
21 minute read
MOVING WITH THE TIMES — AND THE MARKET MOBILE EQUIPMENT, AND WHY IT IS SO IMPORTANT
ENGINEERING & EQUIPMENT Moving with the times — and the market
mobile equipment, and why it is so important
Louise Dodds-Ely
Mobile shiploading – environmentally friendly and efficient
THE PORTALOAD MOBILE SHIPLOADER FROM BÜHLER
Swiss engineering and technology company Bühler has introduced the new mobile shiploader with a capacity of up to 2,800tph (tonnes per hour). The loader features a wealth of functions designed for maximum efficiency, availability and safety. The new design has also been carefully thought through to reduce harmful dust emissions — an increasingly important topic for the health of people and the environment.
The benefits of mobile shiploaders, as opposed to stationary loaders, lie in their flexibility. “Mobile shiploaders provide operators with a cost-efficient solution for a wide range of applications,” says Stefan Anshelm, Product Manager at Bühler Group. “They are ideal for businesses that have an existing berth and possibly share it with neighbouring companies.” Usually mounted on rails, they are connected to a high-capacity pier conveyor and tripper car. High performance and minimal handling help to reduce operating, personnel and mooring costs.
WHAT’S NEW? Bühler’s mobile Portaload has been developed following thorough analysis of existing systems. The complete redesign achieves optimal load distribution, reducing quay requirements. Additionally, wind resistance is decreased, and the robust design offers better protection against storms and earthquakes.
One look at Bühler’s mobile shiploader shows the difference. The vertical pylon is elegantly curved, meaning there is no interference with the fixed feeding conveyor. The construction of the counterweight has been optimized to greatly reduce torque forces. To make maintenance tasks as easy as possible, the open design ensures access to all critical parts. Great care went into optimizing all the movements required for loading, so that berthing times are kept as short as possible.
NO HYDRAULICS — NO LEAKAGE RISK In addition, many features of the mobile Portaload are designed to address
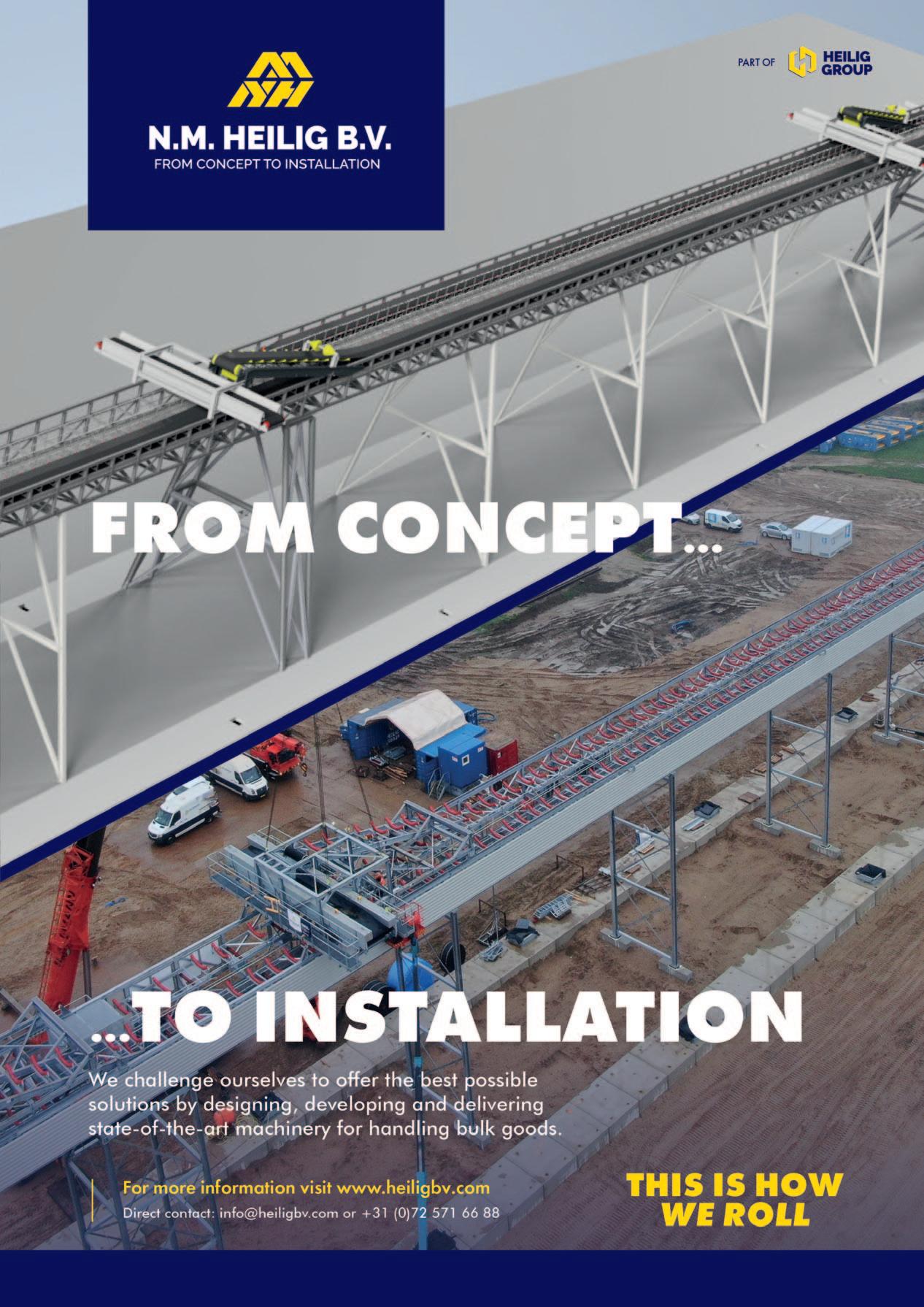
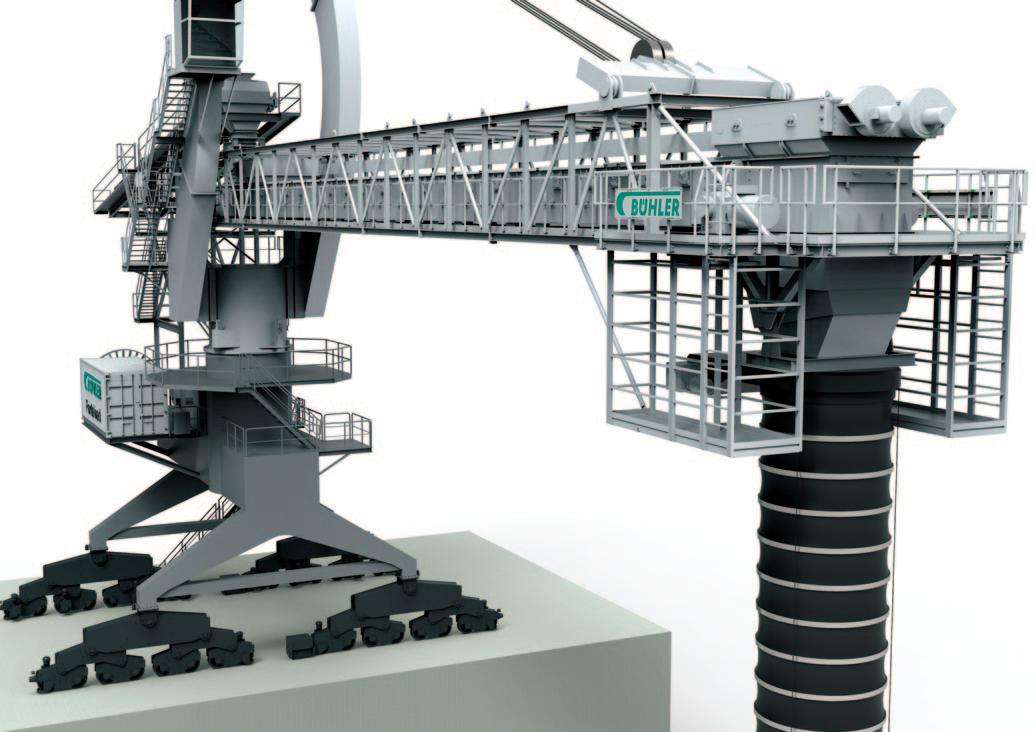
environmental issues.
Most loaders are operated with hydraulic operated kick-systems placed at the tip of the loading beam to extend the range. The Portaload functions without a hydraulic driven kick-in/kick-out system. Instead, it is operated with a winch system that enables the loader to reach into the corners of the cargo hold.
This greatly differentiates the loader from other solutions as it eliminates the risk of spillage of hydraulic fluid into the product or the water. “Leakages do not occur frequently. But if they happen, the consequences are severe. Contamination of the product results in huge wastage. Leakages over water require comprehensive cleaning efforts and must be avoided under all circumstances,” says Andreas Herzer, Head of Market Segment Ship Loader/Unloader at Bühler Group.
The new feature is in line with Bühler’s strategy to reduce the environmental impact of the industries in which it is a player. “The idea to design out the hydraulics sprang initially from a conversation with a customer,” says Herzer. “The customer wanted to address the problem of potential product contamination. The new design was developed following that dialogue.” Removing the hydraulics has other benefits too, as it also reduces maintenance time.
INNOVATIONS TO TACKLE DUST Environmental protection is a key requirement in every industry today. For shiploading and unloading, one area that is attracting increasing attention is dust emissions. The dust created through loading and unloading dry goods can impact on the environment. It can also harm the health of people living close to port facilities and personnel working on the piers. For this reason, regulations regarding dust emissions caused by port facilities are being tightened in many regions. Complying with ever-stricter environ mental governance is becoming a key topic for many stakeholders in the industry.
Bühler’s mobile Portaload tackles dust emissions with a bundle of optional features. The key measure for reducing dust emissions is to control the product flow. By managing product speed and air content within the transported product, dust emissions can be significantly reduced.
Two alternative options efficiently manage the product flow. The Portaspoon installed at the muzzle of the loading spout bundles the product so that loose particles are integrated in the main product stream. Bühler’s innovative dust suppression system delivers even better results. It controls the product flow and can be adjusted according to the requirements of each product. Managing product transportation speed also ensures that sensitive products such as oil seeds, soybean meal or grains are handled safely. The low-speed discharge reliably prevents product degradation.
In addition, the mobile Portaload comes with a completely enclosed belt conveyer, which both prevents dust from escaping and protects the product. The enclosed product transfer points are fitted with spot filters for direct aspiration.
A further serious issue relates to safety. Dust can develop into an explosive atmosphere with catastrophic consequences. By keeping dust emissions to an absolute minimum, the Portaload ensures a safe and healthy environment. This also benefits the product because removing dust from grain results in a cleaner product that can be stored more efficiently and sustainably.
STAYING AHEAD OF THE GAME “It is just a question of time before efficient dust reduction becomes a universal requirement around the globe. Businesses need to future-proof their operations today,” says Herzer. “This is why we took up the challenge and developed a shiploader that ensures that emissions are kept below legal limits, and that efficiently protects the product, the environment and personnel.”
SANY Europe, part of SANY Heavy Industry in China, offers a wide range of high-performance machines. Its product line includes: a broad spectrum of mobile equipment for use in ports; reachstackers; empty container handlers; heavy-duty forklift trucks and cranes; material handlers; hydraulic excavators and other earthmoving machines.
SANY’s equipment is suitable for all types of commodity, and the company prides itself on its ability to transport any cargo from A to B without any difficulties. For breakbulk cargoes, SANY offers a range of heavy-duty forklift trucks, with capacities ranging from 16t to 32t.
For container handling, SANY offers diverse cranes as STS (ship-to-shore), RTG (rubber-tyred gantry cranes) and RMG (rail mounted gantry cranes).
Furthermore, SANY offers mobile container handling machines: several sizes of reachstackers for loaded containers, and ECH (Empty Container Handlers) with a choice of lifting heights and single-box and double-box capabilities for empty containers.
Most of SANY’s sales are carried out through its international dealer network. In addition, there are also direct sales to port operators. The dealer network is stable and SANY has a steadily growing customer base. Personal contact is very important. Winning over a new dealer usually requires discussions over several years. SANY keeps growing the dealer network, making it possible to reach and service a broader base of customer.
SANY operates in a very competitive market, with competing companies that include: Kalmar, Hyster and Konecranes in the segment of mobile port equipment. Kalmar, Konecranes, Liebherr, Kuenz and XCMG are crane competitors. In terms of material handlers, companies such as Sennebogen, Fuchs and Liebherr are major competitors. In order to remain competitive in such a tight market, SANY has a broad product range that always satisfies customer needs and which will be further expanded in 2022. In addition to the know-how from head office in China, SANY Europe has its own R&D department and sources the steel components from its own production. It also works together with many European brand manufacturers.
In essence, SANY benefits from inhouse production of all structural steel components on the one hand, and the use of European-based components such as engines, axles, transmissions, hydraulic pumps on the other. Therefore, the products have excellent durability, and this is supported by a warranty of up to five years.
Electrification is SANY’s greatest ambition for the next years. The company already has 100 empty container handlers and 40 electric reachstackers out in the Chinese and Southeast Asian markets, all running on high hours of autonomy. The experience SANY has already gained in practical use in China and other Asian countries has been permanently incorporated into the further development of the machines. With the adaptations to both European standards and operator habits, as well as the successful certifications, the starting signal in Europe for the electric port machines has now been given. Delivery of the machines is scheduled for the first half of 2023.
ABOUT SANY EUROPE SANY Europe is a company of SANY Heavy Industry based in Changsha in China, which is one of the three largest manufacturers of construction and port machinery worldwide, with a turnover of around US$27 billion in 2021. The company, founded in 1989, offers a wide range of products, with more than 26 product families and over 300 machine models. These are developed, produced and sold by just under 40,000 employees around the world.
SANY’s European site has been in Bedburg, near Cologne, since 2011. The site employs around 90 staff in sales, service and in adapting products for the European market. In 2021, SANY Europe sold over 2,000 excavators in its European sales area. With the help of more than 100 dealers, the turnover across the whole of Europe was over €100 million in 2021.
SANY Europe’s portfolio predominantly focuses on construction machinery such as excavators and wheel loaders, as well as port machinery. The SANY site, measuring approximately 140 hectares, provides space for a production hall and warehouse. Proprietary painting facilities, as well as an administration building and the SANY Hotel are also located on the premises.
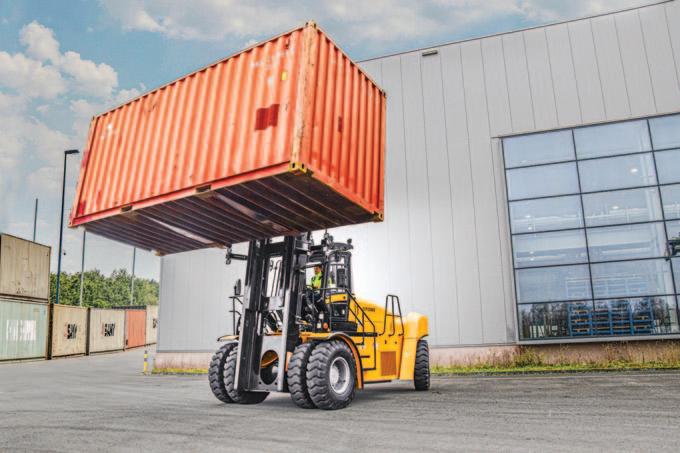


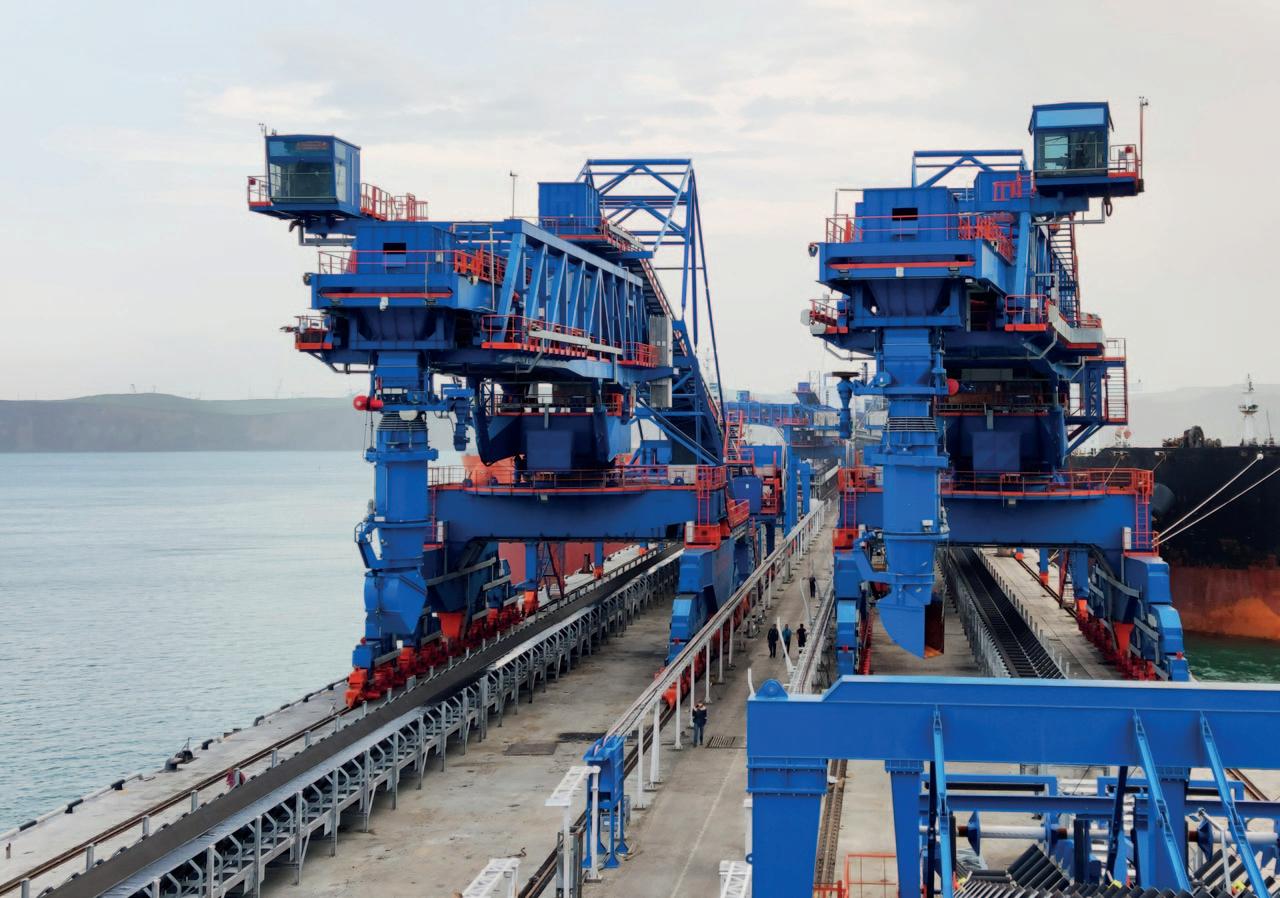
ENGINEERING & EQUIPMENT Liebherr sending three additional LHMs to Noatum terminals in Spain
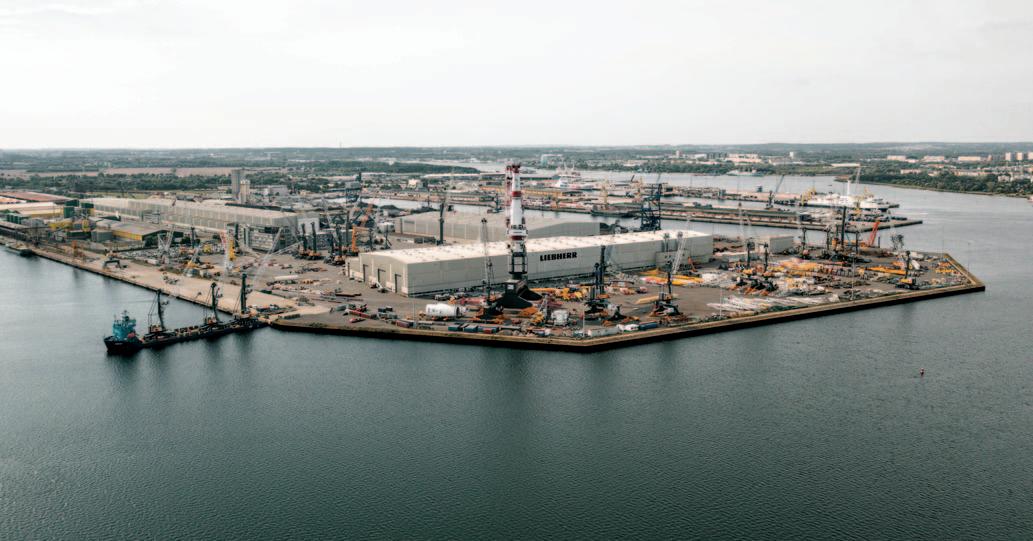
The port of Rostock serves as one of Liebherr’s central maritime production locations, effectively connected to global water shipping lanes.

v Two LHM 420 and one LHM 550 are
v
v being shipped to Noatum Terminals in the West Mediterranean.
The three LHM models are joining an
LHM 420 that was deployed earlier in the year and is operating at Noatum
Terminal Sagunto.
With the flexibility to handle bulk, containers, project cargo, and more,
Liebherr’s LHM mobile harbour cranes are among the most popular in the portfolio due to their adaptability in handling the most common cargo types at port terminals. The first crane arrived on January 5, 2022. Three new Liebherr mobile harbour cranes are joining the fleet at Noatum port terminals in Castellon, Sagunto and Tarragona. The cranes will enable the terminals to improve their handling efficiency for various cargo types.
Boarding the Heavy Load Carrier MERI in the morning hours of 5 September, three Liebherr mobile harbour cranes were prepared for their journey to Spain. Three terminals operated by the Spanish company will benefit from the performance of the LHM 420 and LHM 550 models.
OPERATIONS FOR A VARIETY OF CARGO, SUPPORTED BY LIEBHERR CRANES Port terminals operated by Noatum support a variety of commodities around their global supply chain.
Agricultural goods, minerals in bulk, steel, project cargo, and, containers, and more are all part of Noatum’s logistic network. With their carrying capacity of 124 and 144 tonnes, respectively, the LHM 420 and LHM 550 can lift and handle a variety of cargo.
IMPROVED PRODUCTIVITY AND REDUCED ENERGY CONSUMPTION PART OF HALLMARK OUTCOMES Liebherr mobile harbour cranes offer effective solutions for reduced energy consumption while improving cargo handling productivity. This is in part achieved by Liebherr’s proprietary hydrostatic drive, in which closed hydraulic loops are used for all main functions such as lifting, turning and luffing. The hydrostatic drive allows the operator extremely
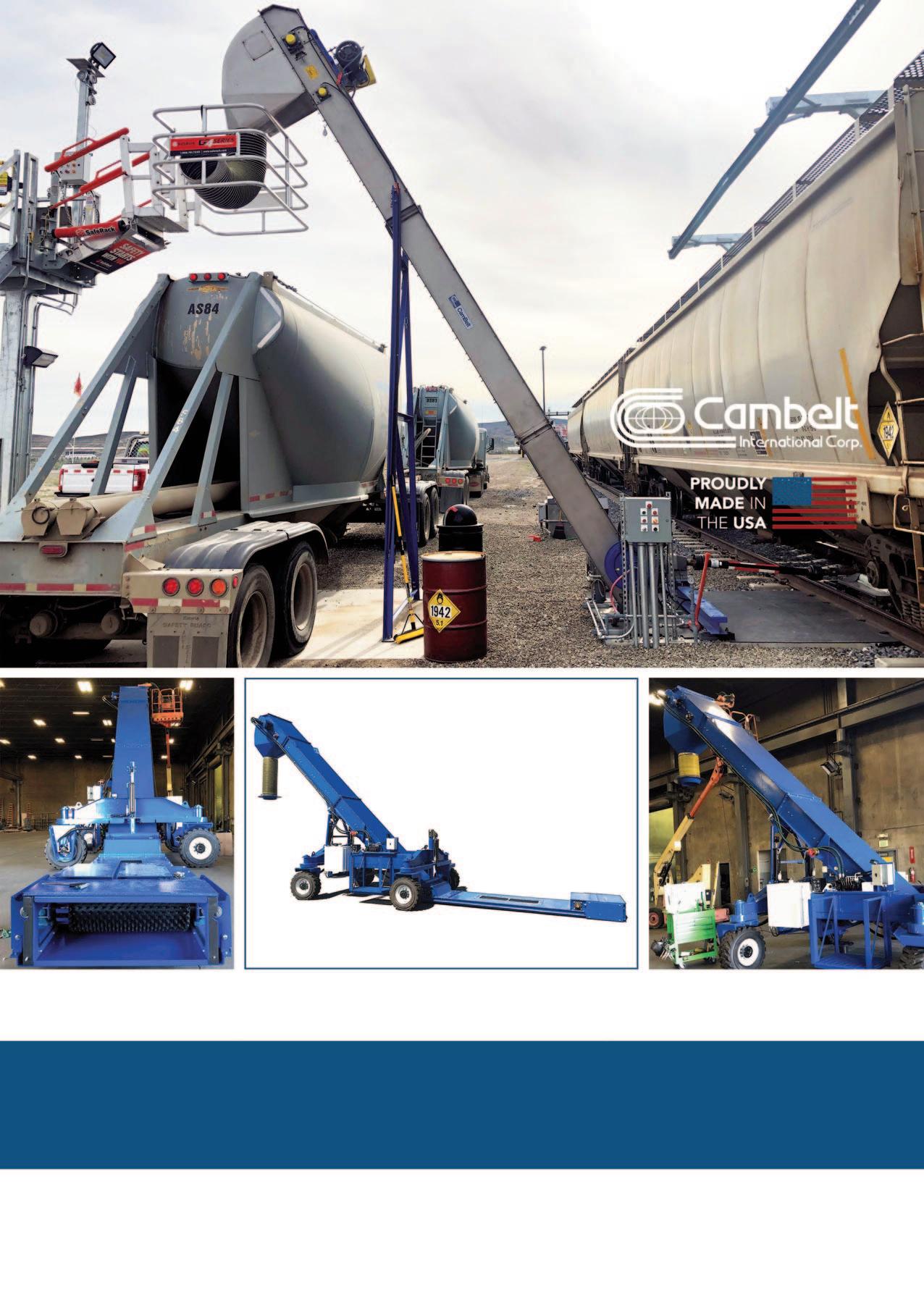

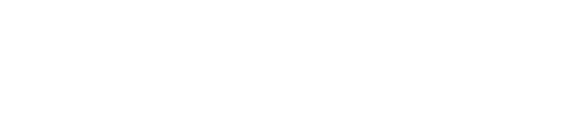
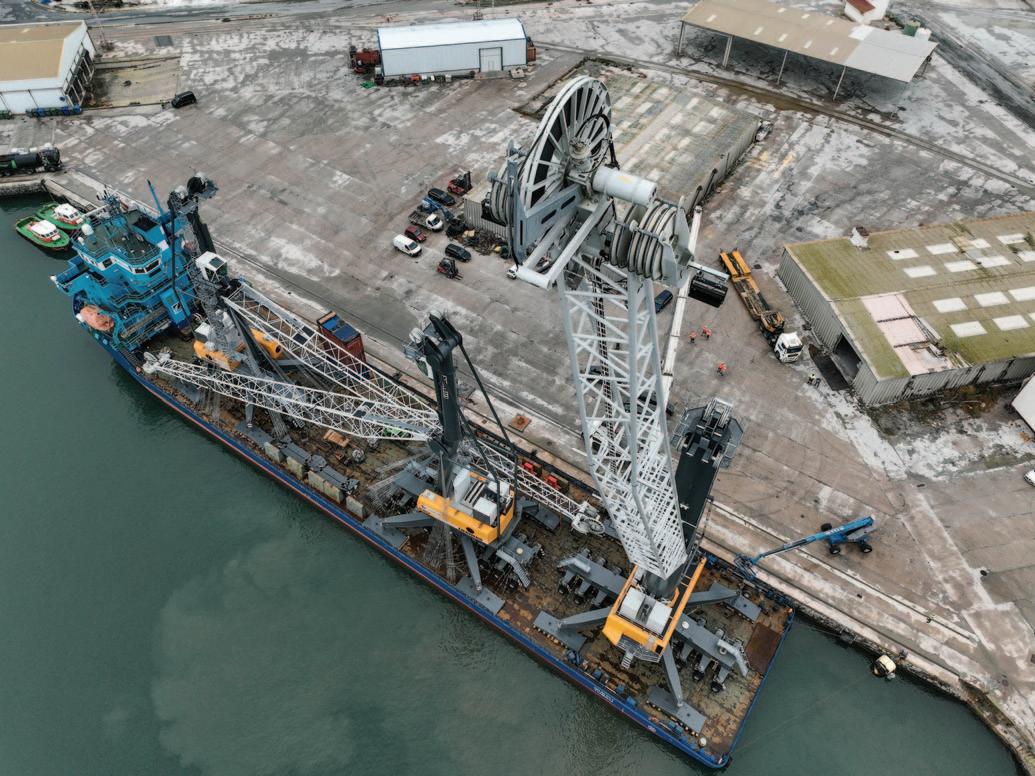
Arriving at the port in Castellon, the three Liebherr mobile harbour cranes get ready to be unloaded in Spain.
precise control. Additionally, service personnel benefit from a minimum number of components, and the operating company benefits from reduced fuel consumption.
Juan Carlos Jiménez, Divisional Manager Maritime Cranes in Liebherr Ibérica, remarks: “Liebherr is pleased to contribute to our customers’ strategic value to provide continuous improvements. For our Spanish client Noatum, this includes supporting them in their aim to reduce their overall environmental footprint while still meeting the demands of increased global cargo traffic both in terms of volume and mass. The LHM 420 and LHM 550 meet their specific tonnage and diverse cargo needs at their Castellon, Sagunto and Tarragona terminals. With the LHM 420 model alone, they anticipate an improvement in productivity of up to 38 containers per hour.”
ABOUT LIEBHERR-MCCTEC ROSTOCK GMBH Liebherr-MCCtec Rostock GmbH is one of the foremost European manufacturers of maritime handling solutions. The product range includes ship, mobile harbour and offshore cranes.
Reachstackers and components for container cranes are also included in the product portfolio.
ABOUT THE LIEBHERR GROUP The Liebherr Group is a family-run technology company with a broadly The two LHM 420 and one LHM 550 join a fleet that will be operating at three different Noatum terminals in Spain (f.l.t.r. Marco Gonzalez, Liebherr Sales Manager for Maritime Cranes at LIB; Juan Carlos Jiménez, Liebherr Divisional Manager for Maritime Cranes at LIB; Oscar Magdalena, Noatum Terminal Manager in Castellon Port; David Jiménez, Noatum Maintenance Manager in Castellon Port).
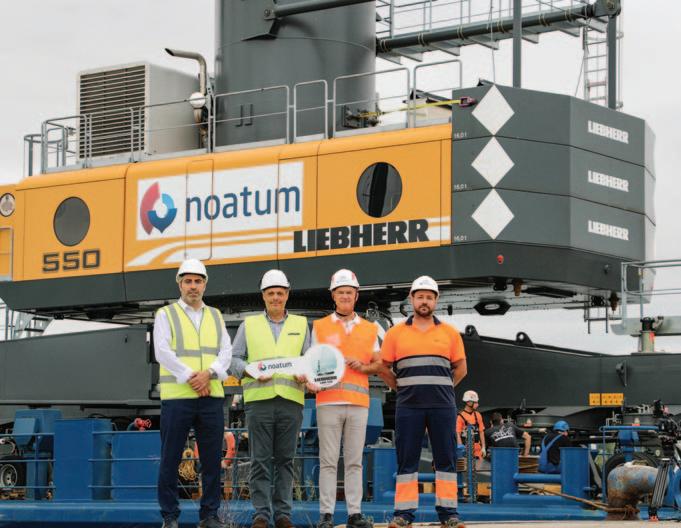
diversified product range. The company is one of the largest construction machinery manufacturers in the world. However, it also offers high-quality, user-oriented products and services in many other areas. Today, the group comprises more than 140 companies on all continents. In 2021, it employed more than 49,000 people and generated a total consolidated turnover of over €11.6 billion. Liebherr was founded in 1949 in Kirchdorf an der Iller in southern Germany.
Since then, the employees have pursued the goal of convincing their customers with sophisticated solutions and contributing to technological progress.
ENGINEERING & EQUIPMENT Hitachi ZW180-7 wheel loader puts customers in the driving seat
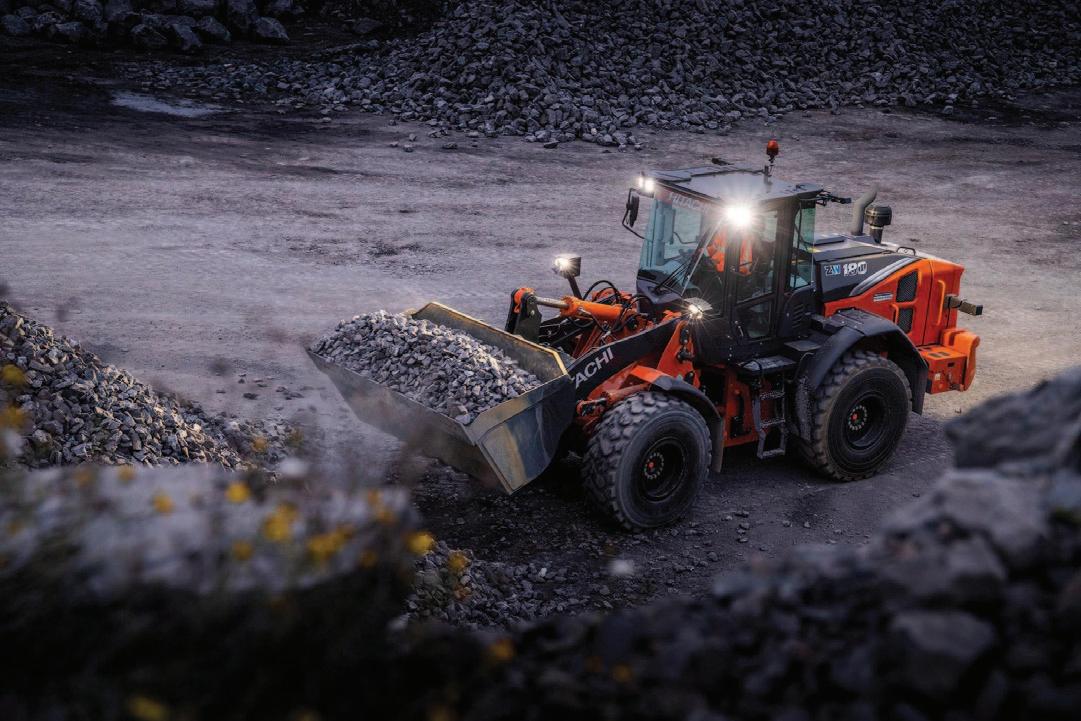
Hitachi has unveiled the ZW180-7, a smaller next-generation model from its Stage V-compliant wheel loader range, which has been carefully designed to appeal to both owners and operators. With industry-leading safety features and unrivalled comfort in the cab, operators feel in complete control of their workspace. Owners benefit from the new model’s exceptional efficiency and maximum uptime, as this gives them greater control over their profit as well as their fleet, thanks to remote monitoring tools and services provided by Hitachi.
FEEL THE DIFFERENCE After spending the day in the spacious, fully redesigned cab, operators will feel

refreshed rather than fatigued, and satisfied at their ability to work more productively. The ZW180-7 epitomizes the ultimate in comfort, with some of the lowest noise and vibration levels in the market. Much consideration has been given to easy operation with the improved seat with mounted electric pilot control levers, ergonomic multifunction lever, anti-slip steering wheel, 40% larger and fully adjustable armrest with integrated controller and convenient side switch panel. The hi-res screen is also easier to view.
Operators will also feel secure in the cab of the new ZW180-7 — one of the safest machines on the market — thanks to superb all-round visibility and intelligent systems. With the Aerial Angle camera system, they have an exceptional 270° bird’s-eye view of the job site and can work confidently in challenging conditions with the full LED work lights package. If anything is close to the rear of the machine, they are alerted immediately by the rear obstacle detection and warning system.
IMPROVE PROFIT AND MAXIMIZE UPTIME Owners will be able to increase their profits due to the impressive fuel economy, efficiency, and versatility of the ZW180-7. This model can be used on a wide range of applications, with three types of lift arms available: standard, high and parallel.
Faster and more efficient short loading operations due to the Approach Speed Control feature, which reduces fuel consumption by 16%, further satisfy owners’ requirements. Productivity is boosted by reduced cycle times gained by the auto power up function. This automatically increases the RPM to maintain travel speed on inclines.
The performance and traction force of the ZW180-7 have also been enhanced by significant improvements to the engine torque. This results in easier bucket filling, faster cycle times, and higher productivity with reduced fuel consumption.
The new ZW-7 model loads trucks more accurately, saving time and money, using the payload monitoring system. In addition, operators can monitor the fuel consumption thanks to the new ECO gauge and performance can be improved with several adjustable functions.
An ultra-reliable performance to significantly boost uptime is possible because the ZW180-7 is built with durable components, intelligent prevention systems and easy maintenance features such as the improved cooling package. The use of highquality Hitachi buckets, customized to suit the application, and robust ground engaging tools that are easy to install and replace, further maximizes uptime.
TOTAL CONTROL AND SUPPORT To support owners and operators throughout the life cycle of the new ZW-7 wheel loaders, Hitachi provides a wide range of after-sales services, and access to vital data and tools so they can manage their machine effectively. These include remote monitoring systems, Owner’s Site and ConSite (part of Global e-Service), and the ConSite Pocket app, which help to monitor performance, track location and plan maintenance.
“With Hitachi ZW-7 wheel loaders, we put our customers firmly in control of their workspace, their business and their fleet,” says Bill Drougkas, Manager Product Management of Hitachi Construction Machinery (Europe) NV.
“The new ZW180-7 offers a superior experience in the cab and exceeds expectations in terms of efficiency and performance. By working in partnership with our customers — providing industryleading equipment, innovative technology and wide-ranging after-sales support — we can help them to create their vision.”
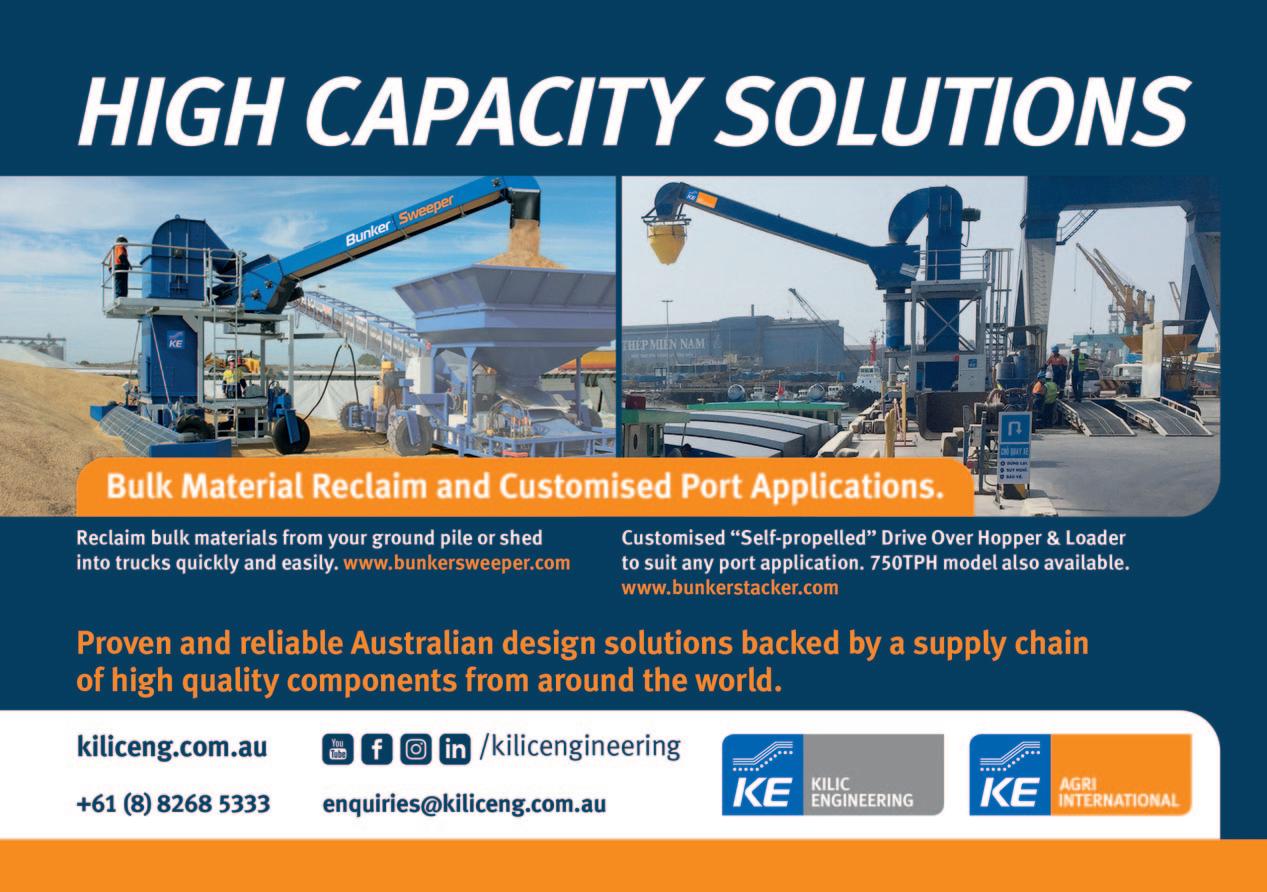
GWS Kraanbedrijf in the Belgian region of Flanders can look back on many years of experience in the provision of bulk and general cargo handling services: constant companions are the now eight SENNEBOGEN material handlers, about which young managing director Stan Goeyvaerts draws an excellent conclusion in the interview.
Walter Goeyvaerts once demonstrated entrepreneurial flair when he restructured and modernized his father’s cargo handling company, founded in the 1960s, shortly after the turn of the century: the result today is GWS, a thriving cargo handling
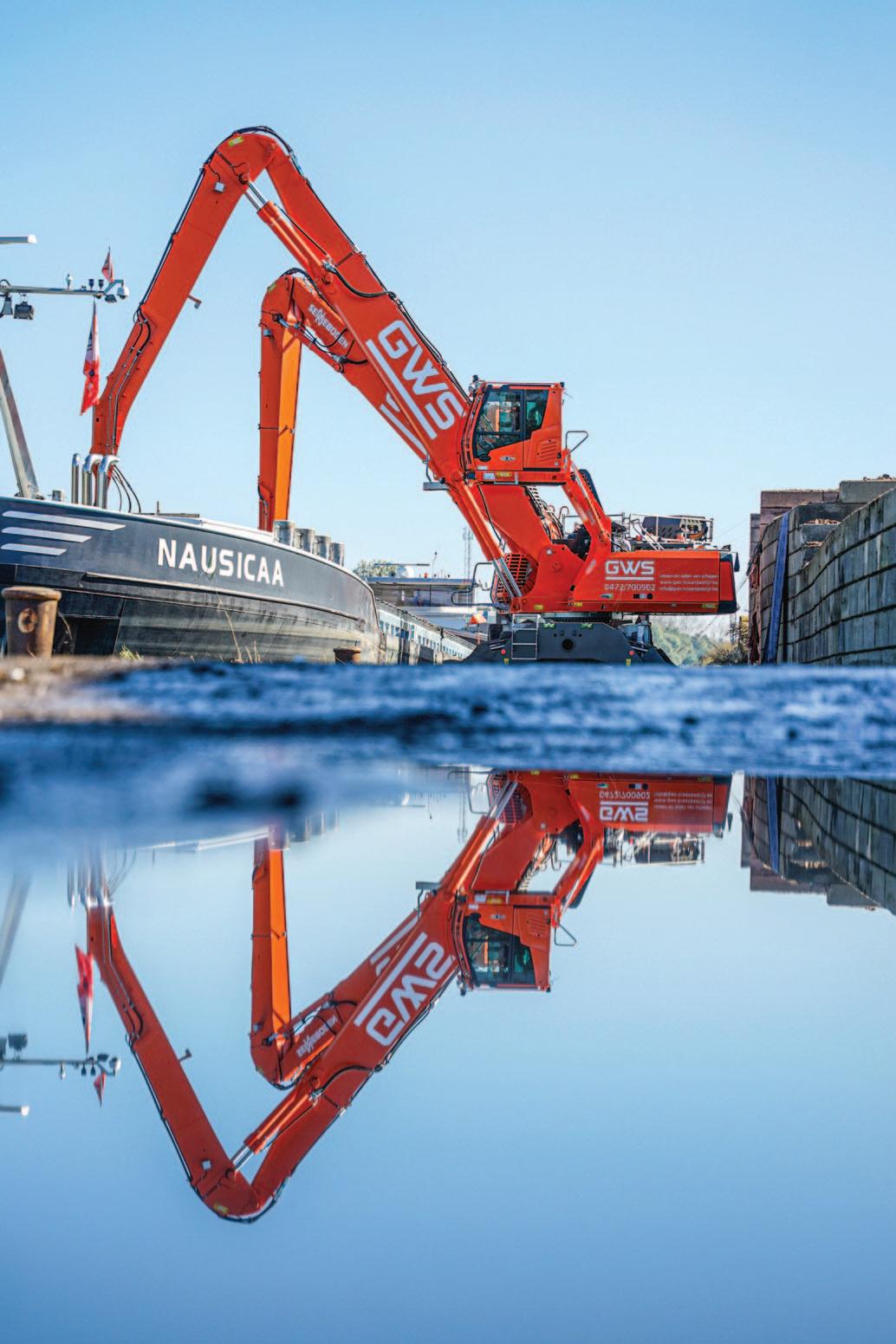
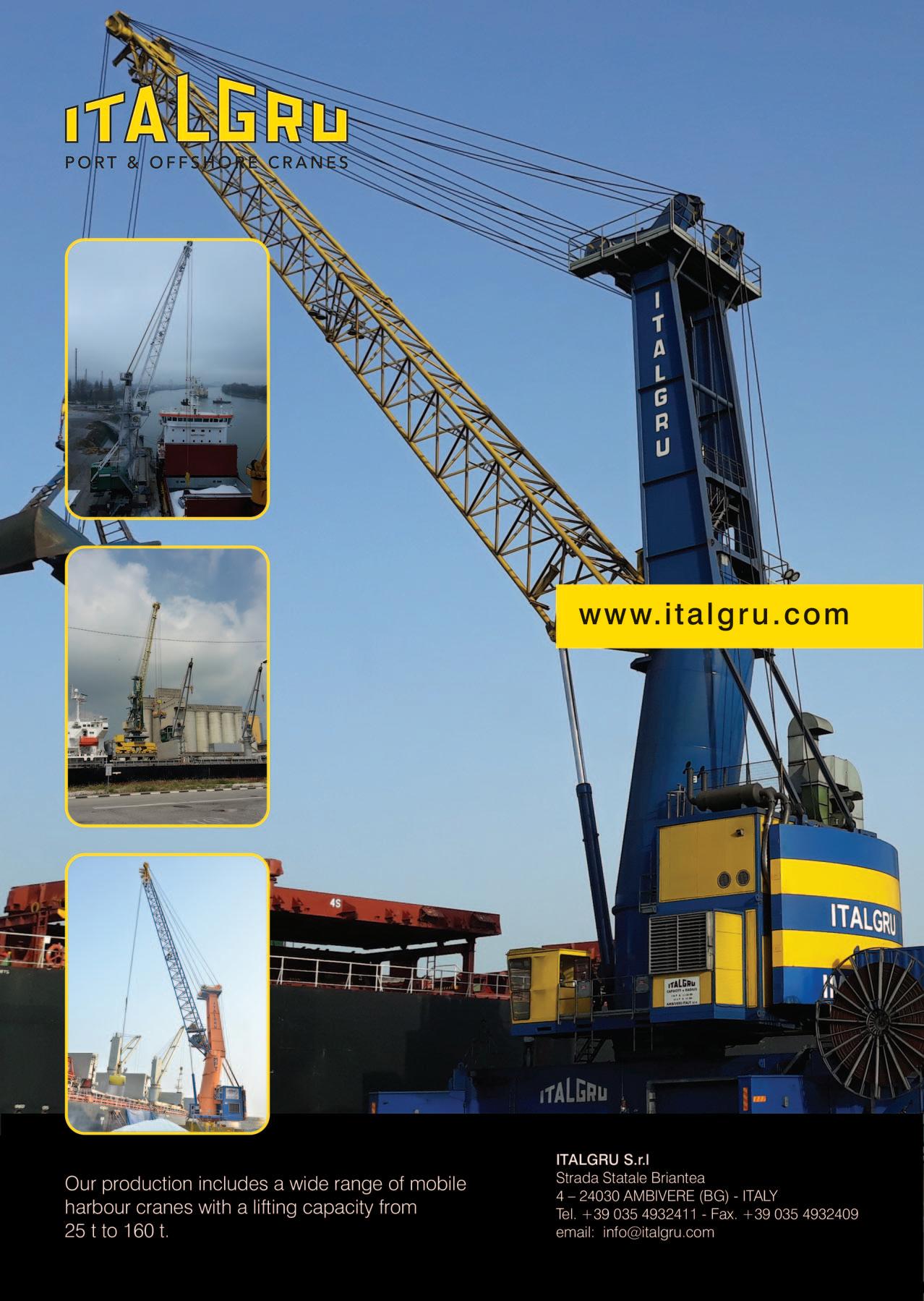

service provider specializing in loading and unloading ships.
His son Stan, the third generation, has now taken the wheel. For him, growth means constantly investing in new handling equipment to respond flexibly to increased market demands. The latest acquisition is a SENNEBOGEN 835 E in the mobile version, which was delivered by the sales and service partner SMT in Belgium. “In terms of size and tonnage, this is the most flexible machine you could ask for,” says Stan Goeyvaerts.
The reestablishment of the cargo handling company GWS took place in 2012 and builds on the experience of the traditional company, whose material handling activities go back two generations. “Initially, we were mainly active in the Antwerp region, but we are now active throughout Flanders,” Stan Goeyvaerts continues. A success story that can be attributed especially to the personal contact with the customer, to which father and son attach great importance. “I still climb into the cabs of our material handlers myself. That also impresses our customers! In addition, we always try to stay on the ball
technically by having an extensive machine park at our disposal.”
EXCELLENT RATING IN TERMS OF HANDLING CAPACITY AND OPERATIONS Ship unloading in a double pack: cargo handling service provider GWS Kraanbedrijf in Antwerp has relied on SENNEBOGEN material handlers since the very beginning.
Today, the GWS machine park has grown to 12 material handlers, including eight SENNEBOGEN machines. “We started with three machines at that time. Two of them were used, the third was already a machine from SENNEBOGEN. We really appreciate the mobility of these material handlers, and that was crucial for our first customers, because they were located in close proximity to each other over a distance of 2km. With SENNEBOGEN, we could easily from one customer to the next, without having to leave the cab. But apart from that, these are machines that stand out for their capacity and their handling . They are very easy to operate and at the same time keep productivity high. My employees enjoy working with them,” says Goeyvaerts, summarizing the strengths of the material handlers.
ENVIRONMENTALLY FRIENDLY AND RELIABLE STAGE V TECHNOLOGY FOR MORE PERFORMANCE ON THE QUAY “In terms of size and tonnage, this is the most flexible machine you could ask for,” explains Goeyvaerts, referring to the new, orange 835 E-Series material handler. In addition, this one operates with a reducedemission, fuel-efficient Stage V engine. “As environmental legislation becomes more stringent, we always include this aspect in our investment decisions.”
Service was also essential for him: “With SMT, we couldn’t have asked for a better partner. They are available to us day and night, if there are ever any problems. As a cargo handling company, we can’t afford any downtime, because a ship has to be able to leave the port as quickly as possible. Thanks to SMT and the intelligent design of the machines with a focus on mechanical components, we can often easily solve minor problems ourselves. In this way, we can always concentrate fully on our customers.”

Hitachi is introducing a larger nextgeneration model from its Stage Vcompliant wheel loader range. The ZW310-7 has been designed to put operators in complete control of their workspace — and master even the toughest job site conditions — with top quality safety features and supreme comfort in the cab. Owners will feel in total control of their profit — thanks to its powerful performance, low total cost of ownership and exceptional efficiency — as well as their fleet and workload, due to remote monitoring tools and services provided by Hitachi.
SAFETY AT THE FOREFRONT The ability to work safely is vital, not only for the operator’s wellbeing, but also for the successful completion of any project. The new ZW310-7 is ideal in this respect, as it’s one of the safest machines on the market, thanks to superb all-round visibility and intelligent systems.
To protect the operator and machine from potential hazards, it allows a superior view from all angles — especially with the excellent visibility to the rear and either side of the narrow engine hood. With the Aerial Angle camera system, operators also have an exceptional 270° bird’s-eye view of the job site, while the rear obstacle detection and warning system alerts them immediately if anything is close to the rear of the machine.
After working a full shift in the spacious, fully redesigned cab, operators will feel less tired and more satisfied at their ability to work more productively. The ZW310-7 epitomizes the ultimate in comfort, with some of the lowest noise and vibration levels in the market. It is especially easy to use thanks to features such as the improved seat with mounted electric pilot control leavers, new monitor controller and convenient side switch panel.
LOW TOTAL COST OF OWNERSHIP Owners will be able to increase their profits due to the powerful performance, low total cost of ownership and exceptional efficiency of the ZW310-7. High levels of productivity are ensured by fast cycle times, a high breakout force and loading capacity, and improved acceleration on inclines thanks to sensors installed on several machine components. The RPM are automatically increased thanks to the auto power up function, which maintains the machine’s travel speed when moving uphill. As a result, the reduced cycle times enhance productivity and reduce fuel consumption.
Faster and more efficient short loading operations due to the Approach Speed Control feature further satisfy owners’ requirements. The new ZW-7 model also loads trucks more accurately, saving time and money, using the payload monitoring system.
In addition, operators can monitor the fuel consumption thanks to the new ECO gauge and performance can be improved with several adjustable functions.
An ultra-reliable performance to significantly boost uptime is possible because the ZW310-7 is built with durable components such as the axles and frame, intelligent prevention systems and easy maintenance features. This can be further maximized by the use of high-quality Hitachi buckets, customized to suit the application, and robust ground engaging tools that are easy to install and replace.
AFTER-SALES SERVICE To support owners and operators throughout the life cycle of the new ZW-7 wheel loaders, Hitachi provides a wide range of after-sales services, and access to vital data and tools so they can manage their machine effectively. These include remote monitoring systems, Owner’s Site and ConSite (part of Global e-Service), and the ConSite Pocket app, which help to monitor performance, track location and plan maintenance.
“The new ZW310-7 wheel loader has been designed to give a powerful performance, low total cost of ownership and exceptional efficiency to European customers,” says Bill Drougkas, Manager Product Management of Hitachi Construction Machinery (Europe) NV. “Built to the highest quality standards, it will significantly boost productivity on busy quarries and large recycling plants, and have a positive impact on profits.”
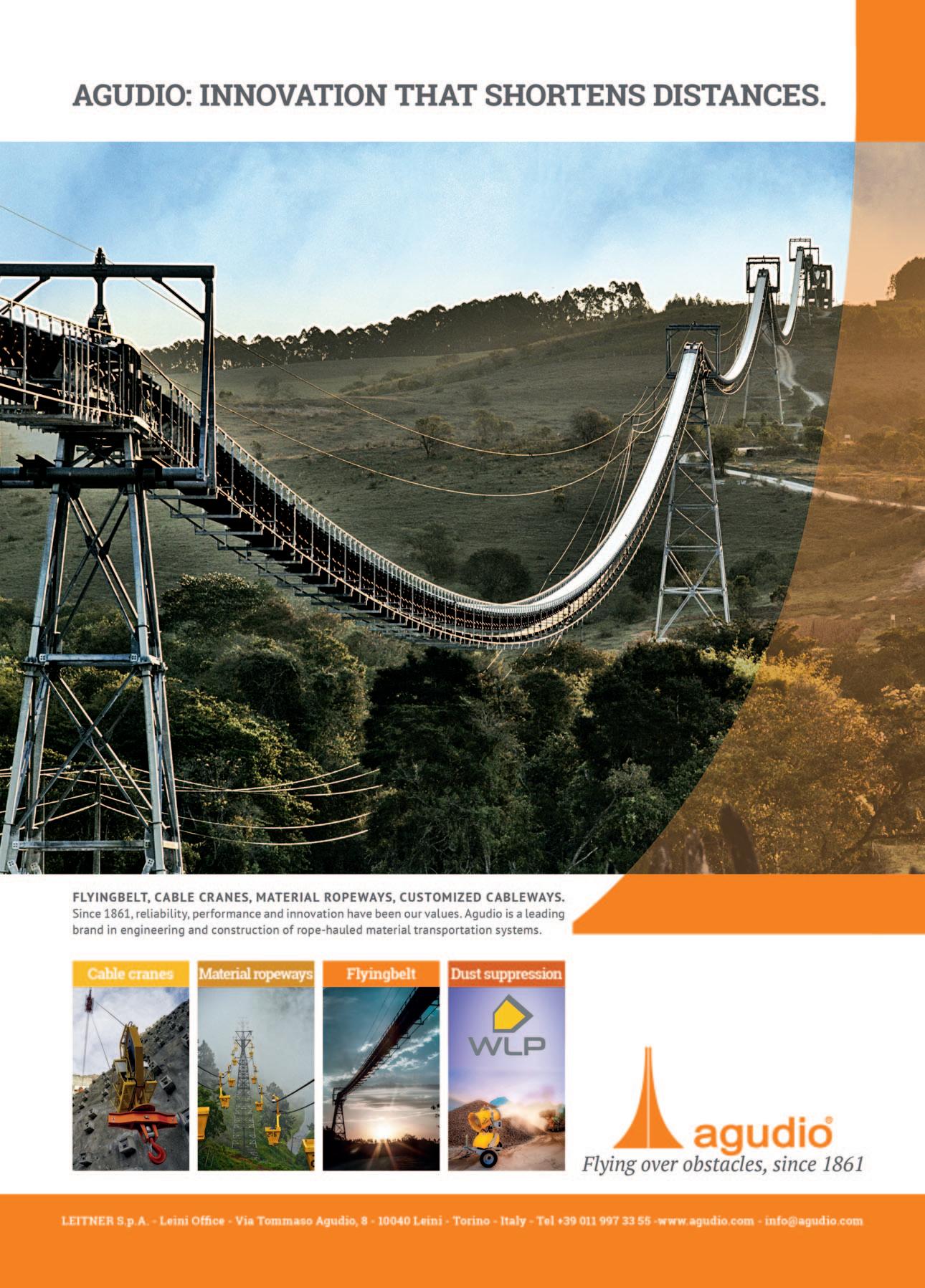