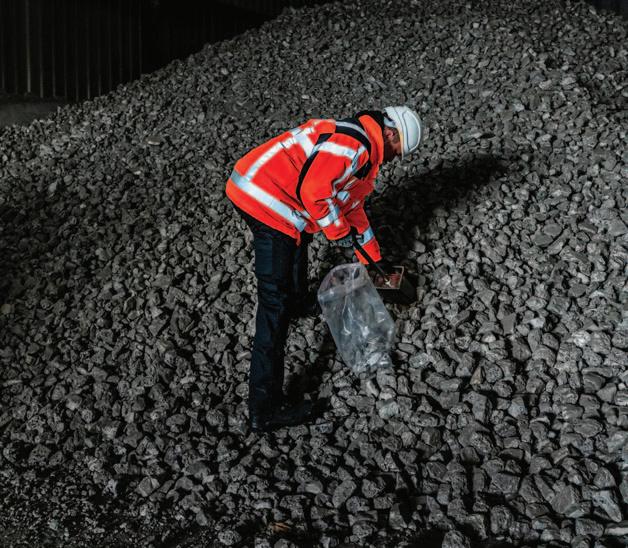
22 minute read
A FINE REPRESENTATIVE SPECIMEN: INSPECTION, ANALYSIS & SAMPLING
Inspection, analysis & sampling A fine representative specimen
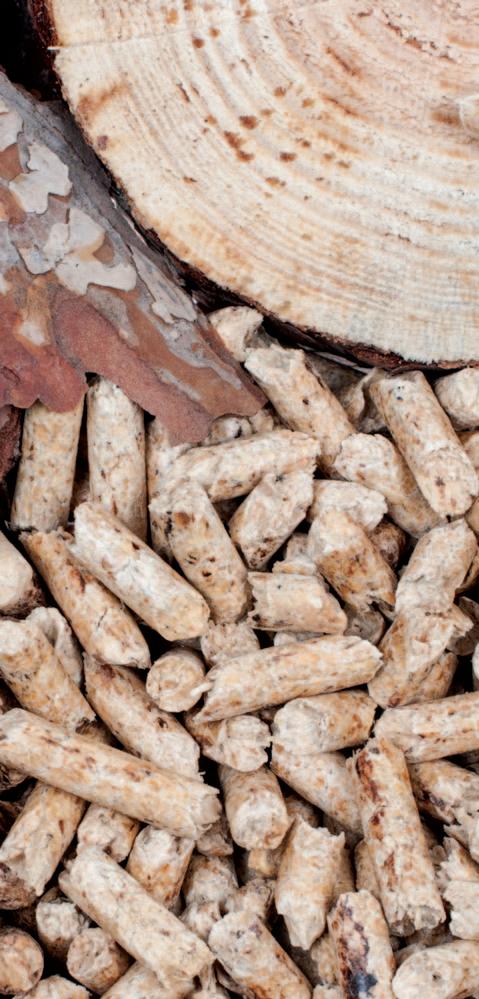
PSB Inspection focuses primarily on coal and coalrelated products, but is also expanding into markets such as biomass, alternative fuels, minerals, metal and slag, flyash and fertilizer.
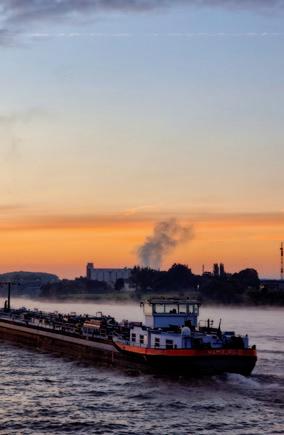
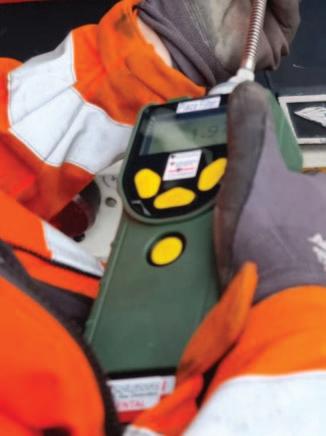
Jay Venter
PSB Inspection – reliable sampling services in a turbulent market
PSB Inspection was established by Peter Bagchus, CEO and owner, in 2017.
The company operates from its head office in Vlaardingen (Rotterdam port area). It has highly qualified and experienced senior surveyors and an experienced sampling preparation team. PSB Inspection runs its own laboratory with highly qualified and experienced laboratory technicians which is all managed by the operational team in close conjunction with the management team members, who have been active in this type of business for decades. Currently, PSB Inspection focuses primarily on coal and coal-related products. However, bearing in mind that the world — and the energy market — is changing vastly and rapidly, it is also working hard to expand into markets such as biomass, alternative fuels, minerals, metals, slag, flyash and fertilizer, which are under development in different phases.
This all takes place with a clear eye on high quality services in the field of inspection, sampling, sample preparation, analytical services and weight ascertainment required by PSB Inspection’s customer base. Recently, the company expanded its service portfolio with gas/toxin measurement (four qualified and certified gas/toxin measurement experts including high quality, certified equipment). More expansion is being planned.
Other than Europe, PSB Inspection can offer its services in various other countries (South Africa, Turkey, UK, LATAM) as well and is also expanding its country portfolio. All is being co-ordinated from its head office, obviously under the applicable ISO standards 9001 and 17025. Certifications to 17020 and GAFTA are on the way. In addition, PSB Inspection also uses its own internal quality procedures.
PSB Inspection continues to focus on the future, a major topic now is the energy transition: the replacement from fossil fuels to products that emit less CO2 than coal. This is quite a challenge. Fossil fuels are still widely used because of past developments: power plants were built, and coal was plentiful and affordable. This cannot be replaced overnight. A direct transition from coal to biomass is impossible. This is mainly due to the technology of current power plants: biomass has a different composition than coal and must be treated differently. Current power plants are completely focused on burning coal. There is also an economic aspect: biomass is much more expensive than coal. Two major steps must therefore be taken before the transition can be fully implemented: power plants must be converted, and it must become more financially attractive to switch to biomass. The fact remains that the energy mix will increasingly consist of renewable energy in the coming years. PSB Inspection is happy to contribute to this development.
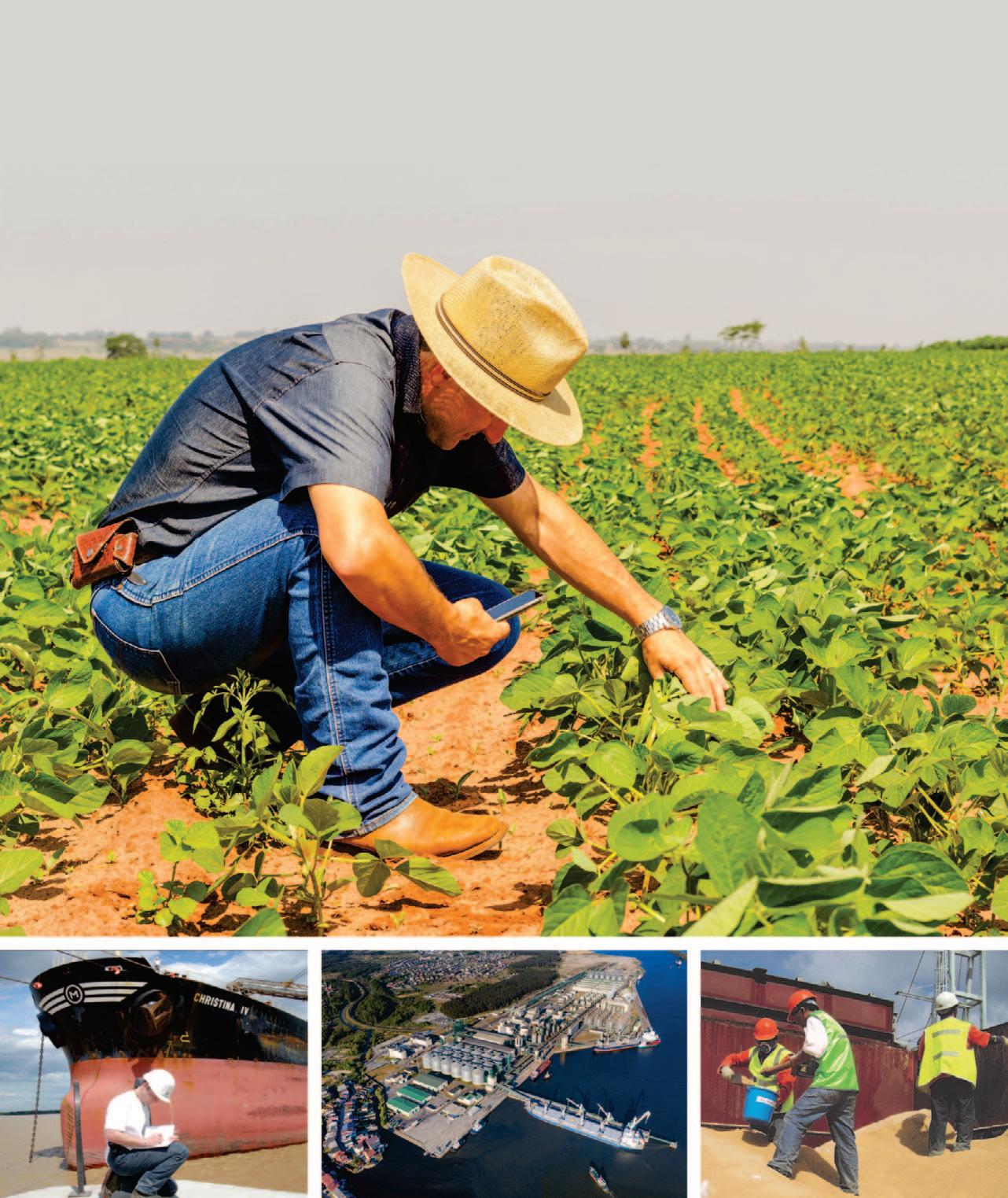
Representative, real time moisture measurement for TML monitoring during shiploading
Transportable Moisture Limit (TML) is typically monitored through sampling and laboratory analysis that complies with IMSBC Code during bulk commodity loading of ships, writes Henry Kurth, Chief Marketing Officer, Minerals Consultant, Scantech International Pty Ltd.
Shiploading may be interrupted until laboratory results are available to confirm average moisture content is below the TML where material type has a high likelihood of nearing, or exceeding, the TML. Where loading is not monitored, moisture content may not be known until after loading is completed. If average moisture from sample testing is then found to exceed the TML, then the ship should be unloaded, in part at least, and drier material added to ensure average moisture is below the TML.
INTERCARGO reported that liquefaction of nickel ore and bauxite bulk cargoes has over the last ten years resulted in five capsize or sinking events causing the loss of 70 lives. It found “that not only were IMSBC Code requirements not being followed, especially in relation to testing and certification of cargo condition, but that there was also lack of adequate assessment and monitoring of the condition of cargoes being loaded in the cargo holds by representatives of all interests ... INTERCARGO is urging all shipowners, operators, and seafarers to exercise extreme caution when accepting nickel ore, bauxite, iron ore fines, ball clay and other cargoes that have the potential to liquefy.”
Technologies exist to monitor moisture content during ship loading operations in real time, and while not able or intended to be used for certifying moisture content, they are nonetheless a useful indicator of free moisture content when correctly configured and calibrated. Loading operations can be paused when measured moisture approaches or exceeds the TML and drier material sought before loading continues.
Representative measurement requires fully penetrative and continuous measurement through the conveyed profile. This is effectively achieved using microwave transmission technology which can often produce measurement precisions of better than 0.5% moisture. This requires a safety factor to be considered when loading a ship, even when calibration is routinely checked and precision verified. If 10% TML is appropriate for the commodity, then an alarm may be raised at 9% moisture from the analyser results. The analysers utilize a belt weigher input to provide tonnage weighted average moisture for the whole load, or loads filling each compartment in a bulk cargo ship. The system is unaffected by particle size, belt speed, segregation or layering within the flow.
Scantech International Pty Ltd TBM200 series microwave moisture analysers have been adopted by most major iron ore companies for monitoring moisture at their mine sites, particularly for hematite and goethite ores. TBMs are used in over 20 commodities for free moisture measurement and appear, from customer feedback, to provide leading measurement performance in the resources sector. Magnetite concentrates are not suitable for moisture measurement using microwaves. A different representative measurement technique called Fast Neutron and Gamma Transmission used in Scantech’s CM100 series analysers achieves precisions of as low as 0.2% moisture on materials where the microwave technique is unsuitable.
Feedback received from the resources sector indicates other technologies, such as surface measurement and conductance systems are not suitable for large conveyed flows as moisture content varies through the conveyed profile and that not one depth within that profile can be relied upon to be representative of the full flow. Vibration, particle size, particle shape, packing of grains, capillary action and ambient conditions affect the moisture distribution through the profile much the same way that tapping a bucket of wet sand causes the moisture to migrate to the surface. In coarser materials the moisture tends to concentrate towards the base as it drains more freely and hence coarser materials pose less risk in liquefaction, but moisture content still varies throughout the conveyed profile.
Measuring moisture representatively and with high levels of confidence in conveyed flows in real time can be a relatively inexpensive and effective way to monitor and manage moisture and minimize potential loss of life and assets when used in conjunction with compliant sampling and laboratory assay practices.
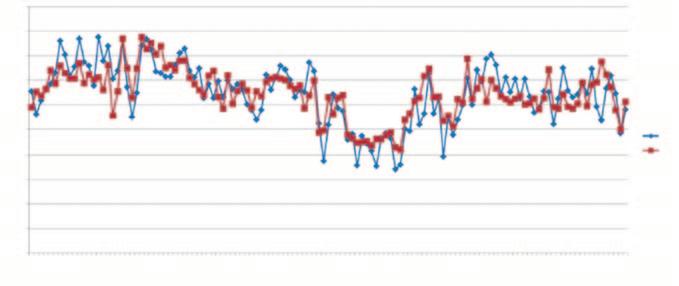
Scantech TBM200 series microwave moisture analyser for monitoring TML during ship loading.
14 13 12 11 10
Moisture (%) 9 8 7 6 5 4
1 10 19 28 37 46 55 64 73 82 91 100 109 118
Sample number Lab TBM
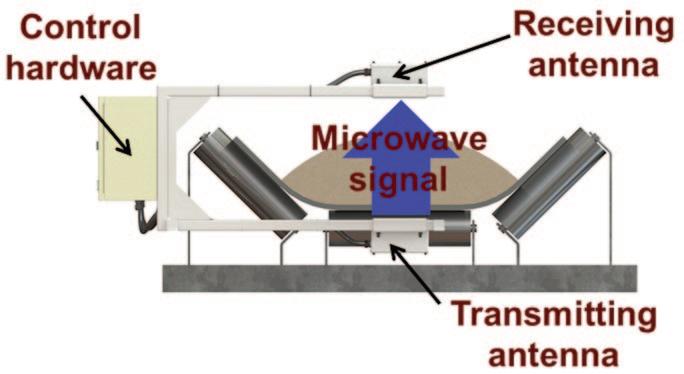
Real Time Instruments (RTI) is an Australiabased company specializing in on-line elemental and moisture analysis of bulk materials providing operators with process data to make pro-active real-time control decisions to improve plant efficiency and bottom-line profitability.
RTI can apply its high-technology products to provide real-time analysis to many industries, assisting companies to identify inconsistencies and help maximize their profits and bottom line — from pit to port and beyond.
RTI’s customers, across the world, have come to count on the company’s suite of elemental analysers and moisture analysers to reap maximum yield from their operations. Having access to real-time results empowers them to make intelligent decisions which means they can recover more, waste less and take full control of their processes.
Across the full spectrum of traditional mining, new and critical minerals, cement production, power generation, food production and shipping, RTI’s suite of globally respected elemental analysers and moisture analysers leads the market in delivering real outcomes which boosts efficiencies and saves millions of dollars!
RTI’s equipment helps customers reach Net-Zero targets through improved efficiency, tighter quality control and reduced emissions.
RTI collects and delivers on-line real time data to operators, meaning they can make critical decisions — on the spot, when it matters.
Below are a few case studies of recent RTI projects, which illustrate the effectiveness of its products.
ALLSCAN DELIVERS BETTER STOCKPILE CONTROL, ON-SPEC ORE AND 5% PA PRODUCTIVITY BOOST
THE CASE: ALLSCAN — IRON ORE, STOCKPILE MANAGEMENT.
The challenge: the customer was processing varied grades of iron ore, but was unable to identify the quality of product once it has passed through the process facility and had been stacked. A comprehensive stockpile management system was already in place. However, operators needed to update that system with lab data as it became available — usually six to eight hours after it had been stacked. This led to an unacceptable lag and an inability to make critical decisions when it mattered. The purpose: knowing the Iron (Fe) content of the product would empower the customer with real-time oversight of the ore blending process. This meant they could gain maximum yield, best exploit ore value and meet content specifications. The discovery: RTI's first step was to understand the customer's processes, systems and specific challenges. From there, RTI developed a high-value, tailored solution which became an integral part of the stockpile software. The installation of an AllScan on the stockyard conveyor belts meant that operators immediately saw the real-time results. As the product was stacked, the stockpile management software logged the same data to include in the result. By doing so, this provided an indepth display showing what product was where, as well as the quantity, and most importantly, where to reclaim it. The result: by tailoring an integrated solution using the AllScan, RTI’s customer was able monitor its stockpile in real time, blend product to specification, and not 'give away' any high-quality iron ore. The ability to blend high-grade ore with regular ore, to create a superior product, in larger quantities, resulted in a profit increase of approximately 5% — and a significant improvement to revenue. Other potential commodity applications: this technology has application in the context of stockpiling, where material composition is a critical factor, across the full spectrum of mineral and ore mining and processing.
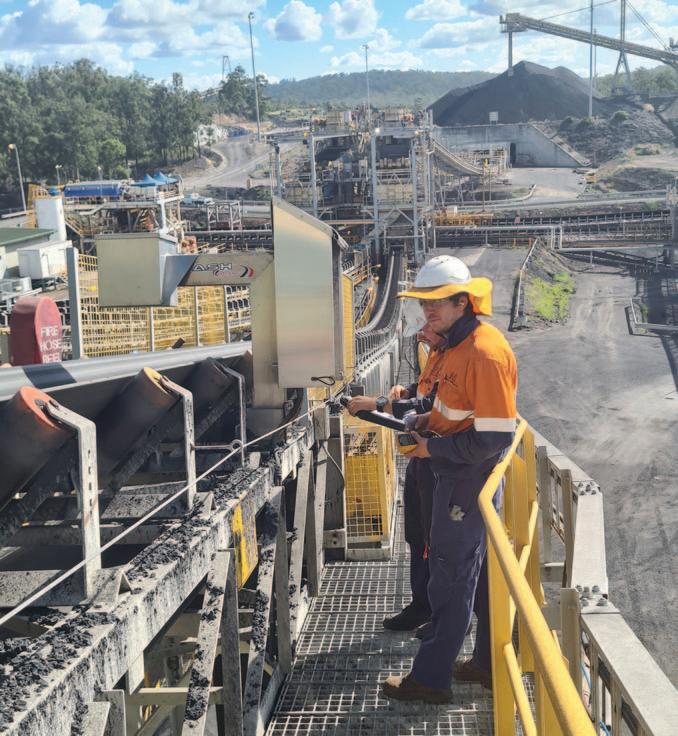
ALLSCAN HELPS MINE OPERATORS DELIVER QUALITY COAL TO POWER STATION IN REAL TIME
THE CASE: ALLSCAN — ASH ANALYSIS
The challenge: the customer needed realtime data about the grade of product being sent to its power station, to help maintain running conditions in the wash plant. The three main results sought were around ash, moisture and specific energy data. However, elemental composition of the ash was also useful. Without the AllScan, the only means of determining these results was to wait for laboratory samples. This usually takes two to three days for critical results, and two to three weeks for full elemental analysis, by which time product has been delivered to the power station. The purpose: knowing the composition of the coal in real time would enable mine operators to make changes to wash plant conditions in situ. Specifically, where product is too low, less coal is rejected,
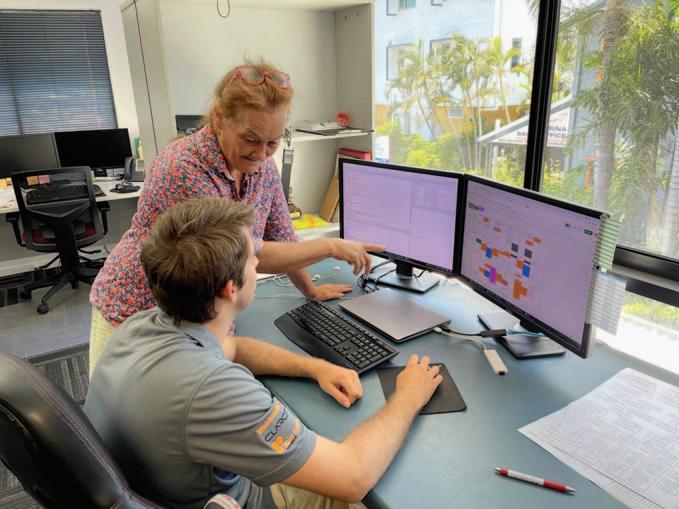
saving money on reclaiming. Similarly, if product was too high and not within specification, this would enable more to be washed or rejected, to bring product back within specification, saving fines from the power station. The discovery: RTI was able to prescribe an AllScan to a targeted install location, enabling real-time analysis of ash, moisture, specific energy and elemental composition of the product. The operators were given full access to the instantaneous results, as well as a rolling 12-hour average, that operators could use to understand the tonnes-weighted average of the previous 12 hours. The result: the application was a success. The operators use the instantaneous results to monitor, in real time, the composition of the product, and minorly adjust the plant accordingly. Additionally, the rolling 12 hour results enabled the maintenance of an average quality for their shift, which remains within power station specification. Daily average data shows the operation was within its specified 28% ash, 74% of the time, and the operation never missed spec by more than 1%. The site is satisfied with the AllScan's performance; such that the customer is now working to calibrate AshScans coming directly from the run of mine. These are placed immediately prior to the entrance of the plant, enabling operators to know product quality received from the mine and being fed into the plant. The AllScan has proven vital to this customer's plant operations; so much so, that if the analyser is not operating, the whole plant is shut down. For this reason, the site has an extensive 24/7 PSA (Product Service Agreement) with RTI to maintain the analysers and ensure they are working at their best. Other potential commodity applications: fundamentally, the same technology can be applied to the delivery of on-spec material in product processing minerals applications.

MOISTSCAN DETECTS HIGH-MOISTURE EVENTS, SAVING 13 HOURS OF PRODUCTION MONTHLY
THE CASE: MOISTSCAN — IRON ORE, STOCKPILE MANAGEMENT
The challenge: persistent 'high moisture events' occurring during plant operation, led the customer to work with RTI in developing a solution which gave it realtime visibility and control. When the customer’s product moisture passed 12%, processes were forced to be stopped and reset to avoid blockage and malfunction of apparatus. This meant unproductive — and costly — downtime; and once the plant was forced to stop, it would take five hours to be restored to full capacity. Further, as moisture was measured by the laboratory, results would typically take between two and four hours to be returned. The purpose: RTI’s primary focus was to give the customer visibility and control over the product moisture operators to increase uptime and minimize downtime on plant feed by monitoring added moisture content to ensure the 12% mark is never breached. The discovery: once the problem of consistent 'high moisture events' was discussed with RTI, the company was able to provide a real-time moisture analysis solution by implementing a MoistScan on plant feed-in and feed-out. By doing so, operators could see the moisture value as it happened, enabling them to avoid breaching moisture limits, meaning the plant could continuously, and more reliably, run at optimum capacity. The result: since the implementation of the MoistScan solution, this site has reported a complete eradication of 'high moisture events', going so far as using the MoistScan to automate the plant. By preventing the constant plant downtime, an average of 13 hours of production have been recovered — which equates to about $2.7m — per month. When throughput is 2,100-plus tonnes/hour, that adds up to millions of dollars in recovered revenue.
Other potential commodity applications: this technology has application in the context of stockpiling, where moisture content is a critical factor, across the full spectrum of mineral and ore mining and processing.

ALLSCAN PROVIDES ACCURATE ONLINE ASH ANALYSIS, IMPROVING AIR QUALITY
THE CASE: ALLSCAN — COAL-FIRED POWER
STATION, ASH CONTROL
The challenge: more than 90% of India's population lives in areas where the air quality is below the World Health Organization's standard, with coal-fired power plants being a major contributor to this pollution. To combat this growing issue in 2014, the Ministry of Environment and Forest had imposed 34% ash limit on all NTPC's power plants. Previously these power plants had to rely on manual laboratory data, taking up to 24 hours to receive a result, by which time the out of

spec coal had already been burnt. The purpose: by knowing the real time ash content of the coal being fed into their bunkers, NTPC can make real-time decisions on the feeding of their boilers. This allows the operators to accurately blend their coal during reclamation to ensure that all environmental targets are being met. The discovery: RTI visited multiple power plants in India to tailor a viable solution for the global issue faced by all coal-fired power stations. RTI was able to identify ideal installation locations for its clients and develop appropriate commissioning procedures that maximized accuracy and minimized disruption to process. This allowed the client to rapidly respond to product changes by blending appropriate coal qualities to ensure that their plant is running at maximum efficiency. The result: in having a high accuracy instrument, the AllScan, on the infeed to its bunkers, the client can monitor their coal quality in real time. This enables the operators to blend their products to ensure the coal fed into their plant is of a lower ash content. This greatly reduces the negative impacts of burning coal to produce power, greatly improving the air quality and the respiratory health of the people living around these power stations. An analyser utilized in this application could see the reduction in more than 1,400t of CO2 and the saving of more than 25,000t of coal per unit per year of operation. Other potential commodity applications: fundamentally, the same technology can be applied in the bio-power sector, where matter is being burned and ash and sulphur content reduction can directly corelate to a reduction in carbon dioxide emissions.
ALLSCAN PROVIDES OPERATORS REAL TIME QUALITY CONTROL OF ORE GRADING
THE CASE: ALLSCAN — BAUXITE, ORE MANAGEMENT
The challenge: out-of-specification product poses costly challenges for operations, leading to the unnecessary waste of time, resources and money with hefty penalties applied for non-compliance. To date, the most effective means of mitigating against this has been through sampling. Traditional laboratory testing was accurate but had a turn-around of two to three days, rendering the data obsolete in this specific context. This is what led the customer to work with RTI in developing an in-situ, online, real-time sampling analysis solution. The purpose: to enable full-spectrum visibility of elemental composition, RTI worked with the customer to deliver highly-accurate data, minute by minute. This informed an ability to achieve the specific, desired outcome, to maintain a specific alumina level, while simultaneously limiting silicon dioxide levels. The discovery: working with the customer, RTI's Research and Development team found the AllScan to have a unique advantage in addressing the challenge, in providing real-time analysis of the product to deliver accurate estimates for the alumina and silicon levels, empowering operators to make key decisions. The result: the AllScan allowed operators to respond to product deviations, in real time, according to the data available to them. This enabled the maintenance of product to specification. The data collected when the MoistScan analyser was initially installed, showed alumina value regularly falling below sites limits. Six months later, having had visibility and control over moisture levels, the site reported an increase of almost 60% in Good Alumina recorded, and a reduction in reject product from 56% to zero. Other potential commodity applications: the challenges faced in the context of alumina are applicable in across a number of ores and bulk materials. Where product quality and elemental composition are key variables in an operations cost and grade control, there is a proven application for AllScan technology.
BAUXITE, ORE MANAGEMENT
Initial data 6-month data Good Al 11% 70% Penalty Al 32% 30% Reject Al 56% 0%
ALLSCAN ASSISTS SCREENING TO IMPROVE MATERIAL GRADE BY UP TO 50%
THE CASE: ALLSCAN — NICKEL ORE, STOCKPILE AND MINING MANAGEMENT.
The challenge: RTI’s customer operates a screening plant that upgrades mined ore before being stored on stockpiles, prior to further processing. Management of the screening plant operations were undertaken based on the results of samples taken of the in-feed material; however, the lag on waiting for analytical results from these samples made making meaningful real time decisions impossible. This limited the customer’s ability to maximize the upgrade of the ore or control the levels of deleterious components. The purpose: by determining the levels of Ni, Fe, SiO2, MgO and other elements in the mined ore, the customer was provided with real-time oversight of the in feed to the ore upgrading process. This meant they could make decisions about in pit operations and screening operations to control and maximize the grade of stockpiled material. The discovery: RTI's first step was to understand the customer's specific challenges. From there, it adjusted the calibrated result of the AllScan to report material parameters defined by the client as best being suited to inform its decisionmaking process such as the SiO2 /Mg, Fe/Ni and Ni/Co ratios. RTI worked with the customer to validate the analyser performance of the AllScan to allow process control decisions to be made based on the generated results with confidence. The result: by tailoring an integrated solution using the AllScan, the customer was able monitor its feed material from the mining operations. The ability to control the ore upgrade process in real time allowed for a 50% increase in the grade of the product at the infeed to the furnace. This combined with the ability to greatly reduce the variation in deleterious competent has had a positive impact on both power consumption costs and CO2 emissions. Other potential commodity applications: this technology has applications in the context of ore upgrading and stockpiling, where material composition is a critical factor, across the full spectrum of mineral and ore mining and processing. DCi
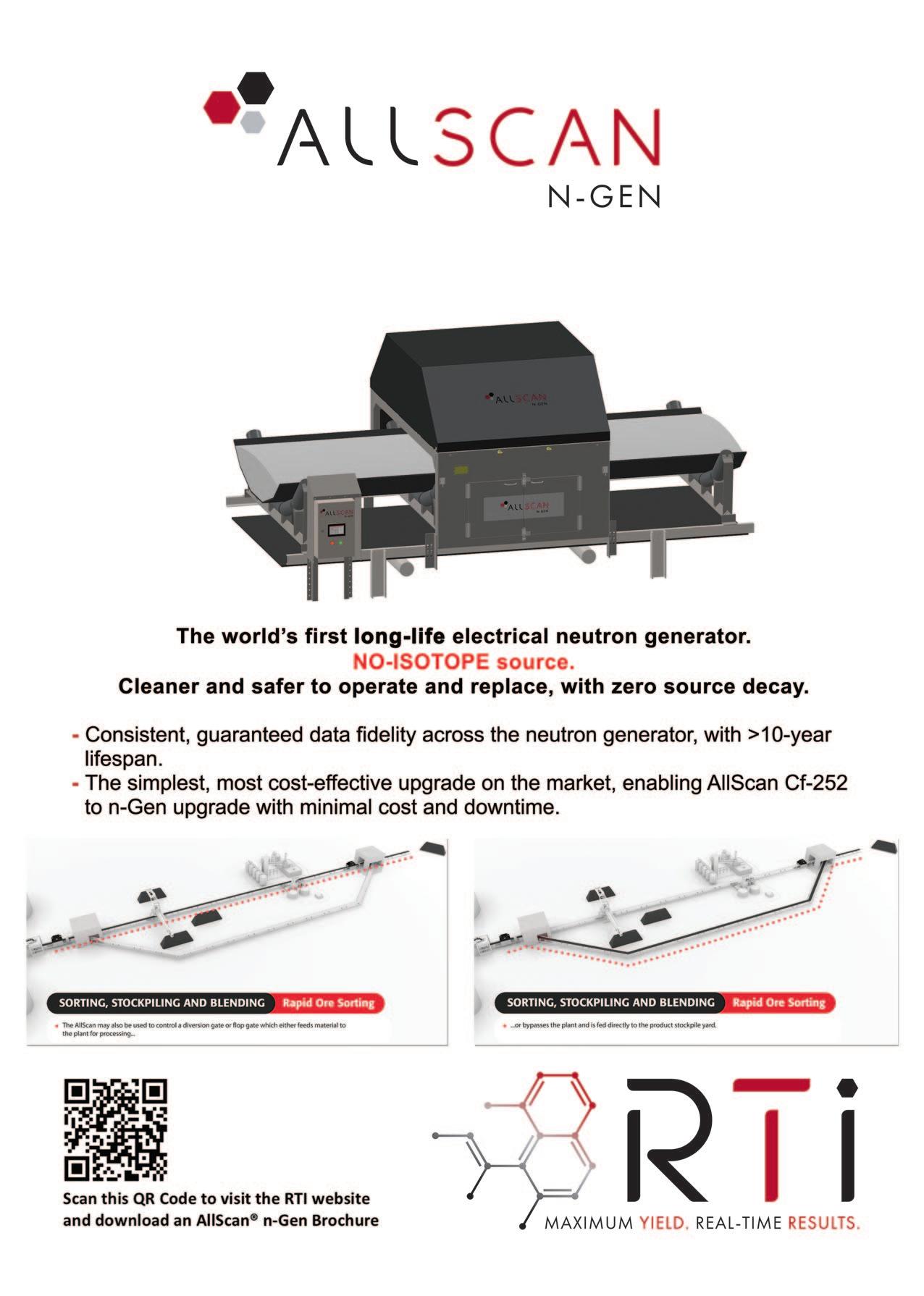
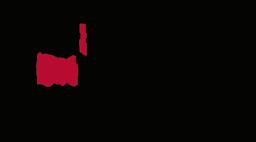
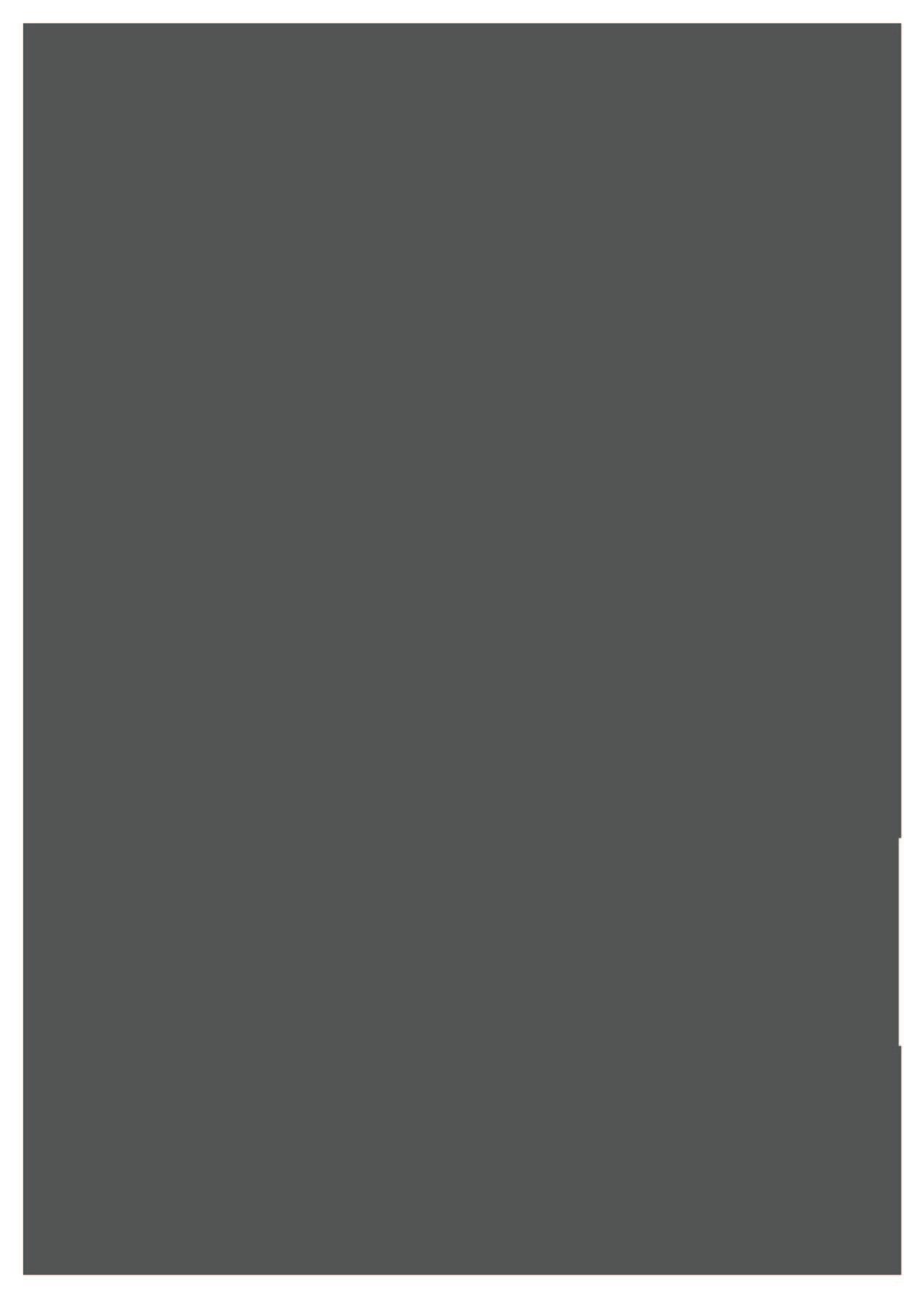
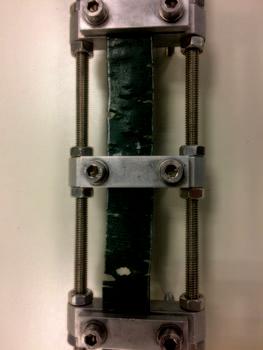
The effects of ozone & ultra violet on rubber conveyor belts
CONVEYING ADVICE
There are two ‘invisible’ and inescapable factors that have a huge influence not only on the operational lifetime of rubber conveyor belts but also their safe operation. Those factors are ozone (O3) and ultraviolet light (UV). Contrary to popular belief, the damage they cause is not limited to high altitudes or sunny climates.
FROM PROTECTOR TO DESTROYER Ozone (O3) occurs naturally in the upper atmosphere. It is formed continuously by the action of solar ultraviolet radiation on molecular oxygen (O2). At high altitude, ozone acts as a protective shield by absorbing harmful ultraviolet rays. Wind currents carry O3 to the Earth’s surface. It is here, at low altitude, that ozone becomes a pollutant. Ground level or ‘bad’ ozone is not emitted directly into the air, but is created by the photolysis of nitrogen dioxide (NO2) from auto mobile exhaust and industrial discharges. The reaction that occurs between the molecular structure (double bonds) and ozone is known as ozonolysis.
Even tiny traces of ozone in the air will attack the molecular structure of rubber. It increases the acidity of carbon black surfaces with natural rubber, polybutadiene, styrene-butadiene rubber and nitrile rubber being the most sensitive to degradation. The first visible sign is when cracks start to appear in the surface of the rubber. Further attacks then occur inside the freshly exposed cracks, which continue to grow steadily until they complete a ‘circuit’ and the product separates or fails. The cracks are always oriented at right angles to the strain axis. The dynamic stress that a conveyor belt undergoes while in operation is considerable. Ozone attack occurs at the points where the strain is greatest.
Although ozone concentrations can differ from one location to another, ground level ozone pollution is everpresent and its effects should therefore never be under-estimated. ULTRAVIOLET LIGHT Ultraviolet light from sunlight and fluorescent lighting also has a seriously detrimental effect on rubber because it accelerates rubber deterioration by producing photochemical reactions that promote the oxidation of the rubber surface resulting in a loss in mechanical strength. This is known as ‘UV degradation’. In belts that are not fully resistant because the manufacturer has neglected to add antiozonants to the rubber compound, the combined effect of ozone and ultra violet not only dramatically reduce operational lifetime, they also cause significant environmental and health and safety problems. This is because fine particles of dust penetrate the cracks and are then discharged (shaken out) on the return (underside) run of the belt. These dust emissions are of particular concern in ATEX regulated areas where materials such as biomass are being carried. ENTIRELY PREVENTABLE The damage caused by ozone and ultraviolet is entirely preventable. Several years ago, we at Dunlop were among the very first in the world to make use of new technology that enabled the effects of ozone to be tested and measured. We equipped our laboratory in Drachten in the Netherlands with the very latest ozone testing equipment and introduced
mandatory testing to EN/ISO 1431 international standards for all Dunlop rubber products. As a direct result, special anti-oxidant additives that act as highly efficient antiozonants and protect against the damaging effects of ozone and ultra violet became an essential ingredient in every Dunlop rubber compound without exception. EN/ISO 1431 TESTING To scientifically measure resistance to ozone in accordance with the EN/ISO 1431 test method, samples are placed under tension (eg. 20% elongation) inside an ozone testing cabinet and exposed to highly concentrated levels of ozone for a period of up to 96 hours (@ 40°C, 50pphm and 20% strain). Samples are closely examined for The first signs — small evidence of cracking at two-hourly cracks appear in the intervals and the results carefully surface of the rubber. measured and recorded. Experience has determined that in order for the rubber to be regarded as adequately resistant, the pass criteria needs to be that the rubber sample does not show any signs of The ‘longer term’ effects of cracking within ozone & UV can occur the 96-hour within a few months. period. Worryingly, from an endThe damage that ozone & UV users point of causes should never be under- view, the vast estimated. majority of samples of our competitors belts tested in our laboratory typically fail within only six to eight hours. It is for this reason and despite its crucial importance, ozone and UV resistance is very rarely, if ever, mentioned by conveyor belt manufacturers and suppliers. This is because the antiozonants needed to protect the rubber cost money. The best advice is to make ozone & UV resistance a constant requirement when selecting any rubber conveyor belt. Dunlop Conveyor Belting