
32 minute read
MAKING THE RIGHT MOVES WITH MOBILE BULK EQUIPMENT
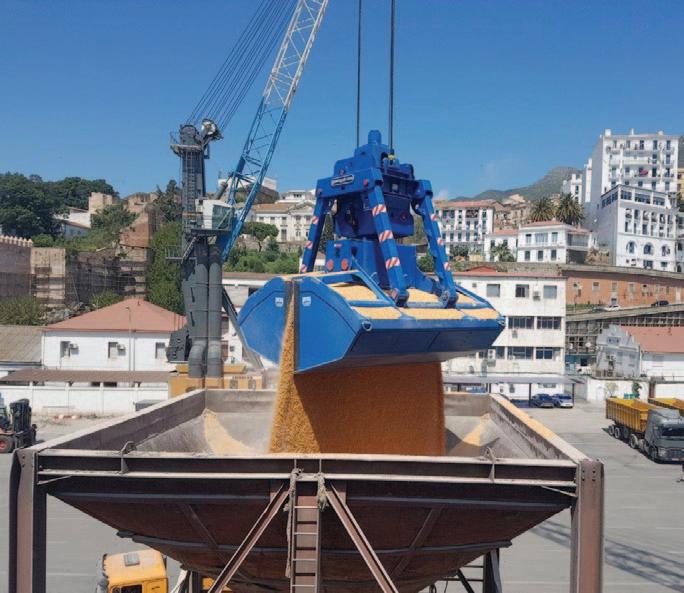
Turkish company, Güven Grab and Machine Inc., manufactures bulk cargo handling grabs for the loading and unloading of various types of commodities.
Ninety-five per cent of its products are exported, China accounting for 65% of its exports. In this context, the import of loading and unloading grabs has been prevented and Güven contributes to its country with a considerable amount of foreign currency input through its exports. The company has designed four types of grabs and registered them with the ‘Industrial Design Registration Certificate’ under the Turkish Patent Institute. There are 12 patent certificates in various fields registered in the name of the company. Güven Grab’s electro hydraulic clamshell motor grab.
DCi
Güven Grab’s radio remote control grab unloading material.
GUVEN GRAB’S GRAB PORTFOLIO INCLUDES:
v radio remote control; v electro hydraulic clamshell motor; v electro hydraulic orange-peel motor; v mechanical clamshell — two-rope and four-rope; v mechanical orange-peel two-rope and four-rope; v hydraulic clamshell excavator; v hydraulic orange-peel excavator; v radio remote control orange-peel; v mechanical clamshell touch down; v mechanical orange-peel touch down; v timber & log; and v dredging facility.
The company also manufactures: v big bag spreaders; and v hoppers. creativity and unique human skills. The fact that these grabs, produced completely in Turkey, have a worldwide user base, has to be some indication of the trust in the company’s products.
THE GÜVEN GRAB FACTORY Production takes place at Güven Grab’s factory, established on an area of 10,000m2 located at Çayırova/Kocaeli.
Manufacturing operates with the most advanced IT, automation, simulation, process control and control systems as well as modelling systems in accordance with Industry 4.0.
INTEGRATED PRODUCTION WITH CNC AND AUTOMATION All products are designed, developed and improved in a 3D computer environment and put into production after performing the necessary tests and computer simulations.
Being furnished with contemporary and modern automation systems, Güven’s factory is equipped with high-level machines that include data exchange and production technologies. Necessary analysis are conducted on the designed products and transferred to the production line with necessary approvals based on the production of the prototype. Once the data is obtained it is analysed and the necessary interventions are made on time for efficient production.
SERVICES Güven professional engineering teams provides worldwide services.
Güven representative can offer customers solutions that will enable them to work faster and more efficiently on any subject.
Güven offers service and spare parts supply to grab users and owners all over the world. Its online support network ensures the necessary determinations are made before the service commences.
Spare parts supply as well as service organizations are carried out within 24 hours.
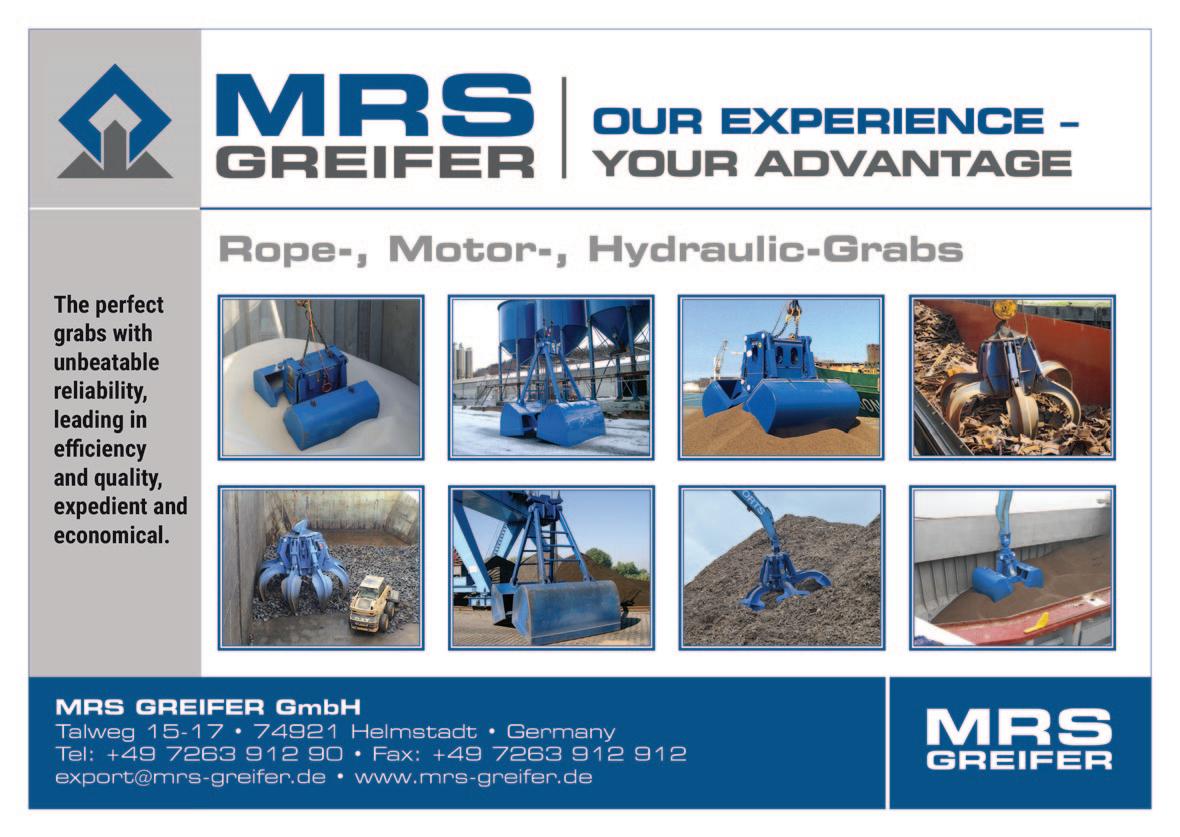
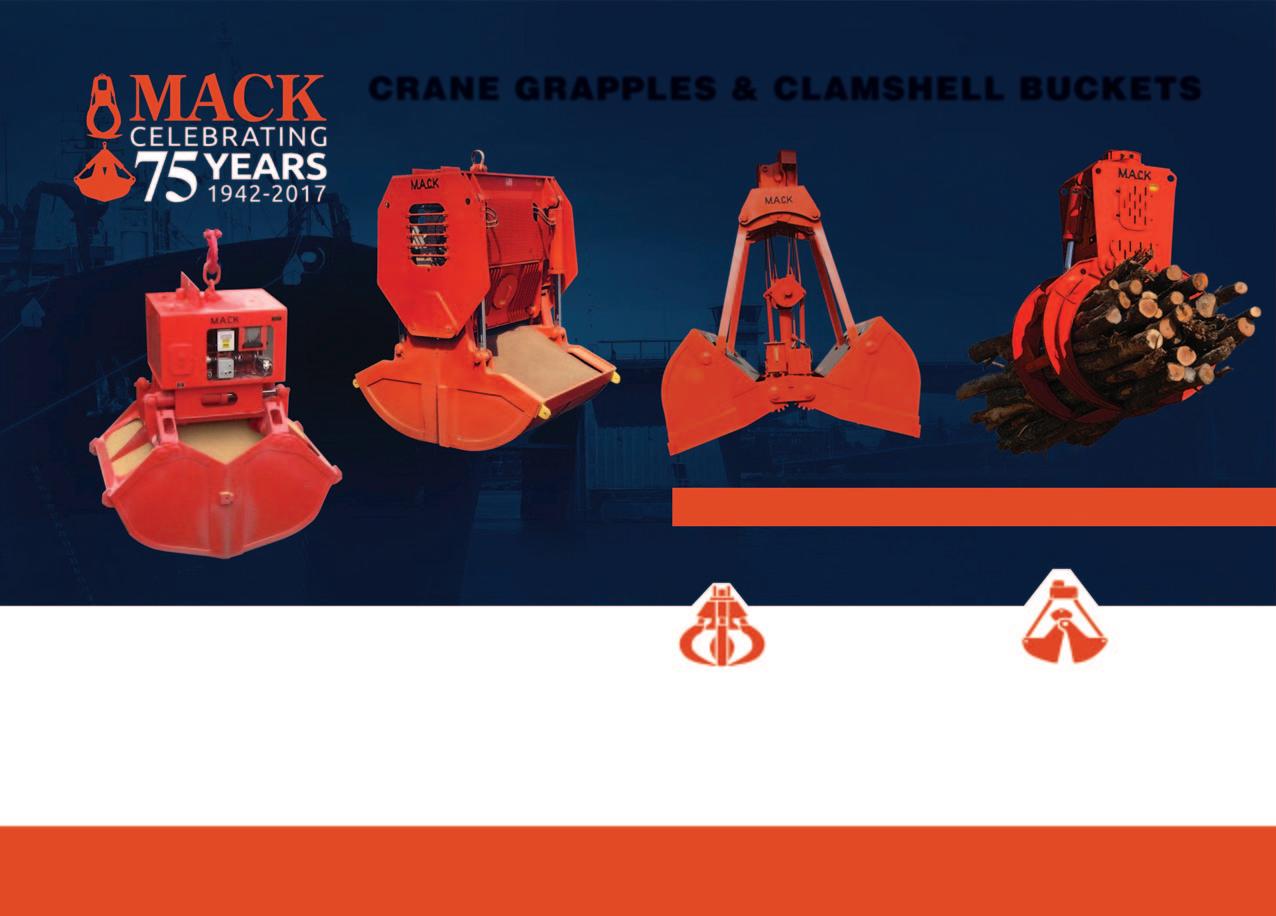
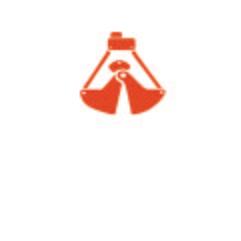
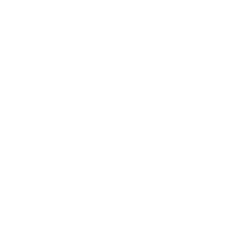


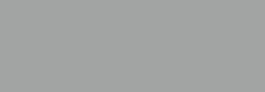
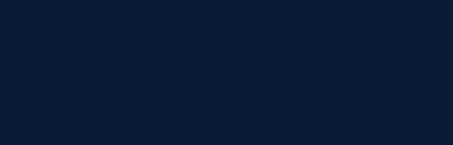
ENGINEERING & EQUIPMENT Making the right moves
with mobile bulk equipment
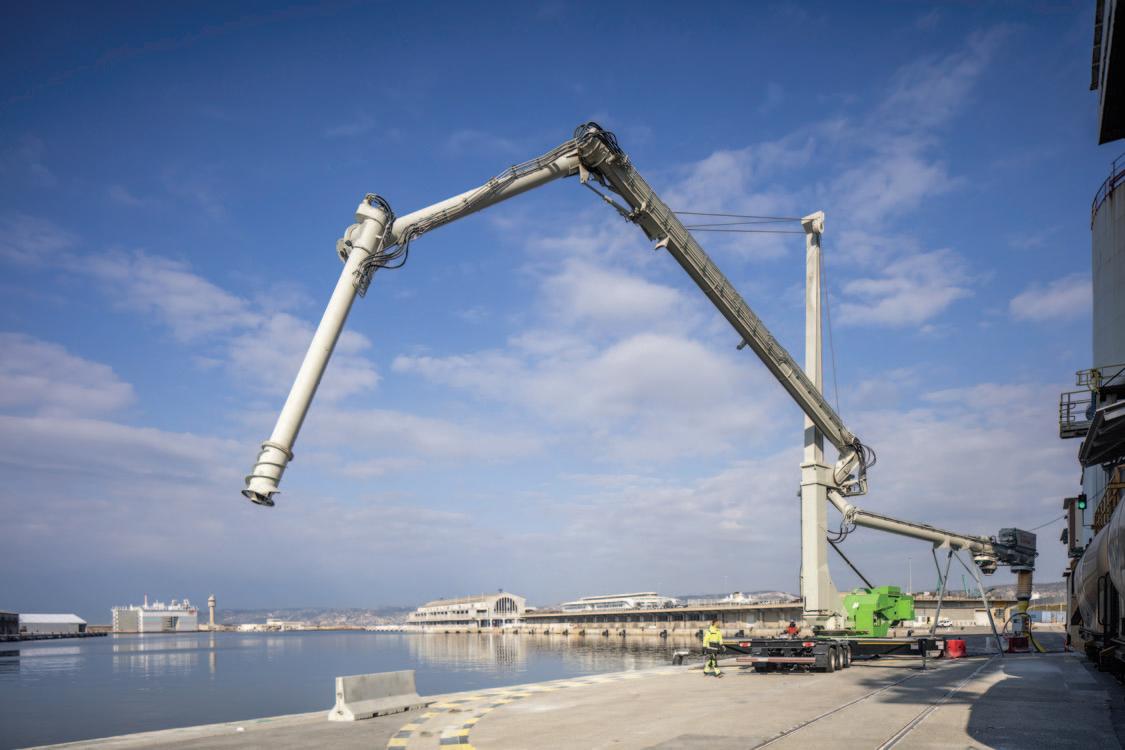
Louise Dodds-Ely
Mobile port equipment can rival efficiency of fixed installations
Agile assets in the port give dry bulk handlers some unique advantages over their fixed counterparts, some systems are even road-mobile, adding to their flexibility; Jörgen Ojeda, Sales Director Mobile Unloaders, Bruks Siwertell, explains.
“When it comes to very large-scale importers, operating out of dedicated dry bulk terminals, fixed, continuous shipunloading systems offer extremely efficient unloading rates and through-ship capacities, reliable cargo flows, fewer delays, less demurrage and therefore cost savings, maximizing profitability.
“But what about smaller-scale operations or those ports where large, fixed installations are not suitable or permitted, or where there are significant distances between working quays? In these cases, smaller mobile ship-unloading equipment is often considered. In-port, or on the road mobility can be significantly advantageous, offering some good cost arguments.
Mobile unloaders should also not just be considered suitable for smaller-scale, niche operations. With multiple mobile unloading units in operation working alongside each other, directly unloading into trucks, dry bulk material can be moved very quickly to shore, dramatically reducing the time a ship stays in port and freeing up capacity for other activities on the berth. Multiple mobile unloaders can offer even higher capacities than a single fixed installation for lower levels of investment.
CHALLENGE TRADITION Today, operators have a wealth of technology to choose from, including some that substantially challenge traditional systems, delivering true, fit-for purpose possibilities that can optimize a port terminal.
Bruks Siwertell has two main screwtype conveyor options when it comes to mobile unloading systems. Its most recent introduction is the Siwertell port-mobile unloader, which was originally developed to offer a more economical solution for grain handling compared with traditional pneumatic unloaders.
The second mobile option is the Siwertell road-mobile unloader, which is effectively a terminal on a trailer and is able to not only move around a port, but relocate to another location entirely. It has a global presence, serving hundreds of installations with extremely flexible, reliable and efficient dry bulk handling.
Both systems offer port mobility, excellent efficiency and rated capacities, very low material degradation rates, smooth cargo discharges, cost-efficient operations and reduced investment costs. They have a totally enclosed conveying line, ensuring environmental protection through no spillage or dust emissions.
DESIGNED FOR PURPOSE Based on a standardized design to keep investment, maintenance and wear parts costs low, the port-mobile unloader is available as a 400tph (tonnes per hour) or a 600tph unit and is able to discharge
vessels up to 60,000dwt.
Siwertell road-mobile unloaders handle a wide range of free-flowing dry bulk materials, and are available in three different sizes: the Siwertell 5 000 S, 10 000 S and 15 000 S; the largest offering an unloading capacity of up to 500tph for discharging ships up to 15,000dwt.
The folding structure on road-mobile systems is mounted on a semi-trailer and the entire unit can be folded down and relocated in under an hour by a single operative, keeping personnel costs low.
Siwertell road-mobile unloader systems can be designed to suit any downstream conveying requirements, and as standard, feature a dual truck-loading system, which delivers continuous, uninterrupted discharge operations as long as there are trucks available.
The port-mobile unloader is equipped with a dual truck-loading system with the option for a third on the 600tph version, all outlets can be used simultaneously. Furthermore, to minimize the impact of truck changeovers and to allow enough time to position the truck correctly, the unloader is equipped with a large-volume intermediate surge hopper.
PROFITS UNDER THE HATCH Total unloading times dictate a terminal’s profitability. All Siwertell ship-unloading units, including the port-mobile and roadmobile unloaders, can reach practically all areas of the cargo hold, including underneath the hatch opening and corners. This is made possible with the ±30° movement in the port-mobile unloader’s vertical arm combined with a ±20° luffing motion in the horizontal arm; manoeuvrability which directly translates into unloading efficiency advances and leaves less material for the payloader to move at final clean-up.
Road-mobile unloaders offer even higher in-hold access with their vertical arms articulated in two parts, delivering ±30° movement in their upper sections, with an additional ±40° movement in their lower sections. These capabilities deliver impressive continuous, through-ship capacities and comfortably challenge the rates of equivalent pneumatic unloaders.
With so much on offer, operators should be considering new technology for their quays and not sleep into selecting more traditional choices. This is a particularly powerful argument with terminals facing the need to be more efficient and sustainable in light of rising populations and climate change.
INDUSTRY UPTAKE Many operators are already making the switch to Siwertell technology and the uptake of mobile unloaders is notable. At the end of 2021, Bruks Siwertell received an order from Swecem AB for a nextgeneration Siwertell road-mobile shipunloader. It will secure dust-free handling of cement in the port of Helsingborg, Sweden.
The Siwertell 10 000 S next-generation road-mobile unit will unload cement at 300tph, discharging vessels up to around 10,000dwt. It will be delivered later this year.
Cement unloader orders continued at a pace during 2021, with two new 5000 S Siwertell road-mobile ship-unloaders contracted to a cement handler in North America. These will also be delivered this year. Also in the US, Cemex US ordered and received a 10 000 S next-generation unit. Another Siwertell 10 000 S nextgeneration unloader, ordered for a Kuwaiti cement operator in 2021 and was delivered in the same year, along with a Siwertell 10 000 S next-generation unloader for an undisclosed cement handler in Israel. It will be taken into operation during the second quarter of 2022.
Furthermore, in 2021, Trimet France ordered a Siwertell 10,000 S nextgeneration road-mobile unloader for unloading dry bulk cargoes of alumina in Marseille, following the lease of an older Siwertell 10 000 S unloader from another Bruks Siwertell customer.
The operator is taking advantage of one particular Siwertell technology attribute, minimal material degradation, reducing the production of powdery fines. Aluminium smelting is energy intensive and is very sensitive to the amount of fines in the alumina; the lower the percentage of fines, the lower the temperature required in the process, which therefore reduces energy consumption.
This system was delivered at the beginning of 2022 and now secures alumina handling at a rated capacity of 130tph, discharging vessels up to 10,000dwt. It also features digital advances that enable extensive monitoring, follow-up, support and troubleshooting through safe, remote access.
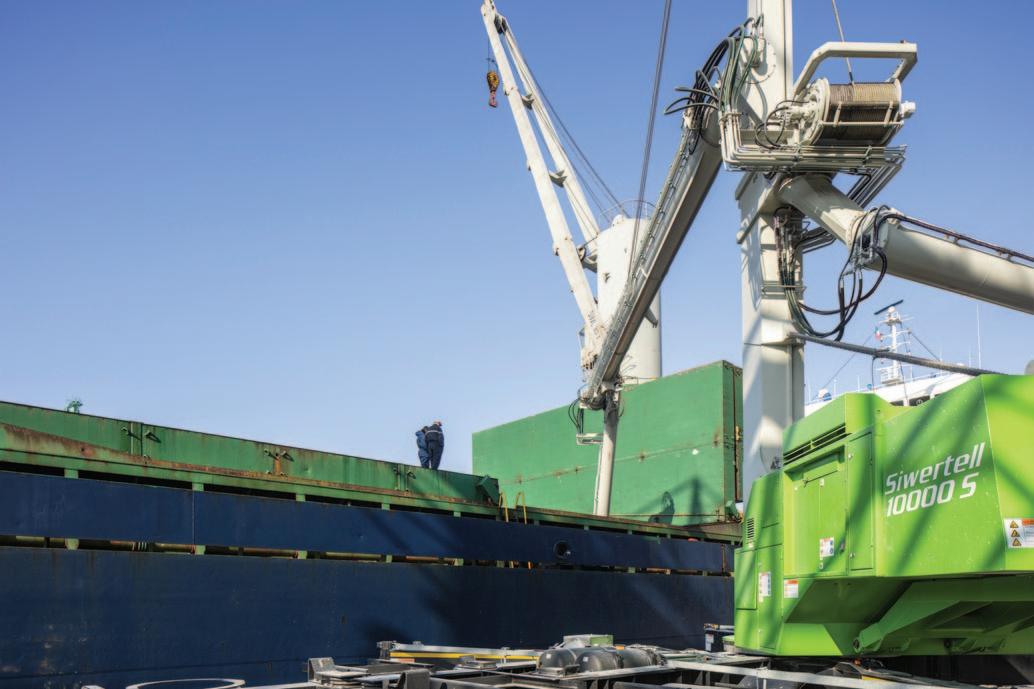

Small is beautiful: NEUERO’s portable pneumatic conveyors offer a flexible alternative when larger machines are unsuitable
Today most articles and advertising are dedicated to discussing large capacity shipunloaders and shiploaders. However, smaller portable equipment still serves as a valuable tool for many in the material handling industry. NEUERO has been at the forefront of field for producing efficient, and long lasting portable machines.
HISTORY The use of portable pneumatic conveyors started a long time ago helping in farms and inland commercial grain storage facilities to store and retrieve grain from every dry space available.
These machines gained worldwide use in the marine shipping industry many years ago. Oil tankers would bring oil to the USA, but in most cases they would need to sail back to the Middle East empty. This was very costly for the shipping companies. It was then decided that grain could be transported back to the Middle East and Africa if there was a way to unload it. This was the birth of using portable pneumatic conveyors in the marine industry. The suction line size was a small enough diameter to fit in the openings on the ship’s deck. Depending on the port, the grain was being shipped to, the grain was either unloaded directly at the port or, in most cases, to a smaller vessel positioned alongside the oil tanker and then the smaller vessel would take the grain to the various ports. The bulk shipping companies took note, and also started using larger vessels to ship the grain knowing that even if the large vessel could not dock at the receiving port they could use the portable machines to offload the larger vessel into smaller vessels for final delivery at the smaller port facilities.
This equipment was useful in the 1970s/80s to help Russia to import grain from neighbouring countries. The rail gauge was different on Russian train tracks than the neighbouring countries. NEUERO designed portable machines with suction booms to transfer the grain from the supplying countries railcars, to Russian railcars for further transit into Russia.
The NEUERO portable machines are still a very valuable tool for salvage operators. If there is a elevator explosion, grain silo fire, grain silo collapse, the wrong grain type put in a specific silo (soybeans on top of corn), removing hot spots, train derailment, or flooding the leading salvage operators all own a fleet of portable machines to solve these disasters.
The portable equipment is still a valuable tool today because it is a flexible alternative to move grain and meals in new regions where infrastructure does not exist, or is needed as backup in case of emergency, and even to help grain clean up from ships that have problem with mechanical unloaders..
One example is the SmartPort mobile barge unloaders. These can work in suction – pressure mode as shown in Figure 1; the grain is sucked and blown to a pressure cyclone that discharges to a truck or railcar. In suction only (Figure 2), the loading part is done via separate conveyor. This machine can be equipped with a filter to capture the dust.
Both machines have a maximum capacity of 200tph. Transport to the client is done in 40ft containers. Once at the client’s site the assembly process, testing, and training is accomplished in just one week.
Figure 2.
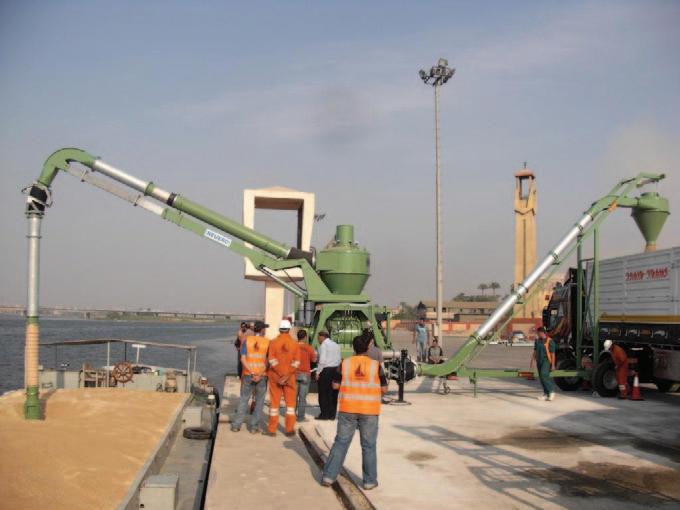
The demand for mobile and portable bulk handling equipment for port or harbour operations has increased significantly in recent times as operators look to increase utilization of berths, minimize capital outlays and cater to a wider variety of vessels. To this end, portable bulk handling equipment often provides more flexible and cost-effective loading and unloading solutions for bulk products. Kilic Engineering (KE) has been producing portable bulk handling equipment for the agribulk commodity and mining industries for over four decades, and it is this experience that has enabled KE to expand its customer offering to now include port and wharf side bulk materials handling equipment.
Since 2018, KE has been manufacturing standalone portable shiploaders for both grain and biomass (wood pellet) loading operations into vessels. As always, KE designs and manufactures equipment which meets each customer’s specific require ments, and this also relates to those customers who require a different solution to the standard shiploaders on the market.
SHIP/BARGELOADING SOLUTION FOR VIETNAMESE CUSTOMER The solution for Vietnamese port operator, Baria Serece at Phu My port, involved the provision of a portable ship/bargeloading machine and utilized KE’s unique design of conveyors, hoppers and elevators to manage the restricted wharf area where the equipment was to be utilized.
KE’s drive-over hopper design which has traditionally been used as part of its patented BunkerSweeper and BunkerStacker range of grain handling equipment, was supplied to the customer to enable direct deliveries for road trucks to the wharf to load corn, wheat and/or soybeans to their seafaring vessels, including barges, primarily for river trade. The receival hopper was equipped with an underbelly conveyor feeding the product into a small bucket elevator onto a swing boom conveyor and through a dust suppression chute into the vessel. Although this was the prime operation requested by the customer, the portable loader was also capable of being fed by ship’s grabs from a transferring vessel or via shipboard grab cranes or jetty based front-end loaders.
The flexibility of the portable shiploader design for its Vietnamese customer was a critical plank in further projects which KE has since undertaken for both Australian and overseas customers.
KE SUPPLIES PELLET LOADING SYSTEM TO
JAPANESE PORT OPERATOR In Japan, a KE hopper/conveyor stacker combination is delivering a wood pellet loading operation for port operator Tokuyama at its port facility of the same name. Here, the customer was keen to find a solution which allowed it to transfer product from trucks and containers into vessels once again utilizing the flexibility of moving the loading equipment along the berth when required to fully load vessels. With berths at the port having multiple users and general cargo services, the ability to remove the bulk handling equipment from the wharf when not in operation, was one of the key benefits of deploying the KE portable machinery.
CARGILL AUSTRALIA BENEFITS FROM KE’S HOPPER Many ports require the flexibility of portable equipment for bulk handling operations where fixed equipment is too restrictive for other port business needs. This was certainly the case when Cargill Australia, part of the food and agri giant’s global operations, identified a need for a portable shiploader that would suit its newly established grain export operations in the South Australian Port of Adelaide.
The proposed shiploader needed to be


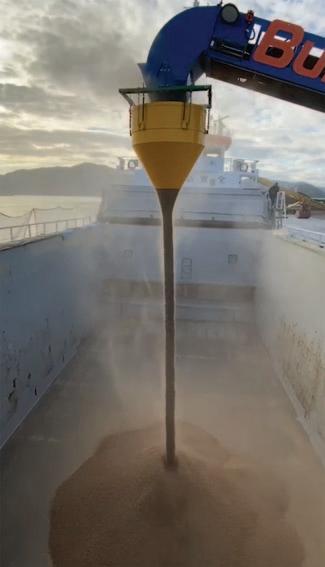
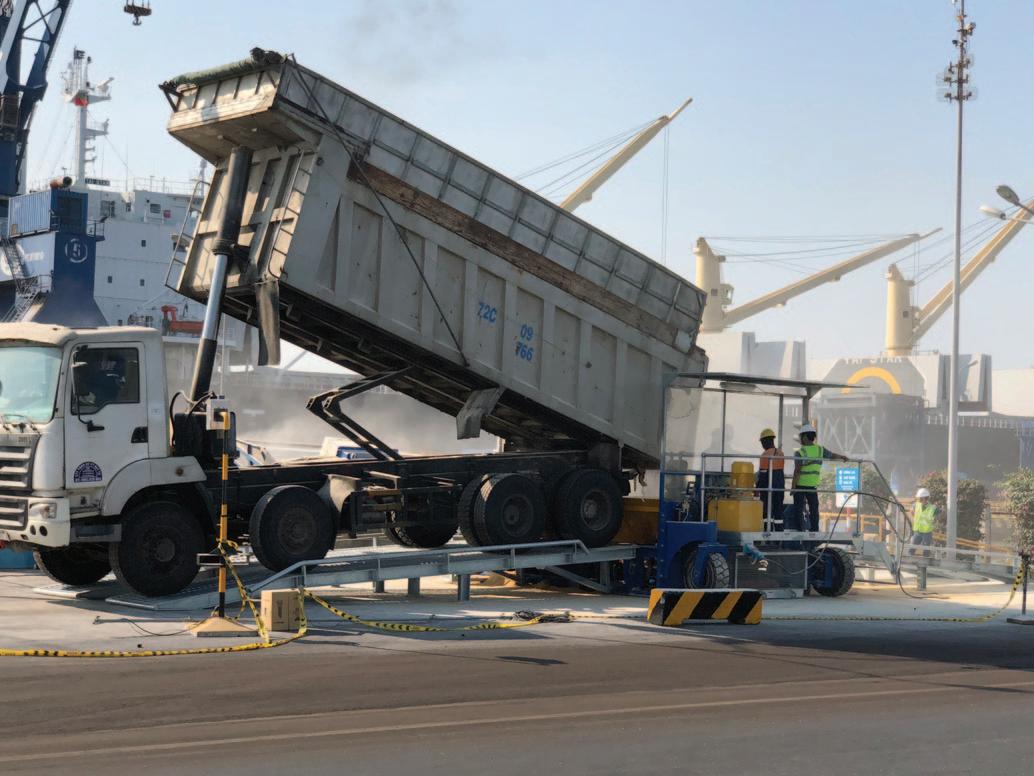
portable as the berth being used for their operations was also required to facilitate other general cargo operations for the Port owner, Flinders Port.
Given that the berth, which would be utilized for Cargill’s grain loading operations, had no access to fixed storage or conveying infrastructure, the company identified a unique design by Italian manufacturer Bedeschi S.p.A. that would meet the loading requirement of 1,000tph (wheat tonnes per hour), but then needed a means of delivering product to the shiploader. It was determined that the loader would be fed from a constant stream of road trucks and this was when Cargill and Bedeschi approached KE to become involved.
Having worked closely with Cargill over many years in supplying portable equipment for its up-country grain receival operations, KE proposed to design and fabricate a large twin/dual above ground hopper that would feed the shiploader to the required 1,000tph specification.
The KE twin hopper is an adaptation of its popular drive over hoppers which form
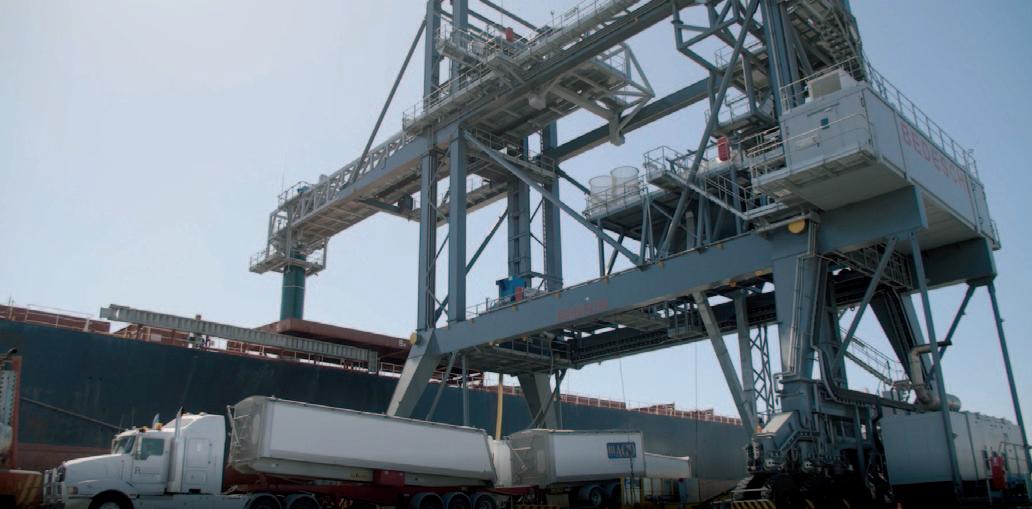
part of the KE BunkerStacker range of portable grain receival equipment widely used across the Australian Grain Industry to fill above ground bunker type grain storages, and utilized in both the Vietnamese and Japanese solutions mentioned earlier in this story.
KE’s concept of a twolane dual drive over hopper to simultaneously receive product from two separate feeds was a simple solution to achieve Cargill’s desired loading rate of 1,000tph utilizing KE’s existing technology and expertise.
However, KE had to ensure its solution needed to be not only strong enough to support two multi-trailer grain trucks unloading but it also necessitated the unit to be light enough to be carried around the port by the Bedeschi shiploader, features that had immediate appeal to both Cargill and Bedeschi.
The Bedeschi shiploader design, which moves on a multitude of rubber tyres incorporating 14 twin wheel bogie sets rather than along fixed rail tracks on the berth, was further adapted to accommodate a dedicated steel rope lifting system attached to KE’s twin hopper set-up to enable efficient and rapid movement of the unit along the berth during shiploading operations.
The portability of the shiploader also allows it to be moved away from the berth when not being used for loading operations to a dedicated parking area.
The dual hopper structure sits just 800mm (31 inches) above ground level with each hopper having a 6m (19.6ft) long dump area to receive the product as it is being tipped from the road transport trucks. Trucks access and exit the hoppers via 9.3m (30ft) long ramps at each end.
Four sets of dual augers feed the grain into the centre of each hopper where it then transfers to an 1,200mm ‘underbelly’ conveyor belt which takes the product to the Bedeschi elevator legs feeding the shiploader.
The Bedeschi machine with its KE twin hopper is now a permanent part of Cargill’s operations at the port with the technology continuing to be supported by KE.
KE: CONSTANTLY IMPROVING AND UPDATING With competition in grain handling and export operations increasing across Australian ports, KE continues to design alternative portable shiploading options for a number of its customers which require cost-effective and efficient solutions that meets their specific needs, particularly where port and wharf access is limited.
Outside of agri and mineral product loading, KE has also designed and preparing to construct a novel hopper and feeder unit that will be used in the unloading of vessels delivering bulk scrap steel products to an Australian port. This machine will deliver significant benefits to an operation that currently clears cargo holds using a combination of ships’ cranes, fixed hoppers, front end loaders and trucks. The hopper/conveyor design will eliminate product double handling and significantly speed up vessel discharge.
KE is a diverse mechanical engineering company based in Adelaide, South Australia, owned and operated by the Kilic family since 1973. The company has a long and proud history of excellence in designing, manufacturing and installing a wide range of material handling systems, the majority of which include its various conveying equipment options.
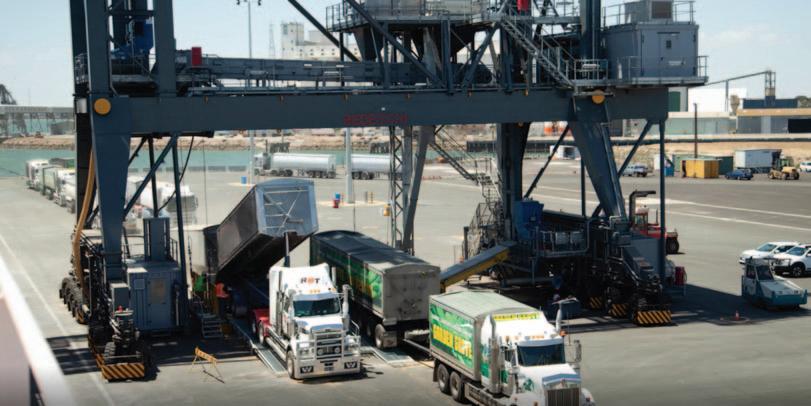
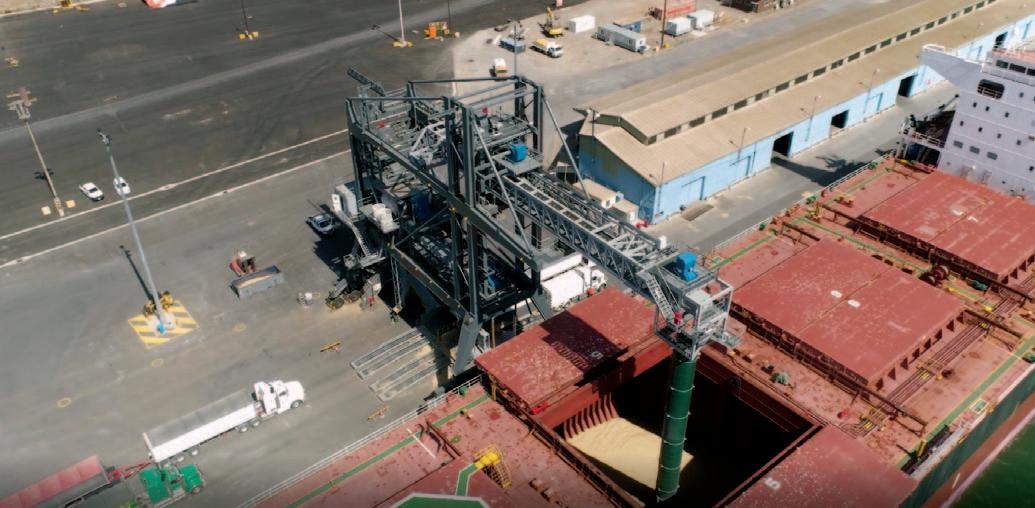
When it comes to handling dry bulk, cargo ports and freight yards are in constant motion moving bulk material between ships, railcars, and trucks. Cambelt designs fixed and portable unloaders and transloaders to maximize efficiency and minimize product loss and degradation along the way.
According to Jeremy Hengst, Vice President, Sales, Cambelt International LLC, what sets the company’s products apart from competitors, like traditional trough-, screw-, and bucket elevators, is that Cambelt is vertically integrated — engineering and manufacturing its own proprietary conveyor belts and conveyors. “By being a vertically integrated conveyor solutions company, we are able to develop unique solutions to resolve our clients’ material transport challenges. Engineering conveyor systems with our proprietary belts allows us to transport materials horizontally, vertically and back horizontally without any transfer points. Designing a system in this manner reduces the number of conveyors in operation while eliminating difficult transfer points, which can be dusty environmental concern areas,” he explains.
CAMBELT TRANSLOADERS: SMALL FOOTPRINT Cambelt’s Scorpion™ line of portable and self-powered transloading conveyors are designed for situations where it is impractical to have a fixed conveying system.
“Due to our propriety belt technology we are able to design conveyor systems with significantly smaller footprints,” says Hengst. “For example, our Scorpion® transloaders loading to discharge point range between 20–27ft, which is less than half of our competitors’ footprint. As transload sites become more compressed, Cambelt’s Scorpion® transloaders can help clients effectively unload in tight transload facilities where a longer conveyor can interfere with traffic patterns reducing overall facility productivity.”
Another benefit of Cambelt’s mobile conveyor systems is their low profile inlet, which requires only five inches (127mm) of clearance, providing unparalleled access underneath railcars or any low clearance loading situation.
These versatile units can be easily moved between various operating lines and are designed to centre load railcars enabling them to have the reach to load whatever is required of them.
They are also environmentally friendly, as Hengst explains, “Cambelt systems have been engineered with dust tight enclosures, minimizing environmental concerns. This design has been at the core of Cambelt’s history, as our conveyor housing is an integral part of our structure design of our conveyor systems. We have engineered our systems to minimize their exposure to the outside environment.”
RANGE OF PRODUCTS OFFERED Besides its Scorpion™ transloaders line, other products offered by Cambelt are: sidewall conveyor belts, high incline & closed conveyor systems, dome reclaimer systems and its CamSpan Gallery enclosed overhead troughing belt conveyors.
INDUSTRIES SERVED “We are a material handling company,” says Hengst, “We specialize in transporting dry bulk materials. Our core business is built around our expertise in conveying dry aggregate materials.
“We work with some of the largest international companies as well as small regional clients throughout the USA, serving industries like agriculture, cement processing, chemical processing, construction and dry bulk cargo handling among others,” he adds. “We are working diligently to develop solutions that address and resolve customer pain points to improve their plants efficiency and operation. “
ABOUT CAMBELT INTERNATIONAL LLC Situated in Salt Lake City, Utah, USA, Cambelt has been in business for over 60 years and at the core of its technology is its unique and patented one-piece flexible sidewall conveyor belting. Its proprietary belt design provides a structurally stronger material that can be transported up steep angles including vertical inclines.
In Cambelt’s custom engineered press, CamBelt, CamWall, and CamFlex conveyor belts are produced with the base belt, the sidewall, and the cleat or nubs moulded together to form a homogenous belt with unsurpassed durability and achieving ultimate adhesion strength Furthermore, the company guarantees that its rugged, one-piece, homogeneously cured products will not delaminate.
Cambelt proudly designs, engineers, manufactures and assembles all of its products in the USA.
On a micro-scale. Hengst believes Cambelt’s core strength is in the team approach to solving customer challenges. The team approach in the workplace as provided the added benefit of “leveraging experience from engineering, manufacturing, field service and operations to developed customized conveyor systems, to solve our clients’ unique material handling challenges.”
Speaking about the current Covid-19 pandemic, Hengst says the company took early steps and gave non-manufacturing employees the option to work remotely, while they reinforced social distancing with its manufacturing team members. He adds “We are fortunate to have a diverse client base, where some are experiencing tremendous growth throughout the crisis.” The company has been maintaining constant communication with its clients and is working with each to accelerate some projects, while putting others on hold until their operations return to a more normal operation. And this has clearly been the right move, as Hengst explains, “The response has been fantastic and our customers are happy to have an alternative to the traditional screw or bucket elevator technologies while having a partner working together to solve their day-to-day material handling challenges.


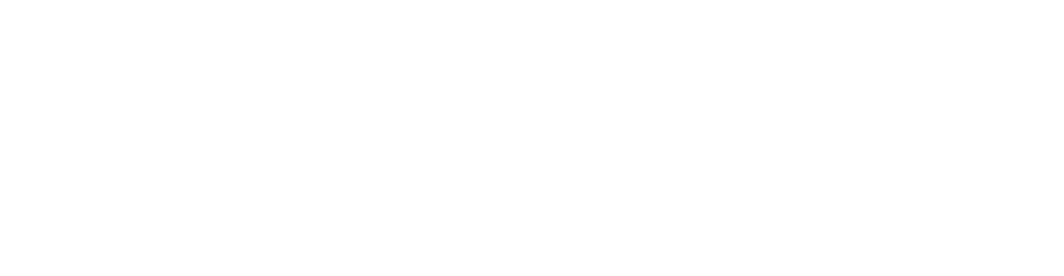
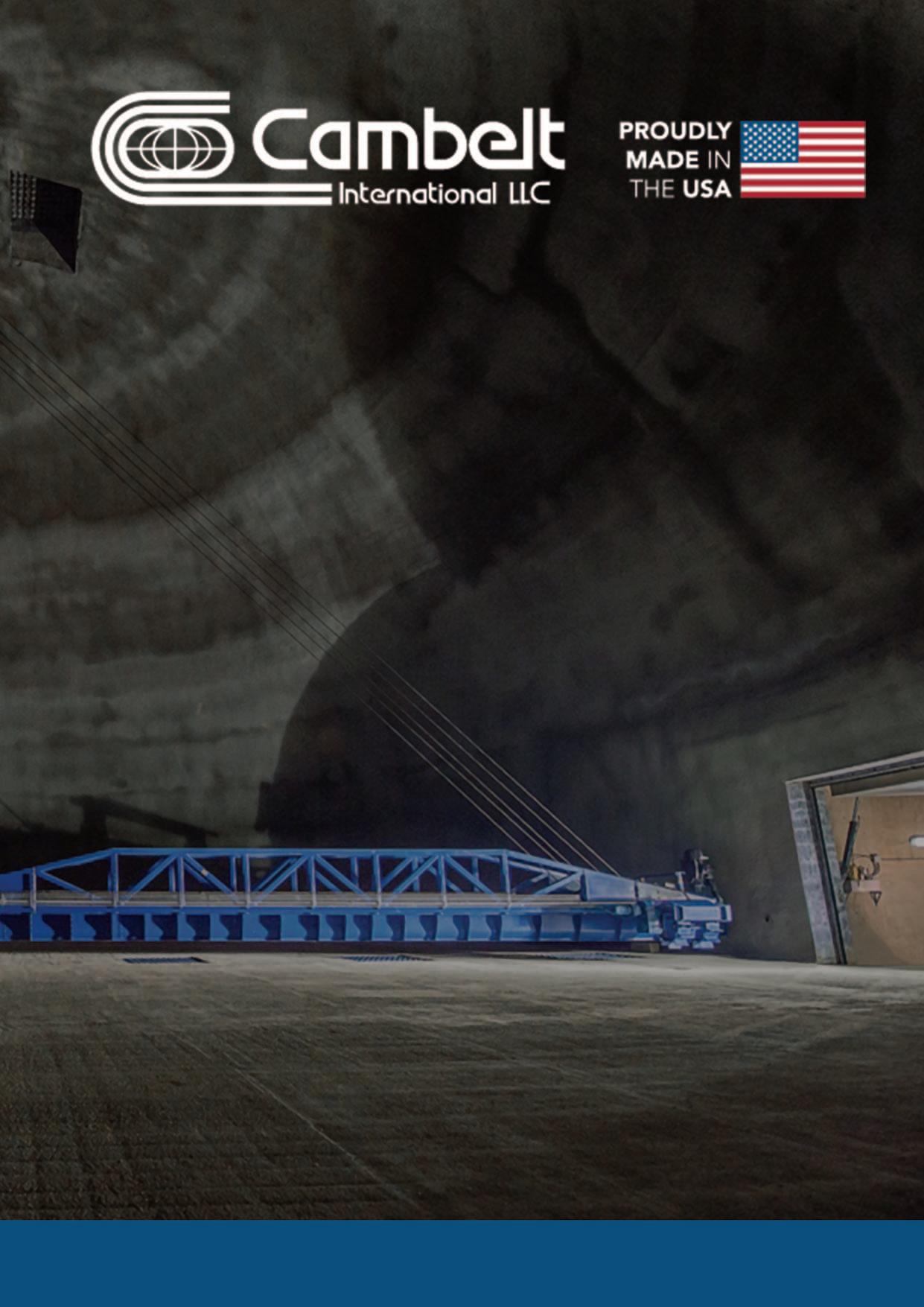

ENGINEERING & EQUIPMENT Next generation: SENNEBOGEN 3.40 G 4 t telehandler unique in its class
It is much more than its little brother: with the latest addition to the Multi Line, the 3.40 G-series, SENNEBOGEN is offering a new telescopic handler with a load capacity of 4t, a stacking height of 7.70m and, as a unique selling point, the most state-of-the-art cab of its kind — infinitely elevating to an eye level of 4.10m for 360° all-round visibility. The new generation of the G series once again sets standards in terms of user-friendliness and efficiency — made in Bavaria.
A Bavarian innovation is entering the telescopic handler market, as SENNEBOGEN is expanding its own Multi Line product line with its second model, the 3.40 G. The completely new development is already visually impressive and unique. In addition to the performance data, the machine also attracts attention in this market segment above all through its comfortable overview. Because, while many claim to offer the best all-round visibility, only one really lives up to this promise.
How? It is all thanks to the modern Multicab, which can be infinitely elevated to an eye level of 4.10m, thus guaranteeing real visibility and safety in everyday work.
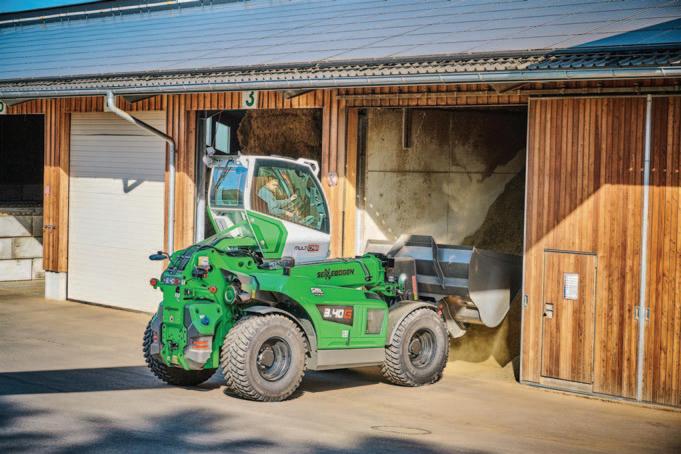
LITTLE BROTHER WITH STRONG GENES: 4T TELESCOPIC HANDLER WITH SML POWER
COMPACT MACHINE WITH MAXIMUM STABILITY
The little brother of the established 355 E has now been developed as an addition to the Multi Line portfolio for use as a telescopic handler and as a multifunctional machine. The four-tonne machine impresses with its compact dimensions of 5.50m length and just under 2.50m width. The stacking height of the telescopic boom is 7.70m. The new SENNEBOGEN 3.40 G offers unique stability with a long wheelbase of 3.10 m and the low centre of gravity of the entire machine at an operating weight of 9.3t.
Throughout the design and construction of all components, special attention was paid to the requirements of multi-shift operation in tough material handling. A
THE BEST BULK TRUCK LOADER IN THE WORLD
Deployed as the most eff ective way to load a truck with bulk goods.
high-strength, solid steel frame and sophisticated design of the telescopic boom ensure that the forces occurring in loading operation are optimally absorbed by the body. This ensures the reliability and durability of the machine, even in demanding continuous operation.
The new 4t telescopic handler from Straubing is equipped with a state-of-theart 100kW diesel engine in emissions category V and can reach speeds of up to 40km/h with its stepless traction drive. The operator can choose from two further modes in addition to road mode. In stacker mode, the machine is even more energyefficient and sensitive, while loading mode mobilizes all power reserves for optimal loading and transport of bulk goods. With the new 4 t 3.40 G model, SENNEBOGEN is expanding its own product portfolio of telescopic handlers with a machine that impresses above all in terms of visibility and operator comfort.
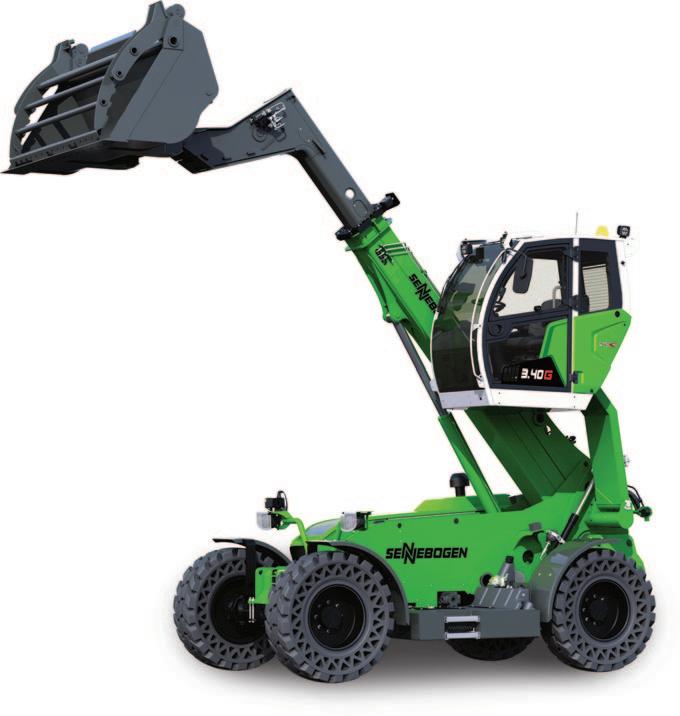
SML POWER AND Z-KINEMATICS — AN
IMPRESSIVE OVERALL CONCEPT
The design of the SENNEBOGEN 3.40 G combines the advantages of telescopic handler and wheel loader technology in one unique machine. The term SML Power stands for optimal power transmission thanks to the Z-kinematics familiar from the wheel loader and multi-functionality in use thanks to numerous equipment options and the manoeuvrability and compactness of the telescopic handler concept. These features are complemented by optimal visibility thanks to the elevating cab, which outshines any traditional wheel loader in terms of overview and safety when loading onto trucks or in logistics.
FLEXIBLE AND MULTIFUNCTIONAL
In the new four-tonne class, the SENNEBOGEN 3.40 G is not only aimed at customers from industry, demanding material handling or recycling, but also at sectors such as biogas plants or contractors in agriculture and municipal services. The various equipment can be operated flexibly at the push of a button, from bucket to sweeping brush and snow blade.
The new SENNEBOGEN 3.40 G also shows its strengths when used with trailers. The infinitely variable travel drive with Compact Drive transmission ensures fast driving or high torque with up to 65kN traction and thrust, depending on requirements.
Like all SENNEBOGEN machines, the 3.40 G can be configured to suit almost any requirement. There is a wide variety of optional equipment available, ranging from the automatic central lubrication system for optimal serviceability to the compressed-air brake system for trailer operation or tyre variants depending on the area of application.
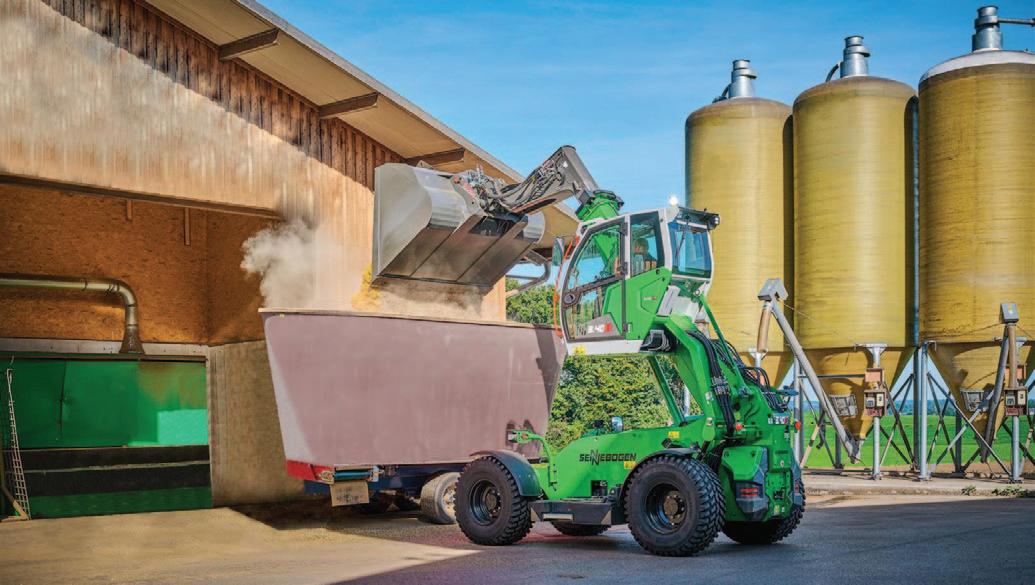
ENGINEERING & EQUIPMENT Steel logistics with SENNEBOGEN 865 E Hybrid at Italian logistics and transport service provider Trailer S.p.A.
The steel handling at the railroad terminal of Trailer S.p.A. should be simpler and more effective in the future: during the renewal of the logistics processes on site, now that the new 865 E Hybrid from SENNEBOGEN has come into play. With support from the sales and service partner Cesaro Mac Import, the Italian company now relies on a material handler with a magnetic lifting beam that can easily handle steel items weighing around seven tonnes.
As early as 1953, the success story of the traditional company Trailer S.p.A. began in the city of Brescia in northern Italy: what once started with freight transports and a single, retired US military transport truck has today grown into a modern logistics service provider with a large fleet of vehicles, specializing in the intermodal transport of steel products.
About a year ago, Trailer S.p.A. started operations in a railroad terminal with five tracks. The machines still in place, some aging crawler cranes and heavy-duty forklifts, urgently needed to be replaced as the processes on site could no longer be performed quickly and safely enough. Together with SENNEBOGEN sales and service partner Cesaro Mac Import, the company found the perfect solution for even more effective and safe handling of semi-finished steel products.
865 E HYBRID SAVES A LOT OF TIME IN STEEL HANDLING AND IN THE LOGISTICS PROCESS This is why the company has chosen SENNEBOGEN’s new 90-tonne model, the 865 E Hybrid. Created for heavy duty port applications as well as for steel handling, the 865 E at Trailer S.p.A. operates with an 18m equipment in combination with a magnetic lifting beam. With the powerful lifting
As of now, the SENNEBOGEN 865 E Hybrid reliably and safely handles steel products with a magnetic lifting beam at Trailer S.p.A., an Italian transport and logistics service provider.
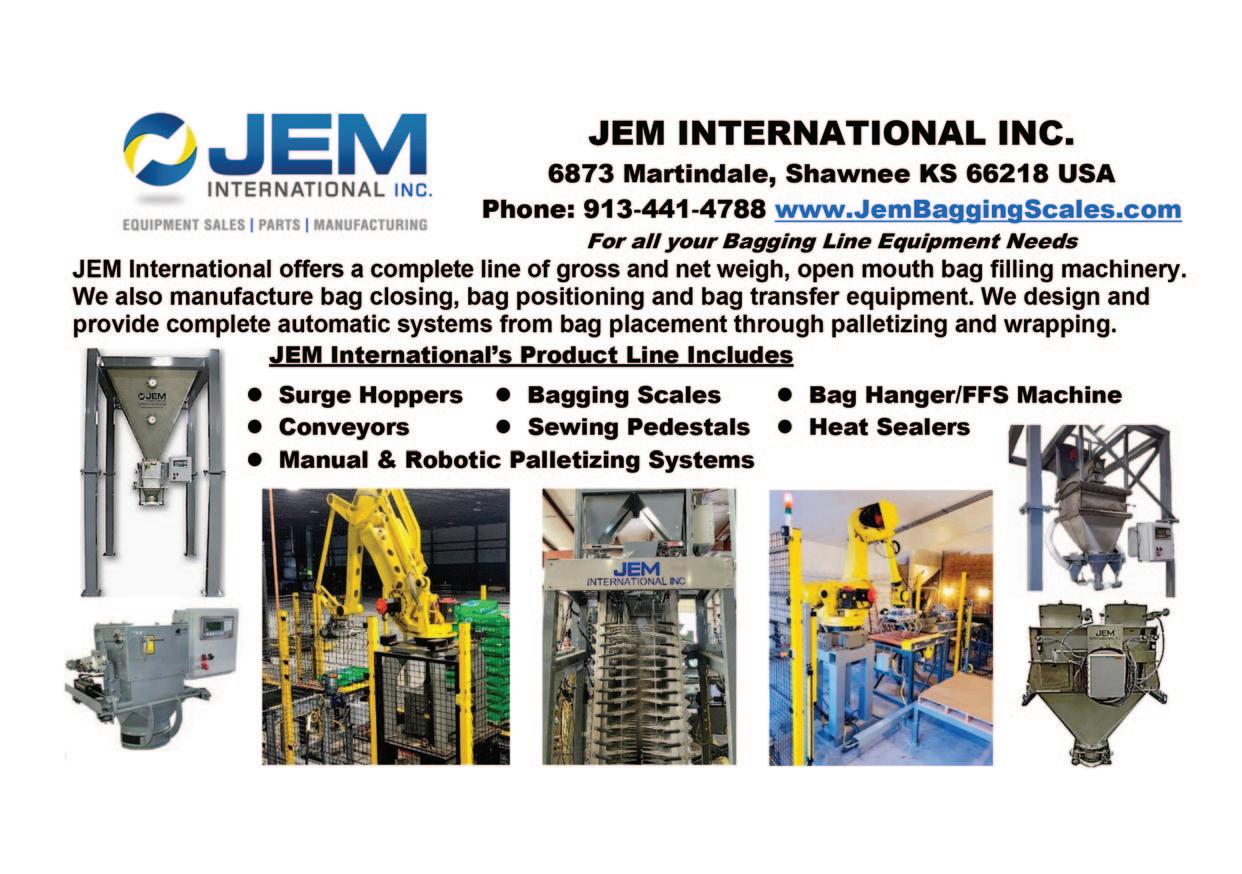
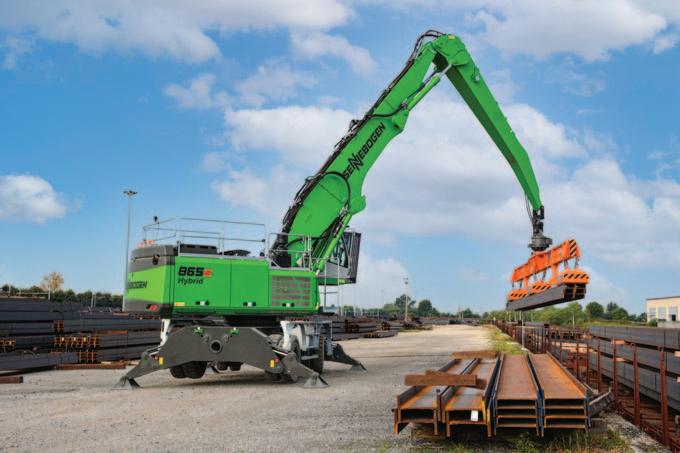
The protective grating as special equipment of the Maxcab Industry cab provides even more safety. ENGINEERING & EQUIPMENT

device, the 865 E moves steel products, such as steel beams or wire rods, weighing around seven tonnes. In the past, the steel products needed to be secured in a complicated procedure by chains and belts when being lifted by a crane, but from now on the magnet completely eliminates the need to secure the load during the handling process. This saves a massive amount of manpower and time, and also makes the daily work routine substantially safer for the operators.
Another highlight is the integrated scale, which allows the operator to check the weight of the handled goods. Directly in the cab, the operator receives instructions from the control centre on how the freight should be arranged to be loaded onto trucks or wagons. And thanks to the integration of the scale into Trailer S.p.A.’s in-house computer systems, the operator receives direct feedback on the correct charging of the transport vehicle. In order to save time, the required transport documents are already prepared in the background and generated in real time.
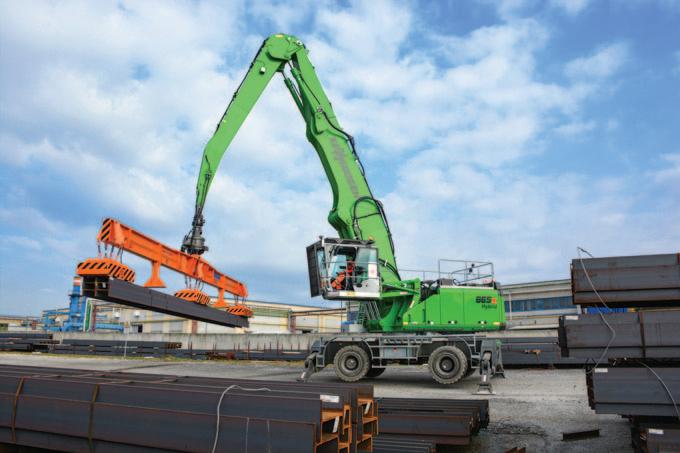
THE 865 E HYBRID NOT ONLY SAVES TIME, BUT ALSO UP TO 50% ENERGY As the name indicates, SENNEBOGEN
About seven tonnes of load can be lifted with the magnetic lifting beam: trucks and wagons are prepared for onward transport in a timesaving manner and with less manpower required. installs the proven Green Hybrid recuperation technology in the 865 E Hybrid, which can save up to 50% energy and thus a lot of fuel when used correctly. Hybrid means that in addition to a fuel-saving 261kW Stage V diesel engine, a second component is installed that significantly supports the engine’s performance.
Here, a separate hydraulic circuit is used, consisting of a third hydraulic cylinder between the two lift cylinders and piston accumulators in the protected rear area of the machine. When the boom is lowered, the repelled oil compresses gas in the accumulators to store this energy until the next working stroke. Just like a spring that relaxes, the boom moves upward without requiring any further energy, and the engine is completely relieved by the temporarily stored energy during the lifting process.
As simple as the system’s operating principle is, the more effective it is in daily operations. Gabriel Hutu, Operations Manager of Trailer S.p.A.’s rail terminal, is also convinced of this and sums up: “For us, this machine is a symbol of the company’s modernization. It changes the way we think and work, increases operational safety and reduces the environmental impact of our processes. Thanks to its large lifting capacity, even at maximum reach, we can transfer loads of seven tons on average from a truck to a rail wagon or vice versa enormously fast and fuel-efficient, too.”

Smart technology specialist RCT and equipment manufacturer Komatsu have delivered a bespoke technology project to safeguard bulk handling operations at a major port in New Caledonia.
The technology transforms the efficiency of operations by allowing local companies to quickly and effectively clear storage areas in bulk carrier ships while protecting port crews from hazardous working conditions within the ship’s hold.
RCT, in partnership with Komatsu, integrated the proven and interoperable ControlMaster® Portable Teleremote solution with a Komatsu PC228 Excavator.
RCT’s customer service team provided comprehensive remote support to Komatsu staff based in New Caledonia to efficiently commission the machine.
The technology package enables the excavator operator to stand at a safe vantage point while accessing the full range of machine functions, as if they were in the excavator’s cab.
The solution includes a pitch and roll indicator which provides the operator with real-time information on the excavator’s status and position within the ship hold.
The pitch and roll indicator will enable the operator to make more informed decisions about the status of the machine within the hold and prevent unnecessary machine damage.
“We really appreciate RCT’s support for this pilot project which is a very good step forward in terms of innovation and safety improvements onsite,” said Komatsu Technical Manager Jean Damour.
“This kind of professional relationship helps us improve our technical skills and ability to adapt to changing site requirements, while focusing on customer needs and supporting their activities.”
RCT Account Manager Wayne Carrington said the project demonstrates how ControlMaster® can be applied to any machine for use in a broad range of industries.
“We empowered Komatsu with the knowledge necessary to commission the equipment and deploy it to site with support from our international Customer Service team,” he said.
“Port staff are pleased with the easy-touse interface and signal strength which enables them to work quickly and effectively.
“We are very pleased to work with Komatsu to deliver this project and we regard them as a competent and highly professional company.
“While ControlMaster® has a proven history in mining, this project demonstrates the technology can meet the demands for bulk handling operations at ports around the world.”
ABOUT RCT
RCT is an innovative Smart Technology company with the expertise to evolve entire industries. It designs, manufactures and delivers technology and service solutions to support clients around the world in multiple sectors including mining, industrial, agricultural and civil. With more than 49 years of success,
RCT leverages knowledge and insight to provide clients the advantage of measurable
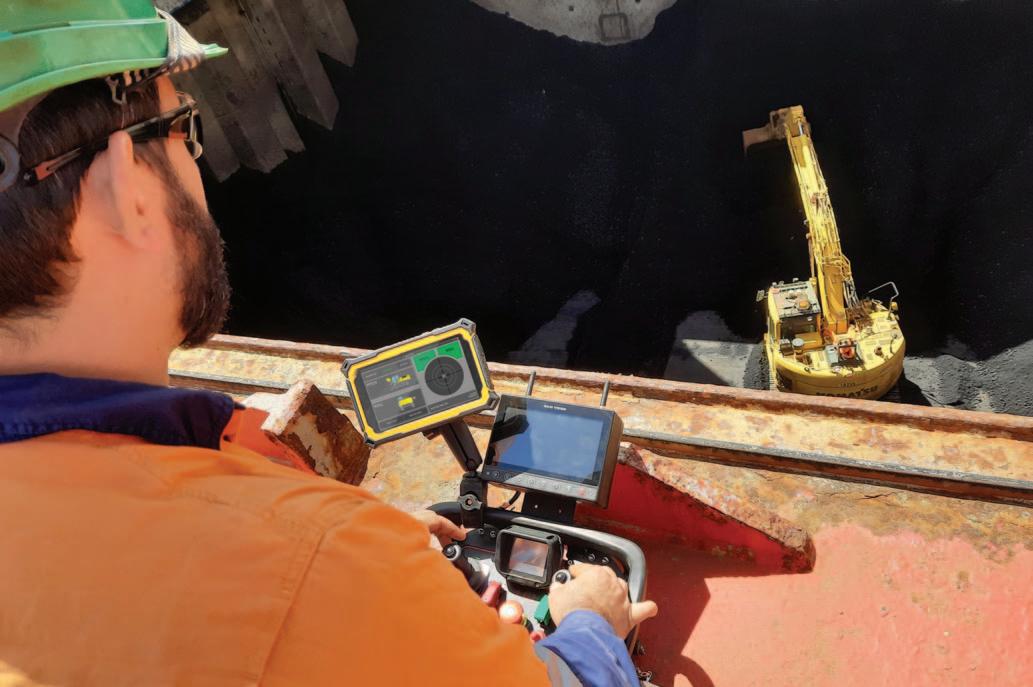
value —increased profitability, productivity, efficiency and safety. Since the 1970s, RCT has traversed all corners of the globe. Its team has grown to 215+ committed people working with clients in more than 71 countries worldwide, from Australia to Africa, Asia, Russia, North America and Latin America.
With its unique way of viewing the world, intelligent solutions and backed by exceptional support, service and training, RCT is globally renowned in smart guidance, teleremote and remote control automation solutions for the mining industry. It continues to listen, see, think, create and evolve solutions that lead to better profitability, productivity and safety for its clients.
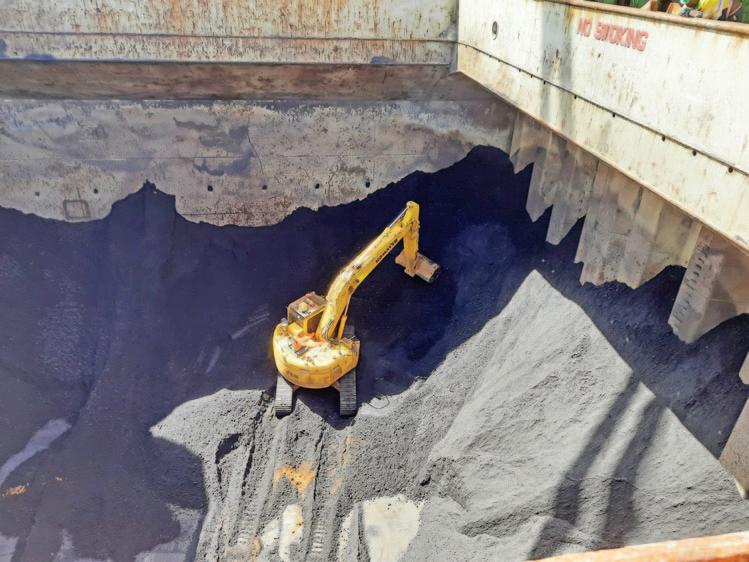
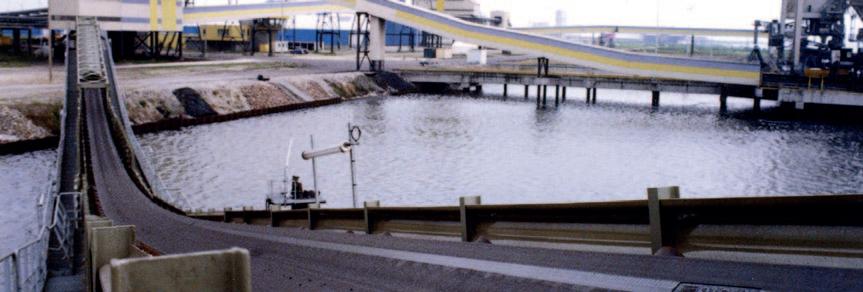
ISO 9001
WE MANUFACTURE IN ITALY TO SUPPLY ALL AROUND THE WORLD
Via A. Colombo, 144 21055 Gorla Minore (VA) - Italy Phone +39 0331 36.51.35 Fax +39 0331 36.52.15 www.sig.it E-mail: sig@sig.it