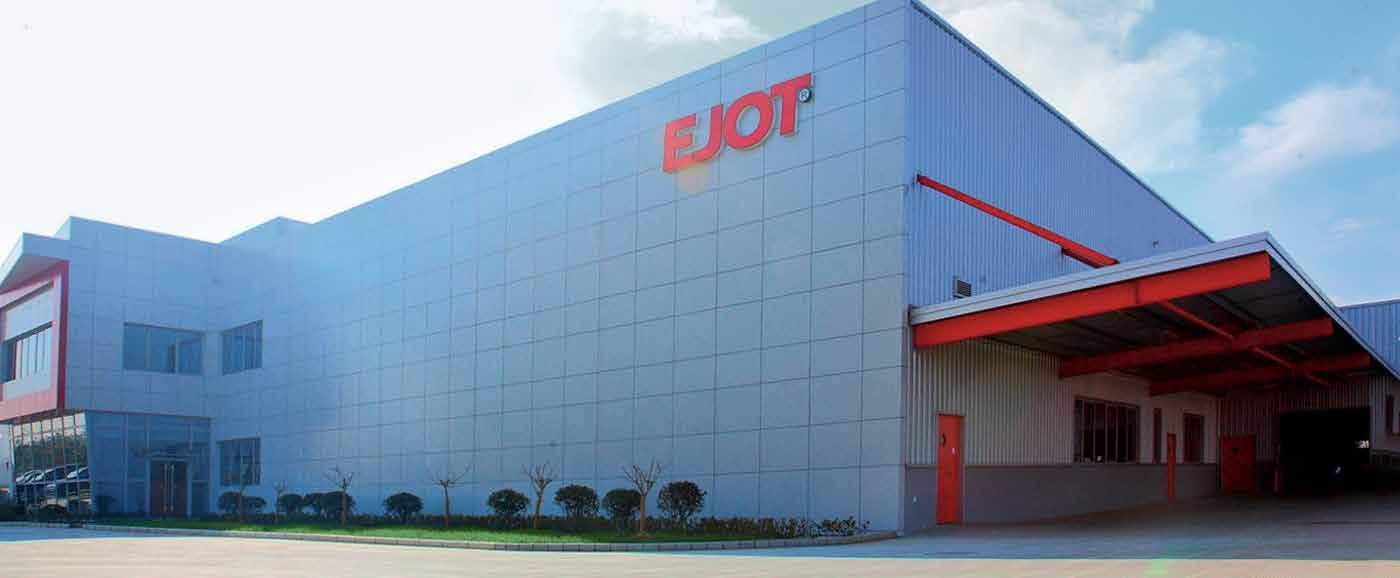
26 minute read
Professional applications for the building envelope
by ejotsverige
Expanding presence in global growth markets
If we look to the future, we will see significant changes in the economy, technology and society. The next generation of automobiles will be primarily electrically driven; perhaps soon in such a way that humans will completely hand over control to the machine, including control over their own safety. Digitalization will continue to establish itself in more and more areas of life at high speed.
>>Text: Dr. Markus Duchardt T hese are just a few of the challenges that we have to acknowledge and overcome as a company. With regard to new product and process developments, there are radical changes and certainly great opportunities that we want to take advantage of. However, the most important technological growing markets are currently in the USA and Asia. The 2020 Annual Report of the WIPO (World Intellectual Property Organization) states that Asia and North America together account for around 75 percent of global patent applications. In addition to Europe, the pacesetters for technical innovations that are relevant for us are therefore increasingly located in Asia and America and must consequently be supported from there.
In the future, mobility will almost certainly be dominated by electrically powered vehicles and aircraft. Global companies in the American and Asian markets will supply a large number of people with electric vehicles and establish a cycle of energy generation and raw material processing, around whose standards we may then have to orient ourselves.
We are not unprepared for this development. We have a broad portfolio of products and product features developed specifically for this application environment. Today, the majority of our application engineers and developers are already working on the conversion of fossil combustion applications to climate-friendly technologies. From battery technology and the increasing number of vehicle sensors, to the lightweight and mixed construction of body shells, to charging stations for electricity and many other areas of application, electromobility offers enormous starting points for our joining technologies and for other complex coldformed and plastic parts from the EJOT Group portfolio.
In addition, the transformation to electromobility goes hand in hand with another major topic: autonomous driving – not feasible without a significant increase in video, radar and lidar systems as well as other sensors and the networking of vehicles with each other. An autonomous driving vehicle has a 360-degree perception of its surroundings, consisting of a network of small sensors with cameras, radar, ultrasound and three-dimensional laser scanning. Here, EJOT also has successfully implemented customised products, for example in the area of micro screws. Numerous technology leaders in these areas are also located in Asia and America.
As the European market leader, the EJOT Group will continue to expand its presence in the growth markets of America and Asia, which it started years ago. With the aim of being the global leader in problem solutions in the areas of fastening and forming technology. Anyone seeking fastening technology solutions thinks of EJOT first. Worldwide. E
EJOT Fastening Systems in Taicang, China
2000
Successes at the joint venture in the USA: Four years after its establishment, the development is very positive. The company now has 80 employees working in a modern production facility. The joint venture is now the market leader for headlight adjustment systems.
2001
Reorganization of the group structure and connection of the companies to EJOT Holding GmbH & Co. KG. The EJOT Group has grown strongly, however, due to the complicated tax circumstances restructuring has been avoided so far. However, with a tax reform comes the possibility of restructuring. With the exception of EJOT France, all companies will be connected below the holding company. At the same time, an advisory board is set up.
2001
Foundation of EJOT Italia s.r.l., Torino, Italy. In the first step, there is only one sales representative. Supply is made through Germany.
2001
Foundation of the UAB EJOT Baltic, Vilnius, Lithuania. The successful three-year business relationship with Hiltus has now given rise to the new company in Vilnius with responsibility for the Baltic States. The focus is on the sale of anchors for external thermal insulation composite systems.
2001
Foundation of the Global Fastener Alliance (GFA). In order to offer customers a worldwide presence, the GFA is founded after a long period of negotiations. In addition to the European companies EJOT and Ribe, the American companies ATF and MacLeanFogg, the Brazilian manufacturer Micheletto, and from Japan the company Owari and from Korea JINHAP are part of the alliance.
Potential and benefit of license management
As early as the 1980s, EJOT started to set up worldwide license management due to the strong demand for its products in direct fastening. In 1982 the first PT® License was sold to the former screw factory Vereinigten Schraubenwerke (VSW). The British PSM was the first foreign company with which a license contract was concluded. One year before, the PT® screw had been introduced in Great Britain for the first time on the occasion of the Birmingham Motor Show.
>>Text: Dr. Markus Duchardt
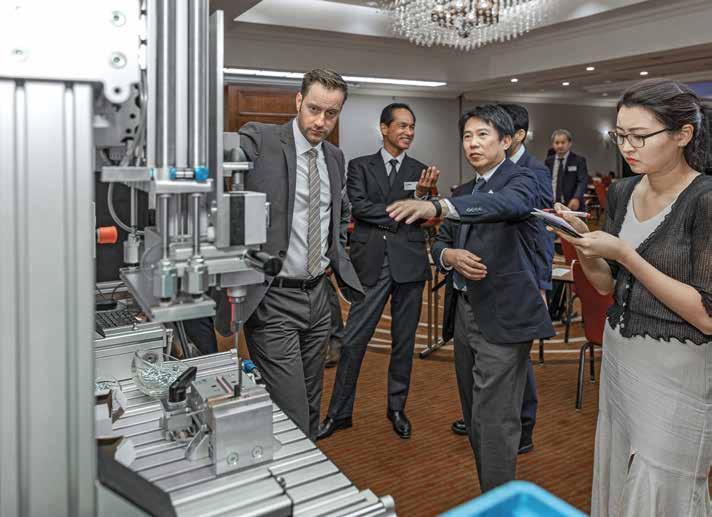
2001
Foundation of EJOT Romania s.r.l., Pitesti, Romania. As a result of further development in Eastern Europe, EJOT is also turning its attention to the market in Romania. With two employees, a small warehouse is set up near Bucharest.
2001
Foundation of EJOT Wostok, Moscow, Russia. The largest market to the east must also not be missing on the EJOT map. A connection of several years with the new managing director of the national company enables the establishment of EJOT Wostok (East Russia).
2001
Foundation of EJOT Spojna Tehnika d.o.o., Zagreb, Croatia. After the foundation of EJOT Austria, the expansion towards the countries of former Yugoslavia is also a logical step. Slovenia can still be supplied from Austria.
2001
Addition of a floor to the EJOT Construction Fasteners building at Stockwiese in Bad Laasphe. In parallel, the exterior facade was finished in the EJOT design.
2001
The stamping and forming division and the raw materials warehouse (construction fasteners) are relocated to the building at Lahnuferstraße in Bad Laasphe. In addition, special machine construction is located there.
The expansion of the license management to the American continent followed. The first order of 30 million screws for a licensee in the Chicago area resulted in further license contracts. In 1989 the first PT® license was sold to Japan. This was followed by the worldwide introduction of further licensed products such as DELTA PT® and ALtracs® Plus. In 2018, the first license for the third PT generation, the EVO PT®, was signed. Today, around 50 licensees in 17 countries act as important multipliers for EJOT. They strengthen our brands worldwide and increase the brands’ availability.
Being an EJOT licensee is interesting for many companies. The trick is to have enough good suppliers in the market. This requires great care in the selection. The worldwide market should be well supplied with the product but not flooded. There are many inquiries by interested companies. But many do not fit in with the EJOT quality philosophy.
The licensee programme also guarantees that EJOT products are available worldwide in a consistently high quality. In order to meet this demand, EJOT provides its licensees with extensive support in the areas of application technology, production and quality and even marketing. In addition to the manufacturing standards, the licensees gain access to licensed tool manufacturers; the basic prerequisite for high-quality end products.
Furthermore, the licensees have exclusive access to digital calculation programmes such as EVOCalc®. This means that torques and clamp loads can be pre-calculated and component optimisations can be made as early as the design stage. This saves time and costs.
Employees of licensees are comprehensively trained and prepared for customer visits or – if desired – accompanied on a regular basis. Comprehensive component tests in the EJOT Applitec are also part of the service programme, as well as training and seminar support. The licensees are intensely familiarised with the product and its application. A broad approach to support that goes far beyond the mere sale of the product – an approach many customers abroad are not familiar with. E
USA: 7 Germany: 1
France: 1
Spain: 2
Mexico: 2 Brazil: 2 Italy: 1
Romania: 1
Turkey: 1 China: 7
India: 2
Malaysia: 2
Singapore: 1
Vietnam: 1
Taiwan: 2 Japan: 6
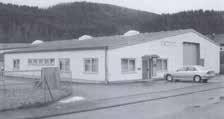
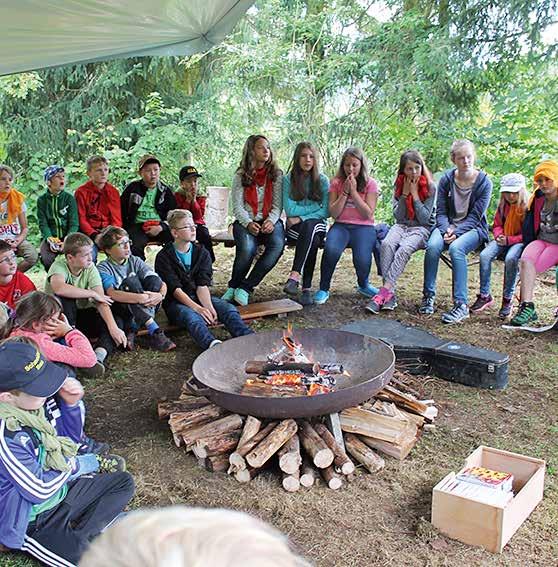
2001
Merger of the companies EJOT Verbindungstechnik GmbH & Co. KG and EJOT Kunststofftechnik GmbH & Co. KG to the EJOT GmbH & Co. KG with the divisions Industrial Fasteners and Engineered Plastic Components.
2001
The kick-off event marks the beginning of the year-long SAP implementation project at EJOT. Together with the service provider KPMG, five sub-projects will be launched, which have to be implemented in different phases until “go live”. After the usual “birth pangs”, SAP becomes normality.
2002
EJOT publishes its first annual report. In addition to the latest developments, such as new products and innovations, current figures, data and facts as well as a management report are also published.
2002
The new ALtracs® screw, a self-tapping screw for light metals, is presented. A patent-protected product with clear product advantages, such as special flank angle thread forming zone and metric compatibility.
2002
First day of training at In der Aue in Bad Laasphe. In cooperation with the Siegerland Metal Industry Association, information is provided about apprenticeships and dual training. With these information events EJOT wants to attract young people for vocational training.
Holiday camp for children of EJOT employees
In 2011, EJOT was awarded the audit certificate “berufundfamilie” (work-life balance) by the non-profit Hertie Foundation for the first time. EJOT had prepared extensively before receiving the audit certificate, which was designed to analyse, evaluate and improve company activities to help employees strike a better work-life balance.
>>Text: Andreas Wolf
The starting point at that time was initially the successful reintegration of young mothers into working life. “The young women were not only very well trained in their respective roles, but, as skilled workers upon completion of their training, they also became an important part of the company”, says Winfried Schwarz, HR Managing Director of EJOT Holding GmbH & Co. KG until 2017. To enable female employees to rejoin the workforce at an early stage following the birth of their child, the company kept in close contact with the expecting mothers both during their pregnancy and while they were off on maternity leave so that individual and flexible working time models could be agreed upon to help them rejoin the workforce. “Back then, that was by far not as widespread and self-evident in the working world as it is today,” emphasizes Schwarz.
More than 10 years later, EJOT has just completed its third re-certification. Efforts to improve the work-life balance of employees have now been expanded to include even more aspects of employee life: holiday camps for employee children, flexible working hours and holiday time regulations in factory and administration positions and the promotion of employee health have been an integral part of an employee-oriented personnel policy for years. Additionally, there are many individual examples from everyday working life which are flexibly implemented in the departments and teams on a daily basis: Swapping shifts and reducing working hours in order to temporarily care for a family member, mobile work from home if a child is sick, parental leave and further training opportunities in the framework of the EJOT Academy and much more.
The main targets of the current target agreement, the implementation of which are checked externally once a year, include, among other things, the promotion of digital personnel development with a view to make the training and further training of employees as well as the career paths of skilled workers and management personnel more flexible. Mobile work is just as much a part of the target agreement as is the flexible organisation of shift work according to special personal or family reasons of employees. Management personnel have a central role to play in this regard. As “service providers and coaches”, they support employees to harness existing potential and perform to the best of their abilities as well as providing advice on issues relating to the work-life balance of employees.
We can only successfully fulfil challenging tasks within the company if our employees can fully concentrate on their work and customers. The future success of EJOT is fundamentally dependent on how well we manage to tie qualified and committed employees to our company. Offering employees a healthy work-life balance plays an important part here, especially for future generations. E
“Career with apprenticeship” putting focus on dual training again
With dual education, an outstanding idea was born in the last century. The German vocational training system is known worldwide for its excellent quality.
>>Text: Andreas Kurth
Distinct self-control mechanisms bring the supply of apprenticeships on the part of companies and the corresponding demand on the part of students into line with each other almost without state intervention and ensure very low youth unemployment, which is envied in many parts of the world. At the same time, a companies’ demand for skilled workers and managers is met precisely and at a high level. Unlike other countries, in Germany “VOCATIONAL training” always has priority over “WORK training”. Through nationally standardised curricula, cross-company and cross-product content and competences are taught, which ensures future employment in other companies as well. With attractive further training opportunities to become a master craftsman, technician or specialist, vocational training can be the springboard to a career. Even studying without an Abitur diploma is possible today due to the vocational training.
Hans Werner Kocherscheidt also discovered the great potential of dual training for EJOT at an early stage. He took on the first apprentices as early as the 1960s. Hundreds were to follow in the course of the decades. Thanks to the initiative of Hans Werner Kocherscheidt, the industrial training workshop was founded in 1975 as an inter-company training facility in Bad Berleburg. The development of the training workshop, today’s Bildungszentrum Wittgenstein (BZW), is still intensively accompanied and promoted by the managing partner Christian Kocherscheidt. As a long-standing chairman of the vocational training committee of the Chamber of Industry and Commerce, vocational education and training is particularly close to his heart. Apprentices as the “future of EJOT”, are a value for the company itself and not just a personnel reserve, but instead they guarantee steady renewal and high-quality performance. Over the years, developments at EJOT have also progressed in leaps and bounds. Analogous to the technological change and the growth of the entire company, the training also changed. In the early years, the apprentices racked their brains in the subjects “technical knowledge”, “technical calculation” and “technical drawing” and worked for months on U-steels until their hands blistered, today the professions and their requirements have changed enormously. Today, EJOT regularly has more than 100 apprentices under contract in 19 different apprenticeship professions. Every year, around 30 apprentices pass their final exams and are taken on as permanent employees. New apprentices are recruited and start their training in the same number. The focus today is not only on traditional professions, such as tool mechanic or industrial clerk. The apprenticeships offered follow the ever more rapidly changing needs of the world of work. New professions such as e-commerce clerk, media designer, chemical laboratory technician or digitalisation management clerk provide new impetus and make a significant contribution to further strengthening already important functions with well-trained specialists in a few years’ time. And if there is no suitable apprenticeship that fits the company’s needs, EJOT goes its own way. With the specially developed combined training to become a “production IT specialist”, the two apprenticeships "machine and plant operator” and “IT specialist” are merged. The increasing convergence of technology and information technology due to digitalisation and Industry 4.0 is thus taken into account with its own dual training course. A unique concept that did not exist before and which was taken up and adopted by other companies quickly.
Further proof that such concepts work are our apprentices like Marius Latt from Bad Berleburg. The “production IT specialist” in training recently completed the first part of his apprenticeship as a “machine and plant operator” with the grade “Excellent” and 98 out of 100 points. The best result of all exams taken in Germany in this profession. One of three “national winners” at EJOT in the last six years. Nevertheless, the dual training system is under enormous pressure. Just ten years ago, local companies were still receiving countless applications from young students who were looking for apprenticeships and dual study programs. At EJOT, too, the now oft-cited “laundry baskets” filled up quickly with job applications.
2002
Innovation Days in Berghausen: Promoting creativity and inventiveness. This was the motto of the Innovation Days. On display were product innovations and in addition numerous suggestions for improvement from a wide range of areas.
2003
EJOT has to cut jobs for the first time due to the crisis. This was followed by a reorganisation of the Industrial Fasteners, Engineered Plastic Components and Building Fasteners Divisions. The new organizational structure is based on a clear division of responsibilities between the holding company, which defines financial and management tasks as well as the strategic direction of the Group.
2003
First digital screw configurator: After entering the fastening data and joining parameters, the customer receives a suggestion for the right screw. Then he can enter the desired delivery quantity and delivery date. This can be sent as an e-mail to the sales department and serves as the basis for a quotation.
2003
New location, new building and new name: After a three-year project period, the new building at the Sherburn-in-Elmet site is finished. The site is located east of Leeds and offers space for expansion on the surrounding land. Last but not least, the name is changed to EJOT U.K.
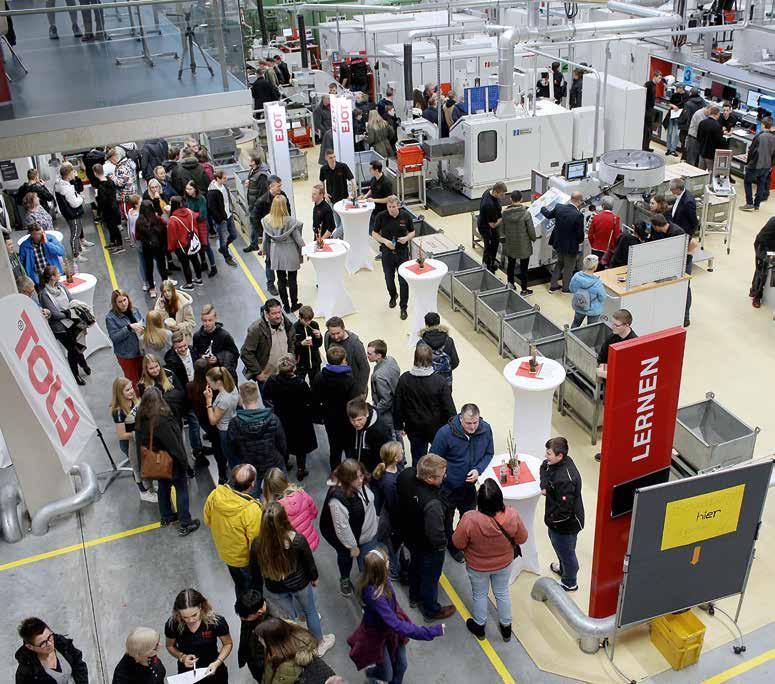
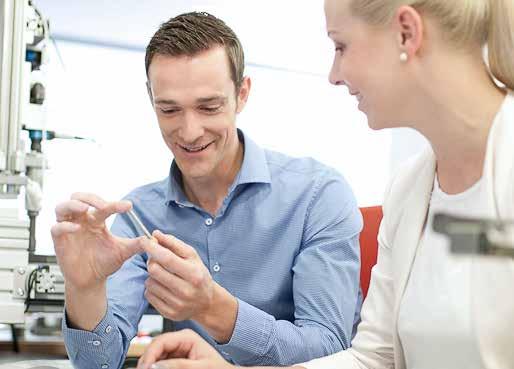
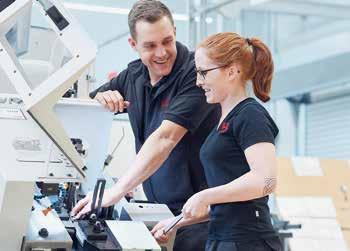
The selection of suitable candidates could hardly be narrowed down, and it was not possible to train as many people as there were potentially available. Many companies remember these times wistfully, because the job market has now completely changed: back then, young people spent a lot of time creating the perfect application portfolio and presenting themselves in the best light, but today it’s the employers who are fighting to recruit young talent. Numerous companies are unable to fill their available training and study positions and are left empty-handed. The reasons for this are complex. In addition to demographic changes, increasing academisation is a major concern. If the drastically reduced number of students also increasingly prefers academic courses to conventional training, this will exacerbate the existing skills shortage long-term.
In the competition for the still existing talents, EJOT prepares itself with great commitment. Just like students did a few years ago, now we try to submit the perfect application to the young people with diligence, effort and creativity and recruit them for training or studies at EJOT. Annual job fairs (hands-on technology) meet with a strong response, as do the activities of our training ambassadors in schools.
Here it is important not only to focus on the smaller number of students who are still interested in education. Rather, the overarching goal must be to increase the basic population of young people willing to undergo dual training again. Since cohorts with a low birth rate can no longer be influenced in retrospect, it is important to put dual training back into perspective. A broad social discussion must succeed in bringing the German education system, which is still envied in the world, back into the focus of young people and their parents. The fact that dual training has turned into a second-class education pathway in parts of society is a development that is more than questionable. A “career with an apprenticeship” is still a “win-win situation” for young people and for businesses. This is impressively demonstrated by the countless apprentices who have been trained over the past decades and who today form the backbone of the EJOT Group as responsible specialists and managers. E
2003
The first General Manager Meeting with the managing directors of the foreign subsidiaries takes place. The main topic is the restructuring and the associated changes for the national companies.
2004
Merger of the Polish organizations into EJOT POLSKA Sp. zo.o The expansion of the European Union is one of the reasons for the concentration process. Due to the retirement of a managing director, the two previous companies are merged.
2004
New hardening plant in Türkiye: After the joint venture was founded in 2000, it quickly became clear that the aging salt bath hardening plant would have to be closed. It is replaced by a modern plant based on European standards.
The advisory board – an important control body for the company’s success
The first meeting of the new advisory board was held on 2 May 2001. For the EJOT Group, the event marked the beginning of a new chapter in its management organisation. With the reorganising of the group structure, the decision was also made to found an advisory board.
>>Text: Andreas Wolf
Alecture held at the University of Witten-Herdecke by Prof. Rainer Kirchdoerfer, a representative of the law firm Hennerkes, Kirchdörfer & Lorz, was to prove key to the later decision. It was Prof. Dr. Hennerkes himself who was tasked with preparing a proposal on the shape that an EJOT advisory board should take.
The advisory board at EJOT was established as an advisory and controlling body for the management of the holding company. The board was also to accompany the new generation of the family business.
In modern “stock exchange language”, the advisory board could also be described as a kind of supervisory board for family businesses. Important control tasks were assigned to the new body in the Advisory Board Rules, such as the approval of annual plans and budgets of individual companies or the approval of major investments. Furthermore, the advisory board was intended to provide a broad background knowledge and a wealth of experience to the management group of the EJOT Group. This was particularly important for the shareholder family, Kocherscheidt, as the members of the advisory board who were not a part of the Kocherscheidt family were themselves entrepreneurs.
The purpose of the advisory board’s control function was to prevent shareholders from making and immediately implementing decisions – decisions first had to be examined and evaluated from several sides. For the EJOT Group, which had just expanded at that time, this was an important step in professionalising the business. And last but not least, the decision to establish the advisory board also made allowances for the risk of a fatal accident involving one or more shareholders. This made for a group management and control system which would continue to function even in the event of such a tragic event.
At that time, the newly constituted advisory board of the EJOT group consisted of the following members. Family: Hans Werner Kocherscheidt, Kathrin Susanne Rörig (today Kocherscheidt), Bernd Frank Reuther. External advisory board members: Dr. Hans Werner Löhr, Dr. Harald Marquardt and Donald E. Surber. Hans Werner Kocherscheidt chaired the board, and Dr. Hans Werner Löhr was the deputy chairman.
In the anniversary year 2022 the advisory board of the EJOT Group is made up as follows: Dr. Hans-Toni Junius (Chairman, pictured), Kathrin S. Kocherscheidt, Jean Dufour, Prof. Dr. Thomas Bauernhansl, Dr. Uwe Böhlke, Andrea Teutenberg. The long-serving chairman Dr. Claus-Dieter Hoffmann who is set to retire will be seen off in August at the centenary celebrations. E
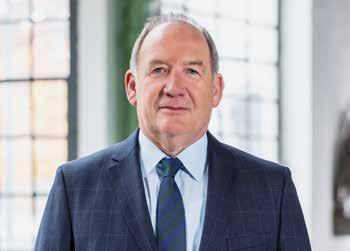
2004
New central warehouse in Gießen: The outsourcing of the finished goods warehouse is intended to optimize logistics costs. The location in Gießen is advantageous due to the convenient transport connections. But the new central warehouse in Gießen does not prove suitable. The logistics of Construction Fasteners and Industrial Fasteners return to Bad Berleburg. The logistics for ETICS products remains in Gießen.
2005
Foundation of Bulgaria EOOD & Co. KD, Pleven, Bulgaria. The EJOT Group has grown with the sales office in Bulgaria. The joint venture partner of the new company based in Pleven is Horizont-Ivanov EOOD.
2005
EJOT has developed special fasteners for the growing market with solar energy. They enable fast and safe installation of photovoltaic systems on roof structures with roofing made of trapezoidal sheet metal, sandwich elements or corrugated fiber board.
The colour doesn’t matter, as long as it’s white
The name EJOT came into being purely by chance: With the acquisition of a teletypewriter, initials had to be given as an address. Margarete Jaeger, the wife of the company founder Eberhard Jaeger, picked the letters “E” and “J”. However, as two letters were not enough, she also added an “O” and a “T” to make “JOT”, the phonetic spelling of the letter “J” in German - and so the name “EJOT” was born.
>>Text: Annemarie Bremer
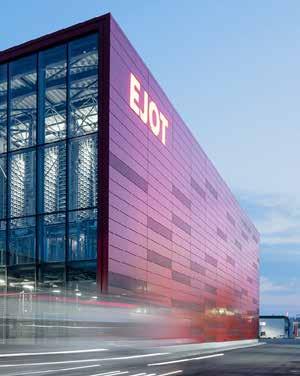
From these four letters, she also developed the first company logo: an upside-down DIN 85 slotted screw in a square field with the name EJOT written across the threaded shaft of the screw. Those not familiar with the company often didn’t understand the letters “O” and “T”. So in the 1980s, the company decided to make a mnemonic out of the abbreviation "EJOT" with the phrase “Eine Jeweils Optimale Technik” (An Always Optimal Technology), which, however, never really caught on.
In 1984, the two companies Adolf Böhl and Eberhard Jaeger were merged under the name EJOT. For the development of a new logo, Hans Werner Kocherscheidt commissioned different designers to come up with several new design ideas. In the end, a proposal by the designer and graphic artist Ulf Höppner from Berleburg, Germany, was chosen - from that day on, a new red logo could be seen on all business papers, and which can still be seen today on every company building and on every company car.
No matter where a building was rented or built, at home or abroad, Hans Werner Kocherscheidt would be there to ensure that his ideas about the image were implemented. Corporate identity was very important to him and he wanted to ensure that the new logo was displayed on all company property. The new trademark had a modern logo, which, thanks to its timeless design, has remained unchanged to this day. The ERAS font served as a base, but the letters were moved slightly closer together so that the text couldn’t simply be inserted in the corresponding font, a mistake that is often made. If the font appears familiar to you, you might already know it from the logo of the CDU, Germany’s Christian Democratic Union party. Here, too, the basis is the font ERAS, with the sole difference being that the letters CDU were tilted to the right, and therefore arranged somewhat differently.
The first version of the design manual, which was typically referred to by engineers at that time as a company standard, was created in the early 1990s. The logos and fonts, like the standard Helvetica font, were also written the same as the first additional logos like “EJOT Qualität verbindet” (EJOT: The quality connection) - and were directly made available in several languages.
For brochures and other advertising material, an inventory was first necessary. Green and purple logo variants existed mostly with Asian licensees.
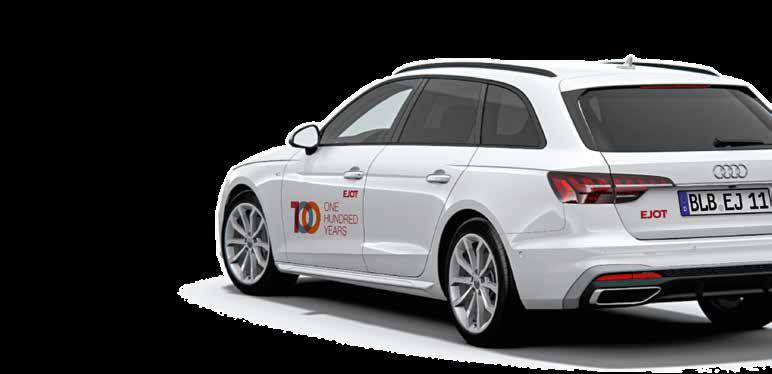
We have of course developed over the years: today, a modern design manual is available where the most important design elements are described, from the logos and business equipment to the description of image worlds. With the design manual, we also want to achieve a uniform appearance of the EJOT brand internationally. This manual is a living document and is continually being developed.
The red EJOT logo even has its own fixed place at the rear of the vehicles that make up the EJOT fleet. When it comes to the colour of the vehicle, the following sentence still applies today: The colour doesn’t matter, as long as it is white. Picking white was a clever marketing decision at the time, because for a long time the colour white was rather unpopular for cars and therefore rare. Consequently, white EJOT vehicles stood out and became somewhat of a unique selling point for the company. Werner Kocherscheidt was always proud of the white EJOT fleet. An attempt to introduce the colour silver to the EJOT company vehicles was unsuccessful. E
2005
Foundation of the new company EJOT Fastening Systems Co., Ltd, Taicang in China. 50 km northwest of Shanghai, Taicang is a central location of German-Chinese cooperation. Other companies such as Waelzholz or Schaeffler are also located there.
2005
Foundation of the subsidiary EJOT Tehnika Spajanja d.o.o. in Serbia. The site is located 15 km from the center of the capital of Serbia, Belgrade. With three employees it is intended to further the southeast expansion for the construction division.
2005
Over the last few years the structured, goal oriented project work has become a steady part of our business processes. For this reason, a project workshop is now held annually. 1.1 EJOT® logo
1.1.2 Free space
In order not to impair the effect of the logo, a free space is defined in which no other graphic elements may be placed.
CORPORATE DESIGN Style Guide
Version 2.4 | 04-2022
Style Guide Version 2.4 | 04-2022
The free space is minimum 50% of the height of the word and figurative mark EJOT. Four "x" correspond to 100% of the logo height.
Style Guide Version 2.4 | 04-2022
2.1 Brochures
2.1.1.1 Cover page > General design
The same print space and the same dimensions of the logo and the claim apply to all cover pages.
| Produkte | Spezial Anwendungen
4
3 1
5
Title head 2020, 34/40 pt Adis di omnimo
Title sub 2020, 18/24 pt, Adis di omnimo
2 Design
1. A large image about the topic or the content is placed in the upper area.
2. The image motif is cut at the lower edge at an angle of four degrees rising to the right. The height of the image motif varies depending on the type of the cover.
3. On the left side of the image motif, there is a trans6 parent area for describing the subject (80% white).
4. Text box for describing the subject
5. For the headline, the defined title head with a font size of 34 pt and a line spacing of 40 pt is the standard.
For the sub headline, the title sub is used. Font size is 18 pt and line spacing 24 pt.
Adobe InDesign Templates
Design templates for Adobe InDesign are available for download in the Marketing Cloud: > Download templates
45
2006
Relocation of the VBT business unit “Fensterbauschrauben” (industrial window fasteners), as Business Unit IFF at Building Fasteners. The windows and glass facades product areas complement the building envelope product portfolio. The product area of window construction deals with products for the industrial production of windows and doors made of PVC, wood and aluminum. In Germany, EJOT is one of the market leaders.
2006
The new company pension plan offers advantages for both the employer and the employee. An in-house collective agreement stipulates that employees can convert a fixed number of overtime hours into the SENECA program, plus a performance-related component. The employee receives an additional retirement benefit and the employer achieves flexibility with overtime hours.