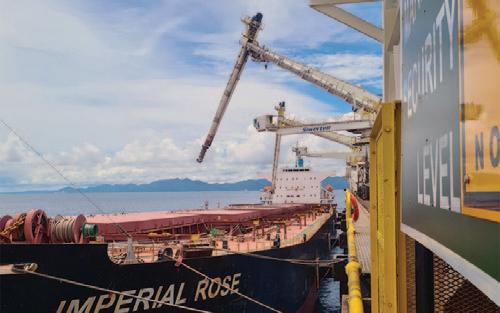
21 minute read
HOLD ON TIGHT: GRAB MANUFACTURERS IN THE SPOTLIGHT
Bruks Siwertell has commis sioned a new Siwertell ST 790 D-type ship-unloader to serve Quezon Power Ltd Co’s San Buenaventura power plant in Mauban, the Philippines. The newly built 500MW coal-fired facility is the country’s first supercritical power station and is located next to an existing Quezon power plant. The operator’s energy output has now doubled, requiring an equivalent doubling of coal intake to around three million metric tonnes a year.
The new and the old power plants use the same import jetty. It is now home to two rail-travelling Siwertell ST 790 D-type unloaders, which share the existing rails and jetty belt conveyors. The first Siwertell ship unloader was delivered in 1998 and has been in operation for almost 25 years.
“The jetty has significant weight restrictions, making the Siwertell unloader a stand-out choice for this installation,” says Per Wahlström, Project Manager, Bruks Siwertell. “Its high capacity to weight ratio was likely to have made it the only equipment with sufficient capabilities that could be installed.”
Environmental protection is also a major priority for Quezon, and any coal spillage is not permitted. Siwertell screwtype ship-unloaders are one of most efficient and environment-friendly types of unloaders on the market. They deliver totally enclosed dry bulk material handling, eliminating spillage and dust emissions, and also ensure long-term value from high jetty utilization rates, reliability and the long service life of wear parts.
“Quezon knows that our machines deliver excellent operational and environmental credentials,” notes Wahlström. “The company’s satisfaction with its existing unloader certainly played a part in it ordering a second one. “Delivery and commissioning went well and the unloader was successfully put into operation, along with operator training,” he adds. “The capacity requirements have also been met.” Both Siwertell screw-type ship unloaders have a continuous rated capacity of 1,400tph (tonnes per hour) and are able to discharge vessels up to Panamax size. The latest unit was delivered, fully assembled via heavy-lift ship, to the site in early 2022.
ABOUT BRUKS SIWERTELL Bruks Siwertell is a major supplier of dry bulk handling and wood processing systems. The company designs, produces and delivers systems for loading, unloading, conveying, storing, and stacking and reclaiming dry bulk materials, alongside equipment for chipping, screening, milling and processing wood for the biofuel, board, saw mill, pulp and paper industries. All equipment is designed to ensure environmentally friendly and efficient operations.
On-belt Real Time Coal Analysers
Saving you coal blending, sorting and monitoring headaches!
Ash, Specific Energy, Sulphur Moisture Over 1,000 installations worldwide Accurate and reliable results Low maintenance, remote support Serviced by local engineers Guaranteed performance
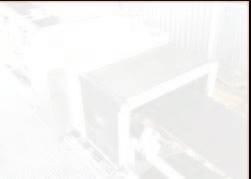
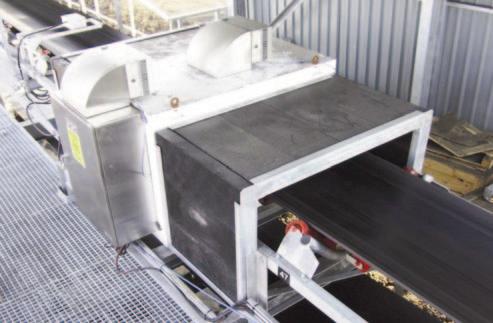
Making your process control easy
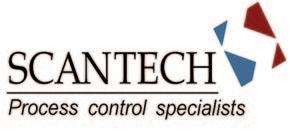
+61 7 3710 8400 sales@scantech.com.au www.scantech.com.au

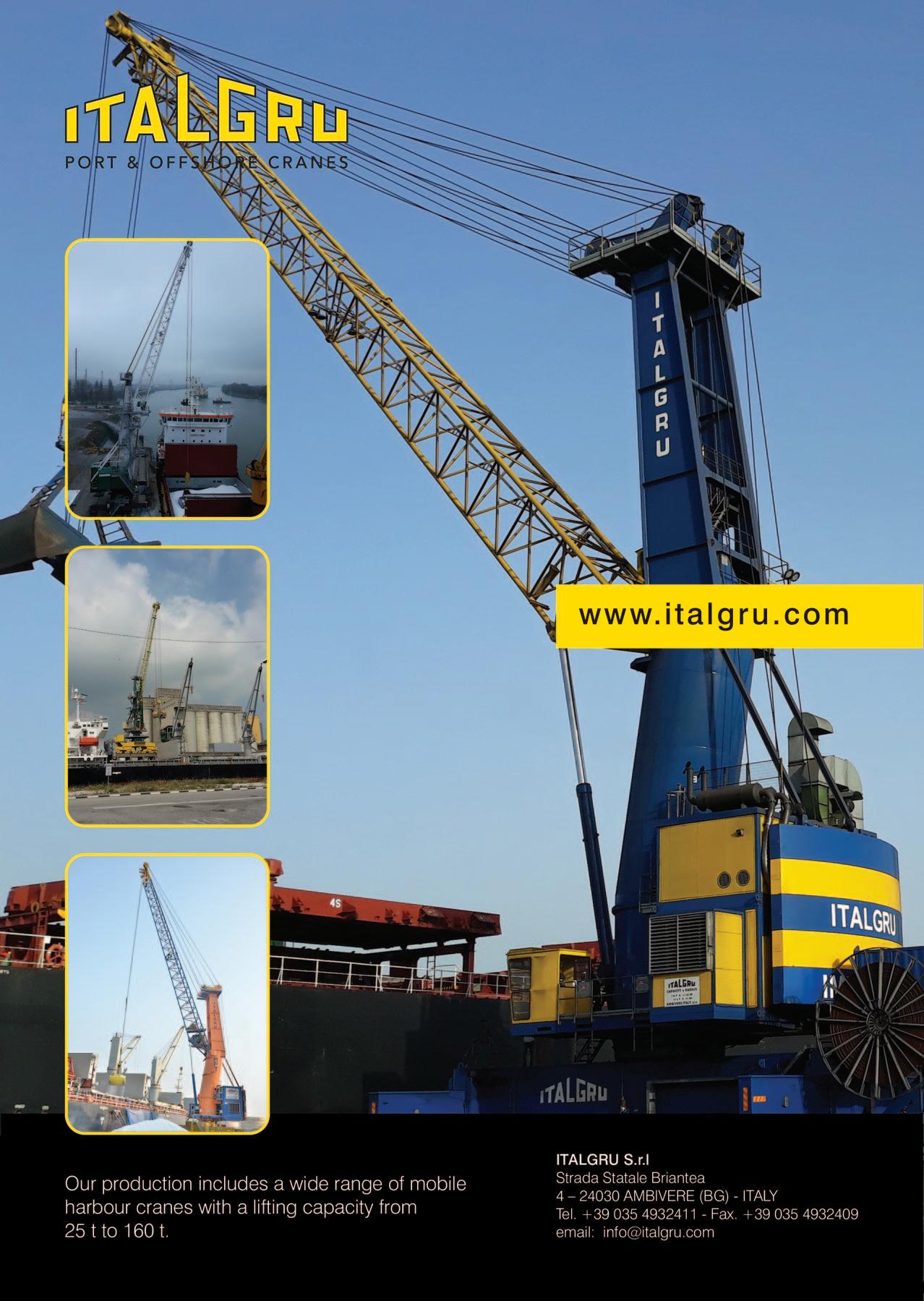
Hold on tight
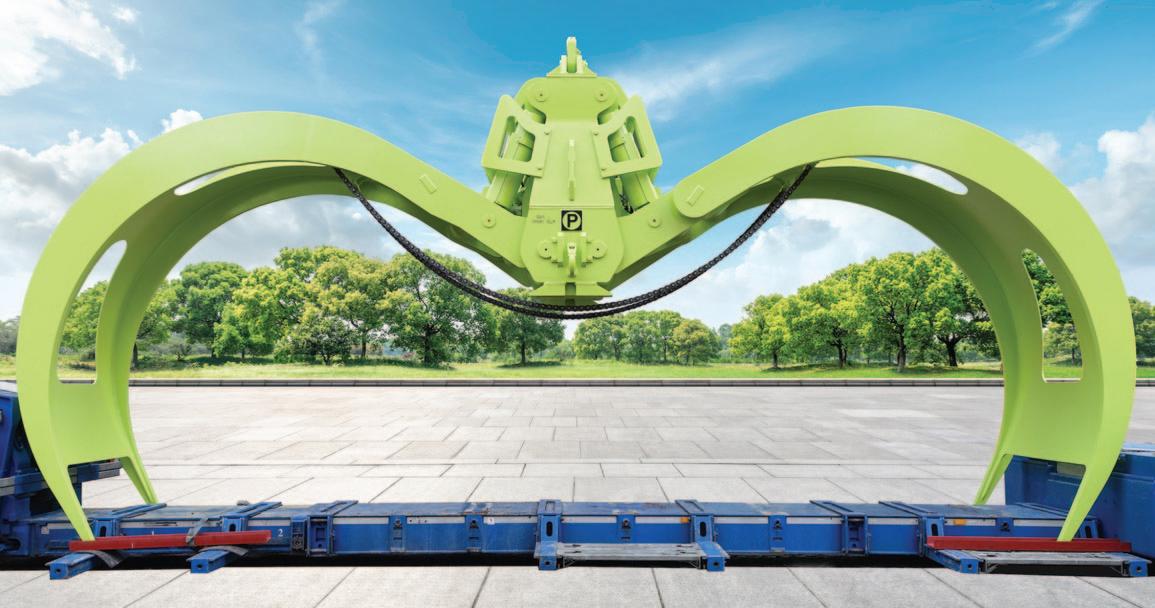
Grab manufacturers in the spotlight
PEINER SMAG sends largest log grabs ever built to New Zealand
Jay Venter

LOG HANDLING IN NEW DIMENSIONS The world’s largest timber grabs have recently made their way to New Zealand.
Three motor timber grabs of type MHG 12500-4 left PEINER SMAG Lifting Technologies GmbH in Salzgitter, Germany, for a long voyage to the destination port. These are the largest log grabs ever built and are unique in the world. They will be used in the ISO port operations in New Zealand.
Each grab is nine metres long, by 1.8 metres wide with a height of over four metres. Weighing 11,000kg each, they have a lifting capacity of 51,000kg, a tongs cross section area of 12.5m2 and a safe working load of 40,000kg.
“Building these world-first, marketleading grabs demonstrates our ongoing commitment to guarantee a safe and efficient operation in timber handling in ports and other environments”, comments Domenic Martinez, Sales Manager of PEINER SMAG.
The giant motor timber grabs (MHG 12500-4) were developed for Liebherr’s mobile harbour crane type LHM 550, a world-first in terms of size and capacity, and are predominantly used for the loading of logs for export. The technology allows to load without the use of ships’ cranes and this enables the operator to handle cargo for a wider range of vessels.
Back in 2021, PEINER SMAG had delivered a number of slightly smaller, but still huge timber grabs with a tong section of up to 8.5m2 to the port of Mount Maunganui in New Zealand. These powerful grabs were so convincing that Liebherr ordered even larger PEINER The world’s largest motor timber grab MHG 12500-4 loaded at PEINER SMAG’s factory for the long journey to New Zealand.
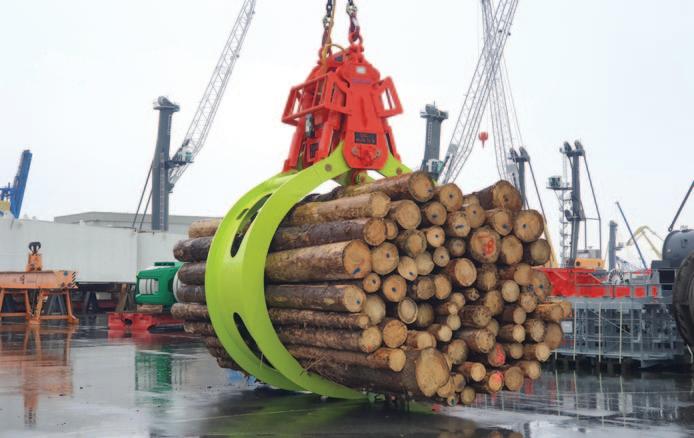
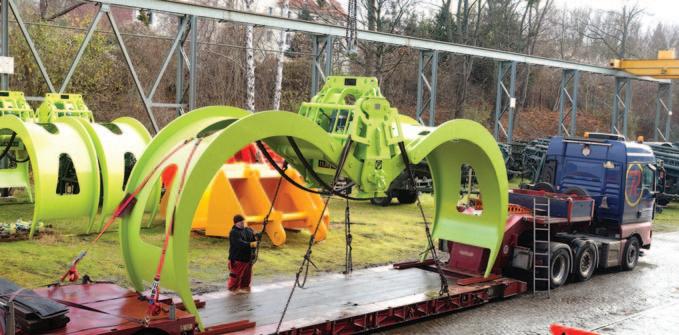
PEINER motor timber grabs underway on the ship to their destination port in New Zealand.
PEINER motor timber grab during port operation, mainly used for the loading of logs for export.
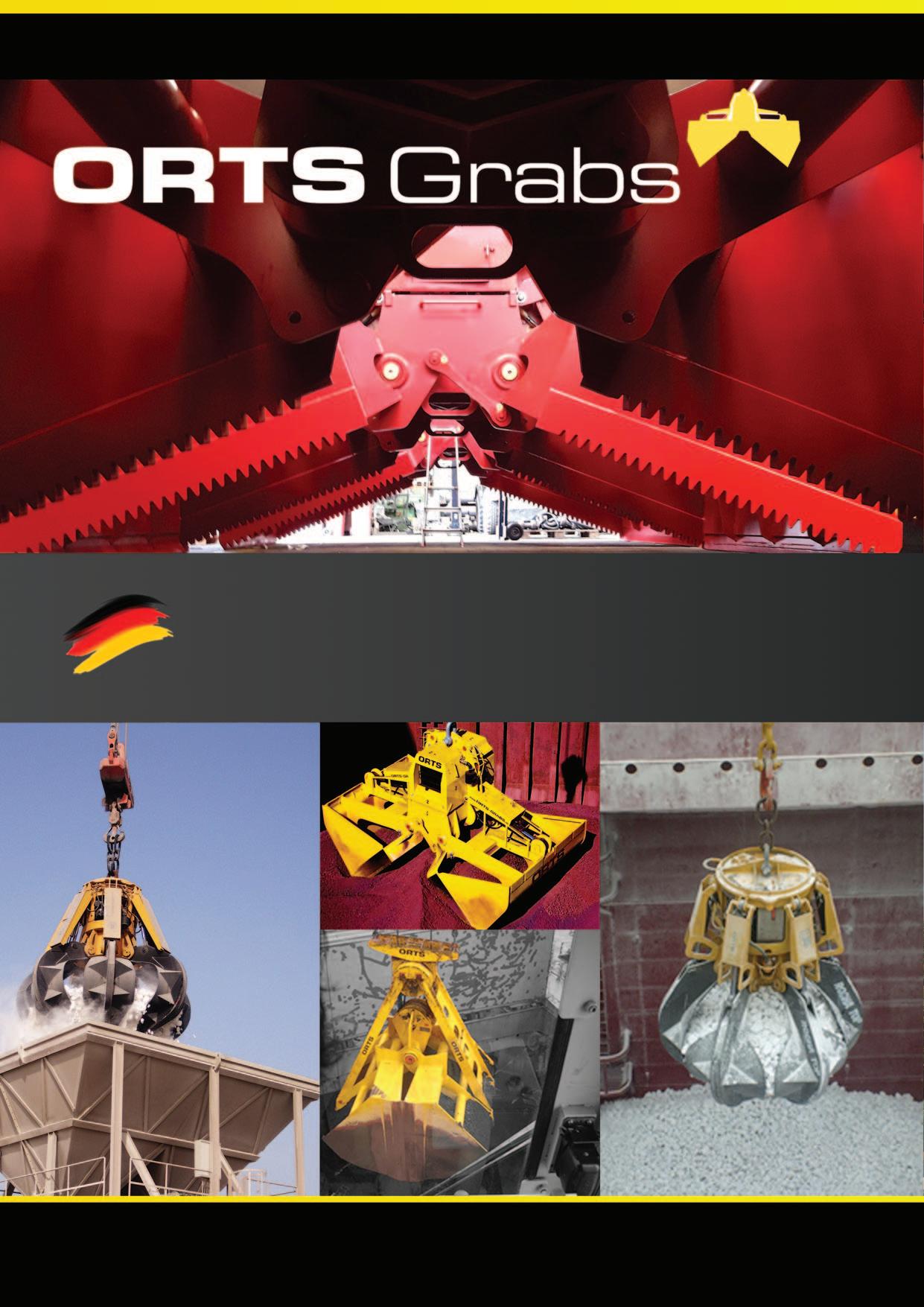
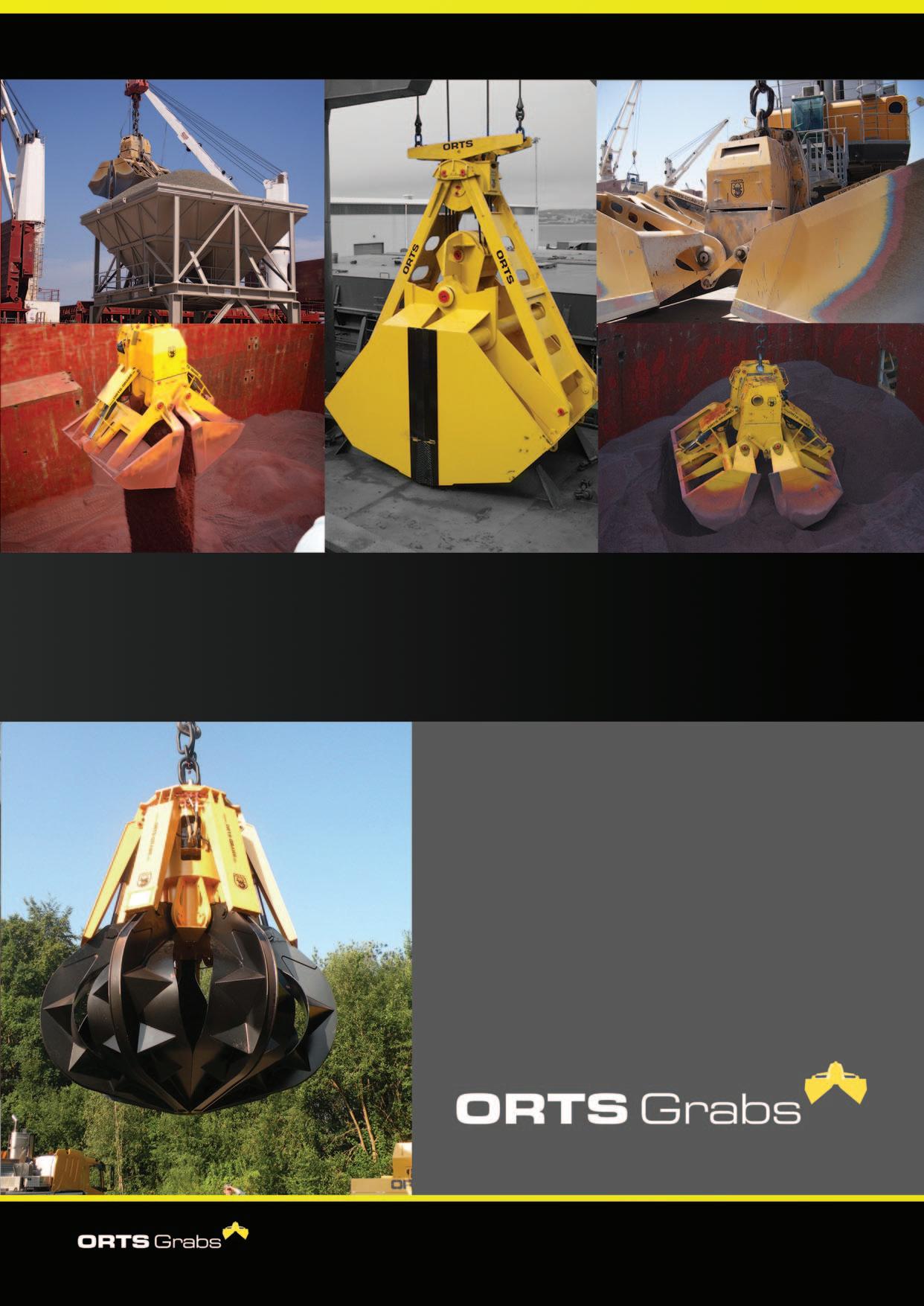

NEW ANALYSIS TOOL FOR MOTOR GRABS The latest development from PEINER SMAG is a data remote system with analogue sensor technology for reading out operating data such as angle, acceleration, oil and motor temperature, as well as oil pressure of the grab. The advantage of this system is that the existing crane system hardly needs to be changed, as the data from the radio system receiver is read out and processed in the existing crane control. No special crane cable is required for data transmission, as the system works by radio. The unit is located in the terminal box of the grab and can generally be used for all motor grab types. Anyone who wants to take a closer look at the PEINER motor waste grab and its accessories can do so at this year’s IFAT trade fair in Munich. PEINER SMAG will be exhibiting at the world’s largest platform for water, sewage, waste and raw materials management in hall C5.228.
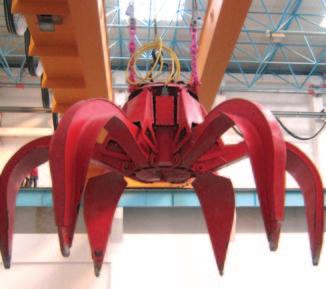
The operating data of PEINER motor grabs can now be retrieved via data remote system. Basic unit of a motor orange peel grab with terminal box for remote data transmission.
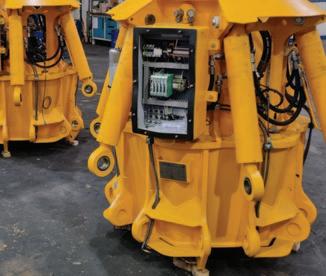
Janus Grab ships three remote control grabs to Indonesia
Southeast Asian countries such as Indonesia, Thailand, Singapore, the Philippines, Vietnam, Malaysia and so on have always been important export countries for Shanghai Janus Grab Co., Ltd (Janus Grab).
According to Janus Grab, customers in these countries are very satisfied with its grabs and the company has been strict in quality, technology and service control and management for many years.
The grabs were loaded for transportation on the 10 March 2022. After two close inspections, nearly four hours later, the grabs were successfully shipped to Indonesia.
REMOTE CONTROL CLAMSHELL GRABS Janus Grab’s remote control clamshell grab is an efficient tool for loading and unloading bulk cargo. The grab can close by lifting up the hook of the crane and open by remote control in the air without any additional power. The hydraulic and electric parts use the plug-in modular design, are easily maintained and repaired and are suitable for ship ocean voyages. The electric system and hydraulic system are designed to be water-proof. Each bulk grab is thoroughly tested by immersing it under water for 24hours. Multi-step buffering reduces the impact to the grab from the crane and ensure rapid unloading. These grabs can work continuously for 24 hours without experiencing trouble.
With more than 30 years’ experience in grabs design, R&D, and manufacturing. and with a group of highly-educated and skilled professionals in steel structure, hydraulic and electric system, Janus Grab has become competitive in worldwide markets. After the grabs were loaded, the fixed point on the grab is tightly connected to the lifting point of the frame box with galvanized steel wire rope and basket bolts to prevent friction between the contact surface and the frame box, caused by the shaking of the grabs during transportation.
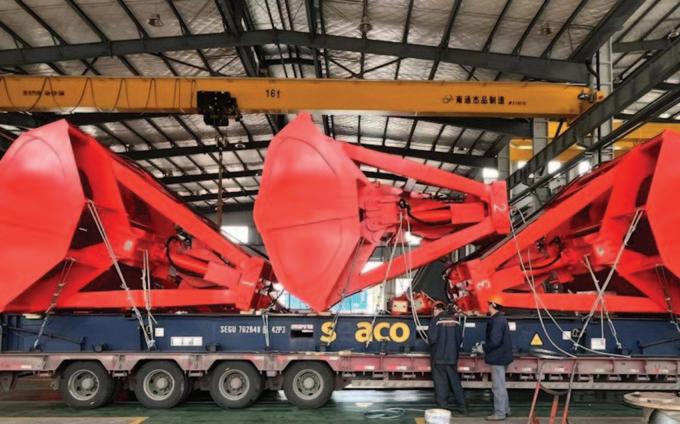
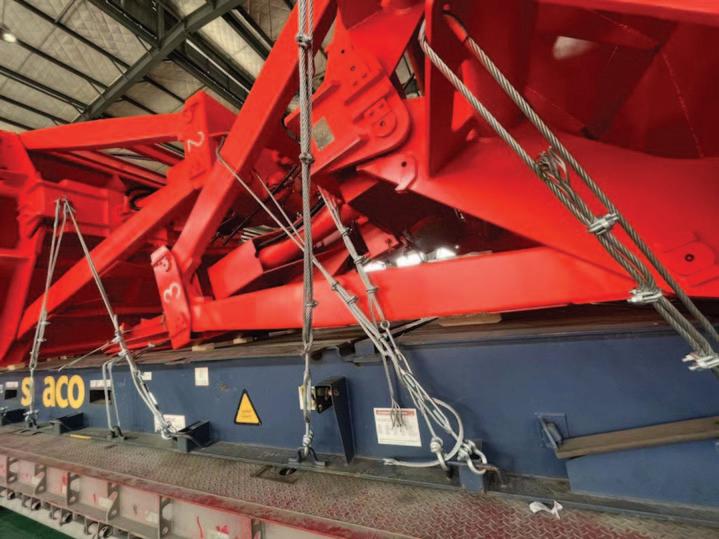
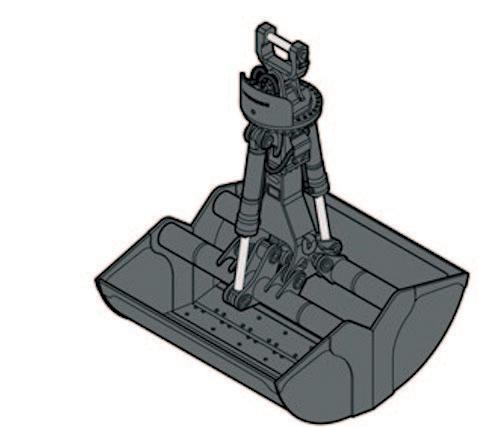
Fully operational for Swiss natural product: Liebherr LH 60 M Port Litronic material handler with GMZ 80 clamshell bucket
An LH 60 M Port Litronic was last year handed over to Aarekies Brienz AG in Brienz, Switzerland. The Liebherr material handler is specially designed for the economical handling of bulk goods and general cargo. The machine will be in operation extracting and quarrying natural sand and gravel in the harbour of the gravel and concrete plant at Lake Brienz. A special Liebherr clamshell with water slots will be used to extract the harbour’s naturally occurring sand and gravel and feed it into the plant.
The Liebherr LH 60 M Port material handling machine will have a very special assignment. It will be assuming a key role in the quarrying and production of the unique Brienzer Sand®, a Swiss natural product. The powerful machine will be handling natural sand and gravel directly at the harbour basin at Lake Brienz, and will also be responsible for the subsequent feeding of the gravel plant.
The machine has just been handed over at the harbour of the gravel and concrete plant. Hans Ulrich Kern and Reto Studer of Liebherr-Baumaschinen AG in Reiden presented a symbolic key for the new Liebherr material handling machine to managing director Dominik Ghelma and the general manager of the gravel plant, Kaspar Thöni.
COHERENT OVERALL PACKAGE Dominik Ghelma is enthusiastic about the new Liebherr material handling machine: “We used to operate a rail-mounted 1970s-vintage cable excavator in the harbour. When we were looking for a replacement, we decided to purchase a Liebherr material handling machine. Quite simply, the overall package is optimally configured for us. We have found an extremely versatile machine with the right attachments for everyday operations in our harbour.”
This overall package is rounded off by a Liebherr service agreement. “Regular maintenance will ensure a long service life and high level of availability of the machine,” stresses Reto Studer. “The service agreement means that Liebherr will perform the maintenance work on the LH 60 M Port, allowing the customer to focus all his energy on his core operations,” he adds.
FOCUS ON HANDLING PERFORMANCE For Kaspar Thöni, handling performance Fully operational for a Swiss natural product: the Liebherr LH 60 M Port Litronic material handler will assist in the quarrying and production of the trademark product Brienzer Sand®.
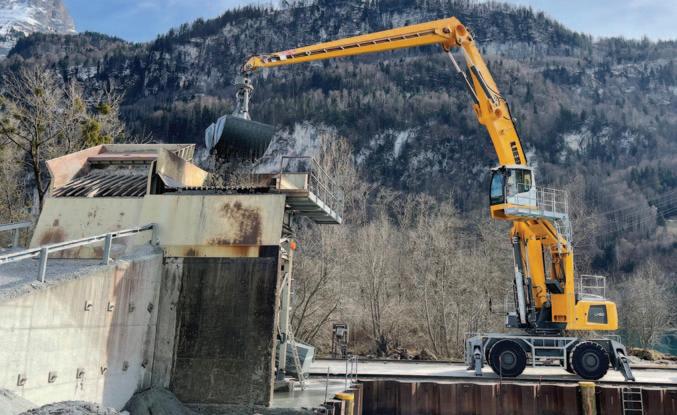
The low dead weight of the GMZ 80 increases productivity and the turnover of material. Furthermore, the optimal shape of the tines allow good penetration and fast emptying. The GMZ 80 is extremely well suited for excavators of the 30- to 110-tonne class and it available with a clamshell bucket. High clamping forces ensure excellent excavation properties.
was especially important in the choice of machine which is expected to remove up to 80,000 tonnes of natural sand and gravel from the harbour basin on an annual basis. The harbour has a depth of up to nine metres therefore it was a requirement that the operator be guaranteed a perfect view of his work area at each of the many different stages of the handling process. The Liebherr LH 60 M in the customer’s configuration meets this essential criteria without problems.
LIEBHERR GMZ 80 CLAMSHELL The LH 60 M Port is equipped with a GMZ 80 clamshell specially configured to meet customer requirements. The GMZ 80 impresses with its optimum design and good penetration, guaranteeing excellent handling performance. The 1,650mm-wide, 2.00m³ clamshell buckets are equipped with teeth on the cutting edge, allowing natural sand and gravel on the bed of the lake to be easily detached and loosened. The water slots on the clamshell buckets allow the water to drain off efficiently during the extraction and handling process. A reinforcement set on the inside of the wear-resistant clamshell buckets enhances durability and at the same time extends the service life of the clamshell.
This type of grab is primarily used with machines of the 60- to 80-tonne class. During the design phase, care was taken when calculating the forces acting on the components to ensure that the flow of forces was optimized and weight was minimized, enhancing the overall performance. This has a positive effect on the machine’s fuel consumption. The two-motor Liebherr slewing drive is equipped with a large-dimension antifriction bearing and impresses with its high torque and lifting force of up to 50t. This allows the grapple to work effortlessly, even under full load.
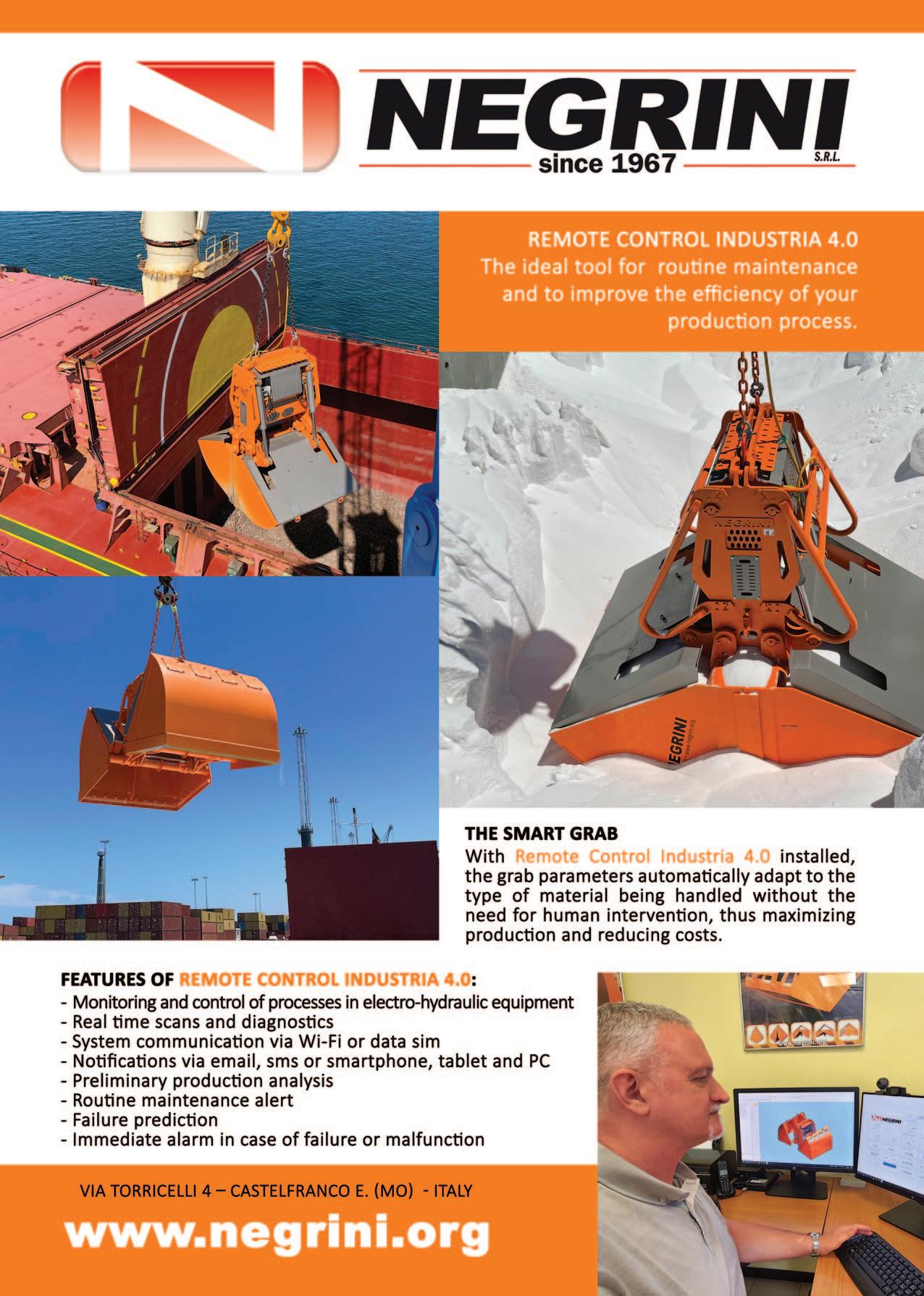
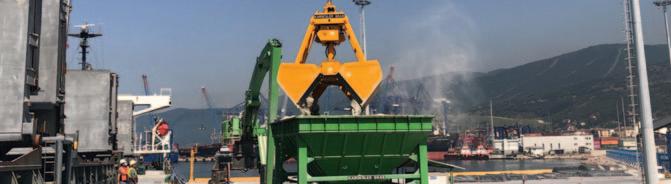
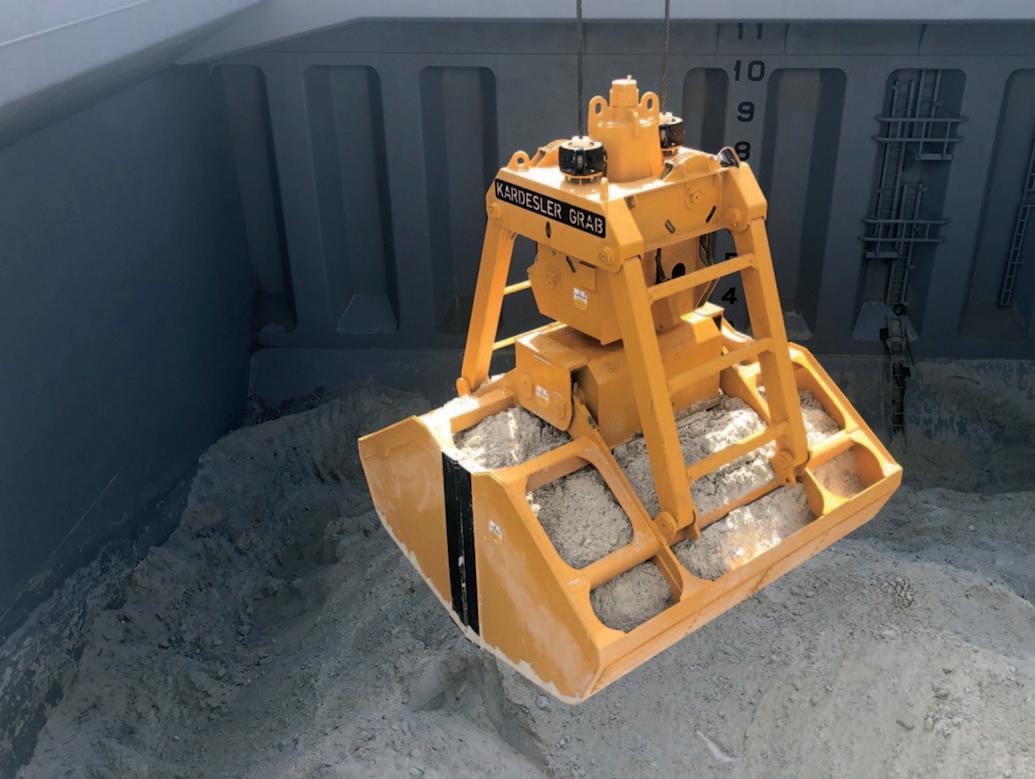


Since 1985, Kardesler Grab & Machine LTD, has been producing a complete range of bulk handling grabs for shipping companies, ports, steel plants and Stevedore companies using radio remote control grabs, mechanical grabs and electro hydraulic grabs, in either clamshell or orange peel designs.
When you have to combine high productivity, flexibility and reliability in handling all kinds of dry bulk cargoes, Kardesler’s independent radio remote control grabs are a great match.
Kardesler grabs are suitable for all types of dry bulk cargo. Usually, different materials need specific kinds of grabs for their operations. “However, in most cases, shipping and stevedoring companies need one unique grab in operations while handling different types of cargo to provide efficiency. Therefore, a radio remote control grab from Kardesler is a great match to meet those demands,” explains, Kardesler’s Mr. Huseyin, adding that scrap, pig-iron, HBI and large stones are also handled with these equipment.
In terms of firmness, Kardesler emphasizes that this is dependent on three key factors; low dead weight, kinematics and closing force of the knives.
The reliability of the grab is also extremely important while discussing firmness. As the saying goes: “I am not rich enough to buy cheap things,” it is pointless to buy a cheap grab which may cost you a lot later. For instance, when an emergency situation or break occurs during vessel handling operation, customers need to have 24/7 service. Kardesler maintains 24/7 service during even during holiday periods for their customers to prevent them losing time and money at the same time. The products could be purchased at any place; however, Kardesler is always ready to serve 24/7 with its qualified engineers worldwide.
Recent contracts have been made with customers in Turkey, Greece, Portugal, Indonesia, Philippines, China and Canada.
The unique independent radio remote control grabs have proved themselves a lot as ‘troubleshooters’. “For instance,” says Huseyin, “so many times, the company’s unique radio remote control grabs have been sent to help unload vessels in need, as the grabs on board and the harbour equipment have failed.”
Kardesler’s grabs are only manufactured in its factories in Turkey; however, Kardesler has many agencies in most parts of the world. Kardesler is proud to manufacture all parts in its own factories and stamp them ‘Made in Turkey’.


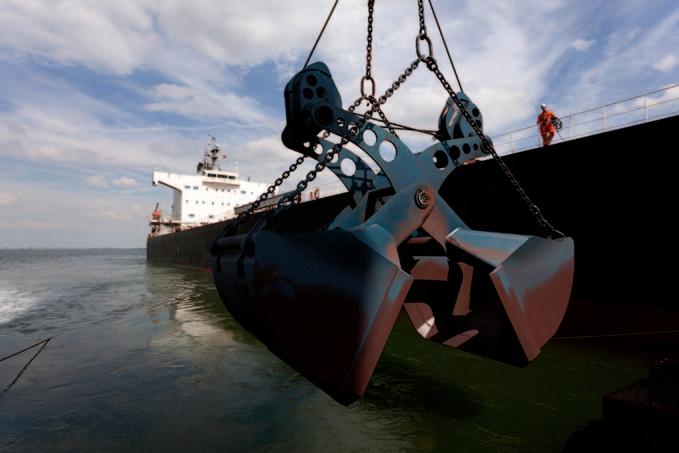
At Nemag, the company believes in the power of innovation to help its customers increase their bulk handling efficiency and decrease their operational costs. In close co-operation with leading bulk terminal operators, crane manufacturers, technical universities and other stakeholders in the industry, Nemag continues to develop new products for the dry bulk industry. Improving unloading efficiency and striving for the lowest handling costs per tonne material transferred are key objectives.
MAKING THE RIGHT CHOICE There are several grab types available, each with specific characteristics and benefits. When choosing a grab, it is important to be aware of the fact that a grab is of fundamental importance on overall performance.
The key challenge is to find the best grab solution and unloading procedure that leads to the highest average unloading performance. In addition, the impact of the grab type on auxiliary equipment costs such as trimming equipment and staff must be considered, as well as maintenance costs.
When it comes to the type of materials it will handle, the choice of grab is more than looking at the bulk material, payload and deadweight. The combination of appearance, density and moisture content of bulk material make it extremely important for terminal operators to choose the right grab. This will avoid overloading the installation, prevent leakages and optimize the overall terminal performance. Choosing the ideal grab also requires a good understanding of prevailing conditions: v Will unloading be with shore-based cranes or floating transshipment? v What is the size of the ship, barge or a bigger vessel? v What type of crane is being used?
THE CLAMSHELL GRABM Nemag’s goal is clear: to create the most productive grabs on the market. One recent addition is its nemaX®, the most productive iron ore grab in the world. Now Nemag is introducing its next innovation — the Clamshell GrabM, the lightest and most productive clamshell grab on the market.
This achievement is the result of combining input from customers from all over the world and the company’s 95 years of experience, supported by state-of-theart design tools such as Solid Works, FEM analysis and TACTON product configurators.
LOW MAINTENANCE COSTS Market research shows that the highest cost of any grab will always be the operating expenditure, OPEX. Nemag wants to keep this as low as possible for its customers, which is why it uses the most durable materials and have also reduced the number of parts that are susceptible to wear and tear. In addition, the company has made it easier to reach and maintain the different parts of the Clamshell GrabM .
This is how Nemag can promise a safer work environment and the lowest maintenance costs per tonne transferred.
COMPETITIVE PRICING By using the latest innovations in engineering, Nemag has further streamlined its manufacturing process and enhanced its latest clamshell grab with modular parts, which all adds up to an extremely competitive price.
SHORT LEAD TIMES & REDUCED LOGISTICS COSTS Nemag’s high-performance Clamshell GrabM has been standardized for production, enabling a shorter lead time from your order to the moment you can start experiencing the increase in productivity that the Clamshell GrabM brings.
After buying a grab, the last thing you want is high transportation costs to bring the grab to your terminal. That is why Nemag’s reinvented clamshell grab has been designed with container shipping in
Nemag’s Clamshell GrabM .
The nemaX is about 15% lighter than any comparable clamshell grab on the market with a deadweight efficiency of only 25–28%.
mind. This drastically reduces the costs of transportation.
The design of the Clamshell GrabM also makes it very easy to assemble and
FULLY CUSTOMIZABLE The Clamshell GrabM is available as a highly customizable modular grab for lifting capacities starting at 20 tonnes up to an 85tonne safe working load.
Building long-term partnerships on trust with the innovative nemaX
CASE STUDY Headquartered in Convent, Louisiana, Associated Terminals (AT) is the foremost stevedore and terminal operator on the Lower Mississippi River and beyond. It operates fourteen midstream river anchorage facilities in the region as well as additional dockside and on-site facilities. “When we first visited AT in 2018, we presented them with a 3D-printed model of our innovative, award-winning nemaX dry bulk grab and they were immediately interested,” explains Rudy Bovée, account manager at Nemag. “They next decided to trial the grab in practice for a month as part of the nemaX world tour. Shortly thereafter, they placed an order. The nemaX simply sells itself!”
Of course, Associated Terminals is not the only terminal to have adopted the nemaX; the dry bulk grab among other things offers versatility, cost-effectiveness, efficiency and ease of maintenance. However, Rudy and his team are particularly proud of the fact that Associated Terminals decided to opt for a Nemag product. Bovée: “AT’s mission, core values and vision perfectly align with our passion for performance. Like Nemag, it highly values customer relations and is always looking for ways to innovate and improve operations. After years of development and cooperation between engineers, customers and users, it is really great that the nemaX exceeds everyone’s expectations. To have a customer actually confirm this is a great source of pride for us at Nemag. Especially such a unique customer as Associated Terminals, with its strong emphasis on midstream transloading activities and the use of floating cranes.”
HIGH PRODUCTIVITY, LOW MAINTENANCE Shortly after commissioning the nemaX in 2019, AT was already achieving the promised productivity increase of 13% and sometimes more. It has also experienced many of the other benefits of the grab. For example, the fact that the nemaX has far fewer moving parts substantially reduces the need for maintenance. Furthermore, it is able to handle 20% more cargo with the same closing cables, further boosting the cost-efficiency of the grab. “Even if the nemaX would have the same productivity as the clamshell, we would still opt for the nemaX, purely based on the operational advantages it offers,” says Zeljko S. Franks II, Senior Vice President of Associated Terminals.
CAPEX AND OPEX
When assessing the financial aspects of a grab, two elements are key: the asset investment costs (CAPEX) and the operating expenditure (OPEX). Bulk terminals with clear insight into maintenance costs have concluded that the total maintenance costs of a grab constitute a more significant factor than its asset investment costs. Calculated over the grab’s lifespan, the average asset investment costs of a four-rope grab amount to around one eurocent per tonne of cargo transferred. In terms of grab maintenance costs, this can however be as much as two or three eurocents per tonne of cargo handled.
MINIMUM DOWNTIME “The nemaX will immediately bring down costs, but other advantages such as maintenance do not become apparent until after a couple of years,” explains Bovée. “Especially when transloading on the water, it is important that the cranes can continuously operate and that downtime is kept to a minimum. For customers such as AT, ease of maintenance is therefore crucial. Since operations take place from a floating pontoon on the Mississippi, any maintenance work will have to be performed right there. So, the less maintenance, the better.”
LONG-TERM PARTNERSHIPS Associated Terminals handles a highly diverse range of cargoes, ranging from dry bulk such as grains, minerals and coal to windmills and project cargo. The nemaX is currently only used for iron ore pellets. Close co-operation with AT and a continuous focus on improvement and innovation will however make it possible to deploy the grab for other types of bulk as well. “We are proud that our grab helps AT to boost productivity and lower the costs,” explains Bovée. “Together with them, we are currently assessing which other commodities might benefit from the nemaX. We do this in close cooperation and based on trust. After-sales is just as important as sales. This is how we build long-term partnerships. In that respect, we are proud to say that AT has placed an order for a second nemaX grab, which will be delivered in January 2022.”
INNOVATIVE DESIGN FEATURES Regular wear and tear can never be fully prevented, but the nemaX allows you to achieve substantial savings in terms of maintenance. This significantly helps to reduce operational expenditure and downtime, crucial in view of the pressure on handling rates that terminals are experiencing due to overcapacity in the dry bulk sector. Through exhaustive computer simulations, the nemaX offers numerous key innovative design features. The most important ones are:
MINIMAL NUMBER OF MOVING PARTS
The nemaX design features a minimal number of moving parts: only two sheaves and 70% fewer moving parts than in a comparable clamshell grab.
ONLY TWO MAIN PIVOT POINTS
The nemaX has only two main pivot points with high quality spherical roller bearings. In comparison, a comparable clamshell grab with slide bearings features 12 main pivot points.
DURABLE CLOSING CABLES
The way in which the hoisting wires have been reeved reduces flexing along the sheave blocks by 75% compared to a 2 x 5-part clamshell grab. Metal fatigue in the closing cables is reduced proportionately, resulting in a longer operational lifespan for these cables. And nemaX’s unique operational design minimizes the clogging and wear of sheave blocks and closing cables and significantly extends the lifespan of the closing cables.
CLOSING CABLES ARE EASY AND SAFE TO SWITCH
The anchor points of the closing cables are located at an accessible working height, making it easy and safe to reeve in new closing cables without needing to set up an elevated work platform of scaffolding.
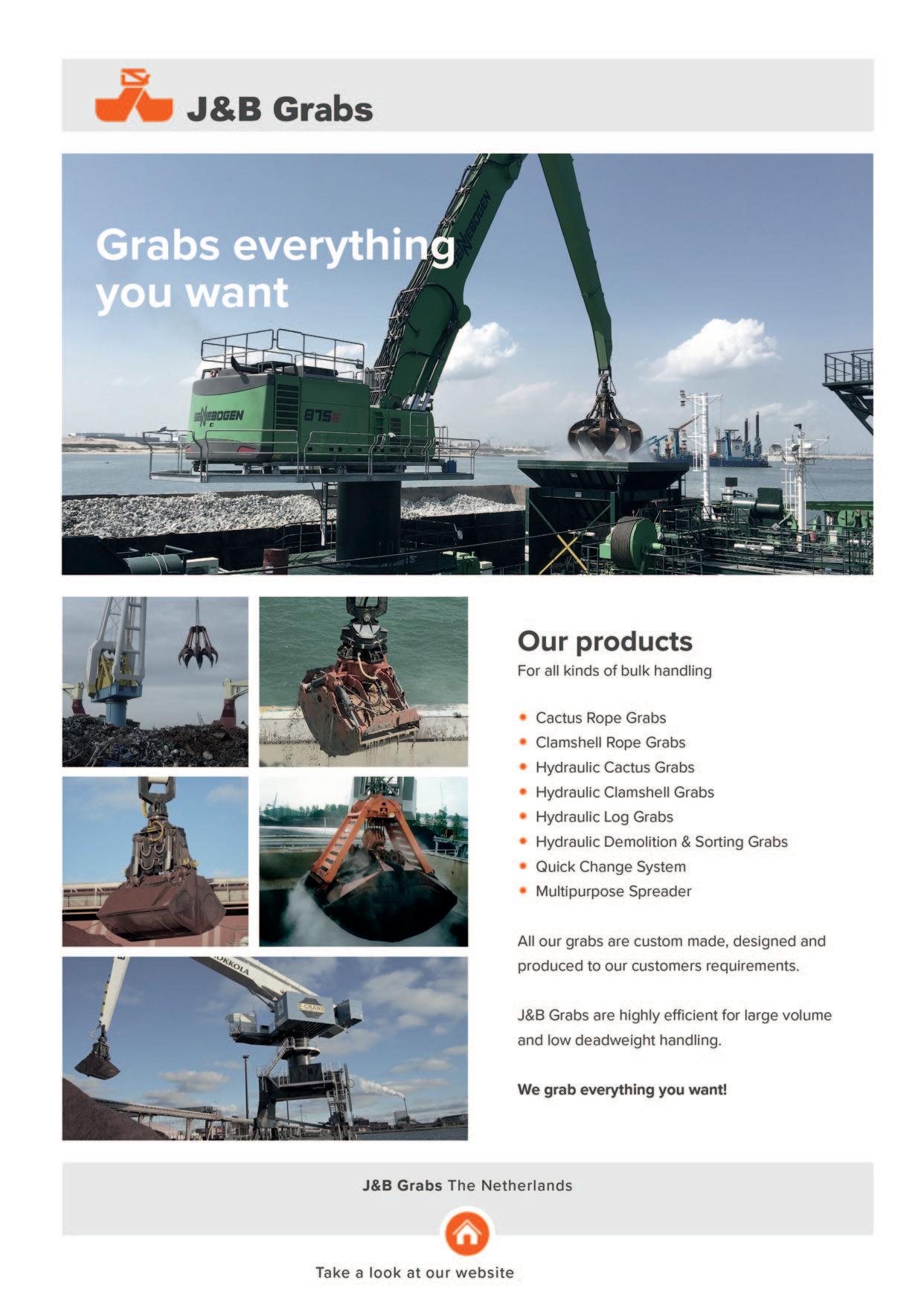