

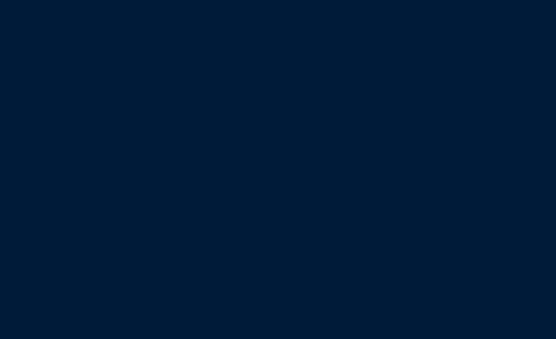
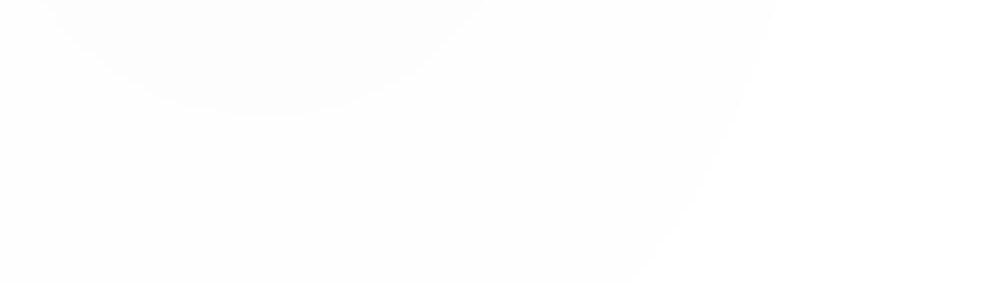
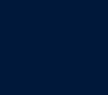

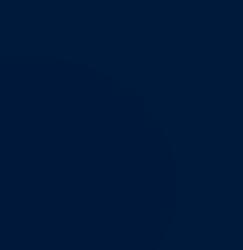

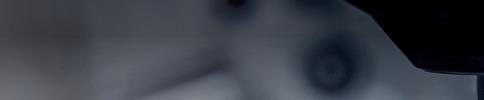

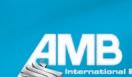
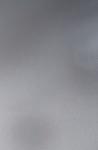


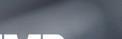
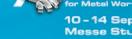
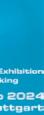
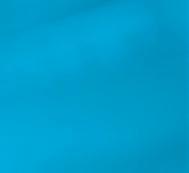



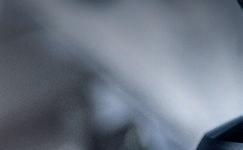

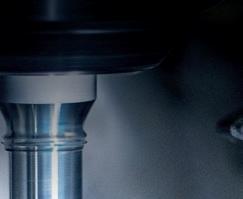
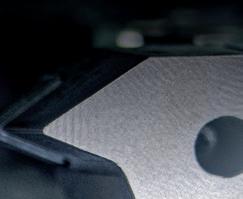
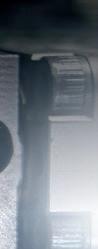


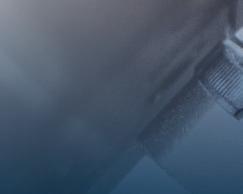
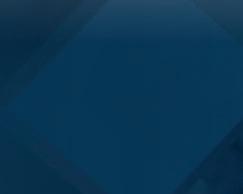
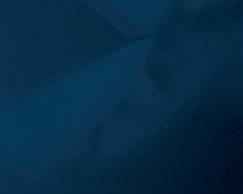
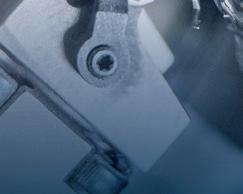


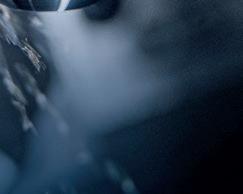
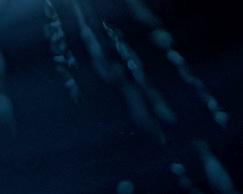
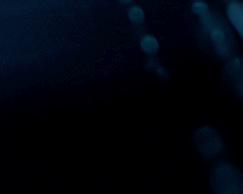
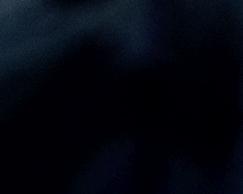
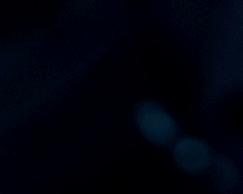
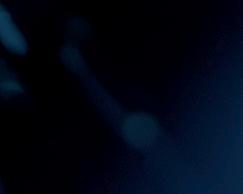



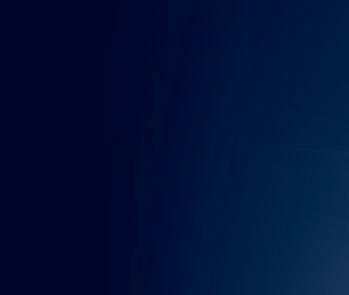
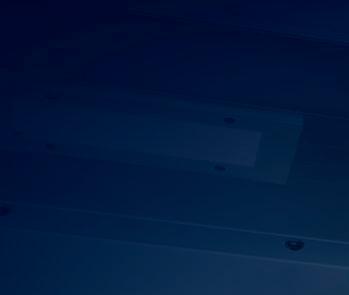
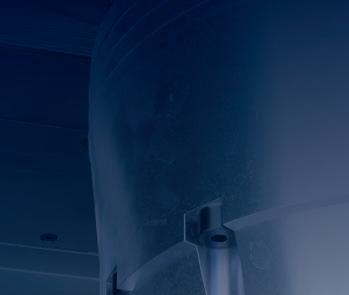
This machining line with two VL 4 vertical pick-up turning machines is characterized by its simple design and high performance. Soft machining of axial piston pump cylinders can be completed in just two operations. The compact design of the line enables the highest productivity level with a minimal footprint.
A number of design details of the VL 4 machines guarantee fast machining processes:
» The machines load themselves using a pick-up spindle. An integrated conveyor belt is available for this purpose.
» The 12-station turret (also for driven tools) delivers by very short swivel times.
» All service units are freely accessible and, therefore, easy to reach.
» The vibration-dampening machine base is made of MINERALIT® polymer concrete, ensuring high stability.
» Vertical machining guarantees optimum chip evacuation.
» With a Y-axis (optional) in the turret, the machines can be equipped for machining complex geometries.
Conclusion: Low unit production costs, high component quality - the VL machines ensure efficient production processes.
» TrackMotion automation system:
The machines are connected using the TrackMotion automation system, which handles both repositioning and turning. Raw parts are delivered to the machines from a storage system.
» OP 10:
The machining of the first part takes place on VL 4 (OP10).
» Parts transport:
The TrackMotion automation system is used to transport as well as turn the workpieces.
» OP 20:
After machining the second side (OP 20), the workpieces are measured by the integrated measuring station in VL 4.
Complete machining in a single setup
In addition to the 12-station turret, the VL 8 is also available with a milling spindle. The milling spindle is mounted in an extra console and off ers extraordinary performance of 52 kW and over 99 Nm of torque. The milling spindle can be used to carry out further, even complex, drilling and milling operations. This signifi cantly extends the range of applications for the VL 8. It can be equipped with a turn-over unit at the pick-up station. This allows workpieces to be produced in two setups directly in the machine. TECHNICAL DATA
MR Components, a medium-sized company from Grigno, Italy, has significantly increased its production capacity and productivity by introducing intelligent automation with EMAG machines. The company, which specializes in the manufacture and supply of parts for diff erential and planetary gears, now produces around 80,000 components per month, with some of the machines running unmanned in the evenings.
In 2011, MR Components invested in the first two VL 7 machines from EMAG, which are characterized by integrated measuring probes and a rigid design. Today, all EMAG machines are equipped with measuring probes to ensure 100% inspection of all components. Additional quality controls are carried out with various measuring devices and in a special measuring room. The current reject rate of only 0.2 percent for 80,000 components is proof of the high quality of production.
Thanks to the high degree of automation, production can continue even after closing time in the evening for 2 to 4 hours, depending on the machine. Thanks to the 100% inspection of components, production is automatically stopped if a part is faulty, which avoids rejects and makes optimum use of production.
» Foundation: 1995
» Production area: 6,000 m²
» 50 employees
» 80,000 components per month
» Quality control: 100% of workpieces are measured
» Reject rate only 0.2 percent
» Workpieces: Components for diff erential and planetary gears
» Predominantly partially and fully automated machines in use
A robot at work on a production system from MR Components. Thanks to automation, additional operations, such as marking, can be carried out flexibly and easily.
Various manufacturing systems are used at MR Components to meet production requirements. VL 7 machines are used in one line, where the operator manually places the workpieces on the automation belt. This method has proven successful for simple workpieces or more complex workpieces with small quantities. In other production lines, VL 4 machines with TrackMotion automation are used, which enable fast automation and greater autonomy, so that the machines can also be operated in unmanned mode. There are also other production systems that are automated with robots to perform additional operations such as marking. These various manufacturing systems enable a flexible response to production requirements and ensure high quality and efficiency.
» Shift model: 2.5 shifts, with the night shift running completely autonomously
Here is the short video about MR Components:
Zona Industriale 3/C
38055 Grigno TN – ITALY
MR Components (MECCANICA REGUZZO)
E-mail: info@meccanicareguzzo.it
Website: www.meccanicareguzzo.it
Whether in the steering system or in the chassis - ball joints are indispensable in our cars. They not only act as a kind of pivot point between diff erent elements, but are also usually in constant motion and exposed to high physical loads. In this context, ball pins and ball sleeves are among the safety-critical car components that have to leave production with a high surface quality and micrometer precision without exception - despite high quantities and general cost pressure.
The machine scores with extreme performance figures. For example, the chip-to-chip time is less than 2 seconds - a ball pin leaves the VST 50 every seven seconds. This speed is made possible by a work area with two workpiece spindles and two optional tailstocks as well as a total of three robots for loading the work area and transporting the components to and from the outside. While one spindle is machining, the other spindle can be loaded and unloaded.
» Comprehensive result:
The recording of the light-band micrometer shows various measured values.
» Live image
With the live image from the work area, the operator can check whether the chip formation is causing a fault in the process, for example.
» Chip-to-chip time under 2 seconds
» Tool change in 90 seconds by robot
» High-speed automation
» Latest SINUMERIK ONE software generation
» Measuring unit including chip detection outside the work area
» Part recognition on the conveyor belt
» Fully automatic tool magazine (incl. RFID)
» High usability via EDNA apps
At this year's AMB, EMAG is presenting the VL 200 vertical turning machine equipped with a CRC robot cell for the machining (OP 10) of planetary gears in the agricultural sector.
Instead of a conventional conveyor belt, the CRC robot cell is mounted directly on the VL 200. This enables the robot to load the workpiece directly into the spindle. The robot takes over the loading and unloading function by means of a double gripper.
FANUC iHMI with 19” multi-touch screen and intuitive user interface.
Advantages of FANUC iHMI:
» Consistent menu navigation: FANUC Home Screen with the applications Planning, Editing, Improvement & Utilization.
» Simple setup: Integration of EMAG-specific masks, e.g. for simplified setup of the clamping device
» Improved diagnostic options: Extensive machine/control documentation directly on the machine control system and easy integration of additional documents
» 3D simulation: Manual measurement of the workpiece possible within the simulation
The workpieces are loaded directly into the spindle!
The vertical pick-up turning machines of the VL series are specially designed for the the production of precise chucked parts. In order to cover the widest possible range of parts, the VL machines are available in four versions for workpieces from 10 mm to max. 400 mm diameter.
Highlights:
» Fully vertical lathe model family with modular design
» All VL machines use direct path measuring systems in all axes
» Ideal for series production - from small to large series
» The complete automation and handling technologies are included in every machine
» Simple automation of several machines possible thanks to uniform automation
» Height Particularly suitable for multi-machine operation
» Minimal non-productive time:
Direct loading into the spindle reduces the loading/unloading time to just 4 seconds.
» Compact automation solution: Space-saving design and easy integration.
» No shuttle required: Direct transfer between robot and machine.
The CRC stacking cell is perfect for components with a diameter of up to 200 mm. It is loaded using workpiece carriers, which are housed in drawers and can carry up to 45 kilograms per drawer. A robot handles the parts and loads and unloads the machines. The machine operator is only responsible for replacing the workpiece carriers, which takes place simultaneously with the main processing time to ensure a continuous production flow.
The MRC robot cell is designed to load and link-up our machine tools. At AMB, we will present a manufacturing system for the machining of planetary gears in the agricultural industry. This system combines turning on a VL 4 with hobbing of the tooth profiles on a CLC 200 from EMAG SU.
For a long time, the separation of raw-parts from the bulk material was only possible manually or using complex mechanical and usually very workpiece-specific solutions such as vibratory conveyors. The chaotic arrangement of the components prevented automated handling directly from the container.
With the new MRC robot cell, EMAG presents a modular automation platform for machine loading and link-up. Thanks to the optional bin picking module, it can also be used to handle raw-parts in bulk in an efficient and resource-saving manner.
» Flexibility:
Fast changeover between different component families, raw-parts and machining processes by using a robot with camera system and optional gripper quick-change system.
» Volume:
Virtually noiseless picking up of components by the robot, no annoying noises due to mechanical separation.
» Economic advantage:
Reduced worker constraints for manual pre-alignment or other preliminary work on raw-parts and, thus, greater autonomy.
» Integration:
Simple integration of handling processes, such as aligning, cleaning or measuring components.
MINIMAL FOOTPRINT:
Compact system with design freedom.
Installation area approx. 2.7 m x 5.1 m.
The MRC robot cell off ers the option of integrating numerous additional functionalities:
» Blow off
» Measuring
» Buff ering
» Labeling/marking
» Read code
» Provision of workpiece carriers for heat treatment by gantry system
» Handling the baskets using the gantry integrated in the SCS 4
» Robots for handling the workpieces including position control
Wire baskets are widely used in production logistics. With the SCS 4 stacking cell, EMAG off ers a highly efficient automation solution for this. It is designed for baskets up to 600 x 500 mm. The baskets are fed into stackers either manually or with an automated guided vehicle (AGV).
Here using the example of a restacking cell for workpieces on hardening grids:
The workpieces are fed from the upstream process via wire baskets, which are buff ered by the SCS 4 and separated for the removal of the workpieces. The workpieces are transferred from the baskets to the hardening grids by a robot, which is equipped with a camera system to detect the exact position of the workpieces.
The hardening grids are handled by a gantry system, which also checks the grids for distortion caused by the hardening process and automatically ejects defective grids. After the hardening process, the components are restacked in the opposite direction: back into the wire baskets and then out of the SCS 4 stacking cell by fl oor roller or AGV back into the subsequent production process.
» Compact complete solution from a single source from EMAG
» Economical production through optimal machine utilization
» Unmanned production
» High storage density with a small footprint
» Comparatively low capital investments
» Simple retrofi tting options
Further information on SCS stacking cells can be found here:
High quantities on the one hand, complex geometric details on the other - shaft machining is a challenge for production planners. In addition, typical components such as rotor shafts, gear shafts or worm shafts require extreme precision, as they are usually something like the "heart" of a motor or pump. How can real leaps in productivity be ensured for these tasks - and on the basis of particularly processreliable vertical machining?
EMAG is providing the answer to this with the VT machine series at AMB 2024 in Stuttgart: The vertical arrangement of VT 2, VT 4 and VTC 100 GT ensures fast production processes thanks to unhindered chip fl ow, fast 4-axis machining, technology combination turning & grinding, scroll free turning, gear hobbing and much more. All of this includes integrated automation for short cycle times. And, because a wide range of options are available for this "modular system", the range of applications for the VT series is enormous.
The gripper in the turret removes the workpiece from the parts storage and transports it into the clamping position or out after machining.
EXAMPLES: VERTICAL SHAFT MACHINING
4-axis machining of a worm shaft
» 4-axis turning
» Threading
» Scroll free turning
» Flutes milling
» Turning helix
Scroll free turning rotor package
» Pre-turning 4-axis (prime turn)
» Scroll free turning with Y/Z axes
The VT 200 CD (Center Drive) with center drive is used for machining the shaft ends. Shafts up to a length of 540 mm and a diameter of 80 mm can be machined on the machine. The machine boasts a large work area and generous travel paths for the two integrated turrets. This enables 4-axis simultaneous machining of both shaft ends. An additional support steady rest can also be used for longer workpieces. The powerful center drive reaches a maximum speed of 3,000 rpm and delivers an output of 19.1 kW at 100% load or 27 kW at 40% load, ensuring effi cient machining of even the most demanding workpieces.
The increasing use of automation in industry, particularly in robotics, is one of the key drivers that will generate strong growth in the market over the coming years. With increasing automation, the demand for powerful and reliable industrial gearboxes is also growing significantly.
The EMAG Koepfer HLC 150 H is a machine specially developed for gear hobbing and worm milling that fulfills the highest demands. It combines state-of-the-art technology with high flexibility and efficiency.
In worm milling, the disc cutter is used to mill each start of the worm subsequently. Existing machines often offer only limited flexibility when selecting an efficient cutting strategy. Idle strokes are often unavoidable, especially when milling multi-start worms. These idle times have a negative effect on the cycle time and, therefore, on process efficiency.
In order to increase the efficiency of such gear cutting processes, the HLC 150 H uses special machining cycles that have been optimised for worm milling. Another advantage is that the deburring operation can also be programmed directly with these cycles in a user-friendly way. This increases flexibility and significantly improves the efficiency of worm milling.
A high-speed gantry loader with a double rotary gripper or a linear gripper in a V arrangement are available for automation.
Efficient gear machining of straight and helical workpieces up to worms and gears with a maximum diameter of 150 mm.
» Enormously wide range of workpieces thanks to innovative cross-slide design and "kinematic Y-axis"
» Gear hobbing machine with impressive performance data
» Worm milling operations are possible due to large milling head swivelling angle
» Various linking options including TrackMotion
» Integrated deburring technology
» FANUC control
The EMAG SU CLC gear hobbing machines were developed for the highly productive machining of precision gears and have been characterized by efficiency, quality and versatility for many years. The spectrum ranges from spur and helical gears, worm gears and crown gears to short gears (splines) in various sizes.
The CLC machines can be equipped with the following technologies:
» Hobbing
» Rough hobbing as a pre-gearing process
» Finish hobbing before hardening and skiving after hardening as a fine machining process
» Milling of individual parts: milling with side milling cutters as a pre-gearing process
The CLC series consists of three vertical gear hobbing machines:
» CLC 200: for workpieces up to 220 mm & module 5
» CLC 300: for workpieces up to 350 mm & module 7
» CLC 500: for workpieces up to 500 mm & module 10
Two ring loader versions with two or four stations are available for the vertical gear hobbing machines in the CLC series. The ring loader offers many advantages. With two NC axes (E and WE axes), the workpiece can be loaded and unloaded directly into the clamping device. But it also makes machine set-up much easier. The two NC axes can be used to move to different positions, which means that only a minimum number of change parts are required when retooling for a new workpiece.
» Conveyor belt with pick-up of the workpieces via a ring loader.
» NC ring loader with swivel arms for the use of hobs with small diameters.
Direct drives in the milling head and tool table for maximum dynamics
Automatically movable counter bearing
Wide range of workpieces: gears, worm gears, crown gears and splines 1 2 3 4 5
Tangential axis with ground and hand-scraped guides for maximum precision
High machine weight for vibration damping
» Maximum fl exibility thanks to large working area
» Tool spindle and work table with direct drive
» High-speed hobbing spindle and worktable
» The worktable can be equipped with a hydraulic workpiece clamping device, with the option of digital monitoring of the clamping path
» also designed for dry machining
» Long tangential axis Y (for longer hobs or multiple tools) - available as an option
» Tactile or inductive measuring probe or sensor for workpiece monitoring
» Scraper chip conveyor for non-ferromagnetic materials (cast iron, aluminium or bronze) or alternatively magnetic chip conveyor
» Tailstock movement by servomotors and preloaded ball screw
» Hobbing arbor with ISO cones
» 2-NC ring loader for minimal set-up eff ortavailable as an option
» Stacker cell with circulating conveyor belt.
» Robot loading from the rear side with loading door.
Further information on the CLC Series gear shaping, gear hobbing and milling machines can be found here:
Precise, compact and cost eff ective - these are the criteria that have made the WPG 7 external cylindrical grinding machine from EMAG WEISS a great success in the market. It requires only a minimal footprint and can also be installed quickly, but at the same time features a whole range of high-tech components for flexibility and productivity.
» Available as a 0° straight or 30° angled plunge-cut machine
» Powerful grinding wheel drive with up to 50 m/s
» Grinding wheel dia. with max. 500 x 80 mm
» CBN or corundum wheels can be used
» FANUC control
» Cooling system with emulsion or oil
» Minimal footprint of only 1,800 x 2,400 mm
» With stationary and moving tip MK4/MK5 or W20/W25
» Optional in-process measuring control (diameter), passive longitudinal
» Longitudinal positioning, automatic balancing system as well as GAP and crash control
» All common grinding cycles integrated in the control system
for the grinding expert Andreas Holstein from EMAG Weiss!
Which applications suit the WPG 7?
This solution may interest many users, who often machine smaller components, like shafts or pinions, in medium quantities. The maximum workpiece length here is 250 millimeters. In this size range, companies often rely on oversized universal cylindrical grinding machines, which take up an enormous amount of space and are also very expensive although, in the end, their functionality is not actually fully utilized.
What characterizes the technology in the work area?
The WPG 7 is basically available in two different versions - for straight grinding or angled plunge grinding with a 30-degree angle. Users must decide between these options in advance. In both cases, they benefit from a powerful grinding wheel drive with speeds of up to 50 m/s and a large grinding wheel with a maximum diameter of 500 millimetres. As a result, the grinding process is very fast and productive.
Is loading manual or automated?
The interior of the external cylindrical grinding machine is easily accessible after opening the large front door.
The external cylindrical grinding machine can be automated by chain conveyor, pallet circulation or robot.
Both are possible. For the automation of cylindrical grinding, we have developed a linear gantry that can be integrated into the enclosure of the cylindrical grinding machine at the customer's request. On this basis, the WPG 7 can be connected with chain conveyor belts, a pallet circulation system or by robot, for example.
BLOG
The complete interview can be found on the EMAG blog:
Sabatti Spa is a renowned family business whose beginnings with the gunsmith Ludovico Sabatti go back 350 years and is, therefore, deeply rooted in gun manufacturing. Today, Sabatti Spa is at the forefront of innovation, balancing time-honored craftsmanship with modern technology, making the company one of the leading names in the industry. The integration of EMAG ECM rifl ing technology into the production of rifled barrels represents a breakthrough for Sabatti that not only improves shooting accuracy, but also combines the tradition of gunmaking with pioneering production methods.
EMAG BLOG
You can find the complete success story on the EMAG blog:
SABATTI SPA
Via Alessandro Volta, 90 25063 Gardone Val Trompia BS – ITALY E-mail: info@sabatti.it Website: www.sabatti.it
Precision plays a decisive role in the manufacture of weapons. One technique that contributes signifi cantly to the precision of fi rearms is rifl ing - the insertion of helical grooves into the barrel of a weapon. The multiple fl utes ensure that the bullet is set in rotation when fi red and produces a more precise trajectory.
With the PI machines, EMAG off ers a powerful ECM rifl ing solution that can be confi gured to customer specifi cations. These machines have a rifl ing module that is integrated into the PI machines. The module can machine eight barrels with a length of 50 to 820 mm in parallel. A new dual module is also now available.
Sabatti uses the PI 2500 with ECM rifl ing technology from EMAG to manufacture highprecision rifle barrels.
Sabatti uses electrochemical machining (ECM) to maximize the precision and performance of firearms with its patented rifl ing process.
The MMR rifl ing process patented by Sabatti stands for outstanding shooting results and underlines the company's pioneering role in the manufacture of rifled barrels.
VISIT US! HALL 4 BOOTH 4C50
This year, we will present our latest automation systems for machine tools. Another area of our stand will be dedicated to solutions for joint machining and manufacturing systems for high-precision tooth profiles. You can also discover interesting topics from the field of hard finishing, such as new external cylindrical grinding solutions and combination machines for hard turning and grinding.
Visit us at our stand 4C50 in hall 4, where you can experience our latest products and solutions up close. Our team is looking forward to presenting our latest designs and developments and answering your questions.
See you at the AMB 2024!
» Free tickets
We are happy to provide you with free tickets for the AMB.
You can order them here: www.emag.com/amb