Flywheel UPS system
myIdea
• Replacing of 10+ Year old Existing Static UPS 11nos- (450 KW) with Energy efficient and sustainable UPS system for critical loads.
• Every 3+ Years Battery replacement and disposal process.
• Lead acid Batteries are prone for fire Hazard.
• Microsoft sustainability target of Carbon negative by 2030.
• Static UPS units replaced by Flywheel UPS system (2x300 KW) having self life of 20+ years.
• Kinetic energy stored in the flywheel is used as back power to connected load during the power interruption.
• No air conditioning requirement for the Fly wheel UPS system and it works up to 50°C ambient temperature with forced air circulation.
• Entire fly wheel system is installed within 250 Sqft area in the premise.
• Elimination of 510 Lead Acid batteries from static UPS.
• Reduction of 8000 MT Co2 Emission over 20 Year Life span of Fly wheel UPS.
• 1000 Sq. ft. RE Space Saving which will be used for Hybrid workplace solution Lab set up.
• Battery risk issues eliminated, No fire hazard, no disposal issues.
• Energy savings to the tune of 20 MWH / Annum.
• TCO of the fly wheel ups is 15 Years.
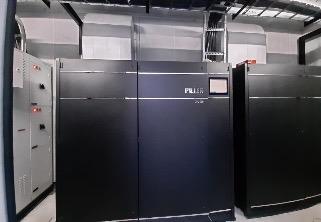
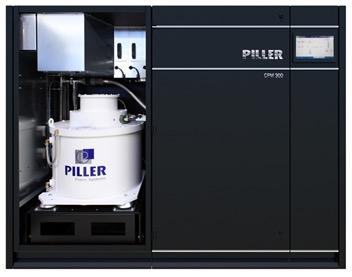
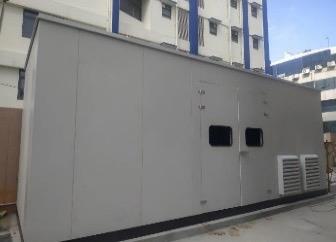

Description of the Innovation:
Bipolar Ionizers & Air Flow switches
CHALLENGE
myIdea
• To choose effective solution for providing treated air in office premises.
• To ensure the solution is effective in neutralizing SARS COV 2 Virus in the facility.
• To ensure that the solution doesn’t require any major modification in the facility.
• To ensure the air purification product is environment friendly.
/ INITIATIVE / SOLUTION
• Market survey carried out along with online research and case studies.
• Installation of Bipolar Ionizers (UL 2998 certified Plasma Air 604) and airflow switches for activation of the Ionizers was finalized.
• Bipolar Ionizers installed at the intake side of fans and Hi wall units, produce positive and negatively charged ions in the air in which the virus can not sustain.
/ ADVANTAGE
• Provision of treated air in the office area across 4 facilities achieved.
• No major modification involved.
• Other effective solution was to install MERV 13 filters which required modification of entire HVAC system in 4 facilities.
• Cost of modifying entire HVAC system of all facilities –Approx. INR 4 Cr. (Saved)
• Cost of installation of Bipolar ionizers with Air Flow switchesApprox. INR 1 Cr. 10 Lakhs.
• Product is UL 2998 certified for zero Ozon Emission.
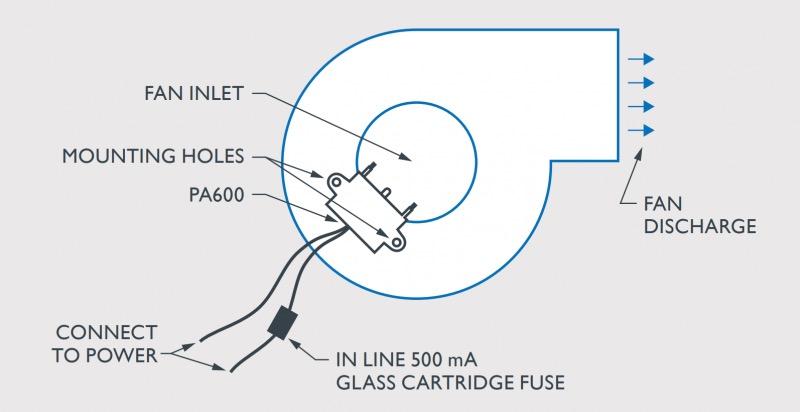
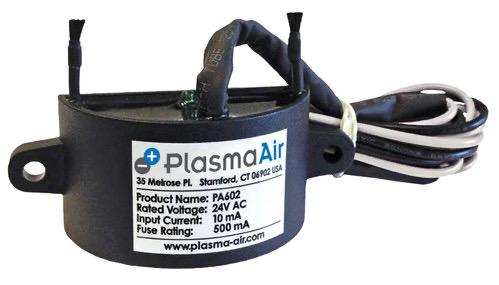
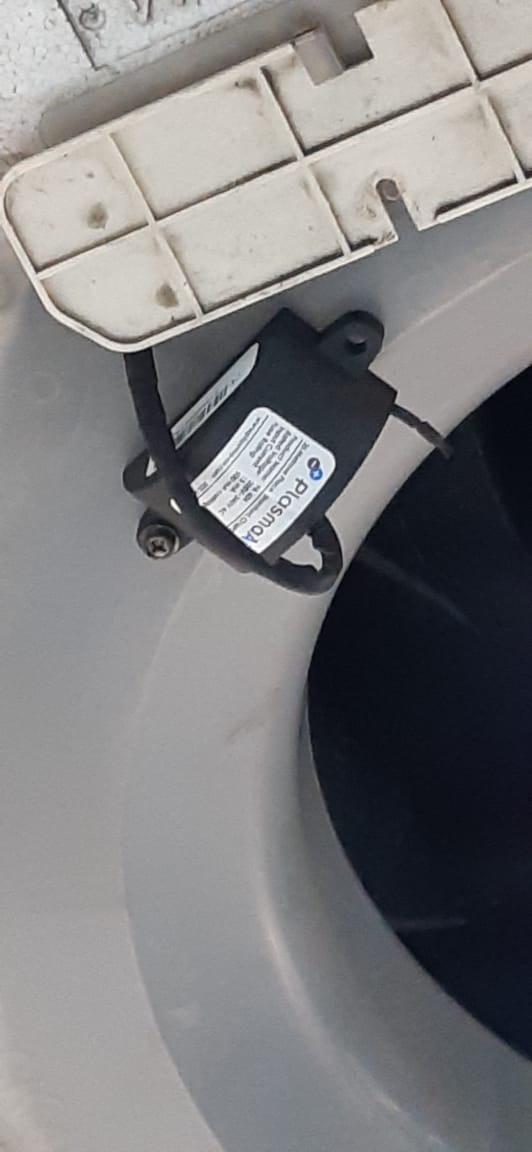
Description of the Innovation:
Hydrogen sensor integrated with Exhaust Fan
• In Battery room lead acid batteries create small amount of hydrogen as by product of charging cycle . Hydrogen is explosive at 4% by the volume of air .If the leak is undetected, it create a potentially explosive atmosphere.
• Battery rooms , like a confined place are frequently unmanned areas and they are often where an accident may take place
• Exhaust : Installation of Hydrogen sensor and interfaced with an Exhaust fan to exhaust the air in the battery room in case of any detection of hydrogen beyond prescribed levels .
• BMS: The hydrogen gas detector would provide 24/7 continuous detection and can provide alert through BMS Systems about any rise in hydrogen levels to site FM team.
• Safety Compliance
• Occupational hazard is mitigated
• Ease of Monitoring : The hydrogen gas detector would offer 24/7 continuous detection (Set point 2 %)
• Automated ventilation
• Risk free atmosphere at Battery room: hydrogen gas detector would also alert BMS, trained personnel about the rising gas leaks before they become hazardous or explosive.
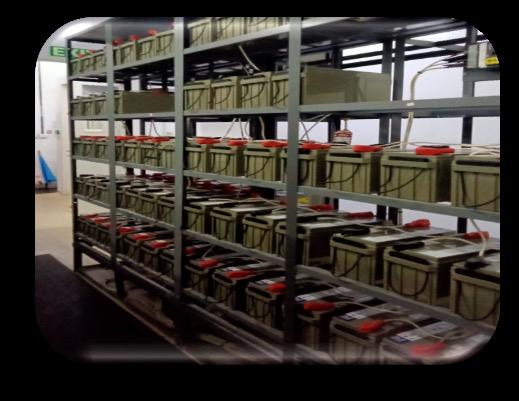
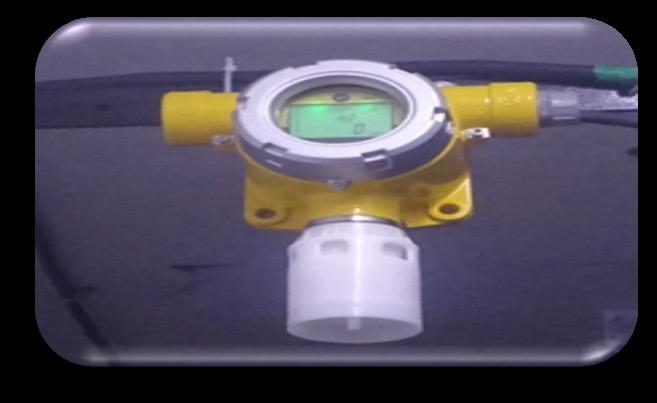
myIdea
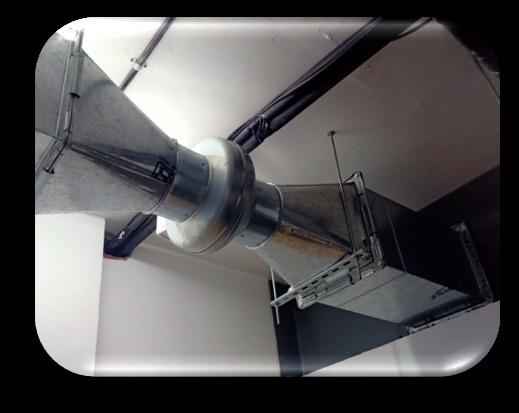
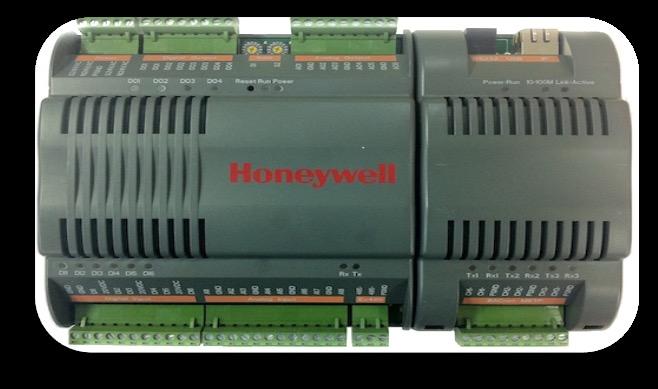

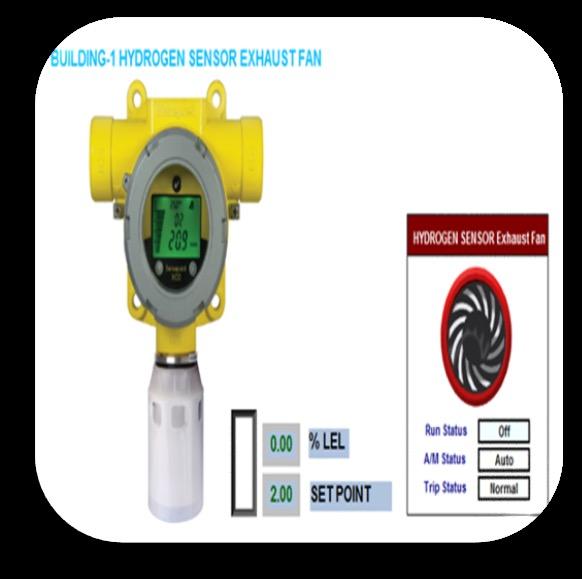
Description of the Innovation:
Daily Facility Report using MS Power Automate
myIdea
• Consolidating the Daily Report of both locations from multiple Stake Holders across different departments.
• Time taking and breaching the SLA timelines for sharing the Daily Facility Report. Numerous data errors and unwanted data redundancy at multiple sources.
• Too many manual entry points of Data & No mechanism of seeing real-time data.
• Creating a live dashboard is a cost-heavy option that requires sourcing to seasoned experts. The average cost for creating such a dashboard is about 2-4Lakhs.
• Created using Microsoft Forms. Forms are then mapped to a common excel file using Microsoft Power Automate.
• The Automated flow gets triggered whenever a response is submitted and populates data in real-time in the mapped excel sheet.
• The responses of multiple forms are not only summarized in a single excel but can also be mapped into a detailed Live/Real-time Dashboard in Power Bi or any other data visualization platform.
• All data being captured is fed into the dashboard as and when the instances occur.
• Infographic outputs that are ready to be shown to Leadership and enable effective decision-making.
• In-House team has made use of existing online tools available in Office 365 suite.
• Saving paper and nature, helping towards sustainability journey
• Multiple data filters and visualization readily available.
• Can be viewed by multiple personnel simultaneously.
• Personnel with no/little experience can use the program and deliver utmost optimal data management.
• Power Automate can be linked into 3000+ applications as of Oct 2021.
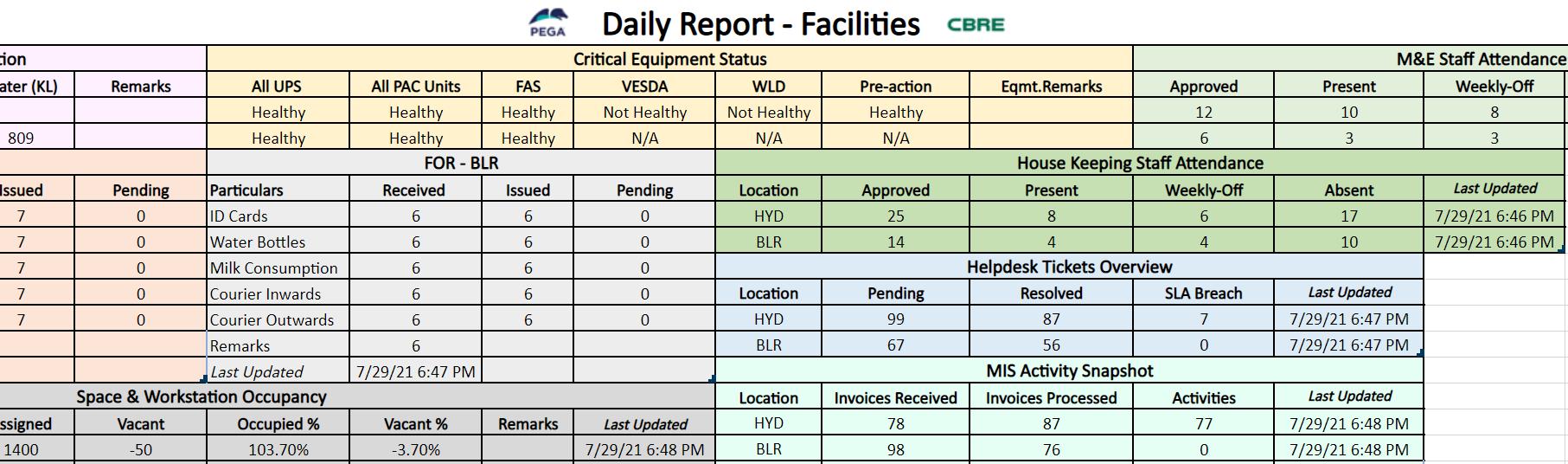
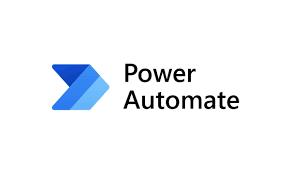
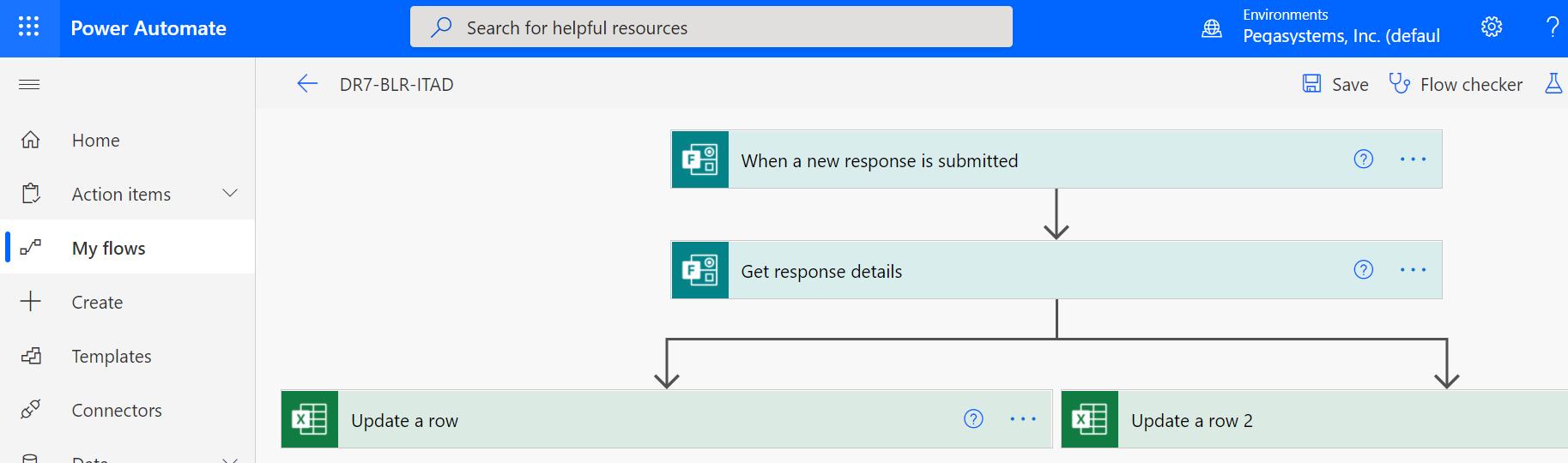
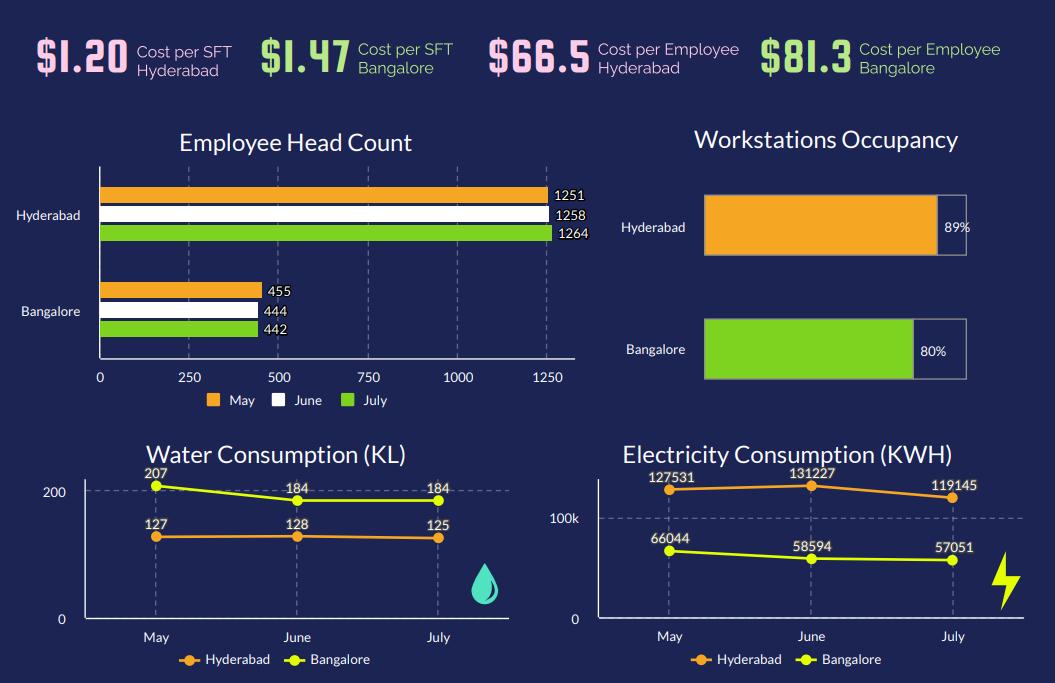
Description of the Innovation:
Green workplace
CHALLENGE
myIdea
• Good air quality index with lower CO2 levels inside the premises.
• Irregularity to add fresh air in the premises due to bad air index in outer area.
• Low-cost sustainability initiative.
• Identification 24 no of plants which are more effective in absorbing CO2.
• Discussed with partner & replaced 2121 no’s of existing plants with higher CO2 absorbing capacity plants.
• Identified locations where we had higher Co2 levels and placed these specific plants.
CO2 ABSORBED PER DAY/ PLANT PHOTO GALLERY
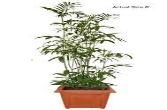
Bamboo Palm, No of plants 10, 0.000259 kg
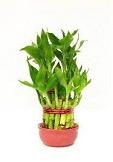
Luck bamboo, No of plants 22, 0.0002011 kg
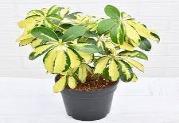
Schefflera, No of plants 41, 0.0002021 kg
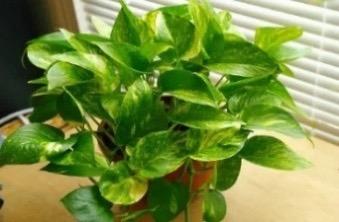
Golden pothos, No of plants 551, 0.131689 kg
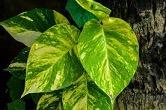
Golden Pathos, No of plants 50, 0.0001865 kg
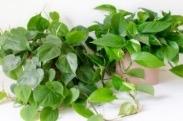
Oxycardium heart leaf, No of plants 70, 0.000201 kg
• Effective low cost, in-house sustainability initiative to reduce CO2 level inside the premises & Reduce Carbon footprint.
• Improved ambience and aesthetics of building / premises.
• CO2 absorbed/ day post selecting & replacing the total no of plant 2121, no’s 0.46772 Kg absorbed per day
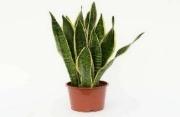
Snake plant, No of plants 72, 0.000289 kg
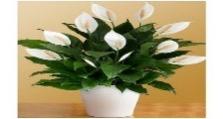
Golden pathos, No of plants 50 , 0.0001868 kg
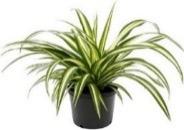
Spider plant, No of plants 45, 0.0000019 kg
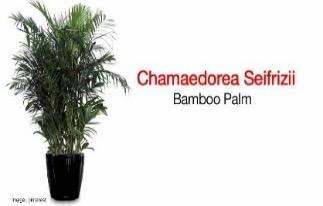
Bamboo/palm, No of plants 289, 0.074851 kg
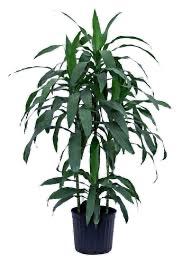
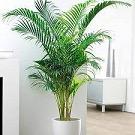
Janet Craig dracaena, No of plants 253, 0.060492 kg
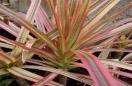
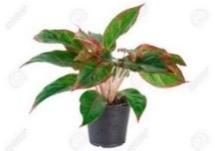
Areca Palm, No of plants 173, 0.047575 kg
Dracaena, Rededged , No of plants 16, 0.0002378 kg
Chinese evergreen, No of plants 130, 0.0002191 kg
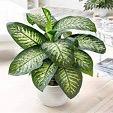
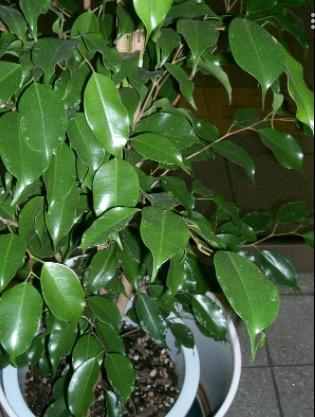
Dieffenbachia, No of plants 95, 0.0002063 kg
Ficus Benjamin, No of plants 78 , 0.0000091 kg
Description of the Innovation:
Active Harmonic Filter
• Previously we were running chiller unit for air conditioner and due to age client has planned to upgrade to VRV
• After VRV implementation, we done separate audit for finding the level of Harmonic and it was very high
• Current Harmonic value is 42%
• Voltage Harmonic value is 7%

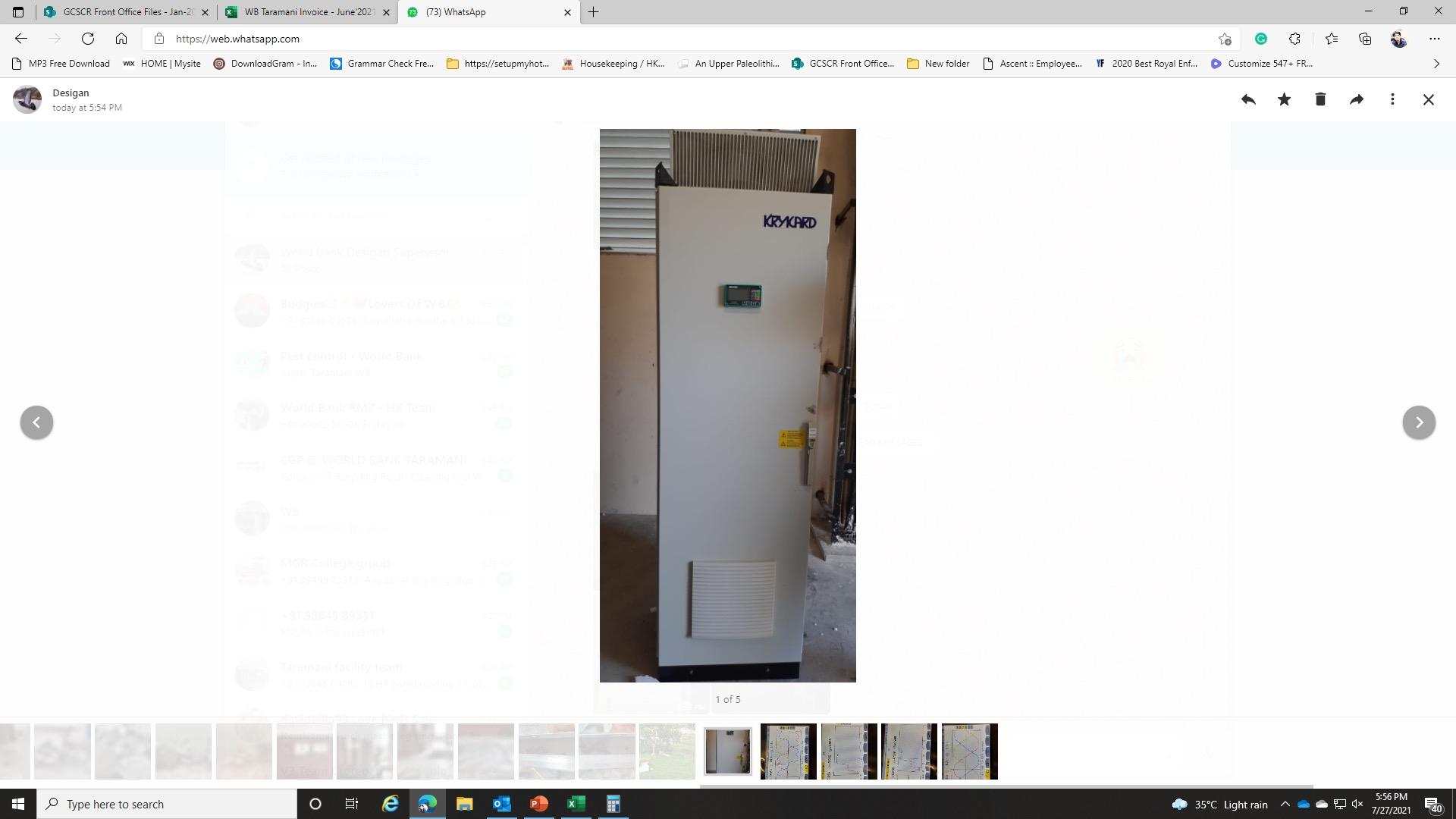
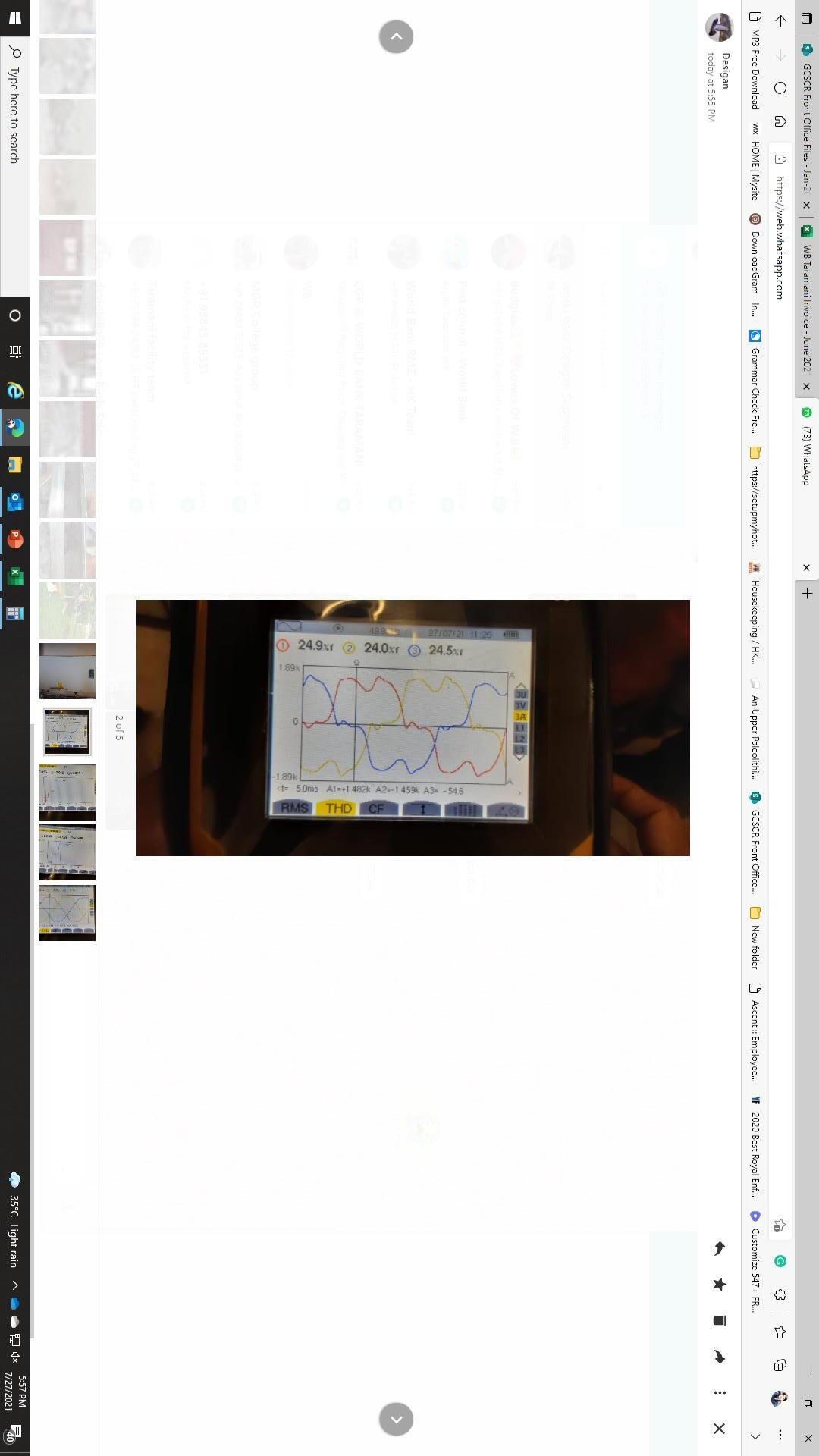
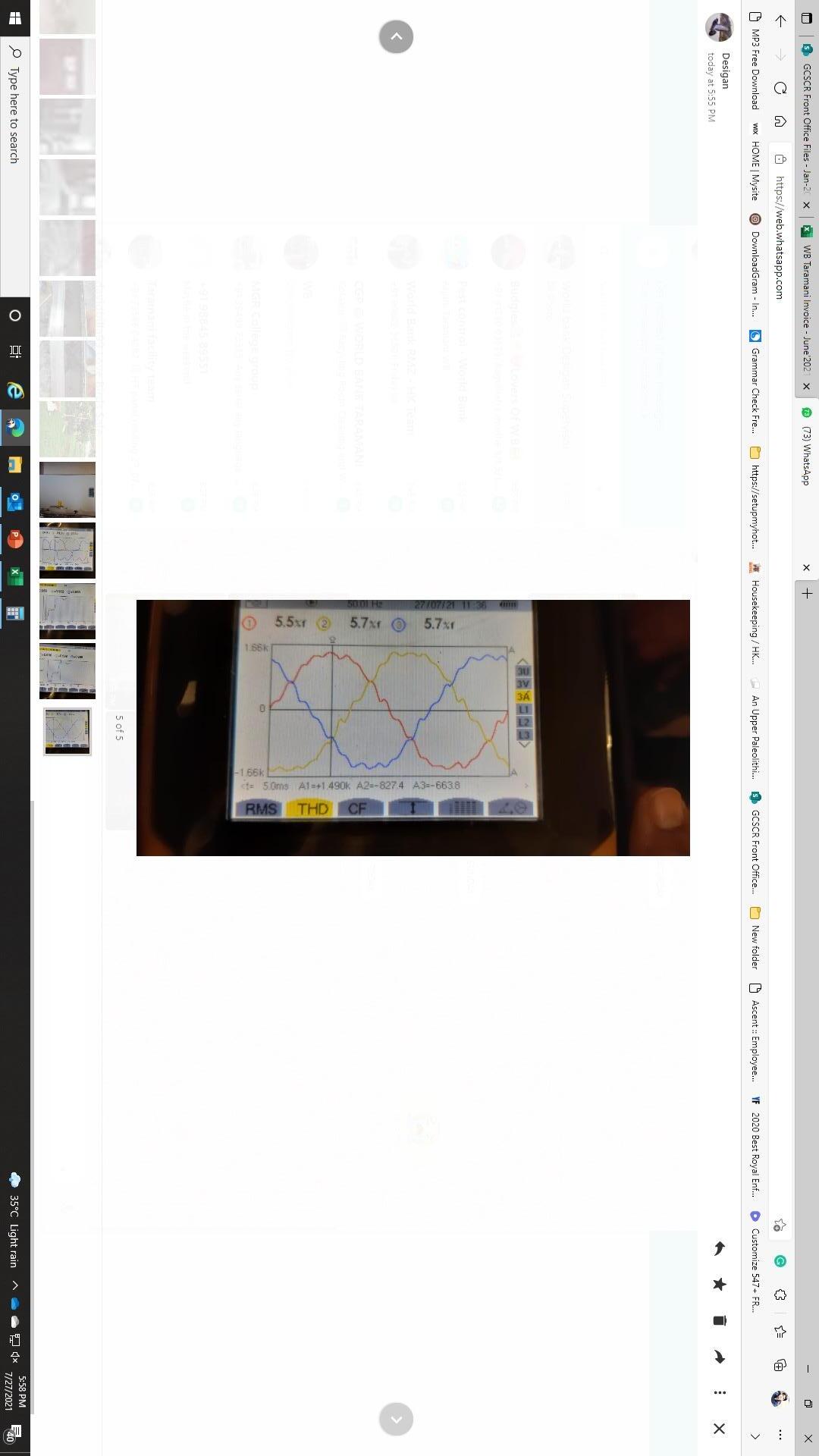
Description of the Innovation:
Sprink Vacuum System for Sprinkler Cleaning
• Dirty Sprinkler heads can cause distorted water spray as grime builds up, become insulated and accordingly will delay in activation of Sprinkler.
• Moreover, we overlook regular inspection and cleaning of fire sprinkler which attracts spreading of virus and bacteria.
• Idea is based on the NFPA 25 Annex A5.2.1.1.2 where it has been written that unless replacing sprinklers that are loaded with a coating of dust or grim , it can be permitted to clean sprinklers with compressed air or by a vacuum that which would not touch the sprinkler. Based on this guideline we explored scope and made sprink Vacuum system which will serve the purpose within less time , complaint and of course without cost.
• Here we have used H/K vacuum machine with pressure regulated valve from old suppression system and one transparent cutout of bottle.
• By implementing this inspection and cleaning procedure inherent risk with the facility which will decrease a lot .
• Transition of Virus and Bacteria will decrease.
• Quickly remove dust and grim so that sprinkler would not be insulated and subsequently reduce risk.
• Accrued a saving of INR120000.00 by implementing it through out east Locations.
myIdea
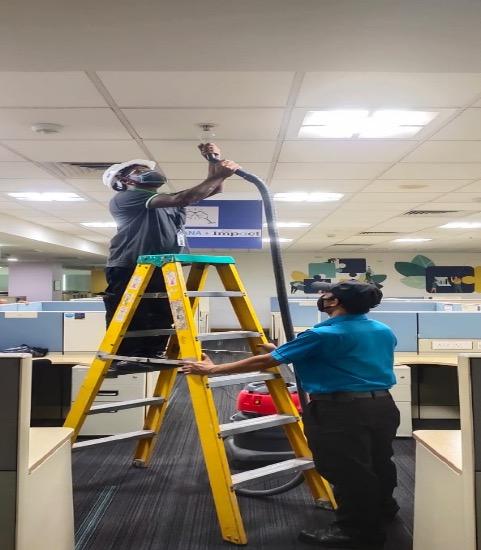
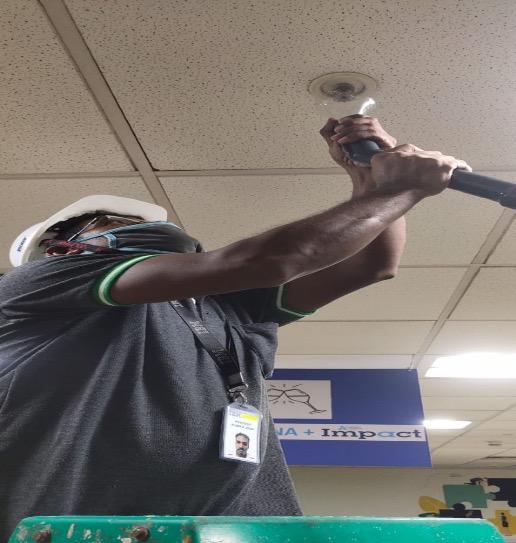
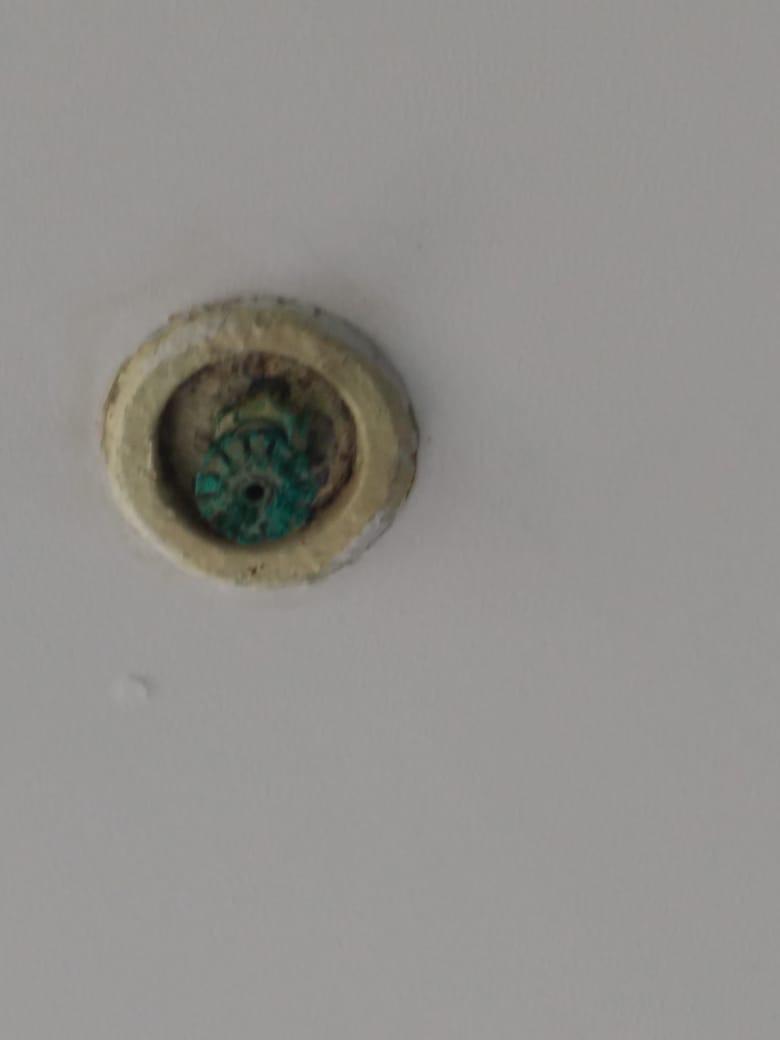

Description of the Innovation:
Retrofit of Conventional AHU system to EC Fan system
• Blower Motor Failure and long lead time for repairs
• Wear and Tear of V Belts
• Power Consumption high due transmission loses.
• Human interface systems
• Blower Noise.
• Frequent breakdown of VFD
• Challenges to clean the Dust deposition on Blower and scroll
• Multiple motor capacities for all AHU’s so difficult to have standby motors
• Introduction of EC Fan Motor directly coupled with composite material which is light in weight and easy to clean with long life along with MCU to replace existing bulky induction motor along with blower, Belt and pulley arrangement.
• Get in MCU and giving up of VFD’s and their huge panels
• Enhance the system efficiency as EC motor has a Unity PF
• Low Electromagnetic noise from motor.
• EC Fan CFM varies as per return air set temp with inbuilt VFD.
• Absolute need base accurate supply of air on the floor increasing the HVAC Energy saving.
• Zero maintenance and minimum human intervention.
• No requirement of motor greasing , belt and pulley alignment, fan balancing.
• Actual Total monthly energy saves is INR.79536 which is 40% of our monthly AHU power consumption.
• Carbon emission reduction by approx. 3.06Ton per annum.
• Man, hours was reduced by 312 hours annually.
• One Single motor and blower can be now standby for the entire building as all the motor capacities are the same
• Total Investment: INR 55 Lacs
• ROI is 6 Years approx.
myIdea

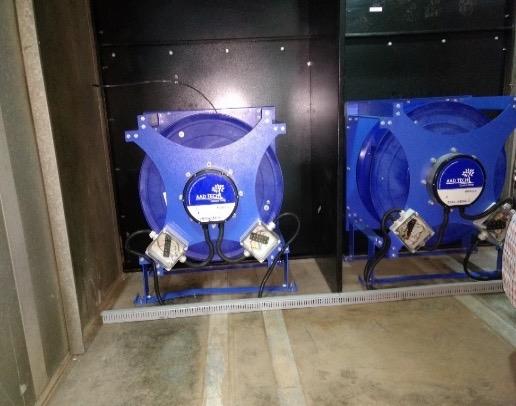
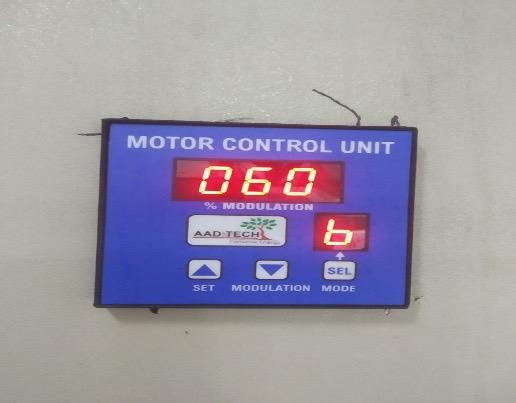
Description of the Innovation:
myIdea
• Social Distancing requirements
• Workstation availability for client employee Return to Office (RTO)
• Identifying Sanitized workstations, meeting rooms, with increased footfall
• Extra resource deployment for sanitization
• These ideas were conceived by the team, proposed & reviewed with client.
• Vendor finalized to execute these changes for “Workstations” and “Sanitization Card”
• Implemented new workstations design with 6 ft. social distance & physical barrier between each workstation and facing away from each other
• The RED side of cardworkstation, meeting room has been used & needs to be cleaned.
• GREEN side of card -workstation, meeting room is sanitized & ready for the use.
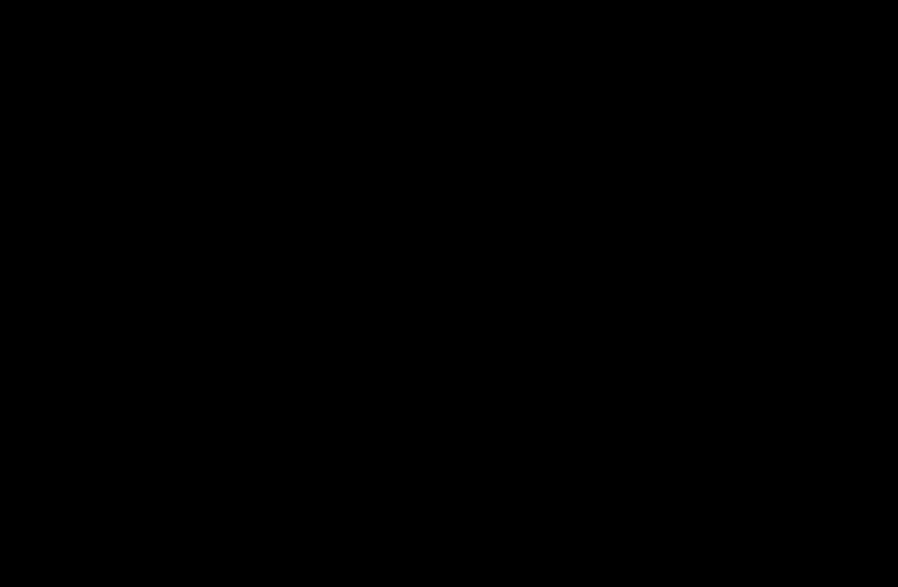
• Increased utilization (114%) of office space from 14 to 30 workstations
• 100% adherence to social distancing norms
• Employee Assurance on COVID safety protocols
• Improved Personal wellbeing and Workplace Hygiene
• Effective resource utilization
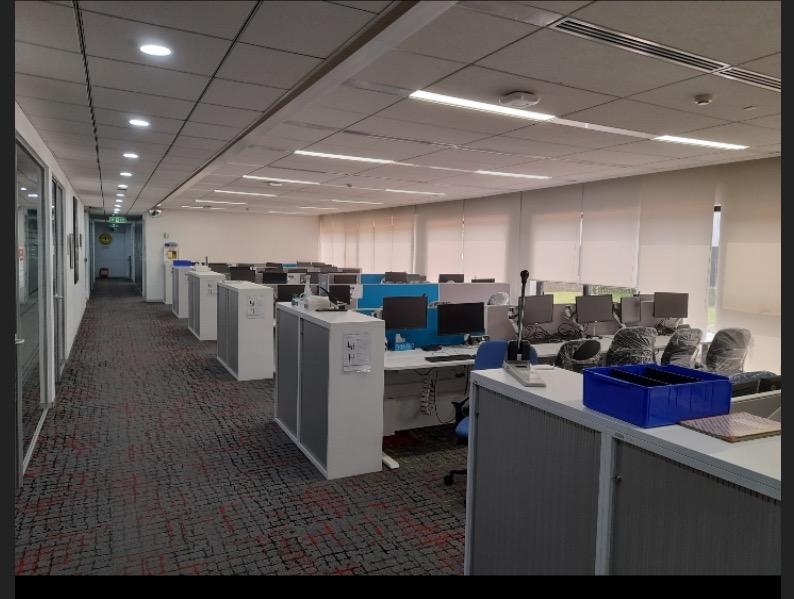

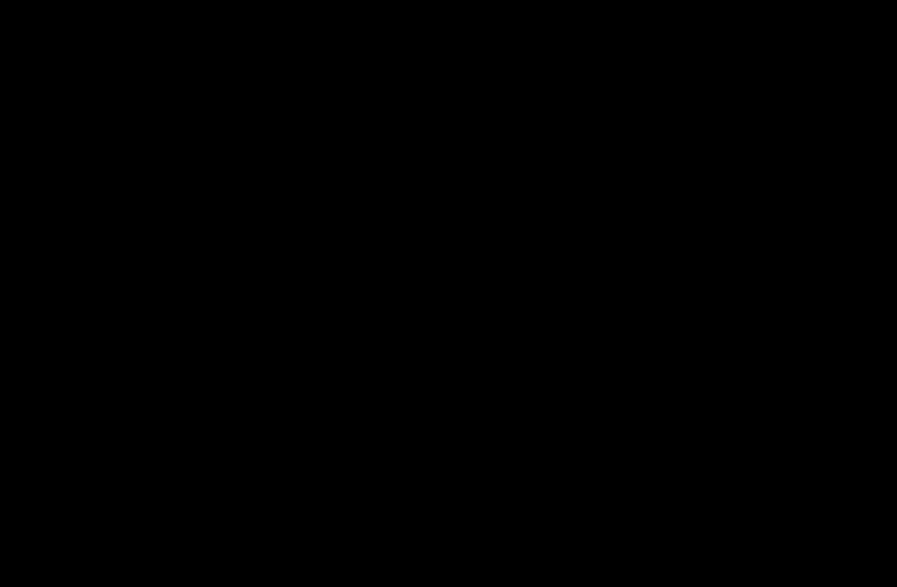
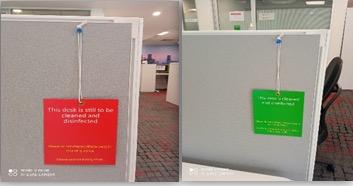
Description of the Innovation:
IOT Based washroom cleaning & Instant feed back on tab
myIdea
• Rest room cleanliness maintenance
• Until then cleaning was being carried out as per predefined timelines
• Despite checklists, there was no way to monitor if cleaning was done or if supervisor had checked the cleanliness
• This technology was used together with employee feedback tab
• Sensors placed at entrance of rest room to count washroom users and threshold of 20 users set for cleaning
• Sensors also placed inside washroom to trigger alarm for maintenance based on ammonia levels.
• Cleaning became need based and enabled digital logging of cleaning records and supervisory checks
• Increase in number of positive responses on instant feedback tab
• Enabled efficient tracking of peak hours and non-peak hours and utilization of HK staff accordingly
• Potential to reduce HK headcounts and reduce costs for client/ CBRE
• Utilization of Manpower increased
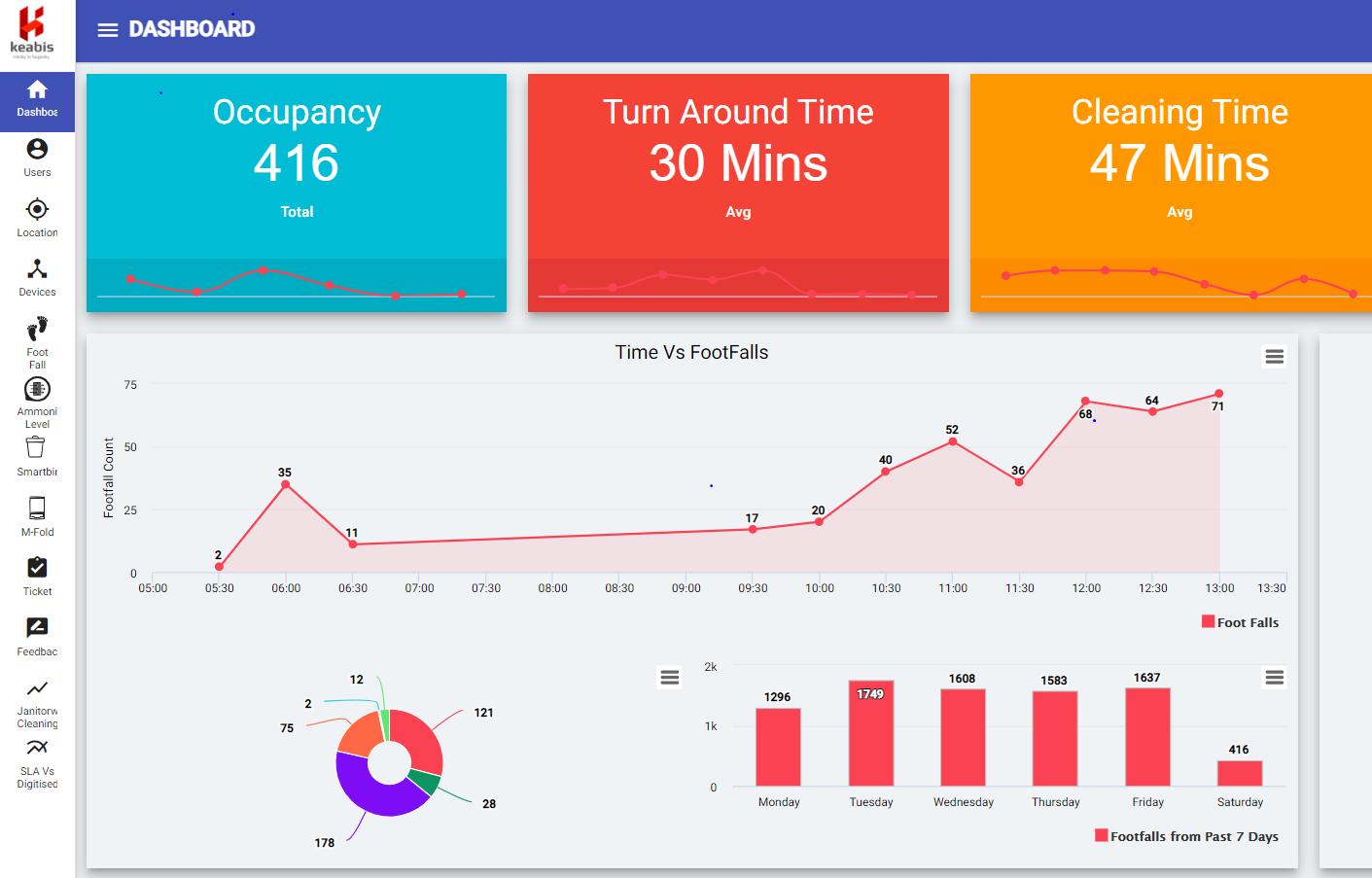


Description of the Innovation:
Air to Water
Harvesting with Touchless dispensers
• Existing drinking water supply for ground staff at security gates is provisioned through plastic water bubbles(20 L cans).
• The supply of these water bubbles again uses a vehicle transport from a third-party vendor
• This method leads to scope-2&3 carbon emissions
• As a pilot Project we introduced 4 No's of 500KLD Air to water harvesting plant with touchless dispensers at these locations inside the campus as a part of strategic Sustainability plan
• These plants harvest 100% clean drinking water from humidity of the air.
• The water is filtered and pumped into the touchless dispensers for consumption.
• Reliable technology giving fresh bacteria-free pure drinking water
• Green Initiative with no depletion to ground or water sources
• Sensor based Touchless dispensers became handy in this pandemic situations.
• Zero Transportation emissions.
• Elimination of Plastic water bubbles.
• Less Repairs and Maintenance cost.
myIdea
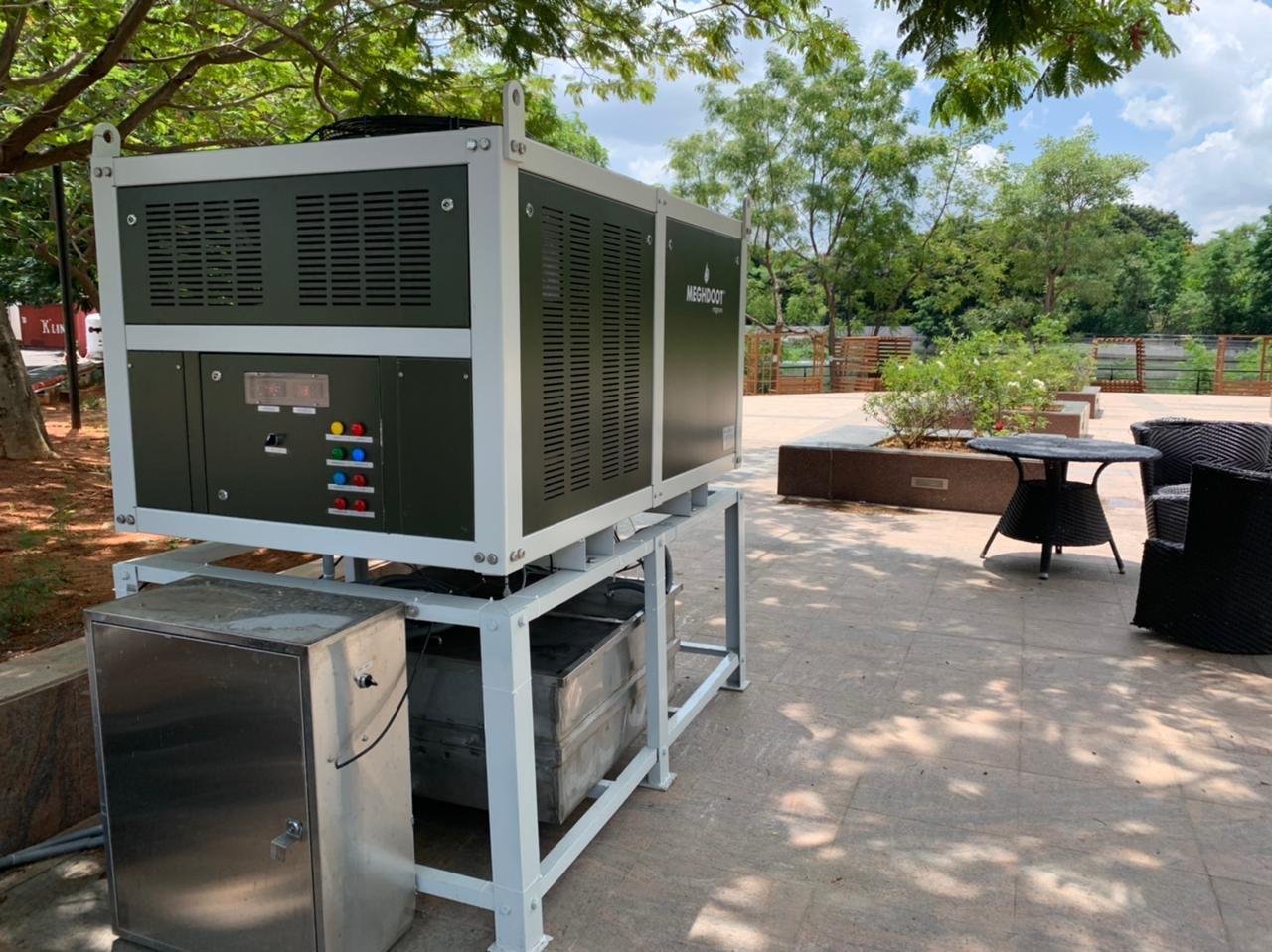
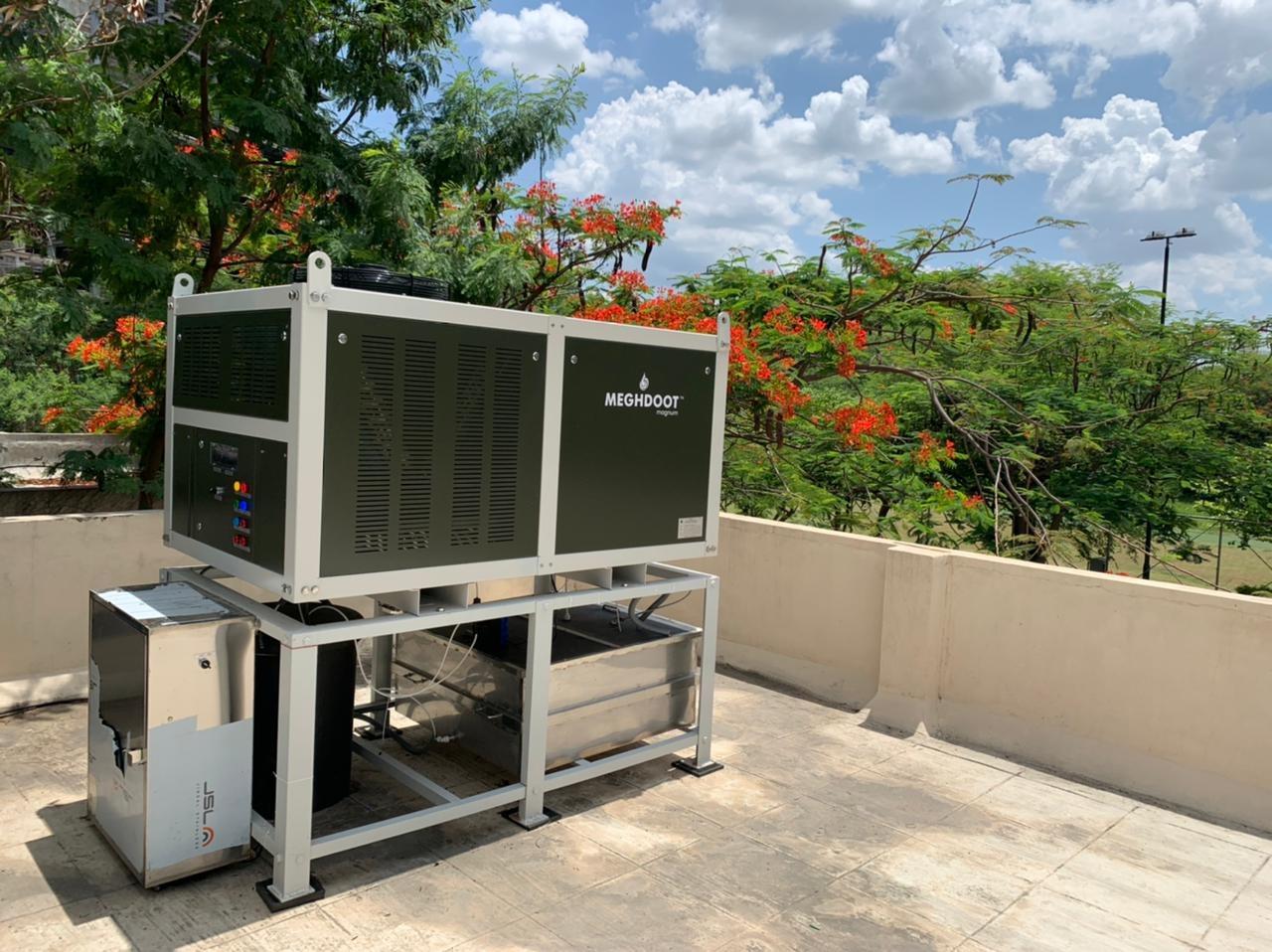
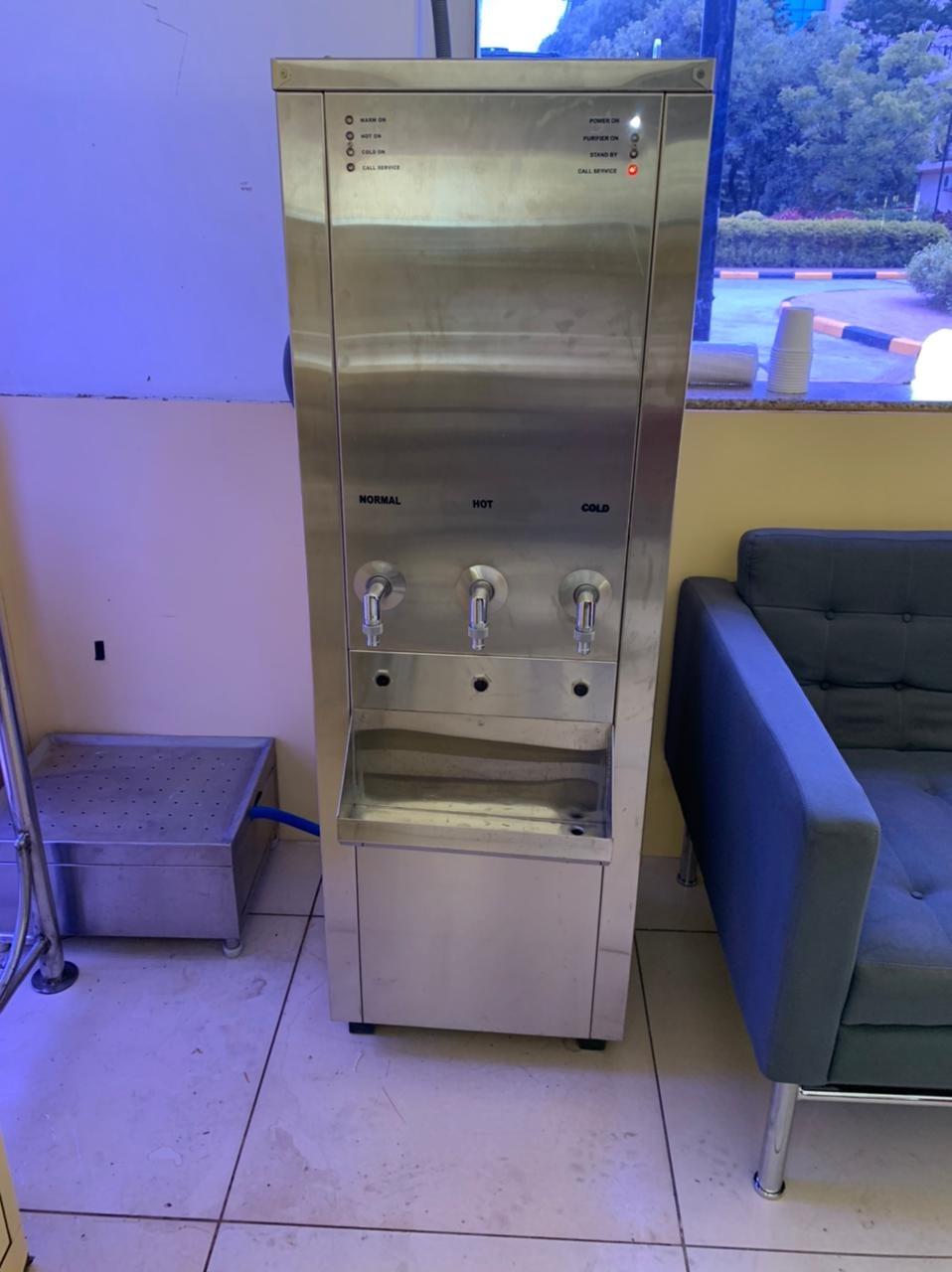
Description of the Innovation:
Conversion of DG Sets- Dual fuel by installing of Optiblend kit (PNG)
• High emission/ curtail Air pollution/ making building eco friendly
• Also curtailed HSD consumptionsubsequently saving in cost
• Total 08 DG sets, combined capacity is 5425 KVA
• Configuration–
• 2 X 1500 KVA
• 1 X 750 KVA
• 2 X 500 KVA
• 3 X 225 KVA
• Initiated pilot project- Retrofitting / modification performed in 750 KVA & 500 KVA, with Optiblend Kit which uses both natural gas (PNG) & HSD
• Also complied with NGT advisory on converting diesel generators into gas based fuel engine
• Post installation of PNG Kit, the fuel ratio is 60-40
• Overall reduction in the HSD consumption by 40%
• On an average 40% reduction in DG emission
• On an average 36% saving in costs,
• Average savings is INR 8/- per unit
• (Earlier cost was 22/- per unit, it has reduced to 14/- per unit)
myIdea
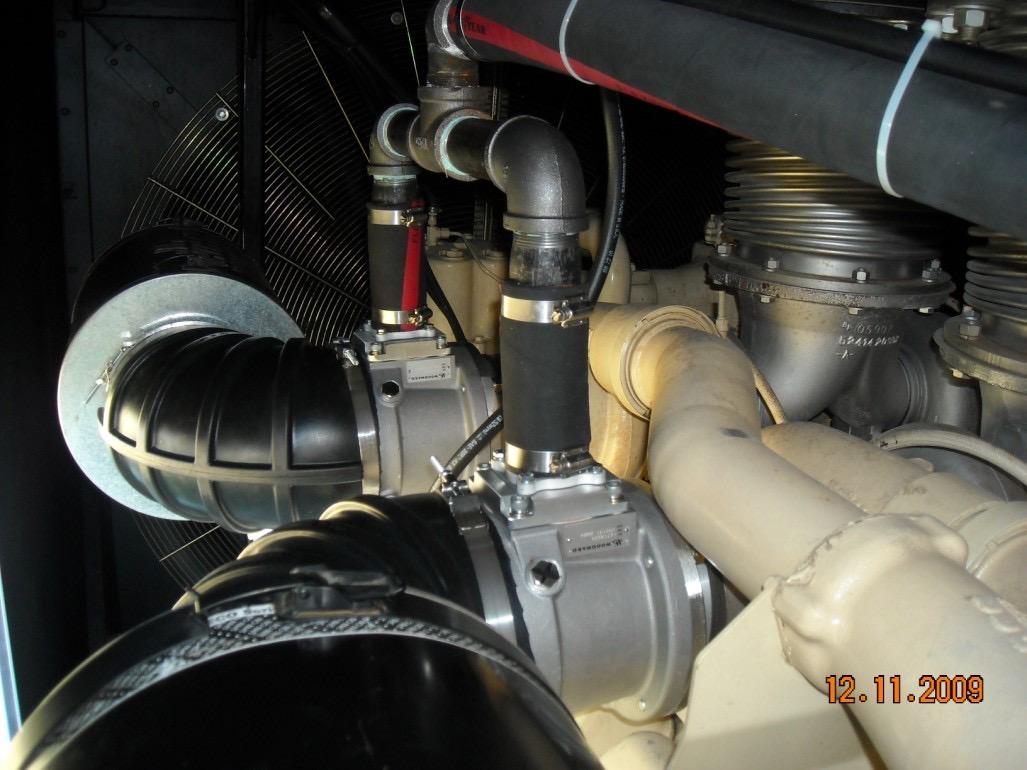
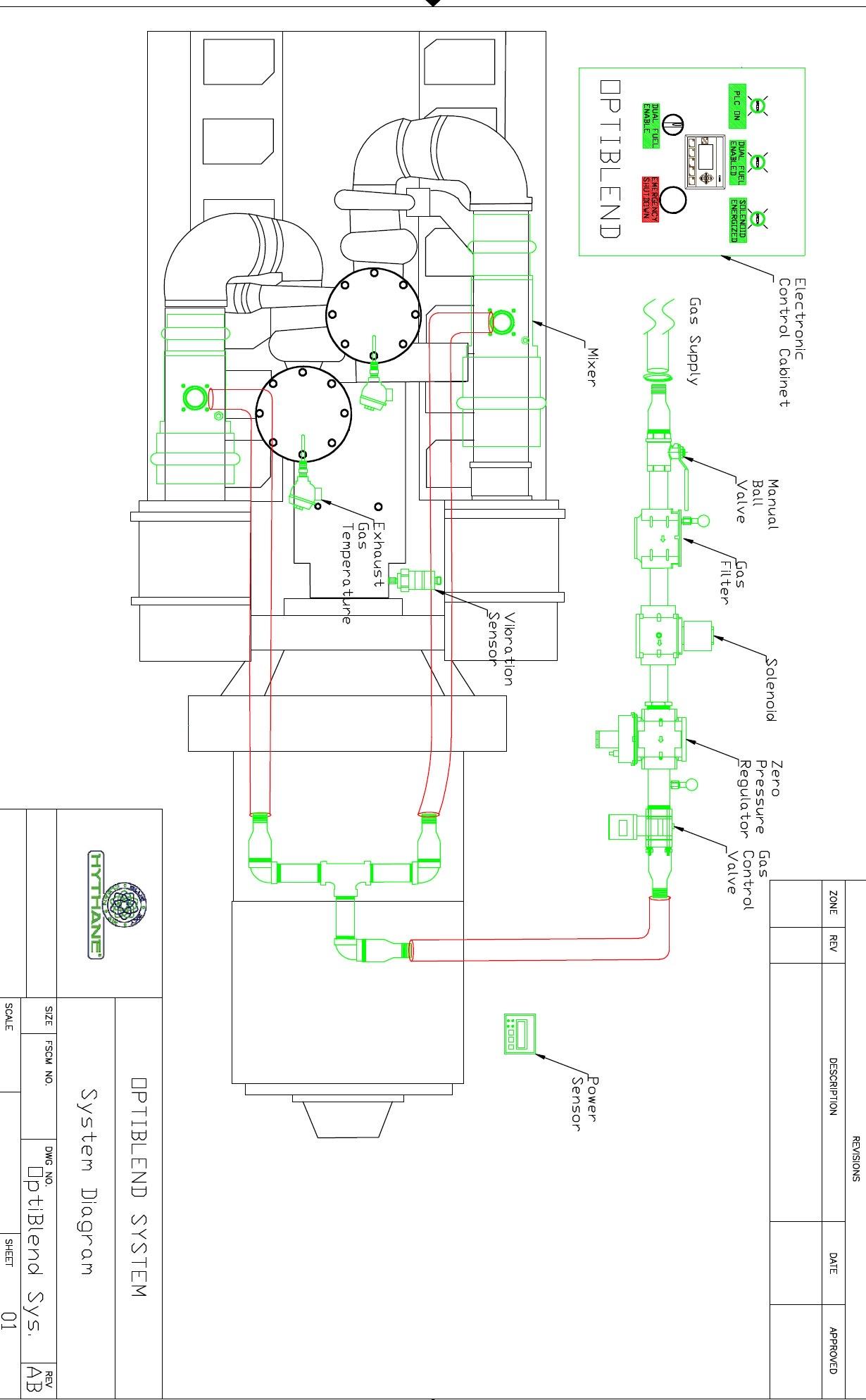
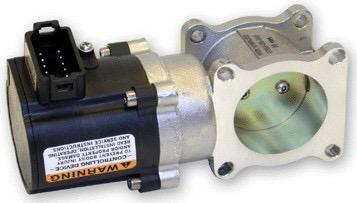
Description of the Innovation:
Automatic
Fire Suppression System in Kitchen Hood
myIdea
• Kitchen being an open source not only for generating of fire but spreading the fire in short span of time
• Increased risk to responders and food makers
• Un-protected infrastructure of the facility
• Higher costs and property losses due to an unwanted accident
• Unavailability of automatic fire suppression system in live kitchen
• Installation of automatic fire suppression system in kitchen hood which is available above hot plat and de-frier.
• Automatic fire suppression system takes the situation under control immediately after detecting the fire within a matter of seconds and once temperature in kitchen hood goes beyond threshold limit i.e., 200’C+
• One step towards ensuring quality of food and safety of food makers
• Automatic arrangement to take situation under control during any untoward fire incident
• Eco-friendly extinguisher filled with F-Class gas to prevent from fire
• Better arrangement instead of having bunch of manual fire extinguishers
• Having a fully protected suppression system establishes the safety of the working staff and the associates availing kitchen services
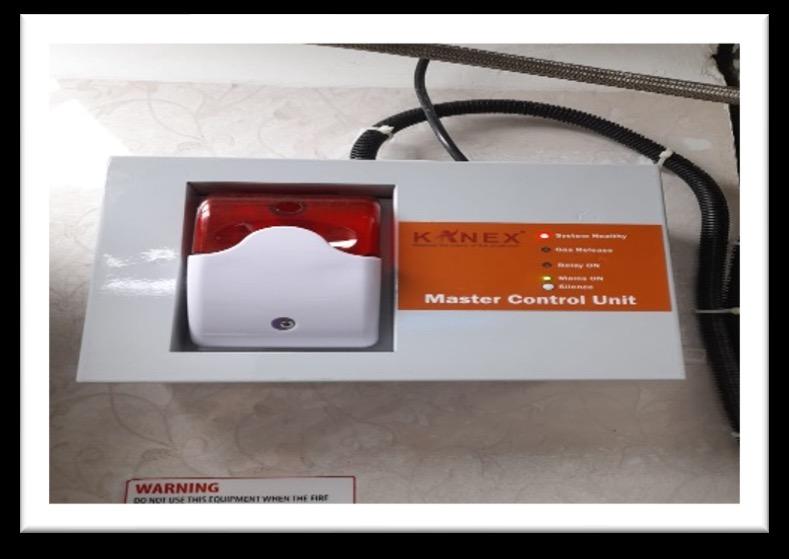

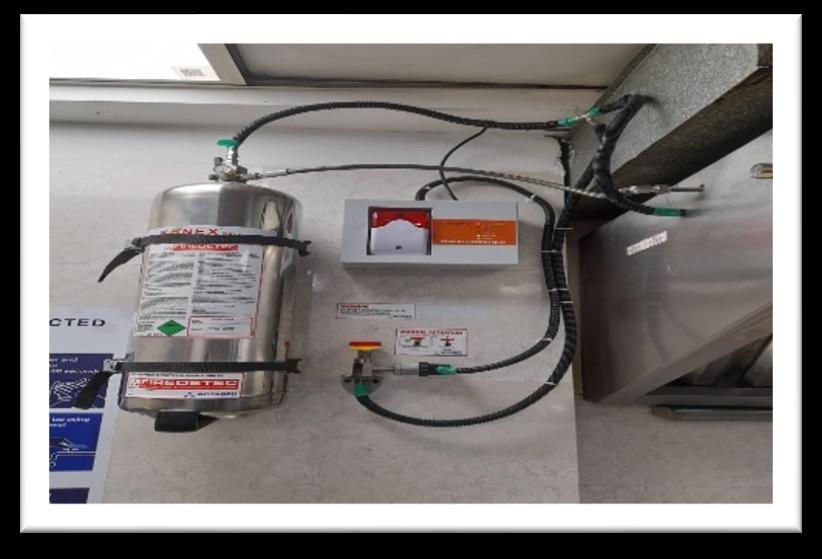
Description of the Innovation:
Implementation of touch free sensor taps
CHALLENGE
myIdea
• We had normal manual water taps in all our breakouts, Pantry’s etc.
• These taps are used to clean crockery & cutleries of employees as well as the office coffee cups by pantry staff
• This had multiple common touch points, which is not safe considering the current pandemic situation
• The cost of sensor tap was 11000 for the existing model
• We tried multiple other options and found better solution to use the same taps
• Installed Protruding Hand free operational sensor Taps with minimum investment
• Easy Installation
• Prevents Infection/ cross contamination
• Dual Sensors for Instant & continuous modes
• Save water with convenience
• Rechargeable battery and it can be used for 5-6 months once its fully charged
• This intelligent sensor also give
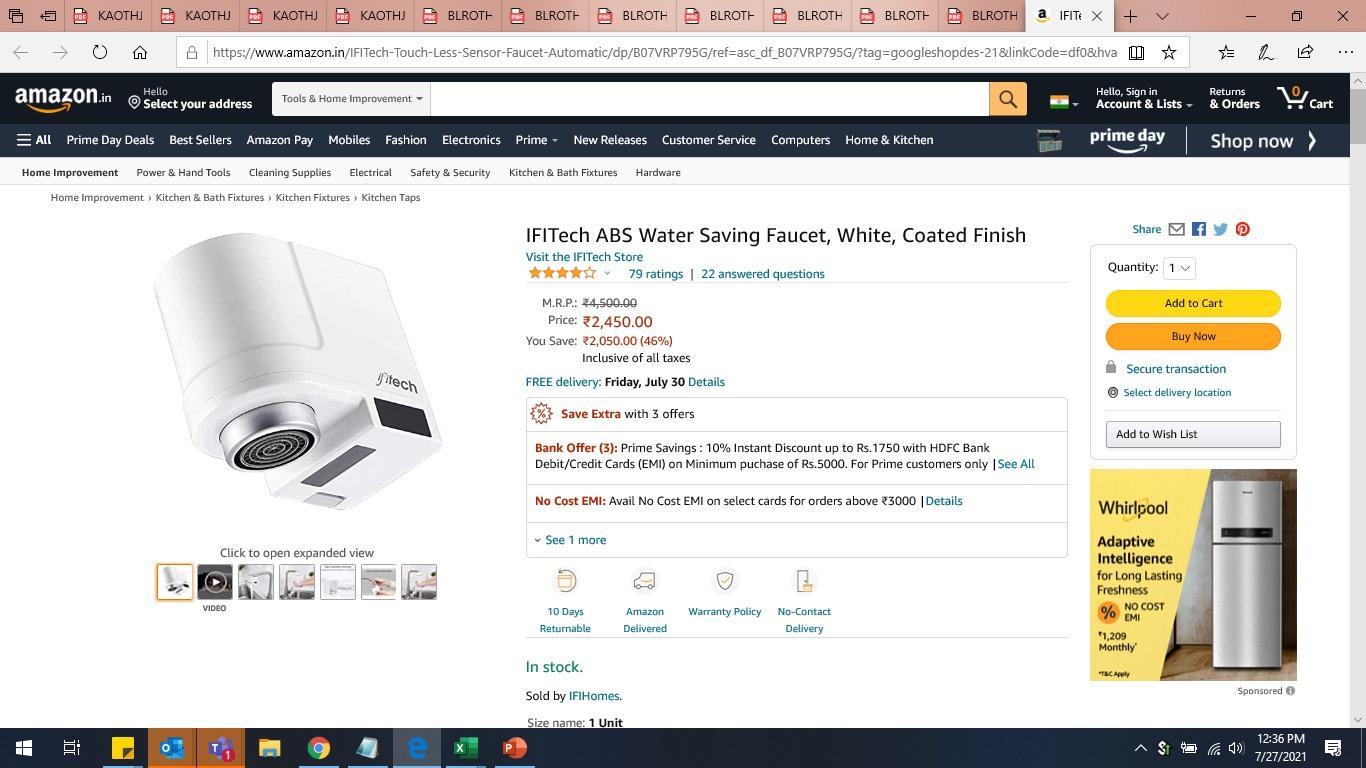
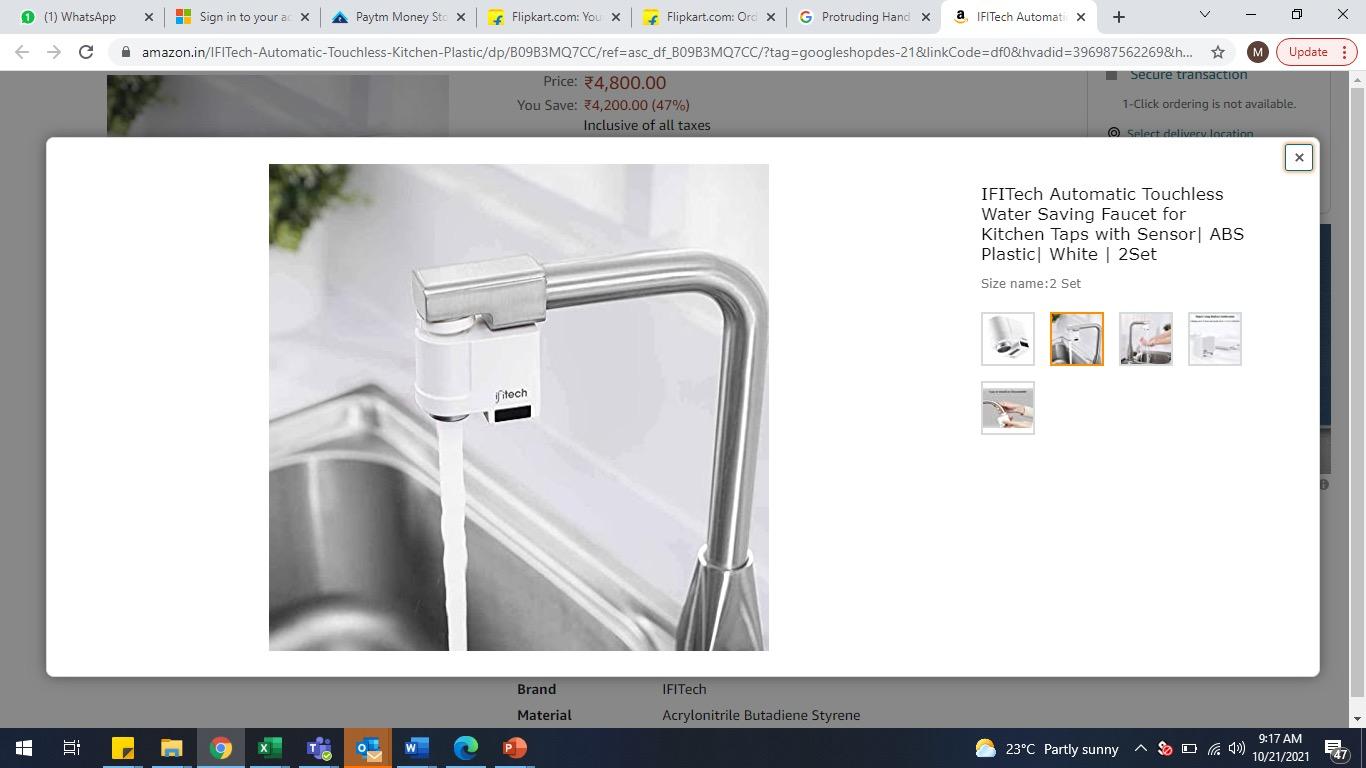
Description of the Innovation:
Sourcing Solar Energy from Open Market
myIdea
• Pursuing Refinitiv sourcing team to rollout the RF for procuring renewable energy from open Market.
• Setting up the reverse auction tool in coordination with Blackstone and solar power contractors.
• Convincing vendors to sign up for the proposed MNDA clause.
• Obtaining approvals from RMZ landlord and BESCOM authorities.
• ABT meter calibration from the builder.
• Vendor registration Refinitiv(Ariba) tool as per payment terms.
• Office located in multi tenant building , out of 10 floors LSEG is occupied 4 floors.
• Find out the consultant to coordinate with the BESCOM, power generator for the smooth transition.
• Organized 7 power generators to get the competitive price by reverse auctioning.
• Coordination with the builder, consultant, client, and power generators by setting up a frequent call.
• Immediate registration after agreement finalization of the power generating company and consultant in client portal for upcoming months renewable energy bid.

• 2.28 million is expected to be procured per year.
• Saving of approx. 1,870 tons of carbon footprint reduction PA.
• Financial savings of approx. $ 118 k PA.
• A veritable step towards CSR
• After the RFP /Reverse auction due diligence contract was awarded to M/s Renew Power with a reduced cost of INR 3.57 per unit.
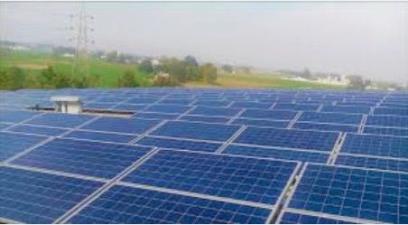
Description of the Innovation:
Virtual Base Kitchen Audit & Healthy Meal Box
• Due to restrictions of movement, base kitchen audits could not be carried out, but safety and hygiene aspects of food preparations could not be neglected.
• It was equally important that associates in office be provided healthy and nutritious meals.
• After detailed discussions with the cafeteria vendor, a process of virtual kitchen audits was established.
• Client Managers were also included in these virtual audits with site checks being carried out using laptop / mobile video cameras and document checks carried out using instant photo shares.
• Ensured associates getting safe and hygienic food.
• Thorough audits carried out without visiting food partners’ base kitchens.
• Undue risk exposure to own personnel avoided.
• Client representatives could also be part of the audit from the safety of their homes.
myIdea
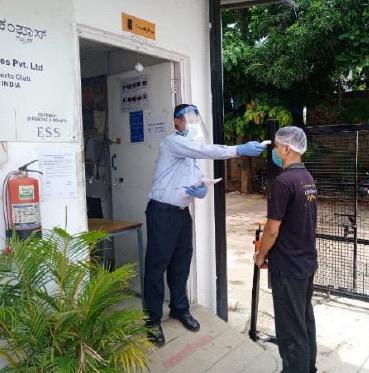
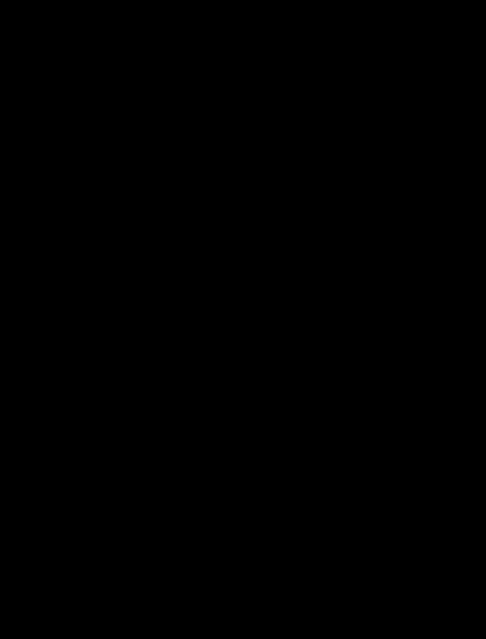
• Healthy Meal Boxes with wholesome food were introduced for associates.
• Special healthy menus were planned which included an immunity boosting drink.
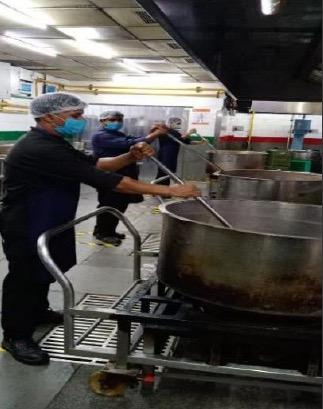
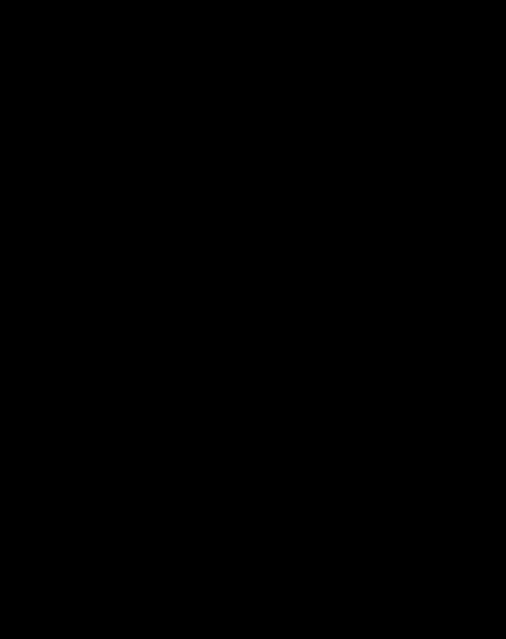
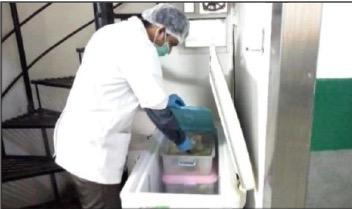

• Healthy menu options for the associates.
• Immunity boosters provided to
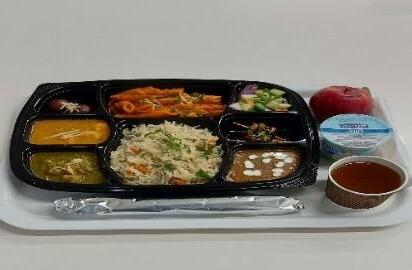
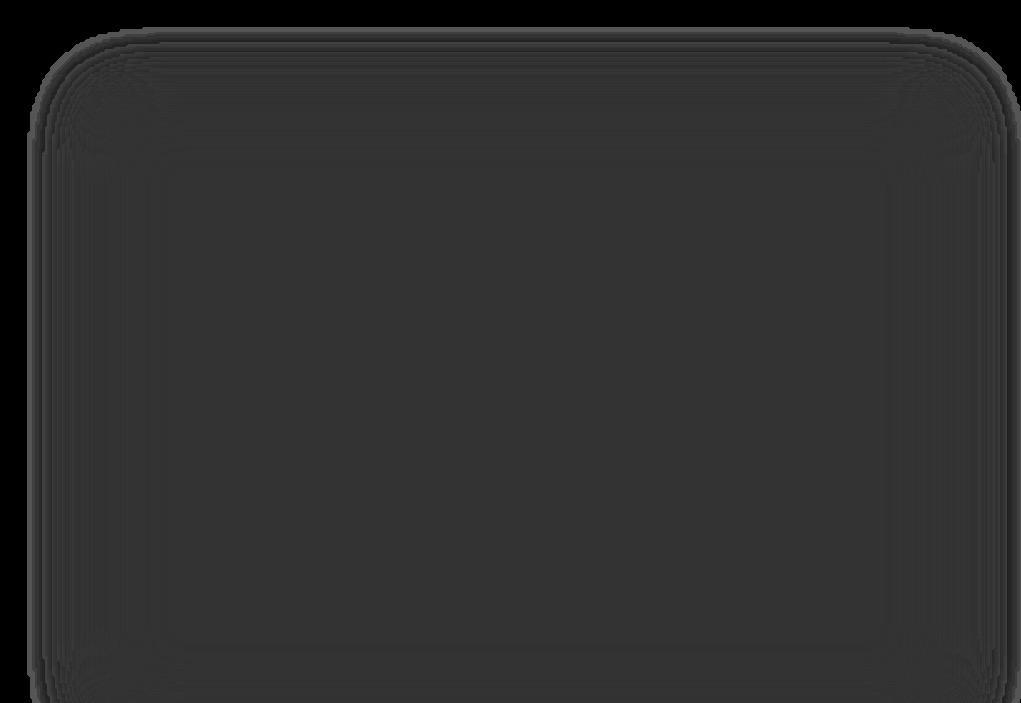
Description of the Innovation:
Robotic Duct Cleaning
myIdea
CHALLENGE
• Planned for air quality improvement in the workplace.
• Need to clean the dust accumulation in the AHU duct.
• Manual cleaning is difficult and same will lead to safety hazard.
• Used Robotic camera to check the level of dust accumulation in the duct.
• With the help of Robot camera vision cleaning materials has been inserted inside the duct and cleaning work was completed.
• Robotic duct cleaning involves with the camera and cleaning accessories, so human direct contact is avoided.
• In Robotic duct cleaning due to absence of direct human contact safety hazards like health issues and accidents can be prevented.
• With the help of Robotic camera before and after image can be captured, to identify the amount of dust accumulated and removed from the duct.
• IAQ test was done after the Robotic duct cleaning and the all the parameters ware found normal.


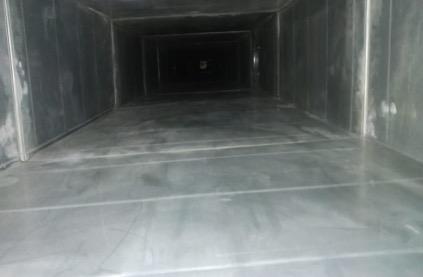
Description of the Innovation:
Water misting system for adiabatic outdoor cooling
myIdea
• During summers, AC units are under constant pressure to circulate sufficient cool air
• When air temperature increases, electricity consumption increases substantially and also the cooling capacity of the AC unit decreases.
• This increased load results in Poor performance, Untimely shutdowns.
• Severe stress for mechanical parts, shortening the lifespan of the air-conditioning unit
• AC Misting System helps conserve electricity and energy by spraying mist on ODU condenser coil.
• Misting system sprays water on the AC condenser in micron sized particles without wetting the condenser.
• Such sprinkler in AC units helps reduce energy and operational cost for the AC condenser units.
• Total consumption of water is 90 liter/ day. We are running this plant mainly during summer months & when ambient temperature rise.
• Pre-cooling helps in reduction in power consumption and increasing the cooling of your existing AC units.
• Outside air temperature into the unit is lowered by up to 12°C.
• Energy consumption drops, saving electricity around 40K units/ Year-thus contributing for sustainability. Increased efficiency of AC units Reduces system downtime.
• Releasing of less greenhouse gasses.
• Yearly cost saving around 3.5 lac/ A. ROI in 2 years
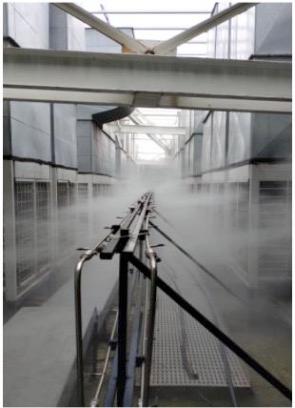
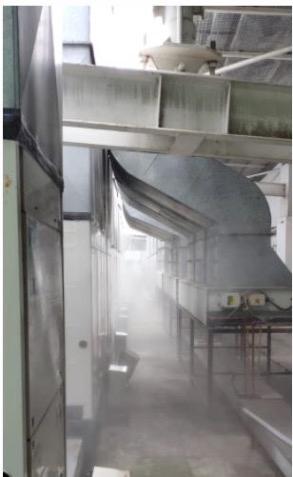
Description of the Innovation:
Introduction of Shycocan Scalene Hypercharge
• The second wave of Covid-19 has had several consequences in the form of rise in the cases, reduced supplies of essential treatments and increase deaths particularly in the young population
• Coronavirus is here to stay
• The threat of the future pandemics is real
• People do not follow social distancing norms consistently
• We need a combination of Vaccine + Technology
• Introducing Shycocan Working methodology
• Shycocan produces Photons
• Photons emanate electrons on striking aerosols, viral particles in the air, solid surfaces and objects in the room
• Due to continuous operation an electron cloud gets formed in the enclosed space where the device is installed
• The electrons get attached to the Coronavirus in the environment in real time and neutralize its positive charge, preventing it from infecting another person
• Up to 99.9% efficacy Immediate Air Borne & Surface
• Constant Protection
• No side Effects Maintains beneficial bacteria and fungi
• One time installation - no consumables
• Effective for all sizes rooms
• Conforms to Regulatory requirements of US, EU, ANZ, META, APAC
myIdea
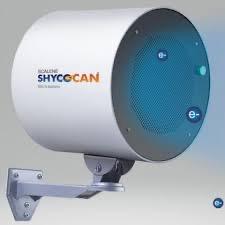
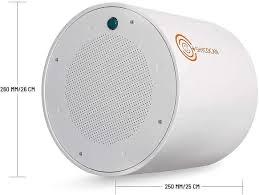
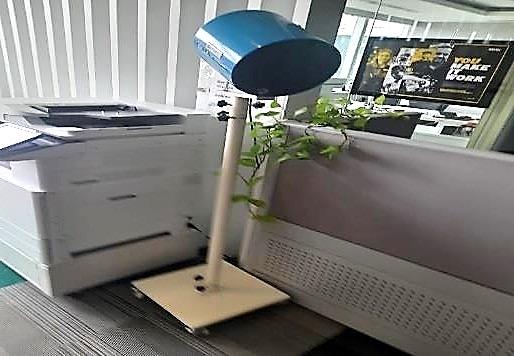
Description of the Innovation:
Employee engagement experience
myIdea
• Due to the pandemic, it was challenging to engage our internal community
• To drive employee experience engagement virtually through activities, workshops and sessions for employees who have been working from home
• To create an environment where mental & physical wellbeing could be enhanced
• Fun Social - This is an event organized to lighten mood & cut the monotony from regular lives
• Now@work - These are fun challenges which is related to employee's day to life & their interests.
• Active wellness classes - This is a daily wellness class where a trained instructor helps an employee to perform Yoga , functional fitness etc.
• Health & Wellness knowledge seriesThese are part of wellness talks & camps specially organized on specific wellness topics which will help our community during these difficult times.
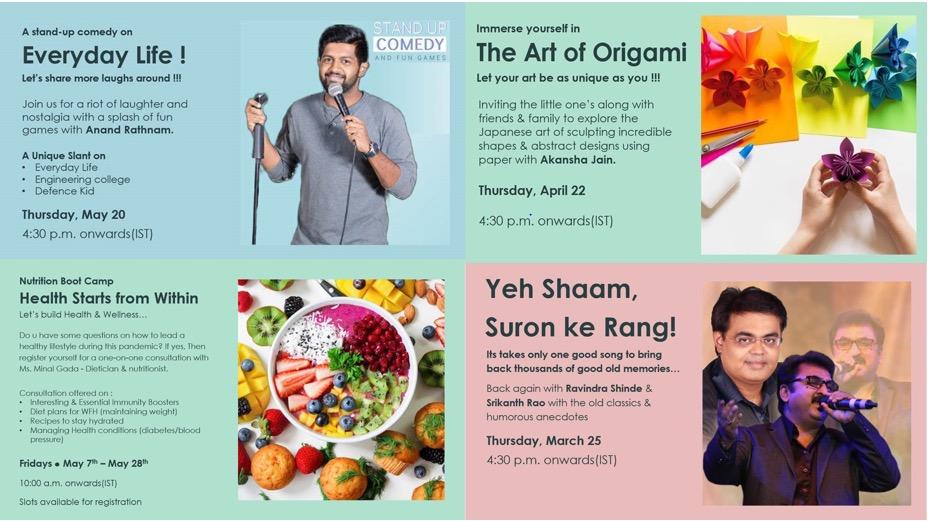
• It helps us to engage better with our community during these trying times.
• It also gives a better working & collaborative approach to the work style
• It give
• Breaks the routine and brings in fun, engagement and learning element between employees, their families as well as with the artist and instructors.
• E sat- Average 94%
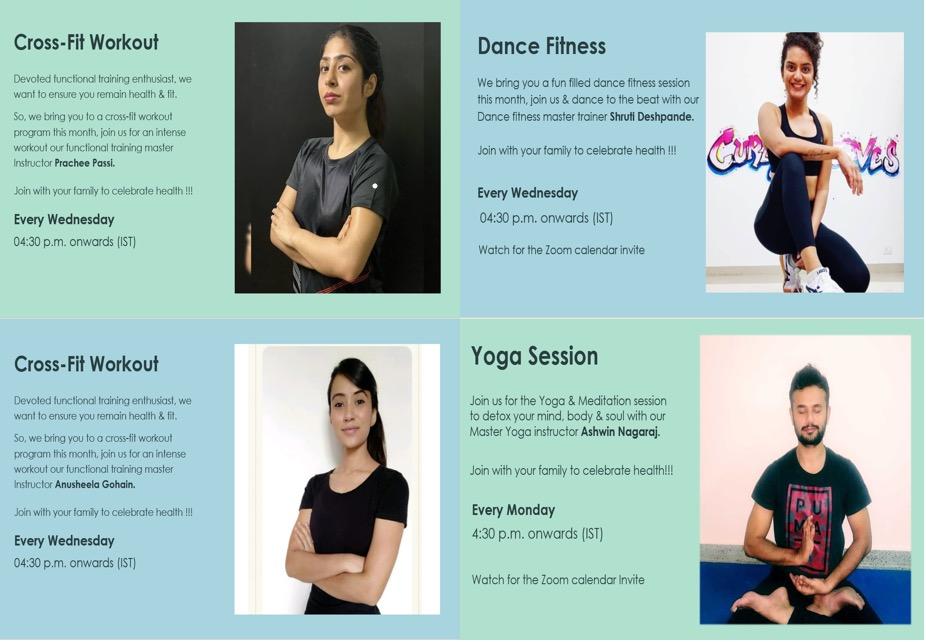
Description of the Innovation:
FPSTAR Tech based STP Implementation
• Activated sludge process works on biological mode with 8-10 hours of retention time.
• No Change in TDS, which results in increased rejection in RO plant
• High peak flow and inadequate storage capacity
• RO water generation cost was high with more consumables
• Addition of salts in softener will increases TDS above 1000ppm consistently which –ve impacts water treatment and reuse
• Total water recovery with RO is only around 60%.
• Space availability constraint for further extension of plant.
• Installation & Commissioning of FPSTAR (Fine Particle Shortwave Thrombotic Agglomeration Reaction) technology working on the principles of elemental specific frequency disassociation.
• As the water passes through the Boom Tower resonator, the elements in the water (except hydrogen and oxygen), will start disassociating from its compounded form to their equilibrium elemental state.
• Elemental frequency breakdown particles and produces clean water with various filtration process.
• Requires minimal storage capacity.
• Continuous operation - We able to get continuous output since retention time was optimized to less than hour for 15KL of water output.
• Meet the peak loads without much difficulties.
• Chemical and Odor free process
• Automated process - No manual intervention required
• Reduction in TDS or salt content
• Ensuring Zero Liquid Discharge Facility
• Additional treated water available for flushing and cooling tower which reduces water procurement by 3000 KL/ Month.
• RO reject can be treated again, which is not possible with ASP technology.
• Meeting Pollution control board norms consistently.
• Reduced O&M cost
myIdea

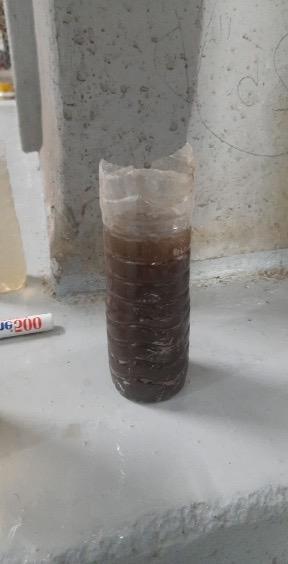
Programmable to meet future water treatment standards without any physical
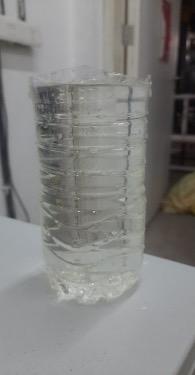
• Estimated Savings – 1.5 Crores per year
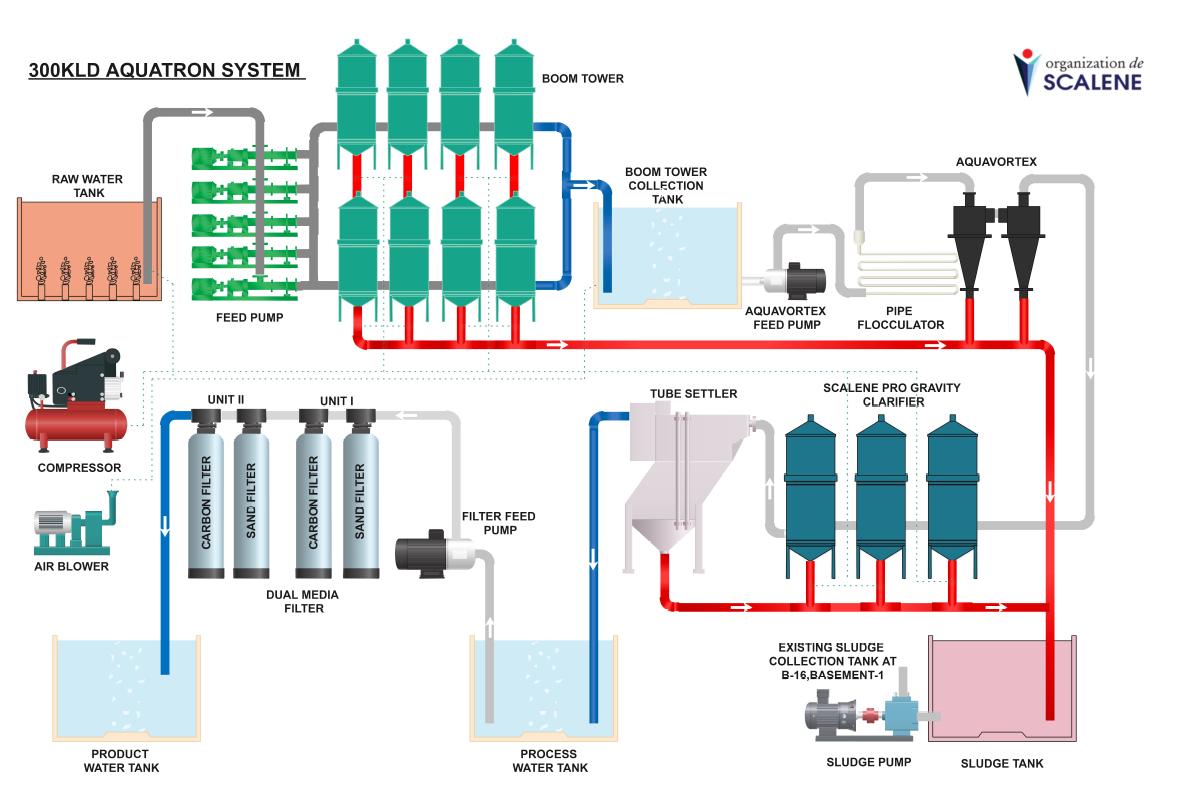
Description of the Innovation: CHALLENGE
• Heavy carbon particles expels into atmosphere while carrying DG exhaust stack cleaning.
• Environment pollution
Carbon collection filter for DG stack cleaning
myIdea
• High chances of Carbon particles getting into nearby residential area.
• Major modification suggested by OEM in exhaust line for re orientation would not prevent carbon particulates into atmosphere which also require Shut down of DG during modification work.
.
• To prevent heavy carbon particles expelling into atmosphere during cleaning activity , Inhouse team has developed a metallic filter which can be used to arrest 90-95
% heavy carbon particles getting into air.
• This has been tested and proved to be 100% efficient.
• It helps us to engage better with our Environmental pollution prevented in great extent.
• Avoided concerns from nearby residents.
• Saving of 28 Lakhs which was proposed for re orientation of Exhaust lines facing residential area.
• Lan lord team approached to support with best technology solution available to incorporate with existing DG stacks to minimize the carbon particles.
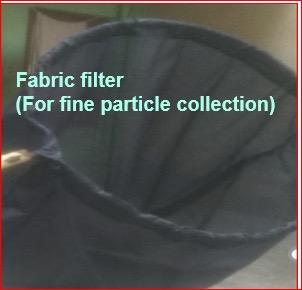
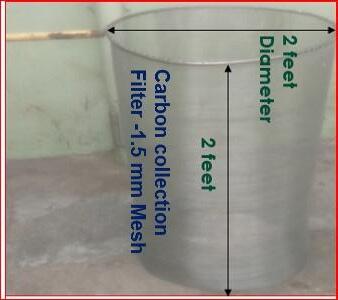
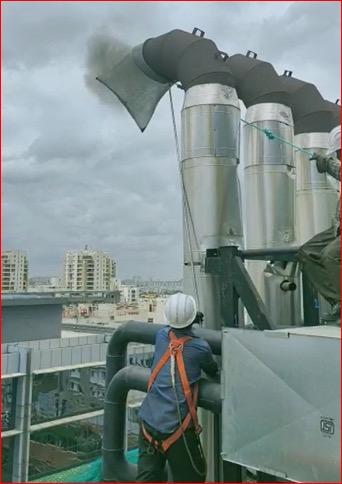
Description of the Innovation:
Fire Detection System in Electrical & Communication
CHALLENGE
§ Fire detection system in the Electrical and Communication shafts was not available.
§ There are chances of fire spreading through cables in shafts and doors to other floors in the event of a real fire.
§ The containment of fire is a challenge even if the floors are concealed with fireproof.
§ To avoid the spread of fire and early detection Smoke detectors installation idea planned at each floor level in electrical & communication shafts.
§ Necessary approval were taken for procurement of detectors and integrated the detectors to existing FAS system. .
/
§ Fast and highly sensitive reaction to incipient fires.
§ Simple handling due to detectors being mounted in easily accessible areas across the shafts.
§ Containment and minimization of impact to site assets and human life.
myIdea

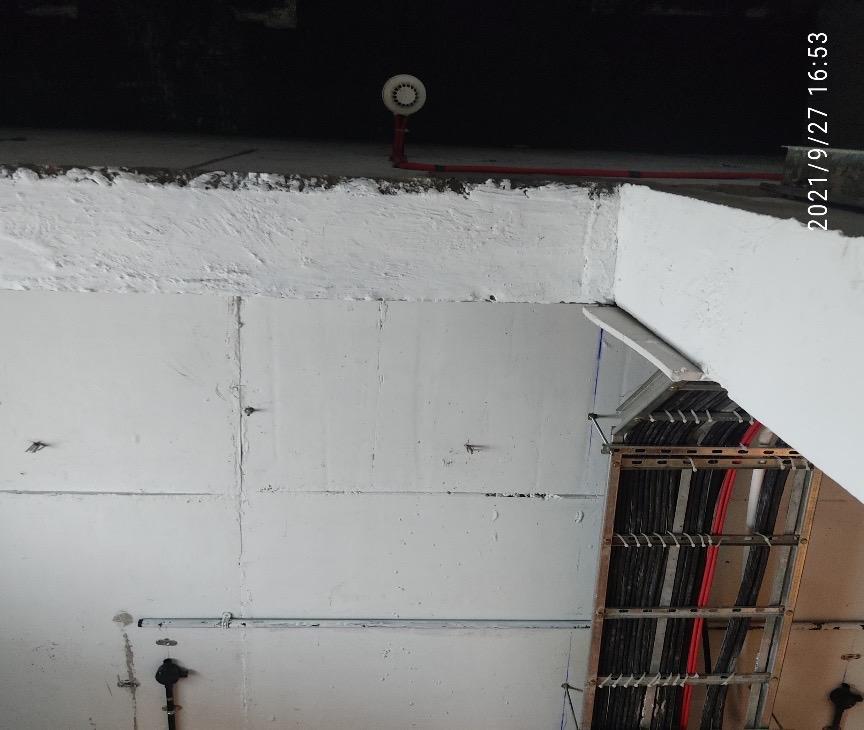
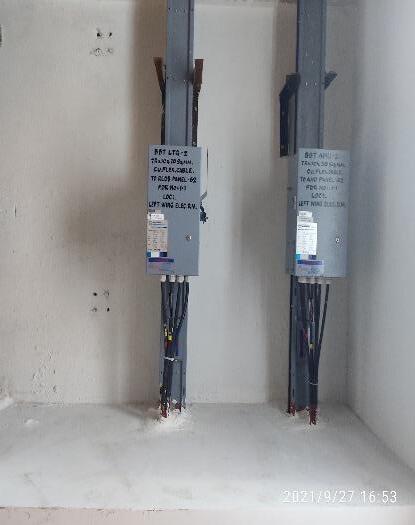
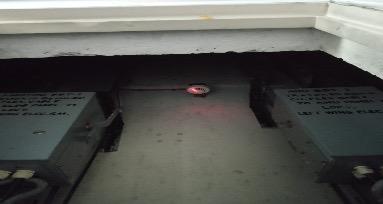
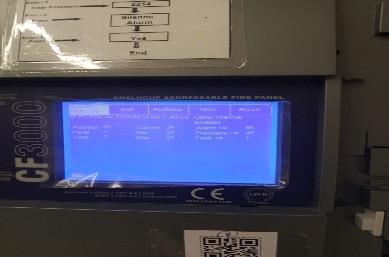
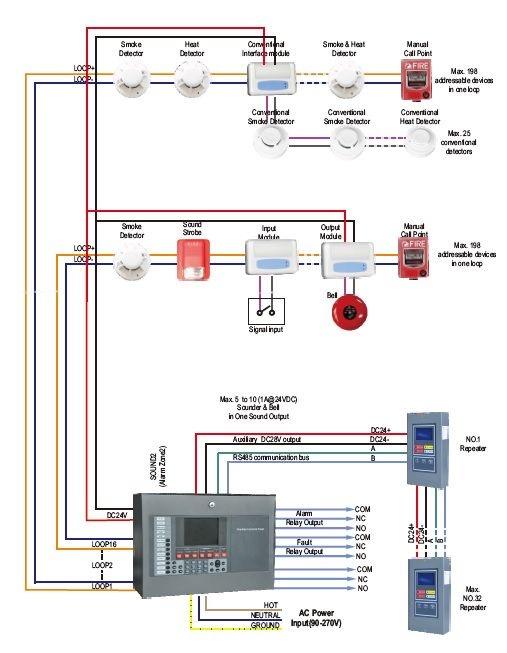
Description of the Innovation:
Public transportation
CHALLENGE
myIdea
§ During the pandemic bringing employees to offices were a big challenge.
§ Employees would find it difficult to travel to office because of Stringent Government restrictions
§ Investment on FM200 for a small server rooms and hub rooms was huge
§ We have contacted BMTC for providing pickup & drops.
§ The proposal were taken to the client and have convinced to them on the safety and security issues as well
§ ceiling mounted sprinkler type gas based clean agent system found more effective and can cover small server rooms/Hub rooms
§ clean agent is defined as the gaseous, volatile and electrically nonconductive fire suppressant that extinguishes the fire
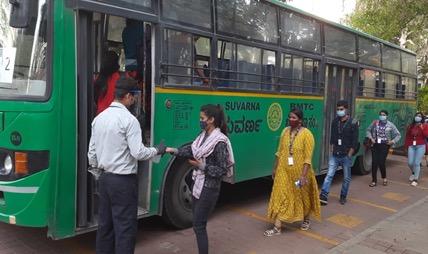
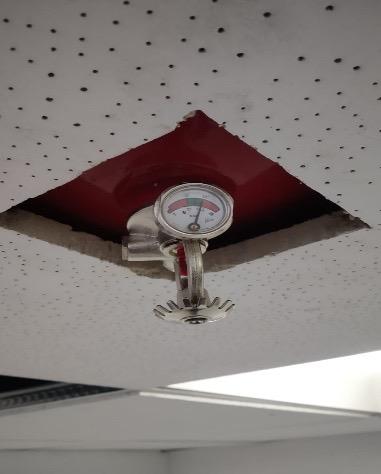
§ Saved an estimated cost of INR 10.00 Lakhs in one quarter
§ Drastically reduced the productions impact to the client
§ Working Pressure (Kg’s per Cm2): 7-10, Area Protection: 3.5 m2 to 4 m2
§ Operation Time in seconds: 10 to 15
§ Extinguishing Agent: Clean agent Gas , Unitization temperature: 57’c to 107’c
§ Cost saving INR 7.00 lakhs

Description of the Innovation: CHALLENGE
§ Existing AC air vent (swirl diffuser) are controlled manually controlled by end user
§ Local temperature demand cannot be controlled in existing centralized Ac concept
Swirl Diffuser Automation
§ Over cooling complaints during partial occupancy
§ Excess power consumption during partial occupancy
§ Hardware to convert the existing CV diffusers will be supplied and installed to make them VAV modulating diffusers.
§ Every Diffuser connected in a daisy chain manner with each other. Group of 20 diffusers connected to individual ports of Group Controller.
§ Group Controller sends requests and responses from each and every diffuser connected in its own network to handle the diffusers data and get ready to transfer over BMS over BACNET Network.
§ In Fault Condition, Diffuser sends alert data to the respective Group Controller. Further Group Controller sends an alert alarm to BMS system with Group ID.
myIdea
§ Local temperature demand can be controlled through automated diffuser modulation
§ Air terminal unit fan running cost savings seen throughout unoccupied times. Example: During lean occupancy or during lunch/breaks when capacity is limited, the diffusers will close ramping down the EC fan on ATU.s
§ Chiller load saving as ATU running speed reduces
§ Estimated Cost Saving: INR 1,66,99,573/Annum
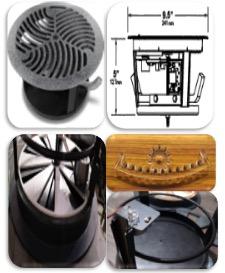
Description of the Innovation:
Diversity and Inclusion in workplace
§ Enhancement required for % of Diversity & Inclusion ratio
§ Improvement for % of women representation in technical role
§ Increase in awareness required in T1 & T2 for DE&I concept
§ Substantial representation required for diverse supplier
§ Scrapping of end-of-life IT assets
§ Outreach to communities and minorities
§ Increase the ratio through a structured roadmap for supported employment
§ Design a program for Internship for women candidates to induct in technical role
§ Collaboration with SME -NGOs for awareness workshops to increase awareness
§ Onboarding of diverse supplier for services as part of responsible sourcing
§ Donation drive for all EOL IT assets to NGOs
§ CSR – Voluntary hours every quarter by employees
§ The ratio of supported employment increased to 4.5% against the target of 5% by end of the year
§ An exclusive Internship program successfully conducted for 13 candidates to prepare them for full time technical role in IFM . Increased ratio of female in technical role to 10%
§ Series of 3 workshops conducted from MS registered NGOs for upskilling in DE&I
§ 2 suppliers onboarded , 2 RFPs in process with focus on responsible sourcing .
§ NGOs utilized IT assets for online education for underprivileged during covid . Client is aligned to make the activity regular across India . Community & Social Impact through
myIdea
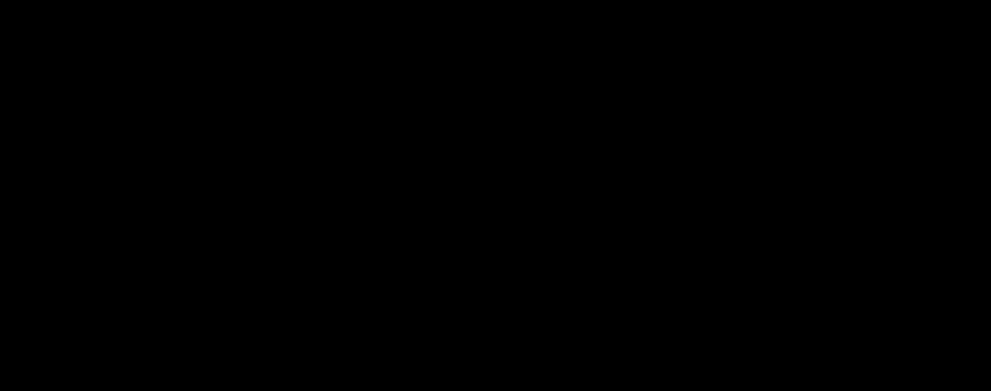
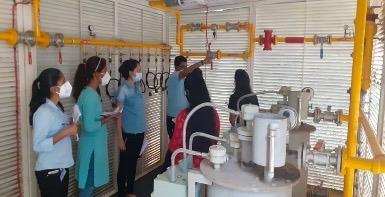
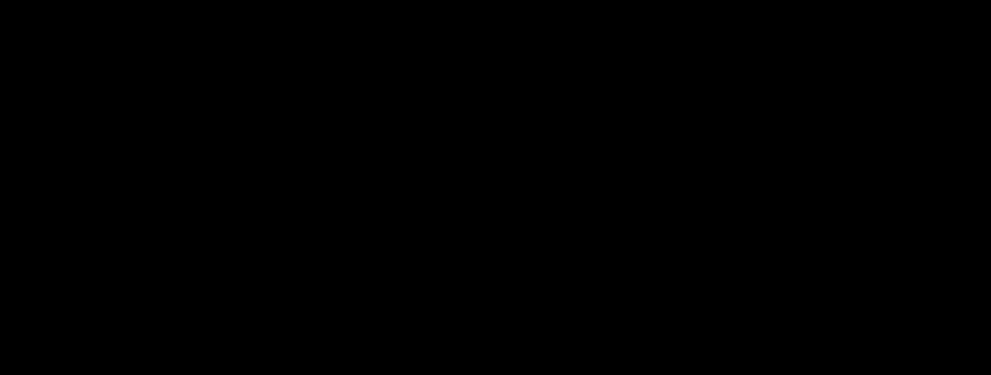



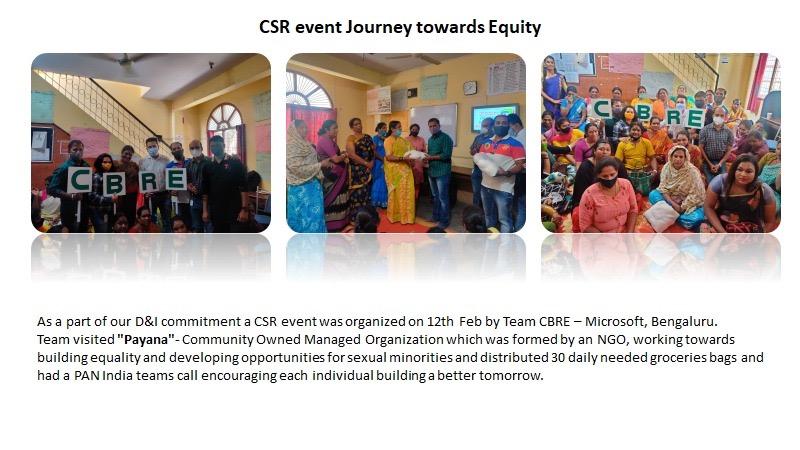
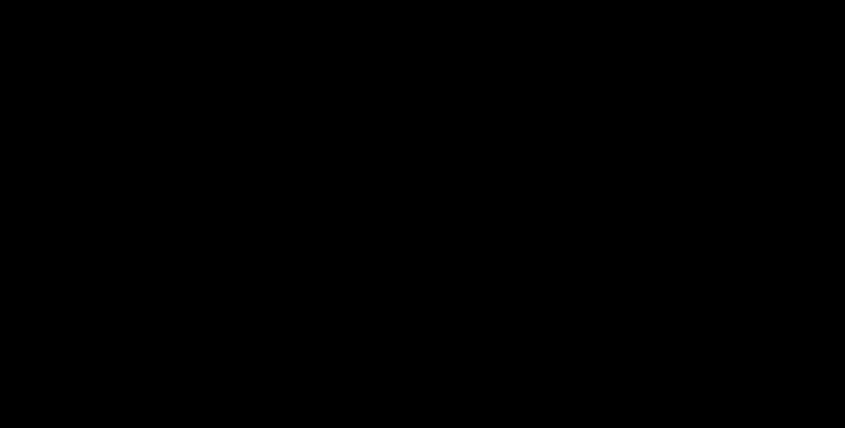

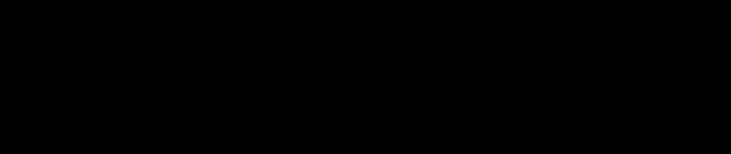
Description of the Innovation:
Waste Plastic Utilization
Bitumen Road
CHALLENGE
myIdea
§ Plastics are non-biodegradable.
§ Burning of waste Plastic causes environmental pollution
§ Disposal of Waste Plastic
§ Potholes & Crack on road
§ More Capex for Construction
§ More Opex Spend for Repair
§ Making Driveway of Waste Plastic
§ Low Polyethylene Crushed Plastic Utilization.
§ Aggregate of 10mm, 20mm
§ Waste plastic in shreds form of size 2.36mm to 4.75mm
§ Stone dust and lime as filler
§ Bitumen 60/70, 80/100 Grade
§ Use higher Percentage of waste plastic. And Reduce 7.5T of CO2.
§ Reduction in Need of bitumen by 15%
§ Generate jobs for rag pickers. Which is ECO friendly.
§ Strength of road increased by 100%
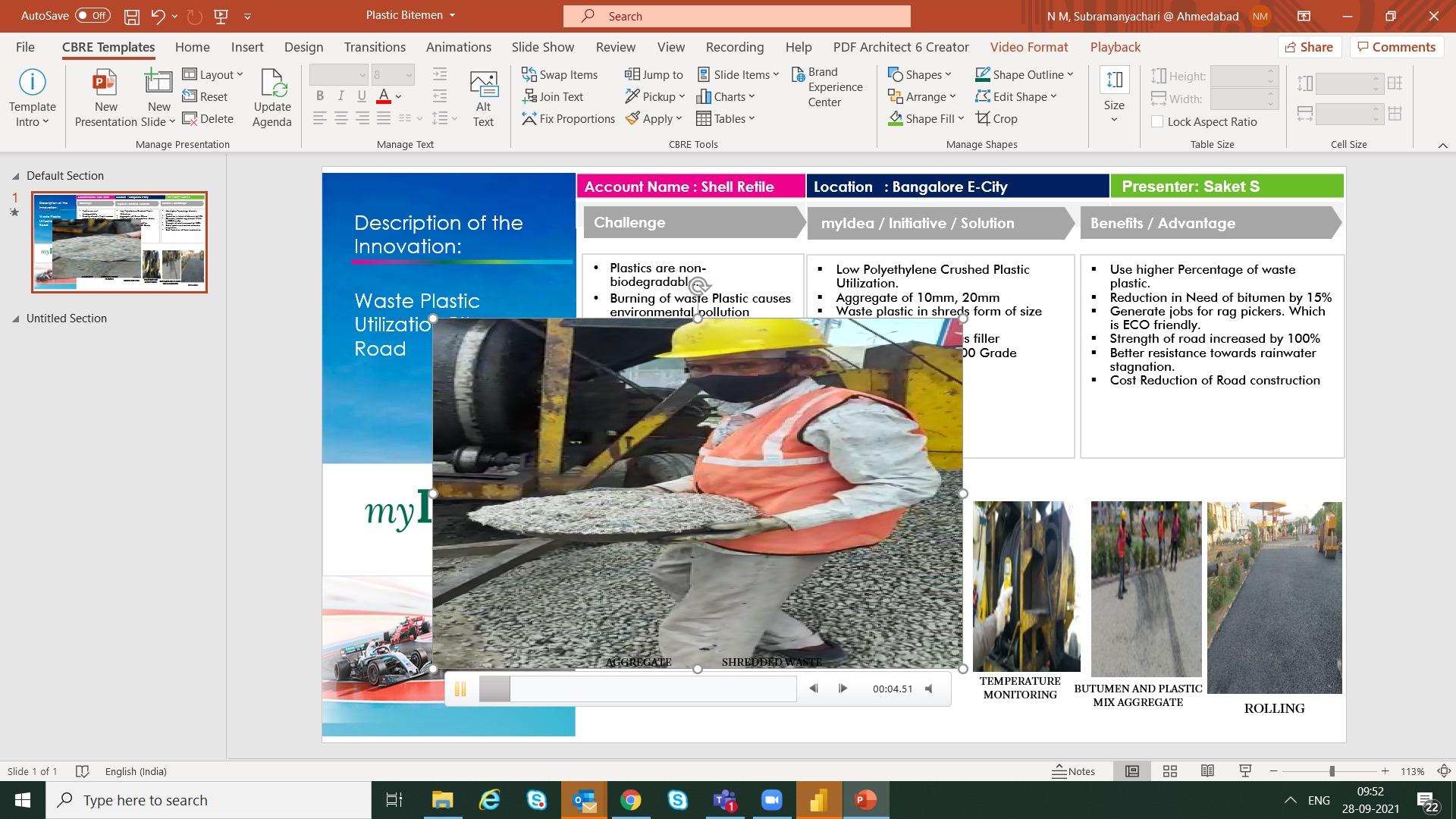
HSSE issues like Vehicle Slip, trip
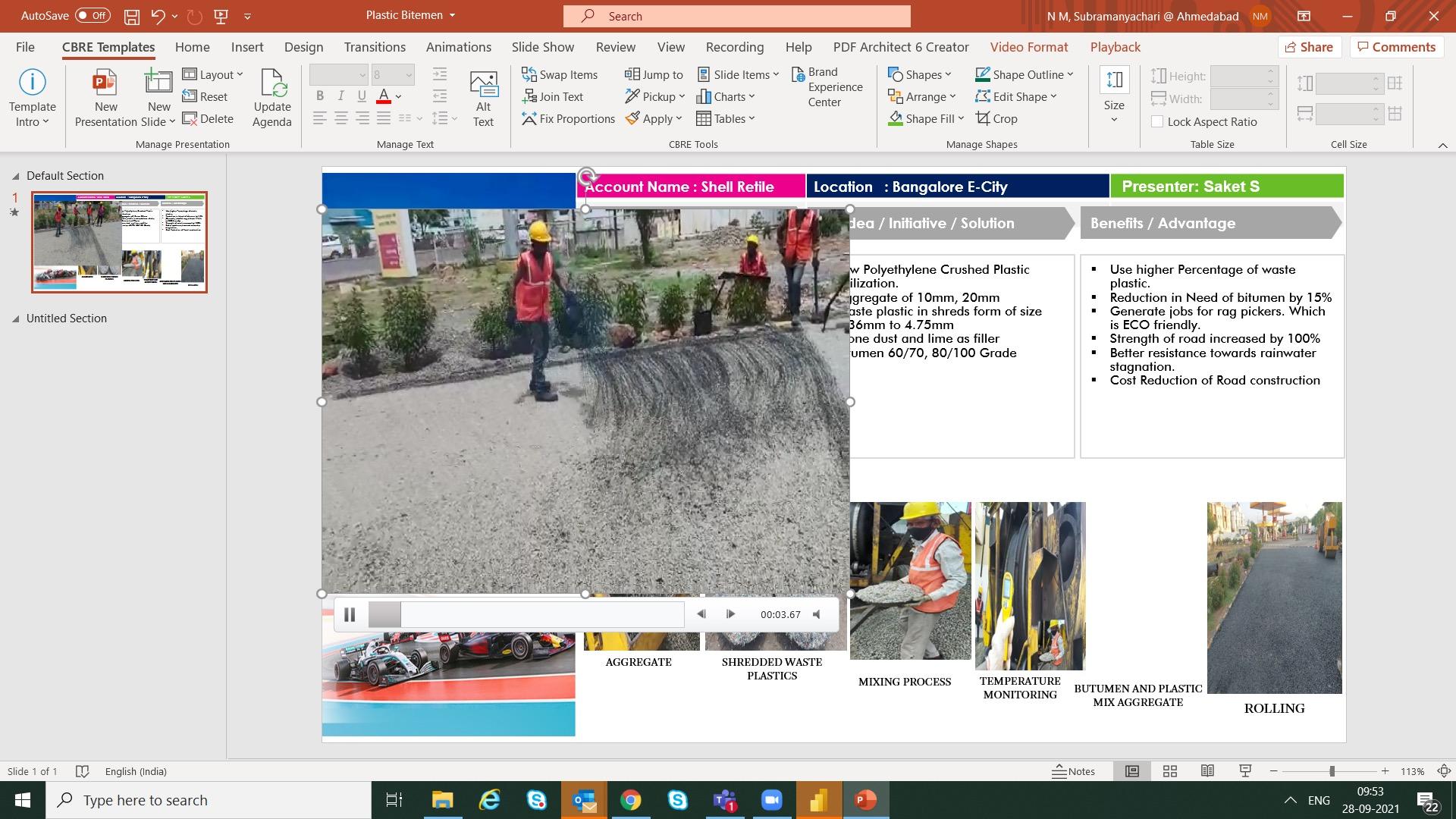
§ Better resistance towards rainwater stagnation.
§ Cost Reduction of Road construction approximate cost of 8cr Savings.
Description of the Innovation:
Stock Management Dashboard in
§ Decrease in Availability Hours of Assets/Equipment
§ Difficulty in accounting Spares in different Regions of India
§ Difficulty in Summarize Inward and outward spare in different region.
§ Unable to access stock details in different region
§ Difficulty to enter data by Field Engineer/Technician
§ Difficult to showcase spare consumption properly
§ Created Smart Sheet and Share Smart Sheet Link Filed Engineers and Technicians to enter in and out material from Containers
§ Creating Power BI Dashboard to Show Case the Summary of Spares available at different region
§ Preparing a mobile based compatibility dashboard and data entry tool so that it becomes more user friendly.
§ Improve in entering & collecting data of Spare inward and outward
§ No additional cost for developing this tools & dashboard.
§ Clear Knowledge on Availability of Critical spares region wise and in-turn helpful to reorder spares immediately
§ Improve in Availability of Equipment
§ Easy to Showcase site wise consumption of spares to the client.
§ Reduction in down time
§ Reduction in the capital cost in terms of stocking spares.
myIdea
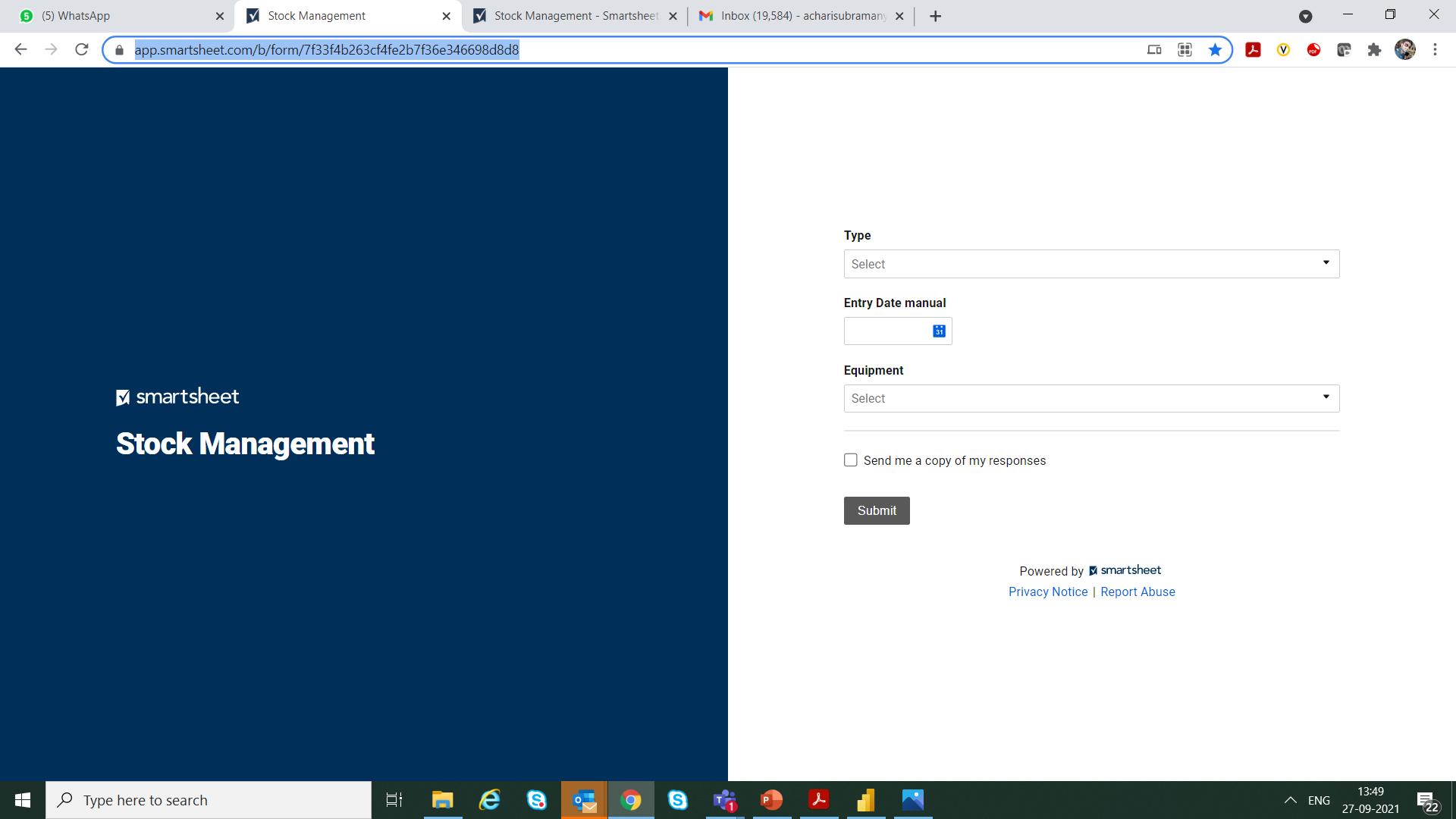



Description of the Innovation:
Rest Room
Hygiene Monitoring
CHALLENGE
myIdea
§ One of the most exposed area of Corona Virus is rest room and it is easily spread from one to others, if no proper sanitization occurs after every use. People may affect by Corona virus, if there is no proper sanitization.
§ Difficult to figure out the used Water closets in terms of safety during higher onsite numbers.
§ Planned to install IC Programmed based Sanitization Status Module in front of rest room.
§ Preparing circuit for Hygiene Monitoring system by using IC,
/
§ All rest room door frames are fixed with a module indicating Hygiene status of the Rest room, RED light indicates as USED and Green Light indicates


Description of the Innovation:
Robotic Lawnmower
CHALLENGE
myIdea
§ Lawn mowing was labor intensive. 12-man hours needed to mow 2200 sq mt of lawn.
§ This was a periodic activity leaving the lawn in non-uniform state.
§ Soil compaction: traditional mower weighs due to its weight ,tends to compress the soil over time. Grass does not grow as well in compressed soil.
§ Lawn cannot be mowed during rains & high temperatures.
§ Cut grass shavings being disposed as garden waste.
§ Battery enabled Robot operates with in a predefined perimeter of the lawn using its sensors to track and trim the grass gracefully.
§ No supervisor needed to monitor the work. The robot works in programmed work intervals and alternates cutting cycles with recharging
§ NO to - fossil fuel, noise & waste.
/
§ In Eco Mode, detects the overgrown grass and trim just that part.
§ Works on uneven terrain - up to 45° gradient
§ Lightweight (15Kgs) - no soil compaction
§ Can also work in adverse weather
§ Reduces Diseases –mowing on a regular basis, reducing the chances of diseases as the lawn is healthy condition.
§ Automatically returns to the recharging base.
§ Mulching robotic cutting -cuts a few mm of grass everyday& return nitrous-rich fertile elements to the soil, eliminate bulky bags of grass.
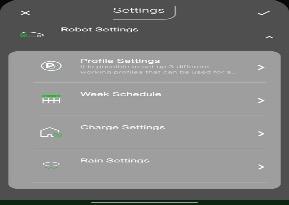
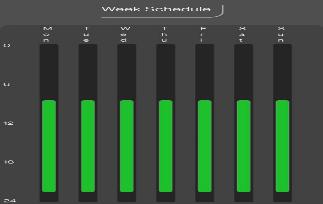

Description of the Innovation:
Introduction of AHF Panel
§ No provision of power factor control panel to maintain the PF.
§ So leading PF. recorded on MSEDCL meter due to high cable distance from main LT panel to HT meter & UPS AC capacitors.
§ High energy consumption resulting in paying more energy charges
§ Also, if the consumer fail to maintain the system harmonics within the permissible level, you have to pay 5% extra energy charges in the electricity
§ Installed power analyzer to the system to identify the leading PF & system harmonics on various loading.
§ Recorded data of harmonics & power factor till 24 Hrs.
§ Accordingly, decided the rating of Anti Harmonics filter to maintain system harmonics & control leading PF
§ Installed AHF panel across the main LT panel & controlled the PF & reduced system Harmonics
§ Maintain data sheet of power factor & energy consumption after installation..
§ Controlled leading power factor & reduced system Harmonics
§ Power quality improved
§ Minimize the system losses
§ Cable heating & unwanted tripping of breakers reduced due to Harmonics control.
§ Achieved savings in the tune of INR 90,000/month.
§ Equipment life & efficiency increased.
myIdea
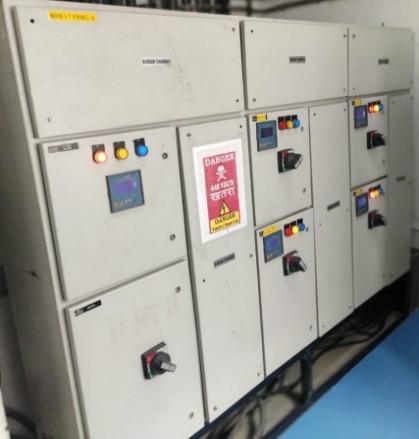
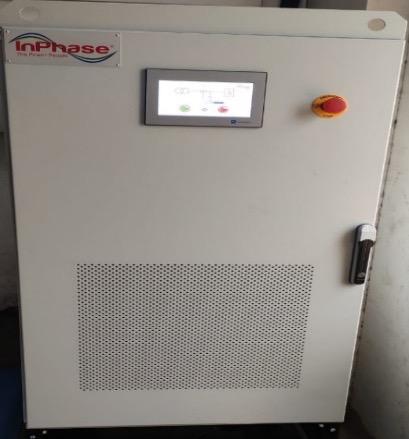
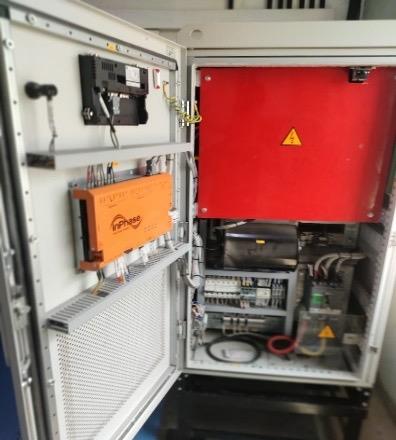
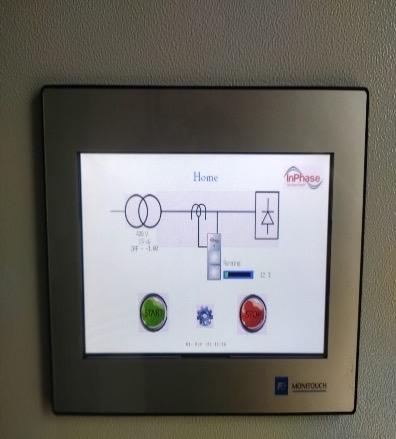
Description of the Innovation: CHALLENGE
§ During Lunch hours cafeteria used to be very crowdy.
§ Difficult to follow social distancing norms.
§ Possibility of close contact
Crowd Management in Cafeteria
§ Employee's dissatisfaction.
§ We advised café digital service partner Hunger box (HB) to come up with innovation for crowd management system.
§ Hunger box come up with crowd management system and their device installed on the entry/exit gates of cafeteria and integrated with access control system & HB app. Max. person allowed at a time capacity set in the device considering social distancing norms..
§ Social distancing maintained.
§ Convenient for employees.
§ Prevention of Covid 19 virus.
§ Close contact avoided.
§ Positive employees' feedback.
myIdea
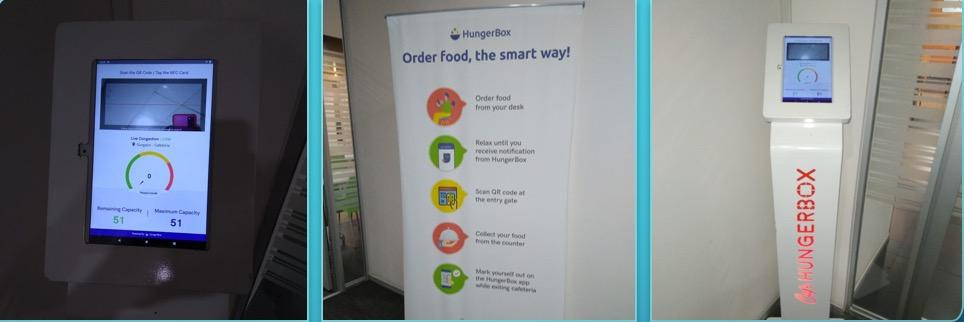
Description of the Innovation:
UPS Optimization at Candor
CHALLENGE
myIdea
§ As we are in planning to increase the heat We had 03 no’s X 80 KVA UPS feeding to workstation, These UPSs were almost 10-yearold & life was getting exceed
§ Repair Maintenance frequency & cost both were getting increased
§ Risk Value was high i.e., it may cause of breakdown in future
§ We have done planning for the shifting of 02 no's X180 KVA modular UPS from Infinity to Candor 2A for the replacement of existing 03 no’s X 80 KVA UPS because Infinity site was in exiting mode
§ These UPS’s 2 X 180 KVA were procured in year 2018, Hence these are new UPS and have remaining long life
§ Re-utilize of UPS ( 2 X 180 KVA )
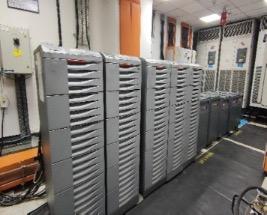
§ Modular UPS are more efficient as compared to ordinary existing UPS
§ Occupying less space from existing structure
§ Cost effective solution to reduce repair, maintenance frequency and Cost
§ Reduce running cost
§ More efficient
§ Easy operation

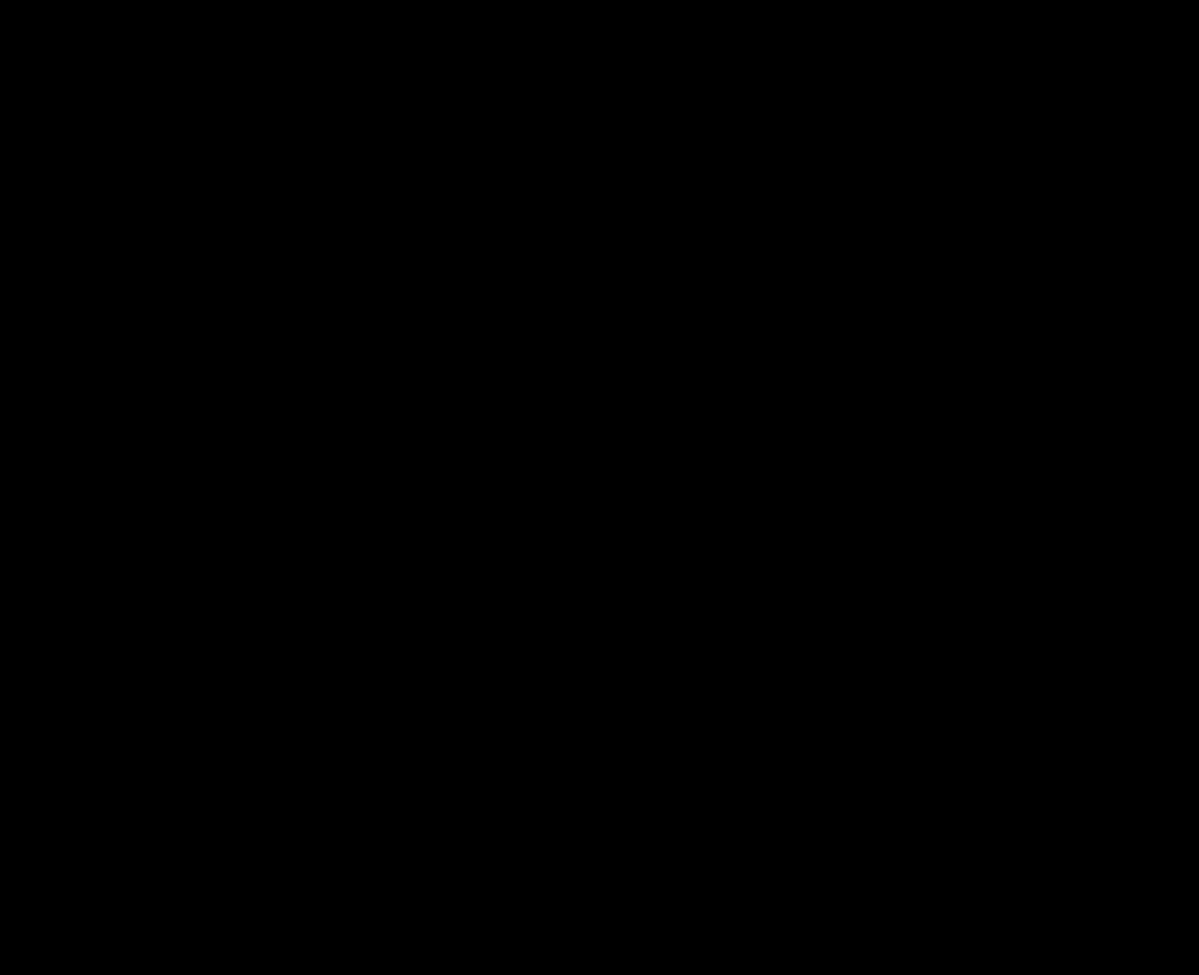
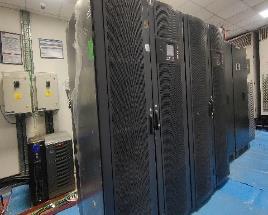
Description of the Innovation:
Cab Sanitization Trolley
myIdea
§ Risk of strain injuries for the HK Staffs’ owing to static load & repetitive hand pumping.
§ Support required to lift the machine from one side and also for refilling the chemical.
§ Trolley wheels get damaged due to heavy loading of unrecognized weight. There is a R&M budget cost for trolleys which is always highlighted for cost optimization by clients. During the facility stand by mode , the repairing cost of any tools and machineries ,need to be optimized.
§ The idea of making cab sanitization trolley has been implemented in ITP with little modification in the design based on the available resource.
§ Trolley has been made with broken pedestal drawer & ply. Separate cabinet storage space has been specified for PPE, HK Chemical & tools and display board for MSDS with work instruction. Power charging outlet provision has been added with the trolley.
§ A damaged and discarded weighing machine was identified from the store. Then the weighing scale part was fixed with the existing trolley. The entire wire setup and fixation work A wooden play was used and fixed beside the weighing scale to keep the materials.
§ Ensuring 100% Human safety by taking into consideration the standard ergonomics factors and reducing musculoskeletal discomfort due to static load.
§ If any chemical leakage happens by chance then there will be 0 impact of contamination to human body. This is cost saving as it is made by in-house team
§ This innovation is saving the recurring R&M cost for trolley.
§ The permissible weight limit in the digital trolley will help to reduce the damage cases and hence it will save the repairing cost. This innovation is considered as a pilot project in Kolkata ITP facility and this will be implemented in across all our facilities

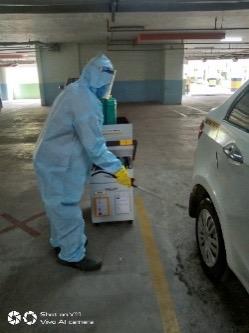
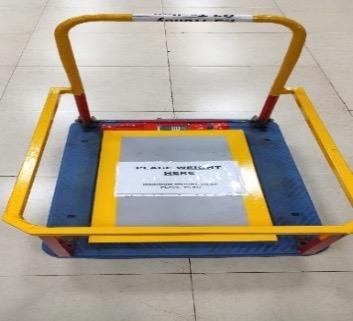
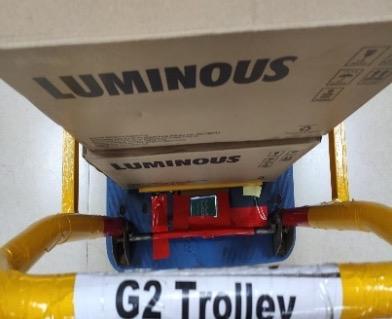
Description of the Innovation:
Rainwater Harvesting
myIdea
§ During rainy season water level will get increased inside the parking area
§ Behind garbage area water stagnation is observed for more than 2 foot
§ Very easily our building get flooded during rainy season
§ By doing this rainwater harvesting will solve the water stagnation in the parking area.
§ 250 KL water tank has been planned to implemented for rainwater storage, can hold normal rainwater which is routed from terrace.
§ Anticipated 3300 KL of rainwater per year will be collected and used for domestic purpose
§ Closed container will not allow to form any algae.
§ These storage water can be used after treatment for domestic, flushing etc.
§ Water stagnation around the building is avoided.
§ Ground water quality improved.
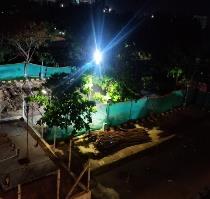
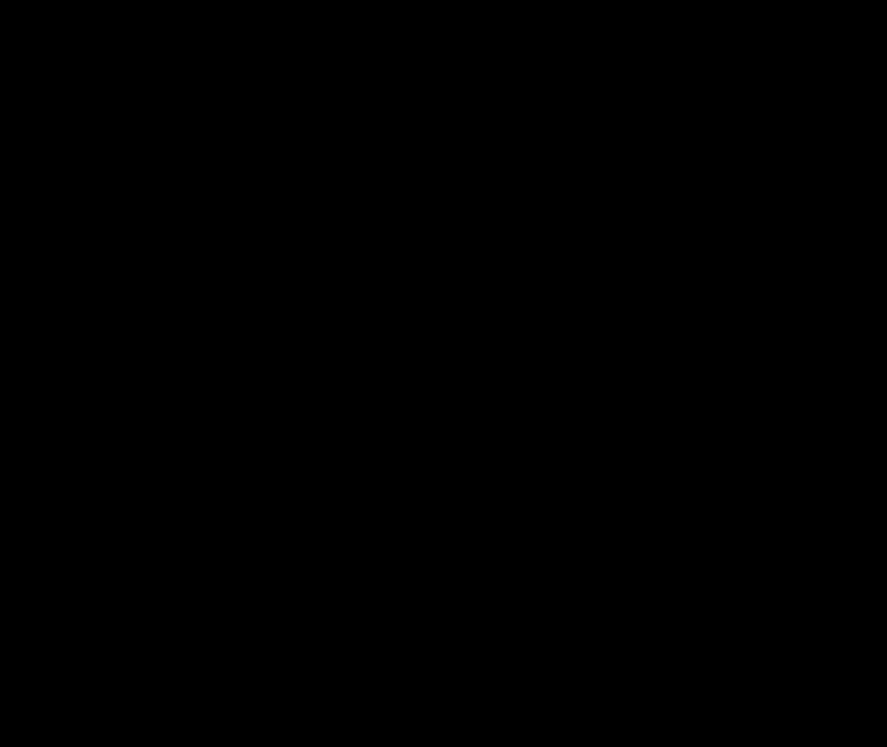
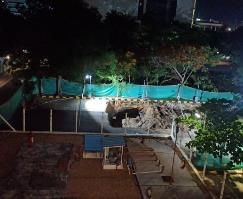
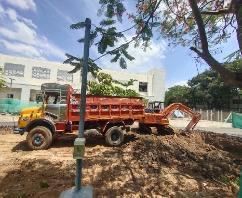
Description of the Innovation:
Automatic Gel Dispensers for Sanitizing the
§ Unhygienic washroom.
§ Chances of getting Infection through cross contamination due to frequent common touch points.
§ Installed Automatic sanitizer gel dispensers with HBT tissues.
§ SOPs pasted how to use the Gel Sanitizer before using.
§ Washrooms WCs found in Hygienic condition.
§ Prevention of Cross contamination of any infection.
§ Cleaning man hours saved.
myIdea

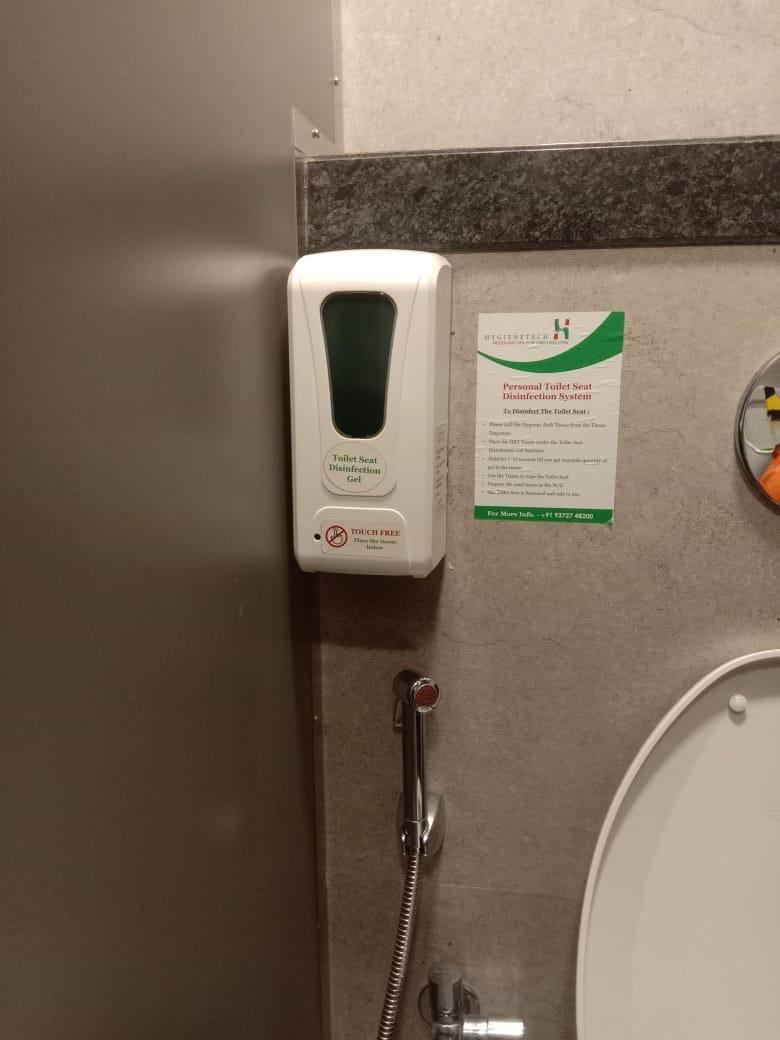
Description of the Innovation:
Zoning of Lights
myIdea
CHALLENGE MYIDEA / INITIATIVE / SOLUTION BENEFITS / ADVANTAGE
§ Workstation lights are operational as it connected with the corridor light.
§ If no one is working on the workstation still lights are operational as corridor lights are on.
§ Team used to connection of lights in such manner so that workstation lights can be used for power optimization.
§ With one circuit workstation light will operational and with other circuit second one will operate.
§ Some amount of electricity will be saved with this initiative.
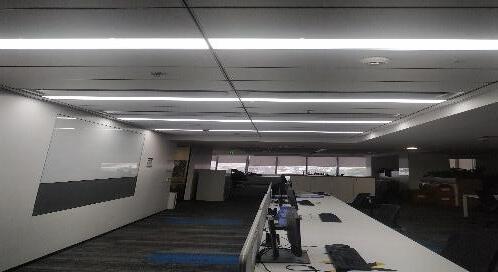
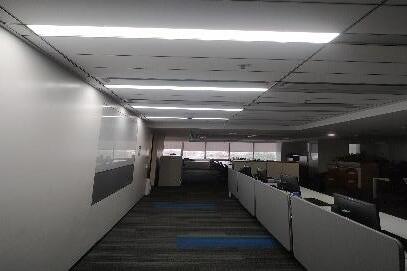
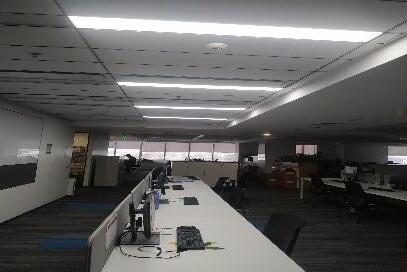
Description of the Innovation:
Online
myIdea
§ Dedicated Manpower required to collect data manually.
§ Authentication of data.
§ Paper Consumption.
§ High Energy losses and poor reliability of power supply to the electrical distribution utilities/ water utilities.
§ Cost involved of a dedicated manpower.
§ Privacy and security concern.
§ We have installed online energy and water monitoring system.
§ Installed monitoring system has been designed to help us to be aware of usage details in real time.
§ By using the installed system overall cost will be saved by approx. 1%.
§ Timely training for on site staff for all new updates.
§ Energy & Water monitoring system help us to become more aware of the energy/water we are using.
§ They give us a better idea of how much we spend on energy/ water.
§ E&WMS help us to spot any devices we didn’t realize were on.
§ Real time water/Energy consumption monitor sequence.
§ Energy monitoring system can prompt us to make energyefficient changes.
§ BMS & Modbus compatible.
§ Authentication of logs.
§ After implementation of the system, we are able to evaluate the improvements/difference if any.
§ Cut operational expenses.
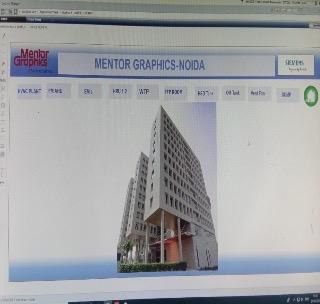
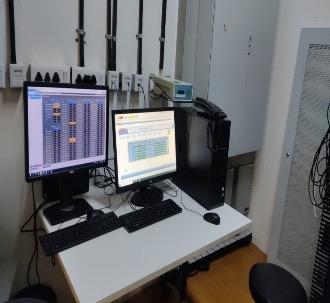
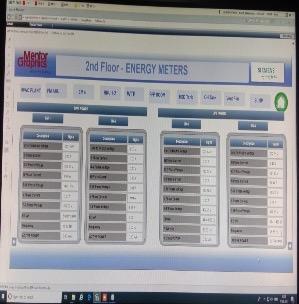
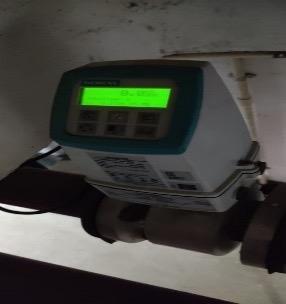
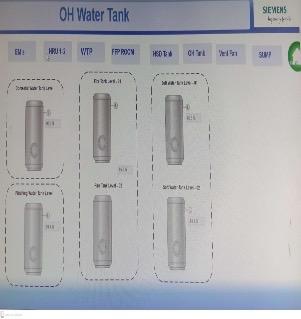
Description of the Innovation:
Installation of Digital water Flow
§ ITP-C1 & G1 are multi-tenant towers and there was no dedicated water flow meters for Cognizant floors for ITP C1 and G1 to measure the raw/flushing water consumption.
§ We were not able to track & measure water consumption
§ Since there is no water charges billed by builder tenants also doesn’t worry much about consumption
§ Monitoring on utilization of natural resource such as water is very important from sustainability point of view
§ We have installed total 12 digital water flow meters for ITP C1 & ITP G1 towers.
§ As these flow meters are installed in plumbing shaft, hence they are integrated with IBMS for capturing the meter readings easily
§ The meters are installed along with digital display also for immediate identification of any error in meter in future
§ We can track & monitor the daily water consumption.
§ Further we observed while doing so that these two new towers are having more water consumption compared to existing ones
§ WC water release in one flush was identified much higher as compared to normal existing ones
§ Water consumption assessment and conservation initiatives are being planned
myIdea
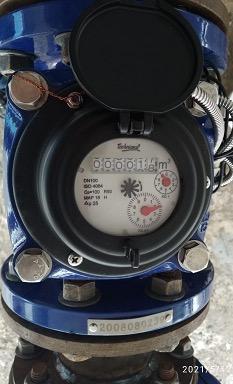
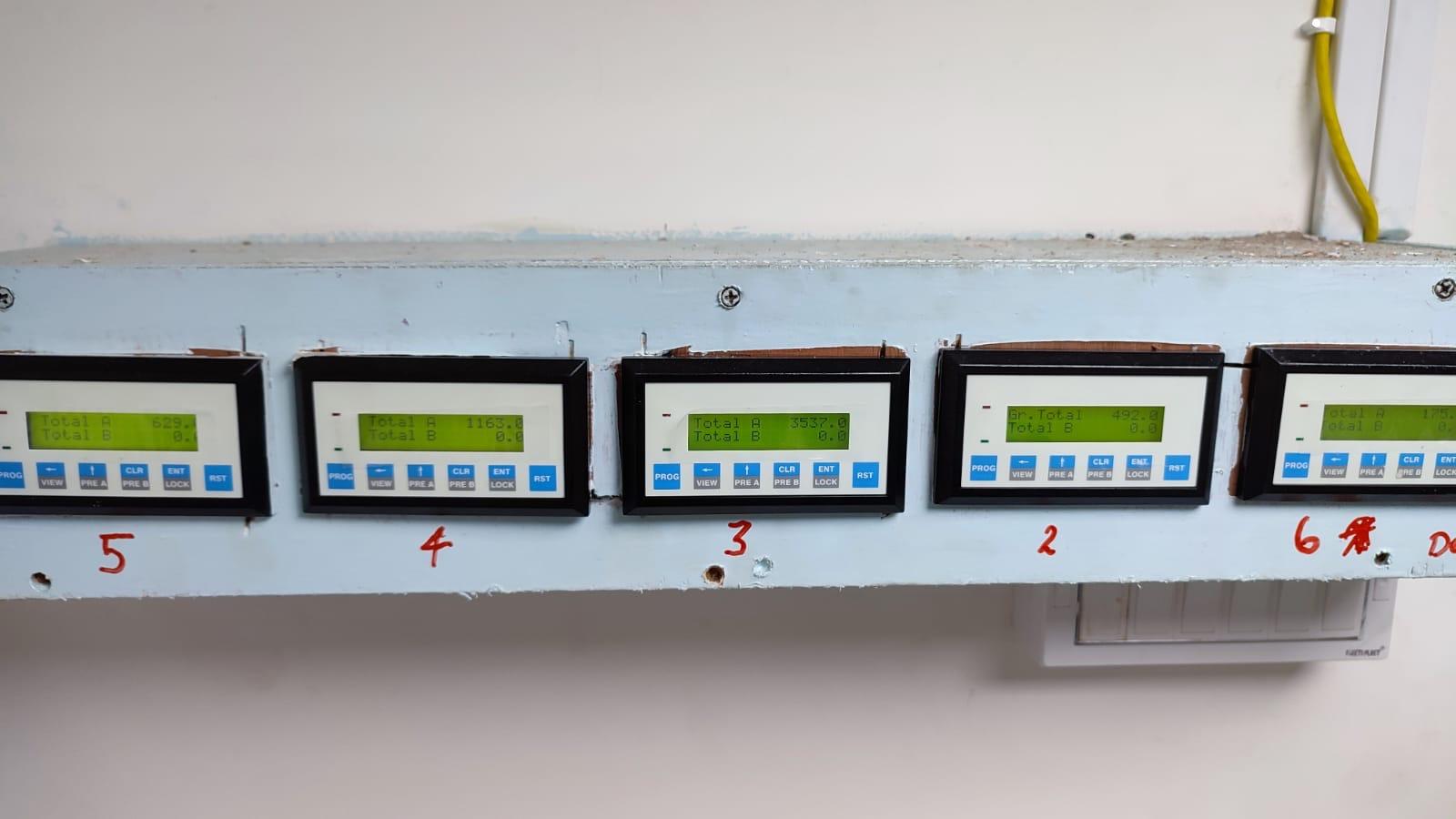
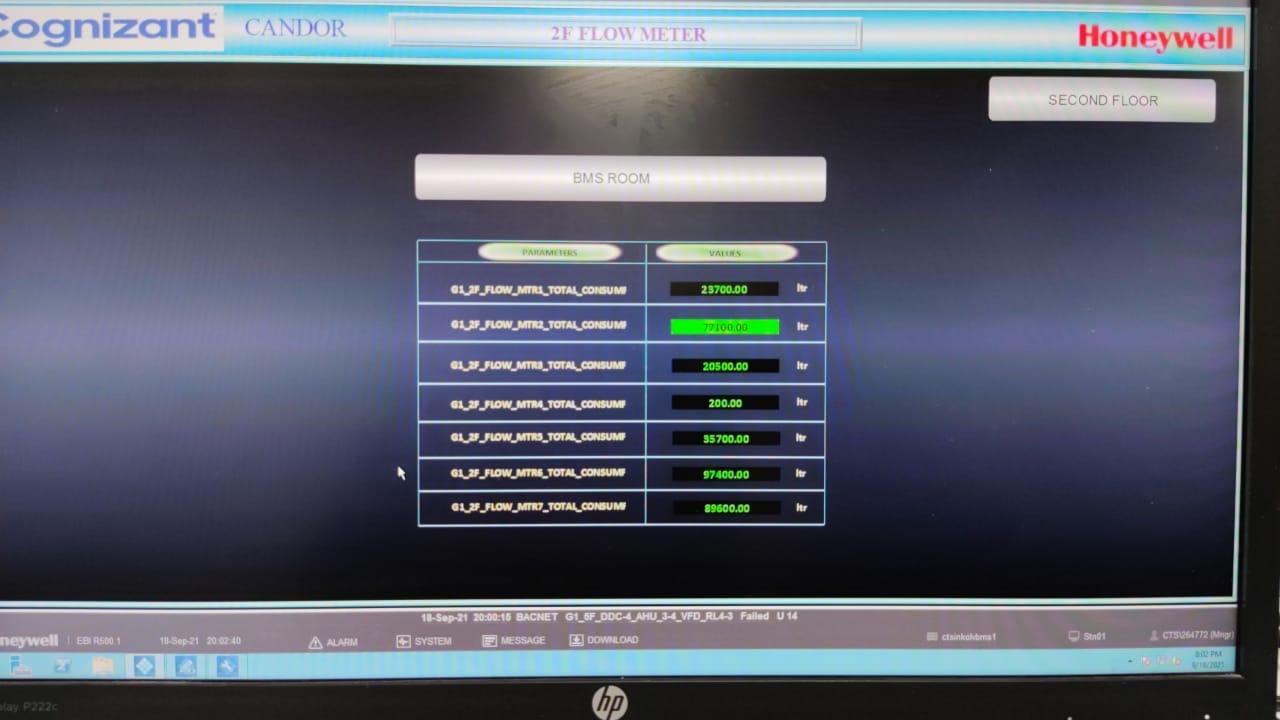
Description of the Innovation: CHALLENGE
§ Detection of weakness in cable Termination/busbars and other related hot spot issues inside the panel were not known unit there is terminal flash or any cable burning issues occured
Panel
Overheating Detection
§ Thermography carried out annually seemed the only avenue to detect cable /bus bar hot spot issues
§ Unscheduled breakdown maintenance were being called for to resolve the issues when they occurred
§ To overcome the issue and identify issues proactively Nicr/nial (Type K) thermocouple wire with Teflon insulation is used as sensor and this sensor is placed inside the panel compartment
§ Thermocouple wire with Teflon insulation has accuracy radius of 5 meters and can withstand temperature up to 200 deg C.
§ This Thermocouple wire is connected to Specially designed Temperature Control unit .This unit can be set from 10Secs to 15 mins.
§ When temperature rises more than the set limit control unit activates the buzzer simultaneously triggers alarm inn BMS.
§ Avoid Un-scheduled breakdown maintenance and business interruptions.
§ Ensuring 100% Human safety and prevent property damage
myIdea
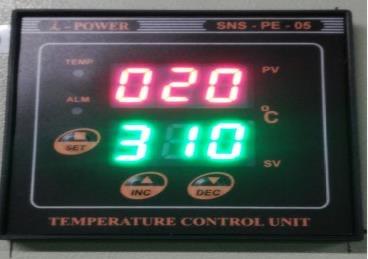
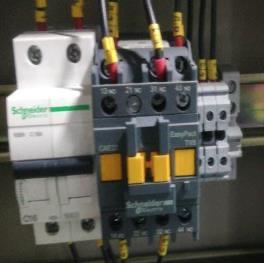
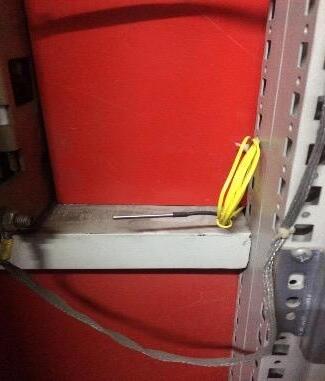
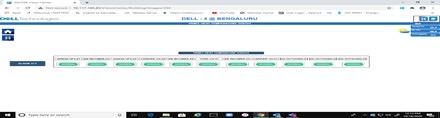
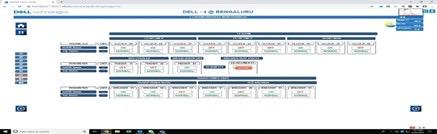
Description of the Innovation:
Use of Recycled Plastics
CHALLENGE
myIdea
§ In present day, the lube bay floor is either having tiles or are coated with epoxy paint to enable smooth cleaning and preventing oil seepage through concrete floors.
§ Currently Epoxy has a limited life of 6 months to 12 months depending on external factors like weather, wear and tear and etc
§ Re-applying of epoxy requires of 5 days of downtime of lube bay. Tiles has a greater life expectancy however it's develops cracks whenever a heavy tools or items falls on the surface
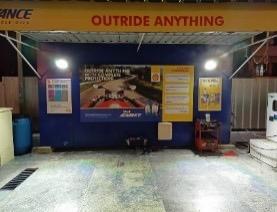

§ In the proposed change the surface will be covered with recycled plastic sheets of 10mm thickness
§ This recycled will be made of used engine oil/Coolant canes generated at the site on daily basis.
§ Future proposal of installation of recycled floor tiles and paver block on the site.
§ Recycled plastic sheets comes at ( lower cost (~35k INR), quick installations (lesser down time), better life ( at least 2 years) and can be further recycled.
§ Reduction in carbon footprint.
§ Direct cost benefit of 2.5cr and overall cost benefit of more than 4cr.
§ Ease of Oil Cleaning with respect to Epoxy and Tiles.
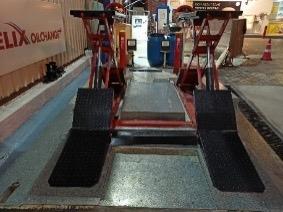
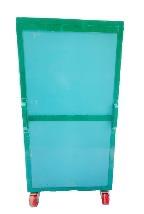
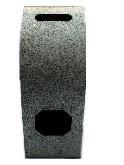
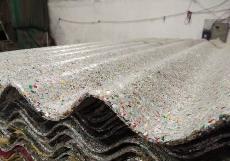
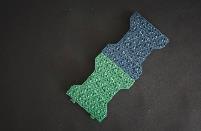
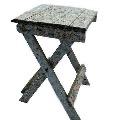
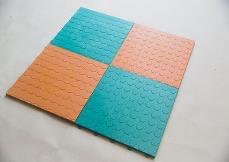

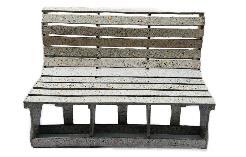
Description of the Innovation:
Replacement of Conventional V-Belt with Polyurethane Belt
myIdea
• Conventional V-belts are used in all AHUs which need periodic replacement due to wear & tear
• Replacement Period is 3 month
• Conventional V-Belt are sensitive to temperatures , oil, grease and common chemicals and solvents.
• Conventional V-Belt After initial run-in and re-tensioning, continues to stretch over time causing belts to become less efficient and slip if not retensioned regularly.
• Heat & frictional losses increase the power consumption
• Team proposed the idea of replacing the of Installation of Polyurethane V- Belt with Conventional V-Belts
• Team identified 4 nos. AHUs and conducted trial project on performance of Installation of Polyurethane V- Bels
• The trial were successful, thereafter, total 124 AHUs were identified for the belt replacement activity in the CDC Facility
• The activity was completed successfully by the in-house team.
• Also, horizontal deployment of innovation is in progress for other CTS facilities.
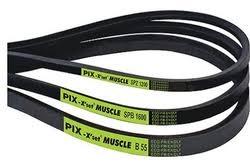
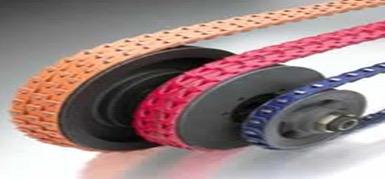
• The activity helped achieve monthly Power Savings in the tune of 81,840 KWH
• Cost saving achieved by installation of PU belt INR 8,18,400/- per month
• As life of belt is also extended ,savings in terms of spares & manpower utilization is achieved
• Improvement in terms of carbon footprint
• Increased equipment performance due to less frictional loss & slippage issues
• The suggestion was well appreciated by the client
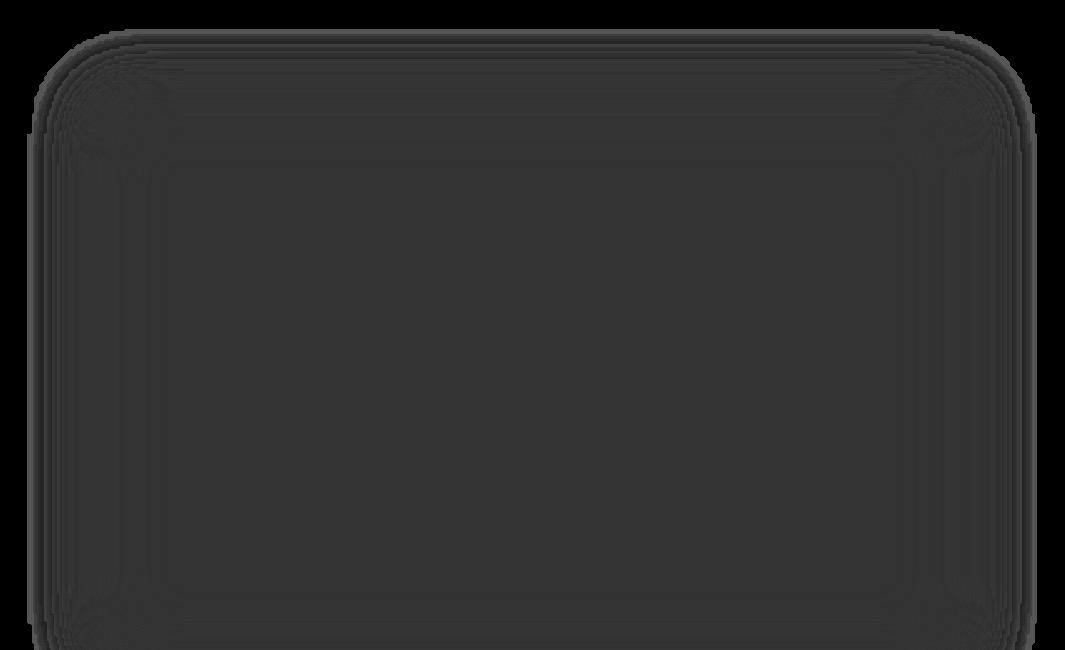
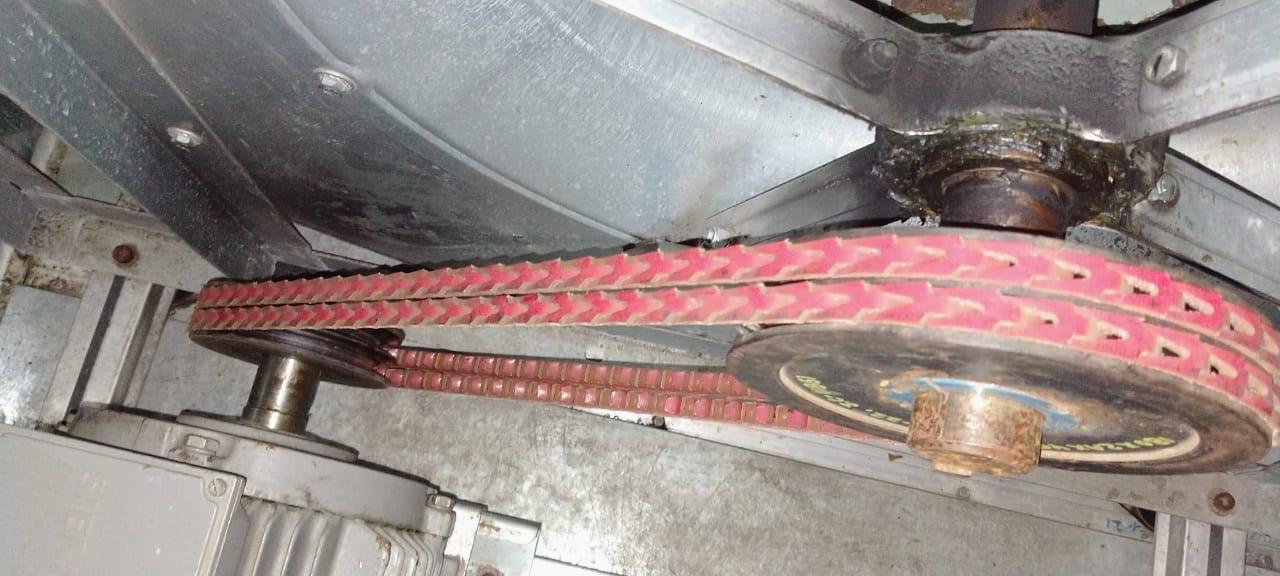
Description of the Innovation:
DG Resilience Panel
• Kosmo One Site energy supply is supported by the land lord team, with the transformers and captive power plant
• The Security of Energy Supply has become a major concern worldwide, and all industry and communication and computer systems depend on a continuous energy supply.
• Our complete system collapses when energy fails and lack of support from building power supply system due to Surges in fuel prices, political conflicts, wars, and natural disasters directly threaten energy supply.
• To evaluate the effectiveness of resilience enhancement strategies for electric distribution new DG resilience panel is implemented in ground floor electrical room.
• DG resilience panel is interconnected with building vertical risers' system with all protective electrical and mechanical interlocks
• Resilience panel is designed in such way that supports 80% to all floor (riser 1,1A & 2&2A)workstation loads and 40 % to common load and HVAC load(5 5A).
• Our own Rental DG supply is fed to the resilience panel during the crisis situation, The focus is, in particular on one specific attribute of resilience, namely, the readiness, i.e., the promptness and efficiency to recover the service without depending landlord team
• Power sustain during disaster. Ability to recover the business.
• Service during crisis with out depending building power system.
• Upgradation in power infrastructure
myIdea
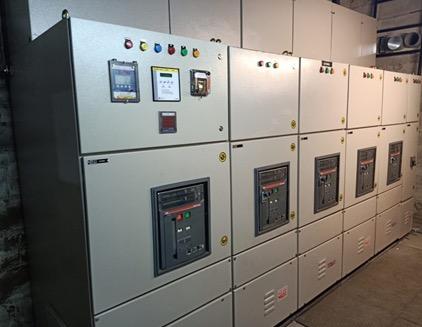
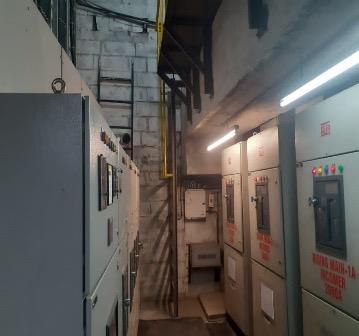
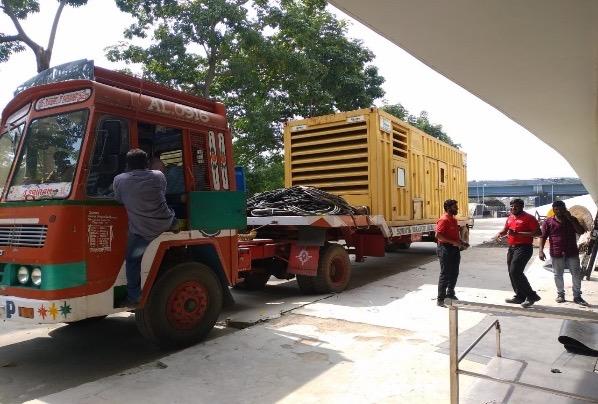
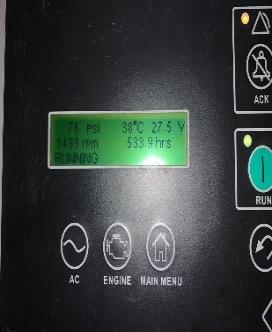
§ To reduce High emission from vehicles coming to premises/ curtail Air pollution/ making building more eco friendly
Description of the Innovation:
Electric Vehicles Charging Stations
§ Initiated for installation of fast charging stations (04 numbers that can be extended up to 10)
§ Each EV Charging station has 02 charging outlets and can charge 08 vehicles at same time
§ For promoting Electrical vehicles, 20 slow charging points were also installed at site
§ Reduction in CO2 emissions up to 30%, 290 Ton/ Annum
§ Reduction in Air Pollution
§ More Sustainable facility
§ Vehicles running cost saving up to 70% , INR 1.15 / KM whereas on fossil fuel INR 4.20/ KM
myIdea

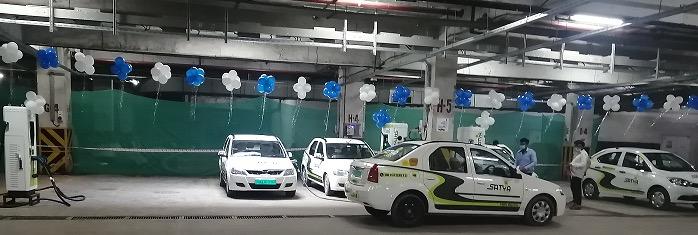
Description of the Innovation:
CHALLENGE
myIdea
§ Workstation lights were equipped with motion sensors but make all lights in the circuit (ON/ OFF) at same time
§ No provision for switching ON/ OFF individual lights in case no occupants.
§ Higher electricity consumption for internal Lighting
§ Explored option of moving away from conventional lights to sophisticated technology.
§ Focused on location where lux level was not meeting required standards and old/ nonfunctional lights
§ Identified 1000 lights (45 Watts), replaced them with 28 Watts high resolution (higher Lumens) lights.
/
§ Each light has inbuilt PIR sensor
§ In case of no occupancy, lights of that workstation will be switched OFF and not all lights in the circuit as was the case earlier
§ 45 watt X 1000 lights replaced with 28 watt having inbuilt PIR sensor
§ Total project cost 20 Lac
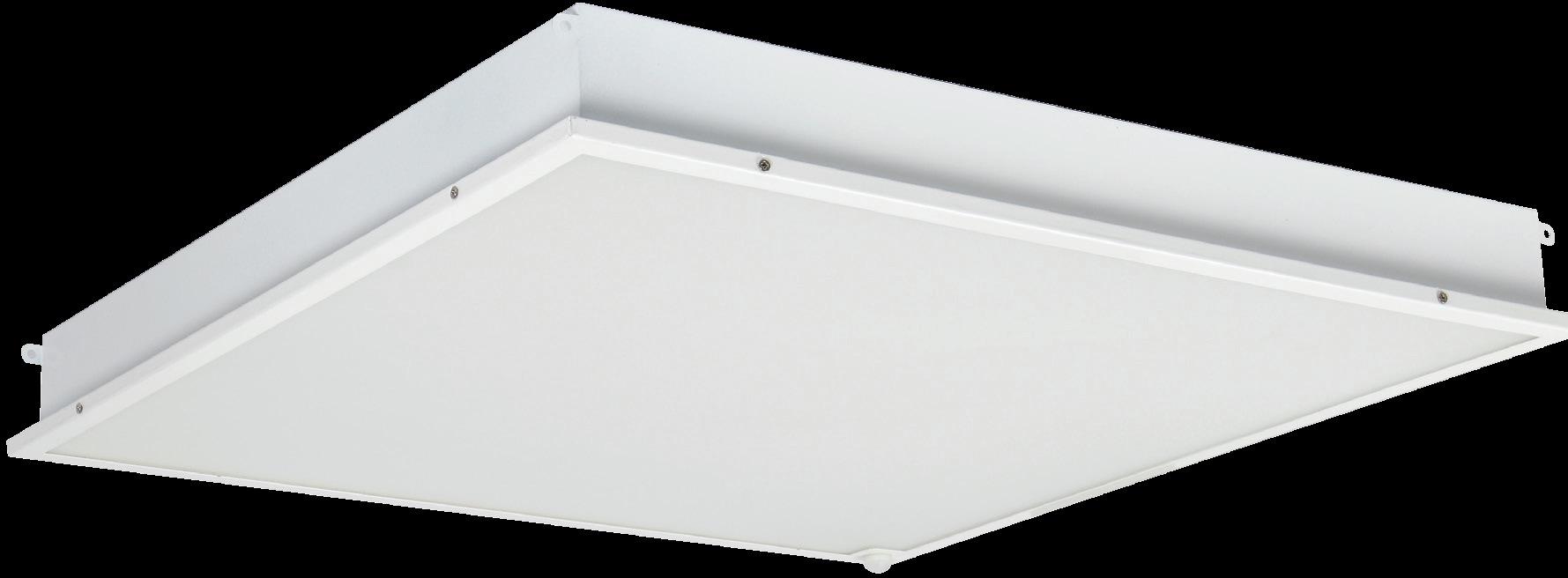
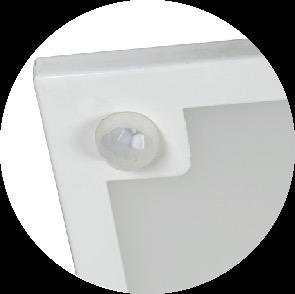
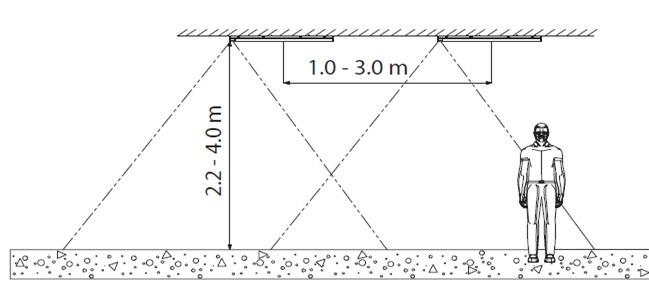
Description of the Innovation:
LEED certification
myIdea
§ LEED Certification rating Gold to Platinum.
§ Be in compliance with environmental regulations and standards
§ Maintain a reasonable site boundary
§ Monitor the energy and water usage data
§ Providing energy performance and promote great indoor air and environmental quality.
§ LEED Certification
§ the LEED for Existing BuildingO&M rating system we improved the operations, policies, procedures, purchasing and maintenance in an existing building.
§ We uses fewer resources, minimizes waste and environmental impact, and decreases life cycle costs to achieve increased productivity and better staff health.
§ Maximum energy savings
§ Efficient use of water
§ Optimum utilization of resources and sensitivity to their impacts
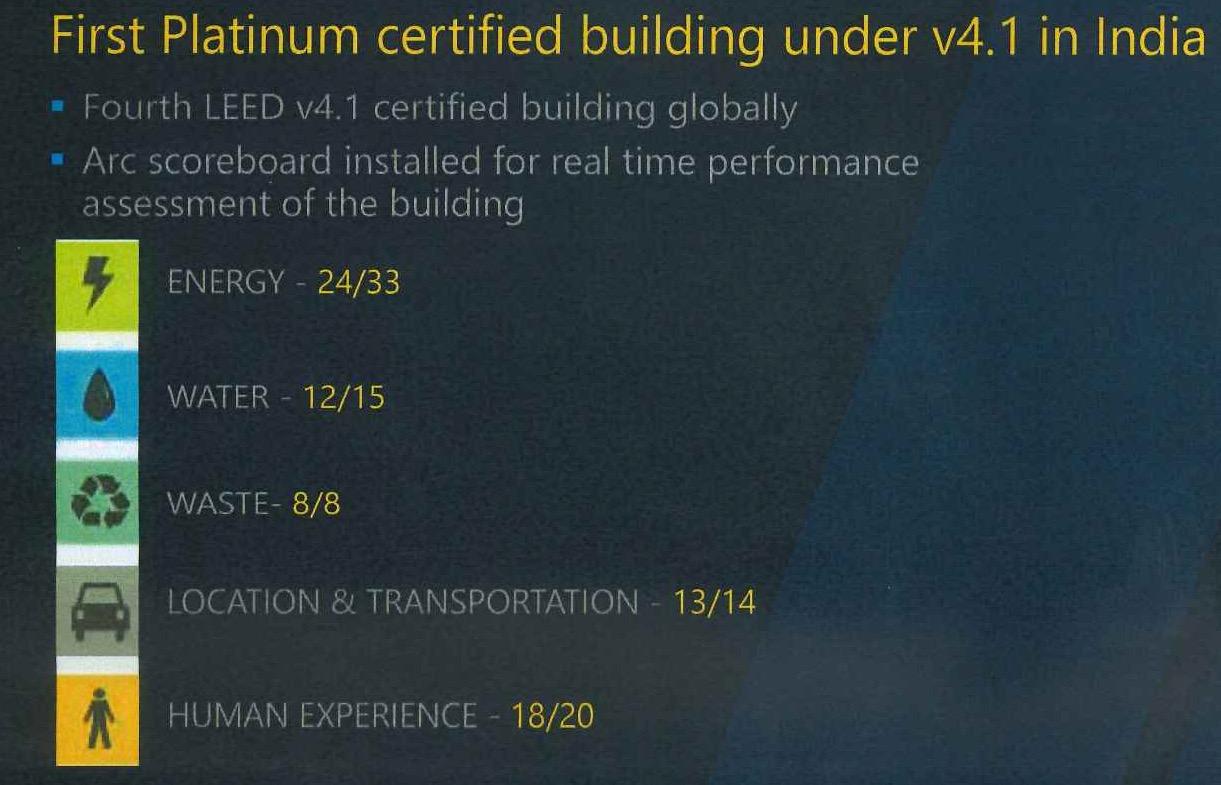
§ First Platinum certified building under V4.1 in India.
§ Fourth LEED V4.1 certified building Globally.
§ Arc scoreboard installed for real time performance assessment of the building
§ Reduced maintenance and operation costs
§ Healthier indoor air quality
§ Increased use of recycled materials
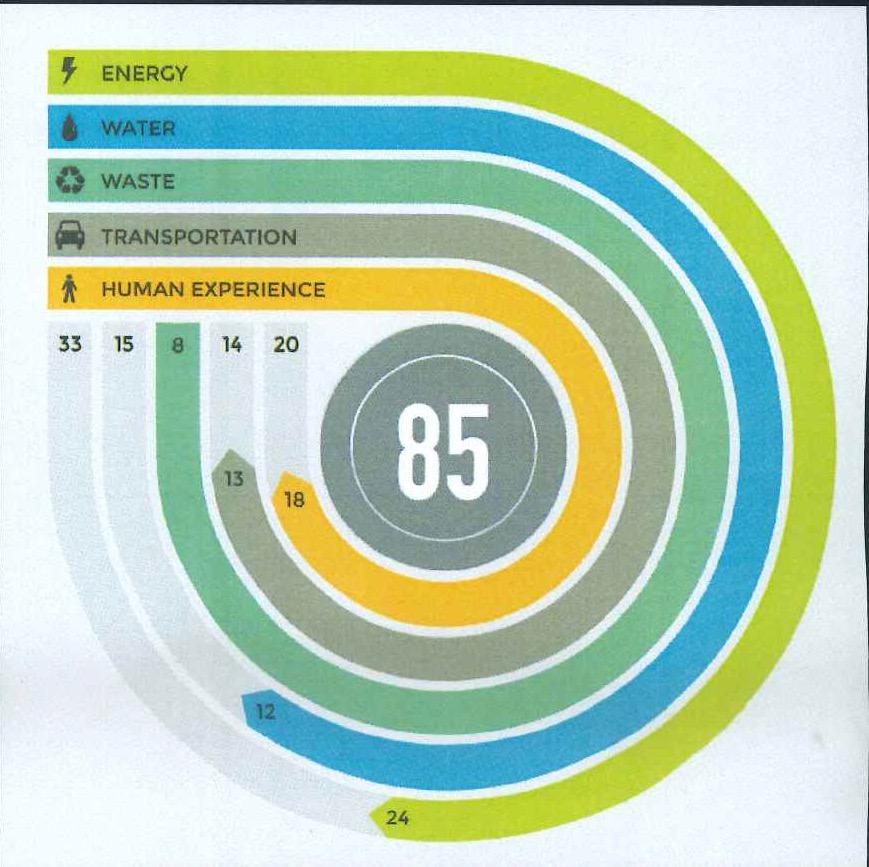
Description of the Innovation: CHALLENGE
§ We have observed that our ground and vendors team facing challenges while performing the Hot work at site. like unavailability of proper PPE or sometime vendor not able to arranged PPE on time.
Portable trolley & PPE for Hot work
§ Secondly, we are facing challenges for providing supply at designated place for welding machine /Grinding machine/cutter machine.
§ Sometimes vendor team doesn’t have the proper PPE due to which permit not issued and work got delayed.
§ Made the portable trolley with single & double phase supply ,fitted Industrial sockets 32 Amp, 30mA ELCB & 100 meter power cable.
§ Welding screen guard made for arc protection & prevent person from eye / face injury.
§ Hot work related all PPE kept in PPE box to provide in emergency case. Due to this fulfill the site Hot work requirement, protect welder to any accident/ mis happening/unsafe act & safe lives.
§ Total cost was 1,46,570 INR
§ Help employee to do the safe work practice at site.
§ Fulfill the site Hot work permit requirement & process implementation.
§ Protect welder to any accident/ mis- happening/unsafe act & safe lives.
§ Resolve the power supply issue with designated place for carrying out any activity.
§ Helps to motivate and promote more innovations in future by the team.
myIdea
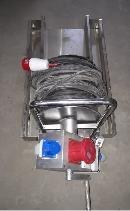
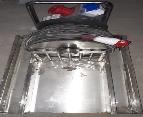
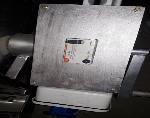

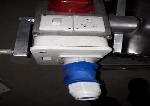

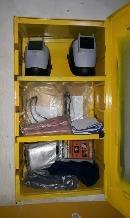
Description of the Innovation: CHALLENGE
§ In-house HVAC & M&E team used to check the cooling tower performance(Delta T) only in the Chiller plant display.
§ We installed the CT performance indicator by install ed a controller in existing temperature sensors installed in IN/OUT pipeline of CT.
§ Ensuring 100% performance of cooling tower and Chiller which is involved in HVAC operation in Block 2&3
Automatic Cooling Tower Performance
Indicator
§ Our Chiller plant is put up in basement 2 and cooling tower is in Ground floor. So, it is little difficult to monitor the performance of CT and some time team missed out the same.
§ Slow response to the system abnormality
§ We programmed the delta T lower limit as less than 3 and upper limit as more than 3.5 in the programmable sensor panel which is installed near the CT.
§ Based on the sensor/Relay out put the lights will glow.
§ If the Delta T value is 3 .5 or more than that the “GREEN” light will glow, and the team will understand that the CT performance is with in the permissible limit and the performance is good.
§ If the Delta T value is less than 3 deg the “RED "will glow and the team will alert that the CT performance is less than the permissible limit and do the needful to fix the issue.
§ To ensure the chiller approach within the permissible limit
§ To Save the cooling tower make up water quantity.
§ This system will be connected with our BMS in future since the building is under construction level. And also 100% efficiency will be achieved when we operate the system with full load. Right now we have only 30-40 % of load due to lock down issue.
Cooling Tower
Performance is within the permissible limit
myIdea
Cooling Tower
Performance is not within the permissible limit
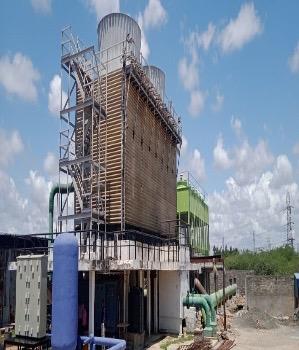
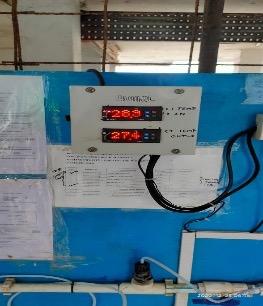
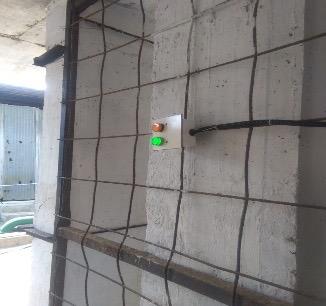
Description of the Innovation:
Critical alarm in LT panel
CHALLENGE MYIDEA / INITIATIVE / SOLUTION BENEFITS / ADVANTAGE
§ Any Trip occurs in LT panel breaker can not be easily identified by Technicians
§ Delay in response of Technician to restore the tripped breaker.
§ Escalations from the client on restoring the power supply.
§ Installed critical alarm panel and also integrated with BMS system.
§ This panel will show the live status of all the breakers in the control room which is manned 24 x 7.
§ Control room operator will further inform the concerned technician to address the issue.
§ LT panel breaker trips can be easily identified at the control room critical alarm panel by the operator.
§ Reduced the response time for restoring the power supply in case of any tripping.
§ Client has appreciated for better response time.
myIdea
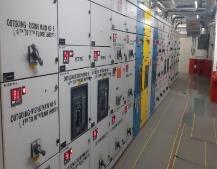
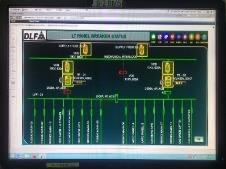
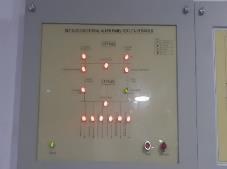
Description of the Innovation:
Conversion of DX unit into Chilled water unit
CHALLENGE
myIdea
§ The existing DX units are more than 10 years old with conventional operation which leads to energy consumption and refrigerant pressure drop due to frequent leak.
§ Also, this DX units were charged with R22 which is having Ozone depletion potential of 0.05 .
§ DX units needs dedicated space for the outdoor units and maintenance cost Is high.
§ Cooling efficiency is low.
§ Installed chilled water units at all lobbies as replacement of DX units.
§ The selection of chilled water units as follows low energy consumption, high cooling efficiency when compared to existing DX units.
§ The losses in pressure of water are accommodated by the sufficient capacity of pump which has low capital and running cost.
§ DX unit consumption of energy 363 khw /day of 8 hrs operations. Where as Chilled water consumption is 143 Kwh /day .
§ Energy Saving is 53,000 Kwh @ Rs 9 .Total Saving is 4.8 Lakhs / annum .
§ Total amount spent is 12 Lakhs & ROI of the spend is 2.5 years.
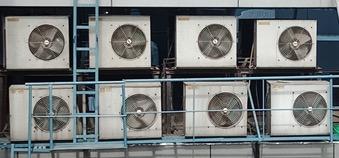
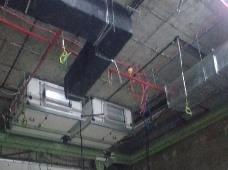
Description of the Innovation:
Automatic tube cleaning system for chillers
myIdea
§ Achieving the standard chiller approach was major concern.
§ Higher Energy Consumption due to raise in chiller approach.
§ Dependency on old traditional method of Chiller De-scaling.
§ Manual De-scaling process involved costing and manpower.
§ Introduction of new technology which should be energy and cost efficient.
§ Automated system for Chiller DeScaling.
§ Automatic Tube Cleaning system to overcome the wastage of cost, Energy and manpower involved.
§ Total energy saving up to 10-15% of Chillers which is around 230000 KVAH yearly.
§ Cost saving.
§ Achieved the standard Chiller Approach.
§ No manual de-scaling.
§ Smooth and automated operation.
§ Time saving.
§ Achieved ROI in less than a years.
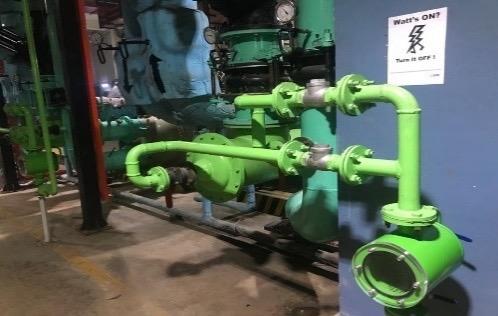
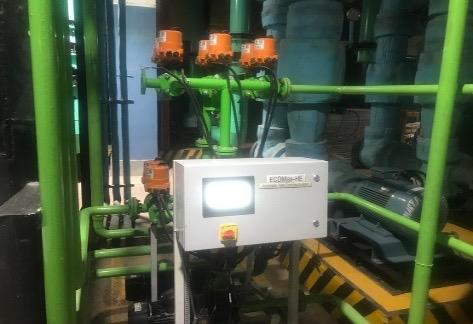
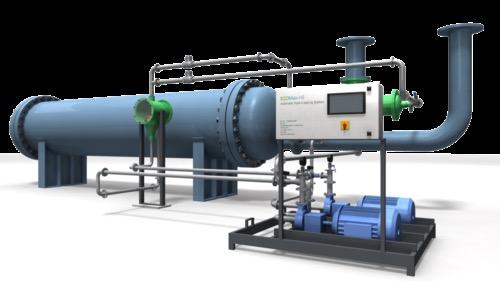
Description
of the Innovation:
British Safety Council Certification
§ Adjustment to new SOP and guidelines and adhering to all the BSC procedure
§ 5 Risk assessments to carry out such as HIRA, CoSHH, Manual Handling, FRA and DSE.
§ PTW with JSA & TBT for all activities, time constraints
§ Communication and participation from top management to task level associates despite Covid pandemic
§ Allocation of resources timely
§ Implementation of safety related activities like Safety Observation, Inspections, Audits
§ Virtual presentation for documents and onsite implementation status
§ Application of PDCA Cycle
§ Lots of trainings and brainstorming sessions
§ On board HSE manager who coordinate all BSC activities
§ Action plan layout
§ Allocating and dividing works with different departments
§ Bringing an idea to make PTW issue less time
§ Budget and allocation of resources in systematic manner
§ Benchmarking with other BSC certified buildings for implementation and best practices.
§ Best safety system with written procedures
§ Compliance for any safety related audits
§ Better proactive process and wider participation and communication on safety
§ Enhanced safety working procedures and protocols adopted for all types of works in the building.
§ It gives a sense of satisfaction to the staff that they are working in the most safe and secure environment.
§ Enhanced reputation for the Client and building in terms of daily operations and maintenance.
§ World class safety standard
myIdea
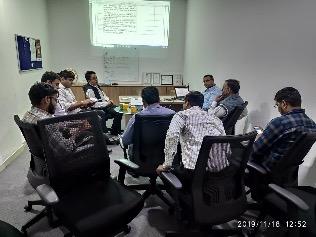


Description of the Innovation:
SOS for women safety in the basement floor
§ The campus has vast basement floors B1,B2 &B3 spanning for 17,23,464 Sq.Ft that are designated as parking area.
§ In the late hours, very minimal movement happens in these basement floors that often causes an insecurity & panic particularly amongst the women employee who works on 24X7 shifts.
§ About 55 nos SOS emergency talk back system is installed in the basement floors of every blocks with visible signages for easy identification & any call that is made from the system is attended by a trained BMS team that operates on 24 X7 shifts.
§ At the BMS operator end, whenever a SOS call is received, the LED indication of the respective zone will turn ON & creates an audible beep sound till acknowledgement.
§ A separate SOP & communication protocols (involving the security team & the ops team) were drafted & implemented to provide immediate help to the person in need
§ The safety & security of the building is enhanced and has created a positive impact particularly amongst the women employees
§ The call points are addressable & Two way communication is possible.
§ Quick assistance for any kind of emergency situation is ensured by channelling the communication through the centralized BMS team to illness.
myIdea
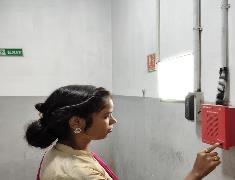

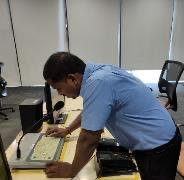
Description of the Innovation:
Equipment Safety
myIdea
§ In-house HK & M&E team & Suppliers uses machineries like Vacuum, Scrubber, Drilling, Cutting, Heating & Welding Machines etc during day to day operation
§ We observed the machines lost their insulating properties over a period or during the transportation, which the suppliers may not be knowing before starting the activity and it can trip the critical circuits or hurt the operator, if not checked in advance
§ The defective machineries can damage both business & human life
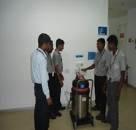
§ Installation of an ELR / ELCB based testing station at the entry locations, which will enable the operator or the vendor to check the machines before connecting to any of the building main circuits
§ There are 2 different light indications in the testing kit
§ Green – Indicates the equipment in good condition
§ Red – Indicates if the machine is defect Indicators will be in OFF condition before & after test
§ MCB & ELCB provided for safe testing
§ In the context of electricity, for its proper conservation, right distribution to the desired points of utility and also to safeguard the precious life and valuable property from damage, it is very important to insulate the point of voltage and the passage of electric current through the conductor
§ Ensuring 100% Human safety and property damage
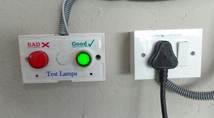

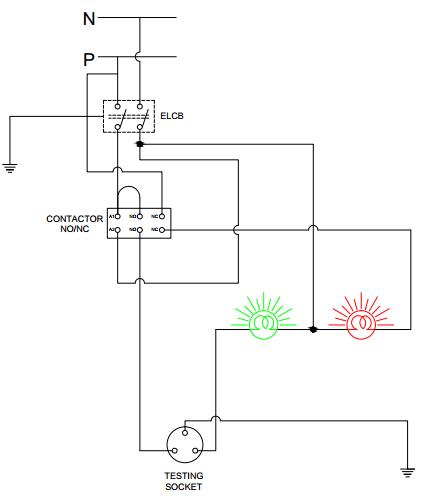
Description of the Innovation:
Light Music in the rest room
• Project was conceived in response to employee feedback about poor overall washroom experience
• Look and feel of washrooms were improved through renovation projects by Dell
• Streaming instrumental music and providing indoor plants inside washrooms was one more effort to improve ambience
• To avoid patent and contract issues regulation on subject were studied and authorities consulted
• Accordingly, soft Carnatic instrumental music is played.
• Project replicated across multiple sites
• Received positive feedback from employees
• Positivity reflected in annual survey results with reduced numbers of complaints/ representations on washroom experience
myIdea
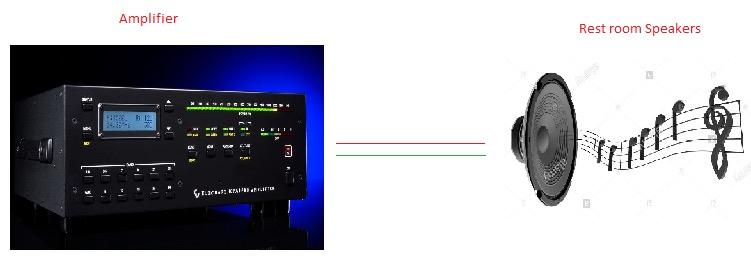
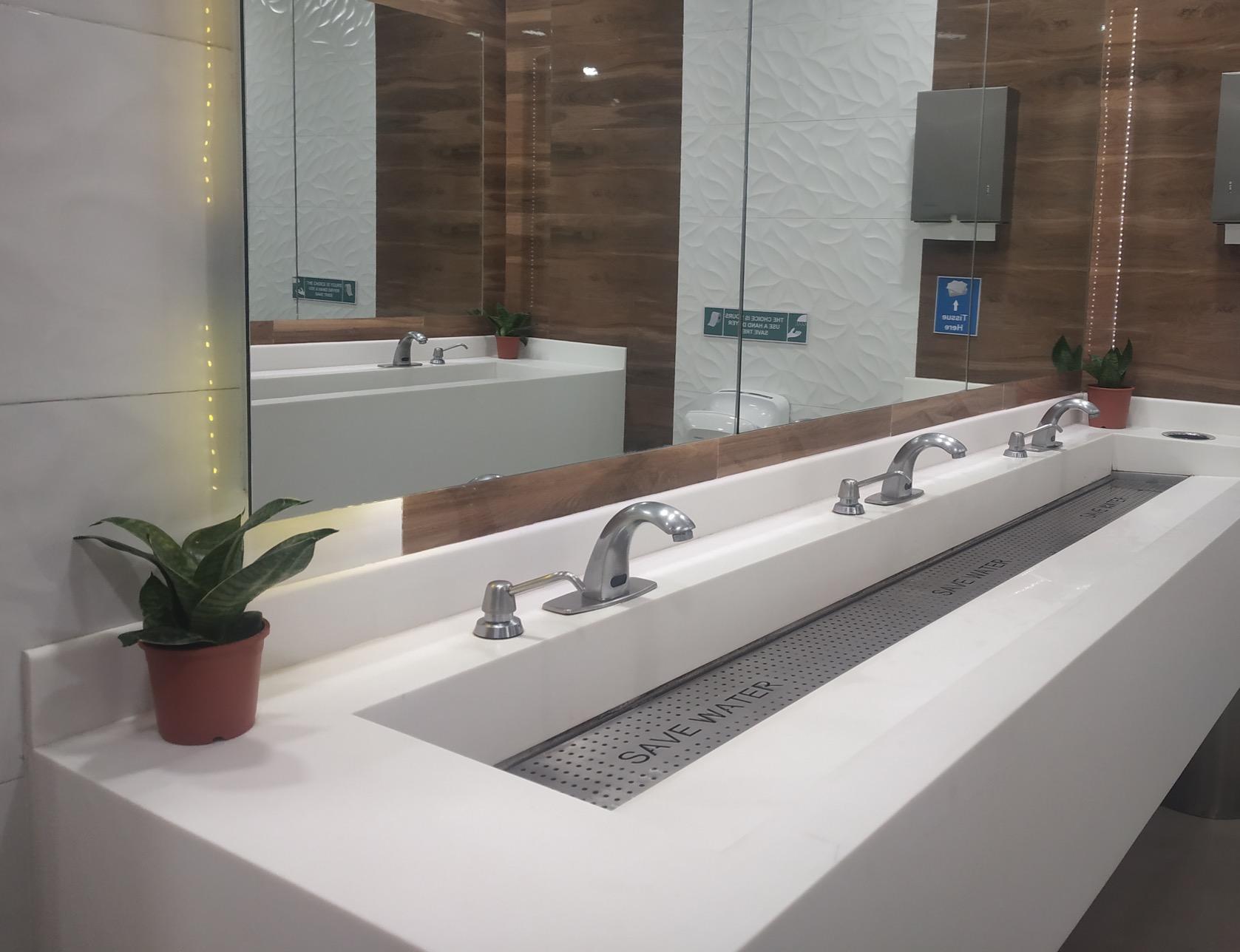
Description of the Innovation:
Conversion of water body into Theme
based Butterfly garden
• Water Body with an area of 2500 Sq. Ft. and 50 KL water capacity necessitates 1200 KL potable water wastage per annum which can feed 15 villages per day with 200 families consuming average 400 litres per day.
• Foreseeing sourcing issue in future, due to water scarcity in city.
• Higher Cost of maintaining the Waterbody
• High expectations to match the standards of the water body by the users.
• Introduction of Theme based Butterfly Garden to match the aesthetics of water body and conserve precious natural resource – Water as a part of CISCO Go Green initiative.
• The Butterfly Garden has been designed to create an environment that attracts butterflies, with a mix of suitable sculptures. The flora in the garden has been specifically chosen, as they are known to draw the attention of our winged friends.
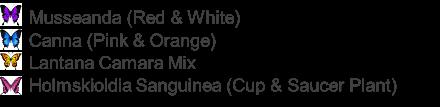
• Saving 1200 KL water can cater 14 villages, considering 200 family Indian village with 400 Litres per day water consumption.
• 100% operation cost avoidance.
$ 10 K USD Maintenance Cost per annum
• 100 water tanker movement avoidance leading to reduction in carbon footprints.
myIdea
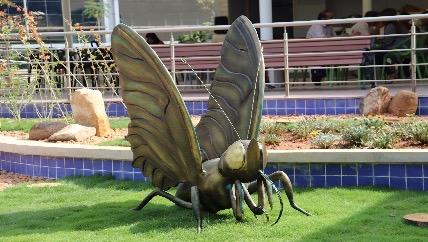

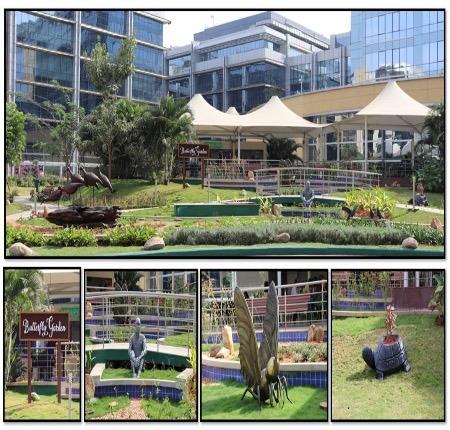
Description of the Innovation:
Portable AC
• The client facility is located in a multi-tenanted occupancy and the timings for running the AHUs are fixed
• Running the AC after office hours costs INR 5671 per hour to base builder as per the agreed terms and conditions
• Running the AHU after the fixed timings are required at least 12 days a month.
• A detailed study has been done and a recommendation has been submitted to client to purchase 3 units of portable air-conditioners to avoid running AHUs after fixed timings
• With client approval, purchased 3 portable AC units and provided to staff during extended timings and weekends
• Purchase of 3 portable AC units costed INR 75,000 which resulted in a savings of around INR 6 Lakhs/ per annum
• Employee comfort not compromised
myIdea

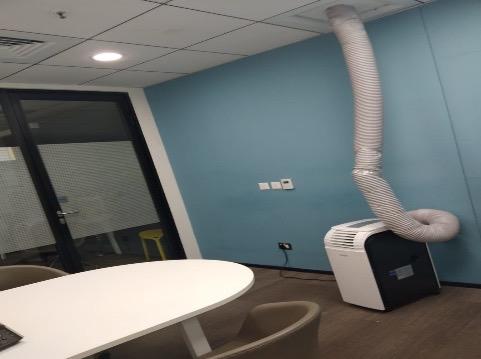
Description of the Innovation:
Indoor Air Quality improvement by Installation of EAC Filters
myIdea
• Existing HVAC system was not designed to filter particulate matter( PM 2.5 & PM 10)
• Poor indoor air quality on floors during peak pollution months
• Challenge of not being able to inject fresh air into the system due to poor ambient air quality. This is required to be done when the CO2 levels increase inside the floors
• New Electrostatic Air cleaner (EAC) filters were installed in all fresh air units and air handling units for controlling the PM levels in the indoor air
• Installed LED screens on each floor for display of real time IAQ parameters to the occupants
• This brought our offices at par with any Global facility in respect of Indoor Air Quality standards
• IAQ parameters ( AQI-8, PM2.5 & PM 10 - Less than 5 Microgram/m3) were achieved on floors post completion of this project
• Treated fresh air is injected into the floors to control CO2 levels
• Enhanced life of AHU coils
• Reduction in the connected chiller load and improvement of chiller efficiency
• Better colleague experience and satisfaction.
• Keeping in view the current COVID-19 situation 100% fresh air injection is possible and can be done

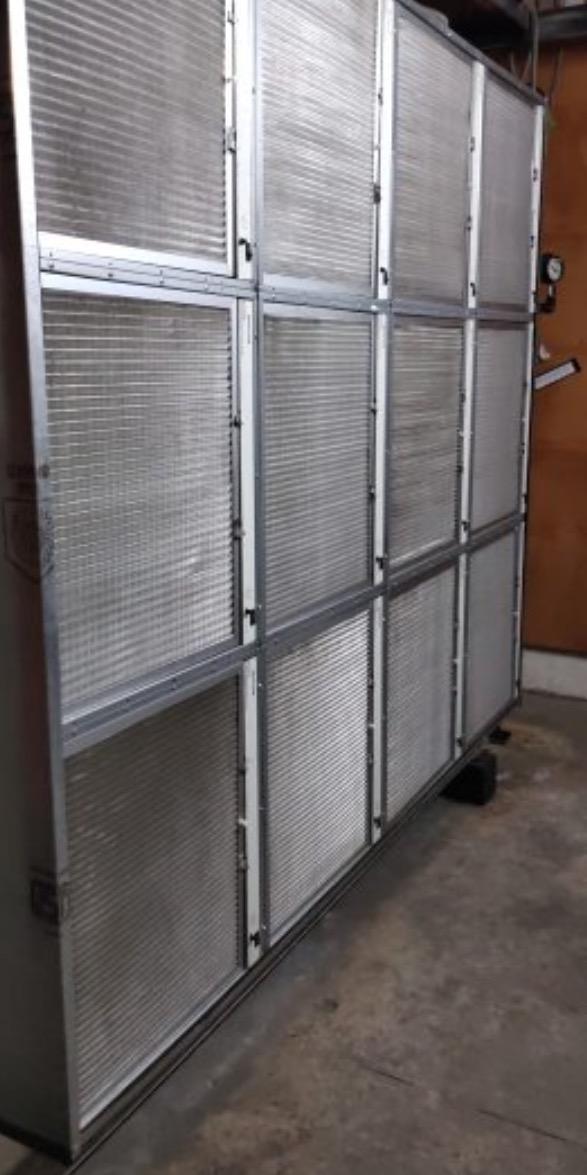
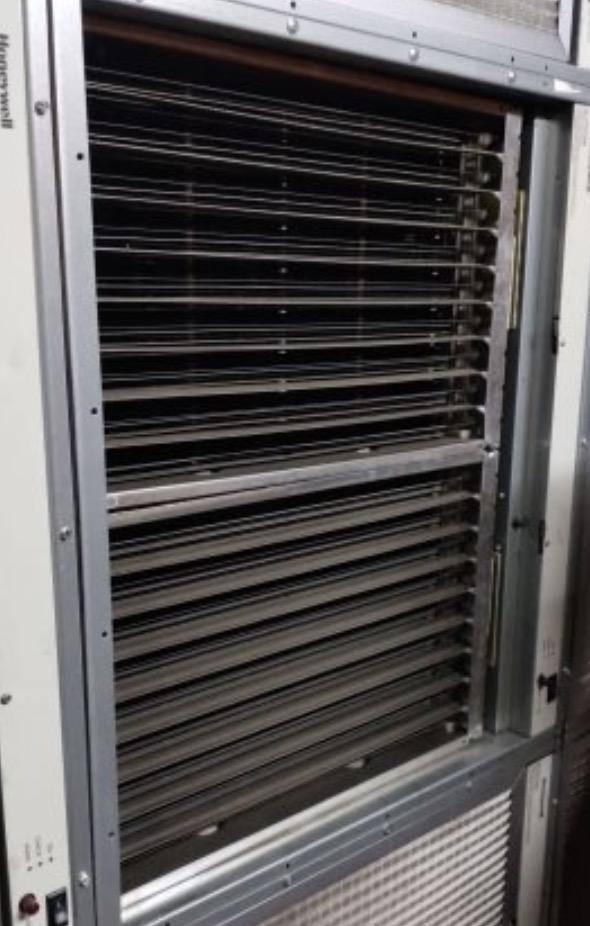
Description of the Innovation:
Use of waste ground coffee beans for bad odor elimination
myIdea
• Risk of bad odour generation in areas vicinity of garbage room, urinal area, WC Dustbins collected garbage in garbage bags, pantries
• Bad odor needed to be eliminated and ensure healthy environment
• Generated daily 8 kg of coffee waste
• Use the waste coffee ground beans in the waste collection points
• Sprinkled waste in the garbage room and in the waste collection bags
• Sprinkled in the artificial planter placed in the washrooms which work odour absorbent
• Reducing Waste - sustainability initiative
• Neuralization of bad odor in the washrooms enhancing user experience
• Coffee beans grounds also used as manure for plants
• Best out of waste
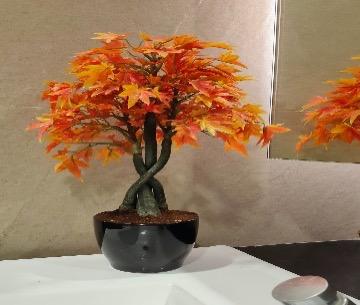
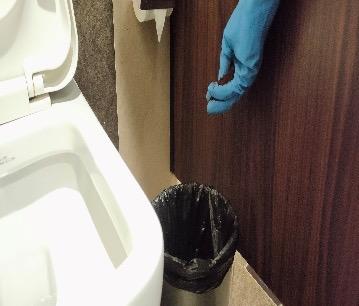
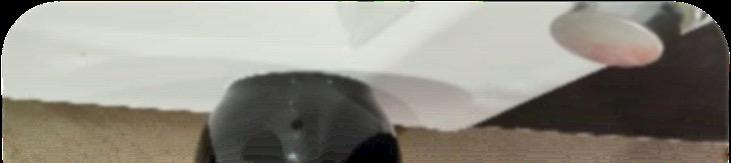
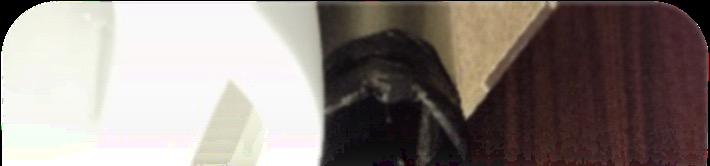
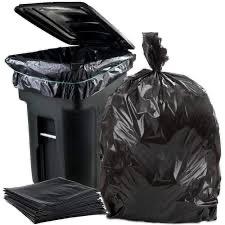
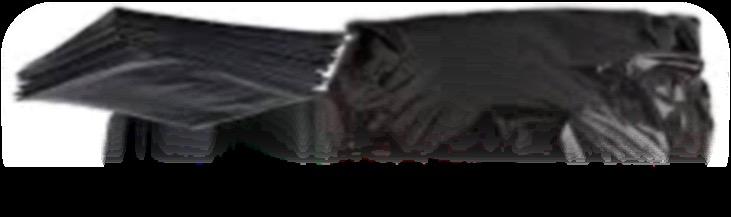
Description of the Innovation:
Labor
myIdea
• No Documentation store for Labor Compliance.
• No preparedness for any Labor Inspector visit.
• Tough situation to arrange the documents from vendors for labor audits.
• Created labor compliance tracker which gives auto calculated vendor wise monthly..
• Re-Engineered the process flow and control.
• Make all the documents available on Centralized share folder for quick access from any location.
• Accessible Labor Compliance Document store from any location within account.
• All sites are prepared to handle labor inspector visit at site.
• Measurable results for comparison from previous months.
• Reduced NC’s and quick closures during labor audits.
• Well Defined and controlled process
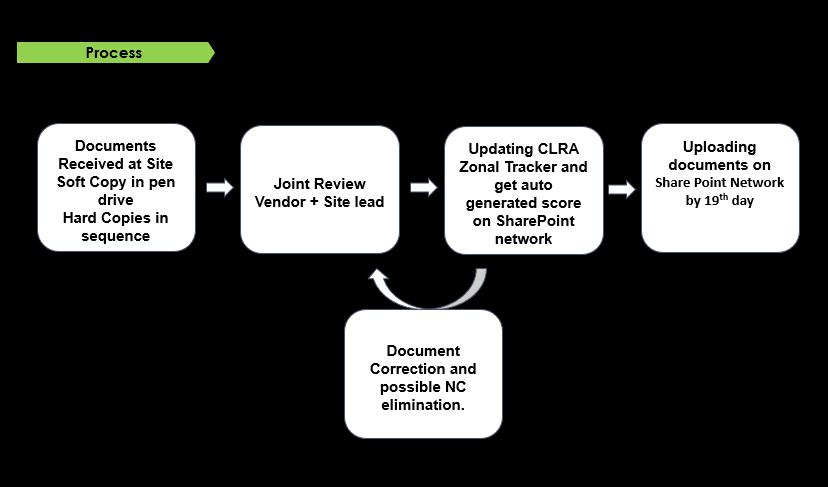

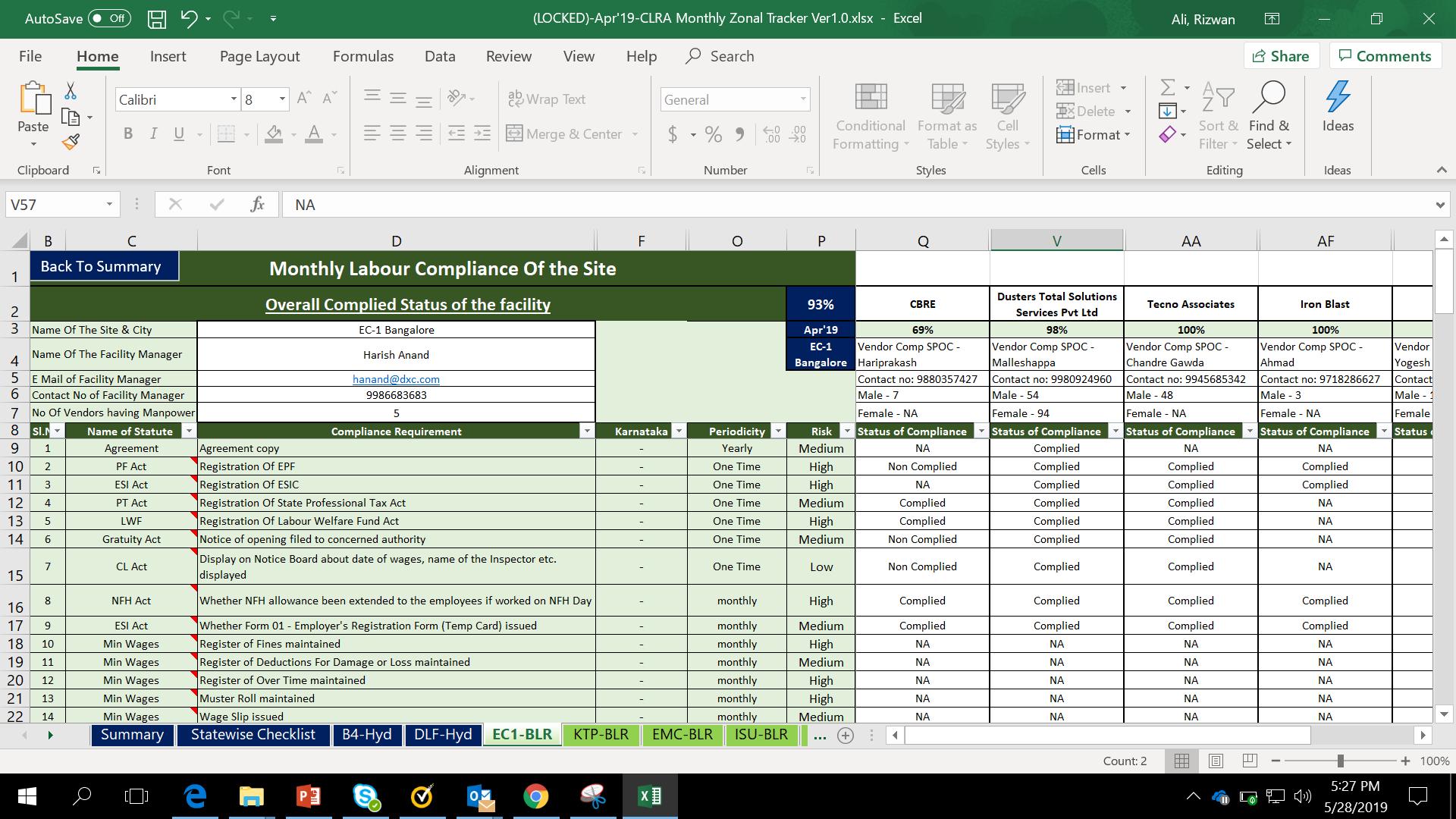
Description of the Innovation:
Cricket Arena :
Wellbeing
myIdea
• Lack of team building and collaboration activities.
• Calling back associates after the pandemic posed a significant challenge.
• Retention Issue: Increase in attrition level.
• Low morale and Engagement activities.
• High stress levels among employees.
• Indoor Cricket Arena - Having an indoor cricket stadium in the office can offer numerous benefits.
• Cost and Funding – Determine the budget for construction, maintenance, and operational costs.
• Space: We all need is Substantial area, preferably with a high ceiling to accommodate a cricket stadium.
• Cost We spent around 385000/for the bowling machine and cricket pitch
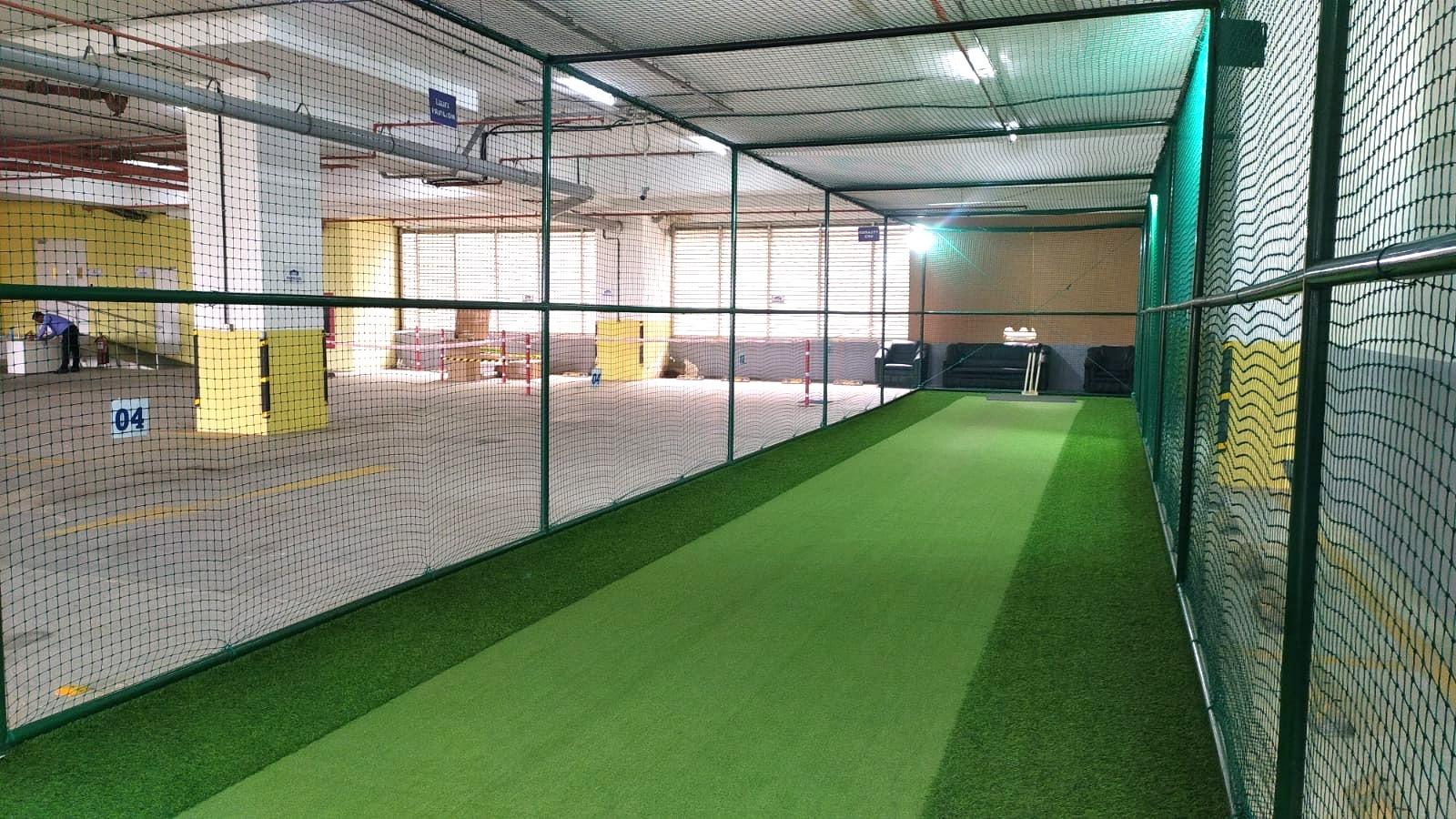
Employee Well-being – It promotes physical fitness, reduces stress, and encourages a Healthier lifestyle among employees.
• Team building – It strengthens teamwork, communication, and collaboration among collogues.
• Health and Well-being programsthey align with company health and well initiatives.
• Productivity Boost- Short breaks for cricket can re-energize employees, potentially increasing overall productivity.
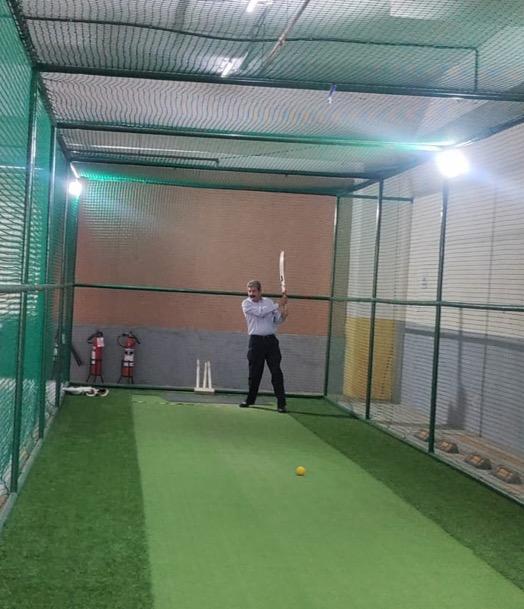
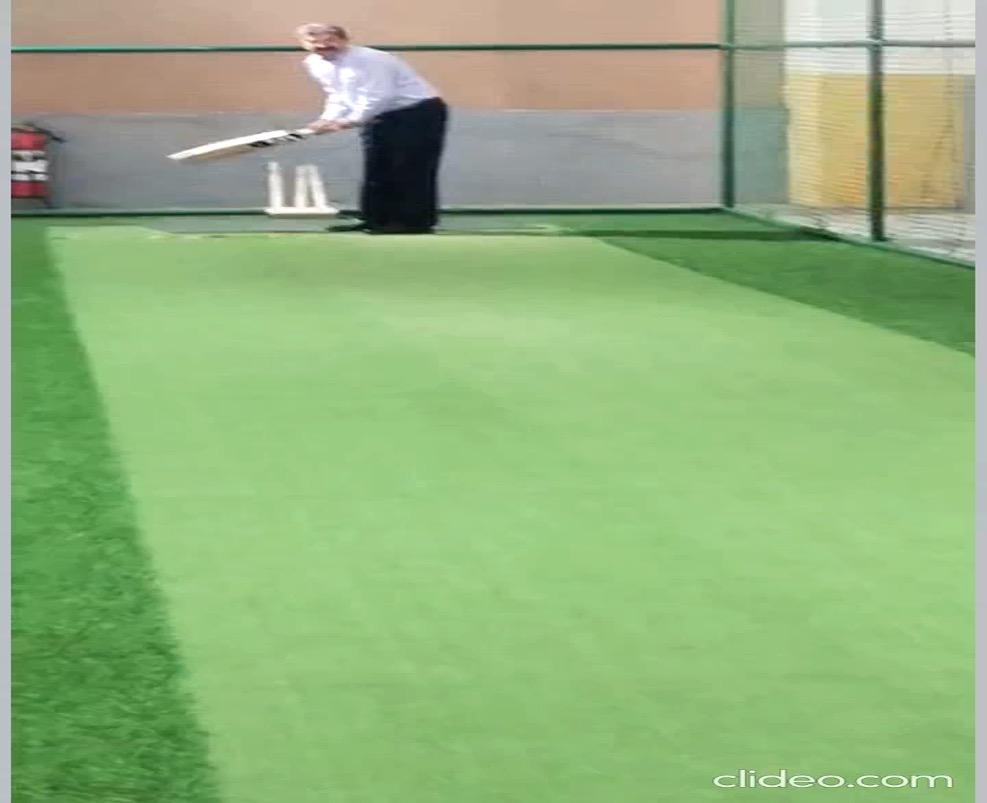
Description of the Innovation:
AC Control Through Occupancy Sensors
myIdea
• Every time we forgot to switch off the AC, we risked getting a steep electricity bill that could add up to a larger sum annually, while also having a detrimental impact on the environment.
Uncontrolled AC usage means
• Higher power consumption
• Electricity wastage
• Reduced life of the AC leading to in-efficient cooling
• Environmental harm (CO2)
• By Investing in the Occupancy sensor which is readily available in the market, the complete building for the standalone HVAC units can be optimized.
• The infrared AC controller controls the AC by using infrared signals just like the AC remote.
• There is no interference with the power supply of the AC.
• Reduces the AC wear and tear, leading to lower maintenance costs.
• Enabling benchmarks to track and save Power consumption positively impacts the environment.

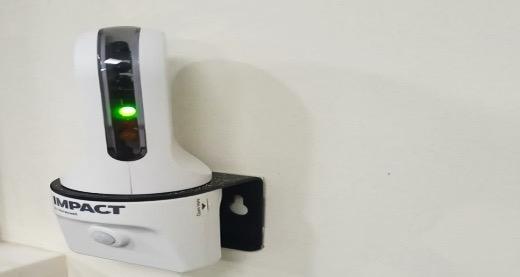

• AC usage comprises 50-70% of the electricity bill with cassette, split, or window ACs.
• In contrast, the infrared AC controller automatically turns the air conditioner on or off depending upon the occupancy in the room..
• Increased AC longevity and lower AC electricity costs
• On average, a savings of INR 426,816/year can be achieved.
• Additionally, by reducing electricity consumption, a significant reduction of CO2 emissions by 38,188 kg/year.
Description of the Innovation:
Enhanced Employee Experience
myIdea
• Launch of Return to Office in April 2022.
• Employees preferred to work from home than coming to office.
• There was a lack of connect between employees of different location.
• Employees lack excitement and participation.
• Building a collaborative ecosystem to foster a richer sense of company culture and bring likeminded colleagues together.
• Design and implementation of 7 regional ‘e-communities’ for Wipro India through their new intranet platform.
• Virtual Engagement to drive participation on the social intranet platform. The content gets posted as per the weekly schedule and special activities on notable days.
• In-person engagements across 43 locations were launched and stabilized with the help of a monthly event calendar.
• Significant growth in employee experience, through virtual and inperson engagements.
• Enablement of a single-channel platform for community engagement.
• FMG communities on The Dot have been recognized for the highest and most consistent engagements.
• Voluntary contribution and involvement from employees has resulted in a 191% increase in the participation rate in 6 months.
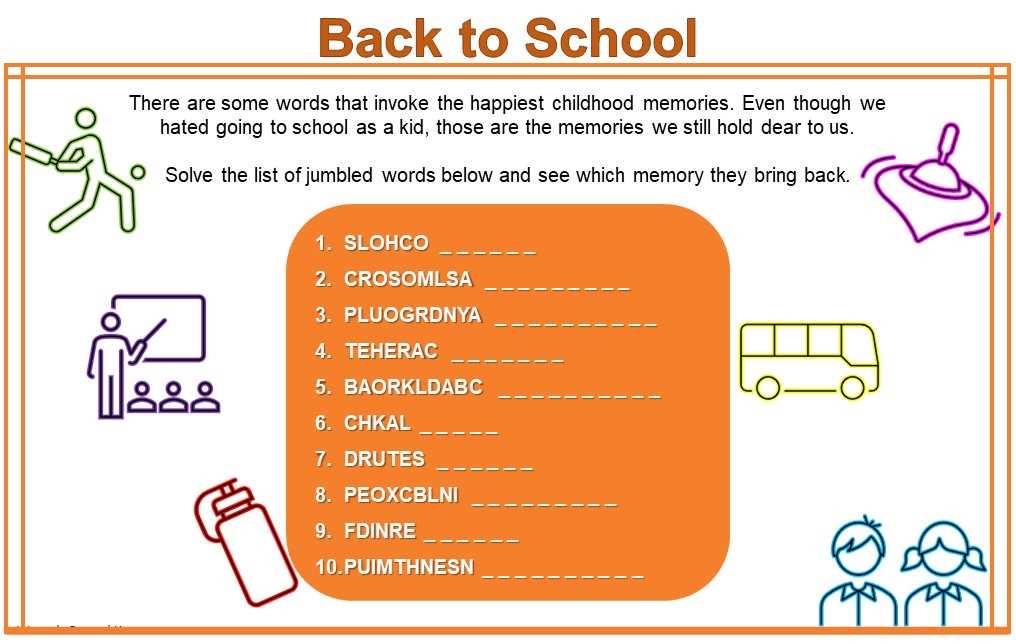
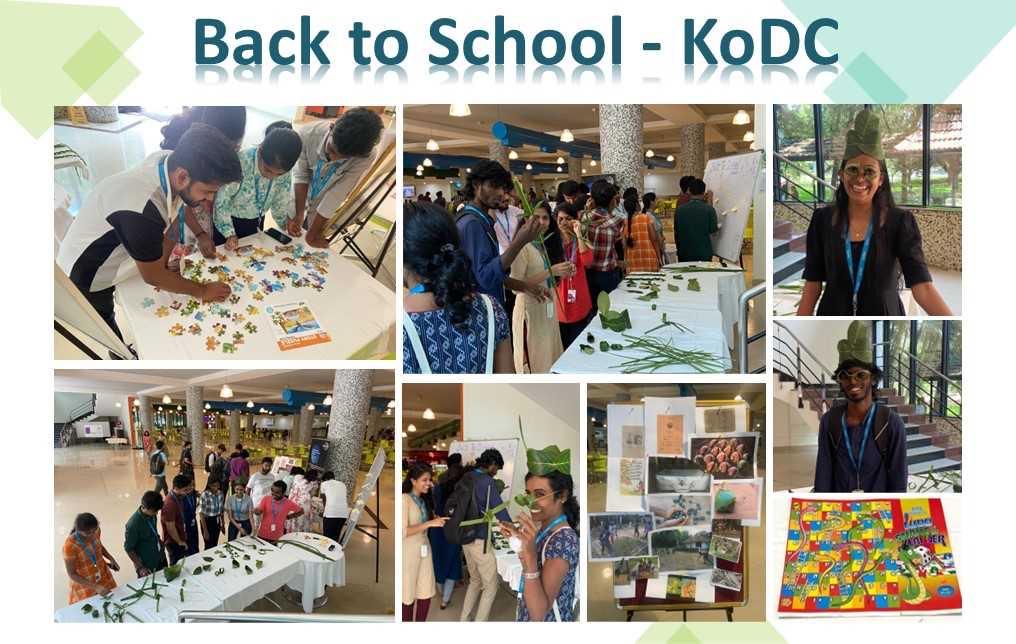
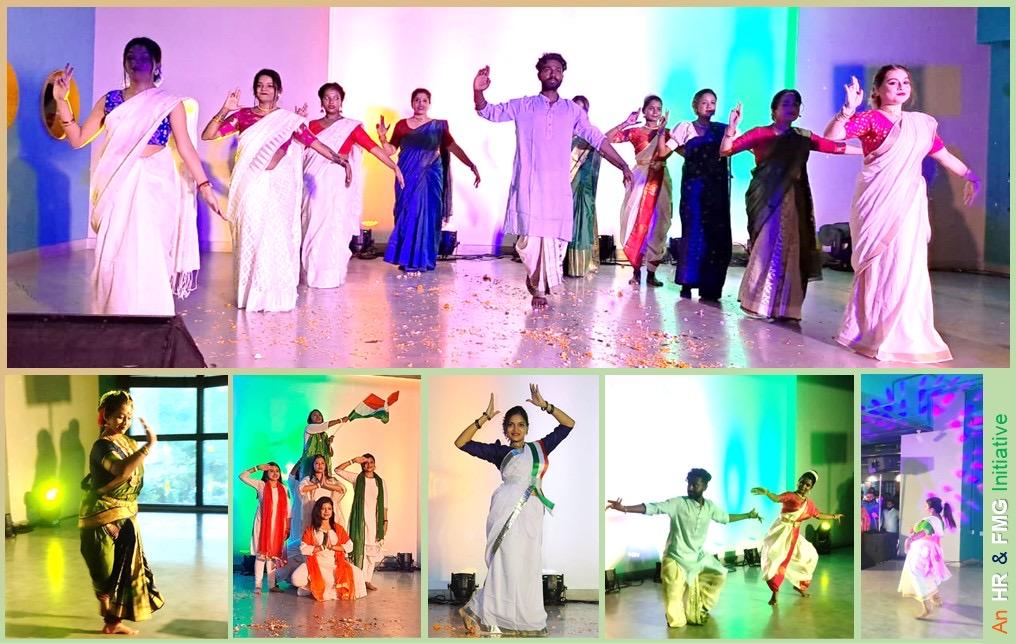
Description of the Innovation:
Health assessment of Rotating Equipment using Portable Vibration Analyzer
• Common problems in rotating machinery include imbalance, misalignment, wear and tear, resonance, looseness or clearance issues, and mechanical faults.
• The absence of a predictive maintenance strategy can result in catastrophic equipment failure due to vibration issues.
• Increased maintenance costs and a shortened lifecycle of rotating equipment.
• Changes in operating conditions such as changes in load, speed, or environmental factors can affect the vibration levels in rotating machinery.
• Irregular, oscillatory movements or motions within the equipment that can affect its performance, reliability, and safety.
• Vibration measurement and diagnostic studies were conducted using a portable wireless tri-axial vibration analyzer.
• Vibration analysis is performed utilizing sensors in the horizontal (h), vertical (v), and axial (a) directions.
• Maintenance strategies: scheduled maintenance can be planned based on vibration level indications of wear or degradation to proactively prevent unexpected breakdowns.
• Systematic vibration analysis for all rotating equipment, including pumps, blowers, and compressors, among others.
• Early detection and mitigation of vibration problems are crucial to prevent further damage to machinery and ensure safe and efficient operation.
• Transition to predictive maintenance: minimize unplanned downtime by adopting a predictive maintenance approach.
• Improved energy efficiency through the identification and resolution of vibration-related problems.
• Vibration data and analysis reports serve as valuable documentation for audits, maintenance records, and warranty claims.
• Safety: proactively preventing unexpected equipment failures enhances workplace safety for employees and reduces the risk of accidents.
• Reduction of Opex cost (CAMC to NCAMC)-$10K/annum.
myIdea
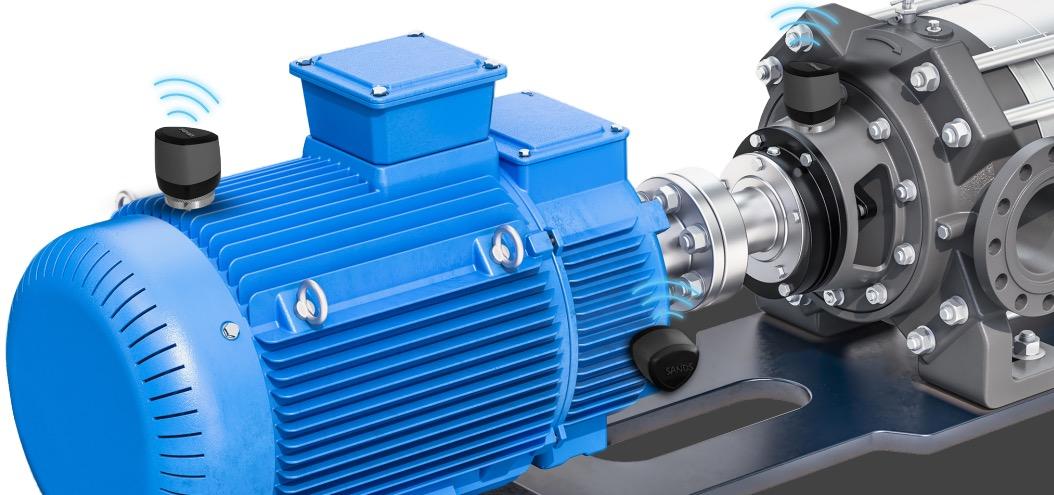
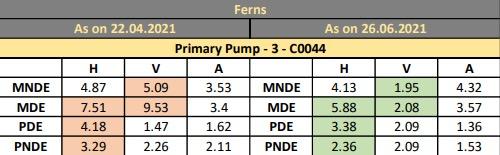
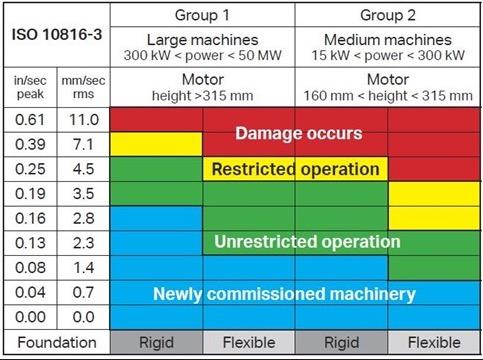
Description of the Innovation:
Enhanced Employee Experience in Transport service
myIdea
• On the first day employees were not able to commute in office cab/shuttle since the profile was not created.
• Employees were missing the shuttles because trips for multiple locations were operating on the same route.
• No Shows were more since employees did not cancel their transport requests in case, they were not using the cab.
• Employees did not have the option to charge their mobile.
• Employees did not have access to drinking water in the shuttle.
• Employees did not have a provision to share trip feedback through the app.
• Employees had challenges identifying the exact pickup point of shuttle routes.
• Implemented the transport facility for new joiners on Day 1 through MS form.
• Implemented the digital signage display on the shuttle.
• Booking confirmation SMS sent 2 hours before reminding employees, reducing no-shows.
• Made provision of mobile charging and drinking water in each of the vehicles.
• We have enabled the employee's feedback through the transport app, and geo-coded boarding location.
• Transport app feature is enabled to get navigation and reach the pickup point.
• Enhanced experience for 510 new joiners with day-1 office transport service extension.
• Ease of recognizing our office shuttle and route.
• It helped to reduce the No Show percentage from 6% to 3%.
• It benefits the employees to locate the shuttle nodal point.
• It helped us to act on employee feedback & and employees can easily locate the shuttle boarding point through the app
• Step towards operational excellence in transport services..
• Enhanced employee experience
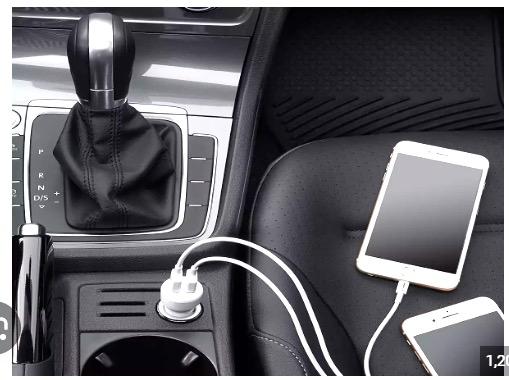
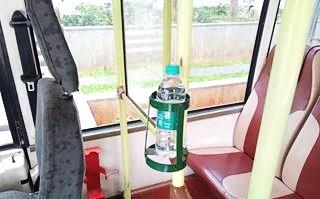
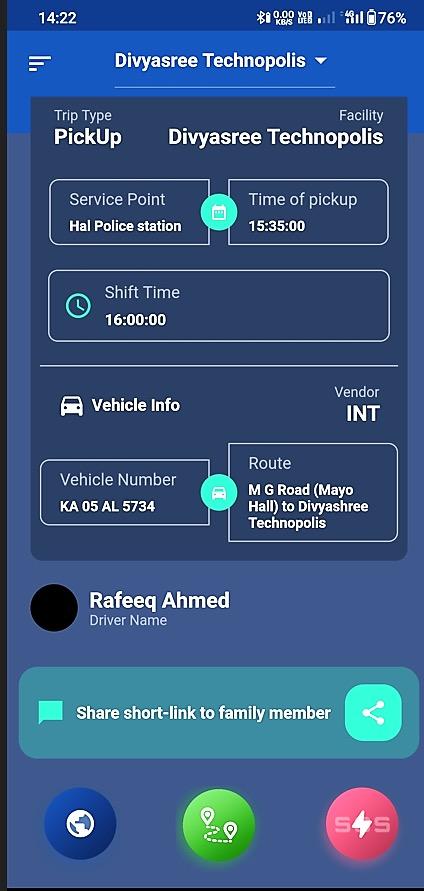
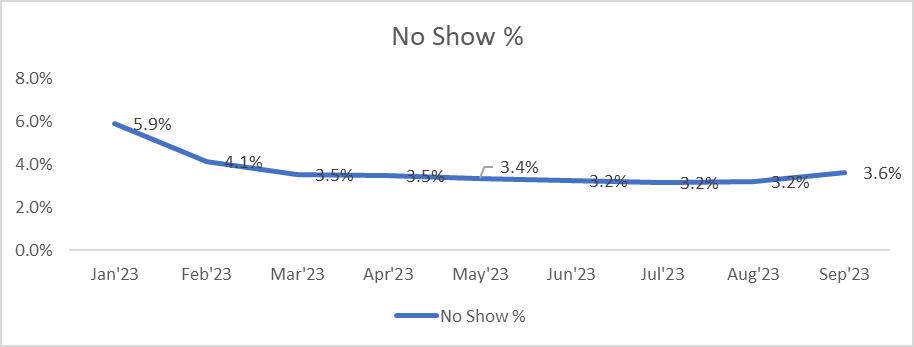
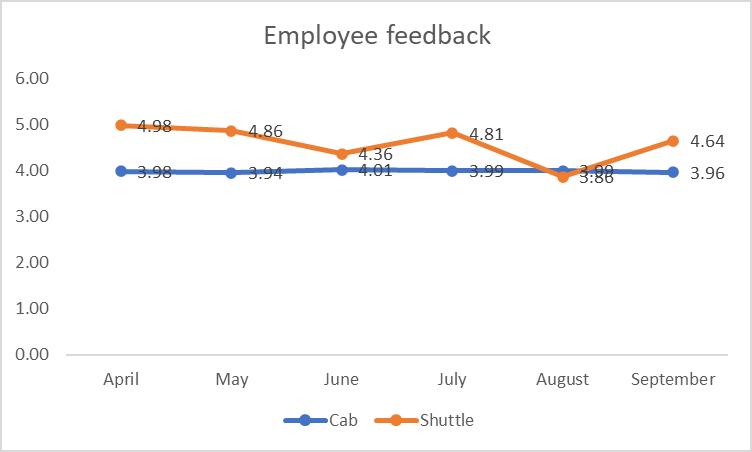
Description of the Innovation:
Leveraging IOT Technology for Monitoring Energy and Space
• Facility energy data reports are taken manually
• Daily basis to arrive facility energy consumption & it’s time-consuming activity.
• Manual log reports need to be maintained for internal audit & future reference.
• Shift wise energy data taken in lean manpower operation
• Manually monitoring of space utilization is difficult and calls for big effort
• Effectively utilized existing infrastructure for the dashboard
• We have created the IOT energy dashboard for effective monitoring and recording.
• Maintaining 3 years of data in the system.
• Easy to demonstrate while auditing.
• Live demand and real-time equipment wise consumption can be monitored in the web browser
• we’ve created the heat mapping based on the VAV thermostat temperature with color differentiation for easy understanding
• Reduction in operations and maintenance costs.
• Web-based monitoring – easily we can monitor the total facility consumption.
• Authenticated reports, can showcase to internal and external auditors.
• Dashboard with graphical representation for easy understanding of daily/hourly facility consumption.
• Space - Physical inspection not required, and we can effectively utilize technician for other activities
myIdea
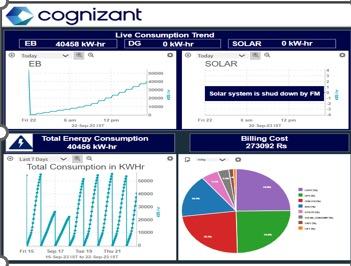
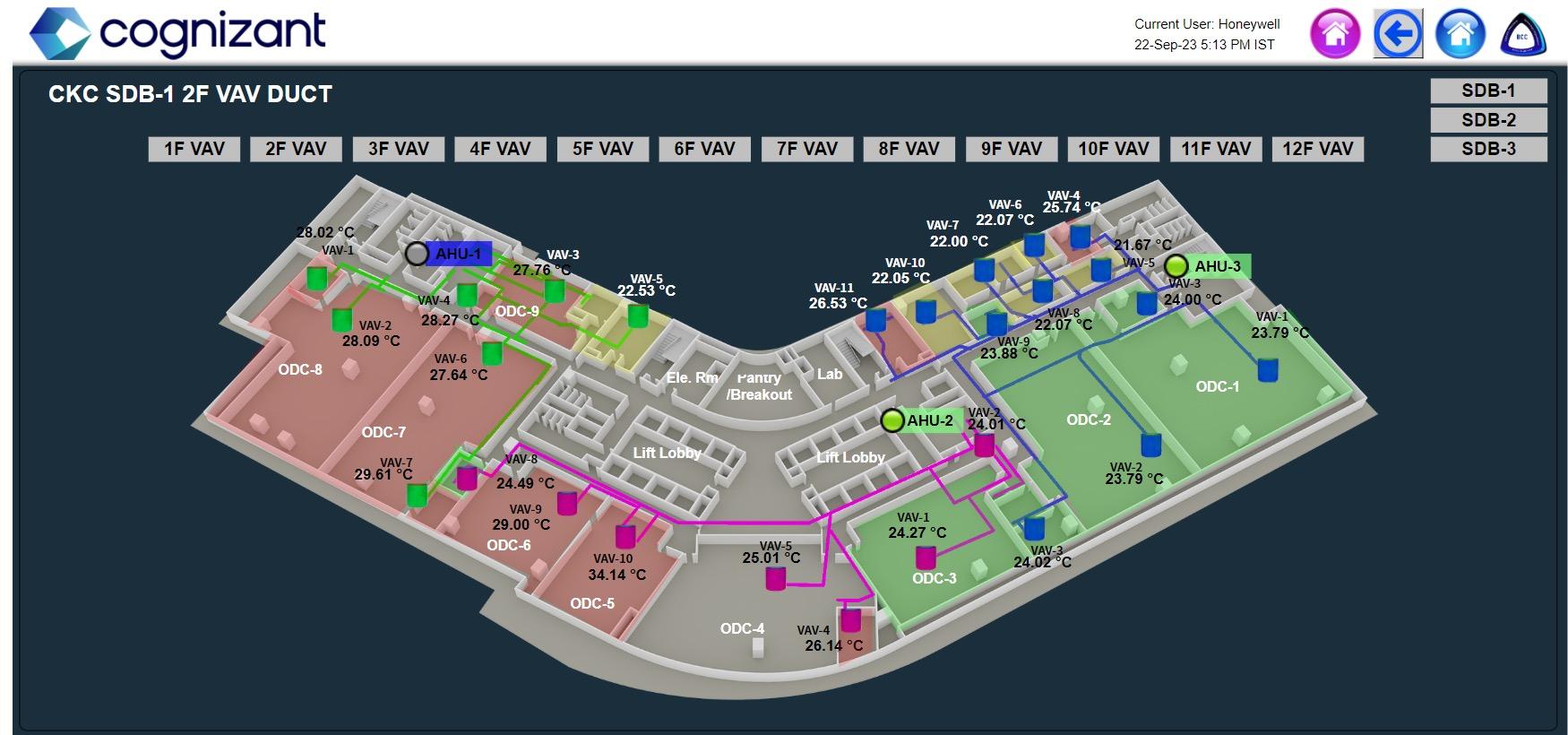
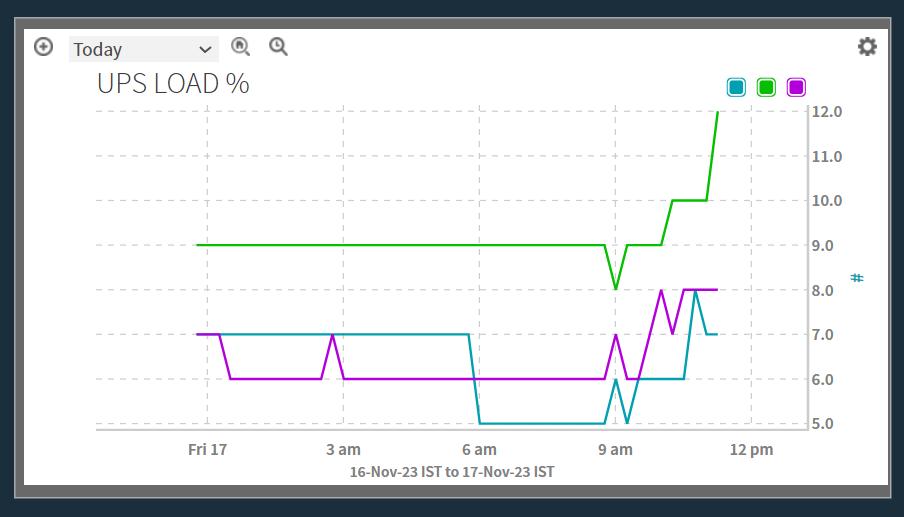
Description of the Innovation:
Safe Handling Of ACB –Material Handling Trolly
• Challenges in loading and unloading of ACB in the panel.
• High possibility of slip, trip & and fall.
• Multiple people handling ACB chances of miscommunication lead to an incident
• Ergonomic issues for staff while handling.
• Repair costs will increase due to damages.
• Increase in R&M & Operation cost.
• Frequent damage to ACB front facia
• Brainstormed with team members and suggested material-handling equipment
• Approached OEM for quotation and obtained necessary cost approval from the client.
• OEM Vendor suggested Manual Hydraulic trolley for easy handling of ACB.
• ACB unloading trolley reduces the manual lifting of ACB with bare hands
• Single person can handle the ACB unloading (200kgs).
• Workplace injury is avoided
• Ergonomic issues eliminated
• Reduced damage to ACB front cover / spare
• Multiple human intervention reduced.
• R&M cost reduced
• Easy to operate
myIdea
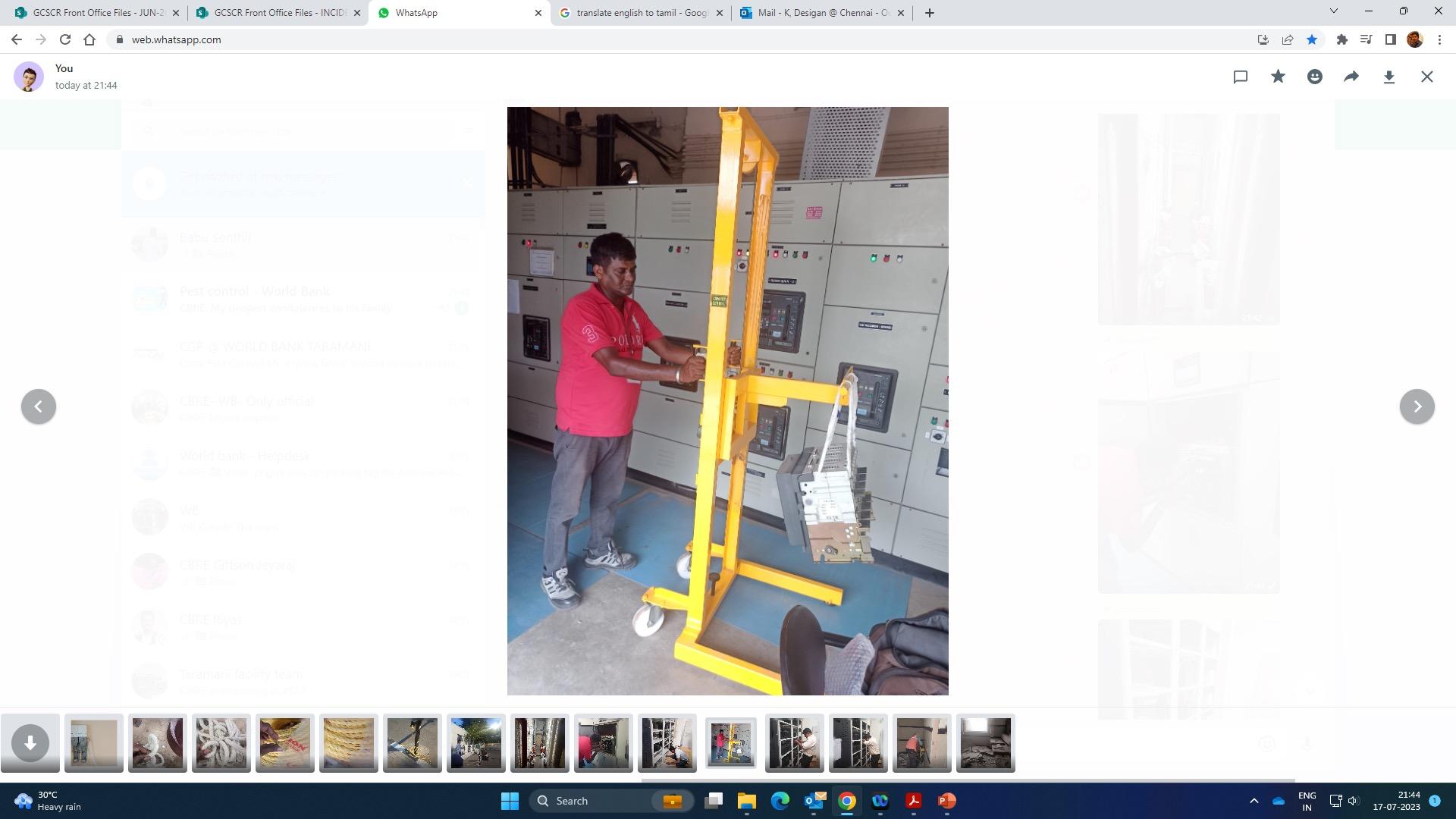
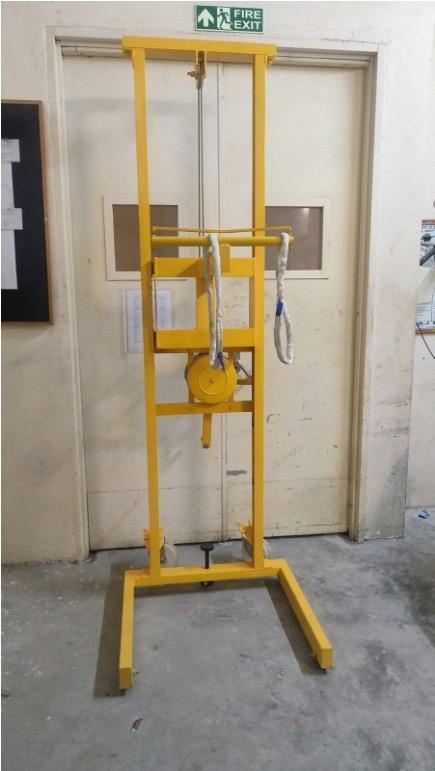

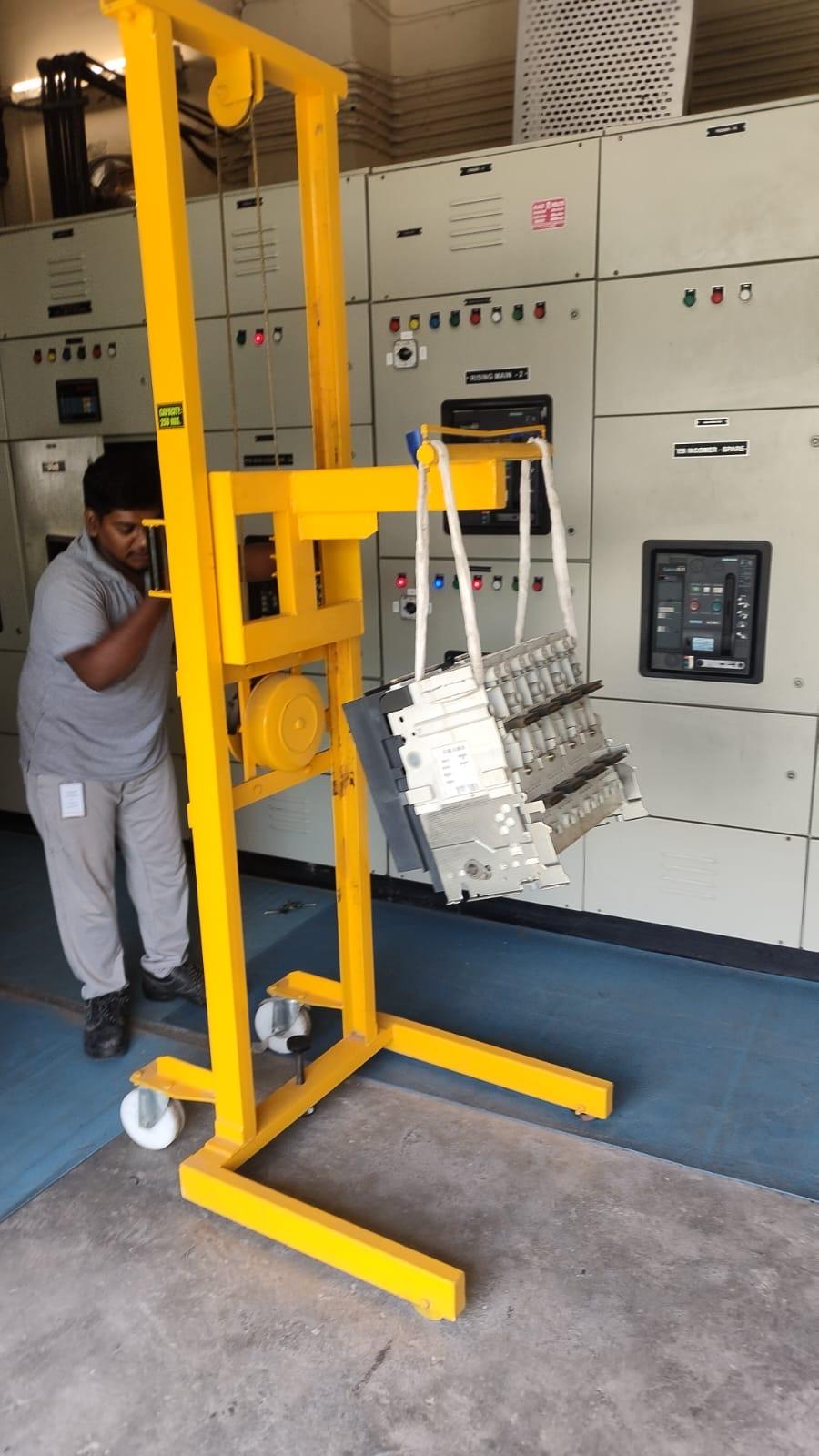
Description of the Innovation: CHALLENGE
Cost-saving Through Electroplating Of SS Fixtures
• Look and feel of the rest room is affected by the faded taps
• SS taps in washrooms are experiencing a rapid loss of shine, attributable to the detrimental effects of hard water.
• This accelerated deterioration is posing an aesthetic challenge and necessitates a solution.
• Maintain the taps appearance for a more extended period than currently anticipated.
• Cost of sensor taps are high leading to increased cost of maintenance
• Brainstormed with team members and planned for electro plating (Electroplating is the process of using electrodeposition to coat an object in a layer of metals)
• By Implementing an electroplating process with a thickness of 15 microns on the taps proves to be an effective solution.
• This method restores the original look and feel, forming a resilient layer that safeguards against the corrosive impact of hard water, ensuring a prolonged and enhanced aesthetic appeal.
• Sustainable solution.
• Enhanced look & feel of washroom,
• Electroplating the taps saved us an estimated INR: 15.59 lakhs compared to purchasing new sensor-based stainless-steel taps.
• It successfully restored their look and feel to a pristine, new state.
• Providing a cost-effective and aesthetically pleasing solution.
• Improved the durability by adding a layer of protection against wear and corrosion.
• Capex cost avoided.
myIdea
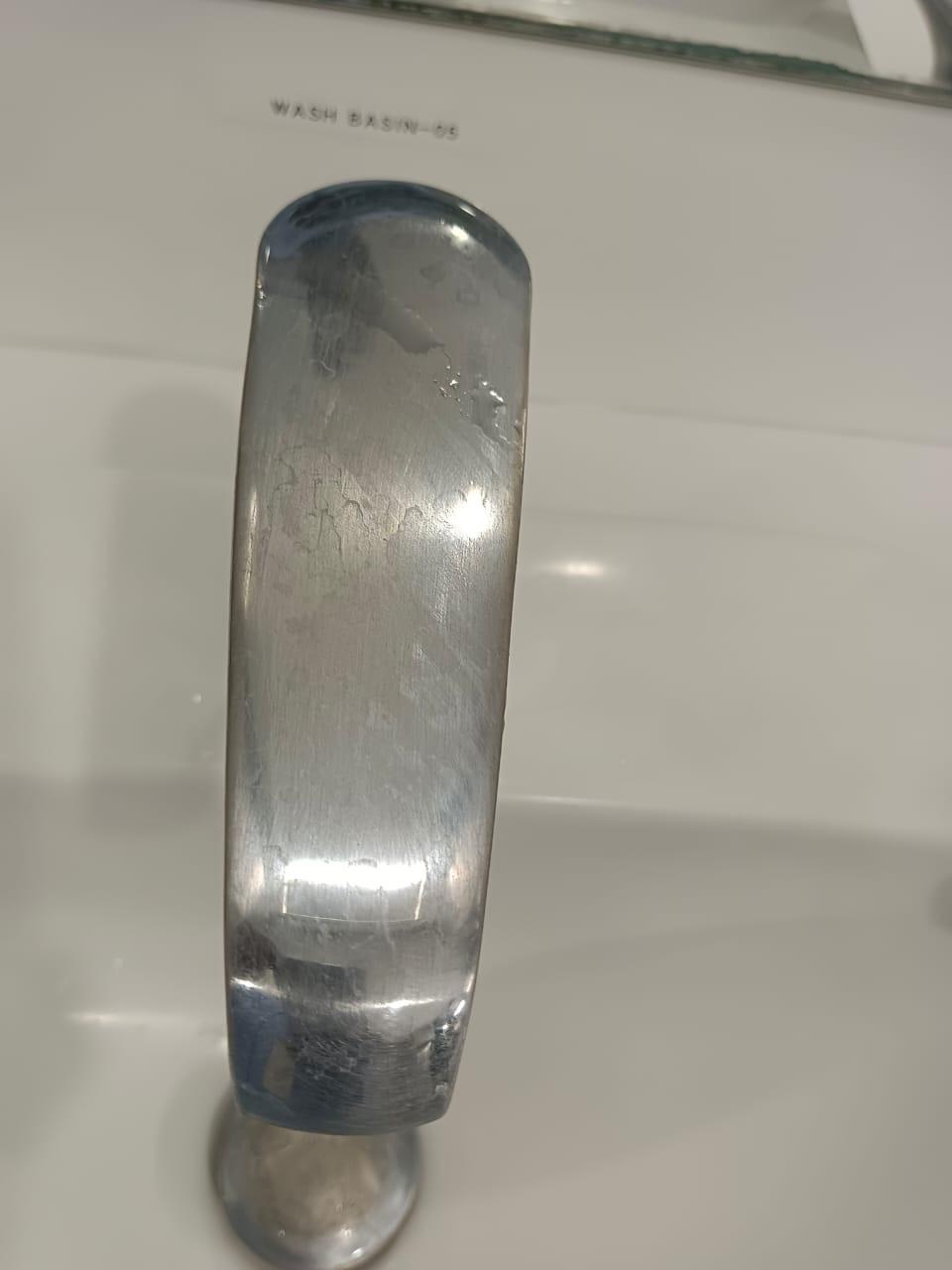


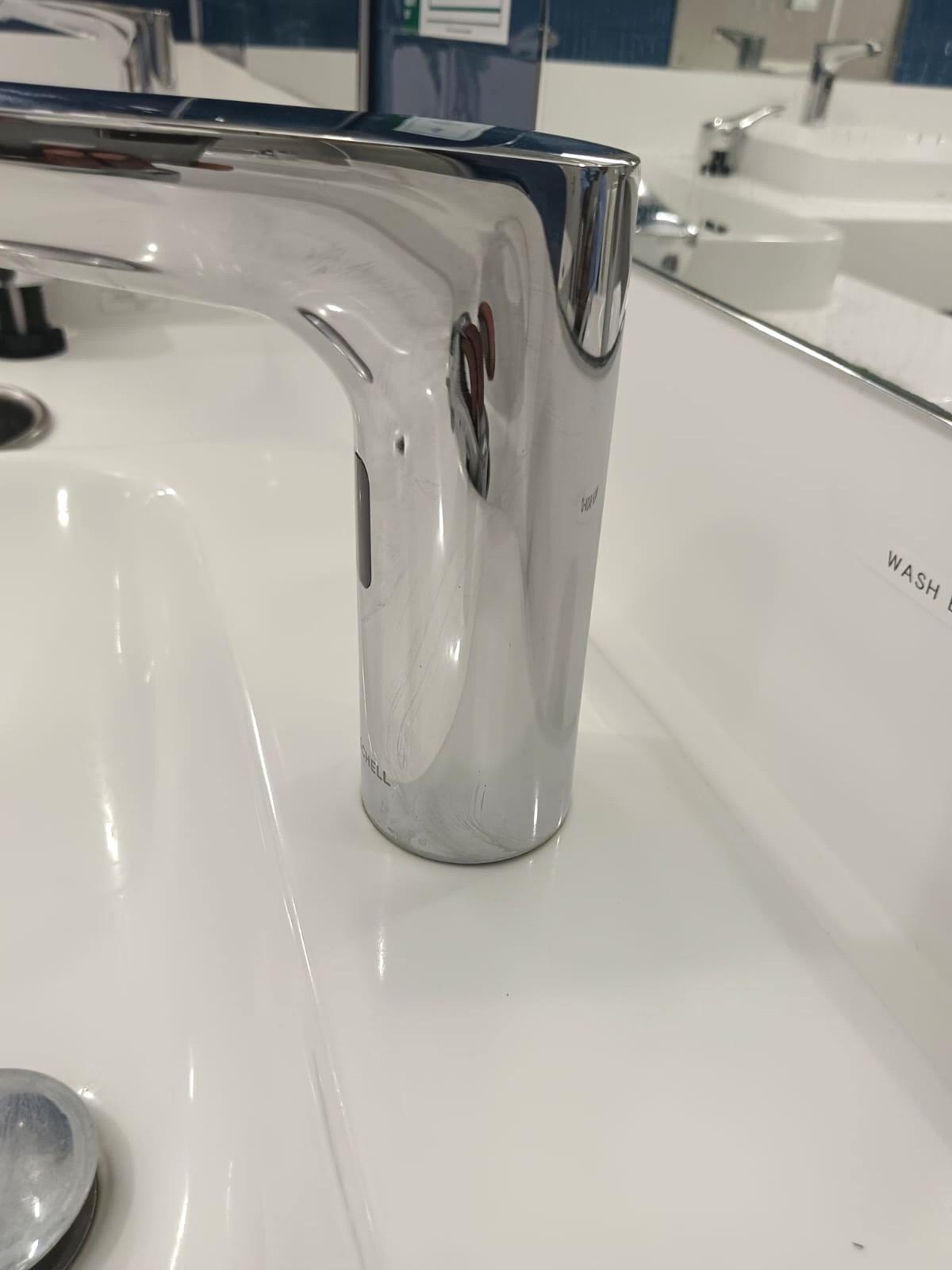
• Our team @Dell is extremely focused on continuous improvement and training is an indispensable element of this process.
Description of the Innovation:
Training Program for Internal teamFault Findings
• This training process has two elements to it knowledge and skill.
myIdea
• Supervisors and executives are required to train the operators/ janitors periodically which demands that they are well aware of the correct processes.
• Supervisors and executives need to have the skill to spot deviations to the approved process when they are being performed by the operator level staff and correct the deviations, if any, instantly.
• Assessment for knowledge is based on awareness of the correct process whereas assessment for skill is based on ability to teach and spot mistakes committed by their teams.
• The training is divided into three segments.
• Pre training assessment reveals knowledge standard of the trainees before the training. This enables us to customize the content.
• During the training, theoretical training is augmented with video based practical training demonstrating what has been taught.
• Post training assessment includes theoretical knowledge and a practical test by way of “fault finding”
• Videos with deliberately committed errors are played and the trainees are required to spot all the actions that are not in line with what was taught
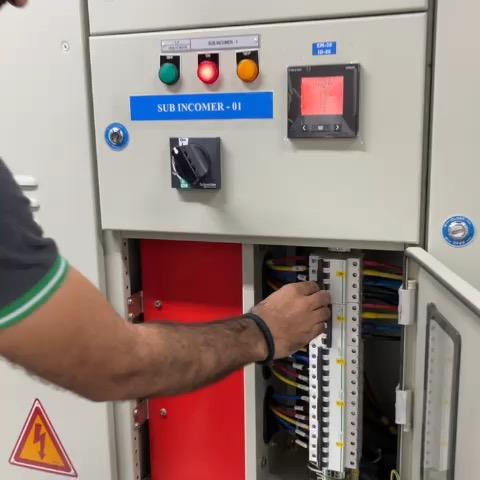
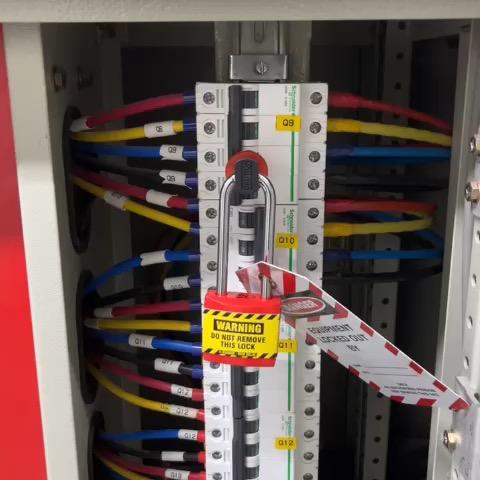
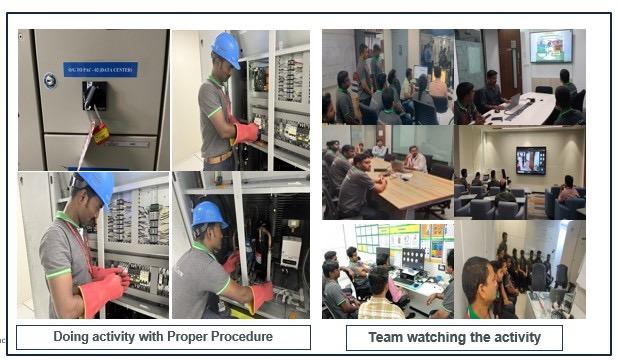
• Online tests at the end of the training provide instant feedback on the effectiveness of the training.
• Standardization of the processes across the account
• Significant difference in test scores before and after training
• Effective measurement of understanding practical aspect of the training
• Significantly higher interest amongst the trainees
• Trainees who have failed to achieve minimum of “BY” standards are encouraged to repeat the training to qualify as “pass”.
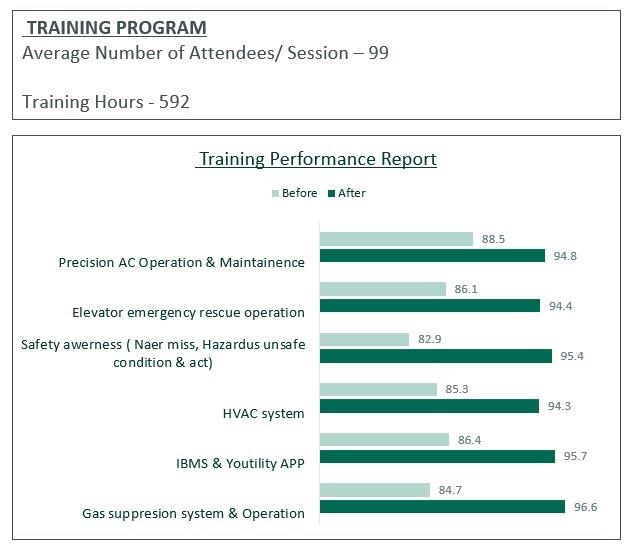
Description of the Innovation:
Zero Landfill
myIdea
• Landfill waste was accumulated at the site which was not fully recycled
• Majority of the food waste and leftovers, plastic, and paper products were going to landfill
• After landing in landfill this waste will leak out toxins that eventually get into the soil
• Contamination of the soil around the area of the landfill
• Plant and animal life may suffer from this exposure to toxic material
• Zero Landfill by 100% recycling
• 1.5 Tons of monthly landfill waste, which included Pantry waste, Tissue rolls, Food waste, Dry waste, etc. recycled
• With the support of the Landlord, all the segregated waste disposed from Bank premises is either getting recycled or recomposted and utilized as manure. LL was requested to purchase new equipment and optimize the utilization of the existing equipment including vermicompost at the site ensuring zero landfill.
• Monthly reports are being shared with CBRE, and dedicated colour-coded bin bags are recommended for client waste calculations
• Helped to achieve existing landfill volume of approx. 18 tons per annum to zero.
• Zero waste facilitates reduction in pollution and reducing environmental impact.
• Reduction of non-biodegradable waste such as plastic
• Zero waste is one of the key parameters for CBRE and Client's ESG goals.
• Reducing carbon footprint
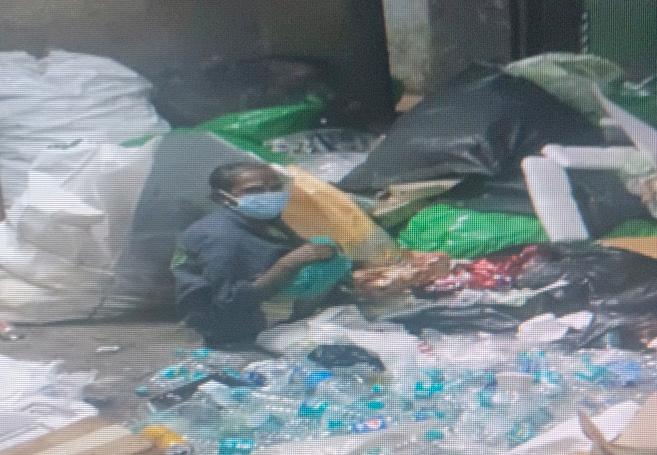
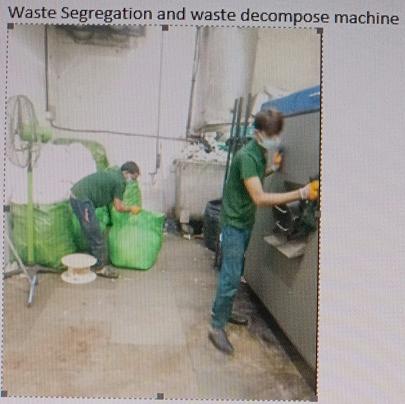
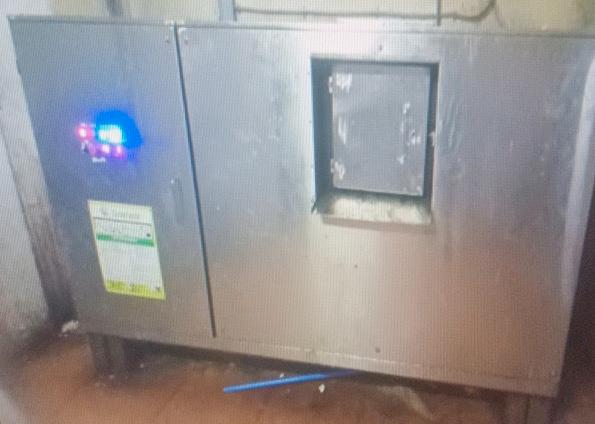
Description of the Innovation:
Parking CO Sensor installed and integrated with basement Jet fan for ventilation
• Difficulty in identifying areas of poor ventilation
• In packed premisesBasements, “0” Ventilation area. Fresh Air Supply is less.
• Working in such areas area can lead to health hazard
• Maintaining fresh air (basement area) was a challenge
• Carbon monoxide detector Sensor works on Electrochemical reactions to measure how much gas is in the surrounding air.
• The Carbon monoxide gas passes from the sensor and reaches the enclosed area this is the unit that converts carbon monoxide input into 4-20mA output. This output gives a signal to PLC and then a PLC command to the Jet fan.
• These detectors are designed to measure the concentration of carbon monoxide in the air in Part per Million.
• To maintain the air levels and good working conditions. CO censors are instilled.
• Once the CO level reaches 25PPM, the sensor senses & and automatically starts the jet fan on auto mode till CO reaches normal
• Carbon monoxide level is increased above 50PPM then Jet Fan is started on High speed.
• Carbon monoxide level is decreased below 25PPM then the Jet fan is automatically off.
• Jet Fan automatically operates and maintains the CO Level.
• It led to maintaining the fresh air all the time in the affected premises.
myIdea
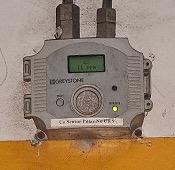
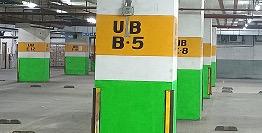
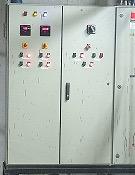
Description of the Innovation: CHALLENGE
Active and Passive Alarm Annunciator System
• Monitoring of BMS systems or individual equipment was not possible in real time.
• There was no warning set off by the alarm most of the time.
• Involvement of human effort for monitoring the systems in case of any issues.
• No backup in case of BMS station PC down.
• The team brainstormed and decided on the below
– An independent alarm system that is directly connected to equipment, not dependent on any network connectivity, has sound and flashing alarms to alert nearby persons.
– Shall be able to accommodate systems that cannot communicate with BMS systems.
– To have an alarm annunciator panel having multiple windows with light and sound output which get activated on potential free single NO or NC contact of any system.
• Supply & and installation cost for annunciator panel, make - minilek, 24 window with external hooter is INR40,679/-.
• Simple status monitoring system.
• Critical systems can be monitored with more trust.
• Multiple systems can be accommodated with simple NO and NC contact integration by wiring.
• No dependency on BMS for any important alert.
• Flashing light with sound gives alert to all nearby person.
myIdea

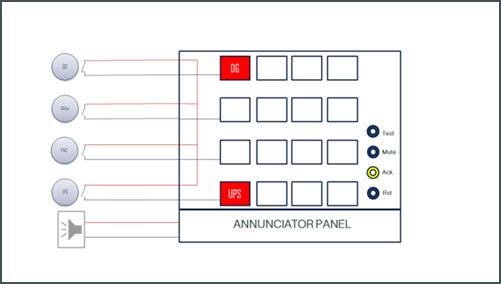
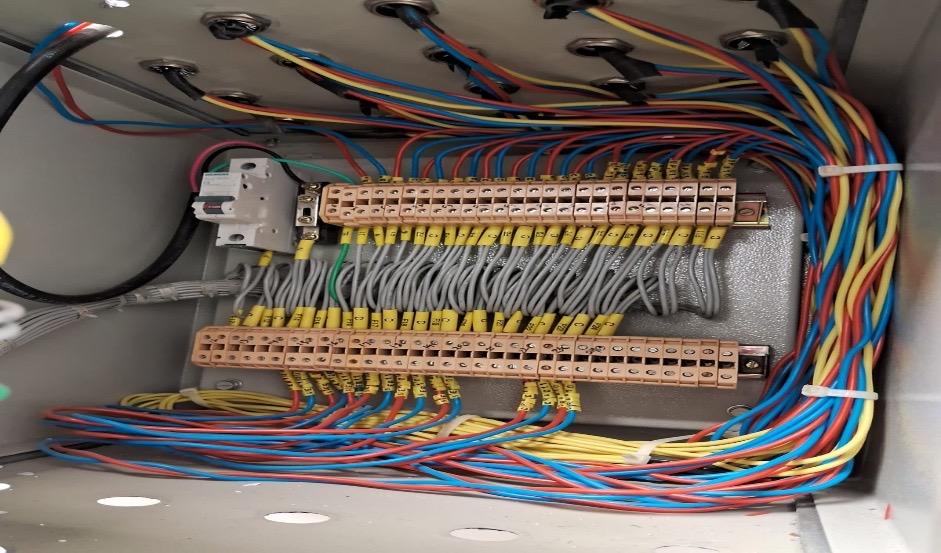
Description of the Innovation:
Modified lighting circuitEnergy Conservation
• Energy Optimization without Compromising Safety
• Identifying Critical Areas for Energy Optimization
• Technological Compatibility and Integration
• ESG Commitments
• Public Perception and Stakeholder Expectations
• Through a meticulous evaluation, we identified that office emergency lights could be managed effectively without compromising safety protocols. We segregated these lights into two categories: lights that could be safely turned off after office hours without compromising safety protocols and those that needed to always remain operational for safety reasons.
• Same has been reviewed and approved by Siemens's EHS Team As well
• Reduction of carbon footprint 3,844 KG Co2e per annum
• Cost saving for Client approx. INR 48k per annum
• Improved life cycle of light fixture considering reduction in lamp burning hours
• Upholding Environmental & Governance commitment
• Encouragement to site team
myIdea

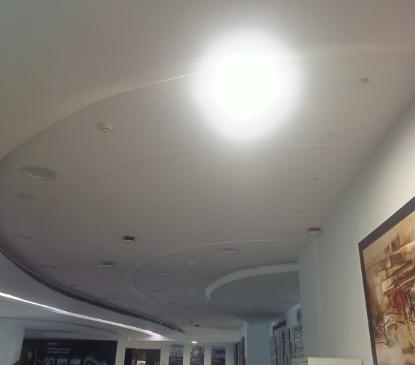
Description of the Innovation:
Temperature Alarm system for Ductable AC units
myIdea
• In the critical room there was no BMS system available.
• Ductable AC units lacked an alarm system for any unit failure or abnormality.
• Additionally, the shift technician's two-hourly physical round time only allowed for failure to be noticed.
• We understood that a delay in attending to AC unit failure could result in critical equipment shutdown.
• For any reason rise in the critical room temperature or Delay in attending to AC unit failure can result in critical equipment shutdown.
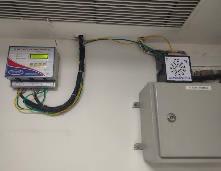
• To address this challenge, we procured an external alarm device and integrated it with the AC switching timer.
• We set low-temperature and hightemperature alarms on the timer for activation of the relay.
• The same was tested manually for any rise or fall in temperature.
• With any reason for an increase in critical room temperature, our team can now immediately address and attend to it.
• Our facility has benefited greatly from this initiative.
• We can now promptly address any AC unit failures, and alarms for high and low room temperatures are available within the range set by us.
• As a result, we have resolved the risk of critical room equipment failure due to abnormal temperatures, and our team can now attend to any AC unit abnormalities in a timely manner.
• The team and clients are now happy and confident as the risk of critical room shutdown has been minimized.

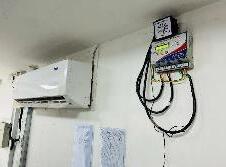
Description of the Innovation:
Interconnection of critical area & comfort cooling chilled water circuit
• Cognizant Deccan Camps (CDC) is an owned facility & 03 no’s different HVAC circuits to cater campus’s entire cooling load
• CDC Facility has a total of 03 no’s 190 TR Air cooled chillers and 02 no's 342 TR Air cooled chillers with separate chiller water lines for both circuits.
• During lesser load in weekends and night operations two chillers are operated due to separate HVAC circuits.
• Higher power consumption for cooling and energy wastage
• Reduction in chiller efficiency due to lesser load on chillers
• Manpower loss due to more equipment operations
• Based upon our discussions & and brainstorming within the team, got an idea and suggested interlinking chilled water line circuits of i.e.,03 no's 190 TR Air cooled chillers (Critical area circuit) with 02 no's 342 TR Air cooled chillers ( comfort cooling - workstation area)
• Accordingly, prepared business case, management of change (MOC), method statement, and risk register with mitigation plan and projected to management for approval.
• Post approval of proposed idea, issued purchase order to vendor & executed the activity
• Switched off one chiller and associated pumps as per loading conditions
• Annual Power Saving in KWH – 18,000
• Annual Cost Saving in INR – 1.8 Lacs
• Reduction in power consumption
• Increase in chiller efficiency due to increase in load
• Chiller backup redundancy level increased
• Interlinking the circuits gives flexibility to run the chillers based upon load conditions
• Reduction in Co2 emissions and saved 14.22 Ton carbon footprints
• Return of investment -1.6 Years
• Supported to sustainability and achieving Net Zero Goals of client
myIdea
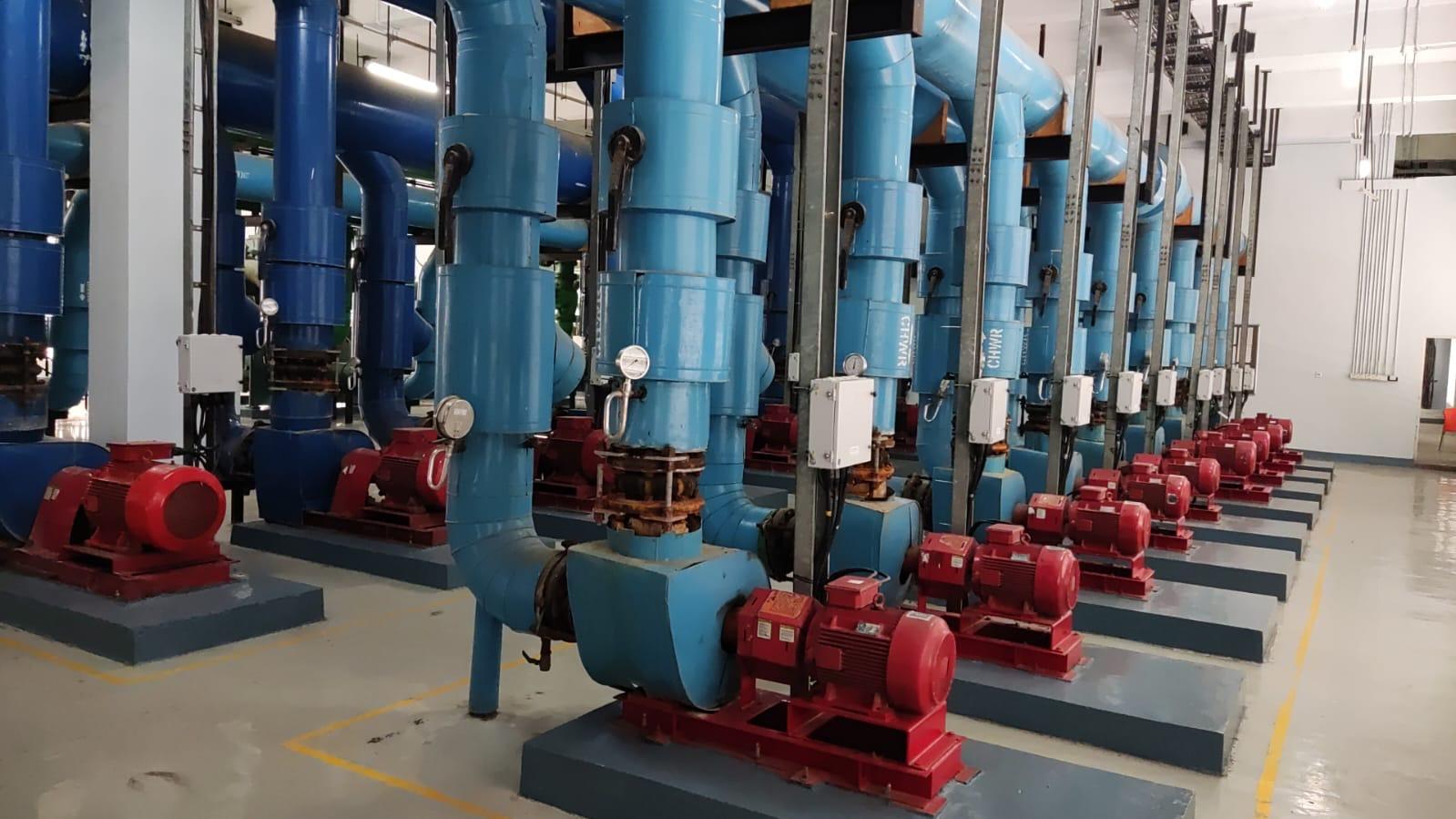

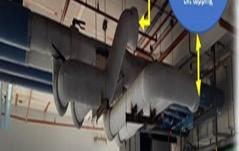
Description of the Innovation:
Provision of bins for Storage in Consumable Stores
myIdea
• We have 2 nos. of M&E consumable stores at Tower S3, Magarpatta, where various consumables were kept in open slotted angle racks.
• There are numerous small items, and it was challenging to keep them appropriately in open racks.
• Earlier, we were using old cardboard boxes to keep the consumables.
• These carton boxes also require to be changed frequently due to durability issues.
• It doesn’t give a good aesthetic look to the store and is difficult to manage.
• Replacement of carton boxes with readily available storage bins was proposed.
• Durable & and withstand rough handling compared to cardboard boxes.
• Available in various sizes as per the rack size and consumables quantity.
• Various color options of these bins are available which allow for category-wise storage of the consumables in store.
• Appropriate storage of consumable material in stores.
• Achieved suitable storage, stacking & nesting of consumables in stores.
• Durable product with minimal damage during handling.
• Various color options assisted in managing the store material category wise like electrical, plumbing, and carpentry within the same store.
• This idea benefitted us to manage the store as per 5S standard in a very better way.
• It saved a lot of time for the ground team for ease of searching for material and managing the store.
• Providing a superior aesthetic look of stores and easy-to-maintain material stacking.
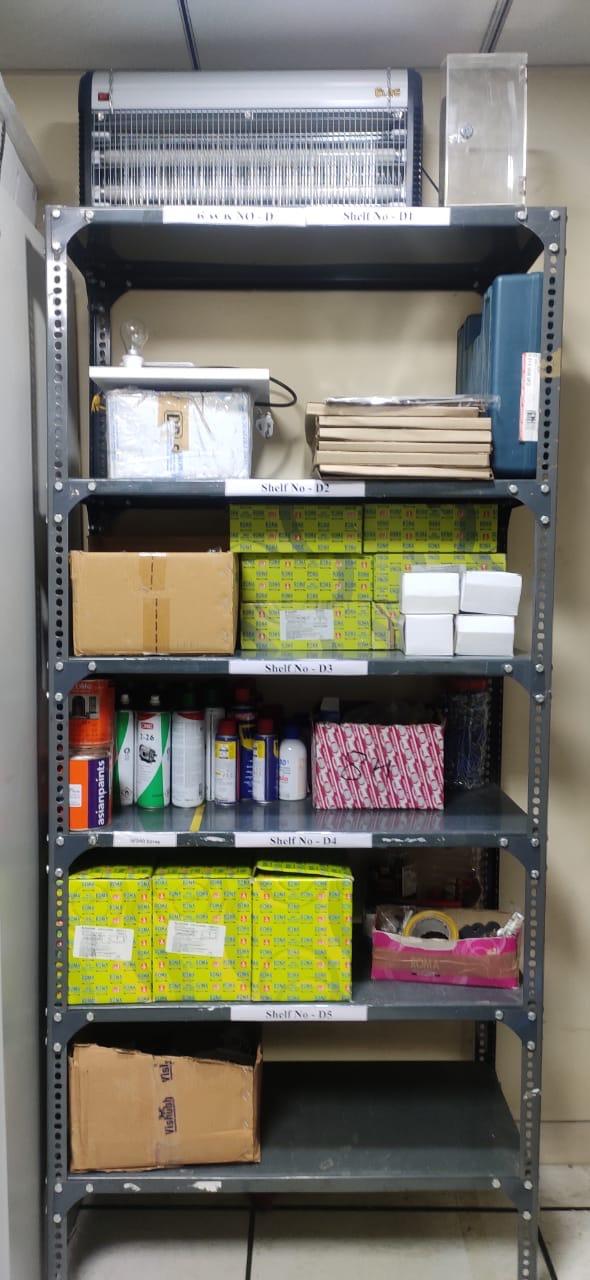
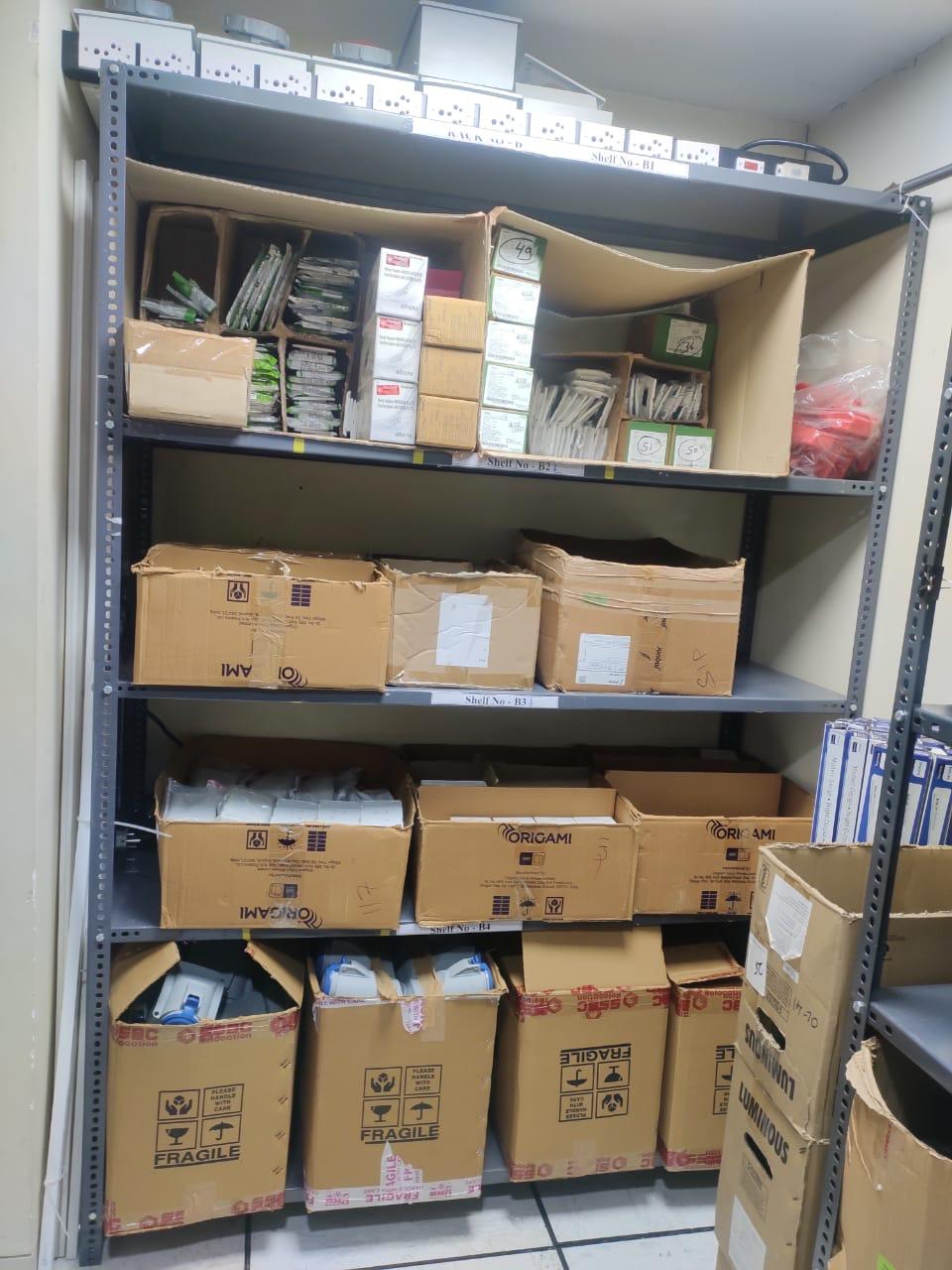
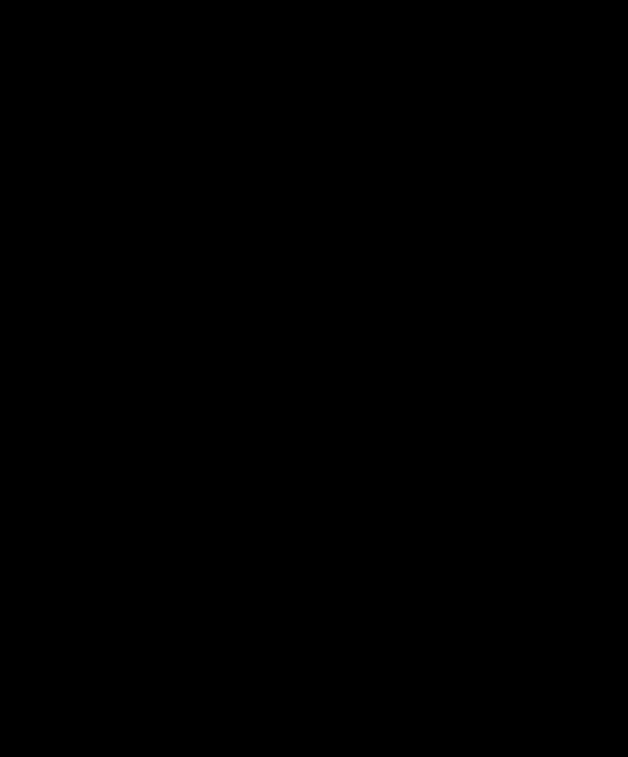



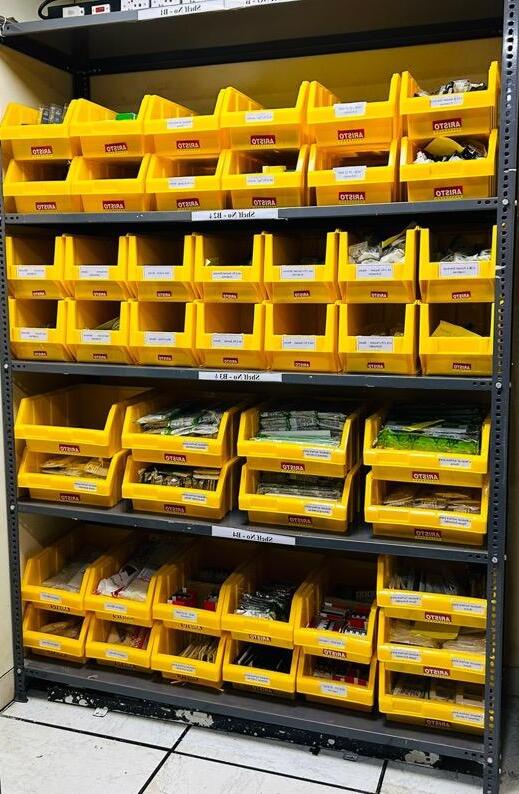
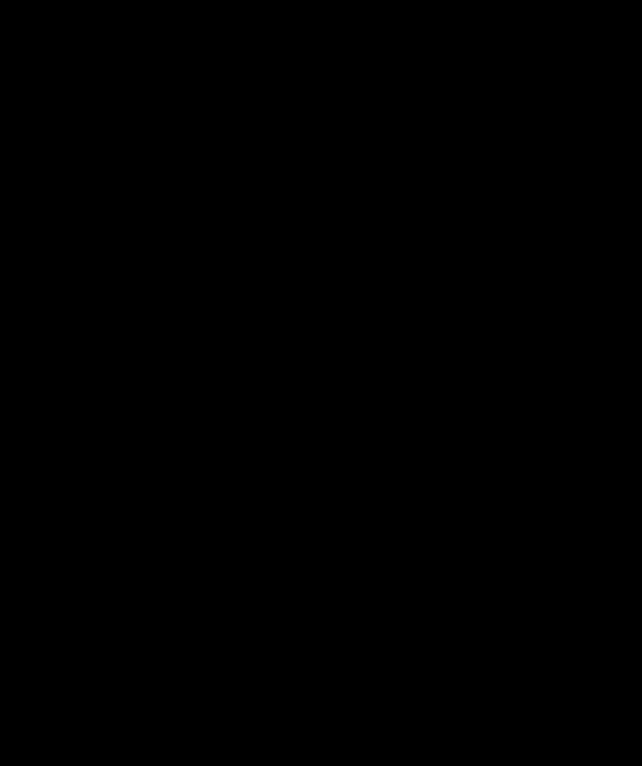
Description of the Innovation:
ESG report on EnergyEnvironmental
CHALLENGE
• Dell has a vision to achieve net zero in sustainability by 2030 and to support our clients in meeting this goal we needed to know where we stand today.
• We used to copy the Excel data and present it through power point where we had to keep updating the slides.
• It was difficult to immediately compare the previous year’s data using PPT
• To make the report real-time we explored various tools available in the market and they were expensive
• Power BI as a mainstream dashboard uses different kinds of connector databases such as Excel, Smartsheet, MS Forms, SQL server, etc.
• We can create interactive visuals to provide an overview and compare the data. These dashboards can be shared over an HTML link
• We developed a Power BI -enabled dashboard, inhouse from the learning modules available on CBRE Talent Coach guided by our CBRE Managers.
• The dashboard that has been developed using Power BI captures energy to include bifurcation of brown, green, and self-generated power, water to include recycled, and water harvested from rain, recycled waste, and Earth Hour savings.
• Creation of the dashboard doesn’t require knowledge of any coding language
• Any MS Office user can create it with various learning modules available on CBRE Talent Coach.
• The dashboard can be presented to external auditors/ leaders/ managers and can be used to preserve data for historical records.
• User friendly
• Enhancing the user experience of the data-viewing to clients
myIdea
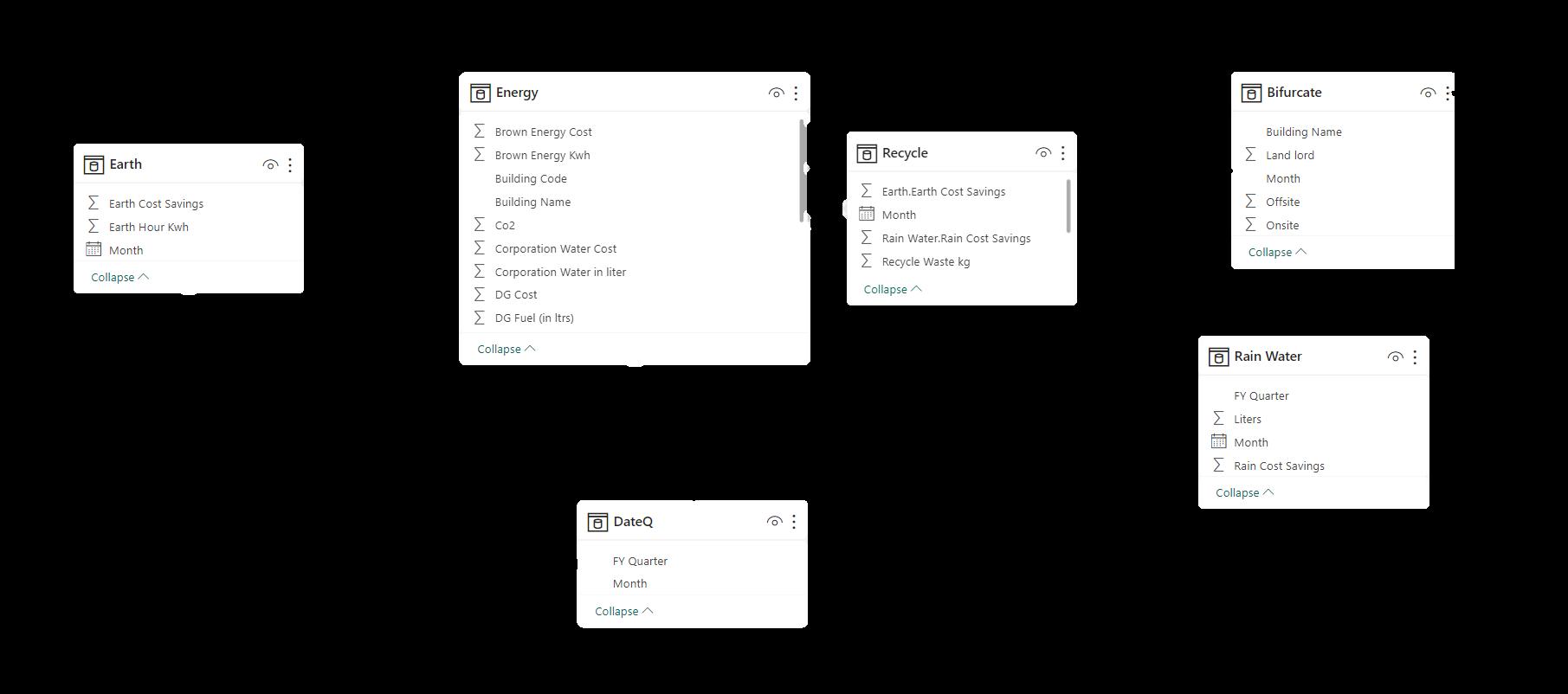
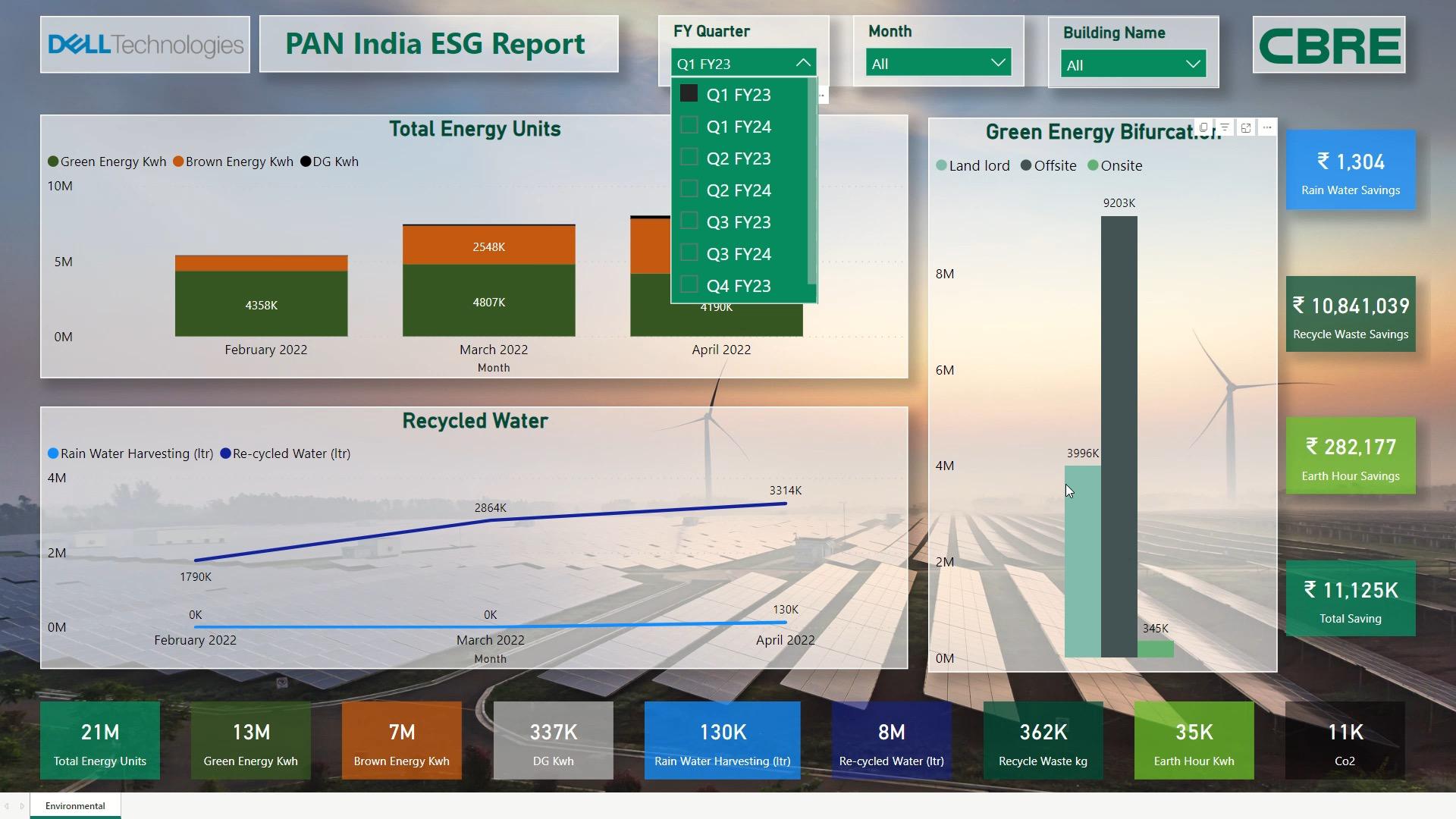
Description of the Innovation:
4G Tracer chemical dosing System for cooling tower
• Corrosion, scaling, and microbiological growth to Chiller System.
• Giving out a foul smell
• Missed or delayed logs
• Excessive Supervision - when done manually these tasks can take up a sizeable portion of highly valuable time of an employee. This system down on over –or under-dosing may occur
• The microprocessor-based control system optimizes chemical dosing & and surface blowdown: improving control and saving energy & and chemicals. In addition, the system provides remote monitoring with PC-based data management software, with data logging, analysis & and diagnostic capabilities with alarms.
• An automated chemical dosing system can adjust the chemical dosing rates in real-time, this ensures the usage of precise amounts of chemicals for the required results.
• At a high level, automated systems reduce the manual workload of managing parameters TDS, and ph.
• Accuracy maintained after implementation in TDS and PH parameters: TDS earlier –3500 -4000 PPM; TDS Current– 27003000; pH earlier – 10 ; pH current – 8 to 9
• Prevention from corrosion, scaling, and microbiological growth.
• No foul smell
• Reduces human error
• Online report monitoring & alarm alerts
• Increase the life of the chiller & and chiller line.
• Increase cooling tower performance
• Improve system longevity
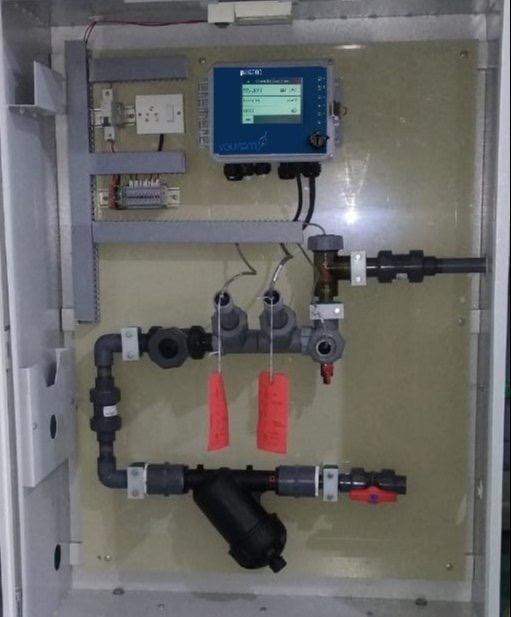
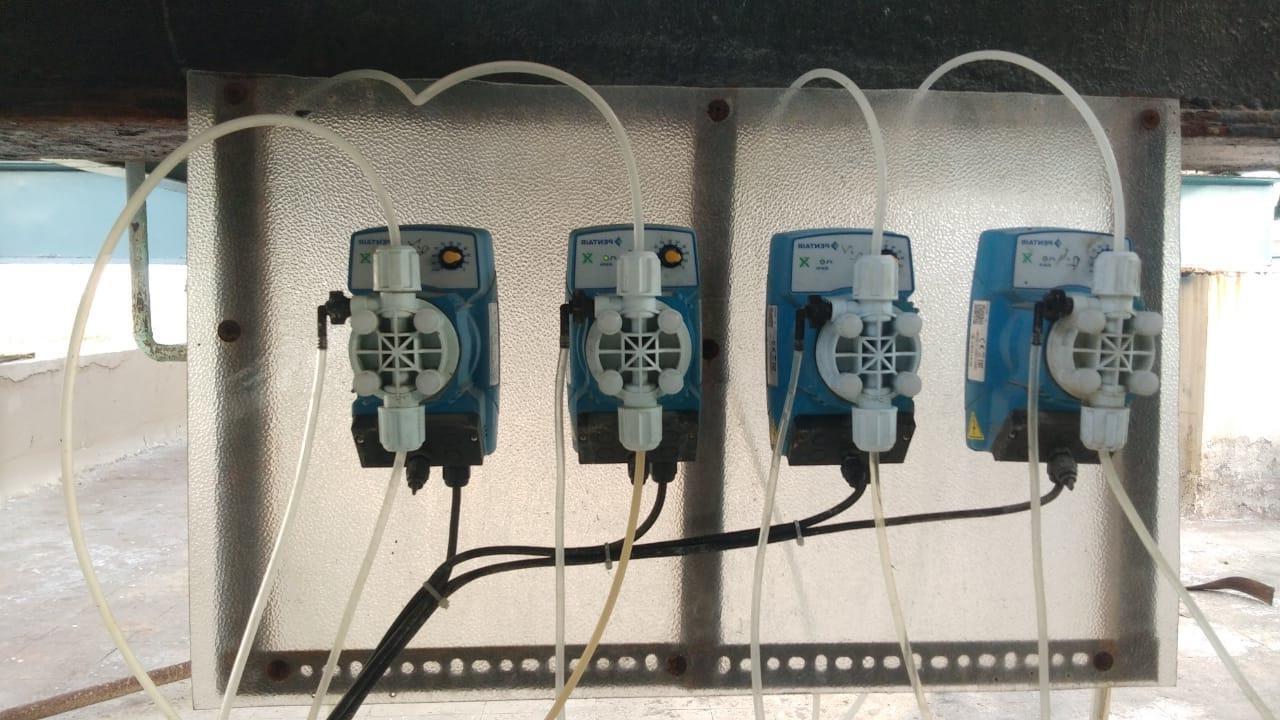
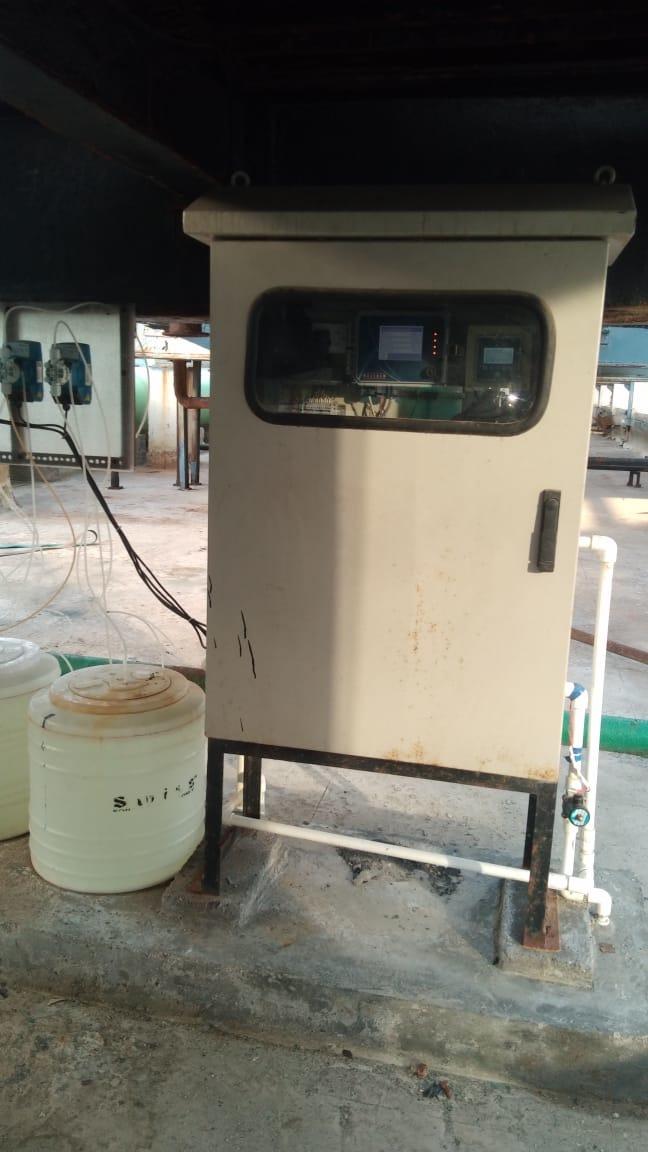
Description of the Innovation:
Video Tutorials
myIdea
• Reaching out to people in remote locations
• Keeping the learners engaged
• Lack of learning format variety
• Access is not available to everyone in the account
• Need to implement a sustainable action
• Difficulty in managing the time available for training.
• Brainstormed for adopting different strategies for fast knowledge absorption.
• We realized that microlearning is an effective approach to this as all lessons are broken down into bite-chunks for better understanding and knowledge retention
• Idea was to bring in a solution that is easily accessible to everyone
• Short reels/videos were made
• Voiceover done in the local language for people to understand
• Easy to understand and motivates the team to focus
• Effective training solution, what we see Is what we retain
• Sustainable solution: Eliminates the need to have paper files of SOPs
• A series of training videos that can be made available to ground staff at various sites, especially remote sites where Vendor / CBRE have limited reach.
• Mobile learning is on the rise as a lot of learners are on the go, and they prefer mobility when it comes to learning
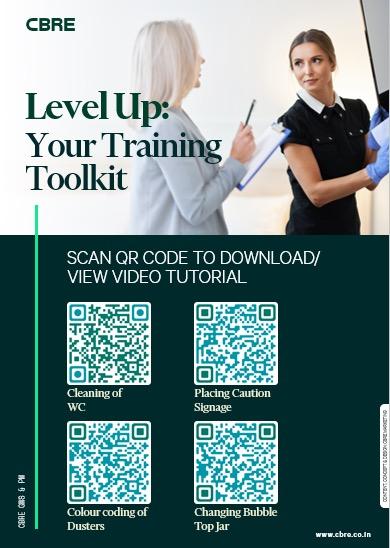

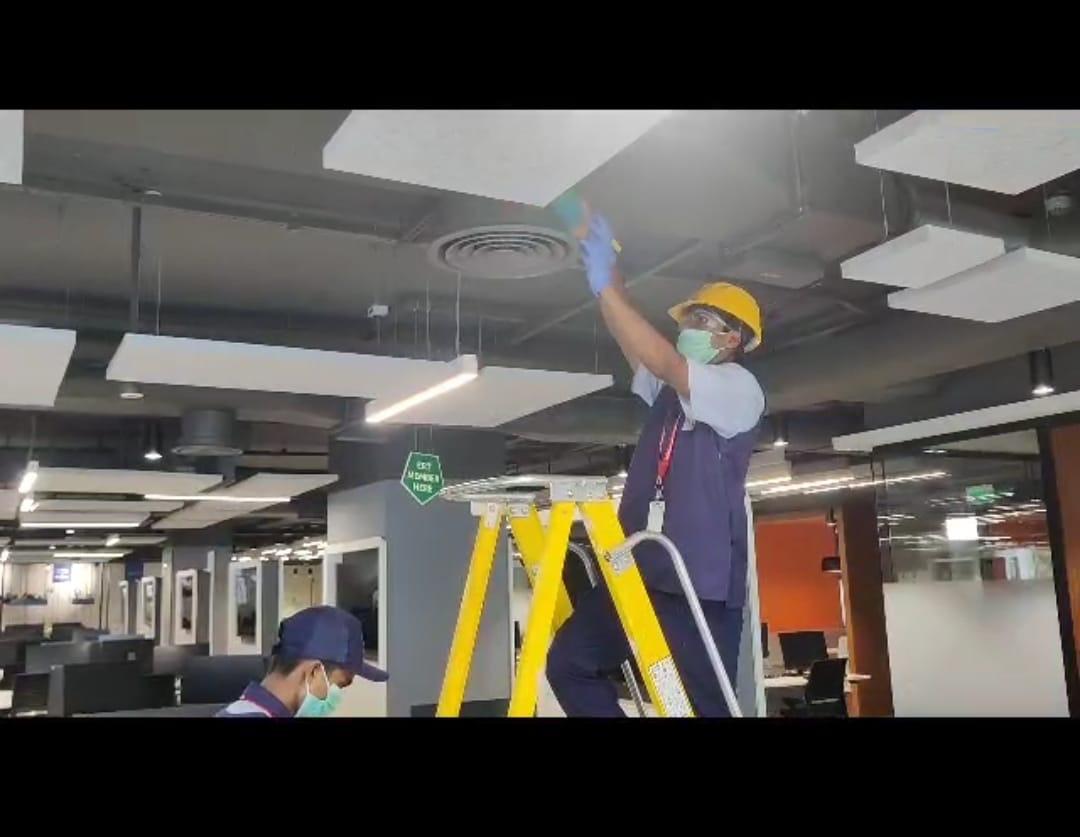
• Breakdown due to multiple leakages.
Description of the Innovation:
Anti-corrosive coating on condenser coils of VRV machines
• Increased maintenance and refrigerant cost
•
• Increased end-user complaints and Increased downtime of critical area machines.
• Implemented anti-corrosive coatings on condenser coils to prolong unit lifespan by shielding against corrosion.
• Prevent the settling down of corrosive substances over tubes and fins.
• Ideal generation & and market research/study on kind of coatings, and application of epoxy/paint.
• Protection against exposure to harsh environmental conditions, as well as against erosion and rusting caused by moisture or chemicals
• It makes the coil & fins cleaning process easy and reduces galvanic corrosion.
• Enhancing Durability: Anti-Corrosive Coatings for VRV (AC) Units
• Ensures sustained efficiency and optimal performance.
• Leakages in AC outdoor coils reduced.
• OPEX cost control
myIdea
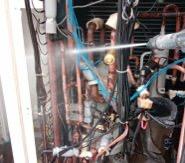
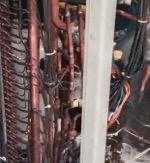
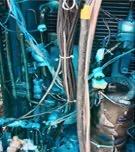
Description of the Innovation:
• Asset breakdowns being manually tracked in excel
• Difficulty in reviewing status of breakdowns
• Trend of Breakdowns and corrective actions records retrieval issue
• Increased manhours in maintaining manual records
• Equipment history not retrievable easily
• No visibility to leadership team on breakdowns
• Approached external vendor team to develop a digitized tool
• New module developed and implemented
• Module captures all details campus, Equipment details, locations, Nature of Breakdown, Expected date of closure, to capture breakdown of Equipment/systems, etc.
• Tools has been enabled with mandatory attachment of service reports and corrective action report while closing any breakdowns
• Automated mail alerts as and when new breakdowns raised or closed in Helix enabled for respective leaders
• Significant Increase in reporting of the incidents after implementing Helix Breakdown module.
• Equipment's Wise breakdown are being analysed
• Based on trends & history discussion with OEM initiated for RCA on issues & reducing the breakdowns.
• Effective governance by reviewing everyday with client , FM team brought out immediate decisions for taking corrective actions .
• History in digitized form is available
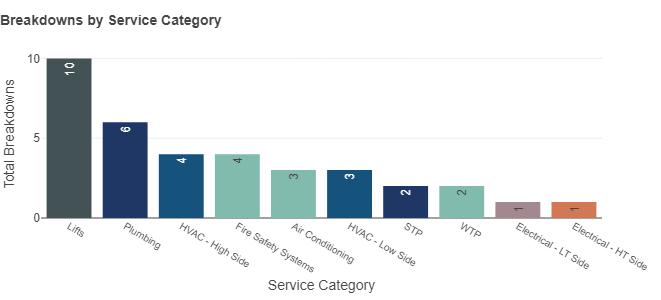
Breakdown Incidents
Description of the Innovation:
Optimum Utilization of Equipment (BMS)
• The existing BMS of Building-3 is 15 years old and is obsolete in the market.
• No OEM Support for Service and Spares replacement.
• Built on propriety protocol (Non-IP based) with multiple on-field controllers not communicating back.
• Unable to Control and monitor the precise HVAC requirements of Critical Areas.
• Replacement with entirely new BMS incl. controllers is CAPEX heavy considering Building-3 Renovation due in FY25.
• Migrating the Non-IP-based BMS to IP Based BMS.
• Re-use of existing controllers from Building-1 (Under refurbishment).
• Preventing potential scrapping and buying new equipment.
• Ensuring the Critical Area/Equipment Operations are maintained as part of Operational Continuity.
• Sauter Race (Non-IP Based) BMS to Siemens Design CC (IP Based) BMS.
• Efficient and Viable Solution considering the Building refurbishment in a couple of years.
• OPEX friendly project.
• A Cost-Saving achievement of approx. INR 4,68,00,000 compared to a full refurbishment of BMS.
• Supports sustainability efforts by extending the life of existing systems and reducing waste.
myIdea
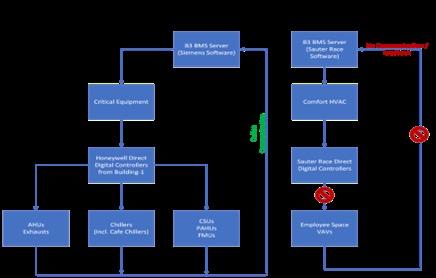
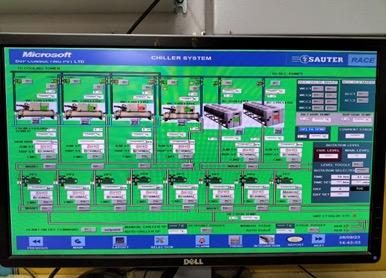
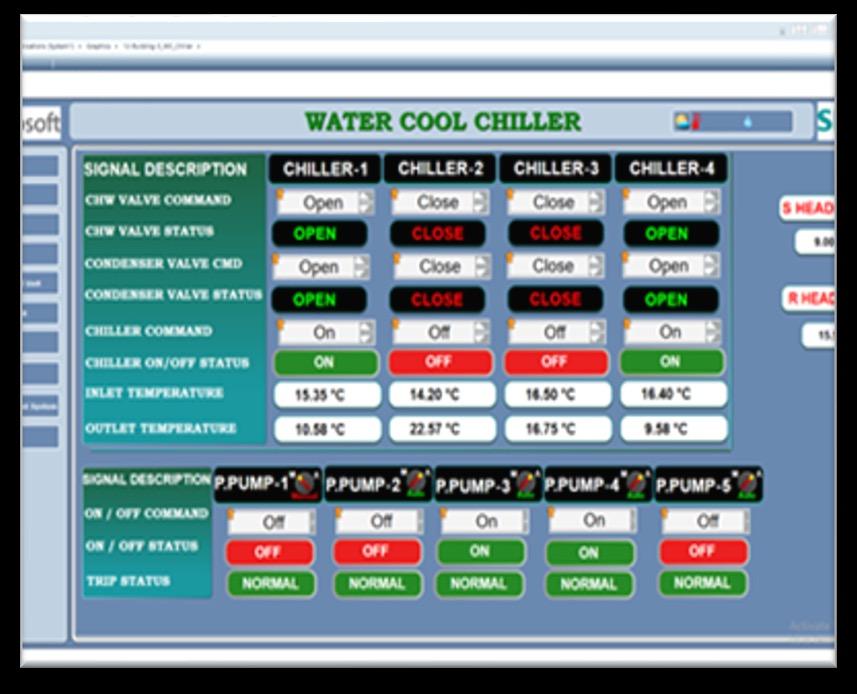
Description of the Innovation:
Robotic Cleaning of Solar Panels
• Solar-panels lose 6-7 % of efficiency due to dust accumulation
• Increased air pollution levels are also responsible for increased dust accumulation.
• This require frequent cleaning of solar panels using water and manual labour both resources are limited and costly.
• Water usage on terrace increase the chance of seepage.
• HK Team is at higher risk due to exposure to High voltage DC in wet conditions.
• Automation has led to resource optimization and better efficiency
• We were deploying 4 members from HK team, daily to clean the Solar Panels with water.
• We have introduced Semi automated robotic solar panels cleaning system, which cleans without water.
• This robot will be operated & monitored remotely using mobile application.
• As the Robot is battery powered, there is no need of external power supply and wires.
• A fully charged battery, is sufficient to clean our installation (125 Running Meters) twice.
• Saving of 280KL (INR 46,000/-) of water in each year.
• Reduced 720 man-days (INR 4,40,000/-) per each quarter.
• Effective and consistent cleaning
• Reducing carbon footprint.
• Reduced EHS risk and safer working condition.
• ROI is 5 months.
myIdea


Description of the Innovation:
Automated Room Cleaning Request System for HK Team
• Back-to-back occupation of meeting rooms necessitate that rooms are promptly re-arrange and cleaned at all the times.
• Cleaning staff needed to be alert to monitor the vacation of the rooms at all the times.
• This was a challenge to the cleaning team as their schedules can’t be aligned to the occupancy schedules.
• This leads to the employee dissatisfaction and complaints on the layout and readiness of the room for next occupant.
•
• An automated solution was required which can inform the cleaning team, whenever a team leaves the meeting room.
• Evaluated 2 different solutions. One using existing motion sensors of HVAC-VAV system and other using separate motion sensor (PID sensor) with minimal electrical components.
• This system lights-up an indication lamp visible to the HK staff externally, signaling necessary action.
• Upon clearing of the room HK staff will re-arm the Indication system, for next use.
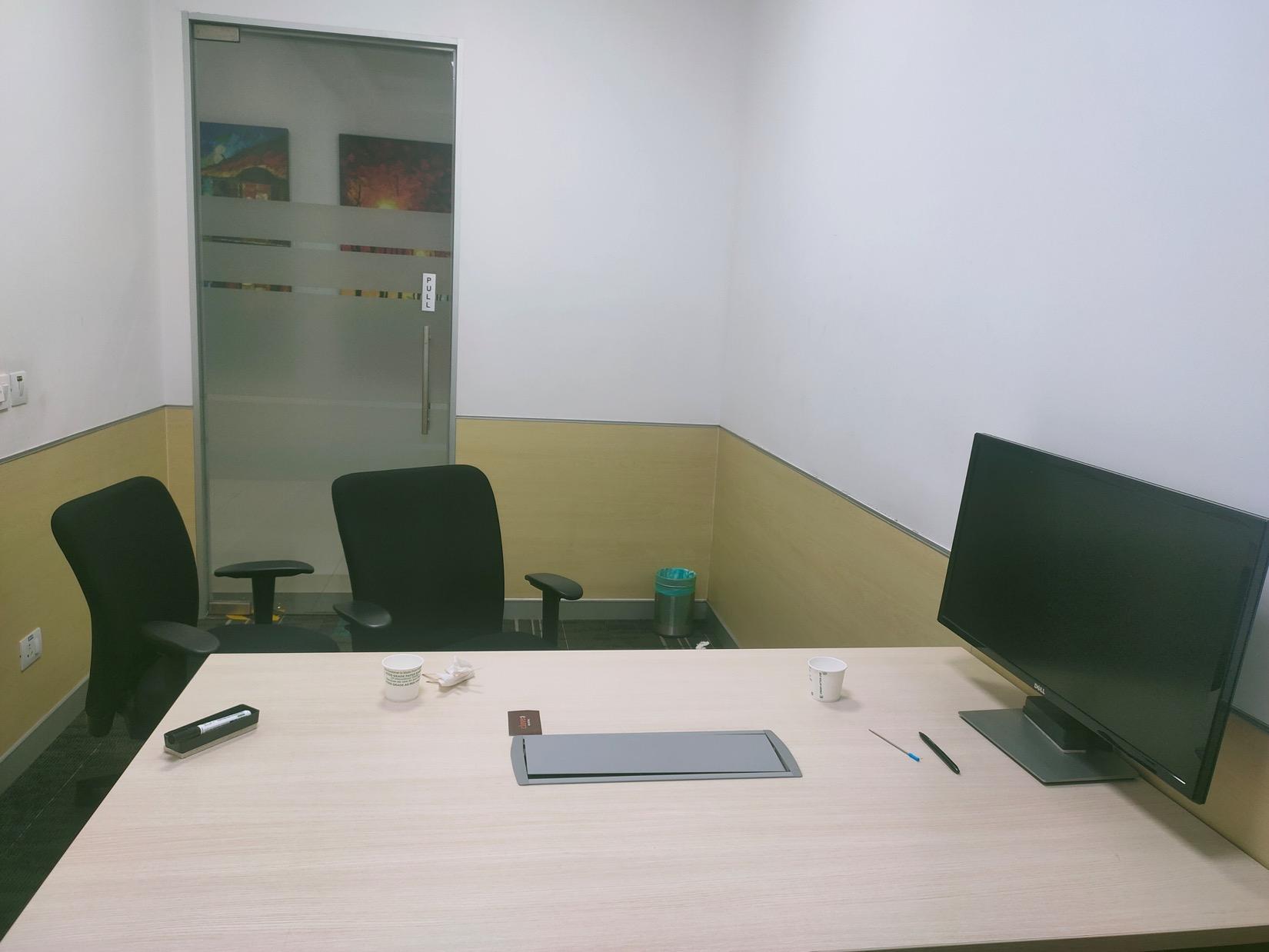
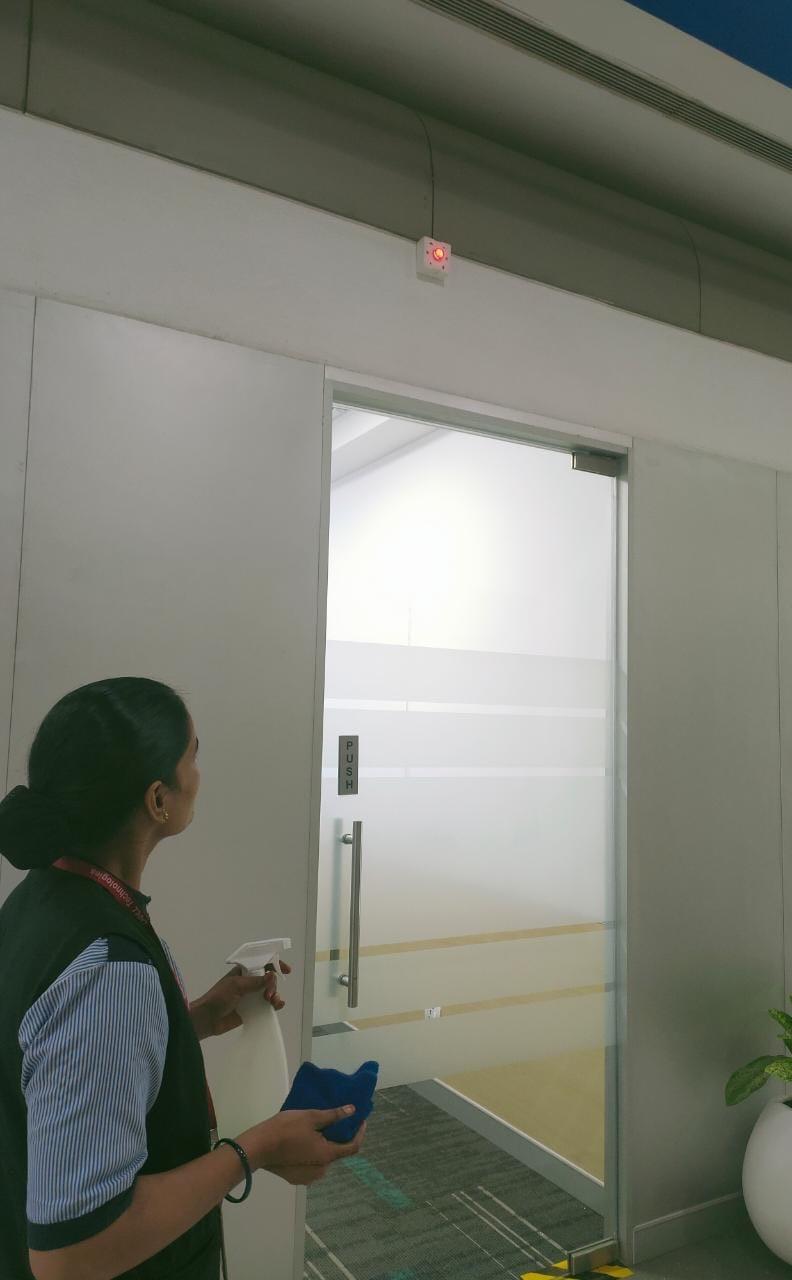
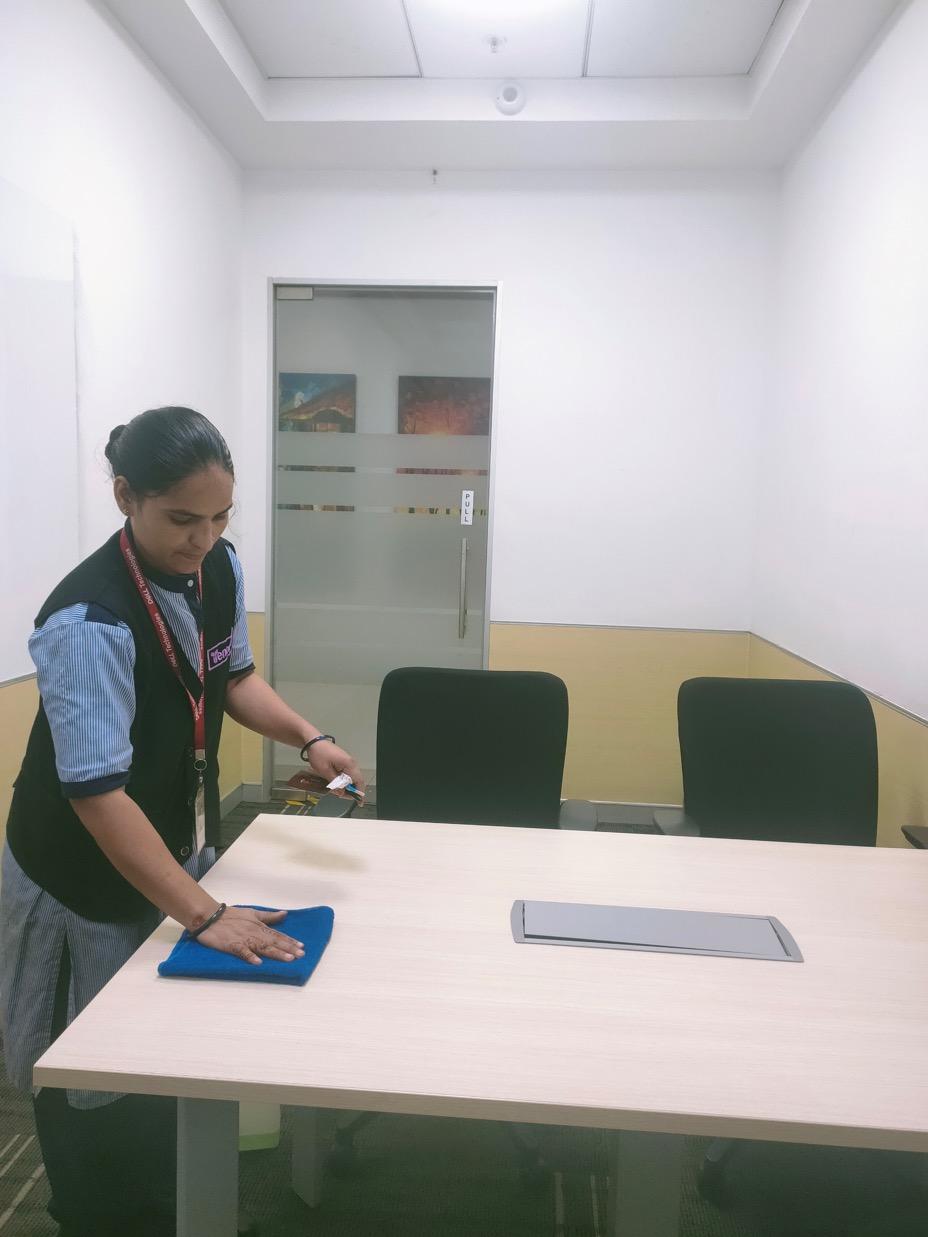
• Improved overall experience of employees
• Increased productivity of HK team as they provide ondemand services, rather than periodic visits.
• Lesser complaints
• Site walk around by HK team takes lesser time and enables them to focus on other tasks.
Description of the Innovation:
Transformation of Garden waste area into Organic vegetable garden
myIdea
• The garden waste area was aesthetically not looking good and was an eyesore for the occupants of Tower 1.
• We need more space to grow more vegetables to help our NGO partners.
• Waste area was becoming a breeding place for mosquitoes and pests.
• Brainstorming done to identify a space as a garden waste area and how to transform the area into an organic vegetable garden.
• The In-house horticulture team cleaned the entire area & and used the seeds of leftover raw vegetables from the cafeteria kitchen, dried them up & ripped them in the in-house nursery & and converted them into saplings. The rest of the portion of the vegetables have been converted into Vermi composed.
• Saplings were planted in the newly developed garden area. A variety of vegetables and herbs like Brinjal / Pumpkin/ladies’ finger / bitter gourd/ snake gourd/ carrot / Spinach & and lots more have been grown.
• No additional cost incurred to develop the space and to grow the vegetables. Moreover, We have saved around Rs. 1 lakh in this process.
• Approx 125 to 130kg of vegetables & herbs harvested every month .
• The vegetables harvested every month is getting distributed to the NGO’s and also distributed among the ground Staffs to motivate them
• The area has become one of the main attraction for the leadership & external client visit as a part of employee experience.
• In other word we are growing vegetables from wastes and giving back to society.
• Added to sustainability drive of Zero Waste moving outside campus by churning the Garden waste into Vermin composted manure utilised in garden as manure.

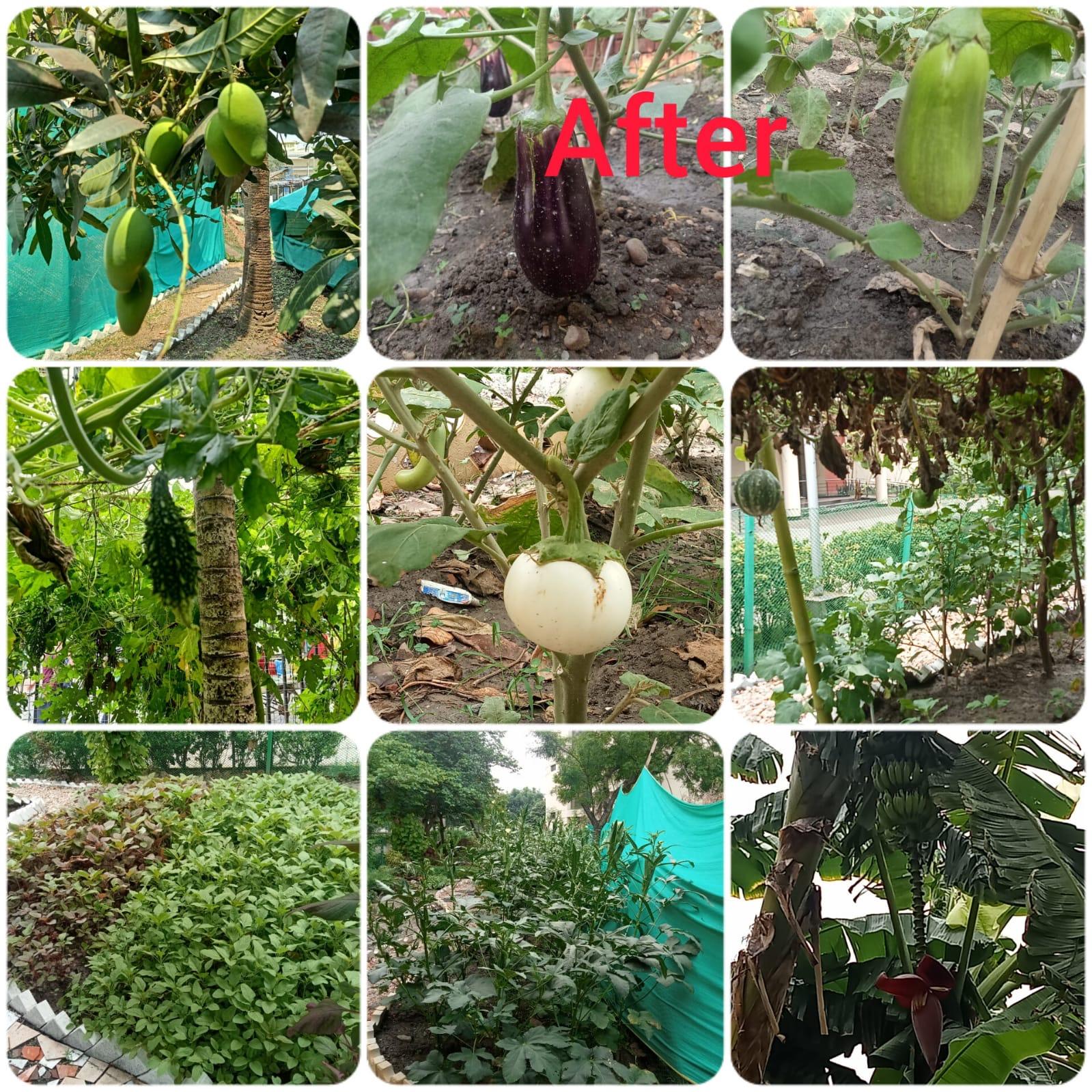
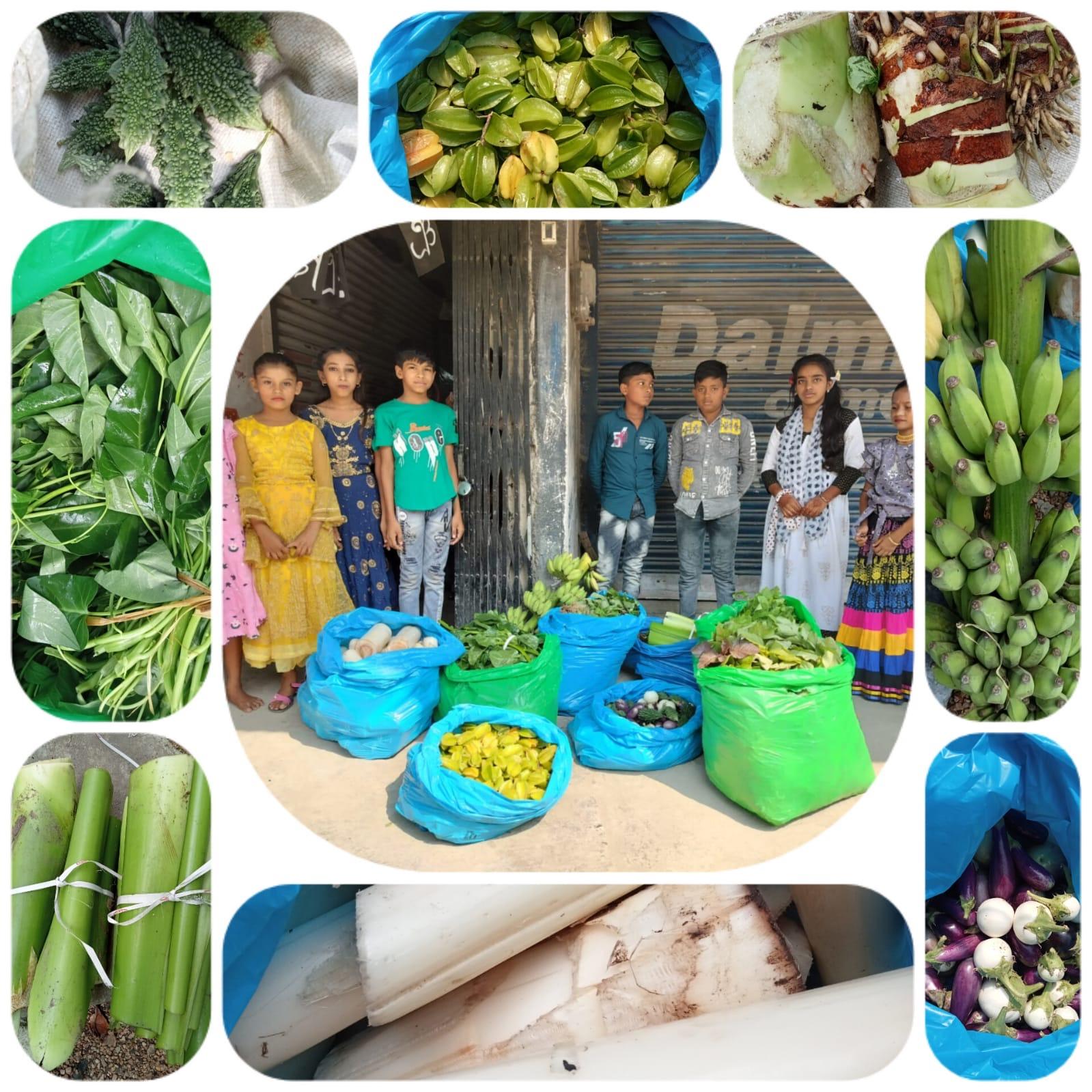
Description of the Innovation: CHALLENGE
Air Purifier with A Fragrance Diffuser
• Insufficient fresh air inside the meeting room.
• Employee well-being hampered.
• Stress levels increased among employees.
• Requirement of constant Air quality monitoring as per IBM Standard (ANSI/ASHRAE Standard 62.1-2022)
• Developing an idea with an Air purifier with a fragrance diffuser.
• Innovative Use of obsolete Materials.
• The In-house team's dedication and ingenuity brought the concept to life with obsolete materials.
• Simple yet effective design with HEPA filter technology.
• Improved Air Quality creating a healthier workspace.
• Enhanced employee experience.
• Design is Compact & Noise-Free.
• Fragrance diffuser enhances air quality with a pleasant scent air.
• HEPA filter technology removes 99.97% of airborne particles.
• Boosts work efficiency & creates a conducive environment for productivity.
• Promotes a healthier & sustainable workspace.
• Client Satisfaction achieved.
myIdea
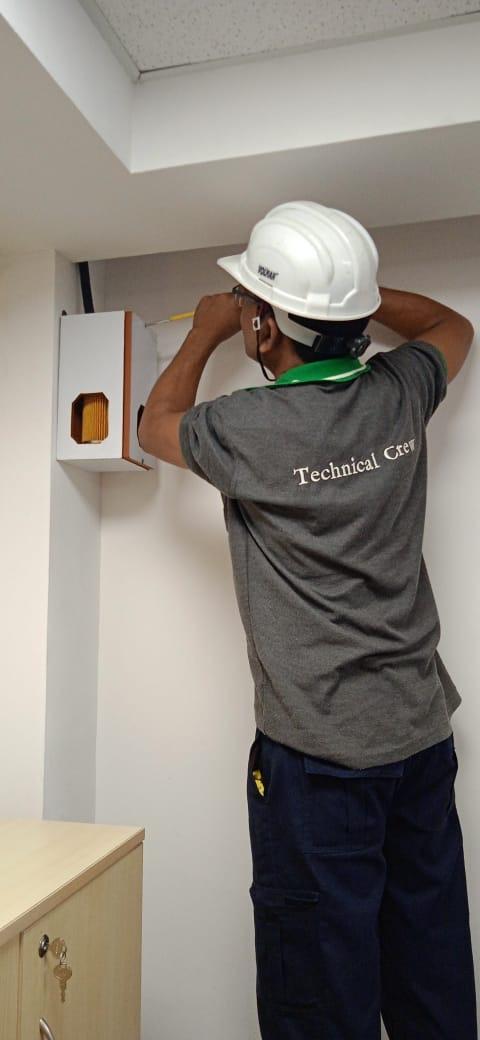

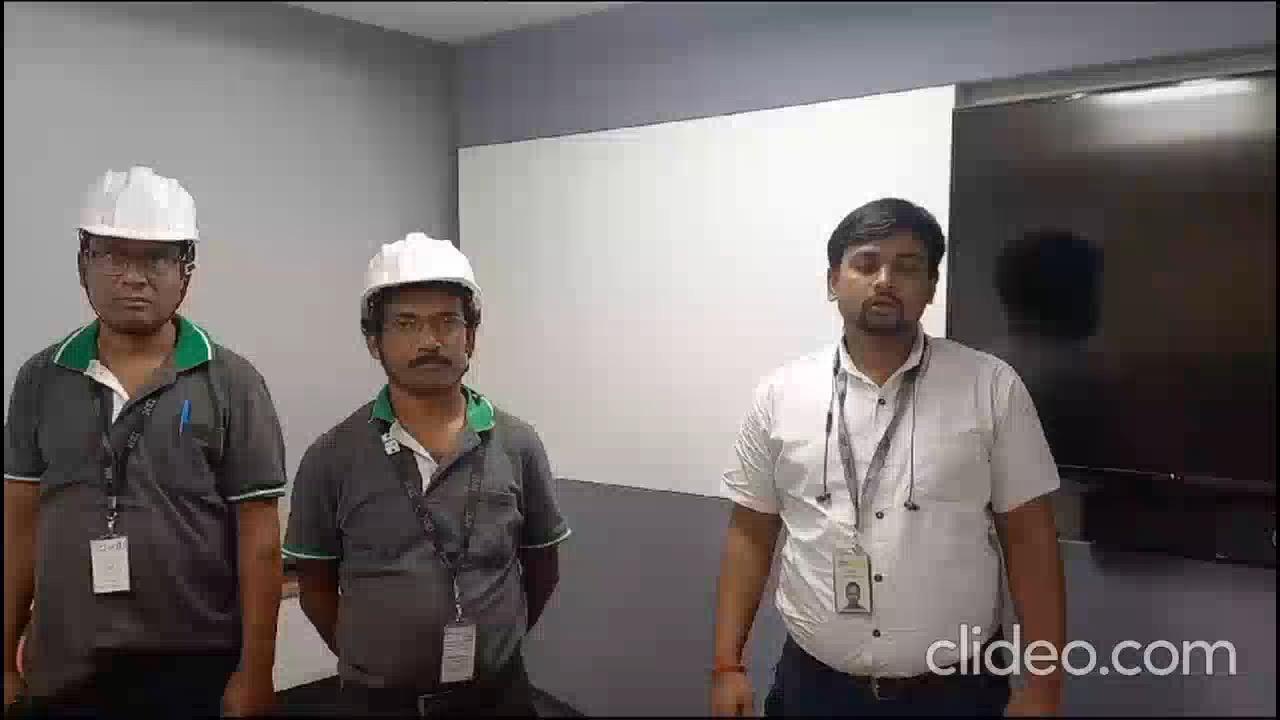
Description of the Innovation:
Special Equipment for Emergency Preparedness
• Lack of equipment for emergency
• When responding to an emergency such as a flood, fire or other, we were experiencing delay in response .
• Lack of agility in our response posed a huge EHS risk
• Life-saving equipment plays a critical role in emergency situations to protect lives and property.
• We decided to have all the essential equipment in place to be prepared for any emergency.
• Some of such equipment which we have includes: UHPS, High expansion Foam Generator, PPV, TIC, Glass center punch, Circular saw, Combi tool, Ventilation fans and
• During emergencies, it is essential to equip and utilize various strategies and resources to mitigate the fire or any such issues and respond effectively.
• Immediate response measures can be taken
• Significant advantage in safeguarding lives and property during emergencies.
myIdea
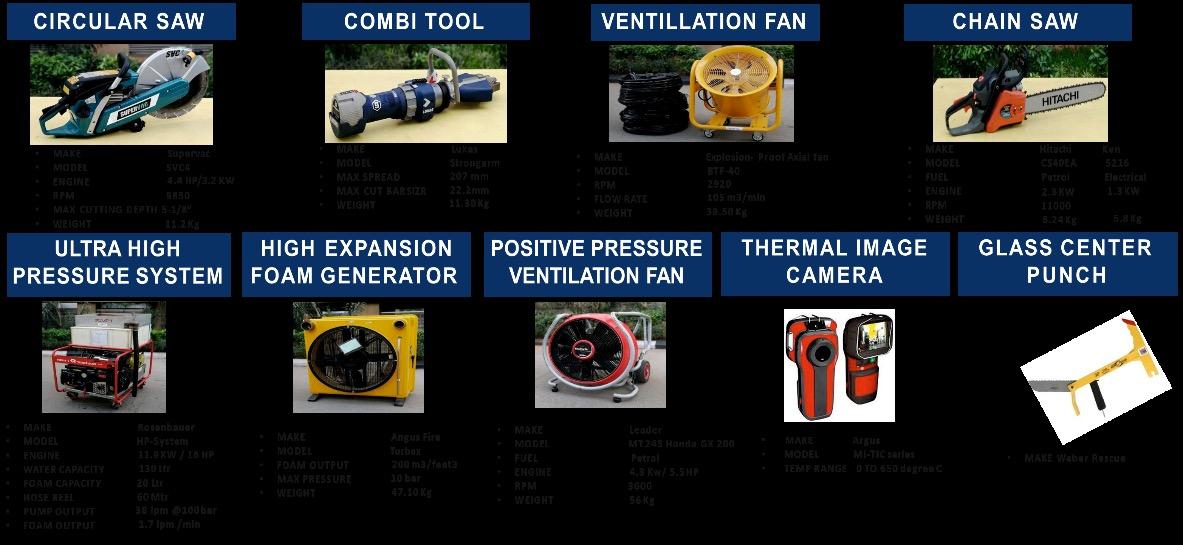
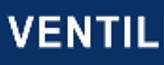
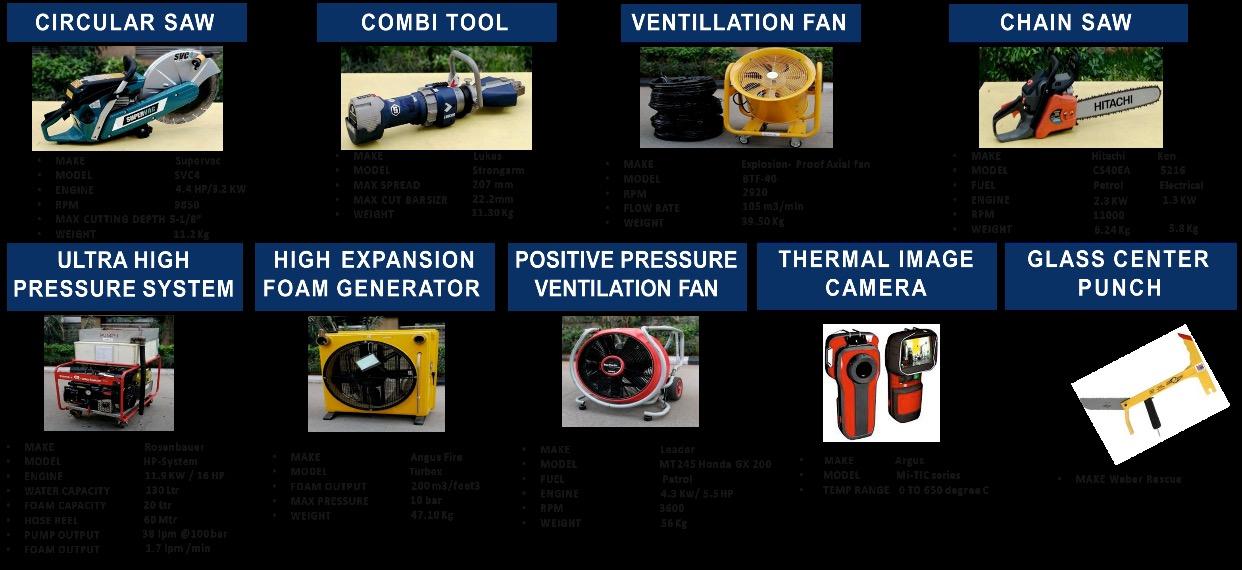
Description of the Innovation:
Employee Training Gallery
• Language barrier in understanding the operation.
• Manhours consumed a lot during training.
• Difficulty in understanding of concepts.
• At times, few of the employees may feel - It’s boring, just sitting and listening to concepts.
• The level of learning is not very deep, subsequently nor is the level of understanding.
• If a learner gets a good mark in the test, are not aware if they know the content. Do they actually understand the materials?
• As a part of increasing employee engagement and enhancing employee participation, visual studios were created for technical and soft services.
• In this way, any new employee joining the organization ( including sub-vendors ) is trained here.
• During their induction, they are shown these areas as a part of the site induction plan and things are explained visually.
• Scan the QR code below to view the video of the training gallery
• Increase in productivity.
• Make learning more Visually Appealing
• Makes Learning courses more relevant to the learner.
• Give learners a better understanding of complex topics.
• Makes it easier for learners to understand and then retain Information.
• Makes it easier to identify patterns, trends, and differences.
• Can be faster for learners to process than text.
• Indeed, a picture is worth a thousand words, as it can help us create meaningful, truly impactful Learning experiences!
myIdea
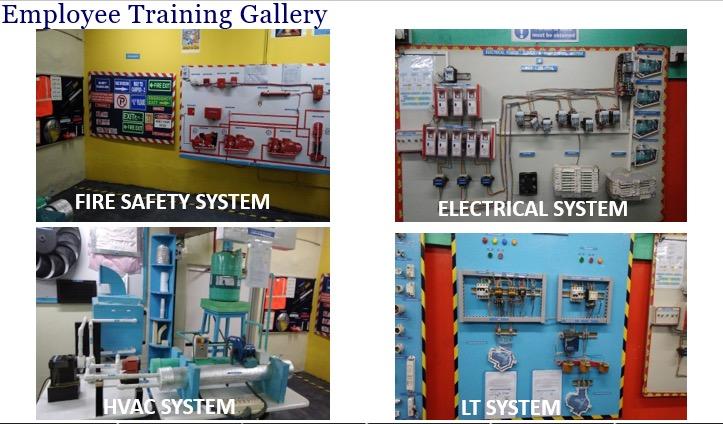
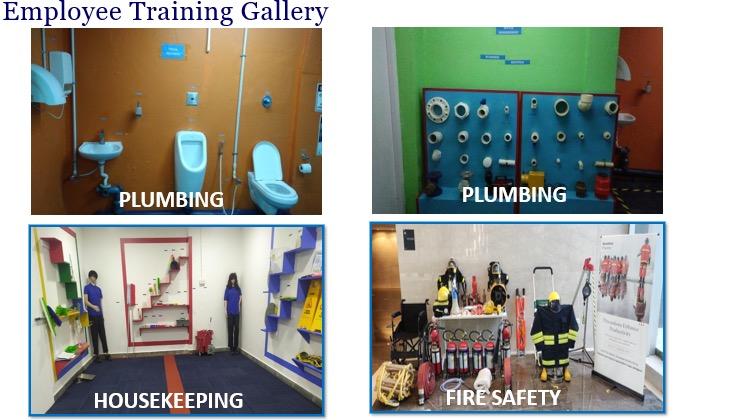
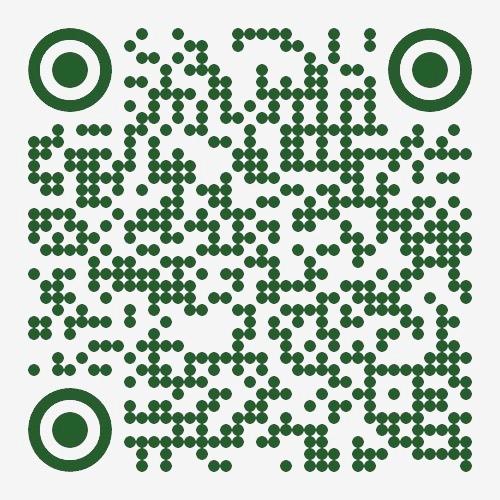

Description of the Innovation:
Employee Engagement : Music Event
• To keep the park environment vibrant & and to motivate the employees to return to office as per various Occupant’s demands.
• We hired External event management agencies fortnightly to conduct employee engagement programs.
• There are time limits and costs involved for every event
• Employees demand more time for Karaoke and other DJ programs every week.
• With an objective to increase the footfall of employees post COVID and to encourage employees to ‘Return To Office’ employee engagement music event was organized.
• The charges obtained by the outsourced team was way expensive (Approx 1lakh/Event) which in-turn restricted the number of events conducted for employee engagement (one event per Quarter).
• CBRE team meticulously planned and took it up with client to purchase Sound Mixer and 4 No of Speakers along with cables and other accessories for a cost of Approx : 3,00,000/- and started to conduct DJ musical events for employees every Thursdays.
• Music and dance event is conducted for employees every week (Thursday) by our CBRE DJs
• Interested employees can come to the stage and perform live singing with Karaoke being played by our CBRE DJs
• Encourages a lot of employees to showcase their hidden dancing and singing talents.
• Thursdays have proved to be the day with the highest footfall for each week.
• Enhanced customer experience and employee productivity .
myIdea
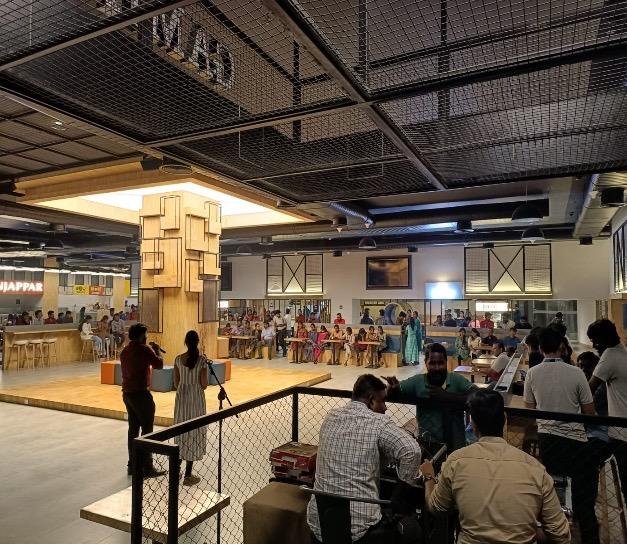

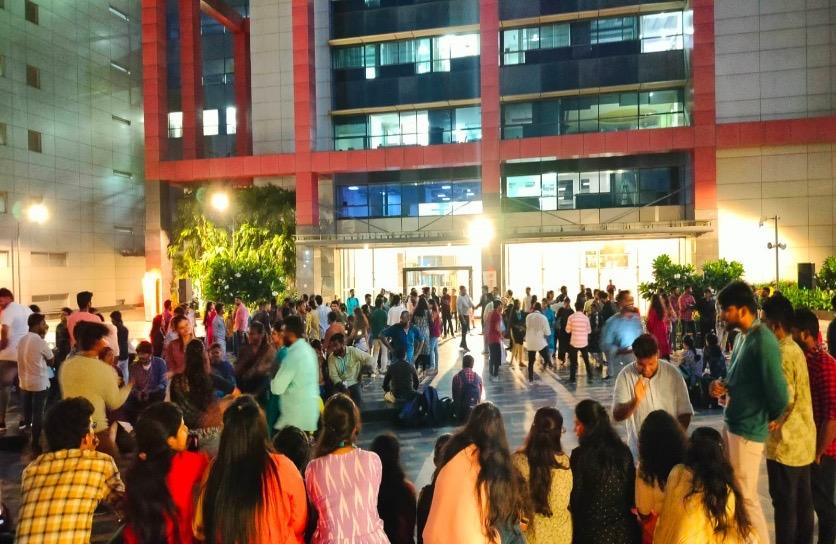
Description of the Innovation:
Lighting Automation Through Building Management
• Indoor Games are booked every day through Portal booking by the occupants
• Technician need to go and switch ON and Switch off the lights as per the schedule of booking
• Manual operation of Lighting at location level is time-consuming
• Energy loss due to manual ON/OFF control
• Increase of overall common area consumption
• Lighting automation is done through BMS system for U-block badminton court.
• This technology helps us to switch ON/OFF lighting load with a single click through BMS system
• Logic created in BMS system and hardware wiring completed for implementation
• Lights are controlled through DDC panel
• Scheduling can be done as per requirement
• Energy Savings of 10,950KWH per annum and cost saving of INR 1,09,500
• Energy Saving and Co2 reduction of 8,979Kgs of Co2 per annum
• Time saving due to remote Control of Lighting through BMS
• Time reduction from 15 minutes to <1minute
• Employee fatigue avoided due to automation
myIdea
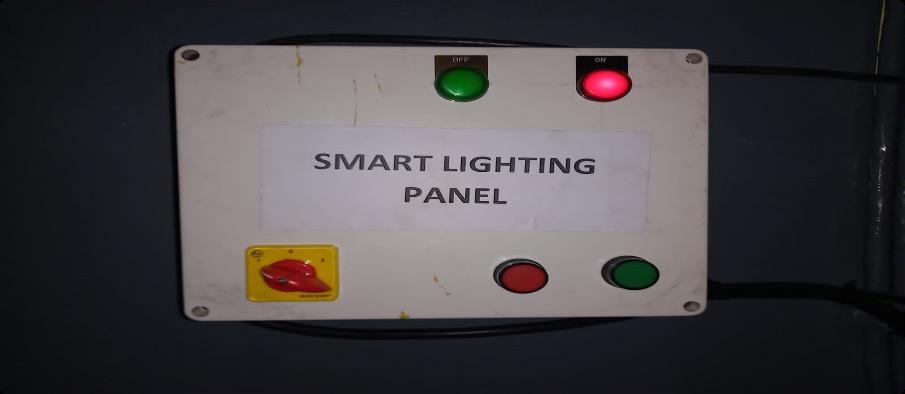

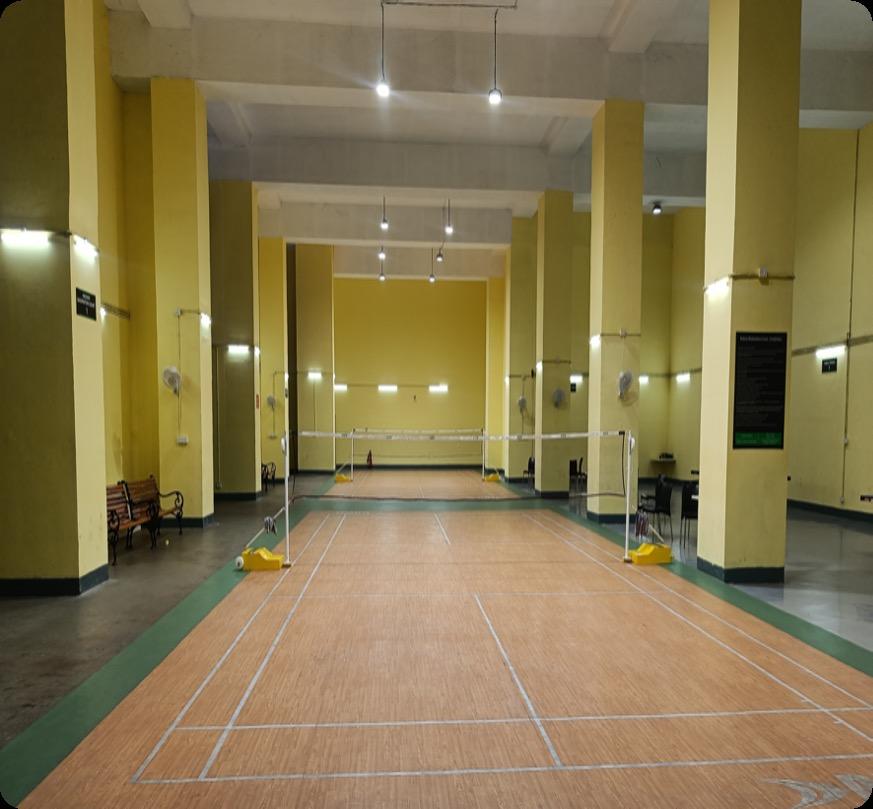
Description of the Innovation:
IoT Based
Smart Water Measurement System
• Lorry water unloading was carried out manually at the Utility block
• Measurement recorded manually at seven unloading points.
• Data analyzing and reporting takes more time due to manual entry.
• Remote monitoring is not possible and chances of manual errors.
• To replace existing mechanical meters with New mechanical meters that have a dual pulse output.
• The dual pulse mechanical meter will be connected individually to communication Nodes, which in turn will communicate the data to the IOT gateway.
• Understanding water consumption patterns is crucial for devising effective strategies to reduce overall consumption.
• Real-time Analysis of Water Consumption.
• Reduced Maintenance Costs.
• Better Communication among stakeholders.
• Predicting Potential Failures. Remote Monitoring.
• End-to-end services.
• Interactive Reports on daily , weekly and monthly
myIdea
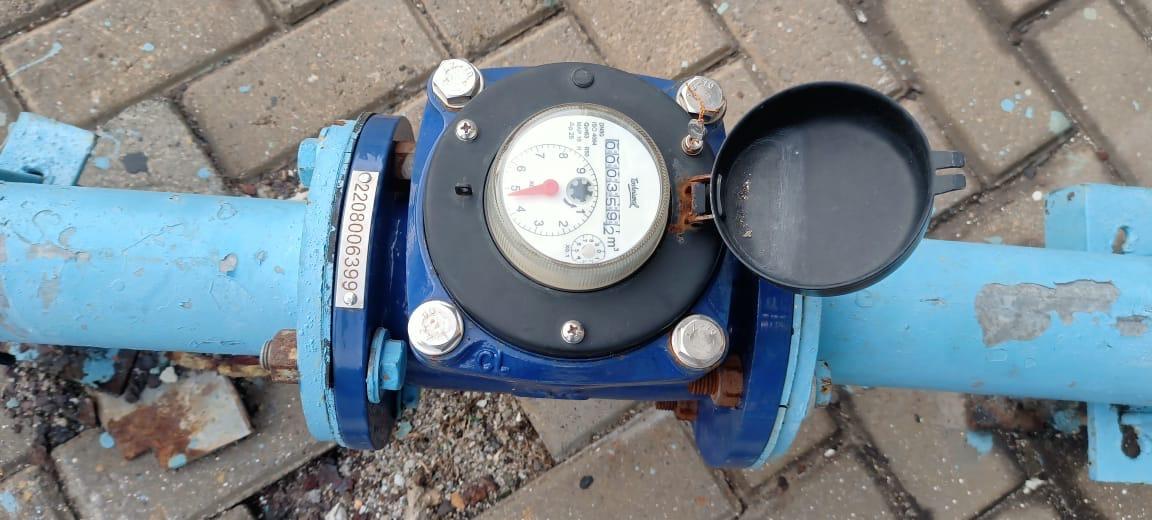
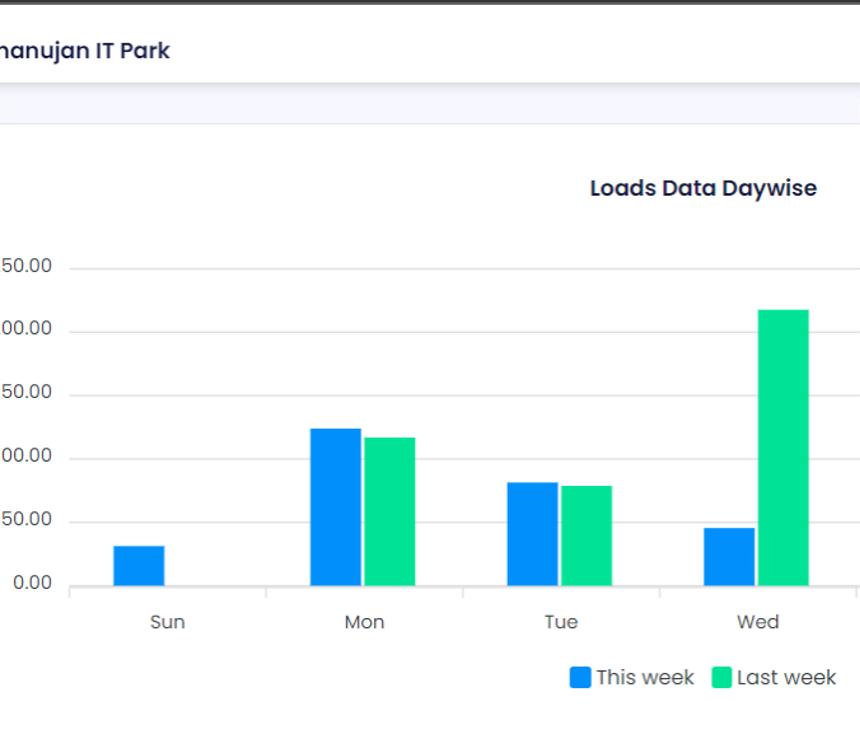

Description of the Innovation: CHALLENGE
Providing UPS Power as auxiliary supply for Energy Meters
myIdea
• The energy meter display was not working during the EB power supply interruption.
• Difficult to get the readings for HVAC billing purposes, while DG is in operation.
• There is a slight variation in the HVAC bill amount compared with the actual.
• HVAC bill preparation will need more calculations if there is any interruption in the main power source.
• The time required to prepare the HVAC bill is more.
• No separate energy meter for chillers, apart from the one in the Main LT panel room.
• Main LT panel has EB supply as primary and DG backup supply as a secondary source, feeding to different locations and equipment. There was no option for the measurement of DG energy utilized while DG is running because the energy meter auxiliary supply is taken from EB and when it fails display will not work.
• These readings would help us to differentiate the load demands during an event of Mains power shutdown and DG back up in operation, as well as the energy consumption.
Since HVAC billing depends on the energy consumption of chillers and pump panels, we couldn’t calculate the energy consumption while DG is operating.
• We have identified that the auxiliary supply of the measuring energy meters (MFM) is fed with only the Mains control supply. Since the meters could measure dual source readings, we removed the control auxiliary supply from the Mains power and connected it with the UPS supply which was utilized for control of AMF and Synch panels.
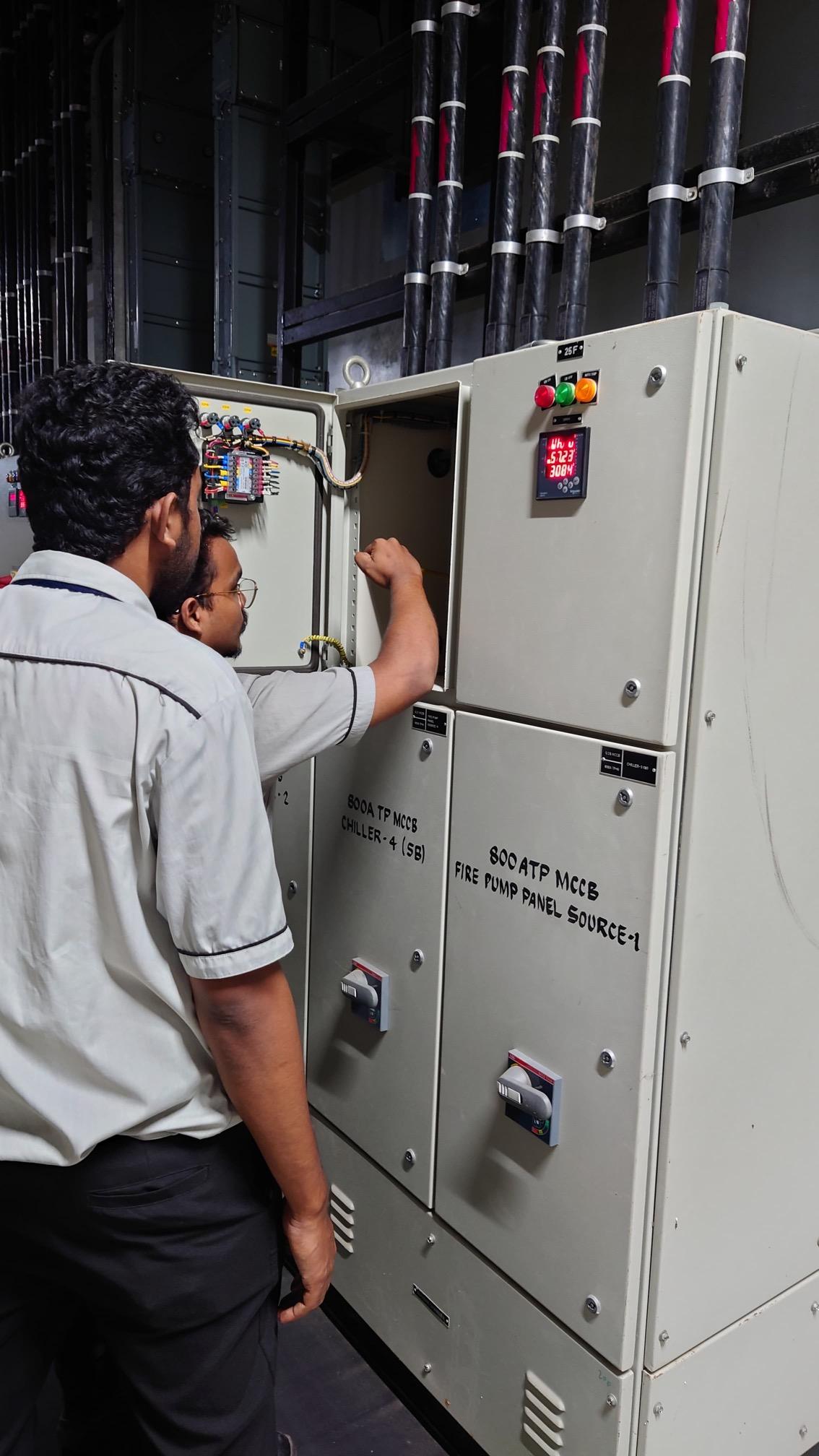
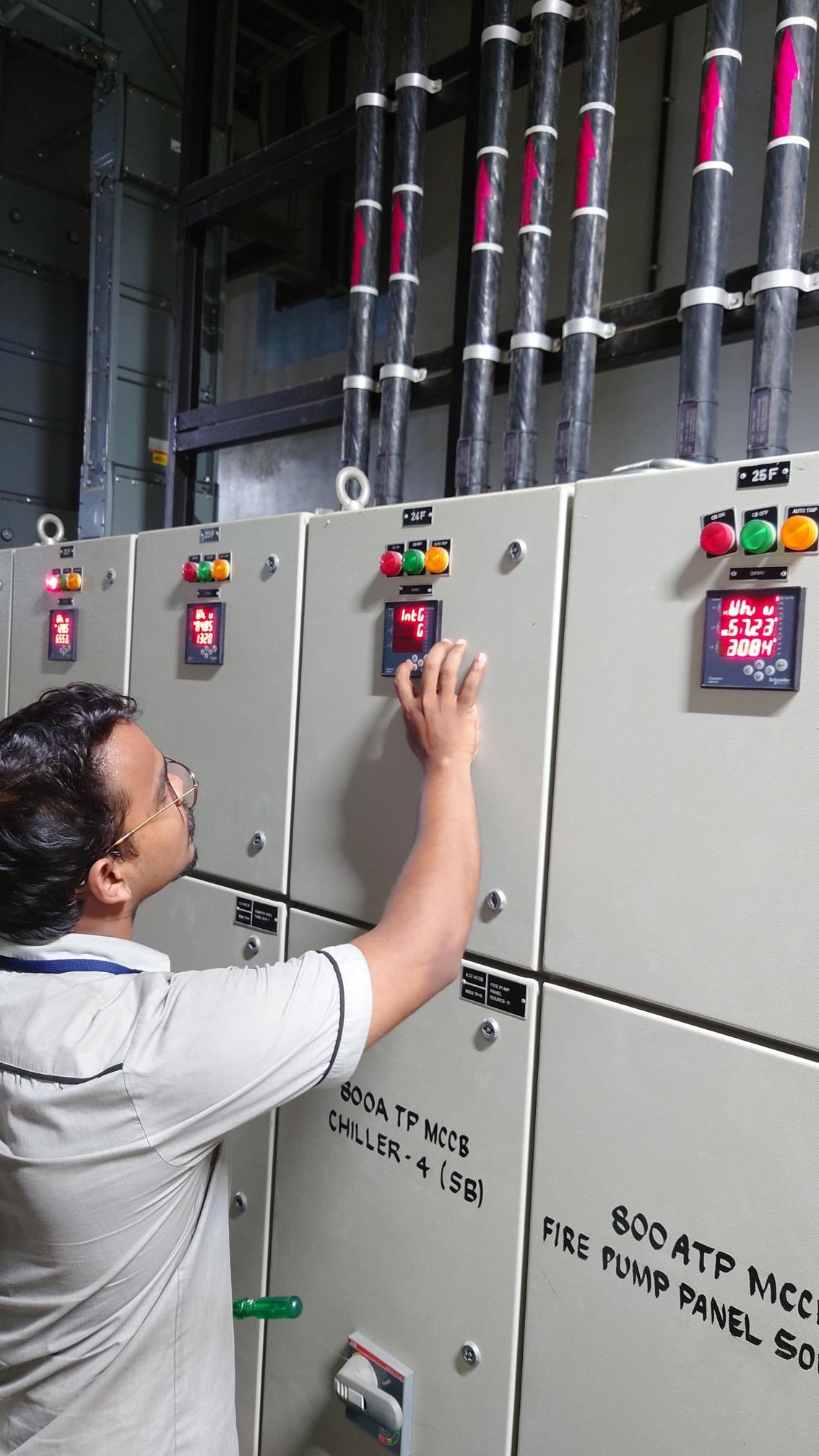
• Zero cost innovation.
• In-house team did the work, with no vendor involvement.
• Accurate measurement of energy consumption of chillers and pump panels.
• Accurate HVAC billing.
• No average data is required to prepare the HVAC bill.
• There is no complexity while preparing the HVAC bill.
• The time required to prepare an HVAC bill is less when compared with the previous method.
• No money loss due to lack of energy meter reading.

Description of the Innovation:
E
ChecklistCreated & Implemented by In-house team
CHALLENGE
myIdea
• Paper being used for the checklist for our daily operational usage
• Occupies more space to store the recorded files
• Difficult to pull out the old data if required.
• Increases the carbon footprint
• To Reduce Paper usage, we have implemented a digital hourly checklist for the HK team.
• Called multiple vendors to execute the E checklist available in the market with various details
• After brainstorming decided to go for an E Checklist by the in-house team.
• The same was created through Microsoft Forms without involving the vendor partner and there was no cost involvement.
•
•
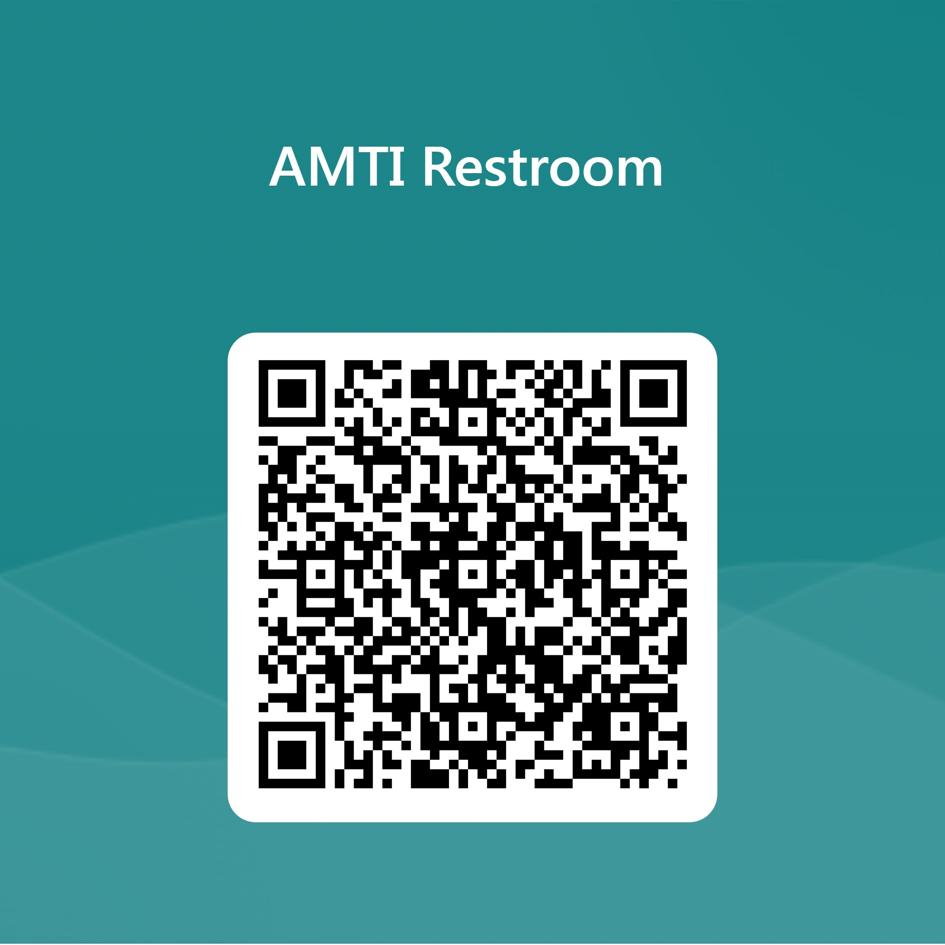
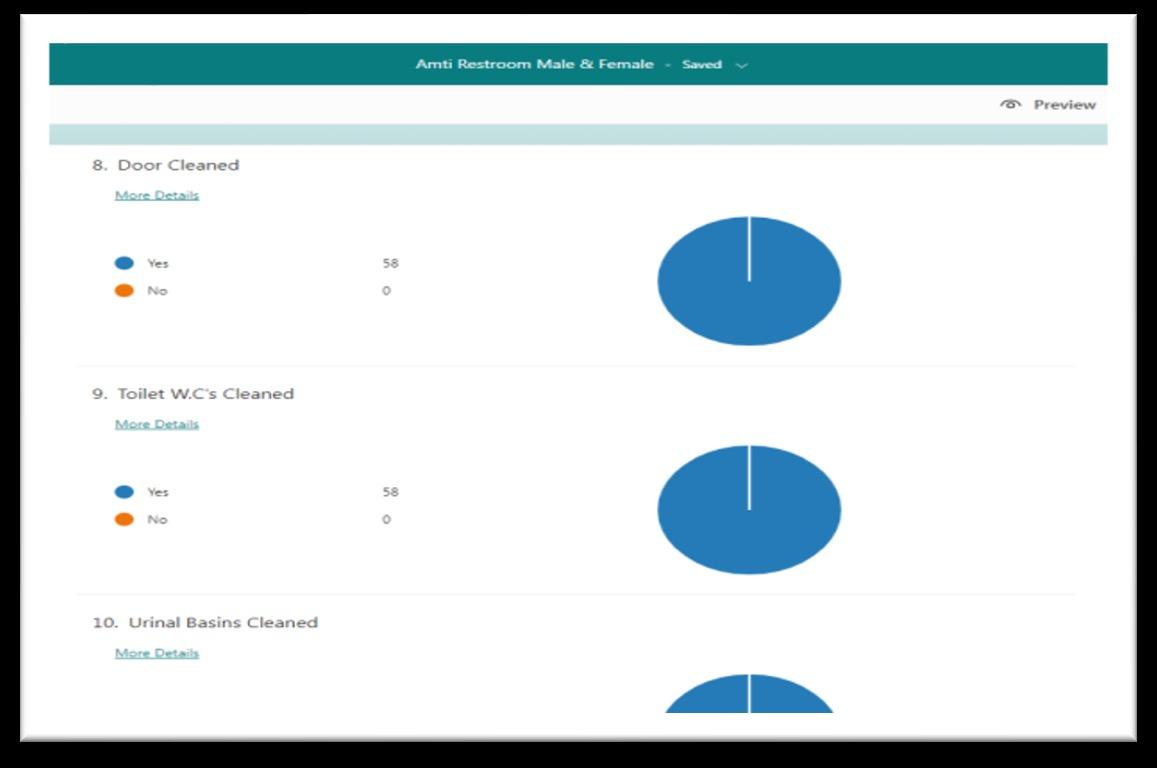
/
• Paper usage has come down drastically
• Same can be downloaded in Excel format
• Status chart can be viewed
• No vendor partner involved
• No cost involved
• Environment-friendly by helping Mother Earth
• Reduced the carbon footprint
• Received appreciation from the client for the initiative
Description of the Innovation:
Centralized e-Learning
Pods for employees & vendors
• Language barrier amongst the task force employees.
• Lack of safety awareness amongst external vendors and labours.
• Document based work instructions/ SOP(s) are difficult to imbibe and implement amongst task force employees including external vendor employees.
• Centralized e-learning platforms using audio-visual tools to enhance understanding of safe work practices.
• Learning Pods are loaded with job-based training modules with interactive audiovisual tools in regional languages.
• E-library with QR code-based pictorial SOP(s) for increasing ease of access to work instructions.
• Rs. 3500/- for printing the board.
• Elimination of language barrier to work instructions and SOP(s).
• Enhanced understanding of the job & job-based safety requirements.
• Reduction of man-hours spent towards training by trainers.
• Ease of access to SOPs and work instructions as it is QR code based.
• Minimal capital investment as it is developed in-house with existing resources.
myIdea
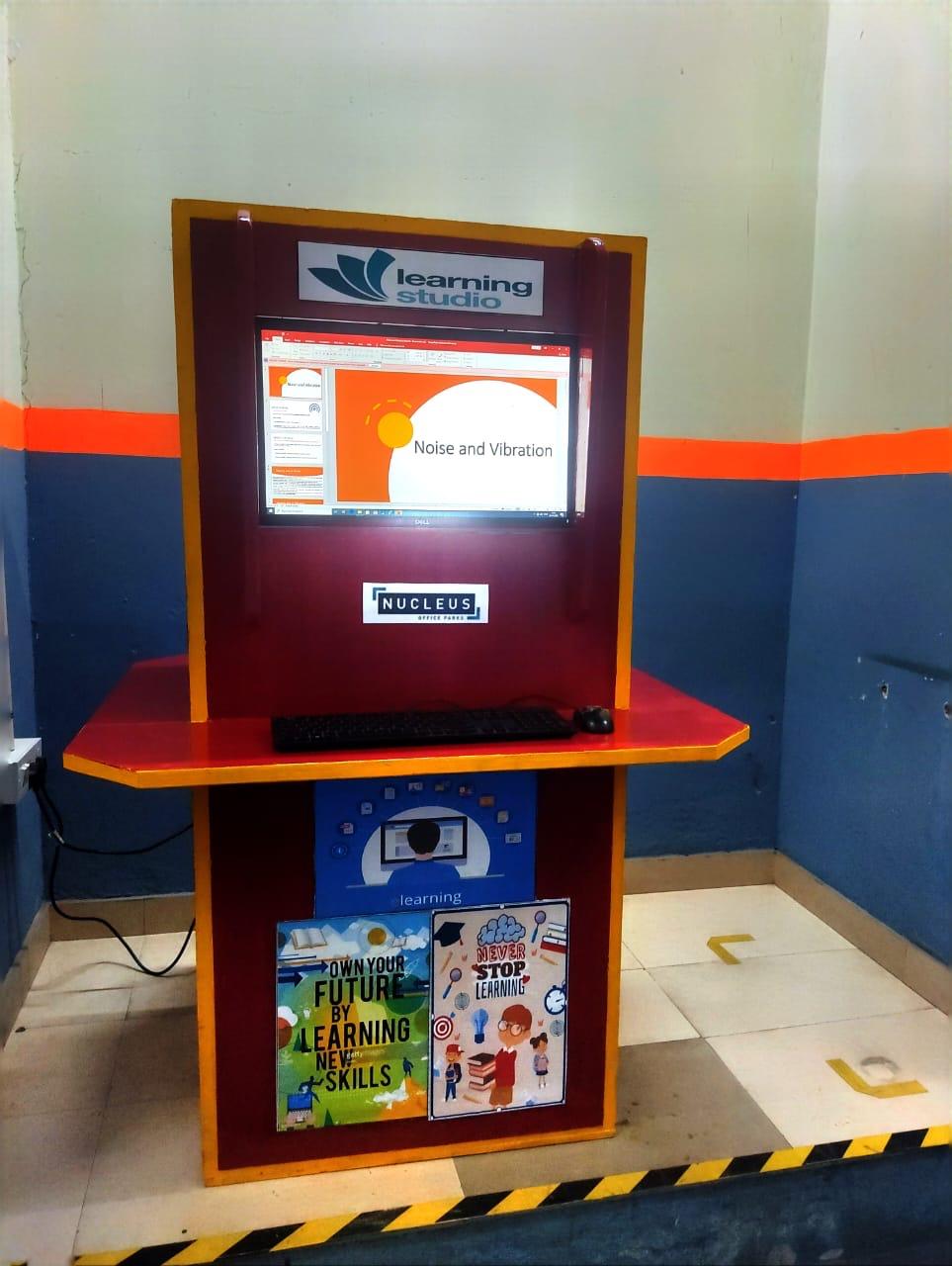
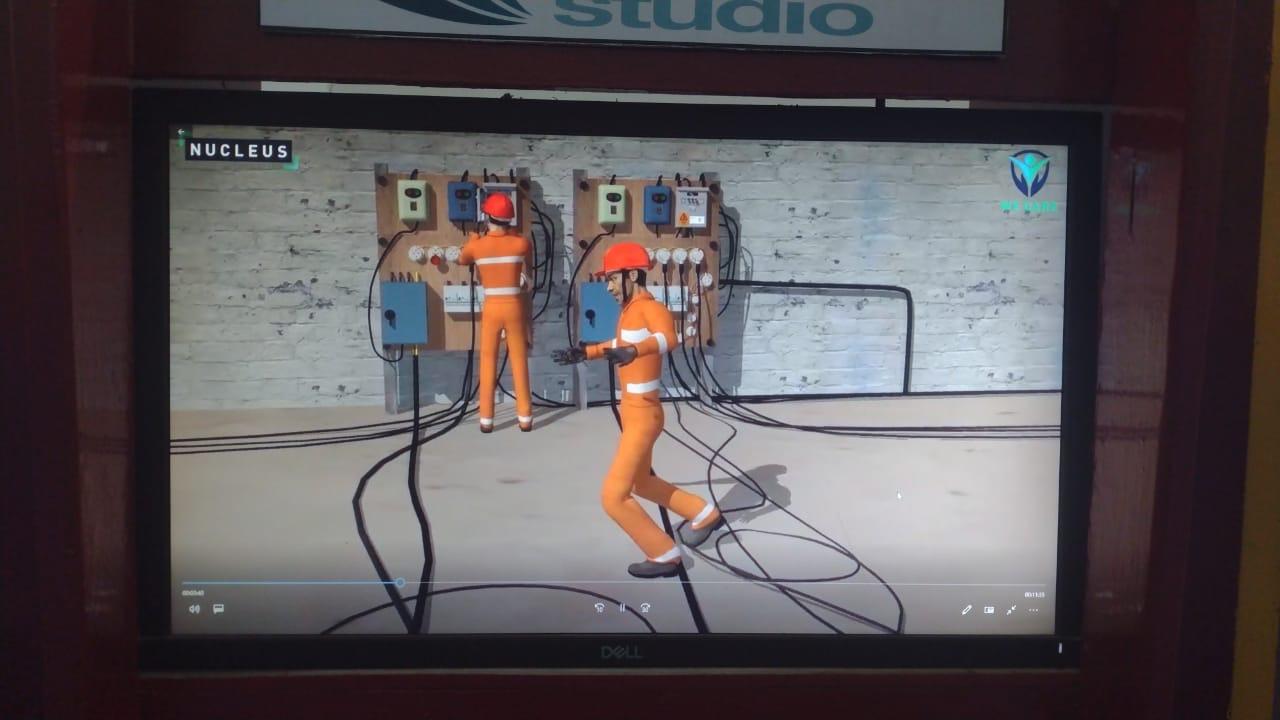
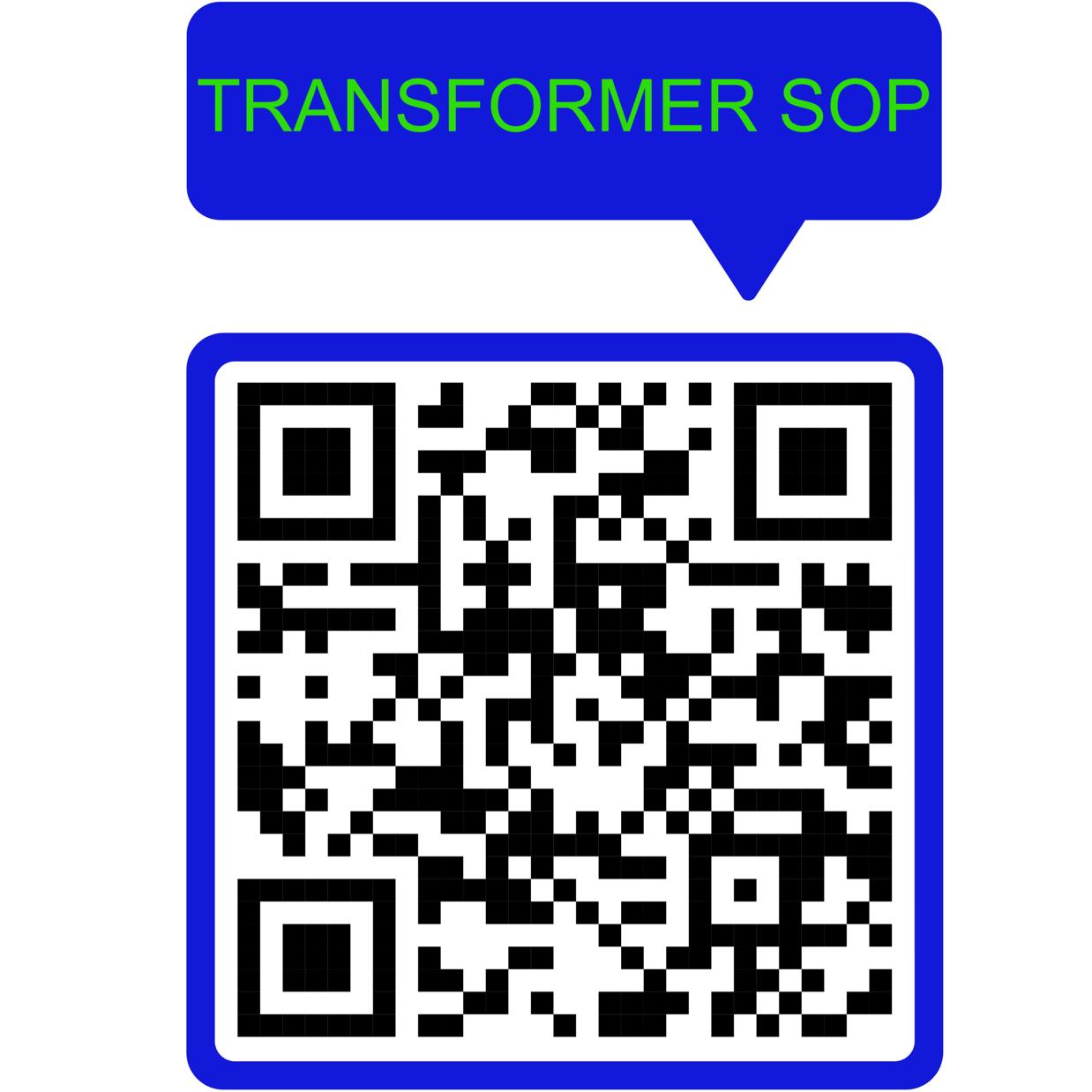
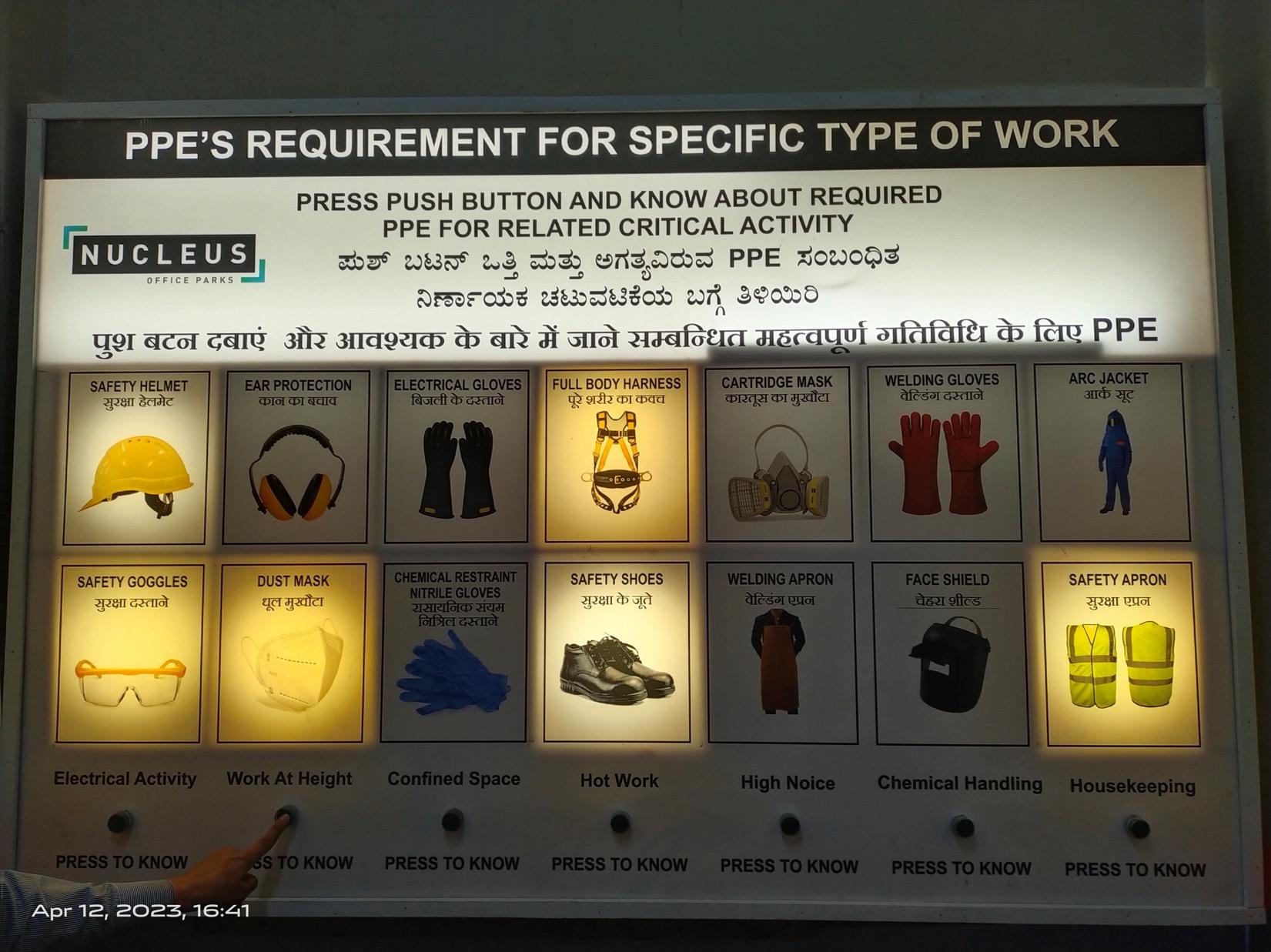
Description of the Innovation:
Self-Watering Plant
myIdea
• Lobby upgradation has been a crucial aspect of the Property Management team. Self-watering plants have been an effective solution
• Daily watering of indoor plants at all 06 receptions and office spaces was a tedious and time-consuming routine daily.
• Increased manpower utilization considering the higher quantity of potted plants and no of locations.
• Ease of access to indoor plants located at a height above the nominal reach of 4-5 Ft was difficult on a day-to-day basis.
• This works on capillary action. It has a reservoir at the bottom that holds extra water.
• A cotton thread pulls water up into the root balls as needed by plants.
• Hence this set-up requires watering once a week or 10 days..
• Multiple drain holes to ensure the roots are moist always and help in watersaving
• Upgrading the lobby by increasing splendor and grandeur of the Building
• Reducing 70% of consumption. Refilling is done once in two weeks. Approx 280 liters of water saved per lobby per month.
• Due to the reservoir setup, results in time-saving and manpower optimization, as the water is enough for a week, and daily watering is not required.
• Easy to maintain the indoor plants.
• Soil is preserved, thereby improving the nutrient-healthy growth of plants.
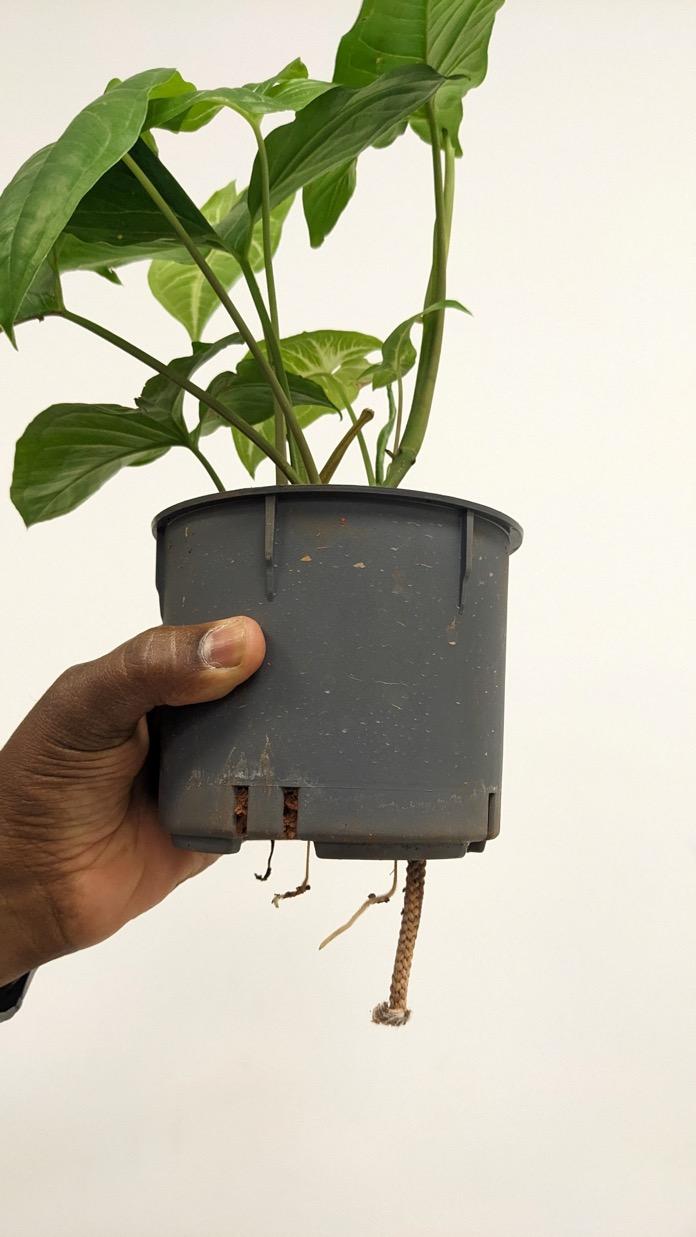

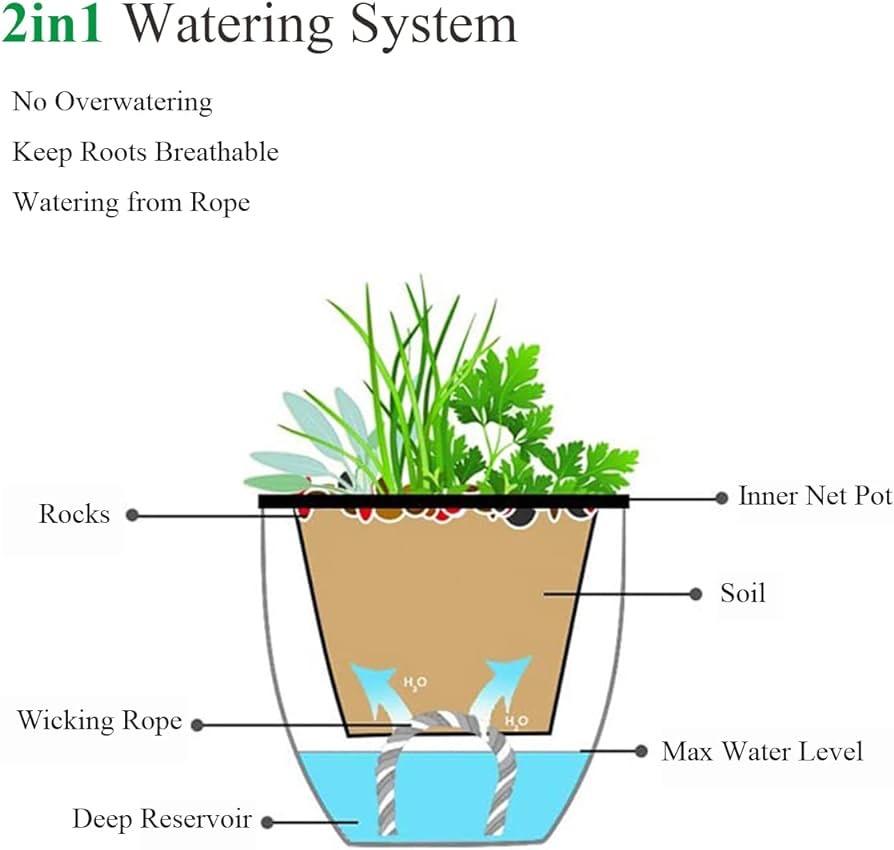
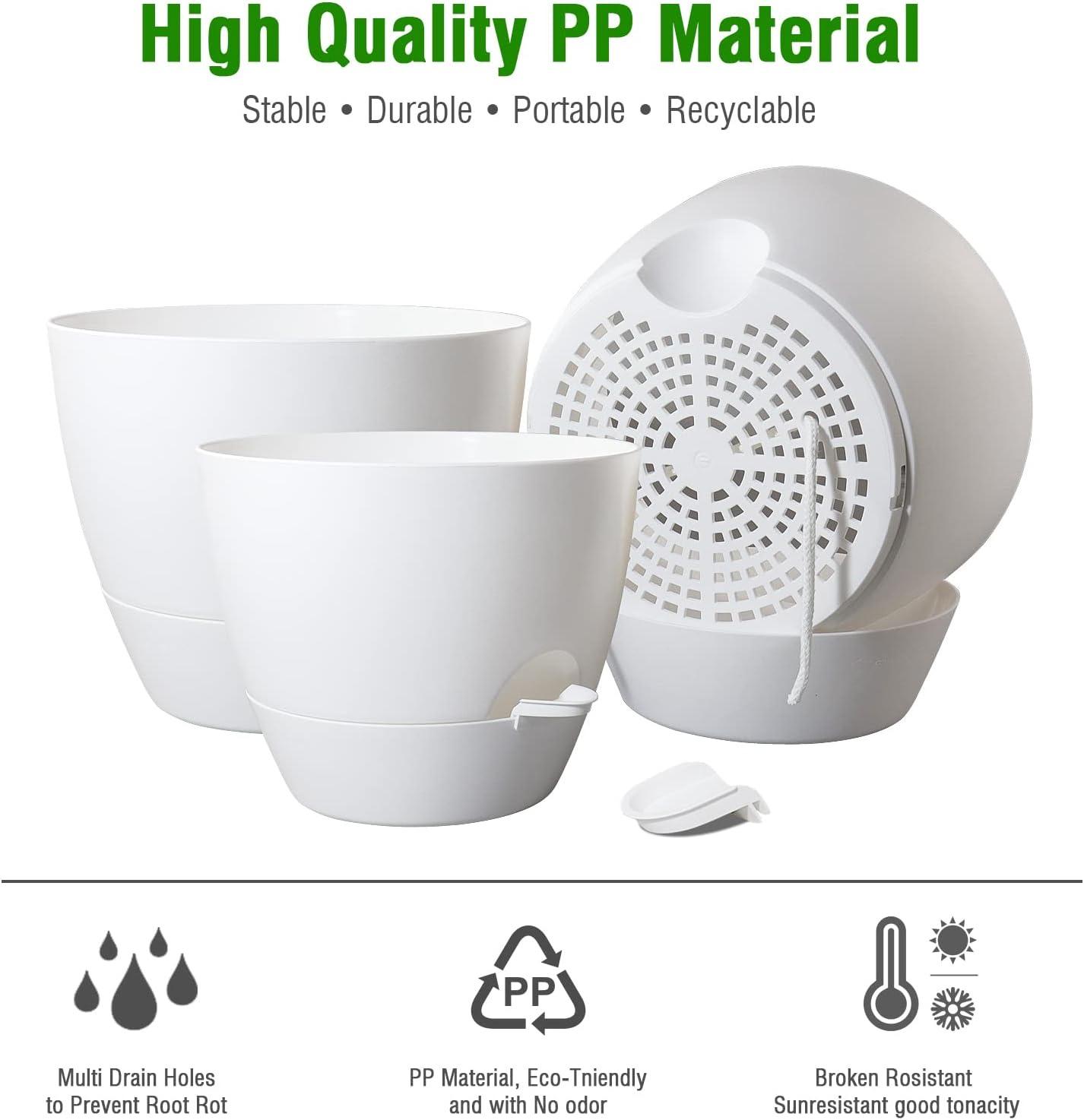
Description of the Innovation:
IOT Based Online Data of Utility
CHALLENGE
myIdea
• Frequent water outages.
• Man-entrapment in Lift.
• Monitoring of PPM activities.
• On-time diesel level status
• On-time re-ordering
• Reduce energy wastage
• Online & real time monitoring of the important utilities at the site
• Like water level ,Diesel Level, Rain monitoring, Lighting system & Security system.
• One window view of all the critical parameters and take appropriate action accordingly
• Viewing Critical parameters anywhere and anytime.
• Monitor the water level, quality and consumption with less human intervention.
• Alerts on WhatsApp in times of critical/ Escalation ex: water level if beyond low level, Fire alert.
• Paperless checklist for both daily reports and PPM activities.
• Monitoring of energy consumption on cellphones.
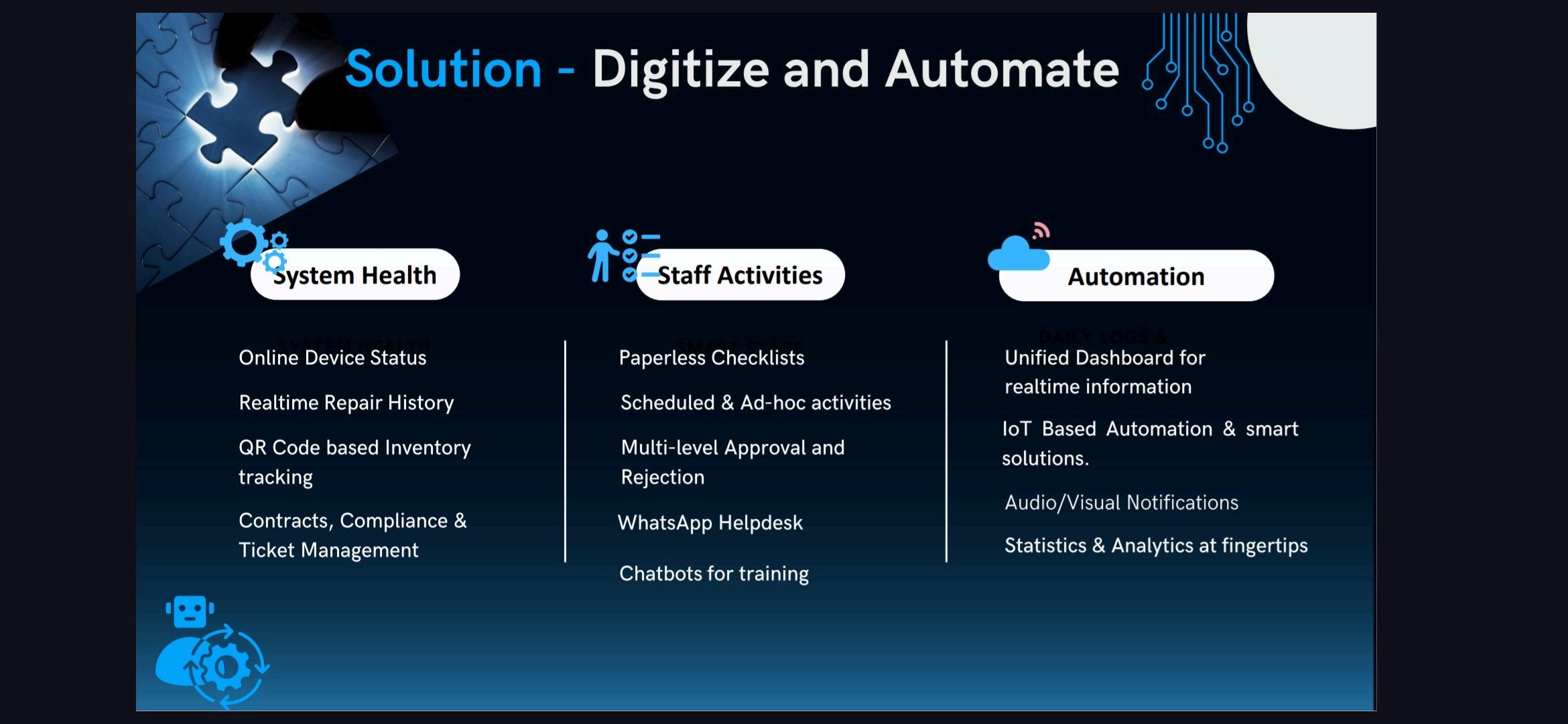
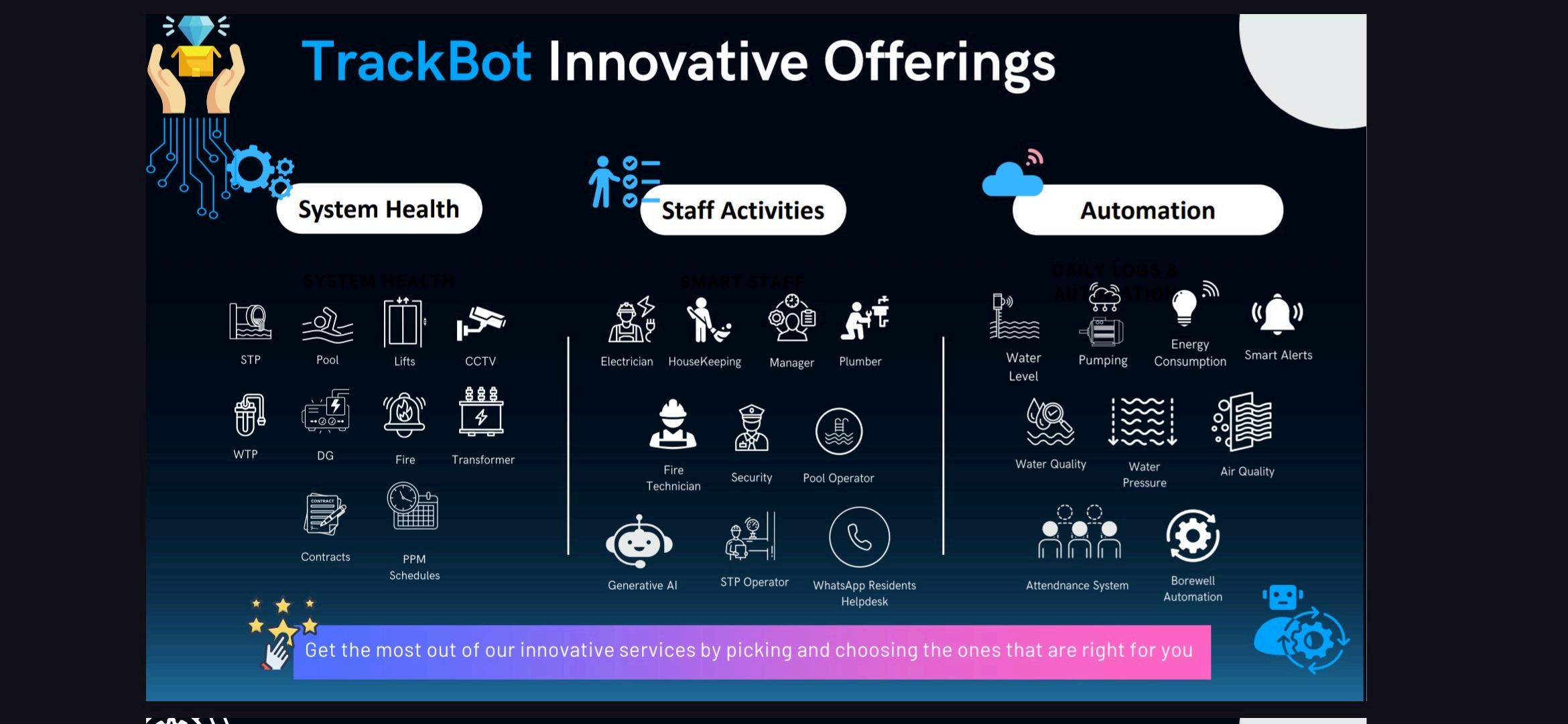
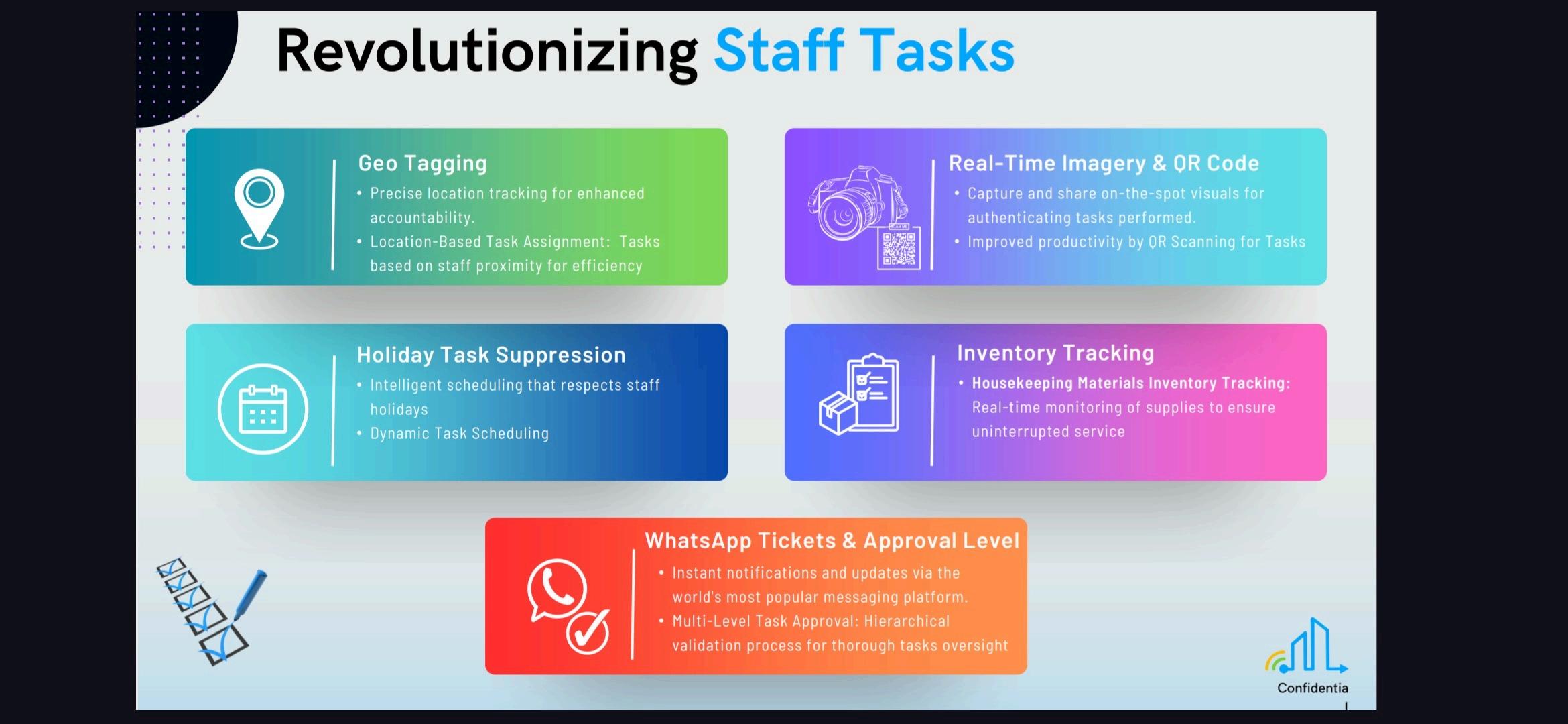
• Hydrant and Diesel driven pumps are high-power and capacity pump
Description of the Innovation:
Fire Hydrant & Diesel Pump
Interlocking
• In case of sudden pressure drop or pressure switch malfunction both pumps can start simultaneously
• This will lead to high pressure in the hydrant line resulting in line damage
• Both the Fire hydrant pump and diesel-driven pump are connected to the same fire line and are in auto mode
• As per IS 15301 – Both pumps should incorporate an interlocking device to avoid simultaneous operation in case of pressure drop
• Electrical inter-locking system (Pla-Relay) installed to avoid both pumps’ simultaneous operation in auto mode
• Immediate implementation i.e. interlocking of pump with PLA relay was done by inhouse team
• Avoid untoward incident in case of emergency due to pump automation
• No dependency on human intervention in case of emergency
myIdea

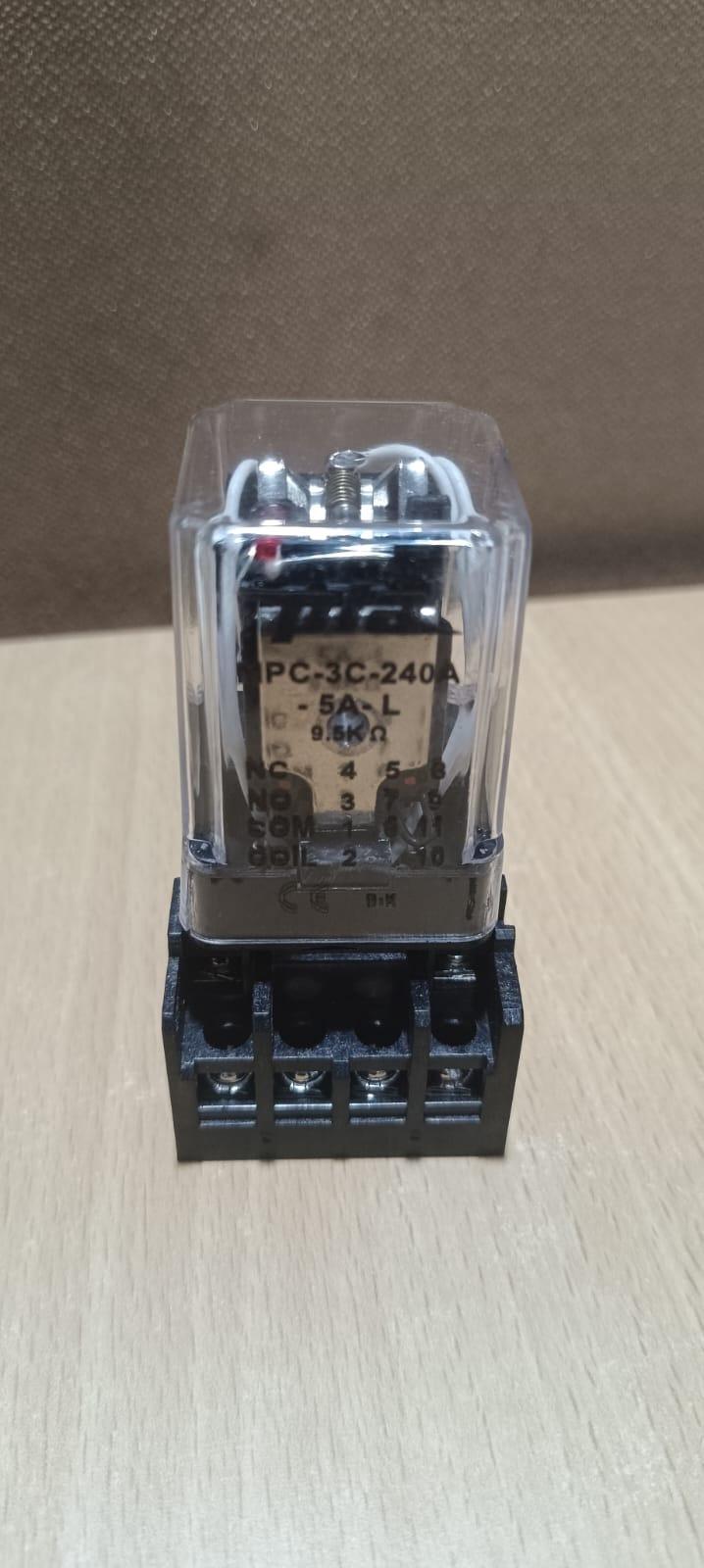
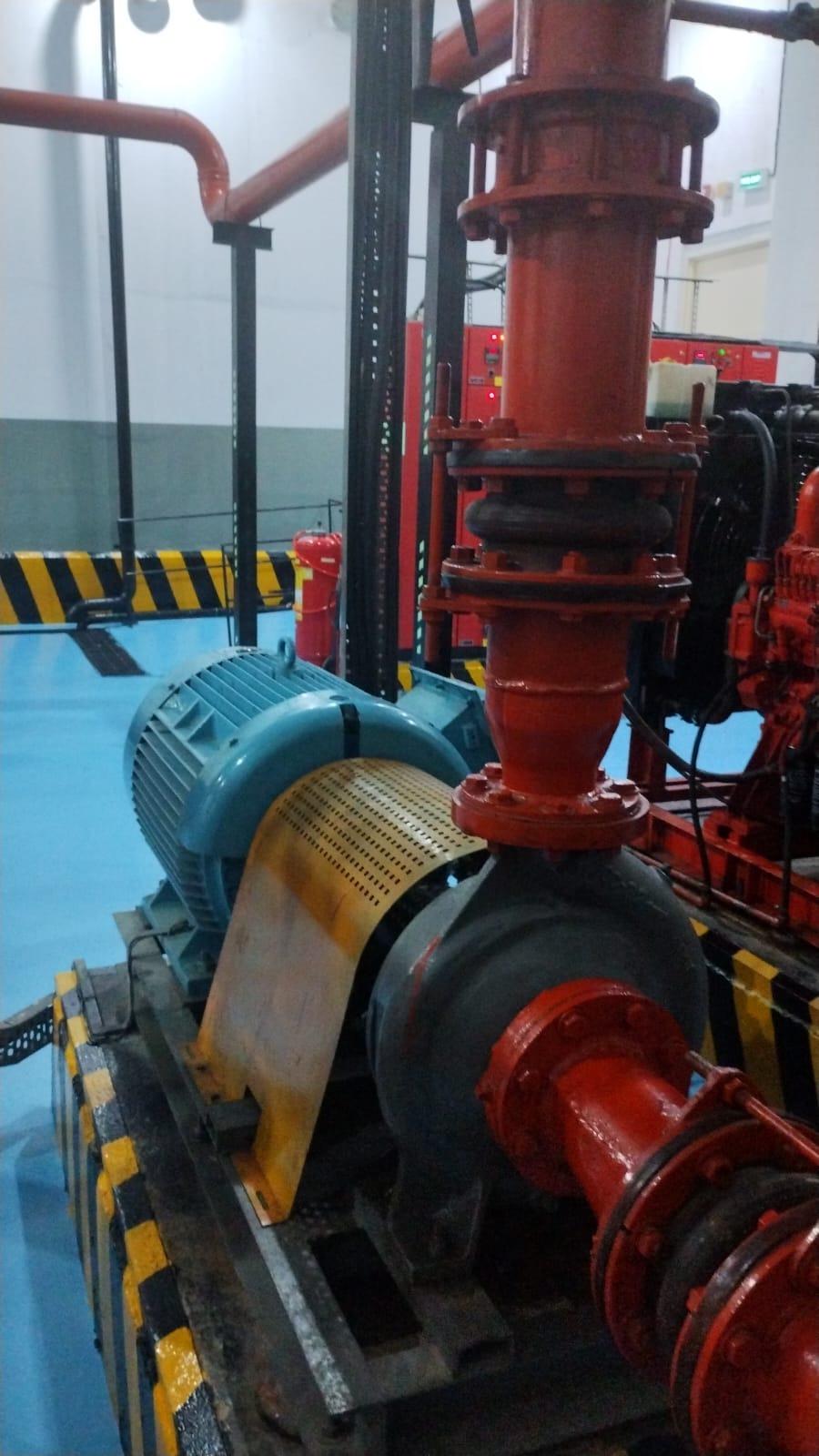
• High Energy consumption of Secondary pump as compared to tonnage delivered
Description of the Innovation:
Secondary Pump Pressure Set Point recalibration
• Pump sizes are always overdesigned
• Chilled water pressure maintained at the farthest end was higher than required by the application
• The secondary pump was operating in auto mode on a set pressure setting of 13 PSI
• As per AHU design 11 PSI was required pressure to maintain the required flow through AHU
• Programming in VFD with pressure set point was reduced from 13 PSI to 12 PSI for all pumps.
• Immediate energy savings delivered without any investment
• Changes in the VFD settings were done by in house team
• Energy saving of 22474 kWh/year was achieved
• Won CII National Award for Energy Management in 2023
myIdea
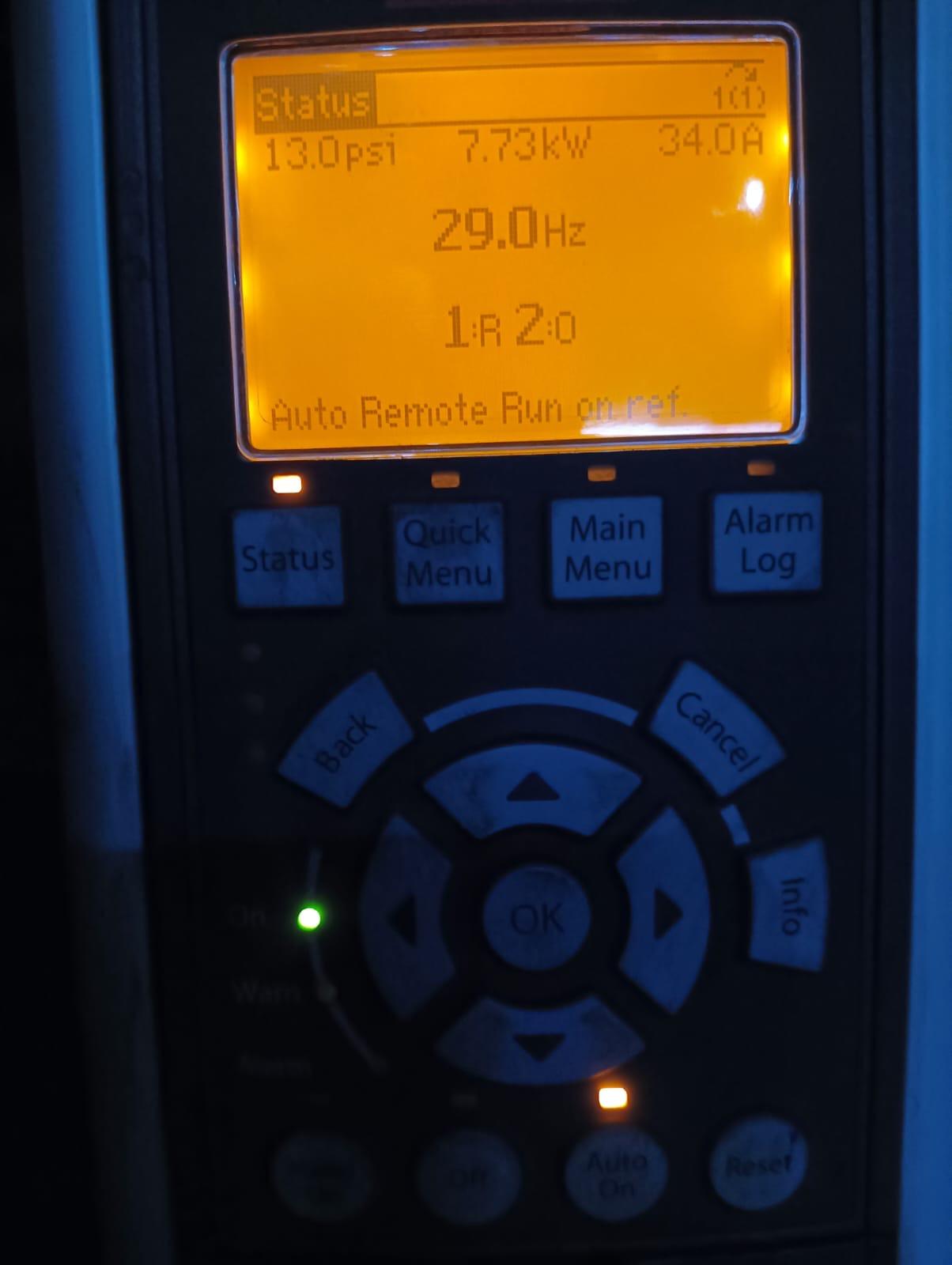
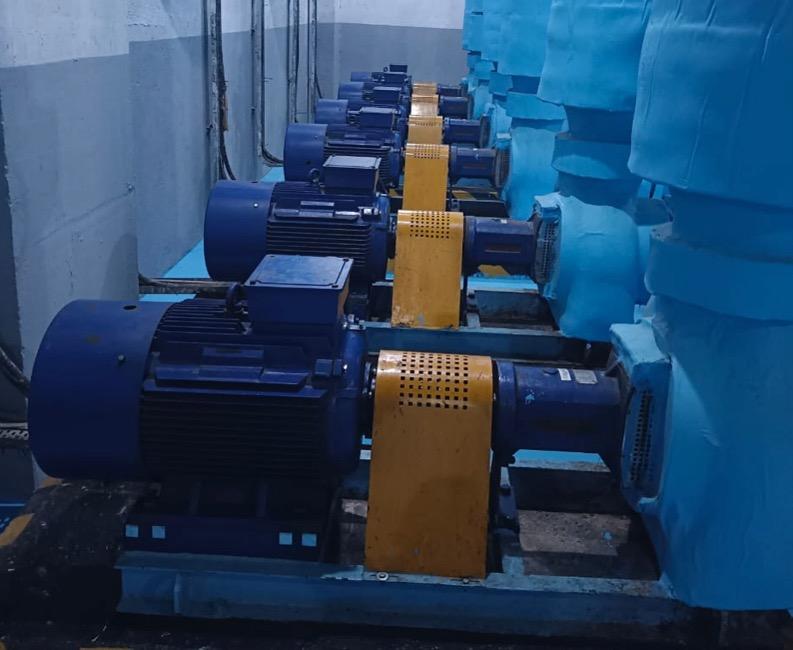

Description of the Innovation:
• Godrej IT Park has SBR type STP plant of 800 KLD
• High Noise level of 110 dB creating discomfort for the STP operator
• Frequent breakdown of air blower resulting in reduced uptime
Trilobe Blower
myIdea
• High energy consumption due to old technology twin lobe blowers
• Air blower system is operated in 4 batches (4 hours/batch/day)
• Air blowers constitute 70% of total STP energy consumption
• The present twin lobe technology is old and inefficient
• Replaced 2 nos. twin lobe blower with efficient Tri lobe blower with IE3 motor
• 15% energy saving in air blower system through Tri lobe blower operation
• Reduction in noise level from 110 dB to 75 Db
• Hazard Elimination: No moving parts are exposed
• Monetary Saving = Rs. 1.5 Lakh/year
• Blower investment = Rs. 9 Lakh
• Payback Period = 6 years
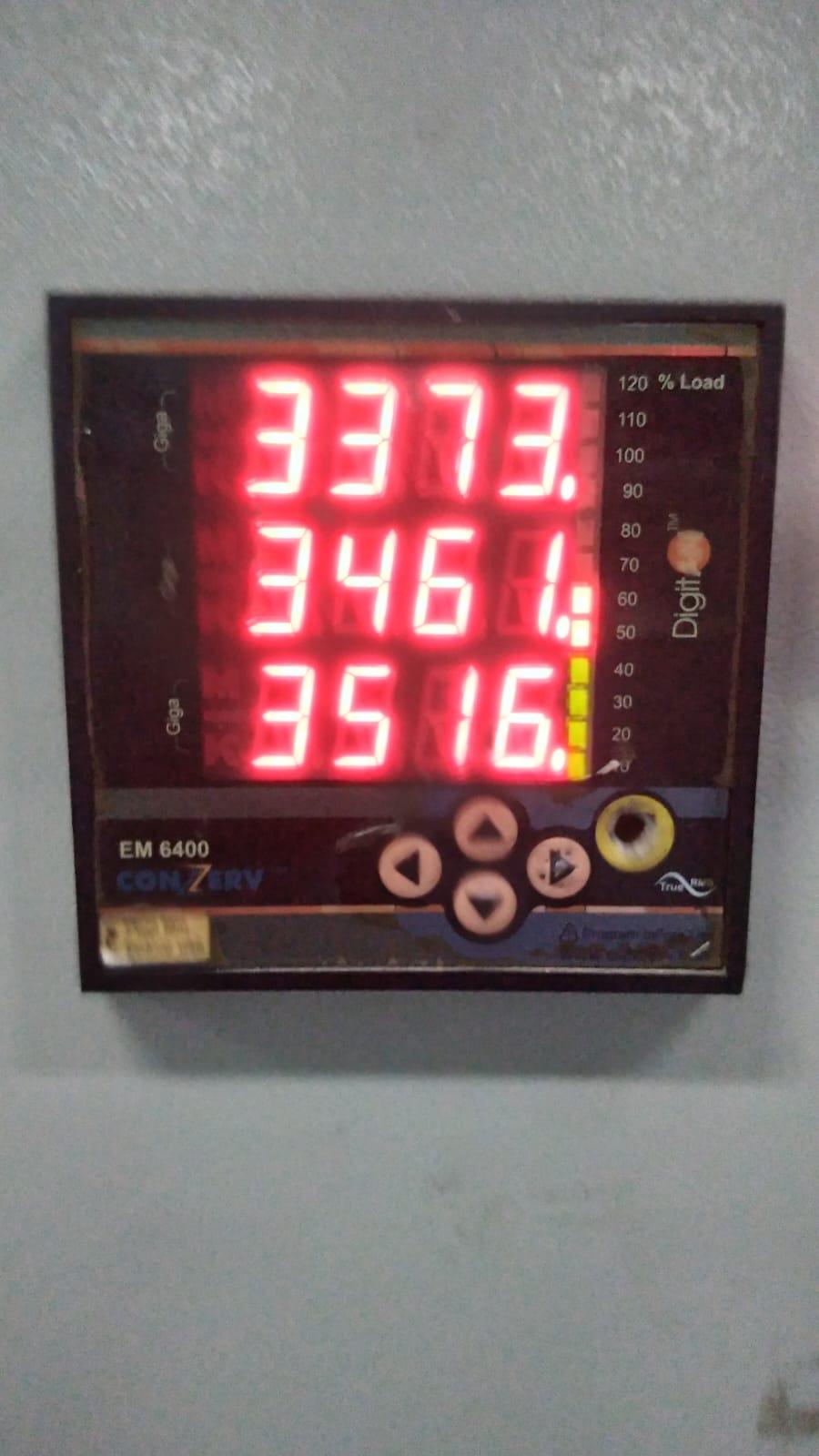
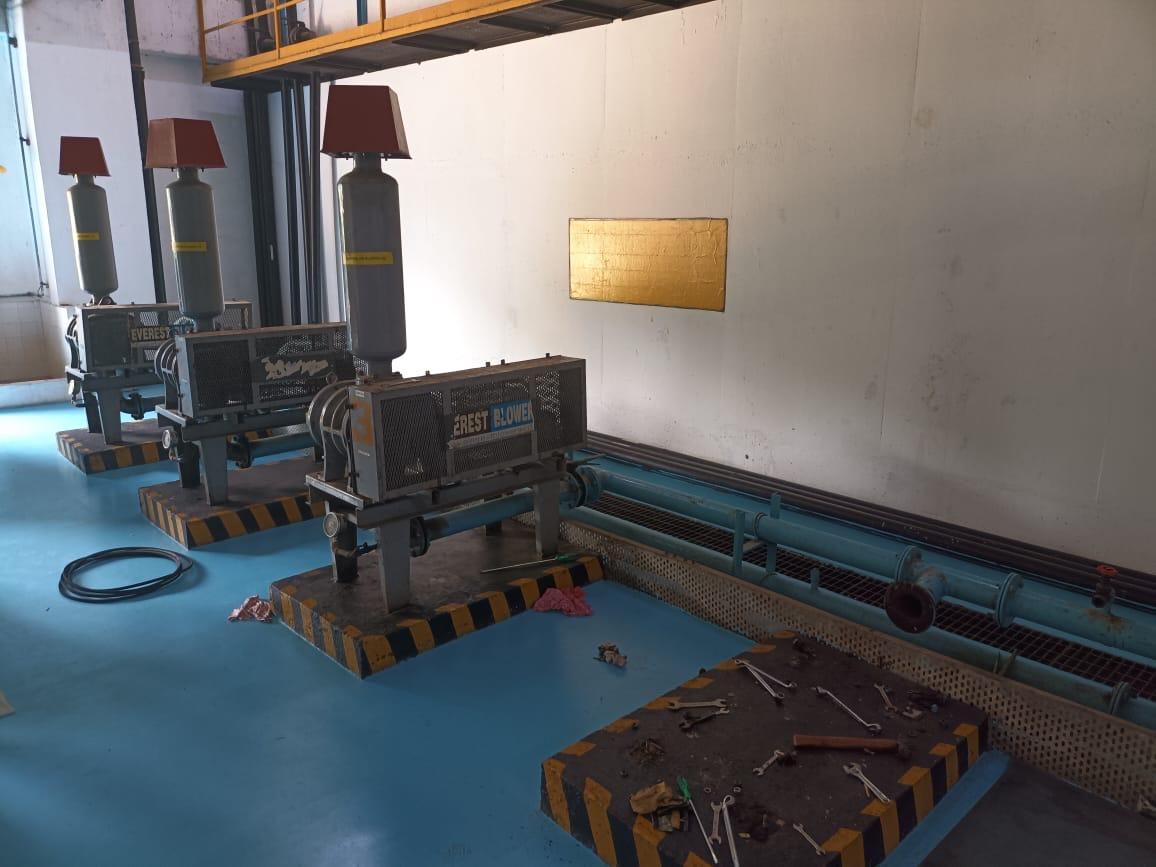

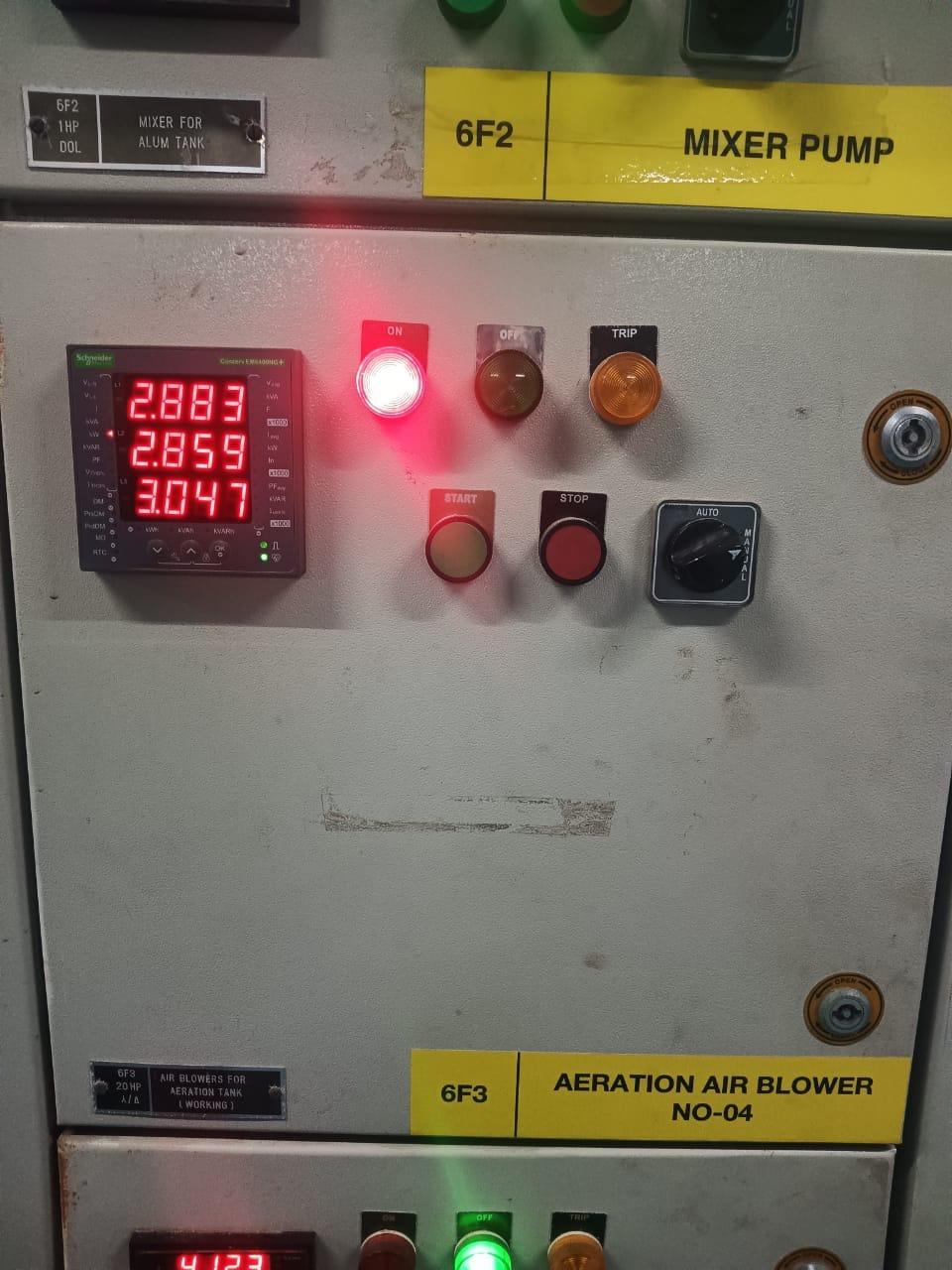
Description of the Innovation: CHALLENGE
Redundancy –
Provision of Secondary Source from HT for building riser.
myIdea
• The iconic wing of the Urmi Estate Building was connected to the HT supply, but there was no redundancy available for Power Failures.
• The newly acquired LT source (2500A) for the building was being partially unutilized. In Tower-A. Since the CD for LT was 250 kVA, a penalty to the tune of 2- 2.5 lakhs was being incurred due to higher MD occasionally during each instance of power failure. The total Penalty paid in FY 22-23 was above 07 lakhs.
• Also, expenses towards Fixed Charges ( 50,000/-) were being incurred monthly when LT supply was not in use.
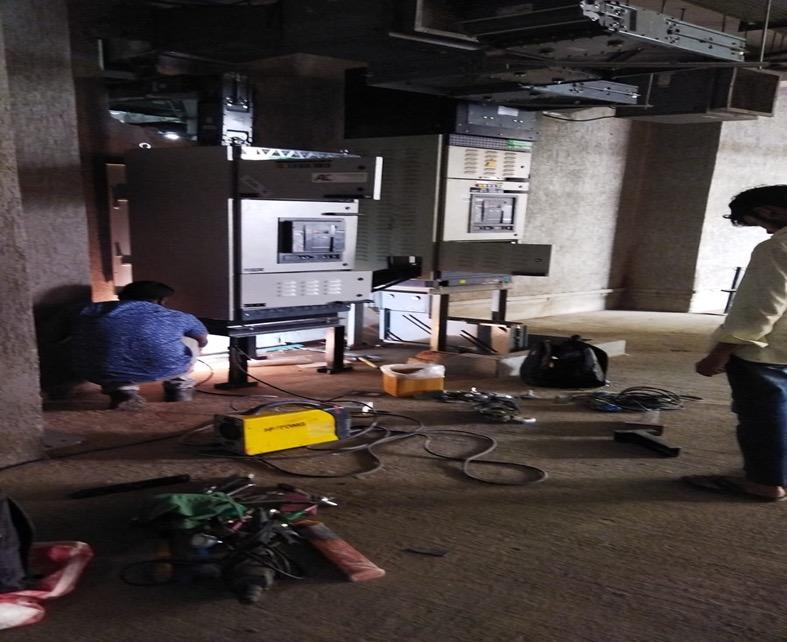
• Iconic building riser (Ground to 12thj Floor) was previously connected to HT source from MV-2 Panel only and there was no redundancy
• The Building had an additional LT source (2500 A) from BEST which was being used only as a backup supply and expenses towards Fixed Charges were being incurred including the penalty due to higher MD occasionally during power failures
• Hence, the LT source (2500 A) was connected to the Iconic Building Bus Duct, and the changeover was provided from the HT source as redundancy to the Iconic Building
• An additional ACB enclosure was installed and connected through the Bus duct with the exiting Bus Duct using a T-joint
• Redundancy created for Iconic Building riser
• Effective use of LT source which was otherwise lying idle
• Savings of 05 lakhs p.a. for Fixed Charges (towards 40% of CD when not in use)
• And avoidance of penalty charges due to higher MD when used as redundancy for multiple loads
• Process enhancement
• Client Appreciation
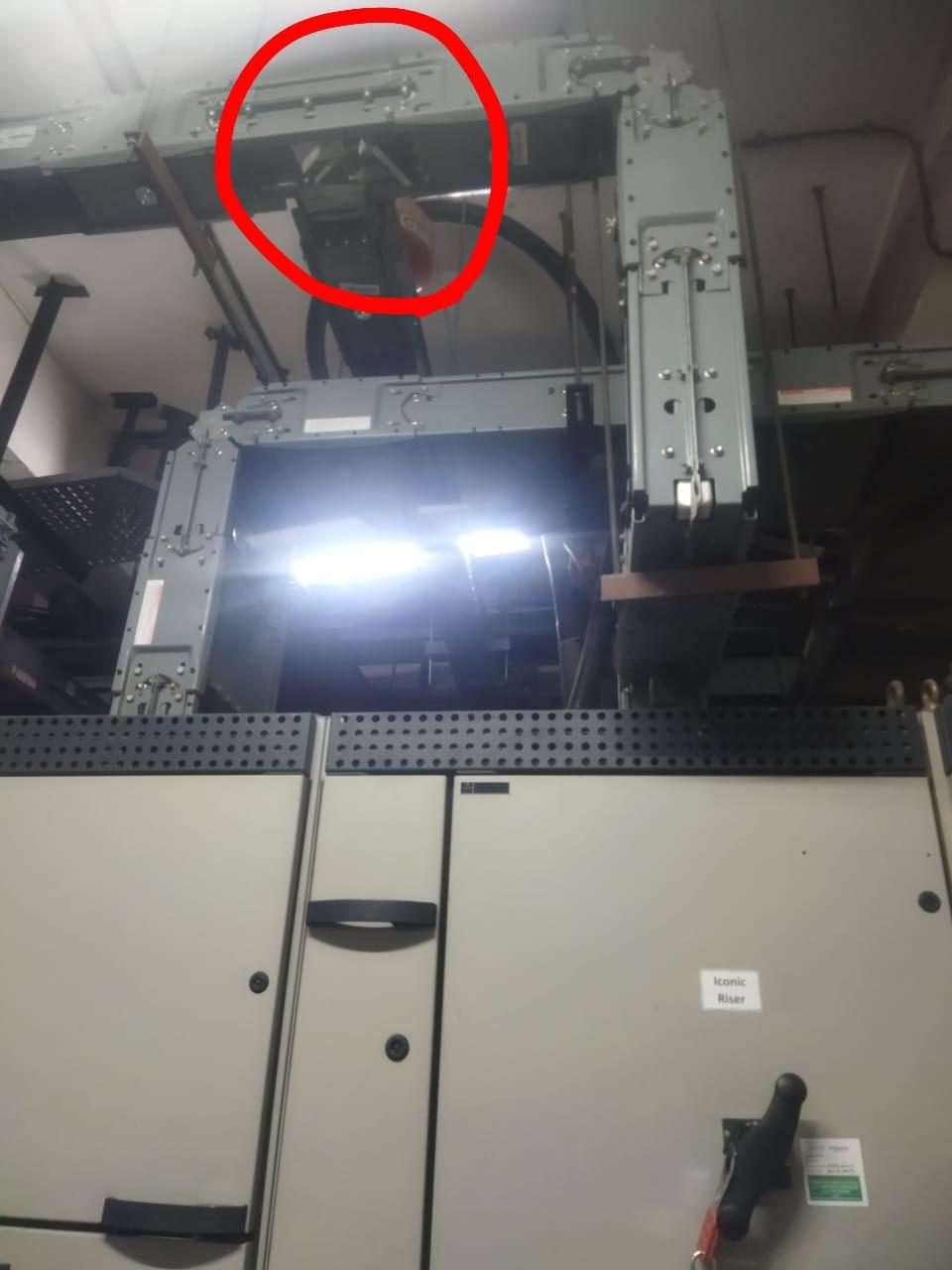
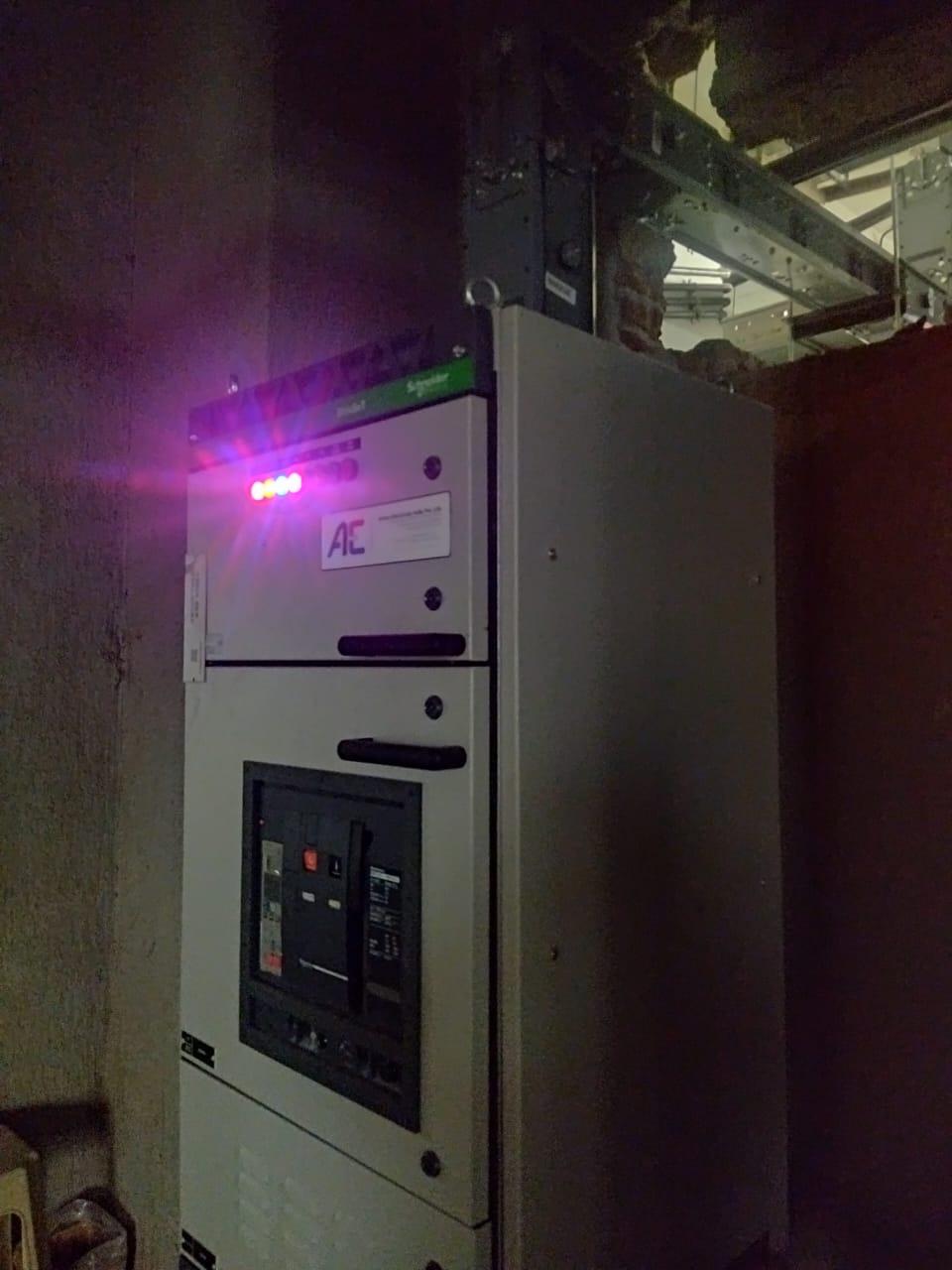
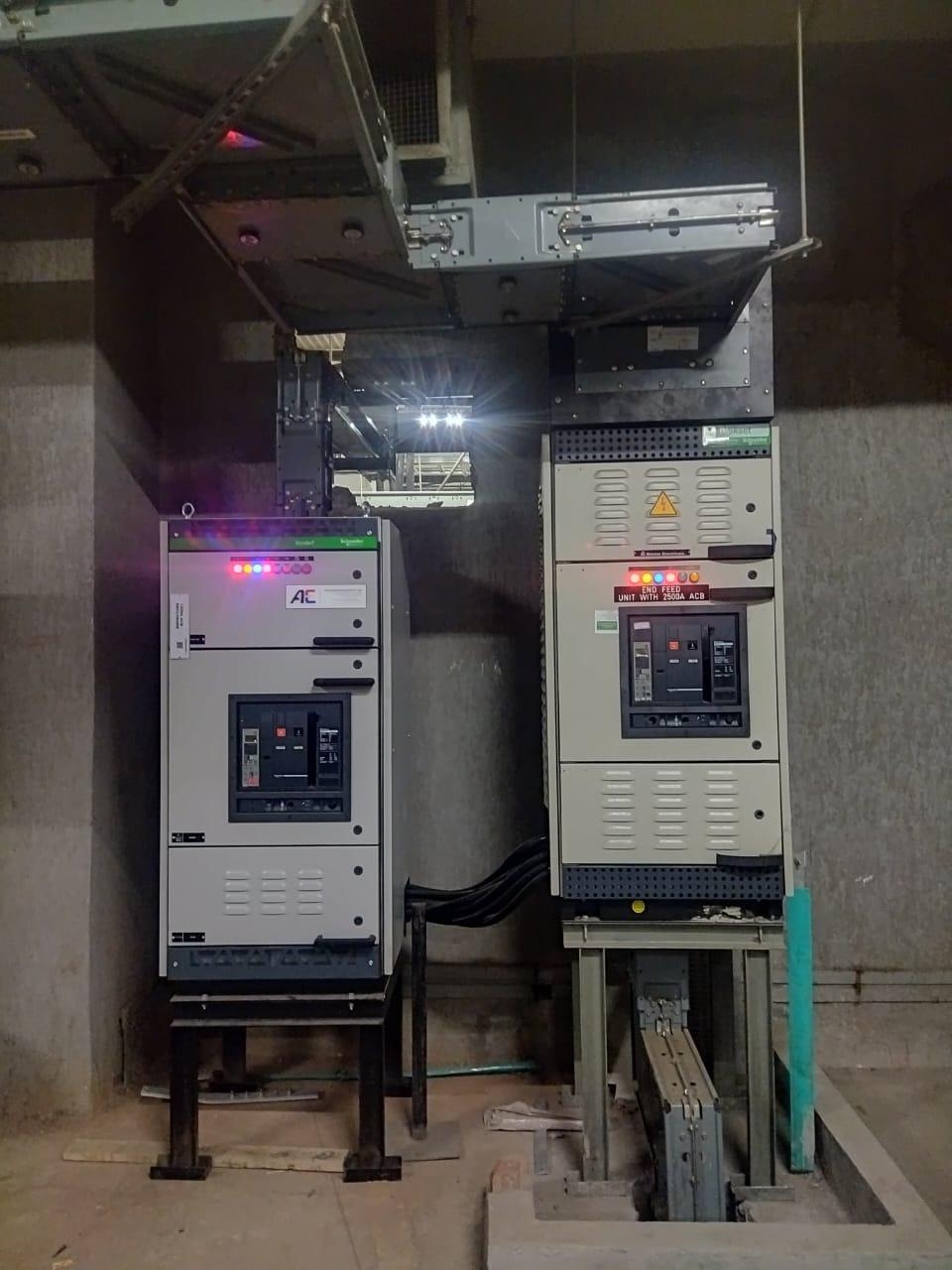
Description of the Innovation:
Elimination of Computer Room Air Conditioning unit & Cooling Tower
CHALLENGE
myIdea
• To provide condenser water to the tenant’s server AC. It was difficult to get shutdowns from tenants for PPM and to attend to any breakdowns.
• It was a major responsibility of the management team.
• After discussion with the Client, decided to allocate open space on the terrace for the tenant’s Server outdoor units.
• We convinced all tenants to install separate AC outdoor units on the terrace for their critical rooms.
• After great struggle and more than a year, this was possible and now all tenant’s critical room AC is operated independently through their outdoor units.
• Air-conditioning is more reliable and cost effective
• This CRAC CT was there for 2 buildings. So, two separate LT energy meters were provided. Now we surrender both these meters.
• Saving of Electricity consumption approx. cost of Rs. 5.75 Lakhs per month.
• Saved CRAC CT operator manpower cost approx. Rs. 1.67 Lakhs per month.
• We saved 8 Security guards for the terrace, costing Rs. 3.05 Lakhs per month.
• Saved water cost of approx. Rs. 2000/- monthly.
• Saving in Dosing Chemicals cost is approx. Rs. 26,371/per month.
• Dependability of critical rooms AC on common CT eradicated.
• Increased availability of open space for future use such as terrace garden/solar project etc.
• Estimated Saving : INR 10,75,371/- per month
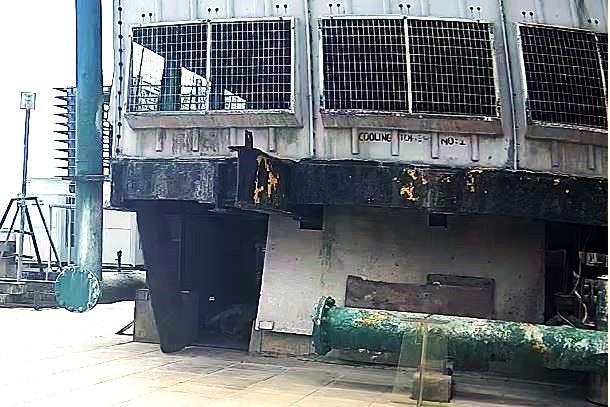

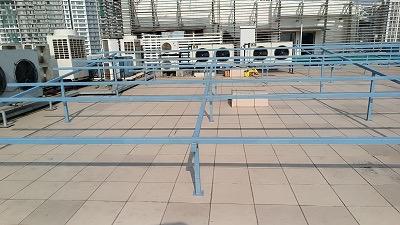
Description of the Innovation:
FRP Coating for Condenser Pipes.
• Condenser Pipes and cooling tower pipeline lines were rusty due to salty weather conditions.
• The approach of the cooling Tower was more them 3.5OC and it varies inversely to cooling tower performance.
• The HVAC Chiller plant frequently tripped due to high Surge.
• Multiple leakages from the condenser/cooling tower pipeline were observed and it couldn’t prevent due to the control valves were not being provided by the developer, resulting 12,600 KL/Year water loss and the tanker water expenses is around 11.34lac /annum
• Daily treated water consumption is around 1lac liters)
• Replaced all the condenser pipes with the new MS pipes.
• Pipelines exposed to the weather were coated with FRP Coatings (Fiberglass Reinforced Plastics)
• *FRP is corrosion resistant, longer life with zero corrosion, and has very high resistance to severe chemical environments.
• Additionally control valve is fixed at all individual cooling tower water supply lines.
• Water level indicators were provided to maintain the cooling tower water balancing.
• Improve Cooling Tower Effectiveness to maintain the approach.
• Zero maintenance and to last at least 20-25 years.
• Pipeline maintenance and painting costs saved.
• Approach achieved is now less than 1OC Temperature difference- Now chiller requires less compressor lift to provide the same cooling capacity.
• Water leakages are arrested and saved water and tanker cost around 11.5lac /annum,
• Daily water consumption saved by 35 KL/day )
• ROI Calculated 4.5years.
myIdea
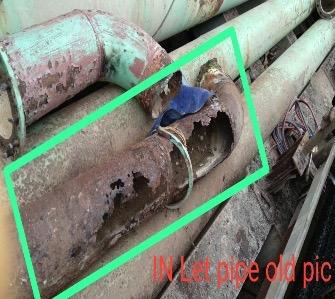
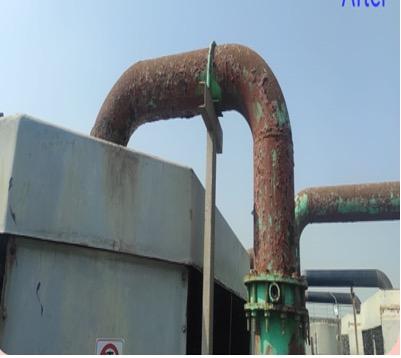
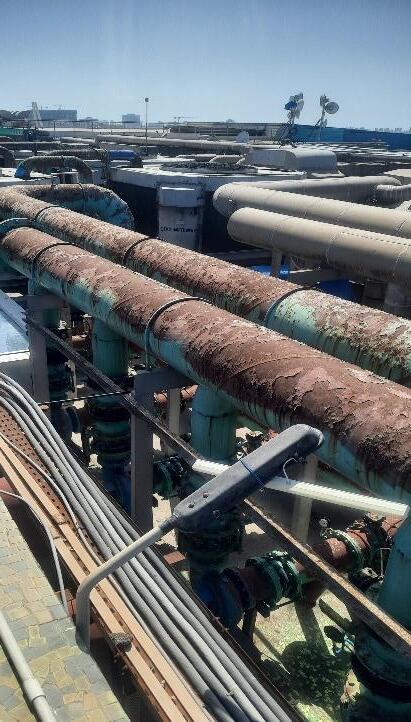

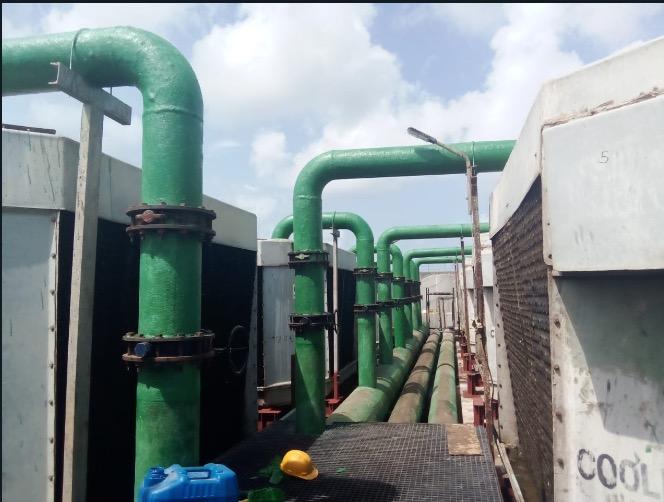
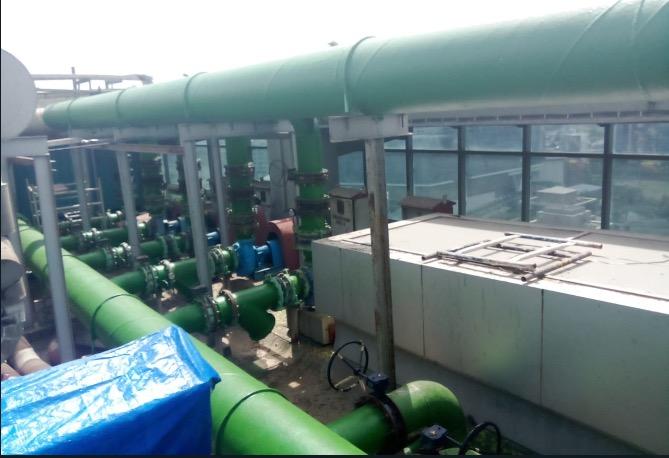
Description of the Innovation:
Digital Water Meters
CHALLENGE
myIdea
• Non-availability of real-time data.
• Less accuracy in data.
• Utilisation of manpower
• Time consuming activity.
• Access for meter reading.
• Paper checklist maintained by manpower.
• Data dependency on manpower and the possibility of human error.
• To mitigate issues in finding real-time data and accuracy, to keep DBR integrated parameters we brainstormed on the solution for the same
• To avoid such an issue, we installed digital meters.
‒ Digitalization of metering
‒ Digital meter installation for submeter.
• Remote monitoring.
• Data accuracy in real-time.
• Manpower cost reduced.
• Acceibility of meter reading eliminated.
• Time saved for meter reading.
• Paperless data with an error-free log sheet.
• Consumption pattern in the dashboard.
• Billing transparency, and ease of integration, help us to find and track peak usages. etc.
• Households can easily monitor their water usage and identify areas where they can reduce water consumption
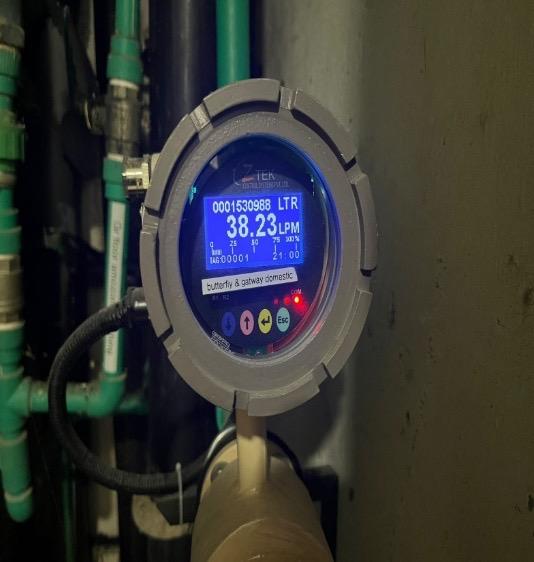
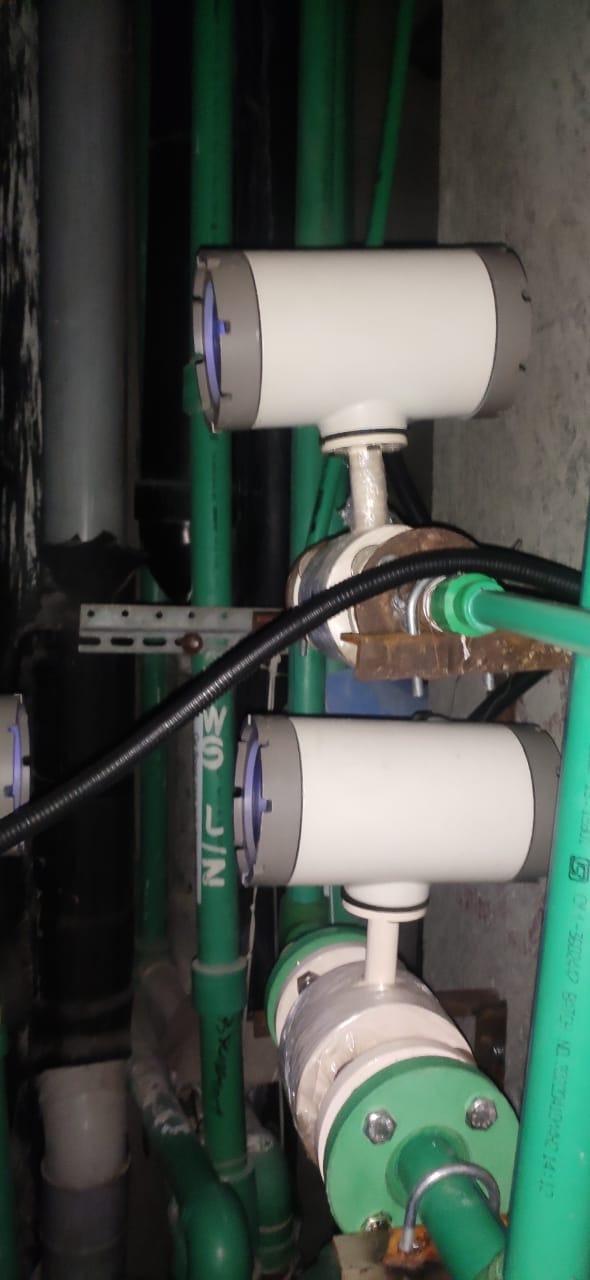
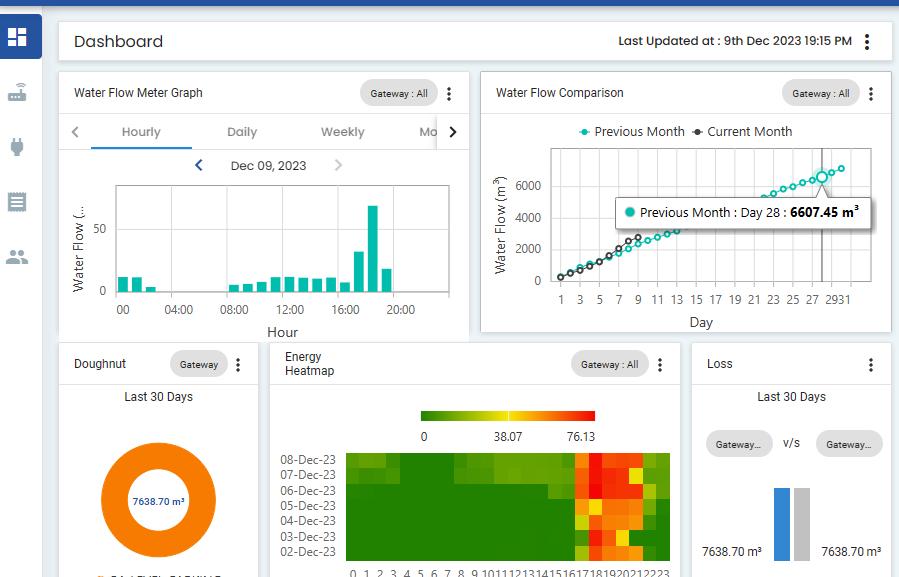
Description of the Innovation:
Server Room Temperature Monitoring Panel
CHALLENGE
myIdea
• The HVAC System is required to monitor for 4 no. server rooms, at the Site.
• Each server room has Split AC units installed.
• Split AC timers malfunction or don’t work properly which causes the temperature is high in the server room.
• A dedicated team is required for Frequent inspection and rounds
• Temperature sensor installed in server room connected to the FM Room.
• Temperature sensors from each server room are connected with the panel, which has 4no’s indication lamp and one hooter installed.
• When ever Temperature raise above 30 °C, alarm is trigged.
• The project was executed by in-house team for INR 5000/-.
/
• HVAC Down time has been reduced. The desired temperature is maintained.
• Whenever the temperature goes up it will indicate and help to find out the problem.
• Frequent rounds are not required to monitor temperature, Due to this manpower is reduced.
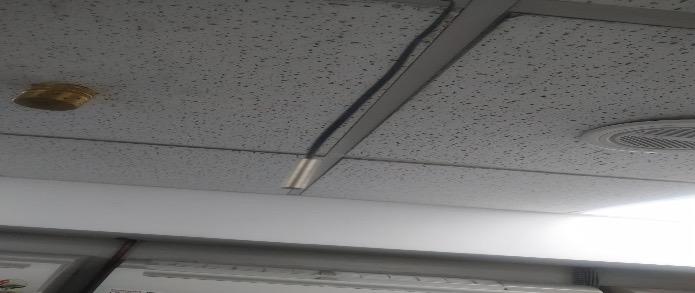
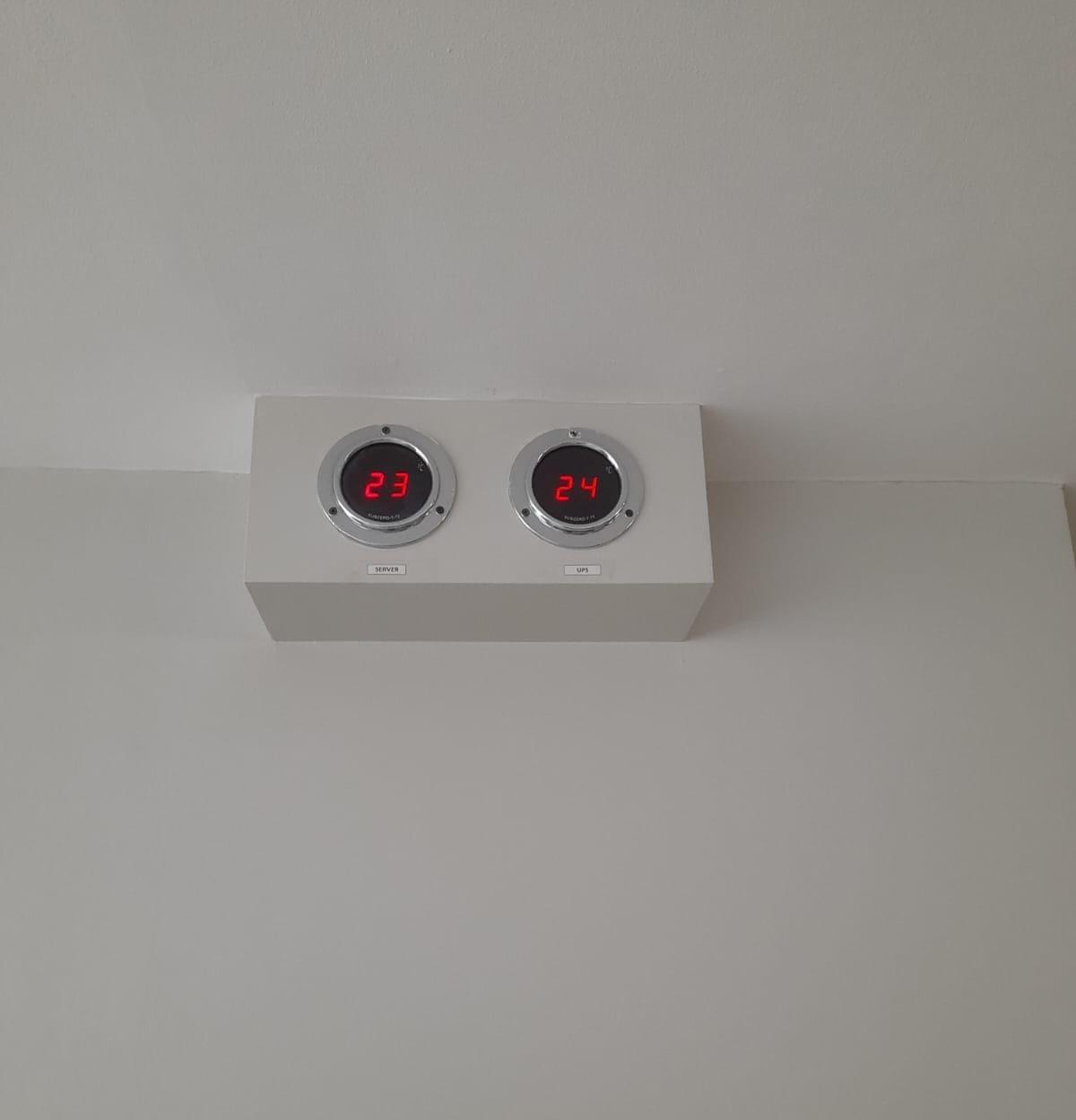
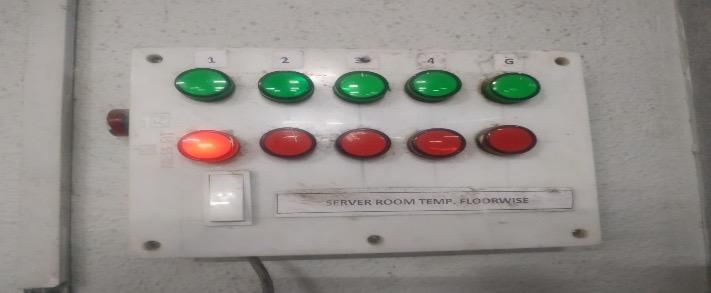
Description of the Innovation:
Water Saving Measures
CHALLENGE
myIdea
• Huge amounts of water are needed to maintain the horticultural area, which occupies 11 acres out of the total 46 acres, as well as to meet the needs of the employees at the site.
• ESG initiatives for Maintaining the groundwater level following regulatory standards.
• To treat the wastewater, there are two STPs (Sewage Treatment Plants, Capacity 300 KLD & and 600 KLD) installed on the property.
• The rainwater was flushed through drains to the nearby stormwater drains. Creating rainwater harvesting pits will enable us to collect rainwater throughout the campus to recharge the groundwater.
• STP treatment of wastewater and use of the treated wastewater for flushing and gardening resulted in an annual water savings of 37,066 KL.
• Using 12 rainwater harvesting pits as a sustainable option the ground water level has raised from 40 meters to 32 meters post monsoons. This is measured with the help of a piezometer .


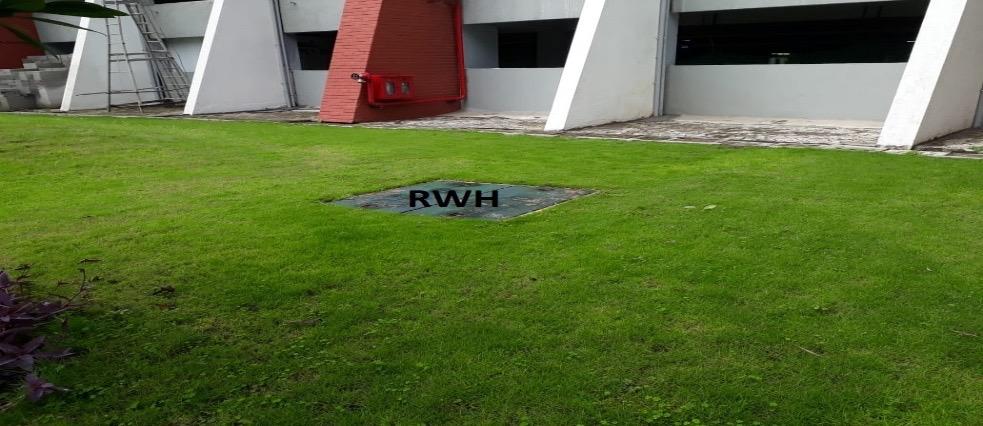
Description of the Innovation: CHALLENGE
Smart Digital PPE Board
• To ensure that all class of workers labors, technicians understand the site safety requirements.
• To Maintain safe working environment in the premises.
• Knowledge of PPE required for respective work.
• To educate workers, technician & labor of the safety equipment in position.
• A easy illustrative board on various types of PPE to be used for any work.
• A digital board with smart interlinking was designed so that with the press of a button the required PPE for particular task would get illuminated.
• The digital PPE board integrated in such a way that. Positioned above each corresponding task, there is a push button integrated with the necessary PP.E.
• Once the button under a particular work is pressed the symbols of each PPE is, reflected through LED lights. .
• This enables individuals to easily identify the required PPE for each task by simply pressing a single button.
• To help maintain a zeroincident/accident/injury record at the site.
• To establish safe workplace and maintain smart working experience for the organization.
• To ensure that even if a worker is not educated, he can understand his safety requirement with the illustrations against type of work
• Cost Impact
• 13,662/-
myIdea
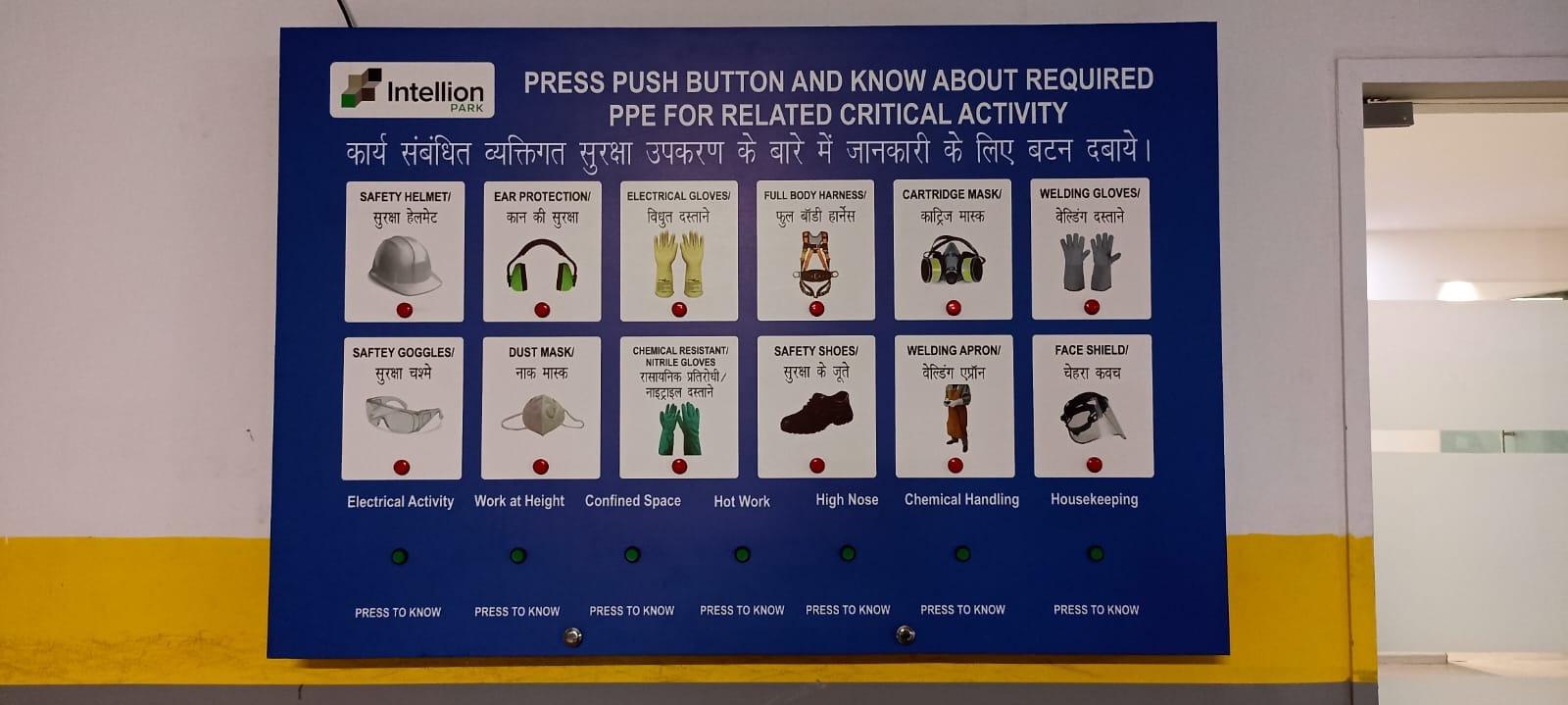
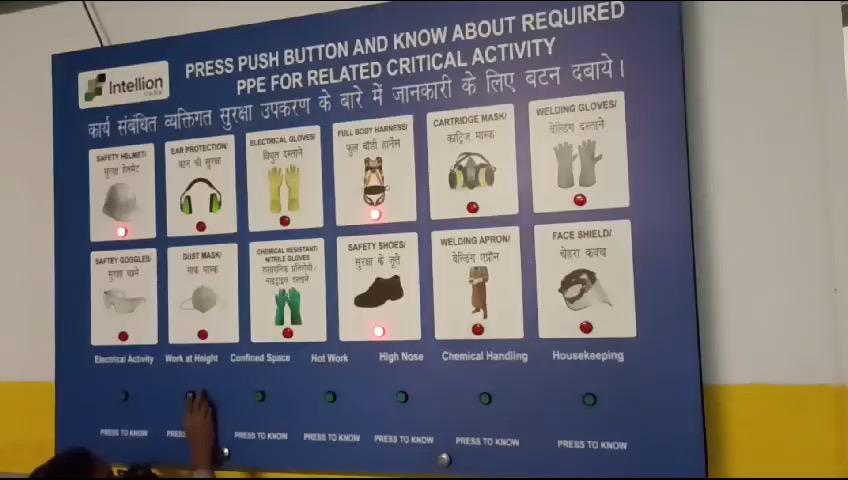
Description of the Innovation:
Indoor & Outdoor Air
Quality Monitoring & Control
myIdea
• To ascertain indoor & outdoor air quality.
• To maintain indoor air quality.
• To maintain the pollution within the permissible levels of Particulate Matter, TVOC, and humidity.
• To ensure employee health and well-being inside the building.
• External –
• Integrated Anti-smog Gun with outdoor air quality monitoring device.
• The anti-smog gun gets activated the moment the sensor of the external outdoor air quality device senses PM2.5 and PM10 levels beyond the safe limit.
• Indoor -
• A portable indoor air quality monitoring device that works on the natural principle as there are no manufactured filters installed inside the device rather it filters the air through the plants.
• Real-time monitoring of indoor and outdoor air quality and outdoor air quality data uploading on HSPCB and CPCB portal.
• Able to maintain EC commitments and data upload to CPCB & HSPCB portal.
• Purifying the Indoor Air in a Natural Way with a Real-Time Air Quality Monitoring System.
• Real-time surveillance system to monitor Particulate Matter, TVOC, and Humidity with Inbuilt sensors for both Indoor and outdoors.
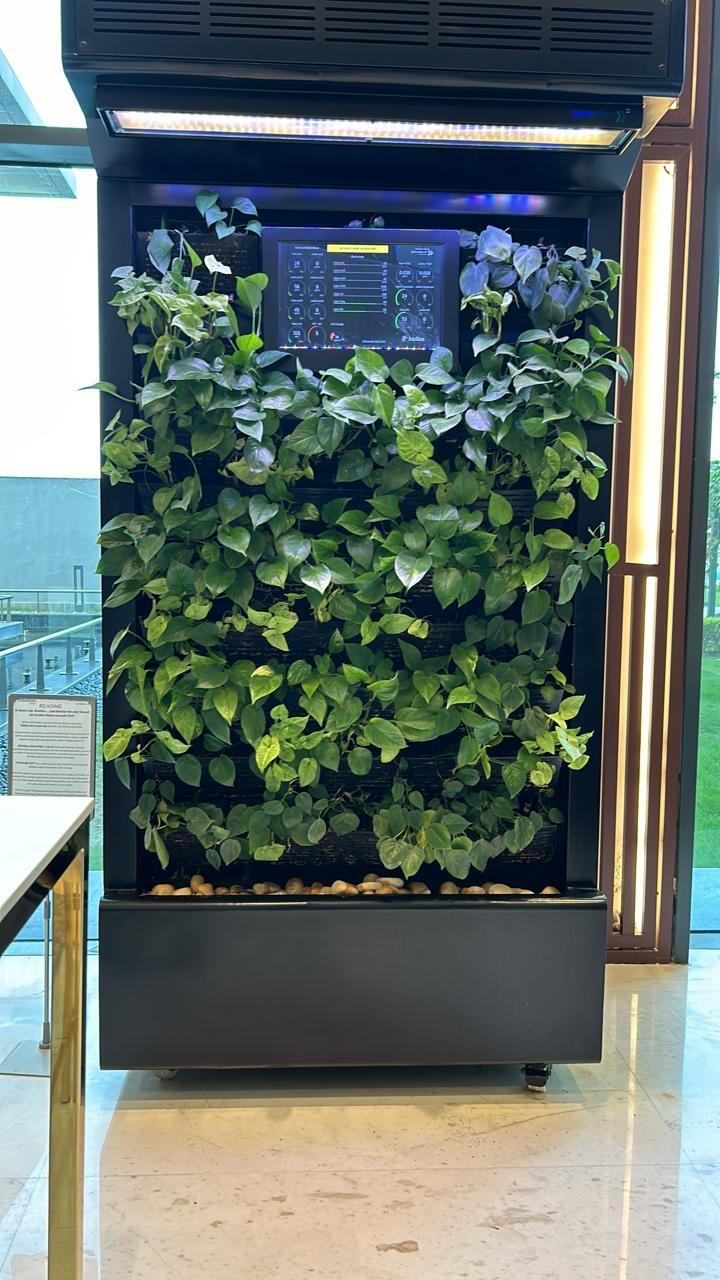

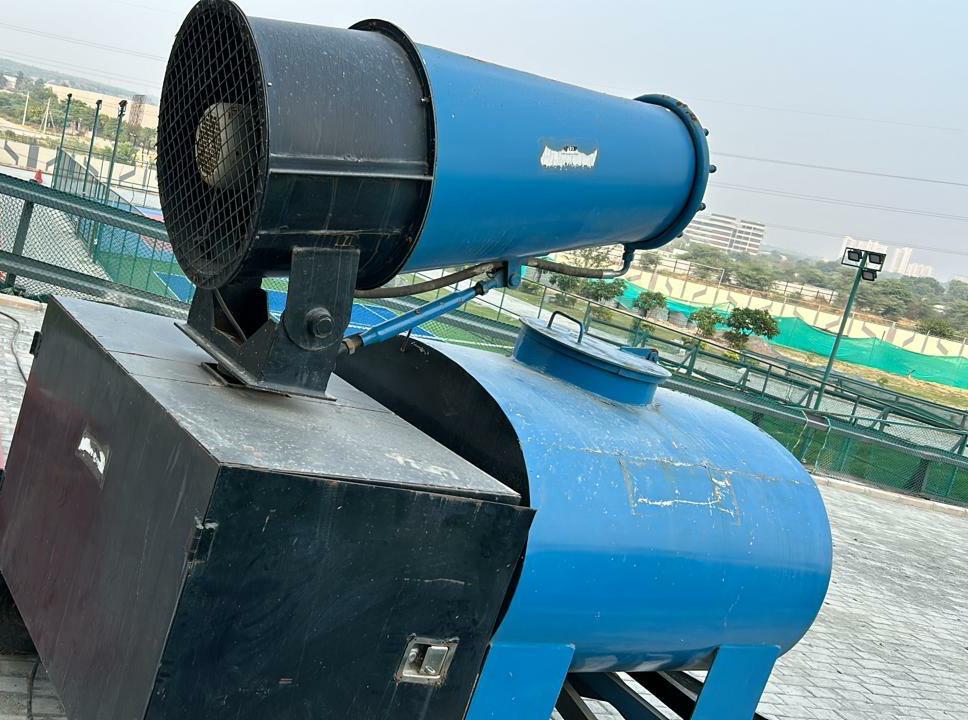
Description of the Innovation:
Mopping Scooty
myIdea
• To Improve Efficiency
• Reduce cost
• Reduce Manpower
• Introduce something catchy and innovative
• The introduction of the Mopping Scooty emerged as a strategic solution to enhance cleanliness within the mall, responding to the escalating footfall. The extensive layout of the mall presented a challenge, prompting the implementation of this innovative cleaning approach. This initiative not only proved effective in saving time but also facilitated an increase in cleaning
• The incorporation of the Mopping Scooty yielded significant cost efficiencies, resulting in a commendable 27% reduction in overall costs. Furthermore, the savings translated to an impressive economic metric of 0.40 paise per square foot, demonstrating a tangible and measurable impact on operational expenses.
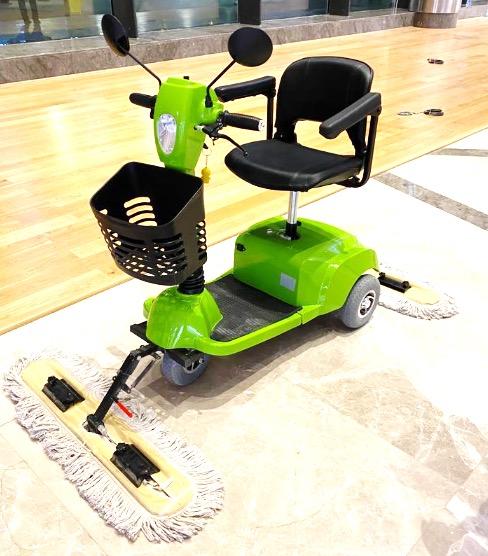
• Recognizing the expansive layout of the mall's atrium and floor walkways as a pressing need, the swift implementation of the Mopping Scooty became imperative for enhancing the cleaning efficiency.
• The Mopping Scooty emerged as a tailored solution, seamlessly addressing the challenges posed by the mall's vast atrium and extensive floor pathways, and thus contributing significantly to the overall operational efficiency of our cleaning procedures.
• This not only underscores the practicality of the initiative but also positions the Mopping Scooty as a cost solution for maintaining cleanliness in the face of burgeoning foot traffic within the mall.
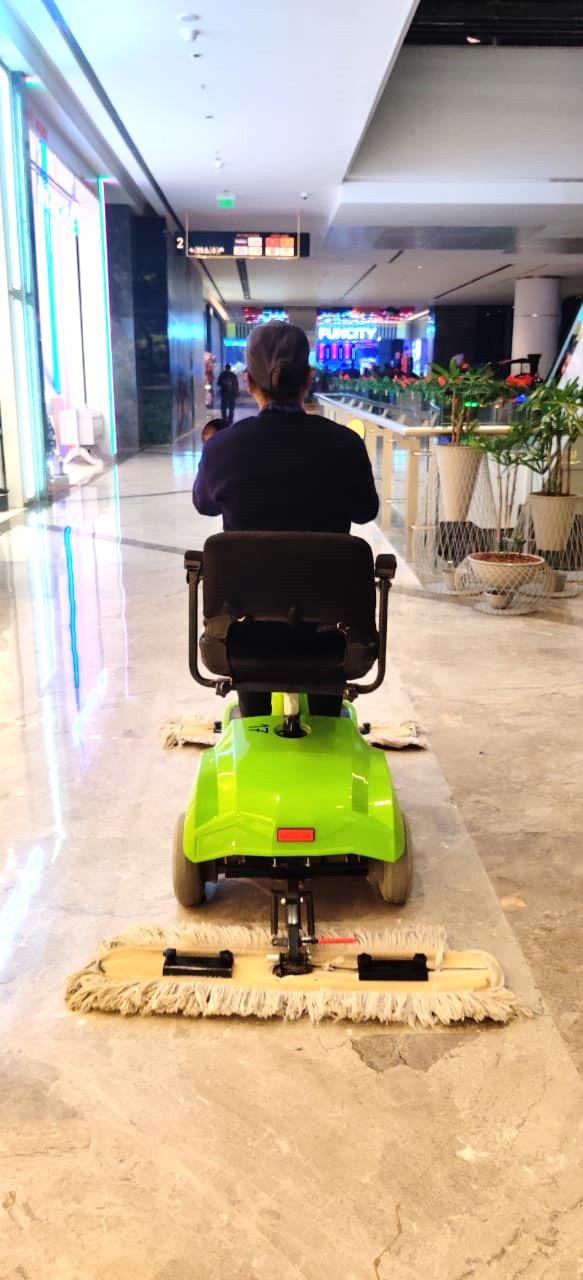
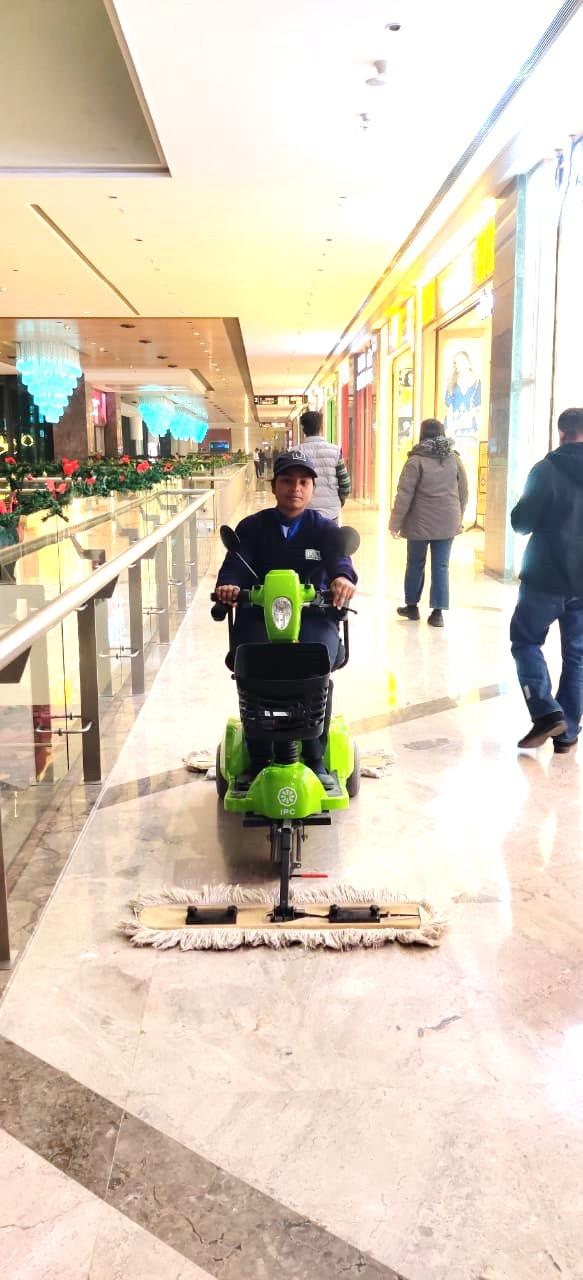
Description of the Innovation:
Mural Painting
myIdea
• On our campus we have Food Court which is adjacent to the Rock Area which gives a dull look
• Brainstormed with our team to make the area look vibrant & and planned for Mural Painting-with Nature Theme for a Good Employee Experience
• In a continuous endeavour to enhance employee experience on the campus, one of the recent initiatives that were taken up is Mural Painting on the rocks
• Mural painting is a large painting done on Walls/Rocks
• There are various themes in Mural Painting. We chose a Nature theme for our campus.
• We’ve contacted various consultants, but the cost was too high. Then, this was done by the local vendor which cost 4.9L. The warranty is 5 years.
• Mural Painting helps in making the dull area look vibrant.
• It is engaging. Attracts employees on the campus.
• In their leisure time, they just come and spend time here. It brings added color, texture & and dimensions to the surrounding area
• Making them visually appealing.
• This helps in the facelift of the campus.
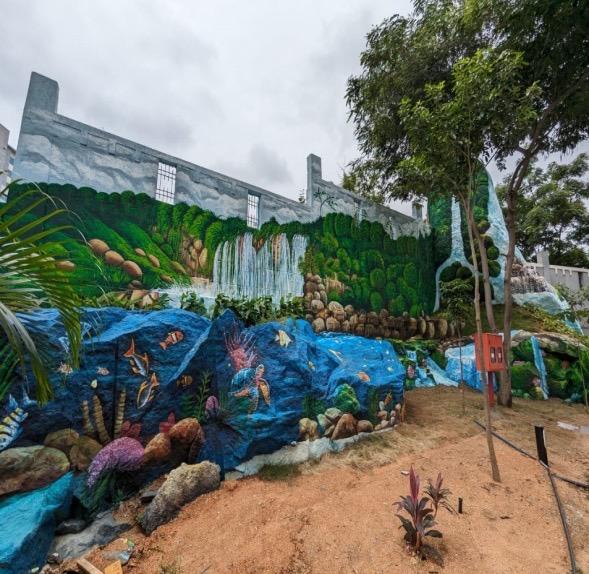
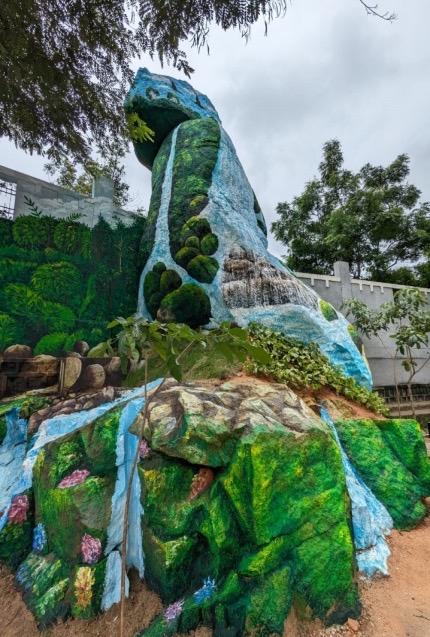

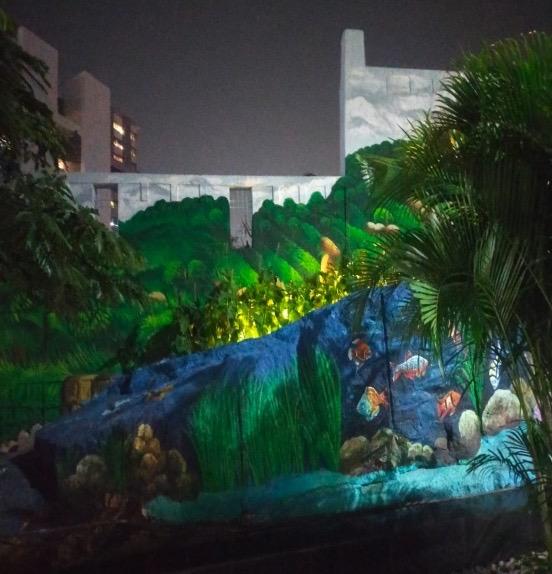
Description of the Innovation: CHALLENGE
Know Your Plants
myIdea
• Identification of plant/tree varieties present within the community because
• Lack of experience with the plants to the residents.
• Unfamiliarity with the varieties
• Complexity of plant varieties and families.
• Absence of resources that will guide them to know their plants.
• Smart plant board – Scanner-based name boards for all the plants and trees.
• Differentiating the plant habits based on different color scanners boards.
• Important facts are written separately for each variety of plant on the name board along with the scanners attached to grab his/her attention.
• Effortless scanning and active learning for the folks.
• Preventing Confusion: Similar-looking plants or species variations can create confusion. Labels prevent misidentification by clearly indicating the specific name of each plant.
• Accessibility: Visitors or individuals interested in learning more about the plants can easily access information through these smart boards without needing external assistance.
• Detailed information about the plant
• Four different color boards for segregated categories i.e. Green – Trees and palms, Yellow- Shrubs, Maroon- Ground covers, and blue for medicinal plants.
• Identification of plants, maintenance, and their uses is just one click away from the user.
• User Friendly interface and can be checked with any smartphone but the only thing you need is an internet connectivity
• Budget friendly and cost is only for the laminating sheet, A4 size paper, and nails to fix on the board.
• Boards and stands are used from the leftover wooden waste from the construction villas.
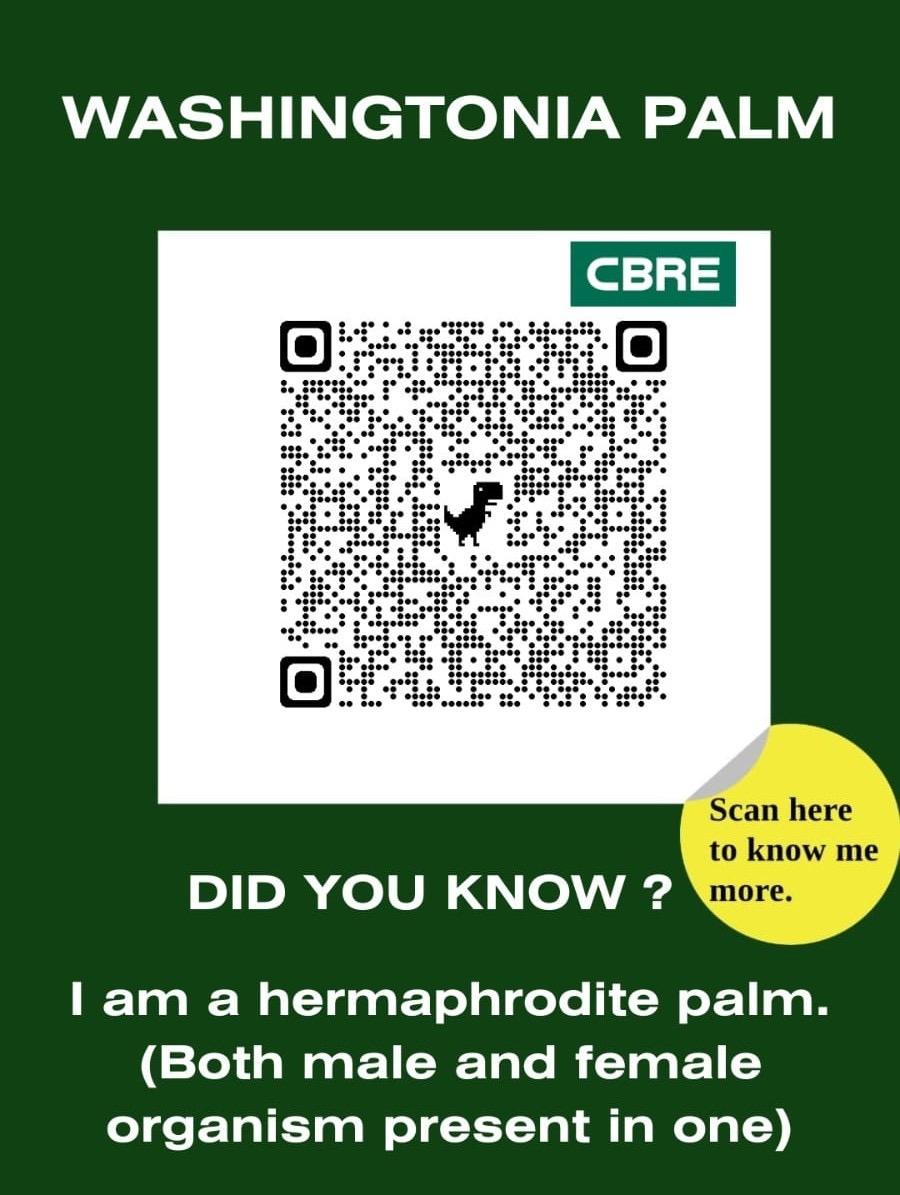
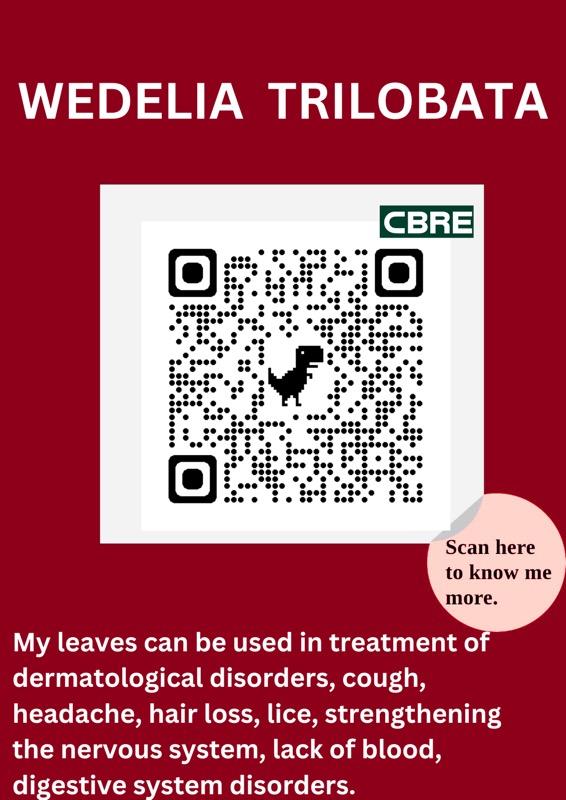
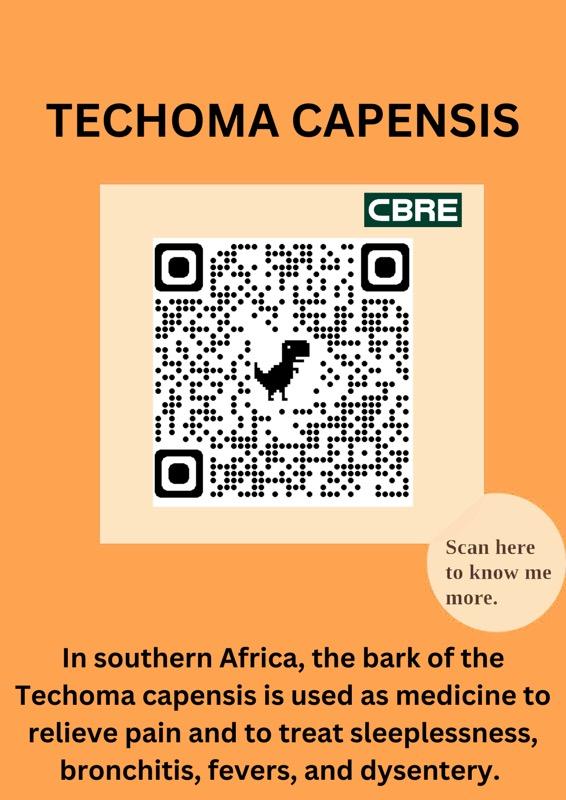
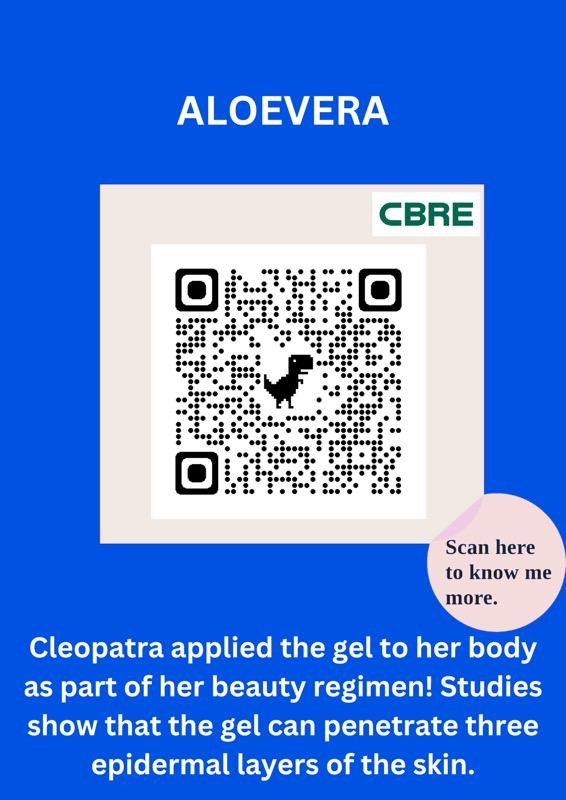
Description of the Innovation:
Power Surge Protection System
• All Blocks are suffering power surges and power fluctuations repeatedly.
• In this issue, all resident’s flats’ electronic and electrical gadgets are affected by high voltage flushing.
• As per builder provision they are not provided any electrical safety for tripping mechanism.
• We have verified all systems and made the provision for the VMR power surge protection system at the Block level.
• We have Made a VMR power surge protection system with a low cost.
• It was resolved over day-to-day complaints from residents of equipment damages.
• All flats’ Electrical and electronic Gadgets are safe high voltages and power surges.
myIdea
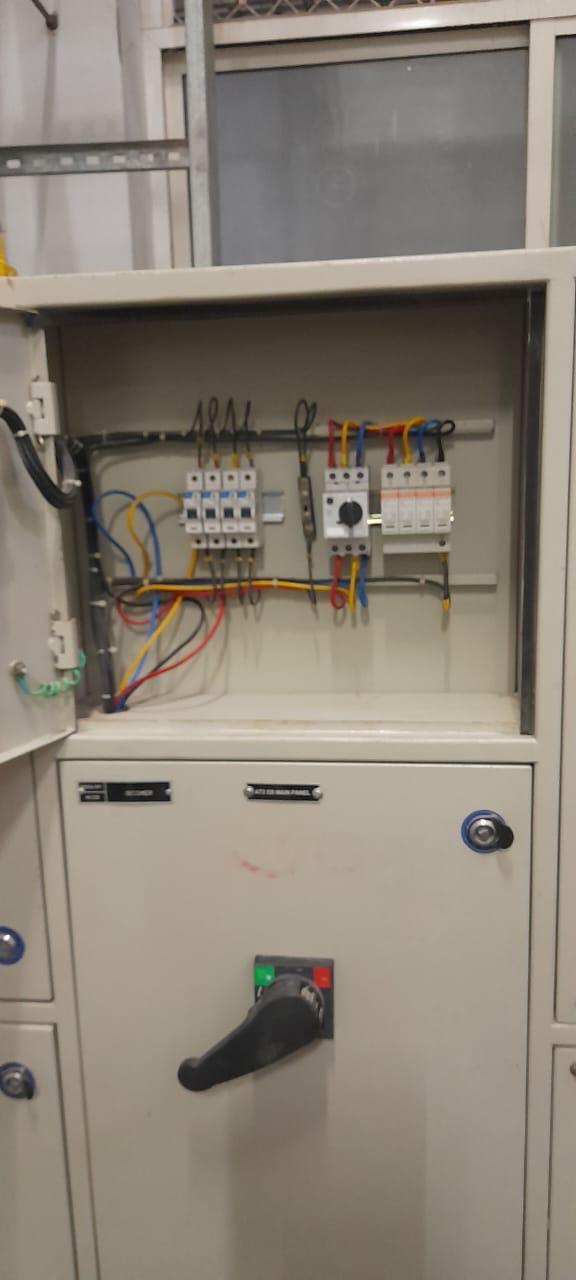
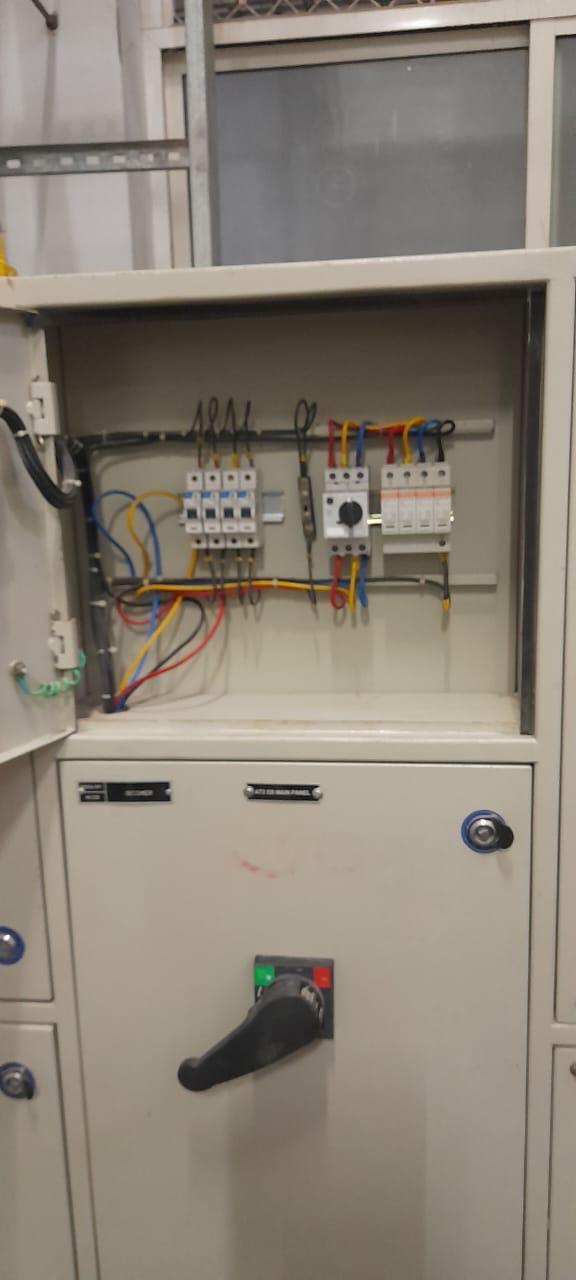
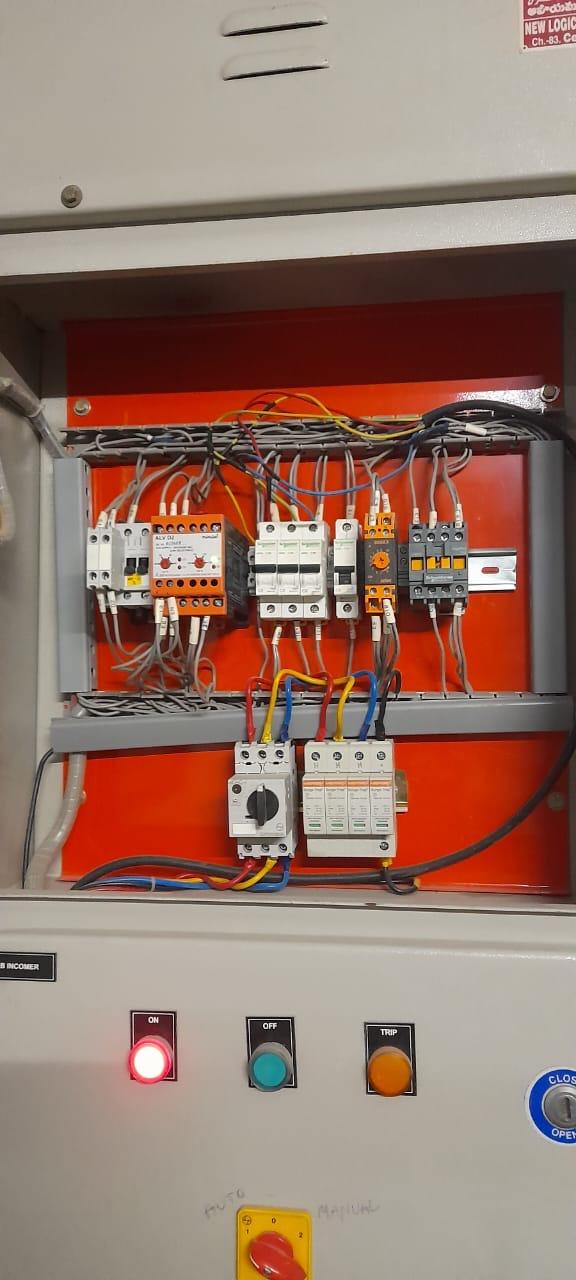
Description of the Innovation:
Installation Of Bucket Type SS Strainer In Cooling Tower
• Faced a few of the chiller's breakdowns on the campus & unable to deliver cooling comfort to the clients,
• Unable to get the costing approval to get the chiller into operations.
• Impacting CBRE SLA
• The Chiller Condenser Approach is increasing gradually due to the accumulation of foreign particles.
• Frequent clogging of chiller condensers & leading to Condenser tubes puncturing and water entering the compressor.
• After inspection we found that the strainers installed in the Chiller Pumps are not sufficient to stop the particles.
• So, we have initiated the source and planned to install the Bucket type SS Strainers in the Cooling tower outlet line.
• With this Condenser approach is maintained.
• It will reduce the cost of Descaling activities to be done in the Condenser.
• It will reduce the tube punctures in the condenser and increase the efficiency of the chiller.
• Zero downtime.
• Approx cost for Procuring the strainers Rs.2.4 lacks /building.
• Value add for the client.
myIdea
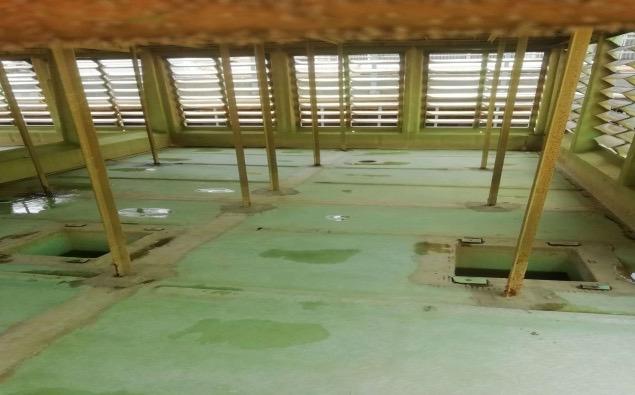
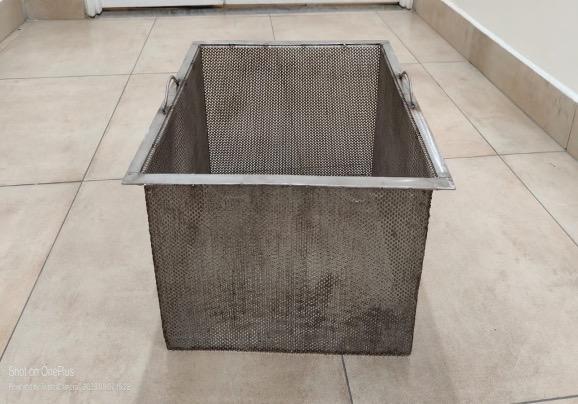
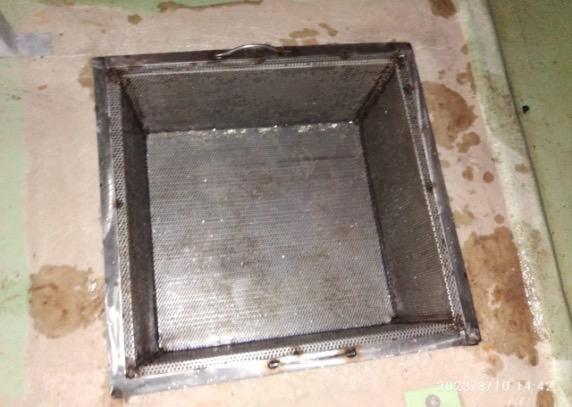
Description of the Innovation:
Wireless Bus-bar Temperature Monitoring System
CHALLENGE
myIdea
• Abnormal temperature increase in bus bars can’t be detected for which potential faults or issues within the electrical system can occur at any time.
• It is difficult for us to monitor the bus-bar temperature inside the Main LT panel regularly.
• During Thermography testing, we saw a lot of hot spots inside the busbars, a few times we found them in melted condition
• A wireless bus bar temperature monitoring system utilizes wireless communication technology to monitor and transmit temperature data from bus bars in an electrical power system.
• Widely temperature measuring range is -50℃~+125℃;
• Regular monitoring of bus bar temperature.
• It can be empowered with a centralized BMS system/ cloud
• The breakdown period of breakers & and other spare equipment will be less
• CT-powered, Sampling frequency 15Sec, Wireless Transmission Distance 100 meters,
• Minimized the fire risk/unscheduled downtime of critical installations
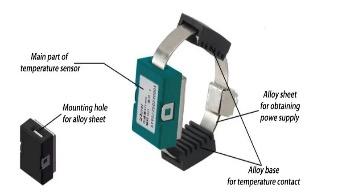
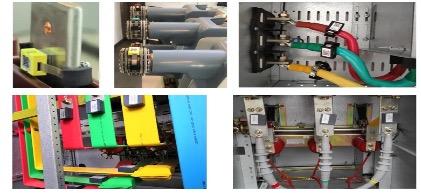
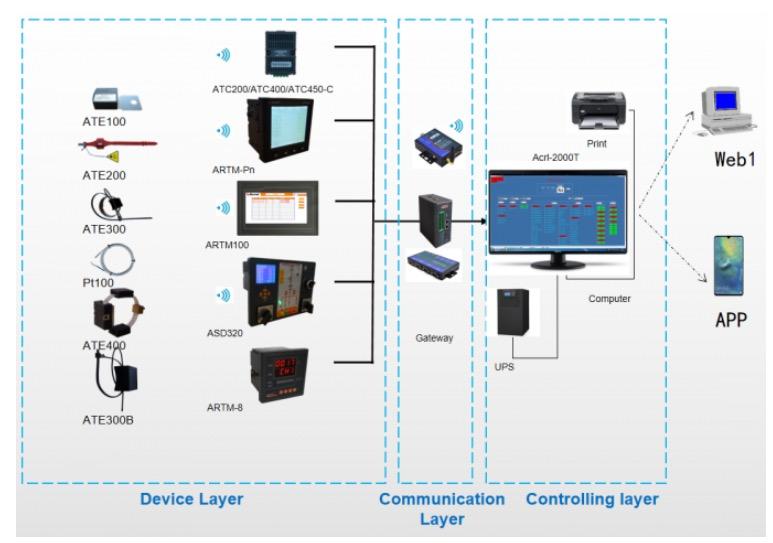
Description of the Innovation: CHALLENGE
• Unexpected system failure due to low DC voltage
• Time delay for power system restoration
• RCA gets impacted due to delay in restoration
DC Voltage Monitoring for HT Panel
Remotely
• Unable to get to know when exactly the system voltage gets down and protection system bypassed.
• Low-voltage alarm circuits is essential to maintaining electrical systems’ safety and efficiency. These circuits are designed to detect and respond to low voltage levels, alerting technicians and operators to potential issues before they can cause damage or disruption.
• A proactive measure taken by Installing DC voltage monitoring relays to remotely monitor, control, and protect the unwanted power system failure
• The low-voltage alarm circuit is designed to alert when the supply voltage of 24-volt drops below a certain level. The circuit consists of a 555 astable integrated circuit that generates an alarm signal. The astable requires a certain amount of voltage to function, which is supplied to pin 4 of the 555 IC.
• Eliminate the manual intervention of periodic checking of DC voltage, which also eliminates human interference.
• Monitoring relays contribute to the overall reliability of the electrical system by providing early warning of potential issues. Detecting abnormal voltage conditions helps to prevent unexpected system failures.
• These are integrated into alarm systems to detect and respond to voltage abnormalities.
• Response time reduced resulting in overall near-to-zero downtime
• Investment: INR 9k, which is negligible in terms of calculating ROI.
myIdea
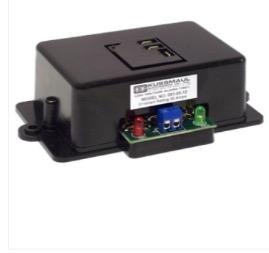
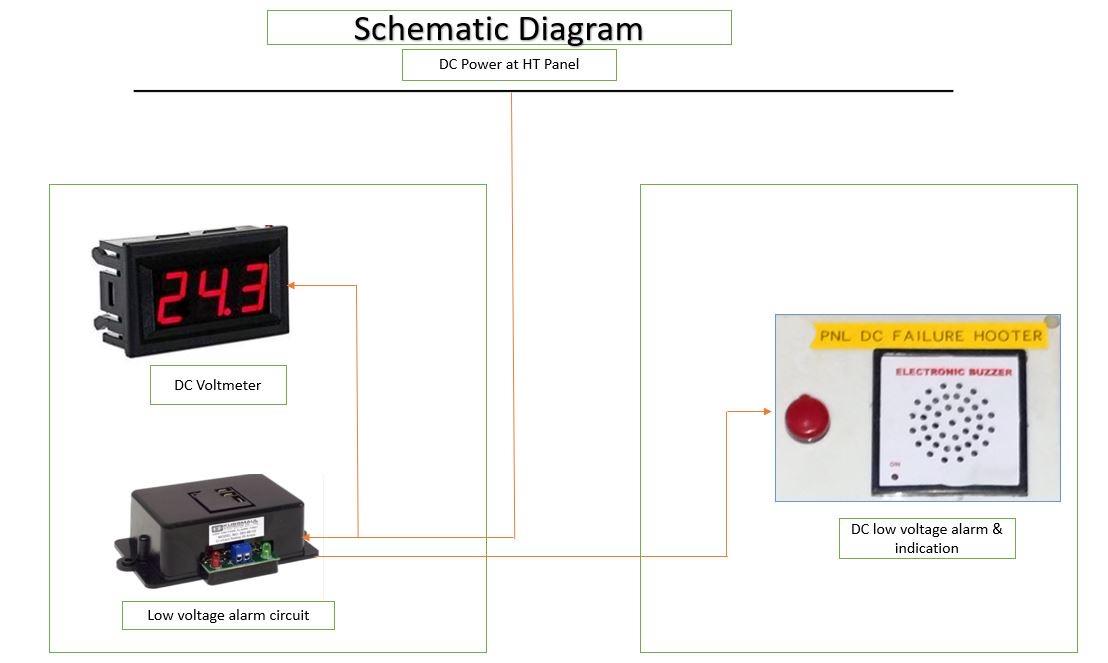
Description of the Innovation:
Zero Water Discharge
myIdea
• Scarcity of Fresh water
• High Cost of Fresh water
• Shortage of freshwater can turn into a business risk
• Water recycle is a sustainability commitment .
• High consumption of fresh water
• STP treated water appx 225 to 250 KL generated every day.
• As per KSPCB all the recycled water to be utilized in the facility and not to be discharges outside the campus.
• Online STP monitoring to meet the KSPCB Compliance .
• Utilization of treated water used for cooling towers
• Implemented water aerators across all faucet at campus
• Rainwater treated with UF and utilized for chillers
Below Initiatives implemented
• Recycled STP treated water at campus is utilized for irrigation
• (50,000 Sq. Mtr of gardening) Appx – 40KL/D.
• Toilet flushing for BGL-15 & 16 . Appx –50KL/D.
• Treated water processed through RO and utilized for water cooled chillers. Appx –150KL/D.
• This meets zero water discharge of the treated water and meets the compliance requirement of KSPCB.

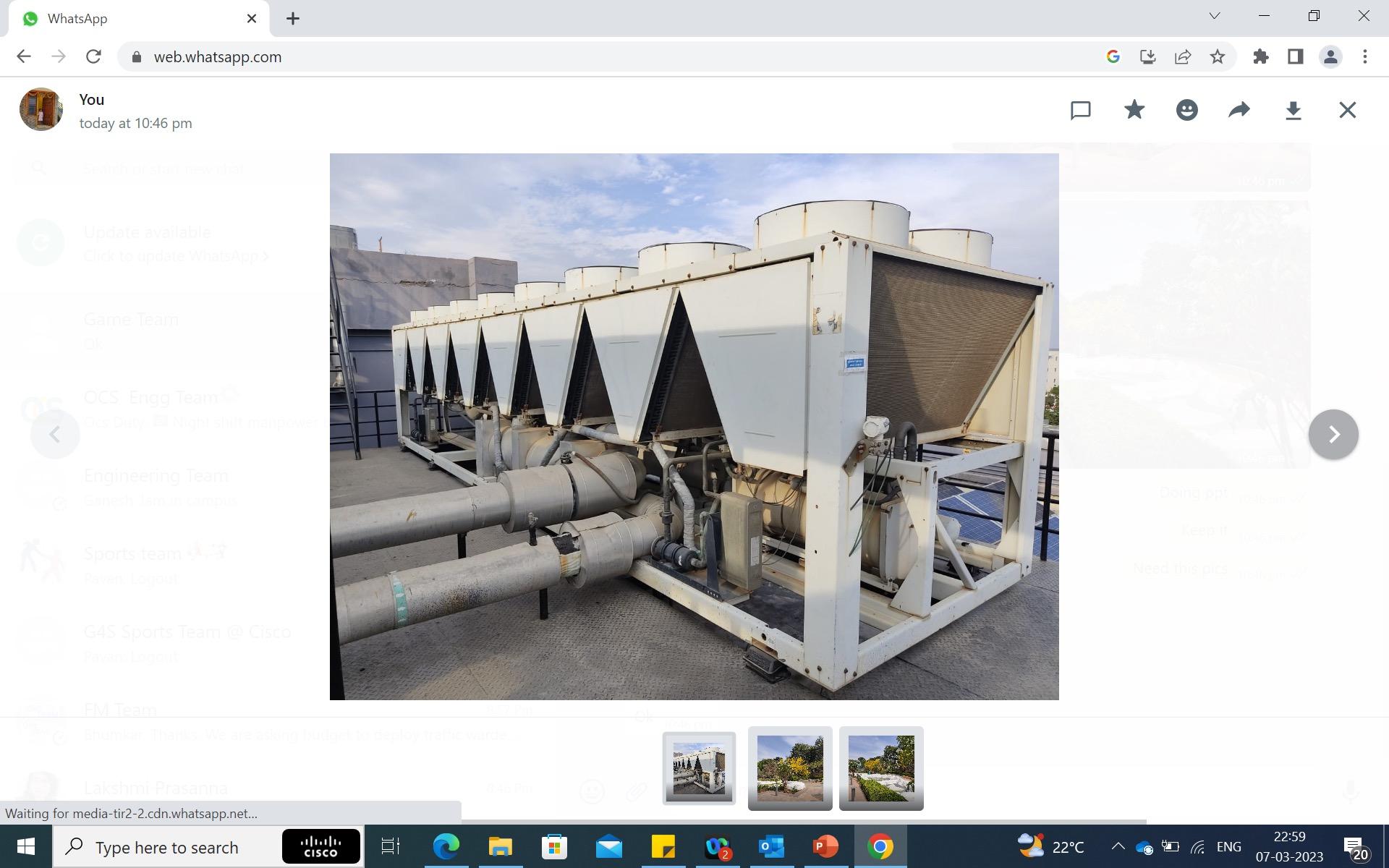
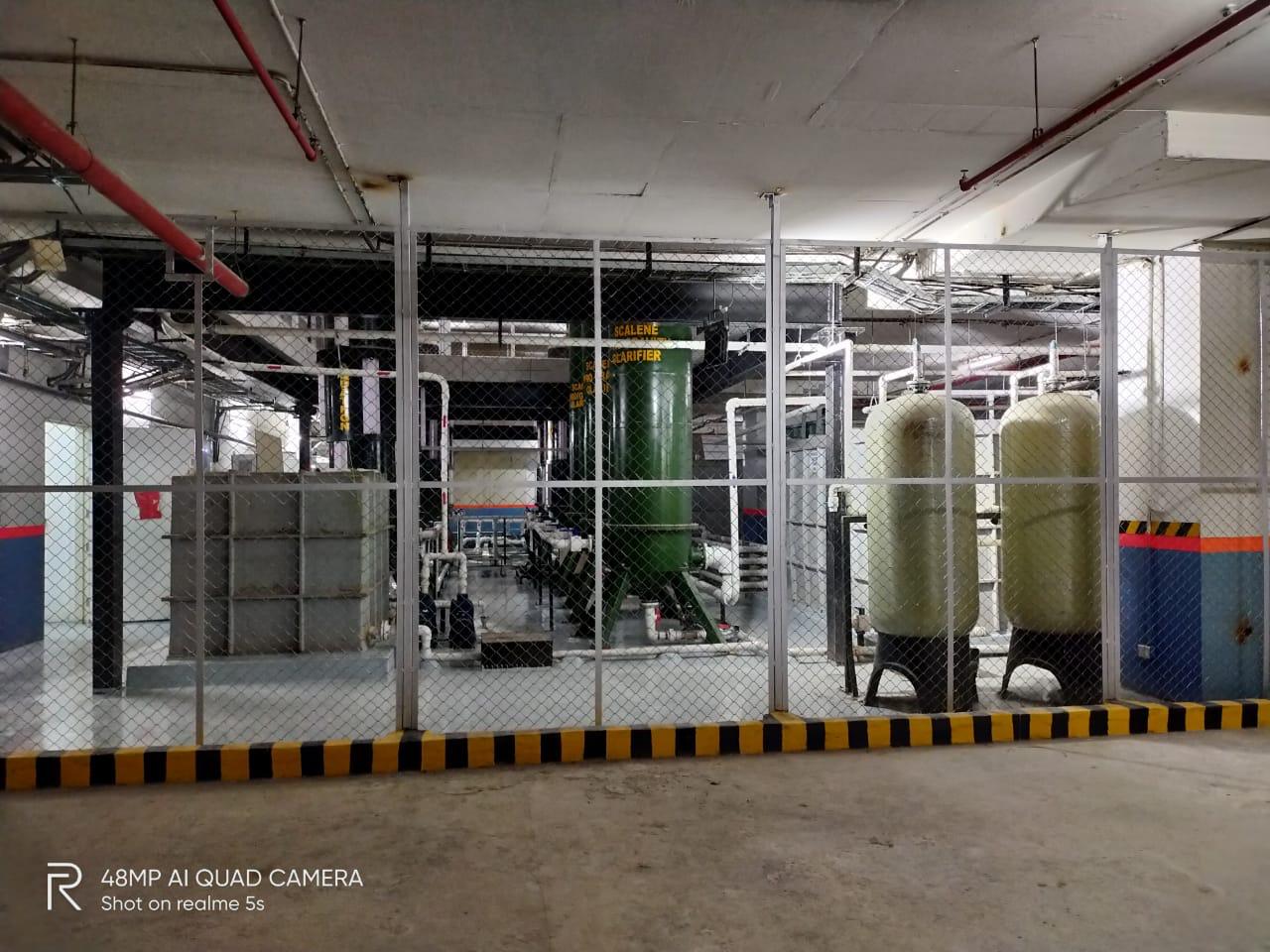
Description of the Innovation:
Smart Flow Meter For Building Plumbing System
CHALLENGE
• What we cannot measure , cannot be controlled .
• Scarcity of Fresh water
• High Cost of Fresh water
• Shortage of freshwater can turn into a business risk
• High consumption of fresh water
• Water conservation is a sustainability Commitment
• Smart Flow meters for the complete building plumbing system.
• Enabling leak alerts on Realtime basis on faulty fixtures to avoid the water wastage.
• Comprehensive Dashboard with Usage Analytics
• Water consumption report with trend on daily basis.
• Enabling benchmark to track and save the water consumption.
• Leakage alarms with instant notifications.
• Identify leakages directly from dashboard & fix leakages, faulty fixtures immediately.
• Complete track on the building water usage.
• Observe spikes/ changes in usage patterns take informed timely decisions.
• Usage analytics, Get detailed reports that provide consumption patterns at every point
• Track water contributed from each riser
myIdea
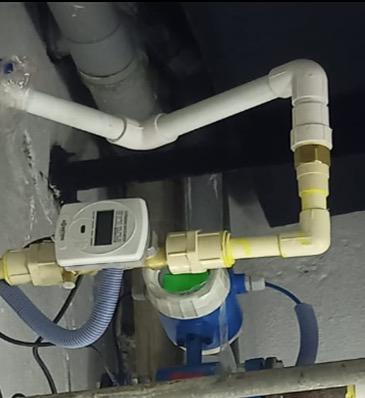
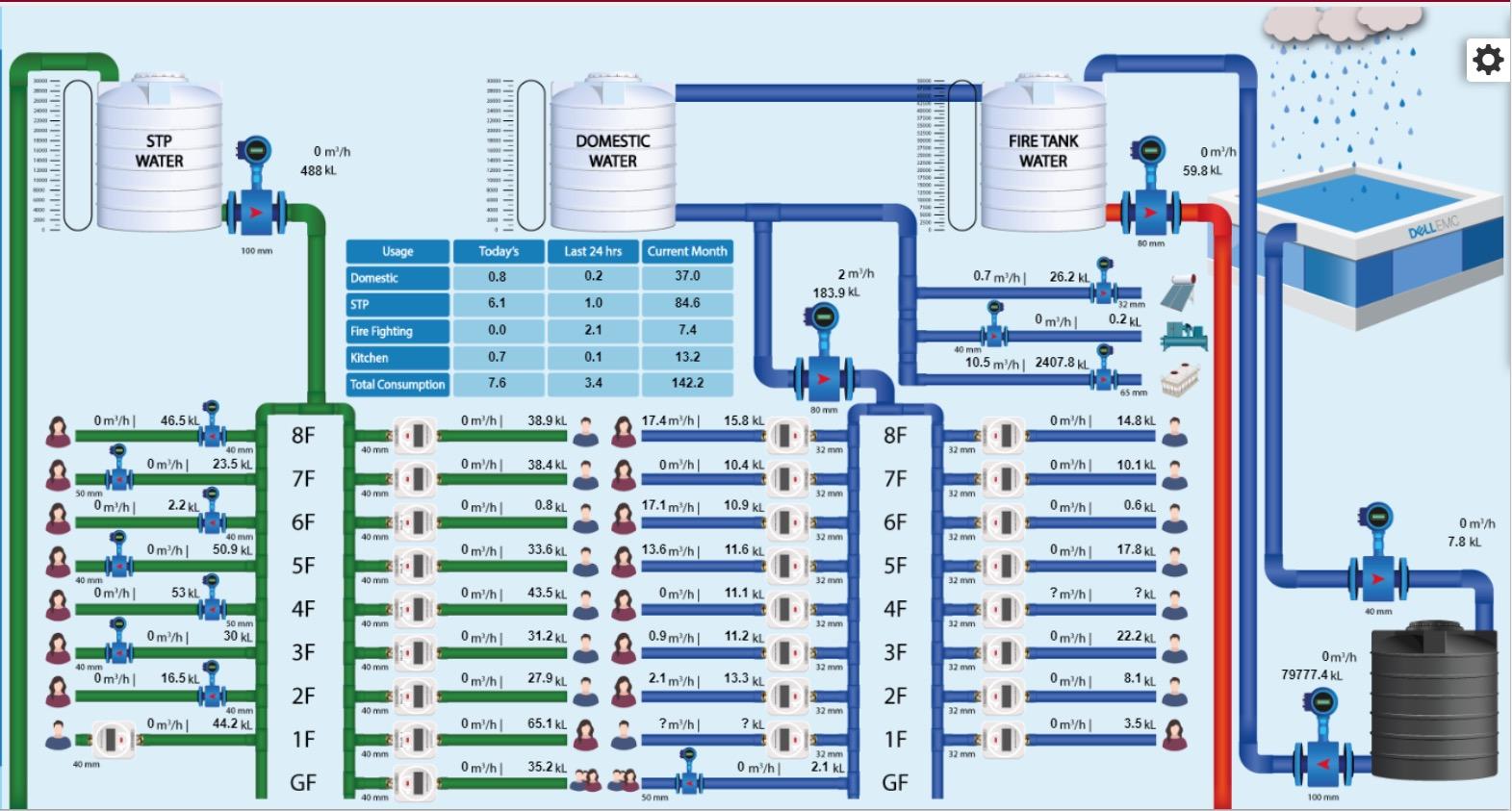
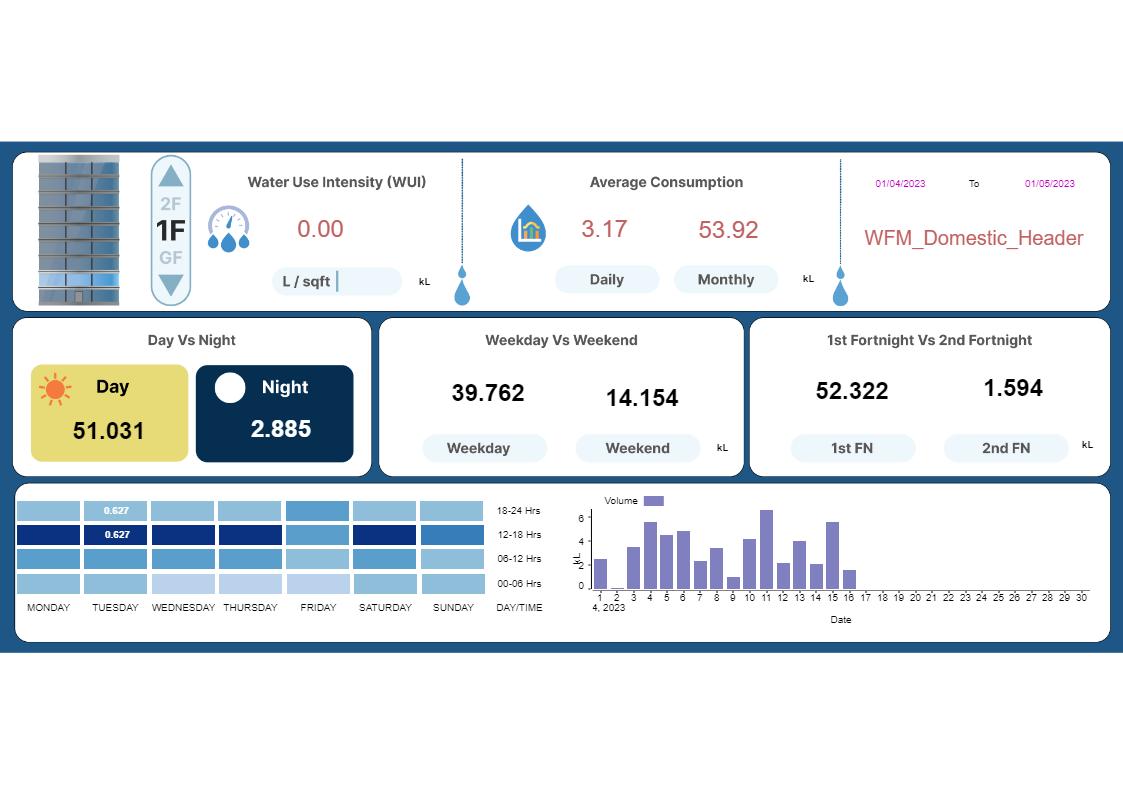
Description of the Innovation:
DC Rectifier Plant Battery Optimization
• High power consumption
• High cost of Battery replacement
• Sustainability Commitment
• High risk of hazardous materials
• At Juniper There are 62 DC Rectifier plants used to provide DC power supply to the lab equipment’s. These DC Rectifier batteries operates at higher Ampere with lesser voltage per cell & widely used across the Networking industries. At Juniper Networks these DC rectifier plants are connected to different Labs. Currently, all these units are operating with <55% load & constant for the last 4 years.
• Hence, it is recommended to reduce the battery capacity across all plants. & there by achieve cost savings from both purchase & battery charging current as well as floor weight reduce and free space across the plants.
• Battery charging current will be less, So resulting savings in power consumption
• This initiative results around $ 45,120 savings during purchase of battery banks without impacting the stakeholders' requirements or present utilization pattern.
• This reduced capacity of batteries will also reduce the impact on environment by lesser usage of Lead & reduces weight on floor plate.
• Reduced quantity of hazardous materials such as plastic, lead, connectors etc while scrapping the batteries.
• Estimated Saving : 36,48,000 INR
myIdea
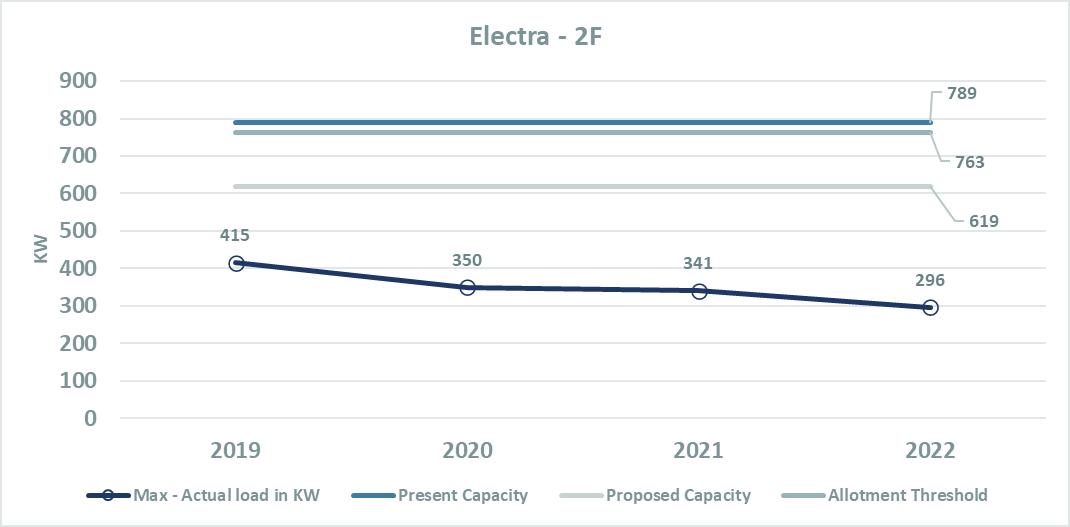
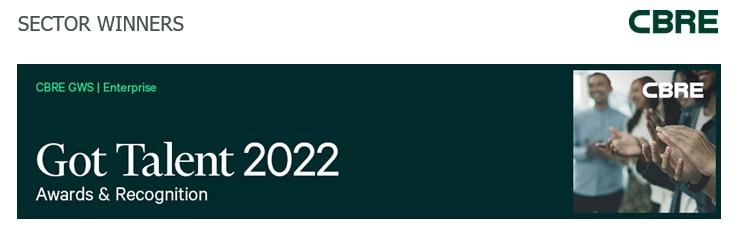
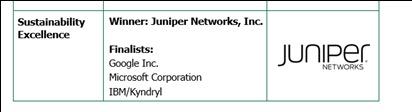
Description of the Innovation:
Best of Waste
• Culture of innovation and creativity
• Waste generation and disposal
• Team motivation
• Client Satisfaction and appreciation
• We have launched on internal initiative to recycle waste as efficiently as possible and bring in change of view – quite literally.
• Used Chemical Container, Gumboots, Dinner plates, Mopsticks,Tissue roll and Packing material are majorly used to create artefacts.
• The aim is to reduce waste generation in the building by 80 to 85%.
• Activity involving support staff apart from regular cleaning can help reduce attrition level and mental/physical stress levels.
• Creativity was the inspiration for support staff team where they had potted out of chemical cans, artistic mirror were made from broken glass, artefacts were created from used coffee grounds and broken mugs.
• Achieved Sustainability goal by achieving Best out of waste.
• The artefacts are displayed in Lowe’s Cafeteria. Apart from amplifying the overall aesthetics of the cafeteria it also has a pleasant view of associates visiting this space.
myIdea

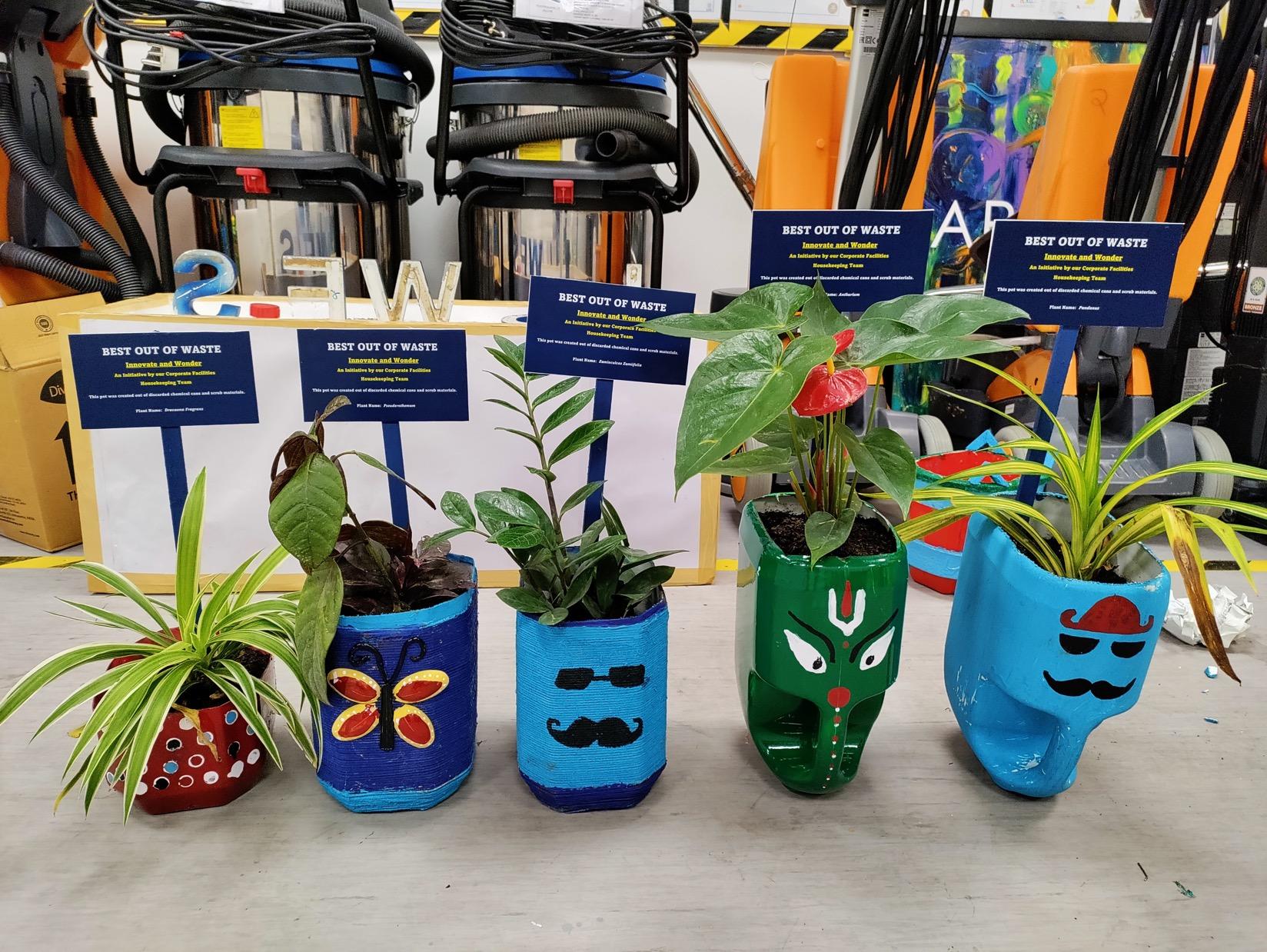
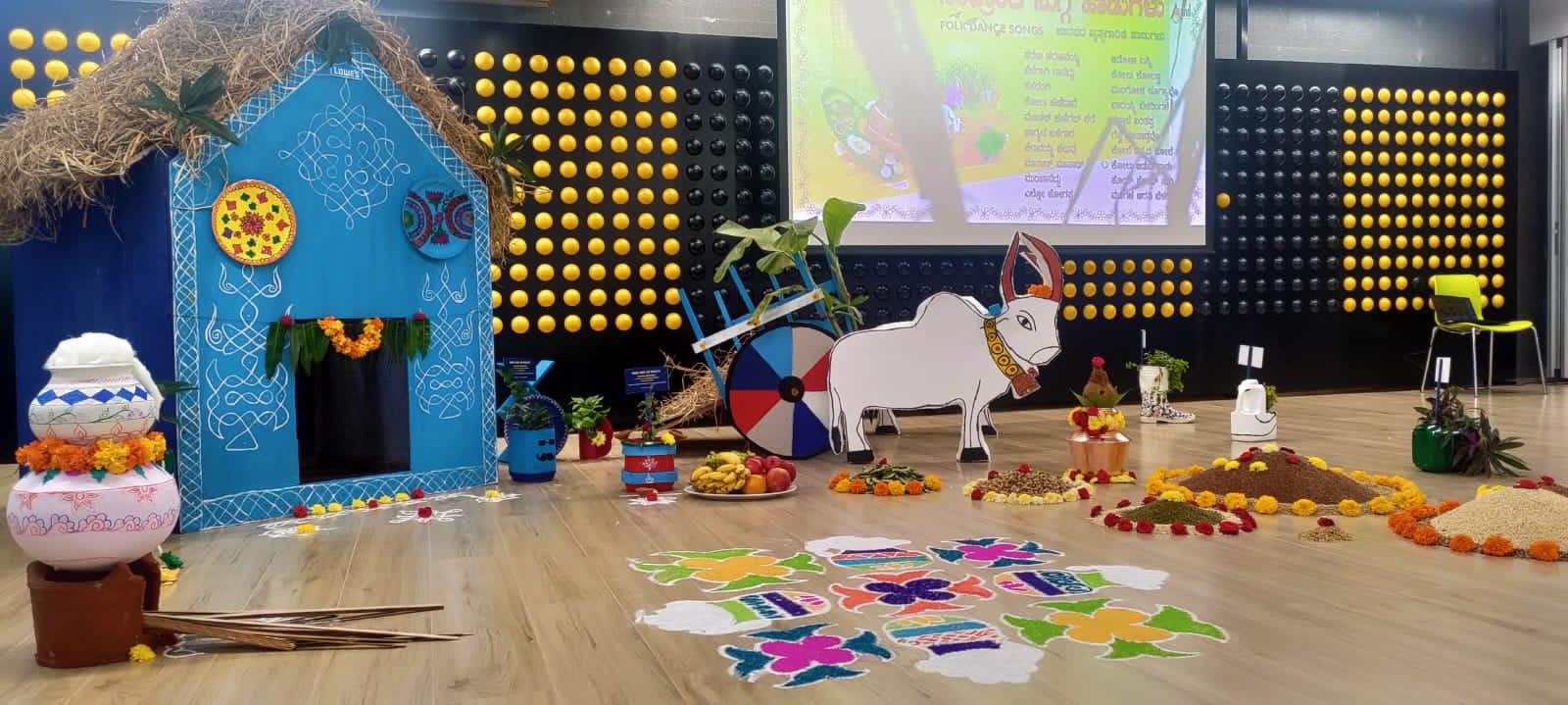
Description of the Innovation:
WOW :
Wellbeing Out Of Waste
• Waste segregation
• Innovative solution towards sustainability
• Cost of fuel
• Commitment towards sustainability
• Initiatives towards protecting mother earth
• Problem statement: Low waste diversion rate of ~65% per month (~1.2 tons (per day) of waste including (Dry, Wet & Landscape waste) mostly ending-up in landfill).
• Solution
• Four-way Bin: Introduced 4-way bins enabling segregation at source, preventing 90% cross contamination before secondary sorting.
• Smart Bin: AI powered bins enabled sorting of the food waste generated in kitchen at source.
• Biogas plant: Utilizing ~18 tons/month food waste into generating ~1.3tons/month of biogas (equivalent to ~0.94 tons of LPG) which is used in our on-site live kitchen.
• Compost Pit: Created 5k Liters of compost pit, recycling landscape lawn clippings, leaves etc., and kitchen scrap to generate 1.3 ton/month of compost fertilizing internal vegetation & landscaping.
• Awareness: Segregation at source training to employees to help increase our diversion rate.
• Increased diversion rate to ~96% – Segregation at source effectively eradicated cross contamination. Additionally, AI powered bins helped further divert waste from landfills and into recycling.
• Soil enrichment - Composting allows recycling of landscape and kitchen scraps into nutrient-rich and organic fertilizing agent.
• Employee Engagement: Waste segregation awareness program helped engage employees with a clearer understanding of our waste management process and awareness about the scope of recycling the waste generated at our offices.
• Clean Energy: We have successfully supplemented the use of LPG in the kitchen with biogas generated on-site, thereby reducing LPG usage.
• Better Environment: Our efforts have effectively contributed to reduction of environmental pollution.
• Estimated Saving : INR 1.29 lacs per annum.
myIdea
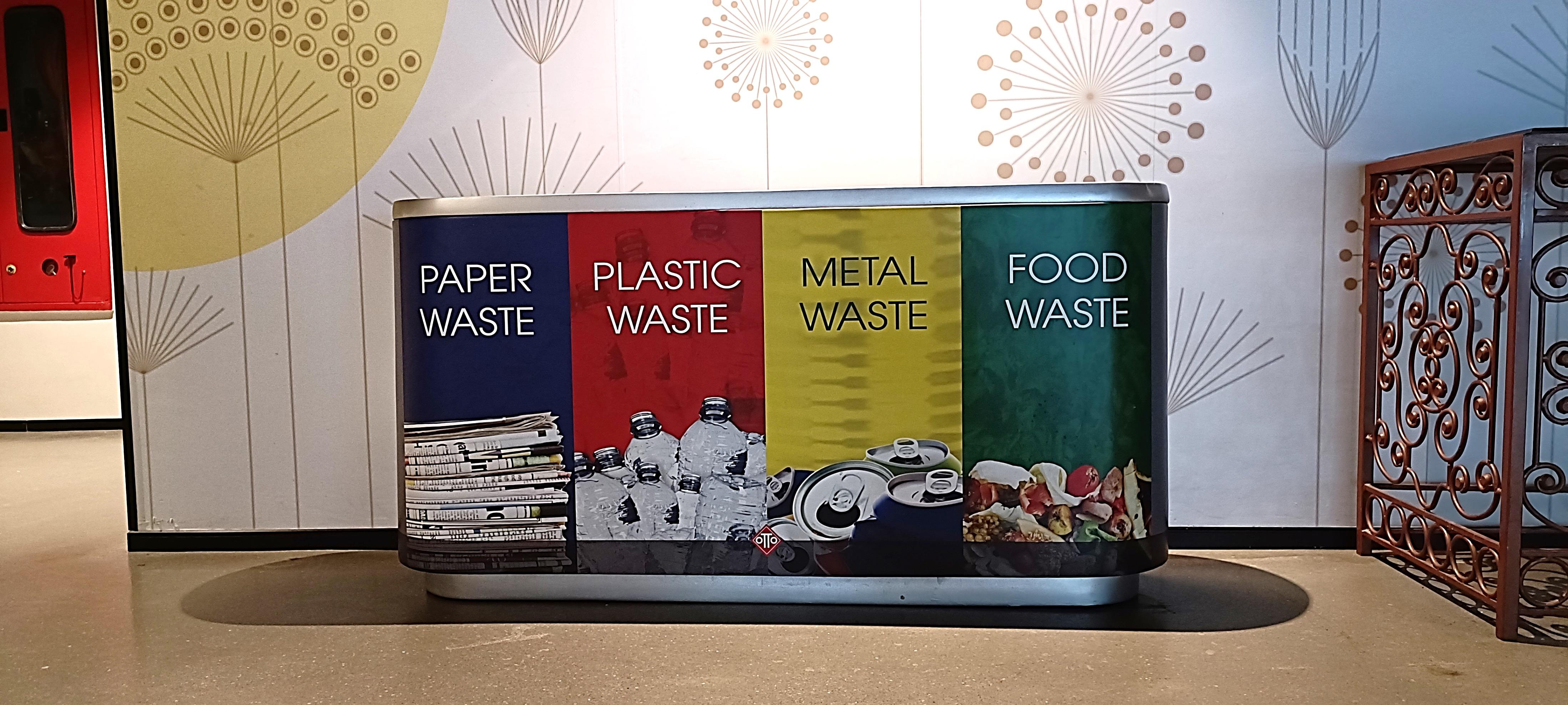
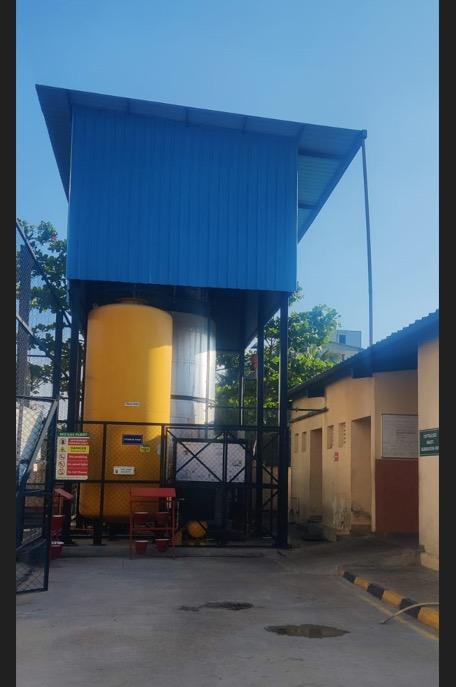
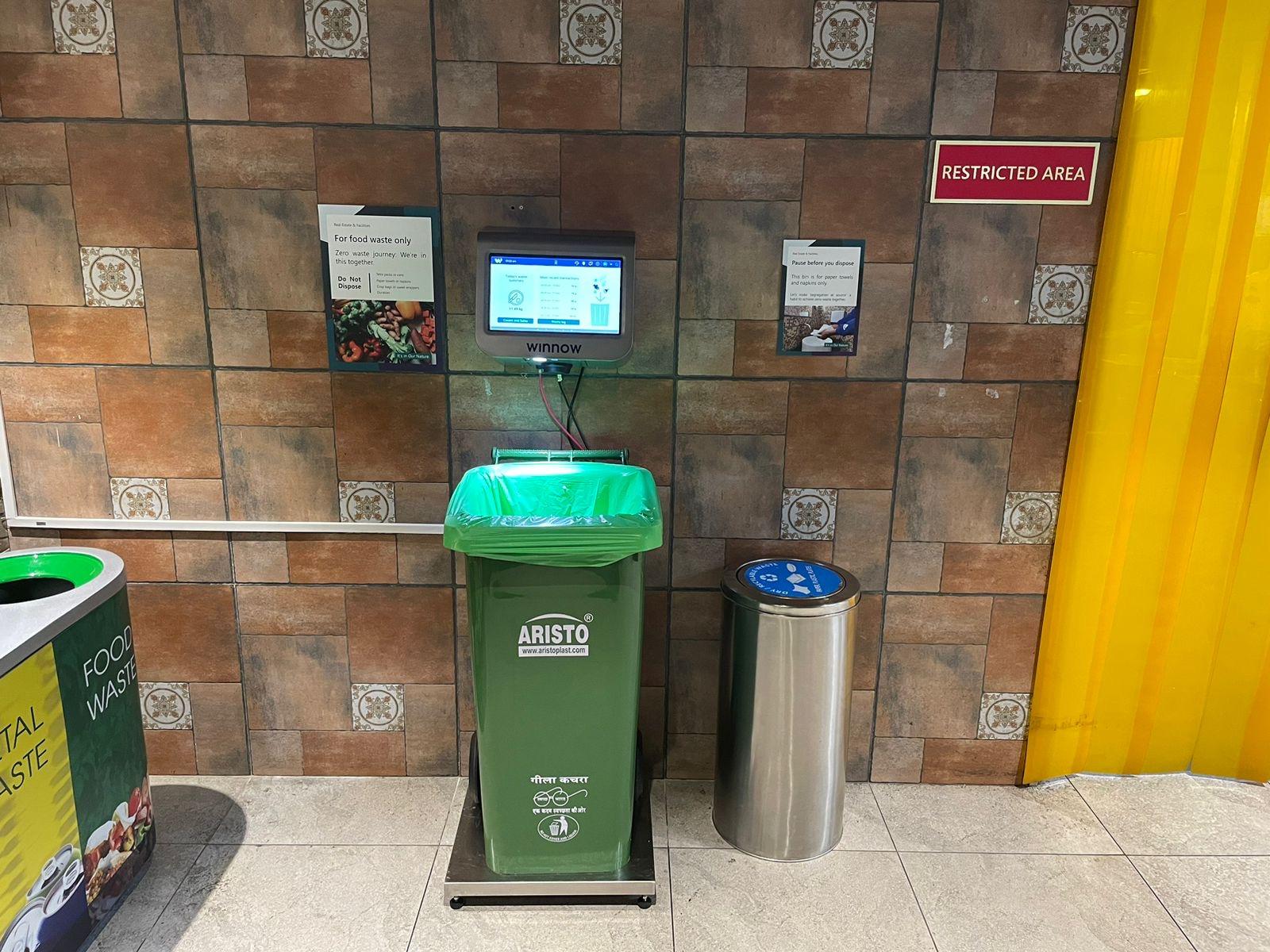
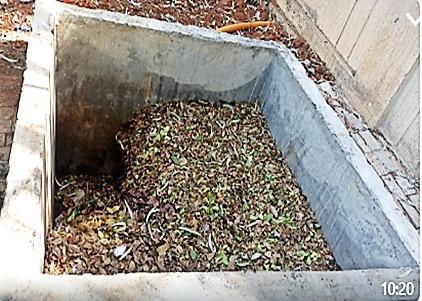
Description of the Innovation:
Chiller Plant Optimization
myIdea
• High power consumption
• Sustainability Commitment
• Inefficient HVAC operation
• Wastages to be controlled
• High cost of energy
• Plant average performance
• 3 no’s of Water cooled chillers are supporting the complete air-conditioning of the campus. All pumping system are conventional and reached EOL.
• 2 no's of chiller are retrofitted with new Magnetic Bearing chillers along with Variable primary & Condenser pumping system.
• All Pumps and Cooling tower fans are with VFD’s and with sensor less pumps.
• Chiller plant are operated with patented Hartman Loop technology.
• Automatic tube cleaning system installed for all chillers.
• Enhanced the sustainable technology of implementing ATCS & Hartman loop CPM.
• Elimination of 860 MT Carbon Emission Every Year. And Energy savings 1075 MWH / Annum.
• 40% Space saving by eliminating Secondary pumping system & optimized chiller capacity.
• Ultra low noise operation of less than 75 Db.
• Improved Plant Performance of 0.42 kw/TR.
• Estimated Saving : INR 8 Mn

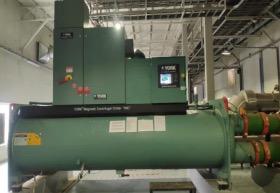
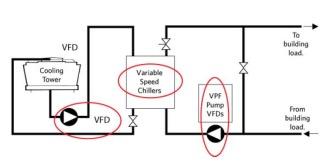
Description of the Innovation:
myIdea
• High Carbon footprint
• High cost of transport
• Lack of useful data
• Low user experience
• Low efficiency of transport
• Low transparency
• Analyzing scheduled Vs actual occupancy.
• Scheduling employees beyond seating capacity.
• Accommodated users over and above max seating capacity of a TT vehicle (12 seats).
• New enrollment request accommodated in existing routes only.
• Identified routes exceeding maximum seating capacity
• Ensuring exceeding users on a particular day are accommodated in alternate backup route vehicles.
• Continuous monitoring and tracking each individual route drivers for over scheduled routes.
• Regular briefing to all these drivers & vendor partner
• Interim option introduced additional vehicles only on Tuesdays & Wednesdays every week.
• Elimination of over all 2945 pickup & drop trips
• Elimination of 8.76 T Carbon Emission over 8 months.
• Ensuring no compromise on user safety & comfort.
• Overall cost optimization close to
• Approved
Description of the Innovation:
Emergency Alarm In Rest Rooms
CHALLENGE
• Inclusivity culture
• Easy of handling emergency
• Promote the culture of health and safety
• Employee experience
• This system would help to locate if anyone stuck inside the rest room cubicles due to lock malfunctioning.
• To avoid incidents of stuck inside cubicles
• During emergency person can press the call button.
• An indication with sound will reach at security desk.
• Security can run immediately to the location and rescue the person.
/ ADVANTAGE
• More accessible to people with disabilities or other special needs by providing audio and visual alerts.
• Increased peace of mind: Knowing that an emergency alarm system is in place can provide users with increased peace of mind.
• Improved communication: An emergency alarm system can facilitate communication between users and staff, allowing them to quickly alert one another about potential hazards or problems.
• Faster response times: With an emergency alarm system in place, staff can respond to an emergency more quickly and efficiently, reducing the time it takes to aid someone in need.
myIdea
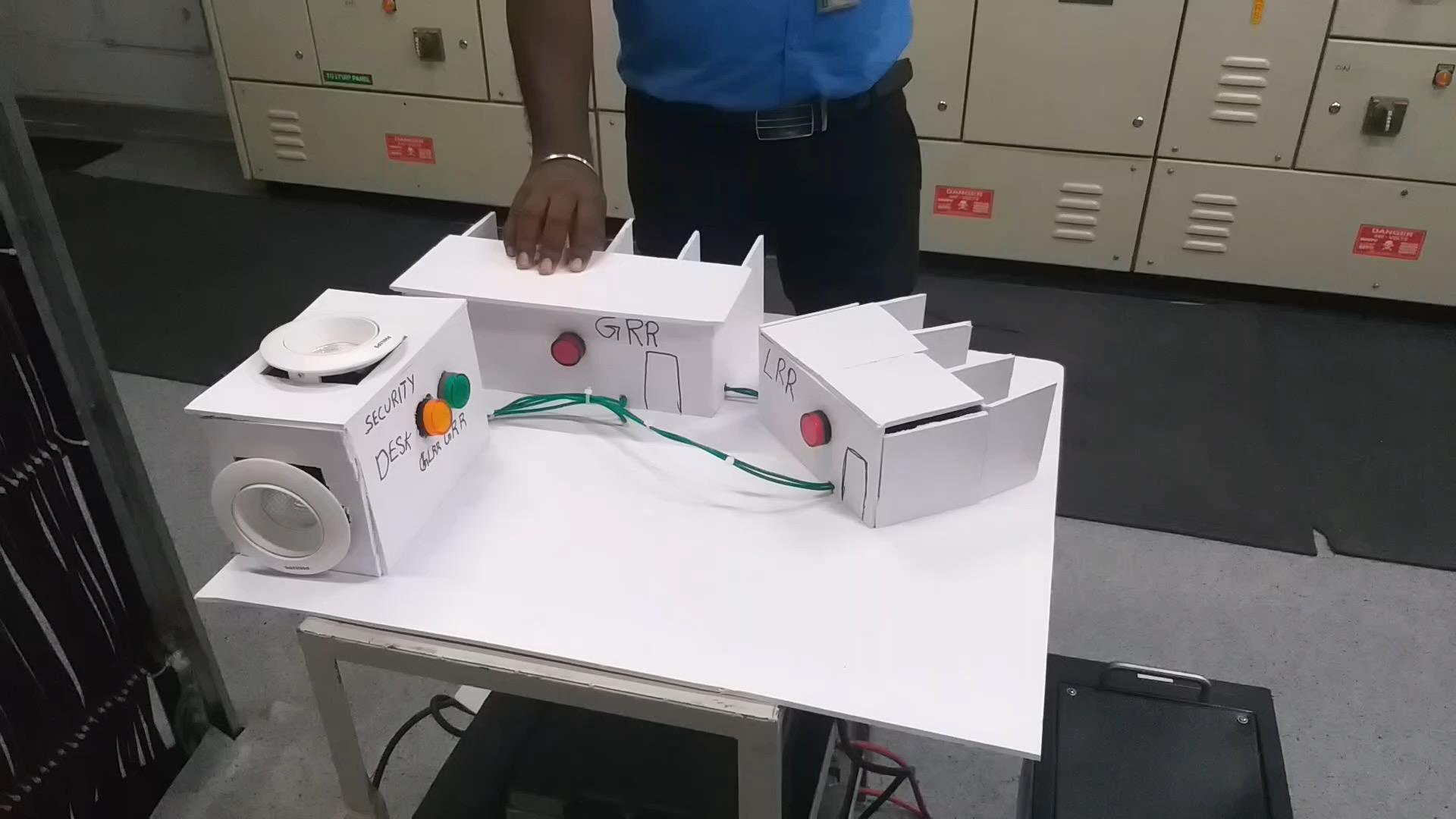
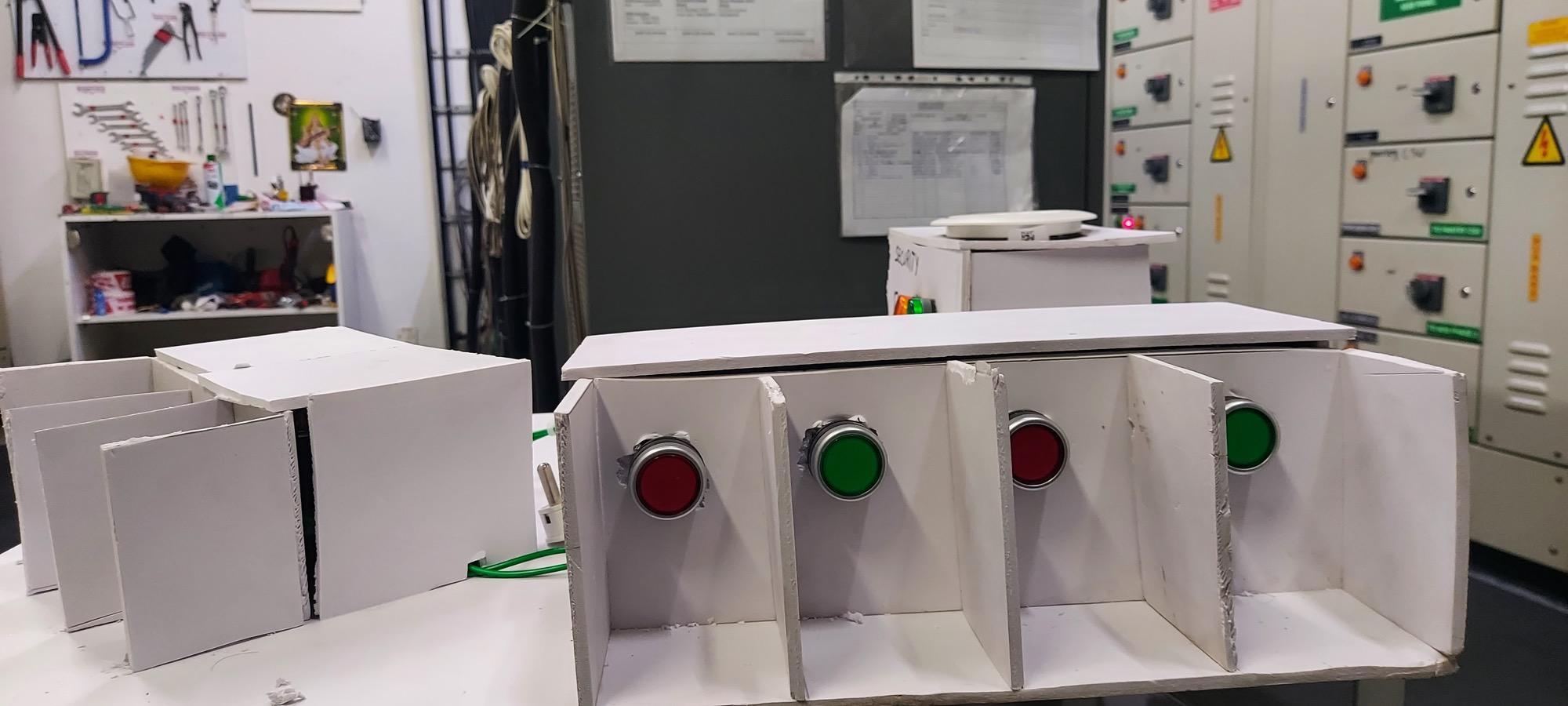
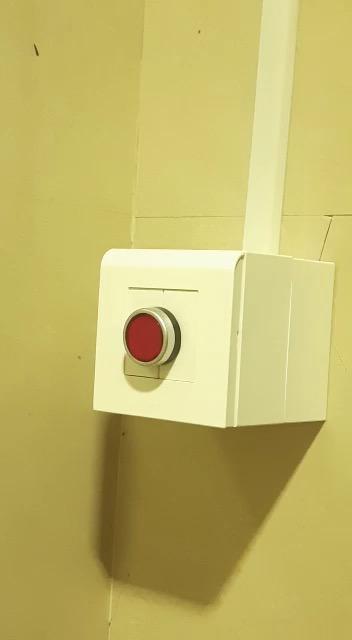
Description of the Innovation: CHALLENGE
• High Cost of drinking water
• Water quality is always a concern
• High dependability on vendors
• Commitment towards sustainability
• To win employee and business confidence
Atmospheric Water Generator
myIdea
• As a part of strategic Sustainability plan
• As a pilot Project we introduced Atmospheric Water Generator
• It generates water by converting water vapour from air in to fresh and clean portable drinking water
• The units contains Electrostatic Air Filters
, Multilevel filtration, UV treatment, Ozonator & Adding Minerals in the output
• Connected with touchless dispensers.
• Reliable technology giving fresh bacteriafree pure drinking water
• Green Initiative to reduce the depletion of ground water sources
• Zero Transportation emissions.
• Elimination of Plastic water bubbles.
• Water test reports meeting the standards of IS10500 :2012
• Getting positive feed back from client that the Quality & Taste of water is good
• Scope 3 energy reduction
• Brown water consumption reduction
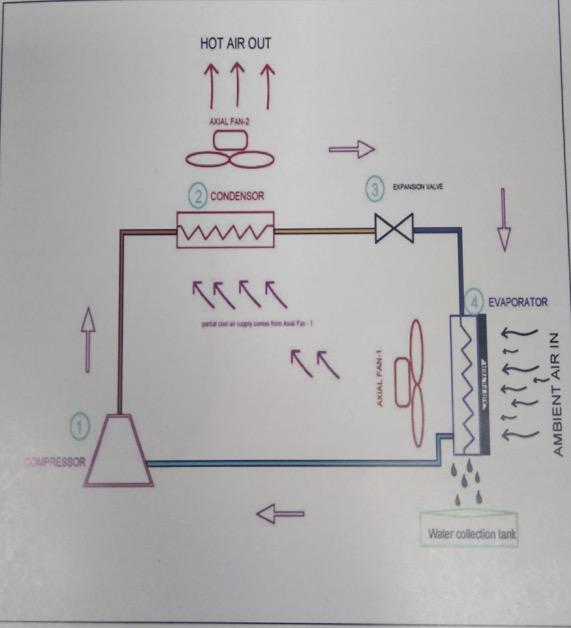

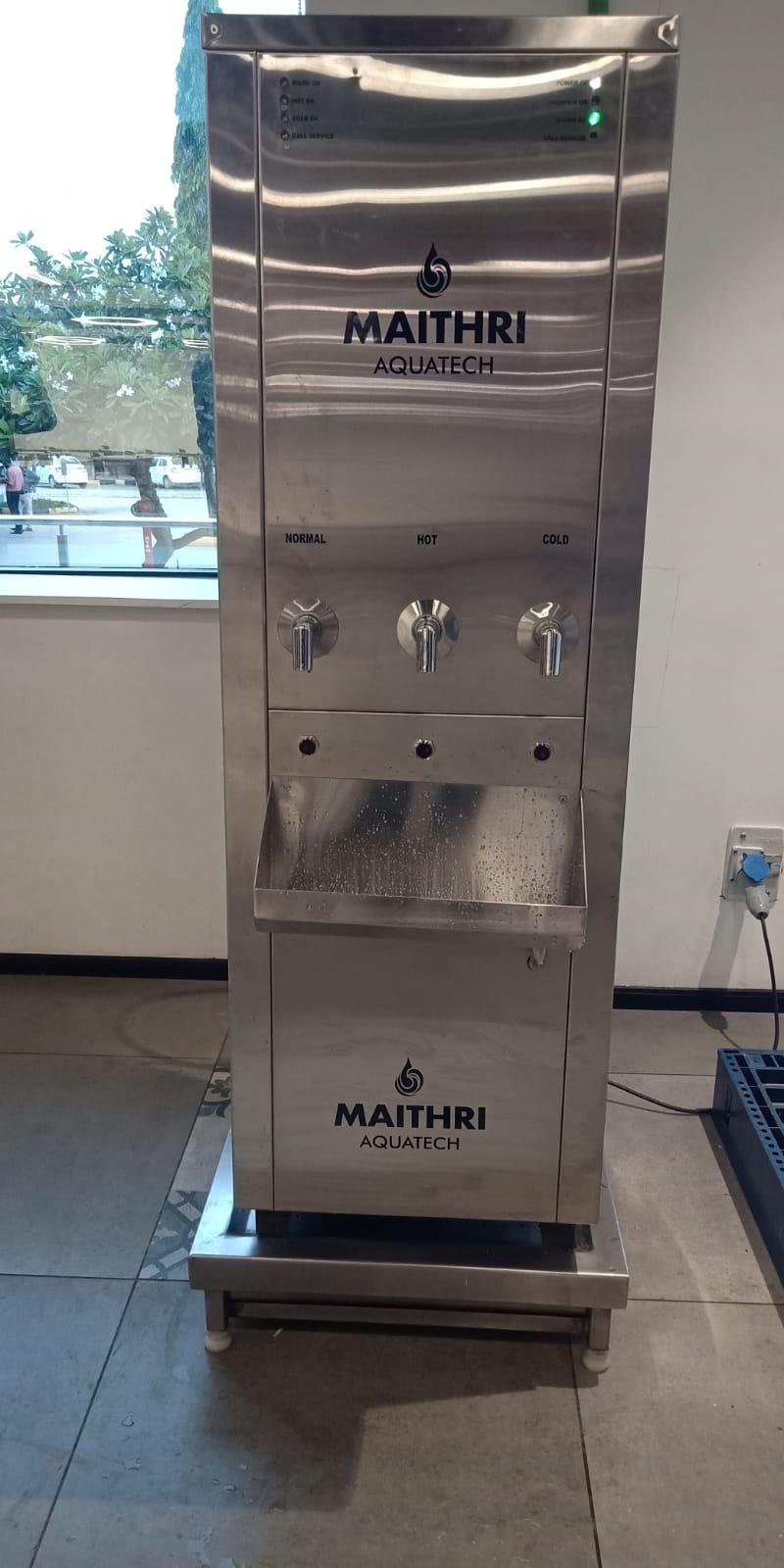
Description of the Innovation: CHALLENGE
Wealth out of Waste
Reduce |
Reuse | Recycle
myIdea
• Culture of innovation and creativity
• Waste generation and disposal
• Team motivation
• Client Satisfaction and appreciation
• Usage of waste in an effective manner
• Due to seasonal Change one of our Spathodea (African Tulip) Tree got spoiled and its almost dead. Instead of disposing the tree we planned to utilize in a useful way. We have transformed the dead tree into few creations in Garden Area.
• Toy Train created in the concept of Independence Day
• Green color of Engine Denotes the tribute to Indian Army
• Flag Drawing at Top shows southern railway flag
• Pink Color Boxes are Tribute to Women
• This Train Created by Team on account of 75th Independence Day
• Tree pots made to place in Alfresco Dining Zone space - Made Wooden type Pots– 7 Nos & Brick –8Nos
• Dessert Garden to replicate a Geographical nature of a Dessert Island.
• Enhance the Garden View
• Reduce & Re-use of waste Materials
• Associates spend enthusiastic time by taking selfies in the locations
• Stress Relieving places at garden
• Carbon Footprint Savings
• Cost Savings
Dessert Garden -
• Cost of Materials spent Inhouse 7338 INR
• Total Cost Benefit by Re - Using Materials INR 17,662/- Approx
Toy Train :-
• Total Cost of Materials Used INR /- 2200
• Total Cost Benefit by Creating In-House – INR/3500
- Approx.
Tree Pots :-
• Total Cost of Materials Used INR /- 500
• Total Cost Benefit by Creating In-House – INR/Approx.4500
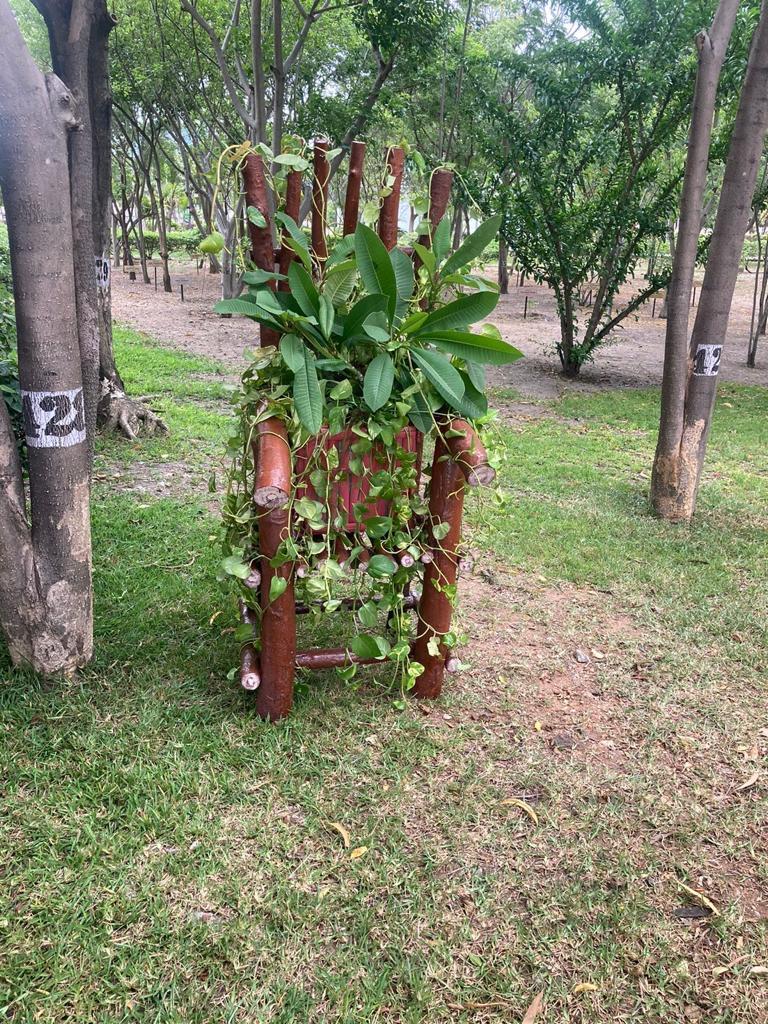
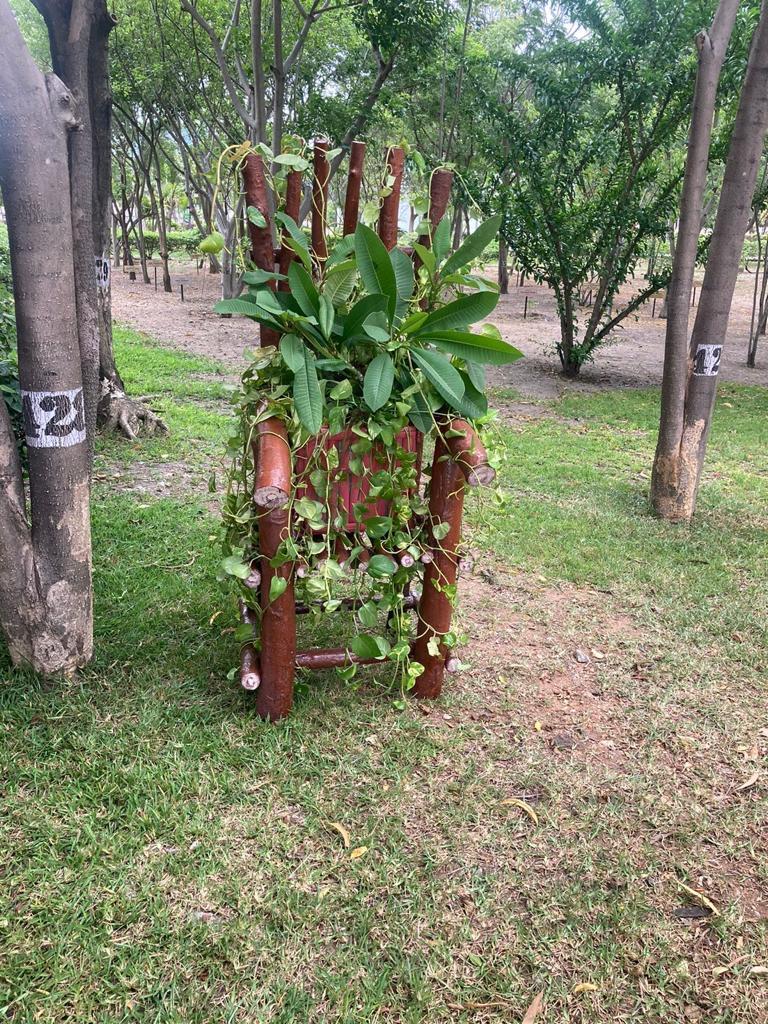
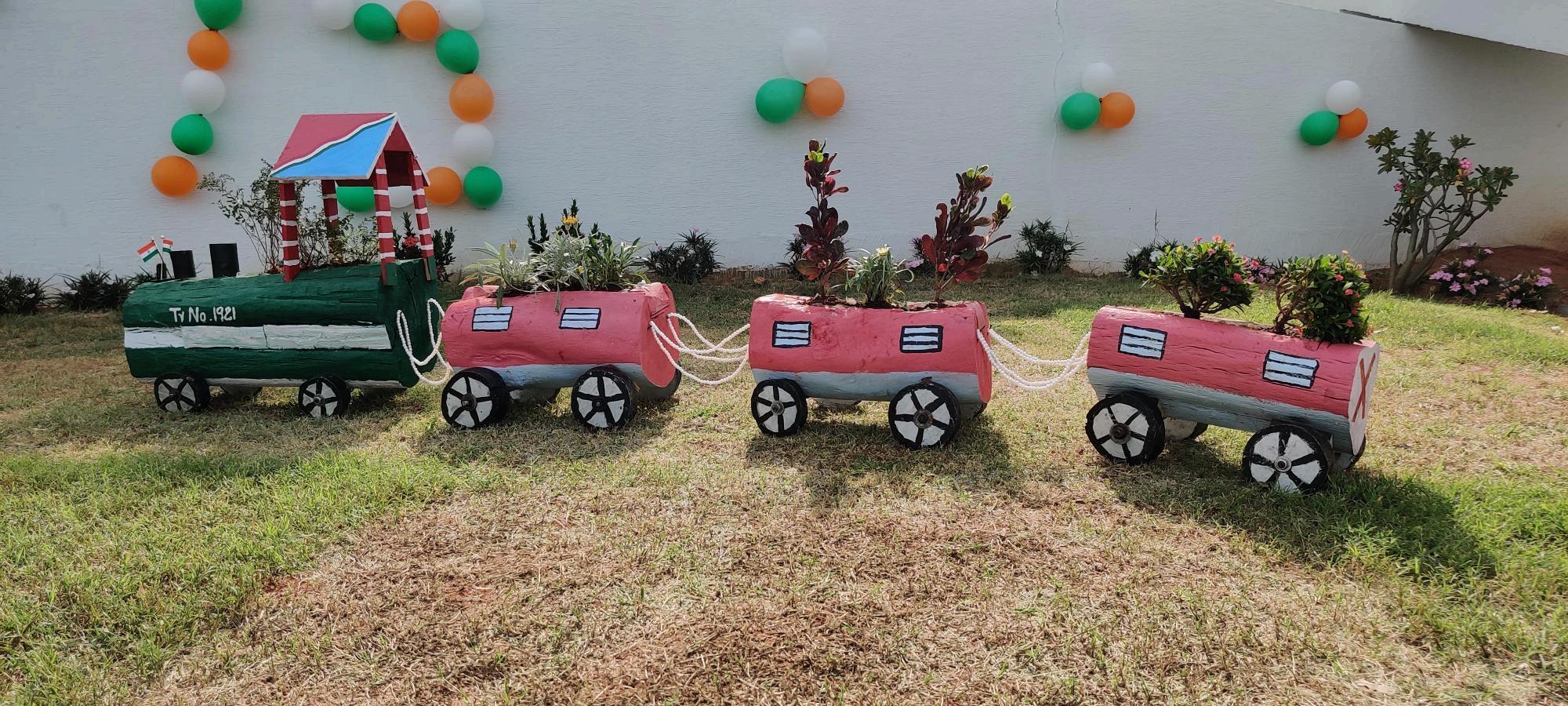
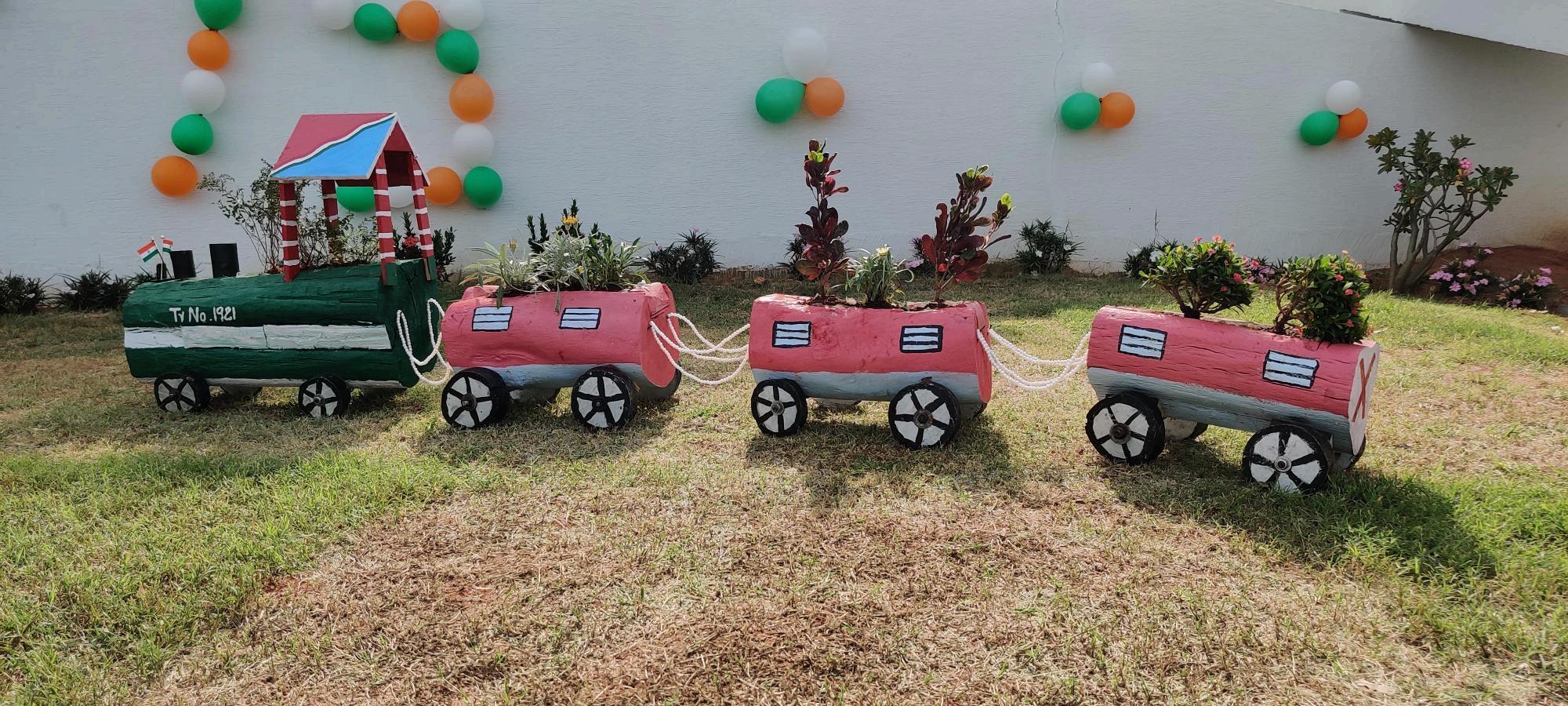
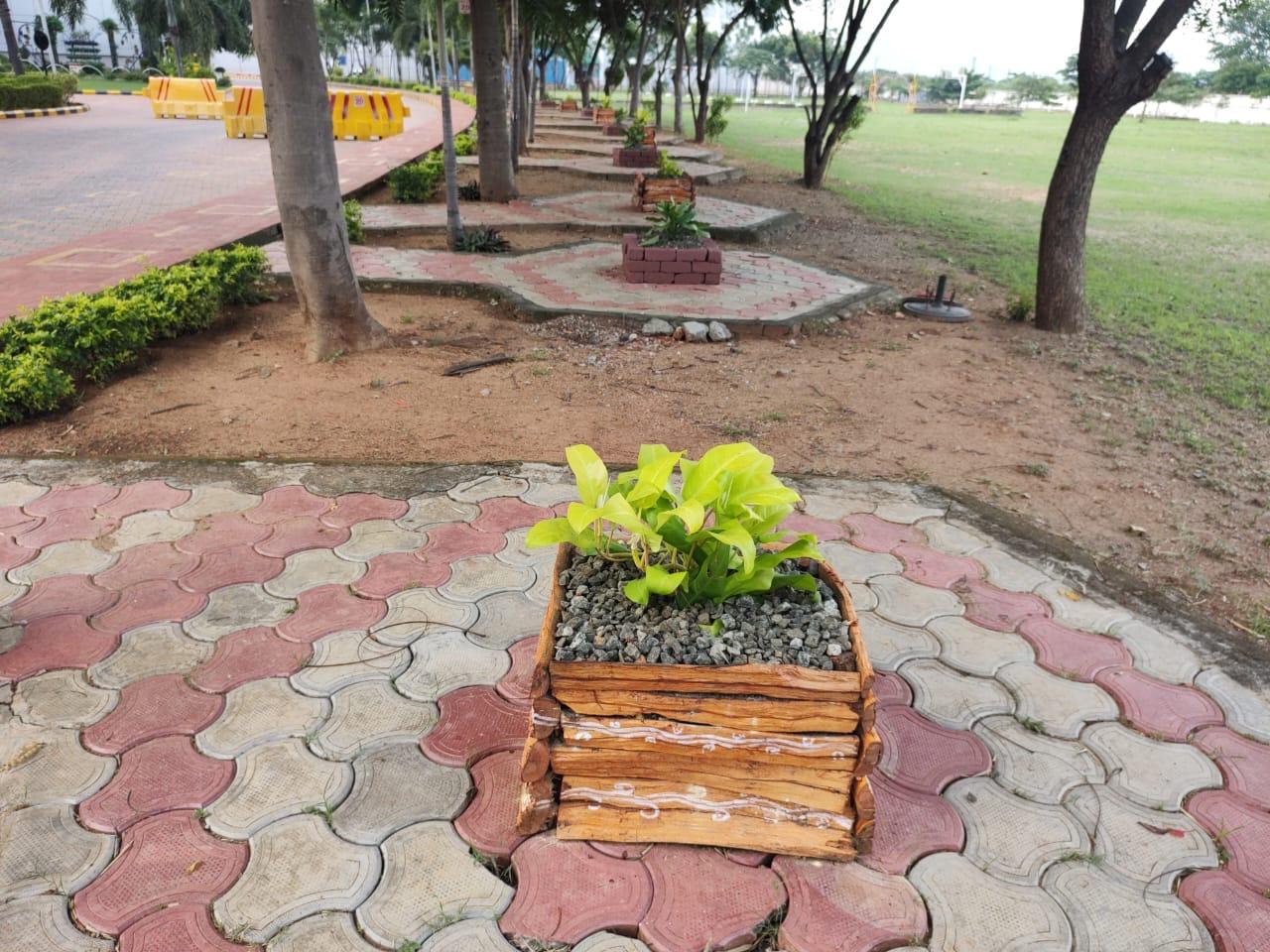

Description of the Innovation: CHALLENGE
• What is not measured cannot be controlled
• Lack of useful data and insights
• Low quality of management ESG report
• Dashboard helps in taking right decision .
UPDAPT Tool For Tracking & Reporting of ESG
myIdea
• Online tool to track and report ESG data on a quarterly basis to the client investor.
• UPDAPT application is user friendly and helps to update data in the tool with ease.
• Simplified process to evaluate the scope-1 & 2 emissions (we just need to update the values in the appropriate fields and tool auto calculates the final values).
• Simplest way to track and report the ESG data on a quarterly basis.
• Dashboard is readily available any time and export custom reports based on the ESG pillars.
• Easily evaluates scope – 1/2/3 emissions.
• Online email notifications and approval workflow.
• Highlights of the quarter can be updated and viewed online anytime anywhere through web login
• Dashboard & report helps to analyse data and bring in efficiency.
• Aligned with Global Climate Change Mitigation action plan.
• Fulfil the investors compliance and transparent governance
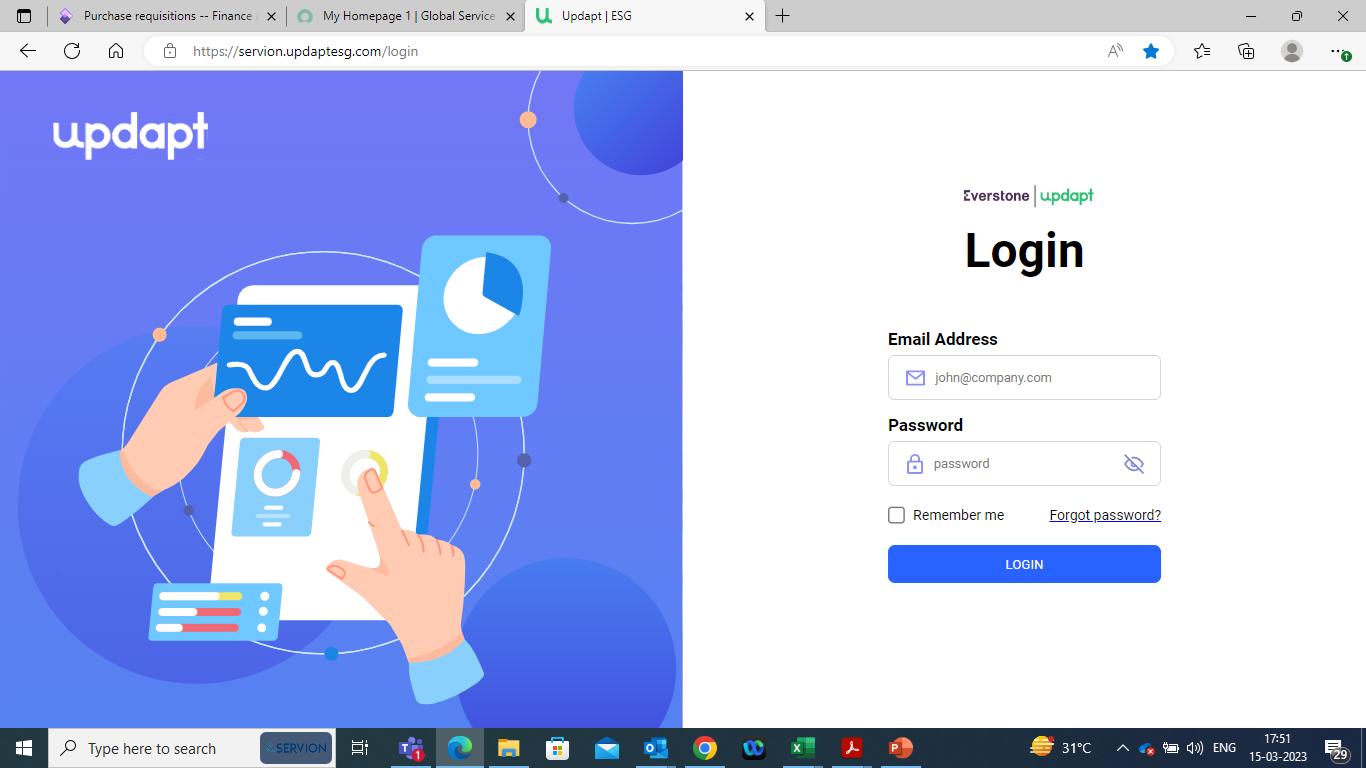
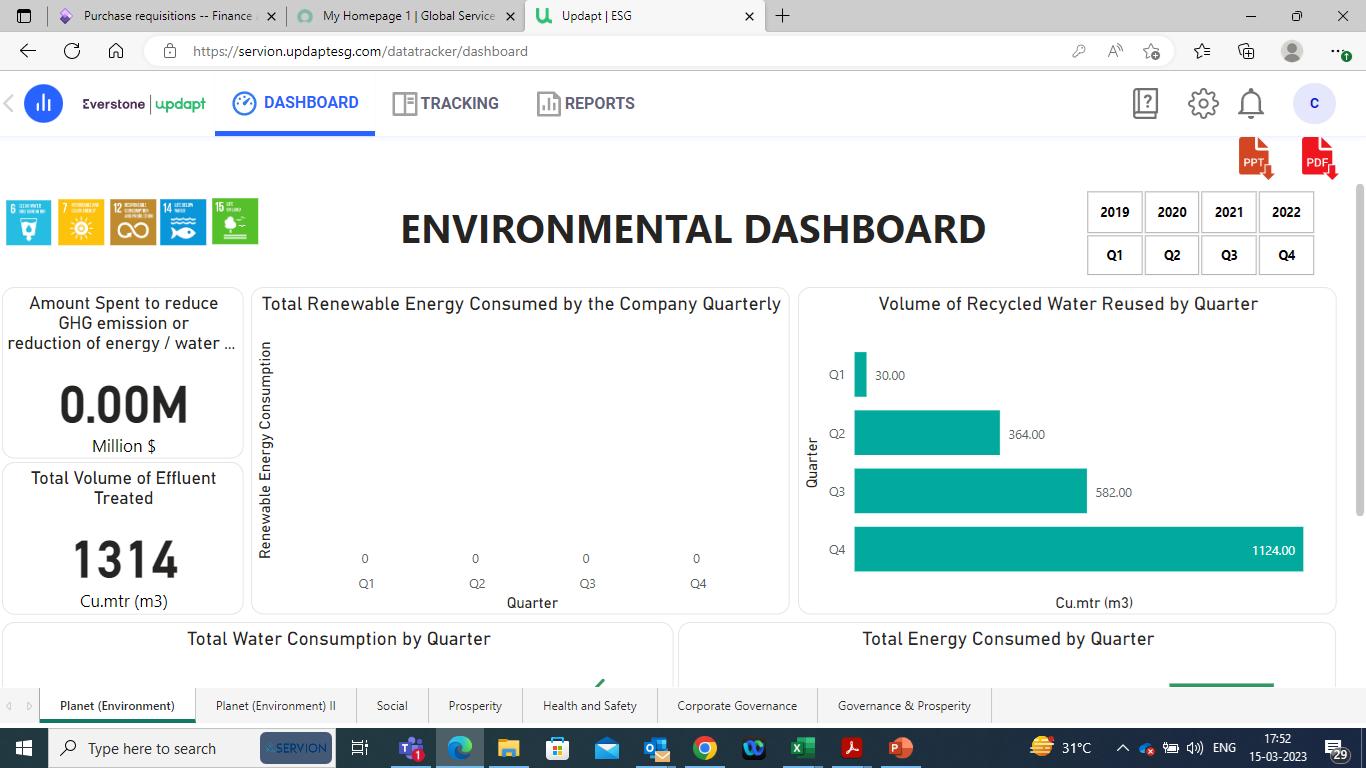
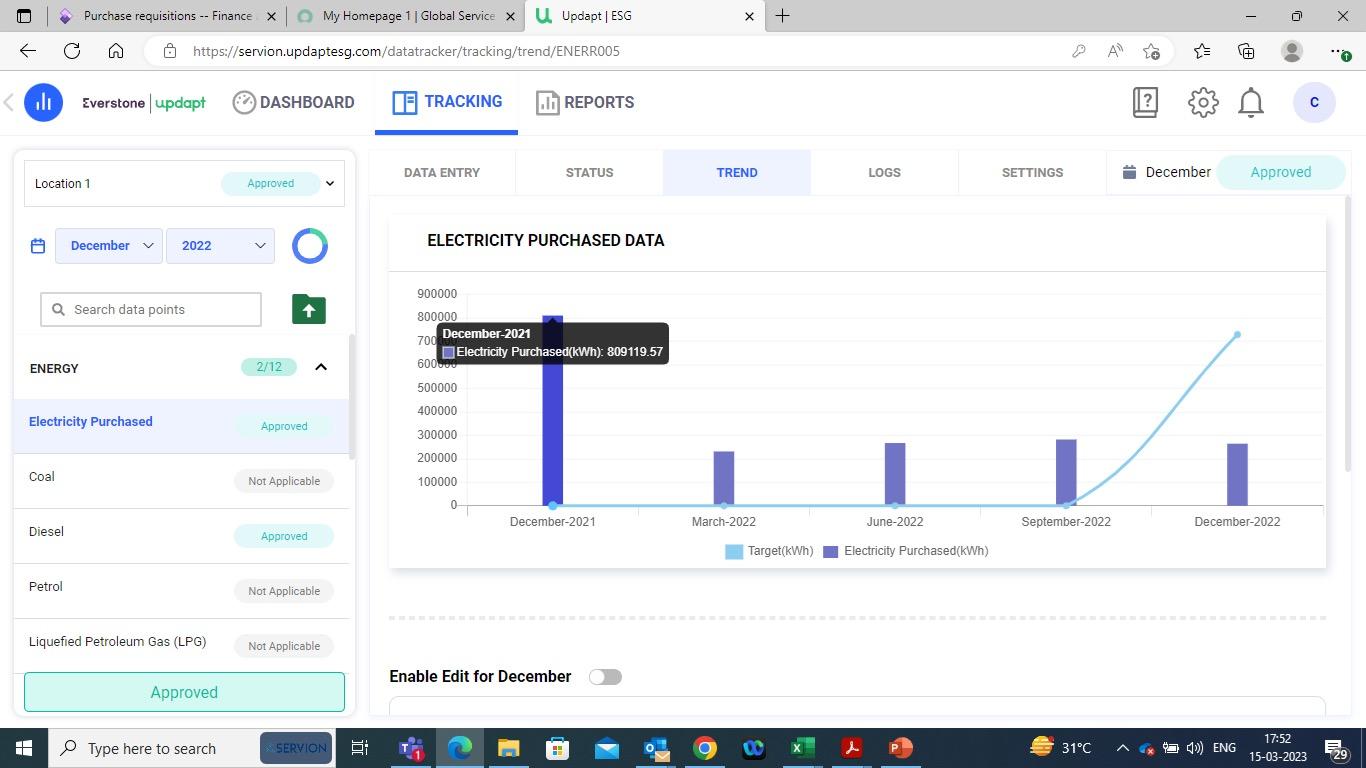
Description of the Innovation:
Wall of Art
myIdea
• Lack of employee engagement .
• Less opportunity for demonstrating employee creativity
• Employee motivation
• Awareness amongst the employee towards environment
• A shout-out to all our incredibly artistic colleagues at GBS India who have time and again proved to be the best, and the Property Team of GBS India does not miss an opportunity to provide a perfect platform to showcase their creativity. A walk around Haddows Campus, Chennai feels like you're walking in an art gallery!
• Several walls adorned with artwork done by GBS Employees. The artists were given an opportunity to explain the creativity and the thought process behind the stunning piece of art that was displayed.
• The 81 creative minds brought out their passion for Diversity & Inclusion, and Sustainability through the canvas & colours.
• Opportunity to Employees to display their creativity.
• Promoting Diversity and Inclusion
• Create awareness of Environment and Sustainability
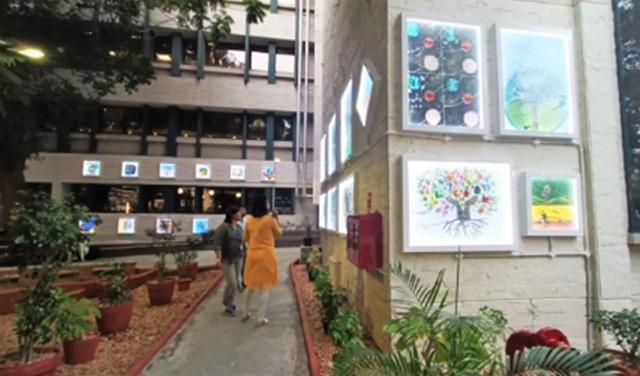
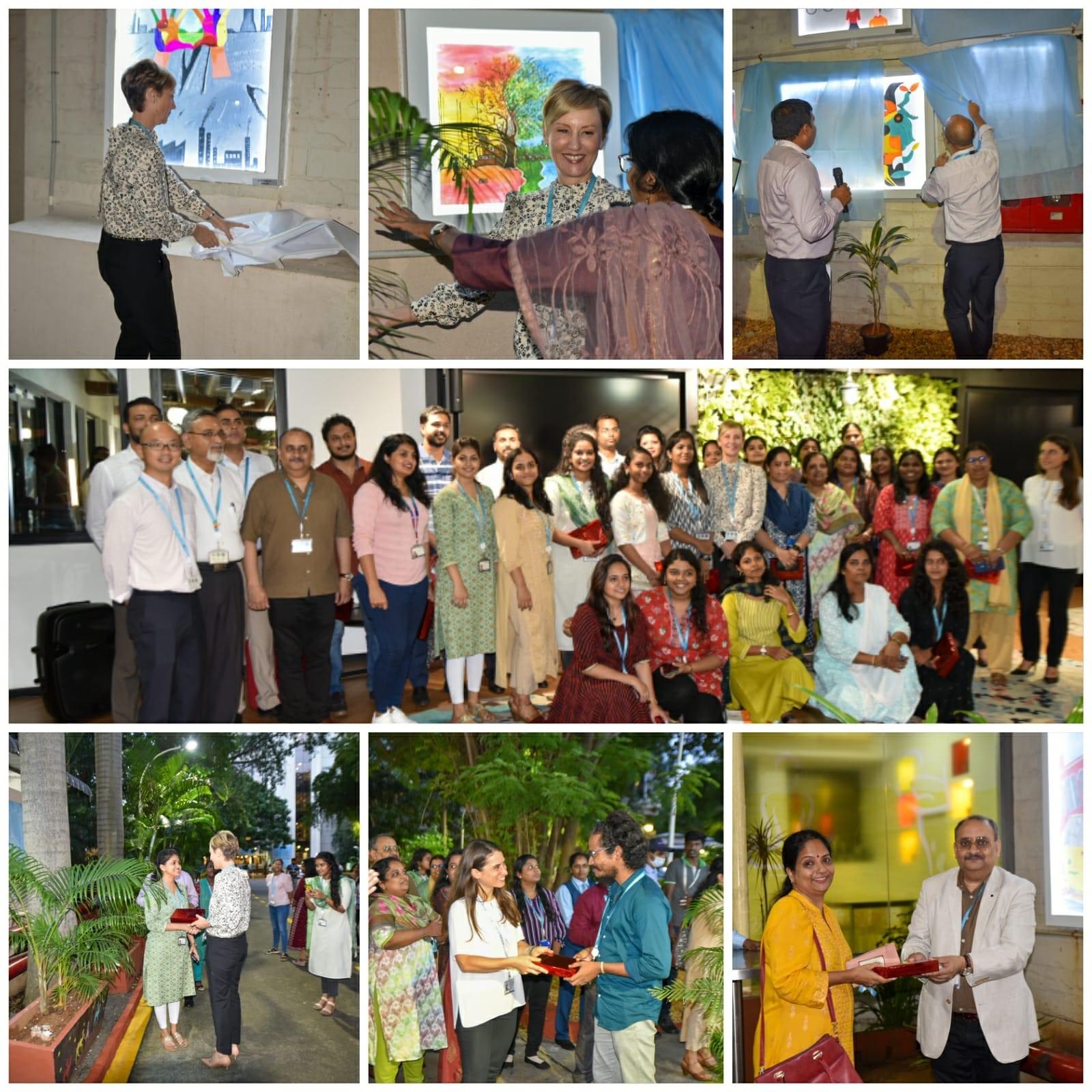

Description of the Innovation:
Rainwater
Harvesting
myIdea
• Scarcity of Fresh water
• High Cost of Fresh water
• Shortage of freshwater can turn into a business risk
• Water recycle is a sustainability commitment .
• High consumption of fresh water
• As part of sustainability project , Rainwater storage project with capacity 250 KL has been completed on Jan 2022 , but rain has been collected from May 2022 to Dec 2022
• Existing parking slot has been utilized for storage tank
• Transfer pump provision is provided, and rainwater will be transferred to raw water sump and can utilize natural resource
• Overflow of rainwater storage is connected to 03 no’s injection bore well each 05 KL capacity
• Major role in upgrading LEED certification from Silver to Platinum
• Natural resource is effectively utilized
• 1781 KL collected from rainwater for period May 2022 to Dec 2022 and same has been utilized
• 74 loads of 24 KL outsourced tanker lorry water has been saved for period May 2022 to Dec 2022
• INR.2,25,000 has been saved due to utilization of rainwater for period May – Dec 2022
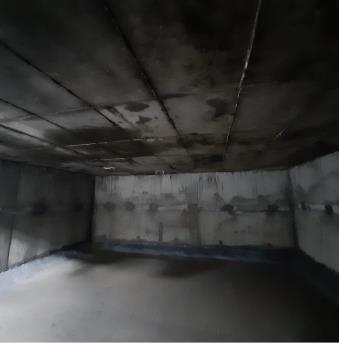
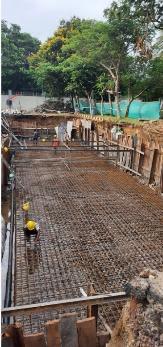
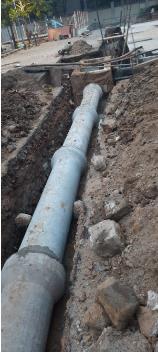
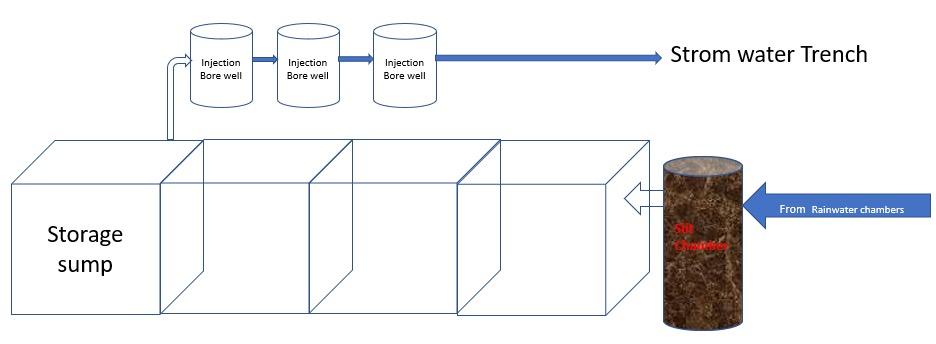
Description of the Innovation: CHALLENGE
Organic Garden
• Promoting sustainability
• Saving the planet
• Promoting Healthy food
• Employee satisfaction
• Creating awareness
• To build Organic garden (720 Sq. ft.) on unused terrace area.
• Growing of herbs & vegetables in the best natural way without the use of pesticides or synthetic chemical fertilizers.
• Utilization of project waste iron scrap for the green nursery innovation.
• Crop damage is prevented by having organic garden structure made from metal pipe covered with green netting to avoid birds' entry.
• Media – We have used soil, vermipost and farmyard compost.
• Availability of fresh herbs as & when required from the source for consumption in office cafeteria.
• Sustainable from a practical implementation perspective.
• In-house team is engaged - sense of accomplishment & ownership
• Onetime overall investment cost – 5,32,000/-
• Types of Vegetables & Herbs with production/yield in initial one month is in below table.
• We use this vegetables in salad, sandwiches, detox water and garnishing.
myIdea


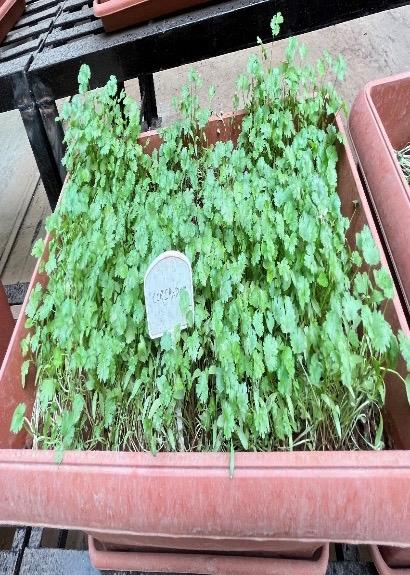
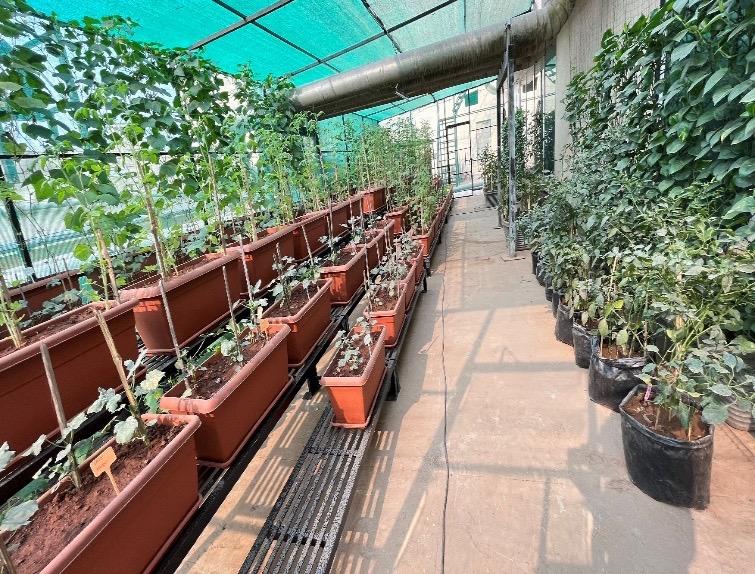
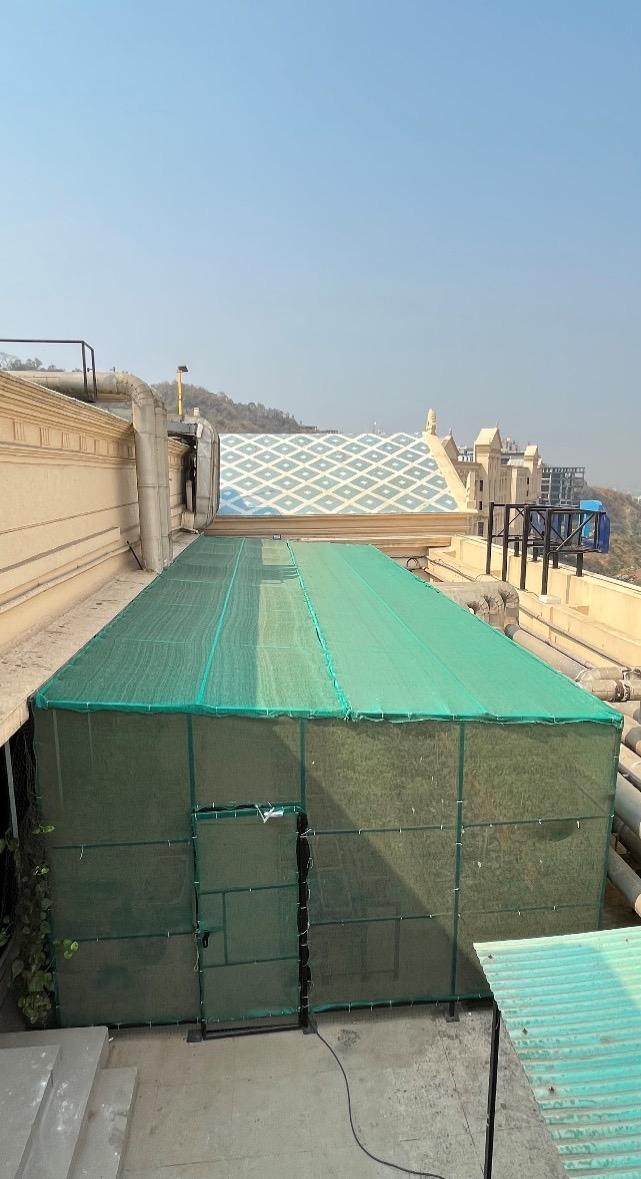
Description of the Innovation:
Chiller Plant Energy Reduction by Booster Pumping System
• High power consumption
• Sustainability Commitment
• Inefficient HVAC operation
• Wastages to be controlled
• High cost of energy
• Plant average performance
• Two separate chiller plants were operated earlier for Airoli B1-B4(Phase 1) & B5B6(Phase 2) respectively
• To reduce energy consumption cross connected Chilled water lines of Phase 1 & Phase2 Chiller plants with installation of two additional booster pumps .
• Two 50HP pumps were installed according to the total area of the campus
• Post installation of Booster Pump, the load can be shifted on either one of the Chiller Plants while one plant is kept Off. there by saving Energy.
• This resulted in power saving of approximately 2000 units per day on weekdays.
• Approximately 480,000 units & INR 5,280,000 @ INR 11 per Unit saved per year.
• ROI. Is 2 Months including all Overheads
• 408 KGs of Carbon footprint saved per Year ( 0.85 KG Per KWH )
• Actively contributed for totally being Net-Zero and one of the first company to achieve & get re-certification as IGBC Campus in India.
• Estimated Saving : INR 52,80,000/-
myIdea
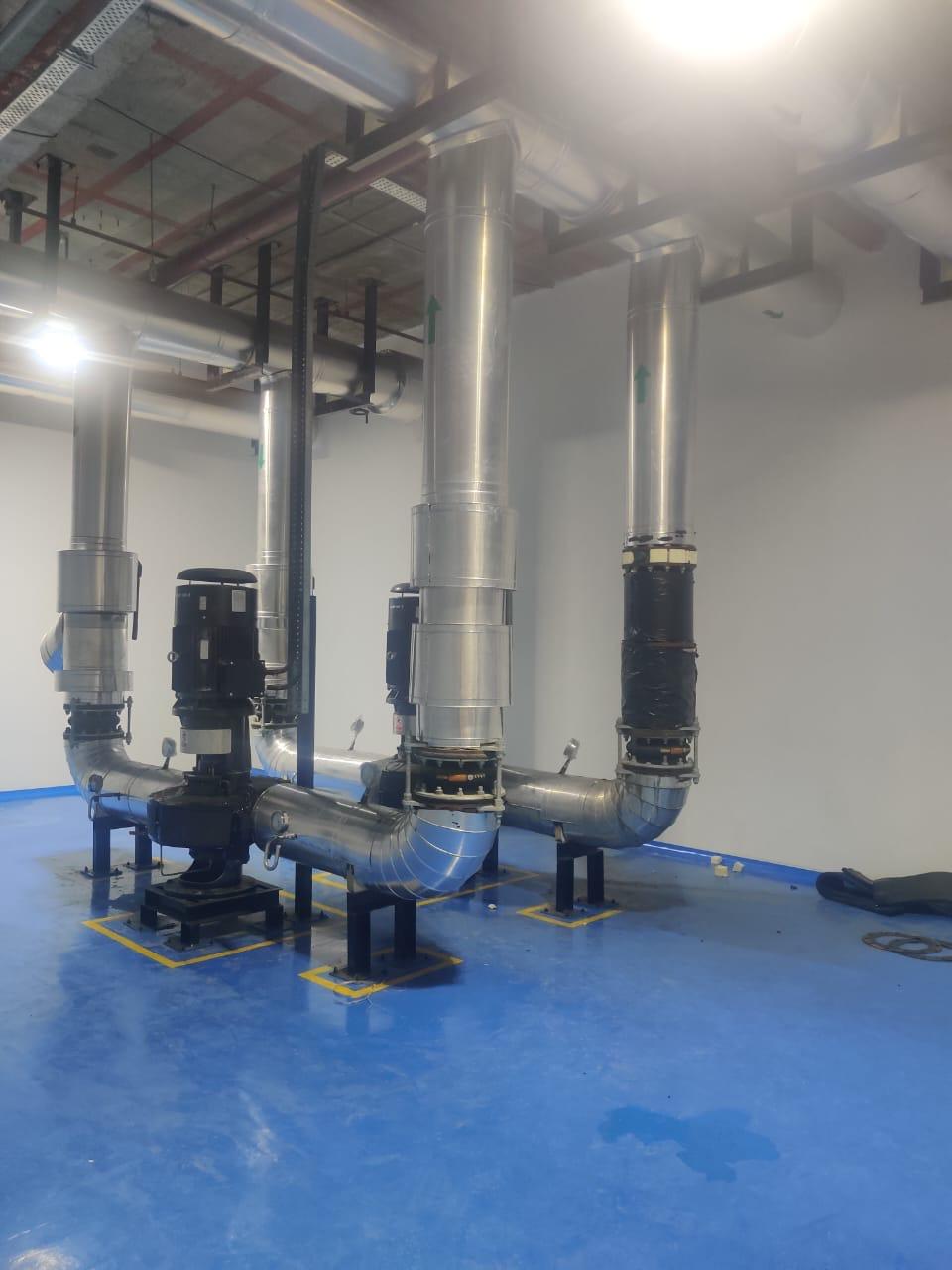
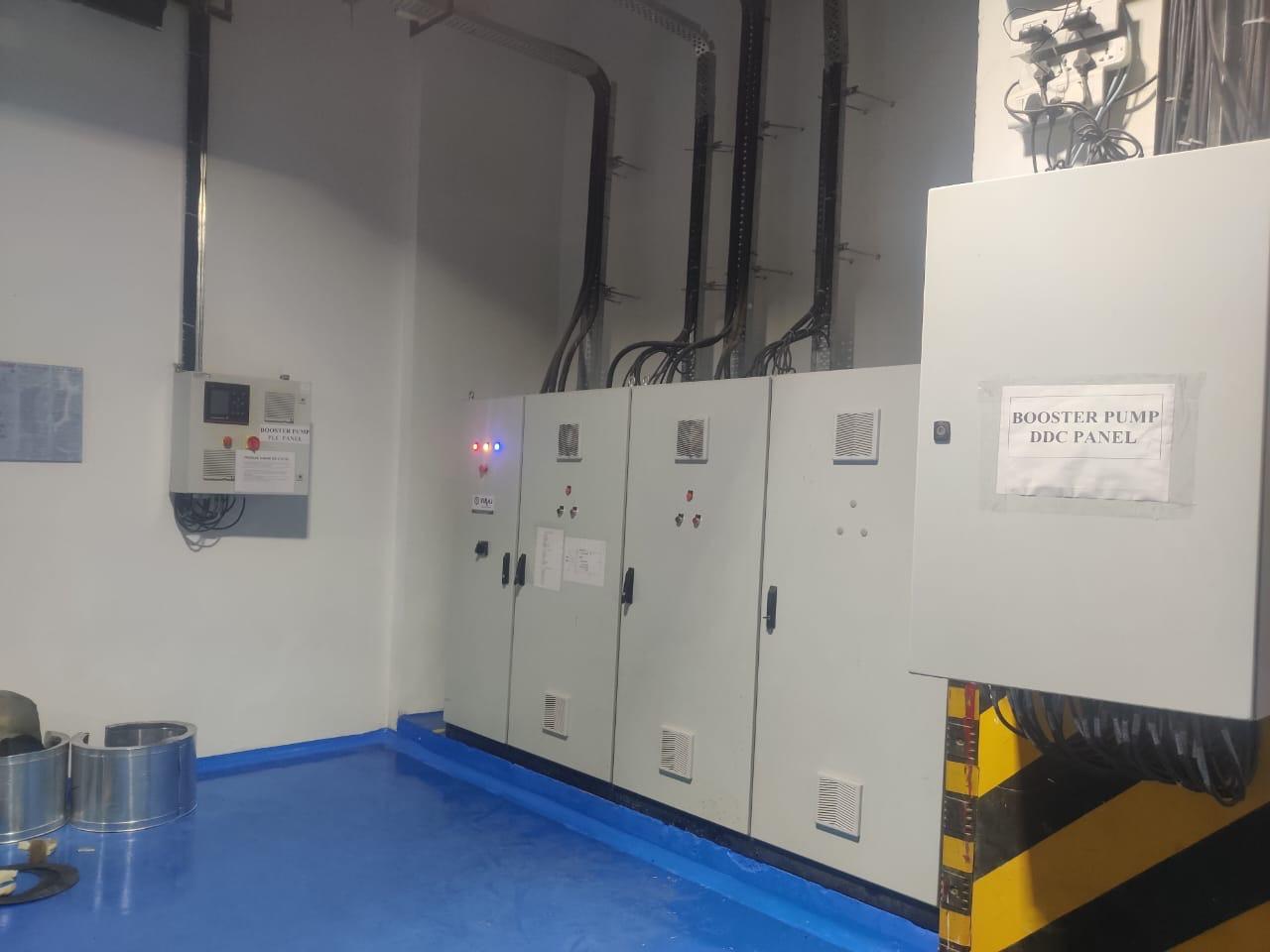

Description of the Innovation:
Saving Of Portable Water
• Scarcity of Fresh water
• High Cost of Fresh water
• Shortage of freshwater can turn into a business risk
• Water recycle is a sustainability commitment .
• High consumption of fresh water
• Controlling the water wastage
• Commitment towards sustainability
• Collection and reuse of HVAC condensation water going to drain line as waste.
• The HVAC condensation water from AC tray drain line is connected through a plumbing lines to the existing 3000 Ltr tank at Ground floor.
• The 1.5 HP pump was connected to the outlet of the tank to supply pressurised water for cleaning purposes.
• Saving cost on precious domestic water consumption
• The waste condensation water is reused for basement area cleaning, HVAC Filter’s cleaning and watering of plants at podium level.
• The cost saving for a sum of Rs 96k- annually ( 20 KL/month) on supply of tanker water.
• Contributing towards Sustainability goal
myIdea
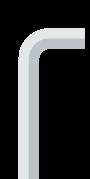
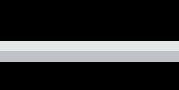
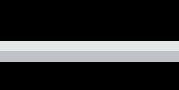
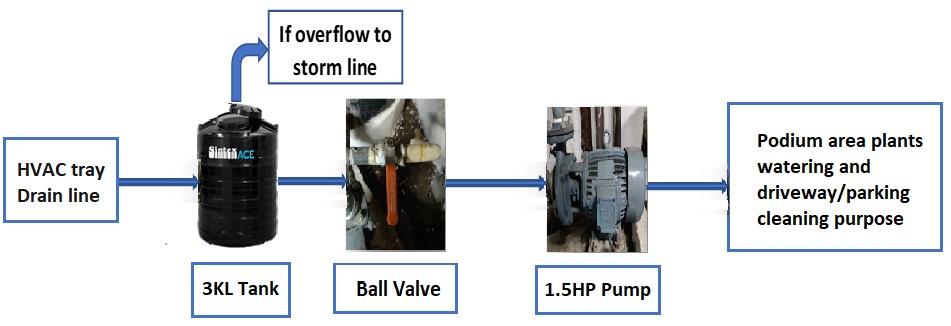
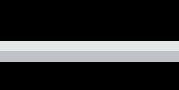
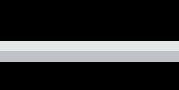
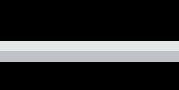
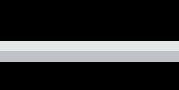
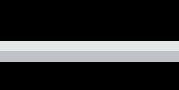
Description of the Innovation:
Condensate Recovery Water System
CHALLENGE
myIdea
• Scarcity of Fresh water
• High Cost of Fresh water
• Shortage of freshwater can turn into a business risk
• Water recycle is a sustainability commitment .
• High consumption of fresh water
• Controlling the water wastage
• Commitment towards sustainability
• To meet the steam demands there is consumption of Raw Water is in large quantity, resulting increase in frequency of regeneration of Softener to almost 3-4 times in a week which was reducing life of the Softener.
• Fuel consumption was going high that is average about 1200 Kg/day.
• Installed condensate recovery water system
• Designed centralized condensate recovery system from all 07 production facilities.
• Provided automatic system with pressure stock level sensors switches for feeding condensate water to feed water tank.
• Enhanced Energy Saving by isolating Electrical Heater to heat Raw Water.
• Reduction in frequency of Regeneration of Softener to 2-3 times in a month which is increases life of softener.
• Gained the feed water temperature from 45 Degree (ambient Temp) to 90 degree.
• Fuel consumption reduced to 1000 –1100 Kg/Day.
• Manpower hours saving for softener regeneration activity.
• Estimated Saving : INR 16,00,000/-
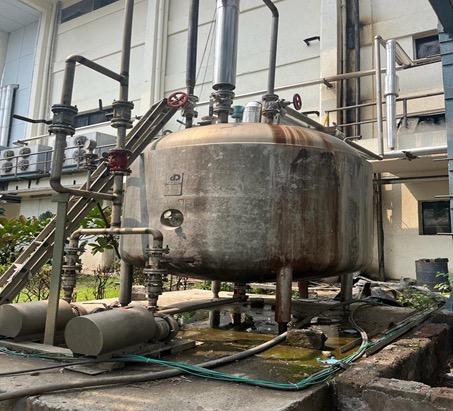
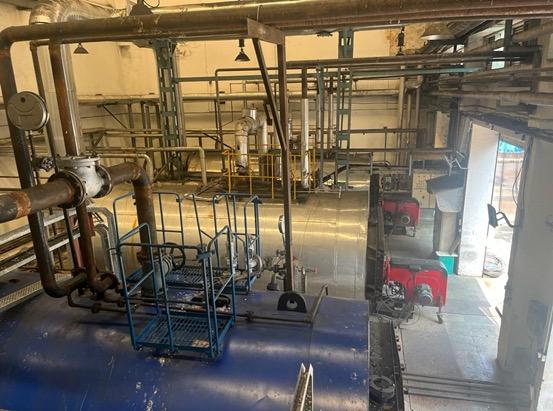
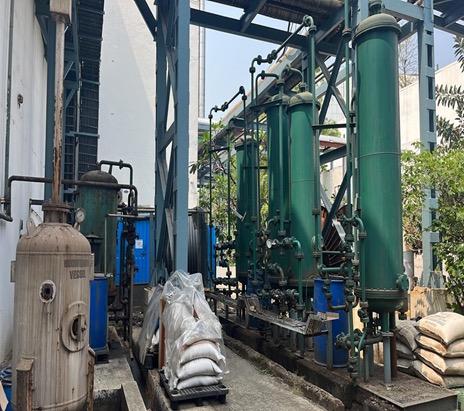
Description
of the Innovation:
Optimization Of CRAC Systems
• High power consumption
• Sustainability Commitment
• Inefficient HVAC operation
• Wastages to be controlled
• High cost of energy
• Plant average performance
• Optimization of Computer Room Air Conditioning (CRAC) operations in UPS room after installation of Lithium - Ion Batteries (LIB) from existing valve regulated lead acid (VRLA) batteries
• In earlier configuration, 2 CRAC units were in operation with 1 standby and after our assessment we convinced client to reconfigured the setup with 1 CRAC unit in operation and 2 standby.
• By auto sequencing operations for CRAC units the room temperature is being well maintained at 25 +/- 1 ° C .
• After implementation, confirmed annual saving of INR 93,951 which was achieved with reduction in energy consumption by 8,541 Kwh units p.a.
• Resilience increased by N+2 from N+1
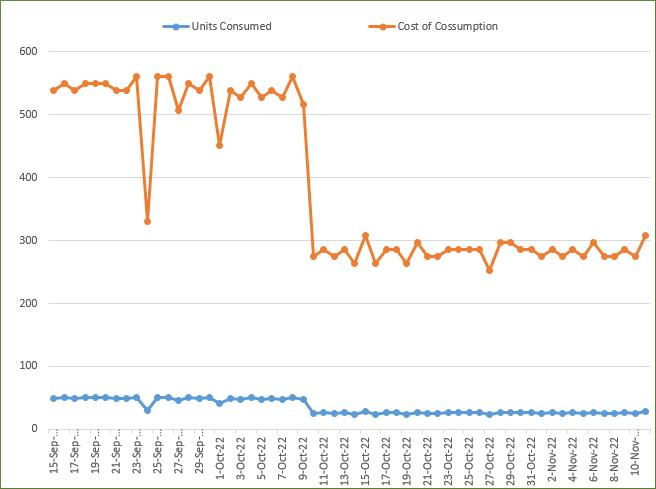
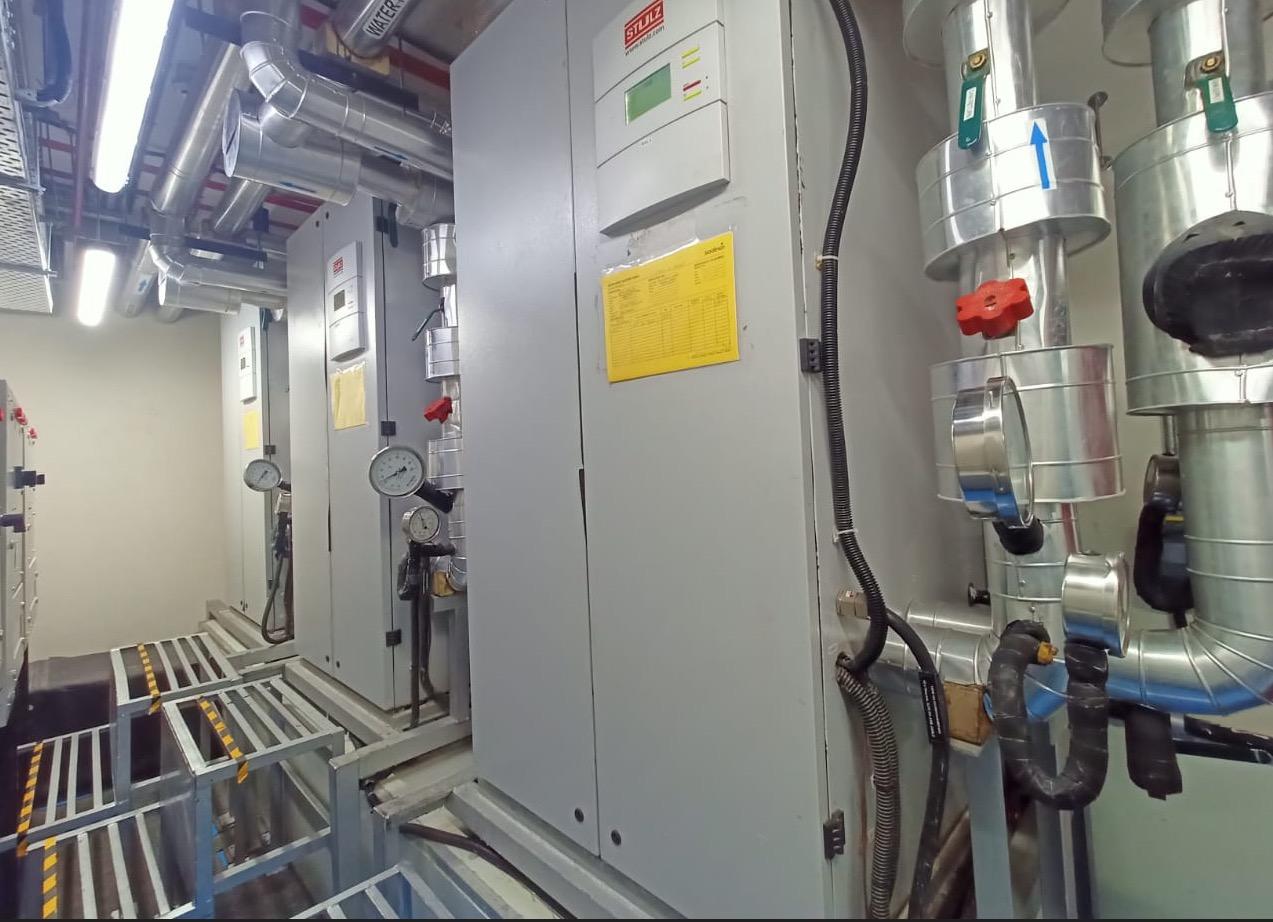
Description of the Innovation:
Onsite Solar Plant Installation And Commissioning
• High cost of power
• Commitment towards sustainable power
• Energy harvesting and conservation
• Dependence on sustainable power
• Additional Solar plant installation planned for Capgemini Talwade Campus
• CBRE Onsite FM Technical Team Coordinated with various service providers for site survey, design details & finalization of additional Solar Power Plant locations .
• CBRE Onsite FM Technical Team shouldered additional responsibility for coordination & monitoring of Vendor project work on daily basis and shared updates to Client Technical Lead for Pan Pune..
• CBRE Onsite FM Technical Team helped client for Project Snagging , Snag rectification and final commissioning of additional 456 KWp Solar Plant
• Onsite solar plant capacity enhanced from 756 KWp to 1212 KWp
• Onsite solar generation increased daily 1800 Units average.
• Carbon footprint reduction 525 tons/ per year.
• Estimated State Electricity Board Energy Bill saving -64.80 Lacs per annum
• ROI of this project 4.5 years.
• Estimated Saving : INR 64.80 lacks/ Annum
myIdea
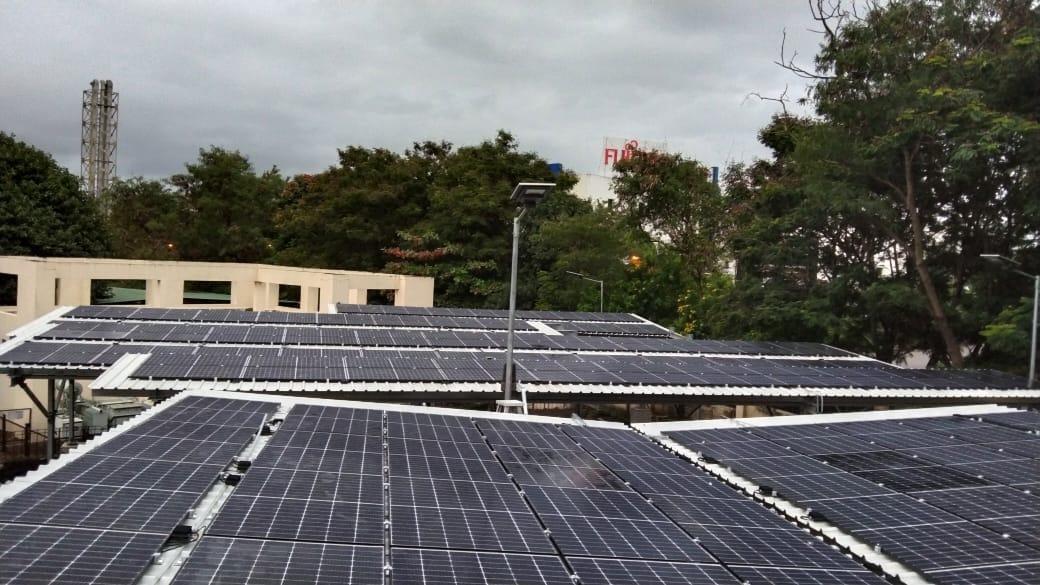

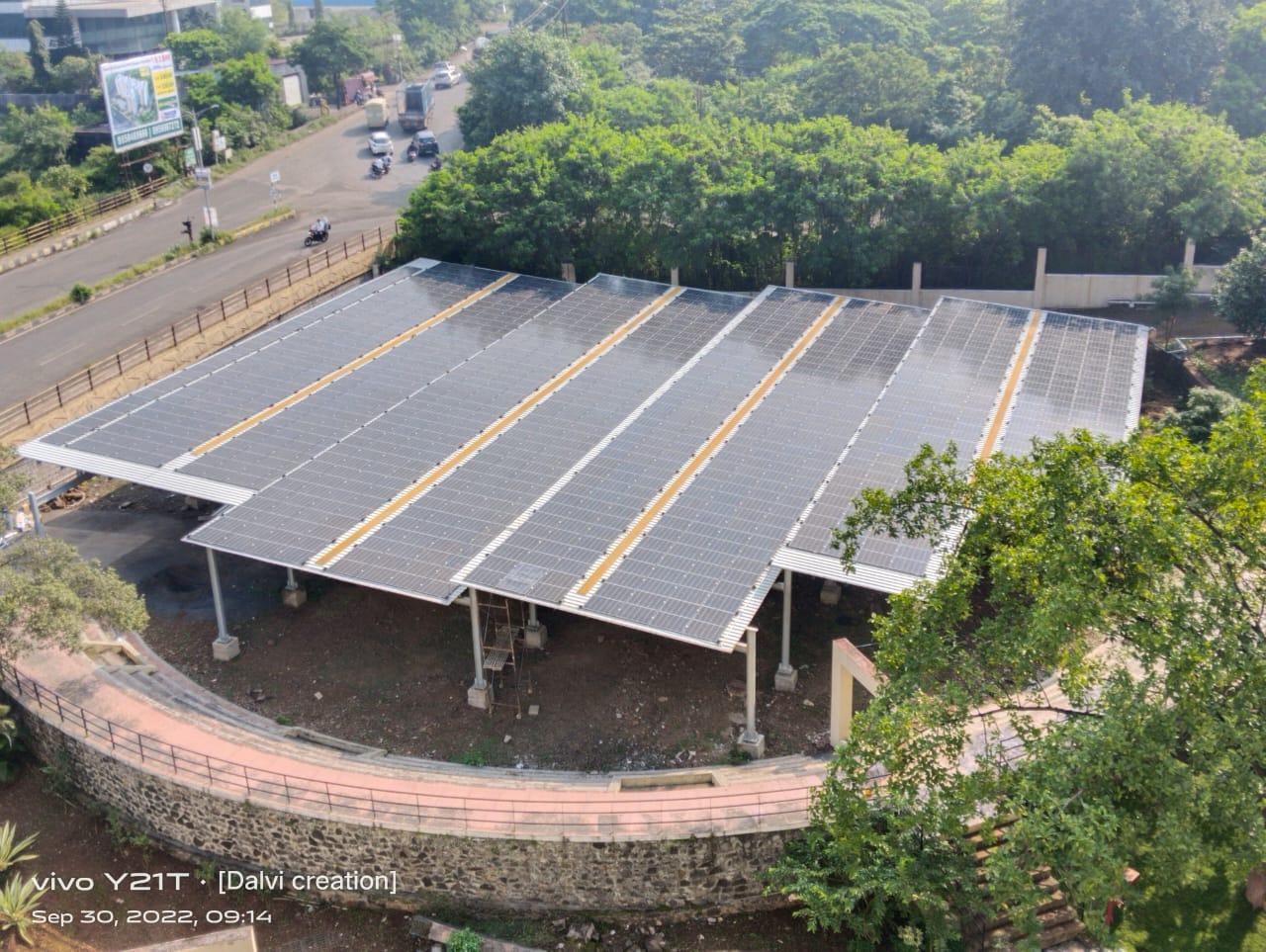
Description of the Innovation:
LEED Certification
myIdea
• Commitment towards sustainability .
• Low knowledge and awareness of sustainable operation
• Inefficiency usage of power
• Reduce wastage of power
• Achieve power consumption
• LEED Certification
• The LEED for Existing Building -O&M rating system we improved the operations, policies, procedures, purchasing and maintenance in an existing building.
• We uses fewer resources, minimizes waste and environmental impact, and decreases life cycle costs to achieve increased productivity and better staff health.
• Maximum energy savings
• Efficient use of water
• Optimum utilization of resources and sensitivity to their impacts
• First GOLD certified building under V4.1 in India.
• Arc scoreboard installed for real time performance assessment of the building
• Reduced maintenance and operation costs
• Healthier indoor air quality
• Increased use of recycled materials
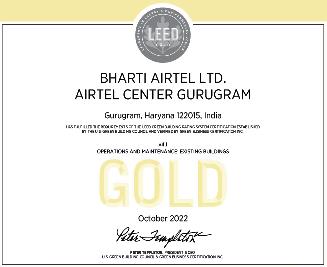
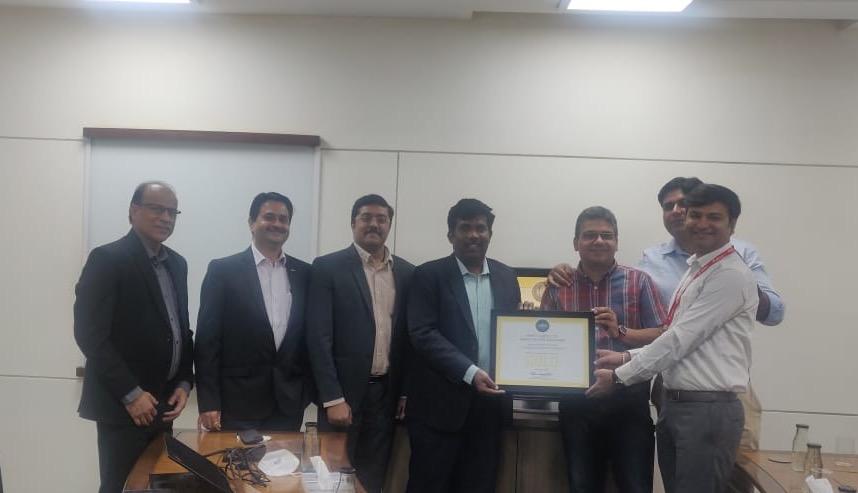
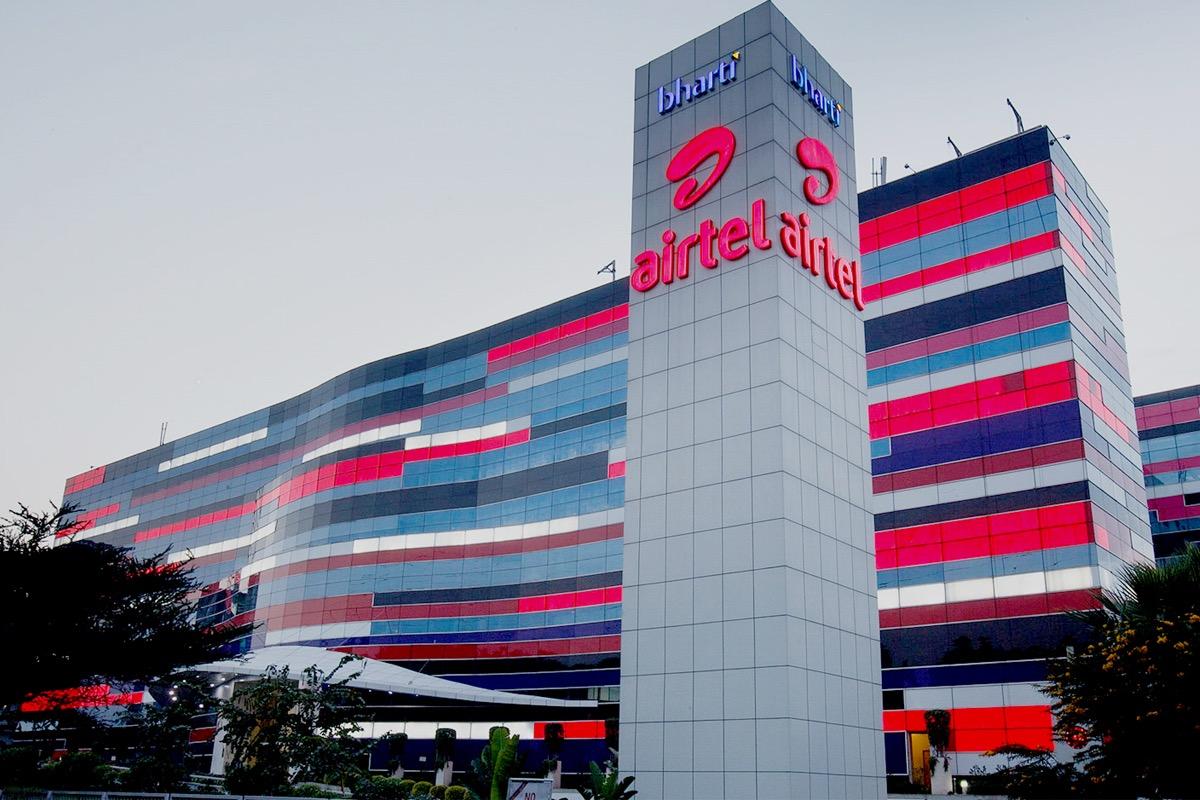
Description of the Innovation:
QR Code-Based PPM Activity Training Video
• High consumption of power towards paper SOP
• Lack of accessibility to SOPs
• Reading is no more an effective way of undstanding for the low skill resources
• Contribution towards sustainability .
• Effective training and gaining knowhow .
• Introduced QR code-based PPM videos with multiple language option
• Standard processes, as recommended by OEM are captured step by step in videos which can be accessed through QR Code pasted on the equipment.
• Technician can scan the QR code & view the training videos, which is a virtual digitized SOP, having multilingual audio and subtitle options
• Standard process as defined by OEMs are readily available for supervisors/ technicians to access before carrying out any PPM activity.
• Increases the PPM effectiveness and equipment uptime.
• New joiners have a handy method to skill up and align with standard practice.
• Multi language audio and subtitle options enable universal application across all states having presence of Dell sites.
myIdea
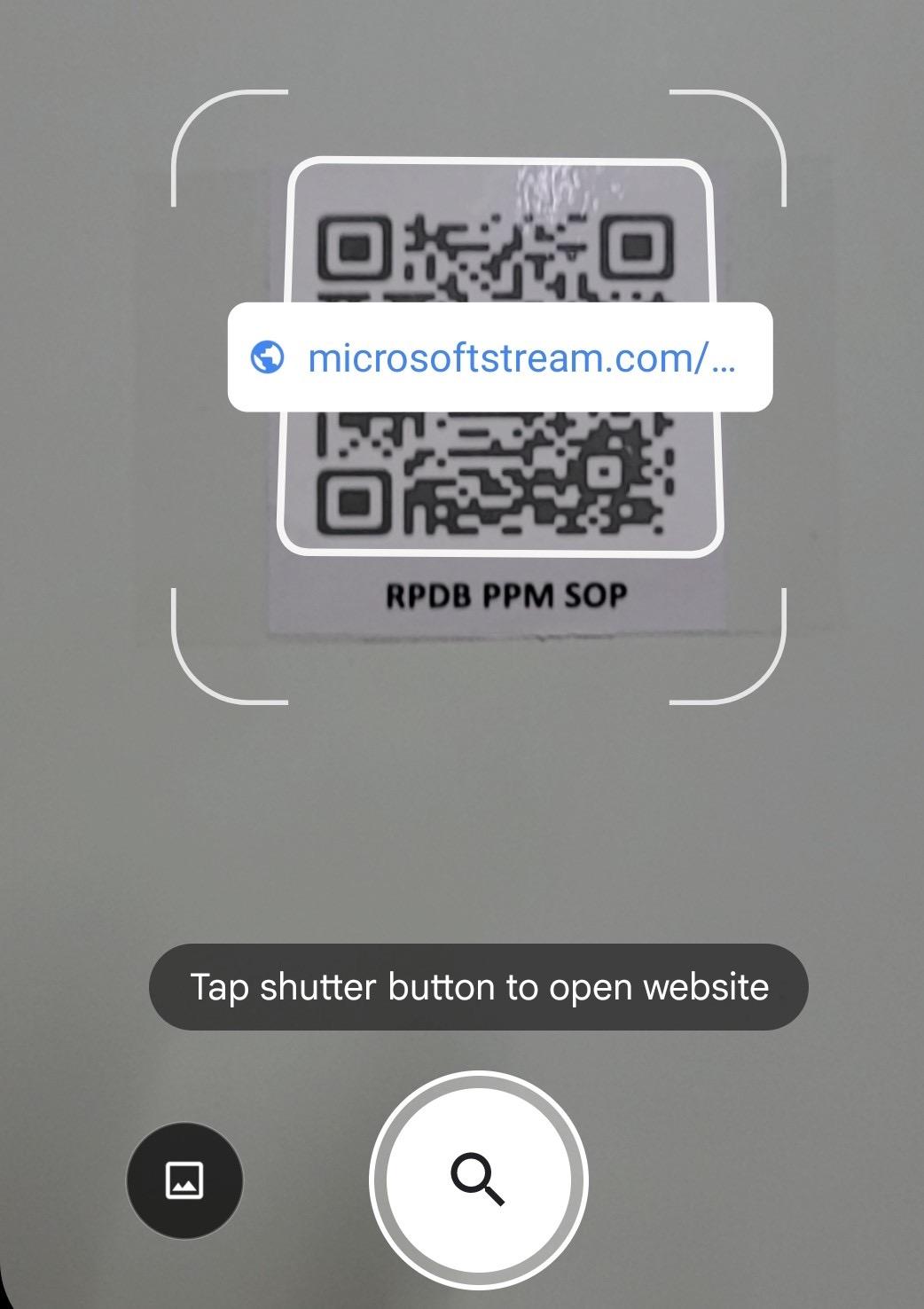
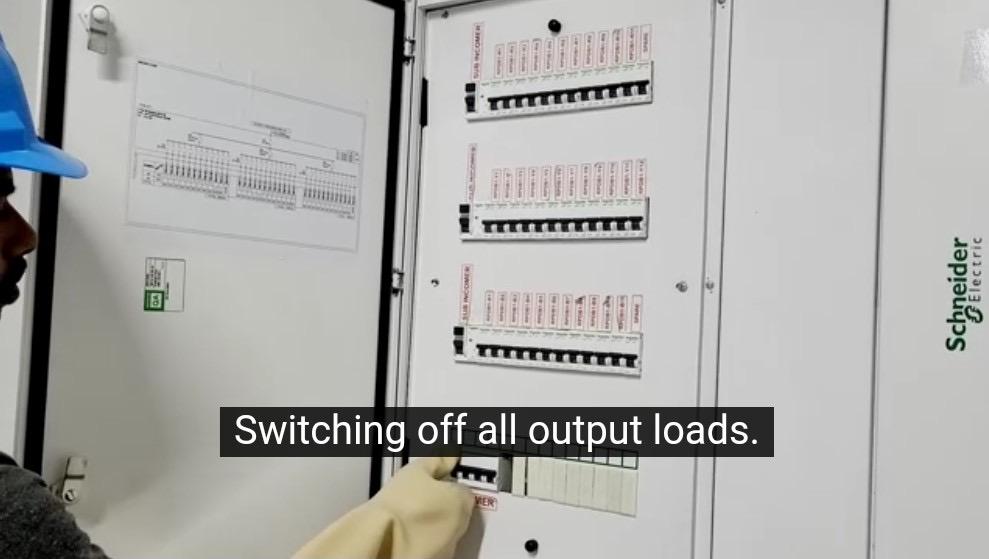
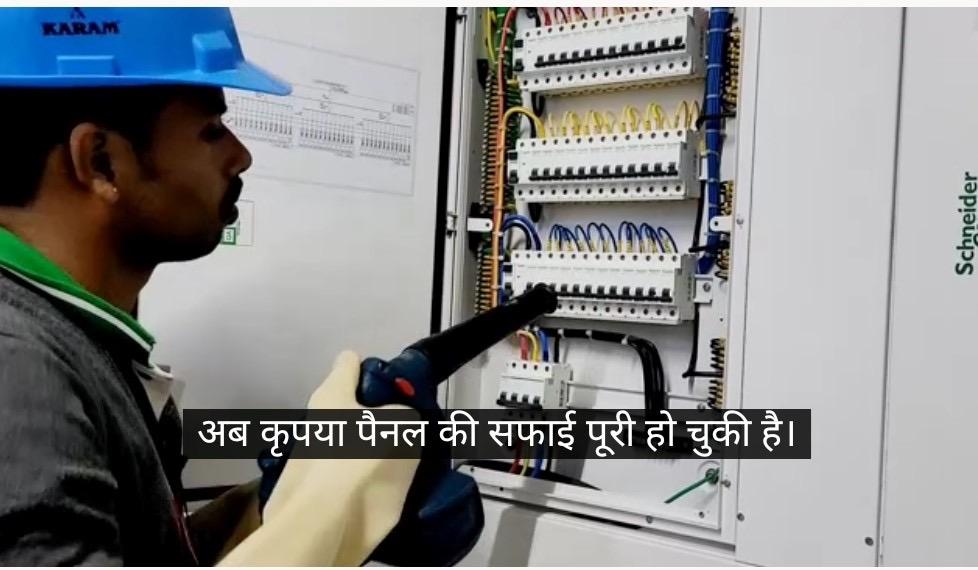
Description of the Innovation:
Smart Bins For Food Waste
• Waste segregation
• Innovative solution towards sustainability
• Commitment towards sustainability
• Initiatives towards protecting mother earth
• Accurate data collection towards waste management
• Lack of Insights and waste reduction initiatives
• Our global commitment is to achieve “Zero Waste” by 2030. We believe that the less we waste, the more we achieve.
• Our immediate focus - reducing food waste (Data revealed that over 70% of average waste generated in the past year from the site was food waste)
• Problem statement/Key requirement
• Identifying source/root cause for food wastage
• Eliminating manual error in weighing the food waste
• Solution
• Smart bin tracks the type and amount of food wastage in real-time
• Impact
• Reduction in overall food wastage
• Increased efficiency in dining operations
• Optimal and appropriate utilization of human capital at kitchens
• Smart bins are AI powered and reinforce effective food waste management. Benefits include:
• Continuous monitoring of food wastage
– increases reliability of data for recording food waste.
• Easy identification of the trend of food wastage – what food gets wasted most and when.
• Supports data-based decision making –AI identifies accurately the type of food being wasted and helps in menu engineering for optimized client experience.
• Reduction in wastage = reduction in operation overheads – Effective food waste management helps reduce costs at critical touchpoints.
myIdea


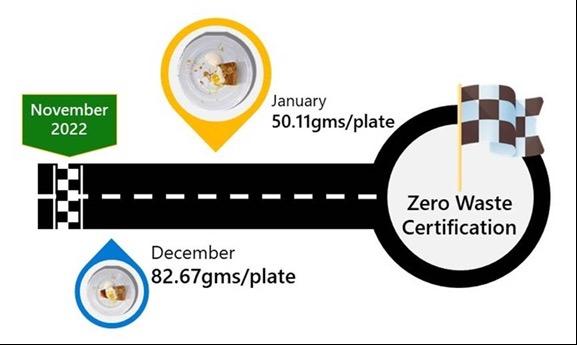
Description of the Innovation:
Wealth out of Waste
myIdea
• Culture of innovation and creativity
• Waste generation and disposal
• Team motivation
• Client Satisfaction and appreciation
• Usage of waste in an effective manner
• Creative way to attain client satisfaction
• Wealth Out Of Waste Activity enables to develop the habit of recycling and recognize their responsibility towards nature and the environment.
• The Best out of Waste simply means to make or to create innovative things from the material we do not use anymore.
• Utilized old newspapers to make window blinds which are shown in the pics # 01 & 02.
• Utilized unused/damaged PVC water pipes to make vertical garden & damaged capacitor cylinders as light domes at breakout area which are shown in Pics # 03 & 04.
• Created value out of waste and discarded material to improve the ambience at site.
• Great feel-good factor to the client and end user employees enhancing better client relationship.
• Controlling the amount of waste sent into landfills, the destruction of forest & other ecosystem with our small little contribution.
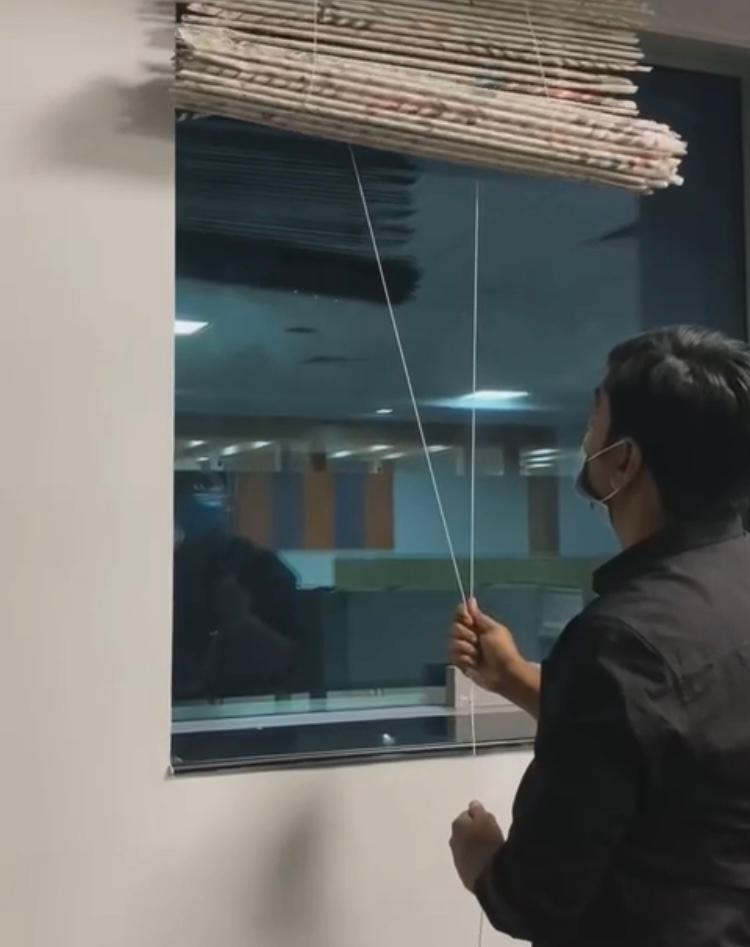
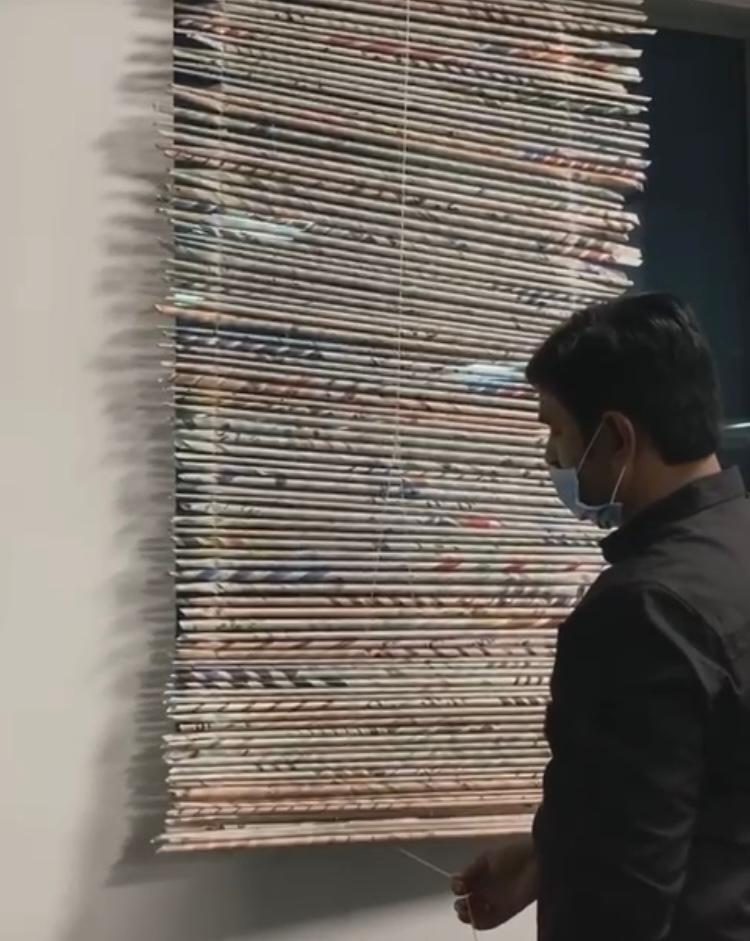

Description of the Innovation:
Pollinator Garden
myIdea
• Promoting sustainability
• Saving the planet
• Employee satisfaction
• Creating awareness
• Creating a balance in environment
• Setting an example towards right sustainable practices .
• BCS is own IBM building where 2800 sft. of unused and monotones landscape areas has been identified
• Our objective to transform existing monotones garden to pollinator garden.
• Initially we started this project with soil digging/filling, checked the nutrient level and used bio-fertilizers according to the local atmosphere and nature.
• Next, we did the most important part which is plantation of selected flower plant and followed by fruit plants along with few aesthetic structures for garden areas.
• As sustainable solution, replenishment of plants according to the seasonal and continuous monitoring is being observed throughout the year for enhancement & promotion of healthy biodiversity at IBM site
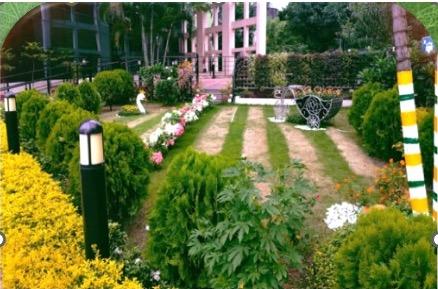
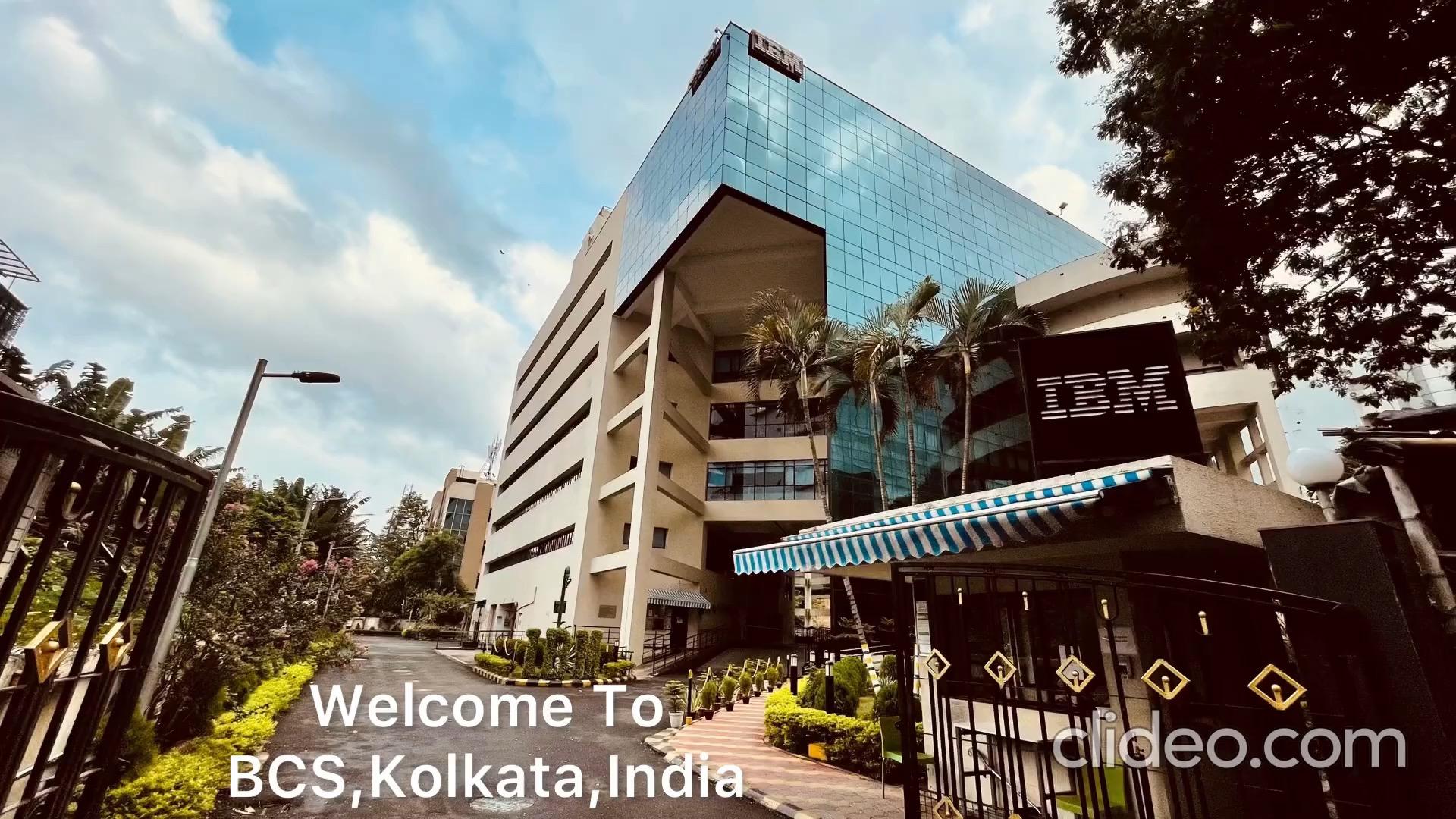
• Pollinators are responsible for over 65% of the fruit's yields and 40% of vegetables production happens that we consume on regular basis.
• Contribute to protect these pollinators and fight against climate change
• Boost ecosystem health by encouraging biodiversity.
• Provide ourselves with an area to relieve mental stress and connect directly with the environment
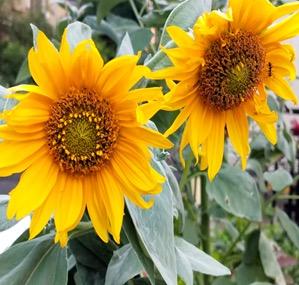
Description of the Innovation:
HVAC Pump
VFD Panel
Ventilation Enhancement
• Overheating inside the panel
• Fire hazard because of overheating
• Lack of circulation of fresh air
• Probability of breakdown of
• HVAC pump motors are operated through VFDs. Due to continuous running, VFDs are dissipating more heat inside the panel which must be removed to prevent overheating of electronic components.
Cooling fan is mounted on the top of the
• It improves equipment safety
• Reduction in operating temperature by 20 deg.
• It eliminates short circuit due to component failure
• It extends VFD life span and creates better
myIdea

Description of the Innovation:
Pet Bottle Crusher
myIdea
• Sustainable practice
• Irresponsible disposal of plastic
• Commitment towards sustainable business operation
• Difficulty in waste segregation and disposal
• Pet bottle Crusher help reduce the volume of plastic waste generated.
• Convenience for consumers: Pet bottle crushers can be placed in public spaces, such as Food Court ,Retail Space in the Premises ,Garden area ,Outdoor Play Area to dispose plastic bottles responsibly.
• Sorting and cleaning of Plastic Bottles.
• Grinding/ Shredding./Crushing.
• Recycling facilitation: Such as Polyester Fibers ,Plastic Pellets or New Bottles
• Resource Conservation: Conserving Energy and raw material like Petroleum
• Educational tool: Sustainable Practices &Awareness for individuals about waste management & Plastic Consumption
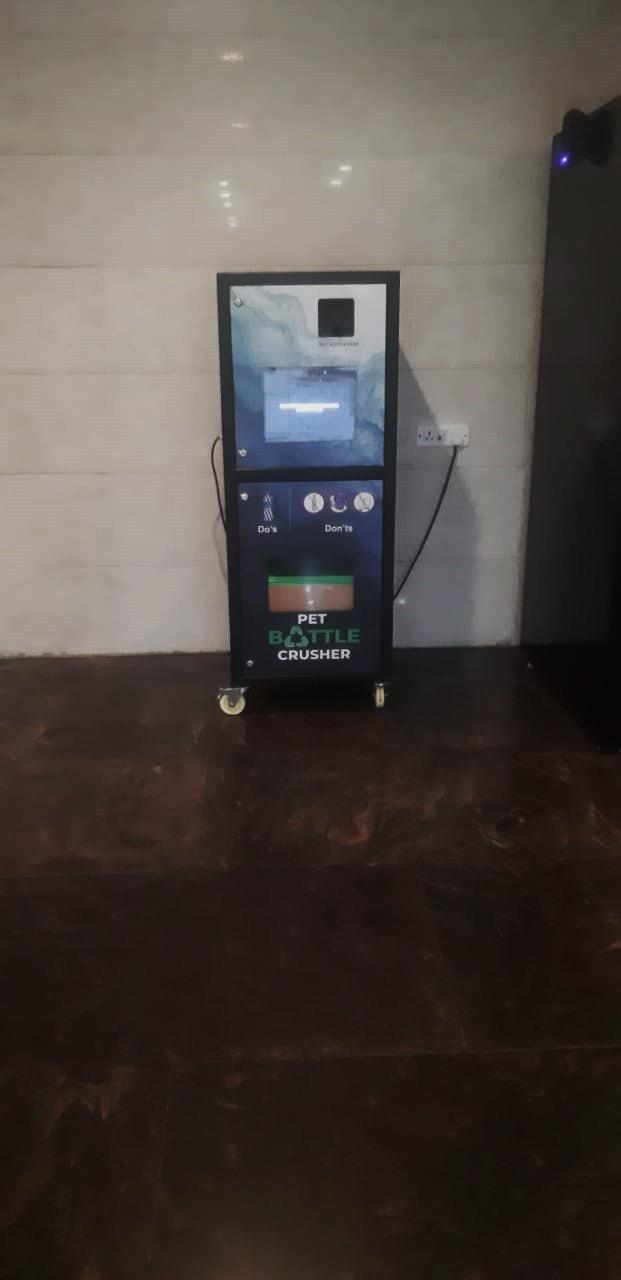
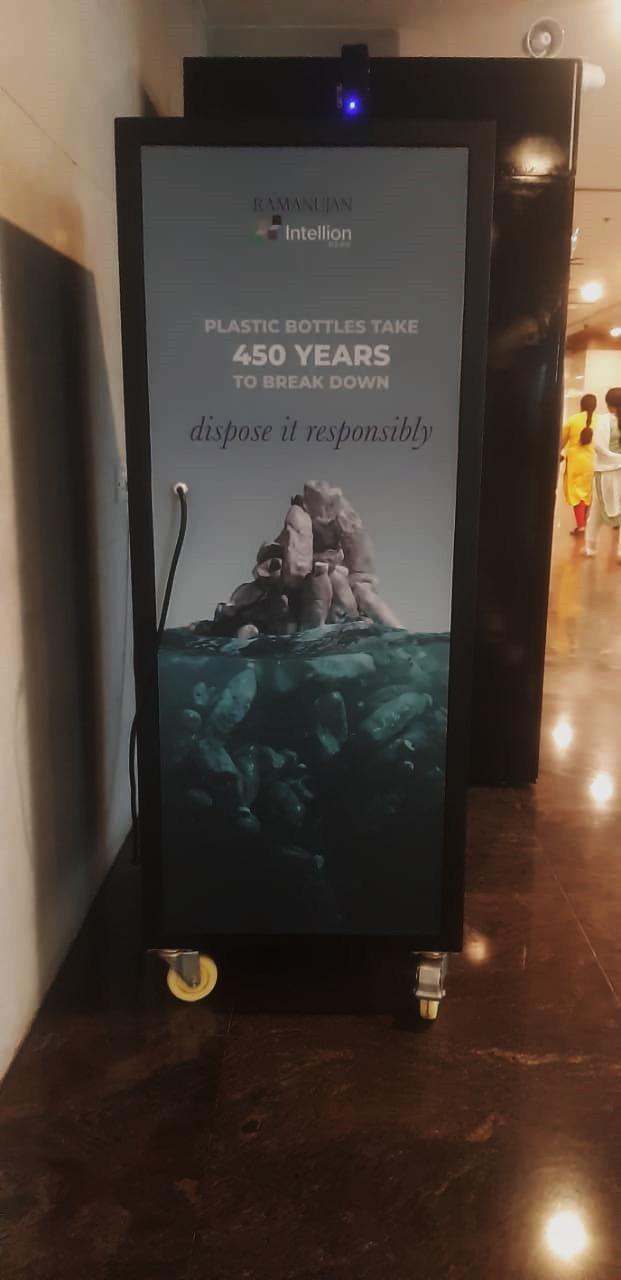
• Recyclable waste plastic.
• Volume reduction of PET BOTTLES.
• Crushing into pieces.
• Eco-friendly and economical collection of recycling materials.
• Low cost and durable long-term solution.
• NO maintenance costs of the shredder.
• Save environment.
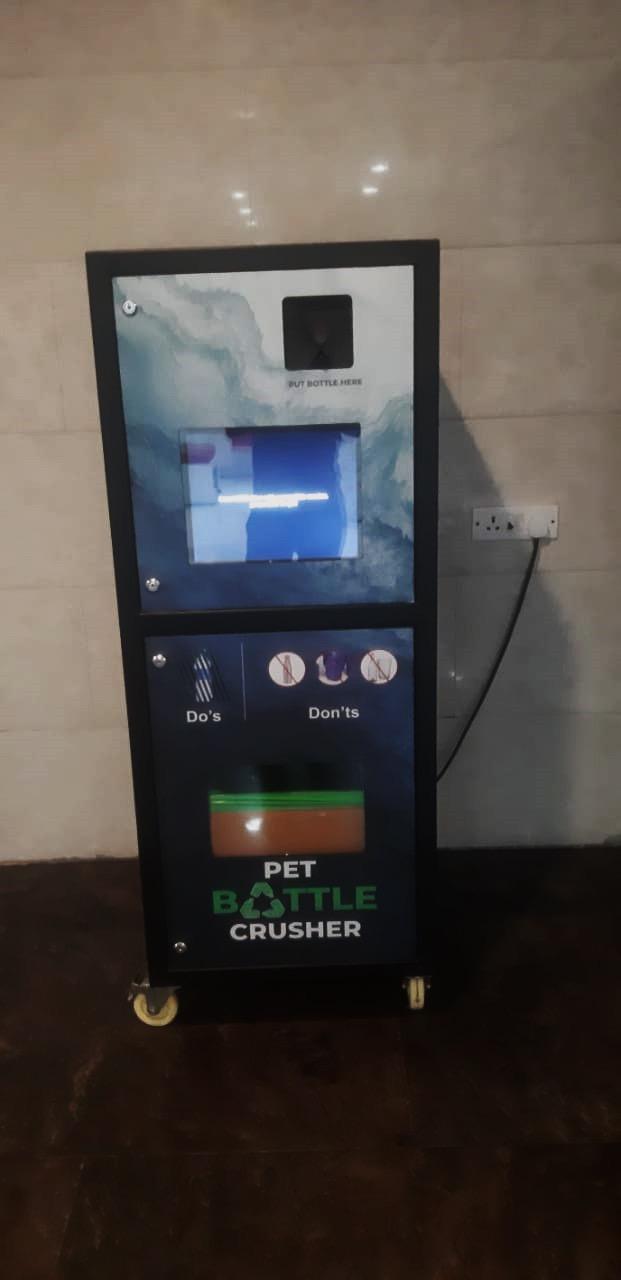
Description
of the Innovation:
Online Energy Monitoring System
• What is not measured cannot be controlled .
• High power consumption
• Sustainability Commitment
• Inefficient HVAC operation
• Wastages to be controlled
• High cost of energy
• Plant average performance
• Help customers in providing accurate electricity bills, minimize their consumption patterns by identifying the excess usage, promoting energy conservation for a sustainable environment.
• There are several benefits to energy monitoring system, including: Improved data for justifying capital investment.
• Identifying peak usage times/excessive consumption as and when it occurs. Increased efficiency and quality of resources due to the ability to identify irregularities.
• Significant Energy Savings.
• Improve Facility Performance.
• Reduce Carbon Emissions.
• Measurement of Results.
myIdea
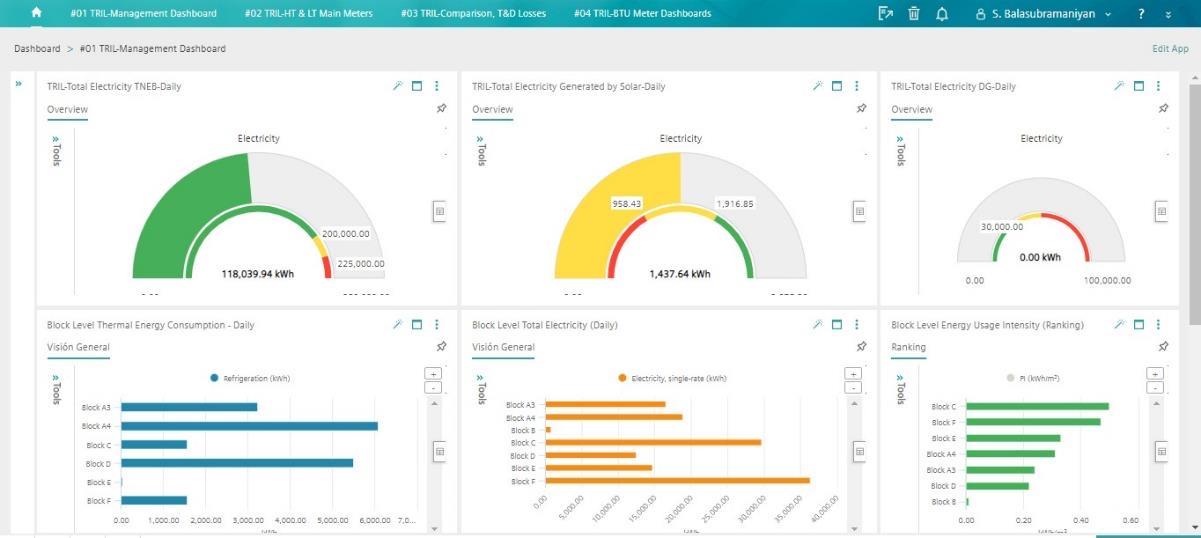
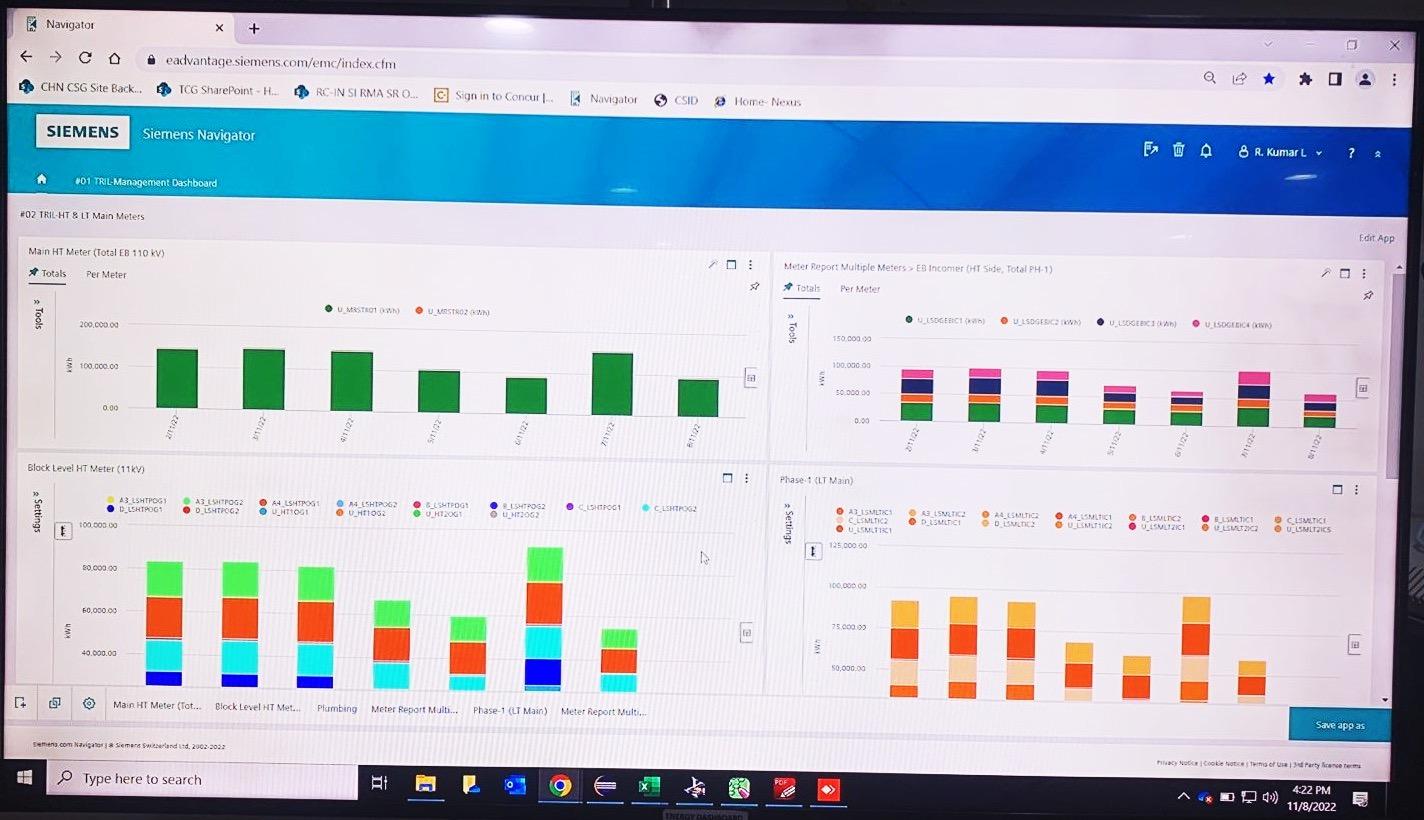
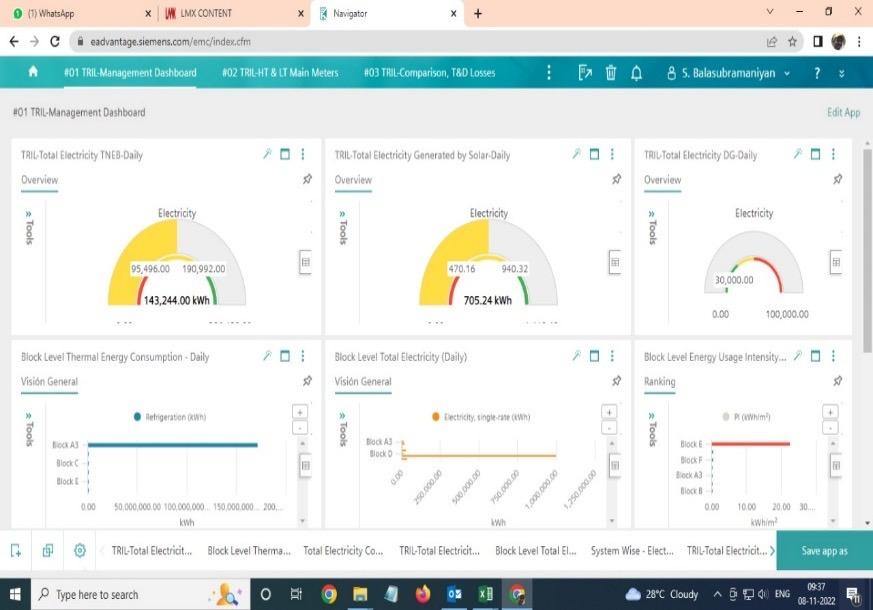
Description of the Innovation:
Language Development Class for Support Staff
• Lack of awareness
• Difficulties in understanding the language
• Lack of inclusivity
• Ineffective way of learning
• Promoting diversity and inclusivity
• Basics being implemented in spoken Kannada and spoken English classrooms.
• Weekly classes stretched total four to Eight hours, with two hours dedicated to English and two hours dedicated to Kannada.
• For English class, we use Anil Sherry's English book, name of the book is Dreamers, Doers, and Achievers, and for Kannada lesson, we refer the Learn Kannada App and YouTube videos
• It supports the ability of person to communicate, and express and understand feelings. It also supports thinking ability and helps them develop and maintain relationships. Language development lays the foundation for the basic understand and speaking skills in our support staff as they enter and progress through daily classes
myIdea
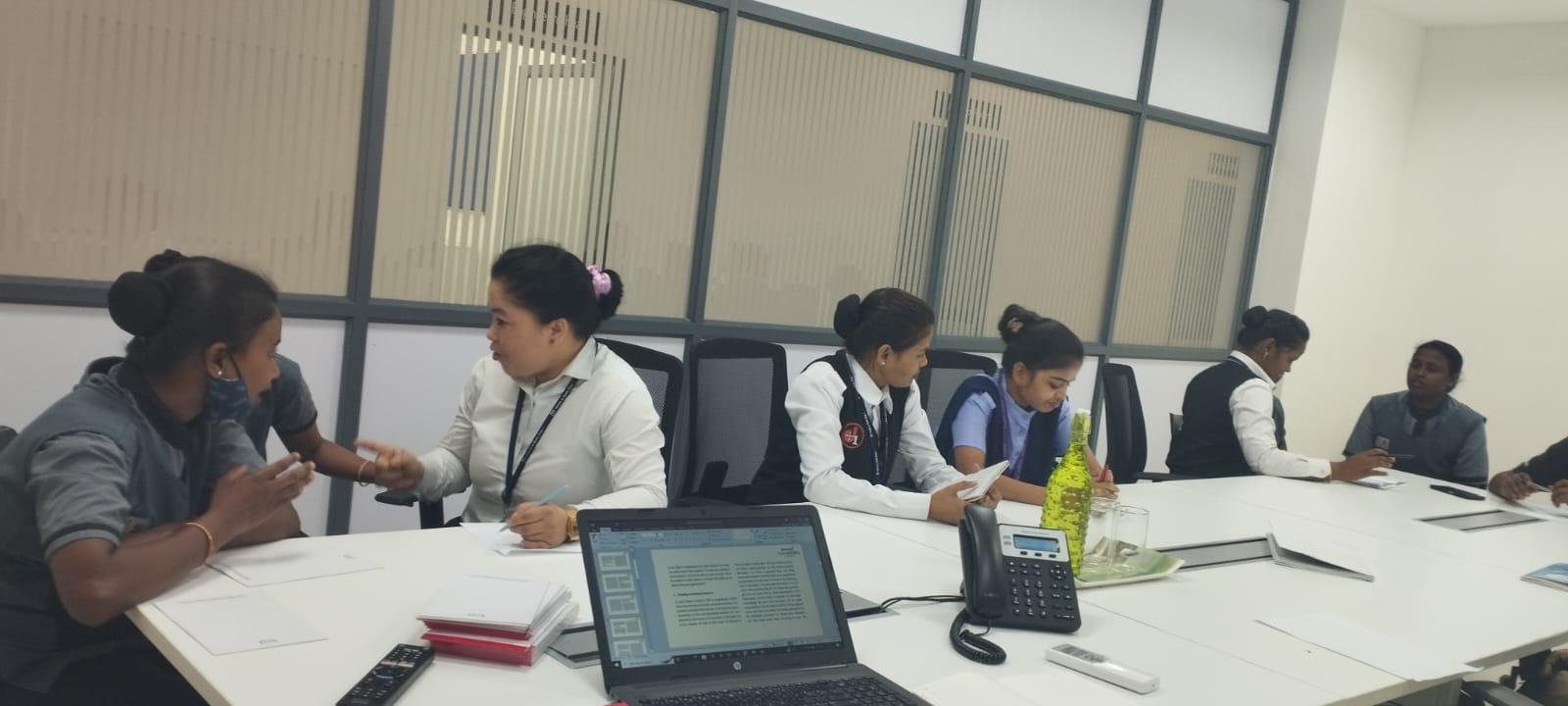
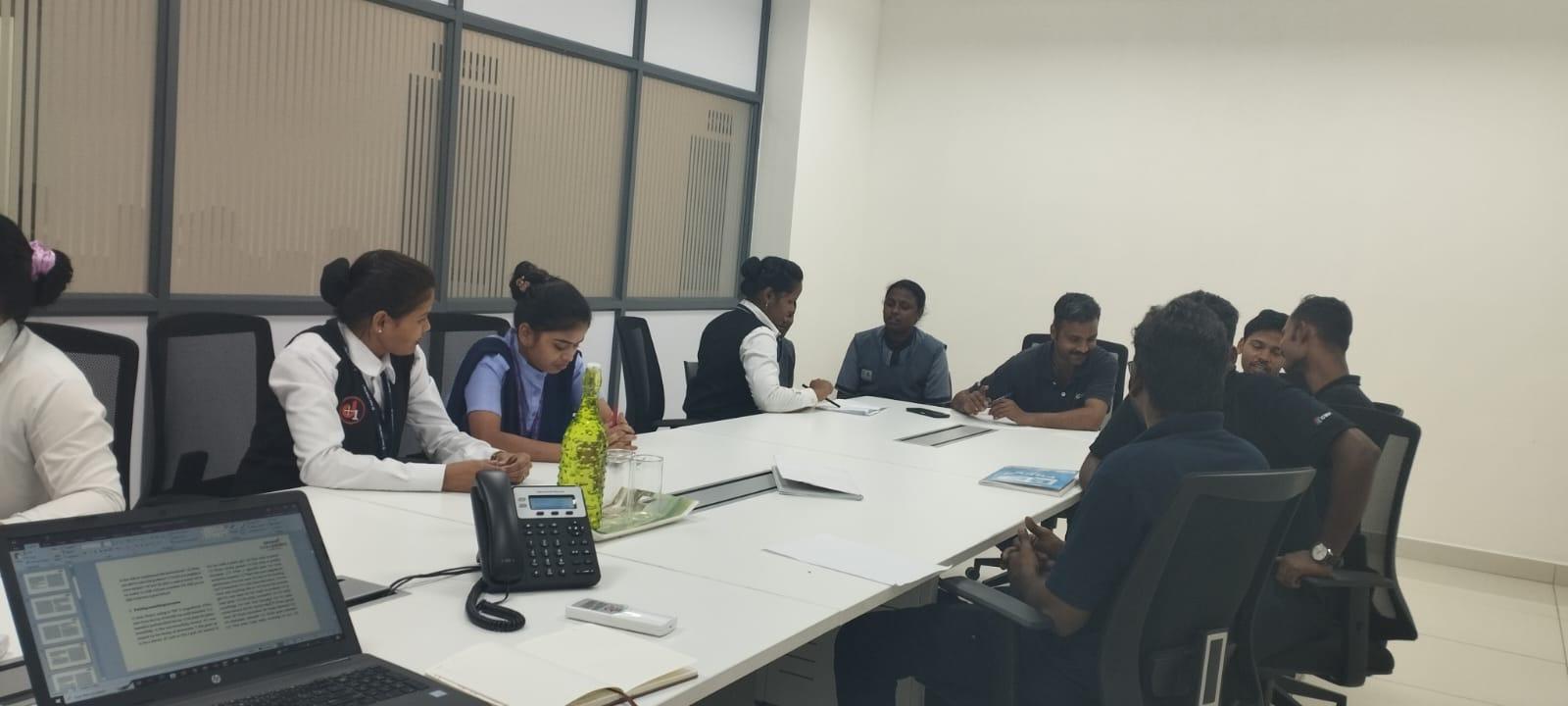
Description of the Innovation:
Healthy Workplace Program
myIdea
• Wellbeing of the employees
• Healthy and happy workplace
• Method of improving the work ambience
• If I have an issue – whom should I reach out to
• Participated in a certificate program consisting of a set of specially designed programs covering prevention of NCDs (Non-Communicable Diseases)
• It covers, Lifestyle Coaching Program covering Training the Trainers program for a group of employees nominated
• Other Programs - Smoke free worksite program and exclusive webinars on Mental Health aim to educate and promote the importance of mental health at the workplace.
• RMZ was awarded silver certification for healthy practices at workplace.
• Outreach to staff for health and well being.
• Multiple programs for .improving workplace habitat
• Improve confidence & morale of the staff
• Certified for healthy workplace
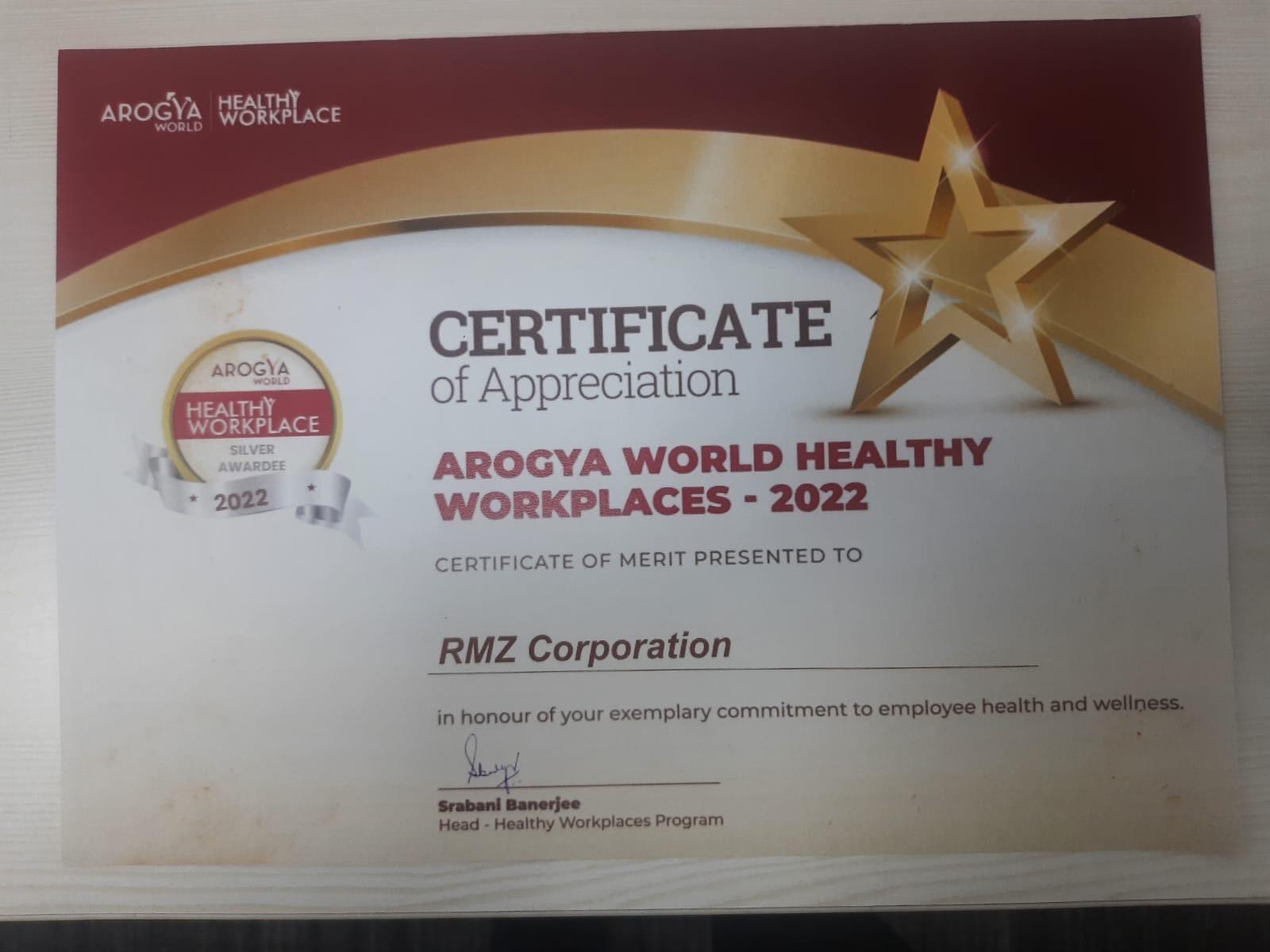
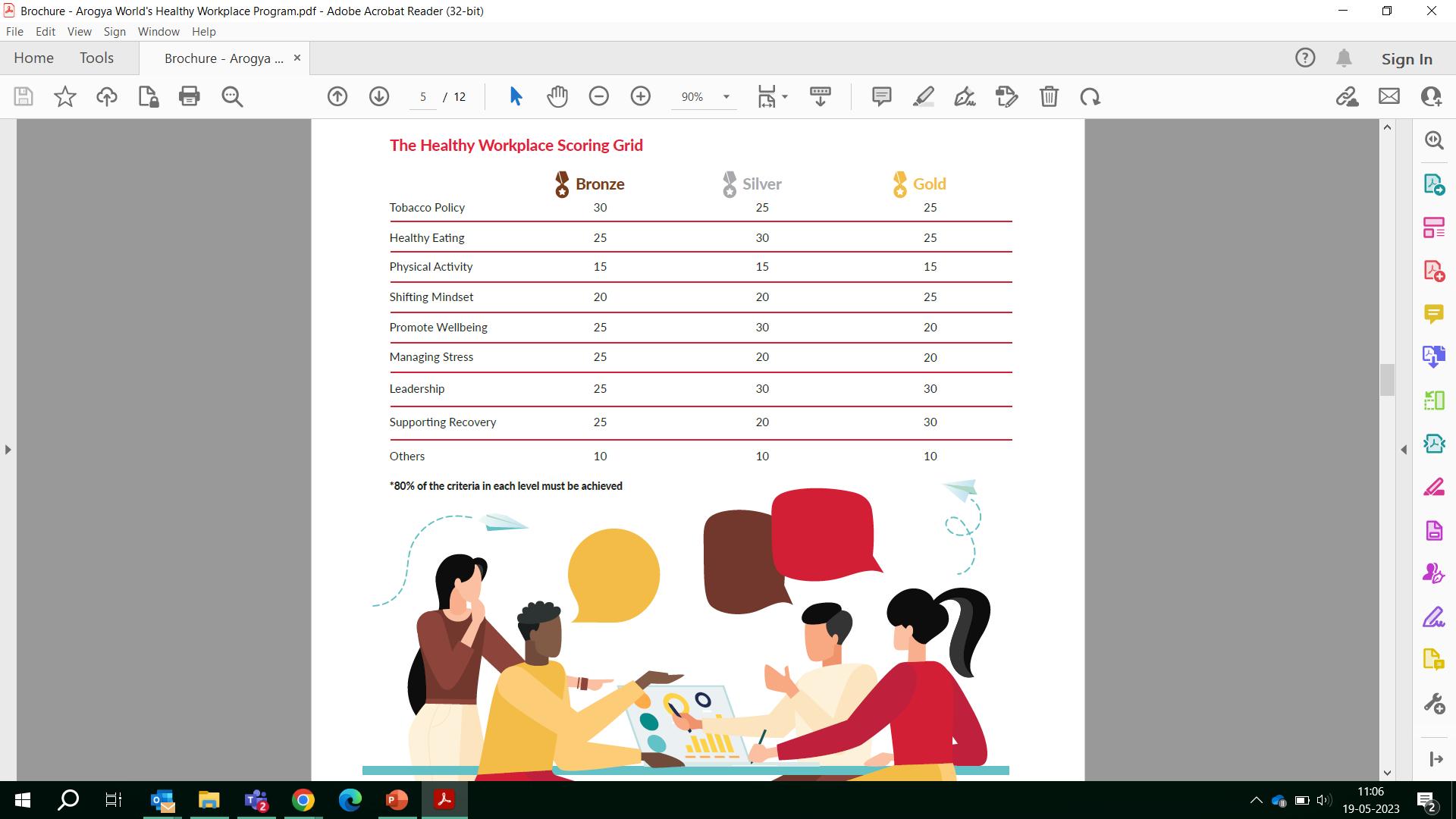
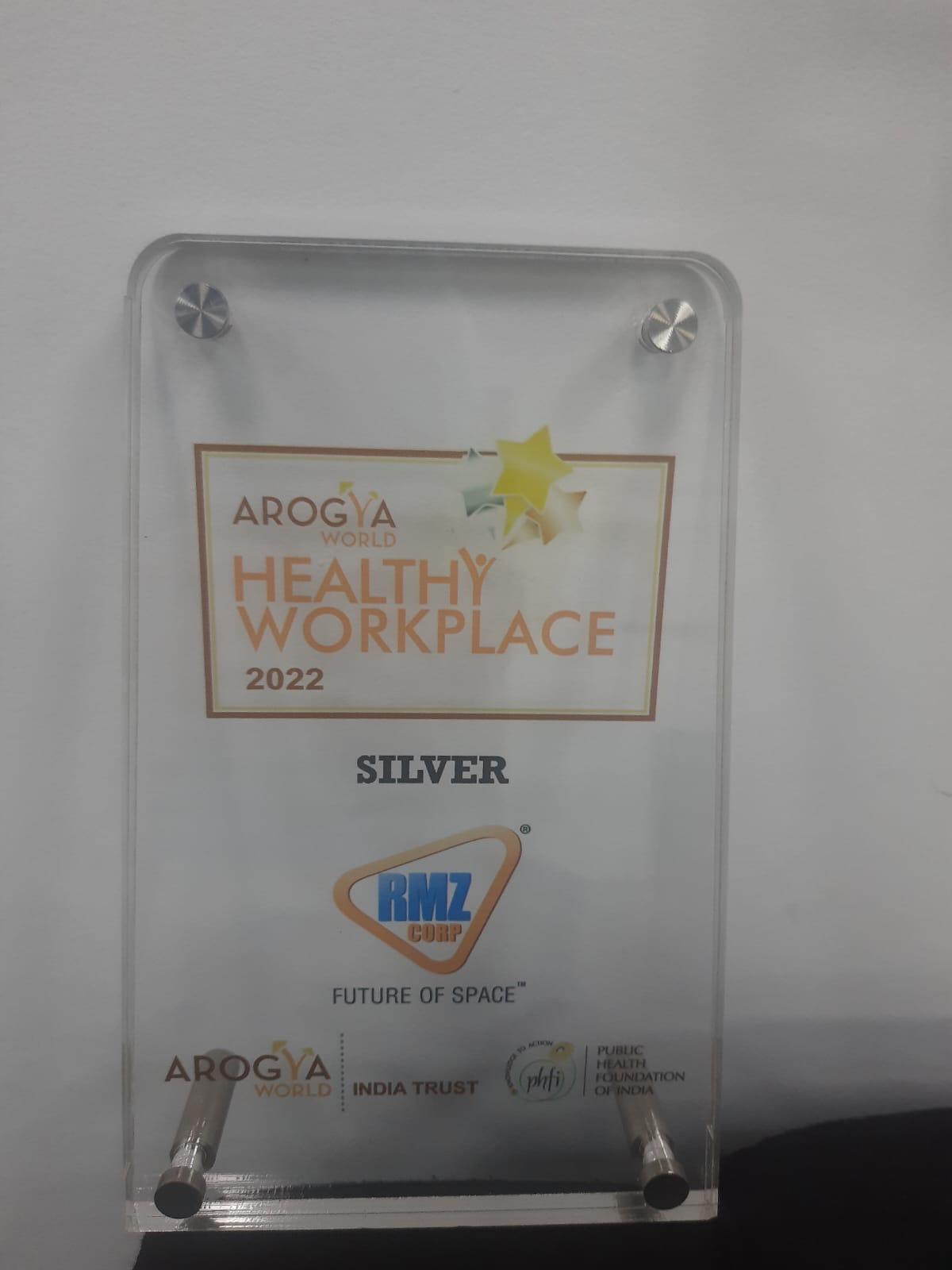
Description of the Innovation:
IoT Based real
Time STP
Monitoring Solution
myIdea
• Lack of real time data
• Inability to take fast response if the plant malfunctions
• Easy and effective reporting
• Ease in handling the internal and external audits
• Improved governance of the plant health
• Software – Can view the information from any laptop/mobile platform
• Data communication through independent GPRS network
• Will get Daily and Monthly reports through mails.
• Reduced operation cost (energy, manpower, consumables, equipment failure)
• Increased STP uptime by enabling better preventative maintenance
• Improved transparency and accountability, reduced reliance on human intervention / human errors / untrained operators / unskilled labor.
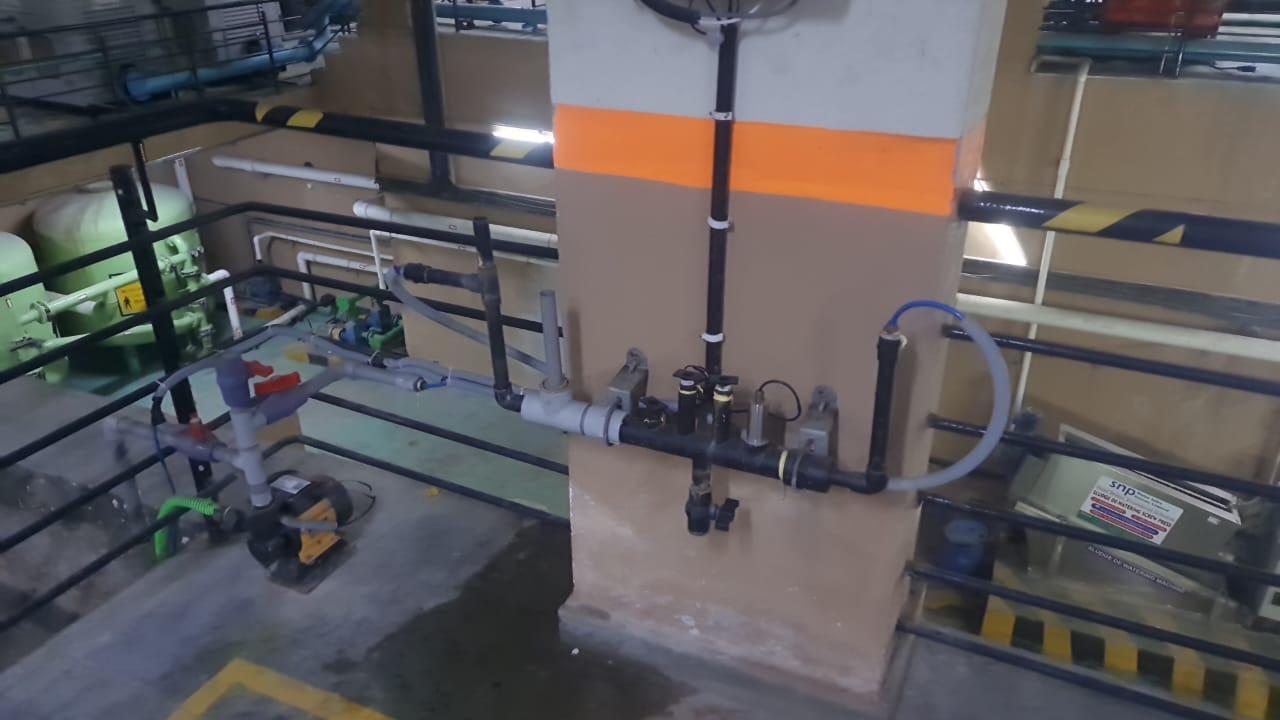
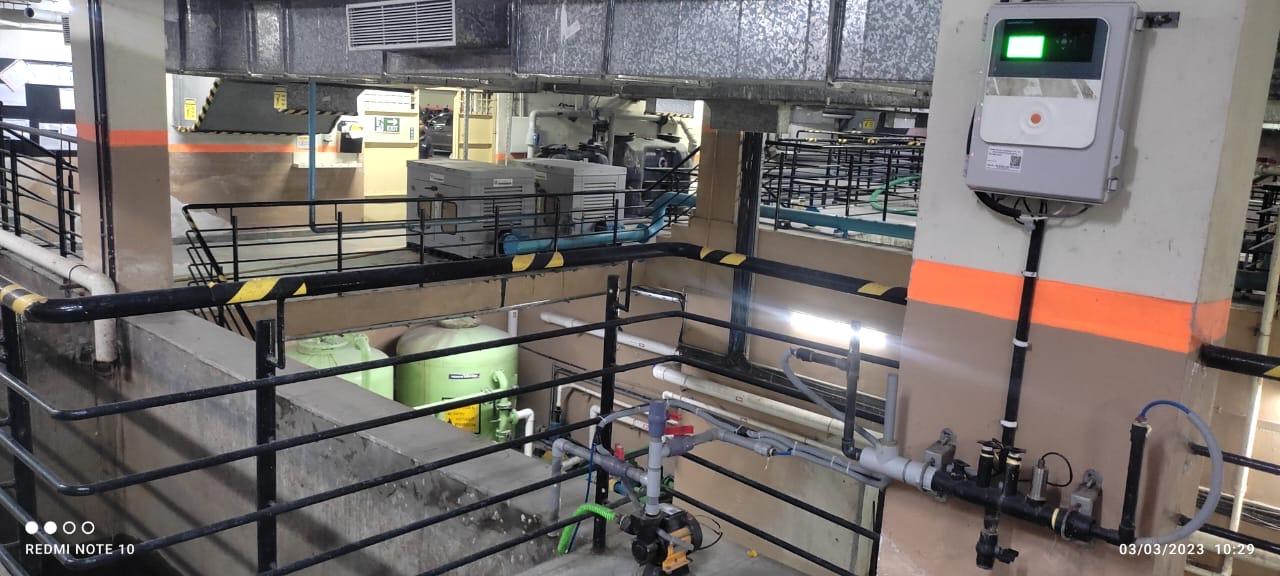
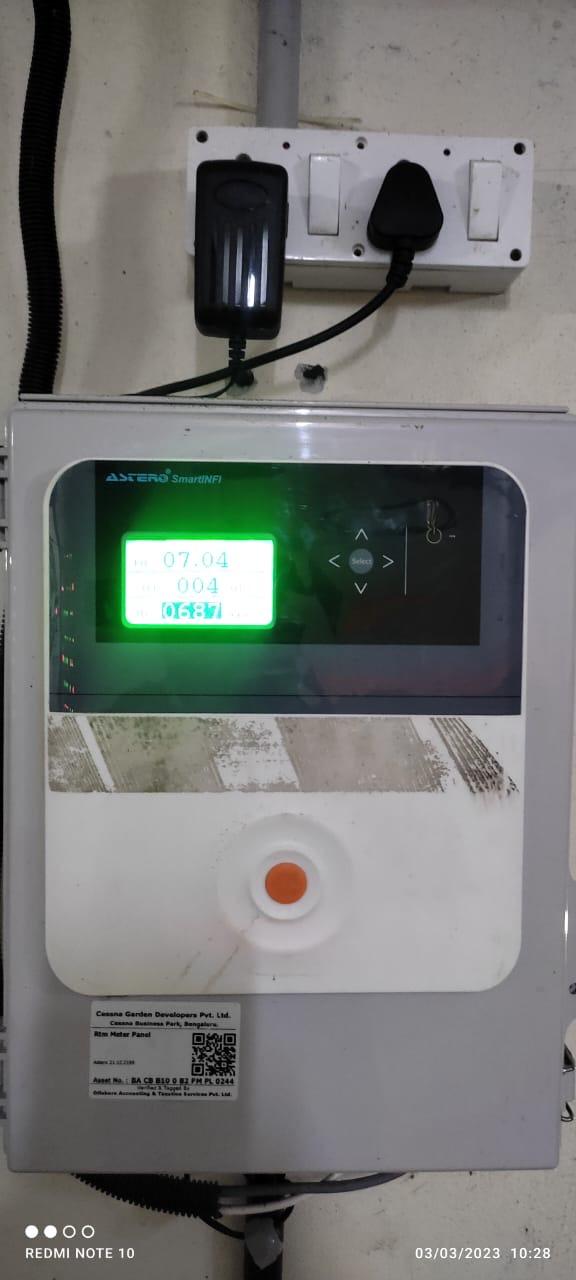
Description of the Innovation:
Centralized SCADA System
• What is not measured cannot be controlled .
• Inability to locate breakdowns on time
• Improve predictive maintenance
• Inefficient HVAC operation
• Wastages to be controlled
• High cost of energy
• Plant average performance
• To know the status of critical breakers like rising main feeders and DG operations during power failure we have installed SCADA System.
• Centralized SCADA will help us to understand the building power sources in one place were 24/7 manpower available.
• Reducing the dependency on Visiting the all systems
• Centralized SCADA System will help us to identify the building power source by sitting one location .
• Time saving
• Zero escalation
myIdea
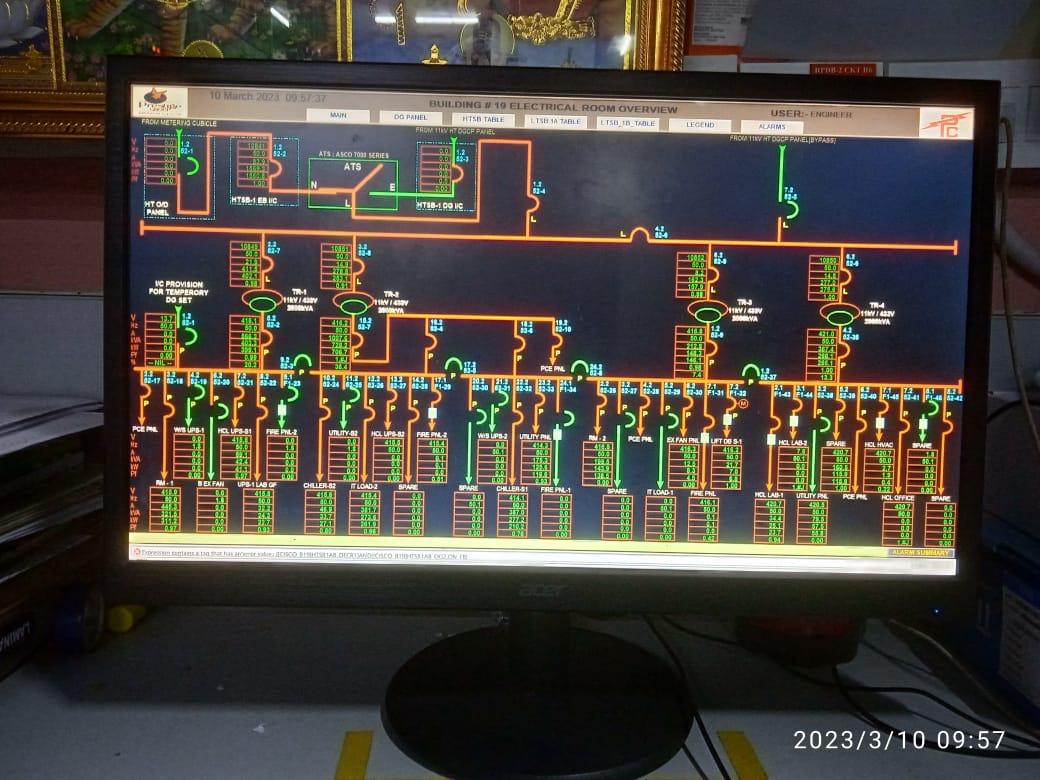
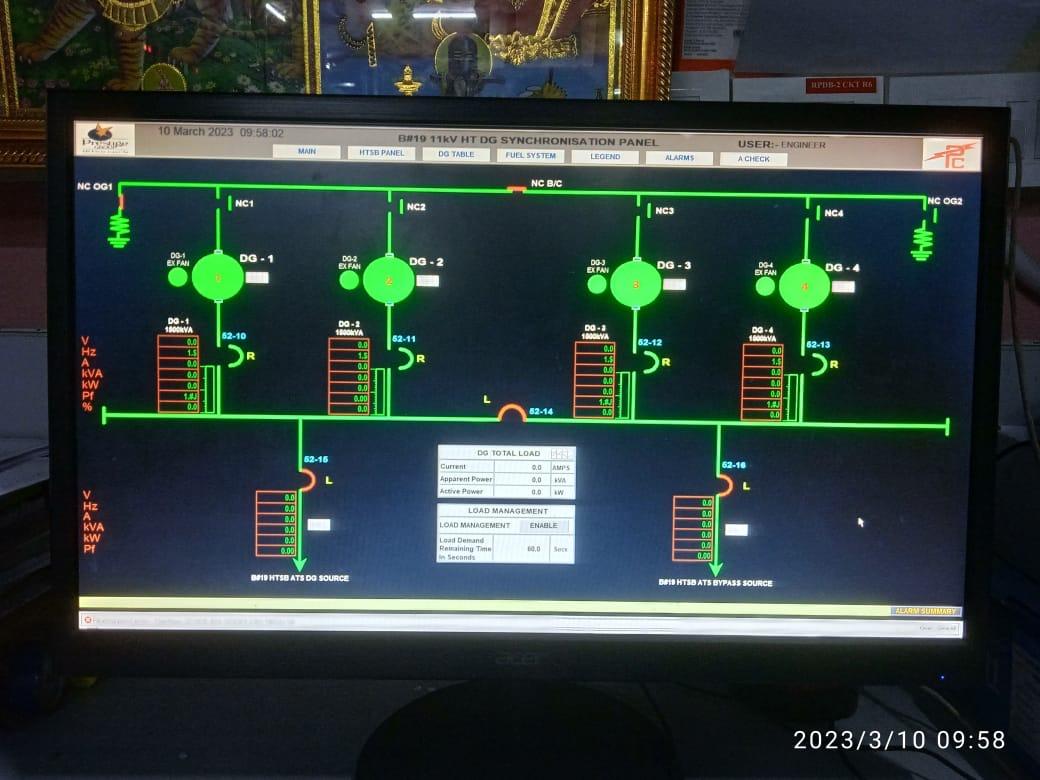
Description of the Innovation:
Utilization Of AHU Condensation Water in Cooling Towers
• Scarcity of Fresh water
• High Cost of Fresh water
• Shortage of freshwater can turn into a business risk
• Water recycle is a sustainability commitment .
• High consumption of fresh water
• Controlling the water wastage
• Commitment towards sustainability
• Utilization of AHU condensation water as makeup water for cooling tower.
• Reduction in temperature of chiller condenser water, thereby saving in electrical energy cost.
• Estimated annual saving in water costs is Rs 110/ KL X 2950 KL, i.e., Rs 3.25 Lakhs per year with an investment of approx. 2.30Lakhs.
• Estimated saving in Electricity cost has not been quantified but assumed to be substantial as the condensation water of AHUs which flow to the cooling tower tub is approx. 12 degree Celsius versus ambient temperature, which is achieved through the cooling towers.
• The energy required to process and deliver it is zero, as the water flow to the cooling tower trays is fed by gravity, while the pumped water consumes approx. .5KWH per KL. [Saving approx. Rs 20K per annum]
• The make up water from condensate is of 16”C in average as against ambient temperature from plumbing system.
• As its pure water no chemical treatment is required for this water.
myIdea
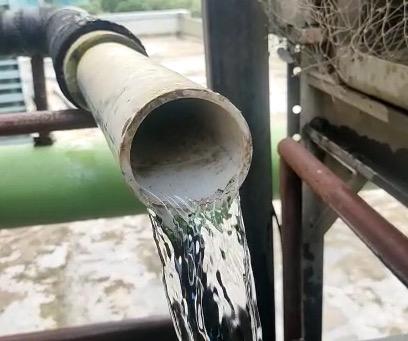
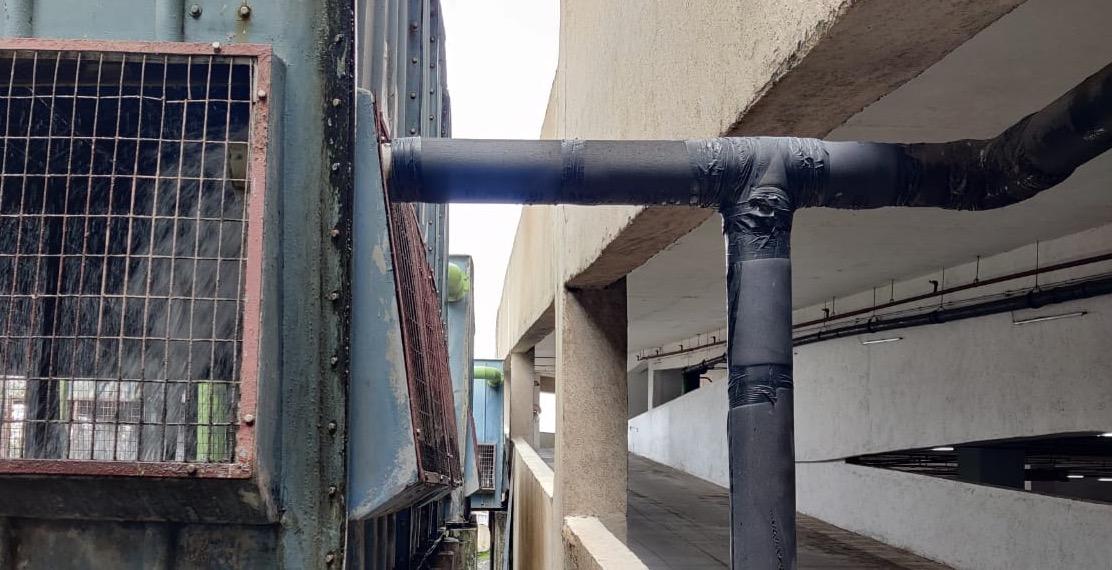
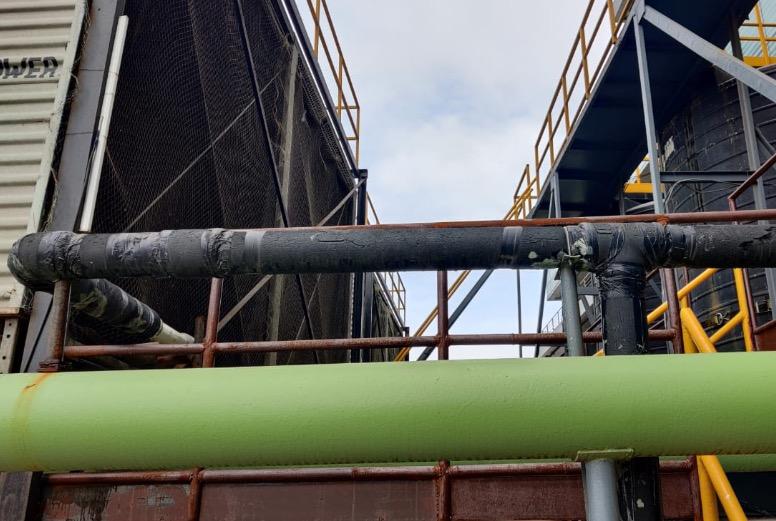
Description of the Innovation:
Chiller Energy Efficiency & Life Cycle Assessment
• High power consumption
• Sustainability Commitment
• Inefficient HVAC operation
• Wastages to be controlled
• High cost of energy
• Plant average performance
• The Chiller accounts for 40% of site energy consumption
• The energy metric which governs the chiller consumption is health of chiller condenser tubes which can be measured as chiller approach
• IT park strictly maintains the water parameters which decides the chiller condenser approach
• Descaling decision is taken if condenser approach exceeds 2 DEGC
• Also to know the life cycle of chiller condenser eddy current test is done on 5 yearly basis
• The affected tubes with reduced thickness are blocked in order avoid any major breakdown during normal operation
• Maintaining chiller approach below 2 DEGC ensures chiller efficiency is maintained
• Eddy current test ensures blocking of affected tubes to avoid breakdown during running condition
• Result of eddy current test enables management for decision in long term for equipment replacement
myIdea
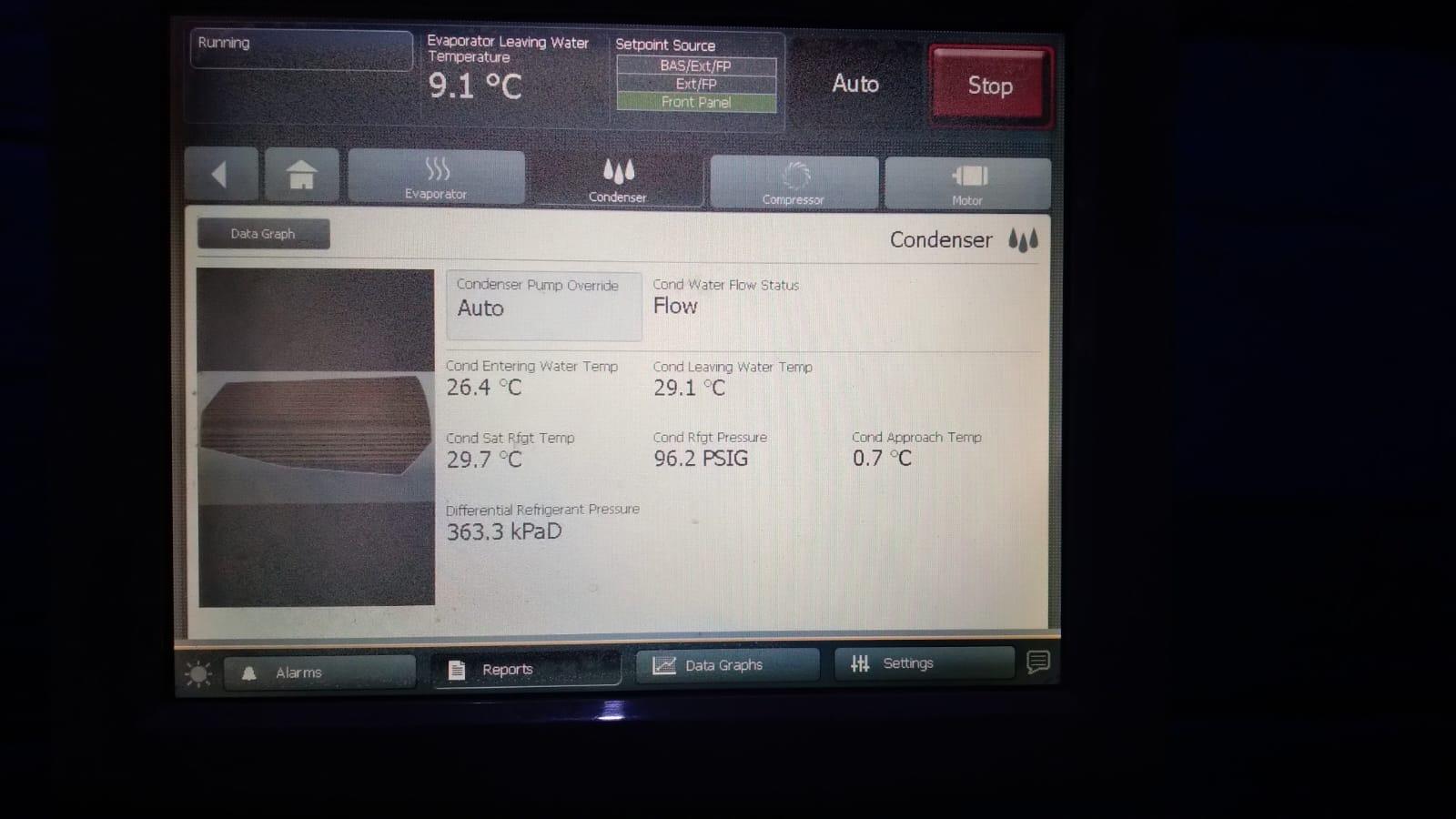
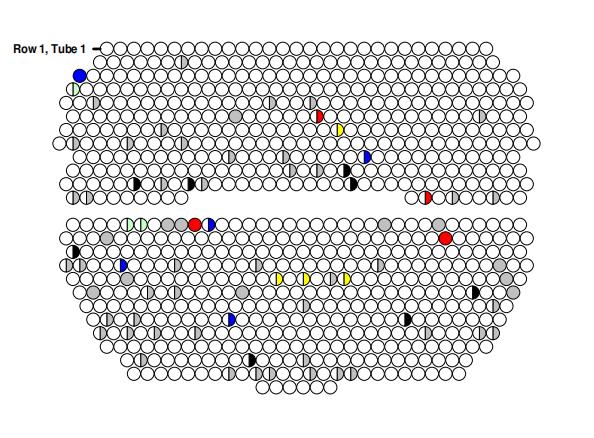

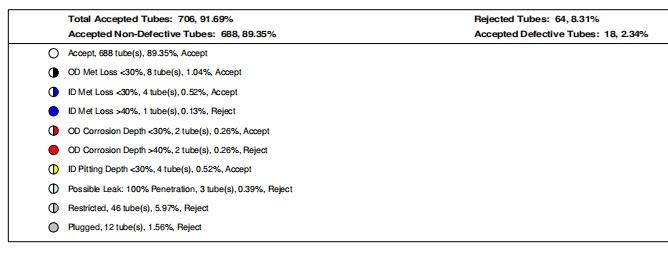
Description of the Innovation:
Vermicompost
• Lack of good soil quality
• Inhouse process to improve the soil quality
• Sustainability commitment
• Improve greenery
myIdea
• Vermi-composting is a process of preparing enriched compost with the use of earthworms.
• Earthworms consume biomass and excrete it in digested form called worm casts, which has been termed as ‘black gold’ due to its nutrient rich properties.
Vermi composting is also regarded as
• Quarterly consumption of 3 brass subsides with the preparation of Vermi compost as these are rich in Nitrogen.
• Vermicompost is rich in NKP (nitrogen, potassium and phosphorus ), micronutrients, beneficial soil microbes and contain 'plant growth hormones & enzymes’.
• Estimated Saving : 50,000/- yearly
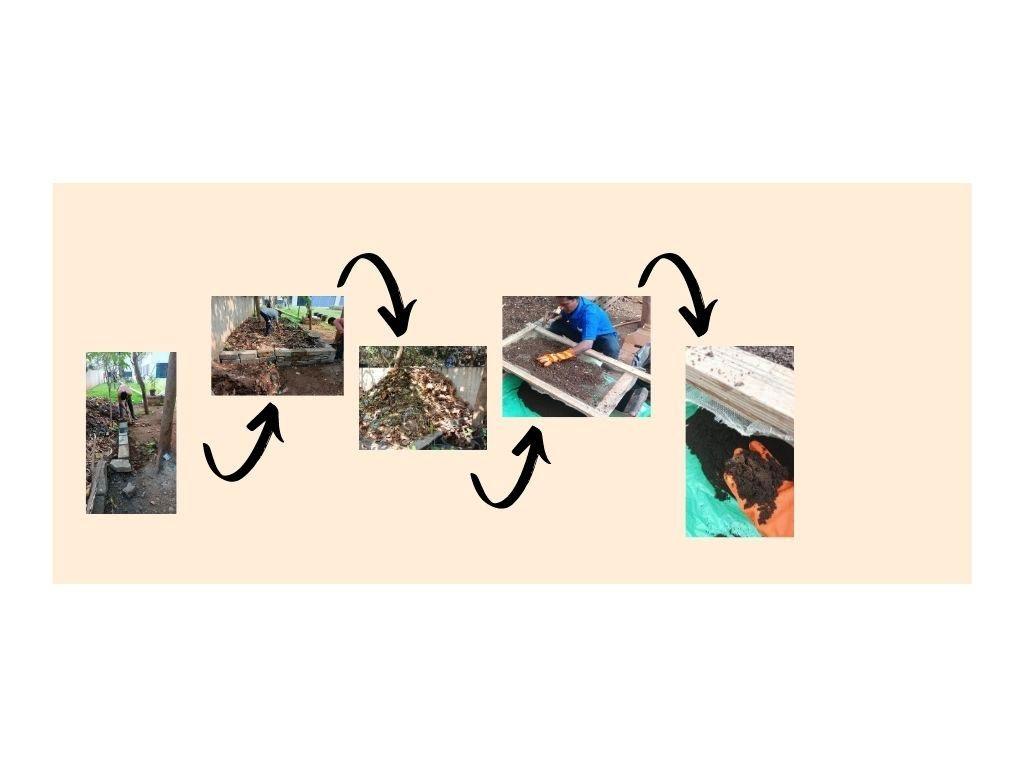
Description of the Innovation:
Integrate Condenser Pump and CT Fans
• High power consumption
• Sustainability Commitment
• Inefficient HVAC operation
• Wastages to be controlled
• High cost of energy
• Plant average performance
• There was high consumption of energy on the chiller feeder due to continuous running of CT fan & Condenser Pumps even after the plant are shut off on attaining set temp.
• In 10 hrs of plant shut down the energy consumption of the CT Fan & Pumps was 60KW/hr amounting to 600unit /Rs 6000/day.
• We Integrated the condenser and CT fan with chiller plant control circuit with help of OEM.
• This ensured that both CT Fan and Pump stopped also on attaining set temp. in a manner that it starts 1 min before chiller restart and shuts down after 1 min of chiller stop.
• Saving of 219000 units annually/Rs 21 lacs annually.
• Shut off condenser pump and Ct fan during chiller off load after getting set point
Temperature .
• 81249 MT Carbon Emission. And Energy savings 219000 KWH / Annum.
• • 35 % energy saving as compared to constant running of CT fan & Pump.
myIdea
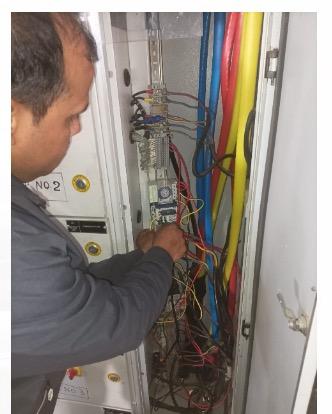
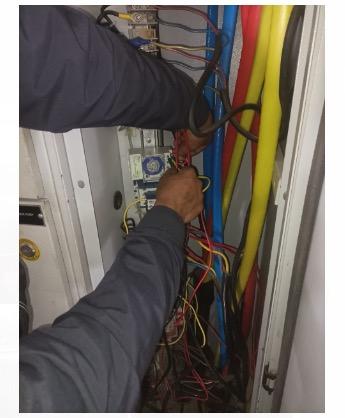
Description of the Innovation: CHALLENGE
• Air pollution
• Commitment toward sustainability
• Government norms
• External air quality
RECD Device in DG Sets
myIdea
• Installation of Retrofit Emission Control Device in DG sets.
• RECD is built on filter-less technology and based on electrostatic precipitation fundamentals.
• It does not require active regeneration and is not affected by exhaust temperature.
• RECD’s clear air filter less solution does not require manual cleaning as there is no choking
• It is highly efficient in improving air quality and capturing Particulate Matter (PM) from air with more than 70 to 90 per cent efficiency.
• This device does not need any water, chemicals, or solvents,
• No adverse impact on engine i.e. back pressure.

Description of the Innovation: CHALLENGE
Switching From 11 KV to 33 KV Supply
• High DG running hours
• High consumption of fuel
• Expensive power cost
• Reducing carbon foot print
• Depletion of fossil fuel
• High cost of operation
• High cost of DG maintenance
• Earlier we had 11 KV GRID supply for our site. Which was coming from a substation about 6km away from our site.
• This is common for 3 sites.
• Frequent voltage fluctuation in 11 KV and tripping was very common during peak load.
• After tripping, a minimum 1-2 hrs. is wasted to resume grid supply.
• To counter this, switched from 11 KV GRID Supply to 33 KV GRID supply.
• Voltage fluctuation and tripping is minimized near to zero,
• DG running for power backup is minimized.
• Burning of fuel is reduced.
• Reduced power losses
• Increased power capacity & Better voltage regulation:
• Discharge of Emission gases from burning diesel is reduced.
• Carbon emission in the environment is reduced.
• Wear and Tears of DG sets reduced
• Diesel consumption reduced
myIdea
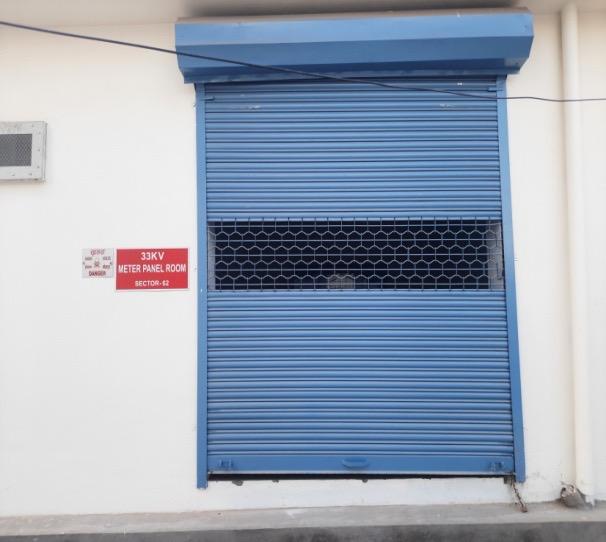
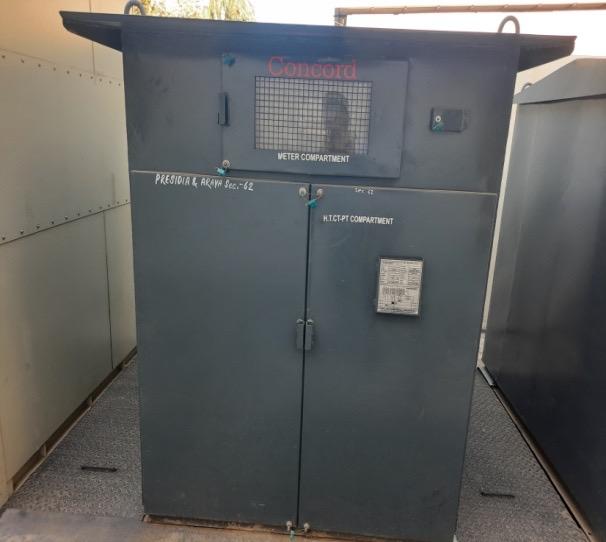
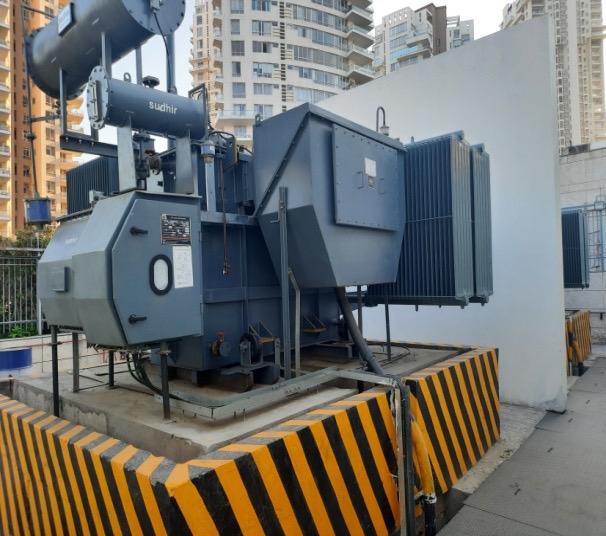
Description of the Innovation:
Green Campus by Using Sustainable Materials
myIdea
• Commitment towards sustainable operation
• Usage of sustainable materials
• Responsibility towards plant earth .
• Reduction of carbon footprint
• Demonstrating the commitment towards sustainability .
• As a green initiative and to have eco friendly campus, introduced Hydro Cleaning Technology in which cleaning solutions generated using Neutral Electrolyzed water
• Generate eco friendly chemicals which are ready to use / concentrated chemicals for daily use.
• This eliminated the usage of hazardous chemicals which helped in providing green environment at our campus
• Allows for disinfection of areas where toxic chemicals are not permitted
• Helped in reducing on stocking of chemicals, as the chemicals can be generated when required in house
• User friendly, safe, non-harmful which uses natural ingredients like Water, Salt and Electricity for chemical generation
• Over-all cost on purchasing of chemicals reduced by 80%
• Machine ROI 18 Months
• Received iNFHRA Workspace Excellence Award 2022 – 2023 under ESG


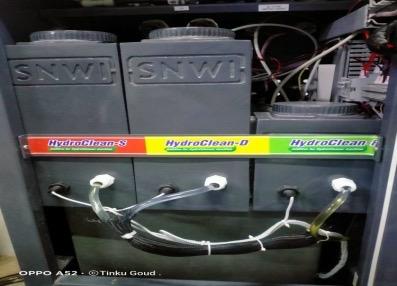
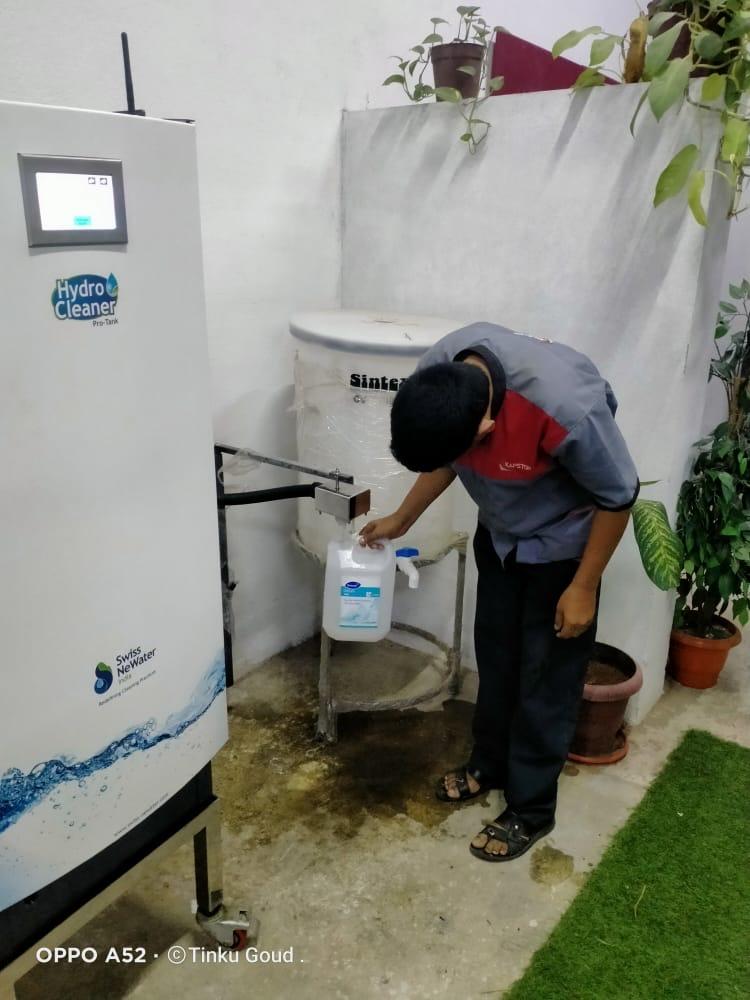
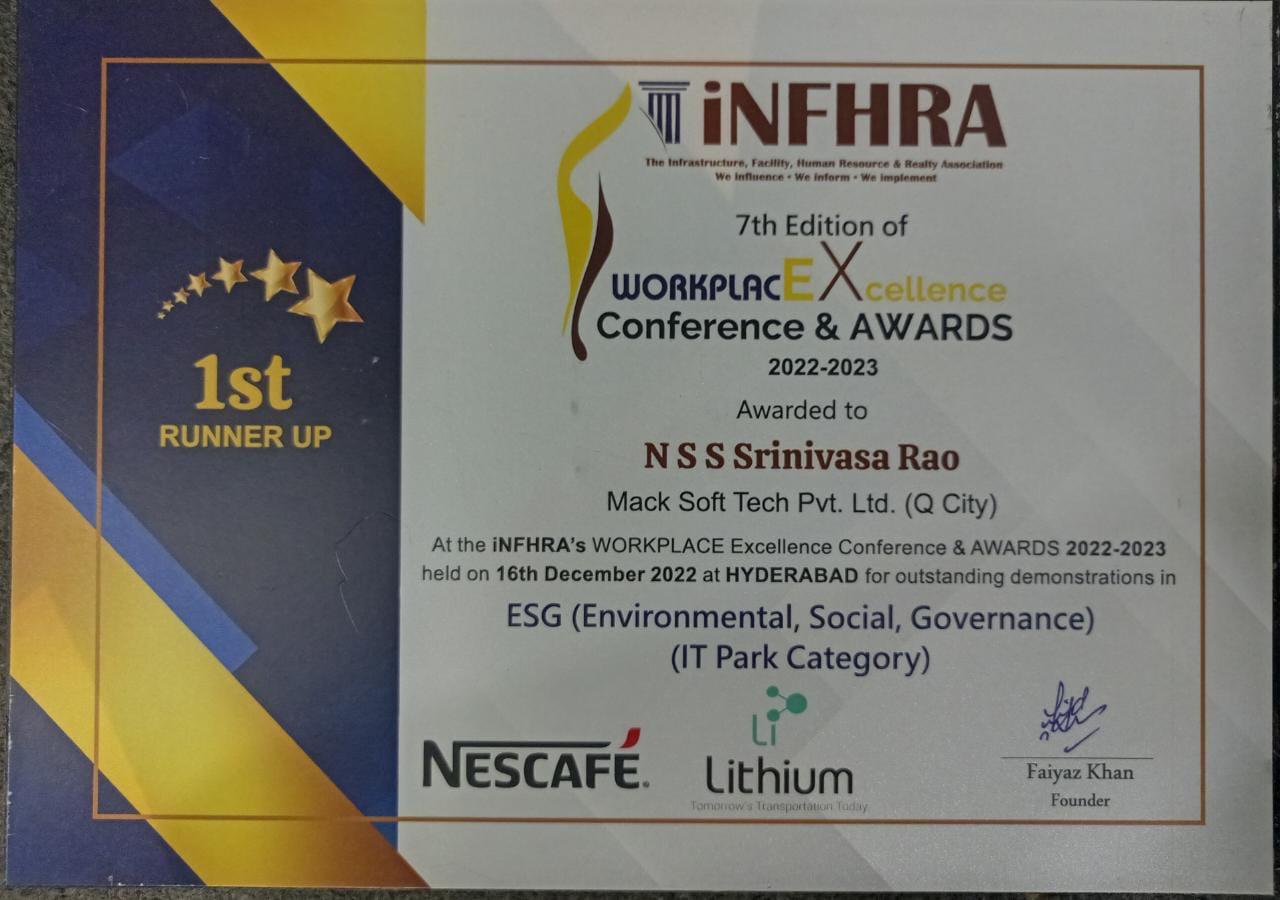
Description of the Innovation:
BMS to Improve HVAC System
• What is not measured cannot be controlled .
• Inability to locate breakdowns on time
• Improve predictive maintenance
• Inefficient HVAC operation
• Wastages to be controlled
• High cost of energy
• Plant average performance
• The building is 10 + years old
• We have 44 AHU’s in campus each with 23K CFM, no VFD’s were installed in AHU’s leading to manually operating the AHU’s on daily basis
• Frequent AHU breakdowns and other on-ground issues
• Introduced BMS to digitalize and improving energy efficiency all the AHU’s
• Installed VFD’s in all the AHU’s with return air sensor control logic
• Provide valuable airside analytics regarding HVAC and fan coil units and variable air volume systems, including identifying unnecessary heating and cooling operation and setting heating and cooling system hours
• Identify valve leakage
myIdea
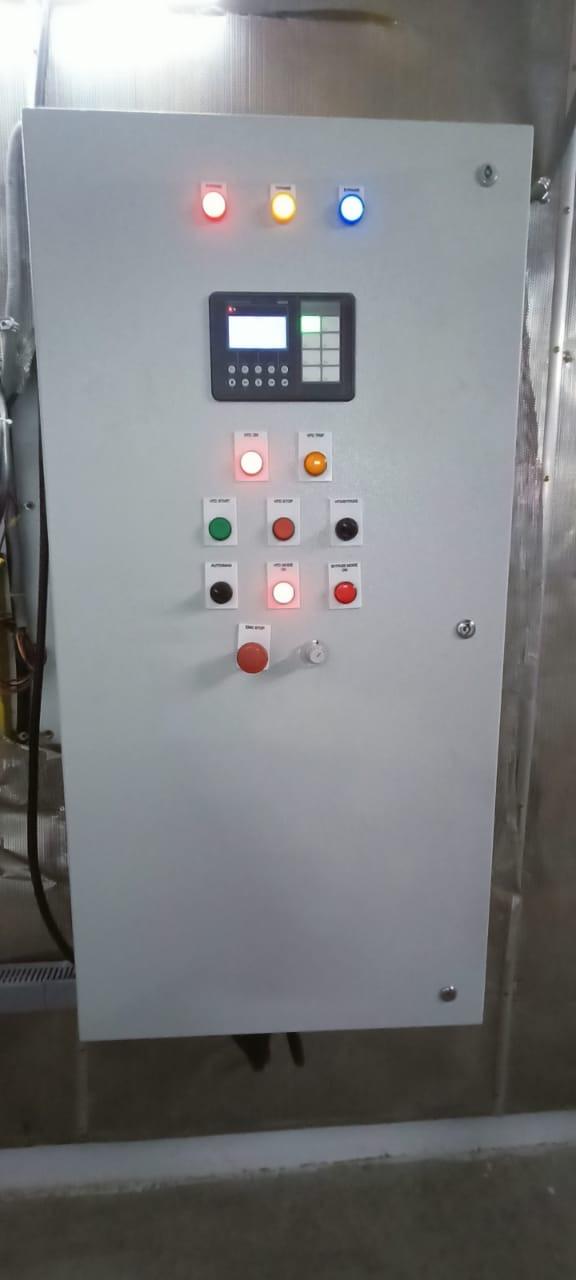

• Monitoring of real time status
• Track energy consumption and produce energy efficiency reports
• Eliminating unnecessary maintenance
• Monitoring equipment and assets effectively to reduce system breakdowns
• Improving efficiency of field service visits and reducing manhours of maintenance teams
• BMS system helped in reducing 5% to 10% of total chillers consumption
• Overall, 6% of savings on chiller units i.e.., 1.2 L KWH per annum, reducing of 98 MT carbon footprint.

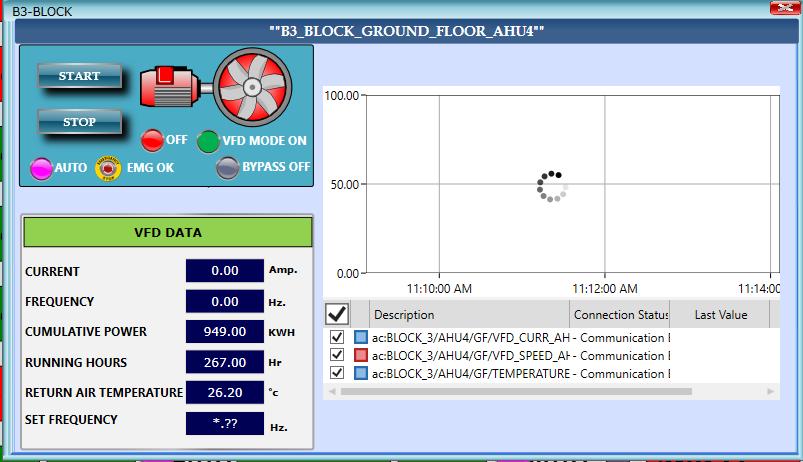
Description of the Innovation: CHALLENGE
• High power consumption
• Sustainability Commitment
• Inefficient HVAC operation
• Wastages to be controlled
• High cost of energy
• Plant average performance
Interconnectivity of Chilled Water Line
myIdea
• Reduction of HVAC pump running hours.
• Increase redundancy of Secondary Pumps.
• Chilled Water distribution header line interconnectivity.
• Energy saving Unit/Month:
• 10,009.2 kwh for T-A & T-D & 11,198.00 kwh for Tower B & C area .
• Direct Cost savings:
• 96,588.78/ month for T-A & T-D & 10,4141.4 /month for T-B & T-C .
• Carbon footprint reduction: 122 Ton/year
• Estimated Saving : INR 1.07Lacs/Month
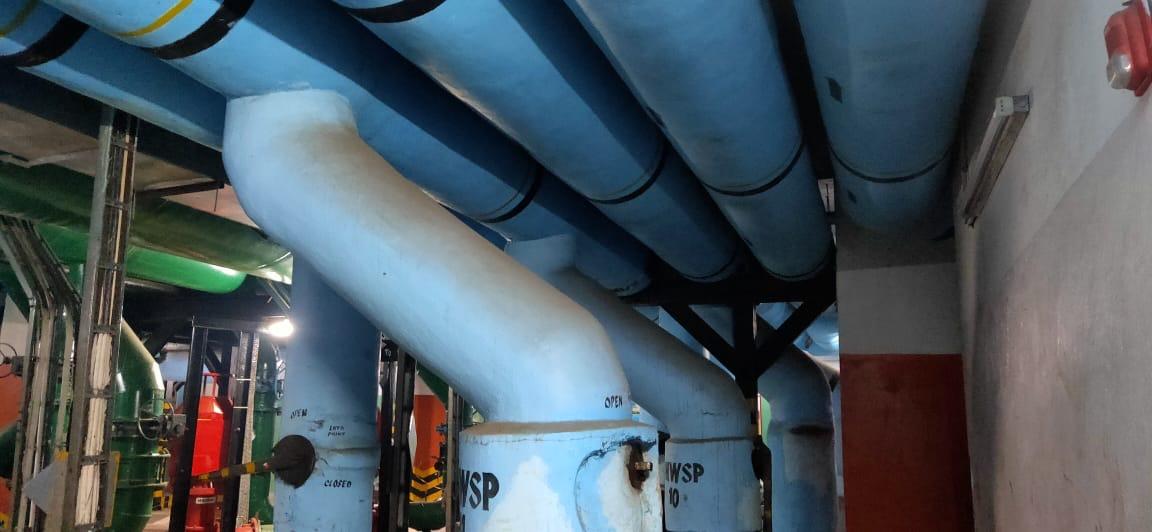

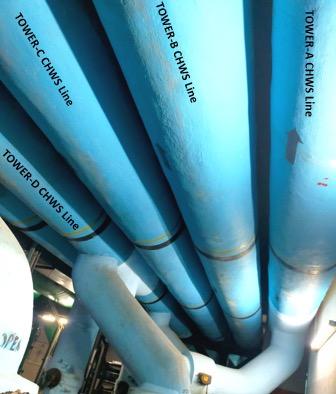

Description
of the Innovation:
• High power consumption
• Sustainability Commitment
• Inefficient HVAC operation
• Wastages to be controlled
• High cost of energy
• Plant average performance
• Replacement of old less efficient condenser pumps to new energy efficient condenser pumps.
• High Energy Efficiency
• Reduce drawing kw power with same delivery capacity
• Less maintenance cost
• Reliability increase of overall HVAC plant
Condenser Pump
• Previously Motor capacity was 93KW and now 75 KW Energy Efficient Vertical inline pumps have been installed,
• Approx. Energy Saving: 1620 KWH/month.
• Amount saving 0.42Lacs/Month.
• Carbon Footprint Reduction: 200Ton/Year.
• Estimated Saving : INR 1.38 Lacs/Month
myIdea
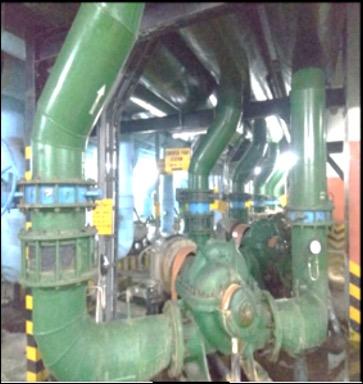
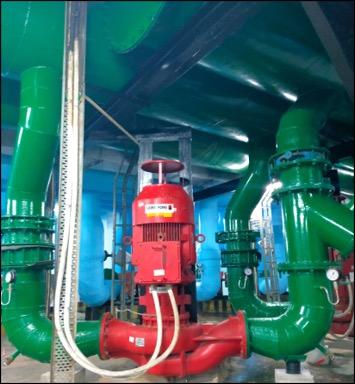
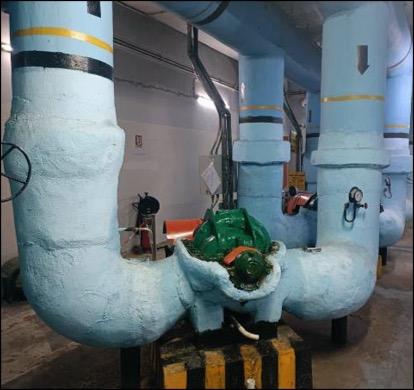
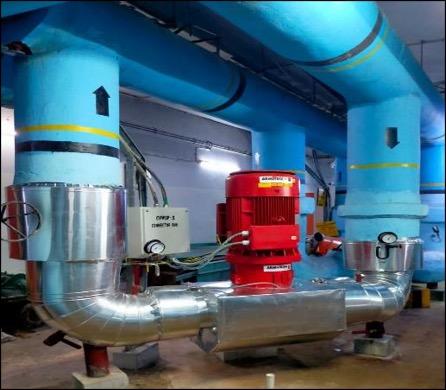
Description of the Innovation:
IoT BMS Application
myIdea
• Juniper Networks Electra building is a 10+ year old office hosting multiple critical infrastructures such as DGs, UPS, Chillers, PACs supporting labs & data centers.
• The BMS system installed during 2011 (project phase) had issues and the data was not reliable.
• Frequent failures of Automation servers & field controllers worsened the situation & made the system unusable beyond a point.
• Warranted frequent visits to the equipment.
• CBRE in partnership with I2I Software Solutions, provided an IoT Cloud based BMS platform.
• Customized UI with input from the frontline users to facilitate better user experience. Platform developed using a modular architecture & topologies as below:
• Data Capture
• Data Normalization & Virtualization
• Cloud Data Aggregation
• Data Visualization
• Policy and workflow
• System configured in IOT
• Chillers,
• DG Sets
• Low Side HVAC
• Smart Meters
• UPS
• Improved, resilient, sustainable Technology
• Reliable & consistent monitoring of critical infrastructure supporting labs & Data Centers.
• Unified, comprehensive and automated data capture system across different types of assets
• System to support different interface types and protocols as needed
• Remote access to data with visualization
• Automated control of assets based on configured set points, and schedule, with override capability
• Support configuration of policies and workflow automation with graphical interface
• Leverage existing HW where possible and augment as needed

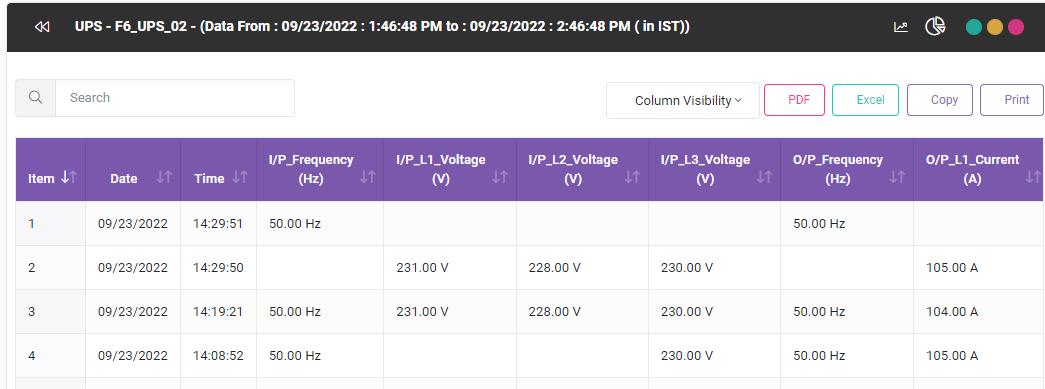
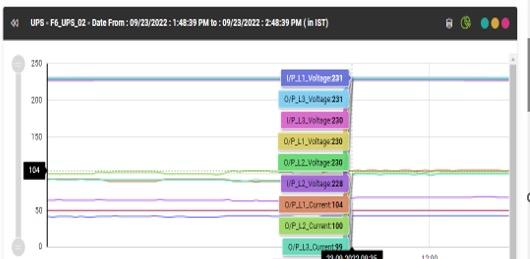
• Limitation to conduct frequent audits
Description of the Innovation:
HOLOLENS -
Virtual Reality Assessment
• Dependency on physical availability of SMEs on site
• Identify a system to reduce dependency on physical presence
• Increases operational efficacy.
• Reduces dependency.
• Conveying instant and accurate information
• Absence of real time feedback
• Technological constraints.
• Providing real-time and efficient collaboration
• Convenient, Flexible, Adaptable.
• Quick turn around time
myIdea
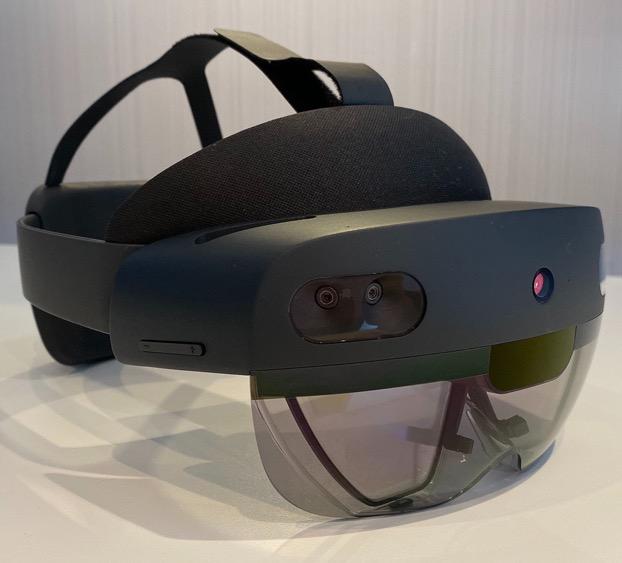
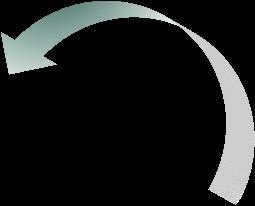
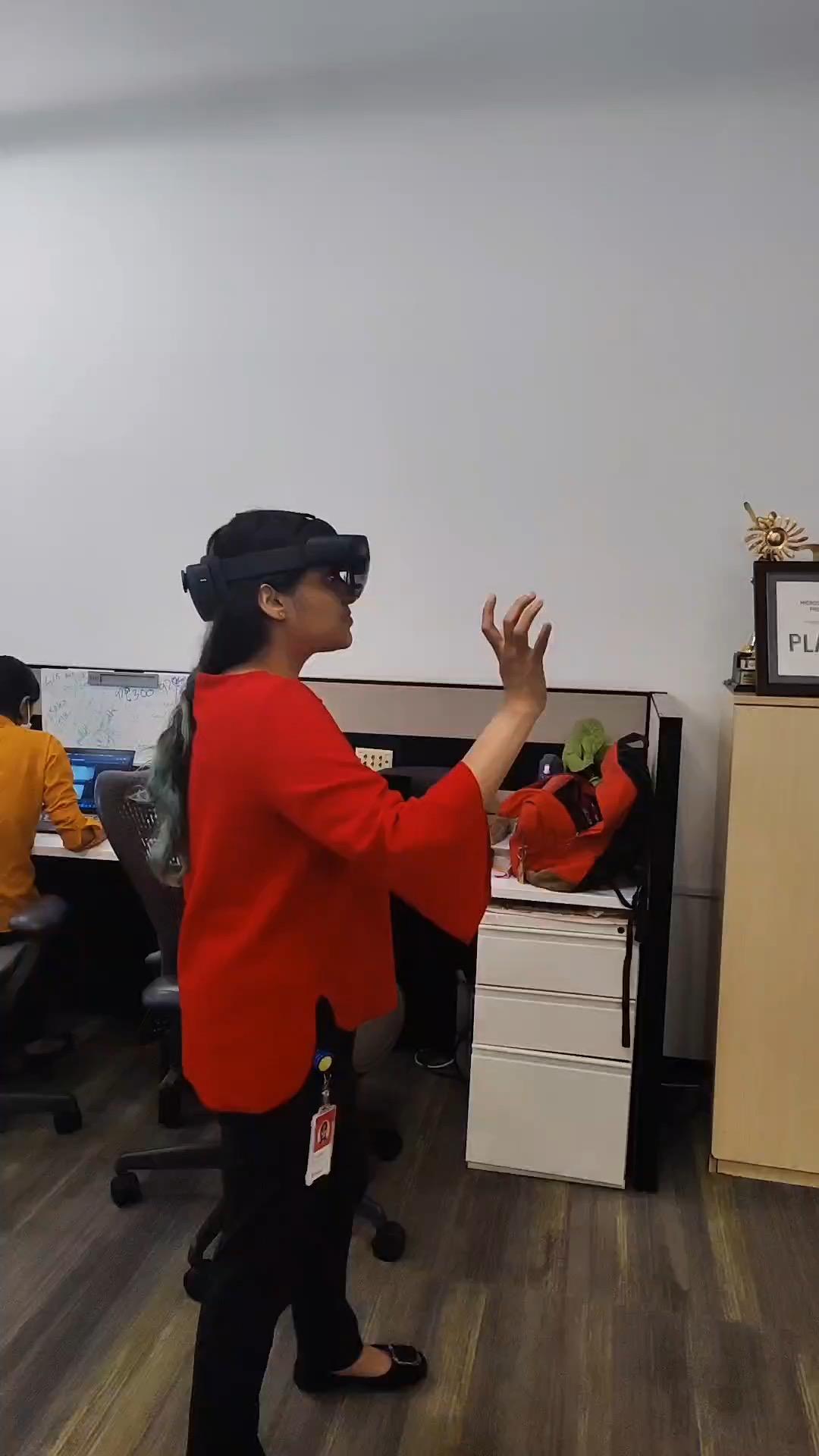

CHALLENGE MYIDEA / INITIATIVE / SOLUTION BENEFITS / ADVANTAGE
Description of the Innovation:
Safety Helmet with Sensor
• During APM work and major project works
technicians find it difficult to identify whether the panels and cables are live or switched Off.
• Also, during excavation for any maintenance works if they come across any cable, they must spend time to know whether the cable is live or not
• Retrofit of power sensor to safety helmet with focus lamp to ensure the user gets alerted as he approaches a live cable/power source.
• Ensuring personnel safety.
• The initiative is a safety tool for the technicians working in the facility.
• We have fixed an infrared power supply sensor to a helmet with focus light.
• Technician wearing this Helmet and moving around the work area will get alerted by the sensor with a beep sound from 2 to 3-meter distance of HT and LT cables and system’s there by ensuring the safety of the person.
myIdea
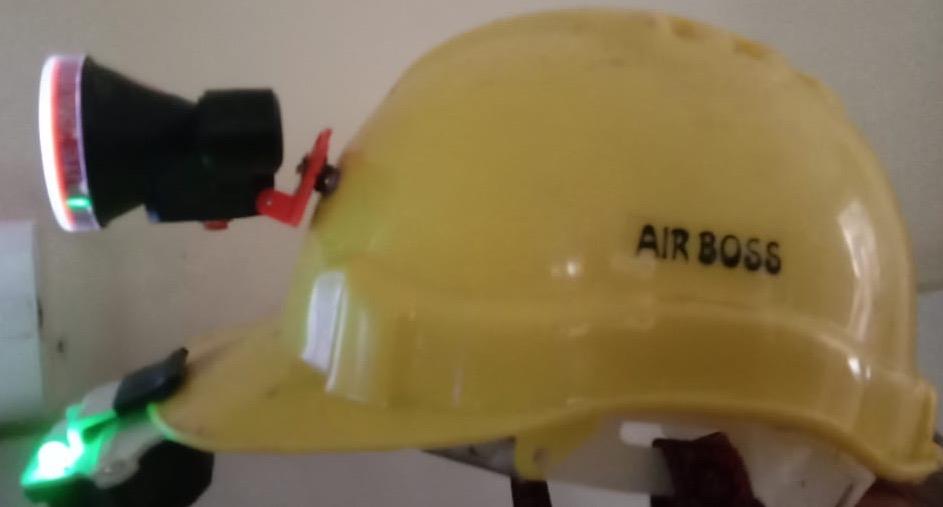
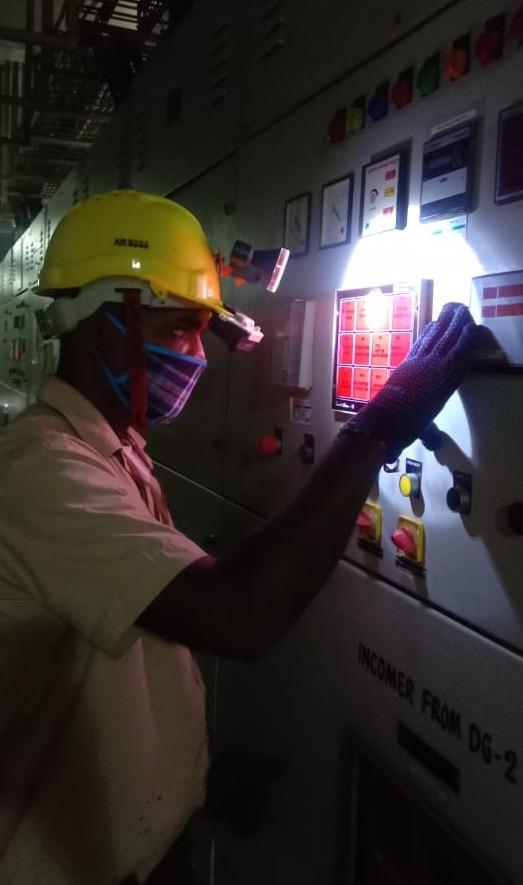
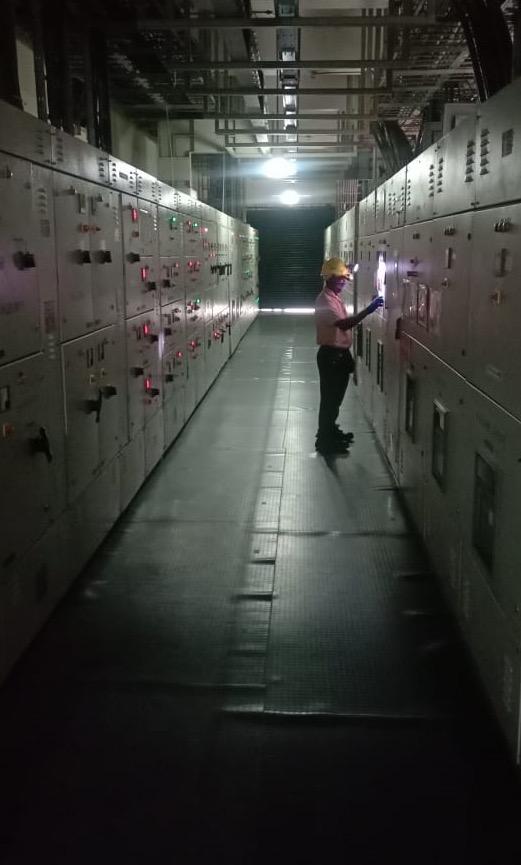
Description of the Innovation:
Lighting Management Through Digitalization
CHALLENGE
• During weekends observed unwanted lights switched ON across the facilities leading to energy waste.
• The shift team was instructed to have a tab over the issue and switch off all unwanted lights to avoid Energy loss.
• Though there was continuous follow ups, due to Monotony factor creeped in and the team started to miss/ignore the energy savings phenomenon causing huge loss of Energy & Cost.
• Client commitment on becoming Carbon Neutral & becoming Net Zero business center becoming a Challenge
• During our Toolbox talk, we did trigger the minds of the team for a solution to save energy & cost.
• During one such Toolbox talk we stumbled upon the idea of saving Energy & Cost remotely, especially digitally.
• Team was motivated and involved to come out with ideas that can help in our commitment for Green & Cleaner Environment
• Stable vibrator has one stable state and one quasi stable state When an external trigger applied to the circuit, the vibratory will jump to quasi stable state from stable state.
• After the period, it will automatically set back to the stable state, for returning to the stable state vibrator does not require any external trigger. The time period to returning to stable state circuit is always depends on the passive elements in the circuit resistor and capacitor
• Connect in seconds. from anywhere in the world
• Access system-any where in the planet
• Control equipment
• To provide an efficient real-time energy use feedback.
• Total energy saved Annually by regulating lightings only on weekends is 29.32 MWH
• Total Cost Savings achieved Annually INR 0.19 Million which is a recurring savings
• Carbon footprint reduction of 134 MT/5 years, again a recurring reduction
• Provide a Cleaner & Greener environment for the future Generation.
• ROI is just 3 weeks-INR 9307
myIdea
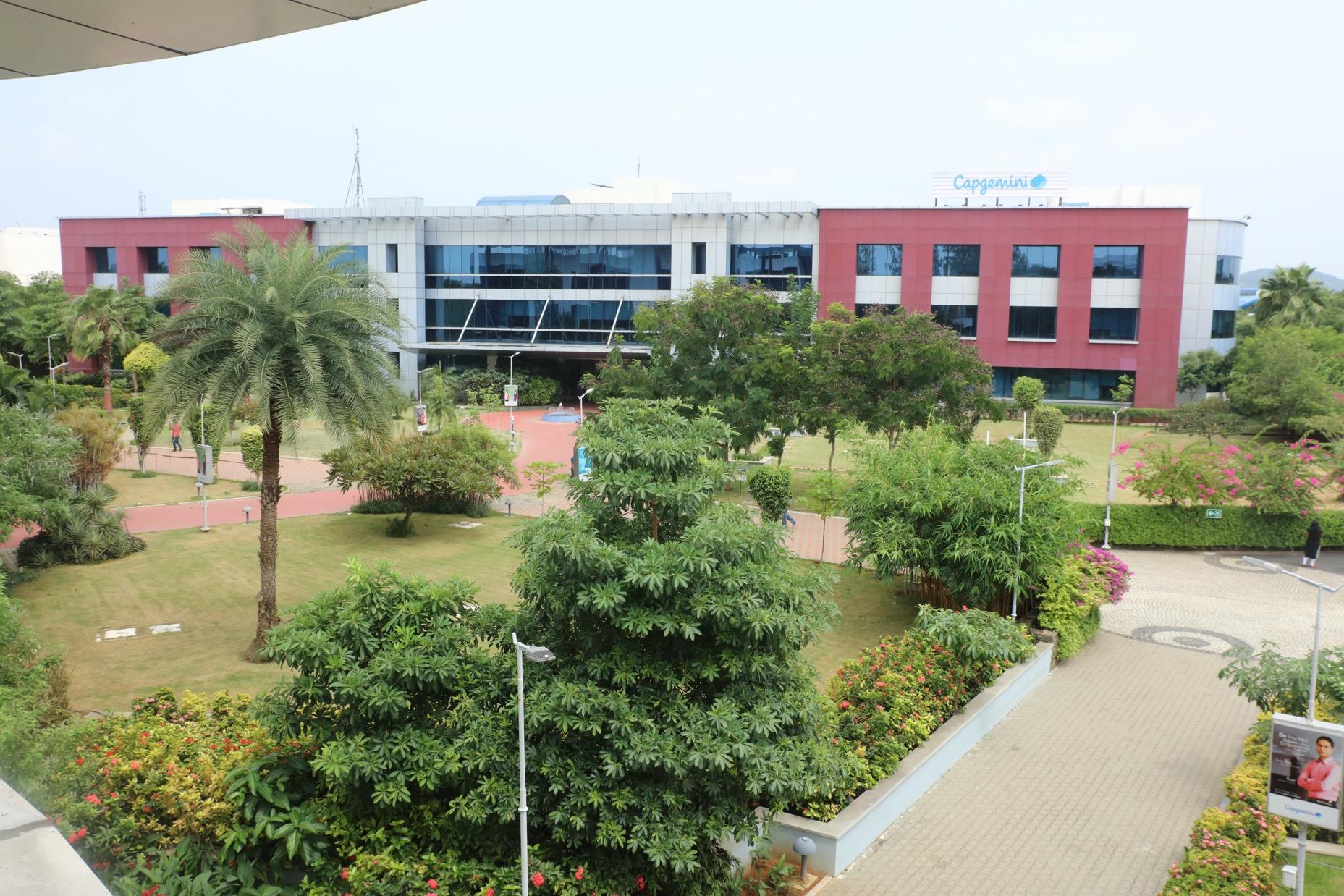
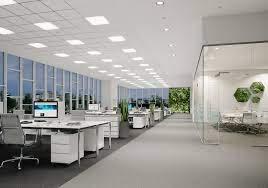

Description of the Innovation:
Employee Safety Tracking Device
CHALLENGE MYIDEA / INITIATIVE / SOLUTION BENEFITS / ADVANTAGE
• Ensuring safety of associates by implementing proper social distancing norms.
• Contact tracing of potential close contacts if anyone in office tested positive.
• Identifying specific targeted areas which needed to be sanitized in case an associate who came to office tested positive.
• Initiated discussions with the client for introducing a contact tracing methodology.
• Prepared floor layouts for implementation of a mapping solution.
• Chosen RTLS solution and the wireless network is created by placing the anchors at key points through out the floors.
• Provided DC power supply and installed the anchors.
• Vendor team completed the calibration and commissioned the system successfully.
• Effective contact tracing
• Track daily movement of associates in office to ensure provisions of social distancing.
• If an employee tests positive or shows symptoms, quickly report on past proximities between associates for the past 14 days or more.
• Ensure that the employees feel safe coming to office.
• Enforces business safety requirements to prevent viral spreading.
• Provides instant alerts for social distancing breaches and disperse congregations.
myIdea
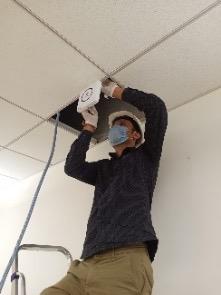

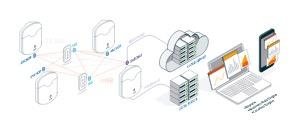
Description of the Innovation: CHALLENGE
• For Events Requirement setups Housemen are utilized to move tables one place to another place.
• Consumes more time for manual lifting
• Risk of Human
• Team gets Tired and exhausted incase of any huge qty movements, Adhoc requirements and Tower to Tower support too may come.
Table Lifting Trolley
• Chances of Slips and Floor Damages
• May Lead to Injury/backache/Muscles and Joint Damage due to heavy weightlifting and when it comes to High Movement risk Increases.
• To overcome the challenges our Innovation team planned to design a trolley keeping base about a browsed item.
• The Initial idea was to produce low-cost product and usage of left behind materials and succeeded with the same.
• Product has been released undergoing many process with all teams support after about 2 month.
• And Before Releasing the product has been reviewed by EHS and concurrence Received as this is safe to use.
• Reduced physical stress/Asset Damage & manpower deployment
• Risks on Weightlifting Eliminated
• Females can also handle this trolley very easily.
• Time Savings Approx. Calculation : Sample 1 Table Distance between South to North End Balcony FC 1st floor - 384 feet
Manpower Required for lifting Manually - 2 Housemen
Time Consumed - 3 Minutes (With Manpower)
Time Consumed - 2 Minutes ( With Trolley)
Savings 1 Minute and one Manpower Per Table
Note We May need to shift 10 to 20 tables minimum per request.
• Time consumption may go high incase of any Huge movement as manpower cannot shift 40kg weight table continuously they can only rest and lift
• Cost Saving :
• Cost of Product If Procured Average - 20000/-INR
• Total Cost of materials used Inhouse 4867 INR
• Total Savings by creating Inhouse INR 15000/ INR Approximate
myIdea
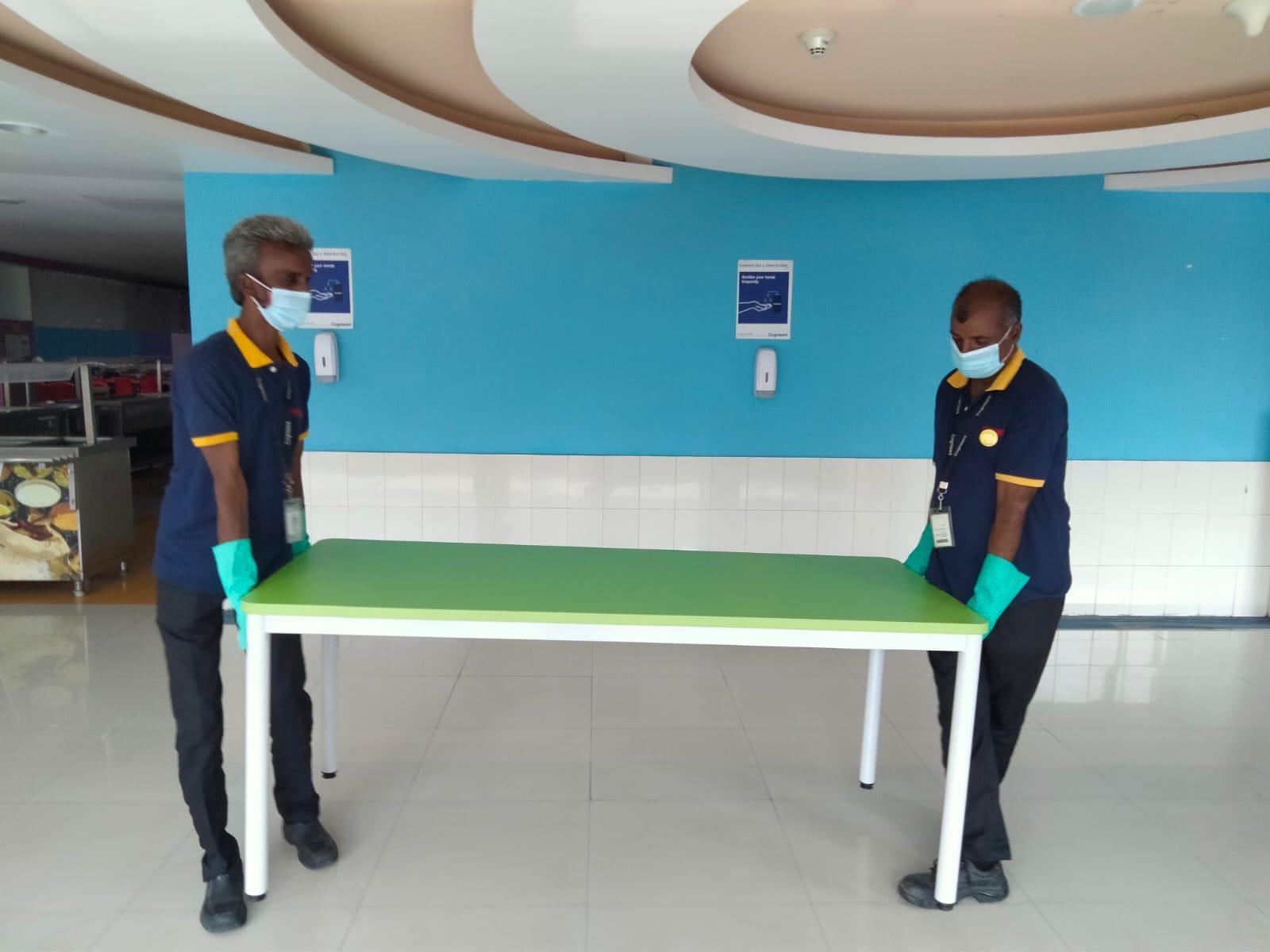
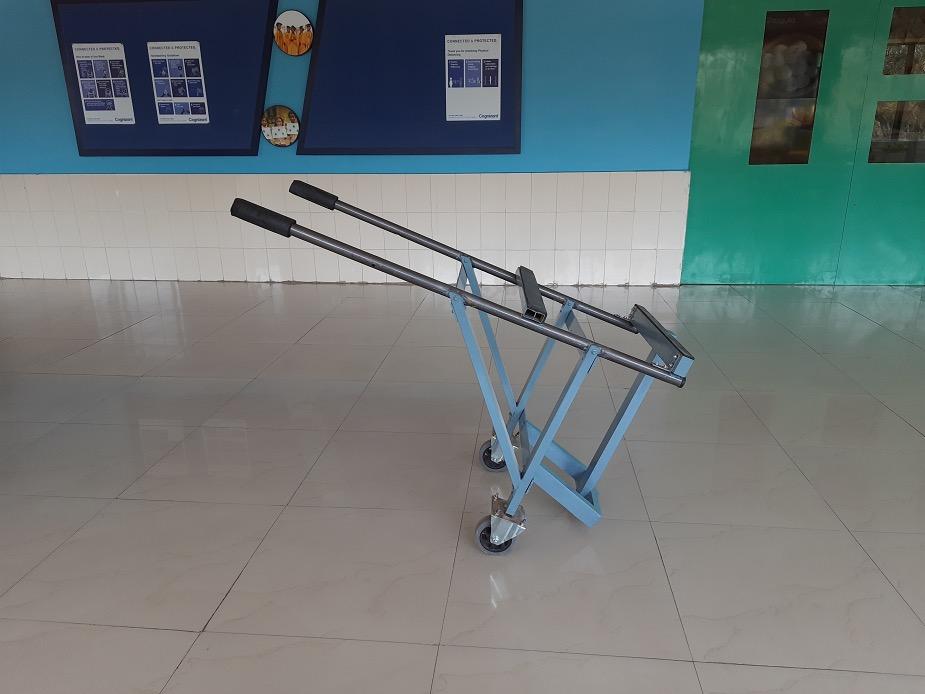
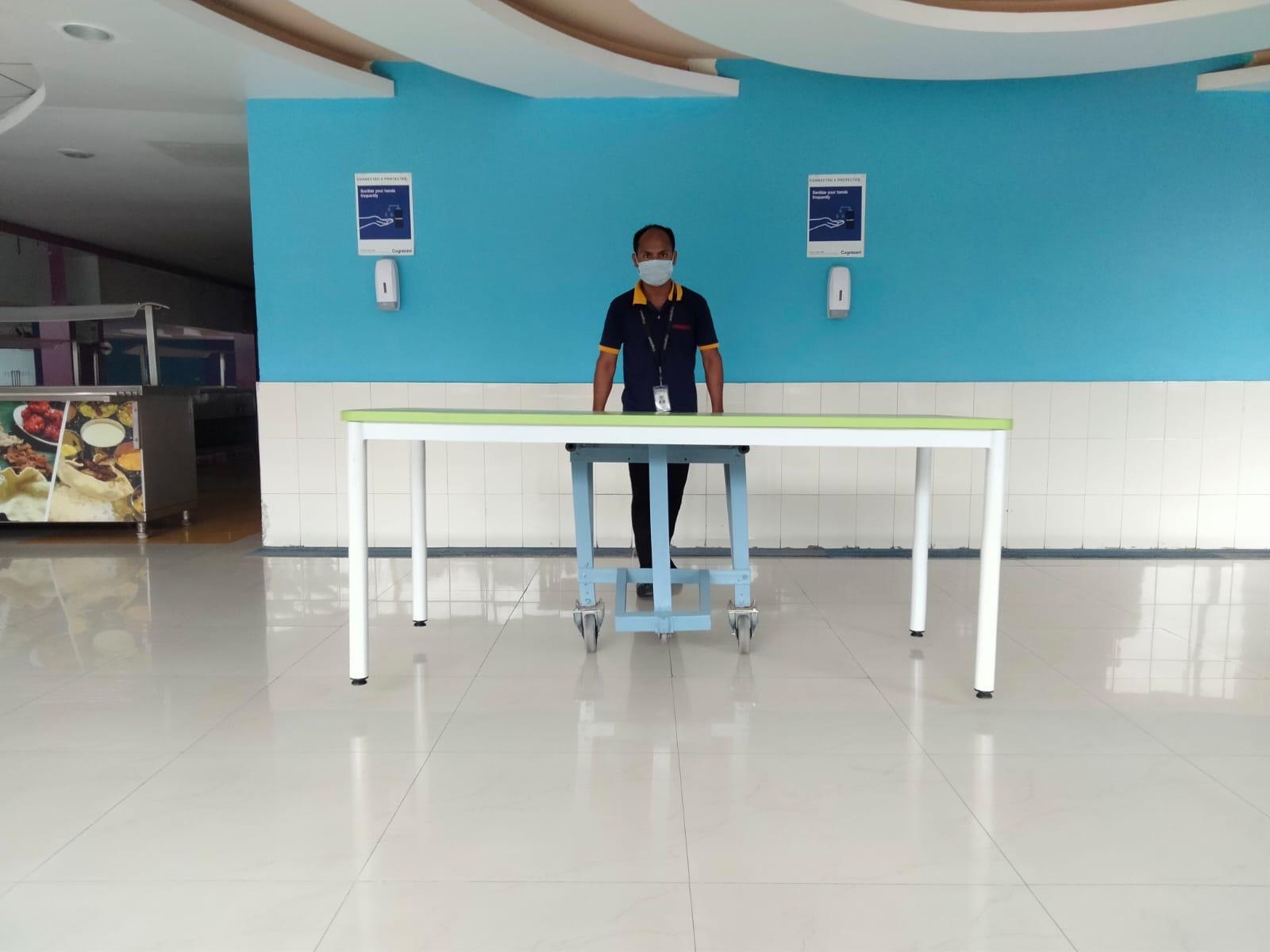
CHALLENGE
Description of the Innovation:
Introduction of Digital Work Permit
• Filling checklist and getting multiple approvals.
• Printing of monthly checklists.
• Tracking of old checklists proved cumbersome.
• Delay in on time permit submission.
• Time delay in getting multiple signatures.
/ INITIATIVE / SOLUTION BENEFITS / ADVANTAGE
• Converted paper checklist to digitalization application.
• Improved Service level.
• Avoiding time delay of multiple approvals
• Increase manhours Productivity
• Eliminate Paperwork.
• Real time updations and get the alerts.
• Inspection, & Auditing made easy with audit logs history.
• Reminders on pending works closure
• Real time monitoring.
• Real time reports generated.
• Sustainable- saving paper.
• Accurate data- elimination human errors.
myIdea
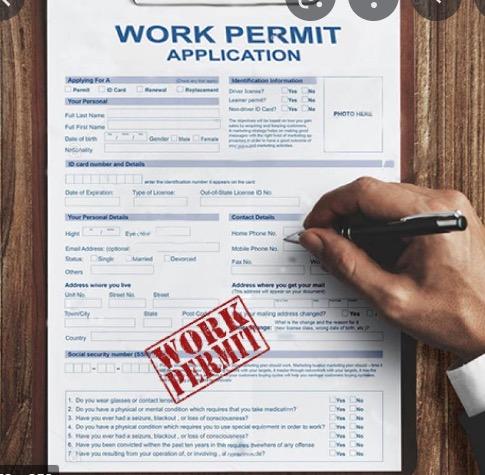
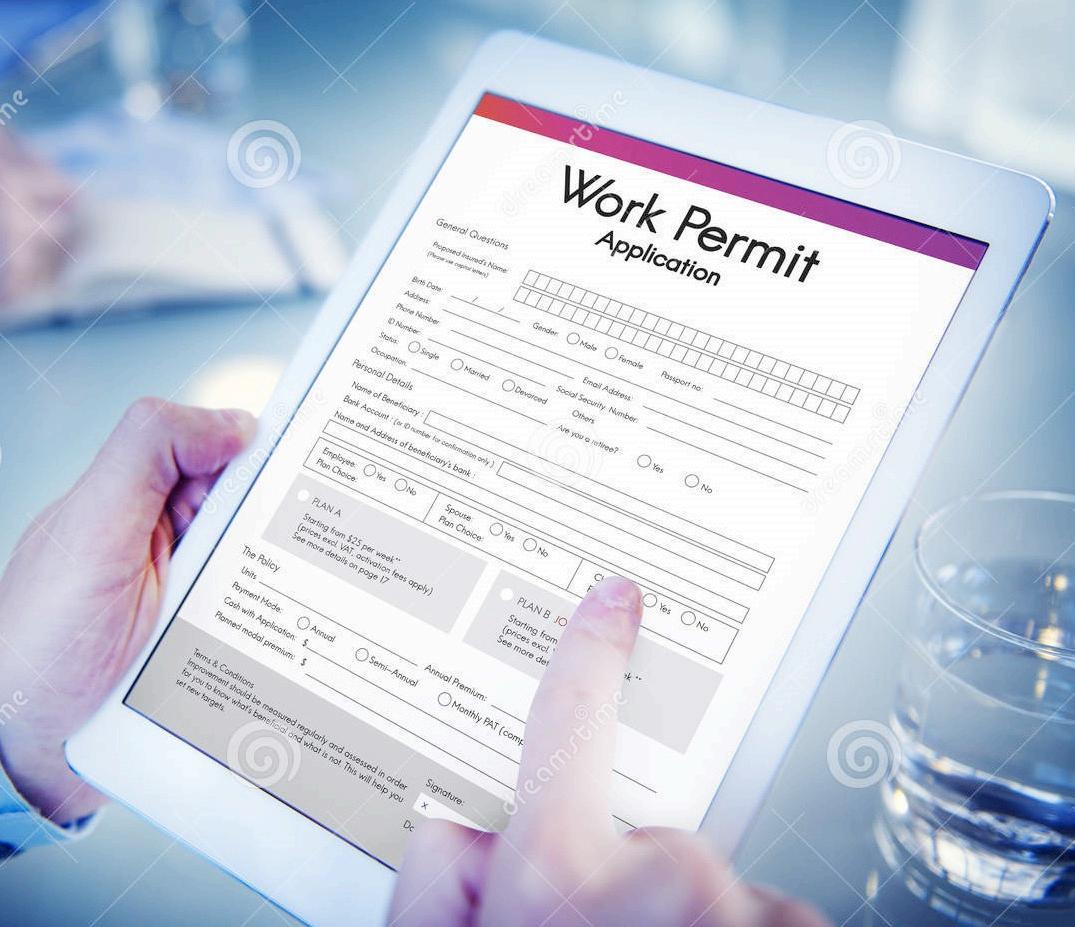
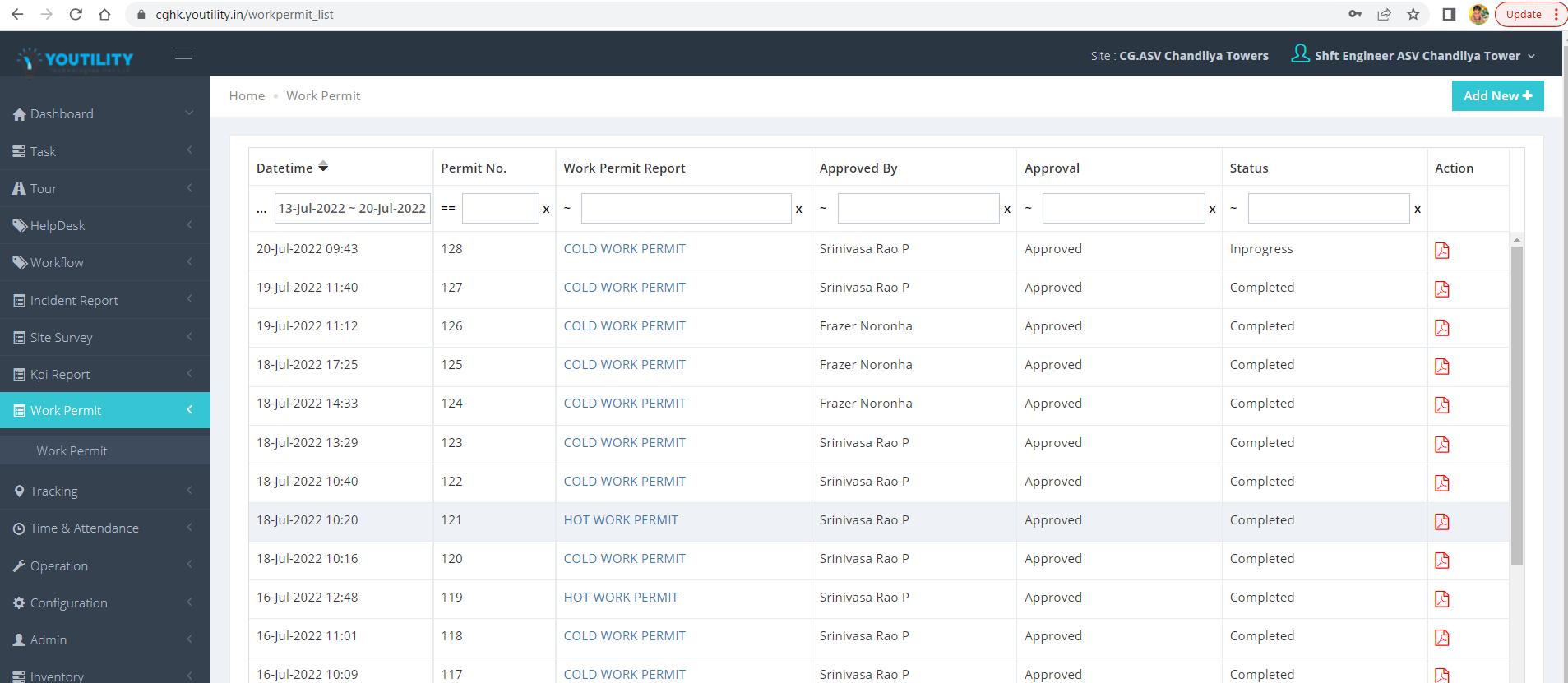
CHALLENGE MYIDEA / INITIATIVE / SOLUTION BENEFITS / ADVANTAGE
Description of the Innovation:
BMS Integration of HSD & Water Meter
• There was no BMS integration for flow meters at municipal water inlet line and diesel unloading as well as transfer line.
• Team has done the monitoring through manual readings which require manpower interventions to monitor the meter readings.
• Any manual error while recording reading will impact efficient water consumption analysis.
• Digital flow meter has been procured for municipal water inlet line and HSD line.
• Necessary controllers and accessories arranged for integrating the meter with BMS.
• Integration of meters has been completed and the meter came online.
• Manual intervention avoided for monitoring the readings of meter.
• Accurate readings can be downloaded through BMS.
• Effective data monitoring and operations.
myIdea
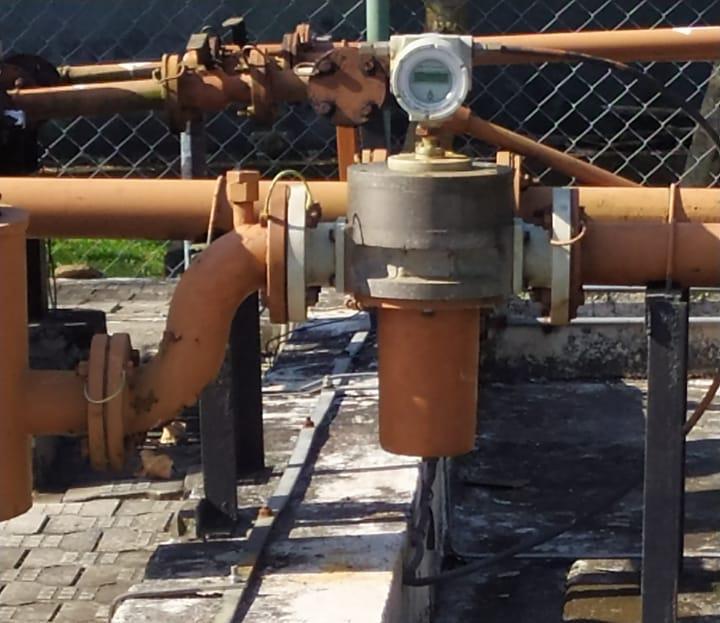
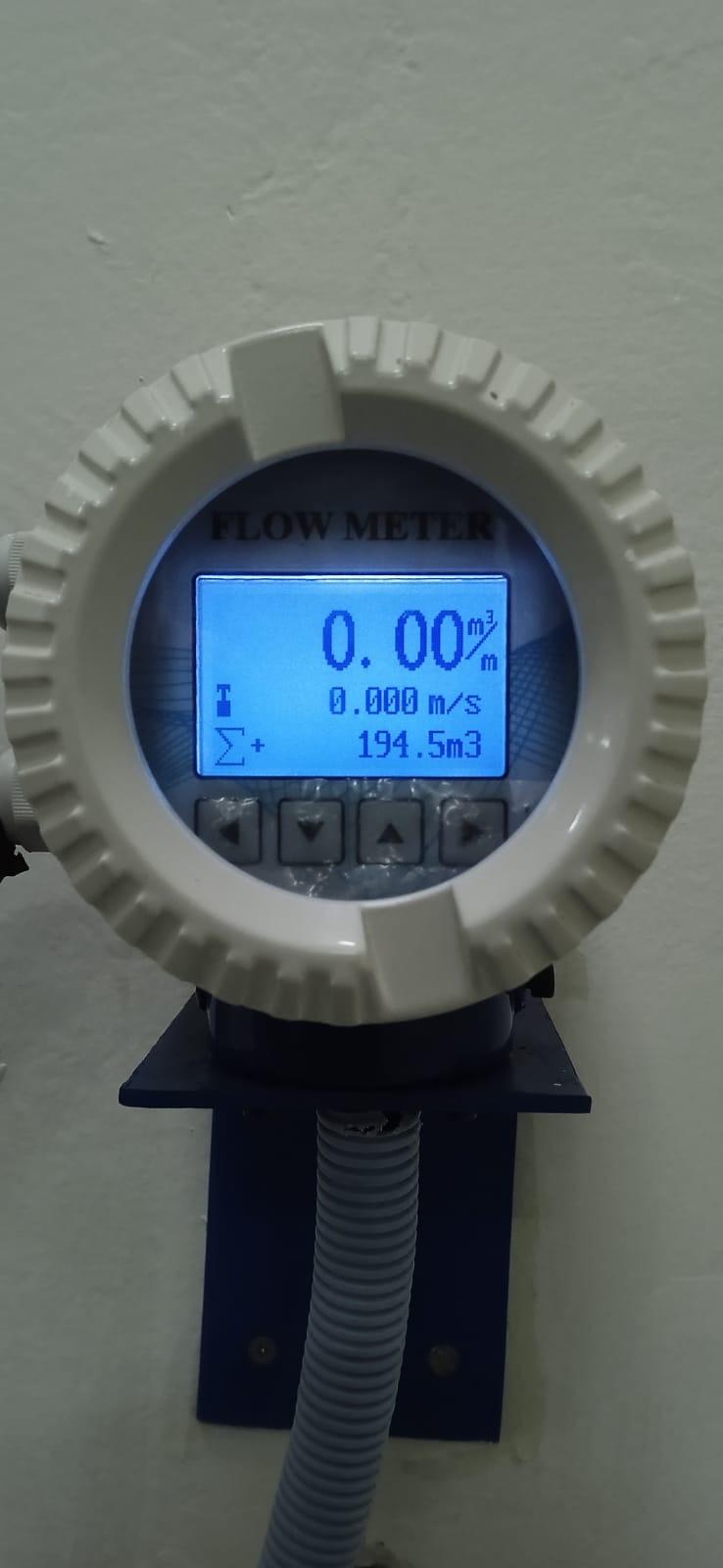
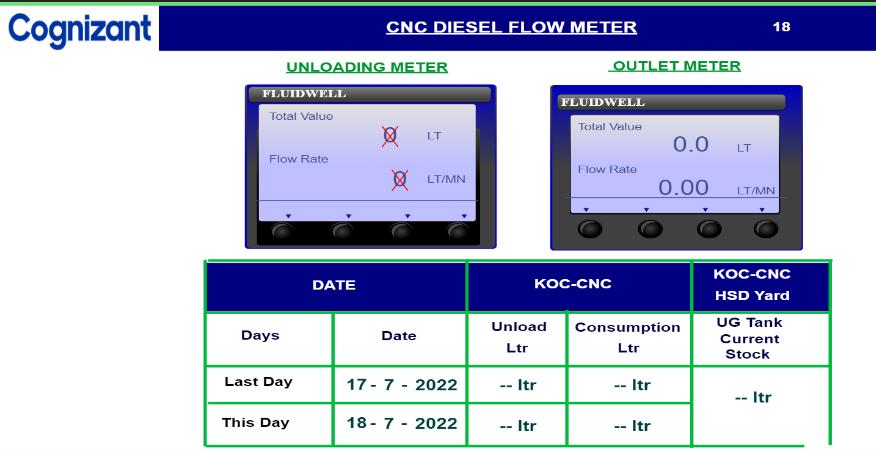
Description of the Innovation:
Safety DeviceSingle Phase
Preventer
• Single phasing is a very dangerous fault to the electrical motor, Which damages the motor stator winding rapidly
• Goal to reduce costs and eliminate downtime caused by unexpected machine maintenance and risks associated with operating faulty equipment.
• Non availability of CW pump for chiller operation due to breakdown.
• Existing control panel was not provisioned with single phase / unbalance preventing device
• In a 3-phase system of supply ,if one of the fuses blows off, single phasing takes place due to the absence of one phase, voltage fluctuates, become low and high causing the equipment connected to it may burn
• Single Phasing Preventer is used for protection and burnouts of pumps and motors against phase unbalance, missing and negative phase sequence. All the phases are continuously checked. A fault trip condition trips the relay - changeover contacts are energized
• This relays are suitable for monitoring incoming 3-phase supply from mains (Electricity distribution line). Being independent of load, it can be used for any HP/KW rating of load.
• All the phases are continuously checked. A fault trip condition trips the relaychangeover contacts are energized.
• Low cost, easily available
• Safety of operator and Life enhancement of pump motors / control panels
myIdea

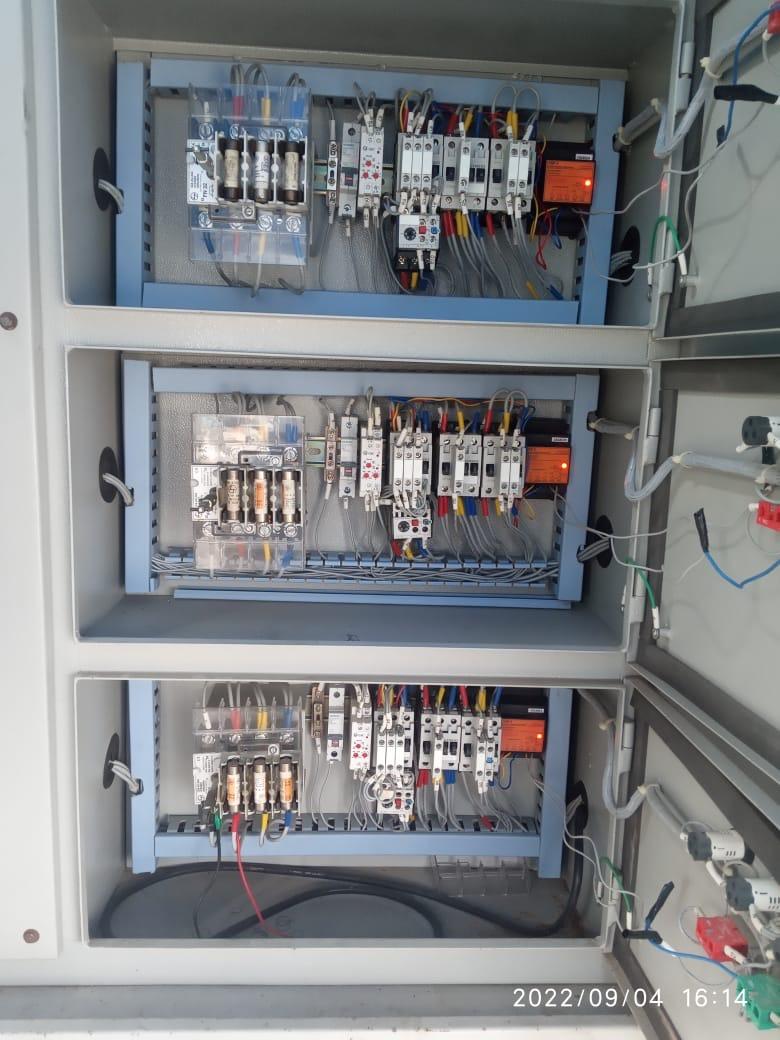
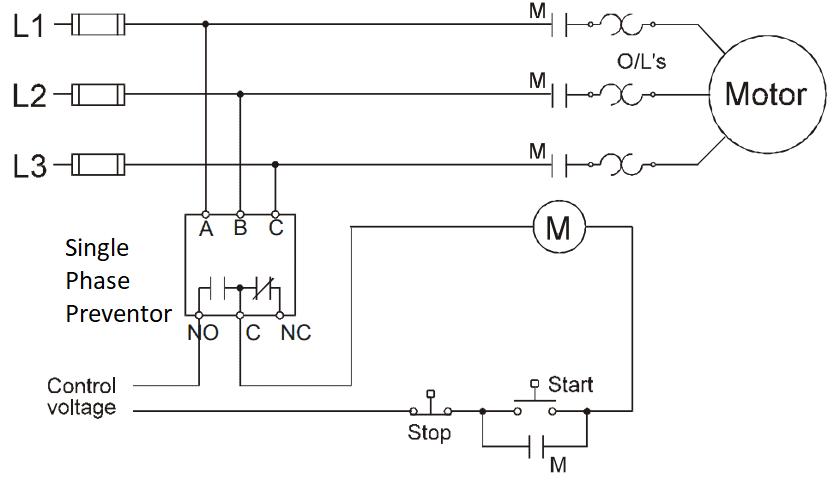
Description of the Innovation:
Interactive Operation Dashboard
myIdea
CHALLENGE MYIDEA / INITIATIVE / SOLUTION BENEFITS / ADVANTAGE
• Tracking open / closed points
closure status
• Difficult to analyze data
quickly in category wise
• No updates in graphical manner
• Initially there was no tracker
• Prepared data in specific excel format as per site condition
• Created pivot table based on various data inputs available in excel format
• Data converted in graphical charts
• Reviewed along onsite CBRE team
• Final review was carried out with Client representative, this was well appreciated
• No cost involve in this task implementation
• Easy understanding of complaints status & site equipment condition
• Quality & quick analysis of recorded complaint
• Helpful for maintaining good relationship due to transparency in data.
• Helps to plan maintenance activities & thereby optimizes resources
• Client Satisfaction
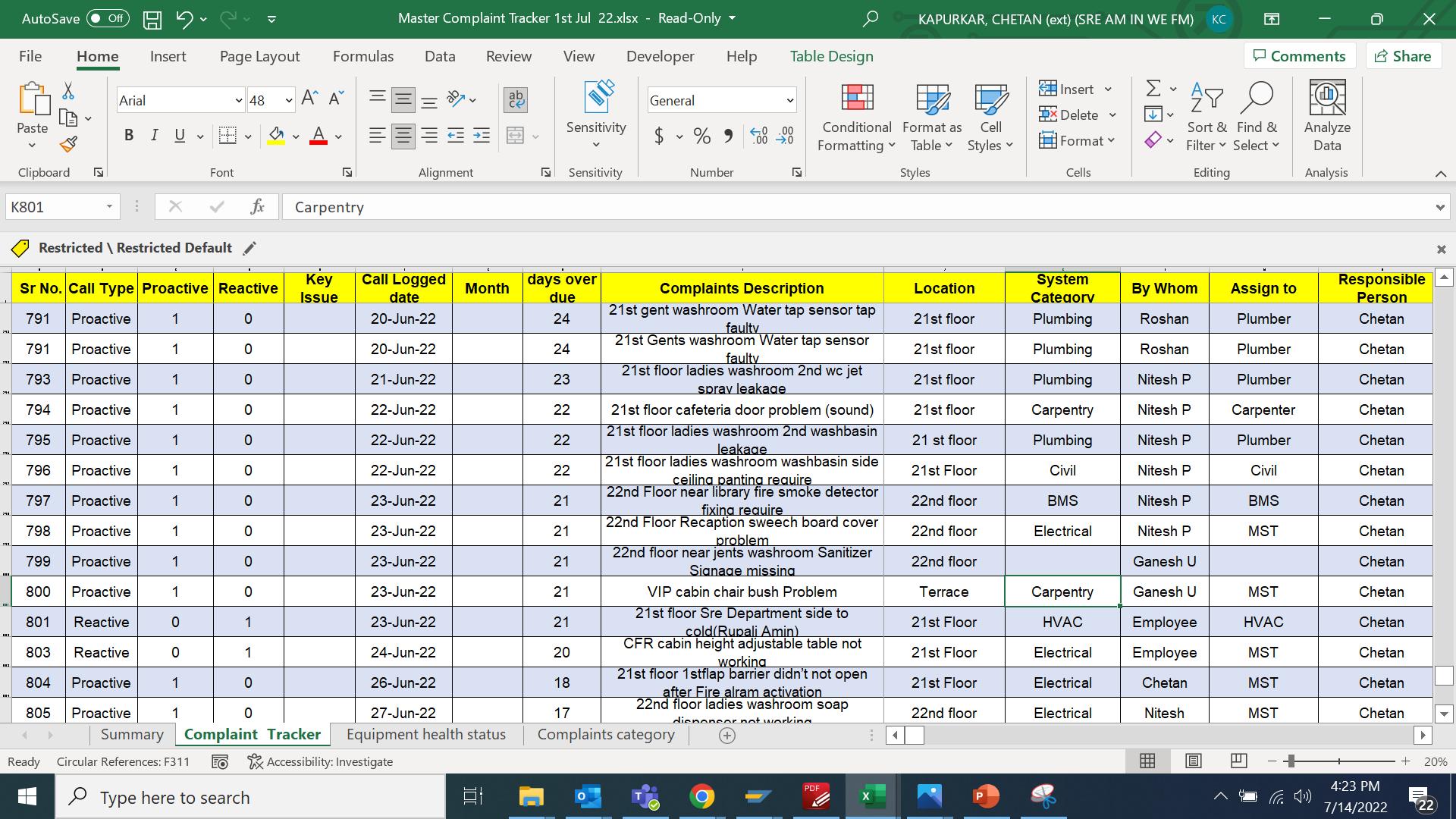
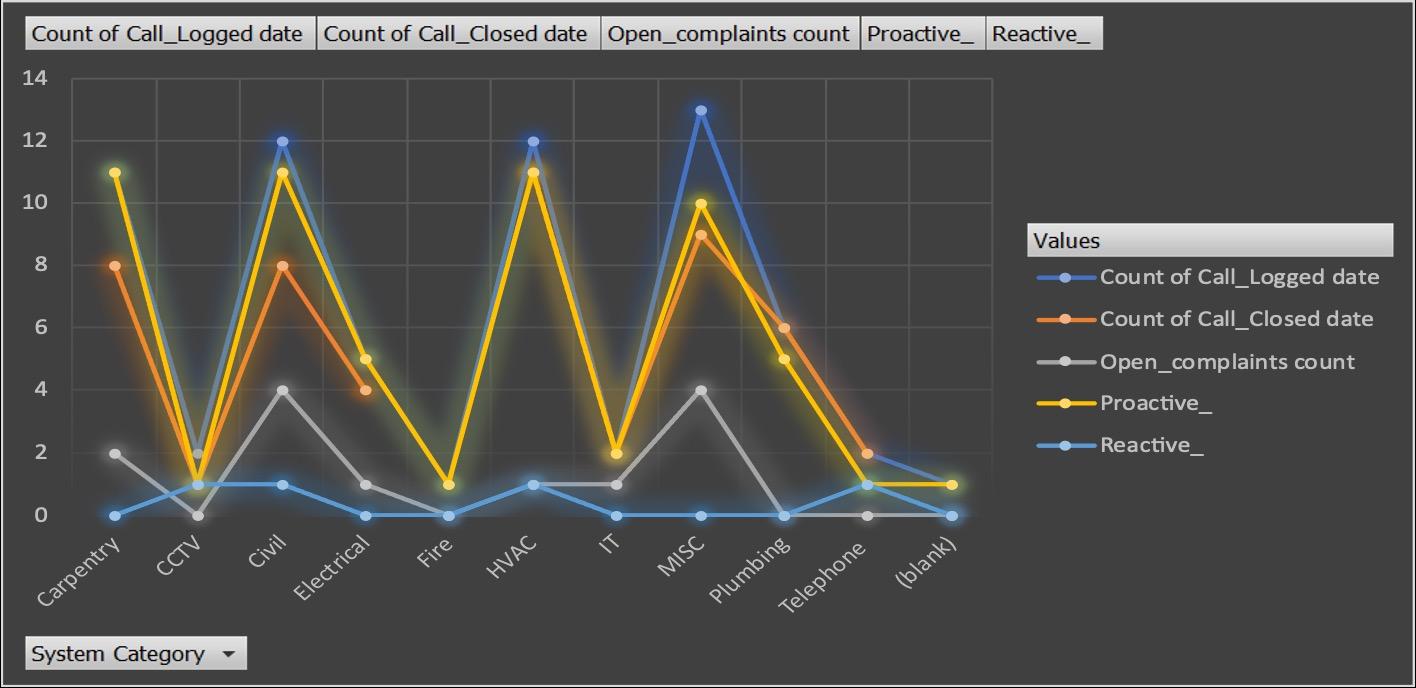
Description of the Innovation:
Power Management of DGs
CHALLENGE
• All DGs (Qty -03) Starting on EB Power interruption for Tower 6
• Turning OFF of DGs done manually by operator depending upon Total Load.
• Manual intervention and dependability on Operator’s judgement resulted into fuel loss and underload running of DGs
• Running of DGs on low load is detrimental to DG life and unwarranted Exhaust Gas generation, harming the environment
• Power management of DG breakers implemented. DG breakers programmed to operate in real time depending upon load requirements
• The DGs set up in Master-Slave configuration. One Master DG continues to be ON and commands other two Slave DGs to be ON / OFF, depending upon actual load.
• DGs running on No load get switched OFF automatically without any manual intervention.
• Elimination of manual intervention and dependability on operator during DG switching / changeovers
• High starting current drawn by chillers, warranted two DGs during EB interruption and with load management now, chiller operation is managed with a single DG
• With micro-processor controls, DG onloading, offloading and changeover being achieved in fraction of seconds, leading to multiple benefits
• Elimination of off-load running and savings of DGs running is resulting into saving of Diesel, reduced carbon footprint and enhancement of DG life
• DGs can be used to their full capacity while delivering maximum efficiency and optimum damage to environment
myIdea
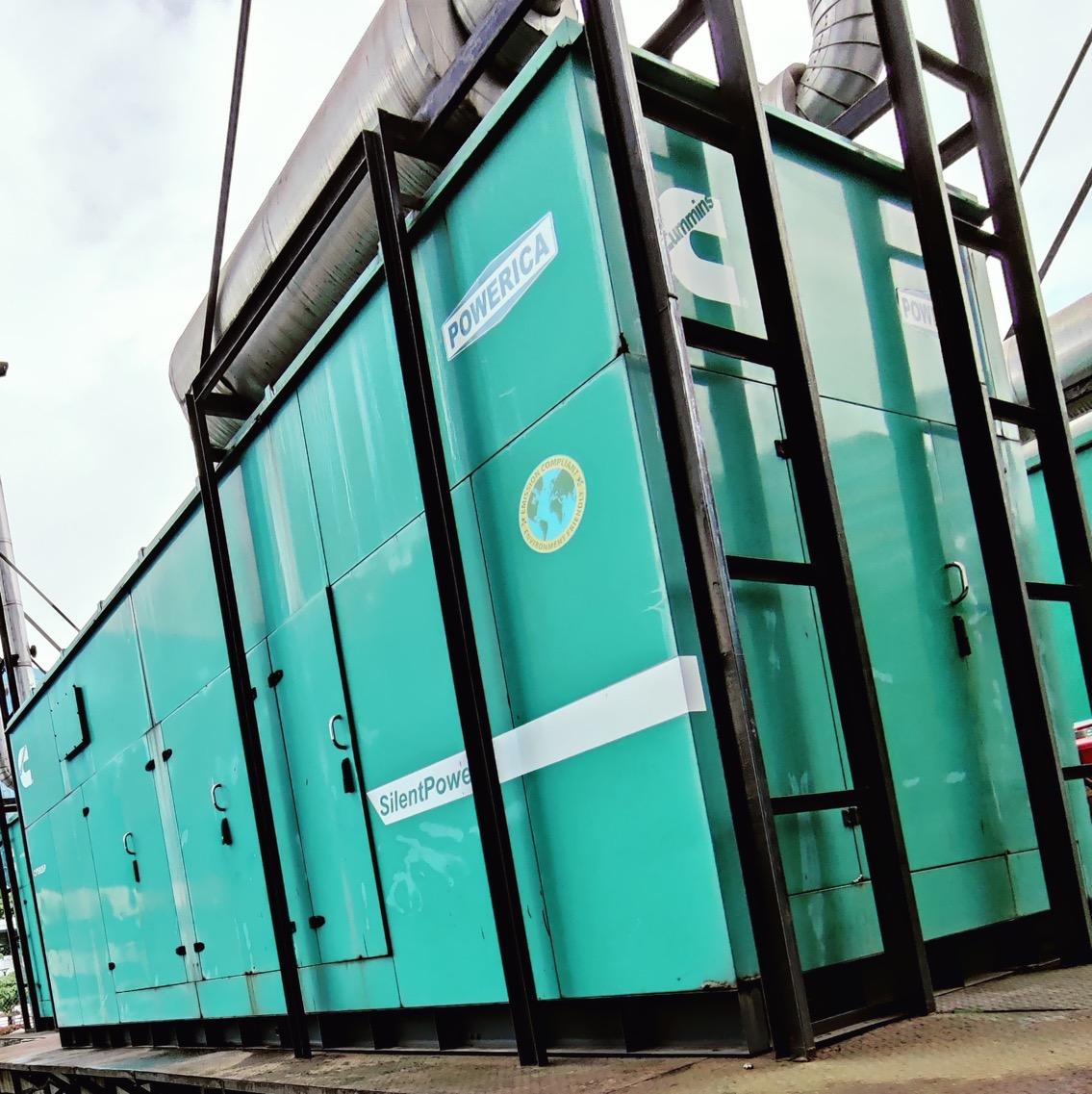
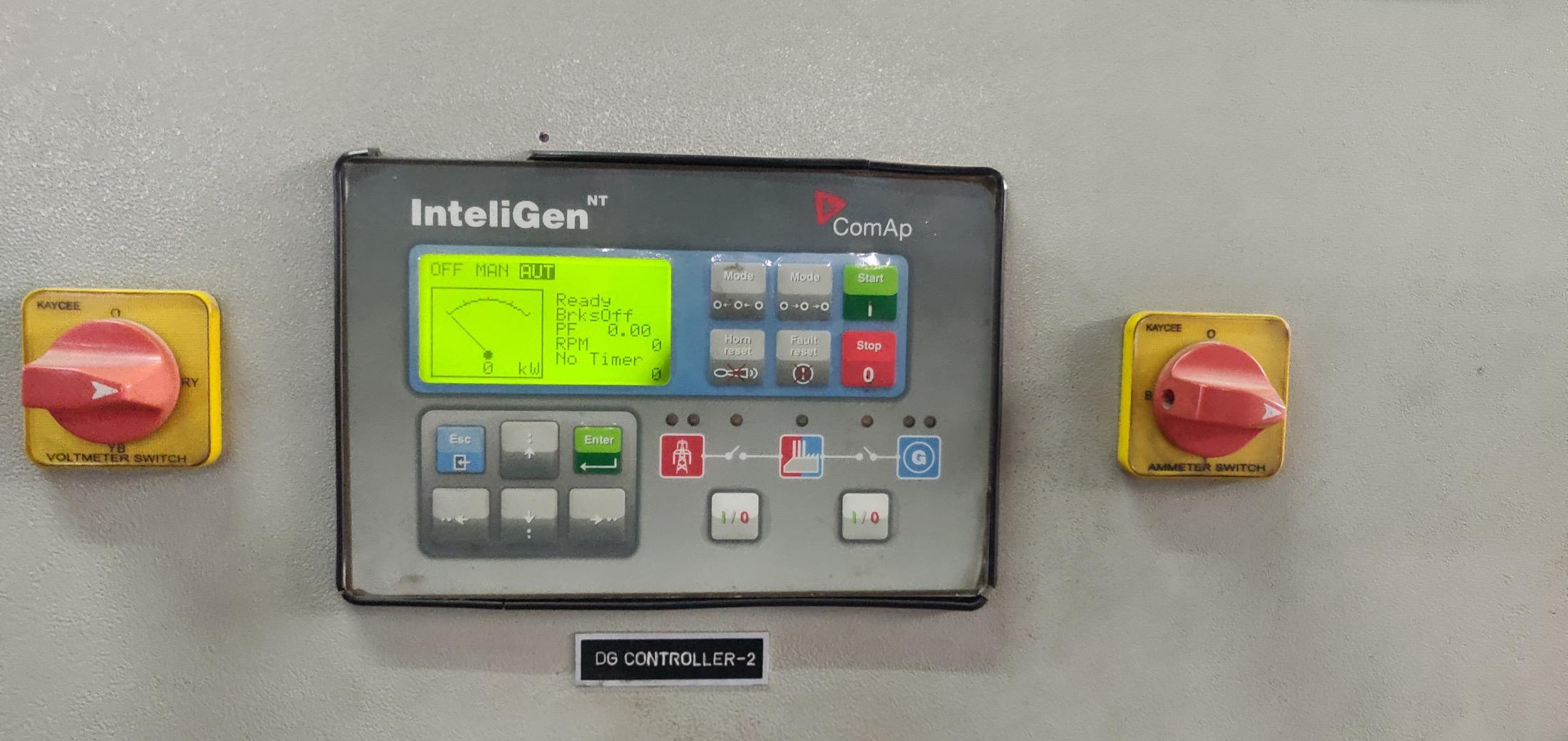
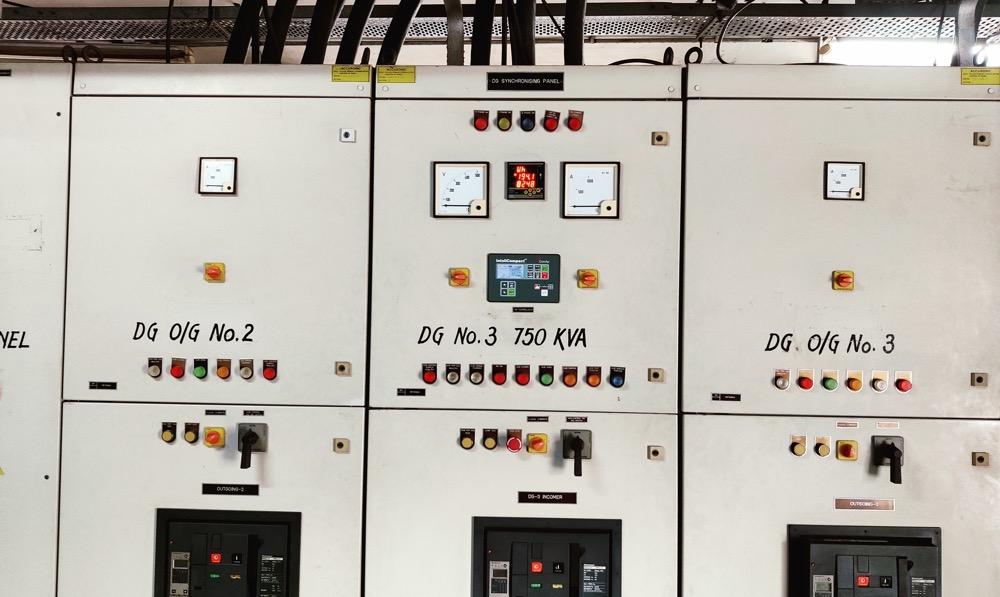
Description of the Innovation:
Highly Efficient CTI Cooling Towers
myIdea
CHALLENGE MYIDEA / INITIATIVE / SOLUTION BENEFITS / ADVANTAGE
• HVAC cooling Towers (3 X 200 TR & 1 X 350 TR) were 12+ years old and were due for replacement..
• Traditional Cooling Towershaving frequent maintenance issues due to aging effects.
• Multiple leakages leading to additional consumption of water
• Frequent fiber coating done.
• CTs running at a low wet bulb efficiency of ~31% only
• So CBRE proposed this idea to the client to replace the existing conventional cooling Towers with CTI approved high efficiency cooling Towers (BCTI-40XE) from Bell Cooling Towers. CTI is the Cooling Technology Institute at Houston,-Texas is worldwide certification agency for CT efficiency
• Validation of the selection of a Cooling Tower can be done from the CTI web site wherein the Matrix of the selection exists.
• They are taller towers with Munter Fills & D-15 Drift Eliminators for higher heat transfer rate and water conservation.
• Larger fan diameter (2200 mm) than traditional ones(1800 mm) handling 73150 CFM/fan than earlier 50200 CFM
• IE2(International efficiency Level-2) motors and FRP blades for high energy efficiency
• Lifecycle replacement with new technology contributing to energy savings.
• Pre-Tested through vigorous norms by CTI and guaranteed to achieve design duty parameters. As per tests conducted this tower has achieved 72% wet bulb efficiency and 124% efficiency compared to design parameters (Report attached for reference)
• 10-15% energy savings on part of chiller consumption (Minimum 100000 KWH savings that is INR 10 Lakhs per annum as per chiller operation trend of full operation of the building)
• Project cost INR 2300000/- with ROI of 2.3 years
• Sustainability initiative with both Energy and water savings with considerable reduction in Carbon Emission.(23314 Kg Co2 reduction)


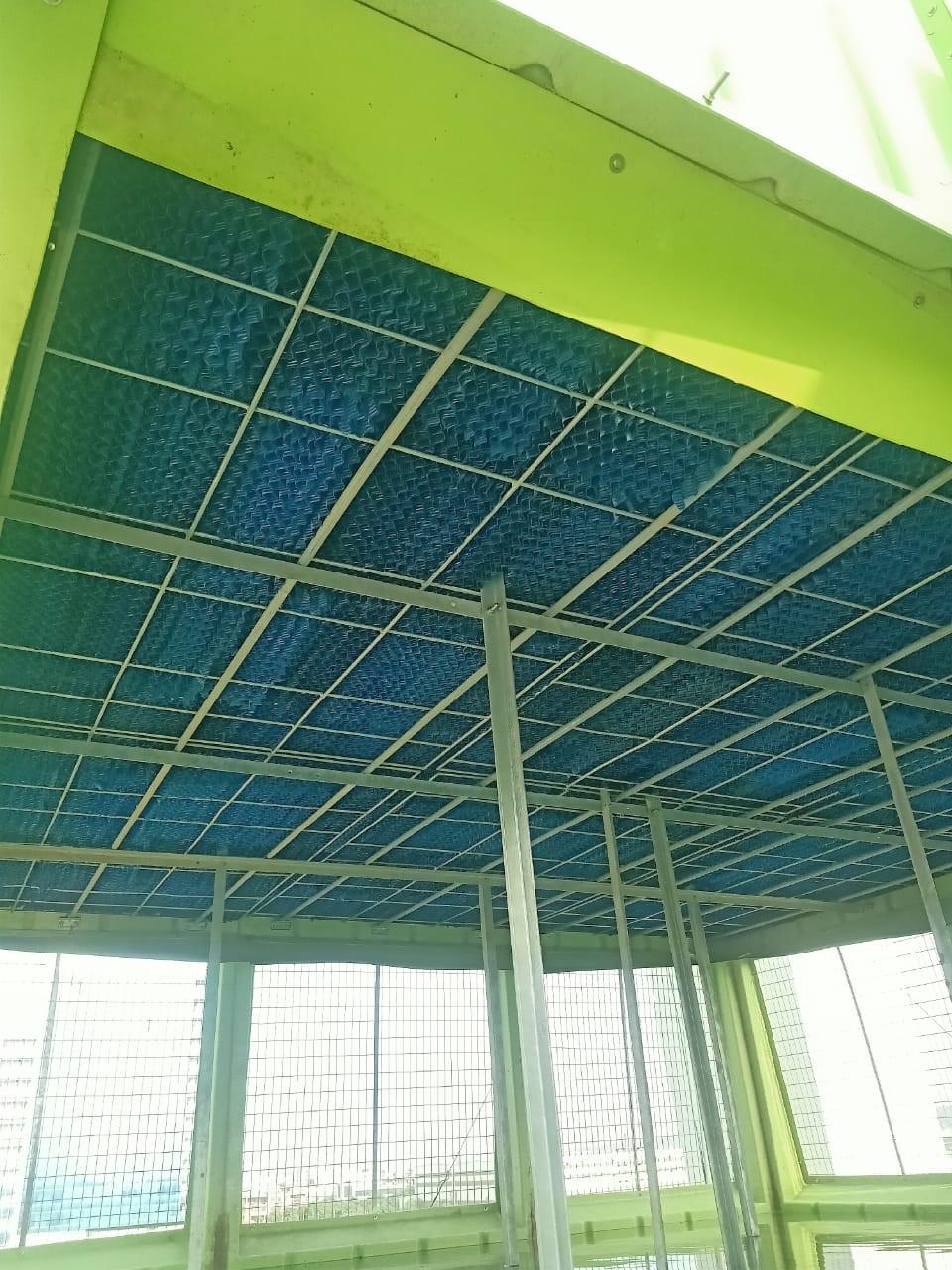
• Critical electrical enclosures (LT panel, Electrical panel) can spark or generating of fire but spreading the fire in short spam of time.
Description of the Innovation:
Fire Suppression for Electrical Panels
• Unavailability of automatic fire suppression system in enclosed Electrical panels
• Increased risk to responders as well as higher costs and infrastructure losses
• Installation of CQRS automatic Fire Suppression System for Critical Electrical panels.
• This is heat sensitive pneumatic polymer tubing system, connected at one end to a Ceasefire extinguishing agent container, while the rest of it runs unobtrusively throughout the area at risk.
• When the flame encounters the heatsensitive tubing and reaches a temperature of 150 - 180°C, the tubing bursts open at that exact spot and forms a miniature nozzle.
• Pneumatic mechanism triggers the valve of the extinguisher and sprays the extinguishing agent out of the tube directly onto the flame, dousing the fire instantaneously.
• A complete set up of an appropriate automatic fire suppression system can minimize the damage cause accidents in critical area
• Entirely self-contained, do not require any power supply and will function normally in the event of a power outage.
• CQRS , the fire can be caught at a single location and extinguished before it can spread.
• 100% Protected automatic suppression system establishes the Safety of Critical operation- LT room, electrical panel
• Better solution instead of having manual fire extinguishers at the time of Fire Incident
• Estimated Expenses: INR- 38 Lacs
myIdea


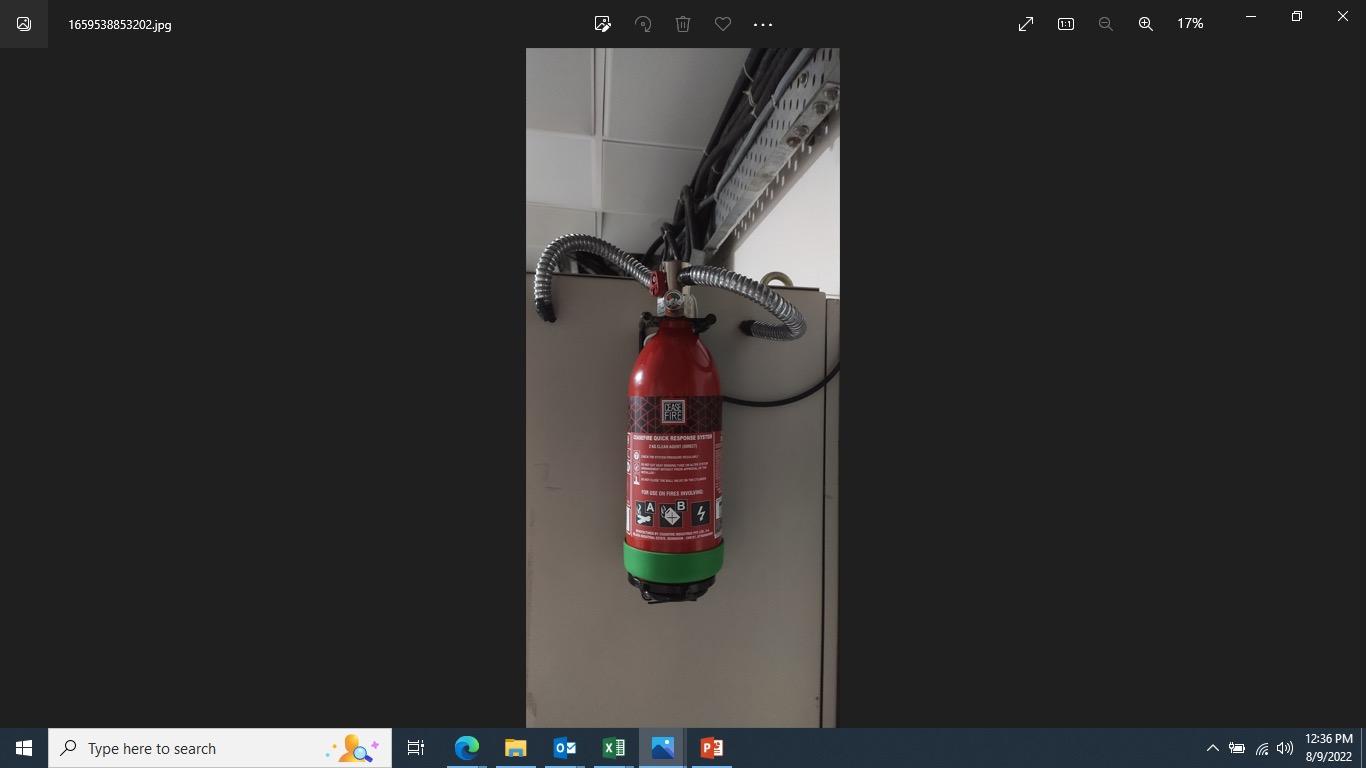
Description of the Innovation:
Integration of CO Sensor
myIdea
CHALLENGE MYIDEA / INITIATIVE / SOLUTION BENEFITS / ADVANTAGE
• The parking area in MGI is located UB & LB
• The continuous car movement lead to increase in CO level in parking
• Ventilation fans are installed in parking area but are not integrated with Co sensor.
• Continuous operation of ventilation fan will lead to unnecessary energy consumption
• While non- operational ventilation fan possess serious health hazard
• The present CO sensor are absolute hence require replacement
• Further this CO sensor are integrated with PLC system installed on each parking level to control ventilation fans
• The CO level were programmed ,as per ASHREA requirement to control fan speed and operation
• Below 25 PPM fan operation stop
• 25ppm to 35 ppm low speed fan
• Above 35 ppm fan operation on high speed
• Co level in parking will be maintained within specified limit of ASHRAE for human safety
• Energy saving in ventilation system to avoid unnecessary operation of ventilation fan based on CO level
• Saving Data:
• Daily Running: 15 min
• Unit Consumed: 3 units
• Total Consumption
• 13 fans x 3 units x 22 days = 858 units
• Monthly Cost: 10,725/- INR
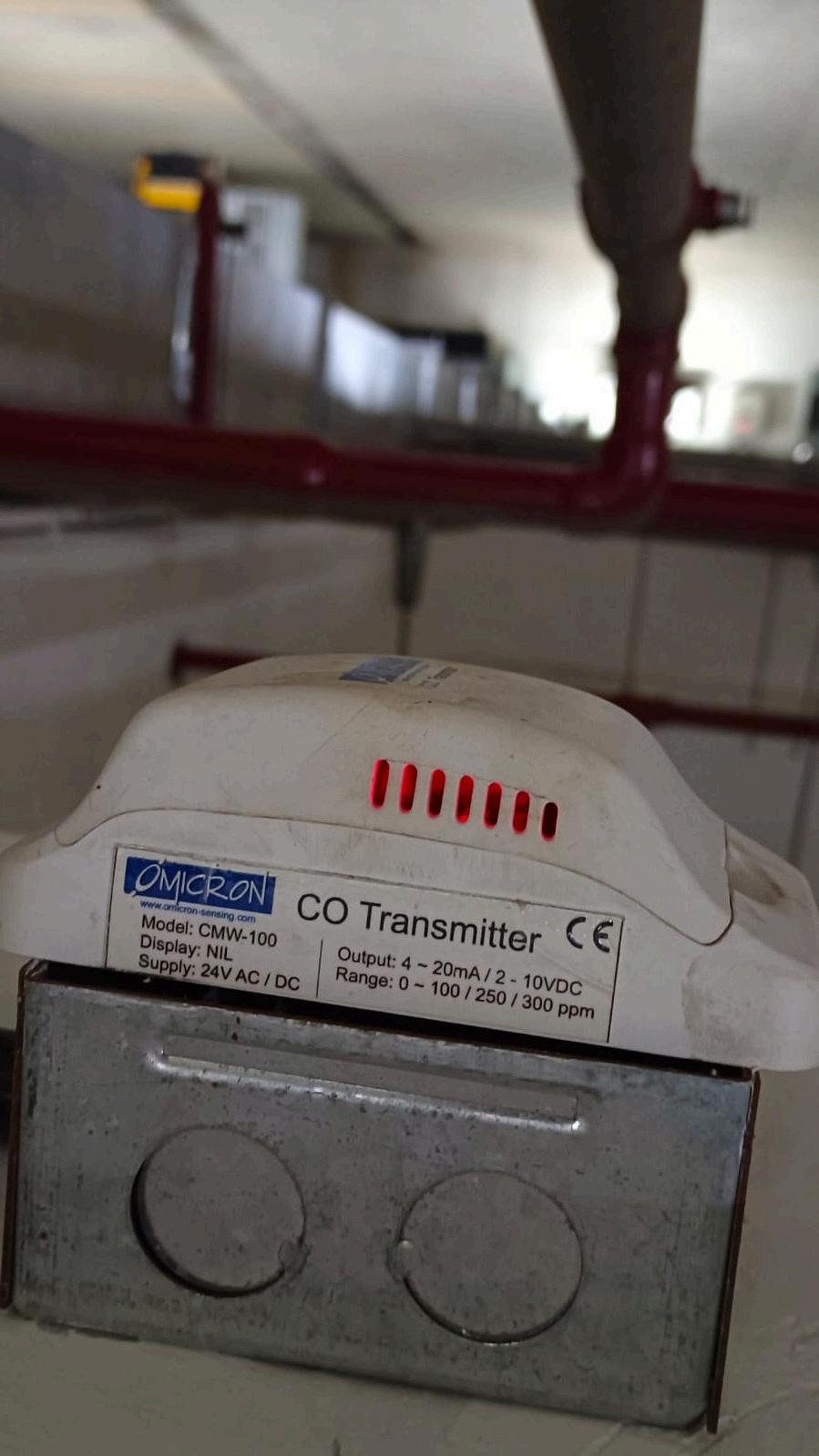
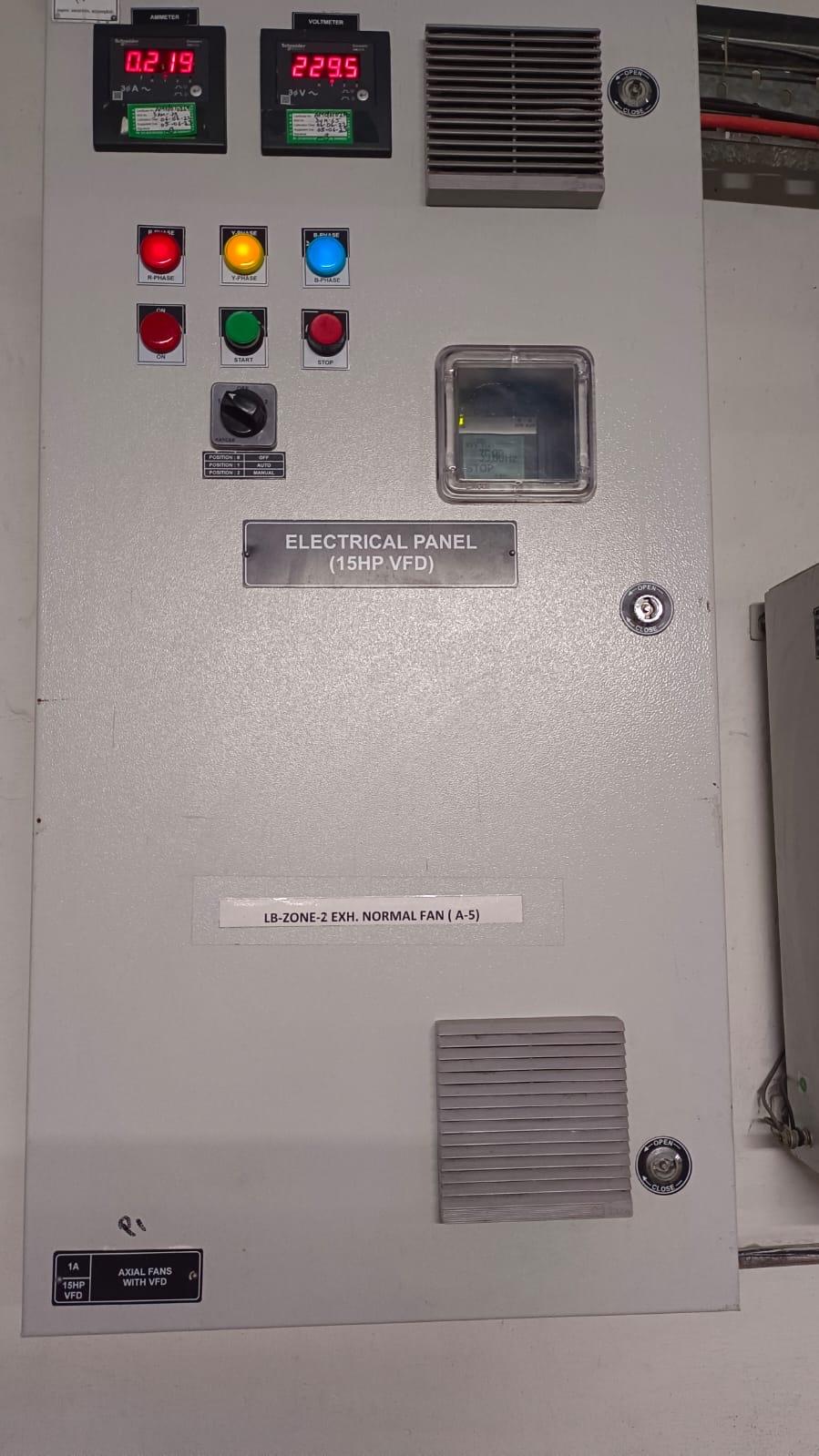
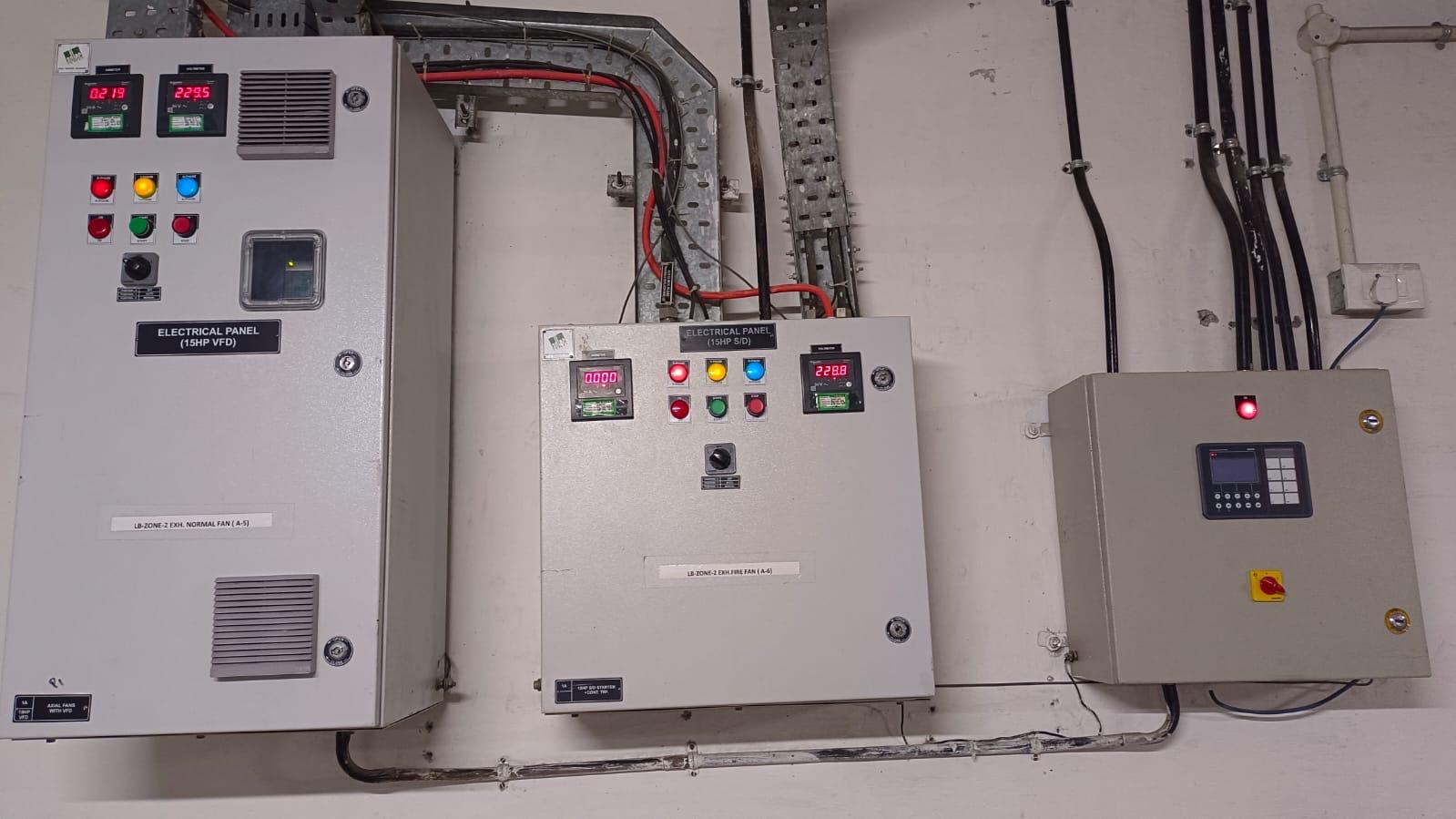
Description of the Innovation:
False Ceiling Dust Collector
CHALLENGE MYIDEA / INITIATIVE / SOLUTION BENEFITS / ADVANTAGE
myIdea
• To maintain the cleaning standard while cleaning the cobweb.
• Take care the employee health and safety.
• Maintain and enhance the daily SS operation.
• Maintenance of cleaning protocol during high dusting activities.
• Adhering EHS guidelines.
• To maintain the cleaning SOP , we have made a transparent cone and fixed it with the cobweb brush stick.
• This cone shape space is working as a dust collector.
• Sheet protector has been used to design this tool.
• Very convenient for regular use and it is washable for multiple use.
• Very minimum cost is involved to design this equipment
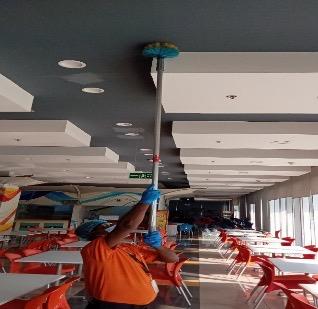
• This innovation helps us to clean the cobweb in effective way and increases the productivity. It does not let the dust scatter that falls on the floor and other exposed surfaces ,which make it difficult to clean repeatedly.
• This container prevents dust explosion in the air and keeps the air fresh
• This initiative encourages good housekeeping practice at site.
• It takes care the employee health and safety aspects.


Description of the Innovation:
QR Code Based
Video SOP
myIdea
• At DLFB facility all equipment like UPS, VFD, PAC,CAC, Micro oven SOP is displayed over notice board as a Large PDF file where to go through each & Every Detailed safe operation procedure of said equipment is time taking.
• When any newly joined technician comes to operate critical equipment, they required to go through different Training modules by OEM to properly operate said equipment safely.
• Time consuming & difficult to conduct chemical safety training for new joinee HK staff.
• We informed to all our OEM / Chemical Trainer & Service technician to provide demonstration about systematic operating procedure of their respective domain electromechanical equipment.
• We Gather all those OEM& Chemical trainer demonstration Video in Quick-Response codes to visualize digital content As well as PDF content by choosing option
• Authorized technician/ HK Boy can come before critical equipment and by scanning the QR code easily visualize OEM demonstrated & handle Chemical Safely by seeing those demonstration video
• By implementing this initiative, we easily can operate electromechanical equipment & handle chemical smoothly where any layman can understand that equipment safe operating procedure
• By implementing this initiative easily saves t by scanning QR code and visualizing OEM /Trainer guidelines
• By implementing this initiative, we easily save printout copies 10 kg which equivalent to 9.42 kg CO2eq) of GHG emissions.
• Cost Saving By Implementing Own Inhouse Team - 5000 Rs.

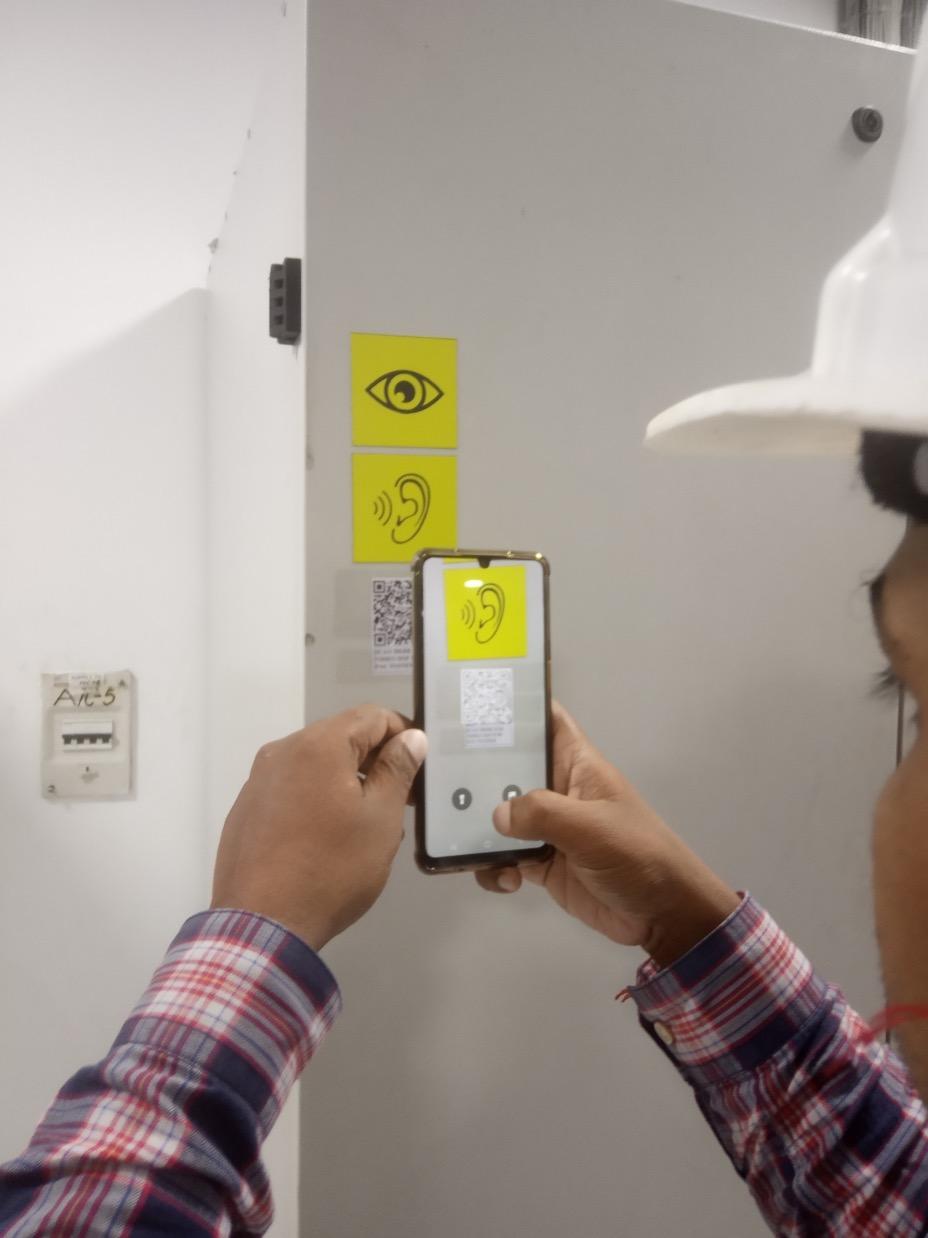
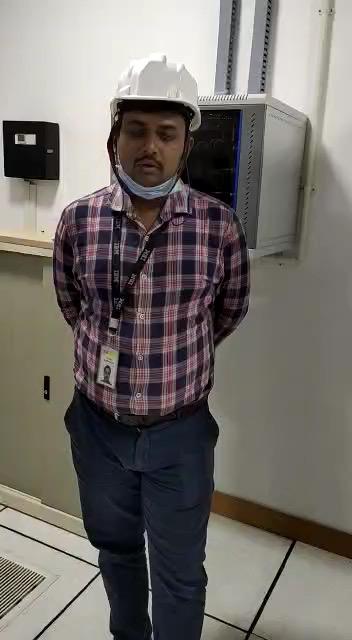
Description of the Innovation:
Chiller Optimization Project
myIdea
CHALLENGE MYIDEA / INITIATIVE / SOLUTION BENEFITS / ADVANTAGE
• Existing B1 & B2 chillers were more than 15 years at EOL.
• Replacing the refrigerant R407C with R134A, as R407C has a glide of 7K.
• Existing IKW/TR is 1.2 for B1 & B2 which increased energy consumption.
• No VFD/VSD system to support part loads.
• The iKW/TR is same irrespective of percentage of load.
• Upgraded version of the system which have IKW/TR -0.7 for efficiency and cost saving.
• Centralized system for B1 & B2 is flexible and changes can be made to accommodate quick changes in demand.
• R134A refrigerant copes better with annual temperature increases.
• Auto tube & condenser cleaning system eliminates corrosion and fouling results in an extended condenser life cycle and energy saving.
• Energy savings of 14,49,026 KWH per annum at 100% load, 17,98,807 KWH per annum at 75% load, 21, 48,589 KWH per annum at 50% load.
• Estimated Saving : INR 1,60,46,718 per annum.
• Low iKW/TR varying from 0.48 to 0.68 based on loads.
• Inbuilt VSD/VFD which supports part loads.
• It has very low noise or no noise (less than 80db).
• It is lubrication free maintenance.
• Variable pumps have higher airflow rate than conventional pumps.
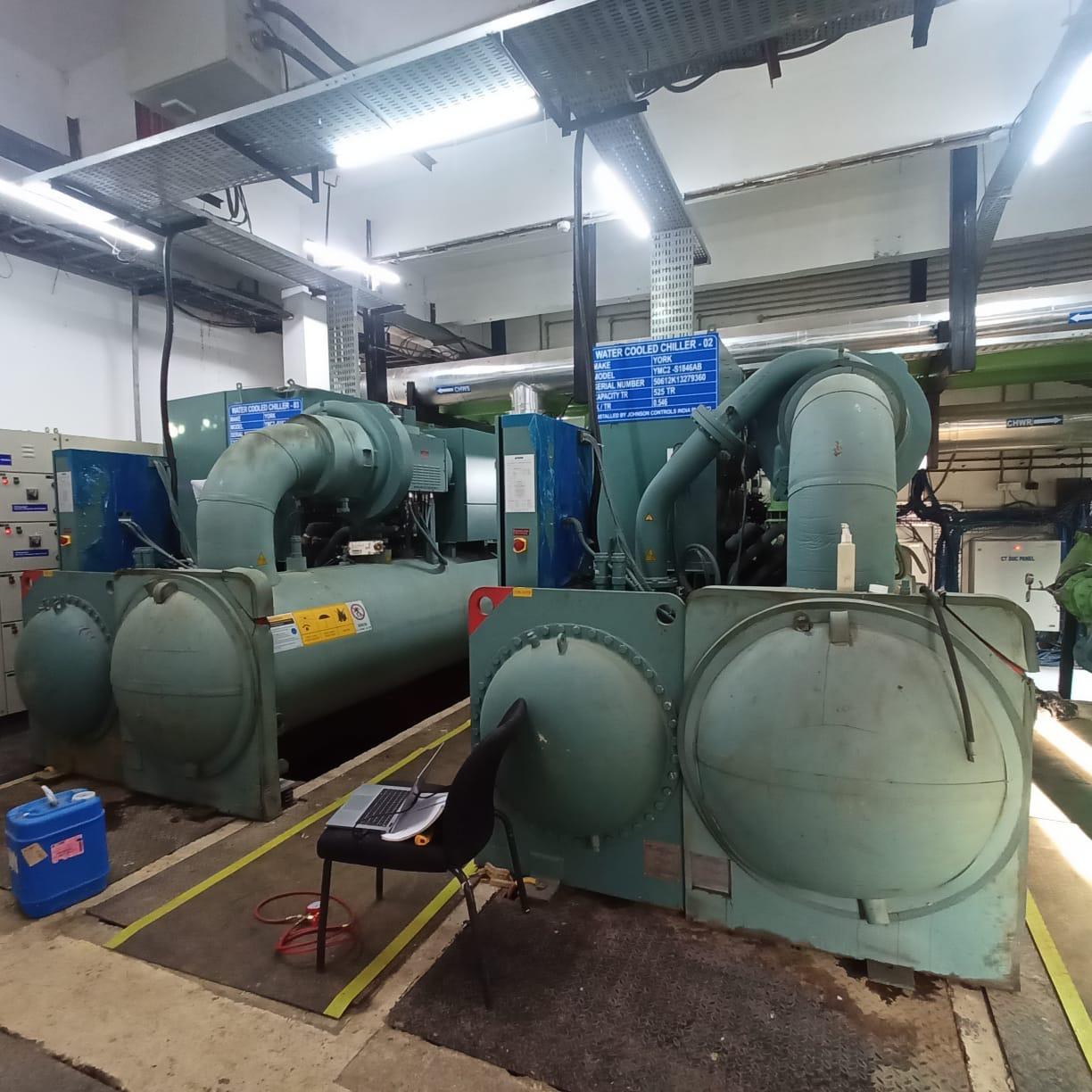
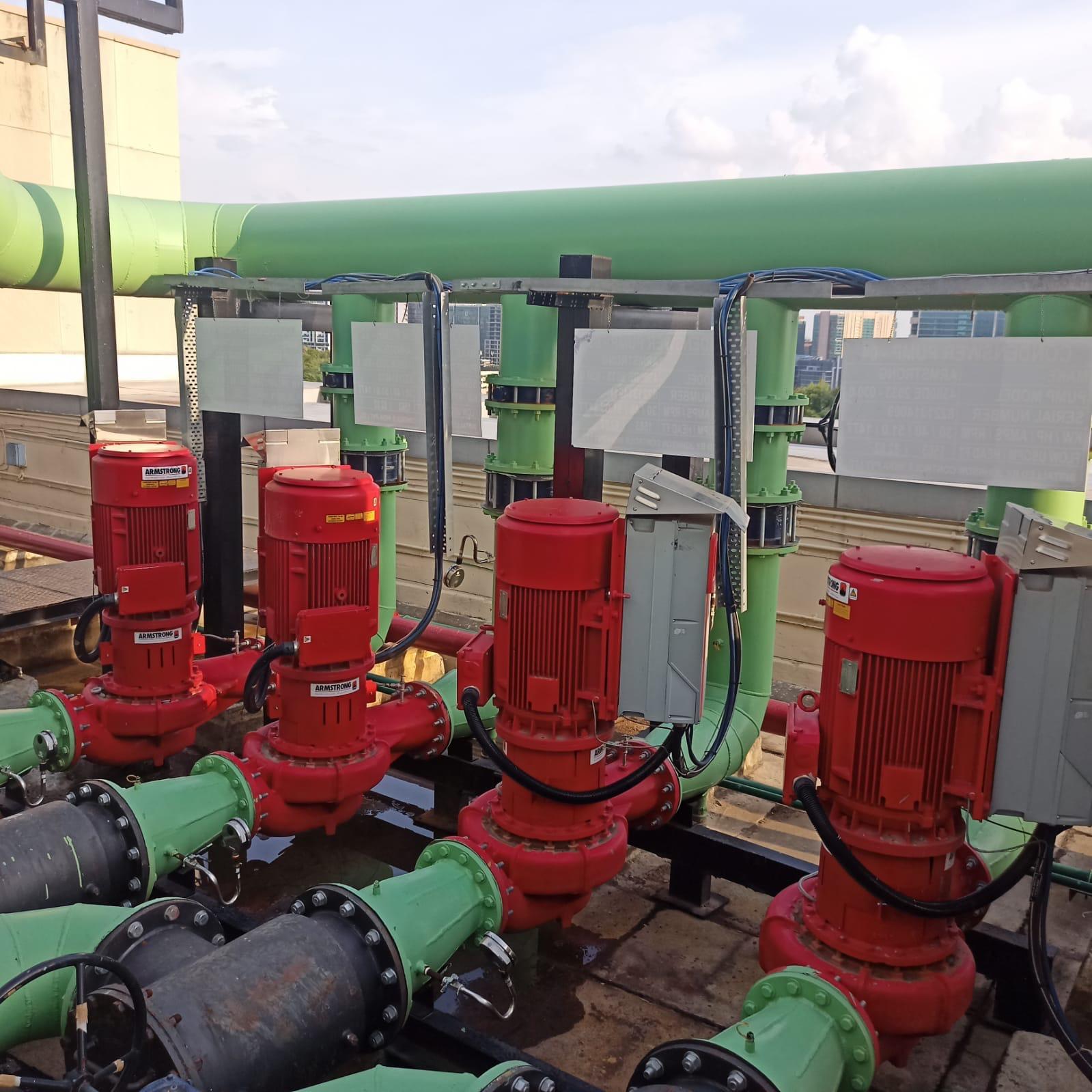

Description of the Innovation:
Employee Safety Handbook
myIdea
CHALLENGE MYIDEA / INITIATIVE / SOLUTION BENEFITS / ADVANTAGE
• Communicate employees on the safety protocols Post covid at Workplace
• Employees guidance during RTO (Return to Office)
• The safety handbook has been issued to the employees who are visiting the office after the pandemic
• The information in the safety handbook has provided guidance to employees on changes/enhancements on Return to the office
• Social distancing in workplace post-Covid
• The safety handbook contains the information on all the precautions that need to be exercised adhering to Covid protocols and signages associated to social distancing while at work
• It also covered the social distancing guidelines and Covid precautionary measures taken at the workplace
• It covered the building protocols, temperature checks, etc



Description of the Innovation:
Eddy Current Test For Chillers
CHALLENGE
• High TDS of water leading to scaling issues in chiller
• Descaling process over a period leads to surface erosion of copper tubes
• Lack of visual methods to inspect condenser tubes for any potential failure
• Predictive Maintenance allows for preemptive corrective actions, and increased asset life.
• Adjustments, and repairs can be performed before the asset fails
• Eddy-current testing (ECT) is one of the electromagnetic testing methods used in nondestructive testing (NDT), making use of electromagnetic induction to detect and characterize surface and sub-surface flaws in conductive materials.
• Chiller tubes inspection has been conducted by ECT test method to find out any surface losses of the tubes.
• All tubes has been analyzed online through the remote monitoring application connected to the eddy current test equipment.
• Observed tube wall losses up to 60% for few tubes and initiated for corrective actions.
• Timely intervention had prevented pre-mature failure of the chiller
• Prevention of unexpected break downs
• Reduced R&M costs
• Improvement of condenser and evaporator approach leading to enhanced chiller performance and energy efficiency
myIdea
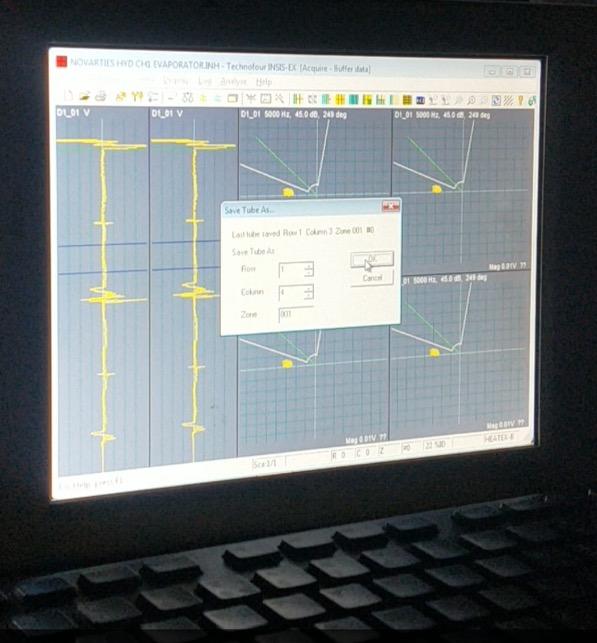
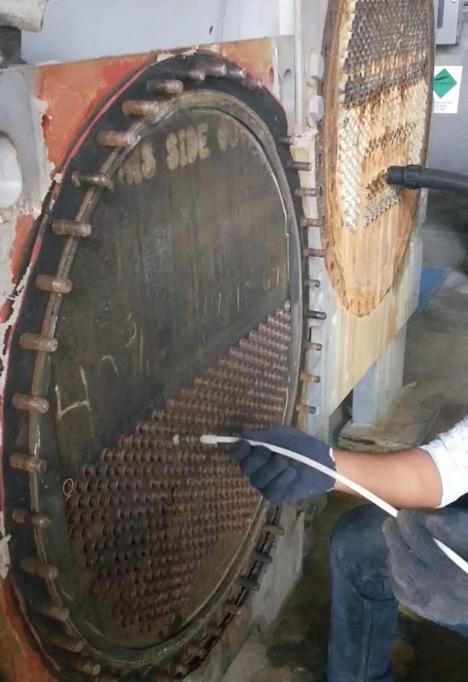

Description of the Innovation: CHALLENGE
Creation of Microsite for End-User
• During the Pandemic- A change Program had to be delivered
• This was to help employees settle from one location to the other.
• They were also moving from assigned seating to unassigned.
• The employees had a lot of pushback as this was a legacy office, hence many stayed close to the office, most leaders had cabins, the location was at the city center, and the location had access to various amenities etc.
• Employees would move in post recovery from the pandemic.
• All the confusion and ambiguities had to be cleared before the move.
• Pandemic wouldn’t allow delivering the program in person.
• Digitized Change Program was the answer.
• TEAMS was leveraged to create a VIRTUAL SPACE to help employees – SEE, UNDERSTAND and get all queries ANSWERED much before the move.
• Live channels were created where anyone, who wanted to know anything about the site had answers ready.
• The impact areas were addressed through channels in TEAMS
• The employees were engaged at every step without blocking much of their time
• Employees felt their voices were heard and addressed.
• Leaders had a live update on the progress of the project and inputs from employees
• We had a cost avoidance of $60K by selfdelivering this inhouse with a very lean team and zero investment
• At the end of the move, we ran a pulse survey and had 100% satisfaction with the project delivery and Change Program
• The employees knew exactly how is their office going to look when they come on the first day
• They know who and how to reach out for any help.
• All apprehensions and confusions cleared and resolved before Day 1 of the move.
• The virtual office was created with only infographics, images and videos
myIdea
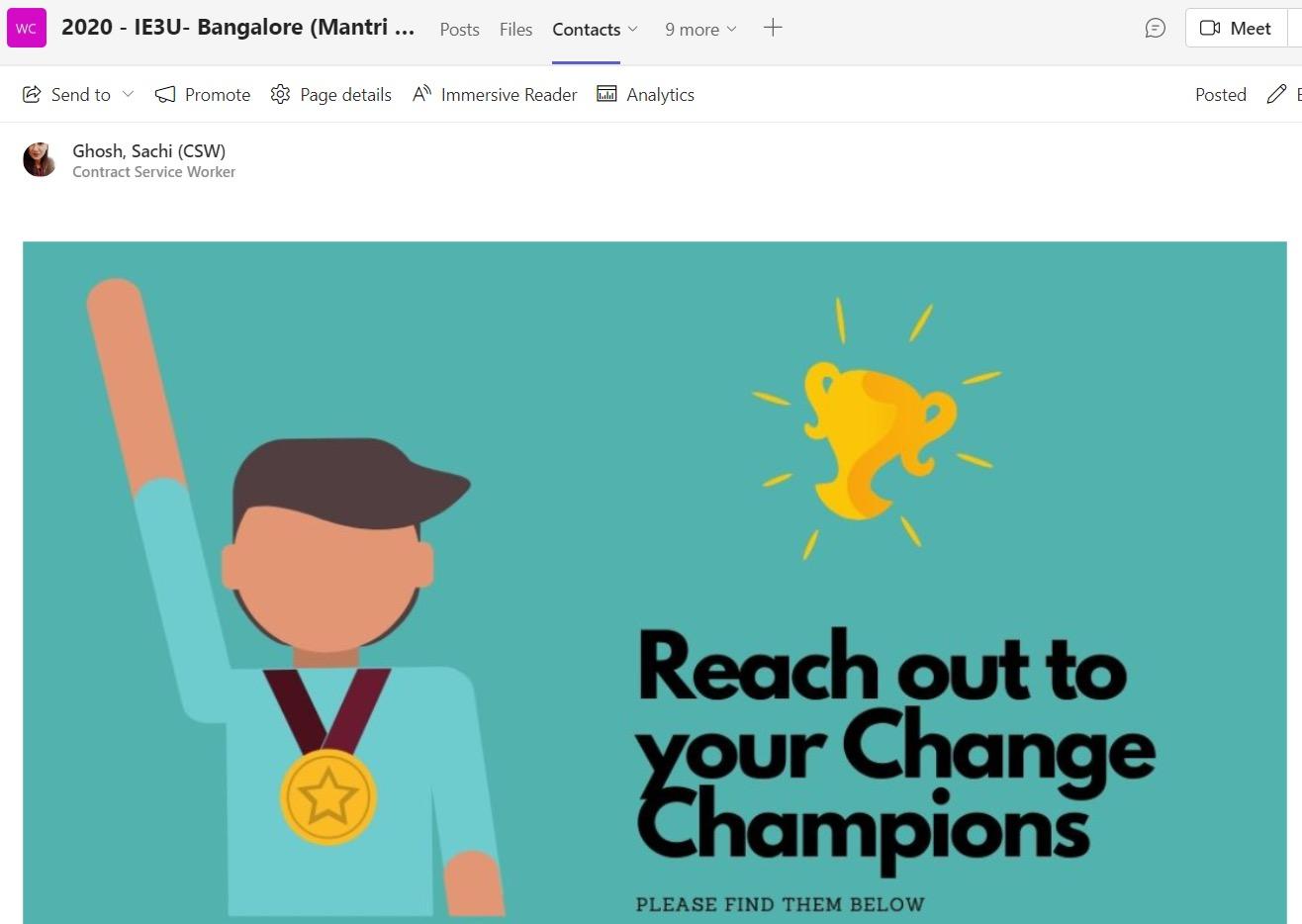
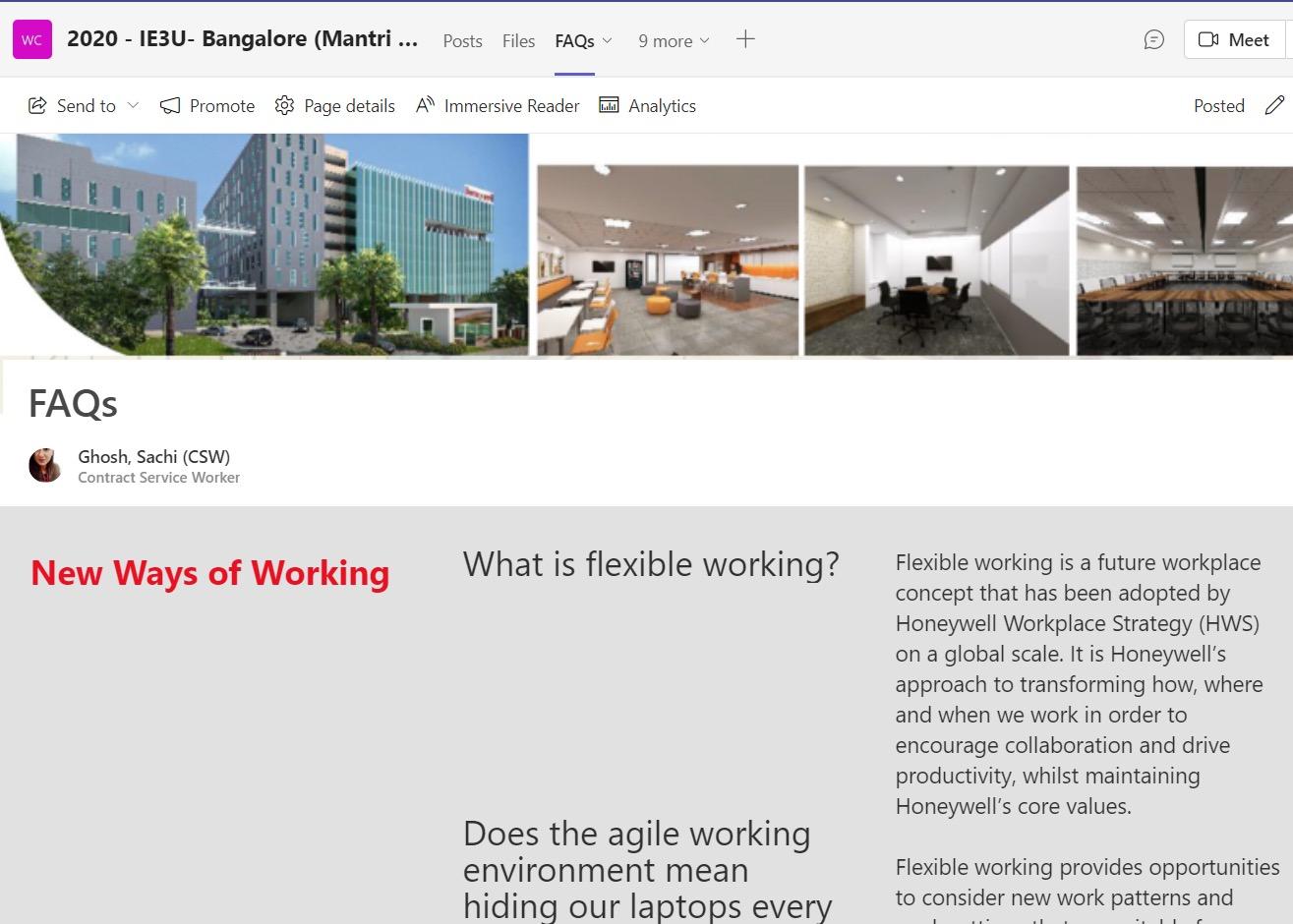

Description of the Innovation:
STP Water Test Lab
CHALLENGE MYIDEA / INITIATIVE / SOLUTION BENEFITS / ADVANTAGE
• Wastewater management is an undesirable task for facility managers and their staff. But it’s an important job, because wastewater problems can quickly turn into a very expensive and unsanitary mess.
• Getting reports from an external agency takes more than a week & we were not be able to take timely action & maintain the water quality instantly as per TNPCB Standard
• Planned & installed, in house water test lab with all supporting instruments like beaker, pipette, kits etc allowing us to take appropriate action in timely manner
• Approximate cost is RS 5.5 Lacs as one time investment.
• Regularly consumable cost of the test kit, approximately Rs10 000 per month
• Real-time information about the water can be collected on daily basis
• Allows to take immediate action to improve the water quality
• By improving the water quality, we can reduce the regeneration time of WTP /back wash of the filtration plant
• By improving the water quality, the chemical treatment is sufficient or not can be confirmed and no further adding of chemicals is possible
• By checking the turbidity/ TSS in pressurebased analysis the back wash time can be increase and power savings through reducing the pump operation and 30KL water approximately can be saved
myIdea
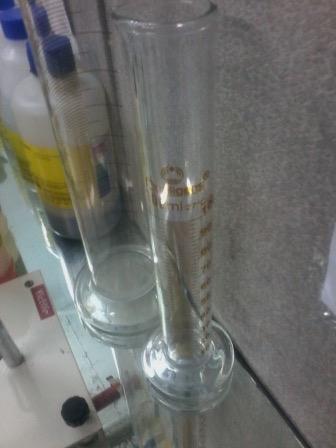

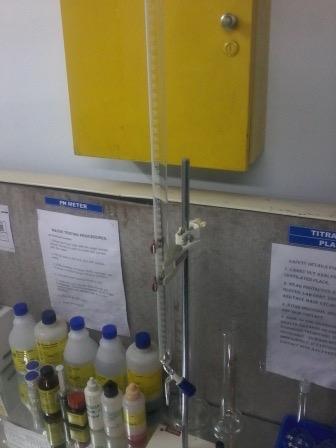
• Contamination due to airborne pathogens and VOC ( Volatile Organic compounds ) in the indoor air
Description of the Innovation:
Indoor Air
Purifier
myIdea
• Toxic gases because of Tobacco and Fragrances
• Windowless office space
• Declined Cognitive performance in the office
• Efforts to reduce pollution have no real time surveillance system
• Installed Just breath air unit in the common area lobby to reduce the pollutant and monitor the real time parameters for taking corrective action.
• Designed for windowless office and no modification required
• Real time surveillance system to monitor particulate matter , TVOC, and monitor humidity with inbuilt sensors for monitoring indoor and outdoor air
• Effectively removes the Particulate matter TVOC and microbial counts by 95% in 2 hrs time
• Zero maintenance No filter change entire solution works on AI technology,
• One stop solution to address all indoor pollutants including monitoring, measuring and managing IAQ
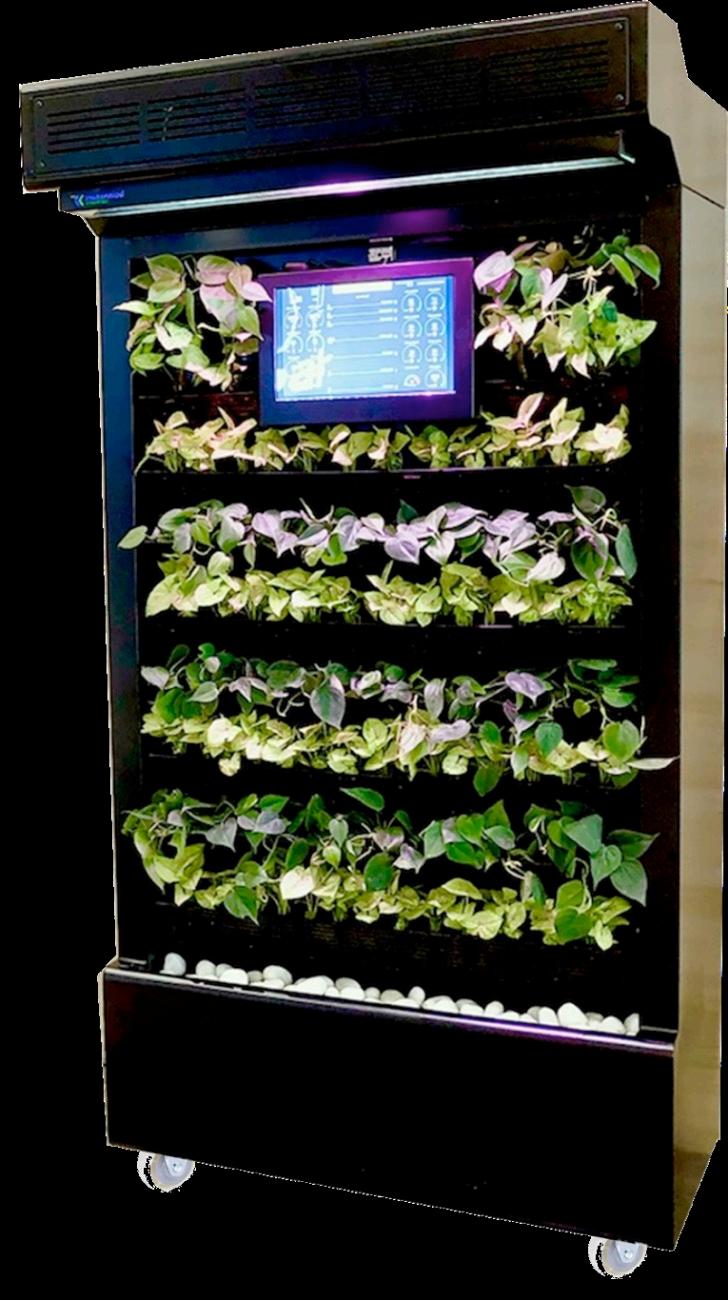
• Odorless Atmosphere Air purifiers enable you to keep your space free from scents.
• Everyone Loves Smoke free Place. Dispose of Volatile Organic Compound and Energy Efficient
• Allergic Microorganisms are Away
• They lighten allergen load in the air and filter harmful chemicals
• They may help with dust and pet dander, And remove mold spores from the air, relieve symptoms of asthma and reduce airborne disease.
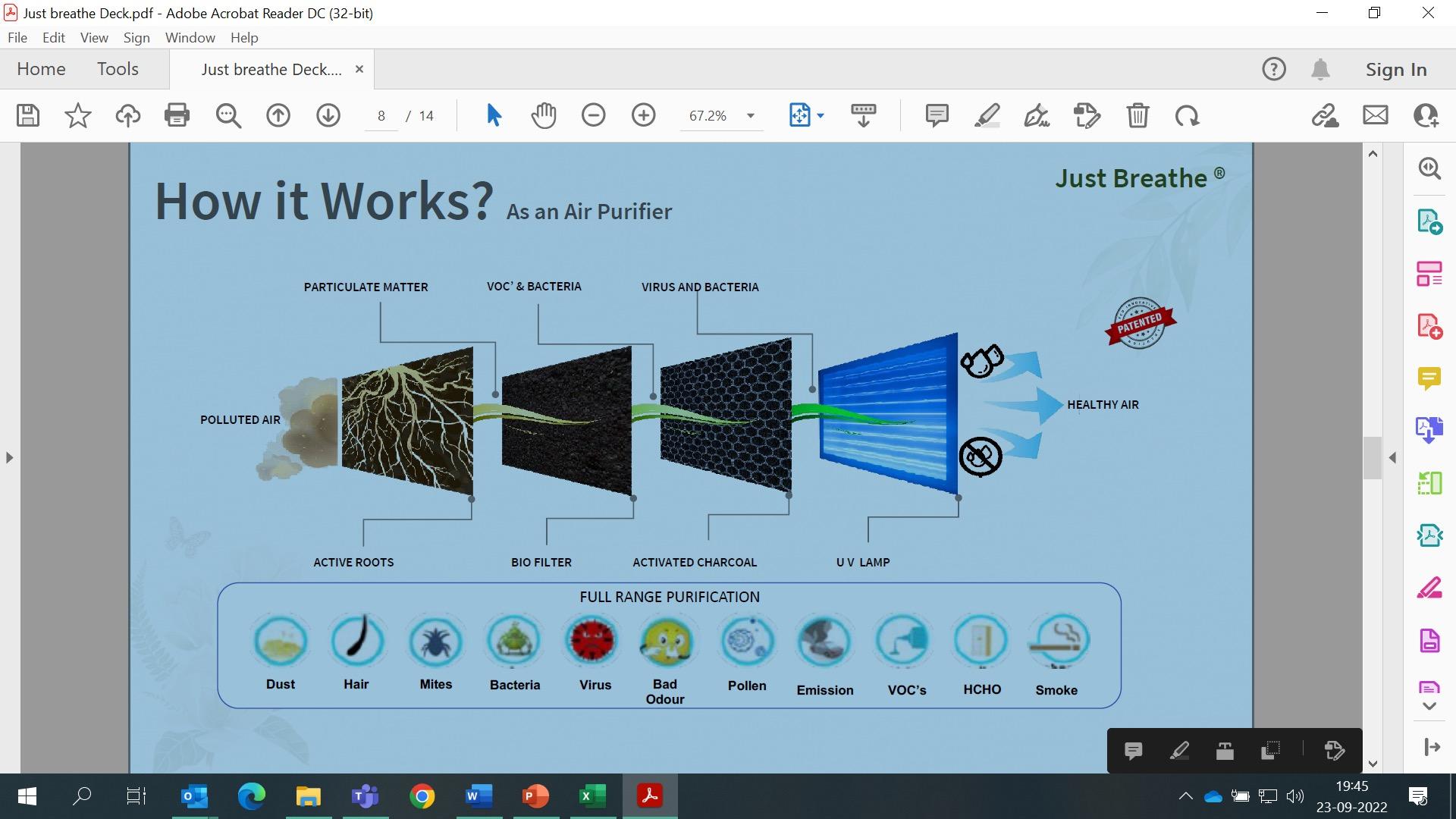
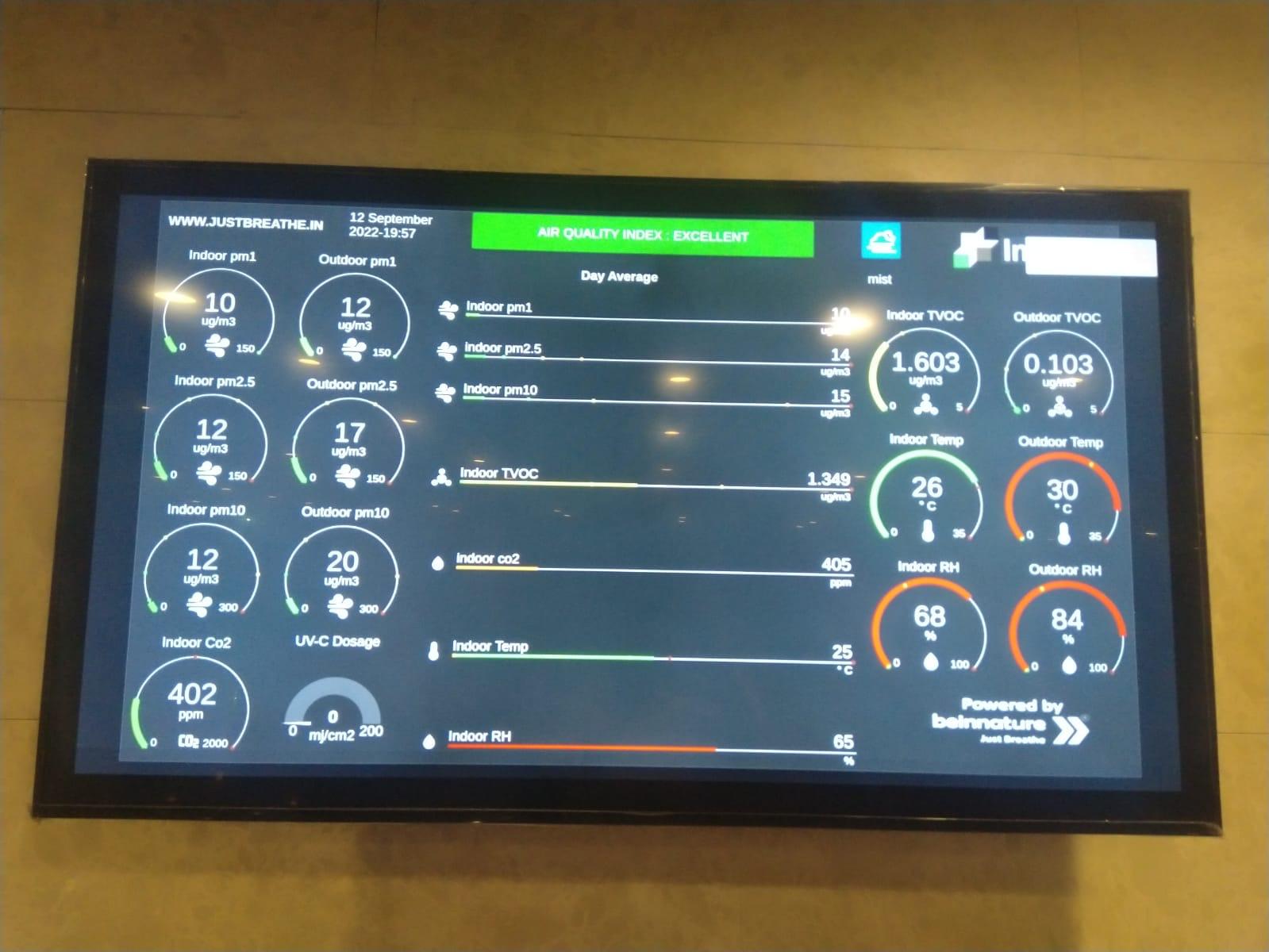
CHALLENGE
Description of the Innovation:
Redundancy System for AMF Panel
myIdea
• Existing system consists of a UPS which provides control supply for the working of AMF panel in automatic mode.
• When the UPS fails or gets faulty, the system fails to work in automatic mode. This requires additional manpower to operate the panels whenever a shutdown/fluctuation occurs.
• The change over operations requires more time and delay in resuming power supply.
/ INITIATIVE / SOLUTION BENEFITS / ADVANTAGE
• The proposal was to bring a redundant supply for the control system with a changeover. The alternate power was taken from DG battery supply which was available in the panel itself.
• A new change over type MCB was installed and control wirings modified accordingly.
• During a power interruption, if the UPS fails, the manpower only need to switch the changeover MCB to DG battery position to work in automatic mode.
• Shut down interval is minimised. When the UPS becomes healthy, it can be switched back to the UPS mode.
• Power shutdown interval can be decreased with the availability of redundant control supply.
• Manpower for the operation of AMF panel can be reduced since the automatic controller will carry out all other functions including breaker closing and tripping etc.
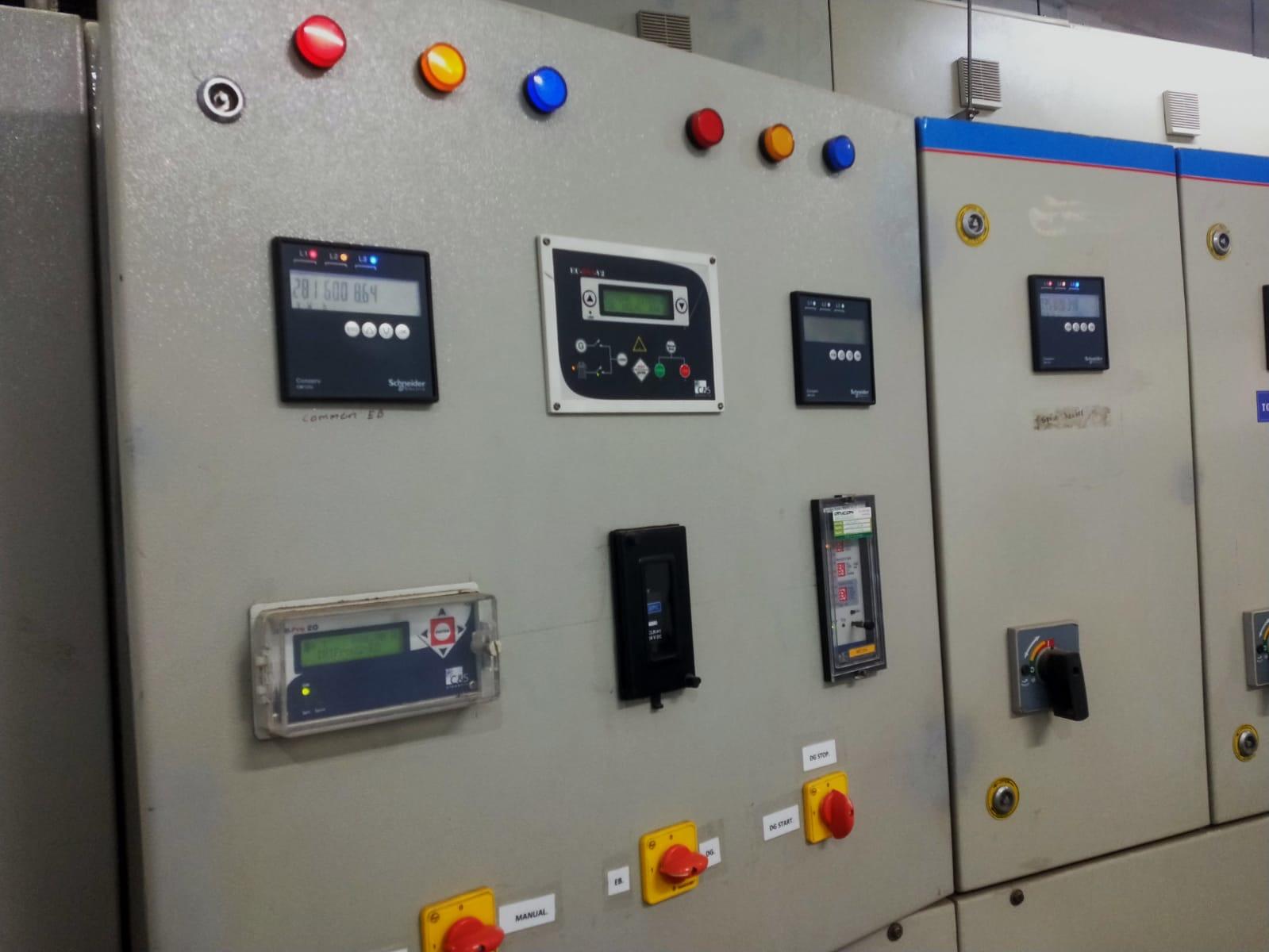
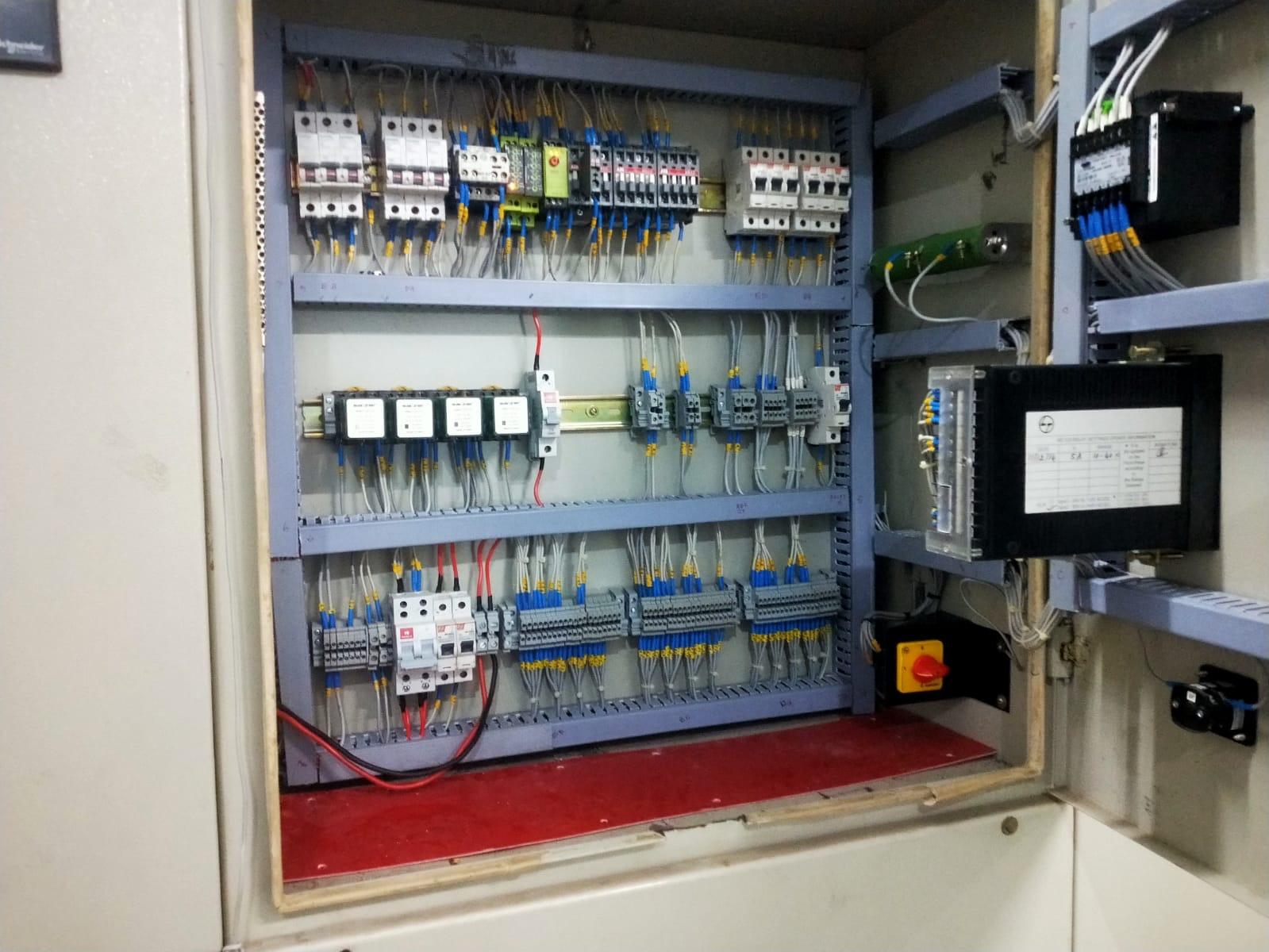

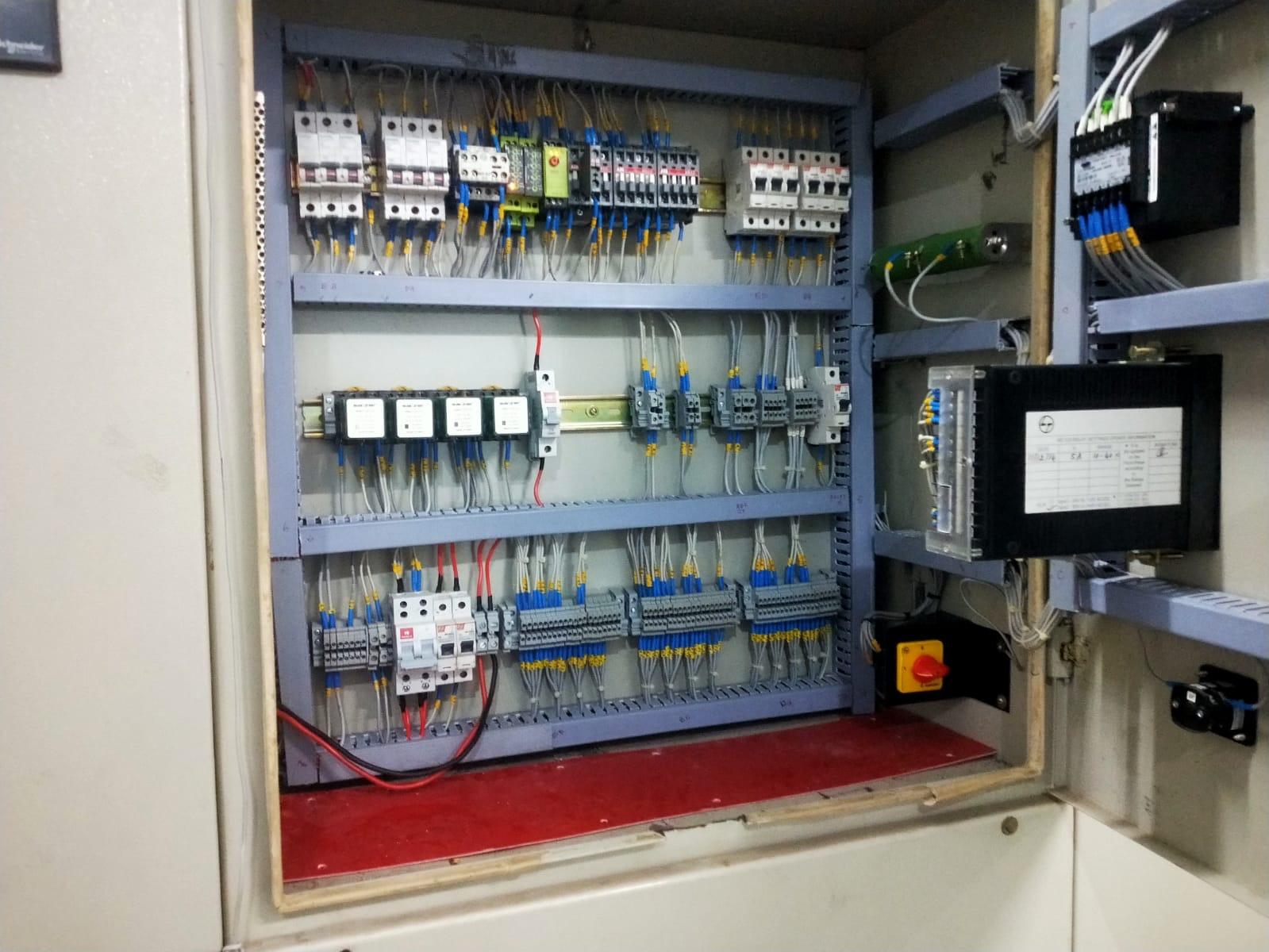
Description of the Innovation:
Solar Smart Bench
myIdea
CHALLENGE
• Difficult to provide charging points at the podium level as it’s difficult to provide wires in granite.
• There is no provision available to delight the employee with digital experience while enjoying the outdoor ambience.
• Lac of sustainability initiative to showcase to the employees at the podium level
• Installed 5 nos of solar benches with provision for 6 no's mobile charging, Free Wi-Fi, laptop charger
• The new solar bench is based on simplicity and minimalism construction provides intuitive usage, while its universal design perfectly fits modern plazas and industrial interior spaces
• Provides adequate lighting during night hours for reading books
• Phone charging
• Safe and free Wi-Fi in public spaces
• Powered by solar energy - free and widely available
• Providing safety at night and highlighting innovation
• Support sustainability in the campus
• Perfect gadget for Employee engagement
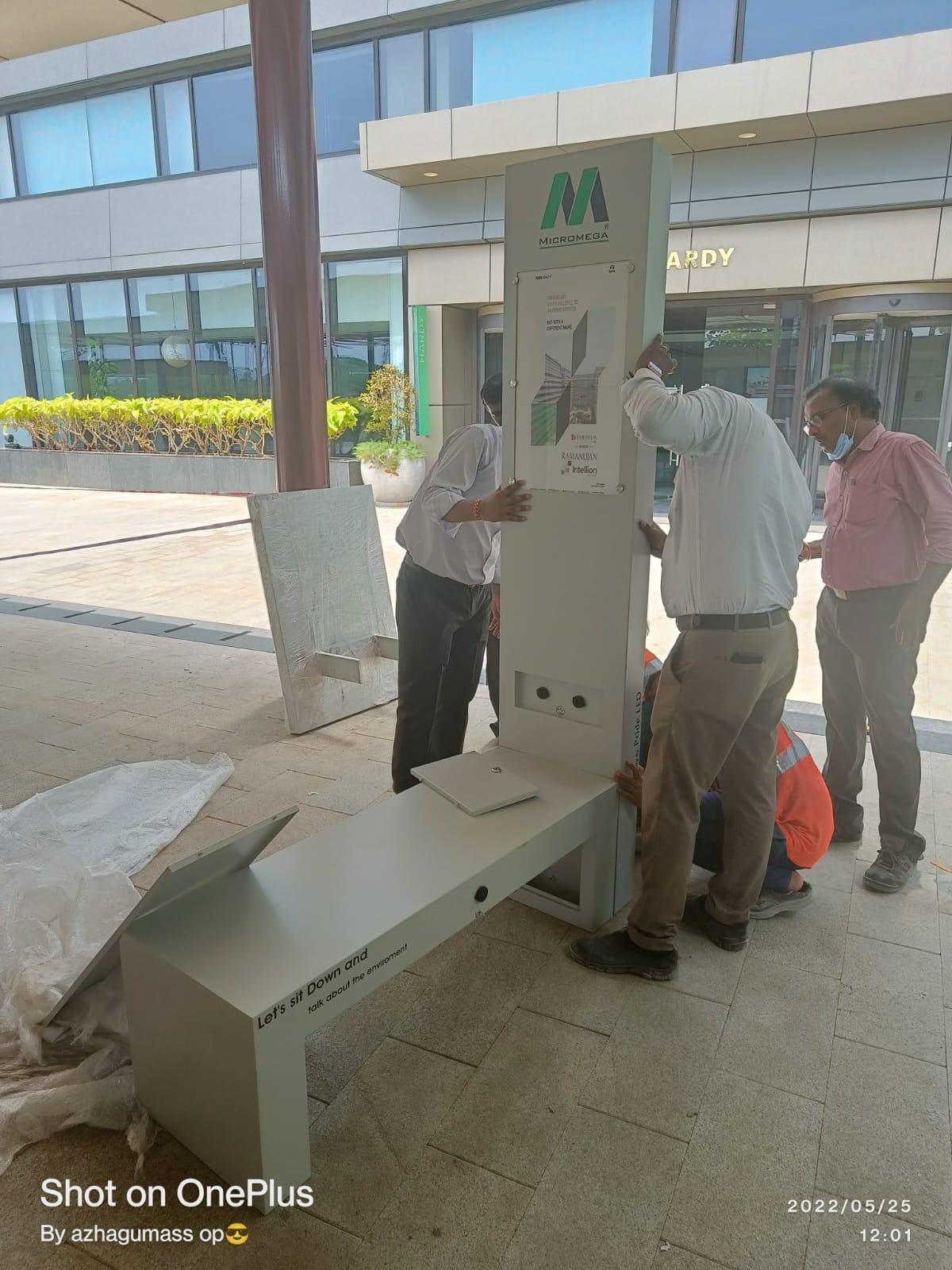
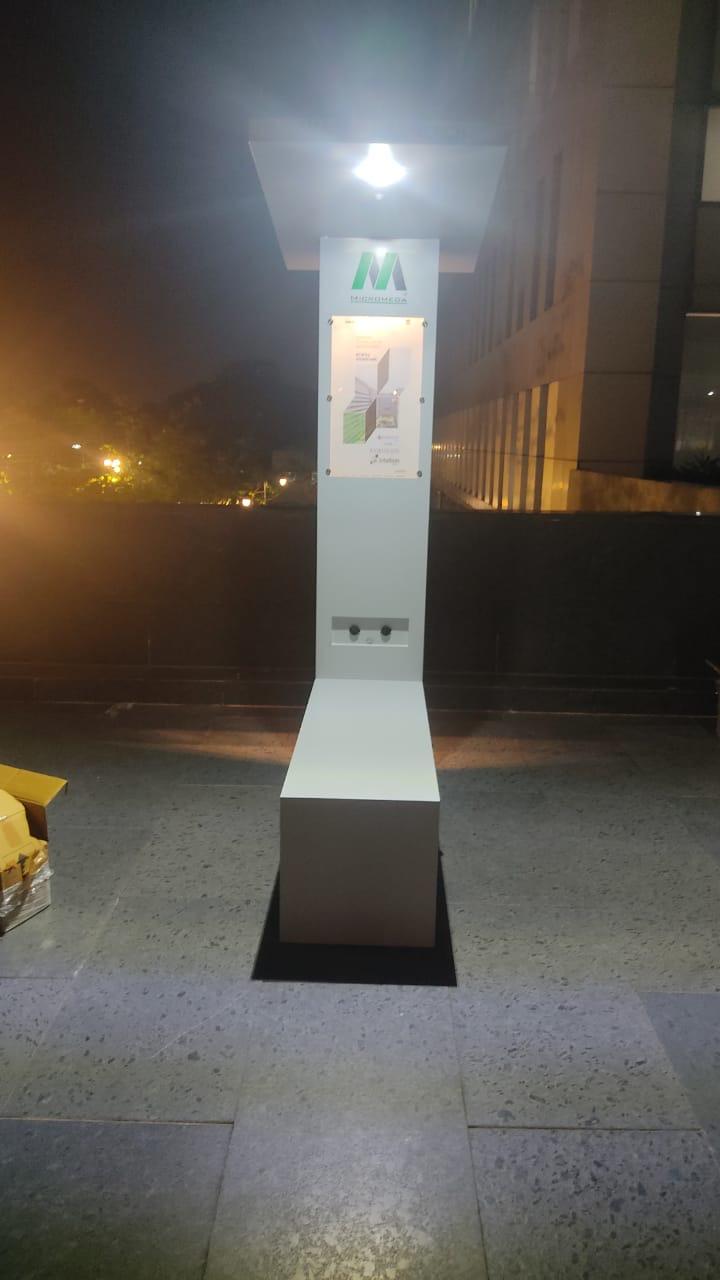
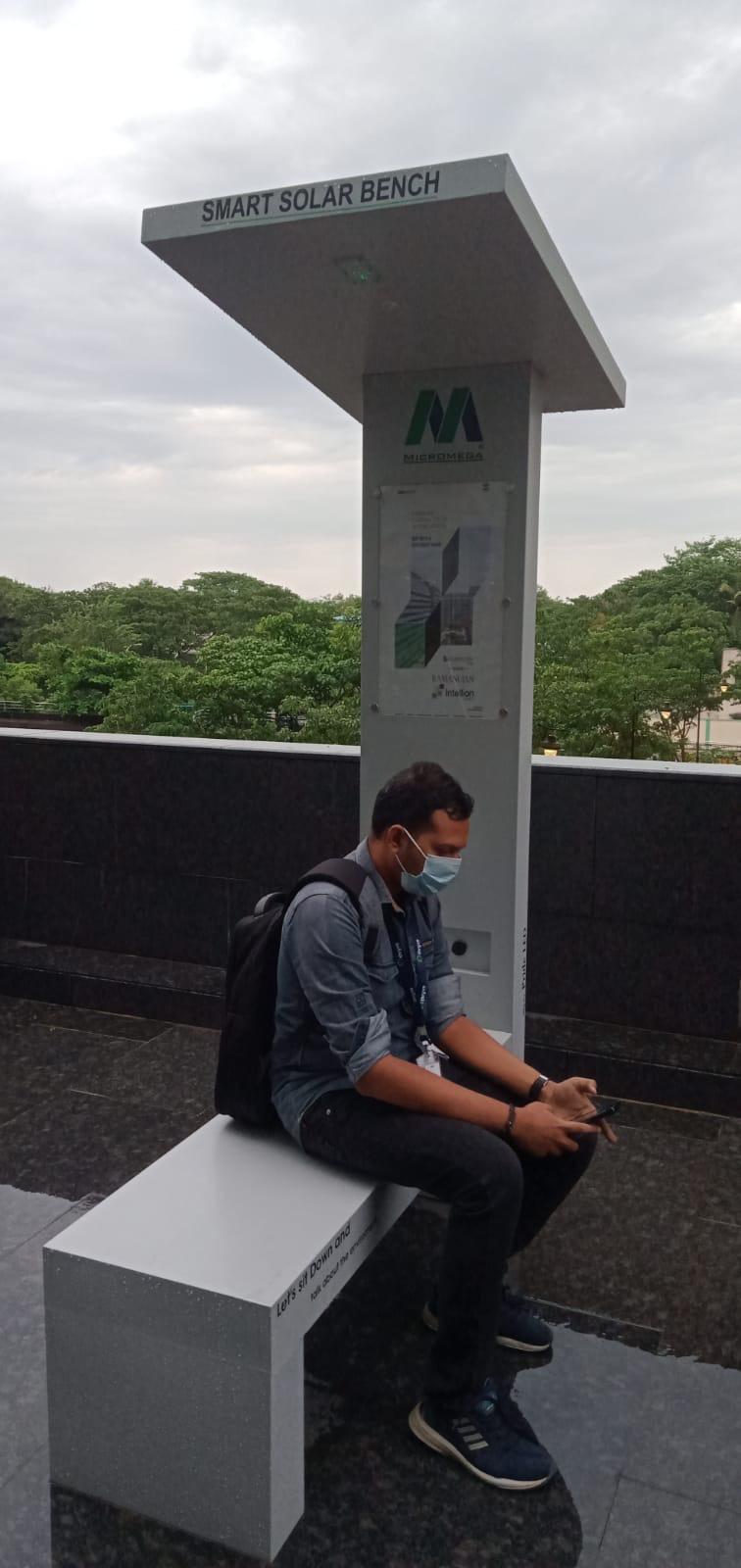
Description of the Innovation:
Smart Cleaning Methodology
CHALLENGE MYIDEA / INITIATIVE / SOLUTION BENEFITS / ADVANTAGE
myIdea
• Housekeeping employees must return many times for bringing cleaning cloths, materials for a single spot cleaning.
• A small dry mop took longer time to clean a larger space such as elevators landing, plaza and lobby
• A wet mop leaving watermarks on the floor
• A bucket of dirty water that gives a negative impression of the property
• Reduce cleaning staff weariness and enhance
property aesthetics
• Reduce water and cleaning chemical consumption
• Reduced cleaning staff work fatigue.
• Cost savings on wear and tear consumables.
• Cleaning efficiency improved.
• Enhanced client's experience.
• Implemented smart saving equipment to get
desired result
• Increased cleaning efficiency, enhanced aesthetics and less job weariness for cleaning staff
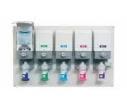

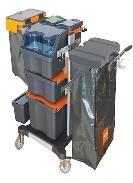
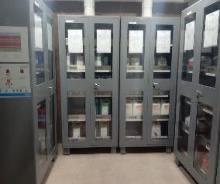
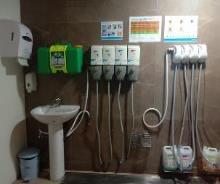
• Ease of work
Description of the Innovation:
• Water accumulation due to heavy rains –turns into a labor-intensive task of squeezing water for the HK team
• Water seepages in Parking are high
• Due to the above reason diverting of the manpower resulting in Compromising of other scheduled works.
Super Sopper Machine
• Inhouse Super Sopper idea makes the job easier with less efforts and speedy work.
• Fall hazard
• Clients are not happy with wet floor
• Invested Rs 8,000/- and creating the machine with inhouse team
• Quality work
• Optimal usage of manpower
• Speed in Work
• Client satisfaction
• Savings of Approx. 38000/- WRT brand new.
• Employee morale raised
myIdea
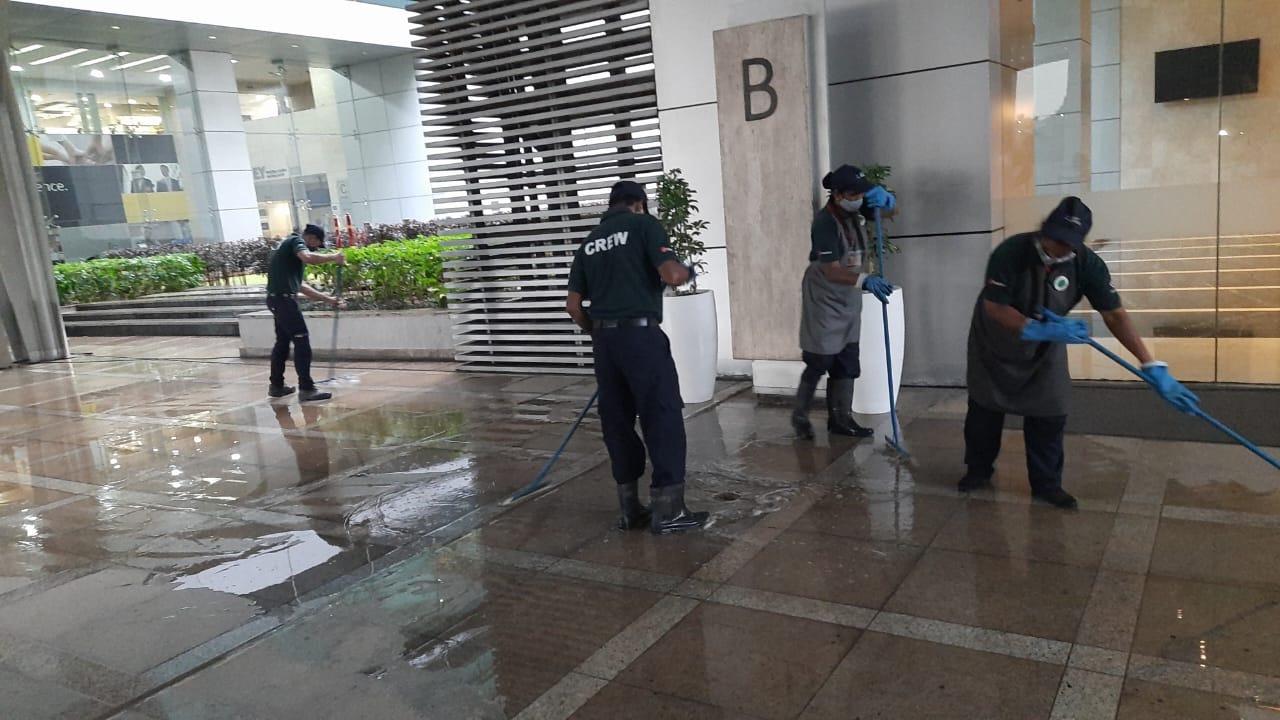
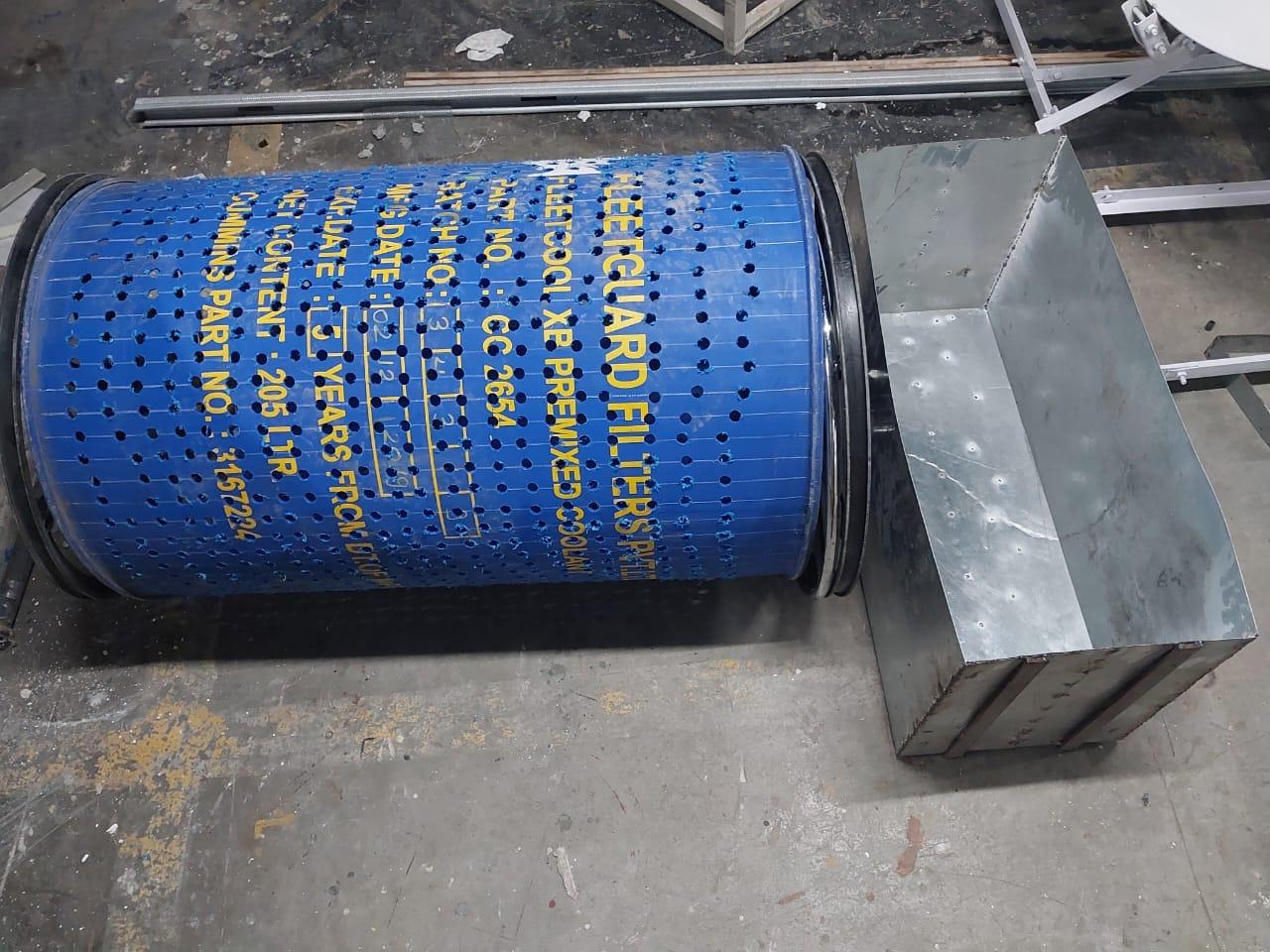
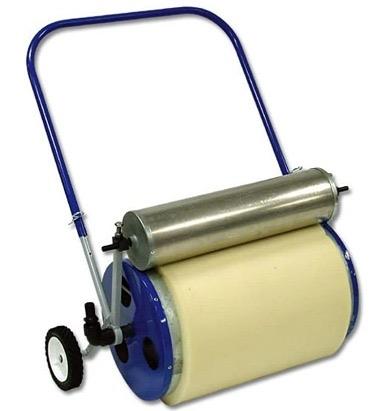
Description of the Innovation:
Bottle Crusher Machine
CHALLENGE MYIDEA / INITIATIVE / SOLUTION BENEFITS / ADVANTAGE
• With rapid urbanization, the amount of plastic waste being generated from various sectors have increased at an alarming rate.
• The used and empty bottles were being thrown in waste which was adding to quantum of waste being generated in the buildings
• Hurdles in recycling plastic waste
• The Bottle Crusher Machine is an effective method to recycle the plastic bottles. It effectively crushes the solid plastics into small pellets which are further used for making usable fabric material/granules for packaging
• Waste management vendor was approached to install 02 machines on FOC basis
• All the F&B outlets and corporate clients were approached to encourage their employees and staff to put the empty bottles in the machine
• Waste Management vendor team too was sensitised to collect any empty bottles found in garbage and put into this machine after cleaning
• “Bottle Crushing Machine” signs where appropriate were placed for awareness.
• PET bottle crusher machines are a boon and help us to achieve sustainability targets and save space in stocking plastic waste before disposing off
• NIL Capex as installed on FOC basis
• Simple to operate.
• Low cost of operation
• Sustainability initiative
• Reduction in ESG impact
• Client appreciation
myIdea
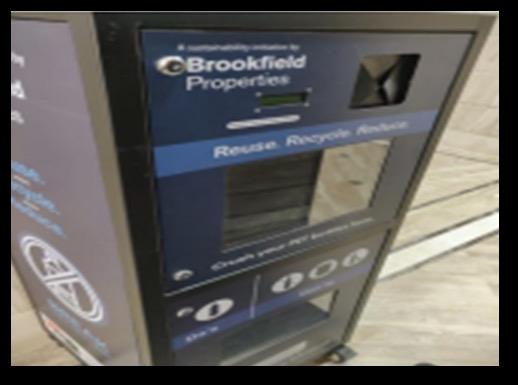
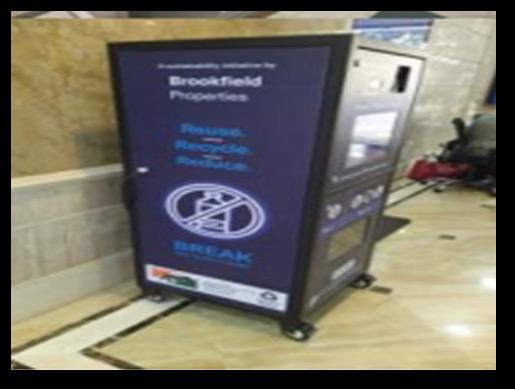
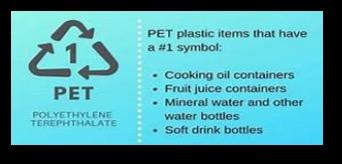
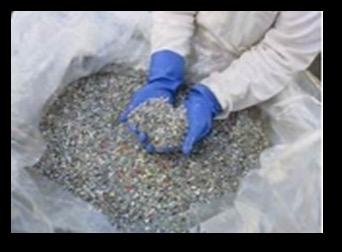
Description of the Innovation:
Portable Fire Extinguisher Trolley
myIdea
• In case of Fire Emergency carrying of right fire extinguishers and fire fighting equipment's on time is very essential.
• Our entire GBD campus is spread across 16 acres.
• Although fire extinguishers are located at prominent location carrying right extinguishers within short span to exact location is difficult.
• Fire extinguishers can be very tiresome and heavy to carry.
• Fire Extinguisher Trolleys offer the solution.
• Customized Fire fighting equipment trolley was made from Scrap items.
• This trolley can be handled by single security guard and within few minutes required fire fighting equipment's can be deployed to location of emergency.
• Following of the equipment’s are accommodated inside trolley
• Fire Extinguishers – 05 (Co2 ABC & Foam)
• Fire Blanket – 01 no.
• Megaphone – 01 no
• Toolbox – 01
• Safety Helmet – 02
• Canvas Hose – 02 with Nozzle
• First Aid Box - 01

• Highly useful in emergency situations and especially in the GBD premises.
• Trolleys is an easy, efficient and safe means of transporting heavy fire extinguishers bank & equipment's in a fast and practical method
• No Cost involved as made from scraps.
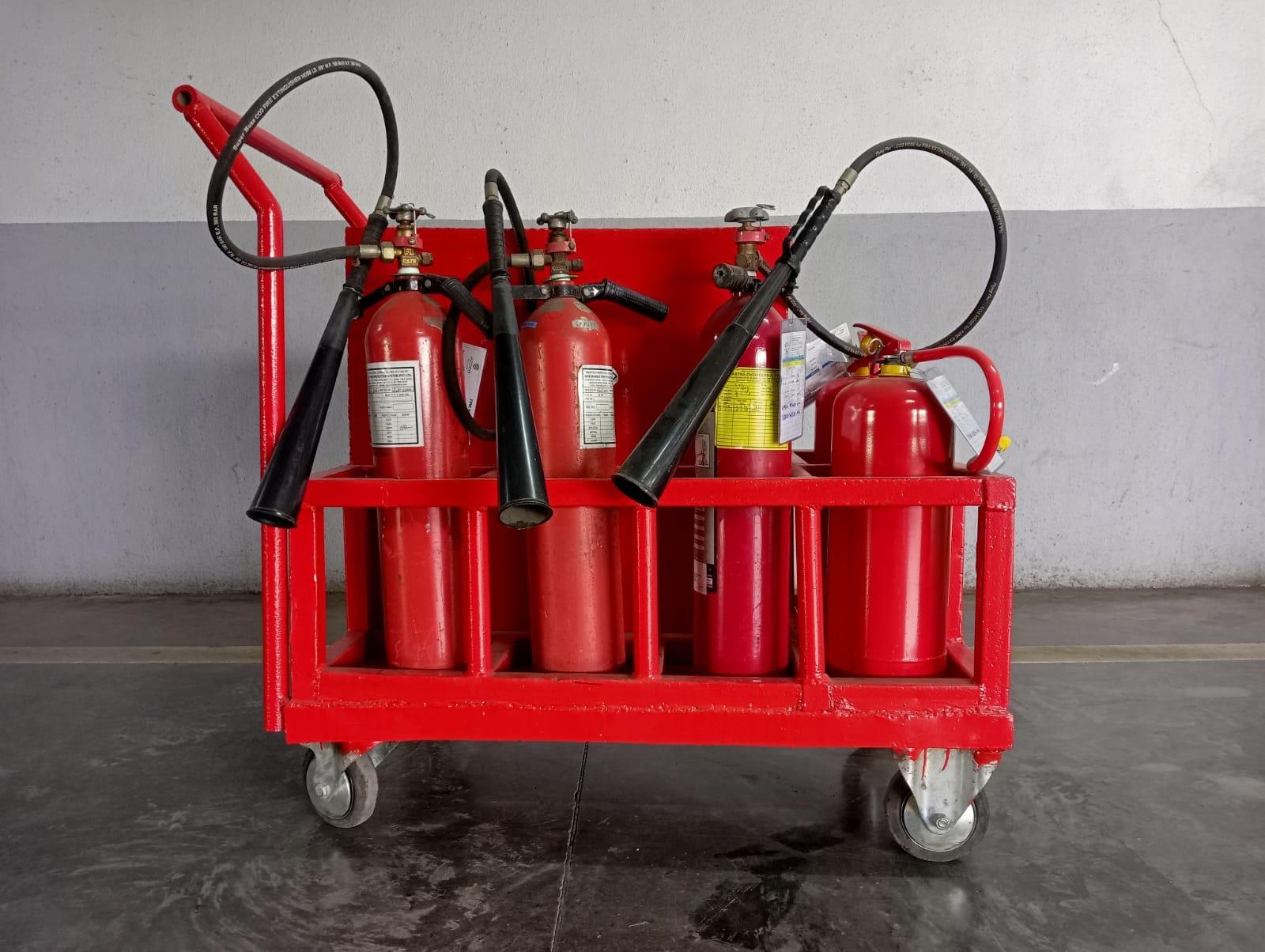
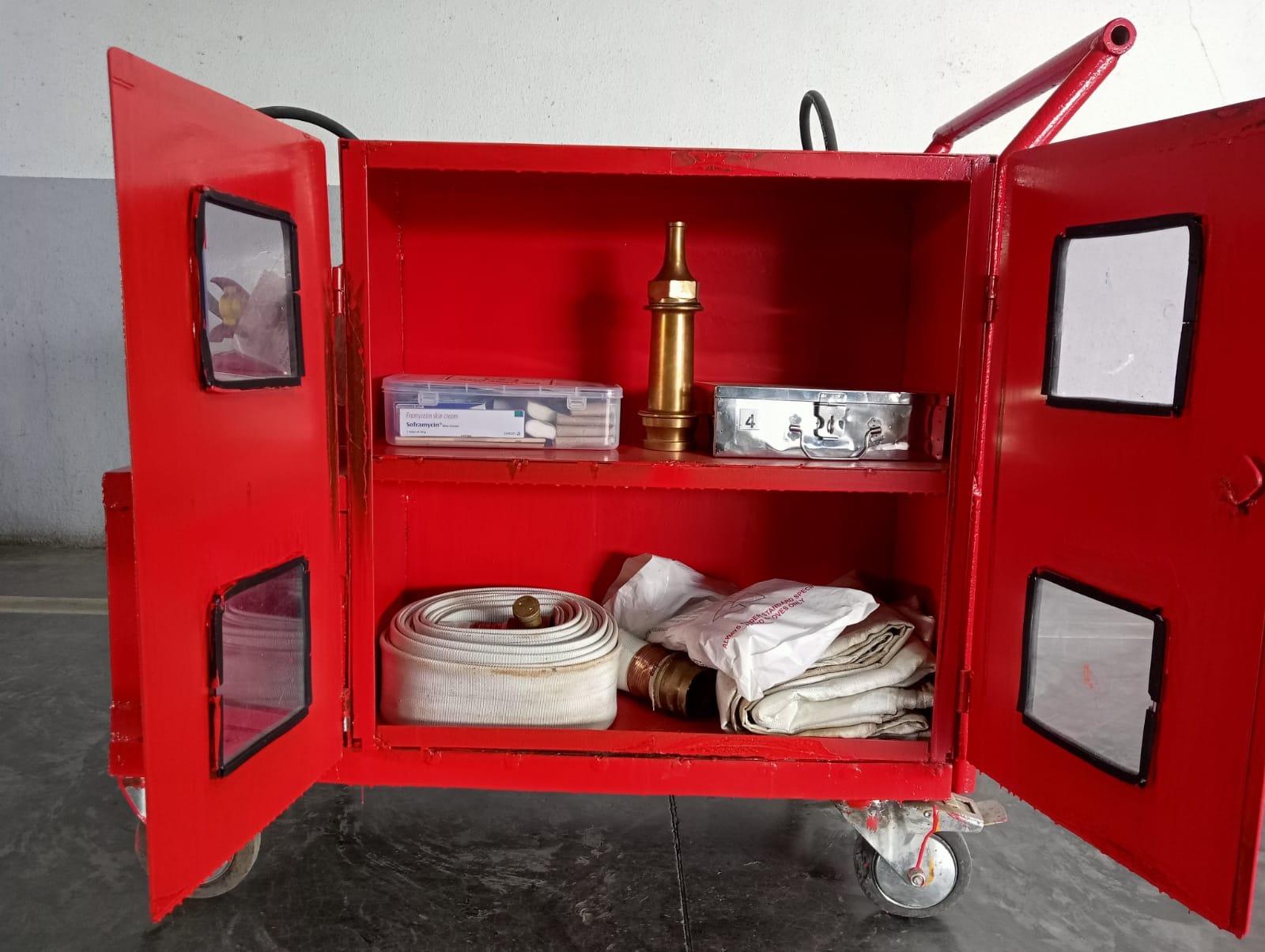
Description of the Innovation:
F-Spanner for Hydrant Valve
CHALLENGE MYIDEA / INITIATIVE / SOLUTION BENEFITS / ADVANTAGE
• Hydrant valve not opening smoothly.
• Problem for maintenance.
• Time & energy wasted during opening the fire hydrant valve.
• Water leakages from the damaged round gasket of valve due to hard of hydrant valve.
• Hard to operate for removing any object that is stuck at the front portion area of male coupling valve of hydrant.
• Continuous leakage of water from male coupling valve as a lot of time is taken while manually operating the hydrant valve.
• Collected M.S. materials from scrap.
• Prepared F-Spanner for smooth operation from scraps.
• F-Spanner painted with red oxide as well as epoxy red paint to avoid any kind of future rust.
• Tried this tool on a trial basis in real time operations.
• Easy to use.
• Its helps in proper maintenance of hydrant valve.
• Reduced time & effort.
• It’s help to avoid wasting water when leakage from male coupling of hydrant valve.
• In an emergency F-Spanner is helpful to open the fire hydrant gate valve smoothly.
• After open the hard gate valve by Use of F-Spanner ,it’s became easy to open with the help of hand in anticlockwise direction.
myIdea
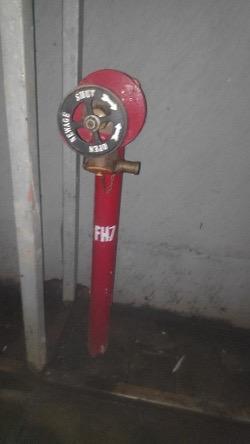
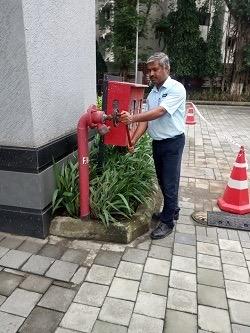
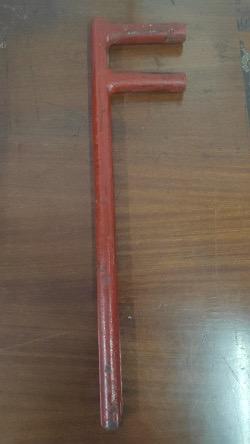
Description of the Innovation:
Conservation Of AHU Condensate
CHALLENGE
myIdea
• Convincing client on the concept of using condensation water from floor AHUs in Cooling Towers, thereby saving on –
-Water Cost
- Electricity Cost.
• Installation of pipe through the building shafts from each of the upper floor AHU Rooms.
• The project completion timeline due to limited working hours for piping works in operational AHU Rooms and floors.
• Utilization of AHU condensation water as makeup water for cooling tower.
• Reduction in temperature of chiller condenser water, thereby saving in electrical energy cost.
• Estimated annual saving in water costs is Rs 110/ KL X 2950 KL, i.e., Rs 3.25 Lakhs per year with an investment of approx. 2.30Lakhs.
• Estimated saving in Electricity cost has not been quantified but assumed to be substantial as the condensation water of AHUs which flow to the cooling tower tub is approx. 12 degree Celsius versus ambient temperature, which is achieved through the cooling towers.
• The energy required to process and deliver it is zero, as the water flow to the cooling tower trays is fed by gravity, while the pumped water consumes approx. .5KWH per KL. [Saving approx. Rs 20K per annum]
• The make up water from condensate is of 16”C in average as against ambient temperature from plumbing system.
• Pure water - no chemical treatment
• Note: Above estimated saving as per present condition (Building occupancy: 56%)
• Currently 50% of the building is looped to this make up setup.
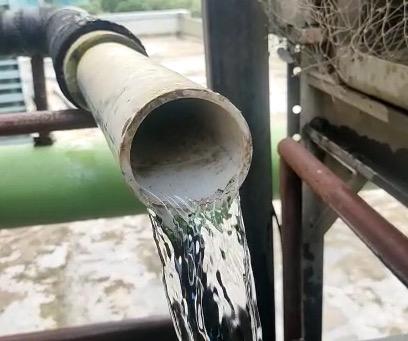
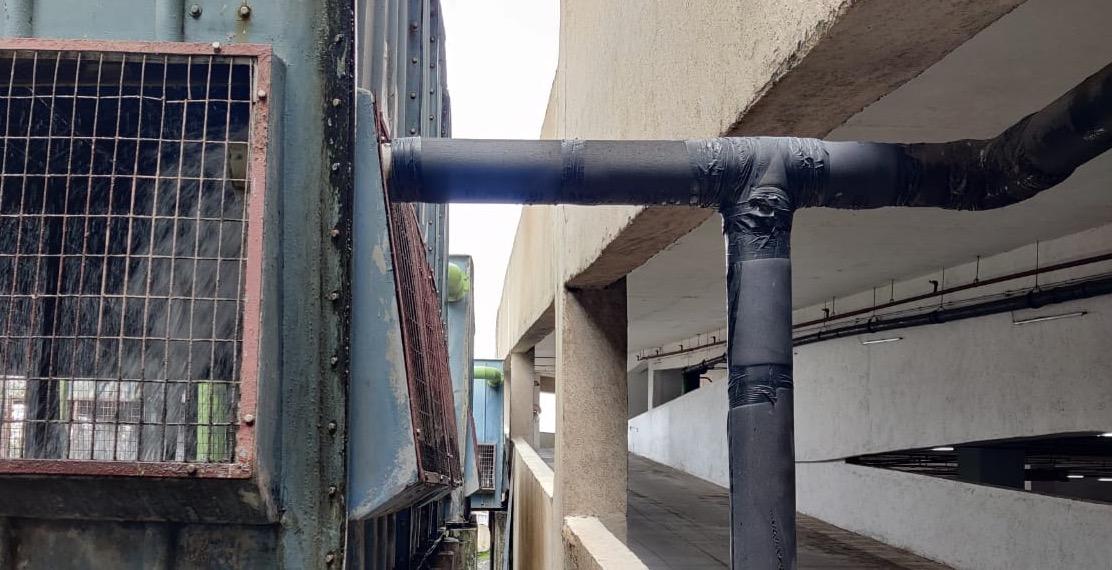
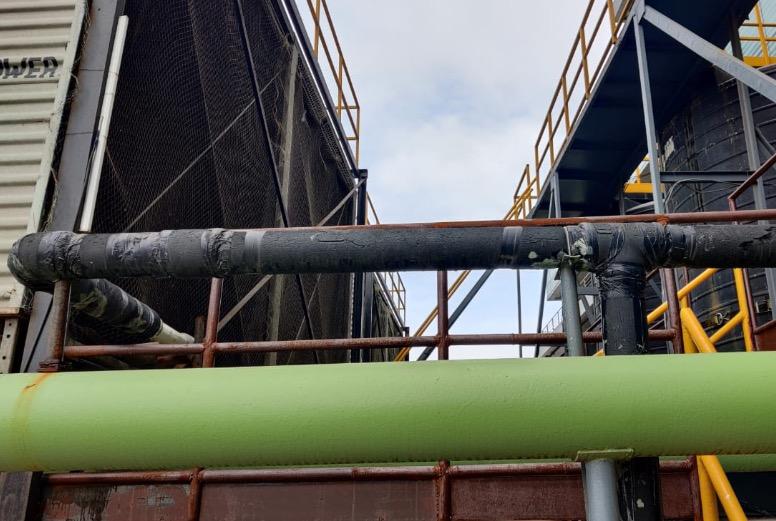
Description of the Innovation:
Automation
myIdea
• The building HVAC system comprises of two zones primary (1-15 floor) and secondary zone (16-30 floors) with Plate Heat Exchangers (16th floor) which provides efficient transferring of heat.
• When space load reduces both the primary and secondary zone’s chilled water pumps does not ramp up/down with respect to tenant’s 2-way valve modulation.
• The chiller load modulates only with variation of chiller return temperature, leaving Vs Set point.
• There is no interface between both zones by which chillers load can be varied by secondary parameters.
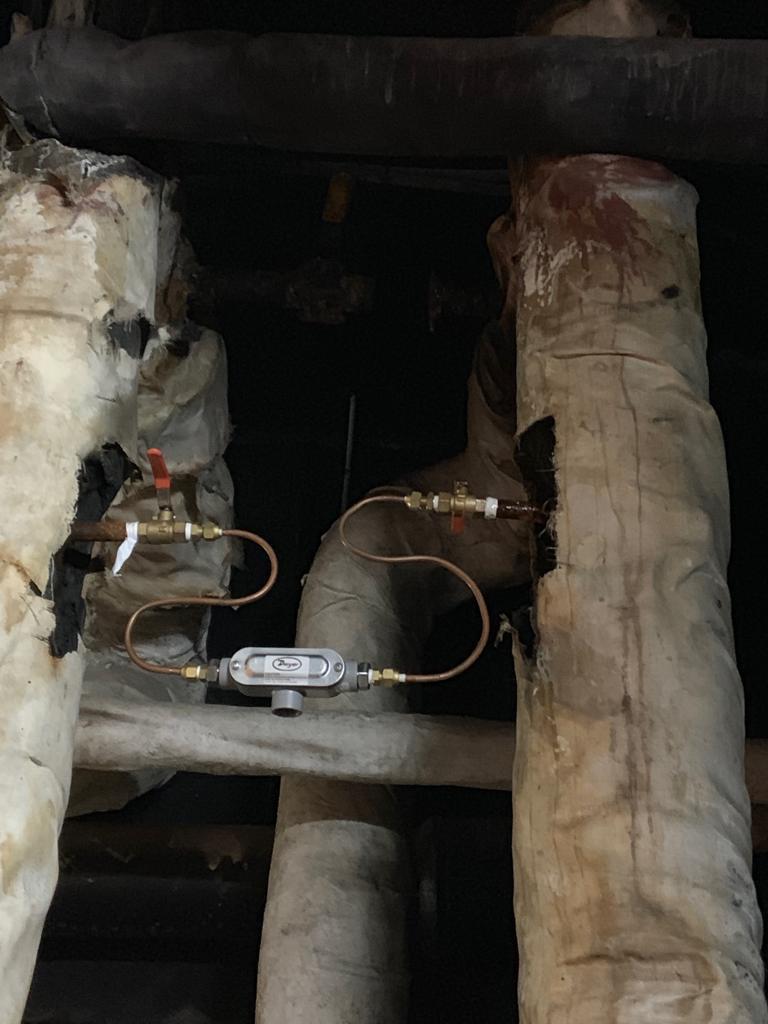
• Secondary zone individual space load decreases,30th floor DP1 enables ramping down of PHE pump. Secondary zone flow < Primary zone flow => approach Temperature between secondary zone and primary zone reduces.
• The temperature transmitter will provide signal to BMS to reduce flow of primary zone supply to PHE.
• Globe Valve1 at 16th floor modulates to reduce the flow, DP2 at 16th floor of primary zone supply to PHE activates and DP3 at 15th floor will activate as per primary zone space load.
• Comparing DP2 & DP3 based on least signal, primary zone VFD ramps down.
• To maintain minimum flow to the chiller, the primary zone pump locked at 30% VFD.
• If further space load decreases, chilled water starts circulating within the bypass line by modulation of Globe valve2 at chiller plant.
• The BMS controller enables comparison of different Differential Pressure Transmitters, Temperature transmitters and regulates the flow of the Chilled Water.
• Regulation of flow of the Chilled Water enables operation of pumps & chiller according to the requirement which in turn results in Energy Savings.
• Capital Expense ₹ 5 lakhs
• ROI 3.8 months.
• Estimated Saving : INR 1566000
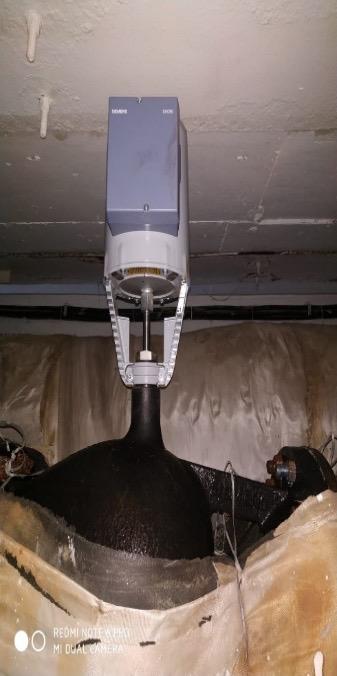
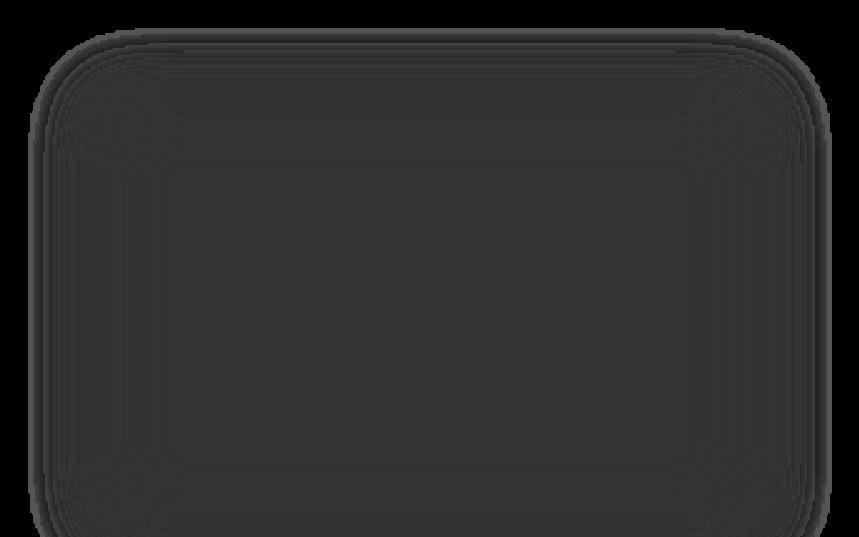
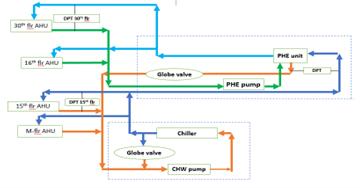
Description of the Innovation:
DG Carbon Collection Tank
myIdea
CHALLENGE MYIDEA / INITIATIVE / SOLUTION BENEFITS / ADVANTAGE
• DG Exhaust outlet is installed above
Terrace level close to Penthouse apartment.
• Initial carbon particle were falling on the Penthouse floor and side walls.
• Due to spreading of fumes in air nearby areas, people's complaints were there..
• Apartments wall getting damaged/black color.
• Installation of DG Carbon Collection Tank.
• It consist of a 5000 ltr water tank, pump connected to sprinkler nozzle and top covered with Wire Mesh.
• When this system starts, water is continuously sprayed across the Tank.
• Water droplets push and dissolve the heavy carbon particles in the water Tank
• Carbon particles are captured in the collection tank.
• Prevented from settling on floor and side walls.
• Reduction in Air Pollution.
• Low cost.
• Easy for installation.
• No more maintenance.
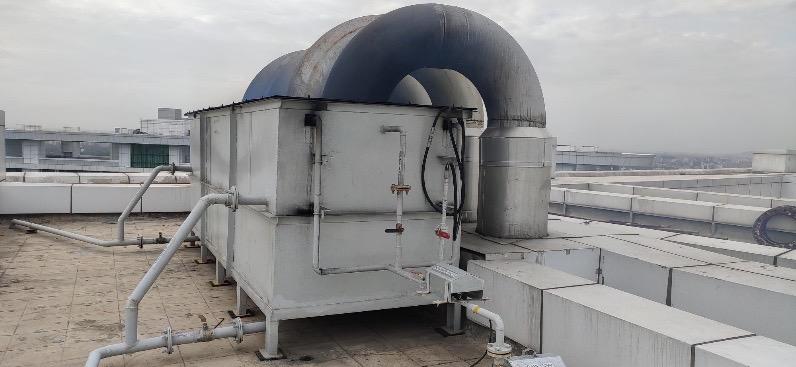
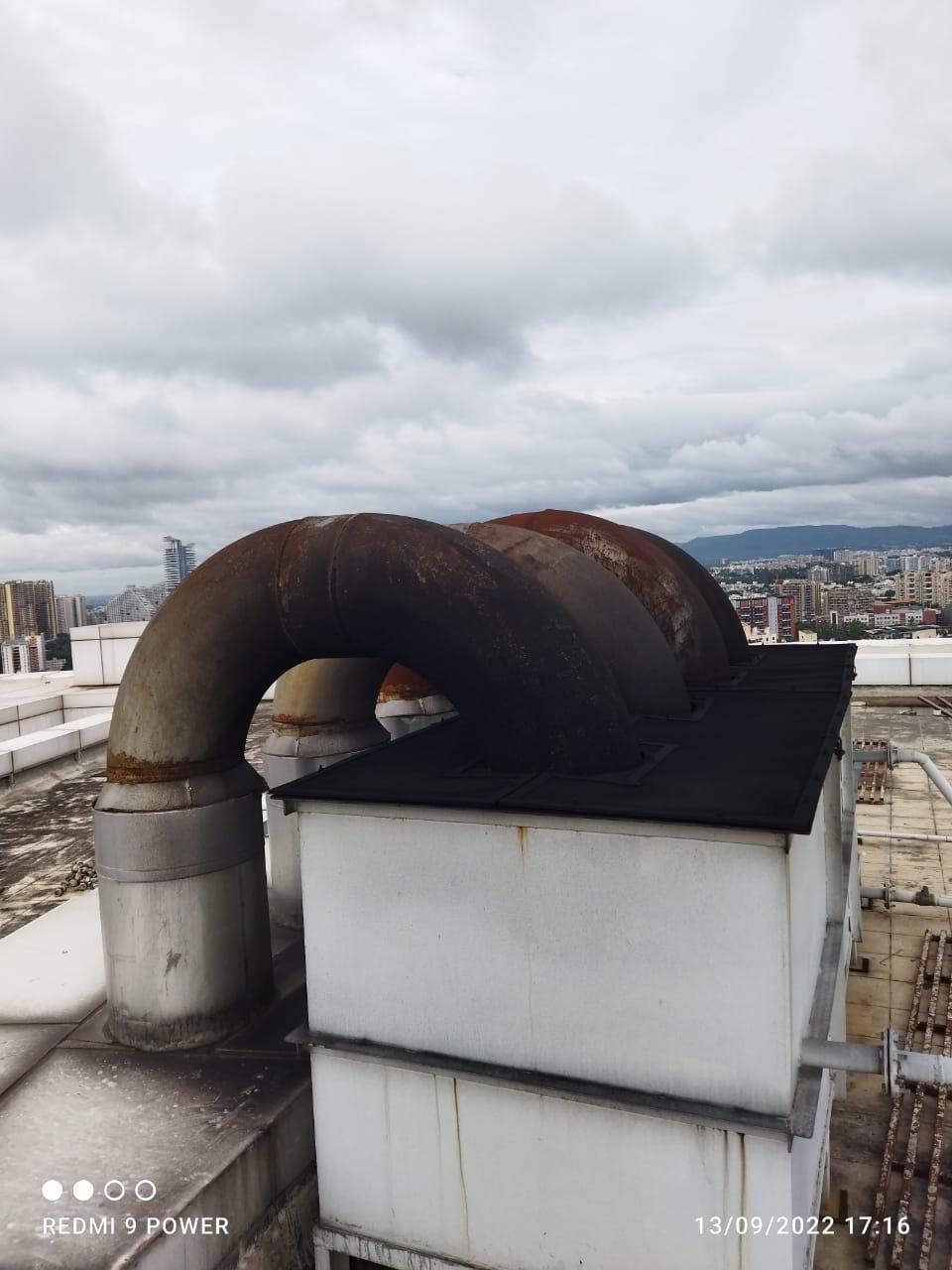

Description of the Innovation:
Chillers & AHU-BMS Integration
myIdea
CHALLENGE MYIDEA / INITIATIVE / SOLUTION BENEFITS / ADVANTAGE
• Our chillers are on the terrace, AHUs are at
each floor & BMS room is located on the Ground floor.
• There was no provision to observe Chiller
& AHU parameters in BMS room
• Time Management
• AHU & pump status with controlling
• The whole chiller system equipment's real time parameters were made available at one point on PC in BMS room
• Optimal control & operation of equipment's was achieved up to certain extent
• Floor-wise AHU operation and cooling control
• Decreased the human efforts & error possibilities
• Easy to get correct Data
• AHU Cooling can be control at single point
• Optimal operation of the pumps, chillers, AHU etc. which increase the life & health of the machineries
• Low losses in the system, as the faults can be tracked & worked upon it
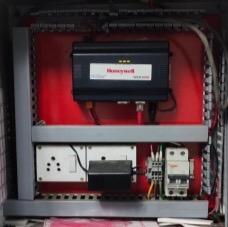
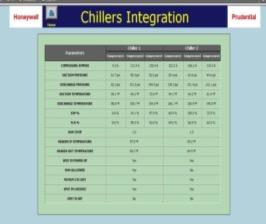
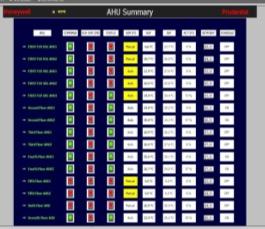
• Small pet relief area.
Description of the Innovation:
Pet Park Creation
• Uneven land with debris material.
• No proper boundary.
• Looked like a backend area.
• No proper garbage bin.
• Unhygienic.
• Pet relief area is extended along with providing proper wire mesh well painted boundary and door.
• Tied up with a vendor to provide required material with any cost by providing him space to display pet friendly advertisements.
• Half area is covered with green grass for playing and half left bald.
• More plants to provide shade in park.
• An old plastic drum is cleaned and painted to use as garbage bin with proper garbage bag layering following the standards of hygiene.
• Creepers are to planted on boundary to cover the wire mesh.
• Improved appearance of Pet relief area and named as PAW PARK.
• No cost load on creating this park, as barter system was used.
• Added value to overall experience of society.
• More space for pets playing.
• More hygienic and easy to clean for housemen.
• Pet friendly and safe leash off area.
• Residents are very happy with this initiative for their pets.
myIdea
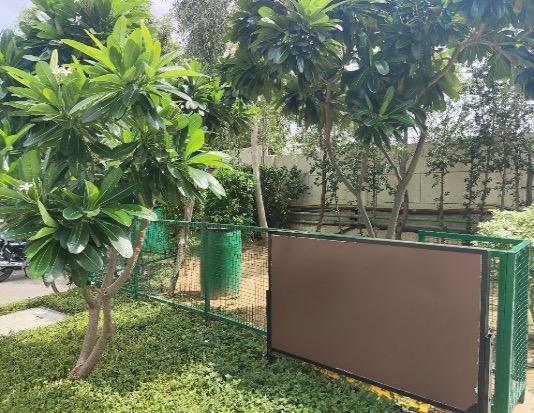
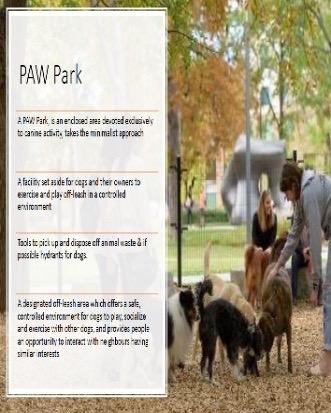
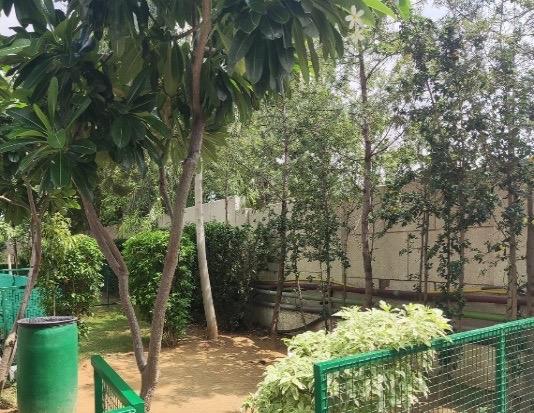
Description of the Innovation:
Pressure Testing Kit
myIdea
CHALLENGE
• As per SOP we need to do the pressure test of the all-delivery hoses (Approx. 700 no’s) on yearly basis at a pressure of 10 kg/cm2 for 1 minute.
• Earlier we were doing this test with the help of hand-controlled branch and due to prolong uses, we were facing leakage issues from the branch.
• There was no pressure gauge available in the instrument, hence we were not sure of the actual testing pressure.
/ INITIATIVE / SOLUTION BENEFITS / ADVANTAGE
• In-house team has made a portable pressure testing device by using a branch pipe, plumbing spares, ball valve (of PN16 category) and a pressure gauge.
• Hose is connected at the branch pipe end and by closing the ball valve we can build the pressure and conduct the test.
• With this innovation pressure testing has become easy, safe & accurate.
• We can now record the testing pressure.
• The cost of procuring the pressure testing kit every time has reduced.
• Wastage of water during testing has reduced.
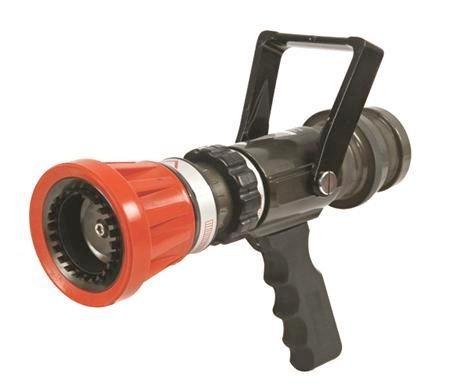
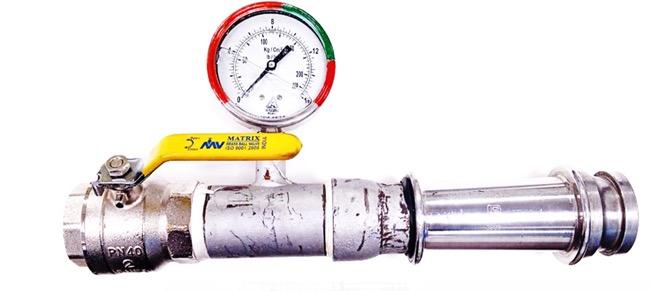
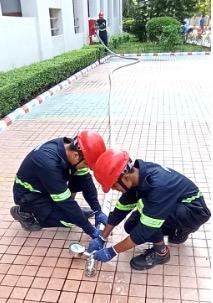
CHALLENGE MYIDEA / INITIATIVE / SOLUTION BENEFITS / ADVANTAGE
Description of the Innovation:
Campus Digitization
myIdea
• Make the campus paper less
• Reduce work-load of the team
• On time data update.
• Manual Errors
• Reviewing methodology
• Process Implementations
• Introducing digitalization in Campus
• Providing Smart Work environment
• Introduced Smart Check Application with which we have digitalized the campus
• Below few modules:
• All Check List
• Inventory Management
• History Cards
• Asset Tagging
• PPM Schedules
• Visitor & Vendor Management
• Helpdesk
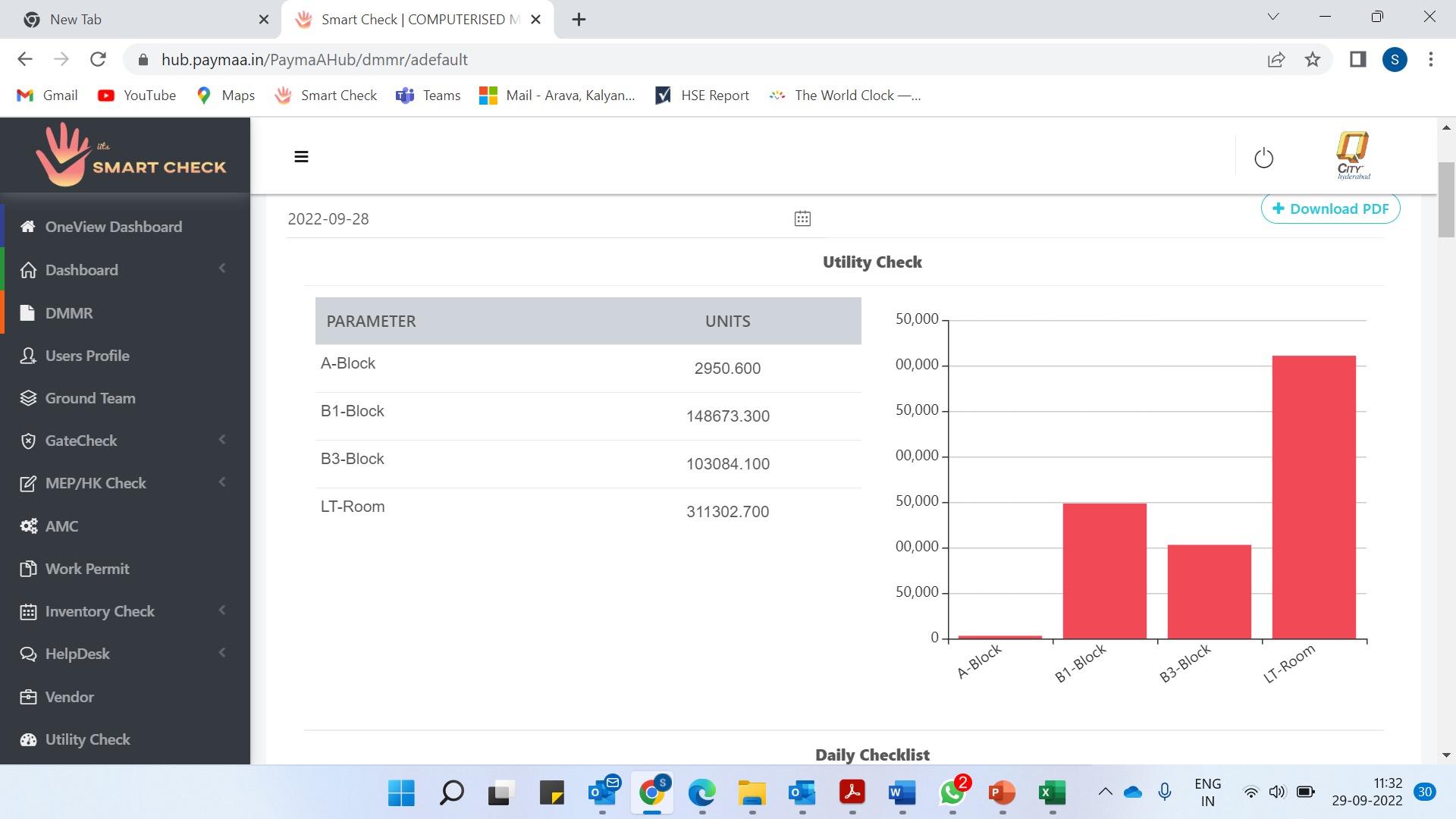
• Real time status notifications are received
• Tracking of day-to-day activities
• Status of schedules on both completed and pending tasks
• Keeping all the data digitally on daily basis
• Tagging of Assets through QR Code from Smart Check – Helps in any asset movement around campus
• Tracking of equipment PPM / AMC
• Generating & approvals of Work Permits online
• Reduced time and paper consumption around campus
• Tenants also raise their request / complaints through helpdesk on smart check app


Description of the Innovation:
Paperless End
User Satisfaction Survey
myIdea
CHALLENGE MYIDEA / INITIATIVE / SOLUTION BENEFITS / ADVANTAGE
• Paper consumption for go green initiative
• Around 3800 families are residing at Mahagun. Printing these many forms were equivalent to 2 trees being chopped down.
• Storing of the papers are difficult, if we want to get a year old or more CSS form that was difficult
• Facing challenges to monitor on timely basis
• Less accuracy
• Requires more manpower to get the CSS filled and tabulated on time
• Maintaining all CSS electronically.
• Used MS office to create CSS forms.
• The results of the CSS can be downloaded in a tabular form.
• Software closely monitors the entire process of CSS
• QR codes were pasted on notice boards and the link for the same was shared online through the automation tool.
• Faster and cheaper process.
• Less time taking.
• Mass reach of audience at a single time.
• Environment friendly, sustainable process.
• Thousands of pages were saved thus a small contribution in saving the environment.
• We can pull the old reports very easily from the tool
• Savings of approx. Rs 4500/- per month
• Reduction in carbon footprint.
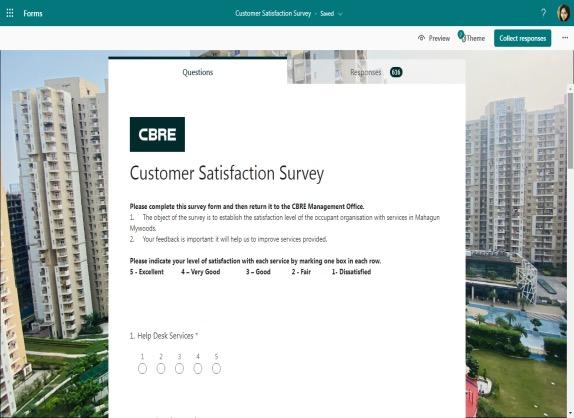
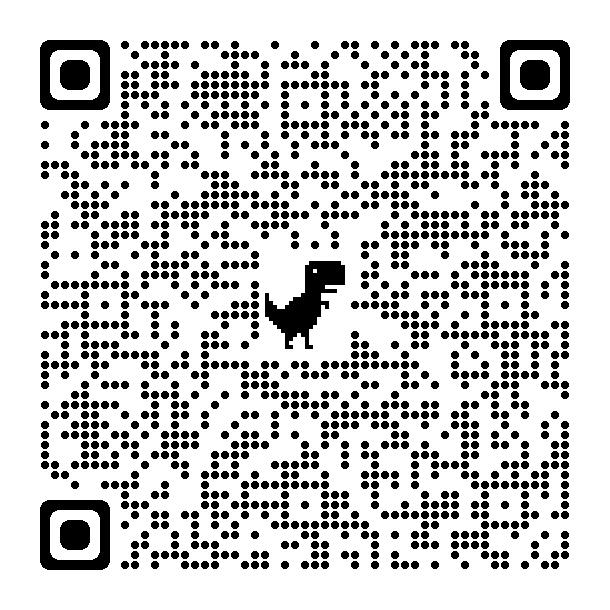
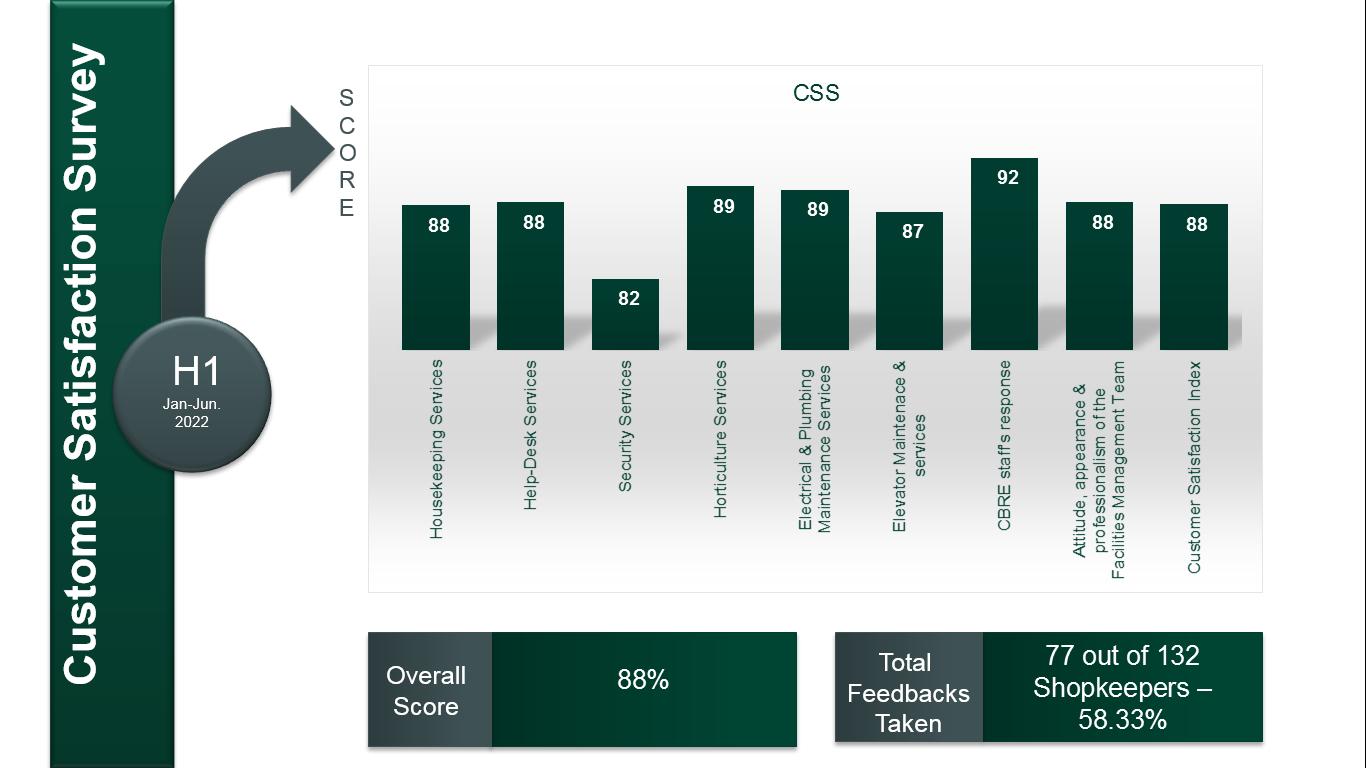
Description of the Innovation:
Power
Redundancy Enhancement
myIdea
• Main ACB tripping due to excess load of Good Earth & Magnum
• Both share load on one temporary transformer
• Temporary transformer capacity 1280 kw
• Occupancy of Magnum increased due to which demand load have gone up by 25%
• Major challenge : after job completion, coordination with Splendor team to run the system
• Dependant on Splendor’s team to keep power switched ON
• Running one 300 TR chiller on Splendor’s DHVBN power
• Laying 192 meters, 300 sq mm 3.5 core cable: from Splendor’s AC plant room to our chiller no 1
• Installing an auto change over switch-toswitch power automatically
• Now we run one chiller 300 TR on Splendor’s transformer and rest two 300TR chillers with our transformer.
• Reduction in the time of running of DG even when DHVBN supply is available.
• Since May 22 to Aug 22 saving of approx. 19.58 lakhs
• Actual cost came Rs 868,912/- for 99,875 EB units
• Else cost would have been Rs 28,31,456/-
• DG cost Rs 28.35 / unit
• EB cost Rs 8.70 / unit
• Total modification cost: approx Rs 5 lakhs
• In 1 month, 4 days: Rs 5 lakhs recovered
• 33 kv will come by 2023 May
• Sept 2022 to May 2023: more estimated saving of 44 lakhs approx
• Total saving in 12 month , approx Rs 58 lakhs.
• Appreciation from client on mail
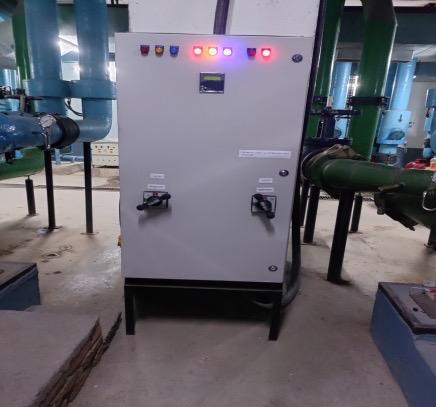
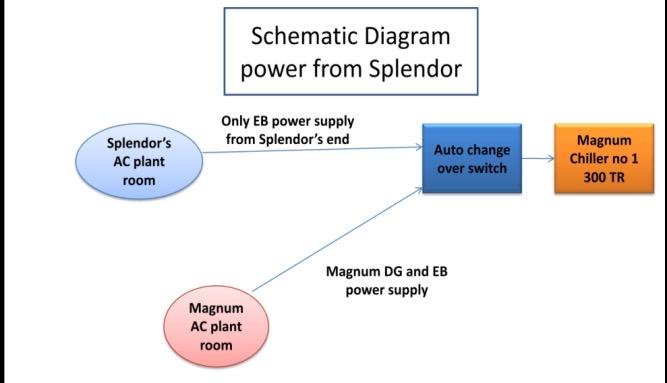

Description of the Innovation:
APFC Panel Modification
myIdea
• We have two sections of LT Panel Each Section have 250 KVRAH Capacitor Bank
• Each Bank of APFC Panel have a 50 KVARH capacitor
• The APFC panel does not maintain the power factor due to the higher capacity capacitor installed in all existing capacitor banks
• We get the high difference in KWH & KVAH consumption in electricity bill due to which power factor of 0.83 to 0.96 during last 12 Month
• We discussed with the client & planned to install small-capacity capacitors (25, 15, and 10 KVARH) in the banks for smooth auto operation. It will help to increase the power factor during less load and reduce the difference between KWH & KVAH
• The Power factor should be between 0.98 to 0.99
• Since we are paying electricity bill charges on KVAH. If Power Factor get to improve the KVAH consumption reduce and reduce electricity billing costs as well
• The difference between KWh and KVAh decreased after APFC panel modification, thus improving the power factor between 0.98 and 0.99 and reducing losses.
• Total savings during 5 Months ₹84364/- & Per month approx. ₹16873/-
• Total Expenditure approx. ₹1.30 Lakh
• ROI = 7.7 Months

Description of the Innovation:
Electrical Room Fans Optimization
myIdea
CHALLENGE MYIDEA / INITIATIVE / SOLUTION BENEFITS / ADVANTAGE
• As part of CEIG recommendations & building compliance, we have exhaust & in-line fans installed across all Electrical rooms (floor shaft rooms) at Elnath & Electra building
• There are 54 fans run 24x7 without any control and circulate the air, though the temperature is normal inside the room.
• These fans help maintaining proper air circulation in the room and ensures the cables & panels are not over heated
• Installation of Thermostat with a relay (sub zero device) to operate the fans based on room temperature
• Temperature set point can be programmed as below;
• Unit start working when temp inside the room is 28 Deg C
• Unit gets cut off once the temperature inside the room is < 28 Deg C
• This results in energy consumption throughout the day, however, the load on these panels is less than 10% with no or minimum heat generation
• This also reduce the life of these motors due to continuous 0peration.
• Numbers of Fans 54
• KWH/Year (Before) 67382 KWH
• KWH/Year (Before) 16845 KWH
• Cost Saving /year 4,54,000 INR
• Cost Investment for this initiative 81,000 INR
• ROI 2 Months
• Timeline for implementation – 1 Week post approval


Description of the Innovation:
Centralized Transport Helpdesk
myIdea
• Helpdesk services managed separately from each location, in total of 21 executives across 11 offices.
• In absence of helpdesk, the calls were handled by other transport representatives where the call protocol was not followed.
• Organization merged with another entity and the transport policy was not the same.
• Data Privacy was a concern for the organization in sharing the contact numbers.
• Companies focus on Diversity and Inclusion.
• Create a HUB to have center point of interaction for query resolution –phone, email and chat all in one place.
• Move from traditional to cloud-based solutions.
• In 2020 the transport policy was one across both entity.
• Hiring women employees to handle the helpdesk calls.
• Inbound and outbound calls handled by dedicated team of 10 members who are all from diversity.
• Advanced features like IVR Option and call recording.
• Existing infrastructure helped to set up a centralized desk in BLR with backup in HYD & GGN.
• As one policy we are able to deliver uniform approach to customers.
• Post deployment we achieved 16% annual saving on Manpower cost. (INR.8,60,400)
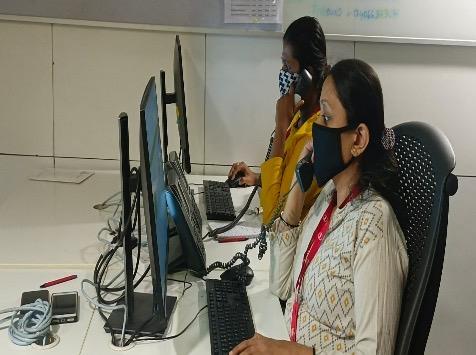
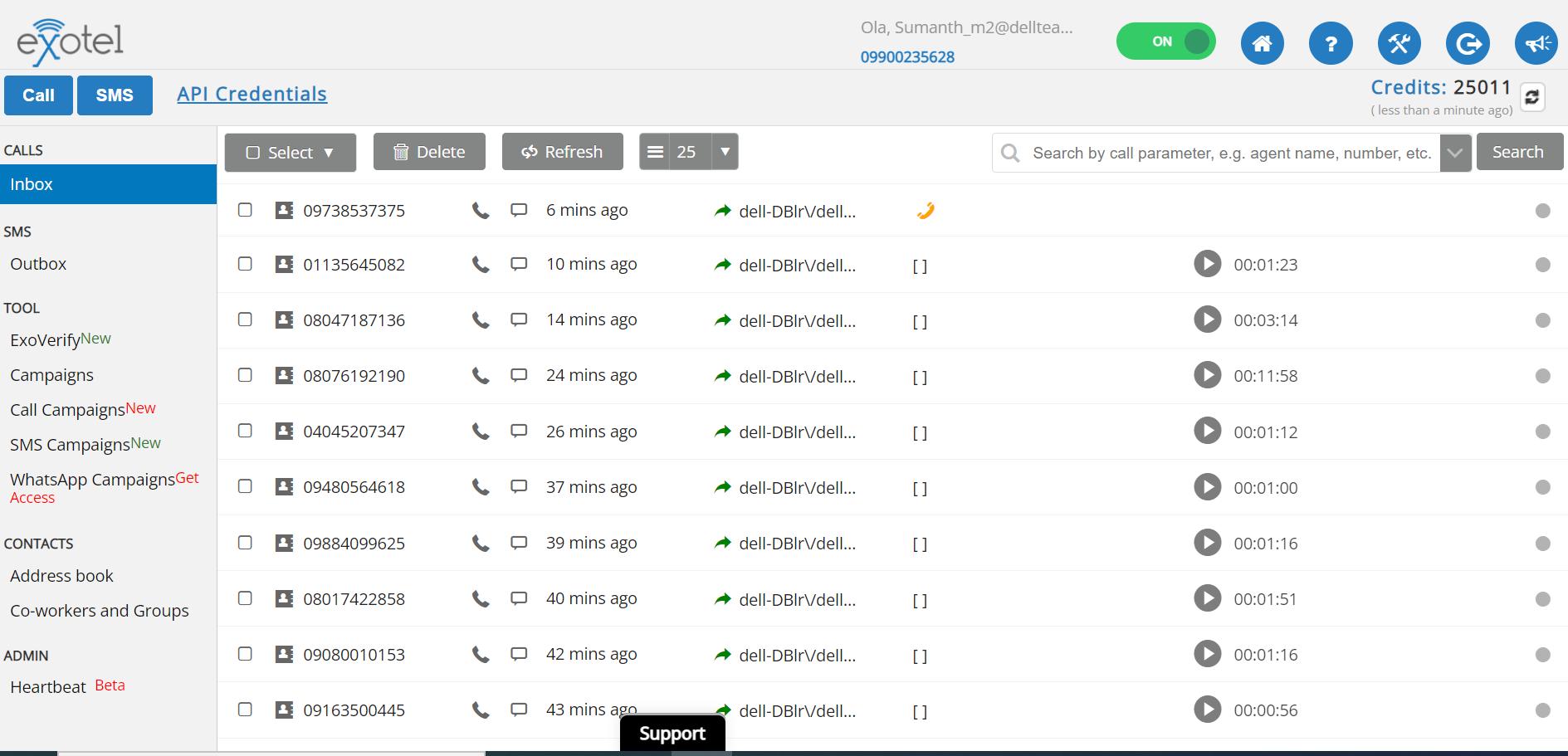
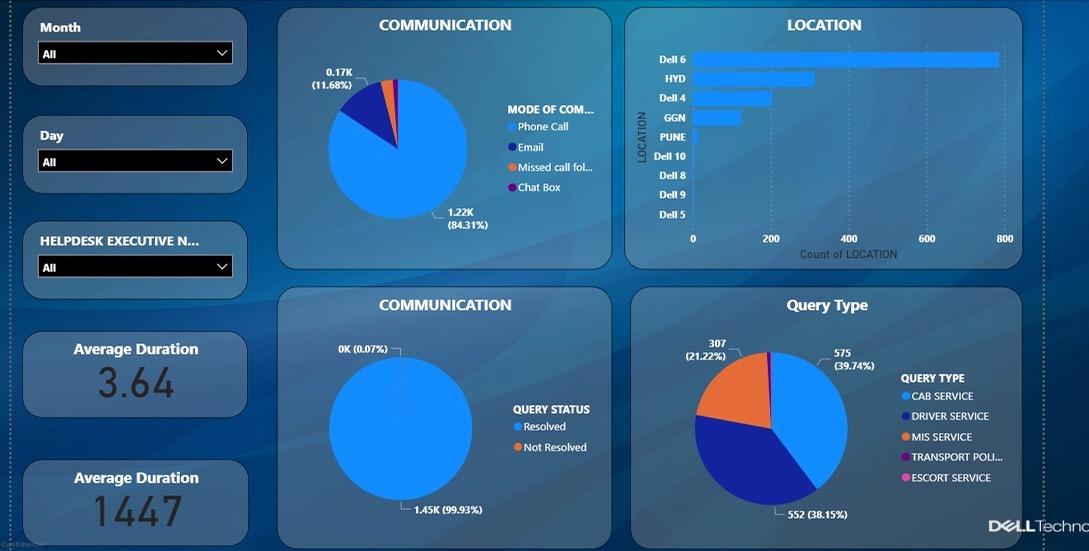
Description of the Innovation:
3D Evacuation Floor Map
• Existing Floor Maps are very old and outdated
• Difficult for users to figure out the floor layout & emergency exits
• Emergency numbers and hotlines need updating
• In 2D map Location identification not mentioned
• Proposed 3D evacuation floor maps
• Prepared artwork and necessary changes and got client approval
• The proposed 3D maps are fluorescent and glow in dark
• All area names mentioned to identify the location easily
• Emergency exit & floor route map highlighted
• 3D Evacuation maps provide good aesthetics and visual experience to users
• People can identify the all the location by viewing the 3D map
• New personnel can easily identify the floor plan.
• Entire floor plan & emergency exit clearly visible in the dark.
• Cost/unit-13840 & Zero maintenance cost.
myIdea

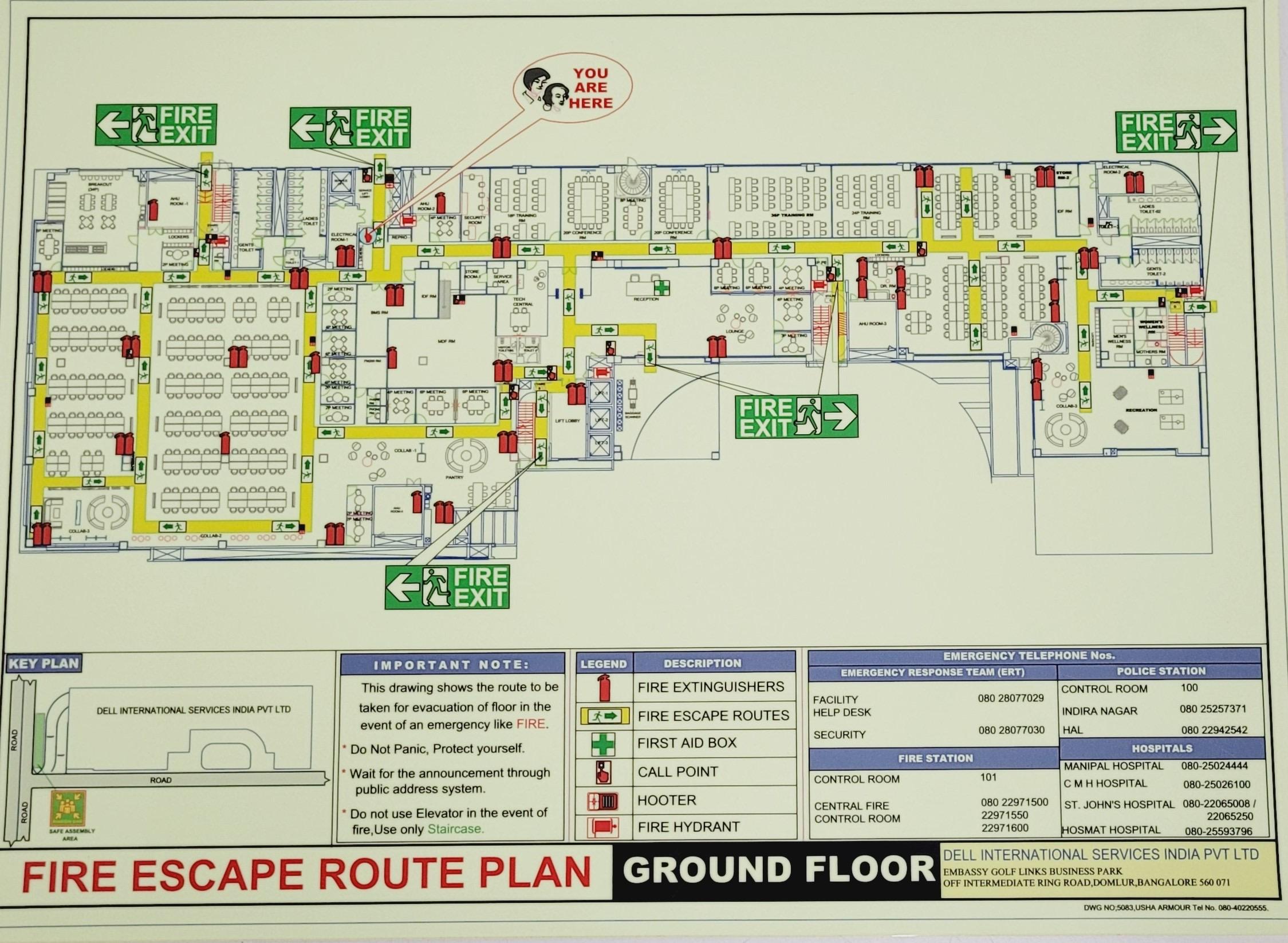
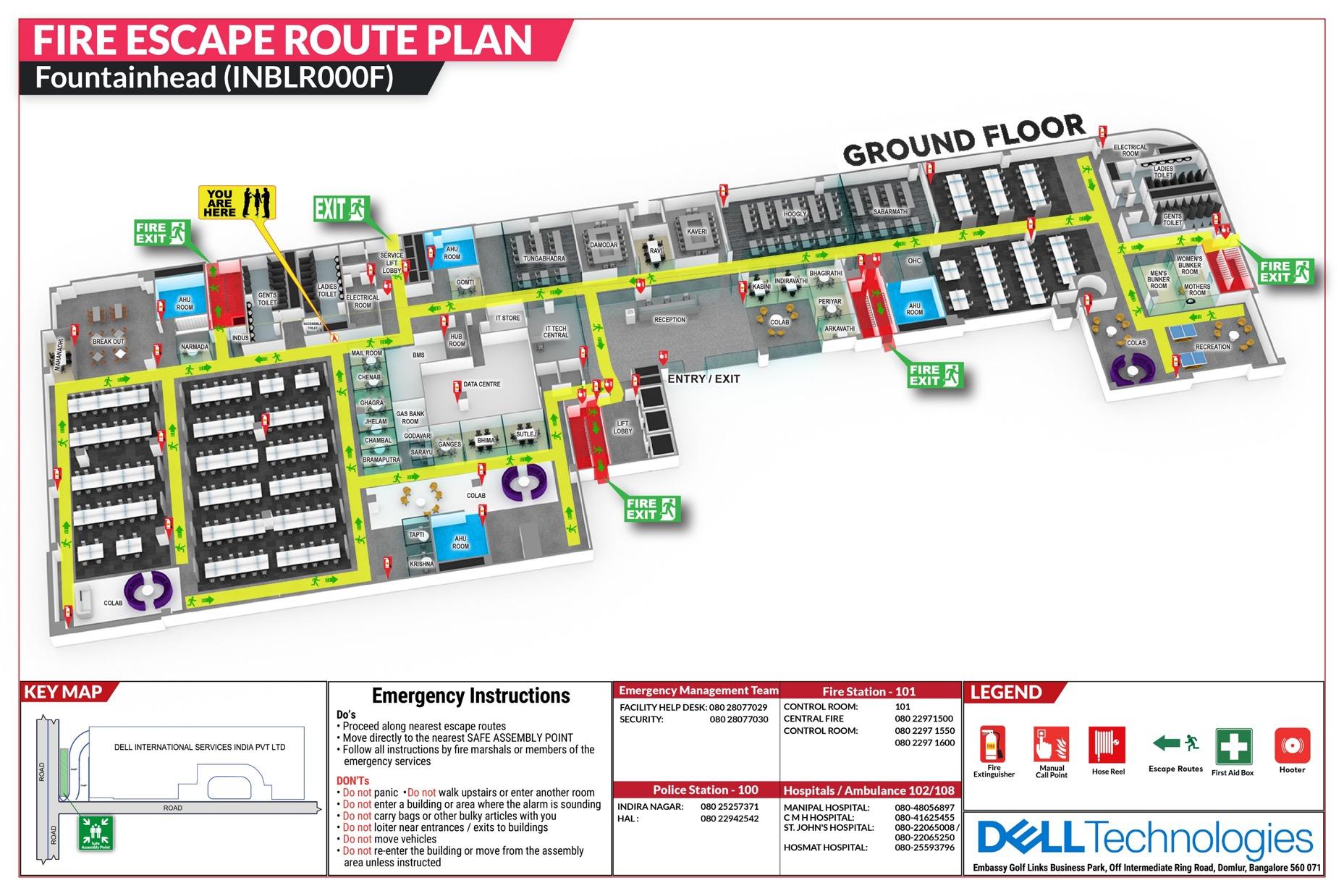

Description of the Innovation: CHALLENGE
OFFICE HOTELING (Mobile
Workspaces)
• Sudden requirement to change from traditional work model to hybrid work model during return to workplace at Stage 6.
• Flexibility to work from any Microsoft offices.
• Optional work from office.
• Survey was conducted to understand employee’ preference to work from office and determine the Hybrid work ratio.
• Hybrid work ratio resulted in downsizing the assigned seat count and a percentage of seats were reserved as ‘Mobile workspaces’ to accommodate the Hybrid work model.
• Mapped ‘Outlook Workspace Tool’ to reserve Mobile workspaces.
• Flexibility ensured for employees to work from any Microsoft office location.
• Optimized utilization of available seats (accommodating ~25% headcount within 5% seats).
• Flexible booking duration resulting into optimized seat utilization (minimum reservation duration of 3 hours).
• Reduced proximity for employees to collaborate.
myIdea
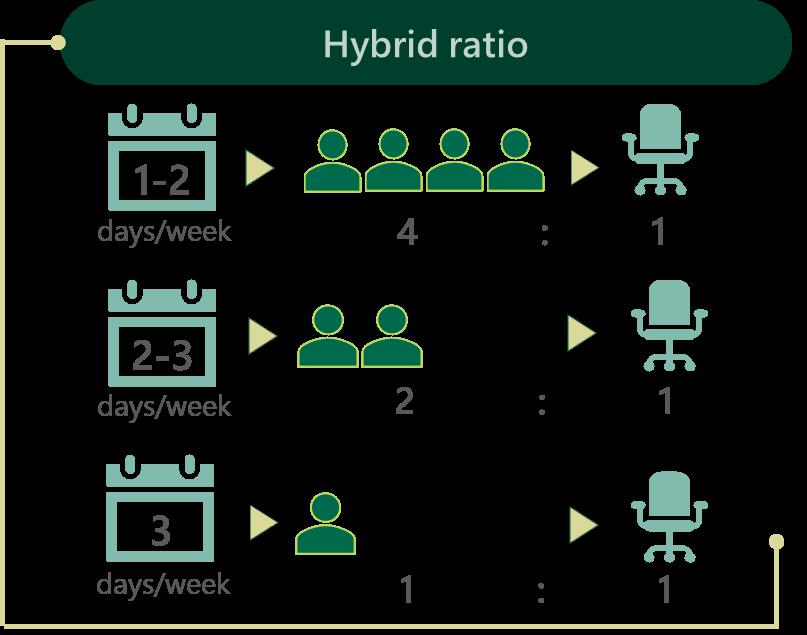
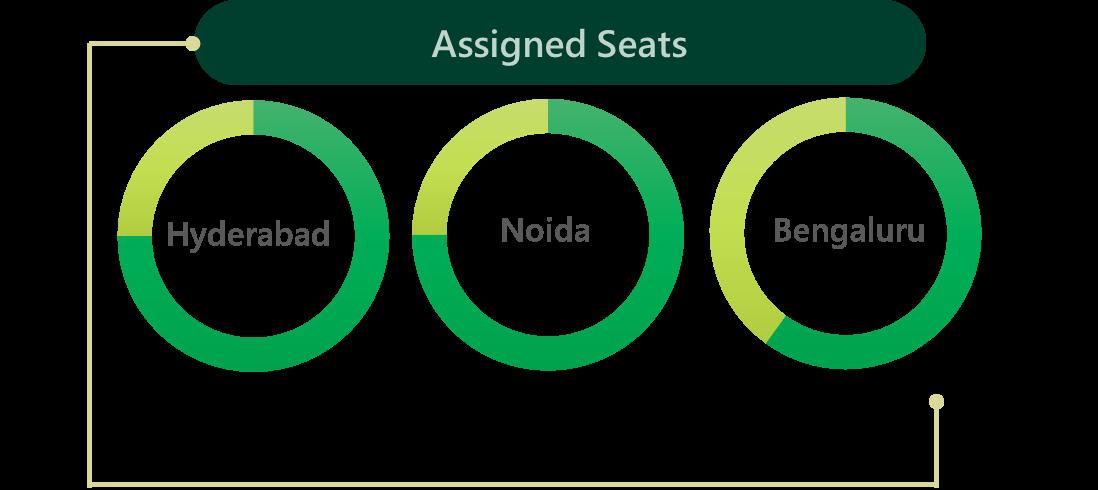
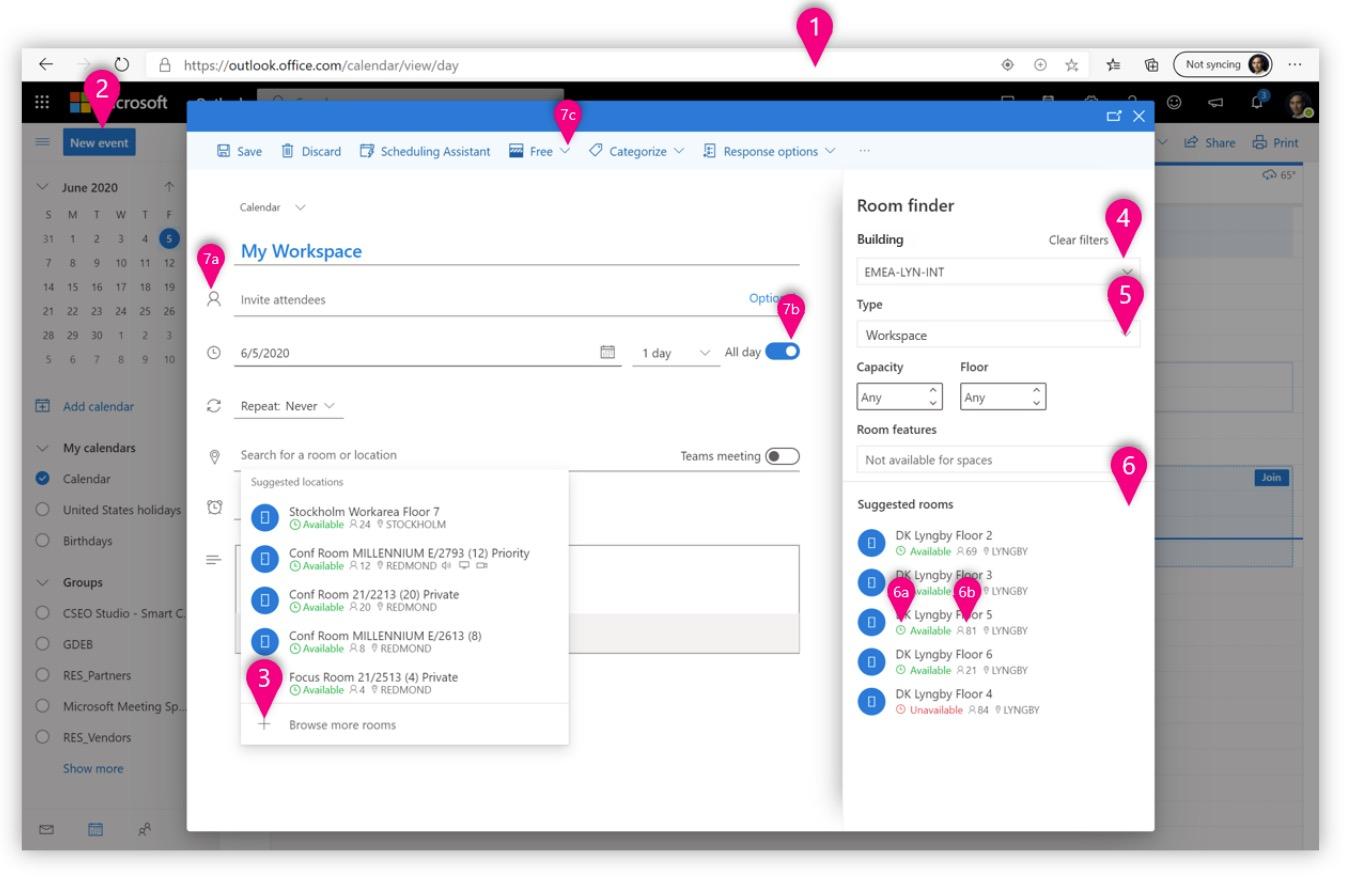
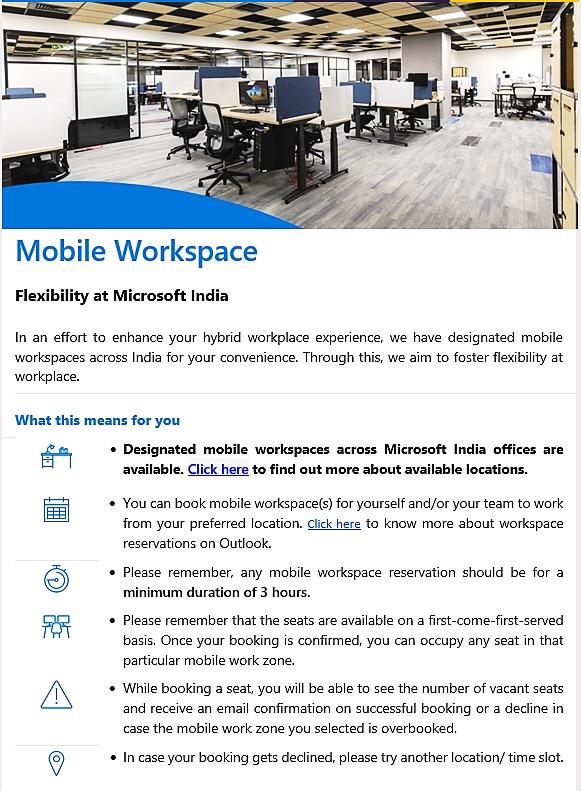
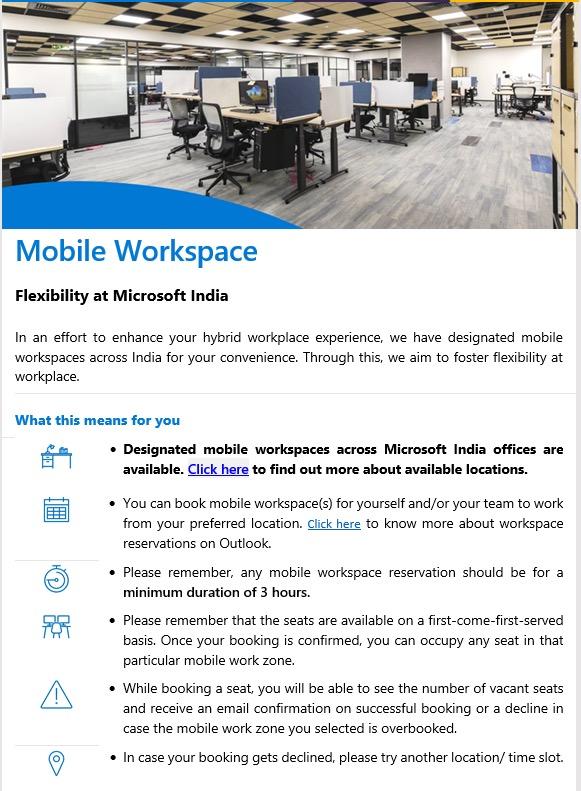
Description of the Innovation:
Stormwater Pump Monitoring System
myIdea
CHALLENGE
• Each building has three stormwater tanks installed with two pumps to evacuate rainwater.
• During a heavy downpour, it is difficult for the operator to monitor the running condition of the pumps as there is no pump monitoring system in the existing setup.
• Any issues in the pump operation will lead to overflow and chances of water getting into the utility basement.
/ INITIATIVE / SOLUTION BENEFITS / ADVANTAGE
• The idea is to monitor the running status of the stormwater pump building-wise from the LT rooms which are manned 24 x 7.
• Prevents overflow of water due to abrupt failure of pumps during rain resulting in water spillage in the basement area.
• Engineering team designed and developed an alarm system to monitor the running condition of stormwater pumps in real-time remotely during a heavy downpour.
• This will ensure the safety of technicians by avoiding manual checking of pumps during rain.
• Effective utilization of manpower.
• Avoid overflow of the stormwater
• Consistency in monitoring the running condition of the pumps during monsoon.
• Real Time alert to the team on pump working status.
• Personnel Safety.
• Inhouse innovation.
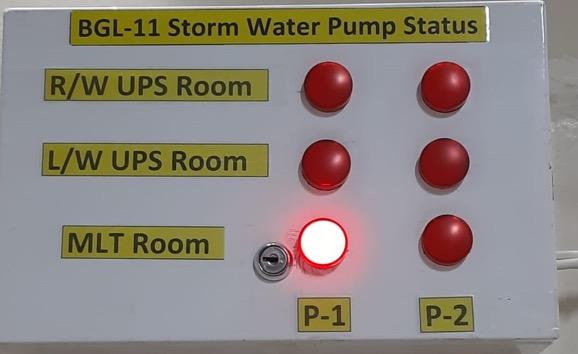

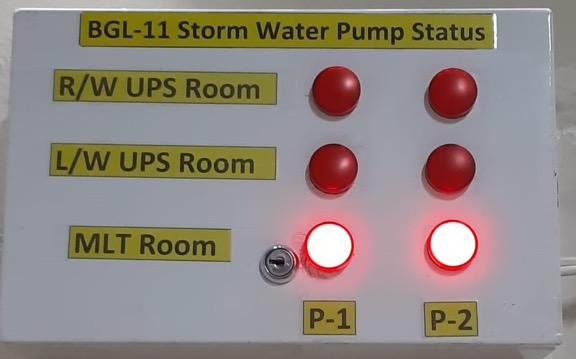
Description of the Innovation:
Well Health & Safety Rating
myIdea
CHALLENGE MYIDEA / INITIATIVE / SOLUTION BENEFITS / ADVANTAGE
• To instill confidence in employees about the safety at workplace as part of return to office strategy
• Pandemic exposure largely occurs in indoor and enclosed environments, where people spend maximum time.
• WELL HEALTH SAFETY RATING by IWBI (International Well Building Institute) on Facility operation and Management
• Third party health & safety certification with scientific evidence-based validation
• Keep Spaces Clean and Sanitized
• Touchless operations/ Cleaning frequency
• Green Cleaning products
• Health Service
• Vaccination Drives / Smoke free environment / Food safety certification
• Air and Water Quality
• Enhanced Fresh Air ventilation/ CO2 level monitoring / MERV 13 filters/ AHU set point changes / IAQ bi-annually.
• Avoidance of high touch points
• Increase fresh air circulations with enhance efficacy with MERV 13
• IAQ improved with green products
• A visible indication of confidence and trust, the WELL Health-Safety seal communicates to everyone entering Cisco Space
• Occupant / Visitors can scan the QR codes and gain insight into how your health and safety is ensured inside the campus.
• Safety work culture promotes productivity, engagement, and employee experience
• Building brand to our clients and investors
• 100% RTO is successfully achieved.
• Long term health & safety needs of people.
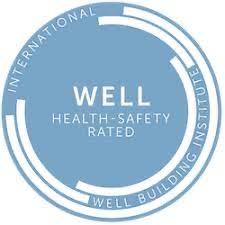
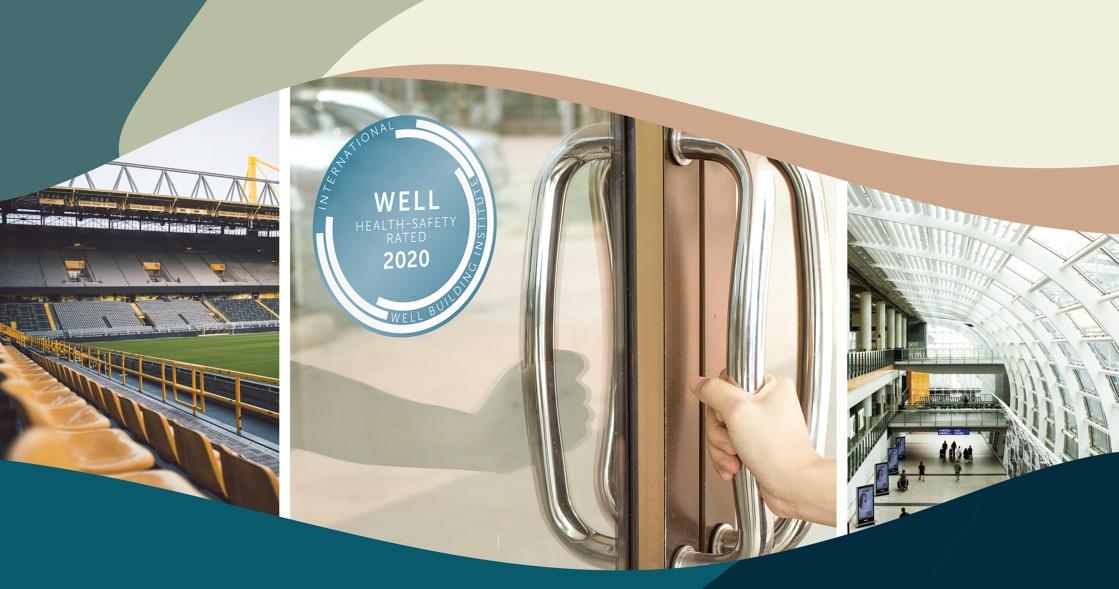
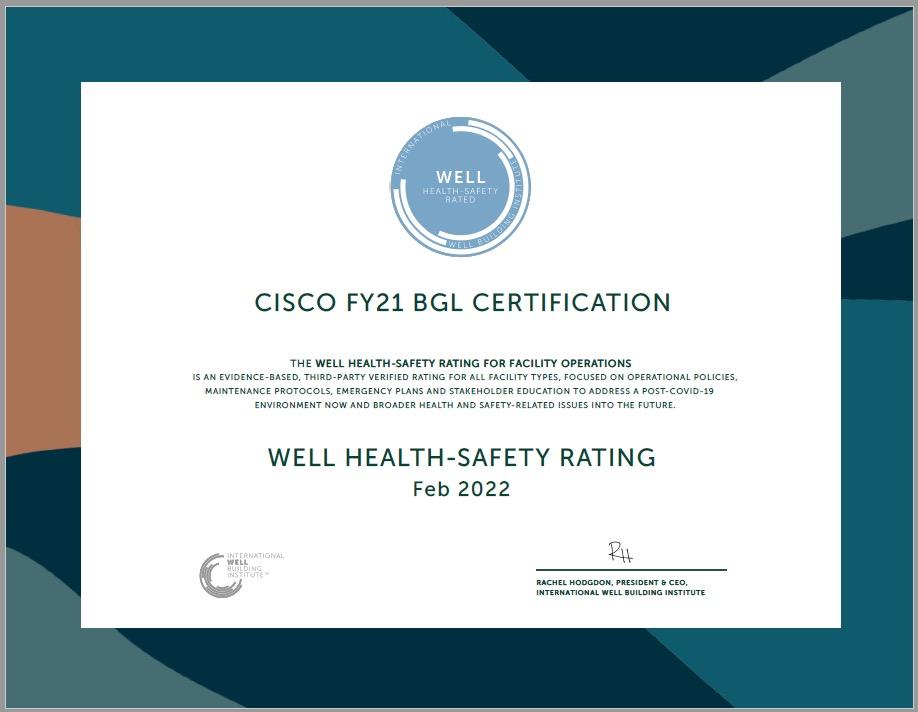
CHALLENGE MYIDEA / INITIATIVE / SOLUTION BENEFITS / ADVANTAGE
• Innovation
Description of the Innovation:
• Upgrade
• Manpower dependent.
• Introduced robotic system at the Workplace
• Time-saving and extra activities will be carried out.
• Manpower optimization
• Automatic operating system using sensors and operated by vendors(BRS)
• Point of sustainability-uniformity in action and effective results
• Cost constrain in consumables
• The machine can be set to clean exactly as required.
• Only we must fill water and chemical from time to time.
• Equally effective for general/deep cleaning tasks.
• High efficiency for larger areas.
• Reduce work fatigue and increase productivity.
• Save the time of housekeeping staff and easy to operate.
• Machine to be charged for 4 hrs a day and utilized for 80 mins per day.
• Operating and maintenance is easy.
• Dry Mop machine manual operationble too.
• Save the time of housekeeping staff and easy to operate.
• Equally effective for daily cleaning tasks.-Dry mop
myIdea
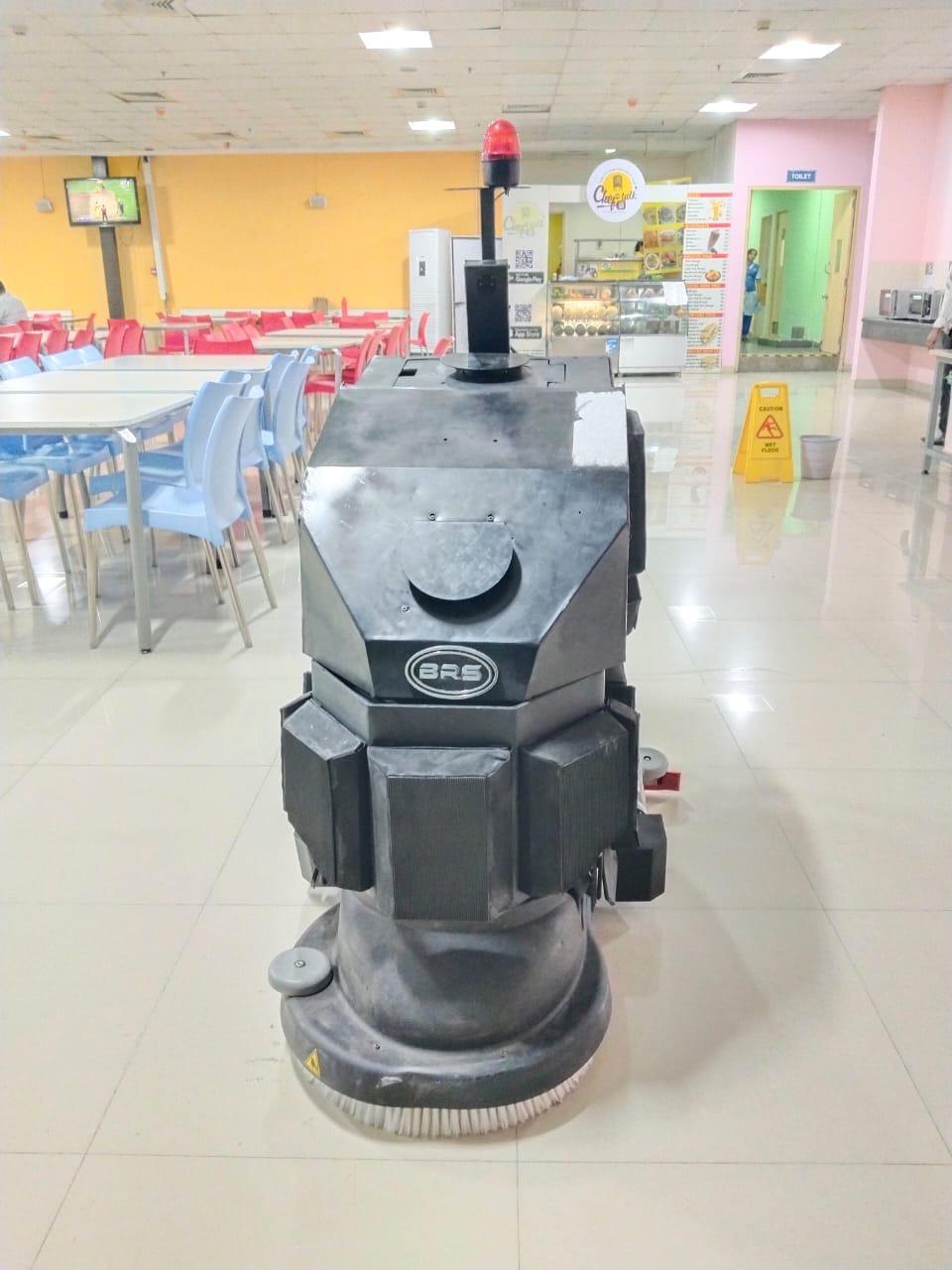
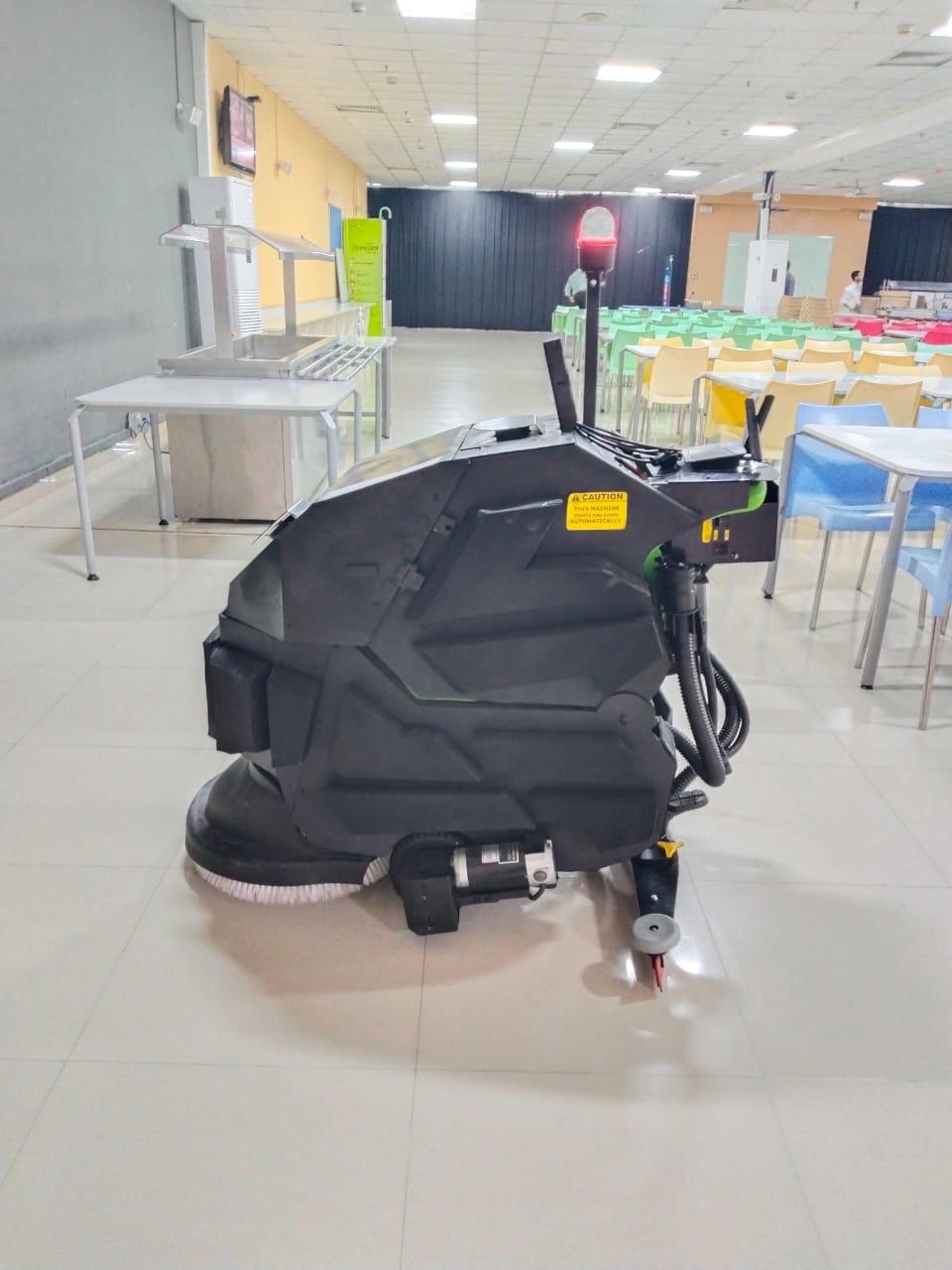


Description of the Innovation:
EC Fan installation for Cooling towers
CHALLENGE
MYIDEA / INITIATIVE / SOLUTION BENEFITS / ADVANTAGE
myIdea
• Maintenance of Blower, Motor and VFD cost more than 1 lakhs per unit.
• Medium efficient fans
• VFD drive losses (close to 3%) which gets dissipated as heat
• Heavy motor lifting shift challenges during servicing
• Getting Site HSE Approval for work execution proving challenging due to Improper documentation for cranes, tools and tackles.
• Replacement of Cooling tower fans with EC Fans are ultimate energy efficiency
• The EC Fans are direct driven motors with inbuilt VFD that improves efficiency
• Maintenance cost will be nil
• Energy savings is due to reduced motor size from the conventional motors. This is due to reduced drive losses and better efficiency of fan.
• Heat reduced with the help of in-built electronics of the EC drive
• Lifting and shifting is very easy due to less weight.
• Reduced Maintenance
• Energy saving will be 30% to 50%
• Simple to connect- minimizes Human error
• Higher reliability – as the EC FAN GRID with 2 or more EC fans will have much lower failure rate than current single fan configuration
• Marginal increase in air-volume if called for since the FANs selected shall have margin for increasing the capacity.
• EC motors have PF close to unity
• Simple to connect. Minimizes human error
• EC motors have high power density
• Extremely low noise and no vibrations
• Soft start with highest torque
• Total annual savings 14.9lakhs with 3.25 yrs. pay back period.
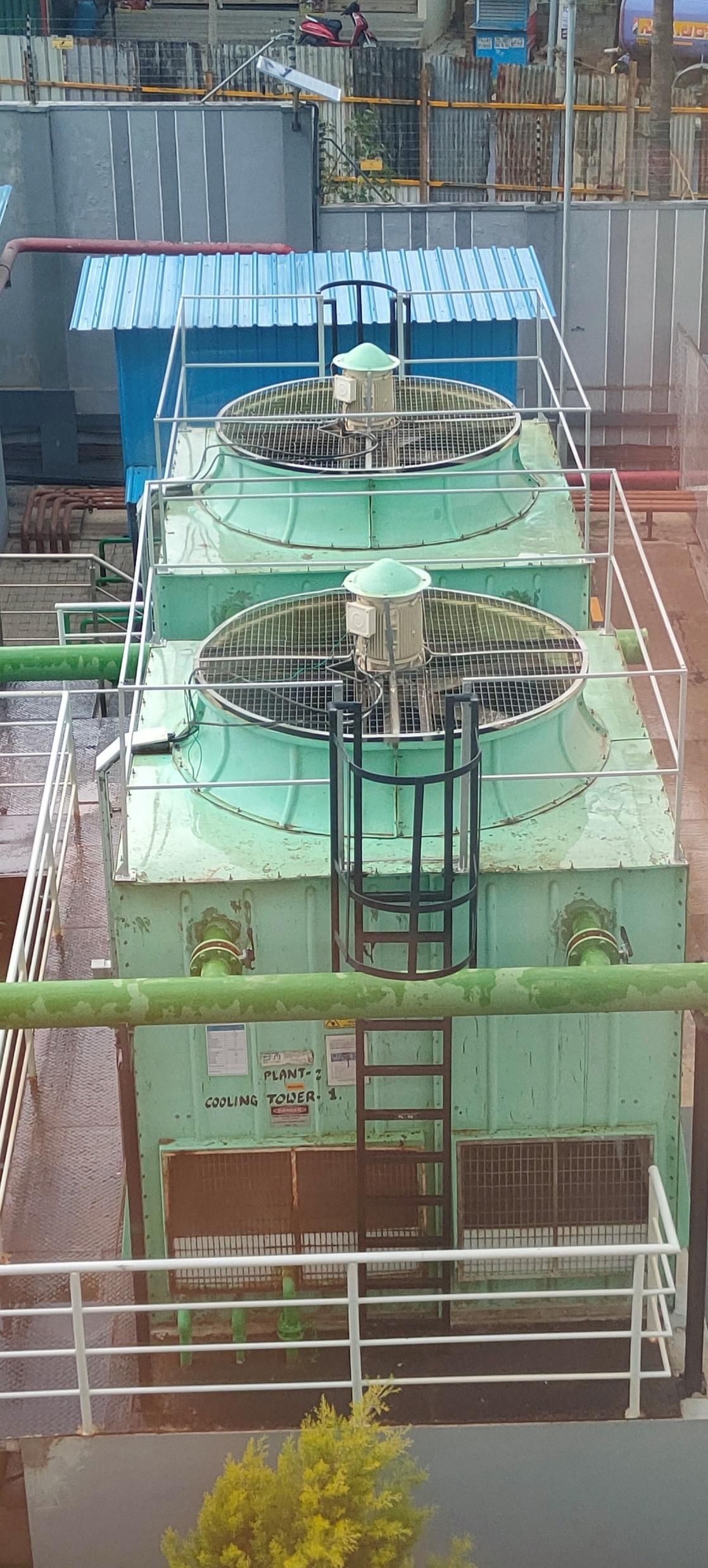

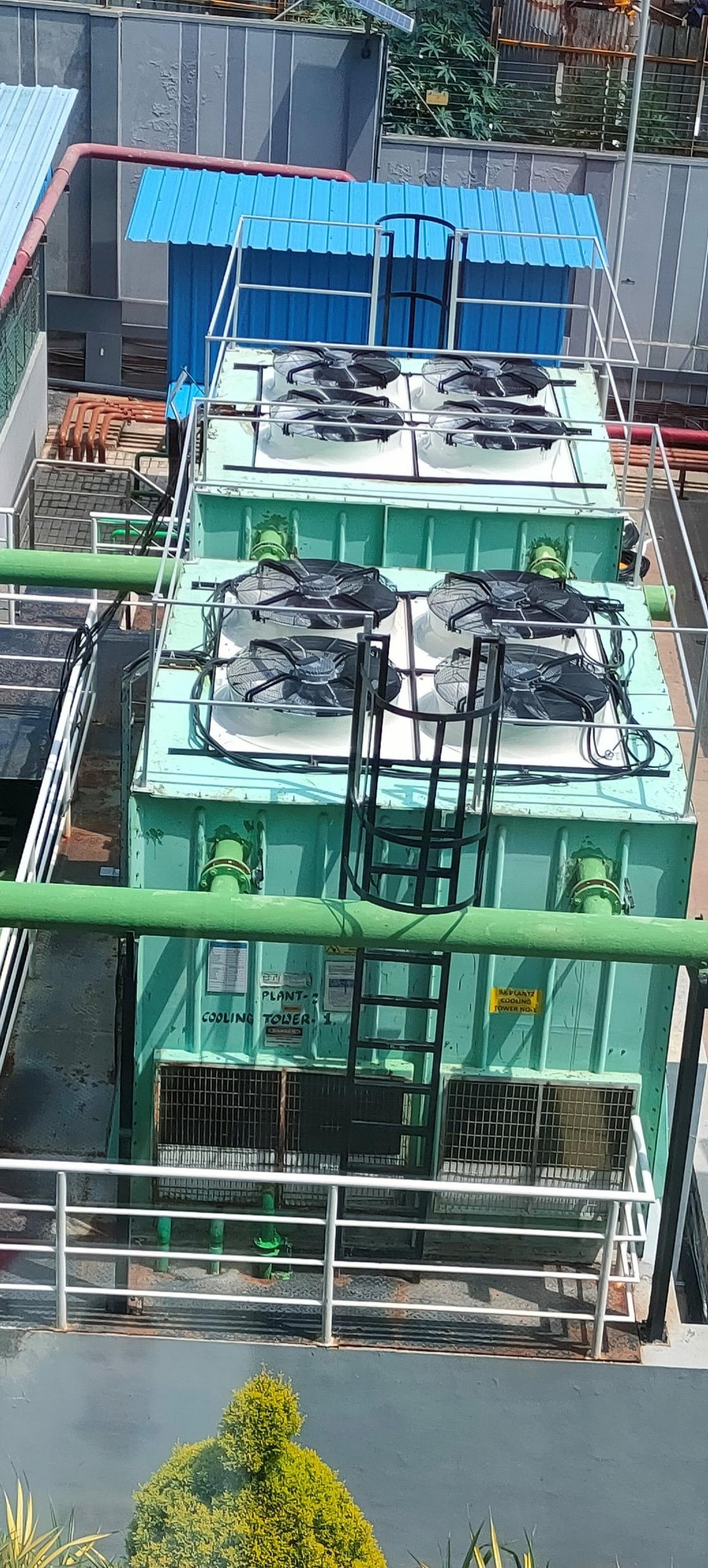
Description of the Innovation:
BI Dashboard to Track inventory
CHALLENGE
myIdea
• Recording and understanding the inventory usage across different sites and different verticals in a single spread sheet was not intuitive.
• After understanding the BI landscape, it was decided that we make use of Microsoft Power BI for creation of inventory usage dashboard.
• In-depth understanding of consumption patterns was unavailable for decision making.
• No standard template, naming conventions, unique identifiers, procedures and process were available for recording data
• Team members collaborated from multiple EM sites to collate the data required for this activity.
• Data cleansing activity was done along with master data creation, so that collection process and procedures can be followed going forward.
• The backend infrastructure was created using Microsoft Share-point that served as the DB for this activity.
• Availability of historical data at one place that helps in descriptive statistics.
• Easy ways to slice and dice your data for research and decision making.
• Date patterns to help team in taking inventory related decisions.
• Quick downloads of graphs and charts for usage related discussions for single product, multiple products, categories, subcategories etc.
• Some of the consumption data were not digitized.
• Acts as a single source of truth.
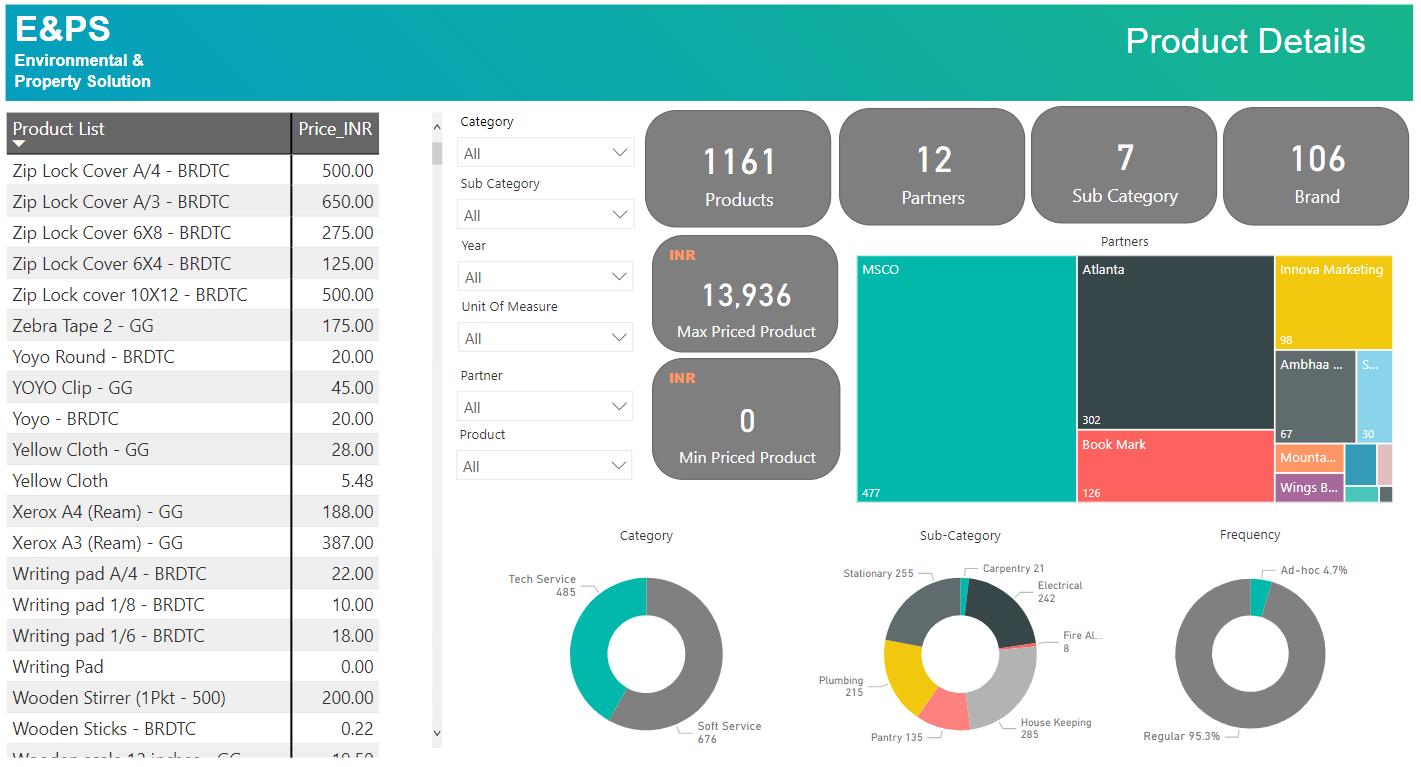
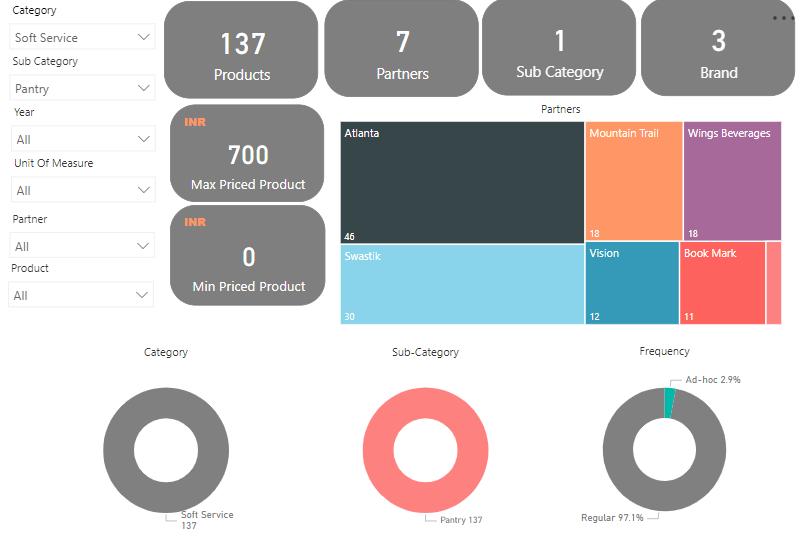
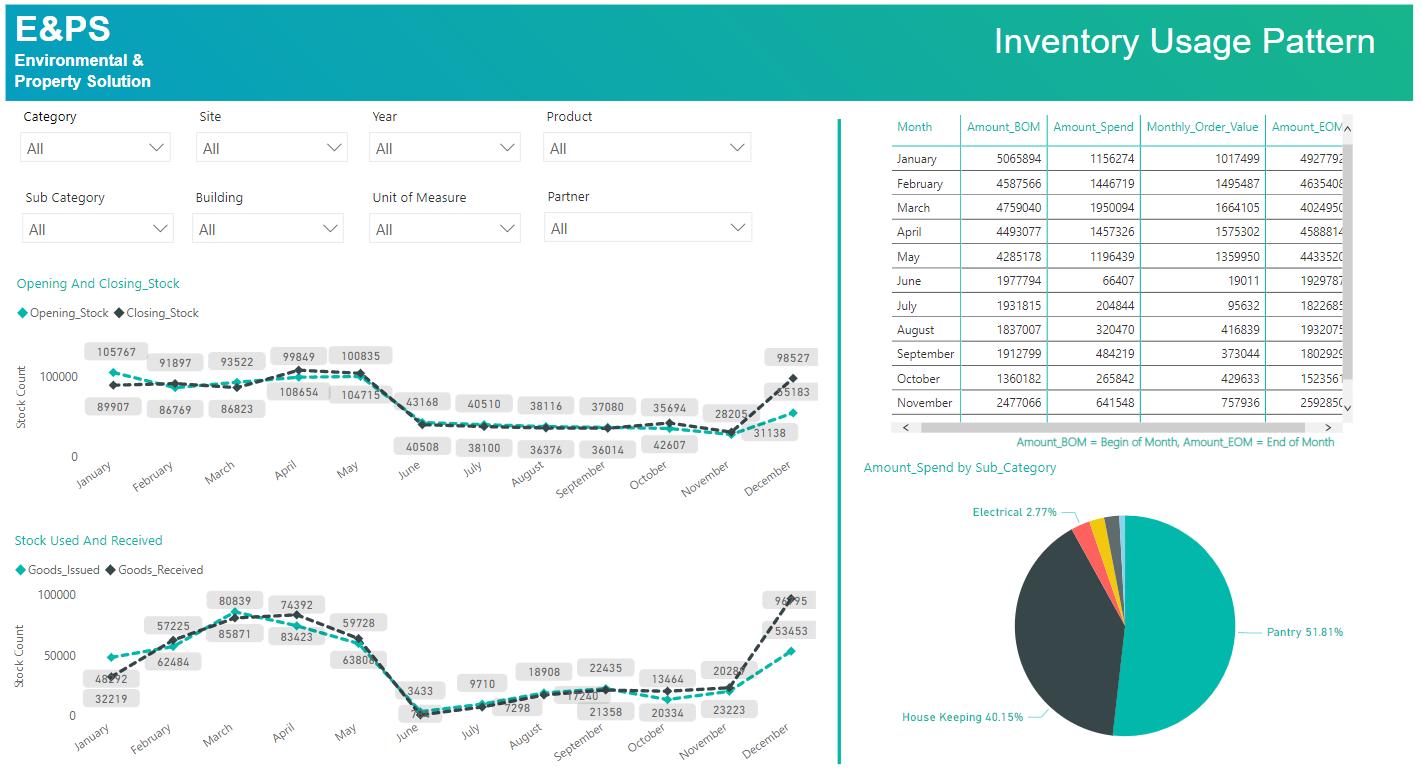
Description of the Innovation:
IAQ Online Monitoring Sensor
• As per compliance standards, it is mandatory to monitor air quality involving 12 parameters within office spaces at least once in six months.
• Indoor air quality is vital to productivity and health.
• Dependency on vendor for getting the IAQ parameter testing and involves high annual cost.
• Results are not real time.
• Nonconformity, if any, is known only post periodic testing.
• IAQ monitoring sensors measuring four parameters installed across most facilities.
• Hence dependency on manual testing remained.
• New technology now measure 12/ 14 parameters real time and pushes information to BMS/ display units.
• Information updated every two minutes through MODBUS.
• Live data on the IAQ in BMS system.
• Parameters like Temperature, Relative humidity , Nitrogen di oxide, CO2 , O2 , Ozone, CO, Formaldehyde, Ammonia, Sulphur di oxide, PM 2.5, PM 10 and TVOC can be monitored online.
• No vendor dependency for carrying out basic IAQ testing – Cost saved.
• As per input received from IAQ sensors, HVAC operation can be turned real time through BMS system.
myIdea
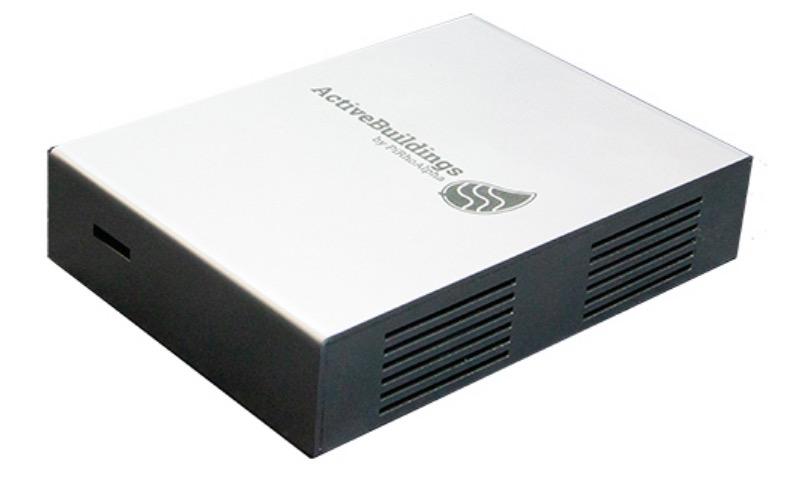
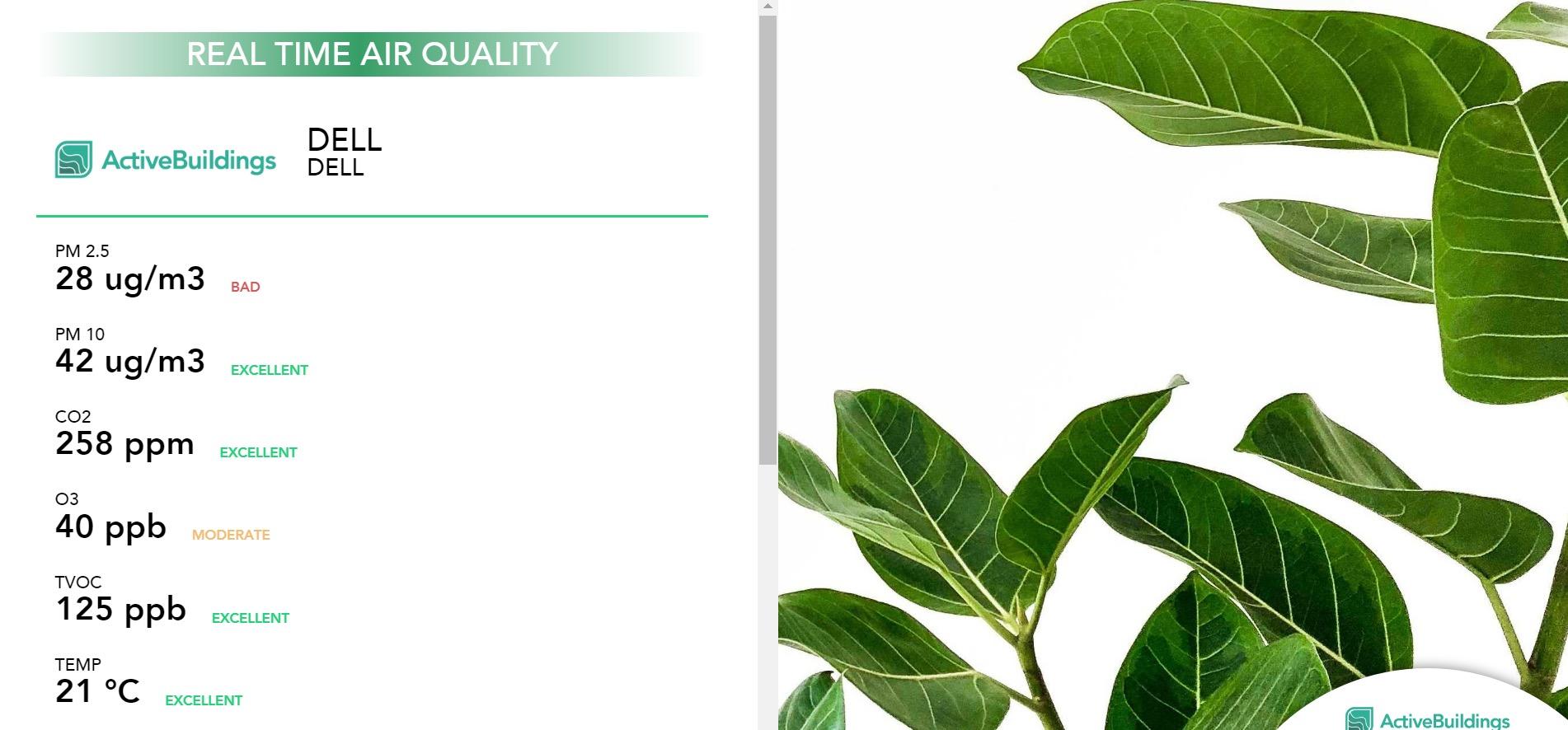
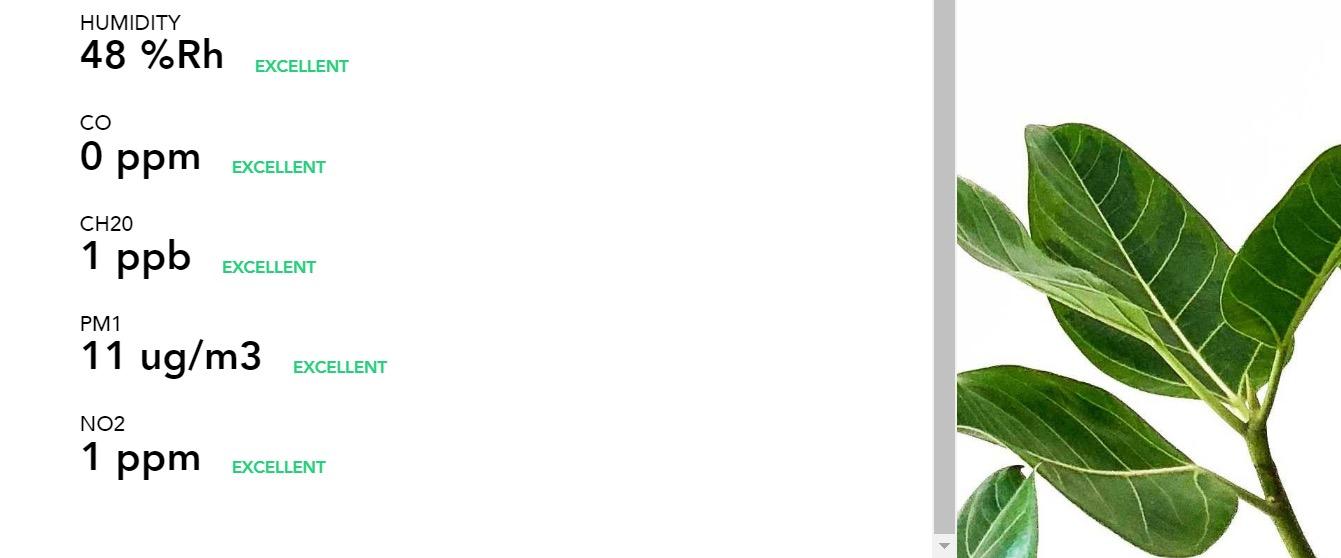
Description of the Innovation:
Rodent control-Rat Hatch Trap
myIdea
• Frequent complaints of rodent in work area
• AV & Network cables damaged by rodent in the office area
• Conventional rat trap are toxic in nature
• Mesh trap not recommended above ceiling
• Odor smell above ceiling
• Rodents will rummage and chewing tiles
• Risk of illness
• Contamination
• Mechanical trap
• Spring mechanism get triggered by rodent movement
• Metal bar falls on the rodent
• Highly efficient pest control system
• Hassle free instalment
• Avoid harming other animals
• Monitor rodent activity
• Maintenance free
• Eco Friendly
• Completely Non-Toxic rodent control device
• Can be used for rats or mice
• Trap can be serviced from ground levelreduction in a need to work at height
• Activation indicator shows when rat is trapped
• Hygienic non-contact removal of the rodent
• Movable trap all over the floor.
• No poison needed
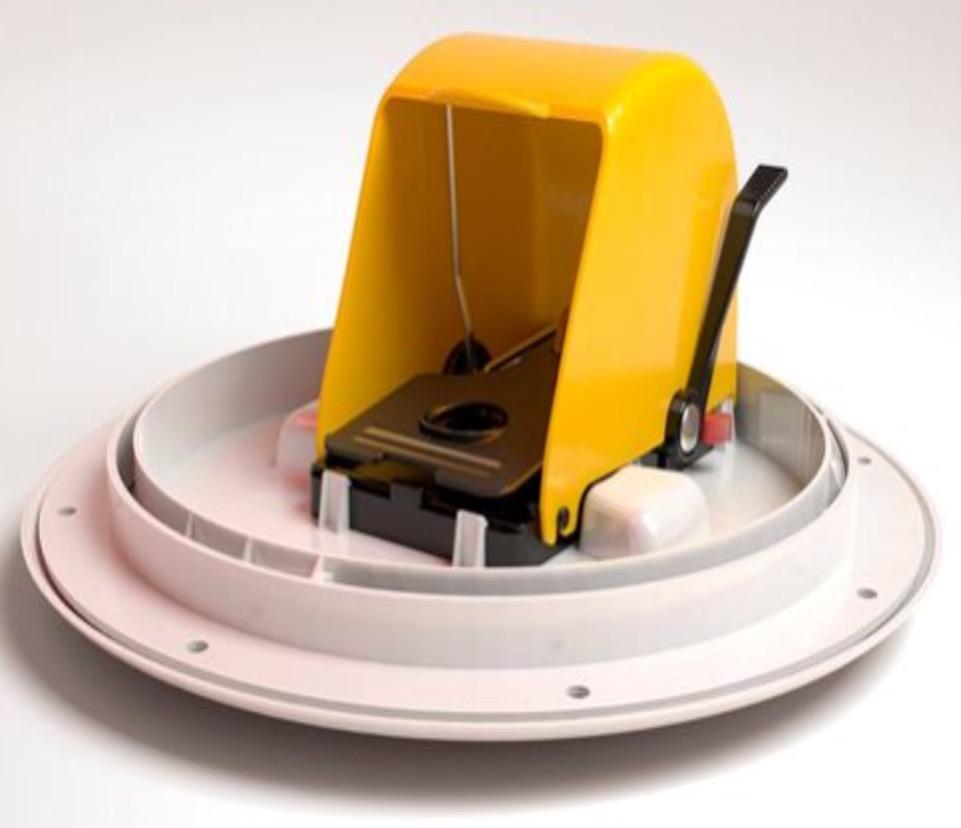
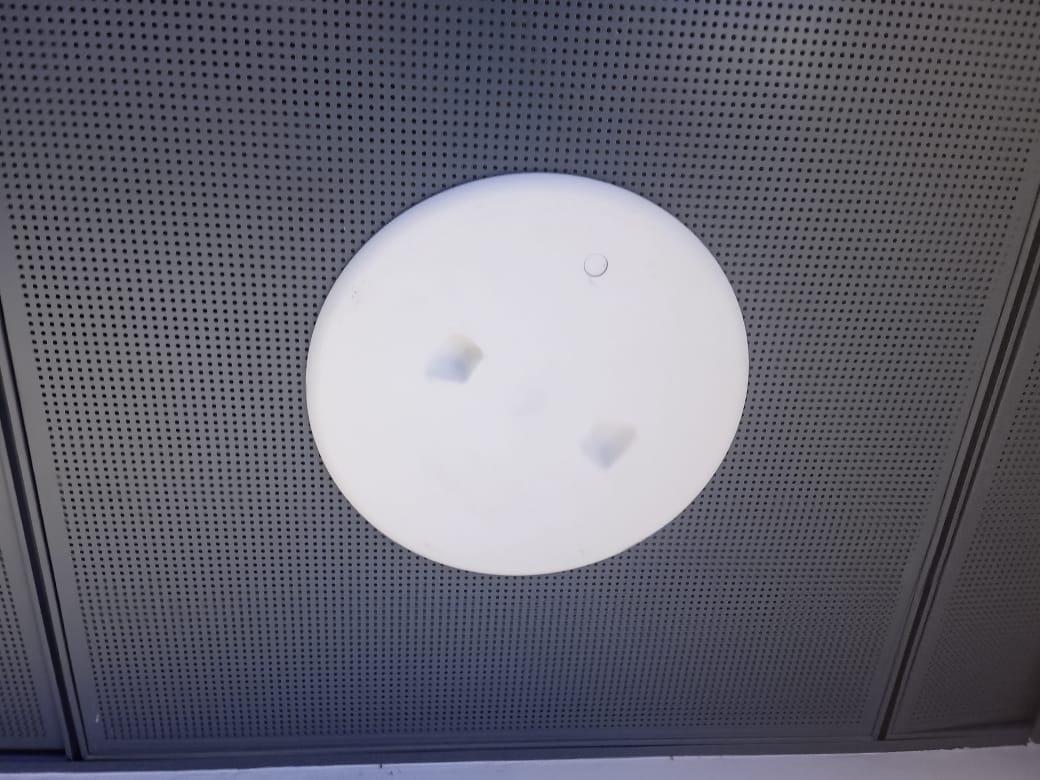
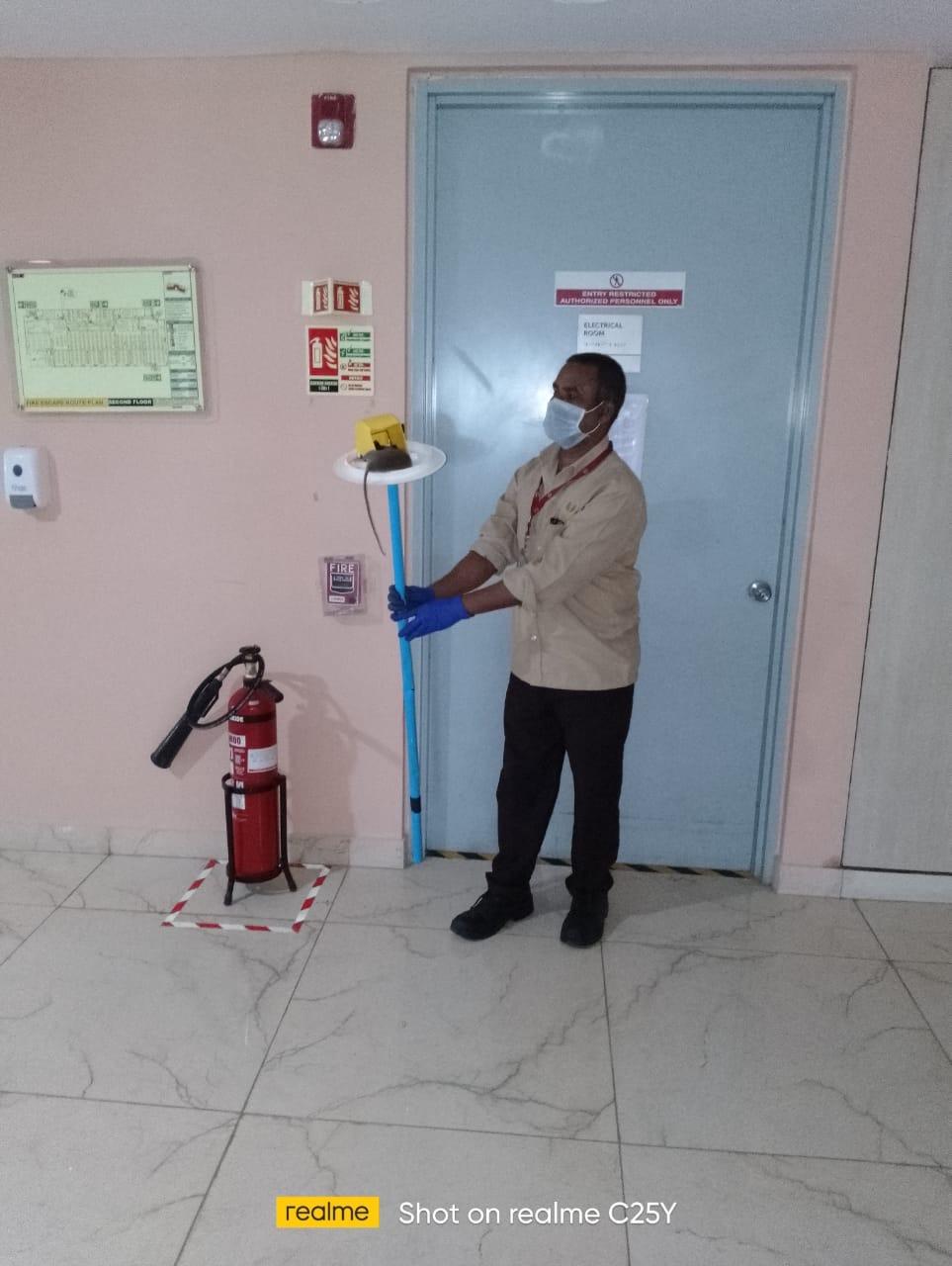
• Dull and plain staircase walls that necessitated frequent painting
Description of the Innovation:
Moss Wall Installation On Staircase Wall
• Encourage employees to use staircase instead of elevators and provide them with a visual appeal and incentive
• To boost acoustic property
• To improve biophilic principles of the building
• We planned to give a new look for staircase walls by adding greenery
• Moss wall implemented across all floor staircase
• Preserved real that is visually as good as live plants and requires no maintenance
• Unique design and shades can be created
• It has been carefully preserved through an eco-friendly process
• Improve air quality and visual ambience
• Guaranteed for three years.
• No maintenance cost.
• Avoids repainting cost
• Stress buster.
• Enables noise reduction
• Absorbs minor air- borne dust
• Stabilized moister level
• No need of irrigation
myIdea

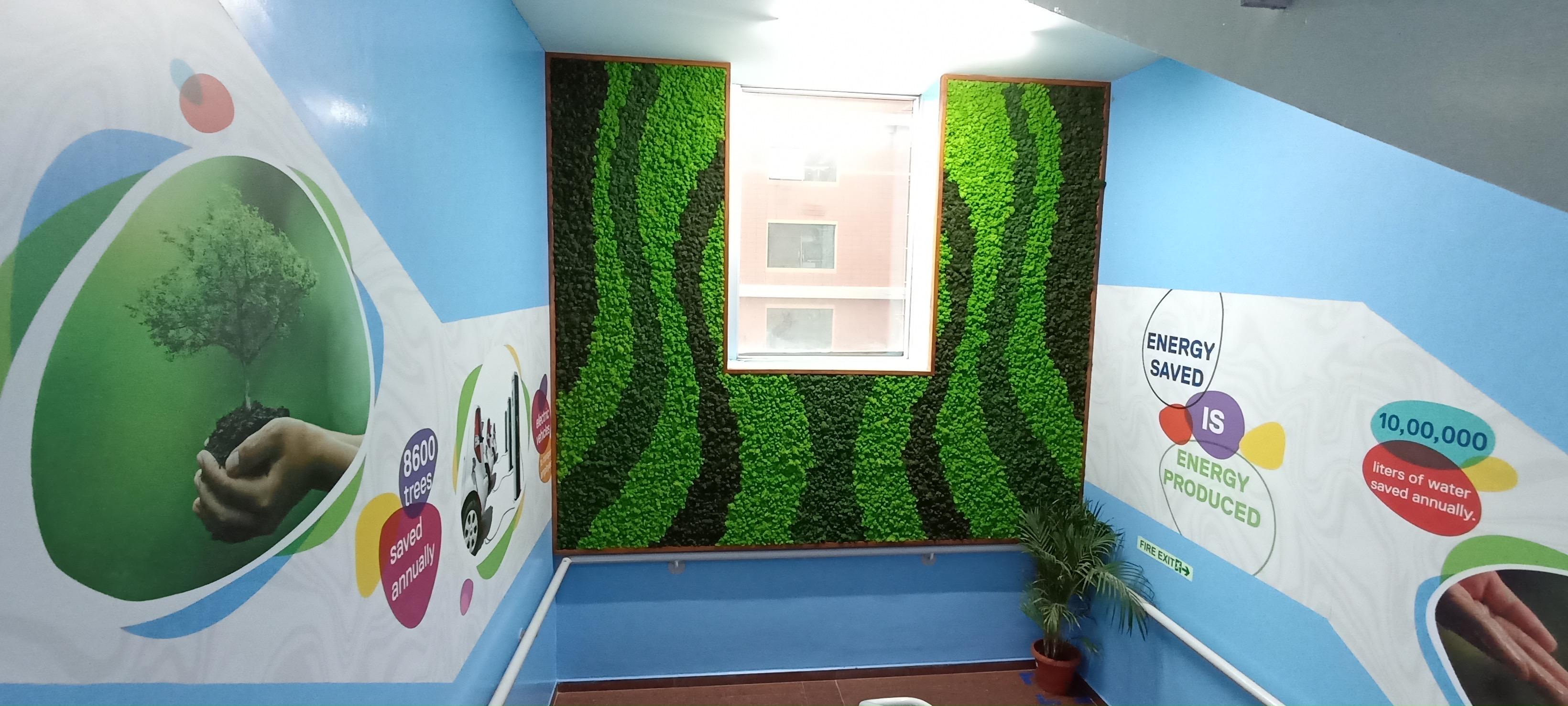
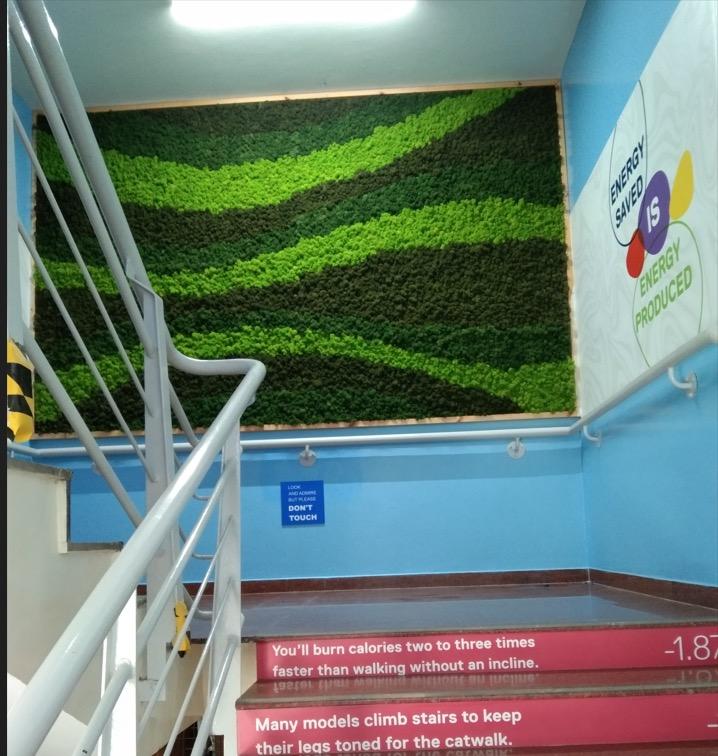
Description of the Innovation:
Multi gas Detector for Confined Space
myIdea
• Confined space is a risk for potential Health Hazards with hazardous gases
• Risk of people getting affected by Poisonous gases, potential to cause Fatal incidents
• Making sure of Staff Health and Safety while entering a confined space was a challenge
• Need to implement mechanism to improved staff confidence and safety awareness while entering confined space
• Initiated procurement of Multi gas Detector to detect hazardous gases in confined space
• Proposed Different models and chosen Honeywell model due to brand value and reliability
• Trained the staff and vendors on importance of safe entry of confined spaces
• Importance of safety while entering confined space was emphasised
• Detectors measures parameters like H2S, CO, Oxygen & LEL
• Staff and vendors can measure the gas levels before entering confined spaces like STP tanks, OH tanks & Storm tanks
• Incidents related to Hazardous gases will be avoided
• Promotes safe practice of entering confined spaces promoting better EHS aspects
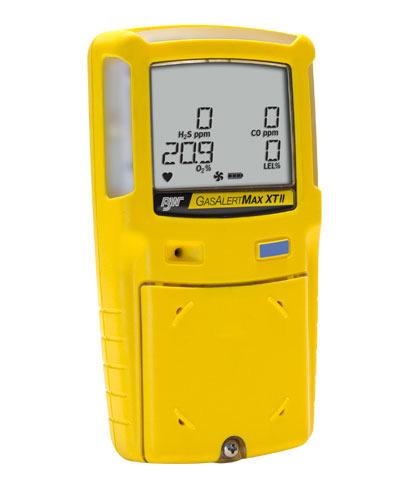
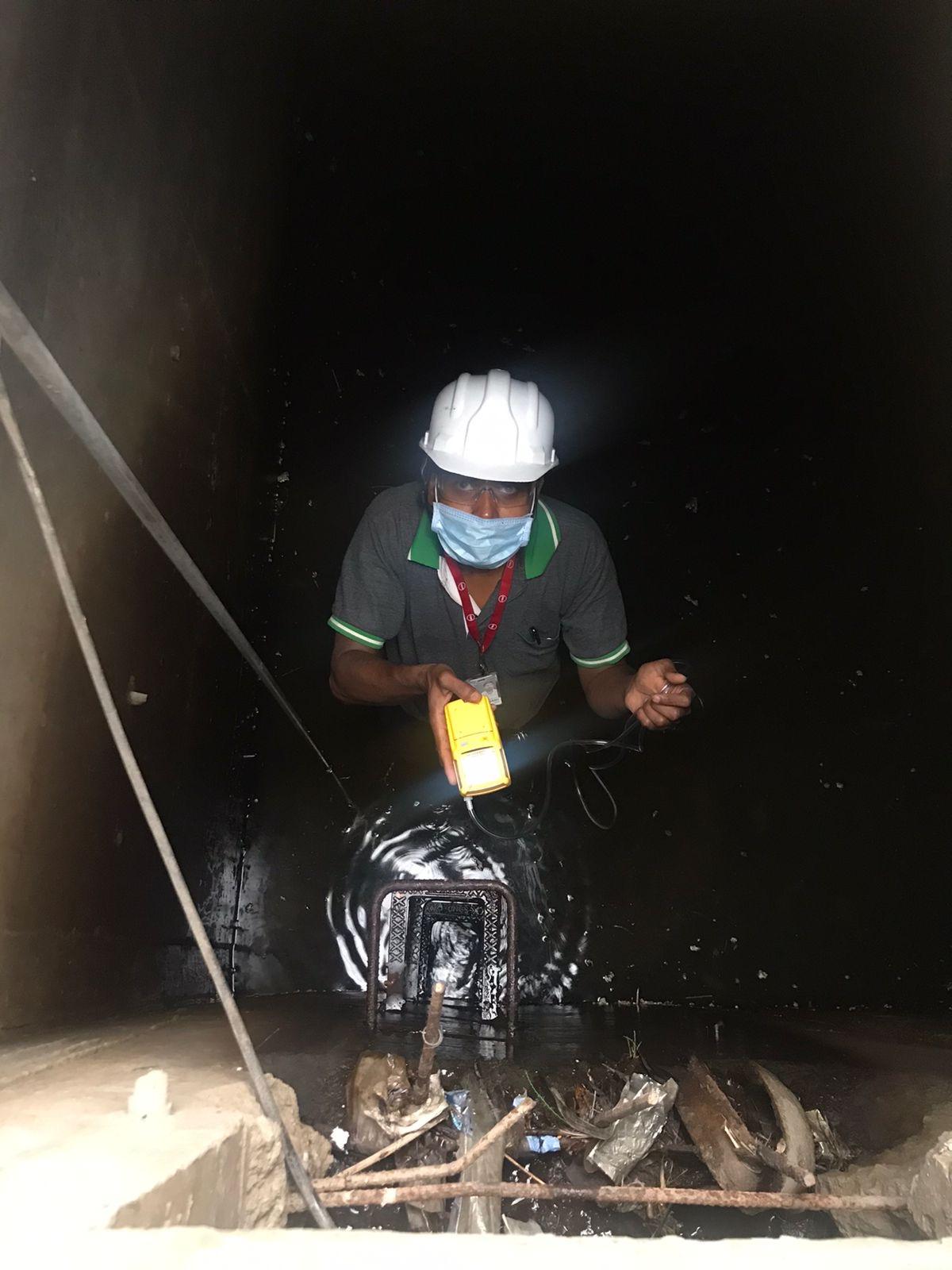
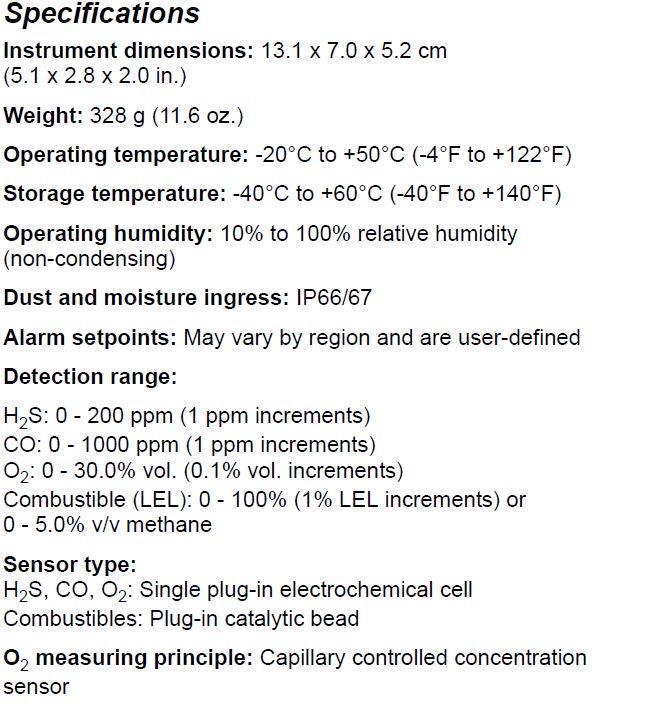
Description of the Innovation:
Drilling Machine Stand
myIdea
• While making wooden (or) metal holes its very difficult to operate the Drilling machine as need to bend
• Long time work may lead to injury and tiredness
• May lead to Musculoskeletal Disorder injury musculoskeletal system affecting the muscles, bones, intervertebral discs due to working over a prolonged period but does not include an injury, illness of disease.
• Sprains, Strains, upper limb disorders which affect the shoulder, elbow, forearm, wrist or hand during the machine handling
• Human error and quality of output may go down chances is too high.
• To overcome the challenge planned to implement an alternative solution for the drilling process.
• This will mitigate human Sprains, will Make
a comfort work bench
• Drilling machine wooden stand has been made with a scrap plywood.
• We were using unused materials for fixing the accessories of wooden stand
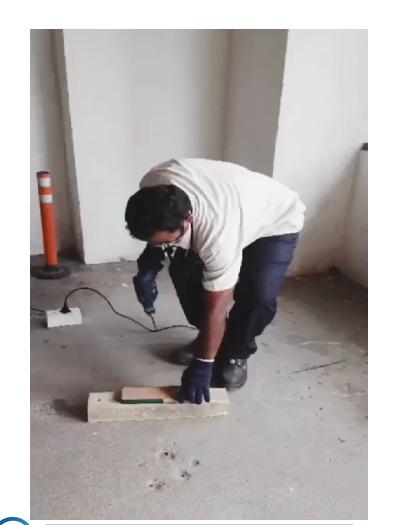
• It Avoids pain in shoulder, elbow, forearm, wrist or hand.
• Eliminates Musculoskeletal disorders
• To eliminate the risk of accident while using the drilling machine
• Bending and twisting avoided while operating machine
• Huge work carried out short duration time saving/Manhours saving
Cost Saving
§ Total Cost Involved : INR 1465/-
§ Total Cost Benefit by Re - Using Materials INR 15000/-Approx.
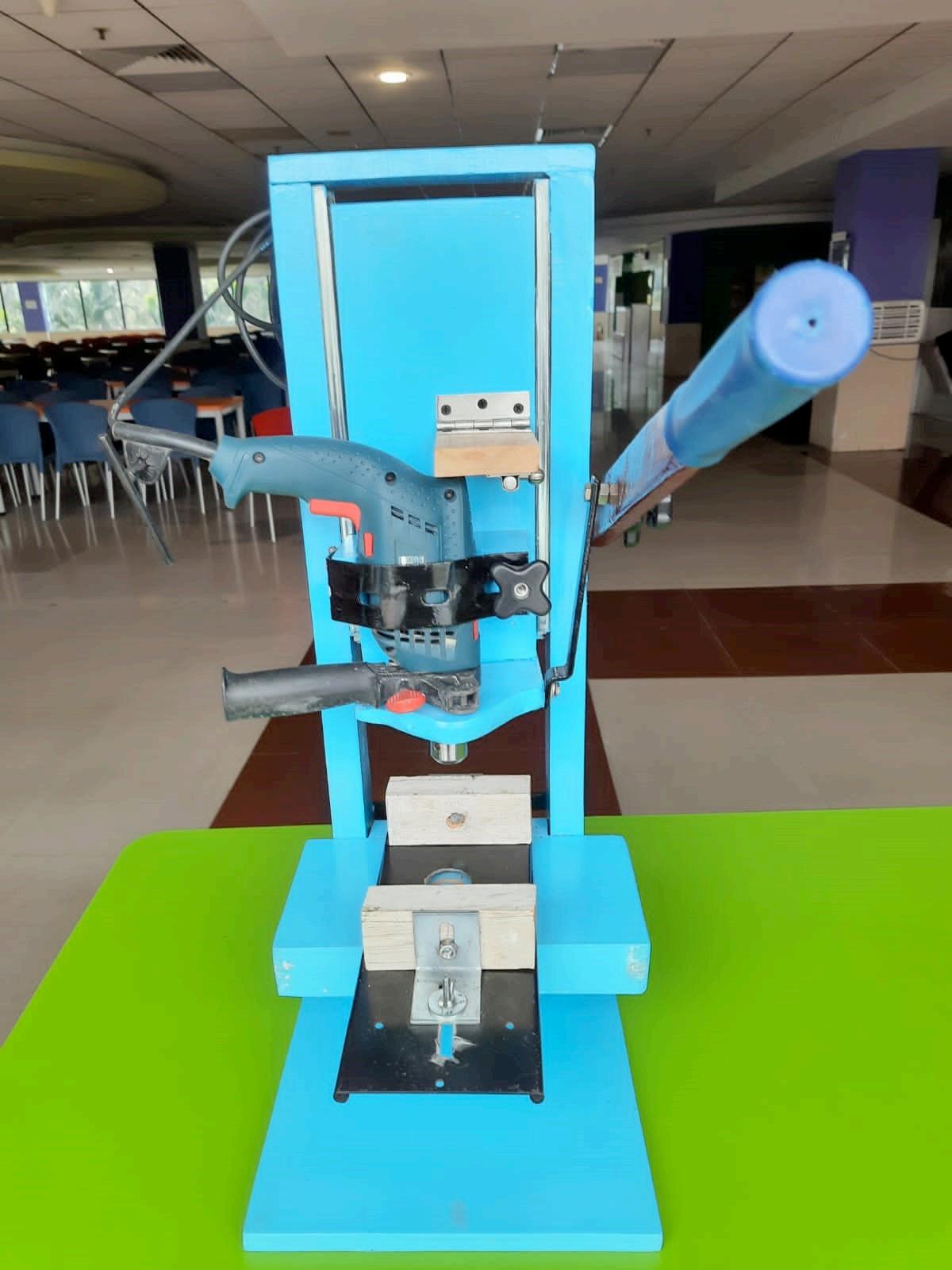
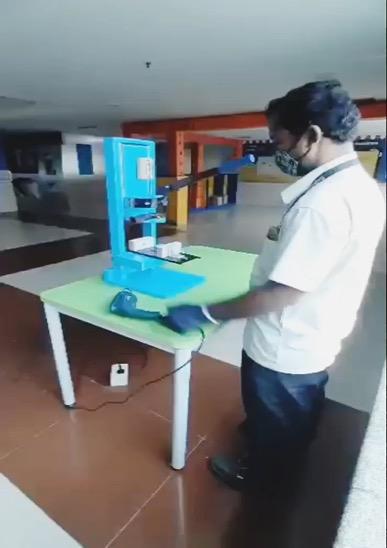
Description of the Innovation:
VFD in Heat
Recovery Wheel Duct
myIdea
CHALLENGE
• It is commonly observed that building fresh air units or HRW units don’t have any VFDs provided. Since most of the HVAC AHUs are CO2 controlled and fresh air dampers are auto operated as per CO2 requirement which create much pressure in duct while dampers are getting closed during operation.
• There was no VFD available in HRW units at cognizant Kochi in which the capacity of motor is 22 KW,
• the pressure was too high in the ducts while its operation that created duct damage. Also energy was over consumed due to full frequency operation even the demand is less.
/ INITIATIVE / SOLUTION BENEFITS / ADVANTAGE
• VFD installation and implementation of the same which prevent asset damage due to excess pressure in duct while auto closing of CO2 dampers, this also contributed energy saving of 1161 KWH/ Month.
• During operation, VFD will modulate frequency of motor and will reduce power consumption as well as pressure in duct.
• Motor load also will be minimized by avoiding full frequency run while all the CO2 dampers are in close position.
• Energy saving of 1161 KWH/ Month.
• Cost saving of 139,392.00 per annum.
• Prevention of asset damage, there was frequent duct damage in HRW ducts due to excess pressure which is prevented after the initiative.
• Chance of motor winding failure reduced since motor will not be overloaded since the VFD will reduce frequency as per the load demand which will help in getting extended life for the critical asset.
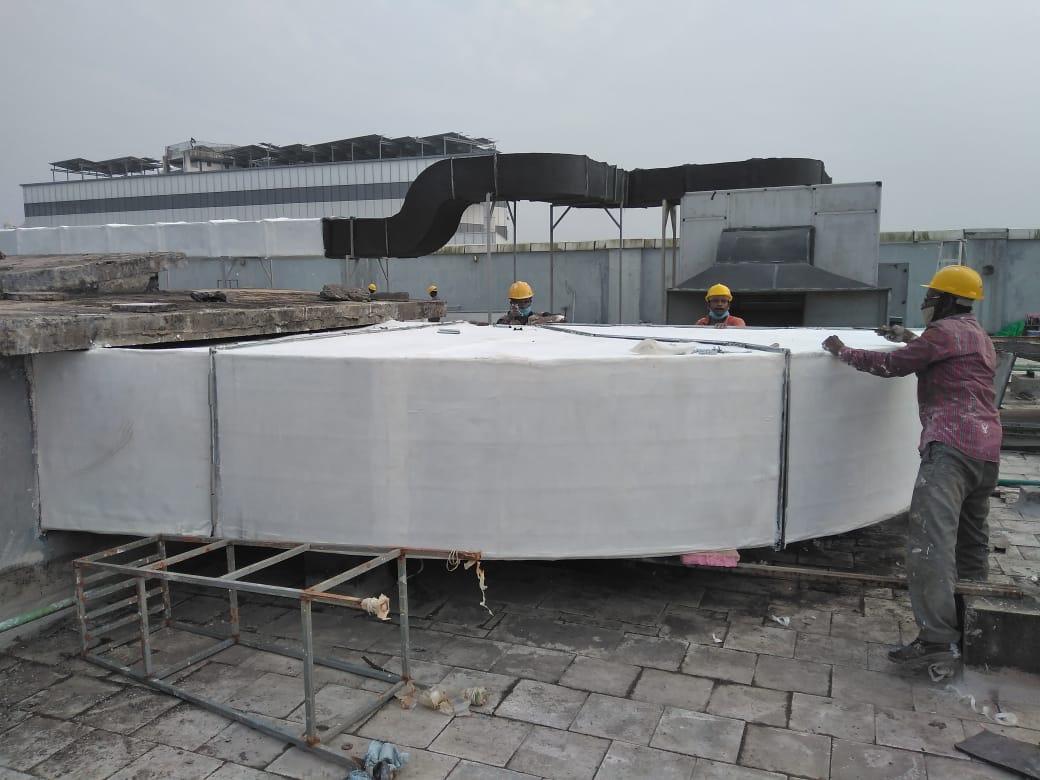
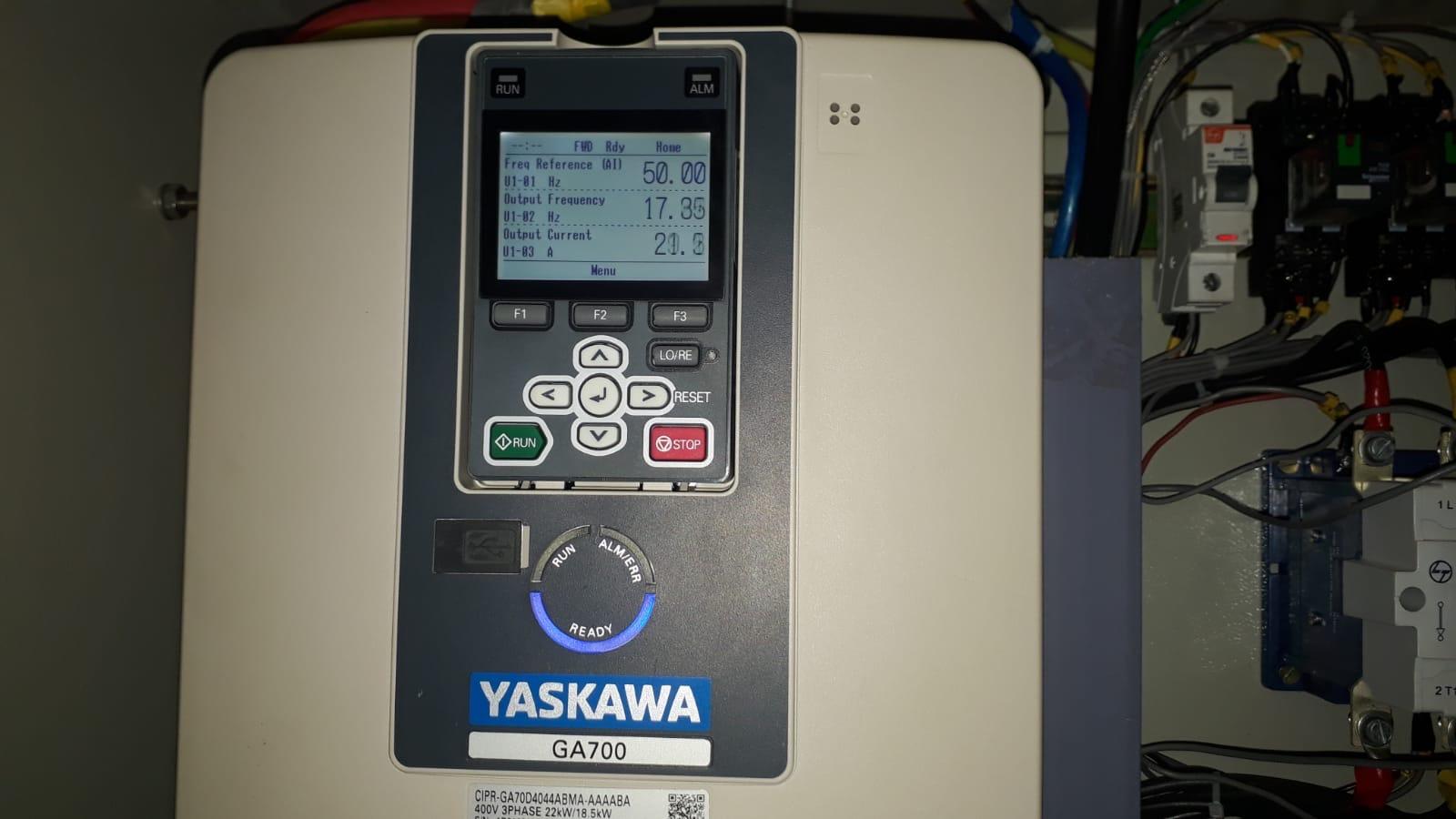
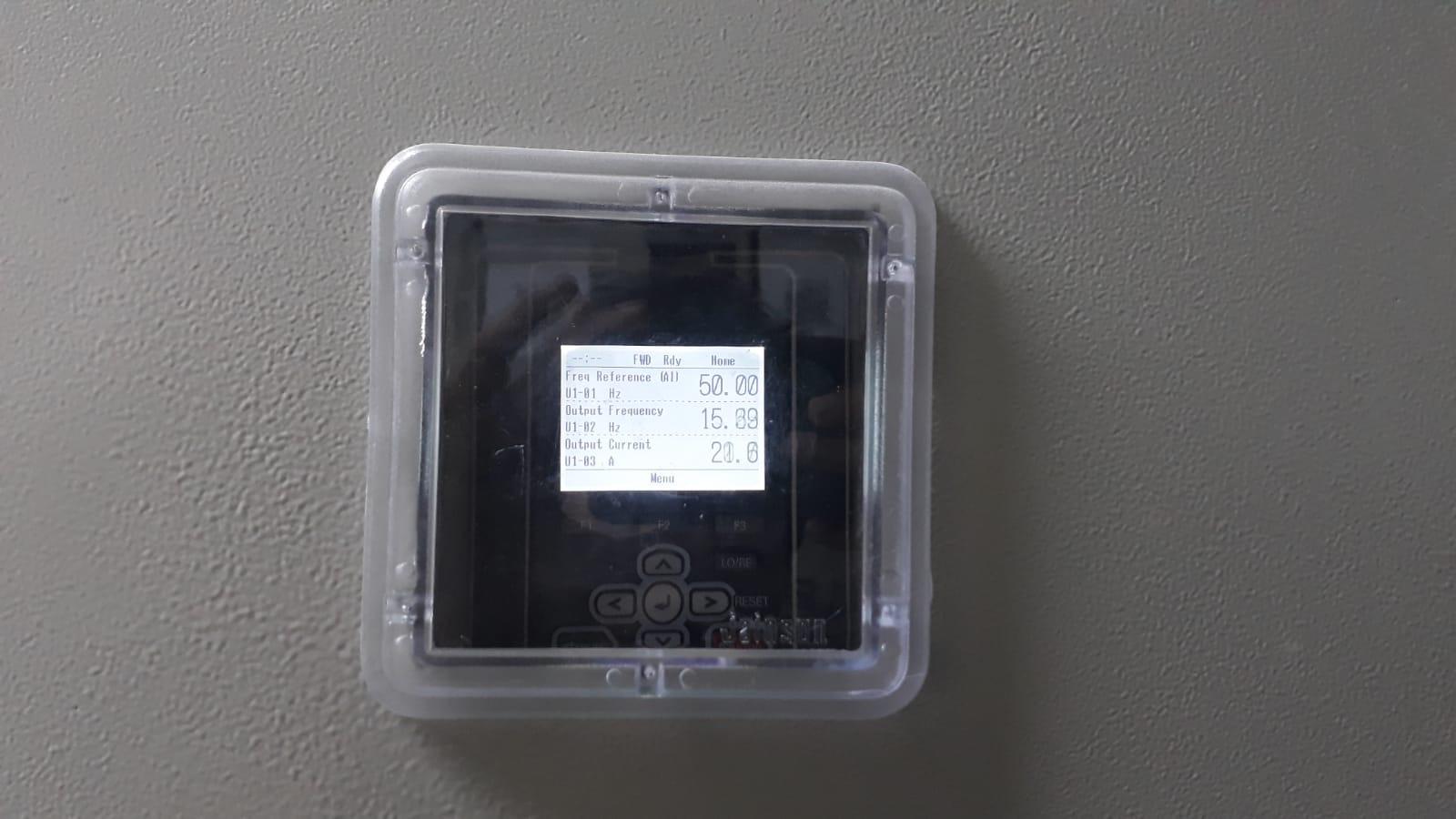
Description of the Innovation:
• Found cement slabs on the trench in the garden were having a dull look and iron handles rusted
Garden
Beautification Project
• Maintaining the cleanliness of these slabs were a challenge
• By brainstorming an idea came of painting the trench slabs
• It has added beautification to the garden
• Painting done with available black paints and added median in the center with white paint .
• Now trench slabs are good looking and free from rust
• The over all work now appears as runway
myIdea
• During watering of garden frequently found soil is sprinkled over the slabs due to water force
• Further added with aircraft structure made from waste wood available in the scarp yard and painted to give good look
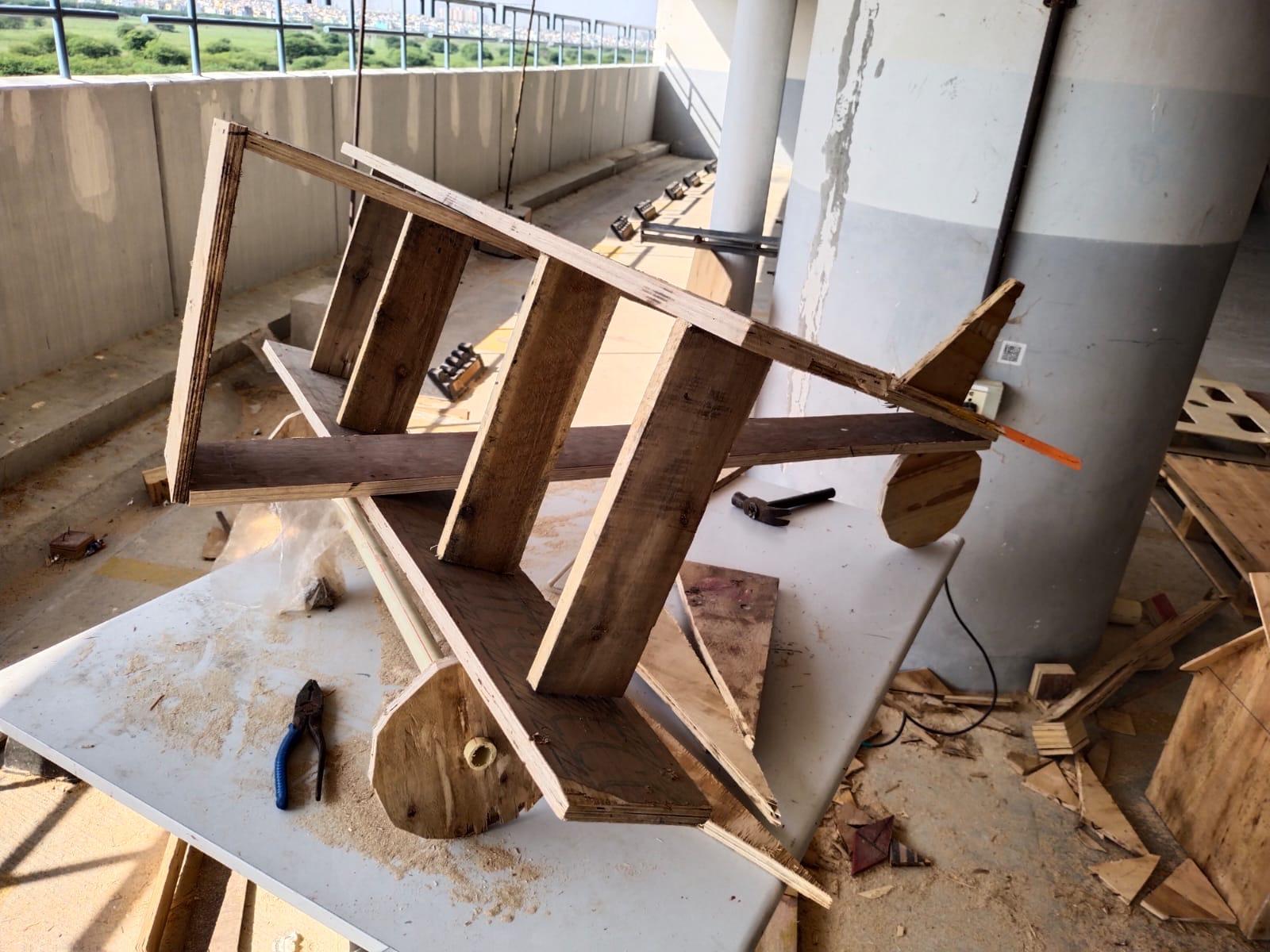
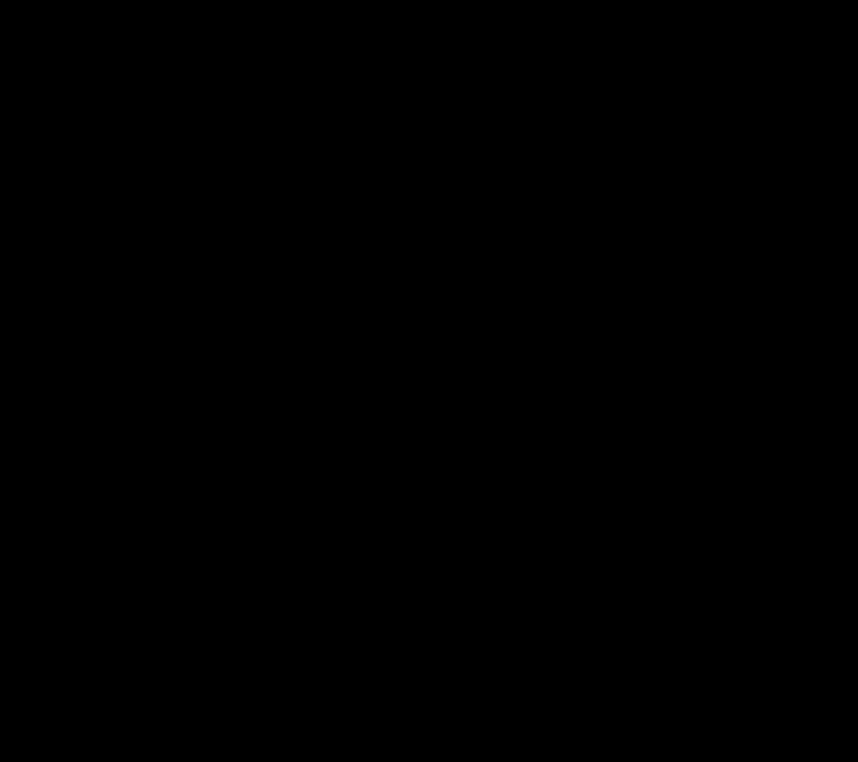


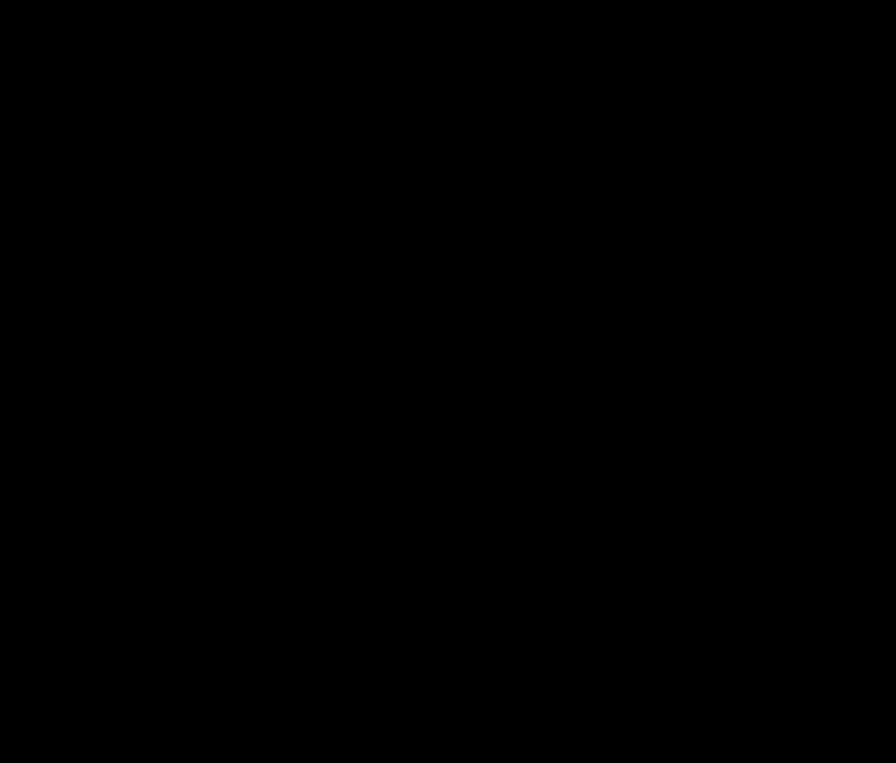
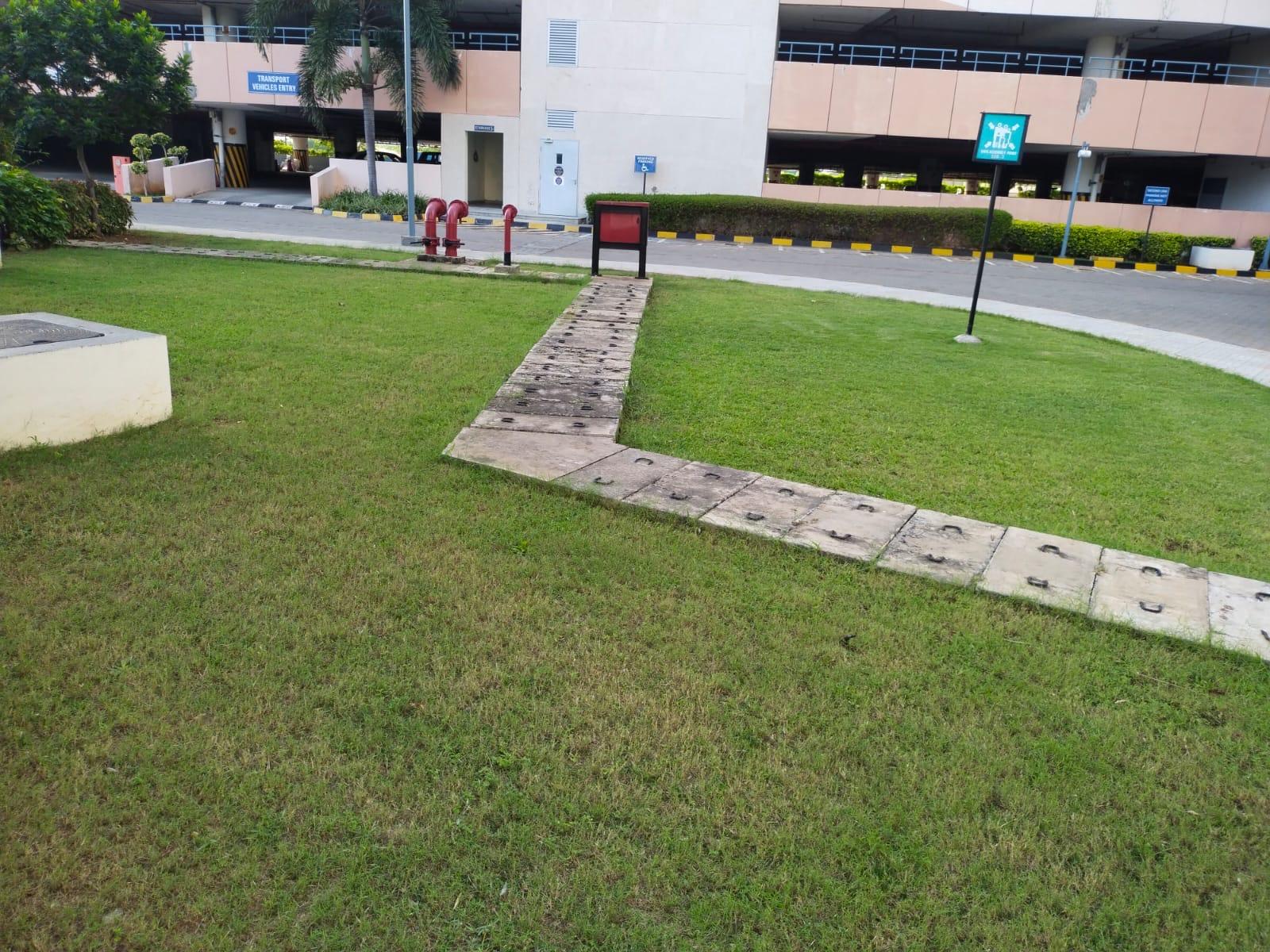
Description of the Innovation:
• As per RTW plan employee started working from office. To overcome from daily stressful & monotonous activity there are no such lively workplace at the facility.
• The regular look of the workstation had become monotonous for the Employees.
• Better utilization of unused space
Collaboration Space in Nature’s Lap
myIdea
• To rejuvenate employee enthusiasm at work place we planned to caste a small agile space of greenery
• Artificial green mat has been utilized as floor carpet which leftover materials were available at site.
• To improves cognitive function, increases productivity, mental refreshment a different or agile workplace is very useful
• The regular look of the workstation had become monotonous for the Employees. To refresh their enthusiasm at work place we planned to caste a small glimpse of greenery at 4th Floor where the employees can relax and breakout from the boredom. .
• All the table and seating arrangement are handmade and painted which has been prepared by our In-house team.
• Since, we have utilised the unused and retrofit materials and the entire job has been carried out by our In-house team. One time cost saving has been achieved.
• Cost Saving – Rs.75000/-(Approx.)
• Client & Employee Satisfaction
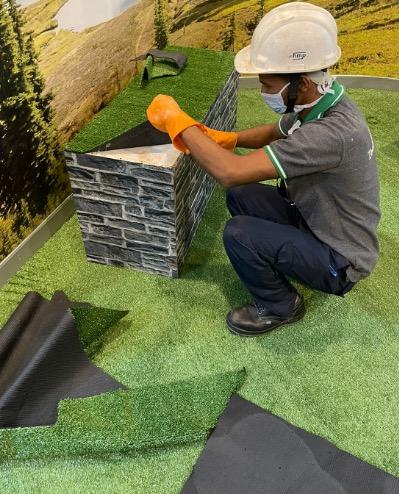
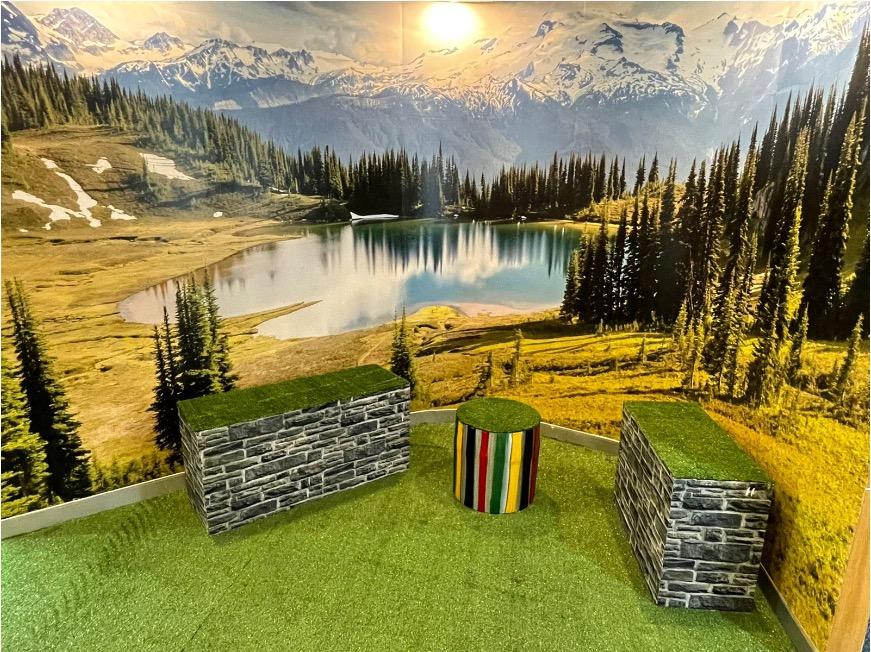
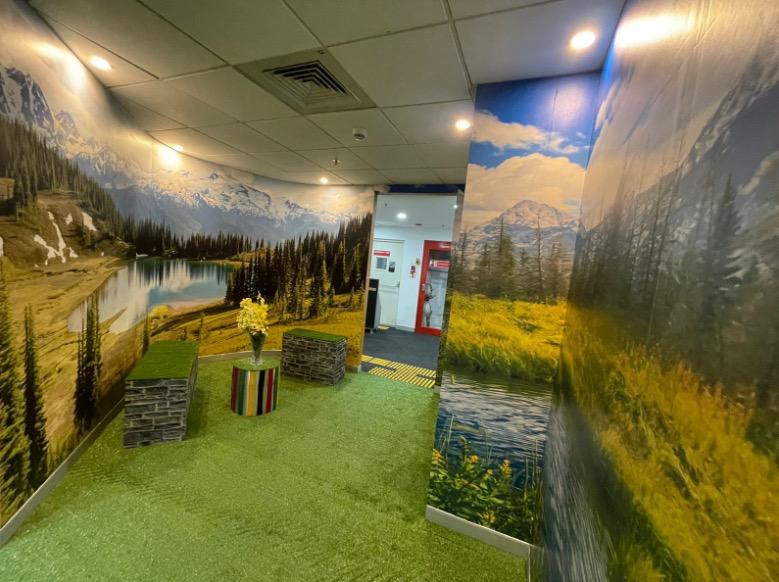
Description of the Innovation:
Golf Kit Holder
myIdea
CHALLENGE MYIDEA / INITIATIVE / SOLUTION BENEFITS / ADVANTAGE
• We have an internal mini golf course, and the kit was available in a different location for employees to pick up and return every time they used it.
• It was a pain point for someone to pick up
• We have moved from individual dustbins to centralized waste bins to improve sorting of waste. There were some bins that were available with us due to the removal activity
• We utilized a pole as centre stand to place bin on a bearing and allow the bin to rotate for the user to pick up desired Golf club and have placed a couple of trays for holding the golf balls.
• A shelter was created for the holder to avoid any damage of material due to climatic conditions
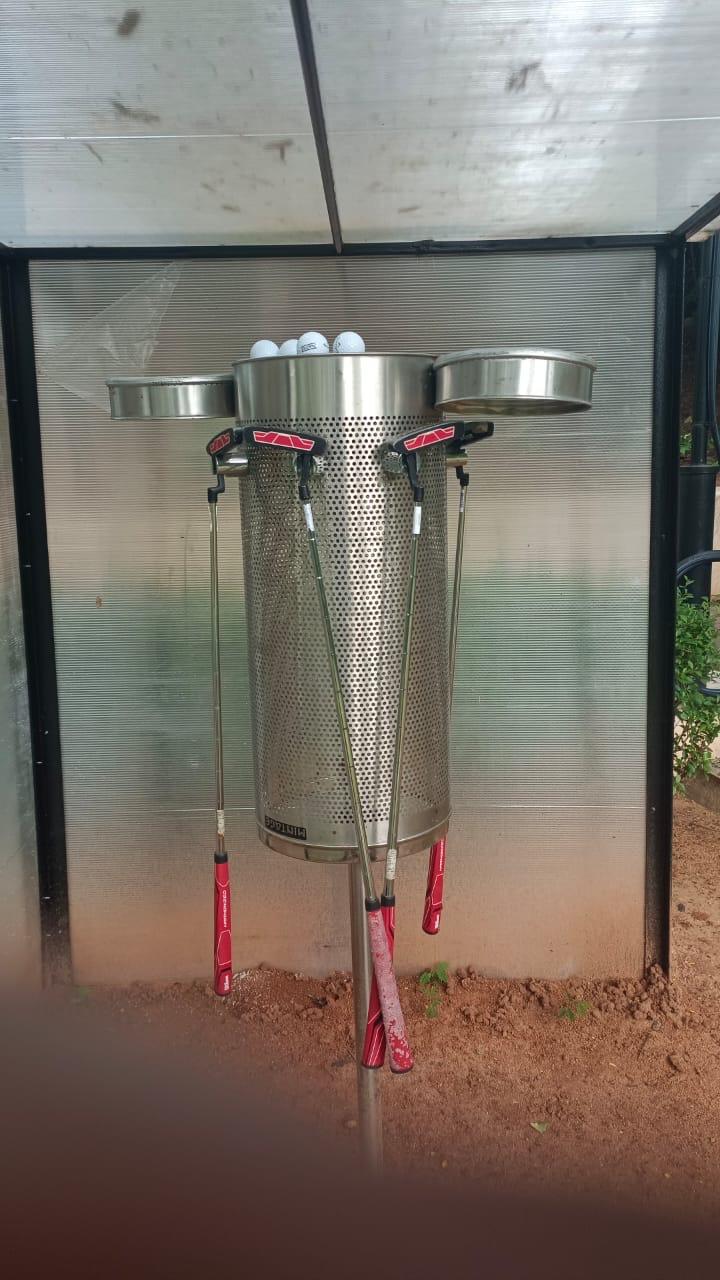

• It was easy for the employees to just walk to golf course, play a game and leave.
• Employees appreciated the proactive approach to ensure workplace experience.

Description of the Innovation:
Pump Dry Run Detection & Annunciator
• Due to negative suction, we are faced frequently air locking issue. For Daily operations, a designated plumber was kept on watch continuously to check the health of the motor and pressure vessel of hydro pneumatic system.
• In the absence of the plumber if the water pressure get decreased in domestic and flushing zone then it may lead to damage of motor bearing, and pump bearing chamber & mechanical seal.
• The Damage of motor and other parts involves high repairing cost and problems in day-to-day operations also equipment down time increased.
• We have installed 4 Pressure switch and Hooters in panel for individual flushing zone and domestic zone.
• The pressure switch kept a track of the water pressure and if the machine went in dry run, then it alerted the plumber by buzzing of the hooter and leading to automatic switching off the motor.
• The hooter was for alerting and take precautionary measures for the plumber
• Increased motor Durability.
• Saved man hours.
• Reduced system down time.
• The process upgradation helped in smoother running of operations in the facility.
• cost effective. Pump dry run detection & Annunciator system.
• Estimated Saving : 150K INR
myIdea

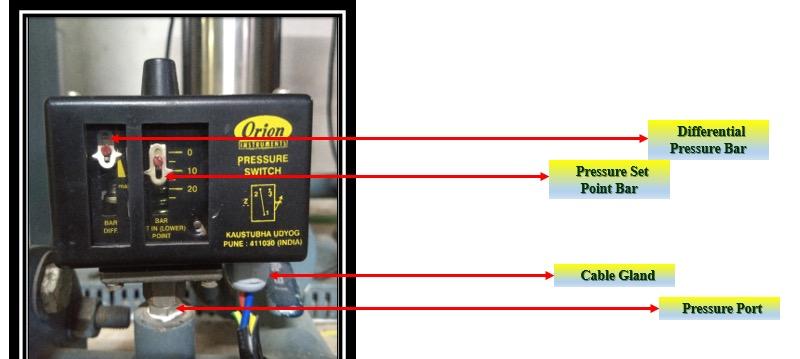
Description of the Innovation:
Fuel Leakage Detection System
CHALLENGE
• Existing HSD Diesel pipeline laid from HSD Storage yard to DG Day tanks had rusted and had leakages due to fair wear and tear which was impacting the flow rate
• Requirement was to detect and avoid the leakage and prevent soil contamination
MYIDEA / INITIATIVE / SOLUTION BENEFITS / ADVANTAGE
• Recommended to client to lay a new pipeline with Diesel leakage detection System.
• HSD Jacketed Pipeline had 80NB outer Pipe & 40NB inner pipe had multiple Leak Detection Sensors along the pipeline to sense the leakage
• External Mounting Type sensors with 24V DC input and RS485 output is transferred to HMI Panel Display
• The sensors detect the leakage and triggers an alarm to the maintenance team about the location of leakage spot..
• Sensors detects leakage of only Diesel by sensing Hydro-carbons present in diesel and will not detect water/ any other liquid.
• HMI Panel provides exact location where leak has occurred thereby making it easy for maintenance.
• Leak Detection System trips the pumps, prevents losses and provides fire safety.
myIdea
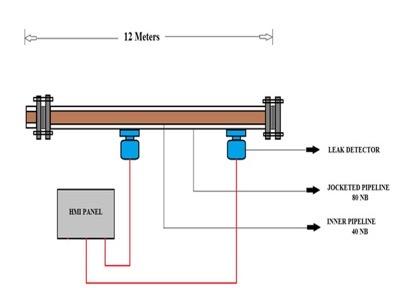
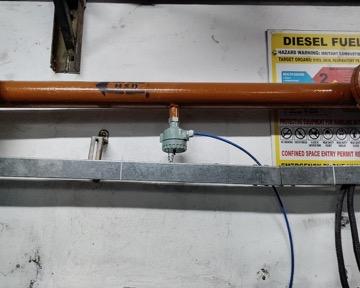
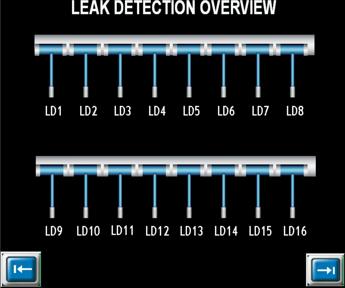
Description of the Innovation:
CHALLENGE
• Employees and visitors with disability was having challenges to access the facility.
• Modifying the existing infrastructure and making easy access for differently abled employees and visitor and achieving the Client ‘A’ level accessible global standards.
Accessibility
MYIDEA / INITIATIVE / SOLUTION BENEFITS / ADVANTAGE
• Modified PWD restroom with fully automated with remote operation.
• Providing tactile indicators for easy navigation to common areas and fire exit staircase.
• All signage standardized to braille format including staircase navigation signage on hand railing, Pantry cupboard, drawers etc.
• All main entry lobby doors of the building are automated including PWD restroom doors.
• Installed ergo car chair in office commute for differently abled employees and for the employees with medical history.
• Employees can experience the innovative range of new features that make Client’s campuses in Bengaluru one of the world’s most accessible workplaces.
• Employees and visitors with any type of disability can access to the building without any support.
• This building is the first facility to achieve ‘A’ level Accessibility global standards across client global portfolio
myIdea
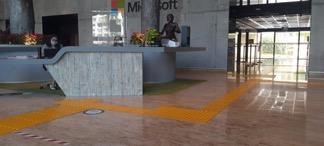
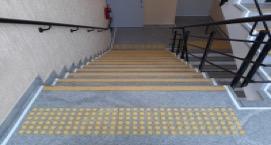
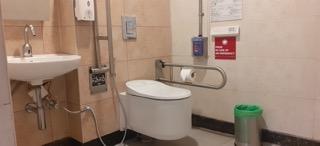
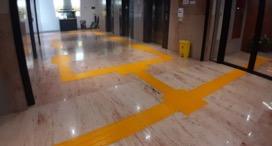
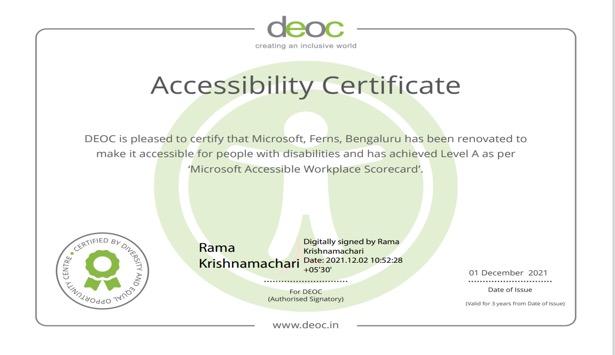
Description of the Innovation:
Handy Mirror
For Contact
Less Inspection
myIdea
CHALLENGE
• Difficult to access and identify the Condenser fan faults when chiller is in operation
• Requirement of visual inspection during Air cooled chillers operations
• If a ladder is used, we need at least 2 manpower
• Involved height work for visual inspection during operation
• Elevated platform occupy more space and involves additional cost
MYIDEA / INITIATIVE / SOLUTION BENEFITS / ADVANTAGE
• Contact less checking arrangement provided.
• We have conducted a HIRA study
• We have fabricated a telescopic mirror and put in to use
• Operator can easily use the telescopic mirror for visual inspection
• By ensuring visual inspection better operational efficiency is achieved .
• Employee safety is enhanced by avoiding a height work
• Cost saved in providing platforms for the air-cooled chillers
• One technician can easily inspect the chiller in shortest span of time .
• Saves valuable time

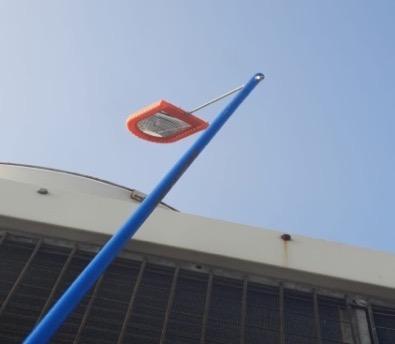
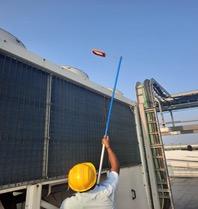
CHALLENGE
Description of the Innovation:
Kitchen Hood Fire Suppression System
myIdea
• It’s related to support staff safety, safety audit concern following National Building Code.
• As we all are aware, the risk of fire, if not mitigated completely can lead towards severe consequences i.e., loss of lives, damage to property etc.
• Kitchen being an open source not only for generating of fire but spreading the fire in short span of time.
• Presence of the oils and grease (which can easily spread) make it a volatile situation.
MYIDEA / INITIATIVE / SOLUTION BENEFITS / ADVANTAGE
• Installation of automatic fire suppression system in kitchen hood which is available above active equipment's as designed like hot plate, deep fryers.
• AFS takes the situation under control immediately after detecting the fire and once temperature in kitchen hood goes beyond threshold limit i.e..160c+within a matter of seconds
• Automatic arrangement to take situation under control during any untoward fire incident.
• Protect the kitchen area including ducts and plenums.
• Protect cooking appliances
• Better arrangement instead of having manual fire extinguisher operations.
• Having a fully protected suppression system establishes the safety of the working staff.
• Trained engineering staff and explained system functional.
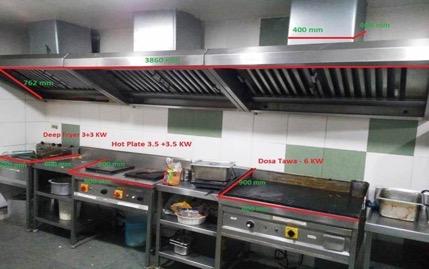

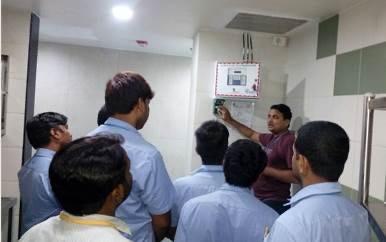
Description of the Innovation:
Virtual Audit Framework
CHALLENGE MYIDEA / INITIATIVE / SOLUTION
• Difficulty faced in conducting real time Health & Safety or Facility Condition assessment due to site inaccessibility during pandemic.
• CBRE team proposed virtual tours that emerged as a viable way to address this unexpected obstacle.
• A remote inspection using a tablet or smart phone, and a conferencing app like MS Teams.
• Facility Coordinator on site would connect with HSE Specialist through a conference call and would go around facility showing all important, critical and even landlord-controlled utility areas.
• HSE specialist can judge problems real time basis or after viewing the recording again and makes suggestion on how to correct problems.
BENEFITS / ADVANTAGE
• Continued focus on improving health and safety of workplace even when travel is constrained.
• Archived inspections recordings for reference.
• Enhanced assessment as any part of the recording can be seen multiple times.
• Sustainable solution even when pandemic is over and can potentially save travel and boarding cost.
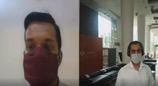
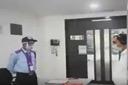
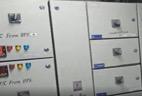
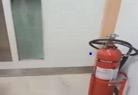
myIdea
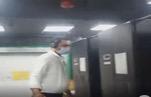
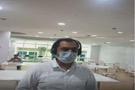
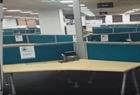
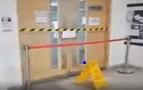
Description of the Innovation:
Hybrid HVAC Solar System
CHALLENGE MYIDEA / INITIATIVE / SOLUTION
• Reduction in Energy Consumption
• Getting to Net Zero
• Meet Sustainability Target.
• Integrating the Solar Panel with the refrigerant circuit of a VRF HVAC System to convert into a Hybrid VRF HVAC Solar System.
• In this system refrigerant is discharged from the compressor with moderate temperature and pressure into solar panel.
• Further solar Panel increases the refrigerant temperature with help of radiant energy obtaining from Sun.
• Refrigerant which is super heated in these Solar Panels increases the temperature difference between the refrigerant in the condenser coil and the air flow induced through the condenser at ambient temperature resulting in better condensation of refrigerant (subcooling) which results in unloading the inverter-based compressor eventually after a few refrigerant cycles, so the partial work of the compressor is got done through the Solar Energy
BENEFITS / ADVANTAGE
• Reduction in Energy consumption up to 30% and proportionate reduction in carbon footprint.
• Taxpaying profit-making company can avail depreciation benefit of 40% every year.
• No maintenance cost hence saves in OPEX
• Contributing towards Sustainability Targets of reducing EUI numbers and Carbon Emission reduction as the HVAC System is being partially operating on Renewable Energy (Direct Sun Light).
myIdea
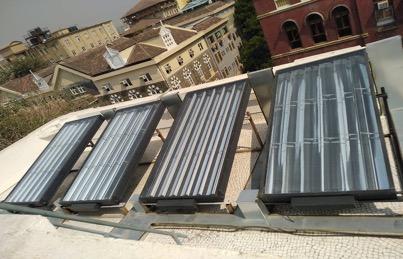
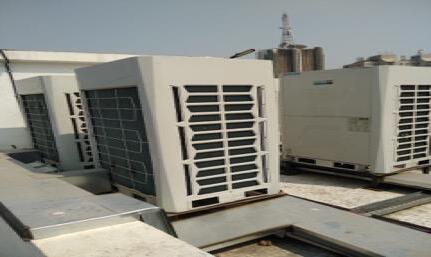
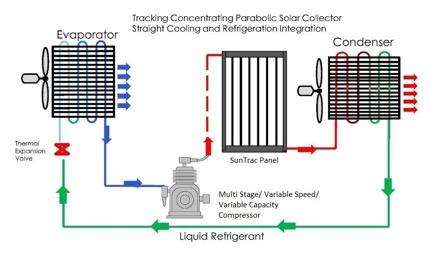
Description of the Innovation:
Lithium-Ion Batteries
CHALLENGE MYIDEA / INITIATIVE / SOLUTION BENEFITS / ADVANTAGE
• Lesser life span
• Weight
• HVAC requirement
• Higher charging current
• Larger space requirement
• Non-ecofriendlyFrequent replacement
• Faster deterioration
• CBRE approached client & recommended to switchover from SMF to Lithium-Ion batteries
• Lithium-ion batteries reduce total cost of ownership, both by doubling battery life and by operating at higher temperatures, reducing cooling requirements
• This lithium-Ion battery solution reduces battery footprint and weight by up to 70%, allowing more effective use of space
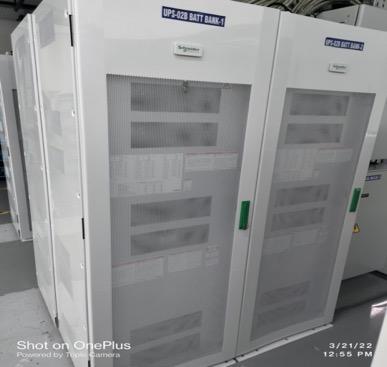
• Real Estate Savings: LIB required 1/3 rd of the conventional battery space
• HVAC Savings: The cooling requirement for the LIB batteries are 60% lesser than the conventional batteries
• Life Span: LIB has 3 times longer life compared to SMF
• Light in Weight: LIB banks are extremely light in weight & can avoid additional floor strengthening which is essential with the conventional batteries
• Energy Efficient: LI batteries draw less power for charging after every discharge cycle. This will reduce the power consumption by 10000 KWH / Month
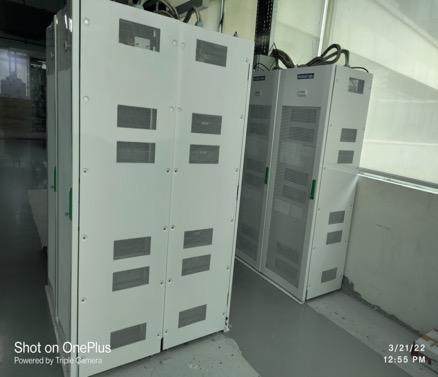
Description of the Innovation:
Touchless RO With Added Minerals
• Conventional RO Purification eliminates essential minerals like Potassium, Magnesium, and Calcium which can turn the water acidic – negative health impact.
• Usage of plastic in the form of Bubbletops used for supply of water
• Increased carbon footprint -High carbon emissions (i.e., air pollution) due to replacement of cans and transportation involved.
• Replacing packaged water cans with inhouse integrated water purification cum dispensation units (Contactless dispensation of Warm, Ambient and Cold water.).
• Remineralization of water with essential minerals
• Remote monitoring of treated water parameters such as TDS, flow and pressure, PH for better control on water quality
• pH balanced potable drinking water
• Touch points will be avoided
• Elimination of plastic bottles usage to store and consume water reduces the risk of microplastic leaching.
• Minimizes water wastage by reporting higher water recovery (i.e. up to 75%) compared to 60% recovery in conventional RO.
myIdea
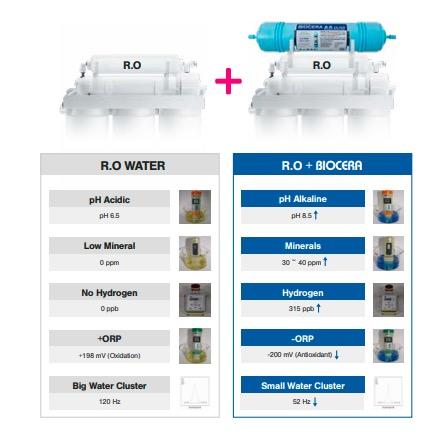

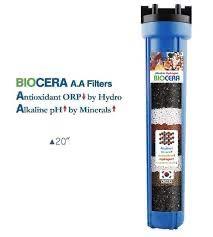
CHALLENGE
Description of the Innovation:
Green Initiative
myIdea
• Being a SEZ campus, disposal of plastic waste and approval from Customs Authorities.
• Eradicating plastic as much as possible and to avoid zero landfill
• Lack of awareness on creation of wealth out of waste
• The process of recycling is not transparent
MYIDEA / INITIATIVE / SOLUTION BENEFITS / ADVANTAGE
• With single bin concept drive across the campus(s) and zero plastic usage , we have removed about 4.5 k workstation dustbins and distributed about 2k of them at the nearest govt schools
• The unused plastic bins were further used for creating planter boxes
• To create more awareness on Ecological Sustainability, we have provided these planter boxes to the NGO partners
• The same has been also used at the campus driveways & common areas to improve the awareness and greenery
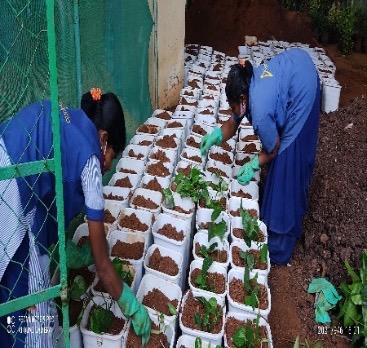
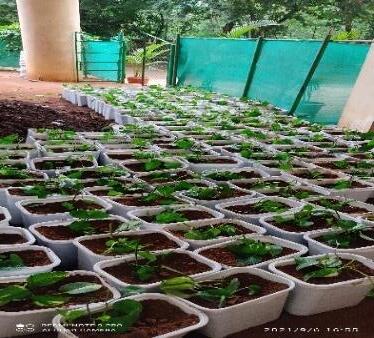
• Optimized the cleaning manhours along with saving of water associated to these bins.
• Minimized the Procurement of new planter boxes .
• Spread of more awareness on the 3R concept
• Under the platform of Community services this initiative had raised the bar of ecological sustainability .
• The said initiative has been

Description of the Innovation:
Duel Fuel Kit
CHALLENGE
• Pollution Board restriction on Diesel generators at Noida
• Carbon Emissions is very high in Diesel generators.
• Cost of fuel (Diesel) is very high
• High cost of Gas-generators
MYIDEA / INITIATIVE / SOLUTION BENEFITS / ADVANTAGE
• Arrange vendor technical and commercial proposals for retro-fit dual fuel kit installation in DG sets
• Arranged Site Survey by IGL to check the availability of PNG supply at NCR locations of client.
• Complete the application and agreement process with IGL to get the PNG gas connections.
• Dual fuel kit installation completed at all 3 NCR locations of Rockwell
• Reduction in Carbon emission – PNG gas CO2 emissions are Nil.
• Fulfilment of NGT/Pollution Board Compliance – Approved by CPBC (DG set usage is banned for winters)
• Reduction in operating cost – PNG is approx. 50% cheaper than diesel.
myIdea

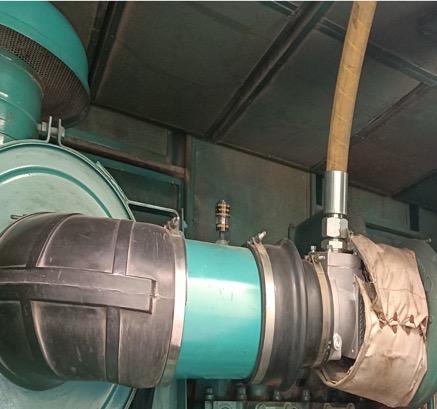

Description of the Innovation:
Smoke Detector Removal Tool
CHALLENGE
• Above false ceiling smoke detector maintenance was a challenge due its height.
• Due to poor maintenance of above ceiling SD there were false fire alarms.
• Tried possibility of additional trap doors which was not feasible as to maintain civil interior aesthetic
• Person has to climbed on heighted ladder to reach above ceiling which could lead to falling.
MYIDEA / INITIATIVE / SOLUTION BENEFITS / ADVANTAGE
• Verified as built layout of floor smoke detector for above false ceiling
• Pointed each single smoke detector on layout which was inaccessible due its location installation
• Checked any specific tools / extension rod available in the market to unlock and dismantle smoke from respective nearest point
• Arranged one suitable extension rod having unlocking female bracket on its head for easy dismantling
§ Enabled 100% maintenance of all smoke detector on regular frequency
§ False alarm trigger reduced resulted in productive office environment
§ Health & safety strengthened during maintenance while ladder arrangement and other height work avoided
§ Improved System healthiness.
myIdea
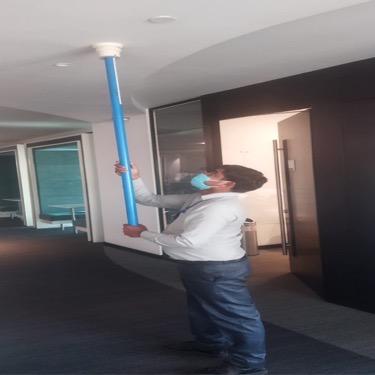
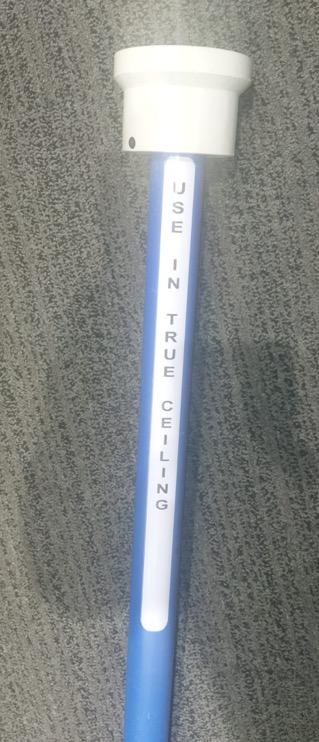
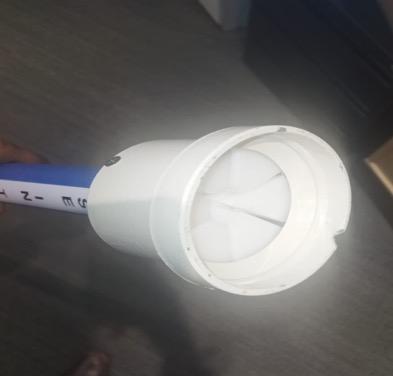
Description of the Innovation:
Portable Fan (Wealth From Waste)
CHALLENGE MYIDEA / INITIATIVE / SOLUTION BENEFITS / ADVANTAGE
• Breakdown of AC and unavailability of cooling
• During AC breakdown due to insufficient cooling, temperature may shoot up in critical areas.
• The rectification time of workstation area VRV cooling system is about 2-3 days depending on the availability of spares. This cause inconvenience to employees.
• To overcome the challenge, we need to place portable fans for cooling of the area as a makeshift arrangement.
• After brainstorming, we come up with an idea of utilizing the outdoor fans to make a high-speed portable fan.
• We have few PAC outdoors which are unutilized and going to be scrapped.
• By using the cut PVC pipes, we made a small portable structure on which we installed the PAC outdoor fan.
• By team effort and using scrap material, we made a high-speed portable fan in-house.
• Refer the image and video below.
§ Zero investment cost.
§ Team engagement to ideate.
§ Made 2 Portable high-speed fan.
§ RPM 1350 capacity, 3 level speed control.
§ Portable and moveable.
§ Safe & Easy to use.
§ Utilizing for cooling of critical and workstation area while AC breakdown.
§ Saved Rs. 60,000/- as a procurement cost of 2 fans.
§ Client Satisfaction.
§ Best out of waste.
myIdea

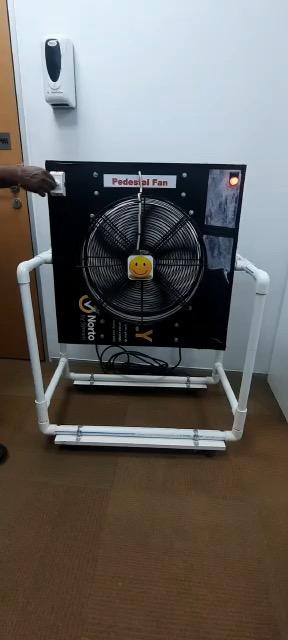
Description of the Innovation:
ERC (Eat Right Campus) Certification
CHALLENGE
• Providing healthy lifestyle, right choice of safe and nutritious food to employees.
• Maintaining high level of food safety standard
• Improvement on three key themes/pillars: –
• Eat Safe - Ensuring personal and surrounding hygienic and sanitary practices .
• Eat Healthy - Promoting diet diversity and balanced diets, eliminating toxic industrial trans-fats from food.
• Eat Sustainable - Promote local and seasonal foods.
MYIDEA / INITIATIVE / SOLUTION BENEFITS / ADVANTAGE
• EAT RIGHT Certification for Campus
• Engaged the consultant to assist us in setting up the process and standard of Eat Right & approach Food & Safety Standards Authority of India.
• Benchmarks have been created on four different parameters (Safe food, Healthy food, Sustainable food, Building awareness) based on which campuses are evaluated and certified as 'Eat Right Campus’
• Based on the result percentage, rating stars will be given, we need to achieve above 85% to get the FIVE STAR rating.
§ Making right choices of food based on the individual requirement.
§ It ensures the food offerings served to the employees is always helps to maintain the health and hygiene.
§ Safe, healthy and sustainable food in the campus would reduce the incidence of food borne illnesses.
§ More than just monitoring food or nutrients It helps handling the high standard practice of the food served in the campus.
myIdea

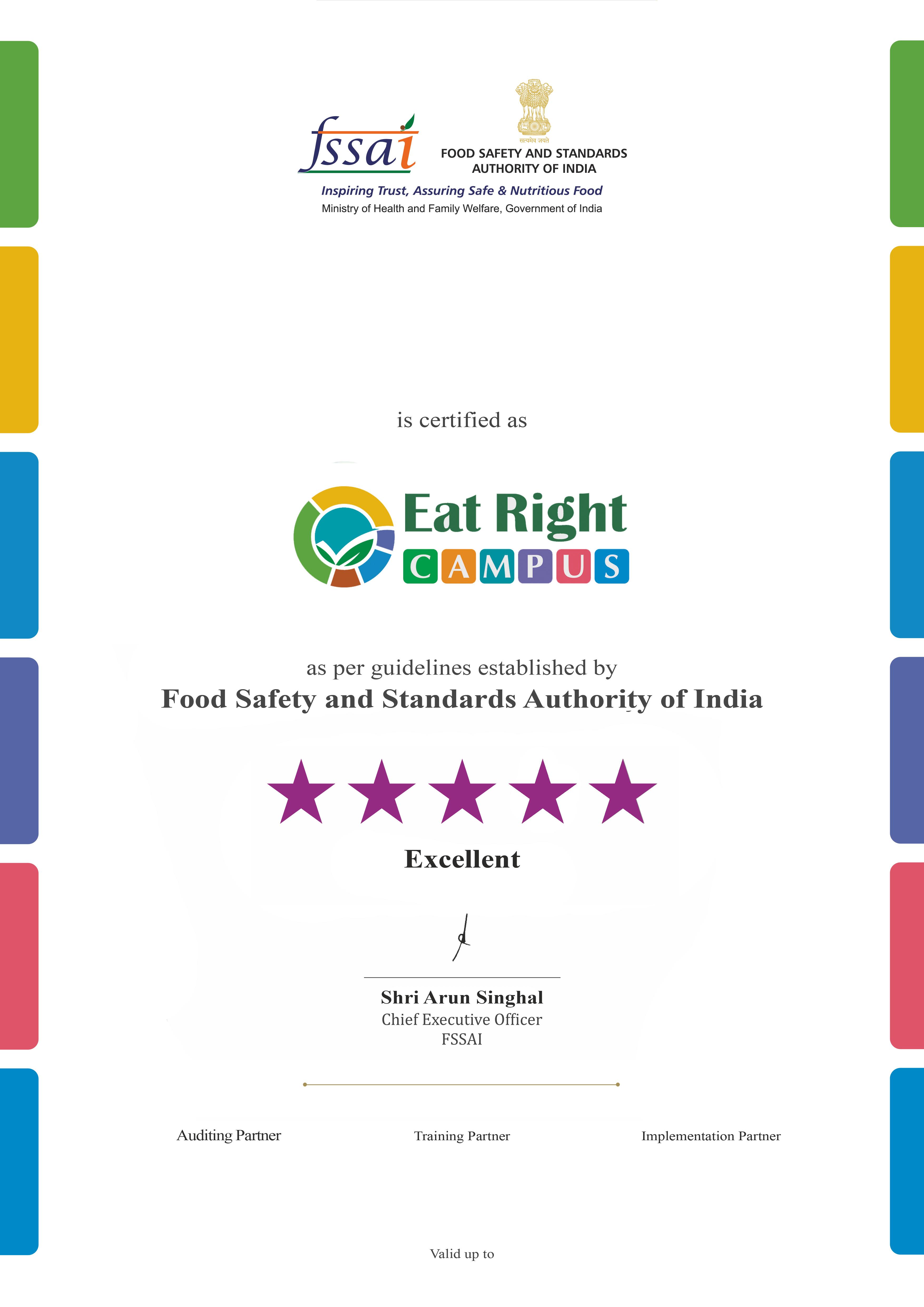

Description of the Innovation:
Restroom Automation
CHALLENGE MYIDEA / INITIATIVE / SOLUTION BENEFITS / ADVANTAGE
• Frequent complaint on cleaning and foul smell
• Real time washroom monitoring was critical
• Restroom users count
• Refilling of liquid and tissue roles
• When everything is located efficiently, maintenance is done on demand, and refills are attended timely - customer experience rapidly improves
• We have installed the sensors for washrooms at various levels
• Installed Tab to get instant feedback
• HK supervisor/Janitors will get notification on their mobile to attend the issues
• Smart facilities management dashboard for data visualizations and alerts
• Get a live view, of geo-specific data across all your washroom facilities 24/7.
§ Need based cleaning,
§ We got real time data
§ Rational usage of manpower
§ Instant feedbacks will provide the insightful data
§ We can get the notifications/escalations through mobile app
§ Optimizing Refills
myIdea
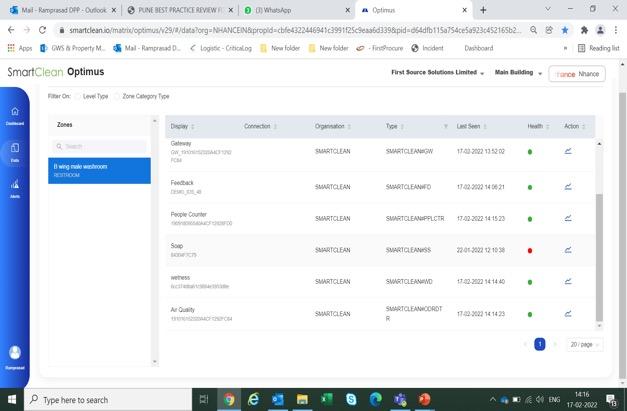
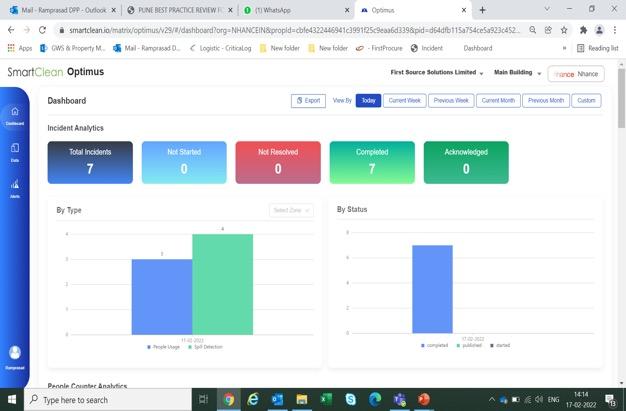
Description of the Innovation:
Work
Safety Card
myIdea
• Self assessment of risk at work for all service staff manually managed.
• Incident escalation only monitored by top level management
• Support partner teams on ground unaware of the process in the situation of an incident occurrence.
• Introduction of Self Assessment Card, with step-by-step instructions that need to be followed prior start of work/ during incident
• Introduction of safety card enhanced awareness amongst FM staff on the safety process to be followed and possession of safety card with the staff at all times
§ Ensures a safe workplace with immediate risk identification around every moment of any activity
§ Nobody gets hurt
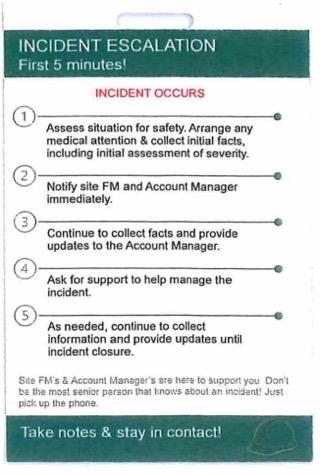
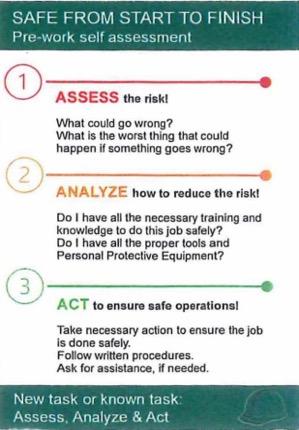
Description of the Innovation:
ACB Replacement & Enhancement
CHALLENGE
• The Air Circuit Breakers (ACBs) were 18 years old.
• Breakers were obsolete – No service support.
• Age related issues could cause unplanned downtime event.
• High maintenance cost.
• The maintenance activity was very difficult due to weight of the breakers.
• ACBs were not BMS compatible and did not have some modern features
MYIDEA / INITIATIVE / SOLUTION BENEFITS / ADVANTAGE
• We initiated discussions with multiple vendors and selected specifically designed ABB Breakers to preserve the existing framework.
• Decided on replacement of obsolete breakers using retrofit kits retaining the existing panels with minor modifications.
• A thorough scope analysis carried out and detailed scheduling done to implement with minimum downtime.
• Successfully completed upgradation of existing GE breakers to ABB breakers within shutdown change window.
§ Improvement of safety and reliability.
§ Low investment costs compared to those required for the installation of a new switchgear panel.
§ Minimum shutdown of the switchboard.
§ Improved System protections.
§ Cost reduction of maintenance and repairs.
§ Continued spare parts availability.
§ Ease of maintenance and functionality of the system.
§ Compatible for BMS integration.
myIdea
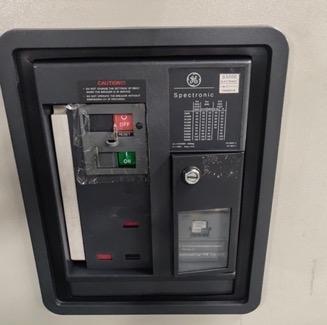
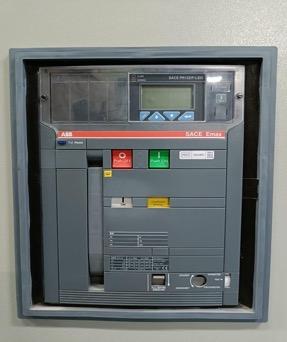
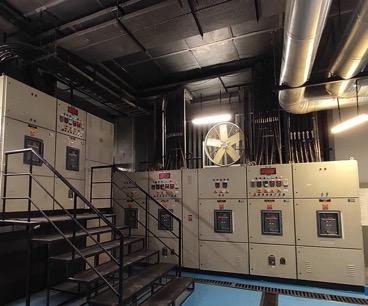
Description of the Innovation:
AFD For Energy Conservation
CHALLENGE MYIDEA / INITIATIVE / SOLUTION BENEFITS / ADVANTAGE
• 150 TR Chillers were operating with max frequency through star -delta starter without feedback control of set points variations
• Observed Heavy noise during full load chiller operations
• Energy consumption without AFD with the star- delta operating model is more
• The depreciation factor of chillers were getting effected
• During less load on Chillers, it was often subject to frequent starts and stops.
• Installed AFD for 150 TR Chillers
• AFD allows the chiller to meet the system load conditions and maintain the lowest possible kW/ton
• AFD control logic is integrated with the chiller controls to optimize chiller efficiency, reliability and drive performance
• Variable torque and soft start reduces the risk of motor and compressor damage. Compressor motor is started using low frequency and voltage
§ AFD helps maximizing chiller efficiency and reduces power consumption , IKW decreased from 0.72 to 0.65.
§ Chiller noise got reduced to almost 12 dBA with an AFD.
§ Energy Savings Calculations as per actuals
myIdea
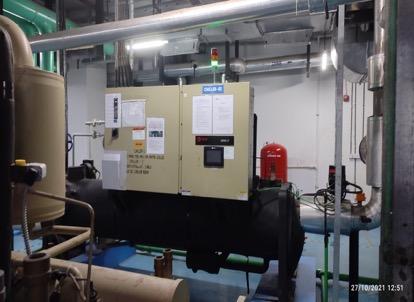
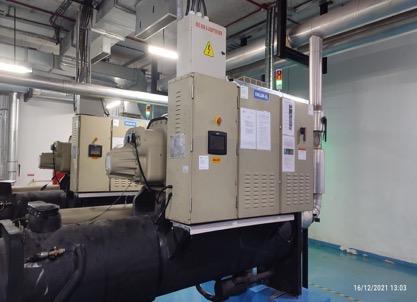
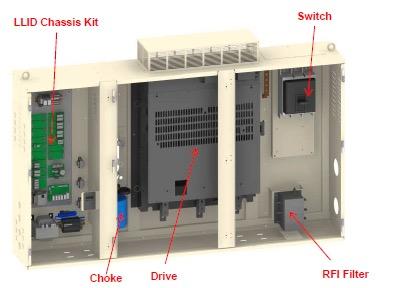
Description of the Innovation:
Adiabatic Cooling System
CHALLENGE MYIDEA / INITIATIVE / SOLUTION BENEFITS / ADVANTAGE
• Frequent maintenance: Need to maintain the Condenser cooling coil clean & tidy.
• Less Efficient: At high ambient conditions fail to deliver required cooling capacity
• Less durability: Life of cooling media reduce due to rust, dust, calcium, limescale build-up and direct sunlight radiation.
• Energy losses: High energy consumption during summer season
• Chiller performance ensures reliability of cooling operations during high ambient condition.
• High evaporation results better Heat transfer between system ( Chiller ) & surrounding ( Atmosphere ).
• Adiabatic Membrane acts as protective barrier for moisture carryover to condenser Coil.
• Higher chiller efficiency with lower electricity consumption with adiabatic system..
§ Compressor life: Protects chiller condensers and prolongs service life of compressors.
§ Carbon reduction of 80.16 MT/Year estimated
§ Enhanced Energy savings of 160 Mwh/Year
§ Cooling capacity- Increase in chiller cooling capacity up to 41%
§ Estimated Saving- 13260 USD/Year
myIdea
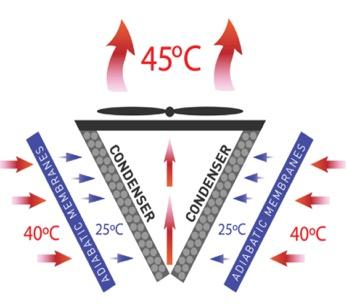
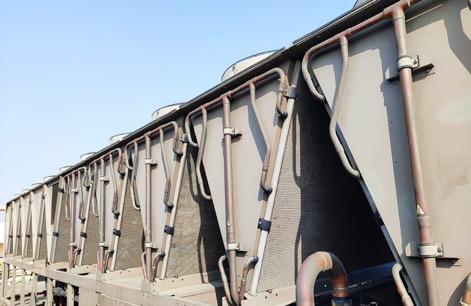

Description of the Innovation:
Hydrogen Sensor Integration With Exhaust
• Battery rooms are almost like a confined place where an explosion may take place whenever the concentration of Hydrogen reaches its LEL
• The concentration of H2 increases during the charging cycle of lead acid batteries
• Hydrogen is explosive at 4% of the volume of air. If the leak goes undetected, it creates a potential explosive in the atmosphere
• Hence, the need for automatic controller is mandatory for larger battery room
• Installation of hydrogen sensor and integrated with an exhaust fan to avoid the potential threat of accidents
• The exhaust Fan will exhaust the air and concentration of h2 only in case of any detection of hydrogen beyond prescribed levels. (2%)
• For higher safety levels, installed standby h2 sensor
• Control panel connected with hooter to trigger the alarm when reach the detection set point 2%
§ Occupational hazard is mitigated
§ Safety compliance
§ Automated ventilation
§ Risk free atmosphere at battery room
myIdea
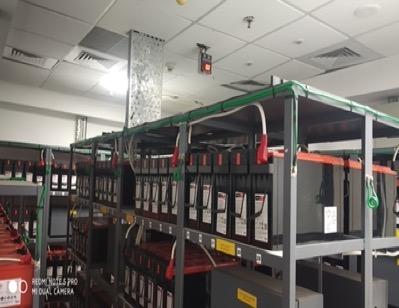
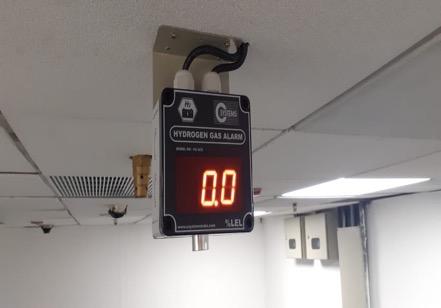

Description of the Innovation:
5S in Energy Conservation
CHALLENGE
• Switches for desk lights are altogether in passage area/pillars.
• Employee finds very hard to choose the switch pertaining to their respective lights .
• As a result, they either turn on/off some other light or they turn on/off all lights.
• Most of time when there are less employees, all lights are on.
• This in result more unit/power consumption.
MYIDEA / INITIATIVE / SOLUTION BENEFITS / ADVANTAGE
• Each switch is connected to the light of a particular area, we decided to provide a specific number to the switch and the same no. is provided to the employee desk as well.
• We connected with the printing vendor for stickers and in 2 days time we were having the stickers with us.
• Same is discussed with internal team and work started phase wise where one sticker is pasted on to the switch and the same sticker was pasted on the desk of the employee.
§ Now employee can easily recognize the light that belongs to their work desk.
§ No wastage of energy.
§ There is a behavioral change in the employees, along with that they now switch off conference room lights, AC, Projector also when they finish off their meeting.
§ Employee now proactively tell us if something is unnecessarily running, and it needs to be stopped.
§ It maximized employee contribution towards energy saving.
myIdea
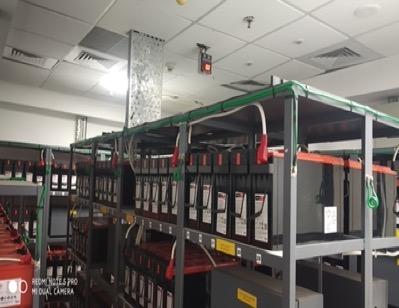
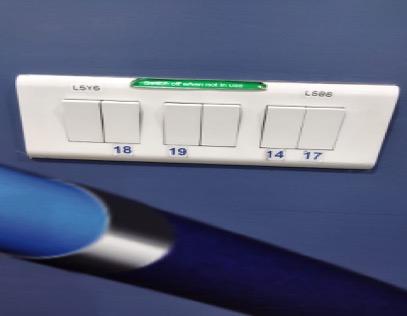
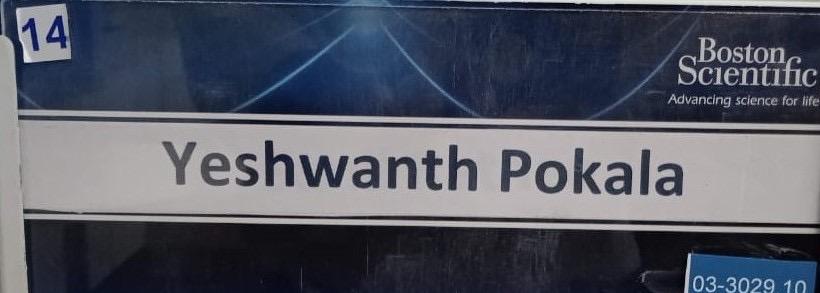
Description of the Innovation:
UVGI System
For Improved IAQ
CHALLENGE MYIDEA / INITIATIVE / SOLUTION BENEFITS / ADVANTAGE
• Poor Indoor and Outdoor Air quality is a major challenge in pollutants seasons.
• Outside Air contains mold, spores, bacteria, viruses and VOCs.
• The virus spreads mainly from personto-person transmission in 3 basic modes:
• Direct air-borne transmission between people
• Indirect surface-borne transmission via contaminated surfaces
• Indirect air-borne transmission through air flows
• UV light photoniser to deactivate DNA of any microbe, pathogens, mold spores, bacteria, viruses, etc., preventing them from re-entering the air
• Improved IAQ in recirculated air (50%99% reduction in airborne microbes)
• No build up of microbial colonies, mold and mildew on the HVAC cooling coil.
• Design based approach - Configurations designed for full coverage of cooling coil
§ UV Light improve Air Quality by killing irritants, which can make people sick
§ Reduce mold and mildew. UV Light develop a robust air purification system and eliminate Fungi, germs, bacteria and viruses.
§ UV light improve the Indoor AIR Quality by eliminating the germs and help eliminate excessive moisture
§ UV Light eliminate organic building on cooling coils and ducts, so it kills pathogens and micro- organisms that would attack other people
myIdea
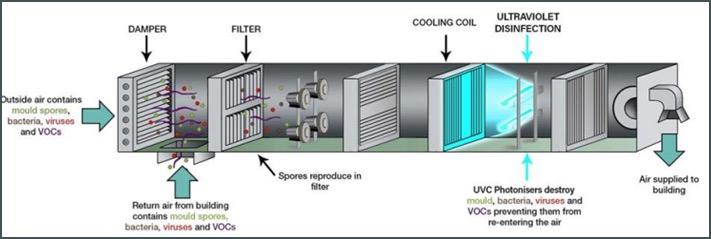


Description of the Innovation:
Integration of all building fire panels
CHALLENGE MYIDEA / INITIATIVE / SOLUTION BENEFITS / ADVANTAGE
• The entire campus has fire alarm panels located individually for all the block which are independent to the command control room
• In event of fire the operator at block level control room receives the information of the fire through the indication on the fire panel which is then notified to main command center over walkie talkie.
• This process might experience unwanted delays in responding during the actual scenario of fire cascading to the quantum of damages caused by the fire
• A structured study was done to identify permanent and effective measures to eliminate the possible delays in containing the actual fire.
• It was imperative to identify the geographic location of the fire and was decided to install a Master repeater/Mimic panel in main command center.
• All the fire panels is integrated with main panel in command center
• In case of fire the alarm/alert will now be communicated to both blocks as well as main control room
§ Considerable reduction in response time during fire alarm notification
§ Fire alarm can be captured in both the control room and Fire station both are 24/7 Operation
§ Pictorial representation of the blocks shows the identification of the fire location clearly.
§ Communication errors will be eliminated.
§ Panel clearly demarcates the detailed view of FCR and other areas like HSD yard, OWC, Gas bank etc. with nomenclature
myIdea
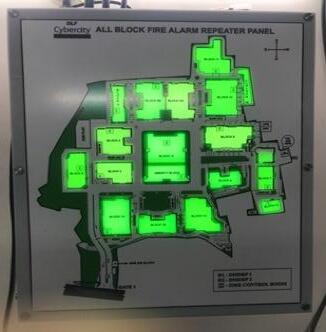
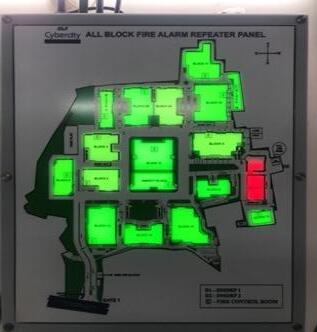
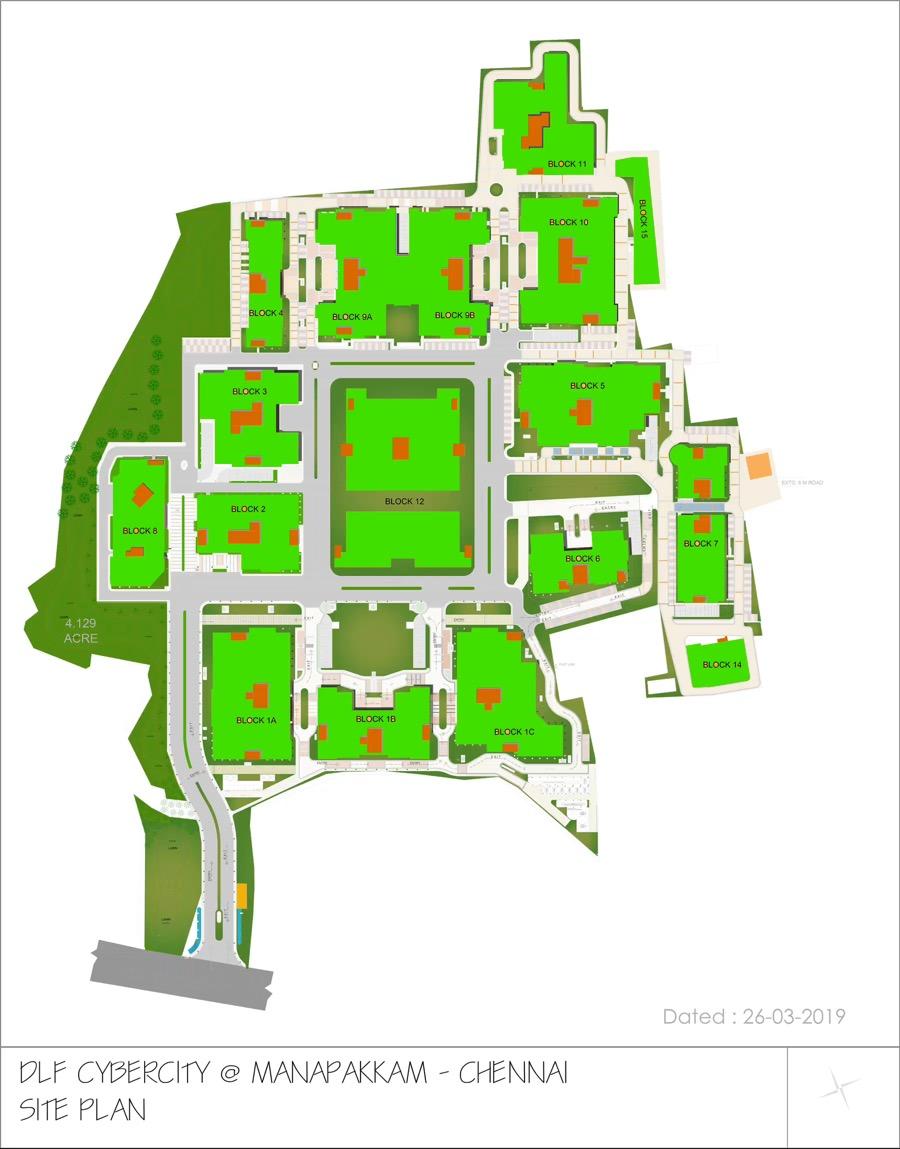
Description of the Innovation:
CertificationUnderwriters Laboratories
CHALLENGE
• In addition to the normal day to day operations we have to spend lot of time in planning and executing tasks related to this certification.
• Already multiple certifications like IMS, Well HSR, 5S etc. were in pipeline within the same period/ immediately following this
• Being 1st of its kind in Asia there was no precedence to prepare for achieving the standards required as per the certification body
• Preparations of various check lists and Process / SOPs as per the requirement
MYIDEA / INITIATIVE / SOLUTION BENEFITS / ADVANTAGE
• Scheduling a broad certification process timeline
• Proactively anticipating the shortcomings in audits and closing the same.
• Allocated team as per their expertise domain to spear head the respective certifications.
• Involvement of clients encouraged to have better results especially in terms of AHU operations and maintenance of indoor air quality
§ 1st Commercial building to get UL certification in Asia, 16th Globally.
§ With the employees beginning returning to work, the certificate is gained the trust of our clients by achieving the certification.
§ Employee RTO increased from 500 to 2000 Approximately and expecting the 50% increase of RTO in the near future.
§ Age of the campus (17 years) has been defied and certification achieved with the existing infrastructure
myIdea
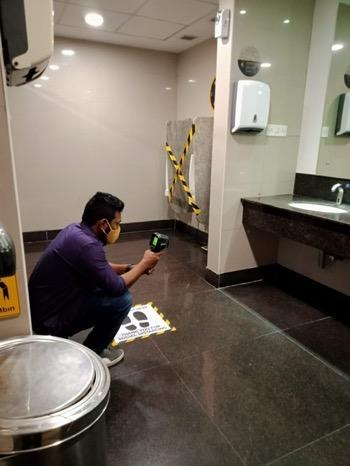

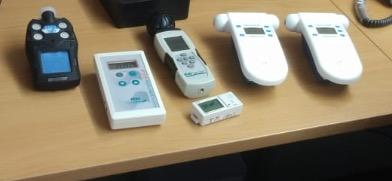
Description of the Innovation:
IOT based breaker status monitoring
CHALLENGE
• Each building having more than 100 LT breakers and it is difficult to monitor critical breakers.
• When there is a power fluctuation or Power changeover from EB to DG and DG to EB monitoring of breakers is difficult.
• Senior team has to visit Electrical rooms when any Power changeover.
• Tracking of changeover time is difficult.
MYIDEA / INITIATIVE / SOLUTION BENEFITS / ADVANTAGE
• Provided indication lamps in parallel to Breakers but it is visible to only person who are in Electrical Room.
• Integrating with BMS is expensive, then also we can't get real time data to everyone.
• Finally decided to go with IOT based breaker monitoring device to know the critical breakers ON/OFF status through telegram application.
• No down time required, only breakers potential free contacts required to know the status.
§ Critical breakers status (ON/OFF) can be monitored remotely, whoever registered in Telegram application.
§ If any Power changeover or Breaker ON/OFF, you will get notification in Telegram app, so that we can have track on critical breaker operation.
§ We can track Breaker ON/OFF timings.
§ Delay in power changeover can be calculated, based on breaker ON/OFF timings.
myIdea
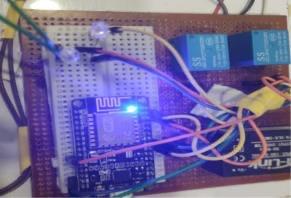
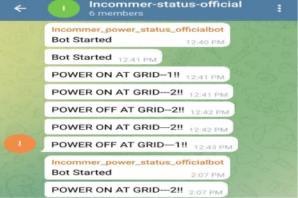
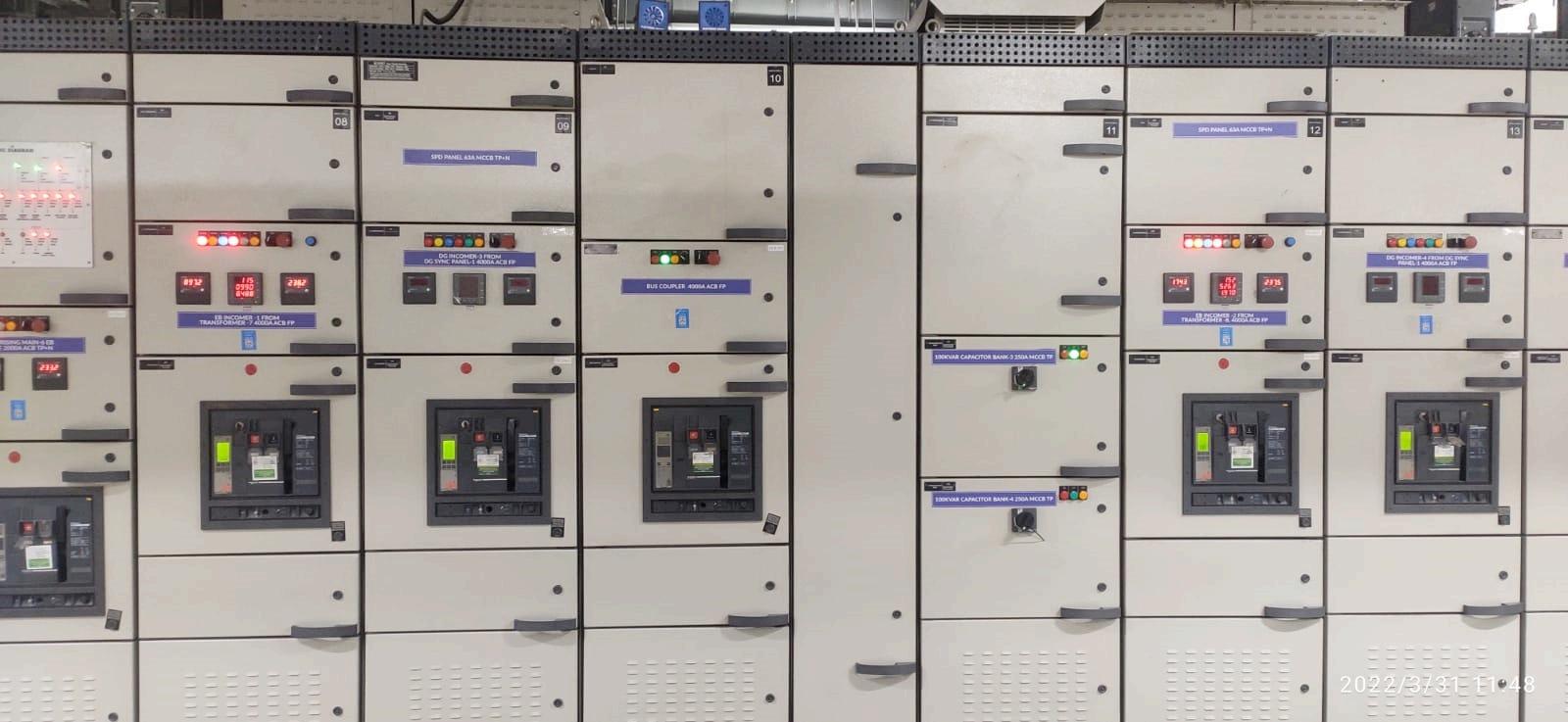
Description of the Innovation:
Phase Sequence
Relay
myIdea
CHALLENGE
• There is lack of safety in the existing Electrical system.
• In case of phase reversal from sub station end or while cable get repaired there were no safeties in our system to monitor phase reversal.
• This affecting the UPS which starts on backup due to unhealthy HT supply.
• Also, motors gets started in reverse direction, lifts & chillers not get operated.
MYIDEA / INITIATIVE / SOLUTION BENEFITS / ADVANTAGE
• To Install a system which can easily tackle the problem of changeover during phase reversal.
• A system which can keep safe our allcritical equipment during phase reversal and phase loss.
• Finally, after having several meetings with OEM & team and after taking client consent. We have decided to Install a phase sequence relay in HT panel to monitor the grid supply.
§ Phase sequence relay will get activated in case of phase loss or phase reversal in grid supply.
§ It help in safeguarding the UPS from unexpected breakdown and to avoid it going to backup mode.
§ Safeguarding of motors to avoid running in reverse directions.
§ Smooth operation of lifts.
§ Smooth operation of chillers.
§ Reduced switching operation of VCB.
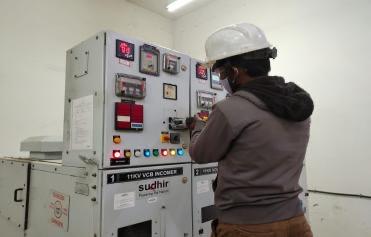
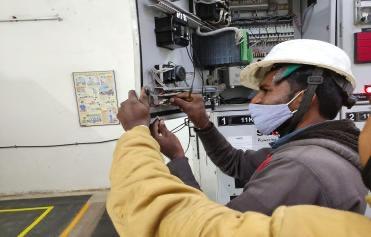
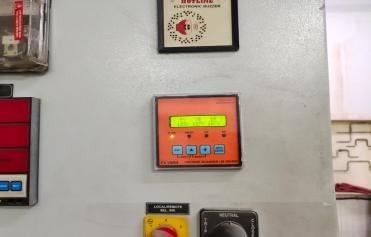
CHALLENGE
Description of the Innovation:
UPS Power for Lifts
myIdea
• Schindler elevators have ARD but work only during Total power failure. ARD does not function during changeover or when power fluctuates.
• Standard practice followed by elevator industry is service engineer attend entrapment issues after 10 minutes of registration.
• Poor ventilation inside Schindler elevators means claustrophobia to passengers.
• Senior citizens, children, ladies may fear to use these elevators due to safety factor.
MYIDEA / INITIATIVE / SOLUTION BENEFITS / ADVANTAGE
• After discussion with OEM, advised them to install an additional UPS connecting only Fans & Light of the elevators with minimum duration of 30 minutes during power outage OR entrapment situation.
• Focusing on Safety resulted in placing an additional intercom inside both elevators and connected it to the building EPBAX.
§ Improvement in Safety, Security & Reliability.
§ Instilled confidence in users.
§ Seniors, children, Ladies comfortable during use.
§ Installation of separate UPS for Lights & Fans ensures uninterrupted power supply if elevators stall.
§ Intercom connected with EPABX provides users ease to ask for help and assistance during any emergency.
§ Intercom connected with EPABX provides ease to connect users with all concerned persons for help
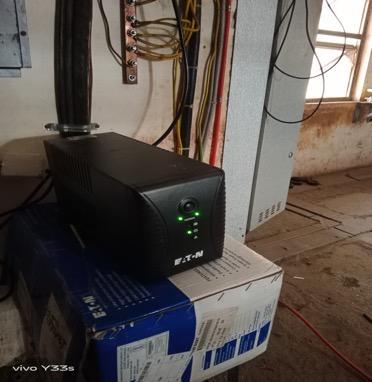
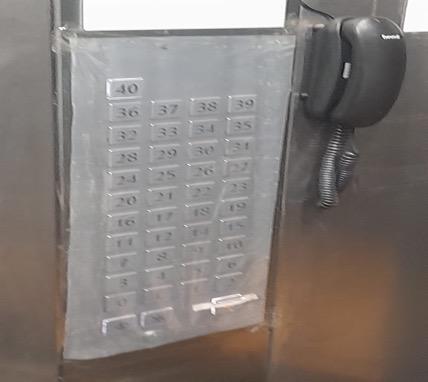
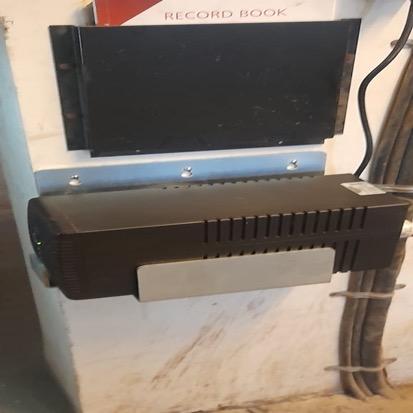
Description of the Innovation:
Power Control Centre
CHALLENGE
• One of our Power Control Center is unmanned.
• In case of any power issues in the outgoing feeders, the same were unnoticed as there was no provision to alert.
• The restoration could be initiated after receiving communications from end users in case of any tripping.
MYIDEA / INITIATIVE / SOLUTION BENEFITS / ADVANTAGE
• With brainstorming, it has been decided to fix annunciator panel with alarm, to identify the faults in the unmanned power control center.
• Same has been initiated with the annunciator panel connected with essential feeders.
• One repeater panel was also installed near Property Management office that is manned round the clock.
§ With the above initiative, an alarm is triggered whenever the essential feeder(s) tripped.
§ The team is able to react immediately by checking the annunciator panel to identify the fault location and initiate rectification.
§ Reduced TAT to respond, without awaiting end user communications.
§ Received appreciation from client on this initiative, that resulted in reduced customer complaints.
myIdea
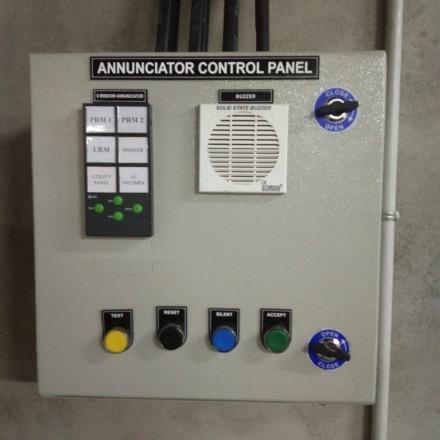
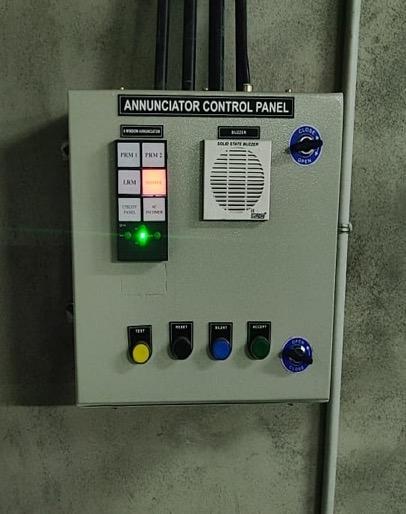
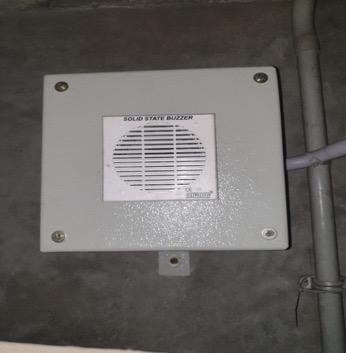
Description of the Innovation:
Automatic Chemical dosing system
CHALLENGE MYIDEA / INITIATIVE / SOLUTION
• The water parameter changes when the blowdown is given at regular intervals and maintaining all key parameters is a challenge by the manual dosing method
• The auto dosing system available product has no flexibility in using the present chemicals and adds up the initial investment cost to 4 times and monthly consumable cost to 2 times.
• The makeup water & Chemical consumption is high in manual dosing
• An Integrated automatic Chemical dosing system is fabricated and installed for dosing three key Chemicals to maintain the PH, Phosphonate residual level, and residual chlorine levels to prevent the Cooling Towers and Chiller system from corrosion, scale, and algae formation in the condenser circulating water.
• This new system monitors the TDS levels in the circulating water and command for blowdown if it reaches 1500 PPM and stops at 1400PPM.
/ ADVANTAGE
§ 25- 30% Reduction in water consumption (40KL/ day)
§ 15- 20% reduction in chemical consumption
§ Increases equipment’s lifespan
§ Reduces/eliminates scale / algae formation and corrosion thereby increasing the efficiency of the chiller system
§ SMS alerts to building manager are inbuilt to raise alarm when water parameter is increased / malfunction in system
§ E.coli and Legionella growth is controlled by monitoring.
myIdea
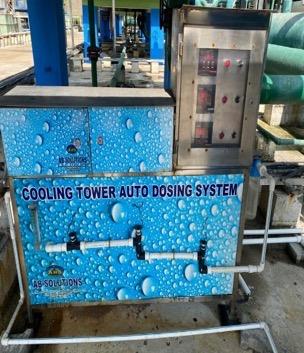
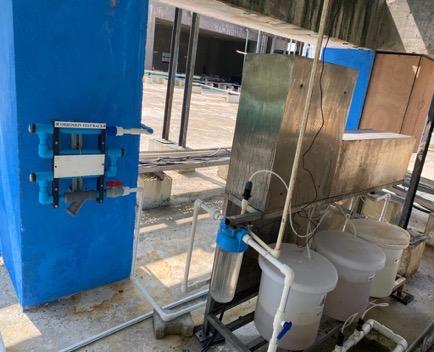
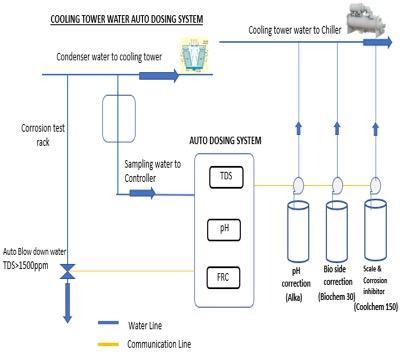
Description of the Innovation:
Innovative Learning Centre
CHALLENGE
• Training security staff about their roles & responsibility during 2 days induction/OJT.
• Undue escalation from tenants and clients.
MYIDEA / INITIATIVE / SOLUTION BENEFITS / ADVANTAGE
• Discussed among the team, our client & senior leadership. Framed a plan to creat Learning Centre :-
• Building miniature with details of floor wise occupation, details of building escalation matrix & entry/exit.
• Wide display board with brief of duties & responsibilities in multi language with pictorial presentation
• Utilise the waste materials like thermocols/plies from scrap yard to bring down the costing.
§ Building miniature with pictorial demonstration easing the understanding of guarding staff.
§ Displaying the details in multi language (Hindi & Telugu) is more easing the understanding.
§ Everything in one room, giving a glance of basic information related to the campus & duties.
§ Reduced the undue escalations and helping the staff to perfrom better, with client satisfaction.
myIdea
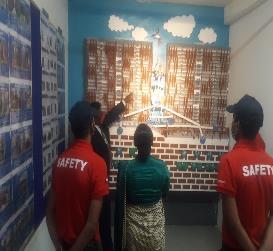
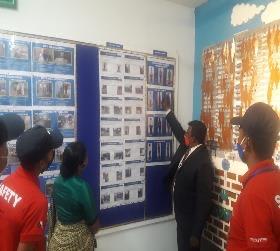
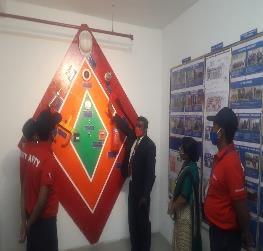
Description of the Innovation:
Play Area –
A Wellbeing Initiative
CHALLENGE
• The area was used as a waste dump-yard in 2018 and we started to work on this to make it into a usable play area.
• No space availability for children to play Ball games.
• Without fence, sometimes Ball hit people walking on the road which leads to injury.
MYIDEA / INITIATIVE / SOLUTION BENEFITS / ADVANTAGE
• As a solution, we converted the space into Play Area.
• Got the MS pipe fixed at a distance of 15 ft*10 ft (3300 Sq.ft) and got the green net tied on the pipes to create fence around the area.
• Kept 2 nos. goal posts at the Play area.
• Also, we have fixed 8 nos. LED flood lights of 50W each on the pipes to enhance lux level.
§ Utilized Space for children.
§ Reduced chances of injuries.
§ Enhanced children safety.
§ Resident and client satisfaction index improved.
§ Aesthetics of the area has improved.
myIdea
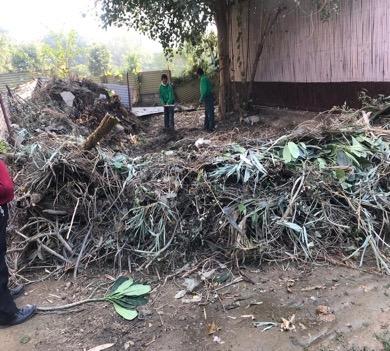
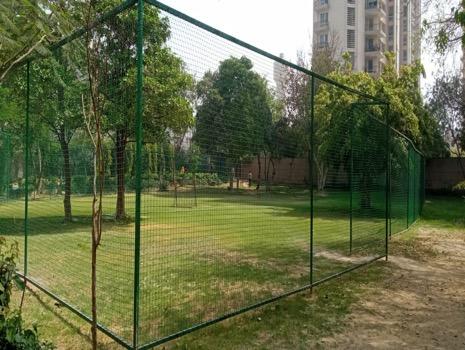
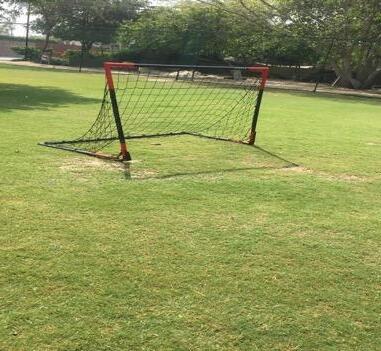
Description of the Innovation:
Replacement of metallic fan with FRP
CHALLENGE MYIDEA / INITIATIVE / SOLUTION BENEFITS / ADVANTAGE
• Metallic fan blade was damaging the gear box and shaft.
• Risk of Damaging the system.
• Break down happening frequently
• Discussed with vendors and evaluated the possible options
• Replaced metallic with new FRP fan blade.
• To avoid to damage the gears box and shaft.
• Installation of this FRP fan blade to save the energy also.
§ Estimated Saving : INR 684000
§ Area : Cooling Tower-Year-2022
§ Power consumption by existing CT Fan (02Nos)
§ Nos of save unit per year with operation of 365days x 24Hrs-KW 33638.4
§ First Year saving Per unit Cost is INR-18 / INR605491.2.
§ Saving in Five Years INR-3027456
§ Total saving in 05 Year after expenditure (LM)INR-2379456
myIdea
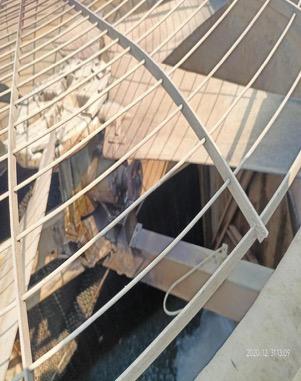
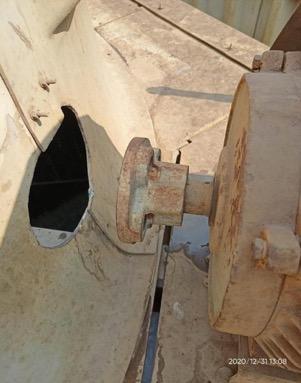
Description of the Innovation:
UPS Functionality
– LIVE Demo for training
CHALLENGE MYIDEA / INITIATIVE / SOLUTION BENEFITS / ADVANTAGE
• To understand operation process it takes more time and at times difficult
• To carry out the root cause during any breakdown
• Inhouse team confidence level not up to the mark.
• Practical knowledge for newcomers in site.
• Organized the team to prepare the model with required materials.
• Few materials taken from scrap to make the live demo.
• The system setup arranged with inhouse team.
• Understand the equipment safety precautionary measures.
• Training has been given to all inhouse team.
§ Get an understanding of the process.
§ Get answer to help technician’s decisionmaking process.
§ Live demo to our team helps to understand how the solution truly solves the pain points and enables them to become more successful in their job.
§ An effective way to address the specific concerns and improve the confidence level.
myIdea
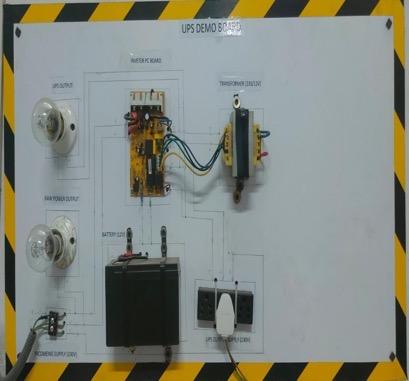
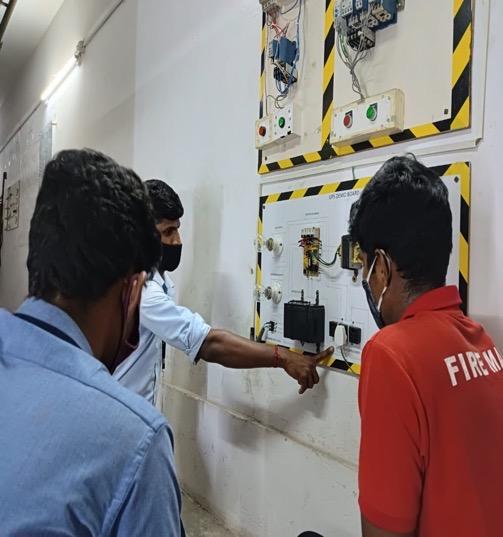
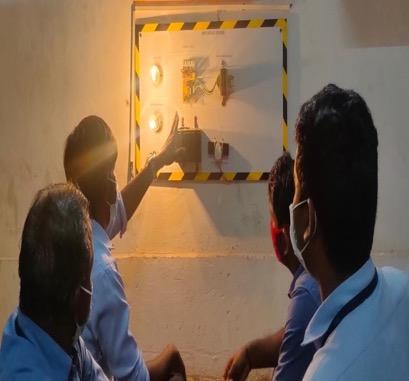
Description of the Innovation:
Energy Monitoring System
CHALLENGE
• Tenants' complaint against high power consumption during COVID time.
• More time consumption in accessing Tenants work area daily to record Energy Meter readings
• Tenants' refusal to give consent for raising the energy Invoice.
• Delay in EB payments seeking frequent clarifications.
• Difficulty in tracking daily tenant energy consumption.
• Difficult in cross verifying consumption between HT and LT units
MYIDEA / INITIATIVE / SOLUTION BENEFITS / ADVANTAGE
• Installation of Energy Monitoring System – ELNET Software Ver 5.3 (EL MEASURE)
• Replacement of Old Energy Meters with New True RMS Multifunction Energy Meters (52no.s) in all Floors.
• Replacement of Old Communication cable with New cables wherever necessary.
§ Easy monitoring of parameters
§ True RMS Measurements
§ Improved accuracy
§ Single User Interface to manage report and monitoring system.
§ Better understanding of energy usage.
§ Collects and records all the data in real time to one single point.
§ Frequent access to Tenants work area is minimized.
myIdea

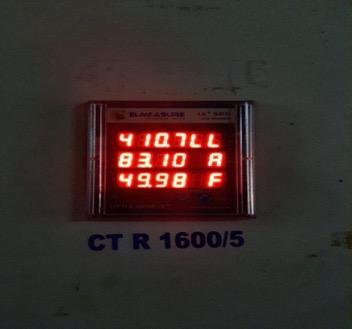
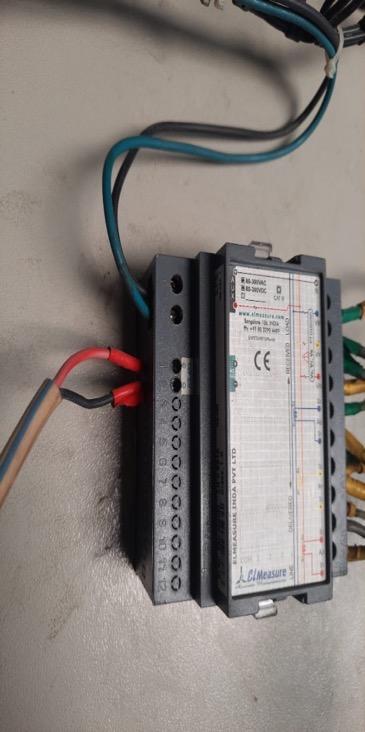
Tenants' satisfaction in Energy tracking system. time
Description of the Innovation:
Protocol for working in Confined Space
CHALLENGE
• Accessing the confined space viz; STP Sump, Fire Hydrant Sump etc. was a huge challenge during maintenance activities.
• Carrying machineries like motors and other cleaning materials was also a tough task.
• Ladders were used to get into the sump for maintenance and cleaning
• Human safety was compromised
MYIDEA / INITIATIVE / SOLUTION BENEFITS / ADVANTAGE
• An idea of fixing a collapsible tripod stand along with winch with 15 Mtr. cable was implemented.
• The tripod along with winch can hold a weight of up to 250 Kgs to mobilize both men and material.
• The winch is equipped with a fall arrest mechanism and the handle can is easy to operate while retrieving.
• After work permits ,O2 level Levels checked and necessary ventilation process ,person who is entering the confined space will be wearing a full body harness and all other PPEs.
§ Men and material can be lowered and retrieved back at ease.
§ Personnel entering the confined space will get into sump with confidence and in case of any emergency, they can be lifted back hassle free.
§ Encourages personnel to work with adequate safety measures.
§ Safe and secure work atmosphere helps to minimize the accidents.
§ Compliance and adherence of safety guidelines to avoid major incidents.
myIdea
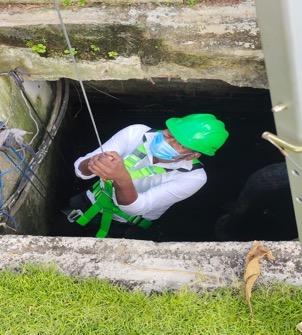
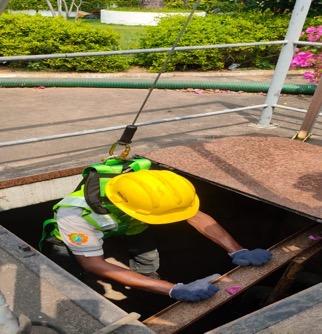
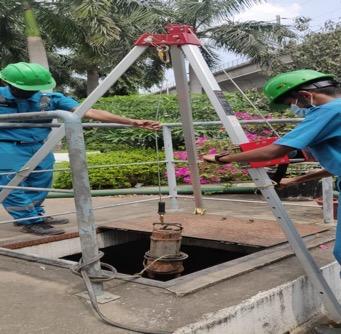
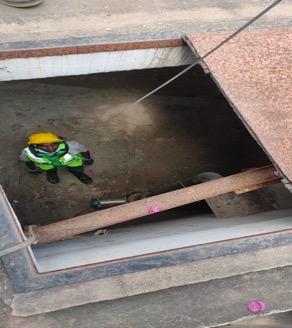
Description of the Innovation:
Shock approach boundary marking
CHALLENGE
• Measures to be taken for enhancing safety of our team.
• To keep site ready for BSC certification in future.
• Each voltage level require a different approach boundary distance from equipments i.e.-HT & LT system to keep the manpower safe.
• We need to have a system in place which any not technical person can understand while entering in utility area.
MYIDEA / INITIATIVE / SOLUTION BENEFITS / ADVANTAGE
• Shock approach boundary marking needs to be done in HT room, LT room, Transformer room and all electrical room.
• The shock approach boundary distinguish according to the voltage level prescribed by British Safety Council.
• As per BSC standard, we created 4 approach boundaries i.e. Prohibited approach, Restricted approach, Limited approach & Arc flash approach boundaries.
§ To improve aesthetic of building equipment's and improve the safety procedure at site.
§ It will help in preventing the electrical incidents at site.
§ To provide a safe distance for personnel from exposed, energized electrical components.
§ Reflective tape prevent accidents at any time of day since it offers superior visibility of hazards.
myIdea
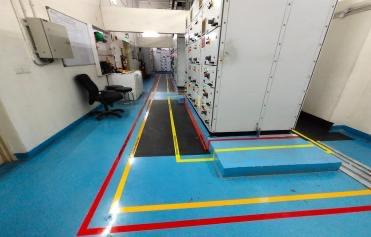
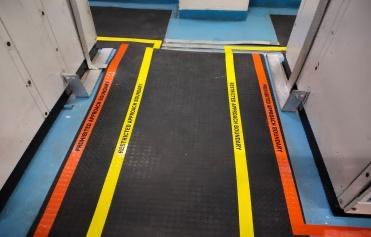

Description of the Innovation:
Chiller Online monitoring
CHALLENGE
• Initially there was no chiller monitoring system.
• Cost saving without the use of smart solutions were not as per expectations.
• The control system cabling and the technical aspects were a challenge to be executed.
MYIDEA / INITIATIVE / SOLUTION BENEFITS / ADVANTAGE
• Logical control panel with online display.
• The whole chiller system equipment’s real time parameters were made available at one point which decreased the human efforts and error possibilities.
• Due to advanced data monitoring the idea to achieve cost saving on our utility bills and optimal control & operation of equipment’s was achieved up to certain extent.
§ OEM & Service support vendor online monitoring system installed and commissioned.
§ Easy to get the data without any lacunae.
§ Financial benefits up to some extent.
§ Optimal operation of the pumps, chillers, AHU etc. which increases the life and health of the machineries.
§ Low losses in the system, as the faults can be tracked and worked upon.
myIdea
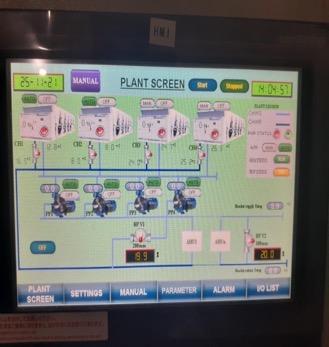
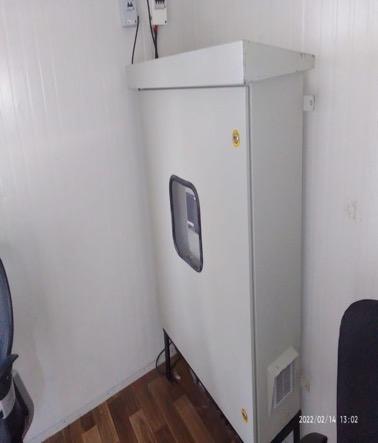
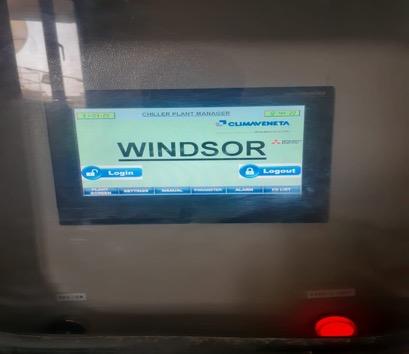
Description of the Innovation:
Sustainability – A holistic Approach
CHALLENGE
• Using scrap for useful work
• Titivation of facility.
• More visibility of Facilities Team around Campus
• Cutting down the dried neem tree trunk which is next to the main entrance, chopping of the tree leaves the area very dismal
• Team Motivation
• Promote sustainability
• Being creative
MYIDEA / INITIATIVE / SOLUTION BENEFITS / ADVANTAGE
• Fountain - Little engineering work with scrap drum combined with a sleek paint job and decorative planters, lighting and live fish.
• Bull Cart - A smart teamwork made an excellent landscape view, from scrap wood, bamboo sticks, colors and creativity to build a beautiful bullock cart as a showcase display.
• Bougainvillea - Created an environment friendly atmosphere, by transforming dried / dead neem tree trunk into a colorful Bougainvillea which enhanced the facility.
§ Recycle / Reuse Reduction of scrap
§ Received positive feedback from the Client and associates
§ Environment friendly atmosphere
§ Eye-catching view of the tree next to main entrance
§ Work Carried out and completed by In-House Team
§ Awarded 1st Runner up at the iNFHRA Workplace Excellence Conference Awards 2021-2022 under Sustainability
myIdea
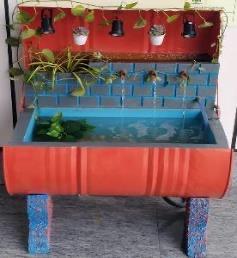
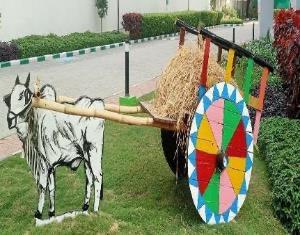

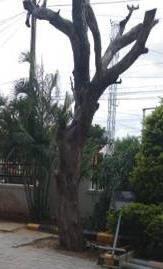
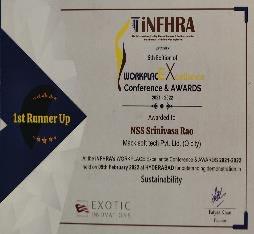
Description of the Innovation:
Inhouse capability of Servicing Breakers
CHALLENGE
• LT & HT Panel ACB's & VCB's were not serviced from last two years.
• Team was facing the problem of tripping.
• During the change over not holding the breakers.
• Team was also facing the problem of breaker rack in and rack out.
• The client has not taken any AMC from outside agency.
MYIDEA / INITIATIVE / SOLUTION BENEFITS / ADVANTAGE
• Had discussion with client to initiate inhouse servicing,
• Make a team and conducted a training about the ACB & VCB servicing procedure and checklists.
• Given servicing Demo to team.
• Planned scheduling and implemented the servicing.
• Successfully completed the servicing.
§ Resolved the tripping/ holding issue.
§ Rectified the breakers rack in/rack out issue and breakers controlling issues were now fixed.
§ Verified the breaker interlocking and protections.
§ Now the team is not facing any problem during the changeover.
§ The cost saved by this initiative approx. Rs.66000.
§ Developing In house capability of breaker servicing
myIdea
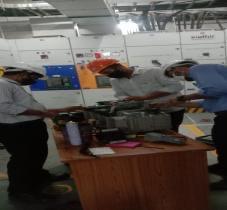
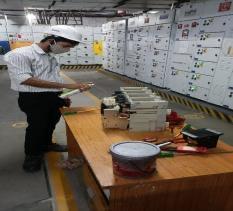
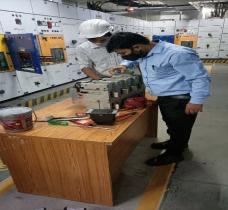
Description of the Innovation:
Automation of Electrical Energy Meter
CHALLENGE
• In 2019 continuously we have 1520% of Energy loss from HT meter to LT sub-meters
• Common area consumption also very high.
• Every month 3 electricians use to go for taking individual flat readings leads to time consumption.
• Individual meter CT coils, Phase sequence of individual coil & cables are not in a proper way.
MYIDEA / INITIATIVE / SOLUTION BENEFITS / ADVANTAGE
• We have 550 Dual Source HPL Energy meters. These Energy meters replaced with L&T meters include with RS-485 ports. RS-485 has been used in a wide range of computer automation systems.
• Total Energy meter Readings are connected to BMS with the help of ERGOMON software, BMS Operator is Monitoring the readings and he would Inform to Technical team if any problem Occurred.
§ Residents also using this Telegram app for Knowing their Energy Consumption.
§ Investing in automation can help to replace manual operations.
§ Automation reduces the fraction defect rate; this will help us at Billing time.
§ Automation improves asset management
§ Right now, we have 5-7% of Energy loss from HT to LT.
§ Residents have appreciated the sustainability initiative being implemented .
myIdea
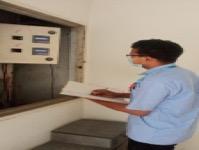
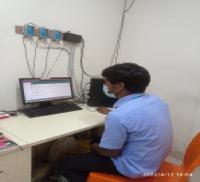
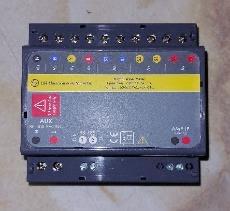
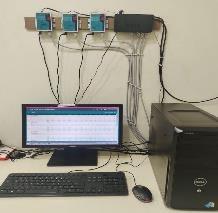
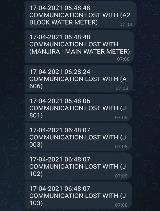
Description of the Innovation:
Ultrasonic Water Sensor
CHALLENGE MYIDEA / INITIATIVE / SOLUTION BENEFITS / ADVANTAGE
• High water consumption due to leakages inside the apartments and some users are not available during their office hours and some users are not aware of the leakages. Also some apartments are locked condition.
• These leakages are not able to monitor and arrest the water leakage on time.
• Leads to heavy water consumption & high billing to individual apartments.
• Installation of Ultrasonic water sensor in the branch line of each plumbing vertical to track & monitor the water leakage in the pipelines & tracking date anytime any where.
• Solid Construction with IP 65 rating with >98% accuracy. Handles High Pressure up to 16 bar, No calibration required, mount in any orientation.
• Detects upto 0.1 LPM of water consumption.
• The sensors are wired in series loop and connected to the LoRa duct unit and the unit receives data from the sensors and relays it to the LoRa gateway and it streams the data to the Cloud via 4G/LTE technology.
§ Recorded water consumption data for every single apartment in the community.
§ Overall consumption reduced by 49% within 6 months of installation. EB charges reduced by 30%
§ The running time of WTP, Pneumatic systems were brought down by 22% from 14 hours a day to 10 hours a day effectively.
§ Mobile app for residents and Dashboard for estate management team for continuous monitoring.
§ The water consumption reduced to 90KL to 50KL per day and for a month 1200KL water saved and the cost is Rs. 1,40,000.
myIdea
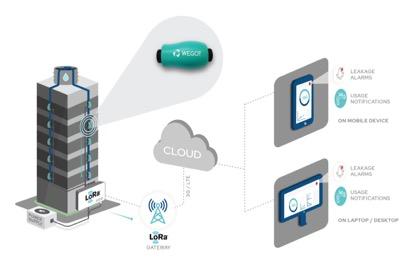
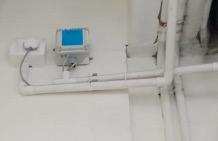
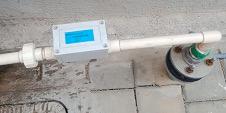
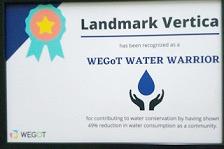
Description of the Innovation:
De-humidifier Water Conservation
CHALLENGE
• OEM recommend to use soft water/RO water for HVAC system supporting Labs & Data Centers IRC units chilled water line with standard quality parameters which can be achieved only with soft water.
• Procuring DM water for the chiller line make-up system is a costliest & vendor dependent solution.
• Existing make-up tank water supplied by the Landlord is not meeting the required parameters and its started spoiling the IRC mechanical valve due to scaling
/ INITIATIVE / SOLUTION BENEFITS / ADVANTAGE
• Client procured new automatic dehumidifier systems for the labs to maintain humidity & Dew Point
• Since the dew point inside labs are higher than the requirement, the de-humidification system started extracting water from the air moisture content
• After multiple brainstorming sessions, got to understand the extracted water from dehumidifier system can be used instead of DM water with the desired parameters.
§ Water Conservation: This initiative helps to conserve water & pay back to the environment
§ Cost Avoidance: Reusing this extracted water will replace the DM water procurement & avoid INR 9,035,838 over the period of 5 years
§ Vendor Dependency: No vendor dependency to procure DM water regularly.
§ Water Quality: This improves the chilled water quality & efficiency of the system.
myIdea

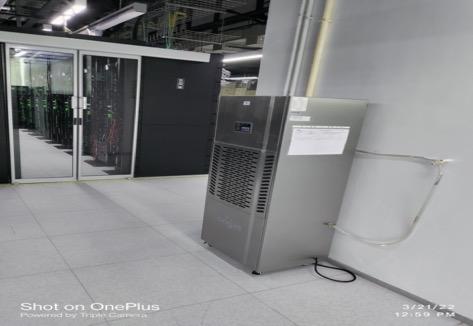

Description of the Innovation:
Centralized RO drinking water plant
CHALLENGE
• Dependency on packaged drinking water from external supplier to fulfill the consumption of 3000 liters per day.
• Challenge to make Plastic free environment at site.
• Carbon emission reduction to meet client sustainability target of carbon negative by 2030.
• Dedicated space required for storage of filled & empty cans in the premises.
MYIDEA / INITIATIVE / SOLUTION BENEFITS / ADVANTAGE
• Installed centralized RO drinking water plant at terrace to feed drinking water to dispenser.
• Individual dispensers installed across the floors in the building at dedicated location to employees for drinking purpose with Hot, cold & normal water dispensing options
• Regular testing of RO water by inhouse test kit & reputed NABL lab to ensure quality of drinking water
§ Contribution towards client’s Initiative towards carbon negative by 2030
§ Reduction of carbon emission 25.83MT/Year.
§ Avoidance of space required for storage of filled & empty cans in the premises.
§ Avoidance of dependency on supplier.
§ Estimated Saving: 40813 USD /Year
myIdea


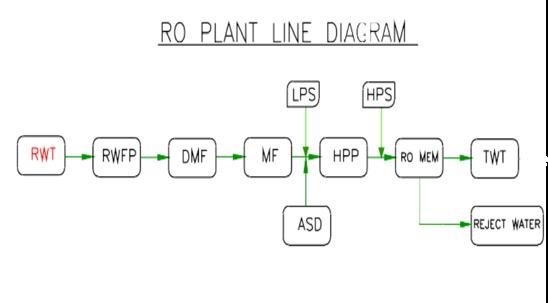
Description of the Innovation:
Skid Mounted Incinerator
CHALLENGE MYIDEA / INITIATIVE / SOLUTION
• The generation of such high quantity of sanitary pad waste creates stress on the waste management syestem and poses a challenge for its safe disposal.
• Mask & Covid PPE kit 12kgs /month
• 250 hygiene bins /month
• GD 1 skid mounted incinerator with burn rate 5kg/h.
• Wax coated or Biodegradable liners provided in bins as per EHS
• Collected liners from different buildings are stored in central waste yard.
• Meeting standards under Waste Management Rules, 2016 (CPCB)
• Biodegradable liners can go directly into the Incinerator by avoiding human intervention.
• One time investment 6 Lakh
myIdea
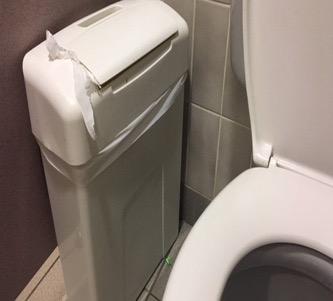
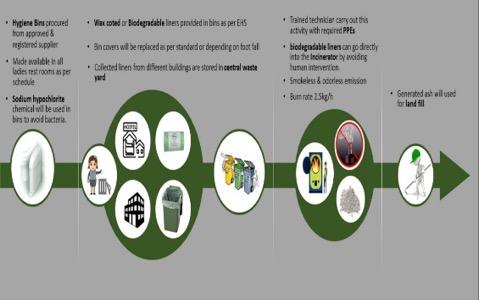
BENEFITS / ADVANTAGE
§ Smokeless & odorless emission
§ Disposing of biodegradable liners without human intervention and also eco friendly approach by following with this method and system.
§ Easy to operate with low maintenance.
§ Ash collected in separate tray with < 5% ash generated per napkin.
§ Generated ash will used for land fill.
§ ROI - one year
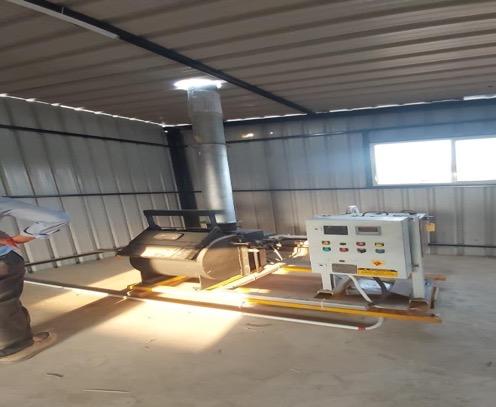
Description of the Innovation:
Culinary Event
CHALLENGE
• Cake mixing event was a regular practice every year during Christmas festival.
• Calling back employees to office for such event was a difficult task.
• Touch points was the major concern as it is a culinary event.
• As it was a live telecast responding back to participant queries was a challenge.
MYIDEA / INITIATIVE / SOLUTION
• We discussed with F&B vendor and planned culinary event through virtual connect.
• We made it live telecast by coordinating with IT team.
• An email was sent to associates to enroll themselves for the event.
• Another email was sent to participants on ingredients and instruction for the event.
• We have sent mail to associates to connect through zoom call and we enabled only chat option to answer their queries.
BENEFITS / ADVANTAGE
§ More number of people were excited and participated.
§ It was the 1st virtual event connect after pandemic.
§ Associates were able to do this activity along with their family members.
§ “Creating delightful workplace experience”.
myIdea
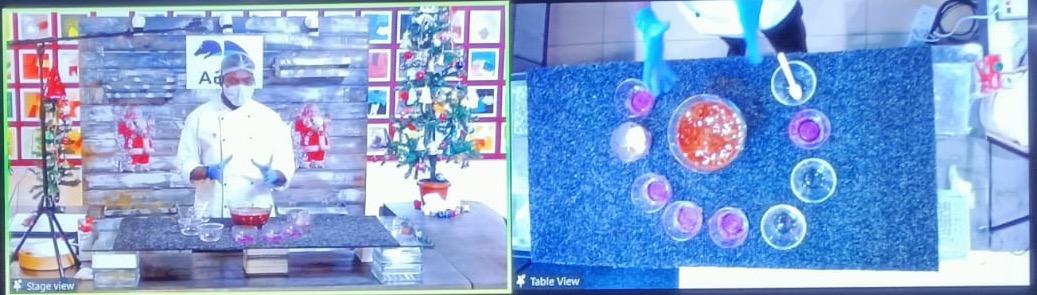
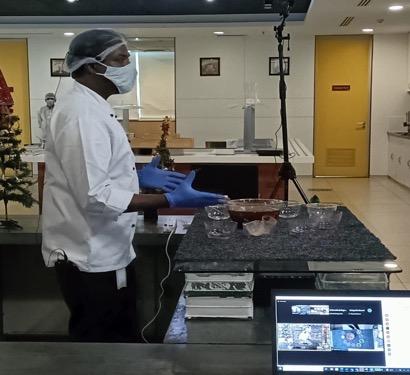
Description of the Innovation:
Upgradation of PLC
myIdea
CHALLENGE
• The Existing PLC control module was 18 years old and not BMS compatible.
• PLC control module being outdated, replacement parts are becoming more expensive and some time not available in the market.
• High risk to business.
• Incase of PLC failure, we would have been unable to operate the DG’s and Electrical Breakers on Auto mode.
• Operating on manual mode would lead to delay in Critical & Non-critical power restoration.
MYIDEA
/ INITIATIVE / SOLUTION BENEFITS / ADVANTAGE
• Worked closely with site Engg team, specialist consultants, vendors to develop a plan and detailed analysis to upgrade PLC.
• Peer reviewed with technical expert.
• Upgradation of existing PLC module and replacement of all controllers with latest version including software upgradation from old version V-16 to the new version V-30 with latest technology.
• Reutilized the field control wirings by relabeling and re-terminating.
• Load trials taken and ensured working as per PLC logic.
§ Significant productivity improvements and reduce risks for business.
§ Higher processing speed.
§ The system can be expanded by adding additional I/O modules.
§ PLC could be integrated with BMS for real time monitoring and alarms.
§ Replacement parts will be readily available.
§ Reduced dependency on manual operation due to auto mode working.
§ Avoided power interruption during the EB power change over and reduced restoration time.

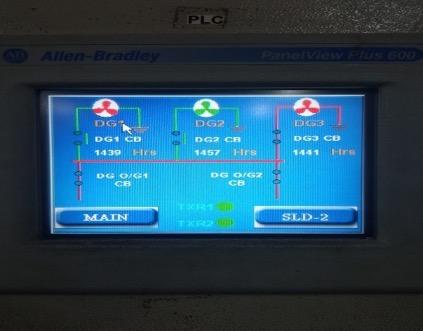
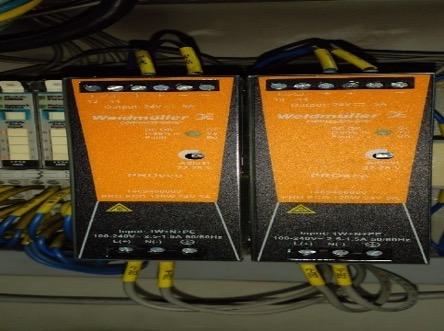
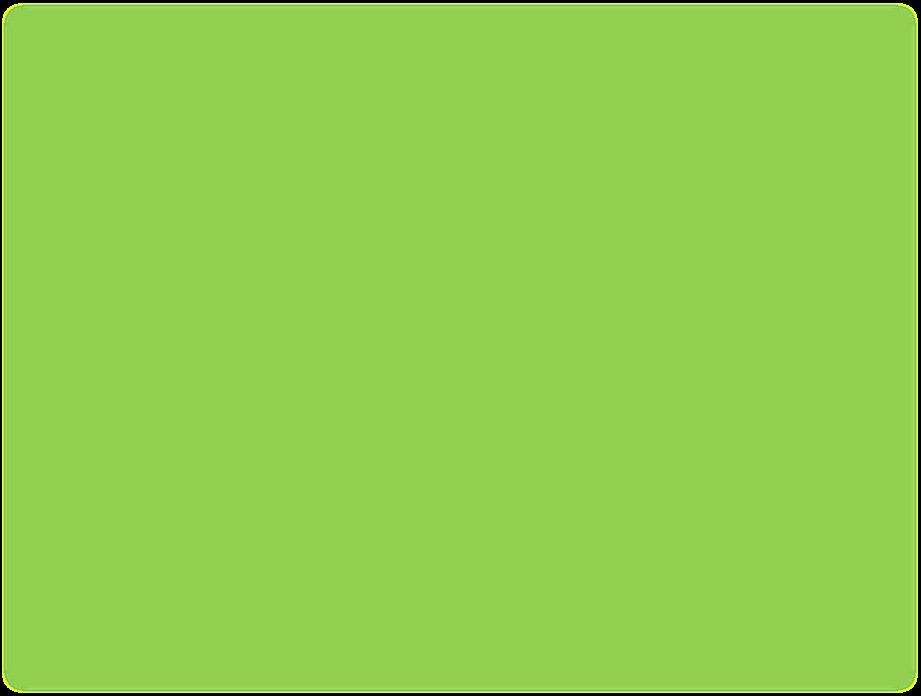
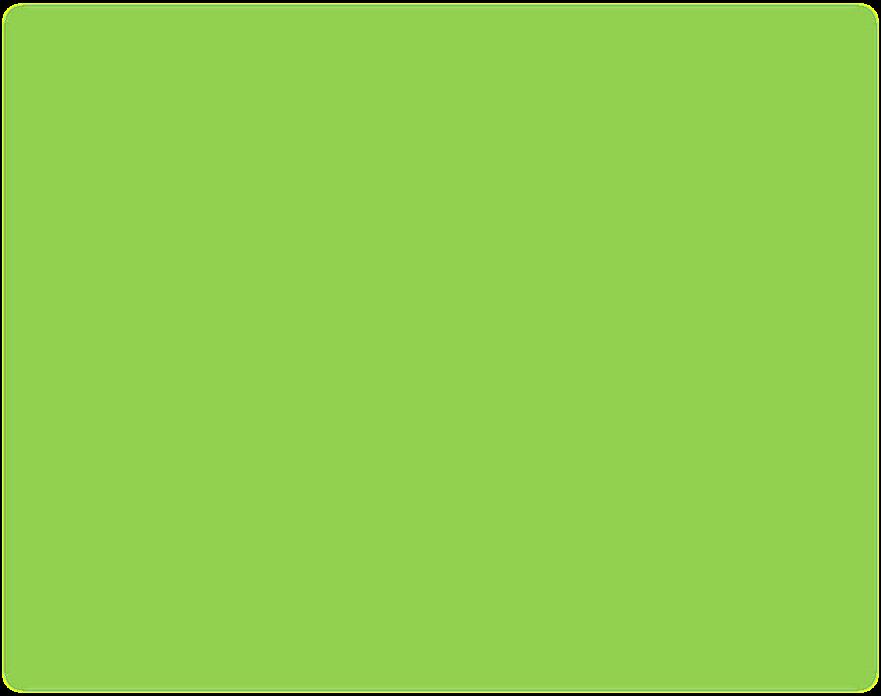
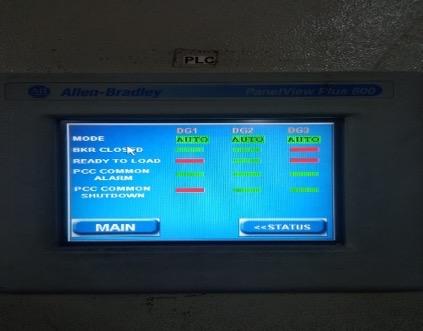
Description of the Innovation:
Capacity Planning Tool
CHALLENGE
• Hybrid Workplace is assumed to be go forward way for offices of tomorrow.
• Arrive at unique solution to meet the organizational requirement.
• Come, up with the best fit option to deliver a rightsized-real- estate portfolio.
/ INITIATIVE / SOLUTION BENEFITS / ADVANTAGE
• Worked closely with DXC Business Groups and IT group to develop Capacity Planning Tool to collect latest employee business and demographic info.
• Information so collected was analyzed in several ways to understand the physical, flexible and virtual ratios in each region.
• Analyzed the scatter of employees throughout India to gauge impact on RtoW.
• Developed scenarios showing seat demand by region / site / floor.
• Provided data points to leadership for decision making.
§ Great insights on controlling the real estate footprint in the country.
§ Nearly scientific way to estimate the seat demand.
§ Data driven policy decisions.
§ Awareness about factors that could influence RtoW decisions / dates.
myIdea
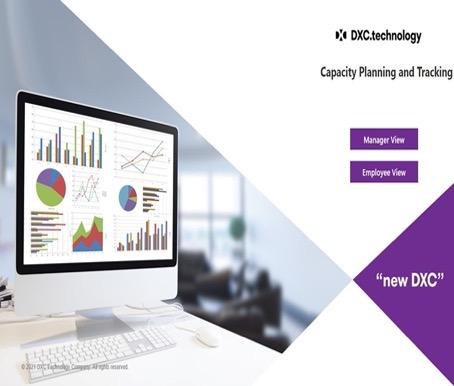
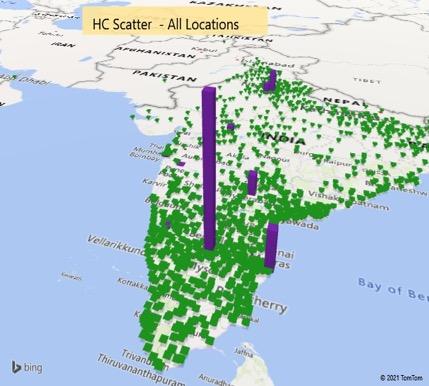

Description of the Innovation:
Automatic
No-Show notification
CHALLENGE MYIDEA / INITIATIVE / SOLUTION
• Delay in NO-SHOW Notification to respective admin supervisors.
• There was a manual validation performed by transport team.
• Total activity was consuming more than 23 hours per day
• Worked with supplier team to utilize the available automation tool to the maximum.
• Detailed study of the tool to understand all the possible ways.
• Worked and changed the configurations in the tool.
• Created testing profiles for transport team and tested the feature for more than a month.
• Finally arrived to save 2-3 hours of transport teams time and reduce manual efforts for transport.
BENEFITS / ADVANTAGE
§ NO-SHOW notifications now REAL TIME using MoveInSync tool to their respective supervisors
§ We have a dashboard for supervisors enabled in Mobile application Which talks about On Time Arrival Delayed arrival, No-shows, No. of transport users scheduled for a day.
§ For Supervisors to access this dashboard transport team will create the profiles in MIS tool and notify the supervisors so that he/she can use the dashboard.
myIdea
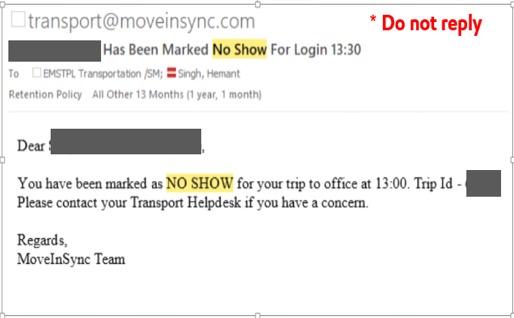

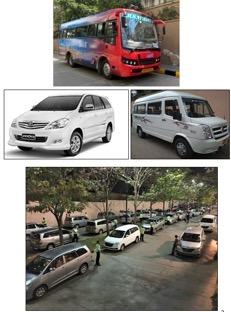
Description of the Innovation:
Air Purifier for Conference rooms
• Common FCU units for Conference rooms
• No Provision of Hepa Filter to purify the air during the pandemic concerns.
• No fresh air as per infrastructure design
• Installation of dedicated Air Purifier with Hepa Filtration.
• Automatic Sensing of contaminated air and purifying in closed rooms.
• Obtained approvals from global EHS Team on the Make & Model of Purifiers.
/ ADVANTAGE
§ Avoiding cross contamination in closed conference rooms between multiple users.
§ Safe & Hygiene environment for closed room users.
§ Helps to improve daily footfall of client operations.
myIdea
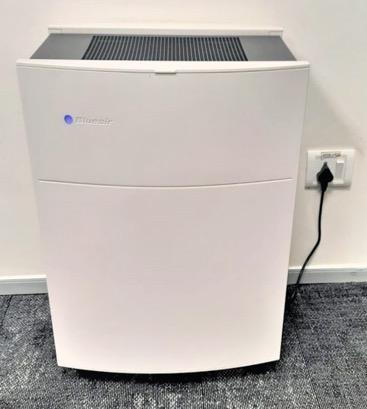
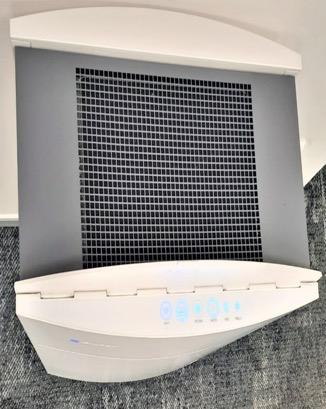
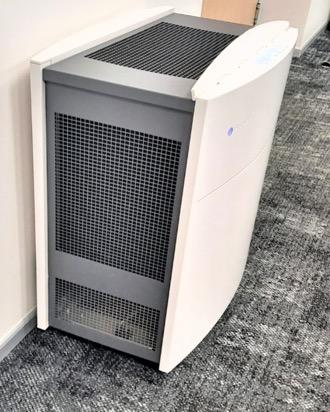
Description of the Innovation:
Chilled water Header modification
CHALLENGE
• Identified minute chilled water leakage from the Victaulic coupling in the main header line inside the critical area, if timely not rectified leads to a heavy water leakage inside the lab that impacts the business operation.
• Around 100KL of chilled water from the piping system must be drained out without any spillages in the critical area. also, there is a constraint in undertaking the welding part in the cast iron Victaulic coupling.
MYIDEA / INITIATIVE / SOLUTION BENEFITS / ADVANTAGE
• Reviewed with designed consultant and client for their concurrence on design change of chilled water line inside lab
• Engaged the OEM for rerouting and feasibility study for execution.
• Obtained the required approvals from lab business units for implementation
• Re-routing undertaken on the delivery line to the PAC thereby giving adequate access for any maintenance
§ Avoid complete draining of chilled water from the system for rectification of any leakage inside the lab.
§ Avoid complete down time of critical Lab operation.
§ Reduction in quantum of treated chilled water.
§ Cost saving in turn of back filling of quantum of water and treatment .
§ Environmental benefit by reduction in quantity of water removal /draining.
myIdea
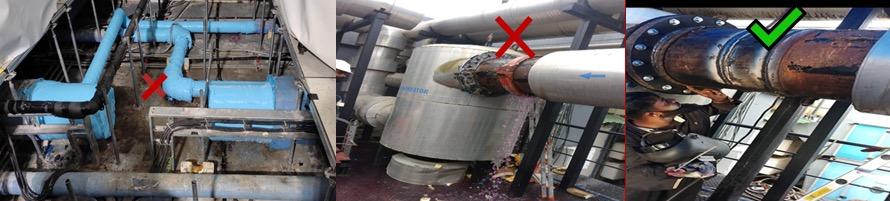
Description of the Innovation:
Sterilization of Coffee mugs
CHALLENGE MYIDEA / INITIATIVE / SOLUTION BENEFITS / ADVANTAGE
• Frequent Usage: Coffee Mugs are frequently used by multiple users.
• Multiple touches: As multiple users touch the Coffee Mug; it gives room for infections.
• Infections : Infection spread across one user to another.
• Cup Warmer ensures reliability of not spreading the Infections.
• Sterilization of Coffee Mugs was implemented keeping in mind the before and after affects of Pandemic
• Machine consists of 200watt Air Heating Coil with Auto Thermo Controller, and the temperature is set to 50 Degree Celsius.
• Higher sterilization efficiency with lower electricity consumption.
§ Stress Free Usage: Users can pickup the cups tension free.
§ Estimated Savings: EHS savings of energy savings (continual working) auto controller: preventing overheating, safe and reliable.
§ Happy Clients: Happy Clients Happy Us
§ Zero Water: Since its Air Heating Coil, the cups washed are wiped and placed on the Cup Warmer Machine for reuse.
myIdea
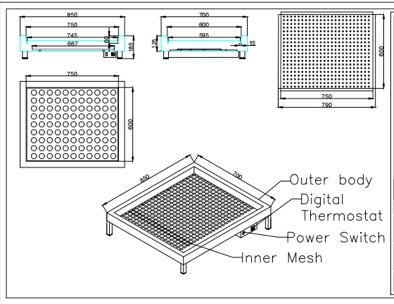
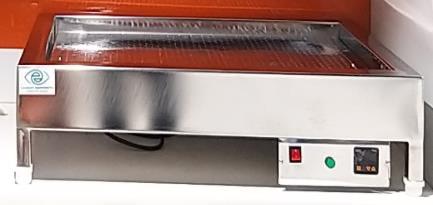
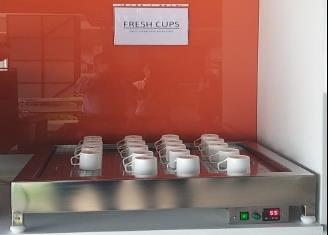
Description of the Innovation:
Isolation Control Valve & Flow Switch
for Water
Sprinkler
myIdea
CHALLENGE
• Isolation control valve and flow switch were not installed for the water sprinkler system at each floor level.
• No testing control at floor level.
• During fire emergency and when the water sprinkler is activated, the water flow of the respective floor cannot be controlled.
• During periodic maintenance, the main valve of sprinkler system had to be closed.
MYIDEA / INITIATIVE / SOLUTION BENEFITS / ADVANTAGE
• Discussed with SME and taken decision to install isolation control valve, flow switch & pressure guage
• Control valves at each floor level to isolate the water flow.
• Scheduled installtion of isolation control valve, flow switch & pressure guage with minimum downtime
• Plan for integrating flow switch and fire alarm system.
§ Isolation valve will control the water flow pressure during water sprinkler activation.
§ Isolation Valve is used in fluid management to stop the flow of water in the pipeline, this is usually for maintenance and safety purposes.
§ Flow switches are used in wet sprinkler systems to detect the flow of water and to send an alarm signal to FAS.
§ Flow switch will also minimize false alarms
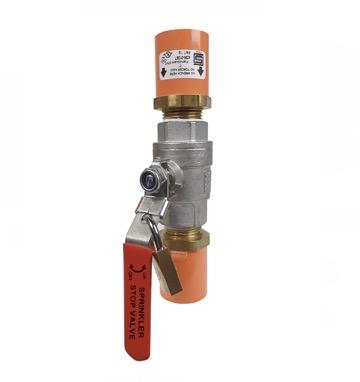
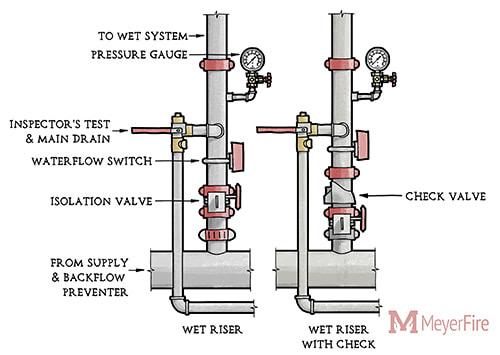
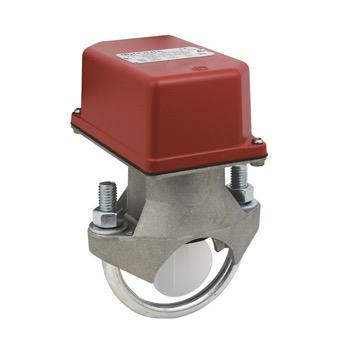
Description of the Innovation:
Provision of Siren to FPS Pumps
CHALLENGE
• Pump operation in auto mode not indicated.
• Pump operation without requirement will lead to high pressure, chances of pipe & pipe fitting crack, may lead to water leakage in the facility
• Continuous operation without discharge will lead to pump & motor failures.
MYIDEA / INITIATIVE / SOLUTION BENEFITS / ADVANTAGE
• Installation of siren at panels to alert the team when the pump starts and to understand the situation to interact with ERT team.
• Identified suitable Siren and installed in FPS panel in pump room
• Different sirens provided for different types of pumps for ease identification.
• Siren alerts the team whenever pumps operated in auto mode and required action ensured by operator / engineer according to the situation.
§ Unusual operation of pumps avoided and eliminated the untoward incidents.
§ Required attention provided immediately to support emergency team.
§ Manual pump operation in FPS system completely eliminated.
myIdea
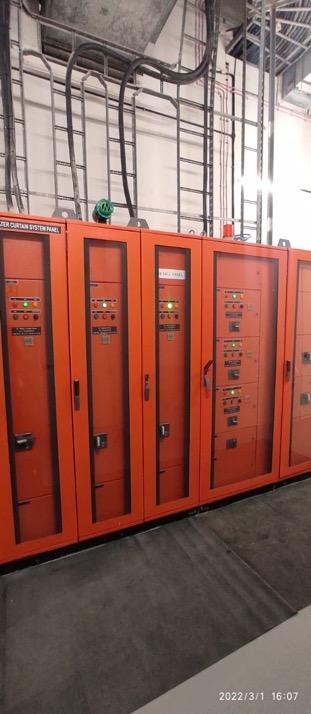
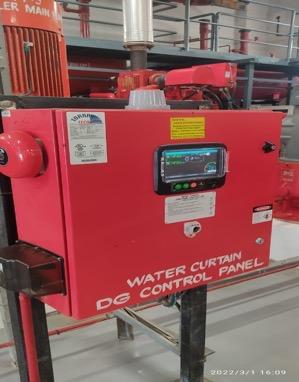
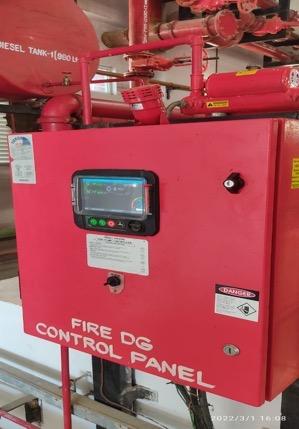
Description of the Innovation:
Redundant
Power Supply
CHALLENGE
• We have two building One building having one main power supply source.
• Incase of any primary power supply breaker failure there no retuned power source to the building.
• As part of BCP it is very critical to run the business.
MYIDEA / INITIATIVE / SOLUTION BENEFITS / ADVANTAGE
• Discussed with Management to avoid the such a criticality allocated Capex fund.
• Redundant Power supply panel installed and modified internal panel and cable laid from utility block to building -2
§ Avoided 100% building BCP critical.
§ Avoided building power failures.
§ Service can take any one of the source.
myIdea
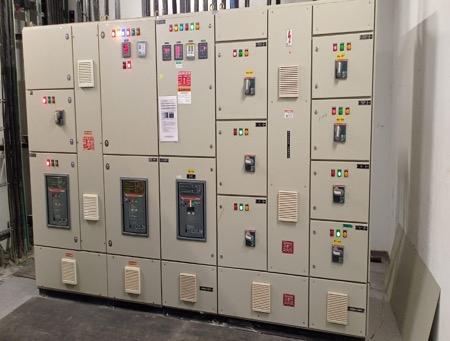
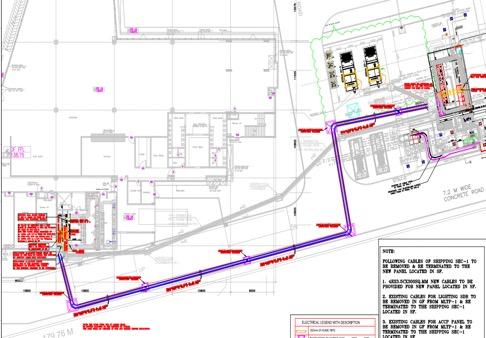
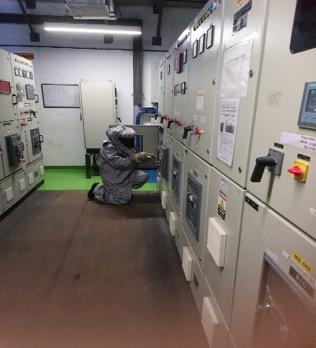
Description of the Innovation:
Vision Software
CHALLENGE
• Maintenance of hard copies of reports on daily rounds – had to be filed accordingly; issue of data pilferage
• Verbal assignment to the staff; issues with information being missed or misinterpreted
• No real time monitoring; no understanding of the presence at a specific location
• Difficult to track, close and account for the observations
MYIDEA / INITIATIVE / SOLUTION BENEFITS / ADVANTAGE
• Securitas Vision is a Security Guard tool which is developed to provide complete control over field operations
• This software enables greater visibility and efficiency; carried out by a streamlined and optimized organizational process
• The tool is equipped to provide the required information on real time basis; enable reports and data points thereof
• NFC tags are affixed at required locations
– tags are scanned onto the phones and detail/ comments are filled in
§ Real time visibility – patrolling as per time schedules; trigger of alarm in case of absence – longer time periods can be accounted for with reasons
§ Process efficiency – human errors negated; pre-designed checklist needs to be ticked
§ Data centralization – storage of files on secure cloud location; no tampering of information
§ Employee accountability – reports furnished as per format; all parameters covered – no manual intervention
§ Paperless operation – no filing of reports
myIdea
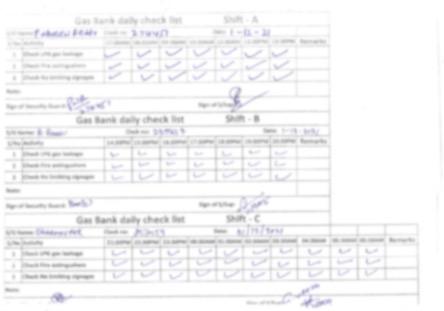
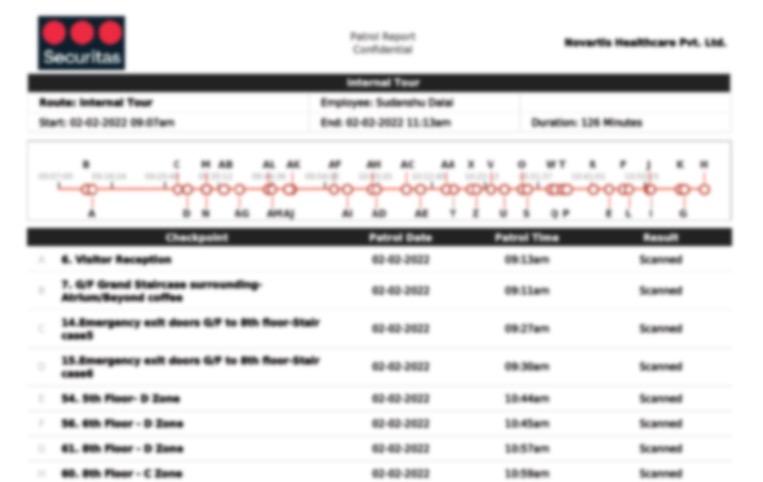
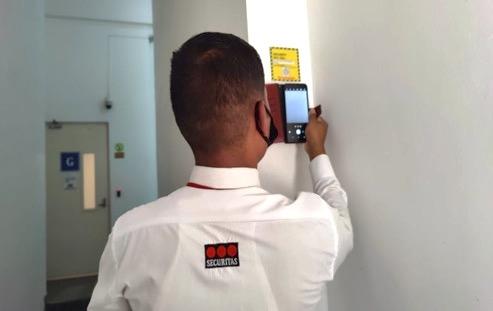
Description of the Innovation:
Thermography test for electrical panels
CHALLENGE MYIDEA / INITIATIVE / SOLUTION BENEFITS / ADVANTAGE
• Unscheduled service interruptions
• Asset failures
• Motor windings overheating
• Imminent motor and bearing failures
• Overheating of equipment
• Heat build up in cable trunking
• Phase load imbalance
• Predictive maintenance programs help prevent surprise failures.
• Infrared thermography is a non- destructive test that can be utilized to identify unbalanced loads, poor connections, deteriorated insulation or any other issues in energized electrical panels or components without dismantling the components.
• Identified observations are fixed much earlier which otherwise might have led to service interruption or asset failure
§ Reduces business downtime
§ Reduces risk of equipment failure
§ Improves system performance
§ Determines whether components and systems operate properly and meet design intent
§ Determines if components have been properly installed and are not damaged
§ Reduces risk of fire hazards and increases safety
§ Reduces excessive power usage
§ Prevents higher maintenance costs
myIdea
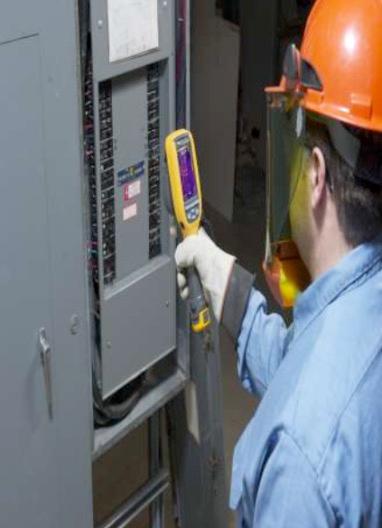

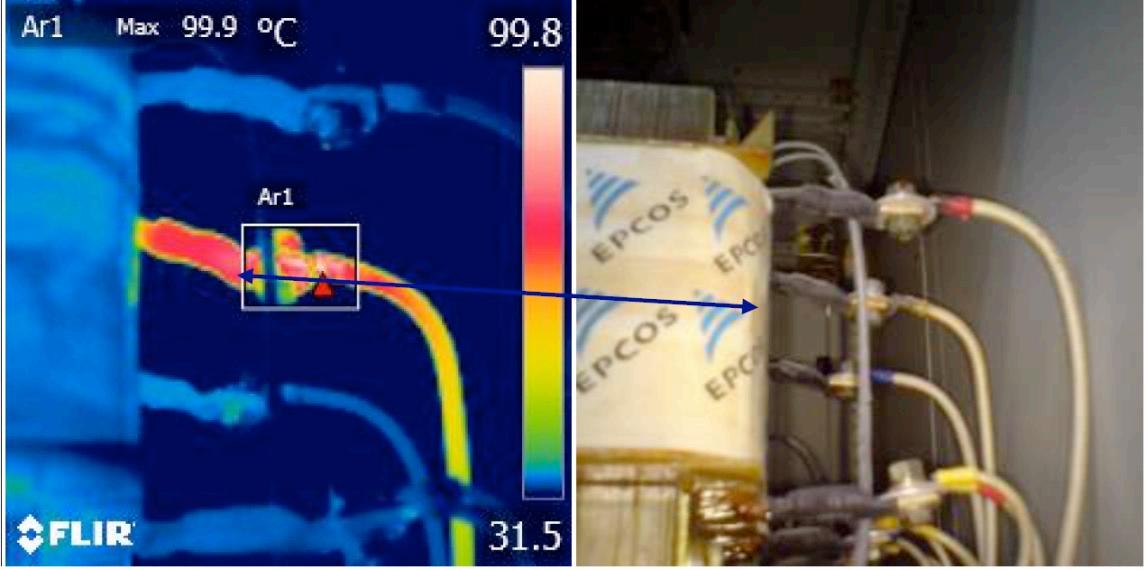
Description of the Innovation:
Drain pump integration with WLD
myIdea
CHALLENGE MYIDEA / INITIATIVE / SOLUTION
• Frequent drain blockage
• Water spreading across the below false floor
• Services below false flooring gets damaged
• Foul Odor spreading to WSTN area through underneath of raised flooring
• Direct Impact on usage of Break out area
• Drainoscopy activity was carried out to clear all the major drain line Blockages
• Concealed drain water lift irrigation by using food crusher and drain pump
• WLD monitoring towards the wet kitchen area
• Inlet water was cut off during the suspected drain blocks / water leaks from drain line by using solenoid valve
• Solenoid valve was then integrated with WLD
• Note: Frequent scheduled drain line maintenance to be considered
BENEFITS / ADVANTAGE
§ Smooth Usage of Break out Area
§ No business or False Flooring Services impact
§ Healthy Plumbing system
§ Reduced Manpower cost in terms of house keeping services
§ No Wet kitchen breakdown

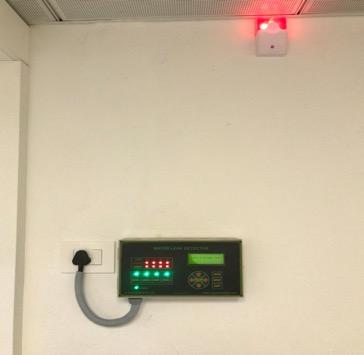
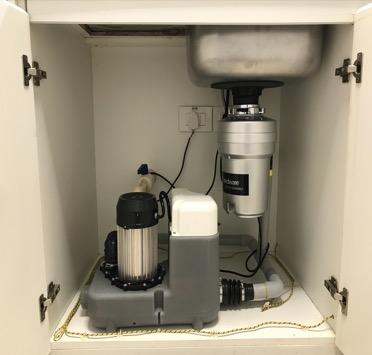
Description of the Innovation:
Sustainability Initiative
CHALLENGE
• Difficult to dispose the debris on weekly basis
• Challenge with Garden debris vendor to follow-up and gate passes too
• Security process involved while loading debris
• Huge Space consuming
• Hazard of Fire and hiding space for toxic incest & Reptiles
• Paling debris all-around
MYIDEA / INITIATIVE / SOLUTION BENEFITS / ADVANTAGE
• Procured horticulture shredder for shredding garden waste, tree branches.
• Easy to handle and reduce the debris space occupancy
§ Chop garden materials into smaller clippings, so gardeners don’t have to deal with making excessive trips to the dump. It’s also easily biodegradable, which, of course, is a huge benefit to our environment.
§ Reduction in no. of trips save transportation and carbon footprint.
§ Increase in nutrient-rich compost generation.
§ Approx. 2-to2.5 lakhs Rs saving on garden debris removal every annum
myIdea
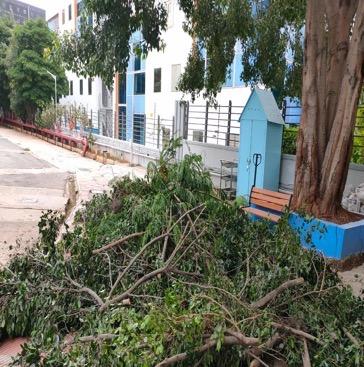
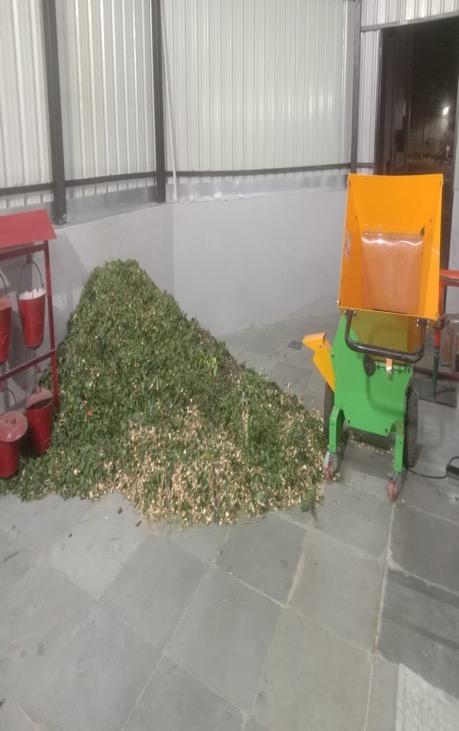
§ they usually take 3 to 4 months to get decomposed. But when you shred them using the garden shredder, the process of decomposition speed-up.
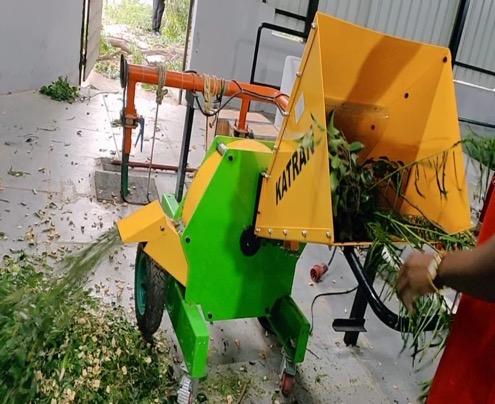
Description of the Innovation:
Digital Feedback Mechanism
CHALLENGE
• Feedbacks and other notifications were shared and captured manually.
• No record maintained or if maintained was unorganized
• Lot of paper usage during Dip stick survey of daily feedback capturing process
• Cost of printing paper was significantly high
MYIDEA / INITIATIVE / SOLUTION
• Digitization of Process
• Better utilization of space More uniformity across the location.
• Save paper as a sustainability initiative
• Optimizing time and manhours
BENEFITS / ADVANTAGE
§ Ease of communication and transparency
§ Process improvement wrt to Data Capture and Analyzation
§ Ease of accessibility
§ Process enhancement of enabling or disabling with new improved SOP as per guidelines
myIdea
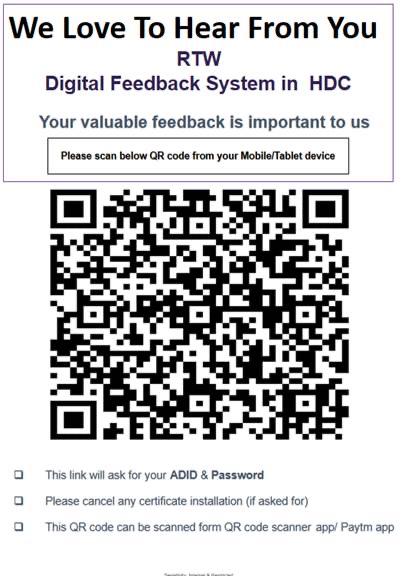
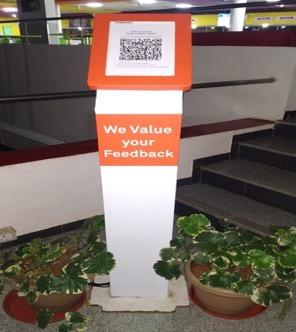
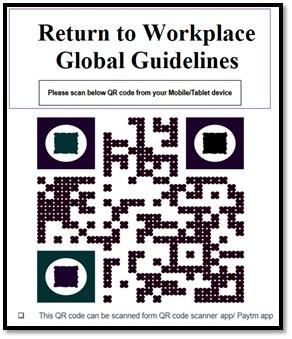
Description of the Innovation:
Waterless Urinals
CHALLENGE MYIDEA / INITIATIVE / SOLUTION
• Conventional restrooms are equipped with high end usage of water for flushing.
• In this time of Covid, water usage has been increased for washing hands frequently for more than 20 Seconds.
• Conventional Hand dryers doesn’t provide purified air for drying hands
• Waterless Urinals have been introduced to decrease the use of water for flushing. A total of 103 waterless urinals system were equipped in Building-3.
• HEPA based hand dryers were installed which removes most of the viruses from the air stream.
• Also, recycled water is being used for flushing as a water conservation initiative.
• The faucets here are installed with an ease of access for wheelchair users. The lighting and the indoor planters are added.
BENEFITS / ADVANTAGE
§ Waterless urinals saves water, thus reducing energy and emissions.
§ An estimated water savings of 2250KL of water per annum on an avg. usage of around 60%.
§ Reduce expenditure on water and related sewerage costs
§ Improve hygiene and urinals are easier to clean.
§ They create no limescale within the plumbing lines.
myIdea
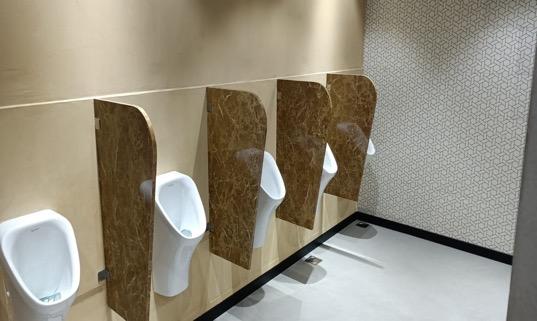
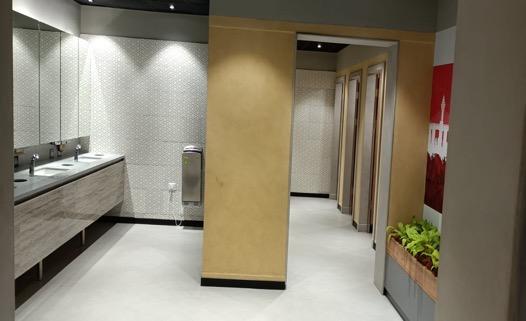
Description of the Innovation:
Employee Experience Enhancement
CHALLENGE
• Hubs or pantries are the places where people get in contact via coffee machines, Refrigerators etc. In midst of this contagious virus, contact word will be scarier.
• In a busy day, hubs are the points of refreshments to charge our batteries and get back to work. Its aesthetic look counts.
• Connecting Bridges though they serve the purpose as a structure, still its performance in the field of material usage, durability, looks stacks up in our minds.
MYIDEA / INITIATIVE / SOLUTION BENEFITS / ADVANTAGE
• All the 6 connecting bridges had undergone a makeover with new carpets, lighting and ceiling all along.
• Atrium is completely revamped with refresh look with new acoustic panels on MPR walls complimenting the new carpet in the atrium, Staircase with decorative lighting, tip wood rafters, moss panels and acoustic paneling, entrance lobby has a welcoming look with new rafter paneling and the new furniture upgrade at Atrium
• The hubs are equipped with touchless RO water dispensers, Coffee machines and Vending machines.
§ Hubs became contactless with touchless RO dispensers.
§ The places which requires contact can be turned down just by scanning the QR. These points are most likely to be vending machines, coffee machines.
§ Waste segregation at the source meant we are participating in the sustainability challenge and helps in building this habit.
§ Aesthetic looks of Pantries, Connecting bridges gets our minds relaxed which can be shown by the increase of our self-performance.
myIdea
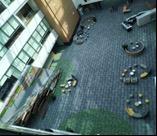
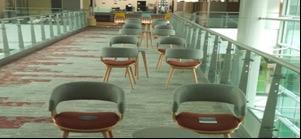
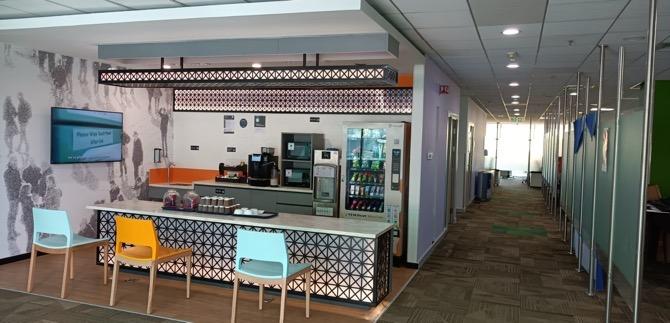
Description of the Innovation:
Energy Efficient LED light
CHALLENGE
• The existing LED light fittings were 6-7 years old.
• Decrease in illumination level of existing 40 Watt LED lights.
• Frequent failure of old LED lights.
• Light fitting was obsolete (3000K) and repair was not feasible.
• Non uniform lighting lux level on floor
• Glare issue because of out of shape anodized reflector
MYIDEA / INITIATIVE / SOLUTION BENEFITS / ADVANTAGE
• Concerns raised with the OEM Philips and had discussion with electrical consultant and internal team, decided to replace the Light fittings.
• Decided to replace old 40W LED light fitting (Sereno RC869B) qty. 240 Nos. with latest 25W LED fitting (RC380B) without changing the existing grid pattern.
• Planned and scheduled the replacement by in-house maintenance team and completed successfully.
§ Low energy consumption, saving of approximately 16,500 Units / Year or INR 1.70 Lacs / Year
§ long usable life & practically no impact to the existing lighting layout
§ Increased illumination enhanced floor aesthetics.
§ Diffused light so no glare.
§ ROI of less than a year.
§ Reduction in CO2 emission approximately 11,550 kg of CO2 (Ref. TPC~0.7 Kg/KWH CO2 emission
myIdea
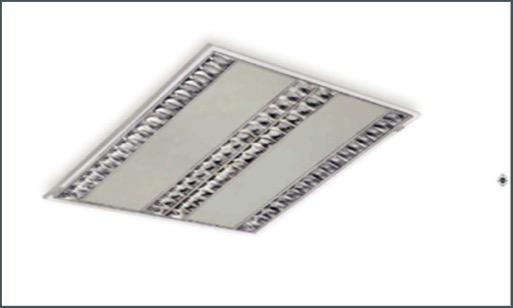
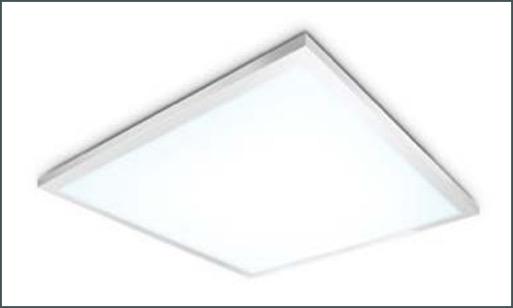
Description of the Innovation:
Replacement of Wet Scrubber to Dry Scrubber
CHALLENGE
• The existing Wet Scrubber are 12 years old.
• High maintenance cost.
• The maintenance activity was very difficult due to Cleaning of inside of Sccrubber.
• Difficulty of Alkali replacement , sludge removal required.
• Regular cleaning of tank and repalcement of fins required.
• Very High Capcity of Blower & Pump used.
• Energy Cosumption is High.
MYIDEA / INITIATIVE / SOLUTION BENEFITS / ADVANTAGE
• More space for operation and maintenance .We have resolved safety issue of congested space.
• Energy consumption is 1/3 than wet scrubbers.
• Yearly approx. Electricity saving would be 14K USD
• water consumption reduction by 3KL / month
• Planned scheduling and implementation with minimum downtime.
• Successfully completed Upgradation of existing Wet Scrubber to Dry Scrubber .
§ Improvement of safety and reliability
§ Low running cost
§ Blower Energy Saving by 30-35%
§ Significant energy saving
§ No floor strengthen is required
§ No drain or overflow line, No leakages
§ Alkali and sludge eliminated & No alkali dosing and storage.
§ Easy for maintenance of Carbon Fillter Cleaning & Increase life of scrubber.
§ Cost reduction of maintenance and repairing.
myIdea

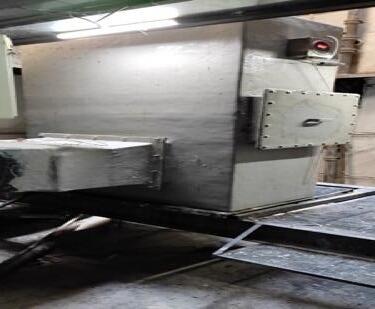
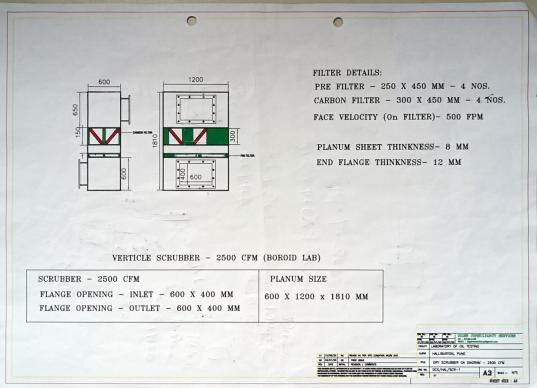
Description of the Innovation:
Advanced Static VAR Generators
CHALLENGE
• There are no APFC panels installed across LT panel floor wise.
• During pandemic due to lockdown only capacitive and inductive load the PF recorded was between 0.3 to 0.5 for different floors.
• MSEDCL changed billing pattern w e f 01.01.2020 & considered KVAH units for Billing.
• KVAH units increased due to LEAD/LAG impact. Though the KWH consumption was constant billing amount increased by 25 to 30%.
MYIDEA / INITIATIVE / SOLUTION BENEFITS / ADVANTAGE
• Approached vendors for Power Quality Test .
• M/s Venus Technocrafts analysed and suggested for installation of Advanced VAR static generator across LT panels.
• Trials conducted for one week and parameters were recorded.
• Approached three vendors for quotes.
• Order placed with L1 vendor for 70KVAR/100KVAR ASVG’s as per contract load.
• Total Qty -04 installed and commissioned.
§ Post commissioning of ASVG’s parameters i.e. PF ,KWH & KVAH were recorded.
§ PF was recorded between 0.96 to UNITY.
§ For HT-1A meters ,difference between KVAH & KWH units was recorded less than 0.5% neutralizing impact of LEAD/LAG on billing.
§ For LT-V meters PF penalty converted in incentives.
§ Overall saving on electricity bill is approx. 30% .
§ For present KWH consumption, Saving in INR is between 80 k to 1 lac/month.
§ ROI - Total spend of 12 Lacks Recovery period is 3-4 months with full load.
myIdea
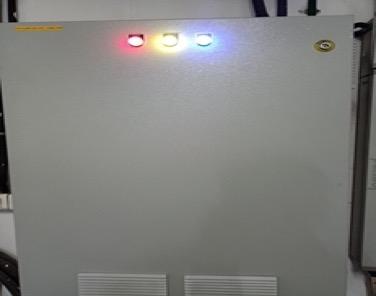
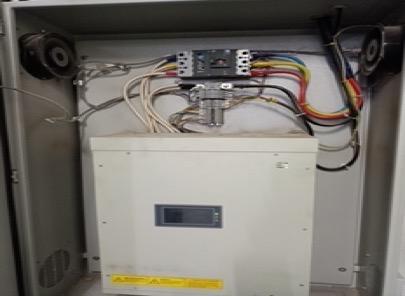
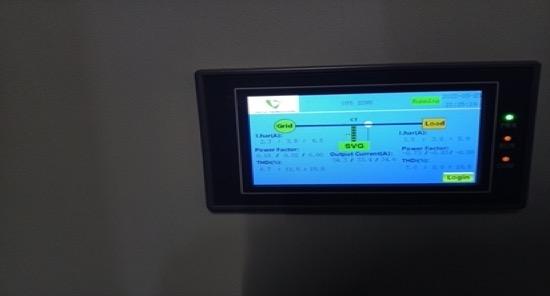
Description of the Innovation:
Data Center
Lighting
CHALLENGE
• Data center was having 4x54 Watt T5 light fittings- Total-90 Nos.
• Lighting power consumption is higher due to 24X7 operation
• EPI and Data Center PUE was higher due to more power consumption
• Maintenance cost of old light fittings is high
MYIDEA / INITIATIVE / SOLUTION BENEFITS / ADVANTAGE
• Data center load being major power consumer at CDC facility
• Team analyzed data center IT and Non-IT load to identify the energy saving opportunity
• Replacing old 216 Watt light fittings with 100 Watt LED found to be smart solution
• Challenges faced for installation inside data center and modification for mounting light fittings over server racks & switches
• Smooth execution by overcoming challenges at data center.
§ Energy / cost savings of 87,194 KWH per year i.e., 8,71,940 INR per year
§ Enhancement in lux levels
§ Reduction in maintenance cost
§ 75 Metric Ton CO2 emission avoided and reduced impact on environment
§ Improvement in EPI & Data center PUE
§ ROI 11 months
myIdea
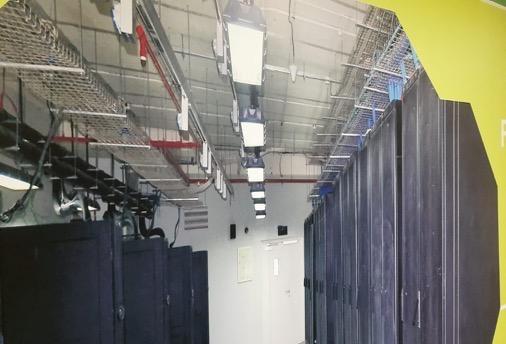
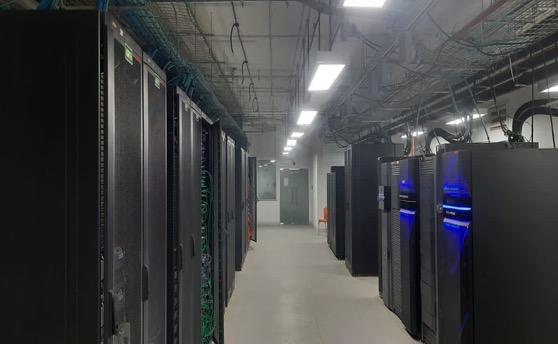
Description of the Innovation:
Touchless Vending Machine
CHALLENGE
• Manual Operation - Multiple touch points.
• Low consumption –employees were not comfortable with manual operation
• MIS – Manual activity for staff
• Cleaning process – Time consume manual activity
• Technical / On call support –When ever there is machine break down there is delay in support form vendor
/ INITIATIVE / SOLUTION
• Introduced Touchless Coffee Vending Machine
• Minimize the touch points and avoid any risk of spreading infection
• User friendly machine, easy to operate on smart phone with 3 easy steps.
• Step 1 -Once you connect the through Wi-Fi
• Step 2 -Scan the QR code on the machine
• Step 3 - You will get the beverage display option on the phone screen in which you can select your beverage option which will de dispensed without touching the vending machine
/ ADVANTAGE
§ Better user experience
§ Daily MIS with easy access to dashboard
§ Inhouse events can be flashed over display screen to market the event
§ Seamless connectivity with quick response time
§ Internet not required - for User as well as Machine
§ Multiple connections same time possible
§ Works well on both Android as well as IOS devices.
§ Fortified machine cleaning procedure
myIdea

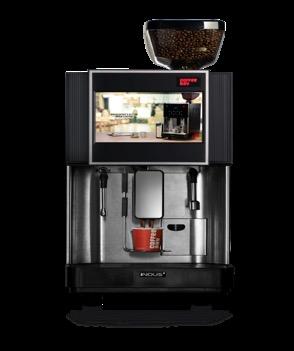
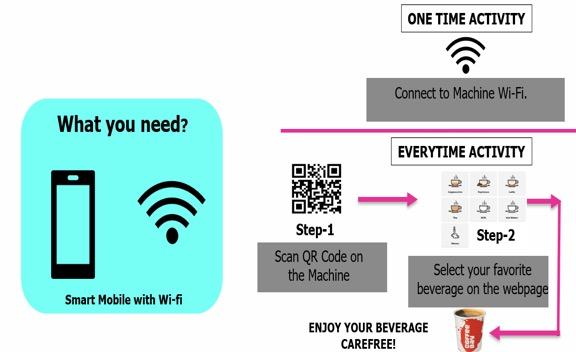
Description of the Innovation: Condeco
Desk Booking and Space Management
CHALLENGE MYIDEA / INITIATIVE / SOLUTION BENEFITS / ADVANTAGE
• No tracking of Space availability and seat utilization
• Planning Space requirement and forecast
• Lack of layout diagram in taking in formed decisions
• Controlling the cost of unoccupied seats
• Demarcate floor-wise space usage or layout drawings for occupancy tracking
• Allocate shared, dedicated and hot seats to verticals or departments for tracking occupancy
• Manage Employee Space Mapping release and movement
• Calculate space cost to charge back users
• Track Real time Space utilization with Access card and log in data
• Take future Space requirements from businesses.
§ Got consolidated information of all floor data
§ Space availability and allocation made easier
§ Accommodating more people in the same space by shift tracking
§ Automation reduced admin team efforts and improved overall efficiency
§ Better Space utilization by Space charge back to businesses
§ Team could focus on their core areas of competence and other value-added functions
myIdea
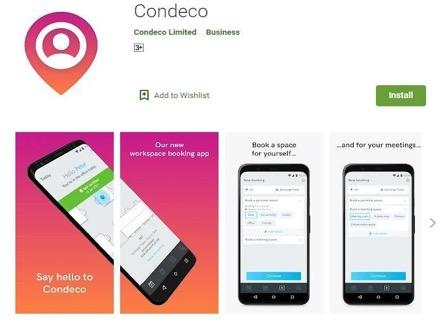
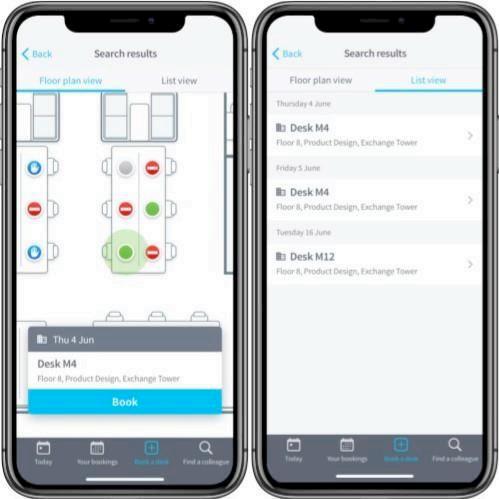
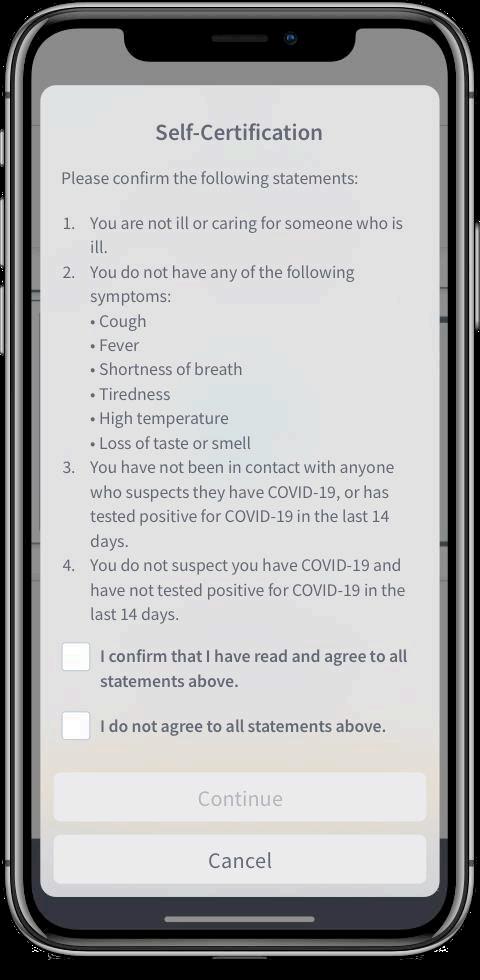
Description of the Innovation:
Interconnecti on of HVAC and DG condenser lines
CHALLENGE
• At Client’s campus, we were to execute the life cycle project of replacement of common condenser water lines of 3 X 1010 KVA DG Sets
• During the work we were having total dependency on a 500 KVA DG set in case of Power failure during the project
• Lack of reliable back up during any issue with the common DG condenser line
MYIDEA
/ INITIATIVE / SOLUTION BENEFITS / ADVANTAGE
• We, as CBRE, proposed to the client to interconnect the HVAC & DG condenser lines
• We could use the HVAC Condenser lines and eventually the HVAC cooling towers for DG Sets in case of any breakdown issue with the DG condenser line/cooling Tower.
• We installed total 6 butterfly valves,
• 2 in the interconnection lines (One in each in/out) and one in each Supply and return of the HVAC & DG condenser lines for local controls and diverting the flow of water wherever required.
§ Improvement of reliability
§ Enhanced and better redundancy on part of Operation of our Captive power Plant.
§ Can now use HVAC cooling Towers as well for the DG sets in case of any emergency
§ Approx. Project cost INR 100000/only
§ Low- cost project to improve the reliability of back up Power
myIdea
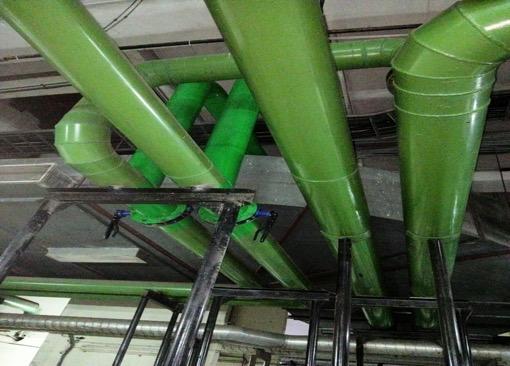
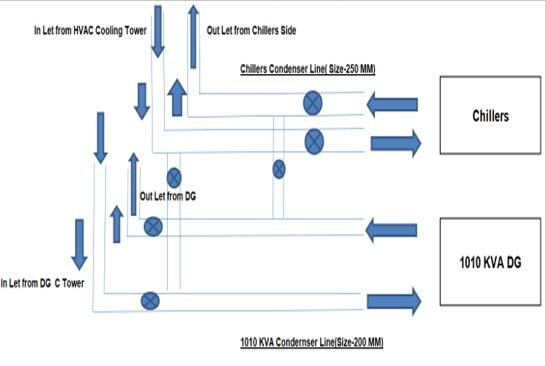
Description of the Innovation:
Space Heater for electrical panel
CHALLENGE
• During rainy season, a breakdown occurred in our main HT Power Supply.
• During root Cause analysis, we observed moisture build up in the incomer section of the VCB inside main HT panel.
• This issue needed immediate resolution as it could frequently cause interruption in Main HT power supply affecting equipment uptime.
• Also causing losses on part of DG running.
MYIDEA / INITIATIVE / SOLUTION BENEFITS / ADVANTAGE
• We, as CBRE, proposed to the client to install a space heater for humidity control within the electrical panel.
• Post client approval, we installed a thermostatcontrolled 100 Watts space heater operating on 220 V AC
• We provided the power supply to the heater through thermostat from a nearby UPS power point to ensure its continued working during rainy season
• Auto sensing and cut off through thermostat, when desired temperature is attained.
§ Easy and low-cost solution to control the humidity within the electrical panel
§ Improvement of safety and reliability
§ Immediate control on the serious issue of disruption to the main HT grid power supply due to high humidity/moisture.
§ Resolution with minimum disturbance to the existing set up
§ Shorter time for installation.
§ Client Satisfaction
§ Cost was INR 3100/- only.
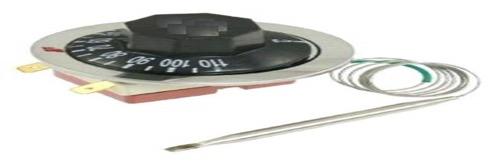
myIdea
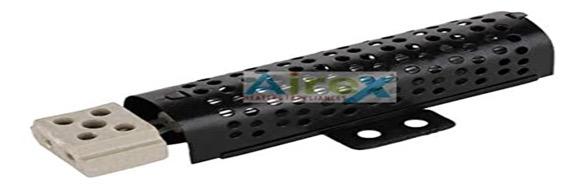
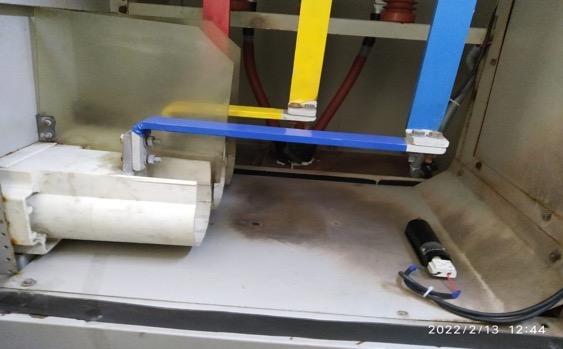
Description of the Innovation:
Installation of central RO plant
CHALLENGE
• Cost of maintenance.
• Cost of service charge & Parts of RO.
• High Water wastage of reject water.
• One of the most common issues is RO water leaking. You may see a puddle of water around your RO on occasion. You may notice this because the pipe couplings have loose connections, resulting in water leakage
MYIDEA / INITIATIVE / SOLUTION BENEFITS / ADVANTAGE
• We have installed a One RO plant in terrace to execute supply of RO water in whole building.
• Use reject water in flush tank & for garding purpose
• You must double-check that all the pipe fittings are securely in place. Call a RO specialist if you see any drips or leaks. If not addressed promptly, leaks in a water filter can cause a slew of issues. The technician will extensively inspect the water purifier to determine the source of the leak.
§ Reduce cost of service & Material of RO.
§ Low water wastage of reject water.
§ No chemicals are required in the process to produce pure water.
§ Reverse Osmosis captures and correctly disposes of the impurities. The membrane removes the impurities without the use of any ions, chemicals, resins, etc.
§ The RO system is very maintenance-friendly as it is a self-contained unit. It requires very minimal operator interaction and only daily monitoring as compared to active maintenance.
myIdea
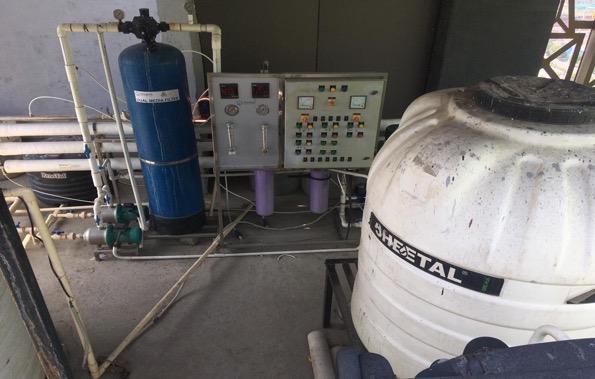
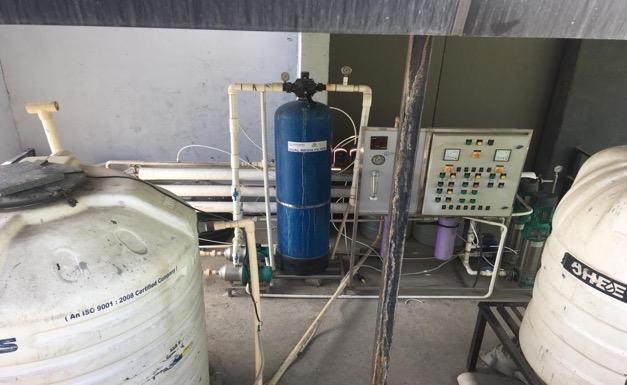
Description of the Innovation:
Movable Trolley for Breaker Maintenance
CHALLENGE
• It was very risky to rack out & rack in the heavy weight breakers.
• Minimum two persons were required in rack-out & rack-in with good balance.
• Potential hazard of falling in case of imbalance. Could cause back bone injury if not lifted with right body posture.
• The whole breaker servicing process was laborious & time taking
MYIDEA / INITIATIVE / SOLUTION BENEFITS / ADVANTAGE
• We found a repairable SS trolly from scrap yard.
• The trolly was refabricated with additional iron channels and wooden top with a required height by in-house team
• While developing the same it was ensured that the trolley is ergonomically fit to use.
• Additionally, a tray was also created to keep the required tools & spares for breaker servicing within the trolly.
§ Since the trolly is designed as per the height of the breaker, hence it’s very easy now to pull out the breaker straight on the trolly.
§ The breaker can be moved easily at any other place for servicing & repairs.
§ Being at an appropriate height, the servicing of the breaker can be done without taking it off the table.
§ All the required tools & spares are available handy at one place.
§ Minimizes the risk of breaker falling
myIdea
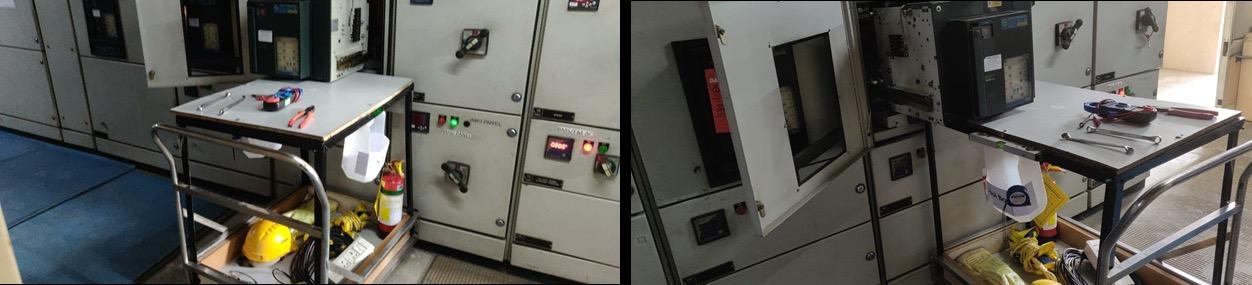
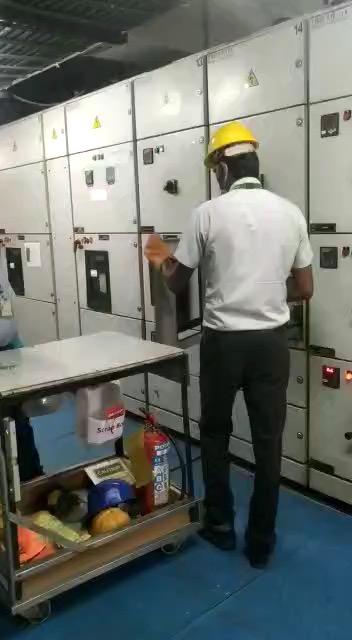
Description of the Innovation:
Provision of Portable AC at reception area
CHALLENGE
• Reception area is provided with 22.0TR HVAC unit.
• During weekend, unit need to be kept running for 12 hours to maintain the ventilation.
• Waste of electricity due to high capacity of unit running during non-occupancy hours.
• High Repair & maintenance cost.
• Requires trained Technicians to switch ON and monitor the unit on regular intervals.
MYIDEA / INITIATIVE / SOLUTION BENEFITS / ADVANTAGE
• As part of Energy saving initiative a thorough study has been carried out and observed only Receptionist occupies reception during weekends.
• Decided to provide lesser capacity Portable AC for reception to maintain the cooling.
• Hence 1.0 TR portable HVAC unit is purchased as per the requirement
• During weekends instead of running 22.0 TR HVAC unit demand of ventilation suffice by 1.0 TR portable AC unit.
§ Energy saving during weekends
§ Estimated cost Saving is INR 90K/ year
§ Low investment
§ Return On Investment is less than 1.0 Year.
§ Quick and Easy installation.
§ Increase in total life cycle of both 22.0TR and 1.0TR AC units.
§ Not requires trained Technicians to switch ON and monitor the unit on regular intervals.
myIdea

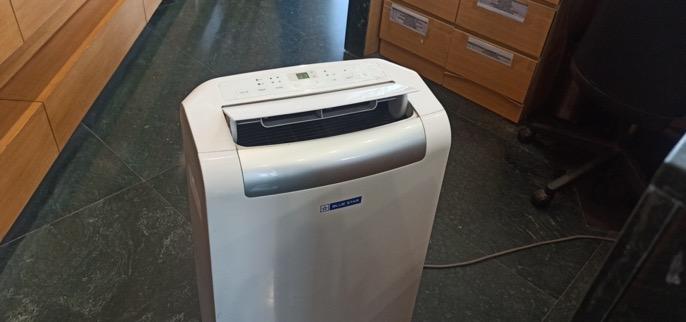
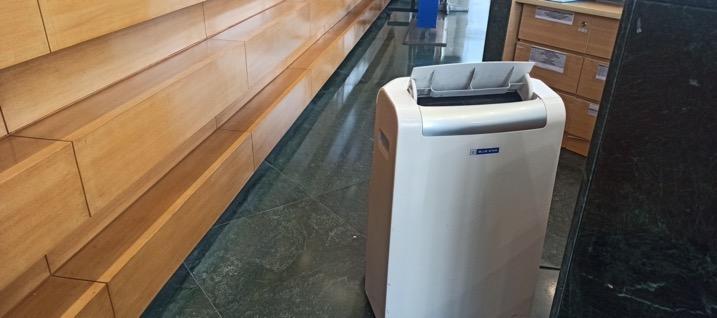
Description of the Innovation:
IoT Device for UPS system
CHALLENGE MYIDEA / INITIATIVE / SOLUTION BENEFITS / ADVANTAGE
• Real time monitoring of the UPS system was not possible.
• Difficulty faced for monitoring of the UPS system
• Remote monitoring of alarms, alerts & parameters of the UPS were not possible.
• IoT (Internet of Things) device was installed in UPS system, which helped to monitor the system remotely over the internet.
• UPS system was connected with IoT through Modbus communication protocol and monitored from central server.
• A system generated mail and SMS trigger to the user/ users for any alarms & alerts of the UPS system on real time basis.
§ Real time monitoring & intimation of alarms and alerts of UPS is possible through the internet and system alerts are sent to the user/ users by mail & SMS, which help to reduce the downtime.
§ No changes of existing UPS system are required as the communication done through Modbus protocol.
§ Increase operational awareness and visibility of the UPS System by continuous and remote monitoring.
myIdea

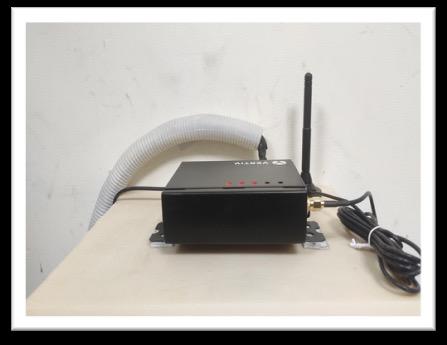
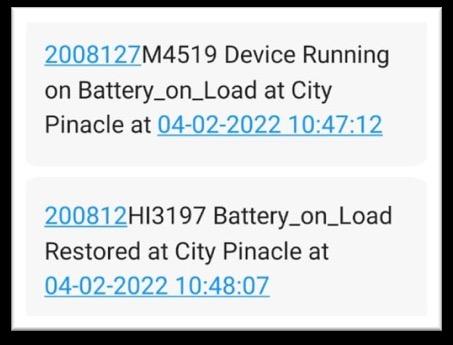
Description of the Innovation:
Introduction of QR codes for Plants
CHALLENGE
• At the time of digital age people have less time to read about a subject and process information.
• Facility has a garden area over 1 Lakh sq feet with various kind of plants.
• No structured database of plants available with entire description of plants.
• It is also difficult to access chemical MSDS for all stakeholders
MYIDEA / INITIATIVE / SOLUTION BENEFITS / ADVANTAGE
• After a brainstorming session , we have decided to introduce QR bar codes that could be linked with each plants.
• Test converter application has been used to convert the entire description of a particular plant to a bar code.
• Smartphone scanner can be used to scan the bar code that is hung on the tree to get the information
• We have made a board of QR code for scanning, HK chemical MSDS details and PCI Chemical MSDS ,will get generated for the given chemical through the link and this is absolutely paperless .
§ With the installation of QR codes ,gaining knowledge about any plants have become more easier as it helps us to save time and efforts to read about a tree from a paper book.
§ Encourage to install a greater number of QR codes to build a digital database for the facility garden area.
§ Also the Chemical MSDS is fast and easily accessible for everyone with this strategy
myIdea
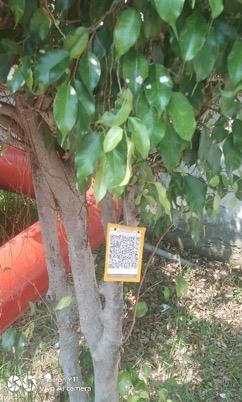
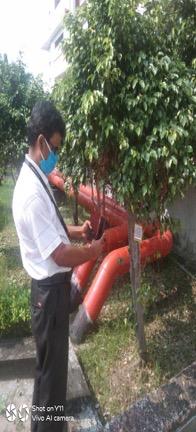
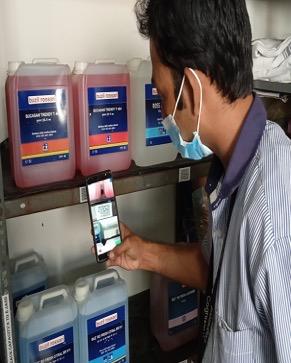
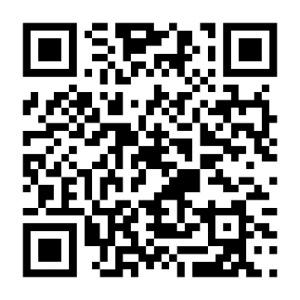
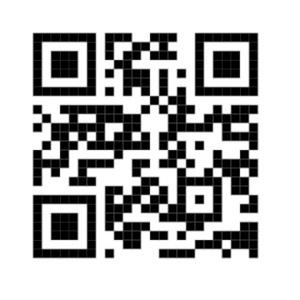
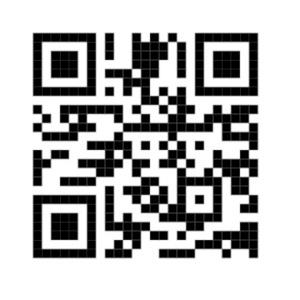
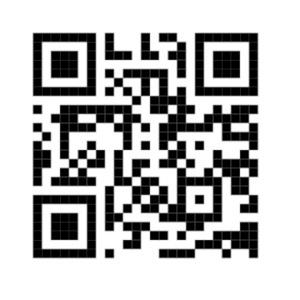
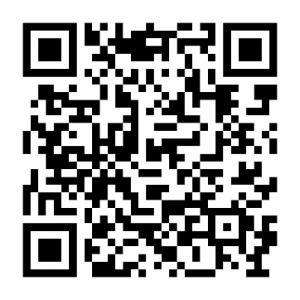
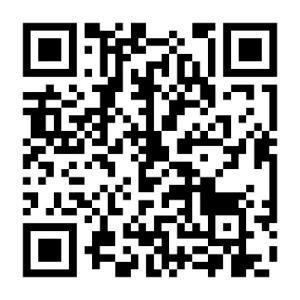

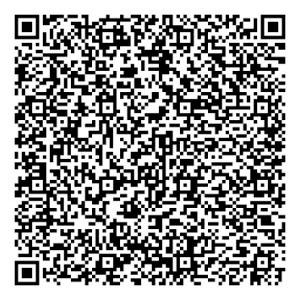
Description of the Innovation:
Annual Rate Contract
CHALLENGE
• Manpower and time loss on account of follow ups with multiple vendors.
• Minimum 3 quotes and comparison is mandatory.
• Building Manager, Asset manager and Internal Audit team approval process was consuming more time.
• It takes approximately 20 to 25 Working days from the date of request to issue the PO.
• We used to get approximately 6 to 8 request in a month.
• Varied Cost for similar equipment across all locations
MYIDEA / INITIATIVE / SOLUTION BENEFITS / ADVANTAGE
• Identification of commonly used M&E consumables and the rates at which it was procured PAN India
• Identification of vendor having PAN India Presence
• Negotiating the best price
• Discuss and close agreement with Client on the process and the rates
§ Reduction of repetitive task thereby increasing efficiency
§ Timely delivery of Materials
§ Best rates are ensured to clientsreduction of 12 to 16%
§ Avoid Dead stock
§ Storage area saved up to 150 Sqft
§ Over all 2000+ materials covered in rate contract.
§ Annual expenses of approx. 42 lakhs
§ Finalizing on at A centralized technology platform in lines with amazon/flipkart model
myIdea
Comparison of Rates

Description of the Innovation:
Cyclic timers and sensors
• High common area Energy Consumption
• Continuous operation of Toilet Exhaust fans, Lift machine rooms and Lighting circuits
• Frequent disputes raised by tenants for excess common area energy billing during full and partial Lockdown period.
• Controlling Non-peak hour energy consumption
• Scheduling all motor loads based on usage pattern
• Installation of cyclic Timers for Exhaust Fans, Ventilation fans, water pumps and in all possible lighting circuits (terrace, staircases building periphery etc.).
• Installation of Occupancy sensors in elevators and ventilation rooms to control lights and fans
§ Increased Energy savings.
§ Reduction in Common Area Energy Billing.
§ Tenant satisfaction
§ Better Utilization of Energy
myIdea
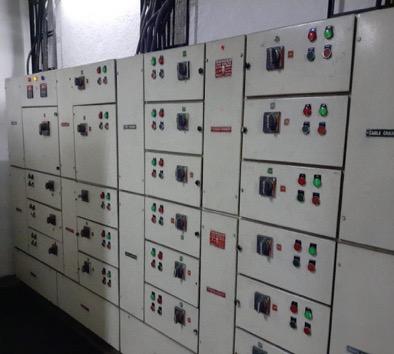

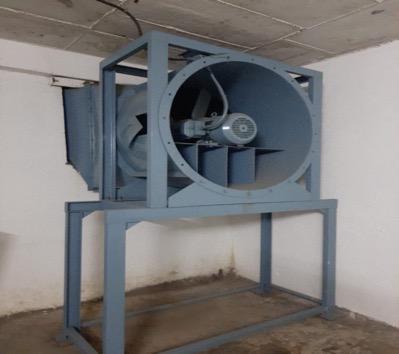
Description of the Innovation:
Electrical Risers tripping alarm system
CHALLENGE
• No information of tripping of breaker to technician
• Occupant critical load interruption until the Engineer got call from concern occupants.
• Unable to meet the Occupant ‘s business continuity
MYIDEA / INITIATIVE / SOLUTION BENEFITS / ADVANTAGE
• Effective utilization of Technology
• Installed indication panel enabled with alarm in control room for instant information of tripping
• Enabling to achieve 100% uptime of occupant's critical loads
§ Indirect saving in terms of service level improvement and sustainability.
§ Occupant critical operation mitigated
§ Power interruption reduced to Zero
§ Customer satisfaction up to the mark
§ Enable to achieve the business continuity
myIdea
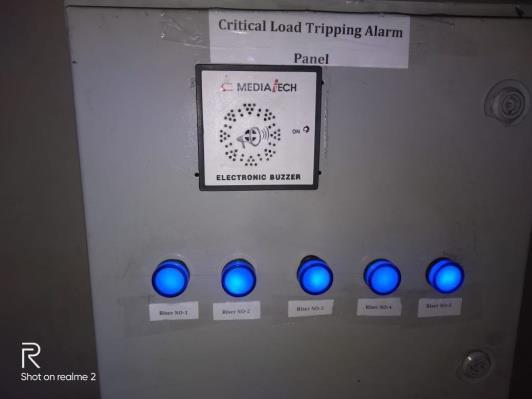
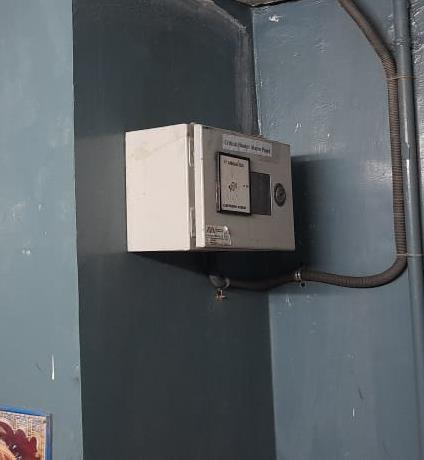
Description of the Innovation:
Digital SOP of Fire Fighting & FAS systems
myIdea
• All the SOP related to Fire Fighting and Alarm Systems are available in office and not close to the equipment
• All the SOP can not be displayed near to the equipment’s
• During the Third-party audit and Clients’ inspection the auditor has suggested different ways to keep the SOP handy such as to be displayed at Panel, Pumps or Pump Room and other locations.
• It was also a challenge to keep all the SOP together at proximity to the equipment. Further, the SOPs were getting dusty after a period
• Keeping all the suggestions in we explored the option of converting SOP to Google Documents and generating QR codes for these
• Subsequently, generated QR Codes for each individual fire pump and alarm panel
• QR codes have been laminated and are displayed on every panels for ease of cleaning
• Further, we will convert our SOP’s in local language for easy understanding for inhouse team
§ The idea was liked and appreciated by the Clients as well as auditors
§ Immediate and easy access to all SOP’s of Fire Pumps and Fire Alarm Panel SOP at the location
§ During the Audit & Inspection is very easy to show and explain the QR Code and very handy at every time
§ Helpful during training, inspection and maintenance
§ No Cost involved in generation the QR code
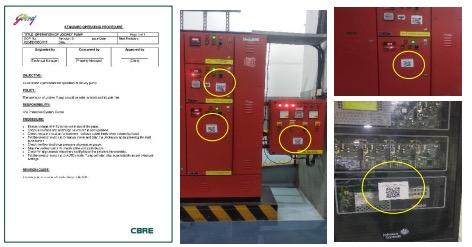
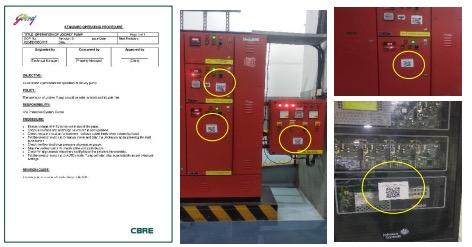
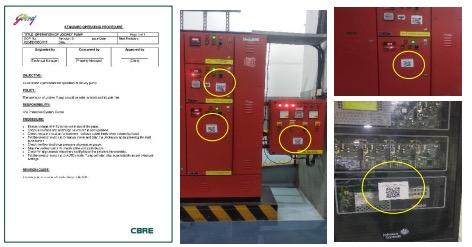
Description of the Innovation:
Wealth from Waste Initiatives
myIdea
• Being a dynamic property , disposing of waste is always a challenge for the P&FM team
• Waste is generated during fit out modification / new fit outs and during execution of R&M works
• There is a cost for disposal of waste and procedure to be followed for the disposal
• Reduction in sustainability score for the quantity of waste being disposed
MYIDEA / INITIATIVE / SOLUTION BENEFITS / ADVANTAGE
• Utilized waste material into useful and meaningful ways like creation of
• Recreation room
• Rock garden
• Fountain
• Flower pot stand
• Covid warrior wall
• with the available materials in the scrap to reduce the disposal of waste


§ Aesthetic improvement in the exit driveway
§ More indoor plants are placed in the same space
§ Creation of staff recreation room with world class amenities for a common man
§ Untapped talents of staff were brought in limelight because of WOW program
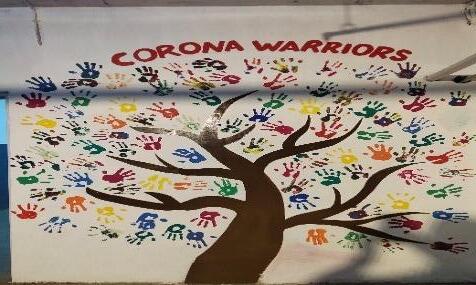
Description of the Innovation:
5S Implementations
CHALLENGE
• Difficulties in managing the paint daily stock/ Consumption in the painter’s sub stores
• There is no integrated training facility available in the campus for the new HK staff for understanding tools/ tackles/ procedure/ safety and chemicals handling etc.,
• Non availability of SLD and flow diagrams in the respective workplace / plant area for quick reference during any breakdown or addition/ alteration work
MYIDEA / INITIATIVE / SOLUTION BENEFITS / ADVANTAGE
• Created a Visual Paint stock dashboard to find the stock available in the sub store quickly
• Created a HK Studio for training and Inducting new HK staff
• Created the SLD’s and flow diagrams in 10ft X 5ft size vinyl boards and placed in the respective locations
§ Pictorial representation provides quick and clear information on the stock and consumption
§ Swift Orientation and effective learning of Housekeeping for new joiners
§ It is easy for the new staff to refer the schematic/ flow diagram by seeing it repletely
§ Easy to refer the flow diagram during any breakdown/ fault finding activity
§ On the JOB Trainings are easy referring the diagram
§ Very useful during the internal / external audits and client visits to explain he system
myIdea
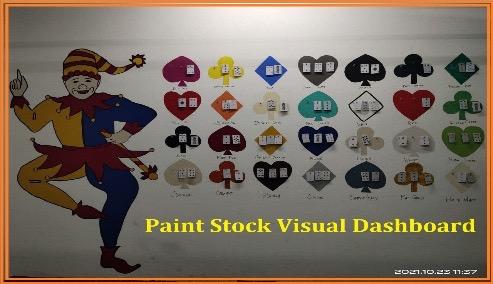
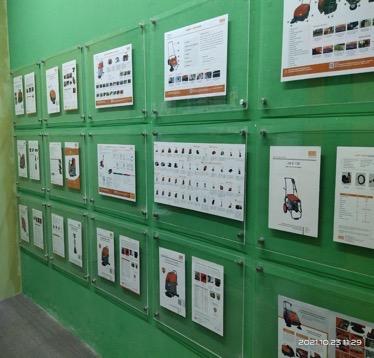
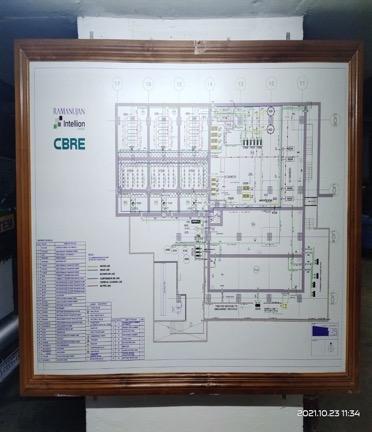
Description of the Innovation:
IOT based Water Levels Indicators
CHALLENGE
• Safety concern in accessing overhead tanks at night and during rainy season using iron ladders and it may lead to slip hazard.
• Opening manual covers for water levels may lead to physical injury.
• No accurate measure of water levels as there are no tank level markings.
• No real-time monitoring
MYIDEA / INITIATIVE / SOLUTION BENEFITS / ADVANTAGE
• Installed IOT based water level sensor using ESP8266 and Ultra sonic sensor.
• Integrate with TELEGRAM app for regular updates.
• Every 3-minutes data will be captured and same will be updated in Telegram App.
• Time Frequency can be changed as per site requirement.
• Circuit and Program done by Inhouse team
§ Monitor Water levels remotely.
§ No manual intervention.
§ Accurate measure of water level.
§ No wastage of water as tank overflow is avoided.
§ Be notified anywhere on your mobile phones through telegram app.
§ Tank levels are getting on mobile, so team can be used for other works.
§ Telegram is an open source, no commercial required and we can add 2-lakh peoples in one group
myIdea

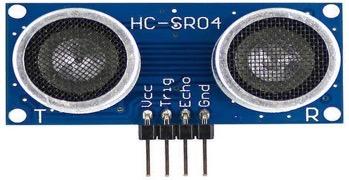
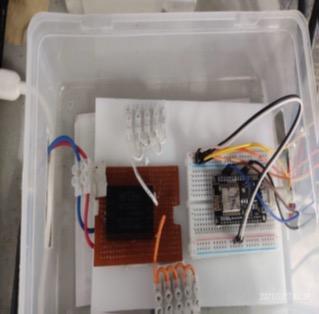
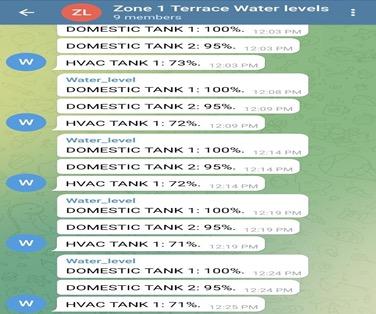
Description of the Innovation:
Wet Waste Sorting
CHALLENGE
• Sort out wet waste
• Difficulty in draining liquid from wet waste
• Difficulty in transferring waste to OWC machine
• Poor quality compost generated from wet waste
• Unable to use such compost for landscape
• Storage of such runny compost was difficult
MYIDEA / INITIATIVE / SOLUTION BENEFITS / ADVANTAGE
• Waste management is primary focus as part of green building
• We sort waste into 6 category in this wet waste sorting is key element
• Trough is equipment use for draining gravies from wet waste
• Mesh frame made by the inhouse team using scrap material
• We have got this idea from civil work happening at site
• We have mesh strainer mounted on the trough with parallel dimensions
§ We are getting right state of wet waste
§ Easy handling
§ Save sorting time
§ Aids in generating dry and right quality compost
§ Compost used for landscape &provide clients for office indoor plants
§ Dry consistency of compost makes it easy for storage
myIdea
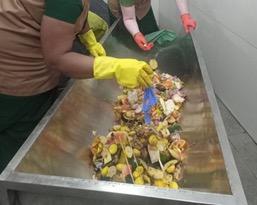
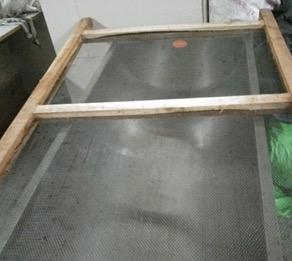

Description of the Innovation:
Vertical Gardens
CHALLENGE
• At our site, we have converted CFL lights into LED lights, repaired the damaged and leakage PVC Pipes and Wooden battens from dismantling of a small occupied area
• Lot of scrap accumulated from CFL fittings, PVC Pipes and wooden scrap. It was a challenge to manage the Scrap and grooming of the building in particular area
• Disposal of scrap is a heavy effort
MYIDEA / INITIATIVE / SOLUTION
• Making use of the CFL fittings, Pipes and wooden scrap for batter use
• Then, we planned to prepare a different types of vertical gardens
• We took the concealed cap of CFL, PVC Pipes and wooden battens and fixed them on a wall and stands made by this Scrap material
• We placed multi-coloured small flowerpots of multiple types of plants
• Placed them in common area gallery and on ventilation shaft wall
BENEFITS / ADVANTAGE
§ A ‘Best from the Waste’ initiative
§ Enhancing customer delight
§ No cost involved to make it
§ Increasing Vertical Green Space
§ Easier to maintain
§ Having amazing environmental impact
§ Appreciated by Occupants and Client
myIdea


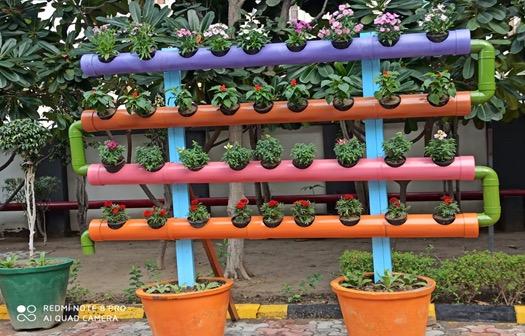

Description of the Innovation:
Portable
Chain Pulley & Mobile Scaffolding
CHALLENGE
• Photo A – Using rope for lifting the pumps
• Involved lot of human efforts
• Not a safe/healthy act. There is a potential hazard for both men and machinery and also consumes more time
• Photo C – ‘A’ type ladders used for all height works in parking areas
• It requires buddy system which consumes more manpower and safety concern as well
MYIDEA / INITIATIVE / SOLUTION BENEFITS / ADVANTAGE
• Used scrap items and come up with an idea of PORTABLE & DISMANTABLE CHAIN PULLEY concept for removing the heavy motors from UG tanks
• All the fabrication and assembling by inhouse team
• Conducted a competition in team and finalised MOBILE SCAFFOLDING
• 1 KW power provision
• Toolbox kit fixed
• Fire extinguisher with stand
§ Safety standards & Employee morale increased
§ Accident-free activity with locking provision
§ Requires less human efforts as well as time
§ Usage of scrap/ value yard materials as a sustainability initiative
§ Savings of approx. Rs 25,000/- by making this product by utilizing inhouse resources
§ Approx. saved 416 man Hrs per month also it could be an intangible benefit
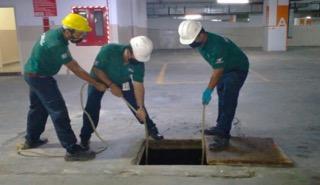
myIdea


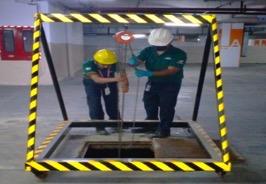
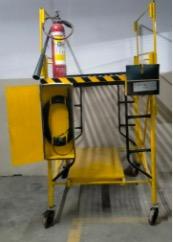
Description of the Innovation:
Block & Bleed
Set up
CHALLENGE
• A Single Isolation valve was installed between the Domestic Water pipelines and Flushing water pipelines
• There may be a chance of Flushing water (STP Treated water) into Domestic water pipeline in case of any pressure drop in the domestic water system and Valve leaking issue.
• It will lead to the Health Hazardous and smell issue to the Residents.
• Installed the Block & Bleed setup by using with additional 3 valves for ensure that there should not pass the flushing water to the domestic water pipeline at any point of time.
• Kept the Block Valves in closed condition and Bleed valve in Open condition
§ The water passing issue has been eliminated
§ We can identify the valve passing issue very easily
§ Residents Comfort level increased
myIdea
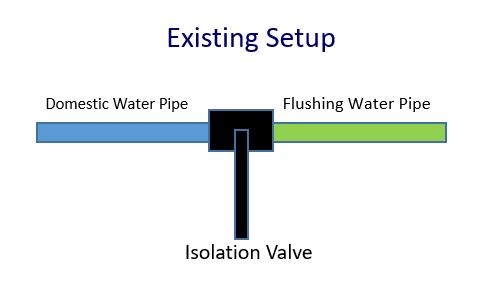
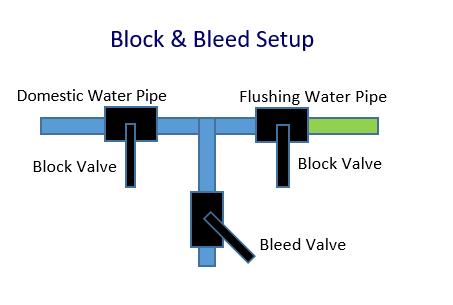
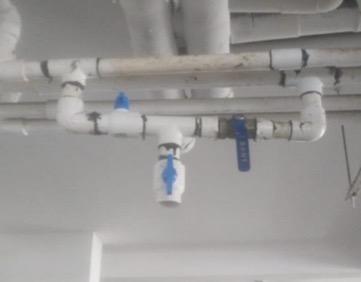
Description of the Innovation:
Touchless Lift
Car Operations
CHALLENGE
• Generally, passengers utilize the lift by pressing the call buttons manually
• On account of COVID-19 there might be an outbreak of this contagious disease through the touch points on the call button in the lifts
• HK team was engaged to clean the touch points with disinfectant in every shift and challenge in tracking the checklist with multiple schedules .
• Option to operate minimum lift have challenges due to grouping and specific programs based on occupation
• Pressing the call buttons using pen, key and many other objects In fear of Covid 19 infection which caused button to damage
MYIDEA / INITIATIVE / SOLUTION BENEFITS / ADVANTAGE
• Installed Bluetooth device in every passenger lift car for easy and touchless operation which can controlled by using dedicated app for the lift movements
• Pictorial SOP is displayed in Ground level lobbies about usage and employee to download the App
• Bluetooth range will be available at the entrance of lobby. Employee have to call the lift using app ,lift will land in the particular floor
• Once entered the lift car ,floors can be accessed through the app
• For Visitors and vendors ,COVID protocols and app usage and procedure is displayed in Security VMS point and encouraged to use the lift through app
§ Easily accessible and minimizes the risk of outbreak of COVID-19
§ Ensuring 100% hygiene is followed.
§ Touching of call button is purely avoided
§ Manual intervention with disinfectant chemicals are stopped
§ These solutions deliver a better experience to passengers that will help employees to feel secure and satisfaction
myIdea
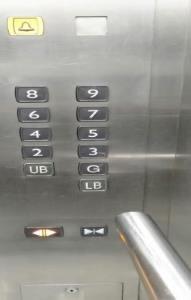
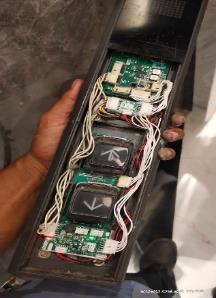
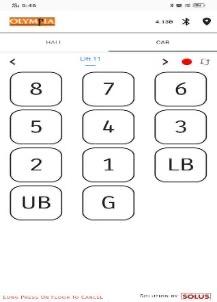

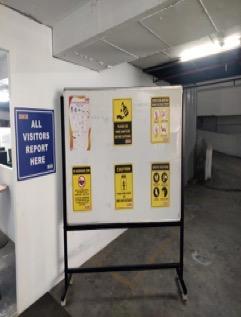
Description of the Innovation:
Locking arrangement of confined space manhole door covers
CHALLENGE
• As per Client’s Confined space safety standard, all the confined spaces should be locked at all time.
• The locks provided for the confined spaces in the driveway were getting damaged frequently due to vehicle movement and most of these confined spaces are on driveway.
• The external locking arrangement has the potential of trip hazard due to the keel, GI flat and the lock protruding above the manhole cover.
• Frequent damage to locks affects the key management system and documentation and results in recurring cost.
MYIDEA / INITIATIVE / SOLUTION BENEFITS / ADVANTAGE
• To eliminate the challenges, implemented an idea of making a locking arrangement inside the manhole cover.
• Used GI material instead of MS sheet to avoid rust, with latch mechanism for locking arrangement
• The GI plate is provided with stiffener rods at the bottom and tested for SWL of 150 Kg
• The arrangement is completely done by inhouse team.
§ Procurement and frequent replacement of locks due to damage caused by the vehicle movement in the driveway and ambient conditions like dust and rain are eliminated.
§ Enhanced safe atmosphere due to avoidance of trip hazard caused by the external locking arrangement..
§ Reduced workload of replacing the external locking mechanism
§ Aesthetically pleasing
§ Savings - Rs 3 lacs per annum
myIdea
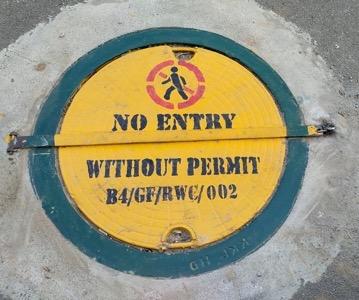
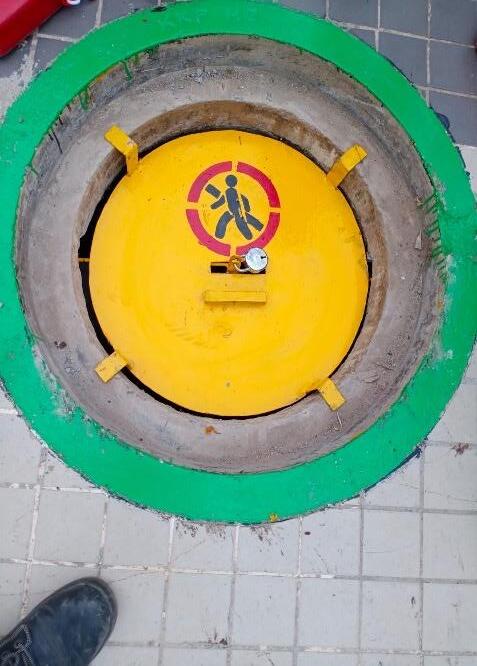
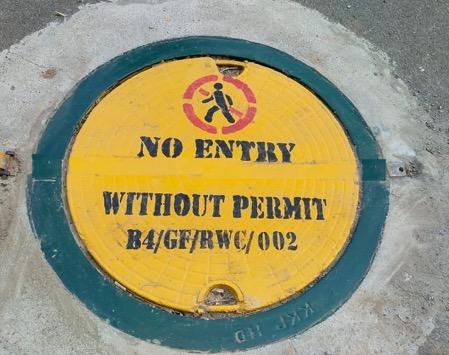
Description of the Innovation:
Open GYM for Senior Citizens
CHALLENGE
• Lack of resources/equipment
• Lack of motivation
• Boredom with regular walking & yoga
• Feeling inactive
MYIDEA
/ INITIATIVE / SOLUTION BENEFITS / ADVANTAGE
• Common open area identified.
• Suitable equipment's selected.
• Equipment's are properly installed
• Usage and its physical benefits posted..
§ Improves overall immune function
§ improve mental health and well-being
§ Social Engagement
§ Prevents from depression
§ Healthy Environment
§ Senior citizens smiley faces said that we (CBRE) are taking care of them.
myIdea

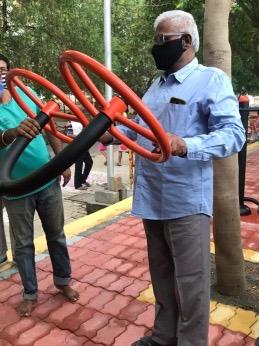
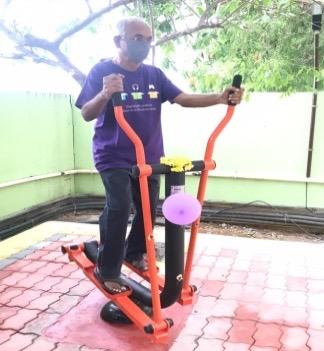
Description of the Innovation:
Wet Scrubber for OWC
CHALLENGE
• The odour of OWC machine was spreading in entire podiums and main entrance of Tower
• Multiple complaints from the residents on regular basis about rotten smell
• Odour of hazardous gas emission was serious point from EHS
MYIDEA / INITIATIVE / SOLUTION
• We put 200 ltrs. drum filled with 50% of water behind OWC machine
• Extended exhaust of OWC with help of PVC pipe in drum above water level. Drum is properly covered from the top
• Installed 1 HP pump for water circulation between drum and exhaust with help of sprinkler to make water curtain
• Small hole (1 inch) is made on top of drum for easy movement of exhaust gases to the nearest chamber through flexible pipe
BENEFITS / ADVANTAGE
§ By installing these system, the spread of odour minimised on great extent
§ Entire material of this project is made available from site debris except motor
§ Customer satisfaction –80%
myIdea
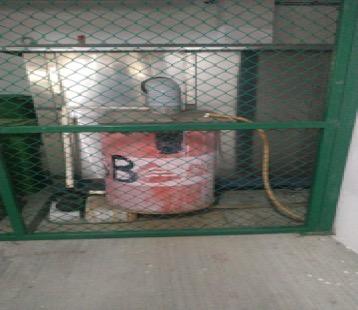

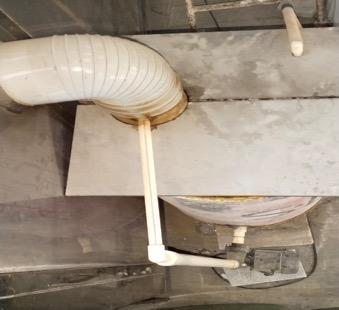
Description of the Innovation:
Centralized CCTV Monitoring
CHALLENGE
• Portfolio spread across 02 Sq. km area
• Each building had Individual CCTV
• Higher cost of monitoring 24X7
• Analogue systems, quite old and of deferent makes in various buildings mostly installed 10 years ago
• Frequent breakdowns
• Network connectivity issues due to different network provider in each building
• High cost for upgradation and set up control room
MYIDEA / INITIATIVE / SOLUTION BENEFITS / ADVANTAGE
• Centralised monitoring at a single location
• Centralized high speed broadband connectivity to all buildings with single network account
• Explored a free software which supports both analogue and IP technology
• Existing CCTV infrastructure used with few modifications
• Compatible NVRs, Switches, Converters, few IP cameras were procured
• 06 Nos 55” screens and 06 Nos workstation machines (PCS) procured to support 284 cameras (64 each)
§ 24X7 monitoring made possible at a single location
§ Considerable reduction in manpower cost
§ CCTV systems maintained by in-house team
§ Process improvement
§ Huge saving in terms of infrastructure, Technology, Manpower & time
§ Implementation Cost INR 10 Lakhs against previous projected cost of INR 1.25 Cr
§ Cost Saving : 1.15 Core
§ ROI -04 months
§ Client appreciation
myIdea
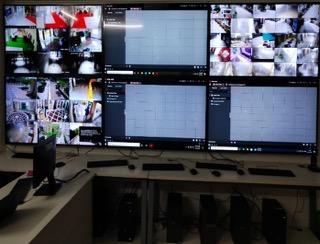
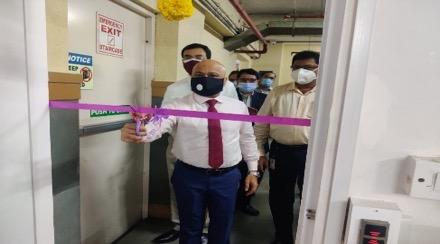
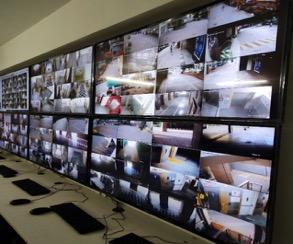
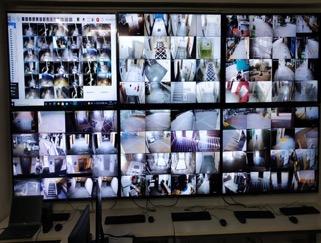
Description of the Innovation:
Ductable Exhaust Unit for LT room
myIdea
CHALLENGE
• Poor ventilation in the LT room
• LT room temperature high (40 to 45 degree centigrade) due to less number of air changes
• Negative impact on Manpower productivity
• Frequent Equipment failures
MYIDEA / INITIATIVE / SOLUTION BENEFITS / ADVANTAGE
• Heat load calculation done for the LT room
• Basis our analysis 3200 CFM exhaust requirement was determined
• The exhaust unit of 3200 CFM with compact ductable design installed
• 11 APCH has been achieved in LT room
• Capex investment around INR 80K
§ Premises Temp. has been brought down by 8 to 10 degree Celsius in LT room. Existing temp is around 35 to 40 degree centigrade.
§ Smell was no longer persistent due removal of stale air
§ Nuisance tripping issue reduce due to controlled temperature
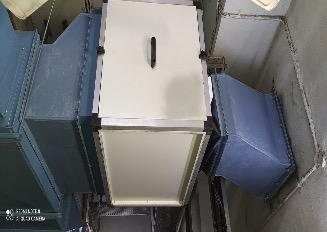
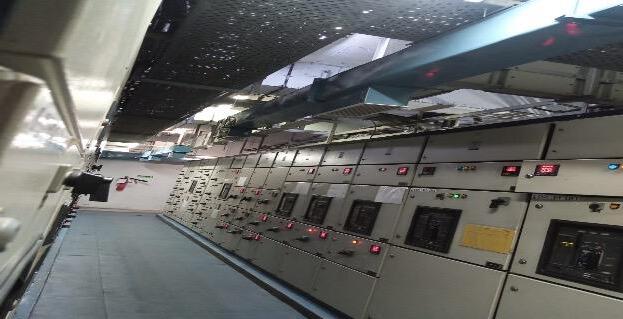
Description of the Innovation:
Test lamp circuit board
CHALLENGE
• Vendors are using electrical equipment’s not in healthy condition
• Motor and Pumps winding issues not able to check
• The defective machineries can damage both business & human life
• As mentioned above issues we don’t have any separate Test board circuit for checking
MYIDEA / INITIATIVE / SOLUTION BENEFITS / ADVANTAGE
• Installation of testing station at the LT Room, which will enable check the Motor and Pumps issue
• 110V Socket – for check motor, pump winding etc.
• If Machine or equipment will is defect automatically ELCB will trip
• For identify motor and pumps fault provided test lamp
§ Mass production can be achieved at lower cost
§ Ensuring 100% Human safety and property damage
myIdea
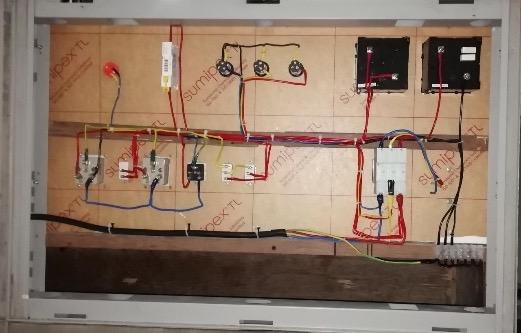
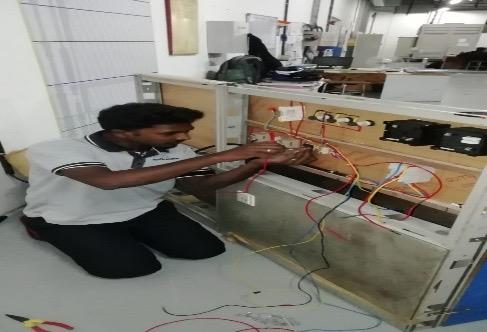
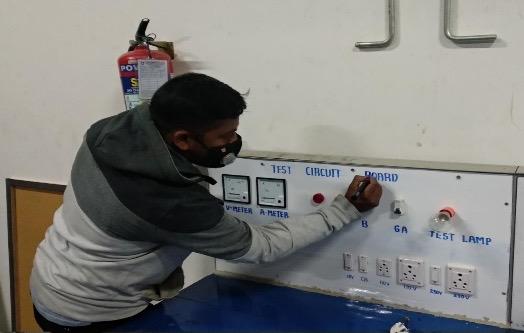
Description of the Innovation:
Safety Studio
CHALLENGE
• IT Park spread across 7 buildings has got close to 1000 task level team members from engineering, housekeeping, security, lift attendants etc.
• Safety plays an important role in managing this campus and every individual has to play his / her part
• Lack of time and resources to look into every corner of the campus by safety team
• Task level team does not have basic knowledge of safety and safety gadgets
MYIDEA / INITIATIVE / SOLUTION BENEFITS / ADVANTAGE
• In order to create awareness on fire safety equipment and components, team has come out with an idea of creating a studio
• Identified a wall to showcase all fire system related components and displayed the tags against each component
• Our Moto is to educate our operation’s team for quick response in case of emergency
§ All new joiners (HK, Engineering, Security) have to undergo safety induction explaining about FAS and FHS components
§ Refreshing sessions are conducted periodically
§ Teams while passing by can have a look at the safety studio
§ This has created awareness among all task level teams working in the campus
myIdea
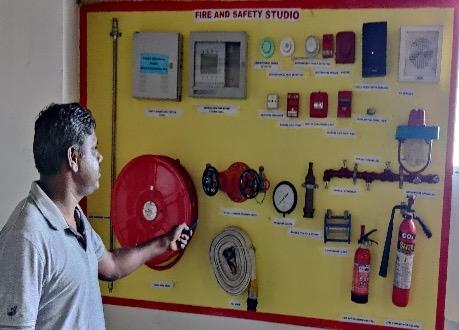
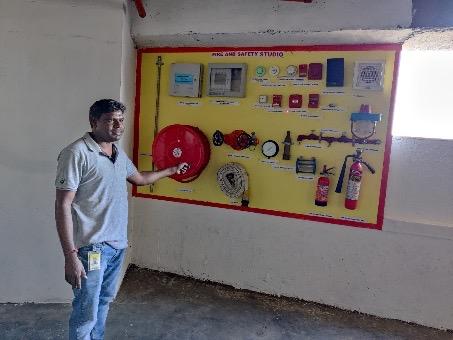
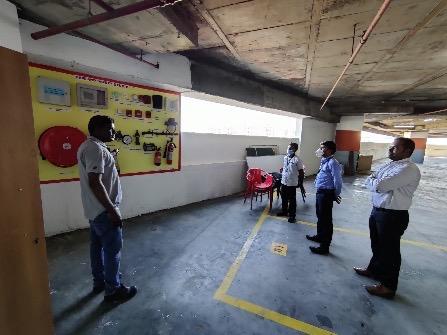
Description of the Innovation:
Motion Sensor for parking area
CHALLENGE
• Building community has got two levels of basements for residents parking and other amenities
• Due to lack of Sunlight Access and Shadow Impact , almost 60% of basement lights need to operate 24/7 (About 500 light fixtures) irrespective of light required or not
• Due to 24/7 operation power consumption is high.
• Due to continuous operations faster burning hours of lights and early replacement
MYIDEA / INITIATIVE / SOLUTION BENEFITS / ADVANTAGE
• Sensor technology incorporating dual inputs of activity and ambient surrounding lighting
• Fit & Forget model with minimal infrastructure changes ,quick and clean install with no disruption to residents. Considerable energy savings from day one.
• Adjustable knobs to control the lux sensitivity(Brightness) as well as the length luminosity (Timer)
• Sensors detect the motion of humans and it is used for both safety and security purposes.
• Phase I completed with one tower, 4 are in process
§ 60 % energy savings achieved by implementation of the initiative
§ In terms of savings 6914 x 9.3 = 64300 per month
§ CAPEX - 250000
§ ROI – less than 4 Months
§ Motion sensors are incredibly durable and long-lasting. They work well with no defects for many years as the technology of them has been working on for a long time
§ Yearly savings KWH – 81000 KWH & INR 7.7 lacs
§ Client & Residents are happy
myIdea
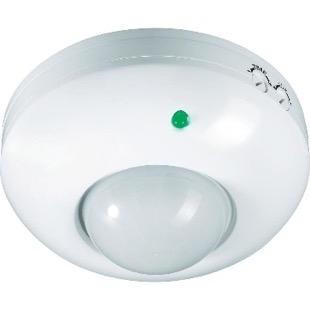
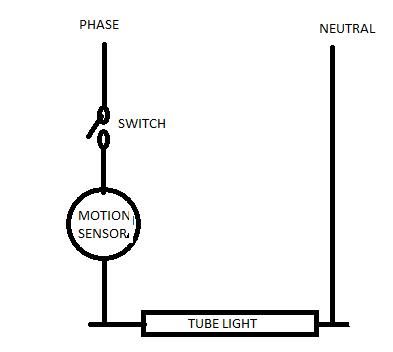
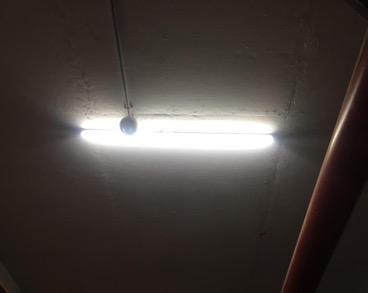
Description of the Innovation:
Automated
Fresh Air Fan
CHALLENGE
• As per the building structure fresh air intake is only through louvers. Which is not sufficient to maintain fresh air level in the occupant's floor considering the pandemic situation
MYIDEA / INITIATIVE / SOLUTION BENEFITS / ADVANTAGE
• To pump fresh air in the occupant's floor automated additional
• Fresh air designed such a way that 15% of AHU CFM will be pumped into AHU room
• Fresh Air fan installed in the AHU rooms with IAQ sensor and operate operates based on CO2 level
§ Due to modulated fresh air intake required fresh air will be pumped into occupants floor
§ IAQ will be maintained
§ Users will get more comfort level
myIdea
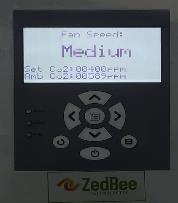
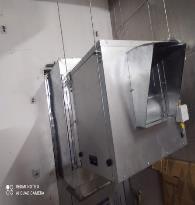
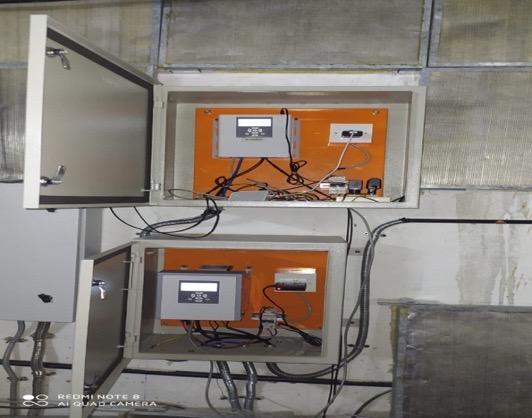
Description of the Innovation:
Recycling of Dry / Wet Waste
myIdea
CHALLENGE MYIDEA / INITIATIVE / SOLUTION BENEFITS / ADVANTAGE
• Resident use to throw mix waste through garbage chute.
• No segregation earlier happened at site either from residents or from vendor.
• Mix Garbage use to go to landfill contributing to land pollution
• Staff and resident were unaware of waste segregation
• No benefit from Waste generation
• SWM 2016 norms weren't met
• Waste Segregation process was made and implemented at site along with penalty for violations, waste collection was initiated through HK staff.
• Second and final level of segregation is done by vendor staff.
• Dry waste is Segregated into Paper, Plastic, Cardboards, Metals, Glass etc.
• Collaborated with MPCB approved recyclers and NGO’s to utilize dry waste
• Wet Waste collected is used to generate organic compost
• Initiated to purchase shredder machine to compost gardening waste
§ 24,823 Kg of Dry Waste Recycled in 12 months
§ 20,980 Kg of organic Compost generated from Wet Waste which is used for Gardening giving results of wining 1st Prize in Horticulture in BMC
§ 10,000 nos. of tetra recycled in exchange got two recycled.
§ 187 Kg E- waste collected and give to recycler
§ Received monthly certificate for recycling
§ In exchange of dry waste to recycler, received green points which is reimbursed to buy A4 size paper rims saving cost of Stationary
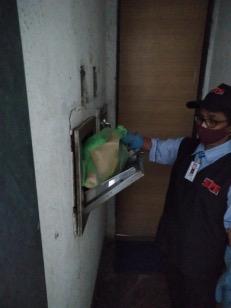
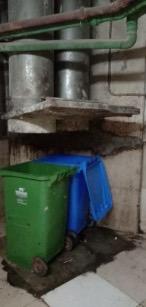
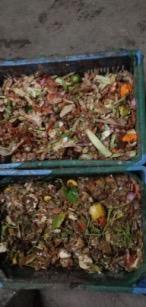
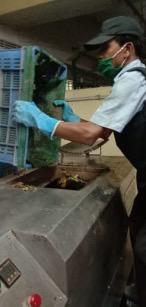
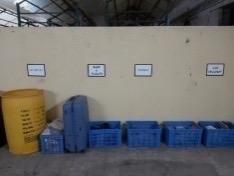
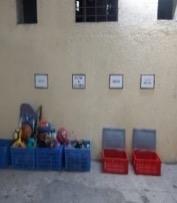
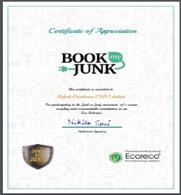
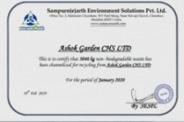
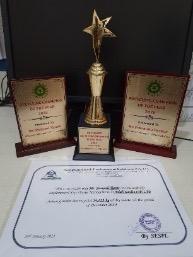
Description of the Innovation:
Vegetable GardenMicrogreen
myIdea
CHALLENGE MYIDEA / INITIATIVE / SOLUTION BENEFITS / ADVANTAGE
• Extend the gardening range and productivity
• Application of new gardening methods called high nutritious microgreens
• Planting a microgreens .They have an aromatic flavor and concentrated nutrient content .Since the space taken is less they can be easily developed in the current gardening structure.
• Session carried out about micro greens to Children's and residents of Springs.
• Micro green method with using of cocopeat, and vegetable seeds.
• BEETS RADISH, BLACK MUSTARD
§ They have an aromatic flavor and concentrated nutrient content .
§ Microgreens contain similar and often greater amounts of these nutrients than mature greens. As such, they may similarly reduce the risk of the following diseases: Heart disease, Alzheimer’s disease, Diabetes, Certain cancers
§ Microgreens may also lower triglyceride & “bad” LDL cholesterol.
§ Suitable for immunity boost ,reduce stress & weight loss
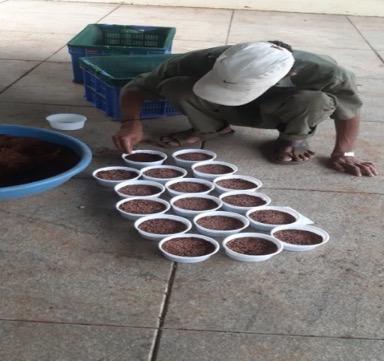

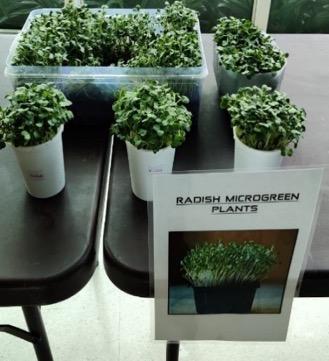
Description of the Innovation:
Plumbing Audit & repair Program
CHALLENGE
• High leakage issues faced at plumbing supply lines due to rusting and other aging issues
• Drain line leakages at various locations
• Water pressure issue at different apartment level
• Internal seepage issue at flat due to wet shaft
• Issues with ball valve & PRV
MYIDEA / INITIATIVE / SOLUTION BENEFITS / ADVANTAGE
• Plumbing in-house audit carried out at site which highlighted the main plumbing issues faced at site and necessary action to be taken to resolve all of it
§ Taking corrective action as suggested in audit will lead to resolving of all the plumbing leakage issues faced at site
§ Water pressure issues will be cleared
§ Seepage issue will be resolved and internal damages to flat can be avoided
§ Easy maintenance and resolution of plumbing system by changing all the old rusted parts, valves, PRV, Strainers etc.
myIdea
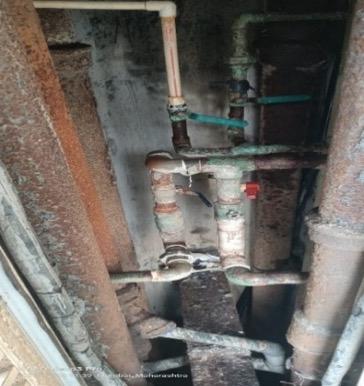
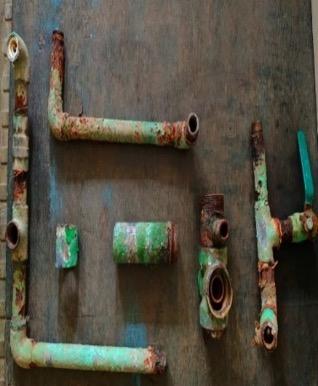
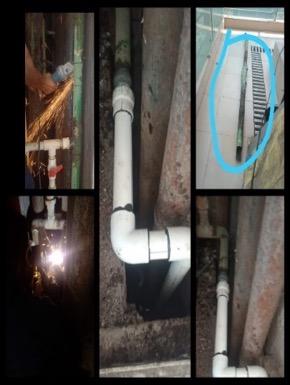
Description of the Innovation:
Fire pump integrated with Fire
Alarm Panel
CHALLENGE
• Currently there is no audio/visual alarm on operation of main fire hydrant pumping system
• Security guard is stationed in the center lobby area which is far from Fire pump room
• In case of emergency or starting of these pumps, the guard will not be able to address the situation
• Also, continuous running of main pumps will lead to untoward incident at pump room affecting other areas of the site
MYIDEA / INITIATIVE / SOLUTION BENEFITS / ADVANTAGE
• available in pump room for detectors, the pumps starting contacts are integrated with FAP to get immediate intimation of Pump Status
• The FAP is installed at CCTV room where 24X7 guard is stationed
• The guard can easily monitor the Fire Hydrant Pumps status as the alarm with individual pump operation will be displayed on FAP whenever the pumps starts
§ Immediate intimation of pump operation status along with operational log
§ Frequent pump operation can be tracked
§ Leakage issue in the system can be address checked
myIdea
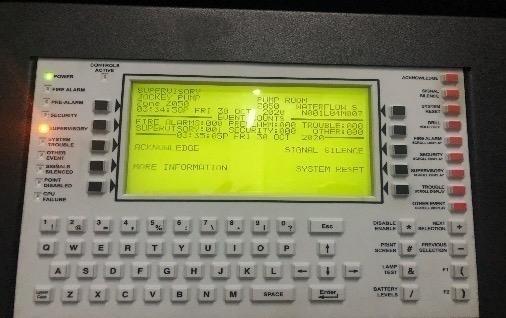
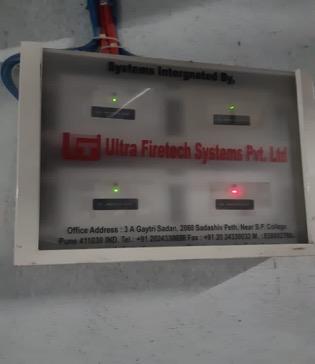
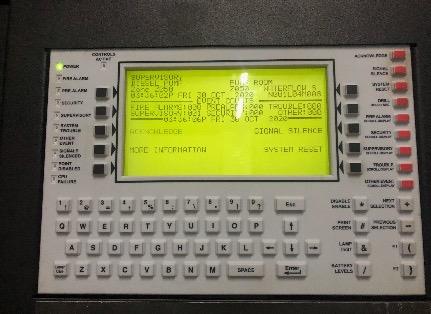
Description of the Innovation:
CHALLENGE
• Very difficult to train the new joiners/ freshers to directly involved into the technical operations and daily routine maintenance at ongoing tasks
/ INITIATIVE / SOLUTION BENEFITS / ADVANTAGE
• Implemented technical live demos for EB / DG Change over system, Motor starters and Basic electrical wiring concept, at PM Training room, to understand the operation and principles of Engineering equipment's, for new joiners/Trainees. All they can learn as practical oriented training from one cubicle
§ Improve the technical skill levels to all freshers/new joiners at site
§ Very familiar to all engineering operations and build quick learning atmosphere at site
myIdea
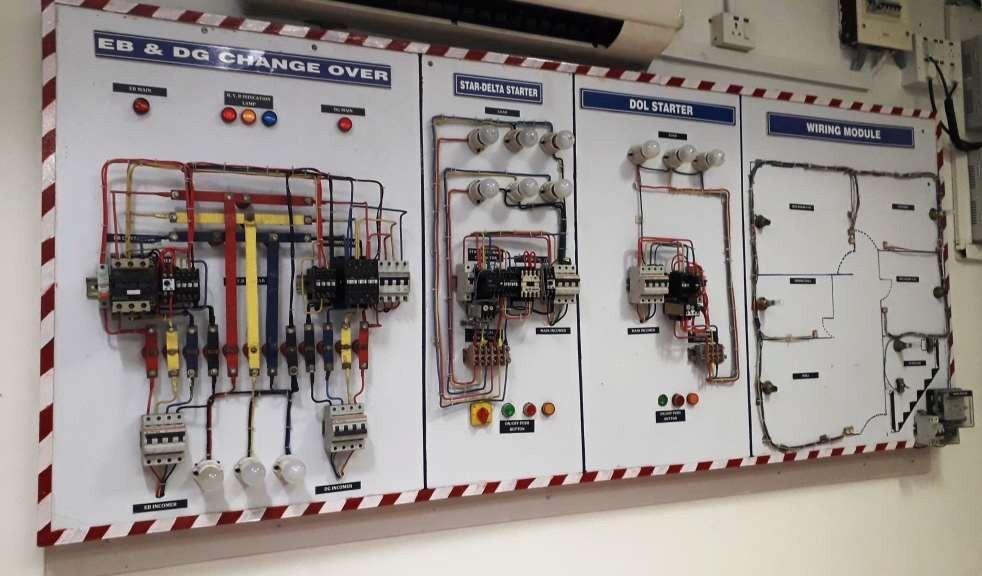
Description of the Innovation:
Lift Regenerative
• Common area energy increase day by day and to control the cost and operate with in the CAM charges
• Regenerative unit
• Installed along with four quadrant Import –Export
• Energy meter installed to capture the regenerative energy
§ Energy saving of 45% achieved
myIdea


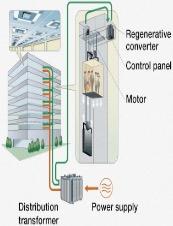
Description of the Innovation:
Bellow for Oil Preservation
myIdea
CHALLENGE
• Entry of oxygen and Moisture. Ingress of Oxygen leads to oil contamination
• Acids and other compounds are formed, this turns to Sludge
• Sludge forms a coating on HeatTransfer surfaces, this reduces heattransfer capacity of the system
• Leads to overheating
MYIDEA / INITIATIVE / SOLUTION BENEFITS / ADVANTAGE
Erected External bellow by Conducting minor alterations to breather pipe for Preservation of Oil in Transformer
• Makes the Transformer a sealed type.
• Provides complete Immunity from Atmospheric Moisture and Oxygen.
• Purging the air breathing system with Dry Nitrogen
§ Reduces maintenance cost.
§ Reduces oil procurement and filtration.
§ Improves BDV and increases Transformer service life.
§ Maintains MoistureFree system
§ Oil degradation arrested Avoid Filtration
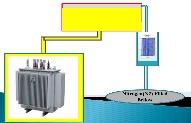
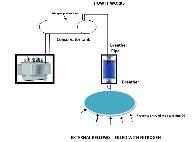
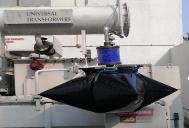
CHALLENGE
• Fire and fire Extinguishing is a huge risk of potential fire related environment
Description of the Innovation:
ELDIE Fire Ball
myIdea
MYIDEA / INITIATIVE / SOLUTION BENEFITS / ADVANTAGE
• People need to come closer to fire base around 6 ft to put off the fire which is a high risk
• Eldie Fire Ball is simple and easy solution which can put off fire without coming in contact with the fire base
• It pushes out oxygen from the fire zone and instantly extinguishes fire immediately after coming in contact (3-10 seconds) with the flame
• Emits a sound warning by its detonation in addition to extinguishing of fire
§ Simple, small /compact safe to use by anyone
§ Suitable for any common fire – class A-B-CE-F
§ No special skill or training is required
§ Safe for humans and property
§ Automatic fire suppression device preventing starting of small fires
§ Only self – Activates when in a contact with a direct flame

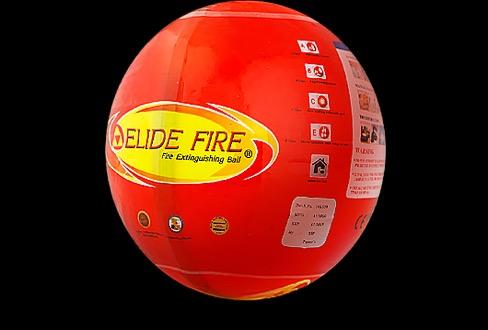
Description of the Innovation:
Telescopic tree trimmer
CHALLENGE
• There are many plants at the premises in which these beans grow half yearly. These beans when dried, open up releasing lots of white colored seeds which falls on the ground and with the wind spreads all over the podium. This looks too shabby and poses a challenge for picking up these dried seeds.
MYIDEA / INITIATIVE / SOLUTION BENEFITS / ADVANTAGE
• Earlier we used to climb on the Scaffolding to remove these Beans from the plants. This not only required manpower (at least 03) but also time consuming and risky.. To avoid this, we have purchased one Telescopic Trimmers for removing of Bean from Plants at Podium Level. The work which required 3-4 manpower is done by a single man
§ Driving efficiency in operations through single manpower and effective utilization of the resources
§ Reduction of cleaning schedules
§ Cost saving achieved in terms of manpower deployment
myIdea
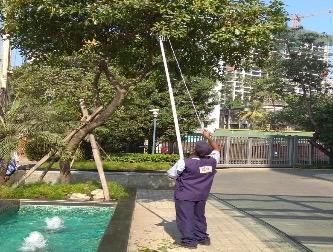

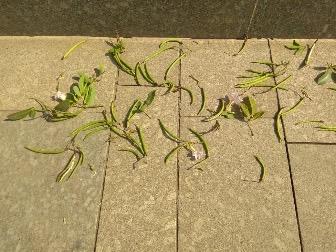
Description of the Innovation:
Sports Zone
CHALLENGE
• Employees often demanded for indoor games to stay fit & recreation. There is only one TT table which generally remains occupied through out days
MYIDEA / INITIATIVE / SOLUTION BENEFITS / ADVANTAGE
• We identified location in basement
• Identified location was such that it will not effect parking area and on going game as well
• Proposal was made to management and approved
• Area was cleaned and marked, Ladder was fabricated and installed
§ Employee delight
§ Employees started utilizing and tenants started inter department matches
myIdea
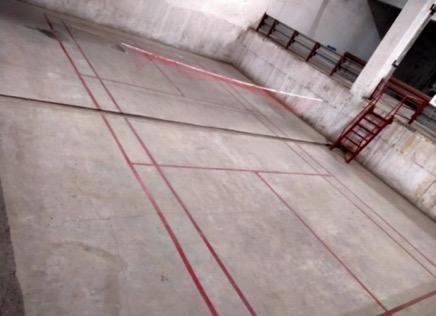
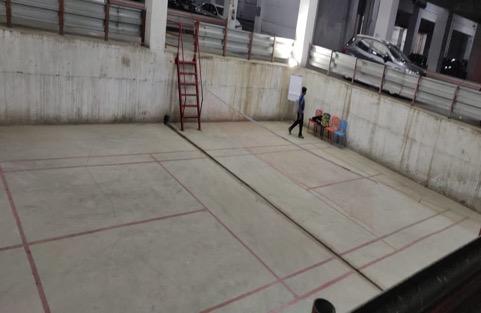
Description of the Innovation:
Revenue Generation
CHALLENGE
• Generating additional revenue through various events & promotional activities
• To attract promoters / advertising companies to get events & promotional activities within premises
• Availability of suitable space for events was major constraint
• Initially there was FIXED RATE for all type of events and activities due to that only 50 thousand income was generated in previous year
• Unavailability of parking space
MYIDEA / INITIATIVE / SOLUTION BENEFITS / ADVANTAGE
• Initially we were facing issues with rates as charging FIXED RATE for all types of activities due to that response was not according to the expectation. Hence the theme was reworked with client for not keeping fixed rate & should be FLEXIBLE which would be based on nature of activities. Therefore, we decided some criteria, upon that we used to charge rates for the events & promotional activity i.e., Product, Required Space & Other
• A major focused on flea market & vehicle display activities which help us to generate more income
§ Generated revenue for more than 14 lakhs from vehicle display ,card events & flea market within a year
§ Additional income can use to upgrade the property or help in reduce the existing CAM charges
§ It is recurring income to property.
§ Overwhelming response from tenants & employees for flea market & vehicle display
§ It encourage employees to take breaks during the day and they will be happier and more productive
myIdea
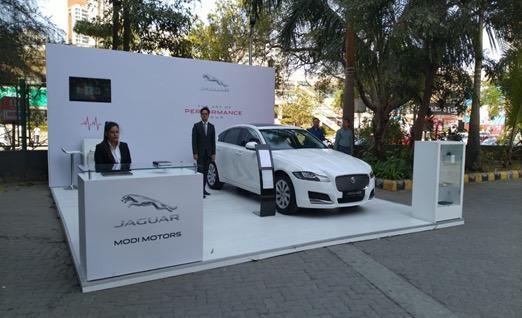
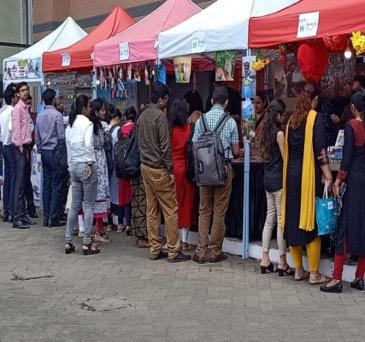

Description of the Innovation:
Automatic Sliding Door integration with FAS
myIdea
CHALLENGE MYIDEA / INITIATIVE / SOLUTION BENEFITS / ADVANTAGE
• Main Entrance Automatic Sliding door of Atrium remains in Auto mode regardless of Fire alarm
• In case of Fire alarm OR fire drill if Door sensor malfunctions, evacuation of people from Building will become difficult
• Manual Intervention is required to open the door posing safety threat for building occupant
• In order ensure safety of all building employees during evacuation it was proposed to
• Install fire module near automatic sliding door
• Connect fire module with Automatic Sliding Door controller
• Integrate and program sliding door to open upon receiving fire alarm signal
• Total Cost of Innovation for 4 nos. sliding door was Rs. 10000/-
§ Safe evacuation of all employees during emergency situation from Building
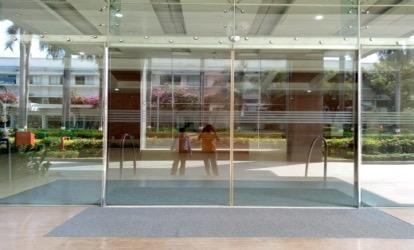
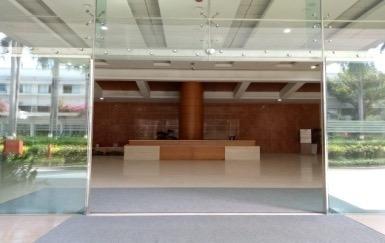
Description of the Innovation:
Overhead Pipeline cleaner
CHALLENGE
• All utility & building’s Basement Overhead pipe line cleaning has been a tedious job, as it consists of multiple pipe lines over 1500 meters in length.
• Even though the cleaning is scheduled once in a week, due to car parking in basement building the dust accumulation takes place & cleaning has to be done multiple times.
• Conventional method involves 2 manpower for basement’s overhead pipe cleaning; one for cleaning and other for holding the ladder is fatigue in nature
MYIDEA / INITIATIVE / SOLUTION BENEFITS / ADVANTAGE
• Introduction of self operated convex shaped Roller brush to clean upper side of pipes. Similarly, concave shaped Roller brush has been introduced to clean bottom side of pipeline.
• These brushes are designed and made by in-house team for customized use, according to the various sizes of pipes (2,4,6 inch. Etc.)
• The trained team executed the cleaning activity with finesse resulting in cost savings
§ Saved Man hours.
§ Enhanced EHS score by eradicating Height work.
§ More areas can be cleaned in fewer time without compromising on cleaning quality
§ Seamless Process.
§ Increased frequency of cleaning with less manpower.
§ Cost savings of ₹ 2,89,245 per year
myIdea
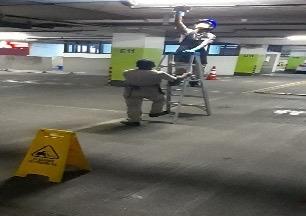
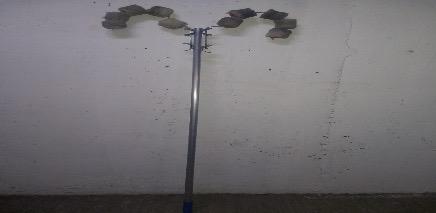
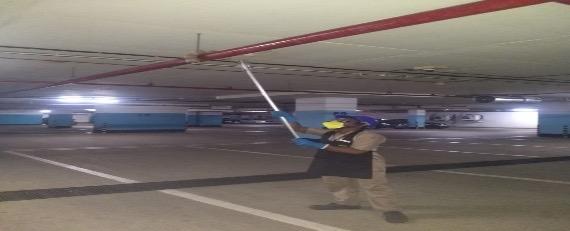
Description of the Innovation:
Neutral Power Factor Compensator
CHALLENGE
• We are getting high difference in KWH & KVAH consumption in electricity bill due to which getting a Power Factor of .98
• Importance of Power Factor -
• Power Factor - Percentage of Electrical Energy being used / total supplied energy
• Power Factor – Real Power / Apparent Power.(KWH / KVAH)
• Power factor should be close to unity (1)
MYIDEA / INITIATIVE / SOLUTION BENEFITS / ADVANTAGE
• We had installed NPFC i.e. Neutral Power Factor Compensator, which help to increase the Power Factor near to 1, also reduce the difference between KWH and KVAH
• Since, we are paying electricity bill charges on KVAH, due to adding the NPFC. The KVAH consumption reduced and reduce electricity billing cost as well
• Total Investment for SITC of NPFC – INR 2 Lacs
§ KVAH & KWH & losses as well which leads Improvement in power factor (close to 1)
§ Saving – Approx. 1.4 Lacs. per year § ROI – Approx. 1.5 Years
myIdea

Description of the Innovation:
Automated Stack Parking System
CHALLENGE
• No. of Parking Slots are less inside the property basements.
• We had to rent parking slots in HUDA Parking at premium
• Costing for HUDA Parking - INR 1.2 Lacs. per month
• HUDA Parking was approx. 500 meters away from premises which was a root cause of customer dissatisfaction
MYIDEA / INITIATIVE / SOLUTION BENEFITS / ADVANTAGE
• Total parking slot available before modification – 47 Slots
• We have installed Automated Stack Parking System for 35 slots total
• Parking Slots After modification –82 Nos
• Total investment – INR 36.75 Lacs
§ No. of Parking Slots inside premises basements increased
§ Total investment – INR 36.75 Lacs
§ Annual Saving – INR 14.4 Lacs
§ Additional Saving by reducing one Security Guard from HUDA parking.
§
myIdea
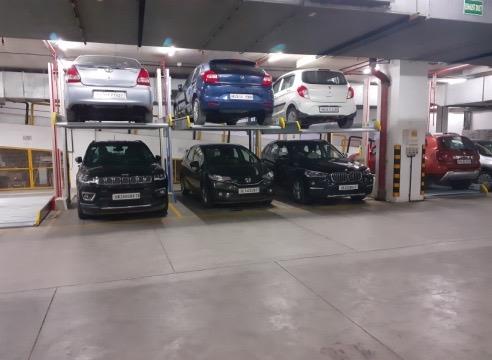
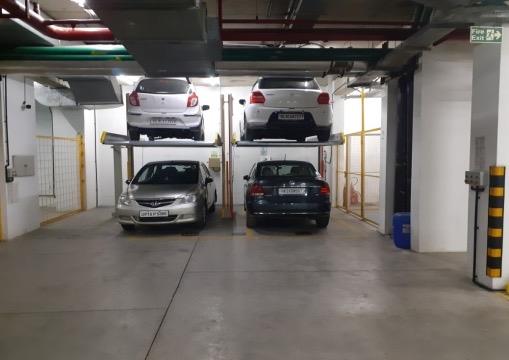
Description of the Innovation:
Digital Checklist
CHALLENGE
• Paper consumption against go green
• Storing of the papers are difficult, if we want to get a year old or more checklist is difficult
• Facing challenges to monitor on timely basis
• Less accuracy
• Requires more manpower to fill the checklists on time
MYIDEA / INITIATIVE / SOLUTION BENEFITS / ADVANTAGE
• Maintaining all Checklist’s electronically
• Software provides a holistic view of all the physical assets and infrastructure components in an organization’s ecosystem. Using both historical and realtime analytics
• Software closely monitors the entire assets lifecycle from design, commission & procurement, to operation, maintenance, disposal, and replacement
§ Software regularly checks asset performance and health, allowing you to service equipment before it affects other assets or results in a failure
§ The E-checklist contains an active maintenance log, recording when the last service occurred, and when the next one is due
§ We can pull the old reports very easily from the tool
myIdea
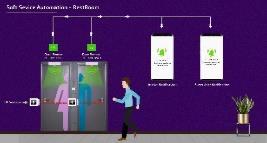
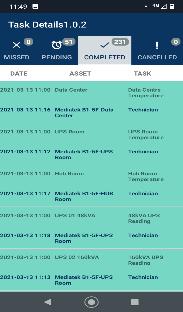
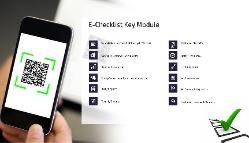
Description of the Innovation:
STP Upgradat ion and Real Time Monitoring
CHALLENGE
• Inappropriate SBR technology adopted for a Micro STP of 50 KLD.
• Equalization tank, was not been provided.
• Air blower capacity was inadequate
• Activated Carbon Filter not found. Several tanks in the STP were oversized, resulting in higher energy consumption than rated.
• This supervision of STP parameters was typically manual, expensive, and not real-time.
MYIDEA / INITIATIVE / SOLUTION BENEFITS / ADVANTAGE
• Rightsizing the STP to 30 KLD, continue to use SBR technology.
• Carbon filter system in addition to existing Sand filter.
• Additional oil and grease trap.
• Addition of air blowers, replacement of diffusers in aeration tank
• Sludge handling system filter press, feed pump and sludge tank.
• EcoChirpTM IoT Sensor based realtime powerful monitoring STP health and quality of treated water.
• Cloud based analytics of parameters
§ Treat entire qty. of 30 KLD sewage generated.
§ Improved water quality & Zero excess sludge disposal through tankers
§ Energy conservation using conventional extended aeration biological treatment and less chemical dosing resulting in reduced cost of water treatment INR 150/ KL.
§ Greater visibility into the health of their STP and quality of treated water on a real time basis. EcoChirpTM enables remote, realtime monitoring of the STP status, allowing for proactive intervention
myIdea
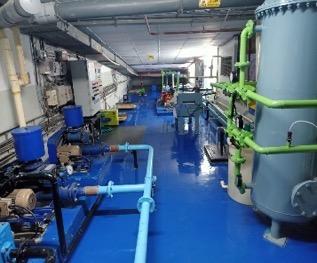
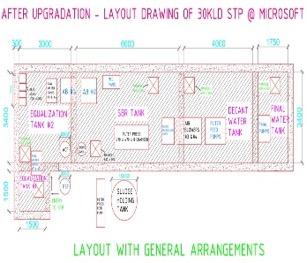
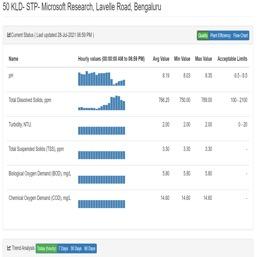

Description of the Innovation:
Bipolar Ionizers & Air Flow switches
CHALLENGE
• To choose effective solution for providing treated air in office premises.
• To ensure the solution is effective in neutralizing SARS COV 2 Virus in the facility.
• To ensure that the solution doesn’t require any major modification in the facility.
• To ensure the air purification product is environment friendly.
MYIDEA / INITIATIVE / SOLUTION BENEFITS / ADVANTAGE
• Market survey carried out along with online research and case studies.
• Installation of Bipolar Ionizers (UL 2998 certified Plasma Air 604) and airflow switches for activation of the Ionizers was finalized.
• Bipolar Ionizers installed at the intake side of fans and Hi wall units, produce positive and negatively charged ions in the air in which the virus can not sustain.
§ Provision of treated air in the office area across 4 facilities achieved.
§ No major modification involved.
§ Other effective solution was to install MERV 13 filters which required modification of entire HVAC system in 4 facilities.
§ Cost of modifying entire HVAC system of all facilities – Approx. INR 4 Cr. (Saved)
§ Cost of installation of Bipolar ionizers with Air Flow switches - Approx. INR 1 Cr. 10 Lakhs.
§ Product is UL 2998 certified for zero Ozon Emission.
myIdea
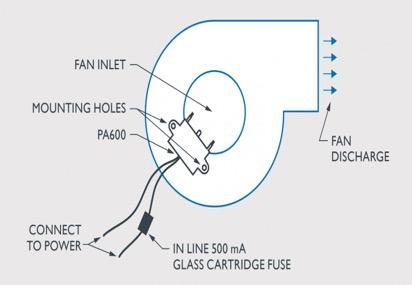
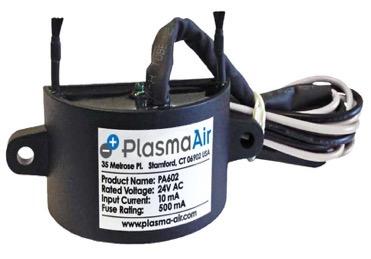
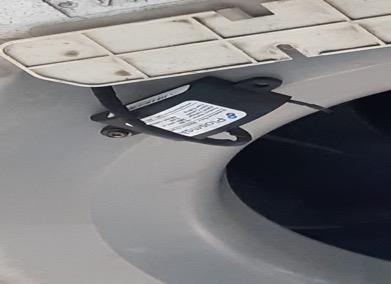
Description of the Innovation:
Green workplace
CHALLENGE
• Good air quality index with lower CO2 levels inside the premises.
• Irregularity to add fresh air in the premises due to bad air index in outer area.
• Low-cost sustainability initiative.
MYIDEA / INITIATIVE / SOLUTION BENEFITS / ADVANTAGE
• Identification 24 no of plants which are more effective in absorbing CO2.
• Discussed with partner & replaced 2121 no’s of existing plants with higher CO2 absorbing capacity plants.
• Identified locations where we had higher Co2 levels and placed these specific plants.
§ Effective low cost, in-house sustainability initiative to reduce CO2 level inside the premises & Reduce Carbon footprint.
§ Improved ambience and aesthetics of building / premises.
§ CO2 absorbed/ day post selecting & replacing the total no of plant 2121, no’s 0.46772 Kg absorbed per day
CO2 ABSORBED PER DAY/ PLANT
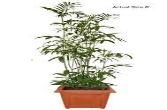
Bamboo Palm, No of plants 10, 0.000259 kg
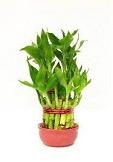
No of plants 22, 0.0002011 kg
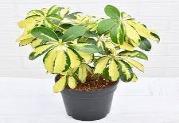
No of plants 41, 0.0002021 kg
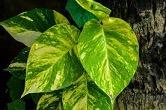
Golden Pathos, No of plants 50, 0.0001865 kg
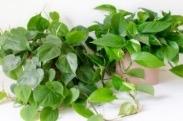
Oxycardium heartle af, No of plants 70, 0.000201 kg
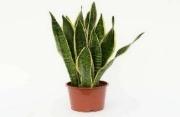
Snake plant, No of plants 72, 0.000289 kg
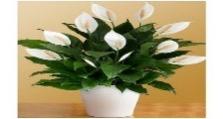
No of plants 50 , 0.0001868 kg
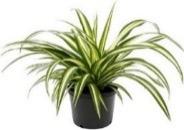
plant, No of plants 45, 0.0000019 kg
myIdea
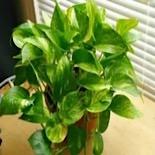
Golden pothos, No of plants 551, 0.131689 kg
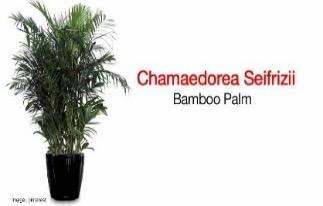
Bamboo/palm, No of plants 289, 0.074851 kg
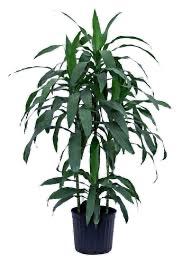
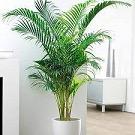
Janet Craig dracaena, No of plants 253, 0.060492 kg
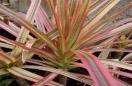
Palm, No of plants 173, 0.047575 kg
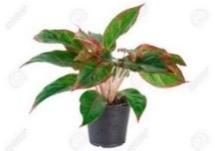
Dracaena, Rededged No of plants 16, 0.0002378 kg
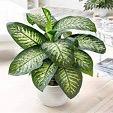
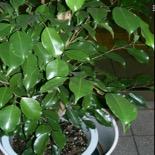
evergreen, No of plants 130, 0.0002191 kg
No of plants 95, 0.0002063 kg
No of plants 78 , 0.0000091 kg
Description of the Innovation:
Vacuum
Cleaner for Sprinkler
CHALLENGE
• Dirty Sprinkler heads can cause distorted water spray as grime builds up, become insulated and accordingly will delay in activation of Sprinkler.
• Moreover, we overlook regular inspection and cleaning of fire sprinkler which attracts spreading of virus and bacteria.
MYIDEA / INITIATIVE / SOLUTION BENEFITS / ADVANTAGE
• Idea is based on the NFPA 25 Annex A5.2.1.1.2 where it has been written that unless replacing sprinklers that are loaded with a coating of dust or grim , it can be permitted to clean sprinklers with compressed air or by a vacuum that which would not touch the sprinkler. Based on this guideline we explored scope and made sprink Vacuum system which will serve the purpose within less time , complaint and of course without cost.
• Here we have used H/K vacuum machine with pressure regulated valve from old suppression system and one transparent cutout of bottle.
§ By implementing this inspection and cleaning procedure inherent risk with the facility which will decrease a lot
§ Transition of Virus and Bacteria will decrease.
§ Quickly remove dust and grim so that sprinkler would not be insulated and subsequently reduce risk.
§ Accrued a saving of INR 1.2 L by implementing it through out east Locations.
myIdea
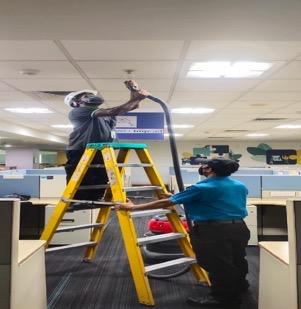
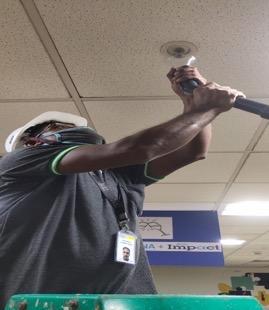
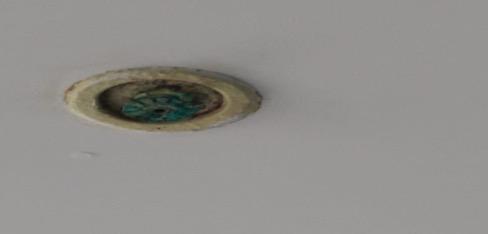
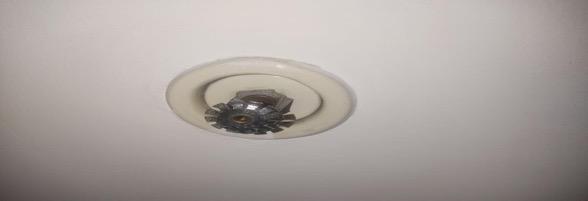
Description of the Innovation:
EC Fan
Retrofit
myIdea
CHALLENGE
• Blower Motor Failure and long lead time for repairs
• Wear and Tear of V Belts
• Power Consumption high due transmission loses.
• Human interface systems
• Blower Noise.
• Frequent breakdown of VFD
• Challenges to clean the Dust deposition on Blower and scroll
• Multiple motor capacities for all AHU’s so difficult to have standby motors
MYIDEA / INITIATIVE / SOLUTION BENEFITS / ADVANTAGE
• Introduction of EC Fan Motor directly coupled with composite material which is light in weight and easy to clean with long life along with MCU to replace existing bulky induction motor along with blower, Belt and pulley arrangement.
• Get in MCU and giving up of VFD’s and their huge panels
• Enhance the system efficiency as EC motor has a Unity PF
• Low Electromagnetic noise from motor.
• EC Fan CFM varies as per return air set temp with inbuilt VFD.
§ Absolute need base accurate supply of air on the floor increasing the HVAC Energy saving.
§ Zero maintenance and minimum human intervention.
§ No requirement of motor greasing belt and pulley alignment, fan balancing.
§ Actual Total monthly energy saves is INR.79536 which is 40% of our monthly AHU power consumption.
§ Carbon emission reduction by approx. 3.06Ton per annum.
§ Man, hours was reduced by 312 hours annually.
§ One Single motor and blower can be now standby for the entire building as all the motor capacities are the same
§ Total Investment: INR 55 Lacs
§ ROI is 6 Years approx.

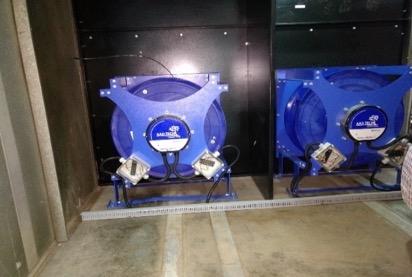
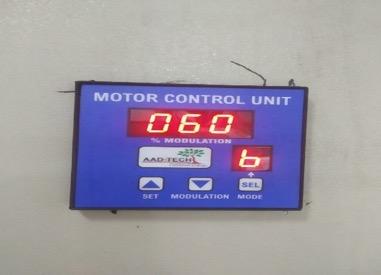
Description of the Innovation:
Air to Water Harvesting with Touchless dispensers
CHALLENGE
• Existing drinking water supply for ground staff at security gates is provisioned through plastic water bubbles(20 L cans).
• The supply of these water bubbles again uses a vehicle transport from a third-party vendor
• This method leads to scope2&3 carbon emissions
MYIDEA / INITIATIVE / SOLUTION BENEFITS / ADVANTAGE
• As a pilot Project we introduced 4 No's of 500KLD Air to water harvesting plant with touchless dispensers at these locations inside the campus as a part of strategic Sustainability plan
• These plants harvest 100% clean drinking water from humidity of the air.
• The water is filtered and pumped into the touchless dispensers for consumption.
§ Reliable technology giving fresh bacteria-free pure drinking water
§ Green Initiative with no depletion to ground or water sources
§ Sensor based Touchless dispensers became handy in this pandemic situations.
§ Zero Transportation emissions.
§ Elimination of Plastic water bubbles.
§ Less Repairs and Maintenance cost.
§ ROI in years: 4 years and 9 months approximately.
myIdea
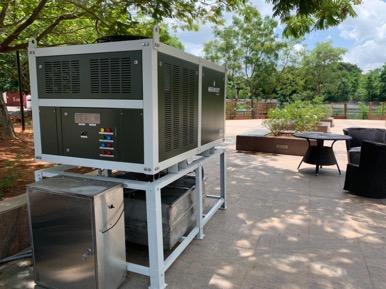
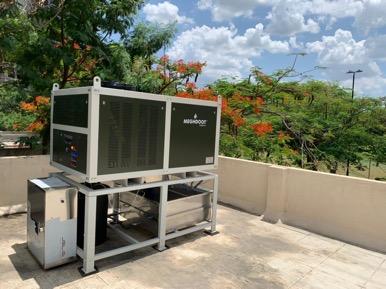
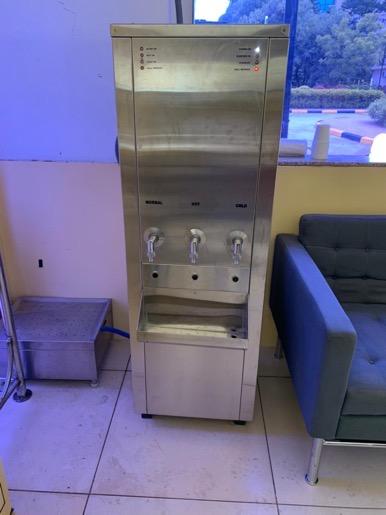
Description of the Innovation:
Implementation of touch free sensor taps
CHALLENGE
• We had normal manual water taps in all our breakouts, Pantry’s etc.
• These taps are used to clean crockery & cutleries of employees as well as the office coffee cups by pantry staff
• This had multiple common touch points, which is not safe considering the current pandemic situation
MYIDEA / INITIATIVE / SOLUTION BENEFITS / ADVANTAGE
• The cost of sensor tap was 11000 for the existing model
• We tried multiple other options and found better solution to use the same taps
• Installed Protruding Hand free operational sensor Taps with minimum investment
§ Easy Installation
§ Prevents Infection/ cross contamination
§ Dual Sensors for Instant & continuous modes
§ Save water with convenience
§ Rechargeable battery and it can be used for 5-6 months once its fully charged
§ This intelligent sensor also give command to the tap to cut-off water supply, if the sensing is more than 60 seconds. This feature helps saving water
myIdea
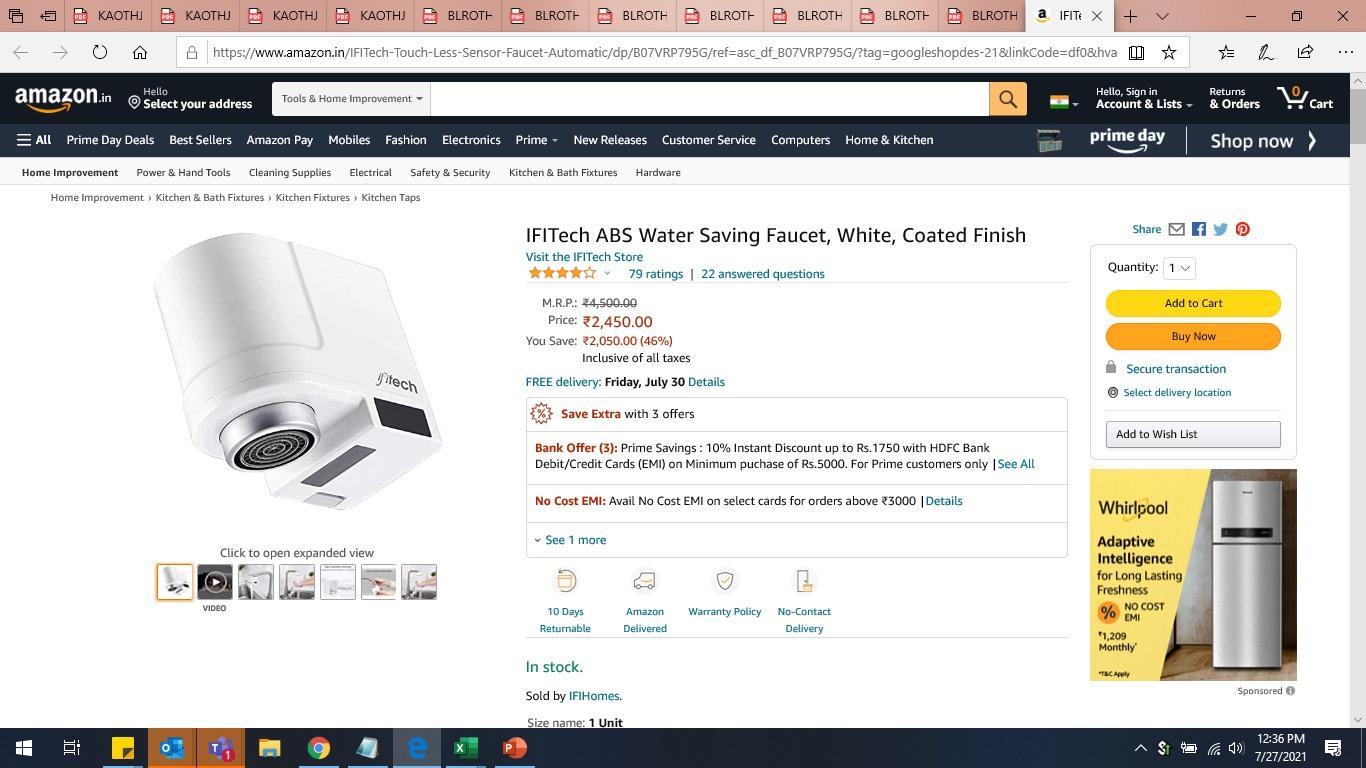
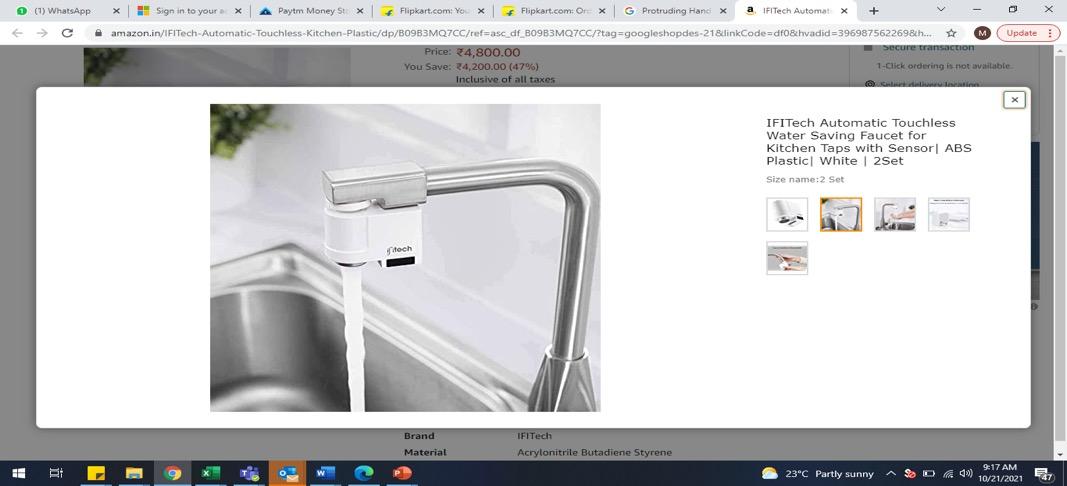
Description of the Innovation:
Sourcing Solar Energy from Open Market
CHALLENGE
• Pursuing Refinitiv sourcing team to rollout the RF for procuring renewable energy from open Market.
• Setting up the reverse auction tool in coordination with Blackstone and solar power contractors.
• Convincing vendors to sign up for the proposed MNDA clause.
• Obtaining approvals from developer landlord and BESCOM authorities.
• ABT meter calibration from the builder.
• Vendor registration Refinitiv(Ariba) tool as per payment terms.
• Office located in multi tenant building out of 10 floors LSEG is occupied 4 floors.
MYIDEA / INITIATIVE / SOLUTION BENEFITS / ADVANTAGE
• Find out the consultant to coordinate with the BESCOM, power generator for the smooth transition.
• Organized 7 power generators to get the competitive price by reverse auctioning.
• Coordination with the builder, consultant, client, and power generators by setting up a frequent call.
• Immediate registration after agreement finalization of the power generating company and consultant in client portal for upcoming months renewable energy bid.
§ 2.28 million is expected to be procured per year.
§ Saving of approx. 1,870 tons of carbon footprint reduction PA.
§ Financial savings of approx. $ 118 k PA.
§ A veritable step towards CSR
§ After the RFP /Reverse auction due diligence contract was awarded to M/s Renew Power with a reduced cost of INR 3.57 per unit.
myIdea

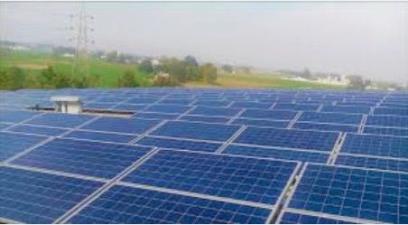
Description of the Innovation:
Robotic Duct Cleaning
CHALLENGE
• Planned for air quality improvement in the workplace.
• Need to clean the dust accumulation in the AHU duct.
• Manual cleaning is difficult and same will lead to safety hazard.
MYIDEA / INITIATIVE / SOLUTION BENEFITS / ADVANTAGE
• Used Robotic camera to check the level of dust accumulation in the duct.
• With the help of Robot camera vision cleaning materials has been inserted inside the duct and cleaning work was completed.
• Robotic duct cleaning involves with the camera and cleaning accessories, so human direct contact is avoided.
§ In Robotic duct cleaning due to absence of direct human contact safety hazards like health issues and accidents can be prevented.
§ With the help of Robotic camera before and after image can be captured, to identify the amount of dust accumulated and removed from the duct.
§ IAQ test was done after the Robotic duct cleaning and the all the parameters ware found normal.
myIdea

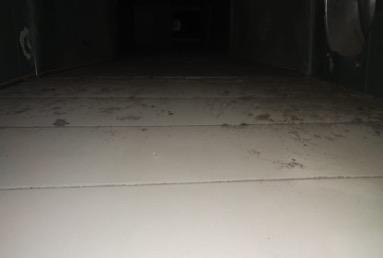
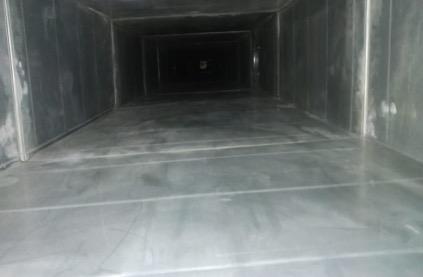
Description of the Innovation:
Water misting system for adiabatic cooling
CHALLENGE
• During summers, AC units are under constant pressure to circulate sufficient cool air
• When air temperature increases, electricity consumption increases substantially and also the cooling capacity of the AC unit decreases.
• This increased load results in Poor performance, Untimely shutdowns.
• Severe stress for mechanical parts, shortening the lifespan of the airconditioning unit
MYIDEA / INITIATIVE / SOLUTION BENEFITS / ADVANTAGE
• Used Robotic camera to check the level of dust accumulation in the duct.
• With the help of Robot camera vision cleaning materials has been inserted inside the duct and cleaning work was completed.
• Robotic duct cleaning involves with the camera and cleaning accessories, so human direct contact is avoided.
§ In Robotic duct cleaning due to absence of direct human contact safety hazards like health issues and accidents can be prevented.
§ With the help of Robotic camera before and after image can be captured, to identify the amount of dust accumulated and removed from the duct.
§ IAQ test was done after the Robotic duct cleaning and the all the parameters ware found normal.
myIdea
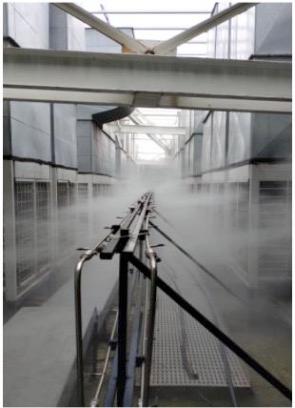
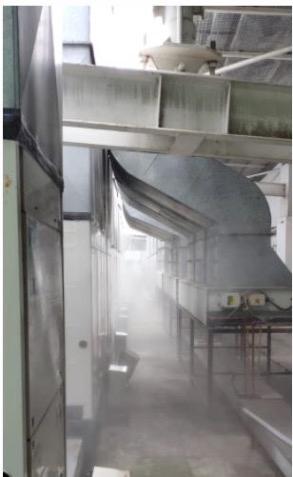
Description of the Innovation:
Shycocan
Scalene Hypercharge Corona
CHALLENGE
• The second wave of Covid-19 has had several consequences in the form of rise in the cases, reduced supplies of essential treatments and increase deaths particularly in the young population
• Coronavirus is here to stay
• The threat of the future pandemics is real
• People do not follow social distancing norms consistently
• We need a combination of Vaccine + Technology
MYIDEA / INITIATIVE / SOLUTION BENEFITS / ADVANTAGE
• Introducing Shycocan
• Shycocan produces Photons
• Photons emanate electrons on striking aerosols, viral particles in the air, solid surfaces and objects in the room
• Due to continuous operation an electron cloud gets formed in the enclosed space where the device is installed
• The electrons get attached to the Coronavirus in the environment in real time and neutralize its positive charge, preventing it from infecting another person
§ Up to 99.9% efficacy Immediate Air Borne & Surface
§ Constant Protection
§ No side Effects Maintains beneficial bacteria and fungi
§ One time installation - no consumables
§ Effective for all sizes rooms
§ Conforms to Regulatory requirements of US, EU, ANZ, META, APAC
myIdea
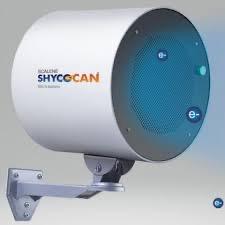
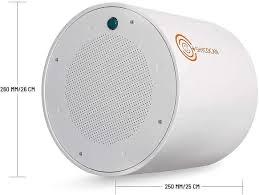

Description of the Innovation:
FPSTAR Tech based STP
CHALLENGE
• Activated sludge process works on biological mode with 8-10 hours of retention time.
• No Change in TDS, which results in increased rejection in RO plant
• High peak flow and inadequate storage capacity
• RO water generation cost was high with more consumables
• Addition of salts in softener will increases TDS above 1000ppm consistently which –ve impacts water treatment and reuse
• Total water recovery with RO is only around 60%.
• Space availability constraint for further extension of plant.
MYIDEA / INITIATIVE / SOLUTION BENEFITS / ADVANTAGE
• Installation & Commissioning of FPSTAR (Fine Particle Shortwave Thrombotic Agglomeration Reaction) technology working on the principles of elemental specific frequency disassociation.
• As the water passes through the Boom Tower resonator, the elements in the water (except hydrogen and oxygen), will start disassociating from its compounded form to their equilibrium elemental state.
• Elemental frequency breakdown particles and produces clean water with various filtration process.
• Requires minimal storage capacity.
• Continuous operation - We able to get continuous output since retention time was optimized to less than hour for 15KL of water output.
• Meet the peak loads without much difficulties.
• Programmable to meet future water treatment standards without any physical modifications
§ Chemical and Odor free process
§ Automated process - No manual intervention required
§ Reduction in TDS or salt content
§ Ensuring Zero Liquid Discharge Facility
§ Additional treated water available for flushing and cooling tower which reduces water procurement by 3000 KL/ Month.
§ RO reject can be treated again, which is not possible with ASP technology.
§ Meeting Pollution control board norms consistently.
§ Reduced O&M cost
myIdea
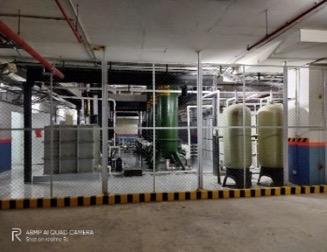
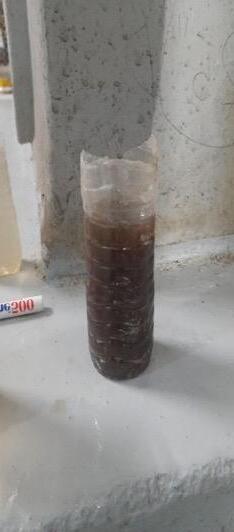

§ Estimated Savings – 1.5 Crores per year
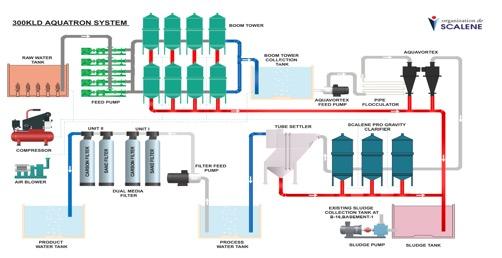
Description of the Innovation:
Carbon filter for DG stack cleaning
CHALLENGE
• Heavy carbon particles expels into atmosphere while carrying DG exhaust stack cleaning.
• Environment pollution
• High chances of Carbon particles getting into nearby residential area.
• Major modification suggested by OEM in exhaust line for re orientation would not prevent carbon particulates into atmosphere which also require Shut down of DG during modification work.
MYIDEA / INITIATIVE / SOLUTION BENEFITS / ADVANTAGE
• To prevent heavy carbon particles expelling into atmosphere during cleaning activity , Inhouse team has developed a metallic filter which can be used to arrest 90-95 % heavy carbon particles getting into air.
• This has been tested and proved to be 100% efficient.
§ It helps us to engage better with our Environmental pollution prevented in great extent.
§ Avoided concerns from nearby residents.
§ Saving of 28 Lakhs which was proposed for re orientation of Exhaust lines facing residential area.
§ Landlord team approached to support with best technology solution available to incorporate with existing DG stacks to minimize the carbon particles.
myIdea
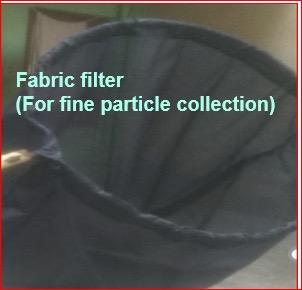
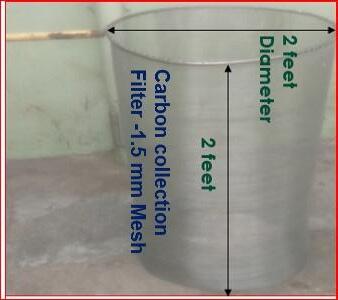
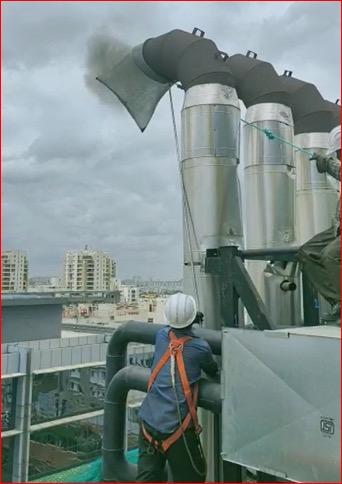
Description of the Innovation:
Fire Detection System in Electrical
CHALLENGE
• Fire detection system in the Electrical and Communication shafts was not available.
• There are chances of fire spreading through cables in shafts and doors to other floors in the event of a real fire.
• The containment of fire is a challenge even if the floors are concealed with fireproof.
MYIDEA / INITIATIVE / SOLUTION BENEFITS / ADVANTAGE
• To avoid the spread of fire and early detection Smoke detectors installation idea planned at each floor level in electrical & communication shafts.
• Necessary approval were taken for procurement of detectors and integrated the detectors to existing FAS system. .
§ Fast and highly sensitive reaction to incipient fires.
§ Simple handling due to detectors being mounted in easily accessible areas across the shafts.
§ Containment and minimization of impact to site assets and human life.
myIdea

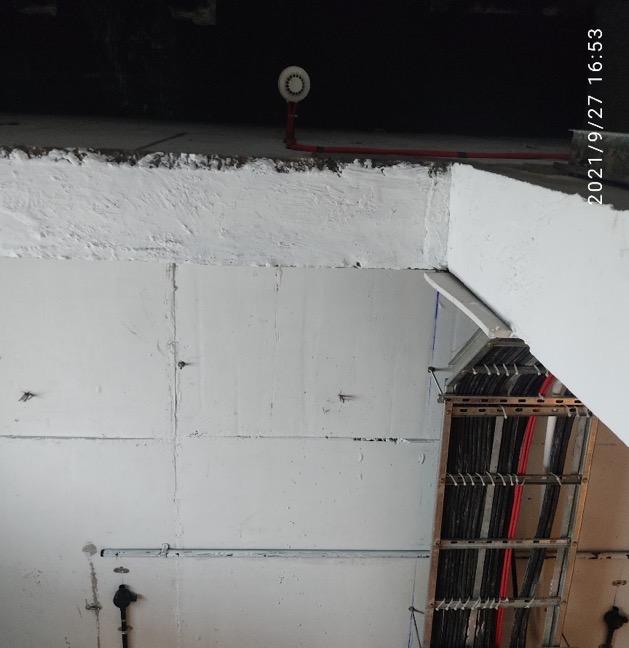


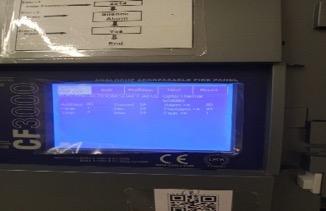
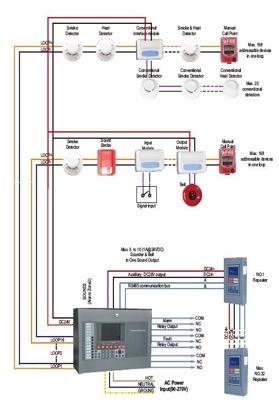
Description of the Innovation:
Diversity and Inclusion in workplace
CHALLENGE MYIDEA / INITIATIVE / SOLUTION BENEFITS / ADVANTAGE
• Enhancement required for % of Diversity & Inclusion ratio
• Improvement for % of women representation in technical role
• Increase in awareness required in T1 & T2 for DE&I concept
• Substantial representation required for diverse supplier
• Scrapping of end-of-life IT assets
• Outreach to communities and minorities
• Increase the ratio through a structured roadmap for supported employment
• Design a program for Internship for women candidates to induct in technical role
• Collaboration with SME -NGOs for awareness workshops to increase awareness
• Onboarding of diverse supplier for services as part of responsible sourcing
• Donation drive for all EOL IT assets to NGOs
• CSR – Voluntary hours every quarter by employees
§ The ratio of supported employment increased to 4.5% against the target of 5% by end of the year
§ An exclusive Internship program successfully conducted for 13 candidates to prepare them for full time technical role in IFM . Increased ratio of female in technical role to 10%
§ Series of 3 workshops conducted from MS registered NGOs for upskilling in DE&I
§ 2 suppliers onboarded , 2 RFPs in process with focus on responsible sourcing
§ NGOs utilized IT assets for online education for underprivileged during covid Client is aligned to make the activity regular across India .
§ Community & Social Impact through CSR activities . Helped talent hunt from minorities to boost supported employment
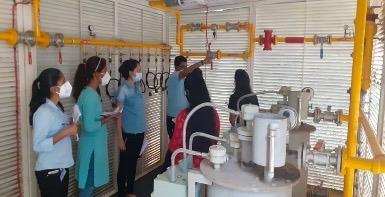
Internship Program for Women in Engg Role
myIdea

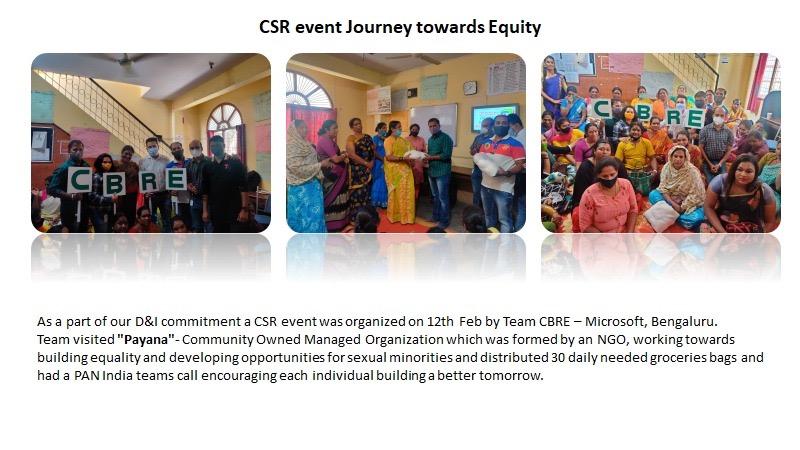
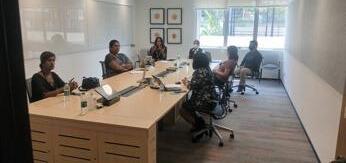
CSR activity for community & minorities.
Interaction with LGBTQAI+
Description of the Innovation:
Waste Plastic Utilization for Bitumen Road
CHALLENGE
• Plastics are non-biodegradable.
• Burning of waste Plastic causes environmental pollution
• Disposal of Waste Plastic
Potholes & Crack on road
MYIDEA / INITIATIVE / SOLUTION BENEFITS / ADVANTAGE
• Making Driveway of Waste Plastic
• Low Polyethylene Crushed Plastic Utilization.
• Aggregate of 10mm, 20mm
§ Use higher Percentage of waste plastic. And Reduce 7.5T of CO2.
§ Reduction in Need of bitumen by 15%
myIdea

Waste plastic in shreds form of size
2.36mm to 4.75mm
Stone dust and lime as filler
Bitumen 60/70, 80/100 Grade
§ Generate jobs for rag pickers. Which is ECO friendly.
§ Strength of road increased by 100%
§ Better resistance towards rainwater stagnation.
§ Cost Reduction of Road construction approximate cost of 8cr Savings.
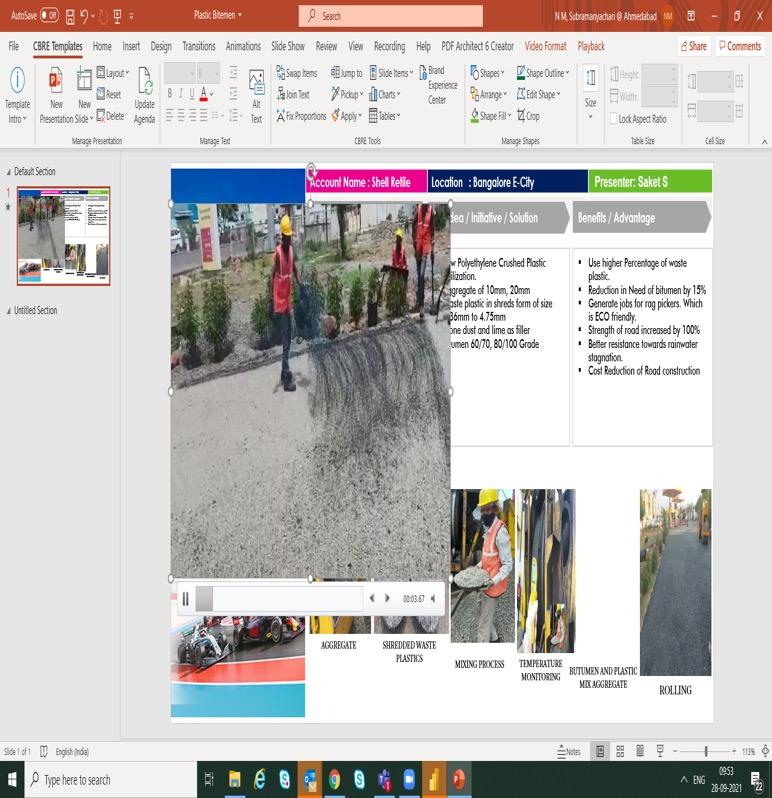
Description of the Innovation:
Robotic Lawnmower
CHALLENGE
• Lawn mowing was labor intensive. 12-man hours needed to mow 2200 sq mt of lawn.
• This was a periodic activity leaving the lawn in non-uniform state.
• Soil compaction: traditional mower weighs due to its weight ,tends to compress the soil over time. Grass does not grow as well in compressed soil.
• Lawn cannot be mowed during rains & high temperatures.
• Cut grass shavings being disposed as garden waste.
MYIDEA / INITIATIVE / SOLUTION BENEFITS / ADVANTAGE
• Battery enabled Robot operates with in a predefined perimeter of the lawn using its sensors to track and trim the grass gracefully.
• No supervisor needed to monitor the work. The robot works in programmed work intervals and alternates cutting cycles with recharging
• NO to - fossil fuel, noise & waste.
§ In Eco Mode, detects the overgrown grass and trim just that part.
§ Works on uneven terrain - up to 45 gradient
§ Lightweight (15Kgs) - no soil compaction
§ Can also work in adverse weather
§ Reduces Diseases –mowing on a regular basis, reducing the chances of diseases as the lawn is healthy condition.
§ Automatically returns to the recharging base.
§ Mulching robotic cutting -cuts a few mm of grass everyday& return nitrous-rich fertile elements to the soil, eliminate bulky bags of grass.
myIdea
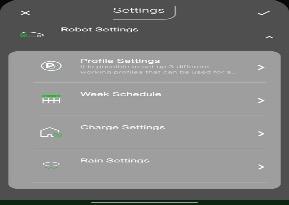
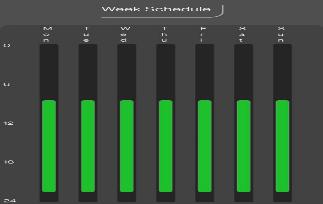

Description of the Innovation:
Cafeteria
Crowd Management
CHALLENGE
• During Lunch hours cafeteria used to be very crowdy.
• Difficult to follow social distancing norms.
• Possibility of close contact
• Employee's dissatisfaction.
MYIDEA / INITIATIVE / SOLUTION BENEFITS / ADVANTAGE
• We advised café digital service partner Hunger box (HB) to come up with innovation for crowd management system.
• Hunger box come up with crowd management system and their device installed on the entry/exit gates of cafeteria and integrated with access control system & HB app. Max. person allowed at a time capacity set in the device considering social distancing norms.
§ Social distancing maintained.
§ Convenient for employees.
§ Prevention of Covid 19 virus.
§ Close contact avoided.
§ Positive employees' feedback
myIdea
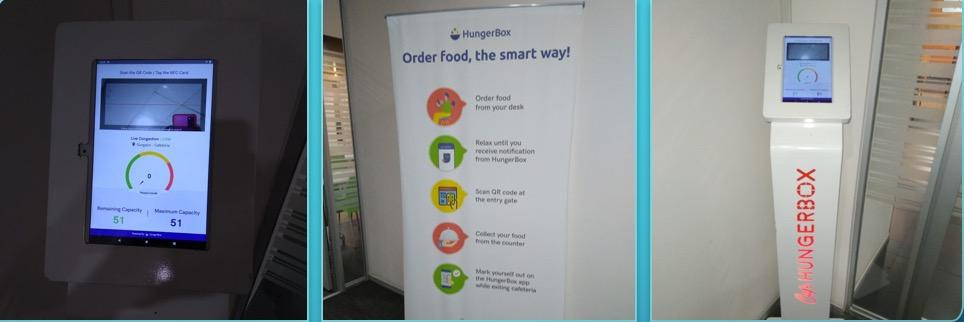
Description of the Innovation:
Rainwater
Harvesting
CHALLENGE
• During rainy season water level will get increased inside the parking area
• Behind garbage area water stagnation is observed for more than 2 foot
• Very easily our building get flooded during rainy season
MYIDEA / INITIATIVE / SOLUTION BENEFITS / ADVANTAGE
• By doing this rainwater harvesting will solve the water stagnation in the parking area.
• 250 KL water tank has been planned to implemented for rainwater storage, can hold normal rainwater which is routed from terrace.
• Anticipated 3300 KL of rainwater per year will be collected and used for domestic purpose
§ Closed container will not allow to form any algae.
§ These storage water can be used after treatment for domestic, flushing etc.
§ Water stagnation around the building is avoided.
§ Ground water quality improved.
myIdea
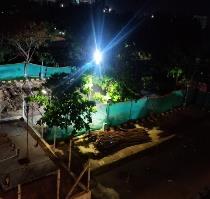
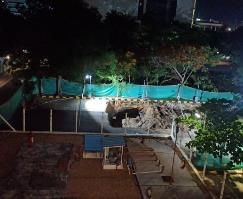
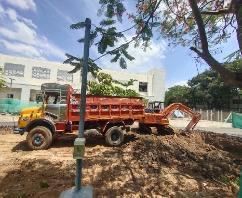
Description of the Innovation:
Automatic Gel Dispensers for Sanitizing
CHALLENGE
• Unhygienic washroom.
• Chances of getting Infection through cross contamination due to frequent common touch points.
MYIDEA / INITIATIVE / SOLUTION BENEFITS / ADVANTAGE
• Installed Automatic sanitizer gel dispensers with HBT tissues.
• SOPs pasted how to use the Gel Sanitizer before using.
§ Washrooms WCs found in Hygienic condition.
§ Prevention of Cross contamination of any infection.
§ Cleaning man hours saved.
myIdea
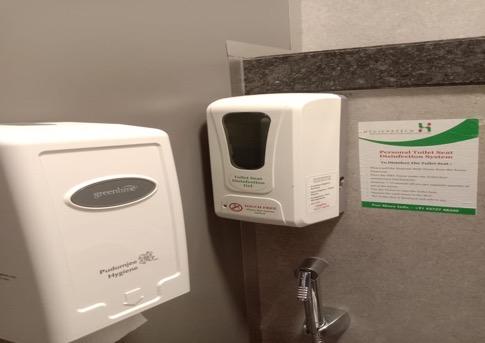
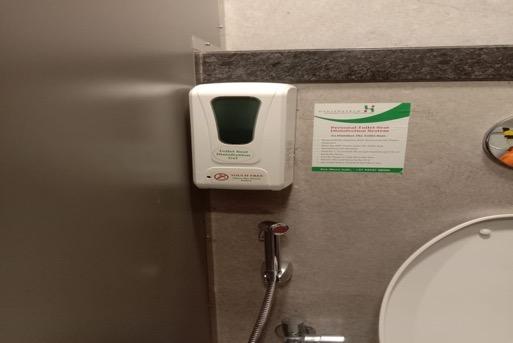
Description of the Innovation:
Installation of Digital water Flow Meter
CHALLENGE
• Buildings are multi-tenant towers and there was no dedicated water flow meters for Client’s floors to measure the raw/flushing water consumption.
• We were not able to track & measure water consumption
• Since there is no water charges billed by builder tenants also doesn’t worry much about consumption
• Monitoring on utilization of natural resource such as water is very important from sustainability point of view
MYIDEA / INITIATIVE / SOLUTION BENEFITS / ADVANTAGE
• We have installed total 12 digital water flow meters for buildings .
• As these flow meters are installed in plumbing shaft, hence they are integrated with IBMS for capturing the meter readings easily
§ We can track & monitor the daily water consumption.
§ Further we observed while doing so that these two new towers are having more water consumption compared to existing ones
§ WC water release in one flush was identified much higher as compared to normal Water consumption assessment and conservation initiatives are being planned
myIdea
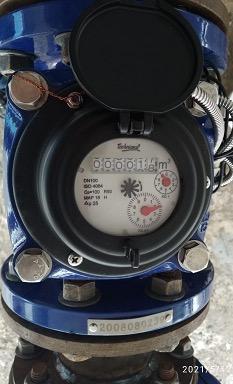
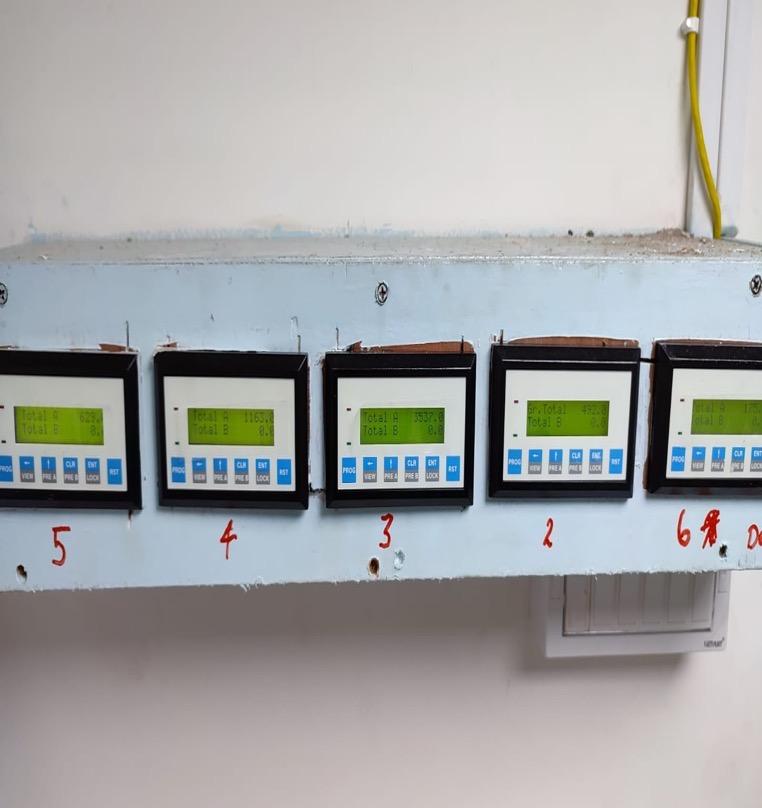
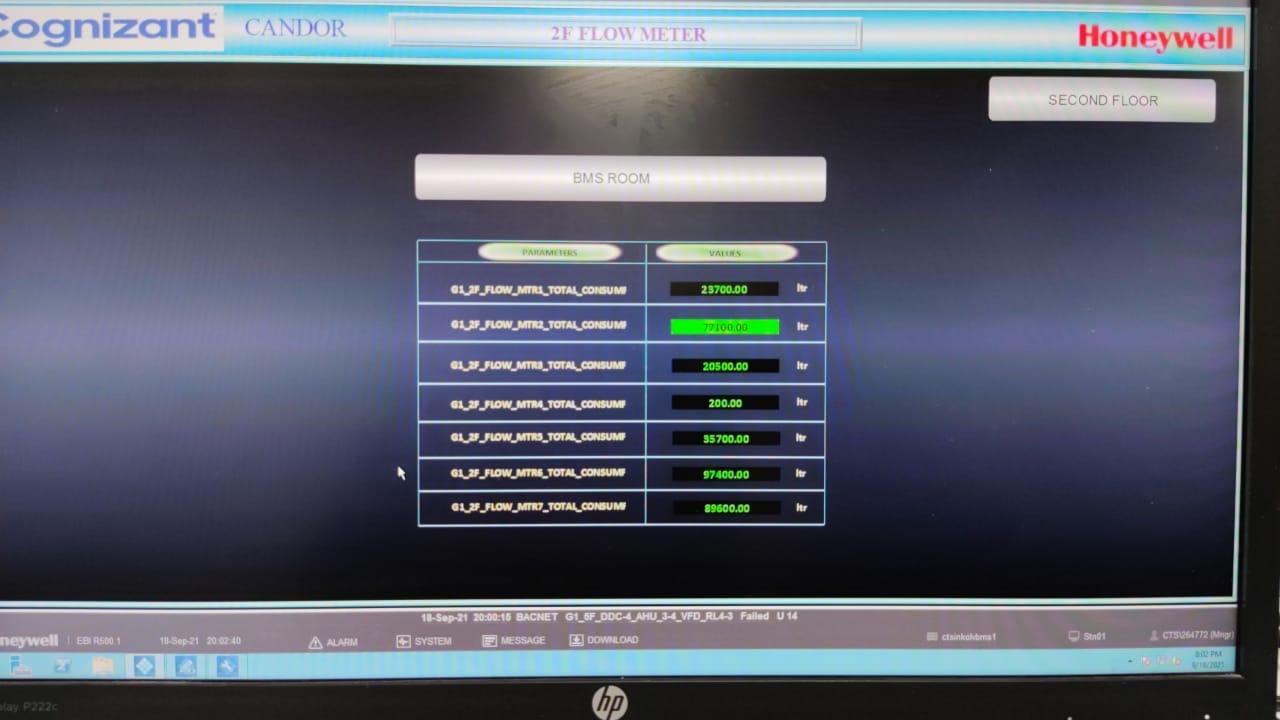
Description of the Innovation:
Panel Overheating Detection Sensors
CHALLENGE
• Detection of weakness in cable Termination/busbars and other related hot spot issues inside the panel were not known unit there is terminal flash or any cable burning issues occurred
• Thermography carried out annually seemed the only avenue to detect cable /bus bar hot spot issues
• Unscheduled breakdown maintenance were being called for to resolve the issues when they occurred
MYIDEA / INITIATIVE / SOLUTION BENEFITS / ADVANTAGE
• To overcome the issue and identify issues proactively Nicr/nial (Type K) thermocouple wire with Teflon insulation is used as sensor and this sensor is placed inside the panel compartment
• Thermocouple wire with Teflon insulation has accuracy radius of 5 meters and can withstand temperature up to 200 deg C.
• This Thermocouple wire is connected to Specially designed Temperature Control unit .This unit can be set from 10Secs to 15 mins.
§ When temperature rises more than the set limit control unit activates the buzzer simultaneously triggers alarm inn BMS.
§ Avoid Un-scheduled breakdown maintenance and business interruptions.
§ Ensuring 100% Human safety and prevent property damage
myIdea
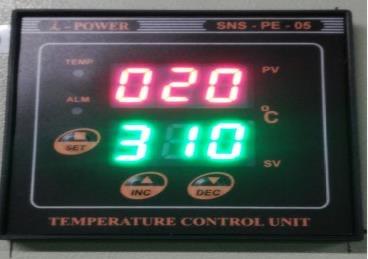
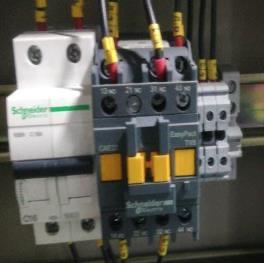
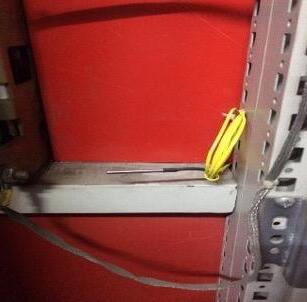
Description of the Innovation:
Use of Recycled Plastics
CHALLENGE
• In present day, the lube bay floor is either having tiles or are coated with epoxy paint to enable smooth cleaning and preventing oil seepage through concrete floors.
• Currently Epoxy has a limited life of 6 months to 12 months depending on external factors like weather, wear and tear and etc
• Re-applying of epoxy requires of 5 days of downtime of lube bay. Tiles has a greater life expectancy however it's develops cracks whenever a heavy tools or items falls on the surface
MYIDEA / INITIATIVE / SOLUTION BENEFITS / ADVANTAGE
• In the proposed change the surface will be covered with recycled plastic sheets of 10mm thickness
• This recycled will be made of used engine oil/Coolant canes generated at the site on daily basis.
• Future proposal of installation of recycled floor tiles and paver block on the site.
§ Recycled plastic sheets comes at ( lower cost (~35k INR), quick installations (lesser down time), better life ( at least 2 years) and can be further recycled.
§ Reduction in carbon footprint.
§ Direct cost benefit of 2.5cr and overall cost benefit of more than 4cr.
§ Ease of Oil Cleaning with respect to Epoxy and Tiles.
myIdea
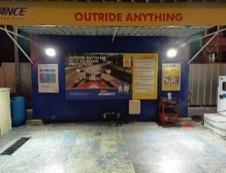

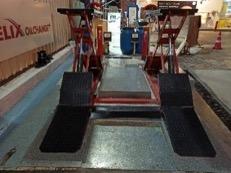
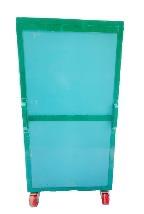
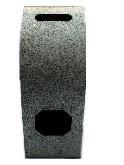
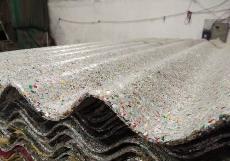
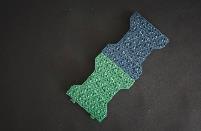
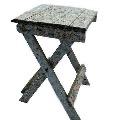
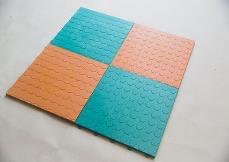

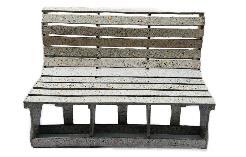
Description of the Innovation:
Polyurethane
V Belt
CHALLENGE
• Conventional V-belts are used in all AHUs which need periodic replacement due to wear & tear
• Replacement Period is 3 month
• Conventional V-Belt are sensitive to temperatures , oil, grease and common chemicals and solvents.
• Conventional V-Belt After initial run-in and re-tensioning, continues to stretch over time causing belts to become less efficient and slip if not re-tensioned regularly.
• Heat & frictional losses increase the power consumption
MYIDEA / INITIATIVE / SOLUTION BENEFITS / ADVANTAGE
• Team proposed the idea of replacing the of Installation of Polyurethane V- Belt with Conventional V-Belts
• Team identified 4 nos. AHUs and conducted trial project on performance of Installation of Polyurethane V- Bels
• The trial were successful, thereafter, total 124 AHUs were identified for the belt replacement activity in the CDC Facility
• The activity was completed successfully by the in-house team.
• Also, horizontal deployment of innovation is in progress for other CTS facilities.
§ The activity helped achieve monthly Power Savings in the tune of 81,840 KWH
§ Cost saving achieved by installation of PU belt INR 8,18,400/- per month
§ As life of belt is also extended ,savings in terms of spares & manpower utilization is achieved
§ Improvement in terms of carbon footprint
§ Increased equipment performance due to less frictional loss & slippage issues
§ The suggestion was well appreciated by the client
myIdea
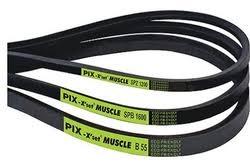
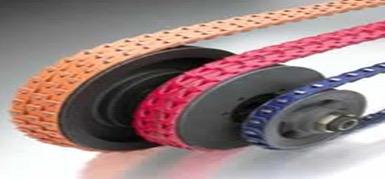
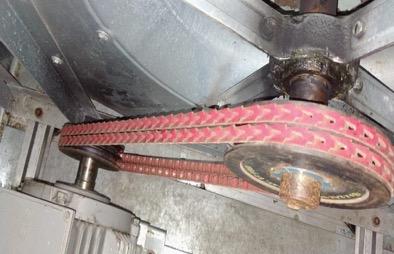
Description of the Innovation:
DG Resilience Panel
CHALLENGE
• Kosmo One Site energy supply is supported by the land lord team, with the transformers and captive power plant.
• The Security of Energy Supply has become a major concern worldwide, and all industry and communication and computer systems depend on a continuous energy supply.
• Our complete system collapses when energy fails and lack of support from building power supply system due to Surges in fuel prices, political conflicts, wars, and natural disasters directly threaten energy supply.
MYIDEA / INITIATIVE / SOLUTION BENEFITS / ADVANTAGE
• To evaluate the effectiveness of resilience enhancement strategies for electric distribution new DG resilience panel is implemented in ground floor electrical room.
• DG resilience panel is interconnected with building vertical risers' system with all protective electrical and mechanical interlocks
• Resilience panel is designed in such way that supports 80% to all floor (riser 1,1A & 2&2A)workstation loads and 40 % to common load and HVAC load(5,5A).
• Our own Rental DG supply is fed to the resilience panel during the crisis situation, The focus is, in particular on one specific attribute of resilience, namely, the readiness, i.e., the promptness and efficiency to recover the service without depending landlord team.
§ Power sustain during disaster.
Ability to recover the business.
§ Service during crisis with out depending building power system.
§ Upgradation in power infrastructure
myIdea

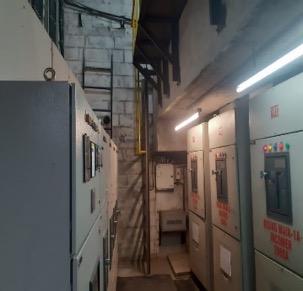
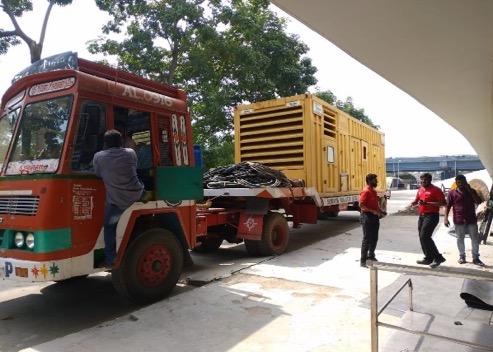
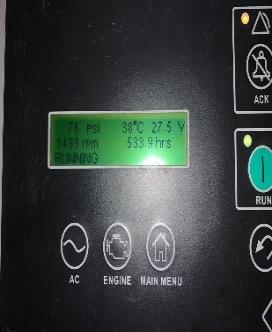
Description of the Innovation: CHALLENGE
• To reduce High emission from vehicles coming to premises/ curtail Air pollution/ making building more eco friendly
Electric Vehicles Charging Stations
• Initiated for installation of fast charging stations (04 numbers that can be extended up to 10)
• Each EV Charging station has 02 charging outlets and can charge 08 vehicles at same time
• For promoting Electrical vehicles, 20 slow charging points were also installed at site
§ Reduction in CO2 emissions up to 30%, 290 Ton/ Annum
§ Reduction in Air Pollution
§ More Sustainable facility
§ Vehicles running cost saving up to 70% INR 1.15 / KM whereas on fossil fuel INR 4.20/ KM
myIdea

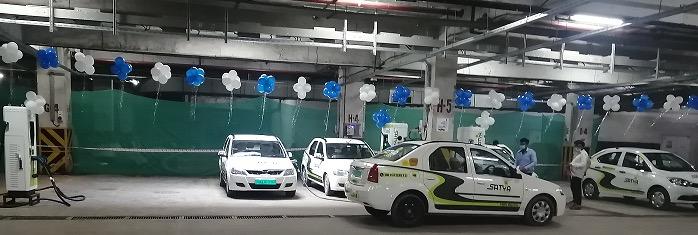
Description of the Innovation:
LEED certification
CHALLENGE
• LEED Certification rating Gold to Platinum.
• Be in compliance with environmental regulations and standards
• Maintain a reasonable site boundary
• Monitor the energy and water usage data
• Providing energy performance and promote great indoor air and environmental quality.
MYIDEA / INITIATIVE / SOLUTION BENEFITS / ADVANTAGE
• LEED Certification
• the LEED for Existing Building - O&M rating system we improved the operations, policies, procedures, purchasing and maintenance in an existing building.
• We uses fewer resources, minimizes waste and environmental impact, and decreases life cycle costs to achieve increased productivity and better staff health.
• Maximum energy savings
• Efficient use of water
• Optimum utilization of resources and sensitivity to their impacts
§ First Platinum certified building under V4.1 in India.
§ Fourth LEED V4.1 certified building Globally.
§ Arc scoreboard installed for real time performance assessment of the building
§ Reduced maintenance and operation costs
§ Healthier indoor air quality
§ Increased use of recycled materials
myIdea
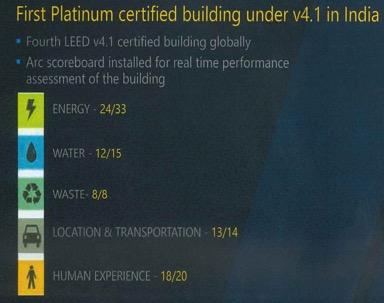
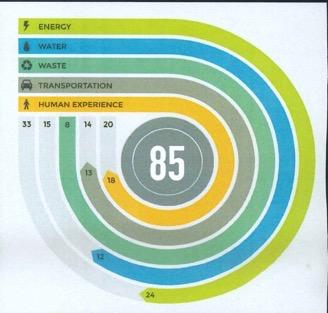
Description of the Innovation:
Portable trolley with PPE for Hot work
CHALLENGE
• We have observed that our ground and vendors team facing challenges while performing the Hot work at site. like unavailability of proper PPE or sometime vendor not able to arranged PPE on time.
• Secondly, we are facing challenges for providing supply at designated place for welding machine /Grinding machine/cutter machine.
• Sometimes vendor team doesn’t have the proper PPE due to which permit not issued and work got delayed.
MYIDEA / INITIATIVE / SOLUTION BENEFITS / ADVANTAGE
• Made the portable trolley with single & double phase supply ,fitted Industrial sockets 32 Amp, 30mA ELCB & 100 meter power cable.
• Welding screen guard made for arc protection & prevent person from eye / face injury.
• Hot work related all PPE kept in PPE box to provide in emergency case. Due to this fulfill the site Hot work requirement, protect welder to any accident/ mis happening/unsafe act & safe lives.
• Total cost was 1,46,570 INR
§ Help employee to do the safe work practice at site.
§ Fulfill the site Hot work permit requirement & process implementation.
§ Protect welder to any accident/ mis- happening/unsafe act & safe lives.
§ Resolve the power supply issue with designated place for carrying out any activity.
§ Helps to motivate and promote more innovations in future by the team.
myIdea
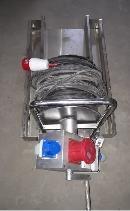

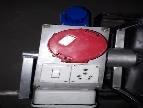
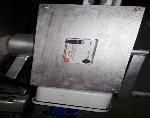
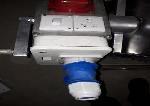


Description of the Innovation:
Automatic Cooling Tower Performance
Indicator
CHALLENGE MYIDEA / INITIATIVE / SOLUTION BENEFITS / ADVANTAGE
• In-house HVAC & M&E team used to check the cooling tower performance(Delta T) only in the Chiller plant display.
• Our Chiller plant is put up in basement 2 and cooling tower is in Ground floor. So, it is little difficult to monitor the performance of CT and some time team missed out the same.
• Slow response to the system abnormality
• We installed the CT performance indicator by install ed a controller in existing temperature sensors installed in IN/OUT pipeline of CT.
• We programmed the delta T lower limit as less than 3 and upper limit as more than 3.5 in the programmable sensor panel which is installed near the CT.
• Based on the sensor/Relay out put the lights will glow.
• If the Delta T value is 3 .5 or more than that the “GREEN” light will glow, and the team will understand that the CT performance is with in the permissible limit and the performance is good.
• If the Delta T value is less than 3 deg the “RED "will glow and the team will alert that the CT performance is less than the permissible limit and do the needful to fix the issue.
§ Ensuring 100% performance of cooling tower and Chiller which is involved in HVAC operation in Block 2&3
§ To ensure the chiller approach within the permissible limit
§ To Save the cooling tower make up water quantity.
§ This system will be connected with our BMS in future since the building is under construction level. And also 100% efficiency will be achieved when we operate the system with full load. Right now we have only 30-40 % of load due to lock down issue.
Performance is within the permissible limit
myIdea
Performance is not within the permissible limit
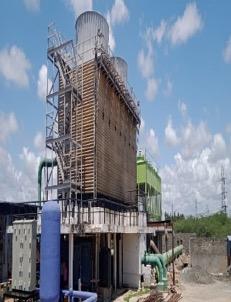
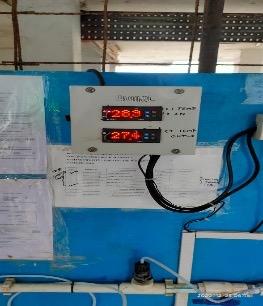

Description of the Innovation:
Critical alarm in LT panel
CHALLENGE
• Any Trip occurs in LT panel breaker can not be easily identified by Technicians
• Delay in response of Technician to restore the tripped breaker.
• Escalations from the client on restoring the power supply.
MYIDEA / INITIATIVE / SOLUTION BENEFITS / ADVANTAGE
• Installed critical alarm panel and also integrated with BMS system.
• This panel will show the live status of all the breakers in the control room which is manned 24 x 7.
• Control room operator will further inform the concerned technician to address the issue.
§ LT panel breaker trips can be easily identified at the control room critical alarm panel by the operator.
§ Reduced the response time for restoring the power supply in case of any tripping.
§ Client has appreciated for better response time.
myIdea

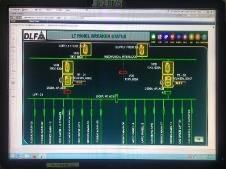

Description of the Innovation:
Conversion of DX unit into Chilled water unit
CHALLENGE
• The existing DX units are more than 10 years old with conventional operation which leads to energy consumption and refrigerant pressure drop due to frequent leak.
• Also, this DX units were charged with R22 which is having Ozone depletion potential of 0.05 .
• DX units needs dedicated space for the outdoor units and maintenance cost Is high.
• Cooling efficiency is low.
MYIDEA / INITIATIVE / SOLUTION BENEFITS / ADVANTAGE
• Installed chilled water units at all lobbies as replacement of DX units.
• The selection of chilled water units as follows low energy consumption, high cooling efficiency when compared to existing DX units.
§ The losses in pressure of water are accommodated by the sufficient capacity of pump which has low capital and running cost.
§ DX unit consumption of energy 363 khw /day of 8 hrs operations. Where as Chilled water consumption is 143 Kwh /day .
§ Energy Saving is 53,000 Kwh @ Rs 9 .Total Saving is 4.8 Lakhs / annum
§ Total amount spent is 12 Lakhs & ROI of the spend is 2.5 years.
myIdea
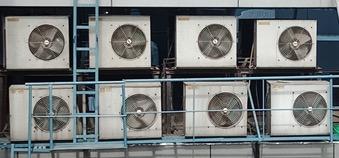
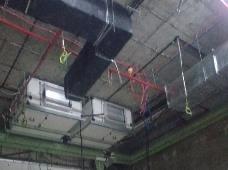
Description of the Innovation:
Automatic tube cleaning system
CHALLENGE
• Achieving the standard chiller approach was major concern
• Higher Energy Consumption due to raise in chiller approach
• Dependency on old traditional method of Chiller De-scaling
• Manual De-scaling process involved costing and manpower
MYIDEA / INITIATIVE / SOLUTION BENEFITS / ADVANTAGE
• Introduction of new technology which should be energy and cost efficient
• Automated system for Chiller De-Scaling
• Automatic Tube Cleaning system to overcome the wastage of cost, Energy and manpower involved
§ The losses in pressure of water are accommodated by the sufficient capacity of pump which has low capital and running cost.
§ DX unit consumption of energy 363 khw /day of 8 hrs operations. Where as Chilled water consumption is 143 Kwh /day .
§ Energy Saving is 53,000 Kwh @ Rs 9 .Total Saving is 4.8 Lakhs / annum
§ Total amount spent is 12 Lakhs & ROI of the spend is 2.5 years.
myIdea
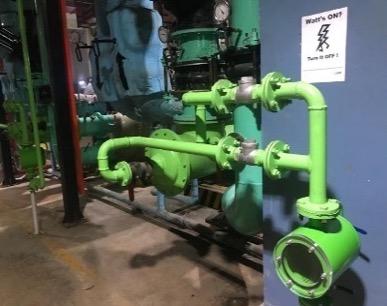
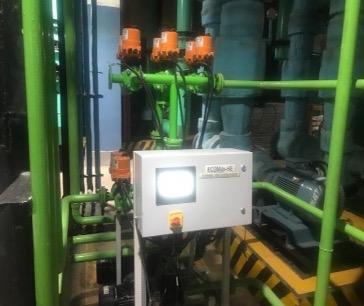
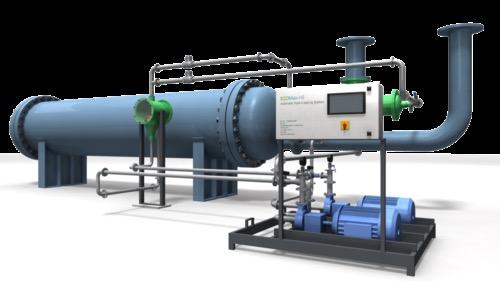
Description of the Innovation:
British Safety Council Certification
CHALLENGE
• Adjustment to new SOP and guidelines and adhering to all the BSC procedure
• Risk assessments to carry out such as HIRA,, Manual Handling, FRA and DSE
• PTW with JSA & TBT for all activities, time constraints
• Communication and participation from top management to task level associates despite Covid pandemic
• Allocation of resources timely
• Implementation of safety related activities like Safety Observation, Inspections, Audits
• Virtual presentation for documents and onsite implementation status
MYIDEA / INITIATIVE / SOLUTION BENEFITS / ADVANTAGE
• Application of PDCA Cycle
• Lots of trainings and brainstorming sessions
• On board HSE manager who coordinate all BSC activities
• Action plan layout
• Allocating and dividing works with different departments
• Bringing an idea to make PTW issue less time
• Budget and allocation of resources in systematic manner
• Benchmarking with other BSC certified buildings for implementation and best practices
§ Best safety system with written procedures
§ Compliance for any safety related audits
§ Better proactive process and wider participation and communication on safety
§ Enhanced safety working procedures and protocols adopted for all types of works in the building.
§ It gives a sense of satisfaction to the staff that they are working in the most safe and secure environment.
§ Enhanced reputation for the Client and building in terms of daily operations and maintenance.
§ World class safety standard
myIdea
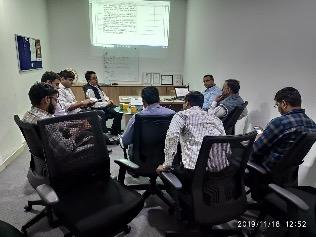


Description of the Innovation:
SOS for women safety
CHALLENGE
• The campus has vast basement floors B1,B2 &B3 spanning for 17,23,464 Sq.Ft that are designated as parking area
• In the late hours, very minimal movement happens in these basement floors that often causes an insecurity & panic particularly amongst the women employee who works on 24X7 shifts
MYIDEA / INITIATIVE / SOLUTION BENEFITS / ADVANTAGE
• About 55 nos SOS emergency talk back system is installed in the basement floors of every blocks with visible signages for easy identification & any call that is made from the system is attended by a trained BMS team that operates on 24 X7 shifts
• At the BMS operator end, whenever a SOS call is received, the LED indication of the respective zone will turn ON & creates an audible beep sound till acknowledgement
• A separate SOP & communication protocols (involving the security team & the ops team) were drafted & implemented to provide immediate help to the person in need
§ The safety & security of the building is enhanced and has created a positive impact particularly amongst the women employees
§ The call points are addressable & Two way communication is possible
§ Quick assistance for any kind of emergency situation is ensured by channelling the communication through the centralized BMS team to illness
myIdea
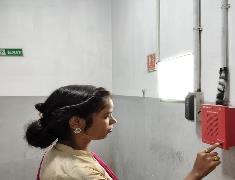
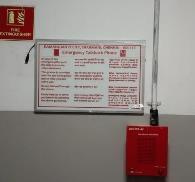
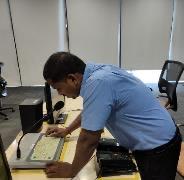
Description of the Innovation:
Equipment Safety
CHALLENGE
• In-house HK & M&E team & Suppliers uses machineries like Vacuum, Scrubber, Drilling, Cutting, Heating & Welding Machines etc during day to day operation
• We observed the machines lost their insulating properties over a period or during the transportation, which the suppliers may not be knowing before starting the activity and it can trip the critical circuits or hurt the operator, if not checked in advance
• The defective machineries can damage both business & human life
MYIDEA / INITIATIVE / SOLUTION BENEFITS / ADVANTAGE
• Installation of an ELR / ELCB based testing station at the entry locations, which will enable the operator or the vendor to check the machines before connecting to any of the building main circuits
• There are 2 different light indications in the testing kit
• Green – Indicates the equipment in good condition
• Red – Indicates if the machine is defect Indicators will be in OFF condition before & after test
• MCB & ELCB provided for safe testing
§ In the context of electricity, for its proper conservation, right distribution to the desired points of utility and also to safeguard the precious life and valuable property from damage, it is very important to insulate the point of voltage and the passage of electric current through the conductor
§ Ensuring 100% Human safety and property damage
myIdea
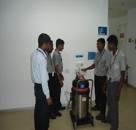
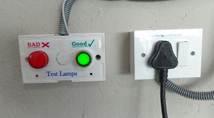
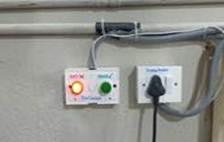

Description of the Innovation:
Theme based Butterfly garden
CHALLENGE
• Water Body with an area of 2500 Sq. Ft. and 50 KL water capacity necessitates 1200 KL potable water wastage per annum which can feed 15 villages per day with 200 families consuming average 400 litres per day
• Foreseeing sourcing issue in future, due to water scarcity in city
• Higher Cost of maintaining the Waterbody
• High expectations to match the standards of the water body by the users
MYIDEA / INITIATIVE / SOLUTION BENEFITS / ADVANTAGE
• Introduction of Theme based Butterfly Garden to match the aesthetics of water body and conserve precious natural resource – Water as a part of CISCO Go Green initiative
• The Butterfly Garden has been designed to create an environment that attracts butterflies, with a mix of suitable sculptures. The flora in the garden has been specifically chosen, as they are known to draw the attention of our winged friends
§ Saving 1200 KL water can cater 14 villages, considering 200 family Indian village with 400 Litres per day water consumption
§ 100% operation cost avoidance. $ 10 K USD Maintenance Cost per annum
§ 100 water tanker movement avoidance leading to reduction in carbon footprints
myIdea
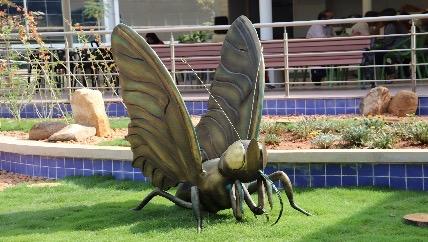


Description of the Innovation:
EAC Filters
CHALLENGE
• Existing HVAC system was not designed to filter particulate matter( PM 2.5 & PM 10)
• Poor indoor air quality on floors during peak pollution months
• Challenge of not being able to inject fresh air into the system due to poor ambient air quality. This is required to be done when the CO2 levels increase inside the floors
MYIDEA / INITIATIVE / SOLUTION BENEFITS / ADVANTAGE
• New Electrostatic Air cleaner (EAC) filters were installed in all fresh air units and air handling units for controlling the PM levels in the indoor air
• Installed LED screens on each floor for display of real time IAQ parameters to the occupants
• This brought our offices at par with any Global facility in respect of Indoor Air Quality standards
§ IAQ parameters ( AQI-8, PM2.5 & PM 10 - Less than 5 Microgram/m3) were achieved on floors post completion of this project
§ Treated fresh air is injected into the floors to control CO2 levels
§ Enhanced life of AHU coils
§ Reduction in the connected chiller load and improvement of chiller efficiency
§ Better colleague experience and satisfaction.
§ Keeping in view the current COVID-19 situation 100% fresh air injection is possible and can be done
myIdea

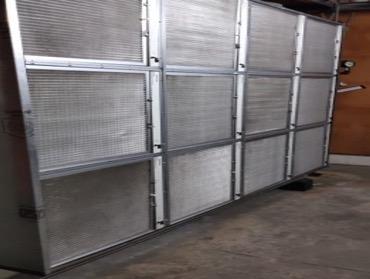
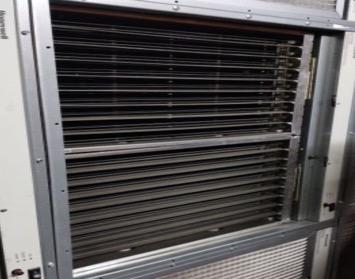
Description of the Innovation:
Energy Meter
Testing Kit
CHALLENGE
• Errors in Energy Measurement.
• Too high or low Consumption
• Frequent Changing of Energy Meters
• Holding of payments due to consumption disputes
MYIDEA / INITIATIVE / SOLUTION BENEFITS / ADVANTAGE
• Preparation of a separate Kit for calibration of energy meters consisting of new current transformers and calibrated multifunction meter(s).
• Offline connection
• Calibration done for 24 Hours or during peak hours to demonstrate the consumption
§ Easy to Check the Correctness of wiring.
§ Easy verification of meter faults and CT faults
§ Complete reduction of errors
§ Improved accuracy of energy billing.
§ Safe to handle due to offline arrangement
myIdea
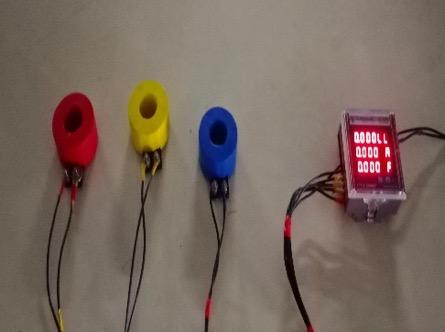
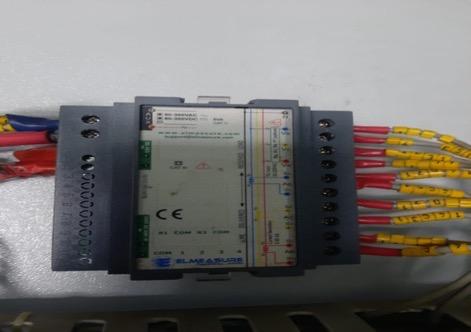
Description of the Innovation:
Monitoring of Air-Quality & Surface Hygiene level
myIdea
• Increase in air pollution across the city
• Poor air quality causing breathing issues
• Bacteria at touch points causing infections
• Implementation of real time monitoring of Air-Quality & Surface Hygiene level in the common area premises to ensure the Air quality and Surface Hygiene maintained
§ Identify Transmission Hotspots
§ Evaluate performance of Maintenance & Cleaning Regime
§ Helps to Monitor air polluting sources to decide on control measure infrastructure installations.
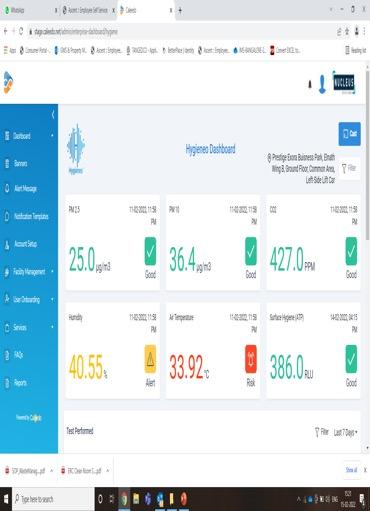
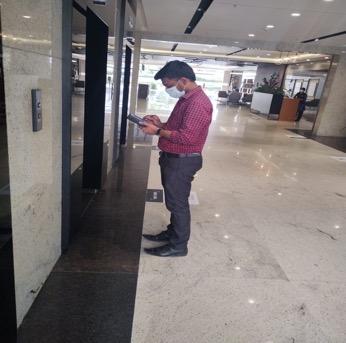

Description of the Innovation:
HVAC optimization
CHALLENGE
• The existing two no’s of Cooling tower are in operation from the day one. Due to stand by CT issue.
• The standby Cooling tower was installed two years back and not connected with main headers and balancing line and not commissioned
• The Softener plant haven’t rewarmed for last three years and the water parameters such as the hardness in the make up and the circulation water are unable to maintain consistently and blow down consumption increased as triple time from usual value.
MYIDEA / INITIATIVE / SOLUTION BENEFITS / ADVANTAGE
• We obtained 38 hrs complete HVAC shut down after a long follows up with client/tenant/vendor and etc, we had completed all defective valve replacement in existing cooling tower and connected all header line with the new stand by cooling tower. And commissioned the new stand by cooling tower successfully.
• The softener plants were rewarmed successfully, and the soft water is being delivered with the hardness of 0 PPM.
§ Estimated Saving would be INR 150000/-| Area 900000 ( Sq ft )
§ Impacted in the water consumption by reduce the blow down water.
§ We are able to blend the high TDS oozing water partially which is available in hand with softener inlet water. And we may reduce water consumption with a sizable quantity.
§ Now chillers are running with permissible limits of all parameters.
myIdea
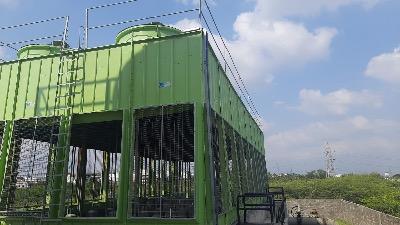


Description of the Innovation:
Waste Water Collection Bins
CHALLENGE
• For maintenance works or When ever plumbing lines blocked, our plumbing team use to clear the same in parking areas.
• It will make the parking area dirty and Foul smell spread over parking.
• Employees and users to give complaints.
• Cleaning of the area required lots of manpower and it’s a hygiene issue.
MYIDEA / INITIATIVE / SOLUTION BENEFITS / ADVANTAGE
• We checked in our ‘VALUE YARD’ for materials to prepare PORTABLE BINs with wheels and valves.
• Converted waste collection bins as below by using minimum materials.
• As a result, more hygiene and safe Portable bins were prepared by in house team.
§ Our SAFETY-FIRST slogan is strengthened in terms of hygiene in parking areas.
§ Client escalations eliminated.
§ Prepared by in house team, we have saved approx. Rs 15K.
§ HK staff requirement reduced from 3 to 1 which is a savings of Rs 2000/- per month which is a reoccurring savings.
myIdea
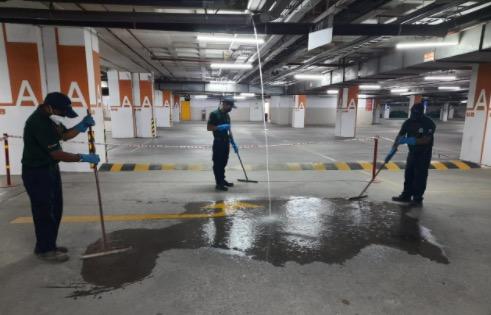
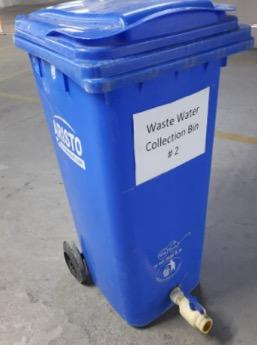
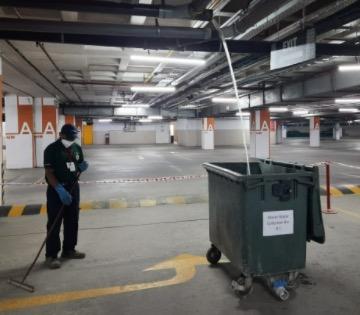
Description of the Innovation:
Utilizing Solar water for common area
CHALLENGE
• Hot water required to common area & Facilities.
• Utilization of Solar Power
• Supporting Sustainability Goal
• Reducing Energy Cost
MYIDEA
/ INITIATIVE / SOLUTION BENEFITS / ADVANTAGE
• Initiated Solar panels for Hot water
• Planed the implementation with the Vendor to best suit our requirement
• Pipelines are implemented to make best use of the usage .
• We have initiated and serviced all motors.
§ Reasons solar panel has great outweighed than any other form of energy is that when it comes to heating water is the efficiency.
§ Reduced the energy consumption
§ Reduced the energy cost
myIdea
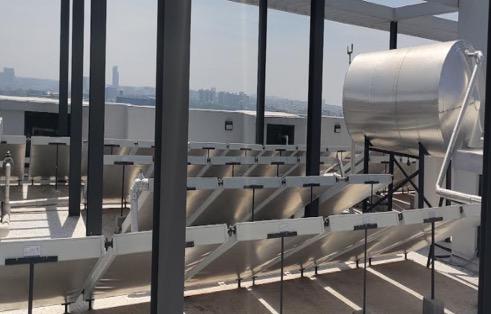
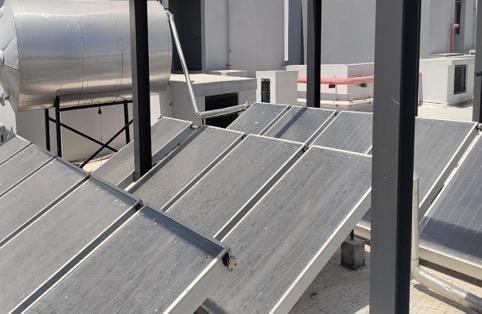
Description of the Innovation:
Snake repellent station
CHALLENGE
• More snakes are entering our property.
• Safety issue for support staff and Employees.
• Very difficult to catch the Snake.
• Landscape staffs are scary to work with.
MYIDEA / INITIATIVE / SOLUTION BENEFITS / ADVANTAGE
• Installed the 05 no’s Repellant stations.
• We made the Snake repellant station.
• Below mentioned contents are used in Snake repellent station and its pure organic materials
• Wild plant extract: 10%
• Organic Additivies 30%
• Acid Insoluble Carrier: 60%
§ Snake moments are gradually reduced at our building.
§ Employee and support staff fear level has been decreased
§ With this organic Snake repellent, get benefits to keep away snakes and not hamper the pleasant environment.
myIdea
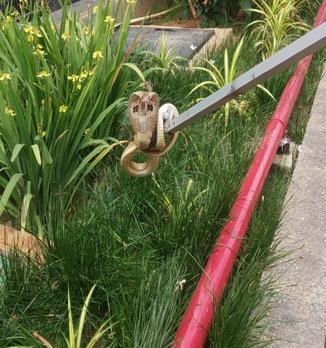
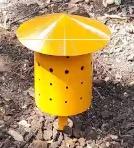
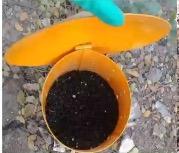
Description of the Innovation:
Timers in Common area lighting system
CHALLENGE
• In order to conserve power consumption & improve light fixtures life cycle
• To ensure Timely switch On and OFF streetlights, lobby lights
• With only one technician we were finding it difficult in switching On & off as Technician was engaged in other complaints
• There were incidents about technician forgetting to switch On and off with excuses
MYIDEA / INITIATIVE / SOLUTION BENEFITS / ADVANTAGE
• Timer Installation in Common area
• Podium Lighting System
• Analogue FM/1 Quartz Timer -6 Nos were installed –Rs.1700 Each
• Lift lobby Lighting System
• Mechanical time switch 15336 timer
• 15Nos were installed –Rs.1700 Each
• Wiring was done with inhouse technician
§ Saved Rs 16,430 for the year, the saving will be carried out further.
§ Maintenance of lighting system to minimize energy wastage.
§ Achieved Environmental benefits
§ Carbon footprint saving
myIdea

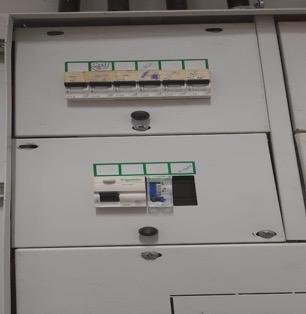

Description of the Innovation:
AHU Valves Actuators
CHALLENGE
• The mechanism for opening and closing a valve. Manually operated valves require someone in attendance to adjust them using a direct or geared mechanism attached to the valve stem. Power-using air pressure, allow rapid operation of large valves..
• Limited output capability
• Large size and weight
• Before BTU Consumption 1200 to 1500 KWH for 1 /60TR-AHU
MYIDEA / INITIATIVE / SOLUTION BENEFITS / ADVANTAGE
• With the stable Floor temperature, the indoor comfort increases. Required temperatures are accurately met, increasing the productivity of office employees
• The perfectly balanced system, under all conditions, increases the energy efficiency and leads to savings on energy costs.
• As the pressure-independent valves ensure perfect working conditions, the actuators mounted on them require fewer movements to keep the temperature stable.
§ Integrated functions as linear temperature control pressure independent and electric regulating into one valve
§ High control accuracy, strong anti interference capacity
§ All temperature and flow can be automatically regulated without any human interference
§ Extremely low energy consumption
§ After BTU Consumption 600 to 800 KWH for 1 /60TR-AHU
myIdea

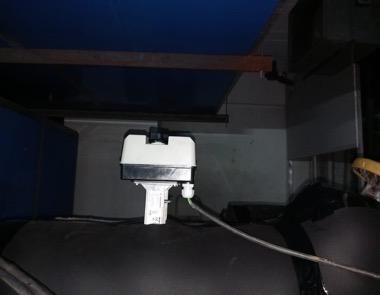
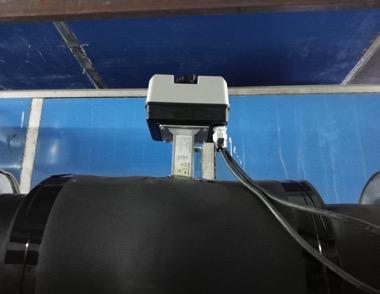
Description of the Innovation:
E Loader EV
CHALLENGE
• Increase in vehicle pollution day by day in the campus due to increase in number of vehicles
• Deployment of vehicle with fossil fuel will create negative impact on sustainability
• Need of the motor vehicle for shifting materials and goods from one place to other for internal works
• Safety of the team is less while shifting the materials and goods by trolley
• Attrition of labour due to more physical work for shifting
MYIDEA / INITIATIVE / SOLUTION BENEFITS / ADVANTAGE
• E loader Electric Vehicle is deployed for transportation of materials and transporting garbage’s from buildings to central storage location which is collected in common areas.
• For full charging it takes 4 hrs., and we can run the vehicle for 60 KM, we can carry 500 Kg stuff in the vehicle.
• The cost of the vehicle is 1.9 Lakhs.
§ This initiative supports the sustainability
§ Reduce the task level teamwork fatigue
§ Creating awareness of Electric Vehicle among the inmates
§ Speeding up the material movement
§ Maintaining the campus clean and tidy ever than before
§ Better and affordable maintenance
§ A low running expenses
§ Smoother and prominent turning sweep
myIdea
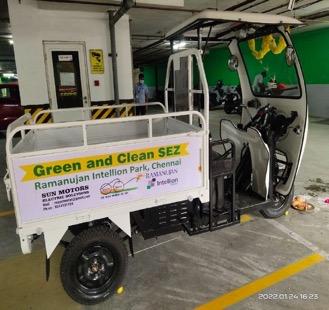

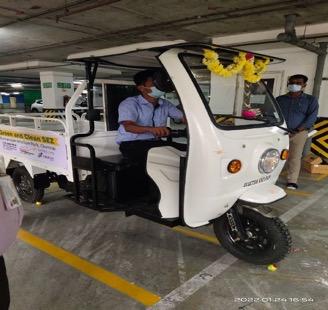
Description of the Innovation:
Emergency exit route Map with Back-lit signage
CHALLENGE
• The basements are larger and less gloomy for finding Emergency exit route Map during real emergency with the existing conventional signage
• When there is no power during an emergency the existing Emergency exit route Map signage is not visible as it is not lit
• As the campus is large and close to 1500 new staff / visits every day it is difficult for them to identify the exit route map itself during emergency as it is not lit and size restrictions
MYIDEA / INITIATIVE / SOLUTION BENEFITS / ADVANTAGE
• We developed a soft copy of the exit route for each locations and made a board with Back-lit display. UPS Power points were provided for Emergency exit route Map signage's
• Installed total 40 Nos of back lit signage's in the basement's common areas at strategic locations
• The new signage is provided in the vinyl sheet it will lost long
• The new signage is easily readable
• The signage board itself visible form a long distance
§ This arrangement enabled the visibility from distance
§ The back-lit provides visibility during the absence of lighting power supply
§ New visitors can easily understand where they are and where to go out even on a normal day
§ Durability of the product is very high as is it made in Vinyl sheets
§ Appreciated by occupant companies on this new arrangement and satisfaction level is increased
myIdea


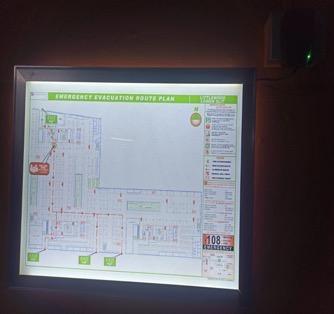
Description of the Innovation:
Airport Trolley
CHALLENGE
• There was no proper platform type trolley available for executing maintenance and attending breakdowns in the chilled water and pipelines and difficulties faced as specially for welding work etc. in the pipelines
• Using a type ladder for continuous work is not safe as they need to hold some materials like valve, pipes etc.
MYIDEA / INITIATIVE / SOLUTION BENEFITS / ADVANTAGE
• Fabricated an Airport trolley for executing the maintenance and attending breakdowns in the basement pipelines both HVAC and waterlines
• The top platform is provided with adjustable side rails for using it during the execution
• The wheels are lockable during the execution of work to ensure safety
§ Quick and safe working platform at heights ensures highest safety
§ The platform can be adjusted to the required height levels
§ It is movable and lockable at the workplace
§ Two to three staff can attend the work on the platform at a time
myIdea

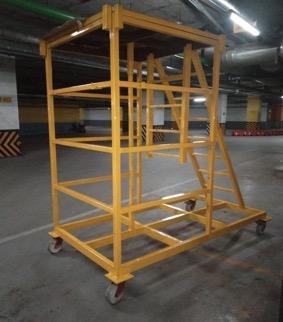
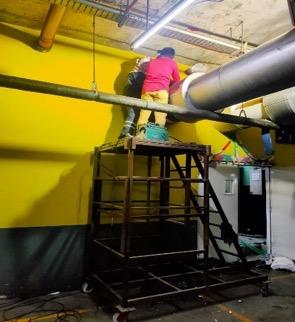
Description of the Innovation:
Chilled Water Temperature Monitoring
CHALLENGE
• Unavailability of Audible alarm for Chilled water supply temperature rise
• Chiller overloading & tripping due to surge in load
• Temperature variance due to failure of pumping system
MYIDEA / INITIATIVE / SOLUTION BENEFITS / ADVANTAGE
• Checked for the available solutions in market for temperature alarming device
• Installed temperature sensing cum alarming device on Header of chilled water supply temperature by inhouse team
• Programmed for desired chilled water temperature range to be maintain
§ Timely & Precise monitoring of the chilled water temperature.
§ Alarm generation to notify the difference in chilled water parameter
§ Decrease the downtime of the system operations
§ Avoid business loss due to breakdown.
§ Help in regulation of chiller set point results in optimization of chiller efficiency
myIdea
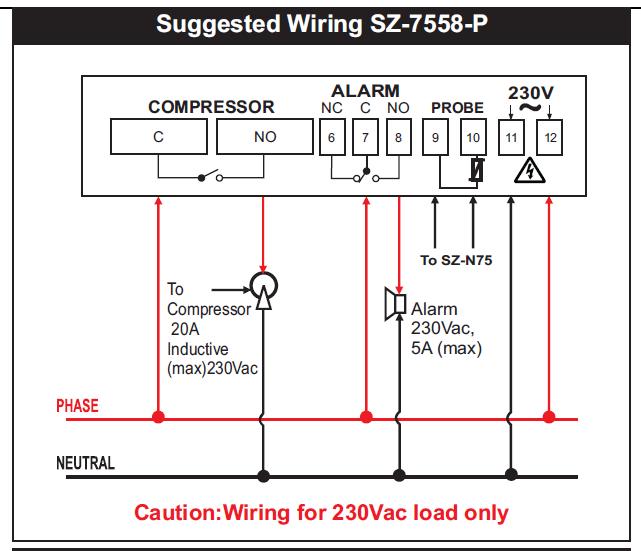
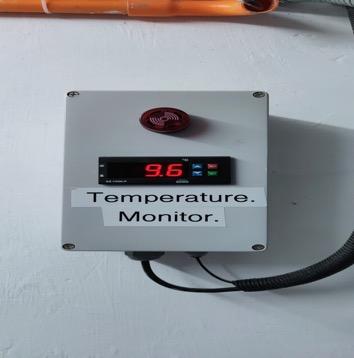

Description of the Innovation:
CHALLENGE
• Fire pump water has been used for parking area cleaning.
• Water tank overflow issue.
• Washroom water leakage issue.
• Plumbing line leakages issue.
• Rain water is not reused.
• STP water is not reused.
• Water flow pressure not set for plumbing lines.
MYIDEA / INITIATIVE / SOLUTION BENEFITS / ADVANTAGE
• Leakages were tracked down, repaired, and closed.
• The refilling of the underground water tank was closely monitored and spillover of water after the tank full condition was completely stopped.
• Timely inspection and repair of water supply system (Once every 15 days)of the washroom in tenants’ offices to check any unreported and unattended leakages inside the offices.
• Maintaining minimum required pressure in the washroom line has been a help in controlling wastage of water.
• Jet machine used for common area cleaning.
• Rain water used for flushing
myIdea
§ All water leakages problem solved hence no water wastage.
§ Water consumption reduces by 756 KL per month.
§ Water bill amount reduce RS.53057 per month.
§ Rain water reused for flushing system.
§ STP treated for grading purposes.
§ Without any cost we achieved this results.
Description of the Innovation:
Mobile Jet Spray
CHALLENGE
• Due to ongoing Construction by Project Team Deep cleaning of basements through normal water wash was very tedious job & required lots of manpower and man-hours, hence use of Jet Spray machine was inevitable.
• Unavailability of Water connection at multiple location in all 3 Basements (approx. 90K each).
MYIDEA / INITIATIVE / SOLUTION BENEFITS / ADVANTAGE
• Arranged pvc water storage tank (700 liter) from Projects team and fixed tap for water outlet at bottom of the tank.
• Water Tank placed on 12 mm thick Wooden ply with ACP, on a Hydraulic trolley and Jet Spray inlet was fixed at Water Tank outlet.
• Cloud Jet Spray Trolley was ready to rain.
§ This Mobile Jet Spray machine can be moved at any location easily by single person.
§ Productivity increased by 300%.
§ 50% Reduction in usage of water supply for cleaning tile grooves, Basement- IPC flooring, Pillar corners, Paving Tiles and other rough surfaces.
§ Team is Planning to design enclosure for beautification of the machine.
myIdea


Description of the Innovation:
Lighting circuit Automation
CHALLENGE
• No Ease of operation in landscape lighting
• Manpower using for ON/Off schedule
• Timely alerts to technicians
• Time control management
• Delay in lighting operation due to human error
MYIDEA / INITIATIVE / SOLUTION BENEFITS / ADVANTAGE
• Identified the possible solutions for challenges.
• Installed astronomical timer to landscape feeder pillars for ease of operation.
• An astronomical timer is one of the convenient ways to manage landscape lighting
• It works by adding information to astronomical timers such as your location, date and time for On and Off. Once it is set and then it will be free from the hassle of turning on and off the outdoor lighting
§ Astronomical timers make use of a preset database that includes timing for sunrise and sunset to guide lighting system about when to switch on and switch off
§ In case of power outage, the device is capable of working.
§ Since the initiative, we have saved approx. INR 5000 by saving the KVAH in the time management of lighting.
§ Cost of one timer is INR 2500/- and we used 3 timers for ease of operations
myIdea

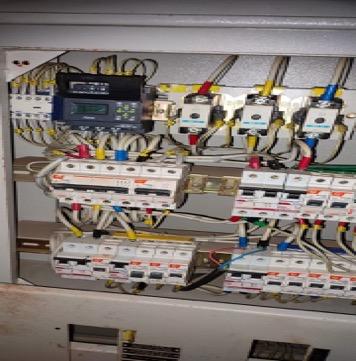
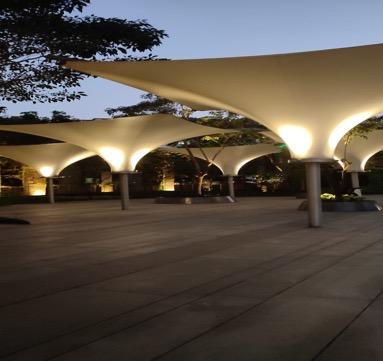
Description of the Innovation:
In-house Manufacturing of D-O-L Panel
CHALLENGE
• No overload protection to the motor.
• Failure of protective interlocks.
• Frequent motor failure.
• Problem for maintenance.
• No indication of limit switch and overload.
MYIDEA / INITIATIVE / SOLUTION BENEFITS / ADVANTAGE
• Control and power Diagram prepared.
• Required material purchased after approval from client.
• New DOL panel prepared in-house.
• Motor and Panel Rewiring done.
• Starter panel replaced
• Panel Installation and testing done.
§ Operations of panel are interruptible according to interlocks.
§ Operator friendly as indicator are available for interlocks.
§ Motor over heating issue solved.
§ In-house prepared so cost effective: Used old box, scrap cables, old materials and few new item purchase of 2800 rupees only
myIdea
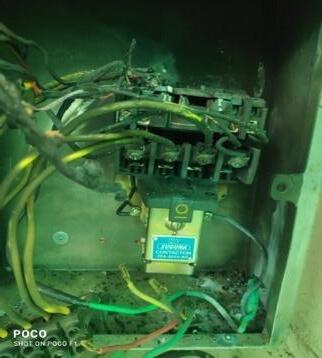
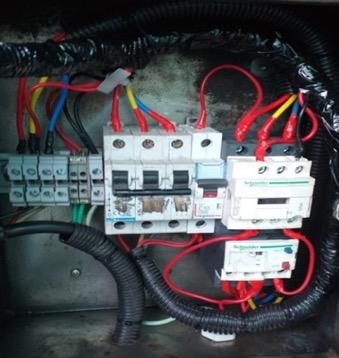
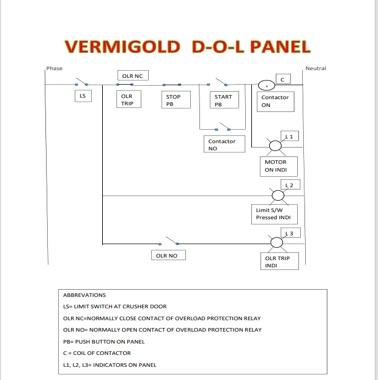
CHALLENGE
• As water tanks manhole doors are located in parking area, checking water levels was inconvenient due o vehicle movement.
Description of the Innovation:
Digital Level sensor
myIdea
• Water tank level were checked manually by opening manhole doors
• While checking the tank level, risk of fall hazard into the tank was anticipated
• Back pain/ injury to plumber while lifting manhole doors
• Continuous monitoring of water tank level was not practical
MYIDEA / INITIATIVE / SOLUTION BENEFITS / ADVANTAGE
• To minimize human intervention and have convenient and continues monitoring of water level, it was decided to install digital level sensors in tanks.
• To avoid EHS issue while performing operation.
§ After installation of digital water level sensors, fall hazard was eliminated by Engineering Control.
§ Ease of continues water level monitoring from BMS by having visual screen.
§ Motivation of technical team improved as initiative is seen as part of their well being.
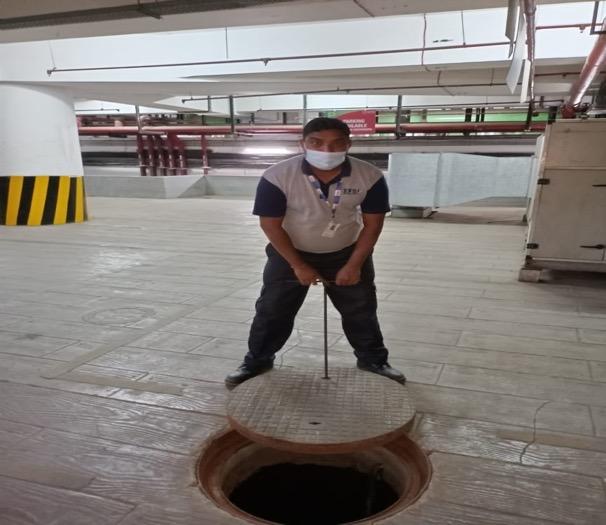
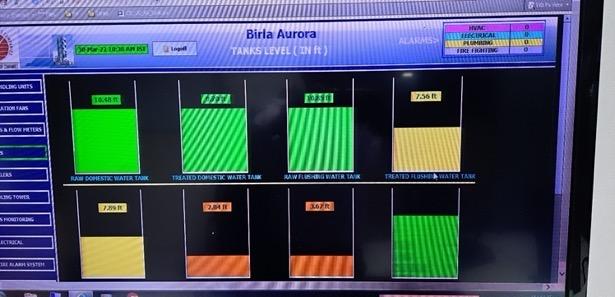
Description of the Innovation:
Replacement of CCTV Server with NVR
CHALLENGE
• Multiple issues with existing server-based camera like missing recording & camera offline.
• Existing server had proprietary software with JCI
• Frequent downtime on camera
• Window based application affects system operation
MYIDEA / INITIATIVE / SOLUTION BENEFITS / ADVANTAGE
• Approached onboard AMC vendor to look out feasibility of system upgradation
• Replaced servers to NVR compatible with existing camera and infrastructure setup
• Resulted in open protocol to reduce rectification downtime
• All recorded footage available & cameras working online properly
§ Enhance Storage capacity of CCTV footage
§ Future ready technology
§ Can withstand in robust ambient condition (Non-Air-conditioned space)
§ Eliminate dependency on OEM for future operations & Maintenance
§ Controlled user login
§ Can receive Intrusion alert
§ Approx cost saving- Rs-5Lacs
myIdea
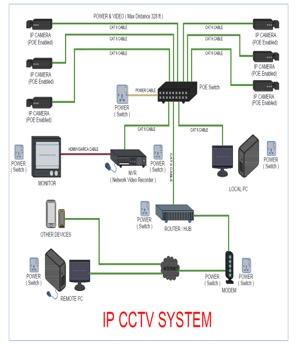

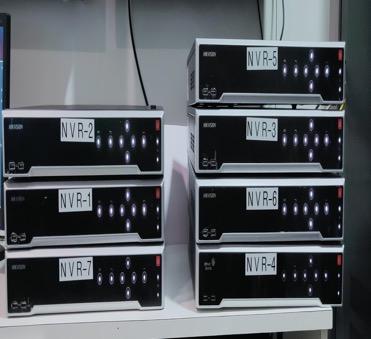
Description of the Innovation:
Ventilation System Automation
CHALLENGE
• Exhaust & ventilation systems-Bad smell all over the cores
• System was manually driven.
• Exhaust systems function and timing poor and unhealthy
MYIDEA / INITIATIVE / SOLUTION BENEFITS / ADVANTAGE
• The challenges was discussed with client with limited cost involved.
• Timer was set and installed in the entire system to function automatically
• Filter was installed to escape from foul smell inside the all-washrooms area.
§ Power saving-Less consumption with the systems automation.
§ Cost saving achieved with the timer used in the ventilation & exhaust panel.
§ Saving of equipment maintenance cost as less wear & tear with fully automation.
§ All foul smell problem solved with all client's expectations.
myIdea
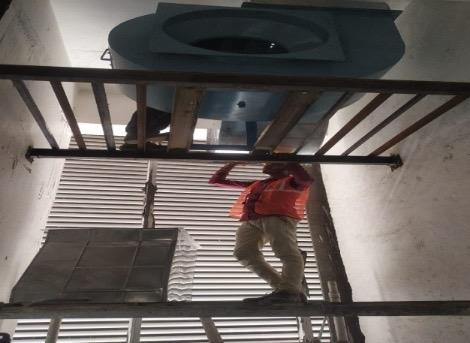
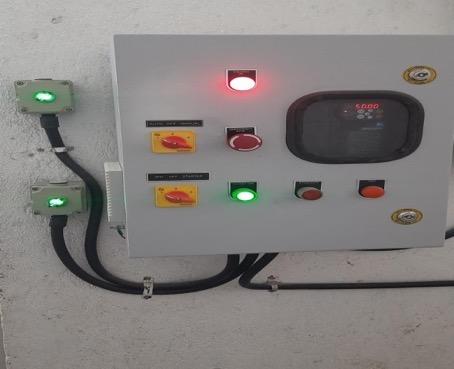
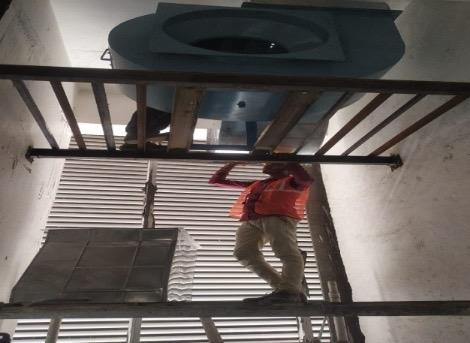
Description of the Innovation:
Floor Motion Sensor
CHALLENGE
• In JK Infotech site we have 3 no clients are here and one of our client was facing problems in the manner of more energy consumption
• Previously lights was kept operational for full day and led to more energy consumption
• Lights/Consumables life cycle was low
MYIDEA / INITIATIVE / SOLUTION BENEFITS / ADVANTAGE
• We have suggested our client to installed motion sensors for lighting operation in working area, washroom, lobbies and lift lobby areas
• The motion detector monitors the presence of people and registers their movements
§ It helped our client in Energy conservation as they have saved up to 2400 kwh or 30% power consumption
§ Life of consumables increased
§ It helped to reduce electricity bill total costing
§ Also, we have discussed to our other clients, and we have planned to implemented with our other client's floor soon
myIdea
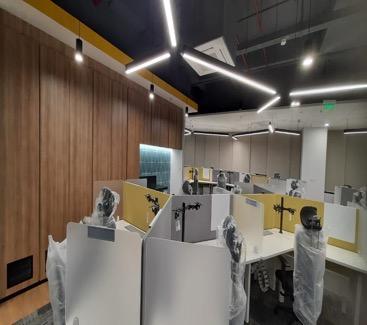
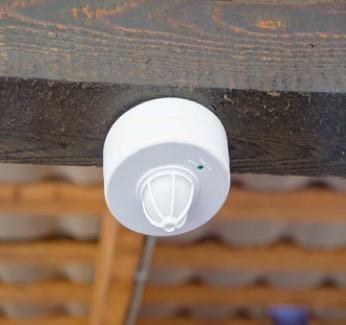
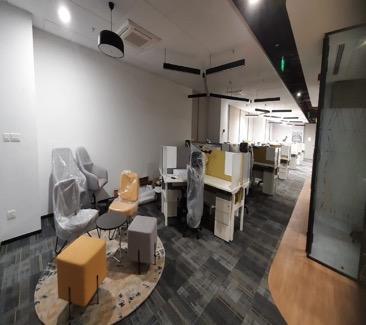
Description of the Innovation:
Fire extinguisher AMC by Inhouse team
CHALLENGE
• Dependent on vendor for foam fire extinguisher servicing, which costs around INR 10K per year.
• Possibility of delay in fire extinguisher servicing due to vendor dependency.
MYIDEA / INITIATIVE / SOLUTION BENEFITS / ADVANTAGE
• Training given to inhouse plumber under the guidance of Nandedcity fire fighting team.
• Due to lockdown period servicing carried out by inhouse team but in future the servicing will be carried out by vendor.
§ Servicing cost on fire extinguisher through vendor annually saved INR 10,000/-
§ Time saved due to non dependency on vendor and follow up required for AMC.
myIdea
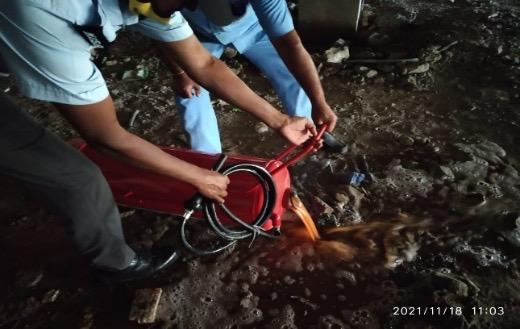
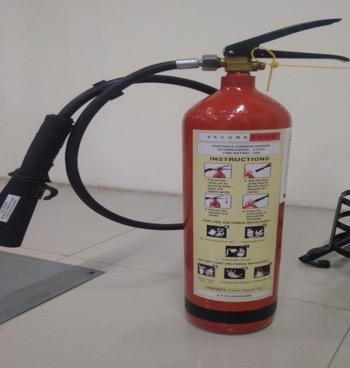
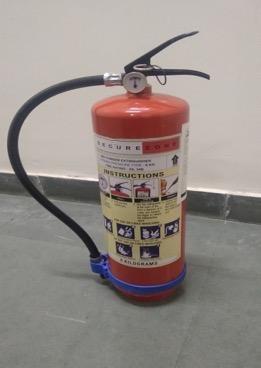
Description of the Innovation:
Access Control Through Facial Recognition
CHALLENGE
• Identification and manual recording of all physical movement.
• Repeated verification at multilevel.
• Deployment of additional manpower at each lobby reception.
• Unauthorized entry into wing.
• Delay due to security screening on multiple levels.
MYIDEA / INITIATIVE / SOLUTION BENEFITS / ADVANTAGE
• Face detection device installed wherein face recognition of residents and their details are captured to enable lobby door access.
• 4 way facial recognition.
• Captures images of each individual accessing lobby.
• Its inbuild with thermal screening to identify COVID – 19 risk.
• Integrated with Video Door Phone calling to desired flat.
§ Secure access & storage of data in electronic platform for longer period.
§ Saving on Manpower cost.
§ Reduced human interference with the help of technology.
§ Restricted entry for COVID – 19 infected person.
§ Capturing record of every movement within the premises.
§ Two-way confirmation/verification of visitors through video calling feature.
myIdea
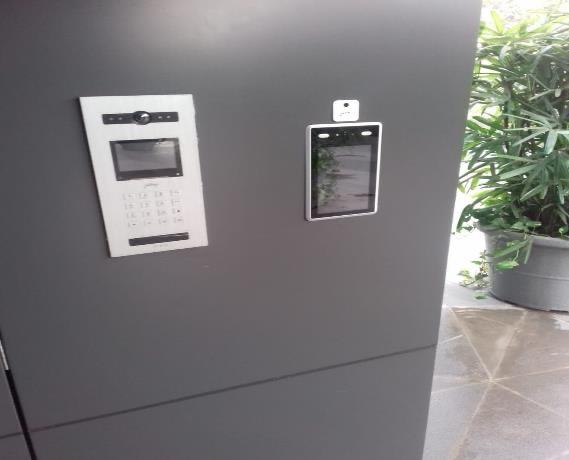
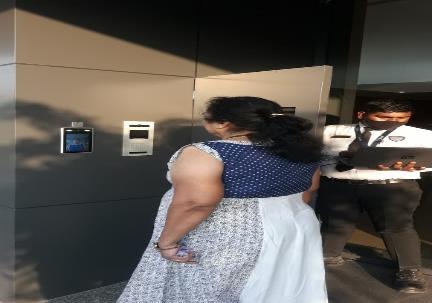

Description of the Innovation:
QR code reader for
Visitor Management
CHALLENGE
• Providing manual access to each visitors.
• One security personnel was to be deployed for providing the access.
• Contactless procedure for smooth entry and exits of visitors.
MYIDEA / INITIATIVE / SOLUTION BENEFITS / ADVANTAGE
• We installed a VMS system where in visitor is provided with link on his cellphone via SMS.
• Once visitor click on the link it provides him with a QR code which he needs to display in front of QR code scanner installed over flap barriers.
§ Smoother and faster visitor register and entry procedure.
§ As per COVID protocol a contactless entry and exit procedure is followed.
§ Easier technique to capture in time and out time of each visitor and maintained record for
myIdea
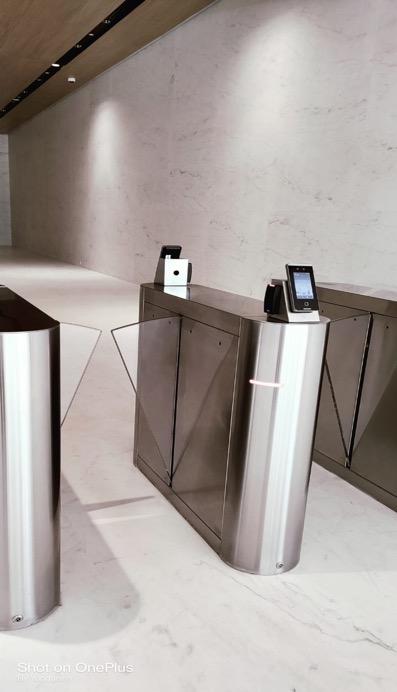
• During the exit he needs to display the QR code once again which enables his check in and check out time on the system.
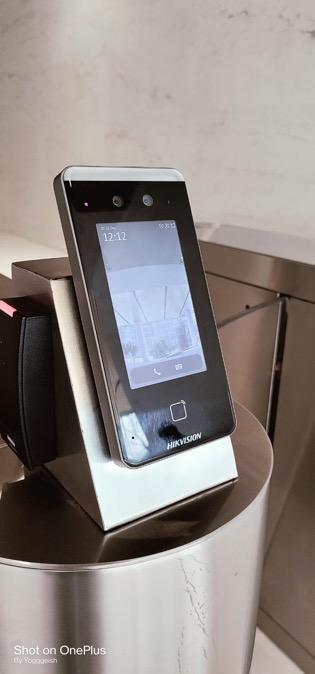
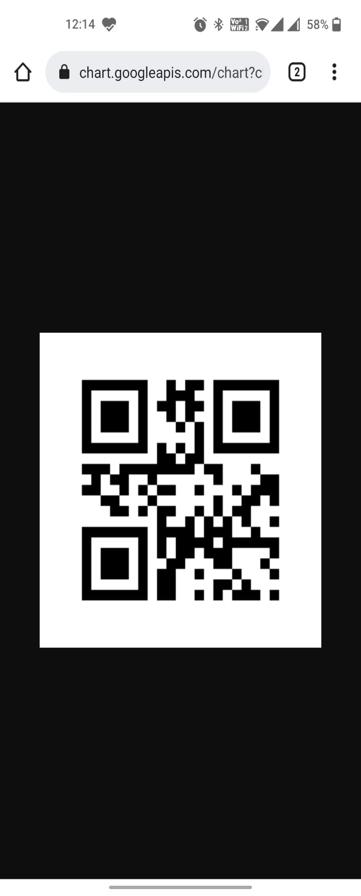
Saved the manpower deployment to operate
Description of the Innovation:
Enhanced Lift Safety with dedicated UPS Power
CHALLENGE
• The two Schindler elevators have ARD but it works only when there is total power failure and not during changeover situation.
• Entrapment issues in elevators during Power change over.
• Delay in addressing the issue causes panic .
• Senior citizens ,children's and ladies were afraid to use elevators as they felt unsafe.
MYIDEA / INITIATIVE / SOLUTION BENEFITS / ADVANTAGE
• Had discussion with OEM and advised them to put additional UPS connecting only Fans & Light of the elevators with minimum duration of 30 m
• Discussed the issue with higher officials , and as the issue was related to safety and security of the passenger, Schindler officials were convinced and did the work at their cost.
• Giving more importance to safety we have placed additional intercom inside the both the elevators and connected it to the building EPBAX..
§ Improved safety & security of the passengers.
§ Users gained confidence while travelling.
§ Post installation of separate UPS for Lights and Fans ,it will ensure uninterrupted power supply whenever any lift stalls.
§ Intercom connected with EPABX will provide ease to connect and will open more options for the passenger to reach for any help.
myIdea
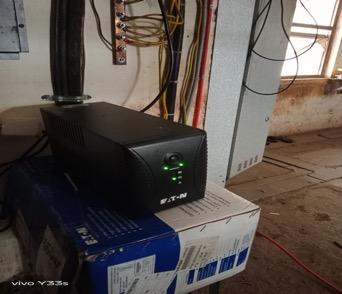
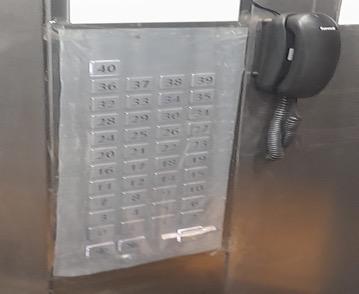
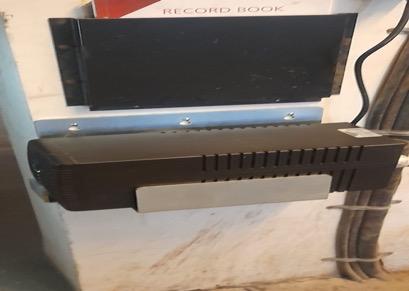
Description of the Innovation:
Upgradation of recreation area
CHALLENGE
• Gardens area Jogging track was completely worn out.
• Plants and lawn dried up, Residents were complaining about shabby look of garden, CBRE is maintaining since 2009. but now it was needed for complete refurbishment.
• During monsoon there was huge water logging at garden and extreme inconvenience for residents/children.
MYIDEA / INITIATIVE / SOLUTION BENEFITS / ADVANTAGE
• FM has initiated beautification and complete refurbishment of garden area..
• Hired the consultant and finalized the vendor with optimum negotiation and done the complete refurbishment of Track, placement of different type of play equipment's/ swimming pool upgradation/ entire foot ball area and parapet wall fabrication work etc.
§ Increased the value of properties.
§ Residents are happy and enhanced engagement at garden area.
§ Area are utilized for Playing game, up-graded kids play area, jogging track, volleyball court, football court, Cabana seating arrangement, upgraded swimming pool, garden with variety of flowers and plants, assigned a place for dog area etc. resident are appreciating a lot.
§ Enhanced User-experience
myIdea
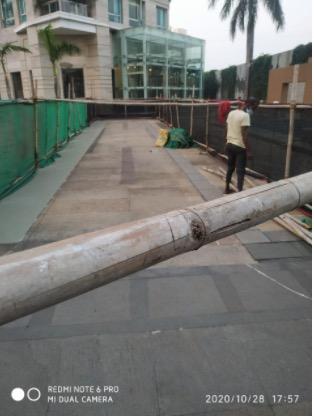
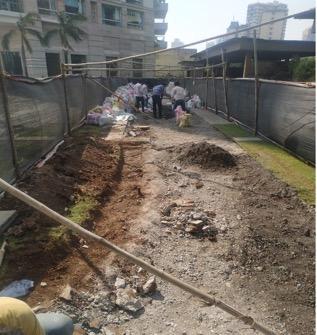
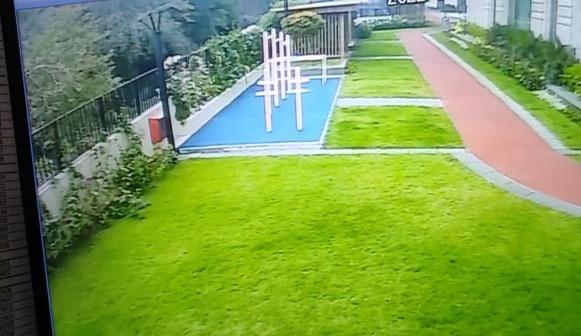
Description of the Innovation:
Lift Real Time Monitoring System
CHALLENGE
• There are 47 lifts of Schiendler make installed in 16 towers.
• Incase of a breakdown or any abnormality, the tower guards informs CBRE office to lodge complaint with OEM
• Chain of communication delays repair and tracking details of PPM, repairs gets difficult
MYIDEA / INITIATIVE / SOLUTION BENEFITS / ADVANTAGE
• Installation of a device called CUBE was discussed with Schiendlers and then approved by client for installation on all lifts.
• This device track operation, parameters, PMS and alarms on its own
• Installed in all 47 lifts successfully
• Worked closely with Vendor to achieve maximum value of the solution
§ Any sensor malfunctioning can be tracked anywhere on its app on phone/laptop
§ Generates service request automatically of breakdown/malfunction
§ Keep tracks of PPM history and the details
§ Easy to calculate downtime
§ Better safety and user experience
§ Better Client Satisfaction
myIdea
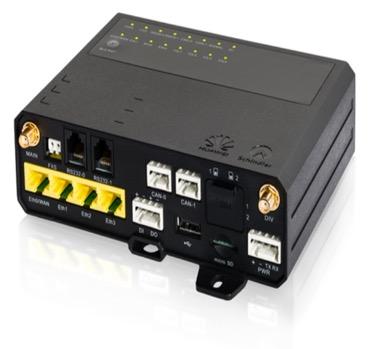
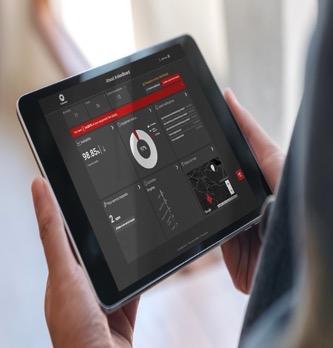
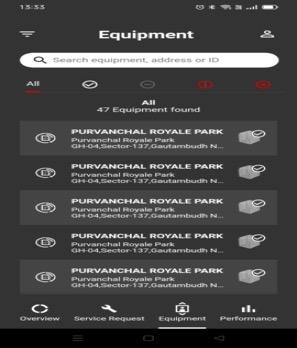
Description of the Innovation:
Breaker Trip
Indication
& Alarm
CHALLENGE
• Monitoring issue with the Air circuit breaker during faults/ Trip (Due to Over Voltage / short Circuit /Ground Faults Etc.)
• Clients are Facing issue of power Failure whereby technicians are not aware of the circuit breaker trip , Getting information from the clients about power failures of their floors due to circuit breaker trip.
MYIDEA / INITIATIVE / SOLUTION BENEFITS / ADVANTAGE
• Implemented a solution of monitoring mechanism on power failures due to circuit breaker trip / fault by providing below .
• Provided control circuit with indication lamps and alarm system when ever power failures due to circuit breaker trip.
• Technician can easily identify location of circuit breaker within seconds time and provide alternative source the client location with minimum timelines.
• Entire activity carried out by internal team with existing material available at stores.
§ Quick response from the team members
§ Client satisfaction
§ With this system we can easily identify which breaker has been tripped with location
§ We have both Audio & Visual system in place now , whereby there are no delay in addressing the fault occurred
§ Cost incurred : Approx. Rs 10,000
myIdea
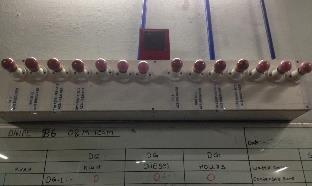
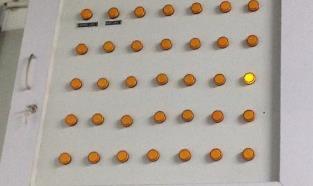
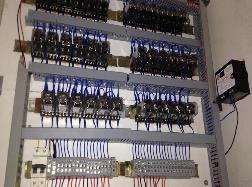
Description of the Innovation:
Water ATM
myIdea
CHALLENGE MYIDEA / INITIATIVE / SOLUTION BENEFITS / ADVANTAGE
• Get the drinking water from external resources at high cost.
• Water Quality not Maintained as per standards
• Water Bottles not Cleaned Properly
• Inconsistency of water supply Excess storage of drinking water
• Discussed with multiple vendors of Water ATM
• Finalized Trident vendor & from the listed water ATM Vendor
• Checked water Samples To ensure good quality water
• Ensure online water quality at any point of time .
• Identified a Place in our campus whereby supply of water to all the buildings is easy without any ergonomic issues
§ 24 * 7 Provision of Pure Drinking water available
§ Water Quality is being maintained as per standards
§ Accountability & Control of water availability & quality is maintained
§ Economical & Cost effective
§ Water is free from all kinds of germs , as it is treated by reverse osmosis process
§ Free From water borne Diseases
§ Reduces dependency on storage of packed Drinking water
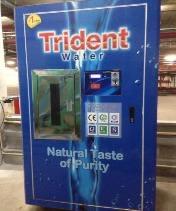
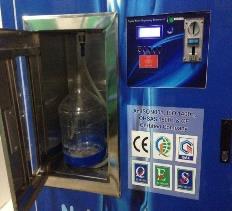
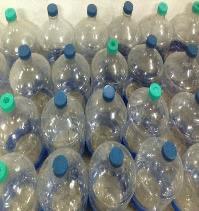
Description of the Innovation:
GAZEBO For Exotica Residents
myIdea
CHALLENGE
• No place for socializing
• Low user experience
• To meet Client’s expectation
• To create value and better the services
• A need for a sitting place within Exotica was felt and Client wanted CBRE team to do the research and look for a space where sitting area can be made, and just bare essential dry snacks and tea/coffee can be served.
MYIDEA
/ INITIATIVE / SOLUTION BENEFITS / ADVANTAGE
• CBRE team suggested the client to set up a Gazebo in B2-B3 park area.
• CBRE team contacted professional vendors to set up the Gazebo and we also contacted various cafes and kitchen owners who can open a small coffee lounge here for the Residents and serve them things at best cost.
• Gazebo was set up and coffee lounge was opened in association with CNA Kitchen. They serve only tea coffee and dry snacks at a very nominal cost. We don’t charge and rental for the same.
§ A place where residents can come sit do their work from home
§ Residents can come and have a cup of tea/coffee at a very nominal cost
§ Residents can come and spend time with their family and enjoy sunny morning
§ No rental is charged thus items rates are very low.
§ Client satisfaction and appreciation.
§ To reduce mental stress

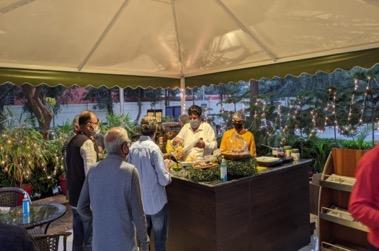

CHALLENGE MYIDEA / INITIATIVE / SOLUTION BENEFITS / ADVANTAGE
• Manual Visitor Management system
Description of the Innovation:
Apna Complex Digitalization
myIdea
• Implemented Apna complex for digitalization.
• Delayed confirmation from client related to vendor

• Through Apna complex app we give awareness to client about any emergency situations like Electricity and in society. any function or activity, we put all notices in same platform.
Give single platform all services like to pay maintenance dues/raise complaints/visitor management.
§ Easy to track complaint status.
§ Communication gets easy with residents.
§ Easy to communicate and notices with client at a short time.
§ It helps security to give access to guest and visitor in the premises on help of feature allow/reject
§ Resident gives feedback of our services on complaints and resolution addressed efficiently
§ Greets residents on festival and special occasion.
§ Residents get auto attendance for maid/drivers.
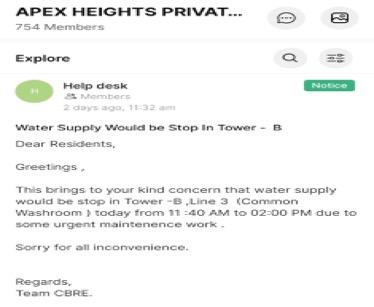
Description of the Innovation:
Maximum Demand Controller
CHALLENGE
• We have Two HT connections (Power) for entire Society.
• MD (Maximum Demand) for each HT Power connection is 150 KVA.
• MD was not sufficient due to electrical load are on higher side in the building.
• No alert in the BMS if there is increase MD.
• While Switching ON Fire Hydrant pumps MD use to cross the limit.
• Had to pay Penalty for crossing the MD limit
MYIDEA / INITIATIVE / SOLUTION BENEFITS / ADVANTAGE
• Had discussion with multiple vendors and selected specifically designed ABB Breakers to preserve the existing frameworks.
• We are paying a penalty regularly whenever MD use to cross the limit which has become a regular issue.
• Planned scheduling and implementation with minimum downtime.
• Decided to install MD controller within the existing panels with minor modifications.
§ Installed Buzzers to incoming panel in the electrical room.
§ Low investment costs.
§ Shorter time for installation.
§ Minimum shutdown for Installation.
§ Cost reduction of maintenance and repairing.
§ After Installation of Demand controller, whenever MD is crossing the limit, with the buzzer, Maintenance staff is able to keep the MD in control.
myIdea

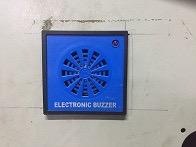
Description of the Innovation:
Automated Grocery Store
CHALLENGE MYIDEA / INITIATIVE / SOLUTION BENEFITS / ADVANTAGE
• Grocery shop which is generally closed 1:00 PM to 5PM.
• Our residents used to face issue to buy the grocery.
• Also, they have no option to check catalogue availability.
• We contacted several grocery store vendors and reviewed their services.
• After reviewing the services, we finalized Gobbly grocery store.
• Most of the vendors did not agree to pay electricity and rent charges.
• While Gobbly agreed to pay both the charges..
• So, launched the Gobbly No Contact grocery store on the site.
§ Now our residents can buy groceries 24*7
§ Residents can find out availability of stock through the mobile app.
§ Gobbly store supports cashless transition. So, no need to carry cash.
§ Gobbly provides Eco friendly Joot bags without any charge. So, no need carry bag to buy the grocery
§ We are generating the revenue Rs 3600 per month from Gobbly
myIdea



Description of the Innovation:
Day light sensors for lighting control
CHALLENGE
• Existing system operate all lights 24 x 7, irrespective of natural light.
• Common area power consumption is high.
• Manual Controlling of individual light is difficult.
• Additional man hours required to control the individual light
• Escalations and suggestions received on lights to switch off when there is a natural light.
• Life of Lights reduced.
MYIDEA / INITIATIVE / SOLUTION BENEFITS / ADVANTAGE
• Identified unwanted lights in daytime.
• Manual controlled the unwanted lights in daytime.
• Planned for circuit separation but cable costing is more.
• Installed Day light sensors in open areas at parking floors to control the lights when there is a natural light.
• Now lights are getting Automatically off when there is a natural light and getting ON when it is dark.
§ Power consumption because of unwanted lights will be reduced.
§ By switching OFF unwanted lights in daytime will increase the fixture life.
§ Day lights sensor cost is low, and installation of this sensor is simple.
§ ROI will get within six months from the installation.
§ Escalation from clients on unwanted lights got reduced.
§ Manhours for lights switching ON/OFF is saved.

myIdea
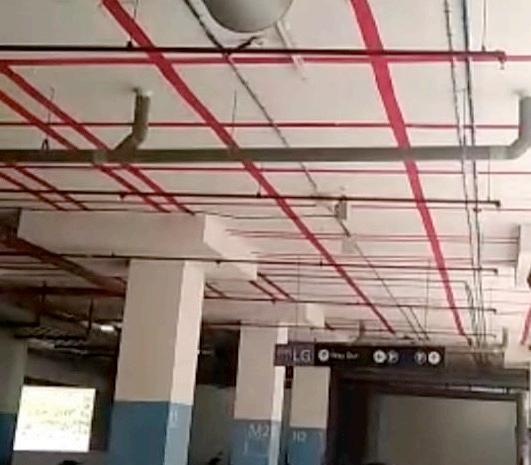
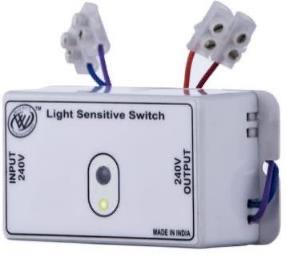
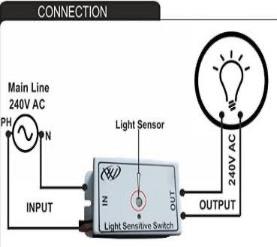
Description of the Innovation:
Security Learning Centre
CHALLENGE
• Being in the building security, each guarding staff should know about the building topology floor wise tenants' occupation and their role & responsibility thoroughly before deploying them to security posts.
• During 2 days induction, to make them understand all things is a major challenge.
• Because of the above, we faced operational issues and undue escalations from the tenants.
MYIDEA / INITIATIVE / SOLUTION BENEFITS / ADVANTAGE
• We discussed among the team and our senior leadership to frame a plan.
• Created Building miniature with occupant details & building escalation matrix.
• Display board with breif on roles & responsibilities, utility areas, parking details, OPLs, grooming standards with pictorial presentation with multi language.
• Security diagram with display of equipment generally used by security.
• To avoid extra expendire, use the waste materials like cardboards /plies lying at scrap yard.
§ Now the team can easly understand about the building, it’s escalation matrix, tenant details and duties & responsibilities.
§ The pictorial presentation with multi language (Hindi & Telugu) is easing their understanding.
§ All the above thing in one room, give a glance of basic things related to the campus.
§ This is helping the staff to perfrom better, with client satisfaction.
myIdea
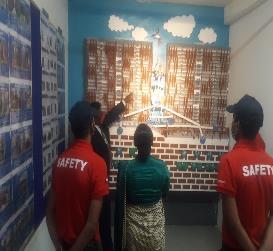
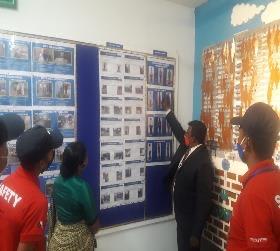
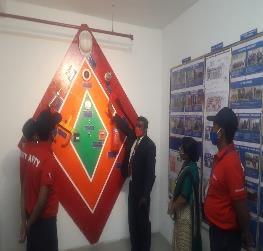