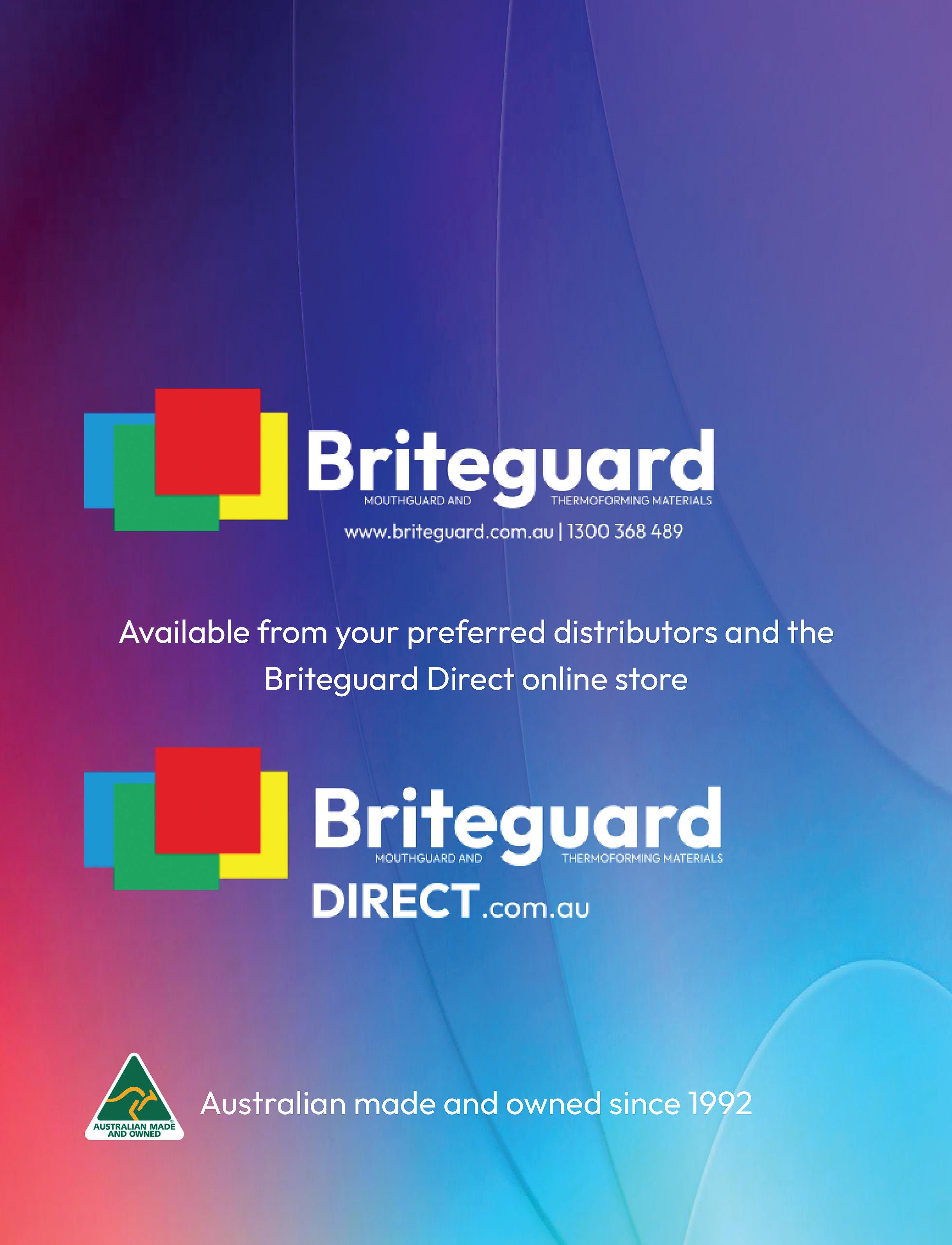

SYDNEY 24-25 MAY 2024
NOVOTEL SYDNEY BRIGHTON BEACH
TWO DAYS OF LECTURES AND WORKSHOPS ON DIGITAL DENTISTRY FOR DENTISTS, SPECIALISTS, DENTAL TECHNICIANS AND DENTAL PROSTHETISTS
TWO DAYS OF LECTURES AND WORKSHOPS ON DIGITAL DENTISTRY FOR DENTISTS, SPECIALISTS, DENTAL TECHNICIANS AND DENTAL PROSTHETISTS
TWO DAYS OF LECTURES AND WORKSHOPS ON DIGITAL DENTISTRY FOR DENTISTS, SPECIALISTS, DENTAL TECHNICIANS AND DENTAL PROSTHETISTS
TWO DAYS OF LECTURES AND WORKSHOPS ON DIGITAL DENTISTRY FOR DENTISTS, SPECIALISTS, DENTAL AND DENTAL
REGISTER NOW and SAVE!
As the new year kicks off, already there are over 350 events listed on dentevents.com with more being added every day. The dental profession is once again spoiled for choice when it comes to getting educated! There are so many opportunities to upskill with everything from face-to-face bespoke hands-on workshops, to lectures to major congresses and exhibitions... so don’t miss this out!
And we’ve been busy too.
After kicking off 2024 with our 3D Printing in Dentistry event, we’re now working hard to finalise our major event for the year, Digital Dentistry & Dental Technology 2024 The 5th edition of DDDT in Sydney will again showcase the talents of our best and brightest clinicians and technicians who work with the latest digital techniques and technologies on a daily basis. The change to digital is unrelenting and this event is the place to connect with the right people and take a giant leap forward in your knowledge and understanding. DDDT24 will encompass 3D printing, intraoral scanning, 3D facial scanning, milling, CAD and CAM software, materials, smile design, digital dentures, implantology, CBCT, restorative, aligners, orthodontics and more. The multi-stream two-day event gives you complete freedom to create a programme that precisely meets your educational requirements. More at www.dentaltechnology.com.au
Leading up to that and if you’re after some tax deductibility to attach to the April school holidays - in New South Wales, ACT, South Australia and Tasmania at least - then look no further than IDEM Singapore 2024 on April 19-21. As a travel hub, there are now plenty of flights at very reasonable prices on offer to Singapore, including from Qantas and also from Singapore Airlines, the official partner airline for the event. When visiting Singapore with kids, you’re completely spoiled for choice when it comes to world class accommodation at reasonable prices, amazing dining experiences ranging from a few dollars at an outdoor market to fine dining... And then there is so much to doUniversal Studios, Sentosa Island, water parks, the Night Safari zoo, botanical gardens and more... plus Legoland and the Bintan Island resorts are only an hour away by car to Malaysia and ferry to Indonesia respectively. Plus, get excited at about the stellar educational line-up and expansive trade exhibition at www.idem-singapore.com.
Rounding off the first half of the year, we have Laurie Walsh presenting a must-attend Infection Control Update 2024 that details all of the recent changes since the adoption of the new AS:5369:2023 Reprocessing of reusable medical devices and other devices in health and nonhealth related facilities published in December 2023. Register at www.icupdate.au
Enjoy the edition...
Joseph Allbeury, Editorand Publisher
Digital Dentistry & Dental Technology is back for a 5th edition in 2024 in Sydney on May 24-25. The two-day, multi-stream event is proving as popular as ever with its unique format, allowing delegates to create their own event within an event.
“We’re looking forward to celebrating 5 editions of Digital Dentistry & Dental Technology with the biggest and best event yet,” said Dentevents’ Joseph Allbeury, the organiser and publisher of this magazine. “We’re already working with sponsors and supporters to bring in top international speakers to present alongside the stellar local talent from Australia and New Zealand we always feature. Back in 2019, we had over a dozen internationals alongside speakers from Australia and New Zealand and now that COVID is behind us, we’re hoping to bring back the international flavour.”
Digital Dentistry and Dental Technology 2023 presented delegates with a choice of over 90 education sessions including 18 workshops - 94 hours of content - in 8 concurrent streams presented by 46 speakers over two days at the Novotel Sydney Brighton Beach.
Topics covered included 3D printing, intraoral scanning, 3D facial scanning, milling, CAD and CAM software, materials, smile design, digital dentures, implantology, CBCT, restorative, aligners, orthodontics and more.
“If you’ve never attended before, have been multiple times or attended every event, we would encourage you to take advantage of the 75% off early bird discount available and register for only $220 until November 24.”
For more info or to register for Digital Dentistry & Dental Technology 2024, visit www.dentaltechnology.com.au
3
UNIVERSAL SIZING
120mm 125mm 127mm
for use with any
or
www.briteguard.com.au
All Briteguard material conforms to the guidelines for the fabrication of Sports Mouthguards Standards Australia International/Australian Dental Association CS 009 2003.
120mm 125mm 127mm
All Briteguard mouthguard materials are manufactured in Australia by Sportsguard Pty
Suitable for use with any Pressure Forming or Vacuum Forming Unit.
Fnent brand in the 3D printing industry and has become a market leading manufacturer in dentistry, best known for their robust and reliable 3D printing technologies.
Not only this, but Asiga have also embraced the rapid development of 3D printing materials by providing their customers with “plug & play” profiles for most, if not all, market leading dental 3D printing materials. Their library now boasts more than 500 qualified material profiles from many of the world’s best known and respected material manufacturers. To offer such freedom in a rapidly evolving industry is testament to Asiga’s objective: to provide their customers the best possible outcome in an everevolving landscape.
At 3D Printing in Dentistry 2024 in Sydney, Asiga revealed two new 3D printers, the Max 2 and the Ultra. The Max 2 is a significantly updated version
of their hugely popular MAX with a major packaging upgrade and a remarkable new user interface. The Ultra, however, is the show stopper stealing, positioning itself as arguably the most advanced dental 3D printer ever.
Housing the latest 4K DLP imaging technology alongside the full suite of Asiga’s robust layer monitoring technologies, the Ultra delivers manufacturing certainty but with a new focus for the sector –design. It is clear that Asiga has taken note and listened to their customers to bring to market a product where the end-user is front and centre.
You cannot help being drawn to the Ultra. It all starts with their new and beautifully designed user interface which feels like something straight from a market leading tablet/phone manufacturer. Menu navigation, infographics and the responsiveness of the user interface screen all have a high quality feel and draw you in for more.
A feature that will most definitely have you hooked is their new touchless entry, an engineering marvel in itself. Asiga
surely had a lot of fun with this and with a simple hand-wave gesture, the hood opens effortlessly and is so silent that it leaves you helplessly opening and closing the hood. Once you have satisfied your desire to play with the hood, it is clear that the attention to detail and build quality of the Ultra is nothing short of exceptional.
A magnetic build platform, simple material tray clamping, internal lighting and wide range of connectivity options all help in the presentation of a cleverly refined 3D printer for both the dental laboratory and dental clinic.
Another key feature to the Ultra is a new infrared heating system which warms materials to 70°C. This opens doors to new polymer technologies where high impact and hardness are key material properties. This is an exciting time for 3D printing and dentistry in general and these new products from Asiga will certainly be turning heads.
For more information on Asiga and these new 3D printers, visit www.asiga.com.
After openings in Toronto and New York City, the Italian company lands in the southern hemisphere with Zirkonzahn Australia
The countdown has started! In the north of Sydney, Zirkonzahn will soon open a brand-new facility: Zirkonzahn Australia - the company’s 14th location worldwide, following the latest openings in Toronto and New York City. Only a few minutes from the city centre, the facility will host educational training on Zirkonzahn products and devices for all dentists and dental technicians who wish to know more about the company’s workflow and work philosophy.
The training courses offered on-site are part of the Zirkonzahn School - the wide, well-structured, and targeted educational programme developed by the Italian company with the aim of teaching the use of its equipment and materials with no knowledge gaps.
But that’s not all - Zirkonzahn Australia will also feature a logistics department
for supplying materials without delivery delays. Moreover, the on-the-ground CAD/CAM expert, Rian Barnard, will support clients and potential customers in the creation of their workflow with Zirkonzahn products, explaining and showing the different components as well as answering all technical questions. With the new opening, Zirkonzahn customers and potential clients from Australia can now see first-hand all the company’s innovations and solutions without flying to the headquarters in Italy (which is, however, always worth a visit: Zirkonzahn’s doors are always open to dentists and dental technicians wishing to discover where all products are manufactured and enjoy the typical South Tyrolean culture that has shaped Zirkonzahn since the beginning).
What started as a one-person business is now a workplace for more than 300 employees all over the world, in various
facilities and training centres. In South Tyrol, Italy, Zirkonzahn has its headquarters, main education centres, a dental laboratory and five production sites. The company also owns 26 facilities and education centres in ten different countries.
In the heart of the Italian Alps, with the core values of discipline, innovation, trust and responsibility, the family-run company Zirkonzahn has been providing solutions and approaches for the dental sector since its foundation in 2003. The know-how and skills developed during the years are inherited from father to son, both Master Dental Technicians, ensuring continuity to clients and building with customers lasting relationships based on mutual trust. 88
BECAUSE WE LOVE WHAT WE DO
BECAUSE
Being a dental technician implies great experience and dedication.
Being a dental technician implies great experience and dedication.
It means pure sensation, attention to the smallest details and observation of all nuances.
It means pure sensation, attention to the smallest details and observation of all nuances.
Striving for perfection requires aesthetics: the desire to imitate the perfect beauty of nature.
Striving for perfection requires aesthetics: the desire to imitate the perfect beauty of nature.
Dental technology is a handicraft and human art which machines cannot replace, but only support.
Dental technology is a handicraft and human art which machines cannot replace, but only support.
This consciousness that stems from our authenticity, is the proud vocation of being a dental technician.
This consciousness that stems from our authenticity, is the proud vocation of being a dental technician.
From patient diagnostics to the final restoration, Zirkonzahn’s main goal is to optimise the collaboration and communication between dentists and dental technicians, providing clinics and laboratories with dedicated instruments forming an optimum match in the complete workflow. Under the motto “Everything under one roof”, all milling units, dental materials, hardware, software, tools and implant prosthetic components are conceived and developed in-house to guarantee constant control over the production process and therefore comply with the highest quality standards. Only in this way, all products can be perfectly coordinated with each other.
From Zirkonzahn, clients don’t just buy “a product”. They buy a whole work philosophy that includes the conception of a seamless and well-coordinated dental workflow - with the possibility of switching from digital to analogue and vice versa - a complete package of services and reliable support. With the company’s multilingual helpdesk, customers can benefit from comprehensive technical support with extremely short response times
provided by a dedicated team, ready to quickly solve all customer’s needs at any workflow stage.
Always developing innovative technologies and searching for smart, unconventional solutions, all hardware components and software modules generate open data formats (e.g. STL, OBJ) which are therefore compatible with all open CAD systems, milling units or 3D printers. Of course, also open data (scans or design files) from other manufacturers can be processed with Zirkonzahn’s wide range of products. In this way, customers can benefit from a complete system which can be personalised und upgraded according to different combination possibilities to meet all one’s requirements. Moreover, the CAD/CAM system design can be customised on request in all colours and different styles, expressing every attitude. With our products, we offer a complete solution to produce high-quality dental restorations.
IAlways at your side to face the future
n dentistry as in the broader world, whoever is up-to-date with the latest news in their field demonstrates competence, professionalism and versatility. Any dentist would be excited to work with a dental technician who, along with the excellent restorations delivered, can offer an incomparable advisory service on the latest effective working techniques to meet all of a patients’ demands. From new working methods to new materials, through the most advanced CAD/ CAM technologies, any new Zirkonzahn invention aims at bringing clinic-lab communication to new levels and finding an ever-increasing balance between function, aesthetics and technical simplification. As in all battles, the duel against the lazy and dull routine can only be won with passion and perception. Looking forward to this new year together, Zirkonzahn will always be at its customers side to walk together. With trust and mutual support, we will be each other’s source of change!
USA
All our
are developed and manufactured in-house,
the heart of the Italian Alps, without compromise: this is our philosophy to ensure the highest quality standards and a smooth
between the different components.
All our products are developed and manufactured in-house, in the heart of the Italian Alps, without compromise: this is our philosophy to ensure the highest quality standards and a smooth workflow between the different components.
We love what we do and we care about passing on our knowledge. With our extensive training programme we show you how to use our digital diagnostic tools, CAD/CAM systems, implant prosthetic components and dental materials.
We love what we do and we care about passing on our knowledge. With our extensive training programme we show you how to use our digital diagnostic tools, CAD/CAM systems, implant prosthetic components and dental materials.
IN 2024 OUR OFFICE AND EDUCATION CENTER IN SYDNEY OPEN THEIR DOORS: FOLLOW US ON OUR SOCIAL MEDIA!
Zirkonzahn Australia
STONEHENGE® – THE HOUSE OF LEARNING HEIDEN, GERMANY
NEW! NEW!
Zirkonzahn Worldwide
ZIRKONZAHN IBÉRICA EDUCATION CENTER IBÉRICA
BARCELONA, SPAIN
EDUCATION CENTER CALIFORNIA IRVINE, USA
STAY UP TO DATE WITH OUR UPCOMING COURSES AND WEBINARS
ZIRKONZAHN HEADQUARTERS GAIS, SOUTH TYROL
NEW!
NEW!
EDUCATION CENTER BRUNICO BRUNICO, SOUTH TYROL
KLINIK DEMEDICI MOLINI DI TURES, SOUTH TYROL
ZIRKONZAHN NEULER
ZIRKONZAHN NEULER
EDUCATION CENTER NEULER NEULER, GERMANY
EDUCATION CENTER NEULER NEULER, GERMANY
EDUCATION CENTER POLAND WARSAW, POLAND
EDUCATION CENTER HUNGARY BUDAPEST, HUNGARY
ZIRKONZAHN FOREST SCHOOL PREDOI, SOUTH TYROL
ZIRKONZAHN MOUNTAIN MONASTERY CAMPO TURES, SOUTH TYROL
NEW!
ZIRKONZAHN MOLARIS I MOLINI DI TURES, SOUTH TYROL
ZIRKONZAHN MOLARIS I MOLINI DI TURES, SOUTH TYROL
NEW!
ZIRKONZAHN HELDENCAMPUS MOLINI DI TURES, SOUTH TYROL
ZIRKONZAHN HELDENCAMPUS
ZIRKONZAHN FORGE MOLINI DI TURES, SOUTH TYROL
ZIRKONZAHN FORGE MOLINI DI TURES, SOUTH TYROL
ZIRKONZAHN RANGER SCHOOL MOLINI DI TURES, SOUTH TYROL
ZIRKONZAHN RANGER SCHOOL MOLINI DI TURES, SOUTH TYROL
ZIRKONZAHN SAFARI SCHOOL MOLINI DI TURES, SOUTH TYROL
SAFARI SCHOOL MOLINI DI TURES, SOUTH TYROL
ZIRKONZAHN MILITARY SCHOOL MOLINI DI TURES, SOUTH TYROL
NEW!
ZIRKONZAHN AUSTRALIA EDUCATION CENTER AUSTRALIA SYDNEY, AUSTRALIA
Workflows for fabricating Full and Partial dentures digitally
NEW 2-DAY INTENSIVE MASTERCLASS
SYDNEY - JUNE 21-22 | AUCKLAND - JULY 26-27
Presented by Sam Dias, Dental Prosthetist
This event is both a lecture documenting why you should choose digital dentures today as the optimal solution for your dental practice or denture clinic together with a LIVE systematic run-through of the process for fabricating both full and partial digital dentures. You will be able to follow Sam Dias as he explains the step-by-step process he uses in his four clinics across Sydney every day.
A demonstration of accurate intraoral scanning and prosthetic design ensures that the outcome won’t be compromised while saving time and money for you and your patient.
The session will conclude with a Q&A session discussing options leading to self-design or aided design as well as the finishing and polishing process.
This course will cover the following...
1. Impression vs Scanning - A discussion and slide presentation comparing intraoral scanning and traditional impressions, including a live scan of dentures will be shown. The scanning process will be shown step-by-step and the many different impression techniques currently used will be reviewed, and details of how these can be carried on to the digital world shown.
2. Clinical workflows for correctly scanning different types of denture cases.
3. Preparing scans before export to fellow colleagues and or labs to minimise errors and patient discomfort, REVIEWS!
4. Adding mesh and articulator adjustment. Combining multiple scans and adjusting the setup of the virtual articulator will be shown.
12 HOURS
5. Wizard and model analysis tools explained.
6. Digital denture teeth selection- How to select the correct digital denture teeth library will be discussed as well as the use of the measure tool plus patient notes and extra scans. Denture teeth library options and applications will be discussed.
7. Digital denture teeth setups - Digital denture teeth setup tips and tricks for faster and more effortless setups will be detailed.
8. Denture teeth options, different materials for multiple applications, such as printed, milled and carded.
9. Denture base design - Key principles to bear in mind when designing your denture bases plus a guide to troubleshooting.
1. Continued denture design with a group discussion and clarification of denture designs.
2. 3D printing - 3D printing techniques plus a guide to material selection and achieving better outcomes.
3. LIVE Carded Teeth modification and milled teeth finishing and tweaking before Bonding.
4. LIVE Carded denture teeth, Milled Teeth and Printed TeethStep-by-step bonding technique with tips and tricks.
5. LIVE Staining technique - Techniques for staining and filling in the gaps.
6. Finishing and polishing - Tips to achieve a great outcome.
7. Discussion + Q&A Session.
Sunshine Dental Lab has begun distributing Trilor ®, a highperformance techno-polymer matrix with multi-directional glass fiber reinforcement for use in creating dental prosthetics. Lightweight and resilient, it’s indicated for copings and substructures and can be utilised for permanent implant-supported frameworks including all-on-x.
TriLor exhibits natural flex and load parameters, making it the ideal replacement for unforgiving metal and zirconia frameworks. The versatility of the polymer also ensures a biocompatible alternative to traditional materials.
TriLor is listed on the TGA’s ARTG as a Class IIa Medical Device and it is certified as a permanent prosthetic material in Europe (CE), the US (FDA) and Brazil (ANVISA). It has tested at “zero sensitivity” according to all ISO 10993 and FDA testing standards.
TriLor has a flexural strength of 540Mpa and the versatility of the product is outstanding. It offers both digital and analogue pathways for use and is available in Ivory or Pink.
TriLor Disc comes in puck form that caters to most milling machines and indications. The fiber-reinforced resin material is designed for suprastructures for full arch restorations and bridge frameworks including All-on-X. This super-strong resin flexes and bends under stress, transferring less energy to the implants, making it an ideal support material for implant-based restorations.
Labs that are analogue can still benefit from TriLor’s qualities with TriLor Arch, a clever and easy way to fabricate implant-supported bars manually using a micromotor and tungsten carbide bur or dental stone. Hence, a lab without digital technology can create substructures without purchasing a mill or a scanner. There are no prohibitive upfront costs to using TriLor Arch and it allows the ana-
n Permanent
n No sintering required
n Contains no metal or zirconia
n Chemically stable, no corrosion or oxydation
n Fatigue resistant
n Reparable with composite
n Bonds to any cold cure acrylic
n 3-5 times lighter than metal/zirconia
n Permanent or provisional bridges
n Removable prosthesis on implants
n Bars for implant-retained dentures
n Fixed orthodontic retainers
logue creation of connection structures between implants that can be embedded in removable prosthetics, as well as frameworks for transferring the position of the implants into the mouth, or simple reinforcement bars for a definitive prosthesis.
TriLor, developed in Italy by Bioloren®, is a techno-polymer that is composed and strengthened by a multi-directional fiberglass matrix, offering high strength and natural load distribution.
Boasting enormous strength while offering natural flex and load parameters, TriLor is ideal for implant-supported bars and superstructures including All-on-X.
Mimicking the characteristics of human bone, TriLor endorses bio-mimetic dentistry with a definitive, metal-free implant bar solution that is aesthetic, comfortable, lightweight and durable.
Any cold cure denture acrylic will bond well to TriLor after sandblasting and cleaning the surface and composite resins can also be used.
For info, visit http://bit.ly/3I6kVNc
In the ever-evolving world of digital technology, one name stands out for bringing innovation right to the doorstep of Australian dental laboratories: Monocure3D. With a commitment to quality, consistency and support, this Sydney-based company is transforming the dental industry, one resin at a time.
Monocure3D’s mission was to provide dental professionals with high-quality, reliable and affordable 3D printing materials. Understanding the intricate needs of dental practices, the people behind Monocure3D have dedicated themselves to developing products that meet modern digital dentistry’s demands.
From industrial beginnings to 3D printing pioneers
The origins of Monocure Pty Ltd trace back to 1979 when Founding Director, Alan Anderson, sold his industrial adhesives company to a multinational. Initially conceived as an industrial chemical development and manufacturing company, Monocure supplied UV-cured inks to traditional printing, packaging and labelling industries, locally and abroad. This foun-
dation laid the groundwork for innovation, quality and support that would define the company’s future.
By 2016, nearly four decades later, under the guidance of Alan’s Son, Charlie Anderson and the Chief Development Chemist, Kevin Jarrett, the first Australian-made resin for SLA 3D printers was developed. Recognising the potential of the 3D printing industry, Charlie steered the company’s focus towards this emerging industry, embracing the challenge with enthusiasm and expertise.
Today, Monocure3D (M3D) remains a 100% family-owned and operated Australian company. With a commitment to 3D printing, the dental industry and local manufacturing, Charlie and his team are invested in pushing the boundaries with the technology’s possibilities and building a community around it.
“We are at the forefront of resin-based 3D printing materials globally,” he said. “Our lab is home to the country’s most talented and experienced photopolymer chemists. Their knowledge is gained from over 40 years of UV-based product development. This highlights a legacy of innovation, family values and the importance of products still being manufactured in Australia.”
mbracing a “set and forget” methodology, Monocure3D’s quality control procedures adhere to ISO 9001, ensuring batch-to-batch consistency across the range. Each batch of resin undergoes thorough lab testing and printing, with a liquid and solid sample retained for the shelflife period (36 months). This approach ensures that an archive of all batch samples is maintained, which can be accessed and tested should a customer experience any issues. This is another example of the dedication to quality and customer satisfaction. Once the resin has been “dialled in” with a 3D printer, each future bottle becomes as simple as shake, pour and print, allowing the end-user to focus more on the job at hand.
“We have developed all our resins at the base reaction level. This allows us to control every aspect of the finished material, giving us the unique ability to create the required properties,” said Kevin Jarrett, Chief Development Chemist.
Monocure3D recognises the risks dental labs can face when transitioning to the new digital age, especially the potential for production stoppages due to material shortages. The recent COVID-19
Opening a world of where the only limit is your imagination...
pandemic highlighted the vulnerability of global supply chains, leading to widespread delays and increased expenses. Making the resins in Australia mitigates potential issues when relying on overseas supply chains.
“Given our position globally, Australian businesses felt more impact than most,” Charlie said. “We encountered numerous reports from our resellers and customers struggling to acquire imported resins. Fortunately, we could switch them to our locally manufactured resins, ensuring their labs continued functioning.”
An integral part of Monocure3D’s innovation lies in the universal compatibility of their resin systems. The chemists and field testers have worked hard to engineer the products to work seamlessly with all MSLA (Masked Stereolithography) and DLP (Digital Light Processing) 3D printers. The dental range has a unique formula for each technology (MSLA and DLP). This development, combined with handy online printer settings, ensures a fast and simple set-up, regardless of the user’s printer technology.
The commitment and approach to new product development are at the heart of the success. Monocure3Ds dental range has been created specifically for the industry, offering properties required for each unique appliance. The team have dedicated themselves to advancing the industry, working with dental technicians locally and globally to develop dentalfocused products.
“I’m immensely proud of my development team,” Charlie said. “Their ability to deliver such high-quality products in a short timeframe, despite the constraints of being in Australia, with limited resources and raw material choice, is nothing short of astonishing.”
In 2022, Monocure3D achieved a new milestone with its GUIDE™ dental 3D resin, marking its first product to be listed on the Australian Register of Therapeutic Goods (ARTG). This highlights the company’s commitment to compliance in the industry. The GUIDE™ resin, known for its biocompatibility and suitability for fabricating precise surgical guides, combines high strength, transparency, heat resistance and odourless/tasteless properties once cured.
Opening a world of where the
Opening a world of where the
Monocure3D views itself as more than just a resin manufacturer; instead as a partner for dental professionals. Australian distributors have been carefully selected in each major city to provide advice and support and to hold local stock. M3D and its partners are committed to supporting dental professionals every step of the way. With local technical support, they can assist in selecting the most suitable material, optimise printer settings for the best results and provide stock rapidly when required.
“We have engaged local, family-owned dental resellers to prove our commitment to providing the best customer service. This partnership ensures that our products are readily available and supported by old-fashioned, ‘feet-on-the-ground’ technical support”, Charlie sid.
As Monocure3D continues to grow and evolve, its focus and commitment to the dental industry are more than evident. The development team are busy researching and developing new products to meet the changing needs of dental professionals and their patients.
Opening a world of where the only limit is your imagination... Opening a world of where the QUALITY
Their latest advancements include specialised resins such as CAST™, a wax-free solution for rapid investment casting. The new biocompatible Try-In Denture Resins available in shades A2, A3, A4 and B5, enabling efficient patient
denture fittings. In addition, the Custom TRAY™ Resin has also been designed for rapid results.
One of the original and popular innovations is ResinAway®, the cleaning solution engineered to safely clean models by turning non-water washable resins into washable ones, eliminating the need for hazardous alcohols. ResinAway is sold worldwide and is compatible with most 3D resin systems.
The new water-based Dental Model SEPARATOR™ has been simplifying the removal of 2-part thermoset acrylic resins from 3D printed models, ensuring effortless separation and workflow efficiency at an affordable price.
Monocure3D has quickly become a pillar in Australia’s dental market. With its innovative products, Australian-made quality and dedicated local distribution network, Monocure3D is an invaluable partner for any dental business investing in 3D printing.
For more info on Monocure3D’s Range, visit www.monocure3d.com.au/dental. For product availability and pricing, contact the distributor closest to you: NSW - Alphabond (02) 9417-6660 and Fabdent 1300-878-336; VIC - Ultimate Dental 1800-636-801 and Durodent (03) 9720-6700; SA - City Dental Supplies 1800-882-412; QLD - K-Lab Digital Solutions 0411-483-575; and WARay Purt Dental (08) 9367-1216.
Question 1. Vita MFT teeth are designed...
a. Using the Gothic Arch Tracer.
b. To aesthetic rules.
c. Using a slide rule.
d. None of the above.
Question 2. Centric position can easily be found with these teeth because...
a. Of the type of acrylic used.
b. An extra cusp is added to the first molars.
c. The occlusal surface design.
d. The MMR was incorrect.
Question 3. The dentures were stabilised with...
a. A soft relining material.
b. Plaster.
c. Compound .
d. None of the above.
Question 4. The dentures were copied using...
a. Photogrammety
b. Silicone matrix
c. Hydrocolloid
d. Alginate
Question 5. MFT stands for...
a. Myo Fossa Teeth
b. Myo Functional Teeth
c. Multifunctional teeth
d. None of the above
Question 6. The intraoral scanner was used to...
a. Take a 360 degree scan of the denture.
b. Take a scan of the intaglio surface of the denture.
c. Take a scan of the ocllusal surface of the denture.
d. None of the above.
Question 7. It’s possible to replace this procedure with a printed copy denture...
a. VMK Crown on a prep.
b. Denture reline.
c. Special Tray.
d. Surgical guide.
Question 8. When printing a denture, it’s important to...
a. Use any material you want even if not approved.
b. Not worry about post curing materials.
c. Follow the manufacturers instruction for use for materials.
d. None of the above.
Question 9. The CAD program used for this article was...
a. 3Shape
b. InLab
c. Up3D
d. exocad
Question 10. A data merge in exocad...
a. Merges and optimises the data ready for printing.
b. Leaves the data in a raw state.
c. Does nothing.
d. Is not needed.
Do you wish to offer your clients a solid and economic prosthetic solution with efficient functional workflows and aesthetic results? That’s possible with VITA Multifunctional Teeth (MFT), which offer all of these features at the same time: reproducible and reliable rehabilitations for a fair price performance ratio.
he morphology of VITA MFT Anterior is designed according to aesthetic rules. Its tooth axis, angle characteristics and dimension of the basal tooth neck simulate the shape of natural front teeth. The surface texture establishes a life-like appearance and the structural composition conforms to the tooth anatomy. The well-arranged neck, dentine and enamel layers lead to an aesthetic play of light and colours with harmonic shade gradients and reflecting mamelon structures.
Due to the occlusal surface design, the centric position can easily be found. This leads to a reliable and time-saving reproduction of the function without extensive grinding. The posterior teeth can be used universally with any occlusion concept because of the multifunctional occlusal surface design. They standardise the workflow of the set-up and provide constant and solid results. This routine helps increase general productivity.
The following case demonstrates how efficient and aesthetic results can be created with the copy denture technique using VITA MFT.
The teeth of the patient’s old, unstable dentures were severely worn. The vertical dimension was diminished and a malocclusion established. The dentures were stabilised with soft relining material in order to find a new, raised centric relation.
• easy and efficient setup, thanks to VITA Easy-Centric
• easy and efficient setup, thanks to VITA Easy-Centric
• multifunctional in a wide variety of shades and shapes
• easy and efficient setup, thanks to VITA Easy-Centric
• multifunctional in a wide variety of shades and shapes
• convincing results with high reliability and VITA quality
• multifunctional in a wide variety of shades and shapes
• convincing results with high reliability and VITA quality
easy and efficient setup, thanks to VITA Easy-Centric multifunctional in a wide variety of shades and shapes
• convincing results with high reliability and VITA quality
• convincing results with high reliability and VITA quality
After that, both dentures were copied with the help of a silicone matrix and articulated in the determined centric relation.
The teeth of the copies were gradually reduced and then set.
Mucodynamic impressions were taken with the new set-ups, which were poured and rearticulated after the successful clinical try-in. Finally, the rehabilitations were processed in polymer, finished and polished. The results were functional and aesthetic rehabilitations which had been manufactured efficiently and economically. The frail patient was very satisfied with the quick procedure and the outcome.
Darius Northey graduated as a Dental Technician in 1993 after working in the family business for many years. In 1997, he established his own dental laboratory in Sydney, Australia and later completed the Advanced Diploma of Dental Prosthetics to graduate as a dental prosthetist. He established Jade Dental Laboratory Pty Ltd with his business partner/ceramist Justin Thompson in Buderim on the Sunshine Coast, Australia in 2006. The Laboratory has a denture clinic on site and also another practice on Bribie Island, Queensland, Australia. They employ 11 staff and are a full
dentists and directly with patients. He has a strong interest in furthering his
and
seminars. He lectures in Australia and overseas on implant overdentures and CAD/CAM
Presented by Emeritus Professor Laurence Walsh AO
BDSc, PhD, DDSc, GCEd, FRACDS, FFOP (RCPA), FDTFEd
This course will discuss recent developments in infection control, with the major focus being on instrument reprocessing, following the release of the AS 5369 Standard in December 2023. The online video component (90 mins) covers New infection control terminology used in 2024; Online resources to support implementing modern infection prevention and control; The journey leading to AS 5369; and an explanation of how the standards system works in Australia, including the interactions between ISO, EN and Australian standards and the concepts that underline the standards landscape. The latter video also summarises the normative ISO and EN standards for AS 5369. As a bonus feature, there is another video on the history of infection prevention and control over the past 150 years.
TOPICS for the 4.5 hour face-to-face session include:
n The importance of precleaning at the chairside.
n What happens when instrument reprocessing is delayed.
n Key requirements for the proper use of ultrasonic cleaners and washer disinfectors.
n How to assess the outcomes of the cleaning process.
n Workflow, PPE and hand hygiene for the reprocessing area.
n Design elements of the reprocessing area and the concepts of physical and spatial segregation of work areas.
n The requirements for sterilising handpieces.
n Proper use of bespoke sterilisers running S cycles.
6 HOURS CPD
n Protocols for using air-removal and steam penetration tests.
n Correct use of chemical indicators.
n Tests for the integrity of packaging systems.
n Implementation of low temperature sterilisation.
n Criteria for load release from sterilisation.
n Definitions of non-conforming items.
n Environmental conditions for instrument storage.
n Record keeping requirements.
n Batch control information, including for high level disinfection.
Laurie Walsh is a specialist in special needs dentistry who is based at the University of Queensland in Brisbane, where he is an emeritus professor. He has been working in clinical microbiology for over 27 years, with more than 200 publications in this field and has been teaching microbiology and infection control at postgraduate level for the more than 25 years, including for the ADA and RACDS. Laurie has contributed to the development of national standards since 1992, including standards for masks, gloves, faceshields, ultrasonic cleaners and most recently, for instrument reprocessing (the AS 5369 standard). He was also involved in the development of
CDNA BBV guidelines, the second edition of the Australian Commission on Safety and Quality in Health Care standards and the ADA IC guidelines.
The title of this article is not misleading; you can actually do most of the work to copy a denture and more in about 10 minutes, with experience, but don’t let that faze you. With the new release of exocad 3.2 Elefsina, named after the city in Greece, exocad in their wisdom have now added the function to easily turn the scan of any denture into separate parts ready for manufacturing using your favourite method, be it milling or printing.
Personally, I think this ability to copy quickly is much more suited to 3D printing as it’s really all about speed and if its speed you’re after, you can print things very quickly if you have the right equipment and know-how. However, some will find reasons to mill and that’s always an option too.
So why would we want to duplicate a denture? The first thought that comes to mind is that this may be a request from the denture patient as they feel they need a spare, but if we start to consider the manufacturing technology available these days and if we think laterally, the duplication and manipulation of the files of the denture could be an alternative to the many day-to-day processes
we now do. For example: repairs, relines, replacing broken teeth and remodelling of dentures could very well be just a thing of the past and be replaced with creating a new denture quickly and easily. I’m sure you could think of other uses as well. I have a few ideas whirring arounf in my head; perhaps we can talk about them at upcoming conferences such as Digital Dentistry & Dental Technology 2024 in Sydney on May 24-25.
So let’s look at the basics of copying a denture.
The first challenge is to take the scan of the denture and this can be done with an intraoral or lab scanner. When using a lab scanner, you may find you need to spray the denture with a scanning spray to dull the surface to stop the reflection. Modern intraoral scanners do not fall victim to this as they will scan shiny surfaces usually without issue. For my experiments, I used the new AoralScan 3 from Shining 3D, a wireless intraoral scanner and the results are spectacular. Using a sensible path approach to scanning the denture so as to optimise the mesh stitching, you will find scanning a denture 360 degrees a walk in the park. Even if you’re a novice, just “go for it” - the scanner is incredibly forgiving and you will still get a good result - it just might take a
bit more time to complete. The real secret to using an intraoral scanner is practice! I also scanned the opposing model and the MMR using the denture and the opposing model as reference.
Once the scans are completed, inspect them for imperfections, edit as needed and then transfer to exocad software. This can be done by a simple stl export.
You can then setup exocad to make a copy denture. Do this by opening the Dental DB part of the software. For those unfamiliar woth exocad, it’s where you set the job up, tell the program what type of job you’re doing and of course adding the clinician’s name, patient’s name and technician’s name. Once you do this, then select the upper arch for an upper denture as per our example. Note that you can also tell the software if you want to print, mill or do a combination of both.
The key here is to select the new buttons, namely the “360 denture scan” and “copy existing denture” button as per Figure 6. Now of course you have the option to copy upper and lower dentures at the same time, but for our example, we are just doing the upper denture as it has a matching partially dentate lower, as I have indicated to the software in Dental DB.
The software will ask to load the files and then the fun begins. You can now do an automatic detection of the denture border, edit the spline as necessary and the software will make a virtual model in seconds from this operation. Next, click on each tooth and it will change colour, detecting the actual denture tooth by name. Rarely it may not be perfect but there is a simple edit tooth to fix any mistakes and then it will detect again perfectly.
Once this is done it will convert the denture teeth from the denture into a fully editable and customisable set of virtual denture teeth that you can manipulate in any way you wish. Change the position, rotate, tip torque, whatever you wish, as well as reform the tooth shape, size or any number of edits you wish to do; you have 100% free control. I personally use the opposing to make sure if I do any changes they are going to be harmonious with the MMR. Of course, you don’t have to do any changes at all if you just want an exact copy of what you had.
Next, the software will create the denture base and of course, you can do a direct copy or you can do any editing and free forming you wish to do and once satisfied, it will generate the base.
After this it will perform a data merge to finalise the baseplate and the teeth. This just merges and optimises the data, joins the teeth together if you have selected to do this and the result will be two files - teeth and base - ready to manufacture in the way you prefer. There is a whole lot more you can do too, but I’m just mentioning the basics. I recommend you try it for yourself to discover all of the features.
Just have a think for a minute how powerful this is and I’m sure you’ll come up with scenarios in your head for this to be useful. I’ll give one example: A patient presents with a denture broken in half due to ill-fitting and a few of the teeth are chipped at the front. Oh, did I mention they’re going on a three month around the world trip tomorrow?
Normally this would be a rush nightmare. So glue the denture together, take a reline impression of the denture with your favourite impression material; if it’s scannable impression material, that’s even better. After the impression, scan the denture 360 degrees and create a copy denture in exocad and while you are doing this, you can, in the software, repair all the chipped teeth. Once finished, send the files to your printer, finish the denture as per resin manufacturer’s instructions and you will have a denture that fits and will be good to go for many months or longer. Charge appropriately.
As I said, I’m sure you can think of many scenarios where this sort of workflow will be a great bonus to your day to day business, don’t think outside the box, work outside it too.
Terence Whitty is a well-known dental technology key opinion leader and lectures nationally and internationally on a variety of dental technology and material science subjects. He is the founder and owner of Fabdent, a busy dental laboratory in Sydney specialising in high tech manufacturing. Using the latest advances in intra- and extra-oral scanning, CAD/CAM, milling, grinding and 3D printing, most specialties are covered including ortho, fixed and removable prosthetics, computerised implant planning and guidance, TMD, sleep appliances and paediatrics.
Popular sports in Australia, such as hockey, rugby and AFL, pose significant facial injury risks and at the adult and elite levels, the strength and consequence is magnified. These risks range from soft tissue damage to serious harm to the dentition and even complete facial structure breakdown in the case of very severe impacts. Specialised high impact mouthguards are designed to minimise oro-facial trauma from the most extreme sports impacts and have proven to be effective over time.
The two mouthguards we will look at are both thermoformed and aimed at minimising the damage from extreme impacts. The manufacturing process is the key difference; one mouthguard formed from a single foil with a single forming and the other mouthguard formed from three foils with three separate consecutive formings.
It is worth noting that both these mouthguards are designed for adult and professional sports people with stable dentition but they are also useful as added protection for sports people with compromised dentition i.e. prominent anterior teeth, implants, etc.
Structure: A single pre-laminated foil. 5.5mm thickness, 1st layer (tissue side) 3.0 mm Erkoflex soft, 2nd (hard layer) 1.0mm COC (cyclo-olefincopolymer), 3rd layer (occlusal) 1.5mm Erkoflex soft. Occlusion: Added when thermoforming by re-distributing the still plastic material. This automatically adds a buccal shield, anterior platform and a flat articulated surface with freedom of movement for support of the lower teeth.
Structure: 3 foils, total thickness 6.8mm laminated one after another. 1st layer (tissue side) 2.0mm Erkoflex soft, 2nd layer (hard) 0.8mm Erkodur-S, 3rd layer (occlusal) 4.0mm Erkoflex soft.
Occlusion: The buccal shield and articulating surface can be ground in after thermoforming or added at the time of thermoforming as per the Triple technique.
Results: The Triple is 32% lighter, has 41% less volume and 20% less incisal thickness than the Heavy-pro. The Triple has less bulk than the Heavy-pro design even though it is made with just under 20% less material. This is due to the reduced palatal dimensions and the redistribution of the occlusal material during the manufacture of the Triple.
Results: The Playsafe Triple and the Playsafe Heavy-pro high impact mouthguards have almost identical measures of resistance to deformation.
Results: The Playsafe Triple has 22% less deformation in the critical anterior area than the Playsafe Heavy-pro, in the posterior the results are almost the same.
* To better distinguish the results, the deflections were multiplied by virtual extension of the roots
The graphs above display the differences in the specification and properties of the two mouthguards.
The Playsafe Triple presents as have having significantly less weight and volume than the Playsafe Heavy-pro while still maintaining the same level of protective potential and in some areas exceeding it.
This highlights the usefulness of quantifying the comparative performance of mouthguards and in this case has allowed us to benchmark and demonstrably develop a smaller, lighter yet equally protective mouthguard than was the current level of design.
Peter Herring is a dental technician, prosthetist and a regular contributor to eLABORATE. He is the Australasian and Indonesian distributor for Erkodent products and spends his time between offices in Perth and Bali. He also operates a busy Australian lab dedicated to thermoformed appliances. He can be contacted at pjh@erkodent.com.au or for general enquires, call Freecall 1800-242-634.
Information contained in this section is provided by the manufacturers or distributors. eLABORATE does not assume responsibility for the accuracy of the data.
RODIN™ 3D Resin is specially designed for various dental applications such as crowns, bridges, all-on-x, full arches, veneers, dentures, models, surgical guides, occlusal splints and try-ins. RODIN 3D Resin has strength and toughness against high impact and abrasion. Users can expect efficiency and profitability in the digital workflow. RODIN 3D Resin is compatible with
popular 3D printers, especially the Ackuretta SOL 3D Printer, which has a validated procedure from printing to curing including the New Ackuretta SOL Plus 3D printer with the XL size build plate.
Available:
CM Medical
Tel: 1300-466-588
info@cm-medical.com.au
www.cm-medical.com.au
The Stratasys DentaJet J5 is a versatile and efficient dental printer that can produce highquality and realistic dental applications in a single print. It can print up to 34 full dentures or 45 full arch models with a layer height of 16.7 microns and a range of 255,000 colours. Load one tray and walk away. It can also outperform
VITA MFT is now available in 16 VITA classical A1-D4 shades and 16 3D-MASTER shades, including 3 bleach shades. VITA MFT (Multi Functional Teeth) stand out due to their outstanding efficiency. The groundbreaking VITA Easy Centric principle simplifies the set-up process. Thanks to the predefined contact points, the teeth find the ideal position almost automati-
cally, saving time and hassle, while also increasing precision. Morphology, incisal design and the shade match with the VITA shade guides also ensure aesthetically pleasing results.
Available:
Henry Schein
Tel: 1300-658-811
lab@henryschein.com.au
www.henryschein.com.au
6-7 DLP printers in terms of output and labour. You can request sample models and see the display machine in action to experience the benefits of the DentaJet J5.
Available: CM Medical
Tel: 1300-466-588
info@cm-medical.com.au
www.cm-medical.com.au
Monocure 3D is the original UV resin cleaning solution that simplifies the post-processing of 3D prints. RESINAWAY offers a non-flammable, user-friendly, long-lasting, cost-effective approach to cleaning by quickly and effectively removing any uncured UV photopolymer resin from your 3D printed parts. RESINAWAY leaves no unwanted
surface cracks, cloudiness or white residue, ensuring your prints retain their pristine quality and clarity. Unlike traditional Isopropyl Alcohol (IPA), RESINAWAY will not ignite at low temperatures, thus making it safe in ultrasonic cleaners. It also doesn’t saturate or evaporate like IPA, allowing for months of cleaning cycles with a single batch. It is the perfect choice for cleaning 3D prints and maintaining build-plates, vats and tools. It is available with a pleasant Rose or Bubblegum scent and now, new Lemongrass and Lime in half litre, 2L, 5L or 20L bottles.
Available:
Monocure 3D resellers
Tel: (02) 9738-5340 support@monocure3d.com.au www.monocure3d.com.au
5-Axis Dental Mill with Disc Changer
Elegant new design
Faster milling of Zirconia and PMMA with High Performance spindle
Sealed chamber to keep milling waste isolated
Built in webcam for real-time mill monitoring
Optional tablet integration
DGSHAPE CLOUD performance visualisation software
DGSHAPE CLOUD performance visualisation software
DGSHAPE CLOUD performance visualisation software
Wet
Bring custom abutment milling in-house
Bring custom abutment milling in-house
Mill multiple restorations at once
Bring custom abutment milling in-house
Mill multiple restorations at once
Incredibly fast output
Mill multiple restorations at once
Incredibly fast output
In-house Production of Custom Abutments
In-house Production of Custom Abutments
In-house Production of Custom Abutments
Simplified production
Incredibly fast output
Simplified production
DGSHAPE CLOUD performance visualisation software
Simplified production
DGSHAPE CLOUD performance visualisation software
DGSHAPE CLOUD performance visualisation software
rolanddg.com.au/dgshape
rolanddg.com.au/dgshape
rolanddg.com.au/dgshape