
33 minute read
A WEIGHT OFF: SHIP-UNLOADING — AND LOADING — AND ALL IT ENTAILS
A weight off
ship-unloading — and loading — and all it entails
Louise Dodds-Ely
Bruks Siwertell commissions new cement unloading system for Colonial
Bruks Siwertell has completed the installation of a new high-capacity Siwertell ship-unloader at Colonial Group’s Georgia Kaolin Terminals, in Savannah, Georgia, USA. The fully enclosed screw-type system now delivers very efficient dustfree cement handling, supporting the company’s strategy for sustainable cement import growth.
“This Siwertell unloader is a great machine, ideally suited for the terminal,” says Bengt Svensson, Contract Manager,
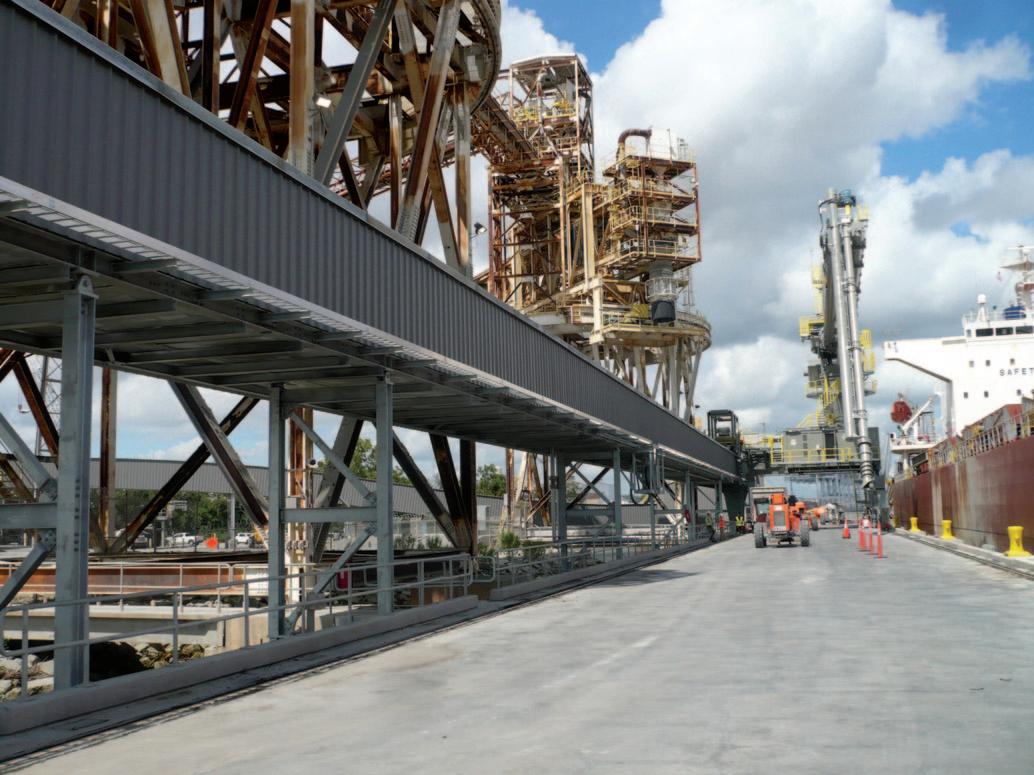
Bruks Siwertell. “It will play a significant role in helping Colonial achieve its ambitious efficiency and environmental goals; early feedback has been extremely positive.”
Bruks Siwertell worked closely with Colonial and its engineering team to develop a customized solution that would successfully integrate with the existing infrastructure at the terminal. “This planning really paid off,” continues Svensson. “We had a very tight window for the installation, to ensure minimal disruption for Colonial’s customers, which meant working long hours, but the result is worth it,” he added.
The flexibility of Siwertell unloader technology enables it to handle various designs and capacities of geared vessels, and supports the company’s switch from bagged cement deliveries to bulk. “Colonial now benefits from the terminal’s increased unloading capacity, which in turn delivers
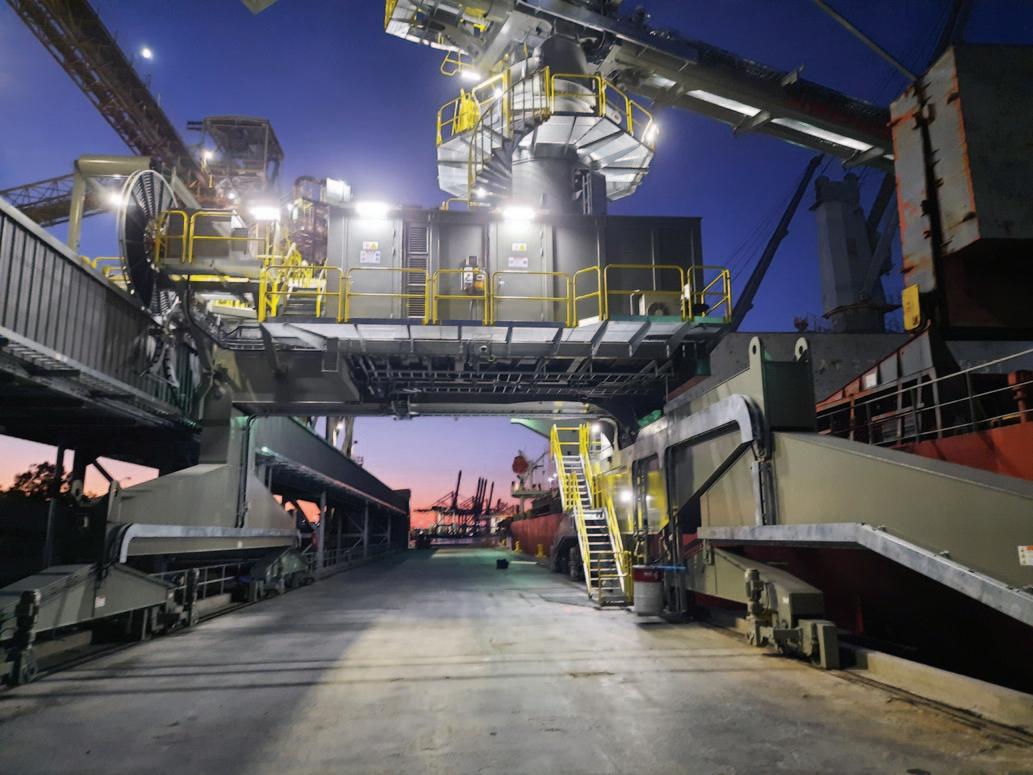
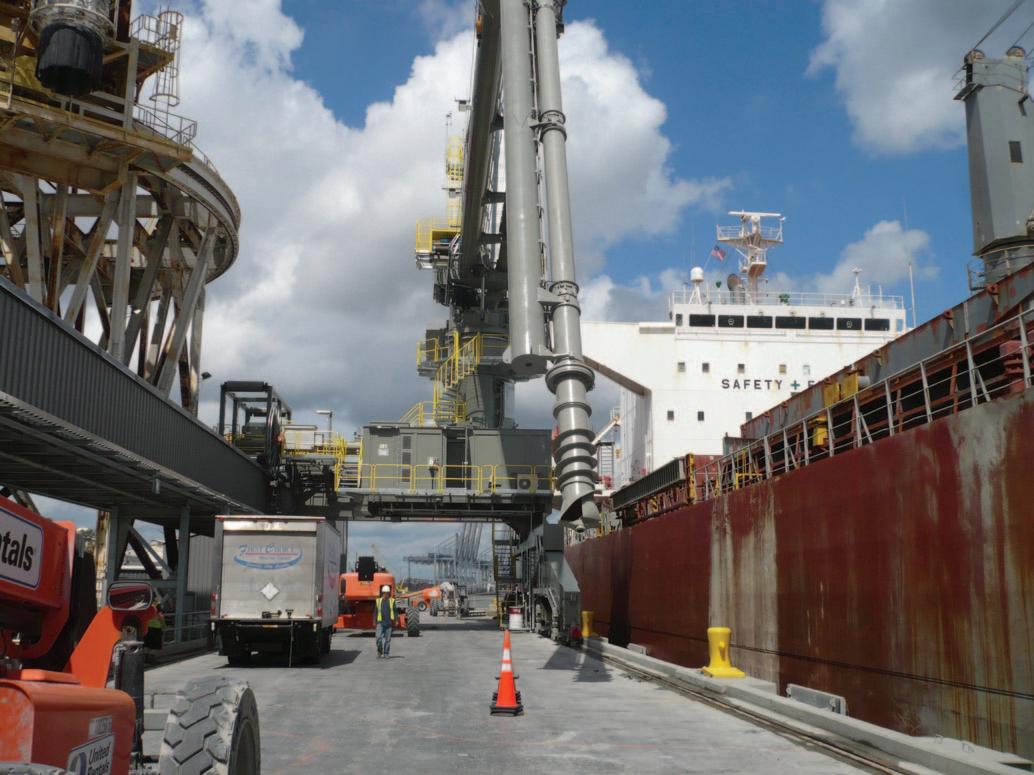
faster vessel turnarounds on the jetty, and with that, cost-savings,” he notes.
Environmental considerations were also a key factor in Colonial’s choice of equipment, and because the Siwertell unloader has an enclosed dry bulk material conveying line, ensuring no dust emissions or spillage, it is permitted to operate within this historic port and complies with its strict environmental regulations.
The Siwertell 490 F-type ship-unloader offers high through-ship efficiencies and a rated cement handling capacity of 800 tonnes per hour, discharging vessels up to 55,000dwt.
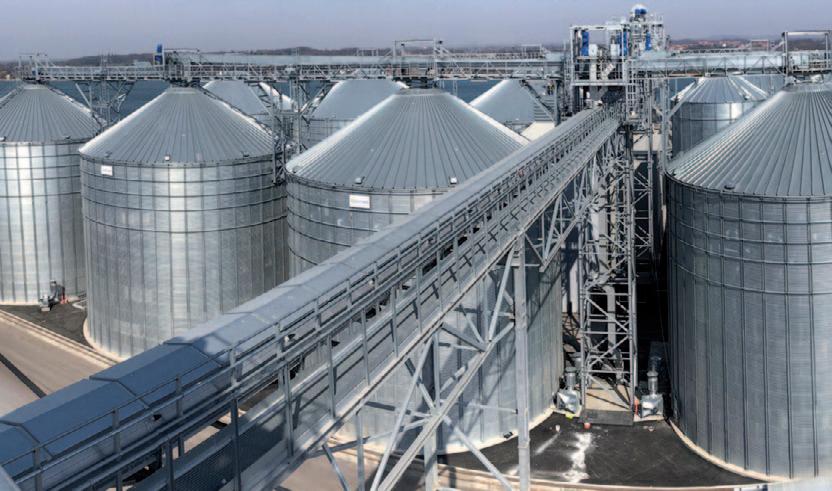

Engineering
BULK HANDLING EQUIPMENT www.buttimer.com
Ireland UK Poland
Buttimer Engineering Cahir Business Park Cahir Co. Tipperary E21 Ireland
BESPOKE BULK PORT EQUIPMENT. FULL RANGE OF HOPPERS AVAILABLE www.docksolid.com
Our DOCKSOLID® hoppers are designed and fabricated in Cahir, Co. Tipperary and are sold under the Docksolid Brand in Ireland, United Kingdom and Poland and branded as Manta in the rest of the world by our partners Terex Prostack www.terex.com/prostack
ENGINEERING & EQUIPMENT NEUERO’s loading and unloading expertise in demand around the world
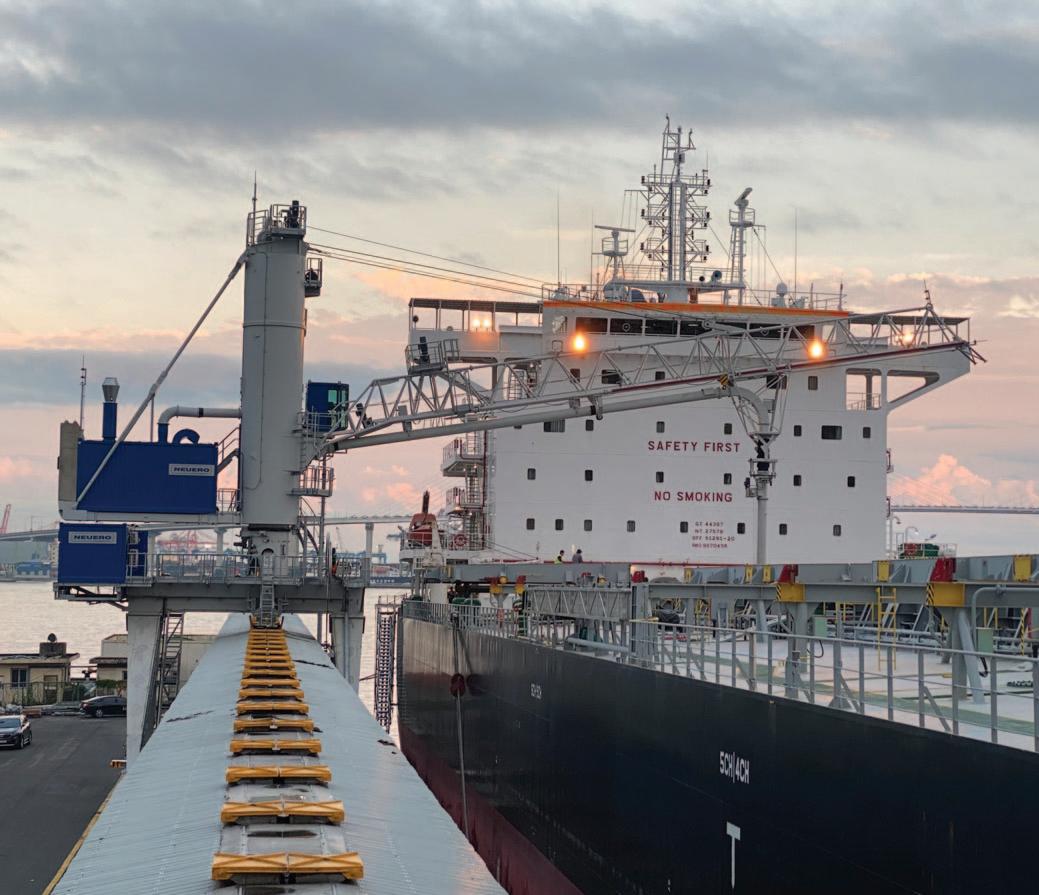
The NEUERO 400tph Multiport M400 ship-unloader at Busan.
NEUERO has been a major manufacturer of mechanical and plant engineering since 1914. It stands for mechanical engineering, innovation and maximum customer benefit.
The company’s aim is to offer the best shiploading and unloading in the world to make it easier for its customers to work at ports and to ensure the supply of goods worldwide. With over 5,000 built references in over 140 countries, NEUERO is a respected manufacturer of shiploading and unloading equipment. Several tonnes of grain are handled every hour worldwide using NEUERO machines.
NEUERO’s machines are characterized by advanced, efficient, reliable and userfriendly design. The systems have the lowest maintenance and operating costs and thus ensure a fast return on investment.
All NEUERO equipment follows the best engineering practices, with quality German manufacturing and on-time deliveries. This high-quality, customized equipment places NEUERO among the most popular global suppliers for the grain and grain by-product market. The company is also seeing great success in its unloaders that are used to handle alumina and petcoke. NEUERO is now also making unloading equipment tailored for wood pellets, PKS (palm kernel shells), as well as other biomass products that are becoming ever more popular to fuel electric power plants that are moving away from coal as a fuel source.
NEUERO’s aim is to supply every client with the most reliable, efficient, environmental friendly, and user friendly ship-unloaders and shiploaders possible. Special attention is paid to using the most advanced and best designed components to make all equipment. The result provides a equipment solution that gives clients the lowest operating and maintenance costs while at the same time giving them the highest operating efficiency.
NEUERO also focuses specifically on environmental issues, and it strives to deliver equipment that offers the lowest possible pollution to the environment. This also makes the work area safer for clients’ employees, as well as giving a clean work area for the neighbours of all clients. NEUERO’s shiploaders and unloaders set standards worldwide.
NEUERO is ISO certified and has guidelines on work safety, health and the environment. More than 300 customers already rely on NEUERO’s expertise. Continuous unloading performance is guaranteed, even during residual cleaning. Less dust is emitted during loading with NEUERO’s special engineered loading head and noise reduction through its insulated machine houses. NEUERO’s lightweight designs make its machines very safe and environmentally friendly for handling.
TECHNOLOGICAL DEVELOPMENTS NEUERO works constantly on ways to improve operating efficiency in both
capacity increases, and power consumption reductions. Just as important, the company is always making changes to make the equipment last longer, and lower maintenance costs. NEUERO studies the flow of material in the conveying line to learn ways to improve the flow which reduces wear on parts, and improves the operating efficiency. Constantly monitoring of temperature and vibration of key bearings helps NEUERO fine-tune its designs, and this information is provided on the clients’ PLC so they can monitor these items and make any necessary repairs when the equipment is not in operation. NEUERO also offers its clients a telediagnostic service so that it can more efficiently assist them with any questions or concerns they have with their equipment.
RECENT DEVELOPMENTS Like so many companies all around the world, operations have been affected by the war in Ukraine. Several projects that were under way in the Black Sea area are now on hold.
NEUERO has recently commissioned a 400tph (tonnes per hour) Multiport M400 ship-unloader at Busan (pictured). NEUERO’s Multiport is available in a range of capacities, and offers the following: v unloading capacity up to 800tph, based on wheat; v supply via the low or medium voltage; v use of diesel generators possible; v stationary, rail or rubber-tyred steerable wheels; v broad coverage of the ship’s hold by horizontal and vertical telescopic tube; v auxiliary winch for residual cleaning on the boom for an excavator or front loader; and v if necessary, with explosion protection concept following ATEX guidelines.
Other continuous ship-unloaders offered by NEUERO include:
FLEXIPORT
v pneumatic ship-unloading for non-freeflowing materials; v the vertical tube can be equipped with a rotating feeder to loosen up the product; and v full coverage of the ship’s hold due to additional extending and kick-in-kickout movement of the vertical boom.
NEUERO developed the Flexiport many years ago, to achieve higher efficiency for non-free flowing materials. The Flexiport unloader combines both a mechanical feeder and pneumatic conveying. The advantage of pneumatic is the ability to unload to the ship hold’s bottom, vacuuming the material and avoiding the need for extra hoppers to lift the material during clean up as required by a mechanical unloader.
The unloading process is different from regular free-flowing materials, because it is carried out with layers instead of positioning in one point and going down (inverted cone).
Nowadays, NEUERO incorporates many features like blower redundancy for high capacity and measurement sensors for vibration and temperature for the bearings. This is also available in the company’s Multiport pneumatic equipment. It is interesting that it is required in all bucket elevators but not in the main drive of a ship unloader.
Efficiency for small ships: for example, when unloading wood pellets from 2,000dwt vessels, an average of 70% was promised and delivered — including clean-up operation. This has already been proven in 2002 at the Essent plant in the Netherlands.
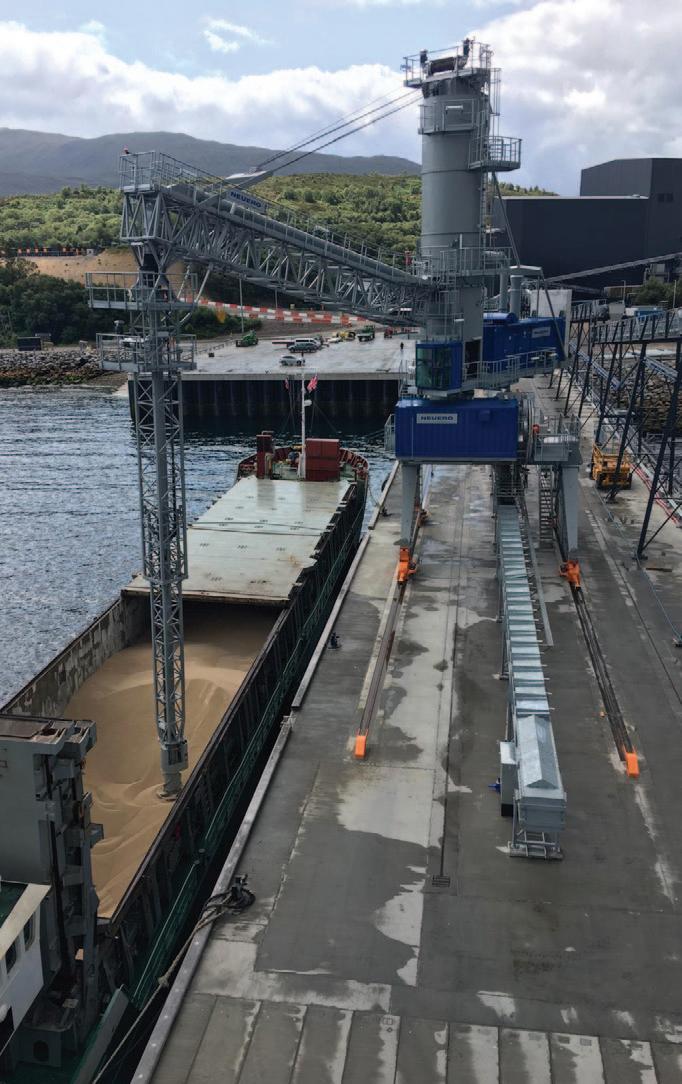
TOWER
v unloading capacity of up to 1,600tph, based on wheat; v movable on rails; v optional with a loading boom; v integrated auxiliary winch per boom; v two separate suction lines (50% each); and v integration of various conveyor elements, such as container scales, magnetic separators, etc.
The Flexiport is ideal for nonfree-flowing materials.
ENGINEERING & EQUIPMENT
Bedeschi expands its ship-unloading portfolio with strategic acquisition
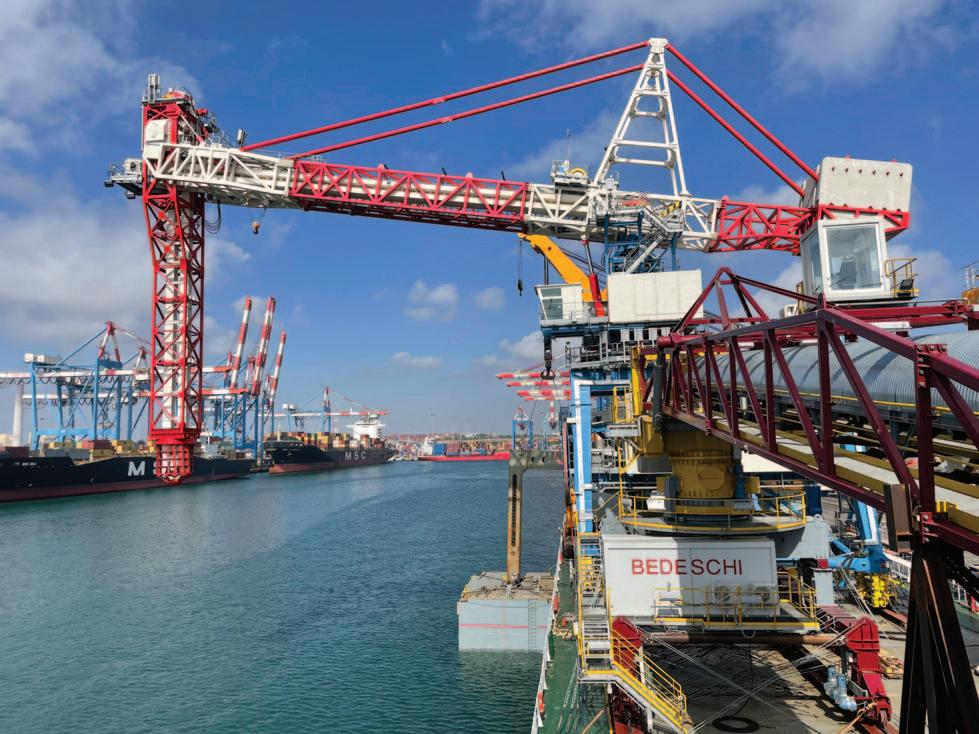
Bedeschi ship-unloader delivered fully erected to Ashdod Port.
Bedeschi is targeting the development of bulk handling business as a strategic goal. Ship-unloading technology has been pushed using in-house know-how, growth, as well as acquisitions.
To complement the bucket unloaders already part of Bedeschi’s line of equipment, mainly applied to highcapacity handling of coal and ores, the company has now added chain elevator unloaders. This technology, even though it was already part of Bedeschi’s portfolio, has been boosted by the acquisition of the grain and oilseeds bulk handling business of Golfetto Sangati (part of GEA). Thanks to this, Bedeschi will be able to handle products ranging from grain to meals, fertilizers to clinker with over 20 machines operating worldwide.
Bedeschi can offer a wide range of mechanical ship-unloaders for vessels up to 120,000dwt, fixed or mobile on rails or wheels with handling capacity from 300tph (tonnes per hour) to 2,000tph, as well as pneumatic ship-unloaders for vessel up to 20,000dwt, fixed or mobile on rails or wheels with handling capacity from 100tph to 300tph.
Bedeschi’s turnkey solutions are designed based on the requirements of its clients, handled material and port structure. Therefore, the company’s R&D department is continuously working to provide the most appropriate solutions.
One of the latest ship-unloaders manufactured by the company has just been delivered to Ashdod port in Israel. In addition to this, Bedeschi recently supplied three automatic dedusting ecohoppers to Ashdod Port. One hopper is used to unload clinker to truck at speeds of up to 800tph, and two are used to unload grain at a rate of 550tph. A filtering system prevents air pollution during filling and discharging.
In the complete process flow, the two conveyors will receive grain material coming from Bedeschi’s continuous shipunloader under operation.
This ship-unloader will operate at a capacity of 1,200tph, and will feature a cutter able to unload free flowing as well as non-free flowing (meals, DDGS) materials.
Enhanced operation with increased capacity can be also achieved with the full environment respect. The shipunloader will be operational by the end of 2022. One new unit will be put in operation in 2023 in UK for Cargill. The supply includes one ship-unloader for grains and meals with an 800tph unloading capacity.
Thanks to the expertise gained with over 20 successful installations worldwide and to the ongoing upgrading process by the design and R&D team, Bedeschi can offer special, custom solutions, for any technical and operational requirement.
Two thyssenkrupp continuous ship unloaders on a vessel for shipping. ENGINEERING & EQUIPMENT

thyssenkrupp has supplied two continuous ship-unloaders to unload coal from vessels ranging from 50,000 to 100,000dwt. The unloaders each have a nominal capacity of 1,250 tonnes per hour, for a subsequent conveyance of the bulk material from the jetty to a power plant. The entire project was carried out by thyssenkrupp Mining Technologies specialists from Germany and China in the face of the special challenges presented by the Covid-19 pandemic.
To minimize the amount of work at the customer’s jetty, the unloaders were completely erected in China and shipped in a fully assembled and pre-commissioned condition. The transport of the 1,300tonne and 43m-high machines from the assembly site to the ship was carried out by a self-propelled modular transporter (SPMT) with a configuration of 120 axles.
The lift from the SPMT to the ship was carried out by a floating crane with a lifting capacity of 3,000 tonnes. Both unloaders were loaded onto one ship and lifted directly onto the jetty at the destination port after shipment.
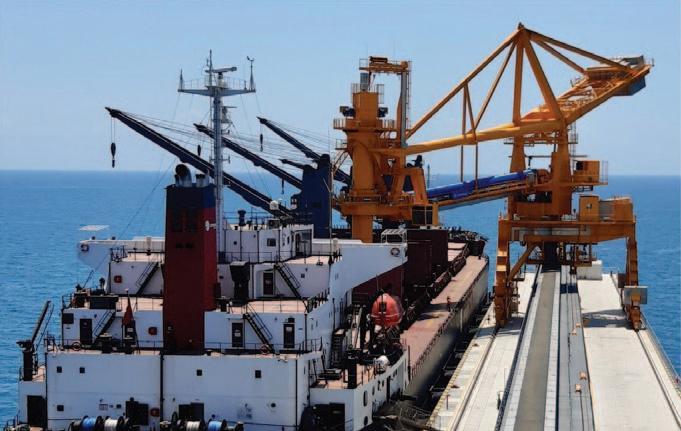
Two thyssenkrupp continuous ship unloaders have started operation (and below, right).
Self-propelled modular transporter (SPMT) moving the thyssenkrupp continuous ship unloader to the jetty for shipping.
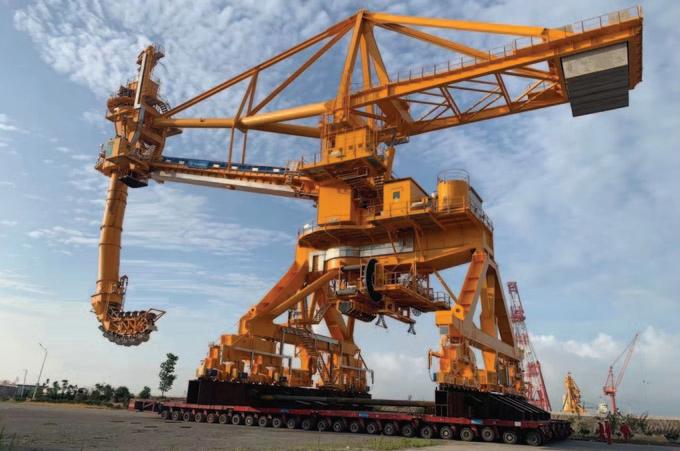
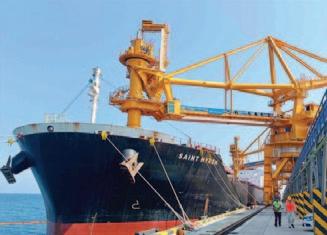

ENGINEERING & EQUIPMENT Keeping ship-unloaders — and loaders — moving reliably
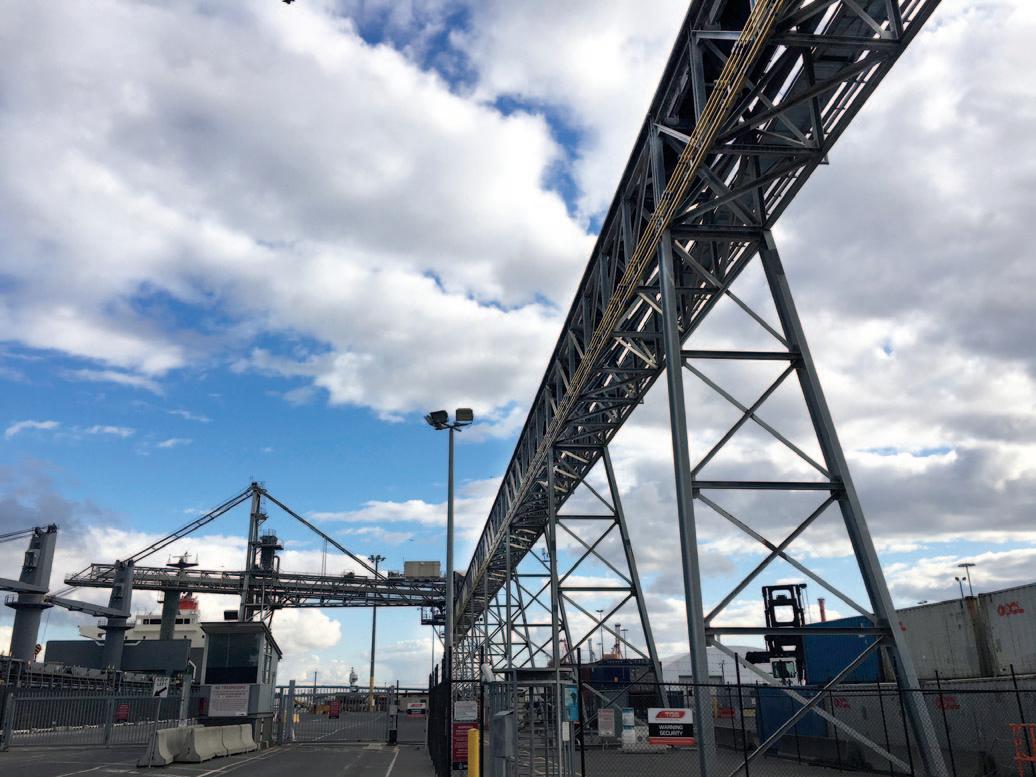


Ship-unloaders and loaders are an indispensable part of the bulk handling market, and their importance and reliable availability is reinforced by the UkraineRussia conflict.
Different routes are explored, and these require investments to modernize existing structures or to engineer new facilities for an efficient handling of raw materials or various types of agricultural commodities like grain for instance.
As a country rich in natural resources and agricultural land, Australia exports a wide variety and quantity of bulk cargoes, for which there are many shiploaders at various terminals. Even when imports are lower, ship-unloaders are in use, too.
Stuart Wheatly, Local Market Manager for Bulk Handling at Conductix-Wampfler in Australia, reports convincingly about products and solutions that Conductix-Wampfler supplies for machines in this market, using some examples:
“We have sold various products for use in grain handling, most notable at grain export terminals. These products include conductor rails, hazardous area sliprings and radio remote controls. Our main customers are all the main players into the market like Graincorp, Emerald Grain and CBH.”
WICET (Wiggins Island Coal Export Terminal) shiploader – level winding cable & hose reels. As part of a shiploader upgrade for Emerald Grain, Conductix-Wampfler supplied a conductor rail solution based on the 0813 series incorporating ProfiDAT® data transmission system to provide a reliable power + data connection to the travelling shiploader. This system replaces a (nonConductix-Wampfler) plastic chain arrangement, that failed regularly — and sometimes catastrophically.
WICET (Wiggins Island Coal Export Terminal) shiploader – level winding cable & hose reels. ENGINEERING & EQUIPMENT
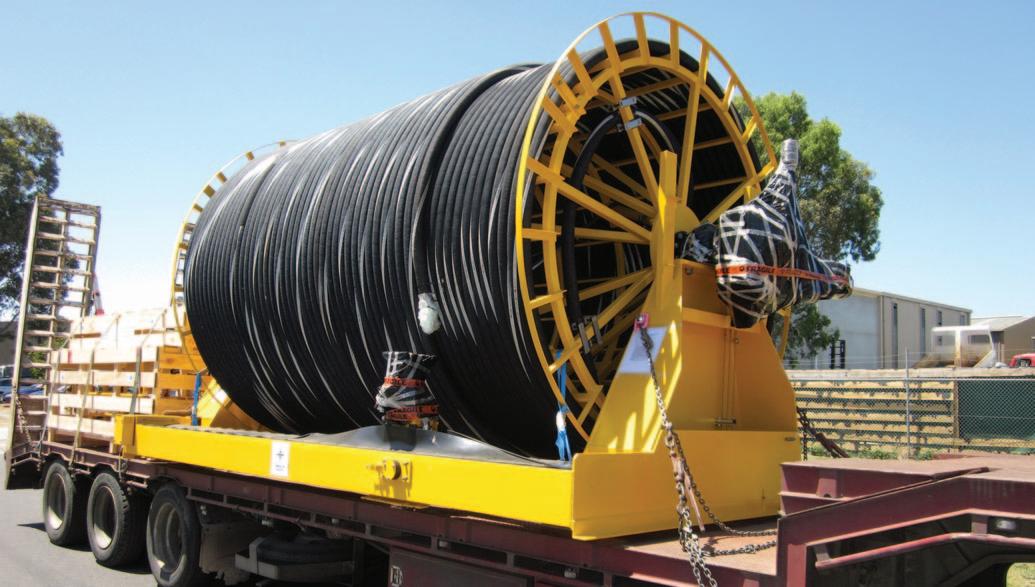
There are several grain-handling shiploaders around Australia which use Conductix-Wampfler Conductor rails for their long travel power supply. Note that this is quite a demanding application since the shiploader can be parked in one location for extended periods of time drawing current when loading a ship. Therefore, it is important that a suitably size high amperage conductor rail system with appropriated number of collectors is used. It is also imperative that the conductor rail systems are maintained and regularly cleaned to ensure no hot spots (localized heating) occur that can lead to damage of the rails.
Wheatly continues highlighting the advantages of the Conductix-Wampfler services for a proper maintenance and to ensure continuous running, long-life reliability and further upgrade of customer equipment.
“Emerald Grain have a shiploader at the Port of Melbourne which was refurbished in recent years. The original shiploader featured power + control connection for long travel via two plastic cable chains. These chains (not sold by Conductix-Wampfler) experienced multiple failures during their service life, including falling from height, which totally disabled the shiploader!” Wheatly said. As part of the shiploader upgrade, Conductix-Wampfler supplied a conductor rail solution based on the 0813 series incorporating ProfiDAT® data transmission system to provide a reliable power + data connection to the travelling shiploader.
“It is interesting to have a look to the whole portfolio. Today Conductix-

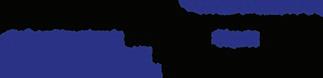

Ship unloaders
Road mobile ship unloaders
Storage & reclaim
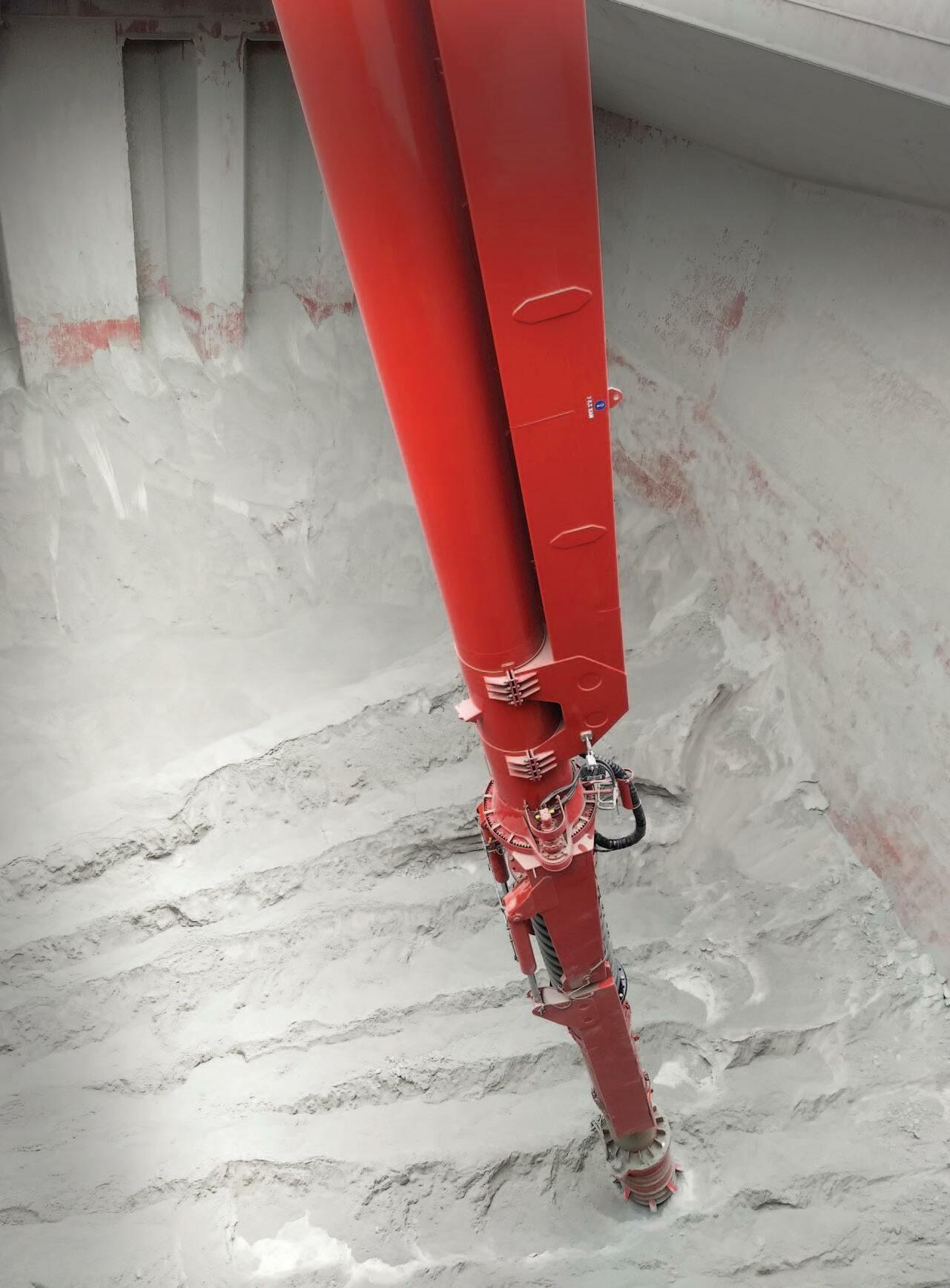
Convey units
Truck loading
Ship loaders
The answer to your bulk handling questions
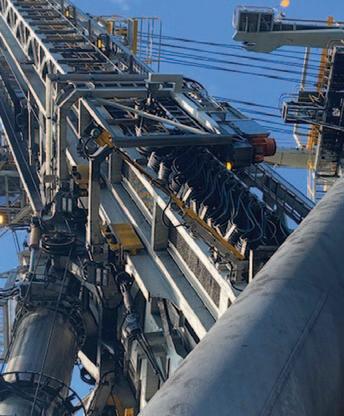
Wampfler has supplied cable reels for long travel power, and hose reels for water supply on various shiploaders and unloaders. These are powered by our proven technology with MAG Drive for mono-spiral spools or alternatively large VFD-driven levelwinding reels. These motor-driven reels are fitted on ship-loaders handling a variety of media e.g. iron ore, magnetite, coal and cement,” Wheatly adds.
Conductix-Wampfler also supplies spring-operated cable reels for use on shiploader telechutes. These spring reels are usually specially epoxy painted to resist the aggressive ‘over water’ seaside environ ment. The company is ready to innovate: “Beside standard cable version, we have recently developed a fibre-optic solution which has been already appreciated and ordered by different customers willingly to handle multiple signals and video connection to cameras on the telechute,” explains Wheatly.
Cable festoon systems are another classical example. Those systems are used on jib booms (both fixed and luffing type) for connection of cables and hoses to a moving telescopic chute (telechute). For fixed booms, the festoon systems are relatively conventional, but for luffing booms the trolleys need to be specially designed to hold the cable as the boom moves through a range of angles. Typically, the festoon systems offered on luffing booms are square track systems, where the trolleys feature rollers that contact on all four faces of the diamond bar track for most positive tracking. Instead of standard cable saddles, these trolleys are fitted with cylindrical pipe sections, which allow the cable to maintain its curved support through all boom angles. “These trolleys also feature a reinforced design to withstand the additional loads exerted due to the luffing action of the boom,” says Wheatly.
Thanks to Stuart Wheatly, and here only using Australia as an example, one can see how broad Conductix-Wampfler’s product range and solution offering is today. With a continuous drive to innovate and propose new solutions, the most demanding requests of customers in the bulk material handling market can be met.
Cable festoon systems at Haypoint coal shiploader and for Portland alumina ship-unloader (pre-assembled).
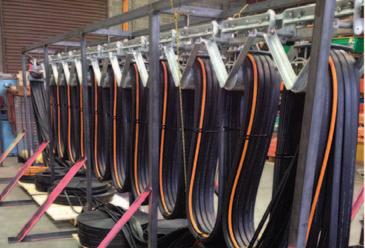
Mexico’s new ultra-efficient agri-bulk terminal underpinned by Siwertell unloader
A new Siwertell ship-unloader in the port of Veracruz, Mexico, is offering such high levels of grain handling efficiency that it is expected to meet its owner’s planned growth for the next 40 years, writes Patrik Henryson.
The Port of Veracruz, in east-central Mexico, is being developed into one of the most advanced port terminals in the world. Accessing global waters via the Gulf of Mexico gateway, the port is undergoing a US$ billion redevelopment project, which will quadruple its installed capacity to reach more than 90 million metric tonnes by 2030. Part of this development is five new terminals and a new cargo processing and logistics area.
Integral to this development is Grupo Gramosa’s Puertos Especializados Transnacionales (PETRA) new agri-bulk terminal. It was planned, designed and built for the specialized handling of solid, liquid and semiliquid agricultural bulk, with a storage capacity of 126,000 metric tonnes of dry bulk and 38,400 metric tonnes of liquids.
PETRA is now operational, and from the outset, its dry bulk import facility has been able to offer unmatched grain handling and environmental protection. Underpinning these exceptional capabilities is a single railmounted Siwertell ST 640-M ship-unloader. It has a continuous rated capacity of 1,200tph (tonnes per hour) and a peak rate of 1,320tph, discharging vessels up to 80,000dwt. The unloader’s seamless flexibility enables it to handle a number of different grains such as corn, soya meal, dried distillers grains (DDGs), and canola seeds without any loss of efficiency.
EFFICIENCY REDUCES COSTS “Grupo Gramosa invested US$85 million in the PETRA terminal as it saw an opportunity to reduce the cost of raw materials for an animalfeed facility, achieved by getting more materials into the plant at a lower cost due to greater efficiency,” explains Jesus Mil Linares, Terminal General Manager, Grupo Gramosa.

All photos: Bruks Siwertell.
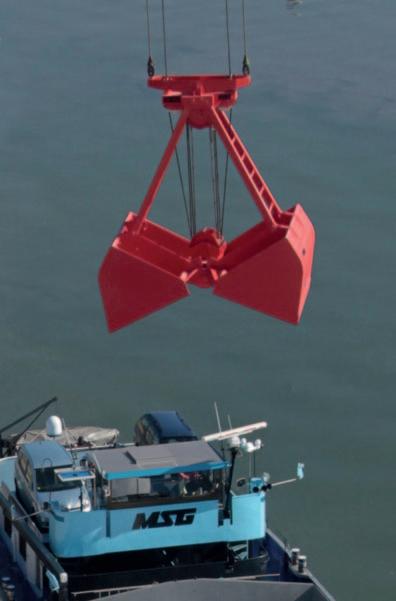
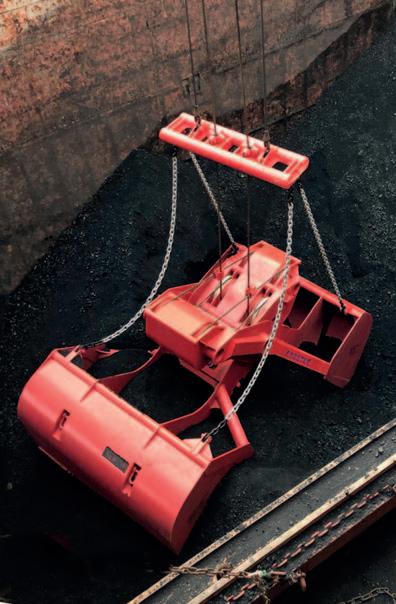
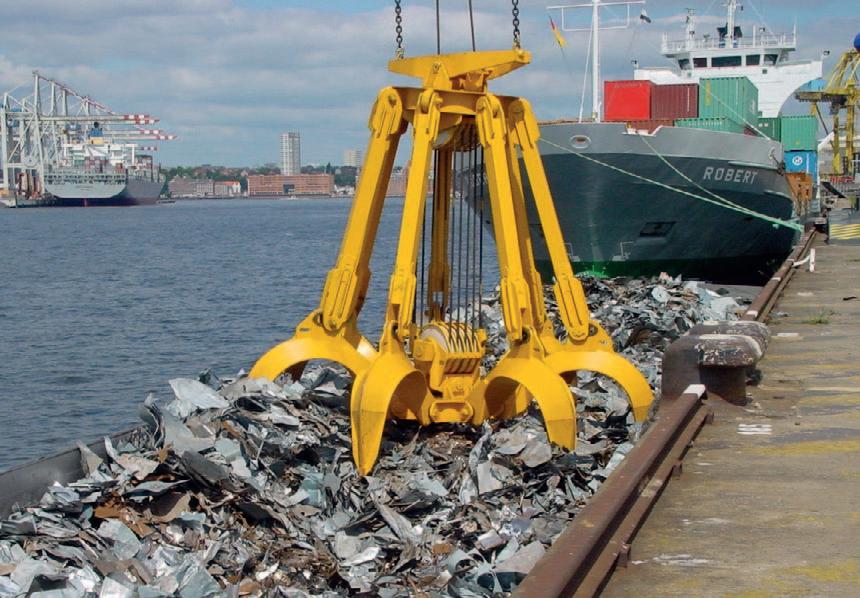

Talking about its new Siwertell unloader, Linares could not speak more highly. “The Siwertell unloader is formidable! With this system we are positively contributing to our beloved country, Mexico, reducing the ‘market basket’ cost by being more efficient in our logistics chain.
“The unloader minimizes terminal operating costs. In addition, there are close-to-zero dust emissions, no disturbing noises, and no spillage,” Linares notes. “This means no cargo losses, which is particularly important when it comes to expensive commodities such as corn, which is currently priced in the region of US$350 per metric tonne and DDGs at US$650 per metric tonne.”
DECADES OF GROWTH “Furthermore, if you consider commodity prices scaled up alongside logistics, with a vessel costing up to US$35,000 a day, we are in a much better position to negotiate more favourable rates. We are faster than any other agri-bulk terminal in Mexico, and offer as low as 0.01% losses, with others reaching around 0.5%, if not more,” he explains.
“One operator is required for the unloader, which means we are using fewer resources as the terminal is fully mechanized from unloading to truck or rail-car loading,” Linares says. “They can comfortably sit in an air-conditioned control cabin, or operate the unloader via remote control, which gives us great flexibility.”
Linares highlights that the efficiency of its Siwertell unloader will meet the terminal’s planned growth for the next forty years. Other benefits include the capability of accommodating an extended draught. “We can cater for larger vessels with a draught of 20m, while other terminals are limited to 13m,” he says. “The terminal also has a highly efficient, looped rail network, which is connected to the region’s two main railway lines, Ferromex and Kansas City Southern de México.”
PETRA’s main Siwertell unloader operator, Eric Marquez Martinez, compares the Siwertell unloader to driving a Ferrari. “A few times the captains have asked me to slow down as I’m going too fast!”
CHOSEN ON PERFORMANCE Grupo Gramosa is a progressive company dedicated to the commercialization and transformation of agricultural bulk, and the preparation of balanced animal feedstocks. It originally ordered the Siwertell shipunloader in 2018. Bruks Siwertell delivered the unit fully assembled in 2019, with commissioning and operator training being carried out in 2021.
Gramosa chose Siwertell technology because it out-performed all other competitor systems during a four-month selection process; particularly the two 600tph pneumatic systems it was initially

LEADING THE WORLDIN BRAKING SYSTEM DESIGN & MANUFACTURING
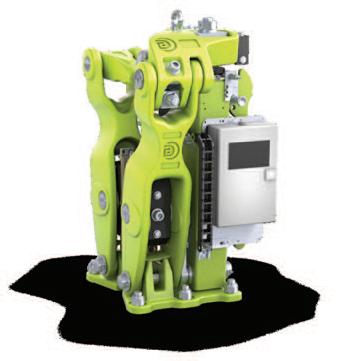
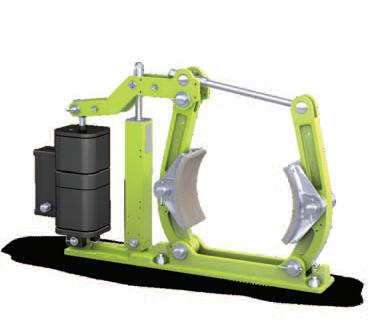
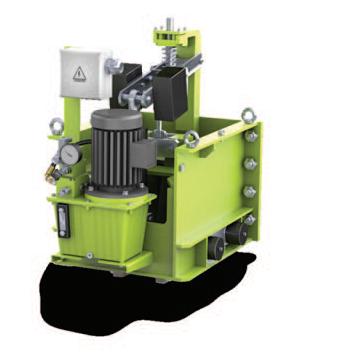
EBN DRUM BRAKES

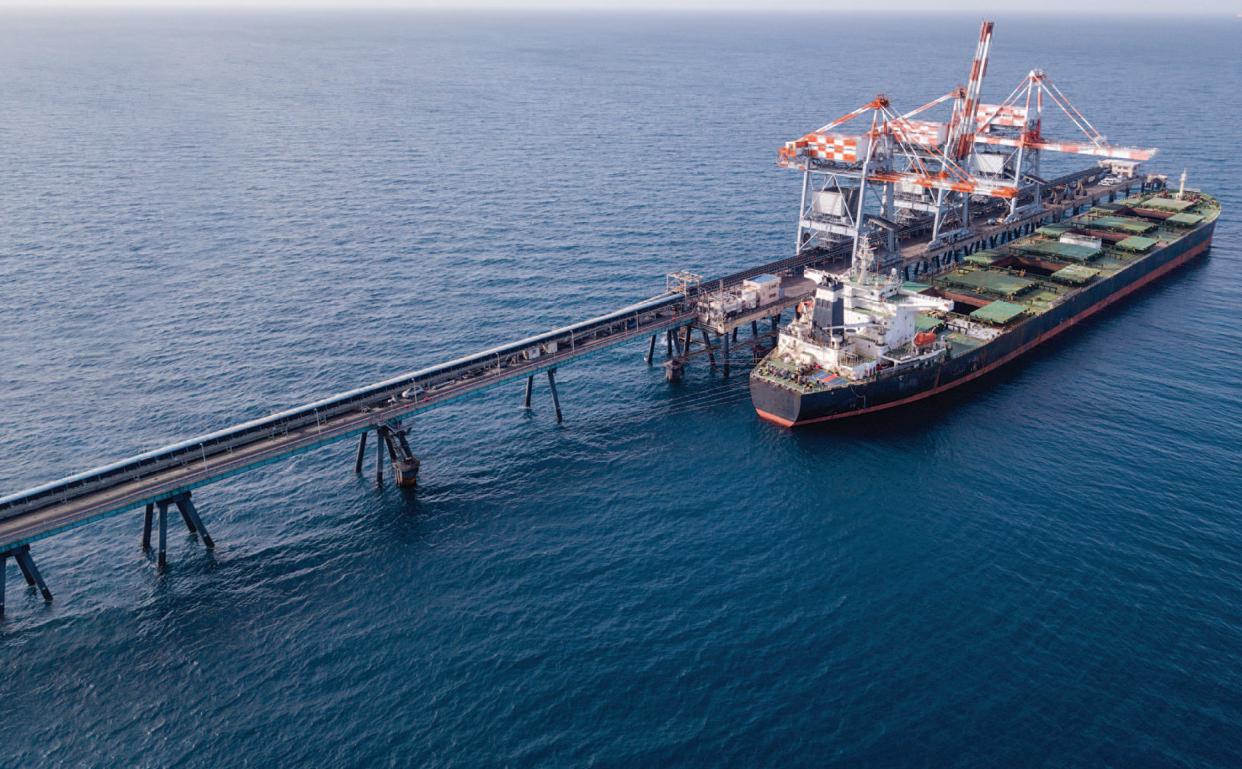
DBSZA RAIL CLAMPS KHD HIGH-DYNAMIC LOAD COUPLINGS CMB-3 FOR SB BRAKES ELECTRONIC STATUS INDICATION SYSTEM
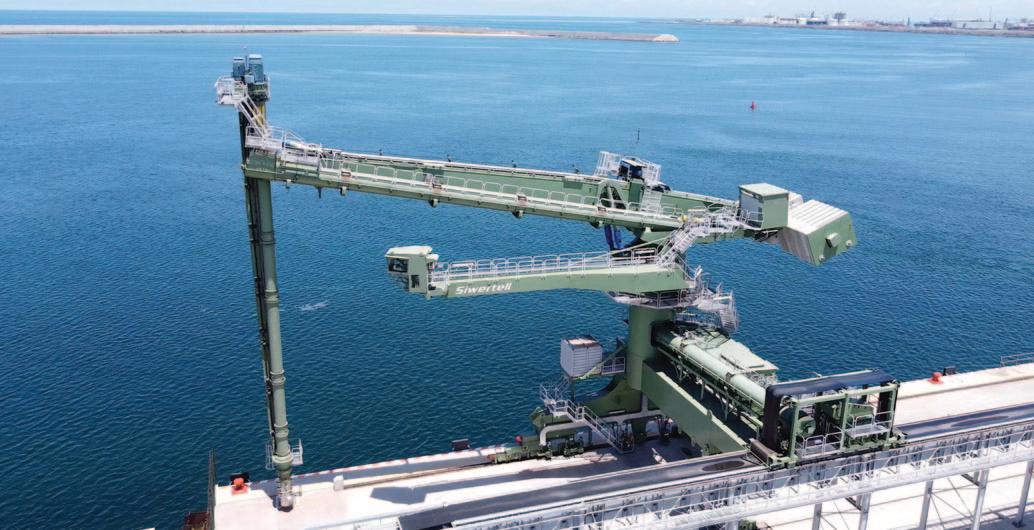
considering.
The analysis showed that a single Siwertell ST 640-M ship-unloader would be a more economical solution in the long term. The operating costs comparing two pneumatic unloaders, delivering an equal total capacity, was lower. Also, the Siwertell unloader offered cost savings from reduced berth occupancy as through-ship efficiency was greater. Furthermore, the quality of grain shipments was also considered.
A statement from Gramosa at the time of the order states that: “The Siwertell system was selected after considering many factors and multiple equipment comparisons. Analysis included operating principles and mechanisms, investment costs, as well as operating costs.
“An important factor was cargo loss and damage. We will handle a number of different grains at the new terminal such as corn, rice, wheat, soya beans and canola seeds. The low conveying speed of the Siwertell screw-type unloader means that the grain is not damaged during handling, which will give us added value and differentiate us from our competition.
“Another consideration in the selection of Siwertell equipment was the balance of performance across multiple grains such as soybean meal and DDGs. Other systems on the market did not compare. For example, in the case of pneumatic equipment, it is very efficient at handling grains, but offers very low efficiency, translating to high operating costs, in soybean meal and DDGS.”
“We are faster than any other agri-bulk terminal in Mexico,” says Linares.
A COMPETITIVE EDGE “It is a great endorsement of our technology, not only for it to be chosen following detailed analysis for several months to compare it with other equivalent capacity systems, but also now that it is operational, for those comparisons to be a reality for the owner,” says Patrik Henryson, Sales Manager, Bruks Siwertell.
“Thanks to the tremendous growth in the agri-bulk segment over the last few years, grain is now the third largest cargo that Bruks Siwertell machines handle,” Henryson explains. “We understand that grain handlers have to meet some of the most challenging dry bulk material demands, and their dry bulk equipment must match these, offering consistently high capacities for maximum profitability, but also maintaining the quality of shipments through sensitive handling.
“We talk about our systems offering grain handlers a competitive edge, and this is exactly what PETRA’s new Siwertell system is now delivering. The unloader is very well suited to the job it has been ordered for. It is so efficient that it directly lowers operating costs, and enables Grupo Gramosa to negotiate better commodity rates.
“The advantages offered are incomparable to other technology, and the Siwertell unloader is so efficient that it will reliably meet the terminal’s growing capacity requirements for decades,”
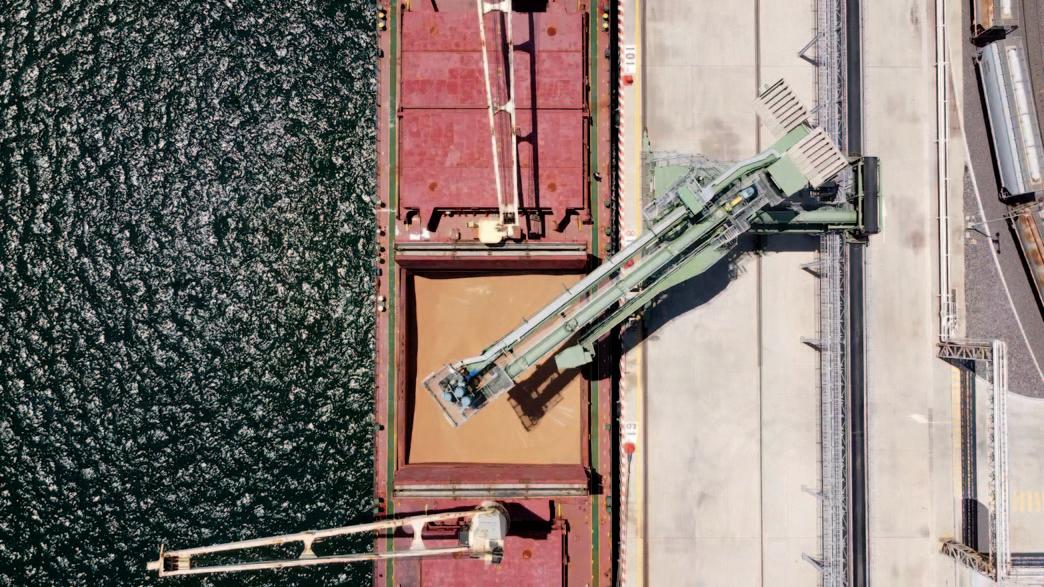

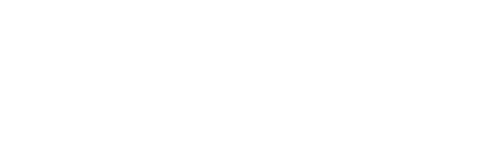
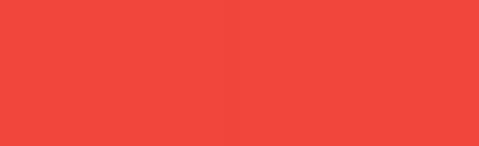


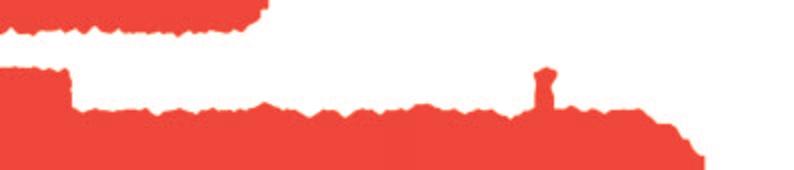
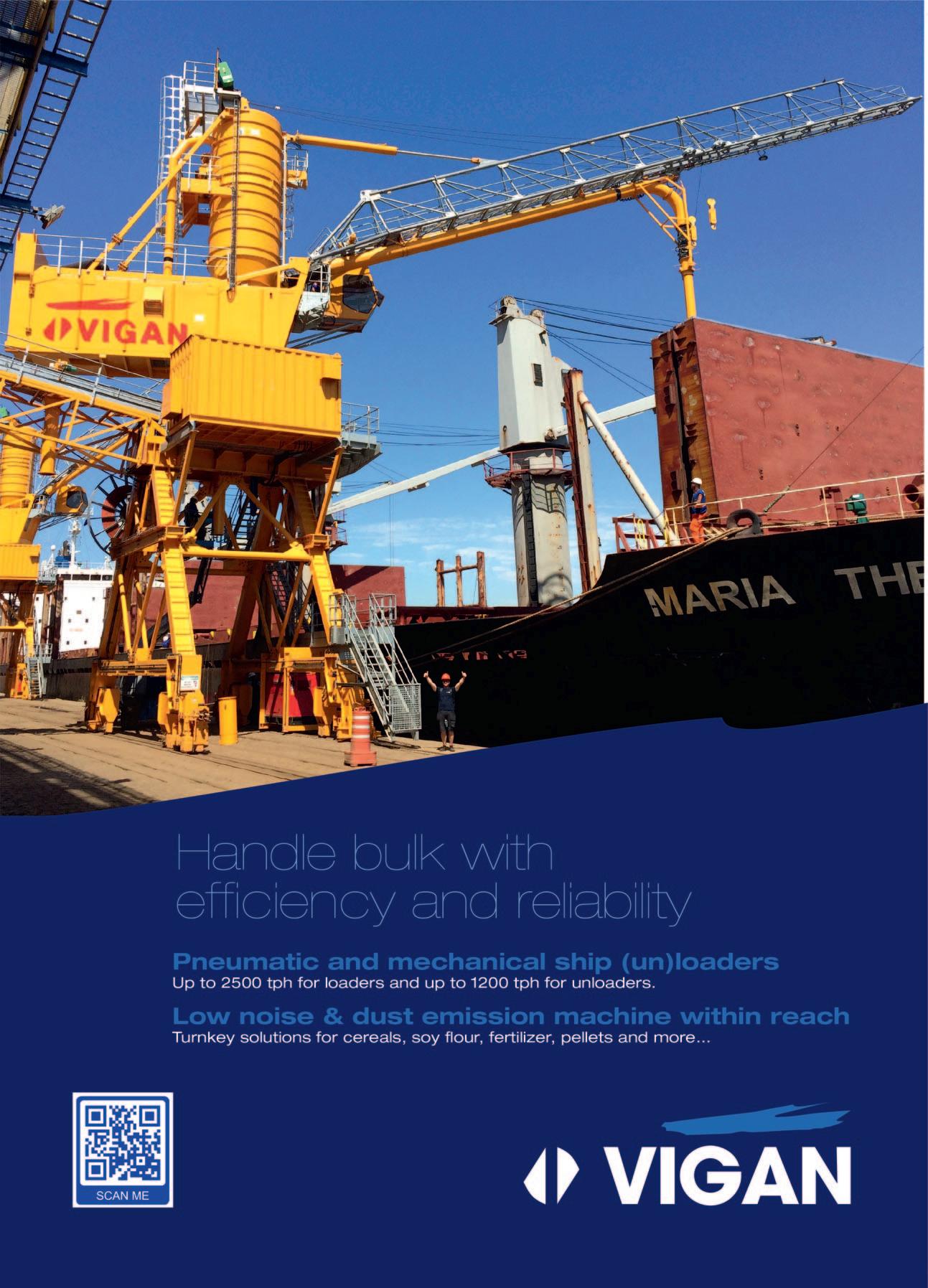
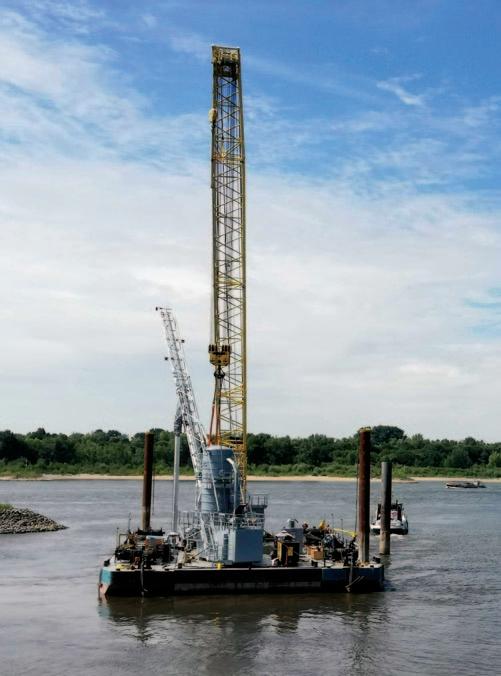

VIGAN oilseed ship-unloader installation on the Rhine (and left).
SOMETIMES, VIGAN MACHINES ALSO ENJOY A WATER CRUISE Just a few weeks ago VIGAN successfully installed a fifth unloader — in less than five years — in Germany, along the Rhine, close to the border with the Netherlands. It was an exciting project in Spyck where many secondary conditions had to be respected.
As usual, the machine was built and completely pre-assembled in the VIGAN factory in Nivelles, Belgium. The customer chose a colour that blended nicely into the environment. Next to strict dust emission specifications, the customer required a low noise emission machine.
Based upon VIGAN’s experiences with its former silent machines and the one recently built for Brüggen in Lübeck (oats unloader, see picture on p66), VIGAN equipped the machines with every possible noise-reducing element: an acoustically sealed piping, a cabin with special noise-cancelling baffles, a specific orientation of the turbine exhausts, specific air thigh sealings… Needless saying that some of these developments will become standard in all VIGAN unloading machines of tomorrow!
In Spyck, erecting the machine on site wasn’t possible because of the facility’s location. On top of that, the area is a natural habitat for birds and the Rhine has strong currents at that geographical location.
Therefore, VIGAN engineers opted to assemble the machine on a spot nearby where the necessary space and access for cranes, forklift and other utilities could be facilitated. During the first two weeks, the machine was completely mechanically built up. A ship’s crane lifted the pneumatic unloader to bring it to its destination, thereby finishing the job in three weeks sharp. So yes, VIGAN also unloaded its unloader by the river!
BUILDING MACHINES UNDER ONE ROOF HELPS FASTER COMMISSIONING A total mounting time of three weeks might seem fast … and it is. This typical VIGAN approach facilitates short mounting times all over the world, whether in Germany, Taiwan, or Bangladesh. Having all parts of its machines being built under the same roof allows VIGAN to have a full overview on every detail of the machine. And all equipment can be pre-mounted completely in VIGAN’s large production halls where its team also realizes the complete electrification.
Customers say that this approach is unique to VIGAN, compared to other manufacturers which choose to build machines — or parts of them — in other places around the world, where labour is cheap(er). Harmonization of every functional part of the final equipment is not an easy task if it needs to be done abroad. VIGAN is therefore sticking to its approach of keeping production in Belgium and to only use the best possible third-party components.
VIGAN machines need to unload from when a ship sails in, until the vessel sails out, and can therefore be operating for long periods. Engineers have reduced wear on components by opting for the most resistant alloys and by minimizing cargo impact through conceptual design and electronics. A real round section elbow, optimal suction control, adapted airspeed through powerful turbines and frequency steering are standard.
All the auxiliary equipment in VIGAN’s machines — moto reducers, high-speed engines, electronic components, compressors, etc. — are all made to the highest standards. Next to their reliability, their suppliers also have good servicing networks along the globe. Globalization also smoothes the connection/interfaces build-up with the downstream part of facility.
Saying VIGAN provides turnkey solutions in unloading is therefore not to be taken lightly. Dry commissioning is taking place at every stage, from the mechanical mounting to the final connection of the machine — until every single device of the VIGAN unloaders
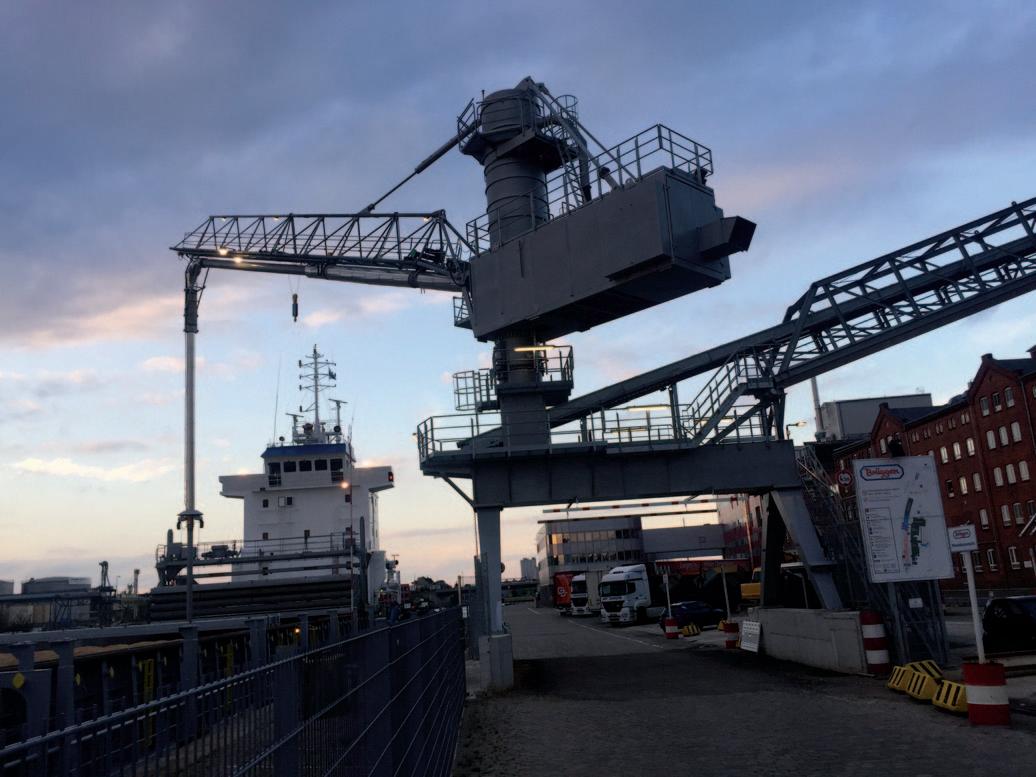
Acoustically insulated machine at Brüggen, Germany.
works properly.
But the customer also requires a ‘suction capacity’ as defined in the offer. As soon as possible, the VIGAN technician will co-operate with the local operators to begin the so called ‘wet’ or ‘hot’ commissioning: proof that the machine can suck the required capacity per hour. Based on this so-called nominal capacity and VIGAN’s experience over the years, the company knows that its machines reach 75–78% efficiency, expressed as a percentage of the nominal capacity. These figures are high compared to nonpneumatic unloading techniques.
In general, one can say that pneumatic discharge became more energy efficient than ever with no damage done to the cargo. The closed-circuit build-up of the machine reduces contamination risk to a complete zero, there are no spillages, and the technique is safe in its features, ATEX rules being covered. It would be said that VIGAN filters almost become air purifiers and, as stated earlier, noise emissions are strongly cancelled.
VIGAN offers fully customizable solutions wherever customers are located, even if its machines have to sail towards their locations.
A ship’s crane lifts the VIGAN pneumatic unloader on its floating platform.
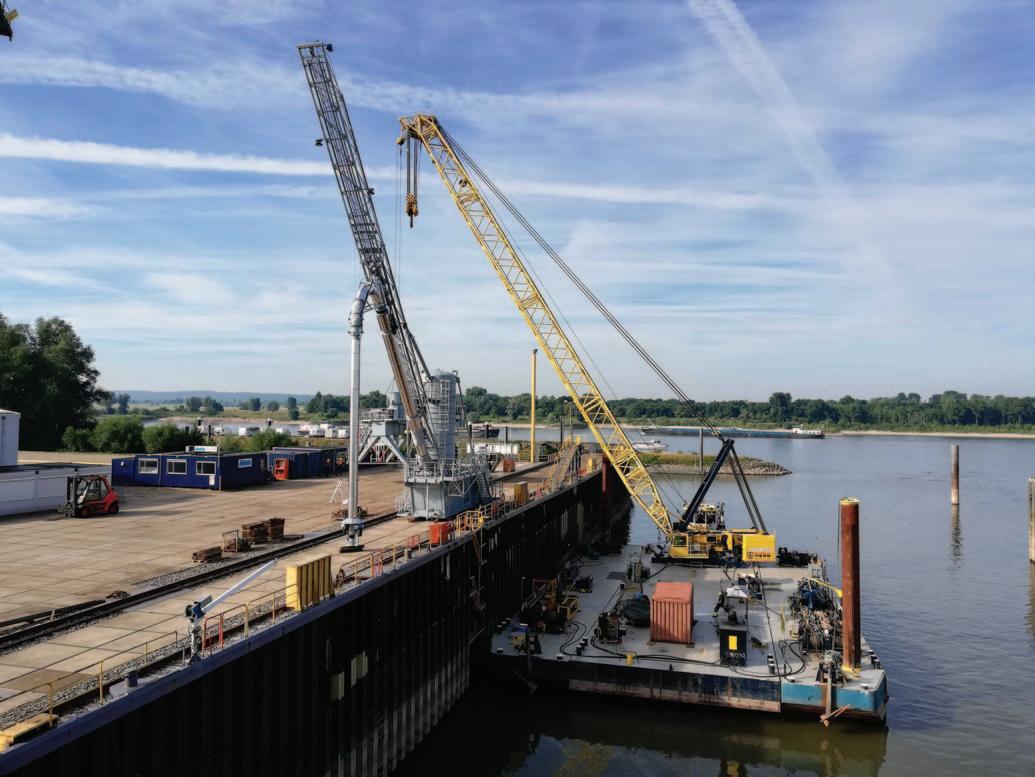
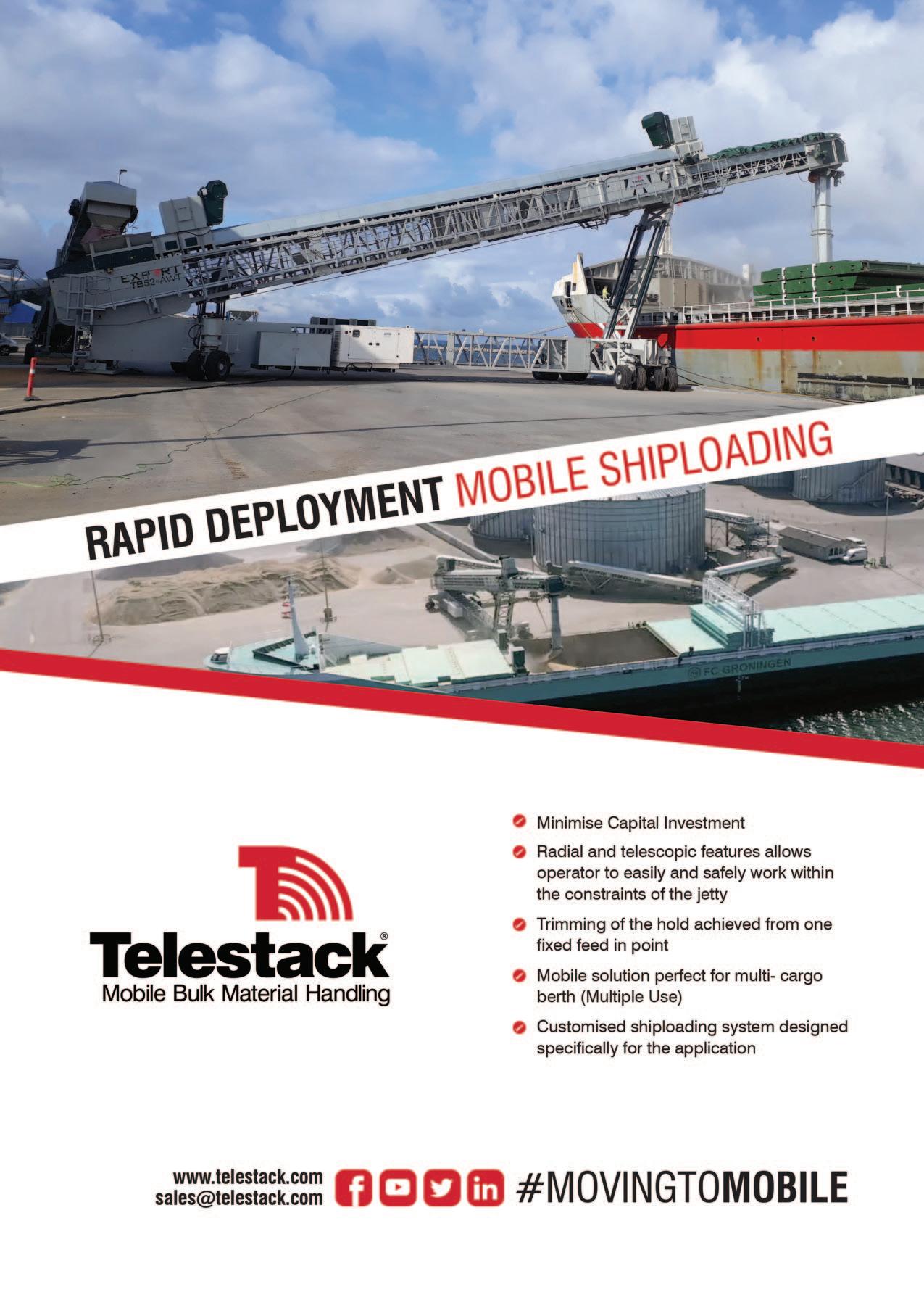
ENGINEERING & EQUIPMENT Road-mobile alumina unloader exceeds expectations in France
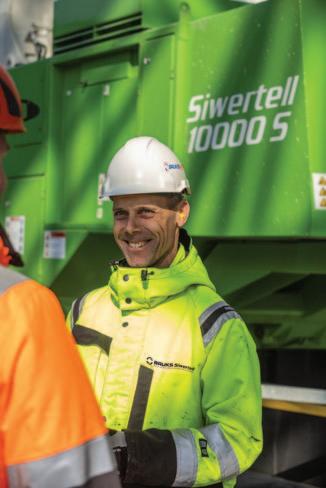

All photos: Bruks Siwertell.
Trímet France’s new Siwertell nextgeneration road-mobile unloader is now operational, handling shipments of alumina so efficiently that it is exceeding owner expectations; the unit’s remote control and digital capabilities are also proving beneficial, writes Jörgen Ojeda.
Handling alumina, the valuable, powdery bulk commodity used in the production of the endlessly recyclable metal aluminum, is a Trímet France speciality. At the end of 2021, Bruks Siwertell enhanced these capabilities further with the delivery of a new Siwertell 10,000 S next-generation road-mobile unloader to the company’s alumina import facilities in France’s largest port, Marseille.
Trímet France, part of Germanyheadquartered, Trimet Aluminum SE, principally receives vessels from Greece and Ireland, with the largest standing at around 14,000gt and the smallest close to 6,000gt. Shipments of alumina are discharged to silos, ready to be sent in rail wagons to a long-established aluminumproducing factory in SaintJean-deMaurienne, south-east France.
SPEEDING UP AT THE BERTH “One of the biggest challenges for us has been to reduce the time that a vessel stays at the berth,” explains a spokesperson for Trímet France. The faster vessels can be turned around the higher the utilization rate of the jetty, delivering better profitability for the terminal. With an expected alumina intake of around 50,000 metric tonnes into the port in 2022, the majority of which will now be handled with the new road-mobile unloader.
Siwertell unloaders are based on screwconveying technology and offer high, continuous through-ship efficiencies. They can reach into the corners of a vessel’s hold, including under the hatch coamings, because of the range of movement in the horizontal conveyor and the pendulum capability of the vertical arm, which also means that assistance from payloaders is kept to a minimum.
“The mobility of the equipment’s conveying arm is definitely an advantage for achieving faster vessel turnarounds, and allows us to operate everywhere in the
We are happy to reduce emissions with this electric Siwertell version holds,” says Trímet France. Trímet France EXCEEDING UNLOADING EXPECTATIONS For around a year and a half, Trímet France leased an older Siwertell 10,000 S unloader from another Bruks Siwertell customer. “We did this before deciding to buy a new, next-generation electric-drive model,” says the company. “Environmental issues have an important place in our mind. So, we are happy to reduce emissions, and the noise of
The new unloader features advanced digital capabilities.
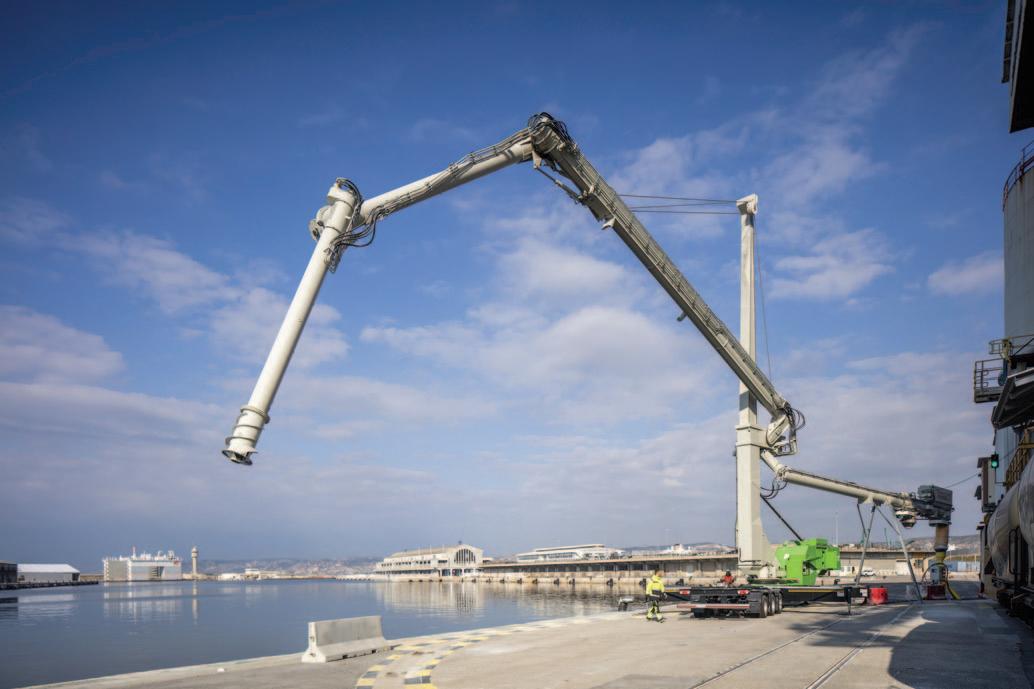
the engine, with this electric Siwertell version.”
The new unloader has a designed rated capacity of 130tph (tonnes per hour) for discharging vessels up to 10,000dwt, it also features advanced digital capabilities. Fitted with the Industrial Internet of things (IIoT) device, CompuLab, owners of nextgeneration models have safe, remote access to extensive monitoring, follow-up support, diagnostics and troubleshooting.
Trímet France highlights the additional performance capabilities of its nextgeneration road-mobile unloader. “The remote control is particularly useful,” says the company. “Operators are able to see precisely if the unloading is efficient, so we can reach a discharge capacity of 150tph. This is over what we expected. Also, the digital capabilities mean that Bruks Siwertell is able to check any problem that occurs on this Siwertell unloader in real time.” They also operate with a layer-bylayer unloading process, which minimizes the chance of airborne emissions from avalanches in the cargo hold. This is further reduced because of the equipment’s excellent hold reach.
For road-mobile unloaders, a dust filter is installed at the top of the loading conveyor. It creates negative pressure and minimizes the risk of dust emissions at the transfer point where material leaves the unloader and enters the receiving equipment. It automatically returns the collected dust to the conveying system.
MINIMIZING DEGRADATION MAXIMIZES PROFITS In addition to offering efficient, environment-friendly alumina handling, with no spillage and very low energy consumption, the Siwertell unloader minimizes material degradation, which delivers a particular benefit to the alumina industry that goes further than the port.
During commissioning Trímet France noted that the remote control needed
Siwertell unloaders minimize material degradation, delivering huge benefits to the alumina industry.
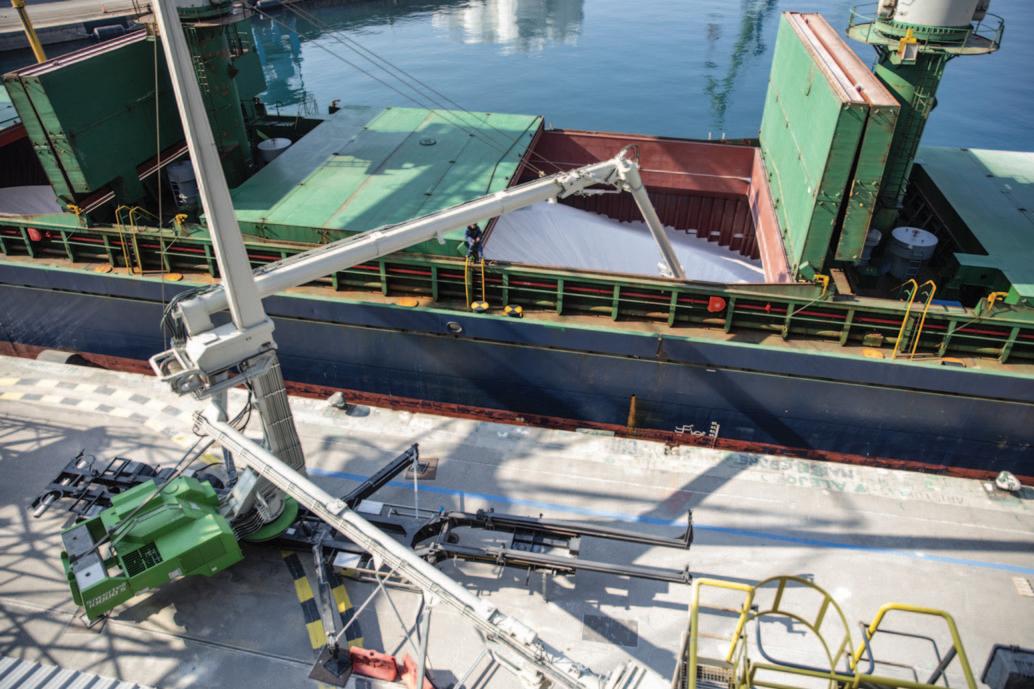
further attention. “We were grateful to Bruks Siwertell for its reactivity to solve the issue, and are continuing to work together to find a solution to reduce noise from the screw because we are situated very close to neighbours,” it adds. Alumina is sensitive to degradation and therefore has a high propensity for the production of powdery fines. These have a significant impact on a smelting plant’s energy consumption; the lower the percentage of fines, the lower the temperature required in the process.
ENCLOSING THE DUST Environmental protection legislation is often a driver for the adoption of enclosed dry bulk handling equipment, and prior to the Siwertell unloader installation, Marseille’s port administration had requested that Trímet France reduce its dust emissions.
All Siwertell ship-unloaders have a totally enclosed conveying line from the hold, where the inlet feeder draws material into the vertical screw conveyor from beneath the surface, to the receiving facility, offering close-to-zero dust emissions and eliminating any wasteful spillage.
“In the midst of soaring energy prices, any reduction in fines has a huge economic impact, and offers better cost control for the plant,” explains Jörgen Ojeda, Sales Director Mobile Unloaders, Bruks Siwertell. “We are not only keen for more port operators to benefit directly from our market-leading alumina handling capabilities, but in addition to this, for these advantages to extend to substantial savings for the global alumina industry as a whole.”
SUPPORT BEYOND DELIVERIES Siwertell road-mobile unloaders provide a flexible, efficient solution for customers that have operations at more than one location. They can be folded down and relocated in under an hour. In the future, Trímet France plans to trial these capabilities, and transfer the equipment to its other sites to test if this solution could be successfully transposed elsewhere.
“We have really had a chance to get to know Trímet France and its operations, initially over its leasing of the older roadmobile,” continues Ojeda. “This was a valuable experience and over this time, we supported the company with any servicing needs.
“We hope that Trímet France will continue to benefit from the enhanced capabilities of its new road-mobile unloader for many years to come, and we look forward to helping the company with its plans for the future,” he concludes.
ALUMINA: A BILLION DOLLAR POINT Bruks Siwertell’s shiploaders and conveyors are well-established as preferred bulk material handling systems for alumina across the world, but it has even more to offer.
Bruks Siwertell can demonstrate that Siwertell screw-type unloaders outperform established alumina unloading methods, including grab cranes and pneumatics, to such a degree that across the global alumina industry, savings could reach the billion US dollar mark.
Alumina is an expensive dry bulk commodity, and its spillage costs the industry millions of dollars every year. During alumina unloading, some grab cranes can spill up to one and a half percent of a shipment. In contrast, independently observed tests with Siwertell road-mobile unloaders showed no loss of bulk material. Eliminating spillage and minimizing dust creation deliver additional savings in cleanup costs as well.
Pneumatic systems do not incur spillage on the scale of grab cranes, but they are less efficient, demand more energy and cause significantly higher material degradation than Siwertell unloading systems. Alumina degradation, and the presence of powdery fines, has a major impact on energy costs in the smelting process; reducing fines, reduces production costs.
Few investments can totally transform an industry, but by making the switch to a Siwertell screw-type unloading system, this is exactly what is on offer, saving alumina plant owners and operators a fortune and delivering major environmental benefits. DCi
