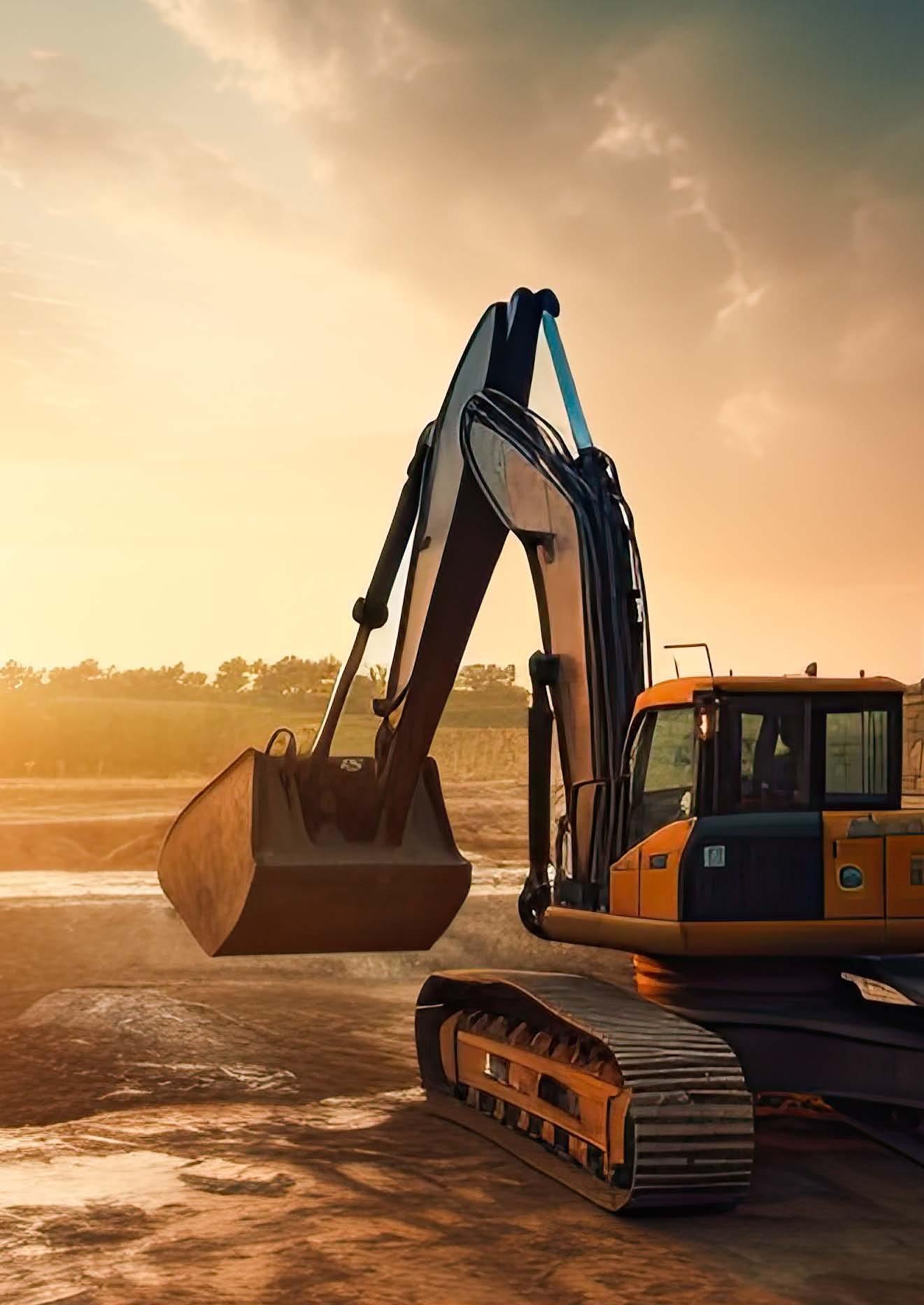
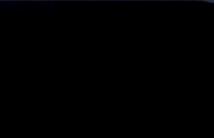
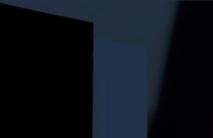
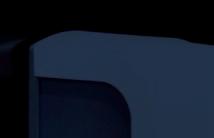
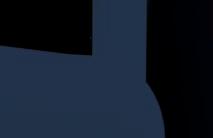
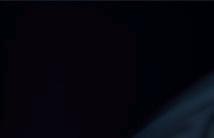
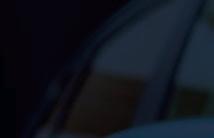
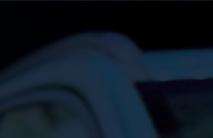
Tel: 604-687-1828
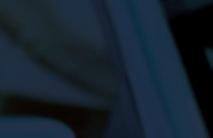
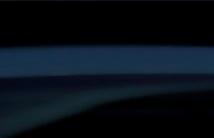
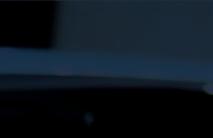
Email: info@argentinalithium.com
Web: argentinalithium.com

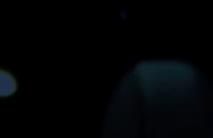
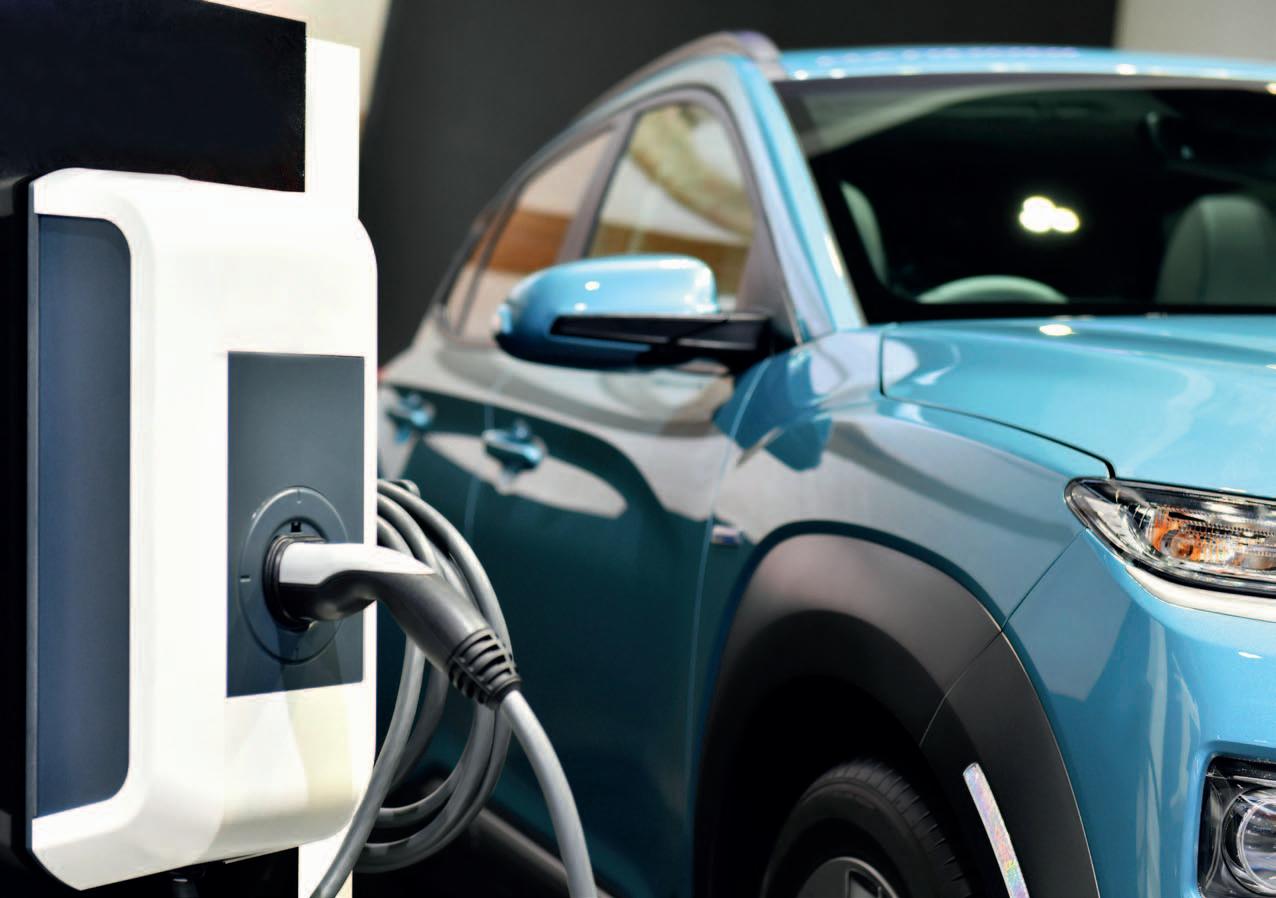
Tel: 604-687-1828
Email: info@argentinalithium.com
Web: argentinalithium.com
Argentina Lithium & Energy Corp is focused on acquiring high quality lithium projects in Argentina and advancing them towards production in order to meet the growing global demand from the battery sector.
The management group has a long history of success in the resource sector of Argentina and a strong track record of government and community relations.
• The Lithium Triangle, including parts of northwestern Argentina, produces about half of the world’s lithium and hosts approximately 60% of the known lithium reserves
• Most lithium in this area is in salt lake (“salar”) brines
• Argentina produces approximately 10% of the world’s lithium, making it one of the top five global producer (2020)
• Government is encouraging renewable energy initiatives
Editor-in-Chief Carley Fallows editor@littlegatepublishing.com
Space Management Emlyn Freeman emlynfreeman@littlegatepublishing.com
Media Coordinator Andrew Williams andrew@littlegatepublishing.com
Lead Designer Alina Sandu Research Kristina Palmer-Folt Editorial Research Amber Winterburn
Corporate Director Anthony Letchumaman anthonyl@littlegatepublishing.com
Founder and CEO Stephen Warman stevewarman@littlegatepublishing.com
For enquiries or subscriptions contact info@littlegatepublishing.com +44 1603 296 100
ENDEAVOUR MAGAZINE is published by Littlegate Publishing LTD which is a Registered Company in the United Kingdom.
Company Registration: 07657236
VAT registration number: 116 776007
343 City Road 60 Thorpe Road London 79 Norwich EC1 V1LR NR1 1RY
Littlegate Publishing Ltd does not accept responsibility for omissions or errors. The points of view expressed in articles by attributing writers and/or in advertisements included in this magazine do not necessarily represent those of the publisher. Any resemblance to real persons, living or dead is purely coincidental. Whilst every effort is made to ensure the accuracy of the information contained within this magazine, no legal responsibility will be accepted by the publishers for loss arising from use of information published. All rights reserved. No part of this publication may be reproduced or stored in a retrievable system or transmitted in any form or by any means without the prior written consent of the publisher.
Copyright© Littlegate Publishing Ltd
The United States is one of the largest hubs of business operations on the globe. With an expansive array of industries across the 50 states, almost every business sector is covered in one way or another. For many companies, expanding their operation into America allows them to access its rich and thriving markets on both a national and international scale. This special USA Edition of Endeavour Magazine focuses on promoting companies which are leading their respective industries, and subsequently adding to the stellar reputation of America.
Despite America being such a big hub of business activity, the country, like the rest of the globe, has dealt with growing concerns regarding population demands, recovering following the global pandemic and making the much-needed shift towards sustainability in recent years. But America takes these challenges in its stride, and we continue to see how companies across the nation are doing their part to meet these demands and continue to strive to be the best.
In Endeavour USA you can expect to see a whole range of industry giants from manufacturing to energy to shipping as much like America’s diverse industries, we are going to cover it all!
82 Cámara Minera de Panamá Over 30 Years of Responsible Mining
88 Arrow Truck Sales Unlocking Potential
94 Association of Marina Industries Educators of Marina Experts
100 PEI Road Builders & Heavy Construction Association Building a Successful Network
106 Massy Stores Deliciously Convenient
With a chief commitment to safety and transparency, Vale is an international mining company that focuses on producing iron ore, pellets, and nickel. Spread across 5 continents, the global mining company works every day to take the natural resources available to us and develop them into prosperous resources; all whilst still working to promote environmental protection. This drive towards sustainable development underpins everything that Vale does, as it believes the safety of people and the planet must always take priority.
Since its establishment in 1942, Vale has grown into one of the largest mining companies in the world with operations across roughly 30 countries all over the globe. However, the foundations of its operations in Brazil, remain the focus for the company operating across both the mining and logistics sectors. The company began under the name Companhia Vale do Rio Doce, where it first extracted ore in Itabira in Minas Gerais. Over the years, the name was shortened, and the company began to take on a larger role across the country’s mining industry by also providing logistical solutions via the country’s railroads, ports, and terminals. It even began operations within the energy industry to promote sustainable electrical production, and now is responsible for producing 54% of its own energy consumption.
Vale’s operations in Brazil centre around iron ore, particularly iron pellets which are used in the construction or manufacturing of many products and services we use every single day. Vale highlights that these ores are working towards the evolution of society as they are used in industries that are developing the world towards the future such as construction for houses and medical facilities, as well as in the technology and manufacturing sectors for things such as cars and household appliances. Also, ore found in the Carajás region in Brazil is considered to be the best quality in the world, at 67% iron content. Therefore, with such a rich deposit of iron ore in Brazil, Vale’s operations play a crucial role in mining and delivering these metals for the development of society.
Vales has multiple mine sites across Brazil, which are involved in the mining, processing, and then logistical movement of the mined products to the steel industries in which it sells the iron. To understand Vale’s valuable role in the mining industry in Brazil, we first must look at the birthplace of the company in Minas Gerais. The state accounts for over 50% of Vale’s iron ore production, with 20 mines currently in operation. Mining in Minas Gerais takes advantage of Vale’s railroad connections between Vitória and Minas.
Vale has invested more the 1.3 billion dollars in the acquisition of trains and freight cars, which it primarily uses for transporting iron ore as well as other cargo. The logistics sector of Vale’s operations allows it to play a more well-rounded role in the mining industry and the distribution of its mined products to the ports and steel-making marketplace. Therefore, the mining operations at
Minas Gerais highlight how the mining and logistical operations of Vale work so closely together to deliver the rich ore to end markets for the betterment of a future planet.
In Minas Gerais, Vale is working alongside the city of Itabira to use its efforts within the mining industry to positively impact the city and build a plan for a more sustainable city. The plan, devised in conjunction with the municipal administration, aims to develop the region with projects which concern the environment, education, and security – all of which are developed with innovation in mind. These projects include the Little Seed of Sport Project, Judo Classes and the Bright Minds Chess Project which is bringing key development to kids across the region all thanks to Vale’s commitment to putting people and the environment at the forefront of its operations.
Vale announced in February that it had entered into an agreement with Anglo American Minério de Ferro Brasil in the Minas-Rio complex in Minas Gerais. The agreement will see Vale acquire a 15% ownership interest in the complex, whilst Anglo
will retain control, management, and operation of the Minas-Rio complex as well as any future expansions. The agreement marks a vital step for Vale and Anglo to develop the mining for iron ore whilst facilitating Anglo’s shift towards low carbonemission steelmaking processes. The Minas-Rio complex has a nameplate capacity of 26.5Mtpy for high-grade iron pellet feed, and the whole complex comprises the mine, plant, as well as geotechnical and supporting structures.
As part of the agreement, the Minas-Rio complex will be able to utilize Vale’s nearby rail line and Tubarão port to expand output as an alternative to the construction of a second pipeline to the port facility at Açu. The partnership between the two companies was celebrated by Vale CEO, Eduardo Bartolomeo, stating in a press release that “Minas-Rio is a Tier-1 asset that will benefit from great synergies with Serpentina’s deposit and Vale’s logistics, and we are confident that this partnership will unlock significant value to all of our stakeholders.”. Bartolomeo’s comments highlight the valuable role both companies can play
Mult Engrenagens has a modern and complete industrial site, operated by trained and highly qualified professionals, guaranteeing customers high quality services in the manufacture and reform of parts. The company has a specialized engineering team and trained and updated technicians with national and international technologies and standards for the development and improvement of high-performance projects. We have experience and tradition in the manufacture of spare parts for multi-brand gearboxes. The manufacture of parts for gearboxes involves reverse engineering with an extensive database already built or according to our customers’ designs, preserving geometric and dimensional interchangeability.
in developing the deposit whilst taking advantage of the company’s existing infrastructural logistics links which will bring economic development for both companies and the respective region.
Pará, the largest mining complex in Brazil, is owned by Vale and represents one of the largest private investments in the country in recent years. The S11D mine complex in Pará encompasses the mines, a processing plant, and rail and port logistic services, which have continued to drive the region’s economic development for many years. The mines are responsible for mining iron, manganese, copper, and nickel across a vast array of mines which span the complex. However, much like in Minas Gerais, Vale also has a vast array of environmental projects in Pará which ensure that the rich biodiversity of the nearby Carajás National Forest is protected.
A key environmental project for Vale is the Vale Amazon Biopark within the Carajás National Forest which works to provide education on the landscape and species which inhabit the forest. The Biopark ensures that more than 270 animals can roam freely, allowing visitors to learn about the animals in
their natural habitats. Over the last decade, the site has seen more than 1.1 million people visiting the site, which has allowed Vale to continue to invest in the protection of the forest which is home to one of the most biodiverse regions in the country.
In Espírito Santo, mining extends back more than 50 years and highlights the vital role the state’s railway and port systems can play in the mining industry. In Espírito Santo, Vale developed a fully integrated strategy for mining logistics which continues to be used every day. Vale’s operations in Espírito Santo highlighted the company for its production of iron pellets, and now the production of pellets by Vale in the region is globally recognised.
Espírito Santo is also home to the largest environmental investment by Vale towards the development of the Tubarão Environmental Master Plan (PDA). PDA aims to control atmospheric emissions and covers 160 projects which are implementing new equipment, improving the environmental controls of its operations, and researching new technologies to reduce environmental impacts. The vast project which encapsulated Vale’s core values, has been successful in its efforts to make vital developments towards the future, whilst remaining clear in its aim to respect the planet, the local communities and the people who live and work across their sites of operation.
Other key mining sites for Vale in Brazil are in Maranhão and Rio de Janeiro. In Maranhão, Vale works with the state to support the logistical movement of ore production through the Carajás Railway to the Ponta da Madeira Maritime Terminal. The terminal plays a valuable role in distributing the ore to consumer markets across the globe, including in China which is currently one of the largest buyers of iron ore products. Then, in Rio de Janeiro, Vale operates the Porto Sul Complex in the Costa Verde region. Vale’s headquarters are based
in the capital, along with a number of terminals which are used for the loading of iron ore. The entire site has the capacity to move more than 75 million tonnes of ore every year through the terminals and towards end markets.
Surrounding the terminals, Vale continues to carry out environmental projects, such as its Fazenda Marinha Project which, much like PDA, monitors environment quality indicators to ensure that the environment is protected as much as possible whilst implementing initiatives which are centres on valuing local culture and promoting education across the region.
Ultimately, Vale’s existence hinges on a passion for improving life and transforming the future for generations to come. To do this, Vale is carrying out mining operations which are essential to life whilst producing ores, pellets and various metals which help to make this possible. However, it is Vale’s commitment to education, environmental protection and innovative approach to the future that has allowed it to play such a valuable role in Brazil for many years thanks to its constant commitment to developing necessary mining operations whilst putting great investment back into the protection of landscapes to support the rich biodiversity of this part of the world.
As part of the SSA Marine and Carrix company, the Tuxpan Port Terminal (TPT) is a privately operated terminal located along the Gulf of Mexico offering a range of services across the cargo and related industries market to the United States. TPT takes advantage of such a vital position, to provide clients from across the worldwide shipping and logistics industry with an alternative cargo handling operation which guarantees a reliable, accessible and high-quality service facilitated through a specialised infrastructure system. Through its team of highly trained personnel, Tuxpan Port Terminal hopes to play a significant role in the development of Mexico’s economy as it expands the country’s foreign trade offerings.
Located 293 kilometres from Mexico City, TPT sits strategically along the Mexico-Tuxpan highway and so provides easy delivery of products from the city into the terminals for distribution across domestic and international markets. The strategic location of TPT utilises the infrastructure links of the region to deliver cargo handling operations that save on freight costs, toll fees and extended transportation times. This reduction in time and distance makes TPT a vital hub that delivers cost-effective benefits for all stakeholders involved in the movement of cargo. By enhancing the operations of stakeholders, TPT hopes to see continued investment into the terminal, which will allow it to maintain its reputation as a reliable and efficient alternative cargo handling service providing vital links to both the Northern and South American markets.
What sets TPT apart from other ports and cargo terminals along the Gulf Coast, is its implementation of cutting-edge technology across its operations. TPT’s operating system has been developed by Tideworks Technology, a subsidiary of the Carrix company, with the aim of providing solutions for the efficient and productive management of the terminal. Tidework Technology’s solutions have already been seen across the world, and in TPT include systems such as Spinnaker which manages yard planning by providing supervision to ship manoeuvres, yard operations, deckhouse activities and the transit of cargo throughout the terminal.
TPT covers a total area of 85.7 hectares (Ha), which is divided into 15. Ha of container storage, CFS and warehousing to handle the high cargo capacities that are travelling through the terminal. In terms of vessels entering the terminal, TPT has a 15-meter (m) depth along its 556m waterfront which has an operational ship capacity of 11,500 twentyequivalent units (TEUs). When vessels reach the terminal, they are met with 2 STS Super Post quay cranes, 30 container trailers, top and side loaders, forklifts, spreaders, 240 refrigeration consoles for containers and the necessary equipment for steel and steel production. All of these facilities, ensure that TPT can seamlessly take cargo from vessels travelling into the Tuxpan port, and move it swiftly off throughout the Terminal complex and then onto
the transportation or shipment companies which will take the goods to their end markets.
To maintain a firm management and standardised system for container merchandise, a Mainsail system has been implemented, which will also enhance the reporting systems across the port. Tideworks Technologies has also implemented traffic control systems which support the effective coordination of cargo across the terminal’s yard. Then, to enhance the connection between the terminal, its customers, shipping lines, transportation companies, and related stakeholders, TPT was installed with a Forecast system to ensure all key players remain updated and in constant communication for the benefit of the smooth flow of cargo throughout TPT.
Typical cargo travelling through TPT includes those in the steel, forestry, project cargo, aluminium and copper industries. All of these industries are global economic heavyweights, and so being the port and terminal of choice for international shipping lines travelling along the Gulf Coast highlights TPT’s
growing role in supply chains for some of the world’s most economically lucrative industries. Therefore, TPT is already highlighting the significant role it has begun to play in the comprehensive economic development of Tuxpan, which in turn will see more importers and exporters utilising the terminals to expand their international distribution network.
Just last year the role of TPT in international markets took a large step forward, with TPT extending its reach across the Gulf of Mexico. TPT announced in June 2023, that it was adding a new multimodal service at TPT, which would connect with Canada, the U.S. and across Mexico. The service will provide exporters and importers with a new strategic channel to enter these markets, supported by TPT’s reputation for efficient and cost-effective cargo handling. This new route will be supported by Crowley, a world-leading shipping and logistics company, which currently provides door-to-door solutions in the U.S., Caribbean, Central American and Mexican markets.
The development of the new multimodal service, will highlight TPT and Crowley’s expertise and professionalism, and provide a competitive advantage for the most modern port terminal complex in Mexico. The General Manager of TPT, John Bressi, outlines in the announcement that “Tuxpan Port Terminal recognises and congratulates both Crowley and CN for the important advantages that the services of both companies will present to foreign trade. Crowley is a premier container line and logistics company that selectively chose TPT for this exceptional service, recognising that this terminal is the best alternative on the Gulf of Mexico coast. This short sea route will offer significant benefits to the BCOs, such as competitive pricing, shorter transit time, reduced CO2 emissions and safer cargo handling. We are delighted to be Crowley’s port terminal partner”.
Bressi’s comments here really solidify the aims of TPT to work with international companies such as Crowley to enhance the shipping and distribution
network for Mexico and bring significant economic benefits to the region. These economic benefits will then provide a wider local and international reputation for cargo handling success, which aims to bring future investment and reliance on TPT for international shipping lines in the future.
Overall, TPT has optimised its strategic location along the Gulf of Mexico to deliver an internationally recognised port terminal which delivers efficient, cost-effective and reliable cargo handling for customers both within Mexico and beyond. With new developments and partnerships, such as with key shipping companies like Crowley, TPT has established itself as the best alternative port terminal serving the Gulf through its specialised systems that ensure every customer’s cargo is delivered with efficiency.
Across almost 20 million hectares of the hinterland, the Port of Itaqui (Porto do Itaqui) boosts the local and national economy of Itaqui through its vital cargo services for a range of products including grains, minerals, and petroleum derivatives. These vital exports have established the Port of Itaqui as a key international hub, which, through a crucial management system, has continued to bring investment into the port and surrounding region. Therefore, the Port of Itaqui continues to provide excellent port logistics to strengthen supply chains, whilst developing new investment projects to position itself at the forefront of Brazilian port development.
Located in the Matopiba region, which brings together the states of Maranhão, Tocantins, Piauí and Bahia, Itaqui has long been a key driving force for economic development along the Central-West of Brazil. Port operations in Itaqui have a long history, and in 1918 saw a decree which would contract the construction of docking facilities in Itaqui which linked the commercial centre of São Luís with a wider international market. However, the grant was not prosperous and was terminated in 1923, with the construction of the Port of Itaqui not beginning until 1960. The construction of piers at the Port of Itaqui was facilitated by the National Department of Ports and Waterways, and the Port began official operations in 1972 following the completion of the first two berths.
Over the next 50 years, the port continued to expand with the development of the pier to cater to further berths, including some solely for the management of petroleum and cellulose products. Now in 2024, the Port of Itaqui has 9 operational berths, which play a vital role in establishing strong supply chains for the region and continue to bring more investment to the region subsequently establishing the Itaqui Port Industrial Complex within both national and international markets.
The Port of Itaqui is overseen by the Maranhão Port Administration Company (EMAP) which provides the infrastructure and management to develop port operations, the quality of services and the establishment of employee and business opportunities. EMPA is responsible for supervising port operations, ensuring that activities are carried out regularly, efficiently, safely and with respect for the environment. It also works to authorise the entry and exit of vessels, including the docking, undocking, anchoring and vessel traffic management across the port area.
As part of this, EMPA oversees the 14 thousand direct and indirect jobs which are created as a result of the port and its operation. Therefore, economically the port benefits both the people and the industry. This management has seen the volume of cargo moving through the port continually rise over the years, with a total of 2.02 million tons of cargo handled by the port in 2023. This is 39% higher than the previous year and highlights the valuable role the port and its management systems continue to play within both the wider port logistics industry and the Itaqui economy.
A key aspect of the Port of Itaqui’s success is thanks to the interconnectedness of the port to
vital railway and highway links. These links include a direct connection with both the Transnordestina (FTL) railway which passes through 7 states across the Northeast and the Carajás Railway (EFC), which connects the capital of Maranhão to Carajás-PA. These routes help the Port of Itaqui to transport cellulose products throughout the region. In addition, the port is also connected with the NorthSouth Railway (FNS) which links the EFC to Açailândia where it transports mineral and vegetable solid bulk and fuels across the states. Alongside the railways, are the federal and state highways including the BR-135, Br-222 and MA-230, which run throughout the north and south of the country. All of these transport services work in lockstep with the Port of Itaqui to take the materials and products handled by the port throughout the country. By utilising the existing infrastructure, the port industry of Itaqui highlights the valuable role they all play in developing supply chains which ultimately brings significant economic benefits to the area.
In recent months the Port of Itaqui announced that it was looking into gaining a new fertilizer
terminal to meet the growing global demand for agricultural inputs. In 2023, the port handled more than 3 million tons of fertilizers, a 22% increase from the previous year highlighting the continued growth in the Brazilian agriculture market. Representatives from the National Secretariat of Ports and Waterway Transport announced it will begin surveys to understand the technical, economic, and environmental possibilities in a feasibility study for the construction of a new fertilizer terminal.
Ellen Brissac, Contracts and Leasing Manager at the Port of Itaqui outlines that “the new terminal, once completed, will bring a significant boost to the development of the Port of Itaqui, a highly demanded port, mainly for transporting grains and solid bulk materials such as fertilizers. The new terminal will further strengthen the position of the Port of Itaqui as one of the main logistics hubs in Brazil”. The new terminals would create thousands of new jobs for locals and increase the revenue for the port and the Brazilian government making significant contributions towards GDP growth. Therefore, the implementation of a new fertilizer terminal hopes Endeavour
NML Tankers has a solid expertize in moving project cargoes from source to destination. NML Tankers & Bulkers supports major project undertakings by combining our shipping and logistics sectors, providing services that include:
• Site survey / feasibility studies (routes, weather, political climate)
• Full / part charter parties (air charters, time/ voyage charters)
• Multi-modal transport (rail, tug & barge, heavy lift)
• Special equipment transport (flat racks, open tops, platforms, tween deck solutions)
• Freight negotiation (COA negotiation, long term rate validities)
• Administrative support (customs clearance, trade documentation)
NML Tankers’s reach provides security through one company control, ensuring strict HSSE, Quality and Compliance implementation throughout the project life. Commitment, flexibility and experience are central to the NML Tankers approach on every project.
nmltankers.com
NML Tankers, combining experience, innovation, commitment and loyalty to hold on strongest and long term partnerships. With over 30 years experience in various sectors of the maritime industry, our maritime traditions combined with our drive for innovation has shaped our organisation and is today the basis of our holistic service approach.
to strengthen both Brazil’s position as one of the main players in the international agriculture market and the Port as a key hub for agriculture business.
Overall, the Port of Itaqui’s mission to provide excellent port logistics for international supply chains including those in the agriculture and petroleum sectors has been very successful. Therefore, the Port of Itaqui has positioned the region as a vital hub for a whole range of local and international markets. The management and development of the port is a key factor in the continued development of the region’s port industry, and so the Port of Itaqui continues to play a valuable role in bringing economic benefits and investment into the region’s maritime sector.
Located in the inner reaches of the Apra Harbour, the Port Authority of Guam (PAG) has spent the last 49 years dedicated to providing maritime, commercial, transportation and recreational services across the Jose D. Leon Guerrero Commercial port. PAG’s dedication to providing full services to the maritime and shipping industry has now established Guam as a vital stopping point for vessels and an import/export hub which plays a significant role in developing the island’s economic development. With goals to continue to expand the port facilities over the coming years, the Port of Guam looks to take the port into the future through key modernisation projects.
Guam has served as a vital port location extending back to the 16th century when the island catered to the ships of Spain, and, following the Spanish-American war, to American interests. Under US Naval administration the island served as a Western Pacific coaling and shipping station, with the only change taking place during the Japanese Occupation of Guam. However, following the transference of command to Guam’s own Department of Commerce after 1951, the Commercial Port of Guam was established. The port continued its role as a busy centre of trade, and it was quickly recognised as one of Guam’s most important economic assets.
To further establish an organisational environment more conducive to providing efficient and reliable cargo service, which was growing Guam’s economy, Public Law 13-87 was passed in 1975 to establish the Port Authority of Guam as a public and autonomous corporation. To make things a little easier, in 2002 the official name of the port in Guam was changed to the Jose D. Leon Guerrero Commercial Port, taking its name from the first commercial port manager who played an instrumental in in getting the US to transfer all port facilities and properties to the Government of Guam at no cost.
Today, the Port of Guam plays a vital role in shipping and cargo routes located along many major Pacific shipping and air routes. As the main and only transportation hub for Guam, it plays a big role in linking the Commonwealth of the Northern Mariana, the Micronesia islands, and the expanding Far East markets which reach not only the US, but the rest of the world. However, due to its location, the port also relies heavily on these shipping lines and foreign contacts to meet the demand for goods for people in Guam via imports – 90% of which are imported from the US.
The port as we know it today reflects a dramatic growth in cargo revenue, having increased its revenue tonnage from $85,677 when the U.S. naval admin turned over the port to the island’s government, to roughly $1.8 million in the 2006 fiscal year. This significant increase in revenue ensures that the port can maintain its operations and continue to expand in the future as the port is entirely self-sufficient. This means that capital
Celebrating 50 Years as Your Leading
funds for construction projects have to be funded through borrowing money on their own credit.
PAG’s financial obligations and administrative operating costs must be funded by money generated from the use of its facilities and services in accordance with the provision of the port terminal staff. This is because the port has no taxing power, so the port is working to maintain a steady flow of operations across the port to generate revenue to handle its expansion, whilst also contributing to the ongoing economic development of the island. To handle these operations, PAG is overseen by a board of directors made up of 5 non-salaried members who are appointed by the Governor of Guam with the consent and advice of Guam’s legislature. The board of directors’ role is to provide and establish policies and directives pertaining to the planning, promotion, development, construction, operation, and maintenance of port facilities.
By the 2008 fiscal year, PAG was processing more than 2 million dollars in cargo revenue, with the bulk of the cargo being containerized. One of the key focuses of the port, as already mentioned, is its cargo. The port is equipped to handle all types of cargo including containerized, breakbulk, unitized, as well as fishery cargo. However, as a major stopping point in the western Pacific region, the cruise ship potential of the port has begun to
grow. Currently, on average 5 cruise ships stop at the island’s port in Piti every year. Cruise porting requires the PAG to coordinate and reconfigure their shipyard each time to accommodate the influx of services needed. However, the port has been establishing a working group to strategize a small cruise ship industry which will reconfigure and develop the port with the aim of increasing the porting potential and opportunities for Guam.
As part of the Port’s development for the future, it is looking to continue to develop its facilities and equipment to expand its cruise porting facilities and continue to meet the demand for increasing cargo shipments. This has been put into motion by the recent passage of Public Law 29-125 which has given the Port Authority conditional approval of its updated Master Plan which outlines PAG’s roadmap for modernisation. PAG wants to transform the port’s facilities into a world-class terminal for Guam and the Western Pacific Region. For the modernisation program, the port is looking to invest hundreds of millions of dollars to transform its commercial seaport ready for the demands of the future. The development has already seen $10 million of investment provided through a Tiger grant to achieve this.
PAG plays a significant role in Guam’s development of its economy through the seamless and necessary movement of cargo through its seaport. Due to its location, it is an island that relies heavily on its international links to bring mutual prosperity to the country and those overseas.
Under American territory authority, it upholds all the same regulations that you would expect from any US port which continues to highlight the port’s reputation on an international scale. With critical developments as the Port Authority of Guam moves toward the future, we look forward to seeing how it expands its operations to facilitate further cruise lines and continues to bring economic development to the region via its increased cargo port potential.
Working with ports across the Gulf Coast of the United States, The Gulf Ports Authority (GPA) promotes the progress of waterborne commerce throughout Gulf ports to bring continued economic development to the region. As a trade organisation, The Gulf Ports Authority provide a forum through which its members receive vital support, education, and networking to uplift the area’s cargo shipment and highlight the region as a key area of shipment.
Since 1945, GPA has been working to progress the waterborne commerce of the Gulf Ports guided by a team of elected officials to promote the continued success of the region. GPA began in New Orleans when there were only 13 public port members in the five Gulf states of Alabama, Florida, Louisiana, Mississippi, and Texas. Over the last nearly 80 years, GPA has provided a forum for its member works where they can address mutual concerns and educate the public and elected officials on the economic impact of Gulf ports. Today GPA covers 36 ports across the Gulf Coast and provides users of the ports with innovatively managed and environmentally responsible facilities with the end goal of promoting the success of each port across the region.
Existing members of the port include the Port of South Louisiana. This is one of the largest tonnage port districts which extends 54 miles of the Mississippi River from New Orleans to Baton Rouge. The port is served by 3 trunk link railroads and 3 major interstate highways. With 50 piers and docks, the ports receive vessels up to 45ft all year round. As a central cargo port, it facilitates cargoto-vessel transfers via its barge system. Every year it moves more than 233mt of cargo upriver to major US markets in the Midwest and Northeast. The Port of South Louisiana is such a complex port, which for GPA is a large member for its role within the industry. However, GPA is concerned with all ports no matter the size as their collective role is what allows the region and the GPA to maintain such a lucrative stream of cargo shipment across the region.
We also see the crucial role smaller ports play in the fundamental role of GPA in the appointment of Walker Smith as the president of the Association. Smith is the port director of the Port of Harlingen Authority and is the first time in the last 30 years that a port director from a shallow draft port has been elected as president of the Association. Smith will lead the Association over the coming months in its pursuit to fund and represent the 36 ports under the association, as it continues to educate elected officials and the public on the importance of waterborne commerce to the US.
A key part of GPA is the bi-annual meeting where all members are invited to meet and provide a space for crucial networking, education, and promotion of the vital role these ports play in the country’s economic development. The next conference is set to be held in May of this year where the 36 ports will gather together under the
Association. However, should conflicts or concerns arise between meetings, GPA will hold gatherings as and when needed to maintain the strength of the region’s port facilities.
A significant partner to GPA is the railway network as these are what allow cargo shipped in from the coast to access markets across America. Companies such as Railworks Corporation provide construction, rehabilitation, and maintenance services to vital rail systems across North America. They recognise the vital role which ports play in today’s economy, as many ports are vital pillars of trade, travel, and industry. Therefore, the company ensures that the railways can be utilised year-round and has implemented custom-built track systems across ports to streamline operations and serve as a vital gateway to the nation and beyond.
Overall, GPA has spent nearly 80 years as the governing authority association across the Gulf Coast of America. Working with all ports from Manatee in Florida to Brownsville in Texas, GPA continues to be successful in its promotion of the region’s waterborne commerce, and, as the demand for cargo and tourism continues to grow across America, the ports will continue to play a vital role in the national economic development. We look forward to seeing how Smith shapes the future of the Association and the crucial developments from association’s conference in a few months.
Petronas Suriname E&P B.V. (Petronas Suriname) is a fully owned subsidiary of the international energy group Petronas, which encapsulates the global company’s operations in Suriname to increase energy potential and optimise the value of the energy industry. Petronas’ energy operations can be broken down into three core businesses: upstream, gas and downstream. These divisions span the company’s portfolio of energy solutions which covers oil and gas, renewable sources, advanced products, and adaptive solutions. Throughout every aspect of its global operations, Petronas has embedded a culture of duty and respect for the planet. This respect for the environment has been implemented firmly throughout its Petronas Suriname subsidiary as it works to bring continued economic development to the region, stable energy, and the development of renewable energy options.
For Petronas, Suriname is a key place for exploration as the country and its surrounding waters have already seen vast discoveries of oil and gas field potential in the region. Therefore, the development of Petronas to its Surinamese subsidiary was an easy decision to harness the potential of the region and continues to expand Petronas’ reach across the world. Consequently, Petronas already have a range of exploration blocks of which it either has full or split participating ownership of.
A crucial development for the company in recent months is the discovery of the Roystonea-1 exploration in the existing Block 52. The discovery is for oil in the block, located 185 kilometres off the country’s coast in a well at a depth of 904 metres. The oil potential was discovered after encountering several oil-bearing Campanian sandstone reservoir packages, which could provide the company with great oil resources. Further evaluation of the well’s resources is currently being conducted to determine the full extent of the discovery. The potential development could work in synergy with the existing Sloanea-1 discovery which was made in the same block in 2020 and could bring significant oil resources to the region.
Mohd Redhani Abdul Rahman, Vice President of Exploration at Petronas, highlights that “The success of Roystonea-1 is expected to drive further exploration for commercially viable hydrocarbon resources in the surrounding areas. Petronas will continue to work closely with the host authority Staatsoli and partners to unlock Suriname’s hydrocarbon potential. We look forward to implementing safe and successful future exploration programs together”. Rahman’s comments highlight the key role Petronas Suriname plays across the region by working with vital stakeholders and companies such as Staatsoli Maatschappij Suriname (Staatsoli), a key oil and gold company in the region, to deliver vital development and investment towards the country’s energy sector. Rahman’s comments also highlight the vital role hydrocarbon resources will play in serving energy demands as the world moves towards more sustainable energy options.
Block 52, in which the discovery was made, covers an area of 4,749sq km and lies in the prospective
Suriname-Guyana basin where Petronas Suriname is the central operator, with a 50% participating interest. However, Petronas’ operations in the region do not end there as the company also has a 100% participating interest in Block 48, as well as a 30% non-operating participating interest in the adjacent Block 53 where the company made the Baja-1 oil discovery in 2022. The continued involvement of Petronas Suriname in crucial development blocks off the coast of Suriname has highlighted its ongoing efforts towards ensuring energy security for the future as energy demands continue to increase at a rapid pace.
In December last year, Petronas Suriname signed a Production Sharing Contract with Staatsolie for the exploration of Blocks 63 and 64 located in the Guyana-Suriname Basin. The signing came during the Suriname Demerara Bid Round 2022-2023 earlier last year. Block 63 covers an area of 5,425 sq km and is at a water depth of 1,700m, whereas Block 64 is shallower at only 1,300m deep. Here, Petronas Suriname has a 100% participating interest in and is the operator of Block 63. Block 64, on the other hand, is operated by TotalEnergies who have a 40% participating share in the Block, with the remaining 60% split evenly between Petronas Suriname and QatarEnergy. This key exploration contract with key players across both Suriname’s energy industry and international energy industries highlights the vital role the country is playing in global economic development and energy potential.
Rahman, Vice President of Exploration for Petronas, highlights that “Securing these blocks is crucial to Petronas’ effort in unlocking Suriname’s vast resource potential in the basin. This underscores the aspiration to build our presence in the country and strengthen our international portfolio, especially in the Americas.” He continues, “We look forward to working alongside the host authority and our partners to achieve more significant milestones while ensuring secure affordable, and sustainable energy to the market”. Rahman’s comments exemplify exactly how Petronas continues to be a leading energy solution provider across the globe as it works to extend its reach across the globe by adding yet another vast region to its portfolio. By helping to establish Suriname in its own right as a vital oil and gas exploration site, Petronas Suriname
adds to the continued investment from companies across the globe into the region.
However, as Rahman notes, throughout every aspect of Petronas Suriname’s operations there is always a keen focus on sustainability, a value passed down throughout the Petronas network. Sustainability is such a key aspect of Petronas’ operations as they are working with finite resources so must be responsible with every aspect of its operations to bring vital development across the energy sector whilst limiting the damage done to the planet. The global Petronas is on a mission to be entirely net zero by 2050, and so this responsibility extends to the Suriname subsidiary to create value, whilst safeguarding the environment with environmental initiatives, supporting social impact
projects, and working closely with governmental agencies to make real change in the oil and gas sectors.
Ultimately, behind Petronas Suriname is a passion for the planet and its people, which is driven by a desire to create sustainable value across all of its sites of operation and exploration. Petronas Suriname has continued to play a vital role in the country’s energy industry, and thanks to its key contracts and projects with stakeholders, it looks set to continue to develop the energy industry in Suriname for many years to come. We look forward to seeing the outcome of the further evaluation of Block 52, and the role the company will play in bringing oil products to market whilst maintaining sustainability as its core focus.
Newmont Corporation is home to a vast portfolio of world-class assets, prospects and talent operating across multiple mining jurisdictions spanning the globe, from the Americas, Australia, and Africa. Newmont is a world-leading gold mining company, with many favourable operations also producing copper, silver, zinc, and lead across the globe. However, Newmont is focused on creating value throughout its operations by following strict safety standards, superior execution regulations and a leading level of technical proficiency that has established it as a leading player in the international mining sector.
Newmont began its operation focusing on the natural resources industry that mines gold, copper, silver, lead, zinc, lithium, uranium, coal, nickel, and various aggregates, as well as helping facilitate key developments in the oil and gas industry. However, today thanks to its continued development since it began publicly trading in 1925, Newmont now has a portfolio that is unmatched across the mining industry with more than half of the world’s Tier 1 assets, including many long-life operations, value-accretive projects, abundant exploration opportunities and world-class talent. This is why it is the only gold producer now listed on the S&P 500 Index. The company’s assets, prospects and people have allowed it to continue to expand its reach across the globe, as it continues to work to create value and opportunities for its shareholders, host communities and employees across every mining operation.
A central mining area for Newmont is in South America where its operations continue to develop the regions on both local and international scales through value-adding mining operations which support employment opportunities across the region. A key site for gold mining for Newmont is the Pueblo Viejo mine in the Dominican Republic. The mine operation is located 100km northwest of Santa Domingo and began construction in 2005, with commercial production beginning in 2013. The site is one of the largest gold assets in the world, however, it also produces silver and copper. The Pueblo Viejo Mine project is jointly owned by Barrick Gold Corporation and Newmont Corporation, with Newmont having a 40% ownership in the project. The site includes two open pits, a processing plant, and a storage facility which is operated by Barrick Gold Corporation.
The Pueblo Viejo Mine project has a 97% Dominican workforce as part of the jointly owned operation’s desire to ensure that all of its operations are creating value for the people that their mining projects affect. By employing a largely Dominican workforce, the companies are making the most of the expertise on the ground and providing those closest to the operations with economic development and growth through employment at the mine site and subsequent processing operations.
To make the Pueblo Viejo Mine project more sustainable the mine’s Quisqueya 1 Power Plant
Since 2008, BGC Engineering has supported the Pueblo Viejo (PV) gold mine located in the Dominican Republic, northwest of the capital city, Santo Domingo. PV is operated by the Pueblo Viejo Dominicana Corporation—a joint venture between Barrick (60%) and Newmont (40%).
BGC’s work on PV includes site investigations, feasibility studies, construction monitoring, and Engineer of Record services for a tailings impoundment that contains conventionally slurried tailings. More recently, we have begun site investigation for a new tailings impoundment to provide required storage for expanded reserves.
Our global experts serve the mining industry from exploration to closure, focusing on the safe and resilient design, construction and operation of mine tailings facilities and open pits. BGC is committed to “mining done right,” delivering projects that benefit our clients and their stakeholders financially, socially, and environmentally. In collaboration with our clients, we aim to develop unique and innovative solutions to often complex problems.
bgcengineering.ca
was converted to natural gas from fuel oil. This conversion took place in 2020 as a measure to reduce greenhouse gas emissions by 30% and nitrogen oxide emissions by 85%. This shift is just one way the mine site is hoping to continue to reduce its environmental impact because, for Newmont, operating in a way that respects the environment as much as possible whilst also using its operation to add value to the mined resources is crucial.
The mine operation at Pueblo Viejo announced just last year that the engineering design of the El Naranjo Tailing Storage Facility that operates within the mine operation will extend its life to 2040 and beyond. This continued development is expected to sustain gold production above 800 thousand ounces (Koz) per year (100% basis) going forward. The extension will require comprehensive engineering, environmental and community involvement, which is expected to be conducted over several years. The hope is that Pueblo Viejo will help to double its existing contributions to the Dominican Republic’s economy and continue to do so for many years to come.
Another key site of operation for Newmont is in Suriname at the Merian Mine. Newmont Suriname LLC is the fully owned subsidiary of the Newmont Goldcorp Corporation which operates the Merian Mine on behalf of Suriname Gold Project CV - a Suriname Limited partnership. Newmont Suriname owns a 75% interest in the limited partnership with Staatsolie Maatschappij Suriname N.V., Suriname’s state-owned oil company, which owns the remaining 35% interest. The Merian Mine is an open pit mine for gold which began construction in 2014. The mine has a mine life of 12-14 years and is committed to partnering with the Surinamese government, the local population, the Pamaka community and the Kawina community, to create value and improve lives through sustainable and responsible mining practices.
As part of Newmont Suriname’s keen commitment to the local community through the Merian Mine,
it established a Community Development Fund (CDF) in 2016 with the goal of regularly contributing to sustainable projects which will benefit the Pamaka community. These projects have included providing drinking water, electrical supply, and agricultural projects to develop the local regions towards success. Furthermore, Newmont Suriname is currently in deliberation with the local Kawina community who have been impacted by the Merian activities to find a way that this community can also reap key benefits from Newmont’s mining activities within its community. Consequently, Newmont is committed to continuing its close engagement with government and local community members to advance the development of the project in a manner that will generate sustainable economic and social benefits for people across Suriname.
A further significant development for the Newmont Corporation in South America is in the Yanacocha Mine located 800 kilometres northeast of Lima, Peru. The project invested more than $1 billion in environmental and social responsibility projects between 1993 and 2012 and remains committed to investing in the local community for many years to come. The Yanacocha Mine is South America’s largest gold mine which is situated between 3,500 and 4,100 meters above sea level and has development activities in four primary basins. The mine is wholly owned by Newmont and remains one of its largest mining operations in South America.
Yanachocha is a surface mine, which poured its first gold ore bar in 1993 and has an annual gold production of 270 Koz. However, whilst being Newmont’s largest gold mine operation it is keenly concerned with creating profitable production that generates sustainable developments and opportunity for the region. It plans to do this through its key guiding values of integrity, trust and respect which saw it establish the Asociación Los Andes de Cajamarca (ALAC) to promote sustainable development in the Cajamarca region. The activities of ALAC are focused primarily on three areas: entrepreneurial development, institutional capacity building and human capital development. Through its ALAC organisation, it can focus on bringing greater development across health infrastructures and services, its farming initiatives, and its nonprofit farming organisation FONCREAGRO, all with the
combined aim of bringing economic development on a local and regional level.
The final key operation of Newmont in South America is in Argentina at the Cerro Negro project. The mine complex sits 600 metres above sea level on the low Patagonian plains in the southern part of the country. The complex includes 3 high-grade underground operating mines including Eureka, Mariana Central and Mariana Norte. However, the complex has many sites of development including 2 underground deposits being developed (Emilia and San Marcos), and 5 other deposits in latestage evaluation which are hoping to expand the existing operations in Mariana’s complex and establish operations across the eastern district. The Newmont Cerro Negro complex is a key site of development for the company with a vast range of deposits currently being developed to continue to bring Newmont and the local community in the province of Santa Cruz continued economic development.
These key mining operations in South America have established the vital role that the region
plays in developing the mining industry towards continued global success. We can see from all of its operations across the Dominican Republic, Suriname, Peru and Argentina that the central focus for Newmont is to develop, support and develop the mining industry in South America whilst always prioritising the impact its operations will have on local communities. By working with the local communities at each respective mine site, Newmont ensures that its operations are always positively impacting the people and the environment. The company’s focus on opening a dialogue and implementing employment opportunities, alongside its implementation of strict regulations and certifications for its operations, has ensured that every aspect of its mining remains governed by national and local environmental standards. We look forward to seeing how Newmont continues to develop its global reach, and specifically how it will develop its South American operations over the coming years as it continues to be a world-leading gold company.
Located in Louisiana, The Port of Lake Charles is a deepwater seaport along the Calcasieu Ship Channel which runs north of the US Gulf Coast. Encompassing roughly 203 square miles of prime channel-side real estate, the port is now the 12th busiest across the nation and annually handles over 56 million tons of breakbulk and bulk cargo travelling along the channel. Therefore, the Port of Lake Charles continues to play a pivotal role in developing the economic landscape of Louisiana through vital cargo shipment and handling facilities.
The Port of Lake Charles is responsible for managing the Calcasieu Ship Channel which runs inland 36 miles and extends out into the Gulf of Mexico a further 32 miles. This Ship Channel drives almost $40 billion of the US Gross Domestic Product (GDP) as it facilitates the shipment of cargo and materials across the Gulf Coast of America. Therefore, the Port of Lake Charles provides essential cargo and landlord services and today is regarded as the 14th busiest port district in the nation as ranked by the US Army Corps of Engineers based on tonnage.
The Port opened in 1926 following its authorization by Act 67 of the Louisiana Legislature just a few years earlier. The official title of the port upon opening is The Lake Charles Harbour and Terminal District, a title the port has kept to this day. However, since its origins the role of the port has continued to expand and now is annually responsible for helping the shipment of vital cargo such as forest material, aluminium ingots, grain, rice, petroleum and petroleum products, frac sand, and heavy lift project cargos. All of these cargos are handled by the port and delivered to the vital land logistical infrastructure across Louisiana.
The Port of Lake Charles is governed by a 7-member board of commissioners who are responsible for overseeing the 2 marine terminals and the 500 acres of property which make up the Lake Charles Harbour and Terminal District. Therefore, serving as the landlord to companies across the port property as well as various other leasable sites near the Calcasieu Ship Channel, the Port of Lake Charles plays an expansive and committed role in ensuring the development of the Louisiana region via the port’s services and land.
A key part of the Port of Lake Charles’ operation is in marine shipping. The port has developed a custom shipping solution which delivers big results for the shipping channel. This includes the City Dock Facility, where the majority of cargo operations take place. It includes 12 deep water berths, where cargo is offloaded or loaded. The berths have a projected depth of 35 feet (ft), with berth 8 having a depth of 40 ft which is used for bulk grain shipments. The facility also includes a 1.6 million square foot of covered storage for warehouse services. The City Dock Facility is located close to essential rail links
making it an ideal location to connect the port to the rest of the state and beyond.
The Port’s Bulk Terminal No.1 provides 7 acres of dry bulk terminals at the Rose Bluff Cutoff along the Calcasieu Ship Channel and can accommodate 2 vessels for loading and unloading. Furthermore, the terminal also operates 2 travelling ship loaders and 2 travelling clamshell bucket unloaders, these include a pet coke ship loader which can facilitate 3,200 short tons per hour, and a calcined coke ship loader with a capacity for 1,200 short tons per hour. Bulk Terminal No.1 provides vessel-tovessel, vessel-to-truck, or vessel-to-open storage solutions. Consequently, the terminal processes more than 3.1 million short tons of dry bulk material annually which includes petroleum coke, calcined coke, barite, rutile, and other dry bulk commodities. In addition, the port is home to Bulk Terminal No.4 which deals in aggregates and is leased to a private company. The Terminal has a 251ft dock face, which can extend to 355 ft with dolphins and has a depth of 35 ft to help move more than 1 million metric tons of imported aggregate annually.
The facilities at the port have been designed to deal in such high quantities of multiple different types of cargo including break-bulk, speciality, heavy-lift, and project cargo from industrial components to forest/lumber products. Whilst the port facilities help to optimise the efficiency of shipment across the terminals, the port is also in a great strategic location just 12 miles upriver from the Gulf Intracoastal Waterway, is close to rail lines (Port Rail) and only 2.5 miles from an interstate. Therefore, the shipment of cargo from the port across land logistical services is made so much easier. Therefore, it is no surprise that the port trades with more than 70 countries around the world thanks to its reputation as the port of choice along the shipping channel.
As the company looks towards the future it is set on developing facilities at the Port of Lake Charles to cope with the $46 billion worth of pre-planned projects set to take place along the ship channel. This will add a further 90.8 million tons of cargo to the existing 56 million tons already travelling through the channel and port every year. The port has already begun inputting new port docks which can accommodate loads of 1500-2000 pounds per square foot, which is almost 4 times the strength of its current berths. This is part of more than $287 million in capital projects which are planned over
the next decade to expand the port’s role and capacity as it continues to be a key player in world trade and speciality cargo.
Another key development for the future is the opening of Cameron LNG (Liquified Natural Gas) Facility which will handle the exports of coke by-products from local petroleum refining, imported lumber, exported bagged and bulk grain, wind energy equipment, project cargo, limestone, rutile, barite, rubber, and chemical products. As this development will take place on the leased land of the Lake Charles Harbour and Terminal District, it will continue to establish the port as a key player for international shipping of cargo.
Overall, the Port of Lake Charles is home to one of the most pivotal ports along the Calcasieu Ship Channel and is responsible for developing a significant part of the Louisiana economy thanks to cargo shipment both into and out of the country. With key developments set to take place over the coming years to meet the growing demand for shipments along the Calcasieu Ship Channel, we look forward to seeing how the port’s facilities continue to expand and meet the needs of the future as a leading port and cargo terminal.
Caribbean Cinemas has spent the last 20 years as a leading cinema chain across the Caribbean, offering a plethora of top international film titles from around the world via its top-of-the-line cinema locations. With roughly 30 theatres and over 260 screens across the company, Caribbean Cinemas delivers top-quality cinema experiences to over 10 million viewers annually.
When you step inside a Caribbean Cinema location you are met with top-quality theatres offering a range of cinema experiences showing some of the most loved film titles from across the world. These titles currently include films such as Barbie, Wonka, Anyone But You and La Pecera. The wide range of titles brings the people of the Caribbean international hits as well as more regional film options ensuring that whether you’re a local or visiting there is always a great film ready for you to watch. Having opened in 2004, the company has spent the last 20 years expanding across the Caribbean bringing top-quality cinema experiences to its expansive range of locations and cafes which have in turn continually developed the Caribbean tourism and entertainment sector.
Caribbean Cinemas believe in creating quality cinema experiences with every visit; therefore, every theatre has been designed with topquality projectors, audio, and comfortable seating. In May 2023, the company conducted a key redevelopment of the Las Piedras Theatre to add premium auditoriums to the cinema location. These integrated three new concepts into the cinema experience; a CXC auditorium, a 4D auditorium and 2 VIP auditoriums, and added to the ever-growing offerings of the Caribbean Cinema chain. This was the first time that the company had ventured into implementing VIP rooms within the traditional cinema setting to provide an all-around top-quality experience with great dining options included. However, the majority of Caribbean Cinemas’ theatres have been designed with stadium-style seating to provide greater space between rows so that every customer can watch in complete comfort and with an unobstructed view.
Caribbean Cinemas works with stakeholders across the digital cinema solutions landscape to deliver top-quality technology and software to ensure every customer gets to experience the same reliably high-quality audio and visual experience the Caribbean Cinema’s name has come to represent. These systems are backed by performance, security, and reliability to ensure a great experience every time. A crucial stakeholder in this is GDC Technology Limited, which is a leading global digital cinema solutions provider that has installed many digital cinema servers and theatre
management systems in the Asia-Pacific region. The company is one of the largest globally and through its comprehensive suite of digital cinema products and services, it provides a comprehensive suite of digital cinema products and services. Therefore, GDC Technology Limited works closely with Caribbean Cinemas to supply a one-stop solution for all of its digital cinema needs.
In addition to top-quality screen and audio systems, Caribbean Cinemas also offer a range of food and restaurant offerings with varied menus to best suit your cinema needs. Across all locations, you can be sure to find concession stands, luxuryfeeling lobbies and a range of LED screens displaying upcoming and current film showings. Furthermore, should you have time before screening some of the locations offer game rooms and birthday party rooms that are perfect for passing time before your film begins or to make the cinema experience a fun group event. For this, the Caribbean Cinema chains offer birthday and corporate event options. The key development at Las Piedras which includes many of these facilities and so has been designed to bring a fun entertainment experience with a range of cinema formats, food and drink options, and titles to suit the whole family.
However, as part of Caribbean Cinemas’ growing sphere across the Caribbean, the company announced at the end of 2023 that it had partnered with students to give them vital access to the film industry. This partnership is with Sacred Heart University (Sagrado) which will enable its students to gain professional experience in the various aspects of film and entertainment, as well as about the company’s development to enhance the student’s professional growth. As part of the partnership, students will showcase productions from Sagrado’s Ferré Rangel School of Communication’s Audiovisual and Film Production program by offering them the opportunity to present their own work on the big screen.
The first of these exhibitions was held at Caribbean Cinemas Fine Arts Cinema Café in Miramar, which showed a compilation of the best student projects from the partnership program at the end of each academic semester. Films included
music videos, commercials, and documentaries with many focusing on community, justice, and peace. Furthermore, the partnership plans to host a competition among students where the winning production will be shown in selected Caribbean Cinema theatres in Puerto Rico in the coming months. President of Caribbean Cinemas, Robert Carrady, comments on this partnership that “Film is an industry with great potential for growth in Puerto Rico, and this collaboration will provide important avenues of development for our future filmmakers and industry professionals”.
Overall, at Caribbean Cinemas you can be sure you are going to have a great film-watching experience. With theatres and services to cater for everyone from small kids to corporate events, the cinema chain continues to provide top-quality cinema experiences to people across the Caribbean. We look forward to seeing how the company continues to expand its reach across the Caribbean as it expands and develops its location to provide even more great cinema experiences.
Whilst striving to provide high-quality tropical produce to fine food suppliers across the East of the United States and Canada, El Sol Brands Inc. has established itself as a key player in the agriculture and retail industry and a company that prioritises quality throughout every aspect of its operations. On a mission to be the premier supplier of tropical roots and produce, the company strives to always provide the highest level of quality across its products, services, and relationships to foster a crucial sense of value in every aspect of its operations.
El Sol Brands began its operations over 20 years ago and has spent the last two decades working to make high-quality and accessible tropical produce readily available across the US. Working across all aspects of produce from planting and fertilising, all the way to packaging and distribution to suppliers across the country. The company works with suppliers to accurately market and provide retail training to bring the same passion for produce that began the company all those years ago.
As El Sol Brands expanded, it began to notice the increasing demand for tropical produce from Latin, Caribbean and Asian customers across the country. Therefore, El Sol Brands shifted its operations significantly towards producing premium-grade tropical produce to meet the growing demands of the population over the last 10 years. Consequently, El Sol Brands is now one of the largest exporters and importers in the tropical produce business and now provides some of the most popular produce from Costa Rica, Brazil, Ecuador, the Dominican Republic, Jamaica, and Mexico to its customers. With a dedicated team of professionals behind the company, El Sol Brands continues to expand its offerings as it brings its passion for produce to suppliers and customers across the region.
For El Sol Brands, maintaining a high level of quality is what separates them from competitors in the market. The company wants customers to feel confident that when they choose products from El Sol Brands or with the El Sol Brands logo, they are investing in produce which has been carefully developed from seed to end product by a team of people who are passionate about making tropical produce exceptional and readily available. The people behind El Sol Brands have an expansive knowledge of the produce and a wealth of experience in the merchandising and marketing of fresh tropical produce so they are well equipped to assist in every aspect of high-quality produce getting to its customers.
The company currently has over 100,000 square feet of warehouse space in Miami and New York which it optimises as packing facilities. El Sol Brands has invested majorly in its packing facilities to ensure that they meet rigid US standards and through its warehouses deliver top-quality produce overnight
www.exfrutec.com.ec
Working in partnership with plus a large number of selected producers, which allows us to supply all our clients with good quality products all year round.
Exporting banana, yucca, eddoes, ginger, plus more from .
Call. 593 999387226 / (04) 2658077 / +1 786 602 3503
Contact: melissa.campos@exfrutec.com.ec – Melissa Campos - CEO andrea.orna@exfrutec.com.ec – Andrea Orna - International Trade Executive
to most places on the east side of North America. As part of the company’s in-depth grading process, products are selected and graded according to its high standards. These standards include a developed proprietary post-harvest method which helps the company to improve the quality and shelf life of products when they reach end markets.
El Sol Brand product packers are trained in the company’s grading and election process with items such as roots, tubers and squashes going through three rounds of grading. This three-step process includes grading at the farm, at the packing facility and then at distribution centres. It is this rigorous process which ensures that over 70% of its produce has the El Sol Brand premium label to represent it has passed the quality standards that the company has become so known for. Therefore, El Sol Brands takes its training right to the retail stores and suppliers as the company believes that training at a retail level ensures that produce managers will inspire the same passion for the product down the entire production line.
In terms of products, El Sol Brands offers a wide range of produce from plantain, Thai chilli peppers, and cactus leaf, to avocados, guavas, and dragon fruits. The range of offerings is vast and has allowed El Sol Brands to remain in step with the growing demands from people across the region for more tropical produce. As the demand for products continues to grow, El Sol Brands’ growers and packers continue to work tirelessly to meet these demands and facilitate the delivery of these products through the logistics systems in place. Therefore, throughout El Sol Brands’ operations, the company thanks to its strong relationships with suppliers, logistical providers, growers, packers, and retailers who continue to allow the company to continue to serve the growing demand whilst maintaining a consistent level of quality throughout every operation.
El Sol Brands is a vast operation which is committed to providing high-quality tropical produce to suppliers across the region. Through its rigorous quality grading systems, it continues to be a significant player and the El Sol Brand is one that is widely trusted and respected for its quality. With expertise in marketing the company provides essential training to suppliers to accurately promote and meet produce demands on both local and regional levels. However, what remains a clear focus for the company is its strong relationships and communication across supply chains to ensure rigid standards of quality are maintained from crop to end products. This focus on relationships is what ensures El Sol Brands continues to provide great tropical produce across the regions, as it believes it cannot truly thrive if its suppliers are not thriving.
Unilever is an expansive brand and one of the world’s largest consumer goods companies. The overarching company is home to more than 400 brands, including many we all know, love, and probably use every day. Globally, Unilever has a network spanning more than 190 countries worldwide. However, one of the current key developments for Unilever is in Mexico where they are investing in new facilities and sustainable programmes to expand their network, whilst providing jobs to support the local community in the process.
Unilever Mexico operates in 11 countries across the Latin American region, working with 9000 collaborators to facilitate Unilever’s manufacturing and distribution needs. The Mexican division of Unilever has a clear purpose to make sustainable living commonplace. Their strategy for delivering this is through achieving consistent, competitive, profitable, and responsible growth. We see these values coming into play in the announcement of a new manufacturing facility to be built in Mexico. The new manufacturing plant in Nuevo Leon comes as part of a $400 million investment in the country over the next 3 years. The plant will be located in the border state of Salinas Victoria, on the outskirts of Monterrey and will manufacture beauty and personal care products. Furthermore, it will provide 1,200 new jobs both directly and indirectly to the local community.
The new plant is set to open next year in 2024 and will bring a crucial expansion for Unilever in the country not far from the border to the United States of America. This investment in Mexico comes as many big brands are investing in facilities there to bring supply chains closer to their final destinations. Consequently, Mexico is a key centre of exports for Unilever to other nations, and so the new plant will be the 5th in the country, adding to the 4 plants which are currently in operation under the Mexican division of the company.
The Unilever brand is known for its sustainable initiatives with 100% of its energy used worldwide coming from renewable sources, and 67% of its raw materials used across its range of products are sourced from sustainable farms. Unilever Mexico maintains this high level of sustainability throughout its work ensuring that no waste ends up in landfill from its operations.
A key focus for Unilever Mexico is sustainability, focusing crucially on the initiatives towards the conservation of soil. To do this Unilever Mexico has established a set of principles focused on ensuring the regenerating agriculture in the country by aiding farmers and small producers across the companies’ value chain. By supporting soil nutrition, the capture of carbon, water care, restoration and regeneration of the land, Unilever Mexico can support the biodiversity of the land. Therefore, the company is working beyond its manufacturing
facilities to ensure that the land around its facilities and across the region is cared for. Unilever Mexico is ensuring that, through its work in Latin America, it is leaving a lasting positive impact beyond its production lines.
Furthermore, over the last 15 years, Unilever Mexico has achieved key advancements in their sustainability programmes and certified production. Now, Unilever Mexico has achieved an 80% sustainable supply across all its key raw materials, and a 100% sustainable supply in its soy, sugar, and cocoa production. Furthermore, 91% of the 13 main vegetables and 96% of the paper and cardboard used by the company are also sustainably sourced. Therefore, throughout Unilever Mexico’s operations they are meeting the sustainable goals of the overarching company, and as a division are leading the way across Mexico for facilitating the manufacturing of crucial health and beauty products in the most sustainable way possible.
FPS Ibérica SA was created in 1987, founded by Beverly John Colson and Alejandro Montero Moscatelli, our enterprising spirit has made us stronger over these almost 36 years.
Since its foundation, FPS Ibérica has grown from a fresh meats, canned meats, beef importer and distributor to a supplier of a wide range of raw materials for the Baby food and food Industries across the world, based on:
Overall, Unilever Mexico continues to expand to meet the needs of a growing health and beauty industry. The investment into the country by Unilever is set to broaden its possibilities and bring with it key jobs to serve the local community. It is clear that even with the expansion of the industry and the need for more manufacturing facilities, Unilever Mexico is still focusing on ways to lead the industry toward sustainability, by promoting the necessary support of the country’s agricultural development.
• Systematic work procedure based on control at origin
• Supply safe (ensuring it is fully tested prior to delivery)
• High quality products (Welfare, Organic, Sustainability)
• Responsible and reliable communication policy
• Committed team
• Logistic and financial solutions
• Market trend info
Commitment to our customers and suppliers • Food safety • Animal welfare and sustainability
Strong, profitable and confident about the future with a solid growth
Range of raw materials:
Meats & Organic Meats
• Beef
• Veal
• Chicken
• Turkey
• Horse
• Lamb
• Rabbit
• Pork
• Ostrich
Dehydrated and food ingredient products
• Freeze dried
• Vacumm dried
• Spray/Flash dried
Ready meals for Industry
• Beef Extract
• Chicken Powder/Broth
• Meatballs
• Seafood pastes
• Chicken/Pork pastes/fats
MEDICAL & PAEDIATRIC NUTRITION
Our range of Powder/Lyophilized Meals with High Protein / High Calories / High Fiber to improve in your SAVOURY flavours.
Fish & Sustainable Fishery
• Tuna
• Hake
• Seabream/Seabass
• Salmon
• Trout
• Plaice
• Gilthead
• Crab
• Lobster
• Shrimps
• Squid
Vegetal & Cereals
• Frozen / IQF / Organics
• Cubes
• Canned
Aromas and Flavours
• Roast Chicken Ar
• Boiled Chicken Ar
• Roasted Meat
• Smoked Meat
• BBQ
• Cheese Flavour
• Mayonnaise Flav.
• Pizza Flavour
• Soya
• Wheat
• Maize
• Rapeseed
• and Mixtures
As Alabama’s only seaport, the Port of Mobile’s role in the state’s financial prosperity can be traced back centuries, having been a crucial step in many supply chains with its expansive growth during World War II. Now, many years later the continued development and growth has seen the region deliver vast investments in manufacturing, agribusiness, and mining. All these industries benefit from the port’s activities, which has allowed the port to become one of the most prominent seaports in the United States. Therefore, the Alabama Port Authority was established in 2000 to position the Port as a strong link and partner across supply chains, facilitating the transportation of goods and materials across the port and connecting them with the crucial rail, roads, river, and runway links.
With 18 diverse cargo handling facilities and a port with direct access to 45-foot deepwater, nine railroads and air, truck and barge movement options, the Port is a vital player connecting the state with the local and international movement of cargo. We know this as annually the Port is responsible for bringing 85 billion USD to Alabama’s economy, providing seamless services to manufacturers and industries around the world. Therefore, the Port provides a gateway for all types of cargo, including aggregates, automobiles, breakbulk, coal, cold storage, containers, forest products, general cargo, liquid bulk, metals, and project cargo.
The connected nature of the port is second to none, and so has been a key area for development to continue to serve and develop Alabama’s cargo industries. Consequently, the Alabama Port Authority has invested over 1.4 billion USD into the port over the last 20 years to modernize and grow its facilities to support its customers’ needs.
In June 2023, the State of Alabama allocated 20 million USD to the McDuffie Coal Terminal to increase the current port incentives to provide greater benefits to businesses. The McDuffie Coal Terminal handles metallurgical and bit coal across rail, barge and truck links. Coal in Alabama is metallurgical and so is a key component in steel making as it is recognised industry-wide as some of the finest metallurgical coal in the world, making it a crucial development for the port to continue to contribute to the state’s overall economic development.
John Driscoll, Director and CEO of Alabama Port Authority commented in a press release for the funding that “At the Port our mission is to help Alabama’s economy grow”. He adds later that “The Port is proud to deliver lower landed costs to shippers through the optionality and fluidity we provide. In addition to these operational advantages, the increased incentives for businesses to use the State’s Port will make Alabama even more competitive in the global market”. We can see from Driscoll’s comments that the Port is striving through every investment to make a mark on a range of industries, to promote both the Ports reputation and the State’s role in the development of the global economy.
This investment comes as Alabama Port Authority announced its 2022 stats a few months early, which saw the port handle 563,191 twenty-foot equivalent container units (TEUs) over the year, which reflects the 9th year in a row that the Port of Mobile has announced a double-digit growth since 2009 at 11%. The intermodal rail volumes continue a 31-month record of triple-digit growth and ended the year with 142% growth compared to the previous year’s figures. Additionally, the container terminal handled a record number of 312 vessels, an increase of 75 vessels from the previous year.
However, Alabama Port Authority is not slowing down its development, and expects to see its capabilities reach one million TEUs upon the completion of the 6th expansion phase at the container terminal, and the deepening and widening of the harbour. Further planned expansions include constructing a fly-over bridge, creating on-dock rail access for the container terminal, modernising the general cargo piers and developing an in-land intermodal facility in North Alabama.
However, Alabama Port Authority is not just concerned with the economic and operations expansion of the port, they are equally as concerned with ensuring environmental standards across all the port facilities and forwarding links. Alabama Port Authority have been Green Marine certified since 2018, which is the largest environmental certification program in North America and provides a framework that the marine industry adheres to, to ensure that the industry can reduce its environmental footprint. Consequently, the Alabama Port Authority is committed to ensuring environmental and sustainable practices and programmes are implemented into all its business decisions, port development plans and daily operations. Its goal is to work towards improving its practices and stewardship regarding the quality of air, water and of soil and sediment. They are also committed to ensuring wildlife habitats are protected, waste management initiatives are followed, and energy consumption regulations are implemented across all operations to improve the environmental conditions in Mobile and the surrounding area of Alabama.
At present, the Alabama Port Authority has implemented electric ship-to-ship cranes at the McDuffie Terminal, Pinto Island Steel Terminal and the Container Terminal. It has repowered locomotives to smart idle/EPA-certified off-road industrial engines to help reduce the particulate matter and nitrogen oxides that are produced from their diesel emission, which has already reduced emissions by 90% and has been further developed with a no-idle policy.
The whole facility also works to ensure that recycling is carried out throughout the port, and twice a week the near-shore and shoreline is inspected. The shoreline work allows the port to monitor the waterways are make sure they are not impacted by environmental damage, and should an instance occur they have the facilities through its environmental programmes to provide clean-ups where releases could have a negative impact on the waterways. However, the Alabama Port Authority is continuing to work to develop the operations of the port towards sustainable success and working to support the surrounding areas through further wetlands developments, conversion to LED lighting and removal of invasive species.
Overall, Alabama Port Authority is working to promote the port’s operations towards global markets through its expansive network of forwarding links due to its ideal geographical position on the Gulf Coast and at the centre of many transport links both by land, sea, and air. As the only port in Alabama, it makes a crucial part of the State’s economic development to aid in the facilitation of import and export cargo whilst providing the local communities with vast employment opportunities. However, the Port Authority is not just concerned with economic success, it is equally as concerned with ensuring that its environmental impact is kept to a minimum and promotes sustainable and environmental programmes throughout its vast range of operations.
Ecolab Specialty Pest Services provides industry-leading expertise to protect your product and maintain a pest-free environment.
Our dedicated fumigation team provides services at ports throughout the United States, including Mobile, AL, with 40+ local fumigation centers. When you need container fumigation, ship fumigation, or other pest treatment for import/export, trust Ecolab to protect your commodities and help meet import/export requirements.
• USDA Compliant
• Quarantine/non-quarantine
• Australian Approved: BMSB
• Communication experts: local, USDA, CBP, state agencies, and freight forwarders
• Documentation for local, state, foreign
LEARN MORE AT: ecolab.com/fumigation
• Perishables: fruits, flowers, fish, vegetables
• Large and small scale fumigations
• Wood packing material (ISPM 15)
• Experienced; licensed; certified
• Grain, nuts, wood, logs
• In-transit fumigation
Alabama contact: Dan Dalton, ACE 561.312.0775 | daniel.dalton@ecolab.com
Chile has a rich and profitable seed industry which has positioned the country as a key figure in global seed markets for its exports. The country is a leading exporter in the Southern Hemisphere and the third in the world for agricultural exports. Therefore, The Chilean Seed Association (ANPROS) was established to be a reliable partner for the country’s seed production. Through its work to support, develop and promote Chile’s seed industry, ANPROS has spent the last 63 years positioning Chile as a reliable and crucial player in global seed production markets.
Founded in 1959, ANPROS is home to 74 members which include producers, distributors, marketers, researchers, and a variety of other organisations which are related to and represent 98% of the seed industry and its operations in Chile. The core operations of the association are divided into various committees which work to develop individual sectors of the Chilean seed industry toward the united goal of developing Chilean Agriculture. ANPROS works to tackle all matters concerning seed activity on national and international stages, whilst ensuring that throughout this they are contributing towards the sustainability of the industry as a whole. The committees are vast and span a range of topics including, specific seed development and production, regional development, intellectual property, marketing and trade procedures to establish ANPROS as a leader in the seed trade industry.
The Phytosanitary Committee is responsible for regulation across the industry and advises on phytosanitary matters, the various daily queries regarding Chilean regulations and the global seed industry. This committee is part of the International Seed Federation, which allows ANPROS to develop in line with global seed regulations. However, the committee is involved in regional associations too, including the Seed Association of the Americas (SAA) to develop the industry on a localised level. ANPROS’s work through this committee establishes the Association into regional and global markets to bring in international standards of regulations, whilst aiding in the unique development of Chilean agriculture. Therefore, working closely with the Phytosanitary Committee is the Commercialization Marketing Committee, which is working to help the distribution of regulated seed towards its end markets. The committee work to ensure the interests of all involved partners in the seed trade industry, to place Chilean seed as a leader in its respective field.
By positioning Chilean seed as regulated, high in quality and easily available via good trade links, which are established by the COMEX and Logistics Committee, it continues to develop the industry’s investment into Chilean agriculture and the economy.
To provide high-quality seeds, ANPROS has a range of committees which focus on various seed types to ensure a future of continued crop success.
The first of these looks at corn, focusing on all aspects of its growth from seed to end markets, to optimize its production and highlight the ways that technology can aid in the production of corn seeds. The committee’s central function is to optimize the member companies’ operations and strengthen their relationship with the network of seed growers across the country to benefit specifically corn seed production. Similarly, the Canola Committee was established in 2003, to organise the companies of the association which produce canola seed. The committee, which now consists of 12 members, works to regulate, supervise and optimize the production and performance of canola seed across the region.
Following this, another committee under ANPROS is the Vegetable Committee, which looks at the regulation of sown products to ensure that throughout the operation there is varietal purity of the seeds. The committee’s main objective, much like the corn committee, is to position ANPROS as a coherent association which is working towards improving the seed production industry across the country. They believe in good communication across the associated companies, which will increase transparency across the productive sector.
One way they are highlighting transparency and communication is through its geographic information system which was developed to highlight contamination, and instances where contamination could occur in the future. By developing this, the Association helps to build a strong and profitable sewn crop industry with its members.
Towards the future of sustainability, ANPROS is crucially aware of the role globalization and climate change play in the agricultural industry. Seed industries are constantly exposed to the entry of new pests and diseases. Therefore, the Biotechnology Committee are working to understand and advise the board of directors on the production, regulation and policies surrounding seed production, whilst actively participating in international discussions regarding genetically modified crops. The committee was created in conjunction with the Agricultural and Livestock Service, the Procedures Manual of the Live Plant Organisms and Modified Propagation. The committee is seeking to protect the environment whilst maintaining the phytosanitary heritage of the seed produced across the association. Consequently,
their work to establish standardised procedures for the importation, production, and evaluation of genetically modified material, whilst ensuring the security of regional Chilean crop production, gives the association a competitive advantage to the industry in this region.
Furthermore, ANPROS leads the way with its insulation system which has been recognised globally for its tool to spatially order the production of seedlings to ensure high-quality, genetically pure and successful crops are produced. The technology was developed by ANPROS and now is managed and supervised across its uses in the industry. It provides crucial knowledge to farmers to help them organise seedlings, seed beds, the use of soil and the compliance regulations with biosecurity to ensure that the seeds are produced throughout the Chilean seed industry to a high standard. This technology was adopted by the National Institute for Agricultural Research (INIA) in a collaboration which incorporates information from AGROMET, an agrometeorological network, into the ANPROS Insulation System to provide seed companies with agroclimatic knowledge to again increase the efficiency of crop production. The combined system
provides ANPROS members, and international seed markets, with innovative technology to help in decision-making regarding irrigation, planting, pollination, and phytosanitary issues. The system ensures that throughout the Chilean seed industry, ANPROS can ensure the profitable, high-quality and efficient development of seed to ensure its sustainability and stability towards a growing seed industry.
Overall, ANPROS focuses critically on various sectors of the seed industry by dividing into committees which work with the seed members to develop the industry towards a high standard of regulation, efficient production, and global status of the Chilean industry. The Association has established itself through its work and development of its Insulation System to leave a legacy of efficient seed production not just across Chile or South America, but across the world as the technologies continue to be adopted globally. Therefore, ANPROS is leading with innovative ideas and close attention to all facets of the seed industry by working with its members towards smaller focused goals which come together to benefit the agricultural development of Chile as a whole.
CURIMAPU is a Chilean seed multiplication company with almost 30 years of experience dedicated to provide high quality service to companies around the world. We are focused in the vegetable and raw crops production, also our facility in Peru, is specialized in under nethouse hand pollination productions.
Curimapu offers on time delivery, confidentiality, security in quality and execution terms with efficient and personalized attention.
Cámara Minera de Panamá (CAMPIRA), or The Mining Chamber of Panama, brings together companies, shareholders, and suppliers throughout the metallic mineral and non-metallic sectors in Panama, to promote the country’s mining industry towards social, economic, and environmental success. CAMPIRA is critically concerned with promoting the mining industry towards sustainable development, by working with mining companies to ensure the efficient and responsible use of mineral resources in the country.
CAMPIRA wants to develop the economy, and Panama’s stake in the world of mining development, however, is critically aware that this kind of development can only take place sustainably. Therefore, CAMPIRA facilitates the sustainable economic development of Panama through a range of practices and standards to benefit the country with the economic profitability of sustainable mining.
Panama is home to an abundance of mineral resources due to its geographical location, with key copper and gold mineral deposits. The country is currently only home to one operational metal mine, Cobre Panama, which is world-renowned for its metal production and so has a significant impact on the economy of Panama. CAMPIRA sees Panama as a key place of development, which has already seen key success in the service sector, and so believes that with such a rich mineral resource the country can take advantage of the opportunity that mining presents the country. CAMPIRA believes that mining can close the productivity gap, promote entrepreneurship, and bring new innovation to the country through new mining projects.
CAMPIRA has been bringing together the public, private and social players in the mining sectors since 1990, to reduce the risks associated with mining, chiefly concerning the environment, whilst enhancing the benefits generated by mining activity. The benefits of mining, particularly in Panama, are positive fiscal developments and the creation of many high-quality jobs to bring economic success both locally to those working at the mines and nationally across Panama by reinforcing the economy. Furthermore, as Panama is located next to the sea on both sides it makes it an ideal candidate for mining metal exports, and so the development of mining in this region will benefit Panama’s economy even further as it can easily export the mined material out of the country. Consequently, CAMPIRA is working on a project to bring together companies relating to mining, to bring a united learning environment and communication to develop the mining industry in Panama towards global success. The companies include those involved in inputs, machinery, engineering, processing, by-products and copper products to ensure that throughout the supply chain from
mined minerals to end products the companies across Panama’s mining sector are working as one fluid machine. The Cobre Panama mine makes a perfect example of the opportunities that can be seen economically, as by consolidating the mining industry into mining clusters, it can promote the development of local suppliers, demand for human capital and infrastructure. Therefore, through CAMPIRA’s work, it is promoting the development of new mining projects to bring strong investment into Panama’s mining sector.
Currently, the metallic mining sector is contributing toward institutional development, with the adoption of better standards and practices. These standards and practices can then positively impact the nonmetallic industry that CAMPIRA is hoping to develop in the country. Consequently, every development and project that CAMPIRA is working on helps to open a new path of shared success in the country at both a national and community level.
Ultimately, the development that CAMPIRA is hoping to see from the mining industry in Panama will contribute significantly towards the sustainable development of the country and its social, environmental, and institutional dimensions.
Overall, CAMPIRA is working to promote the best practices and standards across the sector to ensure that the mining industry is contributing toward the country’s environmental and economic development. CAMPIRA strongly believes that communication across the industry is the best way to promote its development, as this communication can reduce the risks facing the industry whilst enhancing the benefits of shared knowledge across the sector. Furthermore, through CAMPIRA’s aim to bring together all those involved in Panama’s rich mining industry, it can continue to make efficient and responsible use of the natural resource at their disposal. Therefore, as an organising body, CAMPIRA is keenly concerned with the environmental impact that mining has on the world but is working to ensure that operations across the industry are working in the most sustainable and responsible way possible towards the expanding future of Panama’s mining industry.
Experience innovation and excellence with Austin Powder, the world’s oldest privately-owned explosives company. Our commitment to innovation, quality, and safety drives our international expansion and enables us to serve diverse sectors.
Supporting major infrastructure projects in Panama for over 25 years, we value every customer, regardless of size, treating them with equal respect and attention..
Equipped with cutting-edge technologies and a dedicated team, we propel your projects forward while safeguarding people, communities, and the environment.
Partner with Austin Powder today for safe and responsible blasting solutions that deliver unprecedented success in your endeavors.
Since 1833 – Partners in Panama Since 1997
Commitment to innovation, quality, and safety.
Safeguarding people, communities, and the environment. Delivering unprecedented success in your endeavors.
Many would regard a used truck as an outdated and unproductive vessel, and yet, dismissing and reducing used trucks to the scrap heap is an unbelievable waste. This is a strong conviction of Arrow Truck Sales, who with a long history in customer care and a commitment to the haulage industry, are veterans in the buying and selling of semi-trucks. Trying to sell a used truck can be a tricky business, and yet as a reliable source of information and services, they have an unmatched repertoire of business that enables their customers to sell their used trucks for the best price possible!
Since its founding in 1950, they have evolved to become the best source of used medium and heavy semi-trucks in North America. This is evidenced by the fact that they operate across 18 locations in North America and Canada. This is highly valuable to anybody looking to sell their used truck, or trying to find their next trusty vehicle, as they can utilise Arrow Truck Sales’ wide pool of influence and accessibility. Furthermore, their influence is highlighted by the sheer range of trucks that they have on hand for their customers. Indeed, they have access to hundreds of makes and models of semi-trucks, both in manual and automatic transmission. Additionally, all vehicles have at least 400 horsepower and a 12-speed gear system, allowing truckers to have true power and reliability behind the wheel.
The buying and selling of semi-trucks is a fairly narrow business across North America, subsequently, Arrow Truck Sales offer a guiding light for their customers, providing the most proficient and up-to-date semi-trucks out there. Evidently, Arrow Truck Sales do not skip on the quality of
truck. Furthermore, you are also able to trade in your old semi-truck for a newer model, thus reducing the upfront cost of your new vehicle. Once again, this highlights how they put the customer first, and make selling your semi-truck the smoothest process possible.
All of Arrow Truck Sales’ 18 locations are conveniently placed across the country. From East to West, and many sites in between, their friendly and hands-on team are more than ready to help you in the selling and buying of trucks. Moreover, Arrow Truck Sales has a highly comprehensive and up-to-date website that can give you all the information you may need, from semi-trucks to insurance, as well as giving the full list of their locations in North America. Their bustling social media is also great to gain insight into the analytics of each truck, working hard to provide the best of the best in semi-trucks.
Arrow Truck Sales guarantee that each semitruck works well for the customer. Consequently, their entire semi-truck inventory comes with a 90day warranty as well as a 25,000-mile warranty at no extra cost to the customer. This allows drivers to really get a feel for their semi-truck, as well as make sure they are partnered with the best vehicle. And yet, an extended warranty is not the only fantastic service that Arrow Truck Sales provide. Indeed, their help and guidance do not end as you
drive away, as they offer 24/7 roadside assistance giving buyers and sellers accessible protection when they desperately need it. As many truckers will know, roadside protection is no longer an extra bonus but an essential requirement, particularly in long-haulage situations. Accordingly, Arrow Truck Sales offer an Emergency Roadside Assistance Membership Program that is available to every trucker. In this highly comprehensive program, truckers can enjoy towing assistance of up to 50 miles, taking truckers to the service facility of their choice, as well as offering a mobile mechanic service call. The 24/7 roadside assistance also covers tire delivery assistance, since the service call to deliver a replacement tire is covered up to a high price. Thus, alongside many other added benefits, Arrow Truck Sales provide a generous helping hand when the warning lights appear on the dash.
The buying and selling of semi-trucks has never been so easy with Arrow Truck Sales. They see the beauty where others don’t in a used truck. And yet, they do not compromise on the quality and deliverance of the truck, guaranteeing that drivers across North America get the most bang for their buck. Plus, they have lots of economically beneficial initiatives that allow drivers to trade in their used trucks for newer models, whether it be a regional small vehicle or a mighty long-haul monster, Arrow Truck Sales has exactly what you need.
The Association of Marina Industries (AMI) has a strong commitment to the needs and well-being of the global marina industry. Catering to over 1,200 businesses, members include boatyards, yacht clubs, public/private moorage basins, partner associations and marine industry vendors, placing education and networking as a top priority. Therefore, although predominantly operating around the United States, it has a strong membership across the world.
As a non-profit organisation, its sole purpose is to serve the needs of its members. More specifically, it works to bring companies together so that there is an active forum for education and growth. This is most aptly demonstrated by AMI’s Training Institute, which has built a fantastic reputation for the training and certification of marina industry professionals. The institute offers a wide range of benefits for its members, including the globally recognised Certified Marina Manager (CMM) and Certified Marina Operator (CMO) programs and specialised conferences. By obtaining such qualifications, members can demonstrate a deep understanding of the marina industry, as well as enjoy numerous discounted services, industry publications, and legal guidance for any grievance.
Members in the U.S. have further access to brilliant services across the States. Specifically, they have access to forwardthinking and cost-saving business solutions, educational services, updated news, and the latest findings from ground-breaking research. Therefore, AMI is a guiding light in all related legislative issues. Further benefits are also witnessed in the Training Institute, as training is exclusively provided directly to U.S. members, rather than being distributed by partnerships, as is the case for international members.
AMI was formed from the amalgamation of two dominant associations; Marina Operators Association of America (MOAA) and the International Marina Institute (IMI). Although the merge occurred in 2005, the first sparks of AMI occurred in 1992, when a small group of marina industry owners formed MOAA. Significantly, MOAA was born out of a need for a greater advocate in the domestic legislative and regulatory agenda. The Association placed effort into working more in the marina’s interests, in a fair and responsible way. Despite having over a thousand members today, the initial membership consisted of high-end marina managers and owners, exclusively in the U.S.
Nearly ten years later, MOAA had the opportunity of accepting direct sponsorship and support from the National Marine Manufacturers Association (NMMA). This was a major turning point as it enabled
MOAA to curate a healthy domestic profile that was held by major executives in the industry. Moreover, it facilitated a network of strength that was effectively able to combat state and federal issues that were causing great disturbances to the Marina industry. From this initial inkling, it became clear that a proactive voice for change was needed if the industry was going to develop at all, including the building of relationships with national and state organisations to create a tight network.
On the other end, IMI was formed in the mid1980s, which brings to the helm the educational aspects of AMI. The institute was founded to encourage education, training, and certification. Consequently, IMI did just that, as they successfully established and developed numerous management schools, including the highly regarded Certified Marina Manager (CMM) program.
Similar to MOAA, the founding members of IMI were deeply passionate about the marina industry’s consistent development, as the institution strived to educate members to overcome the complex and technical challenges of the day. IMI also has
Scribble Software’s MARINAGO Office is a next-generation cloud-based marina management software providing single and multi-site properties with everything to handle transient, recurring, and seasonal guests.
Always on the cutting edge, MARINAGO Office now offers a state-of-the-art enterprise-level fuel management solution designed to better automate and manage fueling operations.
an impressive portfolio of research and academic published papers. What is great about this particular aspect is the joining together of marina operators, industry consultants, academics, technical experts and governments, that tightly worked together to create an educational network. Accordingly, members could be more prepared to confront the multifaceted issues of the industry.
In 2005, a magnanimous decision was made to join together IMI and MOAA to form a proactive association. Although there were many reasons for the merge, they predominantly wanted to increase active US membership and gather the appeal of consolidating business services; ultimately bringing together the wealth and experience of two strong associations to form the ultimate space for marina membership.
If you were to take a cross-section of AMI, you would find a wide range of marinas, from family-run businesses to large corporations that have become
titans of the industry. As suggested by the name, Marina companies comprise 77% of the membership.
Whilst this does make up a large majority, industry suppliers and honorary partnerships also comprise 15%. Furthermore, the demographic of their membership is spread across corporate chains, privately owned enterprises, and affiliate partnerships with local state trade associations. A recent example of this would be the joining of Alaska Association of Harbourmasters and Port Administrators, which continue to provide a wealth of knowledge to the Association, due to the affiliate partnerships with many trade organisations across the world.
Marinas that are members of AMI offer a wide range of services and expertise, thanks to the guidance and support of the Association. Significantly, 410 marinas, (almost half of the total membership) offer boat repair services to any who stops by. Additionally, 296 marina members conduct
new boat sales on their properties, with another 40 possessing boat-building facilities onsite. Thus, each marina garners the advice provided by AMI, as they help an excess of 1200 businesses make a key difference in the marina industry.
With over 1 million boaters gaining access annually through AMI’s member marinas, they have to cater to a wide selection of businesses and entities. Typically, many boating and logistics associations solely focus on legal issues. And yet, thanks to the joint expertise from which AMI was founded, they have a great passion for the education of their members, exampled by the diligent and highly comprehensive AMI Training Institute, which subsequently provides invaluable certifications. Thus, there is a vast range of benefits to be gained from being part of AMI, as an indispensable network of passionate leaders and hard workers.
Mack David Buildings brings more than 30 years of experience to your marina drystack buildings and outdoor racks.
It is home of the innovative, tool-free, quick-release bolt and adjustable bunker board system that is revolutionizing the drystack storage industry. Contact David Coyle today for responsive high-quality service, design, and construction management for your next marina dry storage project.
Located just east of Canada, Prince of Edward Island is Canada’s smallest province. However, it is also one of the nation’s major maritime provinces with major commerce in lobster and mussels, which gives way to the fantastic trade of seafood. From a tourism perspective, it also boasts idyllic sandy beaches and green pastures, which tempt millions of visitors every year. And yet, the bustling maritime, agriculture, and tourism sectors could not survive without the dedicated efforts of the Prince of Edward Island Road Builders & Heavy Construction Association. They work tirelessly to provide a tenacious voice for the many contractors and suppliers, amongst other industries, across the island, as well as guaranteeing the smooth running of vital operations like road building and infrastructure.
The Association’s predominant strength can be found in the power it has in uniting companies under a common goal. As a collective, the Association totals a staggering 90 companies. This spans many industries, including construction equipment, insurance, and hospitality. Even though there is such a broad variety of companies, every business comes together with one common vision, to create a strong and impactful voice for the heavy construction industry.
As with many construction associations, teamwork is necessary to tackle challenges that occur both in political grievances and construction projects. Consequently, each associate is given equal priority and purpose, and no stone is left unturned in relation to helping others.
Exciting events taking place this month include the 61st Annual General Meeting. This is a fantastic event that allows for many of the Associates to congregate and not only share ideas but celebrate the previous year’s achievements. The Association also provides handy advice for residents by communicating traffic alerts on their website and providing guidance regarding the roads and infrastructure, amongst much more.
As can be imagined, there is a lot of management and expert strategy involved in keeping the well-oiled machine running. Accordingly, the PEI Road Builders & Heavy Association possesses a dynamic Board of Directors, which contains eight representatives from the Regular Member category and two representatives from the Associate Member category. The Board holds monthly meetings to discuss the progress of the Association, as well as briefing the manager who ensures that the dayto-day running of the Association is kept to a high standard. Overall, they work to maintain a strong network of discussion and encourage an open forum that facilitates continuous improvement and innovation within the field.
The Association was first formed in 1962, birthed from a need to have a united voice that could proficiently negotiate with governments to overcome any concerns or grievances. First incorporated by local contractors and their suppliers, the Association has always had the voice of the people at the top of its priorities, allowing for any adversities to be quickly and professionally handled. Case in point, the Association has in
the past negotiated with the PEI Department of Transportation, Infrastructure & Energy in developing numerous successful policy changes that have had a meaningful impact in the region. Furthermore, the Association is a necessary force to allow for the continued success of the sector, which is particularly significant when we consider how many industries and livelihoods it incorporates, including contractors and highway officials.
As commonly known, for any region to reach optimum efficiency, it had to possess an effective network of roads. It is for this reason that the Island’s highway system is of great significance to the Association. So much so, that the highway system is the beating heart of Prince Edward Island’s economy. Evidently, the efficiency of the roads affects every source of financial input.
On the business front, the Association’s work can have great ramifications on many businesses, namely agriculture, fishing, maritime business, and tourism. Perhaps of even greater importance is the safe and quick transportation of the Island’s
residents. These two subsectors come together through the employment of contractors and suppliers, who as a necessity to business, are reliant on an effective network of roads.
The Association has a tight network of channels to drive the local economy forward. Accordingly, they stress that “the number of people who are employed by the contractors, the suppliers and services that the contractors require, the involvement of the private truckers hauling and bringing material to and from the marketplace, and the general amount of money that is left in the various communities by the employees of the member contractors etc., are ways in which this industry affects our economy.”
Some of PEI’s Road Builders most recent projects include vital improvements made to Route 2, a major highway that runs across the entirety of the Island. This particular project needed a range of expert capabilities, such as Earth excavation, the installation of storm sewers, landscaping, hydroseeding, and much more. Consequently, creating a noticeable difference to Route 2 in the Kensington area, last September. Further proficiency is demonstrated the Asphalt Resurfacing as the relaying of the top surfaces of the road is vital for safe passage.
Such projects are a positive impact on a renewed appreciation for the construction industry on PEI. This is most clearly reflected by the approval of $37.7m in special warrants for the Island’s transportation and infrastructure department. This was due to the significant work of the Association, consequently enabling them to effectively utilise the money to overcome previous adversities and rise from the ashes! The funds were primarily funnelled into the expenditure needed to maintain the safety of roads and bridges, and allow the Association to take the lead.
Evidently, the Association oversees and implements essential work for the Island, acting as a key pillar of the community. By supplying an indispensable voice for the construction industry on PEI, many contractors and suppliers can work effectively to build and operationalise an Island that works best for everyone, whilst simultaneously generating significant money for the economy. Thus, the impacts that PEI Road Builders & Heavy Construction Association have are unmeasurable and restore an appreciation for the work of construction workers across the Island and beyond.
As the largest supplier of asphalt in Eastern Canada, Irving Oil can offer various asphalt products, including performance grade, polymer-modified, viscosity grades, cutbacks and so much more.
In addition to building trusting relationships, the company offers a safe and reliable supply network that allows them to respond to their customer’s needs promptly and efficiently.
It is widely known that the acquirement of food is hardwired in the mind as a matter of survival. These days, this instinctual calling is made significantly easier by the creation of the modern supermarket. A weekly trip to the superstore is a regular occurrence for a large majority across the world. Although the notion of the supermarket chain has been an ongoing phenomenon since the 1900s, to this day, supermarkets consistently aim to create affordable and comfortable shopping experiences. This a factor greatly understood by Massy Stores; a leading supermarket chain across Trinidad and Tobago and heralded as the “premier retailer in the Caribbean Basin.”
Massy Stores’ main focus is to provide affordable but delicious food across the nation. As the old saying goes, the customer is always right. As such, their customer base is emboldened by providing the best value products, as well as guaranteeing low costs. This is greatly exampled by the many initiatives that they offer their loyal customers. For example, they provide a trustworthy reward system known as the ‘Massy Card’. This allows customers to get the most for their money, as well as rewarding their loyalty to the store. Although the loyalty system is utilised by many supermarkets, for Massy Stores it represents a continuous building of trust and loyalty to their customers that facilitates a mutually beneficial relationship.
Massy Stores also has a fantastic range of products to offer their customers. From hearty and freshly cooked bread in the bakery, to prime-cut meat in the deli, there is very little that you won’t find in their stores. The freshness of the bakery is emphasised by the fact there is something new every day for customers to look forward to. These include bread, cakes, blueberry tartlets, apple pies, and the signature swiss roll.
Stepping away from sweet treats and on to the fresh produce, it would be hard to miss their innovative fruit and veg. This includes Massy’s ‘One Step… Done’ Microwaveable Potatoes. As their latest product, it is the epitome of delicious convenience. In three steps you can have high-quality and scrummy potatoes in just six minutes. This is one of the many products that Massy Stores offer, putting customer satisfaction at the top of the list. When doing your weekly food shop, it can be so easy to buy the same list of things. Massy Stores provide a solution to the grievance of repeated meals by providing a long list of simple but scrumptious recipes on their website. This includes a wide variety such as Chinese Style Fish Broth, Curry Chicken Pot Pie, and a Vegan Roast. They also provide a section known as Sipsology where there is a step-by-step guide to making the perfect cocktails; these include Martell Eggnog, a breakfast martini, or a twisted sidecar. Therefore, if you are trying to find ways to provide the best food and drink at your next dinner party, then Massy Stores will certainly have you covered. They also offer seasonal recipes that would be great for the Winter period, such as Vegan Pumpkin Loaf, and
even oven-roasted Christmas Turkey, making the Christmas day stress just a little bit easier.
Massy Stores also offer a plethora of other products and services, which include toys, puzzles, medical supplies, and even eye tests! This diversification means that they are there to cater for all their customer’s needs. In fact, some are lucky enough to witness live bands and entertainment in their stores, showcasing local talent and really livening up the regular food shop. Furthermore, much of Massy Stores’ produce is expertly transported and distributed by Alstons Marketing Company (AMCO). The partnership between Massy Stores and AMCO is vital to the running of the store, as AMCO is a leading distributor across Trinidad and Tobago. This means that each piece of produce stays fresh and ready for the shelves.
Alongside its loyal customer base, Massy Stores Associate members support the company’s key integrity. This is achieved by working towards a beneficial and ethical relationship with suppliers. Such relationships are maintained through a network of honesty and trust among the store and suppliers. In particular, the company places great trust in their associate members to conduct their
job to the highest standard. It is only when that foundation of trust is strong that Massy Stores can be confident that they are delivering the best products to their customers. Above all else, they promote fairness and truthfulness, which combine to keep the perfect balance between customers and suppliers sufficiently managed.
Alongside its commitment to its customers and suppliers, the company also heralds a ‘Massy in the Community’ initiative. This means that Massy Stores are an integral component in many local community programmes which work to help the environment and the local area. For example, Massy Stores is part of the vital Plastikeep Recovery Programme, a recycling support programme launched by the government of Trinidad and Tobago government in 2010. In September 2016, the Plastikeep campaign was given a new lease of life thanks to the support of the Massy Stores, which were utilised to “address Trinidad’s mounting problem of plastic waste as well as the lack of consciousness in the general population around proper plastic disposal.”
Necessary contributions to the community are also conducted with Massy’s partnership with Nourish TT, an organisation that works hard to alleviate food depletion and hunger in Trinidad and Tobago by reducing the mounting levels of food waste.
Massy also encompasses an environmental consciousness with their own ‘Go To Green Initiative’ and the #LetsAllDoOurPart campaign. This campaign is mainly geared towards the use of reusable bags and the dedication towards reducing carbon footprint, by exclusively offering reusable bags that encourage customers to move away from their dependency on plastic. This initiative has been put into effect in Massy Stores in Barbados, St Lucia, St Vincent, and Guyana, creating a more sustainable region.
A key part of the superstore chain’s success is its role as a subsidiary of the Massy Group. This wider business provides key expertise to the store, having a rich history in the Caribbean basin since 1923. As such, their varied investment portfolio
means that Massy Stores can really reap the benefits of such a bustling business community. More specifically, their large scale means that they can provide superior value to their subsidiaries, creating a direct path for future prosperity.
Massy Stores’ clear ethos of customer satisfaction has carried them a long way, to become a vital retailer in the Trinidad and Tobago region, meeting both the customer’s and supplier’s individual needs to the best of their abilities. Not only this, but they also play an important role in community events and organisations that work towards a brighter future in the sustainability of the Caribbean basin region.