

STRONG EAGLE
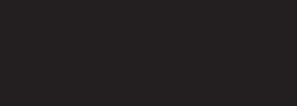
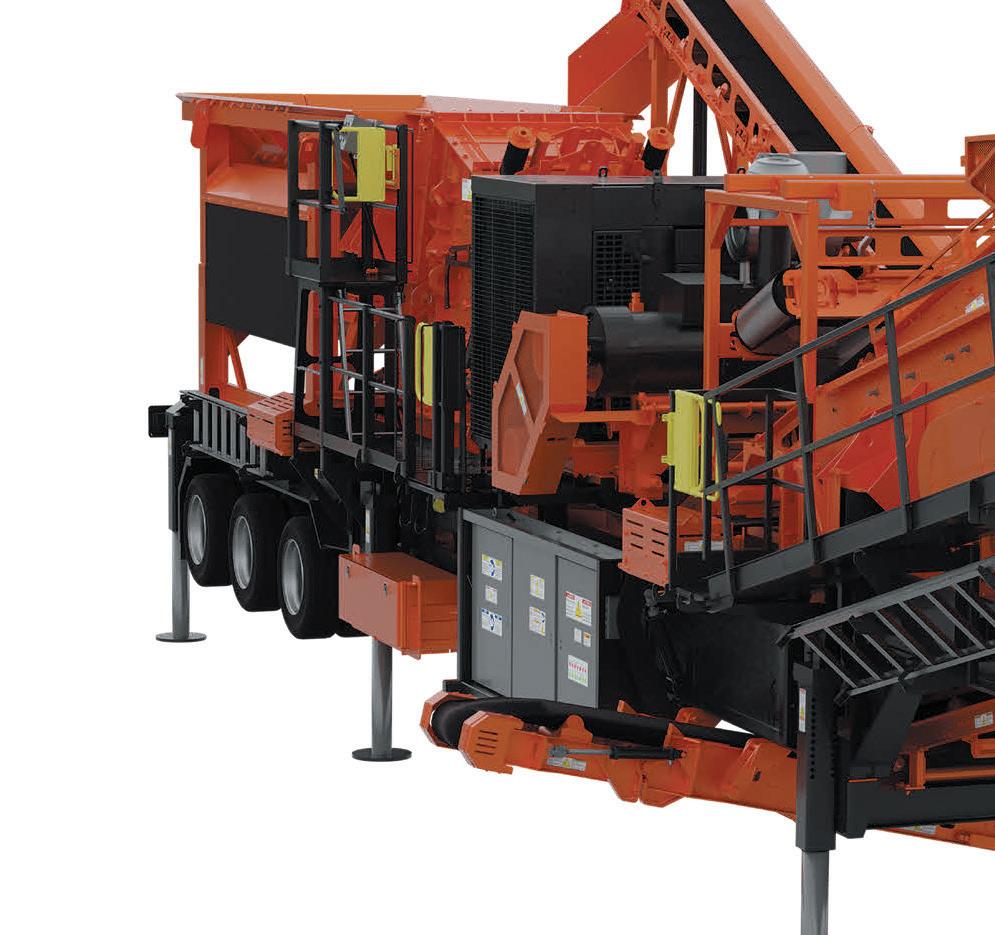

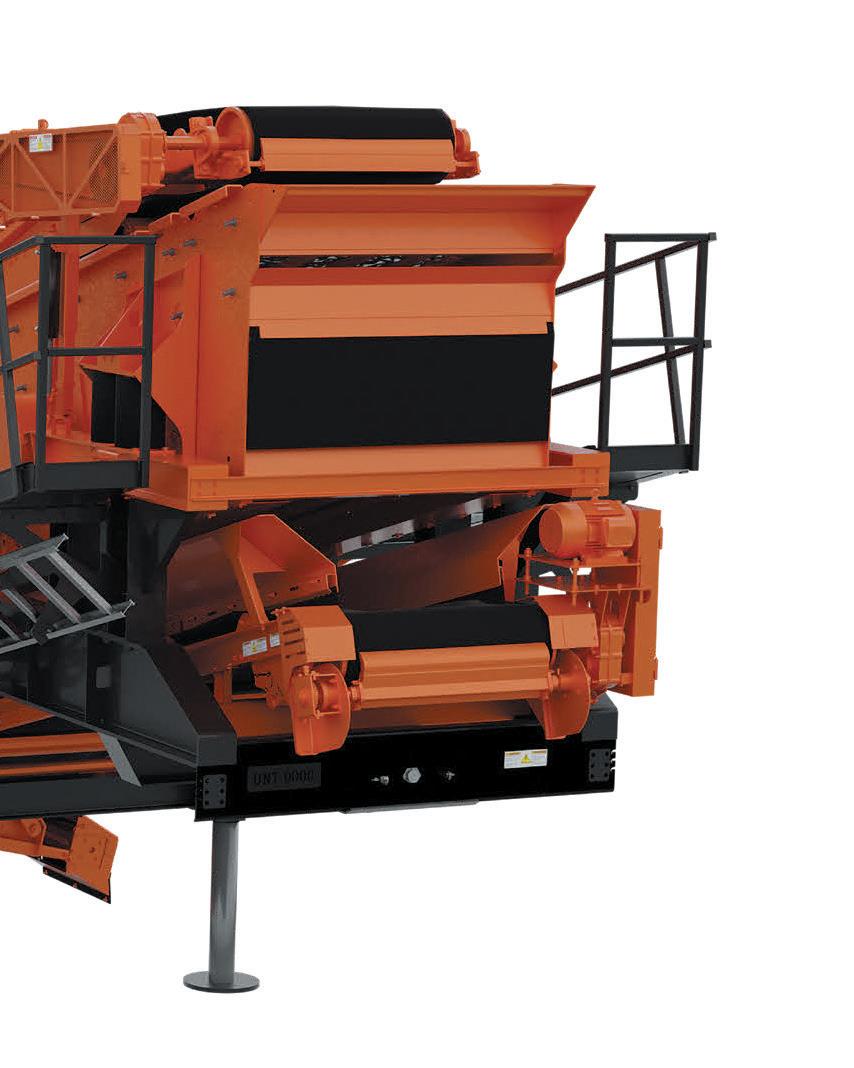

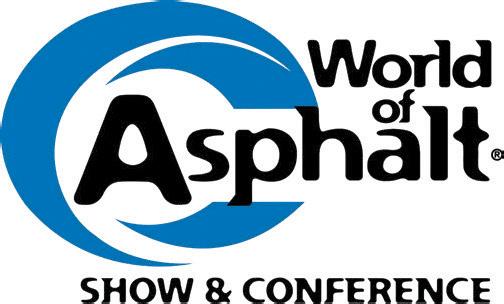


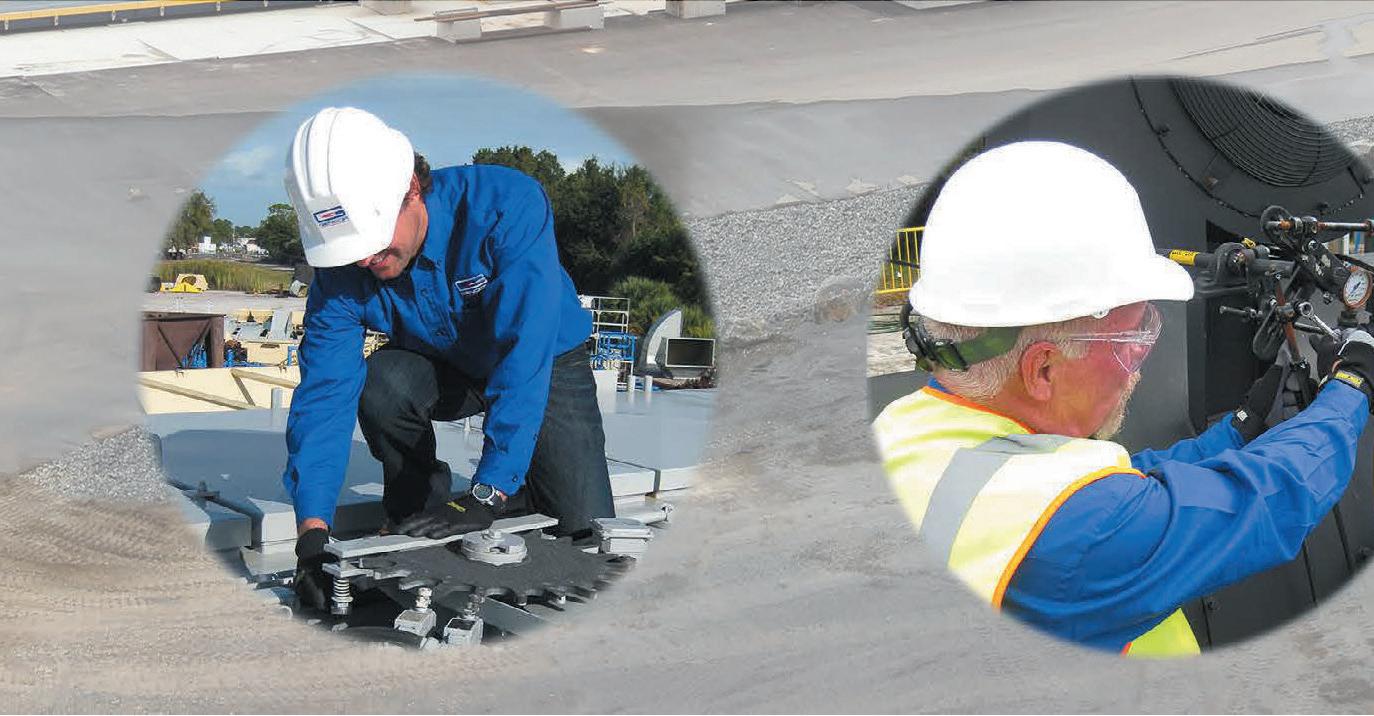
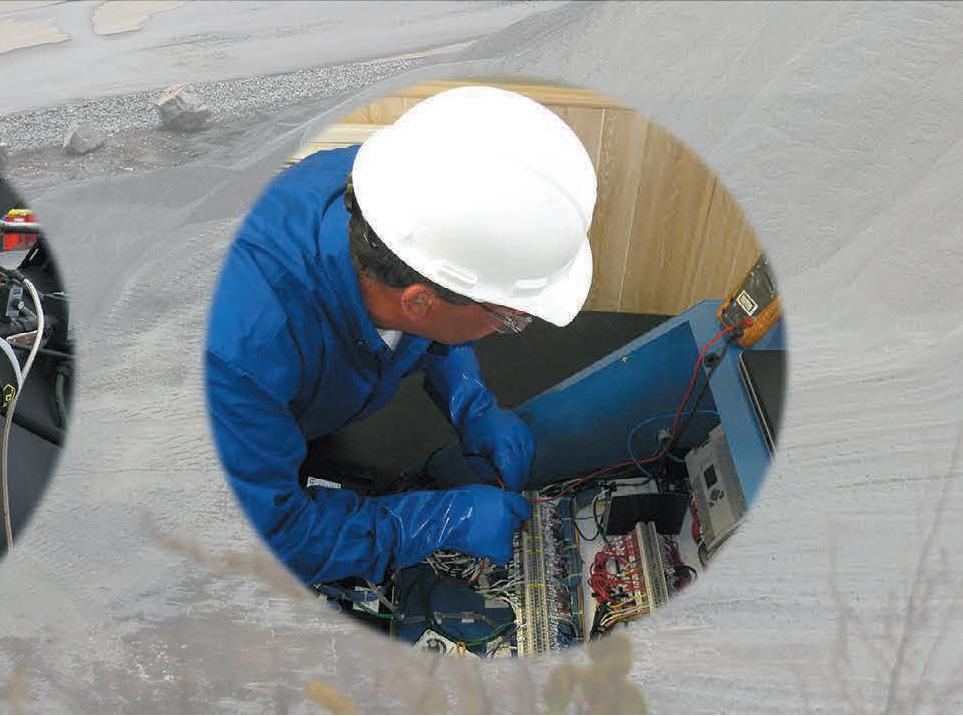
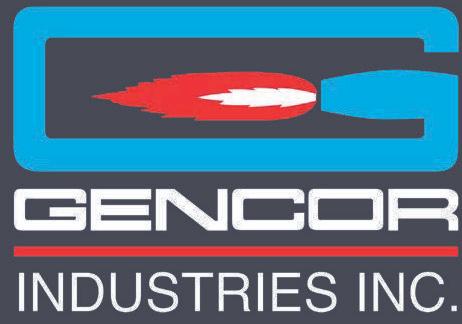
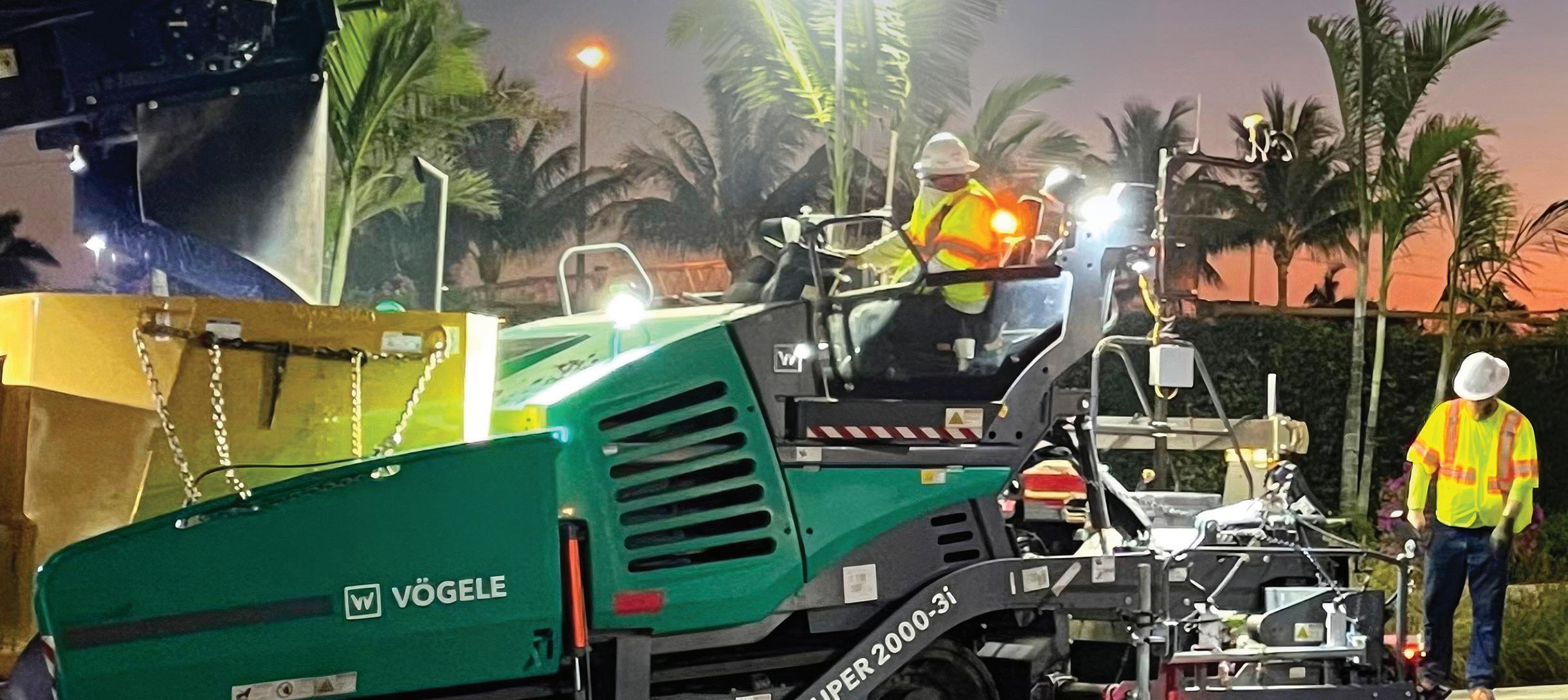



TECHNOLOGY MATTERS
14 Why Reality Capture is the Lynchpin for the Jobsite of Tomorrow
Construction executives have long debated the jobsite of the future built on autonomy and the increased use of technology, and with every day that passes, it’s becoming more than a theoretical concept: it’s now a business necessity.
PRODUCTION NOTES
18 Roadbuilders’ Guide to Crushers
Crushers will only become more popular in the next five years as sustainable building becomes more emphasized across the U.S.
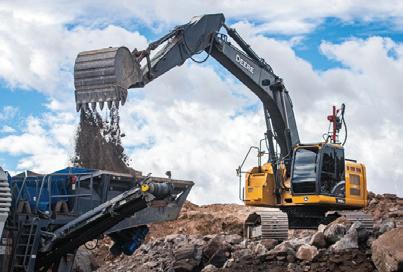
38
FACE OF THE INDUSTRY
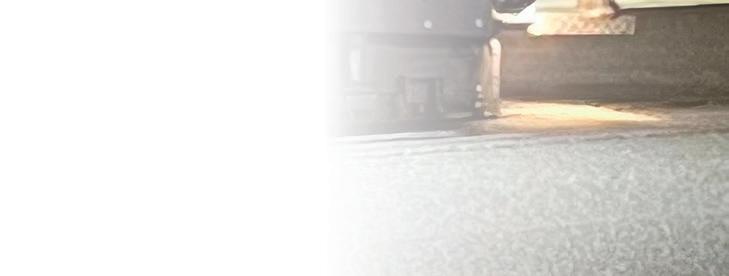
INVESTIGATING INFRASTRUCTURE
The Birth Of The Crushing and Screening Industry
How one CEO’s problem solving challenge launched a new industry in North America, and now their savvy philosophies continue to lead the way.
JOBSITE INNOVATIONS
42 Size Matters
How one contractor’s high tech roller addition improved their pace on jobs of every size.
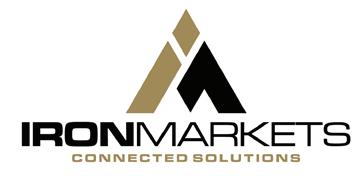
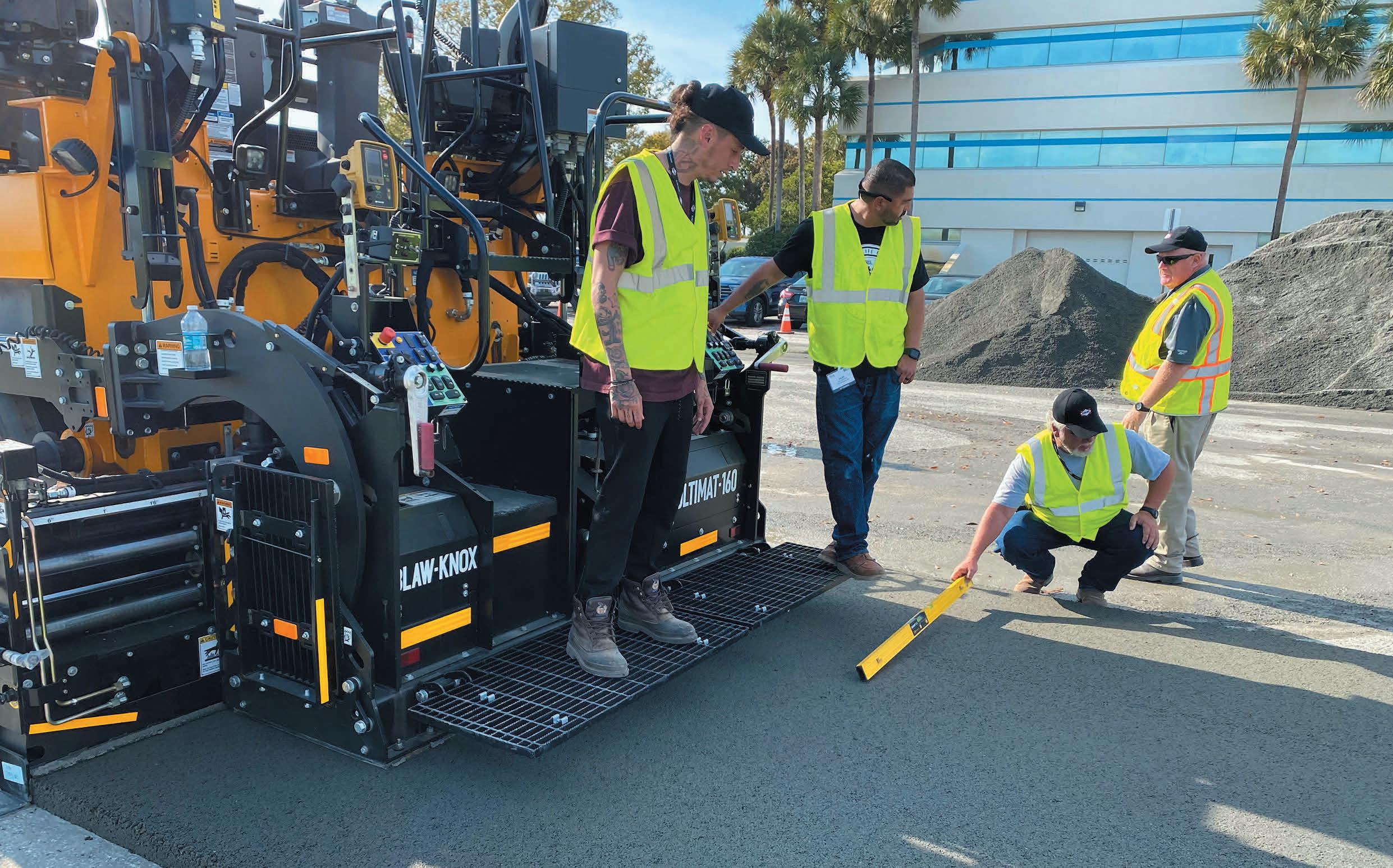
46 PMA vs RMA vs RAP
Pitted up against each other, what does the science say about which makes the best recycled material for your asphalt mixes?
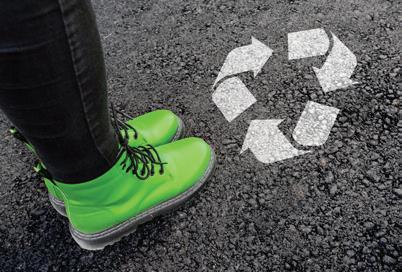
Published and copyrighted 2024 by IRONMARKETS. All rights reserved. No part of this publication may be reproduced or transmitted in any form or by any means, electronic or mechanical, including photocopy, recording or any information storage or retrieval system, without written permission from the publisher. Asphalt Contractor (ISSN 1055-9205, USPS 0020-688): is published ten times per year: January, February, March/April, May, June/July, August, September, October, November, December by IRONMARKETS, 201 N. Main St. Ste 350, Fort Atkinson, Wisconsin 53538. Periodicals postage paid at Fort Atkinson, Wisconsin and additional entry offices.
POSTMASTER: Please send change of address to ASPHALT CONTRACTOR, 201 N. Main St. Ste. 350, Fort Atkinson, WI 53538. Printed in the U.S.A.
SUBSCRIPTION POLICY: Individual subscriptions are available without charge only in the USA. The Publisher reserves the right to reject nonqualifying subscribers. One-year subscription to nonqualifying individuals: U.S. $45.00, Canada & Mexico $65.00, and $95.00 all other countries (payable in U.S.
drawn on U.S. bank). Single copies available (prepaid
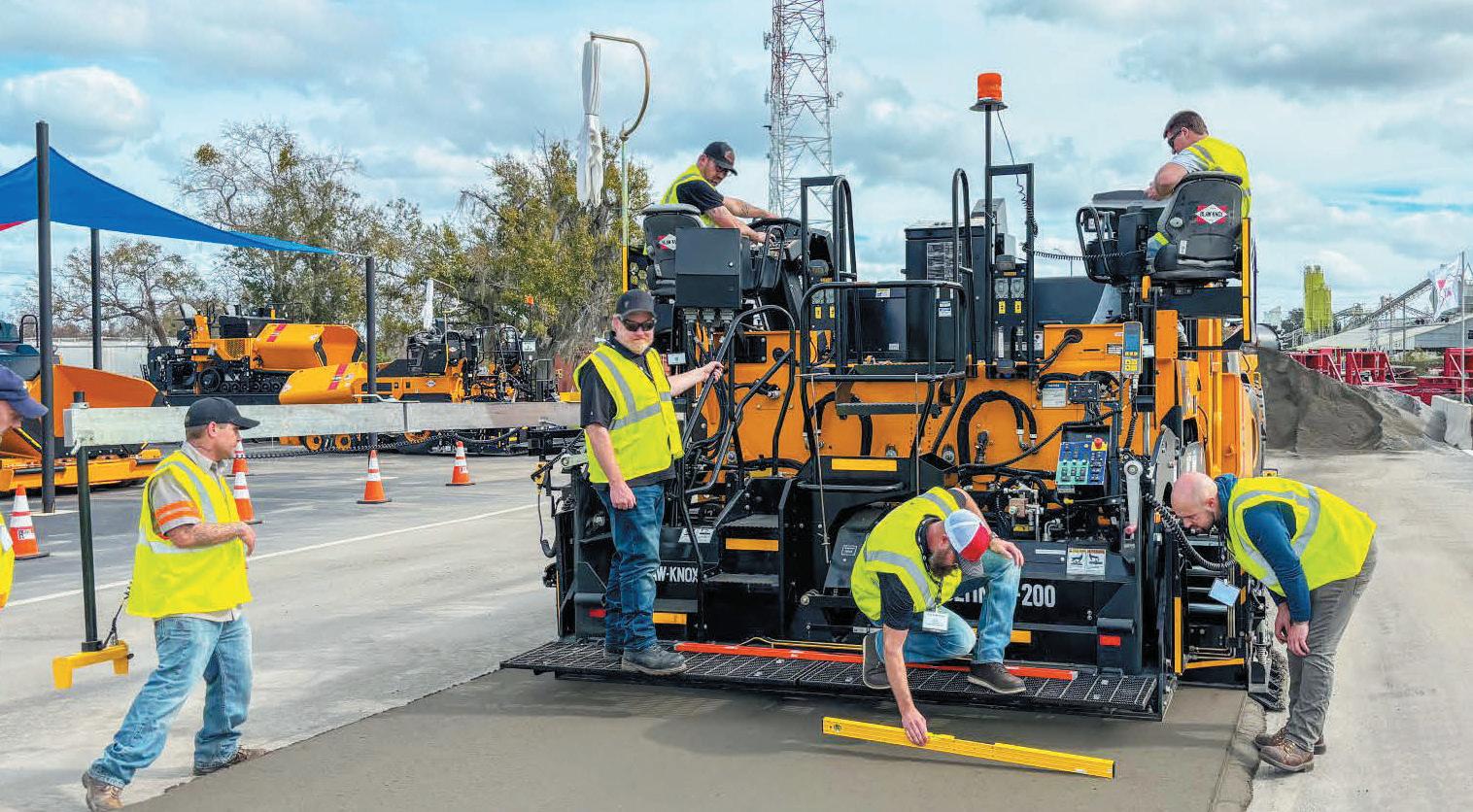
2025 BLAW-KNOX UNIVERSITY TRAINING

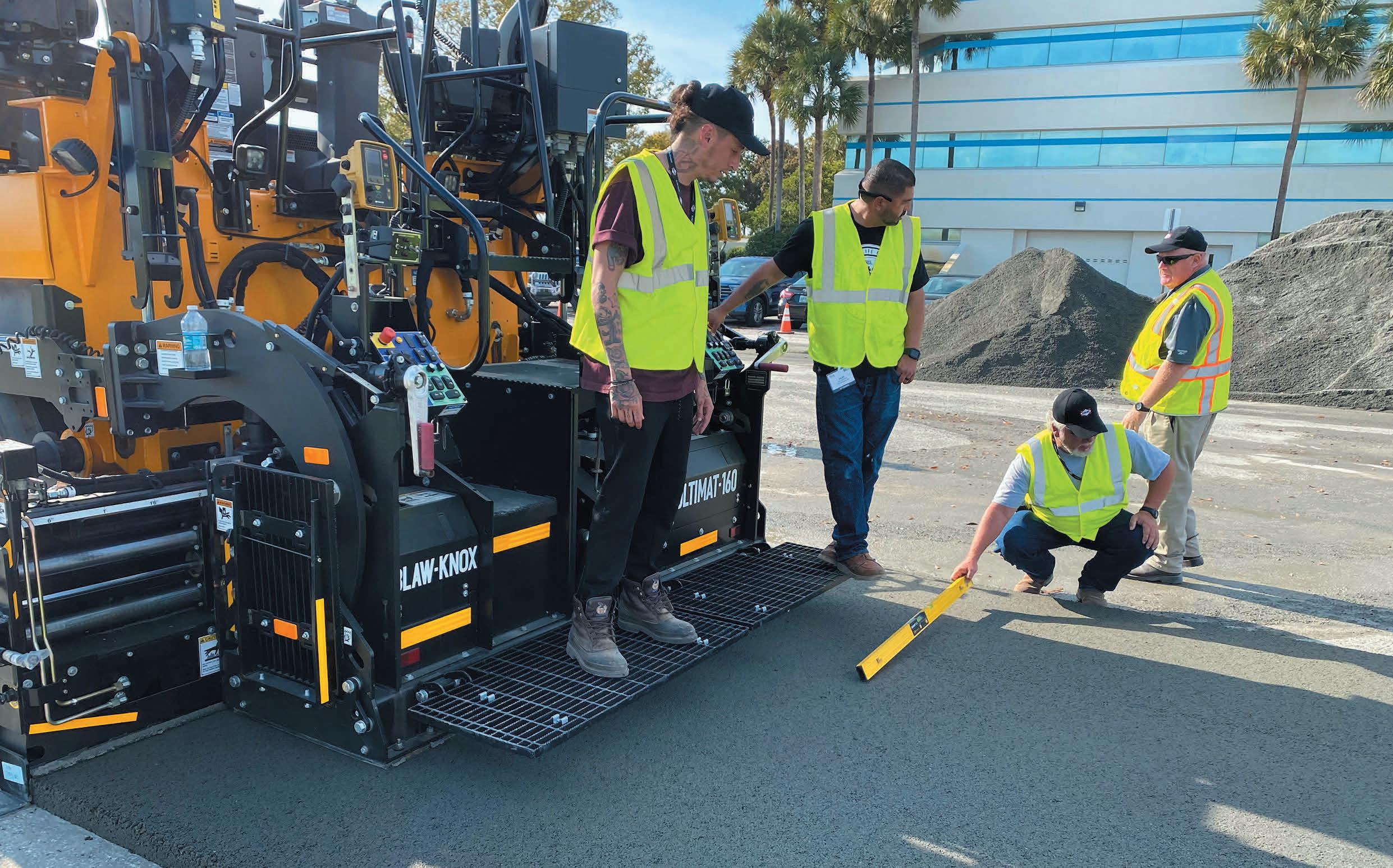
PAVER OPERATION AND MAINTENANCE
2025 DATES
• January 20 - January 23
• January 27 - January 30
• February 3 - February 6
• February 10 - February 13 REGISTRATION
CLASS SIZE IS LIMITED, register today!
DETAILS
All details can be found at www.blawknox.
com/training or contact at (407) 290-6000 ext. 342 or training@blawknox.com
The Blaw-Knox University, is dedicated to training paver operators ad foreman on proper Paver Operation and Maintenance and applied Best Paving Practices through classroom-style and hands-on application courses.
For over a half a decade Blaw-Knox has earned its reputation as the go to source of training and instruction on hot mix paving.
Blaw-Knox provides improved technical and problem-solving skills on a variety of paver operations and maintenance topics. Course instructors share decades of field and teaching experience with attendees, including training on the latest DOT requirements.
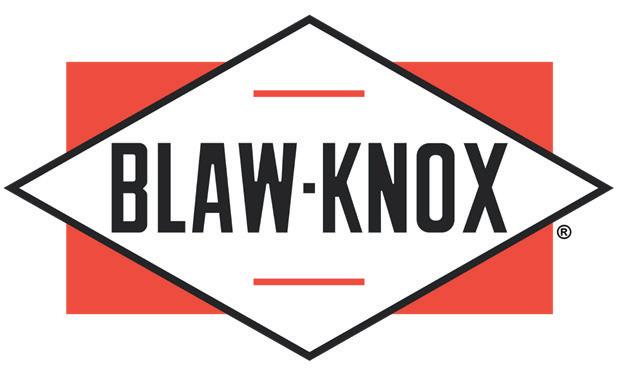
No Edge Lines | Season 2 Episode 4
How do contractors make pavements that can truly stand the test of time? It’s all about that base. Editor Brandon Noel learns how to build a better asphalt mat from the dirt up using the best compaction tips.
Watch the video at:
https://asph.link/ vf2mymeu
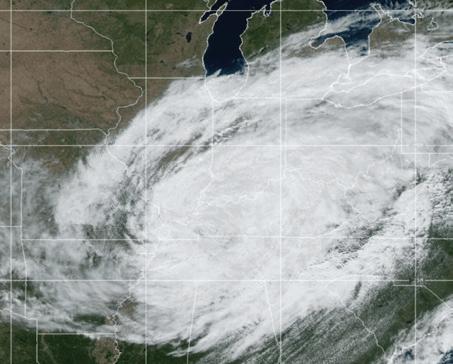
AccuWeather
Puts Hurricane Helene Recovery at $225B-$250B
Buildings, roads, bridges and other infrastructure will need to be rebuilt after Hurricane Helene created catastrophic damage in nine states on the East Coast.
Read more at:
https://asph.link/ w5q9xai7




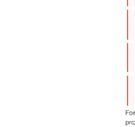
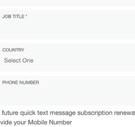
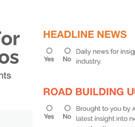
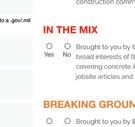
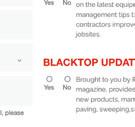
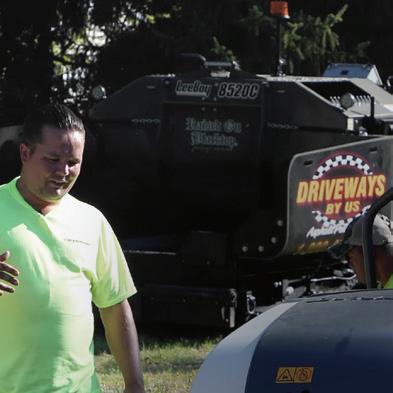
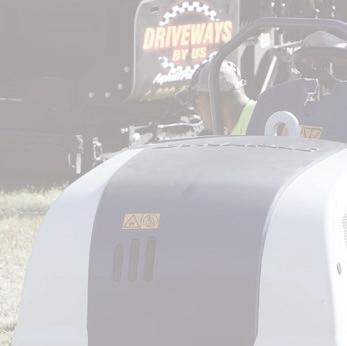
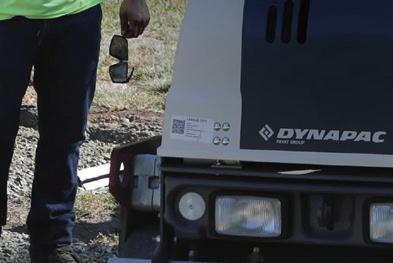
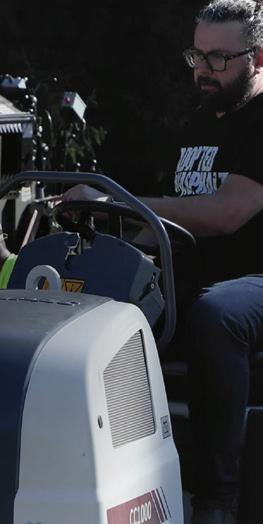

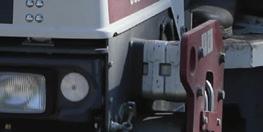
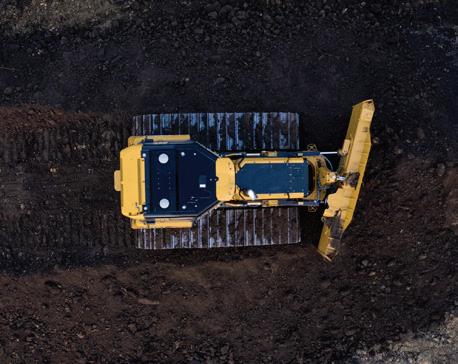
Cat, Trimble Extend Grade Control Collab Agreement
Trimble’s Scott Crozier talked to us about what this partnership means for heavy equipment grade control.

Economic Indicator Highest Since February 2023
The Services PMI, which includes the construction industry, registered 54.9 percent, which is the highest reading since February 2023 and indicates sector expansion for the 49th time in 52 months.

EXCLUSIVE: BOMAG’s Big Bet on New Tech and Customer Connection
The company cast its global vision of success centered on growing smart software, training, and an emphasis on listening to end users at 2025 Innovation Days.
Read more at:
https://asph. link/ftsn79g1
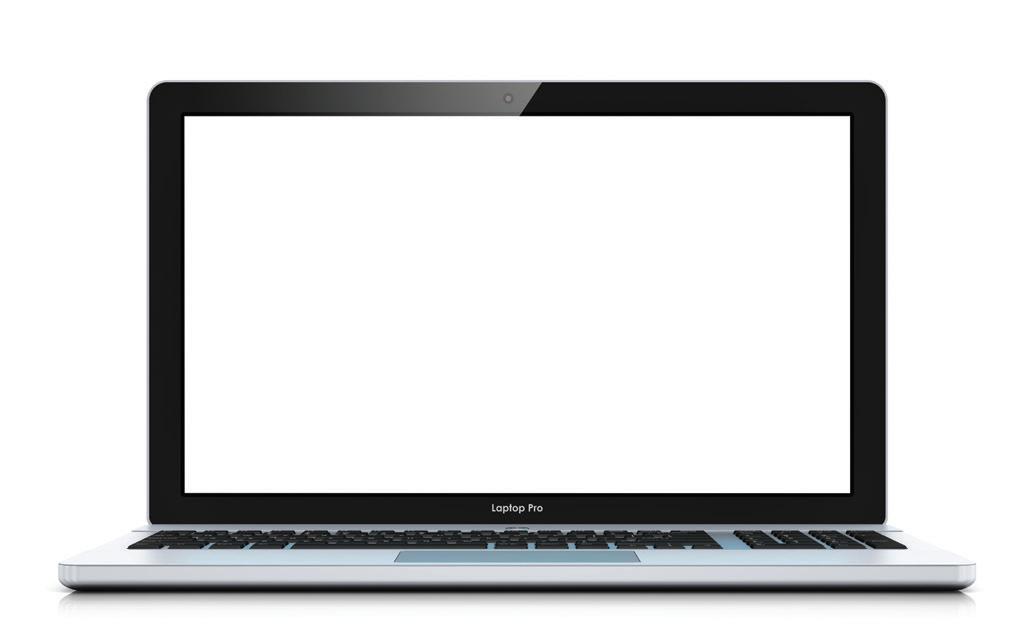
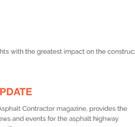
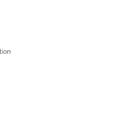
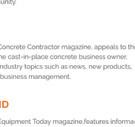


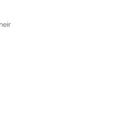
Read more at: https://asph. link/uvcl12gh
Read more at: https://asph.link/ lzsqn0a4
Signup for the Roadbuilding Update, a free bi-monthly newsletter for the most up-to-date DOT, FHWA, asphalt, and other industry news



















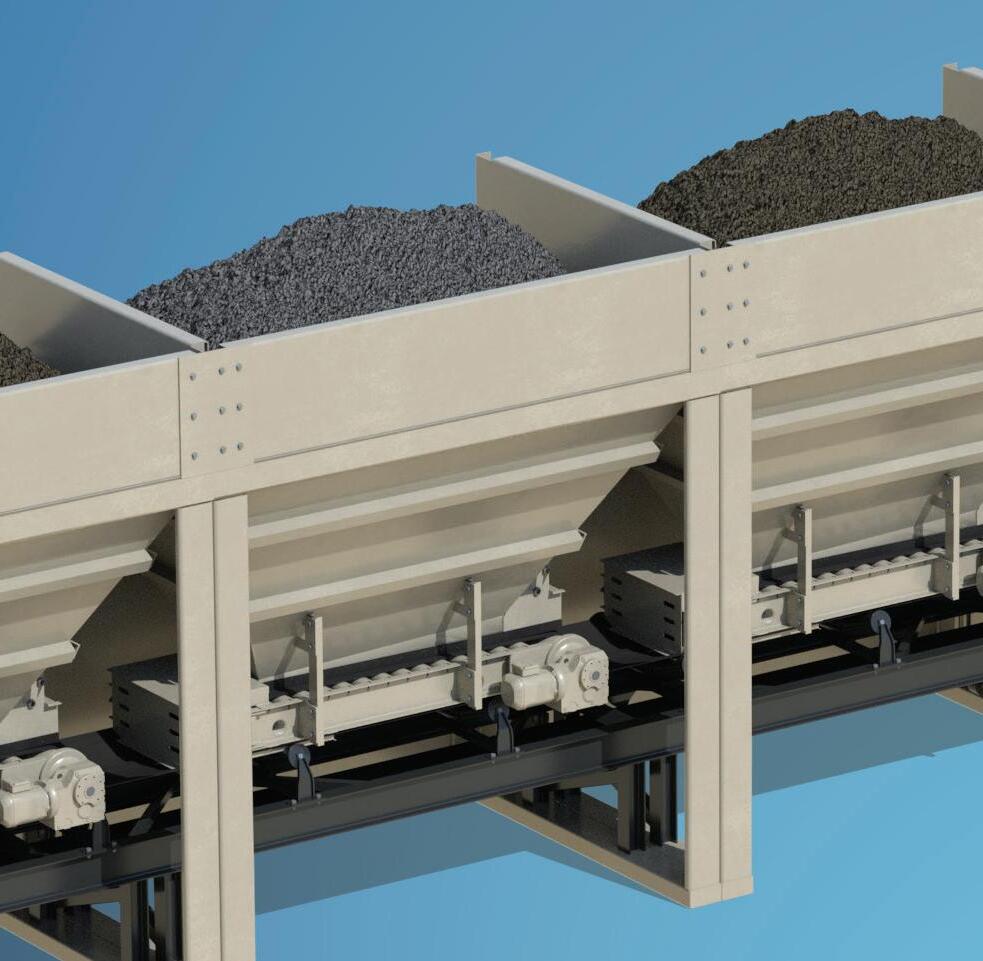

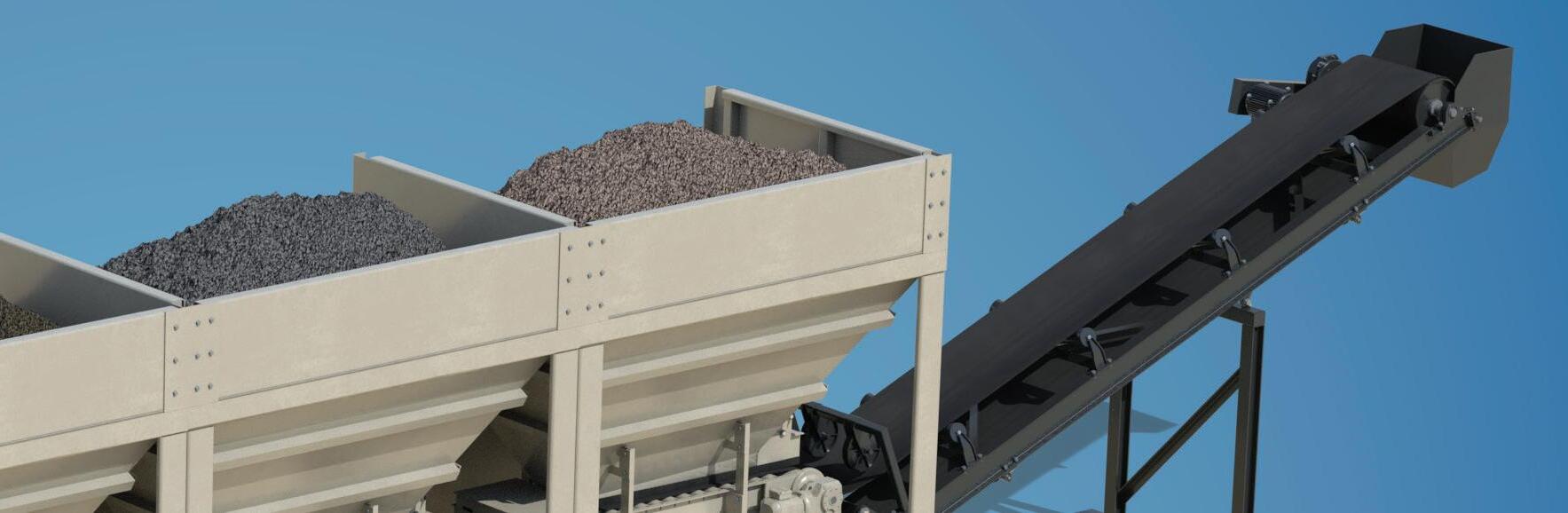
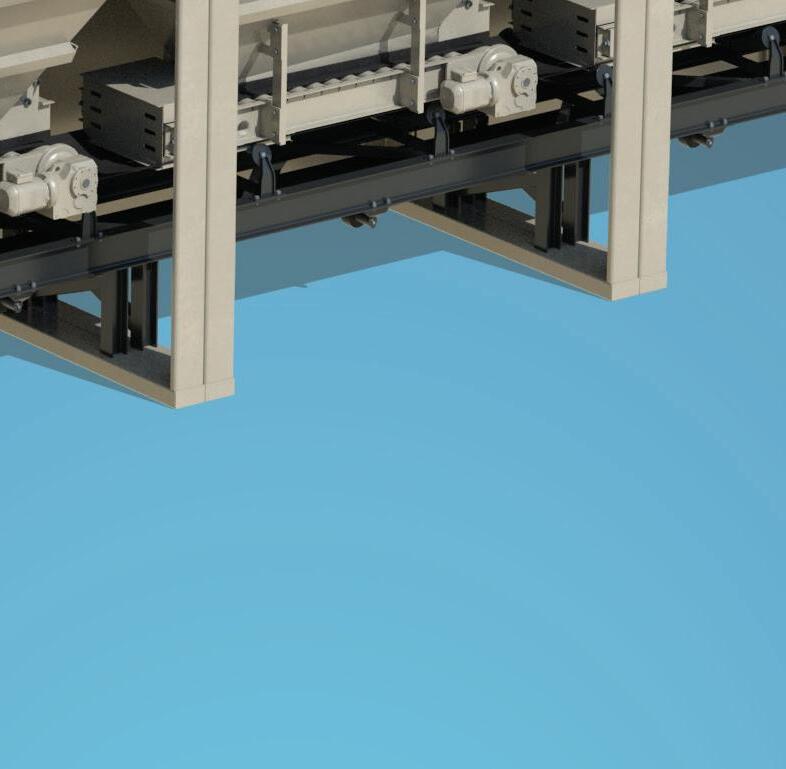
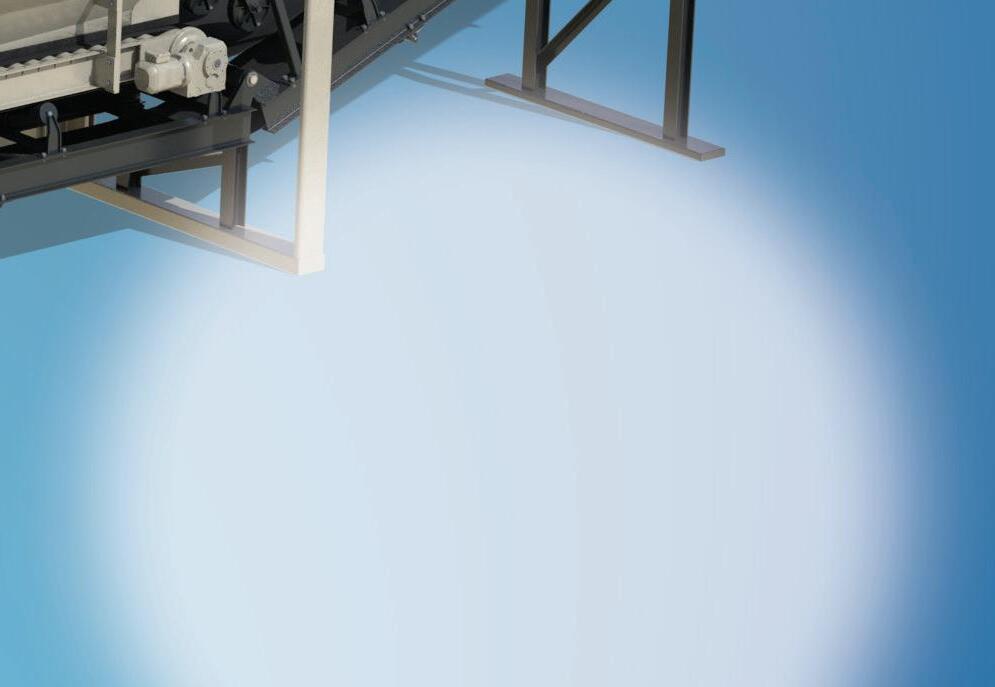
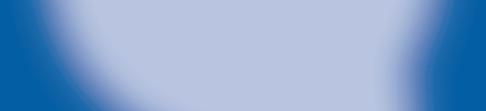

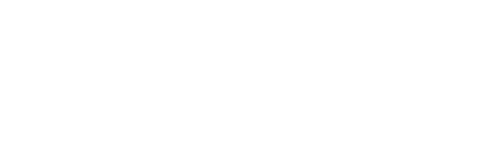
NEW IntelliPac ™ Moisture System
Astec paves the way for sustainable, innovative asphalt plants. The new IntelliPac Moisture System is a revolutionary solution that integrates seamlessly with Astec control systems. This provides unparalleled, real-time visibility into virgin aggregate moisture content. IntelliPac empowers operators to optimize mix design, minimize energy consumption, and reduce environmental impact. With Astec, you get superior asphalt production – better for the environment, better for your business.
BUILT TO CONNECT
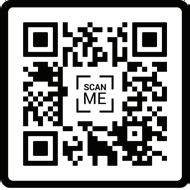
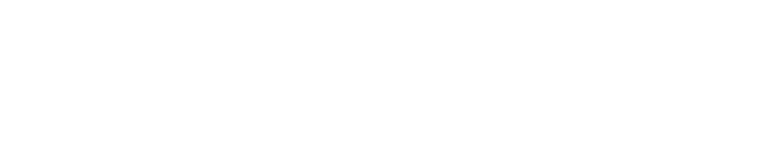
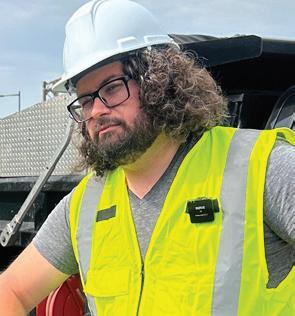
Brandon Noel, Editor
bNoel@iron.markets
234-600-8983
End Of An Era: The Sunsetting Of IIJA
Between it and the Inflation Reduction Act (IRA), nothing has done more for U.S. infrastructure spending in 80 years.
Since the 2021 signing of the Infrastructure Investment and Jobs Act (IIJA), more than 40,000 infrastructure projects have moved forward, and as we enter the second to last year of its funding, there’s still a lot more that will be added to its legacy. I joined the industry about seven months after it became law, and have only known a post IIJA world. I told my predecessor that this past week, and she told me, “You’re really lucky.”
While I acknowledge that, I want to draw attention to some of the important accomplishments that have accumulated in this short period of time, while, also, trying to parse what we might learn from this era and improve upon.
IIJA created 452 different funding buckets containing $850 billion, the source for those tens of thousands of projects completed or currently underway nationwide. Over half of the 5,532 competitive awards have been for less than $1 million, and another 29% fall between $1 - $10 million. It’s hard to overstate how revolutionary that is. It shows how these monies have actually made it down to the local and municipal levels of infrastructure. It has included bridge repairs, safe streets and neighborhood initiatives, and so much more, all the way up to lane expansions for congested highways in smaller market cities.
From 2011 - 2019 the highway, street, and bridge construction sector added, on average, 700 new jobs a month. Since January 2021,
that sector has ballooned to four times that, adding approximately 2,800 new jobs a month. This brought the overall industry workforce back up above the pre-Great Recession high.
Of course, it may not FEEL like the workforce has recovered because of all the issues with labor supply. Both things are true. There isn’t always a new body to fill that new job created.
Another area of concern, heading into the end of the bill’s life, is that inflation has taken its toll on the value of its original funding. What this means is that, while IIJA is undeniably historic and will likely be remembered as such in the future, the contemporary reality might feel slightly underwhelming as it winds down.
This is because, according to the Bureau of Labor Statistics, somewhere between 31% and 40% of the remaining funds could be absorbed by inflation. That is completely without equal precedent.
As the Biden administration comes to an end, it remains difficult to ascertain what the priority of further infrastructure spending will be, despite the glaring reality of its fragility.
As I write this column, my dad is fleeing the second major hurricane to pummel the southern United States inside a month. Hurricane Helene effectively cut off entire communities. It’s clear that the focal points of both the IIJA and IRA will remain in the coming years, regardless of their political popularity, if these types of occurrences become an annual event.
Our road builders, crews, pavers, and asphalt makers keep this country connected. I am hopeful that whatever is on the horizon will continue to bolster our industry’s strength and purpose. See you on the road!
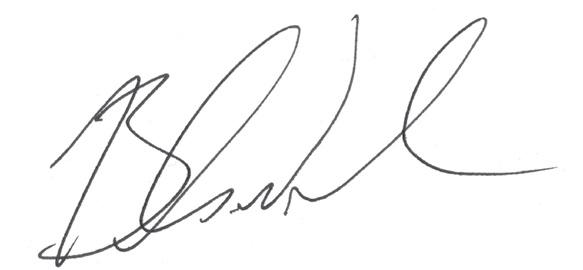
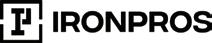

EDITORIAL
Editor Brandon Noel bnoel@iron.markets
Content Director, Marketing Services Jessica Lombardo jlombardo@iron.markets
Managing Editor Gigi Wood gwood@iron.markets
Junior Editor Merina Shriver mshriver@iron.markets
AUDIENCE
Audience Development Manager Angela Franks
PRODUCTION
Senior Production Manager Cindy Rusch crusch@iron.markets
Art Director April Van Etten
ADVERTISING/SALES
Brand Director Amy Schwandt aschwandt@iron.markets
Brand Manager ..................................................... Megan Perleberg mperleberg@iron.markets
Sales Representative ..................................................Sean Dunphy sdunphy@iron.markets
Sales Representative Kris Flitcroft kflitcroft@iron.markets
IRONMARKETS
Chief Executive Officer Ron Spink
Chief Revenue Officer ............................................ Amy Schwandt VP, Finance Greta Teter VP, Operations & IT Nick Raether VP, Demand Generation & Education ....................... Jim Bagan
Corporate Director of Sales Jason DeSarle Brand Director, Construction, OEM & IRONPROS .....................................................Sean Dunphy Content Director Marina Mayer Director, Online & Marketing Services Bethany Chambers Director, Event Content & Programming........ Jess Lombardo
CIRCULATION & SUBSCRIPTIONS
201 N. Main St. Ste. 350, Fort Atkinson, WI 53538 (877) 201-3915 | Fax: (847)-291-4816 circ.asphaltcontractor@omeda.com
LIST RENTAL
Sr. Account Manager Bart Piccirillo | Data Axle (518) 339 4511 | bart.piccirillo@infogroup.com
REPRINT SERVICES
Brand Manager Megan Perleberg mperleberg@iron.markets | (800) 538-5544
Published and copyrighted 2024 by IRONMARKETS. All rights reserved. No part of this publication may be reproduced or transmitted in any form or by any means, electronic or mechanical, including photocopy, recording, or any information storage or retrieval system, without written permission from the publisher.



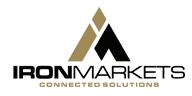
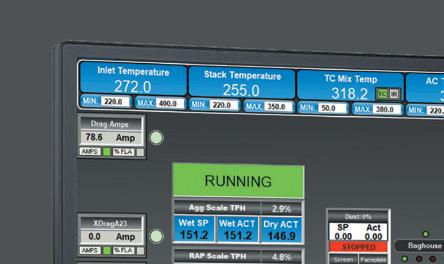


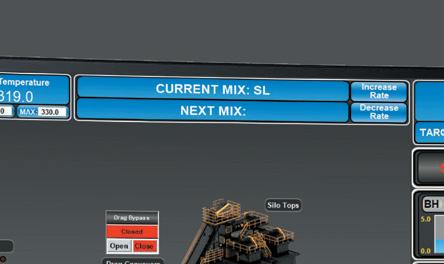
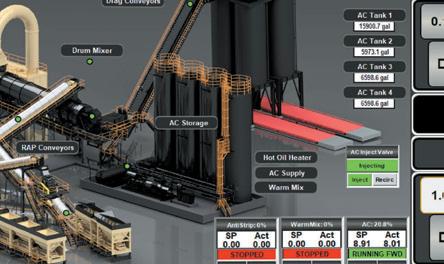
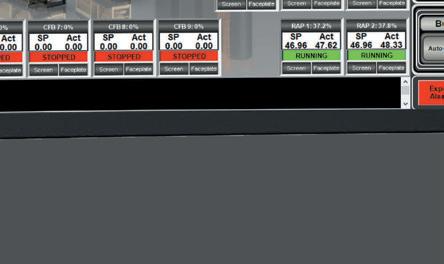

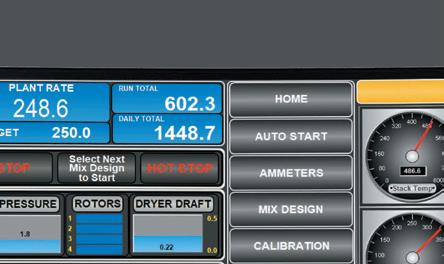


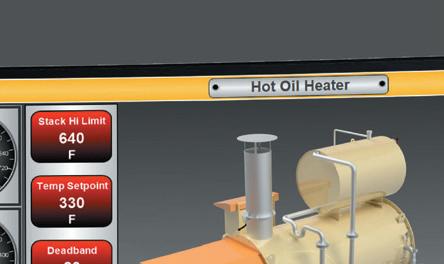
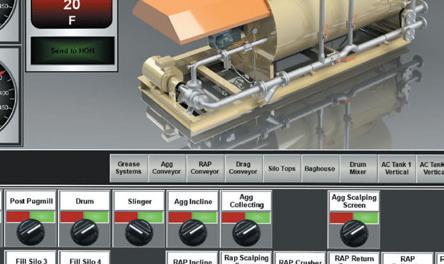


BUILT DIFFERENT BY DESIGN.
The future is connected. That’s why we’ve designed the ALmix Insignia Control System (ICS) around the power of high-speed Ethernet communication. An ethernetconnected facility means our team of programmers have complete visibility into your plant equipment and motor control center for diagnostics and remote troubleshooting. View and control data from your asphalt plants like never before. The Insignia Cloud Platform provides access while you are at the plant, in the office, or on the go. Critical, real-time, plant information is at your fingertips when you need it.
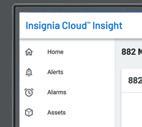
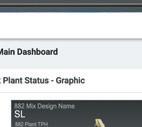

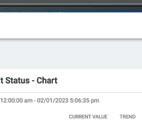
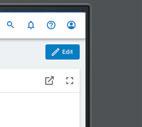

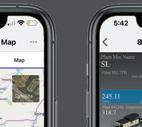
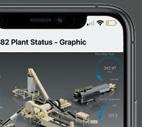
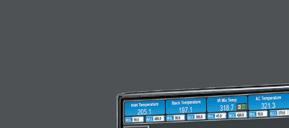

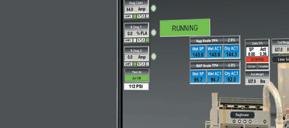

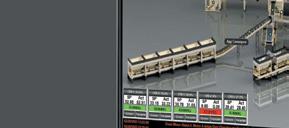
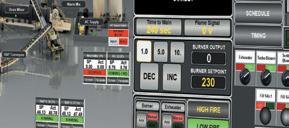
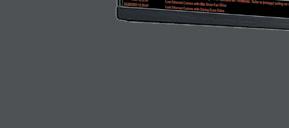
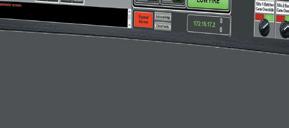
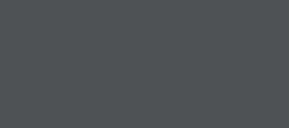

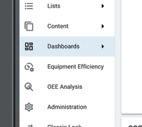
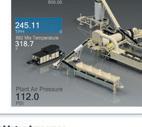
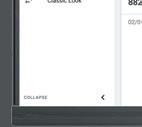
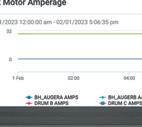

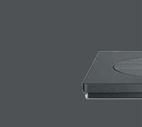
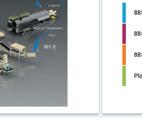

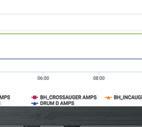
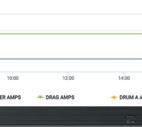
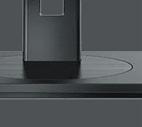
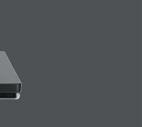
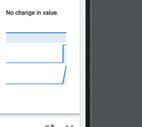
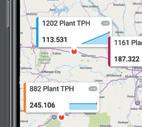
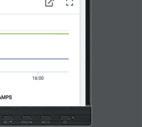
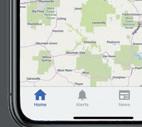

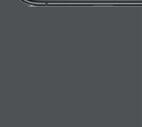
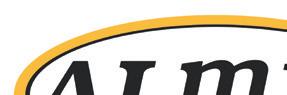

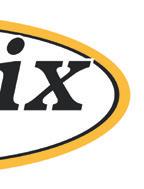
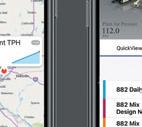

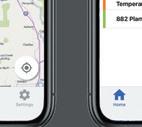
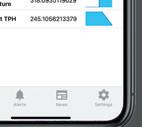
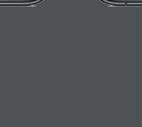
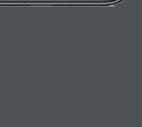
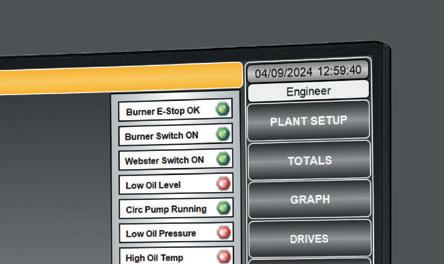

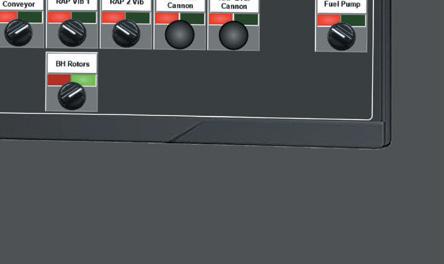
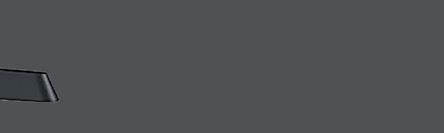
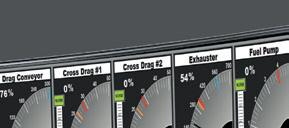




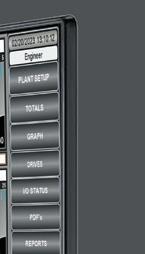
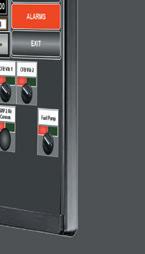
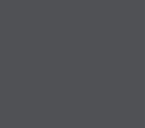
DON’T LET YOUR EXISTING ASPHALT PLANT CONTROLS KEEP YOU GUESSING:
The Insignia Control System is available on all new ALmix Asphalt Plants and is also available for existing plant

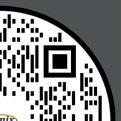

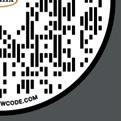
NEW PRODUCTS

Durex Livewire Screen Media
A hybrid-type screen, featuring molded rubber strips that hold high-strength wires in place. Providing better screening action than traditional woven wire and greater open area than polyurethane, this screen media is designed to boost production by reducing costly, time-consuming blinding, plugging and pegging problems – while also delivering good wear life. The Livewire line also features four different opening options: diamond-shaped, alternating “Z” and straight wire, herringbone, and straight wire slot openings for maximum output in a variety of dry or damp applications.
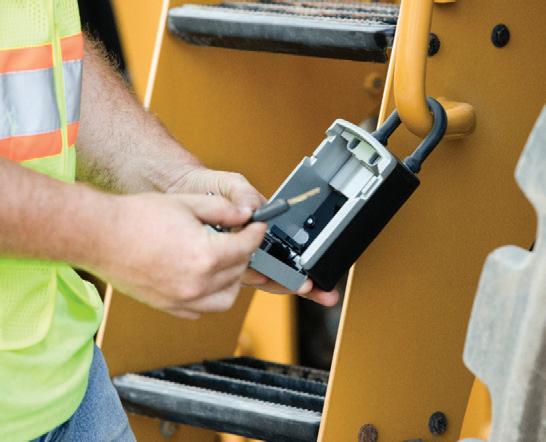
Master Lock Bluetooth Portable Lock Box
With digital access, the 5440EC minimizes the possibility of unauthorized key duplication and losing physical keys. This lock box works with the Master Lock Vault System compatible with both Master Lock Vault Home and Master Lock Vault Enterprise, allowing individuals to open and manage the lock using a phone. The portable lock box is powered by a CR123A battery. Low battery notifications and reminders are available on the lock box and app.
Caterpillar Mid-sized Asphalt Compactors
Caterpillar has announced updates to the mid-sized asphalt compactor line. The Cat CB7, CB8 and CB10 Asphalt compactors are equipped with edge-management options, optional cab, optional split drums and a new mapping display. Features include AM and FM Bluetooth radio and the heated seat combine with seating and legroom, wide sight lines and climate control functions that can help with performance on the jobsite. Proper management of unconfined edges can help optimize density. The vertical edge created by the cut-off wheel helps provide a stable vertical face for joint matching on the next paving pass.
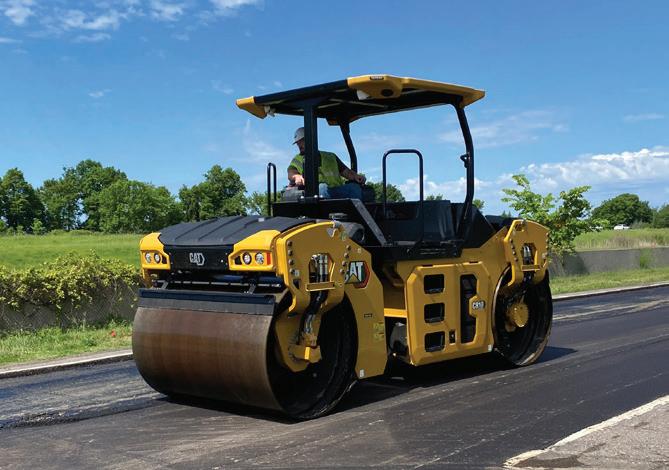
Men’s Enhanced Visibility Dura-Kap®
Industrial Pant
Eager Beaver Equipment Trailers
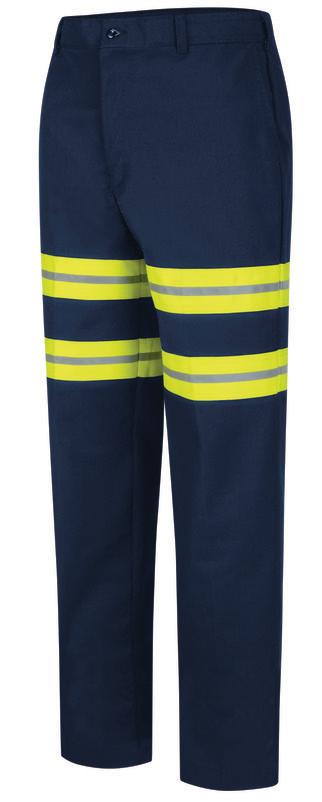
Help make your work environment safer with these durable work pants with enhanced visibility. Made of comfortable fabric in a true-to-size regular fit, the visibility trim above the knee helps draw attention in low light settings. The poly/cotton fabric is engineered to retain its color and release dirt and grease wash after wash, letting them appear bright and stain-free. Be seen and be safe in these attention-grabbing work pants.
Eager Beaver Trailers has released four new equipment trailers: 10SSA, 10SSE, 12SSA and 12SSE. Offering 10- to 12-ton capacity, models with electric or air brakes are available based on operating preferences. These trailers feature adjustable Hutch 9700 three-leaf suspension, as well as Sumitomo tires and hub piloted wheels for reliable transport. Stability is facilitated by double-acting springs and an accessible lightweight ramp for loading and unloading equipment. LED wiring harnesses are sealed for protection from rugged elements on the jobsite. The heavy-duty trailers have a 33-in. deck height, as well as a 19-ft. flat deck with a 6-in. beavertrail.
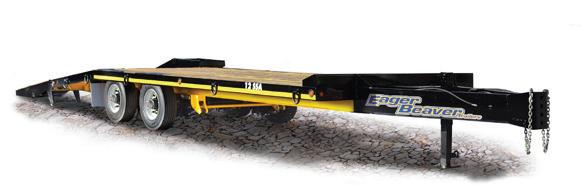
Orbit Screens Series 60 Model 68D Screening Plant
Orbit Screens offers the Series 60, Model 68D for screening materials on construction sites. The Model 68D is powered by a 25-hp diesel engine and comes equipped with a 2-yd. hopper. Built for durability, it handles a variety of materials from topsoil and compost to gravel and rock. Accessible discharge heights include 11 ft. (fines) and 6 ft., 6 in. (overs) depending on the conveyor. When purchasing this model, customers can add an end gate cut off for the hopper, a hopper extension to 4.5 yd. and brush package. It delivers separation of materials for clean output.
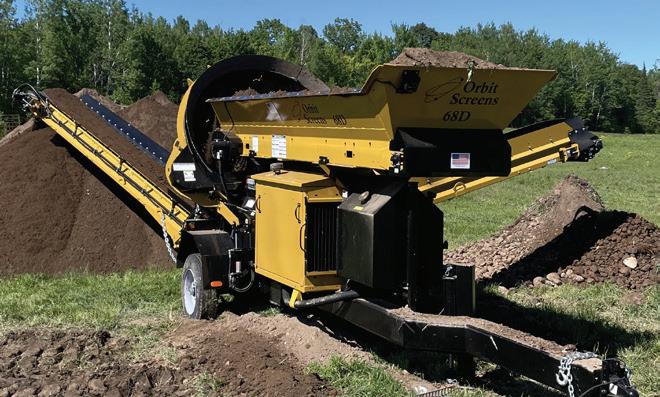

2025 GENCOR TRAINING SCHOOL

2025 DATES
• Week 1: January 20 - 23
• Week 2: January 27 - 30
• Week 3: February 3 - 6
• Week 4: February 10 - 13
REGISTRATION
CLASS SIZE IS LIMITED !
To secure your seat, please register before December 15, 2024
DETAILS
Details can be found at www.gencor.com/training or call us at 407-290-6000 ext. 342.
Improving overall plant production and efficiency are all common concerns for plant owners and operators. Having a well-trained technical crew is vital to maintaining plant performance and efficiency.
Gencor and its training staff represent the biggest concentration of knowledge and expertise in all the sciences and technologies involved in the production of asphalt plants. Customers who attend these seminars benefit by having the support and focused attention of the best specialists in the asphalt industry.
Using Gencor’s state-of-the-art control simulators and actual equipment, our experts take you stepby-step through a comprehensive & intensive concentrated hands-on training program providing the latest techniques on optimizing production efficiency.
NEW PRODUCTS
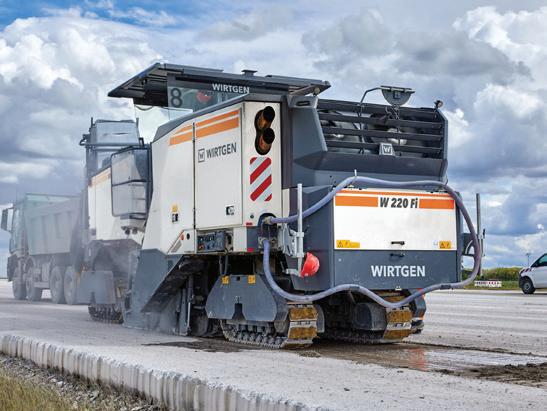
Wirtgen GENERATION C² Round-shank Picks
Developed for milling concrete, they are characterized by high resistance to fracturing, low wear and long service life. Amongst other things, the solid steel body geometry supports removal of material. Pick centering allows milling forces to be concentrated in the top part of the holder and relieves the burden on the clamping sleeve. The shank geometry also increases fracture resistance. In addition to this, the centering function of the grooved profile of the wear plate reduces wear and increases the service life of the round-shank picks and the toolholders.
Volvo CE SD125 Soil Compactor
The 12-ton machine becomes the largest model in the Volvo soil compaction portfolio with an 84-in. smooth-drum and operating weight of 26,565 lbs. (12,050 kg). The SD125 features a powerful Tier 4F 4-cyl. Volvo engine with 147.5 hp (110 kW). Active DPF regeneration eliminates material build-up, reducing emissions. Its specs are similar to the existing SD115 but with a 0.2-in. (5 mm) thicker drum shell and a heavier outer eccentric weight. This results in an additional 935 lbs. (424 kg) of mass on the drum, increasing the static load and eccentric force for a different amplitude profile.
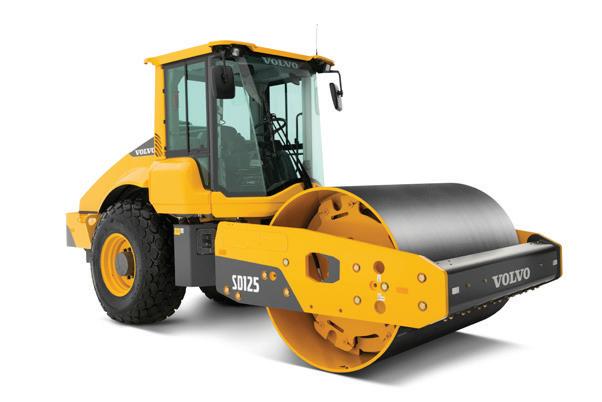
XL Specialized Trailers XL 100 HDG Bus Hauler

The trailer is rated to haul 100,000 lbs. in 10 ft. and designed for moving buses and other recovery loads. The latest lowboy trailer from XL features their classic hydraulic detachable gooseneck, allowing for loading onto the front of the trailer. This lowboy’s main deck is 23.5 in. long. The 22-in. loaded deck height and 6-in. ground clearance transitions with a low incline to the rear deck. The 102-in. wide hauling area has outriggers that swing out to handle wider loads. The rear deck height is 31 in. with 24-in. recessed bolsters and 24.5-in. tires. The 60-in. rear platform in the back of the trailer, in combination with the two 20,000-lb. winches.
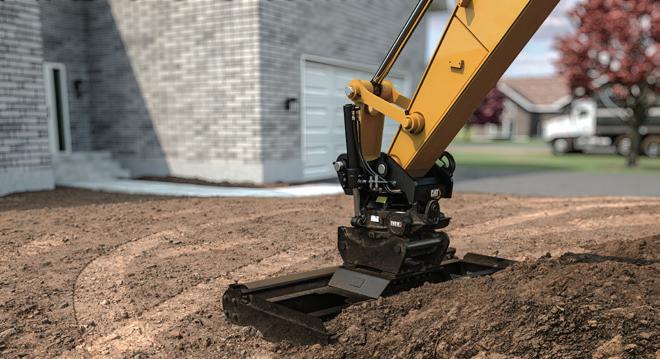
Caterpillar Grading Beams for Cat Tiltrotators
Pairing with Cat Tiltrotators enables 360-degree bidirectional and 40-degree left-and-right rotation of the grading beam for attachment versatility. The grading beams’ mechanically adjustable roller, from 10 mm (0.40 in.) below frame to 20 mm (0.79 in.) above, tailors the desired level of compaction based on material type. Preventing material from sticking to the roller, the adjustable roller scraper allows the attachment to be used with clay, silt and other sticky materials. They tackle a range of applications from grading sidewalks to large site prep applications. The design’s large top opening with solid extended sides and side plates allows the beam to spread, compact and grade materials. Abrasion resistant for long-life operation.

Haver and Boecker Niagara Vibrating Screen Exciters
XL-Class. The company engineers Niagara Exciters to set the required stroke, frequency and exact static moment for each application for screening performance. Customers can choose from a selection of sizes to meet their operating requirements. Options include the following models: HB 25, HB 55, HB 85, HB 115 and HB 150.
Trimble Vehicle Inspection Solution for Fleets
Available through Trimble Instinct, Trimble Inspections adds a modernized truck and trailer inspection application to Instinct’s driver experience. This new inspection application allows drivers to inspect both tractor and trailer simultaneously within the same workflow. It also supports safe fleet performance and fleet maintenance efforts with the ability to connect its inspection workflow with maintenance solutions, like Trimble’s TMT and Penske’s maintenance portal.
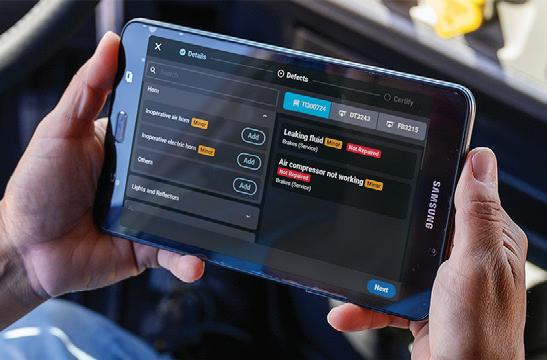
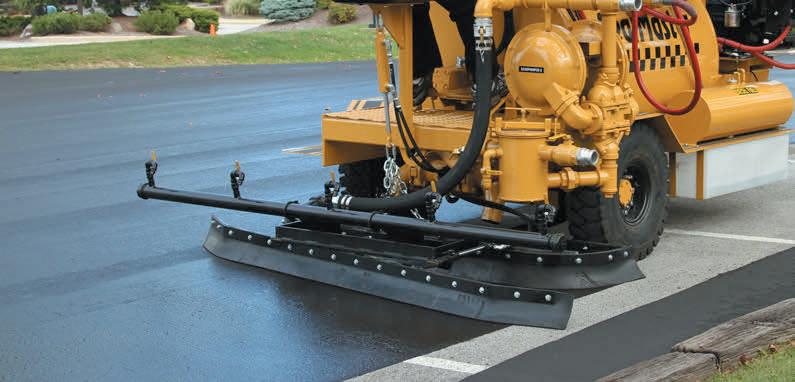
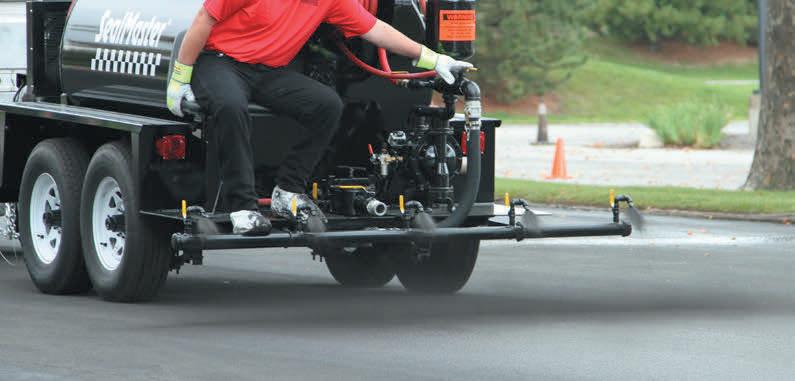

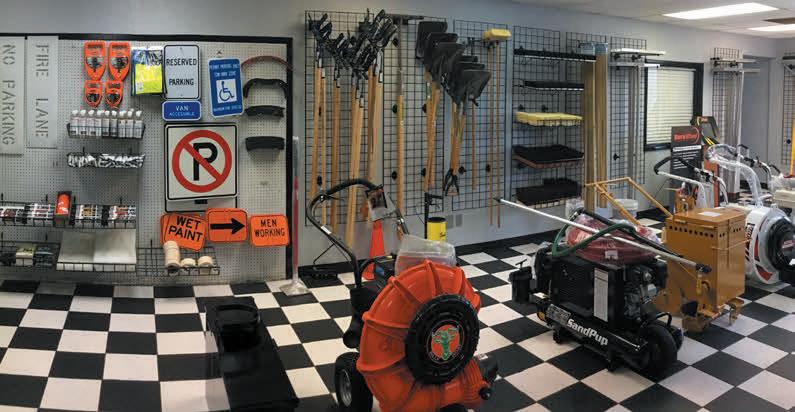

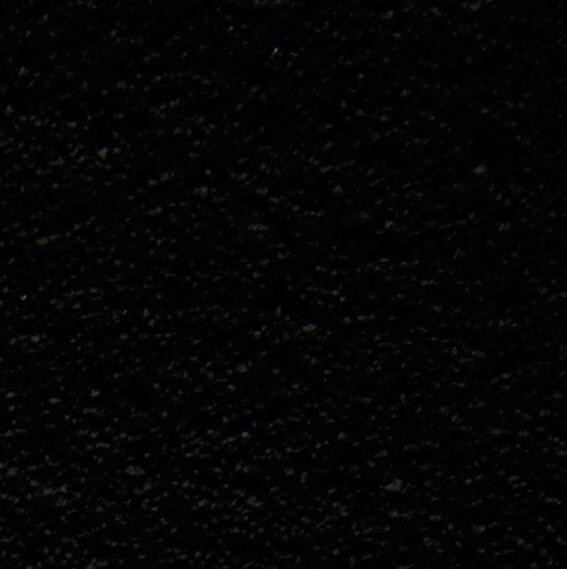
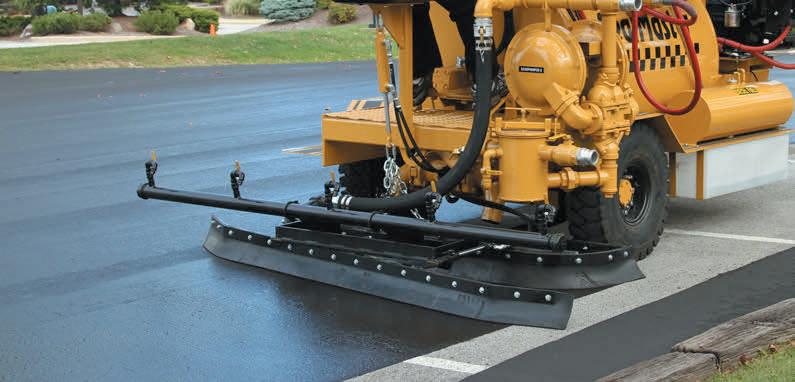
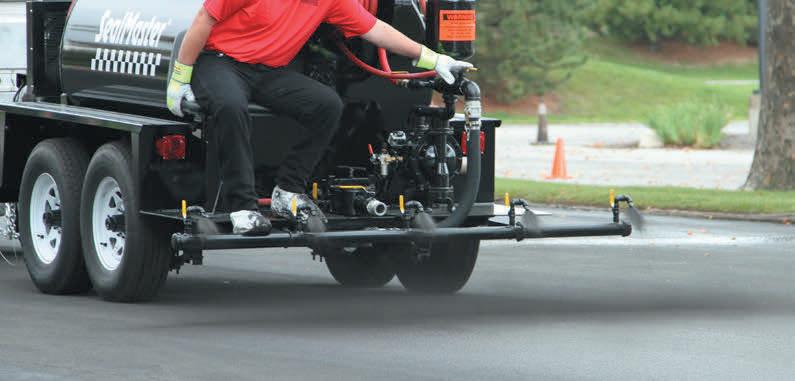
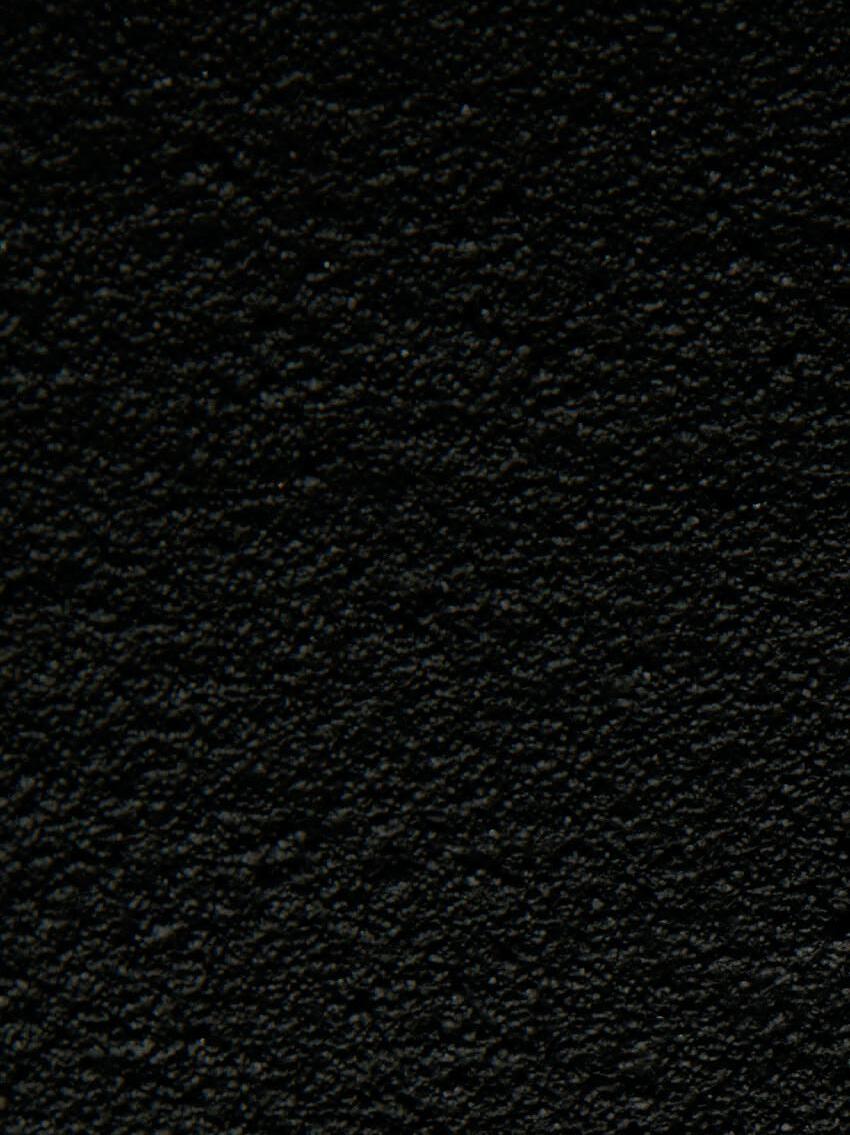
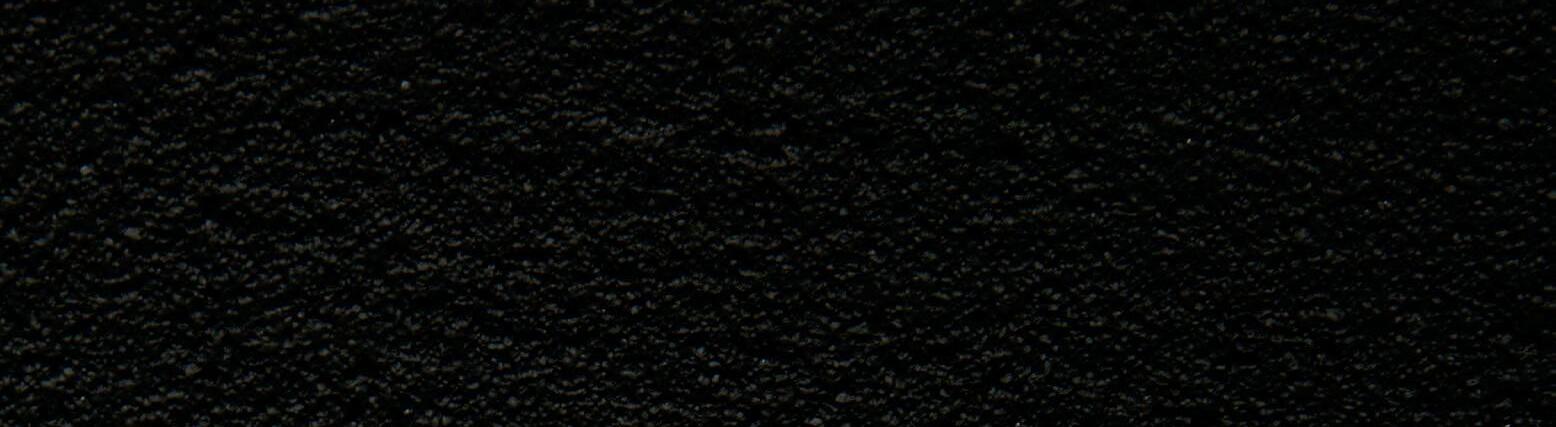

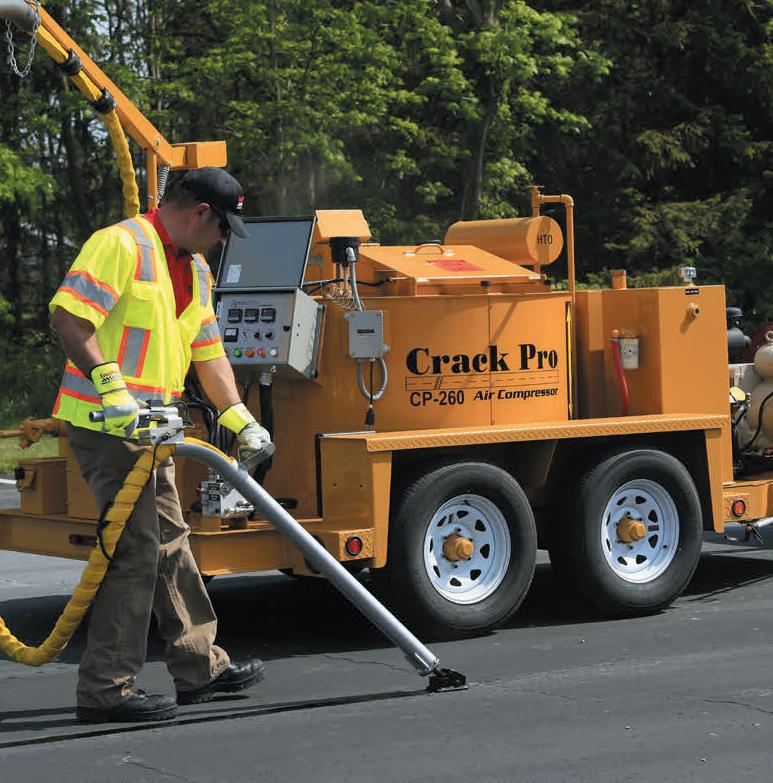
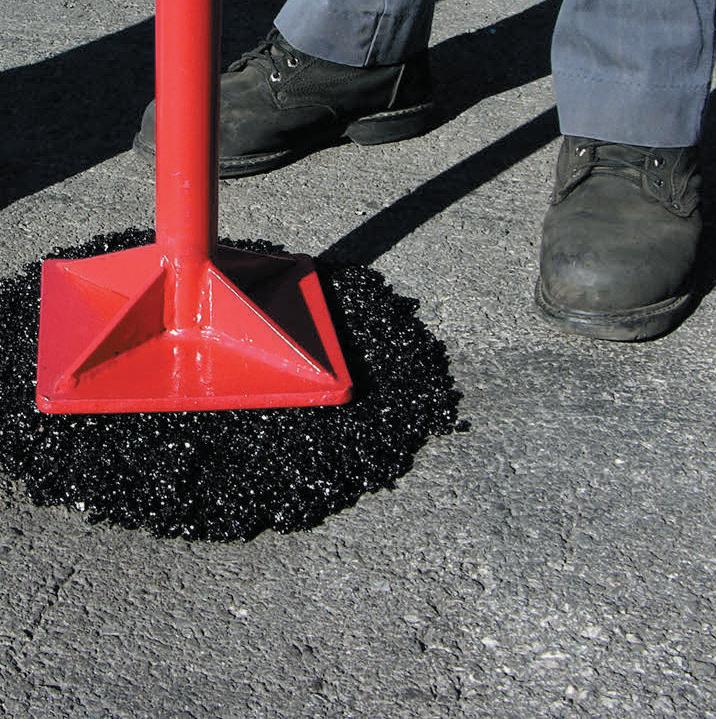

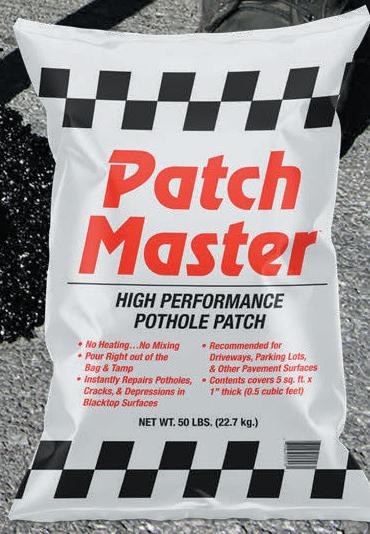
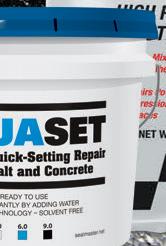

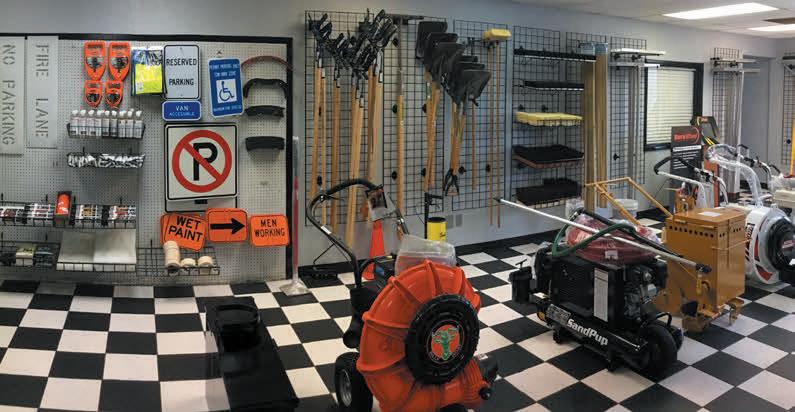
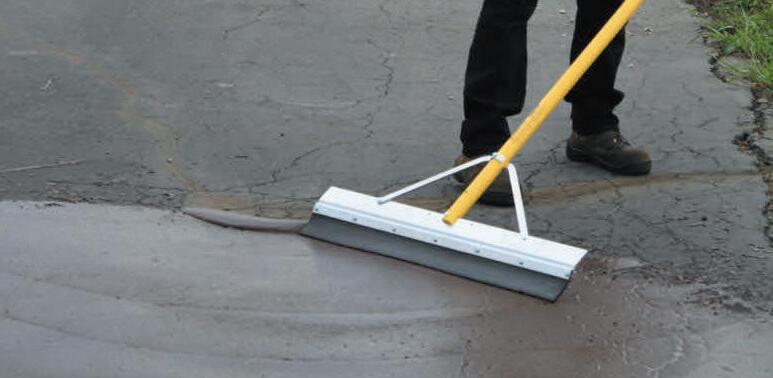
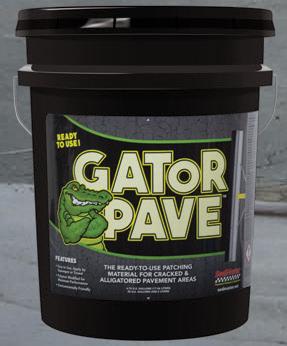
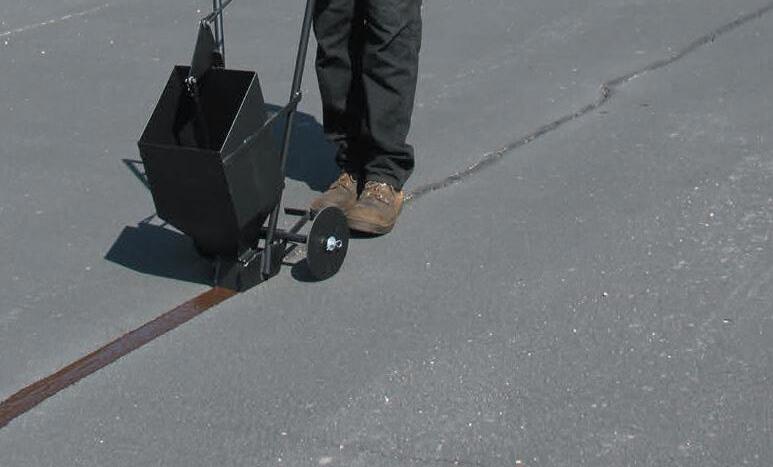
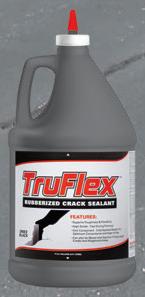
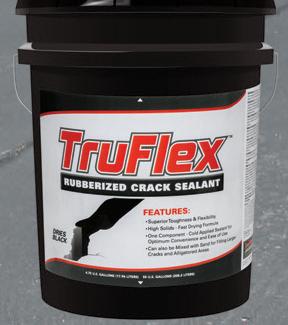
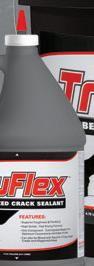
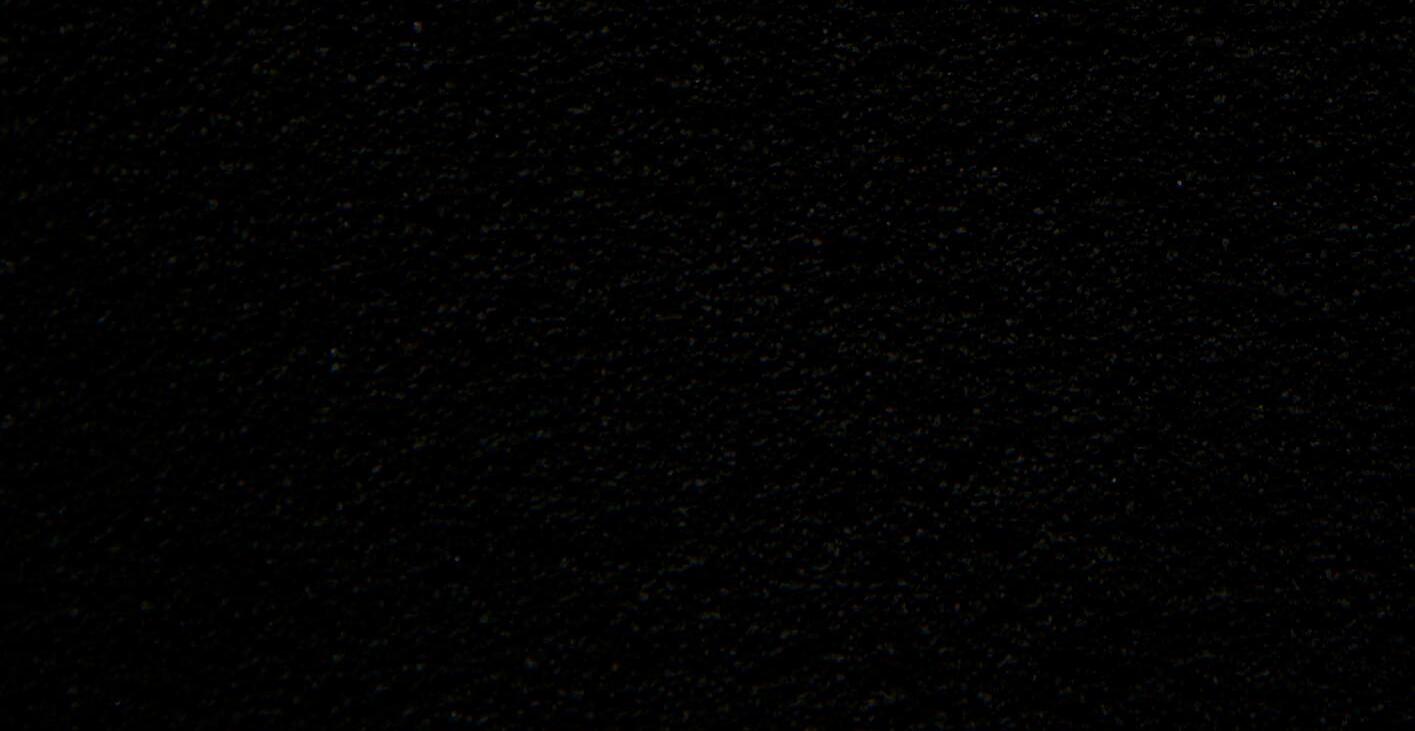
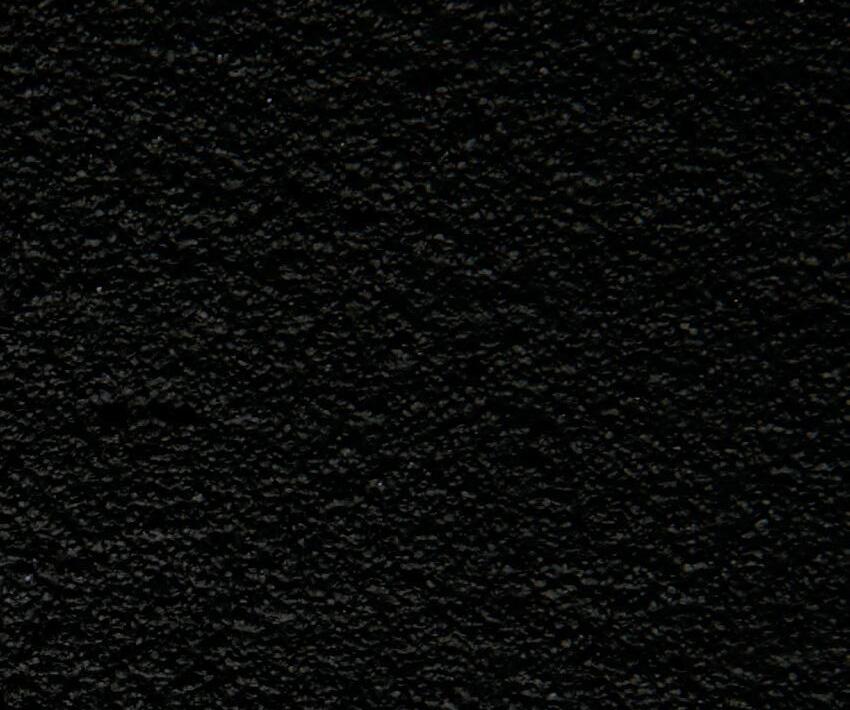

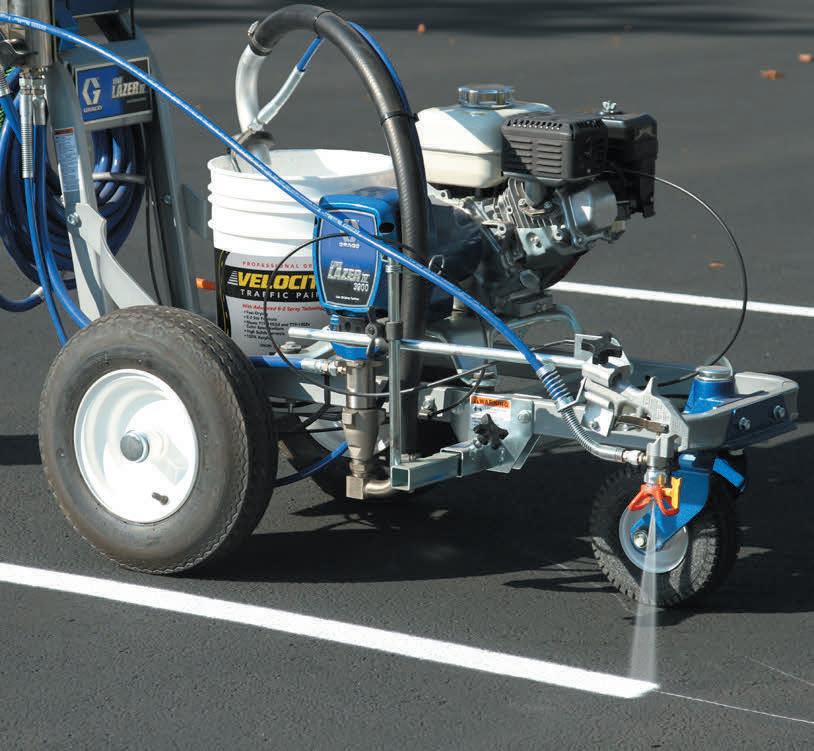




Why Reality Capture is the Lynchpin for the Jobsite of
TOMORROW
Construction executives have long debated the jobsite of the future built on autonomy and the increased use of technology, and with every day that passes, it’s becoming more than a theoretical concept: it’s now a business necessity.
Industries like manufacturing and mining have already automated significant portions of their operations, particularly for repetitive tasks. However, the concrete construction sector has lagged for several reasons, including construction sites’ unique and constantly changing working conditions.
How technology is transforming the worksite is a popular topic of discussion. There is widespread agreement that technology enhances productivity by saving time, materials, and resources.
Reality capture, creating detailed digital twins of physical assets, is the
@Freedy - stock.adobe.com
lynchpin of the concrete jobsite of the future. It empowers teams to quickly capture and analyze spatial data and provides a deeper understanding of site limitations and obstacles.
To address the persistent labor shortage, attracting younger workers and providing training opportunities for current employees is necessary. Incorporating digital technology into a concrete project will not only extend the lifespan of the asset; it will also align with the trend toward technology-focused job sites. Using reality capture technologies for BIM modeling, verification, and
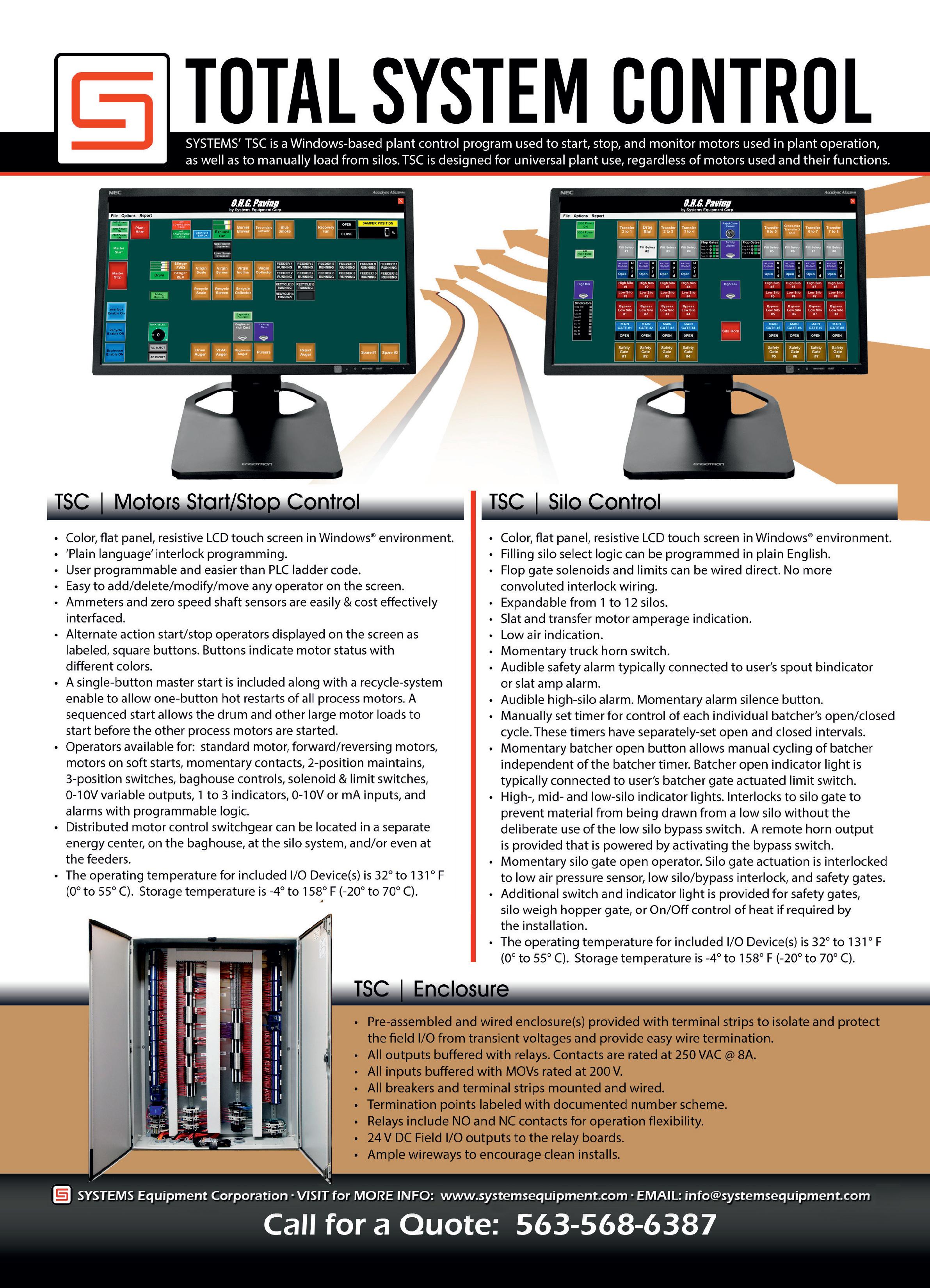
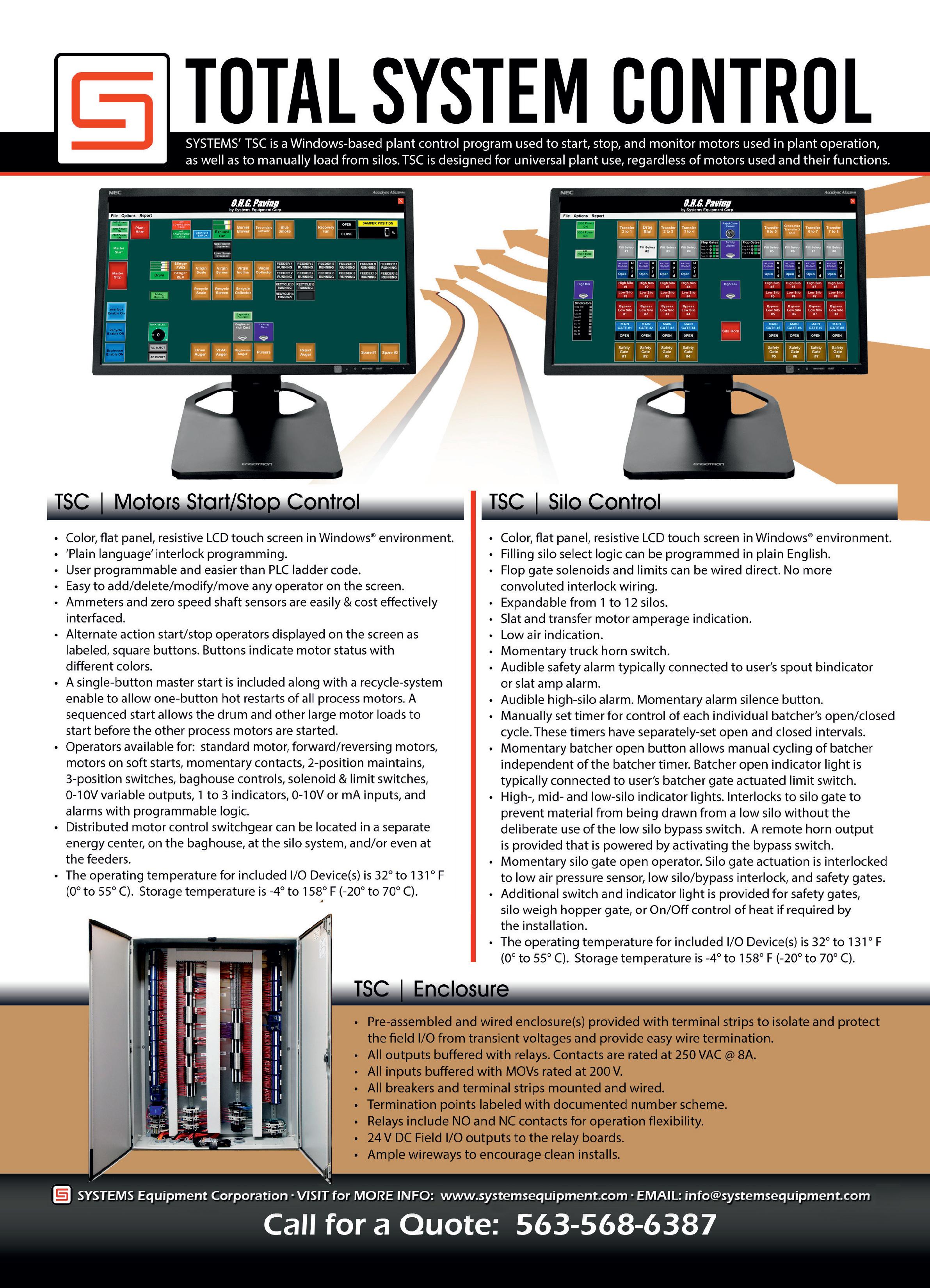
as-built documentation is a benchmark for predictive maintenance.
JOBSITES REQUIRE FOUNDATION OF DATA
Success on the modern jobsite requires intelligence, which relies on constant data collection by workers at every project phase.
Reality capture solutions like laser scanning, mobile mapping, and UAV systems can help a single team member collect site data quickly while minimizing the risk to safety. It also enhances efficiency by organizing the workforce and valuable resources, boosting companies’ profits.
While most business owners prioritize the deployment of technology for its potential to boost productivity and efficiency, it is equally important that these operations contribute to a safer jobsite. Construction executives must ensure that every solution they deploy helps eliminate jobsite mishaps and prioritizes the long-term safety of projects and the teams that make them a reality.
Implementing new technologies may require reconfiguring the value chain, resources, and talent needed for execution. However, with autonomous machinery powered with detailed jobsite data, crews can complete more complex work when they operate.

DECREASING HUMAN ERROR
Many concrete construction workers believe technology can help combat the increasing costs of materials, inflation, and the shortage of skilled laborers.
One of the most significant benefits of automation is its ability to greatly reduce the likelihood of human error, which can lead to unforeseen expenses. A smart digital reality helps reduce mistakes and eliminate the unnecessary use of resources.
For example, automation can streamline the collection and reporting of survey data. Inspections are critical to ensure quality and adherence to contracts. Utilizing digital as-builts during these inspections can improve safety and quality and save time and money.
ELIMINATE THE SILOS
Silos are often created unintentionally through manual processes, and they often limit progress and achievement. Integrating information seamlessly into a system can help eliminate silos and reduce the potential for human error.
For example, a layout specialist working in the field needs access to the design model, and simultaneously the model manager needs data from the field to ensure the model is always updated. But to enable faster and more autonomous field operations, reality capture technology is needed to identify and correct deviations in real time before the concrete is poured or hardens.
A fully autonomous jobsite requires deploying popular and evolving tools that also increase project safety. Teams can use GPS rovers, robotic total stations, concrete detection solutions and laser scanners to capture data, complete calculations, document progress, and confirm quality control.
Reality capture tools allow teams to improve how they track progress, manage schedules and stay on budget while improving the quality of their projects. Autonomy on the jobsite provides peace of mind for everyone, whether in the back-office worker or on the front lines.
By reducing the likelihood of human errors, autonomy enables seamless interaction and ensures that the work teams execute on the jobsite aligns with the project’s plans.
Even before the pandemic, many contractors increased technology adoption and deployment. The use of technology significantly impacts every aspect of the concrete jobsite and leads to critical benefits throughout a project.
Construction project managers should prioritize integrating reality capture technology from the beginning of any construction or renovation project. By addressing potential issues in advance, construction and engineering experts can greatly enhance project efficiency and ensure the completion of projects through streamlined workflows, reduced rework, minimized delays, and reduced site visits.
In the construction industry, executives prioritize the practical uses of new technology. They need to protect their resources and ensure that their investments yield returns. However, it is not wise for any industry or business to adopt technology simply because it is available. Teams should use technology intelligently to simplify and secure jobs and ensure they are completed on budget and according to plan.
Real-time data capture affects every stage of the construction process, including estimating and bidding, construction, project completion, and verification. Smart digital realities can greatly benefit the industry by providing an accurate digital twin of reality, constantly updated with real-time physical and digital data. This access to valuable insight can save time, reduce waste, and improve safety by eliminating human error.
If technology can keep up with modern industry’s ever-changing needs while promoting sustainability, the potential benefits are limitless.
Ted Moberg is the reality capture specialist for building and construction for Leica Geosystems..
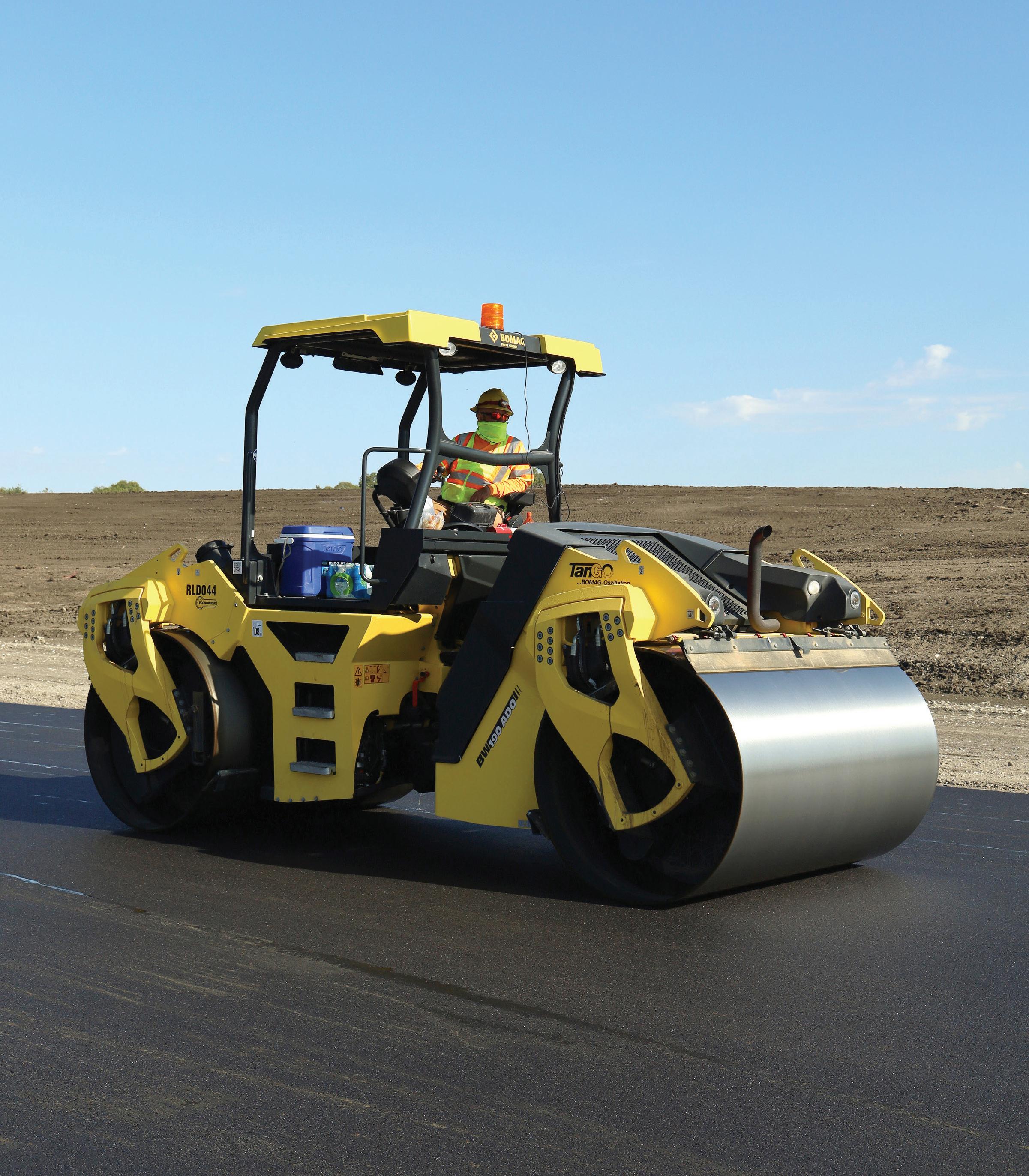
M ANAGER ASPHALT 2
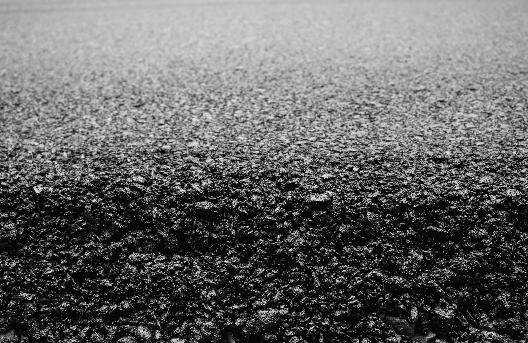
3 Amplitude Options at the Touch of a Button
• ASPHALT MANAGER 2 cuts down on passes and avoids over compaction.

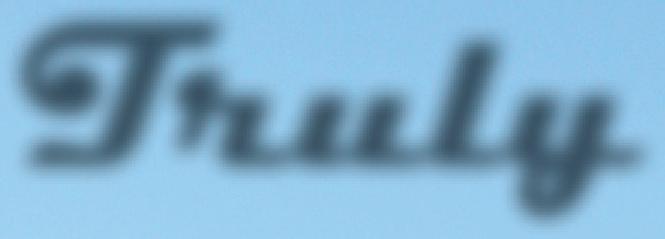
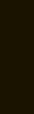
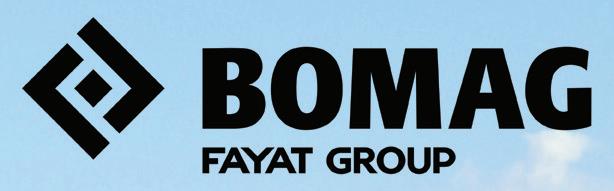

• Delivers professional level compaction results even when a novice is operating the roller.
• No manual drum adjustments required.

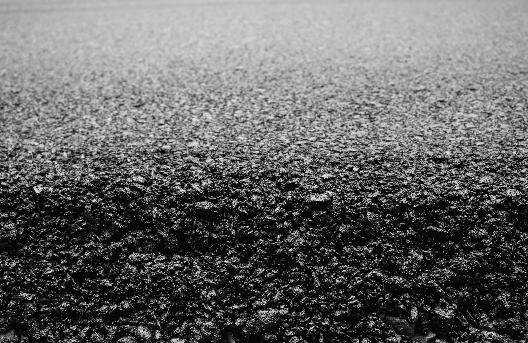
TanGO Takes the Risk out of Compacting near
Buildings
• Tangential Oscillation (TanGO) is simple to operate and safe to run on bridges and near buildings.
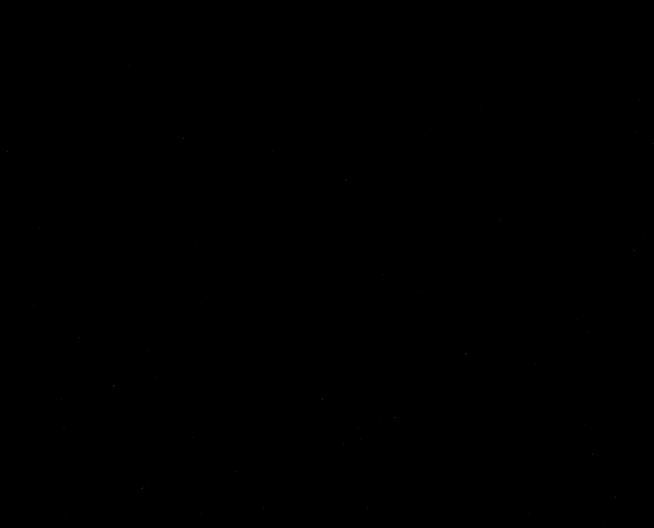
• The TanGO technology creates a smooth mat finish even at higher working speeds.
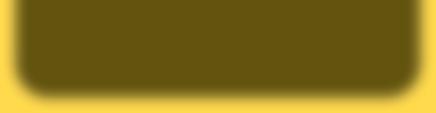
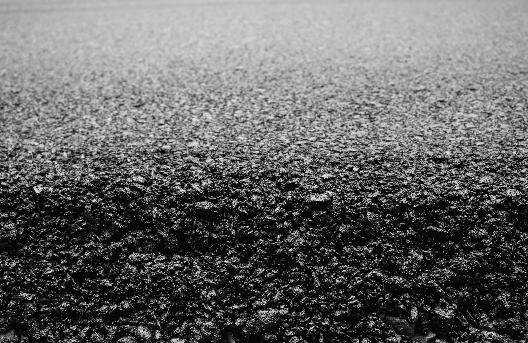

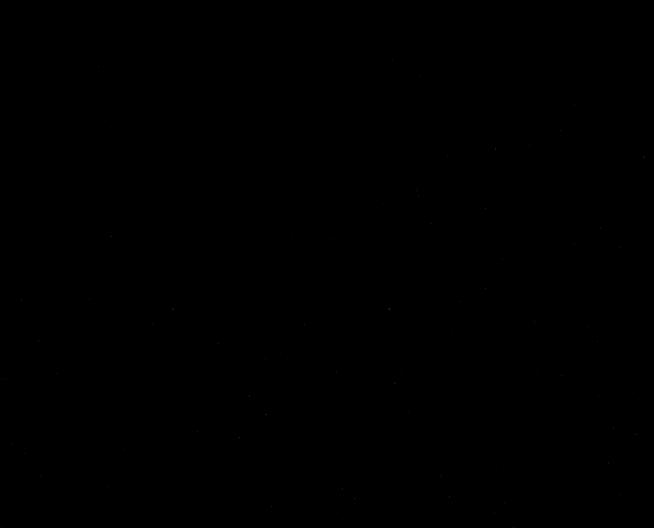
Reduce Passes by up to 40% without losing Mat Quality
• Pair BOMAG BOMAP technology with ASPHALT MANAGER 2 and reduce your number of passes by up to 40% without compromising mat quality.
• Track and document compaction results in real time with the BOMAP App.
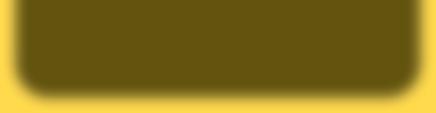
For Truly Intelligent Compaction look to BOMAG Heavy Tandem Rollers and BOMAG advanced compaction technologies like ASPHALT MANAGER 2, TanGO and BOMAP. BOMAG technologies not only improve finish quality but also reduce the number of passes needed and increase your compaction efficiency across the board. Even a novice operator can get professional level results with BOMAG! Contact your local BOMAG Dealer today to learn more. www.bomag.com
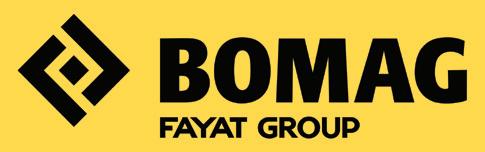
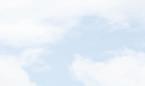
The quality of the aggregates depends on the processing, so original equipment manufacturers have developed crushers in various sizes and capacities.
RDO Equipment
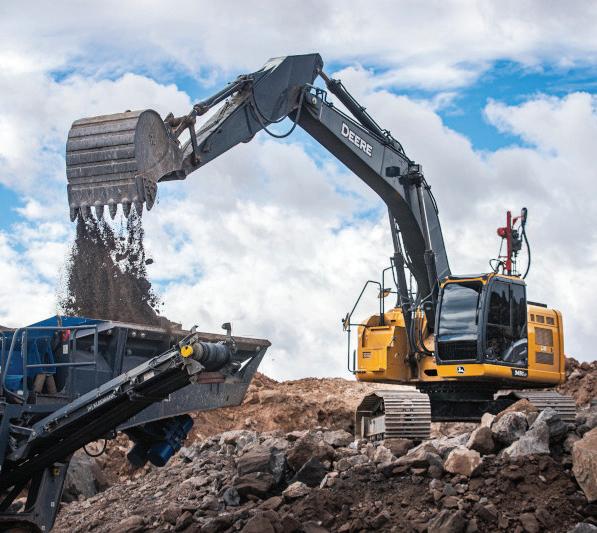
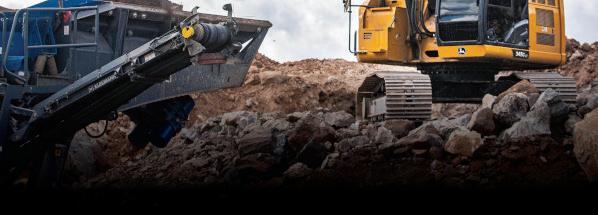
ROADBUILDERS’ GUIDE TO CRUSHERS: Increasing Access to Recycled Materials
Crushers will only become more popular in the next five years as sustainable building becomes more emphasized across the U.S.
I’ve spent lots of time in Utah this year, and among the many takeaways is the steadily increasing value of crushers to a roadbuilder’s fleet. What does Utah have to do with crushers? Historically, Utah’s aggregate market has been robust due to the state’s growing construction and infrastructure development. The
demand for aggregates, including sand, gravel, and crushed stone, has witnessed steady growth in recent years due to population growth, housing projects and infrastructure investments due to an increase in government spending.
In fact, the U.S. Department of Transportation’s Federal Highway Administration (FHWA) announced


Boost Your Silo Performance

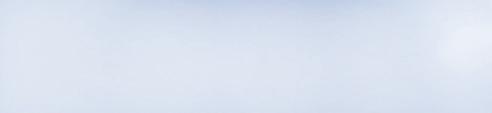

MEEKER SILOS & DRAG SLAT CONVEYORS



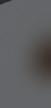

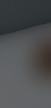




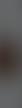



Silo cone opening is 36” wide for ef cient material ow.
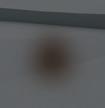




Safety gates on all silos, including long-term and standard options.
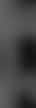
Recessed tub liners prevent silo wall wear, avoiding bulging issues.


Silo bin top batchers feature secure long-term seals.



Recessed wireways on silo tops eliminate trip hazards.
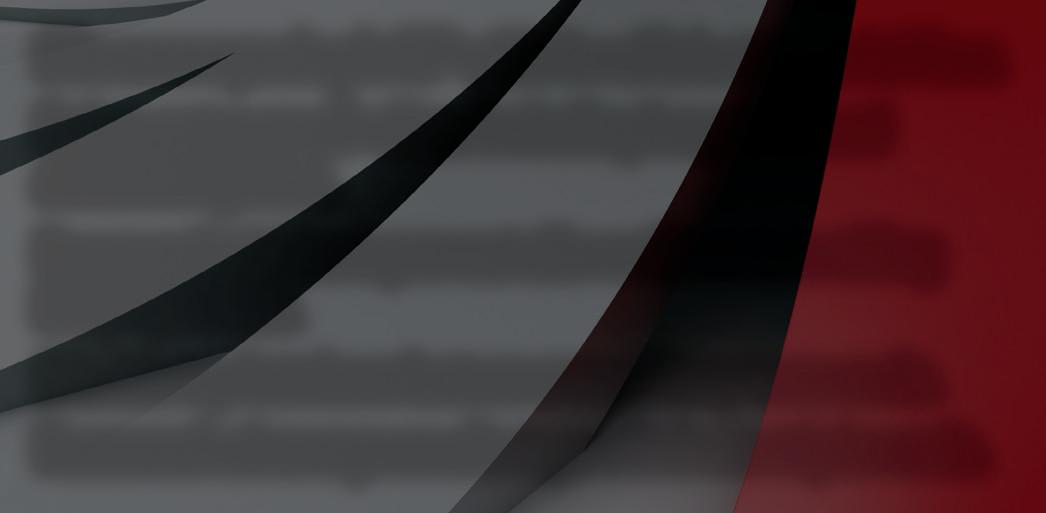


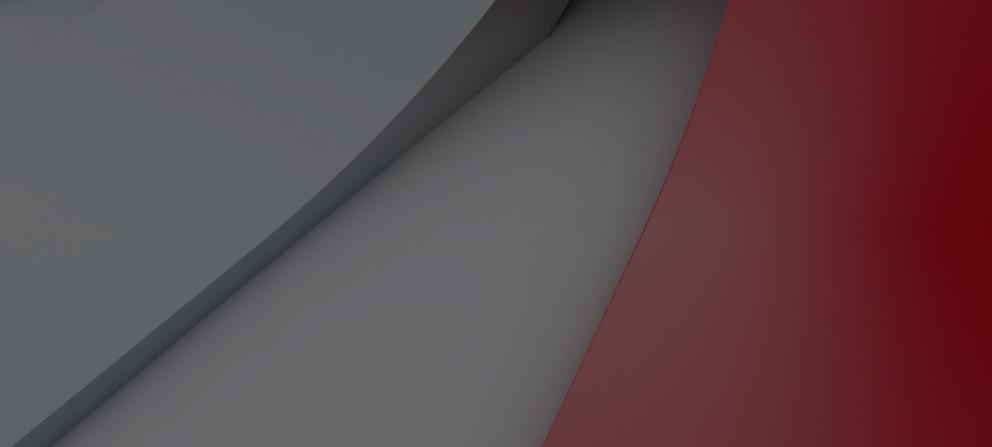
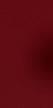

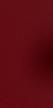



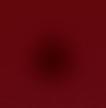
Meeker drag conveyors are larger, allowing slower chain speed and reduced wear.
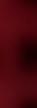
Hydraulic chain adjustment on slats maintains asphalt entry point, minimizing wear.

Visual chain tension indicators on Meeker slat conveyors aid operators.

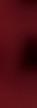
All silos prewired with top and bottom junction boxes.
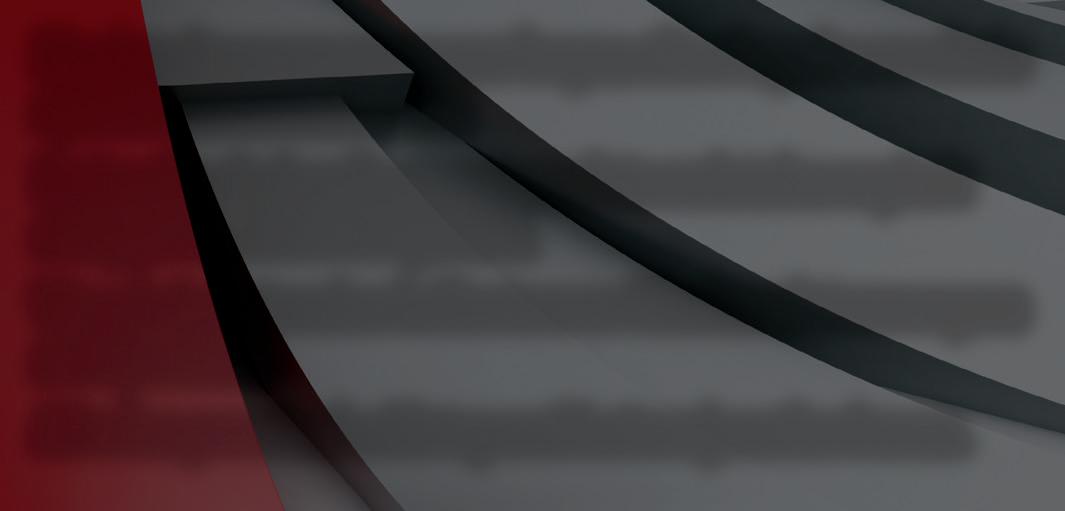
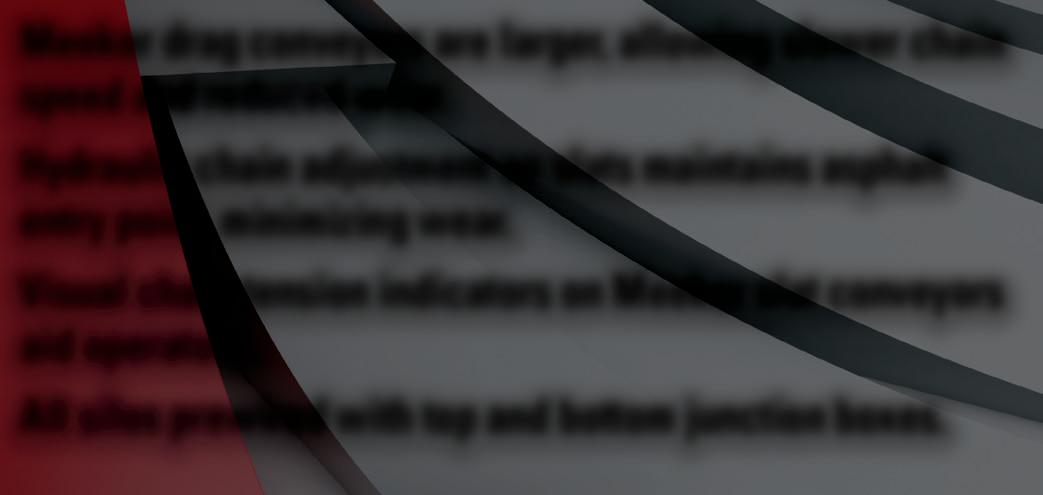


$61 billion in funding for critical road, bridge and tunnel projects as part of the historic Infrastructure Investment and Jobs Act (IIJA). All 50 states are expected to receive some of these funds to improve transportation systems. Most state and regional road-building projects include sustainable construction requirements, with some bids requiring a percentage of recycled aggregates, like Recycled Concrete Aggregates (RCA). Even without government requirements, more and more roadbuilders are interested in RCA because it can decrease input costs and help them manage their bottom line.
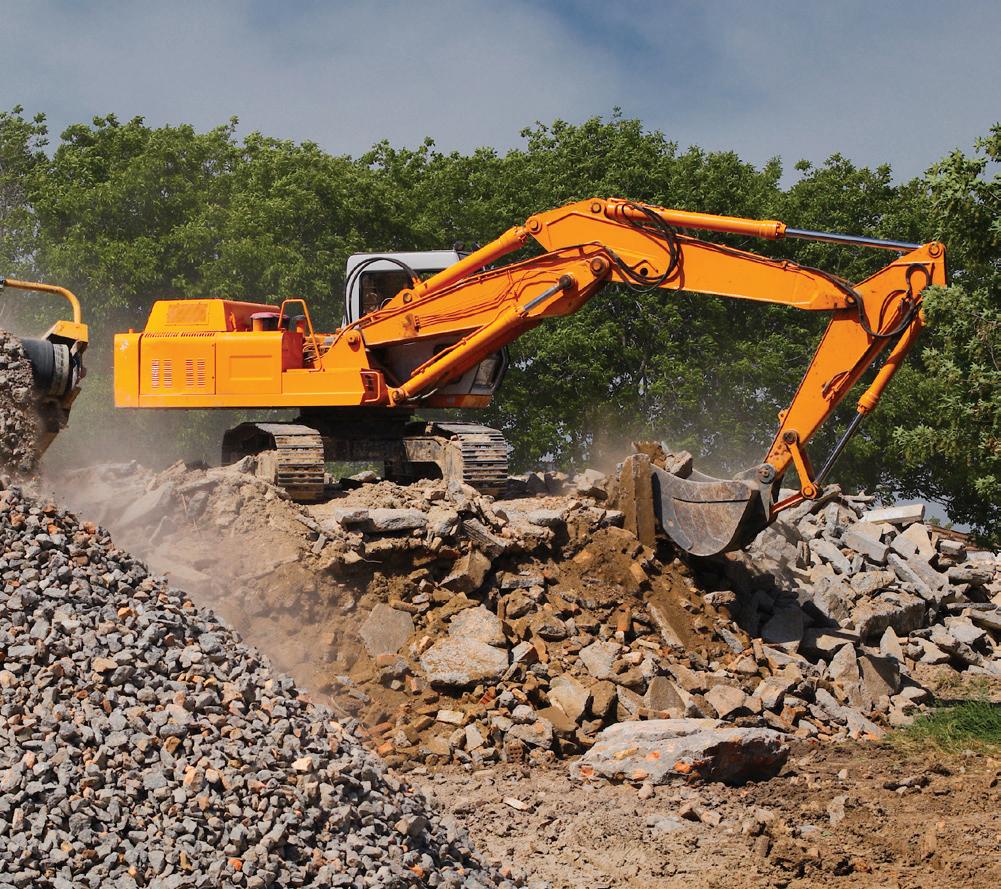
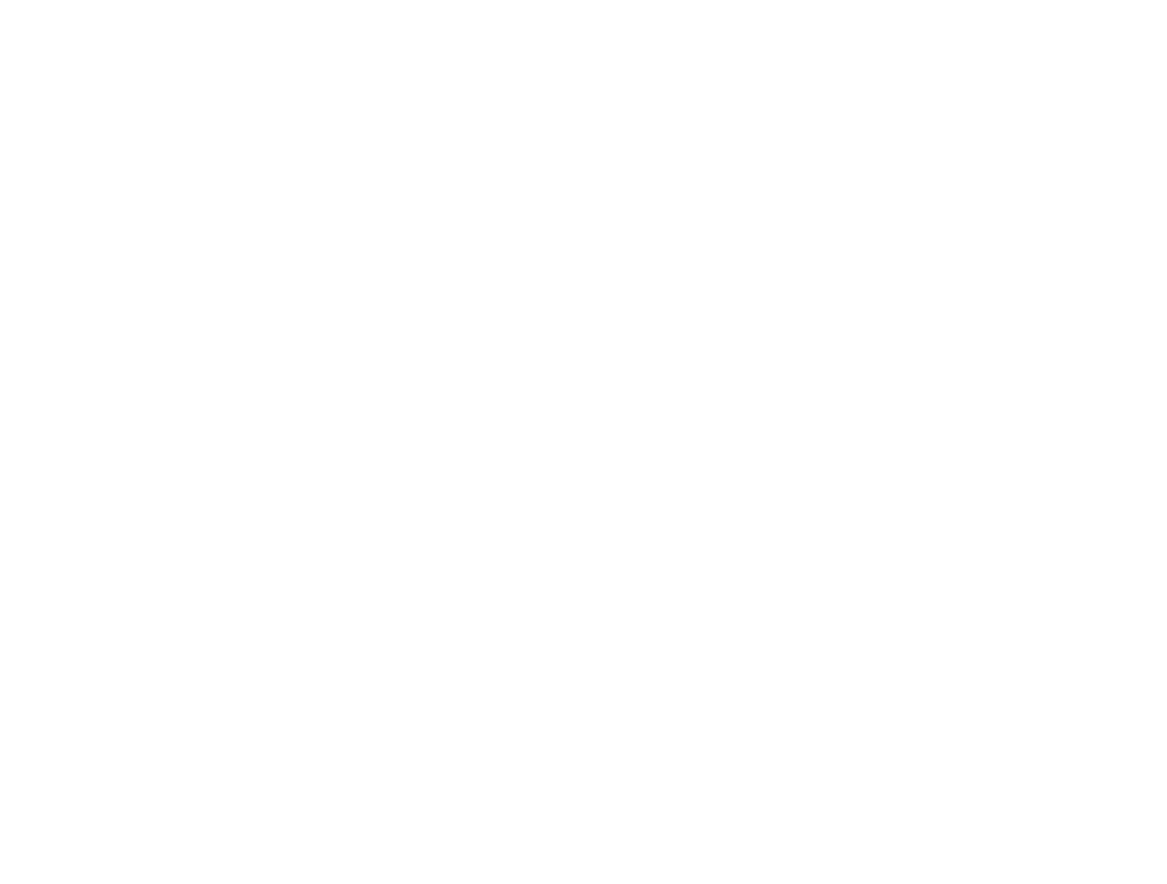
and capacities. Smaller models, like jaw crushers, cost the same as large trucks straight from the manufacturer; while extra-large crushers can cost millions. Crushers are separated into primary and secondary categories. As the name suggests, the following primary crushers perform the first round of compaction.
• Jaw Crusher: These large-scale, heavy-duty crushers use compressive force by feeding material into the “V-shaped” jaw. One side of the V remains stationary while the other side of the V swings against it. The material is forced from the wide opening of the V to the narrowest point, creating a crushing motion. Jaw crushers are widely used to reduce rock into non-uniformed gravel.

People eager to take advantage of government funds and roadbuilding projects will be required to use equipment or technology that improves safety and reduces the amount of carbon emissions. From my time in Utah, I’ve spoken with roadbuilders considering adding crushers to their equipment fleet. While working with team members based in Utah, I discovered crushers are versatile machines that can be crucial for sustainable roadbuilding.
ROLE OF CRUSHERS IN ROADBUILDING
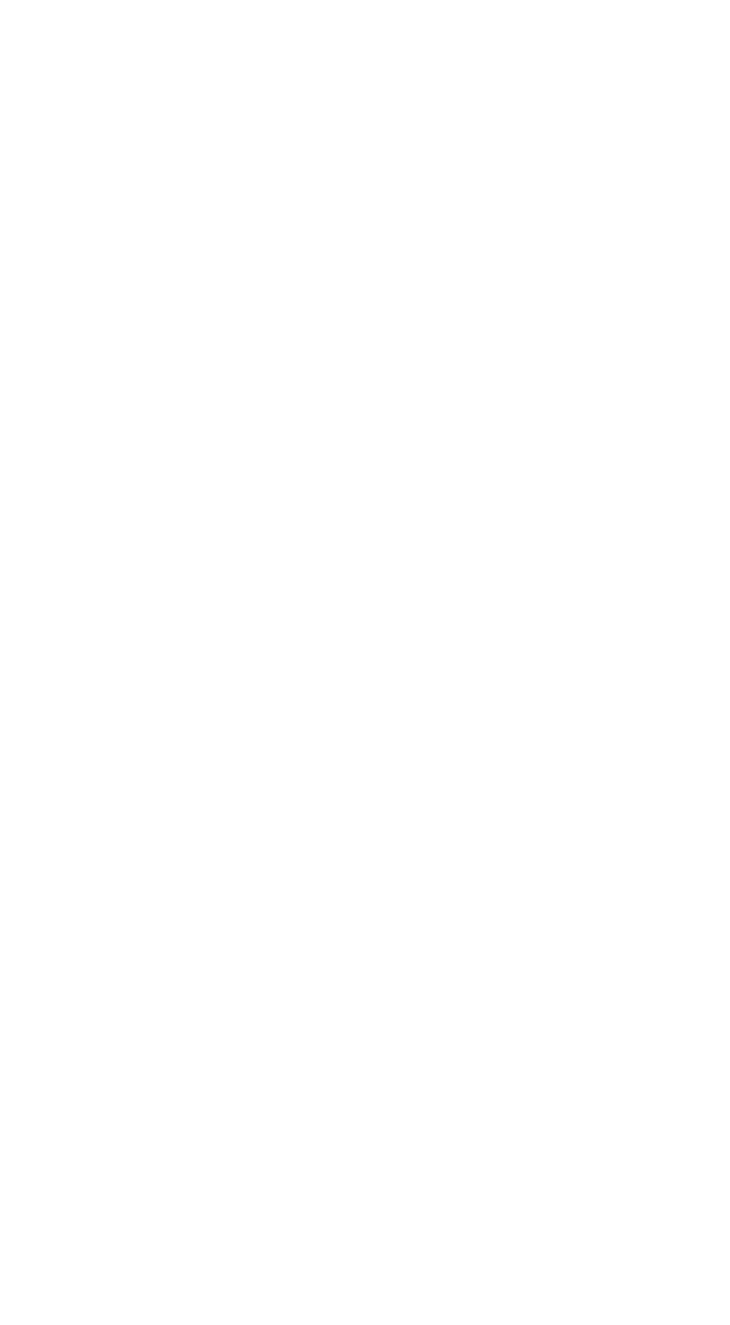
• Gyratory Crusher: This crusher’s hopper is lined with “V-shaped” pieces. The mantle and the concave are shaped like a cone, similar to a jaw crusher. Gyratory crushers are small, precise machines often used for crushing more extensive materials when the desired shape needs to be uniform.
Many government projects require a secondary crusher to refine the aggregate to a predictable, uniform and material. The more uniform the material, the more likely operators will be able to compact materials together consistently and pave smooth roads. The less uniform the material, the more time pavers will take to find the right force to spread the concrete or the asphalt and build a lasting road. Roadbuilders can choose from one of the following secondary crushers.
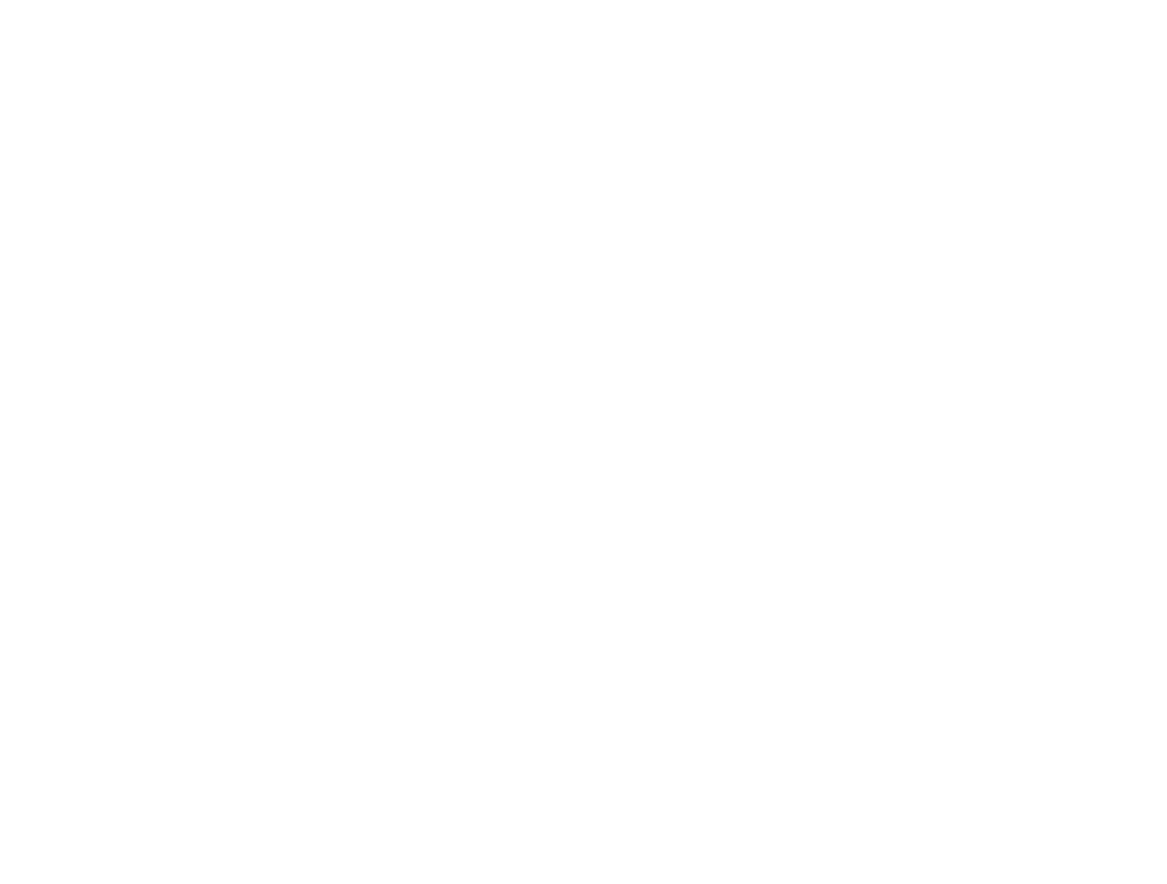
Crushers, as we all know, make big rocks into little rocks. The quality of the aggregates depends on the processing, so original equipment manufacturers have developed crushers in various sizes
• Cone crusher: Used in large-scale industries, cone crushers apply pressure onto the material and squeeze it against a rotating mantle to create compression and force. First broken down at the top of the cone, the material falls into the cone crusher’s lower, more narrow part. This process repeats until the material is small enough to drop out of the bottom opening. Cone crushers are used in asphalt pavement resurfacing or gravel pits to prepare gravel for rural roads.
• Roll Crusher: A Roll crusher reduces material by compressing it between two rotating cylinders parallel to each other. The cylinders are mounted horizontally, resting on strong springs, and the other is permanently framed. The material is then fed between the two.
CHOOSING A CRUSHER
While working in Utah, I’ve met many talented and experienced people building vital roads. When roadbuilders purchase a crusher, they increase their access to recyclable materials, but choosing the right one can be tricky. The right machine will depend on the roadbuilder project’s needs, use frequency, and material type the crusher will break down. Roadbuilders can make a smart investment by considering a specific crusher model’s adaptability, efficiency and reliability alongside the project’s needs. Let’s look at how those factors can help guide the selection of the right crusher. Roadbuilding projects have varying requirements, such as tight timelines, regular reporting progress, or several materials used by third-party parties. However, the project’s profitability may not justify a significant investment in equipment, so a roadbuilder should consider the reliability of a specific crusher model. Roadbuilders can take advantage of opportunities in the aggregate market through a few different options of equipment or technology that can solve challenges. Crushers will only become more popular in the next five years as sustainable building becomes more emphasized across the U.S. Consider visiting with a trusted partner to learn more about Crusher equipment or technology. To see more information about road and bridge projects, check out the Department of Transportation’s Notice of Funding Opportunities on their website.

by Dennis Howard, senior vice president of the construction equipment division at RDO Equipment Co.
Zsolt Biczó/AdobeStock
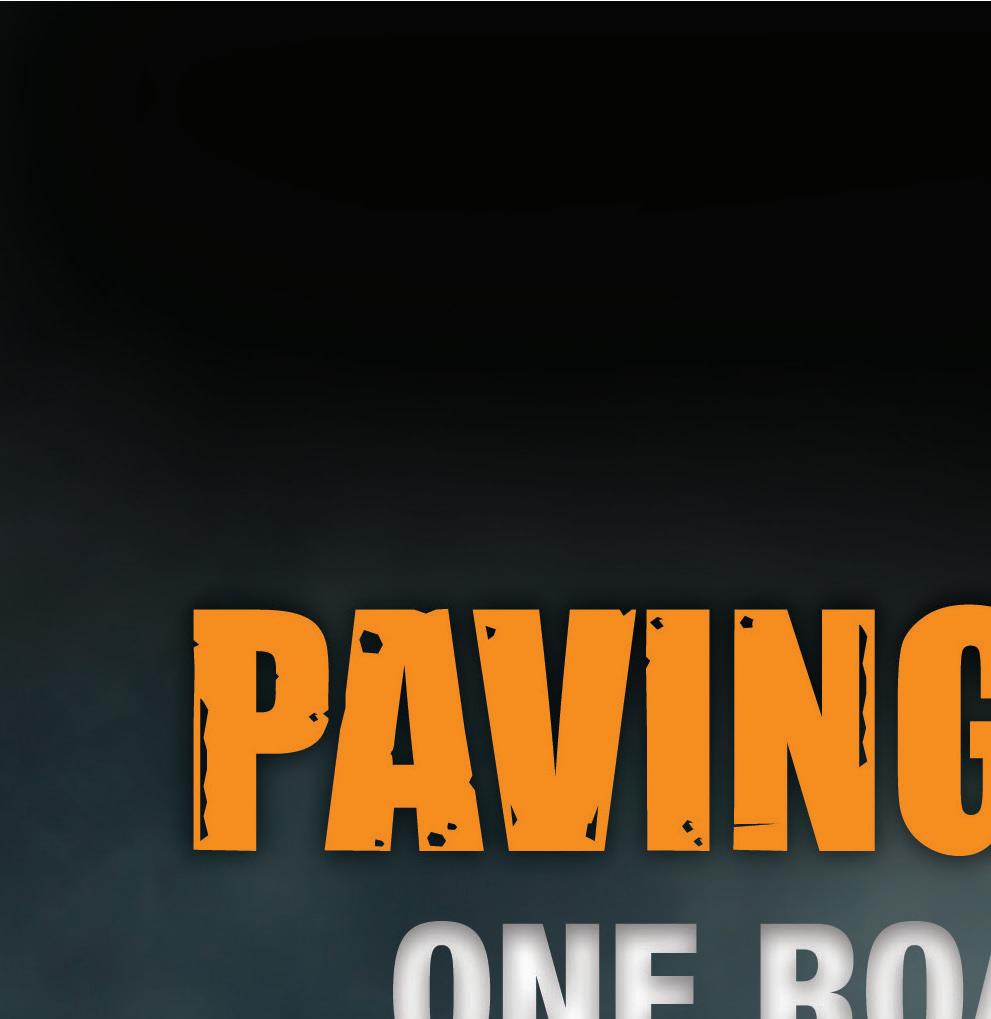



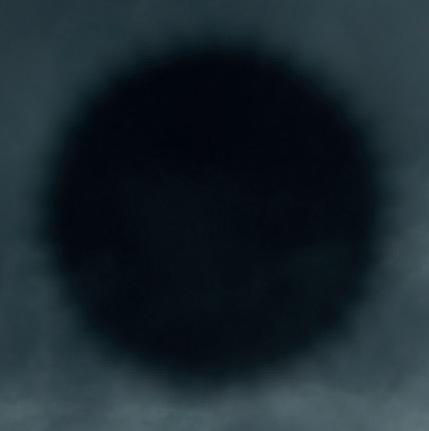


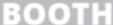

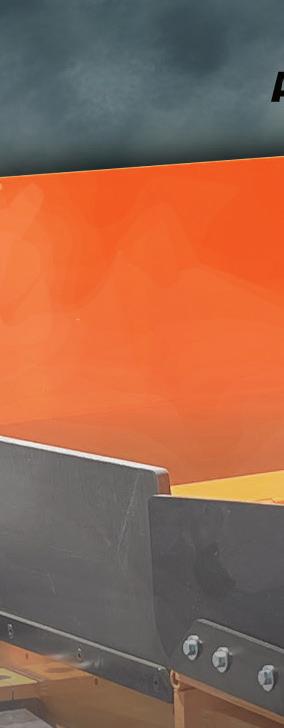
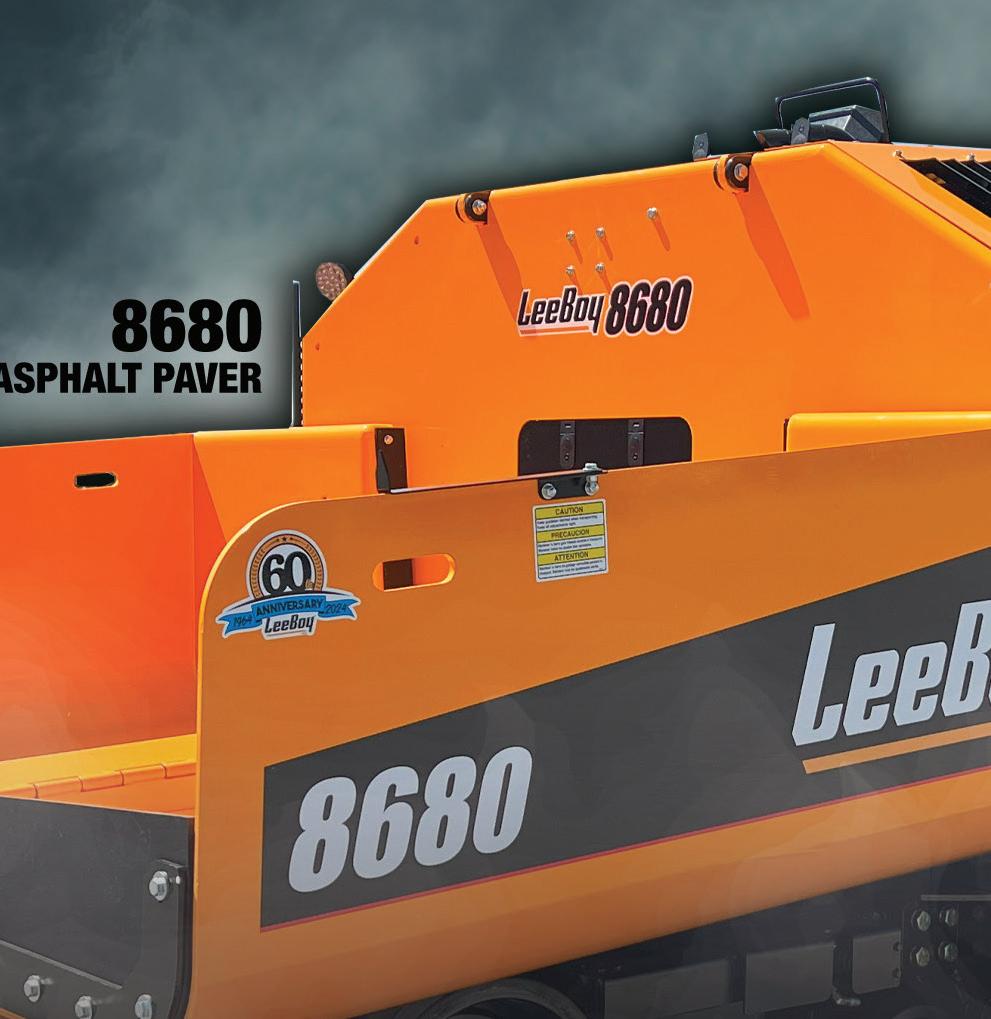
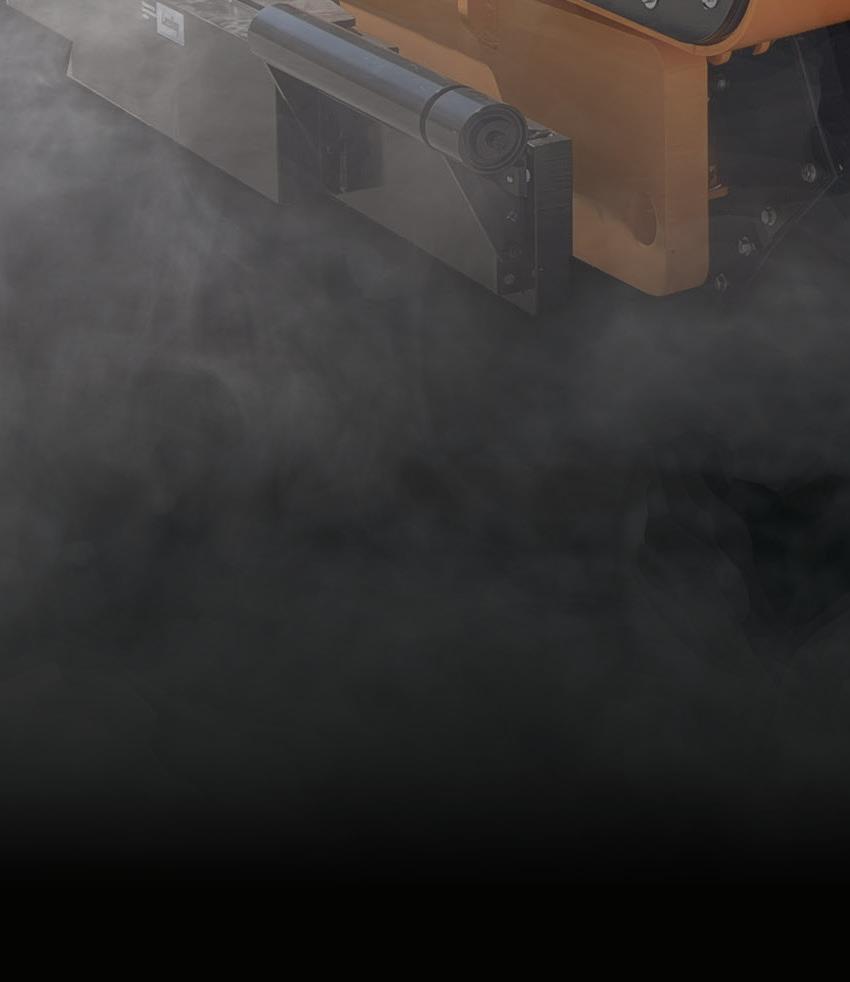
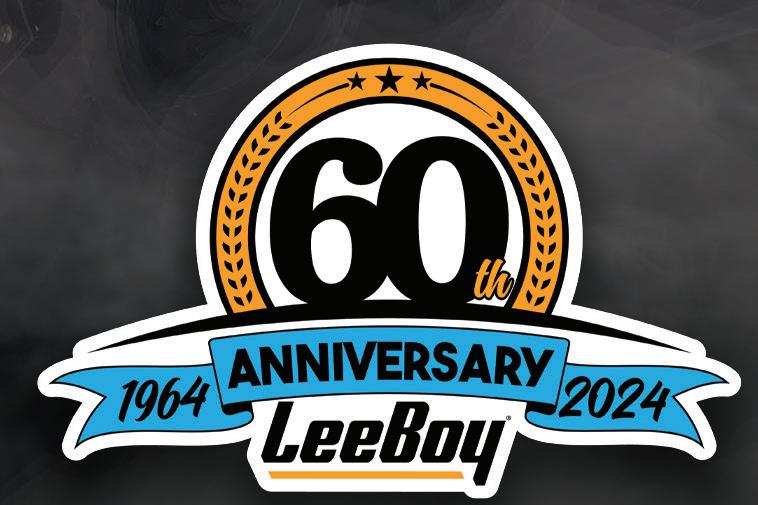
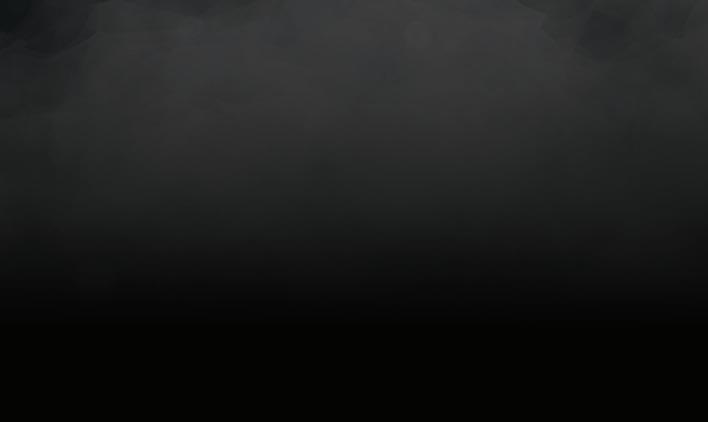




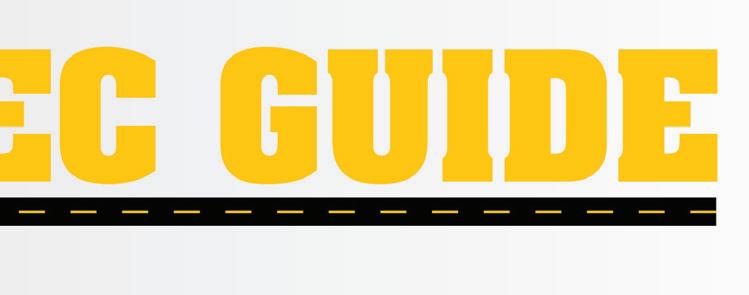
With so many options available, purchasing a new piece of equipment that meets your needs is not an easy decision. Research is an important first step to help you decide exactly what you’ll want to rent or buy. If you’re in the market for an asphalt paver, these next few pages are a great resource. Here, we’ve compiled the industry’s only Asphalt Paver Spec Guide where you can compare more than 75 models. For an even easier way, visit the exclusive, interactive and customizable version of this spec guide at http://www. forconstructionpros.com/specguide/asphalt-paver to sort and rank models based on the specific needs and requirements of your crew.
VÖGELE
With the 10-ft. tracked Super 2000-3, the wheeled Super 2003-3i, the 8-ft. tracked Super 1700-3 and wheeled Super 1703-3i, Vögele is marketing four advanced technology pavers for North American highway and commercial markets. Now, a new app for smart phones, tablets and PCs helps users understand the intuitive and easy-to-use ErgoPlus 3 operating system via animations and step-by-step videos that provide an easy-to-grasp demonstration of work steps, including setting up the screed, varying pave widths, and comprehensive automatic functions. Download at Google Play or Apple store or search Vögele ErgoPlus 3 app.
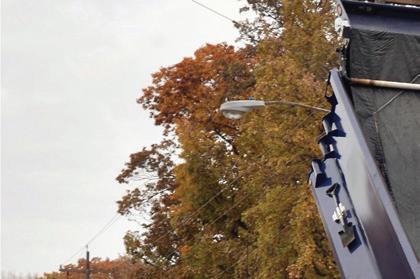
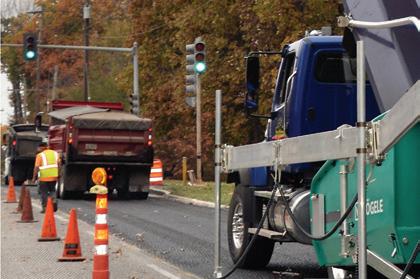



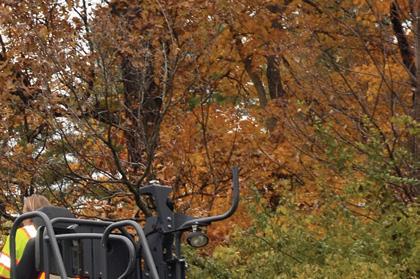
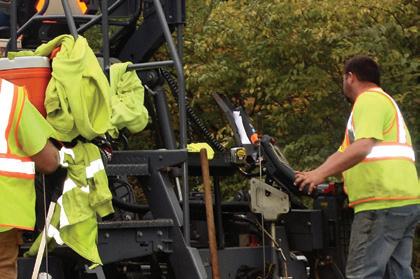
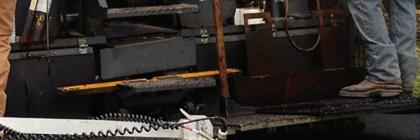
Vögele
Vögele
Vögele
Vögele
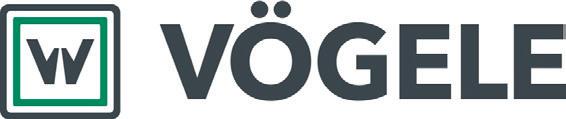
For more information visit https://asph.link/lj2hak
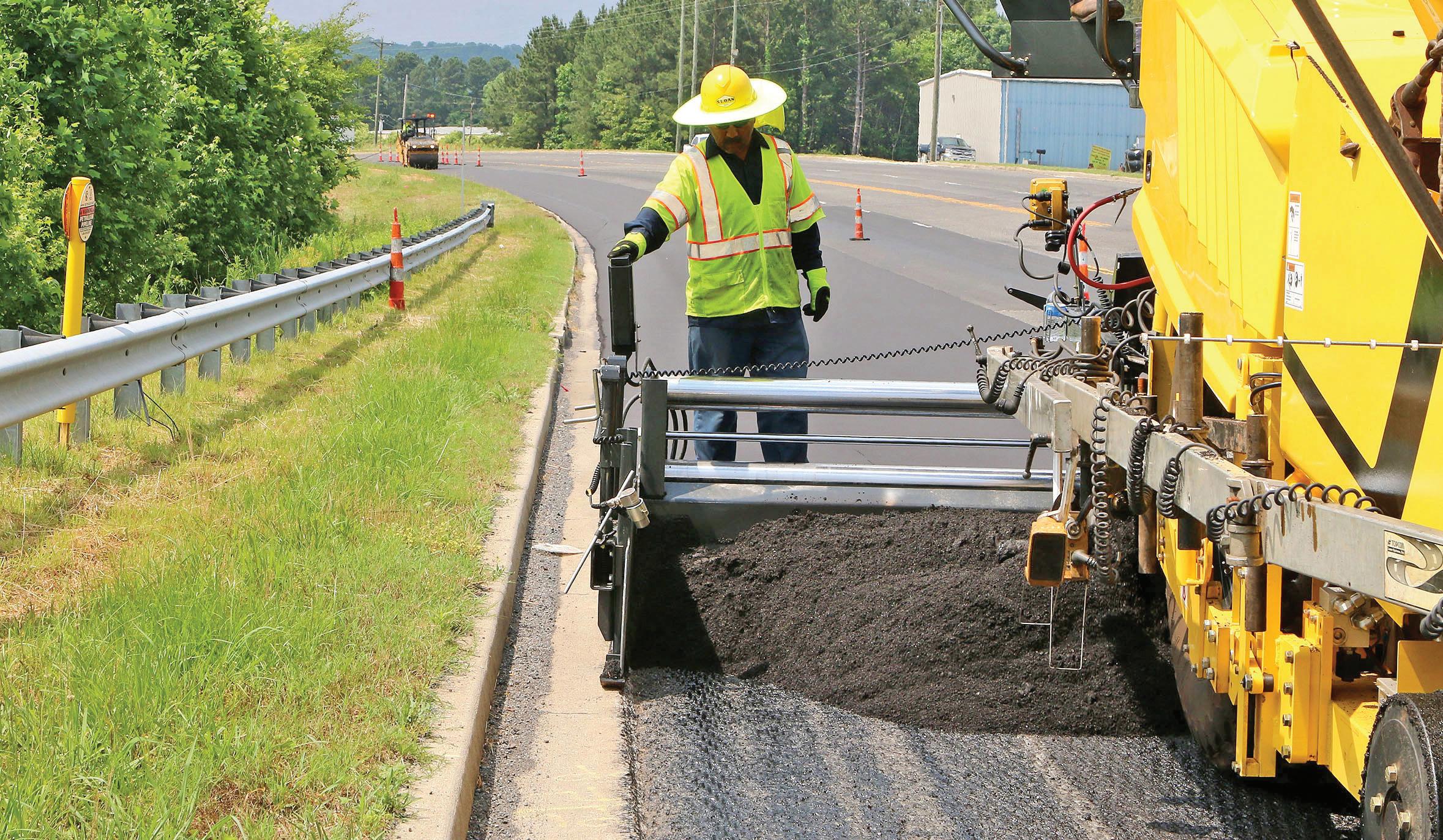
BOMAG
BOMAG is dedicated to asphalt and compaction. While other companies supply products for multiple segments; dirt work, mining, agriculture, BOMAG expertise is solely dedicated to your work and what’s important to you. You’ll be able to rest easy knowing that the support you get with BOMAG products is laser-focused on what is most important to you.

DYNAPAC NORTH AMERICA
Whether on compact city streets or vast highway projects, Dynapac offers solutions to meet all of your paving needs. Dynapac pavers are designed with paving quality, innovation, ergonomics, and innovative solutions in focus. Built with robust screed designs, top pre-compaction and solutions such as PaveManager, Truck Assist, and BPO.
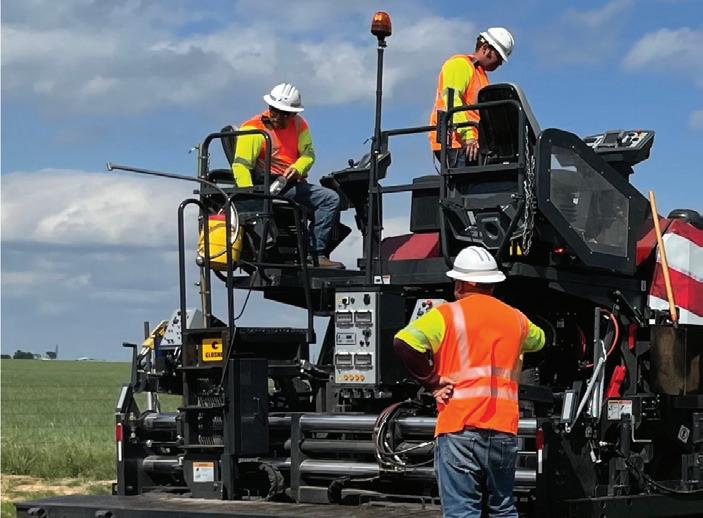
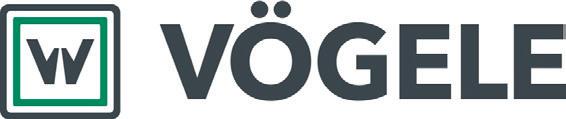
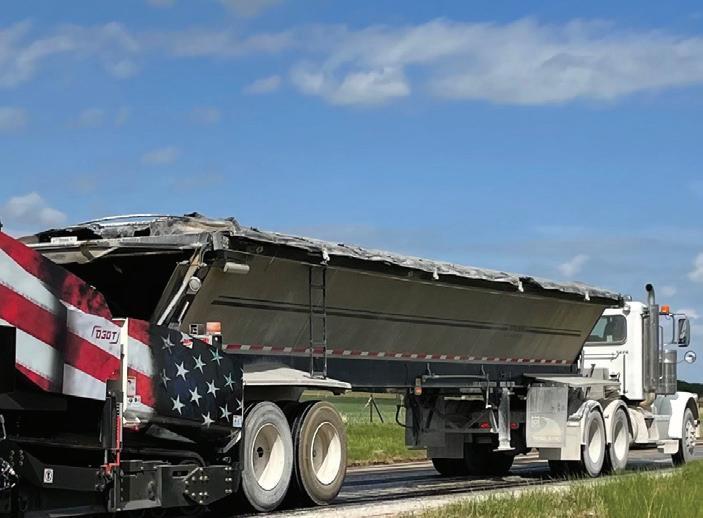



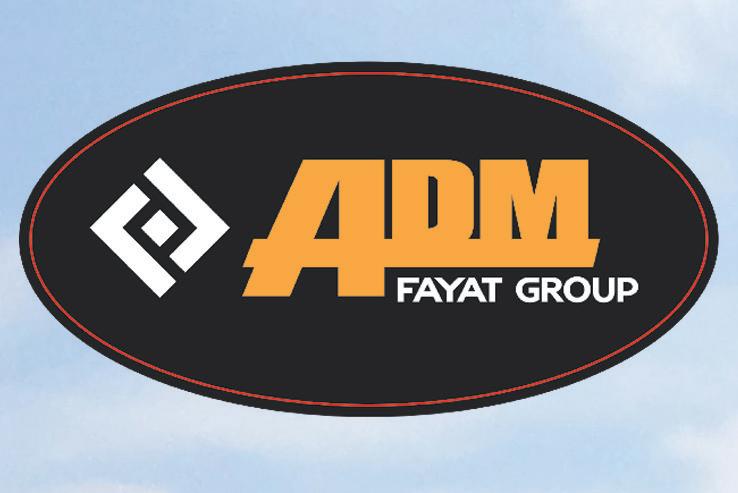
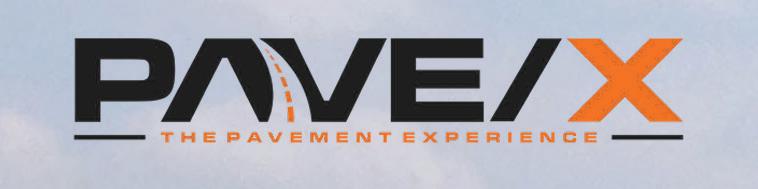

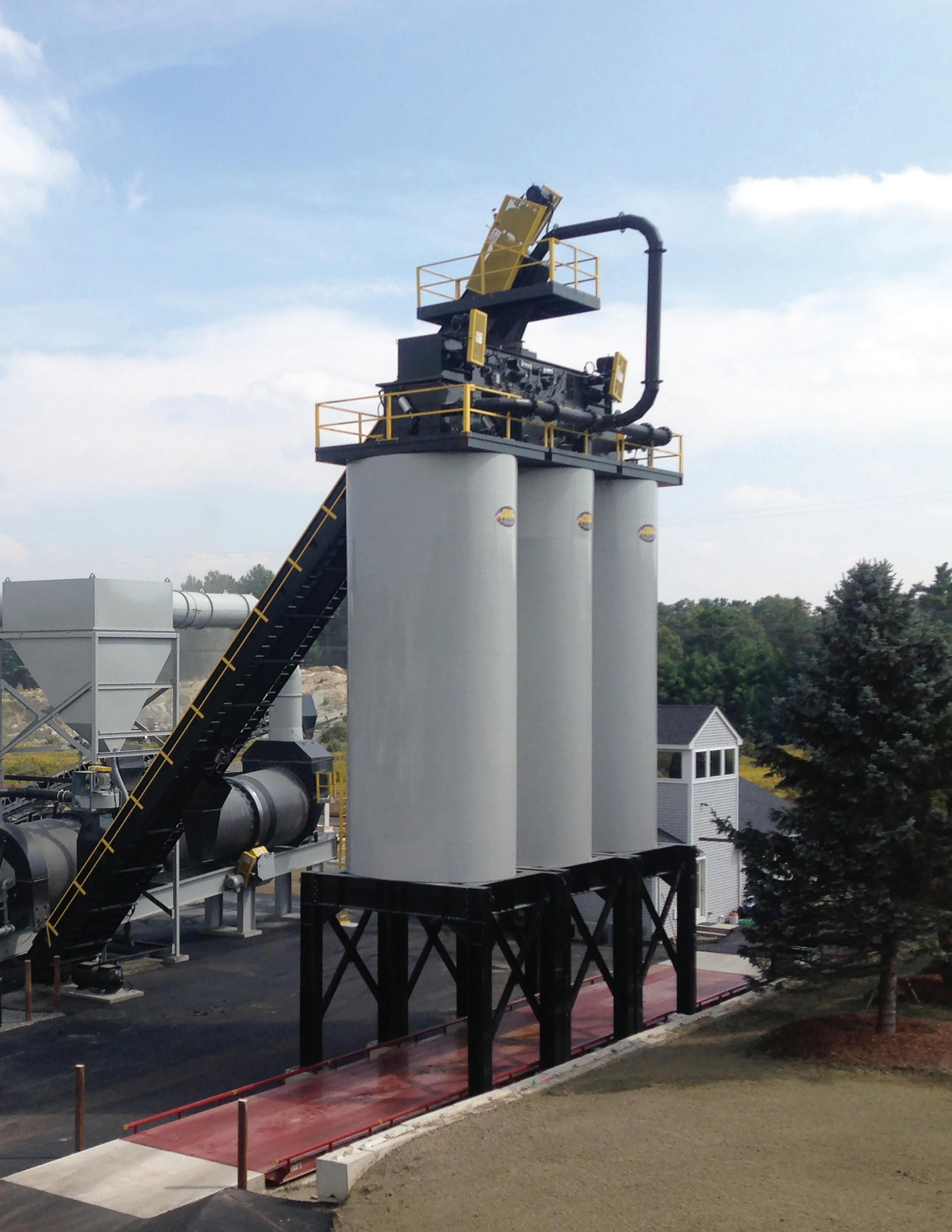
BIGGER PROFITS!

ASTEC
The Roadtec and Carlson paver lines by Astec combine power and functionality with nimbleness and maneuverability. Our highway class tractors can be combined with a variety of reliable screeds that will serve you well for a wide range of applications. The commercial class line provides contractors with reliability and unmatched performance in a compact package. Regardless of your project, Astec pavers produce a quality mat with efficiency and productivity.
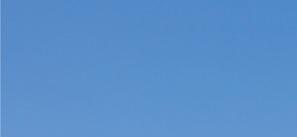
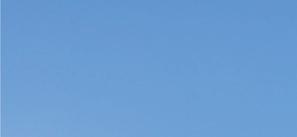
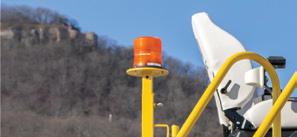
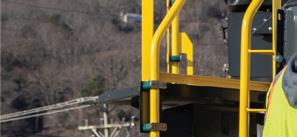
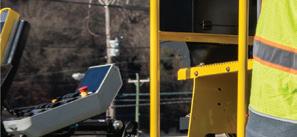
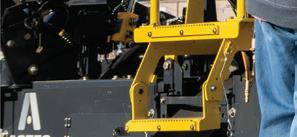
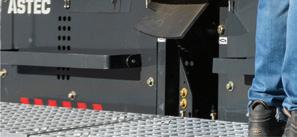
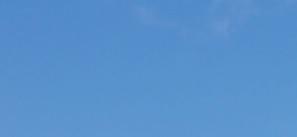
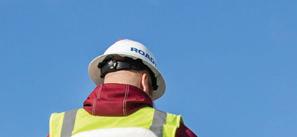
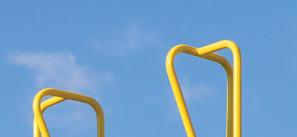

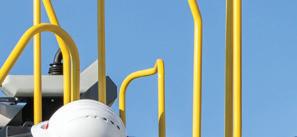
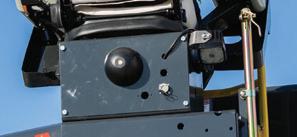

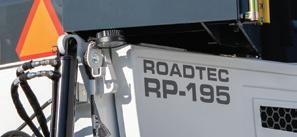
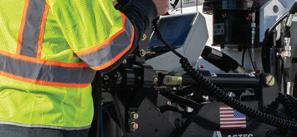

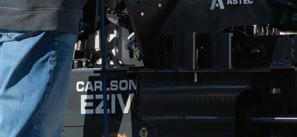
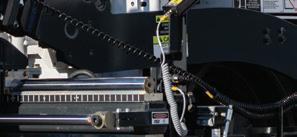

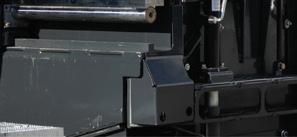
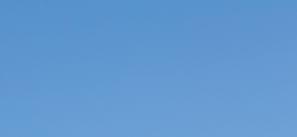
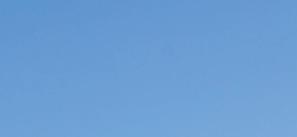
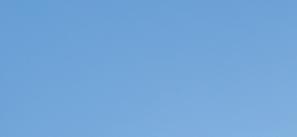
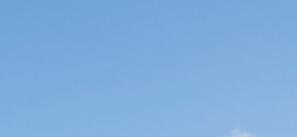
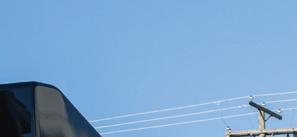
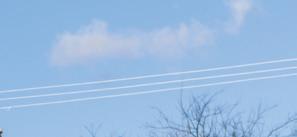

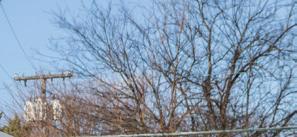
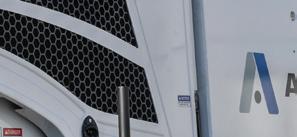
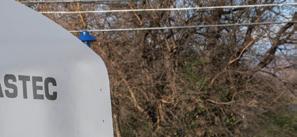
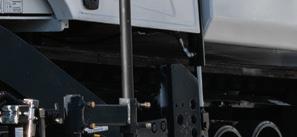

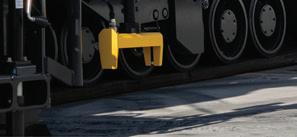
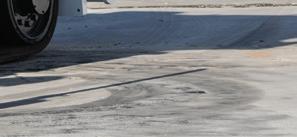

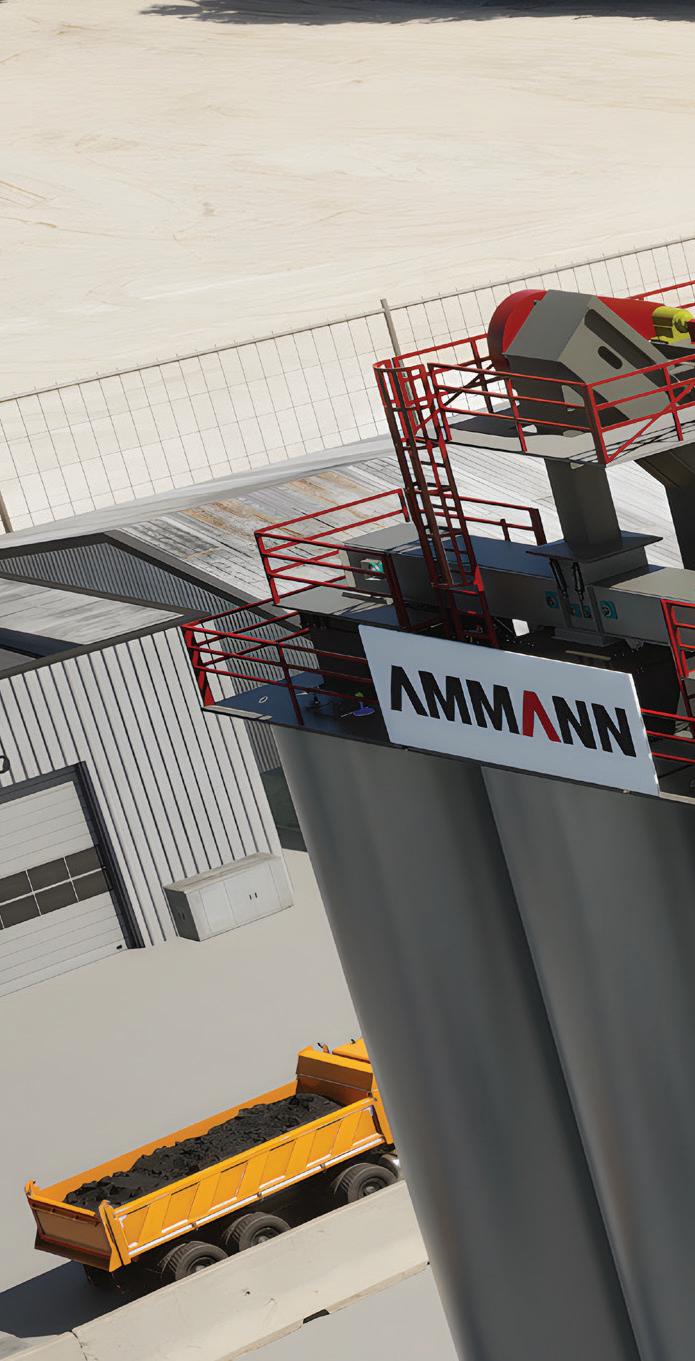
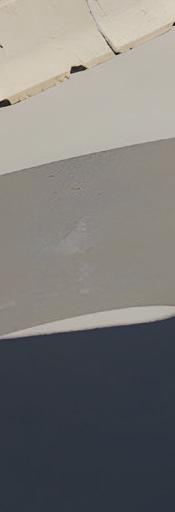
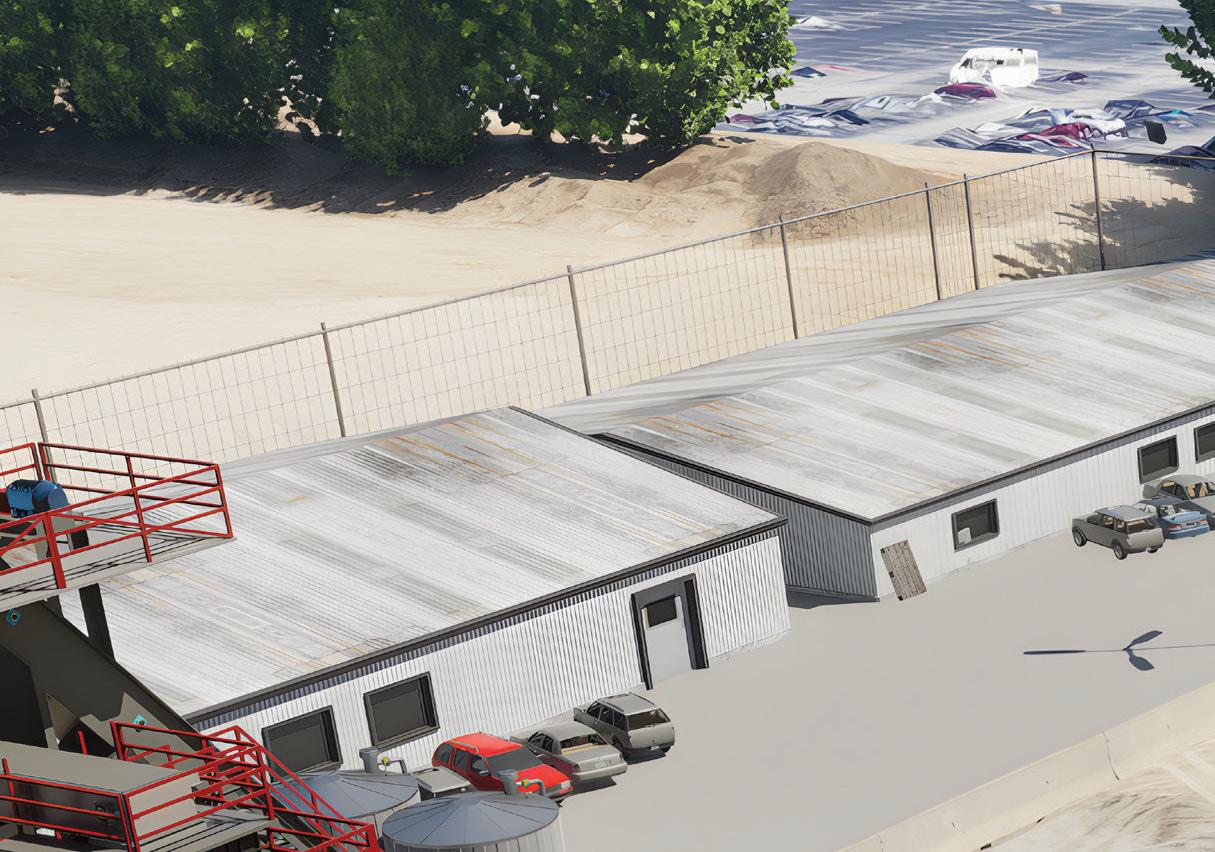
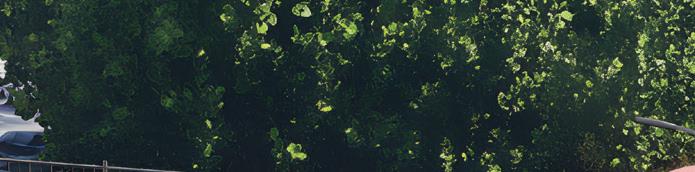
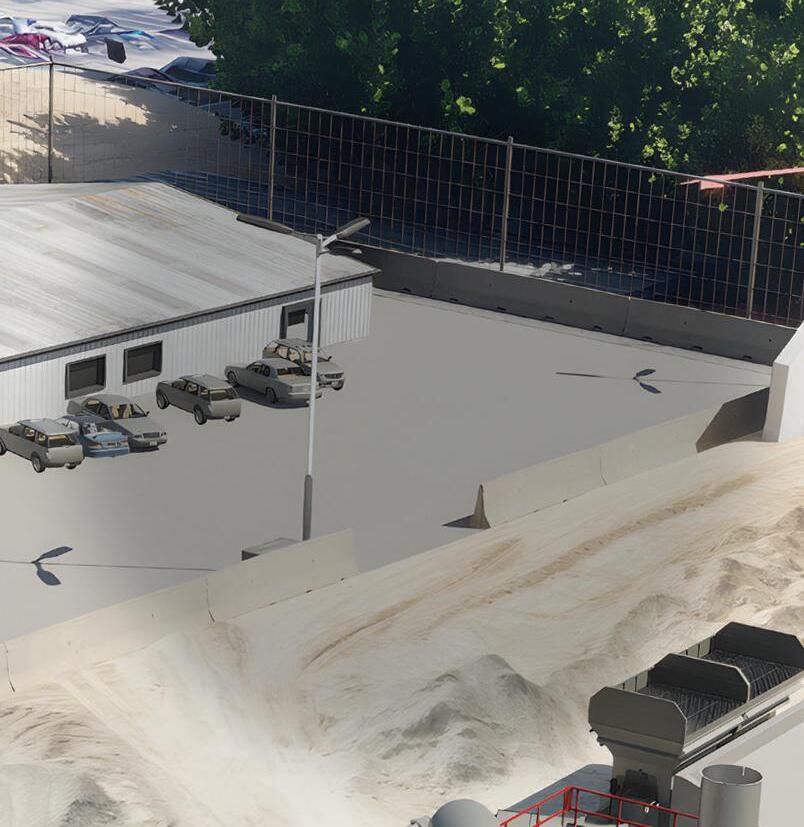
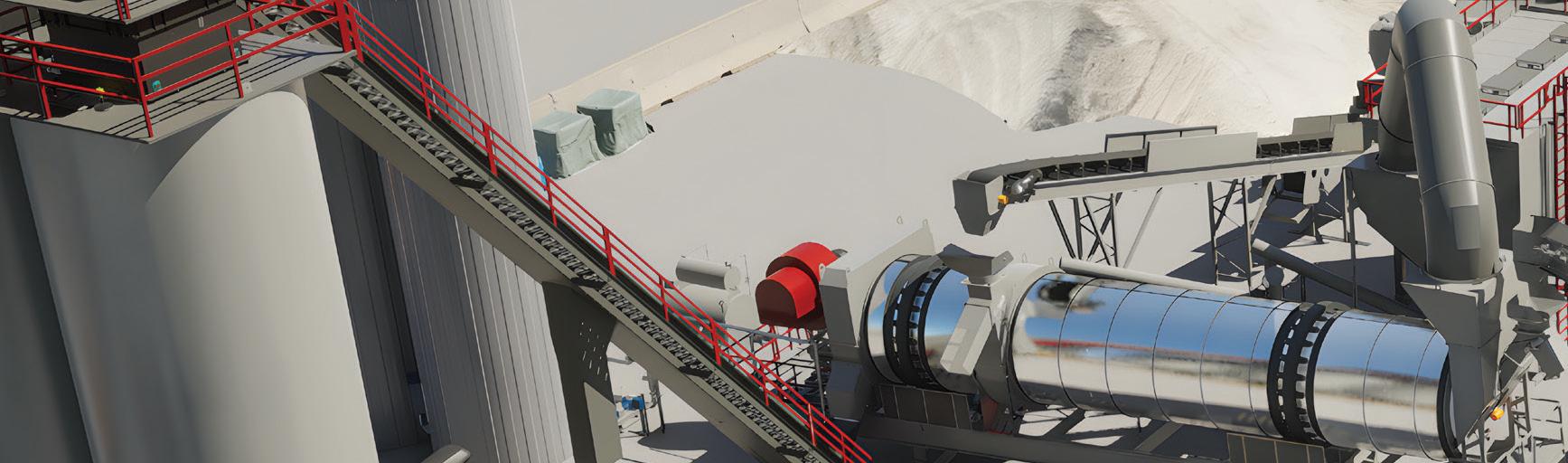



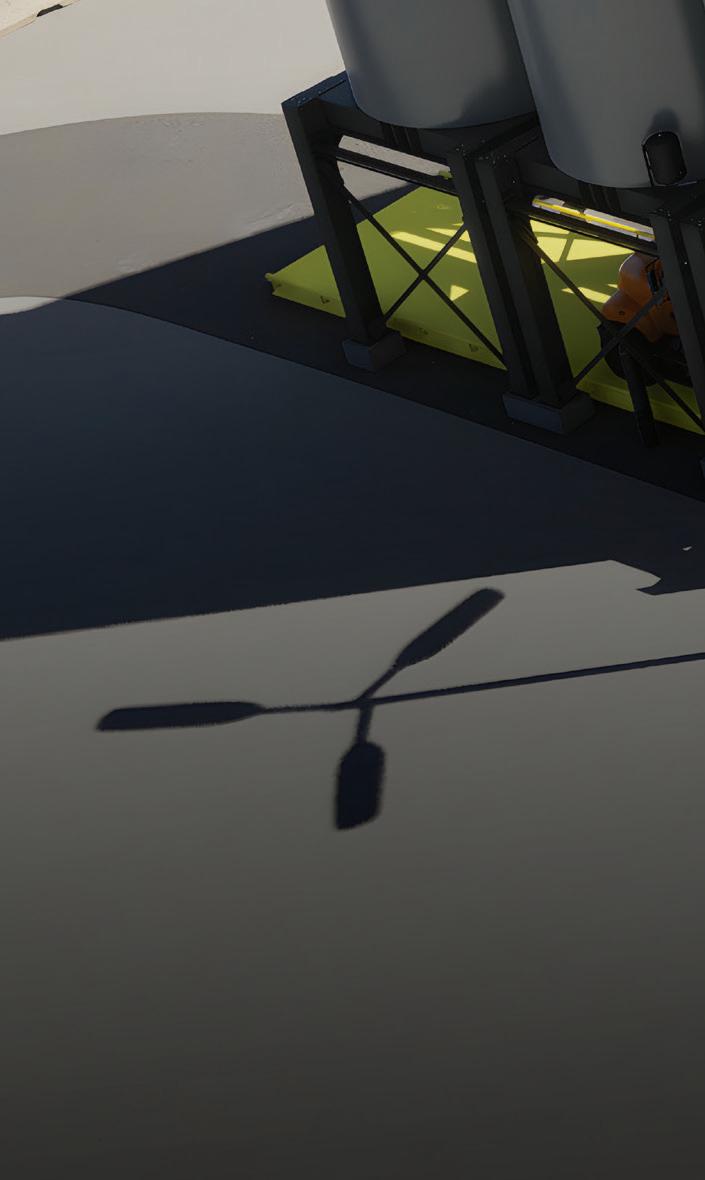
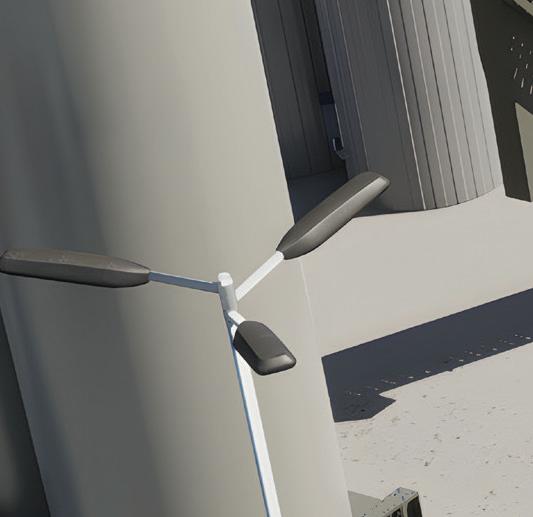
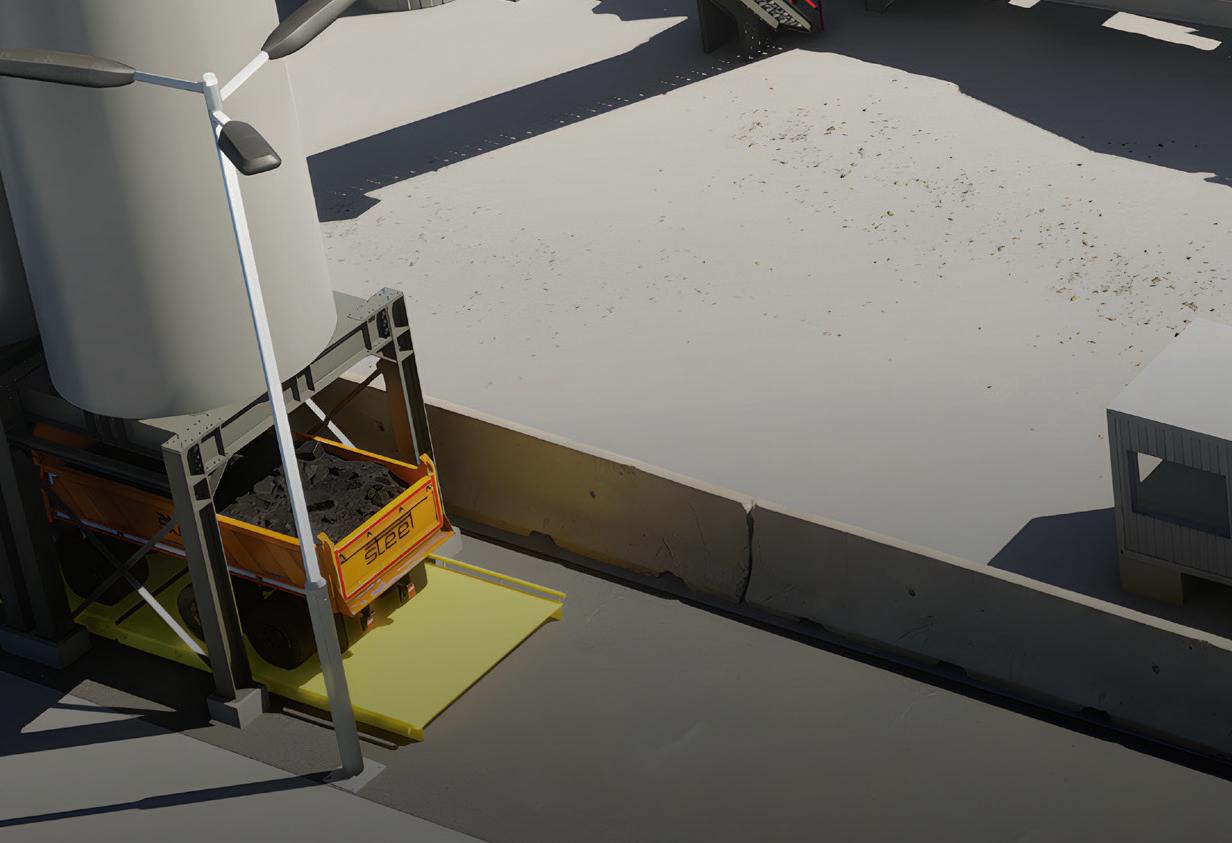
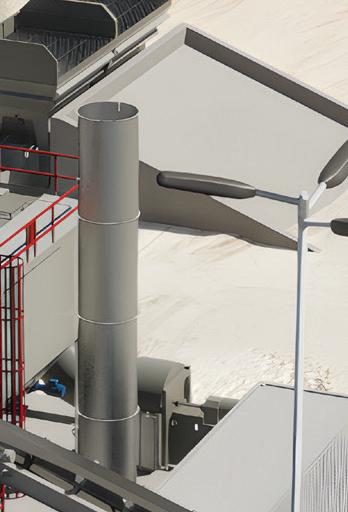
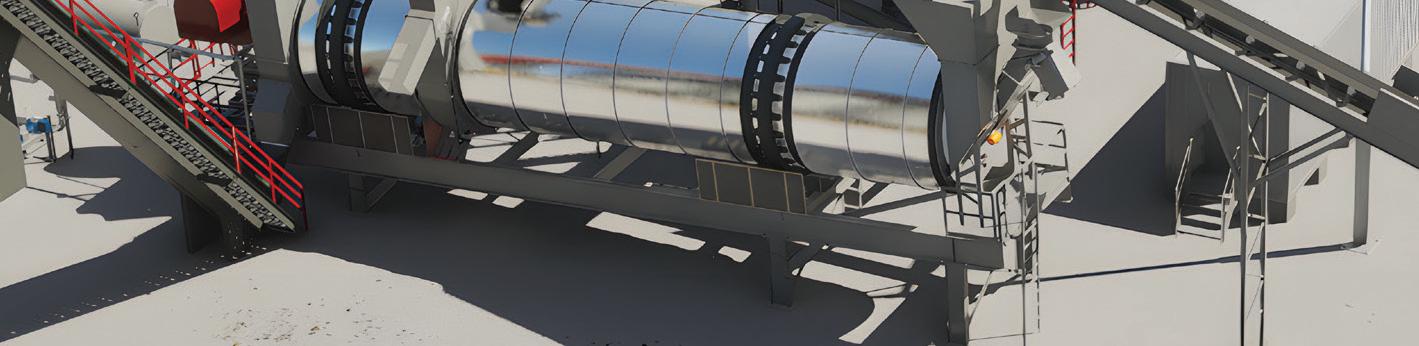


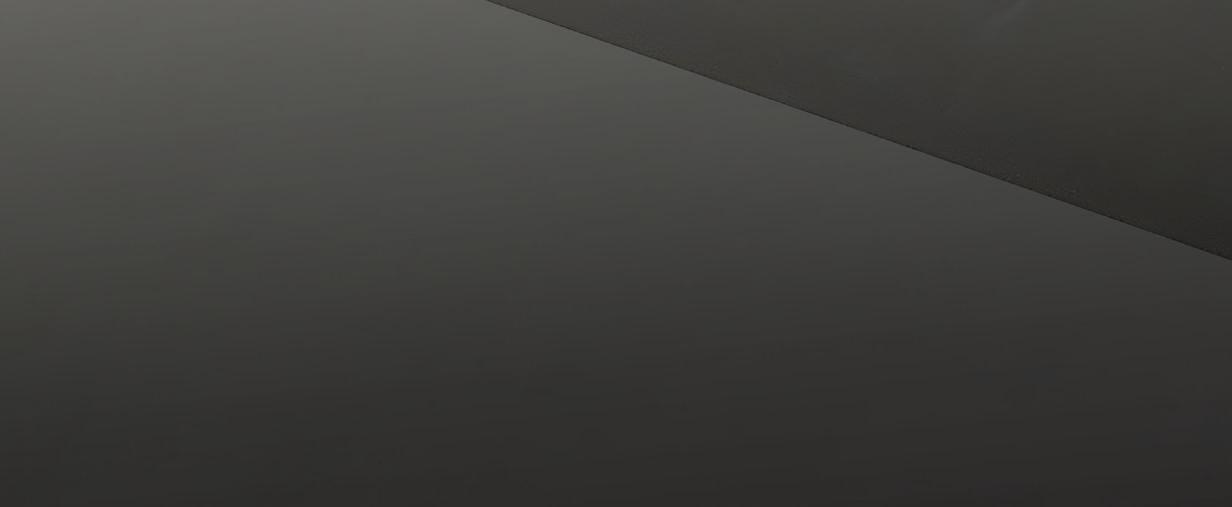




WEILER
Engineered and built to exceed the demands of commercial paving, Weiler pavers incorporate proven designs with new innovations to provide performance, reliability, and outstanding mat quality. Weiler offers six pavers to meet contractor’s needs in a wide range of applications. Weiler equipment is sold and serviced exclusively at Caterpillar dealers throughout North America.
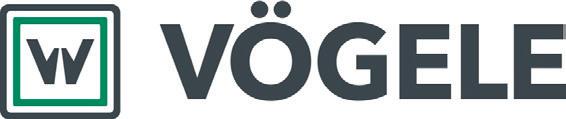

MAULDIN PAVING PRODUCTS
Mauldin Paving Product’s line of commercial pavers ensure superior performance due to three strategic approaches to design. Proven productivity, screed design, and a commitment to quality are the key elements that sets a Mauldin Paver apart. Mauldin Pavers have been trusted for decades by contractors to produce lasting results.

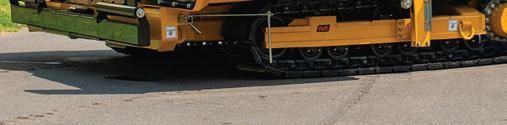

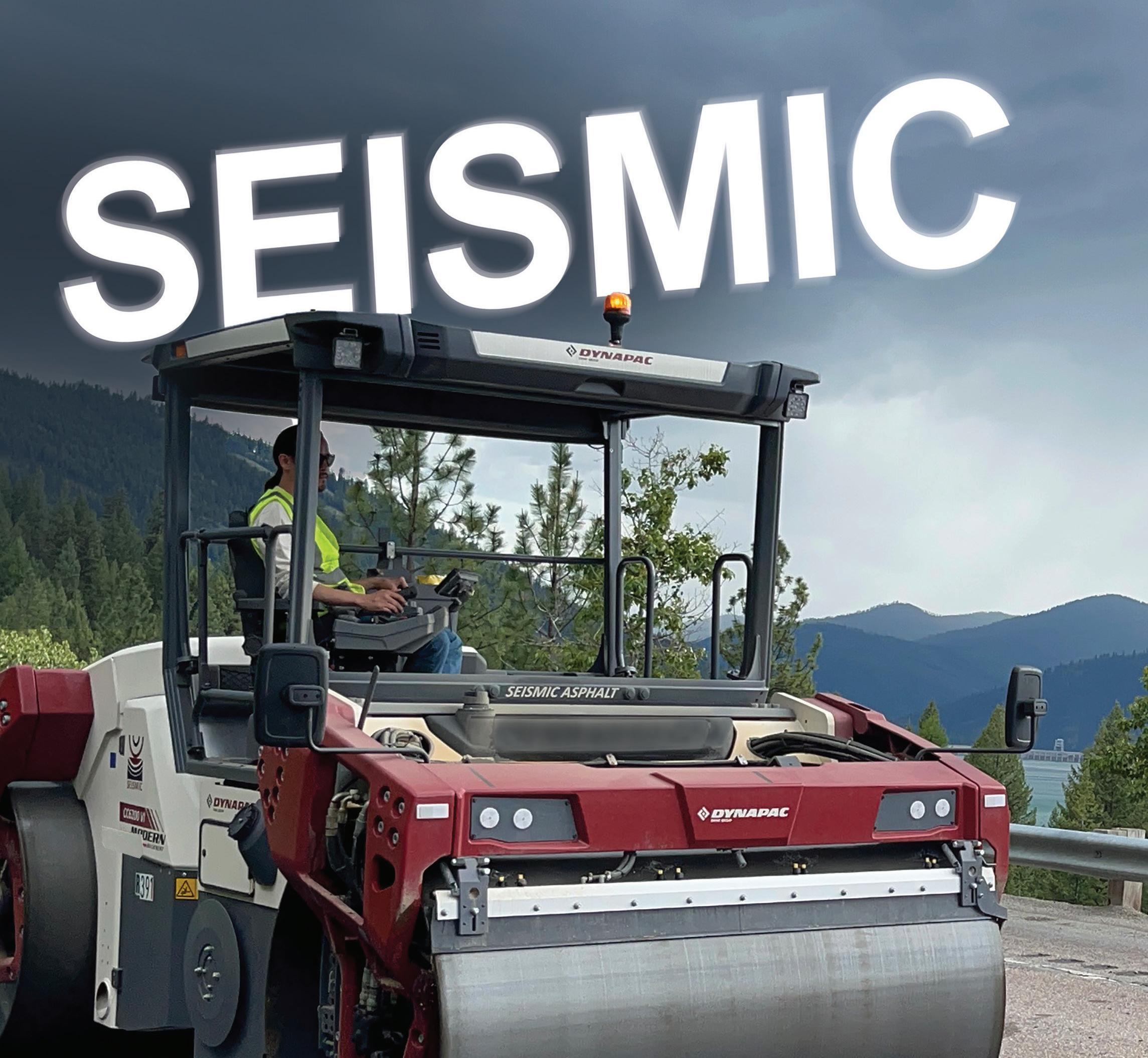
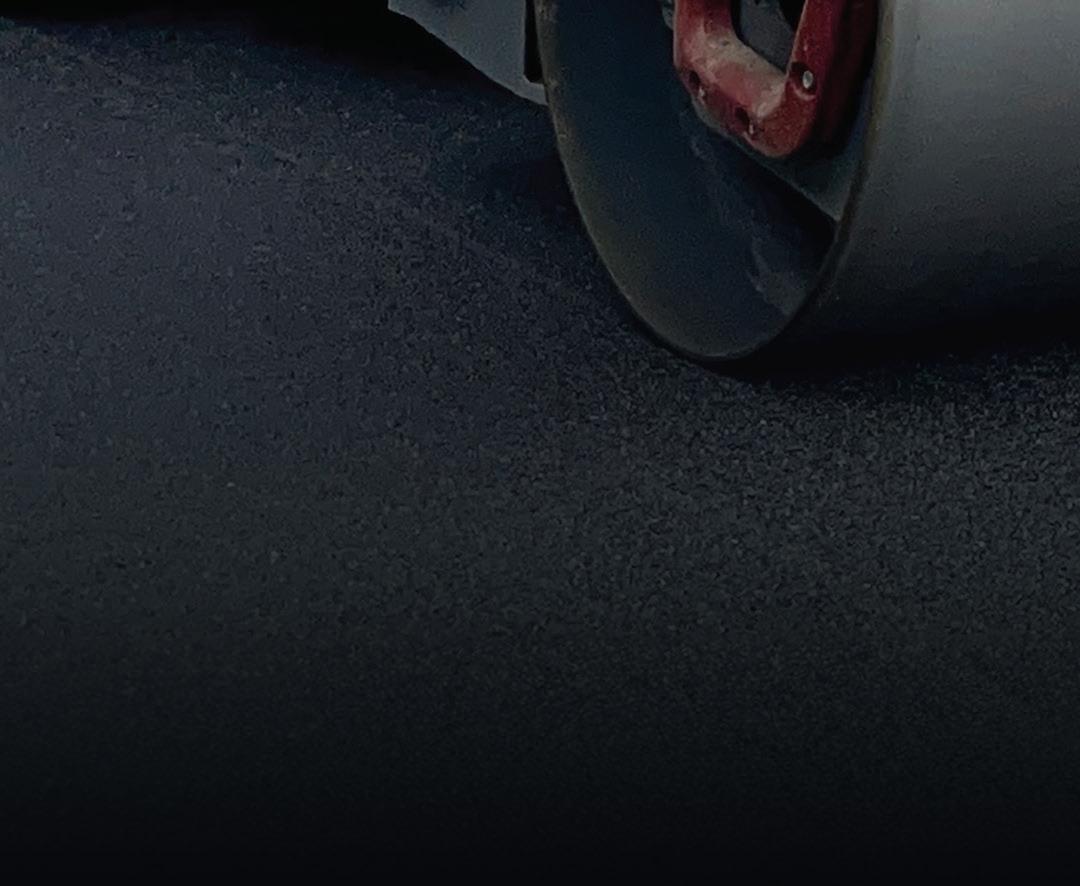
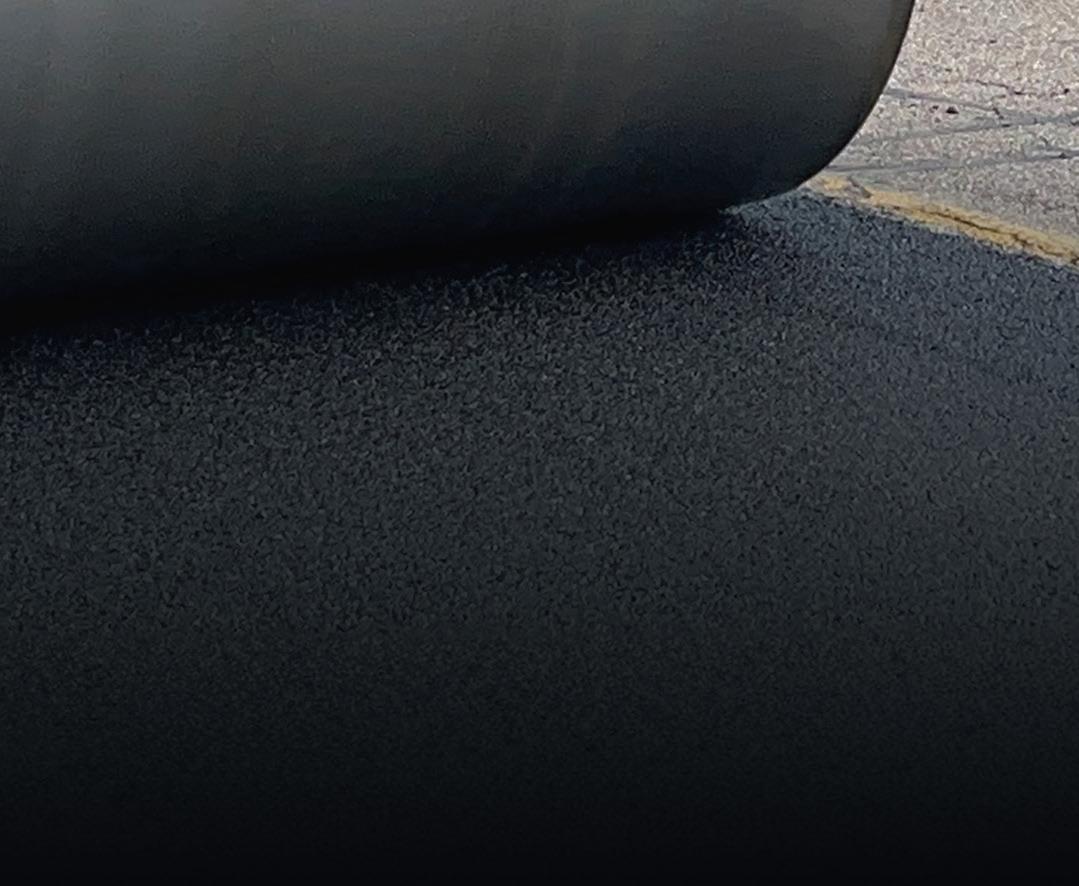

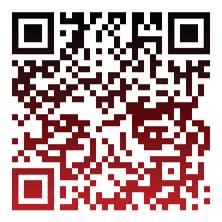


CATERPILLAR INC.
Whether paving pathways or interstates, meeting performance targets is the expectation of all contractors. With a complete line of paver/ screed combinations, Caterpillar makes it easy for contractors to deliver on their promises. And with cleaner burning, more fuel-efficient engines, great parts and service support, application expertise, and outstanding training solutions, Cat dealers offer a one-stop-shop that helps paving contractors meet the needs of their customers.

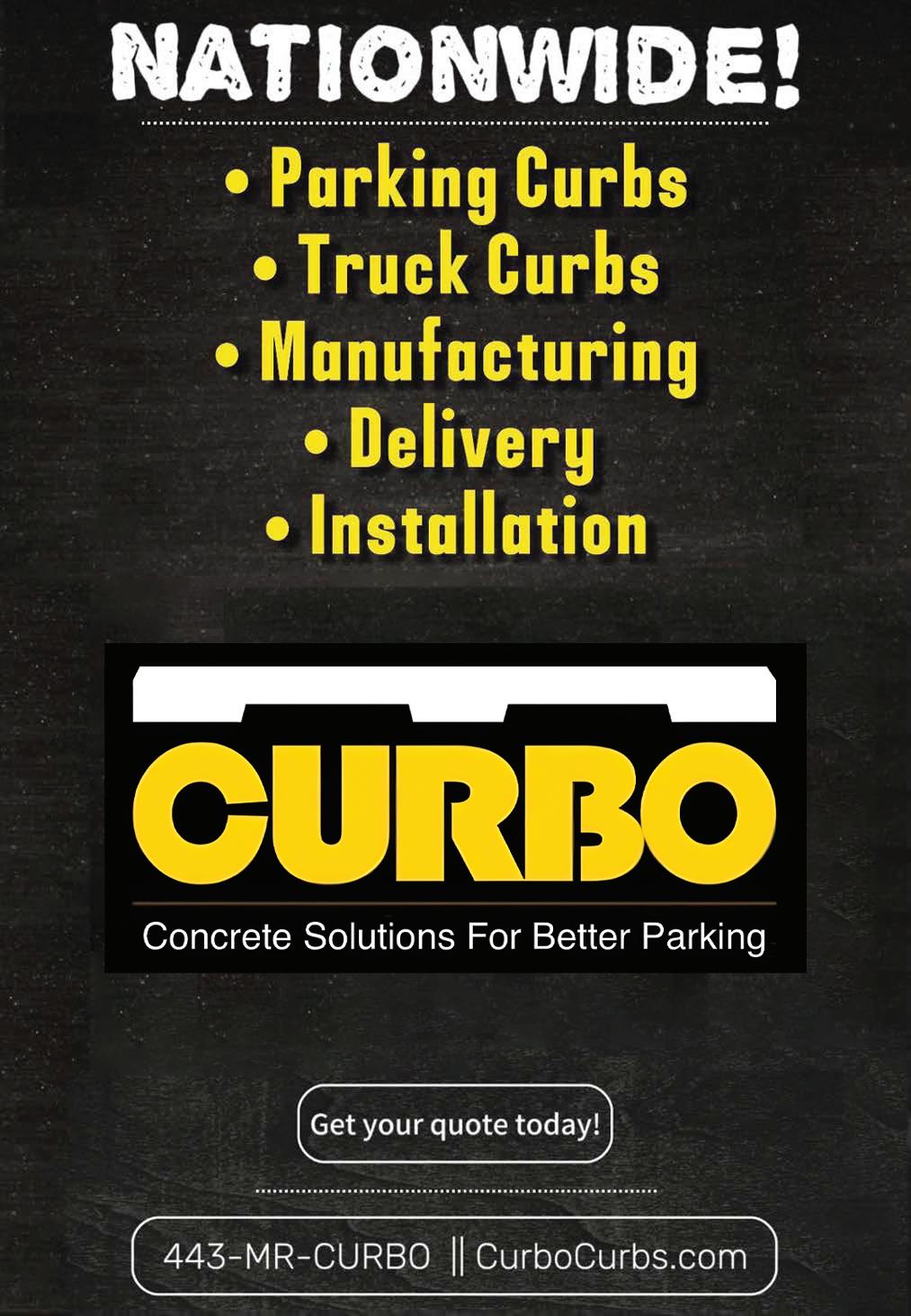
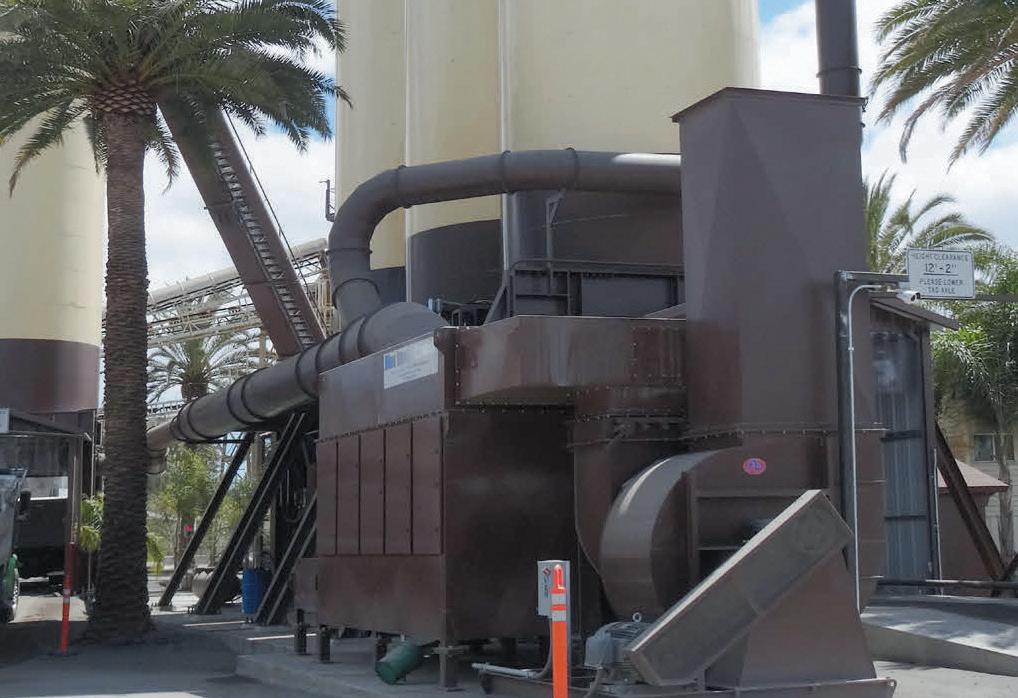




Blue Smoke Control® and X-VOCS™ from Butler-Justice, Inc., capture and filter blue smoke and odors from emission points in your plant — with 99.9% overall efficiency.
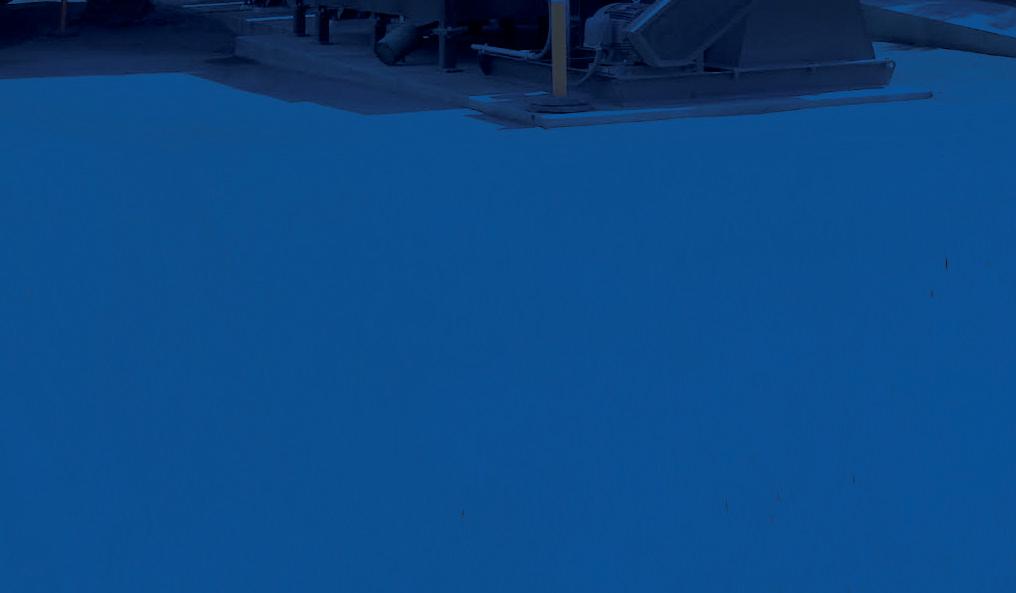

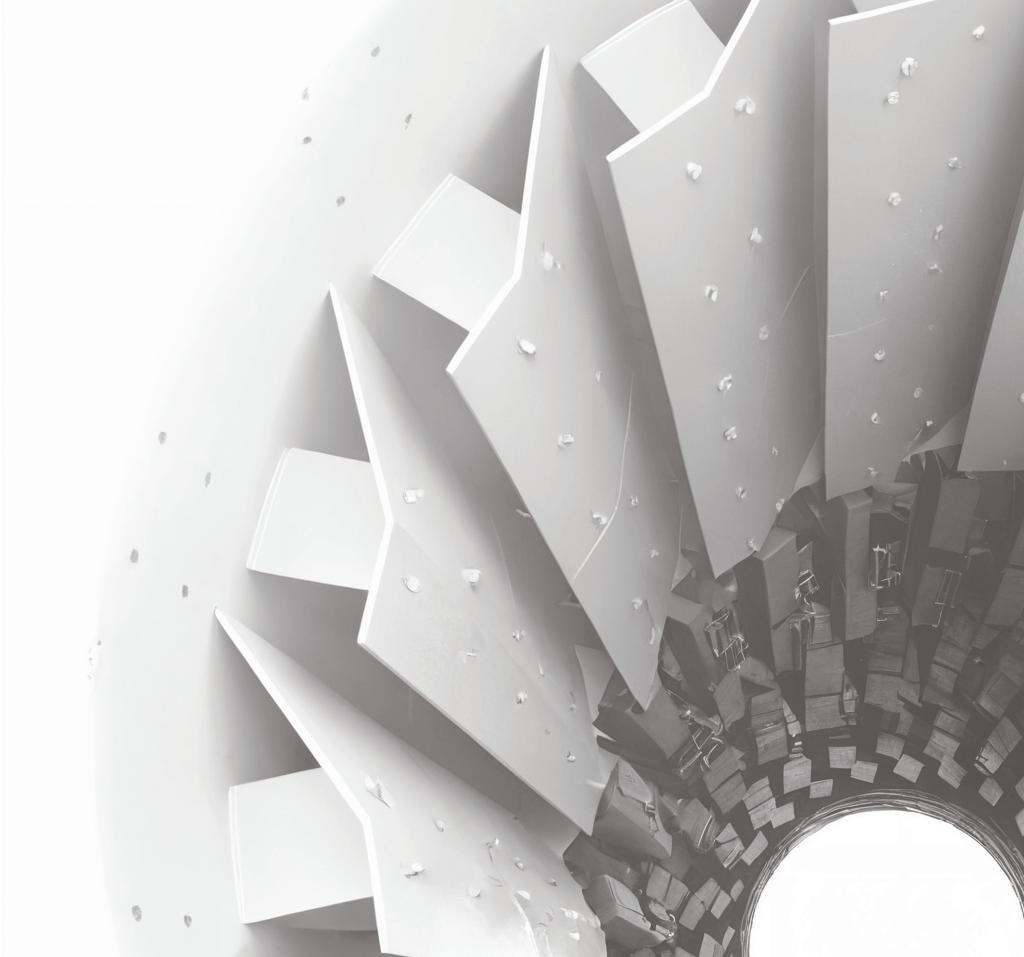
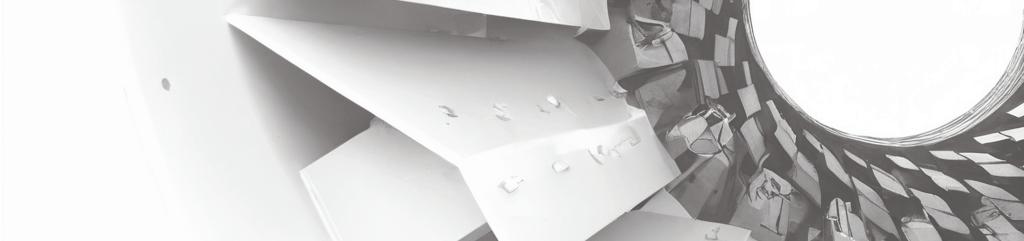
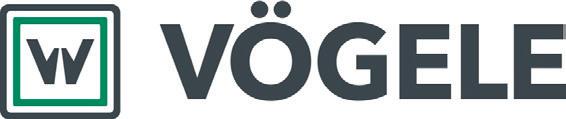
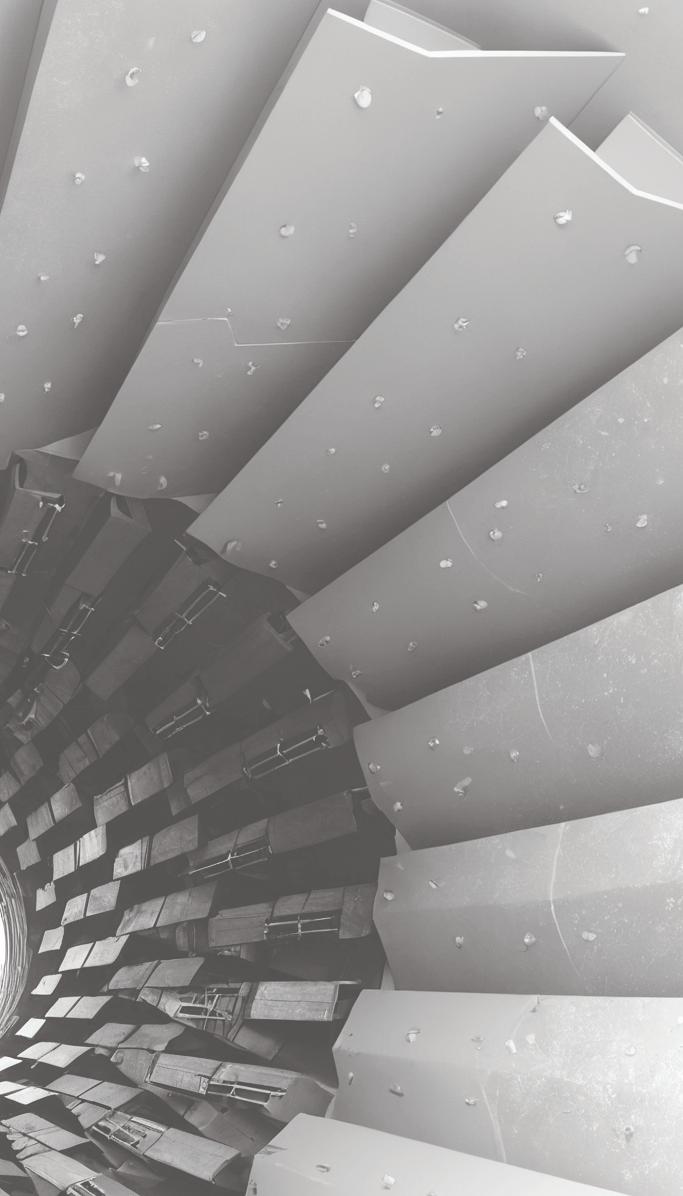

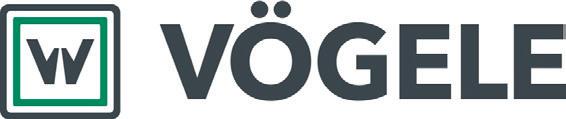
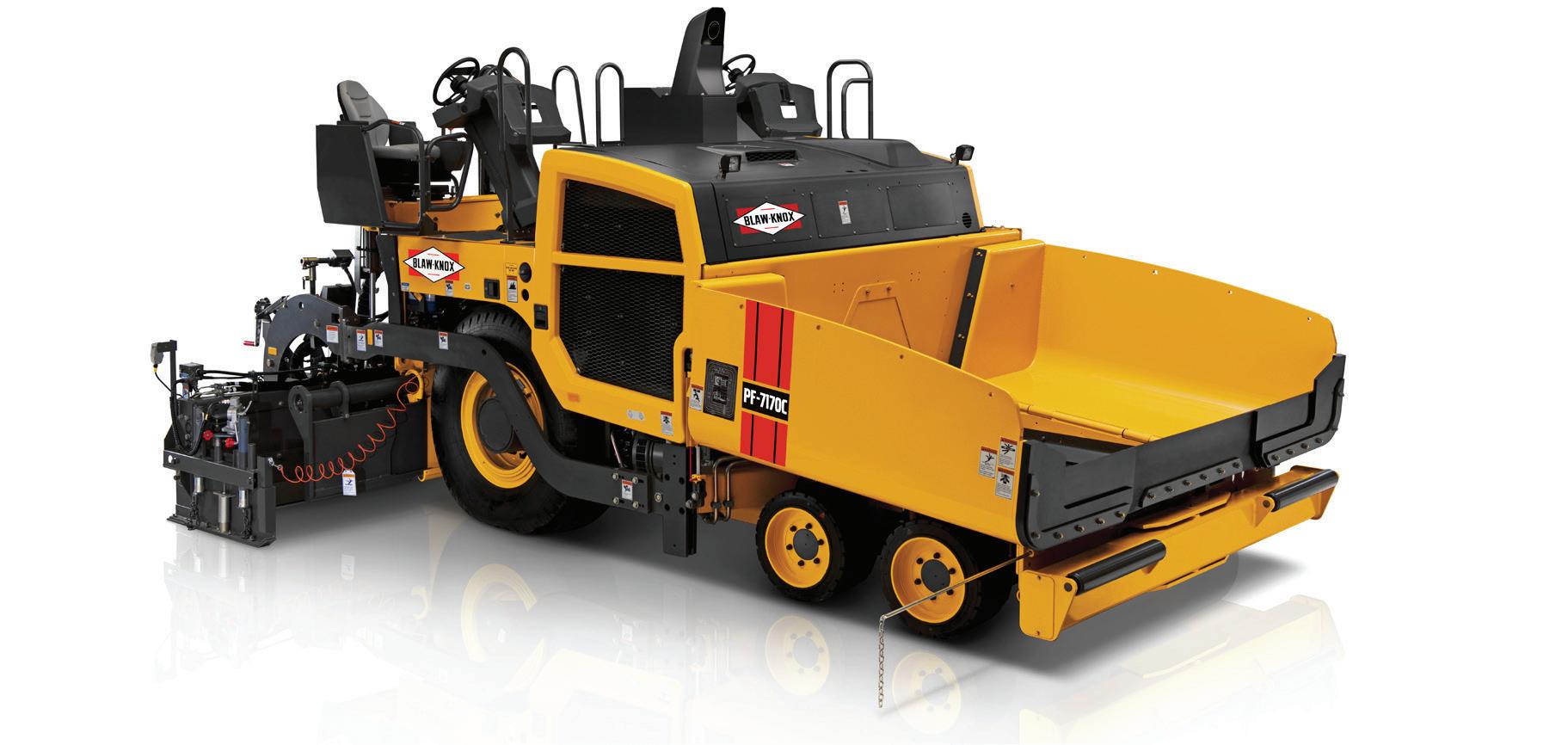
BLAW KNOX
The all-new Blaw-Knox PF-7110C tracked paver combines all-around visibility, ease of operation and a new powerful Cummins 235hp engine for the ultimate in dependability and efficiency. The turbo-charged diesel engine provides more torque and less weight in a more compact package, letting you power through steep grades with confidence. Coupled with the proven Blaw-Knox durable track and automatic tensioning system, the 7110C ensures smooth and consistent paving power on any terrain.
Blaw-Knox, The Legacy lives on.
Blaw-Knox
Blaw-Knox

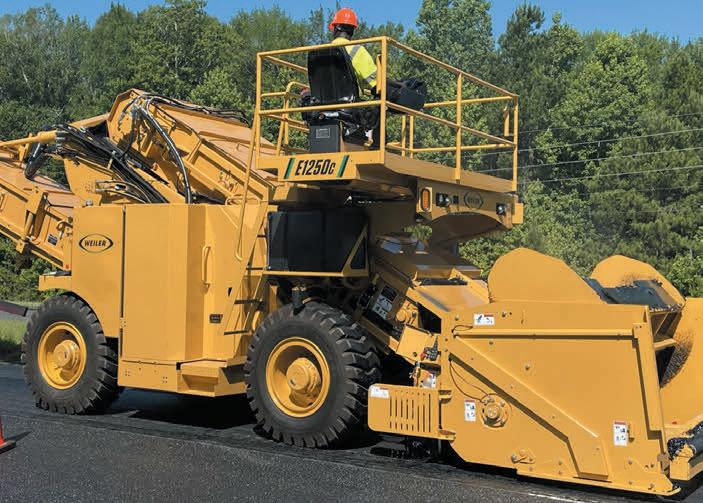
Blaw-Knox
LEADING THE WAY
Weiler Material Transfer Vehicles lead the way with proven innovations to provide the lowest cost per ton of operation.
Innovative and reliable operator friendly features such as paver hopper management system with distance to paver, storage hopper management and auto chain tensioning.

Clam shell doors and full width drop down floors provide unmatched access for cleanout and maintenance.
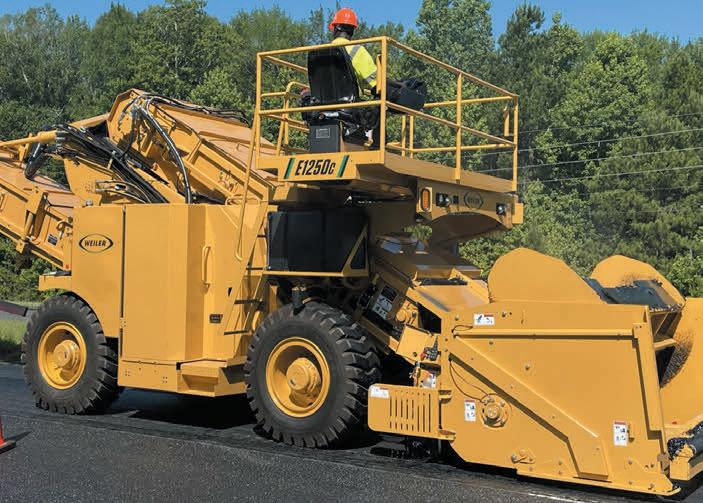
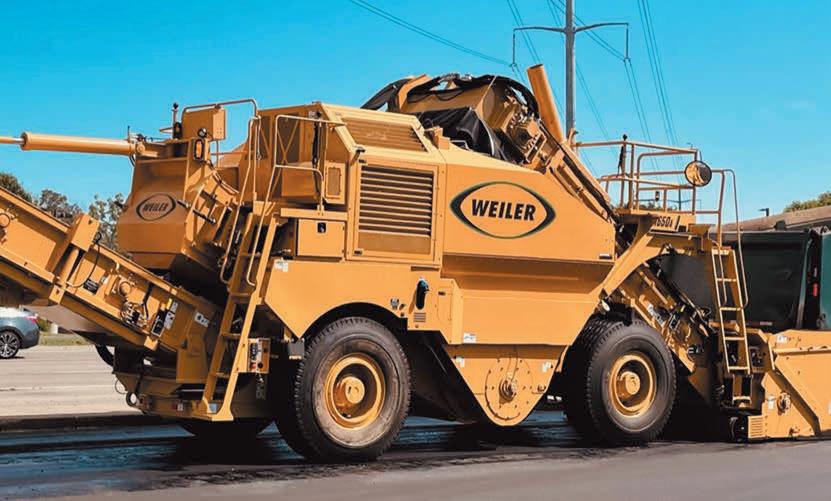
Variable speed elevator and conveyors meet production requirements while minimizing wear.
The multiple, incremental improvements to the 4th generation of chains, sprockets and augers are retrofittable to all machines and provide increased wear life.
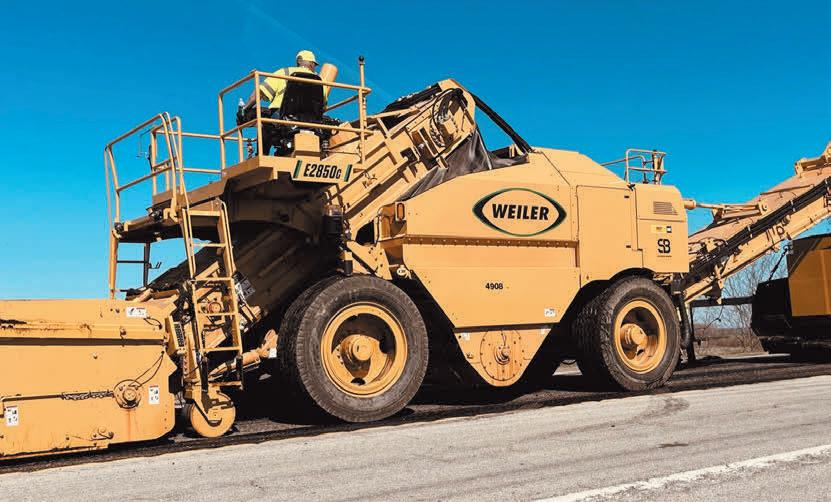
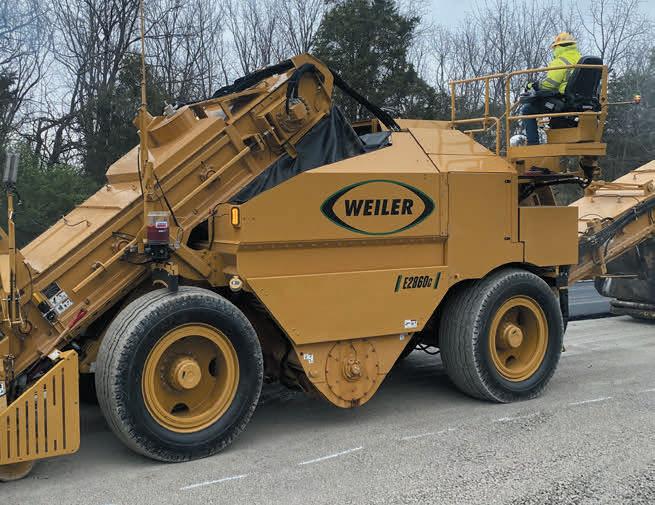

LEEBOY
LeeBoy features a broad range of commercial class pavers to meet any contractor’s needs. All the models are simple to operate, maintain and service while offering top mat quality provided by the Legend Screed.
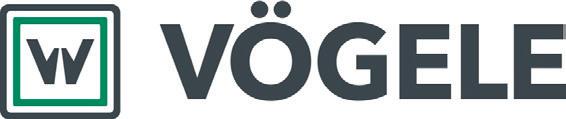
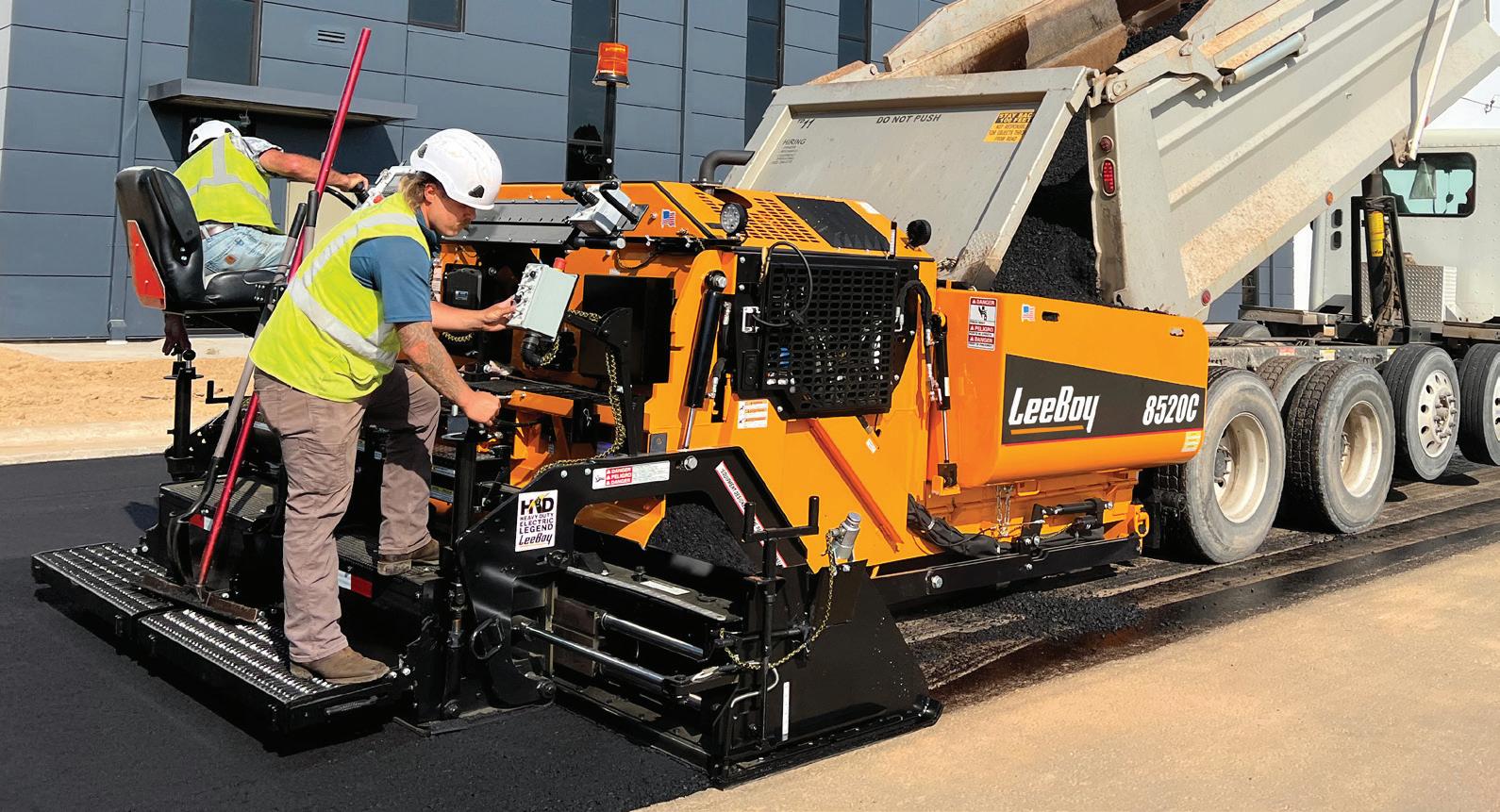
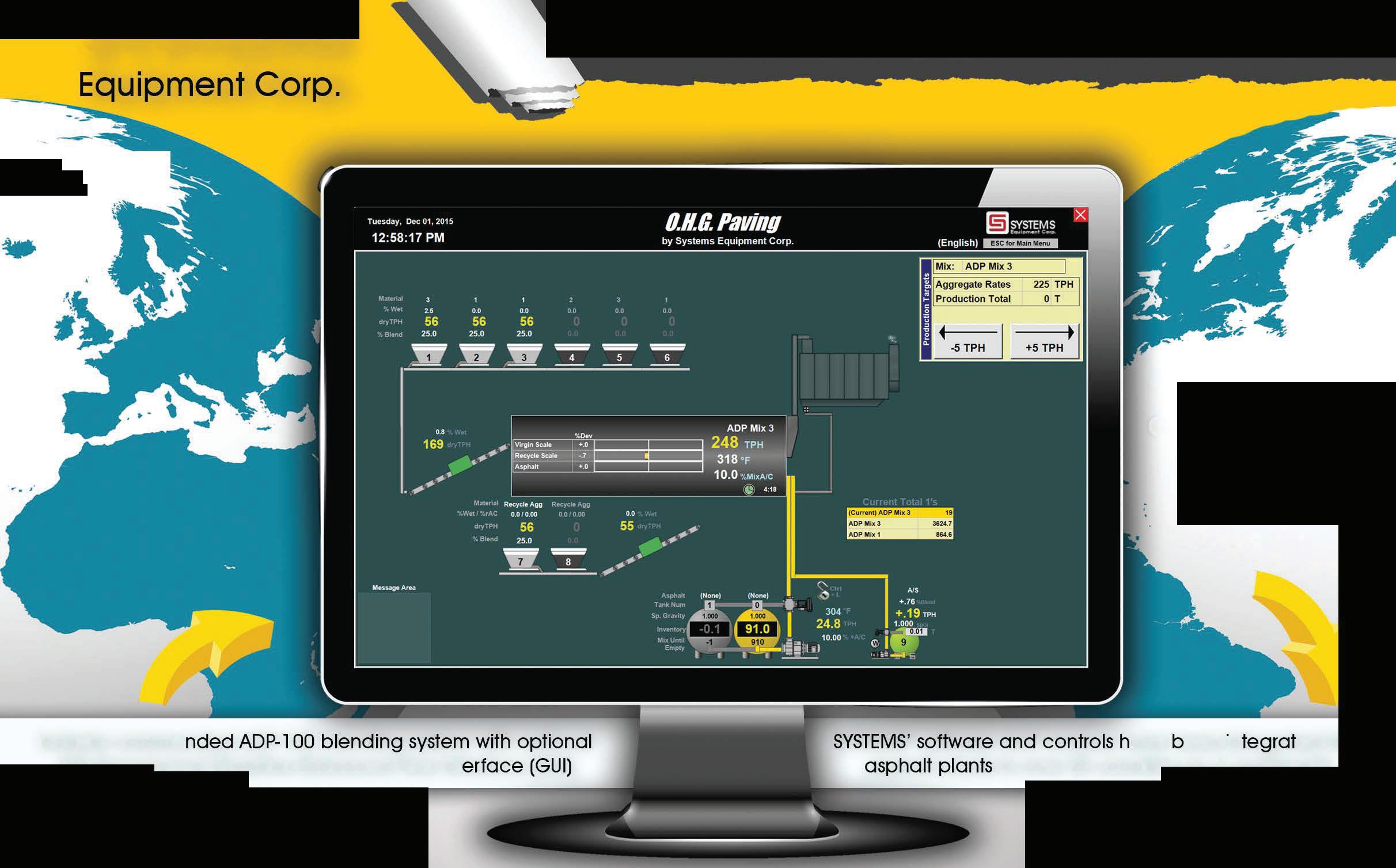

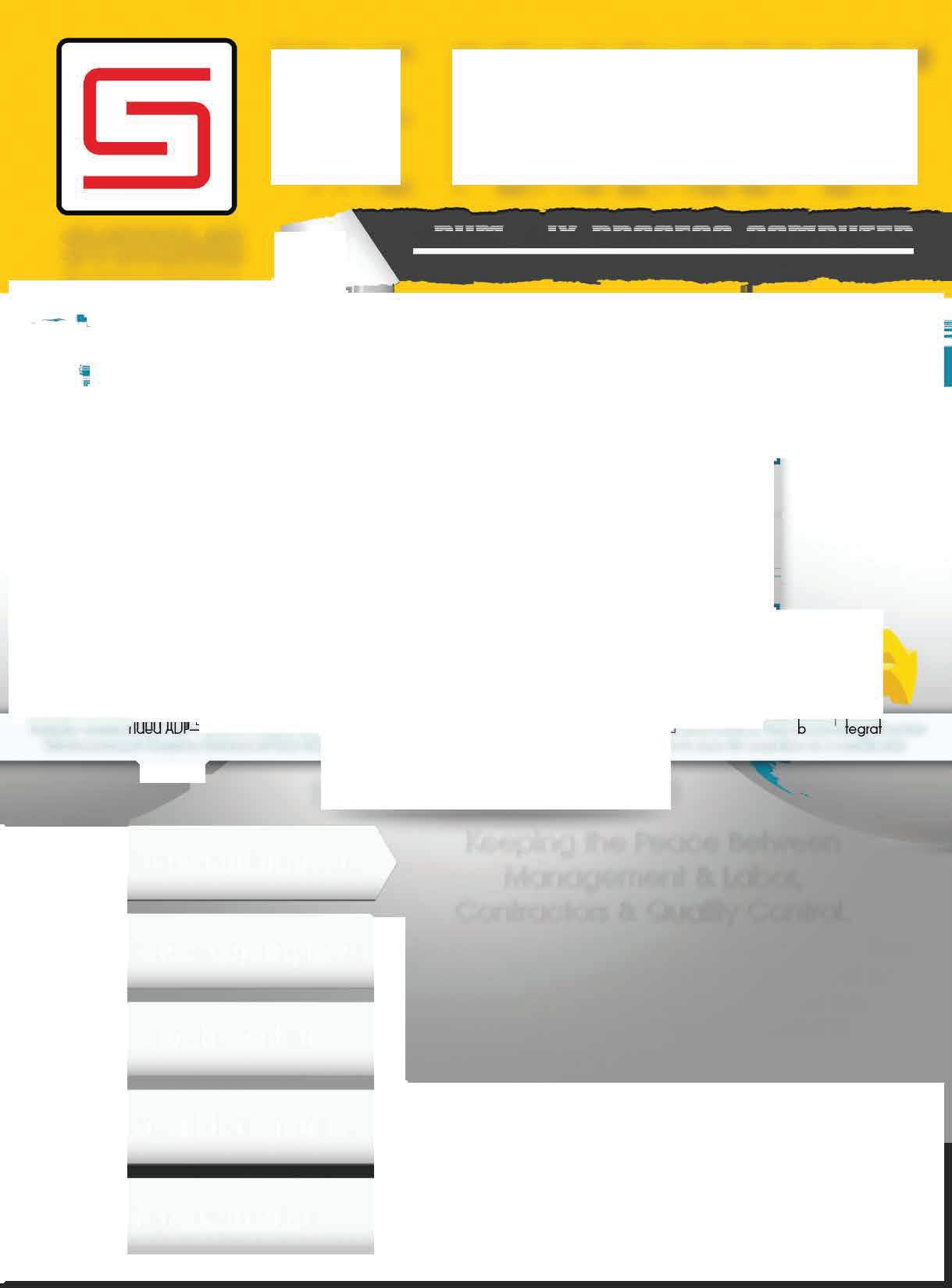

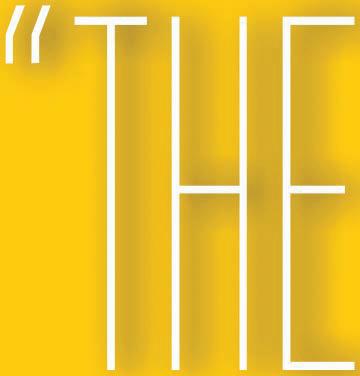
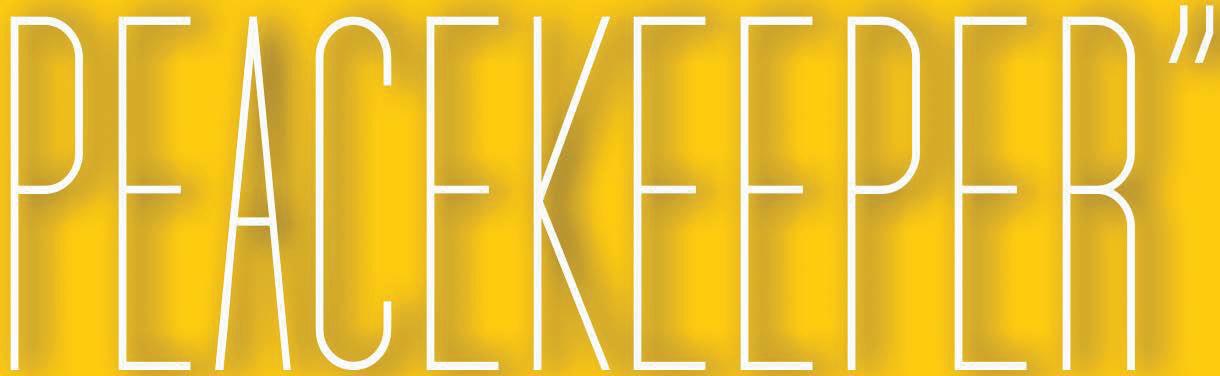
Known For Reliable Automation Systems!
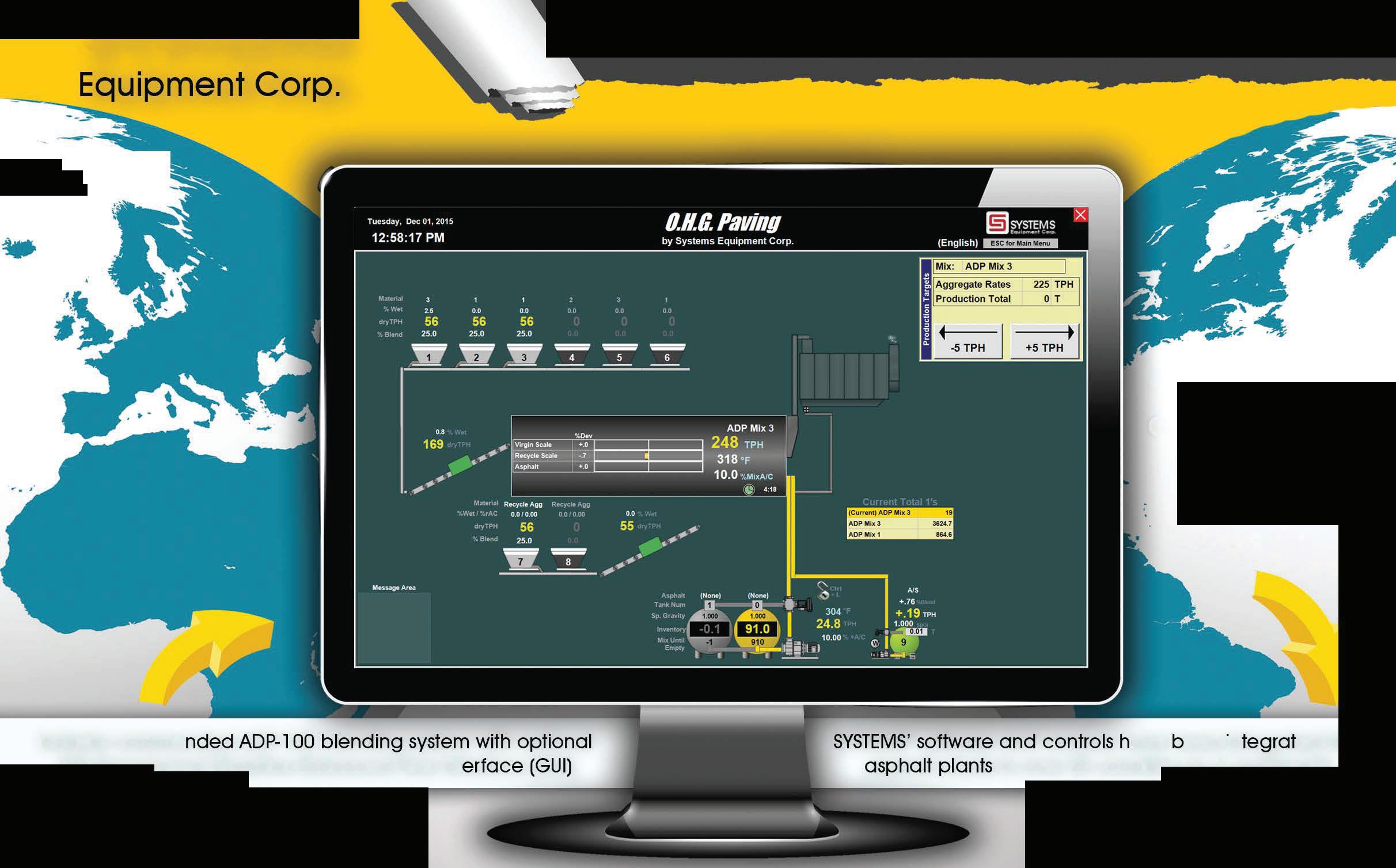
Keeping the Peace Between Management & Labor, Contractors & Quality Control.

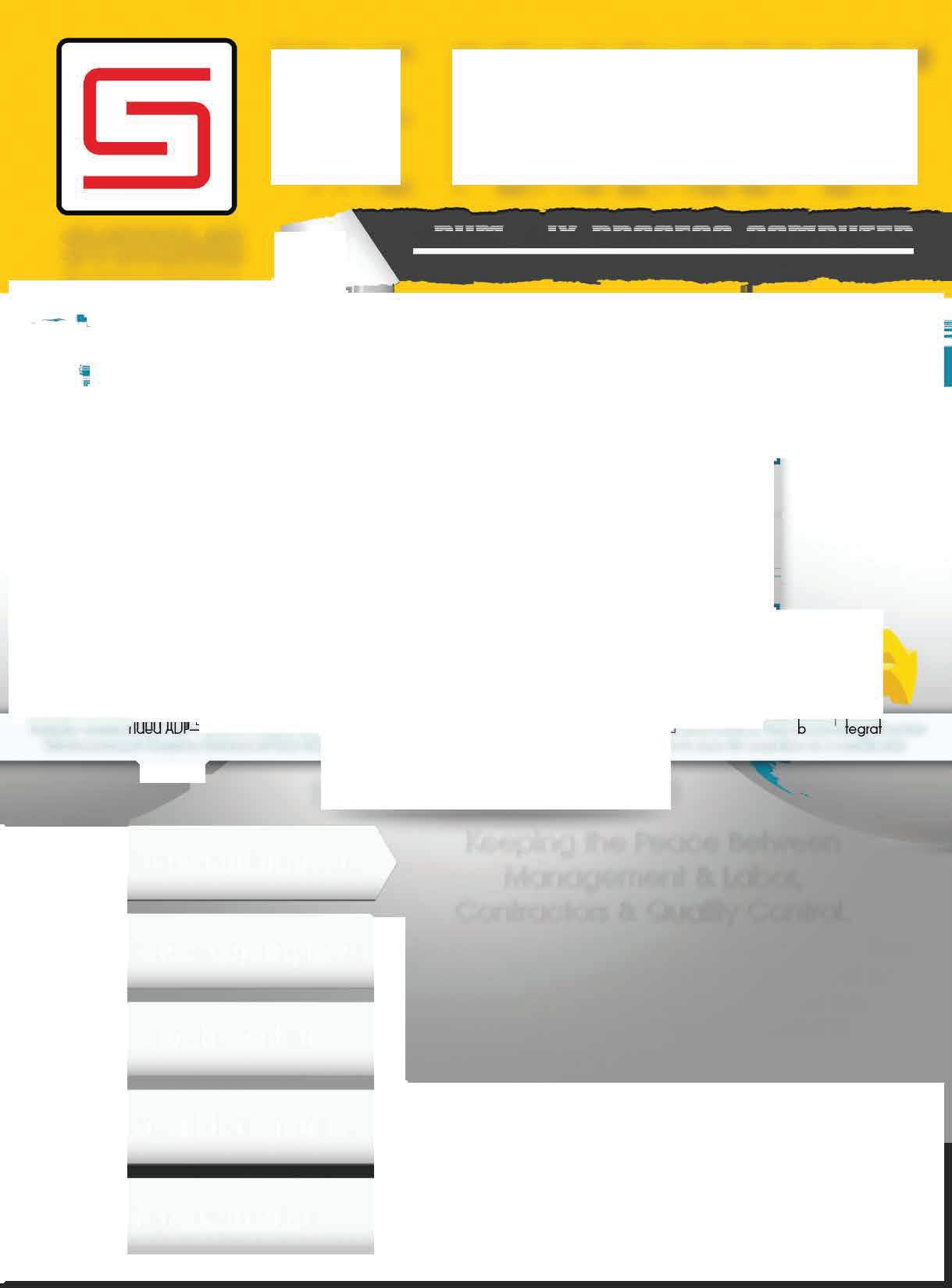
How Crushing And Screening Became A Major Industry
One CEO’s savvy solution started a new industry in North America.
In 1984, Eagle Crusher Company found itself in a quandary. Severe deterioration of company sales caused by the demise of its portable coal-crusher line forced the company to find a new direction. Susanne Cobey, then-vice president of sales and finance, knew of customers’ failures processing asphalt and concrete with rebar with the traditional aggregate jaw and cone, and she set out to find a viable solution as there was not an established recycling industry at the time.
Susanne’s research worldwide led her to a unique Andreas style impactor in Germany that she knew was the answer, as the Andreas impactor had been successfully used for processing debris in war-torn Europe following WWII, but had been forgotten by the time producers here had set out to process asphalt and concrete with rebar using jaw crushers. She then had an Eagle Crusher plant, the Jumbo 1400, designed around the Andreas impactor that had been so successful after the war.
The first Jumbo 1400 customer was awarded a contract rebuilding the runways at Wright Patterson Airforce Base, near Dayton, OH. By recycling the concrete and using it as base material when all the other contractors had quoted only virgin material, the contractor made nearly $1 million on the job. The North American commercial industry for recycled concrete with rebar and reclaimed asphalt pavement (RAP) was born, and the idea of using impactors, again, for recycling resonated around the world.
Despite her father’s insistence that recycled concrete and asphalt was just a
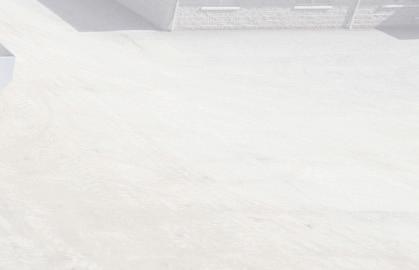
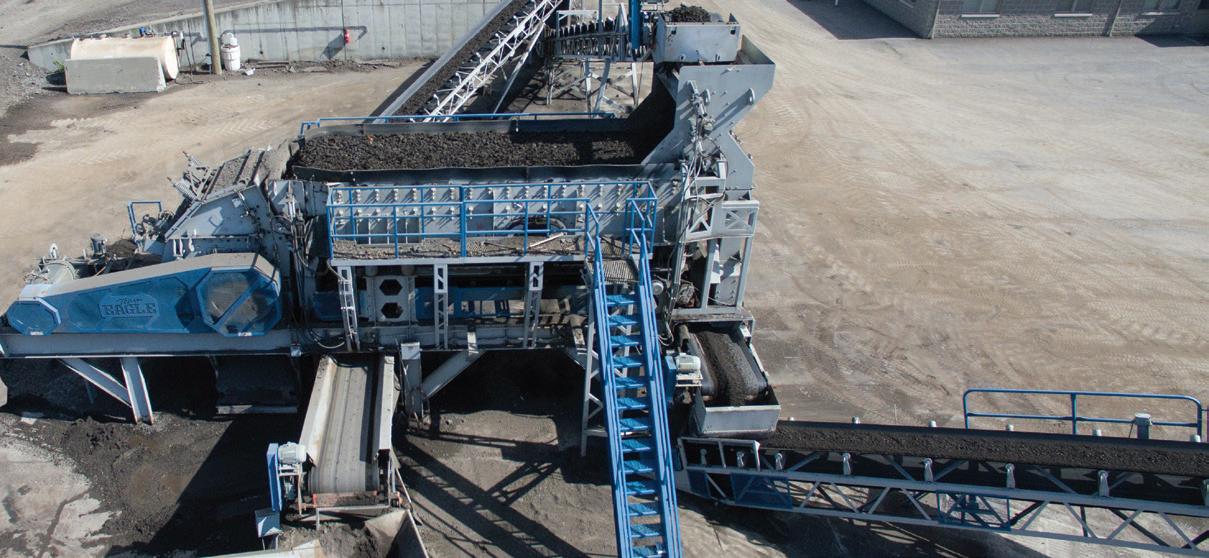
fad like the portable coal crushers had been, Susanne persisted in her vision to build Eagle Crusher’s commercial recycling equipment line into the market’s leading portable recycling equipment that it is today.
MORE INDUSTRY-LEADING ACCOMPLISHMENTS
Also in 1984, Susanne established a new marketing approach that led to producers getting their equipment, faster. Up to that time, crushing-and-screeningequipment manufacturers generally built equipment to customers’ specifications. Instead, Susanne decided to create a line of recycling equipment that she marketed as “Off the Shelf,” readily available for quick delivery. Today, that approach to crushing-and-screening-equipment manufacturing is the norm.
By 1994, Susanne desired to develop an even more innovative and robust impactor. She set her engineers to task to design a new impactor, using three rotor bars instead of four, by combining the solid rotor of a New Holland primary impactor with the three-bar rotor Stedman had perfected for use in its Grand Slam secondary impactor and the basic design of the Andreas impactor. Under Susanne’s leadership, Eagle Crusher introduced its own UltraMax® line of an unequaled, horizontal shaft impactor, featuring a unique, sculpted, solid steel,
The Eagle Crusher MaxRap(R) is an onsite commercial recycling system for crushing and precise screening of RAP for product consistency, productivity, and profitability. Integrates with any asphalt plant automation.

three-bar rotor, the industry’s heaviest, for the recycling and aggregate markets.
PHILOSOPHIES FOR INNOVATION
Understanding early on that a company is only as strong as its people, Susanne uses two business philosophies. One is to believe in yourself, in others, and God, and everything is possible. With this philosophy, Susanne inspires her team by bringing them with her to the table—a table where everyone has a voice, with no one voice stronger than another. Out of this collaboration of equals, great ideas are born, and the solutions to effective implementation, realized.
A second philosophy Susanne practices to achieve great things is what she calls, “Being stupid, crazy, stubborn, and lazy. Stupid enough to think that something can be done, crazy enough to actually do it, stubborn enough to stick with it, and lazy, because no one can accomplish something by oneself.” No matter how good one’s ideas are, it takes teamwork to make those ideas reality.
SUSANNE’S CAREER PATH
The idea for Eagle Crusher began in the early 1900s when C.L. Woods, an Ohio distributor of Eagle Tractors, had a vision. Woods observed that farmers were taking the rocks from their fields and placing them along the

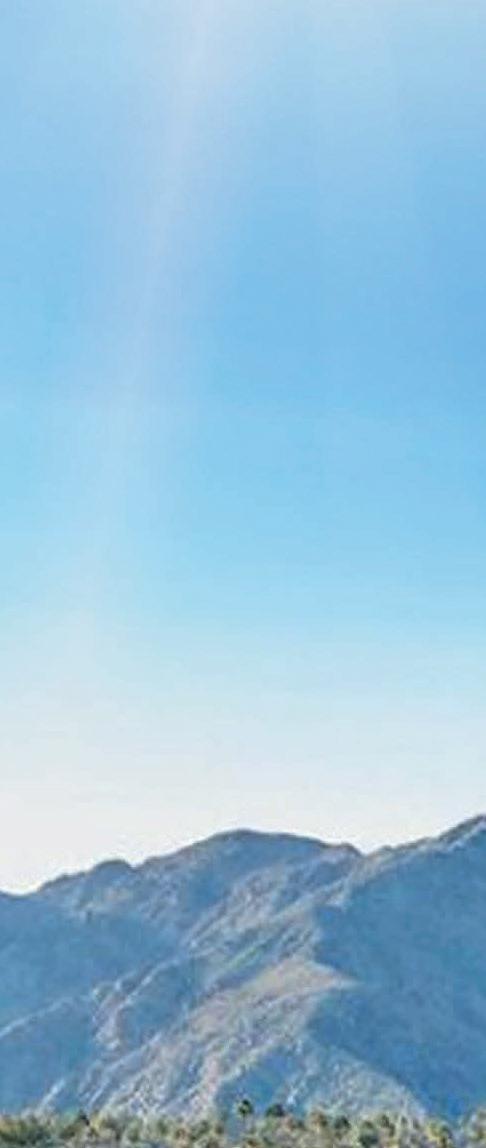
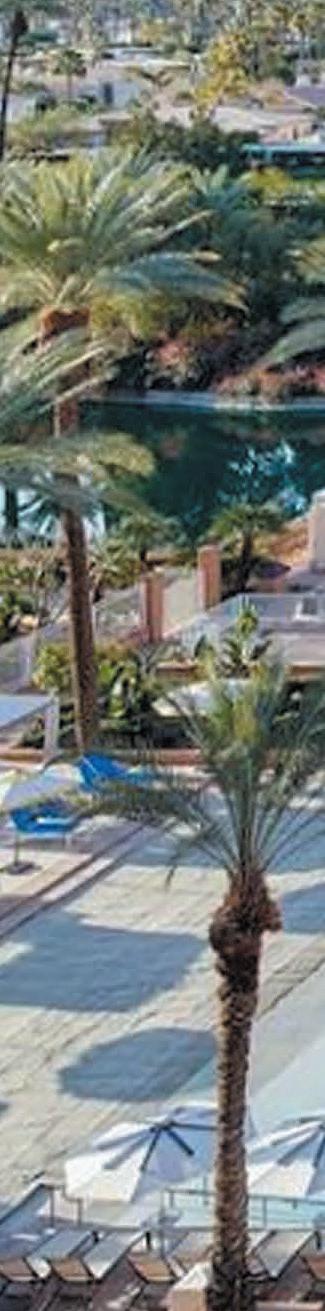
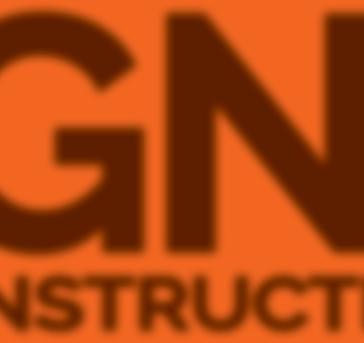

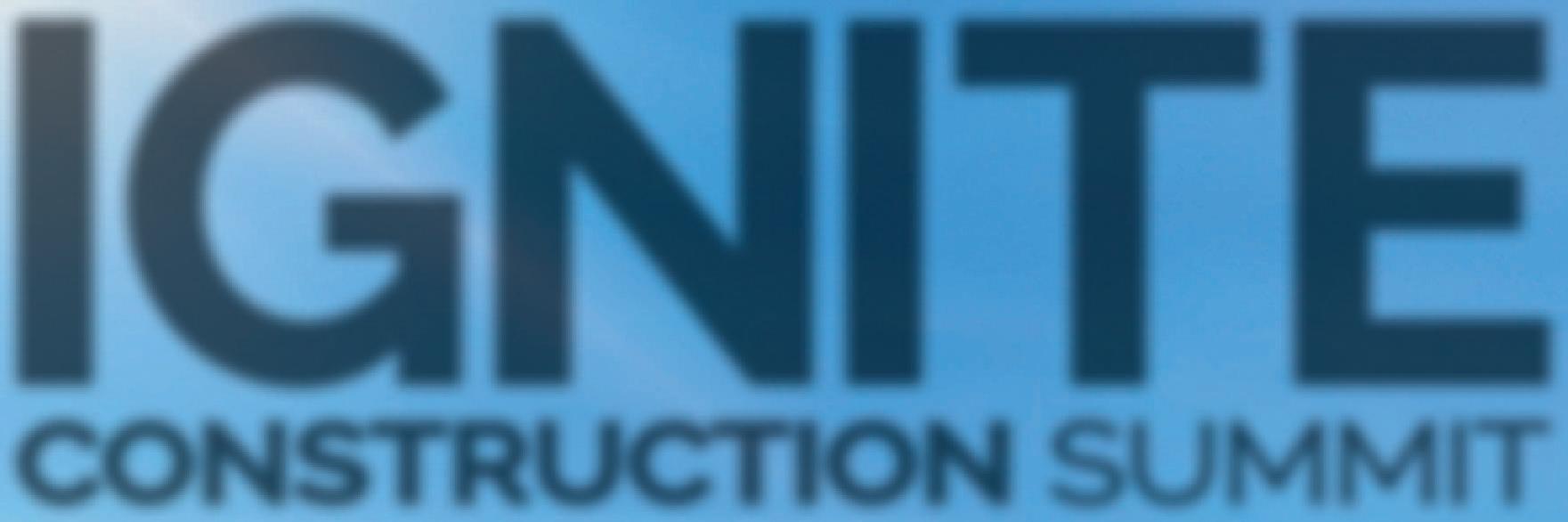
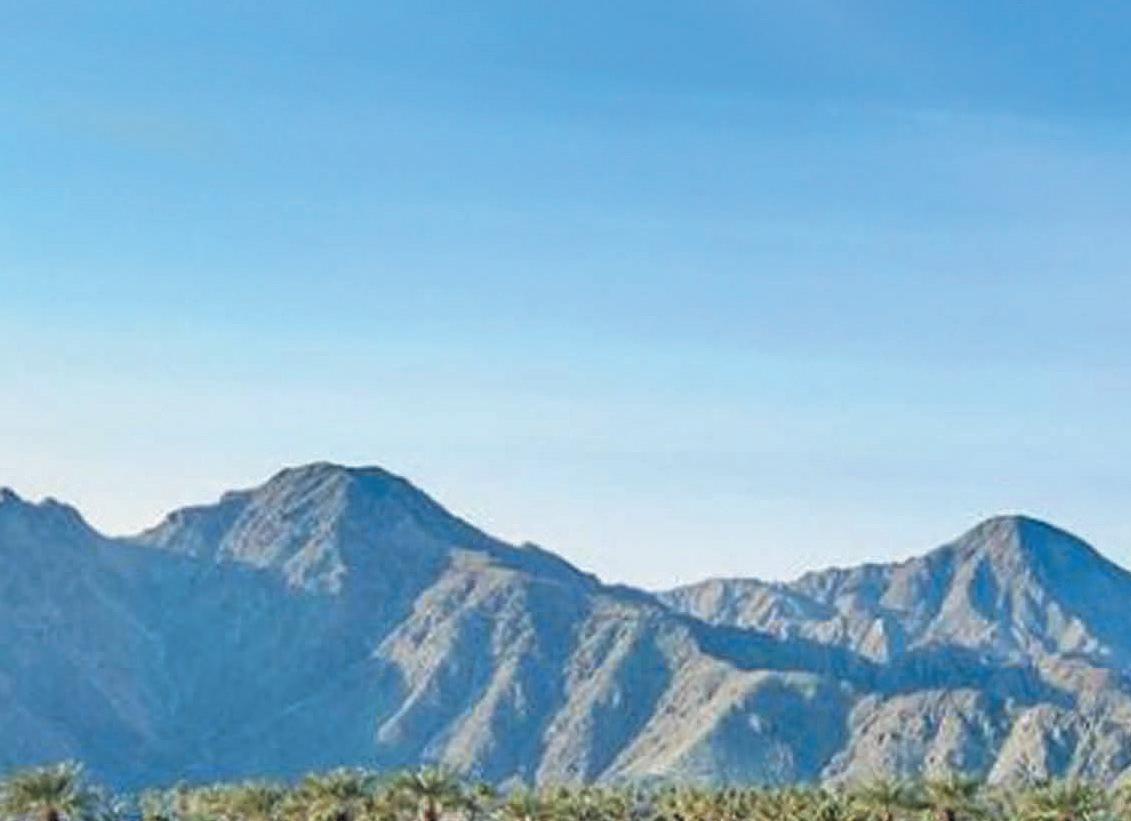

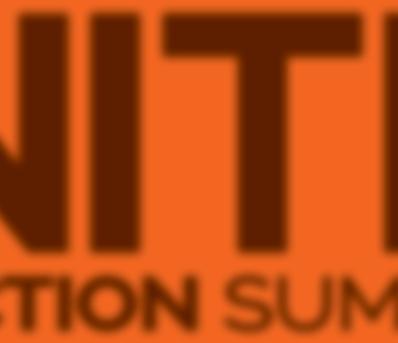
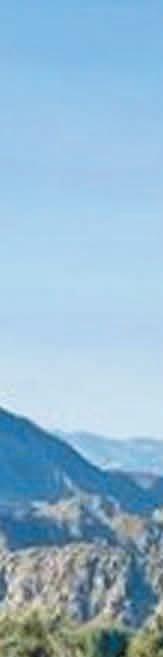
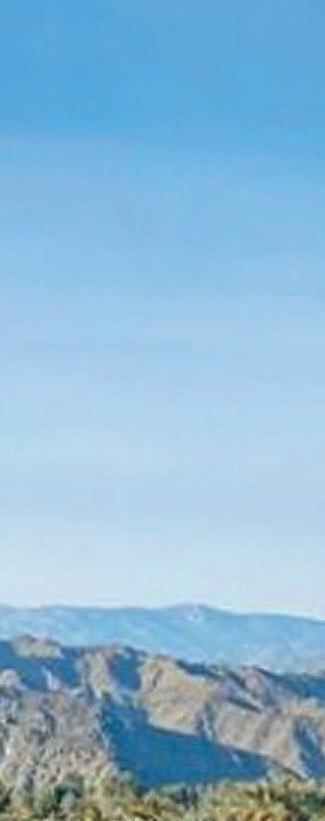

1. A TWIST ON TYPICAL NETWORKING - Engage in Conversations with your peers, while participating in daily networking receptions, and our inaugural golf outing. This event includes corn hole, golf, signature drinks and more!
2. A STAY AT AN AWARD-WINNING PROPERTY - Staying at the Renaissance Esmeralda Resort & Spa will allow the perfect mix of relaxation, fun, and education!
3. EDUCATION LASER-FOCUSED FOR THE FUTURE - Gain access to information and tactics that you can put to use as soon as you get back to the office. Hear from industry experts and receive the resources you need to succeed.
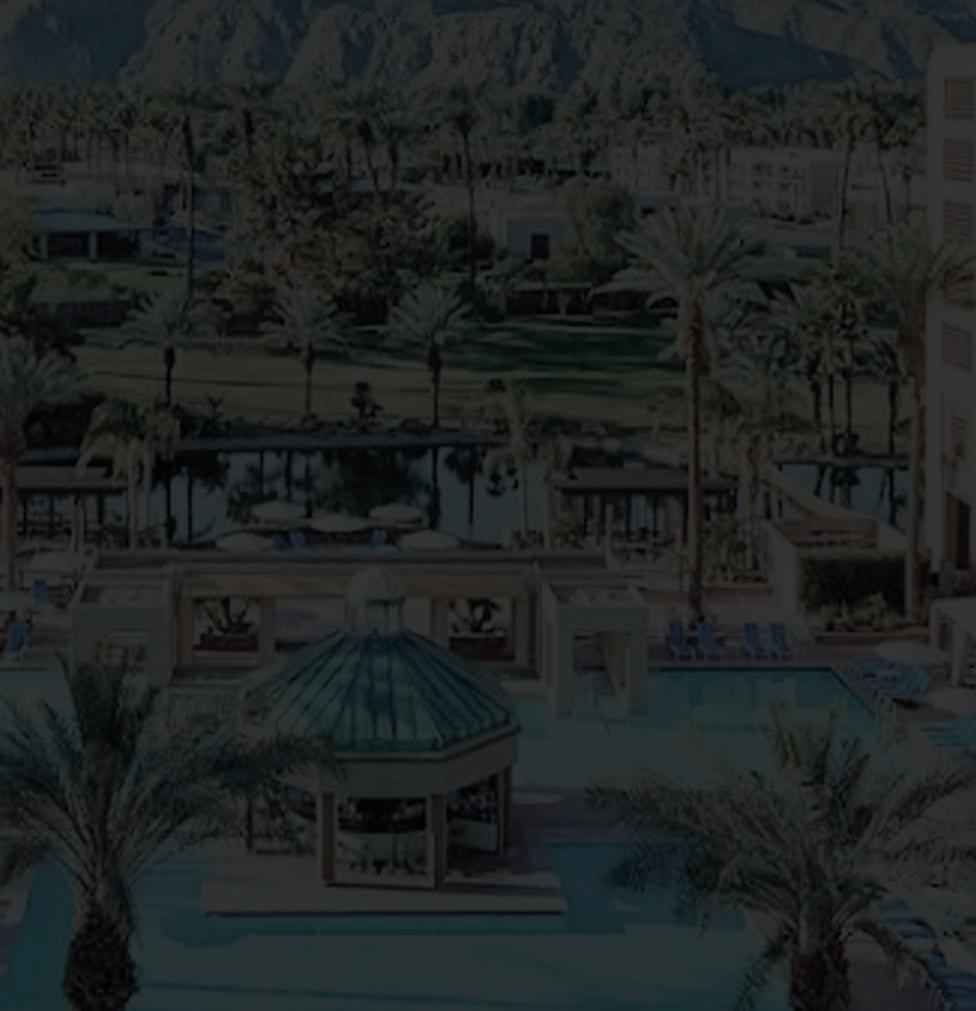


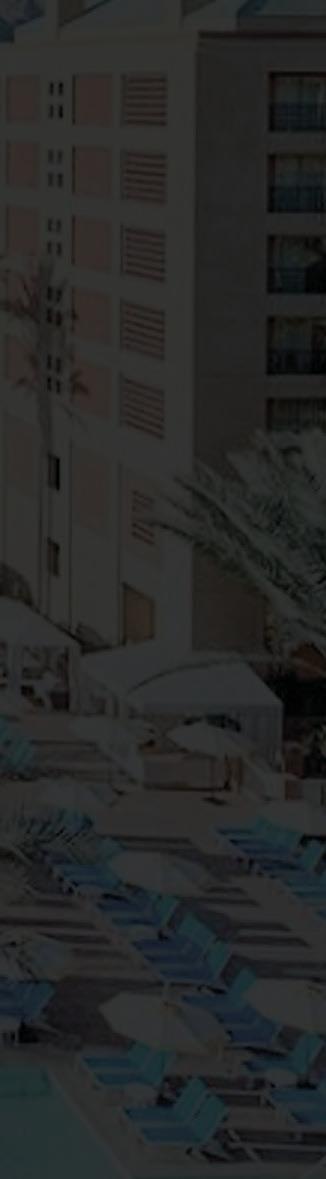
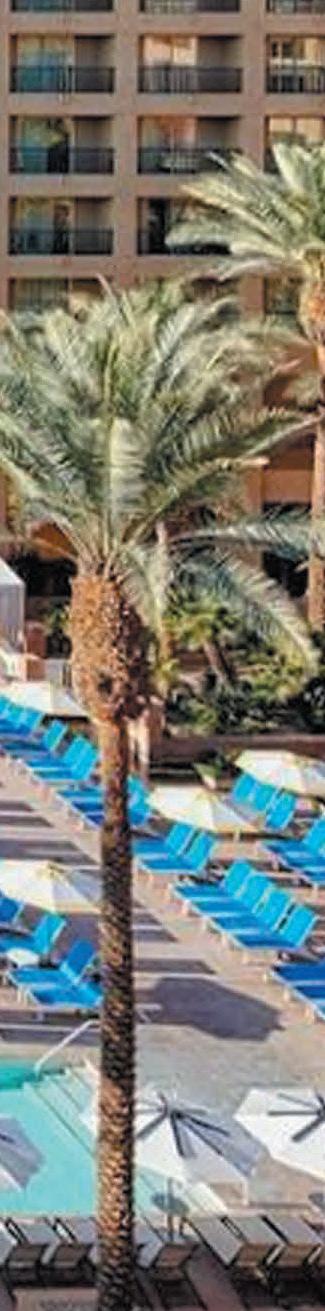
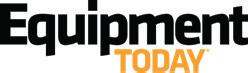
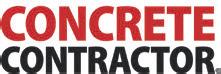
dirt roadsides. He imagined, “What if someone created a small jaw crusher that could mount to the front of a tractor to crush the stone and use it to improve the roads?”
Woods approached Eagle Tractors with the idea, but when the company didn’t share his vision, he founded his own company to manufacture the jaw crusher he had imagined. Thus, in 1915, in Kenton, OH, Eagle Crusher Company was born. While Eagle Tractors eventually ceased production, Eagle Crusher Company continued to innovate and expand. To help with expansion, Woods sold Ralph Cobey, Susanne’s father, a share of the business.
In 1952 after Woods retired, Ralph bought Eagle Crusher Company outright and brought it to Galion, OH where his other businesses were located. Ralph sold Eagle Crusher company in 1964; then, bought it back in 1970 after it had been dismantled.
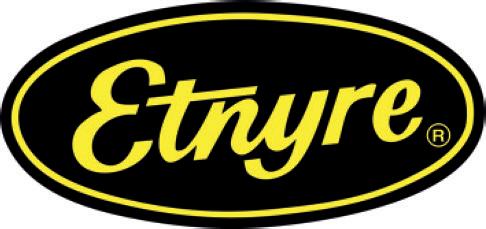
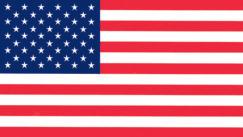
In 1974, Susanne became only the tenth employee when she was hired as parts manager. She advanced to sales manager, VP of sales and finance, and ultimately, president/CEO in 1990 when she was the only female running a company in her industry. In that same year, Susanne purchased the Stedman Machine Company in Aurora, IN.
After graduating from the University of Denver with a BS/BA in Finance and two minors, one in Accounting and one in Economics, Susanne started her career as a financial analyst for the Ford Motor Company. She was the first female ever hired for something other than an administrative support position.
HELPING THE INDUSTRY
In the 1980s, Susanne’s recycling insights allowed her to see the need for a recycling organization focusing on a wider range of recycling businesses than were currently being served. Collaborating
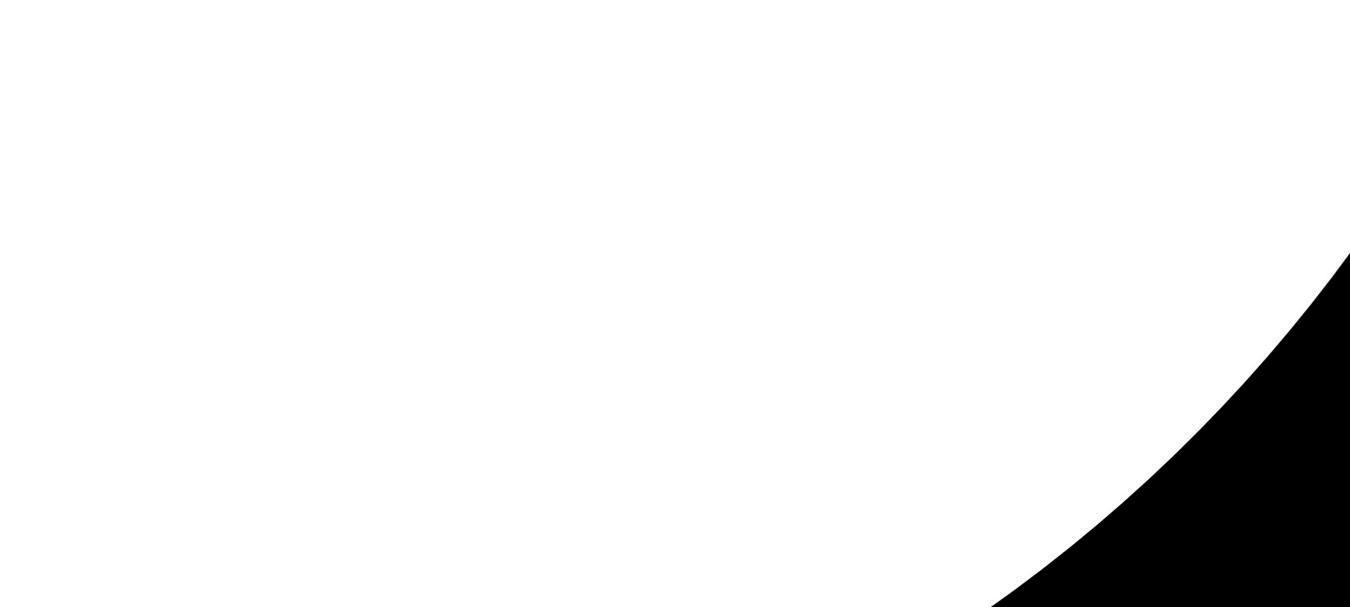
with Bill Turley of C&D World, together they came up with the idea for the Construction Materials Recycling Association, now Construction and Demolition Recycling Association. Eagle Crusher was the founding member.
As a female pioneer in a male-dominated industry, Susanne has dedicated herself to helping other women in the industry succeed, benefitting the industry as a whole to help it grow and thrive. Her advice to them has always been that you may have to work harder than the men to get your due recognition, but believe in yourself, and you will make your mark in the industry for future life success.
To help women overcome the challenges, Susanne has presented at Kaleidoscope Women’s Conference on the battle of breaking tradition, and she has addressed the topic of women in the industry in numerous videos and articles in which she has been featured.

Belt Designed for multiple materials
Truck mounts Available
Standard front to rear Shurco tarp
LiveBottom LiveBottom


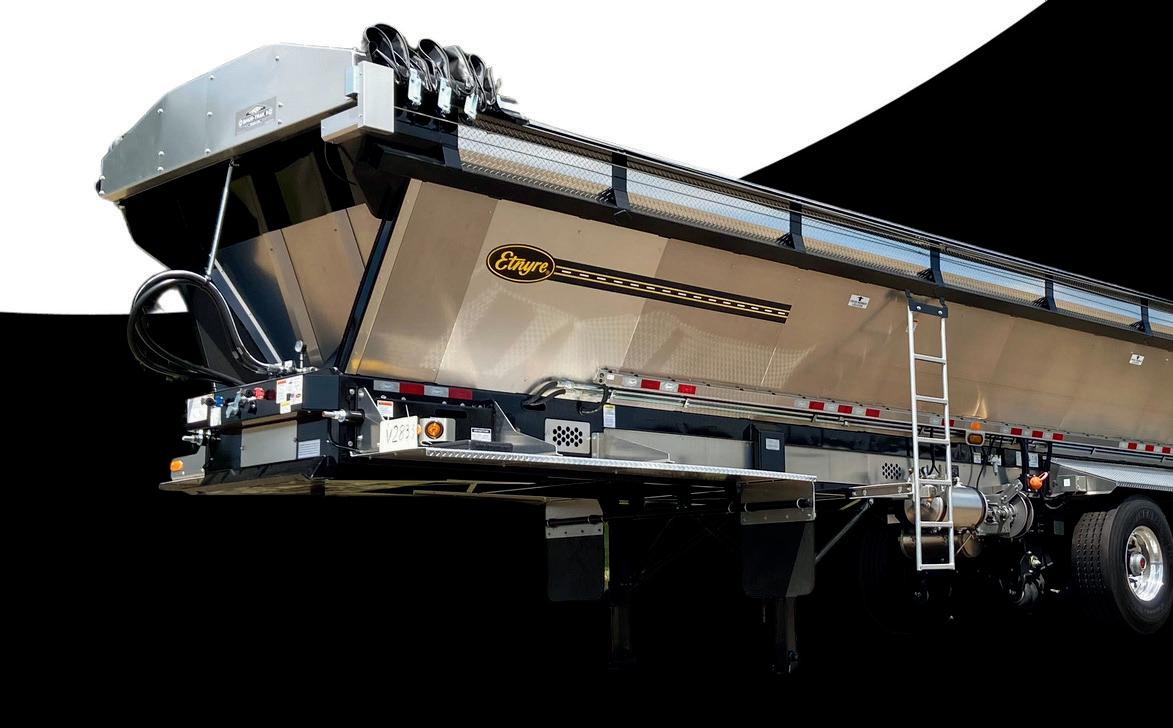

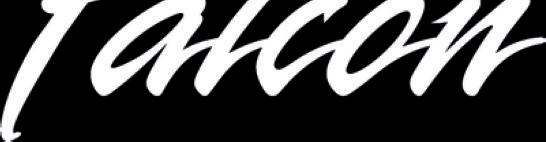
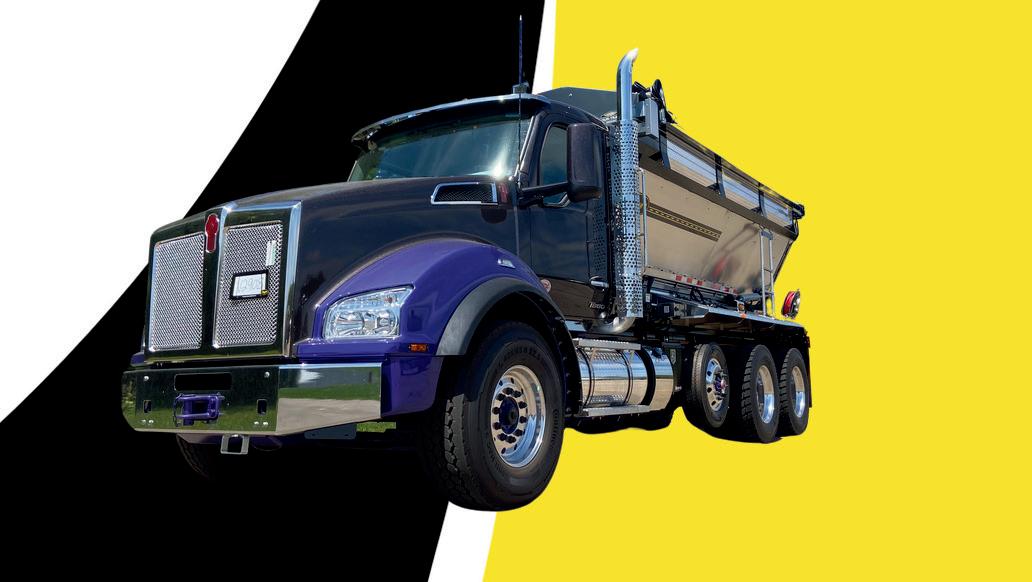
standard electric
Available bin extensions for more Cubic Yard capacity
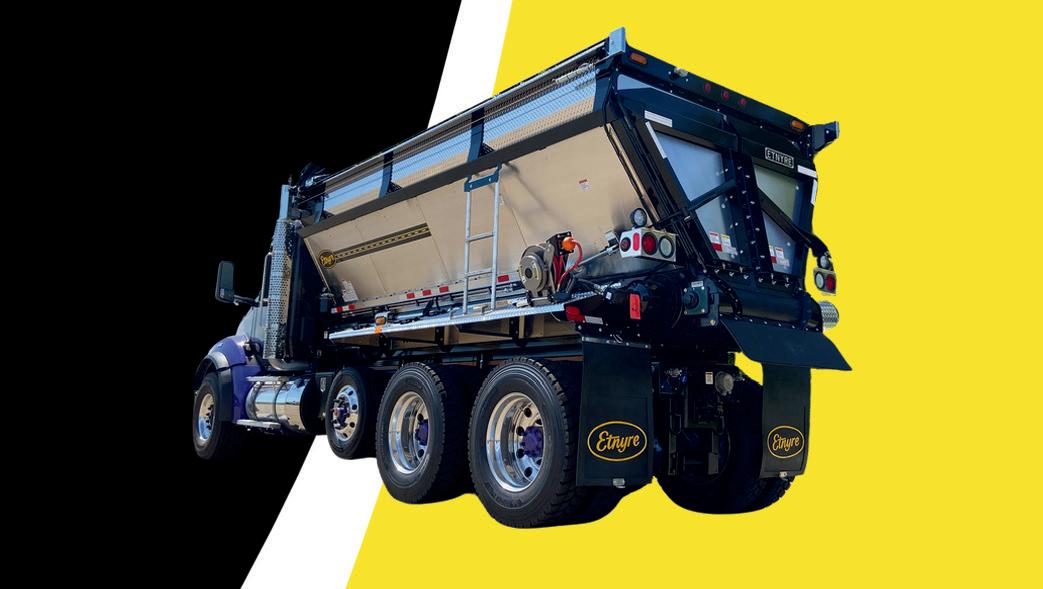


Large range of strandard capacities/lengths availble.
Optional washout tanks availble with electric or air powered pumps
Built for durability with 450 Hardox bin walls & heat retention with 1” Thurmax insulation panels
Multiple axle configurations & capacities
Several rear door options: twin, hilift, hi-lift/bi-fold



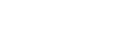
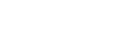




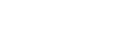

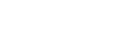
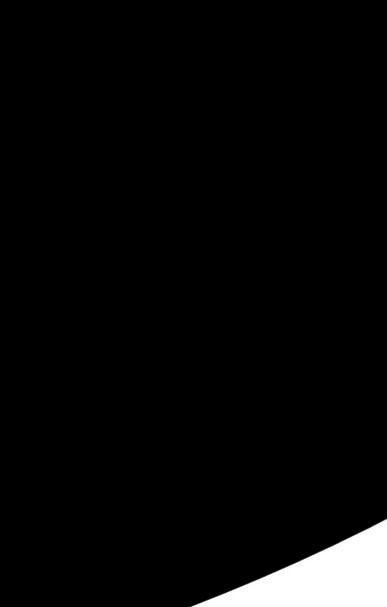

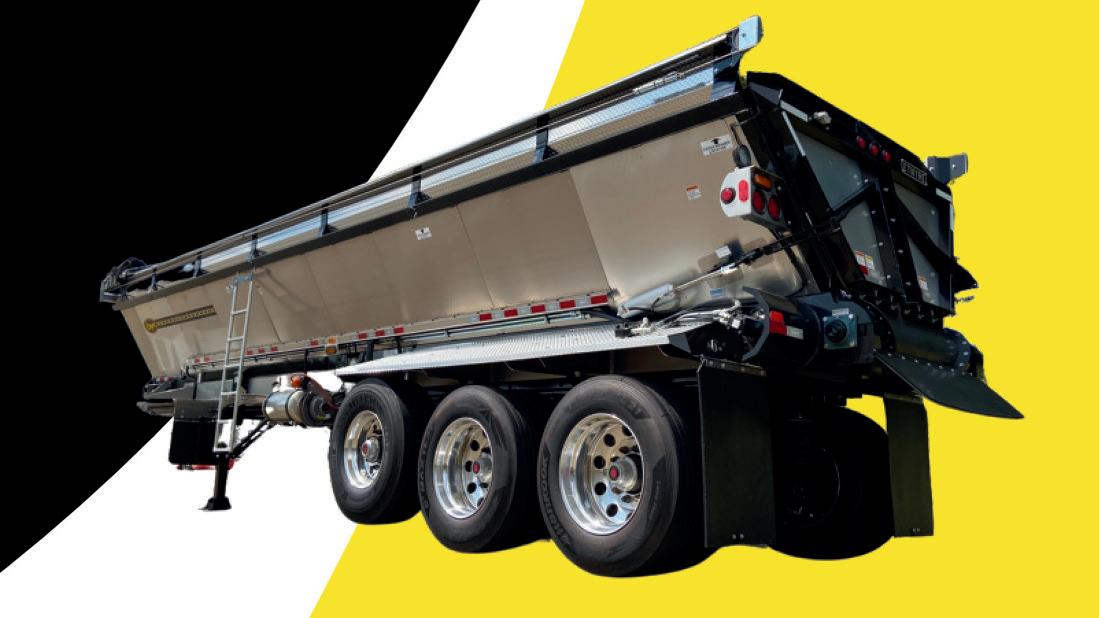
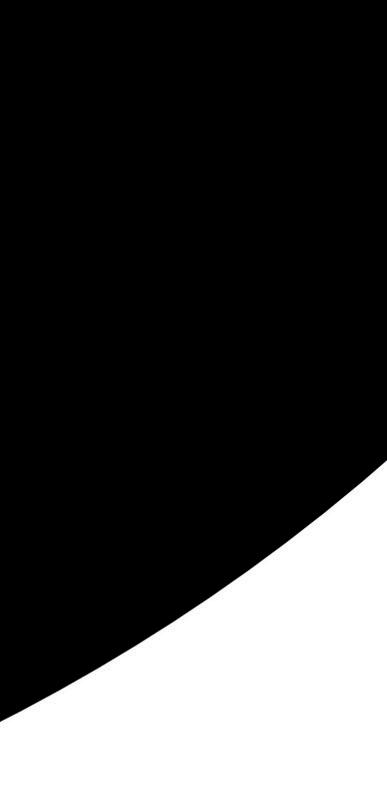
Think safety- No tipping of box eliminates overhead obstructions and potential rollover
42" wide belt helps prevent segregation
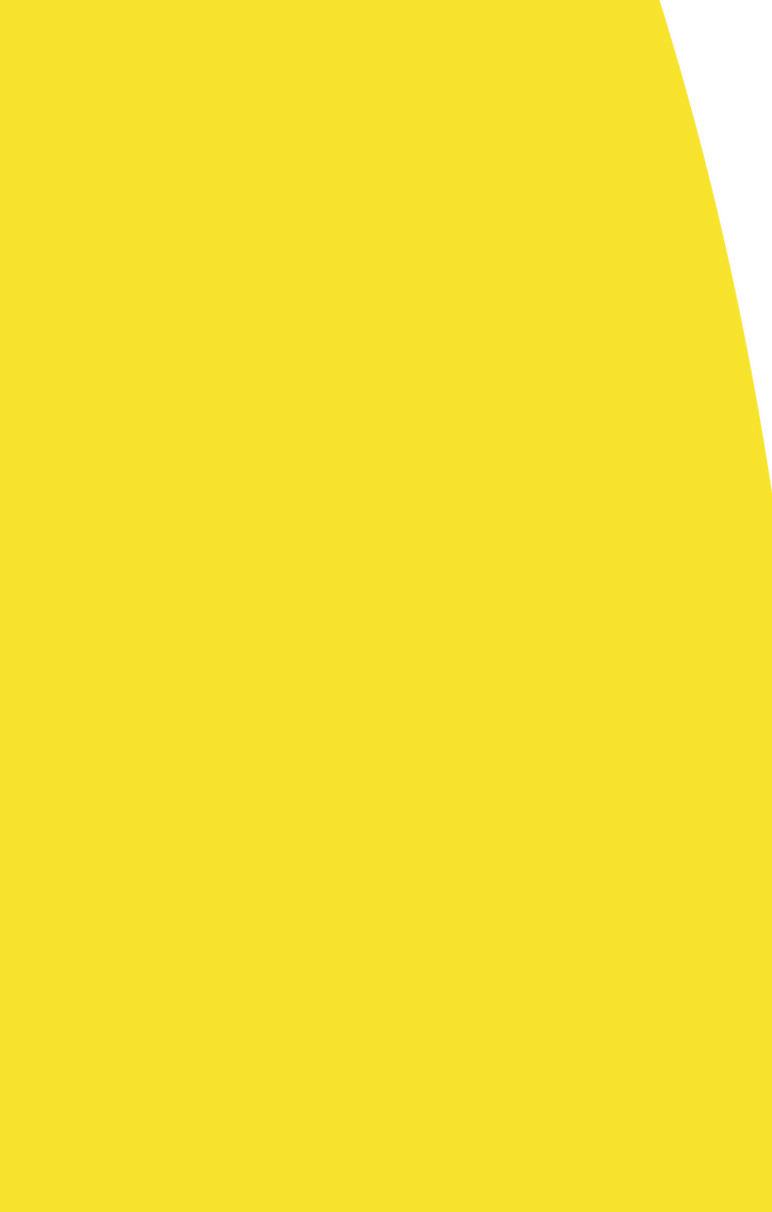


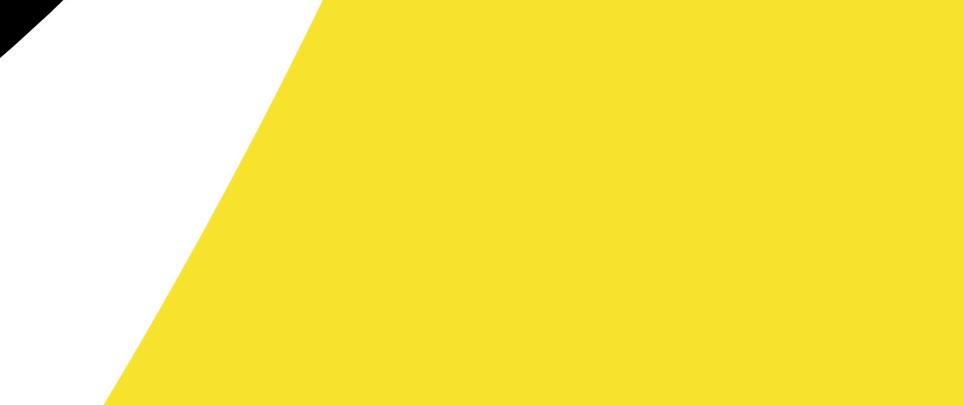

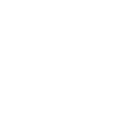
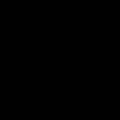
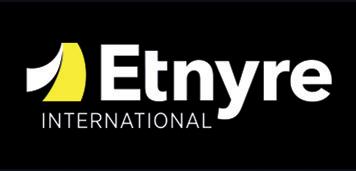
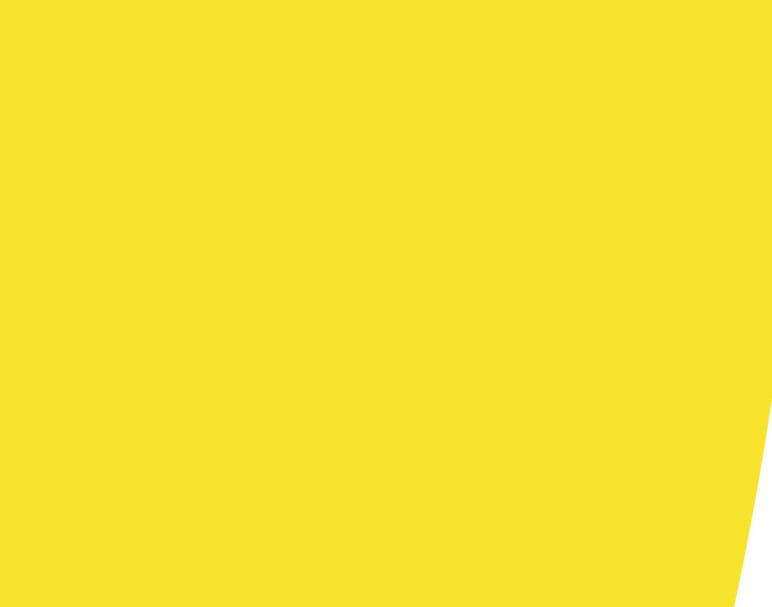
She has also served as a role model for both young women and men in her many commencement addresses and those young people she meets within the industry, sharing sound solutions to help them succeed.
Beyond helping individuals in the industry, Susanne is a believer in helping small communities, as well, especially rural ones, by employing people and improving their quality of life. As Eagle Crusher grew from a small manufacturing company to become a key industry player, it could have been easier to relocate the company from its rural locations to a larger urban area where engineering, management personnel, and skilled labor would be easier to recruit and retain. Instead, Susanne continues to operate in the small, rural communities of Galion, and Bucyrus, OH, making a big difference to rural life there since the company’s inception more than onehundred years ago.
In fact, Eagle Crusher Company recently hosted the Association of Equipment Manufacturers (AEM) Manufacturing Express at its Bucyrus, OH manufacturing facility, celebrating Eagle Crusher’s employees, their families, and the local community, while highlighting the company’s contribution to American manufacturing and the U.S. economy.
AEM’s manufacturing express visited 80 manufacturers on its national tour.
REFLECTIONS ON THE RECYCLING INDUSTRY
As Susanne reflects on her contributions to the commercial recycling industry, especially in light of today’s focus on the three “R’s—reduce, reuse, recycle,” she says, “It’s a good feeling to know that your company is part of an industry that redirects waste into a usable product that used to go directly to landfills.” She continued, “All of you in the industry
should be proud of what you do every day in your recycling efforts.”
Although the idea to find a solution for crushing concrete with rebar and RAP, came about due to the need to diversify her own business, Susanne was savvy and thoughtful with the decision for how she made that happen. She led the way for commercial recycling to become industry mainstays, allowing businesses to diversify and expand existing operations, and for new businesses to be born, with even bigger rewards for the environment. Innumerable tons of concrete and asphalt have avoided landfills, and, instead, are recycled and reused to the benefit of the planet.
by Dan Friedman, vice president of marketing for Eagle Crusher
For more information visit https://asph.link/ laborshortage
NET ZERO EMISSIONS? LO-DENSITY® HEAT PAVES THE WAY

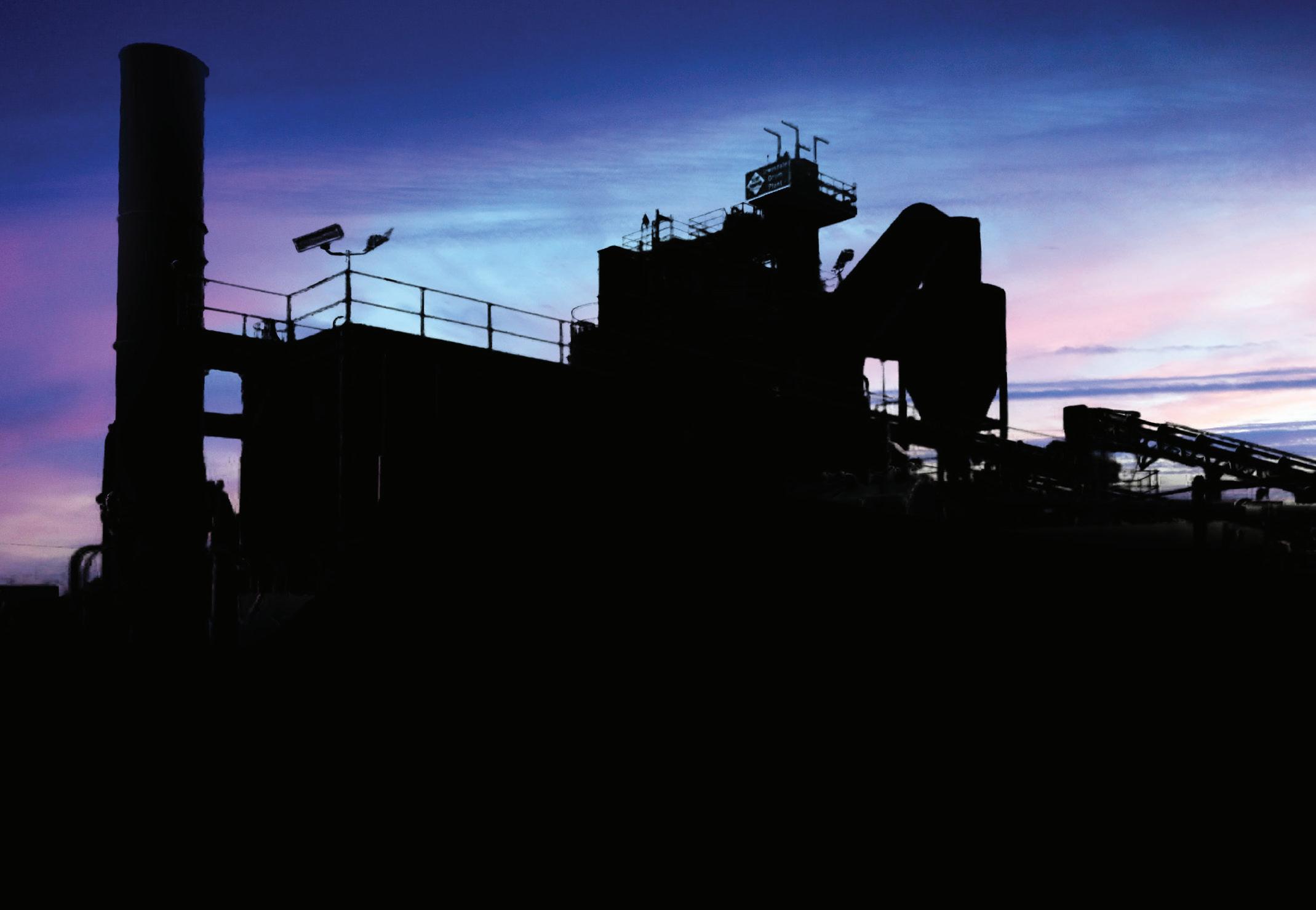
Any source of heat that requires a burner — including natural gas, propane, diesel, or fuel oil — also exhausts emissions into the air. Replace your tank heaters, hot oil heaters, fuel oil preheaters, and distributor truck heaters with our zero-emission, 100% efficient, Lo-Density® drywell-style electric heat. Sustainable PHCo heaters not only operate without combustion or emissions, they also eliminate a source of fuel spills. Find out more:
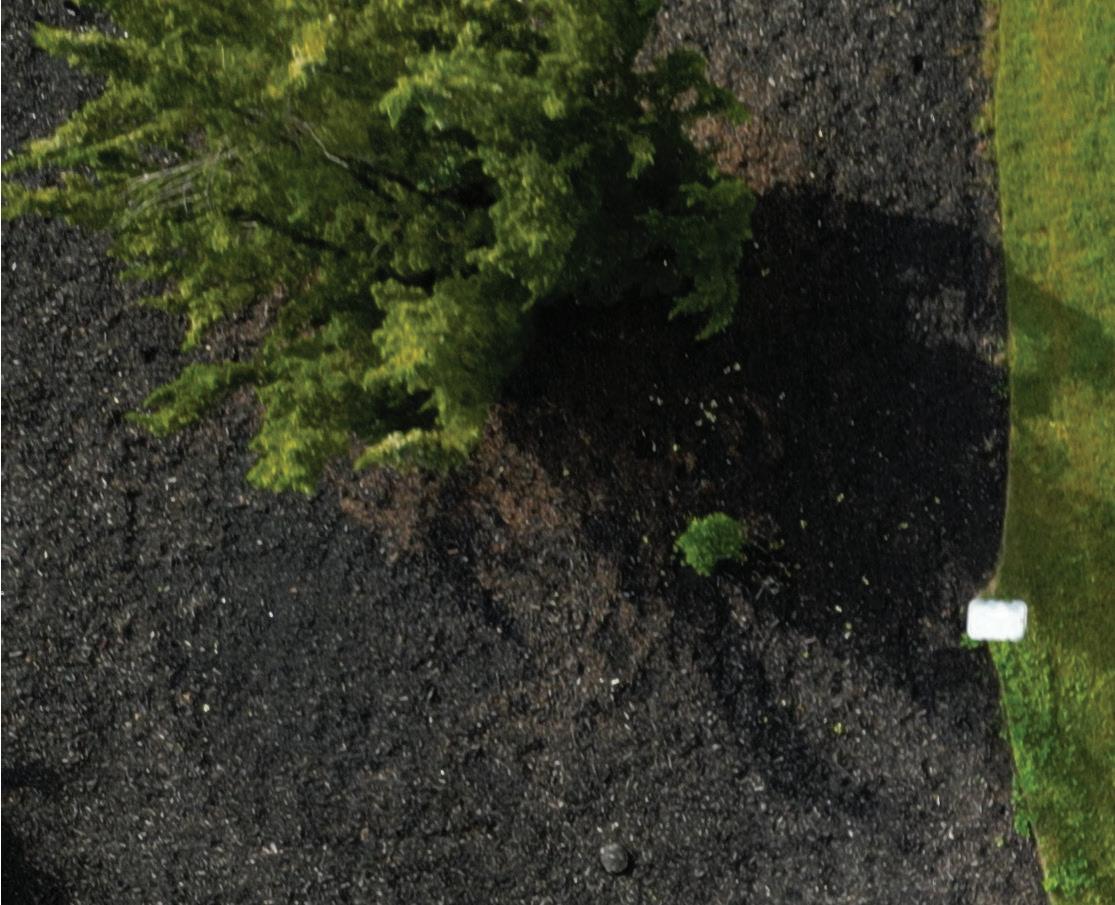

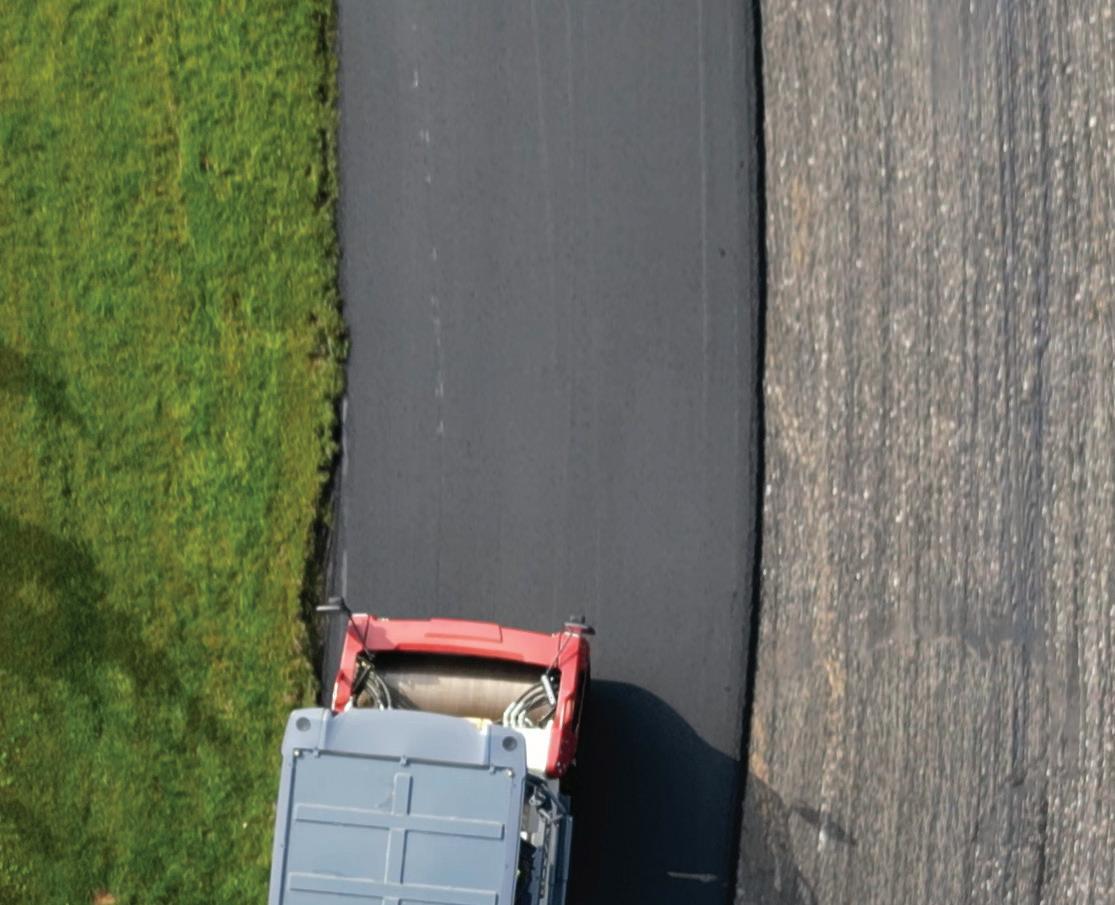
By Brandon Noel, Editor

SIZE MATTERS: Fast And Accurate Compaction
If your business is growing, and you’re quoting more than ever before, it might be time to scale up your iron.
It’s an age old question: Is bigger better? For rollers and meeting your compaction needs, the answer to this question is as nuanced as it is in every other instance. Rollers come in all kinds of sizes and specifications, as well as, with all kinds of various new technology these days. To find out if bigger is better, you first have to ask yourself what types of circumstances and jobsites you need a new roller for.
For the last few years Royal Pavement Solutions (Islip, NY) mostly focused on doing work in the commercial market space, including large parking lots for big box stores and some smaller residential road work when possible. This season they faced their largest road project to-date working for a home owners association.
One of their biggest challenges would be how quickly they could
complete the work, as the HOA wanted to minimize the disruption to the residents daily comings and goings. The neighborhood has only one entrance way, and long stretches of the loop-road that winds through all the houses would be inaccessible. However, the Royal Pavement Solutions team had a brand-new ace up their sleeve in order to ensure an efficient process as possible.
While attending World of Asphalt 2024 in Nashville, TN, Kenny Roy, the owner/operator of Royal Pavement Solutions (RPS), was definitely looking to add a new roller to his arsenal. After seeing what the show had to offer, he landed on the Dynapac CC2200 VI equipped with SEISMIC asphalt technology.
With a max operational weight of nearly 10 tons and 59 inches of compaction width, it’s by far the biggest roller that RPS has at their disposal. It joins their two other Dynapac models, the CC950 and the CC1200, and they regularly bring all three to the jobsite and deployed them effectively in different ways.
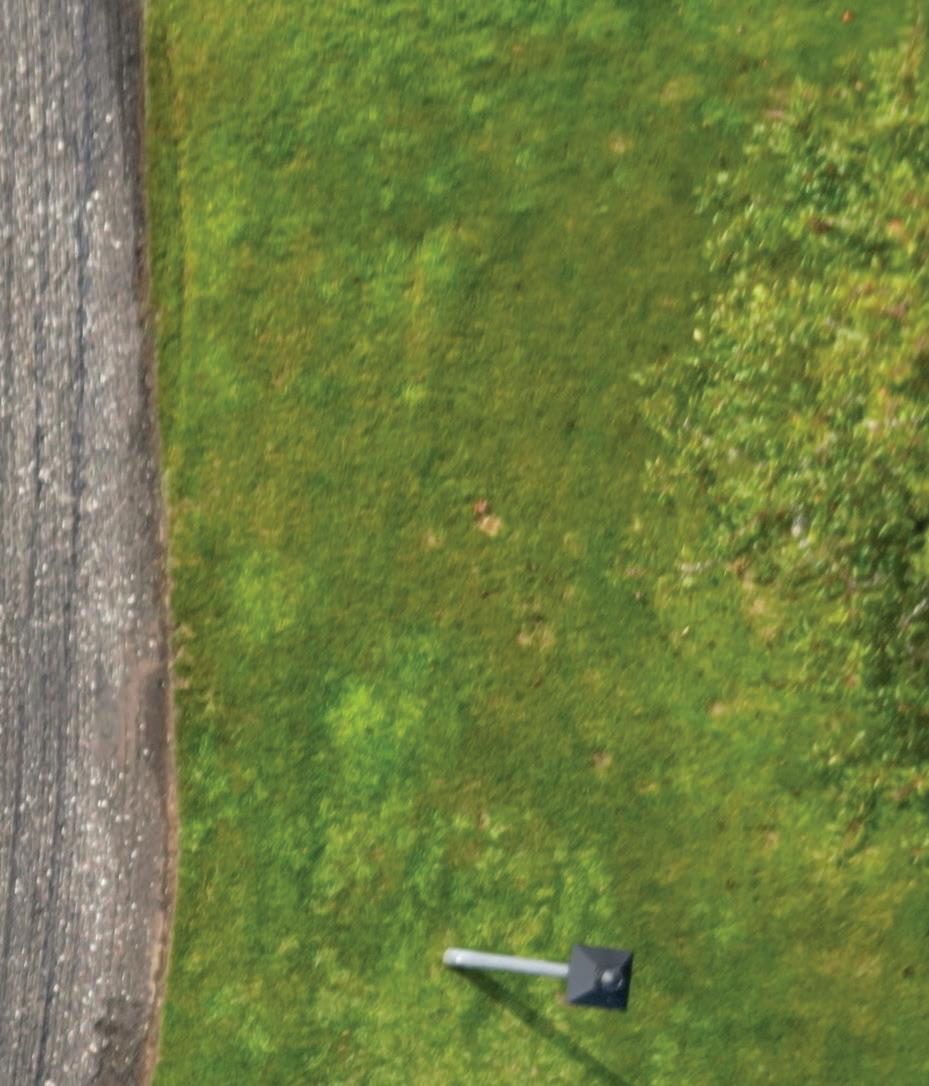

Eagle eye view of the CC2200 VI from Dynapac, equipped with SEISMIC technology.
WHO’S THE BOSS?
The project at Sunken Ponds Estates was greater than 113,000 sq. ft., and included 3 inch depth of milling (1313 cu. yd.) and repaving (2100 tons). It would require full traffic control, minimal disruptions to residents, and no interruption of trash or delivery services. On top of that, due to the age of the community, emergency services access would also have to be maintained. The goal? Complete everything in less than three days. RPS was more than up to the challenge. Day One they would mill and prep the surfaces, cleaning everything up and getting ready for paving on day two. Day Three would be for traffic markings, and the HOA clubhouse parking lot. Now, being a member of an HOA usually comes with some minor concessions to be a part of the community group. It’s not unusual for some members to be a little particular, and,
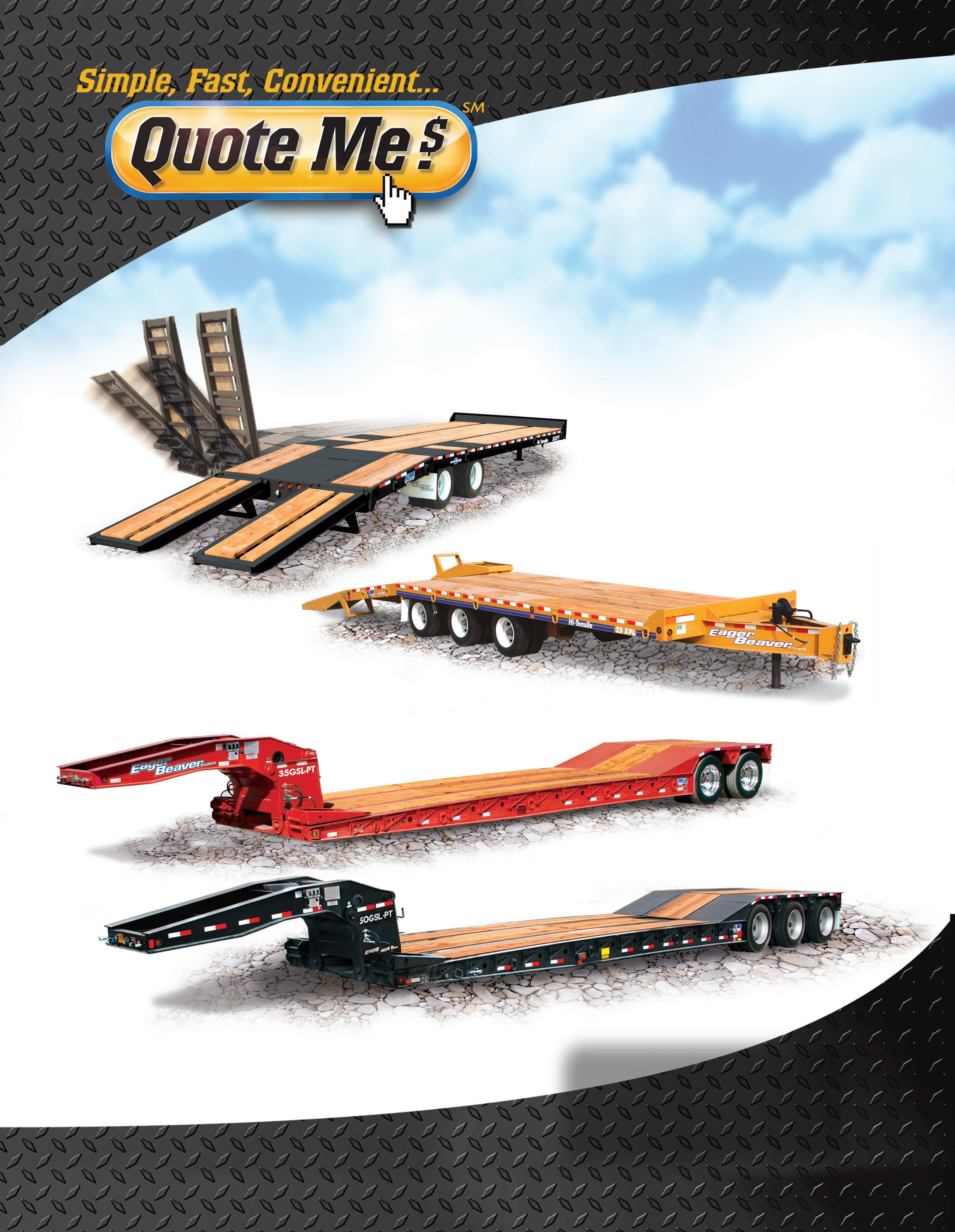
Photo
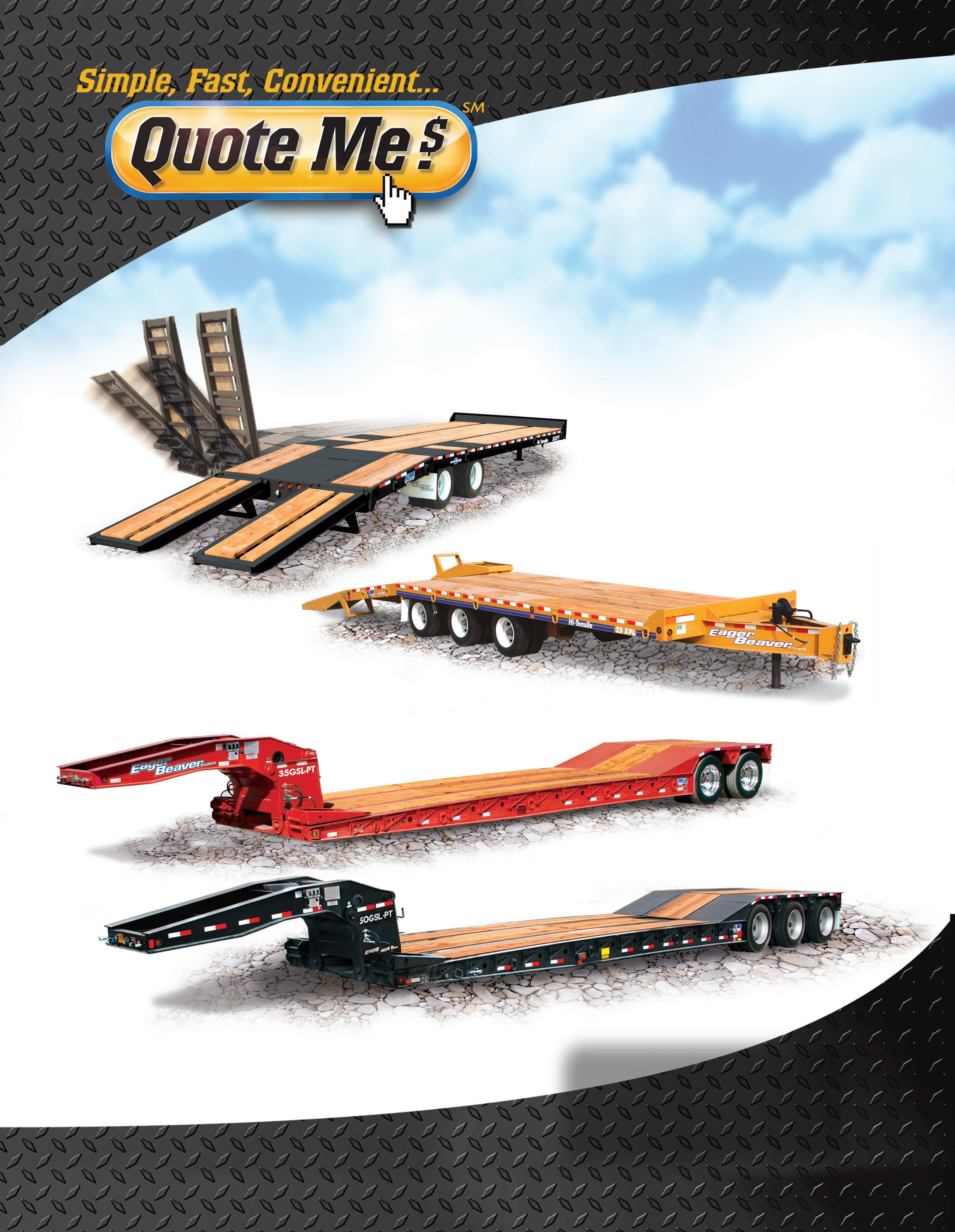
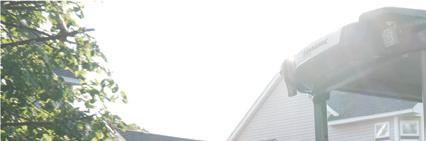
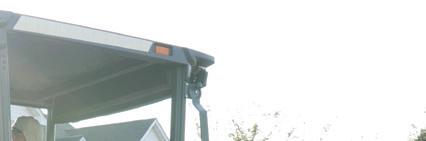

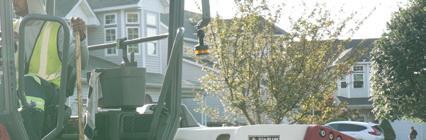
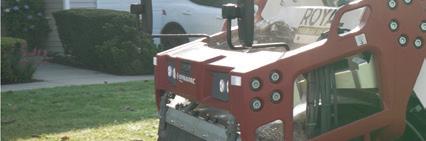
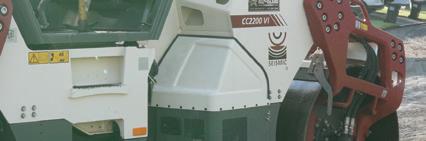
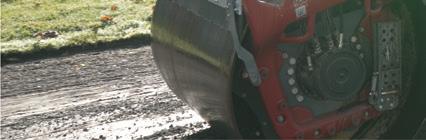

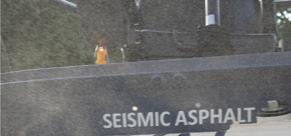

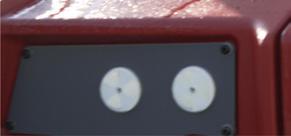
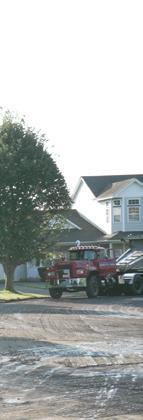
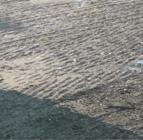
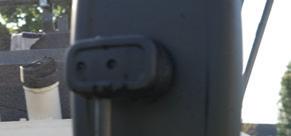
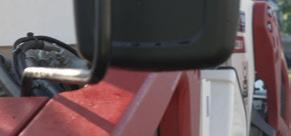
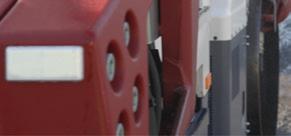
sometimes, that behavior can continue when it comes to contractors trying to get their work done.
“When you come into a private HOA like this, you might have one person as a point of contact, right?” said Kenny Roy, standing next to their brand new roller. “What can be a problem sometimes is that residents have places to be, friends to visit, kids to get to school and back, beach day, or whatever. They’re all bosses then. But we’ve been doing work in this community for a couple of years, and these people have been really great. We haven’t had anything negative at all.”
WHEN LESS IS MORE
One of the big advantages of a smart system for your roller like SEISMIC asphalt is that it can prevent overcompaction. When you over-compact your soil, base, binder, or wear layer past a certain point you’re weakening the overall integrity of the material. That means premature cracking and other breakdowns in quality or strength. Additionally, you end up wasting a lot of fuel, add unnecessary wear-and-tear hours on your machine, and, you’re wasting time that could be spent finishing the job more efficiently.
There are different tech platforms out there that can help prevent
Hector
Polanco, operations manager at RPS, skillfully operating their new rollers through residential roads.
over-compaction and help you track your compaction data, for example: BOMAG’s BOMAP, Caterpillar’s Intelligent Compaction, HAMM’s Smart Doc, and other add-on third party pieces of tech that sometimes require GNSS receivers. There are several options for you to be able to track and measure asphalt stiffness, temperature, and number of passes.
What’s so different about the SEISMIC asphalt technology built into the CC2200 VI is that it takes those readings directly, and then every 0.2 seconds it is assessing any adjustments that should be made to the intensity and frequency of the drum vibration.
“What’s really nice about this machine, why it’s different, is that you get kind of used to the vibration turning up-and-down automatically. It’s signaling to you that the area is ready or not, and you can move on,” explained Hector Polanco, operations manager at RPS. He’s spent the most time using the new roller since it was delivered.
“If I feel the frequency kick up really high, I know it might take another pass, because obviously it’s less compacted and the system is picking that up,” said Polanco. “When it goes down, then I’m already figuring out the next area hit.
Everyone has there own way of doing things, and I’ve got a pattern I normally follow, but this makes a huge difference.”
Hector’s Compaction Pattern:
Step 1: Starting from the edge, no vibration. While backing up, turn vibration on.
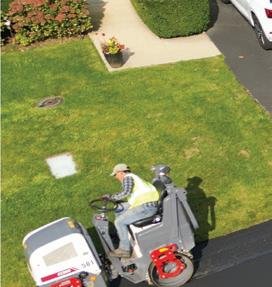
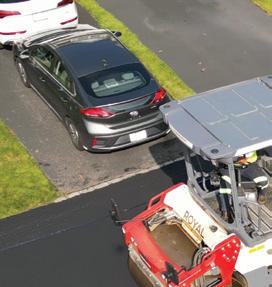
Step 2: 50/50. Align the drum halfway over from the edge of the first pass, putting your water line in the center of the drum.
Step 3: Once you reach a seam, if it’s still really hot and freshly paved, could continue 50/50. However, if it’s already started to cool down, then he works over more gradually using 25/75, or only a quarter of the drum on the uncompacted side. Rinse and repeat.
WHEN MORE IS MORE
Could RPS have completed this project using their two smaller Dynapac rollers? Of course they could. However, their ability to meet the timeline that the client asked of them would have been severely impaired.
“Let’s say we were paving today without the big roller,” said Roy. “At the speed we are laying asphalt today, in order to get this done, the smaller machines would absolutely not be able to keep up with our pace. It’s not just the SEISMIC stuff either. To have 5 feet of compaction width, going back-andforth way fewer times, Hector can keep up with us really easily.”
While the smaller rollers in their lineup followed further behind, finish rolling and working out any potential marks left in the initial passes, with each new truck, the CC2200 and Hector were ready and waiting to go.
“It makes a real difference when you go to bid on a job,” said Roy. “It’s changed the game for us in terms of how much we can do and how fast we can get it done.”
For more information visit https://asph.link/bc1eue
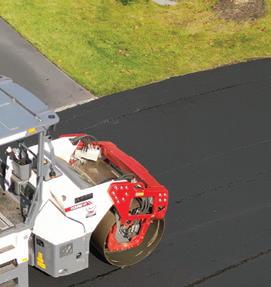
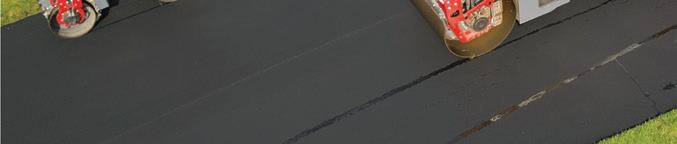
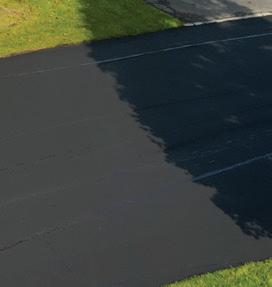
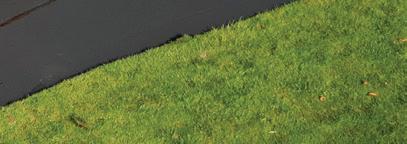
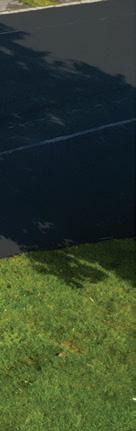
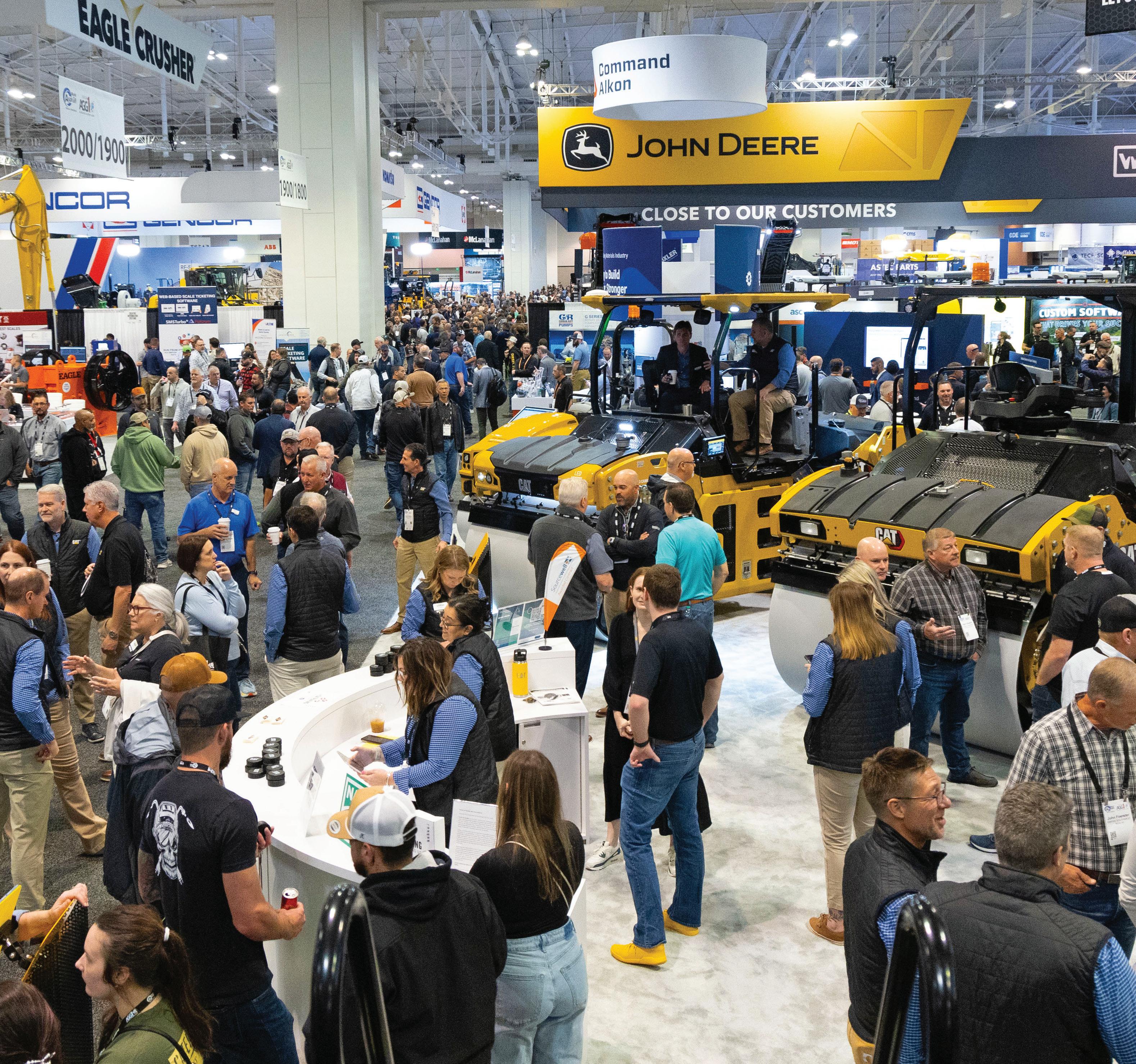
Photo Credit: Pat Brown
Photo Credits: Brandon Noel
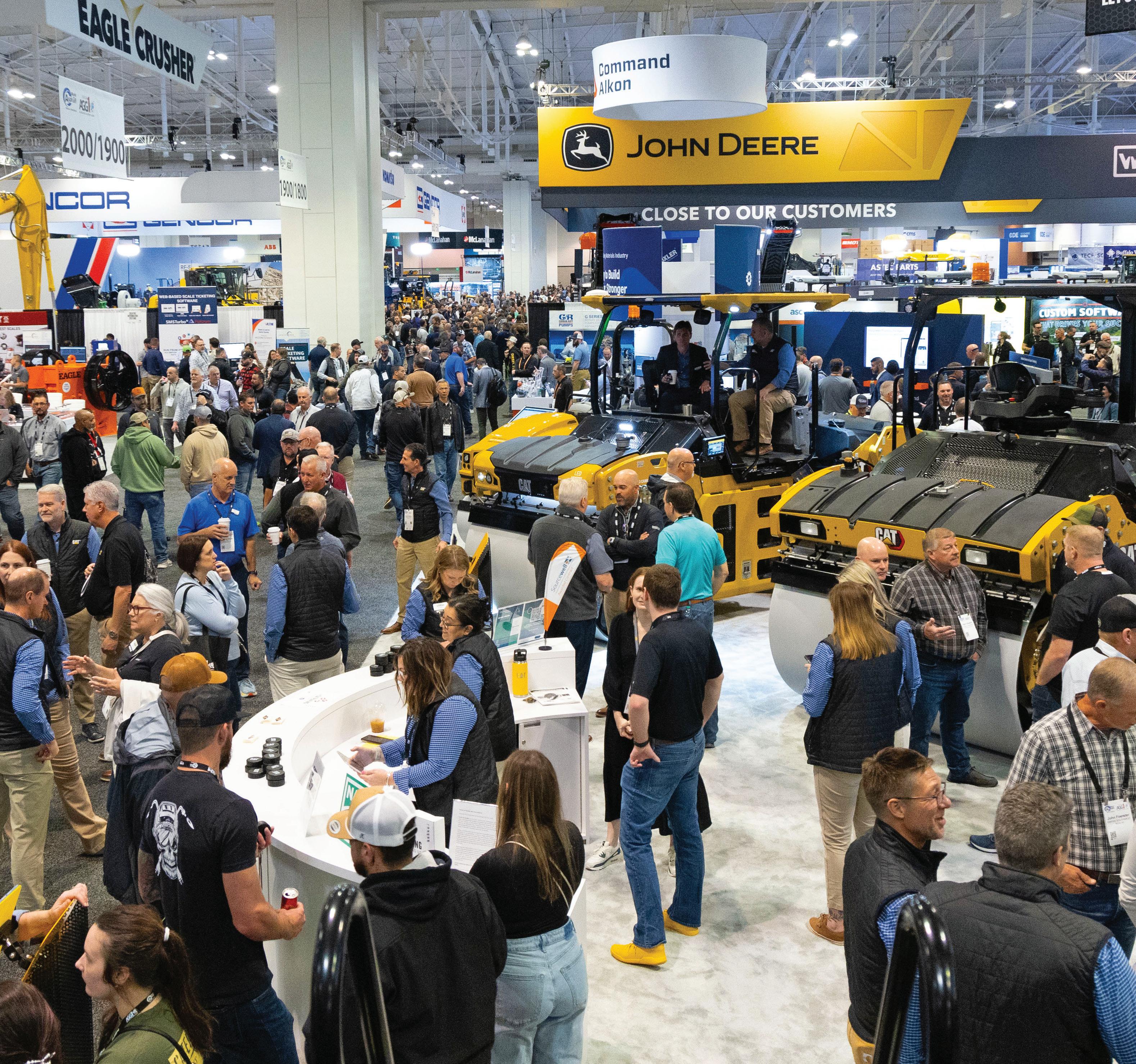
•
•
• Improve your Jobsite and Business March 25-27, 2025 | St. Louis, MO
By Merina Shriver, Junior Editor
A Perfect Circle: Comparing Recycled Materials
Using some form of recycled asphalt mixture in paving projects can be very beneficial and improve the world’s waste problem.
The world has become more invested in reducing its environmental impact and the construction industry has taken its own steps on its journey towards being more environmentally friendly. In the asphalt world, you have the option to use all-new asphalt with virgin materials or you can make a mix with some sort of recycled material. There are a variety of options when it comes to recycled asphalt. The main three are plastic modified asphalt, rubber modified asphalt, and reclaimed asphalt pavement. Not only are recycled asphalt options better for the environment but they are also more economically beneficial.
A REUSED SOLUTION
Replacing asphalt entails removing the old in order to bring in the new. This is not always ideal because it continues to produce more and more waste. Modified asphalt has become much more popular than raw asphalt as of late because of its ability to improve longevity and dependability by modifying asphalt.
Although virgin polymers can be better for asphalt, they aren’t the most realistic option. This is why the industry is starting to use plastic modified asphalt, rubber modified asphalt, and reclaimed asphalt pavement.
PLASTIC WORLD
Plastics have been used extensively throughout the United States for decades and have been mass-produced since before the 1960s. Due to the constant production, use, and disposal of plastics, there is a lot of waste product that is polluting the world. With this in mind, plastic modified asphalt is an
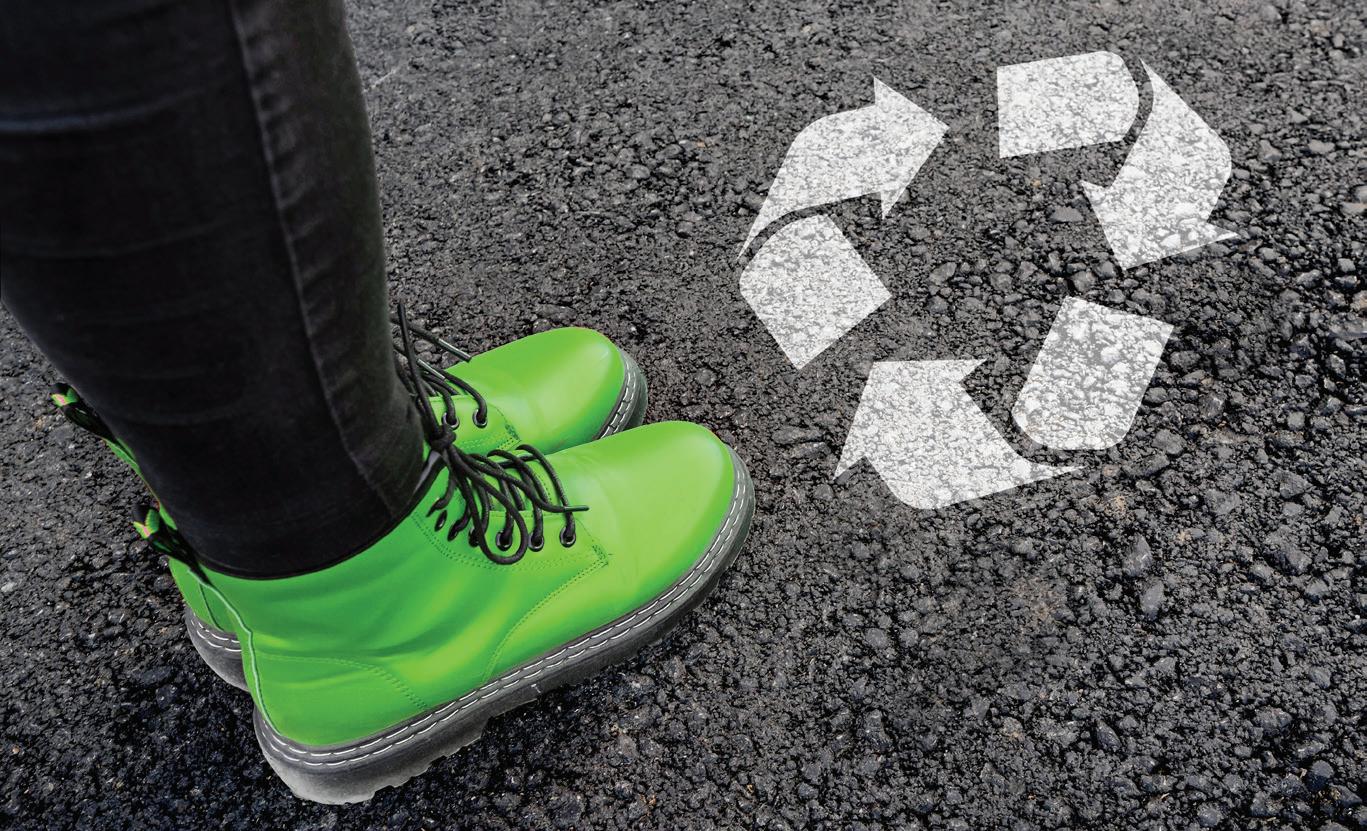
excellent solution. There are various types of plastic waste and some are more suited for asphalt than others. Plastics can be incorporated into mixes in a wet or dry process. Each can be tedious and neither is necessarily better than the other. The main difference is that the wet process requires specific equipment while the dry process does not.
Waste plastics will exist with or without the asphalt industry but using them in modified asphalt mixes is a great way of reducing the impact of such pollutants.
Benefits
The use of waste plastics in asphalt mixes is as straightforward as it sounds. Waste plastics are no longer being wasted and can be used for new purposes. The plastic modified asphalt mixes don’t have a large amount of plastics in them but they are still able to significantly reduce carbon emissions.
@mirsad - adobe.stock.com
Not only are recycled asphalt options better for the environment but they are also more economically beneficial.
Plastic waste has the ability to potentially increase the life of asphalt by resisting degradation and improving temperature resistance.
Improvements To Be Made
While the process of incorporating waste plastics into asphalt mixes is a good idea and can have many benefits, there is still room for improvement. The processing in particular could be better. It is quite a complicated process for plastic waste to be properly processed in order to be used in asphalt mixes. Plastic waste can cause decreases in asphalt’s ability to combat cracking and moisture damage. Not all plastics are the same which results in the possibility of variable benefits and results.
A big challenge posed by plastic modified asphalt is the potential for the plastic to degrade and continue breaking down into microplastics. Microplastics

already pose a huge threat to the environment, particularly aquatic life.
USED RUBBER BOUNCING BACK
Rubber modified asphalt incorporates discarded tire or crumb rubber into an asphalt mixture. Crumb rubber is essentially the scraps from old tires that have been processed into shredded bits. Crumb rubber is mixed with asphalt to create a somewhat resilient product.
Benefits
Rubber modified asphalt can have some big benefits. Like plastic modified asphalt, rubber modified asphalt has a positive impact on the environment. Being able to put waste tires to use and not have them sit in a landfill helps keep pollutants and wastefulness down.
Maintenance frequency is significantly lower than with typical asphalt
mix. This not only saves time but also money. Rubber modified asphalt is considerably cheaper than asphalt mix made only with virgin materials. Rubber modified asphalt can last longer and even improve driver experience. The surface that rubber asphalt forms can be better for preventing tire wear, reducing road noise, and improving skid resistance.
Improvements To Be Made
Rubber modified asphalt can be somewhat problematic in that the rubber doesn’t interact well with the asphalt. During storage, the mixture separates. Therefore, when using this kind of mixture, there is a risk of the asphalt having shortened longevity due to the lack of homogeneity. This causes separation and leaves room for potential life expectancy reduction. When this type of asphalt is at the end of its life, it creates a whole new
challenge because it is a different type of waste. The disposal methods are still trying to be improved.
RECLAIMING ASPHALT
Reclaimed asphalt pavement (RAP) is old asphalt that has previously been used. When repaving, the old asphalt has to be removed and in order to not create too much waste, that old asphalt can be treated and reused.
Benefits
RAP as a method of reusing old asphalt has many benefits for both the industry and the environment.
Kerianne Melillo, chief marketing officer at C.A.C Industries and Green Asphalt Co. said, “Adding RAP into your asphalt mix reduces the amount of virgin materials you need to use.”
Melillo explained that this entails benefits for the environment by
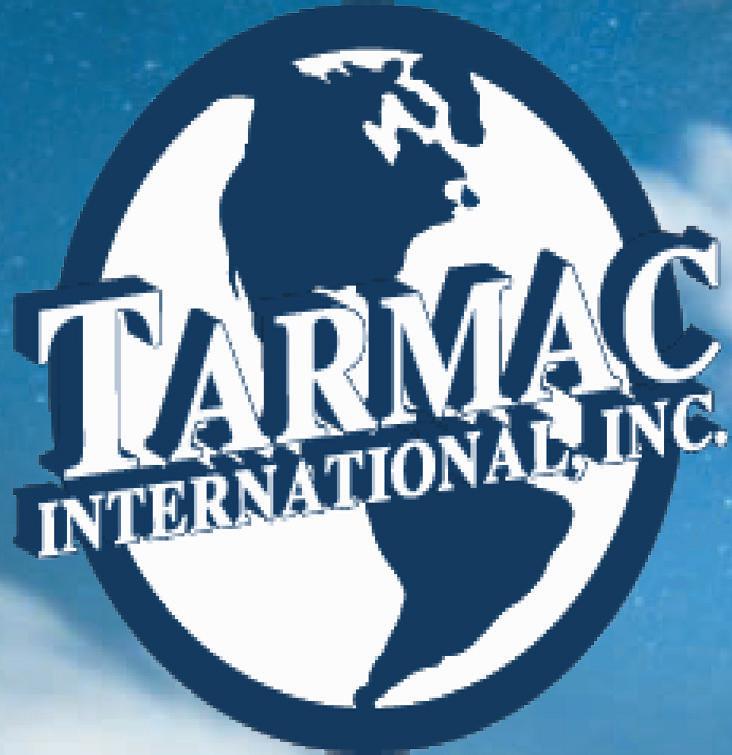

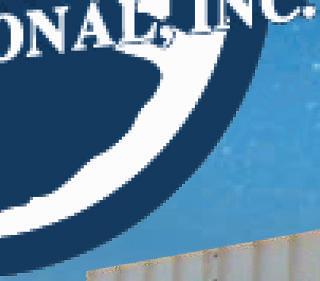
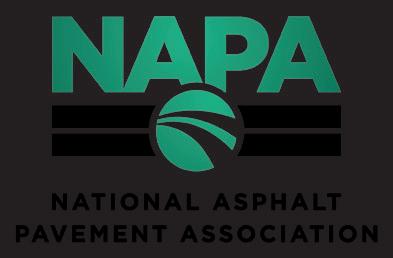
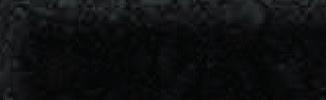

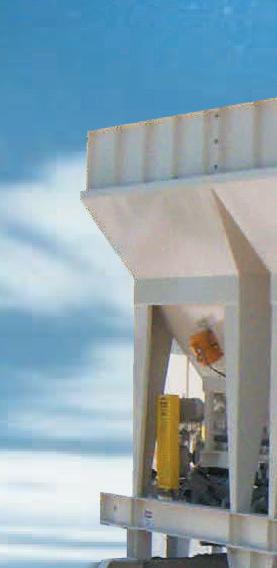

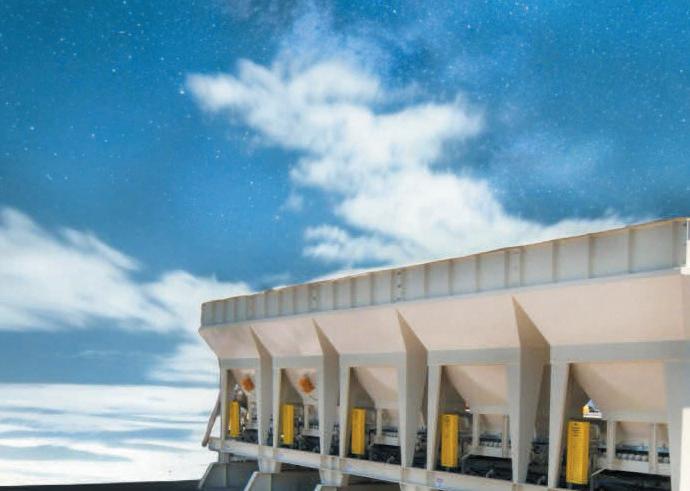
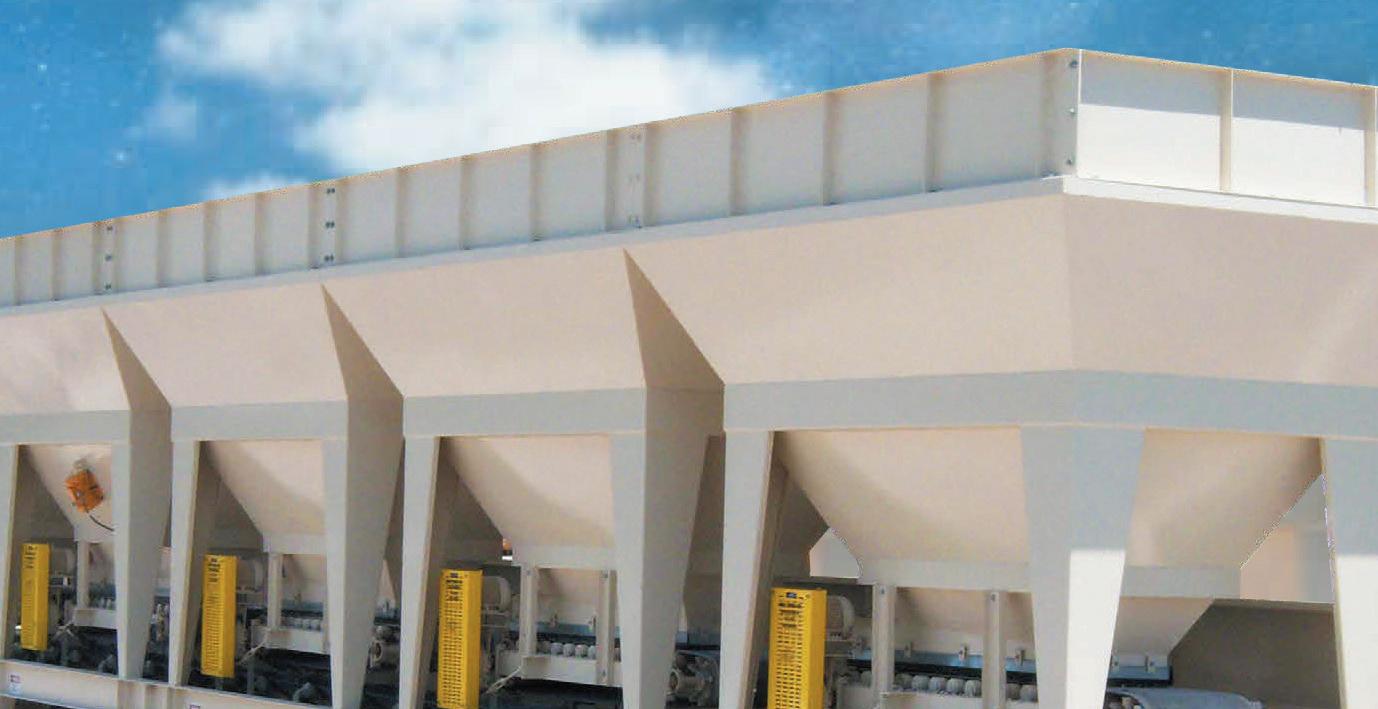

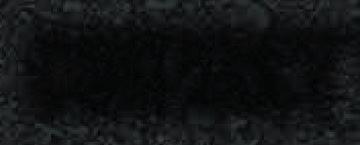


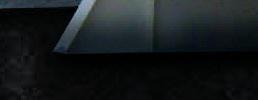

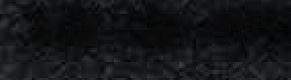

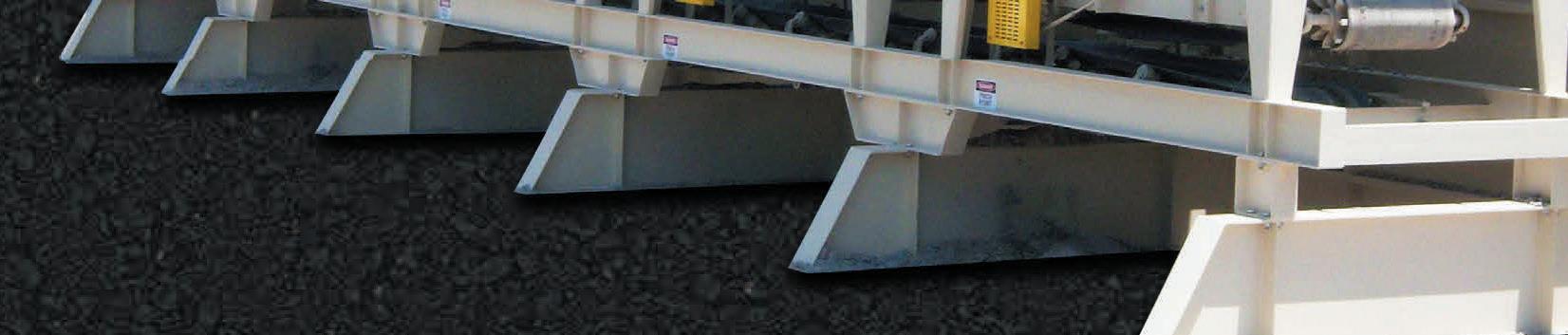
decreasing the carbon footprint for the entire process.
“It reduces embodied carbon within the mix significantly by limiting quarrying, oil refining, and trucking of the virgin materials.” Melillo continued, “It reduces mix cost as the price of RAP is much less expensive than virgin materials – in fact, in certain geographies, asphalt plants can get RAP for free, or even get paid to take it into their facility.”
Using RAP is a great way of reducing the negative impact that asphalt has on the environment. It is also a good way to make life easier in the industry.
“If you have a stockpile of RAP on your land, utilizing it in your mixes can free up space that would otherwise not be useable,” said Melillo.
Improvements To Be Made


difficult for the plant to handle on a consistent timeline.
Melillo shared, “Utilizing RAP can sometimes cause buildup in certain parts of the plant.”
While the issue of higher maintenance frequency is not necessarily a large drawback on its own, it can be more expensive to incorporate weekly or even daily upkeep for the plant.
RAP can lead to deformation of the road if it is in an area of high traffic and extremely heavy vehicles. This can be caused by its slight malleability.
RECYCLED PRODUCTS
Using some form of recycled asphalt mixture in paving projects can be very beneficial and improve the world’s waste problem. Depending on your personal needs, your plant abilities, and the
drawbacks but a lot of it depends on the project and need. Researching and discussing with an expert is always the best way to find out if one of these mixtures is right for you and your business.
Although each of these recycled asphalt methods has its cons and unfavored aspects, there are ways to work with and around each challenge. With a little insight and research, any of these three types could be a great solution to negative environmental impacts.
“If you treat and process the RAP properly, and work with high-RAP experts to fine-tune your mixes, highRAP mixes can be high performing, low cost, and low embodied carbon. Increasing RAP contents in our mixes is a goal the entire industry can get behind, evidenced by the emergence of Balanced Mix Design,” said Melillo.
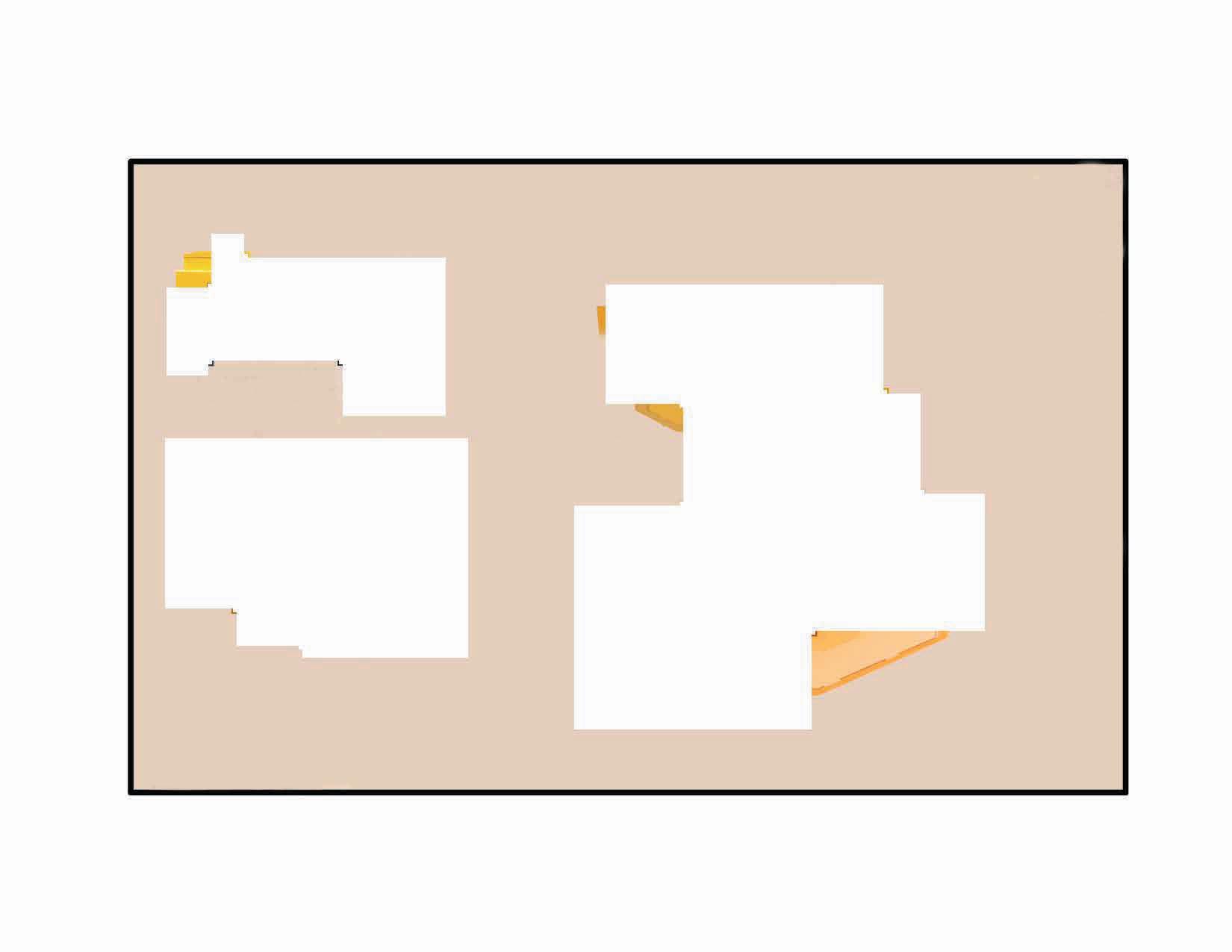
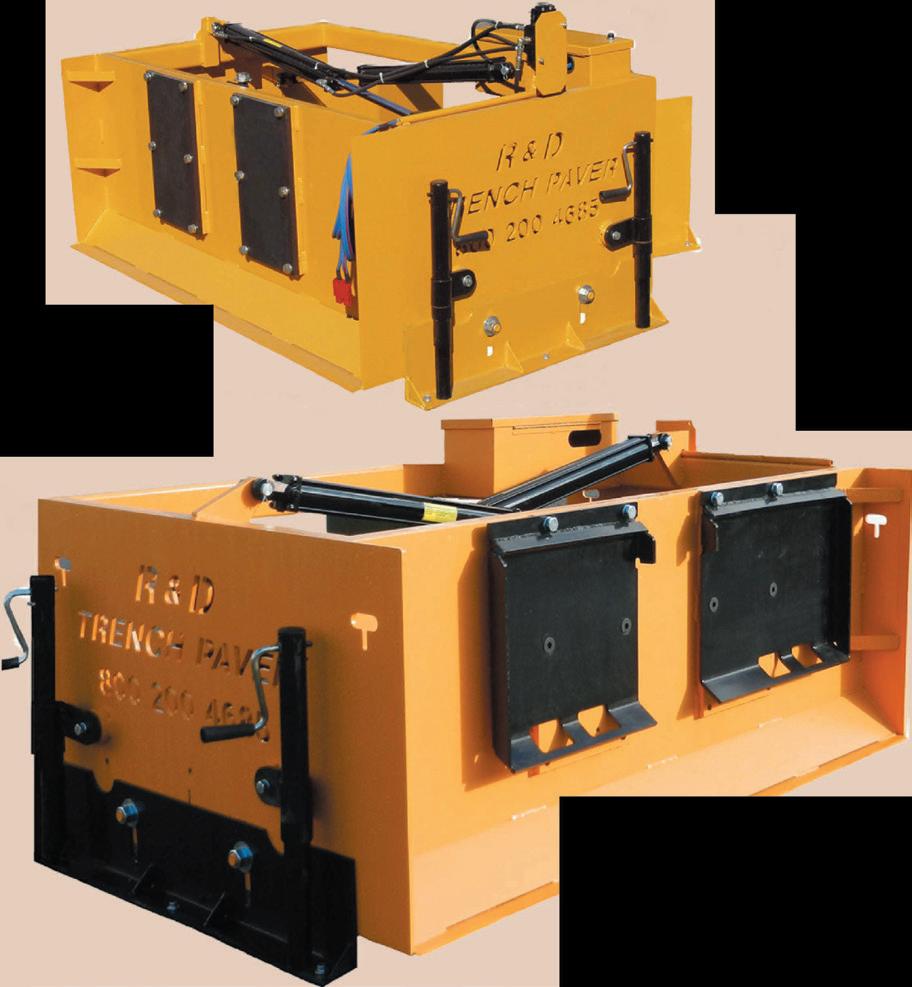
Has Productivity Stalled In The Construction Trades?
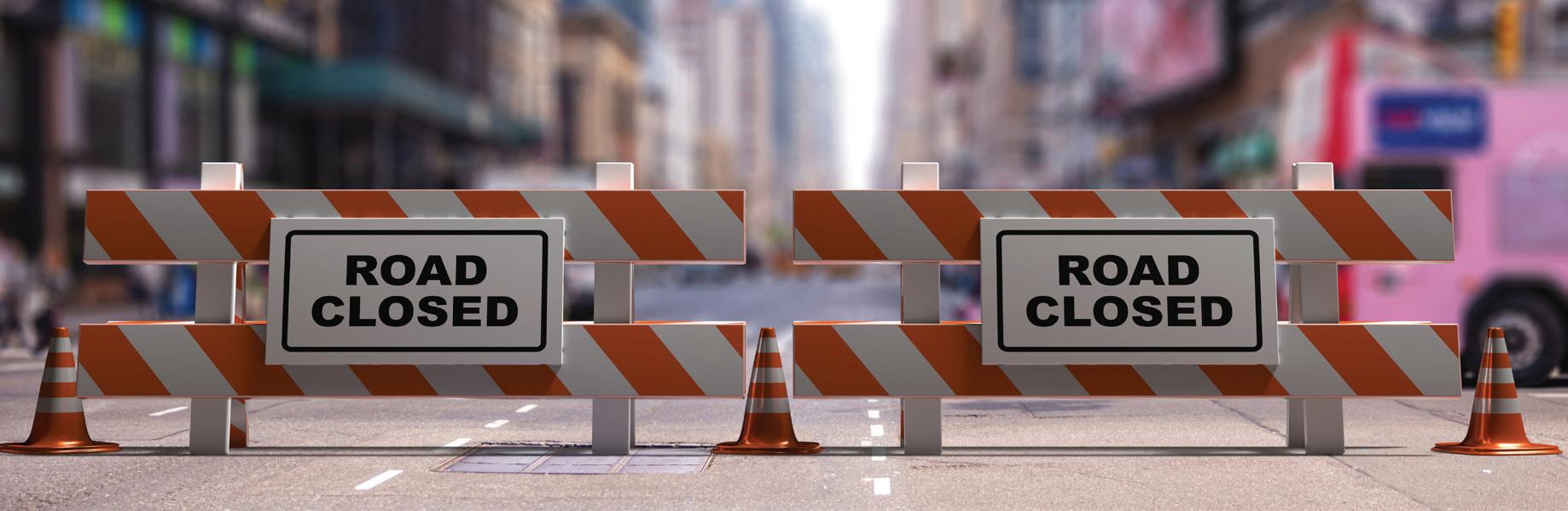
For the past 50 years, while manufacturing and other sectors of industry have seen great leaps in overall productivity, that hasn’t been the same story for the construction trades.
Those of us in the construction industry, whether we want to admit it or not, are faced with an unpleasant truth: we haven’t increased our productivity in more than 50 years. According to a research brief published by the Becker-Friedman Institute for Economics at the University of Chicago earlier this year (The Strange and Awful Path of Productivity in the Construction Industry), “Despite aggregate productivity for the US economy having doubled over the past 50 years, the country’s construction sector has diverged considerably, trending downward throughout that period. And this is no slight decrease. Raw BEA data suggest that the value added per worker in the construction sector was about 40 percent lower in 2020 than in 1970.”
The fact is, construction is the only part of the overall building process, which includes architecture, engineering, manufacturing, and others, that hasn’t advanced significantly in the last 50 years. According to The Economist : “Since 1995 the global average valueadded per hour has grown at around a quarter of the rate in manufacturing… no industry has done worse.”
The lack of significant productivity growth in the construction industry over the past 50 years compared to other sectors is a complex issue with several contributing factors.
HERE ARE SOME KEY REASONS:
Unlike manufacturing or technology, construction lacks a single, standardized approach. It’s a fragmented industry with many small and medium-sized businesses, each with its own processes and workflows. This makes it difficult to implement large-scale changes and adopt new technologies. Difficult, maybe. But not impossible. The fact is, the construction industry is traditionally risk-averse and resistant to change. This can make it difficult to adopt new technologies and implement new processes, even if they offer longterm benefits.
Many tasks in construction are inherently physical and require human skills and judgment. Automation, which has driven productivity gains in other industries, has limited application in construction. While some tasks like bricklaying or welding are becoming automated, the majority of construction work still requires human input.
The construction industry faces a significant skills gap and a shortage of skilled workers. This is partly due to a lack of investment in training and education, as well as an aging workforce. The shortage of skilled labor can lead to inefficiencies and delays, impacting productivity.
Extensive regulations and complex permitting processes can significantly slow down construction projects. Bureaucracy and red tape can create delays and increase costs, hindering productivity. This is very real and experienced in nearly every market. But we can’t blame the government for everything.
Compared to other industries, construction has historically invested less in research and development. This has led to a slower pace of technological innovation and a lack of new tools and methods to improve productivity. This is the real crux of the problem.
AdobeStock/Rawf8
Further, the construction industry often focuses on delivering individual projects within specific deadlines and budgets. This short-term focus can discourage long-term investments in technology and process improvements that could lead to broader productivity gains across the industry. And according to a recent Freakonomics Radio podcast, “when productivity falls, prices often rise.”
The University of Chicago study’s bottom line: “Given its place in the economy, this productivity decline has real effects: Had construction labor productivity grown over the last five decades at the (relatively modest) rate of 1 percent per year, annual aggregate labor productivity growth would have been roughly 0.18 percent higher, resulting in about 10 percent higher aggregate labor productivity (and, plausibly, income per capita) today.”
CLASSIFIEDS
In the area of this industry where I work, pavement maintenance and construction, innovation happens at a glacial pace. But it does happen. A few years ago, a biobased pavement sealer was launched in the Midwest. It has since been proliferated throughout the West Coast and adopted by municipalities, corporations, and government agencies.
This not only due to its environmental/climate benefits—which are many—but also the efficiencies it adds to the pavement construction process: it goes on extremely fast, can be applied overnight, and doesn’t require any specialized training to work with. It’s also stable and cheap to transport—somewhat of an anomaly in my industry.
This product, which is composed of soybean/botanical oils and recycled Styrofoam, can also lengthen the lifespan of asphalt by two to three times—significantly reducing labor and construction costs and freeing up money to be
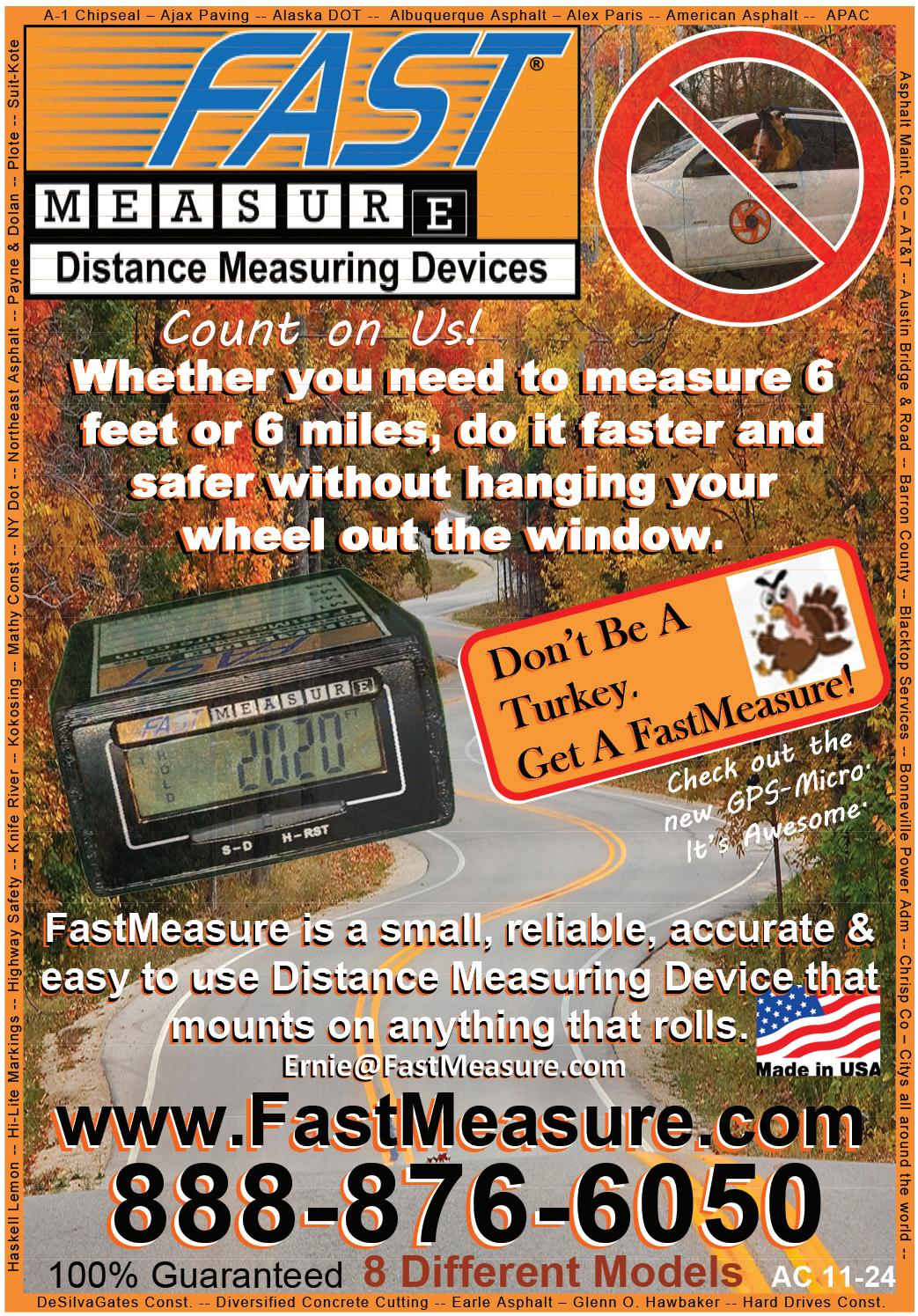
spent on more projects, and—dare I say it—increasing productivity.
We need to change our thinking to accept and encourage more innovations like this.
Overcoming a 20th century mentality and achieving sustained productivity growth will require a concerted effort from all stakeholders in the industry, including policymakers, construction companies, technology providers, and training organizations. And, probably above all, it will demand a focus on investment in and implementation of new technologies in our industry. We can no longer ignore and or fight it. Isn’t 50 years long enough?
by Ken VanDomelen, president and owner, Coast Pavement Services
For more information visit https://asph.link/nvq38x
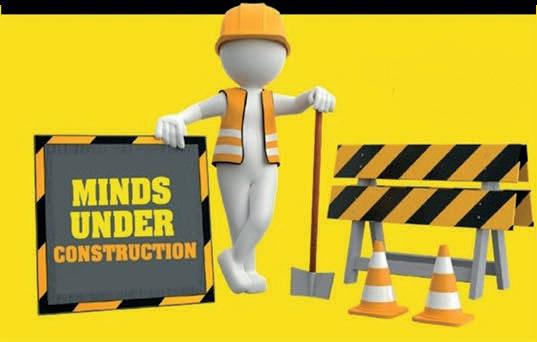
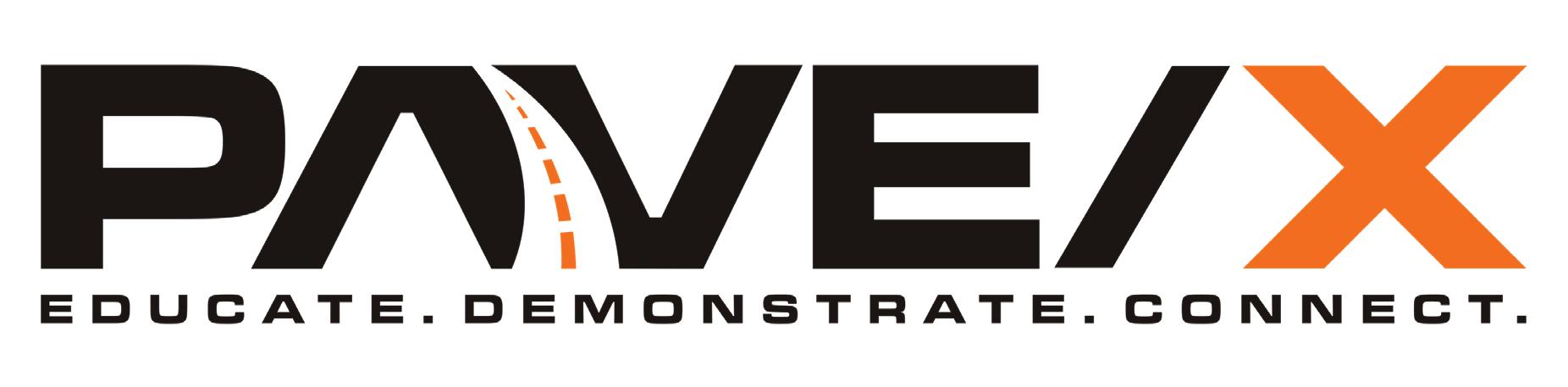
Featuring a robust educational program that is unlike any other learning experience in the market with education covering business management, paving, sealcoating, preservation, sweeping, striping and more.
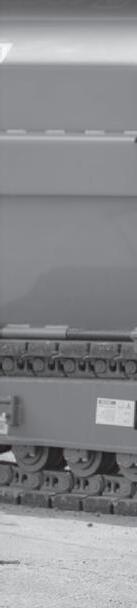
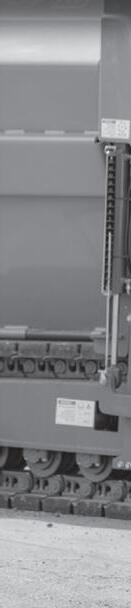


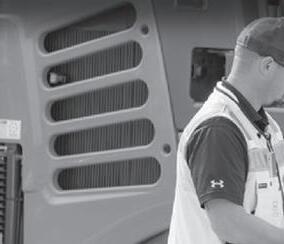
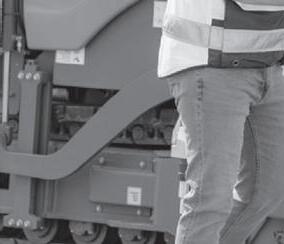
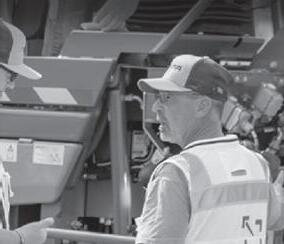



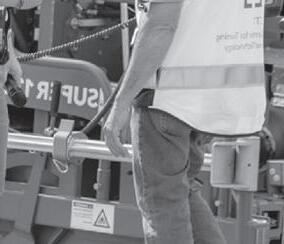
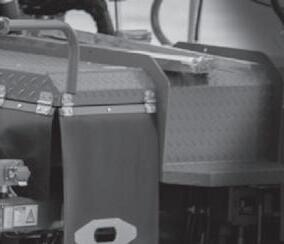
Seeing equipment in action is incredibly important in any equipment buying decision and PAVE/X brings a fast-paced demonstration showcase for attendees to watch equipment at work and ask questions to help ease the decision-making process for them. The Must-Attend Immersive Trade Show Environment Helping Contractors & Business Owners Propel Their Business & Expertise Forward
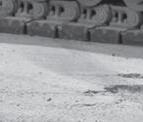



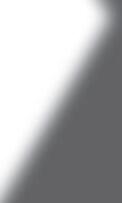
Over the three-day event, there will be an incredible amount of opportunities for next-level networking that will create and strengthen the relationships that are vital to the success of business owners working to grow.

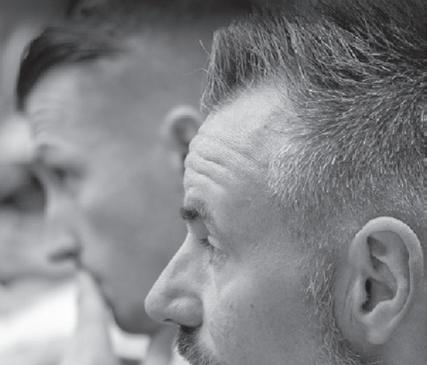
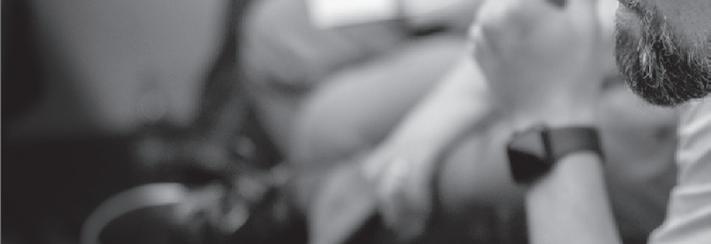


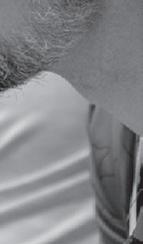


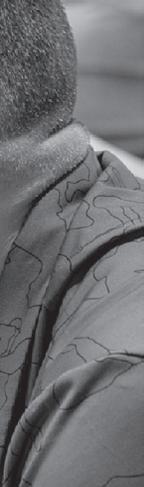

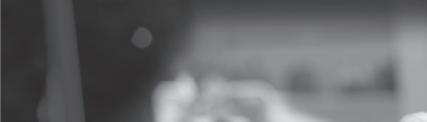
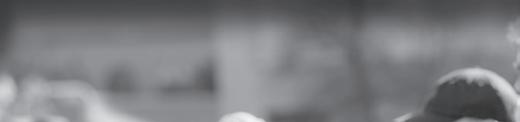

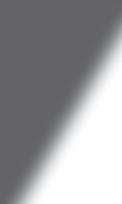
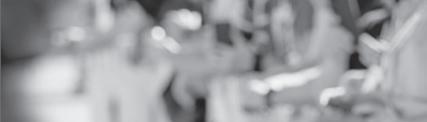
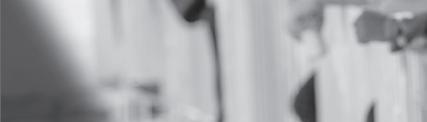
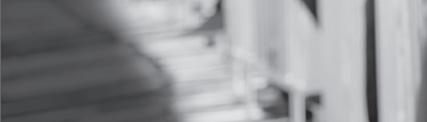
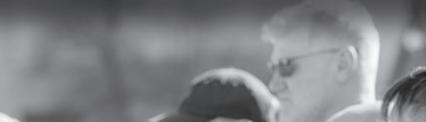
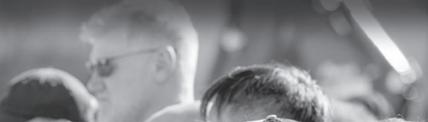
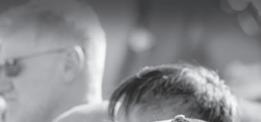
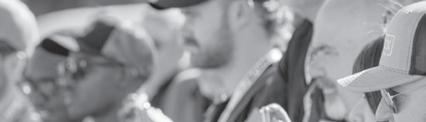
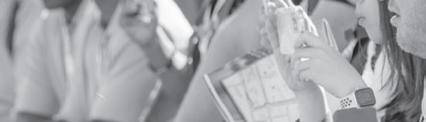
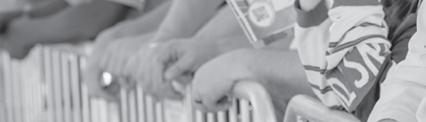

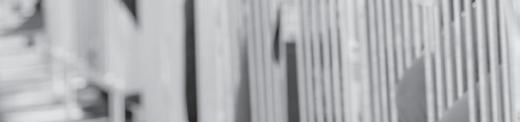





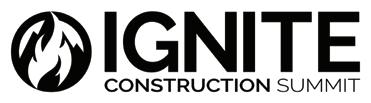
SHUTTLE BUGGY ® SB-3000

Roadtec Shuttle Buggy ® SB-3000
Astec revolutionized the paving industry with the introduction of the Shuttle Buggy, and now the SB-3000 sets a new standard in material transfer vehicles. Effortless maintenance, unmatched performance, and four steering modes for ultimate agility keep paving seamless. Experience groundbreaking innovation with the patented Ground Crew Control Station for the ultimate user experience and protection. The SB-3000 isn’t a machine, it’s a revolution in material transfer, built on Astec’s legacy of industry firsts.