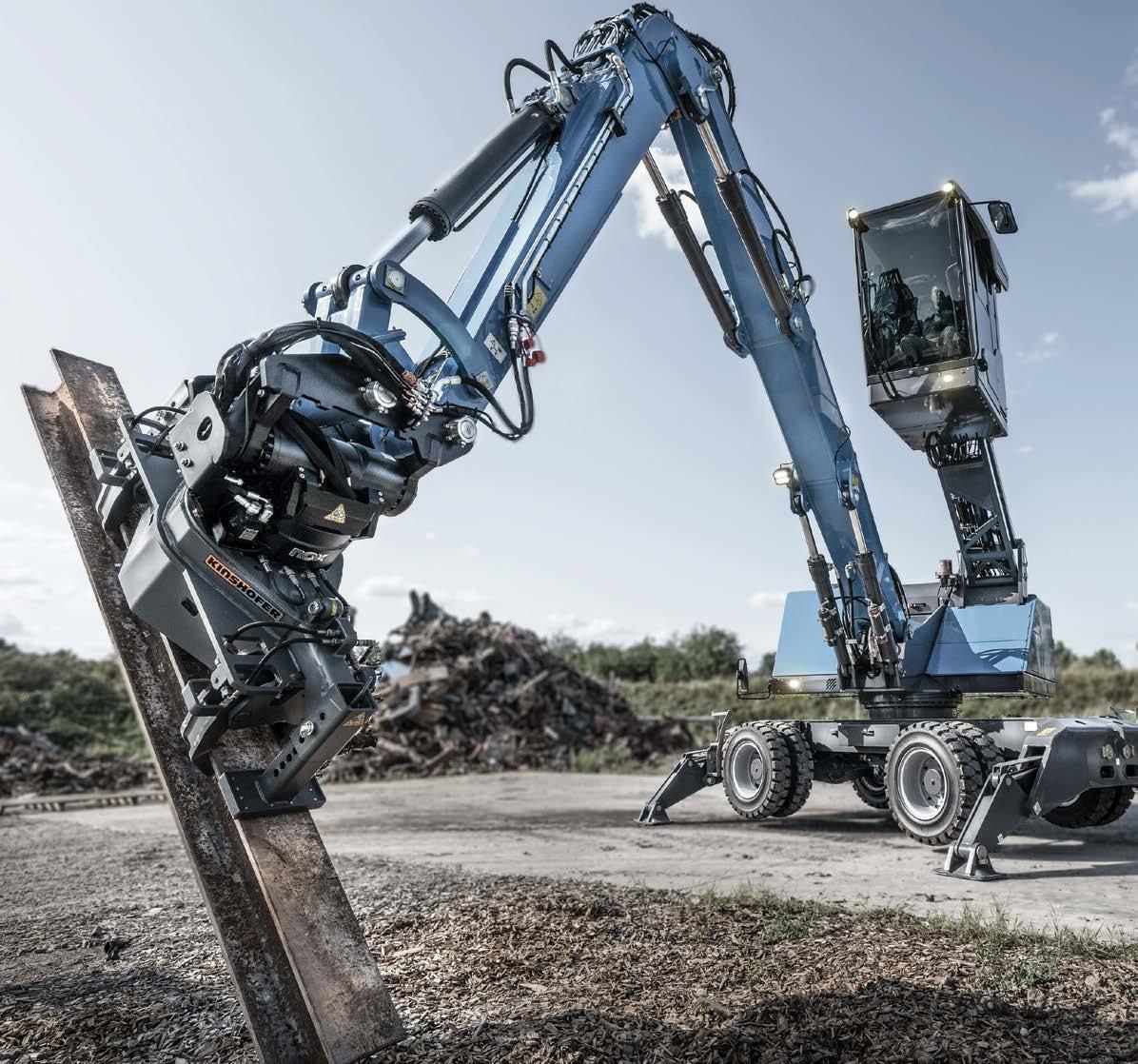
10 minute read
Material Handling Equipment In Mining Industry And Other Industries Scenario
Material Handling Equipment

Advertisement
mateRial Handling equipment in mining induStRy and otHeR induStRieS SCenaRio
One of the most complicated industries is mining, which requires the transportation of vast quantities of bulk materials and minerals at each stage of the mine-tomarket value chain, from the extraction of ore through the delivery of the finished goods to customers. To stay competitive, mining operators need custom, effective material handling and storage systems. They are looking for reliable, low-maintenance hauling, feeding, conveying, loading, unloading, and lifting equipment and storage solutions that are affordable.
To move ore, minerals, or metal products from one place to another efficiently, mining businesses need specialised material handling equipment. Maintaining production and sales volumes while lowering operating expenses could be achieved by selecting the right materials handling and storage systems.
For activities involving underground mining, material management might be complicated. The objective of material handling or mine haulage systems is to move rock masses from one area to another as effectively as possible while preserving production rate and lowering operational expenses. It is crucial to comprehend the proper material handling systems because to the numerous different mining processes, structures, distances, and shifting faces or draw points.
The objectives are set on absolute safety, extreme automation, and
ment P qui e aterial Handling m
lightning-fast, secure network connections when operating in extremely difficult conditions. Modern equipment, facilities, and strict equipment maintenance are required, as well as ongoing risk analysis. Agile and reliable data transfer is also in high demand due to the operating environment, complex business processes, and growing automation. The machines in a mine must operate without latency or interruptions in the network. Valid and trustworthy real-time data, together with asset information management, are crucial because they allow for better revenue to cost ratios, optimal productivity, and more accurate service prediction. Underground Mines Material Handling Conveyors: Due to their high energy efficiency and relative simplicity, conveyor belts can be a useful part of a system for hauling materials. Conveyors can be used as either a primary means of haulage or a secondary method, depending on the size of the mine and the geometry of the orebody. Due to the building of the necessary infrastructure, developing a conveyor system often has a high capital cost, but in mines with extended mine lives, the overall savings can be quite profitable.
Production rate, mine life concerns, ventilation, and ore body geometry are important variables in assessing the viability of conveyor systems. The ore body geometry is the main factor to be taken into account for conveyor system suitability. Material can now be transported over inclining gradients thanks to new conveyor technology. Conveyors, however, work best with ore deposits that are horizontal or shallowly dipping. Uncrushed ore often cannot be transported at a slope greater than 20 degrees. Conveyors take full use of economies of scale since they require production rates that are high and reliable enough to warrant replacing trucks. Conveyors are stationary systems that are difficult to shift.
Locomotive Tramming: The main forms of mine locomotives are powered by compressed air, diesel, batteries, trolleys, battery/trolleys, and to a much lesser extent, flywheels. There are essentially two uses for the subsurface locomotives, Work on the shaft bottom, secondary hauling, and gathering duties and Major highway hauling
The first category often entails brief hauls with relatively few vehicles and calls for a locomotive moving at a speed of 8 km/h. In the latter category, a larger distance is often travelled at a faster pace; diesel and electric locomotives are typically utilised for this task.
The weight and horse power of a locomotive must be chosen in accordance to the load, track grades and curves, track conditions, and the type of bearings on the car. Due to the limitations of the tracks, a locomotive tramming system is typically chosen in conjunction with one or more other transportation methods.
Conveyor systems are the best option for moving mass quantities of minerals underground, but they lack the flexibility of subterranean locomotive systems to move people, supplies, and materials underground in both directions. The locomotive system should be chosen for its versatility if the mine's conditions forbid the use of more than one type of haulage system for both material handling and the transfer of personnel and supplies.
Underground Haul Trucks: In underground mines, haul trucks are a typical means of transportation and are frequently seen in mines with ramp access that are quite shallow. They are the predominant haulage method in mines with annual capacities of less than 1,000,000t,
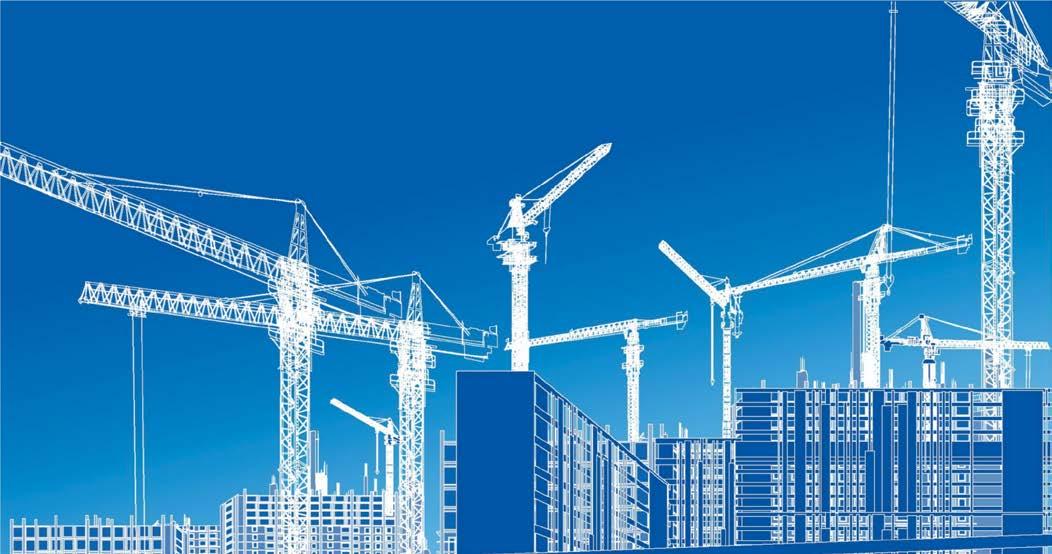
ment P qui e aterial Handling m
spanning from 200 to 400 metres. Because of its great level of flexibility in routing and capacity as well as their comparatively inexpensive initial cost, haul trucks are frequently preferred in mines. Toxic emissions, ramp traffic, noise, heat, and fuel consumption all contribute to the high operational costs of haul trucks.
When haul trucks are used with an LHD, they are frequently loaded at a draw point and made ready for transport outside the mine. Usually, they transport loads to the surface, an ore pass, or a crusher facility where they will be discharged. Haul trucks and LHDs should be mutually adapted for the fleet to maximise loading efficiency.
Depending on the job, underground haul trucks have a wide range of working capacities, although the largest truck made by Caterpillar has a loaded capacity of 60 metric tonnes. The dimensioning of the haul trucks must be considered when designing the subterranean network system. These three factors—width, turning radius, and inclination—should be mutually chosen with the mine design. Operations will be less efficient and unsafe if the equipment and mine design are not dimensioned properly or optimally. Along with design for dimensions, other design factors including a mechanics bay, parts inventory, and ventilation and cooling capacities should be taken into mind. Subsurface haul trucks need a lot of maintenance in order to function properly because of how diesel equipment and underground operational equipment are designed.
LHD Hauling: The LHD or scooptram hauling technique is a flexible way to carry rocks. LHDs are the most typical loading equipment in several mining techniques. In order to continue the production supply chain after mucking underground, LHDs can either load one of the material handling systems already mentioned, or they can truck the material to the next point within the system. Modern LHDs are semi-automatic and designed for manual (on level) operation. They are used to muck ore in hazardous areas or beneath unstable ground. The use of technology to run the through tele-remote operations is also being tested and utilised. With the use of this technology, personnel will be able to control the machinery from a distant place, such as an office above ground. Additionally, operators can simultaneously operate three LHD units
Industrial Trucks: Industrial trucks are used to transfer materials over varying pathways and where there is an intermittent necessity for material flow and usage of a conveyor cannot be justified. Industrial vehicles are not permitted to travel on public roadways. One illustration is the production of lump and fine minerals by mines and quarries, which are then loaded into industrial trucks like dumper trucks and transported to a facility for mineral processing. Because there are no constraints on the area covered and because they can enable vertical movement if the truck has lifting capacity on a steeper route, trucks are more flexible than conveyors and cranes.
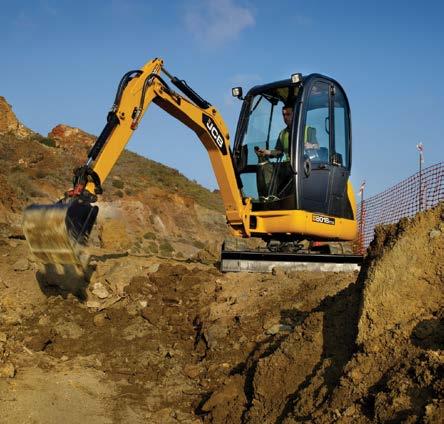
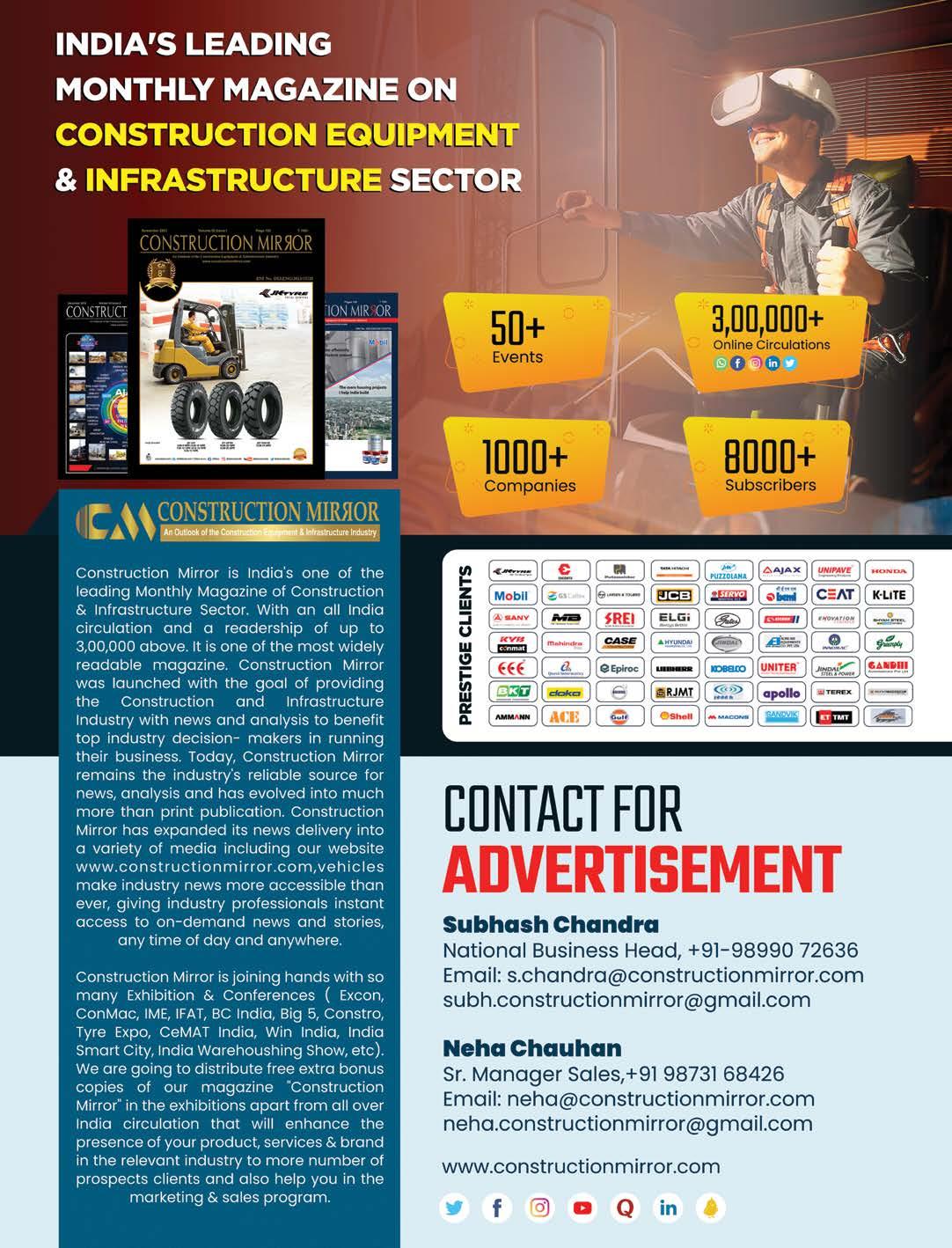
ment P qui e aterial Handling m
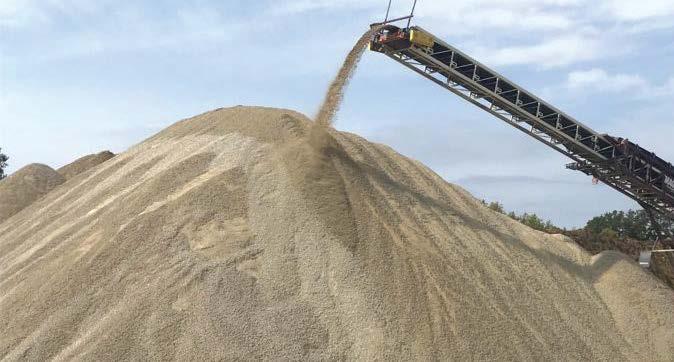
Material Handling In Other Industries There are three equipment use cases in the material-handling market: warehouse management, shop floor operations, and field operations. Accuracy, dependability, and cost-effectiveness are some of the success factors that are similar to these fields. Picking and sorting efficiency as well as monitoring precision are important success factors in warehouse management. Low operating expenses and prompt product delivery to production lines are typically valued in shop-floor operations. The field-operations use case also benefits from mechanical skills like ports, mining, and building, as well as from the ability to manage several operations at once.
The objectives are set on absolute safety, extreme automation, and lightning-fast, secure network connections when operating in extremely difficult conditions. Modern equipment, facilities, and strict equipment maintenance are required, as well as ongoing risk analysis. Agile and reliable data transfer is also in high demand due to the operating environment, complex business processes, and growing automation. The machines in a mine must operate without latency or interruptions in the network. Valid and trustworthy real-time data, together with asset information management, are crucial because they allow for better revenue to cost ratios, optimal productivity, and more accurate service prediction.
The need to achieve cost efficiency in places with higher input costs is what is primarily causing the trend toward increasing automation to occur in the Americas and Europe. Given the lesser influence of e-commerce and smaller investments in infrastructure, the market in Europe is only exhibiting marginal growth in the meantime. However, AGV and ASRS growth is outsized globally, and the COVID-19 pandemic has little effect on growing market shares.
E-commerce expansion and SKU expansion Customers' demands for material handling are always evolving, particularly in the areas of same-day delivery, erratic product volumes, and personalization. However, because of a growth in warehouses and the necessity for locations
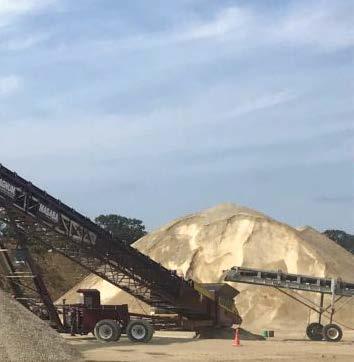
closer to clients, producers must deal with shorter total lead times and more complicated logistics. Additionally, higher risk results in higher proportions of variable and fixed expenses (such personnel and space), but individualization results in smaller order amounts and more frequent unit handling.
Changing demography and increased urbanization. Networks of warehouses, sometimes known as "warehouse footprints," are frequently used by manufacturers. However, rising property values as a result of expanding urbanisation have made it more challenging to find inexpensive warehouses. Additionally, the demand for same-day (or even hourly) delivery is making it harder for distribution hubs to fulfil orders fast. In other words, distributors need more small warehouses close to cities since they want to be closer to end-users. Manufacturers have to deal with an ageing workforce and a general labour shortage due to demography. The former has an impact on the segment as a whole, but the latter has an impact on certain industries that require skilled labour, like crane-and-hoist operations, ASRS, and AGVs.
Increasing infrastructure spending Infrastructure players are funding both new renovation projects and infrastructure renewal in various regions, particularly Asia-Pacific. The construction of new warehouses also needs the necessary supporting infrastructure. Companies are expected to embrace increasingly automated solutions as they relocate to rebuilt factories, especially if they need clean rooms or cold-chain distribution.
Many of these tendencies were already having an impact on material handling, and they have only gotten worse since the COVID-19 pandemic started. Regulations have also changed as a result of increased awareness of sustainability and climate change. It follows that many firms have increased their attention to health and safety. Rigid emissions regulations, for instance, are predicted to increase demand for "hybrid" models in the cranes subsegment, highlighting the need for new cranes or power units that have been retrofitted. Conveyors must adhere to ever-stricter safety regulations, particularly when transporting dangerous goods. Truck safety regulations are also becoming increasingly significant.
Adapting to evolving technologies has long been a goal of material handling. Regardless of whether route is most suitable, manufacturers will need to pursue higher degrees of automation through increased cost effectiveness to free up funds for investments, improved digital technologies, and advanced analytical capabilities. Although the puzzle's pieces may be changing, the objectives are still the same. The only way to be successful is to reach out to clients quickly and correctly, meet them where they are, and cater to their changing demands over time. CM