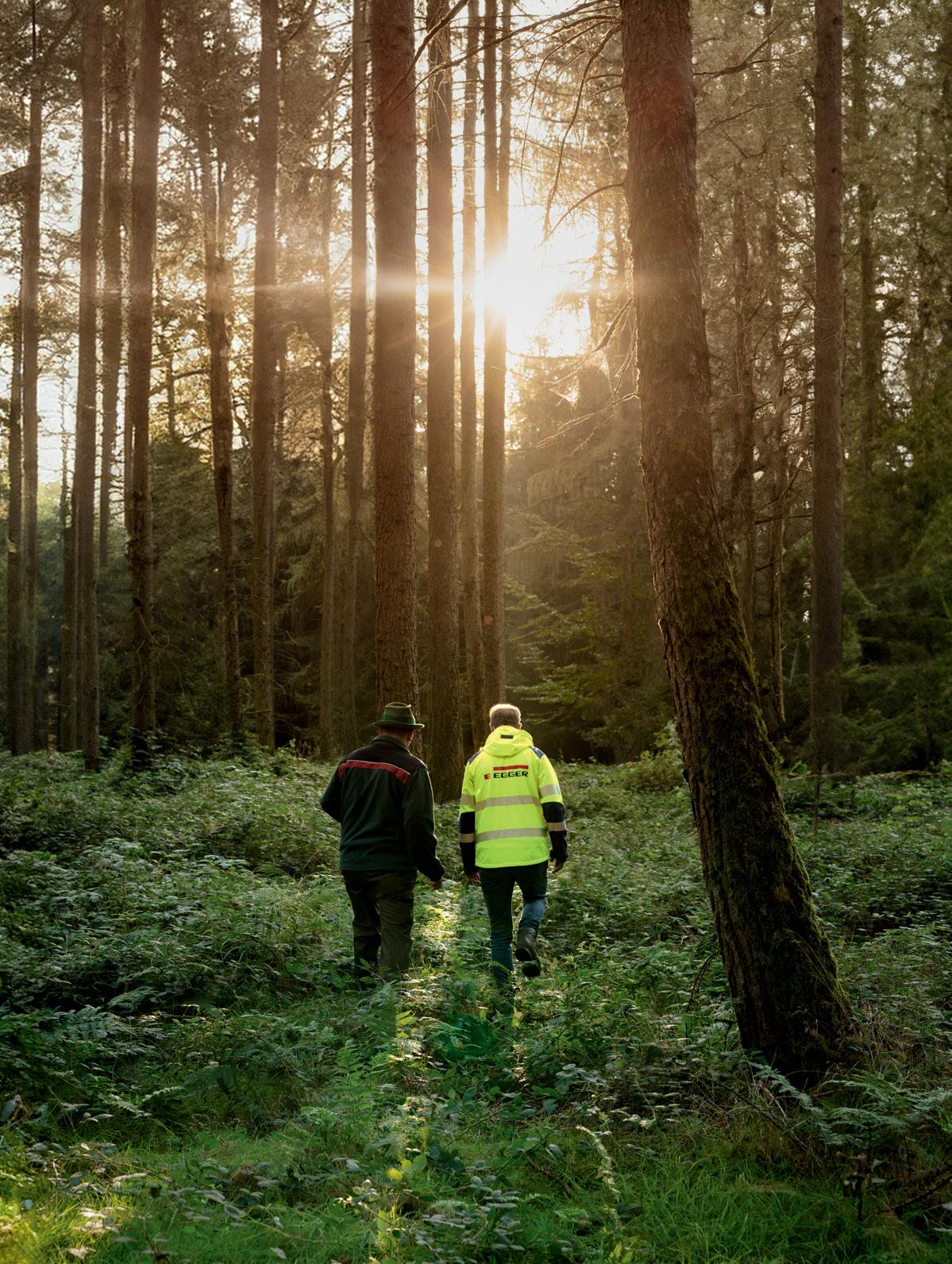
OUR CONTRIBUTION TO PROTECT AND PRESERVE THE FUTURE
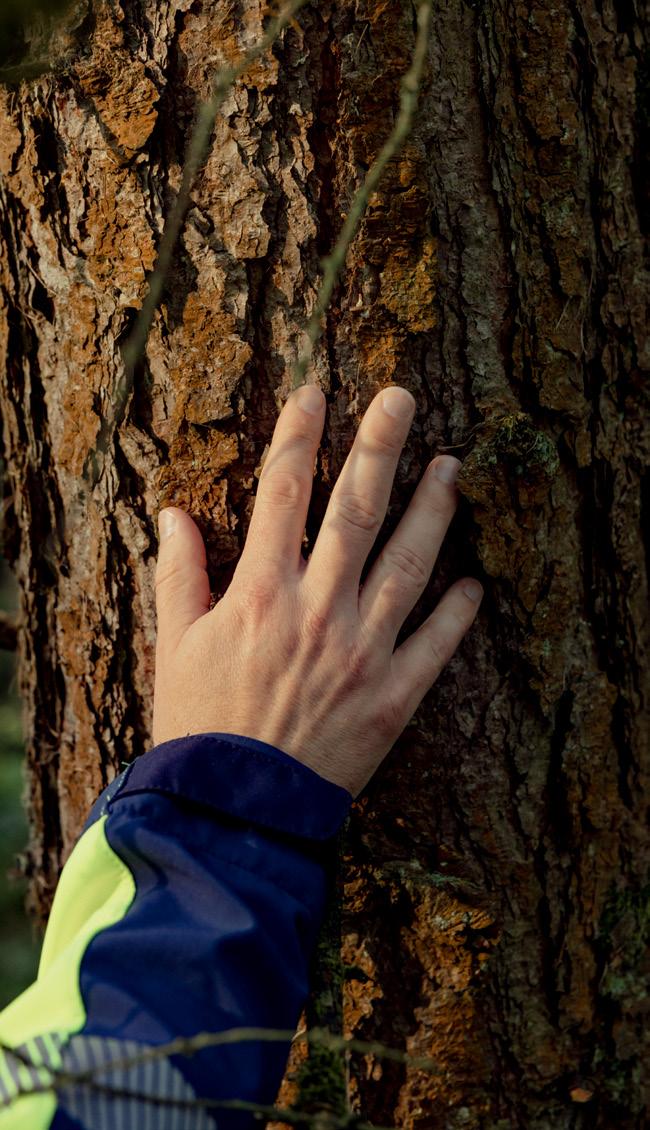
OUR CONTRIBUTION TO PROTECT AND PRESERVE THE FUTURE
Dear Readers,
We are proud to present the first issue of our sustainability journal “VALUABLE”. The title shows what we at the EGGER Group are really all about: We use wood as a valuable resource, in the best possible way and aim to improve the way we do this a little bit every day.
We would therefore like to invite you along on our sustainability journey, a journey which has been especially meaningful for us over the past year. A key milestone was our clear commitment to Net Zero 2050. We are determined to achieve this major climate action goal and are prepared to make significant investments to do so, as can currently be seen in our power plant project in St. Johann in Tirol (Austria).
Another key focal area is sustainable forestry. We explain why a sustainably managed forest is the best climate protector and how the sustainable wood cascade makes an important contribution in this regard. We would also like to show you how we give many lives to wood as a valuable resource and explain how integrated plants make a contribution to the circular economy.
As an employer, it is important to us to provide good jobs. We put importance on workplace safety and consider our employees to be the most important component of our family business. Worldwide, more than 11,000 people work for EGGER, they are therefore an
integral part of the green industry. This also means that we consistently use digitalisation and automation to save energy, to optimise processes and make them safer.
We are proud that all of these efforts enable us to provide our customers with in-depth insights into the environmental performance of our products. In this issue, we explain what a PCF is and why everything is focused on it, we also explain how we will become even more transparent and therefore even better in the future.
With this in mind, we hope that our sustainability journal will provide you with some VALUABLE insights. We know that sustainability is an essential part of our corporate responsibility and look forward to continuing on this path together with you.
EGGER Group Management
Sustainable, of course. Innovative since 1961.
Sustainable business management lies at the heart of the EGGER Group’s corporate DNA. And this has been the case ever since the company was founded in 1961, because even then, wood was far too valuable for Fritz Egger Sr. to simply throw it away. This family company has made a clear commitment to sustainable business management, geared towards future generations.
Supporting goals for a better future
Excellent sustainability performance Prime status in the ISS ESG rating Gold medal from EcoVadis
The EGGER Group is a leading international manufacturer of wood-based materials with more than 11,000 employees and 22 production plants worldwide. EGGER is a full-range supplier for furniture construction and interior design, for structural timber construction and for wood-based floorings, making it a reliable partner for the furniture industry, the wood and flooring trade and DIY
stores. In the 2023/2024 financial year, the EGGER Group generated sales of around 4.13 billion euros and produced 10.4 million m³ of wood-based materials and timber.
Would you like to find out more? The EGGER Group’s Financial and Sustainability Report for the 2023/2024 financial year is available online: to.egger.link/sustainability
7.1 MILLION
EGGER products are climate-friendly and have stored 7.1 million tonnes of CO₂e in the past year.
72 %
of all EGGER products are recyclable, i.e. they are suitable for material recycling after use.
At EGGER the experience of the employees is highly valued – team members have, on average, been working for the company for more than 10 years.
EGGER has established its own apprenticeship programmes in 20 of its production sites. There are currently 476 young people in training.
86 % of all the materials used in the products are made from renewable raw materials.
65 % of the wood used in the wood-based materials comes from by-products or recycling.
69 % of the energy used at EGGER comes from renewable sources.
EVERY PRODUCT LEAVES ITS MARK ON THE CLIMATE. EGGER DISCLOSES THE ENVIRONMENTAL IMPACT ASSESSMENTS OF ITS PRODUCTS AND USES THE DATA FOR CONTINUOUS IMPROVEMENT.
The Product Carbon Footprint (PCF) shows the total greenhouse gas emissions generated during the manufacture of a product and in its supply chain, and is therefore the key climate action indicator. On the path to Net Zero, the PCF from fossil fuel use in particular must be reduced to 0. The PCF is of interest to customers so that they are aware of the carbon footprint of the products they buy and can use it for their own climate strategy. This will be even more straightforward in the future – a pilot project to achieve semi-automated calculation of PCFs per product and plant is currently underway at the Unterradlberg plant (Austria), for even more precise data at the touch of a button.
Center Parcs UK welcomes over 2 million guests to its holiday villages and lodges in its six substantial forest sites every year. It is, therefore, only natural that the hospitality business also applies sustainability criteria to its furniture, as Jerome Baddley, Center Parcs Director of Sustainability, explains: “While quality and price are of course key, wood certifications, recycled content, product carbon intensity, UK sourcing, zero deforestation risk and credentials on the protection of biodiversity are especially important to us.
EGGER Eurodekor Faced Chipboard demonstrates that strong environmental performance does not necessarily mean any offset in terms of higher costs or lower quality. And as a bonus, some of the recycled content contained in EGGER’s boards even comes from our own wood waste!” Transparency is particularly important to Baddley, who carried out a due diligence process at EGGER in Hexham (UK): “The evidence supplied by EGGER was invaluable. It allowed us to establish that the wider environmental and ecological footprint of the timber products that we use reflects the Center Parcs ethos of careful environmental custodianship.”
Here too, the decisive criteria is the product carbon footprint. Binding agents and glues bind wood chips in products such as chipboard. Conventional binding agents are derived from fossil fuels. The goal is therefore to replace them with bio-based binding agents. The challenge here is that although bio-based binding agents are made from renewable raw materials, they usually result in a higher PCF from fossil fuel use during their production than conventional glues. This is often because at this stage, and in most cases their production requires a high input of fossil fuel energy. EGGER is therefore constantly examining alternatives, but will only switch to an alternative, bio-based binding agent if the carbon footprint from fossil fuel used in the binding agents own production is indeed lower than that of conventional binding agents. A first step in this direction will be to use mass-balanced binding agents made from biological waste. EGGER already offers these mass-balanced binders for chipboard products.
Find out more: to.egger.link/epd-chipboard-bmb
EGGER is committed to product transparency through independently verified environmental product declarations. Veronika Auer, product sustainability expert at EGGER, provides an insight into the significance and publication of these documents.
PATRICK MORDA, PHOTOS: RODERICK AICHINGER
Is EGGER unusually transparent in regard to its products?
Ms Auer, what does the term product transparency mean and what is EGGER’s understanding of this concept?
For us, product transparency means that the environmental impact of our products is fully and openly disclosed. This includes providing detailed information about raw materials, production and the associated environmental impact. We want to give customers and other stakeholders a clear and comprehensive overview of the environmental footprint of our products.
Why is this so important these days?
Our customers have become much more aware of environmental and sustainability issues. They want to make sure that the products they buy are environmentally friendly and uphold sustainable practices. Transparency helps them to make informed decisions. Our approach at EGGER, to embrace comprehensive and verified product transparency, gives customers assurance that the information they are given is correct.
Yes, you could say that. We provide detailed environmental product declarations (EPDs). These are drawn up in accordance with a defined standard and verified by independent institutes such as the Institut für Bauen und Umwelt (IBU) (Institute for Building and the Environment). But EGGER’s transparency goes even further. It covers the entire production process. On request, we even offer customers the opportunity to take a tour of our production facilities and gain an insight into our manufacturing processes. This level of openness and the strict verification by independent third parties set EGGER apart from many of its competitors.
What information do these EPDs contain?
An Environmental Product Declaration is a standardised document that presents the environmental impact of a product over its entire life cycle. It contains detailed information on the use of raw materials, energy consumption, emissions, water consumption and other environmental indicators. This data is provided in a transparent and clear format, which makes it possible to assess and compare the environmental impact of different products.
What role do EPDs play in EGGER’s sustainability strategy?
They play a key role. This is because the EPDs not only serve to document and communicate the environmental performance of our products, but also facilitate the continuous improvement of this performance. This detailed analysis and assessment of environmental impact allows us to take targeted measures to optimise the sustainability of our products.
“FOR US, PRODUCT TRANSPARENCY MEANS THAT THE ENVIRONMENTAL IMPACT OF OUR PRODUCTS IS
VERONIKA AUER
How is an EPD created?
An EPD is drawn up in several steps. Firstly, all relevant data along the entire production process is recorded, including the use of raw materials, energy and water and the resulting emissions. This data is then processed by modelling software that carries out a life cycle analysis (LCA). The LCA shows the impact of the product in regard to various environmental parameters, such as its contribution to global warming. The EPD is then independently verified. This process can take up to a year and requires close co-operation between various departments within the company.
The product carbon footprint from fossil fuel use is also a key indicator in this context. Why is this sustainability factor so important?
The product carbon footprint (PCF) from fossil fuel use measures the amount of fossil fuel
-13.8
kg CO₂e/m2 is the total GWP of an EGGER Eurodekor Faced Chipboard
emissions generated by the raw materials, production, transport, use and disposal of a product. This indicator is a key sustainability factor because it quantifies the direct impact of a product on global warming. Reducing the product carbon footprint from fossil fuel use is key to achieving global climate targets and minimising a company’s ecological footprint. For us, it is crucial to achieving our ambitious goal of Net Zero by 2050.
Among
Could you give us some examples of EGGER products for which EPDs are available?
The EPDs cover various types of product – the most important ones for us and our customers are chipboard, MDF boards, OSB boards and DHF boards. Overall, 85 % of all products by sales have an externally verified environmental label, an environmental declaration or an EPD.
What do you think is the most important information in the EPDs?
First of all, the total Global Warming Potential (GWP). This measures the amount of greenhouse gas emissions caused by the product in kilograms of CO₂e per square metre or per cubic metre. In addition to the PCF from fossil fuel use, the total GWP also
“THE EPDS NOT ONLY SERVE TO DOCUMENT AND COMMUNICATE THE ENVIRONMENTAL PERFORMANCE OF OUR PRODUCTS, BUT ALSO FACILITATE THE CONTINUOUS IMPROVEMENT OF THIS PERFORMANCE.”
“WE CAN ALWAYS DO BETTER; THAT’S OUR MOTTO HERE.”
VERONIKA AUER
of all EGGER products have an externally verified environmental label, an environmental declaration or an EPD.
includes the biogenic emissions that are stored while the wood is growing. The acidification potential measures the potential acidification of soil and water caused by emissions such as sulphur dioxide and nitrogen oxides. This indicator is important for understanding the impact on environmental sustainability and biodiversity. Then there is water consumption. This measures the total water consumption that is required, from the extraction of raw materials and manufacture of the product to its disposal. This key figure is particularly relevant in regions where water scarcity is a problem and helps to assess the water footprint of a product.
Besides the EPD, what other documents and tools does EGGER offer in regard to product transparency?
In addition to EPDs, we also provide Environmental Health Declarations (EHDs) and EcoFacts. EHDs contain comprehensive information on the chemical ingredients of the products and their effects on health, while EcoFacts provide a quick overview of the most important environmental indicators
and sustainability features of the products. All these documents and information are easily and publicly accessible at www.egger.com.
How can EGGER become even more transparent in the future?
We still want to make further improvements in this respect. We are currently running a project on the semi-automated calculation of product carbon footprints, we hope to achieve this for of all our products in all versions, depending on the production site in question. Customers will then be able to see the exact footprint of the products they buy. And we, for our part, can identify further areas for potential savings. We can always do better; that’s our motto here.
Documents such as the EPDs are available for anyone to view at www.egger.com
CLIMATE ACTION IS THE MOST URGENT TASK OF OUR TIME.
EGGER IS PURSUING THE TARGET OF NET ZERO BY 2050 AND IS THEREFORE INVESTING MASSIVELY IN THE FUTURE.
Today, 69 % of the energy used throughout the Group comes from renewable sources. The beauty of this is that a significant source of energy comes directly from the own production processes. Wood residues that can no longer be converted into actual products provide renewable energy in the company’s own biomass power plants. They replace fossil fuels in the generation of energy. One of the many advantages of closed-loop production.
The production of wood-based materials is energy-intensive. The EGGER Group’s total energy consumption in 2023 was 9,270 GWh. Around 80 % of this is thermal energy and around 20 % electricity. The good news: 78 % of the heat requirements are already covered by renewable sources. And with electricity too, the amount obtained from renewable sources has risen to 27 %.
On the way to Net Zero, EGGER will, among other things, further reduce its energy consumption and meet its remaining requirements from renewable energy sources. This will require extensive interventions.
Milestones on the way to Net Zero
▸ By 2030, reduction of direct emissions from the EGGER plants (Scope 1) by at least 30 %
▸ By 2030, reduction of indirect emissions from purchased energy (Scope 2) by at least 40 %
▸ By 2030, reduction of indirect upstream and downstream emissions (Scope 3) by at least 10 %
Find out more: to.egger.link/climate-strategy
Although binding agents are just a small component of EGGER’s products, they cause a relatively large amount of emissions along the value chain. That’s reason enough to initiate immediate measures to address the issue: The EGGER glue factories at the Wismar (Germany), Radauti (Romania) and Hexham (UK) plants now only use CO₂-neutrally generated electricity. The external procurement of binding agents for the EGGER board plants in the EU and the UK has also been changed accordingly for both chipboard and MDF boards. A first successful step towards reducing the carbon footprint of the binding agents.
The construction sector urgently needs to become more climatefriendly. A consequence of this: the demand for high-quality construction timber is increasing. At the same time, the yield of felled construction timber is decreasing, also due to climate change. Manufacturing building products from wood qualities that were previously considered difficult to utilise requires innovative thinking and the courage to implement new ideas: The new EGGER EcoBox is a hybrid product made from timber and OSB and replaces conventional building materials. Thanks to industrial production methods, the EcoBox achieves a very high degree of dimensional stability, as well as being straight and even. Compared to solid wood, it requires up to 38 % less wood and is therefore also lighter in weight for the user. The EcoBox impressed the jury of the German Sustainability Award, becoming winner in the Resources category.
Find out more: to.egger.link/ecobox
A state-of-the-art
power
plant that will generate electricity and heat from biogenic fuels is under construction on the company’s site in St. Johann in Tirol (Austria). This represents a further step towards Net Zero 2050. A visit to the construction site, where we met Bernhard Vorreiter.
TEXT: PATRICK MORDA, PHOTOS: RODERICK AICHINGER
The base slab alone, on which the new steam boiler will soon stand, contains a good 120 tonnes of steel. Right next to it, the shell of the turbine house is already beginning to take shape. Each of its numerous concrete pillars of around 20 metres in height weighs 22 tonnes. An impressive backdrop, with Bernhard Vorreiter standing right in the middle. “Here at the parent plant in St. Johann, we have rather limited space in comparison to more recent EGGER plants”, explains the Division Director for Technology/Production of five wood-based material plants in Germany, Austria and Italy. It was therefore necessary to create space for the building that has been under construction here since February 2024 and is scheduled to be connected to the grid in the first quarter of 2026.
“THE PATH TO OUR TARGET OF NET ZERO BY 2050 INVOLVES FAR-REACHING INVESTMENT.”
BERNHARD VORREITER
The EGGER Group has made a clear commitment to the target of reaching Net Zero by 2050. “The path to get there, by drastically
reducing climate-impacting greenhouse gas emissions along the entire value chain, involves far-reaching investment”, Vorreiter explains. At the plant in St. Johann in Tirol, around 80 million euros is therefore being invested in the construction of a new power plant that will use biogenic fuels to supply electricity and heat for production and other areas.
As far back as 15 years ago, Vorreiter managed parts of the first energy and environmental project at the plant. Back then, a biomass plant was commissioned to supply heat to the entire plant, as well as supplying district heating to the neighbouring towns of St. Johann and Oberndorf. “It was a very successful project. We have continued to develop this facility together ever since.”
Things are going well: The power plant is due to be connected to the grid in the first quarter of 2026.
Even back then, the idea for the power plant to generate electricity had already been formulated, which will supplement the existing biomass plant in the future and cover around 80 percent of the St. Johann plant’s own electricity requirements. With a generator output of 14.5 megawatts, it will generate around 100,000 MWh of electricity per year.
The annual fuel requirement for this is around 90,000 tonnes. An enormous amount, but one that has already been procured, as EGGER is committed to the cascading use of wood: “We want to gradually increase the recycled wood content in our chipboard production and have now reached around 65 percent in St. Johann”, elaborates Vorreiter, explaining the complex coordination
of power plant planning with the capacity of the plant. When recycled wood is used in production, there is always a fraction of wood that cannot be used in chipboard production. Bernhard Vorreiter refers to this reject wood as the “thermal fraction”. “This is made up of dusts, granulates and very fine particles that can be used to generate energy.”
But even though 1,600 cubic metres of chipboard are currently being produced in St. Johann on peak days, the resulting thermal fraction alone will not be enough to meet the power plant’s needs – 12 tonnes of fuel will be needed to achieve the targeted key figures – per hour! Similar grades of wood that would otherwise not be further utilised are also purchased from external sources, Vorreiter tells us. “We are installing a highly efficient energy system here, a forward-looking energy concept that is designed for a sustainable circular economy and works towards the grand vision of Net Zero”, Vorreiter explains, with pride in his voice.
The fossil fuel consumption of the St. Johann
“WE ARE INSTALLING A HIGHLY EFFICIENT ENERGY SYSTEM, A FORWARD-LOOKING ENERGY CONCEPT THAT IS DESIGNED FOR A SUSTAINABLE CIRCULAR ECONOMY AND WORKS TOWARDS THE GRAND VISION OF NET ZERO.” BERNHARD VORREITER
plant is already low, even without the planned power plant, thanks not least to the measures undertaken in the first energy and environmental project. “However, our energy requirements have increased in recent years due to the additional output from chipboard production. In addition, the demand for district heating from the local municipalities has grown much higher. We now supply over 100 percent more to the local district heating network than was originally planned”, Vorreiter confirms. The downside: Especially in the winter months, this increases gas consumption at the plant to cover peak demand. “It is precisely this increase in gas consumption that we want to reduce to almost zero with the new power plant project. In general, around 80 percent of the energy required by the plant is to be self-generated after commissioning in 2026.” Around 6,000 tonnes of direct CO₂ emissions from fossil fuels can then be avoided annually at this plant alone. In addition, the biogenic electricity generated by the new power plant has the potential to prevent around 40,000 tonnes of fossil fuel-derived CO₂ emissions. As the new power plant will also increase the
15
“OPTIMISING SAFETY AT WORK IS IMMENSELY IMPORTANT TO US WHEN WE UPGRADE OUR FACILITIES.”
BERNHARD VORREITER
resources for further district heating provision in the region, there is potential to prevent another 15,000 tonnes of fossil fuel-derived CO₂ emissions.
But there are also other goals and positive side effects that the power plant construction will bring. “There was a wood feeder right here for wood chips, sawdust and small slivers of wood. It was one of the oldest facilities at the St. Johann plant”, says Vorreiter, describing the former use of the area, as he crosses the construction site. The problem: the wheel loaders had to drive from the log yard right through the plant. By relocating the wood feeder to the edge of the plant, not only was space created for the new power plant, a major safety risk was also minimised. “Optimising workplace safety is immensely important to us when we upgrade our facilities”, Bernhard Vorreiter underlines. And then there’s an old high-voltage power line – its relocation away from the plant, has been the subject of various considerations over the last ten years. Cranes are often in use, especially during maintenance
of the production facilities, and the line is constantly in the way. “It has to finally go now, and that’s a good thing – once again thinking of safety at work.” This has freed up space for the power plant at a central location on the site, which will optimise the supply to the surrounding production facilities.
The priorities of new power plant could be described, in a nutshell, as keeping in mind Net Zero, the efficient and full use of all available raw materials and the impact of such a project. Vorreiter is always aware of the latter, i.e. its impact: “We use state-of-the-art technology in our project planning and are therefore also providing this as a basis for further projects within the Group”, he says. There are already ideas for other plants that do not yet have their own capacity for energy generation or could potentially expand their capacity.
“We are looking at where it makes sense from an ecological and economic perspective”, explains Bernhard Vorreiter as he climbs out of the foundation for the heavy-duty crane that will soon be put into operation here. Busy workers cross his path. There is work going on all around him. “It’s not just a matter of generating sustainable electricity here in St. Johann. We have the overall approach in mind, the cascading use of wood. We simply don’t want to throw anything away that can still be used”, he sums up, concluding our interview. With its new power plant, the company is well positioned in this respect for the next thirty years.
Project planning with state-of-the-art technology also provides the basis for further projects within the Group.
SUSTAINABLY MANAGED FORESTS STORE THE MOST CARBON. WOOD IS A VALUABLE RESOURCE – EGGER UTILISES IT RESPONSIBLY AND IN MULTIPLE STAGES.
95 % of the wood for the flooring products that EGGER produces in Wismar (Germany) comes from sawmill by-products. They do not have to travel far as they are sourced in the immediate vicinity – from the neighbouring sawmill. This is a prime example of cascading use in practice, as the waste material from the sawmill is processed directly into high-quality laminate flooring at EGGER without the need for any additional transport. Thermal energy from the biomass power plant in Wismar is used to dry the wood fibres. This plant by the Baltic Sea thus perfectly demonstrates how closed-loop production can work.
EGGER’s wood procurement strategy is based on a set of key principles. EGGER sources its wood from the immediate vicinity of its production plants if at all possible. This shortens transport routes and strengthens regional value creation. 73 % of the wood purchases are made in the local region Long-term and stable collaboration with business partners is also very important. The company avoids distributor networks, 92 % of procurement is from direct suppliers. This ensures transparency throughout the entire process and brings favourable solutions for both sides.
EGGER was one of the first wood-based material manufacturers in the world to implement ISO 38200, a globally valid, internationally recognised standard to ensure a transparent product chain for timber and timber products. EGGER therefore fulfils all the statutory requirements in regard to the legality and transparency of the wood it uses. The timber supply chain can be certified as thirdparty verified in accordance with ISO 38200. In addition, EGGER also employs monitoring measures conducted by independent third parties and, wherever available, prefers to use wood from certified forests as proof of sustainable forest management.
Thanks to a new system at the sawmill in Brilon (Germany), EGGER now also uses finger jointing there. This wood-joining technique makes it possible to produce long boards and slats from individual shorter pieces. The background: Due to climate change, the wood qualities available for use are changing. With fingerjointing, defective areas are carefully cut out and a product is created that, in terms of stability, is in no way inferior to the non-finger-jointed alternative. Waste can be reduced and highquality timber products can be manufactured, even from poorer wood qualities. This is how resources are used efficiently at the top of the wood cascade.
State-of-the-art technology and sustainable forestry come together as one in Brilon (Germany). EGGER embraces the cascading use of wood as a valuable resource in its efforts to utilise raw materials efficiently.
Christian Witte wanders through the dense forest in the Sauerland region, where the mighty crowns of the spruce and beech trees stretch across to create a thick canopy above his head: “Brilon is the most densely wooded town in Germany.” The 49-year-old is a regular visitor to the Hochsauerland district, where the fully integrated EGGER Brilon plant is based. Witte, who has been with EGGER since 2006 and has been Head of Wood Purchasing EDP Central since May 2024, plays a central role in a complex wood procurement network. In this role, he manages the Wood Purchasing section and optimises the efficiency of the supply chains for the plants in Central Europe. “EGGER considers it crucial to find sustainable solutions in wood procurement that make sense from both an economic and an ecological perspective”, emphasises Witte.
A well-balanced forest ecosystem
And here in the forest, where EGGER’s key resource originates, Witte explains: “The most important criterion is one of balance: Only wood is harvested that can be regrown.” This principle of sustainable forest management is key for EGGER in order to ensure a long-term supply of raw materials, and is the basic prerequisite for being able to use wood as a climatefriendly raw material. The company is convinced that, in view of climate change, a shift towards mixed forests is a necessary step. As Witte strides across the soft forest floor, he emphasises the importance of diversity for climate action: “We talk about healthy mixed forests, and coniferous trees are just as much a part of these as deciduous trees.” Monocultures are set to lose their future viability.
emissions and strengthens the relationship with our partners. “Through these direct partnerships”, Witte elaborates, “we can also ensure that our high standards are adhered to.” This is because EGGER imposes strict ESG criteria and due diligence checks to ensure that the company is acting in the best possible way in regard to sustainability.
Transparency in the supply chain
EGGER sources wood from an extensive network: Around 3,700 partner companies
“THE MOST IMPORTANT CRITERION FOR US IS ONE OF BALANCE: ONLY WOOD IS HARVESTED THAT CAN BE REGROWN.”
CHRISTIAN WITTE
“Sustainable supply chains are of central importance to us”, says Witte. EGGER puts its faith in long-term, binding collaboration with local and regional wood suppliers. “Our focus is on purchasing our requirements within a radius of 150 kilometres from our plants, wherever possible.” This minimises transport
supply the company’s plants across the Group. These are divided into three main groups: roundwood, sawmill by-products and recycled wood. The wood-based material plants and the Brilon sawmill obtain roundwood from around 1,500 partners, sawmill by-products are supplied by around 1,300 companies and recycled wood comes from around 1,400 recycling companies. And the intensive dialogue between EGGER and its partners is becoming increasingly relevant. New legal requirements such as the EU Deforestation Regulation (EUDR) often demand complex adjustments. EGGER is meeting these challenges with new approaches and is employing digital tools to fulfil the bureaucratic
requirements and make processes more efficient. “We have developed a portal that will enable our partners to retrieve and transmit their data electronically”, Witte tells us. This simplifies the process and increases transparency. “We can also integrate small forest owners with just a few hectares of forest into our systems.”
Cascading use: a model of raw material efficiency
Christian Witte enters the plant premises in Brilon, where modern industry blends into the surrounding forest landscape. The crowns of the trees and the treetops extend all around us, right up to the horizon, flashing every now and then between and above the buildings of the plant. The idea that EGGER had at the end of the 1980s when designing the plant in Brilon was to interweave industry and nature in the best possible way and to directly utilise the surrounding forests as suppliers of softwood and hardwood. Today, the integrated plant extends across approximately 600,000 square metres and combines cutting edge technology with a comprehensive sustainability concept. After all, Witte doesn’t see the forests from which EGGER sources its wood as simply a resource, but rather a legacy that must be preserved.
“THE AIM OF CASCADING USE IS TO UTILISE RAW MATERIALS EFFICIENTLY AND RECYCLE THEM FOR AS LONG AS POSSIBLE.”
CHRISTIAN WITTE
In line with the
the
Here at the fully integrated plant in Brilon, you can see how EGGER implements its sustainable principles. “The aim of cascading use is to maximise the value-added by raw materials and to keep them in the material cycle for as long as possible in successive steps”, Christian Witte explains, as he walks through the production halls. This principle is a core component of the corporate strategy.
▸ At the top of the wood cascade are high-grade sawlogs, which are used to produce timber in sawmills. Not all of the tree trunk can be utilised in this process; sawmill by-products are also created. The sawing process produces wood offcuts, so-called trimmings or wastage, as well as sawdust.
▸ However, these sawmill by-products are by no means waste, but rather a valuable resource for the manufacture of highly durable wood-based materials such as chipboard and MDF.
▸ So-called industrial wood – thin, crooked, knotty trunks, wood arising from thinning, storm-damaged wood or wood from snow breakage – is also processed into woodbased materials.
▸ When wood is reprocessed and reused after it has been utilised, it is referred to as recycled wood. This gives wood, as a valuable resource, many lives and carbon can be stored for the entire period during which it is used.
▸ Only at the very end of its life should wood be used to generate energy.
Since 2008, EGGER has been operating its own sawmill in Brilon, where roundwood is processed and sawn timber produced. This process also produces sawmill by-products such as wood chips and sawdust. These byproducts are processed directly at the same location. Thanks to the integrated conveyor line, the so-called “pipeline”, there are no additional transport emissions. Other woodbased material plants in the EGGER Group are also located in the immediate vicinity of sawmills.
The sawmill by-products generated there are immediately integrated into the woodbased materials process, at the end of which chipboard and MDF boards are produced. “We prevent these residual materials from simply being incinerated and feed them back into our production process. This is the gold standard of cascading use”, says Witte, with pride in his voice.
Recycled wood also plays a key role as a raw material in the production of wood-based materials. Recycled wood is fed back into production and utilised for as long as possible. Only when wood can no longer be processed any further is it incinerated – a crucial step in maximising the efficient use of raw materials. “Wood chips can be recycled up to seven times before they are finally fed into energy recovery”, Witte explains.
The masterplan against raw material scarcity
Witte sees the further intensification of cascading use as central to the future of the Brilon plant and the other EGGER plants. Forests are coming under increasing pressure due to climate change. Ideas and partnerships are needed to make the best possible use of the changed wood qualities and also the damaged wood resulting from storms or droughts, for example. And joint efforts are needed for forest regeneration and to ensure climate-resilient, future-proof forests. “We can also use lower-quality wood for the production of wood-based materials. It may perhaps be too thin for the sawmill, but certainly too good to incinerate”, Witte explains. And then there is also wood recycling. “This allows us
to make the best possible use of wood as a valuable resource and keep it in circulation for as long as possible.” And the carbon remains sequestered in the wood for just as long.
The core of the company’s philosophy is revealed here in Brilon, where state-ofthe-art technology in a fully integrated plant meets a sustainably managed forest environment, with each benefitting from
the other. “The future of the wood industry lies in the intelligent use of our resources and in the digitalisation of processes. This is the only way we can meet the increasing requirements and at the same time make our contribution to protecting the forests”, Witte explains.
At its fully integrated plant in Brilon, EGGER finds a use that makes sense for any quality of wood.
CLOSED-LOOP SYSTEMS EXTEND THE UTILISATION OF WOOD AS A RESOURCE. EGGER MAINLY USES WOOD FROM THE CIRCULAR ECONOMY THAT HAS ALREADY HAD SEVERAL LIVES.
The Eurodekor Faced Chipboard is EGGER’s bestselling product and is popular with customers worldwide with its diverse range of designs and possible uses. Another exciting aspect: it provides a perfect example of the circular economy in action. 76 % of the wood that EGGER processes into chipboard throughout the Group comes from sawmill by-products or recycling. At the end of its long lifespan, the faced chipboard is itself 100 % recyclable and once again becomes a highquality raw material for new chipboard.
EGGER is actively involved with the communities in the areas around its plants. In Romania, the family company provides ongoing support to local schools, for example with new fixtures and fittings. Their cooperation doesn’t end there, however. These schools can also generate a lot of wood for recycling, for example during repair work. EGGER collects old furniture, doors, pallets or wooden packaging, prepares the wood for recycling, and puts it straight back into production. Thanks to substantial investment, EGGER is now the biggest wood recycler in the whole of Romania.
WHAT IS THE IDEAL PERCENTAGE OF RECYCLED WOOD?
The answer to this question depends on a number of factors: EGGER aims to further increase the amount of recycled wood used in its own operations, but a local optimum figure for raw materials needs to be defined for each plant. Issues such as local availability, quality of raw materials, product requirements, availability of the necessary processing technologies and transport distances all need to be taken into account. The all-important yardstick is therefore: which wood mix produces the lowest product carbon footprint (PCF) without compromising on product quality? In the future, the company will continue to need both mainstays, recycled wood and fresh wood – in the optimal mix for each case.
Leeds (UK) was the very first Timberpak site. EGGER now operates its own recycling collection sites in the UK, Germany, Austria, France, Poland, Romania, Italy and the USA. On these sites, wood for recycling from the region in question is collected, sorted and pre-shredded for transport to the EGGER plants. Final processing takes place there. With this successful concept, the wood-based materials manufacturer has also been able to contribute to the development of suitable infrastructure in countries where the recycling of wood was not yet common.
TEXT: NADIA RIAZ-AHMED, PHOTOS: ANNA BAUER
With its consistent use of recycled wood, EGGER has made a clear commitment to the circular economy. This approach is effectively showcased in the interaction between its collection and sorting centre in Leeds (UK) and the production plant in Hexham (UK).
At the Timberpak recycling collection site in the northern English city of Leeds, lorries are lined up one after the other on the vast premises. There’s a constant flow of trucks coming and going and, right in the middle of it all, we find Mark Hayton, an expert on the recycling industry. When he looks around, he doesn’t see wood waste being tipped out of the lorries. “These are recyclable materials, a piece of the future”, he shouts, over the noise of creaking wood, humming machines and roaring engines. Music to his ears. “Wood is far too valuable a raw material to simply be burned. It is not acceptable to burn a resource that takes 45 years to grow in just 45 seconds. By recycling wood, we extend its lifespan and transform it into something new and valuable”, says the Head of Timberpak UK. He has built up 35 years’ experience in the chipboard industry, including 21 years at EGGER, and has an indepth understanding of the circular economy.
“WOOD IS MUCH TOO VALUABLE TO SIMPLY BE BURNED. THROUGH RECYCLING, WE EXTEND ITS LIFESPAN AND CREATE SOMETHING NEW.”
Leeds: A hub for recycled wood
Every year, 150,000 tonnes of material for recycling is processed at the Timberpak site in Leeds. The wood comes from a wide variety of sources – from disused pallets to furniture and construction waste. Here at Timberpak, the material is carefully prepared. “It’s a
fascinating process”, explains Hayton. “The wood waste is sorted, shredded, cleaned and examined, before making its way to the EGGER chipboard plants in Hexham and Barony.” One of the biggest challenges is sorting: Around 40 percent of the wood comes from household waste sites, where pieces of furniture with connected fabrics or other materials often end up in the wood container. The wood-based material MDF (medium-density fibreboard)
cannot be reprocessed either and must therefore be removed. Timberpak’s quality controllers therefore have a key role to play. They ensure that only suitable material is loaded onto the lorries that leave for the chipboard production plants. “At the moment, around 35 lorries leave our yard every day”, Hayton explains.
Timberpak has a central role to play within the EGGER Group. EGGER operates recycling collection sites in the UK, Germany, Austria, France, Romania, Poland, the USA and Italy. New collection sites are being opened every year. “We also explore opportunities in neighbouring countries close to our production sites”, adds Hayton. When he took over responsibility for Timberpak UK in 2003, the
“Our objective is to create products that are not only sustainable, but also aesthetically pleasing”, emphasises the Design and Product Manager.
Her main area of responsibility is understanding the needs of the UK market and identifying trends and opportunities for EGGER products and services. “On the one hand, we have to constantly ask ourselves: How can we make our products even more sustainable? How can we further reduce our ecological footprint?” says Fletcher. “And that’s in relation to the entire production chain and life cycle.” On the other hand, it is also important to meet the expectations of the customers, for example by offering attractive surfaces. The TM surfaces, she adds, are a good example of this. The TM9 PerfectSense Smoothtouch Matt lacquer surface, for example, gives selected decors a natural, matt lacquer look with a pleasant, velvety feel. They bring the matt look, which is popular with customers, onto a recyclable chipboard base. Their anti-fingerprint properties improve usability
immensely, opening up many possible uses in furniture-making and interior design – a combination that is particularly important for architects and designers, as Fletcher has learned from her regular conversations with them.
Produce regionally, think globally
A key element in making these aesthetically pleasing products even more sustainable is the increased use of recycled wood, including material from Leeds. The recycled wood content for products made in the UK plants is around 45 percent. The EGGER Group uses varying percentages of recycled wood and sawmill by-products. The percentage used in each plant depends on various factors:
only site in the UK was the one in Leeds. Over the years, EGGER has established sites in the English town of Washington and in Bellshill (Scotland), and later formed a joint venture with Pearce Recycling in St Albans.
Quality and sustainability: two sides of the same coin
The quality of the materials that Timberpak processes is of crucial importance. “We work under licences from the Environment Agency and the Scottish Environment Protection Agency and are therefore allowed to accept certain grades”, Hayton explains. “We classify our raw material into different categories, from Class A material, which only includes packaging wood, through to mixed wood from municipal collection centres. There are also special classes for solid wood, as well as for demolition wood and scraps from furniture production.” Correct sorting is essential if the wood is to be reused.
Hexham: where wood waste is turned into new products
The EGGER plant in Hexham, just a two-hour truck drive to the north, benefits from the resulting output. In the production hall in Hexham, things are far less hectic than in the yard in Leeds. Nevertheless, Aimee Fletcher has to make herself heard over a certain level of noise. As Design and Product Manager at EGGER, she knows how the processed recyclable materials from Leeds are turned into new chipboard and ultimately finished off to become high-quality design products.
“THE LONGER WOOD STAYS IN CIRCULATION, THE LONGER THE CARBON STAYS SEQUESTERED IN IT.”
AIMEE FLETCHER
for example, the availability of recycled wood and processing technologies, the quality standards of the boards to be used and, not least, the transport distances involved. Overall, the aim is always to manufacture highquality products with the smallest possible product carbon footprint. EGGER therefore not only focuses on sustainability through the use of recycled wood, but also through local production. “To reduce our carbon footprint, we manufacture the majority of our chipboard products for the UK market right here”, Fletcher explains. This reduces long and costly transport routes and contributes to the overall ecological footprint. But the lifespan of the wood also plays a role, Fletcher adds. “The equation”, says the Hexham manager, “is quite simple: the longer the wood stays in circulation, the longer the carbon stays sequestered in it.” Only at the very end of
their life cycle, when the particles become too small for material utilisation, can wood products be incinerated, and they still then provide renewable energy.
Looking at the EGGER Group, 72 percent of all products are recyclable after use and can be reintroduced into the material cycle. “We are proud that we can do our bit. This product”, says Fletcher as she strokes a piece of chipboard with a TM9 surface, “could one day come back to Leeds to stay in the cycle.”
There, in the busy Timberpak UK yard, Mark Hayton is also optimistic about the future of wood recycling: “Recycling is more than just a process”, he says, “it’s a philosophy that helps us to work towards a sustainable future via the circular economy.”
In the showroom, Aimee Fletcher shows customers the velvety matt TM surfaces.
EMPLOYEES ARE THE MOST VALUABLE COMPONENT OF THIS FAMILY BUSINESS. EGGER OFFERS THEM SECURE JOBS AND LONG-TERM OPPORTUNITIES FOR DEVELOPMENT.
In the 2023/2024 financial year, 1,080 employees covered a total of 20,580 kilometres as part of the “EGGER runs” initiative. For every kilometre run, EGGER donates five euros to charitable organisations, thereby supporting important regional projects. This initiative has been ongoing since 2010 and promotes good health and social engagement in equal measure.
In April 2024, EGGER signed up to the United Nations Women’s Empowerment Principles and has set itself some specific targets. The percentage of women employees is to be increased by 5 % annually across the entire workforce of the EGGER Group. The more diverse the teams, the more creative and innovative they are when working together.
The most important thing is that employees return home safely to their families after a day’s work. EGGER has therefore made huge efforts to further improve workplace safety for its workforce. The accident rate was once again reduced in the last financial year to 7.76 accidents per 1 million working hours (internal Lost Time Injury Rate), meaning that the target EGGER set itself was achieved. The long-term vision is “zero accidents”.
20 of the 22 EGGER production plants have their own apprenticeship programmes, even in countries that do not usually offer such dual training formats. Many careers start straight after leaving school. EGGER is currently offering 476 apprentices a long-term job with a future. They are well on the way to starting a career as a skilled worker at EGGER.
4.2 MILLION
EGGER values the commitment and experience of its employees. Employees with many years of service are rewarded with an anniversary bonus. In the last financial year, a total of 4.2 million euros was paid out to employees who have been contributing to the corporate success for many years.
At the EGGER plant in Biskupiec, Poland, three damaged safety helmets are lined up in a display case like valuable exhibits. They symbolise the importance of consistent implementation of safety measures at work.
“These helmets saved the lives of their wearers or at least protected them from serious damage to their health”, explains Barbara Cmiel, Health and Safety Officer at EGGER’s Biskupiec plant. One of the helmets protected an employee from serious head injuries when he fell into a trench during construction of the plant. Another protected its wearer from an even worse fate during unloading when he was hit by a lorry part after a strong gust of wind. The third saved a driver when he hit his head on the tarmac after falling from his lorry.
The stories of the battered safety helmets show how even a brief moment of carelessness can have serious consequences – and how crucial it is to wear the right equipment. Normally, these broken helmets would simply be disposed of, but in Biskupiec they fulfil an important function. They provide a warning and are a motivational tool, a reminder and an encouragement. Above all, however, they underline the importance of workplace safety and show how seriously it is taken at EGGER.
The importance of workplace safety is most clearly reflected in “Vision Zero”. As part of this vision, the company is striving to achieve its long-term goal of zero accidents at work. The short-term strategic goal, to be achieved by 2025, is to have no more serious accidents at work. To achieve this major goal, a comprehensive management system for occupational health and safety has been implemented at all EGGER plants. Since then, accident rates across the entire Group have been significantly reduced.
“Vision Zero shows that each and every individual in the company is important”, emphasises workplace safety expert Cmiel. “At EGGER, we don’t distinguish between internal and external employees or between managers
and production staff.” This respectful and appreciative approach creates a family atmosphere in which people look out for one another.
Leading the way, is Barbara Cmiel, who is passionate about her role and has dedicated her professional life to ensuring safe and healthy working environments. She has been working in occupational health and safety for over a decade and has been with EGGER since 2017, taking on the position of Chief Occupational Health & Safety Specialist at the Biskupiec plant a year ago. In this role, she is responsible for monitoring safety standards, conducting risk assessments and organising regular training sessions.
She also believes that EGGER’s basic principles for working safely together – the four golden safety rules – play a key role:
The life-saving helmets.
TEXT: JAN STRAHL, PHOTOS: STEPHIE BRAUN
1. Safety starts with me.
2. We look out for one another and immediately address any unsafe conditions.
3. I am a role model and I use my personal protective equipment.
4. I adhere to the required safety measures in every step of my work.
“These rules have been kept simple, but they are very effective”, Barbara Cmiel explains. “They encourage all employees to take personal responsibility for safety in the workplace, we regularly communicate them and remind people of them in training sessions and in our day-to-day work.”
Community is the key
“Every employee has a responsibility to look out not only for themselves, but also for their colleagues”, says Cmiel. “We encourage this attitude by creating and nurturing personal relationships and a family atmosphere within the company. This principle not only promotes a strong sense of community, but also a culture of taking responsibility for others.” Employees are encouraged to point out potential hazards and share their observations. “Just like in a real family, we all look out for one another”, Cmiel tells us. Line supervisors play a crucial role in this. “They spend a lot of time with their teams ensuring that the safety measures are adhered to and, of course, they are role models for safe behaviour”, emphasises Cmiel.
Another key factor in EGGER’s successful safety culture is the concept of behavioural safety. “EGGER introduced an awareness programme for safe behaviour a number of years ago”, Barbara Cmiel explains. “It aims to create an awareness of safe behaviour and to get all employees actively involved in our safety culture.” The fundamental idea behind this is that most accidents are not caused by technical failure, but rather by unsafe behaviour. By systematically observing, analysing and
positively influencing this behaviour, risks can be identified and eliminated at an early stage. An example of how a change in behaviour can improve safety is the use of handrails on stairs. “Initially, the topic was ridiculed. Nobody believed that it made a big difference whether you held on to the handrail or not.” To bring about a change in behaviour, Cmiel showed her colleagues statistical data on the number of people who died after falling on stairs during the pandemic in Germany. This figure exceeded the number of deaths caused by road accidents. “After we had presented these statistics, behaviour changed and employees now always use the handrails”, reports Cmiel. Such seemingly small changes can make a big difference. This is why behaviour-based safety is an integral part of the EGGER Group’s overall concept.
EGGER also offers regular training courses and workshops at the Biskupiec plant in order to continuously improve the awareness and skills of employees in regard to workplace safety. EGGER adopts both internal and external measures: The training sessions take the form of both e-learning courses and classroom courses and are held regularly for all employees. “On the one hand, we cover general topics such as safety culture and rules of conduct, health and safety standards, fire prevention and conduct in an emergency”, explains Cmiel, but on the other hand, the training is also tailored to the specific circumstances and risks of the individual workplaces. For example, employees learn how to use personal protective equipment properly and how to handle hazardous materials and also go through the safety procedures for the machinery they operate. In Safety Leadership programmes, line supervisors learn how to act as role models and how to lead by example in encouraging a culture of safety. In our employee workshops on the other hand, employees are shown how to implement safety-conscious behaviour in their day-to-day work and how to recognise and address risks. Barbara Cmiel is delighted with the high level of acceptance and active participation in these events.
accidents. However, the reporting system at EGGER also encourages employees to report close calls, where an accident was narrowly avoided”, explains Barbara Cmiel. “This creates a culture of transparency and enables us to learn from these ‘lucky escapes’ and
“JUST LIKE IN A FAMILY, WE ALL LOOK OUT FOR ONE ANOTHER.”
BARBARA CMIEL
avoid accidents in the future.” The incidents that are reported are analysed and the necessary measures are taken to improve safety. “I share these reports with the heads of department and plant managers. I talk about them in the training sessions and display the reports on our notice boards and information monitors.” This policy of information and communication means that everyone can benefit from these experiences.
The success of this consistent safety culture is measurable and the efforts we make are having an effect. The number of reported incidents in Biskupiec has fallen significantly in the recent period, says Cmiel: “We are on the right track.”
Another essential building block on the way to “Vision Zero” is the accident reporting system. “It goes without saying that we document all
“Vision Zero” is a prevention strategy that aims to create a world with no accidents at work or work-related illnesses. This strategy is based on the conviction that accidents at work are not unavoidable, but in fact have avoidable causes. The focus is on preventing fatal and serious accidents at work. More and more companies around the world are pursuing this philosophy. By promoting physical and mental health in the workplace, companies can not only improve the safety of their employees, but also increase their own economic success. Studies undertaken by the International Social Security Association (ISSA) show that a strong safety culture in companies has a positive impact on product quality and on their ability to meet deadlines on time.
Despite these successes, workplace safety remains a constant challenge and task for Barbara Cmiel. “One of the biggest challenges is still to minimise human error and to continuously improve awareness of safety measures.”
The three helmets in the display case at the Biskupiec plant will continue to provide a daily reminder to employees of the importance of safety precautions in their day-to-day work – and of the fact that they can save lives in
emergency situations. They are visible signs of a corporate culture in which everyone takes responsibility – for themselves and for their colleagues. This is how EGGER is making workplace safety a lived experience, and in doing so, is getting a little closer to its goal of “Vision Zero” every day.
The right protective equipment is available for every task: Infrastructure engineer Marta Kwiatkowska taking water samples. Maintenance engineer Andrzej Wojnarowski lubricating a machine.
DIGITALISATION HELPS COMPANIES TO MANUFACTURE PRODUCTS EFFECTIVELY AND SUSTAINABLY. EGGER BELIEVES IN USING THE BEST INDUSTRIAL BASIS AND NEW IDEAS.
Drones can help with stocktaking in log yards. This means that employees no longer have to go into the log yard to do stocktaking. The drones fly a pre-programmed route and take photos of the piles of wood every couple of seconds. These are then analysed and merged into a map with accurate 3D images. This enables faster stocktaking and provides more accurate data on the individual grades of wood.
EGGER has an integrated management system that covers all plants. It guarantees compliance with clearly defined requirements in all areas and helps to ensure continuous improvement. 19 of the 22 plants have externally certified environmental management systems (ISO 14001). These systems allow environmental goals to be systematically and consistently pursued in an effort to minimise environmental impact and use resources and energy responsibly.
569
MILLION
The EGGER Group regularly invests large sums in its own plants. In the last financial year alone, EGGER invested 569 million euros in maintenance and growth across the Group. In addition to company acquisitions, this expenditure was channelled into all the plants: into increasing capacity and, above all, into the further enhancement of the sustainability performance. In this way, EGGER wants to fulfil its role as a pioneer of new technologies in the future too and to ensure the efficient, closed-loop production of wood-based materials.
40.5 %
In internal logistics, EGGER is in the process of switching over from gas and diesel forklift trucks to electric forklift trucks. Electric forklifts are generally used in new plants. 40.5 % of the forklifts in the fleet are already powered by electricity. There is also a positive trend in regard to cars: The number of electric cars in EGGER’s fleet of company vehicles has increased and now makes up 13.9 % of the total fleet.
As a specialist in process optimisation, Stefan Kohlegger is working on making the interaction between the machinery and the thermal systems in the EGGER plants more efficient. In our interview, he explains how the step towards becoming a Smart Factory is being taken and how the company’s ecological footprint is being reduced.
TEXT: NADIA RIAZ-AHMED, PHOTOS: RAMON HAINDL
Mr Kohlegger, as a fan of outdoor sports, you spend a lot of time outside in nature. At the same time, as a specialist in process optimisation, you are working on making industrial processes more efficient and sustainable. How do you bring these two aspects together in your life and your work? I grew up in Innsbruck (Austria), surrounded by mountains. This gave me an appreciation of nature from an early age. My passion for outdoor activities has developed from this –for me, they mean relaxation and training at the same time. I especially enjoy discovering new adventures, planning new routes and exploring the surroundings. This connection to nature has certainly heightened my focus on sustainability in industry. It makes me proud that I can play a part in making processes more efficient and environmentally friendly through my work at EGGER.
“MY VISION IS AN INDUSTRY THAT OPERATES IN HARMONY WITH THE ENVIRONMENT.”
STEFAN KOHLEGGER
Your specialist area is the Smart Factory, i.e. the digitalisation and automation of processes. What role do people still have to play in this context, if any?
People remain a central factor. I am often asked whether our optimisation solutions will replace human labour. But I don’t see it that way. We provide employees with support and help them to concentrate on their core tasks. People are still needed for many tasks, for example maintenance or creative problem solving. Not to mention social skills – Artificial Intelligence is nowhere near as advanced as we are in this regard.
How would you define the term Smart Factory?
It represents an innovative and futureorientated development in the field of industrial production, which sees humans and machines working closely together. A Smart Factory’s systems are highly automated and closely networked. Technologies such
as machine learning, Artificial Intelligence and modern sensor technology are used to optimise production processes. This results in an increase in productivity, quality and efficiency. But people, with their creative and social skills, still remain an indispensable part of the overall system.
How is process optimisation achieved at EGGER?
Our production plants are equipped with a large number of systems, some of which have been in operation for 10 to 20 years or even longer. The associated control concepts have in many cases remained the same as when they were first installed. With our overarching optimisation programme, we are tackling two challenges: Firstly, we are reworking the existing control concepts and bringing them up to date with the use of the latest technology. Secondly, we are networking the systems, which previously worked independently of one another. This optimised interaction enables us to identify hidden potential and thus increase overall efficiency.
What challenges do you face with automation concepts?
It is important to mention that our overarching energy optimisation programme is not a standard programme that we can simply install and run. Rather, it is a customised solution that is specifically tailored to the needs of each individual system. This is the real challenge: Each system has its own requirements, specific problems and particular framework conditions that need to be taken into account. Although we can draw on a wealth of experience from other projects, we are essentially developing new versions of the optimisation measures for each plant. This requires a great deal of expertise, flexibility and close collaboration with the teams in each plant.
How do your optimisation measures contribute to the general goal of greater sustainability?
Our approach is to make the best possible use of existing systems rather than replacing them with new ones straight away. I consider
that in itself to be an important contribution to sustainability. Instead of costly conversion work, we generally install an intelligent control unit that communicates with the existing systems and ensures that they are perfectly coordinated. By networking the individual systems, we can unlock previously untapped potential, thereby significantly increasing overall efficiency. This then results in tangible savings: We reduce our emissions, lower our gas consumption and ultimately also cut the amount of CO₂ we produce.
Can you give me a specific example where such optimisation has been successful?
At our Scottish plant in Barony, we managed to halve the gas consumption of the peak load boiler within the first three months. The optimised control mechanism for the dryer has reduced our gas consumption by a further 10 %. Thanks to the energy optimisation software, we have cut our gas consumption by an amount equivalent to the annual usage of at least 200 single-family homes every year at this plant alone.
What about acceptance of the technologies by the employees in the plants?
The human element can be a challenge. Each plant has its own culture and its own needs. It’s important to build trust and involve employees right from the start. We see ourselves as longterm partners. At our plant in Brilon (Germany), for example, we have been working together closely since 2019. Of course, there are sometimes reservations when someone from “outside”, who doesn’t work at the plant all the time, looks at the processes. But we always emphasise that our optimisation is a joint effort. And that all plants benefit from the experience of the others.
His task is to make the interaction between the machinery and the thermal systems in the plants more efficient.
“IT MAKES ME PROUD THAT I CAN PLAY A PART IN MAKING PROCESSES MORE EFFICIENT AND ENVIRONMENTALLY FRIENDLY THROUGH MY WORK AT EGGER.”
STEFAN KOHLEGGER
Kohlegger’s strong connection to nature has heightened his focus on sustainability in the industry.
A look ahead to the future: How do you see the role of industry and the use of digital technologies in 2050?
My vision is an industry that operates in harmony with the environment and conserves our planet’s resources. Digital technologies play a key role in this. My wish is that we can create an industry that provides people with optimal support through the smart use of digital solutions. An industry that helps to make it possible for us all to live in peace and in harmony with nature.
Running a business sustainably is only possible with strong partners. Together with them, we want to keep improving the way we do things, which is why we let our customers have the last word.
PHOTO: RAMON HAINDL
“The long-standing partnership between EGGER Holzwerkstoffe and ASSMANN Büromöbel is based on a shared understanding of sustainability and a responsible approach to the use of natural resources. We need high-quality, environmentally friendly materials with a long lifespan. It goes without saying that EGGER procures and processes its wood according to sustainable principles. EGGER’s faced chipboard is one of the key components of our products. Right from the outset at development stage, we pay close attention to efficient product design and the use of environmentally friendly and durable materials. These sustainability criteria form the basis for product certifications such as the Blue Angel and the European sustainability certificate for office furniture, FEMB Level. This means that we are able to meet demanding sustainability standards such as precise knowledge of our materials and products, efficient use of resources and recyclability.”
“IT GOES WITHOUT SAYING THAT EGGER PROCURES AND PROCESSES ITS WOOD ACCORDING TO SUSTAINABLE PRINCIPLES.”
DANIEL KAHNWALD
Daniel Kahnwald, Product Manager – ASSMANN
“The Schmidt Groupe sets high social and environmental standards in line with its ‘Positive Impact’ strategy to contribute to a more inclusive, fairer and regenerative economy. We select our suppliers according to the three pillars of sustainability (ESG). For example, we pay attention to the origin of the products and their certified sustainable supply chain, as well as to their carbon footprint. EGGER provides us with concrete answers and evidence in this regard. We benefit from the high level of transparency and can also identify starting points for further improvements. In the future, we will continue to work on the integration of bio-based or less carbonintensive materials. In EGGER, we have a partner with shared values and aspirations.”
Frédéric Meyer, Director of Transformation and Operational Excellence – Schmidt Groupe
“IN EGGER, WE HAVE A PARTNER WITH SHARED VALUES AND ASPIRATIONS.”
“Our ambition is to create sustainable products that we’re proud of. We make almost 5 million cabinets a year in our own UK factories, so this is a product where our choices can make a real difference. EGGER supply all the chipboard used in our cabinets, and their mix of recycled material (including former Howdens kitchens and Howdens production offcuts!) and re-using virgin fibre from sawmill residues, provide the perfect balance for the highest quality board through our busy factories and for our end product.
Also, EGGER has defined emissions targets, aiming to achieve Net Zero by 2050, with near term 2030 targets, many of which were initiated to support and align to our SBTI targets. EGGER has committed significant investments to ensure delivery of its, and our, Net Zero plan.”
Claire Toomey, Head of Sustainability and ESG Lead – Howdens
“EGGER HAS COMMITTED SIGNIFICANT INVESTMENTS TO ENSURE DELIVERY OF ITS, AND OUR, NET ZERO PLAN.”
Published by: EGGER Holzwerkstoffe GmbH
Weiberndorf 20
6380 St. Johann in Tirol (Austria)
Project leads: Manuela Leitner
Katharina Wieser
Please contact us if you have any questions or suggestions: corporate-communications@egger.com
Publication date: December 2024
Concept, editing & design: loved – a brand of thjnk Germany GmbH www.loved.de
Printing: FRIEDRICH Druck & Medien GmbH, printed on PEFC-certified paper
Notes:
Subject to technical changes and printing errors.
All the decors shown or mentioned are reproductions.
Image credits: Anna Bauer Ramon Haindl Roderick Aichinger Stephie Braun
Additional image credits: Ramon Haindl (p.1, p.2, p.5, p.13, p.43) Anna Bauer (p.25, p.37)
EGGER Holzwerkstoffe (p.3, p.5, p.13, p.19, p.25, p.31, p.37)
The content of this publication has not been approved by the United Nations and does not reflect the views of the United Nations or its officials or Member States.
Weiberndorf 20
6380 St. Johann in Tirol (Austria)
www.egger.com