
6 minute read
AUMUND India rebuilds the world’s tallest belt bucket elevator of 175.3m
Suspended system for testing.
Cleveland Cascades’ production of three vehicle loading cascade systems to be used for loading petcoke is coming to a close following FAT inspection by the client. These consist of a 900-sized system for loading at rates up to 450tph (tonnes per hour), with two further identical 1100 systems for higher rates reaching up to 880tph throughput.
Each design is similar with respect to the setup of the system. A fixed head chute is utilized featuring cascading cones for material control to protect from degradation and dust generation, the cones are enclosed by a shroud encapsulating
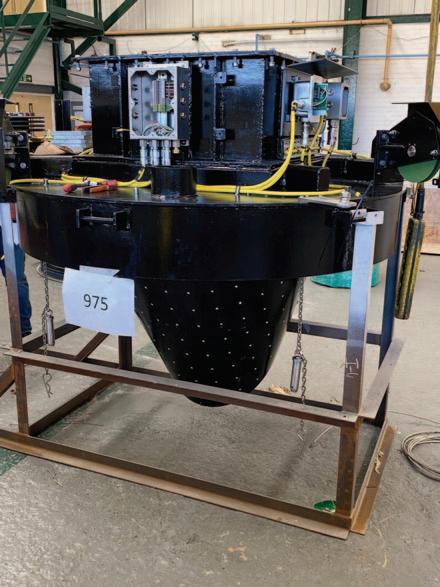
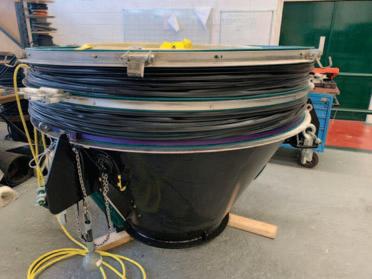
dust laden air preventing its escape to the surrounding environ ment. Finally, a skirt is installed at the chute outlet point creating a seal with the material pile during loading operations.
The 900-sized system has a fully extended length of 5.61m and achieves a retracted nonoperational height of 2.5m For the 1100-sized system, the fully extended length is 6.05m and allows full retraction to 3.0m.
Ceramic tiling is the wear liner of choice within the head chute and cones. This provides Head chute. sufficient abrasion resistance without impeding material flow and gives increased longevity to the wear surfaces.
With the material to be loaded being pet coke, a complex wiring and electrical specification had to be adhered to. The hazardous area classification for the chutes was specified as NEC Class II Div 1, Group F. With this in mind, all electrical components had to be sourced such that they are suitable for operation within the potentially explosive environment.
The pictures show the systems in Cleveland Cascades’ workshops. This is where all pre-installation and any pre-commissioning checks such as trial fits of components take place. Carrier with cones and skirt. Carrier with shroud.
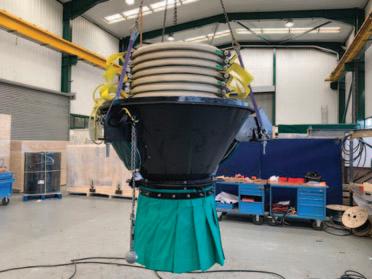
RELIABLE INTERNATIONAL TRADE - OIML CLASS 0.2 (+/- 0.1%)

Features
High precision fully suspended weigh frame
Direct force measurement (no lever arms, pivots or bearings)
Strong rigid beams
Low deflection design 4 load cells 3 or more idler weigh length
Extended Idler Spacing for improved performance
Close Spaced Roller Rack (CSRR) for reduced belt sag and reduced belt dynamic effects (Protected by International Patents)
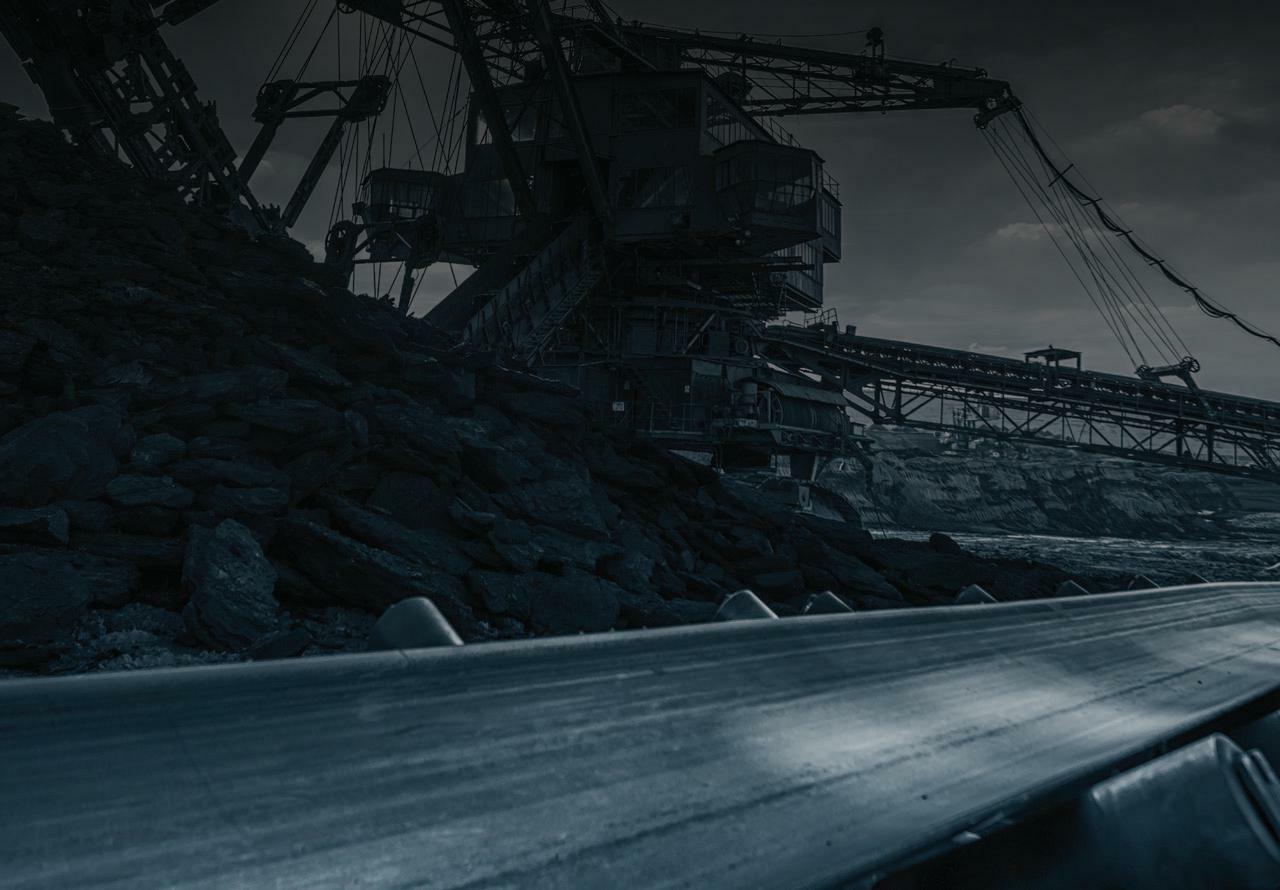
E: sales@controlsystems.com.au T: +61 1 300 784 449
+ Subscribe to Newsletter
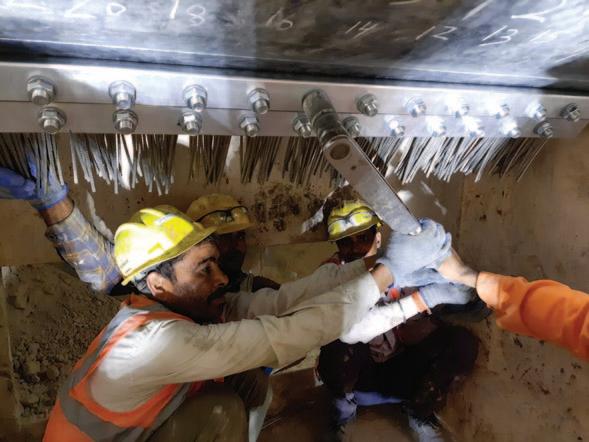
ACC Cement Ltd (Holcim Group) has commissioned AUMUND Engineering Pvt Ltd, Chennai/India, with the refurbishment of the tallest belt bucket elevator in the world, which is 175.3m high. The elevator is installed at Wadi Cement, one of the largest and most modern cement plants in India, for raw meal preheater transport at a continuous rate of 600tph (tonnes per hour). The project is an excellent example of the AUMUND Group rebuild and refurbishment service.
Whilst the machine at Wadi Cement in the Indian state of Karnataka remained in service, a detailed inspection revealed that complete overhauling would soon be required and the company decided to invite bids for the supply and supervision of installation of the necessary components on a time bound schedule preventative maintenance. After due deliberation and looking at performance of various elevators operating at their plant, Holcim decided to award the contract to AUMUND.
Originally, the machine was fitted with a steel cord belt of width 1,320mm and tension rating of 3,150N/mm. After passing the application data through sophisticated computerized selection programme, AUMUND decided to offer an alternative based on its own design concept resulting in a belt width of 1,300mm but with higher tension rating of 4,000N/mm with a bucket size of 1,250mm at bucket spacing of 450mm.
IMPROVED DIRECTIONAL STABILITY AND BETTER TRACKING OF BELT The AUMUND belt concept envisage continuous close pitch longitudinal ropes without rope free bucket mounting spaces but with additional wire ropes running laterally across the width of the belt adding considerable lateral stiffness without significantly changing the belt longitudinal flexibility. This cross-stabilized construction gives improved stability to the belt with improved bucket fixing. This help to avoid the most common cause of elevator failure, which happens at the area of bucket fixing. AUMUND design impart improved directional stability and better tracking of belt.
To make the necessary belt punching, AUMUND has developed a special punching machine design which gives clean fixing holes accurately aligned relative to the belt edge and at precisely the correct pitch. The belt is held in a cassette and advanced automatically under the punching frame using a precision encoder to measure the pitch. The belts are prepared at the AUMUND production in Rheinberg, Germany, and shipped to site at the exact required dimensions including a prepared joint and the required clamping connection.
In addition to the new belt the elevator will be fitted with new drive pulley including friction linings and rubber bucket mounting strips. The casings, inlet and outlet plus the complete drive unit remain unchanged.
AUMUND CONVERSION AND REPLACEMENT SERVICE The conversion or replacement of existing AUMUND conveying equipment, as well as non-AUMUND equipment has been an integral part of the technological expertise of the AUMUND Group for more than 30 years. AUMUND offers the service across the equipment range including belt and chain elevators, pan and bucket conveyors plus plate feeders. A refurbished machine can be supplied with all new moving parts by AUMUND retaining often only the structural elements resulting in a new machine with typically a substantial cost reduction compared to outright replace ment. With minimum changes to the structural parts and chute works installat ion time is significantly reduced and machines may generally be upgraded to the AUMUND standard during a scheduled stoppage. Of course once upgraded in this way the client can expect the usual AUMUND dependability and access to service support and genuine AUMUND spare parts. At the same time AUMUND can offer the possibility of plant capacity improvement with minimum investment.
ABOUT THE AUMUND GROUP The AUMUND Group is active worldwide. The conveying and storage specialists have special expertise at their disposal when dealing with bulk materials. With their high degree of individuality, both its technically sophisticated as well as innovative products have contributed to the AUMUND Group today being a market leader in many areas of conveying and storage technology. The manufacturing companies AUMUND Fördertechnik GmbH (Rheinberg, Germany), SCHADE Lagertechnik GmbH (Gelsenkirchen, Germany), SAMSON Materials Handling Ltd (Ely, Great Britain), TILEMANN GmbH Chains & Components (Essen, Germany) as well as AUMUND Group Field Service GmbH and AUMUND Logistic GmbH (Rheinberg, Germany) are consolidated under the umbrella of the AUMUND Group. The global conveying and storage technology business is spearheaded through a total of 19 locations in Asia, Europe, North and South America and a total of five warehouses in Germany, USA, Brazil, Hong Kong and Saudi Arabia.
Torque tightening of clamping connection nuts and belt clamping finished (photos AUMUND).
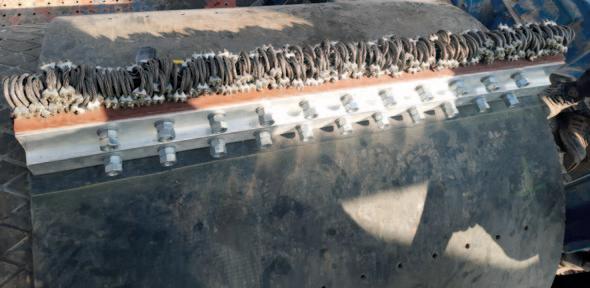