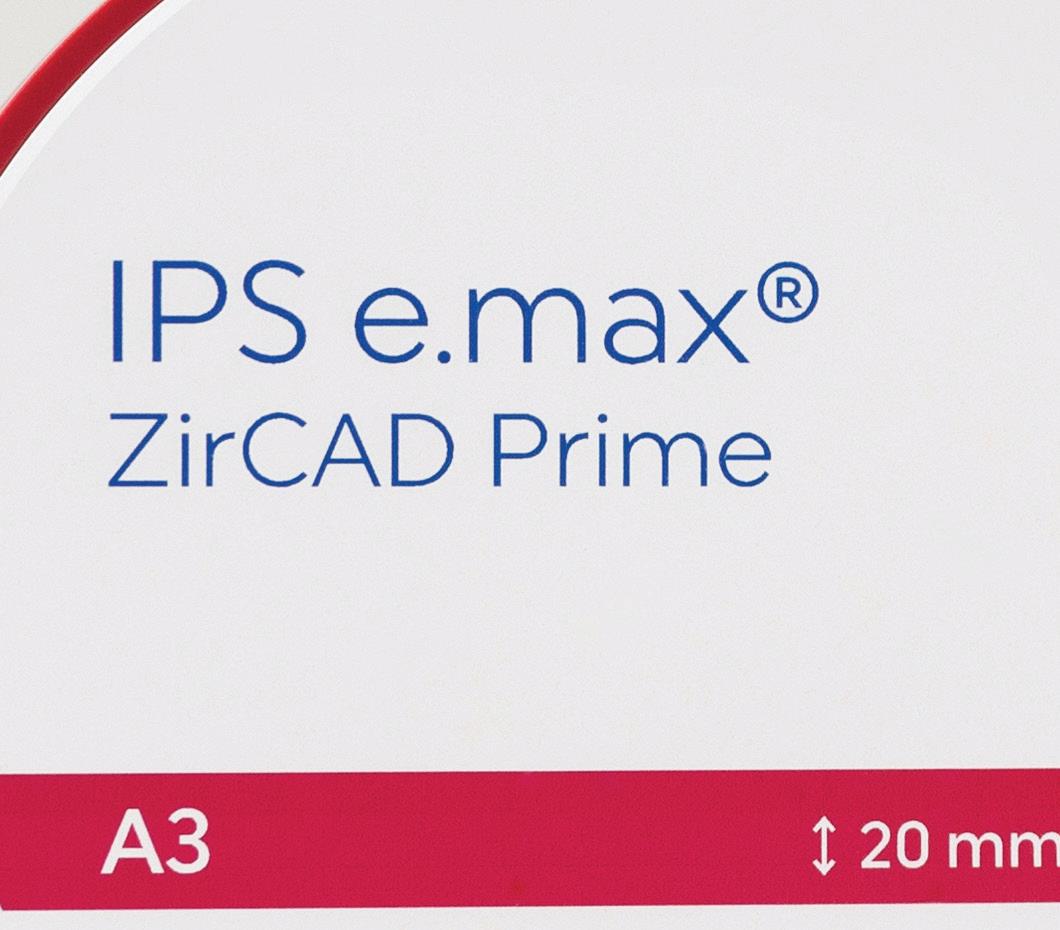
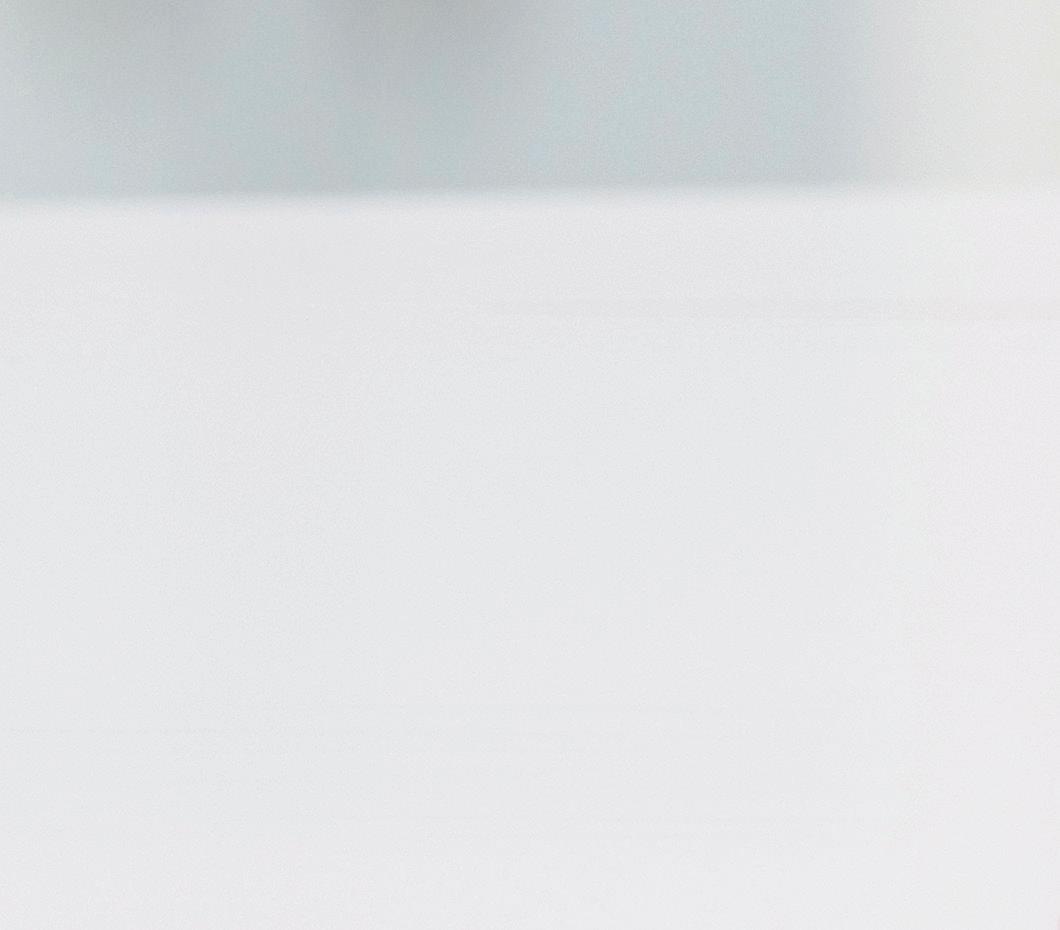

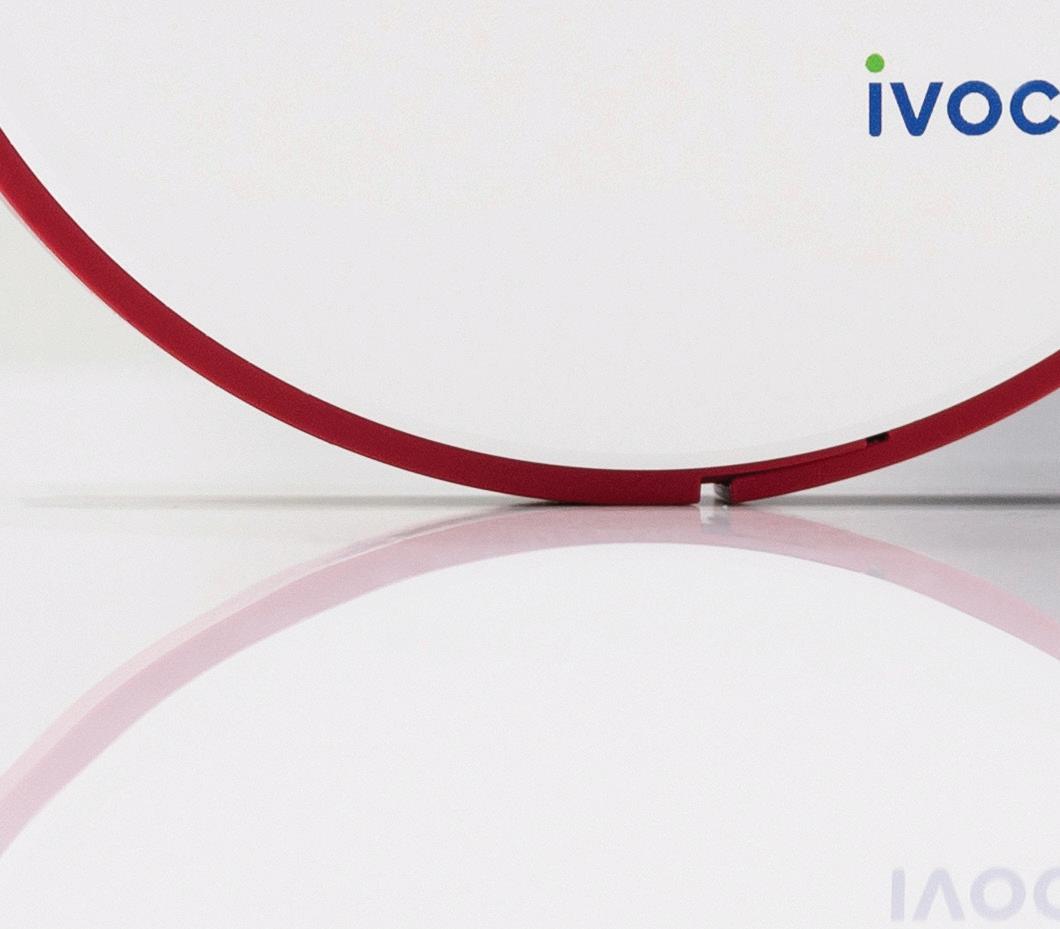
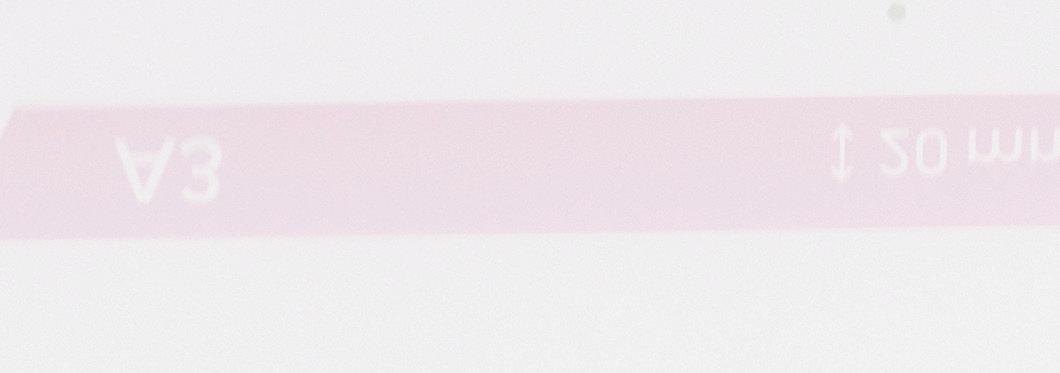
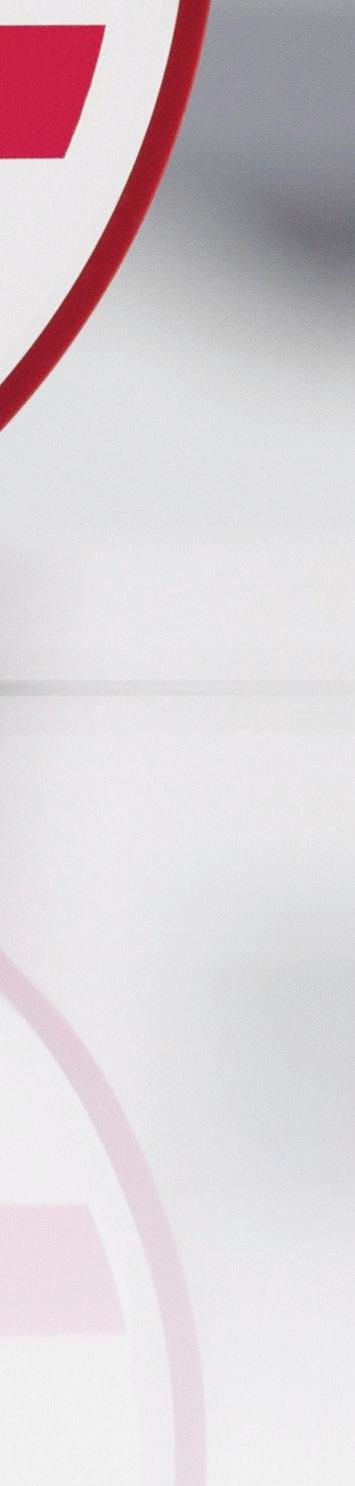
VITAPAN EXCELL: The right tooth for every clinical situation and all face shapes
By Nela Zielonka, Dental Technician
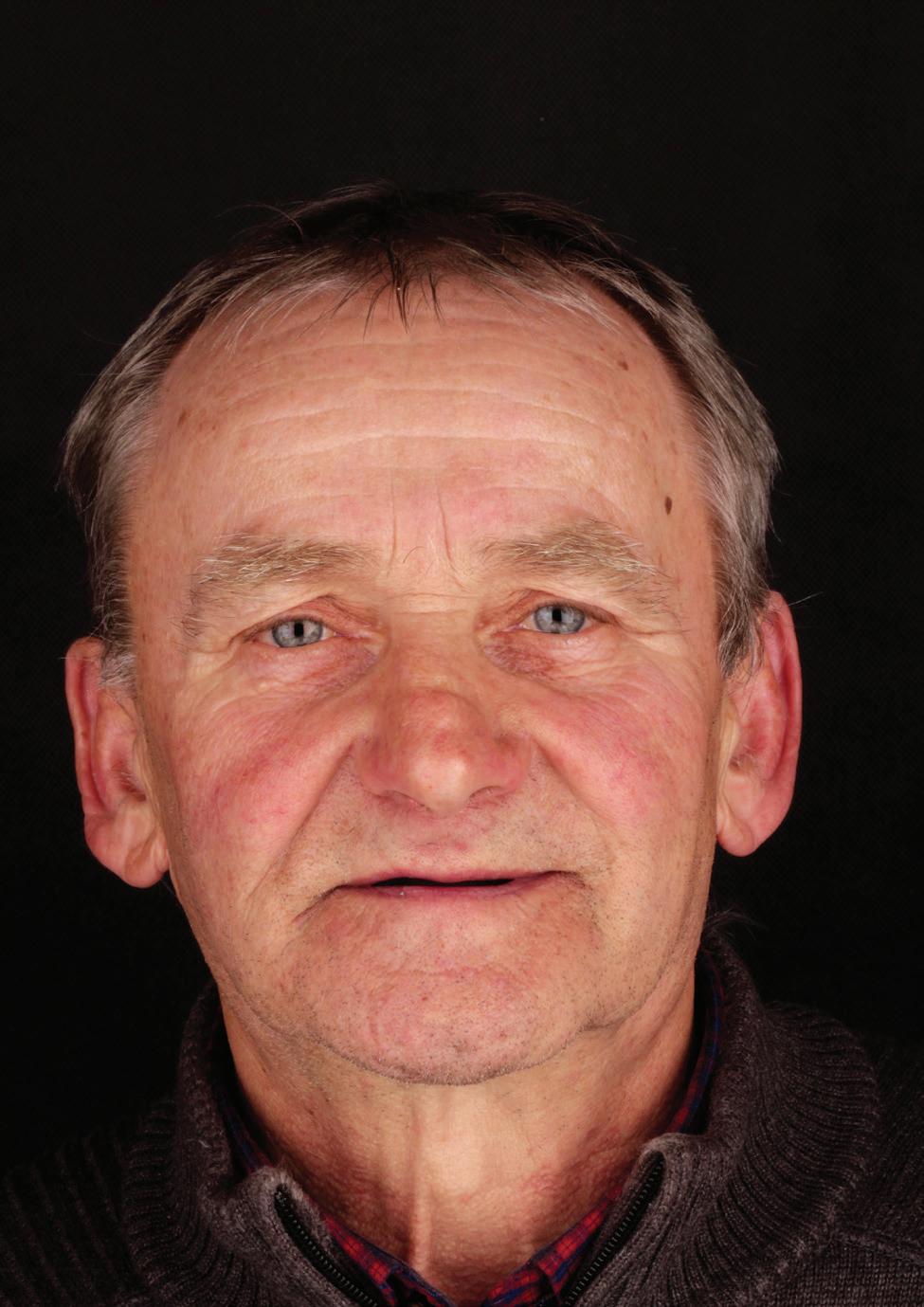
When providing a patient with full denture restorations, the goal is to restore chewing function and phonetics. Full dentures should also give the patient an aesthetic appearance. Selecting the right denture tooth depends on many factors. The width of the jaw ridge and the vertical jaw relation decide which tooth dimension is suitable.
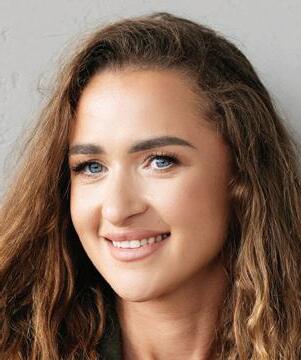
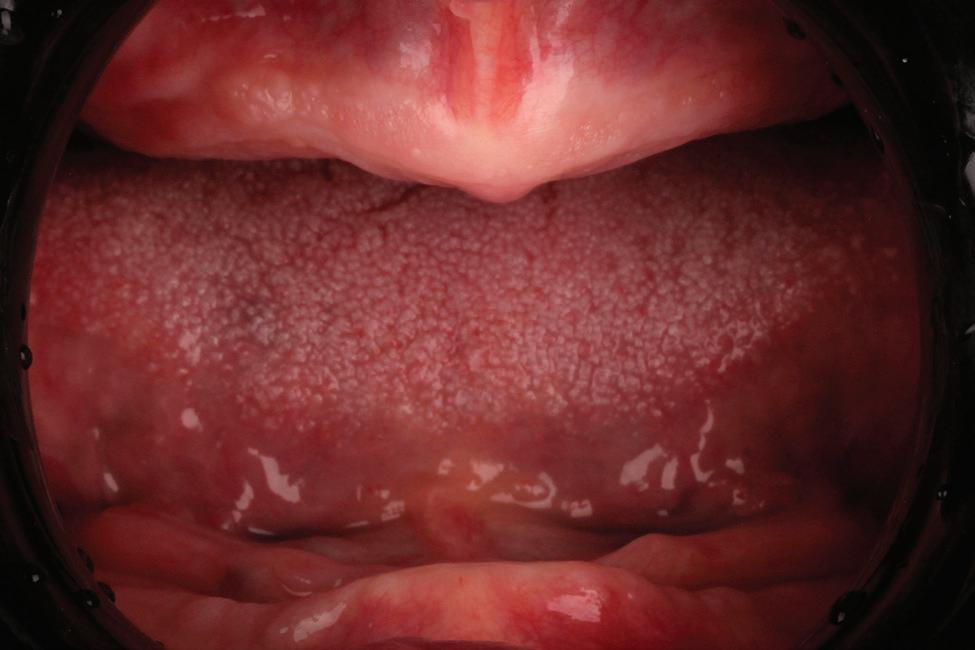
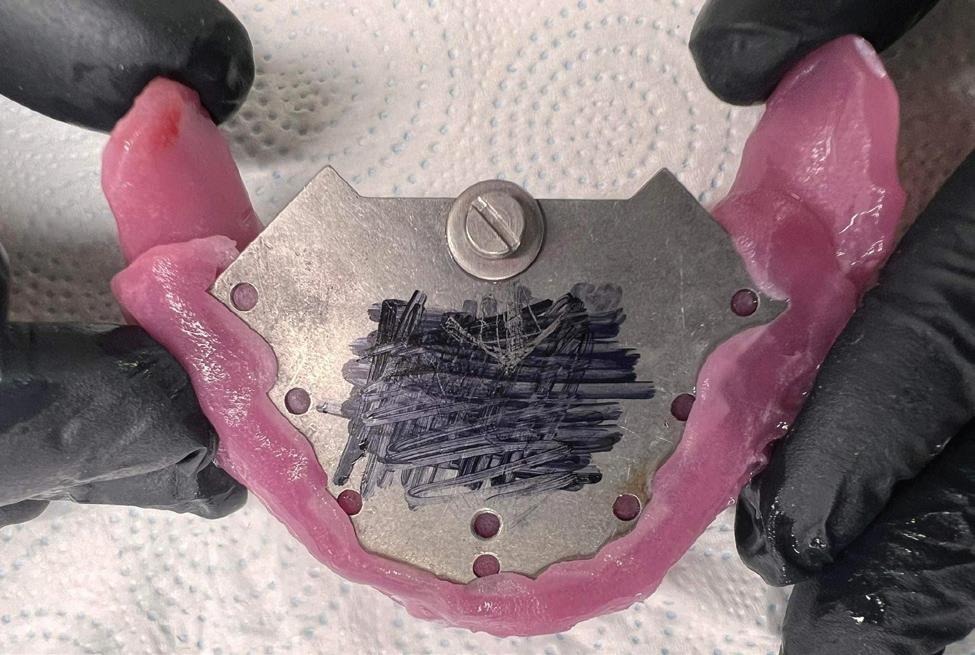
pin registration.
At the same time, the shape of the face and often the natural initial situation must be taken into account based on old photographs. In full dentures, the patient’s desired tooth shade must also be available in the selected shape. Being able to choose suitable denture teeth in the right size, shape and shade is a fundamental step for functional and aesthetic success. In the following report, the dental technician Nela Zielonka (Gaworzyce, Poland) shows how she was able to master a full denture with VITAPAN EXCELL anterior teeth and VITAPAN LINGOFORM posterior teeth.
Figure 3. The centric condyle position was determined with a support
Figure 2. Alveolar crests were suitable for a full denture.
Figure 1. The initial situation with the edentulous patient.
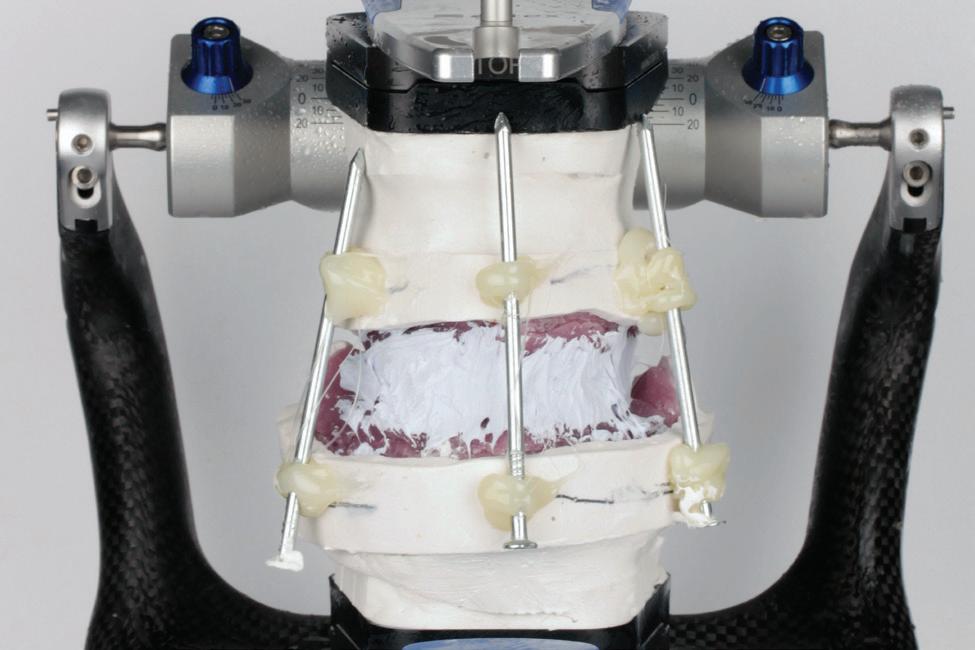

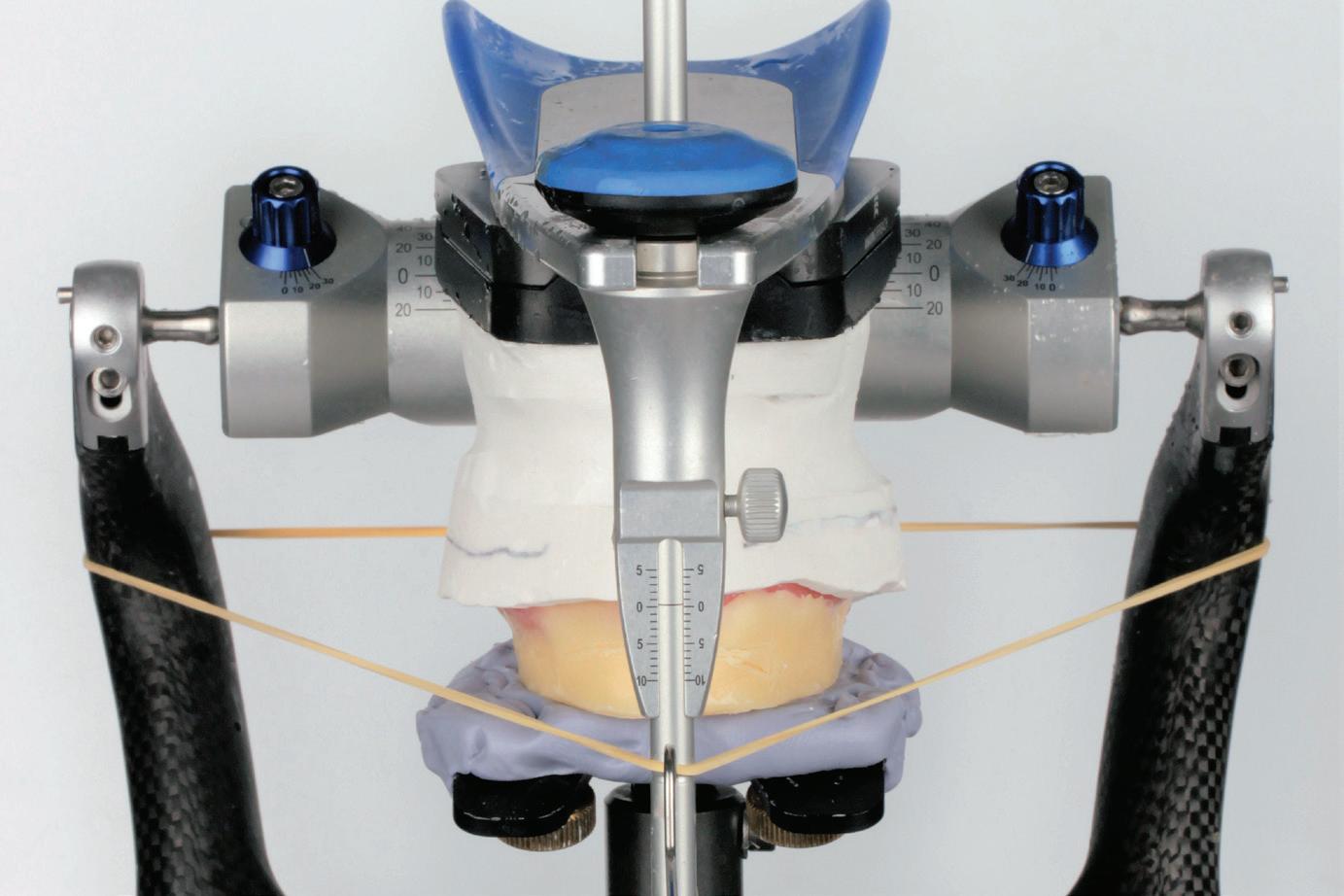
Initial situation and support pin registration
A60-year-old patient presented in the practice because he had lost all of his natural teeth over time. He now wanted to have a full denture fitted for the first time. During the examination, it was found that the alveolar ridges were sufficiently developed to provide a safe, mucosa-supported bed for the planned full dentures, despite severe atrophy in the posterior region of the mandible. In the first step, models were created on the basis of anatomical impressions on which individual trays for the functional impressions could be manufactured. The mucodynamic impression was used to create the master model, which was the basis for the production of a support pin registration, where the centric condyle position was registered, based on the movement paths during laterotrusion and protrusion. This made the centric position visible in the form of the tip of an arrow angle on the registration.
TDetermination of maxillo-mandibular relationship
he master models were articulated using the keyed support pin registration, revealing a significantly sunken vertical dimension. In the registration, the patient did not want to allow for a raised bite; otherwise, he would feel “locked” and uncomfortable.
During the production of the bite templates, it became clear that the vertical height of the prefabricated teeth was limited.
During the final alignment of the wax rims, the occlusal plane was aligned parallel to the bipupillary line and the occlusal plane parallel to Camper’s plane.
The resting position was checked again and the centre line, canine line and smile line were scratched in.
After keying the determination of the jaw relation, it was removed and used for the final articulation, where the new teeth were to be set up.
Figure 6. The new articulation of the upper jaw model, according to the jaw relation determination.
Figure 5. In the articulator, bite templates were produced with wax rims for the jaw relation determination.
Figure 4. The articulation was carried out with the keyed support pin registration.
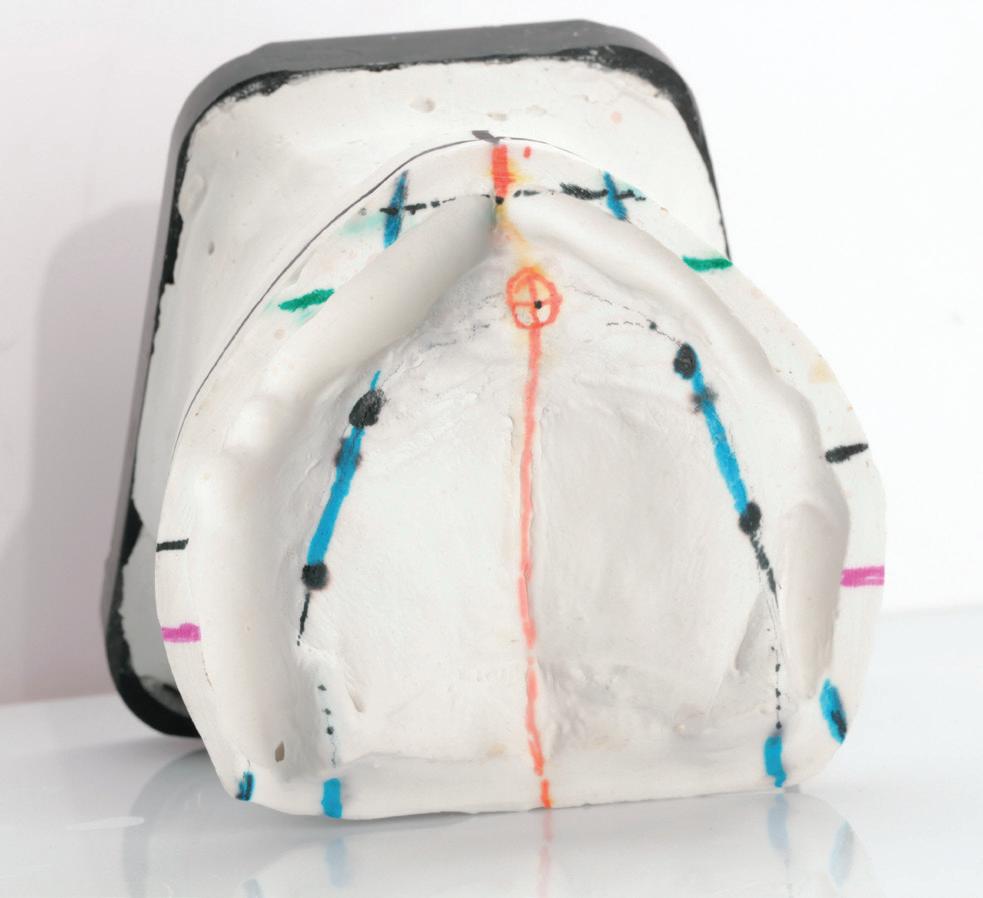
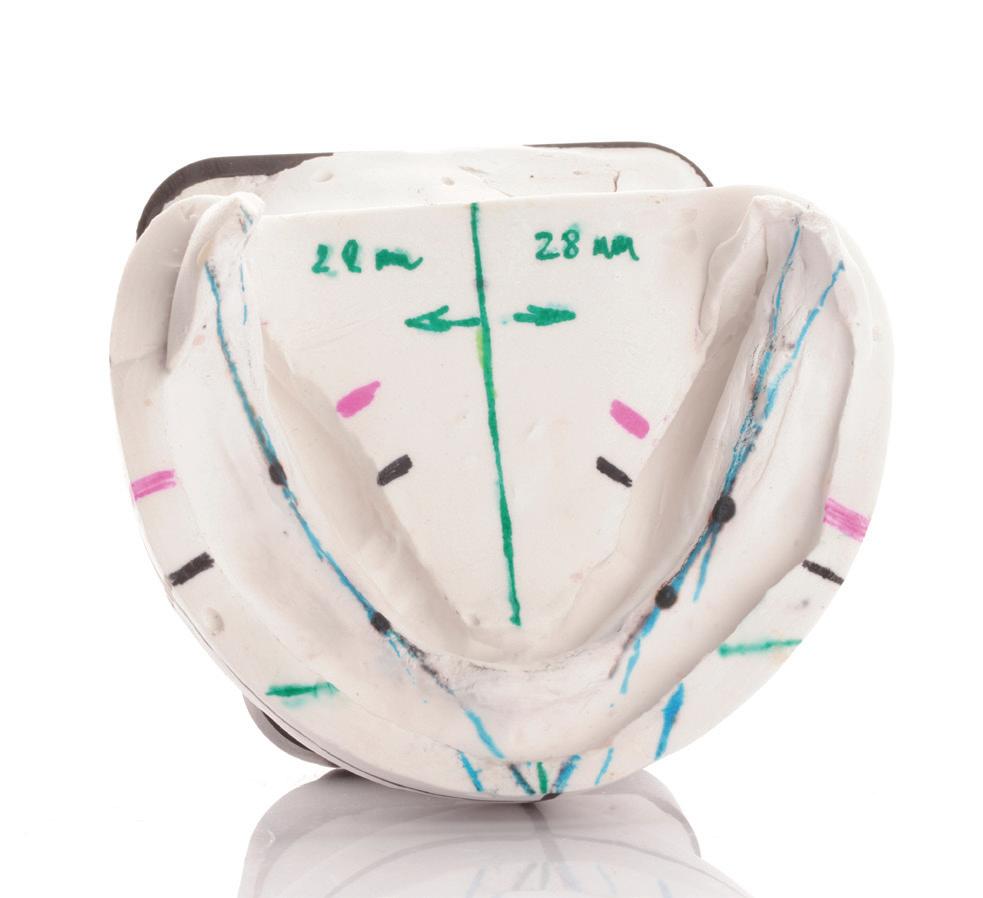

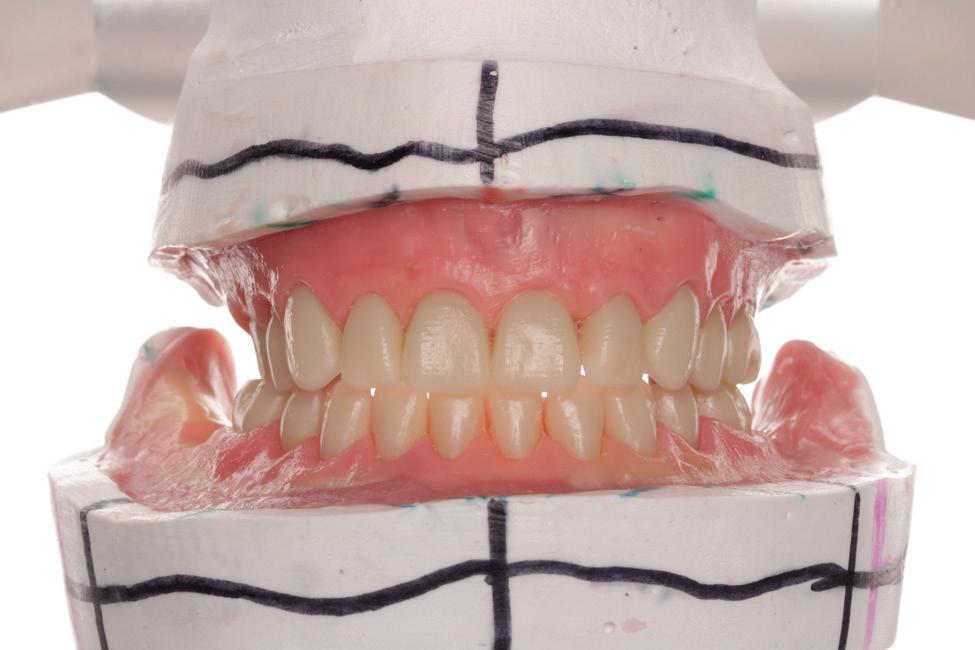
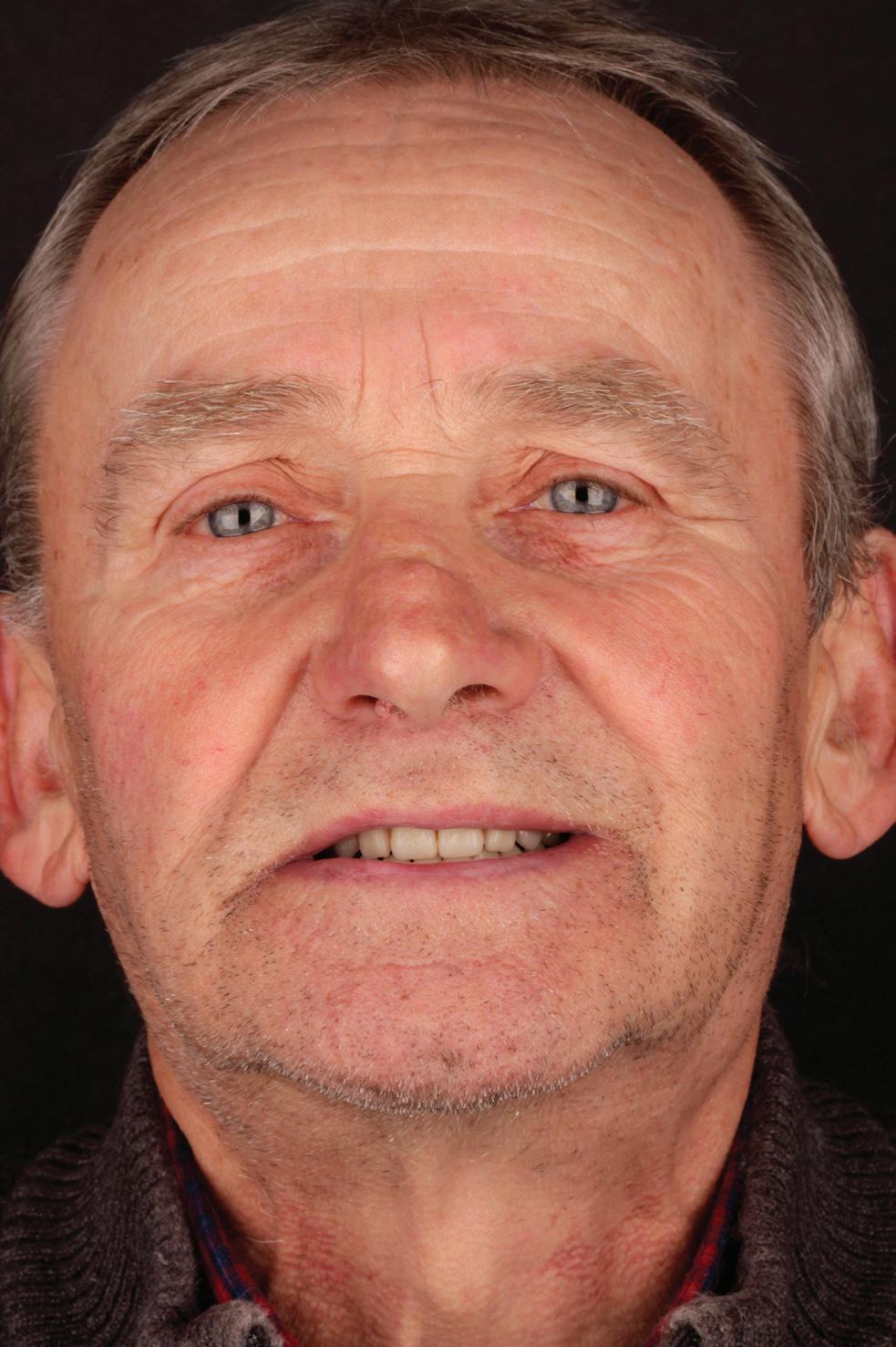
Figure 10. Setup in wax with VITAPAN EXCELL and VITAPAN LINGOFORM.
Figure 11. The patient at the wax try-in.
Figure 7. The model analysis in the upper jaw indicates the necessary steps for setup.
Figure 9. In articulation, the limited vertical dimension is shown in the jaw relation.
Figure 8. The careful model analysis on the lower jaw model.

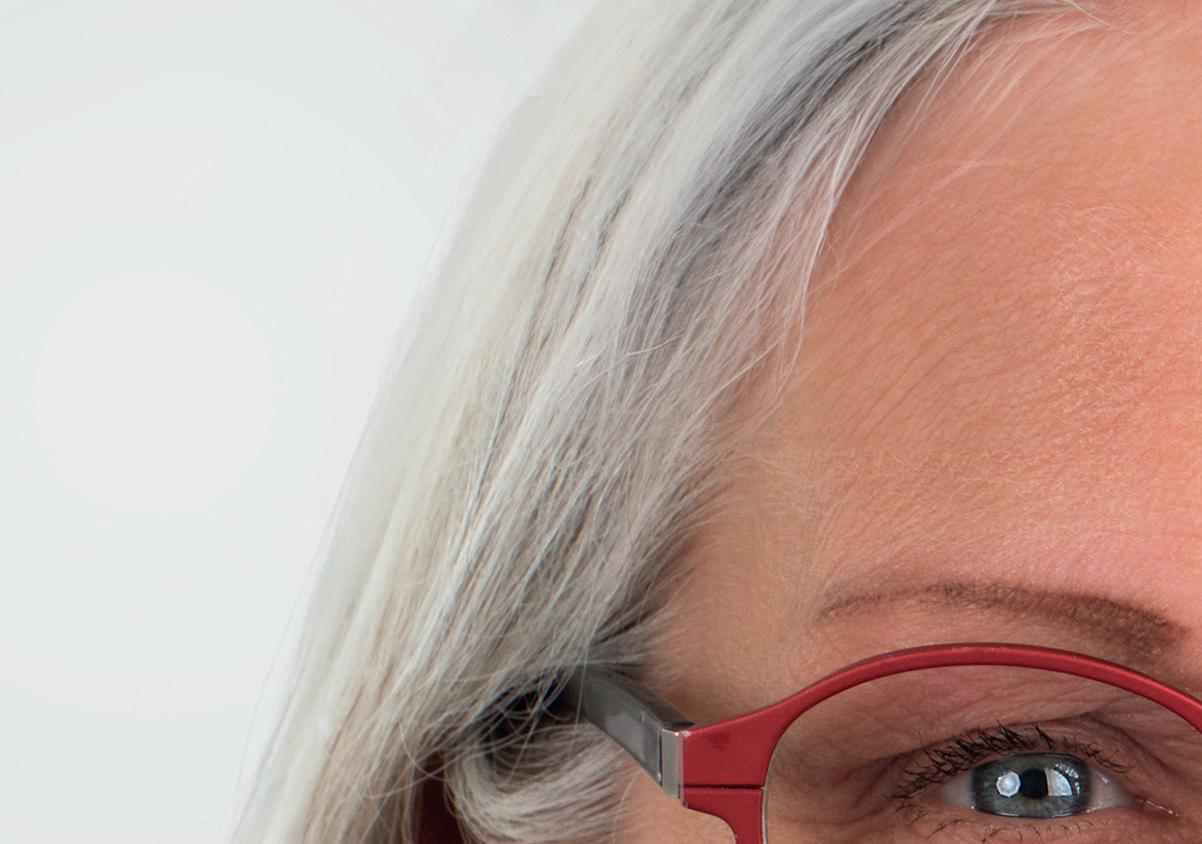
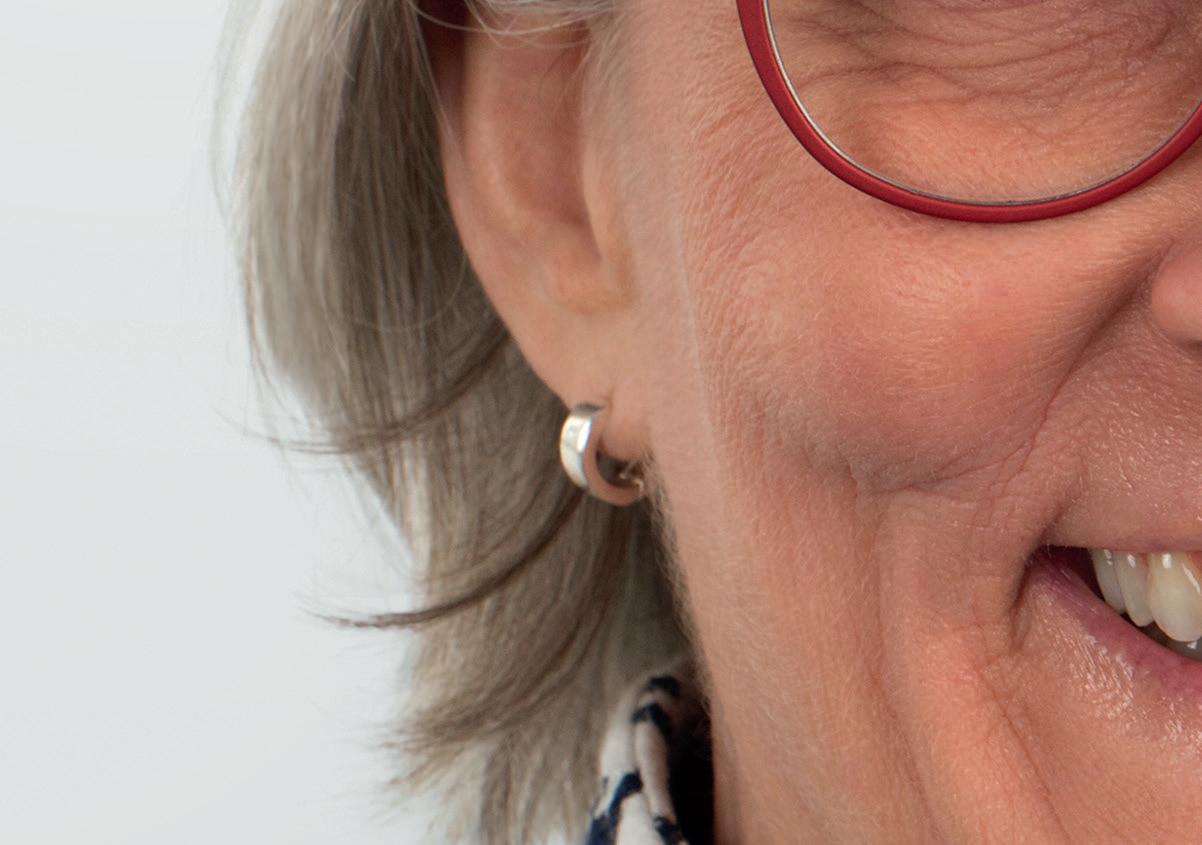

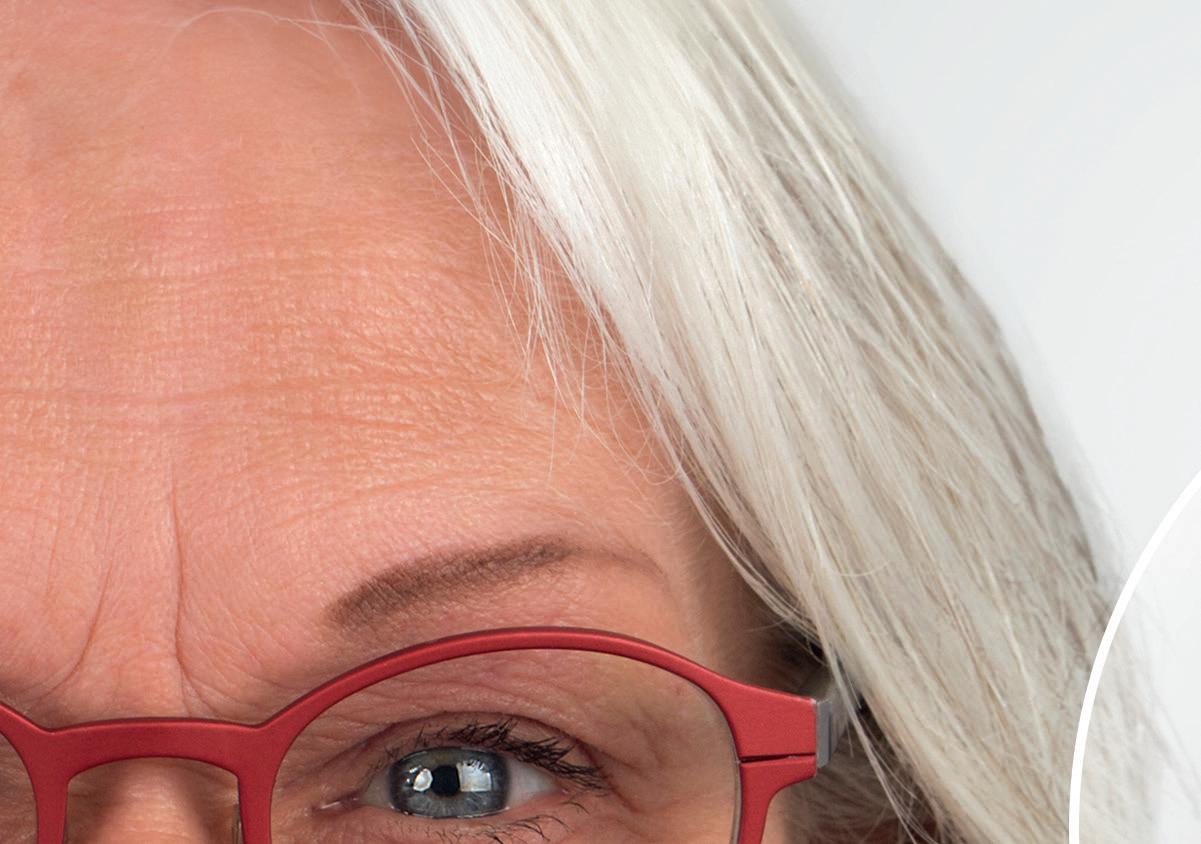
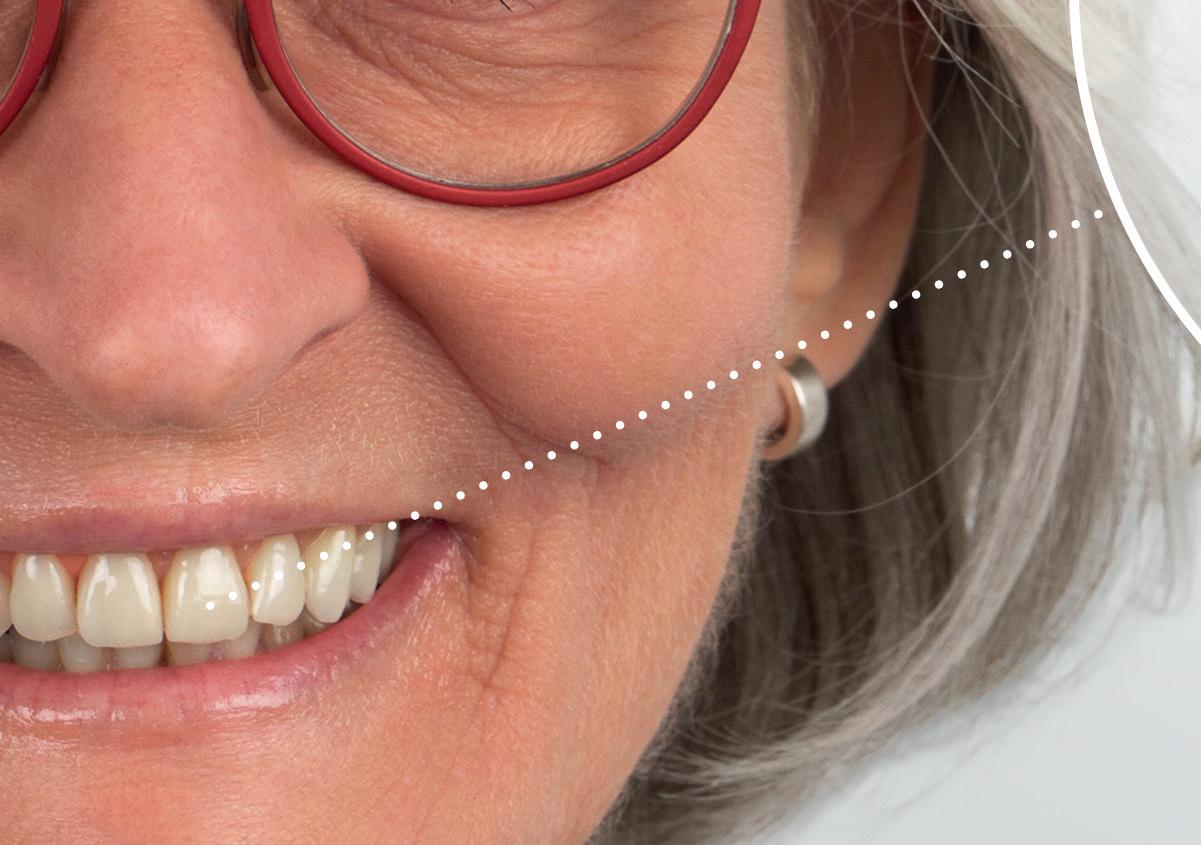
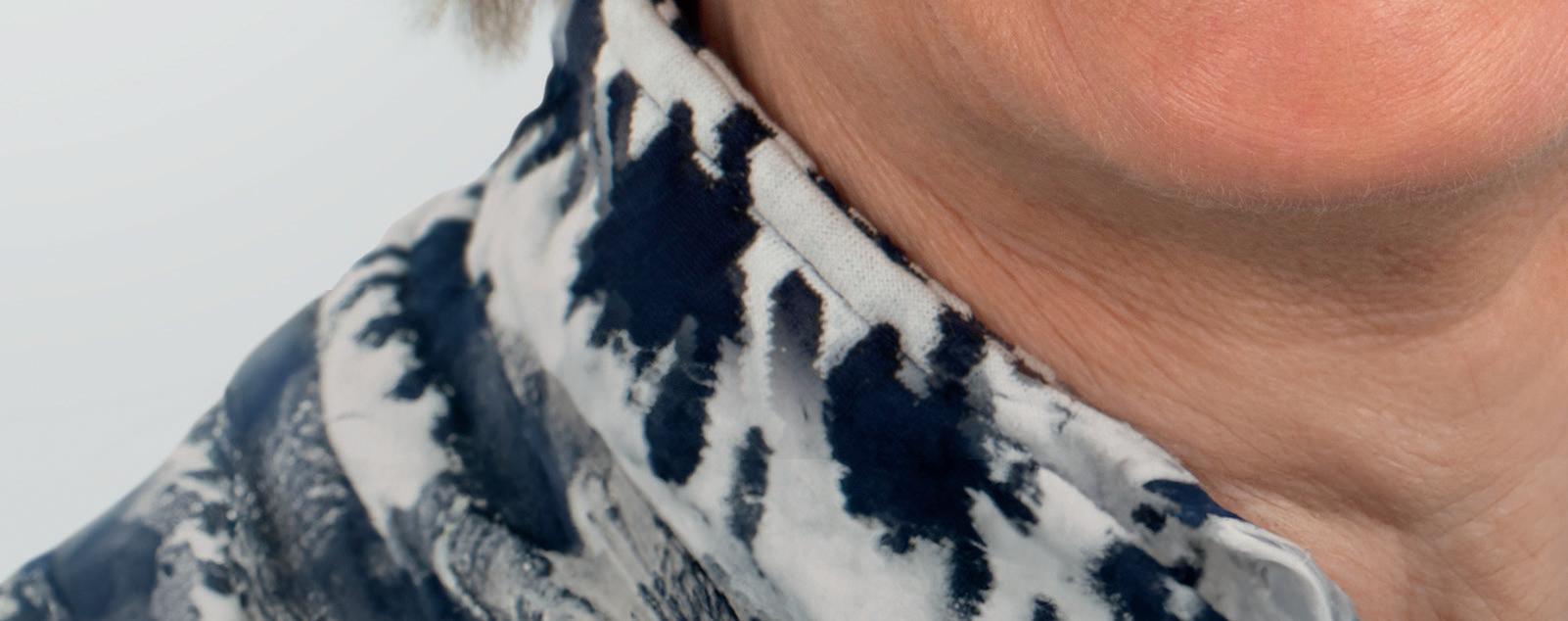
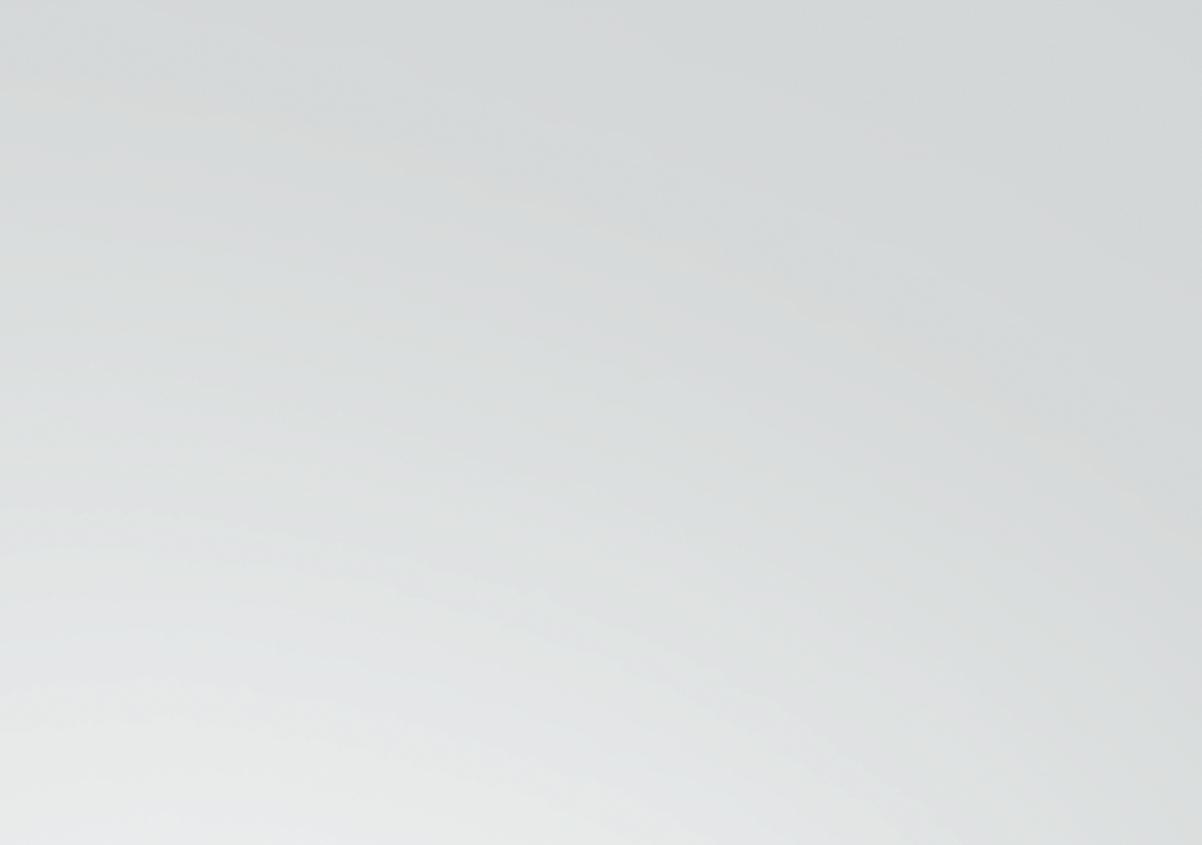
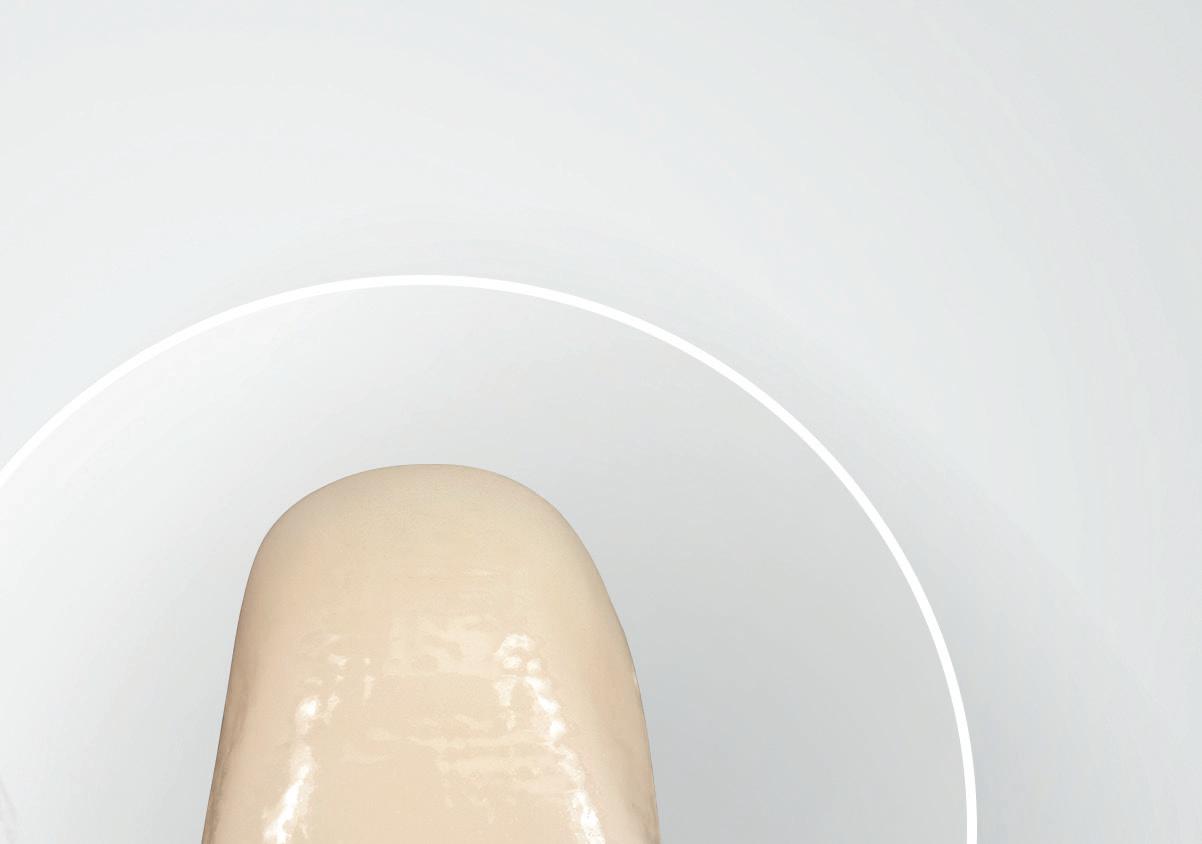
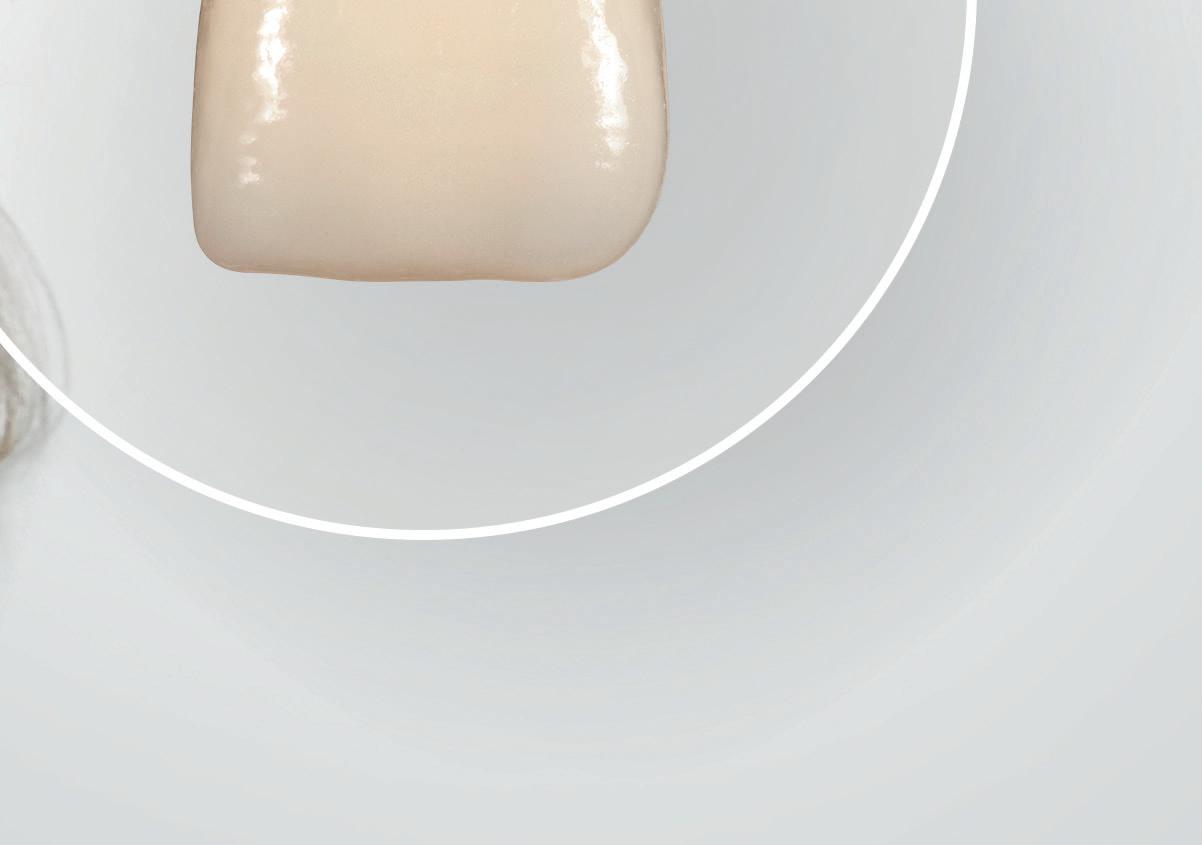
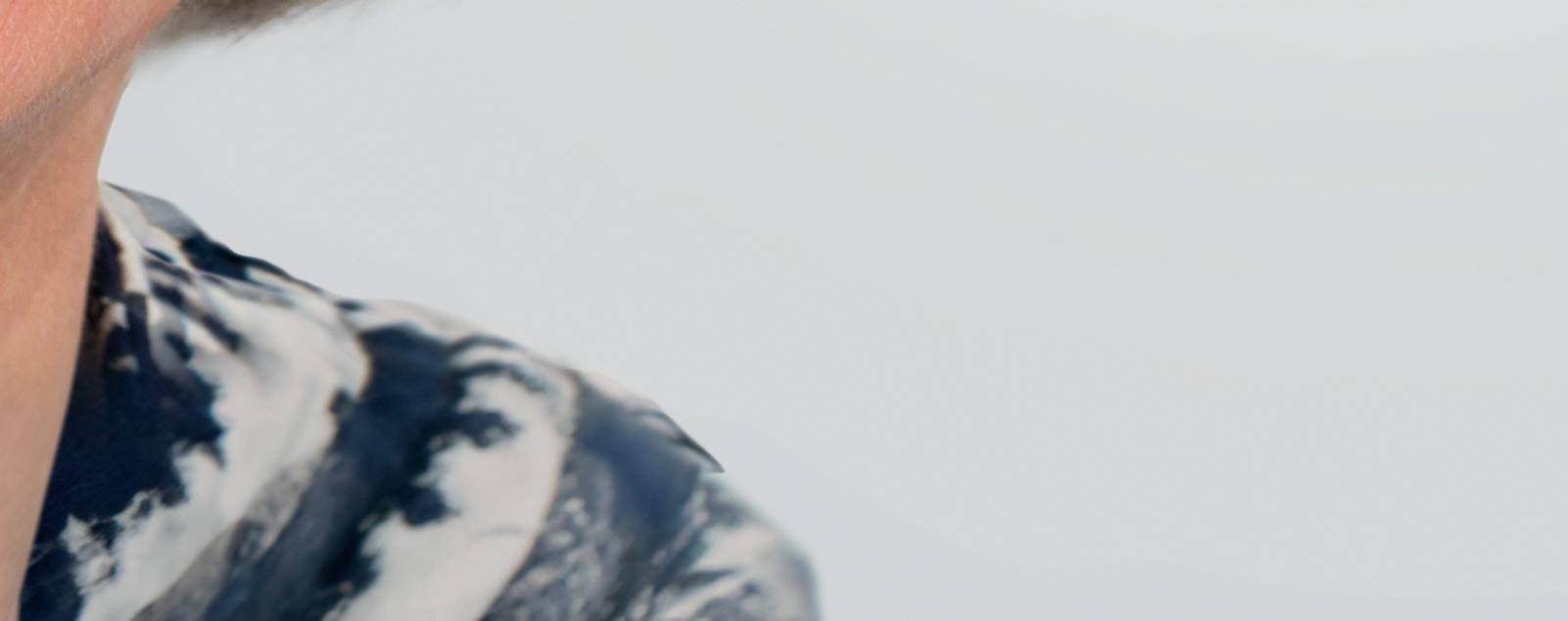
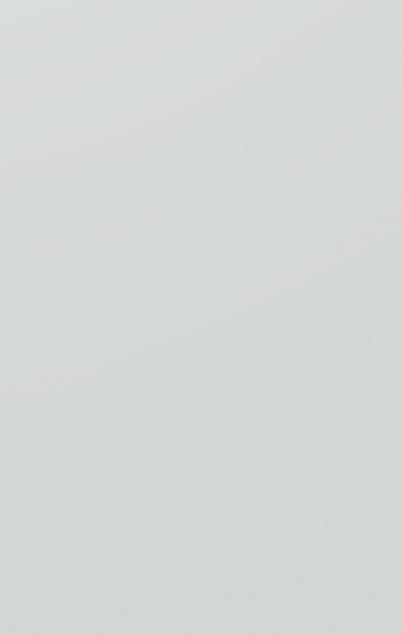
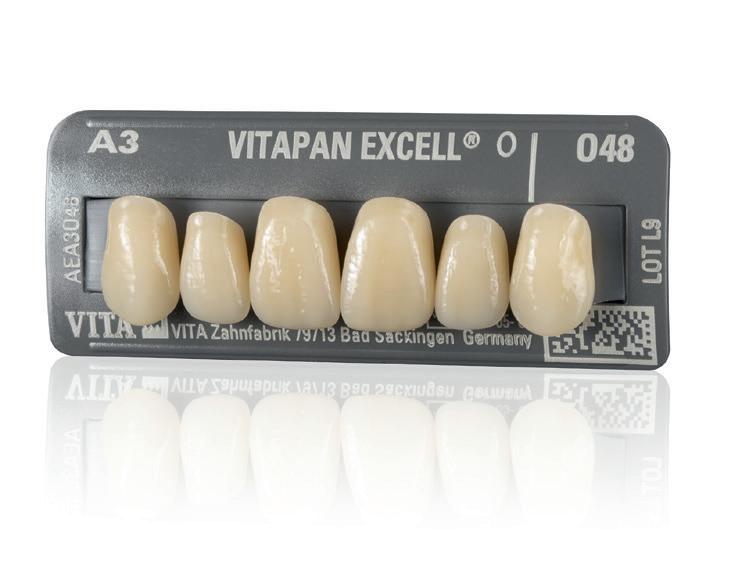
prosthetic

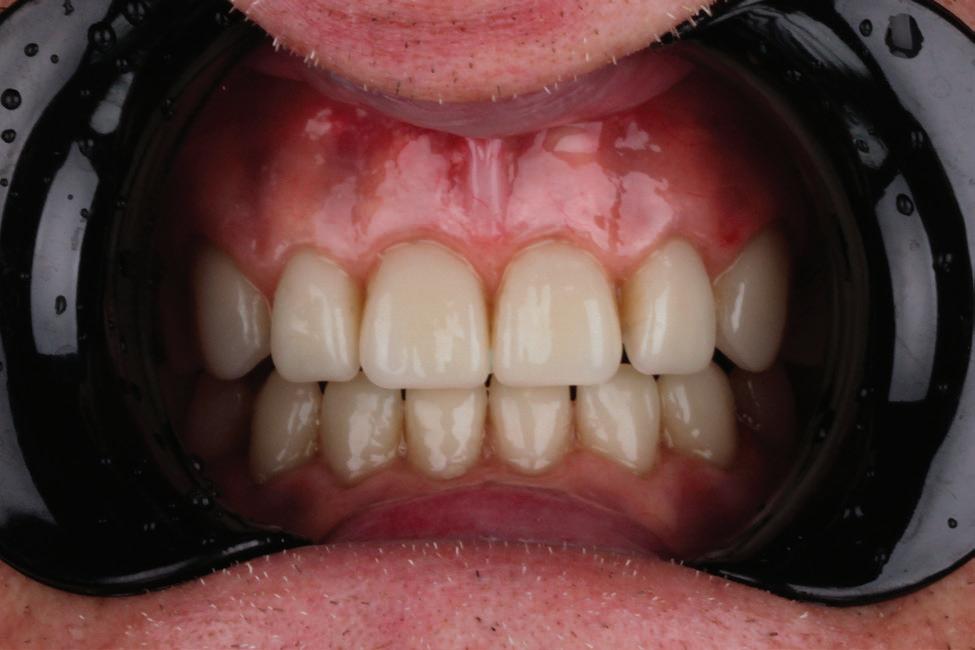
Tooth selection and setup
The right selection of the anterior teeth in the upper jaw is key to the rapid acceptance of a new restoration. In this case, the rectangular VITAPAN EXCELL R45 was selected in collaboration with the patient to fit the small vertical dimension, the smile line and at the same time, the width of the nose and the delicate facial features. The graceful, short VITAPAN EXCELL L33 was selected for the anterior of the lower jaw to match.
For the posterior region, the appropriate universal partner for all setup concepts, VITAPAN LINGOFORM 21L, with a delicate height and mesio-distal dimensioning, was selected. After the anterior teeth had been set up, the posterior set could be efficiently set up with the automatic centric finding, based on the gear wheel principle when the articulator was closed. After the mucogingival anatomy had been worked out, the clinical wax try-in could be done.
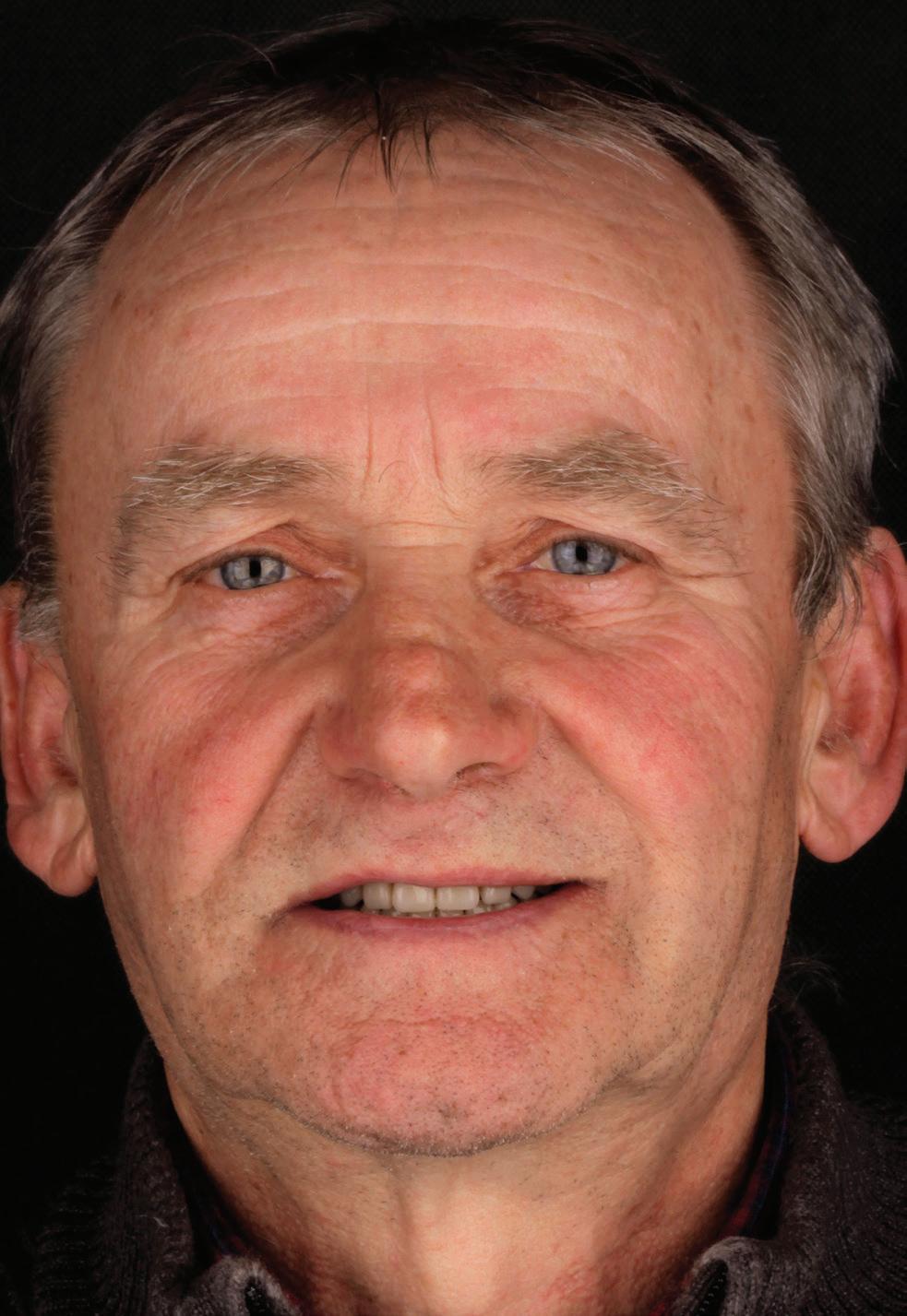
Implementation and integration
After embedding the teeth in cuvettes and wax extraction, they were repositioned and conditioned. Then whitish, crimson, light orange, blue and pink characterisations were made on the labial shield. The base was then inlayed with denture acrylics in shades of orange-red, dark red, light red, pink and dark pink and all the heat-curing resins were pressed from a single mould. After being stored in the pressure pot, the finished dentures were divested, finished and polished. The three-dimensional anatomically layered VITAPAN EXCELL of enamel, neck and dentine material appeared absolutely natural in the reproduced mucogingival anatomy of the denture base. Thanks to the successful aesthetic effect, the patient was able to quickly get used to his new dentures. After a short adaptation phase and minimal corrections in the biodynamic environment, his first full denture fitting went very well and he was completely satisfied.
About the author
Nela Zielonka, is a Dental Technician from Gaworzyce, Poland.
Figure 13. The restoration appeared highly natural in the mouth. Figure 14. The patient and his new teeth were in complete harmony.
Figure 12. The dentures were pressed with heat-curing resins in different shade facets.
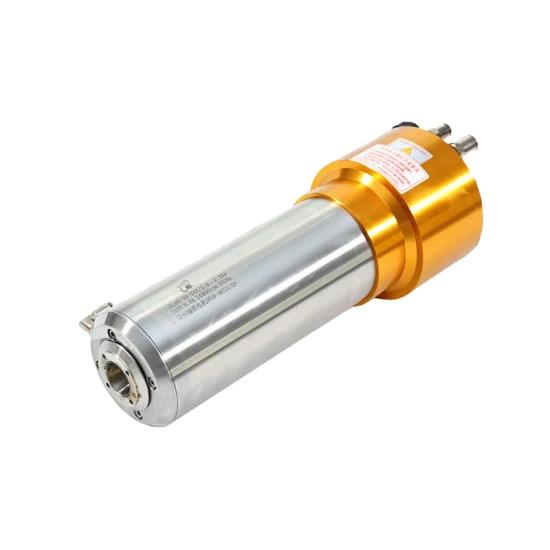
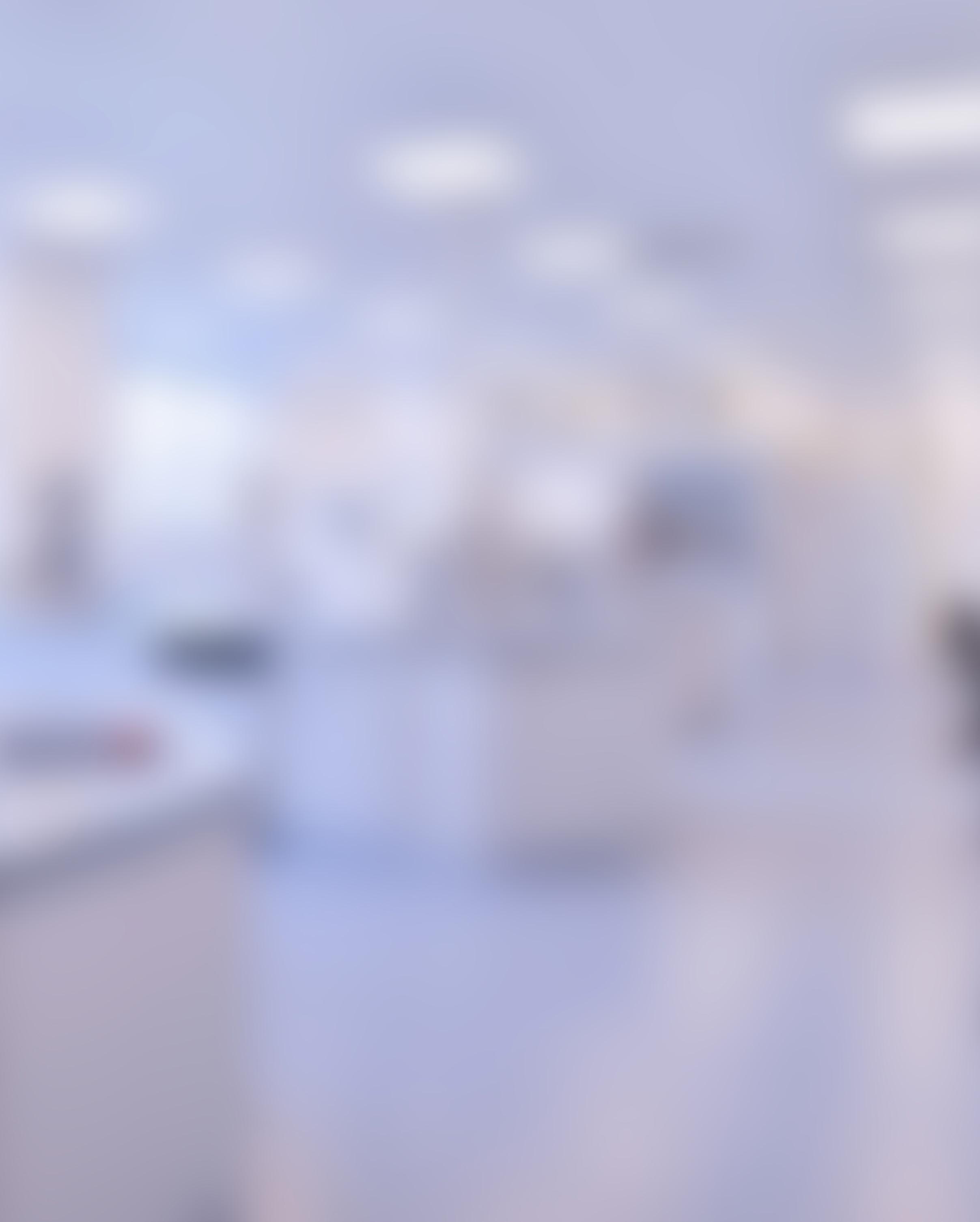
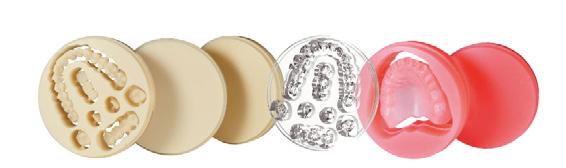
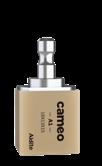

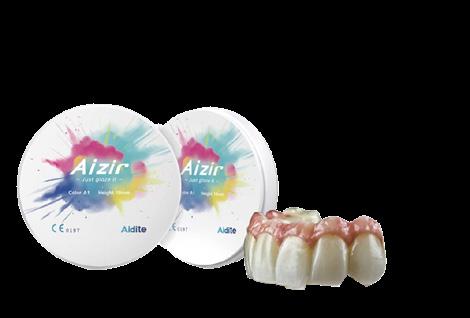
ALL MATERIALS
Create full dentures, Titanium frames and abutments, CoCr frames and copings, Zirconia, PMMA, glass ceramics, PEEK, HPP, and hybrid composite restorations with ease and precision.

The Silensor-sl anti-snoring device
By Peter Herring, Adv Dip Dent Tech, ACCDP
Since the introduction of the Silensor line of anti-snoring devices, hundreds of thousands of people worldwide have relied on it to assist to control their snoring.
The original Silensor was produced from 1997 to around 2012 and introduced the value of non-metal construction, protrusive adjustment using exchangeable arm lengths and repositioning of the mandible by anchoring the arms from the maxillary canines to the mandibular molar region, a design that has the advantage of maintaining protrusion regardless of the mandibular opening.
Building upon the experiences of the previous generation Silensor appliance the current iteration, the Silensor-sl, brings quicker and easier chemical free production, proven base materials (no 3D printing required), easy exchange of the connecting parts by the wearer (Figure 4a-b), increased patient comfort to maximise compliance and reduced mechanical stress on the components by virtue of the unique Double S shaped connecting arms that allows a sympathetic controlled following of jaw movements (Figure 5a-b).
FSubsequent improvements
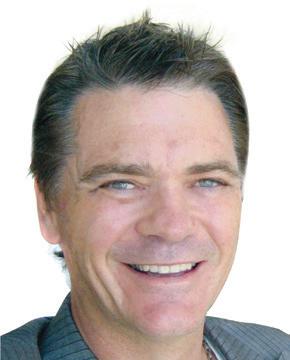
rom its introduction, the thermoformed Silensor-sl has continued to innovate...
Tinted bases: After the introduction of the Silensor-sl, coloured versions of the thermoforming foils used for producing the appliance bases became available. Using a different coloured foil to construct each base works well. For instance, now the wearer could quickly identify the correct orientation of the appliance for insertion, even in dim night lighting (Figure 2).
Occlusal equilibration: The occlusal design has a large bearing on comfort and appliance longevity. The two occlusal faces of the Silensor-sl bases are optimum when modified so that they interact smoothly and are free of jumps and interference in the allowed excursions. This works in harmony with the Double S connectors to reduce stress and increase comfort further. To facilitate this, an optional production step was added to create dual occlusal planes using the Occluform 3 at the same time as forming the bases.
Post Use Occlusal Repositioning - Bite Help Strip: After wearing a mandibular advancement splint overnight, there is a possibility that the masticatory muscles have temporarily assumed a different position. This has no long term consequences, but using the Bite Help Strip will accelerate the return to normal positioning. This is now included with each Silensor-sl (Figure 3a-b).
Figure 1. The Silensor-sl features:
• Adjustable advancement
• Highly comfortable
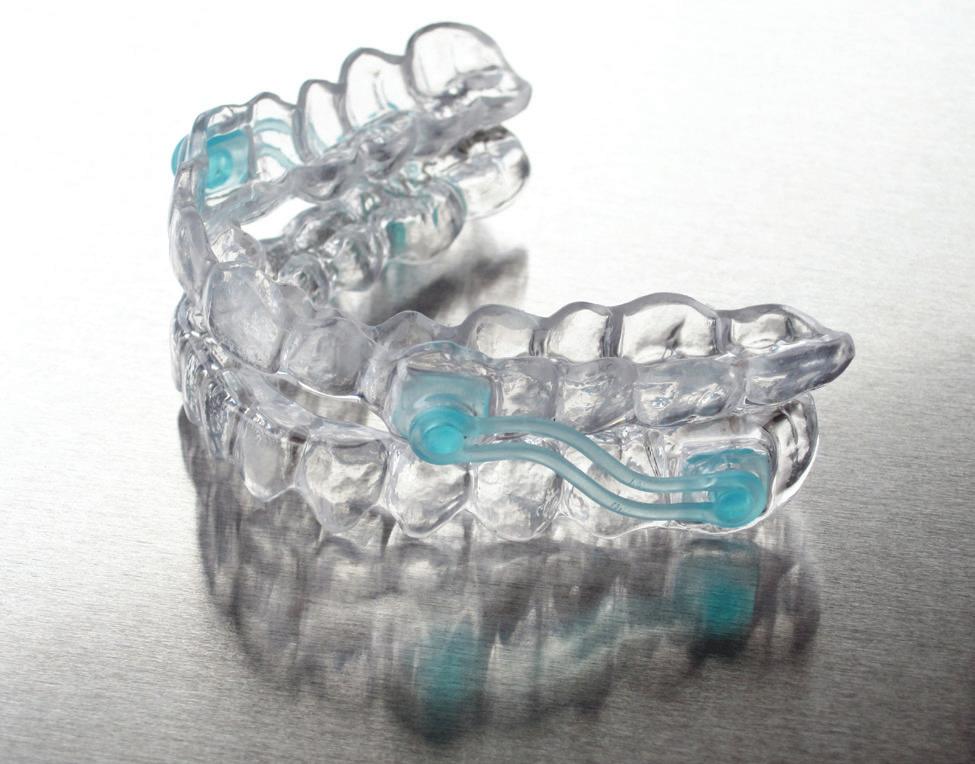
• Effective improvement of snoring symptoms
• Metal-free construction
• Time tested
• Non-toxic
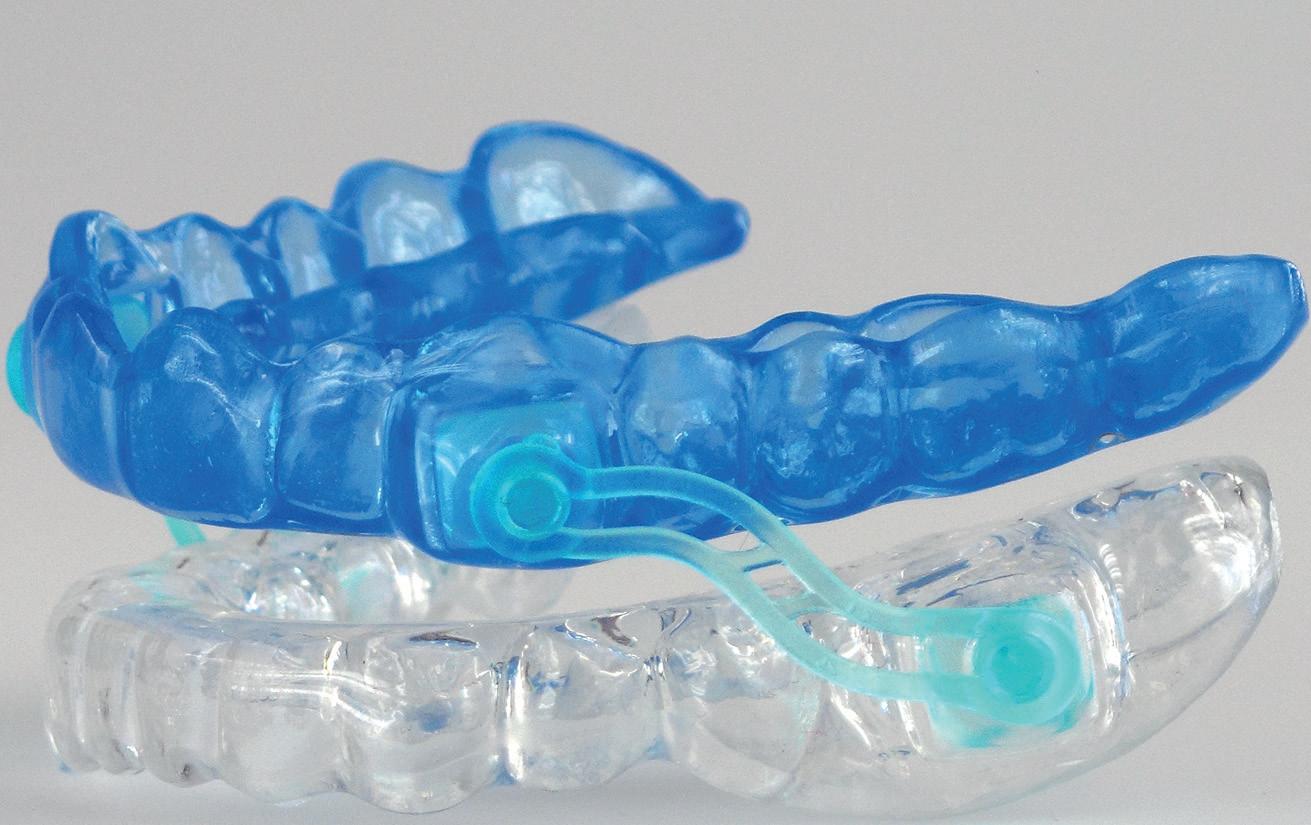
Figure 2. Tinted bases make it easy for wearers to orientate the appliance for insertion.
About the author
Peter Herring is a dental technician, prosthetist and a regular contributor to eLABORATE. He is the Australasian and Indonesian distributor for Erkodent products and spends his time between offices in Perth and Bali. He also operates a busy Australian lab dedicated to thermoformed appliances. He can be contacted at pjh@erkodent.com.au or for general enquires, call Freecall 1800-242-634.

Figure 3a-b. If the occlusion is misaligned after wearing the appliance overnight, the Bite Help Strip will speed the process of return to the normal position. This is included with each Silensor-sl.

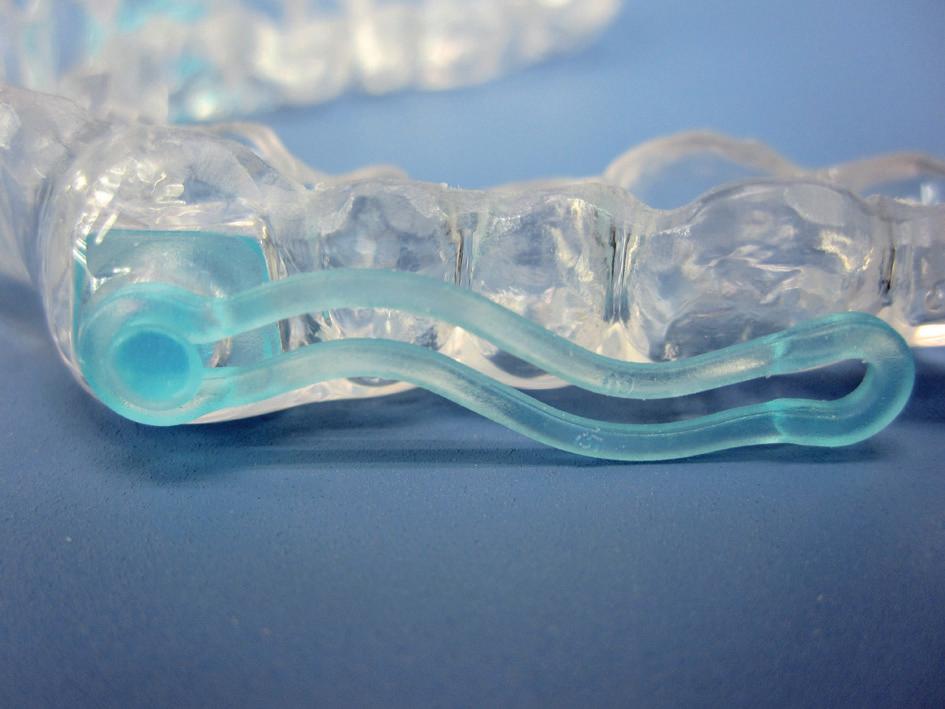
Figure 4a-b. The Double S connectors are exchangeable by the wearer without the need for special instruments.
Figure 5a-b. The Silensor-sl Double S connectors allow a light flexing and mobility of the mandibular fixing point. This improves wearing comfort and reduces load on the connecting area and components.
Information contained in this section is provided by the manufacturers or distributors. eLABORATE does not assume responsibility for the accuracy of the data.
BEGO VarseoSmile TriniQ

Introducing VarseoSmile® TriniQ® by CM MEDICAL, the latest advancement in dental 3D printing materials. Designed for versatility, it supports permanent crowns and bridges, extensive temporaries and denture teeth with exceptional stability and aesthetic quality. Offering 10 VITA® shades, outstanding polishability and superior translucency, it ensures seamless integration into natural dentition. VarseoSmile TriniQ boasts an efficient 3D printing workflow, high bond strength and excellent biocompatibility. Enhance your dental practice or lab with this revolutionary material, providing superior patient care and expanding your treatment capabilities.
Available: CM Medical Tel: 1300-466-588 info@cm-medical.com.au www.cm-medical.com.au
3D Pro zir zirconia blanks by Aidite

3D Pro zir is fabricated using Tosoh zirconia powder from Japan with the most advanced production processes at Aidite, producing a layerless, natural shade gradient, with optimal strength and translucency, transitioning from Cervical to Incisal. With a 3-point test flexural strength of >1050 MPa, 3D Pro zir ensures aesthetic results while being suitable for all indications from veneers and single crowns to 14-unit bridge structures. The 3D Pro zir
range allows fast high-performance sintering, with 2-hour sintering or more conventional cycles for larger spans. 3D Pro zir is available in 98 or 95 mm diameters, 16 shades of the classical VITA® shade guide and 3 bleach shades in thicknesses from 12mm to 25mm.
Available: Alphabond Dental Tel: (02) 9417-6660 info@alphabond.com.au www.alpabond.com.au
DOF CRAFT DRY All-in-One Milling
Introducing the new DOF CRAFT DRY milling machine by CM MEDICAL, designed for precision and efficiency. Featuring an 800W spindle and 5-axis with 90-degree milling, this machine ensures superior performance. The snap-in jig mounting system and automatic tool change with 21 tool pockets streamlines operations. Complete with a builtin operating system, compressor and dust extractor and housed in a sleek cabinet, the DOF CRAFT DRY is your all-inone milling solution for your lab with the latest in milling technology for Zirconia, PMMA and Hybrid Ceramic.
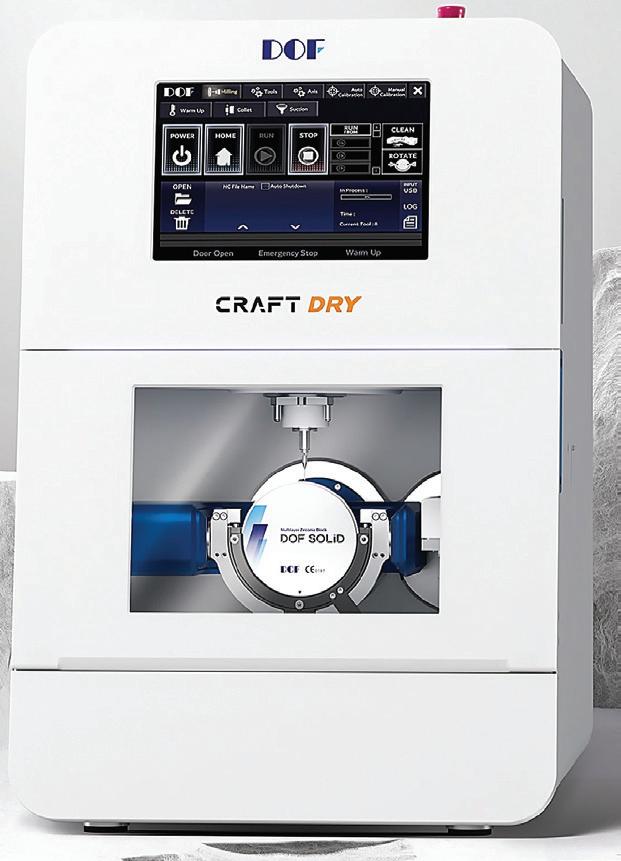
Available: CM Medical Tel: 1300-466-588 info@cm-medical.com.au www.cm-medical.com.au
Scantist 3D Vanishing Scan Spray
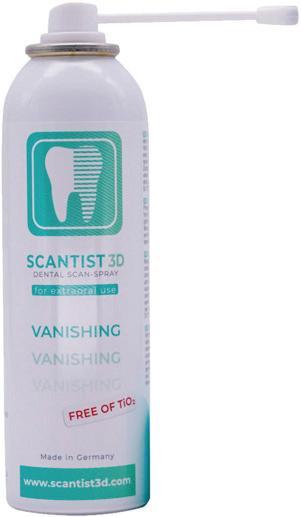
Scantist 3D Vanishing Scan Spray is an extraoral scan spray for use in the dental laboratory to optimise the quality of CAD/CAM recordings, camera/video recordings, structured light scans, blue light scans, etc. Scantist 3D Vanishing Scan Spray evaporates/sublimates automatically after application and contains no pigments or titanium dioxide (TiO2) which results in no contamination of the object, environment or user. The ultra thin, very fine homogeneous coating creates a non-slip surface. It is efficient and economical thanks to precise application using a special valve with fine nozzle and adheres to all materials - even on very smooth surfaces. It also does not have a corrosive effect.
info@alphabond.com.au www.alpabond.com.au
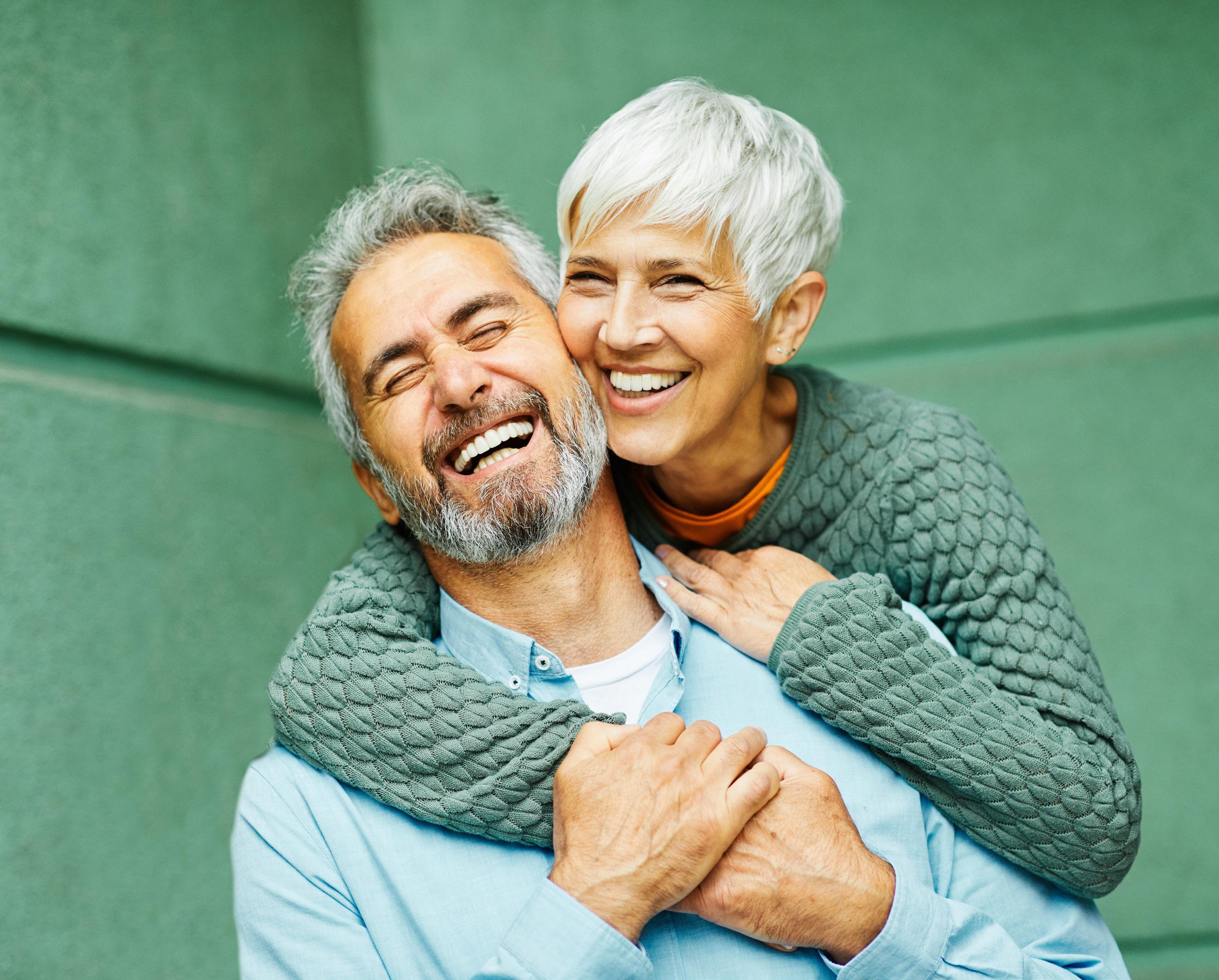
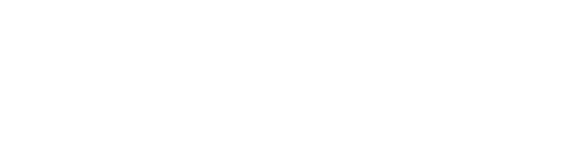
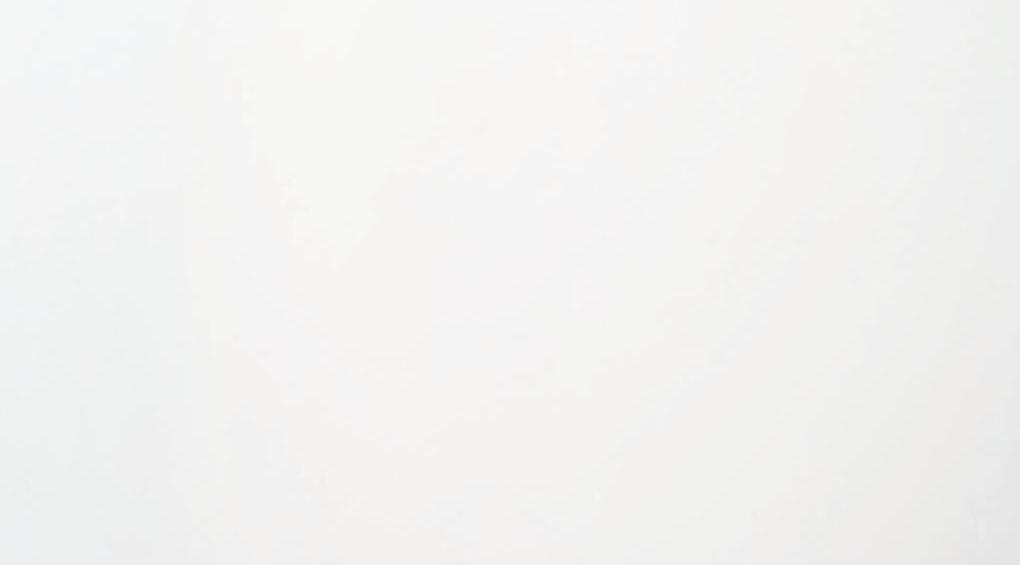
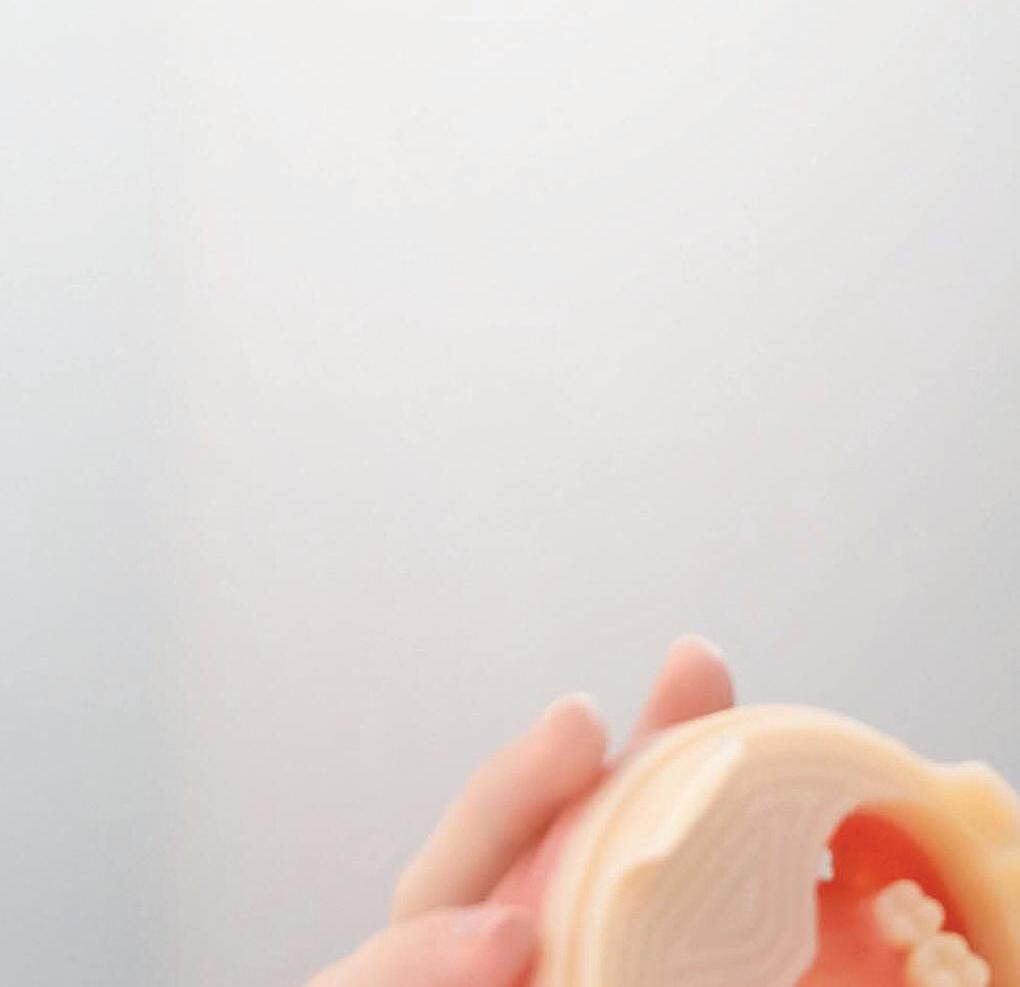
One disc. One denture.



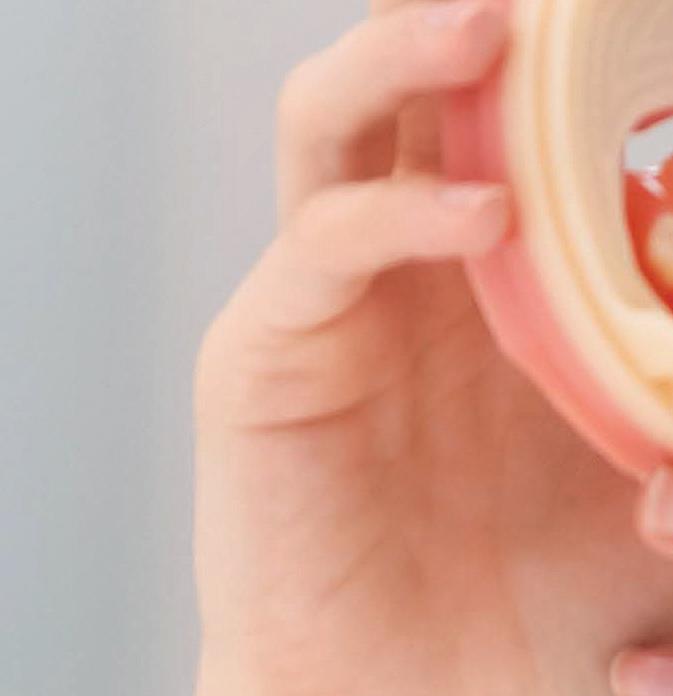
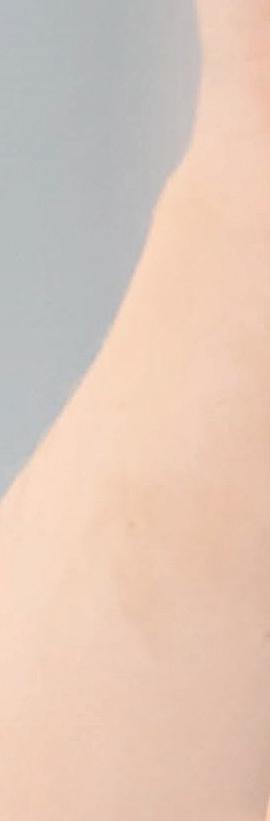
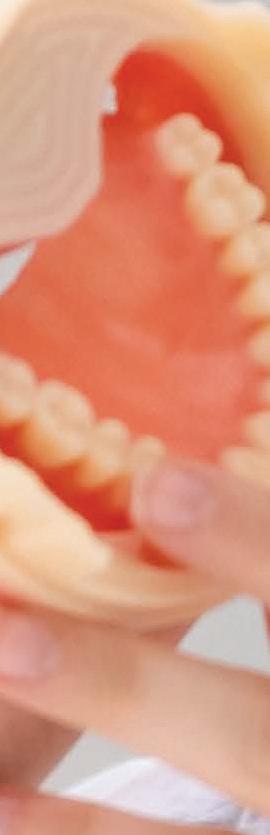

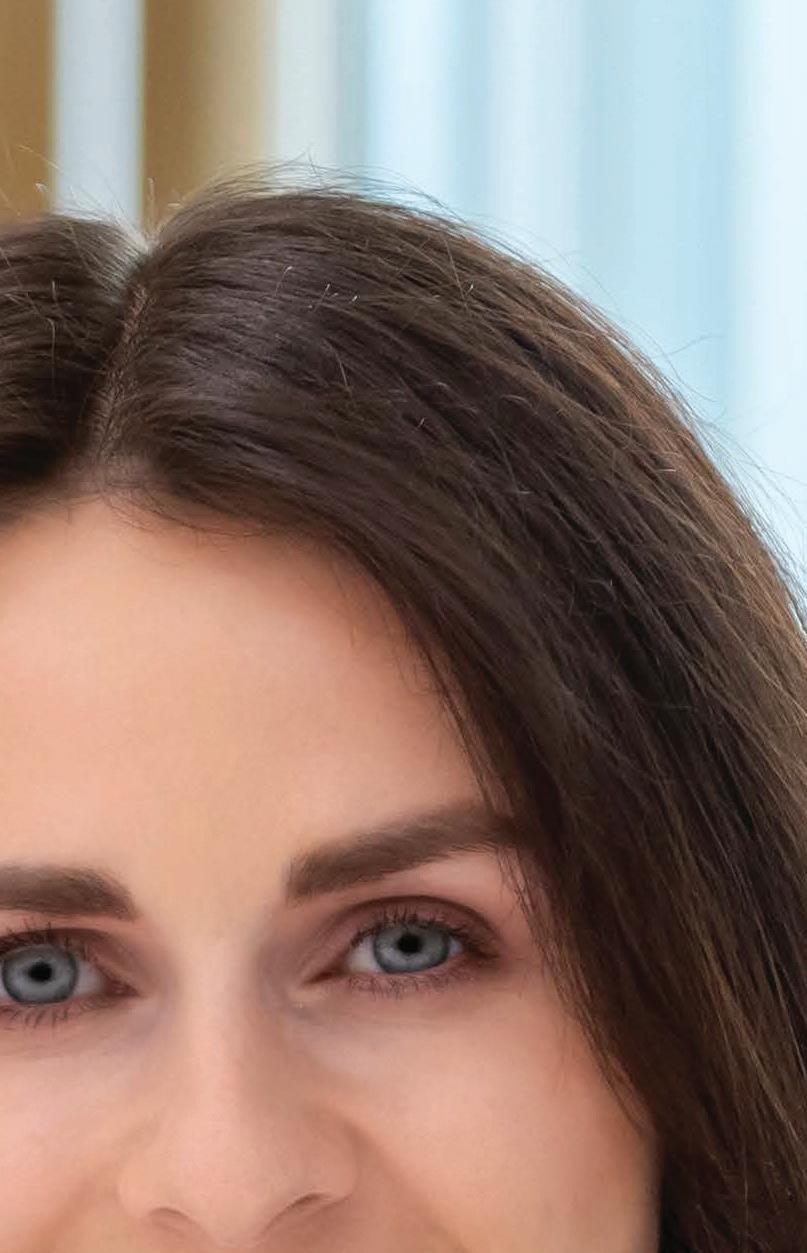
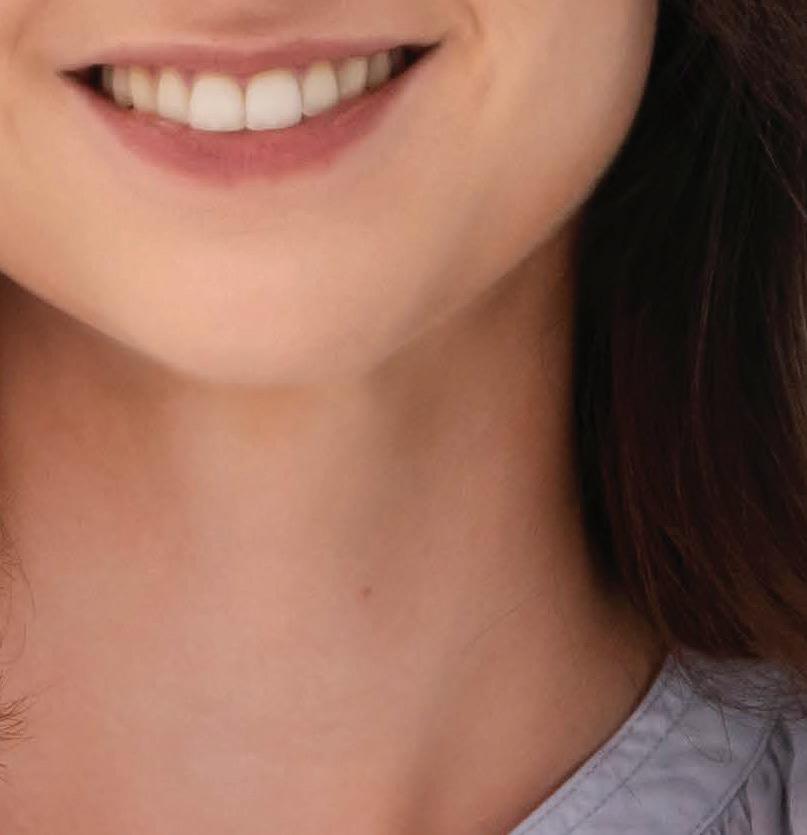
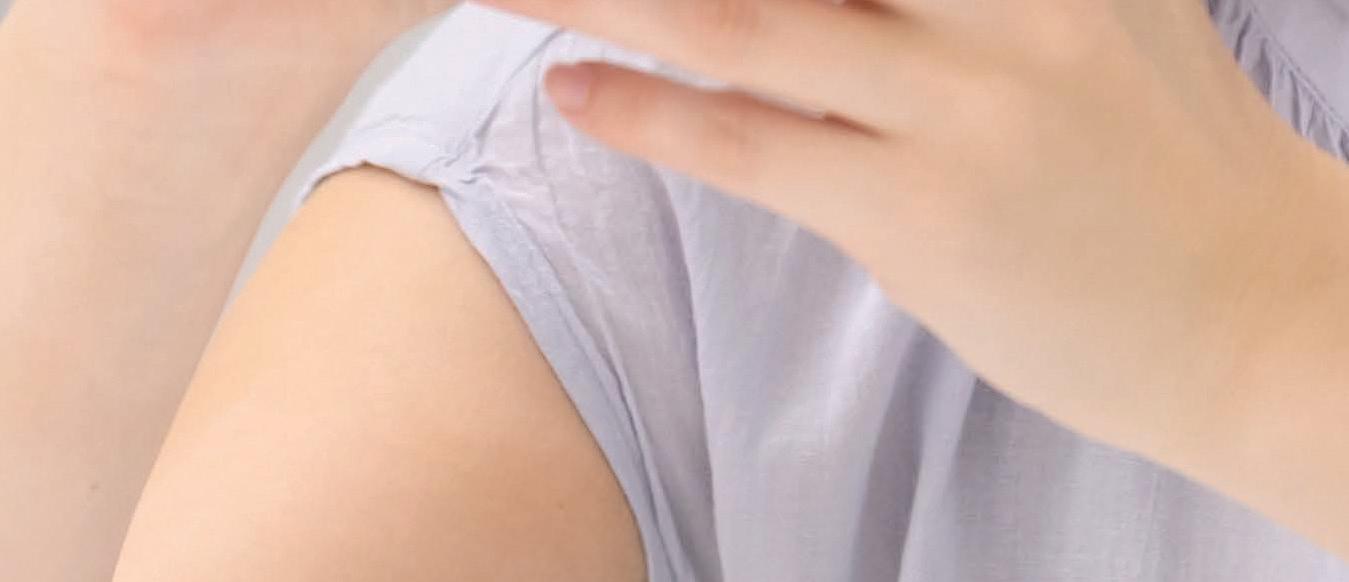
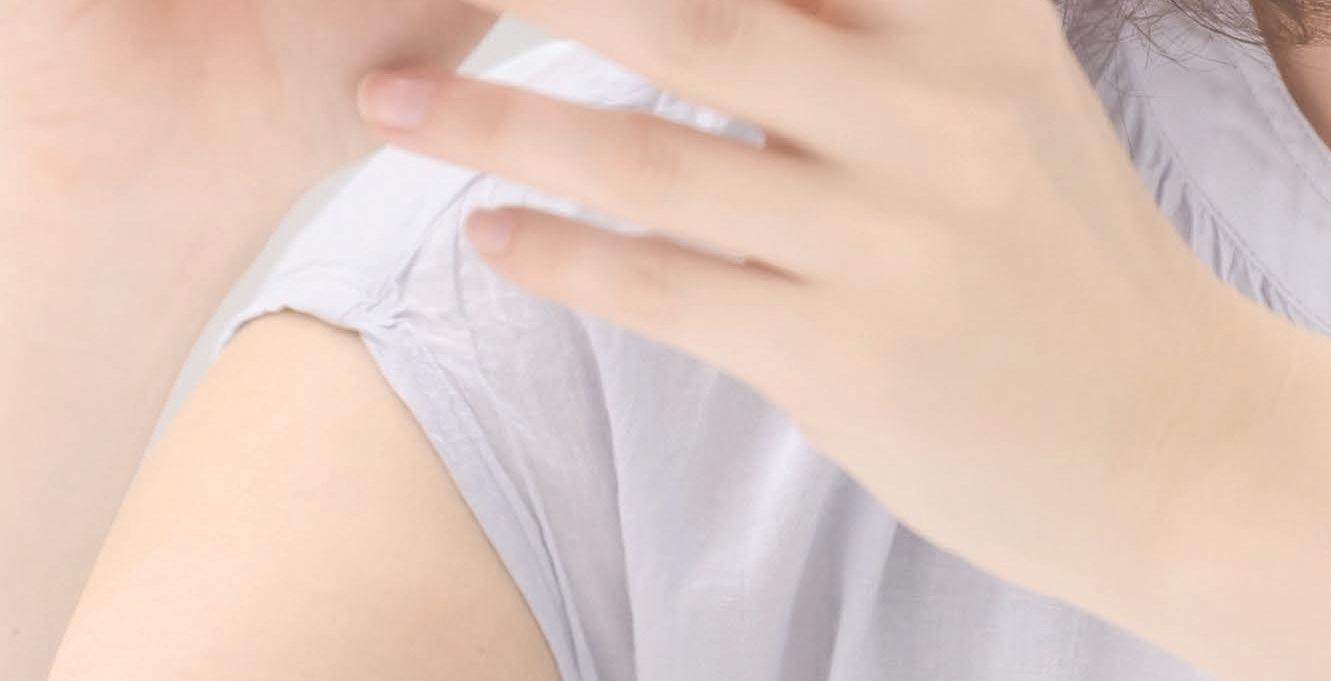
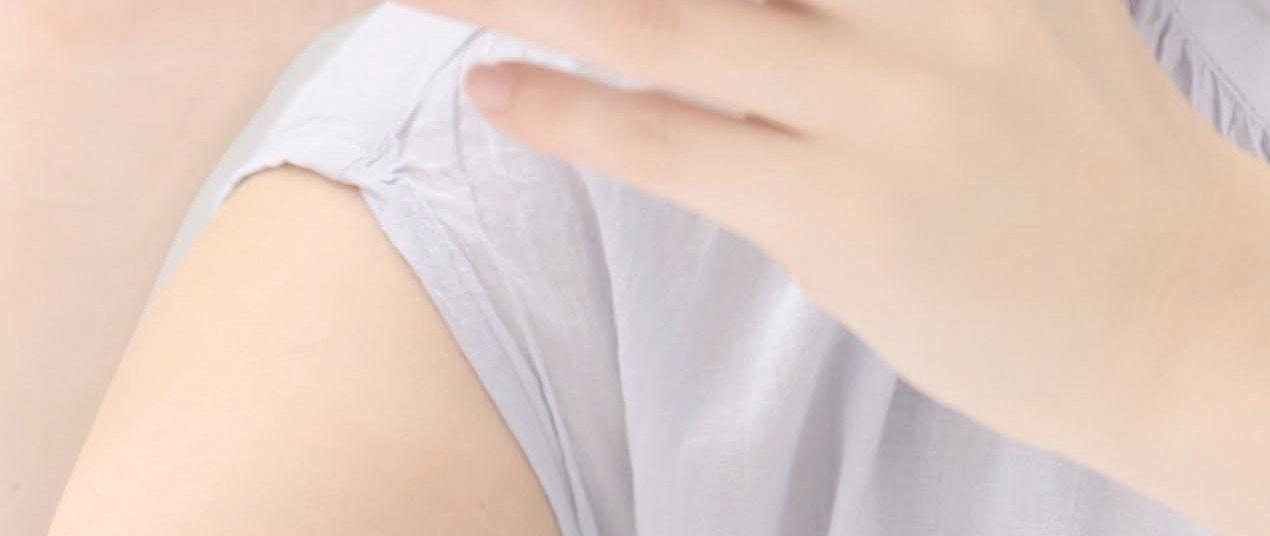



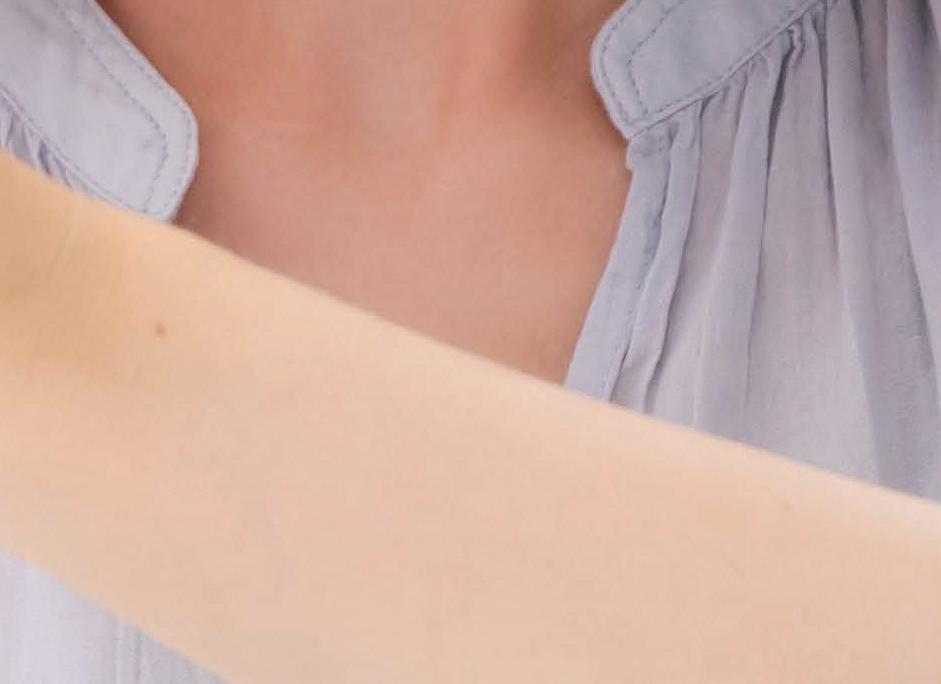
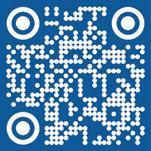


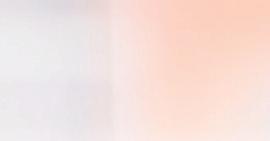
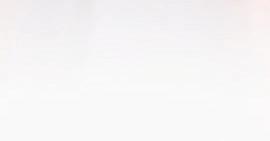
