

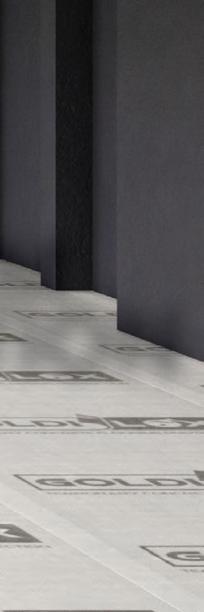

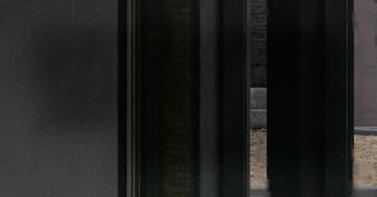

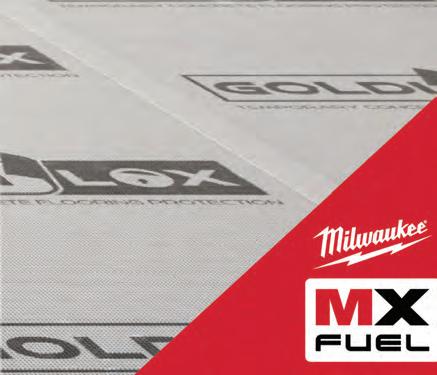




The Stinger electric flex shaft vibrator is rugged, lightweight, and powerful. The 115v electric motor has been designed to run cool with the power and torque to handle todays concrete loads. The stinger attaches to competitor core and casing with quick disconnect adapters.
How
Polished concrete artwork commemorates a family’s history. 20
Looking back at these past two decades of the magazine.
The winning concrete contractors and projects.
The key to saving time, money, and a headache. 38
It may seem like a no-brainer but it’s the wrong choice.
Work smarter, not harder, with the right surface grinder. Here’s what you need to know.
The benefits of restoring concrete through hydrodemolition by repairing, extending, and optimizing the life of the concrete.
A field study evaluated installation techniques, how to deal with adverse conditions, and the troubleshooting of and repair of common issues.
Solving the workforce challenge starts with great employers.
Some financial pitfalls that contractors need to watch out for as you operate your business.
Construction
We can materially improve the nation.
ForConstructionPros.com/22578510
The shortage could swell to more than 160,000 over the next decade.
ForConstructionPros.com/22565116
While attending the ACI 2022 Fall Convention, I was introduced to an interesting construction “meme” based on some commentary of construction projects. As humorous as it was, I think there’s a hidden factor encircling the entire concept.
EDITORIAL
Editor Jonathan Kozlowski jkozlowski@acbusinessmedia.com
Managing Editor Gigi Wood gwood@acbusinessmedia.com
Technology Editor Charles Rathmann crathmann@acbusinessmedia.com
Audience Development Manager Angela Franks
PRODUCTION
Senior Production Manger Cindy Rusch crusch@acbusinessmedia.com
Art Director Marcy Murphy
ADVERTISING/SALES
At one of the hundreds of seminars during the American Concrete Institute Fall 2022 Convention, I was introduced to a particular Venn diagram. The image received a bit of a chuckle from the audience as if it was a well-known trope between construction professionals. Truth be told, it likely is but as I venture more into this industry learning more with each expedition away from my comfort zone, I found the concept quite provoking.
JONATHAN KOZLOWSKI, EDITOR JKOZLOWSKI@ ACBUSINESSMEDIA.COMIf you aren’t familiar, the speaker at the seminar explained it through an anecdote where a contractor spoke with a project owner in a fictitious “don’t you wish” tone with the owner asking for the moon. The situation had the contractor respond with a simple drawing and said, “you can it fast and cheap but it won’t be pretty” continuing through the combinations. The idea was that while the project can and will be done well regardless, good work takes time; good work should be valued; and good work can be as pleasing to the eye as it needs to be.
The hook of it all was that the project can be accomplished with a combination of two of these qualities (fast, cheap, or pretty), just not all three.
Today’s contractors are put to task for each and every project no matter the scope. Where once not too long ago contractors would be able to plan the average sized project a year or more in advance, that lead time now seems to be cut down. Offhandedly, one contractor had recently told me that a six month wait for concrete order is normal. But even then they also ran into the supplier cancelling day-of. (The material went to a higher priority job and the delivery was pushed to the following week. The supplier was very apologetic.)
If we take our three concepts and apply them to the current market: it’s more and more difficult to get concrete fast; tariffs on imported goods as well as the supply chain impacts from the pandemic have all affected many construction material costs; and while a skilled labor shortage has it’s own factor in the supply chain, a limited crew can definitely put a strain on a business’s productivity and efficiency.
Despite the pessimistic “you can have two” outlook, there’s a factor that I think is being overlooked. It’s that regardless of the pairing of options, the work done will always be considered as “good.” Regardless of the challenges of material costs and hard work, I’ve never heard anyone allude that the there was an option to just not do a job well. There’s a pride there and I think that’s something commendable.
Here’s to you for getting through 2022 and working hard into 2023.
Thank you and stay safe.
Kim Basham
KB Engineering Cheyenne, Wyo.
James Baty II
Concrete Foundations Association Mt. Vernon, Iowa
Dennis Purinton Purinton Builders, Inc. East Granby, Conn.
Sales Representative Mike Worley mworley@acbusinessmedia.com Sales Representative Nikki Lawson nlawson@acbusinessmedia.com
Sales Representative Tadashi Soma tsoma@acbusinessmedia.com
Sales Representative Kristin Pride kpride@acbusinessmedia.com
Chief Executive Officer Ron Spink
Chief Financial Officer JoAnn Breuchel
Chief Revenue Officer Amy Schwandt
Chief Digital Officer Kris Heineman
Brand Director, Supply Chain & Green Industry Jason Desarle
Brand Director, Construction Sean Dunphy
VP, Audience Development Ronda Hughes VP, Operations & IT Nick Raether
Content Director Marina Mayer GM, Online & Marketing Services Bethany Chambers Content Director, Marketing Services Jess Lombardo
Director, Demand Generation & Education Jim Bagan Director, Enterprise Sales Kay Ross-Baker
CIRCULATION & SUBSCRIPTIONS
P.O. Box 3605, Northbrook, IL 60065-3605 (877) 201-3915 | Fax: (847)-291-4816
circ.ConcreteContractor@omeda.com
LIST RENTAL
Sr. Account Manager Bart Piccirillo | Data Axle (518) 339 4511 bart.piccirillo@infogroup.com
Tadashi Soma (800) 538-5544 ext. 1267 | tsoma@ACBusinessMedia.com
MEDIA 201 N. Main Street, Fort Atkinson, WI 53538 (800) 538-5544 • www.ACBusinessMedia.com
GCP
VISIT:
Streamlight has launched several new portable lighting solutions, which are wireless and enable mobility while conducting a wide range of tasks, including inspections, equipment installations, work in industrial shops and operating heavy machinery.
• The Dualie 3AA Color Rite is an intrinsically safe work light that provides the option of bright, white light to illuminate large areas or a high CRI light with Streamlight’s Color-Rite Technology for true color recognition. The feature can be used for differentiating color wires, painting and other color-discerning tasks.
• The Syclone Jr. (pictured) is Streamlight’s smallest multi-function work light. Its compact design fits in small spaces to illuminate the work area without getting in the way. Handsfree or hanging, the body of the light can rotate 360 degrees in its U-shaped magnetic base and can be adjusted with one hand. It also provides USB rechargeability.
• The ProTac 2.0 and the ProTac 2.0 Headlamp provide brightness without sacrificing run time. These rechargeable lights are powered with Streamlight’s SL-B50 USB Li-Ion battery pack that charges via USB-C cord inside or outside of the light. Both are dust tight and water resistant.
National Flooring Equipment’s The Rogue provides floor preparation contractors with the power and productivity of a ride-on scraper in the compact size of a walk-behind. The Rogue is an all-electric scraper with precision steering, speeds up to 150 ft/min and a fully adjustable blade angle at the touch of a button.
When developing the Rogue, National Flooring Equipment explored how it could redesign a walkbehind scraper to have all the features of a larger, ride-on in a compact machine. Legacy walk-behind machines are typically difficult to maneuver, using hydraulics to control the scraper. Instead, the Rogue is a fully electric machine, with increased maneuverability and speed—where a traditional walk-behind scraper could work up to 30 ft./min., the Rogue can do up to 150 ft. in the same time. To improve ease of use, the Rogue incorporates simple controls that require less operator input than traditional models. For example, contractors can use toggles on the handle to direct the machine left, right, forward or reverse. In addition, the Rogue includes a button to control blade pitch and angle, unlike existing machines where angle adjustment is limited by a few different attachment options.
In addition, National Flooring Equipment adapted the vibration of the machine to impact floor removal efficiency. Typically, all tooling on National Flooring Equipment machinery oscillates, moving the blade to help remove material—the contractor could not control this. Now, the Rogue features a dial to adjust oscillation, which means that, depending on the application, contractors can choose how the tooling moves to achieve the best result. This means that when removing adhesive, users can turn oscillation off completely; when removing hard goods, contractors can increase the rate of oscillation.
To improve transportability, the Rogue is a modular machine—contractors can remove weights, splitting the machine into multiple parts that are easier to carry. By introducing this new feature, contractors can easily and safely lift the machine, either onto transport to travel to a job site, or upstairs in a job with multiple floors.
https://CONC.me/nvw11b
S3 Barrier SL is a non-portland cementitious based self-leveling material that exhibits ultra-low permeability provides superior chemical bonding performance to existing concrete substrates, and offers moisture protection up to 16 lbs, MVER, and 100RH. It removes multiple installation steps from typical remediation projects that require self-leveling systems, in an all-in-one primer-less subfloor that protects finished floors from high moisture and high pH. Finished floors can be installed in as little as six hours after placement.
Additional uses include: patching compound 1-in. to feather edge, mix with aggregates to repair deep holes and trenches, as a broadcast base for decorative flake or quartz, and as a primerless decorative polished floor overlay system. The formula is safe and environmentally friendly, featuring high levels of recycled material content and emitting zero volatile organic compounds. https://CONC.me/i1ze73
The Multiquip Mayco LS300GK compact, trailermounted concrete pump combines levels of performance with the build quality you would expect on larger pumps. Multiquip designed the LS300GK to be unique and distinct from other pumps with a 30-yard/hour output, handling up to 1 1/2-in. aggregate.
• Oversized 6-in. material cylinders
• 800 psi piston face pressure (max)
• 85.0 HP liquid-cooled Kubota WG3800 gasoline engine
• Ideal for slab work, block fill, shotcrete and more
• 10-cu.ft. capacity hopper, easily removed for maintenance
• Easy to read, solid-state digital control panel
• Optional wireless remote control https://CONC.me/z4qhwz
https://CONC.me/bdbpsu
CarbonCure Technologies’ CarbonCure Express EPD (environmental product declaration) service features a suite of carbon removal technologies, field-leading software, revenue-boosting carbon credits and now reporting—offered as a subscription package and bolstered by personalized customer support.
CarbonCure Express EPD streamlines the complex life cycle assessment (LCA) process required for EPD generation by automating much of the data collection. This enables concrete manufacturers to quickly produce accurate, product-specific EPDs, generated through a secure program and available at an accessible price. With LCA support from objective organizations like Athena Sustainable Materials Institute and final verification from trusted third parties, designers and builders can trust the accuracy of CarbonCure Express EPDs to help them make informed comparisons during procurement.
https://CONC.me/h2dzdk
Ameripolish updated its formula for AquaShield, a waterproofing treatment that provides water repellency to any concrete surface, preventing staining and damage.
• Long-lasting
• Ideal use on any concrete or masonry surface, indoors or outdoors
• Protection from excess moisture and salts
AquaShield was designed for new or existing concrete cast, precast, masonry units, and pavers.
It is a ready-to-use product with excellent coverage rates of approximately 400 sq.ft. per gallon on a broom-finished surface and 2,000 sq.ft. on lessporous concrete finishes.
The water-based and fast-drying product is nonflammable, low-VOC and odor, and will not alter the appearance of concrete.
https://CONC.me/qh1gt4
Scheduled for January 17-19 at the Las Vegas Convention Center, World of Concrete 2023 is dedicated to the concrete contractor and the concrete construction industry, from cement all the way to decorative. Check out these booths and events during the show.
HAPPY BIRTHDAY TO US!
Come join the celebration of our 20-year anniversary at the Concrete Contractor booth! Sponsored by Milwaukee Tools, attendees are able to get a photo taken as if they are on the cover themselves. Come join us in some fun!
FIND US AT BOOTH C4137.
With the theme “Mexican Fiesta”, the American Society of Concrete Contractors is one again hosting its Kick-Off Bash networking event on Monday, Jan. 16 starting at 6 p.m. in Westgate, ballroom C. Online registration will be available until Jan. 5.
FIND THE ASCC AT BOOTHS C4511 AND O40534.
Ideal for concrete inspection and evaluation, the StructureScan Mini XT helps you to easily and accurately locate the position and depth of metallic and non-metallic objects in concrete structures, including rebar, conduit, post-tension cables, pan decking, voids and service utilities. Reduce safety risks, financial exposure, and costly delays and provide the full-range of services to your customers by adding this concrete scanner to your toolbox.
• Rugged compact design, IP 65-rated to withstand a jobsite’s toughest conditions
• 6.5 inch HD touchscreen user interface
• Operation modes tailored for beginner to advanced use.
• Customizable data display, with color adjustments
• Real-time migrated data, onscreen reference markers, and real-time signal floor indicator are also available
Back from popular demand, the Concrete Foundations Association is rebranded its Winter Social as “The Foundation Contractor’s Night,” hosted on Jan. 17 from 6-9 p.m. on the top of the Stratt Tower. Find views of Las Vegas, the fun of amusement rides, high-quality food buffets, and networking galore.
STOP BY THE CFA AT BOOTH C4605.
GSSI WILL BE SHOWCASING ITS STRUCTURESCAN MINI XT ALL-IN-ONE CONCRETE INSPECTION GPR SYSTEM AT BOOTH N1838.
Aquajet will be featuring its Aqua Cutter 750V and the company’s revolutionary Infinity oscillation that moves the water jet in an infinity—or figure 8—pattern, removing more concrete in a single pass while reducing shadowing, eliminating the risk of pipe holes and providing an ideal bonding surface. The 750V’s next-generation Evolution 3.0 Control System includes new functions, including the ability to automatically calculate optimal settings for lance motion for greater precision and efficiency. Like all Aqua Cutter Robots, the 750V cleans and descales rebar without causing microfracturing. It also maintains exceptional horizontal, vertical and overhead reach, making it suitable for a wide variety of concrete removal tasks, such as renovation and bridge and road repair.
Another key feature is remote start and stop of the diesel engine through radio remote control, making it possible for the operator to stop or start the robot from a safe distance and eliminating the need for the machine to run all day.
FIND AQUAJET CO-LOCATED WITH BROKK INC. AT BOOTH C4119.
years business
David Harris and David Forren have attended preconstruction meetings, and for 20 years, as the building team got to the specs for polished concrete—which architects and owners love, but general contractors hate to deal with—he could all but write script.
Harris and Forren are managing partners of Riverbed Concrete, a twodecade stalwart of concrete flooring, and Slick Rock Concrete, manufacturers of precast site furnishings, fire tables, fire bowls, and water bowls. They are also most recently the inventors and managing partners of a new products company called GoldiLox, the peelable concrete floor protection about to turn the building world on its head.
“The GC is put in an impossible situation when polished concrete is specified,” Harris says. “The concrete slab is poured on day one. By the end of the project, that same surface has to be immaculate, on time, on budget—but with no sure way to protect it through the many months of heavy construction.” GoldiLox tackles this problem head-on.
Wait a minute. Doesn’t polishing protect the floor? Why not just polish before walls go up and let the densified concrete bear the brunt of the construction abuse.
Common misconception, Harris says. And a costly one. “For 20 years at meetings we’d educate everyone on what polished concrete is and is not,” he adds. “It’s wear tolerant. It’s durable—no recoating necessary. No
stripping. No rewaxing or buffing. With commercial traffic it stays looking great. But construction abuse is not normal traffic. Polished or unpolished, concrete exposed to oil leaks, oversized construction machinery, metal shavings, dropped tools, chemical spills, and industrial mishaps will absorb stains and show construction abuse in the final product.”
Why not wait to polish the floors when the construction ends to remove
GoldiLox LLC | Photo by Jason Risner of Jason Risner Photographyconstruction damage? Harris says that polished concrete should not be looked upon as a magic eraser to remove construction abuse—it just doesn’t work t hat way. Additionally, by the time the walls are up, the electricians, plumbers, painters, drywall, and other tradespeople make the worksite dangerous a nd difficult to coordinate around the industrial process of grinding and polishing, resulting in hugely inefficient installation and often sub-par results.
To further complicate the argument for polishing after walls, “OSHA recently classified silica dust similar to asbestos,” the 20-year concrete veteran adds. “So many installers are choosing to grind wet. Grinding wet alleviates dust concerns, but grinding wet after walls, with the other trades on site, invites mayhem. “You’re trying to run an industrial process around walls, through every door jamb and opening,” Harris says. “If it’s a new school building, for instance, you’re talking in and out of 100s of classrooms. The process becomes slow and broken.”
For a GC with an eye on budgets, installation quality, deadlines, as well as safety, the ideal is to polish early, uniformly, in an open field of concrete and then frame on top of it. No edging by hand needed, no more hand grinding those last inches near the wall (which never matches the field of the concrete). Fewer inconsistencies in clarity, shine, and uniformity while gaining significant improvements to production rates.
For protection, some contractors in the first months will use OSB (oriented strand board) or plywood, with all the usual plywood problems. “It curls and bows in rain and trips people up,” Harris says. “Leaving it on the slab can often produce ghosting in the finished flooring. The open seams allow in oil and acidic spills. And the cost of sheet goods right now is through the roof.”
Though cardboard is lightweight and typically inexpensive, Harris doesn’t believe it offers enough of a barrier to protect the polished floors. He calls it a “non-starter” especially for the first months of heavy construction, before dry-in. “As soon as you pour, the cranes, lifts, big equipment, and abusive trades are there,” Harris explains. “You can’t tape cardboard to the concrete. It has seams and doesn’t stay down, so dust, metal shavings, dirt, and oil slip in. It turns to mush when wet. The earliest cardboard can go down is after the roof, doors, and windows are up—often months after work begins, and by then the contractor has missed the critical stages of protecting against heavy construction.”
He’s also found
rolls and sheets of plastic ineffective, explaining that “plastic almost always results in ghosting. It’s not seamless, meaning debris and liquids can easily get under it. On top of that, a slip-andtrip hazard.”
For 20 years, by the end of a precon, he explains that he and the GC would lock eyes, one looking pained, the other resigned. Ultimately the GC would ask the big question, “With the budget I’ve got, how the heck do I make sure the concrete I pour next week will look good when I turn the building over to the owner?”
For 20 years, the industry’s best answer has been a shrug.
For a time Riverbed Concrete tried to protect its newly polished floors with a glue-down product. “It’s a great product but with labor, can easily be as much as twice the cost of the floor we’d put in,” Harris says. “Protection is too rarely specified, and builders tend to budget for cardboard, so overly priced alternatives like that can’t come in after the fact.”
This got the Riverbed team thinking. “If we could develop an effective, budget-friendly form of protection we could dramatically improve our polishing production, become more competitive not only in cost but by delivering
GoldiLox LLC | Photo by Jason Risner of Jason Risner Photography• Roll size: 65 in. wide., 1,000 sq. ft.
• 10 gallons of adhesive per 1,000 sq. ft. of fabric (100 sq. ft. per gallon)
• Applicable on day 10
• 2 Years of UV protection
• Antimicrobial and antifungal
• Flame retardant
• Slip, oil, and acid-resistant
• No resin to stain the slab
• A pply directly to concrete, not over coatings or sealants
dependable results that our polishing competitors can’t touch, ultimately landing more jobs per year.” It’s a win for the polishing sub, the GC, the architect, and the owner.
With this in mind, Harris and Forren began experimenting with options a nd adhesives to create a temporary protective covering. The team pressed in and finally found it: the magic combination of non-staining, temporary adhesive and woven industrial textile, creating a durable composite covering that is effective, and easy on budgets.
“Our aim from the beginning was to create a protective covering that could be used industry-wide and on budget for the vast majority of subs and GCs at nearly half the price of other glue-down protection alternatives,” Harris says. The patent-pending invention officially became GoldiLox, the “just right” solution offering the concrete polisher and GC to affordably deliver a final polished concrete floor
that meets the expectations of the owners and architects, with fewer construction damages.
L ooking to help the polishing industry, it was developed to address a missing link in the polishing process. Over the years the team behind GoldiLox hosted a lot of American Institute of Architect presentations for architect CE credits and discovered that architects are getting fed up, with specifying polished concrete only to be delivered a shiny floor that’s riddled with stains by the end of the job.
“The goblins seem to come out overnight, especially with things like hydraulic oil,” he says from experience. “No GC can keep tabs on all of it 24/7. Lines bust. We’ve walked into jobs in the morning
with a 10- by 10-ft.’ oil spill, and that’s the new reality of the finished flooring. Batteries blow up and etch into concrete. Buckets leak. In commercial buildings a big problem is metal piping for fire-prevention systems’ sprinkler lines, oily and full of rusty water. They get cut directly on the slab. Plywood
GoldiLox LLC | Photo by Jason Risner of Jason Risner Photography“Our aim…was to create a protective covering that could be used industrywide and on budget for the vast majority of subs and GCs at nearly half the price of other glue-down protection alternatives.”
—David Harris, Managing Partner of Riverbed Concrete LLC, Slick Rock Concrete LLC, and GolidLox LLC
Industry-leading pumping pressure. Unparalleled quality. Unrivaled customer service. This is the kind of innovation you’ve come to expect from Blastcrete. The RMX-5000 allows contractors to pump harsh materials and longer distances, and features twice the mixer capacity of competitive machines. All this plus user-friendly features for easy maintenance make the RMX-5000 the most productive — and profitable — mixer-pump on the market.
and cardboard are useless to protect against so many of the damages subjected to the concrete during construction but are often the only materials the contractor can afford.”
Affordable, weather resistant, seamless, durable—it temporarily adheres onto the concrete surface like a second skin. Let workers walk on it and
builders build on it. GoldiLox is antimicrobial and antifungal so erect the walls directly on top of it and leave under the framing. Pop lines directly on the white surface. Let cans of liquids topple on the protection and machines roll over it. Let dust, dirt and shavings blow across it. It is flame resistant so welders can work on it. GoldiLox is seamless and NFSI rated
—David Harris, Managing Partner of Riverbed Concrete LLC, Slick Rock Concrete LLC, and GolidLox LLC
Sealing concrete cracks, joints, and other distresses with a rigid repair material often fail as they grow brittle and break over time. The ideal solution provides both strength and flexibility.
TechCrete™ is a highly flexible concrete repair material that not only adjusts with the pavement but delivers the strength to support heavy loads, and the durability to resist cracking, delamination, and spalling.
Have your concrete and repair it, too, with TechCrete™. The most advanced, flexible, long-term repair solution for concrete.
Nationwide sales, service, and rentals. Learn more at crafco.com/sales
“Now what you see at the beginning is what you get at the end.”
as high traction, so rest assured it’s safe to work on. With little to no maintenance, the protection system is the proGC and pro-budget.
The meaning behind GoldiLox name becomes clear. If you consider cheap and ineffective to be “too cold,” and overengineered and overly expensive to be “too hot,” GoldiLox sets right in the “just right” middle. Engineered by polish contractors for polish contractors, GoldiLox protects floors and schedules, reputations, and owners—adding utility into budgets so that architects continue to specify polished concrete with the assurance of a quality final product.
“Now what you see at the beginning is what you get at the end,” Harris says. “In most projects, GCs are walking on eggshells,” he says, “trying their darndest to have a quality floor by opening day. Now they don’t have to worry about it.
Protecting the concrete slab can turn from one of the biggest points of pain into one of the biggest points of pride— providing a “just right” solution to serve the polishing industry.
For more information visit https://CONC.me/n6o6a6
Jim Hanson owns the H & M Saloon, a reception hall on his family’s farmland located in Assaria, Kansas. During construction, a scissor lift left hydraulic oil stains on the floor. Unable to get them out, he hired Troy Vancil, owner of Boulder Polishing in 2021 for a unique stencil in concrete. The result is both awe-inspiring and respectfully honors the family history.
Not able to remove the stains, he was ready to live with them. “But Troy said maybe he could do something else with it,” says Hanson. “I thought it sounded kind of fun.”
The Hanson family was one of the earliest homesteaders on the land, establishing a municipality in the mid-1800s.
Hanson’s matrilineal ancestors immigrated to the U.S. from England in the early 1700s. The father and grandfather immigrated in 1869 from Sweden.
Hanson wanted the reception hall, commemorating his father and mother (Henry and Marguerite), to further memorialize their memory with a oneof-a-kind 13 ft. by 7 ft. installation with stenciled depictions in concrete.
Vancil tapped Shawn Wardall of Specialized Construction Services to help, a nd FLOORmaps Inc. for the customized stencil with Onyx and Dark Brown GemTone Stains by PROSOCO.
Most of the hydraulic stains ended up being straightforward—others remained more stubborn. He used an
oil and grease stain remover to pull most of the stains from the concrete, the remainder were cut out and then filled with micro-topping.
With the art completed, the project fills Hanson with pride. Upon the reveal, “My grandfather was 18 when he came here from Sweden,” he says.
“This picture shows the house where my grandfather lived. It’s the house my dad was born in, and it’s the house I live in now.” What better way to honor your ancestry than by setting it in concrete.
For more information visit https://CONC.me/qoxde3
The creative mind of a polished concrete contractor makes a one-of-a-kind artwork to commemorate a family’s history.
The Rock’N’Roller from MARSHALLTOWN is a roller, weight and spray release system for stamped concrete. Available in 11 patterns, it is available in from 11 1/4 to 36-in. and border rollers. The kit comes with a roller, frame with weight poles, two weights, and a 13/4-in. push-button adapter. This roller has a unique leverage weight system adaptable to different concrete sets and easily creates a push and pull pattern imprint.
https://CONC.me/dmvk20
Solomon Colors explores new depths of decorative concrete with Concrete Dimensions reusable stencils. Embed the specially designed urethane Concrete Dimensions tools in fresh concrete for beautifully crisp medallions and borders. Concrete Dimensions works well with exposed aggregate finishes, texture skins, and flatwork. The durable, flexible urethane means Concrete Dimensions can be removed, rolled up, and reused when the job is done.
https://CONC.me/vd5v0k
Featuring magnets to link the tools perfectly aligning the grout lines, Proline’s SPS system is the culmination of studying and developing for the decorative concrete industry for over 30 years. Once concrete contractors stamp with the Magnetic Seamless Pattern Stamp, they will experience first-hand the benefits it has to offer, no double joints, seamless transition, reinforced composite design, tougher tool with high flexibility, lightweight for less fatigue, no joint squeeze-out and over 4X the coverage of traditional tool.
Available design options:
• Inca Flagstone
• Appian Random Cobble
• Appian Running Cobble
• Blue Ridge Large Ashlar Hammered Edge
• Boston Herringbone Brick
• Boston Running Board Brick
• Carmel Bluestone Ashlar
https://CONC.me/nncynv
• Chesapeake Random Stone
• Monterey Ashlar
• Napa Random Stone
• Pocono Bluestone Large Ashlar
• Sausalito
• Sedona Flag Stone
The BonWay division of Bon Tool Co. Decorative Concrete Border Kits and a 4-piece Border Stamp set provide alternatives to the urethane border mats already available from Bon. The Border Kits each include a Stamping Roller and a matching Border Mat to quickly and easily install patterned borders.
The rollers are 8 or 9-in. wide and offer a simple way to incorporated linear features to decorative concrete jobs and provide a custom look even for curved areas. With the rollers, borders can be rolled out by one person, saving time and money.
• Four border patterns are available: 8 in. Cut Slate; 8 in. Worn Brick; 9 in. Old World Soldier; 9 in. Old Stone Tile
• The rollers are equipped with brackets that attach to threaded Bull Float Handles
• Available in the classic and popular Worn Brick Soldier Course pattern
• The set of four mats is each sized 25 x 8 in., and stamps the exact same pattern
• Three of the mats are standard rigid and one “floppy” in the set is more flexible for easier use against obstacles
https://CONC.me/ddyp9w
The concrete construction industry has changed a lot since the magazine officially launched in 2002. Let’s take a look back at some significant happenings these past two decades and look forward to concrete’s future.
Officially, the Concrete Contractor magazine was originally known as Concrete Concepts. The publication officially became the brand we know today in 2002 and has been celebrating concrete in all its forms since. To celebrate this, we invited a handful of industry insiders for their commentary on these two decades regarding significant changes and challenges—and asked for a bit of perspective on what the future holds.
It’s safe to say that one of the most significant advancements in the last 20 years has been in technology and any useful improvements from technological upgrades should come hand-in-hand with an increase in efficiency. “Today’s technology is much more sophisticated, providing greater efficiency, flexibility, and ease of use,” says Keith Armishaw, North American Business Development Manager at Aquajet. Exemplifying the advancement in the technology of concrete construction equipment to increase the efficiency of today’s contractors, he points out that improvements in the Aqua Cutter 750V’s Infinity oscillation system helps contractors using hydrodemolition for the removal of concrete increase the bonding surface for concrete repairs but also reduce shadowing of the rebar and pipe holes.
Advancements in hydrodemolition coincides with a need for better wastewater management. As more environmental issues gained more awareness over the
years, technology allowed contractors an increased efficiency with water treatment.
“At first, contractors developed elaborate set-ups for collecting and treating wastewater, which was very laborious. In response to the need for an easier and more effective way to clean the water, Aquajet developed the EcoClear, a fully automated water treatment system. Once the water is treated, it is clean enough to be released into the environment or recirculated through the high-pressure pump. Both the robot and water treatment technology have majorly advanced the hydrodemolition segment and contractors’ ability to rehabilitate concrete structures over the last couple of decades.”
There have been also increased efficiencies at the cement plants with upgrades and making them more environmentally friendly. This effort changes the industry’s focus to reduce carbon emissions. The Portland Cement Association (PCA) launched its Roadmap to Carbon Neutrality in October 2021 and Mike Ireland, PCA President and CEO, has seen the changes made by companies already making a difference. “And they will continue to follow the guidelines provided in the Roadmap, which we’re confident will lead us to carbon neutrality by 2050. This is now our industry’s top priority.”
The research and development of lower-carbon cements, alternative fuels, and carbon capture technologies are all under continuous research and development. But to achieve the net-zero goal, the cement and concrete industry has to work together, says Ireland. “We
need everyone in the cement-concreteconstruction value chain to work with us. I also want to mention that Congress and state legislatures are part of this chain, too. PCA will continue to work with elected officials to help develop policies that will assist our companies in their R&D efforts. Effective, meaningful policies will enable us to continue to manufacture materials that are sustainable, durable, and better for the environment.”
Tim Nash, Director of Concrete Products at Wirtgen America has also seen efficiency at the core of the design of equipment as they respond to market changes. With more reconstruction projects and less new construction over the years, for example, he says that the integration of stringless control technologies, increased transportability of slipform pavers, and quicker paving width change times to address any paving run width changes. Changes to these machines have allowed change time to cost contractors hours instead of days.
Over the years, the company has continued its focus on improving smoothness and rideability along with a significant shift focusing more on sustainability, a reduced local emission output, and increased automation of various machine functions as a central theme addressing the shortage of skilled labor.
“In addition to a dwindling labor force, really the one of the biggest challenges has been the nature of the work,” says Nash. “Gone are the days of paving continuous runs all season long.
Jobs are cut up, different paving widths and often requiring constant moving of the paving equipment which can add significant time and cost to a project.”
Undoubtedly, one of the largest impacts onto the construction industry has been the global pandemic. While many contractors were considered essential workers, the industry is still dealing with the adverse effects today. There is a great need for skilled labor but this shortage has been an issue for years prior to COVID—the global pandemic only exacerbated the situation. While private and public programs to increase training will help, PCA’s Ireland thinks that it will likely take some time for meaningful results to materialize.
The same way manufacturers like Wirtgen and Aquajet had made improvements to their machinery, throughout the past decade, contractors had to find innovative solutions to overcome a limited workforce as well as adapting to new health, safety, and environmental regulations.
“The industry as a whole is more aware, for example, of the effects of silica exposure,” notes Armishaw. “To help contractors protect the workforce, manufacturers have responded in a number of ways, such as developing dust suppression systems or incorporating remote operation. In our case, using water to remove concrete eliminates the dust, but we’ve had to help our customers find an efficient way to treat the blast water and meet environmental regulations.”
The simple fact is that concrete is here to stay, even if the substance continues to evolve. Concrete mixes and how structures are built will need to change as materials become harder to source from depletion or cost.
“With greater awareness about sustainability, it’s possible structures will be designed with a longer life in mind,” says Armishaw. “Repair will then be an important aspect of extending the life of the structure, and repair procedures may be something that are considered during the design process.” Like Wirtgen’s
increased integration of automation technologies, Armishaw also predicts that automated processes will affect safety by preventing strain and injury— adding to efficiencies throughout the jobsite.
Similarly, Ireland predicts the further digitalization of everything with a decrease in the reliance of paper. “Whether it’s paper delivery tickets, paper scheduling, blueprints,” he says. Even if you’re a small company with a dozen people or 300 on staff, software options are available to help to meet a contractors needs. Many of which are scalable and budget-freindly.
Further sustainable developments include 3D imaging and carbon capture systems. According to Ireleand there were currently (at the time of his response) four carbon-capture projects being funded currently by the Department of Energy—two of which are taking place at PCA member companies with more on the way.
“All aspects of construction will be quantified for carbon emissions both at the local level and up/downstream and could become significant parts of the bidding process and/or bonus incentive,” says Nash. Additional themes for the future of concrete construction include onsite crushing and reclamation of existing materials, and optimization from machine learning solutions not only at the paver but advancing the process such as batching, hauling, etc.
For the future of the Concrete Contractor magazine, readers can expect the continued coverage of projects and innovations within the concrete industry—in both the constructive and decorative arenas. We will reconvene our Top Products award program announcing the winners in the May/ June issue.
We’ll be always searching for great stories to tell. Our inbox is always open so drop us a line with some information on our latest project. Small or large, we would love to share your story.
Here’s to a new year and the decades to come!
For more information visit https://CONC.me/nsvcip
In looking back towards the magazine’s foundations, Rebecca Wasieleski, Concrete Contractor former editor (2006-2013) was gracious enough to reconnect with us.
Q. What memory stands out from your time with the magazine?
“The strength of the industry and the professionalism of the people in it. I attended many industry events, including the World of Concrete, CFA and ASCC conferences, and even the monthly Wisconsin ACI chapter meetings in Milwaukee. One of the biggest lasting impressions from my time at Concrete Contractor was observing how the leaders in the industry were friends with each other and how they were supportive of people entering the industry. It was a lasting lesson in how quality, professionalism, sharing knowledge, and just being a decent person to others will in most cases bring you success and happiness.
My favorite articles were the cover stories that featured a contractor and a unique project. I typically traveled to a construction site and spent a day with a concrete contractor. We would discuss the contractor’s business and management style, his or her challenges and successes, and the company’s history. Then we would typically tour some recent and noteworthy projects in the area. Those articles gave me the opportunity to visit some wonderful cities and communities throughout the country and get to know some remarkable people.
While my friends and family members thought I wrote about sidewalks and roads, what I was primarily writing about — and learning about — was business management. I absorbed a lot of valuable knowledge about how to run a business and how to be a leader from the contractors I talked with and wrote about over the years. I’ve drawn inspiration from those lessons many times in the last decade, and for that I am forever grateful.”
Recruiting and retaining workers in construction is paramount as the industry grapples with a 650,000 person labor shortage. There are lots of gimmicks, tips and life hacks out there promising to help construction companies attract, hire and keep workers. Successful construction companies know solving the workforce challenge starts with great employers.
To recognize those companies, the staff of Equipment Today, Asphalt Contractor, Concrete Contractor, Pavement Maintenance & Reconstruction, and their digital hub ForConstructionPros.com, hosted the Best Contractors to Work For recognition program, a research-driven analysis that examines a company’s practices, programs and benefits, and surveys its employees for their perspective.
To be considered, employers needed to register, while employees filled out surveys about what it’s like to work for their boss. Entry forms and surveys were handled by the Best Companies Group, which analyzed the data and provided an actionable insights report that companies can use to improve employee recruitment and retention.
To be eligible, construction companies must have 15 full- or part-time employees working in the U.S. The company’s primary business activity must be either general building construction, earthmoving, paving, concrete, or specialty and trades, such as underground, utility, electrical, HVAC, demolition and others.
Want to be considered for the 2023 Best Contractors to Work For?
Please contact Cathy Somers at: CSomers@ACBusinessMedia.com
• The WOW! & Decorative Concrete Awards: Colorado Hardscapes the USAFA Air Gardens
• Cast-In-Place Stamped (Over 5,000 sq.ft.): Connecticut Bomanite Systems —the Downtown Danbury Transit Development
• Cast-In-Place Stamped (Under 5,000 sq.ft.): Beyond Concrete the Dennis Collins Park
• Polished Concrete & Overlays (Over 5,000 sq.ft.): Burgess Concrete Construction, Inc.—the Fruitport Community Schools - High School Addition & Renovation
• Polished Concrete & Overlays (Under 5,000 sq.ft.): Phaze Concrete the Phaze Concrete Office Lobby
• Cast-in-Place Special Finishes (Over 5,000 sq.ft.): Trademark Concrete Systems —the Academy Museum of Motion Pictures
• Cast-in-Place Special Finishes (Under 5,000 sq.ft.): Architectural Concrete Construction—the Norton Children’s Healing Garden
• Vertical/Facades (Over 5,000 sq.ft.): Unlimited Designs —the ASU – Interdisciplinary Science & Technology Bldg. 7
• Concrete Artistry (Over 5,000 sq.ft.): Bomanite International Ltd., the Halong City Carnival Square
• Concrete Artistry (Under 5,000 sq.ft.): Fuscardo Concrete the Rebecca Fuscardo Booth at DecoCrete Expo
• Multiple Applications (Over 5,000 sq.ft.): Hyde Concrete the Tidewater Farmhouse
• Multiple Applications (Under 5,000 sq.ft.: Deco-Crete Supply The Orchard
• Stained & Dyes (Over 5,000 sq.ft.) & Project Video: Desco Coatings — the Fort Edmonton Park Indigenous Peoples Experience
• Stained & Dyes (Under 5,000 sq.ft.): Bob Harris, Structural Services, Inc., and Lee Ann Harris, Decorative Concrete Institute —the Decorative Concrete Institute Facility
• Architectural Cast-in-Place Concrete Structures (Over 5,000 sq.ft.): Colorado Hardscapes, the USAFA Air Gardens
• Architectural Cast-in-Place Concrete Structures (Under 5,000 sq.ft.): Bomanite Artistic Concrete & Pools —the Weststar Tower
• Cementitious Overlays (Over 5,000 sq.ft.): T.B. Penick & Sons —the Legoland Lego Movie World
• Cementitious Overlays (Under 5,000 sq.ft.): Sundek of San Antonio the Aloft Hotel
• Decorative Resinous Coatings: Decorative Concrete of Virginia the Runk & Pratt (Over 5,000 sq.ft.) and the Smith Mountain Lake Garage (Under 5,000 sq.ft.)
• W. Burr Bennett Awards for Safety Excellence: Keystone Structural Concrete; and Shiel Sexton
• Outstanding Safety Achievement Awards, General Contractors (lowest incident rate): Shiel Sexton Co. (over 650,000 work hours); Gregory Construction Services (160,000 – 650,000 work hours); and Wm. Aupperle & Sons (under 160,000 work hours)
• Outstanding Safety Achievement Awards, Specialty Contractors (lowest incident rate): Keystone Structural Concrete (over 300,000 work hours); Vicon Construction (90,000299,999 work hours); and Anderson Commercial Concrete (under 89,999 work hours).
• Outstanding Fleet Safety Records (miles with zero incidents): J. J. Barney Construction (480,000 miles); Schiralli Construction (1,000,000 miles); and Solid Surface Care (4,680,000 miles)
• ASCC Member Owner/Executive Safety Award: Theodore Goloboski III, CEO, Belfast Valley Contractors
• The Overall Excellence in Concrete Construction Winner & Mid-rise Structures: Azzurri Concrete —Chau Chak Wing Museum (pictured above)
• Repair & Restoration: Innobeton, UHPFRC (phase 1), Mediterranee Prefabrication (UHPFRC and slabs, phases 2-4)—the Corniche Kennedy, in Marseille, France
• Decorative Concrete: Shapoorji Pallonji and Company Private Limited— the Aquatic Gallery
• Low-Rise Structures: Spie Batignolles —the Chai Château Haut-Bailly Winery
• High-Rise Structures: Concrete Strategies—100 Above the Park
• Infrastructure: The Concrete Products and Aggregate Co., Ltd.—the SCG-CPAC Ultra-HighPerformance Concrete Bridge
• Flatwork, 1st Place: Larsen & Toubro Ltd.—the MSPT Proving Ground Facility and Test Track
For more on the ASCC awards, visit https://CONC.me/6qg83d
For more on the ASCC awards, https://CONC.me/vxds3k
Choose SET-3G™ high-strength epoxy from Simpson Strong-Tie for your next anchoring installation job. Code listed for extreme temperatures (40° to 100°F), SET-3G is also code approved in concrete holes that are dry, water-filled, water-saturated or submerged. SET-3G is manufactured in the US and immediately available through our distributors, so you can always stay on schedule.
Get a full supply of SET-3G epoxy for your next project. Visit our website at go.strongtie.com/set3g or call us at (800) 999-5099.
A field study evaluated installation techniques, how to deal with adverse conditions, and the troubleshooting of and repair of common issues regarding the surface broadcast of glass aggregate.
Many commercial and residential owners looking to make a striking visual impact on guests often work with designers and innovative contractors alike to create an impressive moment for their home or business. A common request gaining popularity over the years has been the exposedaggregate polished concrete floor. One of the emerging trends in this segment has been the use of glass.
The American Society of Concrete Contractors and Concrete Polishing Council identified the need for a “best practices standard” for the surface broadcast of glass aggregate on concrete flatwork. A field study, performed in late October 2021, was meant to evaluate: various installation techniques; how to deal with adverse conditions, and; the troubleshooting of and repair of common issues found on polished concrete projects utilizing broadcast glass aggregate. While evaluation and testing confirmed many best practice techniques, the study revealed key considerations regarding the practice.
The main difference between a mix design specific to embedding glass into the surface, as compared to a standard mix design used to produce a power troweled Class 7 or 9 industrial floor slab, is the consideration of Alkali-Silica Reactivity (ASR). When using crushed glass, ultimately polishing the surface and when exposed to moisture, a reaction can occur forming a gel that is expansive and thereby potentially creating pop-outs.
Unfortunately, there is no way of predicting how fast or slow ASR will occur. The industry has had good success using pozzolanic materials such as Type F fly ash, metakaolin, and granulated blast furnace slag to help mitigate this reaction in several ways. The amount of a pozzolanic material is often debated and to get the true benefits of mitigating ASR some industry experts have claimed less than 20% pozzolanic replacement will provide little if any benefit. In one honed exterior glass project in 2018, a cement replacement of 50% granulated blast furnace slag was specified
considering the amount of moisture the surface was subject to. After four years, there were no visible signs of ASR.
Other considerations include having the proper proportions of aggregate and cementitious material and creating enough paste to fully encapsulate the glass aggregate. A mix design that does not have sufficient fines and paste can be difficult to fully embed glass aggregate into. With regard to the slump, it is crucial to have a workable mix, considering you are adding a very time-consuming step with the broadcasting of the glass aggregate.
There are four main considerations when placing and finishing a glass aggregate slab.
1. Placing of the concrete and getting the slab ready for the application of the glass.
2. Applying the glass aggregate.
3. Bull floating the glass aggregate completely encapsulating the glass.
4. Finishing the slab via panning, combo and finishing blades and saw cutting.
The industry is still evolving as to the specifics of what would be considered an acceptable FF/FL with the addition of glass aggregate that will ultimately be ground, honed, and polished. Depending on the size of the glass being broadcast (which can range from 1/16 to 3/4-in. in size), it is crucial to have a flat floor. If the slab has low FF numbers, the floor may end up with a wavy surface. It would also be easy to grind through the glass, especially on the smaller-sized glass aggregate.
On a traditional industrial interior power troweled slab, a laser screed is often used to obtain the specified floor flatness and levelness. Most interior polished concrete surfaces specify an FF50 and an FL30 to obtain a uniform class A or B finish, and we have seen specified polished glass projects use these same measurables.
Plan high-profile projects and tackle manageable-sized pours that you can hand screed off of each side of the form, assuring the slab is flat and also making it easier for consistent glass distribution.
Many of the same finishing steps are used as a traditional floor slab such as screeding, jitterbug rolling, bull floating,
Inc.
panning, and ultimately finishing. After strike-off, some contractors prefer jitterbug rolling the concrete prior to bull-floating, with the logic being pushing larger aggregate down while bringing the fines or paste to the surface will make it easier to fully encapsulate glass aggregate. On a commercial project, this can be very challenging considering the workers broadcasting glass have to be working simultaneously with the laser screed and the person bull-floating, while at the same time not interrupting the slab placement.
If site conditions permit, we have successfully used equipment staged outside of the pour area that extended out over the surface and applying the glass aggregate while working out of a bucket. Once the appropriate amount of glass has been applied to the surface, it needs to be floated in. Contractors can use a vibratory bull float for more expeditious embedment of the glass.
Kneeboards or premature walking on the slab surface should be AVOIDED, as the glass can become depressed and the void filled with paste. Once ground, you can see the outline of the depressed area in the finished polished surface.
If panning the surface, timing is crucial. Consider that if you pan too early you can embed the glass deeper, bringing more paste to the surface and making it difficult to grind down to the glass. If panning too late, you will not have enough paste to encapsulate the aggregate and you can expect to pull out some of the glass once ground.
Using combo blades, a tightly troweled surface is desirable as the final finish.
Like any slab, timing is crucial for sawing contraction joints. But, it is especially critical here, considering the glass aggregate is close to the surface and if saw cutting occurs too soon, you can expect some raveling. Like any
slab, curing is an important part of a successful glass aggregate installation. Whether using a chemical cure or, wet blanket curing, the concerns that would normally apply to traditional floor slabs are true here as well. If using a chemical cure, uniform application is important. If curing with blankets, ensure they are lying flat on the surface to eliminate differential curing.
Uniform glass distribution is important to avoid “stacking” the glass. If the paste does not completely encapsulate the glass aggregate, it can easily become dislodged during the grinding phase of the process and can leave voids that will require patching. Although conveyer belt systems are typically used for dry shake hardeners and trap rock applications, it is difficult to obtain a uniform application and not stack the glass using a conveyer with this type of system. For this reason,
broadcasting by hand or using a shovel are the most common ways to apply glass. Note that inconsistent broadcasting will likely not place glass in all areas of the floor and may leave blank spots.
Since there are many effects that can be achieved with a light, medium, or heavy glass broadcast, perform a test mockup, not only to dial in technique but to make sure you get a sign-off from the client on the final appearance. Also, keep a record of how many pounds of glass was used on the given square footage of the mockup so you can calculate how many pounds of glass per square foot will be required for the actual project. This mockup will then become the benchmark for the rest of the project and can be used for comparison purposes.
When applying a slab adjacent to a previously installed slab, precautions need to be taken to slightly recess that day’s pour slightly, as volume change of the concrete will occur when glass aggregate is added. The amount of glass will
determine how far to recess the slab. In one instance, a contractor screeded the concrete flush with the existing slab surfaces and then applied 1 lb./ft.2 of glass. The resulting elevation difference of the glass aggregate slab was nearly 1/2-in. higher than the existing slabs. When the slab was ground flush, a high percentage of the glass was ground out.
All of the previously discussed considerations affect how much grinding will be required to get uniform glass exposure, as well as how the slab was cured and for how long. If a slab finishing process started prematurely—embedding the glass deeper—and the concrete has cured for an extended period, more aggressive grinding will be required. A lower grit metal bonded diamond tool would be required to start to cut through the paste and reach the glass.
Usually, wet grinding is the preferred
method for deeper grinding, as the water keeps the diamond tooling cool for more productive cutting, and the slurry acts as a lubricant, resulting in less aggregate pullout. It is important not to shatter the glass during the grinding and polishing process. To reduce damage to the glass, it is recommended to use an 8 or 10-segment metal bond tool that has beveled edges during and after the glass exposure until you have reached a hybrid or resinbonded tooling sequence. When edging, the same principles must be adopted.
When performing a mockup, it is highly recommended to complete the mock-up in a true mock-up sample that will be removed and replaced, or in an inconspicuous area selected by the owner.
When grinding to expose glass, it is important to run a pass /cut in equal overlapping passes across the floor. Review and inspect the results after each pass to see if an adequate exposure has been achieved. It is extremely important
that the operator does not grind through the glass—this will result in the need timely and costly repairs.
On traditional polished concrete, generally concrete cures a minimum of 21 days prior to the polishing process to prevent aggregate pullout and to have sufficient moisture cure out of the slab to avoid compromising the joint filler’s adhesion. We have heard scenarios of contractors performing the first grinding step within a week to get down to the tips of the glass, however, you can expect the joints to ravel since, and this is too
Above, roller bug and channel/bull floating should immediately follow laser screed.
Left, Concrete being floated slightly lower than form to account for the volume change from broadcast aggregates. Courtesy of Structural Services, Inc.
soon for the application of the joint filler.
Expect sand and in some cases glass aggregate pullout because of the aggressive nature of course grinding. Once the appropriate amount of glass has been exposed and the surface is cleaned and dry, apply a grout coat. Some floors may need multiple applications of grout coat to obtain a void-free surface. Cementitious or polymer resin grout coats can be used.
But cementitious grout coats require longer dry times prior to the next grinding steps, while polymer resin systems usually can be ground off in a few hours depending on temperatures and humidity levels. In either case, it is important to choose a grouting color close to the color of the concrete matrix or sand particles to help mask the voids. Use the representative sample mockup to help determine color selection.
Once there is a void-free surface and uniform glass has been exposed, many of the same steps used on traditional polished concrete can be used, including the application of densifiers and ultimately polishing up to the desired sheen level.
For best results, try and obtain the ingredients that were used in the original mix design of the concrete consisting of the sand, cement and whatever pozzolanic
material was used. Break the weights down from pounds to grams or ounces to make smaller-sized batches.
If you cannot obtain the ready-mix ingredients, there are bagged products you can use to formulate your own mix design. When mixing your powdered ingredients into a resinous material, typically the resin will darken the ingredients. White cement or white pigment can be used to lighten up the mix to the desired color. Expect to have to make several samples to obtain a close color match.
A true representation of the repair is after the repair has been ground, densified, and polished. The color will likely change during each of these steps.
Depending on the depth and width of the repair, it is important to embed the same glass that was originally used into the repair. If the repair is small, it may require crushing the glass into smaller pieces to be able to embed it into the repair material. On larger repairs, glass can be mixed into the repair material and then poured into the recessed area. On smaller repairs, it is better to hand-seed the glass, making sure to get as much glass embedded as possible.
Once the repair formulation has been completed and prior to the application, the next consideration is to prepare the area properly. You must have squared
edges with vertical walls. You cannot feather edge glass. An angle grinder can be used to create a cut but some installers prefer to use a chisel or chipping hammer to fracture the edges, claiming that a raveled edge hides the repair better.
The next step is to use a Nyalox wheel (nylon bristles impregnated with abrasives) to thoroughly clean any residual dust from the repair area followed by vacuuming considering. The use of wire brushes or wire wheels is not recommended as they tend to leave a residual f ilm, potentially compromising the bond of the repair. Once the repair material has had sufficient cure time, a handheld grinder should be used to grind the repair down to the surface prior to passing over the area with walk-behind or ride-on polishing equipment.
The type of sealer used is generally a function of the type of traffic the floor will be subject to and the amount of maintenance the consumer is willing to agree on. Generally, topical guards will darken the surface, bringing out more color. Also, when burnished, guards will dramatically increase the overall gloss.
Penetrating sealers are less topical than guards and do not darken the surface to the extent guards do. In some scenarios a combination of the two types
of sealers can simultaneously be used, with the first application being guard followed by the second application of penetrating sealer. The benefit of using both sealers is enhanced darkening of the polished surface from the guard and increased stain resistance resulting from a solvent-based penetrating sealer.
In all three scenarios, check with the sealer manufacturer for the best daily, monthly, and yearly maintenance methods to preserve the sealers.
Polished glass aggregate projects are no different than traditional polished concrete in that they require some form of maintenance. Having door mats both inside and outside the facility to collect particulate is a starting consideration, as dust or abrasives on a polished surface can negatively impact the sheen on the floor. The type of sealer used will be the first consideration of how the floor should be maintained.
It is important to create a maintenance program to ensure that proper refinement and stain protection remains in tack. The type of cleaning solution used is crucial to preserve the polished surface as well, as floor cleaners that are too acidic or too high in alkalinity can have adverse effects and can quickly degloss a floor.
Be cautious in introducing standard diamond-impregnated pads used for high-speed burnishing in daily maintenance due to the ratio of glass to cement paste exposure. Using flexible abrasives such as diamond-impregnated pads can cause orange peel due to the hardness variation between glass and cement paste, and the paste can become slightly lower than the glass. Typically, incorporating extremely high grit diamond abrasives (above 10,000 grit) into a weekly maintenance program, combined with auto scrubbing with an appropriate cleaning pad, can reduce orange peel, as these methods are truly polishing and not cutting.
It is important to ensure the floor is protected from stains throughout its life cycle, and equally important to schedule the reapplication of stain protection
treatments as often as required based on the traffic and use of the facility.
There are no shortcuts for work done well when it comes to the surface broadcast of glass aggregate on concrete flatwork. With these best practices, contractors should greatly increase the chance of success in their next glass-polished concrete job.
Bob Harris is the DCI President and Founder, Senior Director of Decorative Concrete Consulting, and a Principal for the SSI Team.
Scott Metzger is the owner of Metzger/ McGuire, an industrial floor joint protection and repair products firm. Ryan Klacking is the President of Syncon Inc. Clark Branum is the decorative and polished concrete specialist for the American Society of Concrete Contractors.
For more information visit https://CONC.me/5r4ucu
Every job comes with a unique set of circumstances. But the two things all jobs have in common are concrete and deadlines. Which is why we’ve designed our drills to be the fastest, most accurate, operator-friendly machines on the market, keeping your crew safe and on pace for more jobs. No matter the deadline.
Designed to Beat Deadlines. ezdrill.com
One of the biggest challenges in surface preparation is properly qualifying the application to ensure the right tooling is used for the job at hand. It’s also one of the first important steps and easiest ways to start costing money if not set up properly.
A mismatched tooling to a project can either be not effective or wear out the tooling prematurely. Putting diamonds on adhesive will likely only melt the glue. Put the wrong diamond on an industrial coating and it’ll just ride over the top, not removing anything. Using an abrasive diamond or medium bond diamond on a hard concrete application and the diamonds glaze over.
In the interest of productivity, efficiency, and simplifying the process to help make sure the right tooling is used for the job at hand, it helps to think of surface preparation as three segments: strip, grind, and remove.
Considering the diverse range of tooling available on the market, making sure to choose the correct tooling in any surface preparation project can be a confusing moment. In an effort to try and simplify this, EDCO has developed “Core 4 Tooling.”
“We always talk about it being a recipe for success,” says Tony Calcopietro, the sales director of the rental division at EDCO Equipment Development Co. That problem that we see isn’t necessarily a choice of the wrong grinder, but if the tooling selection is wrong it results in a failed application costing money, downtime, frustration, return of rentals, and customers not getting the job done in a timely manner. I can go on.”
Whether you’re a general contractor that’s just tapping into surface prep, the
man in the truck doing it for the first time, the general handyman doing a bit of everything, or even the weekend warrior – education is key. The project can easily get more complicated than it needs to be if you don’t understand what the tooling and machinery do. Contractors have budgets just like everyone else and there is only so much space in the toolbox. But like there isn’t one wrench, skid steer, or excavator to do every job, it’s the same with surface prep. “People want to just have one tool to do everything, that’s not how it works,” says Calcopietro.
• STRIP – Featuring special sides to make the removal of soft/thick materials and coatings. Use a stripping tooling if you’re project has a soft glue or adhesive, foam rubber carpet backing, flaking paint, soft mastic, or thick industrial buildup.
• GRIND – Designed for hard/thin coatings and to lightly level concrete, grinding toolings should create a smooth concrete surface. A hard thin coating, concrete sealers, mortar-based thinset, light concrete leveling, and smooth/level concrete imperfections all match a tool meant for grinding.
• REMOVE – Since these toolings are designed to remove thick industrialstrength coatings, they will leave a textured surface on the concrete. Use a tooling meant for removal for waterproof
No matter the job, remember your PPE:
• Gloves
• Safety goggles / glasses
• Steel toed shoes
• Respirators
• Hardhat (for certain jobs)
• Vacuum / dust control system (or dust suppression solution, at a minimum)
• Lithium silicates do not require rinsing
membranes, hard thick coverings, pool/cool deck as well as an epoxy and polyurea coating.
Other shows may talk a big game, but only World of Concrete speaks concrete and masonry. We know that a solid foundation isn’t just part of the structures you build — it’s also the key to a more profitable business. That’s why you’ll find everything you need to strengthen your operation here, from new products, innovative solutions, and new technologies to help you capitalize on emerging opportunities.
Pecora-Deck 800 & HB1000 traffic coating systems prevent surface degradation caused by traffic abrasion & the destructive forces of the elements by delivering durable protection to wearing surfaces like concrete & plywood. Whether for restoration or new construction, protect your investment with the Pecora-Deck system that fits your project.
EDCO’s CORE 4 family features the Magna-Trap line of tooling, grouped to simplify the selection process. What they’re doing is correlating the layers (material) one might have on the floor and need to remove to how to get those off. Gary Ondrus, the corporate trainer
Throw a little sand on the surface if the adhesive starts to reactive. Doing this will allow the glue to adhere to itself rather than to the tooling.
at EDCO, and his team trains people regularly to help them be as effective as possible. “We train about recognizing what the layers you’re trying to get up… and what tooling we’d use with what grinder in the Strip, Grind, Remove process,” he says. “The Strip Grind Remove is really just paralleling with working on layers and understanding the layers [you] might be dealing with.”
In a sort of helping-the-helper situation, EDCO has set up a set of questions for dealers to assist contractors to determine the final goal. Through these, dealers can better advise which tooling and equipment will be needed.
Use a Moh’s hardner test. Not all concrete are created equal –even on the same jobsite. Concrete changes from residential to commercial to industrial.
Ultimately, it’s research and education that will help you understand what you’re getting into with surface preparation. If you’re not finding the information you need, ask your dealer. A good dealer should be a great resource for answers.
“There’s so much information out
there – and clickable. Your biggest aggravation is going to be getting the tooling on and it’s not cutting – it just cost you time and money. The biggest thing is to educate yourself,” says Ondrus.
While residential might be under 3,000 psi, commercial might be
3,000-6,000 psi, and industrial might be 6,000+ psi. Knowing where you’re at and the type of hardness of a floor can help.
For more information visit http://CONC.me/36uqby
It may seem like a no-brainer to wax and strip on polished concrete, but it’s the wrong choice for polished concrete.
When properly maintained, polished concrete floors are a work of art. While they are relatively low maintenance, improper maintenance by stripping and waxing can take away from the appearance of the floor and damage polish. It also adds unnecessary labor and cost.
Many building service contractors and in-house maintenance teams fall back onto what they know best when it comes to floorcare. Being used to stripping and waxing vinyl composition tile, it may seem like a no-brainer to use the same process on polished concrete. Unfortunately, while waxing and stripping is a common choice, it is the wrong one for polished concrete.
Stripping and waxing polished concrete floors is a labor-intensive process that requires harsh chemicals and products, including strippers and a wax sealant. The larger the space, the more product and labor required to complete the process. A large warehouse or grocery store could need to shut down for multiple nights to complete the stripping and waxing process, impacting operating hours and the bottom line of a business.
Stripping and waxing concrete floors can also damage floors. Wax is hydrophobic and will not allow the porous concrete to breathe. It traps any leftover moisture and creates a superficial layer over the floor that will not hold up against regular use. Being porous, concrete can act as a sponge. Using water to clean before stripping and waxing will
trap water underneath the wax coating. The water will eventually try to work its way out, causing a whiting effect in the concrete. This diminishes the appearance of concrete floors and creates the need for another round of maintenance. The abrasive pads used to strip wax are also much too abrasive for concrete, causing further damage that wax cannot fix.
Furthermore, stripping and waxing is a long, disruptive and demoralizing activity. Regardless of if the floor is public-facing or back of house, stripping and waxing typically requires shutting down normal processes within the business. Even when completed overnight to avoid closures, crews may require overtime pay, and finding crews willing to work overnight shifts can be challenging. Adding to the labor load, stripping is only the first step—crews also need to apply multiple layers of wax, allowing each to dry before the next can be applied. Even with proper machinery, it’s a process that takes many hours, and crews can become demoralized when faced with the mountain of work.
The good news is that while stripping and waxing is the wrong process for polished concrete floors, a more effective, efficient and cost-effective process exists. Rejuvenating and maintaining polished concrete floors to a high shine can be done during normal business hours and with tools that cleaning and maintenance crews already have in place.
If the floors have not yet had too
The
Ameripolish
much damage, daily maintenance using composite resin abrasive pads that provide the proper level of abrasion on an auto-scrubber or polishing machine can bring back floors’ high-shine finish in a matter of a few weeks.
If the floor is heavily deteriorated from years of stripping and waxing or other damage, it may require a more aggressive approach. A three-step process that includes different levels of abrasion to remove scratches and etching, followed by polishing and sealing t he floor with a breathable product can help rejuvenate floors to their shine.
Maintaining polished concrete floors properly will improve the appearance and shine of floors, while reducing the costs associated with labor-intensive stripping and waxing. It will also help to protect floors and extend the life of polish.
Beautiful floors can enhance customers’ perception of a business. By using t he proper products and techniques for polished concrete, BSCs and in-house maintenance teams can protect a business’s brand—and its bottom line.
Justin Brown is a technical support specialist at Ameripolish.
For more information visit https://CONC.me/8zli1y
darker shows the before with wax and lighter is after the SmartFloor Refinement.Ameripolish ColorJuice - Extreme is the company’s ColorJuice 3D reformulated to give contractors a stronger, more vibrant, and longer lasting color. Turn plain, old, and boring broom finished concrete into illustrious pieces of art. ColorJuice Extreme can be used in horizontal and vertical applications. ColorJuice is ideal for patios, driveways, sidewalks, and pool decks, but can also be used in interior projects like garages.
https://CONC.me/5ujy2j
https://CONC.me/colors-stains
Sundek’s Premium and Premium Plus Finish Coat Systems enhance and increase the longevity of decorative concrete surface areas. Both systems are available with the Classic Texture, SunSplash, SunCoat and new SunLastic Systems. This architectural colored acrylic top coat, when applied along with one of the proven Sundek systems, includes resin and nano technologies which make cleaning and maintaining the surface easier than conventional coatings. The systems are an ideal topcoat for commercial pools, water parks, walkways and residential applications.
• Extended powerful antimicrobial protection, which prevents mold and mildew from ever establishing itself on the surface
• High-performance pigments including UV inhibitors for color retention, and the ability to precisely match exterior colors
• Low VOC and fully compliant in the US
• They also provide the ability to earn Leadership in Energy and Environmental Design points
https://CONC.me/cll53l
Brickform Ultra-M1x is a blend of pure iron oxide pigment and Ultra Fiber 500, packaged in a pre-measured repulpable bag. Ultra-M1x offers a premium color system combined with the added benefit of UltraFiber 500 in the mix. Ultra-M1x can be added at the ready-mix plant or at the jobsite. Brickform Ultra-M1x requires no measuring and disperses evenly throughout the concrete mix. Ultra-M1x is the perfect choice for architectural concrete on residential, commercial and municipal applications.
• 1 bag per cubic yard, 1lb of fiber per bag
• Repulpable bags
• Fiber reinforced
• Reduces plastic shrinkage cracking
• 20 premium colors
https://CONC.me/4w0zjv
Transform dull, gray concrete into a decorative work of art with Consolideck GemTone Stain colors, a set of penetrating, translucent color dyes for interior concrete floors. These non-flammable, water-reducible formulations penetrate and color cementitious surfaces without risk of etching the surface or corroding nearby architectural metals. Safe to use in occupied spaces, GemTone Stain colors will not peel or flake, and penetrate deeper than acid stains or conventional color pigments.
https://CONC.me/nu7ia2
The Lavina L38GRE Concrete Grinder & Polisher from Superabrasive Inc.
98 x 38 x 52 in.1,585 lbs. Kawasaki FX1000, 999 cc, 35 hp
The Lavina L30GEK Concrete Grinder & Polisher from Superabrasive Inc. 76 x 32 x 48 in.794 lbs.
Kohler PCV740, 747 cc, 24 hp, Propane
2,000-3,600 (Engine); 416-750 (Tool Holder) 36.5 in. 898 lbs.
3 x 13-in. Heads, usually a set of 18 metals https://CONC.me/vpkckz
2,000-3,600 (Engine); 570-1,030 (Tool Holder) 30 in.529 lbs. 3 x 13-in. Heads, a set of 9 or 18 metals https://CONC.me/bpvlvo
The Lavina L14E Concrete Edge Grinder from Superabrasive Inc. 31 x 21 x 25 in.132 lbs. 1 Phase, 115 V, 2.45 hp 400-1,00013 in.53 lbs. Single 13-in. Head, a set of 3 or 6 metals https://CONC.me/4tj273
The SDG-11 Single Disc Grinder from MK Diamond Products 40 x 16 x 41 in.212 lbs.
Honda GXV340, 11.7 hp Gasoline 980 10 in.152 lbs. Non-Planetary Single Disc https://CONC.me/fl9eu9
The MK-SDG-7 from MK Diamond Products 34.6 x 17.5 x 32 in.43 lbs. 115 V, 5.2 AMP Electric Motor 3,200 7 in.152 lbs Non-Planetary Single Disc https://CONC.me/ibt2j8
The Helix from National Flooring Equipment
47 x 17.5 x 47.6 in. (max), 27.9 x 17.5 x 29.4 in. (min) 206 lbs.1.5 Engine
Drum: 304 (high), 171 (low) / Motor: 3,339 (high), 1,871 (low) 16 in.128 lbs. 3 Satellites, with 2 Pieces of Tooling Per Disk https://CONC.me/n70suv
The DiamaPro Systems DX-22 from Niagara Machine Inc. 35 x 22 x 42.4 in.465 lbs. 220 V Single Phase Electric Motor 1,400 22 in.275 lbs. Gear-driven, 6 Toolings https://CONC.me/4aeqij
The DiamaPro Systems DX-26P from Niagara Machine Inc. 15 x 26 x 50 in.1,100 lbs. Briggs & Stratton 852 cc, 27 hp Engine 3,600 26 in. 525-675 lbs. Gear-driven, 12 Toolings https://CONC.me/wafcod
The DiamaPro Systems ROG-60 from Niagara Machine Inc. 61 x 31.5 x 38 in.
The Edge from WerkMaster 24.5 x 14 x 33.5 in.
750 lbs. (with stands), 670 lbs. (without stands)
202 lbs. (110 v) / 212 lbs. (220 v)
Briggs & Stratton 18 hp Engine 3,200 60 in.
670 lbs. (plus operator weight) Planetary, 24-48 https://CONC.me/e8ldma
1.5 hp (110 v) / 3 hp (220 v) Electric Motor Options 400-1,16014 in.175 lbs. Multi-disc, 6 Plates with 3 Tools Per Plate https://CONC.me/px7vje
The Raider XL5 from WerkMaster 30 x 17 x 36 in.392 lbs.5 hp400-1,60017 in.362 lbs. Multi-disc, 6 Plates with 3 Tools Per Plate https://CONC.me/y4ezx5
The Titan XT from WerkMaster 39 x 20 x 40 in.600 lbs. Kawasaki (CARB certified) 603 cc, 18 hp Propane 300-900 20 in.526 lbs. Multi-disc, 8 Plates with 3 Tools Per Plate https://CONC.me/o8mliy
The GS24EM M-Series Dual Head Surface Grinder from General Equipment Co. 50.5 x 27.4 x 42 in.
290 lbs. (less grinding tool attachments)
The SG7 SurfacePro Edge Grinder from General Equipment Co. 36.7 x 10.4 x 36.8 in. 39 lbs. (less grinding cup)
The SP8GH9HP Hellcat Series Surface Planer from General Equipment Co.
42.8 x 16.7 x 37.5 in. 227 lbs.
115 VAC, 60 hz, Single Phase 2 hp Electric Motor 250 24 in. not provided
2.3 Kw, 115 VAC, 60 hz Electric Motor 3,400 7 in. not provided
Honda GX270, 4-stroke, 9 hp Gasoline Engine 3,450 8 in. not provided
V-belt / Spur Gear-type Reduction, 12 Tooling Options Available https://CONC.me/9m69sj
Right-angle Gearbox with Single, Multipurpose Grinding Cup (Multiple Aftermarket Options Available)
V-belt, Drum Type with 6 Flail Kit Configurations Available (Kit-Only or Fully-assembled on Drum)
https://CONC.me/67lgna
https://CONC.me/49wkuz
Work smarter, not harder, with the right surface grinder. Here’s what you need to know.
You’ll need more than just surface-level knowledge to achieve the desired outcome on a project with a surface grinder. Errors can lead to more than poor results but can cause costly damage. Getting the job done right requires the proper machine and attachments, as well as understanding the correct way to use them.
Newer high-speed grinders have a higher price tag but they also can complete concrete grinding and polishing jobs more quickly. Of course, with faster grinding performance comes an increased risk of accidentally damaging the floor surface, making these best reserved for the most experienced contractors. Low-speed grinders, the focus of this article, have been available for longer and are an ideal option for operators of all experience levels.
The chosen power source for a surface grinder will often be dictated by the job location. Electric models are the best choice for indoor applications where an electrical source is available. Keep in mind, however, that some models may work with a 115-volt power source, while others require 230-volt. Gas-powered surface grinders may fit the bill for jobsites that don’t have electrical power sources, but these products should only be used in outdoor concrete applications, never inside. For indoor projects with no electricity, whether building or generator supplied, propane-powered models can be used.
A traditional surface grinder design
uses wood or plastic wedges to hold the grinding stones, diamond segments or other attachments in place. Veteran concrete contractors know that it’s not uncommon for grinding elements to shake loose and fall off during operation. Keep in mind, though, that this can be a good thing. If the grinder catches a crack or obstruction, the machine may jump and/or the attachment will release, helping to prevent damage to the machine. The gimbaled head of the grinder will flex/give to provide additional protection in such situations, plus it will follow floor contours for better results.
Magnetic attachments use magnets to hold attachments in place on the surface grinder head. Since attachments may need to be switched multiple times on a single application, this convenience can provide a major advantage. Magnetic systems also have a lower cost compared to traditional style attachments. Furthermore, they attach more securely to the grinder. As mentioned above, having the attachment held too tightly to the grinder can result in machine damage or the grinder jumping when hitting an obstruction; however, a wellengineered gimbaled head design will help minimize these conditions.
Mastering a surface grinder requires experience but there are some basic tips for getting started. For example, many first-time users try to remove material faster by pushing and pulling the machine back and forth. A more effective—and more comfortable— technique is to slowly pivot the machine
The M-series gasoline-powered dual-head surface grinder, model SG24GHM.
General Equipment Companyabout its wheels.
For maximum efficiency, it is also recommended to make multiple passes over a work surface, rather than attempting to make a single deep pass. The highest material removal rates are often achieved by making passes 90 degrees to each other in a waffle-like pattern.
Oftentimes, you’ll need external weight. For instance, the removal of tough urethane coatings is often aided by adding weight to the top of the surface grinder, using objects such as cement blocks or bags of cement, to apply more pressure to the work surface. Add weight gradually until the desired removal rate is achieved rather than stack the maximum weight on the surface grinder all at once and inadvertently causing surface damage.
Be sure to replace or rotate the attachments as needed to ensure maximum productivity. If necessary, contact t he equipment manufacturer to find out the life expectancy of each attachment.
Always consult with the operator’s manual for the specific surface grinder in use. Equipment manufacturers, distributors and rental centers can be helpful resources as well. Take advantage of the knowledge around us to help increase efficiency and lessen the daily grind.
For more information visit https://CONC.me/uuojng
The benefits of restoring concrete through hydrodemolition by repairing, extending, and optimizing the life of the concrete.
We rely on concrete for many aspects of life—the roads we drive on, the dams that help produce power or control flooding, and structures that form our cities, to name a few. This durable, versatile, cost-effective material has had incredible importance to civilizations for centuries. Yet we’re aware production of the material uses a lot of energy and affects the environment. To date, however, there is not a viable alternative. But one way to have our concrete and to be conscious of sustainability, too, is to restore existing concrete structures.
Hydrodemolition offers one of the most ideal methods of repairing, extending, and optimizing the life of the concrete structures while minimizing waste by using high-pressure water jets to precisely remove concrete. The impactfree process eliminates microfractures that jeopardize the integrity of a structure while also cleaning and
descaling rebar without damaging it. In addition to precise removal, hydrodemolition leaves behind a rough, craggy surface that provides an ideal texture for bonding new material. Independent pull-off tests show that the bonding strength achieved through hydrodemolition is much higher than that of jackhammers or other mechanical methods. According to the Swedish Cement and Concrete Research Institute, using hydrodemolition for concrete repair results in a life expectancy of 21-35 years versus 7-12 years with mechanical chiseling.
Hydrodemolition offers an ideal method of repair, extending and optimizing the life of the concrete while minimizing waste.
Aquajet
Hydrodemolition technology also enables a very selective removal process, eliminating unnecessary waste. By using a lower water pressure, a hydrodemolition robot will remove only the concrete that is defective, damaged or deteriorated, leaving sound concrete intact and ready for new material to be applied. Exciting new technology in concrete recycling is even making it possible to reuse the slurry produced from hydrodemolition. A specialty chemical company has developed a new process that incorporates old concrete into new concrete mixes, providing similar performance to traditional material. Minimal removal coupled with the ability to effectively recycle what is removed is a big step toward sustainability.
Concrete isn’t the only thing that can
Hydrodemolition robots can be programmed to remove only unsound concrete, which minimizes waste. Aquajet
be recycled. The water used in the process can also be treated and reused. Some manufacturers have developed advanced water treatment technology. The blast water is captured and treated in a fully automated, high-capacity system that neutralizes the pH and reduces suspended solids from 15,000 to 20-40 mg/L. Some of the blast water is lost through evaporation, but 80% to 90% can be captured and treated. Clean, treated water can then be discharged into the environment or reused for the hydrodemolition process. Not only does this reduce water consumption, it also reduces the need to haul water in and out of jobsites.
Concrete plays a major role in our daily lives and has for centuries. That isn’t likely to change any time soon. But those of us involved in the construction industry are called upon to reduce our ecological footprint, and that is not an easy task. The idea of reusing and recycling, however, can be applied to concrete structures. And as a hydrodemolition equipment manufacturer, we are committed to engineering the most innovative, environmentally friendly products that give concrete repairs the longest possible life.
Keith Armishaw is the business development manager for Aquajet’s North American subsidiary. He has more than 24 years of industry and leadership experience.
For more information visit https://CONC.me/gpdv8a
Some financial pitfalls that contractors need to watch out for as you operate your business.
Construction business owners often start their businesses with good intentions, and they have the know-how, experience, and connections needed to gain clients and carry out the work. However, many contractors and material suppliers overlook how important it is to allocate effort and time to managing finances. Here are some financial pitfalls that construction businesses fall into.
Without clarity on if a project is still profitable after lowering prices to win bids, you might find yourself knee-deep in deliverables without the returns to show for it. Being inflexible with your markup isn’t the solution either. Typically, smaller jobs allow for healthier markups. So, businesses can mitigate the risk of falling into the trap of being booked but broke by having a healthy mix of smaller and bigger jobs. Doing this doesn’t remove the need to ensure that you’re not losing money on the job. After all, the bottom line for any project is to increase your bottom line.
Like the last pitfall, using the same markup for items or overall percentages on all your jobs might simplify the work involved in pre-construction and bidding. However, projects are often wildly different as complex as they are, and this templated approach can cost you big. You have to account for time spent
managing the work on the job site, the in-house personnel who get tied to jobs, and other variable expenses and resource consumption that change depending on the nature of the project. You might be leaving money on the table or even losing money if you don’t do a thorough financial and operational analysis of what a job will entail before you write up your quote, bid, or offer.
Precise tracking for change orders and all the details involved in the project is just good business practice. It is essential not only in managing the project but also in ensuring that you’re able to file the appropriate preliminary notices required to preserve your right to file a mechanics lien in case there are payment issues later in the project. It also helps clients understand the actual costs of what they’re having done. As a result, they’ll be able to make better decisions as clients for subsequent projects and requests for amendments in your current contract. It’s easy for these things to go out of hand, so establishing a straightforward process whenever there are change order requests is smart and essential. Document their requests. Write up a detailed cost breakdown and get on the same page with them before starting any work that’s not in the contract. Absorbing these costs has no real business advantage and is only shaving off from your profits.
Poor tracking for every project is often part of a bigger problem–poor annual financial tracking. You’re dealing with finances on a per-project basis, the business version of living paycheck-topaycheck. You won’t have a clear idea of where your business is financially, what types of clients benefit you the most, and what needs to be done to improve your standing.
There are many reasons why many construction businesses fall into this trap; however common it also is in other business sectors. Construction businesses are often caught up on shortterm cash flow, and ensuring that all payables are covered and plans are correctly implemented. Project continuity, of course, is a crucial focus. However, business continuity can be significantly compromised if a business is not aware of where they are in the medium-term, at least its annual financial performance.
Setting goals helps immensely. Metrics or key performance indicators help businesses have an objective look at numbers to assist them in evaluating their financial health.
Ultimately, the goal is to have a profitable business. With awareness, conscientiousness, and diligence, you’ll be able to stay on the right track as you continue delivering value to your clients.
Patrick Hogan is the CEO of Handle.com.Find the full article at https://CONC.me/dab9c5
Milwaukee Tool’s MX FUEL™ Equipment System was designed to deliver the power and performance concrete professionals have come to expect. It is a fully compatible battery-powered system that goes beyond the limitations of gas and corded equipment, increasing safety and productivity. As a leader in cordless technology, Milwaukee® continues to invest in innovation which allows for systems such as MX FUEL™ to work together to eliminate gas headaches and increase reliability on the jobsite. Zero emissions along with less noise and vibration provide a safer workspace indoors and outdoors while eliminating the hassles of maintenance that come with traditional gas-powered solutions.
Join
www.milwaukeetool.com/Innovations/MX-FUEL
Oztec is proud to introduce the newest edition to its industry leading backpack vibrators. The New BP-45 adds a powerful 2HP option, capable of running vibrator heads up to 2” in diameter, in a lightweight configuration. This backpack maintains Oztec’s Job-Proven Rugged design. Built to withstand the demands of concrete construction sites with a sturdy steel frame, dependable Honda engines, fully adjustable padding system and the highest quality components, all designed for easy maintenance and long life.
The BP-45 is an option between Oztec’s lightest weight model, the BP-35, and Oztec’s most powerful option, the BP-50a. As with all of Oztec’s power units, the BP-45 includes our patented Quick Disconnect for easy interchangeability with Oztec flexible shafts and vibrator heads.
In December of 2019 Oztec Industries, Inc. reintroduced its 1-1/8” & 1-1/2” RubberHeads®. Both of these heads are available with an optional rubber coated extension piece. With Oztec extension pieces, you can greatly reduce the chance of the vibrator head becoming entangled in the rebar. These heads were originally designed to meet the needs of the construction of the Hood Canal Floating Bridge in Washington State, where over 30,000 cubic yards of concrete were poured in heavily congested rebar without a single head getting entangled in the rebar.
Oztec RubberHeads®, ranging in size from 1-1/8” to 2-3/4”, not only protect epoxy coated rebar and delicate form faces, but also produce better consolidated concrete and are job proven to be more efficient and effective than any other vibrator head on the market!
Oztec Industries, Inc. 65 Channel Drive · Port Washington, NY 11050 1-800-533-9055 - 516-883-8857 - Fax 516-883-7857 www.oztec.com
From light- to heavy-duty installations, our broad range of Titen concrete and masonry anchoring solutions has exactly what you need to get the job done reliably. Backed by our long-standing legacy of expert engineering, each of our versatile and innovative screw anchors is designed for maximum ease and efficiency — ensuring a quick, smooth installation the first time, every time. And our skilled field support teams are always available to assist on the jobsite.
To learn more about the full line of easy-to-install Titen solutions from Simpson Strong-Tie, visit go.strongtie.com/ titenfamily or call (800) 999-5099.
Minnich Manufacturing, the leading manufacturer of concrete dowel pin drills, concrete vibrators and vibrator monitoring systems, is dedicated to helping concrete contractors maximize efficiency.
Minnich’s Stinger and Controlled Speed Vibrator (CSV) are just two examples of how the company’s concrete innovations serve customers.
The light yet rugged Stinger electric flex shaft concrete vibrator is a 14.5-pound double-insulated universal motor that can drive the full line of Minnich vibrator shafts and heads from ¾ inch to 2 ½ inches.
The CSV enables contractors to communicate using their cell phone’s Bluetooth to select set speeds of vibrations per minute (VPM) in coordination with the concrete slump being poured. Minnich will continue to bring products to the industry that support the findings of concrete research facilities across the country.
For more information, visit www.minnich-mfg.com
Blastcrete Equipment LLC’s RD6536 Skid Steer Pump attachment is compatible with any skid steer and provides a fast, efficient solution for pumping grout materials, 3/8-inch shotcrete and 3/8-inch structural concrete mixes in a variety of concrete and shotcrete applications. The attachment features Blastcrete’s 3-inch hydraulic squeeze pump.
The RD6536 offers variable speeds of 0-25 cubic yards per hour. Contractors can pump materials 250 feet horizontally and as high as 50 feet with the use of a rubber delivery line. The receiving hopper includes a hydraulic agitator that keeps the mix well-blended, ensuring aggregate and sand stay evenly suspended throughout the mix.
As contractors, we must seek out potential workers at a very early age. This can give you the leg up on competitors not yet recruiting from this employee’s candidate pool.
In this addition of how to find workers, we will explore opportunities to recruit from the post-secondary education systems, and participating on local Career and Technical Education (CTE) Boards.
The post-secondary education system consists primarily of schools that have educational programs for individuals who are out of high school. In some cases, students may have graduated from high school. In other situations, students may have completed their General Educational Development, also known as the “GED.” In either situation, the school is after high school, thus “post-secondary.”
carpentry, concrete, and sometimes even field engineering. (This is not an exclusive list.)
The thing about students attending such technical colleges and universities, that I’m most optimistic about, is t hat the students are attending because they want to learn a trade or skill. They attend with the idea of finding a job in that specialized trade area. In many cases, they are open and available to begin working with a contractor sooner, rather than later.
Let’s address our second “recruitment pool.” If you have a local school district with one or more high schools, you may find that they have a CTE program available to students. In some districts around the United States, you may find students from grades nine through twelve attending.
workers. Depending on your specialty of trade, you may be able to hire students immediately upon their graduation or develop a relationship with a student that encourages their continued learning of a trade by attending a post-secondary technical school.
As contractors, we must seek out the two areas shared in this article. It can give you the leg up on competitors not yet recruiting from this employee’s candidate pool.
Keep fishing for your future workers.
Adobe Stock/gustavofrazaoMany of the post-secondary schools are called
• Vocational School
• Technology School
• Junior College
• College or University
In the State of Texas, one example of these schools includes a chain of technical schools called TSTC, Texas State Technical College. State colleges and universities may have a technical focus for skill training. For many of these technical slanted colleges, there is a vast program of skills training in areas such as masonry, electrical, welding, plumbing, HVAC, diesel engine mechanics,
The CTE has essentially replaced the older shop class that many of us remember. The new CTE is a vast improvement over any shop class you might have taken when you were in high school.
The opportunity for you is that most high schools need contractors, like you, to serve on their Advisory Board.
Most CTE Advisory Boards meet once a month, with members providing helpful industry insights and support for the CTE instructors. The Board Members can play a major role in securing needed resources for the students, including tools, materials, donations, PPE, etc.
As CTE Board Member, you get a first-hand look at the talent coming up during the teen years of future
Brad has been assisting contractors for more than thirty-five years and has earned the name, The Contractor’s Best Friend. Heard weekly on Caterpillar and ForConstructionpros.com’s co-sponsored podcast, The Contractor’s Best Friend Podcast, Brad and team continue to share their experience and love for the construction industry. Brad speaks at national and state conferences including the World of Concrete, the National Pavement Exposition, the International Roofing Exposition, Wisconsin’s ABC annual conference, and many more. Author of several books, Brad has also had more than three hundred articles published to date over his career.
For more information visit https://CONC.me/bestfriend