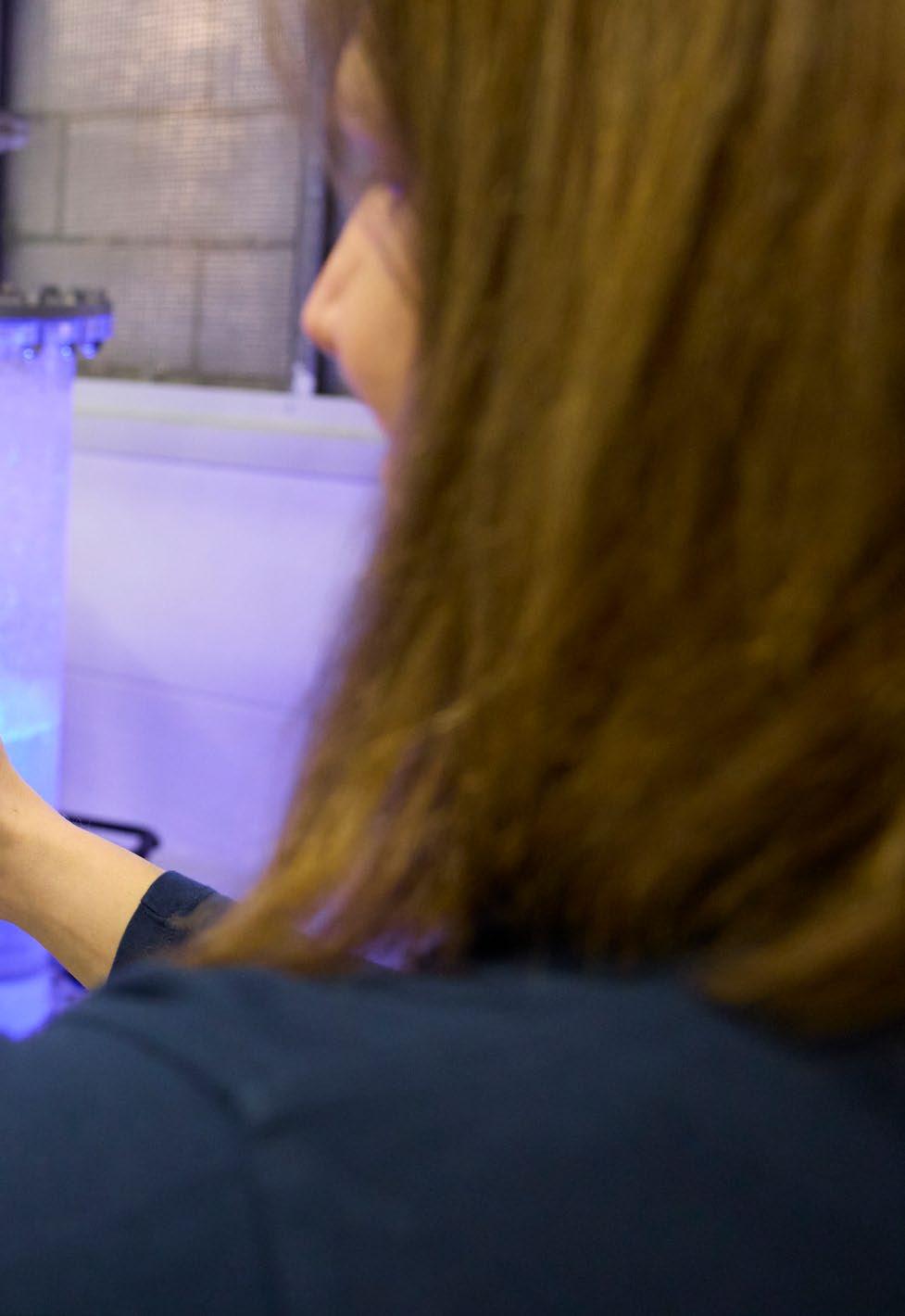
5 minute read
Digital Manufacturing
processes, and technology transform their manufacturing plant into an adaptable, agile, closed-loop Smart Factory, including self-optimising, selfhealing production processes within a connected business network.
In conjunction with our technology partner, SAP, we use some of the world’s most advanced technologies, such as AI and Machine Learning, to create factories that not only orchestrate the manufacturing processes, but actually learn from their experiences.
The combination of SAP’s technology (like SAP BTP, SAP Digital Manufacturing Cloud, SAP Asset Intelligent Network, Team Center) and our step-based approach means our customers can easily adapt at their own pace to meet all sustainability, environmental, productivity and commercial needs.
What Can You Expect?
The shift from single, soiled systems and organisations to networks of capabilities is a game-changer for manufacturers. Our experience in this area means we are the trusted partner for some of the world’s leading manufacturing companies.
Atos’s consultative Smart Manufacturing service gives you:
• A clear strategy and a flexible roadmap with insight on how and where to start, what to expect, and how to scale.
• Advice on how to accelerate business gains, and drive sustainable value and environmental gains.
About Atos
Atos is a global leader in digital transformation with 112,000 employees and annual revenue of c. € 11 billion. European number one in cybersecurity, cloud and high-performance computing, the Group provides tailored SAP endto-end solutions for all industries in 71 countries.
Atos is a Global and Platinum SAP Partner.
• Co-development environments demonstrating proof of concepts and prototypes.
• Integrated solution design and implementation.
Interested in Learning More?
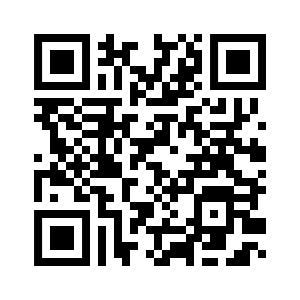
Download our brochure, speak to one of our experts, or request a tailor-made demonstration addressing your specific challenges.
Find out more at atos.net sets up to showcase the digital adaptability of the process, or the fact that a pick-and-pack scenario is running in the warehouse in the background. These combine to lend true authenticity to the experience and deliver real understanding.
“We show that we can speak with the automation layer, and that the automation layer can speak with SAP solutions. It’s about vertical integration, the information technology (IT) and operational technology (OT), and the total integration of those two worlds. It’s really demonstrable,” says Matthias.
C-suite executives, factory managers, IT experts or researchers can grasp the processes quickly, Matthias points out. And experts from different departments within the same company can come to the same place at the same time – virtually or in a hybrid format – without the need for multiple explanations as supply chain solutions are shown in action.
A chief operating officer (COO) or head of supply chain who is familiar with their own production facility can formulate questions about the industry-specific supply chain scenarios within The Factory at SAP Industry 4.0 Center. Convincing a chief financial officer (CFO) to buy in to the head of manufacturing’s enthusiastic appreciation can be harder because they may have less knowledge of the ground floor. Yet sometimes the commissioning process starts at the other end of the business, in the C-suite, before it moves through to the manufacturing team, Ralf says.
“What we try to do is not only address those who are doing the purchasing, but also those who are using the products later on,” says Matthias. That is where a virtual tour alongside the in-person, real-life tour, can be invaluable. For example, two principal decision-makers can stream a live a they want to see our software showcase and talk directly to our management in our headquarters building only 100 metres away from The Factory” element, feed to watch those who have to set up and operate a new process, or vice versa. It means questions or key issues can be pointed out and discussed through streaming technologies in different parts of the country, or the world, simultaneously.
“So, experts on the manufacturing side might want to know, ‘How did the automation of this robot work here? How did you integrate your smart tool? How does it work – show me!’ Then they can deep dive into the systems based on what they can see happening in the real enterprise IT landscape that we have in The Factory. And because everything is real, nothing is fake, it generates trust with our customers,” says Matthias. “People in top management don’t really need the details, but they can see the tangible use cases. It’s something they can grasp and discuss in a very short time.”
Ralf adds that inclusivity across levels promotes communication. For example, a factory worker might point out that glitches could be created if a tool or table is used in a proposed context. Such a small but essential comment might play a crucial role in improving manufacturing or maintenance processes. On the flip side, this immersive experience also provides an opportunity for customers to provide valuable feedback, creating a collaborative community environment.
This sense of collaboration is right at the heart of SAP’s approach. Ralf points out that where competitors might only run a scenario based on one operation or one out-of-the-box vendor, SAP is working in collaboration with many other business partners – small, medium, large, and global. Collaboration in this sense means building bridges, rather than operating in silos – a key mindset for SAP. The Factory is the perfect showcase for anyone needing to see discrete manufacturing, design to operate (D2O), and design to consume (D2C) capabilities, albeit on a small scale, and to visualise how something similar might fit into their own business. One of SAP’s great strengths is collaboration and cooperation, working with both partners and customers to help ensure

Design-to-Operate (D2O) and Design-to-Consume (D2C) Processes
DISCRETE ASSEMBLY
Design, build and operate a discrete unit to produce and mix syrups.
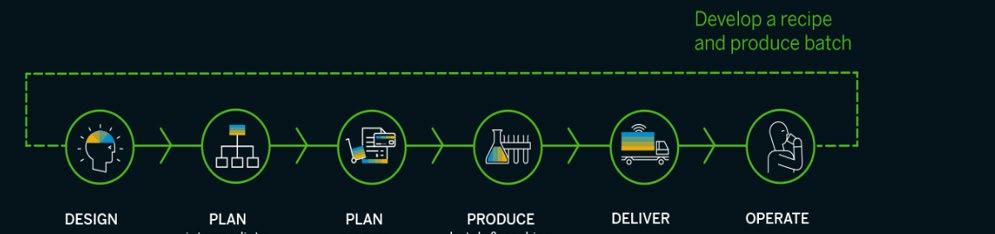
BATCH PRODUCTION the right solutions are available to suit particular needs.
Develop a recipe for a concentrate. Produce, mix and pack the product.
“We would love our customers to run only SAP but – we have to be honest with ourselves – in reality, that is not the case. We are living in a heterogeneous world where the SAP software environment and different cloud companies play an active role. So, it's about connecting and being able to execute the business process end to end in the most efficient and secure way,” Ralf says. He has plenty of experience with companies operating on a silo-based approach, which makes it difficult to connect solutions or software, and so he welcomes the newer outlook of collaboration.
“Times are changing, and customers are pushing for harmonisation and open industry communications standards,” explains Ralf. In a world of mergers and acquisitions, he adds, with multiple vendors across factories, a heterogeneous approach allows for digital transformation, mass personalisation, and configuration, which in turn adds value and futureproofs a customer’s business.
“We have a lot of service and implementation partners, and SAP is powerful because of the partner ecosystem. They are all important partnerships, from the smallest automation-centric, to the biggest as well,” he says. And if there is something that the last three years have shown, it is that no business is an island, and no supply chain is 100 percent secure.
Around 25 or so industrial partners support The Factory setting either by providing service input, supplying hardware, or jointly interacting over a digital supply chain order. Ralf and Matthias emphasise that partnership is SAP’s superpower.
“They all play a crucial, active role in bringing solutions to our end customers,” says Ralf. “SAP has such