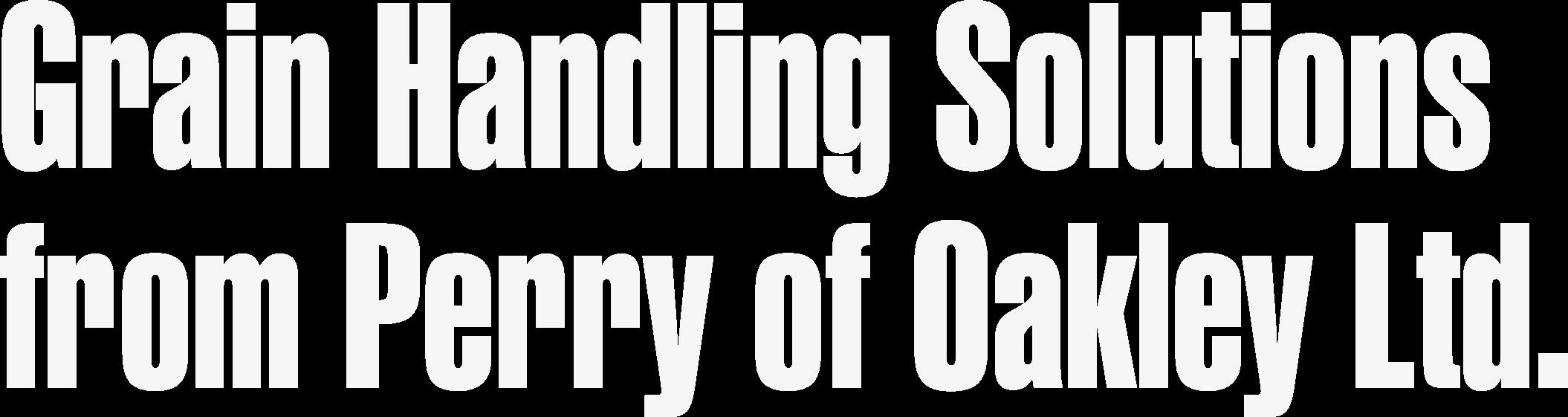
8 minute read
Grain
Grain Handling Solutions fr om Per r y of Oakley Ltd.
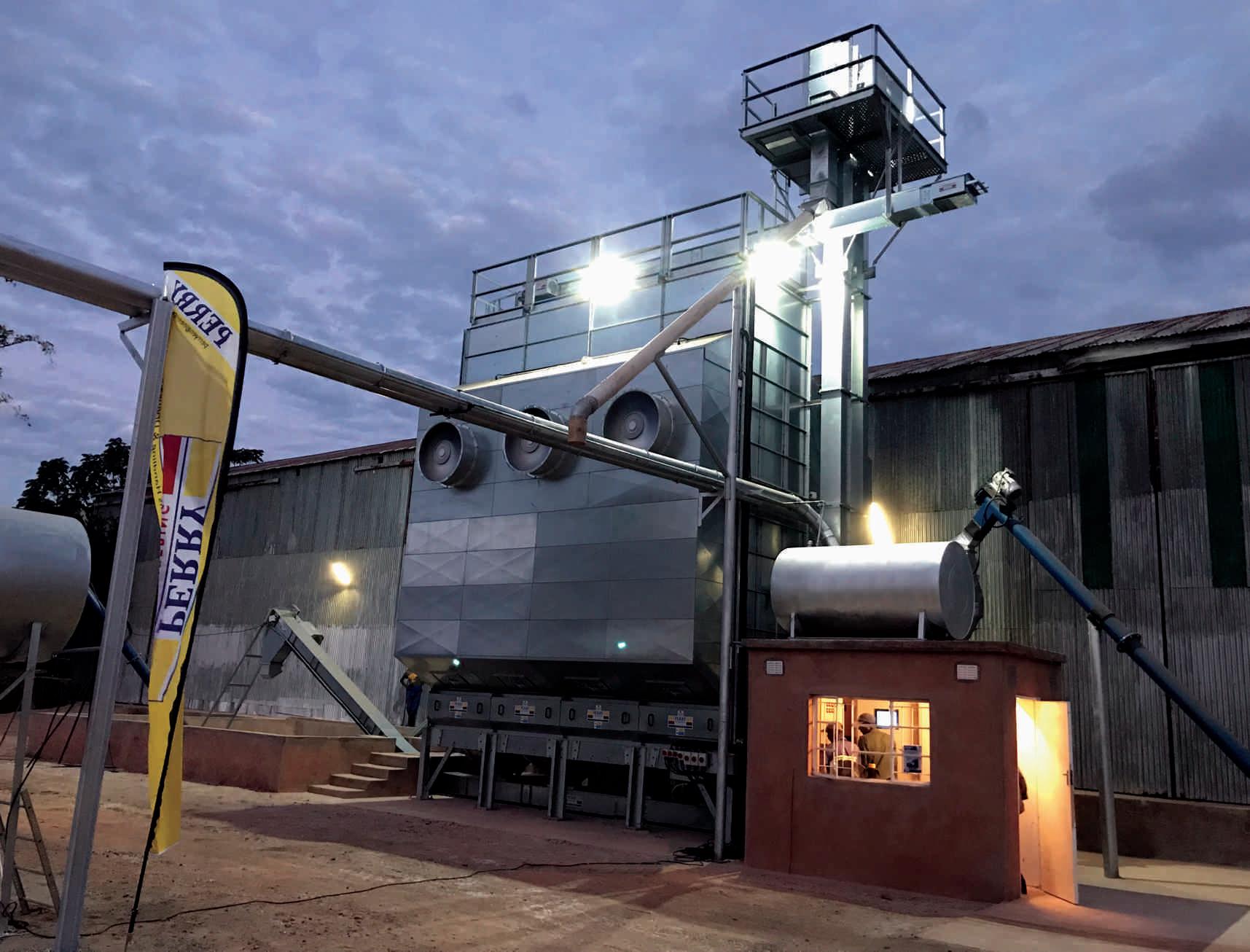
Perry of Oakley Ltd., a 3rd generation family business established in 1947, have significant experience in materials handling, having supplied over 11,000 chain & flight conveyors in over 25 different countries across 4 continents. Perry agricultural chain & flight conveyors come with heavy duty chain, fitted with deep faced flight, perfect for handling cereals, pulses & granular products. The three-piece trough & durable galvanised steel construction provides an exceptional life span, backed up by the Perry 10 year guarantee*. In 1949, Tom Perry built the very first Perry belt & bucket elevator with a capacity of 5tph. Perry equipment can now reach capacities over 1,000tph with an extensive range of handling equipment which includes: reception hoppers, trench intakes, levelling & travelling conveyors, twin trace conveyors, belt conveyors, screw conveyors, and of course chain & flight conveyors and belt & bucket elevators. All Perry products come in three main ranges: agricultural (8-60tph), lightindustrial (60-150tph) & industrial machines (150-1000tph) - each purposefully designed to meet specific requirements. The Perry range of agricultural belt & bucket elevators, can come in either single or double lift, meaning only one elevator is required to transport wet & dry grain, and are supplied with oil resistant low stretch belting as standard. Slatted pulleys help with movement of grain, with the product able to fall through the elevator without creating product build up. Perry elevators are supplied in a galvanised finish (painted optional) & 3mm thick head and boot shell for long life durability. All elevators are available with an access platform using a ladder & hoops to meet all safety standards. Perry also supply an extensive range of silos that include flat bottom silos, with 3m to 32m diameter, and storage capacities ranging from 27m³ to 26,000m³. Hopper bottom silos range from 3m to 13m diameter with either 45° or 60° cones. The hopper silo ranges can be manufactured with either a heavy-duty hip ring or with an internal light weight hip ensuring we can supply the most cost-effective solution for you. With over 70 years’ experience in the manufacture of materials handling, drying & storage equipment Perry have provided a solution for a significant range of projects. Perry provide high quality machinery to a wide variety of industries, including farms, commercial grain stores, waste & aggregate industries, feed & pet food, pharmaceutical & biomass industries, and many others. To find out more about Perry’s range of handling & drying equipment call +44 (0)1404 890300 or email sales@perryofoakley.co.uk *Term & conditions apply.
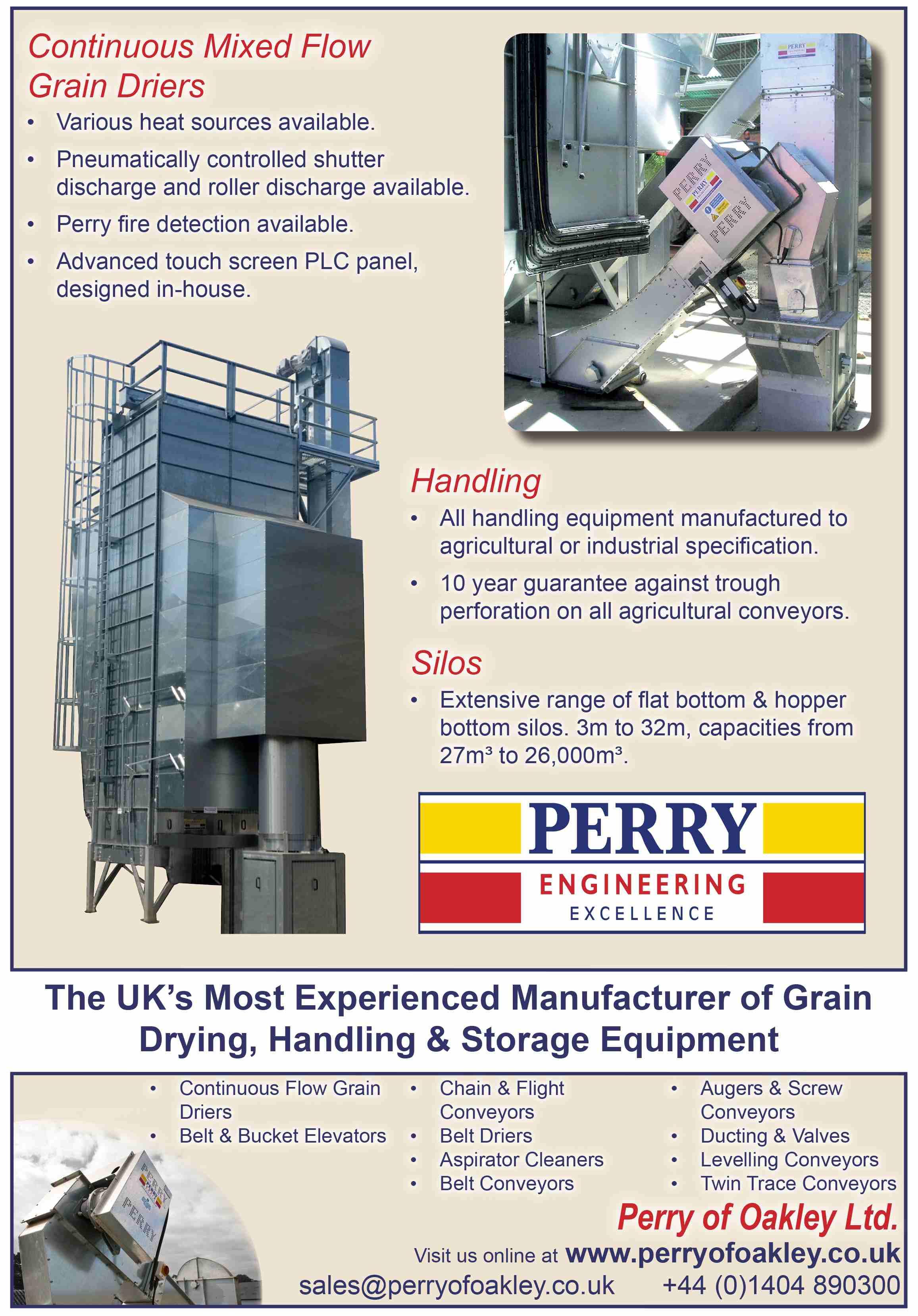
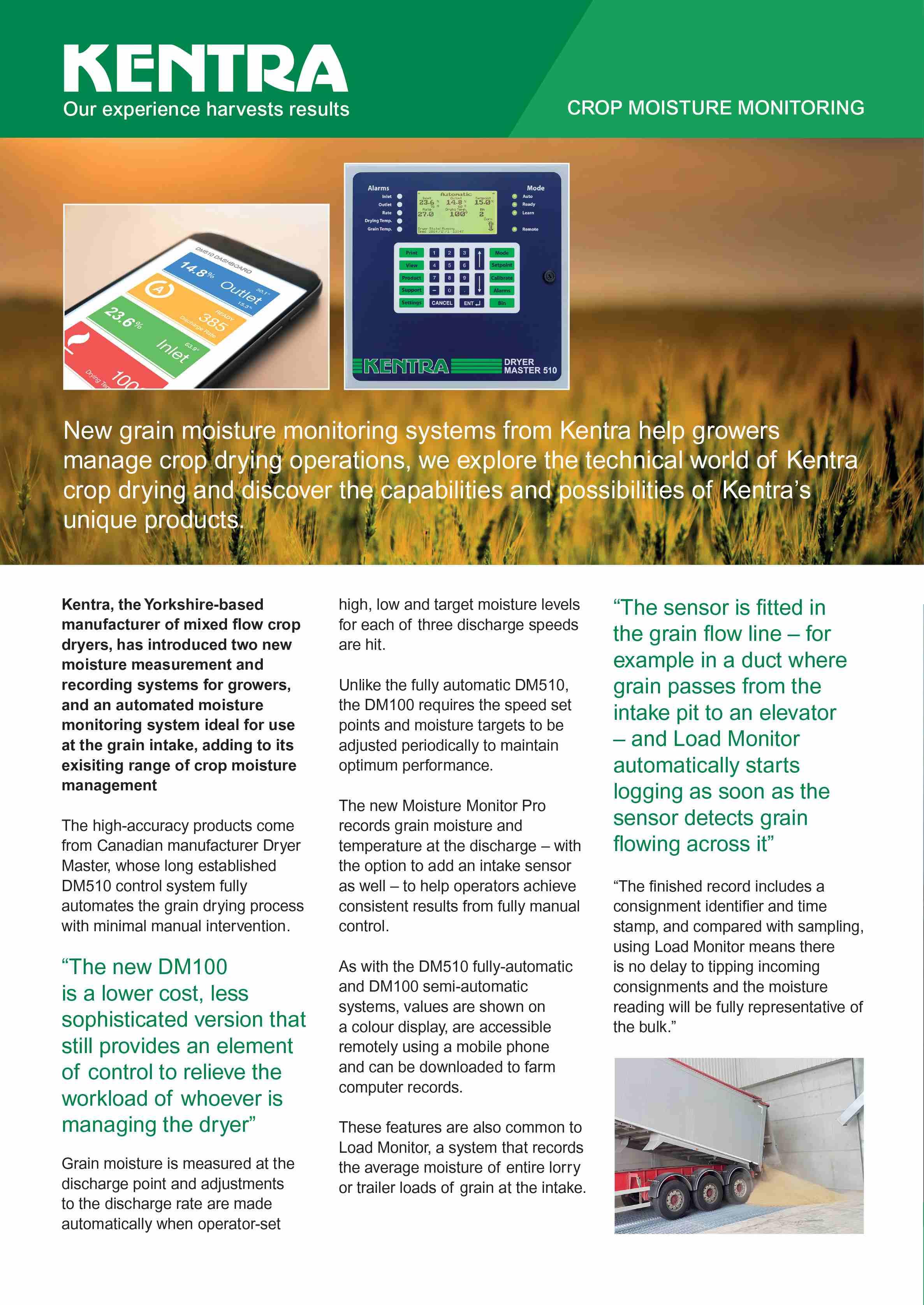
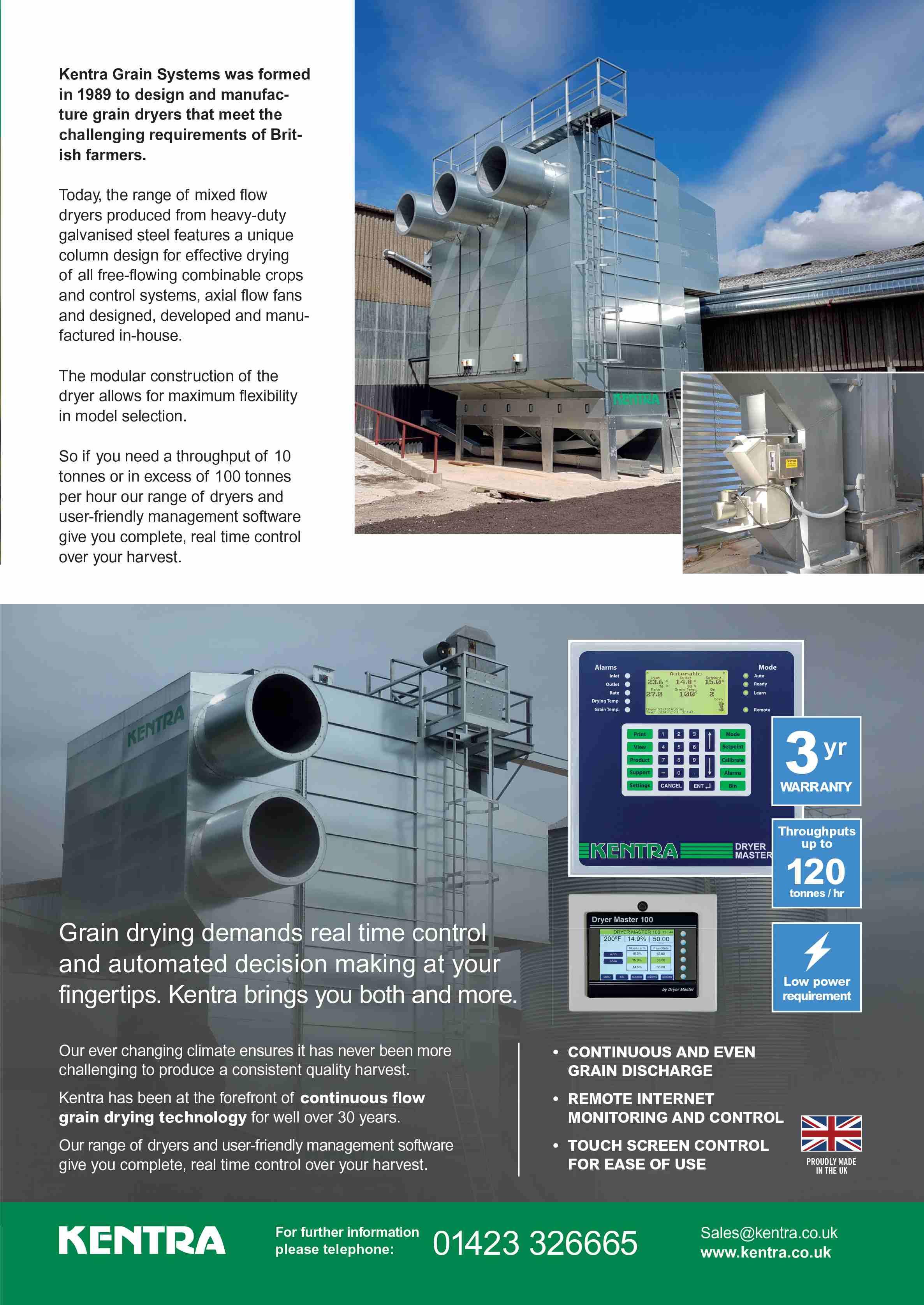
Insects get into grain stores on the back of rodents’, ‘I have a new store so there’s no need to fumigate it’ and ‘grain pests only live in grain stores’….these were just a few of the myths busted in a recent AHDB webinar on the subject of grain storage, drying and pest management. Teresa Meadows, AHDB Knowledge Exchange Manager, shares the discussion and conclusions from the session.
Pest management
Highlighting the importance of thinking about the conditions in and around your store to mitigate against grain pests and, if needed, the best ways to manage insects if found, Martin Cobbald, Managing Director
Busting the myths and sharing the principles of grain storage
of Dealey Environmental Ltd shared his top tips as part of the webinar, which included: • Remove any waste quickly and keep areas around the grain store clear • Ensure your store is completely clean, rodent free and rodent proof • Cool your grain as quickly as possible • If using treatment products, ensure the correct PPE is used, the treatment has penetrated all cracks and crevices and the correct dose is being applied • Continue routing monitoring for insects in grain – pitfall traps and sieves are both good tools to use And the answers to the myths? “If you have a rodent infestation, they can translocate and bring in materials to store that then create ideal conditions for insects (rather than the pests coming in on the rodents themselves); if you have a new store, treating it is important if you have an insect risk, but it should be at a high volume and finally our grain pests found in store can also be found thriving in the wider environment, for example rust red grain beetles in Thetford Forest” says Martin.
Grain storage and management
The importance of calibrating your moisture meter before the season starts to ensure accurate measurements, store hygiene, the servicing of equipment and managing grain to ensure effective drying and cooling were all key points shared by Philip Darke, Operations Director at Camgrain as part of the webinar, in addition. Ongoing monitoring and record keeping through the season is important, said Philip; “Act promptly and don’t forget that your bulk is in the shed when you’re busy. Have a really good programme in place that looks after everything all the time, however busy you are, as once an issue starts to develop, it can very easily get out of control and fast action is essential”. Philip’s three golden rules were: 1. Aeration – most crops can be held with good ventilation 2. Segregation – avoid contamination, eg. ergot, mycotoxins, fusarium, other crops 3. Water leaks – ensure regular careful inspection of roof/floors. Difficult to spot and can be catastrophic. Lastly, “more than ever for this harvest, make sure that you have sufficient critical spares in stock, which you might need and will keep the operation running”, said Philip. Ensuring safe, effective grain storage from start to finish assures crop quality and value. To watch the webinar recording, please visit the AHDB Cereals and Oilseeds channel on YouTube and for AHDB resources on grain storage, please visit: ahdb.org.uk/ grainstorage.
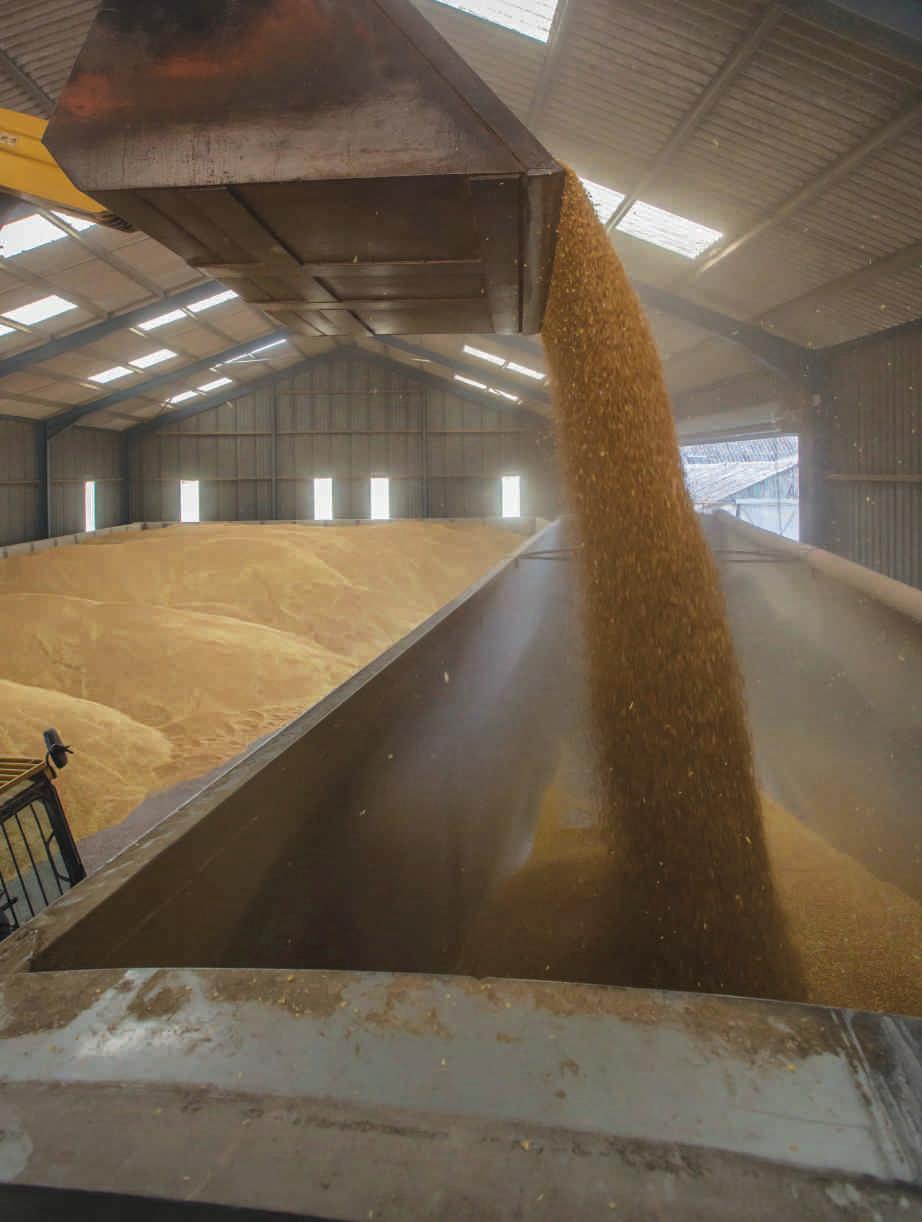
Hit milling wheat bonuses by focusing on nutrition
Growers of high quality wheat are being urged to consider applying a range of crop nutrients at the critical flag leaf stage, as bonuses up to £20 per tonne are being offered for milling wheat with a protein content of 13% or more. With wheat prices currently sitting at £200.00/tonne, FMC commercial technical manager Geoffrey Bastard explains that an extra £160 per hectare could be achieved, for an eight-tonne crop of milling wheat if protein specifications are met. “Boosting grain protein levels is all about correct nutrition,” says Geoffrey. “This is especially important when growing group one milling wheats such as Crusoe, as they have greater potential to meet these specifications but are often more susceptible to diseases, which means they can benefit from extra support.” Although nitrogen is widely recognised as the key driver behind increased protein levels, other nutrients, such as magnesium and sulphur, are equally important. “Applying a variety of nutritional elements at T2 will be fundamental to achieving the bonuses on offer,” explains Geoffrey. “Magnesium is essential for the transport of nitrogen. If magnesium levels are low, nitrogen will remain in the leaves and stems, and won’t be transported to the grain where it’s needed to increase protein and amino acids. Magnesium also helps extend the grain fill period, so ensuring adequate availability in the plant sets the groundwork for optimum nitrogen use efficiency,” he says. “Likewise sulphur also plays an important role in boosting grain protein, as it aids nitrogen uptake and increases flour quality. This is especially important if you’re exporting your grain as flour quality is often rigorously checked via a Chopin alveograph test.” While magnesium is routinely applied to wheat at the flag leaf stage, sulphur should also be applied between flowering and grain milk development to achieve the highest protein content possible.
Geoffrey recommends an application of
Prince®, which contains magnesium, sulphur, and a range of other micronutrients to aid plant health. It should be applied at 3.0-6.0L product/ha from crop GS39-59, dependent on current nutrient status. “Prince® can fit in well with can fit well with a range of other products at the T2 timing as it tank-mixes easily with other products,” Geoffrey says. “In light of the bonus offers available, if you’re growing a group one variety, it’s worthwhile investing in nutrition, as it will pay dividends when it comes to harvest quality,” he concludes.
JWI Ltd intr oduces the Westr up CC -2500 into the UK
It's an exciting time for North Yorkshire based JWI Ltd as they supply the first Westrup CC2500 into the UK marketplace - standing at over 4 meters in height this is one of the largest screen cleaners to be manufactured globally.
The impressive CC2500 boasts: • Total Screen area: 60m2 with below possibilities for flow:
Flow 2 – fine cleaning: 40m2 sand screens and 20m2 scalping screens. • Capacity for pre cleaning wheat at 12t/ m2 scalping screen: up to 480t/ hour wheat, 750kg/m3 with moisture content at 18% • Capacity for fine cleaning wheat at 1,2t/ m2 sand screen:
Up to 48t/ hour wheat, 750kg/m3 with moisture content at 15% • Industrial cleaning of wheat at 6,25t/ m2 scalping screen: Up to 250t/ hour • Capacity for malting barley at 2,2t/m2 sand screen: Up to 88t/ hour
Company Director Charles White, “The JWI team are thrilled to be introducing this high capacity pre-cleaner to our customers – the CC2500 is the largest seed cleaner Westrup can build and it’s capabilities speak for themselves –it’s an exceptional addition to our portfolio and we are looking forward to seeing our customers reap the rewards this machine delivers.”
JWI are the exclusive distributors for Westrup within the UK – a relationship which is valued on both sides as Willem Verbeek, Westrup Sales Manager, explains, “We are very fortunate to have a great distributor network around the world and JWI is a great example of this. It won’t be long before the CC-2500 is making a notable difference to the JWI end customers.”
For more information: www.jwi.ltd charles@jwi.ltd 01325 378008
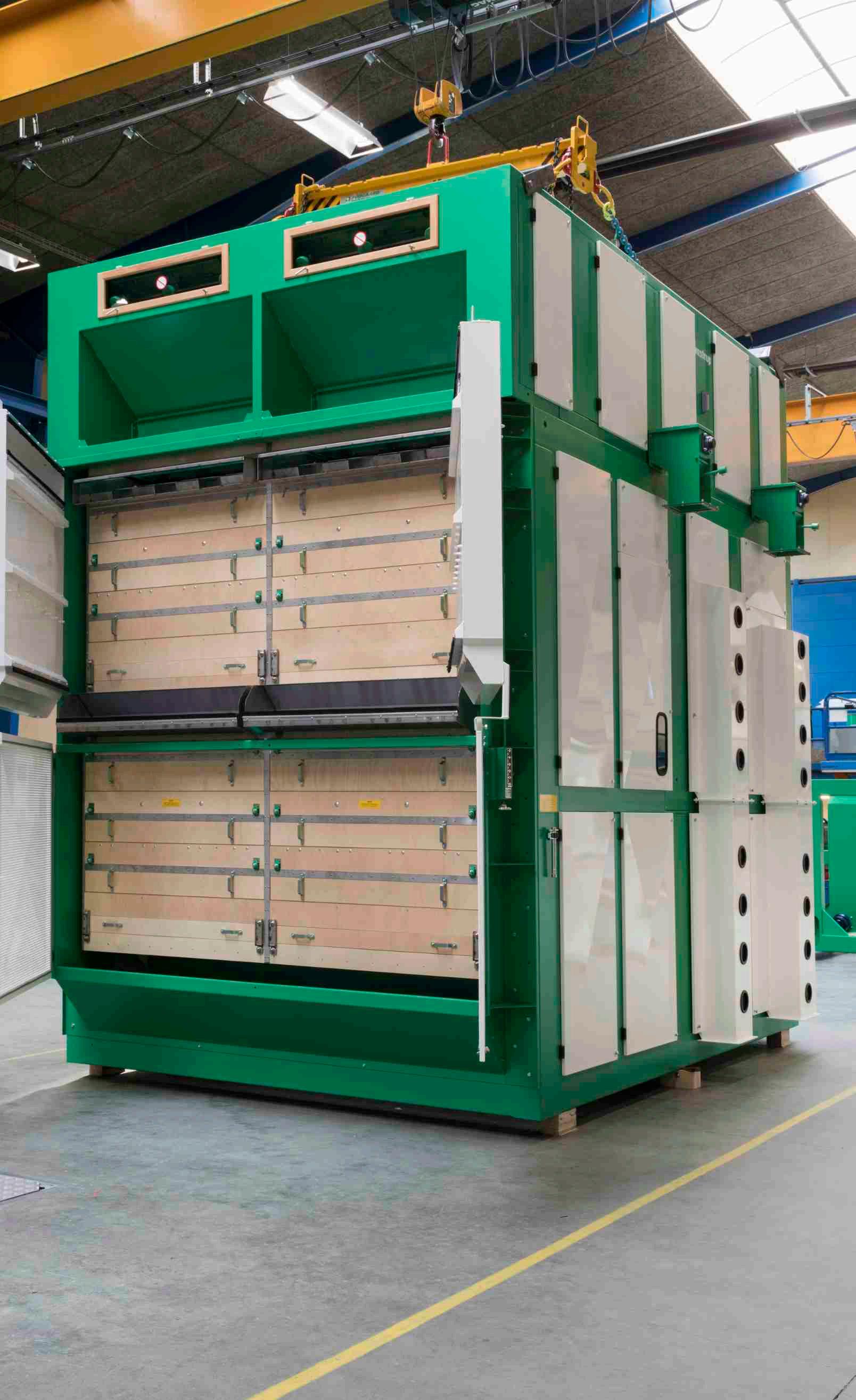