
33 minute read
PARTICLES ON THE RUN: CONTROLLING FUGITIVE DUST
Particles on the run
controlling fugitive dust
LIFTUBE® on the conveyor at Geocycle Belgium.
Jay Venter
LIFTUBE® enables plants to meet safety and environmental standards
Today, industrial sites are subject to increasingly strict standards for the transfer of bulk materials and are looking for solutions to minimize their impact on the environment and increase the safety of their employees. In terms of conveyor belt conveying, the answer to these challenges is the LIFTUBE®. Indeed, this equipment developed by STANDARD INDUSTRIE INTERNATIONAL, perfectly integrates belt conveyors in order to optimize their tightness. This system guarantees the safety of the operators, confines the material by avoiding dust emissions and product losses and drastically reduces maintenance costs. The LIFTUBE® replaces stations equipped with three rollers on conven tional conveyors. In concrete terms, standard onemeter modules can be perfectly integrated into all or part of a new or existing conveyor, keeping the belt, frame and, in most cases, the original motorization. This system is often installed at the right of the chutes and on all or part of the belt length. Available in widths ranging from 500 to 1,600mm, in high temperature, food grade or self-extinguishing versions for ATEX constraints, it avoids any contamination of the transported product with the outside. This watertight system also allows for safe and minimal maintenance by tilting the edges and the central roller.
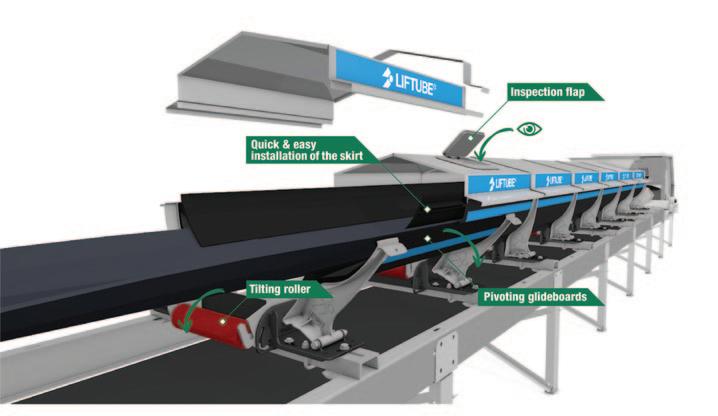
CUSTOMER CASE: LIFTUBE, USED ON WASTE RECOVERY UNIT CONVEYORS GEOCYCLE, SEVESO site, which is at the forefront of the management and treat ment of recyclable waste, recovers used oil cans for its Seneffe plant in Belgium. The product of this recycling (impregnated sawdust) falls on the conveyor belt and is transported over several hundred metres to be used as an alternative fuel in the preheating towers of the HOLCIM group’s cement plants.
Originally surrounded by grids or simply covered, these conveyors regularly spilled over at the level of the chutes and generated significant environmental nuisances (dust and solvent odour) not only for the plant operators but also to the detriment of the nearby urban environment. The customer therefore agreed to equip its three conveyors with the LIFTUBE® 800 special self-extinguishing version.
With LIFTUBE®, the transported material is completely contained. As a result, odour emissions are drastically reduced and there is no material spillage. The LIFTUBE® allows a constant flow of material on the belt and protects the incoming points. Finally, the plant saves considerably on the maintenance of its LIFTUBE-equipped conveyors, since the first conveyor equipped in 2018 has still not required any intervention.
Cleveland Cascades supervising the installation of a spare parts package for Phillips 66.

Cleveland Cascades Ltd. commissioning engineers have recently returned from Immingham in the UK where they were assisting one of its long standing customers, Phillips 66. Acting alongside the planned maintenance shutdown team of Phillips 66, the scope of work was to supervise and oversee the installation of a spare parts package that was supplied earlier in the year.
All components were successfully fitted to the Cascade system which has the capacity to load petroleum coke at rates of up to 620 tonnes per hour.
Following the spare parts installation, cold commissioning checks and function testing of the electrical components was to be performed. Unfortunately, due to unforeseen issues with the shiploader boom ropes, this work couldn’t be completed.
Once rectified, Cleveland Cascades hopes to return for another visit in order to verify the system setup and witness the loading procedure adopted by Phillips 66 operatives, advising on any potential methods to be employed in order to achieve optimal system performance.
Allowing Cleveland Cascades trained personnel to complete the commissioning procedure is invaluable and the results speak for themselves. Doing so ensures that the systems potential is fully realized and that dust emissions from loading operations are drastically reduced, a further benefit is that material degradation is minimal due to the mass flow generated by the cones resulting in a quality product for shipping.

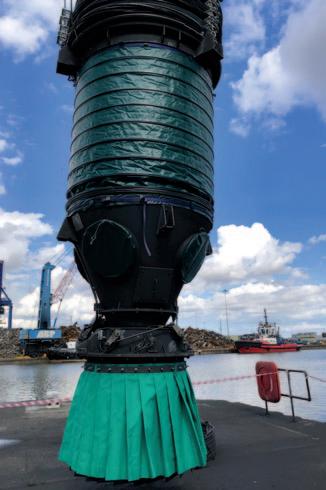
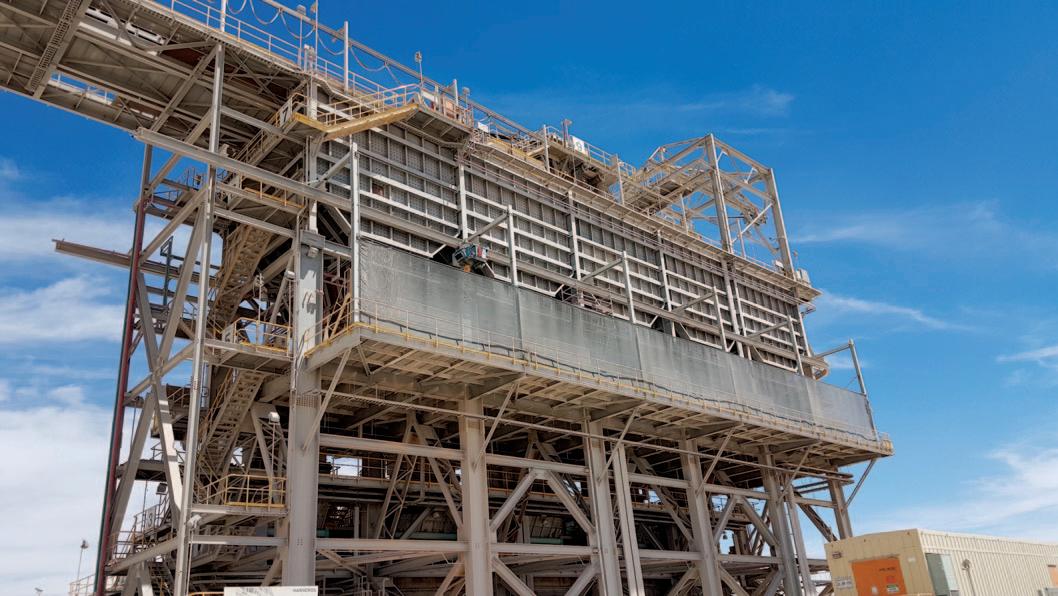
When we talk about dust emissions, what comes first to our minds are industrial sources of emissions, even though dust emissions are part of our day to day lives, writes Gonzalo Campos Canessa, CEO, TRC.
They normally occur because of two reasons: lack of moisture and dirt moving. When dirt is dry, it is easier for its fine particles to become airborne if wind blows or if dirt is being moved somehow.
Mining and other industrial facilities are material handling intensive, which means that the amount of dirt (ore, coal, chemical products, grains, wood by-products and others) being moved around these facilities

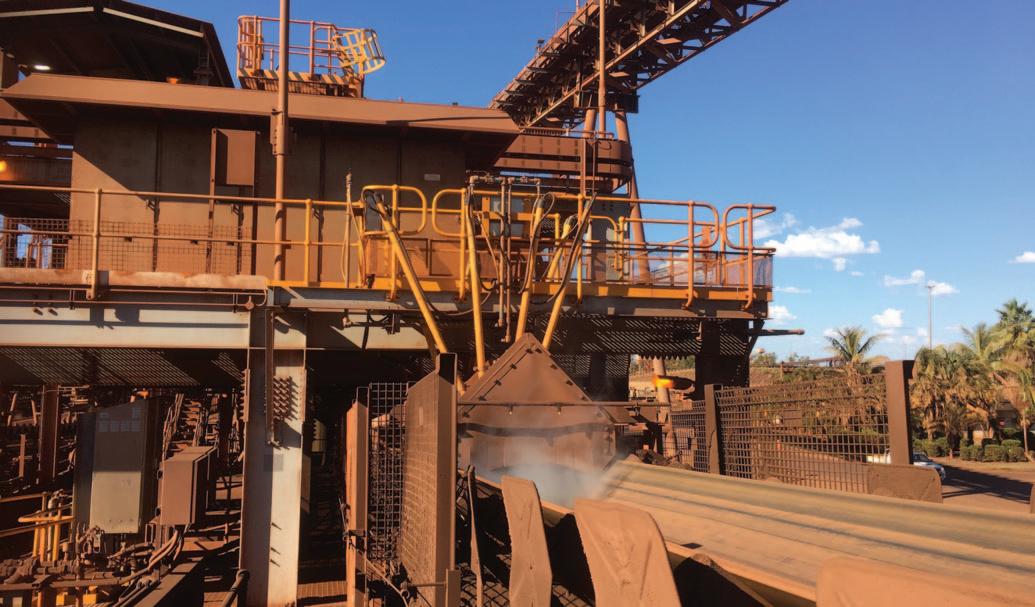
is significant and there is a potential for producing dust emissions and affect neighbouring communities and the environment if they don’t invest on dust control strategies and technologies. Let’s think about the material handling on a hard rock mining plant: 1. The first source of dust emissions comes with the blast needed to break the ground into rocks. This process which creates airborne dust which is difficult to control because of the massive scale and the lack of containment especially in open pits. 2. Machinery is needed to load these rocks into haul trucks. Dust is generated because of material falling down into
the truck’s beds and the impact inside it. 3. These trucks then transport the rocks to the crushing plant, which results in a big number of trucks driving around the plant through dirt roads. The dirt sitting on the ground is moved by the truck’s wheels and generate emissions. 4. The trucks them dump the material on a hopper/crusher. This operation produces emissions when the material falls into the hopper and also because of the turbulence produced inside of it. 5. The ore travels within the crushing plant (multiple crushers, screens and transfer points) before getting to the stock yards. Dust is generated due to the multiple transfers of material. 6. At the end of the process, the ore sitting in the stockpiles is exposed to wind gusts and becomes another source of dust emissions.
In this whole process, miners use different strategies and approaches to keep dust emissions low and controlled. At The Raring Corp, the company offers its clients dust control solutions focused on the crushing plant, from the truck dump to the stockpile, using Agglomerative Dust Suppression Systems (ADSTM Fog) and Water Spray Systems (WSS). Also, we always stress the importance of Passive Dust Control as it was mentioned in our May 2022 Dry Cargo International article: “Passive dust control system, we can say

that it is as important as the Active one, and they cannot work apart because of the high interrelationship of passive and active systems. The Passive dust control system is the key element that creates a controlled volume to isolate the point where dust is generated allowing the Active one to do its job.” Wind fences from our partner WeatherSolve Structures are a good example of Passive Technologies that can successfully be integrated with TRC’s Dry Fog in multiple applications, and to offer our clients integral dust control solutions for their facilities.
Over the years, requests for measuring dust control efficiency have become more common even though it is normally challenging to implement them correctly. Over all these years, we have developed the following procedure for measuring dust control efficiency in transfer points, which can be scaled for other applications.
For determining the efficiency of a Fog based Dust Suppression System the total amount of dust generated needs to be measured using high volume samplers. a) The amount of Base Dust is obtained by measuring the amount of ambient dust in the vicinity of the selected transfer point. This test must be done without any other equipment loaded and running in the neighbourhood of the transfer point being measured. Also, the
Dust Suppression System will remain in the OFF mode until data is gathered. b) The amount of total Ambient Dust is obtained by measuring the ambient dust in the same point measured on a). In this case all surrounding process equipment should be loaded and running. Dust
Suppression System will remain in the
OFF mode. c) The Remaining Ambient Dust is measured with all surrounding equipment loaded and running and this case with the Dust Suppression Systems running
The formula to estimate the dust suppression system Efficiency is the following:

Eff = 100 *((b) - (c)) / ((b) – (a))
Using the methodology described in this document, we have averaged 99.22 % efficiency for TRC’s Dust Suppression Systems in transfer points.
Emissions sources can be anywhere, so in most of the cases the combination of multiple sources is the result of fugitive emissions. This fact makes emissions’ measurements challenging and representative for one specific spot.
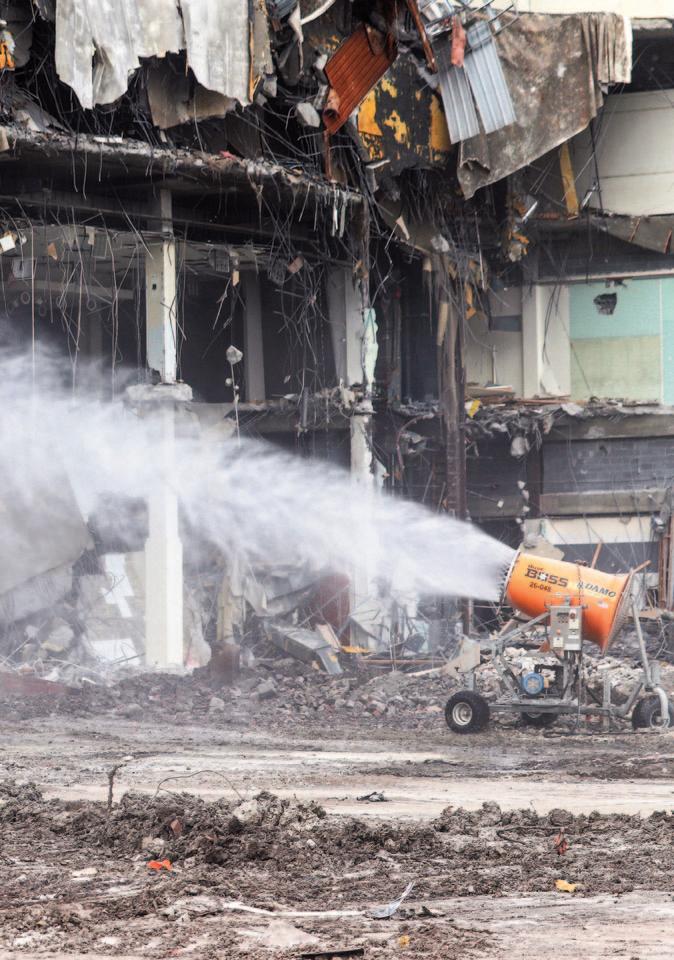

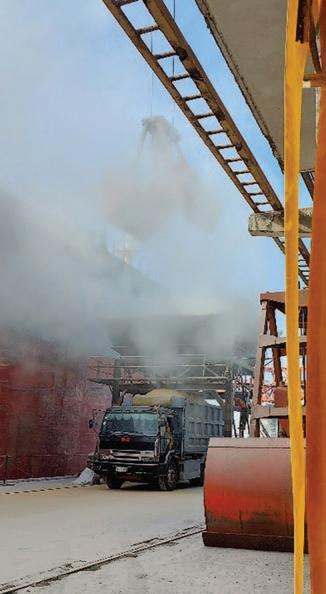
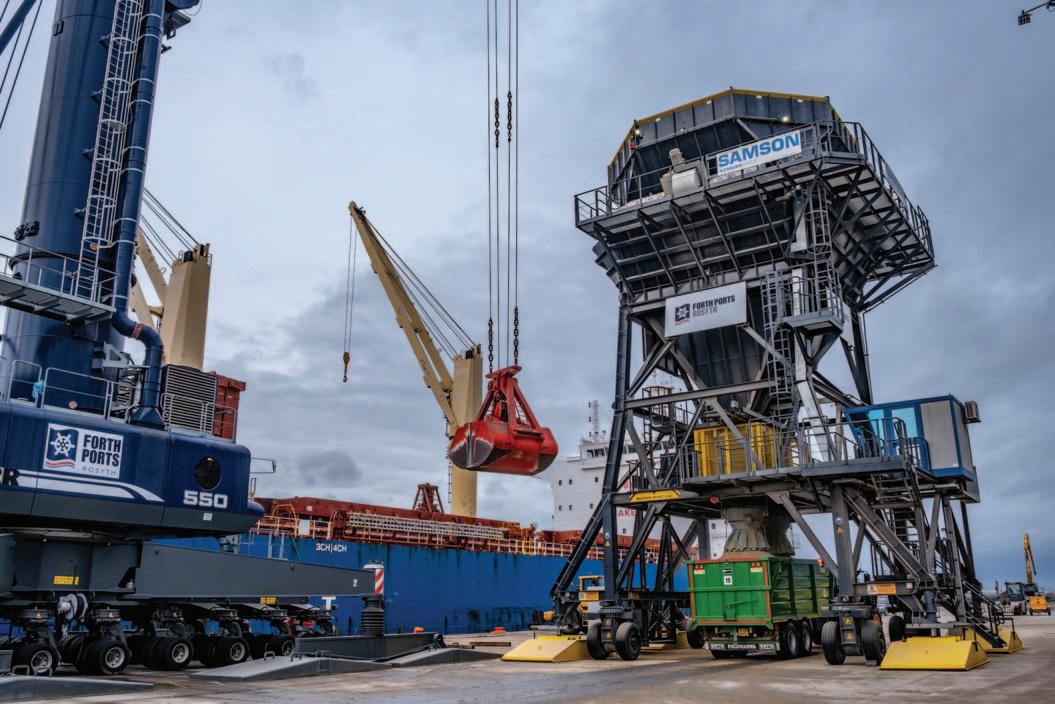
THE PROTECTIVE GROWTH The contemporary bulk material handling landscape continues to impose new practical and low-impact environmental demands on many businesses in regard to ship loading/unloading system, writes Petar Karaivanov, Marketing and Communications Manager, Samson Materials handling Ltd.
Because infrastructure facilities are necessary to allow varied activities, researchers, designers, and managers have focused more on flexibility, adaptability, and eco-friendly solutions.
Many existing industry projects have design lives of many decades and must meet current and future demands by increasing the likelihood of returns on investments while also contributing to sustainability via effective use of resources and equipment.
AVOIDING THE DUST BARRAGE Many dry bulk commodities are prone to spillage and can produce dust pollution, posing issues for ports that will become more and more widespread due to ever tightening of pollution guidelines, regulations and laws. This is especially concerning for low volume operators that work occasionally or seasonally and will not be able to invest in hefty infrastructure projects as easily as operators and ports with regular flow.
Port operators rely largely on cuttingedge low-impact technology in their infrastructure investments to maximize the use and durability of current and future assets. Many of the ageing machinery now used in ports and terminals will lose flexibility and adaptability as a result of ongoing global pollution reduction programmes.
Cereals, animal feed, mineral ores, coal and coke, cement clinker, biomass, phosphate, and other fertilizers are common bulk cargoes in ports. Handling these commodities produces a lot of dust. Environmental effect may be reduced while processing these cargoes by installing new and better dust control filter systems on future equipment, or by converting existing ones.
Ports that handle dry bulk must examine the huge variations between managing containers and dealing with dry bulk items. When handling bulk materials, six major parameters influence dust generation and therefore the equipment used in the process. These are falling distance, loading rate, environmental considerations (rain, wind, and other conditions), mode of transport, material properties (moisture content and particle geometry), and loading/unloading practise. Flexibility and environmentally friendly solutions will raise demand for new infrastructure investments or conversion projects for existing ones.
CASE IN POINT An excellent solution example for bulk materials unloading is an ECO HOPPER (as featured in image 2 below). It is an ecologically sensitive solution fulfilling all
Image 2: Port of Rosyth, SAMSON Eco Hopper with extensive dust control features and filters. Image 1: Example of large quantity of dust generation during bulk cargo unloading while using a regular hopper.
needs for the efficient import of dry bulk cargoes. The hoppers are designed to suit the characteristics and flow properties of effectively any dry bulk material.
Fitted with state of the art dust suppression filters for the lowest possible environmental impact benefitting both port operators and the surrounding environment around the port location.
Eco Hoppers can be suitably designed to receive bulk materials, which will be unloaded at the Quay area via a Crane Grab.
The above featured hoppers, have integrated: v Tapered Inlet Shroud designed to allow for a grab to be lowered within the reception area before opening. This will minimize dust generation created by cross winds and disturbance of airborne dust during the unloading operation. v Inner Hopper Isolation Shield – An inner hopper shield designed to isolate the dust filter elements from the main material flow optimizing the filter media operation. v Flex-Flap Dust Seal System – Special sealing system incorporating braided flexible strips to maintain a negative air pressure within the hopper to contain dust. The Port of Rosyth unloads and stores agri-bulk with a SAMSON Ecological Hopper and their story is one of success. Importing large quantity of bulk materials that need to be handled on site when they arrive, in safe, effective and dust free manner. Considering this, the port invested in a new Liebherr mobile harbour crane for bulk handling capability and to manage dust emissions, a SAMSON ecological hopper is also in place. The eco hopper is the first of its kind in the UK and forms a key component of the new agri-bulk hub facility. As of May 4th 2022 the port has reached its 1million tonnes milestone.
CONCLUSION Future ship loading and unloading systems must offer flexible and environmentally friendly import and export solutions for all bulk materials if they seek to increase the maximum potential returns of investments and increase the lifespan of equipment.
Distinctively tailored designs to match various types of vessels (e.g. from barges to Panamax size) and customer demands will provide an adaptive approach and enhancement in quality of operations at a low price in the long run.
The examples of equipment provided by SAMSON Material handling are equipped with state of the art dust filtration systems which brings the environmental impact close to zero ranking them among the top current experts in the fields of adaptability and low ecological impact of operations in loading and unloading systems.
ABOUT THE AUMUND GROUP The AUMUND Group is active worldwide. The conveying and storage specialists have special expertise at their disposal when dealing with bulk materials. With their high degree of individuality, both its technically sophisticated as well as innovative products have contributed to the AUMUND Group today being a market leader in many areas of conveying and storage technology. The manufacturing companies AUMUND Fördertechnik GmbH (Rheinberg, Germany), SCHADE Lagertechnik GmbH (Gelsen kirchen, Germany), SAMSON Materials Handling Ltd (Ely, England), TILEMANN GmbH Chains & Components (Essen, Germany) as well as AUMUND Group Field Service GmbH and AUMUND Logistic GmbH (Rheinberg, Germany) are consolidated under the umbrella of the AUMUND Group. The global conveying and storage technology business is spearheaded through a total of 19 locations in Asia, Europe, North and South America and a total of five warehouses in Germany, USA, Brazil, Hong Kong and Saudi Arabia.
ENGINEERING & EQUIPMENT Banishing dust with Golden West Industries

Golden West Industries (GWI) is a USbased dust mitigation company specializing in providing custom chemical solutions to mining, shipping and material handling industries globally. GWI works closely with ocean going vessels as well as landbased loading/unloading companies to ensure proper dust abatement, satisfying clients in the US, South America, the Pacific Rim/Asia and anywhere shipping occurs.
GWI’s speciality products are used with self-unloaders as well as non-self-unloaders across the world with extremely satisfying results.
The products are manufactured in the US and distributed via multiple containers including bulk, ISO containers and totes. This allows the vessels to load the product, or be used at ports/ports of loading. The equipment is also in house and is provided to the end user or fleets with an additional cost(s).
Professional technical services directors are part of the equation and are available for installations and 24/7 questions and port of call — maintenance or servicing in all regions of the world.
Golden West Industries provides custom solutions for three main types of dust control problems: v dust control for crushing plants and ore transport systems; v dust control for unpaved roads; v dust control sealant for open areas, stockpiles, hillsides and contaminated areas.
GWI’s dust reductions with coal, gypsum, iron ore, copper (even food grade products), are guaranteed to reduce fugitive dust to 80% reduction levels — however, its standard operating levels are at 90–95% reduction level on average.
Regardless of the size of shipment/cargo intentions/vessel dynamics, Golden West Industries is prepared to handle any and all situations. Its highly trained members of staff are available for any situation and dedicated to the company’s clients.
Generally speaking, GWI’s products are liquid in nature and reduce water consumption by up to 80% with highly favourable results. The equipment is small and easy to operate, install and function for years to come — even in salt water conditions.
GWI has been treating material on ocean going vessels since 1999, and on land facilities since 1991.
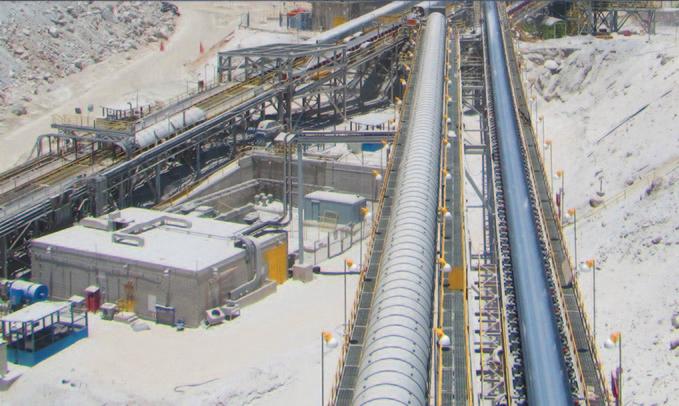

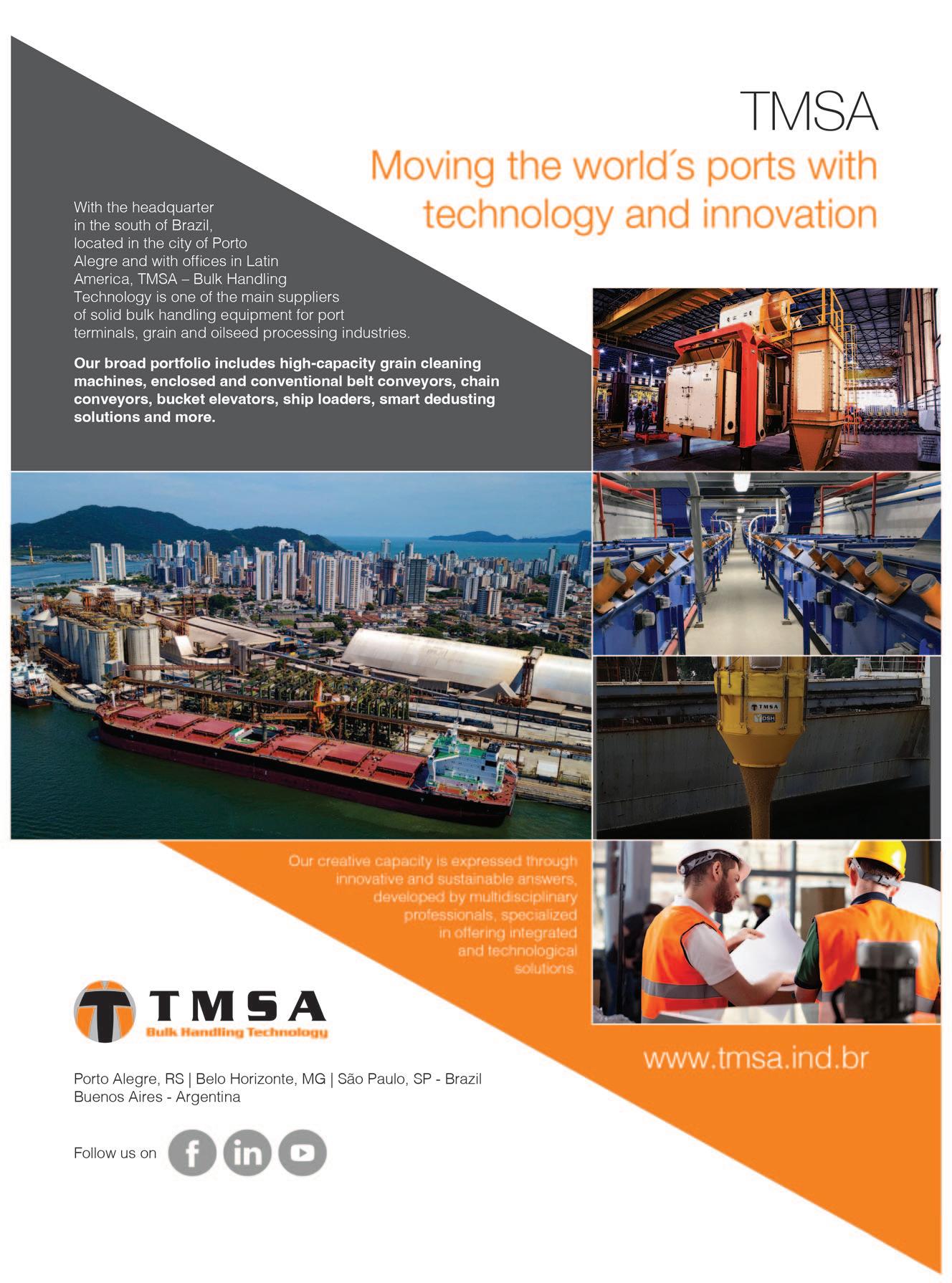

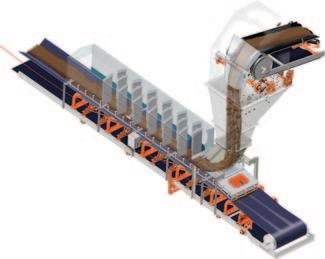
In response to global shortages, fertilizer producers are stepping up production, contributing to higher conveyor speeds and greater volumes of cargo, causing more dust within manufacturing facilities, writes R. Todd Swinderman, P.E., CEO Emeritus, Martin Engineering. For the most part, these facilities are enclosed to prevent odour and dust from affecting surrounding communities, but most workplace safety regulators closely monitor workplace conditions relating indoor air quality.
Some components of fertilizers can produce microscopic dust particles that are invisible to the naked eye which, over longterm exposure, can lead to chronic medical conditions, and thus are highly regulated. Dust can also clog bearings and other mechanical components, requiring more cleaning, maintenance and replacement parts. With this in mind, many fertilizer producers have improved workplace air quality by retrofitting conveyors to better seal the systems and thoroughly clean the belts.
MANY CONVEYORS, MANY RECIPES The manufacturing process for organic fertilizer differs from plant to plant, but most high-volume producers employ a multi-stage system with a throughput driven by conveyors. Many operators generate various mixes of fertilizers by adding precise measurements of different ingredients at specific intervals in the production cycle. Conveying and processing any dry bulk material runs the risk of dust emissions, but many of the hazardous ingredients found in fertilizer need to be ground to a fine powder before incorporation. This lighter, smaller particle size makes the additives more prone to becoming airborne.
Dusty particulate material (PM) can be as small as 2.5 microns (μ) and easily becomes airborne with agitation. At this size, the particles are invisible and small enough to bypass the body’s natural defences, penetrating deep into the lungs. Workplace regulators often test for PM10 and PM2.5 using personal testing devices carried by workers throughout their shifts.
Fertilizer dust can lead to violations because it contains regulated substances. There’s no disputing that fine powder phosphorus dust is toxic to humans and animals, causing serious long-term health issues.[1] Potash is less hazardous, but low dust levels of crystalline silica still appear during testing, which can violate OSHA air quality regulations.
Once a violation is identified, regulators have a number of options. They can set a deadline to solve the problem, issue fines, recommend a medical assessment of the entire staff, or even order a shutdown until the issue is resolved.
SEALING A FERTILIZER CONVEYOR SYSTEM Enclosing the system to contain fugitive dust depends on controlling air flow and ensuring there are as few openings as possible. Two areas to focus on are the discharge and receiving chutes.
Discharge chute with dust curtain and sealed openings.
(all images ©Martin Engineering 2022.)
SEALING THE DISCHARGE ZONE A sealing system that is maintained with no gaps between the belt and skirting is critical to controlling airflow, dust and spillage. Because the process is continuous, the discharging material acts like a fan pulling air into the enclosure. As air is induced into the transfer chute, particles separate, leaving the head pulley and flowing onto the receiving chute.
Installing curtains or barriers where the belt enters the discharge chute and sealing gaps in the chute reduce the open areas where air is drawn in. This air must discharge through the exit of the skirtboard enclosure. The skirtboard enclosure should be designed tall and long enough with intermediate curtains that cause dust to recirculate and agglomerate or collect on the curtains.
Induced air flow is proportional to the throughput, particle size and drop distance, so minimizing the free fall of material in the discharge chute — while still allowing adequate space for belt cleaning — is important. Where air flow is greater than what can be controlled passively, provisions for active dust collection should be included in the design.
SEALING THE LOADING ZONE v
v
v
v
v Regardless of how many belts are discharging onto a single ‘main belt’, the receiving system should be enclosed with sealed chutes. After the last feed belt, the enclosure should be long enough to give dust and fines time to settle, called the ‘settling zone.’ Although fertilizer isn’t a particularly heavy material, the belt support system should be able to absorb the impact of the heaviest cargo to protect the belt. Closely spaced idlers or cradles with support bars help avoid sags in the belt that allow gaps where fines can escape, while easing material disruption. Externally adjustable or self-adjusting skirting traps fine particles in the enclosure and adapts to fluctuations in the belt plane. Easily serviced wear liners can be changed from outside the chute
Heubach Dustiness Index (g/g min) = Dust Collector Filter (g)
Mass or test sample (g) x Test Period (min) x100
Equation: Heubach Dustiness index to measure the amount of dust in a dust monitor. Sealed loading zones might include elements like dust curtains, enclosed discharge zones, and belt support.
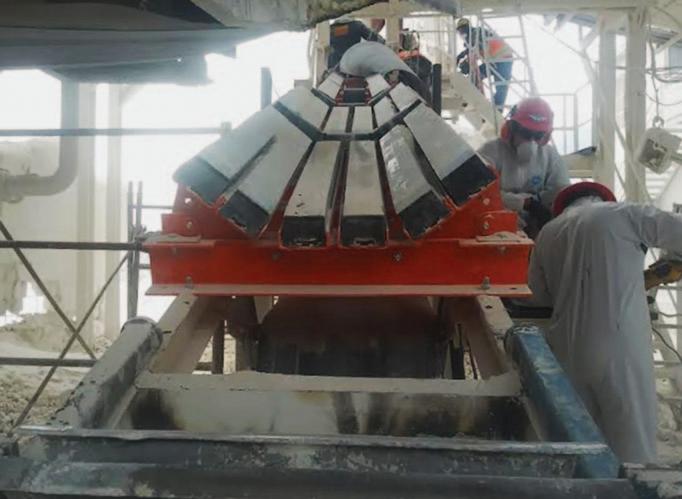
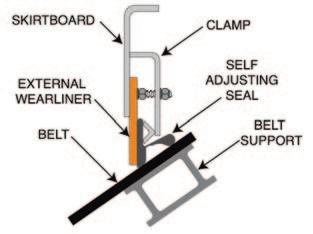
External wear liner and dual self-adjusting seal with belt support.
v
v
v
v without confined space entry. Dust curtains strategically placed throughout the enclosure control airflow and help settle dust. Dust bags or mounted air cleaners collect tiny, highly active particles when induced air flow is too great to be controlled in the enclosure. Inclined belts are common in fertilizer production. A sealed tail box protects the tail pulley from the backflow of fines, dust and spillage. An exit curtain set back slightly from the end of the chute is required to help prevent fugitive dust from escaping at the settling zone and prevent ‘popcorn’ spillage caused by the exit curtain.
CONVEYOR BELTS FOUND IN FERTILIZER PRODUCTION As the belt passes over the head pulley, material generally does not discharge completely due to static, flaws in the belt’s surface, ambient humidity and adherent qualities of the cargo. Whatever is not discharged or removed with a belt cleaner is carried back along the belt’s return and is one of the main causes of fugitive dust. This carryback not only throws off the proportions of carefully weighed additives, but also results in lost product as material drops from the belt along the entire length of the system.
Due to the type of belting commonly found in fertilizer production, dust emissions from carryback are especially problematic. Since the cargo is relatively light, producers rarely use expensive heavyduty belting, instead choosing more costeffective polyvinyl chloride (PVC). Antistatic rubber belts are available with flat top surfaces, but PVC belts are often seen as a lower priced option without considering the cleaning, maintenance and safety costs of dust. This cheaper PVC belt tends to have tiny depressions caused by shrinkage of the PVC into the top layer of the solid woven belt carcass. The belt face resembles a hammered metal surface, with fines getting trapped in the dimples and not falling off during the return by gravity. A primary belt cleaner installed on the discharge pulley will remove heavy build-up, but this does not address the particles captured in a dimpled or damaged belt surface which is a main source of dust on the return run.
The fertilizer production process can also have several inclined conveyors fitted with ribbed, flighted, grooved or chevron belts. These ridges can resemble wheel
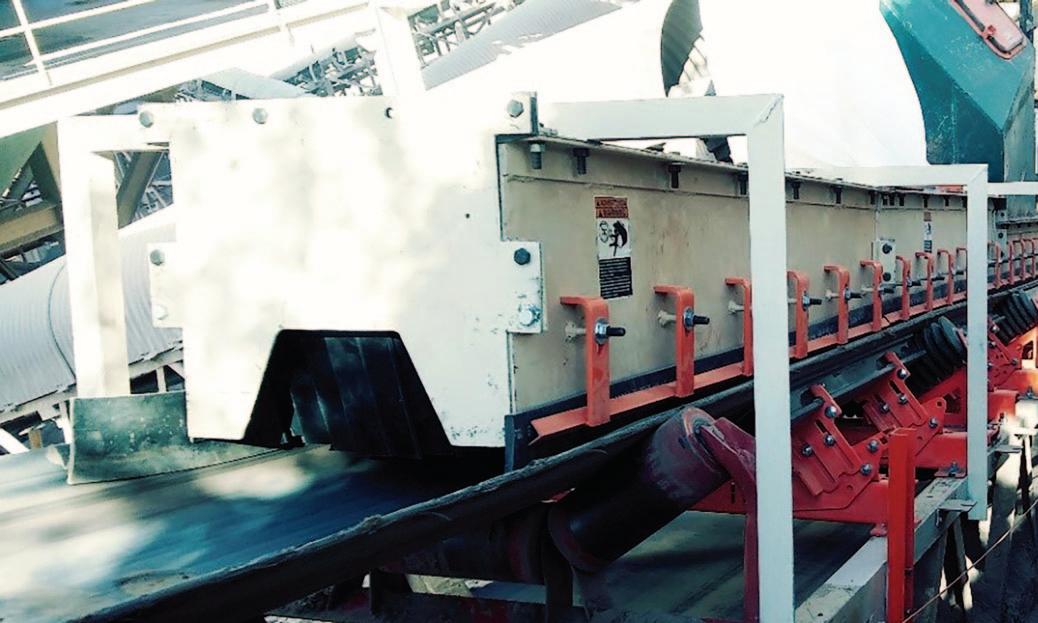
A long, sealed enclosure with cradles, idlers, external skirting and dust curtains.
tracks or tyre treads which the cargo attaches to as it is pulled upward. Textured belting is impossible to clean effectively using a standard belt cleaning system designed for flat belts, so maintenance tends to leave the belt uncleaned. As carryback piles underneath the system, workers typically shovel it back into the material flow, which adds more labor to the cost of operation and exposes the workers to potential injuries.
BELT CLEANING IN FERTILIZER PRODUCTION Because of the tendency of the fertilizer to accumulate static charges, all components in the system — including belt cleaners and chutes — must be grounded to reduce

dislodged dust from re-attaching to the belt surface. Primary cleaners are most effective on a flat (non-crowned) head pulley, and if crowned pulleys are used, segmented precleaner blades are recommended. High quality polyurethane blades can be shaped in a curved ‘constant angle and pressure’ (CARP) design to ensure that a consistent wear surface and pressure are applied to the belt throughout the life of the blade.
The tiny depressions in PVC belting can also sequester material beneath the belt’s surface plane, allowing it to bypass primary cleaner blades. To mitigate this, a specialized mechanically grounded and static dissipating rotating brush cleaner has bristles that can remove trapped dust and fines. The brush is also well suited for the removal of fines and residue from ribbed, flighted, grooved or chevron conveyor belts. The fine polypropylene bristles are rotated using a one or two-horsepower motor (depending on belt width) to dislodge trapped material. Enclosed discharge zones should be designed to fully encase brush cleaners, since the rotating brushes can release dust from dry cargo. The brush cleaner will create generated air and its use may require a mechanical dust collection system. Air cleaners inserted above the discharge enclosure are preferred.
An alternative to brush cleaners is the ‘wash box’. The typical configuration is one or two high pressure spray bars for applying water, followed by two or three secondary belt cleaners, all contained within the wash box housing. The final blade is generally designed for removing water so that the belt leaves the box relatively dry, and most of the water is drained at the base of the unit. In the case of ridged belting, an internal rotating brush cleaner can be used in place of secondary blades.
DUST COLLECTION SYSTEMS When evaluating strategies to control dust in fertilizer manufacturing, some plants may assume that a central collection system is the best or only option, largely because the equipment is widely available. But the cost of these systems is high, and they require significant ongoing maintenance, leading managers to assume that the cost of dust control is going to be prohibitive. In comparison, the mechanical solutions outlined above typically require minimal investment, and there are also highlyeffective options that don’t require massive central collection systems with a cost to match.
Two common pieces of filtration equipment are dust bags and integrated air cleaners. Installed above the conveyor loading zone, dust bags collect particles without energy consumption. In a wellsealed chute with properly controlled airflow, the air is directed through the upper openings, where dust agglomerates in the fine mesh bag.
Once full, a short stoppage in the system allows the bag to relax and the collected dust falls safely onto the belt. Some fertilizer ingredients can emit combustible dust so static-dissipating bags and proper grounding are recommended.
Air cleaners are individual mechanical collectors that use a reverse air pulse in the collection chamber to return dust to the main cargo stream. With low power consumption and easy maintenance , some operators have found air cleaners offer a
The belt passes through a pressure spray cycle, then the water is removed by blades. The tensioner puts enough pressure on the blade to clean the belt but easily pass over splices. ENGINEERING & EQUIPMENT
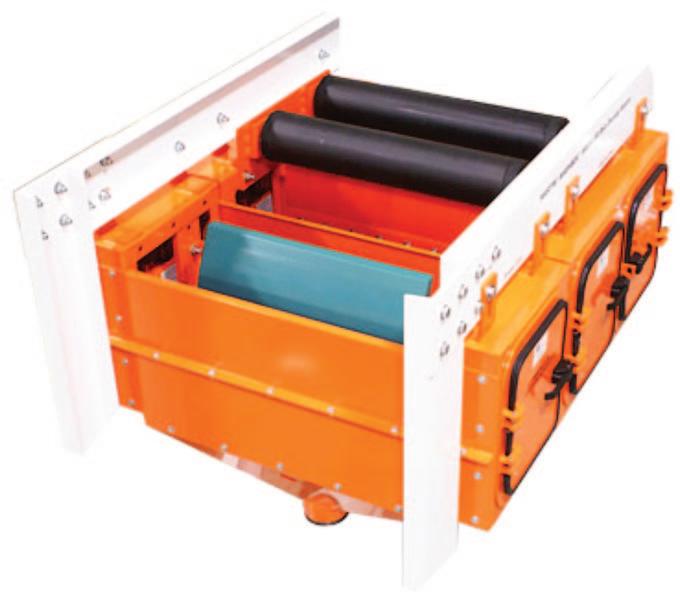

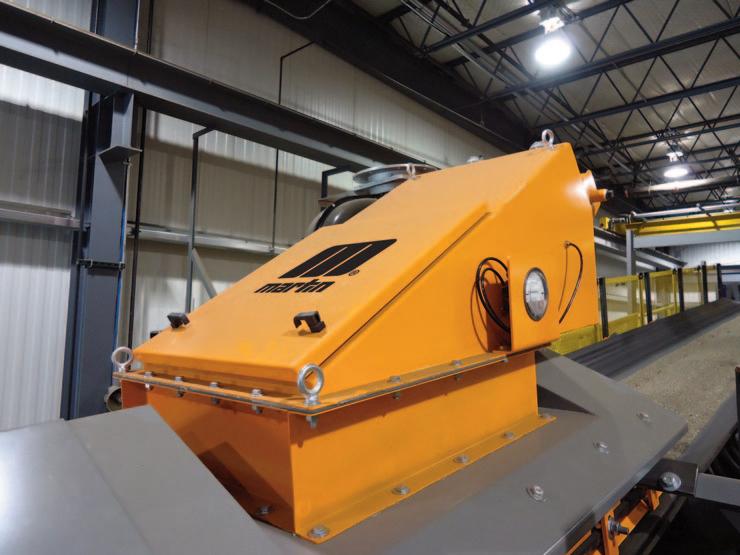
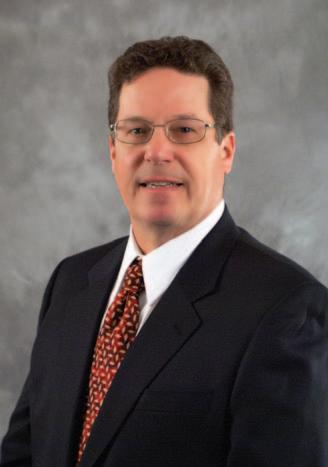
CONCLUSION The current fertilizer shortage has exposed the fragility of the global supply chain, but workplace safety does not need to take a back seat to production. Managers of production facilities are generally aware of air quality issues, but with only a moderate increase in production, operators are often surprised by the dramatic increase in dust emissions these modest changes can produce.
Retrofitting equipment that improves both production and working conditions results in avoidance of dust-related violations, less unscheduled downtime and a lower cost of labour for clean-up. This reduces the total cost of operation and
offers a greater long-term return on investment, and most importantly, results in a safer workplace.
References [1] Environmental Protection Agency (EPA). “Phosphorus”, EPA, 7723-14-0, Sept. 2016. https://www.epa.gov/sites/default/files/2 016-09/documents/phosphorus.pdf
ABOUT THE AUTHOR R. Todd Swinderman, P.E. /CEO Emeritus/ Martin Engineering, earned his B.S. from the University of Illinois, joining Martin Engineering’s Conveyor Products division in 1979 and subsequently serving as V.P. and General Manager, President, CEO and Chief Technology Officer. Swinderman has authored dozens of articles and papers, presenting at conferences and customer facilities around the world and holding more than 140 active patents. He has served as President of the Conveyor Equipment Manufacturers’ Association and is a member of the ASME B20 committee on conveyor safety. Swinderman retired from Martin Engineering to establish his own engineering firm, currently serving the company as an independent consultant.
ABOUT MARTIN ENGINEERING Martin Engineering has been a global innovator in the bulk material handling industry for more than 75 years, developing new solutions to common problems and participating in industry organizations to improve safety and productivity. The company’s series of Foundations books is an internationally recognized resource for safety, maintenance and operations training — with more than 22,000 print copies in circulation around the world. The 500+ page reference books are available in several languages and have been downloaded thousands of times as free PDFs from the Martin website. Martin Engineering products, sales, service and training are available from 17 factoryowned facilities worldwide, with whollyowned business units in Australia, Brazil, China, Colombia, France, Germany, India, Indonesia, Italy, Mexico, Peru, Spain, South Africa, Turkey, the USA and UK. The firm employs more than 1,000 people, approximately 400 of whom hold advanced degrees.
Several dust bags can be utilized, depending on the number of loading zones or dust volume on a belt.
Mechanical air cleaners are low maintenance and improve \ the air quality around the system.
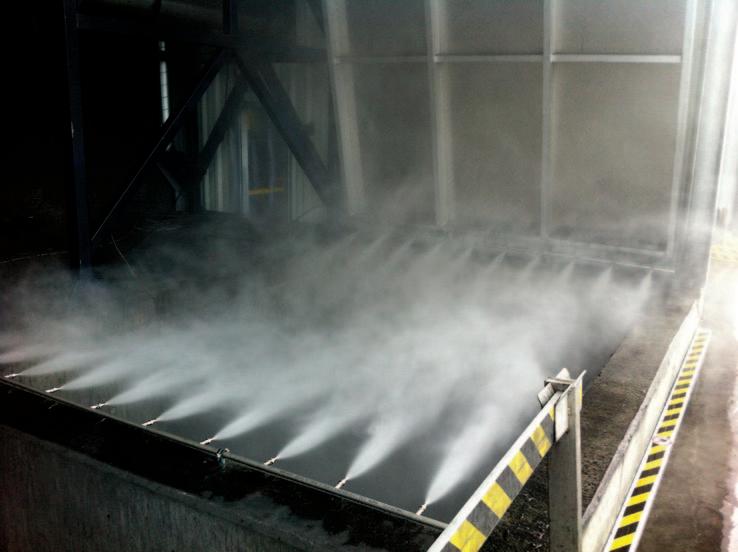
We all like to reside in a healthy, dust-free environment. However, the spread of dust cannot be avoided in some sectors and is harmful to the environment and to health. Health and environmental regulations continue to become increasingly stringent in this respect. In other words: dust control is essential. Spraystream offers cutting-edge atomizer technologies that reduce the spread of dust by about 90%. This allows users to create a dust-free and safe work environment, not only for all employees, but also for the entire neighbourhood.
Spraystream only uses the most reliable technologies of the highest quality in its dust-suppression systems. This means that the company only delivers the most efficient solutions with excellent service. Its ecological dust prevention systems also contribute to a more sustainable world thanks to their limited water and energy consumption. The use of water atomizing allows for the atomizing of the largest possible surface area.
In addition, Spraystream’s innovative technologies help suppress unpleasant odours and allow for the cooling and decontamination of the space. These are always tailored to the extent of the client’s issue and in compliance with the latest industrial standards. Operations like, for example, grain handling, can generate large amounts of dust (above). This is where the Spraystream system comes into its own.
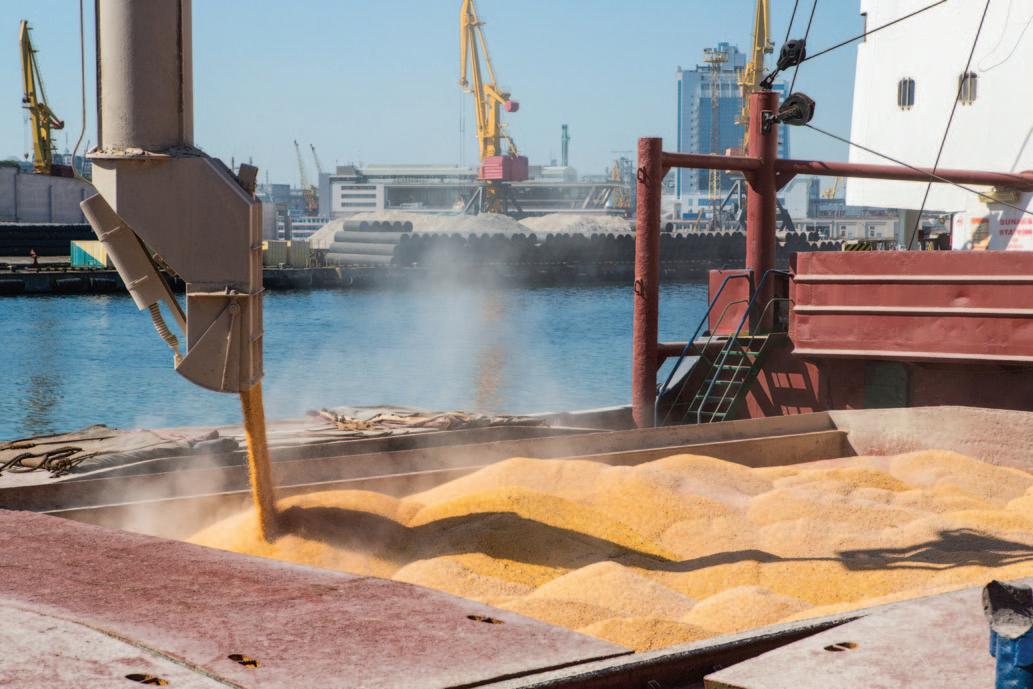
LOADING, UNLOADING, AND TRANSSHIPMENT: THESE PROCESSES RELEASE A LOT OF DUST — SPRAYSTREAM SOLVES THIS ISSUE Port companies load and unload large quantities of (bulk) goods on and from ships every day. They also take care of the safe transshipment of commercial goods. However, these processes release a lot of dust. This leads to unsafe working conditions, the loss of various raw materials, and wear of equipment.
Spraystream has developed various solutions to load, unload, and transship goods in a safe and controlled manner and to control the emission of dust. The company has an extensive range of fog cannons and fixed nozzle systems that absorb the hazardous substances and remove them from the air using the atomizing of small micro-droplets.
Anyone requiring a specific solution should get in contact with the company, which will be able to provide an ideal system, tailored to meet the exact needs of the project.
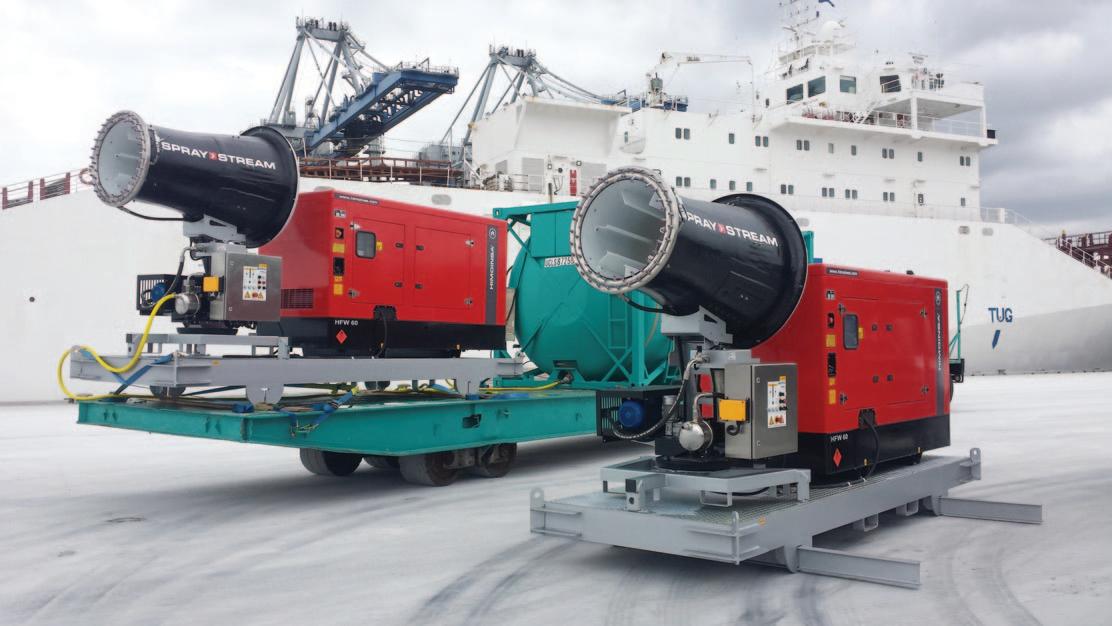
ABOUT SPRAYSTREAM AND THE SAVIC GROUP Spraystream is a subsidiary of the WestFlemish machine builder Savic Group. Mirko Savic, founder and owner of Savic Group, incorporated his company in 2004 with a single mission: designing sustainable, innovative, and high-quality atomizer technologies to handle all odour and dust issues.
As a pioneer in its field, the Savic Group has a its own dedicated internal R&D department and production unit. A team of driven engineers ensures the careful handling of all projects, from quotation to after-sales service. There is also the option to hire one of the company’s cutting-edge machine.
“Our job is to create a healthy and safe environment,” says Mirko Savic.
INNOVATIVE SOLUTIONS OF THE HIGHEST QUALITY FOR ALL CUSTOMERS Cutting-edge solutions of superior quality make Spraystream a global leader in the field of atomizer technologies. Quality has always been, and remains, absolutely paramount to Spraystream as a company, which strives to innovative its technologies every day to sell the best possible systems. Sustainability is key in this respect: Spraystream’s systems are ecological and designed with wear-resistant materials for extensive use. Spraystream always observes the needs of its customers, striving to establish a long-term relationship thanks to its excellent service.
TECHNOLOGY Spraystream uses innovative methods to prevent and control dust, based on the principle of atomizing. Because large surface areas are nebulized at the same time, Spraystream focuses on efficient and sustainable dust control.
MIST INSTEAD OF WATER When micro-droplets (mist) come into contact with dust, both matters merge. They subsequently fall on the floor together, eliminating the dust from the air. This is not the case when using large water droplets; where the dust particles move around the droplets. By controlling the size and quantity of the micro-droplets, Spraystream can create the best solution for customers’ issues.
SPRAYSTREAM FOG CANNONS: A HIGHQUALITY SOLUTION Spraystream offers an extensive range of fog cannons with various options. These machines create a micro-droplet mist curtain with a range of up to 150 metres, in part thanks to the use of high-quality materials: v The patented cone shape is aerodynamic and made from a composite. This high-quality material creates lighter machines, has an attenuating effect, and has a lower risk of corrosion. The cone shape leads to a maximum range with a minimum capacity and water. v Spraystream also uses GRUNDFOS maintenance-free pumps of the highest quality. v Spraystream’s intuitive machines are also very easy to use and can be controlled remotely. v The Spraystream machines have a default electrical oscillation and the fans can withstand high performances. v The wind guides make sure that a turbulent air flow is converted into a laminar air flow. This leads to minimum water flow losses and thus to more targeted and more efficient atomizing. v The atomizers can be replaced easily because rapid-lock systems are used. DCi
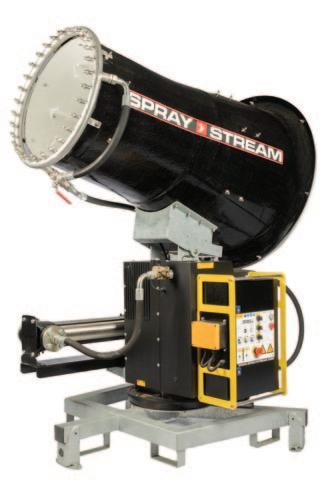
Port Saint John is currently undergoing a quarter billion-dollar infrastructure project which will add a new pier (shown here to the right) with two new cranes and many other significant upgrades. This will be operational in 2023.
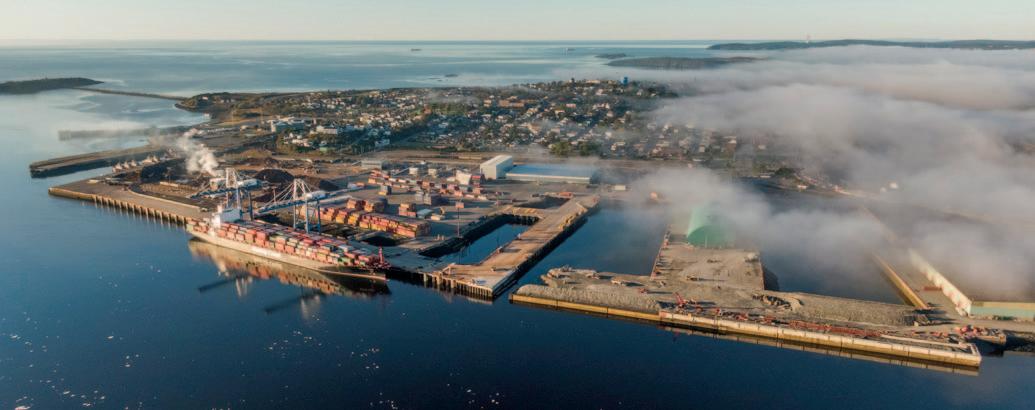
Port Saint John is the fourth-largest port in Canada by tonnage and is located on the East Coast of Canada. Handling a variety of different cargoes, including containers, dry bulk, liquid bulk, and breakbulk, it sees an average annual volume of 27mt (million metric tonnes). This is in part due to a deep-water, year-round ice-free harbour, that remains fluid and uncongested.
However, it also speaks to the partnership with three Class I railways: CN, CP and CSX, regional truckers, three stevedores, and a growing labour force. Together these assets ensure the port is positioned for performance in all sectors, including bulk. The port is also closer by nautical mileage to South America than many of the US East Coast ports giving Canadian exporters, and importers a Canadian East Coast hub for their product to move through.
Specific to dry bulk, Port Saint John currently handles two major commodities: potash and recycled metal, but has room to grow with new materials and products. In 2021, over 1.6mt of potash were exported through the port, a 167% increase from 2020. This bulk operation is made possible through a partnership between Canpotex, Nutrien and CN Rail. These numbers are expected to remain high in 2022. American Iron and Metal saw over 254,000 metric tonnes of recycled metal flow through their terminal in 2021. Outside of these commodities, their Lower Cove Terminal’s 16.8 acres remains open for business as a common user terminal for dry bulk commodities. In the past five years the terminal has seen up to 180,000 tonnes handled at the facility including but not limited to: gypsum, rock, limestone, and salt.
Beyond its common user terminal, Port Saint John also hosts DP World. Its multiuse terminal is currently undergoing a quarter billion-dollar upgrade. New features will include: v Widening and deepening of the overall harbour; v An additional new berth (2,000 lbs per square foot lift capacity, and 17.1m depth); v 21 new acres of terminal space; v 2 additional quay side cranes (superpost-Panamax); v Increased rail capacities; v Technology upgrades.
These upgrades coupled with over 55 acres of existing space, four large on dock warehouses (each over 100,000ft2 in size), and access to CP, CN, and CSX rail enables DP World to offer innovative solutions for moving bulk products around the world including forestry products.
Forestry products are currently primarily moved by container through the Port of Saint John, with the on-site warehouses serving a vital role in ensuring these supply chains remain fluid.
Finally, while many bulk products continue to move in bulk vessels it should be noted Port Saint John is serviced weekly by CMA, MSC, and two Lloyd container services. The most recent addition of a Northern Europe seasonal service by Hapag Lloyd enables Port Saint John to now directly connect to Antwerp and Hamburg.

DCi
The Barrack Point Potash terminal handled over 1.6mt of potash in 2021.
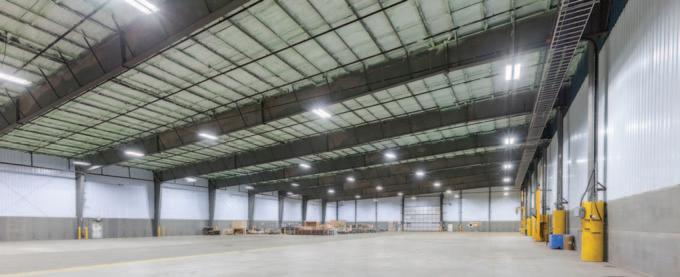
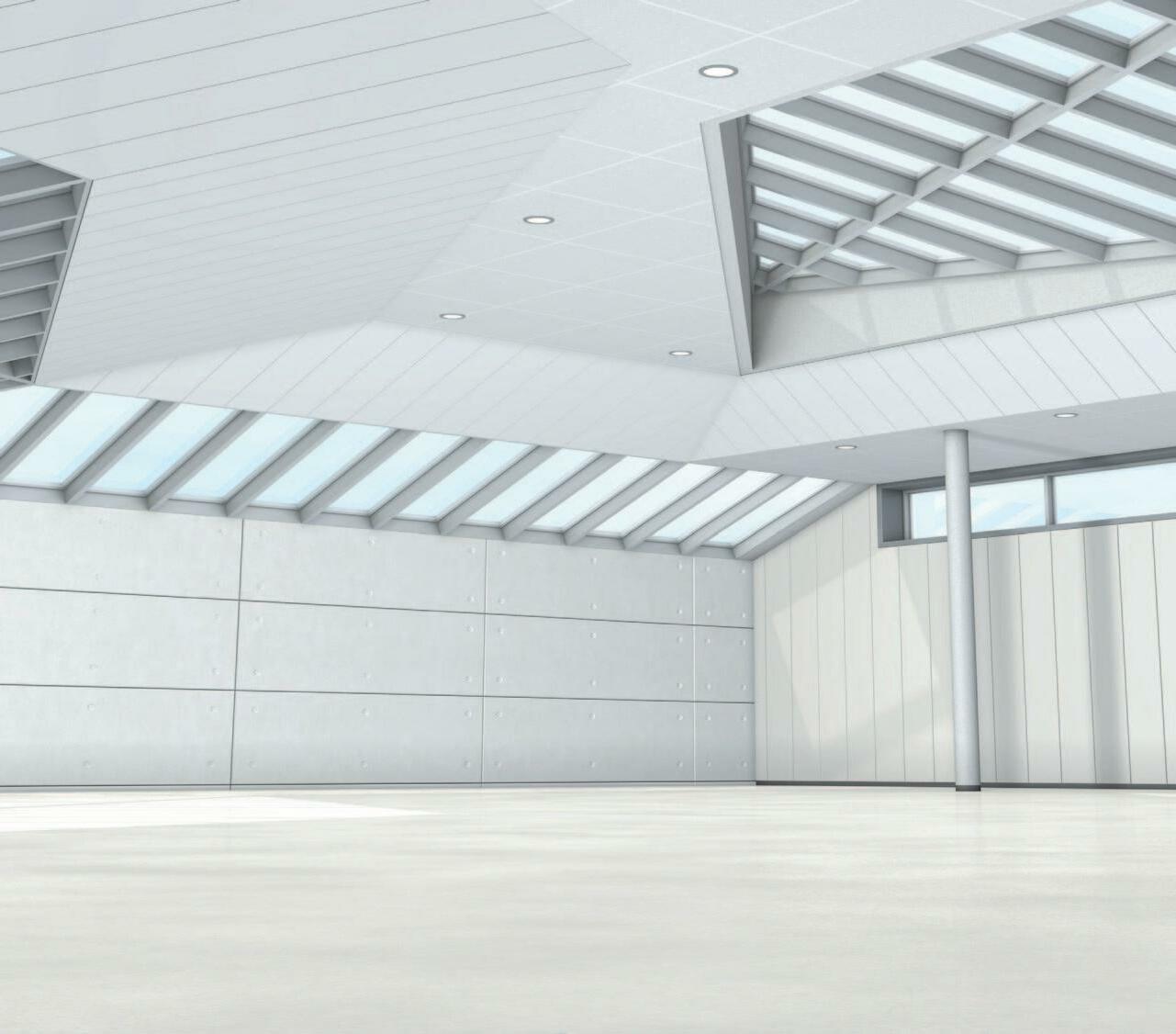

