
8 minute read
A digital revolution in logistics by Pesmel

A digital revolution in logistics - Major savings potential at pulp and paper mills
Advertisement
Article by Kaj Fahllund, Vice President, Pesmel Corporation
Pulp and paper mills all over the world are completely transforming their production processes by automating and digitizing. But what about logistics? Logistics experts at esmel are finding that there are huge savings to be made at pulp and paper mills by using its intelligent Material Flow How® concepts.
«We like to think of lo istics as the lo han in fruit’ at pulp and paper mills. It’s an area here a lot of efficiencies can easily be made. says ony ei as, of esmel. “We have a lot of e perience in the field and have carried out ma or studies on material o s at pulp and paper mills all over the orld. e have proved that ith the ri ht plannin and usin tailor-made lo istic solutions utili in di iti ed automation, there is a potential for hu e savin s and a very speedy return on investment. esmel e perts have not ust studied logistics as a result of their findings they have put hat they have learned firmly into practice. he company has successfully designed and built fully automatic, tailor made systems for some of the most modern and efficient pulp and paper mills in the orld, including ets roup s ne os i, tora nso s matra, and aica aper s l Burgo de bro mill.
ei as adds, “In-mill logistics have a major in uence on the mills’ complete lo istics chain. Our studies have revealed that aitin times of trucks and trains at mills can add up to more than 0 of the total transportation time. here is enormous potential to close these aps usin intelli ent di itali ed automated arehousin . he fact is it’s only hen the rail ay a ons are on the tracks and the trucks on the road that products are movin to their destinations. he aim of esmel systems is to shorten the lead and turnaround times and basically to close those aps.
SHORT PAYBACK TIME
esmel has found that due to the increased efficiencies across the hole logistics chain, ma or savings can be made ith reduced pay bac

2. It’s not just the automation of mill logistics where big savings are made by having an unmanned operation, there is also the short turnaround times where our studies show that millions can be saved in transportation costs.
1. With the right planning and using tailor-made logistic solutions utilizing digitized automation, there is a potential for huge savings.
times on a complete system varying from as little as three to five years. here are all sorts of areas here efficiencies can be made, as ell as many other added benefits, says ei as. It’s not ust the automation of mill lo istics here bi savin s are made by havin an unmanned operation, there is also the short turnaround times here our studies sho that as much as uro - million can be saved in transportation costs.
If you think about a mill that has 1 0-200 trucks comin in and out every day and havin a turnaround time of t o hours each. ith a ell-planned automated system, a 20 minute turnaround is completely viable. dded to this is increased customer satisfaction ith better and more consistent delivery times.
Another bonus of a fully automated logistics system is the reduced damage to bales and rolls due to dramatically reduced for lift and manual handling. esmel s arehousing logistics systems use a series of automatic high bay stac er cranes, conveyors and loading cranes, all connected to its o n arehouse anagement ystem , here the bales and rolls have minimum contact during transportation. Our systems are desi ned to smoothly transport bales and rolls ith the minimum of contact hich means that the customer ill receive the final products in much better shape, says ei as.
WELL PROVEN FORMULA
esmel has its o n ell proven formula for designing and planning in mill logistics solutions. t starts ith a complete mill ide feasibility study ta ing in every area of the mill and beyond, and particularly ta ing into account mill customer re uirements. esmel then selects the right automation components and introduces digitali ation hich is connected for sharing bet een the mill processes.
t the feasibility sta e e like to have as many people from the mill process areas en a ed as possible, often includin the sales teams as ell, says ei as. e like to take a holistic approach as then e can build a model that takes into account all the re uirements the mill lo istics needs mi ht have .
esmel ta es all the e isting data possible from the customer s process areas and builds a simulated model here e act production scenarios

3
3. 3D modelling applications are built replicating customer’s exact logistics situation.
can be vie ed. his is here e like customers to et really involved and en a ed, says ei as. sin their data, e build a D model replicatin their e act e istin lo istics situation. sin a di ital t in as a simulator, e can then clearly
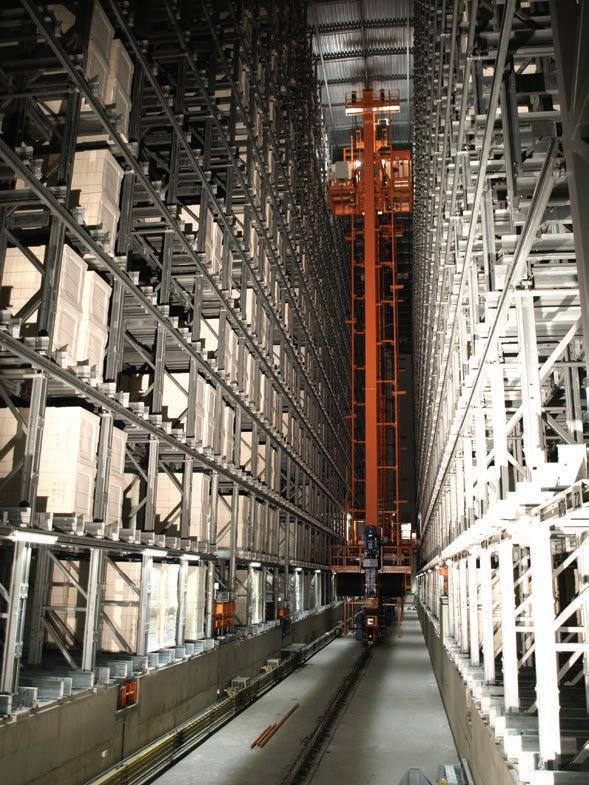

5
4. Pesmel delivered an automated distribution center for pulp bales which includes a 25,000 ton storage high-bay warehouse with a handling capacity of 1,000 ton per hour. 5. Pesmel will supply an automated distribution center with a 65,000 ton warehousing capacity.
illustrate the lo istics possibilities that are available as ell as take into account the future increased demands of the customer.
CASE STUDIES
METSÄ GROUP Äänekoski, Finland
The Challenge o develop an efficient logistic chain for a ne pulp mill producing . million tons of pulp. f the mill output, , tons travel by rail to elsin i for e port and , tons travel by truc s to local customers in inland.
pecifically the mill anted to reduce the round trip time for transportation of , tons of pulp by rail to the ort of elsin i by more than half, from hours to hours. t also anted to reduce e pensive rail ay costs by cutting agon usage from agons and up to five locomotives to agons using three locomotives.
The Solution esmel designed an automated distribution center at the mill hich includes a , ton storage high bay arehouse ith t o stac er cranes ith a total handling capacity of , ton per hour. he design also included automated railroad car loading controlled by the esmel arehouse management system.
esmel delivered an automated distribution center for pulp bales hich includes a , ton storage high bay arehouse ith a handling capacity of , ton per hour.
he installation is completed ith esmel s automated management system hich is connected to the mill s A management information system that allo s instructions, reporting and information sharing across the board from mill to port, and real time trac ing of agons using throughout the delivery ourney.
The Results he ne automated distribution center has achieved significant operational savings
■ nmanned arehouse operations at the mill ■ rain frames have been reduced by ith , tonnes loaded in an average of three hours ■ A saving of , liters of fuel per year ■ ruc loading time has been reduced to less than minutes
Added benefits to the mill are more e ibility in both production and logistics, improved customer service, error free deliveries and improved safety.
SAICA PAPER El Burgo de Ebro Mill, Spain
The Challenge he overall challenge and driver for the investment as to change the operating philosophy from made to order to made to stoc , resulting in improved customer service.
he customer s target as to increase storing capacity and improve inventory control at the mill site. treamlining shipping functions to minimi e turnaround times as e ually high on the agenda. t also anted to improve customer service and provide faster and more e ible deliveries. inally, the customer anted to enhance safety in the storage and loading area. The Solution esmel designed an automated distribution center at the mill hich includes a , ton storage high bay arehouse ith t o stac er cranes ith a total handling capacity of , ton per hour. he design also included automated railroad car loading controlled by the esmel arehouse management system. he installation is completed ith esmel s automated management system hich is connected to the mill s A management information system that allo s instructions, reporting and information sharing across the board from mill to port, and real time trac ing of agons using throughout the delivery ourney.
The Results ■ torage operations ill be completely autonomous. ombined in out handling capacity ill be rolls per hour from three board machines and an off machine coater ■ verything ill be automated in the ne logistics arehouse. arge stac er cranes ith pre and after sorting facilities ill be responsible for placing the paper reels in the most appropriate place to optimi e handling of loads ■ oads ill be prepared for truc loading in minutes after gate arrival, up to five truc s simultaneously, resulting in minimi ed turnaround times at the mill ■ n time deliveries ith minimal product damages ■ he truc loading area has been designed by aica roup specifically for improving truc drivers safety
