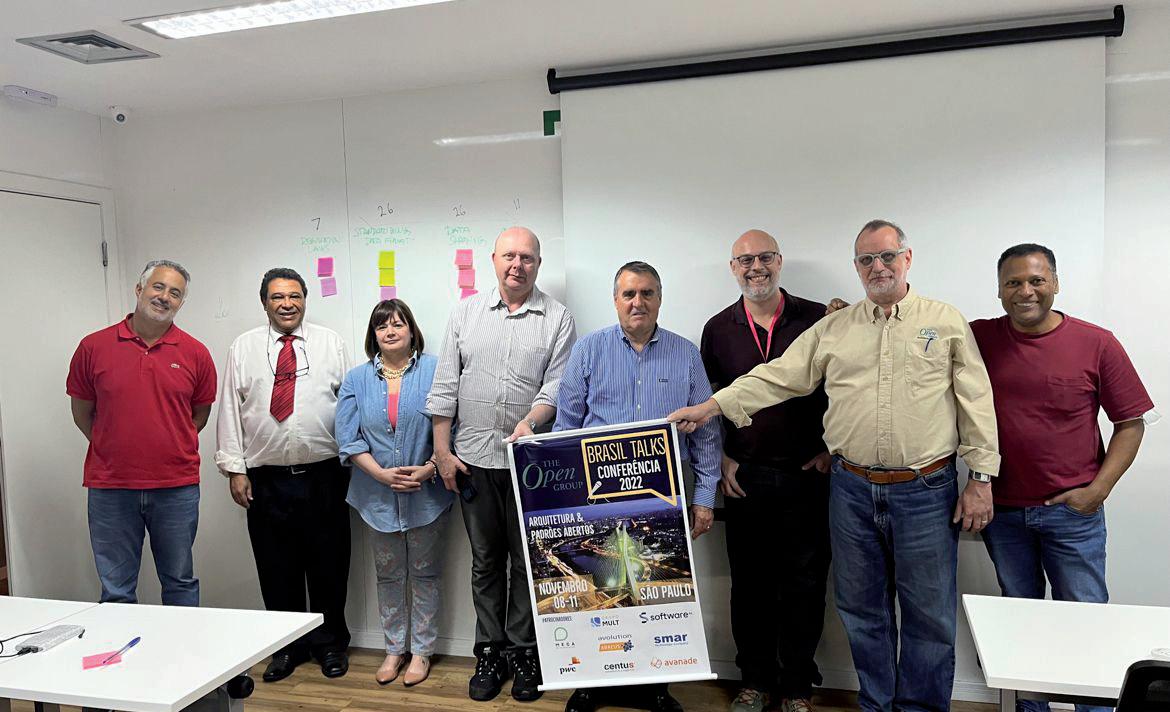
25 minute read
Flash
Open Group Brasil 2022
Como acontece todos os anos, desde 2012, em novembro, aconteceu o “Brazil Talks 2022 – Conferência do The Open Group”, onde padrões abertos foram apresentados através de depoimentos, palestras de empresas, e casos reais. “O evento de quatro dias aconteceu na unidade Paulista da FIAP, universidade parceira e membro do The Open Group, e contou com o registro de 269 participantes, remotos e presenciais, 8 patrocinadores e 93 empresas, de vários segmentos participando, indo, de varejo, até empresas produtoras de petróleo, passando por companhias nacionais de automação industrial, que ajudam a desenvolver o padrão O-PAS”, conta Roberto Severo, Country Manager do The Open Group para o Brasil, Peru e Colômbia.
A Nova Smar, membro do The Open Group, ativa em desenvolver o padrão para o mercado, demonstrou o uso do Open Process Automation Standard, padrão do The Open Group, em campo. O presidente da Nova Smar, Libanio de Souza, apresentou as principais características de uma ferramenta de configuração de um sistema, utilizando componentes projetos, segundo o padrão O-PAS, demonstrando a utilização das tecnologias OPC_UA, IEC 61131, Blocos Funcionais O-PAS e AML. O evento contou com a presença de executivos do The Open Group, como o presidente e CEO, Steve Nunn e o VP de Desenvolvimento de negócios e Segurança, Jim Hietala. Foram 24 palestras plenárias, e 6 workshops em salas de aula, com tradução simultânea (inglês-português), e transmissão em tempo real pelo You Tube.
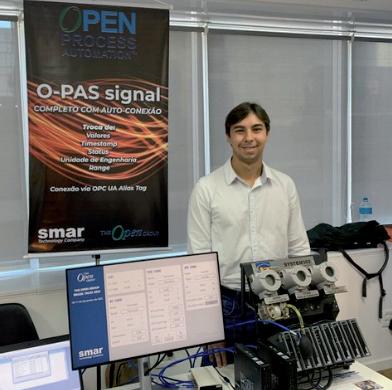
O evento teve um dia dedicado aos arquitetos de domínio e corporativos, que possuem uma profissão muitas vezes confundidas localmente, quando puderam conversar abertamente, e trocar informações, com suporte e mediação da AEA – Associação de Arquitetos Corporativos. Cada dia focou em um tema: Arquitetura Corporativa (TOGAF e ArchiMate); Dia dos Arquitetos; Segurança, Transformação Digital; e Automação industrial, Meio Ambiente e Óleo & Gas.
Destaque-se a apresentação de Pedro Vieira, “A Convergência TI-TO como alavanca da Indústria 4.0” , que pontuou que, para que se chegue efetivamente a uma Indústria 4.0, a partir dos conceitos de Transformação Digital, é necessário investir-se na chave da convergência entre Tecnologia da Informação, Tecnologia da Operação, e Tecnologia da Engenharia. O trabalho apresentou a visão da Indústria sobre a Convergência e o CoE de IIoT da Petrobras.


Expo ISA Brazil

AExpo ISA Brazil International Automation & Innovation, evento anual itinerante da ISA-International Society of Automation Brasil, aconteceu este ano na Unisal Lorena, com organização da ISA seção Vale do Paraíba, e reuniu diversas áreas da indústria, em uma exposição, palestras e Rodada de Negócios, co-organizada com o Sebrae – cujas empresas-âncora eram Embraer, Senai, Basf, PqTec/Nexus, 7COMm, Wipro-Pari, Sabesp, Tekno, Orica.
Flavio Briguente, da Evonik (USA), contou o caminho das pedras para a digitalização de plantas existentes na palestra Improve Proftability through Digital Transformation.
A mesa de abertura foi composta pelo senador eleito, astronauta Marcos Cesar Pontes, contou sobre sua trajetória, a importância de perseverar e estudar sempre; Claudio Makarovsky, Diretor Microsoft e ISA Executive Board Member, que falou sobre que é o #metaverso e suas implicações hoje, no dia a dia; e Ademar Poggio – Vice-Presidente ISA Seção Vale do Paraíba; Nilson Rana – Diretor Evento ISA BRAZIL e Fundador da ISA Seção Vale do Paraíba; Grasiele Augusta Ferreira Nascimento – Diretora Operacional UNISAL-Lorena; Pe. Sergio Augusto Baldim Junior – Reitor UNISAL; Sylvio Ballerini – Prefeito Municipal.
No segundo dia do evento, Gleverson Lemos, da Embraer, contou sobre a robótica utilizada pela empresa; Felipe Carvalho, da Tekno, falou sobre a interface entre TI e TA com Indústria 4.0; Nelson Alves, da Sabesp, discorreu sobre a importância da Automação no Saneamento do Marco Regulatório; Tania Cosentino, CEO Microsoft Brasil, enviou um vídeo sobre a participação das mulheres no mundo da automação e tecnologia; Francisco Sotelo, da Endress + Hauser, falou sobre o Potencial da Espectroscopia Raman; Juliana Favaro, da ABB, mostrou como Iniciar sua Jornada de Digitalização; Marcelo Marino, da Alutal, discorreu sobre a importância do monitoramento de vibração na Indústria; e Erik F. Maran, da Westcon, demonstrou a digitalização de Operações Industriais com Realidade Aumentada – que podia ser experienciada no stand da empresa. Jeremias Rodrigues, diretor Magna Empreendimentos, e Nilson Rana, presidente da seção Vale do Paraíba, fizeram o encerramento e sorteios.


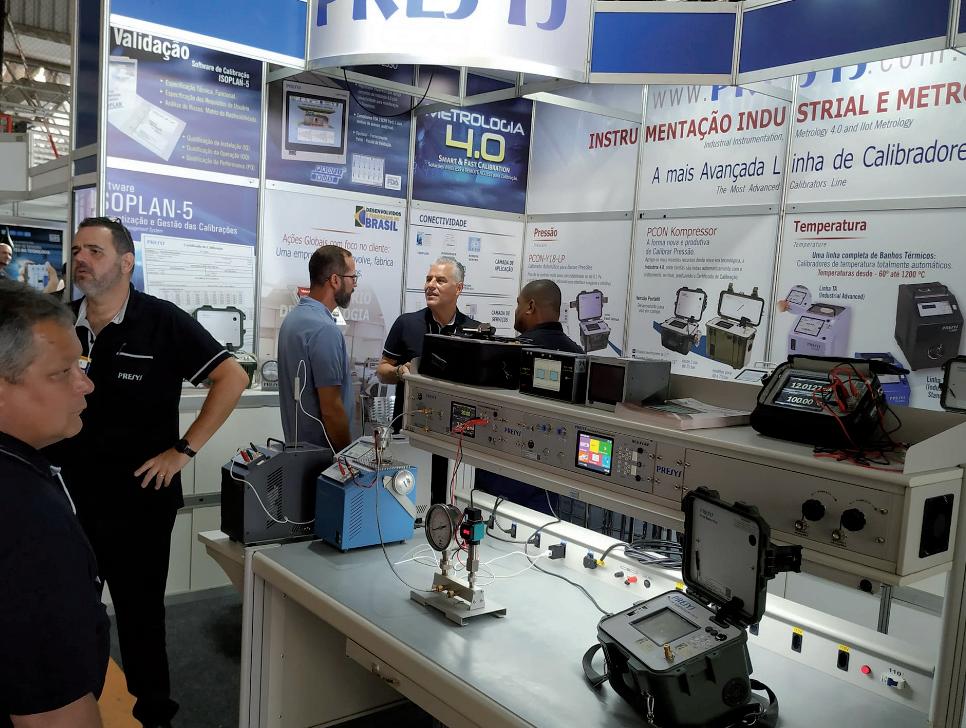
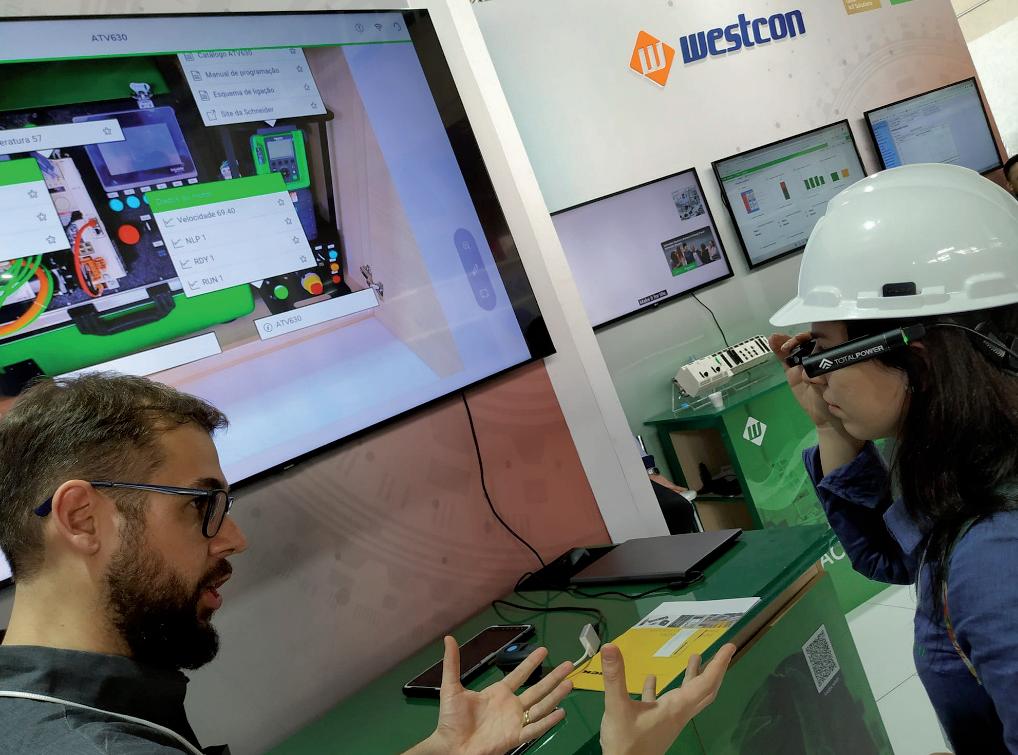
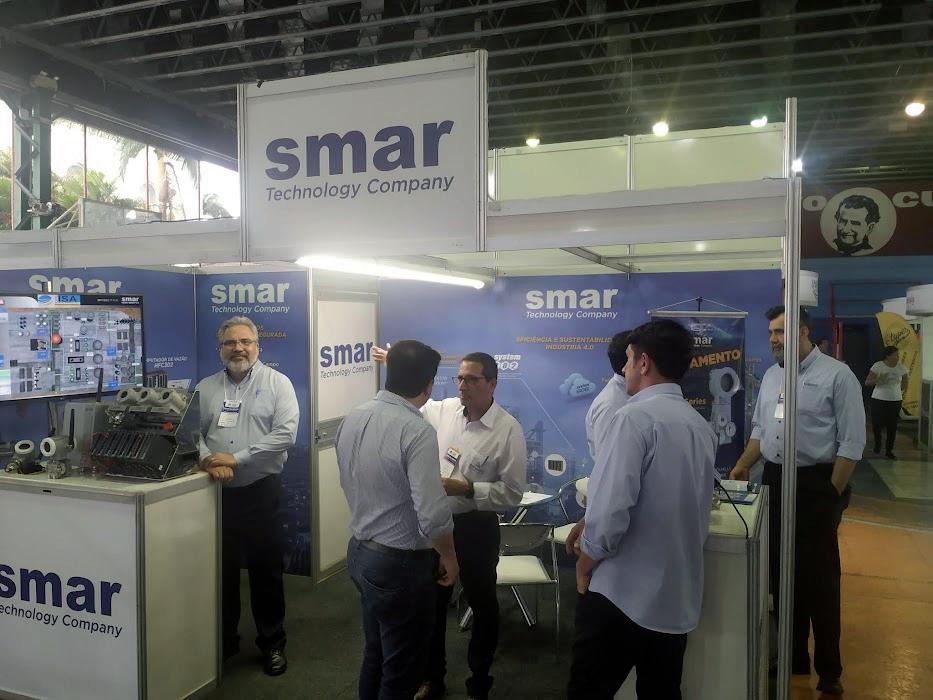

Encontro Técnico 2022 - ISA Seção RS e Grinst-RS
No auditório do Senai em Porto Alegre, com a presença de 60 pessoas, aconteceu, dia 22 novembro, o Encontro Técnico 2022 promovido pelas entidades ISA seção RS e Grinst-RS. O tema do evento foi Inovações em Redes Digitais e Instrumentação. O evento marcou o retorno presencial dos encontros técnicos da organização do Rio Grande do Sul.
“Com um cenário de forte concorrência global e a busca por melhorias nos processos industriais, estamos vendo um avanço exponencial de novas tecnologias aplicadas à Indústria 4.0. É o momento da exploração do potencial da tecnologia digital, de forma segura, confiável, eficiente, robusta, com a mais alta qualidade, maior disponibilidade e proporcionando benefícios na otimização dos processos e controles industriais” conta Tulio Muller, presidente da ISA Seção RS.
O evento apresentou o mercado atual de automação e instrumentação, bem como suas tendências, com o avanço na tecnologia Profibus, e a chegada do APL, Advanced Physical Layer, cenário onde, em uma mesma estrutura de rede Ethernet, se podem ter equipamentos de campo em vários protocolos (Profinet, EtherNet/IP, MODBUS/TCP, HART/IP), e tirando vantagens de algo padronizado e seguro.
O encontro mostrou um pouco da transformação digital em automação de processos, e algumas novidades em medições de pressão, nível, vazão e posicionadores de válvulas.
Patrocinado pela Altus, foi uma intensa troca de experiências, finalizado com um coquetel de confraternização e network.
A Altus e a Vivace são parceiras tecnológicas, envolvendo atuação conjunta no mercado para fornecimento de soluções para automação de processos, utilizando o potencial conjunto das empresas para sistemas de controle, instrumentação e ferramentas de software pertinentes. Esta criativa aliança é uma ousada resposta aos desafios criados pela globalização, alta necessidade de competitividade e modernidade tecnológica, que caracterizam o mercado de automação e instrumentação em nossos dias.

SPS 2022 volta presencial SPS 2022 volta presencial
A SPS, que aconteceu de 8 a 10 de novembro de 2022, em Nuremberg, Alemanha, mais uma vez impressionou. O foco este ano não foi apenas em produtos e soluções, mas também na interação humana – o evento manteve sua plataforma ‘SPS on air’, complementando perfeitamente o evento presencial.
Visitantes profissionais de todo o mundo afluíam para descobrir os últimos desenvolvimentos e tendências de automação, através de 1.000 expositores, que cobriram uma área de 112.000 m2. Os participantes puderam envolverse em discussões sobre avanços tecnológicos, e estabelecer novos contatos. Ao longo dos três dias, o evento atraiu cerca de 44.000 visitantes.
A programação deste ano incluiu apresentações sobre temas de alta relevância para a indústria de automação, como sustentabilidade em automação, segurança, novos métodos logísticos e integração robótica. Também havia muitos painéis de especialistas e, entre os tópicos discutidos, estava o futuro da digitalização e a importância do comércio. O estande compartilhado ‘Automação encontra TI’ também fez um retorno com 23 empresas, aproveitando a maior visibilidade oferecida por esta interação. A exposição do próximo ano acontece de 14 a 16 de novembro, em Nuremberg.
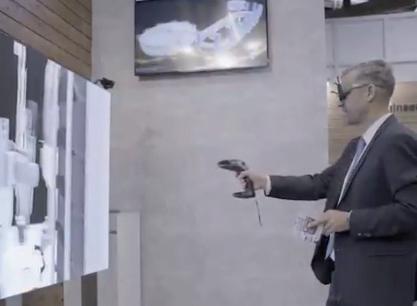
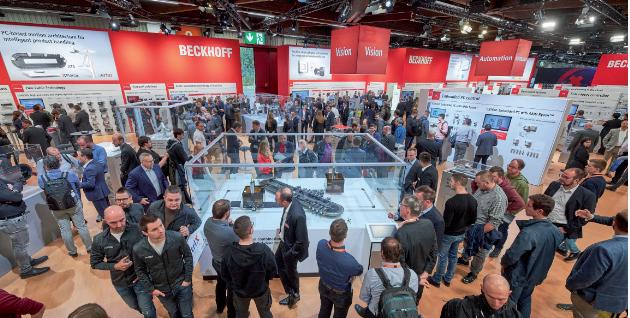
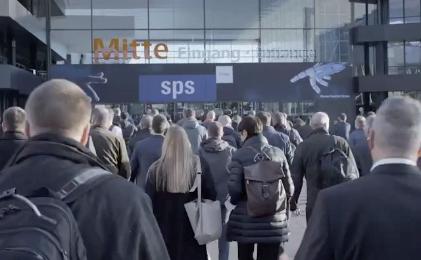
ISA Seção Rio de Janeiro fecha o ano debatendo ISA Seção Rio de Janeiro fecha o ano debatendo transformação digital
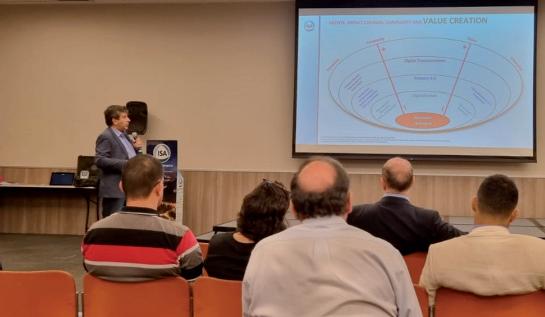
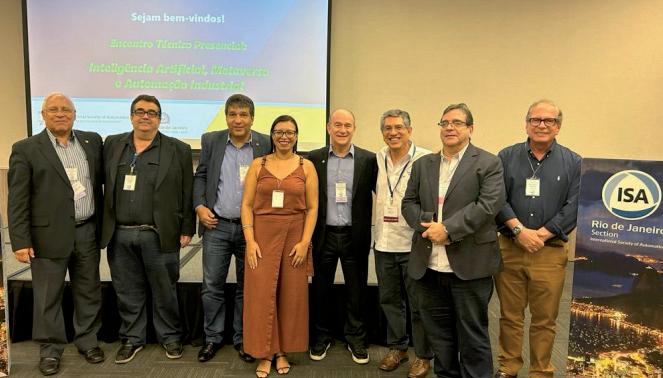
A ISA Seção RJ reuniu mais de uma centena de pessoas no Encontro Técnico Presencial – Inteligência Artificial, Metaverso e Automação Industrial –, no Novotel Porto Atlântico, com a participação dos Keynote Speakers M.Sc Victor Venâncio Dias (IHM Stefanini e Head de Transformação Digital em OI-LatAm), e também do Pesquisador Master de P&ID em Exploração, Ismael Santos (PETROBRAS/CENPES).
Victor Venâncio reforçou pontos importantes sobre transformação digital no Brasil e os desafios a serem superados para ganharmos competitividade em avanço digital no país. Mostrou de forma contundente que 70% dos projetos de transformação digital falham, e o porquê deste fato – e as oportunidades para não fazermos parte desta estatística. Pontos como mudança de mindset dos empresários brasileiros médio e pequeno porte foram abordados.
Ismael Santos apresentou conceitos de Machine Learning e Deep Learning, e abordou um case de Digital Twins, visando à preservação da integridade das plataformas utilizando o metaverso, onde, entre outras vantagens, logrou-se reduzir necessidades de embarques para verificação da integridade de plataformas e manutenções. Pontuou ainda a importância de incentivar a educação com o viés de transformação digital, para desmistificar o falso conceito de que a digitalização irá reduzir ofertas de emprego.
O Gerente de Vendas da Linha de emissões da Durag Brasil, Renato Almeida, falou sobre Sistemas de Monitorização Preditiva das Emissões, abordando controle de queima e combustão, e divisão de emissões, particulados e controle de vazão, mostrando alternativa preditiva da análise de dados de processo, comparando com os sistemas contínuos de emissões por meio de modelagem de dados (PEMS), e assim a previsão de emissões por meio de modelagem matemática.
O evento contou com apresentações institucionais da Aselco, Tormene Group, Superquip e USE, mostrando outras vertentes e suas expertises, e reforçando seus suportes técnicos. A Aselco, Tormene e USE levaram equipamentos de amostra ao evento.
O evento trouxe uma visão atual sobre temas que se integram no contexto de gestão ESG, Governança Ambiental, Social e Corporativa em português.
No final do evento, Jose Guilherme (USE) se despediu da presidência da ISA RJ, comemorou a volta dos eventos presenciais tão caros à comunidade, agradeceu a colaboração da diretoria, ao longo do seu mandato, e reiterou o convite à comunidade de ações de voluntariado e mentoria. Aproveitou para anunciar a eleição de Dayane Lima para o próximo biênio – 2023/2024, em assembleia ocorrida em 30/11/2022. E finalizou com uma lembrança aos queridos membros ISA Pery Ribeiro e Roberto Magalhães (in memoriam), que tanto contribuíram com a organização.
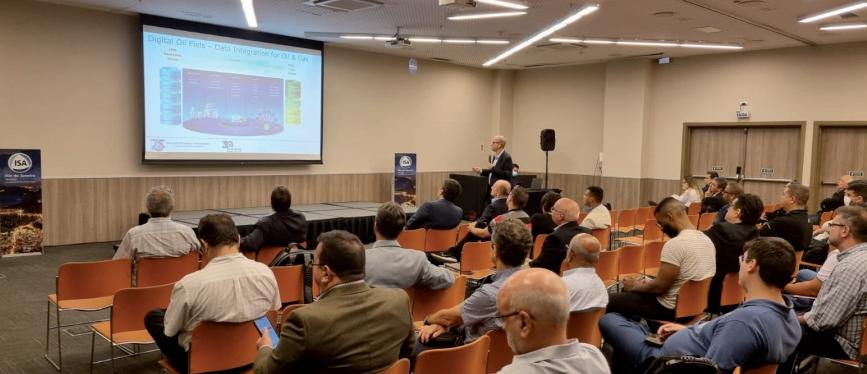
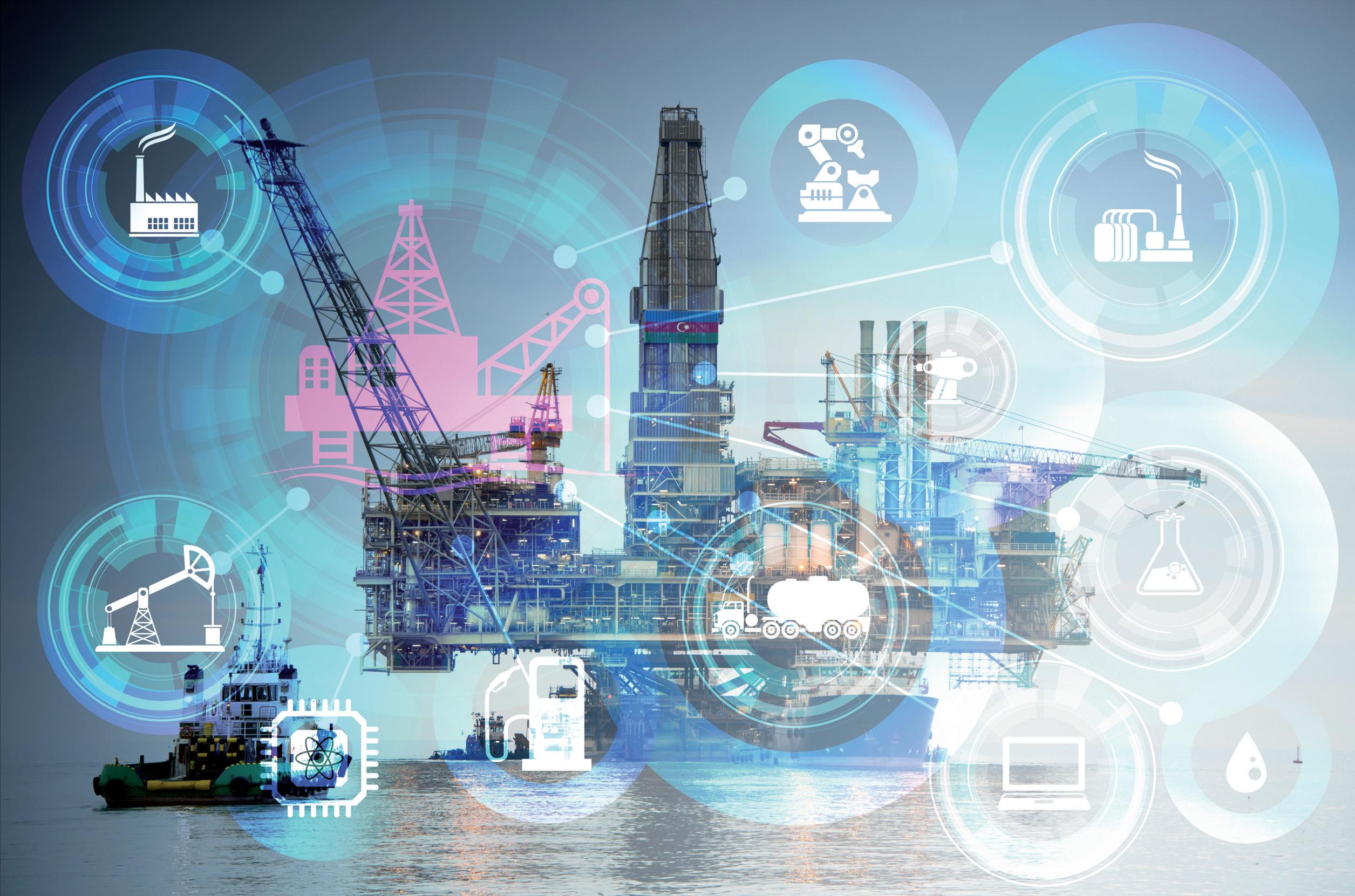
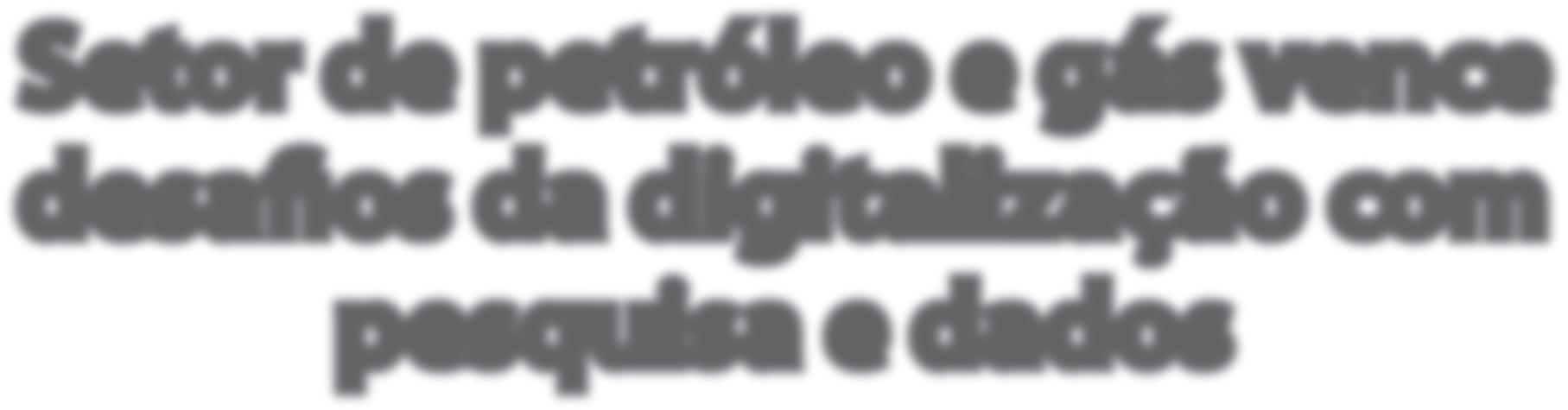
Setor de petróleo e gás vence desafi os da digitalização com os da digitalização com pesquisa e dados
Há algum tempo, os líderes da indústria de petróleo e gás global previam que o setor evoluiria com maior diversificação e uso de tecnologias para inovar – com consequente aumento do risco cibernético. E, como aponta um estudo da BDO Global para a indústria de petróleo e gás, a inovação pode ser uma tábua de salvação – usada para otimizar finanças e operações – ou um calcanhar de Aquiles – ignorado, até que seja tarde demais. Seus analistas apostam que, a inovação, aliada à evolução das prioridades do setor de petróleo e gás, mudará o cenário, com aplicação de nanotecnologia – mas não só ela – em todas as fases do ciclo de vida – da exploração e perfuração de avaliação e produção, transporte e refino. De fato, os analistas veem o mercado digital em petróleo e gás ultrapassando os US$ 20 bilhões, com aumento substancial em segurança cibernética, e esperam mudanças na tributação dos derivados de petróleo, como meio de controlar a demanda e atender metas ambientais.
As apostas tecnológicas não ficam no setor produtivo: espera-se que quase metade de todos os contratos do setor usem tecnologia blockchain para mais rapidez, precisão e menos espaço para disputas – resposta à busca por soluções digitais para os desafios enfrentados nas indústrias de óleo e gás.
Nesse cenário, algumas tendências se destacam na produção, as mais voltadas para a otimização dos processos de manutenção e transição energética, como análise de equipamentos críticos/análise preditiva de falhas; manutenção preditiva e descarbonização. Porque a produção de petróleo e gás deve ser segura, disponível e ter uma pegada de baixo carbono. Mas, o custo de capital
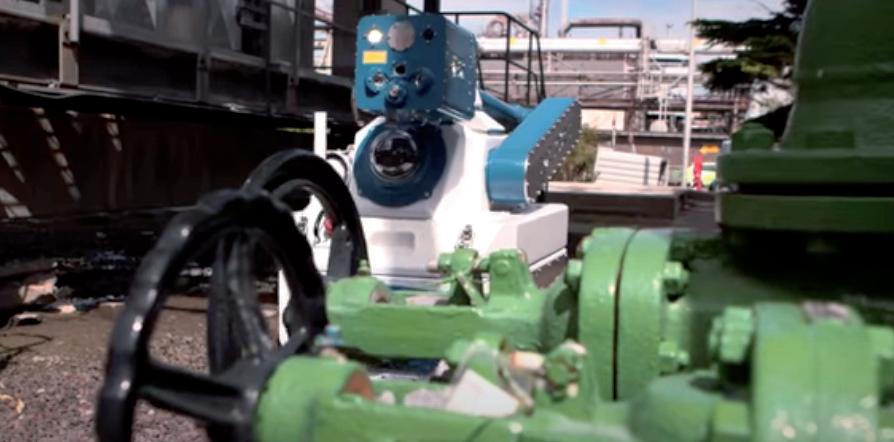

das instalações precisa cair, e isso pode ser feito introduzindo conceitos-padrão e modulares de fabricação inteligente. Estandardização e interoperabilidade de dados, no projeto e nas operações, também podem reduzir os custos de investimento e operação.
Entram aí os conceitos da Indústria 4.0, que oferecem novas formas de trabalhar em petróleo e gás. Eles fornecem uma maneira de introduzir a engenharia digital de ponta a ponta, para toda a vida útil de uma instalação. Dentro dos conceitos da Indústria 4.0, cadeias de valor integradas podem ser construídas, diminuindo custos de engenharia, aquisição, construção, modificações e manutenção de projetos; cadeias de valor integradas abertas para novos modelos de negócios e colaboração na indústria – com base em dados e serviços baseados em dados. A padronização que chega junto com esses conceitos permite instalações sob medida com plantas mais simples e robustas, e um grande potencial para introduzir robótica e autonomia nas operações.
Mais importante ainda, a Indústria 4.0 fornece uma integração vertical eficaz das instalações da indústria de petróleo. Isso torna mais simples a obtenção de dados para o tomador de decisão.
As instalações que implementam os conceitos da Indústria 4.0 perceberão os objetivos do campo do futuro, e isso está sendo facilitado com tecnologias como Redes sem fio, 4G e 5G; instrumentos com sensores independentes para processos e monitoramento, geralmente não invasivos e fáceis de instalar; equipamentos inteligentes; adoção acelerada da Internet Industrial das Coisas (IIoT), que oferece formas alternativas de integração de instrumentação, equipamentos e sistemas de controle; uso de protocolos padrão e plataforma aberta OPC-UA; automação aberta e computação em nuvem.
A diferença é que a Indústria 4.0 propõe uma mudança para uma rede em vez de uma hierarquia, e a IIoT é uma manifestação dessa abordagem de pensamento em rede. A Indústria 4.0 se baseia em automação e controle, tendo como padrões a ISA95 e OPC; a base da IIoT está na ciência de dados, computação e eletrônicos. São perspectivas complementares e necessárias que precisam trabalhar juntas, à medida que TO/TA e TI interagem.
E a implementação da Indústria 4.0 no setor de petróleo e gás envolve a construção dos Digital Twins – gêmeos digitais – para otimizar projetos e operações. E, como outros setores, o de petróleo e gás também enfrenta o desafio de implantar os gêmeos digitais no seu parque já instalado, com o agravante dos descomissionamentos, que envolvem centenas de vertentes e todas com interfaces ambientais. É importante frisar que a Indústria 4.0 não é sobre descontinuação do que existe, mas sobre melhorar o que se faz, automatizar os processos e aproveitar as oportunidades das novas tecnologias, encontrando maneiras eficientes de trazer esses campos para o ecossistema digital, sem desperdiçar dinheiro em ativos que podem ser desativados. De fato, o descomissionamento pode fornecer um incentivo para a digitalização das informações do projeto.
Essa transformação digital que avança no setor de petróleo e gás envolve reconhecer a enorme quantidade de dados que são gerados nos processos, a grande oportunidade que as novas tecnologias proporcionam para transformar a forma de operar o negócio, como descobrir meios para continuar trabalhando em um mundo que está por vir – e ao mesmo tempo já está aí.
É muito interessante observar que essa transformação digital e a aplicação das tecnologias envolvidas não é apenas para grandes estruturas. Pode ser aplicada a sistemas isolados, ou mesmo equipamentos.
Vale ser observado o que uma grande companhia de petróleo fez a partir de uma válvula de controle que falhou e fez o processo oscilar, e acabou por quebrar o corpo da válvula – o que custou algum tempo de parada não planejada. Pensando em como usar os dados já coletados para evitar falhas futuras, o departamento de ciência de dados da companhia usou os dados para elaborar modelos de aprendizado de máquina, orientados para detectar anomalias que não seriam percebidas de outra forma. E o que começou com uma válvula se tornou um teste em outras 15, e depois para milhares de válvulas. Mas, essa é uma
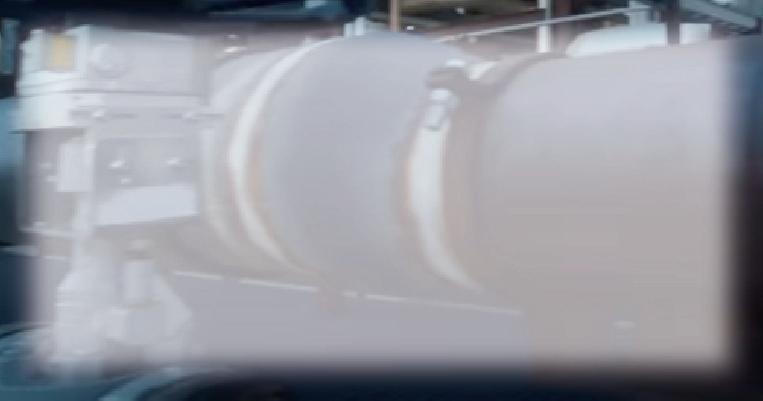
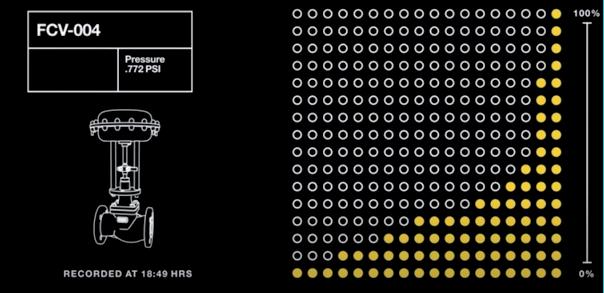
companhia global; como dimensionar e executar isso globalmente? A companhia não fez uso de historiadores de prateleira, e não tendo a pretensão de ser uma empresa de IA, chamou uma empresa de desenvolvimento de modelagem de manutenção preditiva, com quem já trabalhavam em outras frentes. Juntas, as equipes desenvolveram algoritmos, para identificar falhas de concepção com níveis muito altos de precisão, através da tecnologia Predictive Analytics, uma extensão da Inteligência Artificial.
O desafio era dimensionar e implantar a solução em seus algoritmos de aprendizado de máquina para toda companhia porque, ainda que a mecânica da válvula seja simples, o contexto interfere, o que significa que é preciso pelo menos um modelo independente de aprendizado de máquina por válvula. E, ao final, a plataforma da empresa contratada foi capaz de gerenciar 2 milhões desses modelos.
Então, as equipes desenvolveram juntas mecanismos para monitorar mais de 8.000 equipamentos, todos os dias, incluindo dados coletados por robôs, que podem monitorar a posição das válvulas manuais, podem detectar vazamentos, vazamentos de gás, vazamentos de líquidos. E com esse trabalho diário, a companhia de petróleo pode responder de maneira mais rápida e responsável.
Como nem toda empresa tem uma equipe de cientistas de dados, para muitos casos, os sistemas comerciais têm ferramentas que encaminham bem esses problemas – talvez não para dois milhões de modelos, mas com certeza para algumas centenas. E tem muita gente envolvida em melhorar esses processos, e aumentar as capacidades, de maneira segura.
Se quisermos ser realmente bem-sucedidos numa transformação, temos de trabalhar com um ecossistema mais amplo de parceiros, onde todos se beneficiem. Nessa linha, aconteceu uma chamada pública conjunta entre Finep – financiadora de estudos e projetos – e o conselho norueguês de pesquisa (RCN), cofinanciados por empresas no Brasil que compõem o Consórcio Libra, entre elas a Petrobras, e, na Noruega, pelas empresas Shell e Equinor. Esta chamada pública foca na completa digitalização do processo produtivo em gêmeos digitais (Digital Twins), que permitem acompanhar e otimizar todas as condições de produção de uma planta de petróleo. O Grupo de Pesquisa Sistemas de Computação para E&P de Petróleo do INF-UFRGS, e o Sirius Lab da Universidade de Oslo (UiO), ficaram responsáveis por esse projeto inovador.
“Nosso objetivo no Projeto Petwin de gêmeos digais para otimização e gerenciamento da produção de petróleo e gás é otimizar e gerenciar a produção; é um projeto de pesquisa que envolve vários parceiros, cada uma das partes contribuindo nas suas competências. A ideia é fomentar a cooperação internacional para esta área de digital twins, e ter um resultado prático que possa ser aplicado pelas empresas”, conta o professor Dr. João Cesar Netto, do INF – Instituto de Informática da UFGRS – Universidade Federal do Rio Grande do Sul.
Mas, não apenas pelas empresas participantes, para toda a comunidade, incluindo as provas de conceito – obviamente os dados secretos/sensíveis das empresas participantes não serão publicados –, os resultados práticos de ferramentas, relatórios, conclusões e artigos. Nem poderia ser diferente, já que é uma chamada pública para promover a inovação – que virá através de aplicações dessas pesquisas do grupo.
“A gente faz a pesquisa e deixa os resultados num nível de maturidade que prova o conceito demonstrado num ambiente relevante, ou seja, provamos que ele funciona. E aí o desenvolvimento na forma de produto acontece pelo mercado. Estamos na fase em que há a demonstração de conceitos e funcionamento de protótipo em ambiente relevante, porque trabalhamos com dados reais para demonstrar que é possível. Posteriormente, uma empresa pode desenvolver um produto comercial baseada nesses conhecimentos. A função da universidade é justamente permitir que todos tenham acesso a possibilidades de levar inovação para as diversas empresas e setores.”
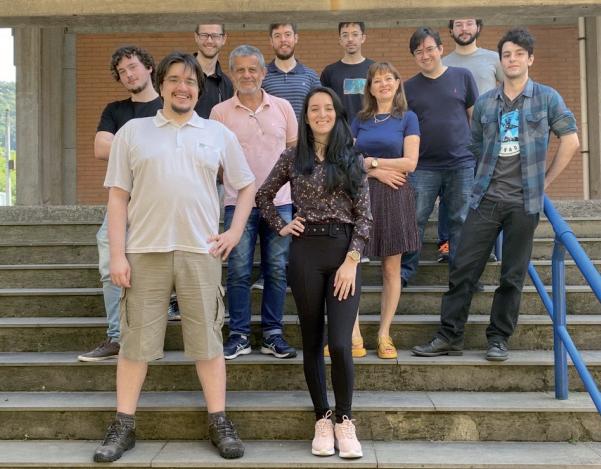
Parte da equipe do INF/UFRGS
Um gêmeo digital é uma representação virtual de um sistema real físico, com os dados desse sistema físico monitorados em tempo real – ou tempo de operação –, ou seja, se acontece um evento no local físico, ele é imediatamente transmitido para o modelo representado, dando acesso a todos os dados que estão acontecendo no mundo físico. É uma representação digital dos equipamentos reais, e daquilo que acontece neles com todos os dados durante a operação, ao longo do tempo. Se muda a temperatura num determinado ponto, isso é registrado no local físico, e também no gêmeo digital, para que se possa trabalhar com eles de forma simultânea com a operação.
O gêmeo digital é um grande concentrador dos dados do que está acontecendo no mundo físico. Ao mesmo tempo que se monitora, se podem tomar ações preventivas, como por exemplo um ponto da cadeia de escoamento está com pressão alterada e, com uma ação preventiva, se pode melhorar a condição de operação do sistema. Ou, a verificação de integridade, como por exemplo, quando a temperatura de terminado equipamento não pode passar de determinada medida, porque isso pode gerar danos sérios – com o gêmeo digital se pode intervir automaticamente.
“Entrando no mundo do Data Science, também posso usar os dados do que já aconteceu, e fazer previsões do que vai acontecer, e o que pode ajudar a sustentar ou aumentar a produção em determinado momento, depois de tomar ações recomendadas para a otimização do processo. Com esse volume de dados, se pode simular “o que aconteceria se” – e as possibilidades acompanham a imaginação, como o que aconteceria se um equipamento injetasse 10 unidades de gás, ao invés de O2? O que aconteceria com a integridade e com a produção? Posso ter aplicações que usam esses modelos computacionais para fazer previsões de cenários, sem ter de experimentar isso no mundo físico – essa é uma das grandes vantagens dos gêmeos digitais. E ainda, usando a massa de dados que fui coletando ao longo de tempo, eu posso aplicar as novas tecnologias de inteligência artificial e machine learning ou Aprendizado de Máquina, para prever comportamento, verificar se existem anomalias, e outras aplicações. Note que, para boa parte das aplicações baseadas em Inteligência Artificial e Aprendizado de Máquina, é preciso ter conteúdo, é preciso ter dados. E o gêmeo digital permite ter esses dados integrados num lugar único – porque tenho como acessá-los de um ponto único – sejam dados do sistema de automação, de manutenção ou das diversas suítes do SAP. E com essa disponibilidade, se pode fazer o planejamento da produção, e colocar algoritmos inovadores de aprendizado de máquina para fazer previsões em diversos pontos das plantas”, conta o Professor Netto.
Existem desafios que o projeto procura resolver, como a unificação da nomenclatura ou a compatibilização dos significados e nomenclatura desses dados. Porque um engenheiro de automação pode denominar um objeto de maneira diferente do pessoal de gestão; cada área tem um jargão, e o desafio é ter uma visão compatibilizada desses dados, ou seja, quando se fala de uma
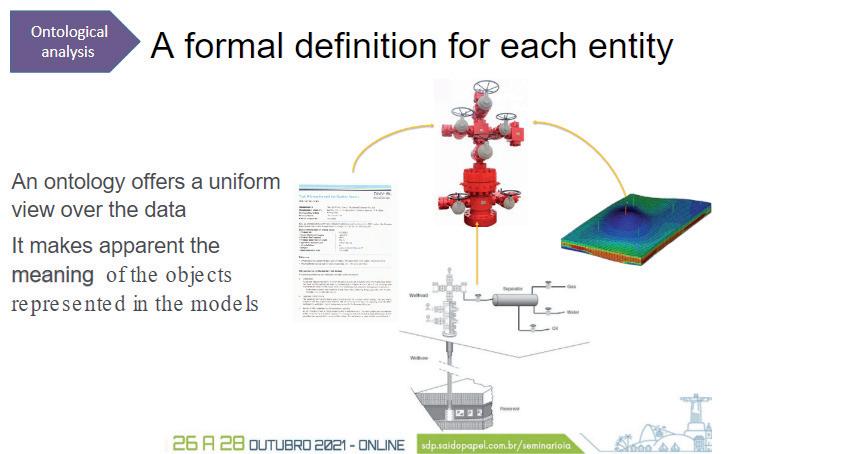
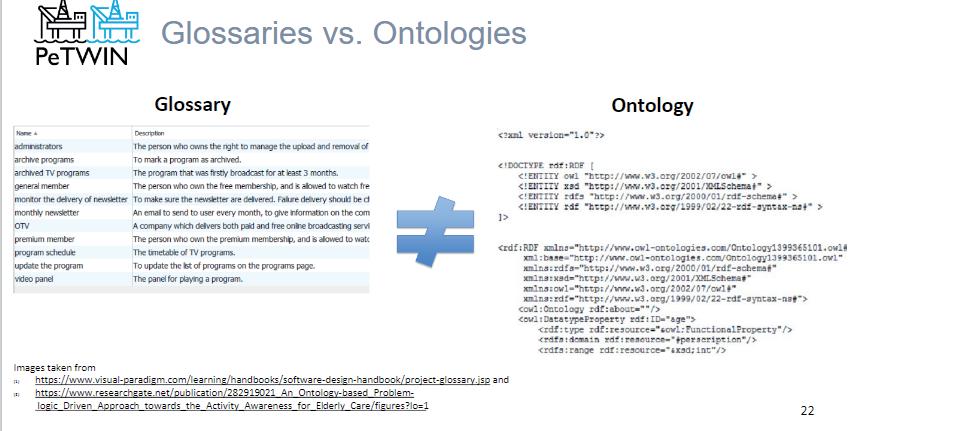
temperatura de um elemento, todos os acessos ao banco de dados vão referir-se de uma forma única àquele objeto e valor associado.
Então, essa unificação utiliza inglês? Sim e não.
O Professor Netto explica que, quando se desenvolve uma ontologia (vocabulário+significado), também se agrupam vários sinônimos, e se orienta a utilização dos dados com base no seu significado.
No PetTwin o foco é demonstrar aplicações que possam dar insights de melhorias e otimização – como um determinado poço vai desenvolver sua produção, por quantos anos, e a partir de qual época é preciso agir para otimizá-lo, e de que maneira. Mas, o projeto não é restrito a isso. Pode ser aplicado à manutenção, e o grupo de pesquisadores já está desenvolvendo uma aplicação, valendo-se do fato de que, para gerar aprendizado, é preciso volume de dados. Mas, como trabalhar com equipamentos com uma falha rara, uma taxa de falha pequena?
“Há dificuldade de aplicar algoritmos de aprendizado de máquina, quando não existe um histórico de base, mas, com o Gêmeo Digital, se pode simular comportamento de falhas e, a partir daí, ter massa de dados para rodar o algoritmo de IA, e fazer predição de falhas em equipamentos que têm baixo índice de falhas, mas alto risco. Por exemplo, pode-se aplicar no Gêmeo Digital de uma válvula subsea, que dura muitos anos sem uma falha sequer, mas que, se falhar, pode gerar derramamento de óleo. Então, através do Gêmeo Digital, se pode modelar o tempo, passando mais rápido que o real, fazendo com que as falhas apareçam no ambiente virtual, coletando esses dados, e colocando para rodar o algoritmo, e aí, então, fazer a predição para a válvula do mundo físico, a válvula real”, resume o professor Netto.
Assim, de maneira segura, se consegue gerar um conjunto de dados, que modelam um grande espaço de tempo, equivalente ao que ocorreria na realidade. Mas, os Gêmeos Digitais se sobrepõem aos já existentes gerenciadores de ativos comerciais?
“Não. Os gerenciadores fazem bem seu trabalho, mas suas bibliotecas estão separadas, às vezes isoladas, ou têm utilização apenas no seu próprio espectro de aplicação. A ideia do Gêmeo Digital é que o historiador que existe nesse sistema comercial seja uma de suas fontes de dados; um CLP seja outra fonte de dados; o sistema de manutenção outra fonte; tudo o que o pessoal fez durante o tempo de projeto, outra fonte. E o Gêmeo Digital busca reunir e prover acesso inequívoco para as aplicações. Então, sempre que se buscar a temperatura de um equipamento, através da unificação e da organização dos dados, independentemente do nome que ele tenha no historiador ou no ERP, o Gêmeo Digital vai saber exatamente o que está usando. Sua interface única proporciona a visão integral de todo o fluxo dos processos – causas e efeitos estão integrados, e são visíveis no Gêmeo Digital”, destaca o professor Netto.
O PetWin está rodando há 18 meses, mas ainda leva algum tempo para terminar. As interações entre os diversos pesquisadores acontecem em reuniões periódicas. Para o desenvolvimento das provas de conceito, protótipos e estudos de caso, a equipe recebe situações verdadeiras, e trabalha com dados reais, porque a ideia é de que, no final dos 42 meses, se tenham definições pertinentes da integração dos dados, que esteja pronta a
@Aveva
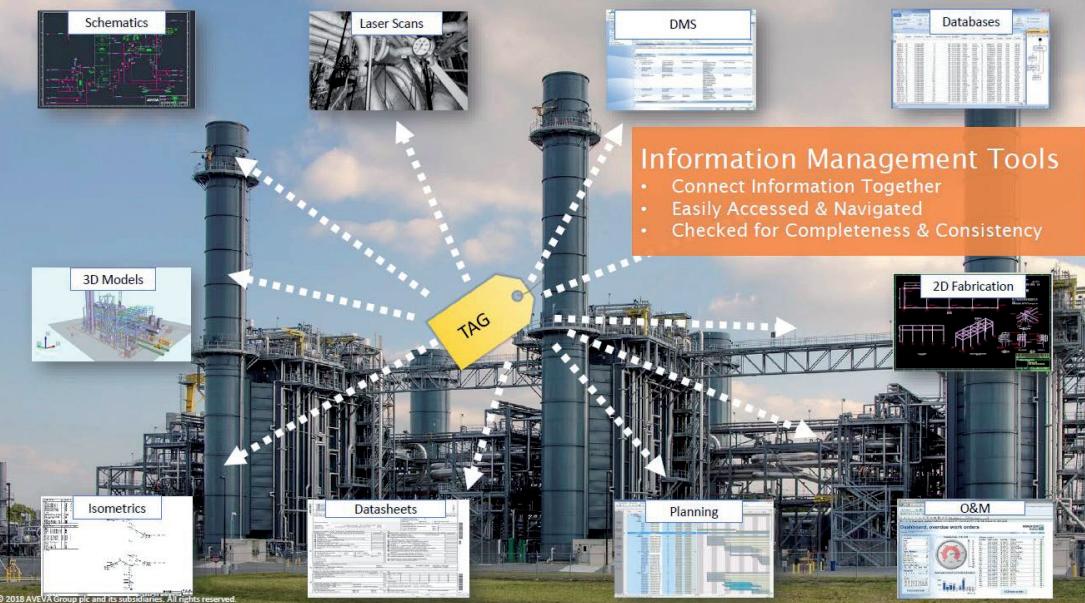

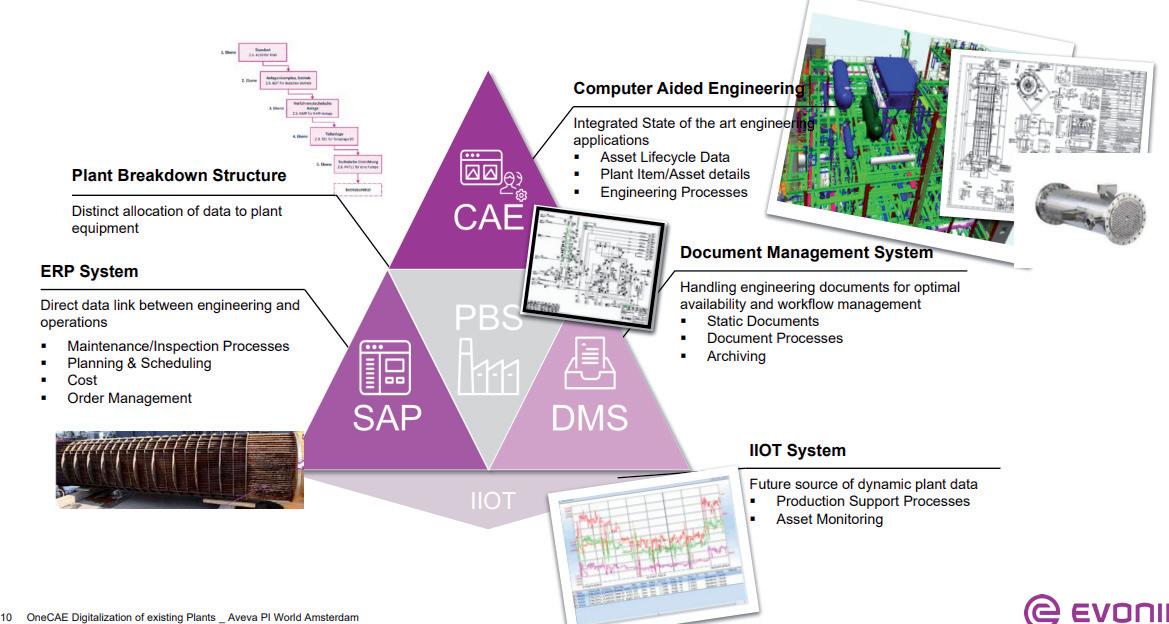
principal parte da ontologia relativa à produção, e protótipos que demonstrem a viabilidade de como desenvolver soluções a partir dele.
O grupo de pesquisadores já tem resultados bem interessantes da conceituação e aplicação do Gêmeo Digital. É bem aguardado o desenvolvimento de como fazer um Gêmeo Digital de uma planta brownfield – que vem sendo elaborado através das empresas parceiras e do professor especialista em modelagem.
Uma empresa que já iniciou o caminho para o desenvolvimento de um modelo de dados para seus ativos (equipamentos, instrumentação e pipelines) e operações é a Evonik. Esses modelos permitem um cenário independente do fornecedor de ferramentas de software. Um aspecto do modelo de dados dos ativos é que ele associa uma sequência de nomenclatura exclusiva, por exemplo, uma estrutura de quebra de planta, a um ativo específico. Uma planta inteira pode então ser mapeada e preenchida com atributos definidos pelo modelo de dados. De fato, outras fontes de dados, como sistemas de gerenciamento de documentos e modelos 3D, também podem ser vinculadas. Isso fornece dados contextualizados para os usuários, que é o valor que se busca nesses projetos.
O modelo de dados é a tecnologia central para um Gêmeo Digital, e um grande desafio para realmente utilizar a tecnologia é a cultura e as pessoas necessárias para modernizar a maneira de trabalhar.
A Evonik reconheceu o desafio adicional de implementar o Digital Twin em uma fábrica que já está em operação e um esforço conjunto está em andamento para criar roteiros específicos das plantas para a implementação de tecnologias digitais – o que vai levar tempo e consumir recursos significativos para implementar a mudança, mas a empresa está certa de que o desenvolvimento agregara valor ao negócio.
As equipes que estão trabalhando com o Gêmeo Digital na Evonik esperam realizar economias em várias frentes: na eficiência de engenharia para projetos de capital, o que é especialmente verdadeiro para otimizações de plantas existentes; na troca de dados com parceiros externos com base em padrões internacionais; na entrega de dados para produção no final de um projeto; no planejamento de manutenção mais rápido, com instruções passo a passo virtuais com os fornecedores; e outras.
O Professor Netto lembra que a necessidade de um especialista para fazer uso de produtos de prateleira, e mesmo de resultados de pesquisas, depende do momento em que se vai utilizar a solução, porque o Gêmeo Digital é aplicado a todo o ciclo de vida de um processo.
O que o mercado pode ter certeza hoje é de que o Brasil tem gente capacitada para atendê-lo. O INF/ UFGRS tem uma equipe com 8 bolsistas BCIT de graduação; 6 mestrandos propondo novos algoritmos; 5 doutorandos trabalhando na fronteira do conhecimento de arquitetura e modelo de dados, além de ontologia; 3 pós doutores, que já trabalharam na indústria em diversas áreas; 2 mestres para suporte. A equipe grande e multidisciplinar tem ainda 8 professores e muitos alunos da graduação, inseridos nos temas afetos ao projeto, que se tornam aptos para atuar nas áreas relacionadas.