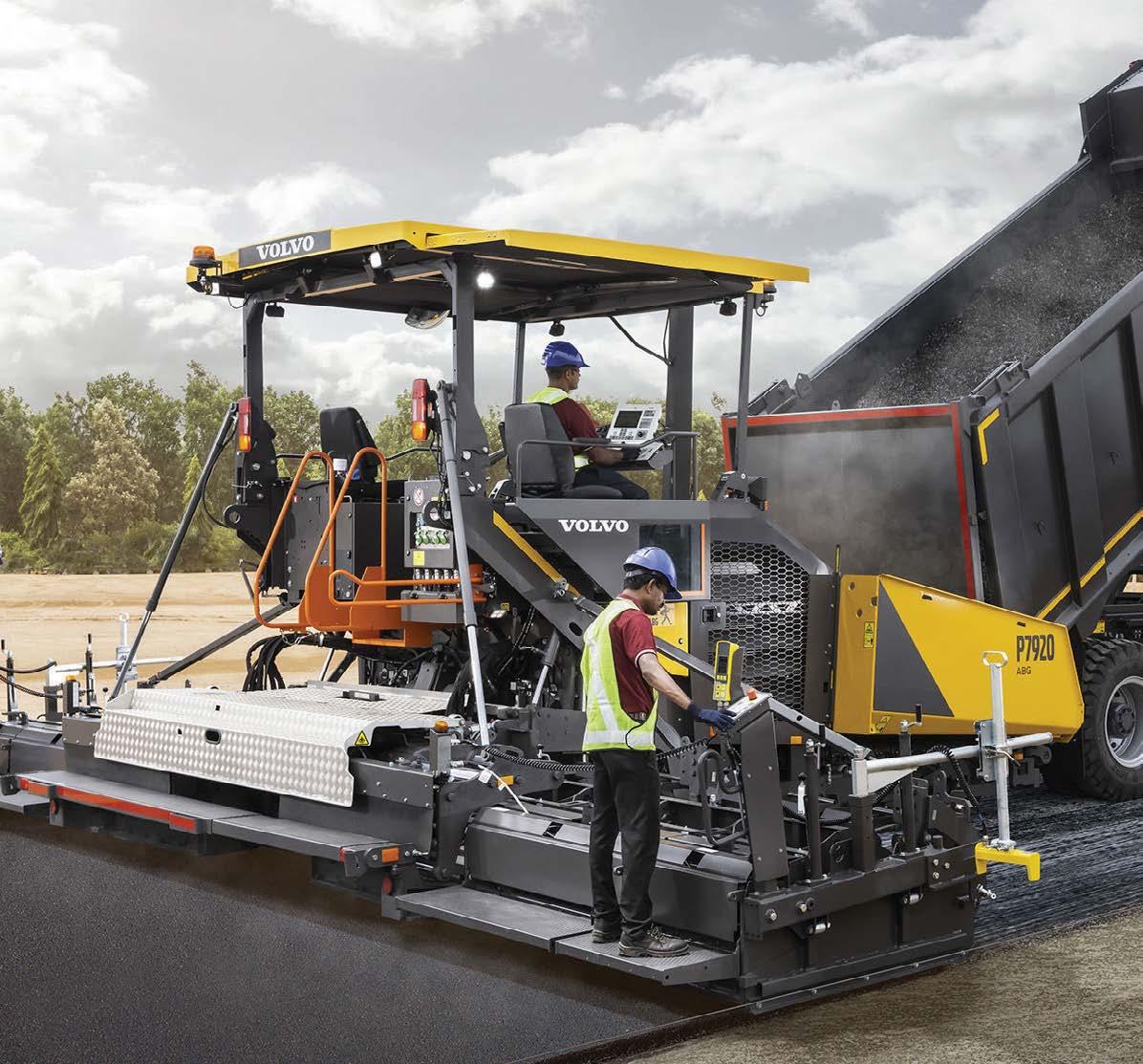
9 minute read
Asphalt Equipment - Process of Making Asphalt Mix
Asphalt Equipment

Advertisement
aSpHalt equipment - pRoCeSS of making aSpHalt mix
Roads have a significant role in economic growth and development and have significant social advantages. They are crucial to the growth and development of a country. The Indian government wants to upgrade its infrastructure, especially for initiatives that involve building roads all around the nation. The asphalt pavements that we use every day are the result of many years of laborious work on the field. The development of better, safer building machinery through trial and error, the use of novel materials, and taking calculated risks to add the finishing touches never stop. In order for a country to thrive economically, its roads are crucial.
Equipment capable of operating without any human supervision handles a large portion of the work involved in laying asphalt pavement. One such is an asphalt mixer, which as its primary components employs a sand and concrete mixture. It resembles a bucket that has been filled with concrete and sand. It employs a technique of mixing and stirring to make sure the mixture is well combined and prepared for pouring. The mixing procedure entails a number of steps, including filling the bucket with the mixture and spreading it out in a layer above the road's surface.
Asphalt Mixing
An essential piece of equipment for building roads is the asphalt mixing plant. The asphalt mixing facility is placed on the site of building the road if the project is significant. In order to create hot mix asphalt, a
ment P qui e alt PH s a
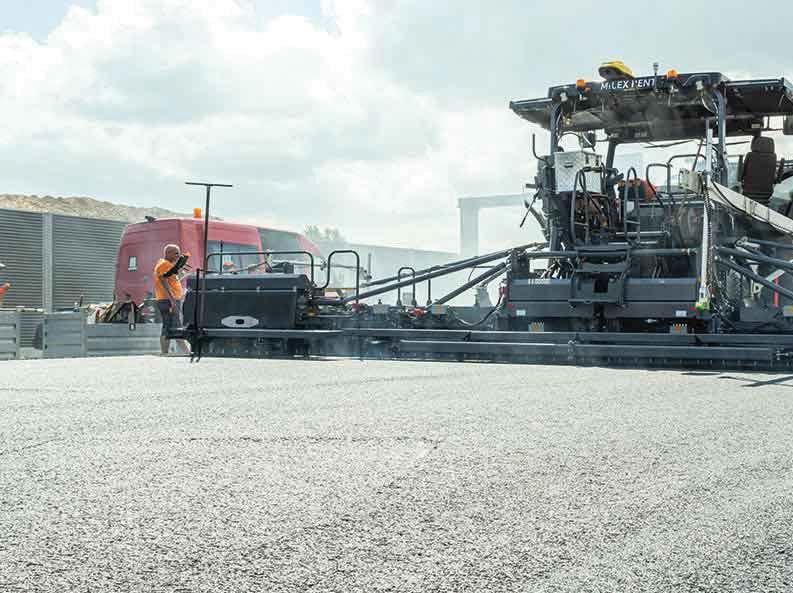
mixture of graded, high-quality aggregates in various sizes is typically heated and combined with liquid bitumen in precise amounts. The paving material asphalt is comprised of bitumen and crushed rocks. Hot mix asphalt's features are influenced by the quantity and quality of bitumen used to create the asphalt, in addition to the types and proportions of aggregate and recycled asphalt pavement. Aggregates must be dried and heated during the manufacturing of hot mix asphalt so that bitumen may easily coat them. The aggregates are dried in a spinning, slightly incline drier drum with a flame during the drying process. The higher end of the drum is where aggregate is first added. The interior of the drum is furnished with several sorts of flights that aid in adequately heating the aggregates and bitumen coating. Process of Making Asphalt Mix Asphalt paving material is a drab, dark mixture of sand, crushed rock, and asphalt cement. It is heated before being discharged hot and steamed into the roadbed, where it is scraped level and then compacted by a large steamroller. On concrete roads, asphalt is also utilised for expansion joints and repair work. Asphalt is also used for tennis courts, playgrounds, airport runways, and building floors. To bind gravel and settle dust, light versions of petroleum asphalt known as road oils are sprayed on roads. Another significant application for asphalt is in roll roofing, which is often made of felt that has been saturated with asphalt. The asphalt aids in the roofing material's preservation and waterproofing. The following are additional uses for asphalt: rustproofing and waterproofing

tunnels, bridges, dams, and reservoirs.
Refining the unfinished: The first step in refining is to pipe crude oil from a storage tank into a heat exchanger or tube heater to quickly raise its temperature for the first distillation. The lighter and more volatile fractions, or components, are taken off through a series of condensers and coolers when the mixture enters an air distillation tower. Following separation, it is refined further to produce a variety of valuable petroleum products, including gasoline (called a "light" distillate), kerosene (considered a "medium" distillate), diesel oil (considered a "heavy" distillate), and many others.
Topped crude is the term used to describe the dense residue produced by this atmospheric distillation process. This refined crude can be turned into fuel oil or other goods like asphalt by additional processing. A "straight run" asphalt is produced when adequate high boiling fractions are removed by vacuum distillation. To manufacture asphalt cement with the proper consistency, solvent extraction, also known as solvent deasphalting, may be necessary if the topping crude includes enough low volatile components that cannot be cheaply removed through distillation.
Cut Back: The next step is to mix or "cut back" the asphalt with a volatile material to create a product that is softer and more workable than pure asphalt cement at lower temperatures. The volatile component of the cut-back asphalt evaporates when exposed to air or heat, leaving the hard asphalt cement, when the material is utilised for paving or construction. The classification of a cutback asphalt as slow, medium, or rapid-curing depends on the relative rate of evaporation or volatility of the cutting agent. For a slow-curing asphalt, heated asphalt cement is combined with leftover asphaltic oil from the previous distillation process, with kerosene for a medium-curing asphalt, and with gasoline or naphtha for a rapid-curing asphalt.
Emulsifying: The asphalt cement can also be emulsified to create a fluid that is simple to mix with aggregate, pump via pipelines, or spray through nozzles. The asphalt cement is ground into globules 5 to 10 microns and smaller in order to emulsify (one micron is equal to one millionth of a meter). Water is added to this mixture. Asphalt and water are less likely to separate when an emulsifying agent is introduced. Colloidal clay, soluble or insoluble silicates, soap, or sulphonated vegetable oils are all examples of emulsifying agents.
Pulverizing: Asphalt can also be ground into a
ment P qui e alt PH s a
powder to create asphalt powder. To achieve uniform granule size, the asphalt is crushed and sent through a series of fine mesh sieves. For the creation of pavement, powered asphalt can be combined with road oil and aggregate. The Asphalt Cement Substance gradually hardens to a consistency like ordinary asphalt cement as a result of the heat and pressure in the road combining the powder with the aggregate and binding oil.
Blowing Air: The asphalt can be oxidised or air blown if it will be used for something else paving, including roofing, pipe coating, undersealing, or water-proofing. A substance that results from this procedure softens at a higher temperature than paving asphalts. At the refinery, an asphalt processing facility, or a company that manufactures roofing materials, it might be air blasted. 500°F (260°C) is used to heat the asphalt. Then, for one to 4.5 hours, air is bubbled through it. The asphalt does not solidify after it is cooled.
Mixing Asphalt: In a mixing facility, aggregate and asphalt cement are blended, heated, and mixed to create the proper paving mixture. Hot-mix facilities can be portable and moved from job to job, or they can be permanently erected (also known as "stationary" facilities). Both batch facilities and drum-mix facilities, which can be either permanent or portable, can be used to describe hot-mix facilities. Different size fractions of hot aggregate are pulled in proportional amounts from storage bins in batch-type hot-mixing facilities to create a single batch for mixing. The aggregate mixture is poured into a mixing chamber known as a pugmill. Afterward, the aggregate and weighed asphalt are thoroughly combined in the pugmill. The material is subsequently discharged from the pugmill into trucks, storage silos, or surge bins after mixing. The gravel and asphalt are heated and blended together in the drum mixer at the same time during the drum-mixing process.
Final Paving: After mixing is finished, the hot-mix is brought to the paving site and distributed with a paving machine in a partially compacted layer to create an even, homogeneous surface. Heavy rolling machines further compact the hot paving slurry to create a smooth pavement surface.
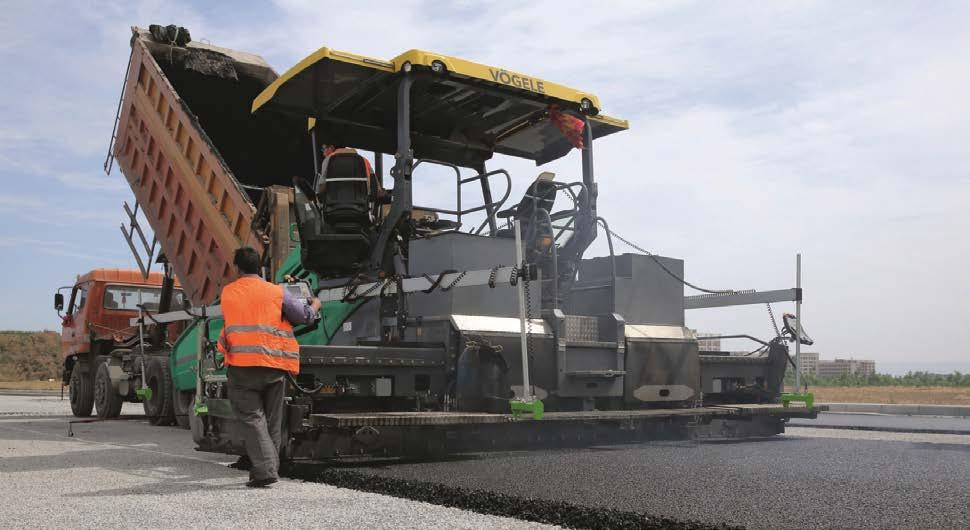

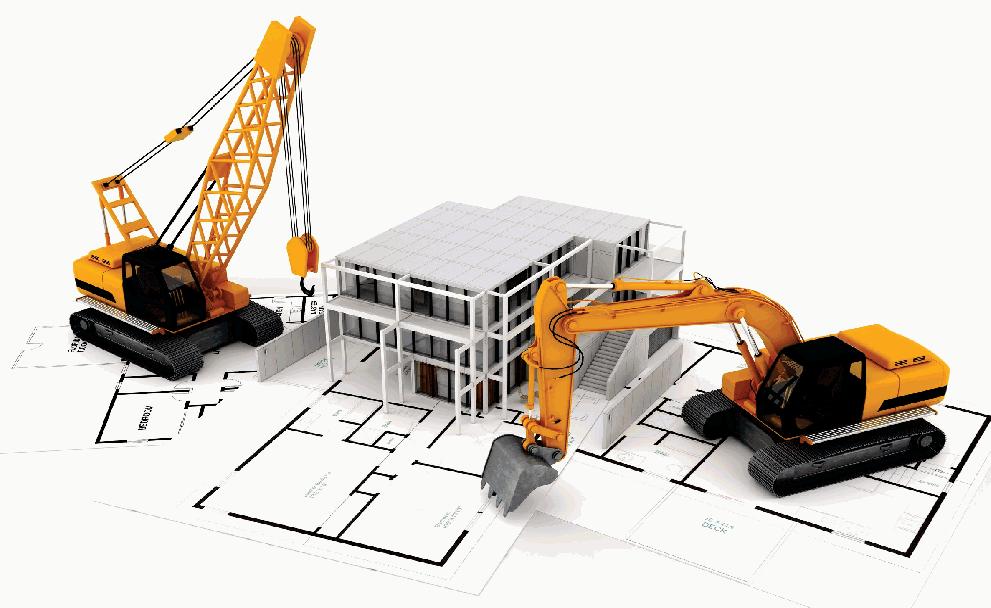
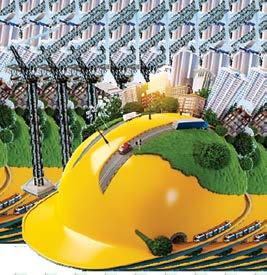
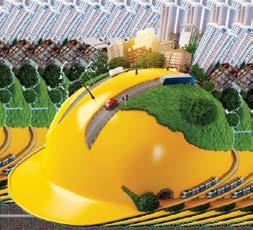
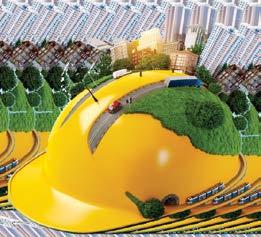

ment P qui e alt PH s a
Asphalt Quality Control The characteristics of the petroleum crude oil used to create asphalt cement have an impact on its quality. Crude oils produced in various oil fields and regions have a wide range of properties. The refinement process has an impact on asphalt cement quality as well. For engineering and construction applications, consistency, also known as viscosity or the degree of fluidity of asphalt at a certain temperature, purity, and safety are three crucial elements to take into account.
Asphalt is rated according to ranges of consistency at a standard temperature since the consistency or viscosity of asphalt cement varies with temperature. Careless temperature and mixing control can harm asphalt cement more during the hardening process than several years of use on a road. To assess the consistency of paving asphalt, a standardised viscosity or penetration test is frequently required. A softening point test is frequently used with air-blown asphalts. Asphalt Waste Water flows, particulate and smoke emissions from oil refineries, and emissions from asphalt production plants are all subject to strict regulations set forth by environmental protection laws. Sulfur dioxides, smoke, and several other emissions must also be strictly regulated, in addition to dust. Equipment needed to regulate emissions includes electrostatic precipitators, primary dust collectors with one or more cone cyclones, and secondary collection units with fabric filter collectors, sometimes known as "baghouses." If left unchecked, hydrocarbons produced during the manufacturing of asphalt produce foul smells and pollutants that will stain and darken the air. Enclosures that catch the exhaust and then recirculate it through the heating process are used to reduce the pollution that comes from the manufacture of asphalt. This reduces emissions while simultaneously improving the process's heating effectiveness. Future of Asphalt Paving The recycling of old asphalt pavements will see numerous new technical advancements in the future, including the use of microwaves to totally breakdown the pavement. Asphalt pavement's crushed rock is heated by microwaves more quickly than the nearby cement, which is then warmed by the rock's radiant heat. The asphalt cement won't burn thanks to this technique. Research is being done on alternative raw material sources, including making synthetic asphalt by liquefying sewage sludge. For the production of modified asphalts and emulsions, new processes are being developed to guarantee constant product quality. For example, high-performance gel-permeation chromatography (HP-GPC), which enables various characteristics to be tested and the data to be collated in only a few minutes, is one of several novel tests being developed to assist define asphalts. Other areas being looked into for improvement include new procedures, more effective mixing and milling equipment, in-line liquid mass flow metres, online monitoring systems, and better safety apparatus. CM
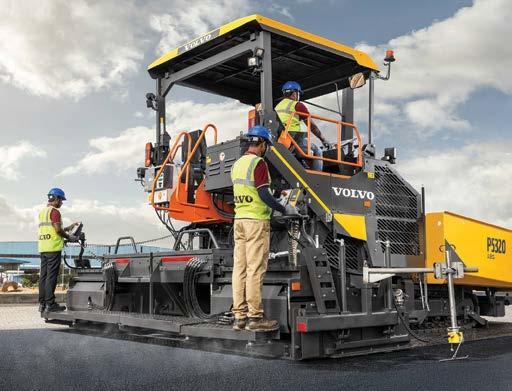
