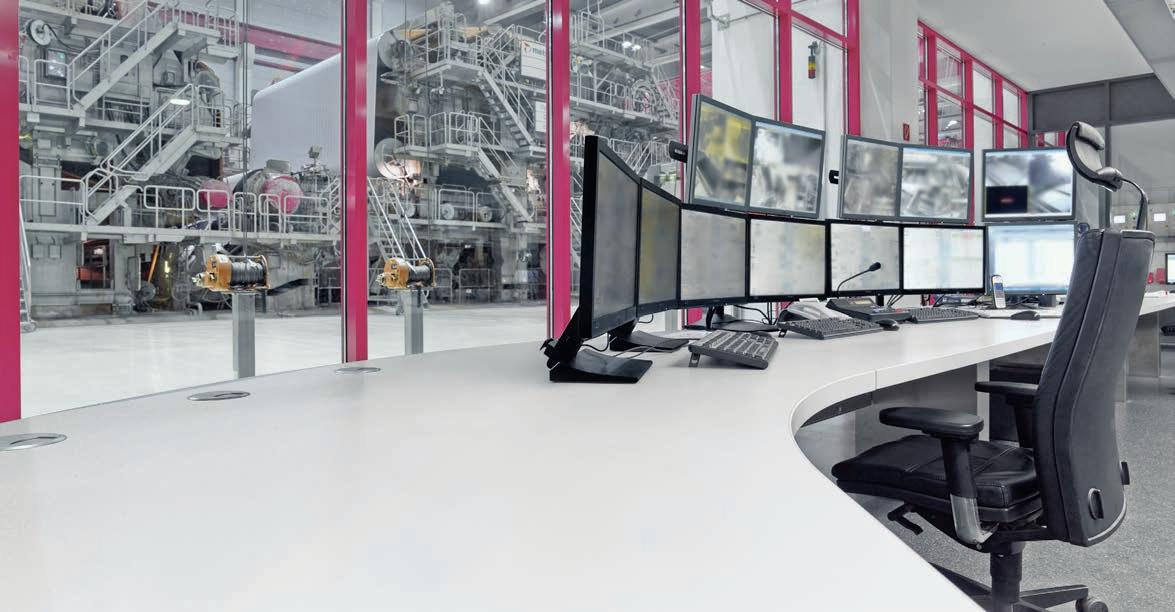
5 minute read
paper machine by Siemens
Water-cooled multi-motor drive for a complete paper machine
Author: Michael Herold, Sales Manager Fiber Industry, Siemens Energy
Advertisement
ENTIRE MULTI-MOTOR DRIVE REPLACED IN NINE DAYS
In April 2018 Siemens put a water-cooled multi-motor drive into operation for Progroup, one of the leading manufacturers of containerboard and corrugated board in Europe. While their paper mill PM1 in Burg near Magdeburg (Germany) was down for ten days for the installation, the opportunity was taken to migrate and combine what had been separate operating areas into the PCS 7 SIPAPER process control system at the same time. The drive system used in the multi-motor drive at PM1 had been running reliably for more than 15 years. To both improve machine speed and enable the mill to maintain its very high availability level into the future, Progroup replaced the multi-motor drive of the air-cooled Masterdrive converter ith efficient, innovative ater cooled converters. This forward planning means PM1 is already prepared for future performance enhancements.
MULTI-MOTOR DRIVE WITH 13 MW INSTALLED DRIVE POWER
With about 41 drive circuits, the new multi-motor drive includes both the variable drives in the paper machine and the pump drives. System compatibility ensured the feed-in points, motors, and most of the cabling could be reused, although selected drives were replaced as a preventive measure or to improve performance. As a precaution, nanocrystalline toroidal tape cores ere fitted to the outputs of both the inverters and converters to protect the motors against bearing currents.
At PM2, its sister paper mill in Eisenhüttenstadt, Progroup has had very good experience with the proven Siemens SINAMICS S120 CM (Cabinet Module) converter series, since the high levels of dynamism and control accuracy of this series make it possible to achieve the drive parameters needed for the paper machine. Progroup also decided to utilize this innovative drive solution for , and ta e full advantage of the benefits of the water-cooled frequency converters at the same time. The presence of a cooling plant for the raw water connection on-site made it easier to set up the converter plant ith energy efficient water cooling. The entire water-cooling system is configured ith redundancy n the event of failure or when required for maintenance purposes, the redundant system automatically takes over. The new, space-saving cabinet arrangement and direct heat dissipation via the water circuit substantially reduced heat losses in the switchgear room.
WHY WATER-COOLING?
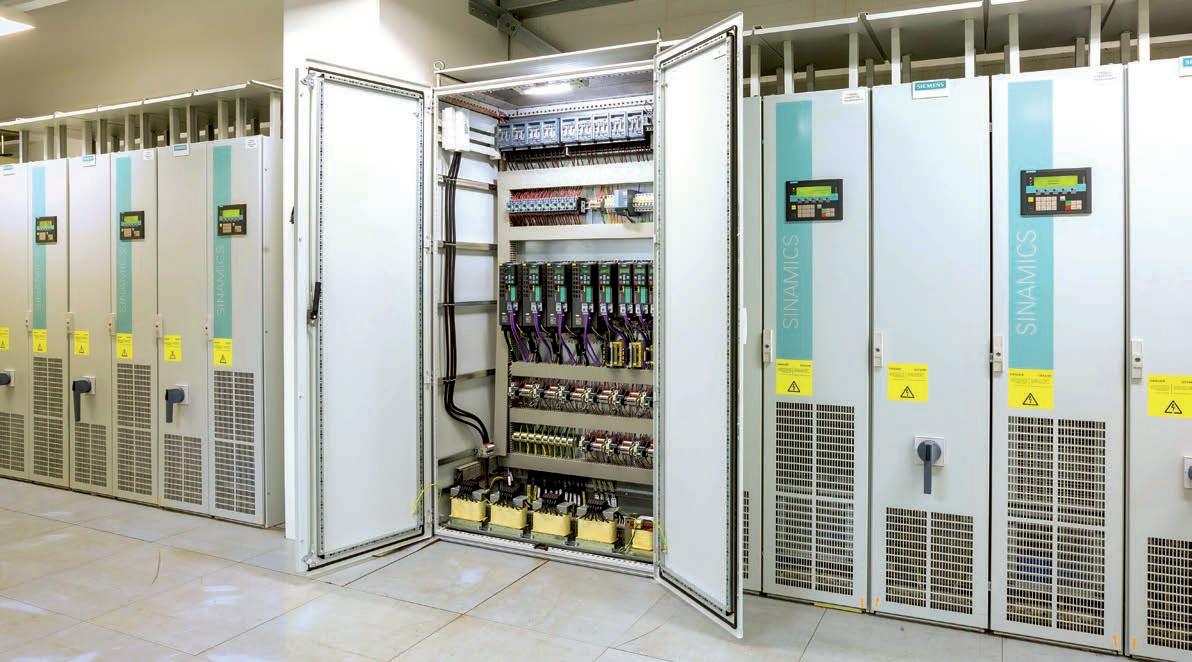
Water is much denser than air, and therefore has a more favorable heat transfer coefficient. eat is directly dra n off to the cooling uid rather than the environment. Unlike air-cooling, water-cooling requires much lower circulation of the cooling agent, which also means the pumps need much lower drive power than fans would otherwise require.
reater efficiency is the result.

Water-cooling substantially reduces the amount of air-conditioning required, which also removes the need to change air filters every year. Additional savings can be obtained from targeted heat recovery for process or heating purposes. This can also reduce maintenance and operating costs for the longer term. The comparatively higher investment cost is amortized over a short timeframe, and lifecycle costs are reduced overall.
UNIFORM PCS 7 PROCESS CONTROL SYSTEM WITH STANDARDIZED SIPAPER APL SECTOR LIBRARY
The entire solution for the automation and drive system is based on the PCS 7 process control
system with the standardized SIPAPER system solution for the fiber industry. ith it, iemens Energy provides a comprehensive tool for implementing process automation, drive controllers, energy supply, IT solutions, and services.
The business areas of multi-motor drives, core cutter, and roll cutter were available separately in various older PCS 7 versions. As part of the upgrade project, these were all uniformly migrated into PCS 7 V9.0 SP1, combined into a single multi-project, and structured within a client-server architecture.
The new multi-motor drive was implemented using the SIPAPER Drives APL standard, the core cutter with the SIPAPER DCS APL standard, and the roll cutter using the SIPAPER Winder APL standard. The main focus was on ensuring there were no changes in function for the system operators. The use of water-cooled frequency converters for the first time made it possible to refine and implement the A rive A standard for the WinCC/panel control system in the redundant water circuits and DC links. The Comfort Panels will be used in the future for onsite operation in the switchgear room.
To ensure a high level of safety for operators and equipment at PM1, the new automation system also includes the fail-safe S7-410 controller. This means the conventional emergency stop components are replaced with fail-safe I/Os. Safety-relevant signals are communicated via the same bus system as the process signals. The standardized, fail-safe PROFIsafe communication protocol prioritizes, protects, and monitors the fail-safe signals. This means safety-relevant functions can be put in place with no additional installation cost, while maintaining a high level of e ibility in terms of signal connections and subsequent adaptations.
NINE DAYS FROM START TO FINISH – HOW WAS THAT POSSIBLE?
To upgrade the existing drive system, Siemens Energy was tasked to replace the entire switchgear during a ten-day downtime. Being perfectly prepared in line with plant requirements was the key to success. The entire conversion was planned beforehand in detail, or o and assembly plans ere dra n up, and assembly tasks like cable runs and piping were also performed in advance. Many different business areas had to be coordinated, from special logistics firms to electrical assembly and assembly of the water-cooling system. Shortly before the mill was powered down, all system components for the multi-motor drive underwent preliminary commissioning on-site, including functional testing, in a separate warehouse adjacent to the paper machine.
Via a temporary direct access to the switchgear room for the paper machine, more than 70 m of control cabinets was moved in the space of two days at the beginning of the downtime. Following connection to the prepared cables, selected water-cooled converters were put into operation on a partially automated basis and in close coordination with third-party business areas, using specially developed scripts and prepared databases.
All these elements ensured the schedule was adhered to and the paper machine was ready to be powered up after just nine days. Using the PCS 7 SIPAPER standard, system commissioning of the paper machine was completed in below ten hours. The lower noise emissions, thanks to the water-cooling installed in the switchgear room, and desired system availability level in excess of 99.8 percent were both achieved.
PROJECT MANAGEMENT, CONTRACTUAL STRUCTURE, AND SERVICE
Siemens Energy was responsible for the project overall, including components and systems from the Siemens portfolio. By making use of regional automation and drive specialists for the fiber industry, the paper mill can rely in the future on short response times and close attention from service employees familiar with the system.
Progroup is very happy with the water-cooled frequency converters, and will therefore also apply this solution not only for its entire multi-motor drive system but also for the larger process drives at its planned paper mill PM3 in Sandersdorf-Brehna.