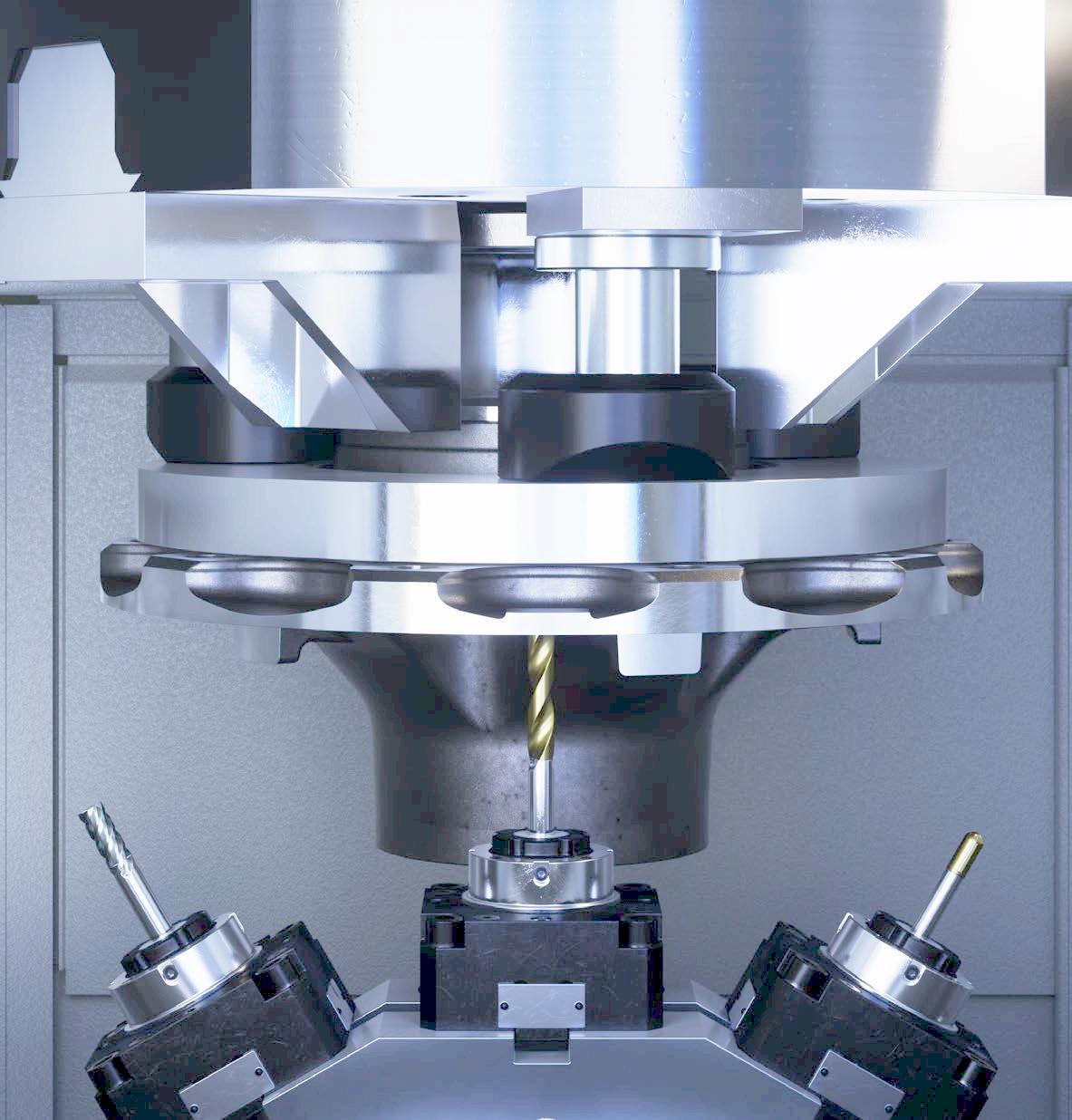
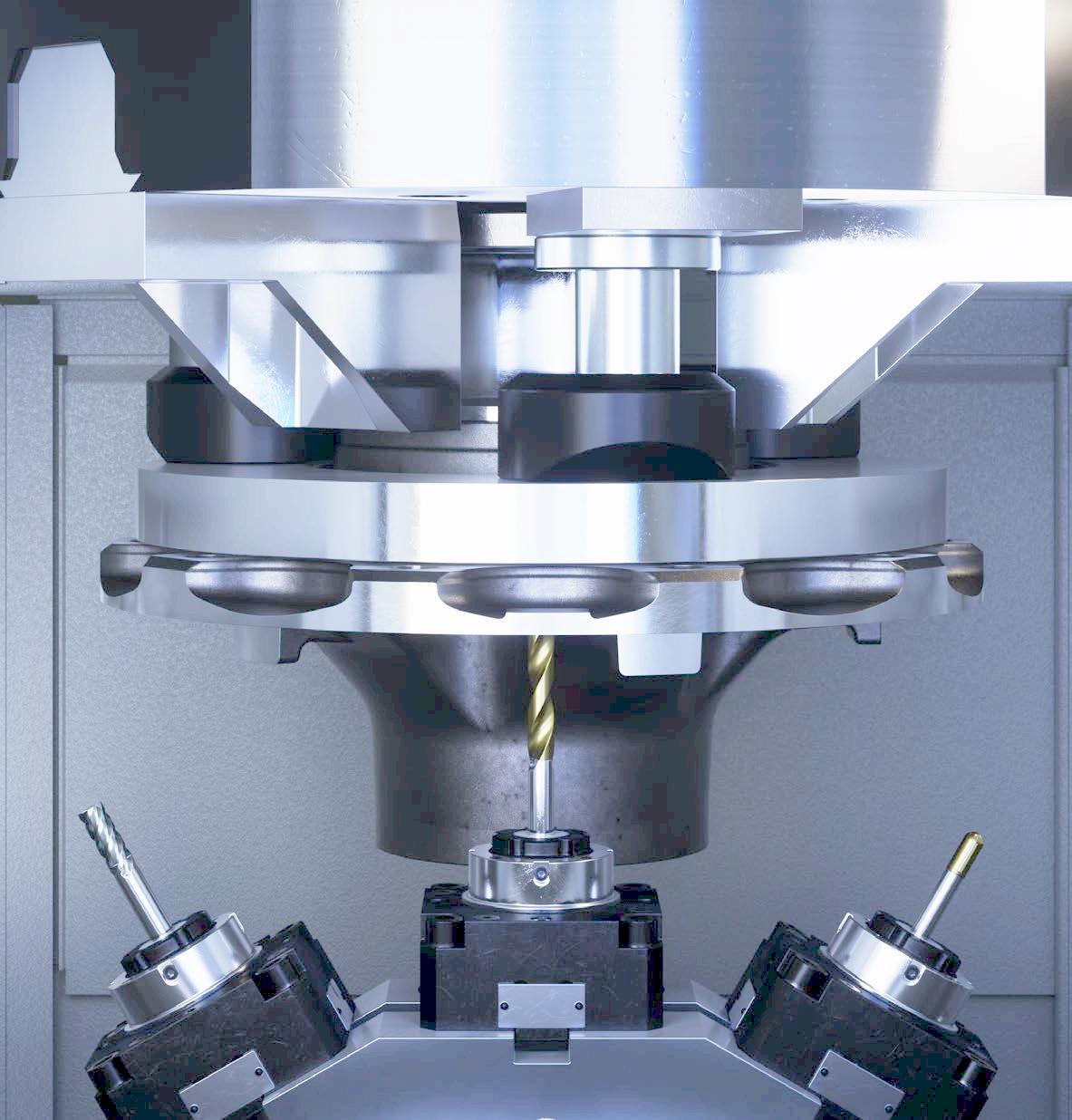
EMAG KOEPFER: BURR-FREE HOBBING OF PL ASTIC GEAR WHEELS
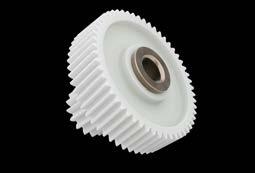
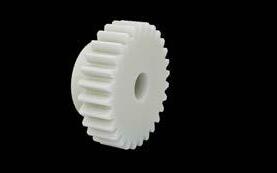
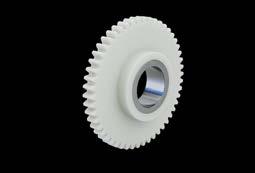
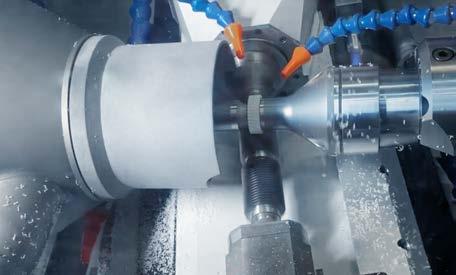
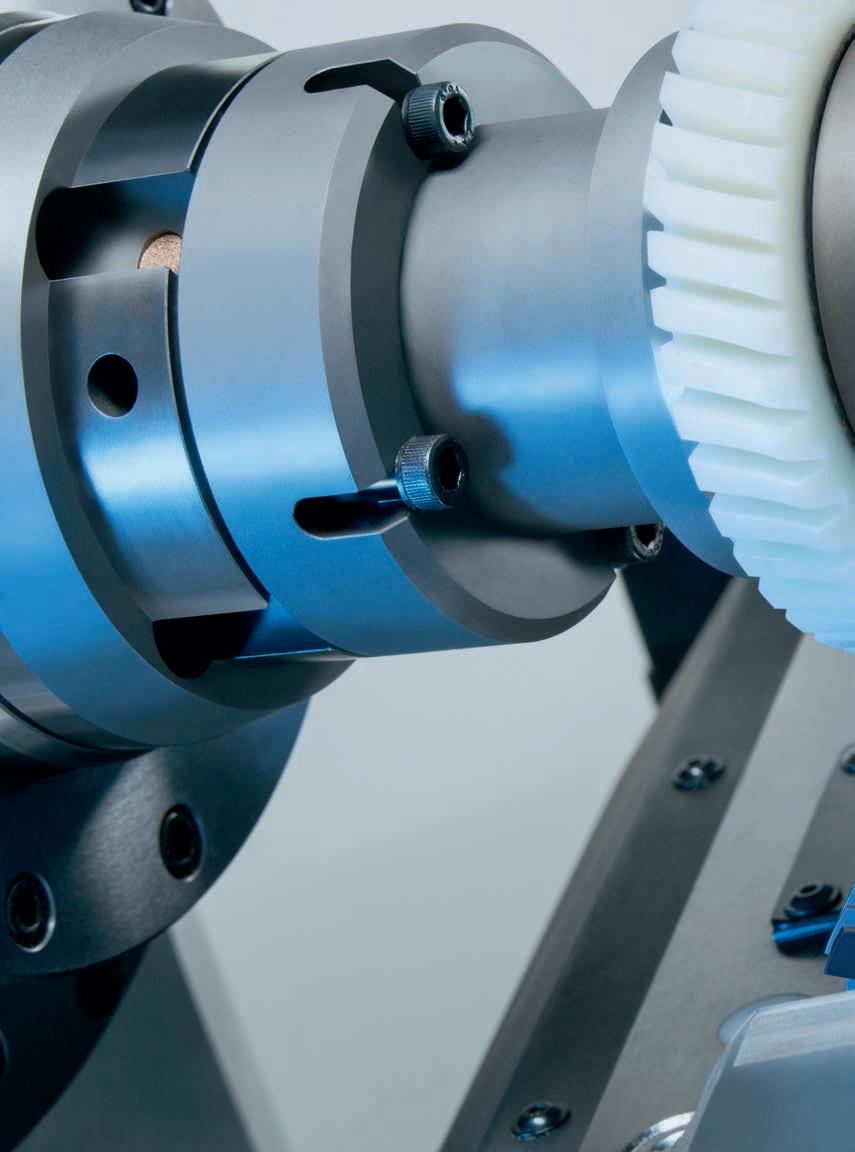
Can tooth profiles be guaranteed to be burr-free? That was the question a Korean gear cutting subcontractor asked the developers at EMAG KOEPFER. The resulting mechanical engineering solution is impressive.
The workpiece is made of the material Delrin – i.e. plastic, which is generally prone to complex burr formation. In order to produce a 100% burr-free tooth edge, EMAG KOEPFER developed the “burr-free hobbing” dialog. The big advantage is that a subsequent deburring process (including parts transport, etc.) is no longer necessary. By the way, under certain conditions, the process can also be used for metallic materials.
There are two hobs with the same profile, which are mounted in opposite cutting directions on a man drel. The first hob cuts the workpiece from one side, stopping cutting before the tool emerges from the back of the component. This is followed by a changeover to the second hob, the direction of cutting changes and the workpiece is milled through completely in synch from the other side. In this way, the tool only penetrates “in the direction of the material” on both sides of the component and burrs are avoided.
Overall, this process can be performed in four different ways, each of which can be selected with user-friendly dialog software.
KOEPFER

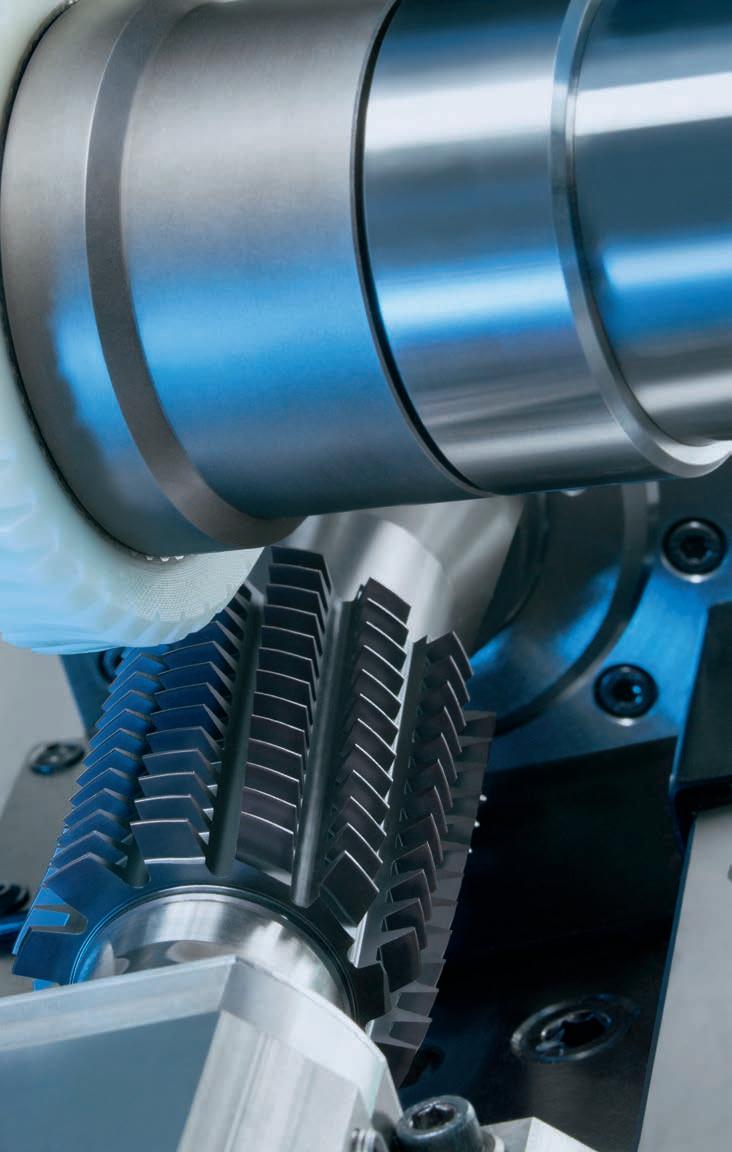
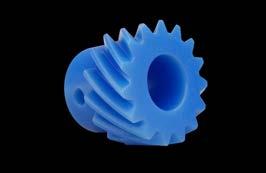
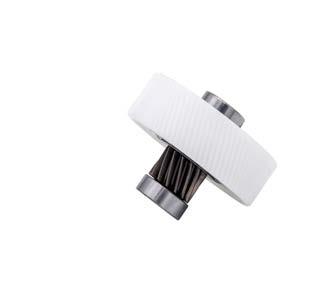
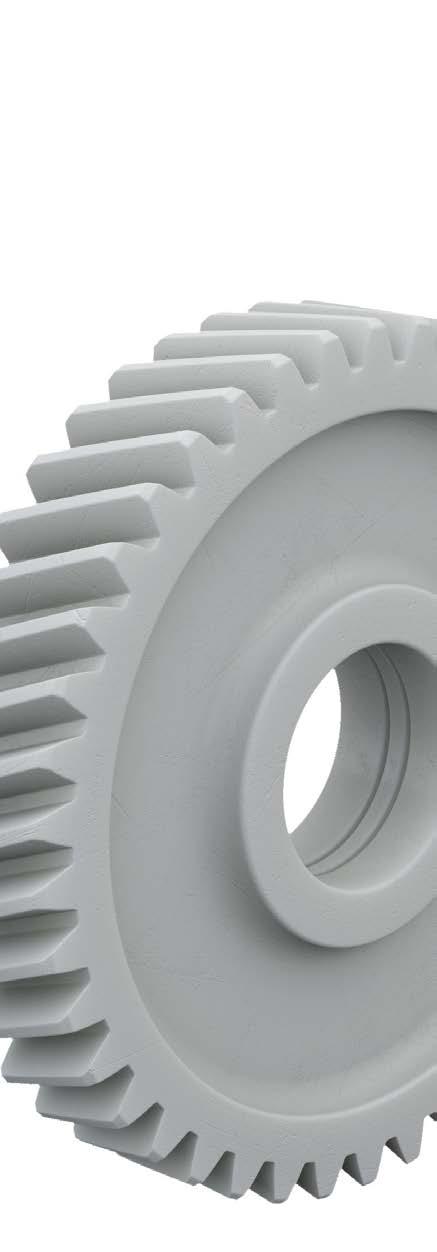
VSC 400 PS: POWER SKIVING AND TURNING FOR COMPLEX GEARING SOLUTIONS
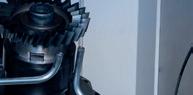
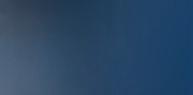

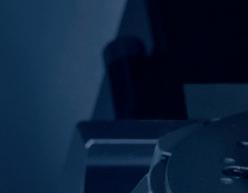
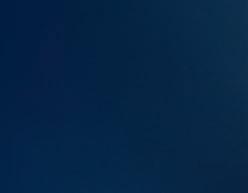
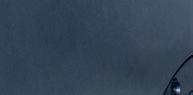
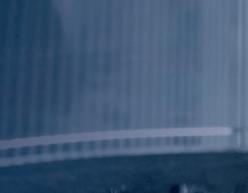
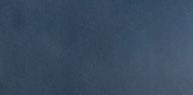


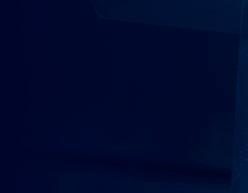

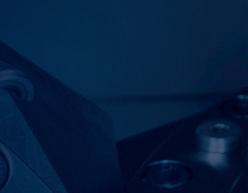
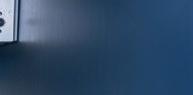

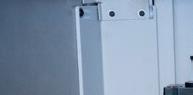
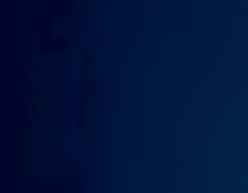
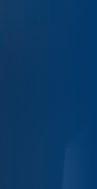



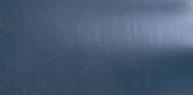
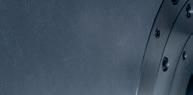
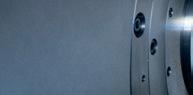
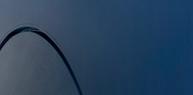
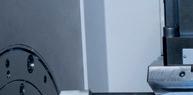
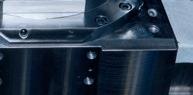
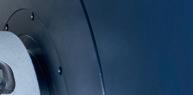
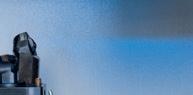
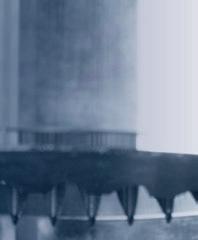
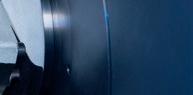
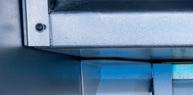
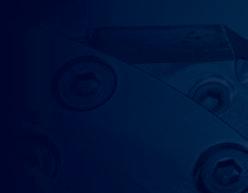
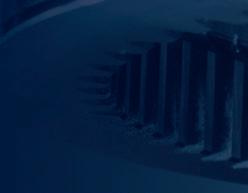
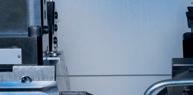
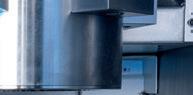
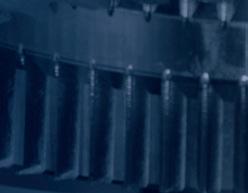

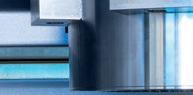
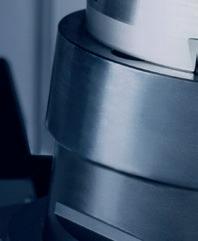
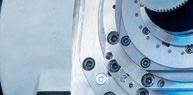
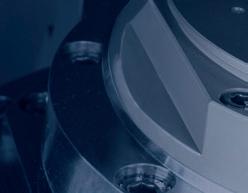
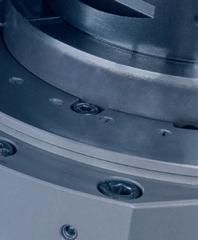
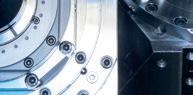


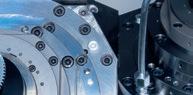
For many users in gear production, power skiving is becoming more and more interesting. Not without reason, since the process is much faster than shaping and more flexible than hobbing and broaching. However, the process was considered to be rather complicated for years.
Against this background, the new development from EMAG is a “game changer.” On the one hand, the VSC 400 PS machine makes power skiving very easy because the operator only has to enter very little data. You no longer have to be a gearing expert. On the other hand, the VSC 400 PS can be equipped with up to four power skiving tools and six turning tools. As a result, users can quickly and reliably finish even complex components in a single clamping operation.
The new VSC 400 PS power skiving machine not only combines power skiving with turning processes, but can also hold up to four different power skiving tools on two spindles. In addition, it can be equipped with up to six turning tools.
PS SHOW ITS STRENGTHS?
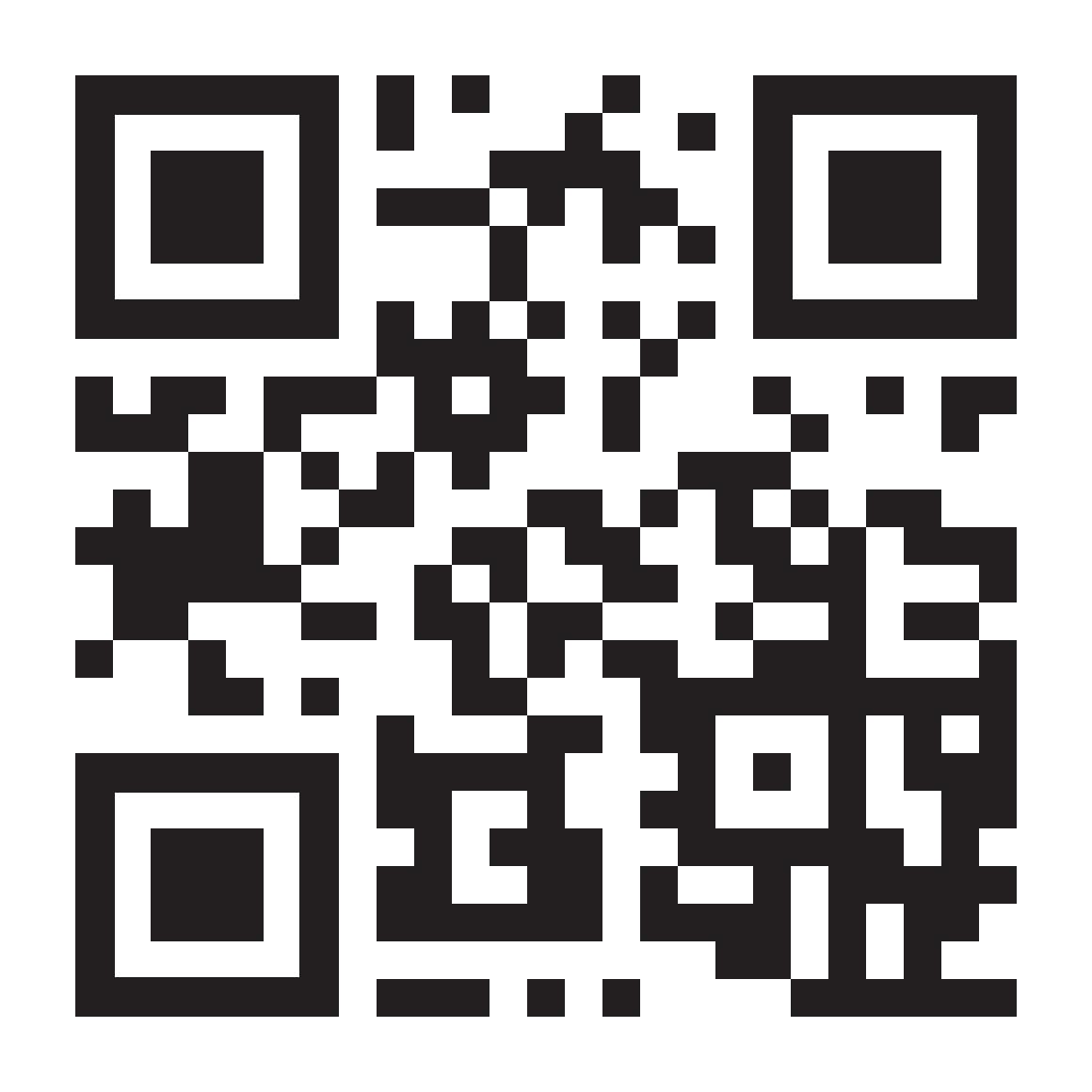
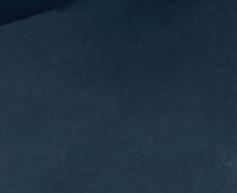

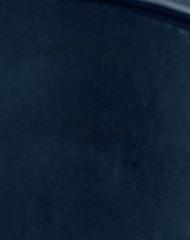
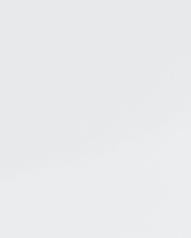
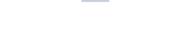
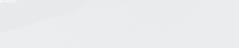
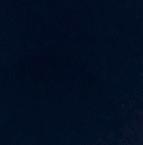
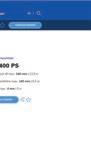
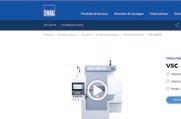
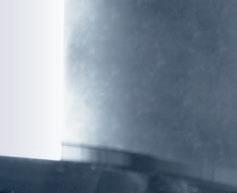
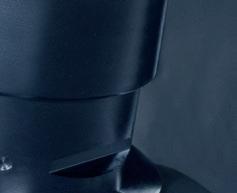
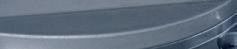
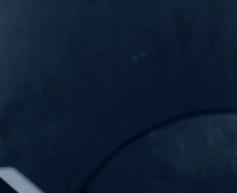
Essentially everywhere where high quality internal and external gears are required, with the machine being primarily designed for flange parts. Where: The more turning operations or different power skiving processes are required on the component, the more effective the machine is.

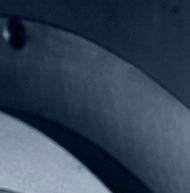

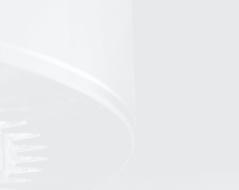

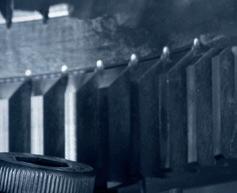
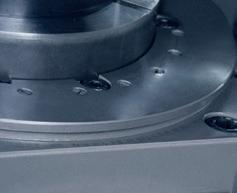
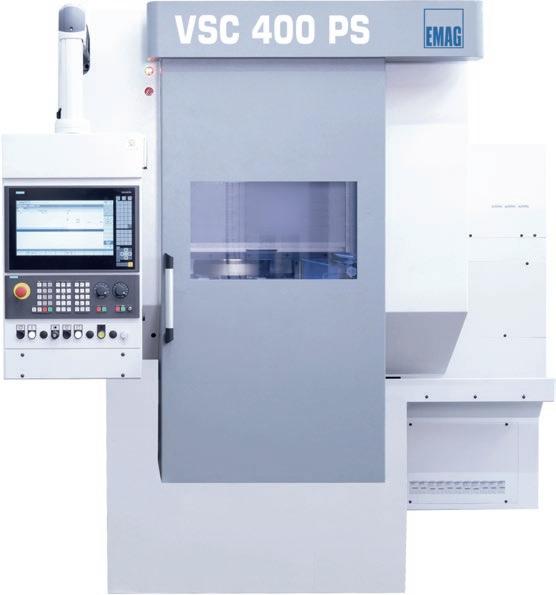
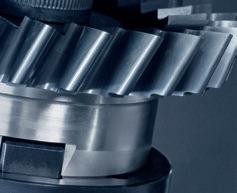
AUTOMATION SOLUTIONS AUTOMATED PRODUCTION SYSTEMS USED BY CONTRACT MANUFACTURERS
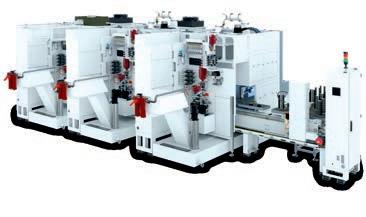
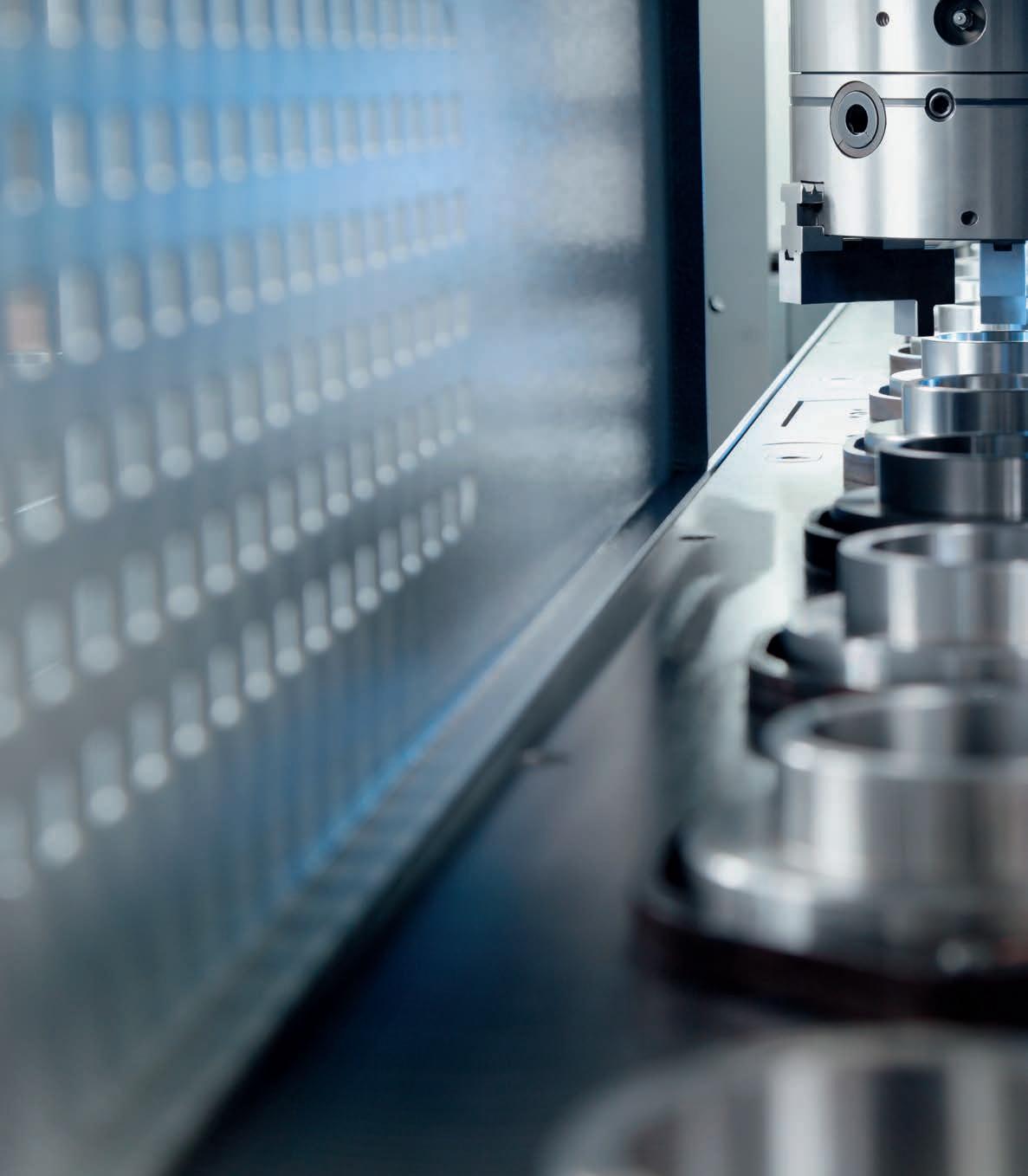
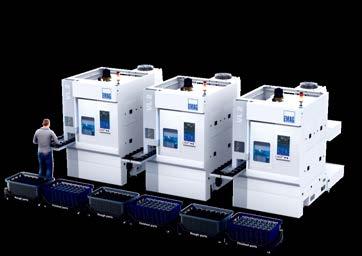
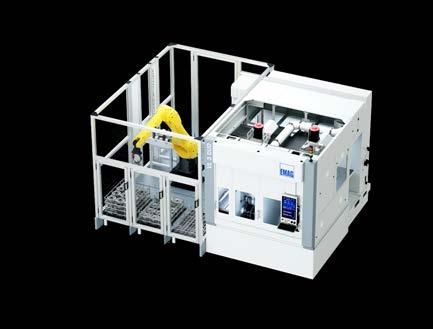
The cost pressure on many contract manufacturers and small manufacturing companies will continue to increase in the years to come. For example, experts expect rising costs when purchasing raw materials, high energy prices, but also increasing price pressure from OEMs. Many see a key solution to these challenges in production itself: Flexible and automated processes must ensure that costs are reduced on the one hand and that competitiveness increases with high component quality on the other. Here, the EMAG Group offers ideal machine and automation concepts to meet these challenges.
» Standalone solution for smaller batches – ma chines with integrated ring automation
The machines have an integrated “O” automation, which the operator loads and unloads manually parallel to the machining process. The component is simply placed on an external conveyor belt with a drag frame, and the automation of the VL machine does the rest.
» EMAG TrackMotion for medium batch sizes – machine + TrackMotion automation + stacker (parts storage)
The TransLift – a lift and turnover unit with a programmable electric gripper – moves extremely quickly on a track between the machines and even through them. The automation is equipped with its own controller, which communicates with the machines via an interface. As a result, the entire process is perfectly coordinated and ensures maximum productivity.
»
Mass
production with robot cells – machine + robot + pe ripheral devices
If necessary, EMAG links its machines with very different robot solutions. The parts are fed into the robot, for example, with feeding and discharge belts, palletizers, drawers or by bin picking – the robot uses these systems when it picks up new parts or puts down finished ones. This comes with a big advantage: The robot then simply has to place the parts on the machine’s conveyor belt. The pick-up automation takes care of the rest.
With its comprehensive automation know-how, EMAG offers its customers solutions that are individually tailored to their requirements. In this example, a robot is used to

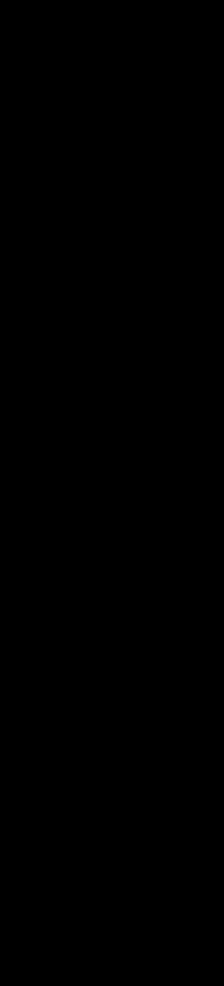
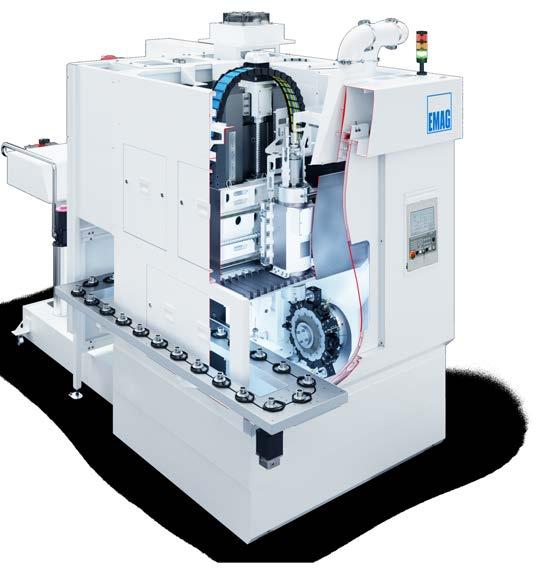
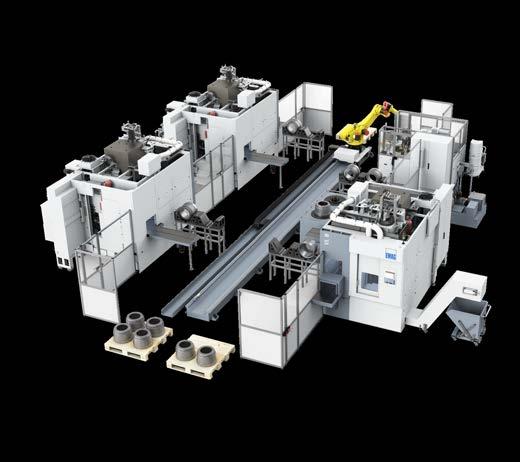
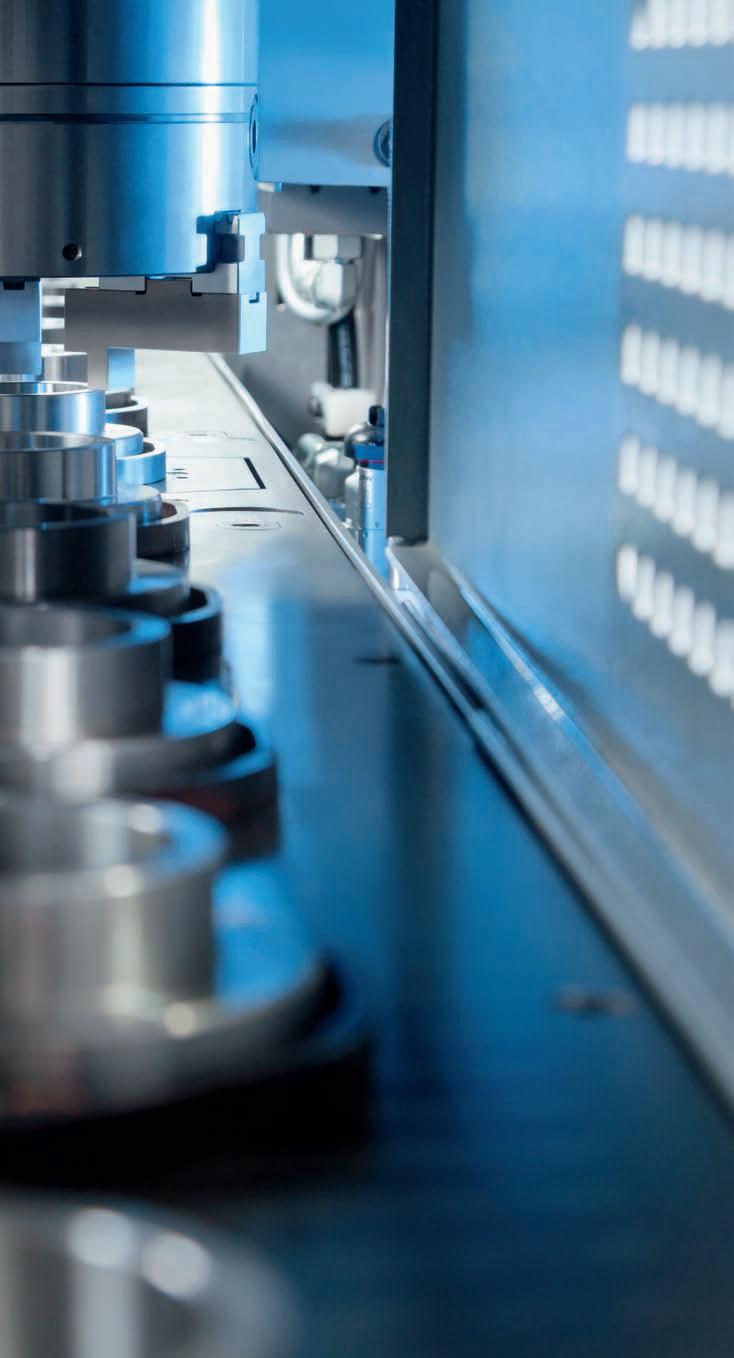
four VL 8 machines – when the component weight is very high (as with the truck brake drums shown here). The robot moves on a track. The basic principle is similar to the “TrackMotion approach.”
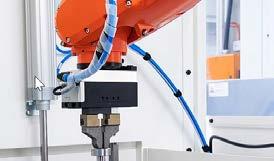
HIGHLY PRODUCTIVE SHAFT MACHINING: 24/7 PRODUCTION WITH AUTOMATION CELL
When it comes to machining shafts, there are few machines that can compete with the performance of the 4-axis shaft turning machines from EMAG’s VT Series. The machine series, which is already highly automated and highly productive, is given a massive boost by the integration of the new stacking cells from EMAG. The result: an extremely compact, fully automated solution for the large-scale production of shaft parts.

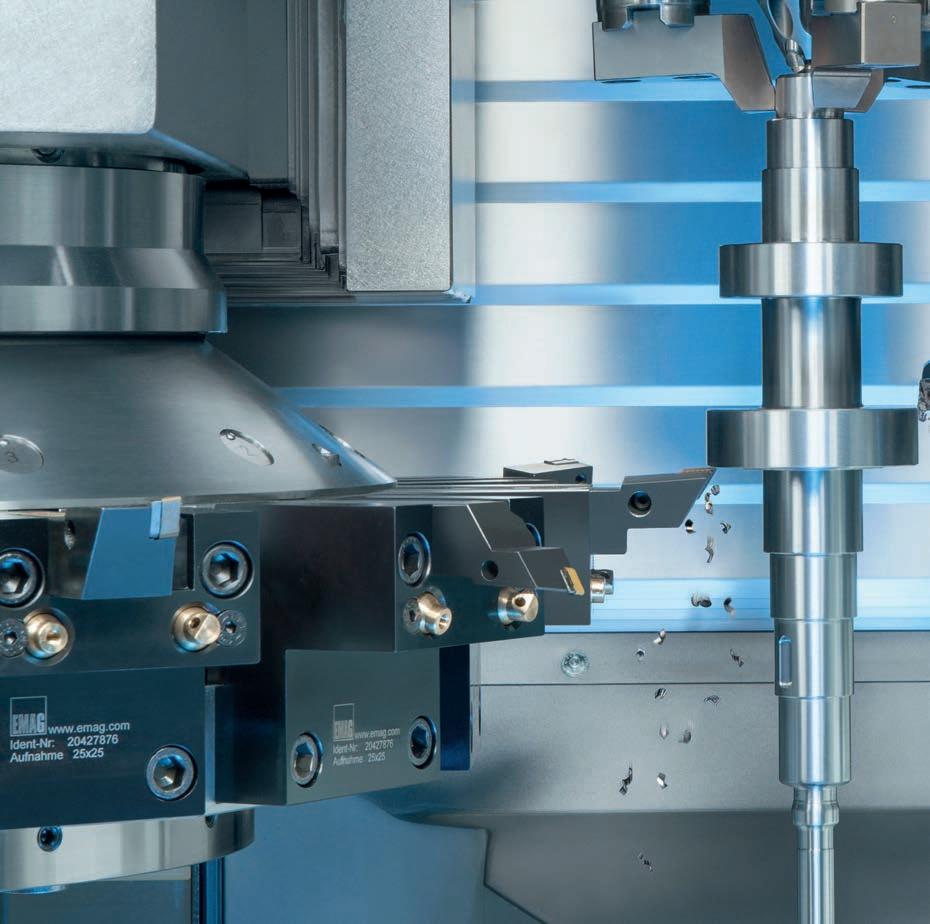
The VT 2 00 vertical turning center is designed for the highly productive manufacturing of shaft parts up to a length of 630 mm and a flange diameter of up to 200 mm. The turning center has two tool tur rets, each with eleven tool positions (one position is occupied by the workpiece gripper). This enables the four-axis machining of the workpieces simultaneously from two sides, which significantly reduces the machining time. The integrated workpiece gripper ensures optimized idle times by loading and unloading the workpieces at the same time.

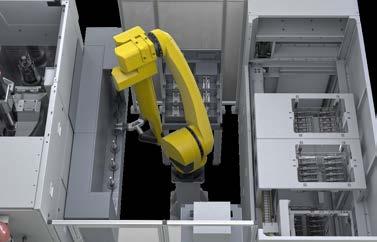

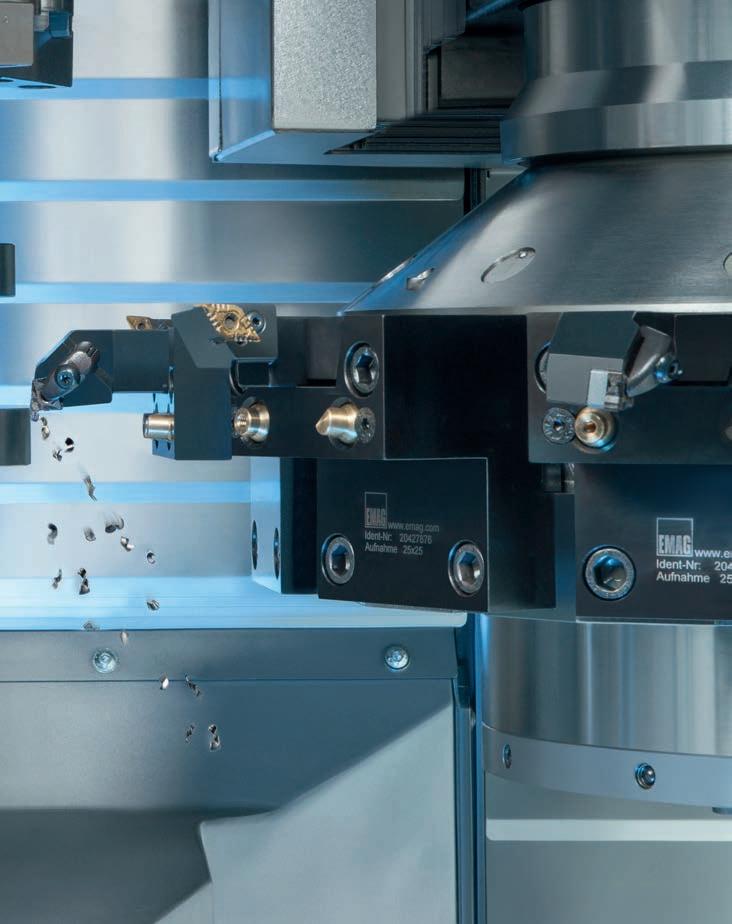
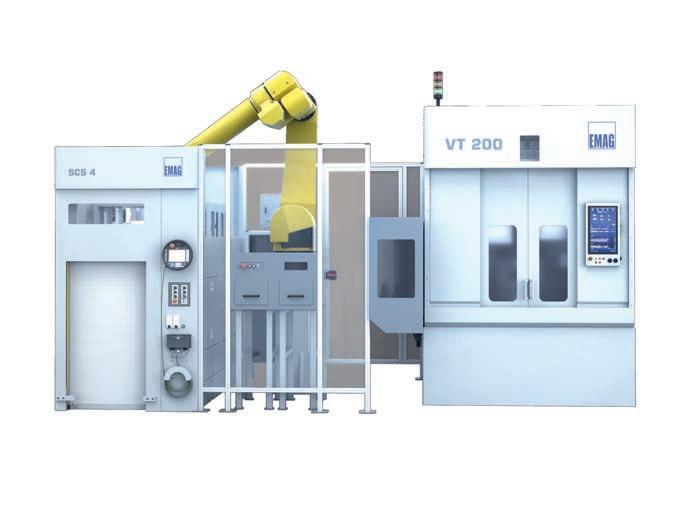
EMAG AT PUCKTECHNIK: GROWTH WITH EMAG TECHNOLOGY
It all started in 2016 with the production of molds for hot presses. Shortly thereafter, the first orders from the commercial vehicle industry followed, and finally a major order for wheel hubs, with which the joint success story of EMAG and Pucktechnik began. Together, a compact manufacturing solution was developed, which today is an important part of Pucktechnik’s corporate success.

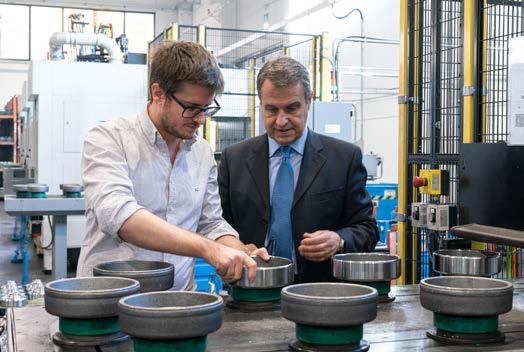
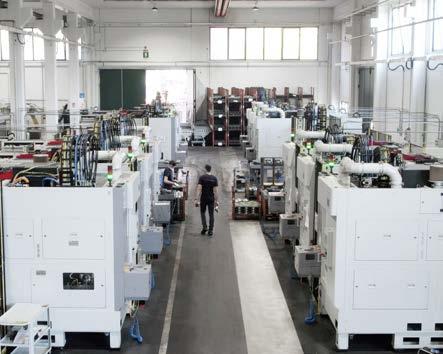
300,000 PARTS PER YEAR ON 11 MACHINES
Using an EMAG system with four production islands and a total of 11 machines (OP 10 and OP 20 machining operations), the customer can machine both sides of the raw part, including drilling and thread cutting. An equipment option on the VL 4 vertical turning machines for driven tools makes this possible. The process itself is easy for the operator. Simply place the raw parts on one of the drag rings of a circulating conveyor belt that functions as parts storage. From there, the TrackMotion automation system takes over and ensures that the machines are loaded and that parts are transported within the system. “The systems are so highly automated that we only need two people per shift to keep all 11 machines running. In addition, they are so easy to use that we can train non-professionals in a very short time, so that our manufacturing experts can take care of the more complex issues.” Dr. Giovanni Carabelli
PUCKTECHNIK
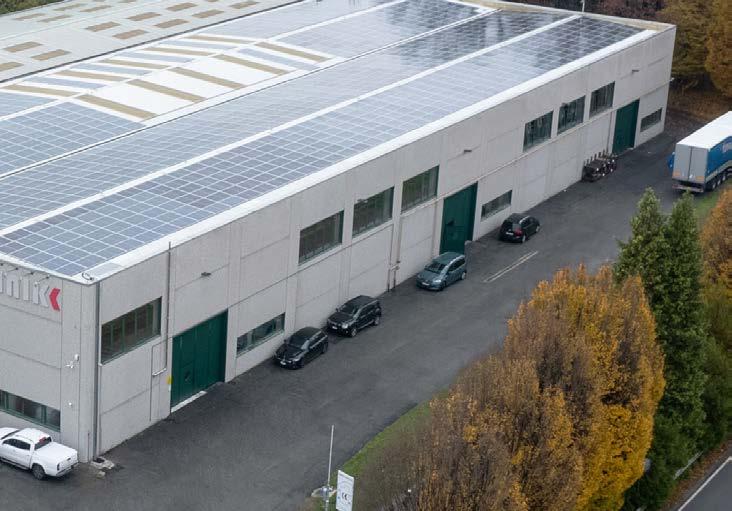
DECLINING COSTS AND VERTICAL GROWTH WITH EMAG MACHINES
“In addition to the production of the wheel hubs, we have also further expanded the production of the forks and invested in a KOEPFER gear hobbing machine, so that we can now also implement the gearing of the components in-house,” says Dr. Carabelli. Pucktechnik has also invested in a VT 4 machine from EMAG. With this equipment, they see themselves as prepared for the automotive industry: “We are currently working on IATF certification so that we can also supply the automotive industry. Since EMAG already has a lot of experience in this area and our experience with the company was very positive, we will certainly continue to rely on EMAG’s expertise and machines in the future. In any case, we look forward to further joint projects.”

EMAG FILM

Here the short video about Pucktechnik:
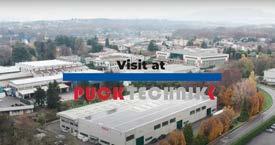
“The manufacturing solutions from EMAG have not only helped us to optimize our costs, but have also brought us further forward in terms of technology.”
Dr Giovanni Carabelli, Pucktechnik CEOMaurizio Colombo (EMAG Milano S.r.l.), Dr. Giovanni Carabelli (Pucktechnik S.r.l.), Christoph Hoene (EMAG Milano S.r.l.).
VSC
COMMERCIAL VEHICLES AND THE LIKE: MACHINING LARGE COMPONENTS EFFICIENTLY
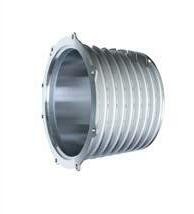
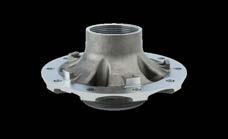
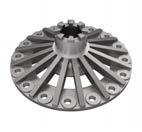

How can particularly large and heavy parts be manufactured efficiently – for example, in the commercial vehicle sector? EMAG provides an impressive answer with the VSC 500 and VSC 500 DUO machines.
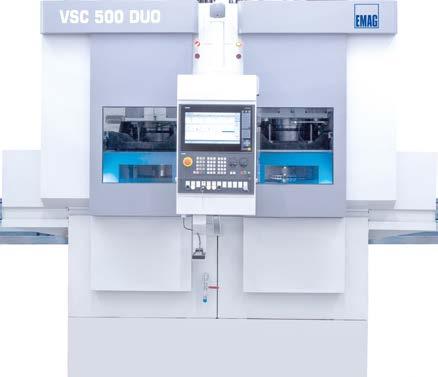
This is what distinguishes the machine in detail:
» The machine body made of Mineralit © has 8 times better damping than gray cast iron and excel lent thermal stability, which increases tool life and precision.
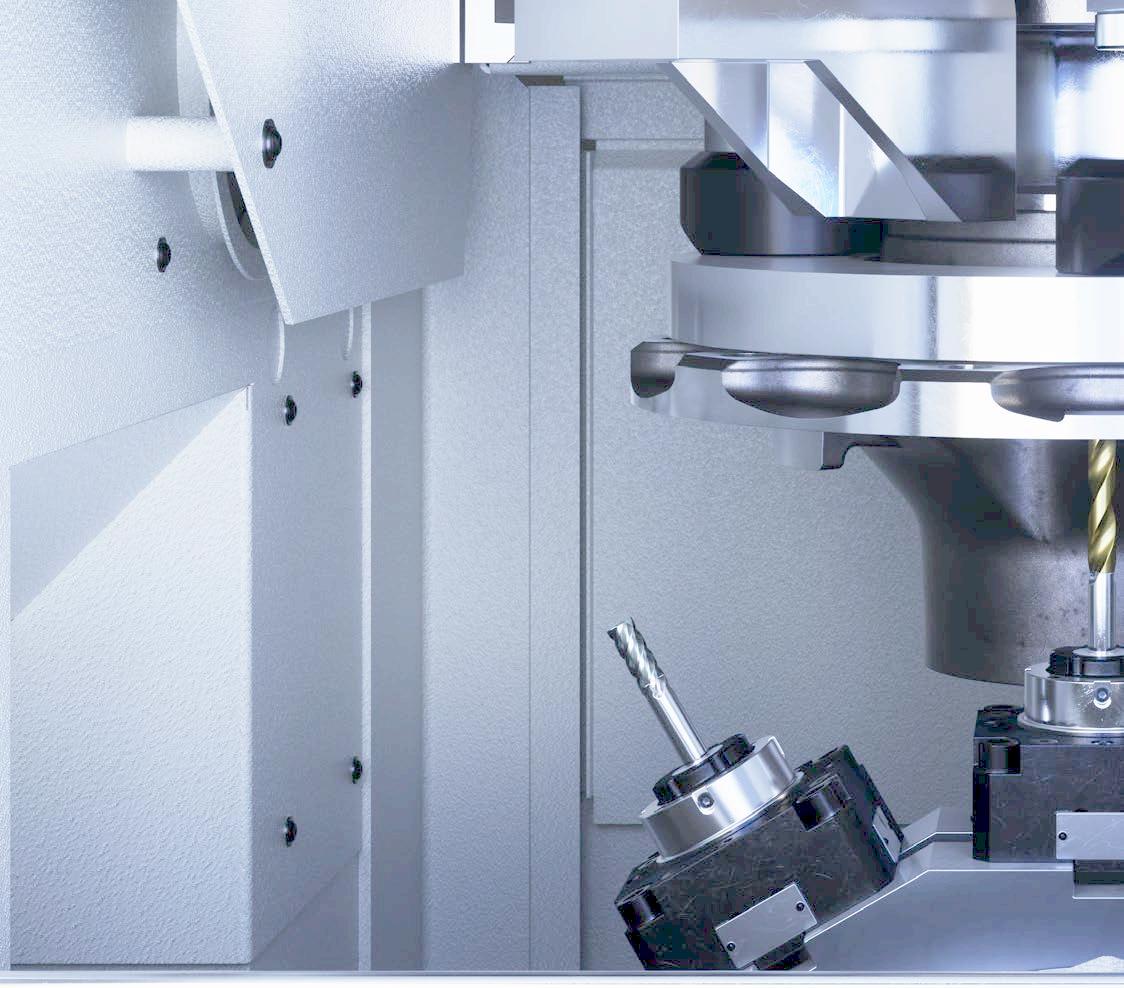
» The hydrostatic guideway in the Z-axis ensures increased stability during, for example, hard machining.
» The symmetrical design of the machine ensures a closed power flow and reduces thermal influences.
DOUBLE POWER
The DUO variant has two spindles in separate bodies. This ensures that the transmission of vibrations within the machine is avoided. In addition, a turnover unit is used between the two operations. Alterna tively, it is possible to manufacture two identical components in paral lel using the same process in order to, for example, increase the out put quantity.
OPTIMIZED

EMAG has further optimized the accessibil ity of the machine. This is why the machining area is now open at the top when the front door is open, for example to drive into the machin ing area with a lifting gear. In addition, a main tenance platform can be installed easily. As a result, access to the overhead slide is very easy for service staff.
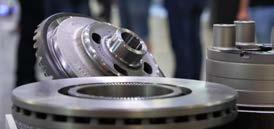
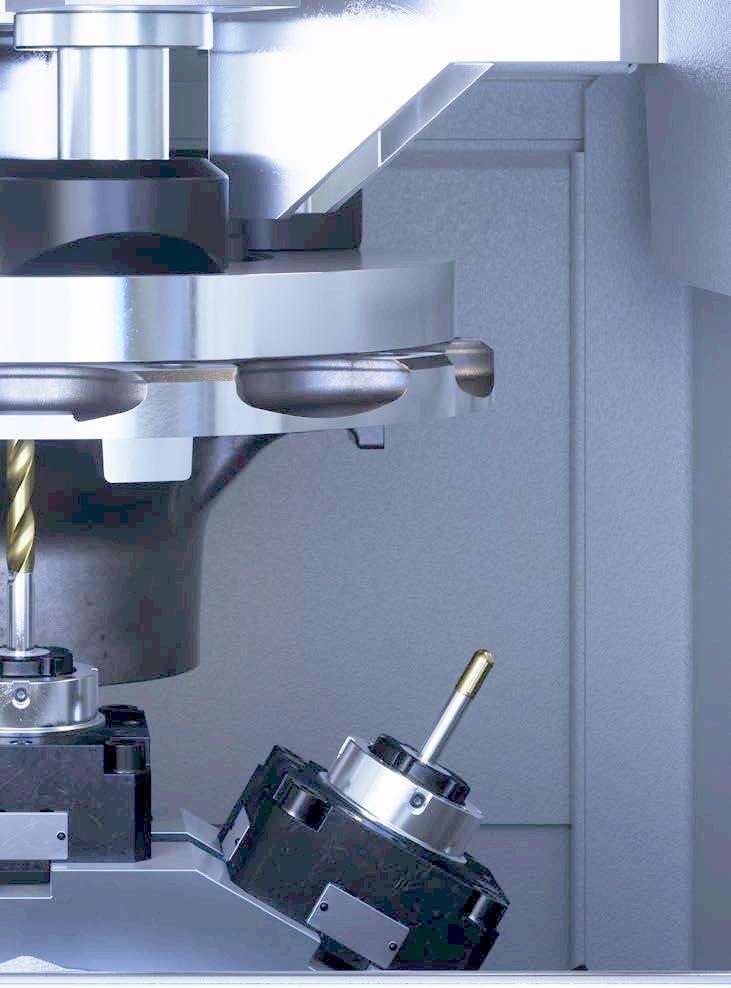
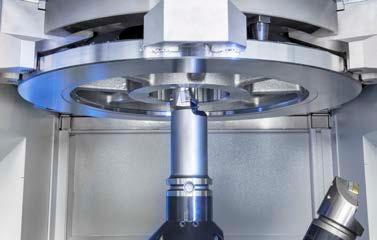
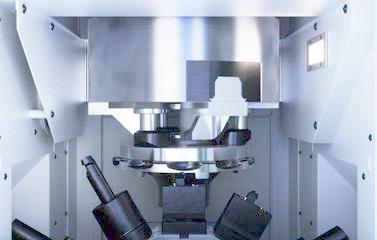
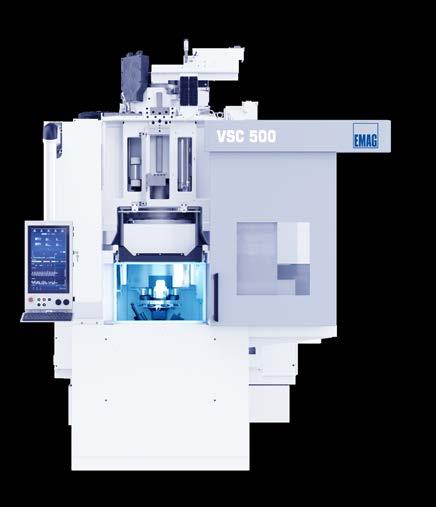
LASER WELDING OF TRUCK DIFFERENTIALS

In a perfectly timed process, housing parts and the ring gear are brought together reliably.
» First, the parts go through laser cleaning. The laser beam removes all impurities and residues.

» After being turned over, the cover, housing, and ring gear are joined. This process is subjected to force-distance monitoring.
» Before the subsequent welding, a seam detection system ensures that the par ticular joint gap is recorded and defined. The welding lens, which is moved along the detected path, is therefore always exactly positioned in the middle of the gap between the two parts to be joined in the process.
» Brushing and ultrasonic testing complete the machining process.
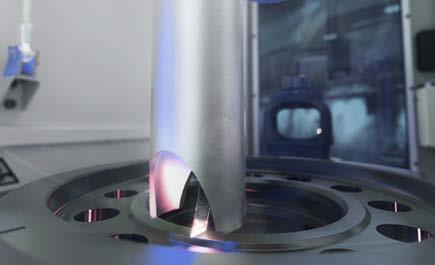
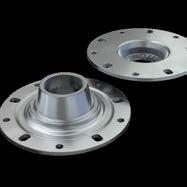


LASER CLEANING OF TRUCK WHEEL HUBS AND THE LIKE
Laser cleaning is traditionally used at EMAG LaserTec to prepare for laser welding. In addition, however, EMAG also offers hand-loaded or fully automated solutions for other areas of application, such as wheel hubs. The special feature of the solu tion is its high flexibility. In this way, 35 different workpiece variants can be cleaned without manual retooling. Many types of contaminants or coatings are removed –from cutting fluids to oxide and graphite layers to rust and paint
“With our laser and joining technologies, we offer individual solu tions that are optimally adapted to the production requirements. This is becoming increasingly important, especially with a view to the electrification of trucks.”
Nikolas Meyer, Business Unit Manager – Sales and Administration at EMAG LaserTec
JOINING
AN CAMSHAFTSS
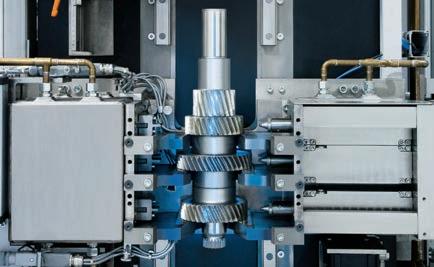
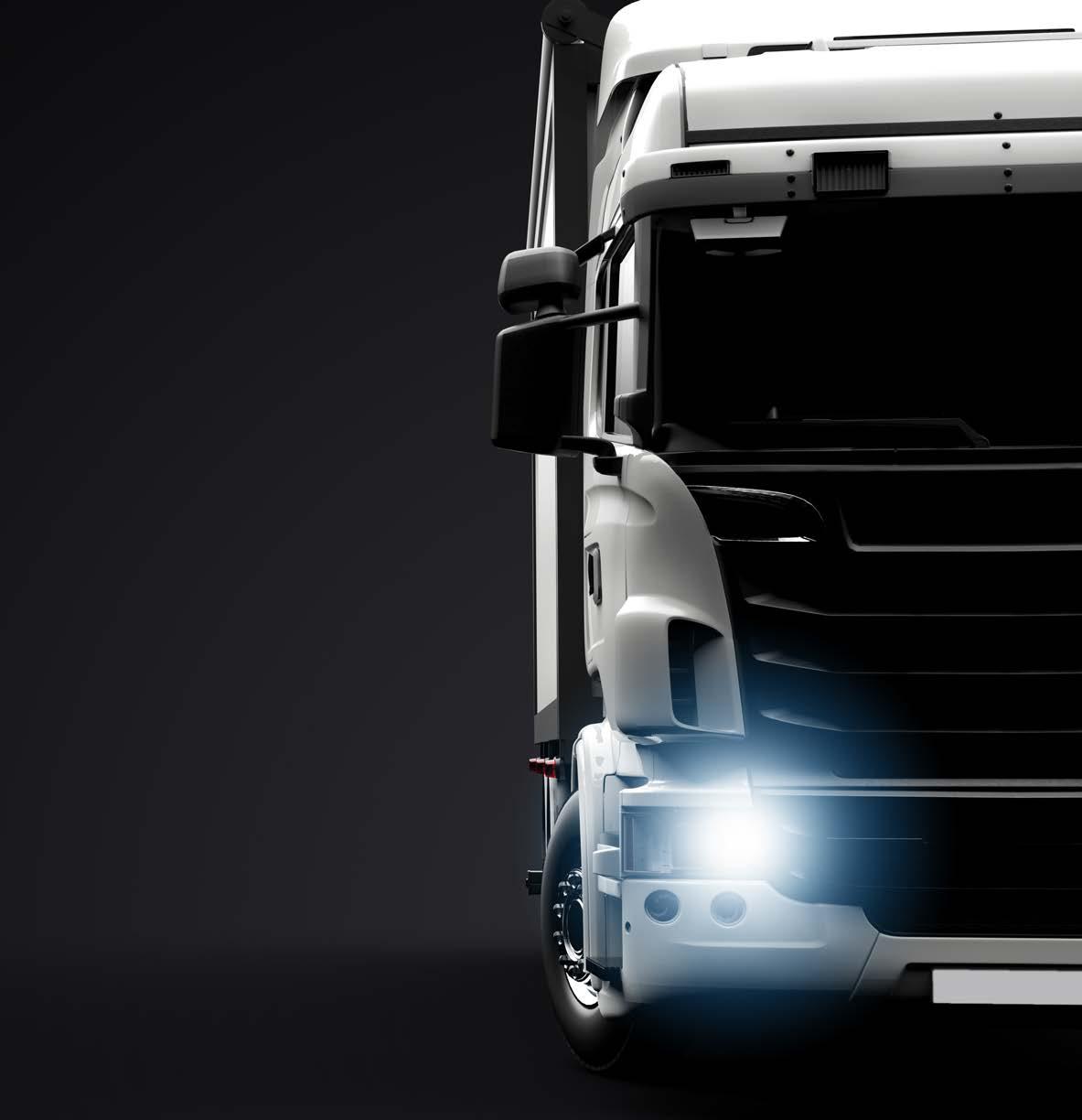

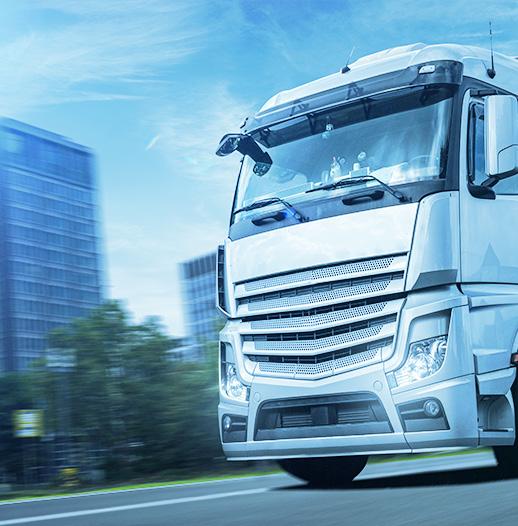
EMAG WHITE PAPER
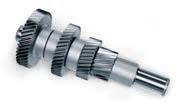
:
THE MACHINE OPERATION OF TOMORROW – TODAY!
How can machine tools be operated intuitively and, at the same time, integrate and display data-driven analyses? With the EDNA panel, EMAG provides a comprehensive answer to this question.
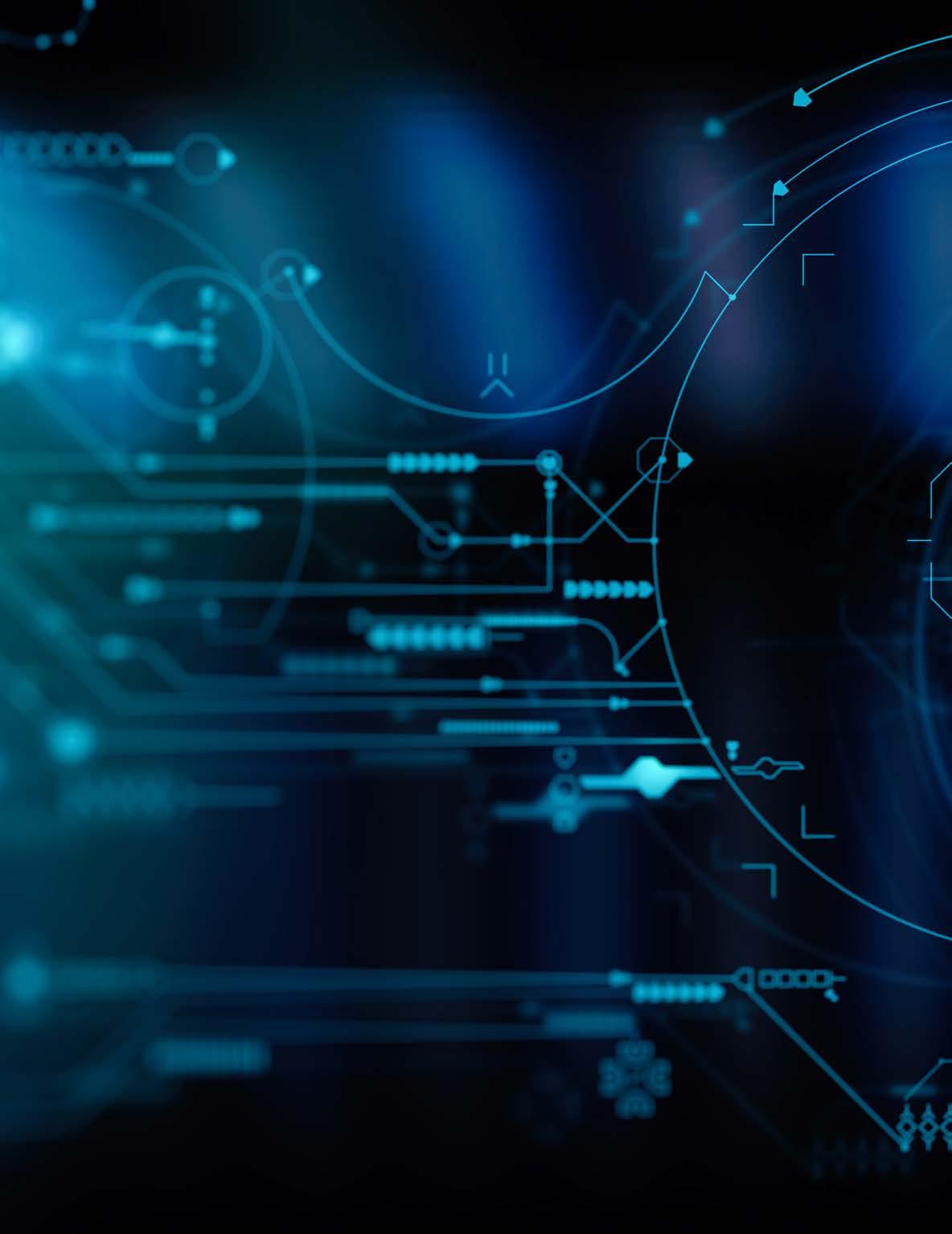
The solution makes it clear what the operation and control of a machine tool should look like today. The large multi-touch screen shows, for example, the user interface of a FANUC CNC SCREEN, user administration, produc tion drawings, predictive maintenance functions, various IoT functionalities, system errors, operating instructions and much more. A changeable and individually adapt able surface is available for this purpose.
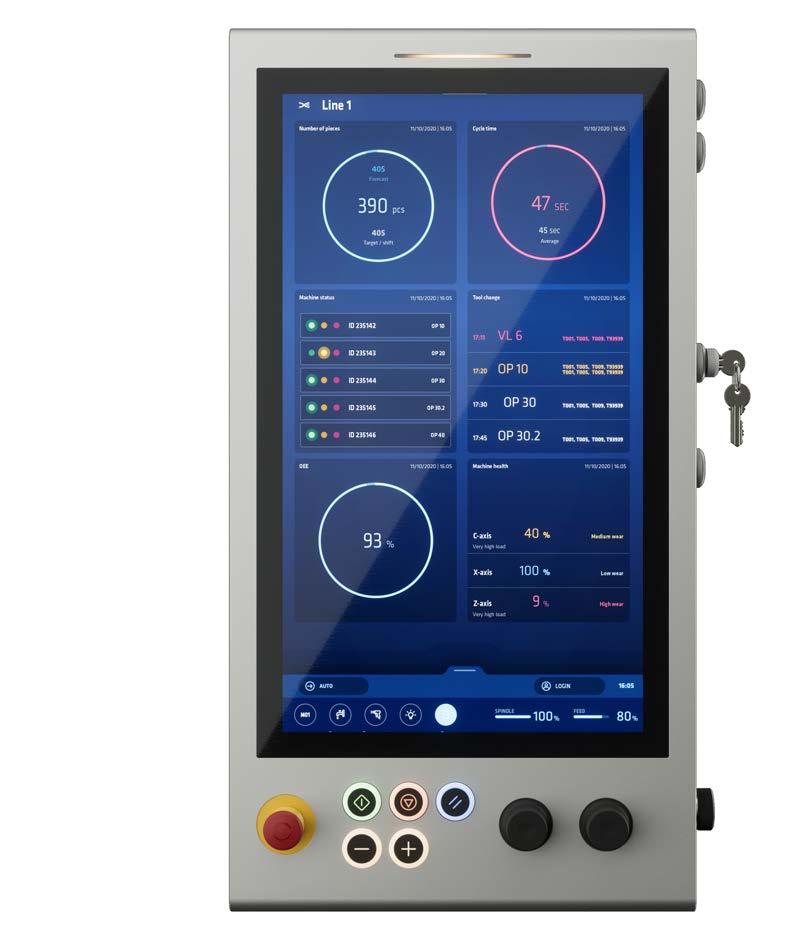
ALL EDNA FUNCTIONALITY AT A GLANCE
With EDNA, EMAG has at its disposal an ecosystem for the digitalization of indus trial production. The basis is the EDNA IoT core, which records a wealth of pro duction and sensor data. The condition of the machine can then be determined, for example, by analyzing regular measurements using the EDNA Health Check.
» Number of pieces produced
» Cycle time average
» Tool change
» Current OEE
» Machine health
Machine lifeline dashboards can be accessed from a variety of devices. As a result, those responsible can survey and evaluate their entire production system.
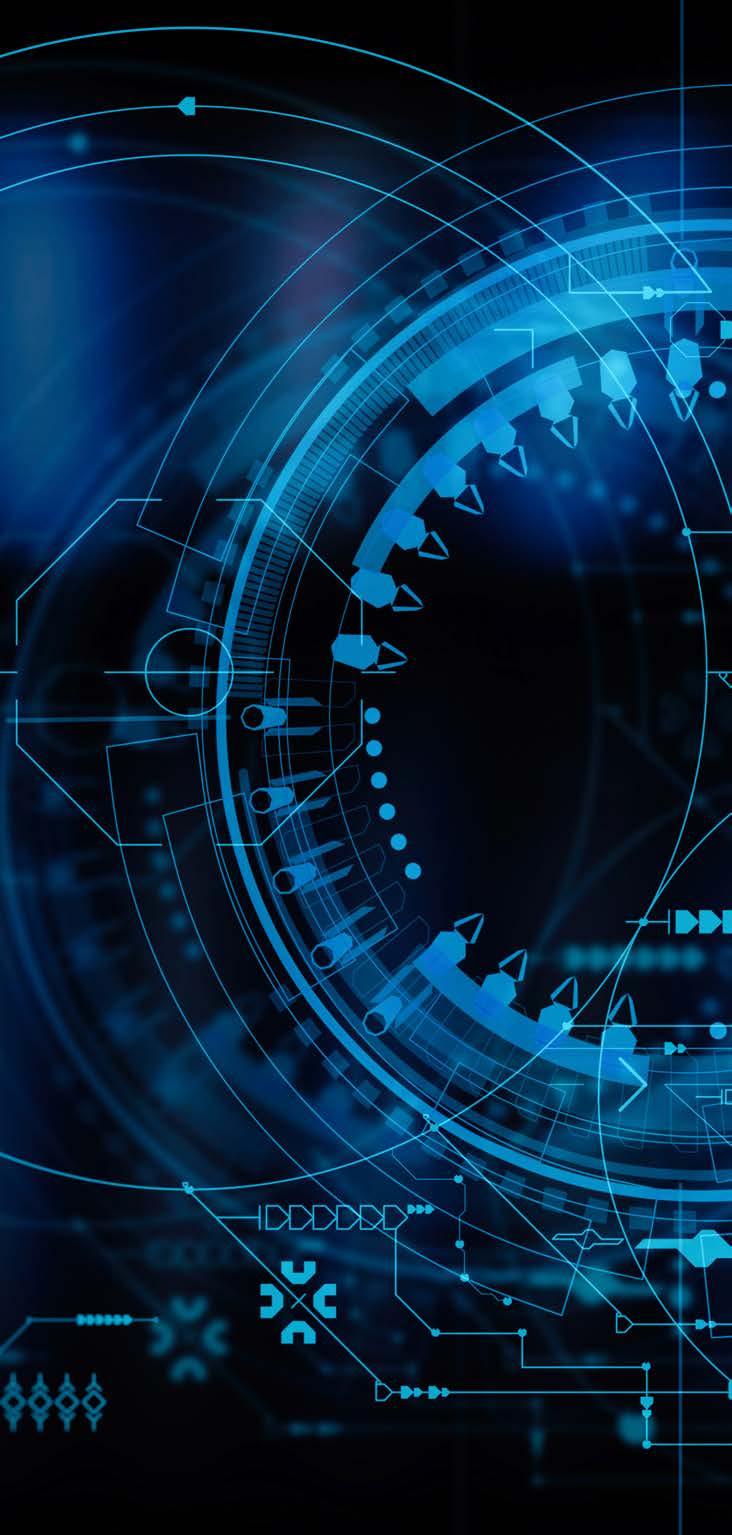
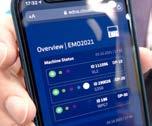
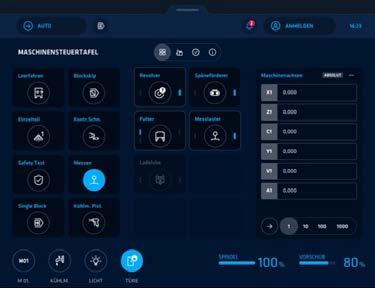
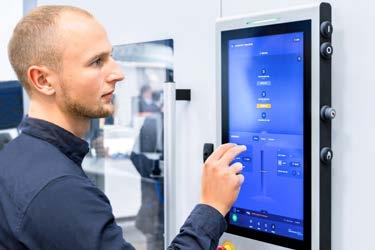
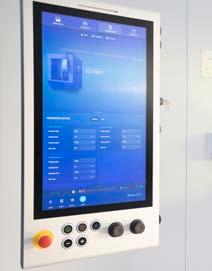
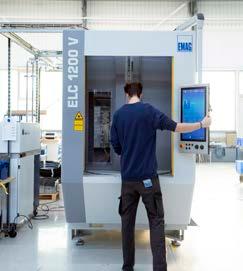

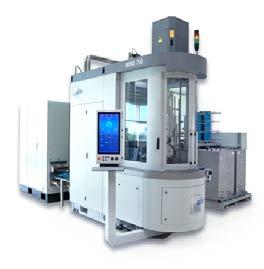
Display of manual functions on the EDNA panel.
An example of workpiece programming from the HMI 4.0 ecosystem.

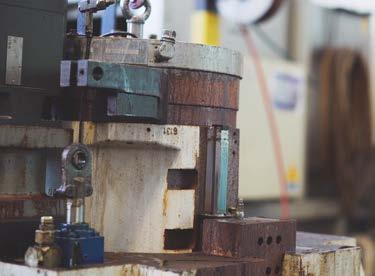
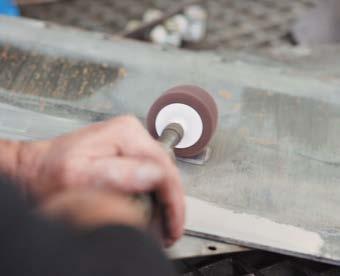
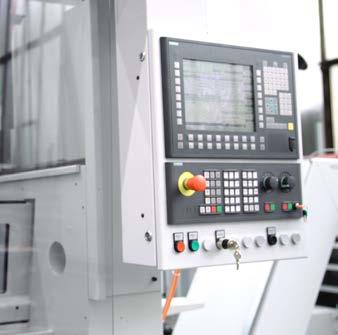
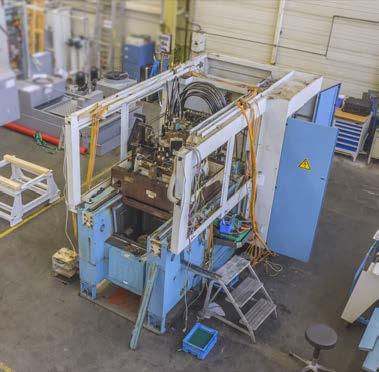
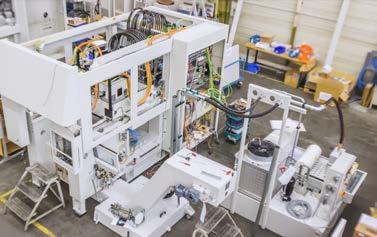
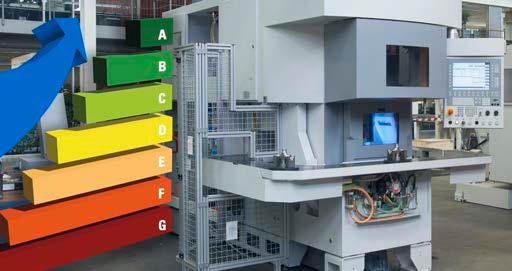
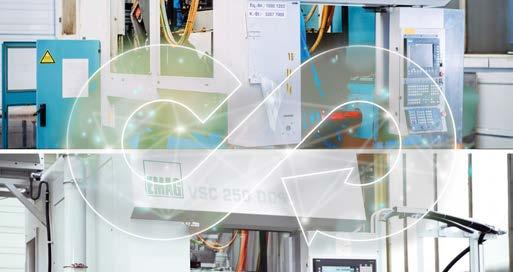
Retrofit at EMAG – the very highest quality down to the last detail. Used machines or other machines in your inventory are refurbished precisely, modern ized, and returned to perfection. Customized solutions for efficient production processes in the usual EMAG quality are created. The spectrum of EMAG retrofits is huge: They range from the replacement of individual assemblies, such as the spindle with new or refur
bished components, to the conversion of the control system, to the complete conversion of individual machines or production lines. At the Retrofit Open House, we will show you the possibilities with retrofitting and which measures makes sense. Retrofit at EMAG: Benefit from the expertise and many years of experience of the original equipment manu facturer!
» IoT
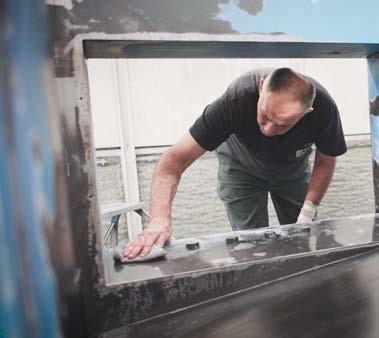
The EMAG retrofit experts can make used machine tools fit again so that they are even ready for IoT. It is becoming more and more common for retrofit machines to be supplemented with new interfaces and IoT applications are also in demand. This ranges from systems for production monitoring to energy consumption analyses and evaluation of the machine health.
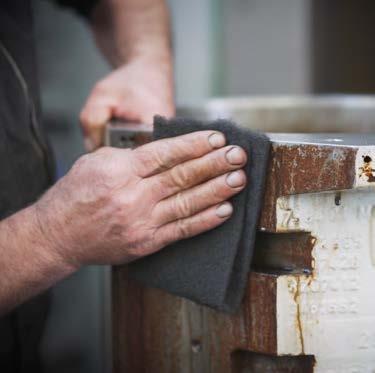

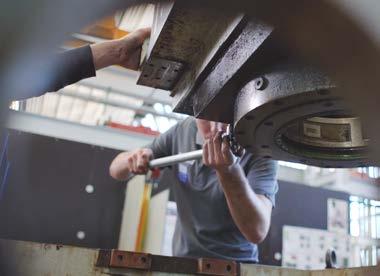

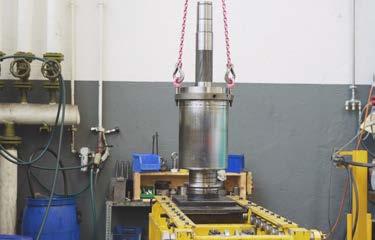
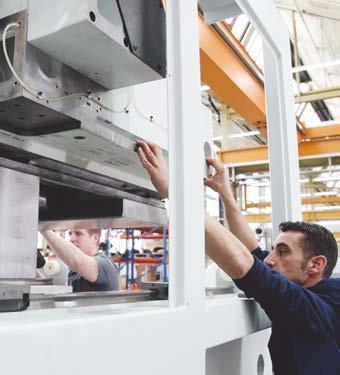

In times of increasing delivery times for new machines, retrofitting is the fast and cost-effective alternative!
EMAG
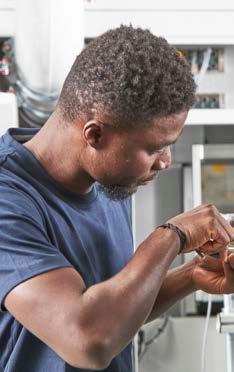
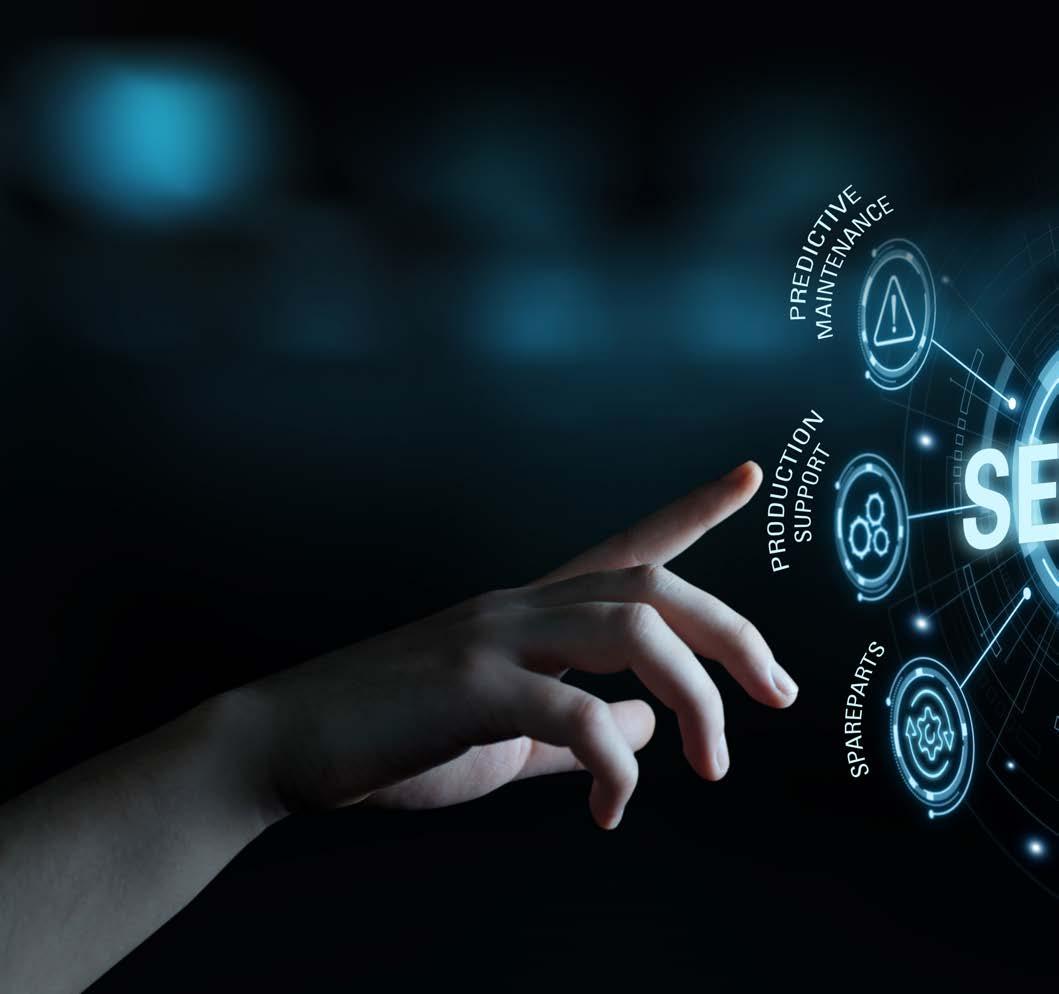


“We see our entire range of services as a part nership and work closely with our
Patrick Theiss
THE DIFFERENCE BETWEEN INSPECTION AND MAINTENANCE:
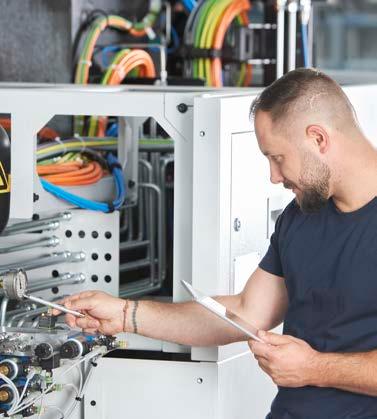
» The inspection involves a comprehensive check, with experts rigorously working through a predefined check list for their respective EMAG technology. Production is only briefly interrupted.
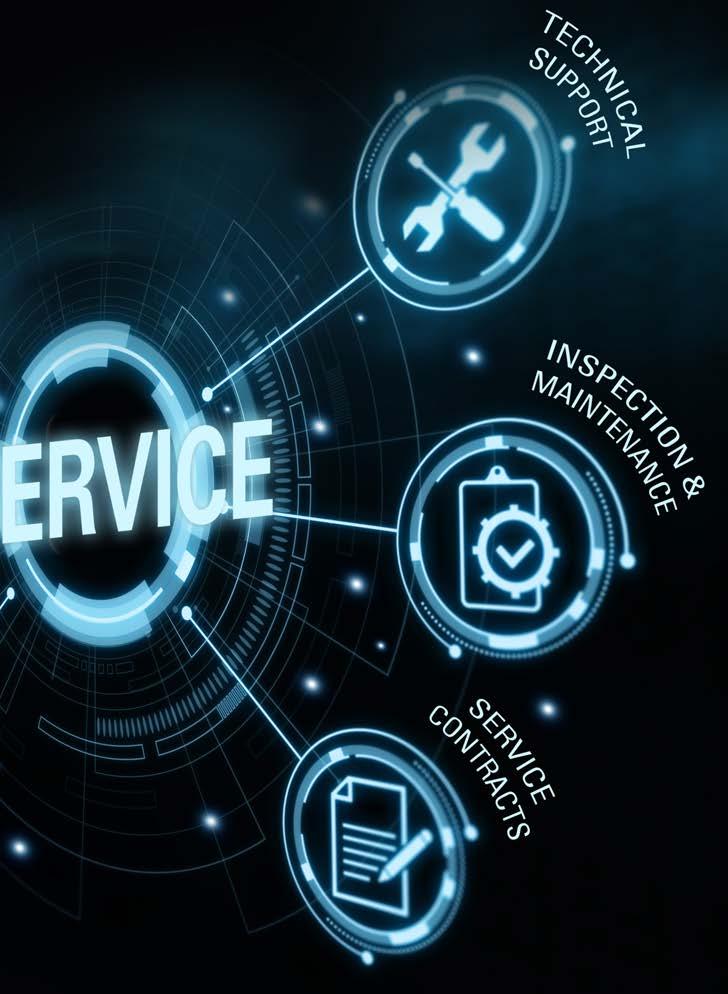
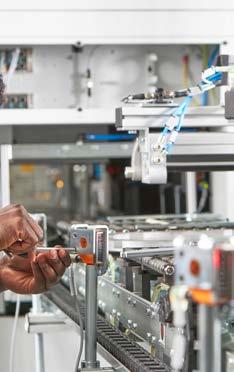
» In contrast to this, comprehensive maintenance is a kind of supreme discipline in the service area, including the replacement of wearing parts, whereby the whole process is planned in great detail – depending on the customer’s production task.
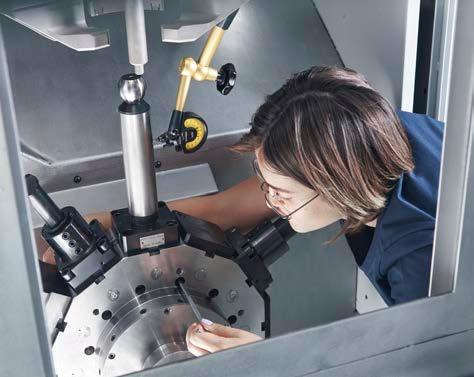
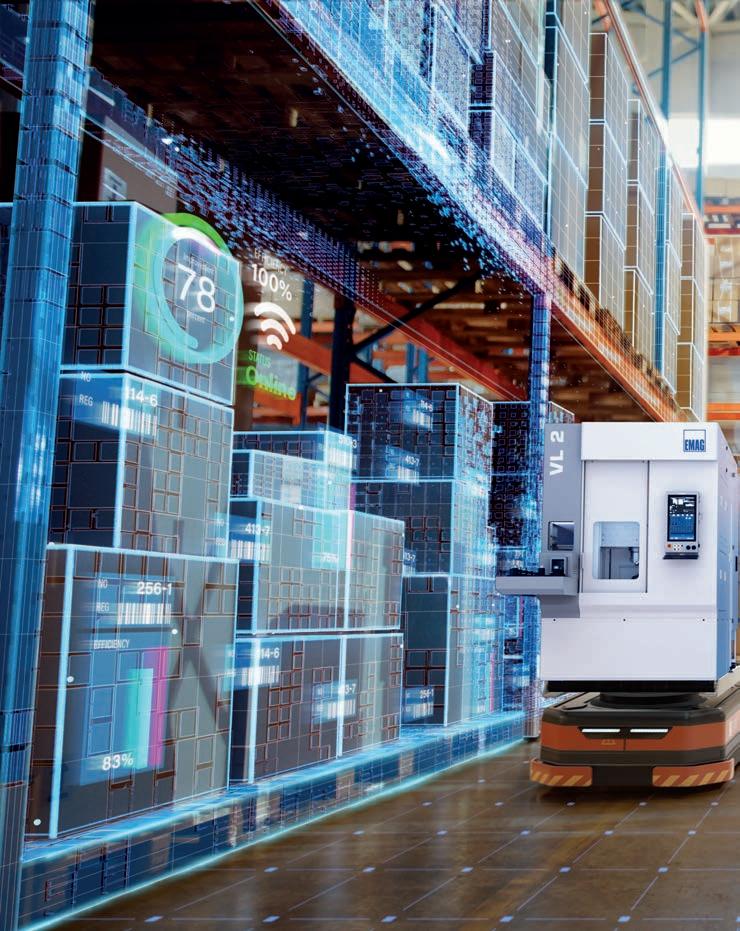

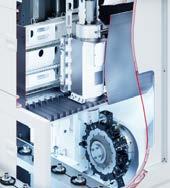
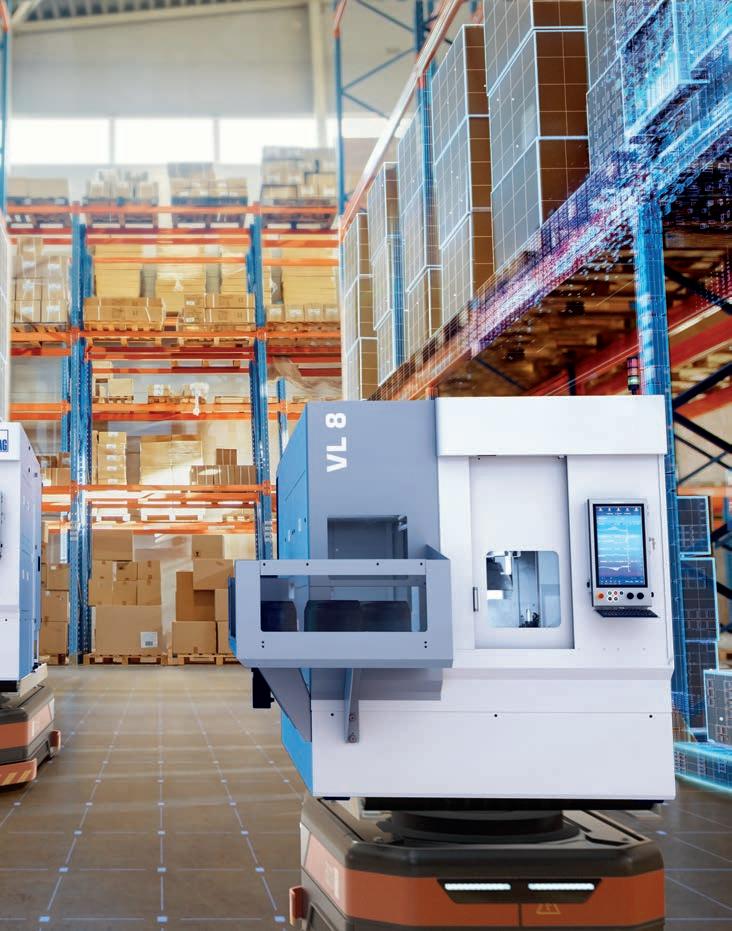



EMAG Salach GmbH
Salach Austraße 24 73084 Salach Germany Phone: + 49 7162 17–0 Fax: + 49 7162 17-4027 E-mail: info@salach.emag.com
Austria Glaneckerweg 1 5400 Hallein Austria Phone: + 43 6245 76023–0 Fax: + 43 6245 76023-20 E-mail: info@austria.emag.com
Sweden
Glasgatan 19B 73130 Köping Sweden Phone: + 46 221 40305 E-mail: info@sweden.emag.com
Hungary Gerenda 10 1163 Budapest Hungary Phone: + 36 30 9362-416 E-mail: lbujaki@emag.com
Czech Republic Lolkova 766 103 00 Praha 10 – Kolovraty Czech Republic Phone: + 420 731 476070 E-mail: mdelis@emag.com
Poland
ul. Krzycka 71A/6 53-020 Wrocław Poland Phone: + 48 728 389 989 E-mail: info@poland.emag.com
Turkey Sanayi Cad. No.: 44 Nish İstanbul Sitesi D Blok D: 155 Yenibosna – Istanbul Turkey Phone: + 90 532 694 54 44 E-mail: ckoc@emag.com
NEWS 35/12.2022 · © Copyright EMAG · Printed in Germany
Market companies
EUROPE
EMAG MILANO S.r.l. Via dei Mille 31 20098 San Giuliano Milanese (Mi) Italy Phone: + 39 02 905942-1 Fax: + 39 02 905942-24 E-mail: info.milano@emag.com
EMAG MILANO S.r.l. Succursale en France 5 Avenue de l’Europe 18150 La Guerche sur l’Aubois France Phone: + 33 02 48 7711-00 Fax: + 33 02 48 7111-29 E-mail: info.france@emag.com
EMAG MILANO S.r.l. Sucursal en España Pasaje Arrahona, n° 18 Polígono Industrial Santiga 08210 Barberà del Vallès (Barcelona) Spain Phone: + 34 93 7195080 Fax: + 34 93 7297107 E-mail: info.spain@emag.com
AMERICA
EMAG L.L.C. USA 38800 Grand River Avenue Farmington Hills, MI 48335 USA Phone: +1 248 477-7440 Fax: +1 248 477-7784 E-mail: info@usa.emag.com
EMAG MEXICO
Maquinaria EMAG Mexico S de RL de CV Av. Hercules 301 Nave 1 Poligono Empresarial Santa Rosa 76220 Santa Rosa Jauregui, Querétaro Mexico Phone: + 52 442 291 1552 E-mail: info.mexico@emag.com
EMAG DO BRASIL
Edifício Neo Corporate Offices, CJ 1503 Rua Enxovia, 472 04711-030 São Paulo SP Brazil Phone: + 55 11 38370145 Fax: + 55 11 38370145 E-mail: info@brasil.emag.com
ASIA
EMAG (China) Machinery Co., Ltd. Sino-German Advanced Manufacturing Technology International Innovation park Building 2, No. 101, Chen Men Jing Road 215400 Taicang Jiangsu, China Phone: + 86 512 5357-4098 Fax: + 86 512 5357-5399 E-mail: info@emag-china.com
EMAG (Chongqing) Intelligent Technical Co., Ltd Building 7, No. 24 Fangzheng Avenue Beibei District Chongqing 400714 China
Phone: + 86 23 49783399 Fax: + 86 23 49783388 E-mail: info@emag-china.com
TAKAMAZ EMAG Ltd. 1-8 Asahigaoka Hakusan-City Ishikawa Japan, 924-0004 Japan Phone: + 81 76 274-1409 Fax: + 81 76 274-8530 E-mail: info@takamaz.emag.com
EMAG INDIA Pvt. Ltd. Technology Centre No. 17/G/46-3, Industrial Suburb 2nd Stage, Yeshwantpur Bengaluru – 560 022 India Phone: + 91 80 50050163 E-mail: info@india.emag.com
EMAG KOREA Ltd. Rm204, Biz center, SKn Technopark 124 Sagimakgol-ro, Sangdaewon-dong, Jungwon-gu, Seongnam City, Gyeonggi-do, 462-721 South Korea Phone: + 82 31 776-4415 Fax: + 82 31 776-4419 E-mail: info@korea.emag.com
Subject to technical changes. Illustration of all machines in trade show versions, may differ from the standard.