
11 minute read
Picking Appropriate Lubricants and Market Trends
Lubricants

Advertisement
piCking appRopRiate lubRiCantS and maRket tRendS
Lubricants are essential in the construction industry. The machinery must function under demanding circumstances, including enormous loads, soaring temperatures, extensive wear, and contamination from dirt and water. Given these difficulties, it is imperative to offer the best possible protection. A maintenance team won't always be close by because construction operations frequently shift locations. All equipment owners and operators strive to minimise machine breakdown because it might result in extended unplanned downtime and unforeseen costs.
Not all lubricants are made equal. In heavy-duty industrial applications, such as those found on construction sites, a high-performance lubricant can significantly influence operational success. Heavy-duty construction tools, such those used to build roads, bridges, and buildings, are subjected to challenging environmental conditions. The performance of the lubricant will be impacted by the weather, whether it is a chilly, foggy morning or a scorching, dry, dusty afternoon. The contribution lubricants make to lowering up-front costs is of great interest. Lubricants may increase engine performance and protection while also increasing fuel efficiency. This is accomplished by minimising the amount of metal-to-metal contact between moving parts and by lowering pumping and spinning losses. The oil flows more quickly because it requires less effort to go through the engine due to its reduced viscosity. Modern engine designs that operate at greater temperatures can also put conventional lubricants under stress and hasten the pace of oil oxidation and degradation. Pick the appropriate lubricant for the task at hand.
Your company depends on you to select the best lubricant for optimal performance because
ubricants l
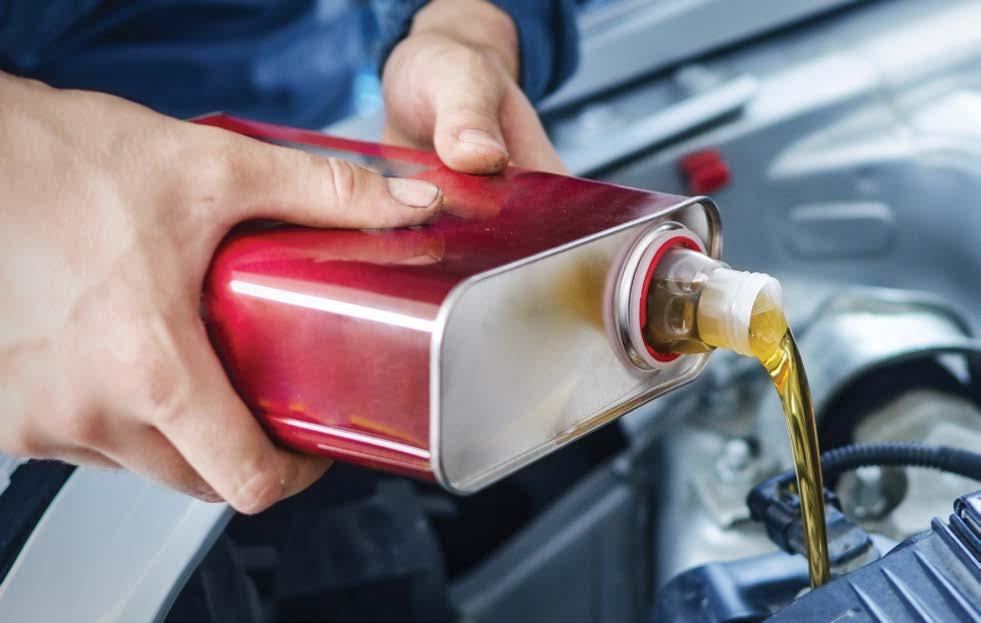
construction equipment operates in some of the roughest settings. However, some lubricants are better suited for particular conditions, much as some projects are better suited for an excavator as opposed to a dozer. For instance, lubricants are available in a variety of viscosity grades that are both intended to function at high operating temperatures as well as the ambient temperature range. Some lubricants are made to function in cooler climates, while heavier-grade lubricants are made to function in hot climates.
To protect moving parts in cold conditions, you need a lubricant that can pump and flow during starting while maintaining viscosity at operating temperature. It's crucial to select a product for hot regions with a viscosity range that prevents the lubricant from thinning out at high temperatures, which could result in metal-to-metal contact.
The lubricants that keep construction equipment operating smoothly have changed along with it over the years. Numerous advantages of lubricant technology have been demonstrated, including increased machinery performance, lower maintenance costs, and longer equipment life. Modern engine oils can improve operational efficiency by consuming less oil overall and offering longer drain intervals, which decreases the amount of old oil that needs to be disposed of. Workplace contamination is less likely when greases are durable and washable. Additionally, hydraulic lubricants can improve hydraulic response while lowering fuel expenditures and pollutants. Therefore, if you haven't given the most recent advancements in lubrication technology for your construction company a second look, it might be worthwhile because it could increase the equipment's lifespan and improve your bottom line. The needs of various construction fleets vary. Therefore, you might want to think about a bespoke lubrication programme that is made to provide the outcomes you require. For instance, our Mobil experts can assist you in streamlining shipping, storage, and handling by consolidating your lubricant product mix. We can assist you in choosing the best products for your fleet and collaborating with your maintenance staff to identify the best maintenance service intervals that keep your equipment operating efficiently on the jobsite, thereby assisting you in completing projects on time and under budget.
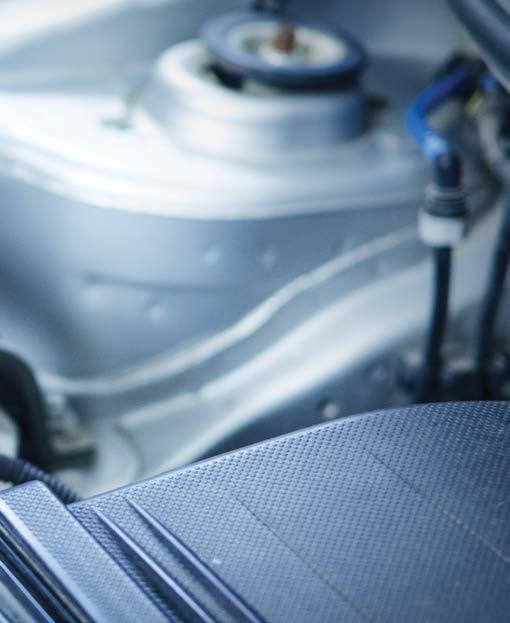
Modern Lubricant Market Trends
Lubricants Without Zinc: Due to their capacity to prevent corrosion of construction machinery and extend the life of equipment, growing demand for zinc-free construction lubricants is developing as a major trend in the industry. Furthermore, zinc-free construction lubricants function well even in conditions of high temperature, high pressure, and high moisture, which in turn is boosting demand for them as the best kind of construction lubricant.
According to the survey, industry leaders in construction lubricants are concentrating on providing high-performance products that will aid end users in protecting costly machinery and minimising unwelcome downtime. Players are making strides with value-added services and offerings in order to provide for a wider end-user base and successfully fulfil their specifications and requirements. In light of the growing end-user preference for environmentally friendly products, construction lubricant manufacturers are also concentrating on broadening their product portfolios by incorporating bio-based variations. The majority of players in the construction lubricants market are already making significant investments to gain a competitive edge, supporting the claim that businesses that develop their digital marketing capabilities to engage end users are likely to gain significant profitability in the long run. Biodegradable lubricants the word "bio-based" describes where a lubricant comes from. This relates to the raw material that is annually renewable and used to create the base stock for the lubricant. These basic stock ingredients include things like soybean, rapeseed, and sunflower goods. These base stocks may have favourable lubricity, flash point, and viscosity index characteristics, but their oxidation stability is frequently subpar. They have a position in some hydraulics, total-loss systems, and environmentally sensitive places, despite their limited use.
Biodegradable Lubricants: Similar to how bio-based lubricants are distinguished by focusing on the front end of the lubricant's manufacture, biodegradable lubricants are distinguished by concentrating more on the back end. It takes into account the purpose and duration for this breakdown to happen, as well as how the environment tends to break down the lubricant, if exposed. Lubricant Specifications
To safeguard engine components and to comply with regulatory requirements, many engine oil specifications currently place restrictions on the usage of certain compounds. For instance, the ash produced when metals like calcium, magnesium, and salt are burned in the engine can clog and harm the vehicle's after-treatment system, putting the environmental protection they are intended to provide in jeopardy. In a similar line, it is well known that phosphorus poisons the catalysts used to burn off unburned hydrocarbons. These elements also have powerful properties, such as the ability to neutralise acids for calcium and magnesium, to prevent wear for components containing phosphorus, and to act as antioxidants for components containing sulphur. Vehicle manufacturers frequently develop innovations that lead to new performance standards for motor oils, which are sometimes crucial to the engine. For
ubricants l
instance, smaller automotive engines have been designed to reduce fuel use and, consequently, CO2 emissions. These engines typically have smaller displacements, turbocharging, and more power than the engines they replace. Sections of the engine's speed load/map may cause a phenomena known as low-speed pre-ignition (LSPI), which can cause severe engine damage, with high compression ratios and optimised fueling. In order to assist prevent LSPI, new lubricant characteristics were needed, and LSPI tests are now being added into the most recent engine oil requirements. Lubricant Selection
The function lubricants play in lowering upfront expenses is a topic of great interest. Lubricants may increase engine performance and protection while also increasing fuel efficiency. This is accomplished by minimising the amount of metal-to-metal contact between moving parts and by lowering pumping and spinning losses. The oil flows more quickly because it requires less effort to go through the engine due to its reduced viscosity. Modern engine designs that operate at greater temperatures can also put conventional lubricants under stress and hasten the pace of oil oxidation and degradation. Implementing a successful used oil analysis programme into a company's fleet management strategy has many advantages. A good programme is a cost-effective technique that can check the oil condition in heavy industrial equipment as part of a solid maintenance regime. Three processes are normally involved in oil analysis: removing a representative sample from the apparatus, sending the sample to an accredited used oil analysis lab, and analysing and acting on the findings. Oil analysis is most successful when carried out on a regular basis so that a trend can be created and used to enhance equipment performance and efficacy. In order to demonstrate operators how and why machinery is wearing down and to help them pinpoint the source(s) of contamination, testing can find contaminants and measure their concentration. Regularly checking the quality of the lubricant and the machinery allows for the early detection of small mechanical issues, which can then be fixed quickly and affordably. It is strongly advised to adopt a used oil analysis programme in order to increase efficiency, lengthen drain intervals, and reduce fuel usage. The choice of an oil that can withstand harsh environments and high temperatures is another important factor to take into account. The equipment used in building operations may be subjected to a variety of difficulties brought on by extremes in temperature, depending on the region. The viscosity of the lubricant can become problematic under such demanding circumstances. Depending on the chemical makeup, the lubricant may start to stiffen or become excessively viscous if the temperature enters the critical zone. This leads to incorrect lubrication of industrial hardware, and over time and in demanding situations, equipment may face catastrophic failure. Construction activities can avoid this by using a lower viscosity oil, which can retain viscosity and flow across a wide range of temperatures. Multi-


ubricants l
grade, low viscosity oils work better in a variety of climates since they don't get too thick in cold weather or too thin in hot, providing proper and sufficient oil flow to safeguard important engine components. In addition, by using the lowest viscosity grades permitted by the Original Equipment Manufacturer's (OEM) ambient temperature standards, the entire vehicle powertrain and hydraulic system can see better operational efficiency. Construction equipment doesn't get to retreat to a garage or shed at the end of a long day. It tends to sit outside, day in and day out, until the job is completely done. It's important to use a product that can withstand both rain and sunshine - and everything in between. Grease, in particular, is susceptible to washout since it's oftentimes most exposed. Finally, don't forget about changing seasons. Though construction may pick up in the summer, many projects go year-round until they're complete. Choosing products that are multi-viscosity or have a viscosity that matches the temperature outside is important to ensure your machinery performs at its best. As a general rule of thumb, low- or multigrade-viscosity products should be used during cool temperatures, and higher- or multi-grade-viscosity products should be used during warmer months. How Are the Lubricants We Use Made?
The base oil serves as the foundation for all lubricants. The three types are mineral, synthetic, and vegetable. I'd rather focus on mineral and synthetic materials because we work with them frequently in industrial settings. Crude oil is used to produce mineral oil, and the refinement process affects the oil's quality. A scale is used to grade oil, and various processes call for different levels of oil quality. The four different types of molecules that make up paraffin, branching paraffin, naphthene, and aromatic are the main components of mineral oil. While branched paraffinic oils have the same structure as paraffinic oils but with an additional branch to the side, paraffinic oils have a long, straight chained structure. Branching paraffinic oils and synthetic oils are both man-made liquids with straight chained structures. One benefit of a synthetic is that, unlike mineral oils, which fluctuate considerably and provide features that are rather predictable, the molecular size and weight are constant in synthetics. The oil flows more slowly the less dense it is. For instance, molasses has a low viscosity and a high density, whereas baby oil does not. A given application's speed, operating temperature, bearing type, and component type—such as whether it uses a gearbox or a motor—all have an impact on the viscosity that is necessary. Dispersants protect components against abrasion by wear products by encasing particles and suspending them in the oil, which makes it easier to flush and remove them from the system. Metal-to-metal contact is avoided by a thin protective layer that is produced when EP additives interact with a component's surface. In some situations, using grease instead of oil provides benefits. Grease prevents dry starts because it doesn't void like oil and locks out adulterants. It is also preferable for insoluble solid additives like molybdenum disulphide and graphite. Contrarily, the grease's broadness restricts bearing speed, reduces component cooling, makes sampling and analysis challenging, and makes it challenging to calculate the proper amount of grease to add. When deciding whether to use oil or grease for a particular application, this is an important issue to take into account. You can understand why using the right lubrication in your machinery has so many advantages with just a basic understanding or knowledge of lubrication. Every organisation strives for greater effectiveness, a longer lifespan, and enhanced. CM
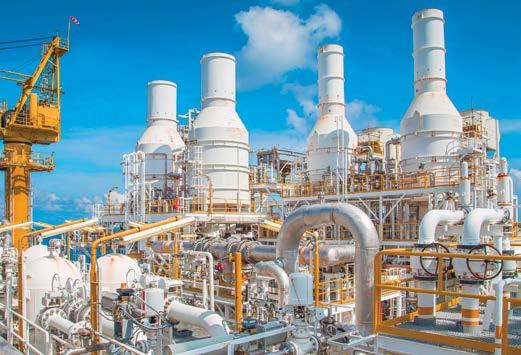
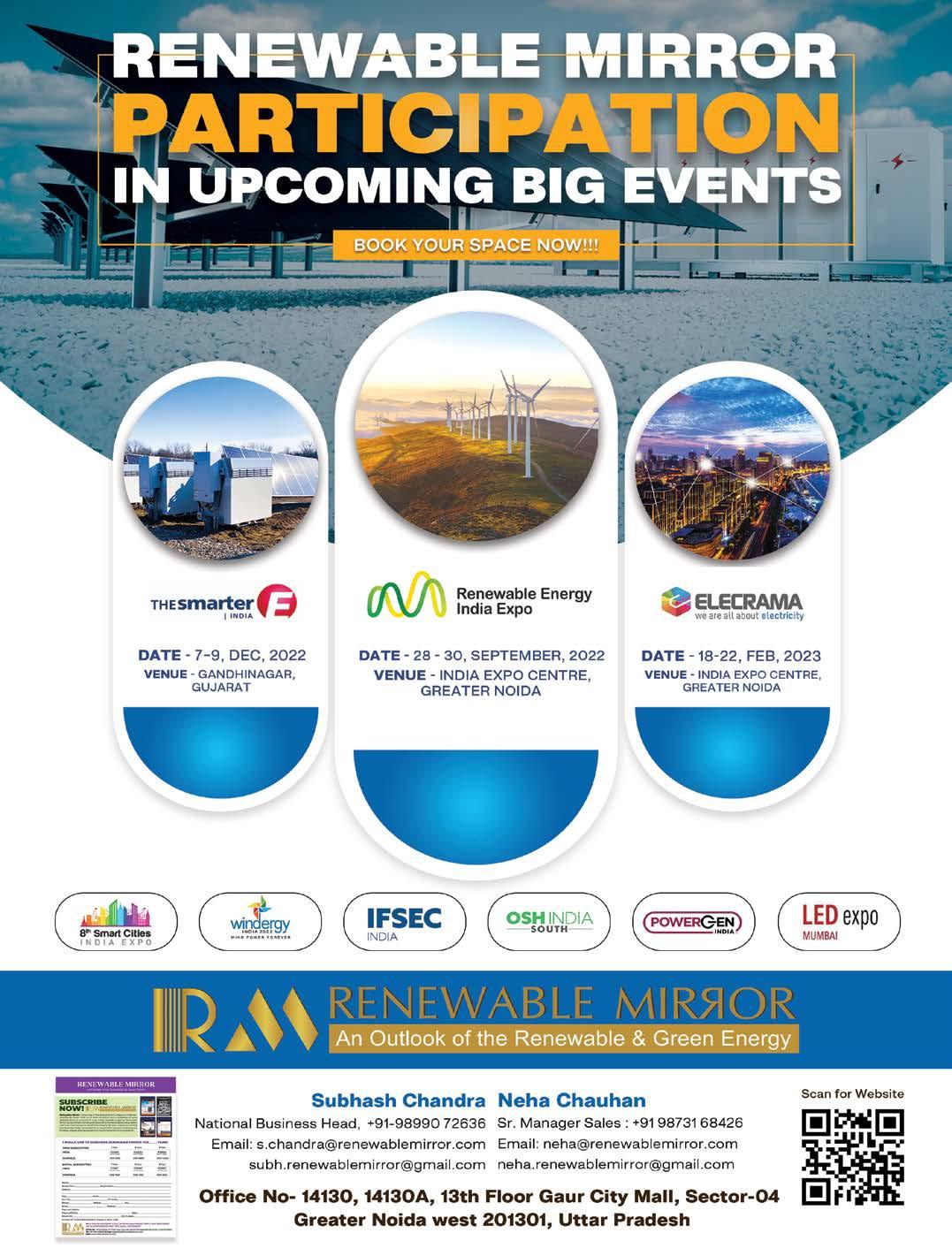