
19 minute read
Um cenário de forte concorrência global e a transformação digital no mercado de Óleo e Gás
César Cassiolato VIVACE PROCESS INSTRUMENTS
Introdução
Com um cenário de forte concorrência global e a busca por melhorias nos processos industriais, estamos vendo um avanço exponencial de novas tecnologias aplicadas à Indústria 4.0.
Processos, fluxos de trabalho, a forma de gerir o desempenho, estão mudando drasticamente. As operações não podem mais funcionar em execução linear ou isolada das diversas áreas da indústria: o mundo, a cada dia, fica mais conectado.
A transformação digital em andamento traz novas tecnologias para apoiar o próximo salto de produtividade e performance na indústria, e envolverá a reinvenção de muitos setores ao redor do mundo, através da utilização de tecnologias de ponta.
Neste sentido, a aderência ao mundo digital tornase um fator decisivo para sobrevivência na competição. A 3ª revolução industrial, conhecida como a revolução técnico científica, foi onde tivemos um grande avanço em termos da eletrônica, principalmente nas décadas de 1970 e 1980 e, que possibilitaram a evolução das redes digitais, com sua consolidação nos anos 2000.
Com o advento da tecnologia digital, a convergência dos dados foi um catalisador para ganhos significativos para a automação e para a gestão industrial como um todo.
Tudo isso criou o caminho para que, em 2011, na Alemanha, se pudessem ter as primeiras conversas de idealização sobre a Indústria 4.0.
Vale lembrar que foram necessários mais de 240 anos, desde a criação da máquina à vapor de James Watt (1769), para ouvirmos, pela primeira vez se falar em Indústria 4.0 pela primeira vez, em 2011.
Já vemos vários segmentos industriais se preparando e se adaptando a esta transformação, deixando a tradicional estrutura de pirâmide hierárquica para a arquitetura estruturada de rede.
Com a Indústria 3.0, os sistemas de negócios foram integrados de forma linear, do sensor ao software empresarial. Embora essa arquitetura funcione, é mais complexa de implementar, pois, todas as informações precisariam fluir por todos os níveis. Também é mais difícil de se manter, pois, requer diferentes conjuntos de habilidades para gerenciar cada camada.
O setor de Óleo e Gás, por sua importância na cadeia de fornecimento, vem tornando-se cada vez mais digital. A transformação digital neste setor vem trazendo uma série de benefícios: a conectividade entre equipamentos, o uso de drones, a inteligência artificial, entre outras tecnologias, que propiciam muitos ganhos em termos de produtividade, eficiência e segurança.
A digitalização e o monitoramento remoto na indústria de Óleo e Gás offshore tem sido uma inovação com resultados operacionais interessantes.
Figura 1 - Estrutura de pirâmide hierárquica x a arquitetura estruturada de rede
Figura 2 - O MQTT cria uma arquitetura segura, altamente escalável para aplicativos industriais e IoT.
A 4ª Revolução Industrial está aqui e remodelando o chão-de-fábrica por meio da transformação digital. Acesso a dados em tempo real, computação em nuvem e aprendizado de máquina são as forças motrizes por trás da Indústria 4.0. Outro ponto fundamental da transformação digital, e como alcançá-la, é arquitetura chamada Unified Namespace (UNS). Simplificando, um UNS é um repositório centralizado de dados estrutura-
dos, no qual qualquer aplicativo ou dispositivo pode assinar ou publicar dados. A arquitetura mais comum para um UNS é construí-lo em um broker MQTT (Message Queuing Telemetry Transport). Um broker MQTT é uma entidade intermediária, que recebe mensagens publicadas por clientes, filtra as mensagens e as distribui aos assinantes. As razões pelas quais a maioria dos fabricantes usa o MQTT como o UNS são porque ele é leve, com payload de mensagens com tamanho máximo de 260 MB, rápido, uma arquitetura aberta, acessível a todos os consumidores, possui relatórios por exceção, apenas as alterações são relatadas (publicadas/assinadas), e é orientado pela borda (Edge).
A transformação digital e o mercado de automação de processos e instrumentação
Espera-se que o tamanho do mercado global de automação e instrumentação de processos ultrapasse os US$ 82 bi, em 2022, com um CAGR de 5,5%. Já o Mercado Global de Automação deve ultrapassar US $330 bi, com um CAGR de 9%.



Figura 3 – A transformação digital no mercado de automação de processos
Tivemos um crescimento enorme de aplicativos e ferramentas de software, aliado às novas plataformas de hardware, com CPUs poderosas (ARMS, Low Power etc.), o que vem garantindo uma maior adoção de produtos de instrumentação e automação de processos em todos os setores.
O mercado de Ethernet industrial deve ultrapassar os US$ 50 bi, em 2022, e cresce a mais de 15% ao ano, principalmente agora com o advento da Indústria 4.0, e onde há a necessidade de uma rede de comunicação eficiente que conecte todos os diversos níveis e componentes de forma escalável, flexível e segura.
O mercado de IoT vem crescendo a uma taxa de quase 20% ao ano, e deve ultrapassar US$ 500 bi, em 2022. A Internet das Coisas (IoT) vem como um agente facilitador da Indústria 4.0, permitindo a conexão e comunicação de vários componentes e em vários níveis, incluindo os sistemas ciberfísicos, sensores, atuadores, máquinas, equipamentos, pessoas, etc. e, mais do que isto, permite a interação entre as partes envolvidas, criando uma nova camada de dados, e tendo informações em tempo real praticamente. Com a possibilidade de dados na nuvem, ganhou-se a flexibilidade tão esperada de acessar as informações em qualquer lugar do mundo, e observar como está o comportamento de seus equipamentos. Quando se expande a conectividade na indústria, é possível observar toda a cadeia movida a dados. É esperado um novo patamar na questão de gerenciamento de ativos com o IoT.
Mas, neste mercado de Iot, alguns desafios ainda são enfrentados em relação a segurança, redes, software e as novas e complexas dependências. Os avanços digitais, se, por um lado, trazem melhorias, agilidades, performance, etc., por outro, criam novas formas de vulnerabilidades, que são exploradas maliciosamente. Vale lembrar que uma maioria dos sistemas industriais não foram projetados para conexão à internet, nem mesmo com a preocupação com a segurança, mesmo diante das mudanças para redes abertas. A IoT é uma tecnologia emergente ainda e, apesar do número cada vez maior de empresas lançando produtos no mercado, faltam padrões e mesmo ferramentas de softwares de segurança em IoT adequados para monitorar os dispositivos legados.
Figura 4 – Os desafios do Iot
Nesse cenário, ainda, onde vemos a aplicação da inteligência artificial e aprendizagem de máquina, a consideração dos fatores humanos torna-se importante e necessária para garantir a segurança. A heterogeneidade do ecossistema apresenta alguns desafios multiníveis e dinâmicos, que precisam ser abordados.
Outro ponto de destaque neste movimento de evolução digital é a utilização dos Gêmeos Digitais (Digital Twins), que utilizam representações digitais das instalações operacionais, por exemplo, no setor de Óleo e Gás, com representações de uma plataforma, reserva-
tórios de petróleo, sistema submarino, equipamentos críticos, refinarias, etc. A tecnologia de Gêmeos Digitais simula cenários e antecipa soluções. Ela trabalha com dados reais da planta em produção e cria uma versão digital, orientando com mais precisão e segurança como os produtos serão fabricados, sem interromper os processos. Tem potencial para contribuir para a redução de custos operacionais, e o aumento da eficiência e segurança nas nossas operações dos processos e relações entre eles.
Por exemplo, no mercado de Óleo e Gás, existem uma série de aplicações, como por exemplo, monitorar em tempo real o desempenho operacional da planta ou áreas específicas, além de orientar a tomada de decisões em diferentes cenários. É a tecnologia auxiliando a otimização do cumprimento do plano de produção, com a máxima rentabilidade.
Sem contar ainda com uso da inteligência artificial e aprendizagem de máquina com modelos mais cada vez mais precisos, onde se consegue garantir a operação no seu ponto de maior resultado econômico. Recursos poderosos de integração de aspectos de projeto e de operação, simulação e predição. Além disso, tem-se o acompanhamento em tempo real, aumentando a possibilidade de identificação de desvios, e a necessidade de ajustes e correções com maior rapidez e eficiência nos processos.
A capacidade dos Gêmeos Digitais de manusear e realizar operações com um volume de dados considerado é outra vantagem na possibilidade da simulação rápida e avançada.
Além disso, a convergência da TI e TO, tecnologias de Big Data, Iot e o advento do 5G impulsionarão o crescimento do mercado digital na área de processos industriais: alta velocidade, largura de banda e baixa latência. É o momento da exploração do potencial da tecnologia digital, de forma segura, confiável, eficiente, robusta, com a mais alta qualidade, maior disponibilidade e proporcionando benefícios na otimização dos processos e controles industriais.
E ainda, os equipamentos de campo envolvidos em medições e controles poderão manusear uma grande quantidade de dados, com grande facilidade e tempo de resposta, poderão permitir atualizações de firmware e funcionalidades de forma automática, poderão armazenar manuais e mesmo arquivos de interfaces, com ferramentas de configuração como DD/EDDL/FDI (Intelligent Device Management (IDM) – carregará automaticamente os arquivos, quando o equipamento estiver conectado, e desta forma evitará erros de versões e poderá sempre estar atualizado). Fácil configuração através de webservers. Novos equipamentos, sensores e novas funcionalidades serão desenvolvidas. Com mais flexibilidade com consumos de energia nos equipamentos, permitindo interfaces mais poderosas, do tipo IHM.
Mas, e o parque instalado? Vai ser descartado?
Antes de respondermos a estas questões, é importante ter em mente que uma grande parte da indústria de processos do Brasil ainda está no estágio mais simples de automação. Mesmo daqui há 10 anos, pode ser que uma boa parte ainda não terá seus processos com as vantagens da indústria 3.0.
Certo é que, em novas fábricas, estas têm uma maior probabilidade de serem projetadas e construídas, pensando em automatizar ao máximo seus processos. E, existe, hoje, uma jornada de introdução a essa nova realidade, processo muito particular a cada companhia, e com etapas diferentes de maturidade em direção à indústria 4.0.
Esta transição para o mundo digital 4.0 não deve ser encarada como um projeto, e sim como estratégia pelas empresas, e mais do que isso, não exige necessariamente o descarte completo do antigo em favor do novo. O importante é analisar o mercado, o ambiente de seus negócios, de forma a ganhar pontos relevantes para produzir, gerar e gerir alinhados com a estratégia do negócio, e que se possa garantir a competividade. Esta tem sido a estratégia das empresas de Óleo e Gás.
Certamente, em plantas críticas e com grandes volumes de negócios, este processo deve ser cauteloso. Pensando no parque instalado com tecnologia já desatualizada, e lembrando que a Internet não foi desenvolvida inicialmente com foco na segurança em mente, e sim, na velocidade e disponibilidade, e que além disso, muitos sistemas industriais já existem há muito tempo, como uma colcha de retalhos de sistemas de controles e redes novas e antigas, vários equipamentos, e que foram instalados ao longo do tempo, fica clara a vulnerabilidade em questão, em todo este legado. Essa interconectividade se estende além dos sistemas operacionais e das redes de controle industrial para as redes de negócios, e viceversa. Consequentemente, existem, potencialmente, milhares de pessoas com acesso direto e indireto a sistemas críticos e, literalmente, dezenas de milhares de maneiras de invasores atacarem esses sistemas. Vale lembrar ainda que nas últimas décadas, as redes de TI (tecnologia da informação) e de automação convergiram entre si, ou seja, integraram-se uma à outra, na chamada arquitetura integrada. Isso estabeleceu condições favoráveis a ataques cibernéticos, já que as redes de automação têm pouca “maturidade”, em relação aos controles de segurança cibernética.
Outro fato que merece destacar é que, em redes in-
dustriais, nem sempre se estabelece controle de segurança de borda, o que já garante uma certa proteção. A zona industrial DMZ tem sido utilizada. Uma Industry DMZ (zona industrial desmilitarizada) é uma camada de segurança de rede adicional entre as redes de TI e Industrial OT (Operational Technology). O IDMZ fornece uma zona de buffer entre zonas de segurança não confiáveis (por exemplo, TI) e zonas de segurança confiáveis (por exemplo, Industrial) para intermediar as conexões, para que nenhuma comunicação de rede direta seja permitida entre zonas de segurança não confiáveis e confiáveis. A infraestrutura IDMZ consiste em vários dispositivos de rede, incluindo, entre outros: dispositivos de segurança/firewalls, servidores IDMZ, servidor de rede virtual privada (VPN), switches e roteadores. Além disso, podemos ainda citar algumas regras e padrões que merecem atenção: • Segurança de ponta a ponta, edge devices com
TPM (Trusted Platform Module) e protocolos seguros (MQTT, AMQP); • Hardware de computador padronizado com um plano de ciclo de vida; • Sistema operacional padrão com correções rotineiras; • Ferramentas de software comercial padronizadas e homologadas; • Solução de gestão de acesso e identidade suportada para usuários e ativos; • Meios suportados e atualizados para um ativo identificar e defender-se de um ataque; • Segurança de rede, Plataformas de firewall, Tecnologias de servidor virtual; • Fortalecimento do sistema; • Segurança de aplicativos; • Segmentações com níveis de acessos e autenticações; • Funcionalidade e segurança de domínio; • Métodos de transferência de arquivos e dados protegidos; • Métodos de acesso remoto protegidos; • Uso de equipamentos Iot padronizados e homologados; • Uso de normas ISA95 e IEC62443.
Na questão deste processo de transição para a transformação digital e o parque instalado, deve-se atentar que nem todas as tecnologias incluídas na Indústria 4.0 devem ser aplicadas e, certamente, vai depender de cada empresa, seu ambiente de negócio, e o nível de competividade que sua estratégia possui. O fato é que existem inúmeras possibilidades de uso dessas tecnologias para a transformação dos negócios em cada setor industrial. E mais do que isto, o uso destas tecnologias, além dos benefícios de performance como um todo, pode estabelecer novos patamares nas áreas de serviços e nas relações entre empresas.
Industria 4.0 e a Manutenção Inteligente
Na cadeia de valores da indústria, a manutenção tem um papel fundamental, que é manter o maior grau de disponibilidade produtiva com segurança, e permitir o uso dos ativos em todo o seu ciclo de vida, no menor custo operacional.
A manutenção preditiva, no contexto da transformação digital, é uma abordagem de monitoramento técnico proativo estabelecida, e que usa recursos avançados de análise de dados, baseada em aprendizado de máquina e inteligência artificial para monitorar dados de equipamentos e ativos. Os modelos de aprendizado de máquina são treinados usando dados históricos para detectar qualquer comportamento anormal que pode indicar sinais precoces de falha. Ao detectar um problema precocemente, ações preventivas oportunas podem ser tomadas, e possíveis adiamentos não programados ou paradas não planejadas podem ser evitadas.
Figura 5 – Equipamentos desenvolvidos com Inteligência Artificial
Com as tecnologias da Indústria 4.0, por exemplo, o uso de Iot, podem-se ter facilidades e benefícios na gestão dos ativos que, somados à Inteligência Artificial, podem levar a mais assertividades na tomada de decisões, em relação à manutenção. Os sistemas aprendem baseados na coleta de dados dos ativos da planta. Os dados são enviados para a Nuvem, e com uso de algoritmos de predição baseados em Mineração de Dados e/ou Aprendizado de Máquina, vão gerar as metodologias de aprendizagem que permitirão maior eficiência, maior disponibilidade, paradas programadas, menores custos de intervenções, ou seja, a manutenção inteligente.
Tradicionalmente e de forma geral na indústria, cuidar de equipamentos e ativos em uma planta tem contado com a substituição de equipamentos ou partes e peças, após um tempo definido, e esta abordagem às vezes significa que esta substituição é feita sem necessidade, e em momento de impacto na produção. Outra estratégia é a manutenção corretiva, onde se espera falhar para tomar a ação, e aí, sem dúvidas, o impacto pode ser grande.
Figura 6 – Posicionador Inteligente x Diagnósticos Avançados
Na Figura 6, temos um posicionador VIVACE, o VVP10, que tem diversas funcionalidades e diagnósticos avançados. Os dados brutos alimentam a análise preditiva incorporada ao posicionador de válvula. Como os sensores são integrados ao posicionador, a atualização dos dados pode acompanhar a dinâmica rápida dos movimentos da válvula de controle. Esses sensores monitoram continuamente o controle de movimento, as mudanças de pressão, condição da válvula e atuador, condição do posicionador e condição do ambiente operacional. Isso significa que o desempenho da válvula de controle pode ser mantido em níveis ideais, monitorando continuamente e tomando as ações preventivas necessárias. Os diagnósticos são exibidos na forma de contadores de eventos, gráficos específicos e tempos de operação, oferecendo limites, configuráveis pelo usuário, para geração de alarmes que ajudam no gerenciamento de ativos e redução do custo total de propriedade (total cost of ownership), reduzindo assim os custos gerais com manutenção.
No mercado de Óleo e Gás, as grandes companhias vêm cada vez mais em busca de metodologias e facilidades que possam facilitar a manutenção. Neste viés, podemos citar a Shell, que utiliza a manutenção preditiva em seus ativos para melhorar sua confiabilidade e, portanto, sua eficiência. Um exemplo são modelos de aprendizado de máquina para monitorar válvulas de controle, com a intenção de identificar tendências de desgastes e falhas, que possam causar impacto com a interface com o fluido do processo. Com o tempo, as partes mecânicas da válvula de controle, como o plugue, a sede, a gaxeta, podem degradar e causar vazamentos, ou aumentar a variabilidade do processo.
A Shell, através do uso da inteligência artificial, detecta situações iniciais nas válvulas de controles e, desta forma, pode ter condições de fazer a manutenção inteligente.
Cientistas de Dados da Shell desenvolveram modelos de aprendizagem de máquinas que podem analisar milhares de dados simultaneamente e, assim, permitir que seus engenheiros possam extrair insights desses dados. Usando dados históricos, estes modelos são treinados para reconhecer anomalias nos conjuntos de dados. Os alertas são acionados quando pequenas anomalias são detectadas, para que uma investigação mais aprofundada e mais assertiva com a manutenção proativa possa ocorrer. Estes modelos possuem alta confiabilidade na identificação de falhas.
As análises de manutenções preditivas das válvulas de controle pela Shell: – Melhoram os controles, diminuindo a variabilidades dos processos; – Ativam a detecção precoce de falhas, antecipando possíveis reais problemas; – Reduzem custos de manutenção, ao fornecer informações mais assertivas e confiáveis sobre a real necessidade de intervenção; – Melhoram a produtividade, disponibilidade, desempenho de forma geral, com segurança operacional.
E, o mais interessante para o mercado é que estas soluções de manutenção preditiva foram recentemente liberadas para as operadoras da indústria de energia no mercado aberto, via Open AI Energy Initiative, que foi lançada pela Shell e parceiros Baker Hughes, C3 AI e Microsoft. É um ecossistema aberto de soluções baseadas em inteligência especificamente para a indústrias de energia e processos.
Ao trazer suas soluções para o mercado, a Shell busca incentivar que outras empresas façam o mesmo, e assim se acelere a adoção da tecnologia de inteligência artificial em toda a indústria. A Iniciativa da Open AI Energy fornece uma estrutura aberta para a construção de soluções interoperáveis, como modelos baseados em inteligência e física, bibliotecas de diagnósticos e serviços.
A Shell planeja acelerar seu programa de manutenção preditiva também explorando casos de uso adicionais no C3 AI Suite, incluindo integridade de ativos, otimização de produção, otimização de sistema, segurança e sustentabilidade.
A manutenção preditiva com inteligência artificial e aprendizagem de máquina permite que a Shell identifique a degradação e as falhas dos equipamentos antes que elas aconteçam, permitindo que os operadores tomem medidas proativas, e evitem paradas não planejadas dispendiosas, interrupções de produção e riscos potenciais ao meio ambiente e à segurança humana. O equipamento monitorado inclui válvulas de controle, bombas, compressores e outros componentes críticos.
Como parte do programa de manutenção preditiva
da Shell, a equipe do projeto modelou o posicionamento esperado da válvula, com base nas condições do processo, e então, começou a monitorar suas posições reais e previstas. Subsequentemente, a manutenção preditiva para válvulas de controle, através da ferramenta, detectou um desvio entre a posição real da válvula e sua posição prevista, e disparou um alerta. Na Figura 7, a linha azul mostra a posição real da válvula obtida do controle, e a linha verde mostra a predição. As caixas verdes mostram quando ocorreram os desvios.
Figura 7 – Posições x Anomalias (Fonte: “THE SHELL JOURNEY TOWARDS Global Predictive Maintenance”)
A linha vermelha na Figura 8 mostra a saída do controlador. A linha verde mostra a do feedback de posição da válvula de controle, e a linha azul mostra a variável de processo. A variável de processo se manteve linear, em relação ao feedback da posição da válvula. Em resposta à saída do controlador, foi tentando trazer a variável do processo de volta ao valor definido. Consequentemente, a análise deste monitoramento pelo usuário recomendou uma investigação sobre a saúde da válvula de controle. A investigação revelou que a válvula estava oscilando de 5% a 10%, até seis vezes em menos de um minuto, e então o movimento quase parava e começava de novo. Isso se repetia continuamente. Como resultado, a substituição ou reparo da válvula, e até mesmo do posicionador, está sendo considerada. Essa detecção precoce de um problema potencial fez com que a manutenção pudesse ser planejada no melhor momento, antes da falha causar um impacto maior.
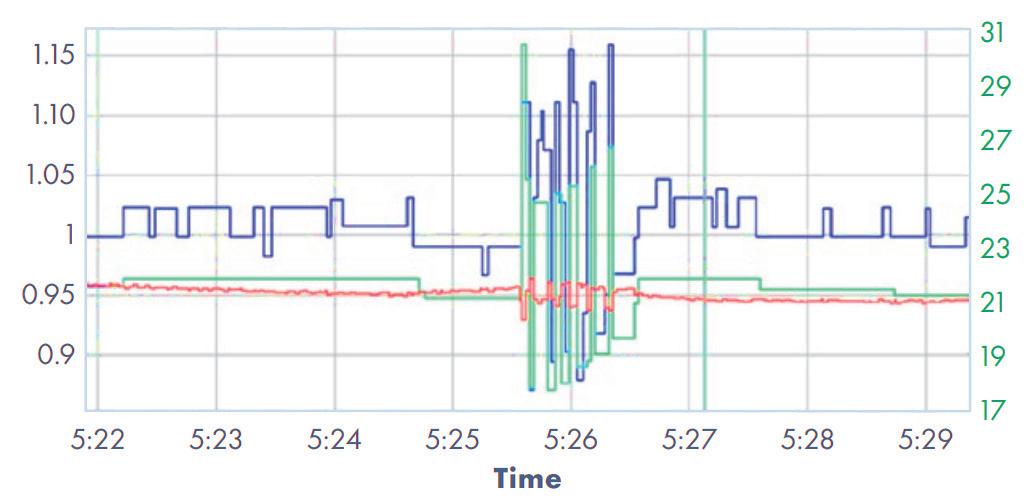
Figura 8 – Dados do Posicionador de Válvulas (Fonte: “THE SHELL JOURNEY TOWARDS Global Predictive Maintenance”)
As vantagens são inúmeras, e podem reduzir significativamente os custos, eliminando a necessidade de tempo de inatividade planejado em muitos casos.
Ao prevenir uma falha com um algoritmo de aprendizado, pode-se ter a continuidade de funcionamento, sem interrupções desnecessárias, em muitos casos.
A manutenção preditiva também leva a uma vida útil remanescente mais longa dos equipamentos, uma vez que danos secundários são evitados, enquanto uma força de trabalho menor é necessária para realizar os procedimentos de manutenção.
Com a inteligência artificial e aprendizado de máquina, aumenta-se a segurança operacional, e se podem otimizar ainda mais os processos com base em dados em tempo real.
Conclusão
Estamos passando por uma transformação digital que parece ser somente o início de uma revolução. Este novo mundo permite a exploração do potencial da tecnologia digital em vários segmentos e, principalmente, no mercado de Óleo e Gás, de forma segura, confiável, eficiente, robusta, com a mais alta qualidade, maior disponibilidade, e proporcionando benefícios na otimização dos processos e controles industriais.
A tecnologia embarcada nos produtos que atendem a Indústria 4.0 permite o próximo passo na melhoria de performance da instrumentação com alta confiabilidade, e rumo à excelência operacional: habilidades preditivas e cálculos complexos que proporcionam melhorias significativas de performance, e facilitam a manutenção preditiva.
São habilidades built-in, e onde os equipamentos aprendem a partir de dados, sem a necessidade de programação explícita do usuário, e onde permitem detecção segura, automatizada e autônoma no tratamento de dados dos sensores, de anomalias na gestão de ativos, entre outros.
Vários equipamentos possuem algoritmos para facilitar a manutenção preditiva, antecipando falhas, e criando condições aprendidas quando em operação, para maximizar o tempo de operação, aumentando a disponibilidade até a parada programada.
De maneira simples, utilizar inteligência artificial nos equipamentos de campo leva a melhores resultados: custos, otimização de tempo, menos falhas, paradas não programadas e manutenções preventivas.
Referências
– Material Indústria 4.0 – César Cassiolato – https://www.vivaceinstruments.com.br/pt/neuron, acessado em 26/11/2022 – https://nossaenergia.petrobras.com.br/, acessado em 26/11/2022 – Velthuis Klein, Nikki, “THE SHELL JOURNEY TO-
WARDS global predictive maintenance” – www.shell.com, acessado em 26/11/2022