
7 minute read
Adding 30% capacity with little investment by AFT


Advertisement
2
Creativity compliments major rebuilds at APPM… Adding 30% capacity with little investment
Article by Roman Smorgunov and Lyubov Lyubimova
Located near the White Sea, about 1,000 kilometers northeast of St. Petersburg, Arkhangelsk Pulp and Paper Mill (APPM) is one of the largest producers of containerboard in the country. They produce over 500,000 TPY of fluting and Kraft linerboard and have a total mill capacity of over 900,000 TPY, including bleached market pulp. An important player in the European market, their containerboard is considered a benchmark for quality, having a “noble” brown color, reaching over 60 countries. Their domestic market share has risen along with export markets in Italy, Spain and Turkey being strong as well.
Over the past several years, they have invested over EUR 100 million on both board machines, improving quality and reducing environmental impact. BM2’s rebuild for linerboard and corrugating medium started up in 2016, including a new wet end, improvements to the drying section, a new pope reel, slitter, and wrapping and handling system. A new control system was also put in place. Earlier, in 2014, BM1 underwent a comprehensive rebuild, including a new wire section for raftliner production. rom refining and stock preparation were completely updated. Within the framework of each of these projects, all guarantees for end products were met. Environmental goals from 2013 to 2021 include water consumption cut in half, pollutant emissions down by 65%, discharge water reduced by 75% and greenhouse gas emissions lowered by 18,000 tons of CO2 equivalent. Alongside the significant containerboard investment, the mill is always in search of ways to improve quality and increase capacity with little money spent. Dmitry Khrapach, board production manager, challenged his team to wonder: what if the bottleneck in BM1 screening could be overcome to open the way for higher productivity.
FOCUS ON THICK STOCK SCREENING FOR THE BOTTOM PLY
Says Khrapach, e need strate ic e ibility because packa in is al ays chan in . iber yield and optimi a-

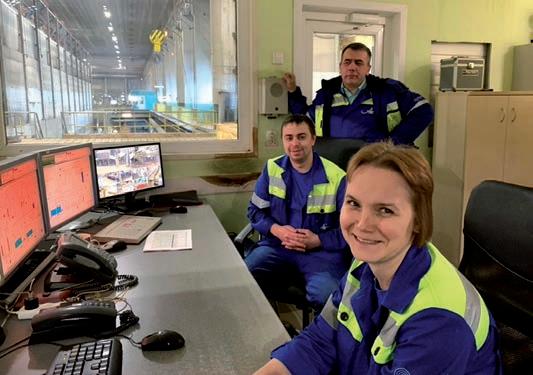
4

tion is a must. asy chan es from one rade to another have to be smooth. roduct appearance must be consistent. et, sometimes e had akes and shives in the pulp causin problems on M1. uality problems, too. s a result of comprehensive measures performed on the machine, e increased the production rate above desi n capacity. o ever, this caused limitations in thick stock screenin capacity. So, e needed to increase the screenin capacity, hich as accomplished ithout bi capital investments. or this purpose e chose , kno in that they have the kno led e and e perience in tacklin such tasks. AFT’s Roman Smorgunov, Jussi Karppinen and Tarmo Karioja helped APPM with modelling BM1’s bottom-ply thick stock screening and mapping out o changes inside the screens. A imAudit mass and o balance analysis revealed that major productivity and quality gains were possible. The screen room was limited by inefficient rotors and insufficient open area in the cylinders. AFT recommended changing over to new high efficiency rotors and cylinders ith optimi ed open area and profile in all three stages to improve pulp throughput, hile not sacrificing the accept pulp quality. All three stages employ acro lo cylinders and high efficiency rotors. APPM went with the recommendations and also made necessary engineering modifications to the BM1 thick stock screening system, including pumps, pipes, valves. The project was completed in 2018 with all expectations met. Says Khrapach, ho says screenin is borin Sometimes you in bi by bein creative. Simple, bold moves inside our screens improved o to allo us to ma imi e output and uality. e achieved a 0 ain in screenin capacity, and stable properties of the end product - that’s a bi in
INTELLIGENCE INSIDE EXISTING SCREENS
Roman Smorgunov, sales manager at AFT, points out that the new rotors achieve lower reject thickening than the OEM rotor, meaning that rejects are reduced despite similar re ect o s. A still closely monitors for uctuating consistency, but can do so calmly, even during peak production of the board machine. Khrapach says, Since makin the chan es, the screens have run smoothly for over a year, so far. Operators and the maintenance team can focus on other obs. Khrapach continues, Our discussions ith applications e perts are al ays productive because of the ay e brainstorm ideas. he best results are reached throu h creative problem solvin and cooperation. e kno our mill ell and has an in-depth understandin of pulp and paper processes.
With a laugh Khrapach concludes, ecause every production site is a livin or anism, there are never-endin challen es. ut that’s a ood thin as it keeps us alert at all times
1. Dmitry Khrapach, board production manager, (right) and Roman
Smorgunov, AFT specialist. 2. BM2 operator observes quality as the sheet comes off of BM2. 3. A wide range of hardwood and some softwood is used at APPM, coming from expansive forests within a 350 kilometer range. 4. Denis Sergeev and Elena Saiko, pulp mill control room operators with their boss, Vadim Moseev. 5. Vadim Moseev, pulp production manager at Arkhangelsk Pulp and Paper Mill.


7
6. The human touch is part of APPM’s consistent quality approach to bleached market pulp.
7. Located near the White
Sea, Arkhangelsk Pulp and Paper Mill (APPM) is the largest producer of cardboard in Russia, as well as a key player in bleached market pulp.
MAXIMIZING FIBER FOR MARKET PULP
Producing over 1,000 t/day of pulp, including ECF (Elemental Chlorine Free) since 2019, they cook, screen, wash and bleach birch and aspen for their own machines and produce bleached market pulp for customers. When they bleach, they use hydrogen peroxide as a bleaching agent, replacing sodium hypochlorite.
According to Vadim Moseev, head of APPM pulp production, their ecologically pure product allows for greener, safer pulp production and end products. e considers this to be a competitive advantage of Arkhangelsk APPM on both the Russian and world market. Of note, however, he believes that market pulp requirements demand constant attention to even the smallest issues in the process.
Recently, Moseev and his team decided to reduce fiber deposits on evaporation e uipment and increase fiber recovery. Moseev remarks, Small problems can become bi problems, so e address them early. e decided to repurpose an old screen to handle all black li uor o for our hard ood and soft ood Kraft production, hich runs at 80110 C. he oal of the conversion as to recover more fiber from the black li uor stream and meet capacity ob ectives. e looked to to make this happen.
According to Tarmo Karioja, AFT project manager, who provided technical support for the project, ith our ussian team, e reconfi ured the inside of the screen and ho the unit as controlled. he up rade included an Cb rotor and lectrobeam drilled cylinder alon ith preliminary layout, pipin and process en ineerin . In addition, ne control valves and operatin lo ic ere built around the old ooper pressure screen and e istin DCS system. All objectives for this screen conversion project were achieved, including: ■ reduction of fiber deposits on the evaporation equipment ■ ncreased fiber recovery and returning the fiber to the pulp output ■ Running the system in a hermetic environment, without any emissions ■ Running a single screen to handle all of the mill s blac li uor o
Continues Moseev, ecause has been a partner for a lon time, our pulp mill has ained many advanta es from their kno -ho , especially around cylinders for screenin . heir kno led e is valued by our team as an e tension of us. Back to the point about problems, Moseev quips, hen unsolved problems and little issues are accumulated, it ets messy. I ill say it another ay... there are no little issues in our business. ll the issues that arise in the course of our business re uire a prompt response.
WHAT’S NEXT AT APPM?
ookin ahead, optimi ation could include replacin screens for paper production. Says Khrapach, ith our productivity ains helpin pay for ne t steps, e are al ays lookin for ne ays to meet market needs as they chan e. very production site is a livin or anism. here are al ays never-endin challen es. hat’s hy e count on the people to discuss problems, and help us solve them. Our recent advances make it possible to fi ure out the ne t steps. According to Risto Weckroth, general manager with AFT, M has become a star in packa in in ussia. hey are part of an increasin ly dynamic and e citin marketplace. e plan to support their ro th ith innovation, especially ith e istin e uipment that can reach a hi her level of performance.