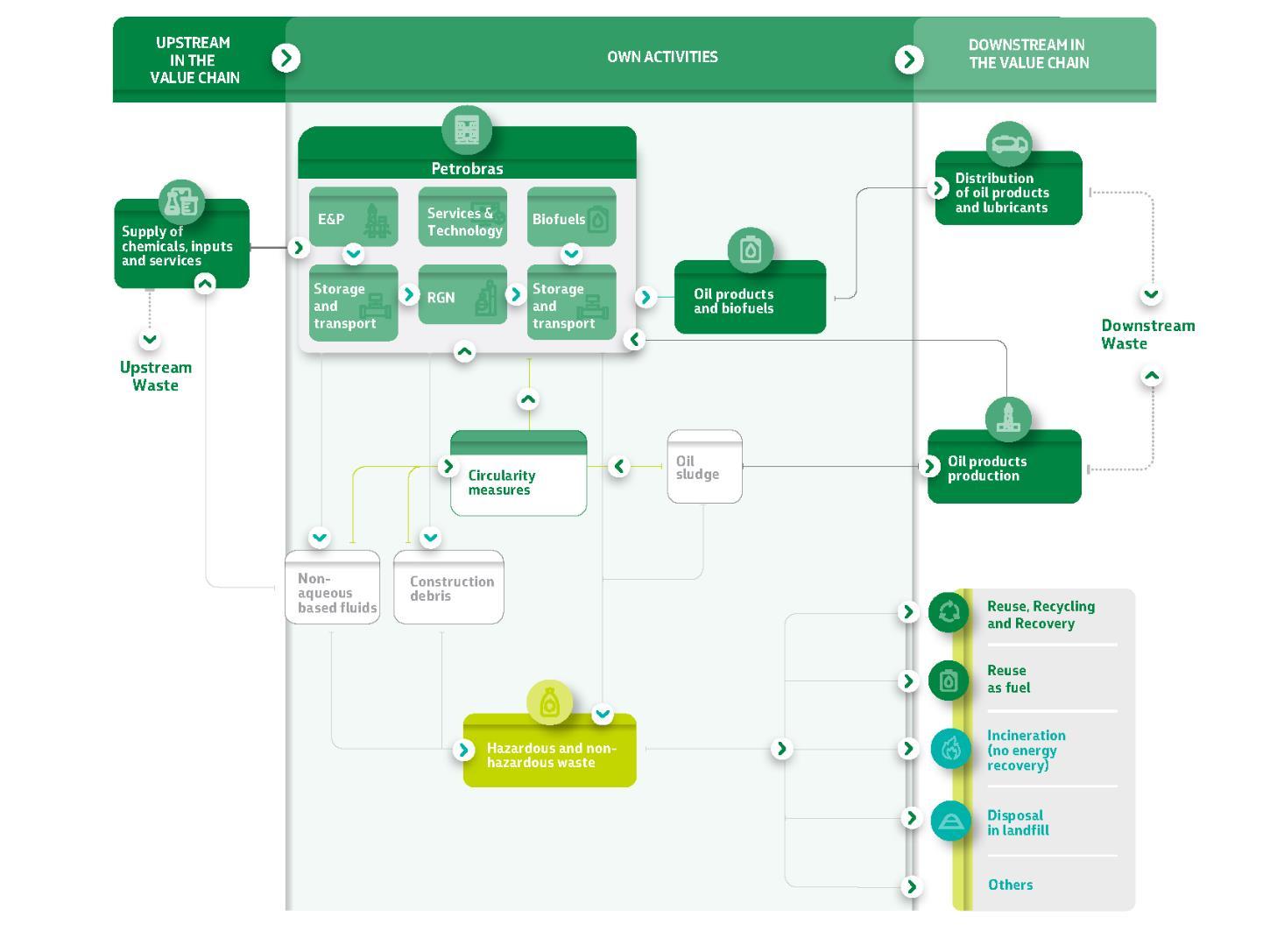
15 minute read
Waste management and decommissioning
Waste management covers measures for the proper management of solid waste throughout the lifecycle of our businesses, including circular economy practices, which seek to prevent generation, reduce, reuse, recycle, treat hazardous and non-hazardous waste and environmentally appropriate disposal of waste to value materials and resources while avoiding or mitigating possible impacts to the environment and human health. This material topic includes the decommissioning process related to dismantling, transportation and disposal of equipment, structures, and waste, as well as its risks and opportunities. It also includes the proper planning and execution of studies and projects, all while seeking sustainability, environmental protection, safety, and care for people.
The linear production model has placed great pressure on the environment and natural capital, generating impacts related to the extraction of natural resources and the generation of solid waste. In view of this, we have undertaken efforts to continuously improve the management of our products throughout their life cycle and have sought to close our processes in light of the circular economy, reinserting waste into the production cycle in order to minimize its final disposal in the environment and the need for of raw material extraction.
We recognize the relevance of sustainability for our business throughout the production chain. Therefore, we have advanced in relation to our previous commitment of zero growth in the generation of waste from processes by 2025, and we are now committed to a 30% reduction in the generation of solid waste from processes by 2030, with the allocation of 80% of this waste to routes for use, recycling and recovery (RRR) by 2030.
To this end, we have developed circularity actions to allow the reuse of our waste as raw material for petroleum products, and in other production processes. The effectiveness of these initiatives is monitored through indicators that measure the amount of waste generated and the percentage destined for use, recycling, and recovery routes.
Our activities generate solid waste that may contain mixtures of hazardous and non-hazardous substances; therefore, when not properly managed, they can be sources of potential adverse impacts on human health and the quality of the environment, such as:
▪ Pollution of soil and surface or underground water sources, due to the environmentally inadequate disposal of waste, which may compromise the availability of ecosystem services for use by society, productive sectors and biodiversity;
▪ Decrease in the useful life of landfills due to the disposal of waste subject to RRR, reducing the area available for the disposal of waste that does not have an economically or technologically available route at the time of its disposal.
Our supply chain may also occasionally be responsible for possible impacts due to inadequate waste management, which is why, in addition to seeking only suppliers licensed by the competent environmental authorities, audits are planned for qualification in the contracting and inspection process during the execution of the services.
As an example of waste generated in our processes, we have: oily sludge, drilling fluids and cuttings, industrial effluent station sludge, catalysts, used lubricating oils, spent acidic or basic solutions, fuel filtering elements, paper, plastics, wood and debris from civil construction. In our units, the sources of waste generation are the activities of production and processing of raw materials and intermediate currents, effluent treatment, preventive and corrective maintenance processes of equipment, engineering works, as well as administrative activities. The figure below illustrates the simplified process flow of inputs, activities and outputs related to waste management.
PROCESSES FLOW FOR INPUTS, ACTIVITIES AND OUTPUTS RELATED TO WASTE MANAGEMENT
Management of waste-related impacts
Proper waste management in accordance with current legislation and good practices in the oil and gas industry is part of the principles of our Health, Safety, and Environment Policy, and our environmental, social and governance (ESG) position to protect the environment, highlighting the theme “Circular Economy with a focus on waste minimization” present in our Strategic Plan 2023-2027 (SP 2023-27).
Our solid waste management follows the waste management hierarchy established in current legislation: non-generation, reduction, reuse, recycling, and treatment of solid waste, and environmentally appropriate final disposal of waste, with the aim of avoiding or mitigating possible environmental impacts.
Since 2013, we have adopted circular economy practices in our activities to prevent the generation of solid waste, with emphasis on the reuse of oily sludge in the production of shale oil and green petroleum coke. These practices made it possible to reduce the generation of hazardous waste by more than half, from
260,000 tons to 98,800 tons in nine years, minimizing any negative impacts on the environment and people1 .
As for non-hazardous waste, in 2022 we internally recycled 569 m³ of construction debris for the purpose of using these recycled aggregates in paving access roads and topographic conformation at the Gaslub Cluster works site. 1 In this chapter, information on waste is presented in thousands of tons, for a better understanding of the quantitative data.
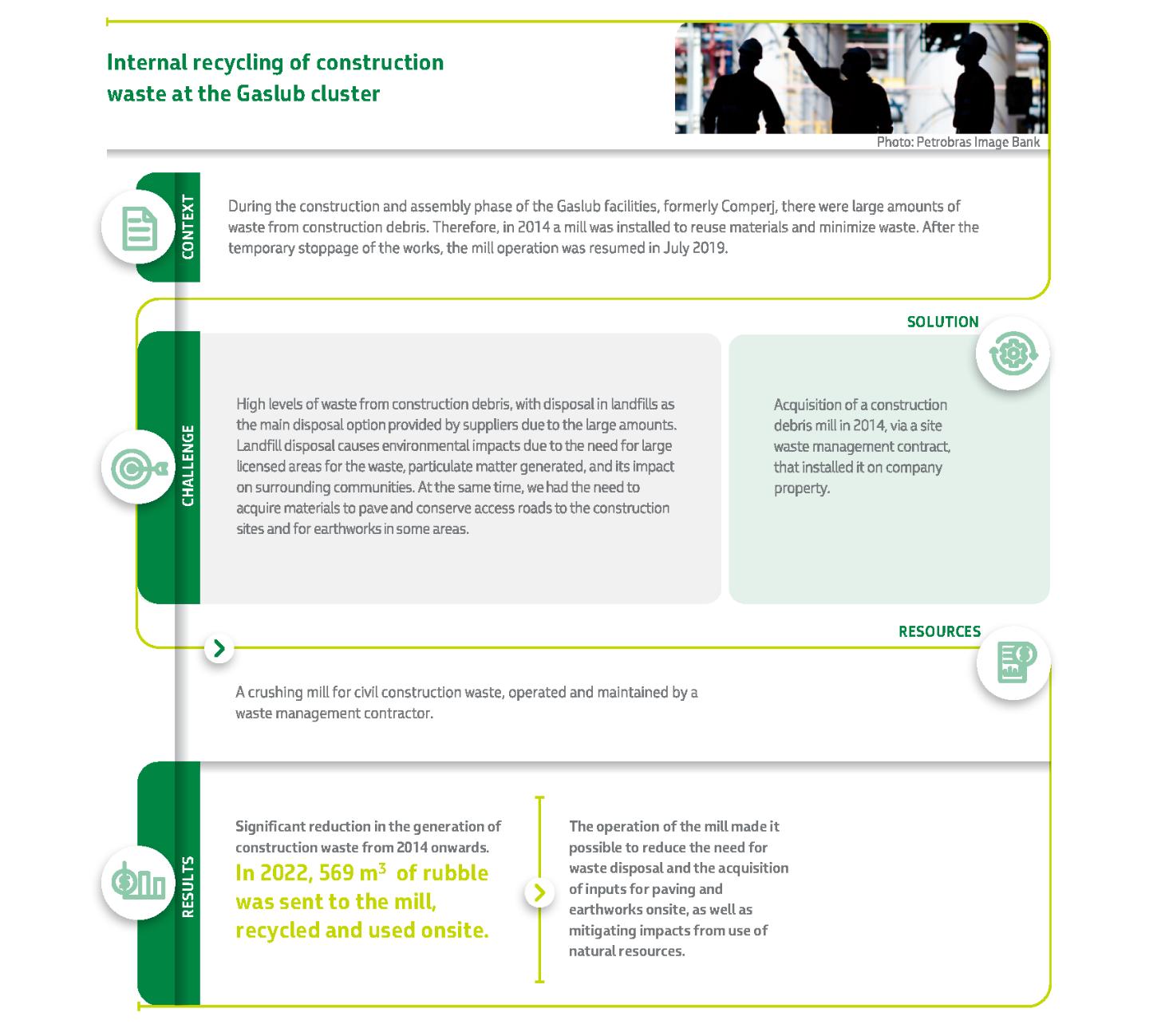
In our operations in the Amazon, proper segregation of organic waste and carrying out the composting process, allowed us to recycle waste using the compost generated in reforestation activities and recovery of degraded areas in the oil province of Urucu.
More recently, we changed the contractual model for supplying non-aqueous-based drilling fluids from marine wells for servitization (products as a service), so that the fluid is returned to the manufacturer after use, further favoring the reuse that was already practiced internally.
In 2022, three social projects focused on the collection and proper disposal of recyclable solid waste were addressed through a pilot public selection process carried out with a focus on the metropolitan region of Rio de Janeiro. Together, the projects add up to an investment of BRL 8.9 million to be disbursed over the next three years.
Through this partnership, we will allocate recyclable and reusable solid waste generated by four of our properties in the metropolitan region of Rio de Janeiro to three cooperatives who won the bid, with the potential to receive around 600 tons of recyclable materials per year. In addition to the materials, the cooperatives will receive resources to be invested in training and improving the schooling of the collectors, the maintenance of vehicles, sheds, and equipment, and in environmental education actions.
Additionally, to mitigate the potential adverse impacts generated by waste, we implemented preventive and corrective actions described in our process standards and specific internal technical standards on the subject, in addition to following Brazilian and international technical standards.
For the development of new projects, we use the Front-End Loading (FEL) methodology for planning and approval of each phase of the project based on technical, economic, and environmental feasibility, in which technical criteria related to minimizing the generation and optimization of the destination of waste. Routinely, several studies are carried out as part of the environmental licensing process to identify and assess the socio-environmental impacts throughout the development's life cycle, thus mitigating impacts related to solid waste management. Preventive, mitigating, and compensatory measures are defined in the installation, operation, and decommissioning phases of the projects.
We also invested around BRL 3 million in research and development projects on topics related to the minimization, reuse, and environmentally sustainable disposal of waste at our Research Center (Cenpes). We made progress in studies of solutions that make it possible to use our waste as an input for highvalue-added products, such as the use of oily sludge to produce asphalt products, which are in the planning phase for pilots on an industrial scale.
Information related to solid waste management is recorded in proprietary information systems that cover all stages of management, maintaining an up-to-date corporate database that is used to carry out our annual inventory.
We routinely assess our environmental performance in waste management through the monthly assessment and monitoring of four indicators Process Generated Hazardous Solid Waste (RSPG), Process Generated Non-Hazardous Solid Waste (RSNPG), Hazardous Solid Waste Destined for RRR routes (RSPD RRR) and Non-Hazardous Solid Waste destined for non-RRR routes (RSNPD NRRR).
Our performance is periodically evaluated by our management system and governance structure, from the technical level to senior management, as described in the Risk Management and Corporate Governance chapter. Critical analysis of the results allows us to incorporate lessons learned into subsequent action planning cycles.
As one of the forms of external evaluation of our solid waste management and performance, we participate annually in the evaluation process of the Dow Jones Sustainability™ World Index (DJSI World). Within this aspect, in 2022, we obtained the highest score in the DJSI World in questions related to Waste Disposal and Hazardous Waste of the “Operational Eco-efficiency” criterion. This recognition reinforces the quality of our management for this topic.
Generated waste
We adopt the system of classifying waste as hazardous or non-hazardous following the protocols reported by the Brazilian Association of Technical Norms (ABNT), Norma Brasileira (NBR) 10004, which is based on the Code of Federal Regulation – Title 40, Protection of Environmental – Part 260-265, Hazardous waste management. It should be noted that Law No. 12305/2010, which establishes the National Solid Waste Policy, also adopts the same criteria for classifying waste as hazardous and nonhazardous, excluding radioactive waste.
In 2022, the generation of hazardous and non-hazardous solid waste in our processes was 98.8 thousand and 150 0 thousand tons, respectively, totaling 248.8 thousand tons of waste. The generation of waste from processes in 2022 was the best performance in the last four years, the result of the sum of the circular economy actions implemented and the occasional reduction in non-continuous cleaning and maintenance activities.

In order to achieve our new ESG waste commitment, we are planning new circularity actions, operational optimizations, sustainable hiring, and workforce training and awareness, to reach 2030 generating a maximum of 195 thousand tons of process waste.
In 2022, we held the “Sustainability Journey – Conscious Consumption and Waste” training, with 3,072 participations from our workforce.
HAZARDOUS AND NON-HAZARDOUS WASTE GENERATED3 (consolidated)
Regardless of the classification, the waste mass is determined by direct weighing or estimation considering technical and engineering criteria (density and volume). When they are estimated, we try to make conservative estimates by overestimating the masses, which are later corrected after weighing them at the time of shipment for final disposal, which may occur from one year to the next. Finally, in 2022, the result of hazardous solid waste generation was 18% below the established internal limit of 120.0 thousand tons and the generation of non-hazardous solid waste was 27% below the target of the internally established limit of 204.8 thousand tons.
Waste disposal
In 2022, we disposed 110.3 thousand hazardous and 161.8 thousand non-hazardous tons of waste from our processes6. The proper management of our solid waste allowed 88% of the hazardous waste mass generated in the processes to be sent to RRR routes. The total hazardous waste from processes destined for non-RRR routes was 13.1 thousand tons, therefore, lower than the established limit for the year (22.2 thousand tons).
Also in 2022, 68% of the mass of non-hazardous solid waste from the process was destined for RRR routes. The disposal of non-hazardous waste from processes for non-RRR routes was 51.8 thousand tons, therefore, lower than the established limit for the year (91 thousand tons).
In total, 76% of the mass of hazardous and non-hazardous solid waste from the process was destined for RRR routes, which reiterates our efforts to adopt circular economy practices and puts us on track for our new ESG commitment to dispose of 80% of waste process solids for RRR routes by 2030.
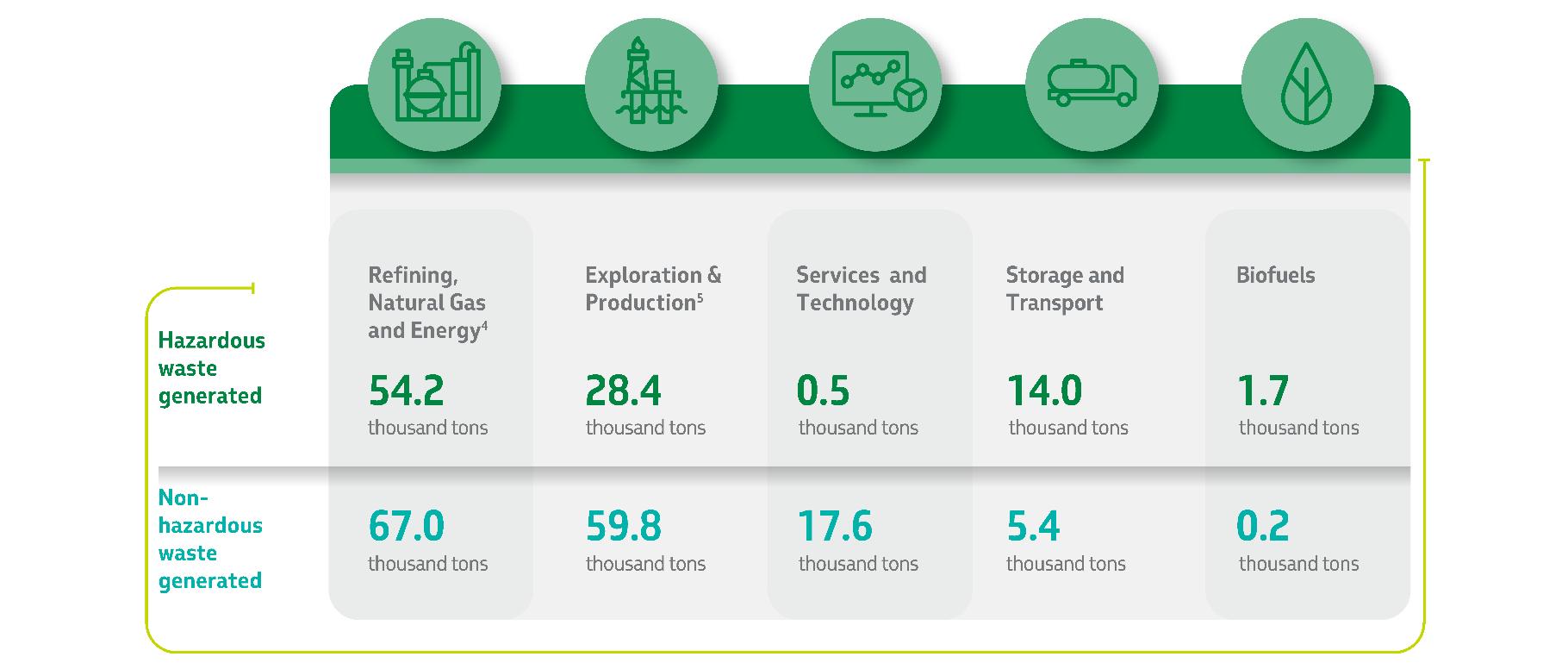
We determine waste disposal methods and enter into contractual agreements with contractors who are specialized and licensed by the environmental authorities for this purpose, and who must follow our regulations and standards.
All the disposed hazardous and non-hazardous waste was transported to allow for the environmentally appropriate treatment or final disposal to take place. We employ, both for the transport and disposal stages, authorized suppliers licensed by the competent authorities (environmental, transport, and health inspection). In 2022, 110.3 thousand tons of hazardous waste and 161.8 thousand tons of non-hazardous waste from our processes were transported nationwide. In the year in question, we did not make any international waste shipments7
The difference between the mass of waste generated and disposed of occurs as part of proper waste management, since a portion is temporarily stored safely in our units to await disposal where normally batches are formed for transport and may occur from year to the next. —
7 Law no. 12.305/2010, which establishes the National Solid Waste Policy, does not cover radioactive waste that is treated with specific regulations (for example, the norm of the National Nuclear Energy Commission (CNEN) No. 8.01/2014). Despite this, in 2022, approximately 551 tons of Class 2.2 radioactive waste, according to CNEN standard No. 8.01/2014, containing naturally occurring radioactive material (NORM) were disposed of by a licensed company in Texas-USA. There was no obstacle for this process by CNEN and the transport plan was licensed by Brazilian Institute for the Environment and Renewable Natural Resources (Ibama) and by CNEN.
8 Data include Petrobras Parent Company (units in Brazil and abroad), Transpetro and Petrobras Biocombustível

9 Considers engineering works in the Refining, Natural Gas and Energy units.
10 Considers the Production Development activities.
11 Waste submitted to unconventional disposal technologies or to more than one type of treatment.
Drilling fluids
We adopt actions related to operational efficiency in line with the practices of the offshore oil & gas industry, maximizing the use of the inputs used and minimizing landed waste. Some practices allow increasing the useful life of non-aqueous-based fluids, such as solids control and storage for evaluation of characteristics to allow their reuse in other projects. In addition, the use of dryers to reduce the content of adhered organic base has allowed the classification of gravels for environmentally adequate disposal in accordance with current legislation and the determinations of the competent authorities.
In 2022, we generated 2.6 thousand tons and disposed of 2.1 tons of cuttings and water-based fluids from exploration and production processes in land operations or landed from offshore operations12. We also generated and disposed of 4.7 tons of cuttings and non-aqueous based fluids. We adopted alternatives for environmentally appropriate treatment or final disposal of these materials.
TECHNOLOGIES FOR DISPOSAL OF WATER-BASED FLUIDS (WBF) and NON-WATERBASED FLUIDS (NWBF)13 (consolidated)
Oily sludge
Oily sludge is one of the main hazardous wastes generated in the oil & gas industry, mainly in cleaning activities of storage tanks for oil and oil products and effluent drainage and treatment systems. As reported in this chapter, in recent years we have adopted circular economy practices for reusing and valuing this waste.
In 2022, 38.7 thousand tons were generated, and 41.5 thousand tons of oily sludge were destined for disposal. For this portion that is not reused as raw material for petroleum products, environmentally appropriate treatment or final disposal alternatives are adopted.
Divestment processes
In 2022, we continued the plan for the transition of the units that make up our portfolio management to ensure full compliance with all the units' emergency preparedness and response requirements. This way, a culture of contingency and accident prevention was reinforced to prepare the teams involved with this new scenario.
We have systems for decommissioning and divestment of assets and companies, in addition to HSE policies, guidelines and standards, which establish procedures for planning and executing these activities in offshore and onshore assets. Accident and leak prevention actions are carried out on all assets in which we are operators or have a stake, throughout the entire life cycle of the project, from planning to decommissioning, including the asset sale processes (divestments). This is always done under the supervision and with the participation of control and inspection bodies. In the case of divestments, strict criteria are applied in the selection of potential buyers to ensure the technical, financial, and operational capacity to provide business continuity. Compliance with all commitments, requirements and accident and leak prevention programs are disclosed to potential buyers and maintained by us throughout the process until the asset is transferred to the new operator and the transaction is closed (closing). The new operator, upon receiving the asset, takes on the responsibility for all commitments and requirements related to the prevention of accidents and spills. These commitments and requirements are established and supervised by various control bodies (National Agency of Petroleum, Natural Gas and Biofuels - ANP), Brazilian Institute for the Environment and Natural Resources (Ibama), Brazilian Navy, Fire Department, state agencies environment, among others), that participate in the divestment process.
Decommissioning process
The E&P portfolio active management process must take into account issues related to the decommissioning of assets. This is a legal requirement when the life cycle of the production system ends, or within the scope of area revitalization projects, replacing old systems with new ones. It is thus a natural process within the production cycle of the oil and gas industry.
Once the need for decommissioning has been confirmed, we plan and carry out activities in compliance with current regulations, following strict safety standards and carrying out multiple criteria analysis (environmental, technical, safety, social and economic), which allows us to objectively identify the alternative that best reconciles the various criteria considered.
In this analysis, we also consider a vast material of studies and guidelines on the best practices of the oil and gas industry worldwide.
In compliance with resolution no. 817/2020 of the ANP, the Facilities Decommissioning Programs (PDI) are evaluated and approved by the ANP, Ibama and the Navy, within the limits of their attributions. In summary: Ibama analyzes the solution for decommissioning and disposal of structures from an environmental point of view; the ANP verifies the technical compliance of the proposed solutions, confirming their alignment with the industry's best practices; and the Navy examines whether issues related to navigation safety and other uses of the sea are ensured.
The Facilities Decommissioning Programs contain information regarding the company's social responsibility management system, which includes: social diagnosis; social responsibility plan (with measures to mitigate identified risks) and initiatives supported under the Petrobras Socio-environmental Program. The adoption of these actions supports the entire business lifecycle, demonstrating our commitment to carrying out decommissioning activities safely. The social risks of decommissioning projects are evaluated, and mitigating measures are implemented, according to the internal standard Manage Social Risks throughout the Business Life Cycle.
>> Information on the minimum notice period for operational changes and programs for improving employee skills and career transition assistance can be found in the Labor practices and equality of opportunity chapter.
Closing operations and decommissioning activities can impact the environment and communities located around the sites due to the processes of dismantling structures and facilities. During the execution of these activities, waste is generated such as plastic and metal scrap inherent to lines, subsea equipment, and platforms, as well as debris, oily sludge, cleaning residues contaminated with oil and hydraulic fluids. To mitigate these possible impacts, we have systems for the development of asset decommissioning projects, in addition to HSE policies, guidelines and standards, which establish guidelines, processes and activities to plan and execute decommissioning of offshore and onshore assets. Compliance with decommissioning obligations involves various activities carried out in accordance with the decommissioning program approved by regulatory bodies and in accordance with applicable legal requirements.
In 2022, an Executive Decommissioning Committee was created to monitor the evolution of the best global practices and assist with the creation of strategic guidelines for implementing the decommissioning projects.
In 2022, we obtained approval from the Brazilian regulatory bodies for the decommissioning of FPSO Capixaba, in the Jubarte field, in Espírito Santo, as well as completing the unmooring of the P-07 platform in February. In addition, we have progressed with approval stages for decommissioning of other production systems, such as the P-33 and P-26, and we continue to carry out disconnection operations and removals of subsea equipment already approved for decommissioning projects underway in the Campos Basin, highlighting those related to the project to revitalize the Marlim field. We also abandoned 13 wells and disconnected 50 risers.
Over the next five years, we plan to decommission 26 platforms, 360 offshore wells and approximately 2,500 km of risers and flowlines, and we want to become a global reference for this activity, focusing on sustainability, safety and care for people and the environment.
It should also be noted that since 2022, the strategy for the disposal of our floating platforms that will undergo decommissioning has been implemented. This process considers a green recycling policy for these units, in line with the best global industrial ESG practices with a focus on sustainability, in order to guarantee the appropriate recycling process with protection of the environment and human rights. The P-32, a unit with interrupted production, will be the pilot project of this new policy, which has the following guidelines:
▪ Implement actions to minimize waste generation, prevent impacts on biodiversity, as well as reuse equipment and encourage the circular economy;
▪ Recycling in shipyards equipped with technological solutions, such as dry docks or impermeable land with an effective drainage system, which guarantee the containment of contaminants resulting from dismantling activities, preventing their release into the environment; do a prior inventory of the existing materials on the vessel, to ensure the proper preparation of a recycling plan by the shipyard;
▪ Recycle the fleet of vessels safely, protecting the environment and people working in the recycling yards;
▪ Consider quality certificates, requirements of resolution no. 1257/2013 of the European Union Ship Recycling in the case of international shipyards, and/or in the case of Brazilian ones, the operating licenses and compliance with applicable legislation, rules and regulations on the environment, safety, and health of workers, including management of subcontractors;
▪ Act in accordance with agreed upon commitments, including measures to control corruption and respect for internationally recognized human rights
Onshore decommissioning processes
As with offshore decommissioning activities, the abandonment of assets located on land is subject to the same corporate system, obeying the same criteria to ensure the execution of the best alternative to the dismantling of onshore installations.
In the case of onshore assets, the process involves several stages such as inspections, cleaning and decommissioning of pipelines, permanent plugging of wells, razing and environmental recovery of locations with authorization from regulatory bodies and in accordance with applicable legal requirements.
Analogously to offshore assets, we submit all our decommissioning projects to the ANP, however, the environmental licensing for decommissioning projects in onshore environments needs to be authorized by state environmental agencies, linked to the State Environmental Secretariats.
In 2022, we decommissioned 44 onshore wells in several concessions.