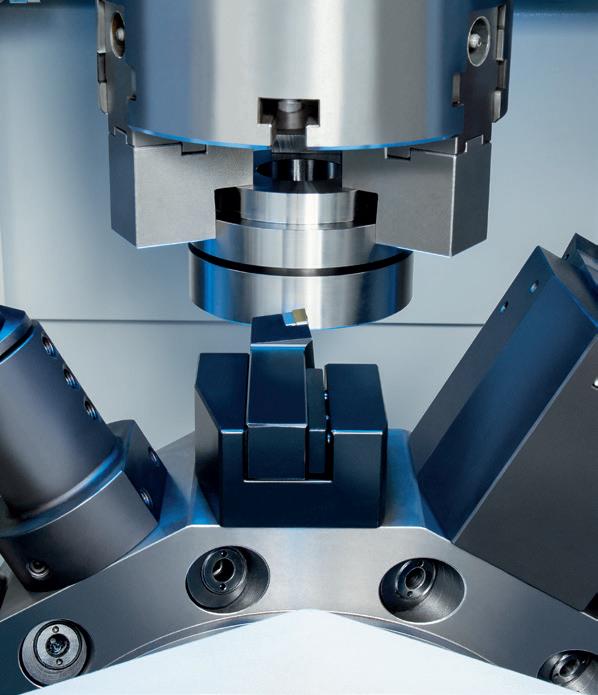
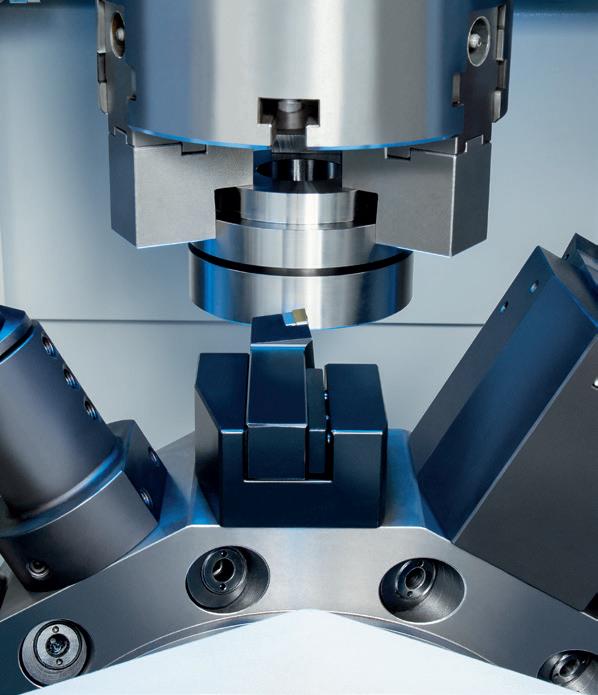
BUSINESS UNIT TURNING
Turning machines for chucked and shaft parts


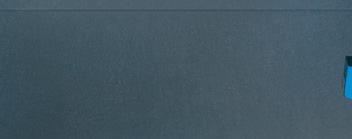
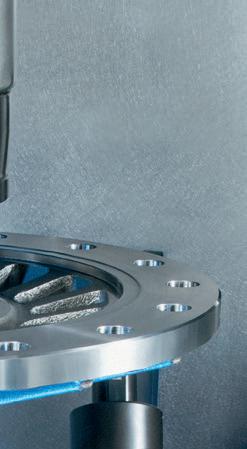

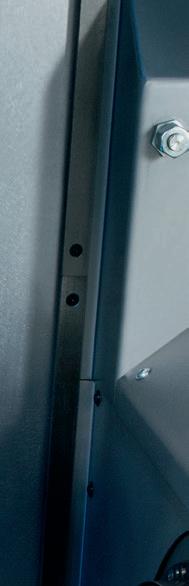
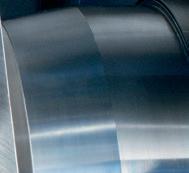
CONTENTS
Turning machines for chucked parts
VL Modular Solutions p. 6
VLC Modular Customized Solutions p. 12
VSC Customized Solutions p. 14
Turning machines for shaft parts
VT Modular Solutions p. 24
VTC Modular Customized Solutions p. 26
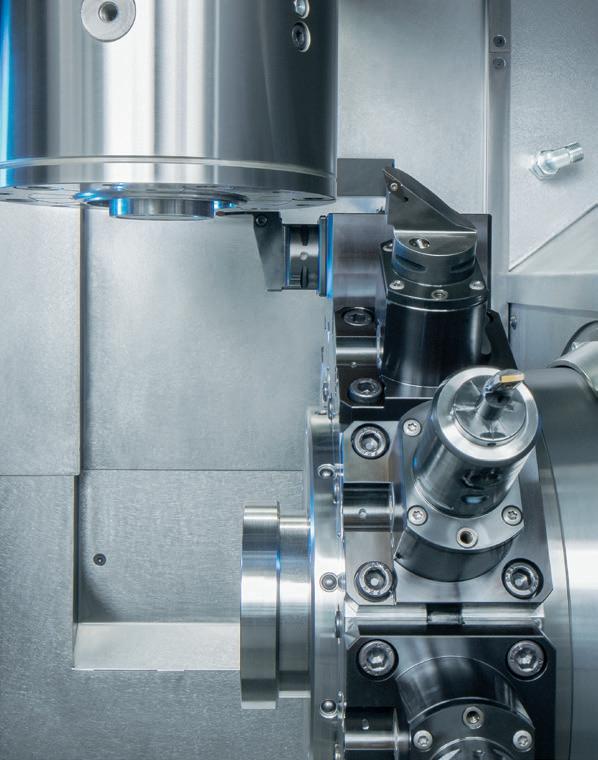
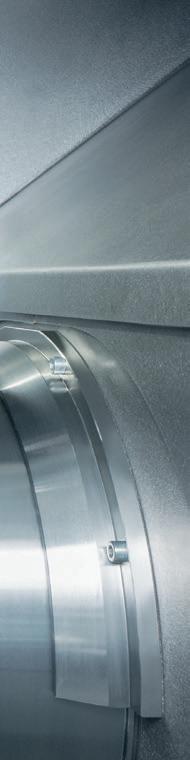
TURNING MACHINES CHUCKED PARTS FOR
VL MODULAR SOLUTIONS
The VL Series vertical pick-up turning machines were specially developed for manufacturing precision chucked components. To cover as wide a range of parts as possible, the VL Series is available in four versions for a workpiece diameter ranging from 10 mm to 400 mm.
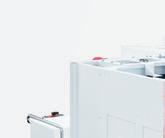
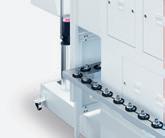

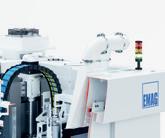
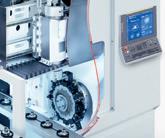
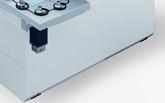


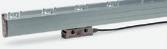
MAXIMUM PRECISION – DIRECT POSITION MEASURING SYSTEMS

M/MIN

THE PATENTED EMAG TURRET
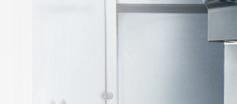
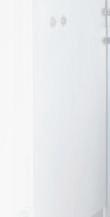
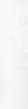
+ Glass scales – Fully encapsulated linear glass scales in all linear axes.
+ Standard – Glass scales come standard on all EMAG machines! Measuring




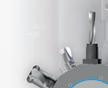
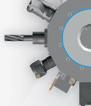
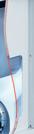







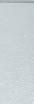
+ Fast, with zero play and wear – the EMAG turret is equipped with a direct drive (torque motor) for swiveling.
+ Precise – Thermal stability is ensured thanks to an ambient temperature controlled cooling system.
+ Flexible – The turret has space for twelve tools (featuring either a VDI or BMT interface). Driven tools can be used in all tool stations. The optionally available Y-axis ensures maximum fl exibility.
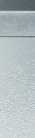
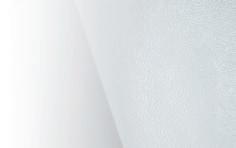
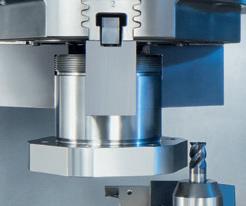
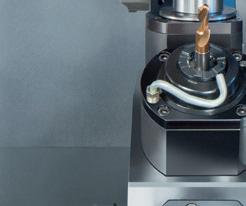
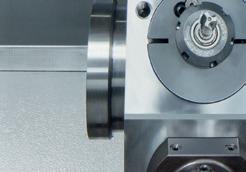
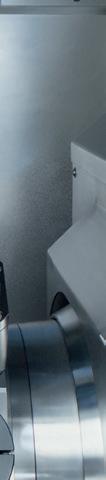
BENEFITS OF THE VL SERIES
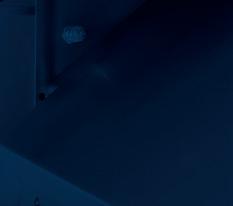
+ High strength
Large working spindle bearing diameter + MINERALIT® polymer
concrete machine body
+ Complete automation
Including raw and finished parts storage areas
+ Simple handling
All the service units are easy to reach
+ Minimum footprint
Compact machine design
+ Maximum performance
Short distances between the machining area and pick-up automation system
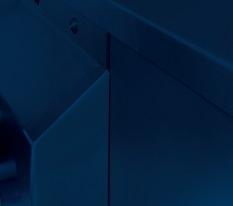
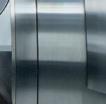
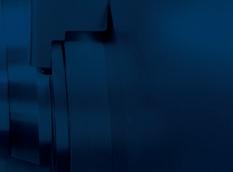
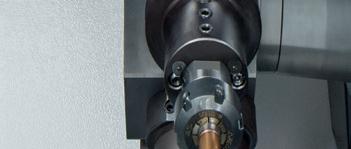
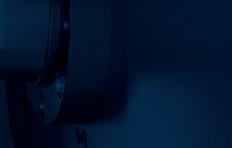
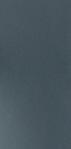
VL MODULAR SOLUTIONS
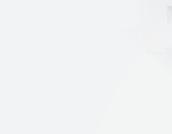
VL 2 and VL 4 for small and medium-sized workpieces
The VL 2 and VL 4 pick-up turning machines are ideal for workpieces with a diameter up to 100/200 mm. They feature integrated automation and a parts storage area, which enables them to operate completely autonomously, relieving the strain on production personnel. Efficient mass production of varying batch sizes is possible and, thanks to flexible clamping systems, they can also easily machine whole part families.

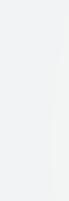
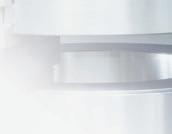
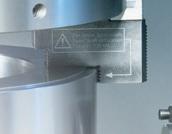
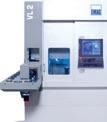


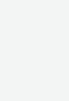

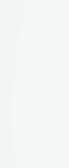
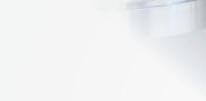
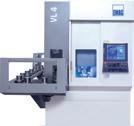

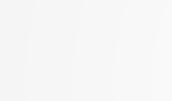

Cover
Machines: VL 2
Sawn part diameter: 100 mm
Material: X5CrNi1810 2 OPs

Main hub
Machines: VL 4 Forged part diameter: 120 mm Material: 16MnCr5 2 OPs
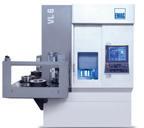

Intermediate gear
Machines: VL 2
Sawn part diameter: 60 mm Material: C45 2 OPs

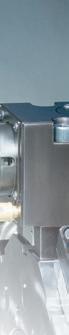
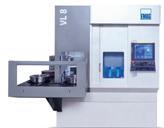




Sprocket
Machines: VL 2
Pre-forged part diameter: 50 mm

Material: 16MnCr5 2 OPs




Piston
Machines: VL 4
Sawn part diameter: 100 mm Material: 46S20 2 OPs








VL 6 and VL 8 for large workpieces
Machine larger workpieces, or achieve maximum flexibility in production with a VL 6 or VL 8 pickup turning machines. Integrated conveyor belt makes loading the machines with heavy parts a breeze. Place parts on the conveyor belt by crane and the machine takes care of everything else.
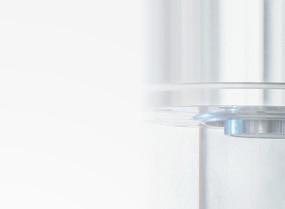
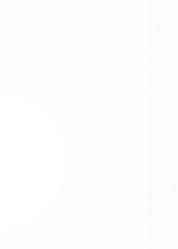



Drive gear
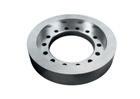

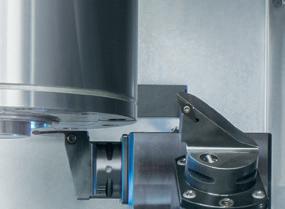
Spur gear


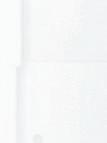
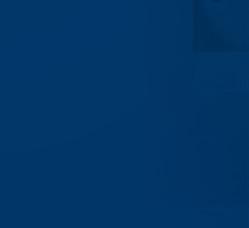
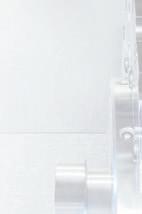




































Main spindle
»
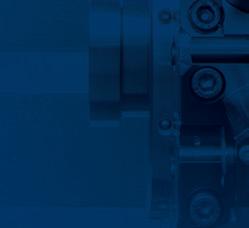
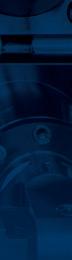
VL MULTI-SPINDLE MACHINES – VL 3 DUO
EMAG has extended the VL Series product range with the VL 3 DUO, a twin-spindle machine solution for the highly productive manufacturing of chucked parts up to 150 mm (6 inches) in diameter.
The VL 3 DUO integrates all of the most recent EMAG technological developments (including self-loading spindle, the TrackMotion automation system and the modular design of the machine) to create a highly productive manufacturing system with a minimum footprint.
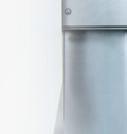

automation system
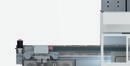
Spindle 1
Parts storage area
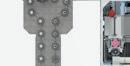

Access to e-container and hydraulics



HIGH-PERFORMANCE TURNING WITH THE VL 3 DUO
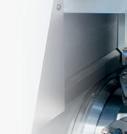
Spindle 2 OP 20 NC shuttle Central machining area extraction unit


The VL 3 DUO scores highly for heavy-duty machining due to its rigid machine design. High feed forces with a large cutting depth reduce the machining time.
Standard spindle:
ap = 4.75 mm
0.2 in
f = 0.4 mm/rev 0.02 in/rev
v c = 250 m/min 1,000 in/min
High torque spindle:
ap = 8.5 mm
0.3 in
f = 0.4 mm/rev 0.02 in/rev
v c = 250 m/min 1,000 in/min
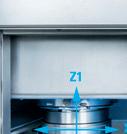
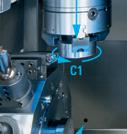
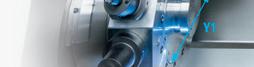



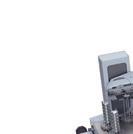
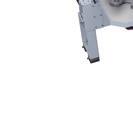
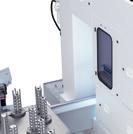
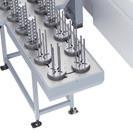
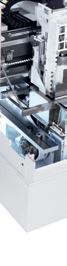


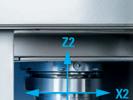


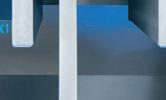













MACHINING AREA OF THE VL 3 DUO:
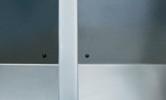




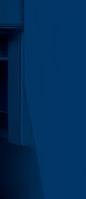
VL 3 DUO FOR DEMANDING TURNING WORK
+ Working spindle with 5,000 rpm/32 kW/255 Nm at 40% duty cycle
+ Sturdy mechanical design – spindle bearing, front: 100 mm (4 in) in diameter, spindle fl ange to DIN 55026, size 6
+ Motor spindle with DirectDrive for minimum run-up times, maximum true running and diameter tolerances
+ Maximum torque over large range of speeds –baseline spindle speed: 1,408 rpm (at 100% duty cycle)

Highly productive machining of chucked parts with a diameter of up to 150 mm (6 inches) with minimum space requirements




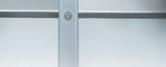
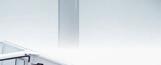


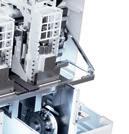
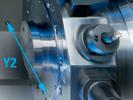
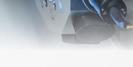
Maximum precision
Machine base made of MINERALIT® polymer concrete, machine weight 10,000 kg, size 45 linear roller guides and direct position measuring systems in all axes
Integrated automation
Pick-up working spindle for loading and unloading
Unique machine concept
Two working spindles and two high performance tool turrets with torque motor
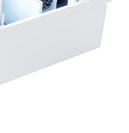
Optimum accessibility
Short distance to the turrets and working spindle ensure optimum accessibility.
Maximum flexibility
Parts storage area for up to 400 workpieces and TrackMotion automation system for high speed part transport between the parts storage area and machining areas as well as for turning the workpieces
Minimum floor space requirement
24.5 m 2 for the complete machine: VL 3 DUO + TrackMotion + parts storage area + chip conveyor
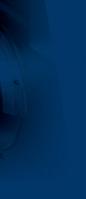
+ Water-cooled motor spindle for maximum thermal stability
TECHNICAL DATA
Travel distance, X (machining stroke)/ Y (optional)/Z
Main spindles (2x) – Standard
» Power rating, 40%/100%
» Torque, 40%/100%
» Speed, max. rpm 5,000
» Spindle flange to DIN 55026 Size 6
» Spindle bearing dia., front
100 4 High torque spindle – Option
» Power
» Torque, 40%/100%
» Speed, max.
Turrets (2x)
» Turret tool positions Qty 12 Rapid-traverse rate, X/Y/Z
MODULAR CUSTOMIZED SOLUTIONS
VLC pick-up turning machines – more than just turning
Various manufacturing technologies can be used flexibly on these machines. In addition, they are extremely compact and have powerful drive units in their spindles and axes, which ensure they have plenty of capacity at all times. The great flexibility of the equipment and powerful working spindles are supplemented by the integrated automation solution using pick-up spindles.
The machining area in VLC machines can be configured flexibly. For the turning process, the twelve tool positions in the tool turret can be equipped with conventional and driven tools.









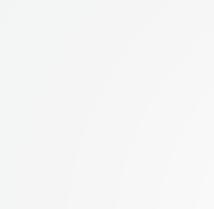
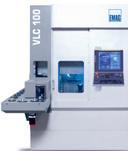
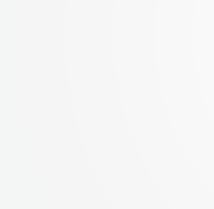
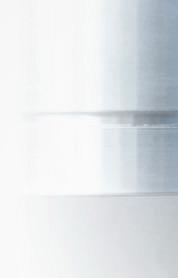
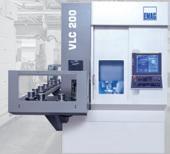
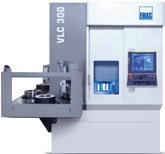
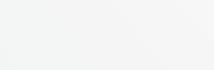
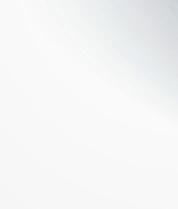
TECHNICAL DATA
Tool turret (driven as an option)
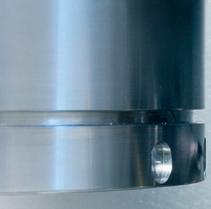
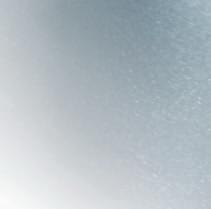
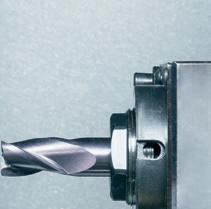
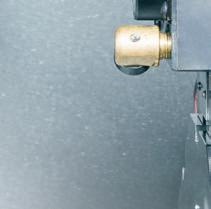
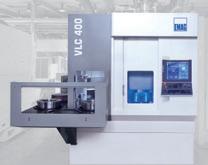

TECHNICAL DATA
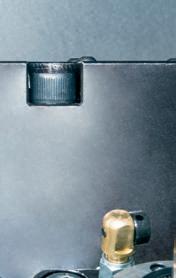
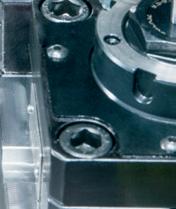
VSC CUSTOMIZED SOLUTIONS
VSC – Multi-functional production centers
Machining + automation + measuring: The machines of the VSC Series are configured for individual production requirements. Their patented design guarantees the shortest travel times between the pick-up station and the machining area, reducing idle times The MINERALIT® polymer concrete machine base and the twin-wall construction have an excellent vibration damping effect and offer outstanding thermal stability.
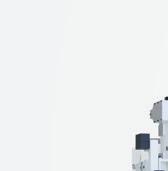
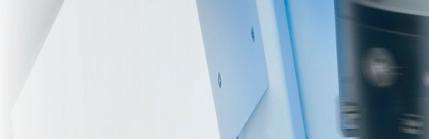
Measuring station
Energy container Automation
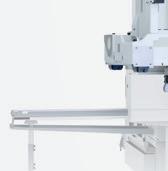
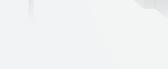
TECHNICAL DATA
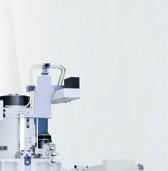



Hydrostatic guideway (standard)
Machine body made of MINERALIT® polymer concrete
Working spindle
Pick-up station
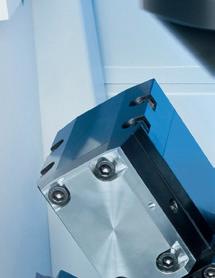

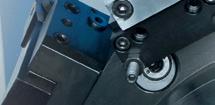
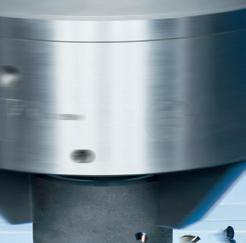
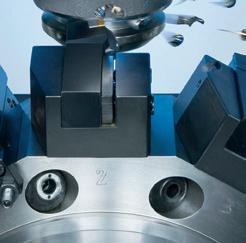

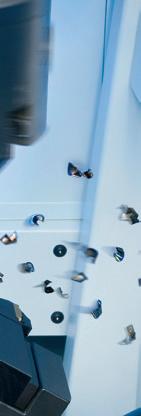
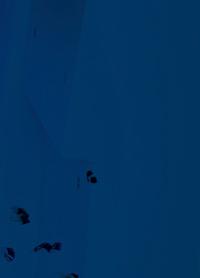
THE EMAG TURRET
The high-speed 12-station disk-type turret features very short swiveling times. Driven tools can be used on all twelve turret stations for drilling or milling operations. The EMAG turret gearbox combines high speeds with high capacity while requiring minimum fl oor space.
+ Very high speed
– Very short swiveling times
– High speeds when using driven tools
+ Very high capacity
– Very small design with high torque
+ Very high precision
– Turret firmly embedded in the machine base = High rigidity
– Very high degree of repeat accuracy when indexing from tool position to tool position
+ Very high availability
– Inured to collisions, owing to the use of torque motors
– No raising of the turret for swiveling. This means that no chips or dirt can get into the turret.
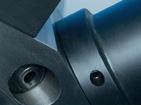
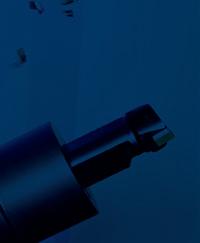

VSC MULTI-SPINDLE MACHINES
VSC DUO – the twin-spindle machine for sequential operations
The VSC DUO principle offers a highly efficient solution for the machining of medium to large numbers of parts on a minimal footprint. The work areas are completely separated. This allows the axes to be programmed independently of each other. This makes it possible to realize sequential operations in one machine.
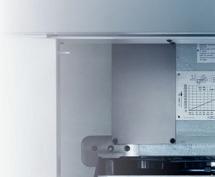
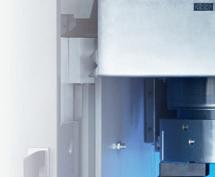
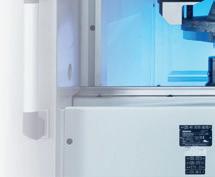
TECHNICAL DATA
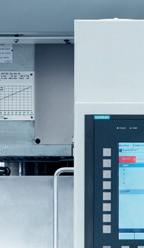
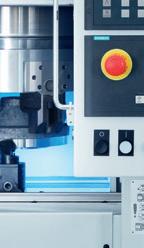
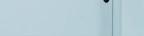
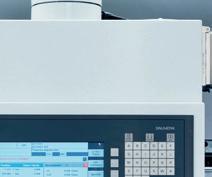
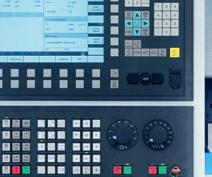
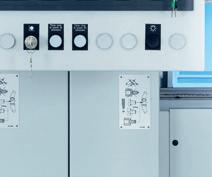
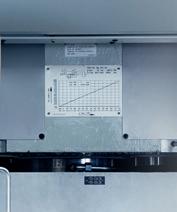
TURRET

Both turrets accommodate not only stationary turning tools but also driven drilling and milling tools. This allows for either identical or different operations to be carried out in the two spindles:
+ After the first set of operations have been carried out on the workpiece, using the first spindle, the back of the component is machined in the second one; or the second spindle could be used to machine the workpiece in the same clamping position.
+ Two workpieces can also be machined with identical operational sequences.
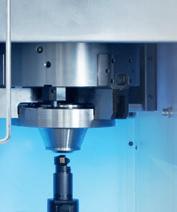
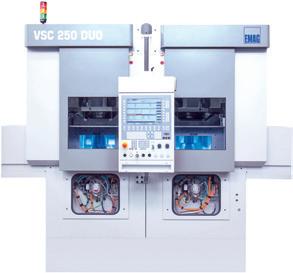
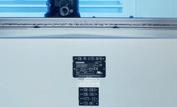

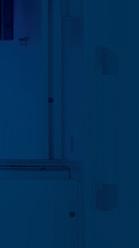
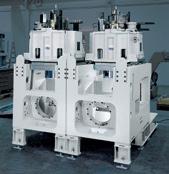


VSC 250 DUO: Separate, extremely sturdy machine bodies made of MINERALIT® polymer concrete; the two overhead slides are independently programmable.
Machines shown with
VSC MULTI-SPINDLE MACHINES – TWIN MACHINES
High-speed turning machine for large-scale production
Over the years, EMAG has developed vertical turning machines that load themselves by moving the main spindle and performing various operations in a single clamping operation. In addition, there is a consistently symmetrical slide and machine structure for thermostable production. The VSC 160 TWIN is one of the fastest turning machines on the market for components up to 130 mm in diameter.
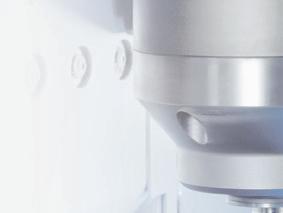
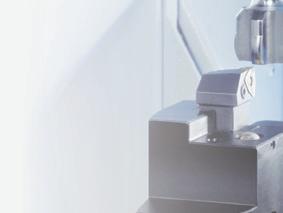
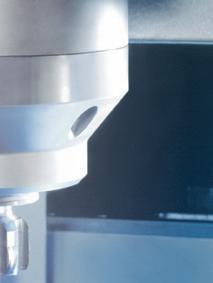
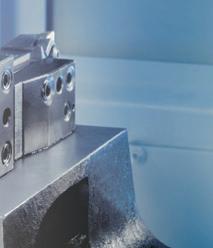
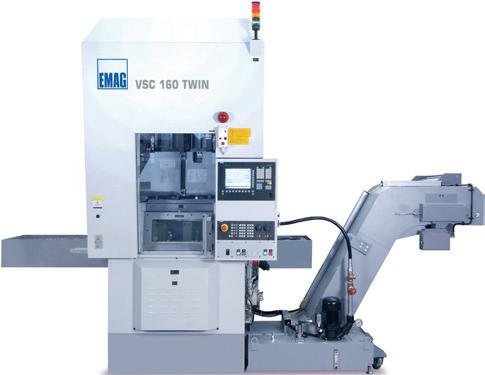
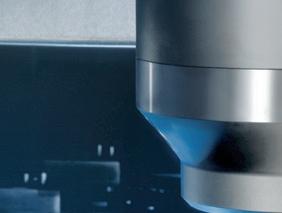

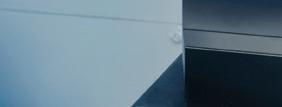
SIMULTANEOUS MACHINING
+ A single machining area with two working spindles
+ Simultaneous machining of two workpieces with identical operational sequences
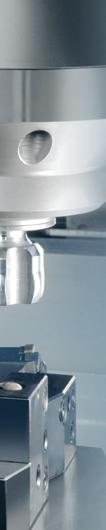
+ Machining operations for workpiece diameter and length can be corrected for each working spindle individually

HIGHLY DYNAMIC, PRECISE AND RELIABLE –THE VSC 160 TWIN
+ The working spindle with hydrostatic bearings in the Z-axis ensures outstanding component quality and a high tool service life for soft and hard machining operations.
+ Closed, thermosymmetrical structure with machine base made of vibrationdamping MINERALIT® polymer concrete.
+ Good chip fl ow thanks to the vertical design » Low-wear guiding elements
+ Cooling system for spindle motor, machine body, spindle, and turret
+ Turret for 2 x 4 tools
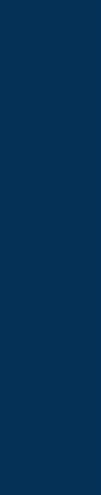


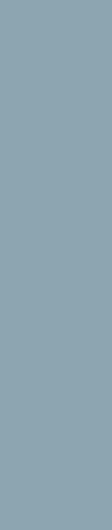
TECHNICAL DATA
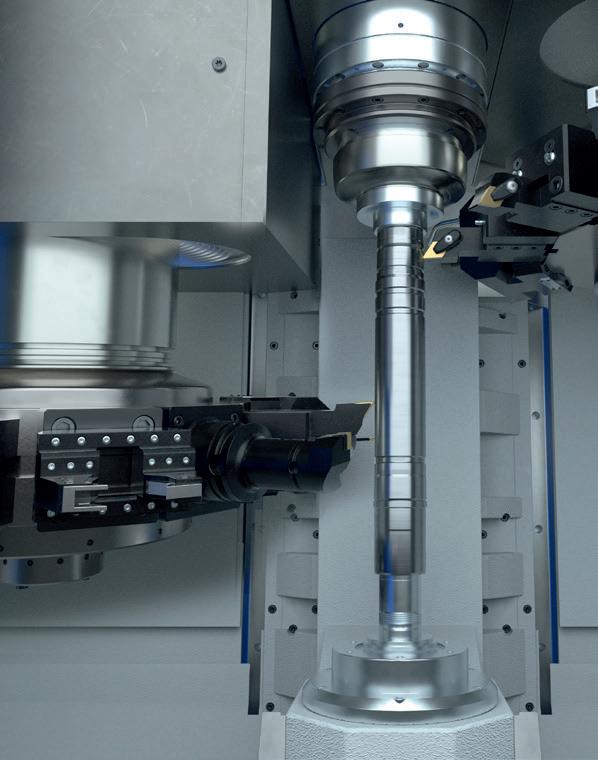
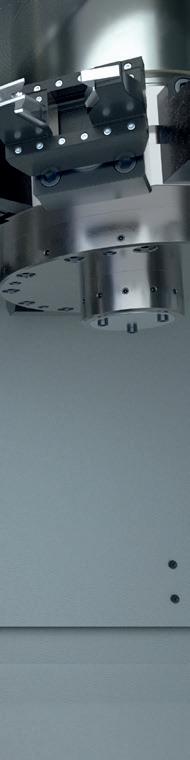
TURNING MACHINES SHAFT PARTS FOR
VT MODULAR SOLUTIONS
Fast processes are required for machining large quantities of shafts. Both the machining process and the loading and unloading processes must be completed extremely quickly. The VT 2 and VT 4 machines are guaranteed to achieve the maximum performance you require.
Four axes, short distances, and a powerful main spindle – these are the strengths of the VT Series. The full effect of these can be felt, in particular, when machining large quantities. A key factor is the machining of parts from two sides. This greatly reduces the machining time. Two tool turrets, each with eleven tool positions which can be equipped with turning tools or driven tools, ensure machine fl exibility.
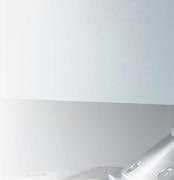
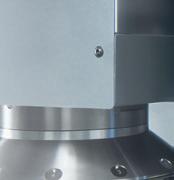








AUTOMATION SEQUENCE


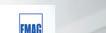



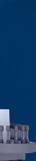
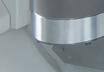
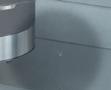
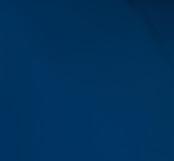
SIEMENS 840D SL NOW AVAILABLE

THE BENEFITS
+ The standard machine comes prepared (“tunnel”) for integration with the TrackMotion automation system.
+ Reduced machining times due to four-axis machining
+ Shorter idle times with simultaneous loading and unloading of components


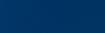

+ Lower investment costs thanks to integrated automation
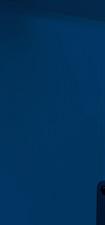
The gripper in turret 1 takes the workpiece from the raw parts storage area and transports it to the main spindle/tailstock. At the same time, the gripper in turret 2 takes the machined workpiece from the main spindle/tailstock, transports it to the finished parts storage area and deposits it there.
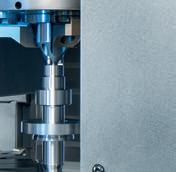
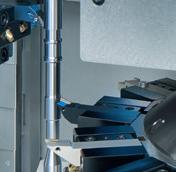

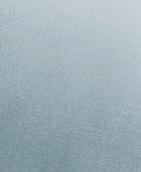
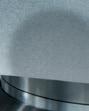
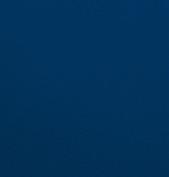
WORKPIECE CHANGEOVER TIME 6 SEC.
THREE KEY SUCCESS FACTORS
+ Reduced machining times due to four-axis machining
+ Shorter idle times with simultaneous loading and unloading of components
+ Highly productive shaft manufacturing thanks to integrated automation
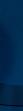
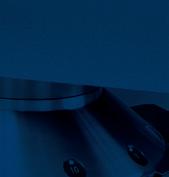
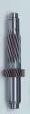
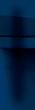
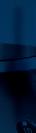
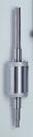
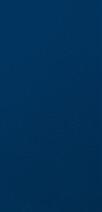
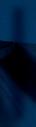

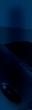


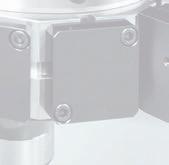

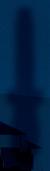
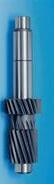


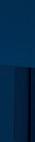

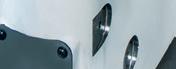
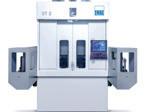
Workpiece
Workpiece
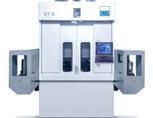
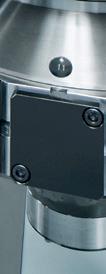
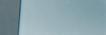
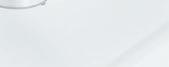
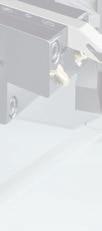
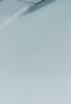
Workpiece
Workpiece
VTC MODULAR CUSTOMIZED SOLUTIONS
VTC machines are available in either a single spindle or DUO version.
With a DUO version, this single machine operates like two four-axis turning machines, and offers a variety of machining technologies in its two stations. These machines are increasingly being converted into multifunctional production centers that include finishing operations such as cutting to length and centering. These operations prepare the parts for additional four-axis turning or more processes downstream. All of this is completed in a fully automated cycle on a single machine.
The spindle motor, main spindle, tool turret and electrical cabinet are all fl uid-cooled. With their great power, high spindle speeds and sturdy turrets, the machines of the VTC Series are highly productive turning centers for shaft machining. In addition to workpiece grippers, every turret can be equipped with stationary turning tools or driven drilling and milling tools. Furthermore, the machining area can be fitted with additional technology modules if required.
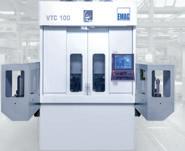
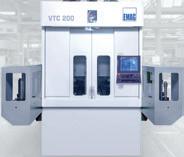
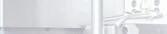

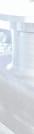

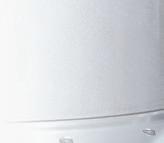
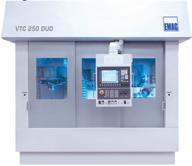
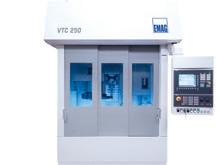


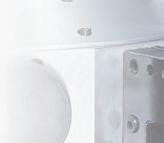

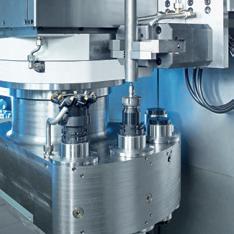

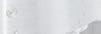



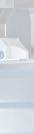
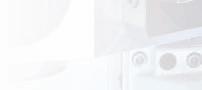

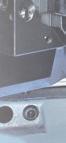
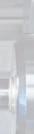


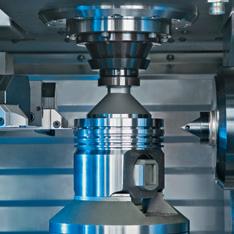
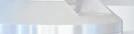
Shaft machining: Centring, drilling, end machining
Machining a steel piston: plunge-cutting the grooves
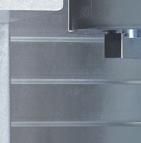
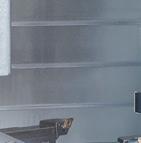
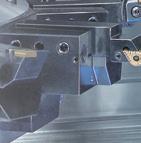

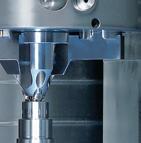
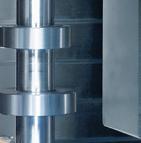
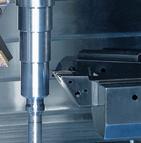
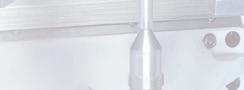
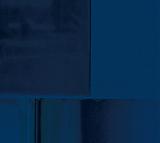
Main
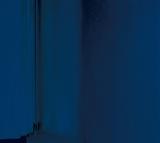

Torque of driven tools, 25%/100% Nm ft-lb 24/12 18/9 30/15 22/11
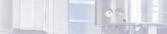

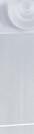

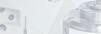
Component changeover: The finished




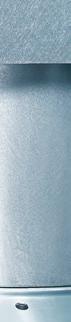
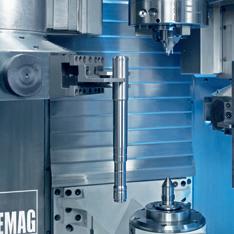

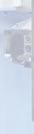
is removed and taken to its storage area. The new raw part is loaded (sequence from right to left).

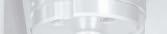

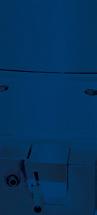
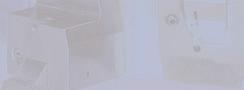

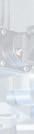

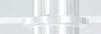
Rotor shaft machining: Skiving


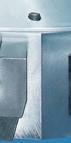
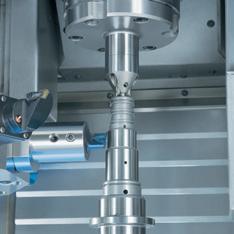

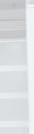
TECHNOLOGY. CONNECTED.
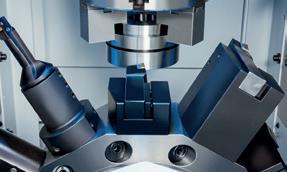


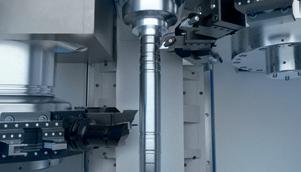
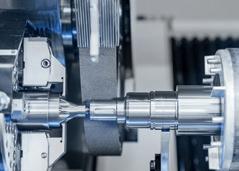

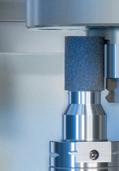
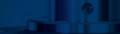
Turning Chucked Components
Turning Shafts
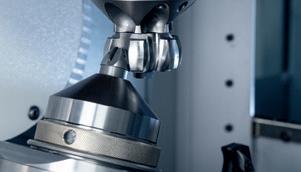
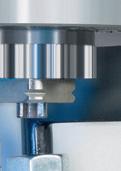

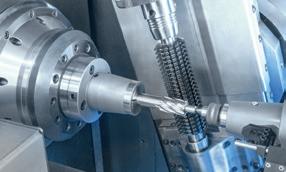
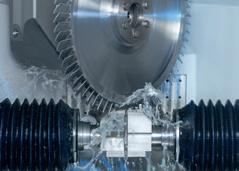

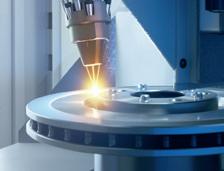

Milling Gear Hobbing Grinding


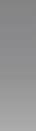
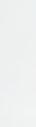



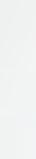
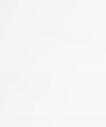





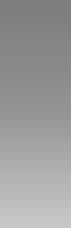
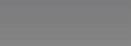
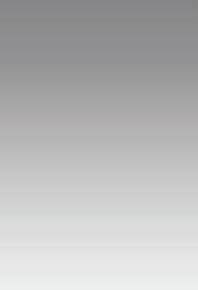






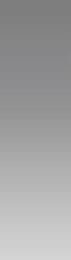




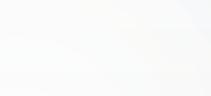





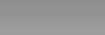


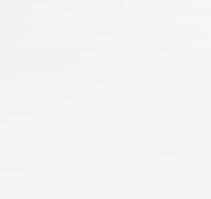
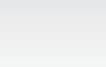
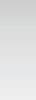








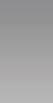


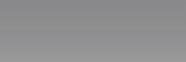
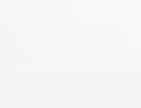
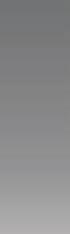



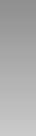
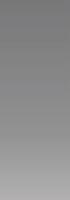


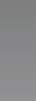




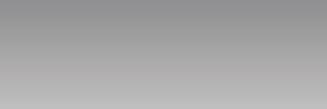

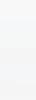
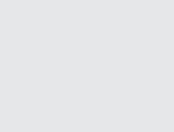

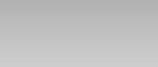


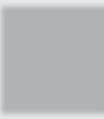
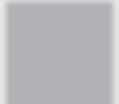
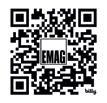

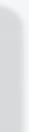
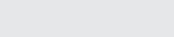

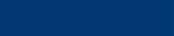
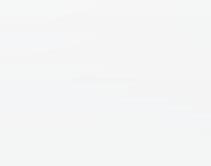
