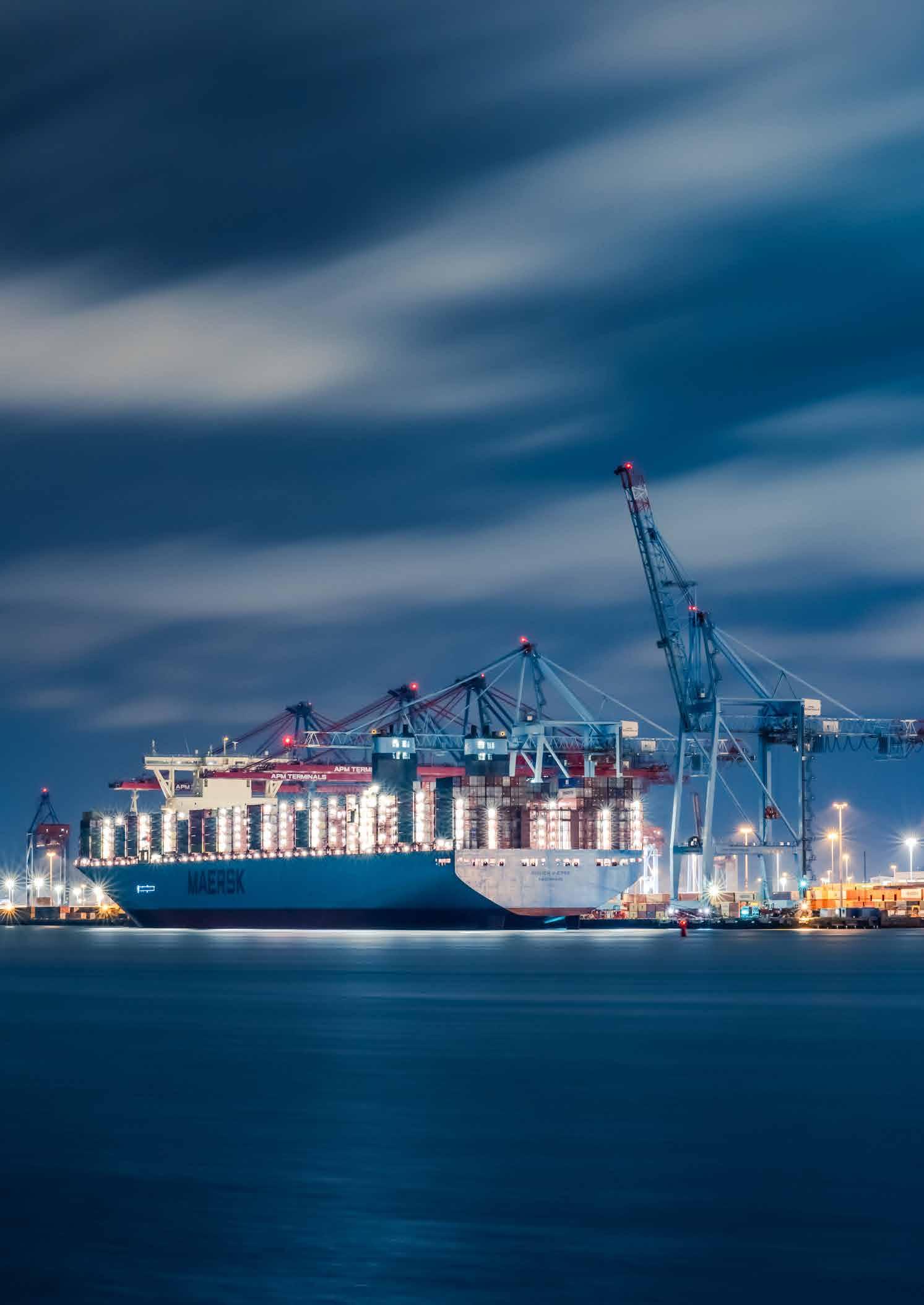
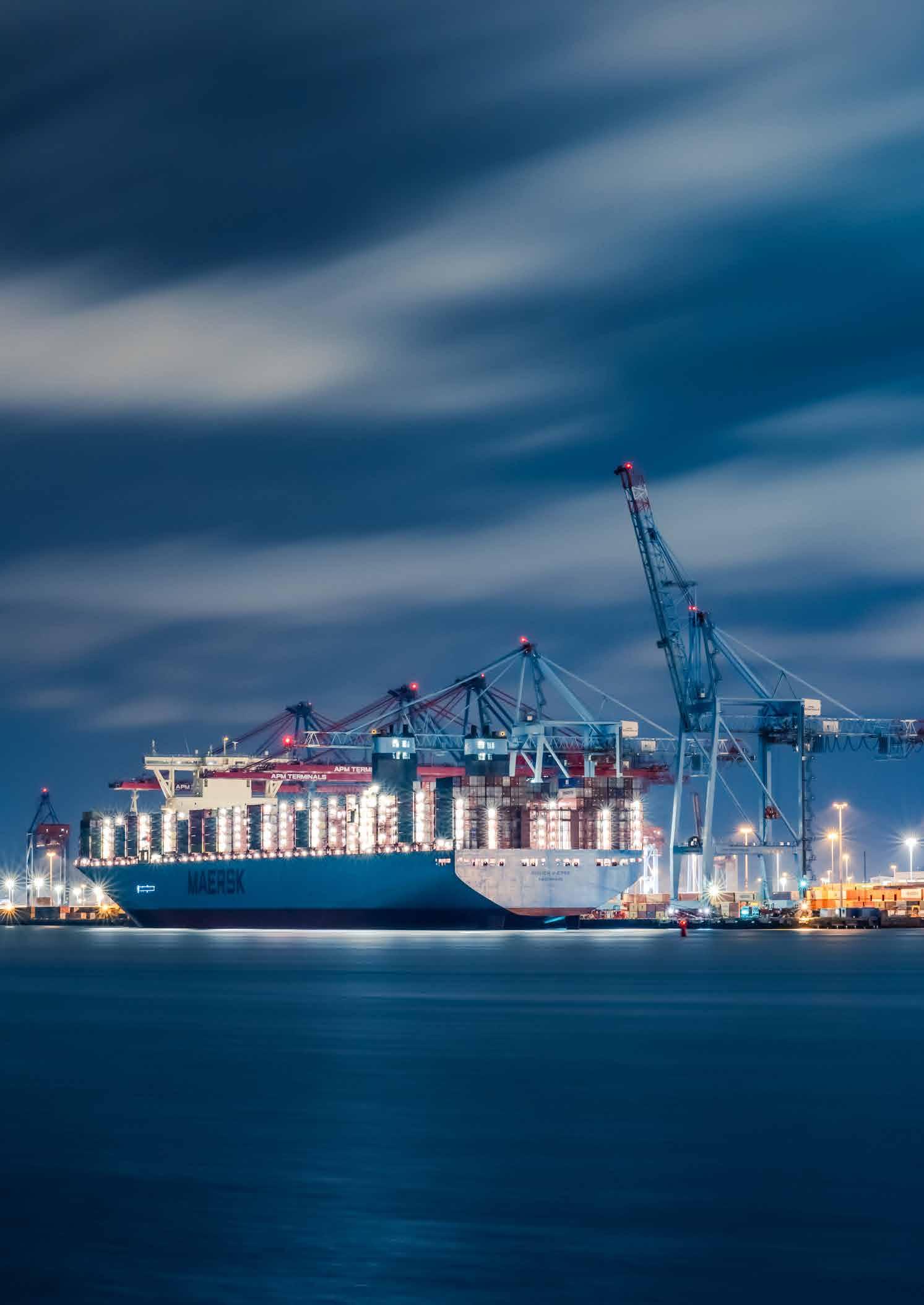
Release Your Potential
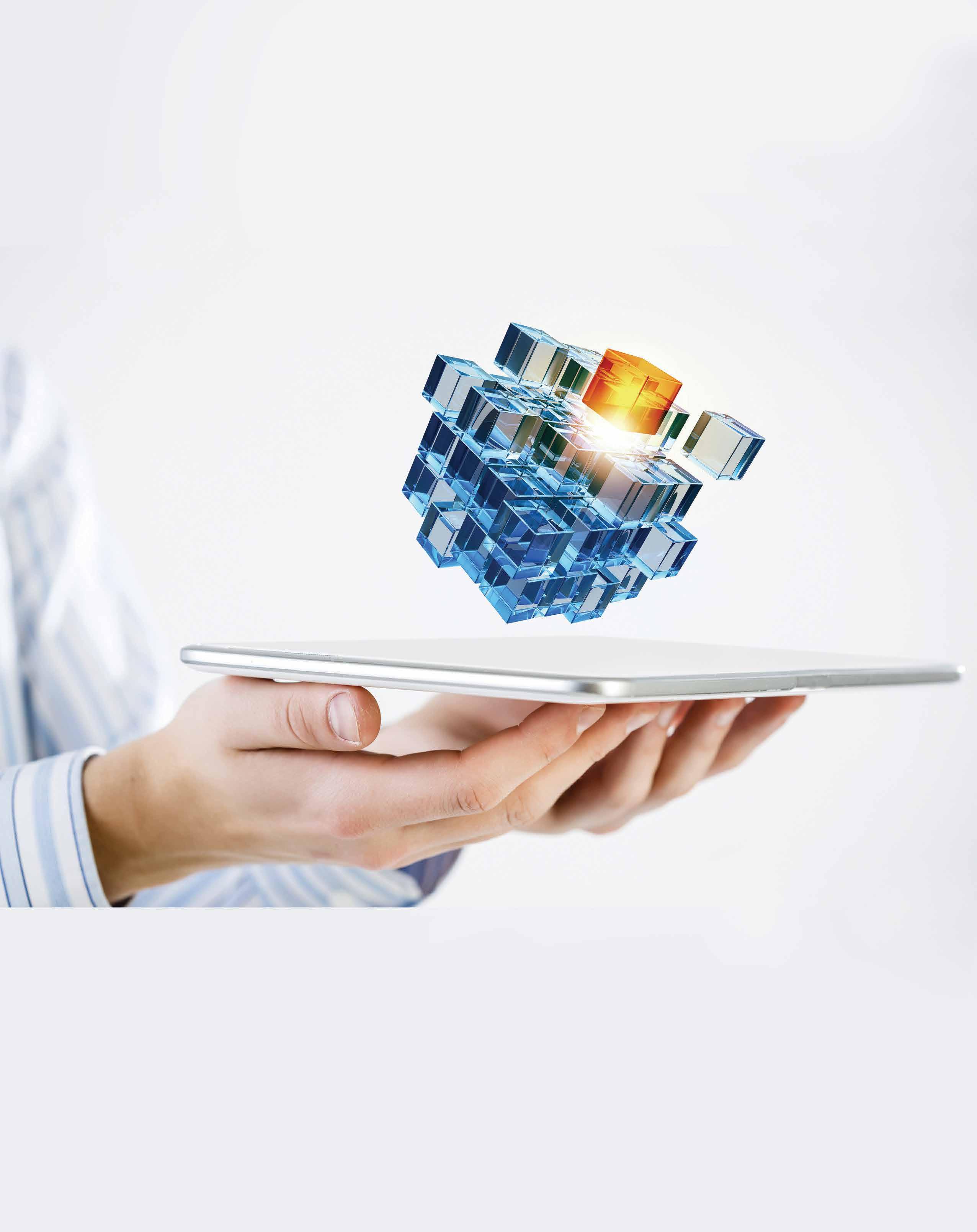
It starts with the right software
A modern propane business presents unlimited opportunities for growth. Let ADD Systems help you realize all those possibilities as we meet today’s challenges of customer experience, speed, accuracy, mobility, and ever more important, scalability.
ADD Systems has been providing solutions to the energy distribution industry –retail and wholesale fuel, propane, convenience stores and more – since 1973.
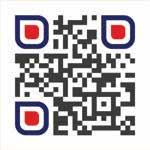
Heads of Departments
Editor-in-Chief Carley Fallows editor@littlegatepublishing.com
Space Management Emlyn Freeman emlynfreeman@littlegatepublishing.com
Media Coordinator Andrew Williams andrew@littlegatepublishing.com
Lead Designer Alina Sandu Research Kristina Palmer-Folt Editorial Research Amber Winterburn
Corporate Director Anthony Letchumaman anthonyl@littlegatepublishing.com
Founder and CEO Stephen Warman stevewarman@littlegatepublishing.com
For enquiries or subscriptions contact info@littlegatepublishing.com +44 1603 296 100
ENDEAVOUR MAGAZINE is published by Littlegate Publishing LTD which is a Registered Company in the United Kingdom.
Company Registration: 07657236
VAT registration number: 116 776007
343 City Road 60 Thorpe Road London 79 Norwich EC1 V1LR NR1 1RY
Littlegate Publishing Ltd does not accept responsibility for omissions or errors. The points of view expressed in articles by attributing writers and/or in advertisements included in this magazine do not necessarily represent those of the publisher. Any resemblance to real persons, living or dead is purely coincidental. Whilst every effort is made to ensure the accuracy of the information contained within this magazine, no legal responsibility will be accepted by the publishers for loss arising from use of information published. All rights reserved. No part of this publication may be reproduced or stored in a retrievable system or transmitted in any form or by any means without the prior written consent of the publisher.
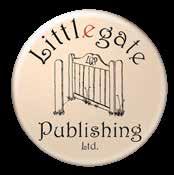
Copyright© Littlegate Publishing Ltd
Editor’s Note
When you think of the Asia-Pacific region, you would probably imagine beautiful beaches and forests, alongside amazing wildlife and marine animals. Although this is most certainly true from a tourism point of view, in a business mindset, all these specialised resources make it the perfect place for technological and industrial growth.
Consequently, across Asia and the Pacific region, what can be witnessed is the rapid increase in new technology, globalisation, and market-orientated reform. This points towards vast innovation and enhancement of industry. Thus, here at Endeavour, we have been very lucky to witness how such companies have drastically grown, as business advancements have swept across the vast region. This is also helped by the growing demands of a rapidly increasing population. This means that the Asia-Pacific region can afford a greater workforce and economic advancement.
It is for this reason that the Asia-Pacific region deserves its own specific publication. Within this issue, you will find out about brand new innovations in engineering, sailing and biscuits! Thus, we will not only discover the business behind the lavish and decadent Asian skylines but how such companies face the challenges of the ever-modernising world.


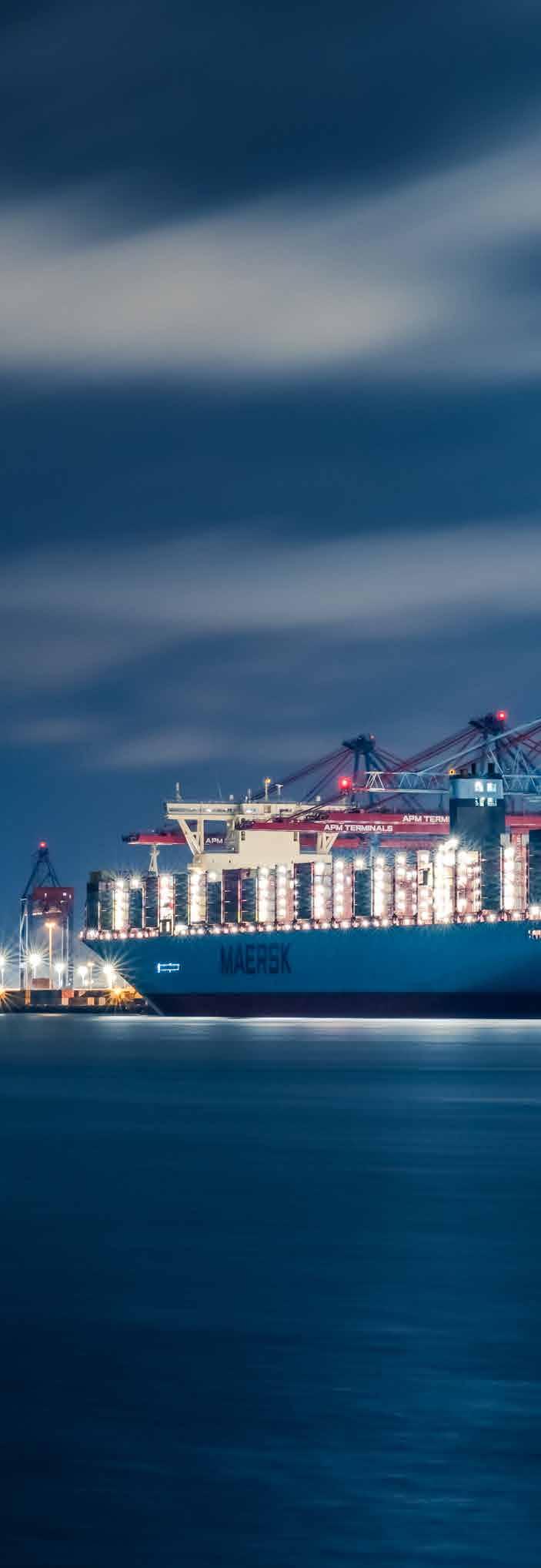
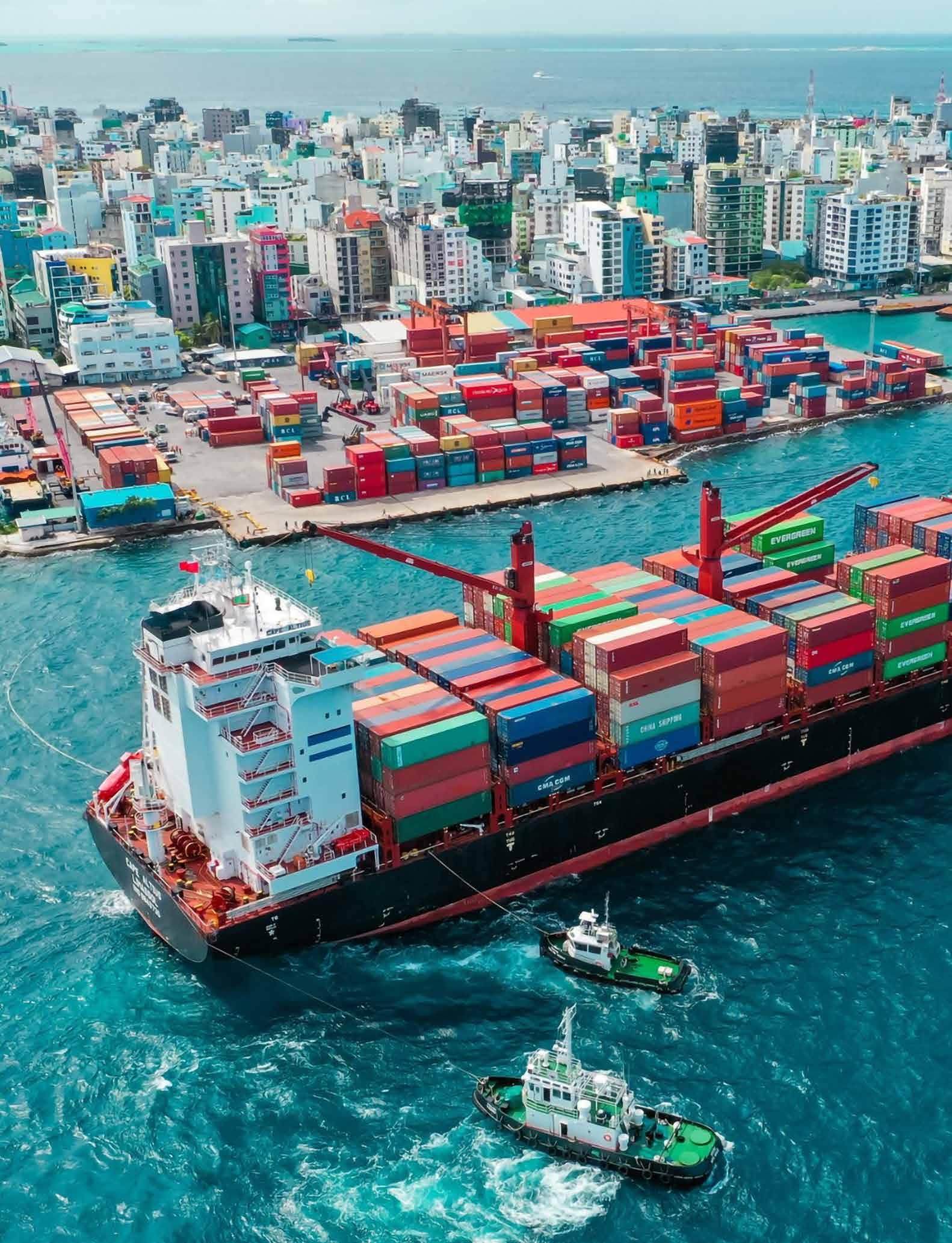
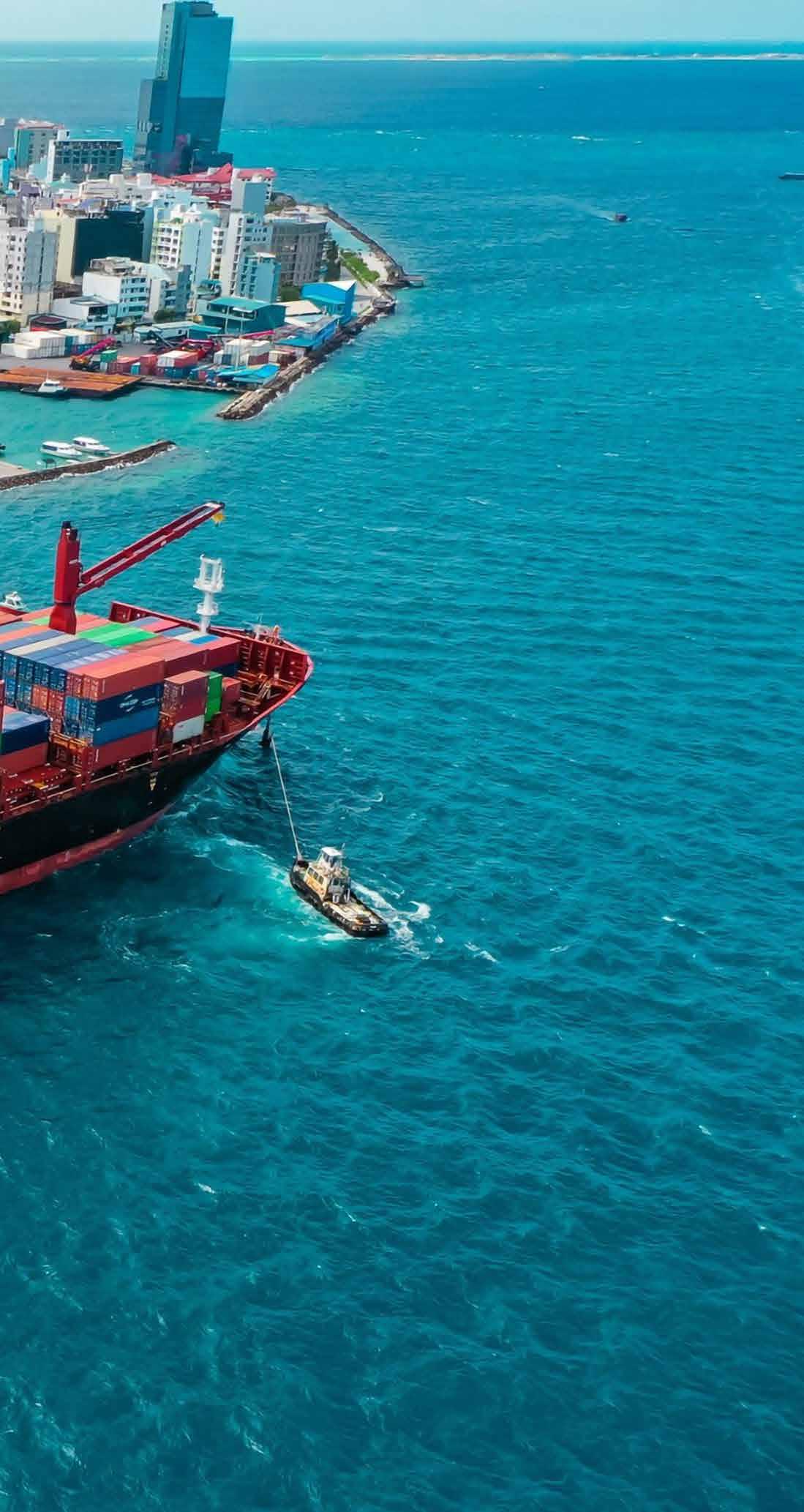
Established as a beacon for reliability and efficiency across the commercial cargo imports of the Maldives, Maldives Ports Limited (MPL) develops, manages, and operates the ports across the islands. The Maldives has become such as popular tourist destination, which sees an increasing number of cargo shipments needed to meet the needs of these visitors whilst also maintaining the existing cargo supply chains operating between the region and the rest of the world.
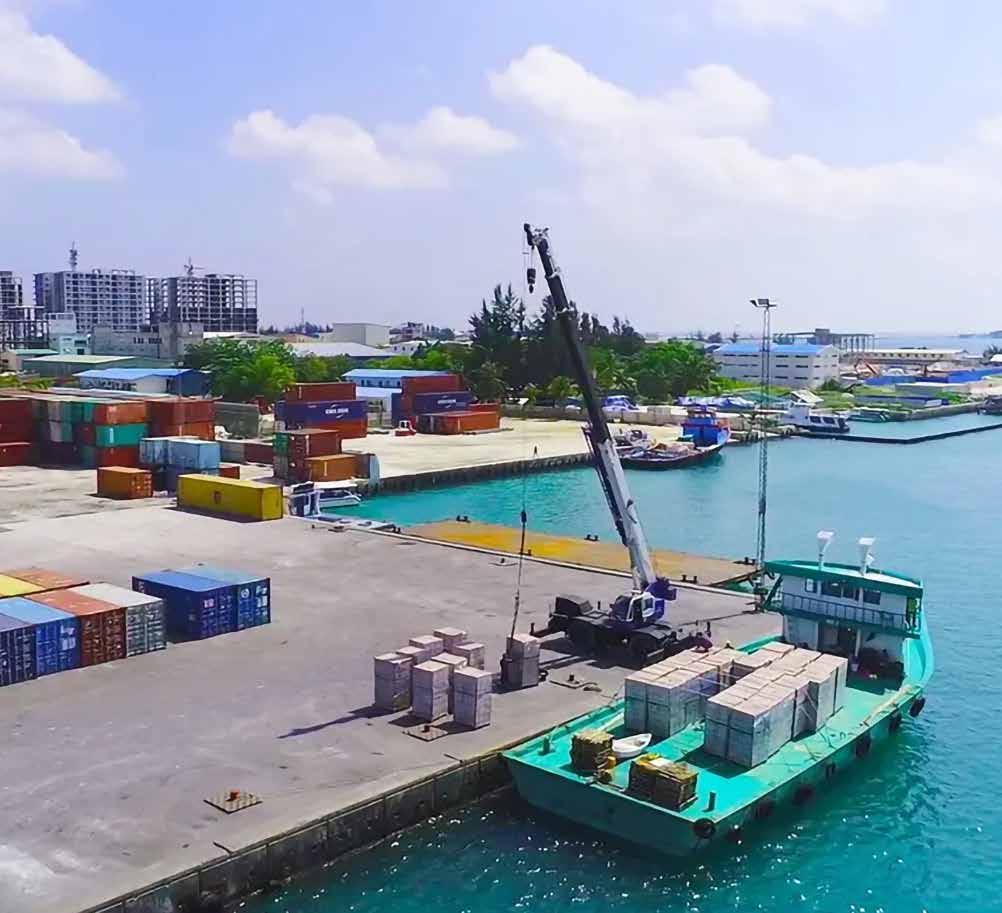

Instituted by a presidential decree, MLP was established to oversee the ports of the Maldives and regulate them as a hub for international maritime and commerce operations. MPL offers a wide range of port services across its ports and terminals, with cargo services covering a large part of this. For cargo, MPL works to provide container unloading, ship-to-shore, stuffing/unstuffing, container inspection and clearance services to vessels visiting the ports across the Island region. This cargo is then facilitated through MPL’s transit cargo department which is designed to move this cargo from anchor to other boats and land transport partners which keeps supply chains moving with such an efficient service. Throughout these operations, MPL has implemented a set of regulations to ensure the safety and security of its port activities, whilst also providing the essential navigators and pilots to help every vessel arrive safely into the port’s wharfage.
MPL has a range of ports under its operations, including Malé Commercial Harbour, the main port for the Maldives. The port is located in the north-western corner of the Malé Island and is a key player in international maritime operations as the ‘gateway’ to the Maldives. The port’s location close to the capital of the Maldives means that cargo travelling into the port can then be distributed across the islands and onto further international markets through MPL’s network. Malé Commercial Harbour has a quay length of 102M with a depth of CD-9.25m. The port provides docking and clearing, as well as storage operations at the Malé Commercial Harbour facility.
The Hulhumale International Terminal is another key port terminal under MPL’s operations which is owned and operated by MPL. The terminal has been in operation since 2013 and is a focal point for the smooth transport of cargo through the Maldives. Hulhumale International Terminal works with the Malé Commercial Harbour to help prevent container congestion that often occurs at the central port of the island. The terminal has an existing storage capacity of 500 TEUs and operates two warehouses and 5 plug points for reefer containers. The port specialises in the handling and storage of perishable cargo, and so has the facilities to accommodate the conditions needed to keep this kind of cargo including food safe and temperate.
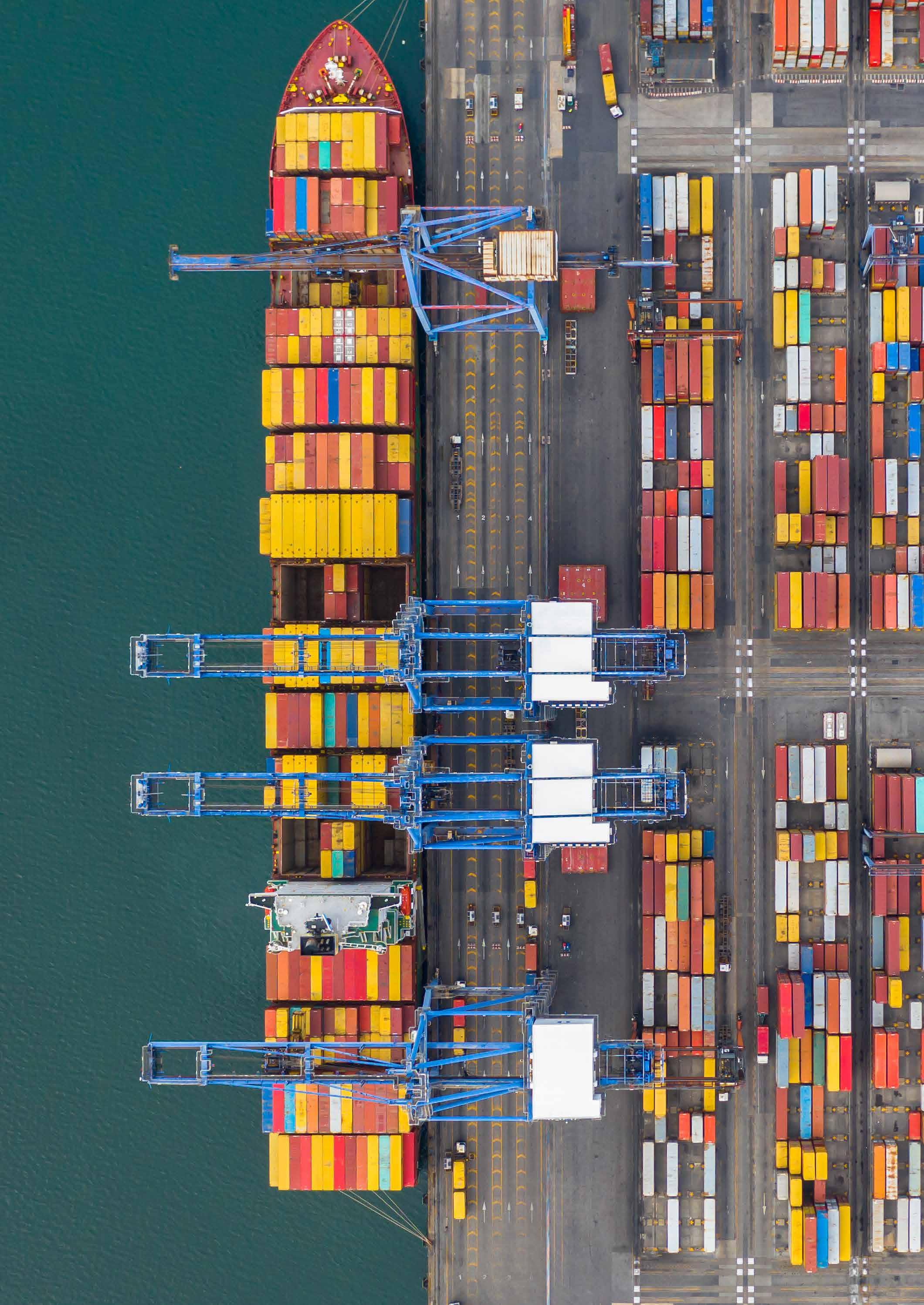
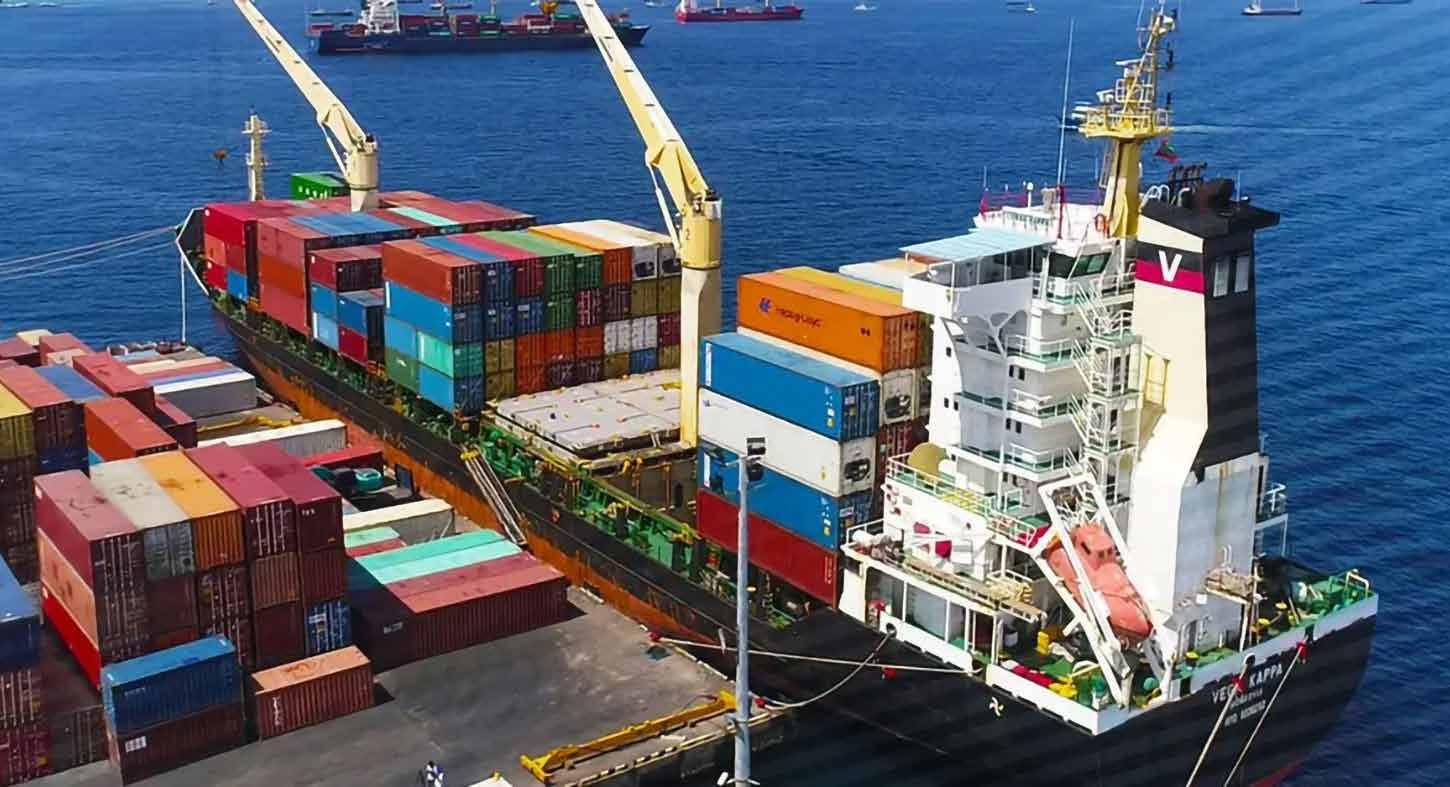
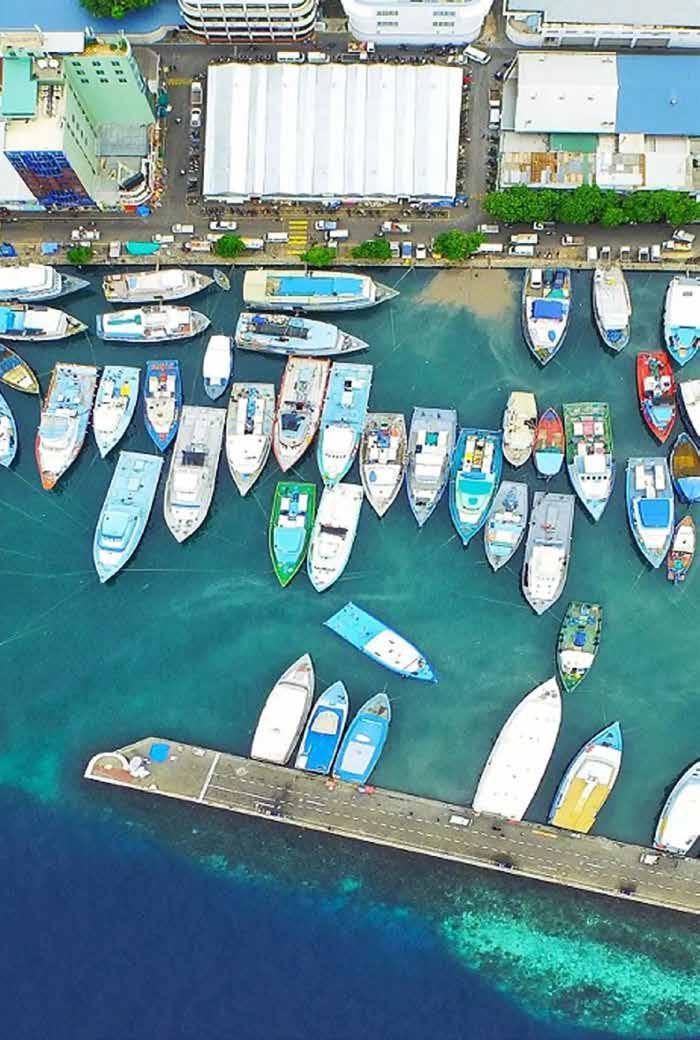
The third port operation under MPL is the Kulhudhuffushi Regional Port (KRP) which is located in the north of the Maldives. Its operations span back almost 20 years and support the Kulhudhuffushi Island which is known as the central economic capital for the north of the islands. The port’s main role is across the domestic, inter-island and distribution activities to support the movement of goods and merchant trade from Malé Commercial Harbour and to the north area of the region.
MPL has developed new plants for KRP to expand its port so that it can receive cargo directly from India via the Cochin Ferry Link. This would expand MPL’s role in Indian markets and allow perishables and other consumer goods to be transported directly into the port to bring continued benefits to the island communities. Whilst it will offer greater accessibility to these goods to the Maldives, it opens up a vital connection between India and the Maldives which will bring continued economic benefits to the region. Additionally, KPL benefits international customers with fast clearing speeds through its warehousing facility in up to 10 days, and at a 30% tariff on imported goods making it a competitive choice for exporters to the Maldives.
The final central port operation under MPL is the Hithhadhoo Port Limited (HPL) which oversees the Hithadhoo Regional Port located in the south of the
Maldives. The HPL operates as a distribution hub for the sound of the islands, providing cargo handling and storage-related services for businesses and industries established in the south. Much like, KRP, the port also has a 30% tariff on imported goods, which is designed to help encourage cargo processing through the port by minimising the cost of warehousing and double handling from the Malé Commercial Harbour.
As we have seen, MPL covers the entire span of the Maldives with vital ports, terminals, and warehouses under its operations to promote the vital role of the Maldives in international trade routes and shipping lines. However, as MPL moves towards the future, it has just announced the appointment of Mohamed Wajeed Ibrahim as CEO. Ibrahim brings with him 9 years across the MPL family and aims to steer MPL towards its next phase of development. The future of MPL is set to focus on excelling with innovation and operational optimization to make all port activities even more seamless, efficient, and competitive in international markets. Therefore, the appointment of Ibrahim to see the company into
the next phase of its development highlights MPL’s commitment to providing essential stability and leadership across the Maldives maritime landscape. Ultimately, MPL is uniting the Maldives industry with a leading force to promote operational excellence across the region’s maritime industry. With a range of cargo handling, warehousing, pilotage and stuffing/unstuffing services, every port across the Maldives is equipped with stateof-the-art equipment and services to make all handling efficient. With such a vast spread across the Maldives’ cargo industry, MPL is therefore vital in bringing economic growth to the region from the import and export markets. Therefore, with MPL’s implementation of internationally recognised regulations and standards, the Maldives maritime industry continues to thrive. We look forward to seeing how the new CEO Mohamed Ibrahim will take MPL into the future, as he continues to focus on developing port optimization.

Offering a world class logistics service
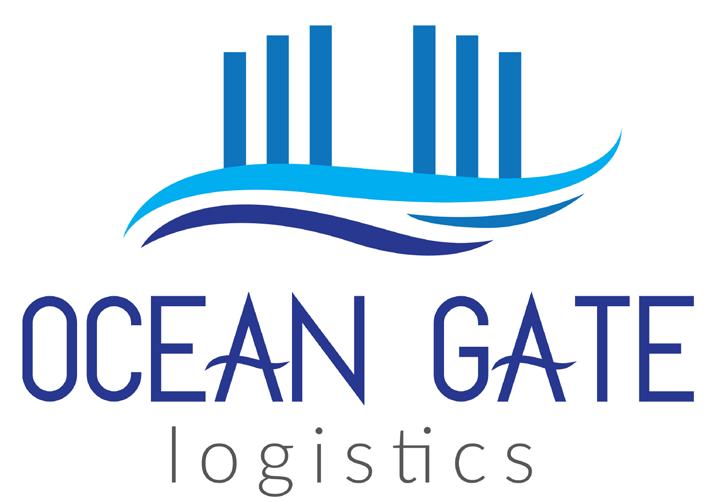

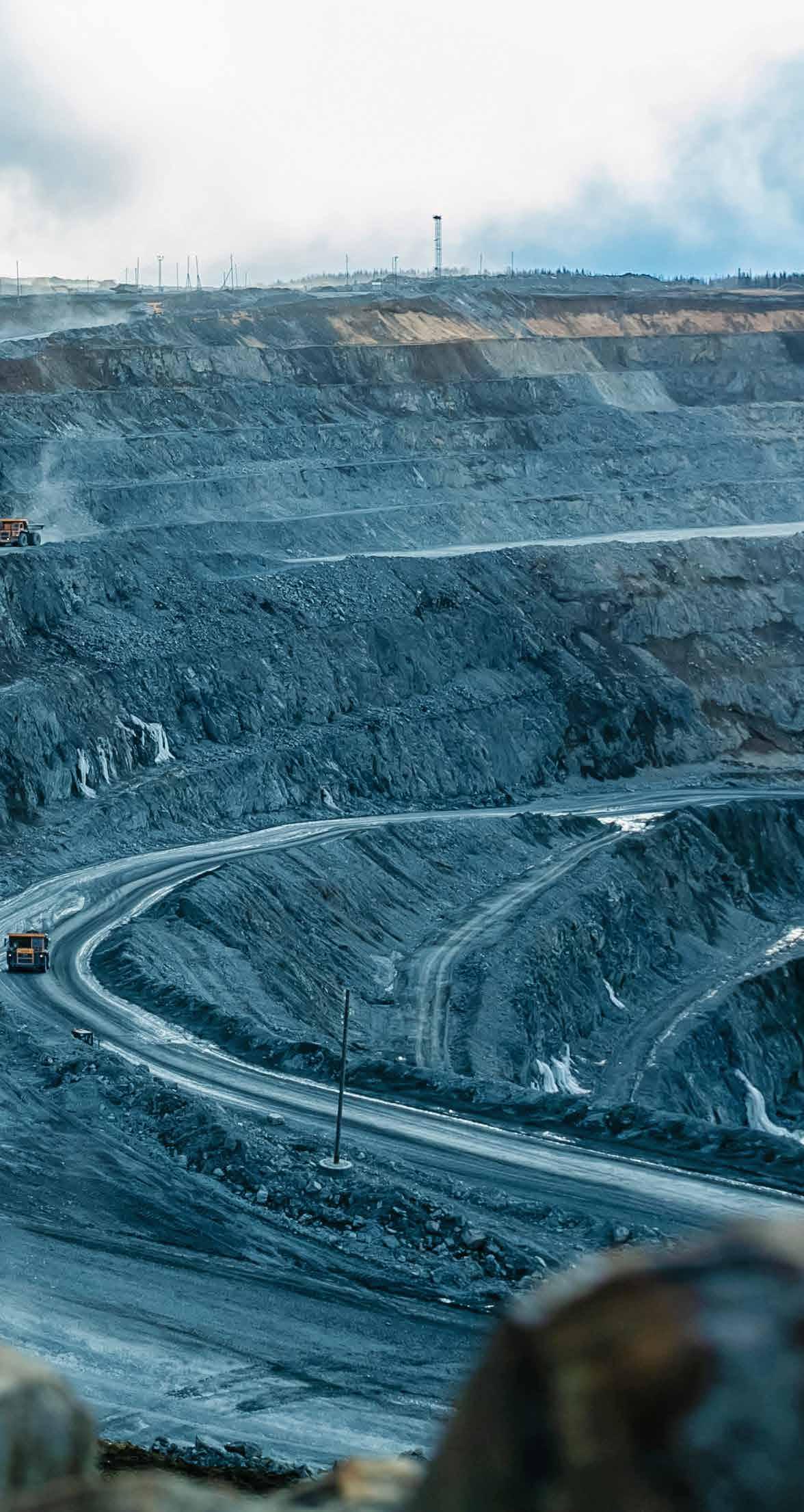
Newmont Corporation
With a portfolio spanning world-class assets, Newmont Corporation has spent almost a century as a leading mining company operating in every corner of the globe. The company focuses primarily on gold mining, however, it has many vital mining operations spanning the metal industry from copper, to silver, zinc and even lead. Throughout its operations, Newmont remains focused on developing each deposit to create value that meets strict safety standards and internationally recognised regulations, all of which are backed by its leading technical proficiency to remain a key player within the international mining sector.
In 1925, Newmont began its operations with a central focus on enhancing and developing the natural resources of gold, copper, silver, lead, zinc, lithium, uranium, coal, nickel and various aggregates across the mining industry. These vital deposits sought to bring economic development to their respective regions, whilst working to enhance the company’s role as a leading mining and deposit exploration company. This commitment to development was also seen across the oil and gas industry, as it worked to utilise its expertise in the mining sector to bring value to the energy resources to market. Today, all of this remains the same, however, Newmont now has one of the largest and most expansive portfolios across the mining industry.
This portfolio covers more than half of the world’s leading Tier 1 assets – many of which include long-life operations, value-accretive projects, as well as many exploration opportunities. With such a vast array of assets, prospects and people behind its operations, it’s no surprise that Newmont is the only gold producer currently listed on the S&P 500 Index. This listing highlights Newmont’s vital role in developing assets towards the future, whilst working closely with shareholders, supply chains, host communities and its network of employees together to bring significant benefits across every single mining project under its operations.
A central mining area for Newmont is in Papua New Guinea, on Lihir Island where there is a significant gold deposit. Lihir Island is located on a geothermally active extinct volcano crater and is home to the Lihir Gold Mine. The mine one the largest producing gold mines in the world, and began its life almost 30 years ago with the aim to bring economic value to the people of Papua New Guinea through employment opportunities, investment in infrastructure and local supply chains. The mine is estimated to contain 310 Mt of combined proven and probable reserves grading 2.4g/t of gold with the in-sit gold of 23Moz as of June 2020.
The island consists of 5 Miocene Pleistocene volcanic units of which there are volcanic calderas and two sequences of mafic volcanic rock. The geothermal activity remains present in the Luise caldera, and so the orebody is contained in a hydrothermally altered porphyry gold system. Therefore, the gold is hosted in the volcanics, intrusives and breccias within the caldera and consequently, most of the gold is contained in sulphides. Consequently, the ore produced from the mine is refractory and is therefore treated with pressure oxidation before the gold is recovered using leach processes.
The mine contains several defined deposits which are adjacent or partly overlapping, including the Lienetz, Minifie, Coastal and Kapit. These are adjacent to the Borefields and Camp deposits, all of which are connected by areas of low-grade mineralisation. The current mining of the deposits will take place over a 13-year period during which higher-grade ore will be fed directly for processing and lower-grade ore will be stockpiled. It is expected that it will be processed during the following 17 years to oxidize and carry out cyanide leaching, and so gives a total projected life of 30 years to the mine. The mine utilises an autoclave for direct feed ore to reduce the proportion of ore fed through the flotation circuit to increase gold recoveries and increase total gold production. The processing facility treats the sulphide and oxide ore and now can output more than 6Mtpa of ore and an output capacity of 800,00oz of gold a year. This ensures that Newmont can accelerate its processing rates and produce more gold with maximum value.
In October last year, Newmont became the first company to list on PNGX (Papua New Guinea
Supporting Mining in Papua New Guinea
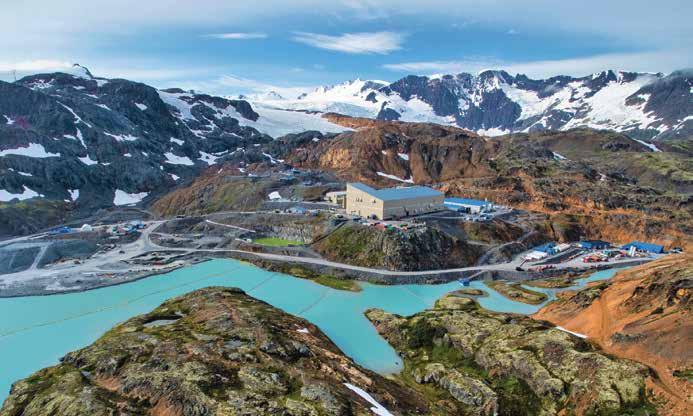
Exchange Market) with its depository interests. This highlights the valuable role Papua New Guinea continues to play in establishing the region as a key gold resource in international markets. This is supported by the vital role Papua New Guinea plays in developing Newmont’s global gold deposit portfolio. This listing highlights Newmont’s commitment to the future development of the nation.
In recent news, Newmont announced that it would be partnering with John Wood Group plc, commonly known as Wood, to expand the current Lihir Gold Mine and deliver concept and feasibility studies. Wood, a multinational engineering and consulting business, will facilitate the detailed design and construction management services as
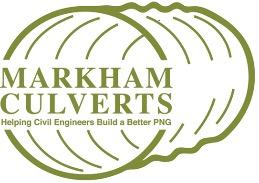
part of an $18 million contract with Newmont. The consulting and engineering services will bolster the company’s working capital programme and work to bring continued economic development to Papua New Guinea.
For Newmont, Papua New Guinea adds yet another valuable mining project to its growing portfolio of world-class assets, prospects and talents across the world. Its mission to create value across all of its operations can be clearly seen with the Lihir Mine in Papua New Guinea where it has implemented safety standards, superior execution and technical expertise all for the benefit of those in the region. With roughly 4,500 residents and fly-in fly-out workers, it’s clear the role the mine plays in supporting Papua New Guinea and its development on both a local and international scale cannot be understated. We look forward to seeing the growing role the company will continue to play in Papua New Guinea and how vital partnerships with international consulting and engineering services such as Wood, will take the mine into the next level of its value creation development.
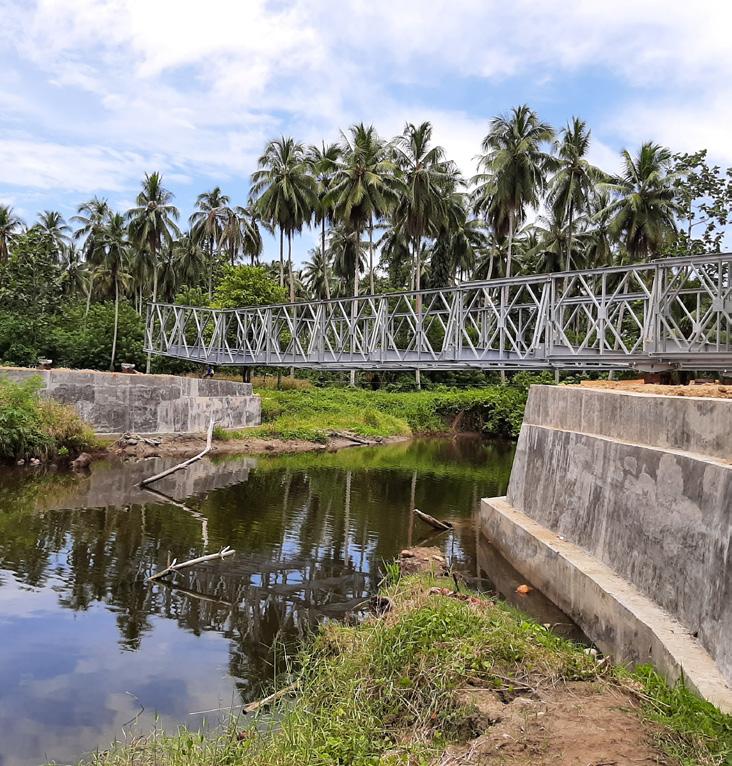
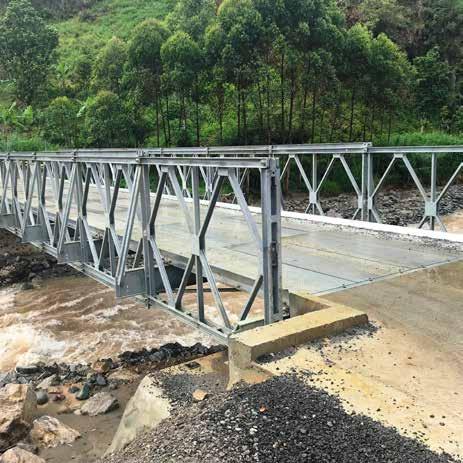

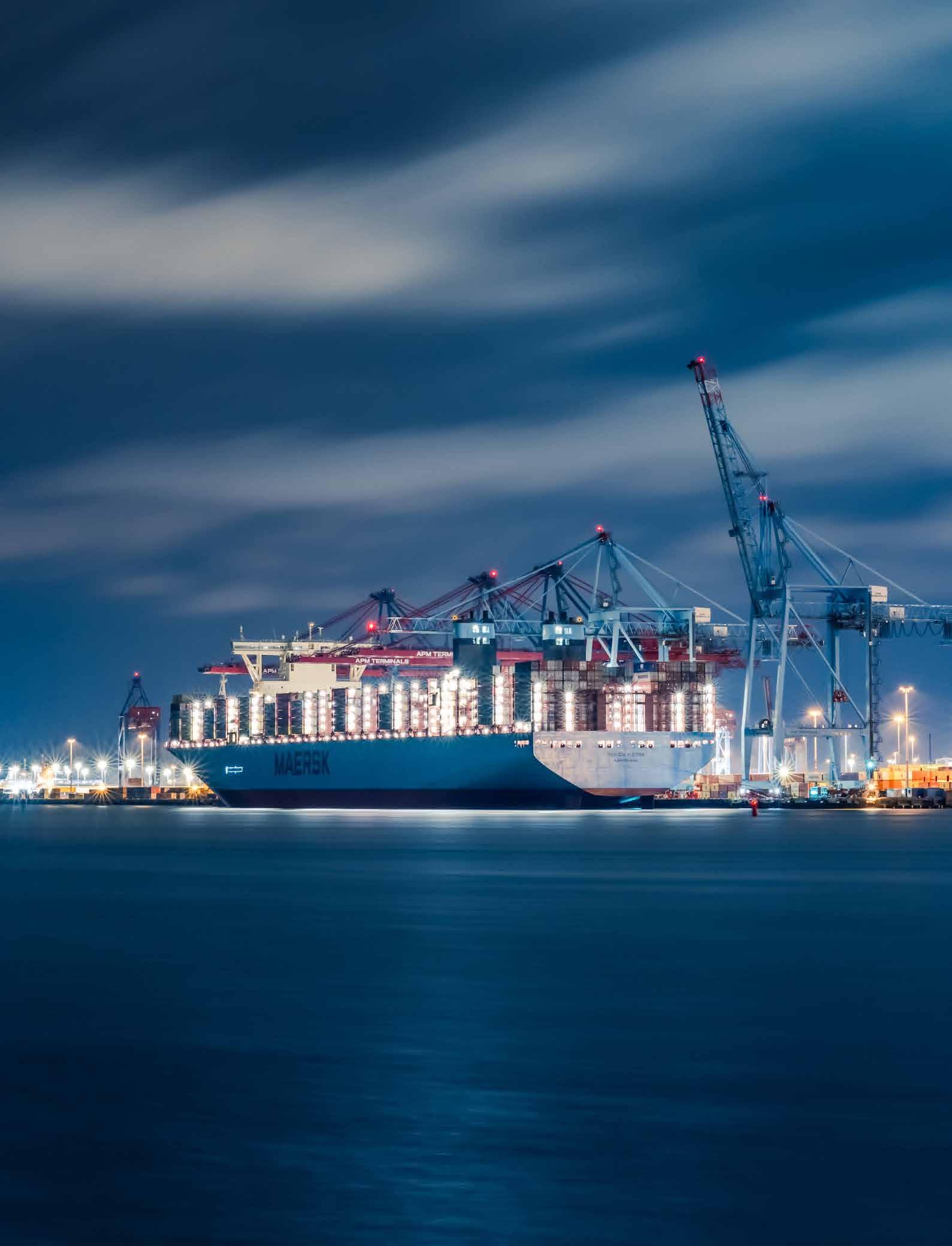
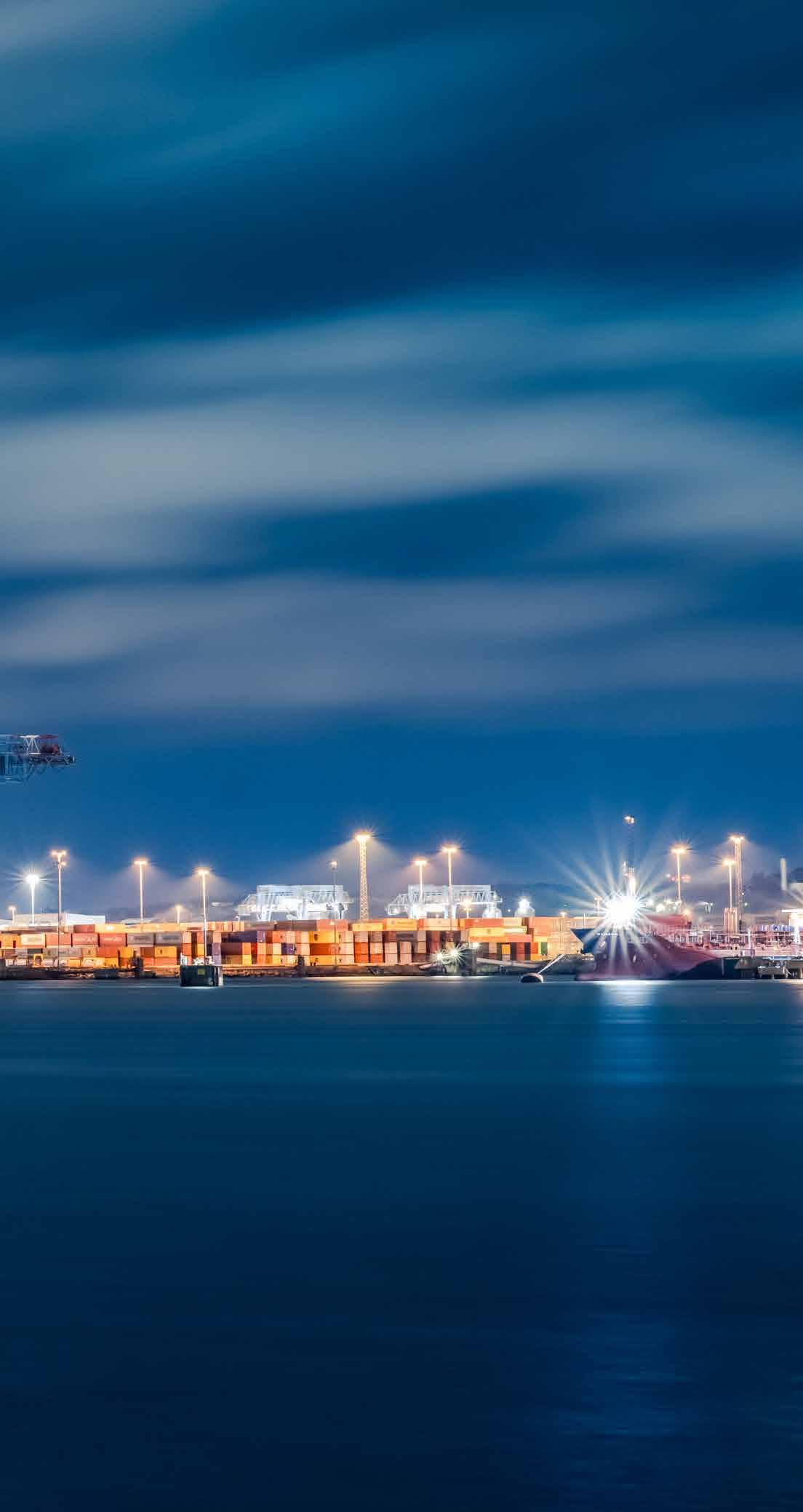
As one of the largest shipping companies globally, A.P. Møller –Mærsk (Maersk) provides an integrated transport and logistics service committed to connecting the world to help businesses thrive. For Maersk, the development of companies on an international scale is underpinned by efficient logistics solutions which require expert knowledge and seamless integration into businesses worldwide. With a reliable, efficient and secure logistical network, businesses have the opportunity to move vital cargo to new markets to bring economic development and strategic partnerships for the benefit of trade internationally. Therefore, when businesses, whether large or small, partner with Maersk they are accessing an international network of transport and logistics experts who are committed to getting their customers’ cargo delivered quickly, cost-effectively and securely every time.

With such a vast logistical footprint, Maersk is committed to delivering more connected, agile, and reliable logistical solutions supported by its international network. Therefore, as global markets continue to evolve, Maersk is a leading shipping company providing greater flexibility and security to its customers, so that they can unlock their potential in international markets. Currently, Maersk has over 100,000 employees across its global operation spanning 130 offices worldwide covering many rich and thriving industries. Across its vast network, Maersk has many vital locations which are developing each region’s logistical sector for the benefit of the businesses that continue to thrive and contribute to their respective economies.
What separates Maersk from its competitors is its commitment to delivering effective transportation solutions no matter the industry, commodity or market. To achieve this Maersk operates one of the largest shipping companies in the world responsible for delivering 12 million containers every year to regions spanning all corners of the globe. Once these vessels reach ports, Maersk then also provides full inland services which move this cargo from major terminals and onto its target markets via roadways, railways and riverways. However, should cargo need urgent transportation or require specific cargo needs, Maersk also operates an air freight division which aims are reduce the cost of urgent and critical cargo requiring air freight delivery.
With such a wide array of logistical offerings, Maersk remains committed to ensuring that every customer can find the right solution for their needs, even if their cargo requires specialist requirements. To achieve this, Maersk works with its teams across the globe to communicate with local suppliers to provide complete and integrated supply chain logistical solutions which cover cargo from the start to the end of its journey. This end-toend logistical service offering is backed by Maersk’s digital solutions system which ensures that its customers can achieve their goals with systems uniquely designed and implemented by its teams. These supply chain solutions also include warehousing to help businesses strengthen their reach with strategically located storage facilities
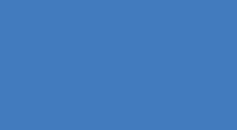
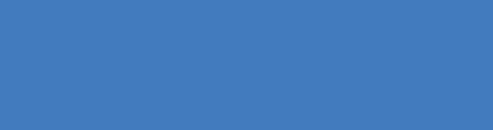
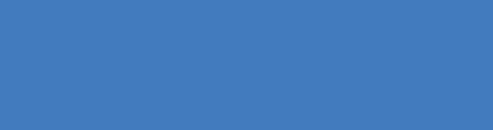
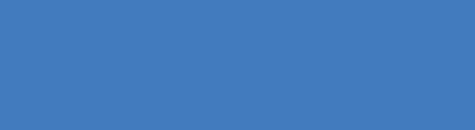
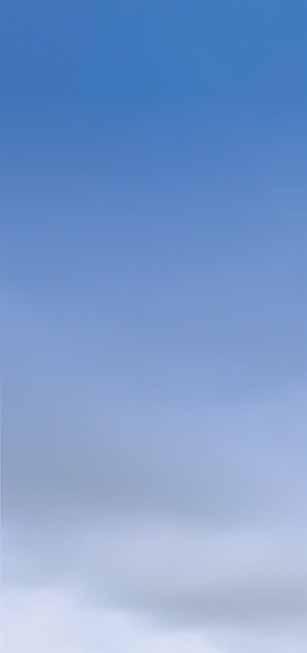
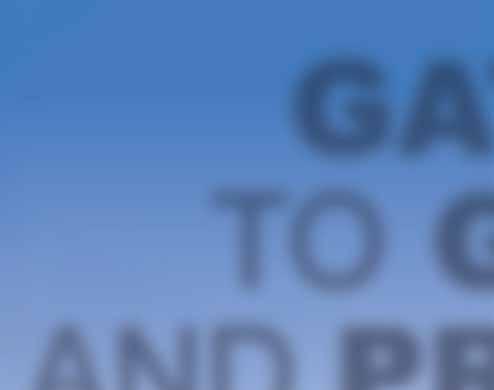
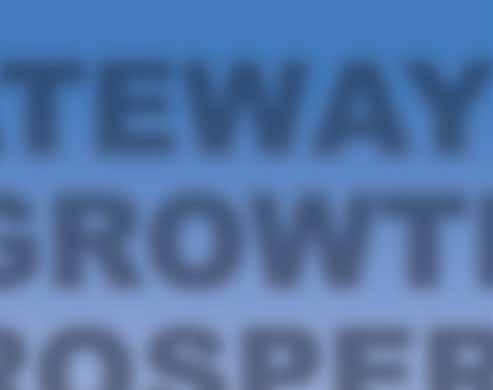

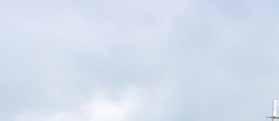
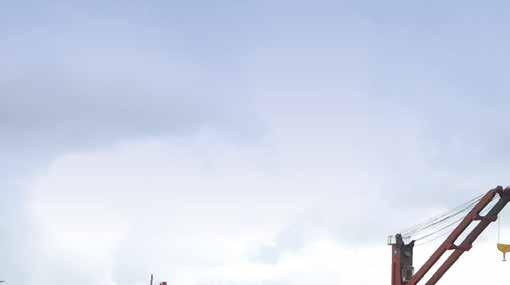

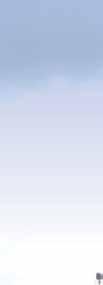
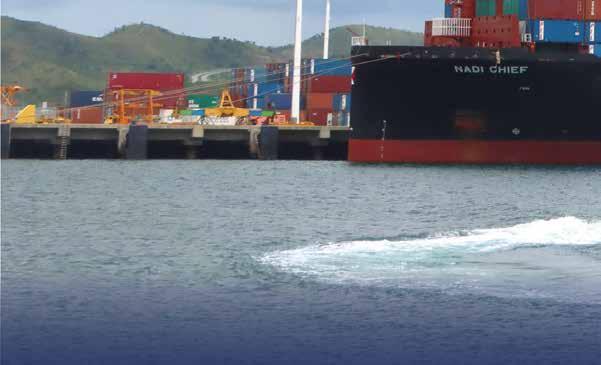
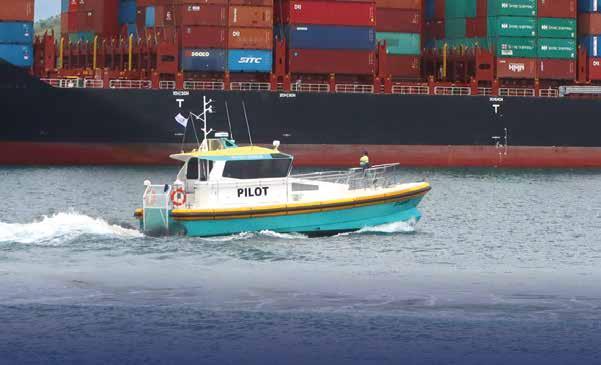
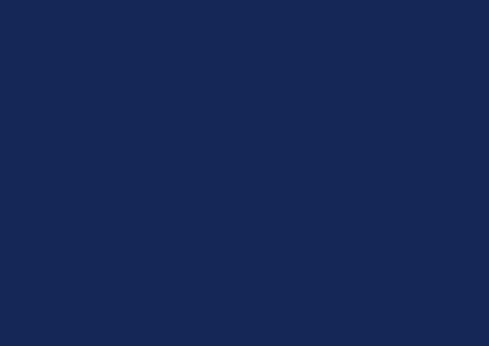
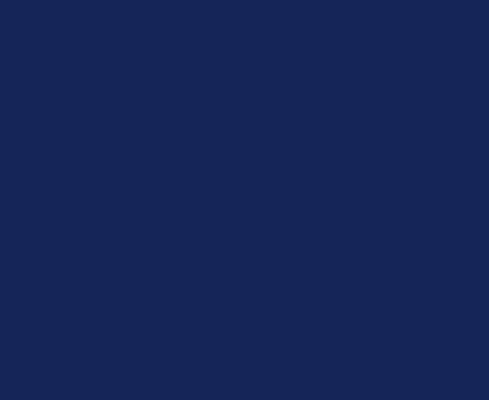
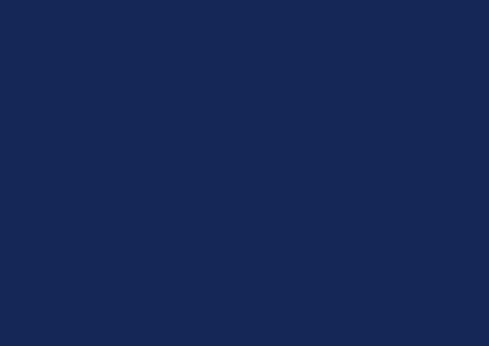
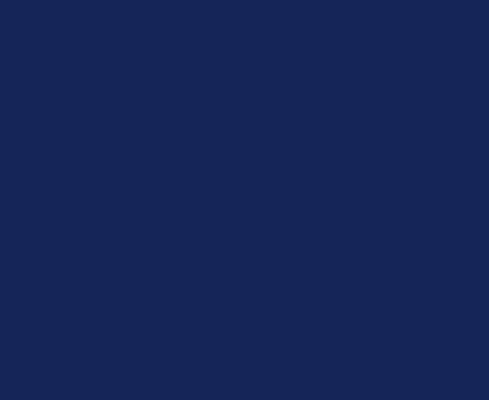
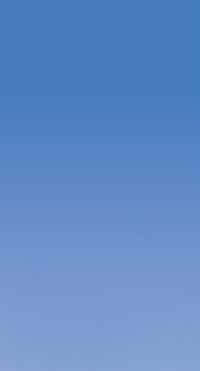
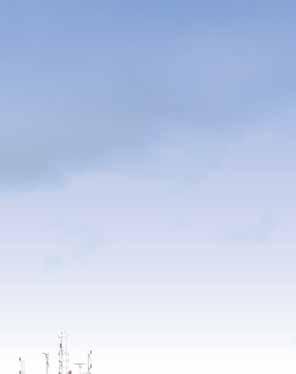
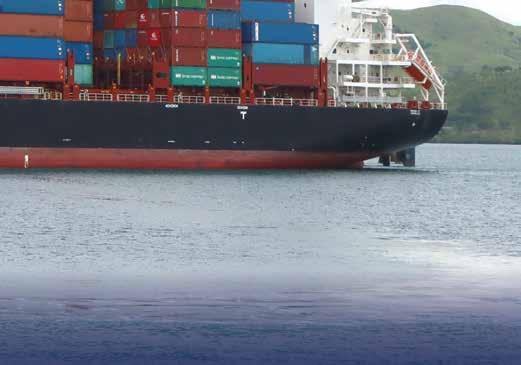
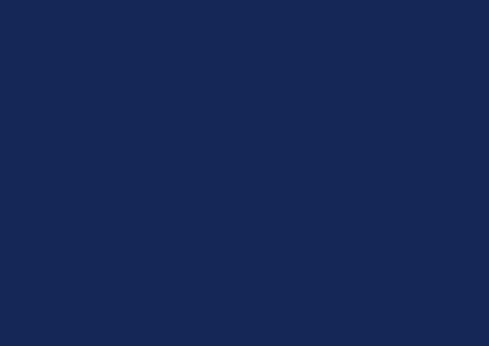
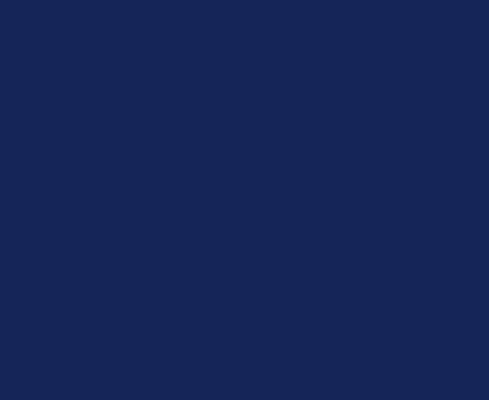
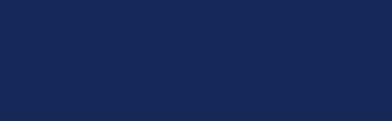
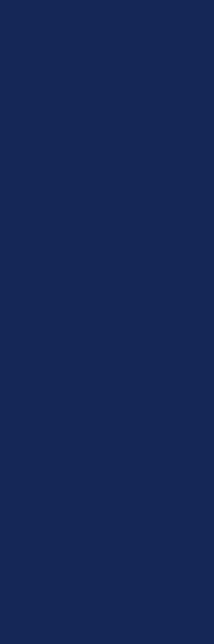

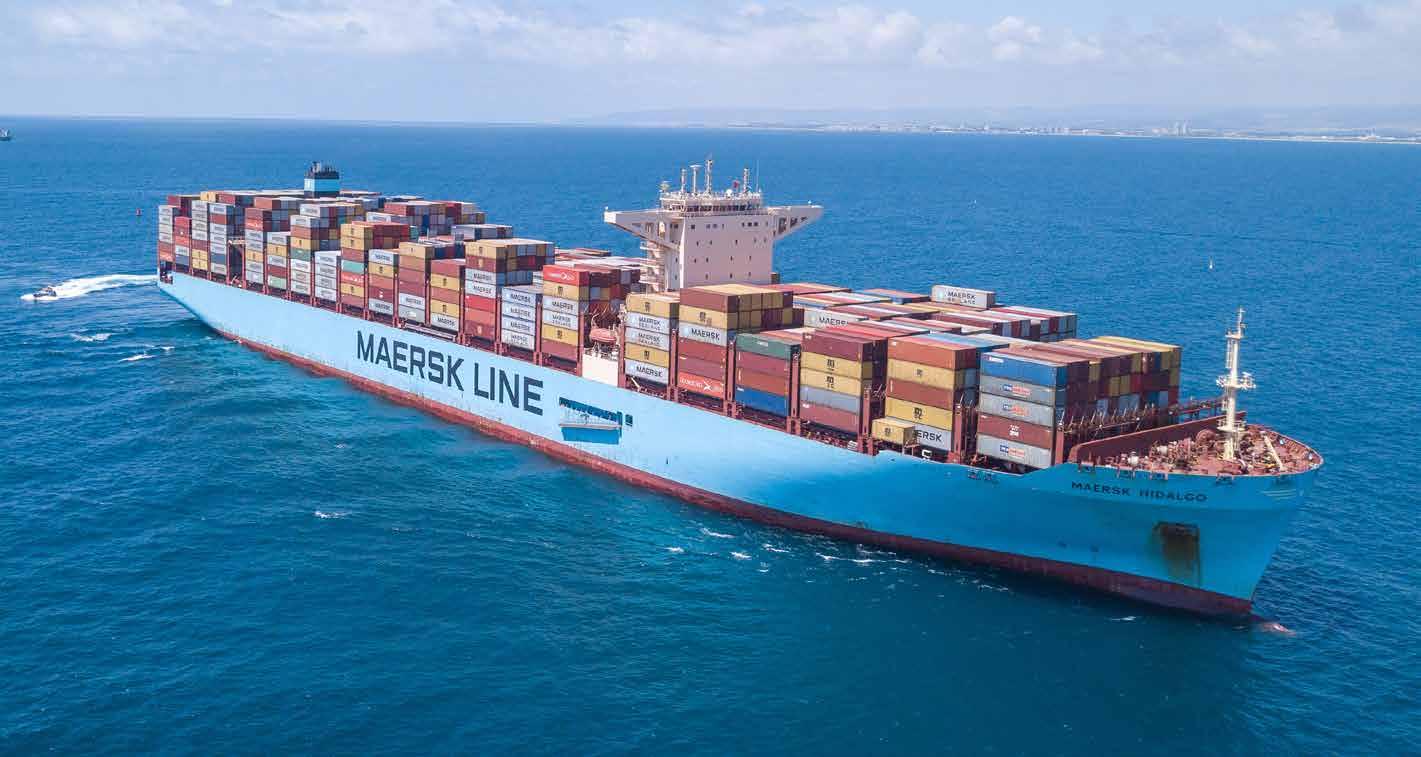
from which Maersk ensures the timely delivery of its customers’ goods to its supply chains. It is clear that across Maersk’s operations, the planning, orchestration and management of all transport and logistics services are met with the company’s stellar reputation and industry-leading expertise in the shipping industry to ensure that every single customer can find a logistics solution that works to help them, and their business thrive.
A key country that Maersk services is Papua New Guinea where Maersk is the leading shipping company. For over 10 years, Maersk has provided essential shipping and logistical services to both large and small businesses and customers facilitated by its on-theground teams. These teams work effectively with local supply chain facilitators to ensure that all logistical operations across the country are met with seamlessly integrated transport services throughout every step of the shipment process. Currently, Maersk operates two vessels which run on an 18-day rotation taking cargo from the central hub of Tanjung Pelepas and then calls at ports across Papua New Guinea including Port Moresby, Noro (Solomon Islands), Lae, Madang, and Wewak, as well as feeder services, to ports such as Kimbe and Rabaul.
These services are backed by Maersk’s international network and team of skilled experts in the shipping field, to ensure that businesses in Papua New Guinea can make the most of global
trade. Therefore, as the leading shipping company in Papua New Guinea, Maersk plays a vital role in developing the region’s economy on a global scale by ensuring that businesses can access the services and networks available to many larger international companies. Therefore, the businesses of Papua New Guinea can continue to expand their offerings and enter new markets for their economic benefit, and in turn the reputation of Papua New Guinea in international trade.
To expand its coverage of Papua New Guinea’s shipping industry, Maersk is also working with Inchcape Shipping Services to bring even greater coverage of the country’s ports. By working with another giant in the shipping industry, Maersk can continue to expand its coverage across Papua New Guinea and enable faster transit times from ports across the country and onto international markets. This, in turn, aims to bring further economic benefits for the country and its trade across even more parts of the globe.
As the global company look towards the future, it is working to implement green initiatives and sustainable practices into its shipping services. This was recently highlighted with the arrival of Maersk’s second-largest vessel, the Astrid Maersk which runs on green methanol. The vessel sister to the initial Ane Maersk vessel, arrived in Koper, Slovenia and marks a key step in the company’s mission to achieve net-zero emissions by 2040. Ivić Vodopija, Country Manager for East Adriatic and Central Europe at Maersk, outlined the vital development of the vessels, as “The launch of this class of vessels is a key milestone for Maersk in
Connecting and Simplifying Supply Chains
our journey to decarbonise ocean transportation. Astrid Maersk, together with her sister vessels, embodies our ambitions in the areas of sustainability and innovation”. Vodopija continues that “…this decarbonisation journey requires collaboration from the entire ecosystem including customers, partners, regulators and all other stakeholders and Port of Koper is one of our key partners. We are in this together and today we have visible proof that we can move in the right direction”.
Vodopija’s comments highlight the vital move towards sustainable forms of energy which can be utilised by the ocean transportation industry. As such a key global player in the shipping industry, Maersk’s strive towards net-zero emissions signals to the entire industry that it is possible, and that the future of the logistics industry does have a green future. This is a key area that Maersk will continue
to work on over the coming years as it strives to hit net-zero greenhouse gas emissions by 2040.
As a major player in the world of integrated logistics solutions, Maersk is committed to ensuring that no matter the cargo, it will find a solution to help its customers meet the needs of international trade and achieve recognition in international markets supported by Maersk’s vital logistical solutions. As we have seen in Papua New Guinea, Maersk is committed to ensuring that every region and country is supported by its network of offices and local suppliers to ensure that supply chains run efficiently. However, as the world moves towards a more sustainable future, we look forward to seeing how the milestone of the Astrid Maersk will continue to be replicated across its vessel as it shifts its focus to more sustainable transportation options.
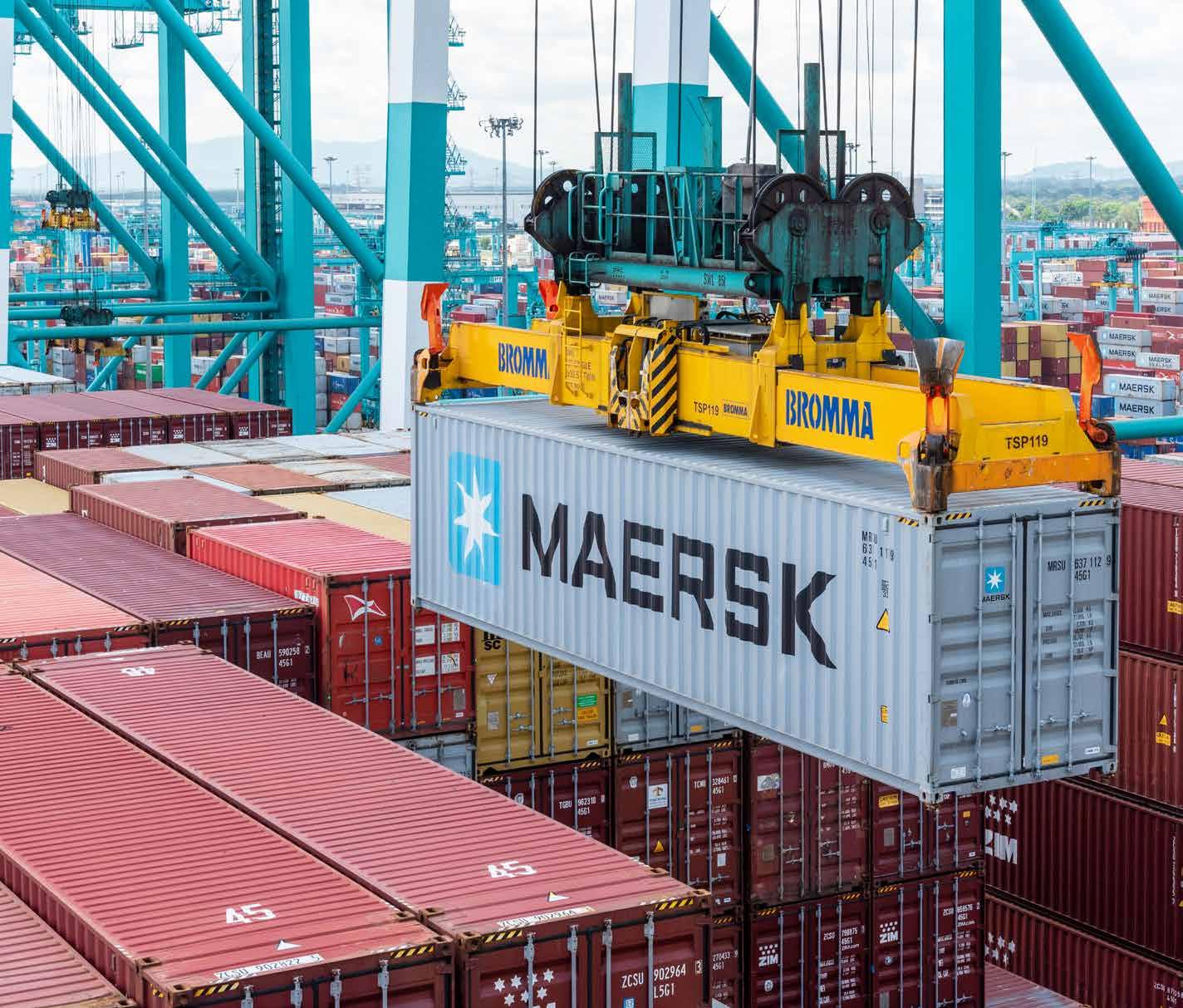
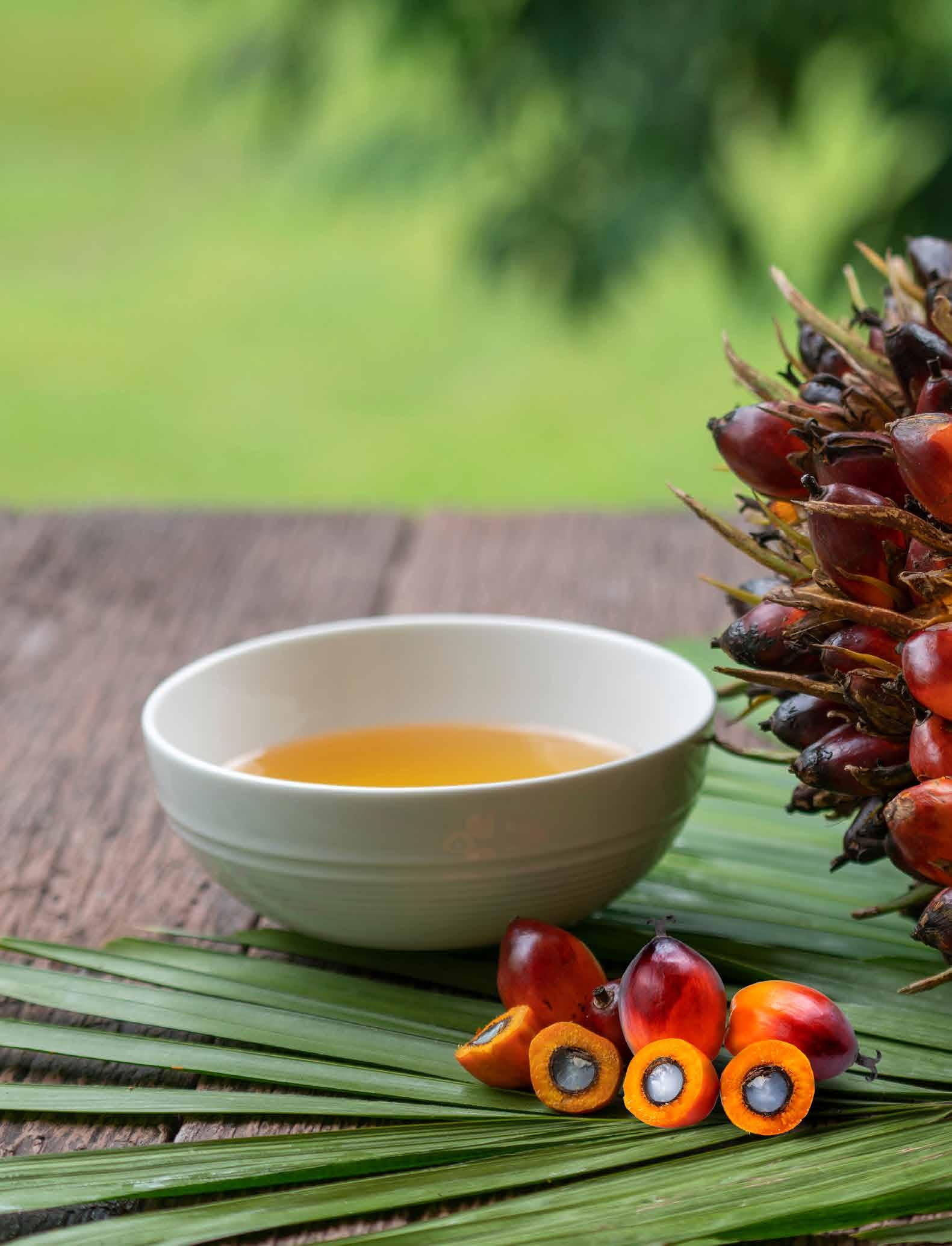
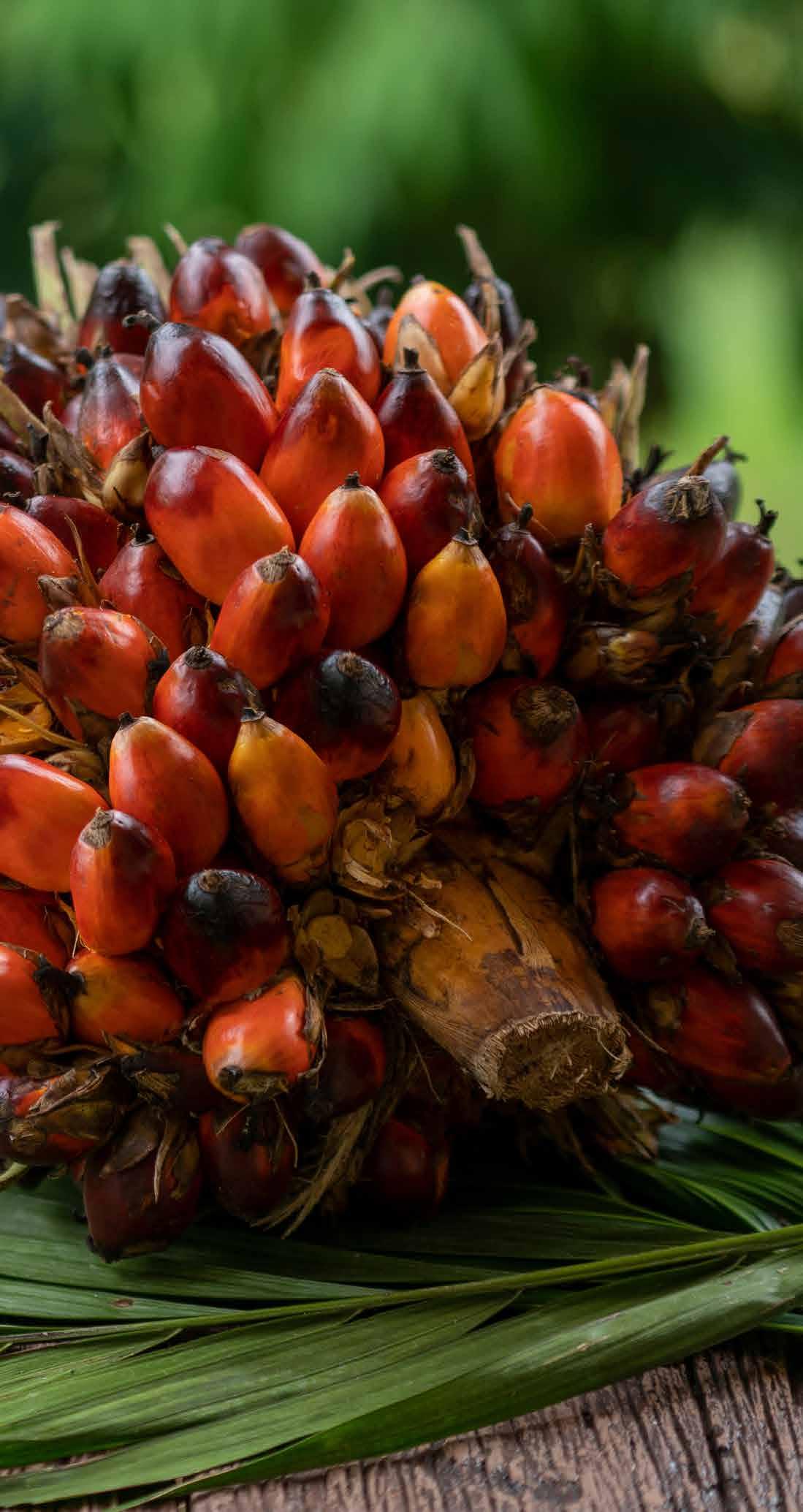
Malaysian Palm Oil Association
Palm oil has continued to play an increasingly popular role across industries worldwide, with the global consumption of palm oil reaching 78 million metric tons in 2023. Malaysia is responsible for producing more than 80% of this global supply and is currently the second leading producer of palm oil in the world behind Indonesia. Therefore, as such a lucrative and growing industry for Malaysia, the Malaysia Palm Oil Association (MPOA) was established to bring together all aspects of the industry and work towards ensuring its long-term profitability and stability by providing a single unified voice across the country’s palm oil industry.
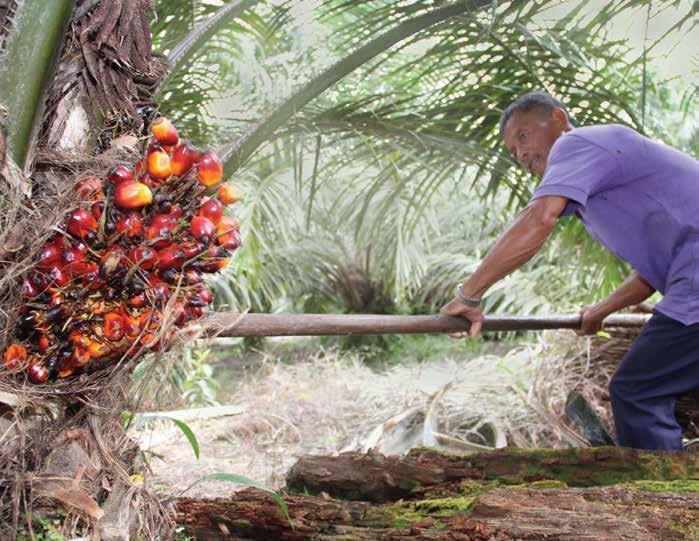
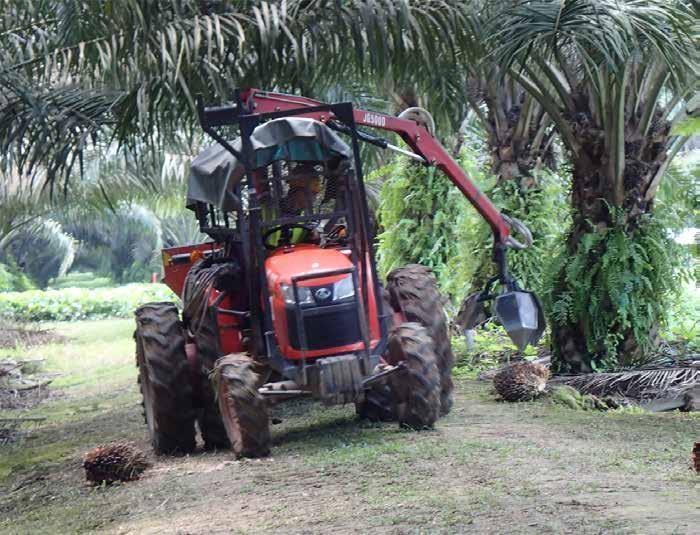
MPOA was established in 1999 as a unified voice for the palm oil industry in Malaysia, taking over from three large plantation sector associations: the Rubber Growers Association, the United Planting Association of Malaysia, and the Malaysia Oil Pal Growers Council. With the support of the government, MPOA unified these associations and councils into one overseeing body which would bring together all aspects of the industry from farming to the production and marketing of palm oil. Therefore, over the last 25 years, MPOA has played an important role in supporting the needs and interests of businesses, stakeholders and people working across the Malaysian palm oil industry. This support has ensured the continual synergy and development of the plantation industry on a national and international scale.
Under MPOA are a range of members who span the entire palm oil industry, these members include individuals and corporate bodies spanning across the crop plantation sectors which are planting and farming palm, rubber, coconut, sugar cane, cocoa, tea, banana and pineapple crops. These members play a vital role in ensuring that every step of the Malaysian palm oil and agricultural industry’s supply chains are represented from the planting, marketing and development of palm oil and associated crops to their harvesting.
To achieve this united voice for the palm oil industry, MPOA is governed by a council consisting of a Chairman, Vice Chairman, Secretary, Treasurer and 13 members. Across the council are three major committees which are working to control the developmental role of palm oil. The first committee is Stakeholder Affairs which oversees governmental figures and landowners across the industry. As part of this committee’s operations, it reviews federal and state laws and regulations, whilst lobbying proposals and presentations to enhance the industry for legislative and regulatory bodies. The second major committee under MPOA is the Sustainability, Research & Development Committee which is responsible for maintaining close relationships with research institutes such as the Malaysian Palm Oil Board (MPOB), to ensure that technical knowledge is made readily available across the industry. Through the support of
Murrin Corporation
In Murrin Corporation, part of the Danec Group, our philosophy is that inspired by you, we improve lives. This purpose drives us to perfect and develop the best materials in oil palm seeds.
With over 40 years in the market, conducting research and development alongside important institutions such as CIRAD in France, we have acquired enormous experience in constantly improving oil palm seeds and their various versions. Both E. guineensis (Dorado Plus) and interspecific hybrid OxG are genetically enhanced to provide great characteristics. A proven higher productivity, higher oil extraction rate, annual height growth of 20 to 25 cm which facilitates their management and harvesting cycles of 21 days are a few of the many benefits of our seeds. Making it an attractive and sustainable alternative for farmers.
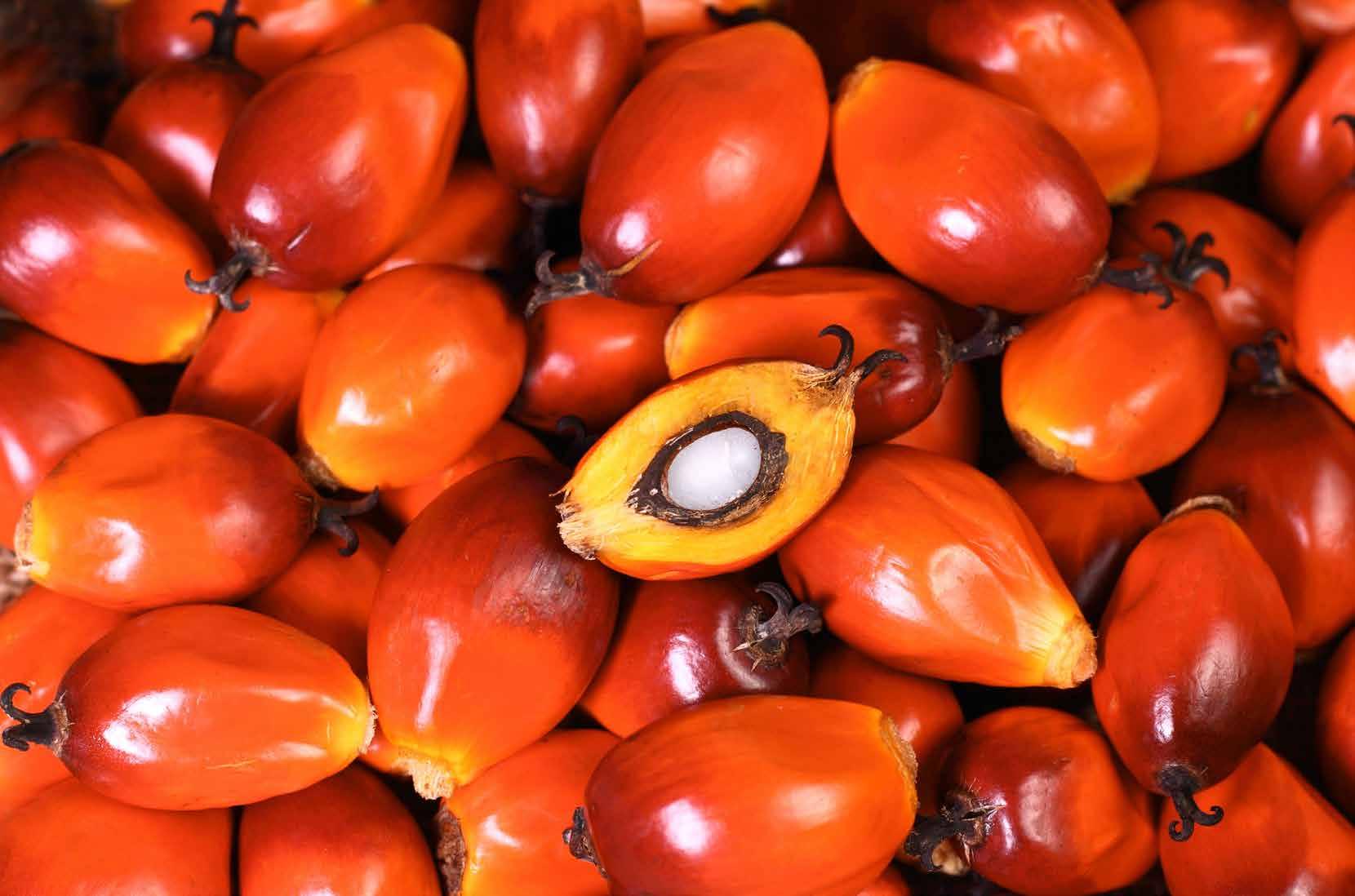
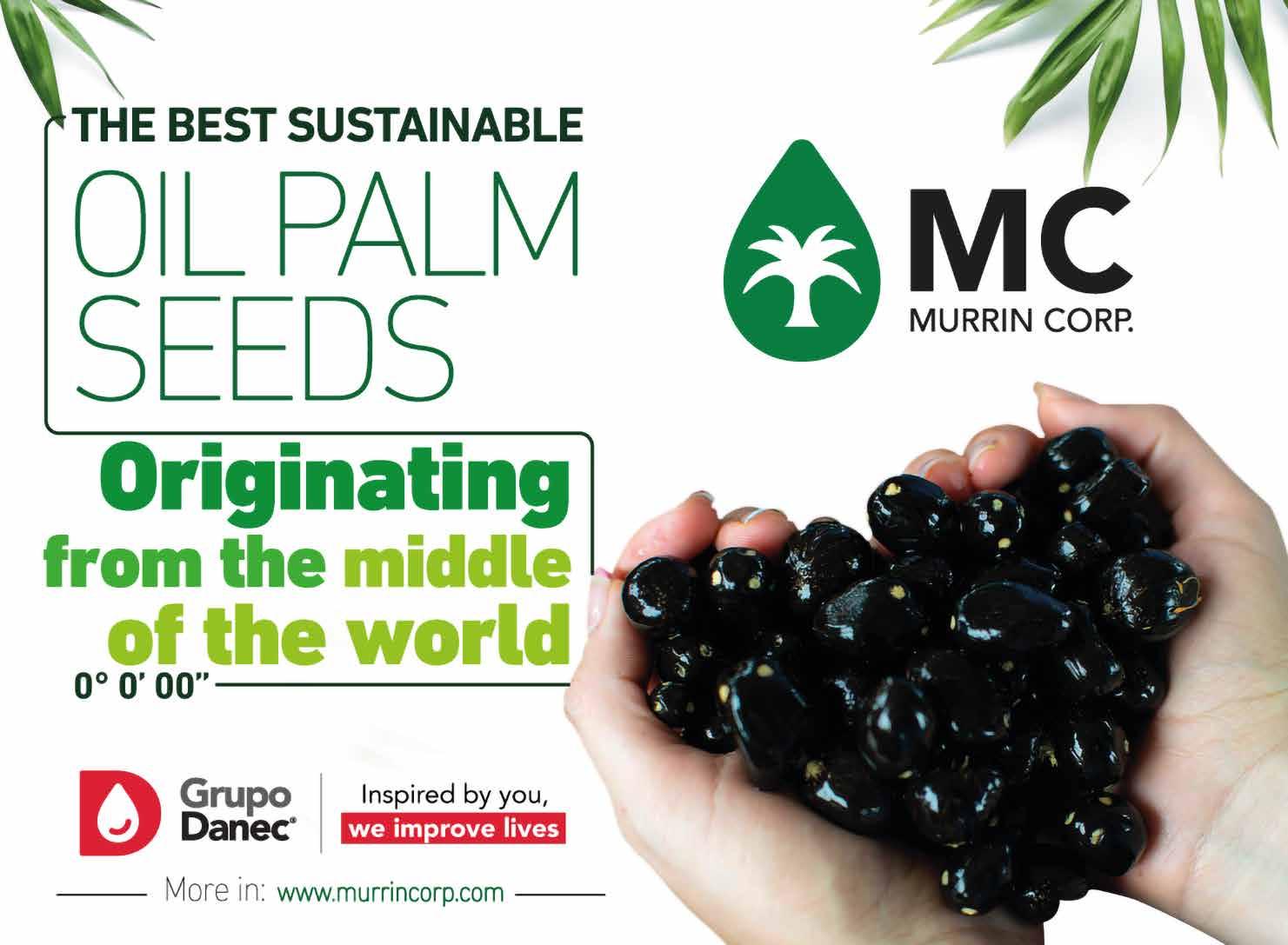
Malaysian Palm Oil Association
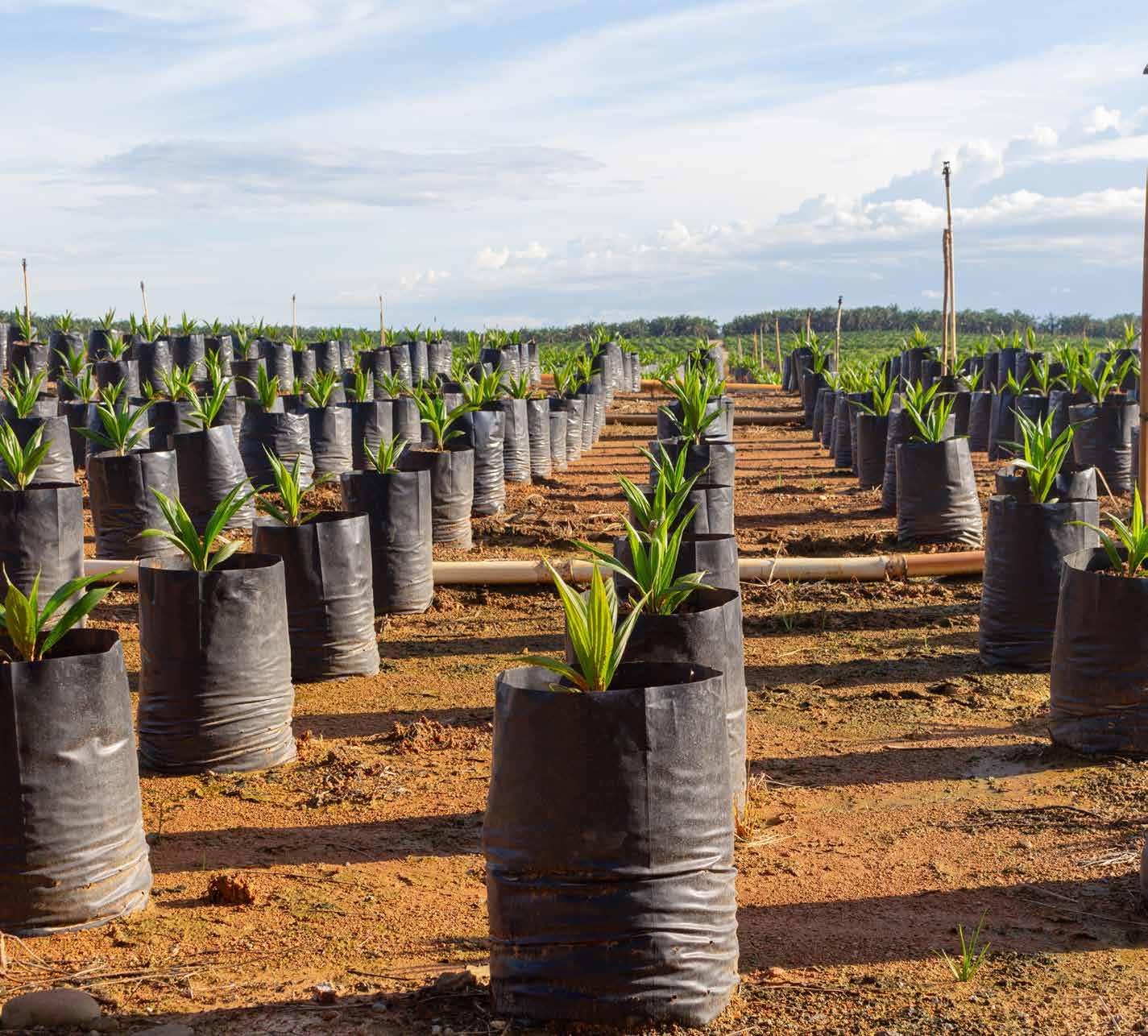
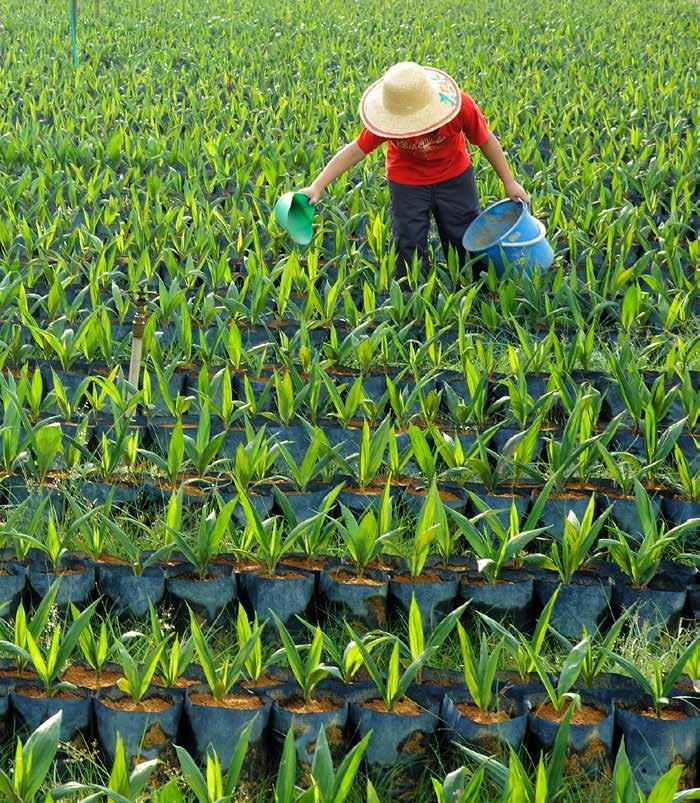
research and expertise, MPOA is continually pushing towards the development of the sector to meet the demands of the palm oil markets. A key part of this committee’s operation is towards sustainability as the palm oil industry has seen increasing pressure from environmental movements worldwide which are pulling away from palm oil usage due to its links to deforestation. Therefore, MPOA is focused on ensuring that all operations across the country make the most of every drop of palm oil produced while mitigating excessive environmental damage in the process.
However, the environment is continuing to play a vital role in the future of palm oil production as the kind of extreme weather we’ve seen across the world with both droughts and mass flooding has led to lower crop yield. With lower crop yield less palm oil can be produced, and so Malaysia’s ability to meet the global demand could be reduced. Therefore, the Promotion, Market Intelligence & Analytics Committee under MPOA are working to continue to
promote and enhance the image of Malaysian palm oil and its other commodities towards international markets by working with the Malaysia Palm Oil Council (MPOC) to ensure that it can continue to position Malaysia as a leading palm oil producer.
A key way MPOA promotes the palm oil industry of Malaysia is through working with vital players across the industry and providing a channel for which communication between research sectors, stakeholders, government officials and farmers is more readily available. By sharing vital palm oil crop information, farmers can produce greater yields, and then through the formation of vital relationships with stakeholders and government bodies, these can be marketed and supported by legislation to ensure that the industry remains a prominent and vital driver of the Malaysian economy.
As we have seen, MPOA plays a vital role in ensuring the long-term profitability of the Malaysian palm oil industry, by supporting farmers, research and networking between all the vital players across the industry. With a vast network of members under the Association, MPOA provides an essential unified voice to ensure that the infrastructure and development of the industry remain a priority concern for key figures across the country. As the industry looks to deal with climate change struggles and environmental pressures, we look forward to seeing how MPOA continues to bring a unified voice to the Malaysian Palm Oil Industry and how it continues to meet and sustain palm oil demands across the world.
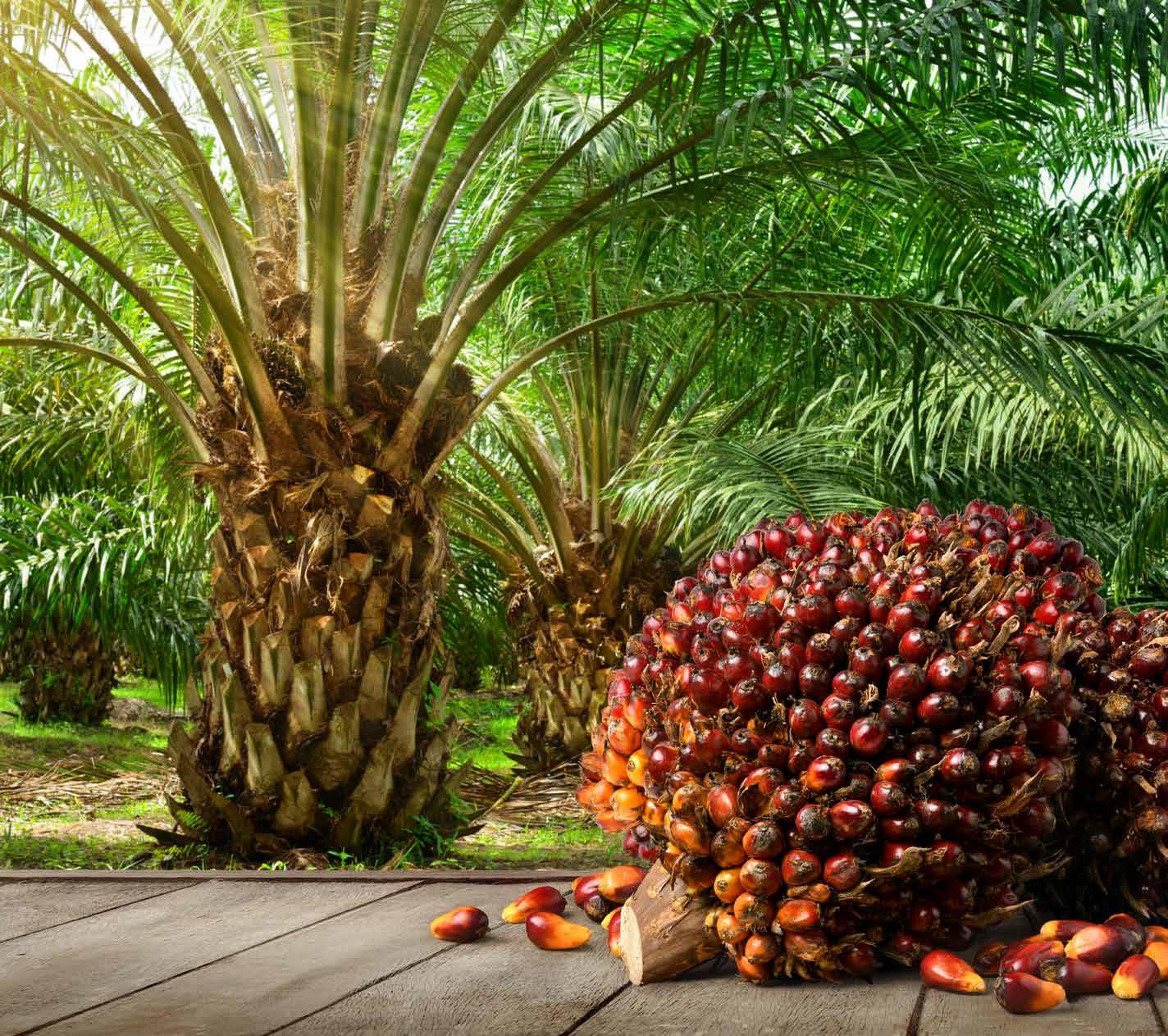
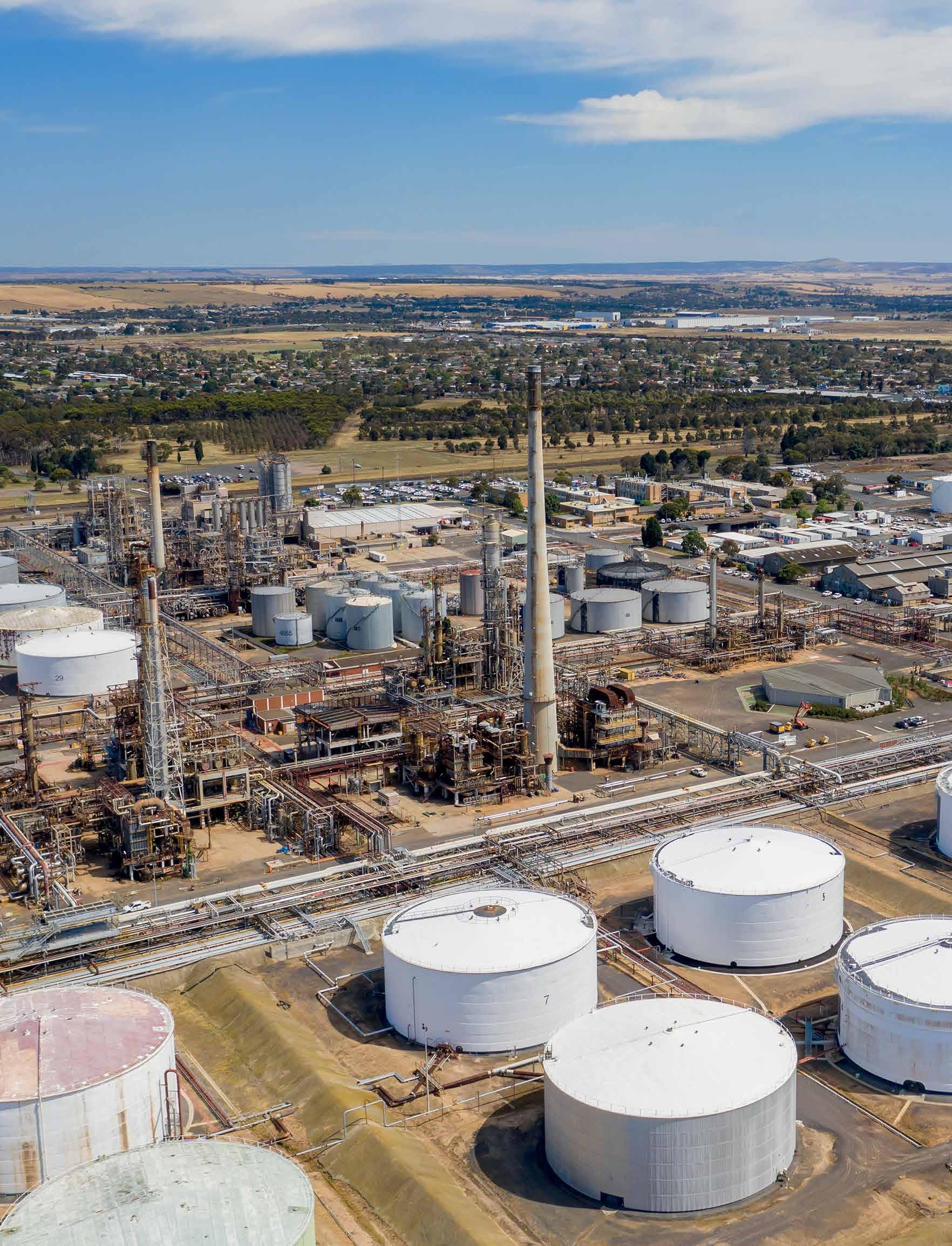
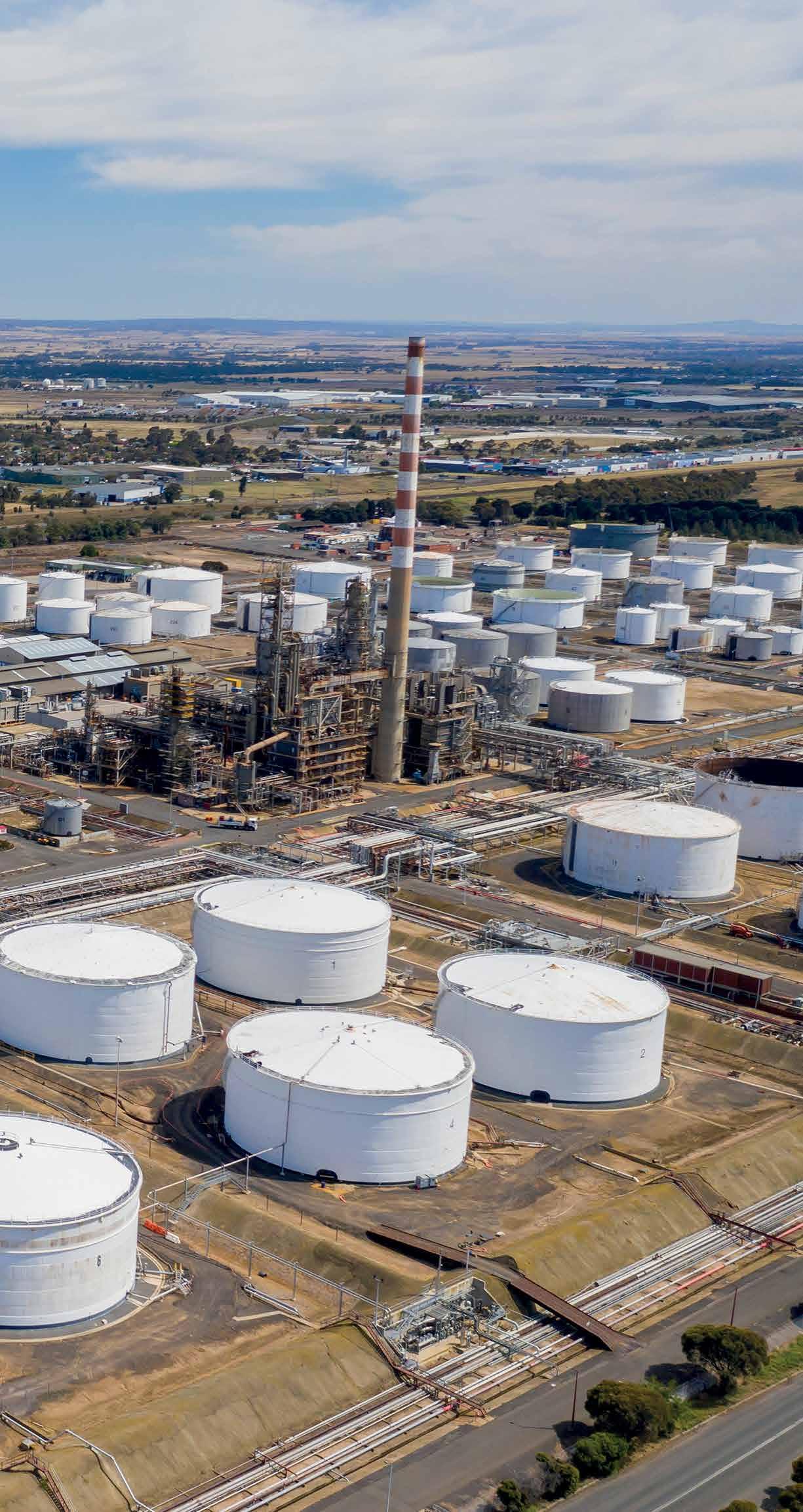
Clarke Energy Australia
Specialising in low-carbon, efficient, and flexible energy systems, Clarke Energy Australia delivers a range of energy solutions, with a focus on ensuring quality products, solutions, and services across a wide variety of sectors. Therefore throughout its operations, Clarke Energy Australia leads the Australian market through its complete engineering, procurement, and construction of its energy solutions. As a subsidiary of the global Clarke Energy company, Clarke Energy Australia is a leading provider of power generation and storage solutions across Australia, New Zealand and Papa New Guinea. Throughout every aspect of its operations, whether on a global or regional scale, Clarke Energy is committed to safety, quality, and the environment as it continues to serve its customers with quality products.
Clarke Energy began its operations in 1989 and has worked over the years to now be a world-leading company in the design, installation and long-term maintenance of gas and diesel engines for power generation applications. From this substantial base, Clarke Energy opened its Australian division in 2001 with its first premises in Adelaide which today is the head office for the whole of the global company’s South Pacific regions. Since 2001, the South Pacific region has grown expansively, and it is now an award-winning specialist in gas-fuelled technology with a whole range of engineering, project management, sales, service, ports, and administration personnel ready and waiting to serve its customers every need.

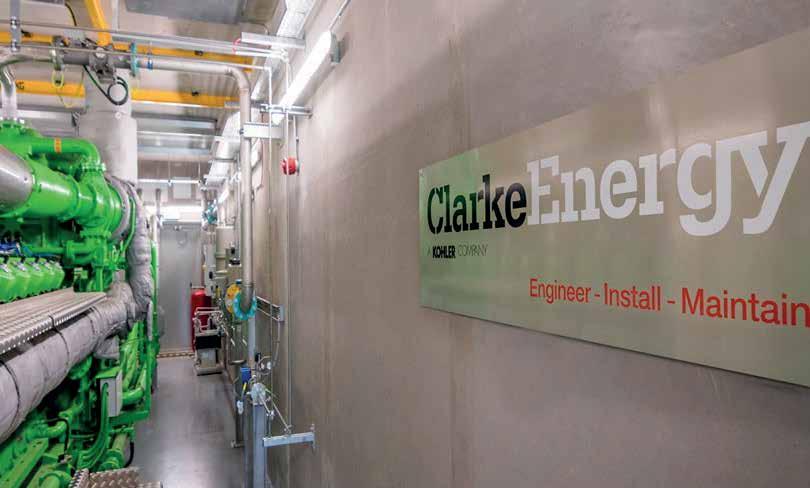
Clarke Energy Australia provides complete engineering, construction, and procurement (EPC) services to suit the supply and maintenance of gas engines or other power generation systems to help make its customers’ energy projects a reality. In engineering, it creates computer-aided designs and provides mechanical and electrical engineering to make these a reality through installation. For installation, Clarke Energy Australia has dedicated teams which help to bring these designs to life with their top-quality project management, installation, and commissioning of the entire energy solution. Once the company has designed and implemented a range of energy solutions it continues to add value to its business through the installation and maintenance of the system all under one company.
Clarke Energy Australia’s supply can range from the sale of a single engine, a completed combined heat and power plant, to a fully engineered power plant, as well as the integration of other power generation and hybrid or microgrid solutions. The vast array of solutions that Clarke Energy Australia offers all under a single company allows them to follow every project from concept to its implementation and maintenance to ensure that customers are receiving solutions which are best suited to their needs. Then, all of the EPC will be completed by the company which boasts over two decades of expertise in the field, and a whole host of substantial projects behind them. Clarke Energy is a part of KOHLER Energy, which means that throughout its energy systems, the
Energy Solutions for Every Situation
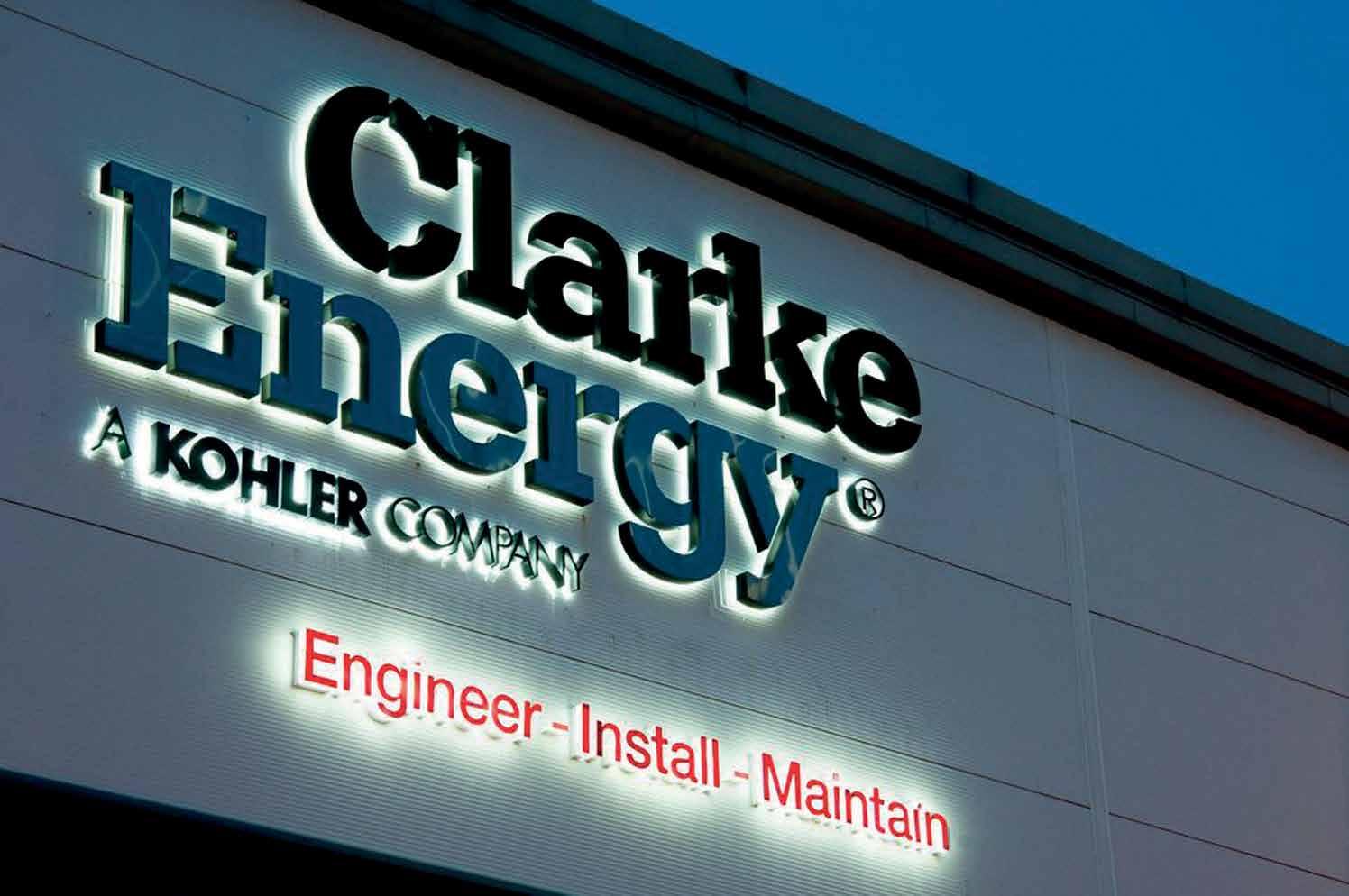
company can deliver a range of KOHLER’s gas engines, biogas upgraders, battery energy storage systems, carbon dioxide captures and heat pumps. However, Clarke Energy Australia is also the largest and sole authorized distributor and service partner for INNIO Jenbacher gas engines in Australia, which along with the KOHLER systems, has established the company as a key player in energy solutions providing top-quality engines.
Already within its portfolio are many turnkey power stations in remote areas, and now it has over 20 years of experience across such a vast array of applications and conditions that for energy solutions, Clarke Energy Australia is the leading choice to meet and exceed its customers’ needs. This has been seen with Clarke Energy Australia undertaking a range of energy solutions across the mining, oil, and gas industries to deliver efficient, low-carbon energy solutions that are uniquely suited to the needs and conditions of its customers.
Clarke Energy Australia provides gas engine fuel sources to the mining sector which can accept a variety of fuels including natural gas, coal bed methane, coal steam gas, liquified natural gas (LNG), diesel and crude oil. These allow mining facilities to remain resilient and functional whilst
improving efficiency which in turn hopes to reduce carbon dioxide emissions. Then for the oil and gas sector, Clarke Energy Australia engineers, installs, and maintains a range of solutions for oil and gas wells, hydrocarbon separation plants, drilling rigs, gas compression plants, dehydration stations, and oil treatment plants.
In recent news, Mineral Resources Limited (MinRes) has chosen Clarke Energy Australia as its preferred partner for a second project. The two companies reached an agreement on a new 26.9-megawatt (MW) power station for MinRes’ Onslow Iron Project. The work will take place in Ken’s Bone Mine which is planned to produce roughly 35 million tonnes of iron ore per year. The mine is expected to commence operations in June 2024, and Clarke Energy Australia will design and supply mine and process-related infrastructure. This will enable the processed ore from the mine to be hauled by private road to Onslow, where port operations will transfer the product to transhipment vessels destined for international markets.
Clarke Energy Australia

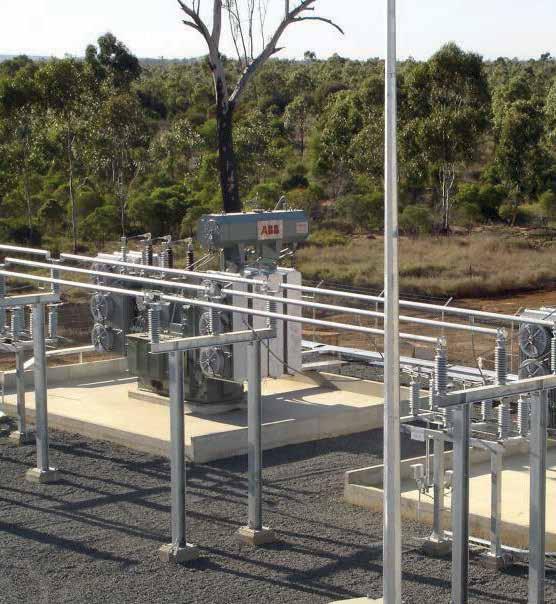

Experts in Industrial Electrics
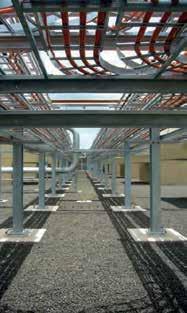
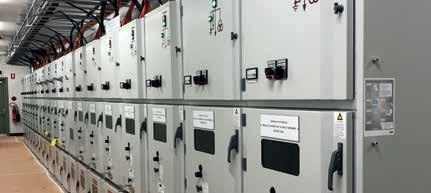
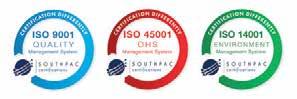
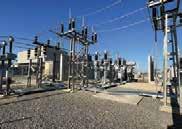

Therefore, the contract will see Clarke Energy complete a ‘power wrap’ of the Ken Bone Mine and port which will feature tailored solutions at both ends of the operations. 9 Jenbacher J420s will supply the highly variable load of the Onslow port operations whilst 8 J620s will power the comparatively high load transients of mining operations 150km inland. One of the key aspects of Clarke Energy Australia’s operations is ensuring that its solutions are futureproofed for hydrogen. All of the Jenbacher Series 6 engines can operate on up to 25% blended H2/ CH4 without the need for retrofits or special orders. Furthermore, from 2025 direct injection options will be available through Clarke Energy Australia which will achieve 100% H2 operations to help move industries towards a future of decarbonisation in and across supply chains.
Clarke Energy Main Board Director and Australasia Managing Director Greg Columbus commented in the MinRes and Clarke Energy Australia press release announcing the partnership that “From our humble beginning in Australia 25 years ago it is very pleasing to see growing recognition amongst WA Tier 1 miners and energy producers for the Jenbacher 6 Series generator and the exceptional quality of our design and builds in remote, islanded applications”. Greg Columbus highlights the expansive and widely recognised role that Clarke Energy Australia plays across the industry as it continues to build on its portfolio of projects across the mining, oil, and gas industries.
Overall, Clarke Energy Australia is an all-inone engineering, procurement and construction company that provides pivotal energy frameworks and solutions to help establish reliable energy infrastructure that suits and supports its customers for now and in the future. As Clarke Energy Australia continues to develop its implementation of engines that are future-proofed, it looks set to grow expansively as the company moves both its customers and its operations towards a future of decarbonisation – an essential move for the mining, oil and gas industries which so often use natural resources. Therefore, throughout Clarke Energy Australia’s systems and solutions, it is providing efficient solutions which are actively working to help its customers’ projects and move the energy industry towards a world of reduced carbon emissions.
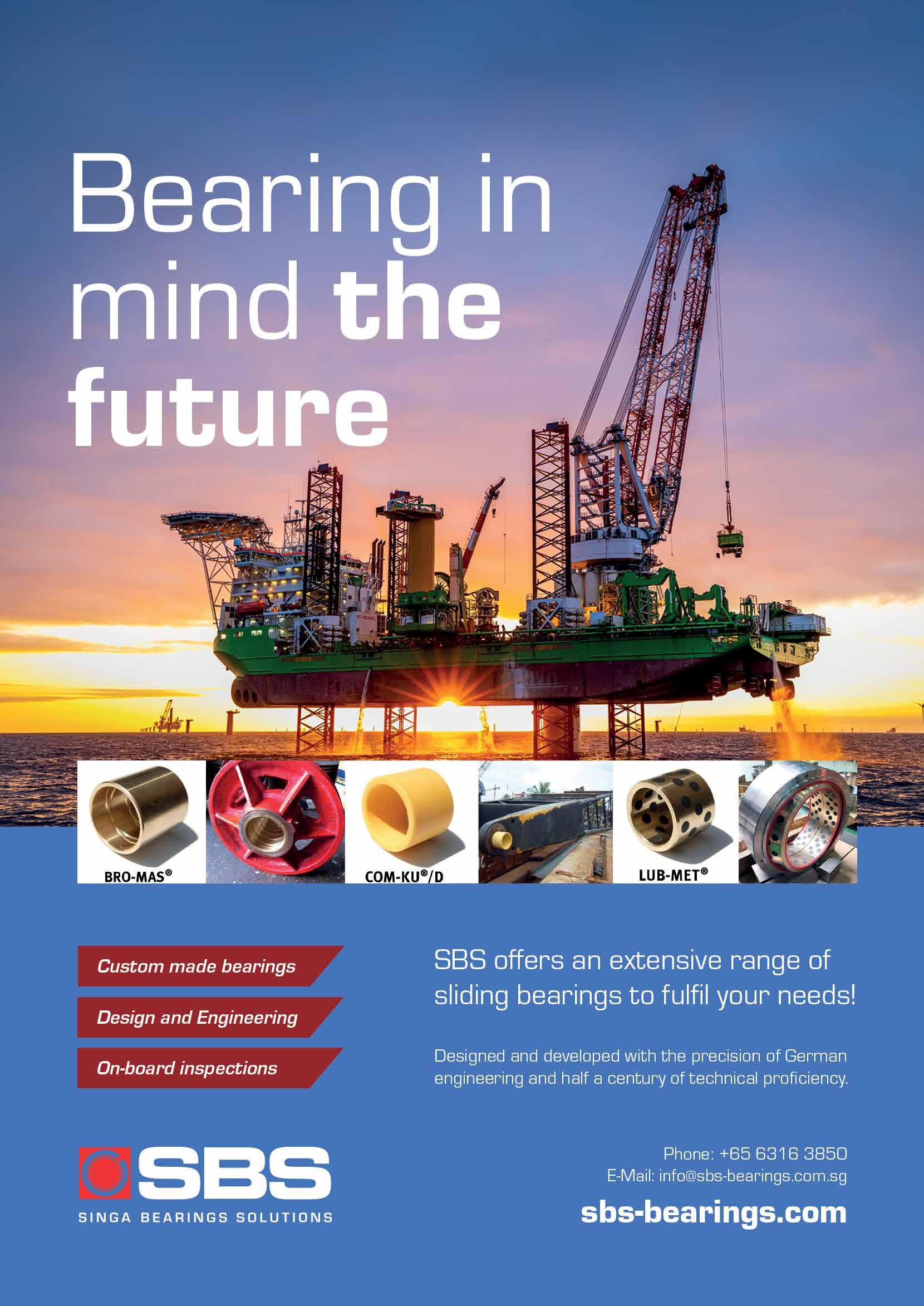
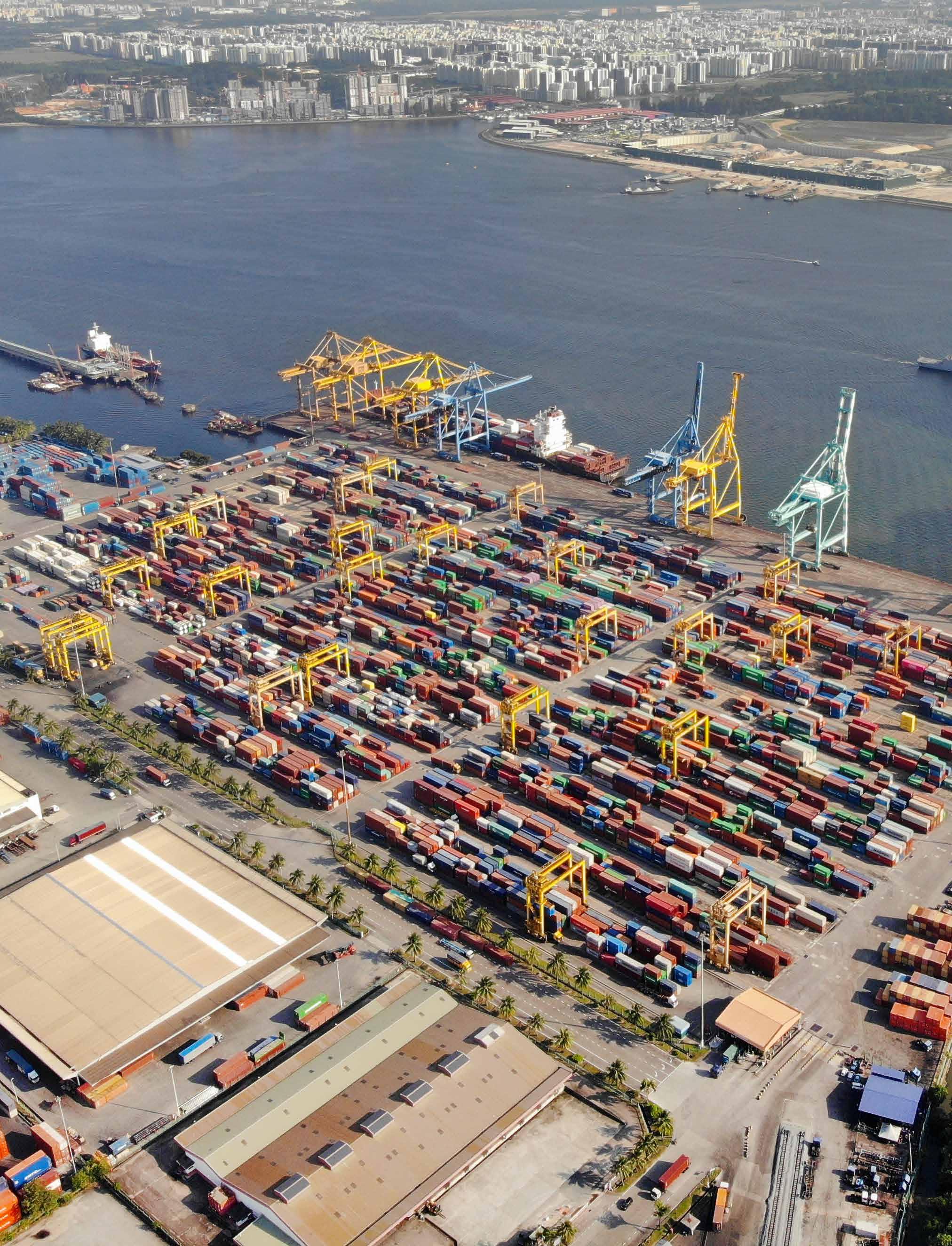
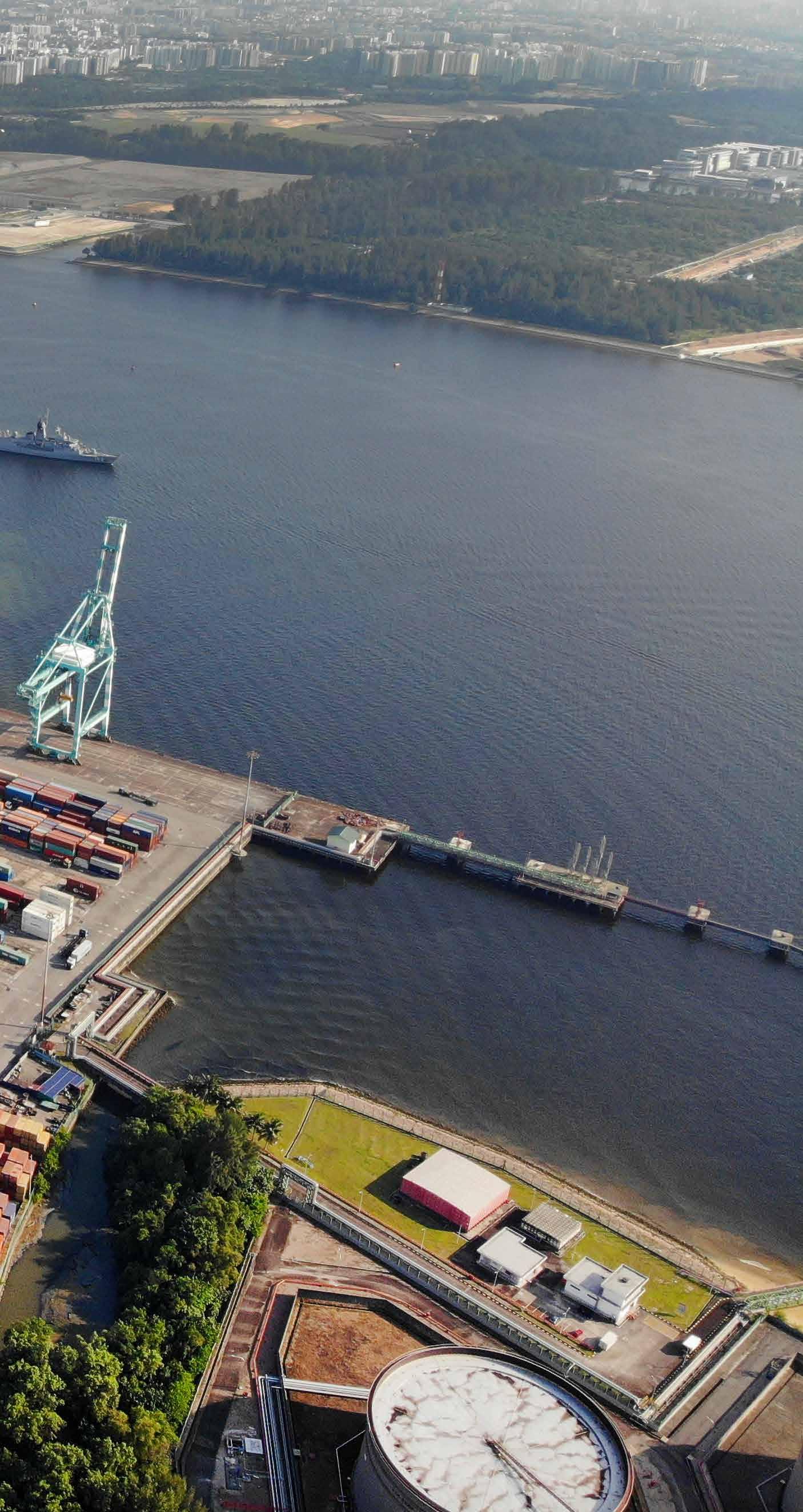
Located on the southern tip of the Malaysia Peninsular, Johor Port Berhad provides vital maritime services to vessels travelling along the coast and porting in Malaysia. With more than 100 acres of land, the port serves as a vital hub for the shipment of some of the country’s vital industries spanning the petrochemical, engineering, furniture, telecommunication, electronic goods and food products markets. Therefore, with the Port on a mission to become the most efficient integrated multi-purpose port in the region, Johor Port continues to invest in its service to remain ahead of the game with cutting-edge solutions designed to revolutionize the market.
Johor Port Berhad, a member of MMC Group, has long played a valuable role across the Malaysian shoreline located just 32km from Johor Bahru city centre, and close to the 8000 acres of the Pasir Gudang Industrial area. The port, built by the Johor Port Authority, was the first port developed in Johor and saw continued development to expand its facilities to reach new and lucrative markets. A key development for the port came in 1977 following the development of a Breakbulk Terminal and Liquid Edible product Jetty. These facilities allowed for the expansion into the edible oil markets, a market that is vital for the port because it is now one of the largest states producing palm oil in Malaysia. Therefore, with the development of the terminal and jetty, the port became an essential port for oil refiners who have continued to use the port for over 40 years as a key gateway for delivering oil products across the world. In addition to this, the port has its own free trade zone, making it a valuable route for all types of cargo shipments to make the most of the economic advantages of the port and not face additional taxes.
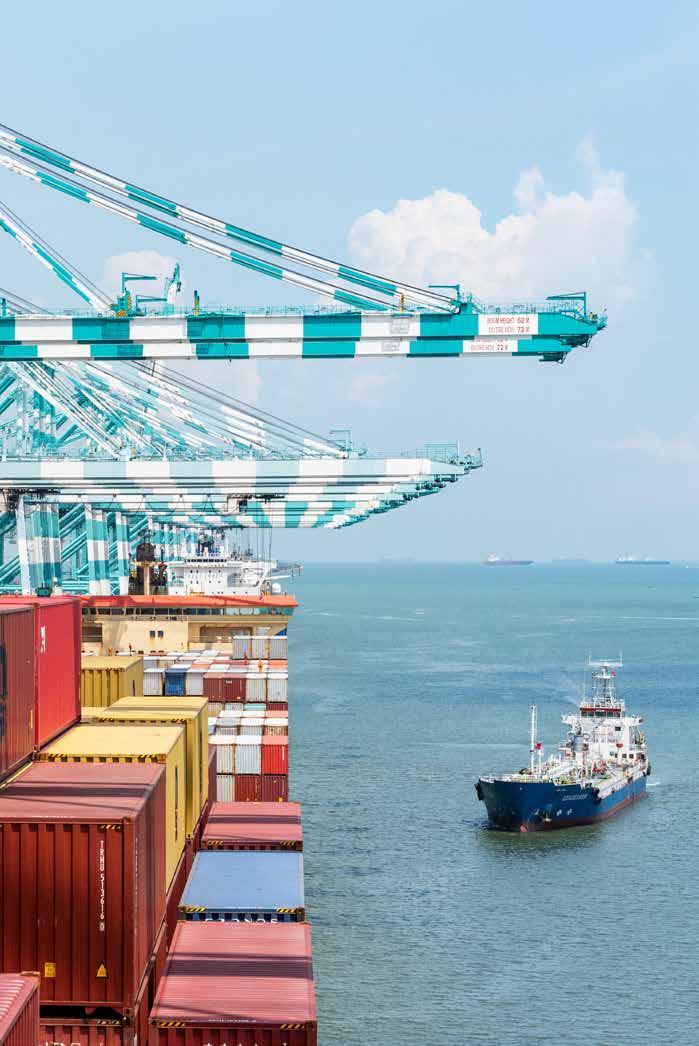

A Strategic Hub for Maritime Development
Johor Port Berhad is committed to providing customer-friendly solutions that are costeffective, and play a valuable role in the import and export activities of Malaysia and its neighbouring countries. Across 3 berths and 700 metres of quay length, the port has a max capacity of 1.45 million twenty-equivalent units (TEU) serving major shipping lines every day. Additionally, the port has Dry Bulk Terminals and Break-Bulk terminals which handle cargo ranging from non-edible dry bulk to general, project, heavy lift and even gas-related cargoes.
The port has the largest palm and edible oil terminal in Malaysia which helps manage the country’s large palm oil production and exports across the world. Malaysia is a leading palm and edible oil producer, and so Johor Port Berhad has developed specialised facilities to cater to liquid bulk cargo. This includes the vital equipment to load and unload edible oil, petroleum, and even petrochemicals. The cargo is then sent to different
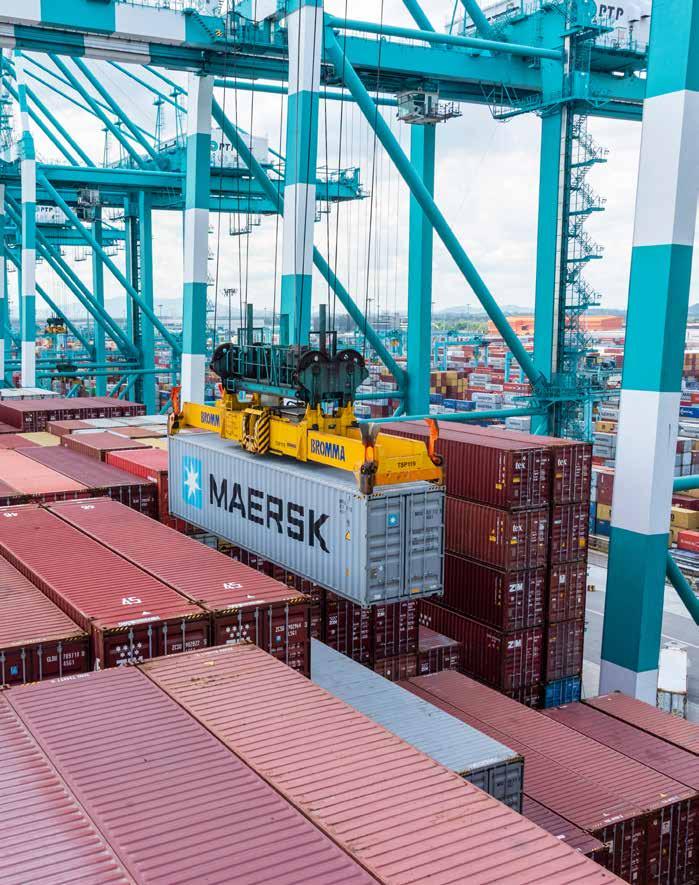
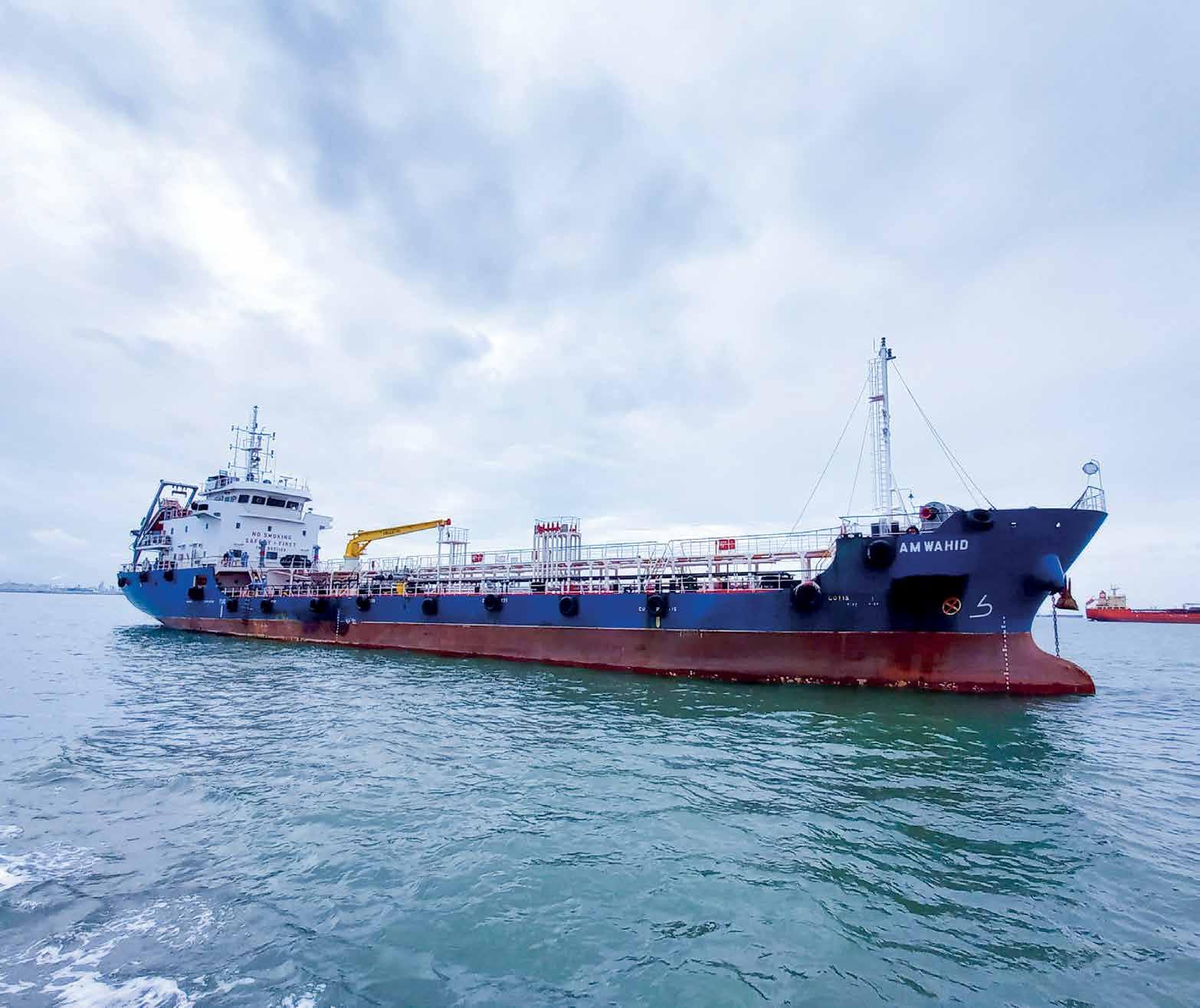


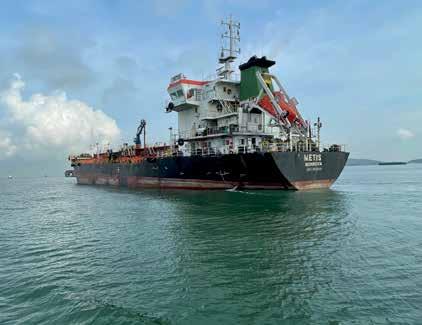
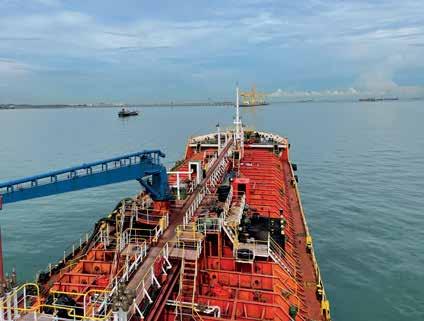
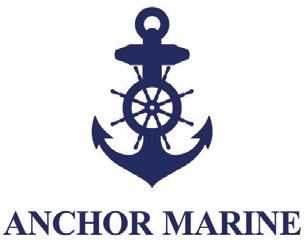
Johor Port Berhad
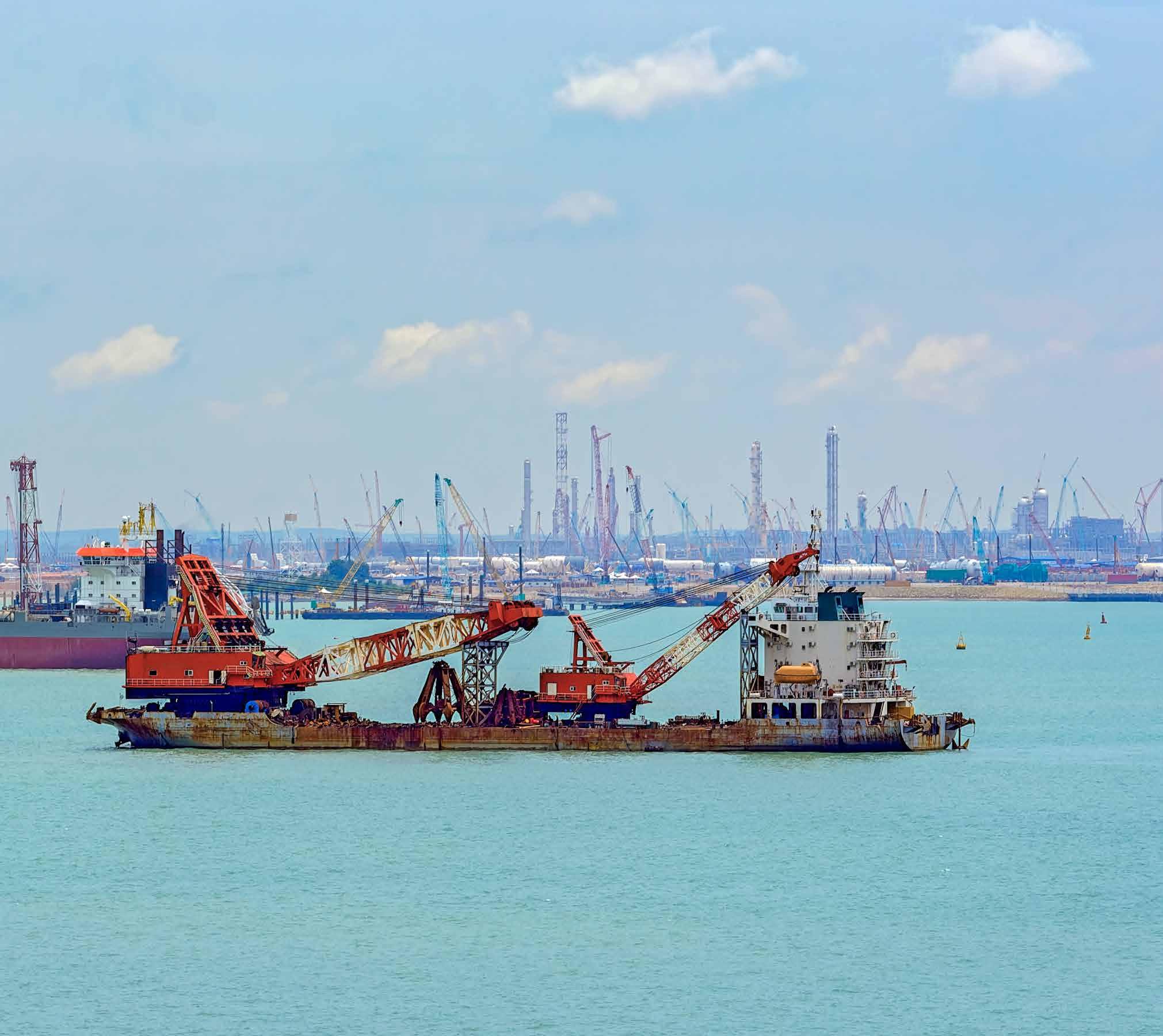
facilities depending on whether it is edible or non-edible oils. These types of cargo can then be stored in the terminal tank farm with almost 1 million megatons (MT) in capacity.
As a hub for Malaysian exports and imports, the port also delivers vital marine services to vessels with pilotage, bunkering, transhipment, towage, berthing, and vessel traffic monitoring. However, a vital service Johor Port Berhad offers is its Offshore, Inspection, Maintenance and Repairs Centre (OIMRC) which provides a comprehensive scope of services and facilities directed towards the oil and gas industries. This includes manpower supply, onshore equipment, parts mobilization/ demobilization, maintenance and repairs.
Once cargo reaches the port, Johor Port Berhad facilitates complete logistical services, many of which are made possible through its One Stop Total Logistics Centre. Johor Port Berhad provides innovative, customizable and competitive logistics solutions and packages to its customers every
day, which help to support customers in delivering their business operations more smoothly. As part of this, it facilitates inventory and supply chain management, shipping freight arrangement and storage solutions. In all of these areas, Johor Port Berhad aims to deliver cost-effective solutions which meet and exceed its clients’ expectations, whilst building its reputation as a key logistics and supply chain manager across Malaysia.
A key way that Johor Port Berhad remains ahead of its competition across Malaysia is through its implementation of technology across every aspect of its operations. The implementation of ICT has remained a crucial aspect of its planning and execution of day-to-day operations, including the development of multiple systems. These systems include the Johor Port Container Terminal System (JCTS), Multi-Purpose Terminal System (MPTS), Free Zone Information Processing System (FZIPS), Vessel Clearance System (VCS), Marine Service System (MSS), and Port Safety Management System (PSMS).
A Strategic Hub for Maritime Development
These systems work across the Port to provide a fully integrated and seamless operations, which ensure that every person interacting with the port is met with the same top-quality services supported by reliable, secure and efficient technological systems.
As Johor Port Berhad moves towards a more technologically advanced future, it recently announced the development of a Port Access Management System (PAMS), which is designed to revolutionise the process for gate and permit access. It will streamline the application process for vessels and feature enhanced security measures to safeguard the port and its users. Additionally, the online platform will make the process more userfriendly to make applications easier to submit. With the development of digitalisation and technology across its operations, Johor Port Berhad can
continue to meet the growing demands of the port and remain a key multi-purpose port facility serving the growing export and import markets of Malaysia.
As we have seen, Johor Port Berhad is a thriving port that plays a vital role in the development of the country’s shipping industry. With a particularly vital role in the movement of edible and non-edible cargoes, the port serves Malaysia’s import and export industries, and so throughout every aspect of its operations, it is striving to position the port as a vital hub for accessing Malaysia’s diverse markets. However, what remains the same throughout every aspect of its operations, is Johor Port Berhad’s commitment to delivering customer-focused solutions. It is this commitment which has allowed it to firmly solidify its place as one of the most reliable, efficient and integrated multi-purpose ports in the region.
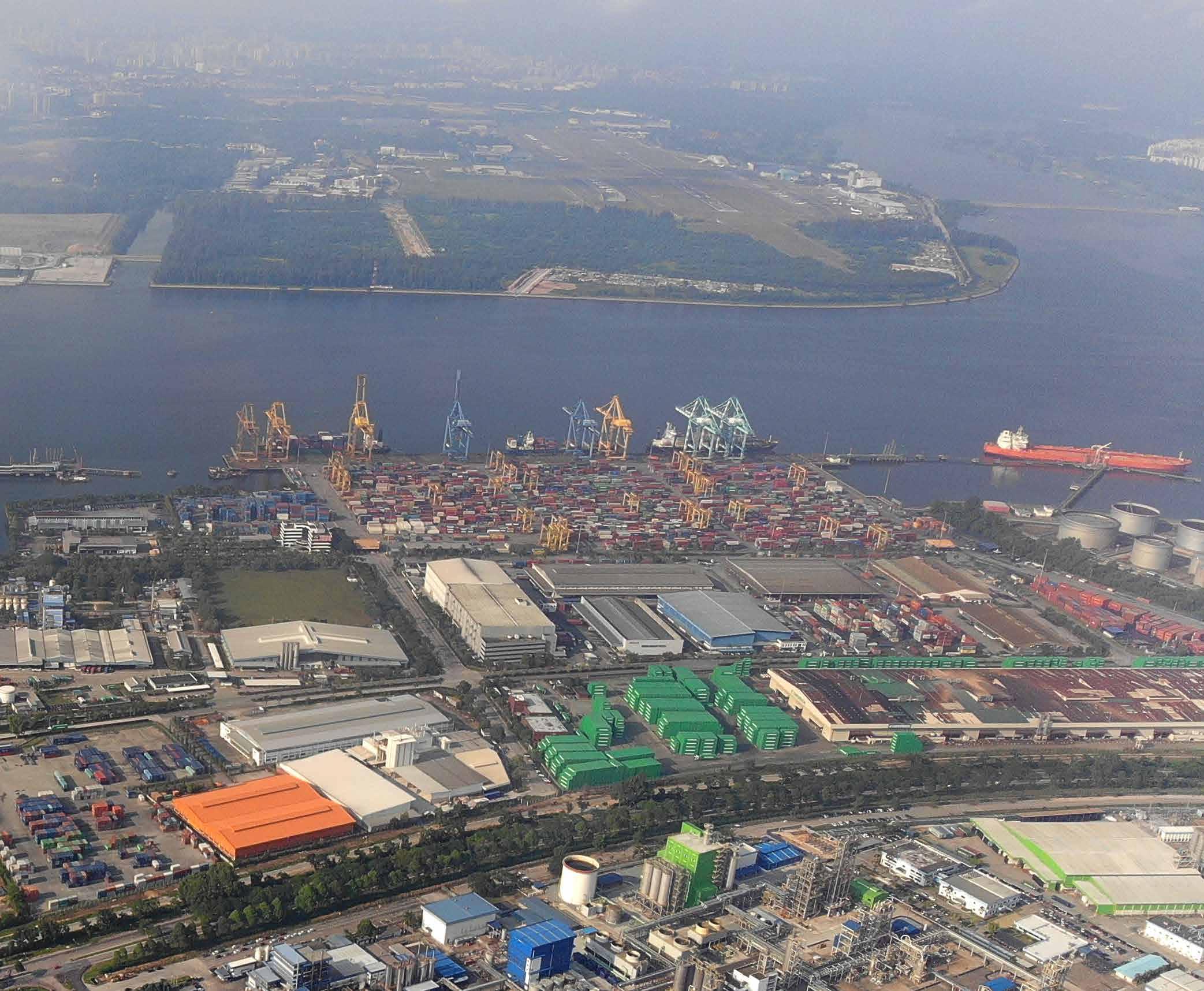
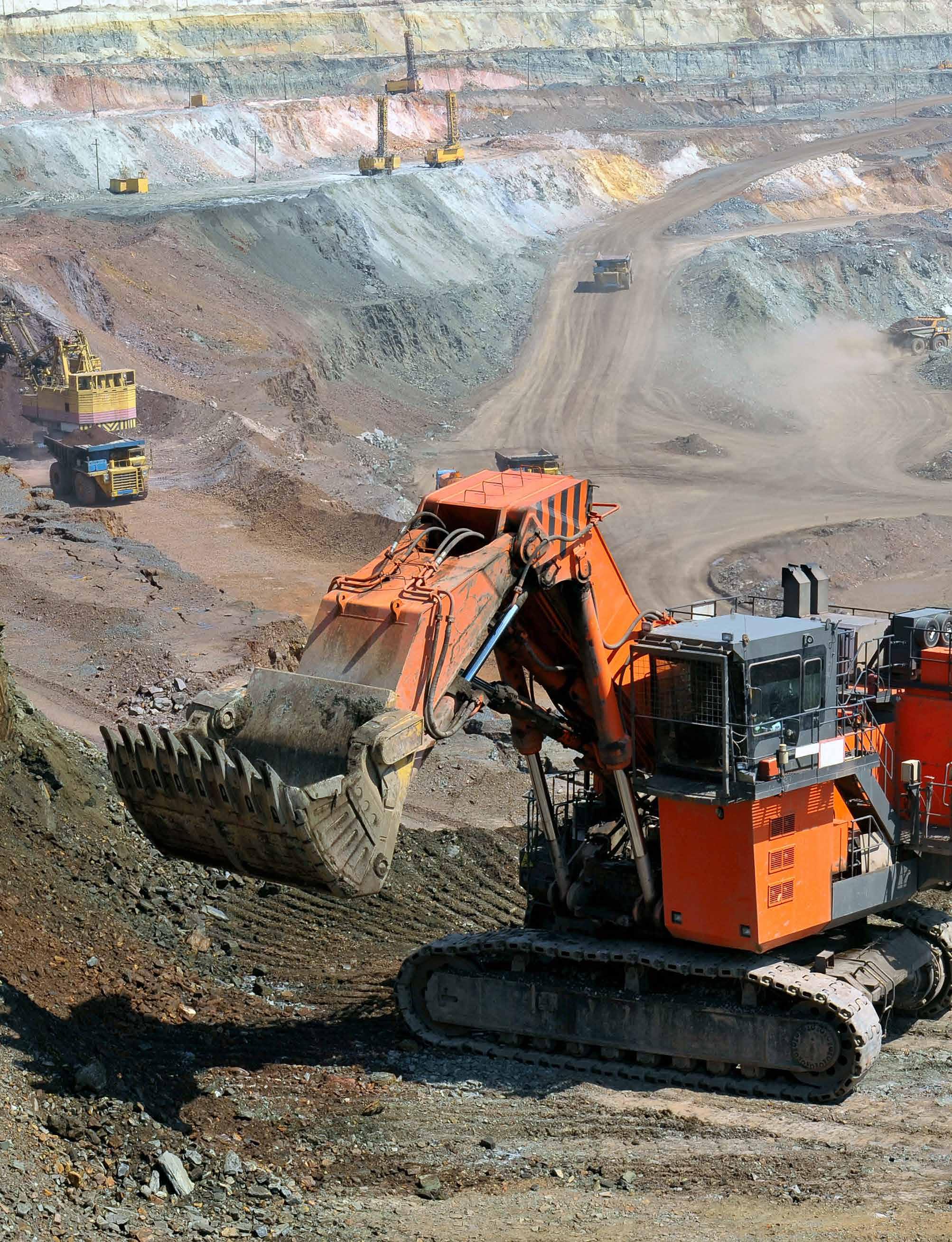

The demand for green energy has seen a vital increase over the last few decades, as companies worldwide take on the responsibility to reduce emissions and build infrastructure better suited for a carbon-neutral society. However, many of these vital infrastructural developments, including the development of renewable energy, electric vehicles and sustainable farming, require mined metals and minerals. This a tricky balance to play for companies, who seek to drive the world towards the energy transition whilst also participating in the necessary mining activities required to source such resources like copper, nickel and iron. However, companies like BHP are world leaders in these resources but operate with a key focus on building a better and cleaner future to support the renewable energy industry and the planet.
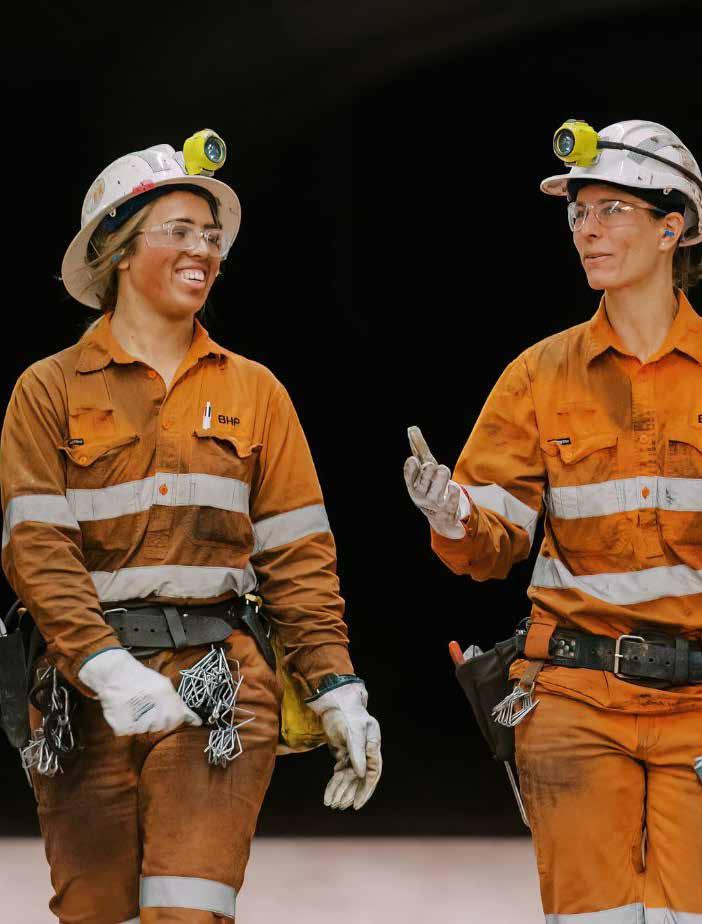
BHP is a world-leading mining company, which produces iron ore, copper, metallurgical coal and nickel, as well as potash. Its operations span the globe and include a complex portfolio of large, long-life quality assets which are focused on delivering value as well as sustainability. BHP is focused on the need for decarbonisation efforts to take effect immediately, so have established themselves as a responsible body that manages commodities which are vital in the development of a renewable energy future.
To understand the valuable role BHP plays we must understand the role of each of the metals and minerals which they mine and the role they play in energy transition targets. Iron ore and metallurgical steel are vital for the development of global infrastructure, and so are crucial resources needed to support the future implementation of renewable energy on an infrastructural level. Copper and nickel also play a vital role in making renewable energy possible, with copper covering the vast majority of electrical wiring. Nickel is a prominent metal used in the development of rechargeable batteries which are used in electric vehicles worldwide.
A crucial aspect of development for BHP in recent years has been towards potash, which is utilised across the agriculture industry to see higher crop yields which contribute to the production of biofuel on an international scale. Therefore, these metals and minerals are crucial throughout all of BHP’s work to ensure that their mining, processing and transportation services for these products are always working towards the betterment of the future of the planet.
BHP manages some of the world’s most resilient long-term portfolio assets which continue to grow in value thanks to the company’s discovery explorations, development of resources and acquisition of assets. Across its array of assets and mine operations, BHP develops and implements mining operations and then oversees the processing and refinement of ore before it transports these resources to customers. In addition to the mining, processing and logistical movement of the resources, BHP also focuses on waste management to ensure that its environmental impact on the planet remains at a consistent minimum.
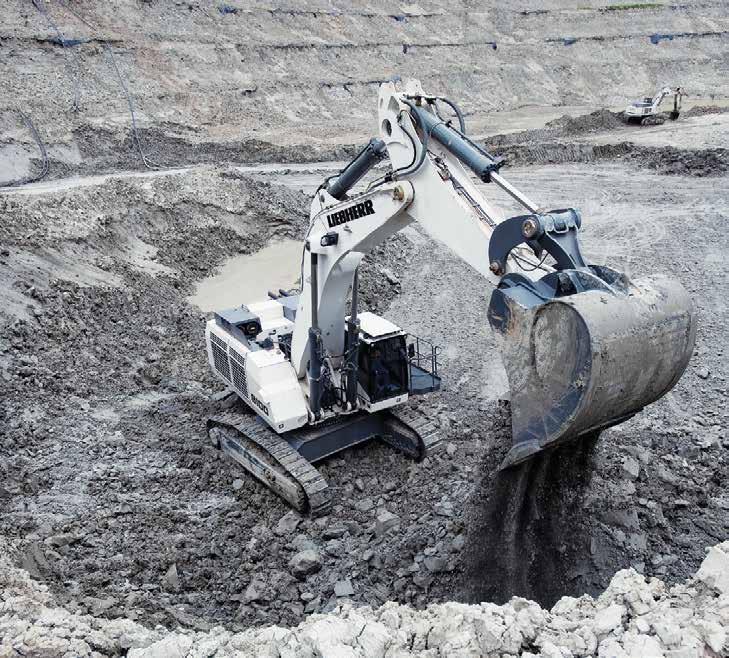

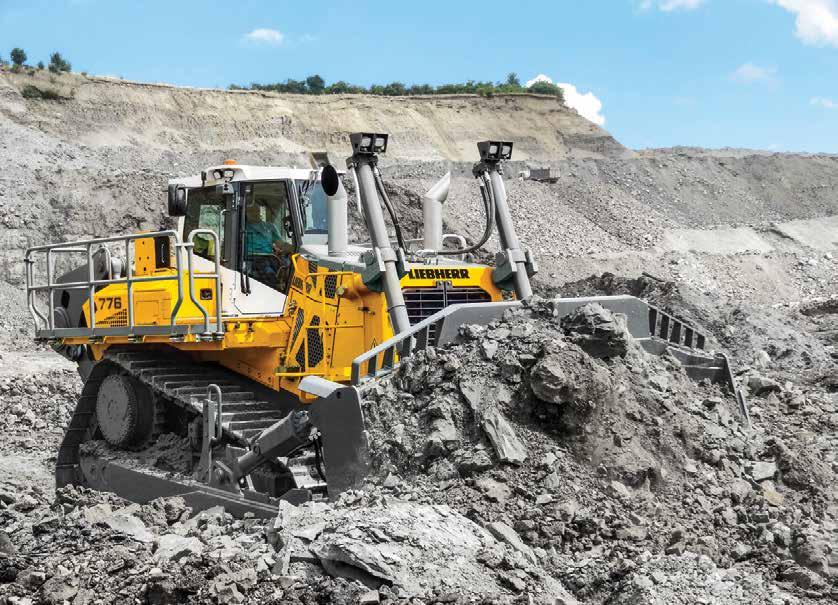

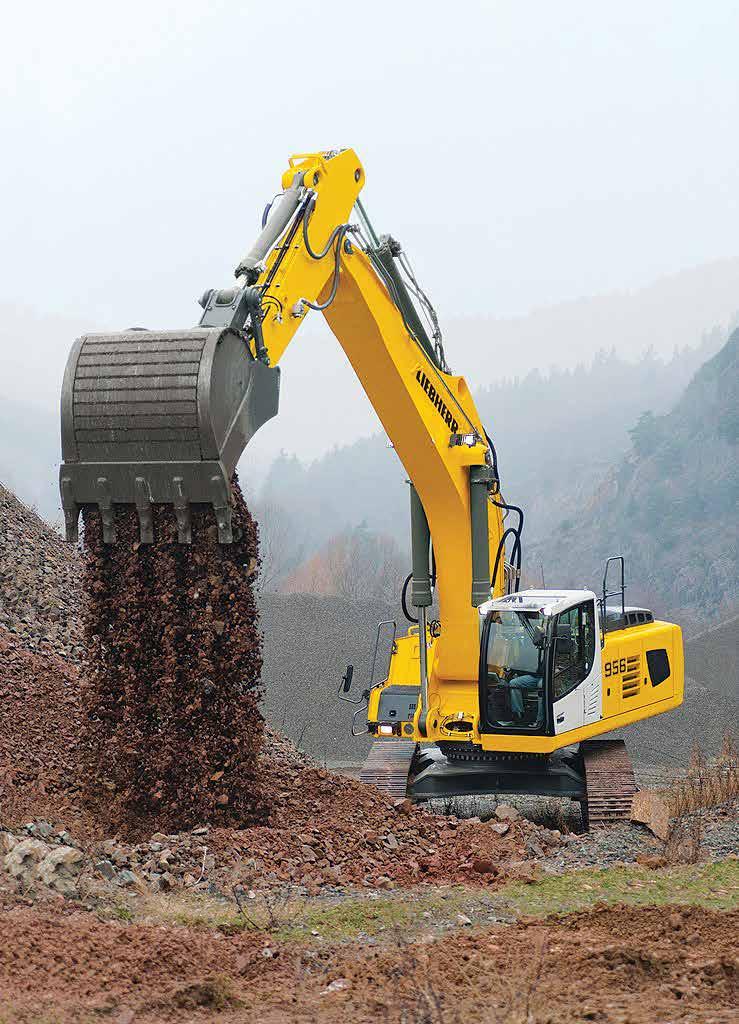

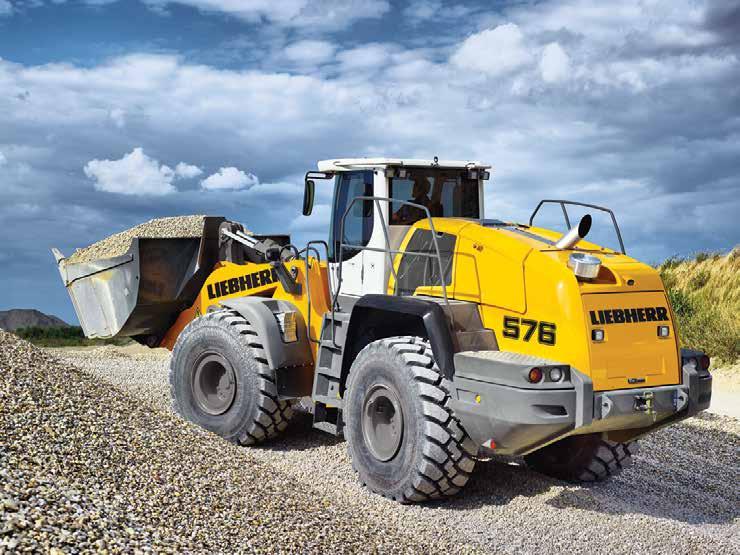
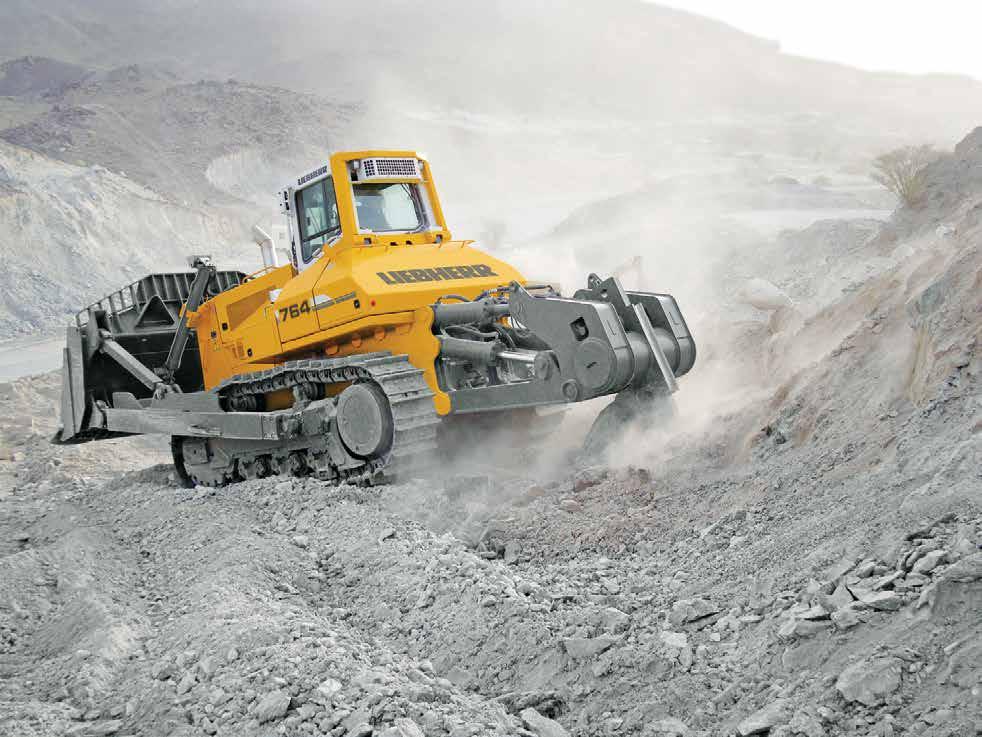
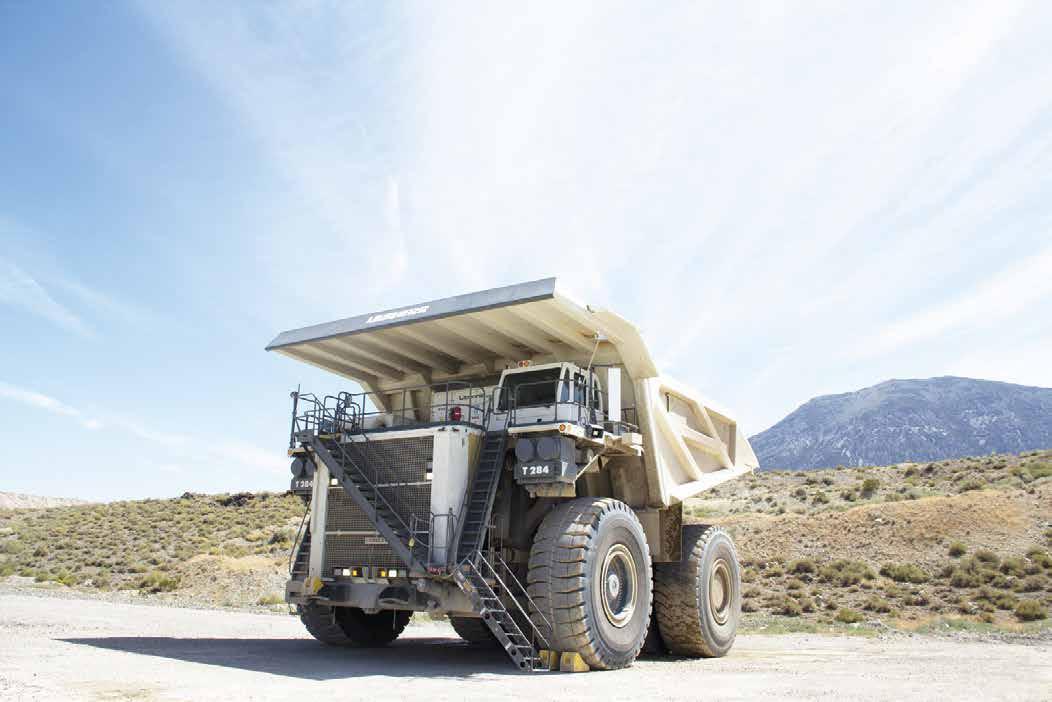
www.liebherr.com
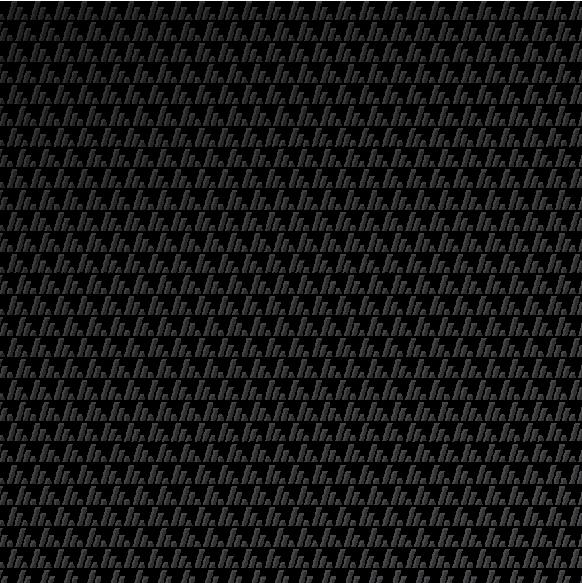
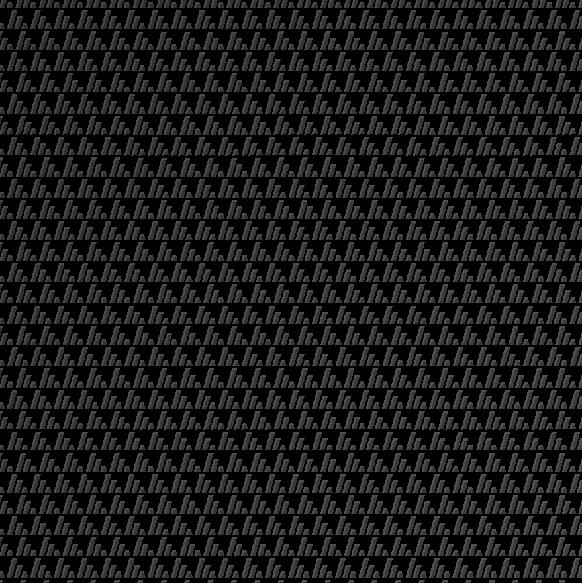
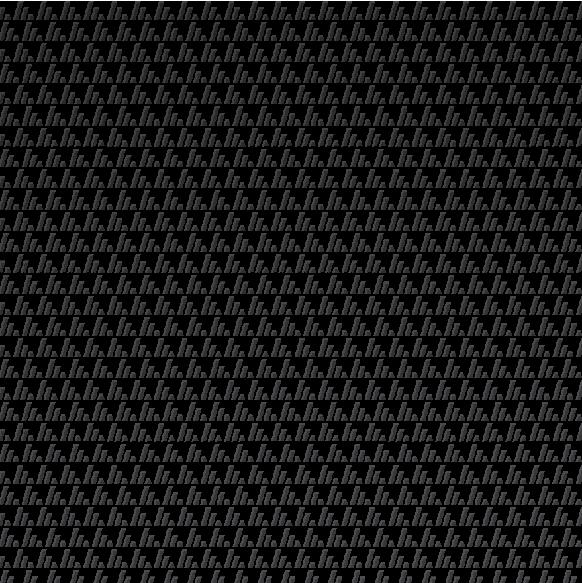
PARTS ENGINEERED TO PERFORM IN HARDROCK MINING
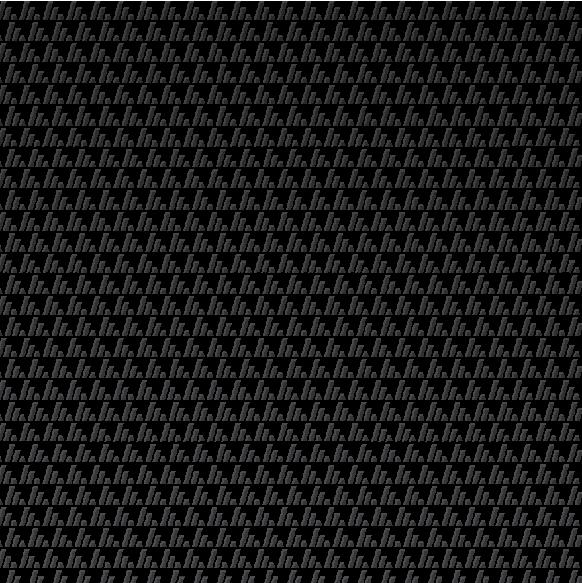
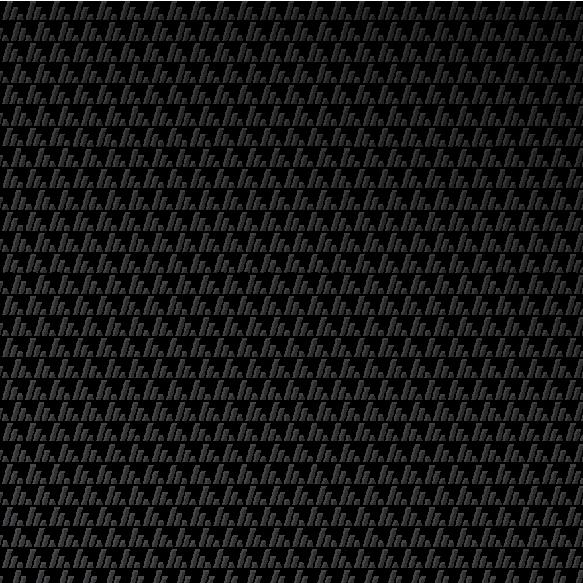
SURFACE PARTS SPOTLIGHT
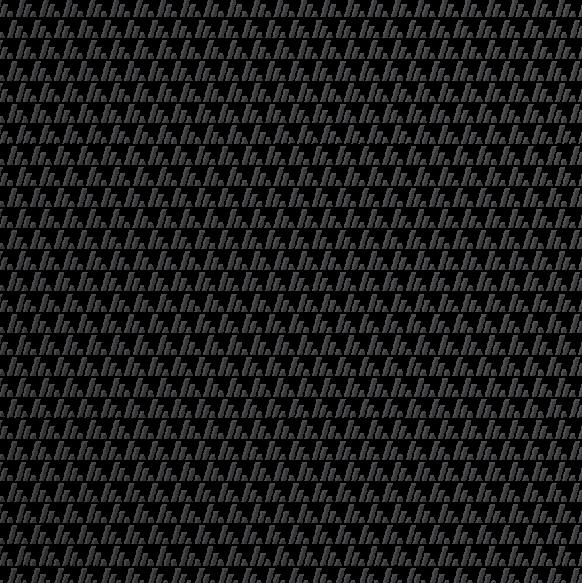
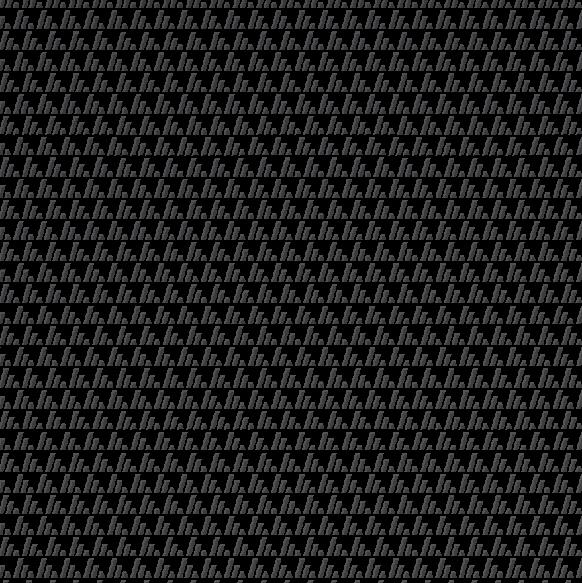
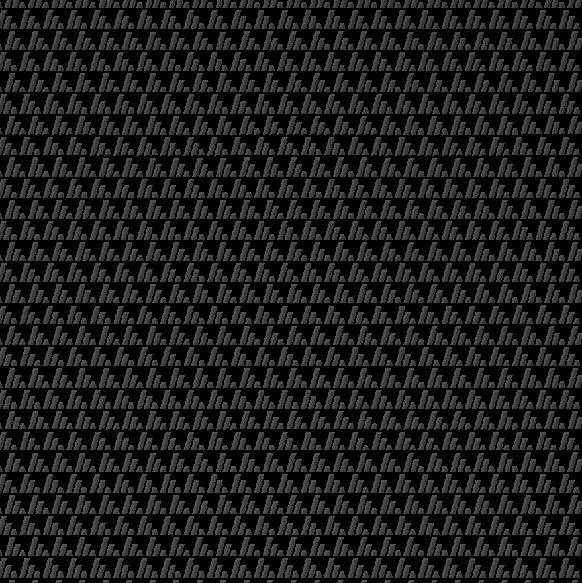
MASPRO is a leading provider of cutting-edge engineering solutions for underground and surface operations in the hard rock mining industry. What sets us apart is our unwavering commitment to optimising the parts we produce to increase safety and reliability. Our team works closely with customers to ensure that their machinery performs at its peak, even in the harshest mining conditions. If you’re looking to drill deeper, move more ore, and push your equipment to the limits while maintaining the highest standards of safety and operational reliability, talk to the MASPRO team today!
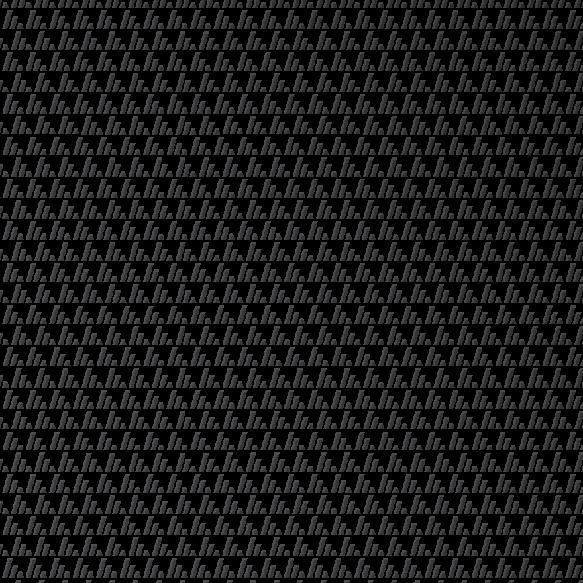
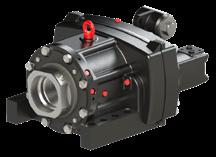
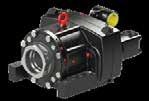
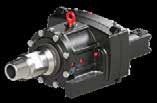

UNDERGROUND PARTS SPOTLIGHT

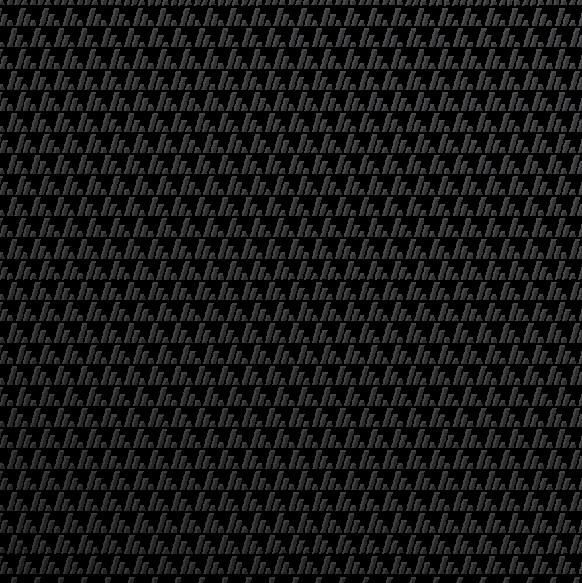
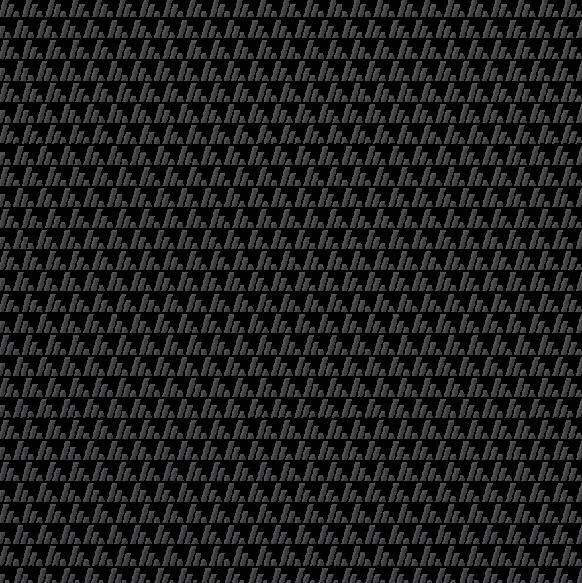
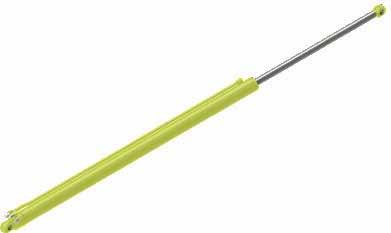
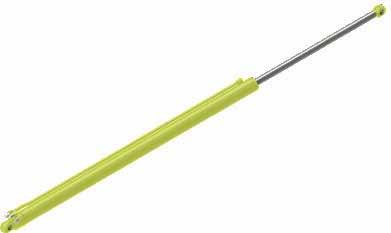
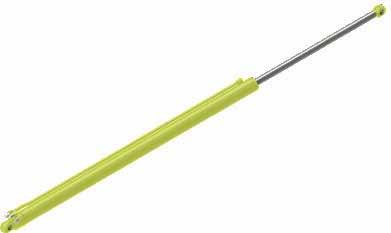

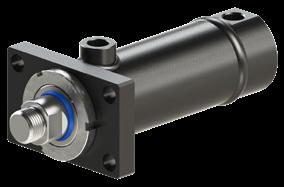
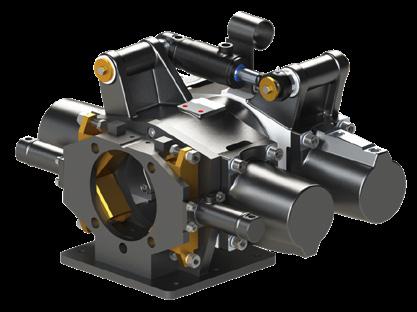
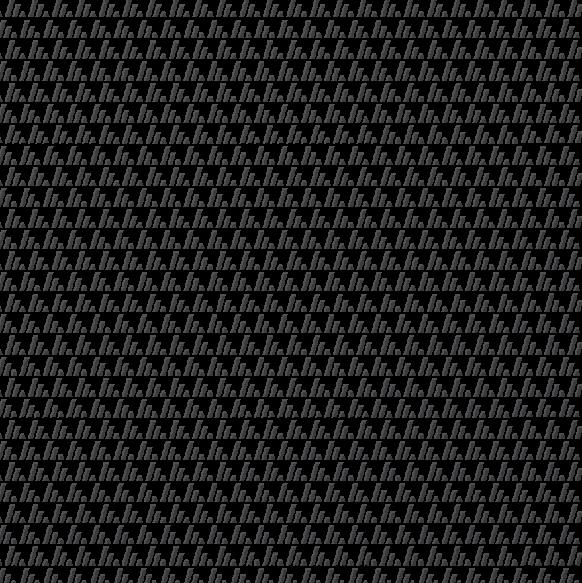
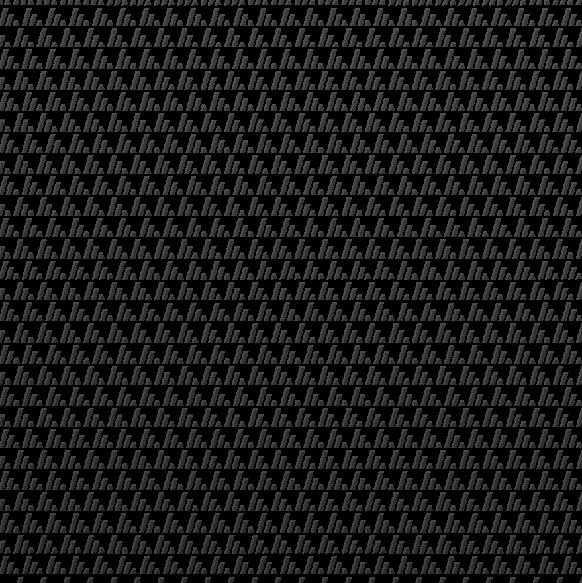
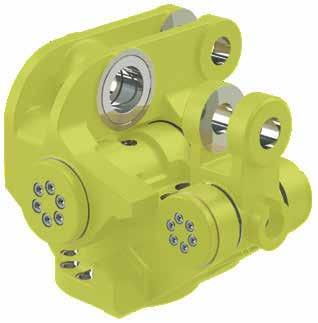
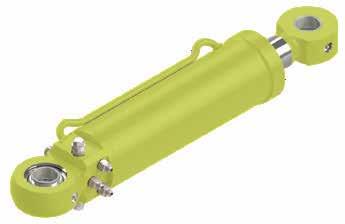
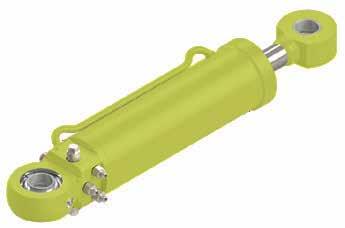
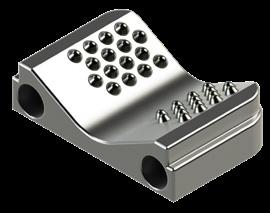
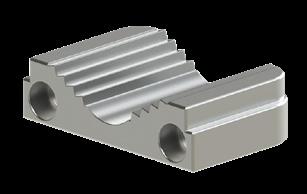
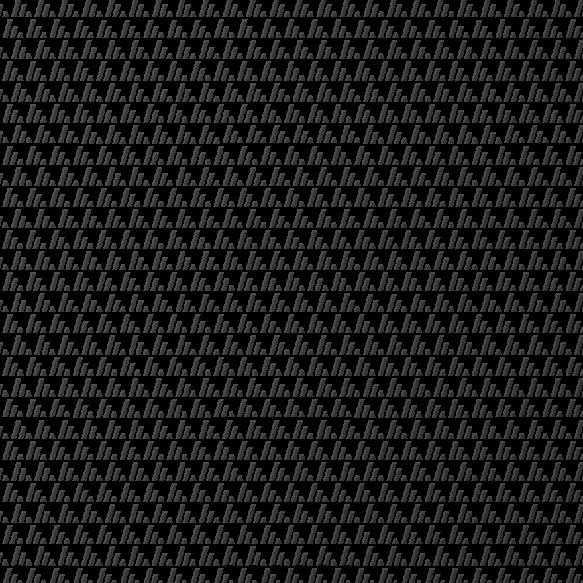
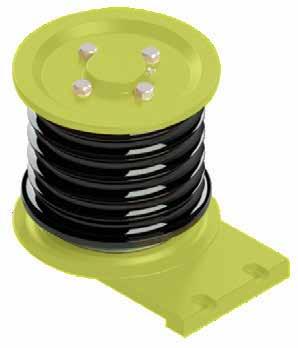
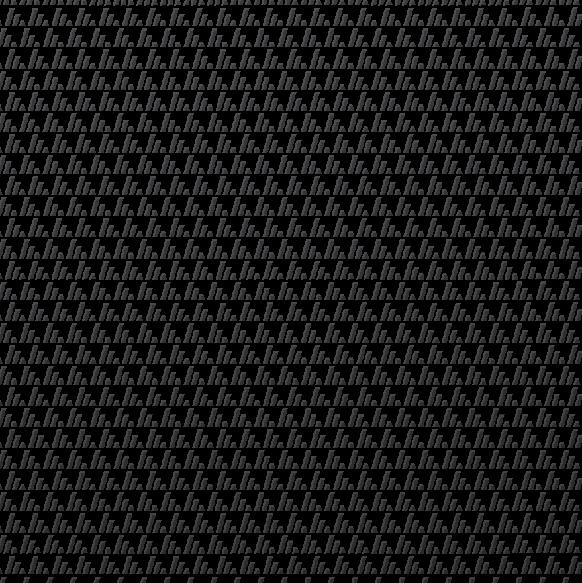
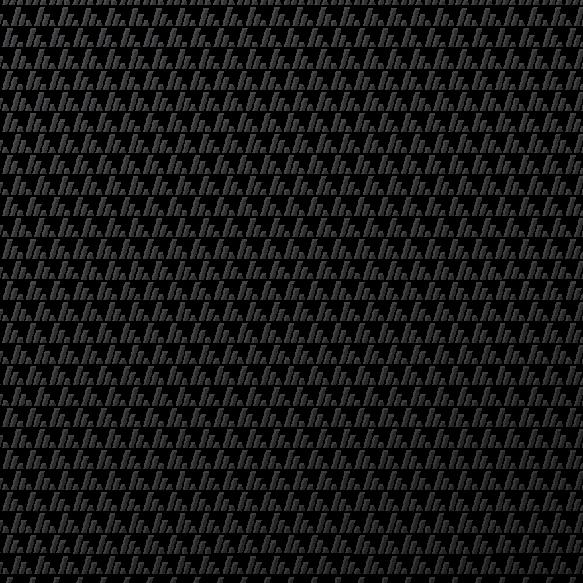
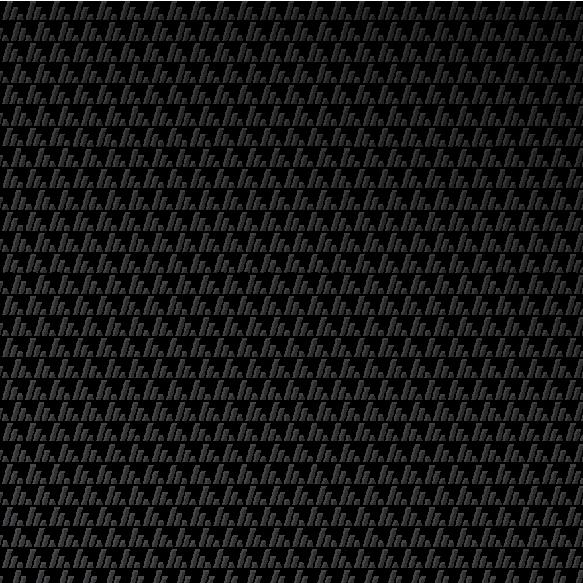
MASPRO
Building A Better World
Having leveraged reverse engineering to fully understand the best way to manufacture high-quality mining products, MASPRO delivers innovative solutions designed to meet the needs of even the most challenging of mining environments.
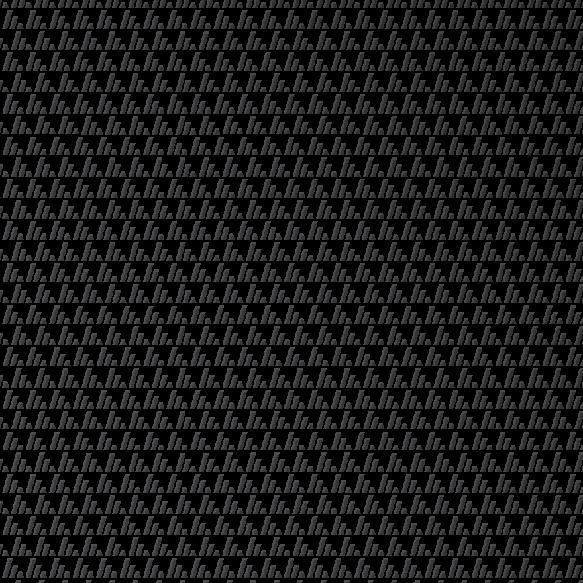
Established in 2006, MASPRO is a family-owned and operated company based in Condobolin, Australia that is passionate about delivering precision-engineered mining parts to the world. MASPRO, , has spent the last 18 years focused on creating flexible solutions for the mining industry which aim to reduce recurring failures and help to keep its clients’ mobile mining equipment safe, reliable and operating optimally.
This focus on success is what has bred a culture of innovation across the company as it works to utilise its expertise in the underground and surface mobile mining equipment industry to create world-class engineered, manufactured, and tested products which rival OEMs on the market. By investing in cutting-edge technology, digital software design, 3D optical scanning equipment and comprehensive metallurgical knowledge, MASPRO has been able to re-engineer and perfect its mining parts and equipment for the needs of the mining sector. www.maspro.com.au
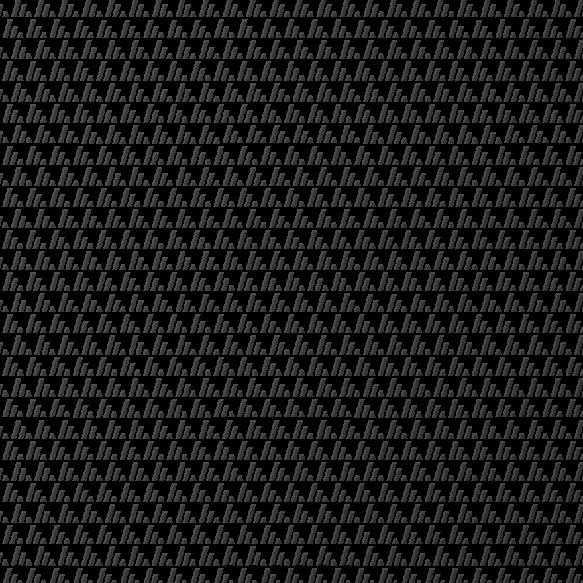
Whilst the mining and transport of its ore play a vital role, BHP is also heavily involved in the sales, marketing and procurement of assets to bring continued investment and expertise into the mining sector. It achieves this through a close understanding of the markets, customers and suppliers’ needs. By close attention to global mega-trends, BHP can cater its operations and acquisitions to seek out the most vital and profitable assets which will contribute greatly to the renewable energy transition.
Australia is a key site of operations for BHP with assets covering metallurgical and energy coal, iron ore, nickel and copper operations spanning the entire country. In Western Australia, BHP has the West Musgrave Project which covers the Nebo and Babel nickel-copper deposits, as well as the Succoth copper deposit. The project has an expected mine life of 26 years, with a proposed ore production rate of 10-14 Mtpa. Also in western Australia is BHP’s Nickel West operation which is part of its Minerals Australia business. Nickel West covers a variety of locations across traditional lands with a fully integrated mine-to-market operation spanning both open-cut and underground mines, as well as concentrators, a smelter and a refinery all within the complex. The asset is a crucial driver for renewable energy markets for BHP with 85% of its nickel being sold to battery suppliers across the world.
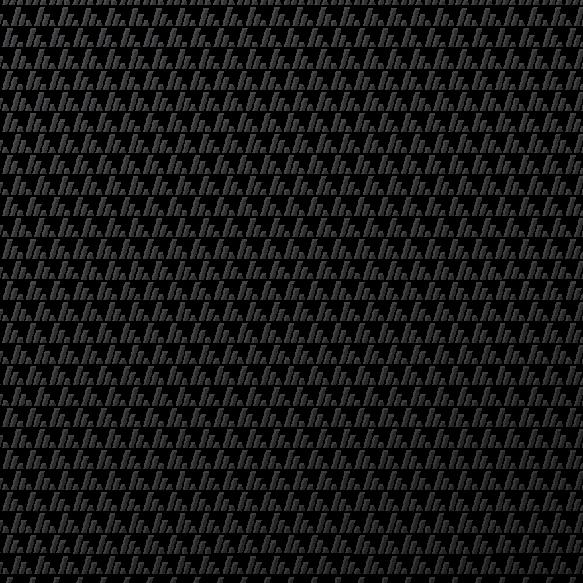

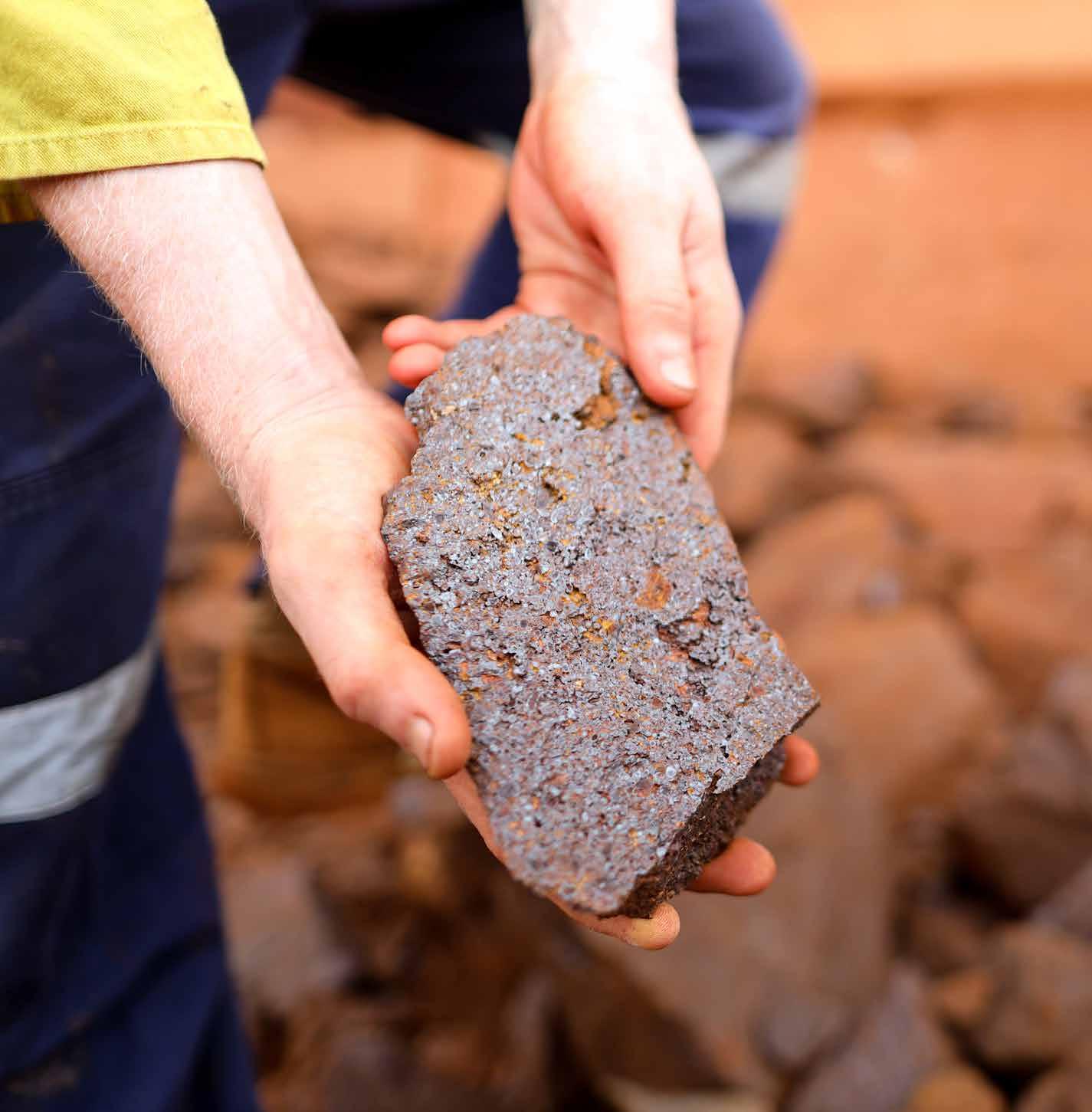
Whilst BHP develops vital metal production at Nickel West, part of the company’s mission is to make its operations just that little bit more sustainable. Therefore, BHP has been implementing a range of sustainable projects aimed at improving the overall impact of the complex’s operations on the region. These projects include the Northern Goldfields Solar Farm and BESS Project with Tansalta, which incorporated two solar farms and a battery energy storage solution. The project aims to support the mine and concentrators needs of the Nickel West complex.
The Goldfield Solar Farm began construction in 2021 and built upon the existing Merredin Solar Farm which was a power purchase for BHP in agreement with western Australia’s largest solar farm. Then
in 2022, BHP announced another power purchase agreement with Enel Green Power for the Flat Rocks Wind Farm which once completed will power the Kalgoorlie Smelter and Kambalda Concentrator on the Nickel West Complex. This investment in utilising renewable energy across BHP’s operations shows the company’s commitment to mitigating its environmental impact on the planet as much as possible.
In Queensland, BHP mines metallurgical coal across 7 assets in the Central Queensland Bowen Basin. The asset is owned in a 50:50 partnership with Mitsubishi Development, and is regarded to be one of Australia’s largest producers and suppliers of seaborne metallurgical coal. The site includes the Hay Point Coal Terminal which can handle more than 55 million tonnes of coal which the mine exports every year. In addition to BHP’s operations in the coal industry in Queensland, BHP also operates the Mt Arthur Coal Mine in New South Wales which produces coal products for an international customer base across the energy sector.
As BHP look towards the future, along with the rest of the world, it is hoping to significantly cut its carbon emissions by 2030, and achieve net zero greenhouse gas emissions (including both scope 1 and scope 2 emissions) across its operated assets by 2050. By working with its partners in the steel and maritime industry, BHP hopes to reduce its emissions across its BHP-chartered shipping operations for BHP products by 40%. To achieve this it is working with key stakeholders, and is backed by US$400 million in investments from its Climate Investment Program to significantly improve the low carbon steel making and low-emission technologies of the future.
With BHP you can feel throughout every operation a need and drive to make real change in the world. Through the acquisition, operations and development of BHP’s long-life assets continue to play a crucial role in developing the world towards a more sustainable future. Therefore, BHP’s goal to bring people and resources together has been largely successful and has built a steady foundation ready to meet the renewable demands of the future.
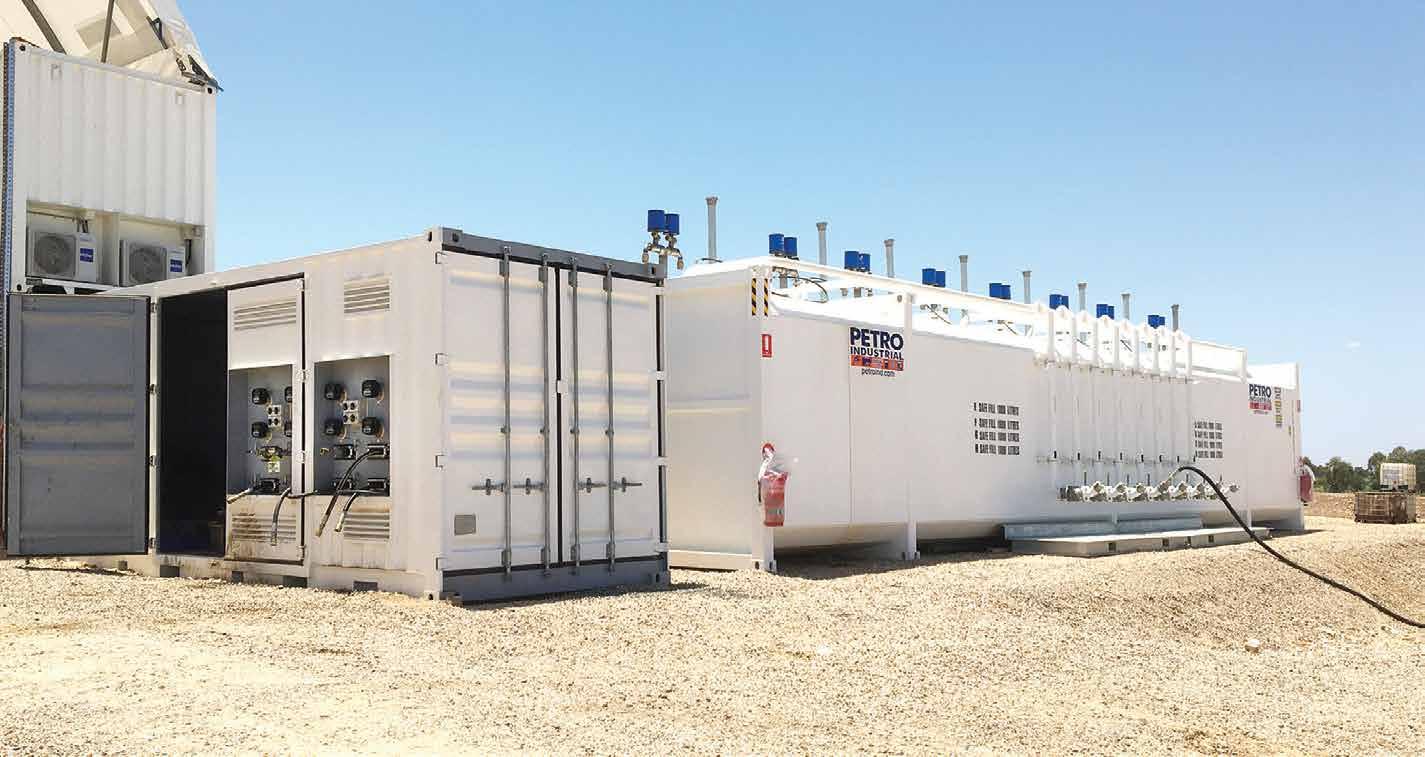
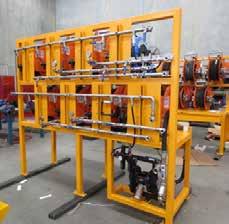
BULK FUEL & LUBRICATION Storage & Dispensing Solutions
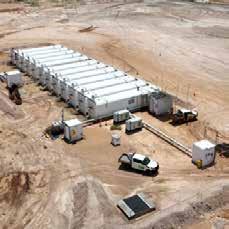
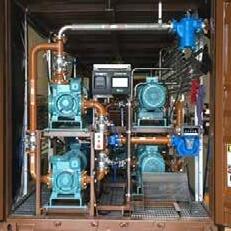

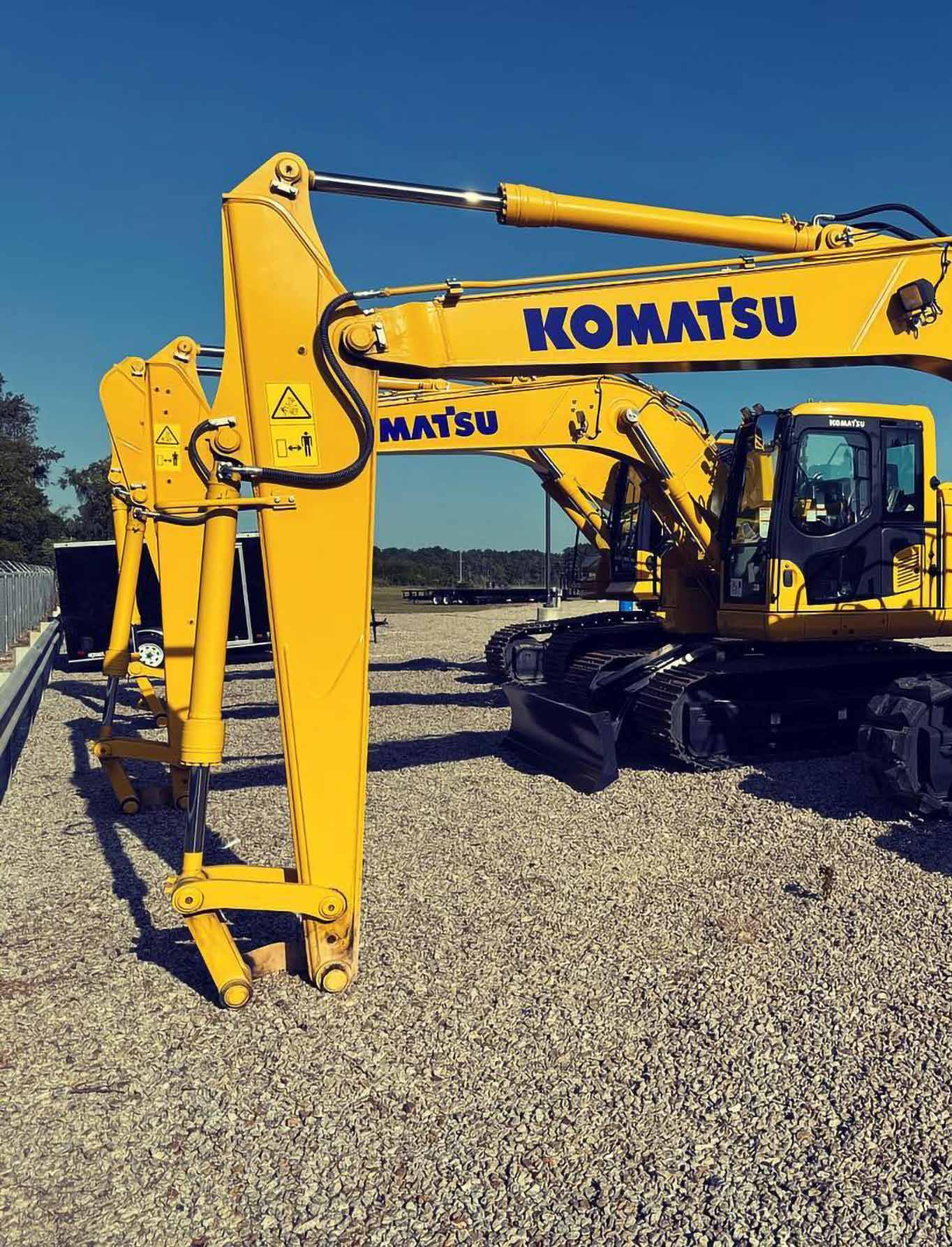

Over the last 100 years, Komatsu Mining Corp. has continued to invest in its equipment solutions and services which has established it as a leading manufacturer of machinery for the construction, mining, forestry, and industrial equipment sectors. Across the company’s portfolio of equipment and machinery, Komatsu’s products are designed to deliver value, thanks to its implementation of innovative technologies to take its equipment into the future. Therefore, Komatsu aims to create value throughout its operations, which will bring continued economic benefits for its customers and empower industries worldwide to develop towards a more sustainable future.
Komatsu was founded in 1921 with the goal of providing those in the local community with employment opportunities following the closure of a local copper mine. This passion for supporting people in the local community provided the vital foundation from which the company we know today could form. Having built from a small operation in Japan, Komatsu today is now a multinational corporation which manufactures equipment and machinery across a wide variety of industries.
However, this passion for supporting people can still be seen throughout every product it manufactures as each one is designed with innovation to deliver top results for its network of customers. Its customers are working on some of the most complex projects across the world which are delivering essential infrastructural changes for the betterment of people and the planet.
A key sector for Komatsu’s operations is the construction industry, where Komatsu has developed a range of equipment which champions performance, quality, and reliability. Komatsu’s equipment offerings to the construction industry cover things such as dozers, excavators, motor graders, trucks, and wheel loaders. However, what sets Komatsu’s construction equipment apart from its competitors is its inbuilt smart technologies available across its range of equipment, which are designed to help customers deliver projects with speed, safety, and cost-efficiency as a priority.
To help Komatsu deliver excellent equipment offerings supported by the latest technology to the construction industry, it announced in December 2023 the acquisition of iVolve Holdings Pty Ltd. iVolve is an Australian-based technology company
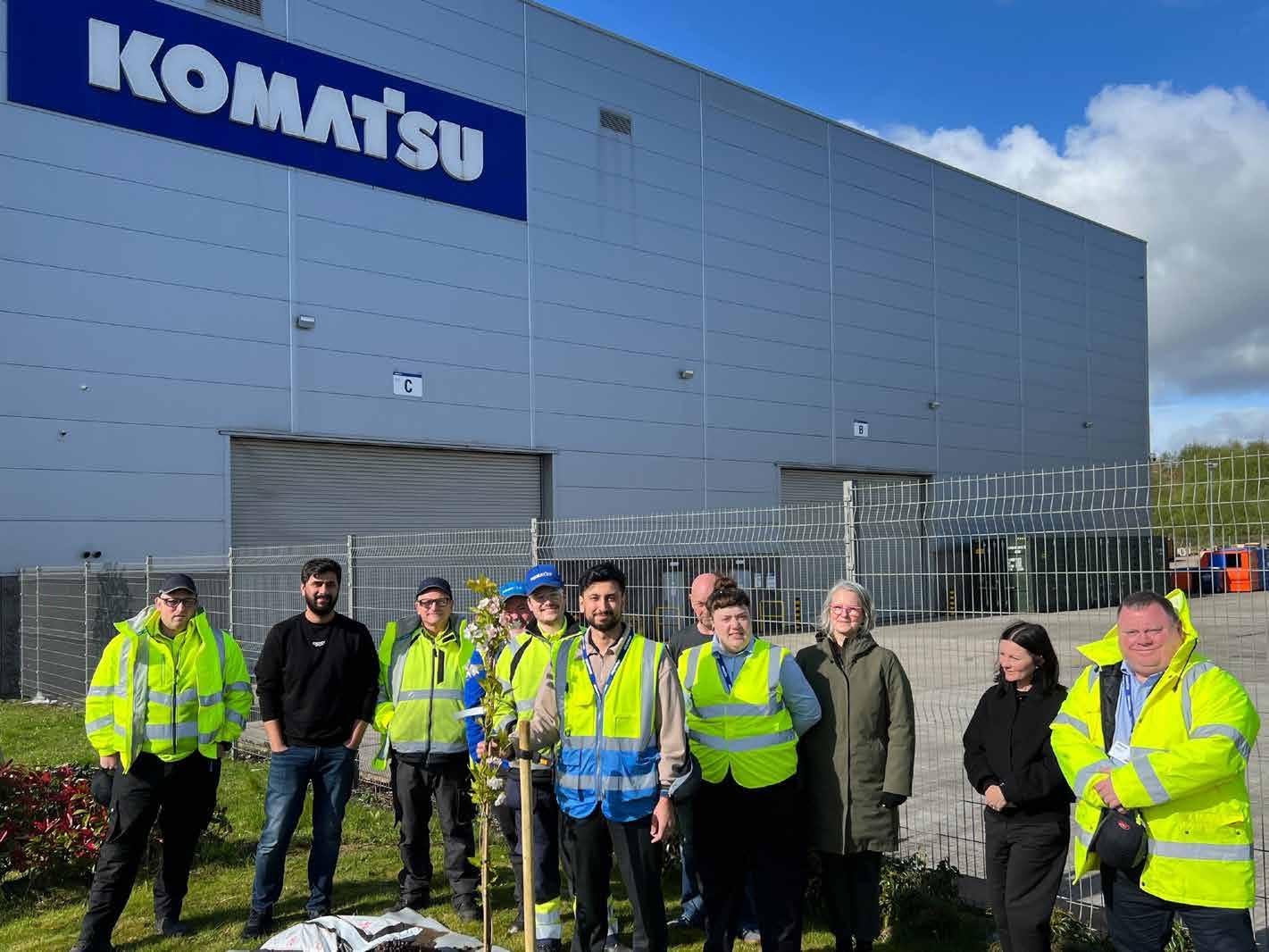
Mining Equipment for the Future
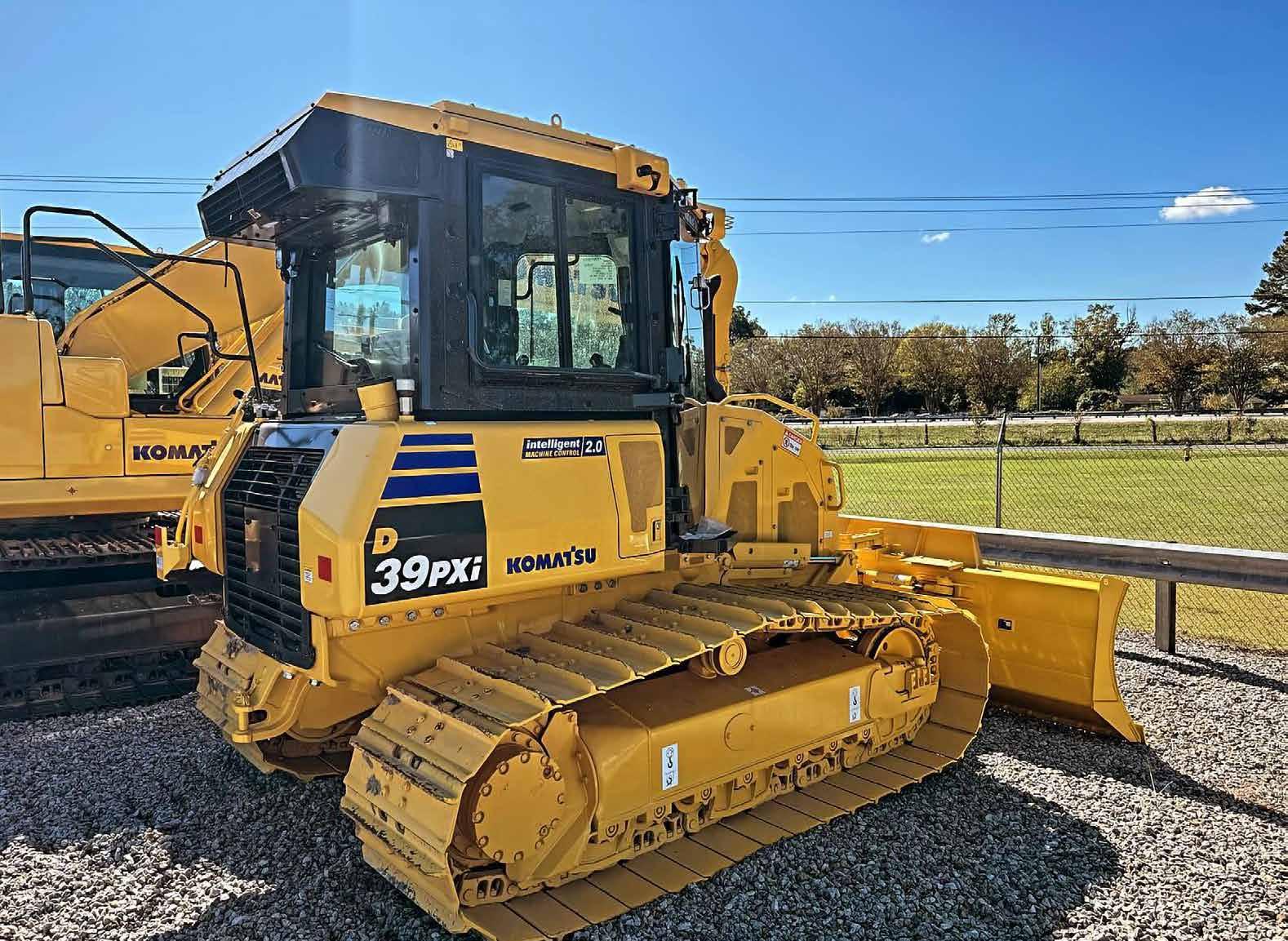
that provides top-of-the-range fleet management solutions perfect for equipment within the midtier quarry, mining, and construction industries. Komatsu looks to adopt these technologies into its equipment to allow its customers to have greater control over its fleet on the job site to increase productivity and heighten safety concerns.
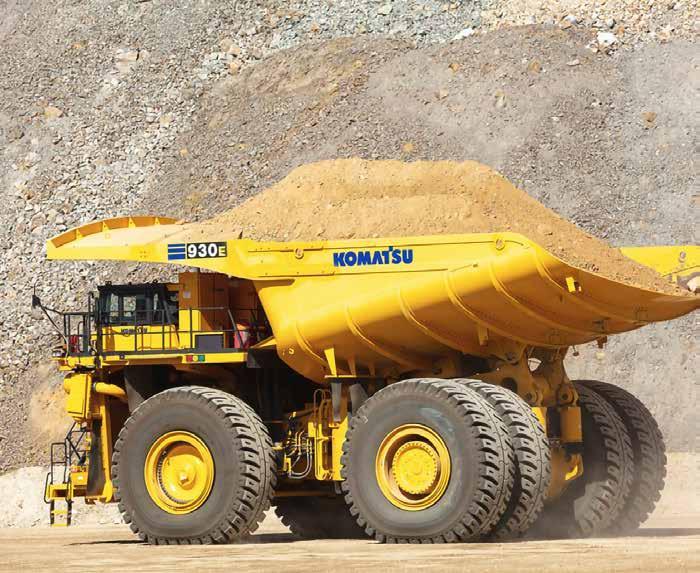
Komatsu already has a range of smart construction technologies with iVolve which have been implanted throughout some of its equipment. These include its Smart Quarry Site Technology which utilises pre-shift inspection to allow managers to identify issues across its fleet of mobile equipment to provide a detailed view of the health and status of each machine’s performance. This system helps managers to make the most of equipment and reduce downtime. Therefore, with the new acquisition of iVolve, Komatsu can continue to implement these fleet management technologies across its construction equipment, and its entire product line offering to provide greater transparency and management of fleets across complex construction sites.
Mike Gidaspow, Vice President for Products, Service and Solution for Komatsu in North America highlighted in the press release that “iVolve have been great collaborators and this acquisition offers exciting potential to further our world together”. Gidaspow’s comments focus on Komatsu’s overall mission to deliver products that will provide essential services to help world-developing
Komatsu
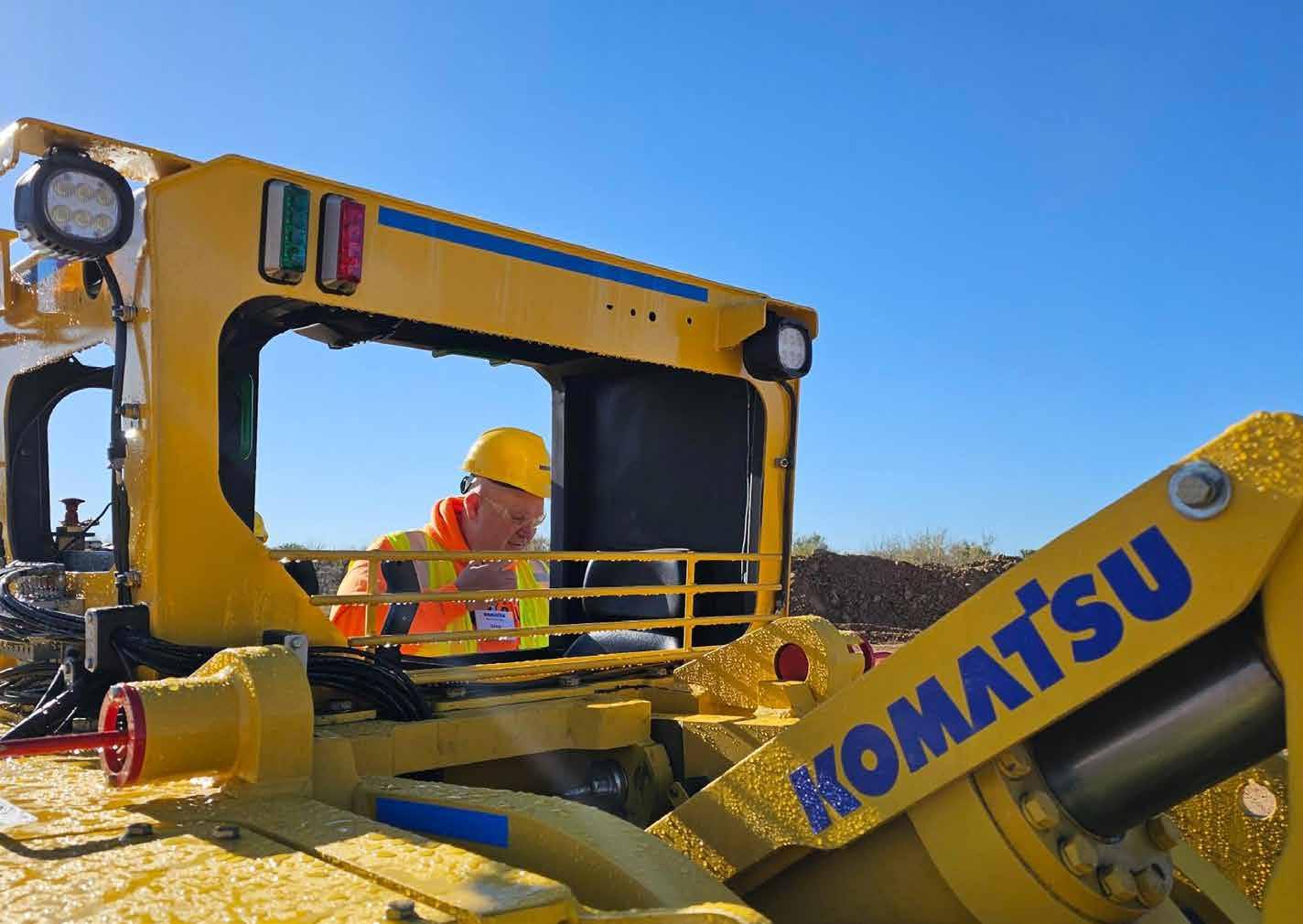
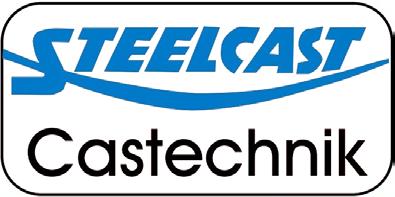
STEELCAST LIMITED
Regd. Office & Works: Ruvapari Road, Bhavnagar, Gujarat, India 364 005
Phone: +91-278-251 9062,
Fax: +91-278-242 0589, 251 9831
E-mail: pns@steelcast.net, Website: www.steelcast.net
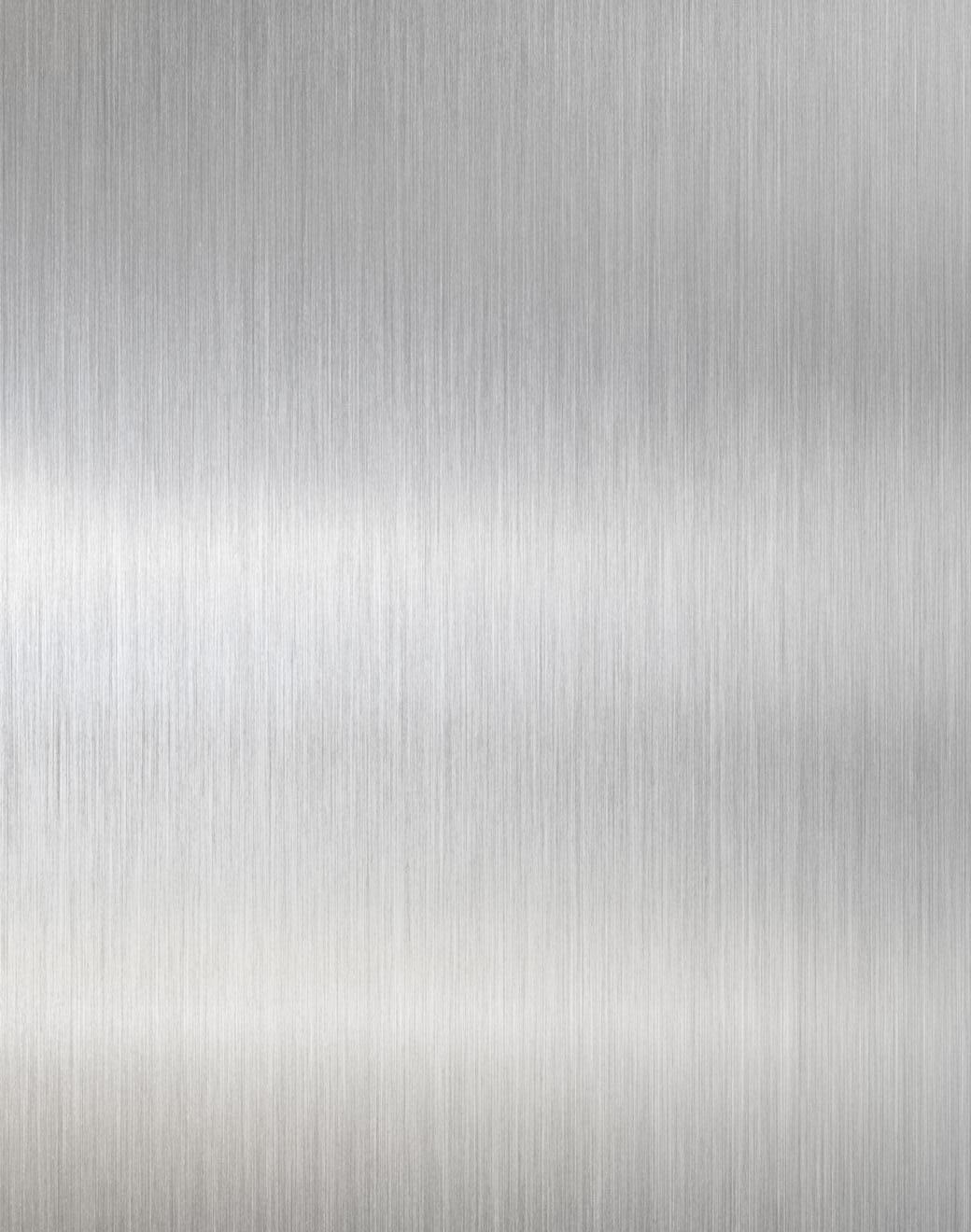
In Service to Komatsu Group of Companies
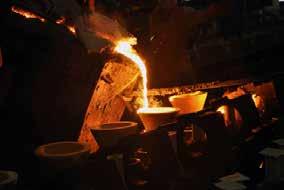
Steelcast Limited thanks
Komatsu Germany GmbH
Komatsu America Corp., USA
Komatsu Limited, Japan
Komatsu Mining Corp., India
Komatsu Mining Corp., USA
Hensley Industries Inc., USA
We are a leading steel foundry in India, boasting an annual production capacity of 29,000 tons of steel and alloy steel castings. Our facilities include in-house CNC machining, along with comprehensive manufacturing and testing capabilities such as Heat Treatment, Induction Hardening, and NDT. We cater to various industries including Construction, Mining, Earthmoving, Locomotives, Steel, Cement, GET, and Railroad sectors.
RECOGNITIONS
• ISO 9001-2015, ISO 14001-2015 & ISO 45001-2018 certification by TUV NORD, Germany. • EN 9100-2018 certification for Aerospace by TUV NORD, Germany • Accreditation by Association of American Rail Road (AAR)
projects remain on track. The iVolve system is planned to be rolled out across Komatsu’s offerings across North America.
One of the most vital industries that Komatsu serves is the mining industry, as its role in global development cannot be understated. The mining industry has seen increasing demands over the last few decades as metals and minerals have taken on a new role in moving the industry towards the future. We have seen this with the use of metals such as lithium used in lithium-ion batteries which is driving the electric vehicle market. Therefore, Komatsu is focused on delivering products which make mining operations run more smoothly for the betterment of the future, and so offers a wide range of operations across both the underground and surface mining sectors.
Komatsu is the leading provider of electric and hybrid rope shovels, walking draglines, automation solutions and connected mining technologies for the surface mining sector. In the underground mining sector, it has a range of shaft sinking equipment, underground rock bolters, underground hard rock drills and underground hard rock bolters. With every piece of mining equipment offered by Komatsu, customers gain access to Komatsu’s team of experts across its global network of dealers who
Mining Equipment for the Future
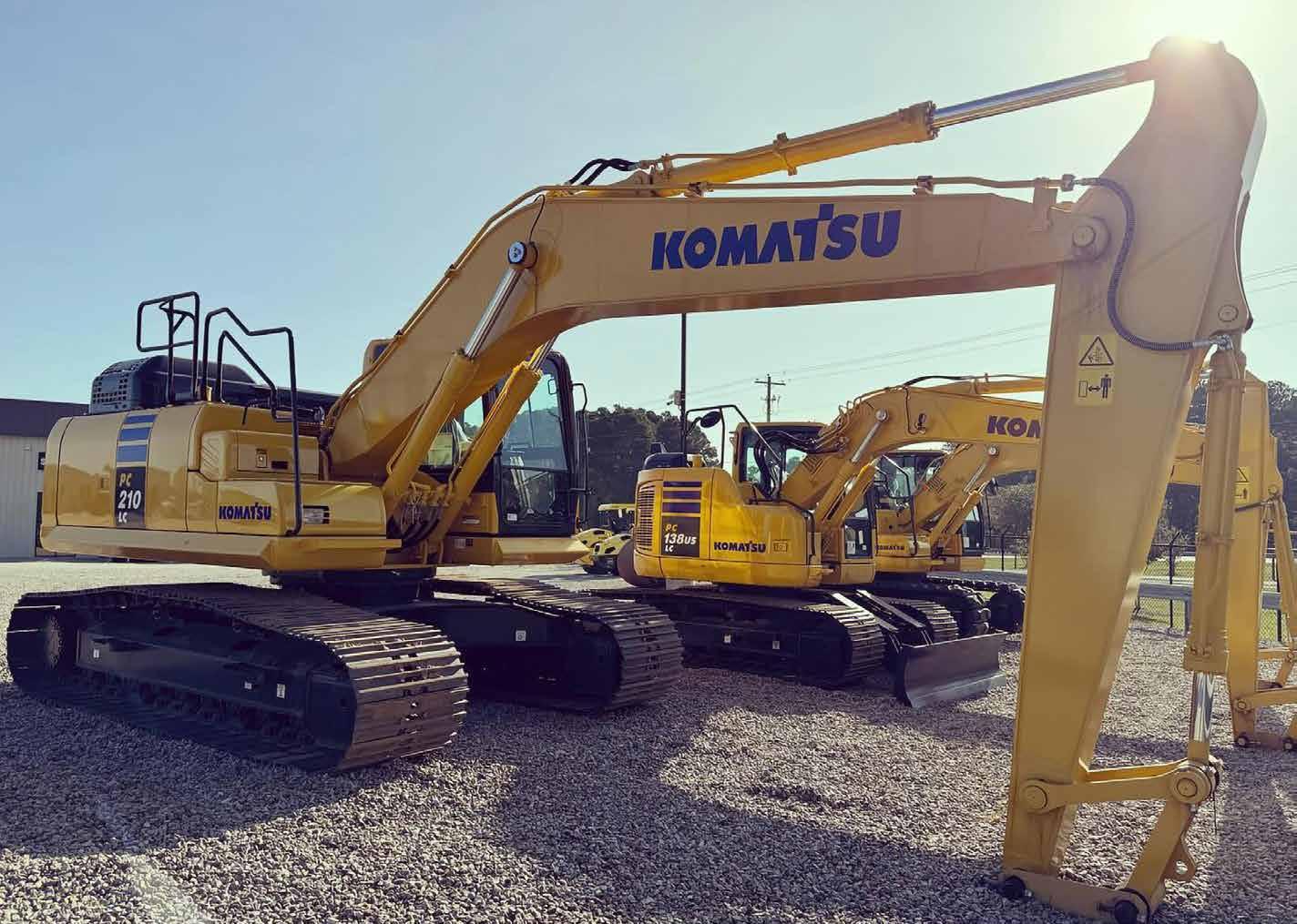
are always on hand to help customers choose the right bit of equipment for a job and then remain in contact to ensure each one continues to deliver results for its customers.
With the ever-evolving nature of mining, and as demand continues to soar, Komatsu is committed to providing equipment that continues to meet the current demand of the mine site. Therefore, in February Komatsu introduced the WX11 LHD into the underground hard rock lineup, which offers the best-in-class breakout force and payload. The 11-tonne machine is designed to boost productivity whilst providing lower costs for its customers. Ryan Karns, Director of LHD and Truck Products at Komatsu, highlighted in the press release that “The WX11 is a game changer for hard rock miners. Developed through a close partnership between our experienced team and our longtime customers, this product reflects a shared commitment to design excellence”. Karns comments highlight the founding passion behind Komatsu again, that every bit of equipment is designed for the benefit of its customers as helping them achieve success brings greater success for the world.
The WX11 exemplifies Komatsu’s commitment to providing mining equipment that can be integrated into the next generation of mining capabilities. The
WX11 joins the introduction of the GD955-7 Motor Grader just a month before. The GD955-7 offers operators all the control and precision they need to build and maintain haul roads for truck fleets of 100 tons and up. The machine provides powerful horsepower and exceptional blade downforce pressure to make grading so much easier. We can see with both of these offerings Komatsu remains committed to providing innovative equipment and technologies to reduce overall machine maintenance and keep costs at a minimum, all whilst driving powerful operations to make even the most complicated of jobs a reality.
Every time we cover Komatsu, we are reminded why it is a key player in the machine and equipment manufacturing sector on a global scale. Throughout every new product offering, Komatsu is committed to helping its customers achieve their project success which in turn will develop the world towards a better future. We look forward to seeing what new project offerings Komatsu will develop over the coming years as it continues to meet the growing demands across the mining, construction, forestry, and industrial sectors.
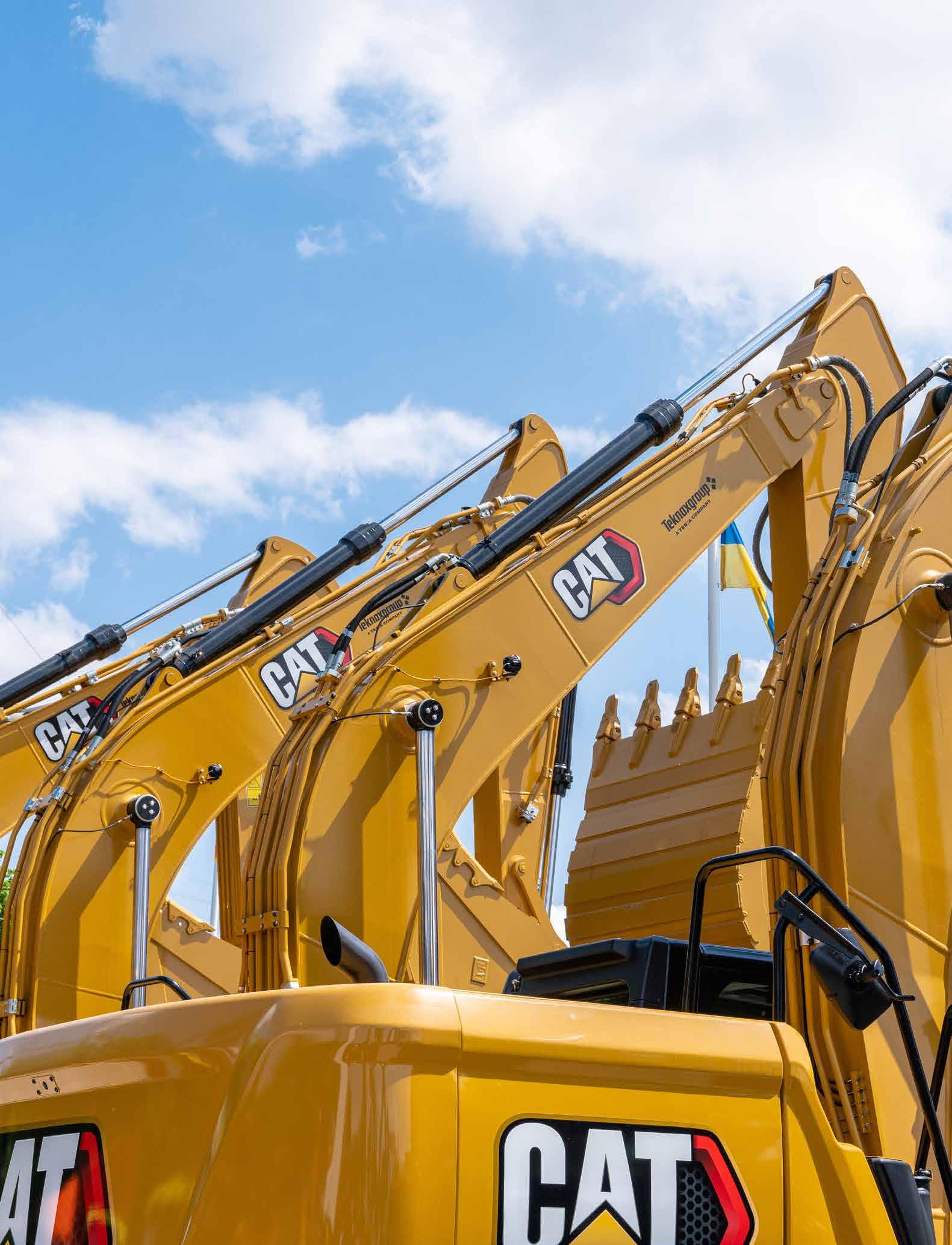
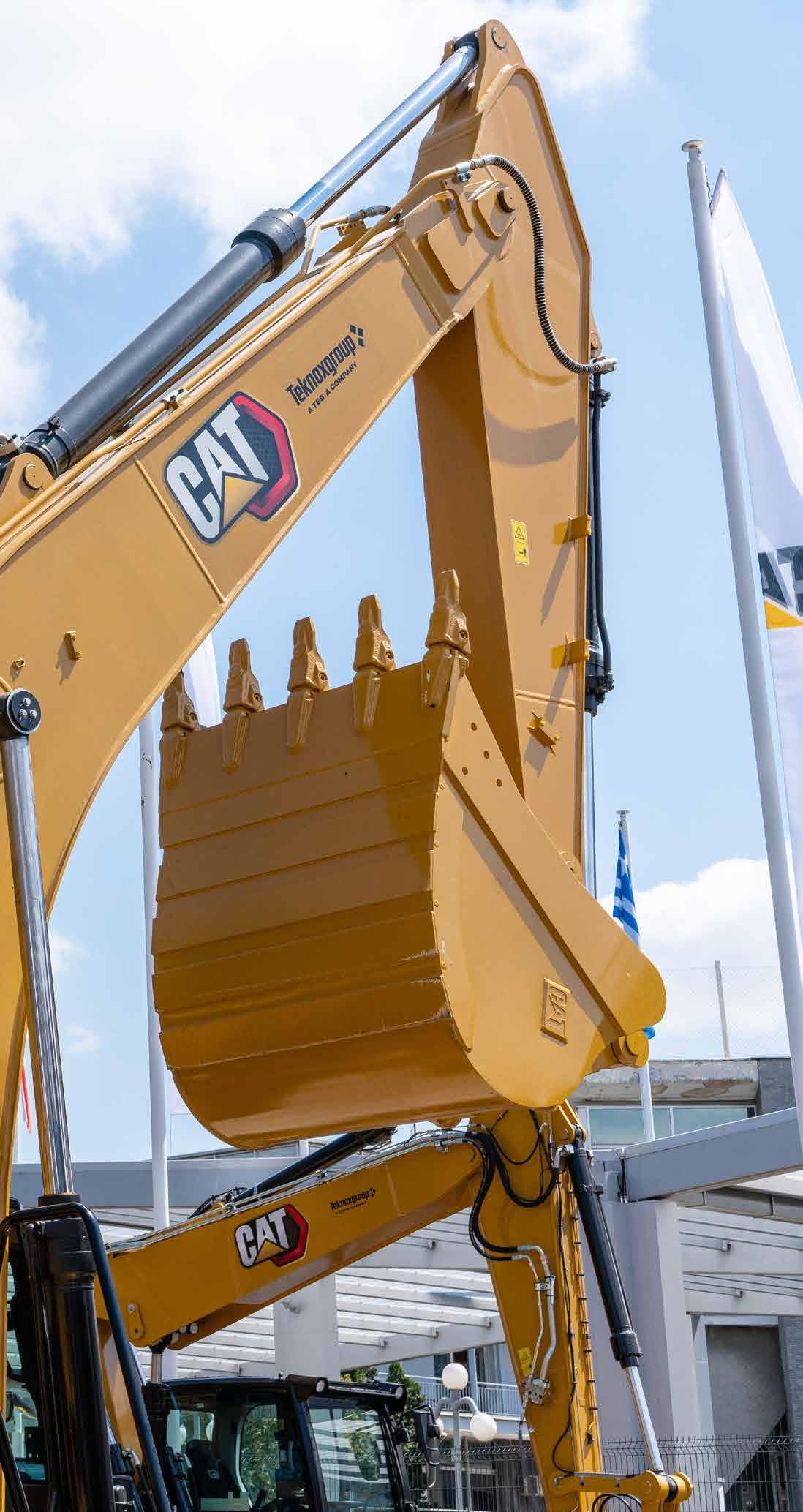
Caterpillar Inc.
The Caterpillar Inc., brand is one you will be very familiar with if you’ve ever stepped foot onto a construction or mine site. With its iconic yellow branding and ‘Cat’ logo, Caterpillar is a world-leading manufacturer of construction and mining equipment, off-highway diesel, and natural gas engines, as well as industrial gas turbines and diesel-electric locomotives. With almost 100 years of experience behind its operations, Caterpillar is committed to delivering innovative products and services across its global network that are shaping the future of the mining and construction industries.
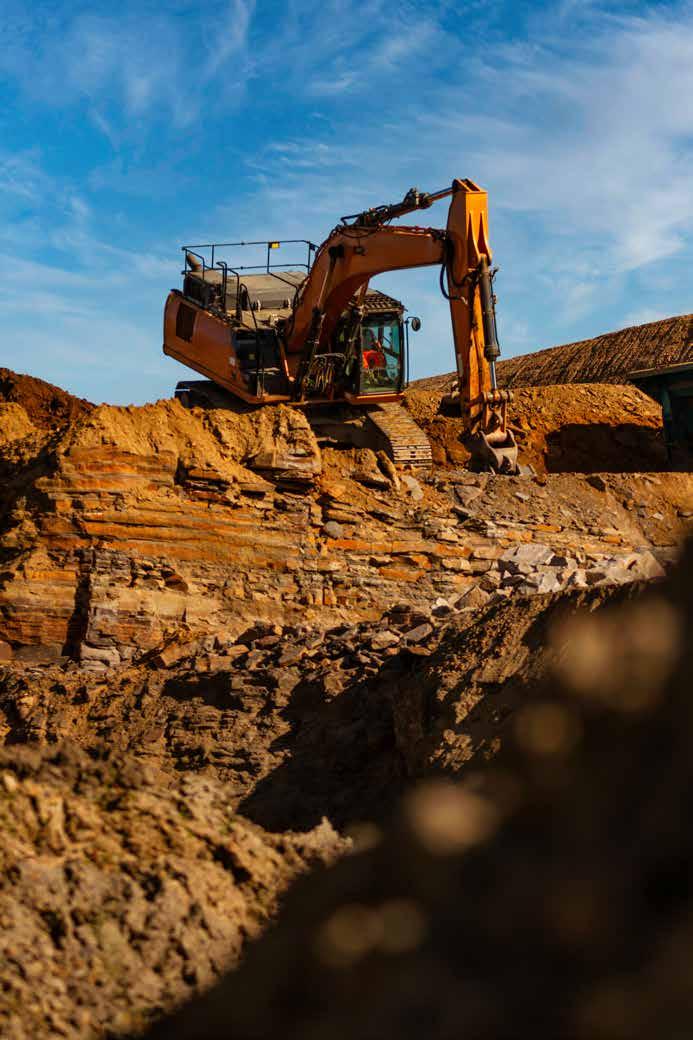
When you buy a product from Caterpillar you are buying top-quality machinery, which is backed by industry experts who are focused on ensuring that its customers get the most out of every bit of equipment they purchase. To achieve this, Caterpillar believes in bringing together the right people, products, technologies, and services needed to provide solutions which meet the needs of every project. The reputation of Caterpillar’s machinery and equipment speaks for itself, with business operations now spanning every continent on the globe and in sectors such as construction, mining, energy, and transportation.
With every development for Caterpillar, its operational efficacy, cost, reliability, and work site safety are of paramount importance. We see this in the Mining sector, where Caterpillar has its Cat® product line for surface mining which spans the drilling, digging, loading, hauling and maintenance of mine sites to ensure efficiency. When buying one of its vast collection of heavy-duty mining equipment, whether it be a large wheel loader, dozer, motor grader or truck, customers can be sure that every machine has been developed with performance in mind. To achieve this, Caterpillar offers Cat MineStar™ Solutions with its mining equipment, which provides the industry’s most comprehensive and thoroughly integrated suite of technology offerings.
Cat MineStar™ Solutions ensures that customers can have optimized control over fleet management, whilst getting real-time feedback on the health of their machinery. This solution is aimed at improving operations and maintenance of these heavy pieces of equipment so that Caterpillar can continue to deliver results of value for its customers. The MineStar solution is available across its drilling, loading, hauling, dozing, and grading machinery and is aimed at enhancing the efficiency of its mining equipment to make mining operations more productive for its customers.
However, as Caterpillar moves towards the future it is increasing its product offering to meet the mine sites of the future. In May 2023, Caterpillar introduced the Cat® D10 Dozer which is designed to be more productive, efficient and durable to meet the harsh conditions of the mine site. The D10 features industry-leading technology, which reduces the fuel burnt, and increases the productivity and uptime of the machine. With a stator clutch torque converter and load-sensing hydraulics, the D10 is designed to be more efficient than previous models and provide
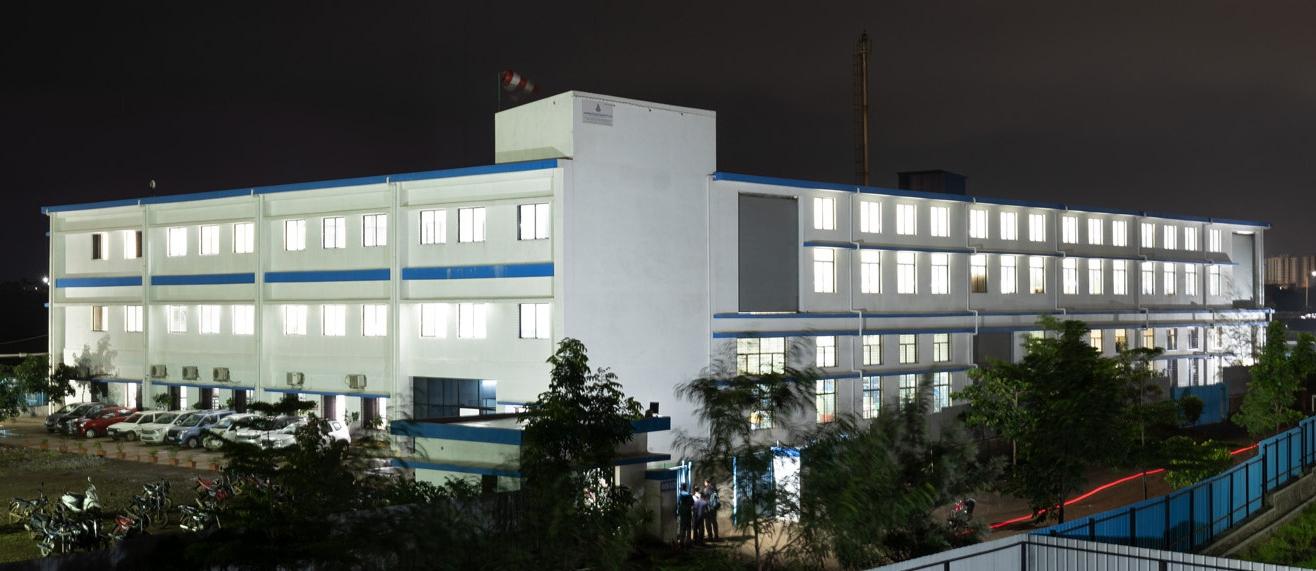

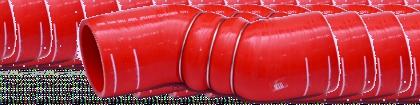
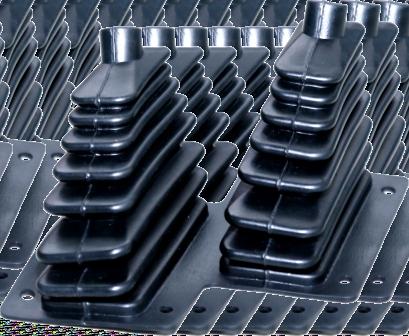


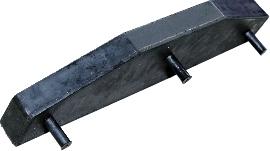
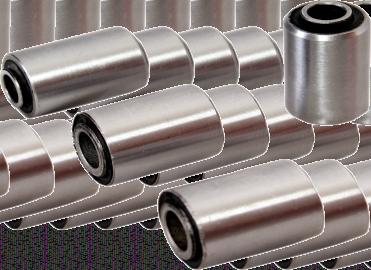
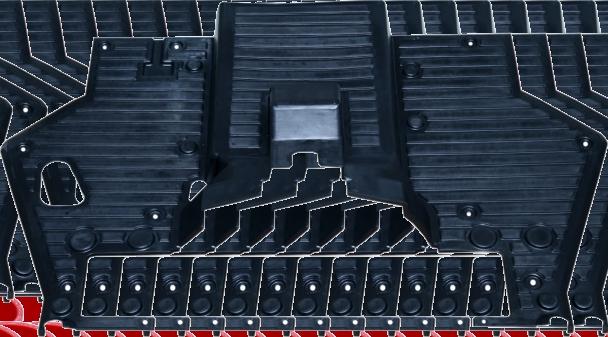


Caterpillar Inc.

a longer component life with reduced oil changes and reduce the need for maintenance and repair costs.
By significantly reducing cycle times thanks to the focus on maximising material moved per litre of fuel, the D10 has been designed for the future but is ready to integrate into customer’s projects tomorrow. Consequently, the D10 highlights the focus by Caterpillar to make machinery which provides optimum efficiency for its customers now, whilst integrating technologies which will allow the dozer to have a prominent role in the future of mines.
Much like the mining industry, the world of construction is just as challenging, but now with more project restraints, schedules, and heightened safety concerns. Therefore, Caterpillar has developed a range of industry-leading construction equipment which is designed to handle the challenging confines of construction projects and deliver efficient productivity for its customers. Machines spanning Caterpillar’s construction range include excavators, mini excavators, dozers, wheel loaders, skid steer and compact track loaders, backhoe loaders, telehandlers, articulated trucks, and motor graders – to name just a few!
With every purchase of construction machinery from Caterpillar, customers can take advantage of its Global Dealer Network which supports them throughout their projects. The network provides customers with access to partners, services, and guidance from a team of construction industry experts. Therefore, when customers buy from Caterpillar, the machines do not lose their value as the network works to maintain the efficiency, health, and productivity of the equipment for its entire operational life.
What separates Caterpillar’s equipment from its rivals is its Cat® Command Remote Control Technologies which provides the construction industry with equipment that can be remotely controlled without the need for the machine operator on site. The Command Remote Control Technologies is reshaping construction projects for the future, but removing the need for operators which improves operational safety whilst reducing downtown which drives bottom-line benefits for the customer.
For Caterpillar, its Command Remote Control Technology is pushing the future of autonomy into the construction industry. The automation technology began almost two years ago following
the acquisition of Marble Robotics of San Francisco. Marble Robotics had developed a range of small delivery robots for use in dynamic environments, and so Caterpillar adopted this technology and infused it with the rugged durability of its Cat Construction range to deliver construction equipment that is equipped with completely remote systems for greater site automation. This development allows Caterpillar to jumpstart its lightweight and costeffective autonomous equipment range, which has allowed it to remain ahead of its competitors.
Using Caterpillar’s Command Remote Control Technology, customers can operate up to 5 machines at once, with machines able to deliver precision operations. To achieve this all operators need to do is assign the machine to a drop point, which the machine will then navigate to alone. Once jobs are completed the machines leave the material and then navigate back to the pickup area where the operator can then take back control. This allows for multiple points of development to take place at once, as the operator does not physically need to be with the machine for it to operate. This
Optimized Equipment Solutions
reduces downtime and increases efficiency, whilst removing the opportunity for safety risks across the construction site.
For Caterpillar, it aims to deliver machinery and equipment which delivers results for its customers. This is something we can see throughout every piece of equipment produced, and every new technology introduced. With a network of dealers behind its products to ensure that customer satisfaction and machine health are guaranteed, Caterpillar has established a world-renowned reputation for reliable machinery which can be seen across mine and construction sites all over the globe. However, it is with this reputation that Caterpillar is striving towards the future, to adopt new and innovative technology to enhance performance and reduce environmental impacts. With this in mind, Caterpillar is focused on making equipment that will be seen across the future of the mining and construction industries, however, it is implementing these technologies now for the benefit of its customer’s projects today.
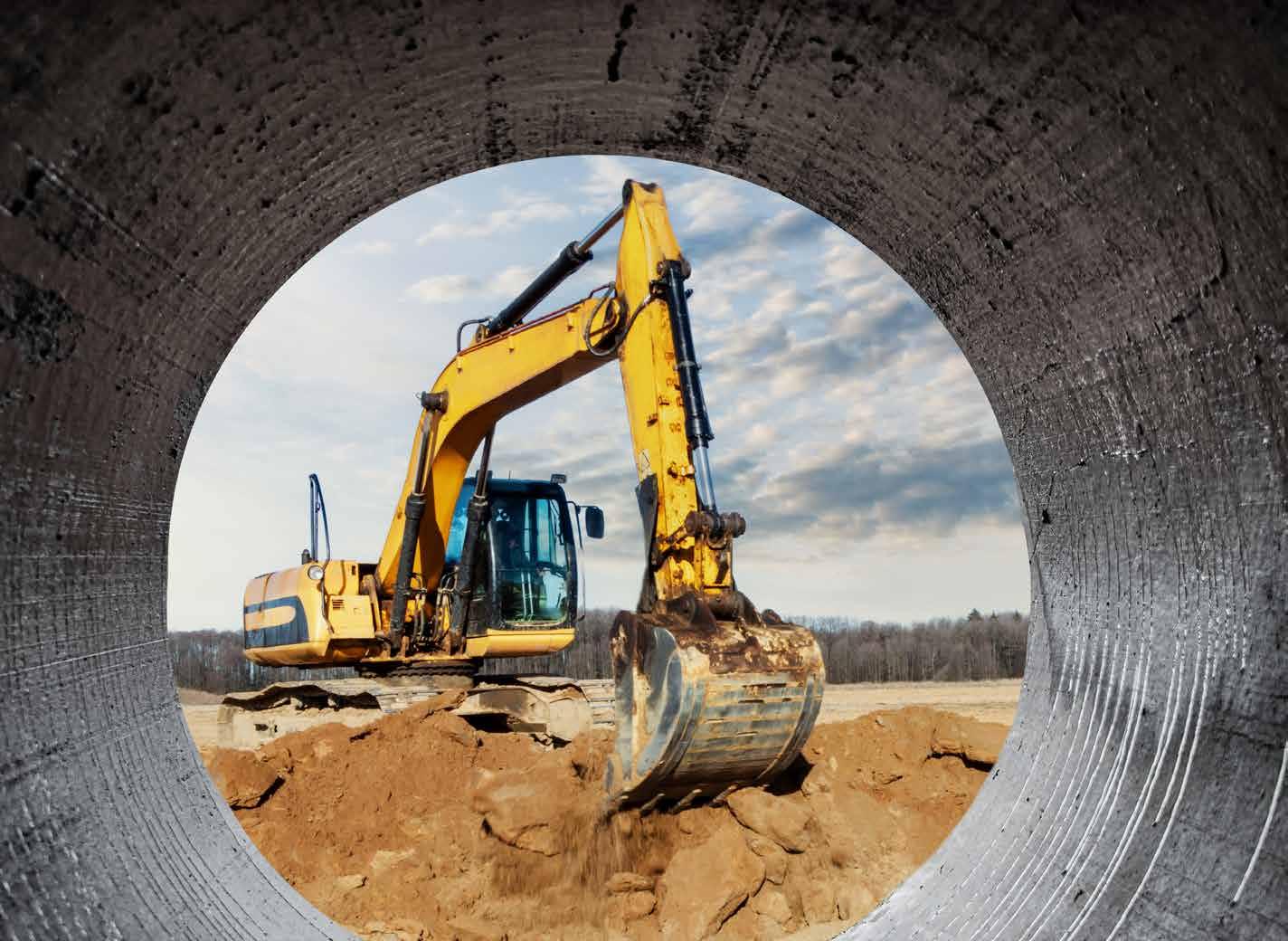
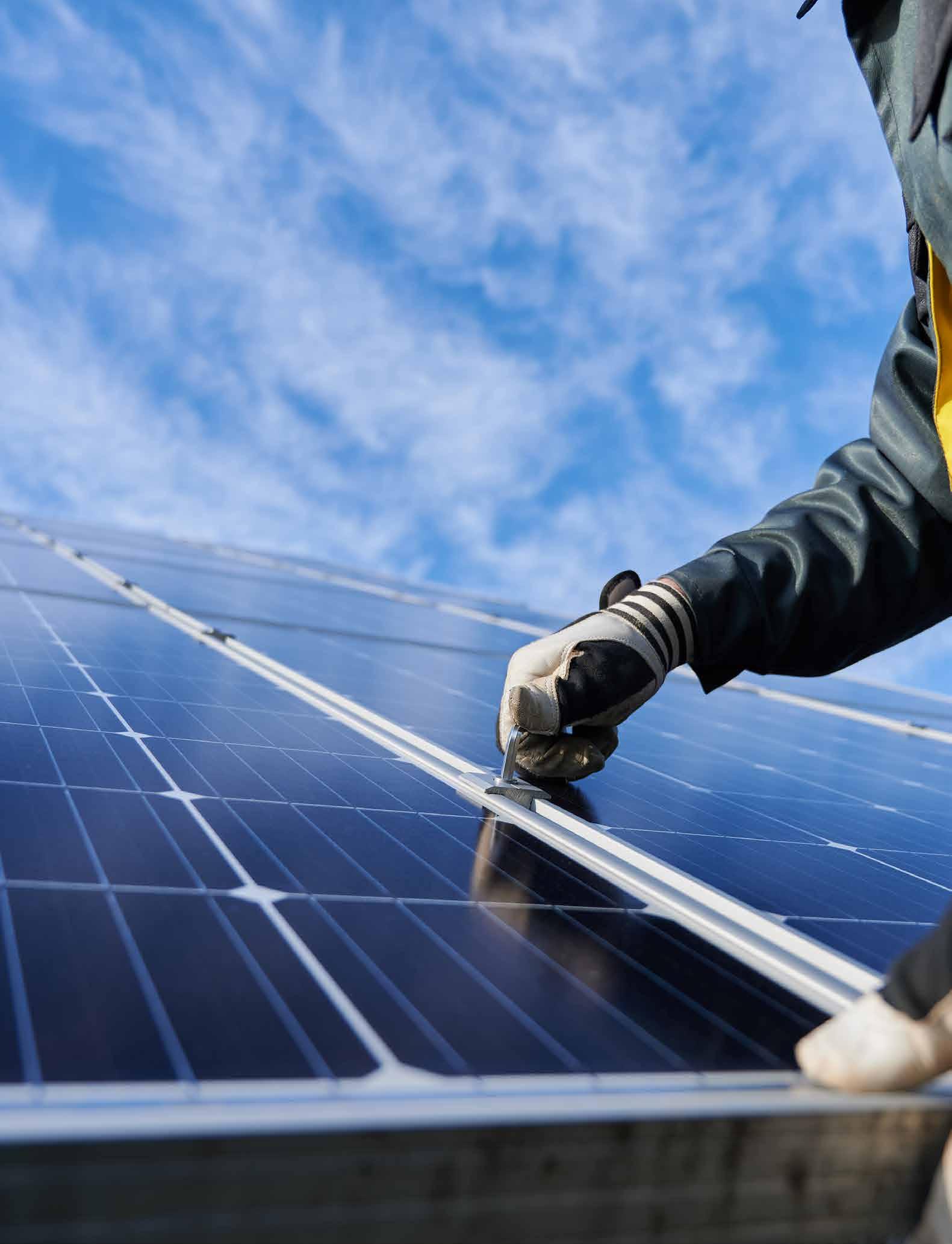
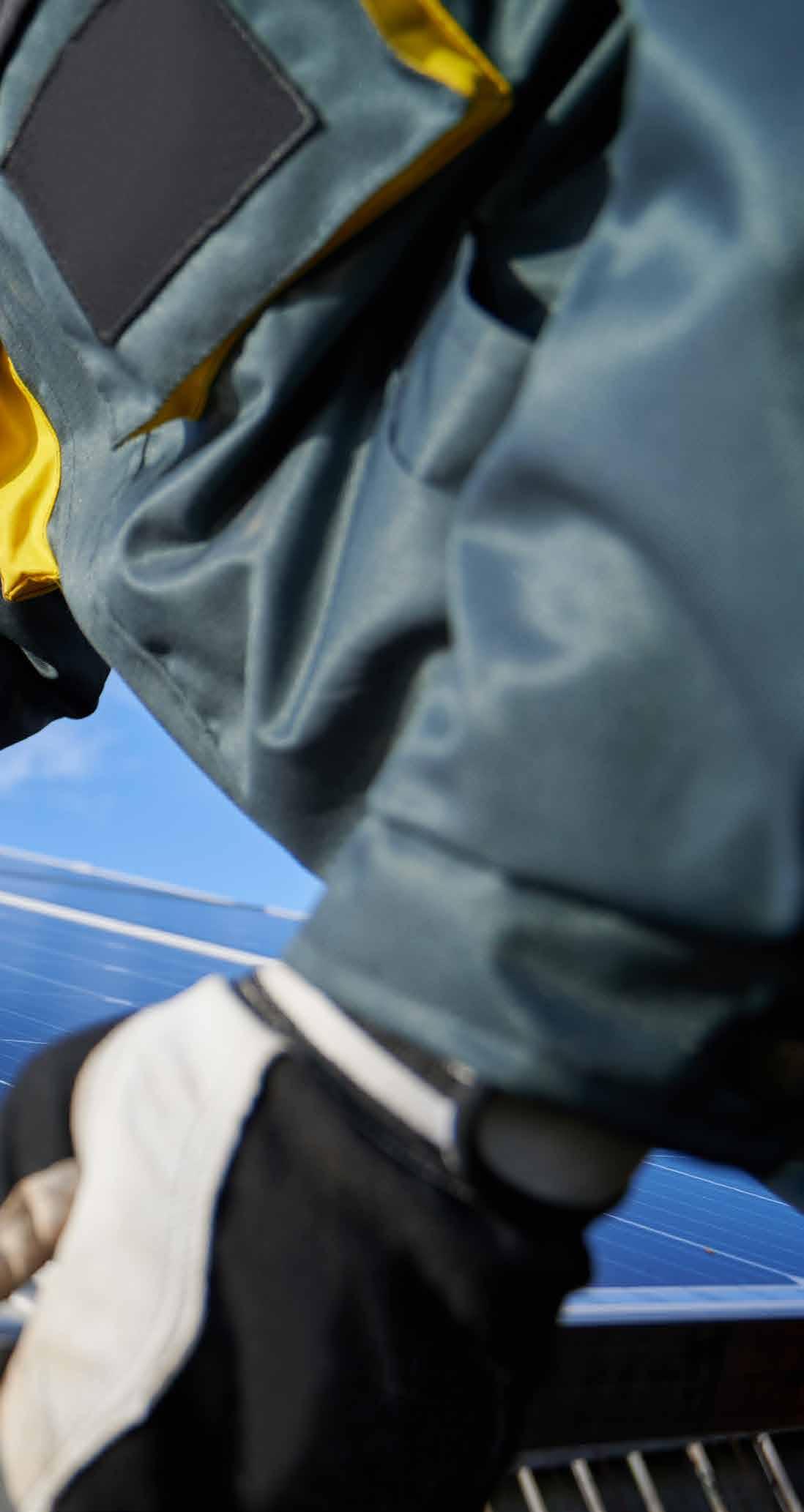
Malaysian Photovoltaic Industry Association (MPIA)
The solar industry has seen a vast uptake of solar photovoltaic (PV) systems across the globe in recent years to help reduce environmental impacts and increase the number of houses and businesses to facilitate their daily functions via renewable energy. In Malaysia specifically, the last 20 years have seen the development of the solar PV industry spearheaded by the Malaysian Photovoltaic Industry Association (MPIA). MPIA’s role engages with the energy ministry, regulators, and authorities to champion the development of the solar PV industry and expand its operations for a more sustainable future.
In 2006, the Malaysia Building Integrated Photovoltaic (MBIPV) Project, made up of the United National Development Program (UNDP) and the Ministry of Energy, Water and Communication (KTAK), funded a seed grant which established MPIA. The project was crucial to driving both energy efficient and renewable energy initiatives, with the mission to reform and democratize the electricity supply industry in every aspect from generation to transmission and distribution. MPIA’s operations work with key governmental figures to make solar PV prices competitive, reliable, and sustainable to ensure their efficiency as an energy source for the country. It is MPIA’s main vision to create a climate of renewable energy availability, where everyone can reliably generate their electricity via solar PV systems to remove reliance on fossil fuels and reduce the daily running cost of electricity for people across Malaysia.
To achieve this mission, MPIA brings together key players across Malaysia’s photovoltaic industry to promote the distribution, education, and regulation of the industry. When the Association began in 2006 there were only 45 members under MPIA, however, today there are close to 200 active members which highlights the current push towards the application of solar PV systems already evident across the country. This is confirmed by the approval of more than 350MW of solar PV projects implemented by SEDA under the Net Energy Metering (NEM) programme in 2020. This covers more than 400 completed new installations by the end of 2020. This positive growth of the industry is

also reflected in the large-scale solar (LLS) program which since 2016 has accumulated more than 850MW in operational capacity.
One of the central focuses of MPIA is education, as the Association hopes that through education it can help successfully achieve Malaysia’s national target of 40% renewable energy capacity by 2040, with the goal of increasing this to 70% by 2050. To achieve this, MPIA has developed its Solar Roadshow 2024, which is hoping to make these governmentally established targets a reality through education and networking. The roadshow focuses on sharing knowledge to help better spread awareness and necessary development into grid readiness, how to enable the energy transition, and discussing the future of electric vehicles in the motoring landscape.
The roadshow will stop at cities all over Malaysia to share the work of MPIA and bring into conversation the role of solar PV moving forward. It is hoped that through the workshops, which will feature speakers from governmental organisations to big organisations, such as the Green Technology and Climate Change Corporation (MGTC), the Association will bring greater awareness to the solar PV market and its member companies. The goal is to bring economic development for the country and MPIA members, whilst pushing the country towards a necessary energy transition.
A Voice for the Malaysian Solar Industry
In January this year, the work of MPIA was highlighted with the signing of a Memorandum of Collaboration with Bursa Carbon Exchange (BCX), to establish awareness of the Renewable Energy Certificates (RECs) market all whilst educating project developers on how to monetise it through BCX. This will mark the first collaboration between the two organisations, and through the MPIA Solar Roadshow 2024, MPIA and BCX hope to create a more transparent market for RECs in Malaysia.
Overall, MPIA has spent the last 20 years developing the solar PV market in Malaysia by promoting its members and education surrounding the renewable energy industry to encourage greater uptake of solar PV systems. For MPIA, development throughout its members continues to bring vital investment into Malaysia and in turn, continues to push the country towards a greater application of renewable energy supported by reliable energy infrastructure for future-proof energy generation. Therefore, through the Association’s focus on education and collaboration, MPIA looks set on easily achieving its renewable energy targets whilst establishing Malaysia as a hub for solar PV development.
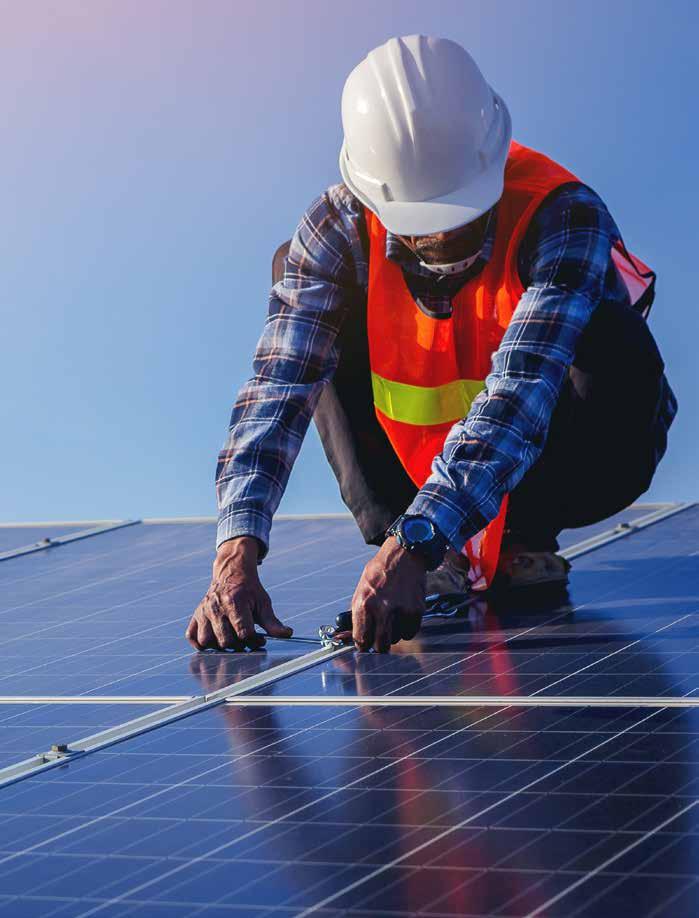
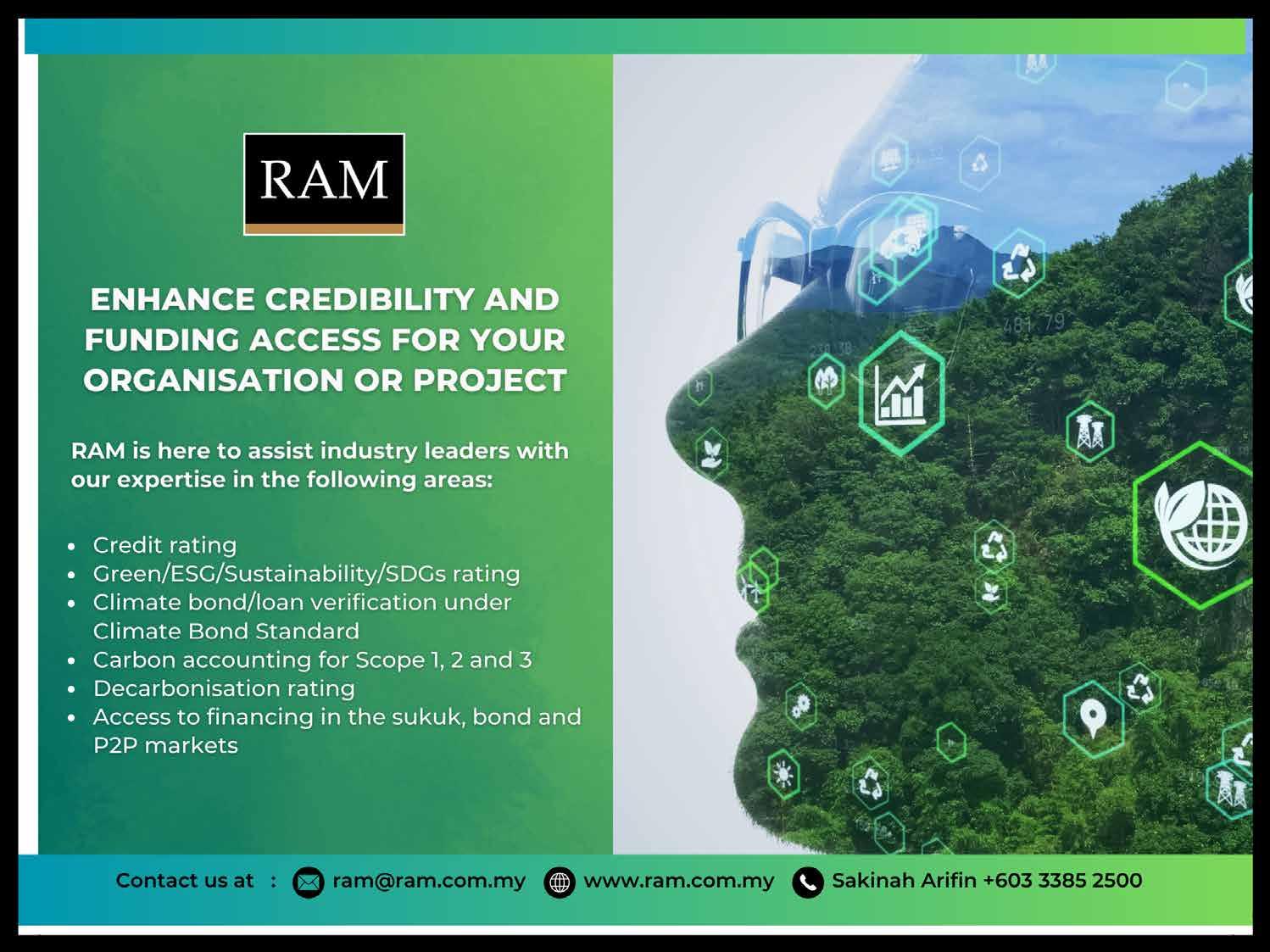
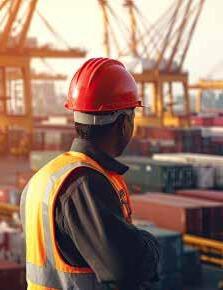
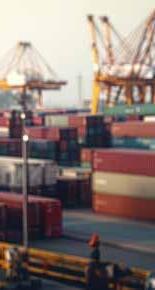
Port Authority of Guam
Located in the inner reaches of the Apra Harbour, the Port Authority of Guam (PAG) has spent the last 49 years dedicated to providing maritime, commercial, transportation and recreational services across the Jose D. Leon Guerrero Commercial port. PAG’s dedication to providing full services to the maritime and shipping industry has now established Guam as a vital stopping point for vessels and an import/export hub which plays a significant role in developing the island’s economic development. With goals to continue to expand the port facilities over the coming years, the Port of Guam looks to take the port into the future through key modernisation projects.
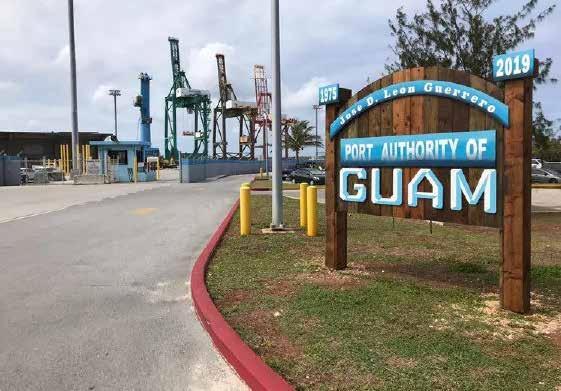
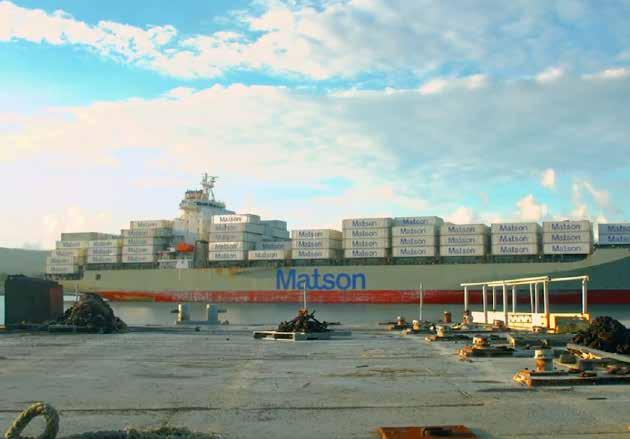
Guam has served as a vital port location extending back to the 16th century when the island catered to the ships of Spain, and, following the Spanish-American war, to American interests. Under US Naval administration the island served as a Western Pacific coaling and shipping station, with the only change taking place during the Japanese Occupation of Guam. However, following the transference of command to Guam’s own Department of Commerce after 1951, the Commercial Port of Guam was established. The port continued its role as a busy centre of trade, and it was quickly recognised as one of Guam’s most important economic assets.
To further establish an organisational environment more conducive to providing efficient and reliable cargo service, which was growing Guam’s economy, Public Law 13-87 was passed in 1975 to establish the Port Authority of Guam as a public and autonomous corporation. To make things a little easier, in 2002 the official name of the port in Guam was changed to the Jose D. Leon Guerrero Commercial Port, taking its name from the first commercial port manager who played an instrumental in in getting the US to transfer all port facilities and properties to the Government of Guam at no cost.
Today, the Port of Guam plays a vital role in shipping and cargo routes located along many major Pacific shipping and air routes. As the main and only transportation hub for Guam, it plays a big role in linking the Commonwealth of the Northern Mariana, the Micronesia islands, and the expanding Far East markets which reach not only the US, but the rest of the world. However, due to its location, the port also relies heavily on these shipping lines and foreign contacts to meet the demand for goods for people in Guam via imports – 90% of which are imported from the US.
The port as we know it today reflects a dramatic growth in cargo revenue, having increased its revenue tonnage from $85,677 when the U.S. naval admin turned over the port to the island’s government, to roughly $1.8 million in the 2006 fiscal year. This significant increase in revenue ensures that the port can maintain its operations and continue to expand in the future as the port is entirely self-sufficient. This means that capital
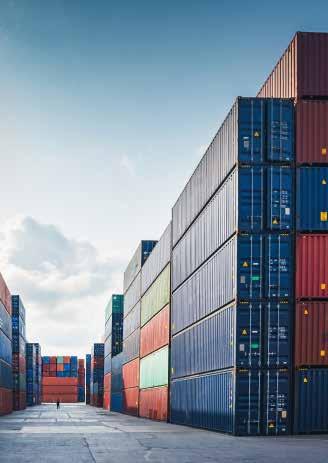
Port Authority of Guam
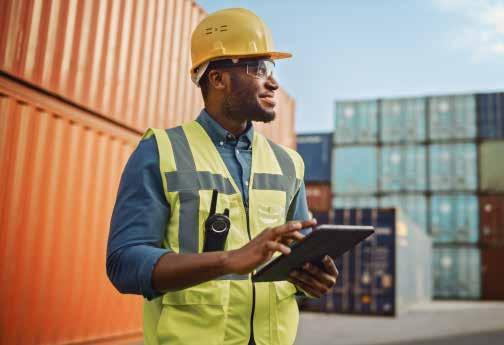
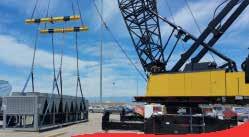
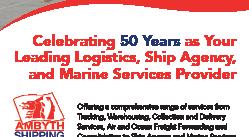
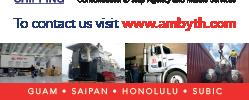
funds for construction projects have to be funded through borrowing money on their own credit.
PAG’s financial obligations and administrative operating costs must be funded by money generated from the use of its facilities and services in accordance with the provision of the port terminal staff. This is because the port has no taxing power, so the port is working to maintain a steady flow of operations across the port to generate revenue to handle its expansion, whilst also contributing to the ongoing economic development of the island. To handle these operations, PAG is overseen by a board of directors made up of 5 non-salaried members who are appointed by the Governor of Guam with the consent and advice of Guam’s legislature. The board of directors’ role is to provide and establish policies and directives pertaining to the planning, promotion, development, construction, operation, and maintenance of port facilities.
By the 2008 fiscal year, PAG was processing more than 2 million dollars in cargo revenue, with the bulk of the cargo being containerized. One of the key focuses of the port, as already mentioned, is its cargo. The port is equipped to handle all types of cargo including containerized, breakbulk, unitized, as well as fishery cargo. However, as a major stopping point in the western Pacific region, the cruise ship potential of the port has begun to
grow. Currently, on average 5 cruise ships stop at the island’s port in Piti every year. Cruise porting requires the PAG to coordinate and reconfigure their shipyard each time to accommodate the influx of services needed. However, the port has been establishing a working group to strategize a small cruise ship industry which will reconfigure and develop the port with the aim of increasing the porting potential and opportunities for Guam.
As part of the Port’s development for the future, it is looking to continue to develop its facilities and equipment to expand its cruise porting facilities and continue to meet the demand for increasing cargo shipments. This has been put into motion by the recent passage of Public Law 29-125 which has given the Port Authority conditional approval of its updated Master Plan which outlines PAG’s roadmap for modernisation. PAG wants to transform the port’s facilities into a world-class terminal for Guam and the Western Pacific Region. For the modernisation program, the port is looking to invest hundreds of millions of dollars to transform its commercial seaport ready for the demands of the future. The development has already seen $10 million of investment provided through a Tiger grant to achieve this.
PAG plays a significant role in Guam’s development of its economy through the seamless and necessary movement of cargo through its seaport. Due to its location, it is an island that relies heavily on its international links to bring mutual prosperity to the country and those overseas.
Under American territory authority, it upholds all the same regulations that you would expect from any US port which continues to highlight the port’s reputation on an international scale. With critical developments as the Port Authority of Guam moves toward the future, we look forward to seeing how it expands its operations to facilitate further cruise lines and continues to bring economic development to the region via its increased cargo port potential.
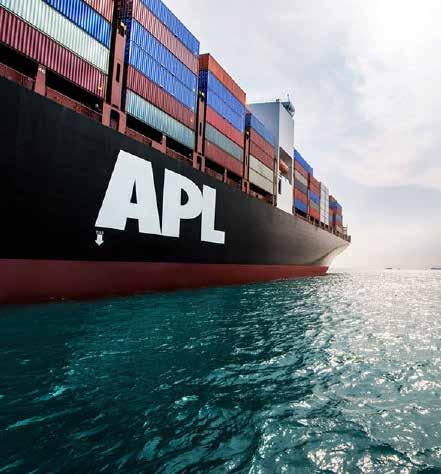
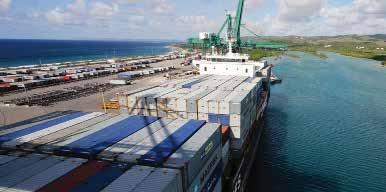
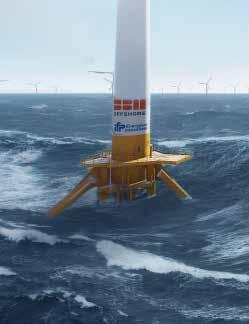
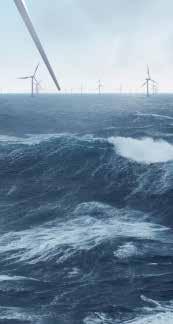
As the energy demand continues to soar across the globe, companies such as SBM Offshore are working to create new and innovative solutions which hope to make energy more accessible. However, SBM Offshore is doing this by harnessing the ocean to move the world towards a future of renewable energy. SBM Offshore utilises its vast expertise across the sector to bring energy to some of the world’s biggest cities whilst constantly working to protect to planet and its people.
To achieve carbon neutrality across the energy sector, SBM Offshore uses its technological expertise to design, build, install, and operate offshore floating facilities across the worldwide energy industry. According to SBM Offshore, twothirds of the world’s cities are located near a shoreline, therefore the need for energy solutions on coasts has the potential to bring significant local prosperity. However, a key focus for SBM Offshore is harnessing the natural power of the ocean to bring energy to local communities whilst not putting these communities or the environment at significant risk. This attention to protection and energy infrastructure building is what positions SBM Offshore as such a significant player in the future of energy development.
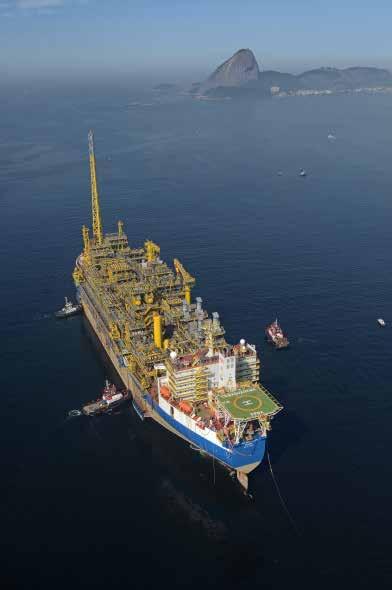
SBM Offshore specialises in a range of offshore deepwater solutions including floating production storage and offloading (FPSO), oil and gas production operations and installation services, offloading terminals, TMS LNG, wave converters and floating offshore wind terminals. It has positioned itself at the top end of the FPSO market and deals with some of the largest and most complex projects in the sector. SBM Offshore focuses on using innovation to deliver high-performance solutions which always aim to meet and exceed its client’s expectations, often going beyond what is available across the market. Its deepwater systems work to tackle unique sets of engineering challenges and make energy infrastructure possible through its comprehensive research and development teams.
A key pioneering strategy of SBM Offshore’s operations is its Fast4Ward program which includes its Multi-Purpose Floater (MPF). The MPF is a generic hull which can accommodate an internal turret, external turret, or spread-mooring solution to facilitate topsides for increased production capacity. The Fast4Ward program has been designed to transform its operations by reducing the cycle time to energy delivery by de-risking projects and improving the quality and safety of its solutions. Therefore, the resulting energy solutions produced by SBM Offshore are paving the way towards future generations of FPSOs across the energy sector.
The Fast4Ward program hopes to add value to its clients’ operations by improving the economics of their deep-water projects which in turn will lower break-evens. To achieve this, SBM Offshore has leveraged its experience by standardising its designs to improve execution of multiple projects which has knock-on benefits across the deepwater
Connecting the future: Cables International leads the global market through innovative cable management
Becoming the world’s leading supplier of specialty cables for the marine and offshore sectors is no mean feat. Yet with more than 50 years of experience, research, and innovation behind them, Cables International have firmly established themselves as global market leaders. Their history, however, is only part of the story. Today, the company’s exceptional range of partnerships has allowed Cables International to continue building momentum: a steadfast customer-centric focus provides a continuous impetus to pioneer new, creative solutions.
One such partnership, namely with the Prysmian Group, has resulted in Cables International’s marketleading offering of offshore cables.
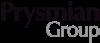

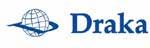
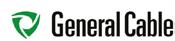
Required to deliver reliability and quality results in the harshest environments, these cable solutions provide high-performance power, instrumentation and control systems. Offshore oil and gas locations all around the world are served from Cables International’s distribution centers in Singapore, Malaysia, China, Australia and Dubai.
Meanwhile, Cables International’s extensive range of cable cleats from industry leaders Ellis Patents has been designed specifically to meet the gruelling needs of the energy sector.
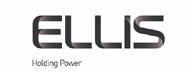
These products provide enhanced protection against the intense forces associated with short circuits, pulling and slamming that are often found in industrial environments. Manufactured from superior metallic and composite materials, the components have international industryappropriate certifications, making them a vital addition to any high-risk, high-load energy installation.
Similarly, through working closely with cable specialists Tecnikabel and APS Finland, Cables International’s portfolio of telecommunications cables now satisfies the widest range of customer requirements and meets or exceeds the strictest international standards. Reliable and longlasting performance is thus a given no matter the conditions.
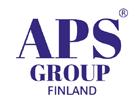
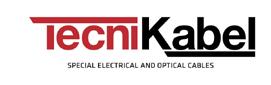
In addition to offshore cabling solutions and cable cleats, Cables International also provides plugs and sockets, an offering that the company has diversified and honed with expert support from partner Marechal Electric.

As a matter of course, the design is driven by safety, and the products are measured against stringent quality standards. Designed for heavy-duty use, they can be relied upon consistently in the most testing environments.
While safety and longevity are at the core of Cables International’s entire product offering, these design pillars also support one of their core values – sustainability. The first industrial company in Southeast Asia to achieve carbon neutrality, they are strongly committed to maintaining an environmental focus throughout their business and supporting their customers in their own sustainability goals.
Sustainability, in fact, forms a key part of Cables International’s strategic partnership with SBM Offshore, a global frontrunner in the supply and installation of Floating Production, Storage and Offloading (FPSO) vessels and a pioneer in developing a sustainable and affordable energy source from the world’s oceans. Significant collaborations to date include the supply and installation of cables for the FPSO Almirante Tamandaré, Mero 4 and FPSO One Guyana.
A crucial factor in making the collaboration run smoothly has been Cables International’s flagship program, Cable Management Solutions. This service guarantees that a customer’s cables and wiring are carefully devised, exactingly installed, and meticulously overseen, ensuring that every system works at maximum efficiency from day one. The company’s team of experts offers support with every aspect of design, engineering, procurement, installation, and ongoing maintenance for all kinds of cable management systems, providing regular and detailed communication with customers throughout the entire process.
Through their continued focus on developing productive partnerships and anticipating customers’ needs, Cables International have earned their place at the head of the cable industry. With so many changes, developments, and innovations happening throughout the sector, however, they refuse to leave space for complacency. Look out for more exciting news from Cables International in the coming year. www.cablesinternational.com
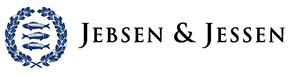
SBM Offshore
solution industry due to their repeatability. In addition to this, SBM Offshore has worked to seamlessly incorporate digital solutions into its offshore solutions, which allows its models to constantly improve their performance whilst also remaining continually optimized for the specific needs of its client’s operations. At present, SBM Offshore has completed the construction of two Fast4Ward hulls with more planned in the future.
In addition to this, SBM Offshore has its Ocean Infrastructure program which delivers value platforms that are safe and sustainable, whilst also creating a more affordable energy solution. This includes a fleet which has been made increasingly efficient by SBM Offshore to lower the carbon footprint of its solutions and produce a leading uptime and safety track record. Therefore, SBM Offshore leads the market with its leased FPS solutions and currently has multiple units in operation across the globe which continue to provide the company with a unique breadth of operations experience across the energy sector.
However, everything that SBM Offshore does is framed by climate change mitigation which can be seen throughout its operations with its strong commitments to net-zero by building facilities and infrastructure in a carbon-reduced way. A key way SBM Offshore does this is through its emissionZERO program which aims, as the name suggests, to
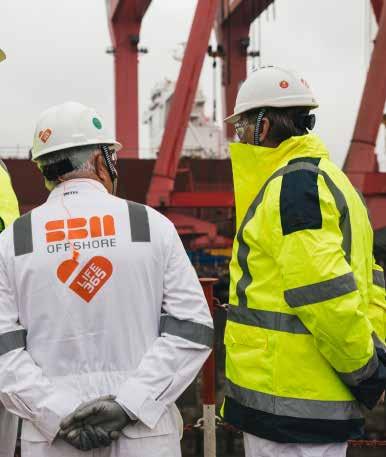
achieve near-zero emissions from its operations. To do this SBM Offshore has set targets in line with the net-zero emission of its key stakeholders and continues to develop products in an emissionreducing way. This is seen in its continued product developments which not only provide a platform for stakeholder engagement but uses the development of its FPSOs to show the energy industry what is possible when strict emission targets are put into place across such a global company. Its Fast4Ward programs are the foundation of this for SBM Offshore.
Furthermore, SBM Offshore remains committed to these carbon-neutral goals through its 3 key strategy pillars of environment, social and governance. As we have seen, in terms of the environment, SBM Offshore is continually investing in energy-efficient technologies whilst also working to bring environmentally friendly solutions to a global market. In addition, the company continues to work closely with its suppliers to encourage innovation and ensure that sustainable solutions encompass its supply chains at every level. We see this in its zero-emission solution for hydrocarbon production which, as the company moves towards the future, is hoped to continue to create value for all of its stakeholders as it leads the market with carbon-zero energy solutions.
Additionally, SBM Offshore fosters a safe and inclusive environment where the people are at the heart of its every function. The company aims to inspire and empower people by focusing on strict guidelines on workplace health, safety and security, community relations, human rights, diversity, and inclusion. It is this keen focus on its people that has earned SBM Offshore global recognition as a responsible corporate citizen. In turn, those who choose to use SMB Offshore as their energy solutions provider, know they are working with a company that has a reliable reputation as a reliable and supportive partner across international markets.
Throughout SBM Offshore there is a strong commitment to achieving high operation performance which focuses on a value-based approach. This approach prioritizes strong leadership, clear decision-making processes, effective communication between management and stakeholders, as well as strong ethics and

SBM Offshore
compliance. All of these factors are part of the company’s ongoing commitment to continuous improvement which helps it achieve operational excellence and consistently high-quality solutions. As the company moves towards the future, it has continued to incorporate digitalization into its operations and governance to help it remain ahead of the curve. However, what remains the same about SBM Offshore is its central values of integrity, care, entrepreneurship, and ownership which can be seen throughout every single aspect of its operations.
As SBM Offshore looks towards the future its key focus is on its new-build FPSOs with oil production volumes of up to 250,000 barrels per day which previously was the focus of the Fast4Ward FPSO. The large conversion FPSO with an oil production volume of up to 150,00 barrels per day will rival traditional FPSO markets as it continues to convert oil tankers to FPSOs. Furthermore, SBM Offshore will continue to take a selective approach to market opportunities
with a key focus on the main FPSO markets in Brazil and Guyana where the majority of low breakeven oil-price prospects are concentrated. In addition, SBM Offshore continues to develop its business across the globe which hopes to see up to 35 FPSO projects reach a Final Investment Decision (FID) between 2021 and 2023.
Overall, SBM Offshore continues to strive to keep pushing the boundaries across the energy sector to produce solutions which respect the planet whilst also bringing essential energy infrastructure to coasts across the globe. What separated SMB Offshore from its competitors is it commitment to sharing its experience with the industry to continually deliver safe, sustainable, and affordable energy solutions from the oceans which can provide essential energy for many generations to come. We look forward to seeing how SBM Offshore continues to develop the offshore energy industry and continues to show the industry how crucial sustainability is in the energy sector.

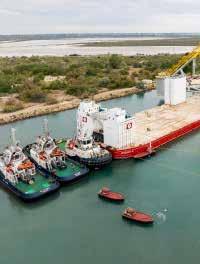
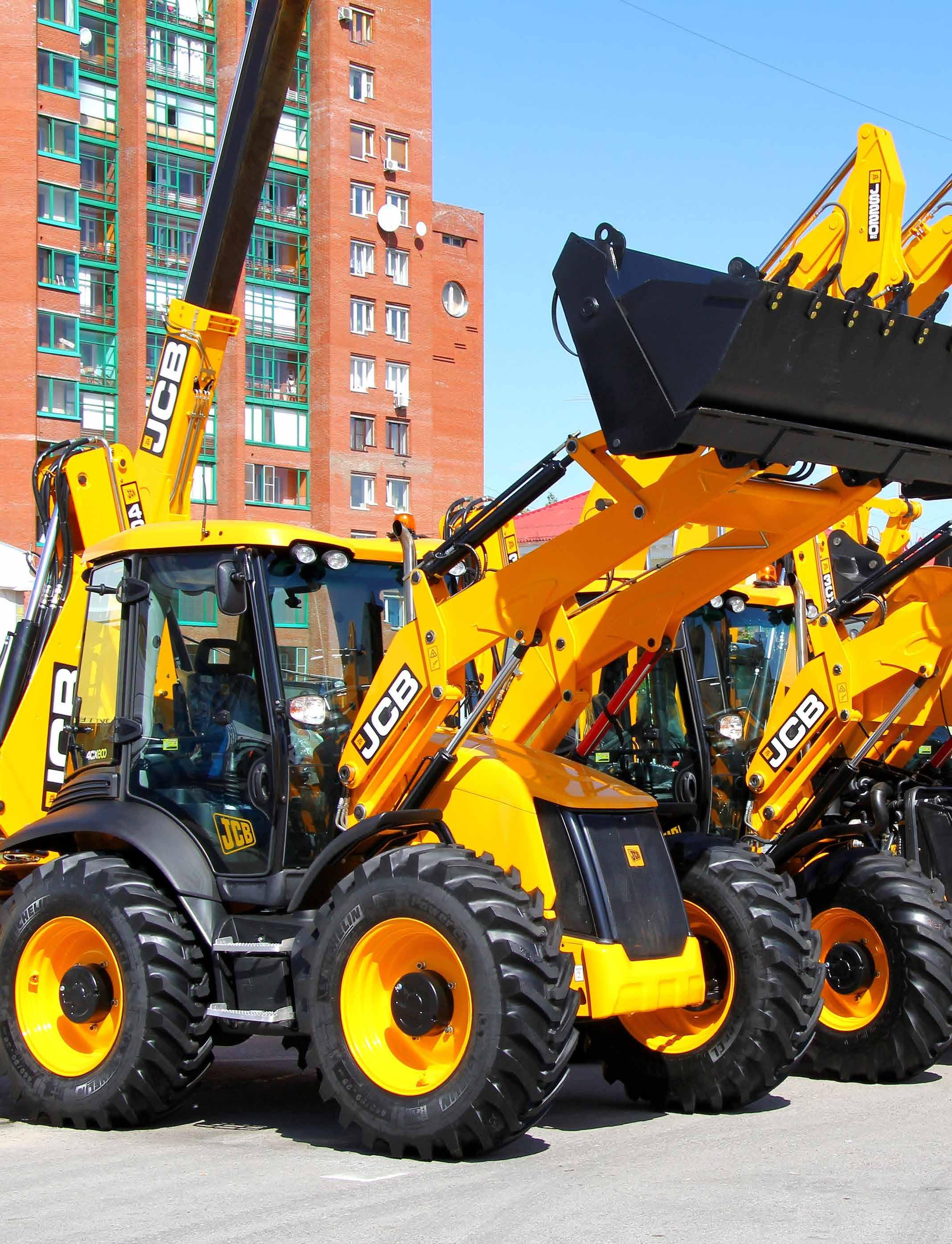
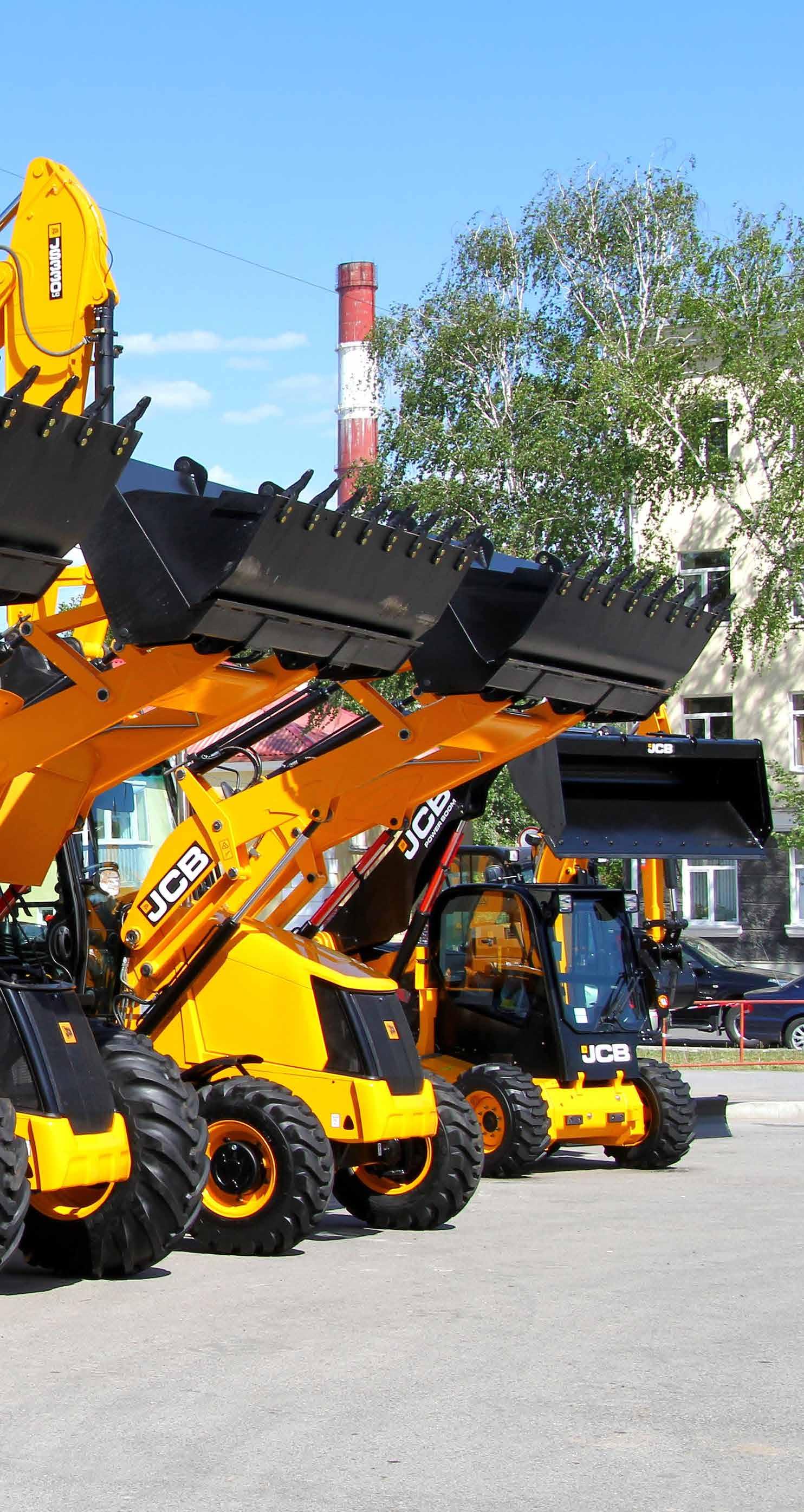
As a leading manufacturing company that pioneers all of its operations with innovation, it is no surprise that JCB is a globally recognised brand playing a vital role in sculpting the modern world. JCB is trusted for its reliable machinery, and, thanks to this reputation, its products can be seen across project sites all over the world. However, more recently the company has been making vital developments towards sustainability as it works to meet global demands for decarbonisation. Therefore, with its legacy, reputation, and experience behind it, JCB is stepping into 2024 with its sights set on introducing renewable energy options across its machinery and equipment portfolio.

JCB found its origins in agricultural tipping trailers and has spent the last 79 years developing its manufacturing offerings of heavy machinery and equipment, and now is a globally recognised brand with 22 plants in operation across 4 continents. In addition to the plants, JCB has more than 750 dealers globally with roughly 11,000 employees in over 150 countries around the globe. Therefore, as the company approaches its 80th birthday next year, we simply can look back over all of the projects that JCB’s equipment and machinery have been a part of to see the vital role the company continues to play across the world.
Having established itself as a leading manufacturer in the world of construction, agriculture, waste handling and demolition, JCB is now focused on developing renewable energy machinery. The push towards sustainability starts all the way at the top with Lord Bamford, Chairman of JCB, who outlines that “I set the challenge that we should be making hydrogen engines for the construction industry and for agriculture. Two years later, we have hydrogen engines working in the kind of equipment that JCB makes. A solution that delivers power in the same way as conventional engines, but with none of the fossil fuels. We’re proving daily that hydrogen does work, that it’s clean, renewable, transportable fuel”.
Bamford’s call for zero-carbon alternatives has propelled the company’s mission to find ways to replace fossil fuels whilst still fuelling heavy machinery that can meet the same high-demand workloads of its carbon-emitting counterparts. This high demand payoff means that batteries are not the solution JCB were looking for as they can weigh too much, are costly, and then need the time and infrastructure to recharge. Therefore, the alternative green energy choice for JCB is hydrogen, and so JCB Power Systems has developed the first hydrogen motor in the industry. The hydrogen motor takes advantage of existing technology and adapts it to establish a new engine technology with readily available components. The motor will combust and deliver power in exactly the same way as a diesel engine but with zero emissions.
To make the most of this hydrogen engine development, JCB has made a Backhoe Loader with can do everything its diesel-powered equivalent
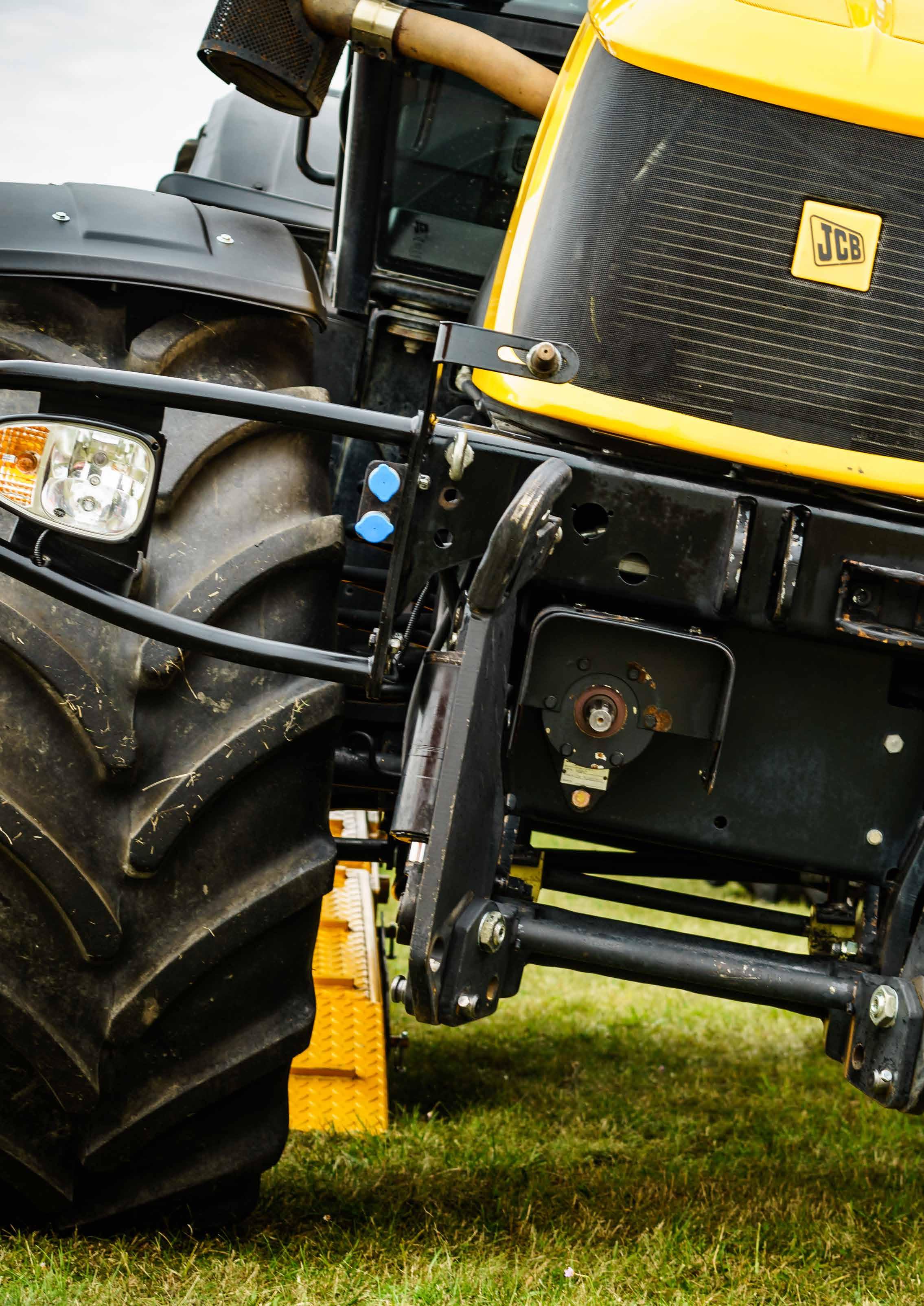
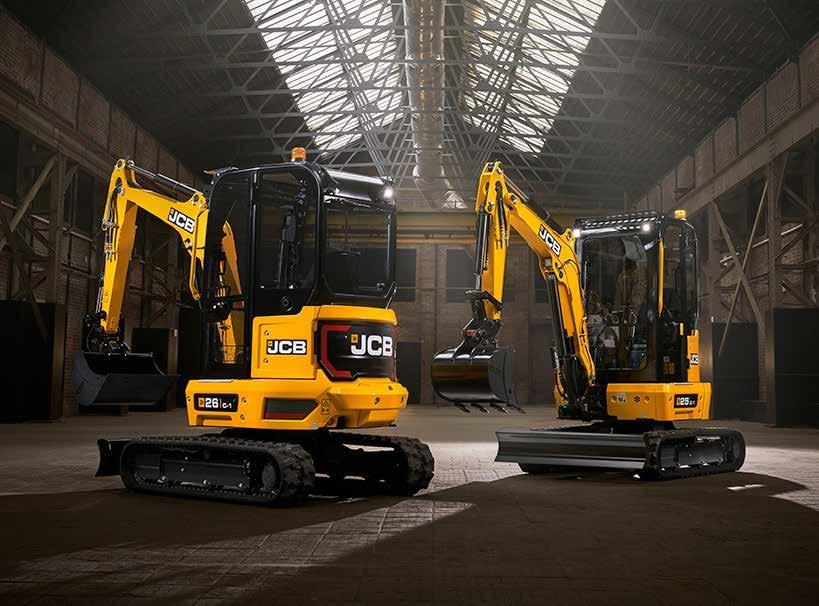
can do but is a lot less complicated than hydrogen fuel-cell technology and emits no steam from its tailpipe - so no carbon dioxide is released at the point of use. To support the Backhoe Loaders and future hydrogen-powered machinery, JCB has also developed a mobile hydrogen refuelling unit which allows for easy transportation of hydrogen on-site. This will increase the efficiency of its fuel delivery and continue to make the hydrogen-powered solutions a preferable choice over previous fossil fuel options. In 2023, the 50th JCB hydrogen combustion engine came off the production line and continues to move the company towards a sustainable future.
JCB has also been making waves in the electric equipment sector, and last year saw the company launch two articulated boom aerial work platforms which give its customers the choice of having fully electric or diesel-electric hybrid drivelines. JCB’s A45E is a fully electric option which produces zero emission whilst not compromising on performance. In addition, JCB has also expanded its equipment line further with the launch of a compact 403E, which is the first full electric wheel loader for the company. It boasts the largest standard battery pack in its class which matches the productivity seen by the popular 403 diesel model. The strong focus on
renewable and green energy sources shows the innovation that has allowed JCB to remain ahead of its competition across the globe. The company continues to strive for the best technologies, and with the help of its global network, it can achieve these and move the industry towards sustainable solutions.
A crucial aspect of JCB’s worldwide network is its subsidiary in India, where JCB began its joint venture in 1979. The now fully owned subsidiary of J.C Bamford Excavators has 5 state-of-the-art factories where it manufactures an array of the company’s world-class equipment for the domestic market in India, as well as for exports overseas. These exports are delivered to more than 124 countries worldwide, via a network of 60 dealers and 700 outlets and thanks to its 8,00 employees. The headquarters for JCB in India can be found in New Delhi where the company has its Ballabgarth Factory.
The Ballabgarth Factory is the world’s largest factory for Backhoe Loaders and also manufactures Skid Steer Loaders, Telehandlers, Diesel Generators and Diesel Engines. However, for India, a crucial
focus is ensuring local workers and companies are benefitting from the company’s operations. Therefore, JCB in India has close to 380 world-class Indian suppliers throughout its supply chains and manufacturing lines. This, along with a range of community initiatives, ensures that JCB’s operations in India are always looking to bring economic and infrastructural development to the region for the benefit of those who live there.
Overall, JCB is a brand that fosters innovation as it works to supply sustainable and efficient machinery to make projects a breeze for its customers whilst helping them to achieve carbon reduction in their projects. For JCB, the future of heavy machinery needs to be geared towards sustainability to keep up with the worldwide demands for carbonreduced options throughout every industry, but especially in industries such as construction which was previously very fossil fuel-dominated. We look forward to seeing how such a global company continues to lead the manufacturing industry and exemplify how focusing on sustainability is key to continued success.
The Future of Construction

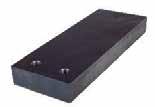
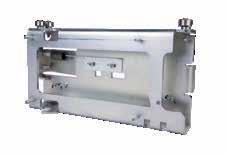
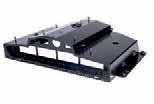

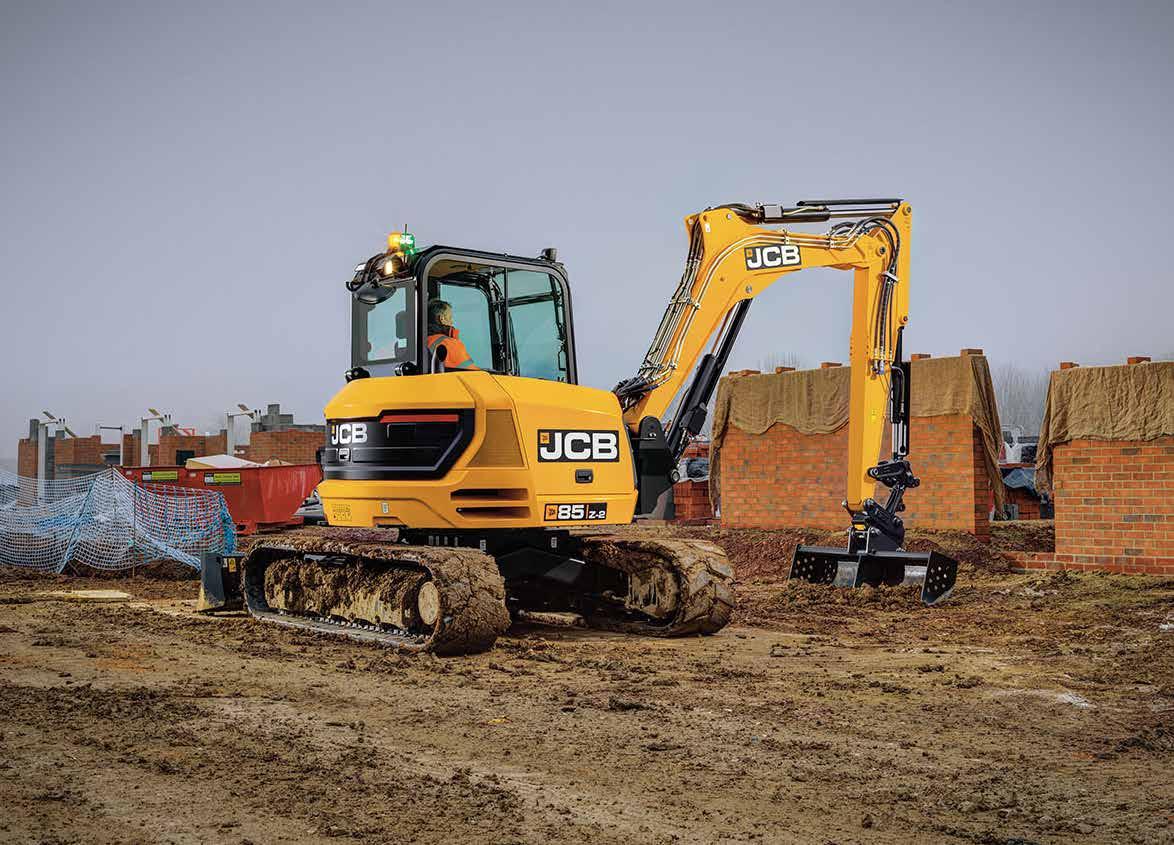
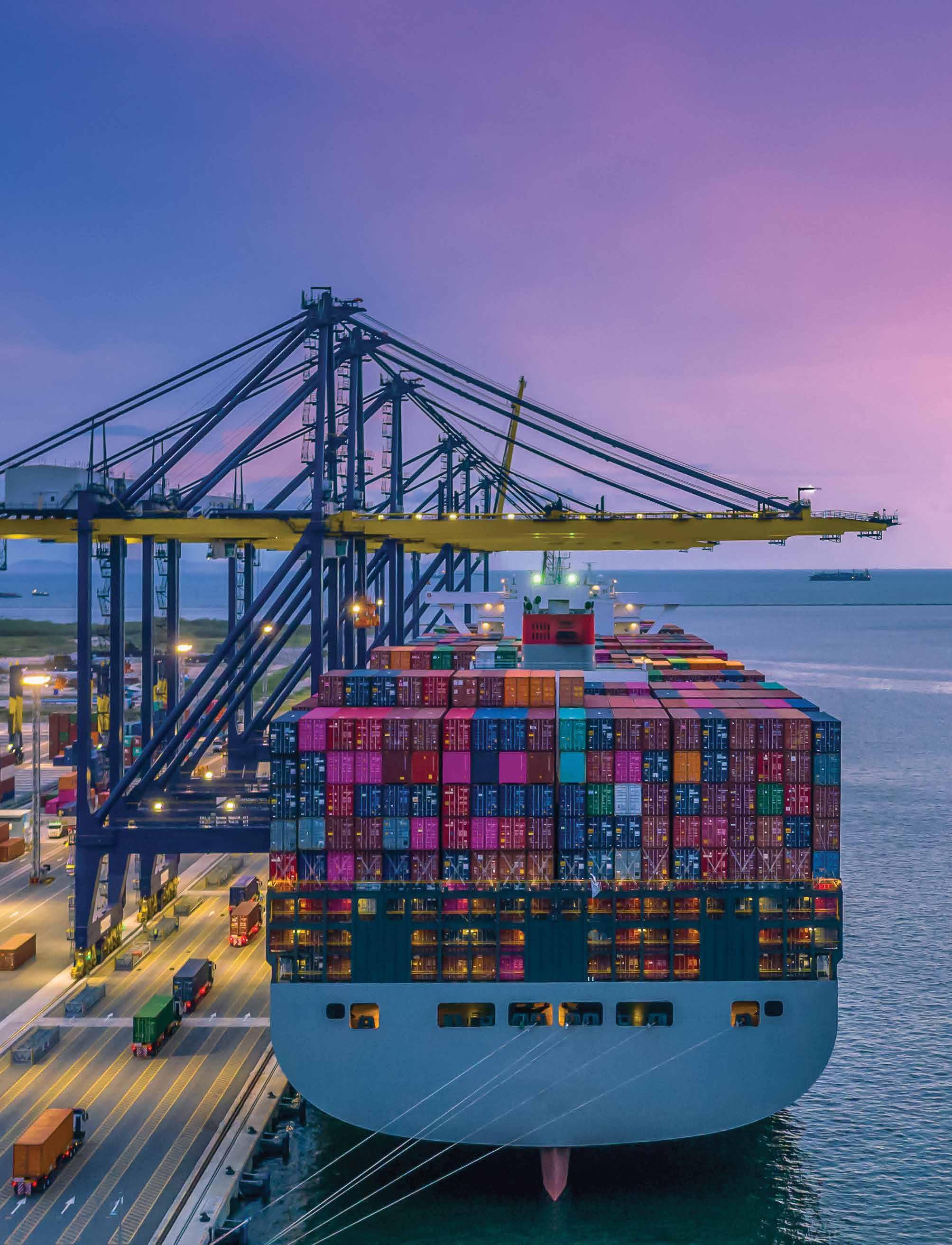
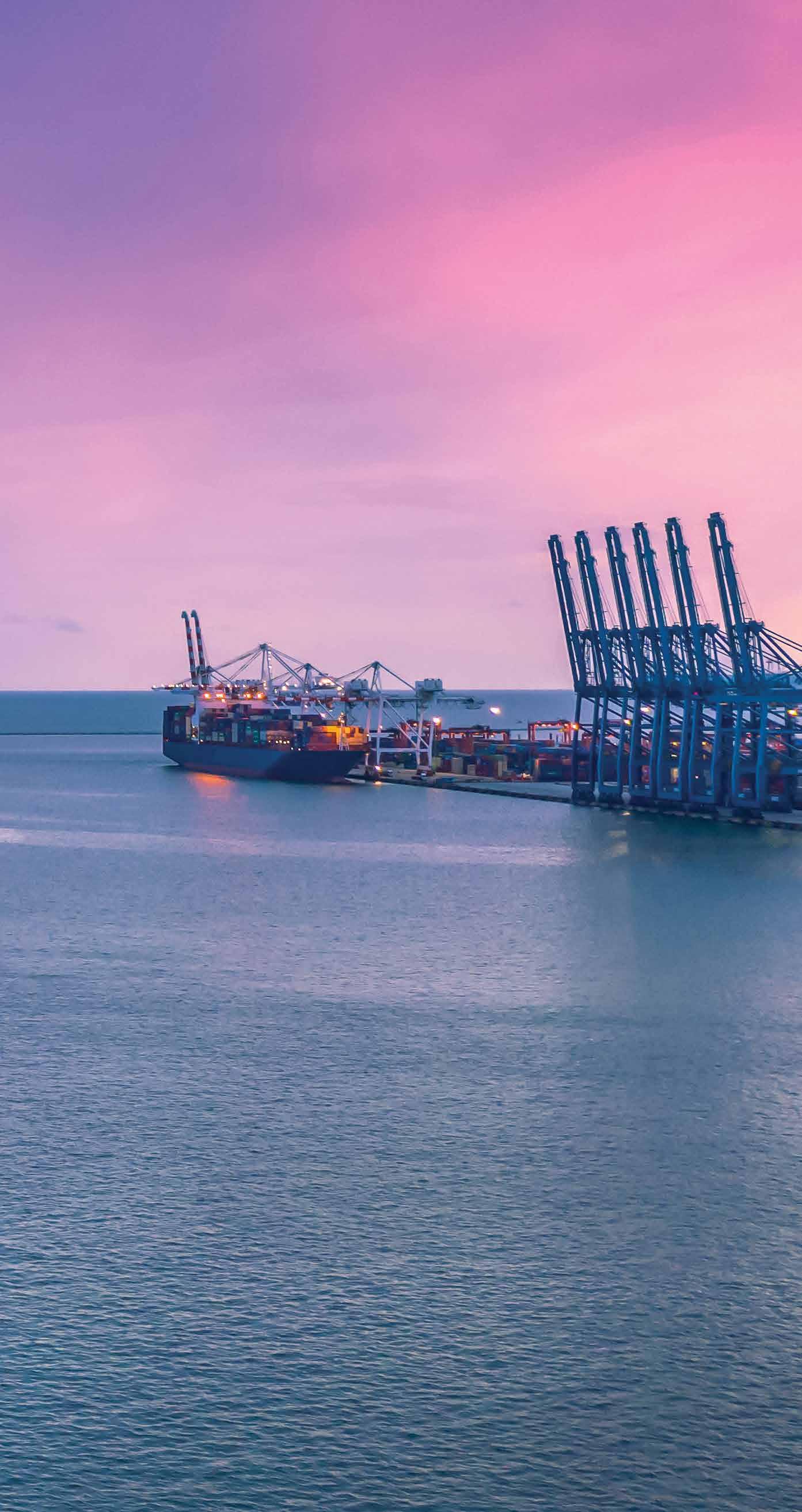
Operating the world’s largest transhipment hub, PSA Singapore provides unrivalled connectivity in the heart of Southeast Asia. PSA Singapore is a world-leading ports and terminals group which handled 37 million twenty-foot equivalent units (TEU) of containers in 2022. Therefore, as the flagship terminal of PSA International, PSA Singapore leads the industry across the region providing handling, management, depot, and warehousing services to a whole range of container vessels.
PSA Singapore began as the Port of Singapore Authority, which was a statutory board responsible for regulating, operating, and promoting the Port of Singapore in the 1960s. However, in the 1970s its container port and handling facilities were established which over the next few decades saw expansive growth reaching 5 million TEU by 1990. By this point, Singapore was the largest container port in the world, and so in 1996, the regulatory functions of the original company were transferred to Singapore’s new maritime regulator, the Maritime and Port Authority of Singapore (MPA). In 1997, the Port of Singapore Authority converted into an independent commercial company which kept the PSA initials and added Singapore removing the original acronym meaning. Since the container port and handling services began as the central focus for PSA Singapore, it has continued to expand and play a vital role in the overarching multinational PSA International group.
The core business of PSA Singapore is the movement of cargo from one vessel to another whilst in transit to its destination. This vital role is due to its strategic location at the heart of

SUPERCHARGE YOUR SUPPLY CHAIN EFFICIENCY
Following DHL Supply Chain’s investment of EUR350 million in Southeast Asia, find out more about how DHL in Singapore is unlocking the future of logistics for our customers.
As the leader in green logistics, we are committed to carbon neutral facilities and a full EV fleet by 2025.
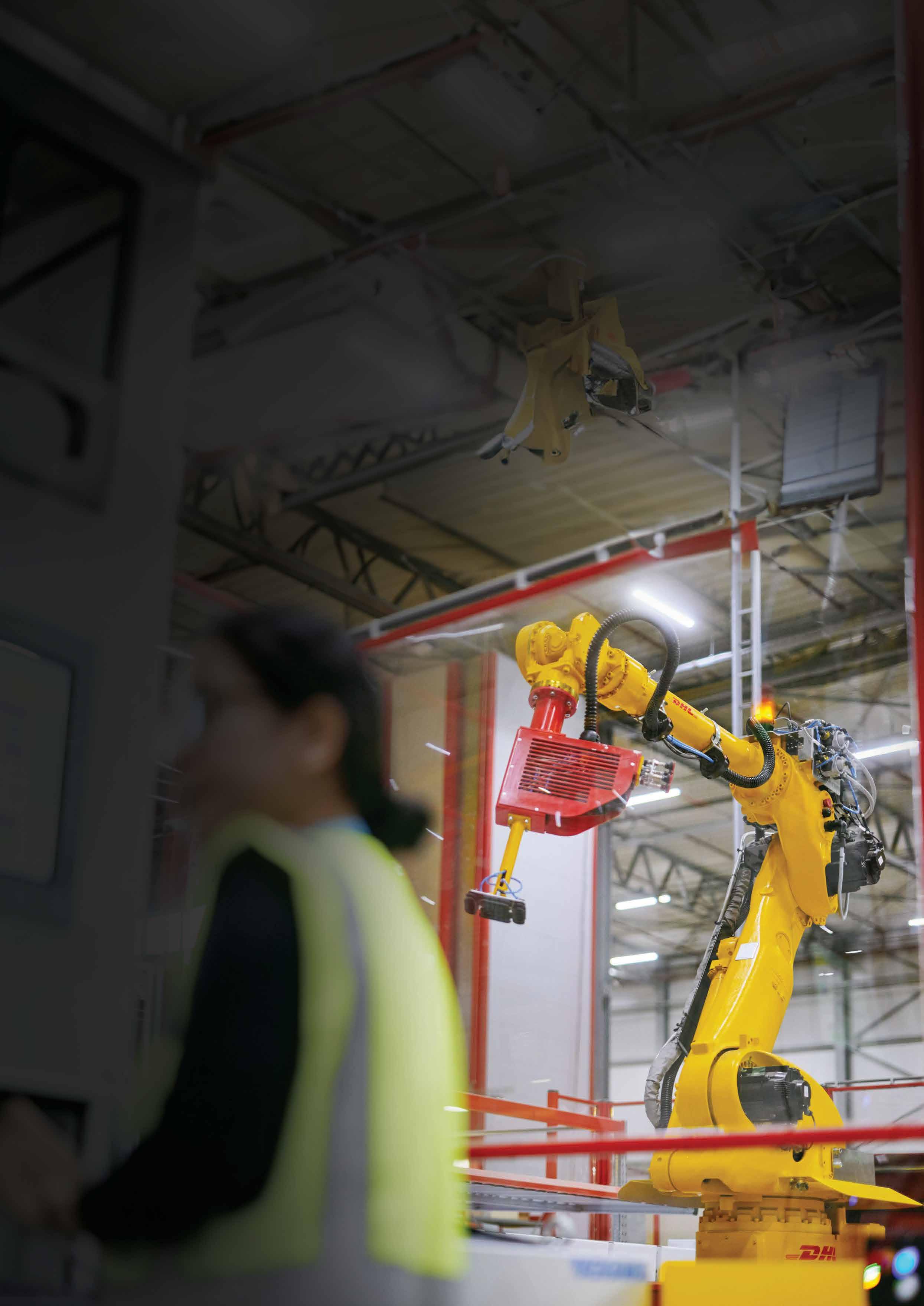
Our investments in digitalization are driving productivity and value for our customers with innovative technologies and services including:
Automated pallet storage and retrieval systems
Goods-to-person picking robots
Automated Guided Vehicles
Warehouse Automation Systems
Connected Control Towers
Whether your business operates in Energy & Chemicals, Engineering & Manufacturing, Life Sciences & Healthcare or Technology, visit our website to find out more about how we can supercharge your Singapore supply chain efficiency.
Contact our supply chain experts today at nazher.khan@dhl.com or xubin.liu@dhl.com.
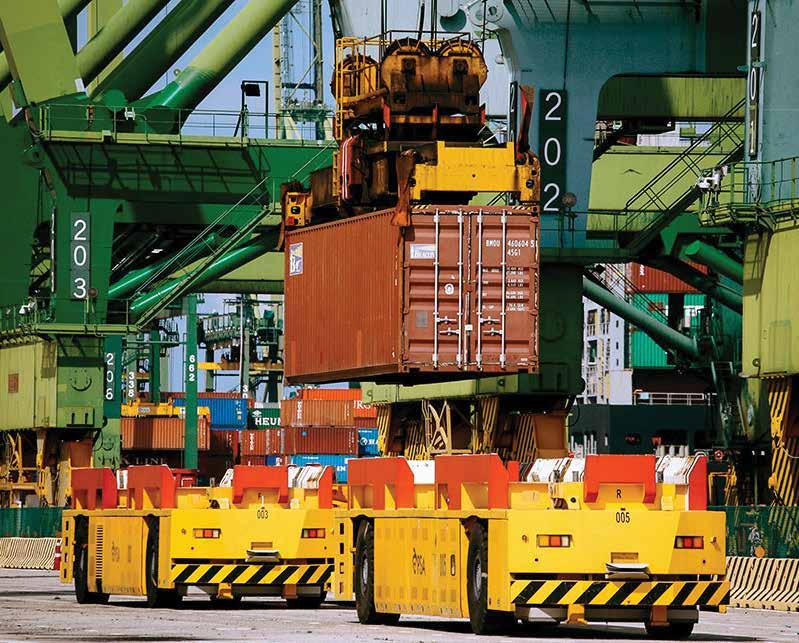
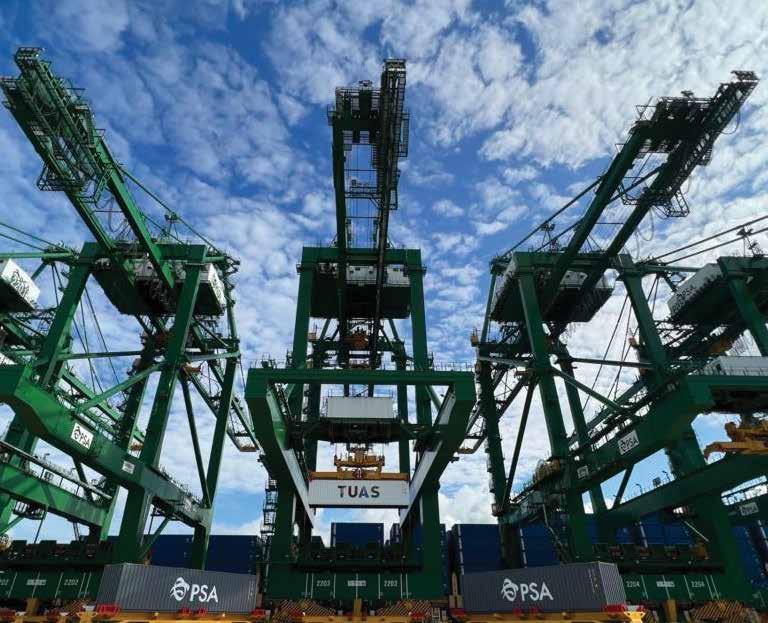
Southeast Asia, at the crucial crossing point of many major shipping routes. Therefore, the PSA Singapore has become an important hub for global supply chains as feeder vessels bring containers to the Port of Singapore which are then loaded onto larger vessels which are then taken on shipments to their final destinations.
This transhipment method is both costeffective and efficient because it allows vessels to make a single voyage to the port, rather than multiple journeys to each individual destination. Consequently, approximately 85% of the containers that arrive in Singapore are transhipped to another port of call, and so the role that PSA Singapore plays in facilitating and maintaining this system of transhipment can be felt across the local and international cargo industry.
Across PSA Singapore there are 55 berths at the Tanjong Pagar, Keppel, Brani and Pasir Panjang ports. These ports all are equipped with container handling equipment and have a combined capacity of 50 million TEUs. The largest facility is at the Pasir Panjang Terminals (PPT) which has 3 dedicated births and is supported by an open car yard and multi-storey car storage yard which accommodates 20,000 car park lots. In addition, PSA Singapore has its Jurong Island Terminal which is located on the western corner of Jurong Island and has 2 berth terminals with a capacity of 400 TEUs.
A significant part of the development of PSA Singapore is the Tuas Port which is currently under development to consolidate all the company’s container terminals into a single location on the western seaboard of Tuas. The finished port is planned to have an automated and integrated operations system which will be deployed to tackle the next generation of cargo demand. Construction of the first set of berths began in 2021 and is expected to be completed by 2040. The entire project is part of PSA Singapore’s vision to form a holistic ecosystem which will bring goods anywhere in the world faster and more reliably.
For PSA Singapore sustainability is not just an option but a responsibility. It is working constantly to ensure that in order for the business to retain its resilience and continue to grow without compromising the environment it has set out on a mission to reduce greenhouse gas (GHG) emissions for the next generation. It has committed to a range of targets which are in line with Singapore’s climate ambitions. A crucial step towards these initiatives came in a recent partnership between PSA Singapore and the Pacific International Lines (PIL). As announced this month, the two companies have signed a Memorandum of Understanding (MOU) to jointly develop sustainable solutions to cut carbon emissions and optimise maritime efficiency. This includes the development of a set of low-carbon emission routes for containers shipped by both companies.
PIL is the largest home-grown carrier in southeast Asia with strong shipping links in Asia, Africa, the Middle East, Latin America, and Oceania. As leaders in their respective industries, the partnership signifies a crucial move towards sustainability throughout the shipping industry. Mr Nelson Quek, Regional CEO of Southeast Asia for PSA International discusses the partnership between its flagship
Singapore division and PIL in the company’s recent press release, stating that “PSA is pleased to partner with PIL as we take the bold and essential step towards decarbonising the global supply chains that power our economy. We remain committed to working hand-in-hand with likeminded stakeholders as we spur concerted action towards our transition to a cleaner and sustainable future beyond the areas served by our ports”.
Therefore, this crucial partnership is set to drive change across the industry and allow each company to meet the common goal of achieving net zero carbon emissions by 2050. It is these joint ventures with other respected stakeholders within the shipping and cargo industry, that have allowed PSA Singapore to develop its operations and establish itself as a crucial hub for these industries on a global scale. Through strategic partnerships, PSA Singapore continues to deliver productivity and efficient terminal services.
Overall, PSA Singapore has worked tirelessly over the last 50 years to move from a regulatory board into the world-leading ports and terminal group,
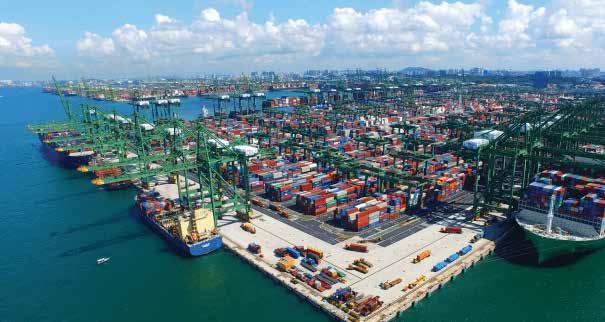
which has continued to expand across the globe. PSA Singapore plays a crucial role in an international network of port and container handling services both under PSA International, but also in the shipping industry as a whole. Consequently, through this work to develop its facilities and through strategic partnerships with significant stakeholders across the industry, PSA Singapore continues to foster a leading supply chain which is powered by its innovation, technology, and sustainable practices.
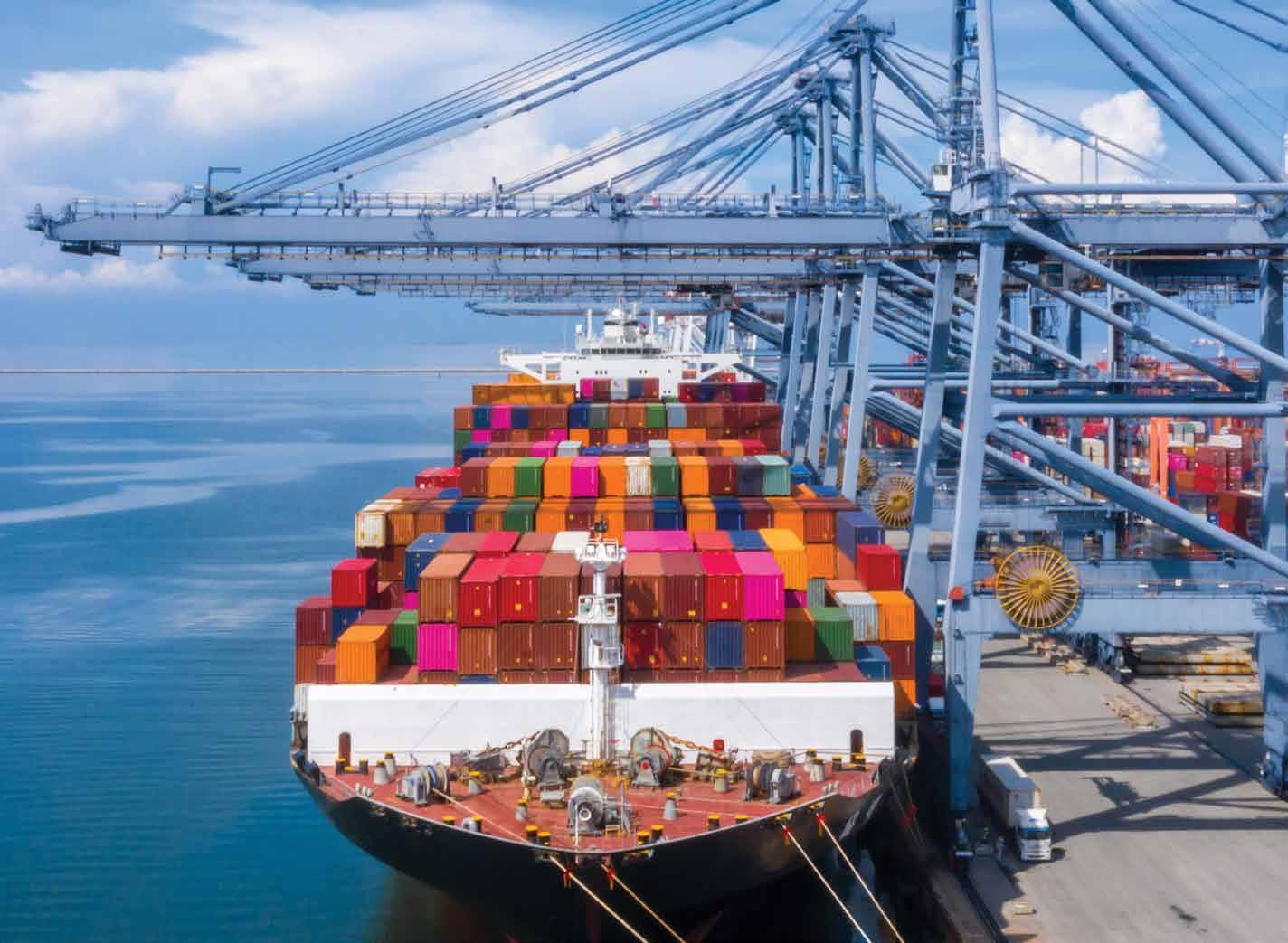
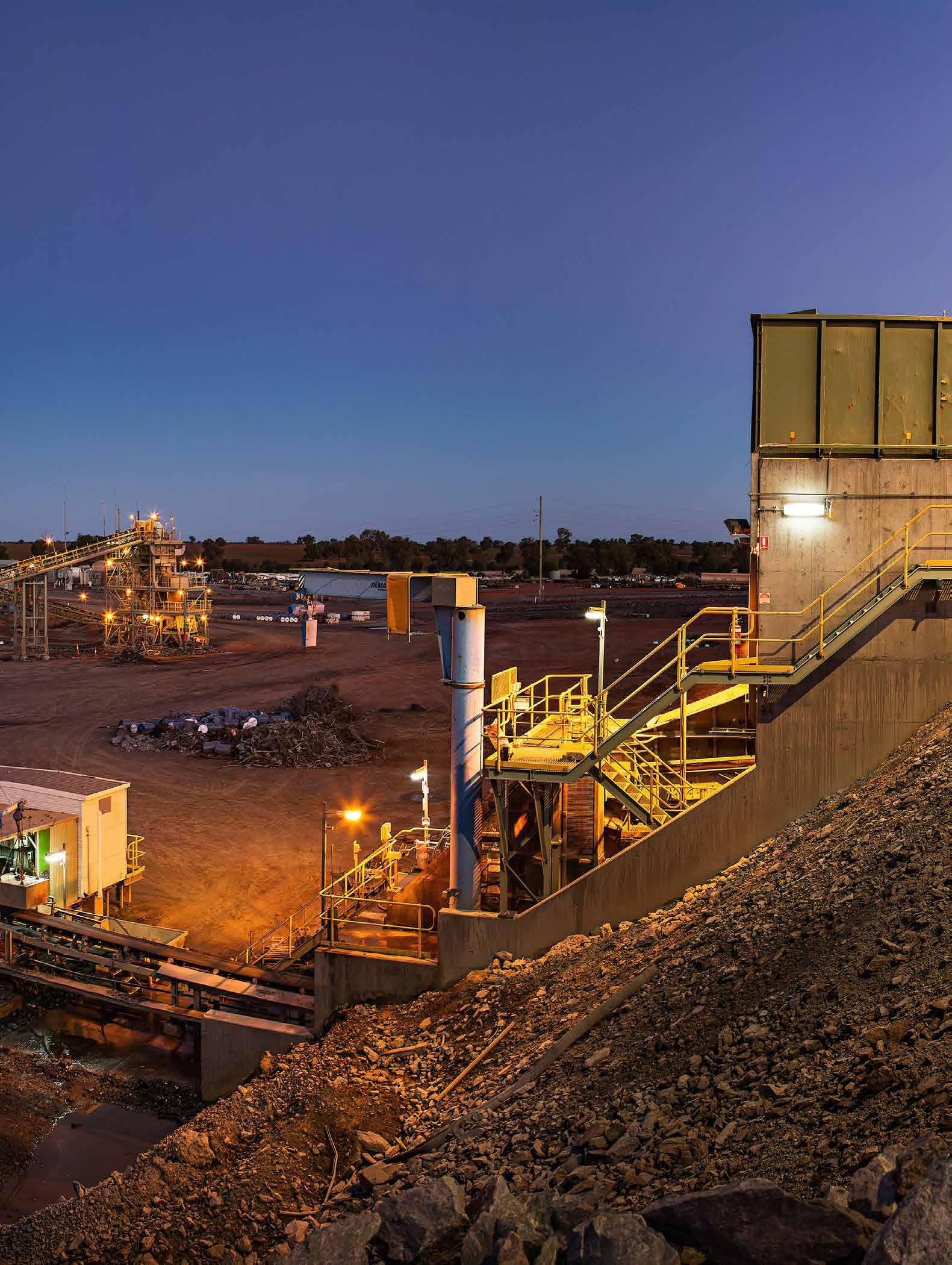
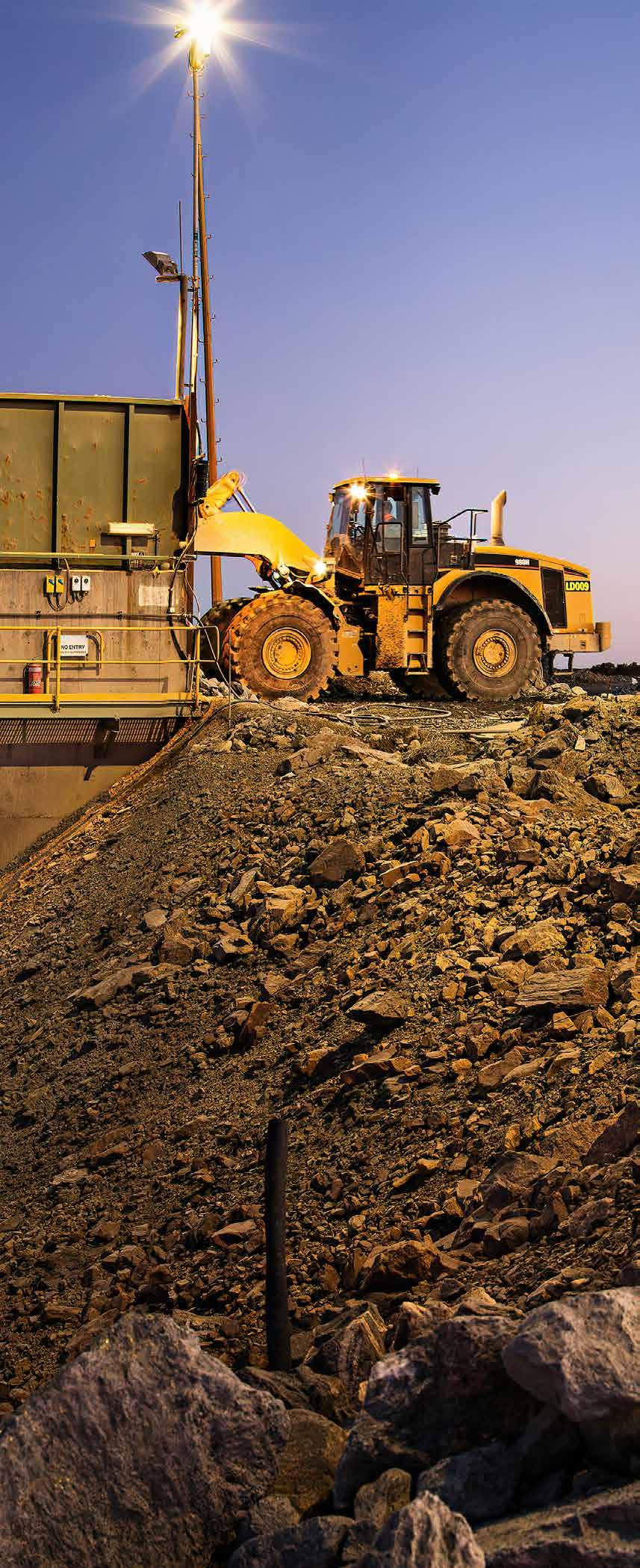
Gold Fields Australia
The Australian mining industry is one of the largest in the world, bringing significant profit to the nation. Gold Fields’ collection of mines certainly stands as a key contributor to the Australian mining industry. Operating across four mines in the Southwest region of Australia, a lot can be said for the rapid growth that the mining entity has experienced in the last 20 years, reaching an unprecedented position in Australian mining.
As suggested by the name, Gold Fields mines are located across the Eastern Goldfields region in Western Australia. The company is comprised of four mines: Agnew, St Ives, Granny Smith and Gruyere. The first two mines were acquired over 20 years ago, operating a tiny production, before growing into the mining entity it is today. Such success was further advanced with the attainment of Granny Smith and Lawlers gold mines from Barrick Gold towards the end of 2013. Furthermore, in 2016 Gold Fields created a vital joint venture with Gold Road, so that the Gruyere mine could be utilised more efficiently, in the form of an open pit. Such an acquisition was a solidifying moment of Gold Field’s success.
IPP(WA) have proudly been supplying Gold Fields Australia their PPE and Safety products for over 20 years now. Keeping people safe is what we do best.
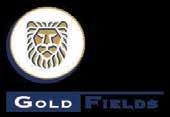
The prosperity of Gold Fields is represented by the Yilgarn South Assets, which is a measurement of the company’s contributions to the Australian mining sector. Currently, the Yilgarn South Assets provide an additional 452,000 ounces of annual production to the country’s mining sector, with 2.6 million reserve ounces and 1.9 resource ounces. In reference to the former, this is the projected figure of materials that are expected to be recovered and produced at the four mines. Alternatively, resource ounces refer to the economic interest in mining operations. This is indicative of the external investment in Gold Fields operations, and how this translates financially. It is therefore no wonder that Gold Fields Mines is the largest regional Australian production centre, responsible for 40% of total production.
If we take a closer look at each individual mine, we can begin to see how each site has a specialism which contributes to the bigger picture of Gold Fields success. For example, St Ives is the oldest mine out of the four mines. Having been in operation since the mid-1980s, it has produced over 10.5 million ounces of gold. This makes it the leading gold producer out of all the mines, as it produces more than 350,000 ounces of gold each year. Such discoveries are made through the successful exploration of the extensive greenfields project

Gold Fields Australia
pipeline, as the mine is characterised by both underground and surface mining. Over the years, St Ives has had many significant findings, such as the discovery of an impressive high-grade deposit, which was viewed as such an impressive venture, that it earned the name of ‘Invincible deposit’.
Moving on to the Gruyere Mine, it is heralded as one of Australia’s largest underdeveloped gold deposits. Located about 200km east of Laverton in Western Australia, it has an accumulated mineral resource of 148 million tonnes, grading at 1.2 grams per tonne for 6.2 million ounces of contained gold.
The Gruyere Mine is so successful that is projected to become Australia’s deepest open-cut gold mine. Currently, the mine consists of one main open pit which will be developed in stages to incorporate an approximate depth of 500 meters below the surface. The main mining activities that occur at Gruyere mine include loading, hauling, drilling, blasting and equipment maintenance, which is carried out by specialised contractors. Subsequently, the Gruyere Mine is projected to continue prosperous exploration until at least 2031.
Located to the northeast of Perth, is the third mine; Granny Smith Mine. This particular mine
demonstrates the unwavering dedication of the Gold Fields team, as four days a week the team fly to the site via a chartered jet from Perth Airport, taking nearly an hour and a half to travel to work.
Thankfully, Gold Fields recognises the strain that this may have on employees, consequently, some members of the team live in host community towns such as Laverton and Kalgoorlie. Granny Smith’s most active mine can be found at Wallaby, where the Granny Smith Carbon-in-pulp processing plant is located and metal ores are processed under campaign milling conditions.
Finally, the Gold Fields Australia mining network is made from the Agnew Gold Mine. Located in the Eastern Goldfields region, it produces more than a quarter of a million ounces of gold a year.
The Agnew mine was acquired by Gold Fields in 2001, which allowed the mine to source gold from underground and be processed by the CIP plant. Similar to Granny Smith, the 650-man workforce flies in from the outpost location of Perth. The commitment of the Gold Fields team stems from underground production, development, and maintenance, to low-voltage electrical works.
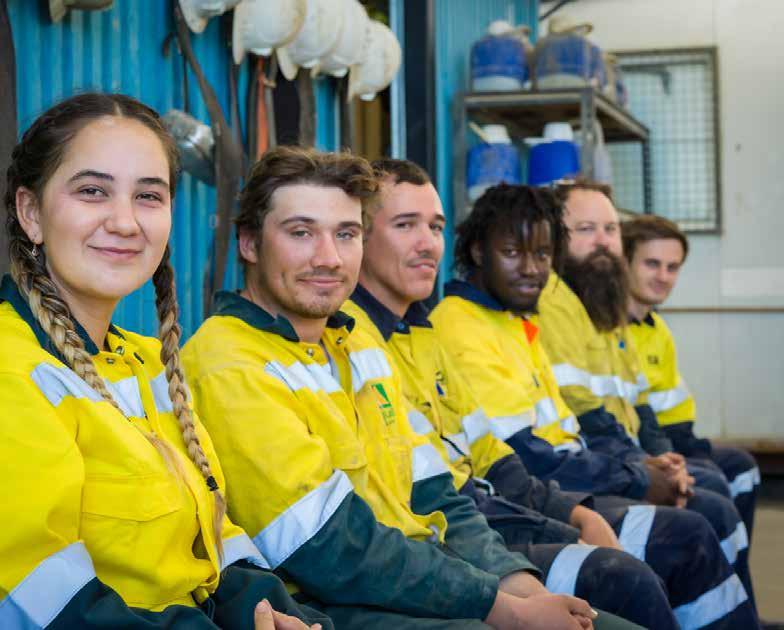
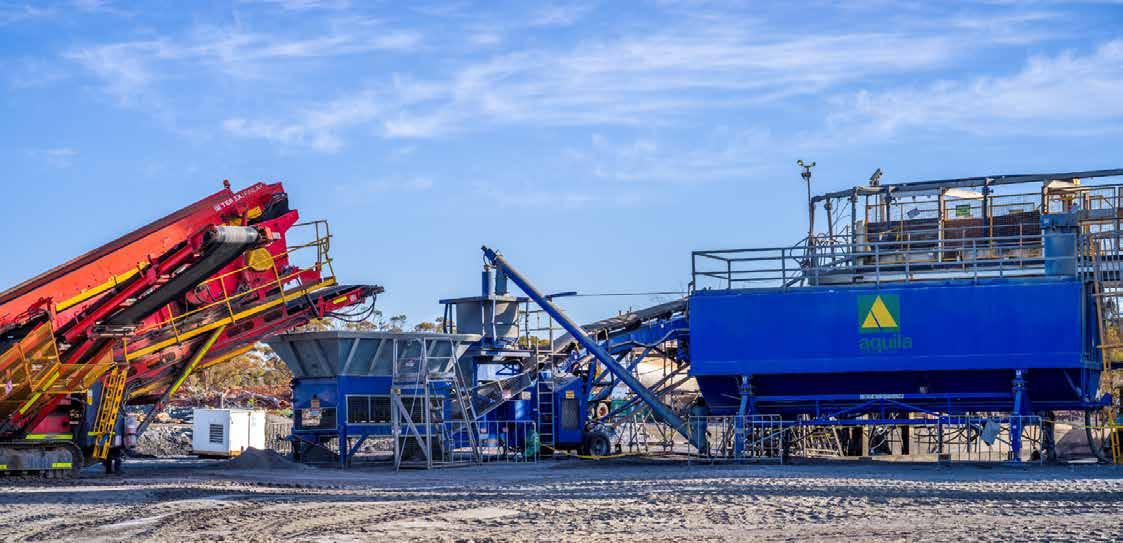

Gold Fields has a clear devotion to diversity and inclusivity in the company. The company has a strong belief in a rich culture throughout the organisation. Consequently, diversity is not just a tick box, but a valued contribution to the company, as the experience, knowledge, and creativity of each individual is a key asset to the success of the business. This is demonstrated by the meritocracy system that the company operates on, as each employee is encouraged to reach their full potential.
This is refreshing to see when the company is placed in a mining landscape where indigenous Australians, as well as women, lack overall representation. In response to this, they have created initiatives that help support these groups, which include bursaries, and trainee apprentice and graduate programs, which help mentor the next generation of talent in Gold Field mines. In particular, the conviction in a women-led workforce is coming to fruition: over 45% of the Perth office comprises of women, with 40% of women in leadership roles. The notion of gender equality is so deeply rooted in the value of the company, that they are working hard
towards the representation of women in all roles, with the goal of 25% representation by 2025, and 30% by 2030. This is further indicated by the indigenous populous that makes up 3.6% of the entire workforce, with clear efforts to expand in the future.
Overall, Gold Fields Australia has created a tenacious reputation in the Australian mining industry. With a wide variety of services available, spanning across mining sites, they are going through a period of exponential expansion. Consequently, they are one of the most valued added mining companies in Australia, with no plans of stopping!

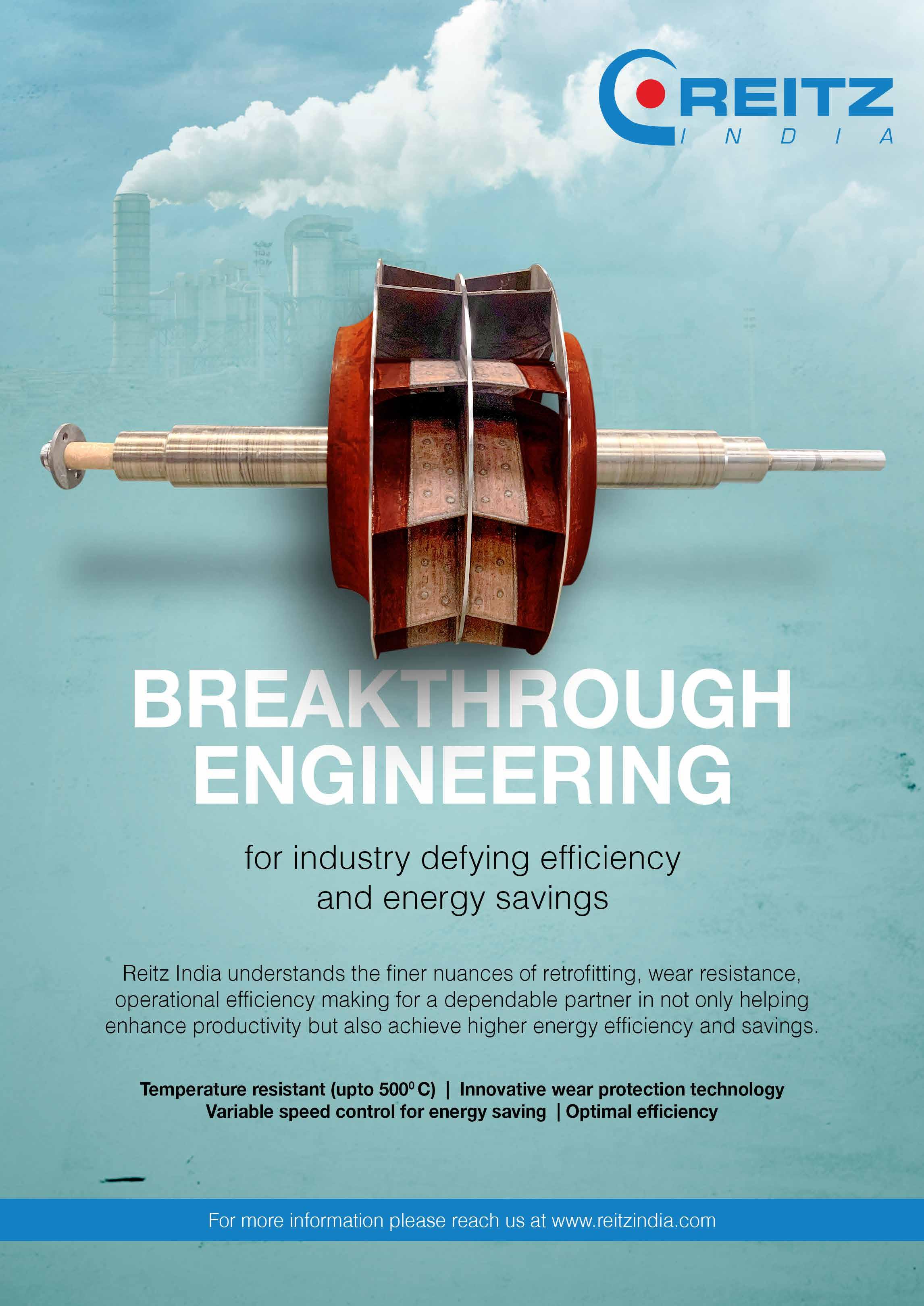