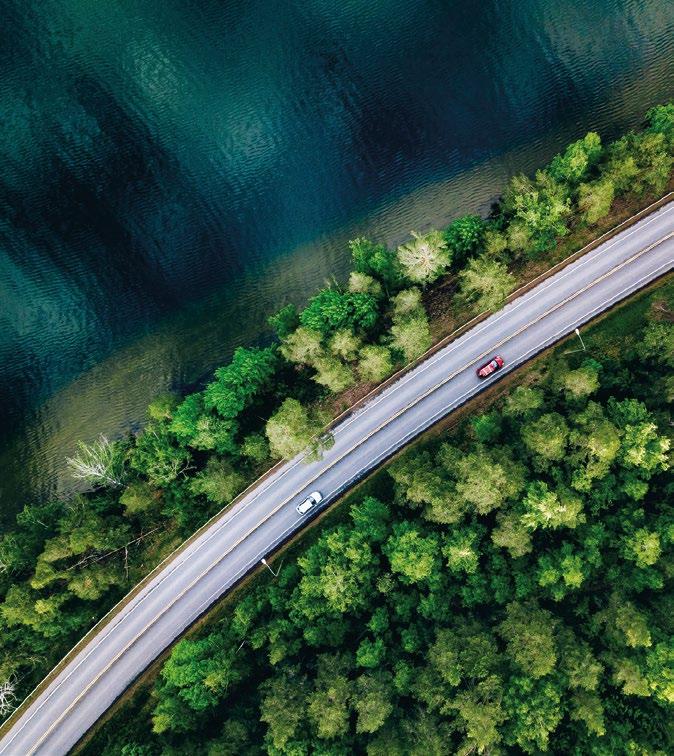
12 minute read
SISTEMI AUTOMATICI DI PESATURA
BIO-serie può essere utilizzato in materiali di riempimento gel con meno plastificante rispetto ai convenzionali HSBC, in applicazioni di alta elasticità offre un eccellente recupero elastico, dovuto alla sua basa perdita di isteresi, e in applicazioni con caratteristiche di aderenza, quali suole per calzature, si rivela un’ottima alternativa alle classiche gomme SBR e BIIR offrendo un più alto coefficiente di frizione statica in condizioni di asciutto e bagnato.
ELASTOMERI TERMOPLASTICI APPLICAZIONI
COPOLIMERI STIRENICI A BLOCCHI IDROGENATI CON ALTO RECUPERO ELASTICO
L. Rodriguez-Guadarrama, L. Ortega-Álvarez, M.L. Sánchez, Dynasol Group, Madrid, SpainRUBBERWORLD, ottobre 2022, pag. 45-48
La tecnologia di polimerizzazione vivente anionica è in grado di produrre polimeri con stretta distribuzione di peso molecolare, strutture polimeriche a blocchi e una microstruttura controllata adatta ad una grande varietà di applicazioni. Nel caso dei convenzionali polimeri stirenici a blocchi (SBS), i segmenti polibutadiene, che contengono doppi legami insaturi, possono subire un’ulteriore modifica chimica con questi doppi legami selettivamente idrogenati per produrre copolimeri stirenici a blocchi idrogenati SEBS, che offrono eccellente resistenza ai raggi ultravioletti, all’ozono e all’invecchiamento e un’ottima stabilità termica. Sfruttando i vantaggi menzionati, il gruppo Dynasol produce una vasta gamma di SEBS che, opportunamente addittivati con olio, una o più poliolefine, cariche, resine etc. permettono di ottenere elastomeri termoplastici TPE. Questo articolo si propone di esaminare l’influenza della macrostruttura di SEBS ad alto peso molecolare, lineare e/o radiale, in mescole SEBS/polipropilene/olio, con un approccio reologico per analizzare il recupero elastico e la processabilità di SEBS e delle mescole SEBS/polipropilene/olio. Scelti tre tipi di SEBS Dynasol, uno commerciale a struttura radiale e due a struttura lineare messi a punto in un impianto pilota, spiegata la preparazione delle mescole SEBS/polipropilene/ olio e illustrata la loro caratterizzazione, l’articolo espone dettagliatamente i risultati ottenuti con questi copolimeri stirenici idrogenati ad alto peso molecolare. La conclusione dell’articolo è che i materiali SEBS ad alto peso molecolare e struttura radiale offrono un’eccellente prestazione nella formulazione di mescole, a cui si chiedono resistenza ad alta temperatura, stabilità dimensionale dei manufatti stampati ad iniezione, processabilità migliorata e ottimizzata ritenzione di olio. In pratica il grado Dynasol commerciale esaminato possiede un ottimo bilanciamento di recupero elastico e processabilità, dimostrando che i materiali SEBS radiali ad alto peso molecolare offrono nuove possibilità di formulazione di mescole elastomeriche termoplastiche ad alta prestazione. Senza dimenticare che questi materiali costituiscono un’alternativa sostenibile per produrre materiali riciclabili.
GOMMA AD ALTA VISCOSITÀ - PARTE 3
O. Krieger, B. Klie, U. Giese, Deutsches Institut für Kautschuktechnologie e.V., Hannover (Germany) - email: benjamin.klie@dikautschuk.de - KGK n. 4/2022, pag. 47-54
Si tratta della terza parte di un accurato studio sulla calandratura (la recensione della prima parte è stata pubblicata sul numero di dicembre 2021 e quella della seconda sul numero di marzo 2022). Ad uso di chi non si ricordasse bene l’argomento, anche in questa terza parte l’introduzione ribadisce che la calandratura è un processo normalmente usato nella gomma per produrre fogli di alta qualità con elevata ed accurata geometria e basso spessore. È opportuno tenere ben presente che il flusso fra i due cilindri corotanti della calandra consiste nella combinazione di flusso di trascinamento e di flusso opposto di pressione, che dà luogo a vortici di rotazione. L’intensità del flusso opposto di pressione dipende dalla viscosità della mescola di gomma, per cui una mescola con viscosità più alta richiede una adesività minima più alta sulla superficie del cilindro per evitare scivolamenti sulla parete e per essere convogliata attraverso la zona di alimentazione. Quando poi il foglio calandrato lascia la prima zona e viene portato alla seconda zona, la forza di adesione alla superficie del rullo deve superare la relativa forza di ritenzione e il successivo gradiente di pressione della zona per evitare un distacco prematuro. Il corrugamento e la ritenzione del foglio di gomma di fronte alla seconda zona, causati dal distacco prematuro, causano inclusioni di gas, alte fluttuazioni di pressione della zona e, di conseguenza, l’insorgenza di fluttuazioni geometriche in spessore e larghezza.
Lo studio affronta per primi gli spetti teorici della calandratura e le difficoltà di lavorazione nella calandratura di mescole di gomma molto viscose. Specificato poi che la calandra di laboratorio scelta per le prove è la KQF200 di Troester a quattro cilindri e che il polimero utilizzato è l’NBR Krynac 3330, con una formulazione comprensiva di una resina fenolica adesivante, lo studio affronta gli argomenti pratici del processo, ossia: determinazione del comportamento al rigonfiamento del foglio, una volta superata la zona di alimentazione; implementazione di una metodologia alternativa di calandratura per mescole di gomma ad alta viscosità; calandratura di fogli ad altezza aumentata; influenza della velocità e della temperatura del rullo della calandra; aumento della velocità della linea di calandratura con l’utilizzo di resina adesivante. Nella conclusione dello studio si ricordano gli inconvenienti delle convenzionali tecniche di calandratura (corrugamento e formazione di bolle), che possono essere evitati con l’utilizzo di una metodologia simile al frizionamento o alla scrematura. In pratica le zone due e tre sono usate come una specie di zona di stiratura senza rivoltamento della gomma, ossia come zone di calibratura. Fatte alcune considerazioni sull’importanza dell’adesività della mescola, si evidenzia che la geometrica accuratezza di ±0,02 mm, per un’altezza del foglio di 1,4-2 mm, evita difetti di superficie, mentre con la mescola formulata per le prove si ottiene una velocità massima della linea di calandratura pari a 6 m/min senza compromettere qualità del foglio e stabilità di processo: aggiunti alla mescola 4 phr di resina fenolica adesivante, la velocità può aumentare a 8 m/ min. Tuttavia, trasferire i risultati delle prove e applicare la metodologia alternativa su scala industriale comporta fattori e limitazioni da prendere in considerazione, tra cui la velocità della linea di calandratura e il comportamento di alimentazione della prima zona, entrambi inferiori rispetto a quelli della piccola calandra di laboratorio.
PROVE E MISURAZIONI
PROPRIETÀ DINAMICHE MECCANICHE DI ELASTOMERI PVMQ RETICOLATI CON PEROSSIDO E MODIFICATI CON RADIAZIONI ALLA LORO FREQUENZA NATURALE
M. Şen, D. Aksűt, Achettepe University, Department of Polymer Chemistry Division, Ankara (Turkey), I. Saltuk, N. Akgerman, Tavdi Company, Barrington (USA) - email: msen@ hacettepe.edu.tr - KGK n. 4/2022, pag. 55-61
Lo studio inizia con un’introduzione interessante non solo per l’esposizione dell’argomento trattato, ma anche per la presentazione dell’ultima versione dell’oscillografo dinamo-meccanico Yerzley (DYMO), migliorato con sensori addizionali, acquisizione elettronica dei dati e controllo a mezzo computer con valutazione automatica dei dati. In accordo con la norma ASTM D945, il DYMO funziona come un dispositivo di movimento armonico e può eseguire prove di compressione dinamica e di taglio alla loro naturale frequenza, nonché di isteresi statica e di scorrimento. La frequenza naturale di un dato campione, dopo mescolazione e vulcanizzazione per le condizioni dell’uso finale, è determinata dal DYMO sotto modalità di compressione o taglio. Il campione può rappresentare un tipico componente isolante per vibrazioni in vari settori quali, per esempio, ferrovia, trivelle di esplorazione petrolio e gas, ponti autostradali, grattacieli antisismici etc. (la lista riportata nel testo è molto lunga ed esaustiva). Per quanto riguarda invece le radiazioni, è risaputo che la radiazione ionizzante è uno strumento importante per la preparazione di nuovi materiali con proprietà superiori. Benché fin dal 1980 siano state fatte indagini sulla gomma siliconica irradiata, tuttavia in letteratura non ci sono rapporti sugli effetti di radiazione a frequenza naturale sulle proprietà dinamiche, meccaniche e ammortizzanti di elastomeri PVMQ, reticolati termicamente con perossido in presenza di coagenti, in questo caso TAIC (triallilisocianurato). In questo studio vengono determinate le proprietà dinamiche e meccaniche e la densità di reticolazione di elastomeri PVMQ, a reticolazione perossidica e modifica con radiazione ionizzante, per mezzo del DYMO, esaminando in dettaglio l’effetto del coagente TAIC sullo smorzamento di energia ed altre proprietà dinamomeccaniche alla naturale frequenza di questi elastomeri. Questo lavoro, inoltre, è il primo studio che spiega l’utilizzo del sistema DYMO come analizzatore della densità di reticolazione per elastomeri.
Per le prove viene utilizzato un grado PVMQ di Shin-Etsu di durezza 50 Shore A, il perossido Trigonox 101-45S di Nouryon e il coagente TAIC fornito da Sigma Aldrich: con questi materiali vengono preparate due mescole, una senza ed una con TAIC. Per quanto riguarda l’apparecchiatura di irradiazione, si usa un acceleratore di elettroni lineare ALID-7 con un’energia media di 6 MeV.
Il lavoro si articola in vari paragrafi, che prendono in esame: caratteristiche di vulcanizzazione delle due mescole; effetti di coagente e radiazione sulla comprimibilità, sul fattore di perdita tan delta e sulla proprietà di dissipazione di energia degli elastomeri PVMQ.
Dalle prove effettuate risulta che tutte le proprietà meccaniche sopraccitate, compresa la resilienza, possono essere alterate con l’aggiunta del coagente TAIC alla mescola e con l’irradiazione a fascio elettronico degli elastomeri: i relativi cambiamenti possono essere attribuiti alla variazione della densità di reticolazione degli elastomeri. L’aggiunta di TAIC aumenta le reazioni di reticolazione dei gruppi vinilici della struttura chimica, mentre l’aumento di gelificazione è probabilmente causato dal completamento delle reazioni di post-vulcanizzazione del coagente per irradiazione e dalla reticolazione specifica delle catene del silicone. L’aumento della densità di reticolazione degli elastomeri PVMQ è la causa delle diminuite proprietà di smorzamento o dissipazione di energia, dal momento che esso aumenta l’elasticità e riduce la comprimibilità.
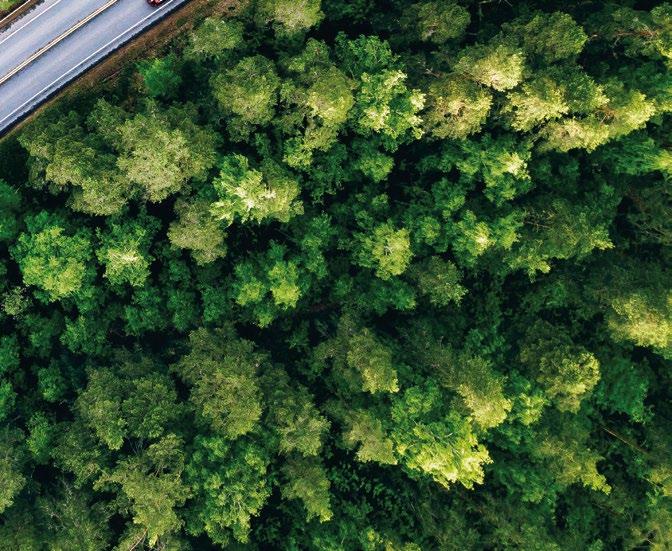
Materie Prime E Applicazioni Aumentano Le Opportunit Per Le Cariche Naturali
D. Vink - RFP n. 4/2022, pag. 28-31
Le cariche rinnovabili offrono numerosi vantaggi in gomma e plastica e sono ormai in fase di valutazione in una vasta gamma di mescole di gomma, come alternativa alle convenzionali cariche minerali o sintetiche.
In quest’ambito l’azienda UPM Biochemicals, unità operativa della della UPM forestry and paper production, fondata in Finlandia nel 1996, nell’ottobre del 2021 ha annunciato l’introduzione sul mercato delle cariche a base lignina Biomotion RFF (Renewable Functional Fillers). Fino alla metà del 2022 la produzione dei materiali RFF si è limitata a piccoli volumi su scala pilota, in attesa della produzione su scala industriale nella bioraffineria UPM di Leuna in Germania, che sarà operativa entro la fine del 2023 con un potenziale di 220.000 ton/anno di prodotti RFF, glicole monoetilenico (MEG), glicole polipropilenico (PPG) e zucchero industriale da legno di faggio. I materiali di legno, utilizzati da UPM, derivano dalla gestione di diradamento forestale, da scarti industriali e da segatura di segherie.
La scelta della lignina come carica naturale per la gomma è stata presa da UPM dopo avere confrontato Biomotion RFF e carbon black in mescole con diversi gradi di carbon black. Si è così verificato che l’utilizzo di carbon black N990 comporta un potenziale di riscaldamento globale GWP (Global Warming Potential) pari a 4.500 Kg di anidride carbonica equivalente per metro cubo di mescola di gomma, vale a dire il 27% in più rispetto al carbon black N772, che ne sviluppa 3.500, a sua volta il 27% in più rispetto ai 2.600 Kg di Biomotion RFF sostituito al carbon black. Un ulteriore incentivo a questa scelta è stato il risultato della collaborazione con l’azienda tedesca Rosta, che ha prodotto un’unità di sospensione in gomma/ metallo con una mescola prodotta dalla svizzera Compounds AG: in questa mescola Biomotion RFF ha sostituito tutto il carbon black nella gomma naturale, ottenendo una riduzione del peso della mescola e un’impronta di carbonio più bassa di 420 Kg/m3. Anche se il costo della mescola è risultato leggermente più alto, ci sono stati però benefici, quali una possibile riduzione delle cariche bianche, una densità più bassa, nessuna conducibilità elettrica e un buon rinforzo meccanico. Sono risultati però più bassi l’allungamento e il carico, forse per la relativamente bassa area superficiale specifica (40 m2/g) del grado RFF scelto (X40), che si cercherà di migliorare con la silanizzazione della carica stessa.
Esistono già molte applicazioni di Biomotion RFF, tra cui tubi (IVG Italia), rivestimenti per applicazioni ferroviarie come isolamento acustico e per correnti vaganti (Sealable Solution Germania), articoli tecnici (Wiele Rubber Belgio), pavimenti e suole (Nora Systems Germania) e O-ring (Wallstabe & Schneider Germania). La più interessante, tuttavia, è probabilmente quella della Standard Profil Automotive (Turchia), che produce tubi in EPDM con densità più bassa del 10% rispetto a quelli con carbon black N990 e con riduzione del talco da 80 a 60 phr, sia pure con un carico più basso ma migliori allungamento e resistenza a lacerazione.
Anche nel settore dei termoplastici Biomotion RFF ha già trovato applicazioni, come rivestimento per pavimenti e articoli medicali, grazie alla sua elevata purezza per basso contenuto di IPA (0,1 mg/ Kg) e di zolfo (<0,2 wt%), che ne consentirà l’uso anche in articoli a contatto con alimenti ed acqua potabile.
Per quanto riguarda il settore automotive, UPM, sulla scorta della possibilità di abbassare il peso delle portiere auto del 50% minimo con il ricorso ad alluminio o magnesio, sostenuta da Orion Engineered Carbons e Dow Europe, afferma che Biomotion RFF è in grado di sostituire carbon black e altre cariche pesanti nelle guarnizioni portiera, offrendo il 10% di riduzione in peso e un’impronta di carbonio inferiore del 50%.
Considerando la difficoltà di competere con gli alti valori di resistenza all’usura offerti dalla silice nell’ambito del pneumatico, UPM preferisce focalizzarsi sugli ar- ticoli tecnici in gomma. Tuttavia nel 2020 Pirelli Tyre ha già iniziato ad utilizzare lignina nei pneumatici bicicletta, considerando le sue qualità di carica di basso peso, il suo più basso depauperamento di acqua e le sue più basse emissioni di anidride carbonica rispetto alle cariche che sostituisce.
Macchinari E Attrezzature
ULTIMI SVILUPPI NEI MACCHINARI DI LAVORAZIONE DELLA GOMMA
D. Vink - RFP n. 4/2022, pag. 34-37
Attualmente c’è molto fermento di novità nell’industria della gomma per quanto riguarda macchinari e attrezzature per la sua lavorazione: questo articolo offre una panoramica aggiornata, che vale la pena di leggere (la riportiamo lasciando i particolari ai lettori interessati) per rendersi conto delle novità e delle tendenze che stanno prendendo piede. A parere di Thomas Gradl di Engel (Austria), produttore di presse per stampaggio ad iniezione, le aziende che lavorano la gomma siliconica solida HCR (High Consistency Rubber) dovrebbero valutare l’opportunità di passare dallo stampaggio a compressione a quello ad iniezione, utilizzando le attrezzature esistenti fino a quando è possibile. Tuttavia è senz’altro necessario avvalersi di un sistema di riempimento dello stampo più adeguato: nello specifico, stampare silicone solido ad iniezione consente una più alta portata, una maggiore produttività e meno personale addetto.
Stefan Herzinger di Wickert Maschinenbau (Germania) obietta che il sistema ad iniezione è adatto alle produzioni di grandi quantità, mentre quello a compressione si rivela migliore per la sua capacità di produrre, per esempio, articoli farmaceutici senza il fenomeno del flash (segni di flusso) e permette di stampare facilmente articoli con inserti di metallo o tessuto. Catene di gomma rinforzate e corrimani di scale mobili stampati in continuo sono altri esempi di miglior prestazione dello stampaggio a compressione rispetto a quello ad iniezione, senza dimenticare la necessità di una pressione costante nella cavità dello stampo, critica a volte nel secondo sistema. Oggigiorno i problemi della catena di approvvigionamento sono peggiorati, vuoi per i com- ponenti elettronici o per parti in acciaio, e trovare le soluzioni fa parte del servizio, che un produttore di macchine dovrebbe fornire ai clienti, come nel caso di Wickert, che offre equipaggiamenti ausiliari a completamento del sistema di stampaggio. Sigma Engineering (Germania) offre il sistema Sigmasoft per la simulazione e l’ottimizzazione dello stampaggio ad iniezione di termoplastici, TPE e LSR: con la nuova versione 5.3.1 il software consente una visione dettagliata di tutto il processo di stampaggio a compressione, poiché la simulazione comprende l’influenza termica di stampi aperti, la plastificazione dell’elastomero e l’analisi della vulcanizzazione, fino ad affrontare lo stampaggio di articoli gomma/metallo. Hägglunds Drive Systems (Germania) offre trasmissioni idrauliche semplici, economiche ed esenti da manutenzione, anche come ammodernamento di una macchina esistente. La sostituzione di trasmissioni elettro-meccaniche con le sue più recenti trasmissioni elettro-idrauliche su estrusori, mescolato- ri aperti e calandre consente un funzionamento con risparmio di energia.
Deguma Schütz (Germania) ha abbandonato la tradizionale costruzione del mescolatore aperto, dotando la macchina di un alloggiamento degli ingranaggi, posizionato all’esterno della zona dei cilindri e dotato di una più efficiente trasmissione con riduttore epicicloidale del servomotore raffreddato ad acqua. Questo nuovo assetto elimina la necessità di una grande ruota di trasmissione, elemento costoso soggetto ad elevata usura, rende più facile l’accesso ai singoli componenti per la manutenzione e consente il riscaldamento delle mescole per frizione alla temperatura desiderata, facendo funzionare i cilindri a velocità differenti.
Troester (Germania) offre un nuovo macchinario di estrusione molto automatizzato con combinazione di calandra cilindro-testa, che permette di ottenere fogli estrusi e calandrati perfettamente dimensionati. Maplan (Austria) ha introdotto la nuova serie di presse ad iniezione verticali
Easy+, in cui la chiusura a quattro colonne è sostituita da un telaio a C, che consente l’accesso allo stampo da tre lati. Queste nuove presse sono più veloci e consumano meno energia, grazie alla trasmissione idraulica MAP.cooldrive con servomotore dinamico e a reazione rapida. Inoltre l’azienda ha introdotto il concetto MAP. autocell, che grazie al sistema MAP.commander controlla l’intero processo produttivo fino a sei presse, senza interfaccia con altri controlli. IMG (Italia), distributore dal 2009 delle presse cinesi Haitian, vuole promuovere la vendita delle proprie presse a compressione ed iniezione più attivamente in tutta Europa, in particolare sul mercato tedesco. La sua nuova pressa verticale GUMvert VCV 300/1000 combina funzionalità a compressione ed iniezione, passando da una all’altra con un semplice pulsante, e dispone di una chiusura a pistone rovesciato, che assicura un risparmio del 30% sui tempi di chiusura/ apertura, con una conseguente riduzione dei consumi energetici.