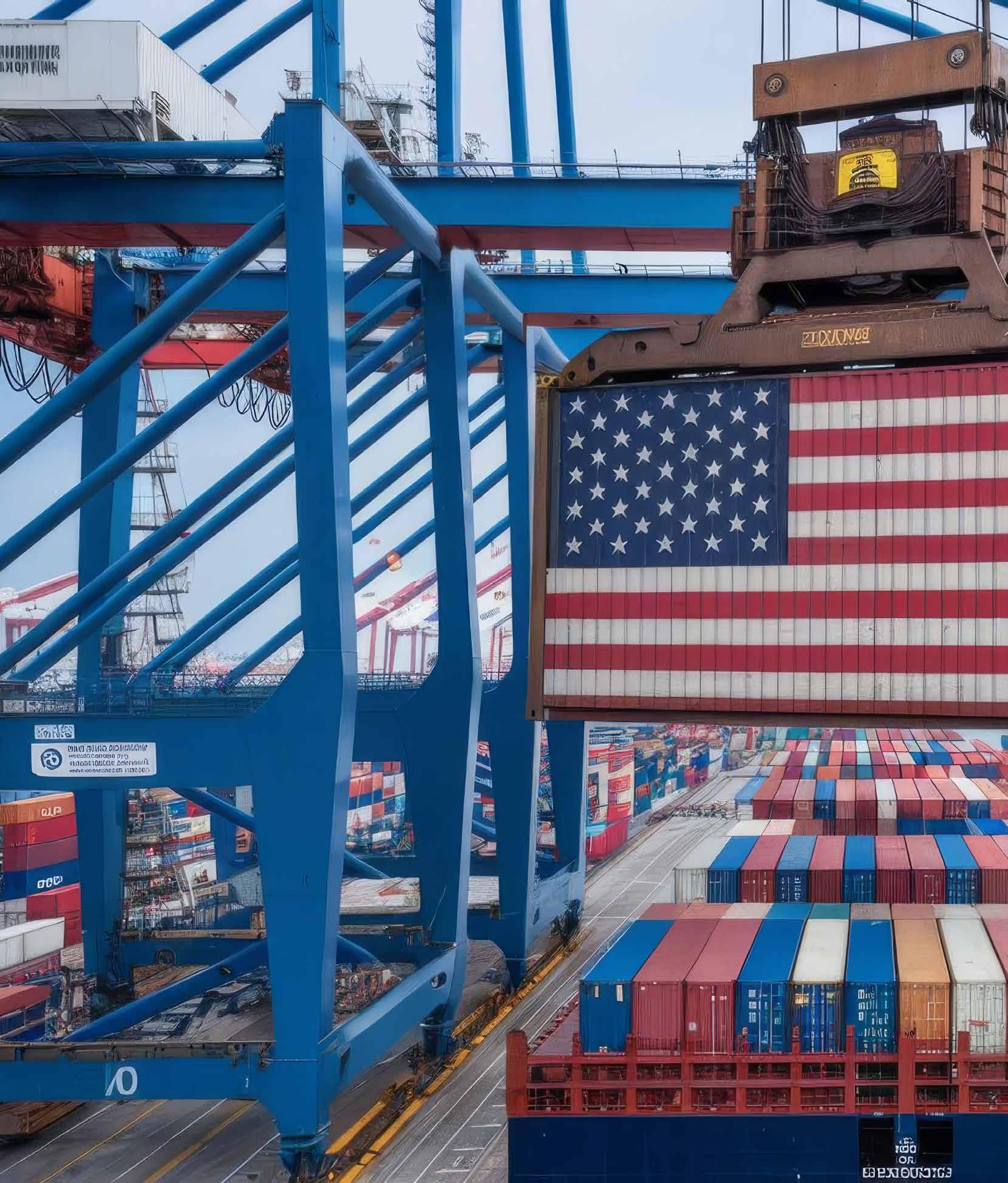
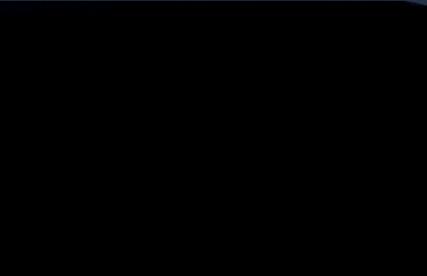

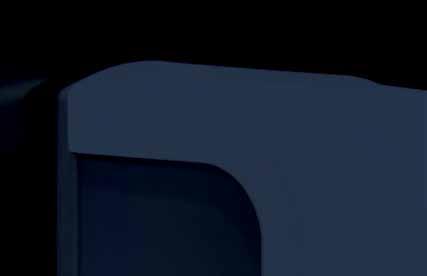
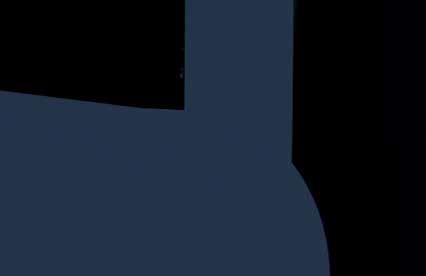
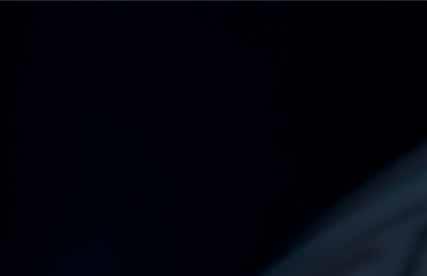
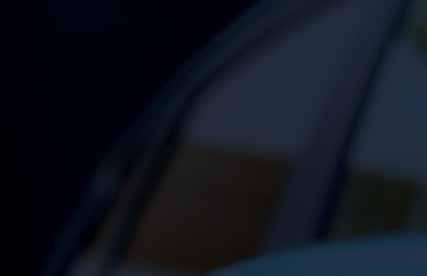
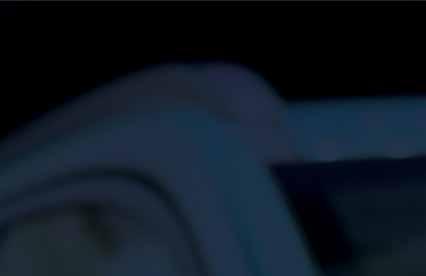
Tel: 604-687-1828
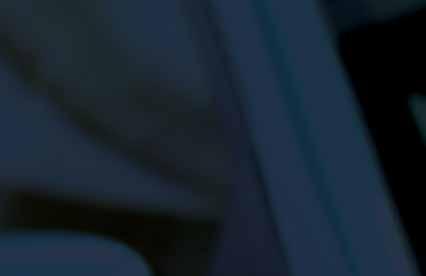
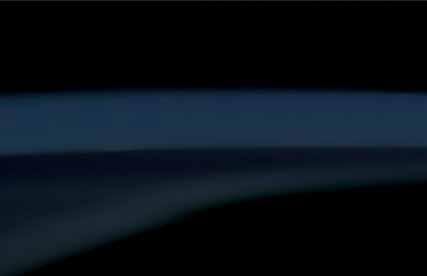

Email: info@argentinalithium.com
Web: argentinalithium.com
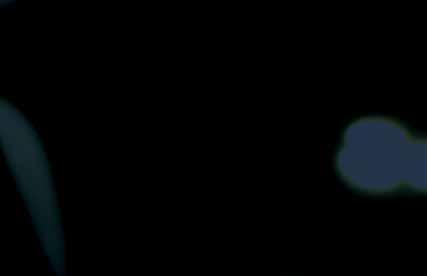
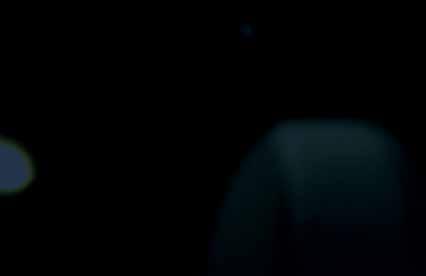

Tel: 604-687-1828
Email: info@argentinalithium.com
Web: argentinalithium.com
Argentina Lithium & Energy Corp is focused on acquiring high quality lithium projects in Argentina and advancing them towards production in order to meet the growing global demand from the battery sector.
The management group has a long history of success in the resource sector of Argentina and a strong track record of government and community relations.
• The Lithium Triangle, including parts of northwestern Argentina, produces about half of the world’s lithium and hosts approximately 60% of the known lithium reserves
• Most lithium in this area is in salt lake (“salar”) brines
• Argentina produces approximately 10% of the world’s lithium, making it one of the top five global producer (2020)
• Government is encouraging renewable energy initiatives
Editor-in-Chief Carley Fallows editor@littlegatepublishing.com
Space Management Emlyn Freeman emlynfreeman@littlegatepublishing.com
Media Coordinator Andrew Williams andrew@littlegatepublishing.com
Lead Designer Alina Sandu Research Kristina Palmer-Folt Editorial Research Amber Winterburn
Corporate Director Anthony Letchumaman anthonyl@littlegatepublishing.com
Founder and CEO Stephen Warman stevewarman@littlegatepublishing.com
For enquiries or subscriptions contact info@littlegatepublishing.com +44 1603 296 100
ENDEAVOUR MAGAZINE is published by Littlegate Publishing LTD which is a Registered Company in the United Kingdom.
Company Registration: 07657236
VAT registration number: 116 776007
343 City Road 60 Thorpe Road London 79 Norwich EC1 V1LR NR1 1RY
Littlegate Publishing Ltd does not accept responsibility for omissions or errors. The points of view expressed in articles by attributing writers and/or in advertisements included in this magazine do not necessarily represent those of the publisher. Any resemblance to real persons, living or dead is purely coincidental. Whilst every effort is made to ensure the accuracy of the information contained within this magazine, no legal responsibility will be accepted by the publishers for loss arising from use of information published. All rights reserved. No part of this publication may be reproduced or stored in a retrievable system or transmitted in any form or by any means without the prior written consent of the publisher.
Copyright© Littlegate Publishing Ltd
The United States is one of the largest hubs of business operations on the globe. With an expansive array of industries across the 50 states, almost every business sector is covered in one way or another. For many companies, expanding their operation into America allows them to access its rich and thriving markets on both a national and international scale. This special USA Edition of Endeavour Magazine focuses on promoting companies which are leading their respective industries, and subsequently adding to the stellar reputation of America.
Despite America being such a big hub of business activity, the country, like the rest of the globe, has dealt with growing concerns regarding population demands, recovering following the global pandemic and making the much-needed shift towards sustainability in recent years. But America takes these challenges in its stride, and we continue to see how companies across the nation are doing their part to meet these demands and continue to strive to be the best.
In Endeavour USA you can expect to see a whole range of industry giants from manufacturing to energy to shipping as much like America’s diverse industries, we are going to cover it all!
As pioneers of solutions across both land and sea, Carver Companies is an umbrella company operation which spans the construction, maritime and aggregates industries. With 12 companies under the Carver Companies brand, it provides superior logistical, cargo handling, construction, management, and materials development services which are united in Carver’s vision to provide these services whilst maintaining its commitment to honesty and integrity every single day.
Carver’s operations can be split into three main divisions: construction, maritime and materials, with plenty of companies spanning these main sectors. However, the first company that kicked off the Carver brand name was Carver Construction which was founded in 1989. The company began with a single crew facilitating digging projects, however today it has expanded into a diversified construction company working across all aspects of site development. This expansion brought together more the 30 years in the industry under the construction company, and today has a combined 130 years of managerial experience across the sector with its employees. Carver Construction now is a regional leader in all aspects of public, commercial and private sector construction across America.
Another key company under Carver’s construction division is Canaday Property Management Services which provides highquality and reliable maintenance services across the greater Capital District. The company has been in operation for over 25 years and works alongside Carver’s construction business to deliver superior services to facilities to keep them looking and functioning at their very best. This service is available through Canaday in over 14 countries and operates more than 20 sweeper trucks across these areas.
Since Carver began, its maritime sector has vastly developed, and now covers a massive section of its overall operations. Under Carver’s Maritime Sector, there are 8 companies spanning from cargo handling and stevedoring to steelworks and industrial park management. A key company is Carver Maritime Charleston which specialises in handling bulk and breakbulk cargo. Carver Maritime Charleston is known internationally for its diverse range of maritime services which serve vessels travelling from local and international markets. Then following the success of Carver Maritime Charleston, Carver Companies began Carver Maritime Manatee in 2018 which delivers the same level of high-quality cargo and maritime services, but in an even more strategic location in the Tampa Bay Channel. The newer facility accommodates larger vessels with a 40ft water draft. Carver Maritime Manatee is also the closest deep-water port near the Panama
We are proud to be associated with Carver Companies, and congratulate them on their achievements, wishing them continued success for the future
Canal, and so it plays an increasingly vital role in connecting America with international shipping lines and markets.
Carver Companies is also the owner of the Port of Coeymans Marine Terminal and the Coeymans Industrial Park. The marine terminal is the central industrial waterfront property for New York and its operations span from handling the modularization of power plants and bridges to the manufacturing and construction of marine projects. Part of the success of the marine terminal comes from it being privatelyowned so throughout its operations the owner and employees can work much closer together to deliver a top-quality service to its customers across shipping, processing, warehousing, and logistical needs. The Coeymans Industrial Park, thus, was established with built-to-suite warehousing and facilities to help with the cargo coming from the Coeyman Marine Terminal. The industrial estate now has easy access to all major access points in the Northeast via river, truck, and rail. Therefore, Coeyman Industrial Park provides a fast, efficient, and effective logistical service to help with the development of the Coeyman Marine Terminal.
The final key division of Carver’s operation is in the materials and aggregates sector where it has Carver Sand & Gravel, and Carver Canada. Carver Sand & Gravel began its operations in 1996 as a
natural transition for the company from product to service alongside its construction business. The company began by purchasing a rock quarry and focused its operations on developing an Aggregate Industrial Business. Today, this business has grown exponentially, and now covers multiple quarry sites, as well as sandpits, and blacktop plants. These sites are supported by the Carver’s fleet of trucks, which work to take the materials from the quarries and towards end markets. Under Carver Sand & Gravel, there are now 10 locations which are serving vital markets on the Atlantic and Gulf coasts of America.
The final, and newest addition to Carver Companies, is Carver Canada a granite quarry and port facility. The company’s operations, located in Bayside in New Brunswick, cover almost 100 acres of waterfront real estate and serve 20 miles of nautical coast along the Atlantic Ocean. Its essential
maritime services continue to spread Carver Companies’ reach further into North America.
As we have seen from the vast array of companies under the Carver Companies umbrella, Carver has a stake in multiple of the largest markets operating across America. All of these companies are utilising the knowledge and expertise of the Carver teams to bring an internationally recognised superior service no matter the operation. With each company, Carver boasts multiple projects which are bolstering many local communities across America, and so with this long-term vision for development across the construction, maritime and aggregate industries, Carver Companies is set on transforming each one respectively to create a unified and internationally recognised reputation for Carver Companies in the process.
The inland waterway systems across the U.S. play a valuable role in generating exports and delivering them as imports across the country via the river system. Therefore, the inland waterways help to develop the economy of America, with 502 million tons of freight worth more than $134.1 billion moving throughout the river systems every year. With a large part of the nation’s economy resting on its waters, the Inland, River, Ports and Terminals (IRPT) works to maintain the economic prosperity of the inland waterways, whilst working to be a force for dynamic growth in America.
Based in the state of Missouri, IRPT is a nonprofit trade association working for the benefit and development of the nation’s inland waterways, ports and terminals. IRPT was charted as a non-profit corporation in 1974 under the laws of Missouri, and so is only a fairly young company compared to the historical role of the waterways systems across the U.S. However, despite its young age, the Association works across the U.S., marine transportation system (MTS) which comprises approximately 12,000 commercially navigable miles of both inland and intra-coastal waterways. Transportation along these waterways is achieved through the use of locks and damns which allow the water levels to be regulated by IRPT to keep vessels moving and cargo reaching its intended markets with reliable speed, safety and efficiency.
A key sector which relies on the inland rivers, ports and terminals is the agriculture sector, which utilises the waterways system to transport its products to and from states spanning the water system. These products can then be transported through the Inland Marine Highways to serve both domestic and international exporting channels. Consequently, the U.S. economy relies on the agricultural sector and its use of inland waterways systems to continue to remain competitive in the global export marketplace. Therefore, in such a vital industry as agriculture, IRPT’s passion for growing the economy through the development of the country’s inland ports is crucial. The association’s passion for building economic growth brings together the multi and intermodal transport links throughout the waterways through the river, rail and road network, which subsequently continues to contribute towards the U.S.’s international export market.
Under IRPT are over 300 members ranging from port professionals to terminal operators, shippers, carriers, firms suppliers and other associations. These members work with IRPT to enhance the waterways systems that span across the nation’s river basins. Members from IRPT span the Missouri River Basin, Great Lakes Basin, Arkansas-White-Red Ouachita River Basin, Pacific Rivers Basin, Upper Mississippi Basin, Ohio River Basin, and Illinois Basin. These basins and subsequent river systems are what divide up the members of the association, as they work to enhance the industry across each region. IRPT encourages cooperation between these members and those who use the waterways for essential cargo transportation. By establishing a strong relationship between these key
stakeholders, IRPT’s members cohesively support the development and reputation of the system as key facilitators for the nation’s economy.
However, IRPT’s network does not just end with those who manage and facilitate the operations across the inland waterways of the United States. Instead, IRPT also meets with and collaborates with governmental agencies to develop the local and national economies of each state along the waterways, whilst enhancing the overall reputation of the country’s vital transportation system. By working with the government, and other stakeholders within the maritime and transportation industry, IRPT provides the essential network for its members to thrive, whilst encouraging both private and public investment to enhance the system which plays such a vital role in the nation’s economy.
Over the last few years, IRPT has been working on a range of initiatives which continued its mission to be a resource of vital change to the inland river, ports and harbours systems. These initiatives are working to bring vital education, funding and personal development to the region. These aim to educate the
Storage and distribution facilities at ports and terminals require the interior to be expansive and dry. Calhoun Super Structure specializes in manufacturing durable fabric structures tailored to suit your needs. With over three decades of expertise, our structures feature high-density polyethylene (HDPE) fabric for ample natural light and hot-dipped galvanized steel frames for superior corrosion resistance. Additionally, our structures offer wide-span interiors up to 250 feet, maximizing storage capacity.
www.calhounsuperstructure.com
general public on the industry, develop those within the industry with the latest expertise and establish a solid foundation for the industry’s future.
With the backing of IRPT, the waterways industry and the Association’s members are continuing to see great economic benefits from the waterways’ reliable and efficient management. This was highlighted in February with the Ports of Indiana which are a member of IRPT seeing 12.6 million tons of cargo travelling through its ports every year. This is the second-highest total tonnage in 63 years, second only to the 14.8 million tons that travelled through its ports in 2018. The prominent role Inidana’s ports play in developing the inland waterways as well as Indiana’s industry, highlights what a valuable role the members of IRPT play in developing the industry across the country.
Indiana also plays a key role in the agriculture industry, with its fertilizer handling seeing an 11% increase last year, alongside the increase in demand for its soy products, minerals, ethanol, DDGs and cement. Therefore, the Ports of Indiana is just one example of a member of IRPT which has
seen a vast increase in product demand, particularly in the agriculture field, which utilises the inland waterways, ports and harbours across the country to deliver significant economic benefits for Indiana year on year.
Overall, IRPT continues to promote the healthy growth, operations and development of the inland river ports, terminals and harbours which are serving the U.S. every single day. The waterway plays such a vital role in advancing the American economy, across a variety of industries and sectors. Every single member under IRPT plays a vital role in achieving the success of the waterways, and alongside the rail and road links, each one is steadily establishing the inland waterway network as one of the most vital assets to domestic shipping for the country.
At the epicentre of Georgia’s commercial hub, the Georgia Ports Authority (GPA) serves as the gateway into America’s markets via vital ports along the Southern Coast of the United States. GPA’s operations aim to enhance the business of the region and strengthen relationships between industries, communities and the people at the heart of the thriving economic hub of Georgia. Connected to key railroads highways and inland ports, GPA makes the perfect partner for logistics and shipping companies hoping to access the thriving economy of the United States.
In operation since 1945, GPA is a key player serving local and international markets with vital trade links and significant investment to bolster the role of Georgia’s ports across the maritime industry. To achieve this role, GPA is committed to providing its customers with efficient, productive port operations which create jobs and support the almost 10 million Georgians that its ports serve.
Supported by a 13-member board of directors, GPA hopes to maintain its competitive edge through the development of leading-edge technology, marketing and operational management to highlight what is needed to create and sustain the growth and security of Georgia’s industry for tomorrow.
Under GPA are two vital ports, one of which is the Port of Savannah, the largest single-terminal container of its kind in North America. The facility has two modern deep-water terminals; the Garden City Terminal and the Ocean Terminal. At the Garden City Terminal, GPA operates one of the largest container handling facilities in the US covering 1200 acres of land and is responsible for moving millions of tons of containerized cargo every year. The terminal is served by 37 weekly container ship services, which are supported by the largest single-operator terminal in the nation. The terminal ensures a more efficient connection between international markets and the US. This terminal is supported by the Ocean Terminal which provides vital cargo services to more diverse vessels and cargo offerings. With roughly 10,000ft of berth space across its 5 berths, the Ocean Terminal is strategically placed to provide flexibility to shipping companies utilising large vessels. Collectively these terminals work to provide flexible, efficient and reliable cargo handling operations for vessels travelling into the Port of Savannah.
The other major port under GPA is the Port of Brunswick which comprises 3 GPA-owned deepwater terminals, of which 2 are directly operated by the Authority. The Port of Brunswick is known for its auto and heavy machinery operations, as it works with more than 12 major manufacturers. These services are primarily operated through the Colonel’s Island Terminal within the port, which is one of the fastest-growing export and import operations in the South Atlantic. The operations at the Colonel’s Island Terminal support the Brunswick Mayor’s Point Terminal which focuses on agricultural products entering Georgia and the US grain belt. The Colonel’s Island Terminal and Brunswick Major’s Point Terminal support a further marine Port terminal operated
by Logistec U.S.A., which specialises in handling breakbulk and bulk commodities.
These vital ports are working to ensure that the flow of goods from the US to international markets, and from international markets to the US are met with efficient, reliable and effective port operations. With specialised and port offerings, GPA is well equipped to manage shipments in the refrigerated cargo, cars, machinery, bulk, breakbulk, project cargo and reefer sectors. However, one of the vital aspects of GPA’s operations is that they connect these maritime operations with efficient and reliable national links through the railroad and highway system. The Garden Terminal at Port of Savannah is the region’s busiest intermodal gateway serving 38 trains per week with import and export cargo. This is facilitated through the Mason
Mega Rail which is the largest intermodal rail facility for a port in North America. This facility and other vital railroad links are therefore essential in the movement of cargo from ports such as Savannah, Mayor’s Point and Colonel’s Island can be moved across the country and onto destinations in the Midwest, Gulf States and California.
The movement of cargo across America is vital to allowing GPA to play a valuable role in the development of Georgia’s economy as a key cargo port across the Southern American Coast. However, when highways and railroads are efficient, GPA also operates a key inland port model which allows the Authority to take containers on shorter distances or strategically place them in intermodal yards within the country. By utilising the inland waterways of America, GPA has been able to extend
its operations across the country and meet the growing cargo needs of its clients. GPA achieves this through the Appalachian Region Port which is a joint effort operation between the State of Georgie, Murray Country, GPA and CSX Transportation. The terminal opened in 2018 and has continued to bring significant economic benefits to Georgie by facilitating a new way for cargo to enter directly into America and across global markets.
As we have seen, GPA is continuing to expand its operations and now has vital ports across the coast of Georgia which are working together with inland ports and logistical infrastructure to ensure that cargo can be freely moved across the country, and onto international markets with ease for growing economic benefits across Georgia. However, as GPA moves towards the future it is set on implementing a range of improvement and development projects to further enhance its infrastructure. These projects include a $1 million infrastructural improvement to the Port of Savannah to link the on-dock rail yards which are served by CSX and Norfolk Southern. This
will expand the port’s reach across Mid-American markets and increase its rail lift capacity to 2 million TEUs from 500,000. On the Ocean Terminal, GPA is increasing the berths and renovating the container yards so it can serve two large container ships simultaneously. The renovation for a 1,325ft berth aims to be completed by January 2025, with the second berth’s completion coming in June 2026, adding 2,650 feet of berth space to the existing port infrastructure.
The developments across GPA’s operations highlight its commitment to ensuring that the ports of Georgia are well-equipped to meet the growing cargo shipment demand from both local and international markets. This increase in demand was highlighted in June when GPA reported it has seen a 22% increase in containers travelling through its ports. These containers provide essential cargo for the retail market and have continued to drive growth across the Port of Savannah.
GPA Board Chairman, Kent Fountain, outlined the vital role of GPA in growing markets with “The
teamwork among our GPA employees and our supply chain partners delivers unmatched service for our customers”. Fountain continues, “In order to press Georgia’s logistical advantage, the Board is investing significantly in new capacity across our docks, container yard, truck gates and rail connections”. Here Fountain highlights how as the company continues to expand, it remains focused on achieving this alongside its valuable supply chain stakeholders, to ensure combined success for all.
Ultimately, GPA is strategically developing the ports across Georgia in order that they can better serve growing international and local markets. With specialised developments to enhance the existing infrastructure of the ports, GPA has expanded its reach across the US to establish Georgia as a pivotal and thriving economic and trade hub within global markets. We look forward to seeing how GPA continues to expand its operations across the US to strengthen industries, empower entrepreneurs and sustain communities for years to come.
Cargo Group greatly appreciates the Georgia Ports Authority work to expand their footprint in the global supply chain. GPA’ s efforts have a direct impact on every industry in the area and Cargo Group is here to help.
The announcement of many southeastern electric vehicle plants and GPA’s ability to service these massive plants has been great for us. Cargo Group specializes in project cargo, flat racks, open tops, and crating. We are able to offer these plants local drayage, transloading, and delivery of products that most warehouses in the area cannot handle due to the size and weight.
Governed by a seven-member board of Harbour Commissioners, the Port of Milwaukee works to promote the shipping and economic development of Wisconsin and the surrounding states thanks to its commitment to stimulating trade on both a local and international scale. Working with its tenants, customers, transportation providers, logistical experts and other supply chain experts, Port of Milwaukee sustains the water-centric city of Milwaukee with a thriving cargo industry, reliable transportation links and the continued development of the leisure sector to see significant economic growth in the region for many years to come.
Located to the west of Lake Michigan, the Port of Milwaukee serves as a hub for the distribution of cargo and materials travelling from the Gulf Coast, and into vital US states such as Illinois, Minnesota, North Dakota, South Dakota, Nebraska, Missouri and Indiana. Thanks to its strategic location just 1,021 nautical miles from the coast of Montreal in Quebec, Canada, the port also serves as a vital link with Canadian markets, including those in Alberta, Saskatchewan and Manitoba. Therefore, in its role to promote the shipping and commerce of the region, the Port of Milwaukee’s operations are influential in both domestic and international markets.
One of the major advantages of the Port’s location is its excellent infrastructure links with the railroad and highway systems. The Port of Milwaukee is served by two Class I railroads; the Union Pacific (UP) Railway and the Canadian Pacific Kansas City (CPKC) Railway. These provide an essential link to other states, and so vessels stopping in Milwaukee can use the port to distribute its products throughout the region and onto the national marketplace. This reliance on the railroad infrastructure has been further developed by the Port of Milwaukee as it also owns and maintains 14 miles of its own rail track, which connects up with the UP and CPKC railways.
In addition to the railroads, the Port of Milwaukee is also directly served by the Federal Interstate Highway System with the I-94/794 which allows trucks to drive directly into the port. This ease of access to the port for the land freight forwarders and trucking companies allows for a quicker turnaround on shipment pick-ups and therefore a speedy delivery to customers. Consequently, through almost 350 miles of highway connection, the Port of Milwaukee provides direct from its ports to crucial trade hubs such as Chicago, Minneapolis, St. Paul., Peoria, Des Moines, Moline, Indianapolis, Madison and Green Bay.
Annually, operations at the Port of Milwaukee see 2.3 million metric tons of cargo handled through the port, which adds roughly $106.5 million in economic activity and $68.1 million in income generated. In addition to these regional economic benefits, the Port of Milwaukee also provides 1,309 jobs
For over a century, the partnership between M.E. Dey & Co. and the Port of Milwaukee has played a significant role in shaping local trade in the community. Our founder, Mae Elizabeth Dey, established an office as a Customhouse Broker in 1907 by request of the district Director of Customs to provide brokerage services at the port. The role of a Milwaukee broker at that time relied heavily on collaboration with the port to facilitate shipments arriving through the Great Lakes. Mae’s relationships with other brokers at major seaports helped connect Wisconsin shippers to the rest of the world. As transportation methods evolved and intermodal became a reality, M.E. Dey and the Port of Milwaukee have maintained a strong partnership in addressing challenges unique to inland ports and securing Wisconsin’s place in the global marketplace.
which continues to bring both personal and local economic benefits for the region.
The history of the port dates back to 1835 when it was known as the Great Lakes port, dealing with commercial cargo vessels serving the struggling new village on the west shores of Lake Michigan. The area provided access to the Milwaukee, Menomonee and Kinnickinic rivers which join Lake Michigan within Milwaukee’s harbour. Therefore, the port slowly began to grow in size as settlers and traders were drawn to the region to take advantage of this vital port at the heart of three rivers and Lake Michigan. Over the years an ‘inner harbour’ was developed, and a comprehensive plan was formulated to build a lakefront area within the outer harbour. This harbour, under municipal control, played a crucial part in the development of the port into the modern port that we see today. Today, the port has built on this success and today is overseen by a board of commissioners who work everyday to strategically promote the port’s operations, and work with those across the industry to devise plans
to help the port maintain its role in the future of America’s economy.
Within the Port of Milwaukee, vessels are offered a range of services to offload and unload cargo, whilst providing 330,00 square feet (sq ft) of covered warehouse space for bulk, steel and general cargo, as well as 30,000 sq ft of climate-controlled space. Key cargo moving through the Port includes a variety of breakbulk and non-containerized cargo including steel, wind turbine components, brewery tanks, mining equipment, yachts, forest products, transformers, farm and construction machinery, manufacturing equipment, bagged materials and other project cargoes. Therefore, as we can see, the Port of Milwaukee is involved in a whole number of sectors from manufacturing, to renewable energy, mining and agriculture, which each play a vital role in enhancing the American economy.
As the Port of Milwaukee moves towards the future it has implemented major developments across the port, including the development of facilities for the agricultural sector. In July 2023, the Port of Milwaukee announced a partnership with the DeLong Co., Inc. to open a $40-million Agricultural Maritime Export Facility on Jones Island. The facility is aimed to handle agricultural commodities and transport them via the Port’s truck, rail and international vessel network. These agricultural commodities include animal feed supplements derived as a byproduct of ethanol due to its high nutrient value.
The facility will allow Wisconsin’s maritime and agricultural economies to play a greater role in international markets. It is hoped that with the successful implementation of the facility, Wisconsin will develop into a vital trade hub for its home-grown soybeans, corn and grains which it can deliver to a wider international audience. The Director of Port of Milwaukee, Jackie Q. Carter, highlighted this in the press release announcing the facility saying that “Port Milwaukee is an integral link in the Wisconsin economy. In this case, we are connecting Wisconsin farmers, growers and producers with new international markets”.
Carter continues, “The combined support from local, state and federal officials affirm the importance of this new asset on Jones Island. The development of this facility at Port Milwaukee is a great addition to the city’s marine commerce, and I’m excited to witness the benefits it will create for our maritime economy”. Carter’s comments highlight the growing hub that the Port of Milwaukee
continues to expand into, and with vital investments with key players in the sector such as agriculture, the Port can continue to provide significant economic benefits for both Milwaukee on a regional level and Wisconsin on a state level.
The continuous development and promotion of activities at the Port of Milwaukee is what has marked it as such a vital port within both domestic and international markets. Dealing with cargo from a vast array of industries, the Port’s services, and then vital logistical links via the railroads and interstate, allows the port to remain a key player within the state-wide economy. With such a reputation for development, whilst meeting the demands of the cargo, tourism, and logistics industries, the Port of Milwaukee has been successful in promoting the shipping and commercial cargo aspects of the region. We look forward to seeing how the port continues to expand and put the development of Wisconsin industries at the forefront of its development in the years to come.
For over 50 years, Universal African Lines Alliance (UAL) has been providing dedicated shipping services to take vital cargo from Europe and the US Gulf Coast to West Africa. This shipping operation has allowed UAL to establish a leading and reliable logistics service which works directly with its customers to make transporting cargo across the Intra-African shipping lines so much easier. A vital aspect of this operation includes serving the Oil and Gas industry, as it works with key clients across these coasts to deliver energy resources backed by UAL’s reliable, flexible and professional service.
UAL provides a complete logistics, shipping, and management service which takes its expertise across the shipping industry and utilises this for its fleet management and cargo shipment solutions. UAL offers services between Europe often departing from Aberdeen or Antwerp, as well as in North America leaving from Houston, and from Mexico via Veracruz. Vessels from these ports then travel towards the West African coast with break-bulk and containers which are crucial for the oil and gas industry. Through UAL’s Inter-African services, it has created a seamless lane for cargo flow between the African ports and Europe/the Americas.
To achieve this seamless flow of cargo, UAL utilises its shipping agents under the Universal African Lines B.V. shipping lines. Agents working across this division of UAL provide modern multipurpose transportation options to its customers supported by its fleet of vessels. These vessels have been designed with innovation and environmental
sustainability in mind, and so UAL operates 5 fuelefficient vessels which aim to reduce the overall emissions of UAL’s operations. These Eco-Trader vessels include UAL Africa, UAL Bodewes, UAL Houston, UAL Texas, and UAL Cologne, and have a specially designed axe bow which helps to provide a more streamlined shape to the vessel and reduce the amount of fuel needed for propulsion.
In May this year, UAL highlighted its continued development of performance optimisation to reduce carbon emissions further across its fleet. The announced developments aim to provide greater efficiency and include the implementation of silicone antifouling paint across its vessels and the utilisation of specialised additives for lube oil. These adjustments hope to make operations more efficient and durable. In addition, UAL has also rolled out new software systems across its vessels to optimise engine load and weather routing. The implementation of these measures highlights UAL’s mission to reduce its carbon footprint and deliver sustainable shipping services which support both its own and its customers’ sustainability goals.
Harald Maas, Managing Direction of UAL, outlined the vital role of the EcoTrader vessels which are “sailing with a 30% lower fuel consumption compared with similar size tonnage. It is no surprise then that our fleet has a CII rating A label already”. Maas continues by highlighting the ‘stringent’ rules of the CII rating, and so sees the developments that UAL are putting in place as a way to retain this status for many years to come.
These vessels play an essential part in UAL’s cargo operations, which have an international reputation as a reliable and fast cargo handler, specialising in finding a shipping solution to meet all its customers’ cargo needs. UAL provides complete cargo handling operations to its customers to see each of their cargo projects through from start to finish. The operations are overseen with UAL’s commitment to planning, coordination and top-quality management systems all supported by clear and honest communication. For cargo, UAL provides complete container services with a fleet of containers including boxes, refers high cubes, open tops and flat racks. These services are
provided throughout UAL’s door-to-door solutions offerings which are predominantly supplied through UAL’s K5 Freeport & Oil Centre which controls all the company’s cargo handling and stacking. This use of K5 stevedores helps UAL to deliver cargo resources efficiently which reduces potential risks associated with cargo handling.
However, a key perk of UAL is that it offers a variety of specialised transport solutions geared specifically to help its clients move cargo which may be hazardous, heavy or require extra measures to be transported safely. For this, UAL utilises its vast network of agents and staff to guarantee its customers a cost and time-efficient delivery of goods, even to the most remote areas. To ensure this is possible, UAL is committed to ensuring clear communication between its operations and destination ports across Europe, the Gulf Coast and Africa. This is essential as UAL relies on its partners and local companies situated across its area of operation, which helps UAL to continue to deliver specialised cargo needs across such a dynamic and developing industry.
In recent news, UAL announced that it was expanding its operations and introducing new shipping services in Guyana. This expansion into
South America highlights a strategic move for UAL which is leveraging its expertise across the shipping industry to provide greater shipping and logistics solutions to a new market for the company. This is particularly exciting as Guyana has seen rapid growth in its energy sector, and so UAL is strategically placed to help deliver these resources to international markets. This development adds to the existing development of UAL across South America including Brazil, and so highlights the vital role UAL continues to play as a leading shipping and logistics company for the Gulf Coast.
Ultimately, UAL is a leading and dedicated shipping service taking hold of shipping along the Gulf Coast, Europe and Africa. With the vital expertise to manage, deliver and develop shipping operations, UAL is committed to finding a shipping solution to ensure that its customers can keep their operations running smoothly. However, as the world moves towards a greener future, UAL has already begun to develop its fleet and shipping logistics to implement more sustainable and renewable designs and features to help protect the planet. We look forward to seeing how UAL continues to expand its role across the shipping industry and increase its logistics offerings across these vital coasts.
MARITIME AGENCY, STEVEDORING, HANDLING & CUSTOMS CLEARANCE
Nouadhibou • Nouakchott • Rosso And all other customs offices in Mauritania
Certified ISO 9001 version 2000 since 2005 & HSE underway
Email: ekhyarhoum.medlemine@snim.com msbeije.samma@snim.com / sidahmed.samma@snim.com
Mobile: +222 4490 3035 / +222 4490 6590 / +222 4490 6591
Website: www.samma.mr
As many of us are aware, having topquality transportation links, reliable roads and accessible bridges is one of the most vital parts of everyday life. Almost every single industry relies on transportation of some kind to ensure that daily operations can function well – this includes everything from public transport to large cargo shipments for a whole range of industries. With such a vast spread across industries which are pivotal in keeping the economy running, the role of keeping the highways, railways, and port links running smoothly cannot be understated. This role is even more vital in Virginia, in the United States of America, where the country’s third largest state-maintained highway system is in place. Therefore, the Virginia Department of Transportation (VDOT) play a vital role in supporting the transportation sector of Virginia, to ensure that it can continue to support the businesses that rely on these vital links every day.
Established in 1906, VDOT is the state highway commission for Virginia which is committed to ensuring that the operation, maintenance and development of Virginia’s state transportation system remains responsive to the needs of the state. Across Virginia, VDOT is the operator across almost 60 miles of highway systems, made up of interstate, primary, secondary and frontage roads. However, its role does not end on the road, instead, it is also responsible for overseeing the management of bridges, signs, signals, and ferry services, as well as commuter car parks and various rest areas across the state. These include more than 11,900 bridges, 7500 culverts, 6 tunnels, 4 tolling facilities, 3 ferry services, 41 rest areas and 100 car parks. Therefore, VDOT’s operations cover every corner of the state, and ensure that whether people are travelling by car, bus or ferry they will be met with the best quality transportation infrastructure possible. One of the current major projects being carried out by VDOT is the development of the I-95 in Fredericksburg, where the commission has 7 projects underway. These include the development of express lanes and access ramps connecting Route 17 and Old Courthouse Road to serve more motorists. This aims to dissipate the existing gridlock that frequents the I-95 and keep people moving more freely throughout the area. In addition to this, VDOT is also currently expanding the capacity
on the I-64 interchange with the goal of reducing congestion across the Southside Hampton roads. The development of this plan underwent thorough research under VDOT to ensure that all improvements would mitigate the existing problems, whilst also working to ensure that the environmental impacts from such a development were monitored.
This attention to detail throughout every project by ensuring that it is thoroughly researched and mapped out ensures that every dollar spent on the development is justifiably utilised for the benefit of the state’s transportation infrastructure. However, VDOT also remains focused on ensuring that safety remains a top priority throughout every development project. This was highlighted with its current Pedestrian and Bicycling Program which aims to provide safer routes for pedestrians and cyclists across the state, particularly in areas surrounding schools across the state. To achieve this VDOT has implemented neighbourhood traffic programs, highway safety corridors, a safety service patrol and a Virginia statewide traffic incident
management system to ensure that pedestrians and cyclists are protected at all times.
To achieve such widespread projects, VDOT relies on businesses across the state with contractors, consultants, and suppliers to help them achieve these vital infrastructural developments. We saw this just last month with the Commonwealth Transportation Board, part of VDOT, awarding a $361 million contract to Branch Civil Inc. for the widening of Interstate 81. The work will see both the north and southbound sides of the interstate widened providing three lanes between exit 143 in Roanoke Country and exit 150 in Botetourt Couty. The project is expected to begin in 2025 and is part of VDOT’s Corridor Improvement Programme (CIP) which aims to improve safety, increase reliability and foster economic growth for the State.
Program Delivery Director for VDOT, Dave Covington, outlined the project as “…the largest contract that we’ve awarded for I-81 to date, and it reinforces our commitment to improving this vital corridor”. As Covington outlines, the I-81 is a vital
link spanning over 300 miles within the state, making it the longest interstate highway within Virginia. Therefore, the interstate provides essential transportation links across the state and allows for people and cargo to be able to travel into and out of the state down this vital network.
VDOT is a vital service which keeps the transportation infrastructure functioning at its best. Covering a vast network of road, rail and even ports, VDOT’s operations play a significant role in almost every industry within the state by providing efficient, reliable and functional transportation networks to get people where they need to be going faster but more importantly safer. With the essential help of local businesses to help with the engineering, procurement and construction of these improvements, VDOT can ensure that no matter where you go in Virginia you have access to one of the best transport networks in the country.
Sitting strategically on the Northern Gulf of Mexico is the Port of Mobile, a deep-water port serving Alabama’s economy through inland waterways, highways and railways. The port’s well-connected nature, and being the only seaport in Alabama, makes it an essential gateway for cargo travelling to and from the state from both local and international markets. The port is overseen by the Alabama Port Authority (APA) which manages all port operations and ensures the seamless movement of cargo from the port and across all 67 counties in the state and beyond into the national American market.
APA’s operations span the 18 diverse cargohandling facilities which are supplied via rail, road and barge to and from the Port of Mobile’s 45-foot deepwater berths. The wellconnected nature of the port means that it is a key player for shipping lines travelling along the Gulf Coast as cargo can seamlessly be moved from the port, into the state and even beyond the state’s border thanks to the vital transportation links at the Port’s disposal. Over the last 24 years, the Port has continued to expand this role, and today, with the help of APA, is now responsible for bringing almost USD 100 billion into Alabama’s economy in a single calendar year through its cargo services and seamless supply chain operations.
As a vital cargo port to the United States, the Port of Mobile deals in all types of cargo from aggregates, automobiles, breakbulk, coal, cold storage, containers, forestry products, general cargo, liquid bulk, metals and project cargo. This
At CSA, we specialize in providing exceptional service for forest products, break bulk, and heavy-lift operations. Our offerings extend to comprehensive terminal operations, including expert loading and unloading of rail cars, trucks, and river barges. In addition, our Container Services division ensures seamless handling and storage of your goods.
Our Services Include: Expert Stevedoring & Break Bulk Handling Efficient Terminal Operations Comprehensive CSA Container Services
Choose CSA for unparalleled reliability and efficiency in all your cargo needs.
Contact Greg Schruff, CSA General Manager M: 228-323-2427 • O: 251-441-0230 • E: greg.schruff@ssamarine.com For more information visit our website www.csaports.com
was formed in 1999 as a joint-venture between The Cooper Group and Stevedoring Services of America (SSA Marine).
ability to handle such a wide variety of cargo types provides APA with a strategic edge over other ports across the Gulf Coast, not only because it has vital rail, road and inland waterway links, but its ability to move cargo throughout supply chains supported by the vast experience in the shipping and maritime sector. Therefore, no matter the industry, businesses rely on the Port of Mobile knowing it is supported by such a reliable operation.
Earlier this year in March, APA announced that the Port of Mobile had the highest container volume on record since the port first opened in 2008, moving 53,608 twenty-equivalent units (TEUs). This figure represents a 27% increase from the same period the previous year, contrary to expectations with the market reportedly softening. This continual increase for the Port signifies how it has expanded its cargo offerings and in return has seen significant growth in its container services year on year. Consequently, APA’s Port of Mobile has remained one of the fastest-growing container terminals in the US, and so solidifies its place in both national and international markets.
However, APA aims to continue to build upon this growth and announced a channel-deepening project that will make the Port of Mobile the deepest container port in the Gulf. The project, which is
currently in operation and aims to be completed next year, will allow much larger vessels to port the container terminal. Allowing larger vessels to port will not only increase the capacity of the port’s operations but will add yet another competitive edge to the Port of Mobiles offerings. The project hopes to attract new shipping lines too large to berth at competing ports along the Gulf Coast, and so should bring significant economic impact to Alabama with an influx of new vessels arriving in the Port of Mobile.
APA also recently announced its partnership with CSX Transportation; a leading American railroad company that specialises in the movement of freight across the eastern side of America. The partnership will support APA’s Intermodal Container Facility (ICTF), which is positioned in Decatur, with rail connectivity supplied by CSX. The partnership will redevelop a portion of CSX’s existing facility which will expedite its ability to serve customers in North Alabama. This partnership is a key milestone for APA as it works to bring even greater rail transport links across the state. Alabama Port Authority Director and CEO highlighted in the announcement of the partnership that, “The expansion not only signifies our confidence in the local economy but also reflects our ongoing efforts to meet the evolving
needs of our customers while contributing to the growth of the communities we serve”. Driscoll’s comments here highlight how APA is constantly working to develop Alabama’s port infrastructure to make its customers’ operations and supply chains flow easier to bring significant economic development to businesses and the state in the process.
Ultimately, Alabama’s Port Authority has taken the strategic location of the Port of Mobile and transformed it into a thriving and competitive hub that benefits from the vital road, barge and railway links across the state of Alabama. With partnerships and investment to develop the port’s facilities, it is clear to see how APA has continued to see yearly growth in its container services which have contributed towards significant economic development for Alabama. As APA look towards the future, it looks to continue expanding its port offerings to make it the port of choice along the Gulf Coast.
Ecolab Specialty Pest Services provides industry-leading expertise to protect your product and maintain a pest-free environment. Our dedicated fumigation team provides services at ports throughout the United States, including Mobile, AL, with 40+ local fumigation centers. When you need container fumigation, ship fumigation, or other pest treatment for import/export, trust Ecolab to protect your commodities and help meet import/export requirements.
• USDA Compliant
• Quarantine/non-quarantine
• Australian Approved: BMSB
• Communication experts: local, USDA, CBP, state agencies, and freight forwarders
• Documentation for local, state, foreign
• Perishables: fruits, flowers, fish, vegetables
• Large and small scale fumigations
• Wood packing material (ISPM 15)
• Experienced; licensed; certified
• Grain, nuts, wood, logs
• In-transit fumigation
Responsible for the North, Central and South American shipping division of the global COSCO SHIPPING Line, COSCO SHIPPING (North America)
In. has long provided a stable and reliable business presence spanning the shipping industry of the US, Canada, Mexico, Panama, and the Caribbean for the last 8 years. Supported by the global network of COSCO SHIPPING Lines, COSCO SHIPPING (North America) provides integrated services across container, transportation, engineering and logistics sectors in North America. As COSCO SHIPPING (North America) moves towards the future, it has set its sights on enhancing its operations with technology to continue to position it as a leading, reliable and efficient shipping provider across the region.
info@register-iri.com www.register-iri.com
COSCO SHIPPING (North America) was established in 2016 through the integration of China Shipping North America Holdings and COSCO America Inc. These two companies formed into COSCO SHIPPING (North America) which today is headquartered in Secaucus New Jersey. The foundations of COSCO SHIPPING (North America) are built on the success of the Chinabased COSCO SHIPPING Corporation Limited, which operates across the globe with a fleet of over 1,300 vessels, with a total container fleet capacity of 3.12 TEUs and 129.40 million TEUs at its container terminals. This makes COSCO SHIPPING CORPORATION the world’s third-largest ocean carrier, and first among container terminal operators in the world. Therefore, in the development of shipping lines across the Americas, COSCO SHIPPING (North America) governs the Americas sector of its global operations through close to 30 subsidiary and joint venture companies operating across the region.
Today, COSCO SHIPPING (North America)’s operations are vast spanning so many aspects of the shipping industry, with multiple intersecting operations that combine to make it a key player in the shipping solutions delivered to customers across the region. A key way that COSCO SHIPPING (North America) achieves this is through its whollyowned subsidiary COSCO SHIPPING Lines North America, which provides end-toend solutions across the shipping industry. These include multi-modal transportation operations and comprehensive logistics which have established its reputation for efficient, reliable and cost-effective container shipping to the US, Canada, Mexico, Panama, and the Caribbean.
Once container vessels reach the shores across North America, COSCO SHIPPING Terminals (North America) provides efficient terminal services to container vessels arriving at ports across America. COSCO SHIPPING Terminals (North America) is a wholly owned subsidiary of COSCO SHIPPING Inc. Pacific Maritime Services, which is a joint venture between COSCO SHIPPING Terminals, Stevedoring Services of America, and CMA Terminal Links. A key terminal for the company in the United States is in Long Beach, California, where it has the Pacific Container Terminal (PCT). The terminal covers 256
acres and operates 14 ZMPC gantry cranes and 39 fully automated truck lanes.
In addition to PCT, COSCO SHIPPING Terminals (North America) also has the West Basin Container Terminal, LLC (WBCT) which is a joint venture between COSCO SHIPPING (North America) Yang Ming Marine Transport Corporation, and Port Americas, Inc. WBCT is a mega ship capable of servicing up to 14,000 twenty equivalent units (TEU) vessels, offering 4 berths, 315 acres of land, 15 gantry cranes, and ondock facility, and on-site full-service maintenance and repair service. Across all of these aspects, WBCT can handle over 1 million lifts per year, ensuring that COSCO SHIPPING Terminals (North America) can continue to service the industry.
As part of one of the largest logistics companies in China, COSCO SHIPPING Logistics (North America) was established as a joint venture between COSCO SHIPPING Logistics in China and COSCO SHIPPING (North America) to provide world-class logistics solutions including warehousing, as well as first and last critical touch point solutions in the Americas. The integrated logistics solutions ensure that customers have to deal with only one company to achieve a seamless supply chain network, meaning that each one can work quickly and reliably, for cost-effective logistics solutions. Across logistics, COSCO SHIPPING (North America) is constantly working to better its service to deliver customised and efficient logistics, forwarding, warehousing,
and distribution management to reduce its clients’ operating costs and maintain its reputation as an all-in-one logistics solution provider.
For Cargo, COSCO SHIPPING (North America) also provides shipping for general, dry and breakbulk cargo. These are made possible through its subsidiaries; COSCO SHIPPING Bulk (North America) and COSCO SHIPPING Heavy Transport (Americas) Inc.
The global COSCO SHIPPING Bulk is one of the largest and leading dry bulk shipping companies in the world, and so with this framework behind it, COSCO SHIPPING Bulk (North America) provides vital dry bulk services to the US, Canada, Mexico, Colombia, Venezuela, Brazil, Uruguay, Argentina, Peru and Chile. Across these countries, the companies prominently moved grains, coal, pet coke, iron ore export, steel, fertiliser and cement import across the region and into international markets. Then, COSCO SHIPPING Heavy Transport (Americas) Inc. specialises in the handling of high-value cargo through its float-on/ float-off, roll-on/roll-off, skid-on/skid-off, and lifton/lift-on operations. The company brings with
it more than 35 years in the shipping industry and is considered to be a leader in the world of semisubmersibles.
Across the entire cargo industry, COSCO SHIPPING (North America) aims to provide the same level of expertise, efficient transportation, and seamless logistics that the global COSCO SHIPPING provides. The Americas division continues to develop the industry, and today is a leading shipping company operating across the region. However, its services extend beyond just cargo and also encompass tinkering, bunkering, equipment leasing and marine engineering services. Across these services, COSCO SHIPPING (North America) offers leading vessel services to keep shipping lines running smoothly, and vessels operating at their very best. This includes companies such as CHIMBUSCO Americas, a joint venture between China Marine Bunker (Petro China) and COSCO SHIPPING (North America) it provides bunkering and petroleum trading services acting as a broker between vessel operators and bunker supply companies. Its operations span the
Build bigger, higher, better premises right here! Whether multiuser building, high-bay warehouse, picking and packing or distribution centre, anything goes. Take advantage of our proximity to Germany’s only deep-water container terminal – with regular liner services and weekly container trains to the hinterland.
DIRECT AND
Since January 2024 Hapag-Lloyd‘s AL4 transatlantic service connects Wilhelmshaven with Mexico and the US-Coast.
Americas and even help handle bunkering inquiries from American customers to ports in China.
As COSCO SHIPPING (North America) moves towards the future, it continues to expand its offerings by carving out strategic partnerships with key shipping companies across North America. A key partnership was announced by the company in August, which saw COSCO SHIPPING and TCL launch a warehousing operation, which would enhance TCL’s supply chain in the North American market, whilst boosting logistics efficiency so that customers can gain access to fast, reliable and high-quality services supported by COSCO SHIPPING (North America)’s expertise in the regional, and global shipping sphere. The partnership marks a significant milestone in the growing relationship between the two shipping and logistics giants and sets both companies up for a new chapter in their strategic operations together.
This focus on expanding operations, to deliver even more integrated shipping and logistics solutions was highlighted in June, when COSCO SHIPPING (North America) launched its cross-border transportation service which would operate between the United States and Mexico. The transportation services would see COSCO SHIPPING (North America)’s
IBT trucking subsidiary, deploy a fleet of 53-foot trailers in Texas, which are specifically engineered for cross-border operations and offer enhanced loading capacity. The trucks are designed to deliver superior transportation efficiency, and so are ideal for making vital trips across the border to deliver seamless transportation services. The partnership will utilise IBT’s network and access the main factory cities in Mexico to deliver these products throughout the US and Canada. This expansion would see COSCO SHIPPING (North America) add yet another vital transportation link to its growing network across the Americas to enhance its customers’ operations and get products to their end marked more cost-effectively.
Ultimately, COSCO SHIPPING (North America) continues to leverage its foundation under one of the largest global shipping companies in the world, to harness the shipping, logistics and transportation potential of North America. With a plethora of subsidiaries under its operations spanning almost every sector of the shipping industry from start to end of supply chains, COSCO SHIPPING (North America) has established itself as a key player in the North American shipping market for many years to come.
As a well-respected industry leader, Titan Cloud today works with some of the largest names across the retail petroleum industry and commercial fleet market. This extensive network, which spans roughly 50% of all U.S. consumer gasoline companies, enables Titan to provide its customers with reliable data and analytics that can help manage risk and fuel profit. Consequently, with an industryleading Fuel Asset Optimization software platform, Titan Cloud Software provides its customers with the tools to effectively manage a range of operations, including environmental compliance risk, reducing maintenance costs, and increasing revenue.
Founded in 2021, Titan Cloud connects people, equipment, and facilities to maximise operational efficiency and minimise the environmental impact of the petroleum industry via fuelling facilities. Titan Cloud achieves this through its industry-leading software solutions which focus on environmental compliance, advanced fuel analytics and facility management. These solutions mean that its customers can effectively manage risk and run efficient, profitable businesses.
Titan Cloud’s software interacts with tanks, dispensers, sensors, and other devices to provide its customers with a comprehensive and bespoke service to effectively monitor their fuelling operations. These systems are designed to work with fuel equipment across all major manufacturers to deliver flexible solutions and premium services to help grow fuelling businesses. One of the key perks of the Titan Cloud software is that it is an all-in-one system that gives clear feedback on operations directly to its customers via Titan Cloud’s secure system.
In convenience store settings Titan Cloud provides a seamless software platform which allows companies to track and monitor everything from the forecourt to the back-office operations. In addition, one of the main focuses of Titan Cloud is its environmental compliance checking software. This helps owners, operators, and regulators streamline the compliance process, cut down on fines, and maintain an efficient system of compliance.
Using intelligent fuel monitoring and insight data systems, Titan Cloud works to make every drop of fuel count. Titan Cloud does this to boost the profits of owners and operators by providing them with round-the-clock access to gauge data for improved flow rates and reduced downtime. These are all essential for fuel at convenience store businesses to ensure that they remain profitable and efficient in delivering refuelling services to customers. In addition, the systems set up by Titan Cloud allow clients to manage vendors, technicians, and work orders remotely more easily. The remote nature means that operations can be tracked for their status to continually streamline the work order of its clients.
Another significant section of Titan Cloud’s operations is to improve the software of fleets. Today, Titan Cloud is the industry’s leading software provider for fleets, which works to simplify environmental compliance for its customers. Titan Cloud works throughout fleets across the world to
make fuel delivery accurate every single time. The company’s systems work to provide visibility into the tank inventory of fleets to provide vital data in realtime. These systems help customers to streamline their fleets, maximise uptime and minimise loss of fuel, as customers can use Titan Cloud’s systems to implement work order flows and help customers follow up with vendors automatically. Consequently, Titan Cloud’s systems are so widely trusted that its fleet software is used in the top 3 car rental fleets in the United States.
For service providers, Titan Cloud provides a built suite of tools and applications that help companies work smarter. A key aspect of this is to provide a comprehensive system where all documents, files and spreadsheets can be accessed in one secure location. Its Advanced Facility Inspection tool allows Titan Cloud customers to digitize all paper files for better efficiency for data inspections. The system then digitally can transpose inspection results onto state forms when required. In addition, customers can set up alarms which allow Titan Cloud to connect directly to equipment and get visibility into their alarms. This allows for remote troubleshooting and gives the customer clear insights into the issues and how to fix them. This comprehensive service allows Titan Cloud to remain the partner of choice for its customers as they can gain a much more indepth view of their equipment and get important data, tracking and e-filling systems to make the whole fuelling process much more seamless.
As we have seen, Titan Cloud is such a vast company that is working to greatly improve the retail petroleum industry through its key Fuel Asset Optimization software platform. However, just last September they acquired Leighton O’Brien, a global fuel analytics software and field technologies provider, which continues to expand Titan Cloud, and solidifies its place as a global leader in the downstream fuel software market. The acquisition hopes to bring the two company’s expertise in environmental compliance site maintenance and fuel management solutions together to expand the global company’s footprint to 6 continents and 43 countries. Furthermore, the acquisition adds 20,000 sites to its fuel monitoring capabilities which means it can provide a faster return on investment and a more streamlined experience to its 85,000+ gasoline solutions worldwide.
CEO and Chief Product Officer of Titan Cloud, David Freese commented in a press release on the acquisition that “Titan Cloud is committed
to connecting people, equipment and facilities to maximise operational efficiency and reduce the environmental impact of every fuelling facility on the planet. With this acquisition, we will accelerate our global growth, extend our product portfolio, and expedite our Fuel Asset Optimization roadmap”. He continues, “Customers will benefit from the industry’s best and most complete Fuel Asset Optimization Platform for operational scale, performance and ROI”. Freese’s comments highlight the expansive role that Titan Cloud continues to play, and this acquisition is just another step in providing the best Fuel Asset Optimization Platform for its customers.
This was echoed by the CEO of Leighton O’Brien, Chris Cooper, “We’re excited to unlock the next stage of growth by leveraging our complementary strengths to deliver the best solutions on the market – creating more value for our customers and opportunities for our employees”. Cooper will join Titan Cloud as the President of International to lead global expansion serving fuel retailers, fleet operators and service providers across
both established and emerging markets. Cooper continues, in the press release that “Titan’s deep product portfolio, robust platform and financial backing, combined with our global footprint, rich wetstock IP, and decades of experience, strengthens our collective position and provide the operating scale needed to serve our growing international customer base”.
Overall, Titan Cloud provides an expansive Fuel Asset Optimization software platform which is designed to make the whole petroleum retail industry seamless. Its crucial software allows its customers to stay connected throughout its operations from its forecourts, head offices and throughout its fuel fleets. The company’s secure and reliable data software allows the company to lead the software industry across this sector with a reputation for expertise and efficiency throughout all of its systems. This is why with key acquisitions, such as Leighton O’Brien we look forward to seeing how Titan Cloud continues to expand its role across international markets as it continues to provide its customers with leading software solutions.
Located in Louisiana, The Port of Lake Charles is a deepwater seaport along the Calcasieu Ship Channel which runs north of the US Gulf Coast. Encompassing roughly 203 square miles of prime channel-side real estate, the port is now the 12th busiest across the nation and annually handles over 56 million tons of breakbulk and bulk cargo travelling along the channel. Therefore, the Port of Lake Charles continues to play a pivotal role in developing the economic landscape of Louisiana through vital cargo shipment and handling facilities.
The Port of Lake Charles is responsible for managing the Calcasieu Ship Channel which runs inland 36 miles and extends out into the Gulf of Mexico a further 32 miles. This Ship Channel drives almost $40 billion of the US Gross Domestic Product (GDP) as it facilitates the shipment of cargo and materials across the Gulf Coast of America. Therefore, the Port of Lake Charles provides essential cargo and landlord services and today is regarded as the 14th busiest port district in the nation as ranked by the US Army Corps of Engineers based on tonnage.
The Port opened in 1926 following its authorization by Act 67 of the Louisiana Legislature just a few years earlier. The official title of the port upon opening is The Lake Charles Harbour and Terminal District, a title the port has kept to this day. However, since its origins the role of the port has continued to expand and now is annually responsible for helping the shipment of vital cargo such as forest material, aluminium ingots, grain, rice, petroleum and petroleum products, frac sand, and heavy lift project cargos. All of these cargos are handled by the port and delivered to the vital land logistical infrastructure across Louisiana.
The Port of Lake Charles is governed by a 7-member board of commissioners who are responsible for overseeing the 2 marine terminals and the 500 acres of property which make up the Lake Charles Harbour and Terminal District. Therefore, serving as the landlord to companies across the port property as well as various other leasable sites near the Calcasieu Ship Channel, the Port of Lake Charles plays an expansive and committed role in ensuring the development of the Louisiana region via the port’s services and land.
A key part of the Port of Lake Charles’ operation is in marine shipping. The port has developed a custom shipping solution which delivers big results for the shipping channel. This includes the City Dock Facility, where the majority of cargo operations take place. It includes 12 deep water berths, where cargo is offloaded or loaded. The berths have a projected depth of 35 feet (ft), with berth 8 having a depth of 40 ft which is used for bulk grain shipments. The facility also includes a 1.6 million square foot of covered storage for warehouse services. The City Dock Facility is located close to essential rail links
making it an ideal location to connect the port to the rest of the state and beyond.
The Port’s Bulk Terminal No.1 provides 7 acres of dry bulk terminals at the Rose Bluff Cutoff along the Calcasieu Ship Channel and can accommodate 2 vessels for loading and unloading. Furthermore, the terminal also operates 2 travelling ship loaders and 2 travelling clamshell bucket unloaders, these include a pet coke ship loader which can facilitate 3,200 short tons per hour, and a calcined coke ship loader with a capacity for 1,200 short tons per hour. Bulk Terminal No.1 provides vessel-tovessel, vessel-to-truck, or vessel-to-open storage solutions. Consequently, the terminal processes more than 3.1 million short tons of dry bulk material annually which includes petroleum coke, calcined coke, barite, rutile, and other dry bulk commodities. In addition, the port is home to Bulk Terminal No.4 which deals in aggregates and is leased to a private company. The Terminal has a 251ft dock face, which can extend to 355 ft with dolphins and has a depth of 35 ft to help move more than 1 million metric tons of imported aggregate annually.
The facilities at the port have been designed to deal in such high quantities of multiple different types of cargo including break-bulk, speciality, heavy-lift, and project cargo from industrial components to forest/lumber products. Whilst the port facilities help to optimise the efficiency of shipment across the terminals, the port is also in a great strategic location just 12 miles upriver from the Gulf Intracoastal Waterway, is close to rail lines (Port Rail) and only 2.5 miles from an interstate. Therefore, the shipment of cargo from the port across land logistical services is made so much easier. Therefore, it is no surprise that the port trades with more than 70 countries around the world thanks to its reputation as the port of choice along the shipping channel.
As the company looks towards the future it is set on developing facilities at the Port of Lake Charles to cope with the $46 billion worth of pre-planned projects set to take place along the ship channel. This will add a further 90.8 million tons of cargo to the existing 56 million tons already travelling through the channel and port every year. The port has already begun inputting new port docks which can accommodate loads of 1500-2000 pounds per square foot, which is almost 4 times the strength of its current berths. This is part of more than $287 million in capital projects which are planned over
the next decade to expand the port’s role and capacity as it continues to be a key player in world trade and speciality cargo.
Another key development for the future is the opening of Cameron LNG (Liquified Natural Gas) Facility which will handle the exports of coke by-products from local petroleum refining, imported lumber, exported bagged and bulk grain, wind energy equipment, project cargo, limestone, rutile, barite, rubber, and chemical products. As this development will take place on the leased land of the Lake Charles Harbour and Terminal District, it will continue to establish the port as a key player for international shipping of cargo.
Overall, the Port of Lake Charles is home to one of the most pivotal ports along the Calcasieu Ship Channel and is responsible for developing a significant part of the Louisiana economy thanks to cargo shipment both into and out of the country. With key developments set to take place over the coming years to meet the growing demand for shipments along the Calcasieu Ship Channel, we look forward to seeing how the port’s facilities continue to expand and meet the needs of the future as a leading port and cargo terminal.
Located on the Mississippi River, the Port of Greater Baton Rouge is strategically located to provide crucial access to the nation’s heartland via nearly 15,000 miles of inland water transportation, as well as to the Gulf of Mexico and ocean trade lanes to Latin America and beyond. Consequently, the port is an integral part of the national maritime industry and a significant player in developing Louisiana’s economy. The Port of Greater Baton Rouge now is one of the top ports in the US dealing with a significant tonnage of cargo every single day.
Before 1920, Greater Baton Rouge was just a docking facility, which consisted of wooden wharves along the Mississippi River Edge but had no levee system. However, as the river levels were relatively stable, the port made docking at the port simple and efficient for mooring. Therefore in 1926, the Greater Baton Rouge Municipal Dock was completed on the east bank of the Mississippi bringing greater cargo docking possibilities to the region, which in 1952 saw new legislation introduced to establish the Greater Baton Rouge Port Commission. Then just 2 years later construction began on a general cargo dock, grain elevator, and a grain dock on the west bank of the river allowing the port to begin to play a vital role in Louisiana’s growing economy.
Today, the Port of Greater Baton Rouge provides a wide range of products and services including the handling of forest, agricultural, steel, pipe, and petroleum products, as well as ores and coals and bulk and liquid bulk chemicals. Due to the port’s diverse shipping options via its vast network of water and road links, the port has established itself a reputation for outstanding service. This service is backed by the Port’s highly experienced business development staff which are on hand to transfer products and various types of cargo in a timely, safe, and secure way. The Port of Greater Baton Rouge’s commitment to excellence for its customers has earned the port a reputation for productivity and damage-free cargo handling that you can rely on.
Facilities at the port include deepwater docks, export grain elevators, liquid bulk terminals, midstream buoys and anchorage, warehousing, inland river terminal and a range of different facilities to make sure the port efficiently moves cargo to benefit the local region and continues to develop Louisiana for continued future development. Currently, the Port has 4 deep-water draft ships which can berth and unload/load at the same time. However, the Port has recently undertaken a $15 million rehabilitation project which aims to rehabilitate an existing fifth berth at the northernmost end of existing deepwater docks. The project has been designed, approved, and partially funded. It is the first major berth expansion since the completion of the Port’s doc extension in 1986.
Louisiana’s logistical advantages have placed it at the epicenter of world trade for centuries, providing access to global markets, international shipping lanes and major ports through 15,000 miles of the Mississippi River. A key anchor is the Port of Baton Rouge, boasting a 45-foot deepwater channel and direct connectivity to ship, barge, truck and rail systems
The port today is known for its growth and expansion, which has seen its jurisdiction expand to include Pointe Coupee Parish which includes the Port of Pointe Coupee in Lensworth, as well as the ‘old ferry landing’ on the west side of the Mississippi River. The Port of Greater Baton Rouge has seen in recent years American Queen Voyages making regular stops at the landing, which takes passengers on excursions around the parish and across the river to St. Francisville and West Feliciana Paris. Furthermore, American Cruise Lines and Viking River Cruises began departing from the port in 2022. The port was attractive to these companies due to its commitment to upgrading and improving the old ferry landing to make it better for passenger traffic and the coach buses which transport visitors to places of interest in nearby towns. The profitability of the port has seen a significant boost in tourism across Greater Baton Rouge.
The port is looking to expand its facilities to enable port partners to increase capabilities and create more economic opportunities. The port is currently undertaking plans to rehabilitate and expand its northernmost deepwater berth in Mississippi with the aim of increasing its ship size capabilities and making docking into the existing deepwater berth safer. Currently, berths at the port have been experiencing increased congestion with the increasing demand for cargo across Mississippi. Therefore, additional infrastructure is needed to service the growing demand for liquid bulk commodities. Funding for the dock facilities expansion is in place and is permitted with work being completed and hopes to increase container handling. However, The Port is requesting more funding from the US Department of Transportation’s Maritime Administration (MARAD) as well as other funding sources which hopes to see more efficient affixed container handling pieces of equipment to increase port container handling facilities of the Gulf Intracoastal Waterway.
Looking towards the future, an exciting development for the Port of Greater Baton Rouge is Grön Fuels, a Fidelis company, which announced on Earth Day 2021 the development of a $9.2 billion carbon-negative renewable fuel complex at the port. The facility will be designed to be
the world’s largest sustainable aviation fuel and renewable diesel production facility. Construction commenced in 2022 and is hoped to achieve full commercial operation by 2025. Renewable energy for the port is a key development, and so Grön Fuels will be using proven and bankable technologies from renowned global technology providers to manufacture sustainable aviation fuels (SAF) and renewable diesel (RD). The facility is also planned to produce other renewable materials, as well as green hydrogen.
The project will be completed in conjunction with its on-site 200MegaWatt (MW) renewable carbonnegative electric power plants will produce carbonnegative SAF and RD. The entire system at the Port is the flagship Fidelis Climate GigaSystem™ and is expected to mitigate over one gigaton of carbon dioxide from facilities located at the Port over the production facility’s lifetime. Construction at Grön Fuels LLC is anticipated to begin in 2023.
As we have seen the Port of Greater Baton Rouge is an expansive operation that has seen such a strategically located port continue to expand its
operations to develop towards a more sustainable future that is critically concerned with ensuring that the importing and transporting of cargo across the port is consistent. The port is continually committed to refurbishing its existing infrastructure and developing further berths to be able to continue to meet the demands of the future. Consequently, the Port of Greater Baton Rouge continues to play a significant role in developing Mississippi and the port towards continued economic success.
The Exmar Group, headquartered in Antwerp, is a diversified and independent shipping group which serves the international gas and oil industry. Within the expansive Exmar Group is Exmar Offshore Company (EOC) which is an innovative owner, offshore designer and engineer which serves providers across the global energy industry. The EOC division is headquartered in Houston, Texas and provides multi-disciplinary maritime and offshore solutions which it designs and delivers to achieve sustainable and efficient value to its customers worldwide.
Whilst the global Exmar Group focuses on shipping needs, the EOC is a global maritime company which delivers tailormade technical and crewing services to the maritime and offshore industries. EOC focuses its operations on the building, owning, leasing, managing, and operating of high-specification assets. EOC designs and develops solutions for its customers across the oil and gas industry for production, storage, supply, and transportation needs. Having built its operations on the back of decades of offshore experience, EOC has moved from exploration to production across the development spectrum to begin facilitating the vastly expanding need for energy worldwide. Therefore, EOC is an expert in designing the best offshore solutions for its customers’ needs. What sets EOC apart from peer companies is its focus on innovation, and it believes that innovation is the key to providing its customers with solutions that have a competitive edge.
EOC provides a range of floating production solutions which they have developed for unique commercial and technical solutions. The in-house expertise of its vast array of engineering staff means customers can be sure that solutions provided are made with every detail considered, and for the most efficient timeline, all whilst remaining cost-effective and practical. The engineers provide complete engineering, project management, construction, supervision, and field management across its renowned solution offerings.
One of the most crucial developments by EOC is its OPTI® Production Semisubmersibles which are a hull and deck truss form which aids in the execution of projects and is designed to lower life cycle costs. The OPTI® proprietary hull form and single deck truss feature combine to provide superior hydrodynamic performance with payload weight efficiency, ease of construction and a simple integrated, rapid, and flexible project execution. The main reason the OPTI® system is so innovative is that it provides a complete solution that is proven, scalable, flexible, and repeatable within the industry’s leading cost, schedule, and mission performance. Consequently,
EOC provides complete strategic solutions which are carefully engineered to suit the commercial and operational tools to reduce project cycle times with uncompromising safety and quality performance.
The OPTI® submersibles are made with innovative features to withstand the most extreme of weather circumstances. These solutions are built with multi-side columns which are designed to reduce drag forces and lead to lower mooring forces vortex-induce motions (VIM). Consequently, the proprietary ring pontoon shape reduces the heave motions. However, the reduced motion structure still maintains a simple construction design as all solutions are made and designed by EOC to be made with minimal structural shapes, thickness and steel materials grades which have all been expertly chosen to reduce fabrication costs and increase shipyard efficiency.
The truss structure of EOM’s OPTI® Submersibles has a flat upper desk which allows for modular equipment skids to be integrated near-ground level
in a flexible sequence. All of the solutions designed by EOM are scalable, flexible, and repeatable so that the hull forms and deck truss can be best suited for a broad selection of global fabricator capabilities. Structurally the columns, pontons and nodes are all repeatable and allow for easy repetition across projects for easy scalability. Therefore, EOC’s design allows them to facilitate energy solutions for the future to easily scale and reshape the existing models to be scaled up or scaled down to suit its customers’ needs.
Some examples of EOC’s include its OPTI-Micro™ which was introduced in 2016 for limited recoverable reserves or as an early production system. It offers flexible development solutions with upside production potential. This system has a 40,000 barrels per day (bpd) production capacity which offers a strategic alternative to a complicated, expensive tie-back and at a lower price point than its larger conventional counterpart hubs. The OPTI-EX® is the industry’s first speculative build semisubmersible floating production system, and now a decade after this system was first established, it has a capacity of 60,000 bpd a day. Additionally, the OPTI-1100™ has up to 100,000 bpd and is now an industry-leading and award-winning Delta House facility which is operated by LLOG Exploration.
As EOC looks towards the future they have developed a hub to deal with the increasing energy needs of the world. The OPTI-1600™ provides rates of 120,000 bpd, and the space and load capacity for water flood, gas injection and subsea boosting equipment. This design features all the same technologies and features of previous and original models making it cost effective, but with a much larger service capacity to meet the growing energy needs of the future.
However, for EOC floating production storage and offloading (FPSO) facilities are still the main development solution across the world where local markets, export pipelines and facility infrastructure either do not exist or cannot deal with an increasing demand for energy needs. Therefore, companies such as EOC are providing dedicated FPSO facilities including some notable ones including the FPSO Farwah and the FSO Luxembourg which shows the company’s adaptability across the globe for all its customer’s FPSO needs.
Additionally, EOC is recognised as a specialist and reliable partner in the market of accommodation barges for which it owns, operates, crews, refurbishes and maintains a fleet of barges for international and national oil companies. Under EOC is the Wariboko, which was built in 2010 and later purchased by Exmar, and accommodates 300 POB with a dynamic gangway, 900km2 of clear deck and a 68 metric tonne (mt) crane.
The Nunce is also a barge under EOC featuring its proprietary design which was delivered in 2019. The barge is able to accommodate 450 POB and can be quickly converted to a DP unit. It has a 900m2 clear deck and a 25mt crane. However, the final accommodation barge of EOC is a new build which is being developed to accommodate 500POB using its in-house design systems to innovatively make a barge for the future. It is hoped that through this barge it can meet the offshore project challenges of the future with its proprietary designs for both barge and semisubmersible efficiency.
Overall, Exmar Offshore Company are leading the offshore solutions industry with its innovative designs which are able to bring a range of monohull, barge and semi-submersible systems for use in floating production, mobile offshore drilling and a range of other vessel needs. Through its development over the years, we have seen how its renowned OPTI® systems have forged a new path towards the future of energy solutions. However, what has remained the same for EOC throughout every offshore solution is its commitment to facilitating every stage of its renowned engineering and design process. Therefore, EOC’s customers can be sure that every detail of its solutions offerings will be delivered using top-quality systems, all whilst supported by an expansive team of experts.
As a provider of exceptional quality flour and plant-based ingredients, Bay State Milling has developed its network of suppliers to facilitate every step of the process from grain to end packaged products. Supplying their high-quality ingredients to retail and wholesale bakeries, food service operators, distributors and food manufacturers, Bay State Milling has a wide reach across the industry in the United States with an expansive and reliable nationwide distribution network. However, the basis of Bay State Milling’s operations is family, as it has been passed down over the last 175 years through five generations of one family, who have remained committed to providing access to healthy, delicious, responsibly sourced and produced food ingredients.
Established in 1899, Bay State Milling started as a company that predominantly milled wheat flour for bread and snacks. However, over the years the way people eat has changed; not only are allergens such as gluten catered for in a more diverse way, but people are more conscious of the ingredients used in products for health reasons. Therefore, Bay State Milling has adapted over the years to diversify its product offerings in line with consumer demands. Now they produce wheat and rye flour, oats, seeds, spices, and unique varietals all with varying options including gluten-free, high protein or high-fibre diets. As the food system and the way we eat continues to change, Bay State Milling is prepared to evolve to always stay ahead of its customers’ needs to provide a variety of options, which taste great and are affordable. All whilst maintaining the trust that the company has built with customers and across its supply chains for generations.
For Bay State Milling a trusted and reliable supply chain is crucial, as the company works across every aspect of their ingredients’ lives from seed to end products. All products are responsibly sourced from its dedicated supplier and grower partners, which are expertly processed and milled to meet the exact specifications for its product uses. Consequently, the company has an expansive network of research and development teams, commercial teams, as well as state-of-the-art milling and production facilities across North America and Canada.
Bay State Milling has strategically placed its milling and production facilities across North America to ensure that it minimises freight costs to deliver competitive ingredients that seamlessly integrate into its customers’ operations. Bay State Milling operations have therefore perfectly positioned themselves to supply expansive markets geographically, whilst also ensuring that the products it does supply are constantly evolving with consumer needs.
A key focus for Bay State Milling is innovation, as the company has established a dedicated team of food and cereal scientists, culinary experts, nutritionists, and sensory experts to ensure its products are always high in quality. These teams are working to improve the quality of all ingredients produced and milled across the company’s network.
Semear Group is a family farming production company of 3 generations that is totally involved with the delivery of the best quality products. Our experience is focused on Chia and Quinoa.
We are a company with a lot of experience in the international market. Located in Santa Cruz de la Sierra, Bolivia economic and industrial center of the country. Our production has a strict quality control plan in all its stages, from sowing to the time of export. Semear sows, harvests, processes and exports organic chia seeds of the highest quality to the world.
Our mission is to produce food in strict compliance with the quality standards agreed with the client in the committed deadlines, but also in a responsible way with the Society and the Environment, watching over the conditions of our collaborators, assuring sustainable markets for our associated products.
This has provided the company with a proven track record of formulating top-quality products and commercialized ingredients that are used in many of today’s leading brands. A lot of this work is being facilitated in the company’s Rothwell Grain Essentials Center to develop its ingredients, whilst working directly with its partners and customers.
By working with its customers, the company can use its real-time feedback to continue to develop its ingredients and keep tabs on the changing eating habits across the nation to better supply them for the future through this direct communication. The Rothwell Grain Essential Center takes product development from concept to commercialisation, whilst ensuring that throughout every stage of a product’s life from seed to end product is critically managed with the most advanced technology and agricultural knowledge. This is what ensures the trusted quality throughout its production that Bay State Milling is known for.
One product development that sets Bay State Milling ahead of its competitors is its HealthSense® line which has disrupted the market to allow consumers to enjoy their favourite foods such as pizza, pasta and bread whilst also meeting their dietary requirements for healthy fibre. The HealthSense® Wheat Flour allows people to be more engaged with their food, to know what is included and where it came from. The range is aimed to help the consumer to feel more in control of their food. Consequently, the Bay State Milling Company announced the launch of Wingold® Wellness multipurpose flour in May 2023, which is marketed as a better-for-you blend with three times the guthealthy fibre of traditional refined wheat flour. The new blend has the same taste, functionality, and quality that customers know and love from Bay State Milling, but it has been innovatively developed to provide a more gut-friendly option. This announcement highlights the company’s commitment to evolving in line with consumer preferences, to ensure it remains ahead of the game across the industry.
Overall, Bay State Milling provides its diverse and growing array of customers with innovative,
distinctive, and high-quality grain-based ingredients. These ingredients have established the company as changing the game for the grainbased ingredient industry as they are remaining in touch with its consumer base to ensure that its products are serving both their needs and dietary requirements. However, it is the familyowned quality that really makes this company stand out as throughout its operation the company’s sense of care and ownership is the foundation for every product’s expansion and development. Consequently, Bay State Milling continues to evolve with the changing tide of customers’ food requirements, and so remains ahead of the industry by actively working throughout supply chains for the benefit of its customers.
As an expert in the oil industry, Renkert Oil attracts the most capable industry veterans who focus their expertise on solving customers’ technical and logistical problems. Renkert Oil also provides guidance for their clients on the oil to choose that will best suit their needs. Renkert has the capability to meet nearly any specification, regardless of how niche it may be. By supplying their customers with advice, security, and the right products – they are a vital partner in each customer’s success.
As an established oil distributor since 1987, Renkert’s customers depend on them to provide industry-leading customer service. With supply terminals across the USA and in Europe, they serve an array of international partners, providing consistency on a global scale. Alongside the distribution of speciality oils from world-leading producers, Renkert produces its own food-grade oil products to match international demands. This is exemplified by the awarding of the global Quality Management certification, SQF, which highlights their dedicated quality focus.
Process oils are used either to aid processing, improve safety or improve the quality of finished Serving
goods. Renkert Oil serves the rubber and ThermoPlastic Elastomer (TPE) industry with extender oils which improve the softness and pliability as well as the cost of these products.
Mineral oils are key to lubrication and higher quality oils have added benefits. For example, Renkert supply Nexbase synthetics that improve fuel economy in passenger cars as well as heavier-duty engines. Furthermore, their advancements in Isoparafins have a reduced environmental impact, due to their biodegradable quality.
As part of their innovation strategy, Renkert developed the capability to produce very high purity, crystal-clear mineral oils. In fact, the US government’s FermiLab chose Renkert Oil as the highest quality in the sector and won the company a large contract to support their NOvA physics experiment, which used Renkert oil to detect Neutrinos. Based on that project, they have grown to be the third-largest Food Grade Mineral Oil producer in North America. Much of their USP quality mineral oils are used in sensitive Food Processing, Cosmetics, Medical, Agriculture, and many more applications.
Renkert Oil has become one of the biggest white mineral oil suppliers, producing specially selected products to meet a wide range of industry needs. Many of their customers want the assurance of FDA approved, food grade quality of their Renoil colourless and odourless mineral oils. Customers are therefore guaranteed the most state-of-theart products that are internationally recognised for their quality.
Renkert Oil’s broad client base reflects the innovative solutions that Renkert provides, as they are not just a distributor of process oils, but also invest in industry experts, inventory, and the facilities to make custom products. The close industry relationships that Renkert has acquired over the past 35 years ensure supply security for their customers. The technical expertise that Renkert provides simplifies product development. Whether it be distribution, consulting, or production, they are always on hand to support specialised projects for their customers and international clientele.
Receiving a diagnosis can often be a daunting experience, making the option of a second opinion vital in the early stages of diagnosis, as it helps patients gain a greater understanding of their health. At MediGuide International, members have access to world-leading healthcare consultants who can provide top-notch second opinions and care, whilst avoiding the hassle of waiting lists or geographical limitations. By providing services across 152 countries, MediGuide has the most knowledgeable health experts on hand quickly and effectively, helping millions of people across the world.
MediGuide understands that the value of a second opinion is unmeasurable. As such, they provide easy access to the world’s leading healthcare professionals from the top medical centres around the world. Such a lifechanging service can be accessed with a few clicks of a button, allowing patients to easily obtain a remote medical second opinion. In 2018 alone, out of 97% of their evaluated cases, 5% of these cases resulted in an altering of diagnosis, whilst in 84% of cases, there was a turnaround in treatment. Such statistics are telling of the unimaginable service that they provide, that is unmatched by the world’s leading healthcare institutions.
MediGuide was first founded in Delaware, the US, in 1999. Since its inception, MediGuide has amassed an active membership of 10 million that stem across jurisdictions in 5 continents. Evidently, from the beginning of the millennium, it has endeavoured to build a system of trust with its members, so they have full faith in the knowledge and solutions of diagnosis.
MediGuide offers a triad of excellent healthcare services. Alongside expert second opinions, patients can also gain optimal access to digital healthcare services and an international medical concierge facility. As aforementioned, receiving a remote second opinion means that you can access healthcare professionals from across the world, which would otherwise be unobtainable. Accessing a second medical opinion is very quick and efficient, as the service is proactive in facilitating a full review of your diagnosis and treatment plan in just 10 days. Patients can also rest assured that the diagnosis and proposed treatment is based on the latest clinical research from top medical professionals. All of these fantastic services can be accessed via a simple phone call, opening a world of triumphant healthcare.
The notion of unlimited and completely accessible healthcare is a big part of why MediGuide is so successful. As such, their unmatched digital health services are really something to marvel. In the healthcare field, a digital platform to access records is not unique. However, MediGuide go even further than this by offering a comprehensive Preventative Health Program and Telehealth service to ensure that health conditions are effectively managed. The Preventative Health Program is a
great option for those that are searching for a routine appointment, whilst being put in control of their healthcare. This demonstrates how MediGuide is there for their patients, even when they are not in urgent situations. Telehealth is alternative form of advice for those who wish to receive quick and easy face-to-face help, so you have medical advice on demand. Thus, rather than joining an endless waiting list for a doctor, MediGuide’s Digital Healthcare mean that you can talk to a doctor anytime, anywhere.
Just in case you do need to travel to receive renowned treatment, MediGuide is also happy to cover the cost of travelling to one of the stateof-the-art medical centres. Known as LifeLink, it ensures that members receive the best treatment, regardless of their geographical location. Their hospitality extends further as members can receive business class flights, accommodation for the patient and a plus one, as well as other related costs covered up to $1 million. A big plus is provided by offering alternatives to staggering insurance costs that are usually associated with healthcare.
Alternatively, MediGuide also provides a Navigator package, which perseveres to make sure that the patient’s journey is as hassle-free as possible, utilising a re-pricing and cost containment blueprint
Finally, to round off a thorough diagnosis and treatment plan, a care manager is available to guide you through the next steps of your treatment. This means that they provide specialised help through your medical needs. And yet their help doesn’t stop there! MediGuide will organise a specialist doctor at your local medical clinic, and oversee the entire process, from pharmacy medication to insurance. Therefore, patients can relax knowing that MediGuide will be with them every step of the way.
MediGuide has been able to achieve such medical prestige due to a combination of dedicated clinical practitioners that guarantee the 24/7 supply and demand of medical care across the world. So much so, that it is not unheard of for nurses and doctors to take a call in the middle night if urgent care required it. And yet, such relentless work does not go unrecognised. As part of an appraisal system,
Providers, and state-of-the-art technology through expert systems, medical rules and digital platforms. The company delivers first class service that maximizes operational efficiency, cost containment, transparency and profitability. Moreover, Best Assistance serves various National & International clients within the region: insurance companies, TPAs, self-funded schemes, Mutual funds, Orders, Syndicates.
(Health Insurance Management System) that aligns with the company’s and clients’ business strategy. HIMS® consists of structured Modules & functionalities covering TPA & Insurance cycle and needs.
Lebanon - France - UAE - KSA - QatarEgypt - Türkiye - Nigeria - Iraq - S. Korea
Hubbell Incorporated leads the way in the manufacturing of utility and electrical solutions by enabling its customers to operate critical infrastructure safely, reliably, and efficiently. With a focus on delivering high-quality and dependable products, Hubbell Incorporated positions itself as an ethically and sustainably conscious company, even being recognised as one of the 2023 World’s Most Ethical Companies by Ethisphere. Therefore, it’s no question why Hubbell Incorporated is such a crucial player in both the world of electrical and utility manufacturing and in the wider sphere of ethical business practice.
Hubbell Incorporated began by developing equipment and tooling to serve the growing demands for new assembly and manufacturing machinery as part of the industrial revolution. This core value of development has remained with the company, and as of 2022 boasts US$4.9 billion in revenue. The foundation of Hubbell Incorporated’s success is to serve customers, whilst operating with discipline to growing the enterprise as a company that is respected by customers and provides a place for employee development. The company has positioned itself, since its beginning, as a global player in the world of electrical and utility manufacturing; now with a collection of 75 respected and well-known brands in its portfolio, all managed and processed by its almost 19,000 employees across the globe.
As a company, Hubbell Incorporated aims to provide solutions that help its customers to succeed, including solutions in energy saving, safety and security, extreme environments, ground bonding, wire and management, and foundation repair. As part of their operations, they work in a great variety of markets, therefore the recognition as one of the leading companies for ethical practices exemplifies the excellence that Hubbell Incorporated has instilled throughout all its operations since its origins.
A central philosophy of Hubbell Incorporated is ethics and sustainability, and as previously mentioned they have been named, for the third time, as one of 2023 World’s Most Ethical Companies. This title was given by Ethisphere, who conduct a review of companies internationally asking questions about their practices. This includes more than 200 questions on culture, environmental and social practices, ethics and compliance activities, governance, diversification, and initiatives that support a strong value chain. Consequently, Hubbell Incorporated stands out as one of 135 companies internationally that was given this title and exemplifies the practices towards ethical and sustainable development in the business.
Hubbell Incorporated is keenly aware of its responsibility to manage the environmental, social and governance (ESG) factors that are impacted by its operations. They believe that sustainability is a meaningful driver for business resilience and growth. Therefore, their sustainable efforts reflect
their commitment to energizing and empowering the communities that support the work they are doing. Since its founding 130 years ago, there has always been an emphasis on long-term performance and impact on the environment which has guided the company and its decision-making. To ensure the company is sticking to and meeting its aims in terms of sustainability, they conduct regular ESG materiality assessments.
Hubbell Incorporated has been smashing its sustainability targets. Two of their initial key sustainability targets were to reduce their absolute Scope 1 and 2 greenhouse gas emissions and absolute water consumption by 10% by 2025, when compared to the base level set in 2019. However, as of 2021 they have already achieved both targets and continue to work towards reducing water consumption and greenhouse gas emission. Therefore, as part of their 2023 sustainability report, Hubbell Incorporated has committed to reducing Scope 1 and 2 greenhouse gas emissions by 30% by 2030. Also, they are aiming to reduce water usage by 25% and reduce hazardous waste by 30% by 2030. As we can see, Hubbell Incorporated is always trying to improve and better its goals to drive its sustainability performance.
Furthermore, the company also achieved the title of one of the most ethical companies in the world for 2023 due to its dedication to social responsibility. As a company, they strive to provide
a positive and inclusive work environment by continually fostering a culture that supports its employees’ health, safety, diversity, and well-being. However, their work does not end at the edges of the business, instead, they have expanded their commitments to the communities in which they operate and to the stakeholders they engage with.
Hubbell Incorporated is actively giving back to its immediate communities by putting employee volunteering and gift matching in place. Additionally, social responsibility is a key concern throughout their supply chain, and in a further effort to give back they have set up corporate donations via The Hubbell Foundation. Which, as of December 2021, has donated US$1,000,000 annually to benefit science, technology, engineering, and math programmes, as well as a variety of additional charities.
Overall, Hubbell Incorporated champions efficient and reliable solutions and leads the way in electrical infrastructure. They align themselves with sustainable goals that they strive to actively achieve in everything they do. It is clear to see throughout its operations that they are a company that believes in environmental change, whilst promoting a safe, productive, and inclusive work environment. Their recognition by Ethisphere again exemplifies the role they play globally, and we wouldn’t be surprised to see Hubbell Incorporated on their list for many more years to come.
Shiv-om Brass Industries has been the overall business pioneer for over 30 years. It was commenced in the year 1992 with a small manufacturing area & with the hard work from our director & teamwork. We have over 1 600 000 sqm of manufacturing facility. We serve the industry by manufacturing customized Brass parts all over India and additionally, seaward our products in countries like the USA, UK, Europe, Australia, etc. We have the large-spaceoccupied manufacturing unit at Jamnagar with the best machinery for manufacturing brass components in-house, brass components, and a fully assured quality control panel. With the best-in-class hardware, talented and experienced team members, adequate measuring instruments, we are serving the best quality product, at the best costs.
Shiv Om Brass Industries is an ISO 9001: 2015 certified company in the field of manufacturing activities. We remain contemporary with advanced technologies and arranging learning opportunities for all workers. By the years of experience and broad vision towards total quality in every aspect, the company has earned its name in the Brass Industries, worldwide. With modern machinery, skilled labour, enough measuring instruments, and well-qualified management, we always serve better quality at the best prices. We are dedicated in our efforts to give you total satisfaction in terms of quality product and service.
Mr Yash Gohel, Managing Director, Shiv Om Brass Industries.
Factory Address: Plot No. 3690, Road No. 7, Near Pramukhswami Circle, G,I.D.C., Phase-III, Dared, Jamnagar-361004, Gujarat, India Tel: +91-288-6643600 | Email: yash@shivombrass.co.in