
5 minute read
Mar et p lp line n ersi n t p lp line by Bellmer
2

Advertisement
3
Market pulp line conversion to uff pulp line at tora nso kutsk r ill weden
Article by Ahti Peiponen, Winder specialist, Bellmer GmbH
Stora Enso converted one of its bale-based market pulp lines into a so t ood u pulp line and increased its u pulp capacity at Skutskär Mill in Sweden. Bellmer as selected as their technology partner.
The 26 million euro investment enhanced uts r ill s profitability and long term competitiveness by increasing uff production by tonnes annually. he mill s total uff pulp capacity after the investment is 415 000 tonnes.
“Both hygiene and non-woven products are a fast-growing market. This investment has enabled us to support the growth of our customers and further develop this business together

with them,” states Stora Enso’s Biomaterials Division.
Stora Enso’s Skutskär Mill in eastern Sweden is a modern pulp mill that primarily produces uff pulp for diapers, other hygiene products and non ovens, but also pulp for li uid pac aging board and speciality papers. he mill s total annual capacity is tonnes of B pulp, soft ood uff pulp and bleached hard ood birch pulp.
FLUFF PULP “NATURAFLUFF BY STORA ENSO”
According to the company, atura luff by tora nso is the idest range of uff pulp grades on the mar et, including a completely chlorine free bleached uff pulp. After the investment, uts r ill no produces tons of uff pulp per year.
1. Fluff pulp by Stora Enso. 2. Fly over.


5
4. Operador desk. 5. Empty spool lifting.
Skutsk r Mill started manufacturin uff pulp in 1969. We have long been the largest manufacturer of this pulp in Europe. In the last couple of years, we have only strengthened our position. Demand for uff pulp is ro in by per cent a year globally,” says enri olm, irector of tora nso uts r ill.
tora nso studied the transformation or for four years ith various e uipment suppliers before deciding to carry out the pro ect ith Bellmer. he moderni ation as large and included a ne dilution controlled headbo , ater removal improvements at the ire section, a ne reel and a inder, including complete automation and controls. he reel delivery also included an automatic return system for bringing empty spools bac to the reel spool storage. As this is a s ing dryer machine that can produce both sheets and rolls from pulp, the pro ect included a y over section to pass the eb over the cutter lay boy to the ne reel at the dry end.
TurboWinder by Bellmer
Bellmer s scope of the turn ey delivery as very detailed. It included:
■ Automatic set change ith tape applicators to fasten shipping roll tails to the roll body. ■ A traversing cutting device. ■ eb holders to maintain tension during set change. ■ ffective and reliable eb separation after the slitters, ith t o spreader rolls mounted in an ad ustable frame. ■ An automatic core feeding table and pivoting device to load ne cores bet een the drums. ■ ast and accurate automatic slitter positioning for pairs of bottom and top slitters. ■ eparation fingers after the slitting to force the ebs to separate. ■ eb feeding ith vacuum and driven belts. ■ A parent roll transporting system, B ransporter from reel to un inder. An automatic empty reel spool return system was also included.
he formation of the uff pulp must be ood and the quality must be just right, since the pulp is used directly in the converter’s end products. hat is hy e needed to make si nificant improvements also to the production line’s wet end. We replaced the wire section and installed a new headbox,” says Henrik Holm.
“A key part of the conversion was, however, the new winder, which Bellmer supplied seamlessly in co-operation ith us. ellmer as e ible, as when we had an idea, they were quick to develop it. Solutions emerged smoothly,” says Holm.
CUSTOMER-FOCUSSED PRODUCT DEVELOPMENT
“Effective threading through the winder is crucial for a uff eb due to its thickness 0 m2). We improved the web threading to wind-up section by installing driven belts instead of air blows,” says Bellmer s sales manager Ahti eiponen.
“Fluff pulp, winded to the desired customer reel dimensions at the automatic winder, is de-
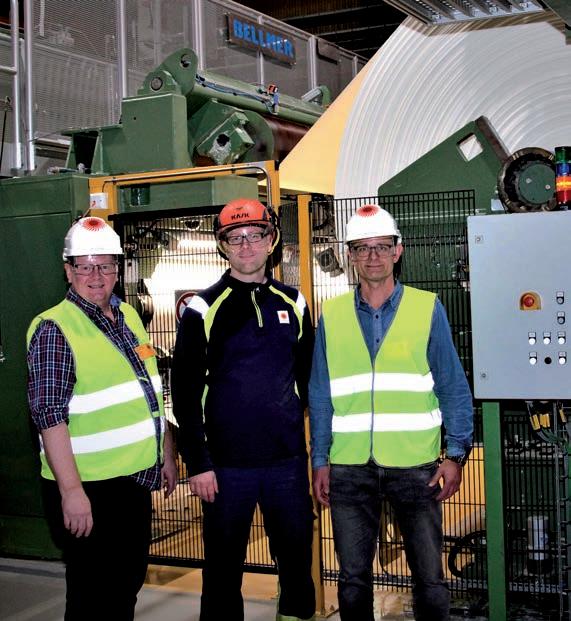

6. At the middle Lasse Aspelin, StoraEnso Skutskär, right Frank
Schorzmann and Ahti Peiponen from Bellmer.
livered directly to the converting plants manufacturing hygienic products; therefore, Stora Enso only needs to apply medical tape used in hospitals to bind the tails of the customer reels, instead of the typically used hot-melt glue. R&D was required to invent this medicaltape solution, which was successful, and the outcome is that 28 tape dispenser units units do the job required during the automatic set change” says eiponen.
“Occupational Safety and Healthy requirements ere fulfilled by takin the necessary measures to avoid excessive noise levels and improve ergonomics,” he adds.
Our main criteria ere that ellmer fulfilled our technical specifications and uarantees, had the right delivery time – and price, of course,” says production manager asse Aspelin.
“The targets were to reach several scheduled points, such as the start-up time, rollin test uff pulp the first time and mi in bet een uff and bale pulp. When the line was ready, we started re ular uff pulp production and periodically in bales in order to fine-tune the inder packin line,” says Aspelin.
s this as ellmer’s first modern, ne - eneration reel and winder delivery to a Scandinavian customer, the project was important to us. At the same time, we are pleased to be Stora Enso’s partner in Skutskär as a leading headbox manufacturer,” says yr i trengell, of Bellmer inland y.
STORA ENSO
tora nso says its strategy is to support customers to meet consumers demand for sustainable products based on rene able materials. art of the bioeconomy, tora nso is a leading global provider of rene able solutions in pac aging, biomaterials, ooden constructions and paper. tora nso s business divisions are onsumer Board, ac aging olutions, ood roducts and Biomaterials.
he Biomaterials ivision offers a ide variety of pulp grades to meet the demands of paper, board, tissue, te tile, and hygiene product producers.