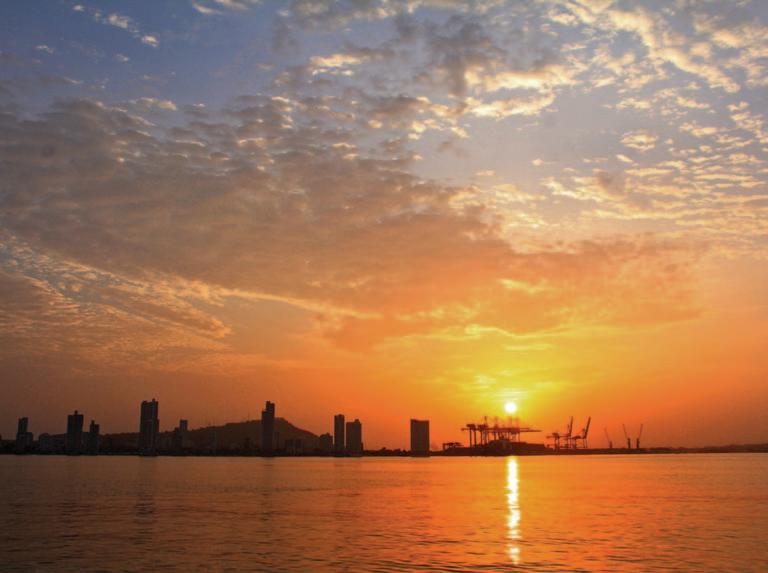
8 minute read
Gdynia and Riga Freeport sign memorandum on coal
The Russian Port of Vysotsk is to build a new grain terminal, which will have an annual capacity of four million tonnes.
As per its planned design, it will be able to handle rakes of six rail wagons at a time and have storage on site for up to 240,000 tonnes. It will serve grain producers in the Leningrad Region, which are increasing production all the time, and the new terminal will help them focus more on export markets. Total investment will be around $91 million.
A further two grain terminals are already under construction in both Vyborg and Kingisepp districts of the Leningrad Region. Barry Cross
Spain’s Mediterranean Port of Cartagena reported total traffic of 18.25mt (million tonnes) in the half year to 30 June. This is its best result since 2005 and represents yearon-year growth in the region of 18%.
Dry bulk performed well in these first two quarters, with imports up 16.85% based on traffic of 3.4mt and around 1.5mt being inbound grain. These originally came from Ukraine, but new sources have since been found, given the difficulty in getting grain out of Ukrainian ports because of the war with Russia.
According to the port, “Cereals continues to generate very good figures thanks, first of all, to the fact that our farmers (…) were very far-sighted and concentrated imports in the first months of the year, but also because we have (…) established commercial relations with other booming markets such as the United States, Germany, Brazil or France.”
Clinker and cement also did well, with 100,000 tonnes more imported in 2022 than in 2021, equivalent to a 60% uptick. Customers in Spain and Italy remained in place, and new alliances established with Algeria and Turkey.
The port points out that the new rail connection at Escombreras with central Spain has also boosted traffic, especially cement traffic generated by Cementos El Tajo. This new line means that clinker now flows from the port to different parts of Spain. Barry Cross
Dry bulk imports up in Cartagena
Gdynia and Riga Freeport sign memorandum on coal
Gdynia Port Authority and Riga Freeport have signed an Memorandum of Intent that will pave the way to enable greater co-operation between them. One of the results should see the Port of Riga handling at least five million tonnes of coal by the end of the year.
The two ports hope to take advantage of the unstable situation in the global energy market and disruptions in freight supply chains by leveraging spare capacity to be found at the Latvian and Polish ports.
In particular, Riga wants to better use the state-of-the-art multi-purpose Krievu Island terminal, which became operational at the end of 2018. This facility has equipment to handle and crush coal, as well as transport and store it. It has the most up-to-date infrastructure in the Baltic region as well as being very environmentally friendly.
Coal handling, for example, is effectively a sealed activity, with an automated wagon dumper system. Furthermore, a closed conveyor belt network transports coal to and from docked vessels. In order to reduce dust escaping into the air from open coal storage areas, the coal is regularly misted; in winter, snow cannons are also used for the same purpose. There is also a 23-metre-high dust fence to prevent the spread of coal dust into the immediate environment.
The port authority has also placed an air quality monitoring station on Krievu Island.
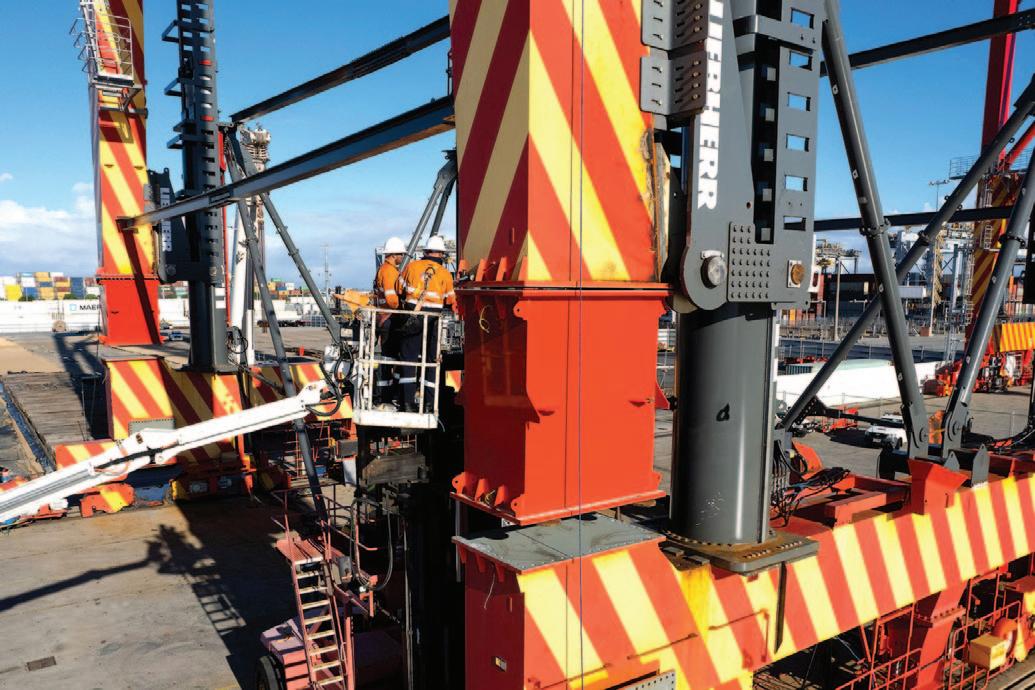
Liebherr Transform is the new upgrade, modification and overhaul service that has a tailor-made solution for customer needs. It is available for ship to shore container cranes, rubber tyre gantry cranes, rail-mounted gantry cranes, mobile harbour cranes, offshore and ship cranes.
The new Liebherr Transform provides tailored solutions that respond to the continuously growing demands on today’s businesses. A range of ingenious upgrades, clever retrofits, machine overhauls and service modifications breathe new life into customers’ existing machines. Using the latest technology and years of experience, Liebherr brings a combination of sustainability, smart technologies, maximum productivity and cost-effectiveness in one complete solution. This allows existing equipment to reach its full potential.
New service solution includes overhauls, upgrades, retrofits and much more It is inevitable that equipment becomes outdated over time but that does not mean it has to be replaced.
As the name suggests, existing machines are transformed using affordable complete or partial machine overhauls, retrofits and upgrades. This not only saves the increased capital expenditure of investing in new machines, but also reduces the carbon footprint by avoiding the need for new equipment through the extension of the service life. A number of retrofits and upgrades are available which increase versatility and performance, or ensure compliance with more stringent regulations, and so open up a wider spectrum of opportunities. At the same time, operators do not have to get used to new machines and can continue to benefit from their vast experience with existing equipment. The Liebherr team of expert engineers takes care of the entire planning and implementation of Transform projects — from consultation, through to installation and technical support and service.
STRONGER, FASTER, SMARTER, GREENER Companies are under pressure to increase volume and performance, widen scopes, or reduce emissions and costs, the list is endless. Liebherr Transform helps to lighten the load through a comprehensive range of structural, electrical, mechanical, ergonomic or digital modifications. Through the application of new technologies and expertise, Liebherr machines are transformed for the workplace of the future. They are stronger, faster, smarter, greener, and ultimately...better.
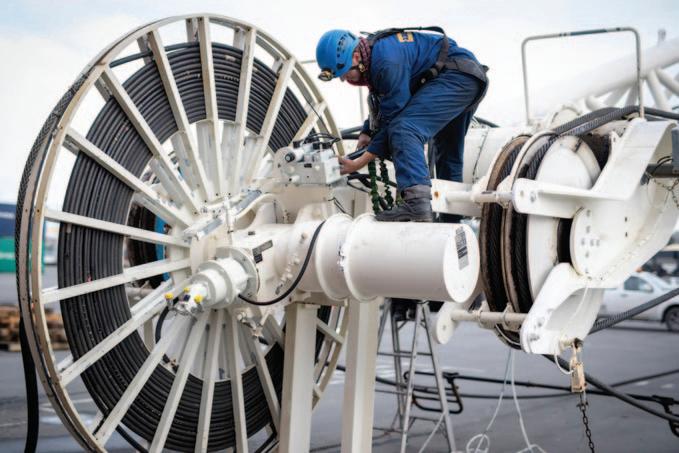
Muller Beltex BV, V.A.V. Aandrijvingen BV and Germany based Bechtel GmbH have announced their strategic alliance. By a transfer of shares, the owners Lars Muller and Emiel Schoutsen have established this co-operation.
The know-how and expertise in components for bulk handling equipment is not limited to the Netherlands and Germany, where the three companies are located. They operate worldwide and the close co-operation between the three companies will therefore provide major benefits for their entire, geographically widespread, customer base.
Both owners emphasize that this alliance is not a merger and that the companies will retain their own identities. Company locations and contact points will remain unchanged.
The advantages arising from the collaboration are, in particular, the bundling of their expertise and the use of each other’s network, especially abroad. In certain markets or geographic regions, the one partner is better represented than the other. “This collaboration will enable all three of our companies to better position themselves in the market and to provide our customers with materials, knowledge and service in an even better and more efficient way,” Muller and Schoutsen state.
V.A.V. Aandrijvingen is globally known for its chain applications in the feed and grain handling industry. It is able to deliver immediately from stock, or within days, all components for chains as well as elevator components and parts for various screw conveyors.
Muller Beltex providing solutions for the bulk handling and process industry and specializes in bucket elevator trouble shooting. Further to this its components, Polysur® elevator belts, Kryptane abrasion resistant polyurethane liners, and the Atex approved monitoring systems are known worldwide.
Bechtel GmbH is a strong service related supplier of components for bucket elevators and chain conveyors. Its knowledge of chain conveyors and problem solving capacity enables it to build, for the entire German industry, all types of chain conveyors even for the most complex applications.
The alliance of the three companies wishes to further improve their already very high service level to the bulk handling industry, and thus securing quality and continuity of their efficient supply chain.
Bobcat unveils its most powerful compact loaders
Bobcat has expanded the company’s next generation RSeries range of products with the launch of the new S86 and T86 compact loaders. The new S86 R-Series SkidSteer Loader and T86 R-Series Compact Track Loader replace the previous 700 and 800 M-Series loaders and complete the current R-Series loader line-up.
Commenting on these new product introductions, Mike Vought, Vice President Product Management at Doosan Bobcat EMEA, said: “The S86 and T86 are exceptional machines — the most powerful compact loaders we have ever built, providing even more versatility as both tool carriers and workhorses.”
TOP-OF-THE-RANGE: THE S86 AND T86 COMPACT LOADERS Delivering a higher engine and hydraulic output, the Bobcat S86 and T86 are the most powerful compact loaders the company has ever built. Both machines use a well-proven Stage V compliant 3.4 l Bobcat engine – producing 78kW (105 HP) at 2,600RPM. Just like all R-Series loaders, the engine is mounted in-line with direct drive, which improves the cooling capacity of the engine and hydraulic components. This change increases reliability in high-intensity applications such as road construction and forestry work.
John Chattaway, Loaders Product Manager at Bobcat, commented: “The S86/T86 follow on from the very successful introduction of the smaller S66/T66 and S76/T76 loaders. The S86/T86 top-of-the-range models continue the same trend by setting new industry standards in every area, from incab comfort and safety to available power and attachment versatility. The S86/T86 take what is possible with compact loaders to a whole new level.”
The new S86 and T86 workgroup design increases the ability to lift more, carry more and reach further. This is achieved by a new workgroup geometry that improves lifting capability throughout the lift arm’s range of motion. When combined with the high hydraulic performance and the lighter and stronger cast-steel lift arm sections, the loaders offer higher capacity throughout the lift cycle — even at full height. Along with the S66/T66 and S76/T76 models launched over the last two years, the S86/T86 set new industry standards for incab comfort. This includes the low noise and vibration levels inside the one-piece sealed and pressurized cab, together with the intuitive SJC controls as standard, and the informative displays. The cab also has an HVAC system as standard and increased operator visibility, which can be further enhanced with the innovative Clear Side cab option.
With the latter, 75% of the side windows are mesh-free, ensuring an unobstructed view from the cab. Bobcat has also added a rear-view camera as standard equipment to the list. In addition to the standard five-inch in-cab display, Bobcat offers as an option, an advanced seven-inch display that provides even more detailed machine information and unprecedented device connectivity.
