
12 minute read
FLSmidth announces completion date for the acquisition of TK Mining
CREATION OF A LEADING GLOBAL MINING TECHNOLOGY AND SERVICE PROVIDER On 11 August, FLSmidth announced that all conditions and requirements for the acquisition of thyssenkrupp’s Mining business (TK Mining) have been met. In accordance with the sale and purchase agreement, final closing of the transaction will take place on the last business day of the month. Accordingly, the transaction will close on 31 August 2022. All regulatory clearances have been obtained without imposition of any competition-related remedies.
TK Mining is a leading full-line supplier of solutions for mining systems, material handling, mineral processing and services. The combination of FLSmidth and TK Mining will create a leading global mining technology and service provider with operations from pit-to-plant with a strong focus on productivity and sustainability.
FLSmidth Group CEO Mikko Keto commented: “Today’s announcement marks a significant milestone in the history of FLSmidth. We are very excited to soon welcome our ~2,000 new colleagues and TK Mining’s customers to FLSmidth. The completion of the acquisition contributes to FLSmidth’s strategic growth ambitions within Mining. Our combined company will offer customers a stronger, complementary value proposition, while creating significant aftermarket opportunities, driving value creation through compelling synergies and further strengthening our sustainability and digitalization agenda.”
Further impact of the transaction, including updated financial guidance for 2022, will be communicated no later than in connection with the release of FLSmidth’s financial results for the first nine months of 2022 on 8 November 2022.
Van Beek introduces ‘Sisca’ online customization configurator
With the introduction of Sisca, an online configurator for screw conveyors, Van Beek once again demonstrates its ability to innovate. This unique customization tool enables Van Beek’s knowledge and expertise to be available 24/7. “With Sisca, we offer customers in our sector an unrivalled opportunity to receive a customized quote, including delivery times, in near real time,” says Perry Verberne, Van Beek’s managing director.
With its innovative configurator Van Beek takes a stride forward in the configuration procedure for screw conveyors. Sisca enables Van Beek customers to independently configure a customized solution, which is beneficial in terms of both price and delivery time. This makes it possible to configure a screw conveyor within the available budget, and without compromising on the high standards of quality for which Van Beek is recognized.
REVOLUTIONARY TOOL Verberne: “We can now share with our customers the expertise that is inside the minds of our engineers. The online engineer is certainly not a replacement for our sales engineers. However, it collates our customers’ initial information requirements regarding price and delivery time.” The Managing Director is very proud of this revolutionary tool, which was developed in-house. Whereas existing configuration tools in mechanical engineering only offer the possibility of linking standard modules, Sisca excels in well-thought-out customization. The online engineer always takes into account the customer’s specific product and production process. It offers a wide range of possibilities when it comes to specifications, such as the required design, the type of material, various cleaning options, and whether the screw conveyor will be located in an environment where, for example, ATEX guidelines may be in force.
3D-MODEL In short, the innovative online engineer is extremely userfriendly, has a logical structure, and allows users to manage projects via their own account. Sisca offers the opportunity to be advised at any time of the most suitable screw conveyor system. Within an hour, the designed configuration is emailed not only as a quote, but also as a fully developed 3Dmodel. “Personal contact with our specialists remains possible at every stage of the configuration process. After all, Sisca is a unique addition, not a replacement for, the more than 80 years of knowledge and experience that Van Beek has accumulated,” Verberne explains.
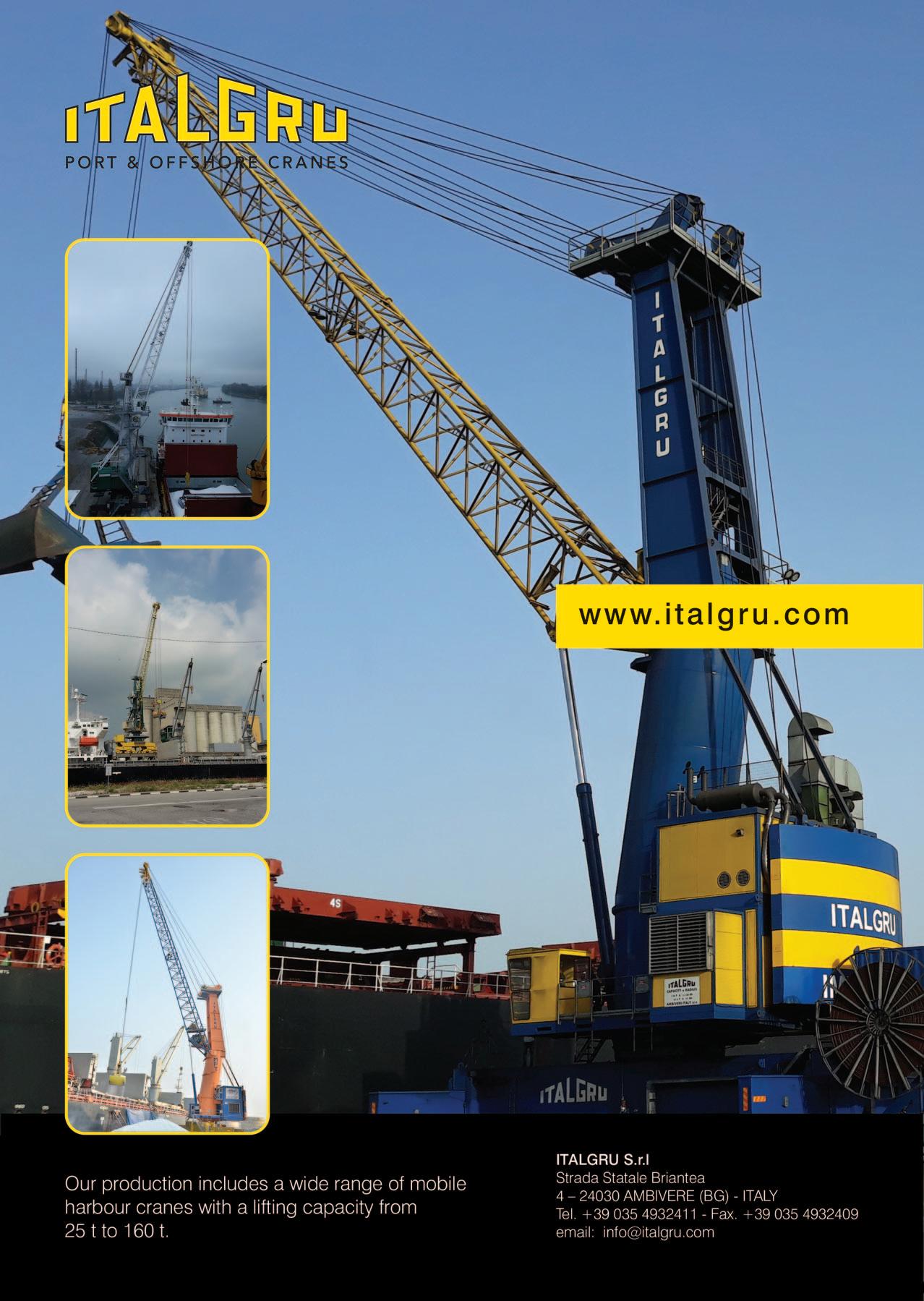
PREMAS® 4.0 by AUMUND
more and more customers are opting for Predictive Maintenance
A display installation of PREMAS® 4.0 on a bucket elevator in the AUMUND showroom in Rheinberg. The main components of the Predictive Maintenance Solution are mounted on a life-size model of a bucket elevator boot (photo AUMUND).
The digital Service, PREMAS® 4.0 Predictive Maintenance Solution, which was launched at the beginning of 2021, has already proved its viability in practice in many installations all over the world. The online maintenance system, which was developed for the AUMUND Group with the technical participation of PREMAS AG, Switzerland, has been brought to market over 100 Systems in shortest time. AUMUND Fördertechnik, Rheinberg, Germany, SAMSON Materials Handling, Ely, GB, SCHADE Lagertechnik, Gelsenkirchen, Germany and all the international AUMUND subsidiaries have each installed and successfully commissioned PREMAS® 4.0 Systems in their sales areas.
Currently the majority of applications of the Predictive Maintenance Solution are on AUMUND machines such as belt and chain bucket elevators, pan conveyors and the silo discharge system CENTREX® . Customers of the AUMUND Group member companies SCHADE Lagertechnik and SAMSON Materials Handling also use PREMAS® 4.0 on their stacker and reclaimer equipment and mobile material feeders respectively. PREMAS® 4.0 users include concerns such as Dyckerhoff, Sabanci Holding, HeidelbergCement, Saudi Cement Company, Fujairah Cement, Union Cement, Aditya Birla Group, Shree Group, Holcim, Votorantim and Conch Cement.
Although the current focus is predominantly on cement industry customers, the PREMAS® 4.0 system is of interest to any industry with operations which depend on 24/7 reliability of conveying technology, as demonstrated by many AUMUND reference installations.
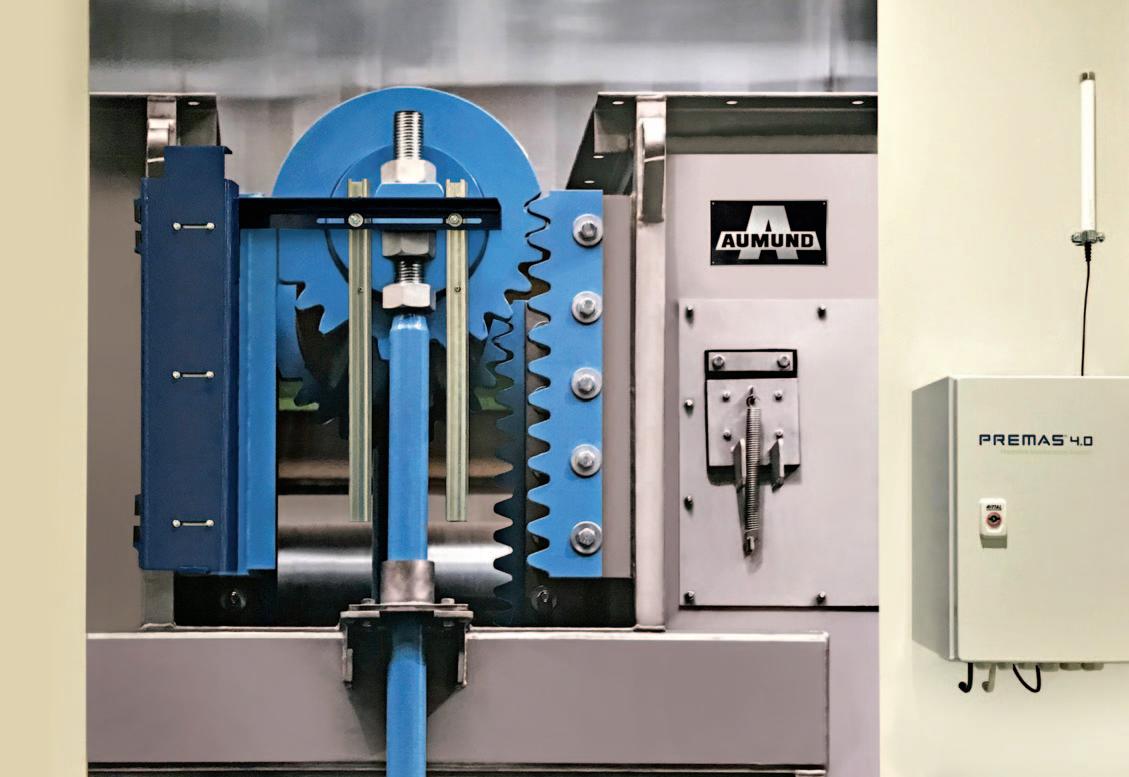
PREMAS® 4.0 INSTALLED DURING CONVERSION OF THE WORLD’S HIGHEST BUCKET ELEVATOR AUMUND India incorporated PREMAS® 4.0 in February 2022 into the conversion of the highest bucket elevator in the world, at 175.3m, at the ACC Wadi Cement Plant (Holcim Group). [See ‘AUMUND India rebuilds the world’s tallest belt bucket elevator of 175.3m’ on p68 of the April
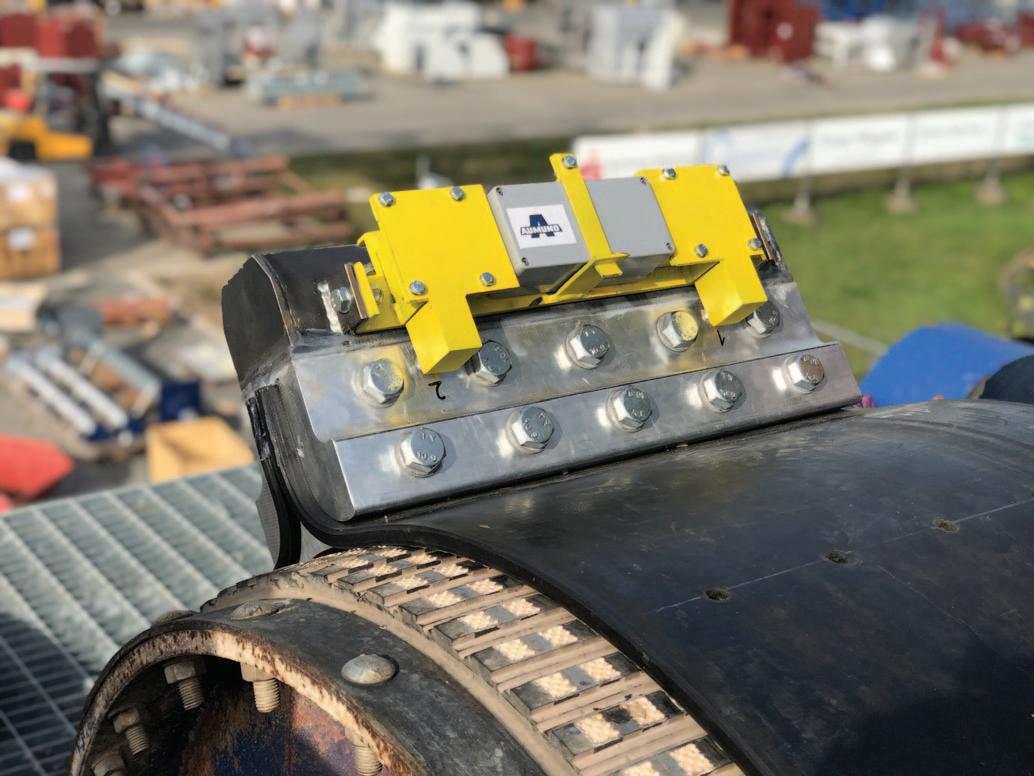
issue of Dry Cargo International.] Titan Cement in Greece is benefiting from the advantages of the digital system in the conversion of a chain bucket elevator not originally manufactured by AUMUND. With PREMAS® 360° Maintenance Packages AUMUND USA was also successful with conversions of AUMUND bucket elevators for Lafarge Ravena (also Holcim) and Nevada Gold Mines, as was AUMUND Asia, Hong Kong, with Sampyo Cement in South Korea. The AUMUND Group PREMAS® 360° Maintenance Packages: Basic, Advanced and Premium are adapted to the various maintenance strategies, requirements, and budgets of customers.
Soon AUMUND will also be able to monitor the clamping connection on a bucket elevator with PREMAS® 4.0. Tests by development engineers at AUMUND and PREMAS have been successful, and a trial application of clamping connection monitoring is currently underway at a cement plant in Poland.
PREMAS® 4.0 – MUCH MORE THAN
JUST DATA COLLECTION The digital service combines the latest sensor technologies with data collection and analysis, enabling early recognition of wear and ageing of important machinery components of conveying equipment. PREMAS® 4.0 gives 24/7 online information in real time about the condition of the machine, provides a forecast of the estimated remaining lifetime of critical components, and enables planning of maintenance and spare parts requirements in advance, which in turn allows action to be taken in time to prevent potential problems.
SERVICE CONCEPT OF THE AUMUND GROUP BUILT ON TWO PILLARS PREMAS® has been the flagship of the customer service strategy of the AUMUND Group since 2004. The purpose and objective of PREMAS® is to offer a comprehensive maintenance programme for all kinds of bulk materials handling equipment in the cement industry, in power plants, in the iron and steel industry and in many other key areas.
The service concept of the AUMUND Group is today built on two pillars, the classic in-person analogue on-site inspection of PREMAS® Preventive Maintenance Service, carried out by certified personnel, and the new predictive digital monitoring system PREMAS® 4.0 Predictive Maintenance Solution. The PREMAS® 4.0 online monitoring solution which was launched at the beginning of 2021 has already proved its viability in practice in many installations all over the world. At the same time PREMAS® 4.0 is part of the PREMAS® 360° Maintenance Packages which have been on the market since the end of July 2021.
ABOUT THE AUMUND GROUP The AUMUND Group is active worldwide. The conveying and storage specialist has special expertise at its disposal when dealing with bulk materials. With their high degree of individuality, both its technically sophisticated as well as innovative products have contributed to the AUMUND Group today being a market leader in many areas of conveying and storage technology. The manufacturing companies AUMUND Fördertechnik GmbH (Rheinberg, Germany), SCHADE Lagertechnik GmbH (Gelsenkirchen, Germany), SAMSON Materials Handling Ltd (Ely, Great Britain), TILEMANN GmbH Chains & Components (Essen, Germany) as well as AUMUND Group Field Service GmbH and AUMUND Logistic GmbH (Rheinberg, Germany) are consolidated under the umbrella of the AUMUND Group. The global conveying and storage technology business is spearheaded through a total of 20 locations in Asia, Europe, North and South America and a total of five warehouses in Germany, USA, Brazil, Hong Kong and Saudi Arabia.
Test device for sensor monitoring of clamping connections on bucket elevators (photo AUMUND).
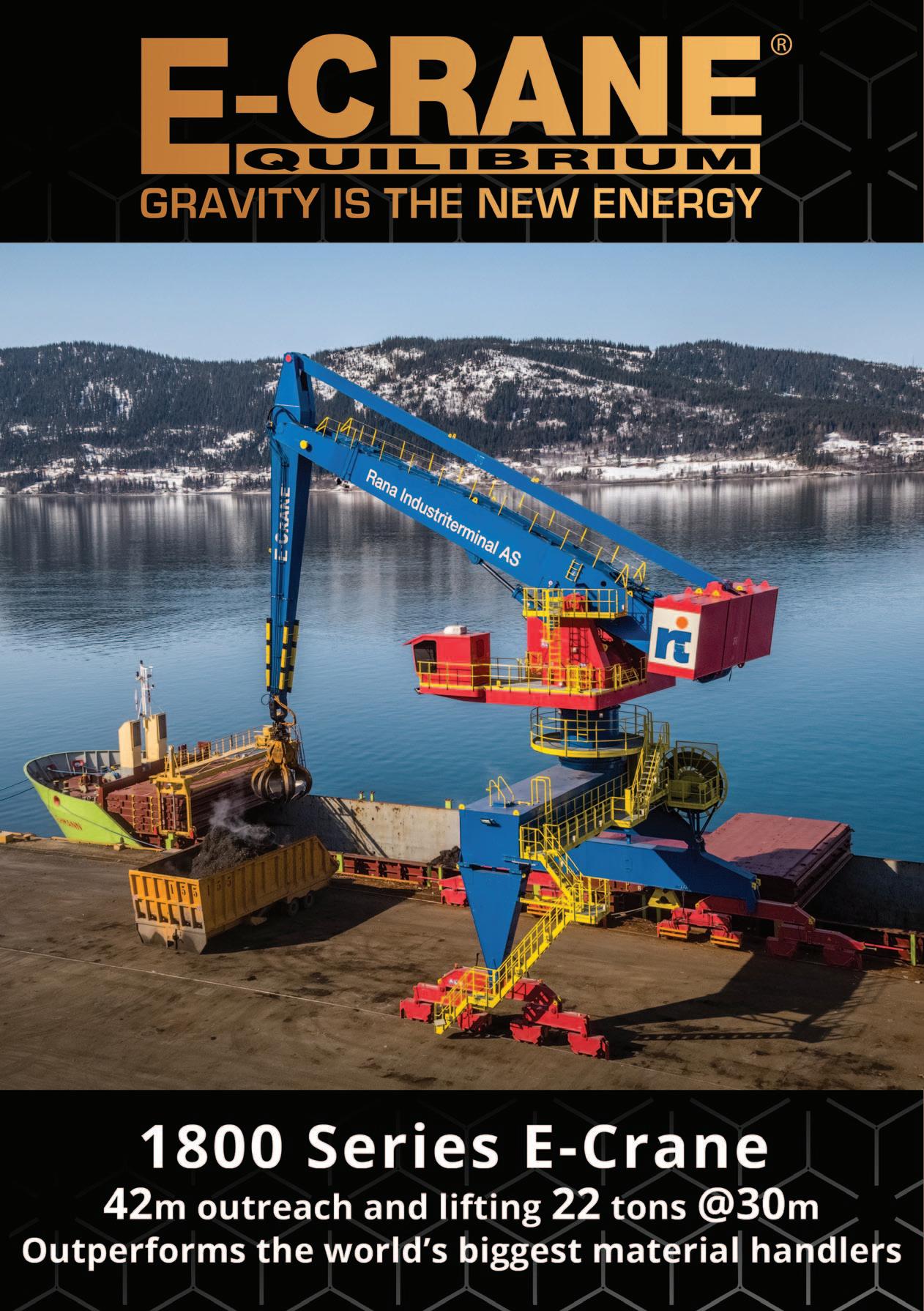

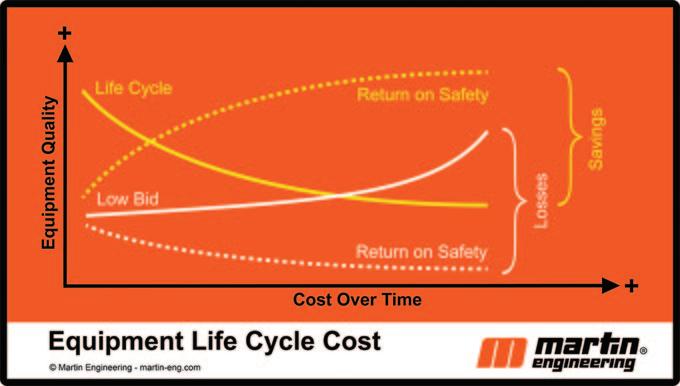
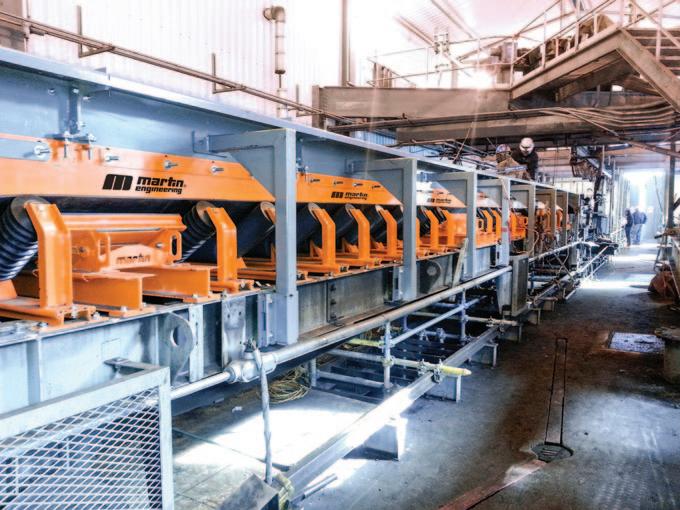
A well-designed conveyor system controls the maximum load at the highest achievable volume, with the safest possible work environ ment (all images ©Martin Engineering).
The economics of
workplace safety
Conveyor safety is not a modern trend bred by government regulation; it’s a common-sense idea as old as the first conveyor design, writes R. Todd Swinderman/ CEO Emeritus, Martin Engineering. In the modern age, safety is a key factor in worker protection, reduced insurance rates and a lower total cost of operation. There are several hurdles to the installation of safety equipment, the biggest of which is the nearuniversal use of the Low Bid process.
When companies buy on price (Low Bid) the benefits are short-lived and costs typically increase over time. In contrast, when purchases are made based on lowest long term cost (Life Cycle Cost), benefits usually continue to accrue and costs go down, resulting in a net savings over time. [Figure 1] Safer and more reliable equipment is easier to service, has a longer life and is less expensive to maintain.
Organizations that embrace safety show significant performance advantages over the competition. The proof is reflected in reduced injuries and greater productivity, along with above industry average financial returns and higher share prices.
Justifying safety investments is greatly enhanced by quantifying what most financial managers refer to as “intangible costs”, i.e., injuries, lost labour, insurance, morale, legal settlements, etc. However, managers and accountants have been trained to think about saving direct costs to justify investments.
When conveyors don’t operate efficiently they have unplanned stoppages, release large quantities of fugitive materials and require more maintenance. Emergency breakdowns, cleaning of excessive spillage and reactive maintenance all contribute to an unsafe workplace.
SAFETY PAYS Numerous case studies revealing the positive relationships between safety and productivity are backed up by organizations that gather global statistics on accidents and incidents. The simple formula for return on investment (dividing savings by cost) does not capture the potential savings from safety investments. Several organizations provide detailed and regional statistics on the cost of accidents [Fig. 2]. Lacking specific historical data, managers can turn to numerous reliable sources that provide the probability of incidents that can be used to estimate tangible and intangible future costs [Fig. 3]. The financial technique used to compare options is called a ‘net present value’ (NPV) analysis. NPV compares different investment options with varying costs and savings (cash flows) over time, discounting them by the company’s cost of
Inefficient conveyor operation leads to unplanned downtime, fugitive materials and increased maintenance.
Figure 1: Life cycle costs.
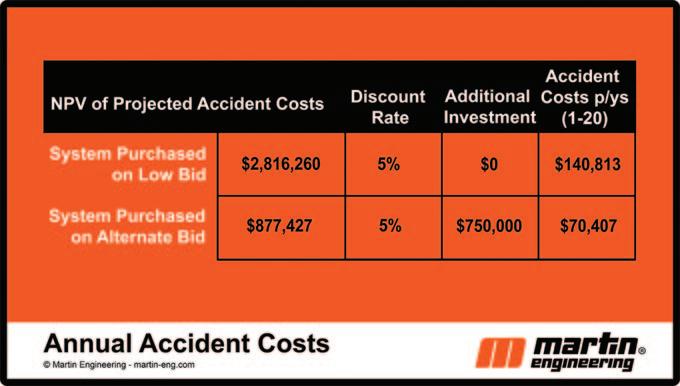
money. For example, an internal risk analysis shows a facility has 30 workers exposed to conveyor hazards. The estimated probability of the different classes of accidents (fatal, lost time and first aid) is multiplied by the cost of these accidents to reveal what could be invested to reduce the incident rate by half [Fig. 4].
Assuming the life of the conveyor is 20 years and the cost of money (discount rate) is 5%, the available additional investment would be about $750,000 more in design time to accomplish the 50% improvement in safety. By choosing the lowest-priced bid to meet the minimum safety requirements, the short-term expenditure ends up costing considerably more over the 20-year lifecycle [Fig. 5].
By spending $750,000 more to exceed the minimum safety and design requirements and reduce the accident rates by 50%, the annual projected cost of accidents drops from $140,813 to $70,407.
Measured in today’s dollars — including the additional investment of $750,000 — the projected savings over the 20-year term at 5% are about $1.2 million by investing more upfront. If, after further analysis, the savings are found to be less — perhaps only a 25% reduction in the cost of accidents — the upfront investment is still justified over the long term. Even though it takes a little more effort to collect data and do a financial analysis, in the end, NPV consistently proves that safety does indeed pay.
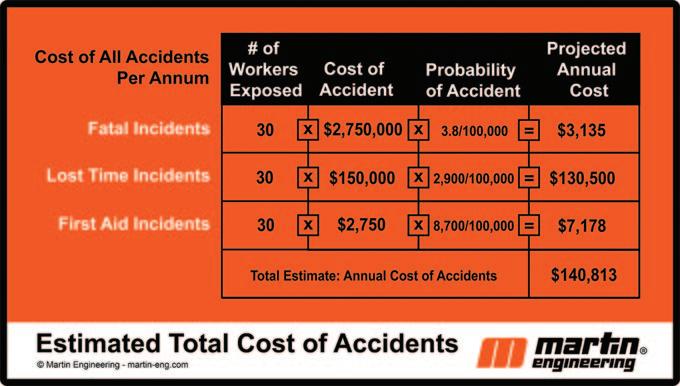

ABOUT MARTIN ENGINEERING Martin Engineering has been a global innovator in the bulk material handling industry for more than 75 years, developing new solutions to common problems and participating in industry organizations to improve safety and productivity. The company’s series of Foundations books is an internationally recognized resource for safety, maintenance and operations training — with more than 22,000 print copies in circulation around the world. The 500+ page reference books are available in several languages and have been downloaded thousands of times as free PDFs from the Martin website. Martin Engineering products, sales, service and training are available from 17 factoryowned facilities worldwide, with whollyowned business units in Australia, Brazil, China, Colombia, France, Germany, India, Indonesia, Italy, Mexico, Peru, Spain, South Africa, Turkey, the USA and UK. The firm employs more than 1,000 people, approximately 400 of whom hold advanced degrees. Figure 3. Accident rates
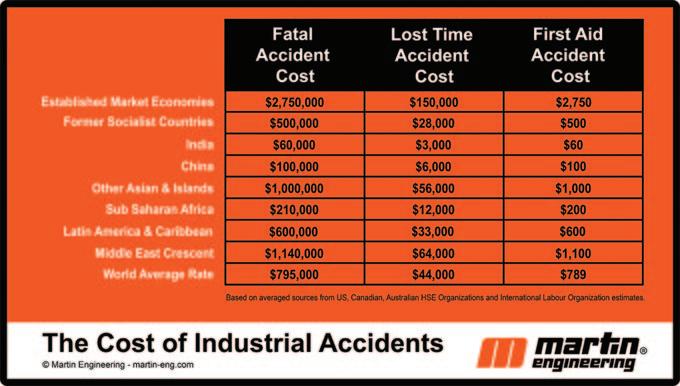
per 100,000 industrial workers per year.
Figure 4. Estimated total annual cost for all accidents.
Figure 5. Annual accident costs for years 1 to 20.
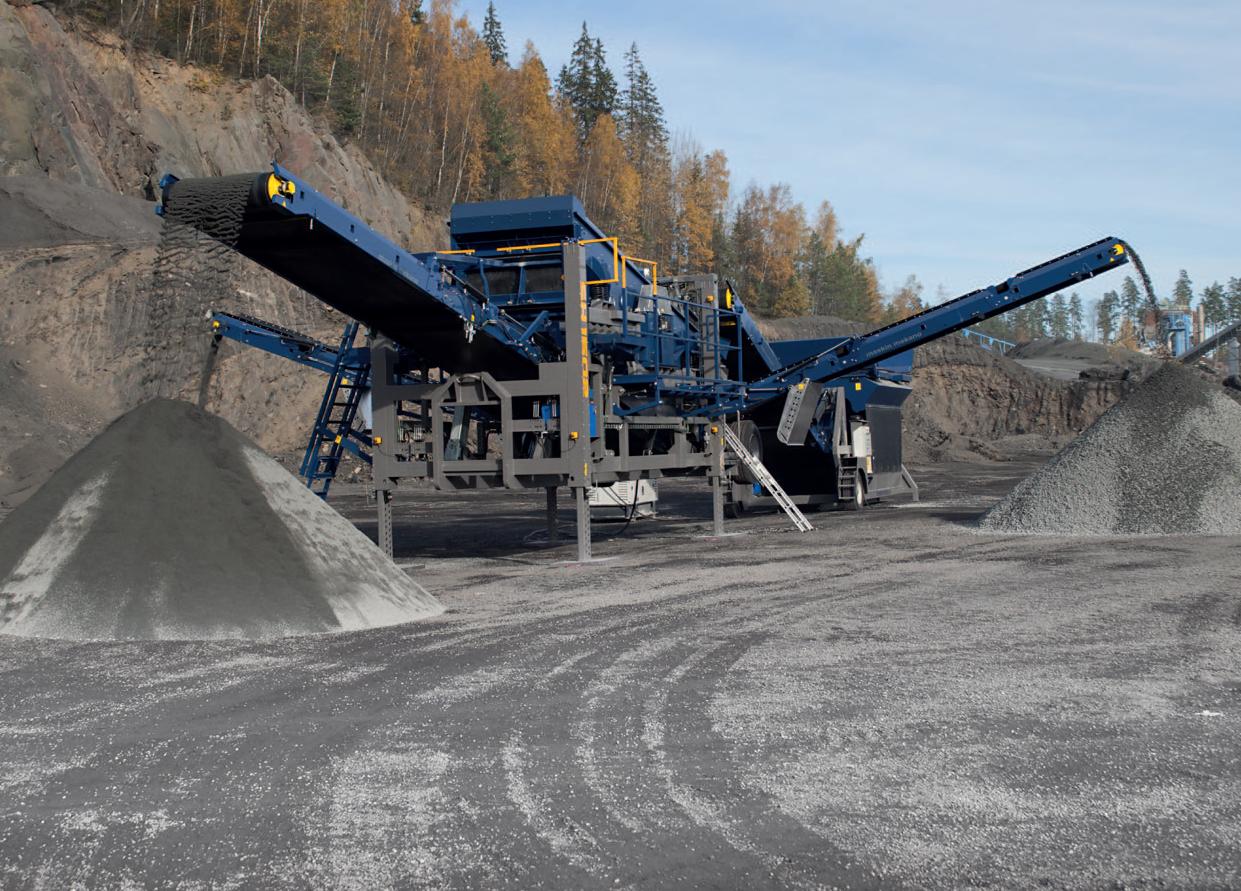
