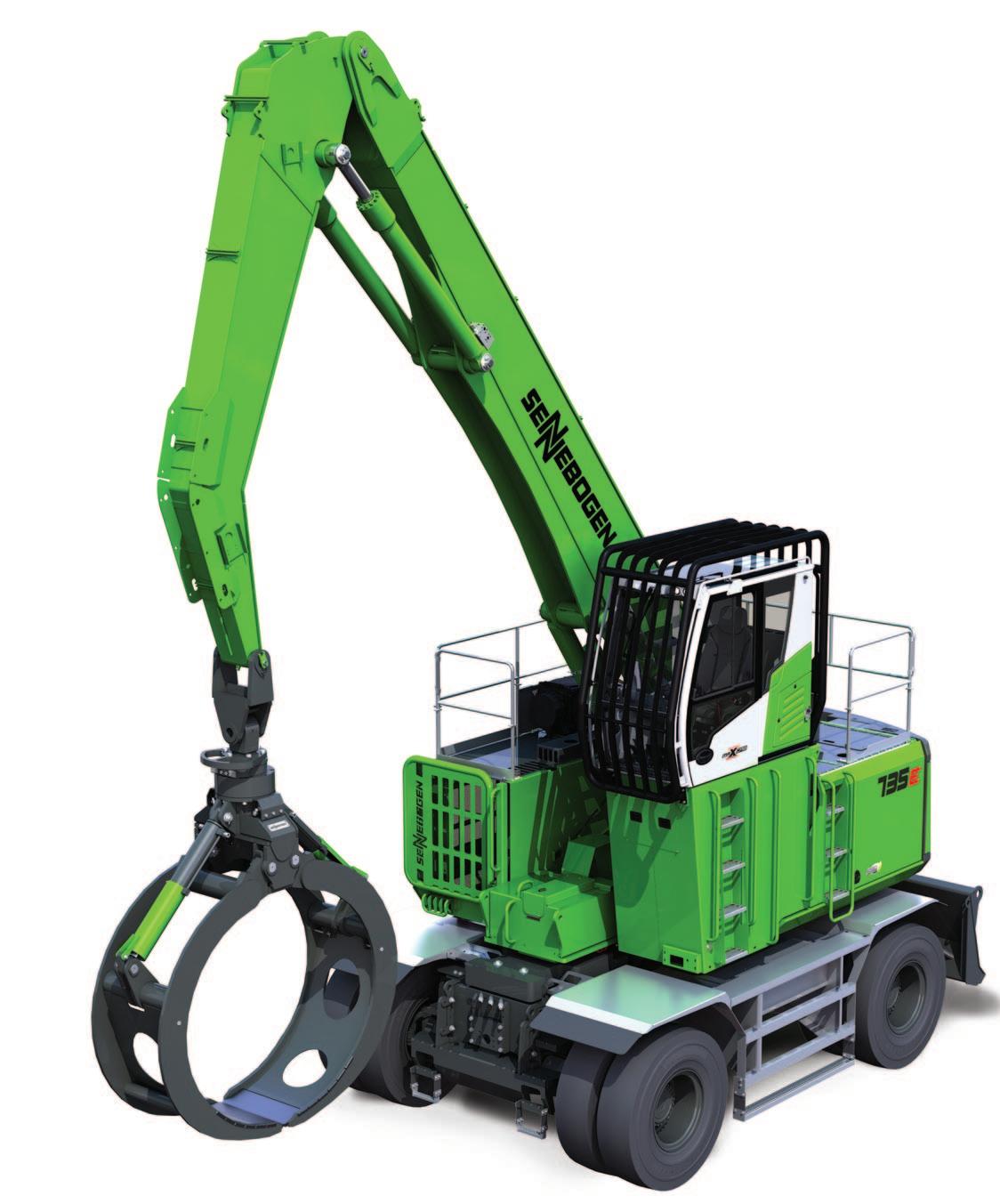
9 minute read
EFFICIENT TIMBER HANDLING: MATERIAL HANDLER WITH ELECTRIC TRAVEL DRIVE FOR PICK & CARRY
SENNEBOGEN will be presenting the 735E with the Green Efficiency Drive electric travel drive at bauma 2022.
Efficient timber handling
Material handler with electric travel drive for Pick & Carry
Hybrid technologies are not only on trend, they can also significantly save energy if used correctly. With the Green Efficiency Drive (GED), SENNEBOGEN has developed a drive technology that represents a hybrid system with a mix of diesel and electric drive. The GED is an electric travel drive for material handlers, which is particularly useful when the machines are designed for continuous operation, for example in sawmills, timber handling or log yards. The 735 GED saves up to 30% in energy with the same performance. This not only significantly reduces operating costs, but the machine is also more dynamic and quieter.
The Green Efficiency Drive is used where the largest share of energy demand is generated — when driving. Material handlers in particular do quite a lot of driving, which is why there is the greatest potential for savings here.
Equipped with the GED electric travel drive, the 735E saves up to 30% energy and therefore significantly reduces operating and service costs.
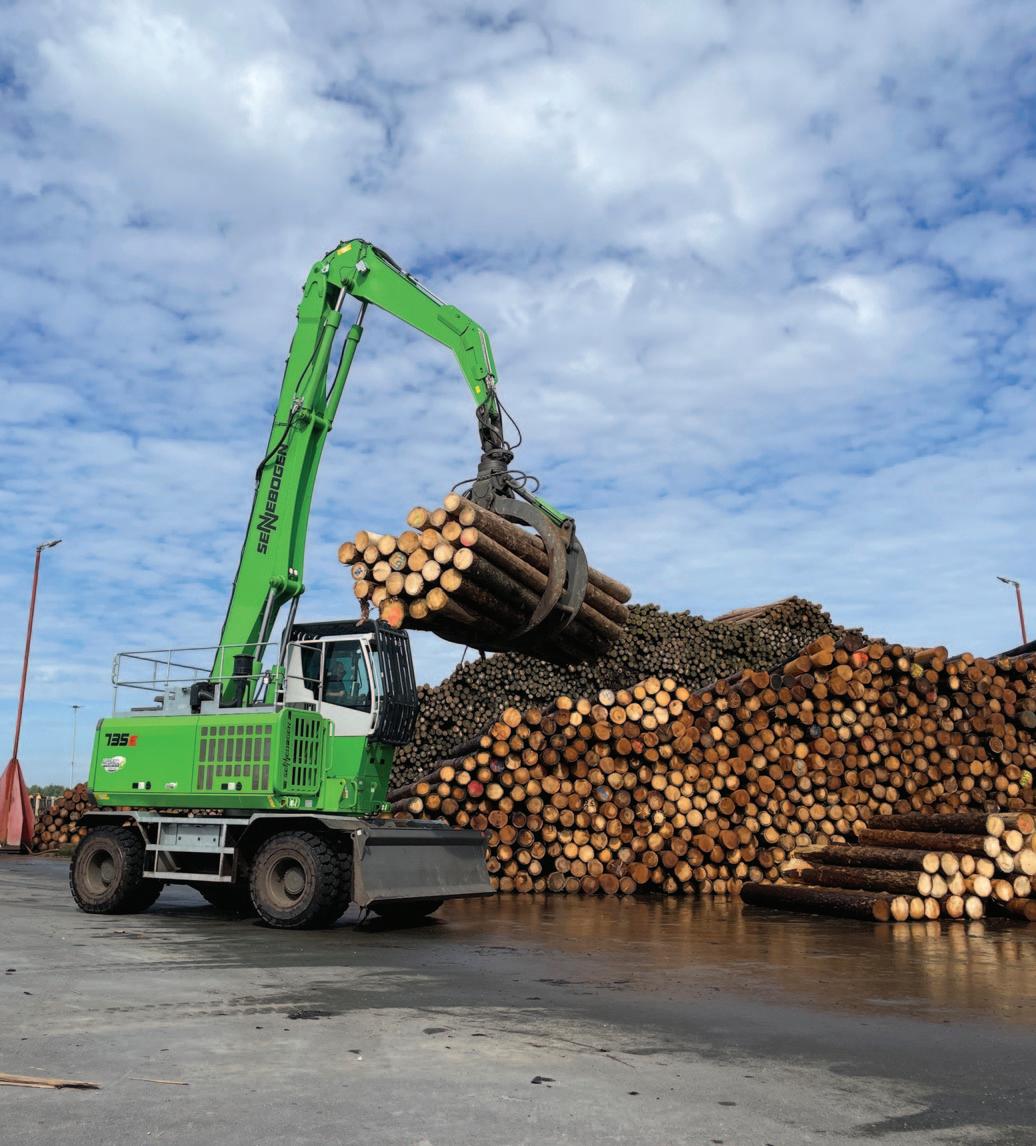
ENERGY RECOVERY VIA ELECTRIC TRAVEL DRIVE The system solution, based on Bosch Rexroth components, was jointly developed into a marketable product, and was launched by SENNEBOGEN under the name ‘Green Efficiency Drive’. The Pick & Carry material handler 735 E is the first machine to contain the series production technology for electric travel.
While the machine is moving around the log yard, the diesel engine drives a generator, which generates the necessary electricity for the electric engines. During deceleration, the electric drive engines act as generators. This means that they supply the auxiliary equipment with the energy required and relieve the diesel engine. The recuperated energy can even be stored for a short time, increasing the drive power.
Another advantage is that the use of modern components in the electrical system reduces heat loss. This can also save engine power for system cooling and achieve higher working dynamics.
GOOD FOR NATURE AND WALLETS — UP TO 30% ENERGY SAVINGS AND LOWER EMISSIONS Over the entire product life cycle, the 735 GED saves up to 30% energy with the same performance level and therefore saves operating and service costs on a large scale. Rightsizing the engine makes it possible to save on the machine’s consumption and thus also on emissions. Vibrations and noise are also significantly reduced — for pleasant and quiet operation, which relieves strain on people and the environment in the long term.
IMPRESSIVE HANDLING Thanks to the electric drive motors, the 735 GED also has outstanding responsiveness when moving off and positioning. This results in a vehicle that can be moved dynamically and precisely, but that is also a pleasure to drive.
Supporting the transition to greener steel
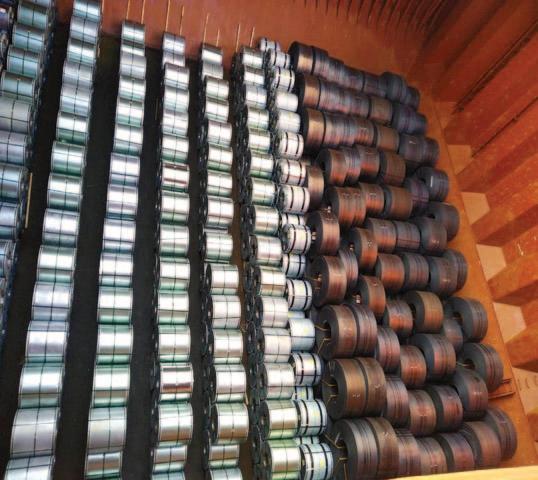
... if the industry is to meet its target of halving emissions by 2050 sustainable steel production is essential...
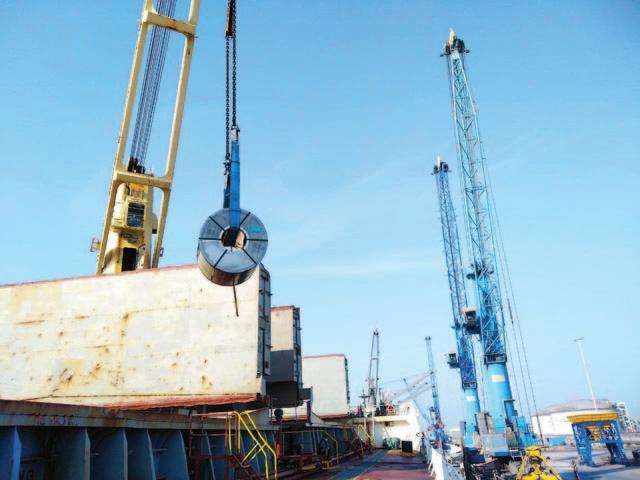
With green steel being touted as a potential solution for the steel industry’s decarbonization goals, the industry is looking to capable partners to support their efforts.
Steel remains one of the most sought-after commodities in the global economy due to its role in most engineering and construction projects, as well as in the growing development of renewable technologies such as wind turbines and solar panels.
According to the World Steel Association, more than 330mt (million metric tonnes) of steel and steelmanufactured goods were traded in 2021: a sharp increase compared to 270mt transported the year before.
The materials needed to produce steel using traditional blast furnace processes — specifically iron ore and coking coal — have also seen noticeable upticks in global trade over the past two years.
As a result, the steel industry now accounts for approximately 8% of total global carbon emissions, with every tonne of steel produced emitting about 1.85 tonnes of carbon dioxide. It is no surprise that the industry is now under pressure to become more sustainable.
According to the International Energy Agency (IEA), the steel industry is predicted to grow 33% by 2050 and has to at least halve its carbon emissions to meet global climate goals by the same year.
However, doing so economically, while keeping up with growing demand, is a challenge.
GREEN STEEL ‘Green steel’ is being touted as one solution that could push the industry towards a long-term sustainable future.
To make green steel, coking coal is replaced in the production process with more environmentally friendly products, such as hydrogen, while electric furnaces take the place of traditional blast furnaces.
Hydrogen has proven to be an effective replacement for traditional coking coal in the steelmaking process. In April 2020, Swedish steel maker Ovako’s trial at its steel mill demonstrated that hydrogen is a viable source of energy with no negative impact to the steel quality produced.
A 2020 report from the European Parliament noted that replacing coal with hydrogen could decarbonize the steel industry. However, in doing so, it would drive up global steel prices by about onethird, although further refinement would reduce that gap in the following years.
EFFORTS SUPPORTING GREEN STEEL Projects involving green steel have popped up around the world. Europe, in particular, has seen a vast number of steel production companies producing or transitioning to green steel, including SSAB in Sweden, Tata Steel in the Netherlands, and ArcelorMittal in Germany, as the continent looks to become a technological powerhouse for the industry.
In Asia, South Korea is set to be a major player in the development of green steel, with leading steelmaker POSCO creating a new entity to develop more sustainably produced steel.
India has also started on projects to reduce its dependence on coking coal. National steel producers Reliance and Adani have begun hydrogen-based production, while the Steel Authority of India and Rashtriya Ispat Nigam Ltd are striving to reduce carbon emissions from their production process.
Several other producers have taken similar steps. British Steel is looking into the use of green hydrogen to develop netzero steel, Australia’s BlueScope Steel is upgrading its traditional blast furnaces, and Germany’s Salzgitter just approved a significant funding proposal to produce low-carbon steel by 2033.
CHANGING COURSE The development of green steel is likely to impact the global dry bulk cargo trade, including iron ore and coking coal, particularly when it comes to total commodities and its freight routes.
Currently, the majority of the world’s iron ore (54%) is shipped from Australia to China, which produces about 53% of global steel for smelting, with similar levels of coking coal finding their way to East Asia. However, with Europe leading the charge for green steel production, these commodities could soon find themselves changing course.
“Dry bulk cargoes are often not subject to major geographical shifts,” says Lars Hardeland, GAC Group Operations Director – Shipping. “Australia and the Far East remain the engine of the steelmaking industry but as new technology comes online and processes are refined, we could well see these patterns change.”
Despite dry bulk freight rates sliding from a recent high of 5,650 in October 2021 to 1,002 in September 2022 based on the Baltic Dry Index, demand for dry bulk remains high and is expected to grow for the steel industry.
EXPERIENCE IN DRY BULK As one of the world’s foremost providers of shipping, logistics and marine services, the GAC Group has six decades of experience handling dry bulk vessels, with a very high level of expertise and a global network that can adapt to changing industry trends without impacting supply chains. As a major dry bulk agent, it is active in a diverse range of dry bulk markets and is ideally placed to handle increasing demand, particularly for the steel industry.
As green steel becomes more viable and commonplace, the need to ensure that hydrogen supplies are in the right locations will become even more paramount: a challenge that GAC is ready to take on.
“Having been providing tanker agency services since the 1970s, our tanker pedigree is also unmatched. Just as with the dry bulk industry, we are a global specialist agent for all tanker types. As customers explore the adoption of alternative fuels, we recognize the need to adapt to changing supplies, both in terms of the amount of cargo and where it is being shipped to,” says Hardeland.
PROVING THEIR METAL GAC is already demonstrating its value around the world as a dry bulk partner as the sector embarks on it decarbonization journey.
“We are seeing increasing amounts of cargo arriving at Sohar to meet global steel demand,” says Ashan Silva, GAC Oman’s Business Manager at the port of Sohar.
“As ship agents, we are committed to supporting bulker operators and managers to enhance their efficiency by ensuring a fast turnaround time through cost-effective solutions. We are here to remove any bottlenecks from a vessel’s operation while at port. Our team works closely with terminals round-the-clock to support cargo operations, sharing information with key stakeholders and keeping the global bulker fleet moving.”
In South Africa, GAC has noted a steady incline of dry bulk cargo arrivals as the economy reopens following the pandemic.
“Turning a vessel around quickly is vital for port operations due to the high demand for berths. Our role is to monitor operations and readjust operational plans where needed to mitigate problems and optimize efficiency for our customers,” says Theodale Johns, the company’s Business Development Manager.
Meanwhile in India, the world’s secondlargest steel producer, steel production capacity is set to treble by 2030, which will have significant energy, environmental and economic ramifications.
Sankar Narayanan, Senior Manager –Shipping at GAC India, says GAC’s local experience and capabilities in handling dry bulk cargo vessels means that they are prepared for changes.
“Our well-planned loading and discharging operational expertise enable us to adapt to the changing demands of the dry bulk industry. Our market research tools, including commodity-based line-ups, delay analyses, tonnage updates and industry trends, help customers stay abreast and plan for operations intelligently,” he adds.
On the challenge of fast turnaround times, Narayanan adds: “Our research desk runs 24/7 and is committed to providing customers with information analyses to facilitate smooth planning and minimize waiting times.”
SUSTAINABILITY GAC supports the steel industry’s bid to decarbonize with its own corporate sustainability efforts, which set the goal of becoming net carbon zero by 2050. A Sustainability Roadmap is in place to guide its operations towards an environmentally friendly future.
As the green steel transformation gathers pace, GAC aims to become knowledgeable and experienced in the development of this new-found technology, as well as standing ready to support industry partners in the transition and when green steel becomes mainstream.
The transition will not be cheap but the industry is gradually realizing the long-term benefits. And by working with reliable ship agents who embrace sustainability, the transition will undoubtedly be smoother, easier and trouble-free.
As a renowned and respected ship agent, GAC looks to be ideally placed to support the steel industry, as well as the wider dry bulk community, with its decarbonization efforts through costeffective and modern solutions that keep global trade moving and turn around vessels at port in record times. DCi
Lars Hardeland, GAC Group Operations Director –Shipping.
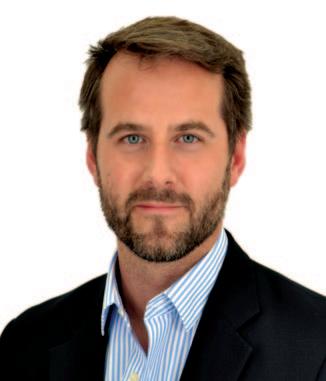