
1 minute read
6: PERFEKTIONIERUNG DES SCHWEISSPROZESSES AN DER GEBAUTEN ROTORWELLE
from EMAG NEWS #36 (DE)
by EMAG Group
So schätzt etwa die Internationale Energieagentur (IEA), dass in diesem Jahr 14 Millionen E-Fahrzeuge verkauft werden; dies entspricht einem Absatzplus von 35 Prozent im Vergleich zum Vorjahr. Der Anteil am gesamten Automarkt beträgt damit bereits fast ein Fünftel. In der Folge rückt die Herstellung zentraler Bauteile des E-Motors wie die Rotorwelle in den Fokus von Produktionsplanern. Gesucht werden innovative Lösungen „aus einer Hand“, mit denen sich das Bauteil in immer größeren Stückzahlen besonders effizient und prozesssicher bearbeiten lässt.
EMAG LaserTec setzt dabei aktuell mit der ELC 6 ein Zeichen im Markt: In der ganzheitlichen Technologie dieser Laserschweiß-Maschine werden Füge-, Reinigungs- und Schweißprozesse an einer gebauten Rotorwelle kompakt zusammengeführt, wobei ihr Rundtischsystem für optimale Taktzeiten sorgt.


» Laserreinigung
Ein Portal entnimmt die Einzelteile vom Transfersystem und legt sie auf den Schwenktisch. Im ersten Schritt erfolgt eine Laserreinigung der Bauteile, wobei die zwei Rohlinge von Arbeitsstoffen und Schmutz befreit werden. Dabei trifft gepulste Laserstrahlung auf die Oberfläche und das Material verdampft schlagartig. So ist die zurückbleibende Oberfläche perfekt für die Weiterbearbeitung vorbereitet.
» Vorwärmen und Fügen
In den nächsten Schritten (Vorwärmen und Fügen) sorgt zunächst Induktionstechnologie für eine ideale Bearbeitungstemperatur am Bauteil, bevor anschließend die beiden Bauteile zusammengefügt werden.
» Prüfung
Vor dem Schweißen erfolgt eine Prüfung der SchweißnahtLage und eine Nachregelung der Bauteilposition. Dabei wird die Kontur präzise gescannt und die Daten der Schweißoptik und den NC-Achsen mitgeteilt.
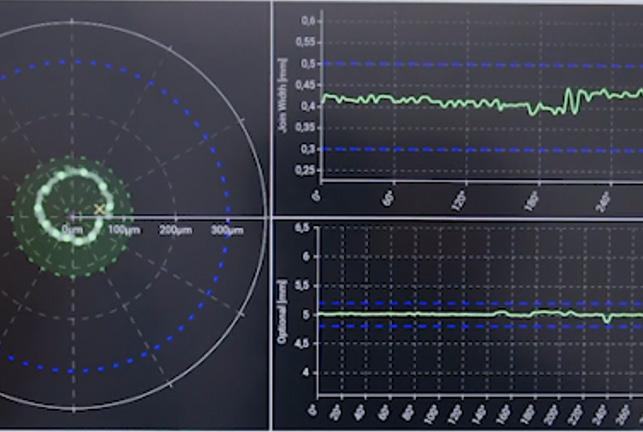
VORTEILE DER ELC 6:
Insgesamt weist die ELC 6 eine enorme Produktionsgeschwindigkeit auf – unter anderem, weil die Maschine mit ihrem Rundtisch während des Schweißens (und damit hauptzeitparallel) be- und entladen wird. Zudem sind die einzelnen Teilprozesse perfekt getaktet und das Prinzip „feste Optik/ bewegtes Werkstück“ führt zu einer hohen Betriebssicherheit. Darüber hinaus gestaltet EMAG LaserTec diese Lösung für den Kunden sehr flexibel in Bezug auf Technologie, Leistung und Automatisierung, wobei Werkstücke bis zu einer Höhe von 300 Millimetern in der ELC 6 bearbeitet werden können.


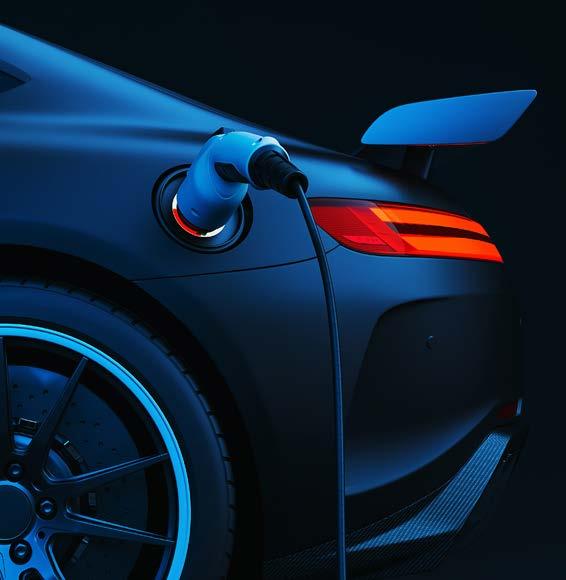
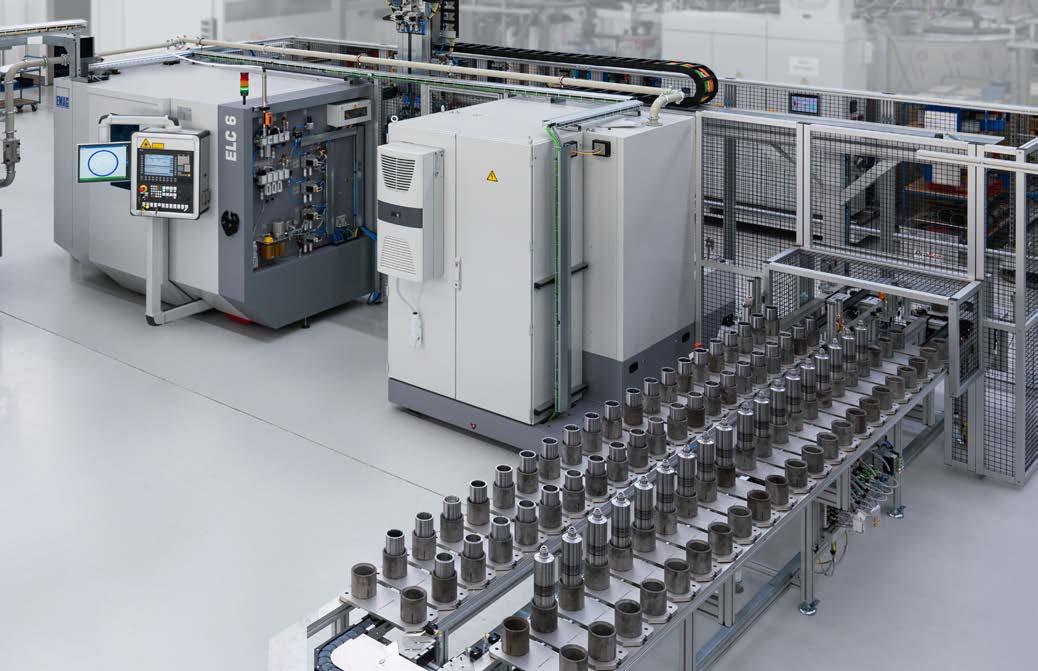
