Vertical centrifugal immersible pumps
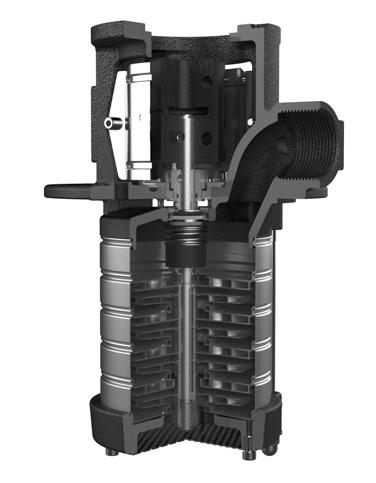
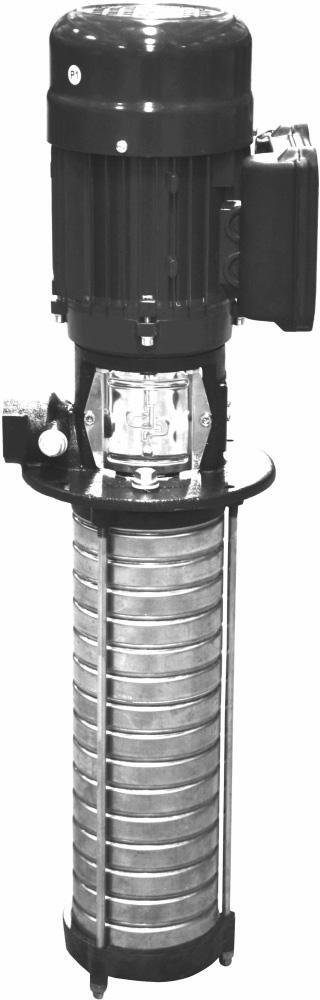
Technical specification booklet
series: DPVCI 2 - 4 - 6 - 10 - 15 50Hz / 60Hz (DIN/IEC)
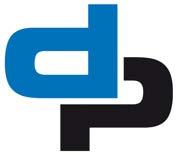
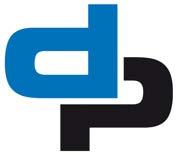
Technical specification booklet
series: DPVCI 2 - 4 - 6 - 10 - 15 50Hz / 60Hz (DIN/IEC)
The vertical, single or multistage centrifugal immersible pump series is designed for pumping water, filtered cooling fluids or lightly aggressive, watery mediums from a storage tank. The suction side at the bottom of the pump is equipped with a stainless steel strainer. The discharge side is located at the motor stool.
Where the required duty point corresponds with the amount of stages, in some applications the immersible length has to diver from this. Therefor it is possible for the DPVCI range to use empty stages to create the required length. In that case the impellers are mounted in the casings closest to the suction casing.
The hydraulic assembly is driven by an electric motor. All hydraulic parts of the pump are made of stainless steel.
Table 1: Model key Example DPVCI 10/8(18) B
During centrifugal operation of the pump an negative pressure is created at the inlet of the first impeller. This negative pressure enables the medium to enter the pump at the suction connection at the bottom of the pump. Every impeller is placed in a stage casing. The passage of this stage determines the capacity of the pump. The diameter of the stages is related to the centrifugal forces and its “stage pressure”: the more stages, the more pressure.
This total capacity and raised pressure will be guided to the outside of the pump at the motor stool.
The pump is provided with plugs for measuring and venting, both located at the pump outlet connection. These connections are meant to vent the pump system when the pump is not in operation or to measure the discharge pressure of the pump using a G 1/4 connection. Also on the motor stool two connections are available to vent the storage tank.
The working range is depending on the application and the combination of pressure and temperature. For specific and detailed limits please consult the working ranges as described in the paragraph 1.8. The overall working range of the pumps can be summarised as follows:
Table 2: Specification of the working range
1.If the ambient temperature exceeds the above value or the motor is located more than 1000 m above sea level, please see 1.5.3
2.Deviation in viscosity and/or density could require an adapted motor power. Please contact your supplier for more detailed advice.
3.The free space above the motor cooling fan must be at least 1/4 of the diameter of the inlet of the cooling fan in order to have a sufficient flow of (cooling) air.
4.Pumps that are intended for 50 Hz operation, may not be connected to 60 Hz power supply.
For minimum capacity at medium temperature of 20 oC, see table 3: for higher temperatures, see table 4 .
A minimum capacity has to be secured to prevent the pump from overheating, gathering gas, cavitation etc. The minimum capacity corresponds to all percentage of the optimum flow Qopt in relation to the temperature of the liquid pumped. Also a minimum medium level needs to be taken into consideration.
For ambient fluid conditions the minimum fluid level for the pumps in the storage tank is mentioned at the dimensions pages. In case of an increased required vapour pressure for fluids at higher operation temperatures, a system analyses is recommended to determine the required NPSH to avoid cavitation and air enclosure inside the pump.
If the ambient temperature exceeds the maximum allowed value, or if the motor is located more than 1000 m above sea level, the motor cooling is less effective and could require an adapted motor power. See below table for the change in power output or contact your supplier for more detailed advice.
Table 6: Basic material variants
* see medium handled list for correct seal material
Medium lubricated stage bearing Tungsten Carbide against Ceramic
To suit almost every application the pump is assembled out of modules which can be selected depending on the required working range.
Basic modules are:
• Basic pump model, which defines the capacity, pressure and basic material. Temperature range -20 up to 120 oC
• Total stages, which defines the length of the pump suitable for the storage tank.
• Sealing, which define the elastomers and the mechanical seal. A cartridge seal construction is equipped as default. Temperature and pressure range, see chapter 4.1
• Electric motor, which defines all requirements of the motor such as motor size, power, voltage, frequency and all possible motor accessories.
For assembling the total amount of stages to the motor stool an additional upper stage casing is required. Therefor when all visible stage stages are counted from the hydraulics, the sum will be the total amount of stages added by 1.
CE Conformity with European Safety Directive
The performance diagrams give a global overview of all the pump models the shaded models are mentioned in this documentation. Detailed characteristics are given for each model showing the hydraulic efficiency, NPSHreq, and shaft power as well.
The performance of the pump depends on the number of stages. As per example:
DPVCI 4/20(18) B:series 420 stages with 18 full head impellers
The detailed performance curves are in accordance with ISO 9906:2012 (Grade 3B).
The pumps van be configured with multiple types of motors. Therefore the performance data, like Q/H, efficiency and shaft power used for published curves are converted to the average speed per motor power. To refine this data the published data has to be corrected accordingly.
The characteristics given are based on:
• De-aerated water at a temperature of 20 °C
• Density of 1,0 kg/dm3
• Kinematical viscosity of 1 mm2/s (1 cst)
Per January 1st 2015 for multistage pumps (reference 50Hz and 2 poles) a new Commission Regulation (EU) No547/2012 as part of the Directive 2009/125/EC is mandatory.
According to this the pumps need to apply to a new Minimum Efficiency Index (MEI). This value is set to be >= 0.40
For the design version 2 - 10B, 15C immersible pump range the following values are applicable:
Table 7: Minimum efficiency index
The minimum frequency of the DP motor should be limited to 30 Hz to ensure sufficient cooling. When the rotational speed exceeds the nominal speed of the motor, make sure that the power output of the motor is suitable to drive the corresponding pump model.
The performance of the pump differs from the fixed speed performance according to the recalculation scheme.
To find the required hydraulic information from the published curves, it is important to know the application in which the pump has to be installed. There are two main distinction to be made:
AFlow determined (like booster sets and cleaning) Opening taps
BPressure determined (like boiler feed and reverse osmosis systems) Facing counter pressure.
Pump size / no of stages. Installed motor power Capacity @ Pressure
NPSH (m)
Hydraulic efficiency (%)
Required power (P2)
O Calculated duty point
Actual hydraulic performance
A Flow determined
B Pressure determined
To determine the correct length of the pump see both following explanation and table.
length incl. motor length excl. motor
Full stage pumpF1 F2
Pump with empty stagesF3 + F4 F3 + F4 -LB
The length F3 corresponds with the length of the applied motor power. F4 corresponds with the total number of stages. Example: 2/16(30) F3=396mm, F4=732mm.
Table 8: General dimensions
*including packing
To determine the correct length of the pump see both following explanation and table.
length incl. motor length excl. motor
Full stage pumpF1 F2
Pump with empty stagesF3 + F4 F3 + F4 -LB
The length F3 corresponds with the length of the applied motor power. F4 corresponds with the total number of stages. Example: 4/16(22) F3=442mm, F4=560mm.
*including packing
To determine the correct length of the pump see both following explanation and table.
length incl. motor length excl. motor
Full stage pumpF1 F2
Pump with empty stagesF3 + F4 F3 + F4 -LB
The length F3 corresponds with the length of the applied motor power. F4 corresponds with the total number of stages. Example: 6/12(26) F3=442mm, F4=740mm.
Table 10: General dimensions
*including packing
To determine the correct length of the pump see both following explanation and table.
length incl. motor length excl. motor
Full stage pumpF1 F2
Pump with empty stagesF3 + F4 F3 + F4 -LB
The length F3 corresponds with the length of the applied motor power. F4 corresponds with the total number of stages. Example: 10/8(13) F3=455mm, F4=445mm.
Table 11: General dimensions
*Decreased motor power: Qmax = 19 m³/h
**Power input based on a V 15/3 C of this hydraulic speed design
To determine the correct length of the pump see both following explanation and table.
length incl. motor length excl. motor
Full stage pumpF1 F2
Pump with empty stagesF3 + F4 F3 + F4 -LB
The length F3 corresponds with the length of the applied motor power. F4 corresponds with the total number of stages. Example: 15/3(15) F3=445mm, F4=498mm.
Table 12: General dimensions
*including packing
1.Decreased power
To determine the correct length of the pump see both following explanation and table.
length incl. motor length excl. motor
Full stage pumpF1 F2
Pump with empty stagesF3 + F4 F3 + F4 -LB
The length F3 corresponds with the length of the applied motor power. F4 corresponds with the total number of stages. Example: 2/3(22) F3=315mm, F4=560mm.
Table 13: General dimensions
*including packing
To determine the correct length of the pump see both following explanation and table.
length incl. motor length excl. motor
Full stage pumpF1 F2
Pump with empty stagesF3 + F4 F3 + F4 -LB
The length F3 corresponds with the length of the applied motor power. F4 corresponds with the total number of stages. Example: 4/7(16) F3=396mm, F4=431mm.
Table 14: General dimensions
*including packing
To determine the correct length of the pump see both following explanation and table.
length incl. motor length excl. motor
Full stage pumpF1 F2
Pump with empty stagesF3 + F4 F3 + F4 -LB
The length F3 corresponds with the length of the applied motor power. F4 corresponds with the total number of stages. Example: 6/2(18) F3=340mm, F4=540mm.
Table 15: General dimensions
*including packing
To determine the correct length of the pump see both following explanation and table.
length incl. motor length excl. motor
Full stage pumpF1
Pump with empty stagesF3 + F4
The length F3 corresponds with the length of the applied motor power. F4 corresponds with the total number of stages. Example: 10/1(6) F3=343mm, F4=287mm.
Table 16: General dimensions
To determine the correct length of the pump see both following explanation and table.
length incl. motor length excl. motor
Full stage pumpF1 F2
Pump with empty stagesF3 + F4 F3 + F4 -LB
The length F3 corresponds with the length of the applied motor power. F4 corresponds with the total number of stages. Example: 15/4(11) F3=587mm, F4=392mm.
Table 17: General dimensions
*including packing
Table 18: Seal code, dimensions according EN24960
Q1 E GG11Ca / SiC / EPDM *EPDM
Q1 V GG12Ca / SiC / FPM FPM
B E GG13SiC / Ca / EPDM EPDM WRAS / ACS-20 - 10025
B V GG14SiC / Ca / FPM FPM
U3 X4 GG15TuC / TuC / HNBRHNBR
U3 V GG16TuC / TuC / FPMFPM
B E GG18TuC / Ca / EPDMEPDM 559236-20 - 120 (140)25 (16)
B E GG23SiC / Ca / EPDM EPDM
MG-G606Q1 Q1 V GG24SiC / SiC /FPMFPM
Q1 X4 GG28SiC / SiC/ HNBRHNBR
Q1 E GG29SiC / SiC / EPDM EPDM
*default seal type, code depends on max pump pressure
12010
The standard DPmotors are produced conform the latest technical design, and comply with the international standards and EU directives regarding safety measures.
The motors can be specified as:
• Standard IE3 >= 0,75kW
• T.E.F.C. (totally enclosed fan cooled) Squirrel cage.
• AC induction motor.
• Protection IP55.
• Insulation class F.
• Temperature rise class B.
• Duty class S3 (50% or S4 (40%), maximum starts per hour, see motor tables).
• Noise levels conform IEC 60034-9.
• >= 3,0 kW default 3 x PTC.
The motors come in 2 different configurations depending on power rate. Up to 4kW a V18 mounting type is used. For power 5,5kW and up a flanged motor type V1 is default. Mounting in acc. with IEC60034-7 and dimensions in acc. with IEC 60072-1
• Standard motors as per above, in single phase (1x230V)upto and including 2,2kW.
• Provided with 10 pole industrial connector “Harting stecker” HAN 10, mounted in stead of the motor connection box, <= 7,5kW.
• Provided with Rain cover on top of the fan hood.
• For motors < 3kW provided with 3 x PTC and/or anti condensation heater (1x230V).
• Motors from other manufacturers like Siemens and VEM.
581xM20x1.5300
37161510303230/4009.6/5.57.60.91+25%/-10%349587.5 612xM20x1.5300
37161520303400/6905.6/3.27.60.91+25%.-10%349587.5612xM20x1.5300
37161510404230/40012.5/7.280.92+25%/-10%351588.5622xM20x1.5300
37161520404400/6907.2/4.280.92+25%/-10%351588.5 622xM20x1.5300
37161510555.5230/40017/9.87.80.93+25%.-10%352588.5672xM25x1.5300
37161520555.5400/6909.8/5.67.80.93+25%/-10%352588.5672xM25x1.5300
1.Note: The indication of the material designations to ASTM / AISI is not binding
1.Note: The indication of the material designations to ASTM / AISI is not binding
P.O. Box 28
2400 AA Alphen aan den Rijn
The Netherlands
t +31 172 48 83 88
www.dp.nl
05/2023
Original instructions
97004475 F
Subject to modifications. Digital alteration, publication or distribution of the content of this document without prior notice is strictly prohibited. Permission for use, copying and distribution of this document as published by DP-Pumps is granted on the condition that no part of the document is used for information or commercial purposes outside of the DP-Pumps organisation or one of its recognised dealerships.