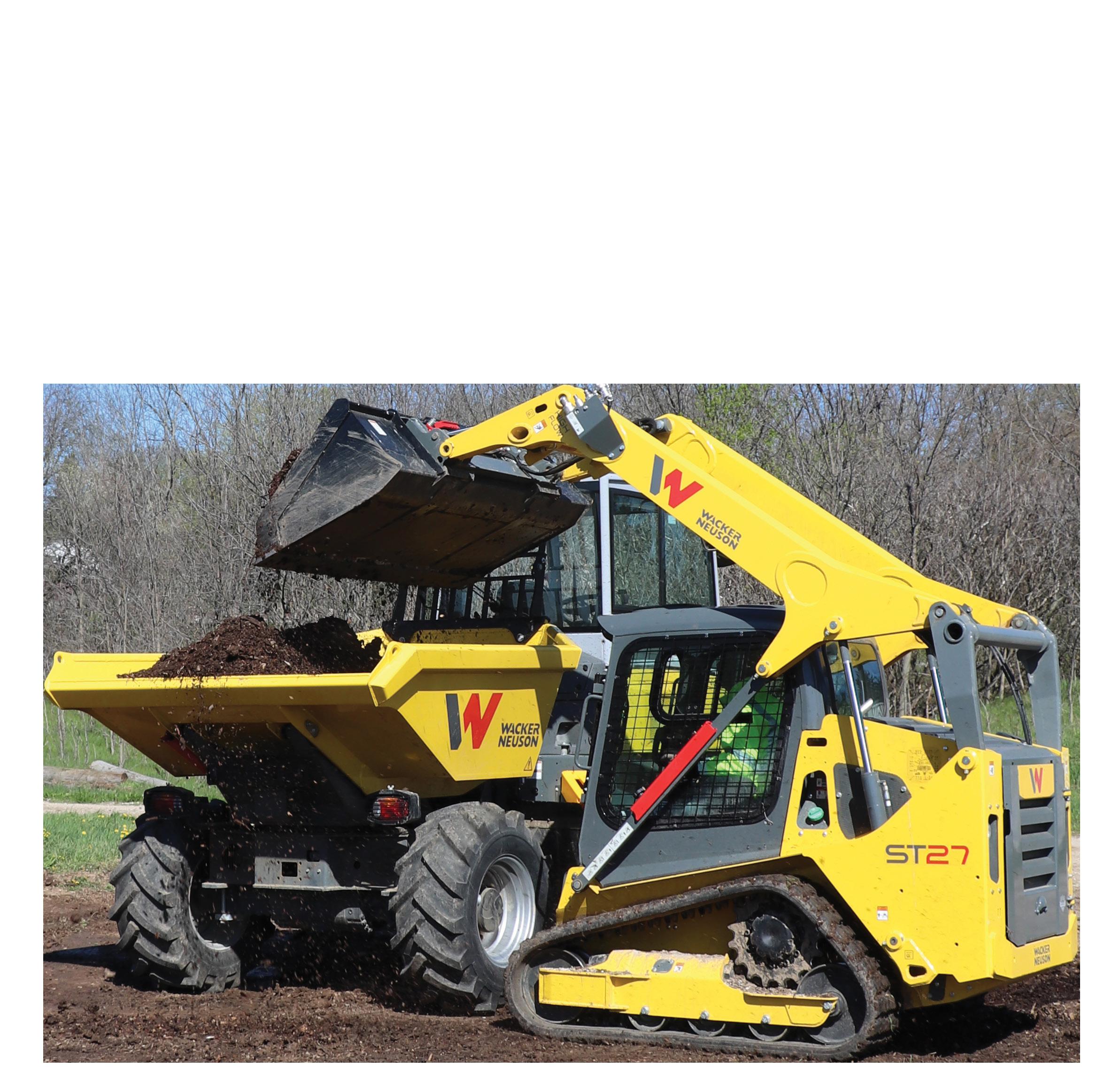
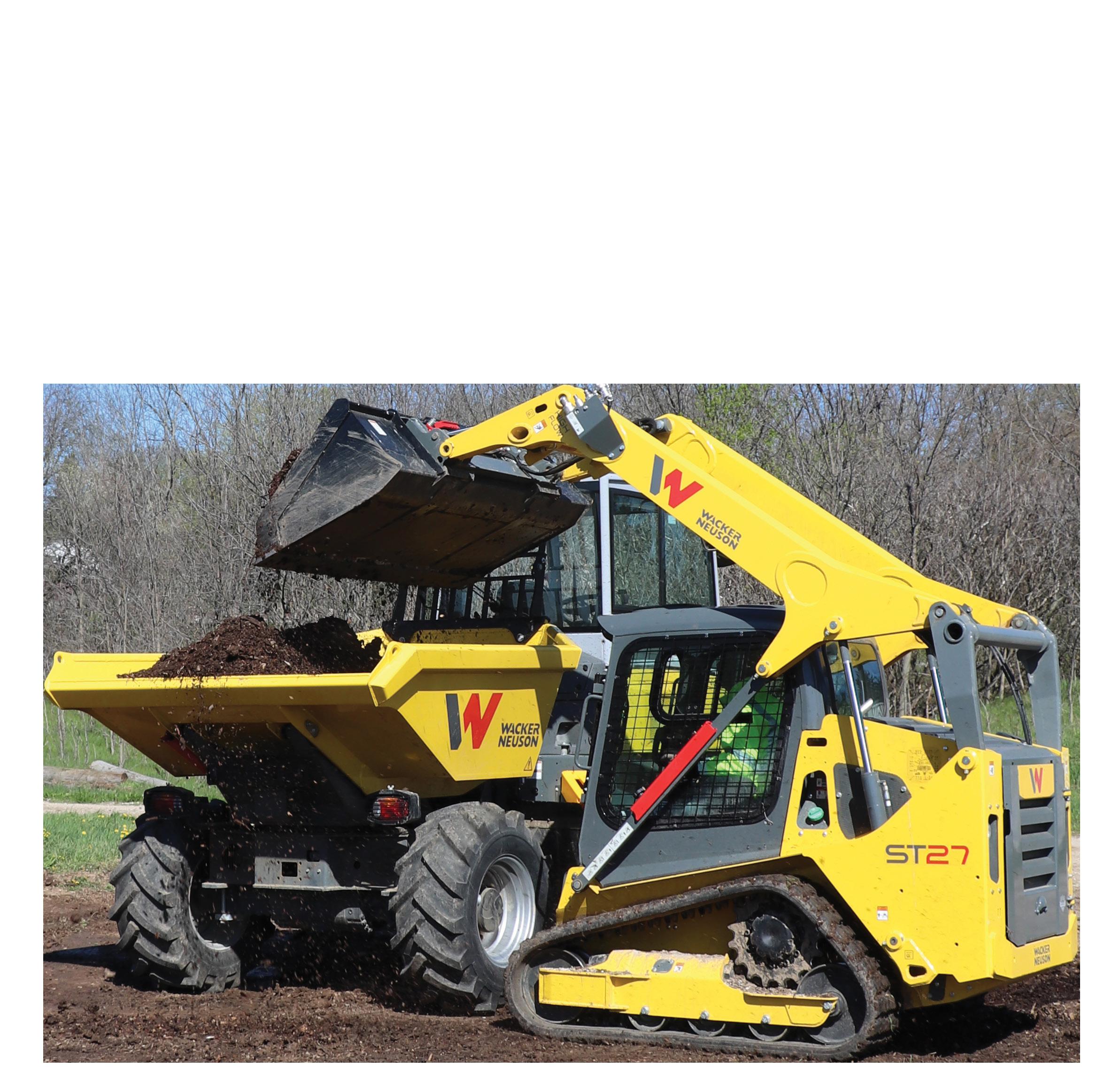
LOADER
SPEC GUIDE
LEARN ABOUT ALL THE LATEST MODELS
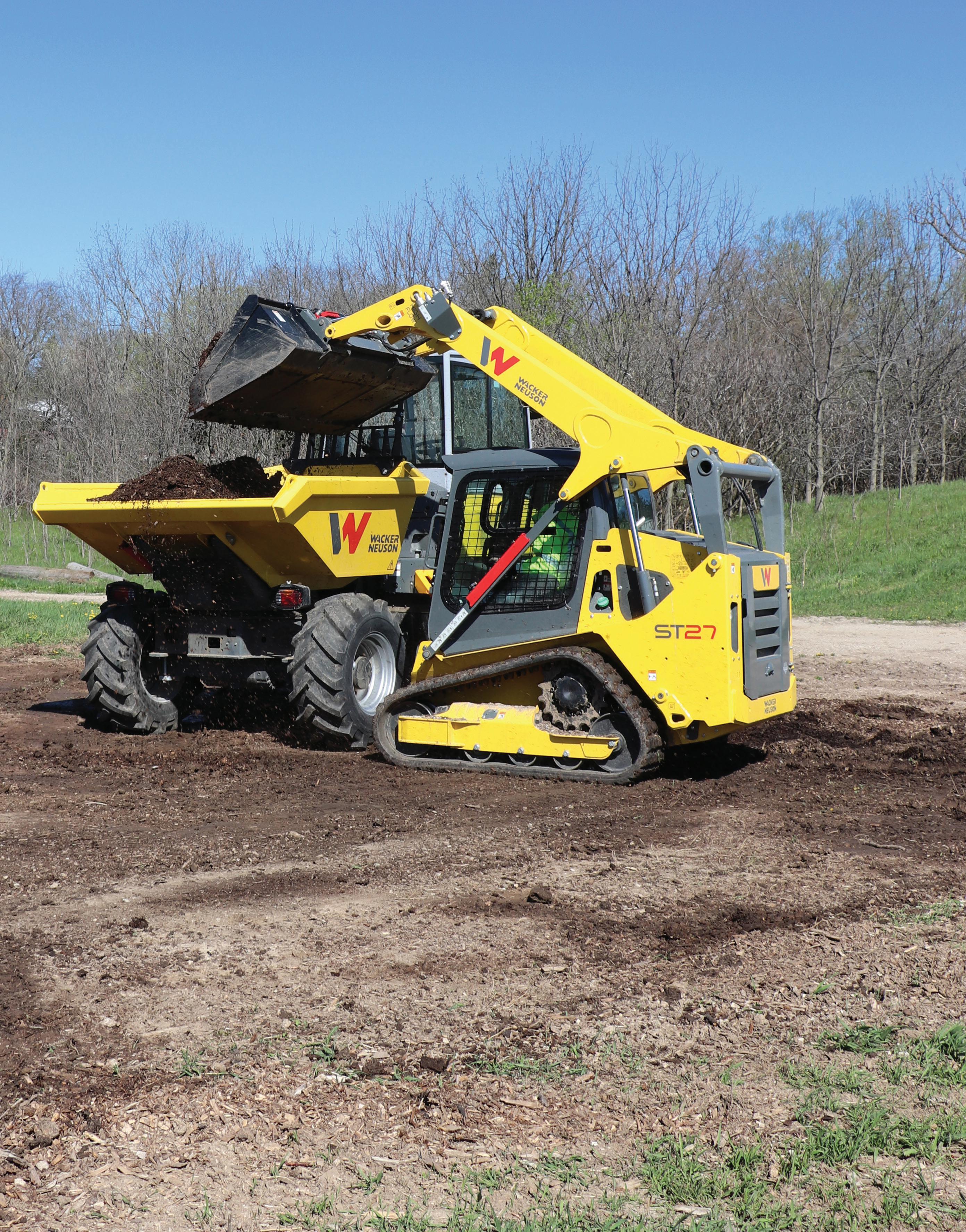
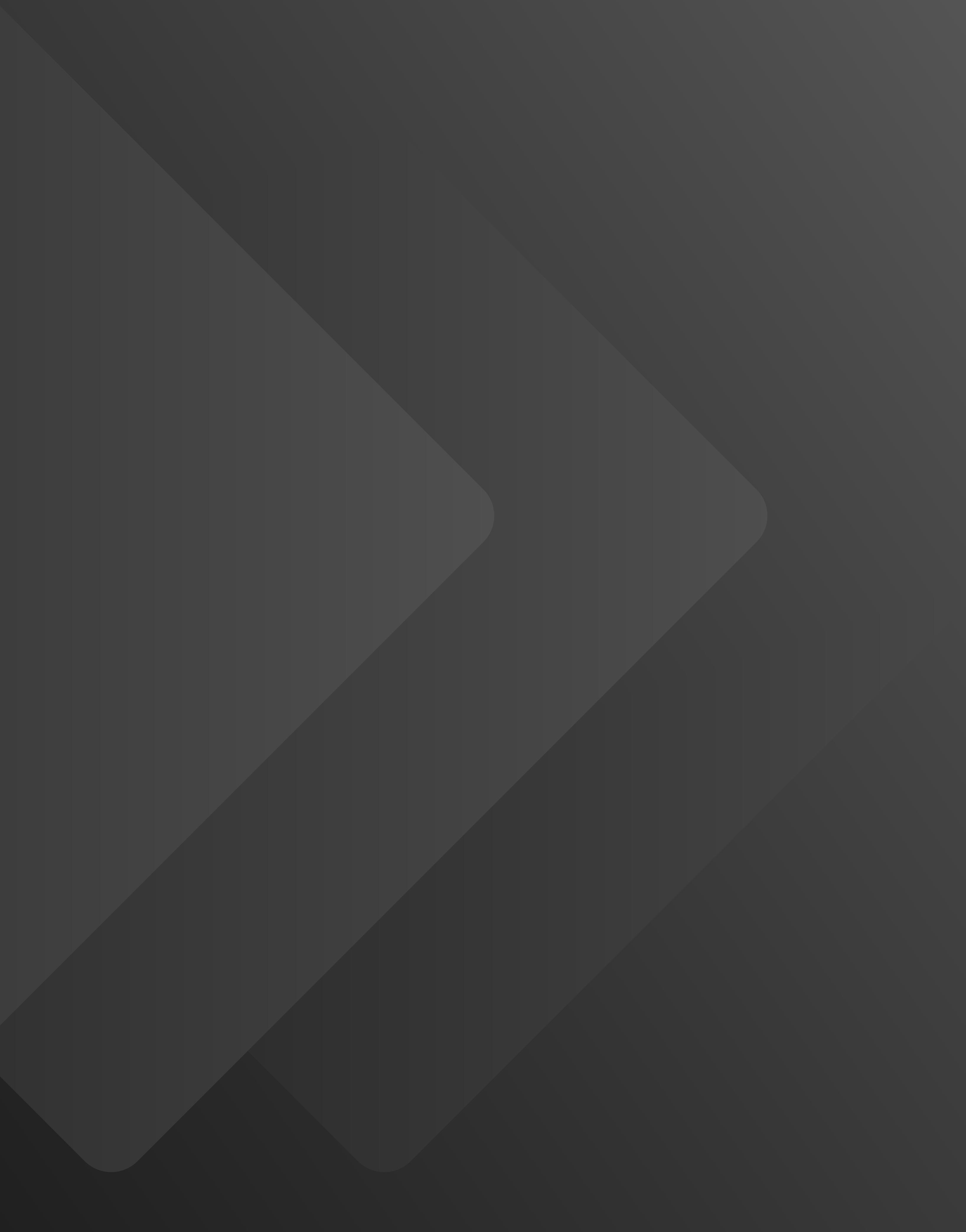
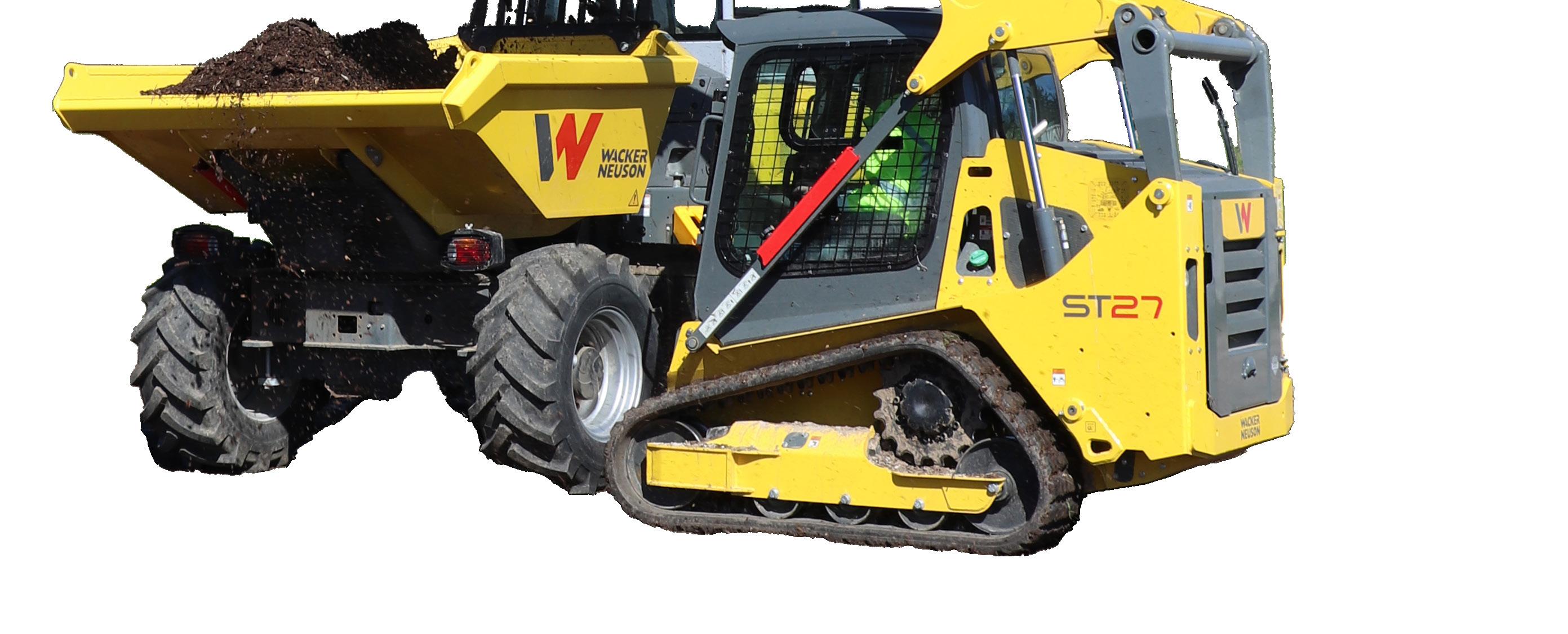
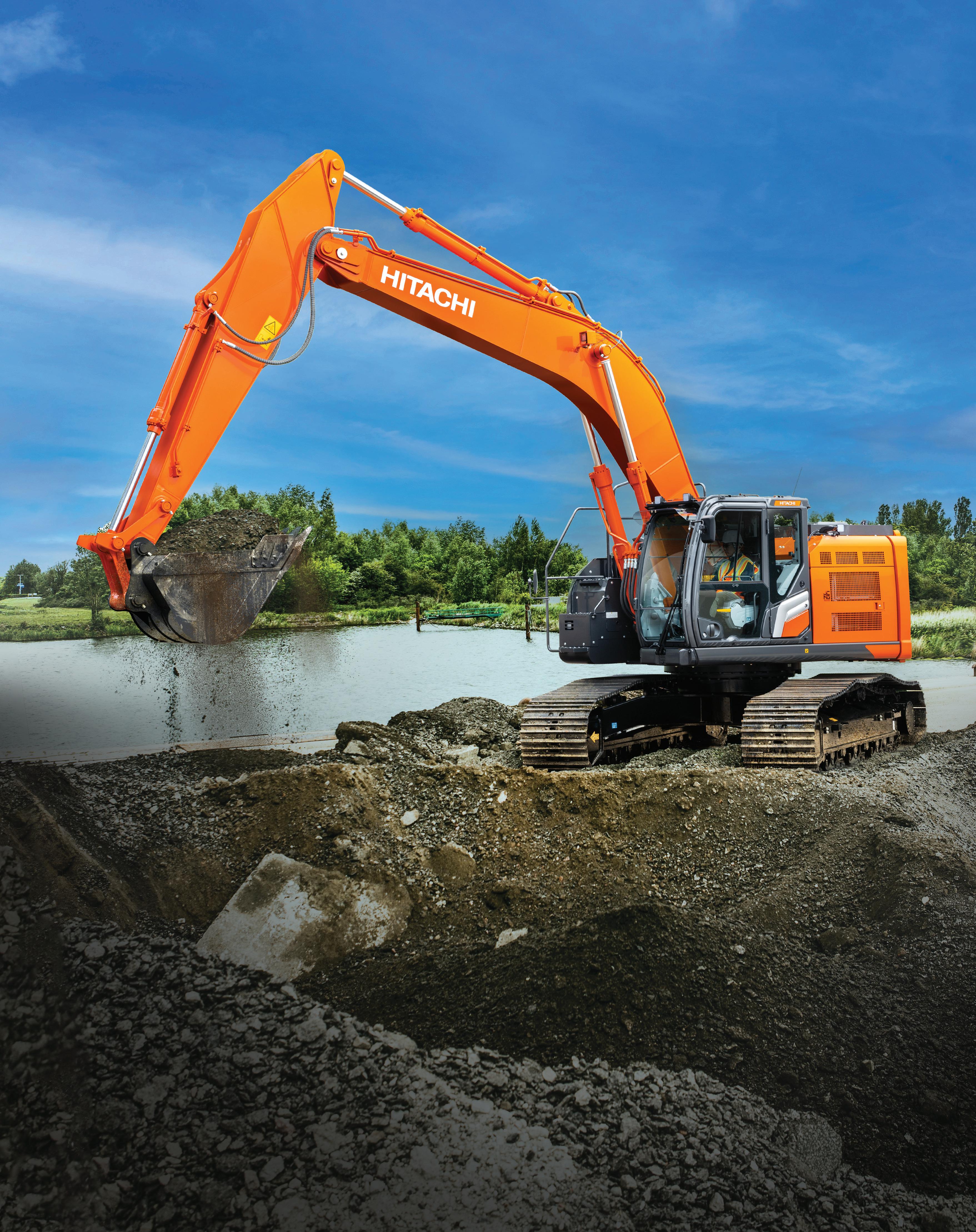
BUILT TO WORK, BUILT TO LAST
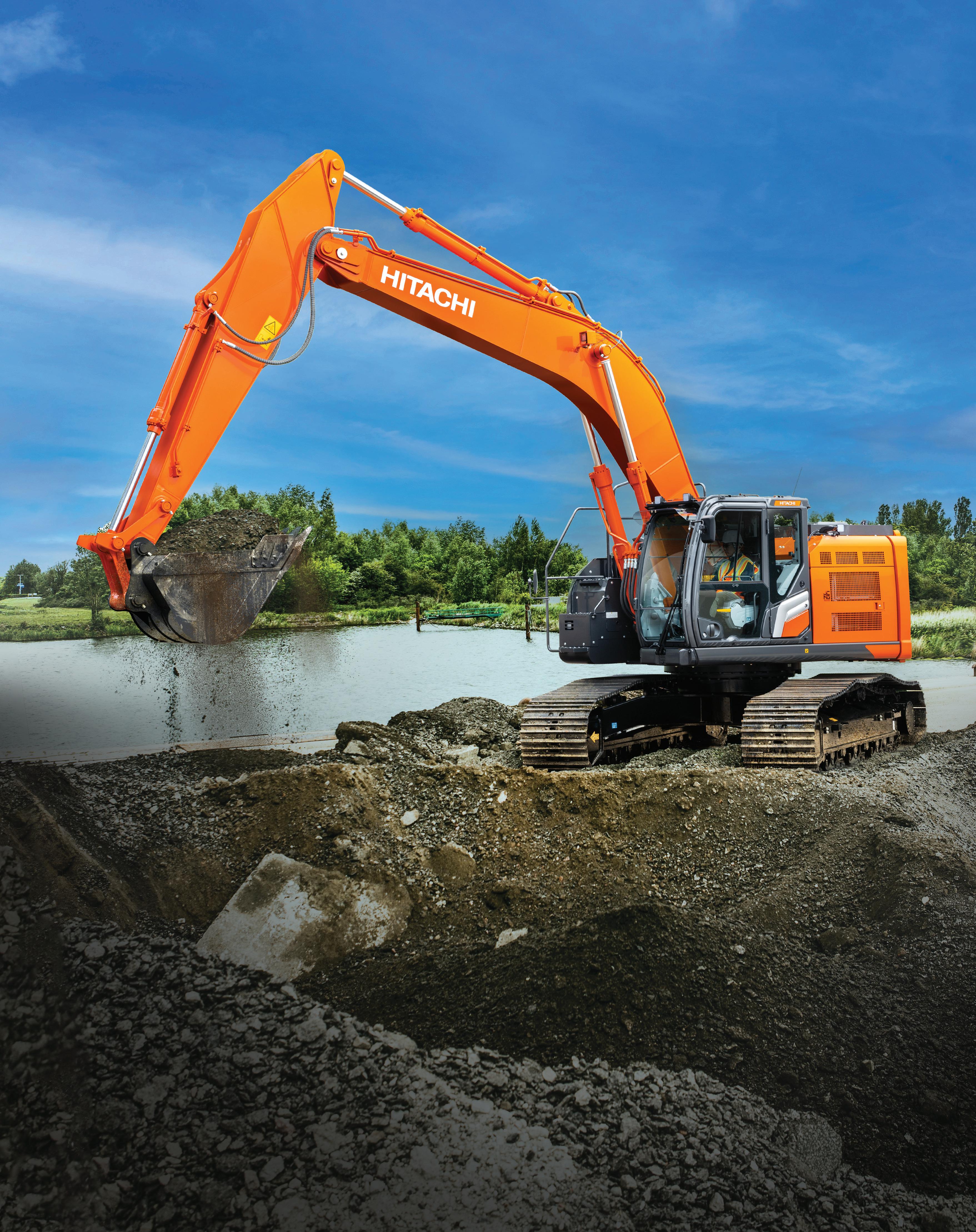
WORKSITE EQUIPMENT
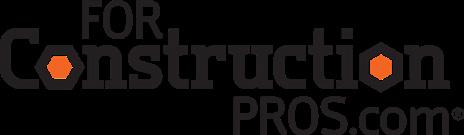
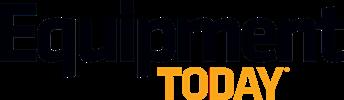
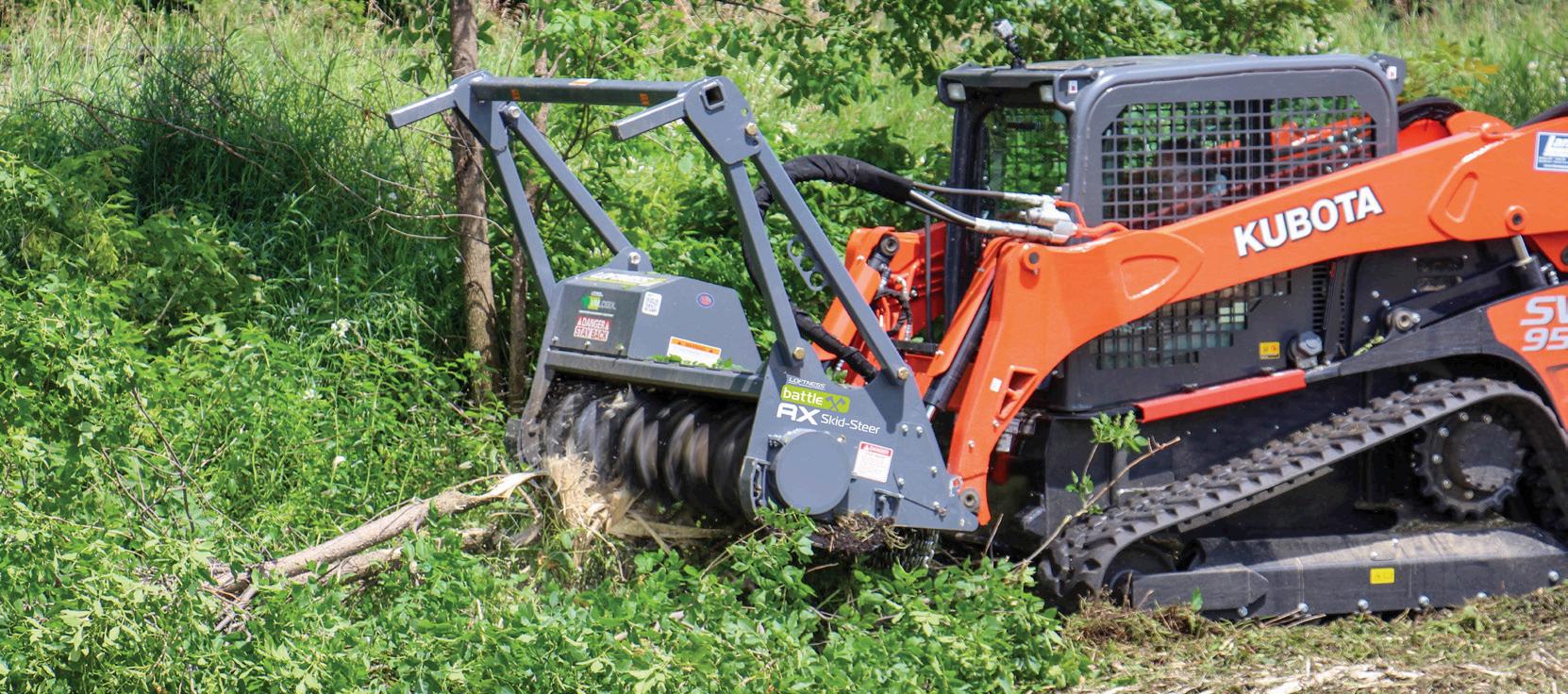
COVER FEATURE
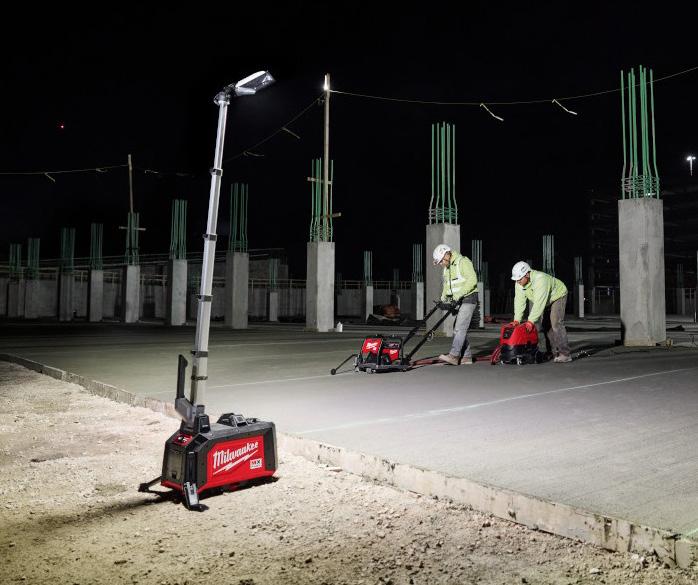
CONCRETE EQUIPMENT
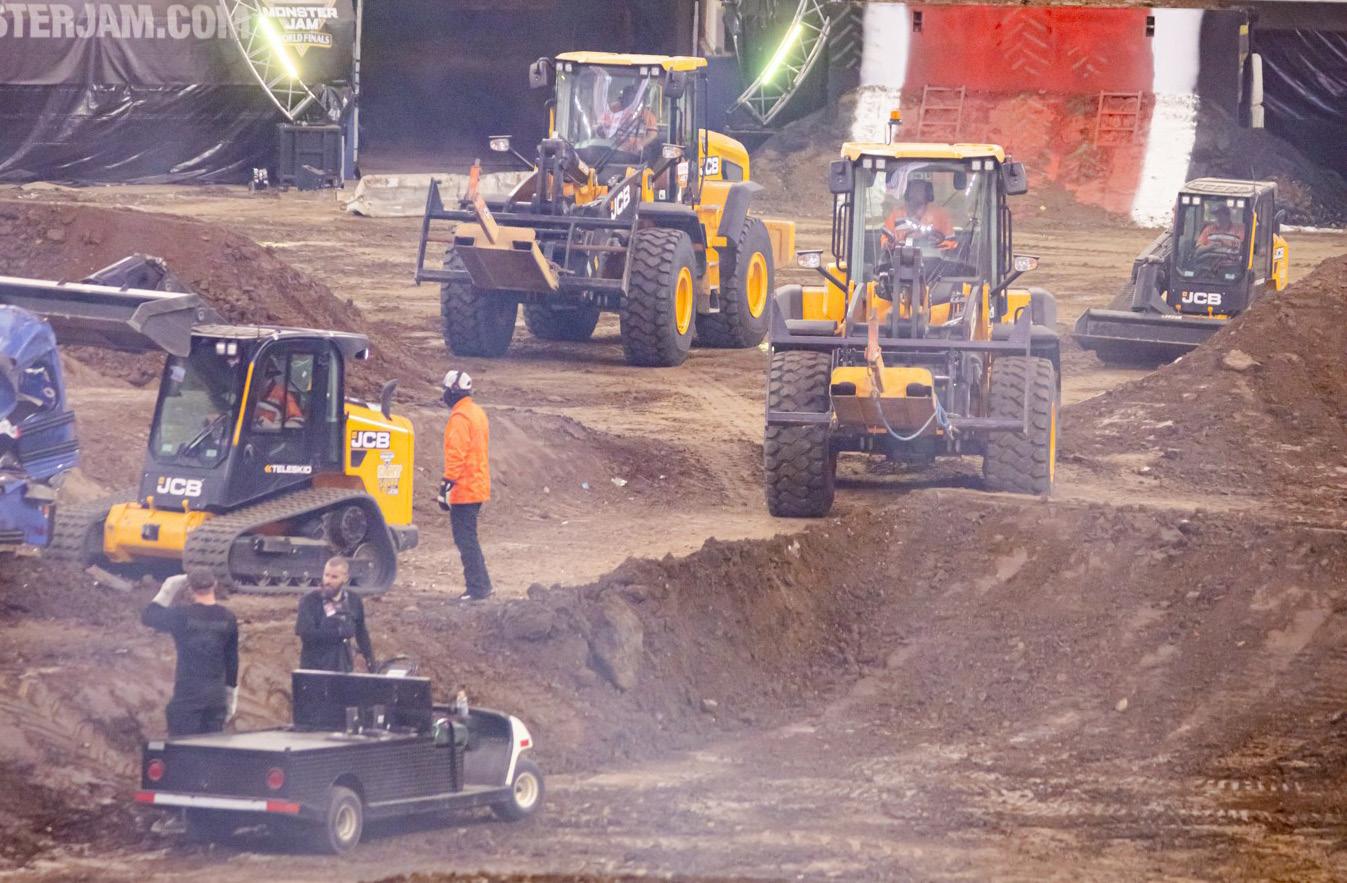
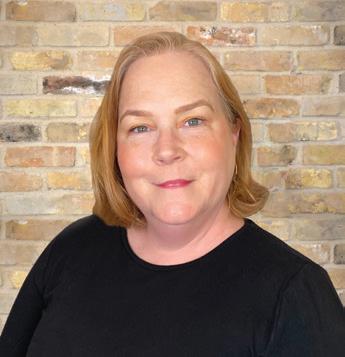
Monster Jam Finals Features JCB Earthmoving Equipment & the JCB Monster Truck DIGatron
Driven by
champion Tristan
England, the DIGatron’s first year as a participant ended with tons of fans and a second-place race finish.
The crowd, the trucks, the music, the noise … what could be more fun? Learning how the track and the event came together, especially for dirt enthusiasts everywhere! Being invited to a media event at a fun experience like this was a thrill, and getting to go behind the scenes and talk to some of the experts organizing the show and JCB’s involvement in the Monster Jam family was a unique opportunity.
WHY MONSTER JAM?
The evening of the Monster Jam Finals, Alice Bamford, daughter of JCB Chairman Lord Bamford shared the origins of the Monster Jam partnership. The idea stemmed from Bamford’s son’s love of Monster Jam.
“Monster Jam is such a fun event,” said President & CEO of JCB North America Richard Fox-Marrs during an interview at the event. “It’s something that involves the whole family. .”
Alice Bamford also loves that Monster Jam is family friendly.
“Every generation can come,” she said. Monster Jam also strikes a chord with JCB’s customers, dealers and service techs. Also, according to Bamford, “JCB is fully integrated into Monster Jam.”
In addition to providing equipment for the Dirt Squad, JCB’s engineering team designed DIGatron, a JCB Monster Jam truck, inspired by a backhoe loader. It is driven by the reigning Monster Jam World Finals racing champion Tristan England.
WHY MODEL DIGATRON ON A BACKHOE LOADER?
Fox-Marrs pointed out that the backhoe is JCB’s signature product.
“It’s the product that the company was founded on. It’s the product that
the company is renowned for around the world. Today the backhoe and the loader are two products that the company is renowned for around the world. But the backhoe was the original product and very much piece of construction equipment. And that’s what made [us] go with backhoe,” FoxMarrs said.
The backhoe also makes an appearance during the competitions, but more on that later.
HOW IS THE TRACK BUILT?
In addition to DIGatron, JCB is also the official heavy equipment partner of Monster Jam, Jayme Dalsing, senior director of global operations for Monster Jam, said. Dalsing has been with Monster Jam for 10 years.
Wheel loaders, compact track loaders and other equipment move 5,000 cubic yards of dirt (stored onsite in the parking lot from the last event at SoFi Stadium two years ago) to build two tracks on which the trucks will race and perform stunts. According to Dalsing, the 2024 World Finals track was similar to a motorcross track.
The dirt squad uses the earthmoving equipment to build the track with driver safety in mind. When building the ramps, the squad must include enough room for turns and enough space away from the walls.
After the first three events comes the freestyle competition. For this competition, multiple earthmoving machines come up and reconfigure the track. This involves tearing apart the track that the trucks have been using and adding new areas where they can jump and stunt. It was interesting to watch how quickly the field changed.
Dalsing said that JCB is a committed partner, and the Dirt Squad personnel is extremely happy with

the JCB equipment. In addition to earthmoving equipment, JCB loaders are used to recover incapacitated trucks. This includes a specially designed loader named Scoopz, a crowd favorite.
WHAT’S
NEXT?
JCB is committed to the Monster Jam Partnership for five years, according to Fox-Marrs.
“[It’s] a five-year partnership, which is great … It will take time to establish and develop and hone and refine and, you know, to make investments on things like diecast toys and the merchandise feasible. It has to be done over a longer period of time as well. It’ll be a sustained approach for you know, what’s hopefully the first five.”
Quarter one of 2025 will see merchandise in stores. “There will be diecast models, Lego models, remote control models. ... that’s another piece that’s going to ... help get the JCB brand out there, which is ultimately … the mission, Fox Marrs said
Reader Survey
We want to hear from you. Please take a couple minutes and answer this brief survey. Use the link or QR code.
Read more at:
eqtoday.co/ReaderSurvey
Subscribe to Our Newsletter
Don’t miss our informative content. Sign up for the Breaking Ground. Don’t delay. Subscribe today!
Read more at: eqtoday.co/BGSubscribe
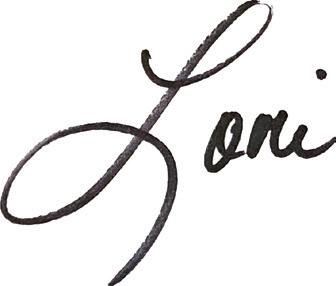
Audience
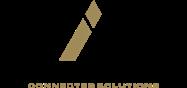
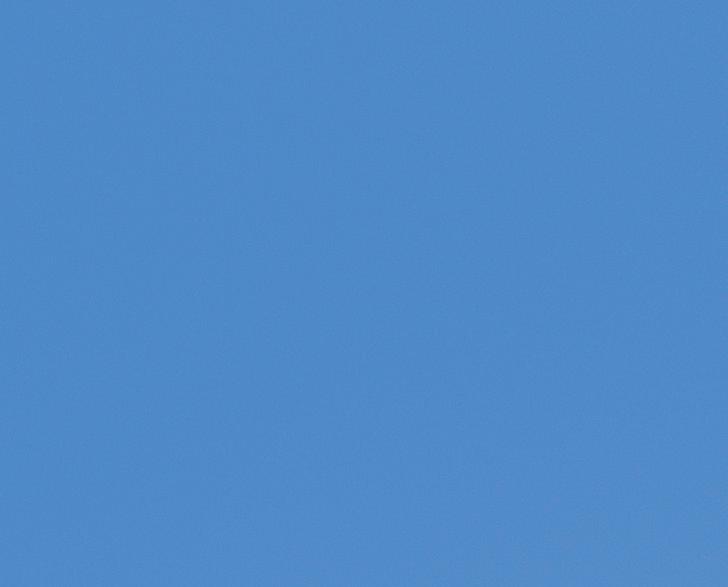
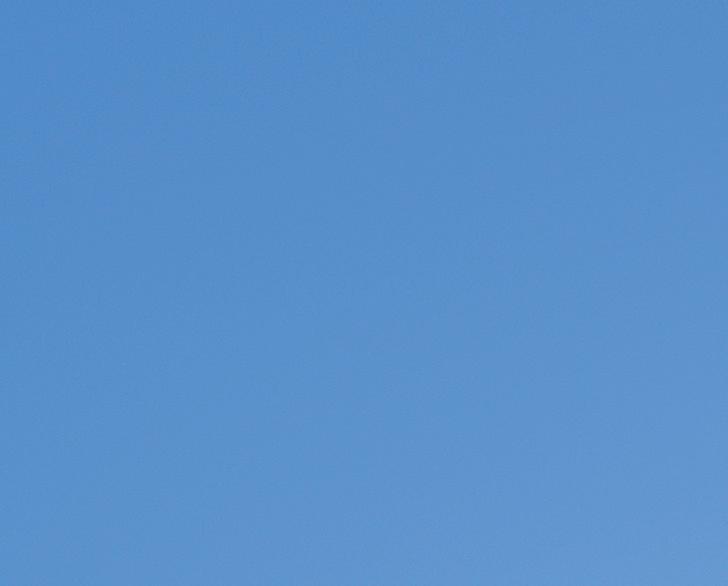
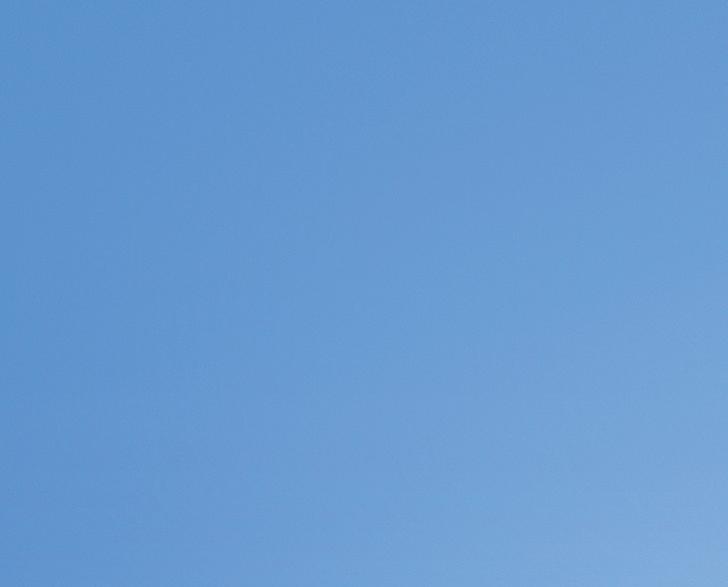
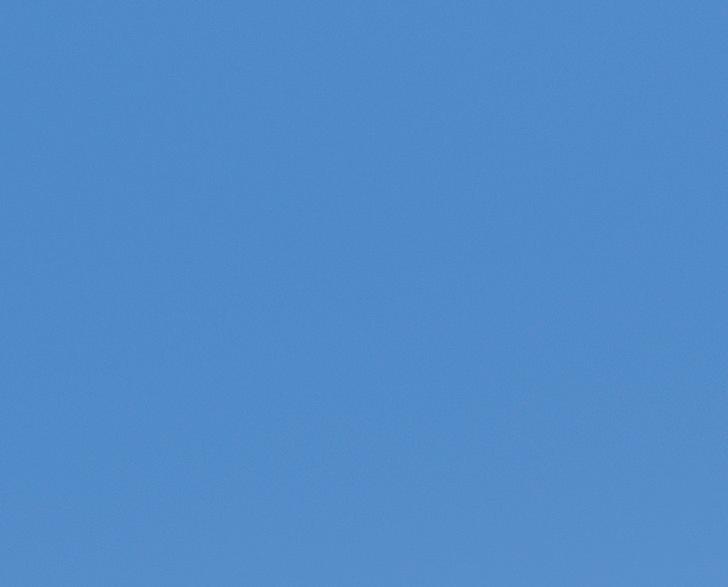
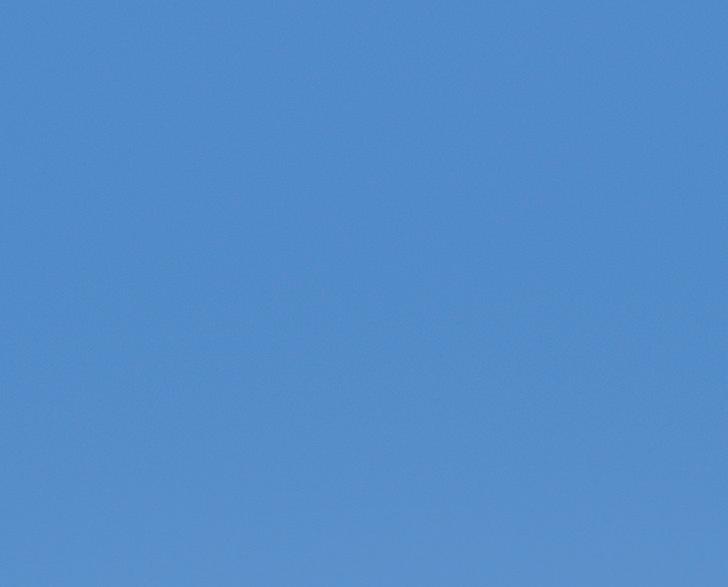
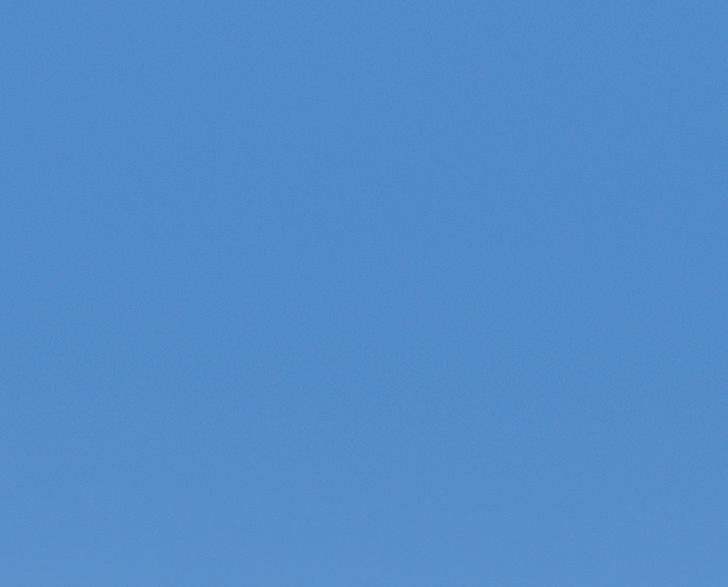
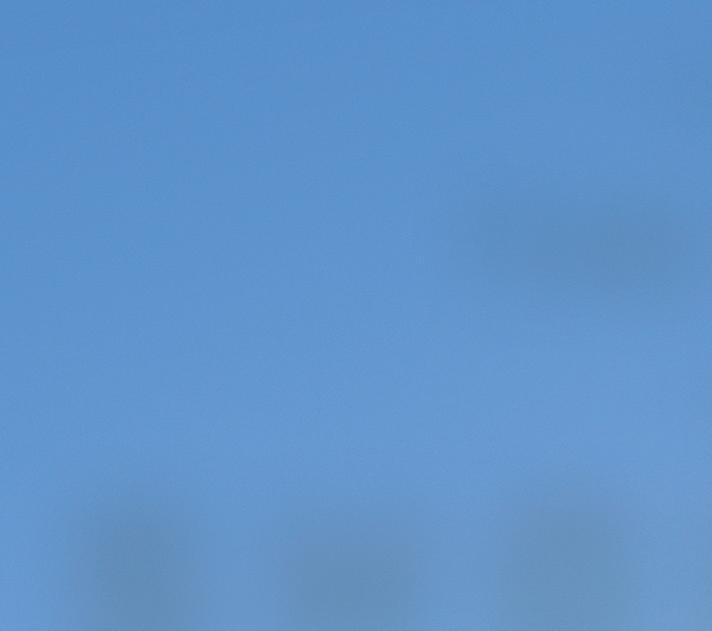

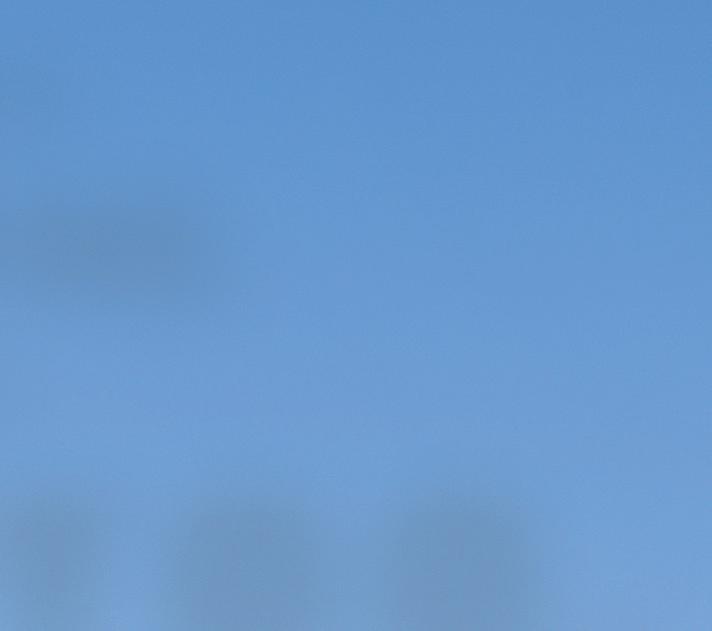
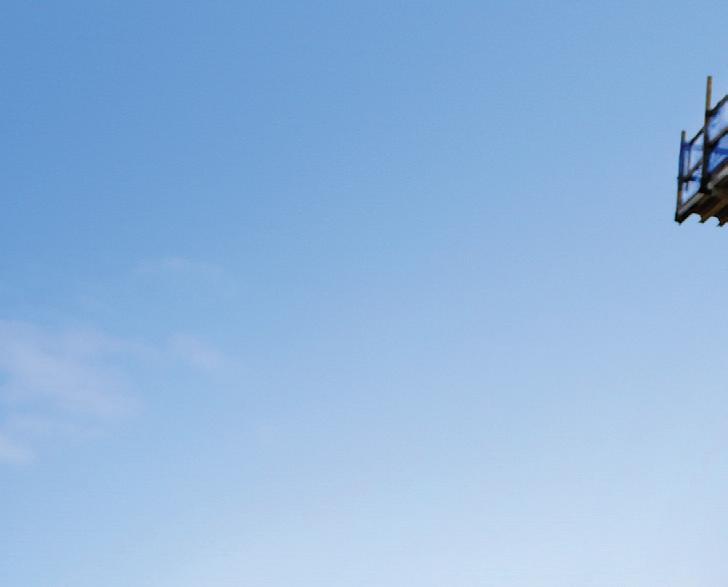

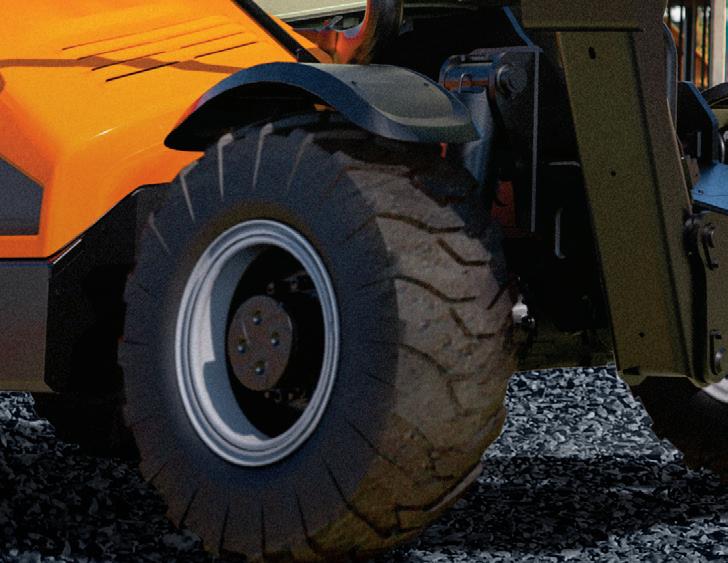

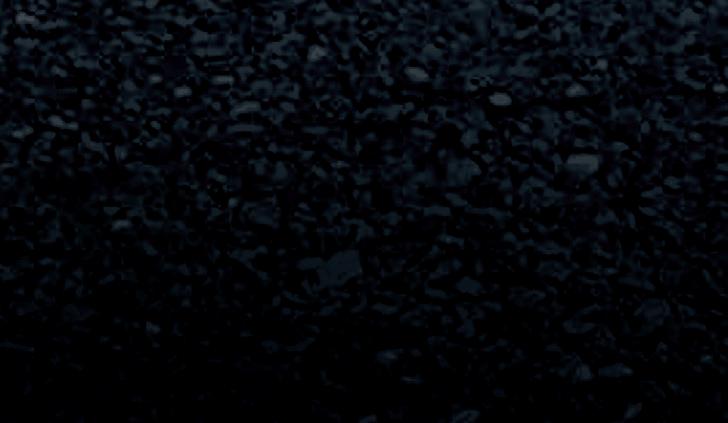
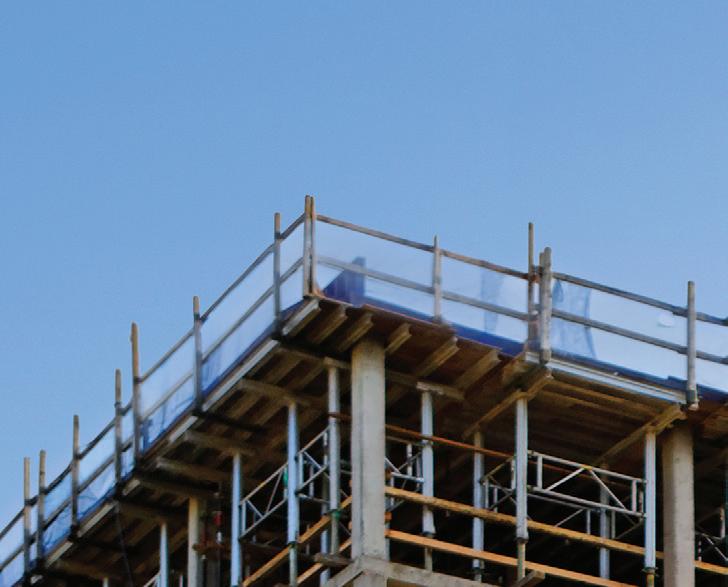

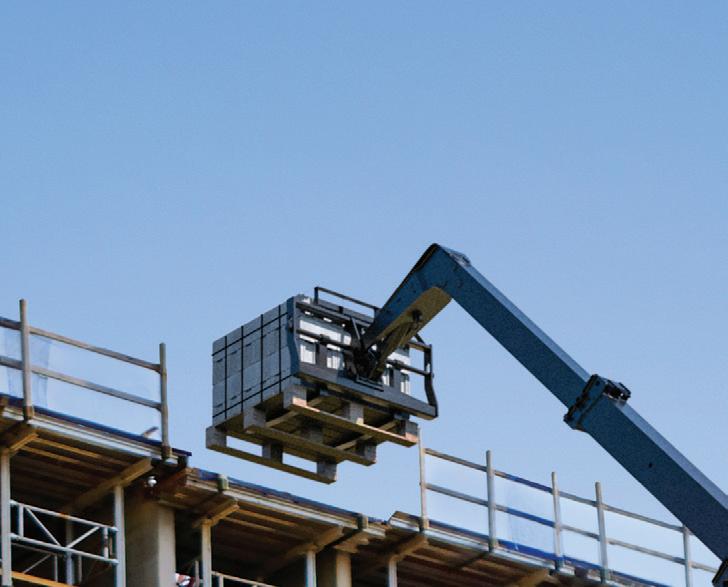
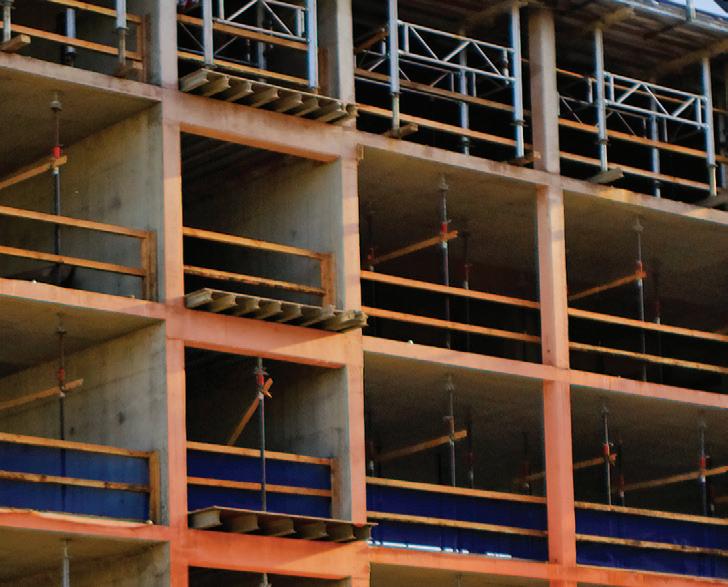
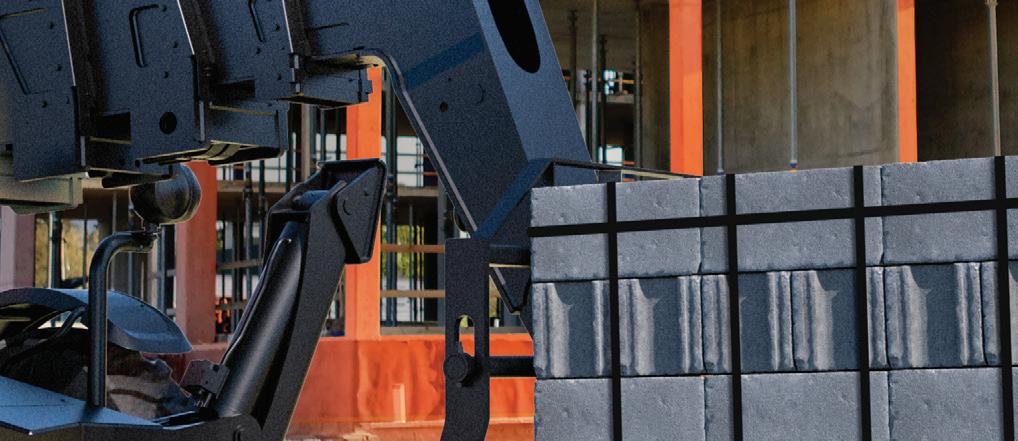

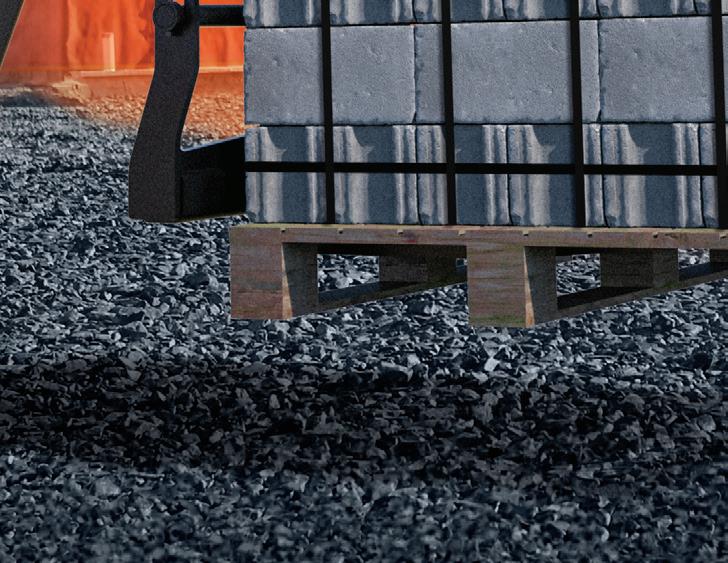
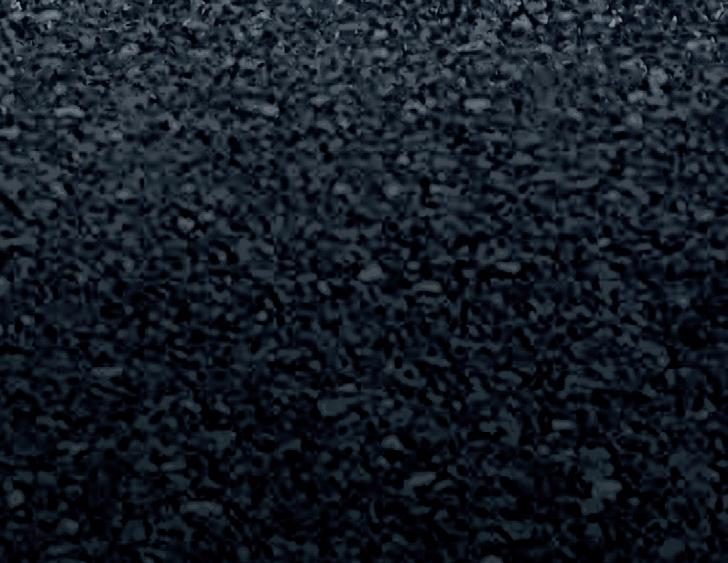
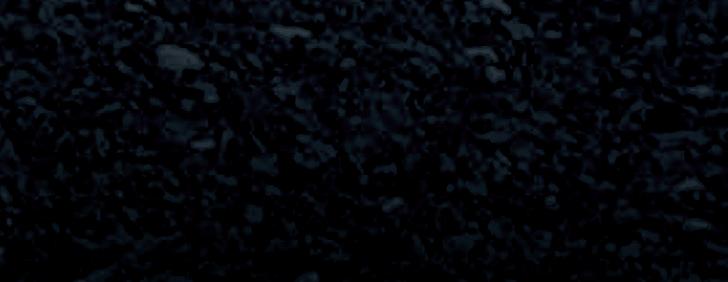
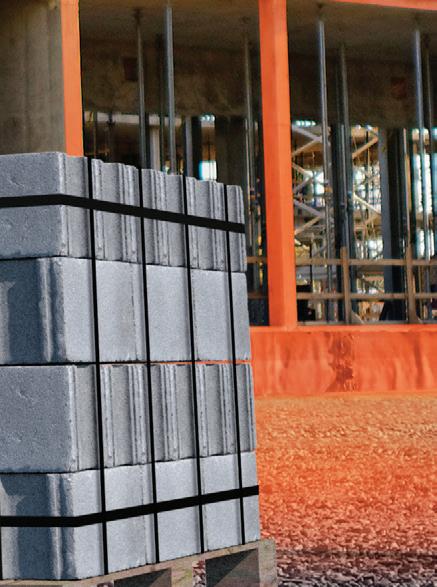
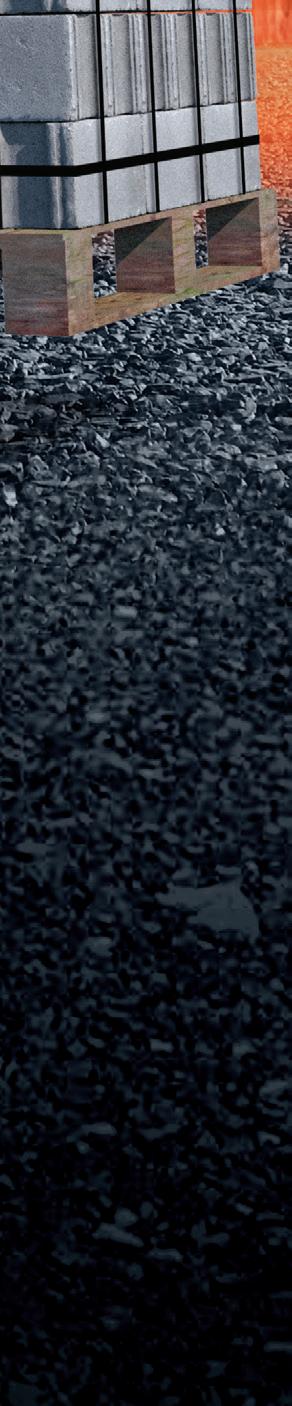
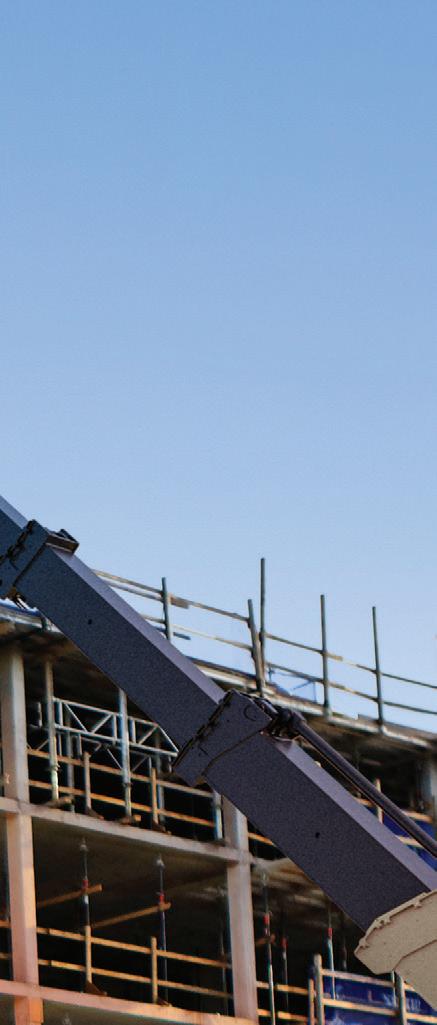
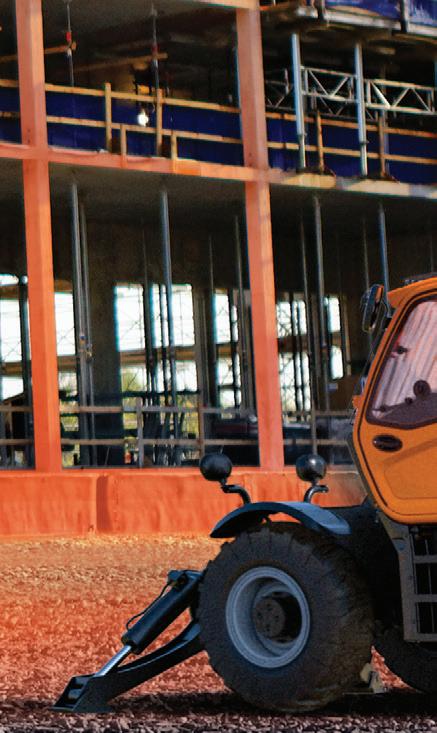

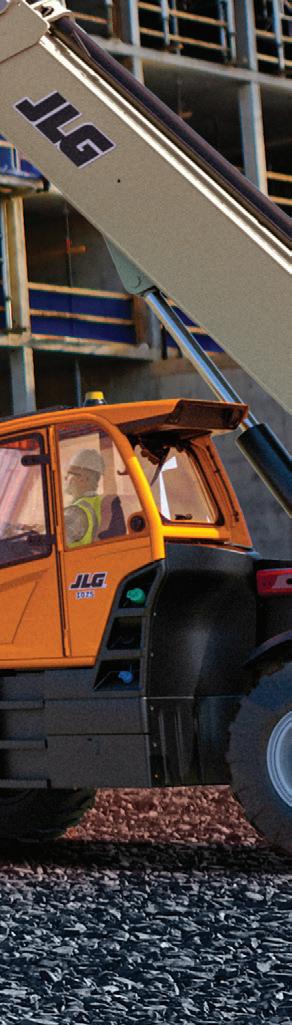
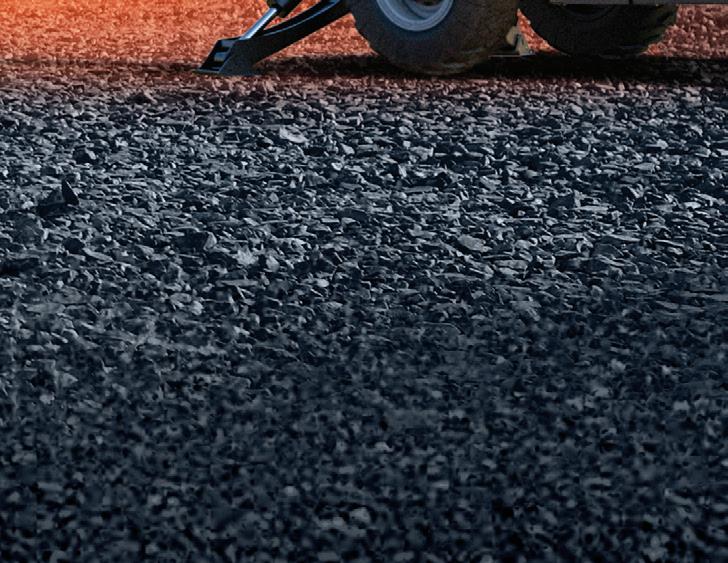



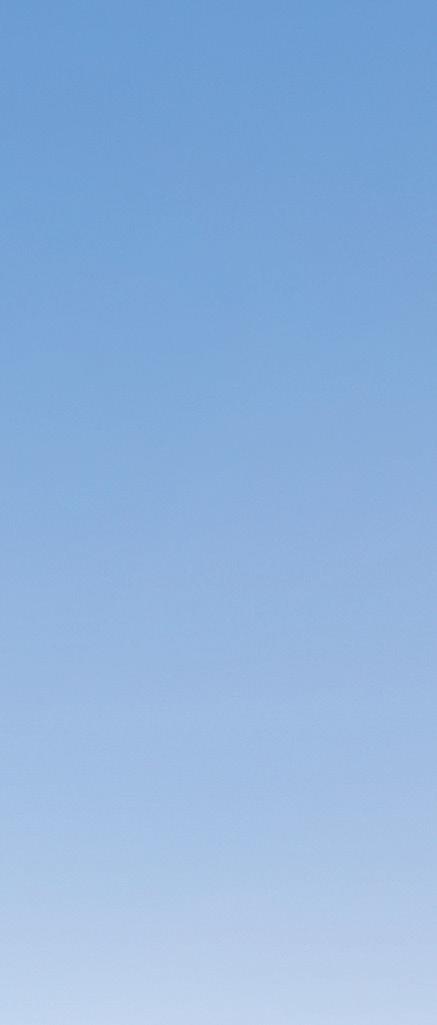

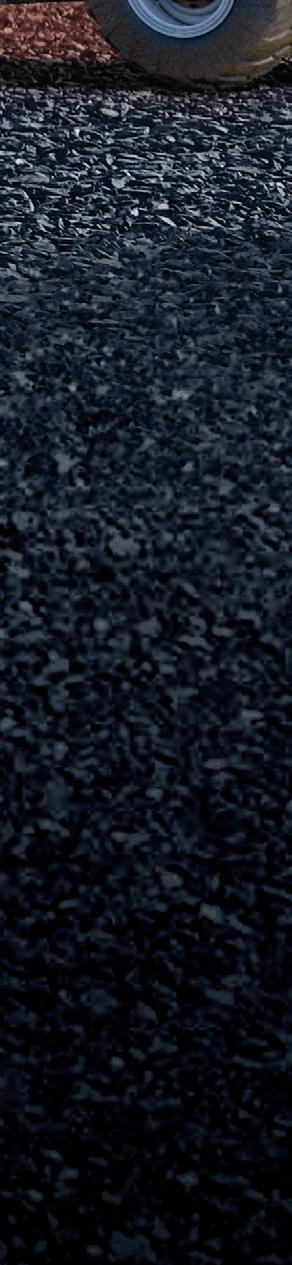
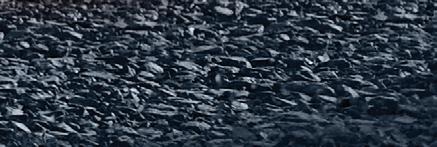
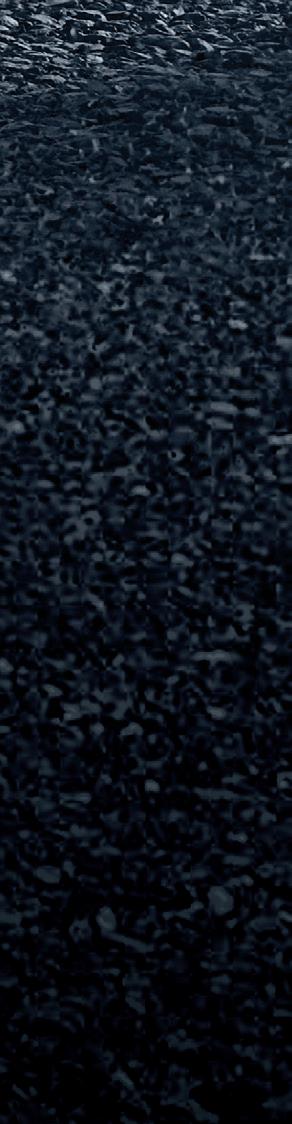
These pages feature some of the latest equipment available. For more information on these products, scan the QR code shown.
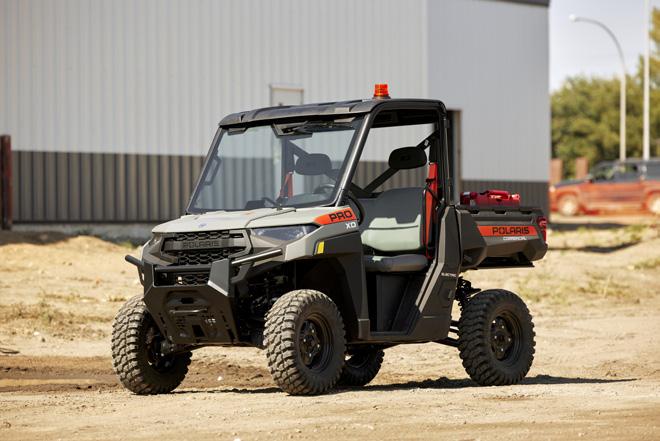
Polaris Pro XD UTV
Featuring an all-electric powertrain through Polaris’ exclusive 10-year partnership with Zero Motorcycles, the Pro XD Kinetic offers the same 1,250-lb. cargo and 2,500-lb. towing capacity as a full-size gas or diesel Pro XD UTV, while its allelectric powertrain is designed to deliver instantaneous torque and precise handling.
An electric powertrain also requires less maintenance. Heavyduty boots, bearings and bushings, Kevlar-backed seats, thick 8-ply tires and a rust- and dent-free poly bed ensure that the electric model is built to last from the headlights to the tailgate. A rugged, long-lasting 14.9-kWh lithium-ion battery; an electric motor; and 140 lb.-ft. of instant torque provide the power operators need to tow up to 2,500 lbs. and haul up to 1,250 lbs.
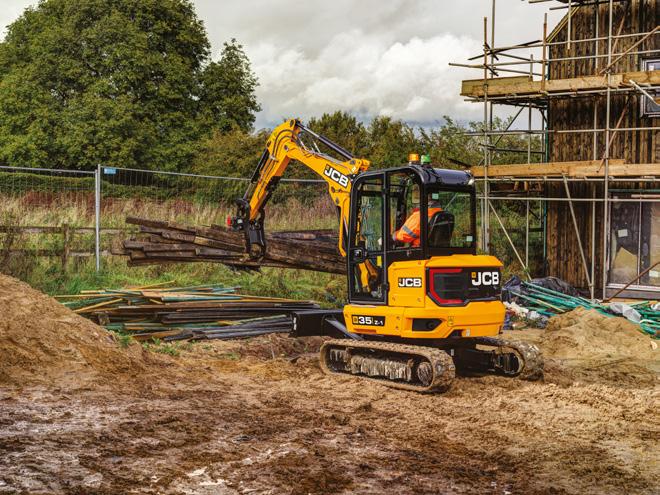
JCB 35Z MEX Mini
Excavator
JCB offers the 35Z Mex mini excavator for compact digging, lifting, transporting and excavation in tight spaces. It is a zero-tail swing, rubber-tracked, 3.5-T machine that comes tiltrotator ready with a standard thumb attachment and two- and four-way dozer options.
The 35Z delivers 24.7 hp and 7,284 lbs. of breakout force with a dig depth of 10 ft., 6 in. A new dig end geometry and visibility facilitate dumper loading. Inside the machine, the cab provides a flat floor and a hands-free Bluetooth radio with media socket.
Read More at eqtoday.co/4u5fygls
Werk-Brau FX26 Forestry Mulcher Attachment
The FX26 Forestry Mulcher is for excavators from 8,000 to 16,000 lbs., with a direct-coupled motor which provides power during use. A heavy wall 14-in. rotor is fitted with 21 fixed knives to shred brush, limbs and standing trees up to 6 in. in diameter. The bite-limiting tooth design maintains drum speed and prevents stalling. Material is passed through two breaker bars to create fine mulch. The FX26 weighs 785 lbs. and requires 15 gpm to 35 gpm of hydraulic flow to power the gear motor but features a 26-in. working width for production. With two grease points and no additional drive components, this simple design can be maintained on jobsites.
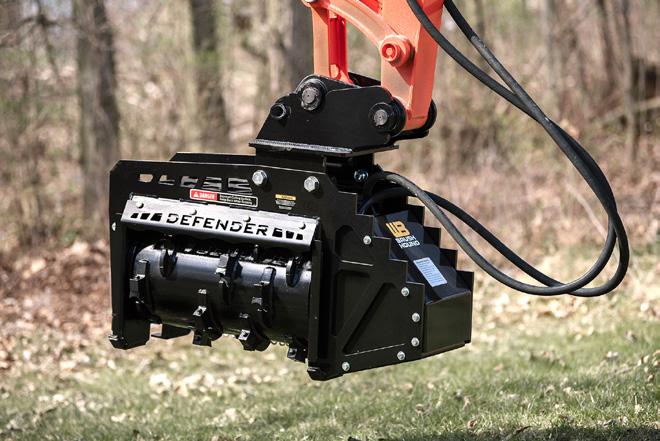
Kubota RTV-X1130 UTV
Kubota offers the RTV-X1130 utility vehicle for transporting cargo and materials. Powered by a 24.8-hp diesel engine, the RTV-X1130 features a 6-ft. long bed that has several configuration options to handle different types of cargo.
The cargo bed has the ability to divide into different sub-compartments. It offers 26 cu. ft. of storage and cargo capacity of 1,212 lbs. Using the new Pro-Konvert system, the bed and its three sides can be configured without tools allowing operators to drop the two sides and/or the back tailgate for loading and even converting it into a flatbed. With the inclusion of a hydraulic dump bed and bed lock feature, users can have control and safety over their load control and achieve material placement.
Trimble TDL450B Radio

Read More at eqtoday.co/d0t78swm
The Trimble TDL450B Radio is a next generation 450-MHz external radio with Bluetooth for transmitting, receiving and repeating GNSS corrections. It provides configuration options and reliability for GNSS use on jobsites.
Designed to support Trimble and third-party RTK base stations, the TDL450B is a wireless UGH data radio built for use in harsh conditions and includes an add-on fan tray for impact and weather resistance. The interface makes it possible to set up and configure. Access to diagnostic data in the field also makes it possible to solve signal strength challenges and make adjustments when needed. The TDL450B radio is available through the SITECH distribution channel and is compatible for use within 12.5-kHz or 25-kHz bands.
Read More at eqtoday.co/yj7yzc08
CASE 651G Wheel Loader
The CASE 651G wheel loader delivers a breakout force of nearly 24,000 lbs. and a lifting capacity of more than 16,100 lbs. It also features a large hydraulic pump for increased cycle times, a curved bucket for material retention and high hinge pin for dumping clearance.
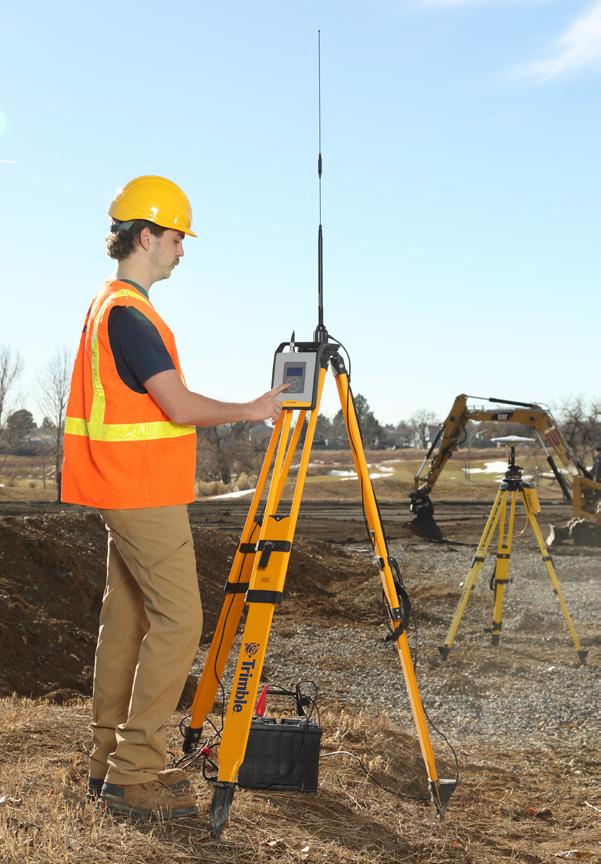
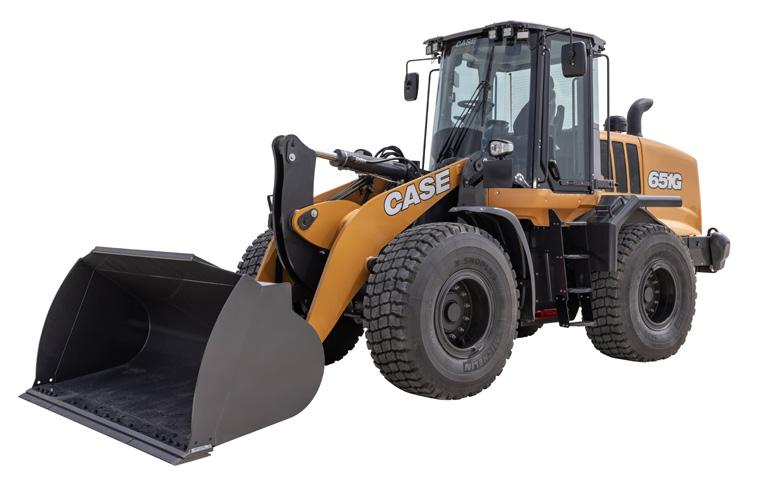
The 651G is powered by a 172-hp FPT Tier 4 final diesel engine and equipped with a 65-gal. fuel tank. It has a touchscreen display and adjustable electrohydraulic controls that allow the operator to independently set boom and bucket responsiveness to smooth, moderate or aggressive. Operators can weigh loads and track material moved with an integrated onboard scale.
New Holland ML35T & ML50T Telescopic Loaders
Two new telescopic reach models—the ML35T and ML50T—are designed to give operators reach and hinge pin height when loading or moving materials is required. With their compact design, low ground clearance and balanced weight distribution, the machines allow operators to navigate tight spaces and minimize ground disturbances.
Read More at eqtoday.co/dc1xathe
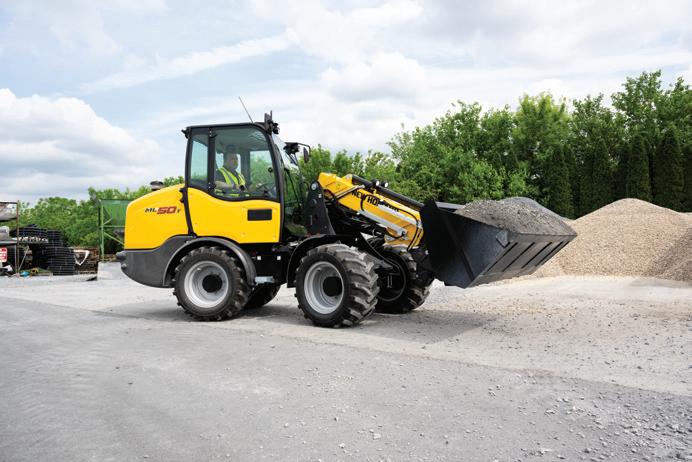
The telescopic boom design of the ML35T and ML50T models redefine reach capabilities for SAL models. The flexible nature of these booms allows operators to retract and extend as needed to handle jobs with various height needs. With increased elongation of the boom, these models are designed for space-limited sites, delivering horizontal and vertical outreach. Operators also use the telescopic boom to maneuver and handle materials at elevated heights, such as loading concrete debris over dump truck box sides. Both models feature a hinge pin height of around 170 in. (4.3 m).
Read More at eqtoday.co/k39axkqi
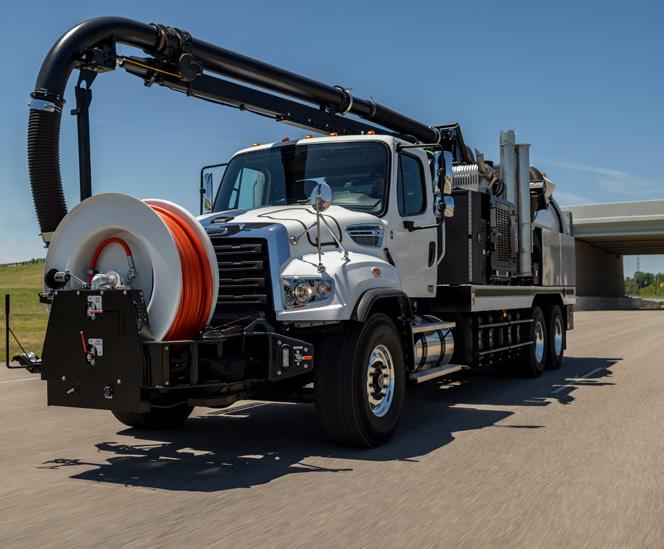
Freightliner 114SD Plus Truck
The 114SD Plus is designed to deliver advanced powertrain and active safety technologies, comfort features that keep operators working hard and the QuickFit Electrical System that makes upfit simpler and more efficient.
With a 2,500-sq.-in. windshield for visibility, extra-wide door openings that make entry and exit easy, a factory installed backup camera with reverse proximity sensors for added rear visibility, and the optional Bendix Intellipark Electronic Parking Brake system that helps prevent rollaways, the 114SD Plus is purpose built for safety. New powertrain options provide horsepower and torque ratings that make the 114SD Plus productive on jobsites.
Read More at eqtoday.co/s3cpnnuk
Stellar NXT68 Hooklift & Bumper
Stellar Industries showcased the all-new NXT68 Hooklift and a 90,000-lb. pull capacity bumper for servicing, rental and lifting applications on jobsites. The NXT68 offers a load height of 12.5 in. and various capacities, including 68,000 lbs. at 62-in. hook height, 57,000 lbs. at 54-in. hook height and 68,000-lb. dump capacity.
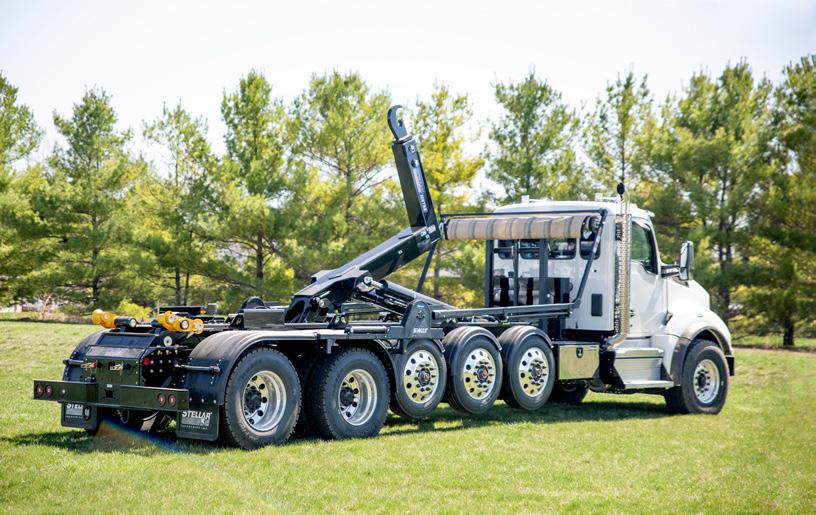
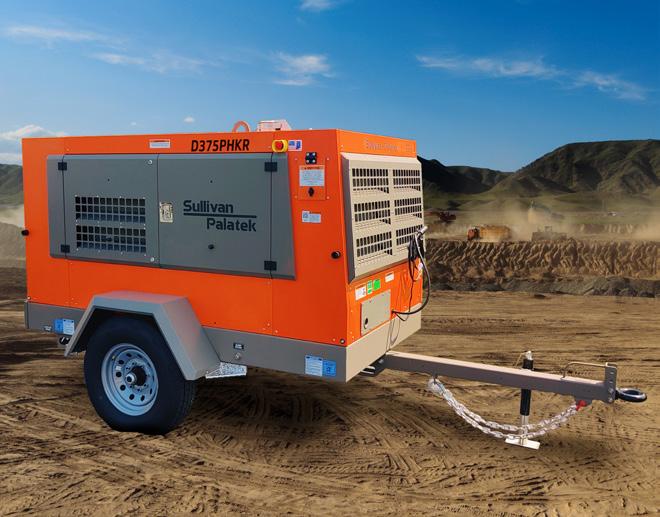
Sullivan-Palatek D375PHKR Portable Air Compressor
Powered by a 134-hp Kohler Tier 4 final engine, the D375HKR delivers 375 cfm at 150 psi during use. It is simple to operate with Sullivan-Palatek Electronic Controller, a large display of readouts for control over power consumption, pressure range and more. Maintenance is also simple with the swing up pneumatic-lift service doors to access the unit.
Used in environments where no alternative power source is available, in the heat of the desert or freezing temperatures of a mountain slope, the portable air compressor is protected by a powder coated exterior finish for rust and corrosion resistance.
The Sullivan-Palatek D375HKR meets U.S. Environmental Protection Agency emission standards. For transport, the air compressor is equipped with two wheels at the base and can be towed to desired locations.

With a power range of 50 hp to 160 hp, the flail mulcher can be used with AEBI tractors because of its low weight and close center of gravity to the tractor for use on steep slopes. S7 base is a mulcher designed for tasks that do not require lateral displacement.
Available for 16-ft. to 22-ft. containers, the NXT68 Hooklift offers reliable material handling capabilities. An electronic joystick control system is available on the NXT52, enabling operations with a single joystick that governs all hooklift functions. Stellar introduced new standard bumper options for its hooklifts, catering to diverse chassis specifications.
The rotor shaft of the S7 base is equipped with SMO or SMW flails, which mulch grass and woody material up to 7 cm in diameter. Due to its construction and the spirally arranged flails on the HELIX rotor, forces are distributed evenly, promoting smooth operation at speeds of up to 10 km/h. The housing contains hardened counter cutters, which are interchangeable in the S7 series. The combined protection device of chains and flaps prevents twigs from getting tangled and protects against stone impact.
The newly designed belt housing corresponds to the sturdy construction of forestry equipment and features deflectors to protect passing plants.
Curry Supply Utility Truck & Trailer
Product Line
Read More at eqtoday.co/bpj53v24
With a 20,000-lb. pull capacity, the 20K option offers two versions: an economical version using chassis take-off lights and a full version featuring built-in lights for Class 3 to Class 6 chassis applications. Meanwhile, the 90K option features built-in lights and a 90,000-lb. pull capacity for Class 7 and Class 8 chassis applications.
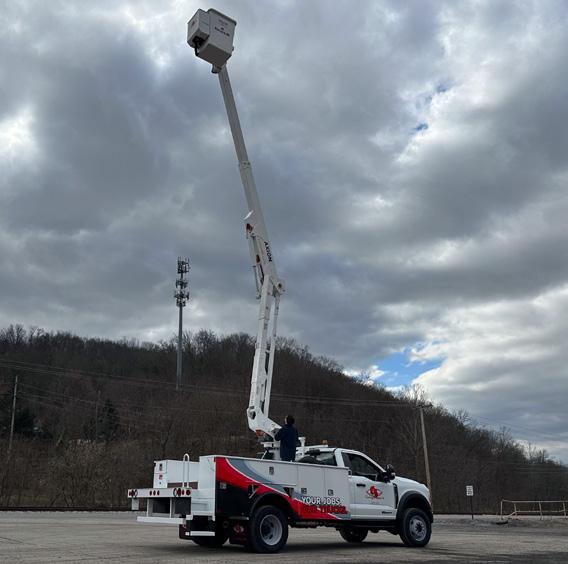
Curry Supply’s new utility truck and trailer product line is an expansion into the utility vehicle market made possible through partnerships with Dur-A-Lift, Stellar Industries, Posi+, Axion and Dakota Bodies. With these partnerships, Curry Supply has curated a selection of trucks and trailers that can be customized to fit specific customer requirements.
The line includes products ranging from insulated and non-insulated aerial lifts to crane service trucks, digger derricks and utility trailers, the new line offers solutions for tasks from electrical work to heavy lifting and sign and signal maintenance to roadside repairs. The trucks and trailers are designed to withstand demanding jobsites and weather conditions with safety as a priority. Each product can be tailored for different needs, offering a range of configurations, body styles and equipment options.
Volvo CE ECR145, EC210, EC230, EC370, EC400 & EC500 Excavators
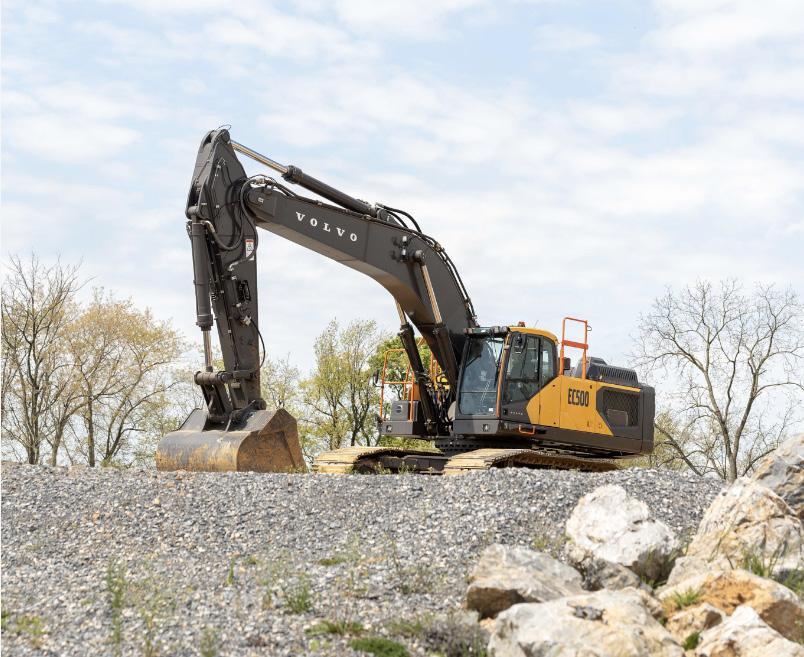
Volvo CE introduced a new range of excavators with upgrades in safety, performance and operator features. The initial launch includes multiple medium and large excavator models in North America—the ECR145 short swing, EC210, EC230, EC370, EC400 and EC500 crawler excavators.
An upgraded electrohydraulic system and other features—like a smart cooling system and engine speed regulation for high torque at a low rpm—offer better performance compared with the previous generation while outperforming the prior models. The hydraulics enable better machine control and movement of the boom, bucket and other hydraulic components. Work modes expand to 10 settings, including two specific to power and four specific to automatic ECO modes.
A new creep travel mode with boom and arm shock reduction settings give operators tight command of loads and reduce spillage. Volvo Smart View with Obstacle Detection gives operators 360-degree visibility of the machine’s surroundings. It also combines camera technology and a new radar detection system to distinguish between objects and humans.
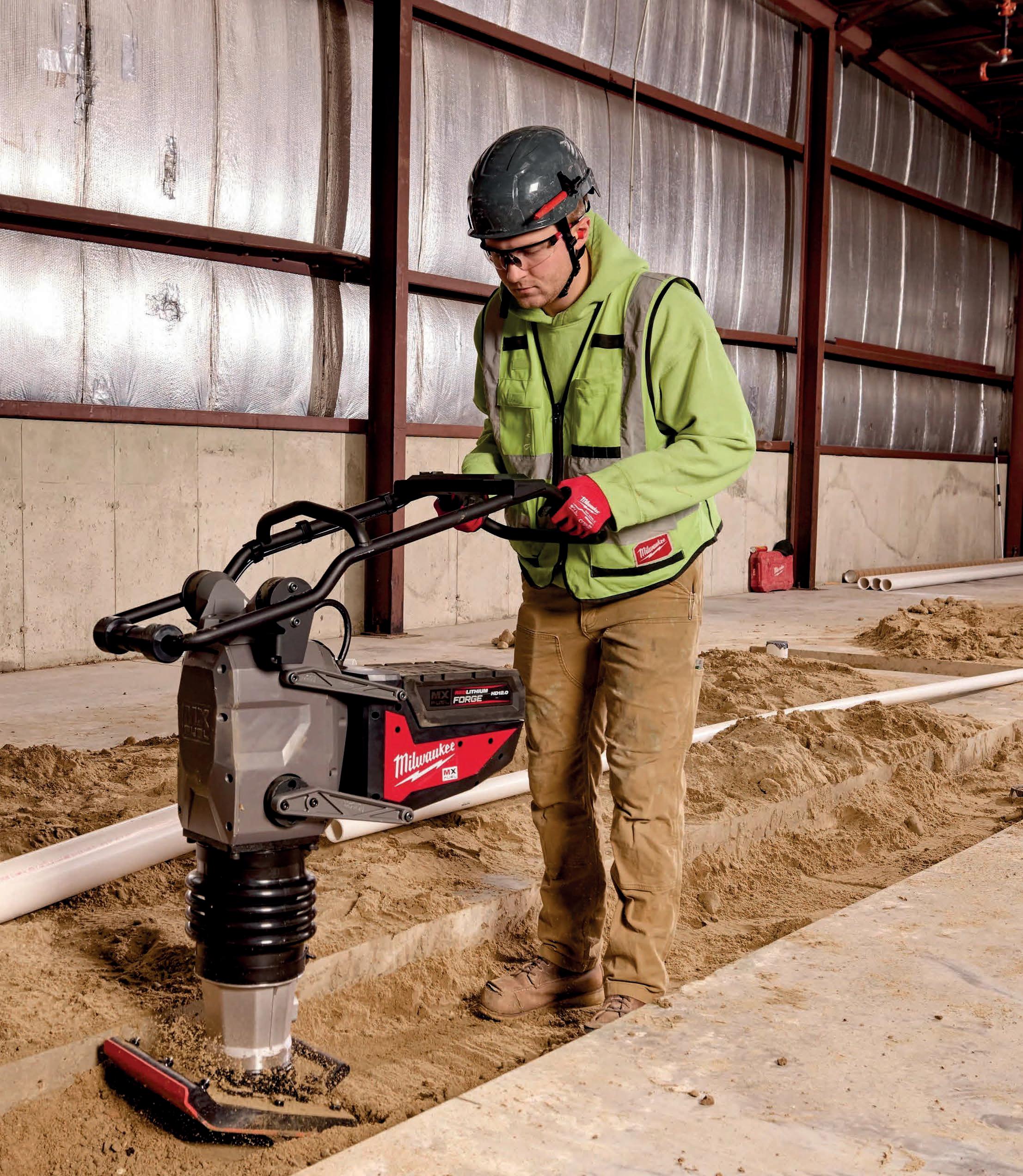
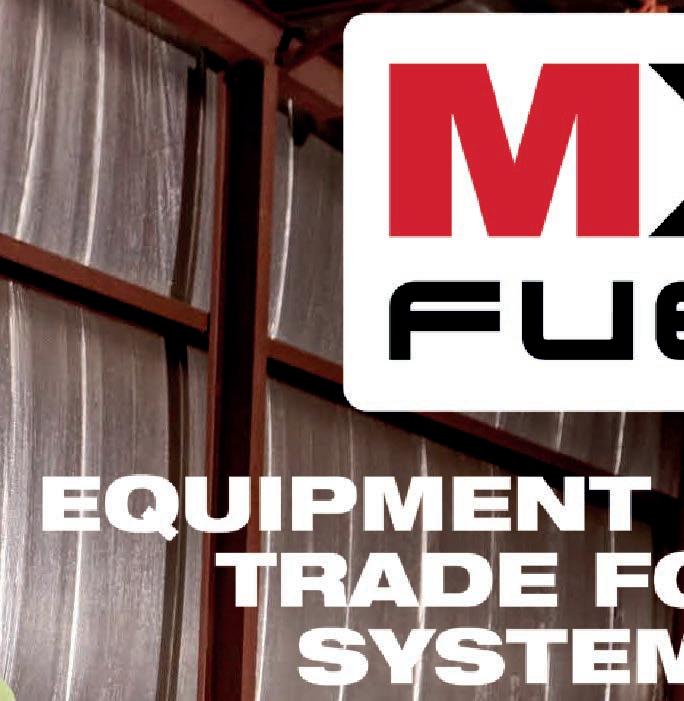
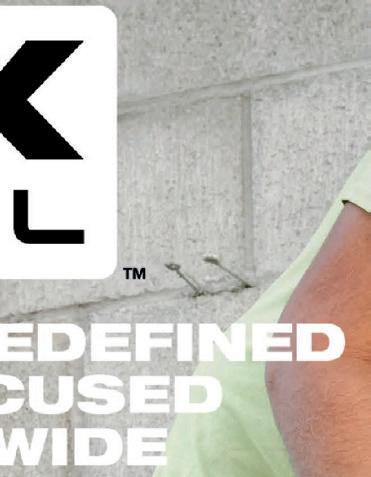
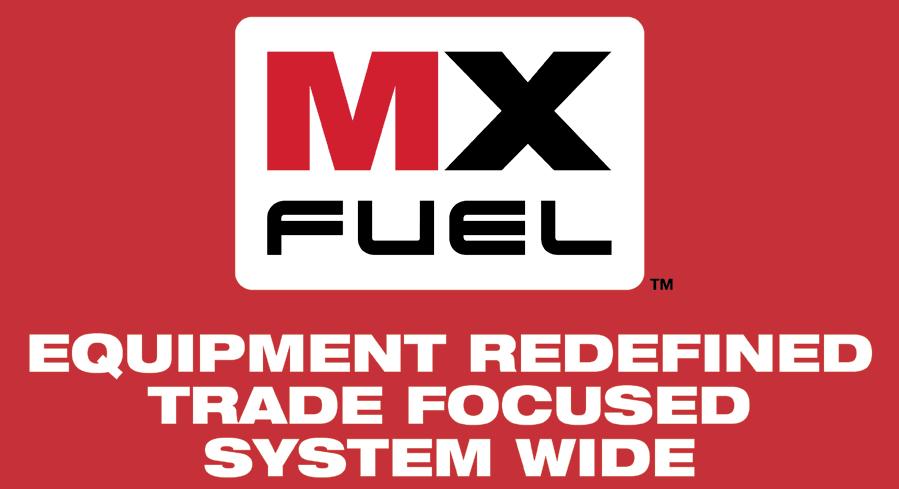
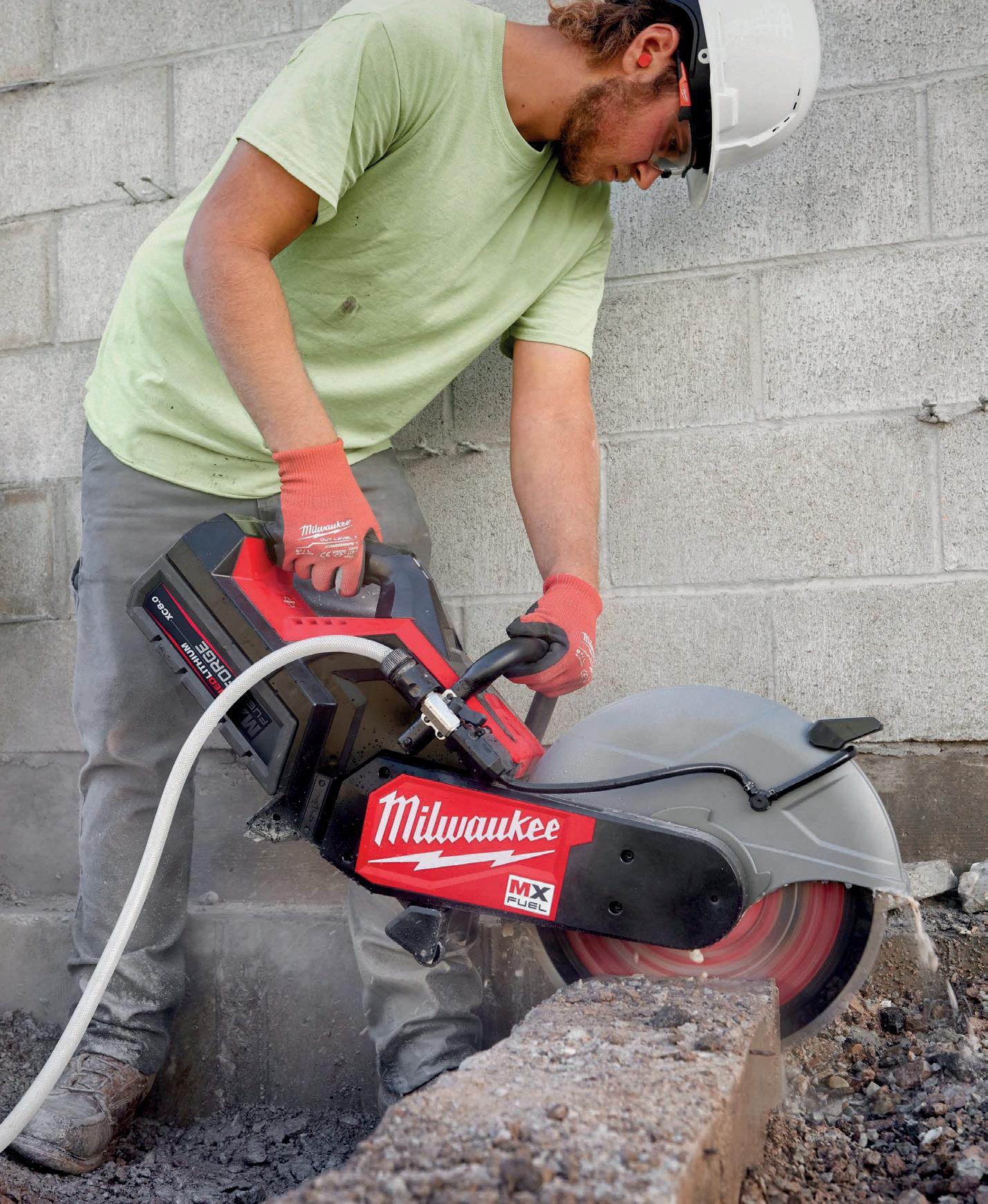
FROM POUR... TO FINISH
SOLUTION FOR EVERY STAGE | FORGE BATTERIES + SUPERCHARGER
From pour to finish, the MX FUEL™ Equipment System by Milwaukee Tool provides an innovative battery-powered solution for every stage of the concrete process. With the most consistent starts and most reliable pours, MX FUEL™ eliminates the emission and noise headaches associated with traditional gas-driven tools.
A world leader in cordless technology, Milwaukee® is committed to disrupting the gas-powered equipment space with battery-powered alternatives that are integrated with cutting edge electronics, REDLINK™ intelligence, and POWERSTATE™ Brushless motors.
FROM POUR…
Streamline site-prep with solutions like the MX FUEL™ 70kg Rammer. Delivering the power to hit harder and travel faster, this rammer delivers maximum productivity without sacrificing compaction performance. Providing no gas headaches and greater control, this rammer offers a centralized user interface, allowing for easier control adjustments and maneuverability in trenches of confined spaces.
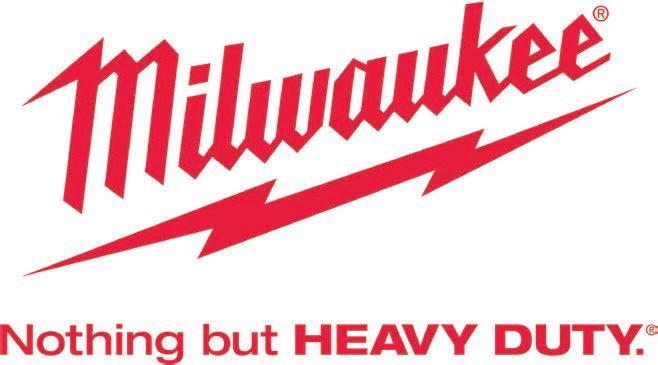
…TO FINISH
The cordless MX FUEL™ 14” Cut Off Saw w/ RAPIDSTOP™ also provides the power and performance of a gas-powered unit, cutting through reinforced concrete and rebar with ease. A push button start allows users to start the cut off saw in seconds, eliminating the strenuous, repetitive motions of priming, choking, and pulling the engine to start. Meanwhile, the RAPIDSTOP™ Brake offers enhanced safety, stopping the blade within three seconds. The tool also features advanced safety features like Milwaukee’s revolutionary AUTOSTOP™ Kickback Control, which senses severe kickback and automatically shuts off the saw to reduce strain or injury to the user.
Each product within the MX FUEL™ system can be powered by the cutting-edge MX FUEL™ REDLITHIUM™ FORGE™ line of batteries—Milwaukee’s most powerful, fastest charging, and longest life batteries. Pairing these batteries with the MX FUEL™ Super Charger, professionals can maximize their productivity, being provided up to 2X faster charging. The Super Charger is also COOL-CYCLE™ Capable, providing high-speed battery cooling and increased duty cycle for less downtime.
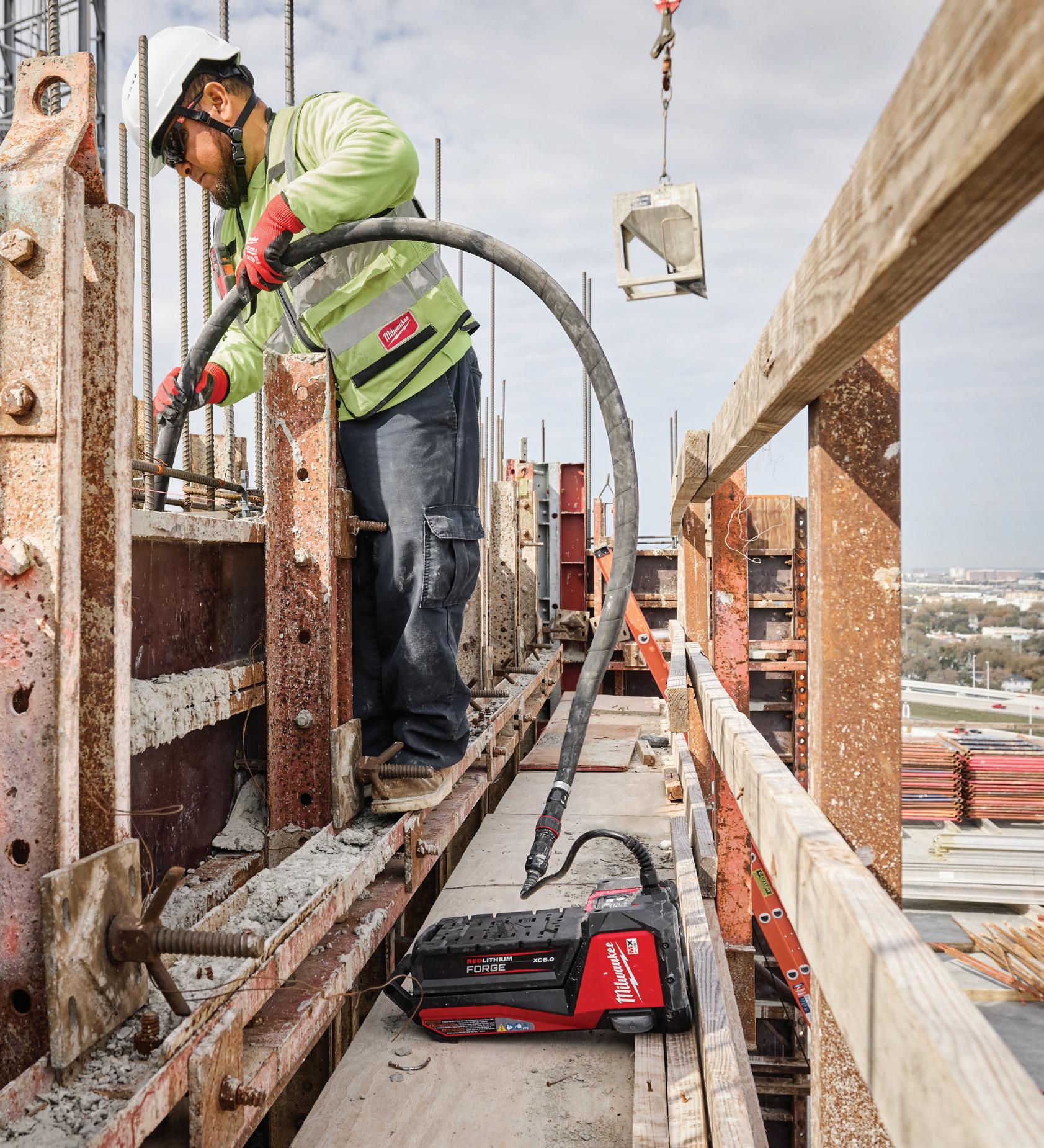
MOST MOST CONSISTENT CONSOLIDATION POWERFUL ,
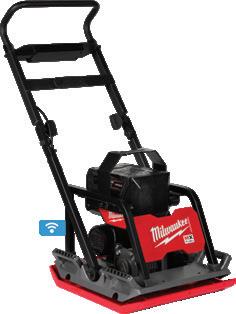

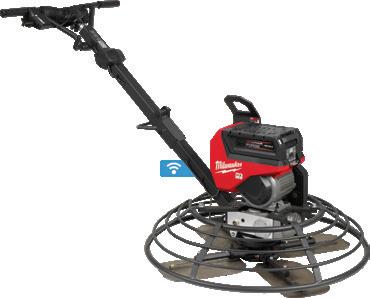
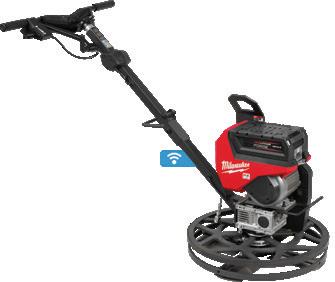
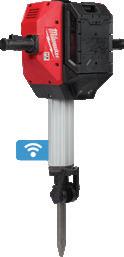
1.75" HEAD, 7' WHIP PER CHARGE, 130 YDS3
MX FUEL™ High Cycle Concrete Vibrator Kit
MXF372-2XC
LEARN MORE SETUP
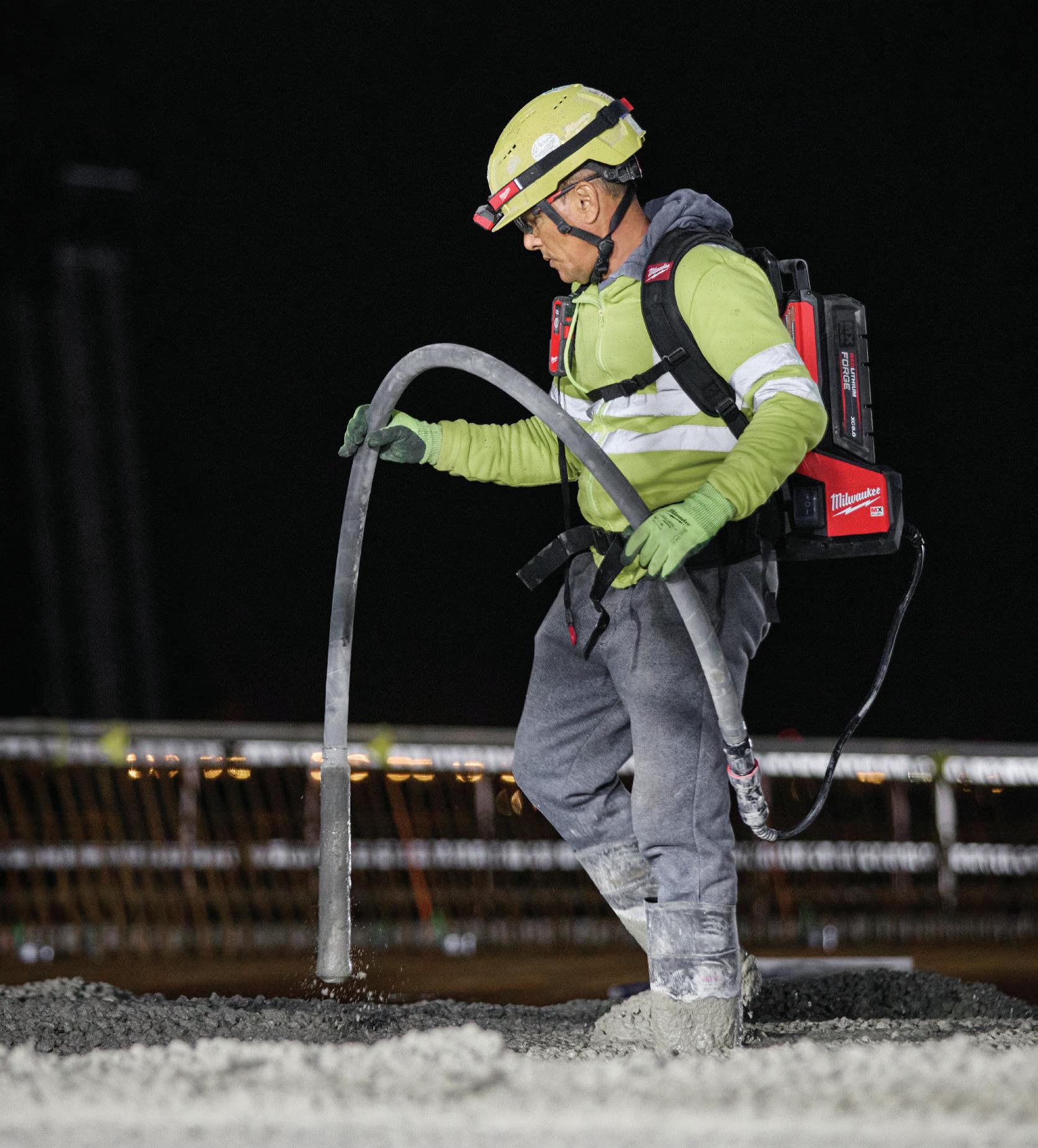
MX FUEL™ Backpack High Cycle Concrete Vibrator Kit w/ 7' Whip / 1.75" Head
MXF372-2XCB
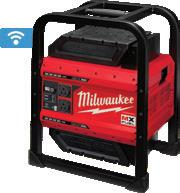
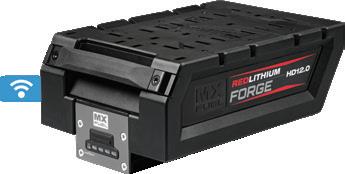
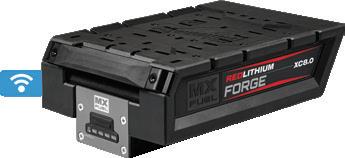
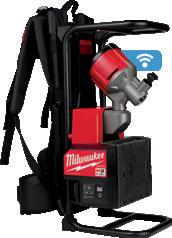
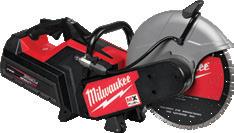


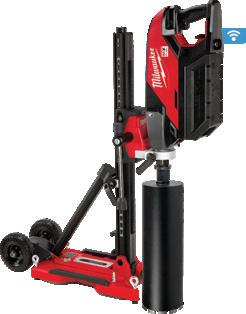

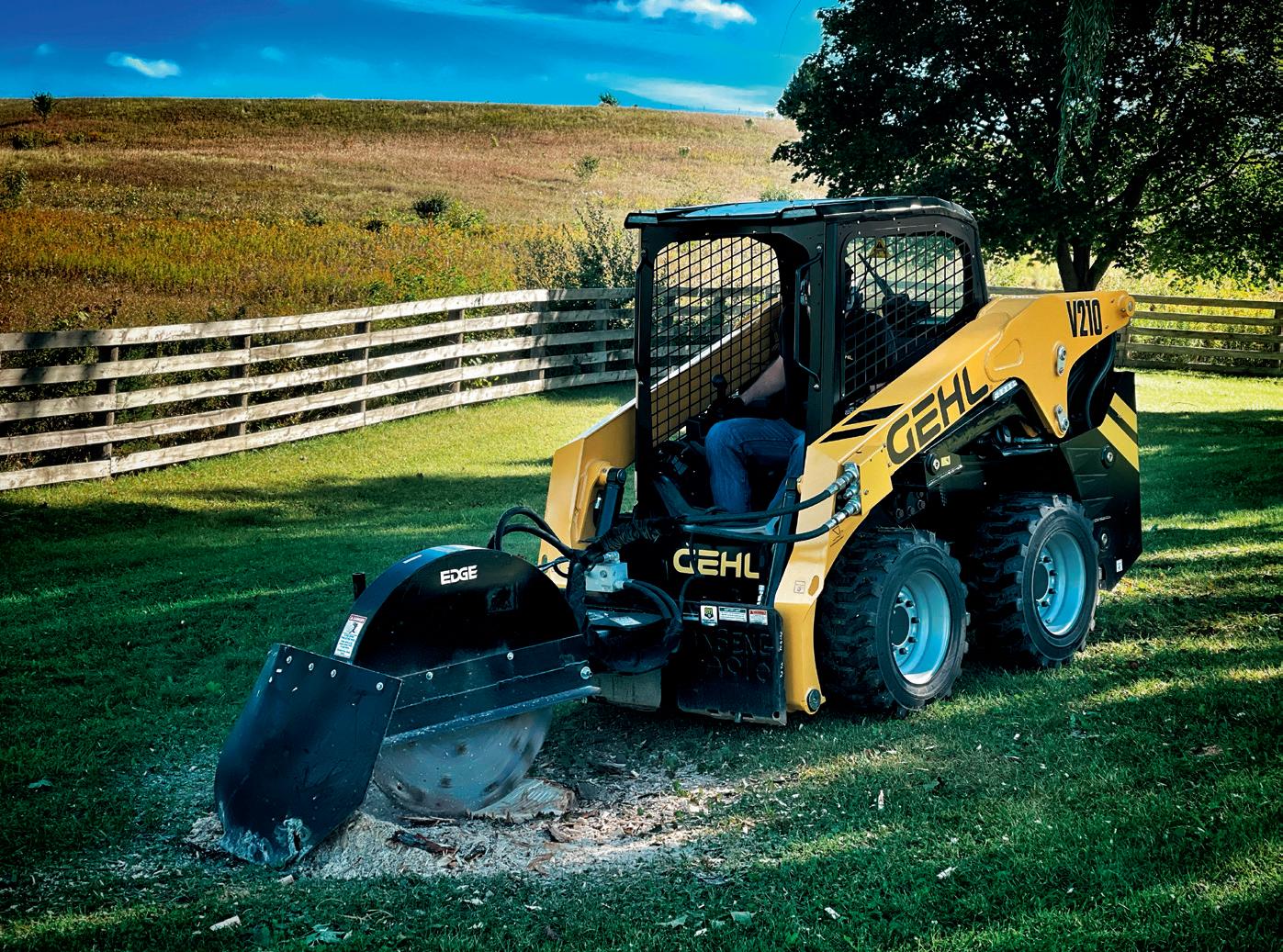
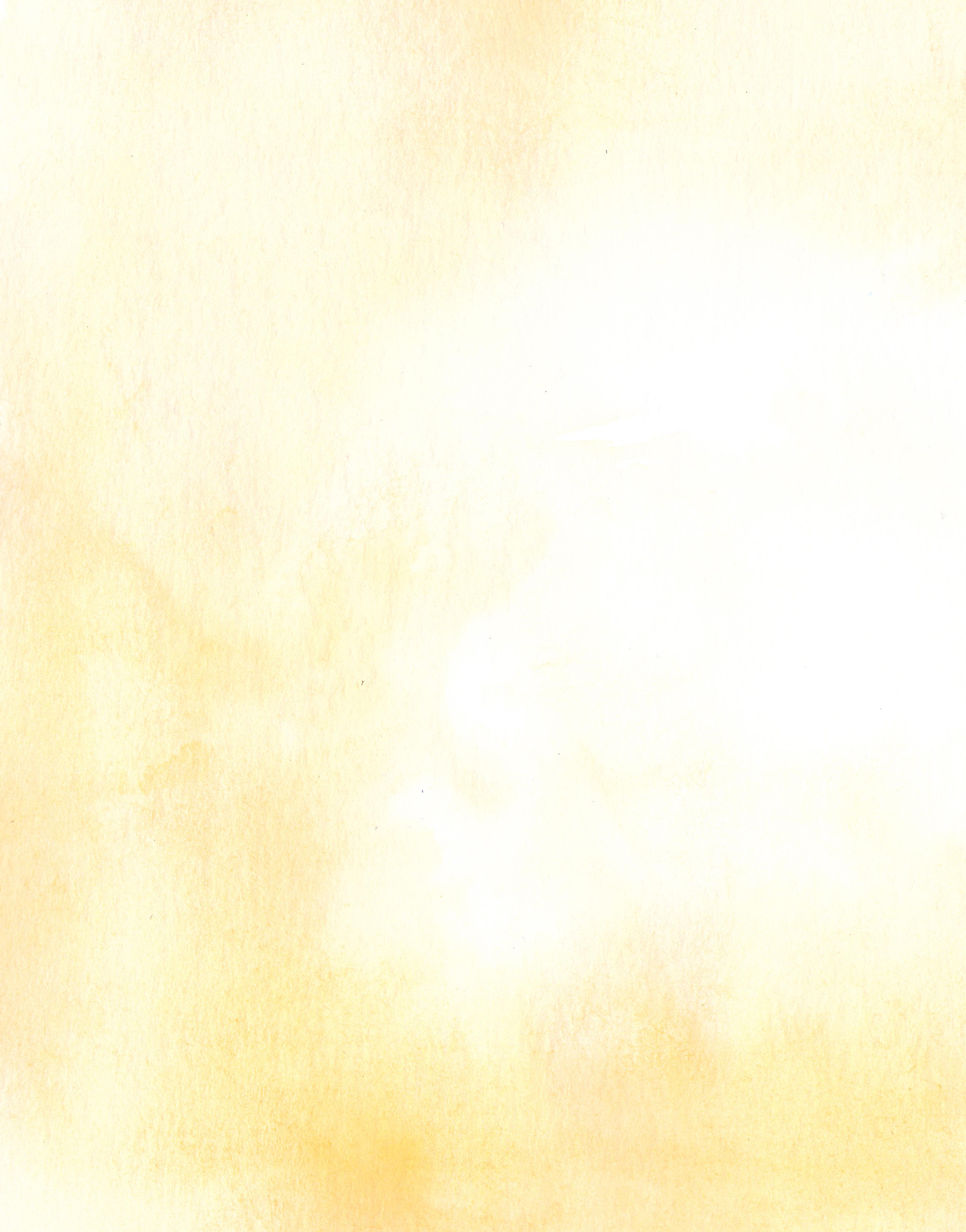
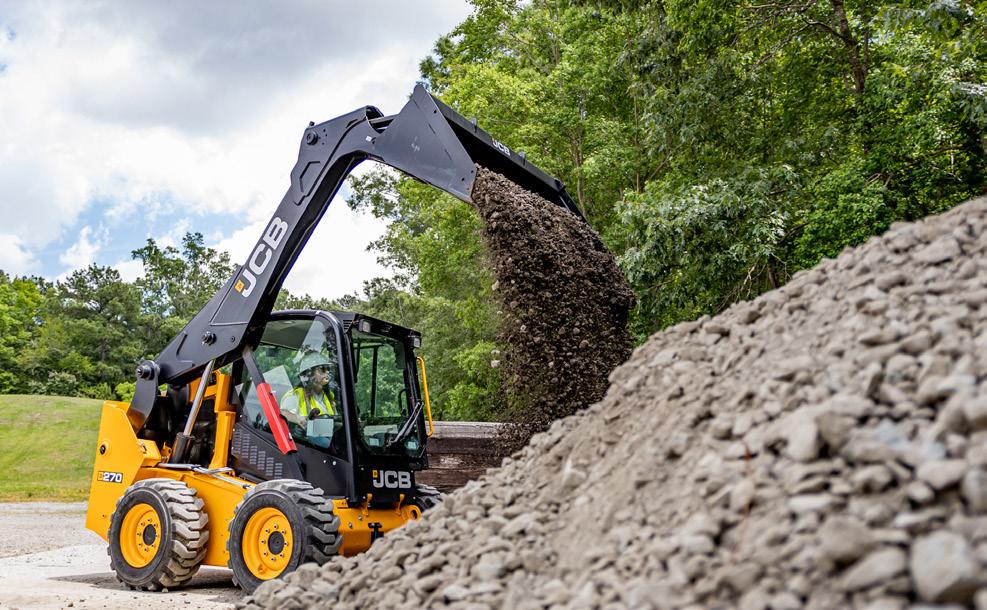
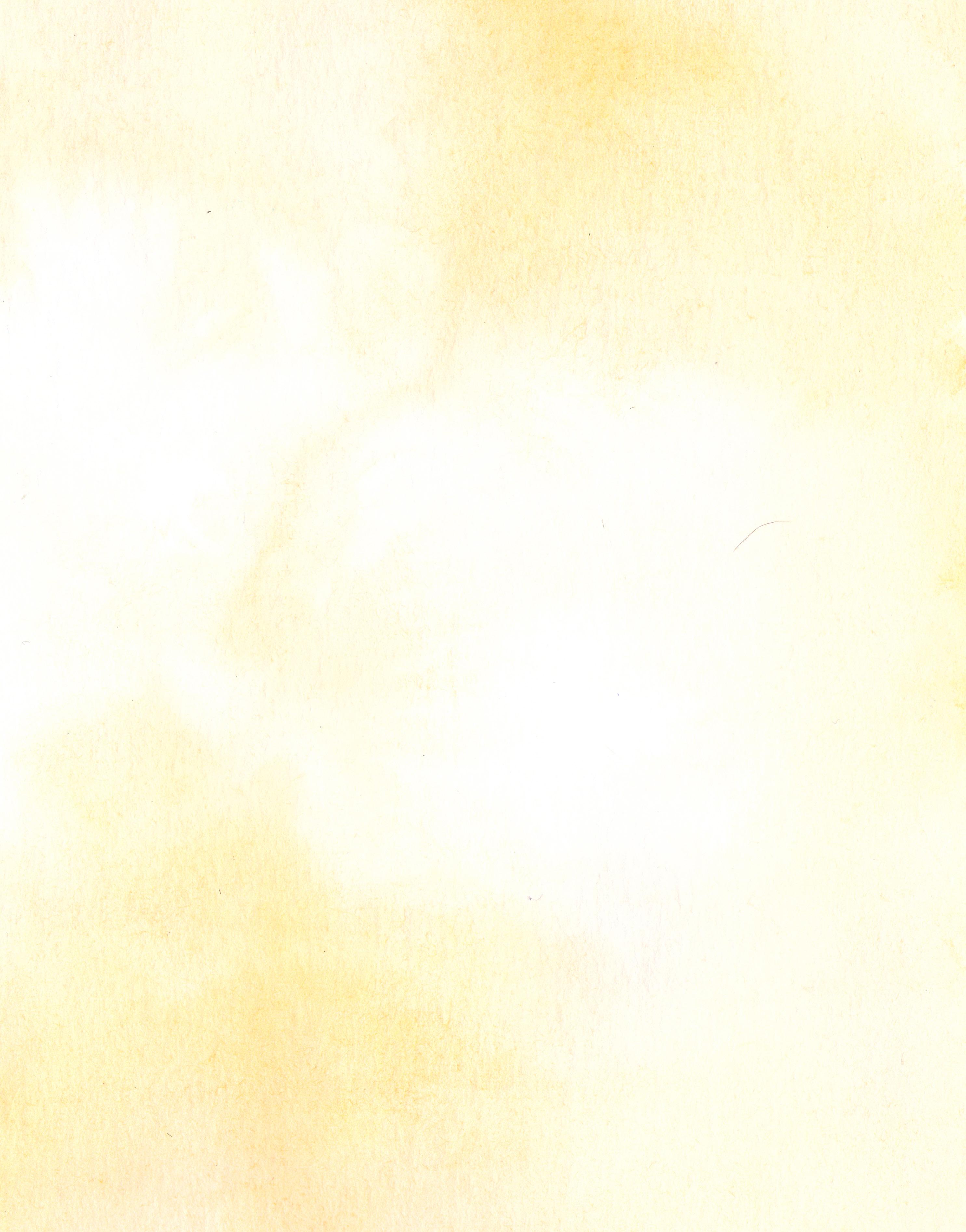
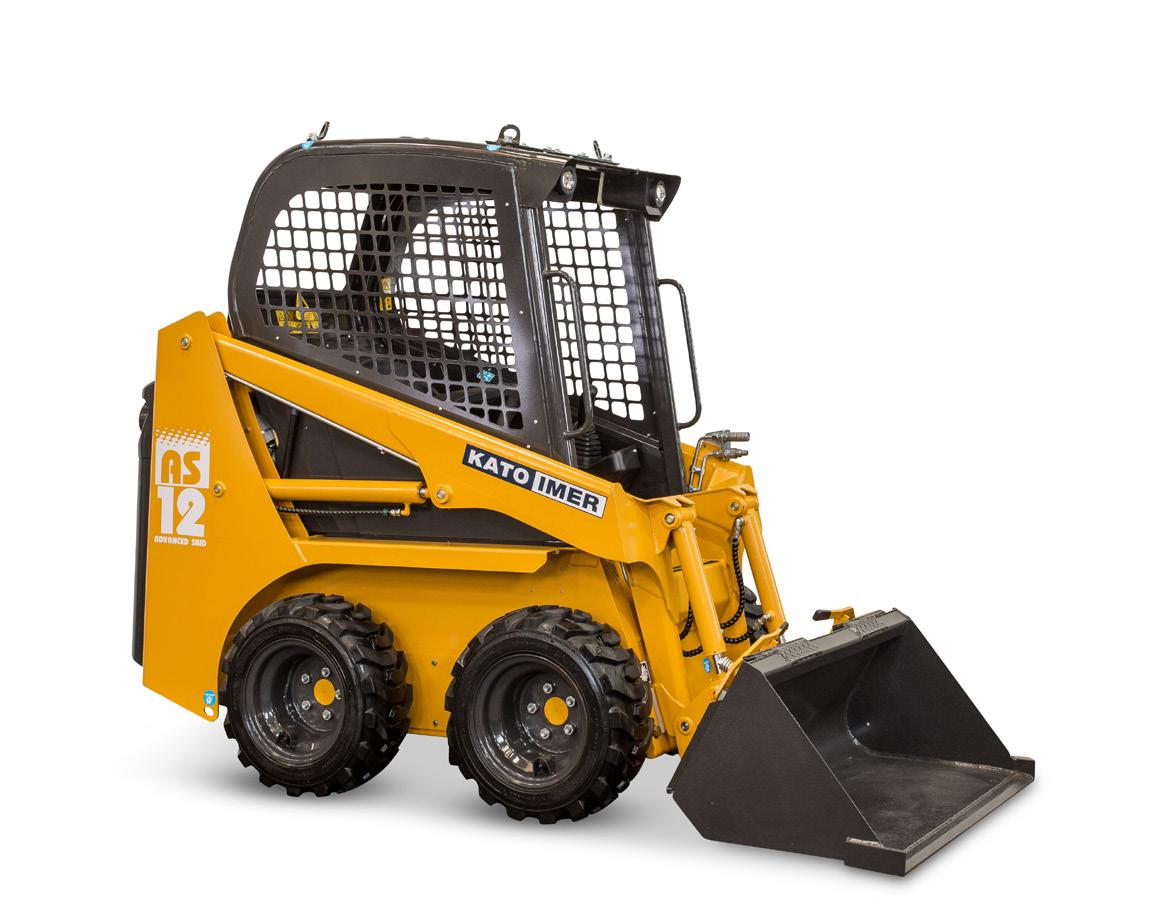

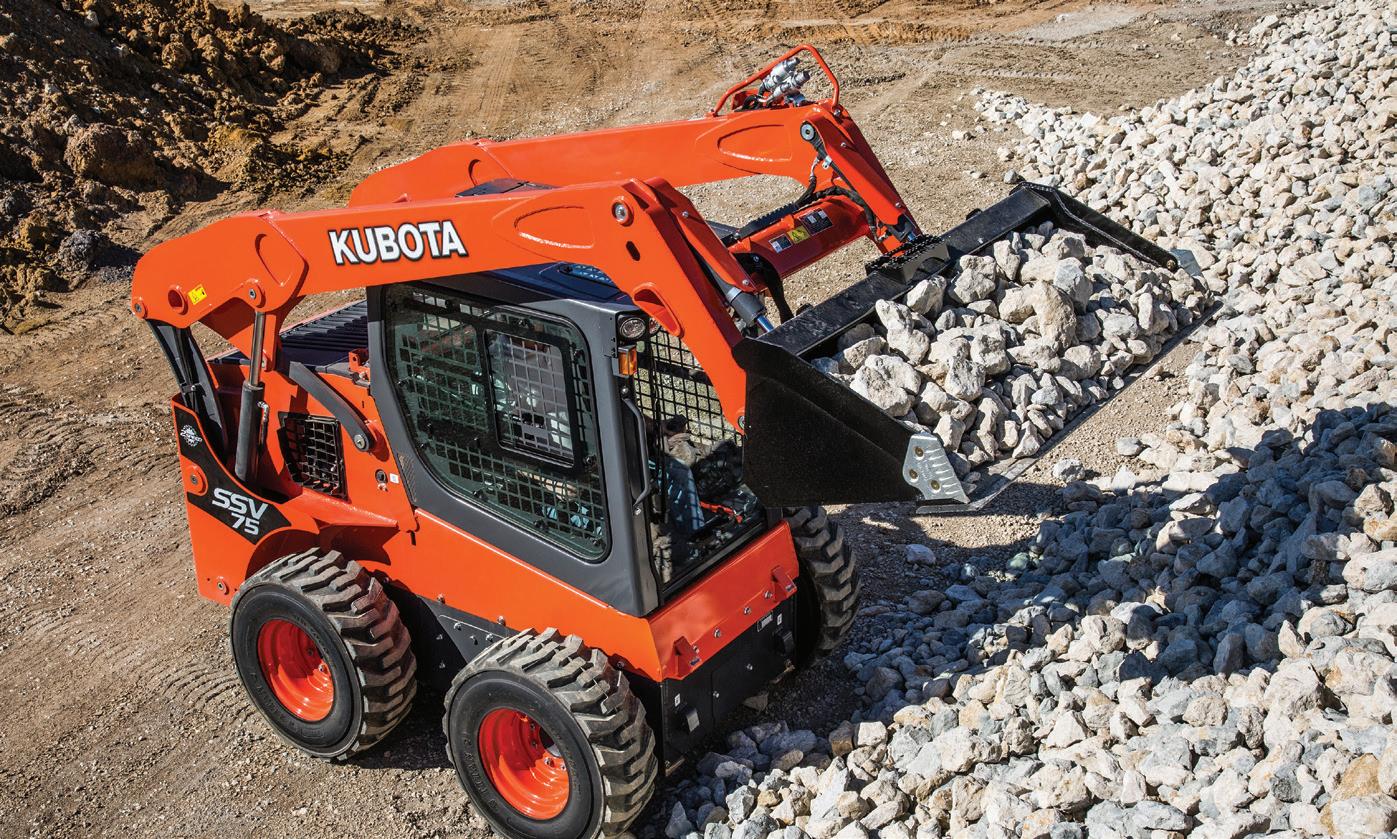
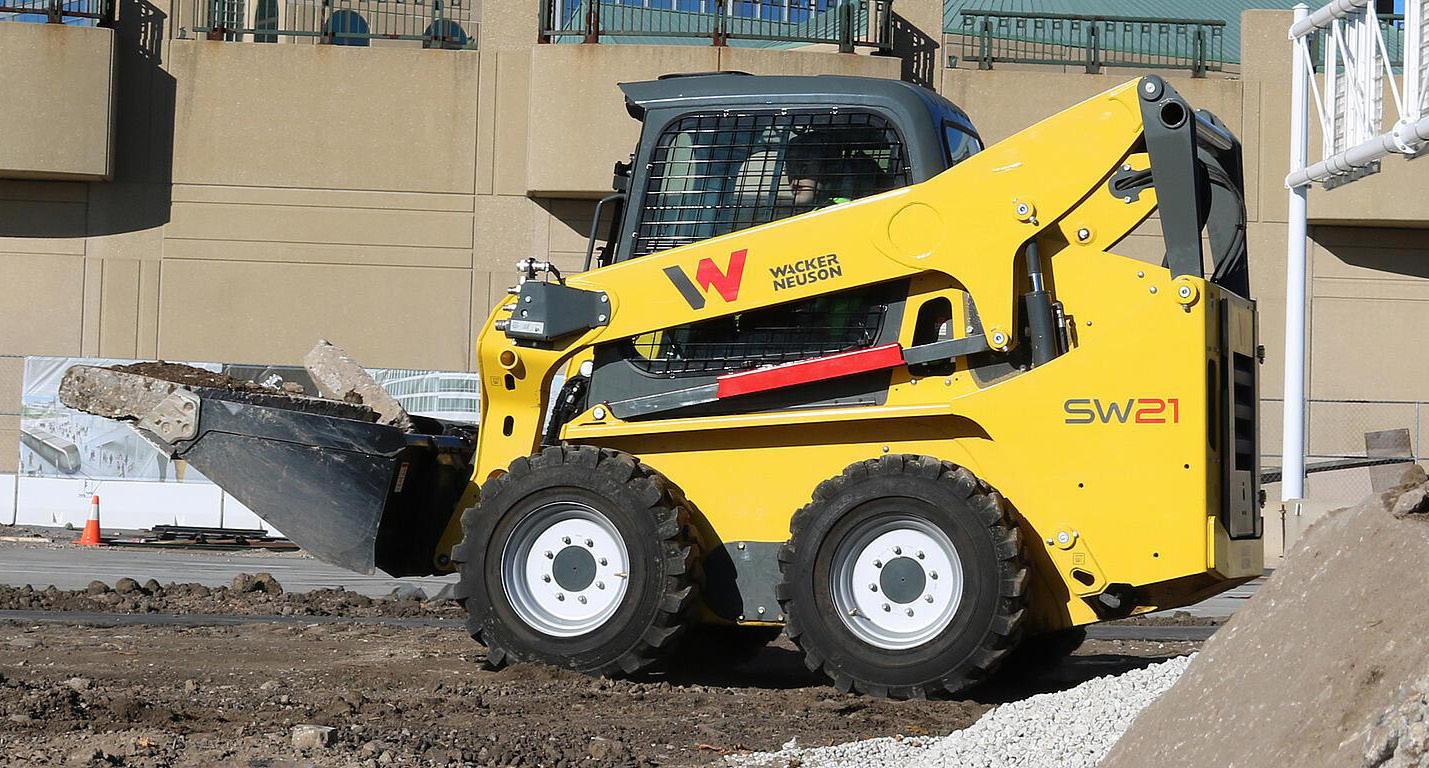


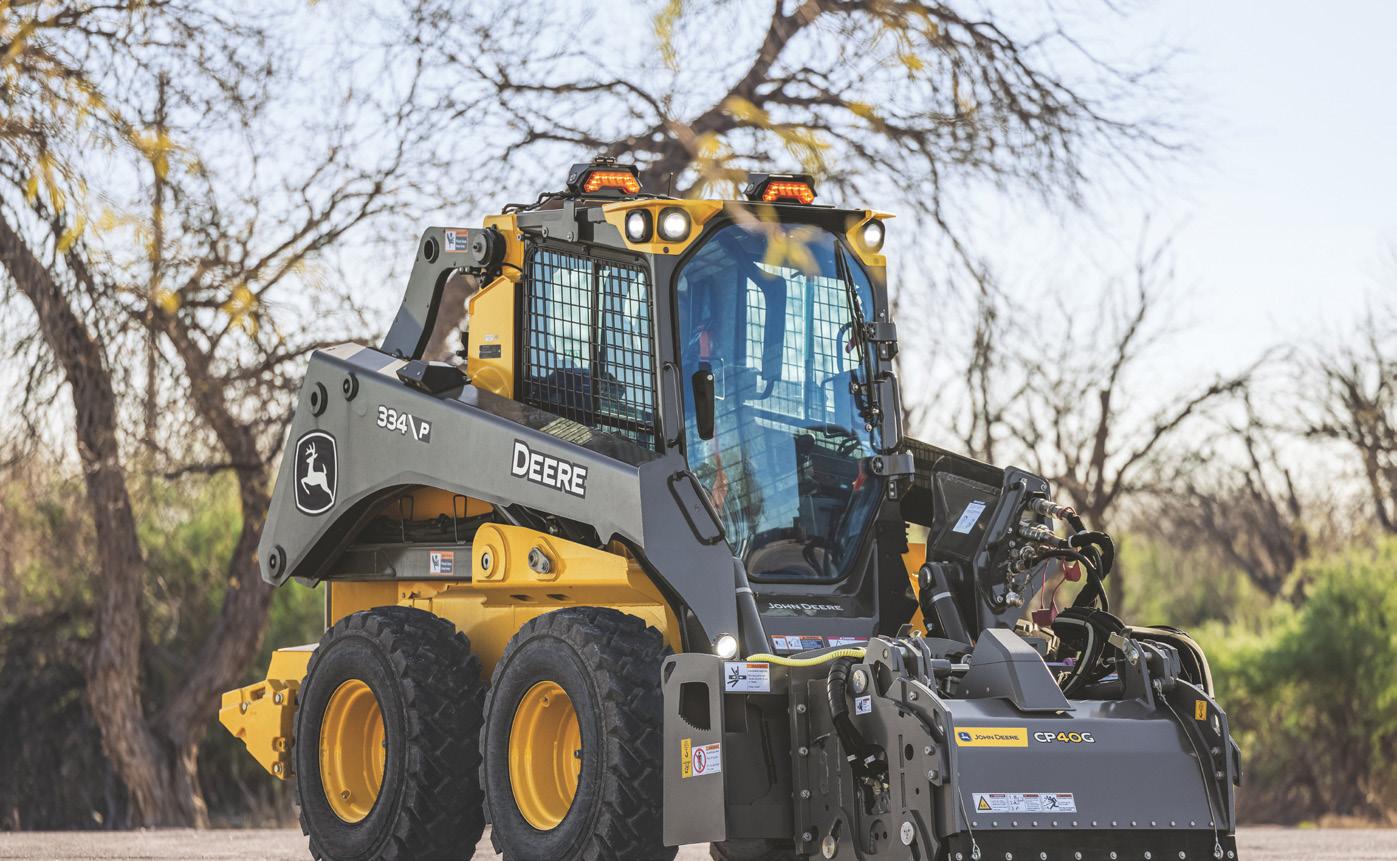
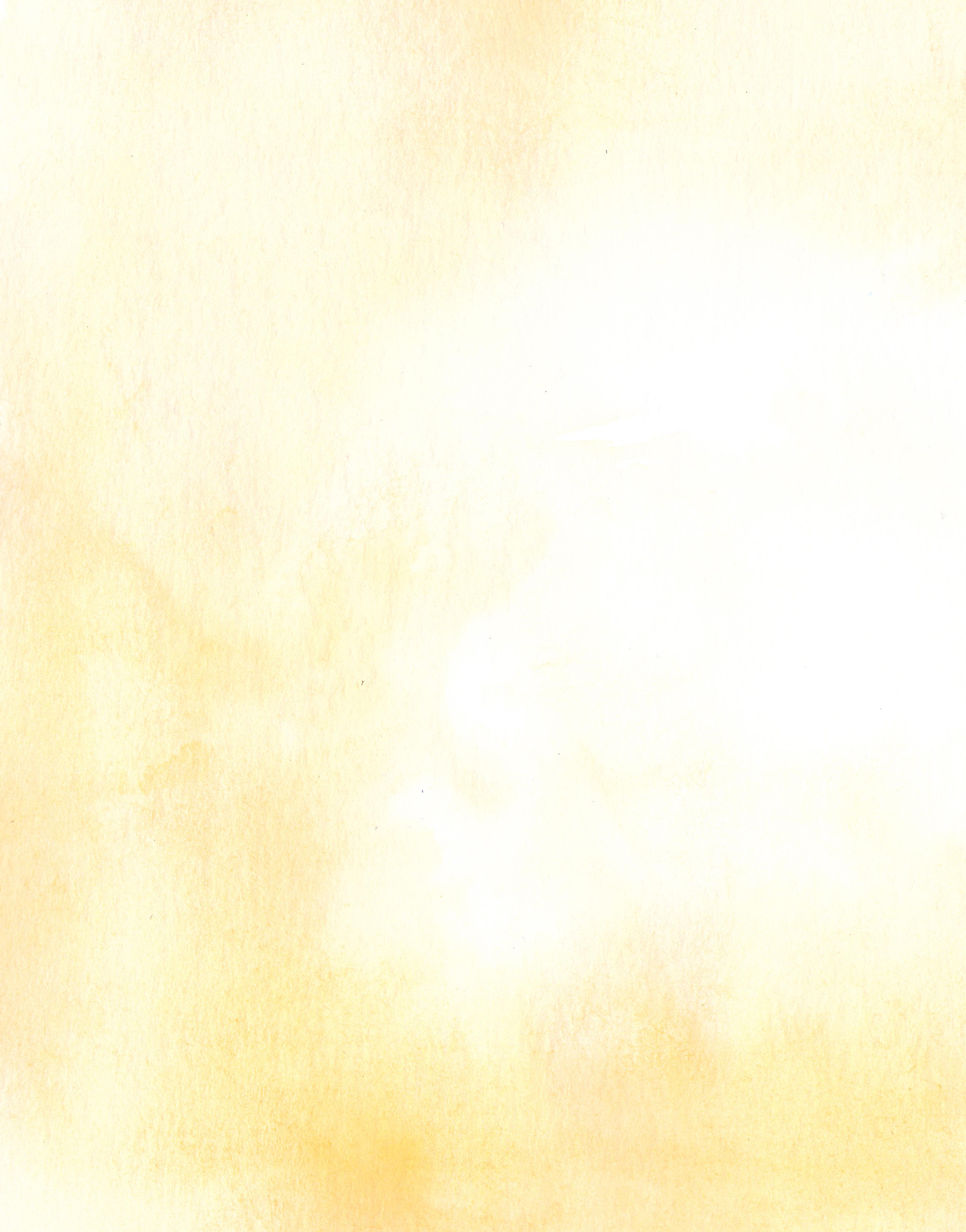
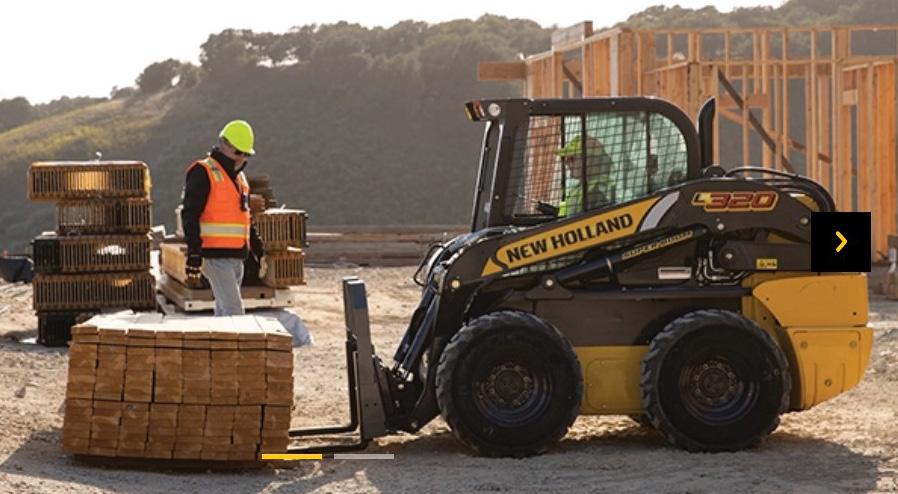
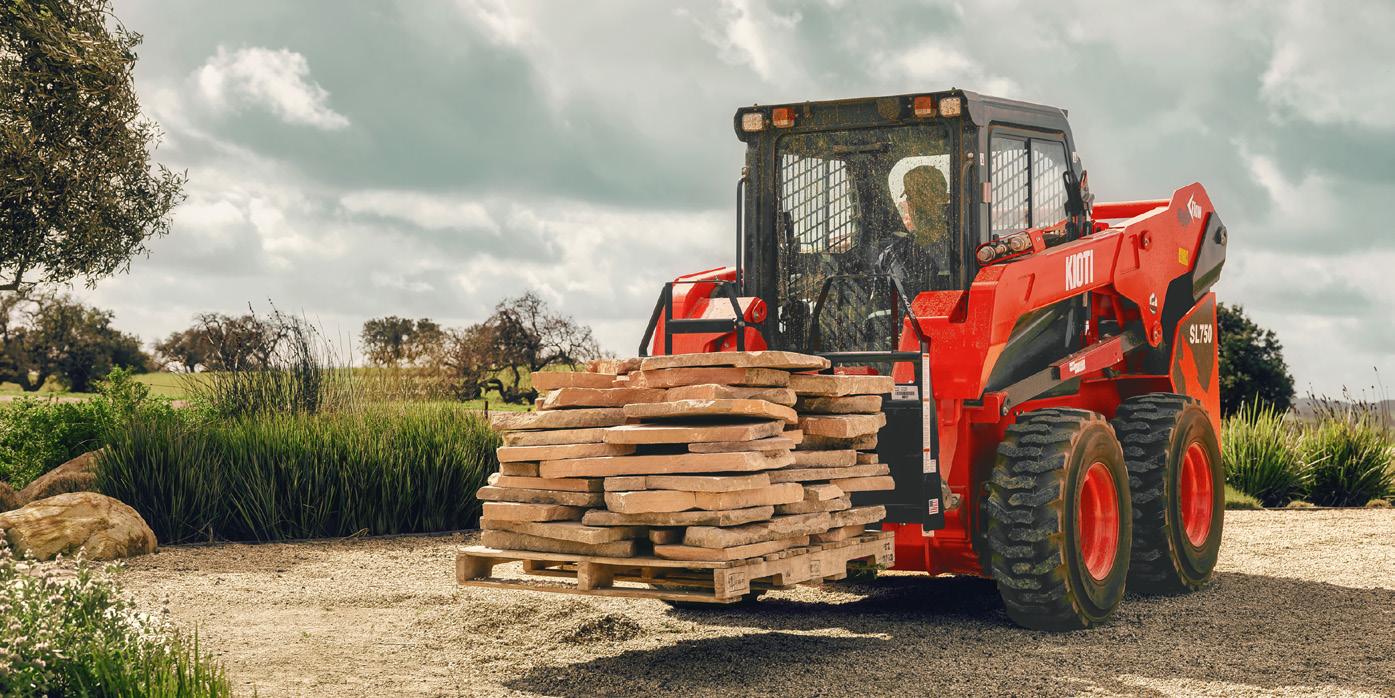
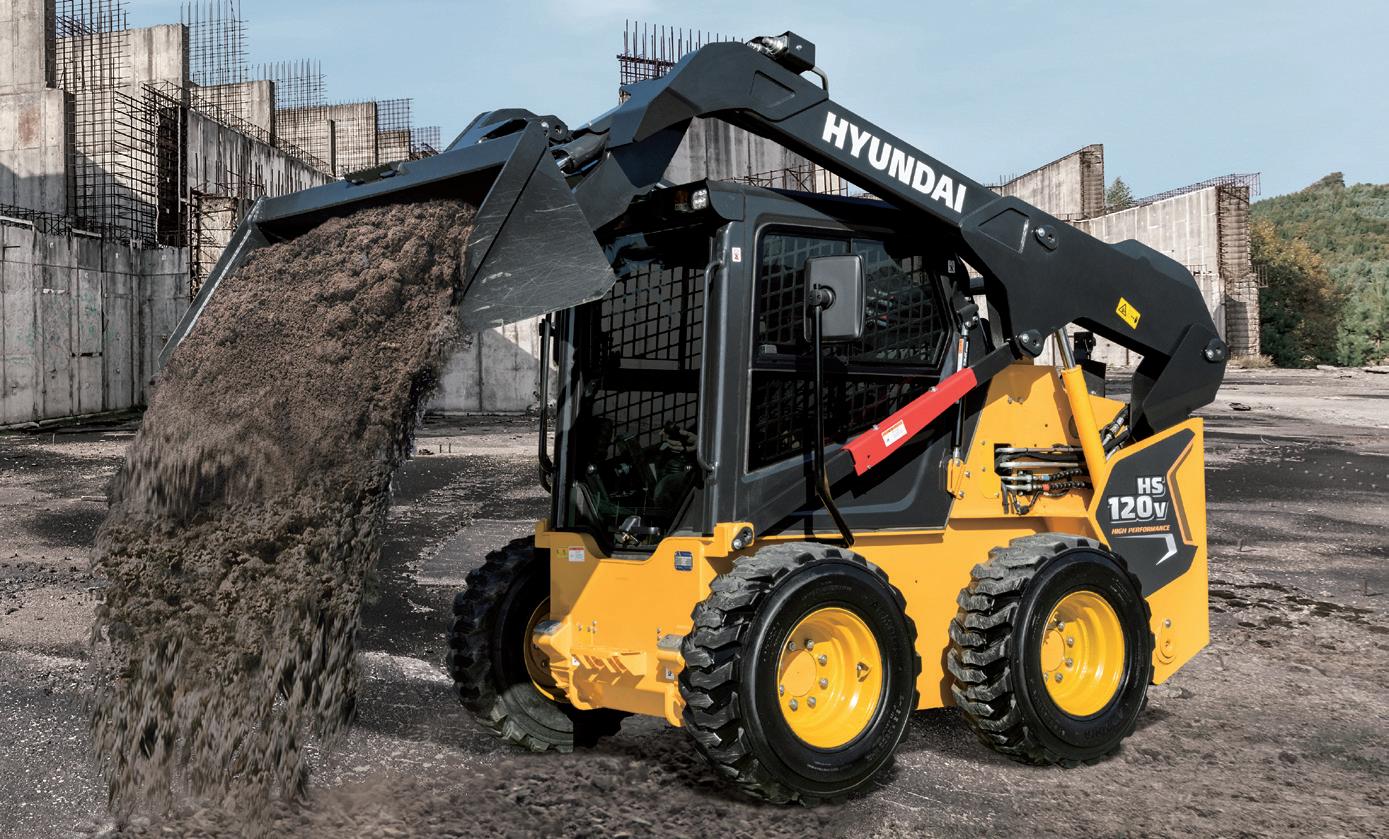
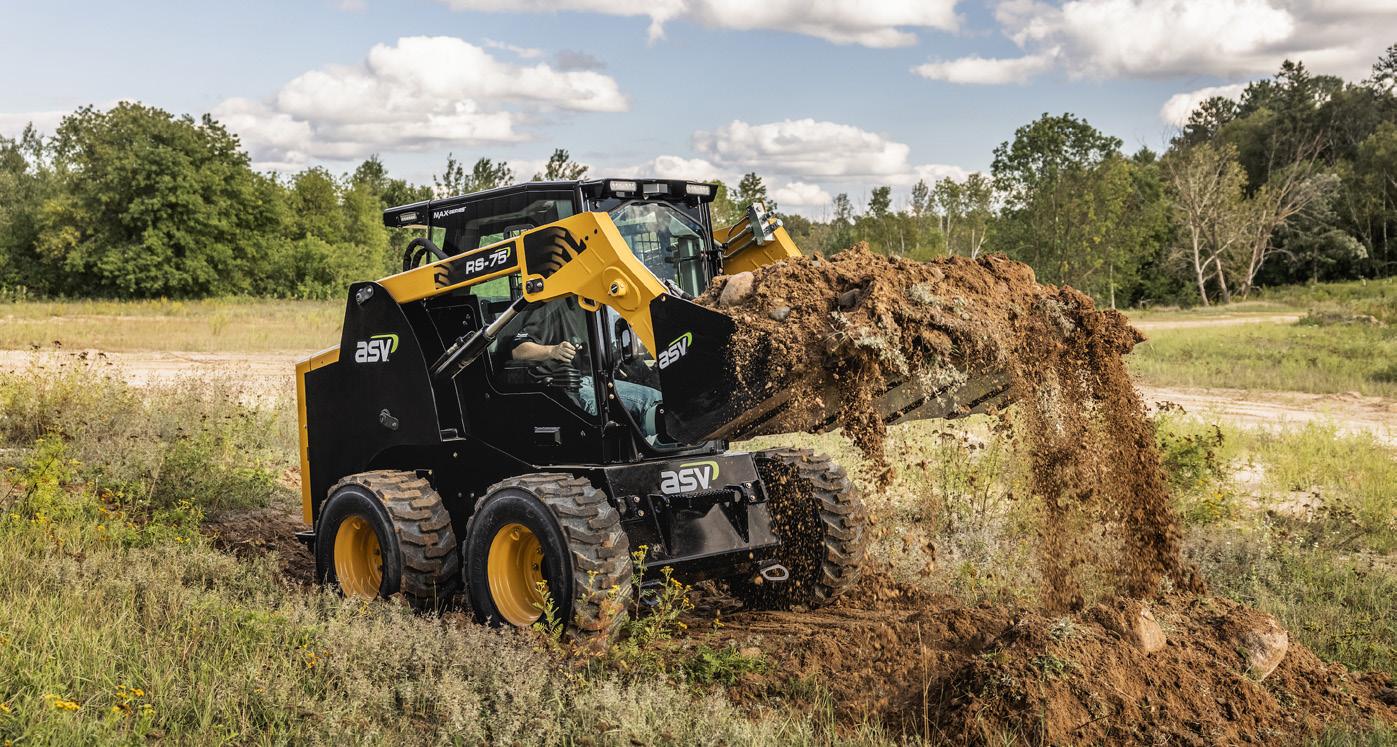
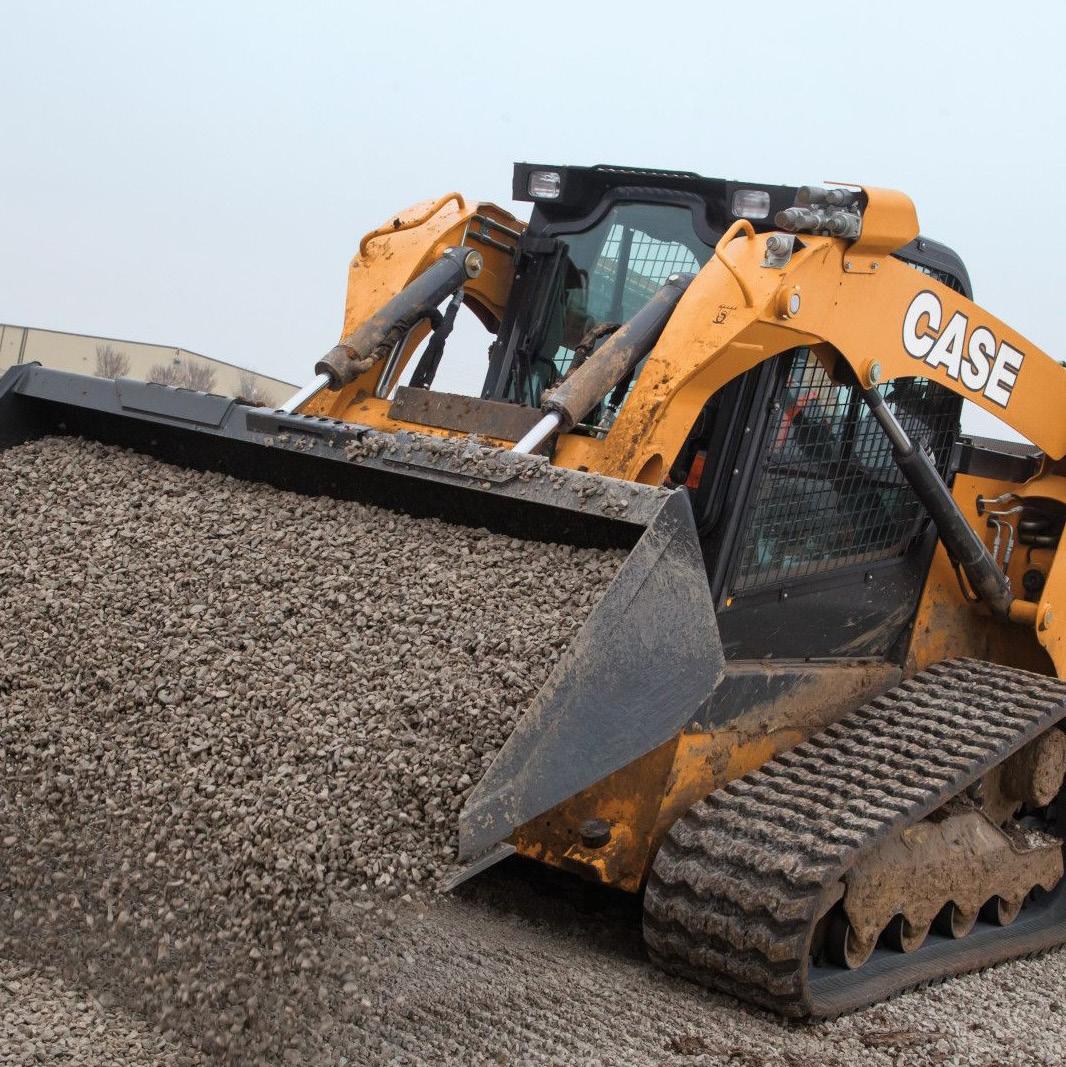
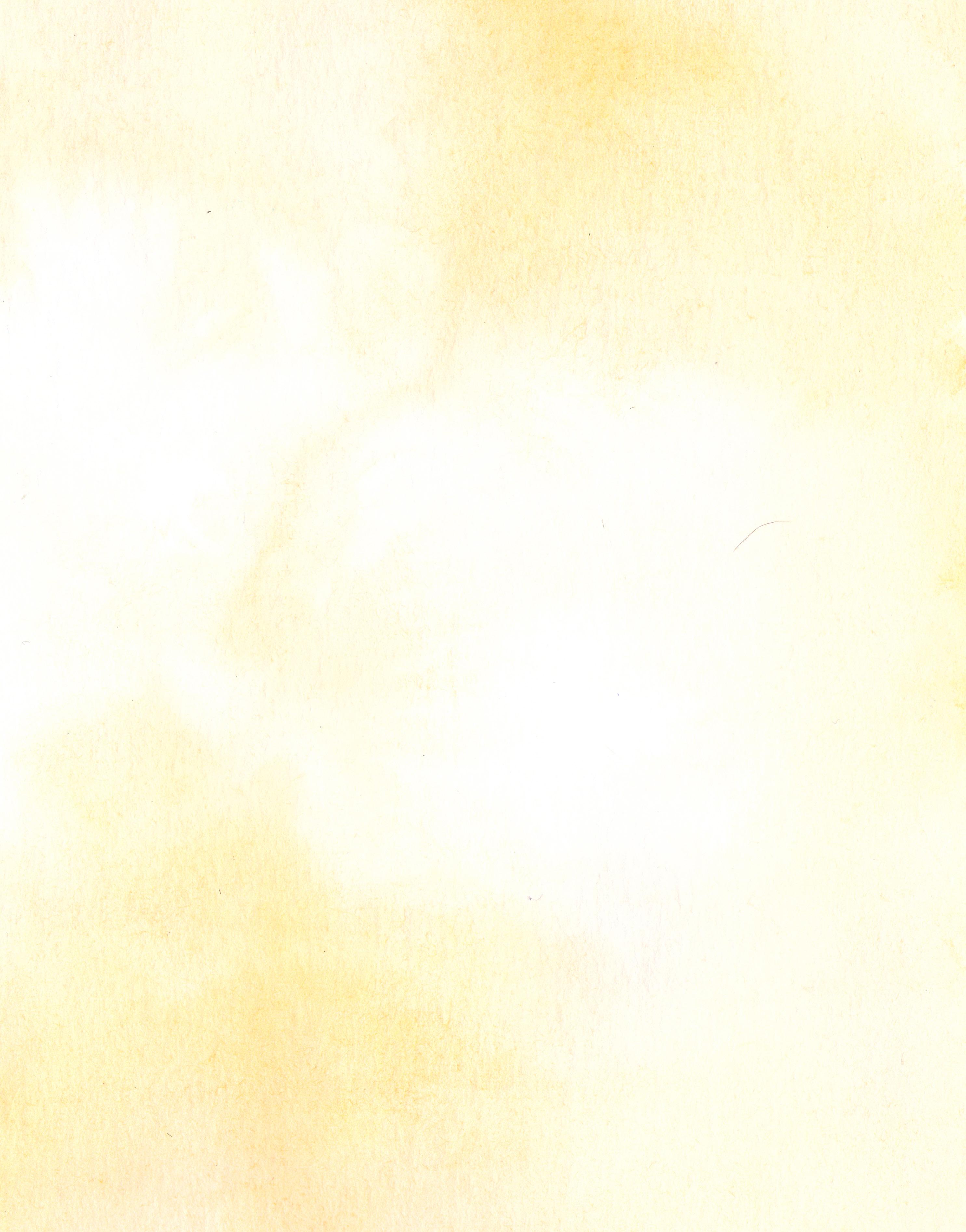
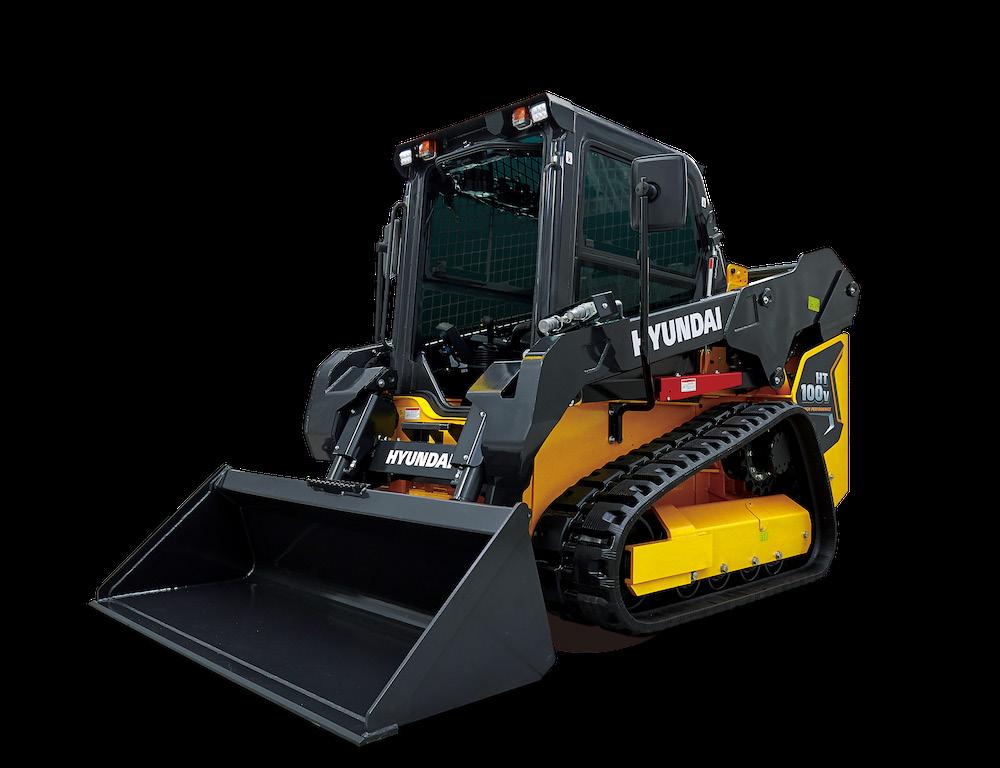
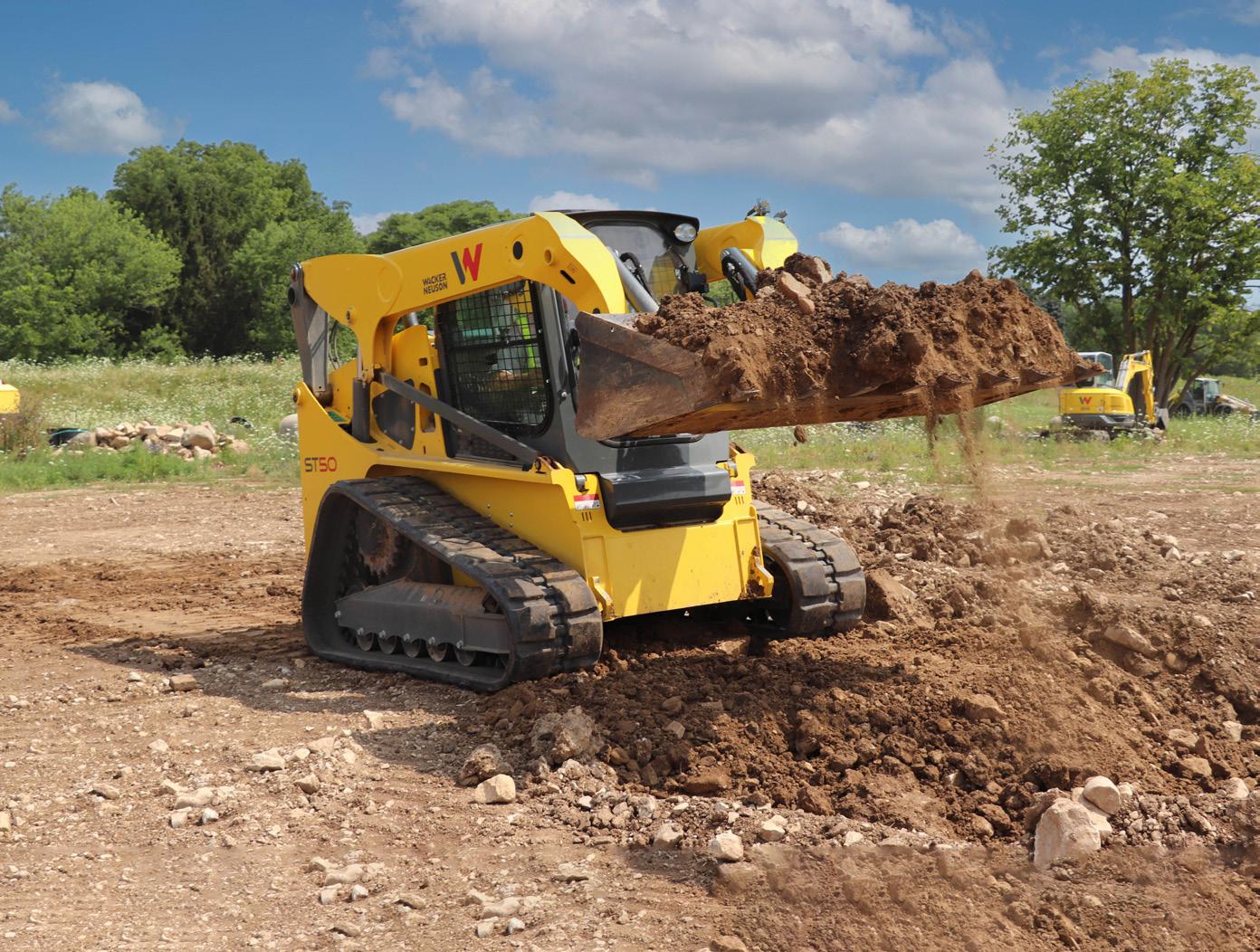

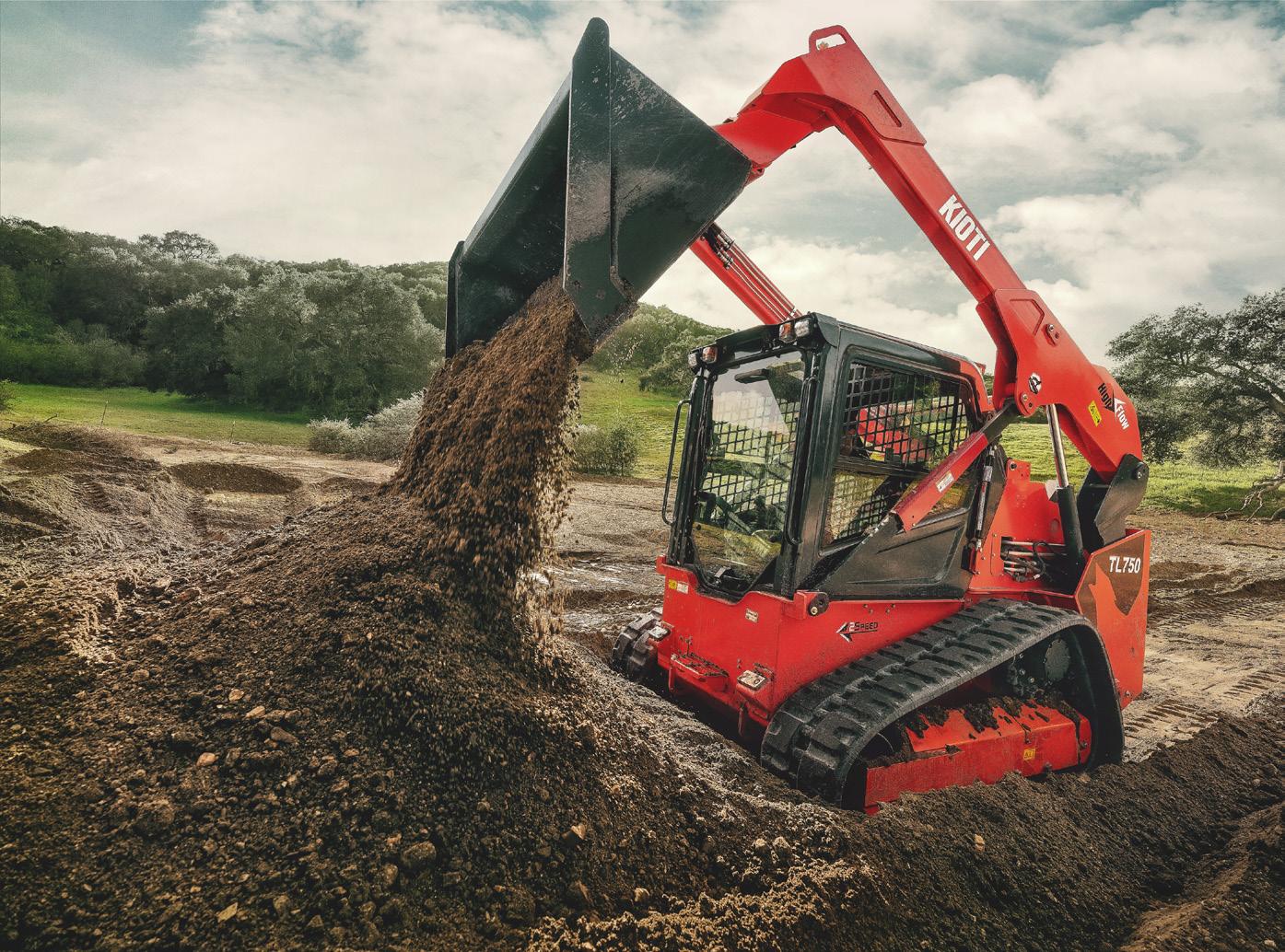
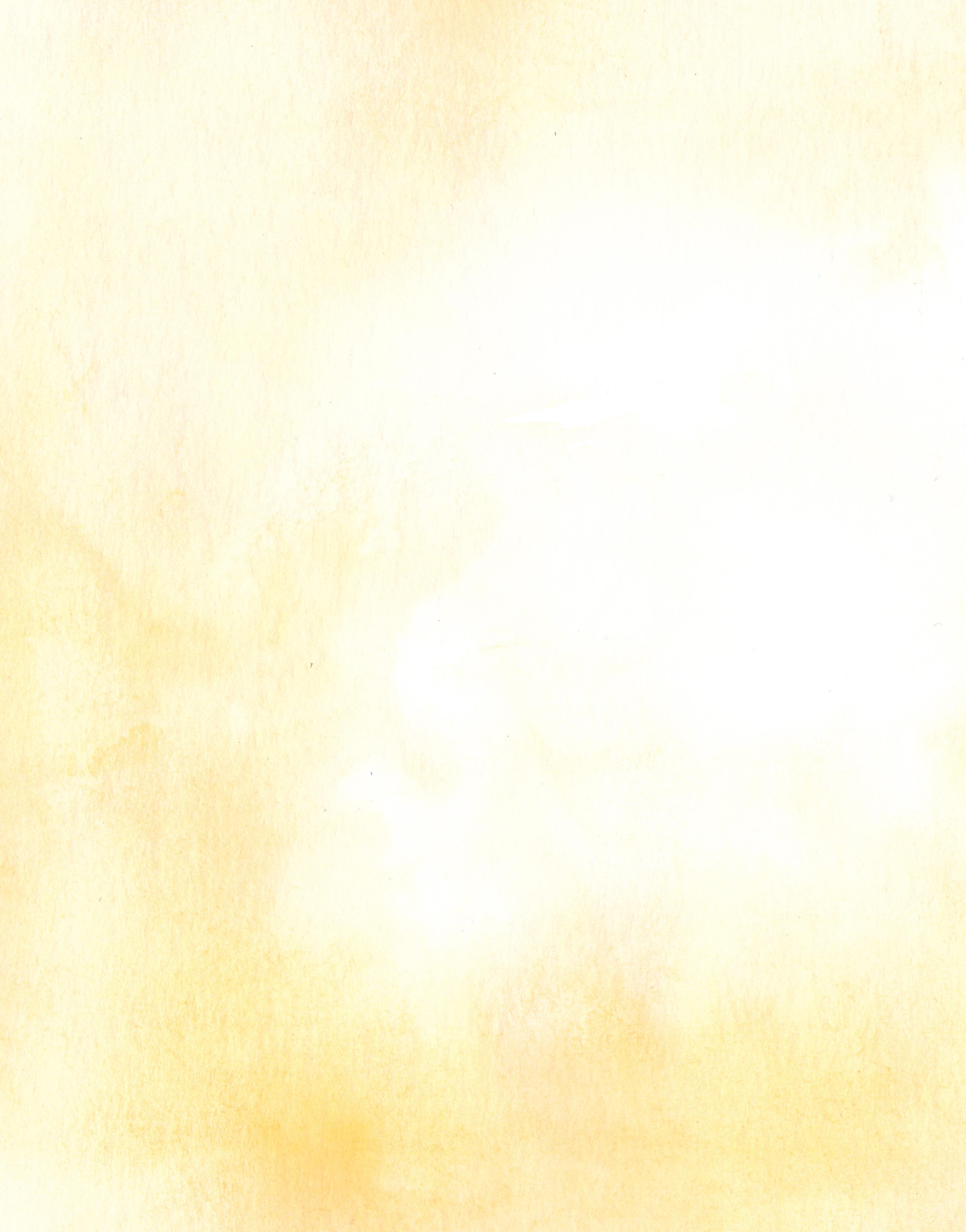
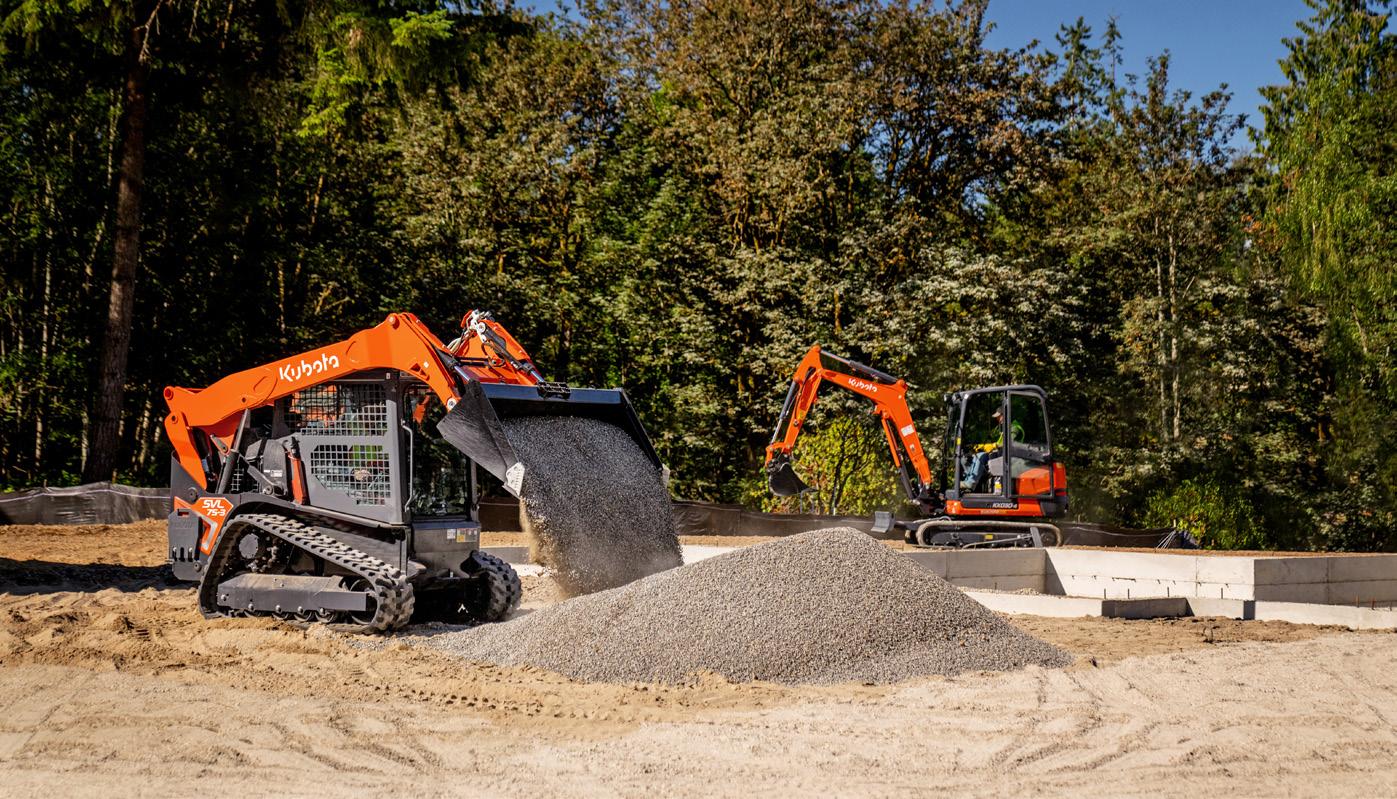
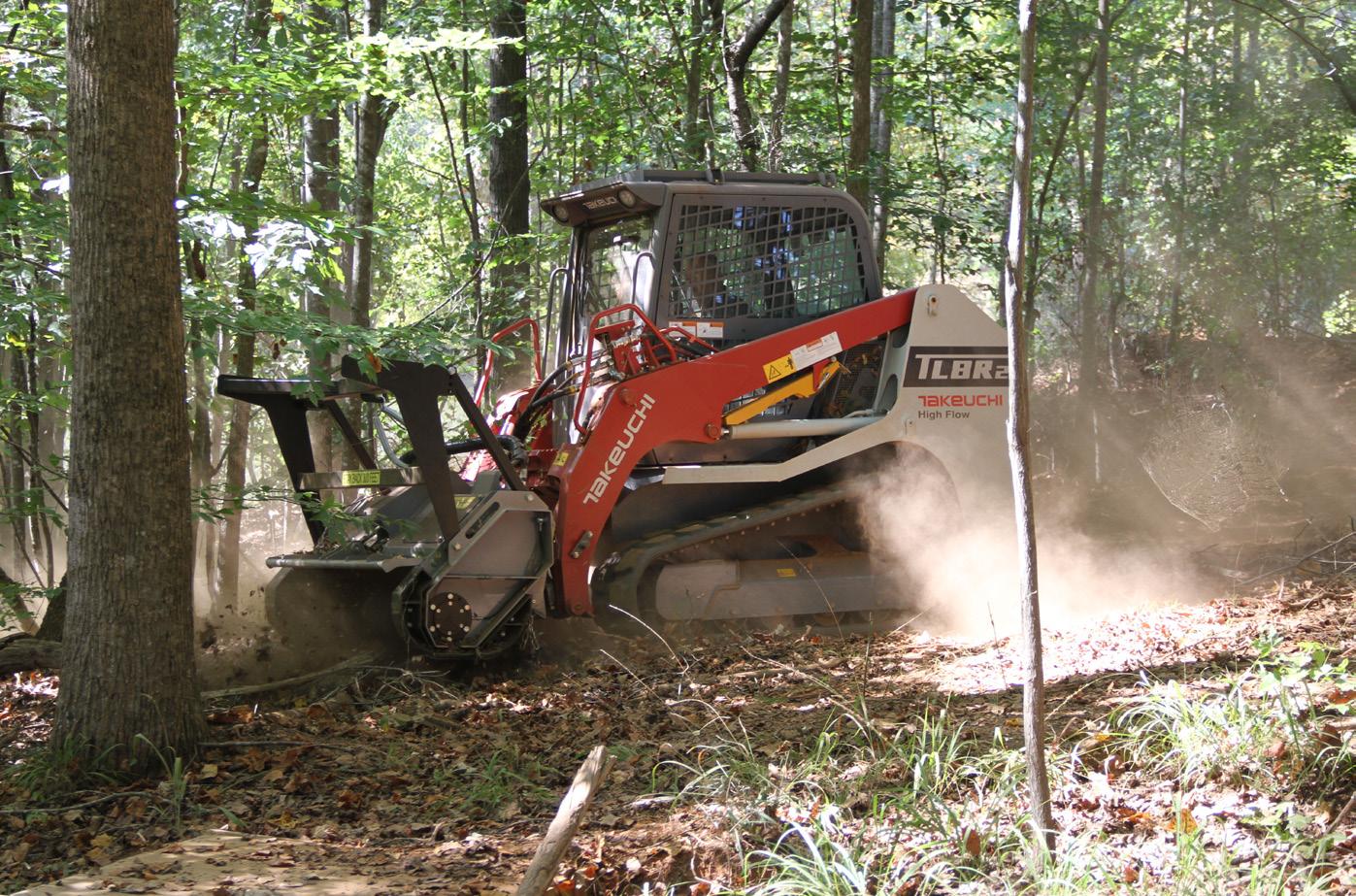
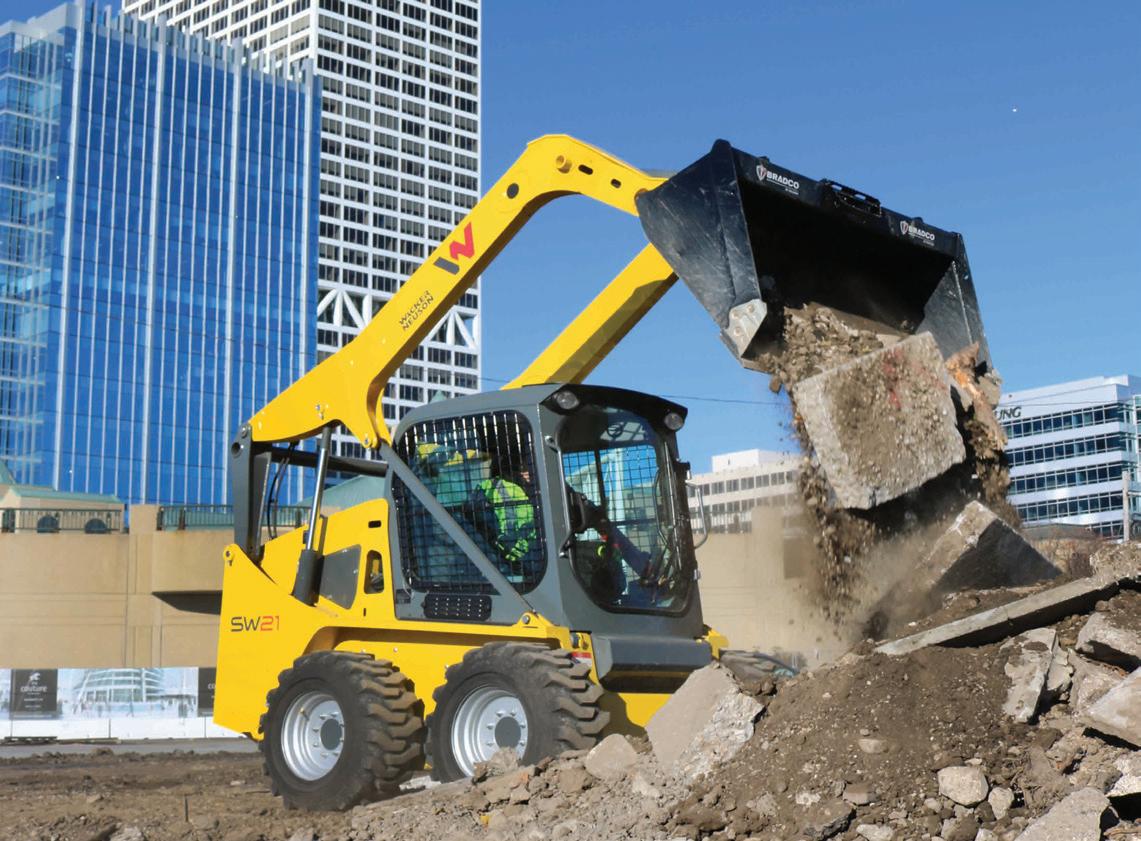
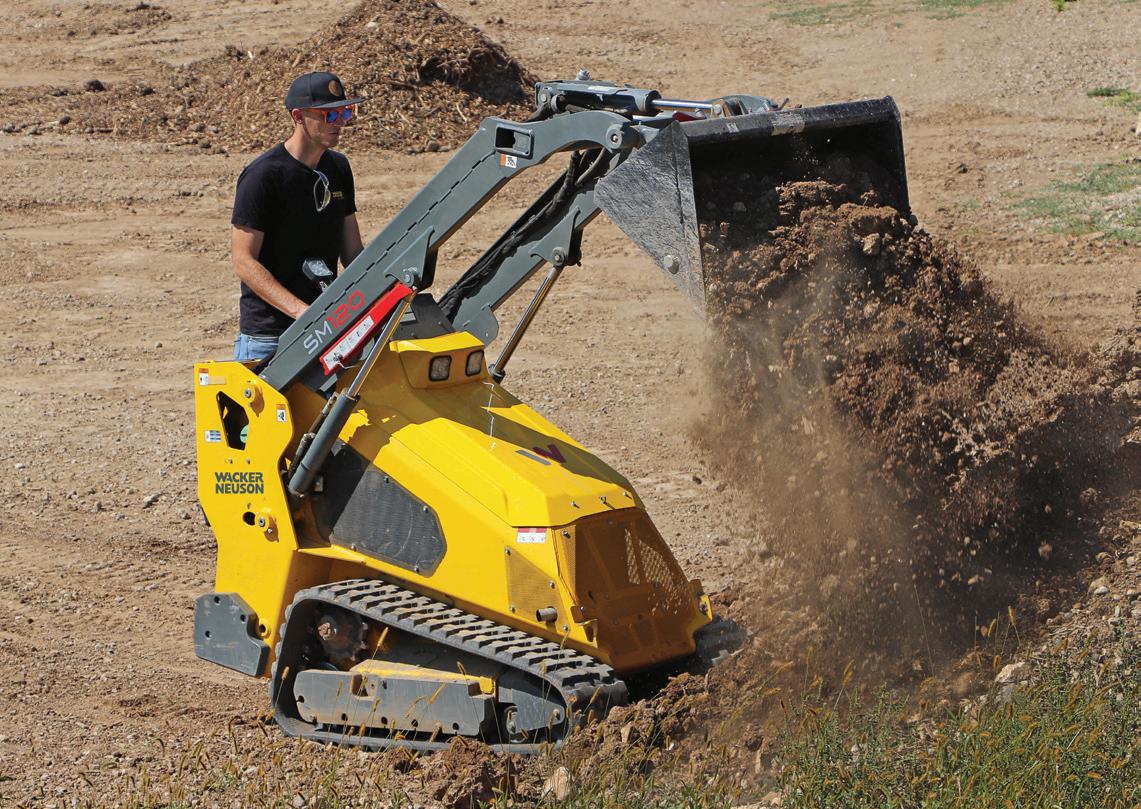
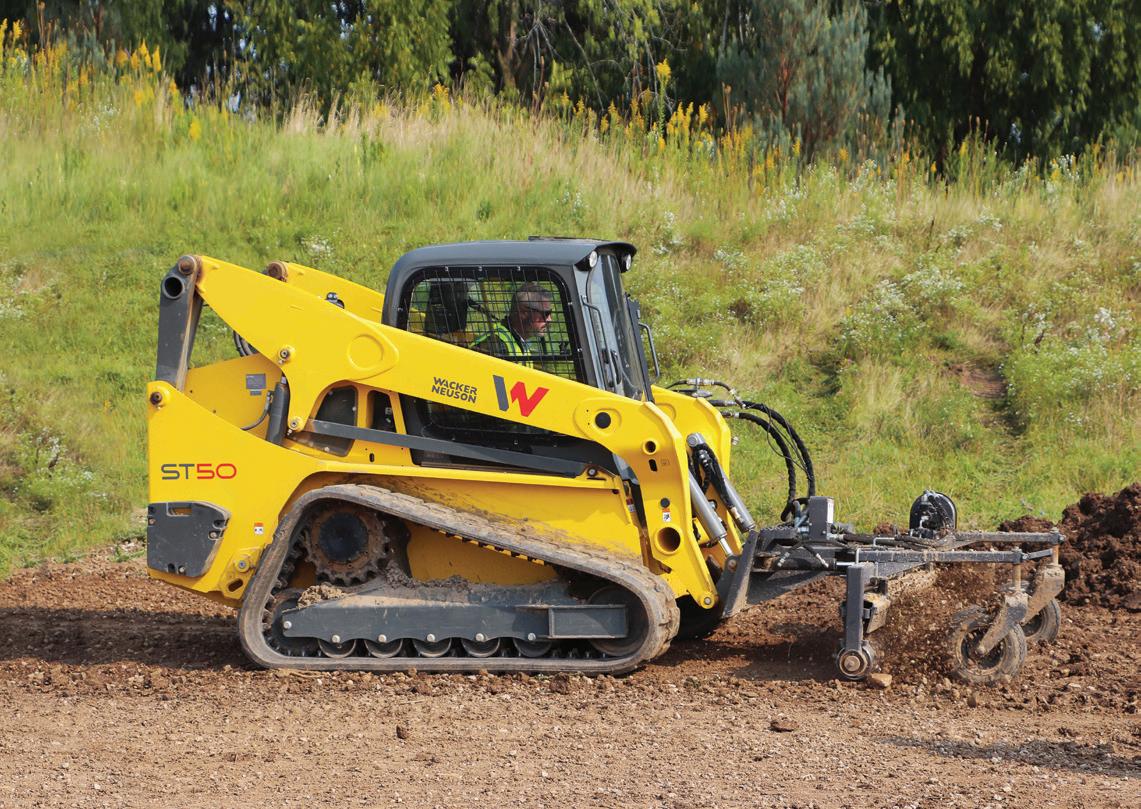
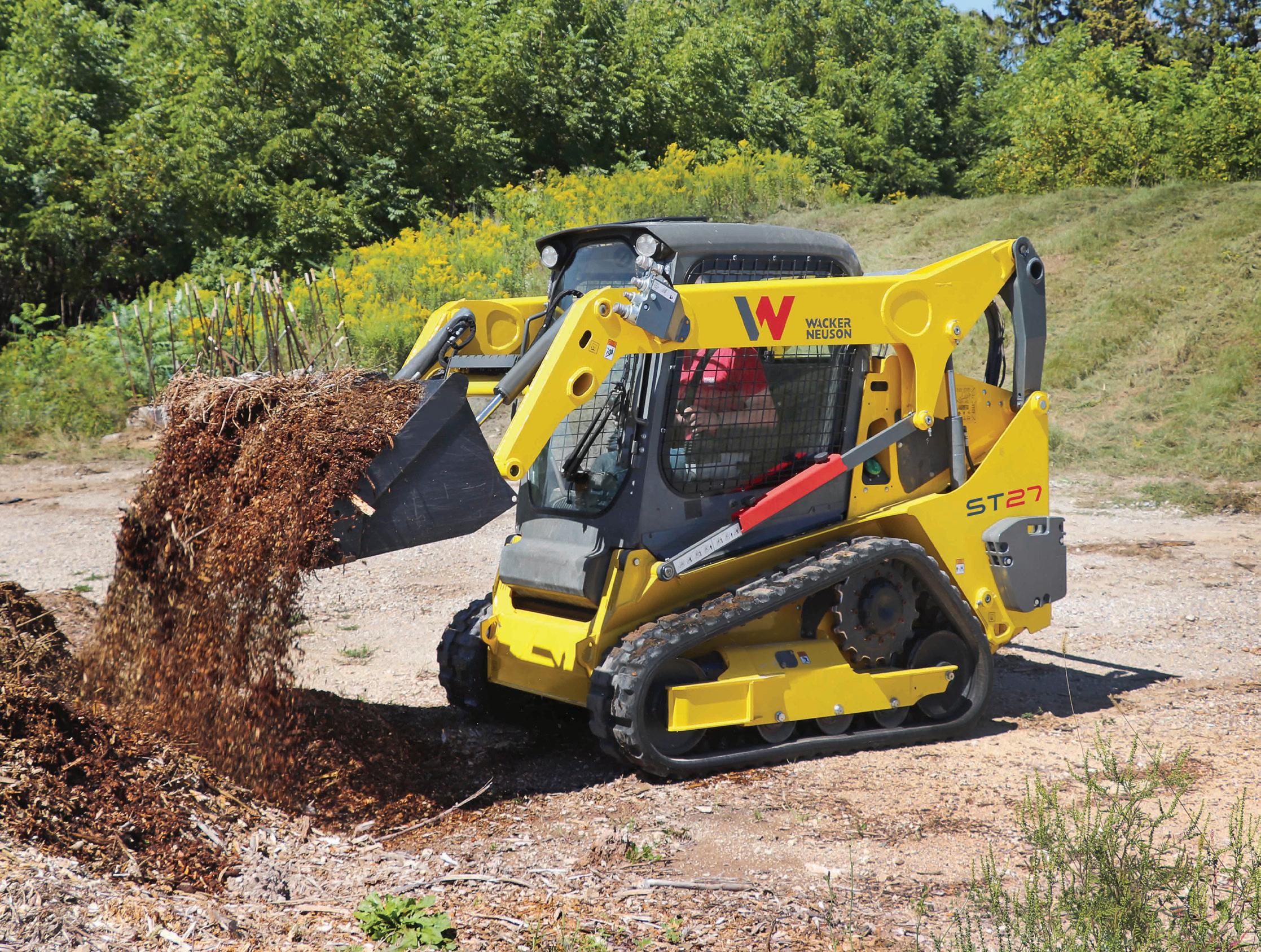
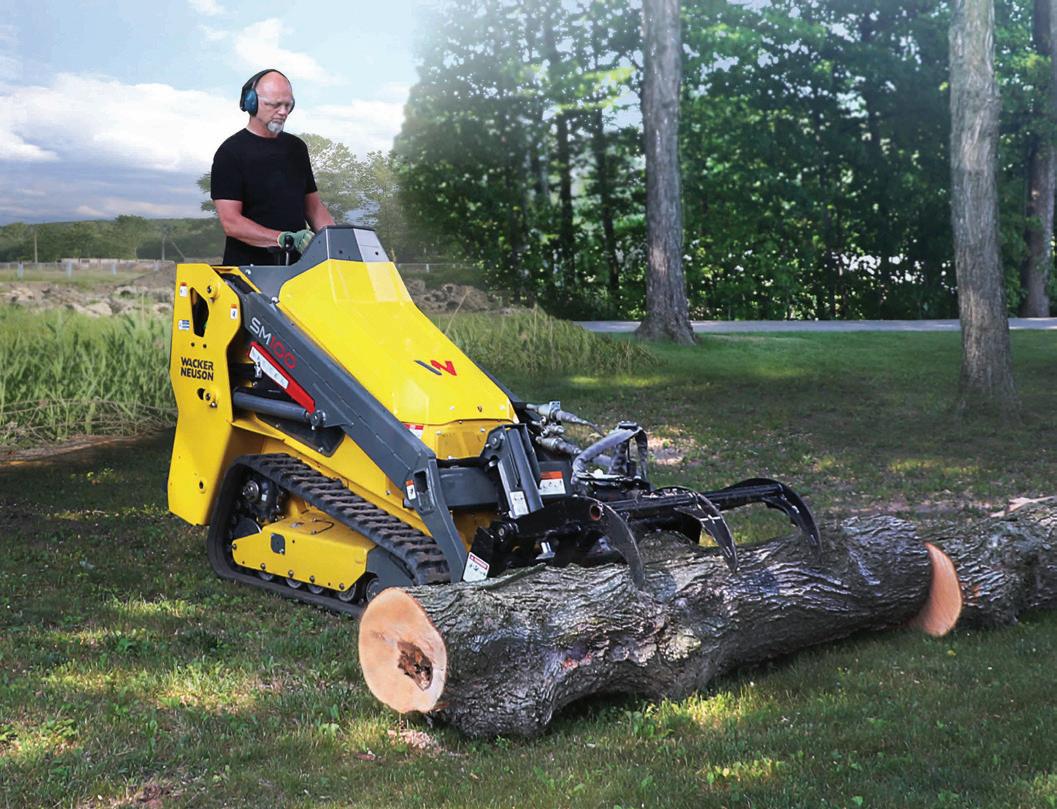
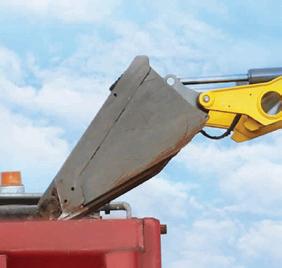
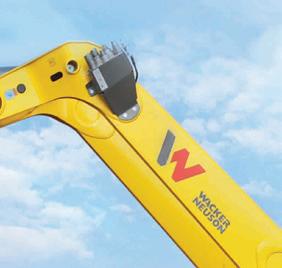
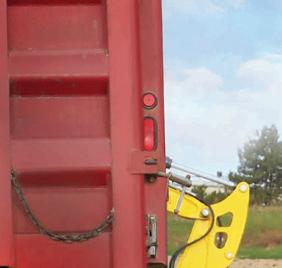
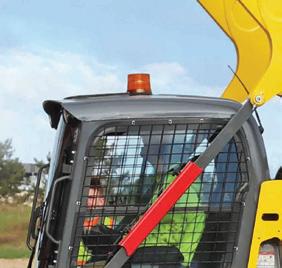
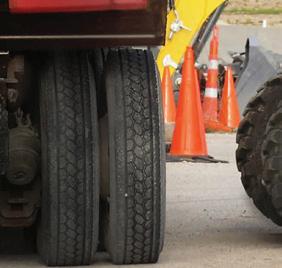
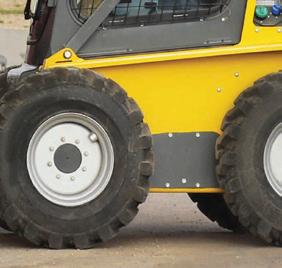
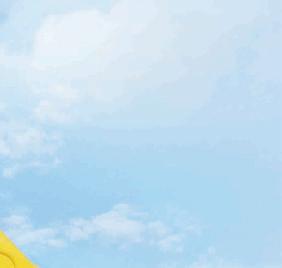
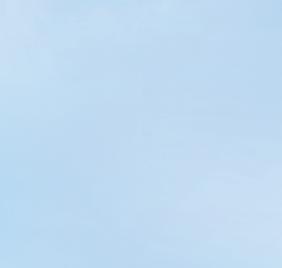

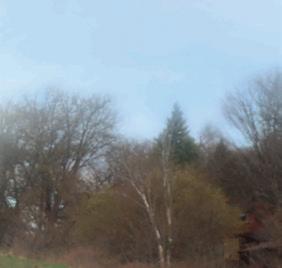
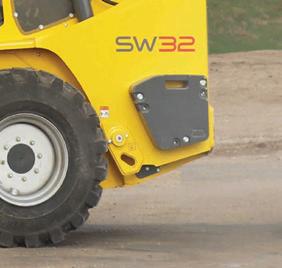

Moving, lifting, digging or loading, Wacker Neuson vertical lift skid steers and compact track loaders are designed to handle tough applications. In addition to high hinge pin heights, these versatile machines also feature the best service accessibility in the industry and comfortable cabs with simple, intuitive operation. For lighter-duty work, as well as commercial or residential landscape projects, Wacker Neuson’s stand-on utility track loaders are the perfect fit in confined spaces.
Put your job site challenges to the test. Contact your local Wacker Neuson dealer or visit us online today.
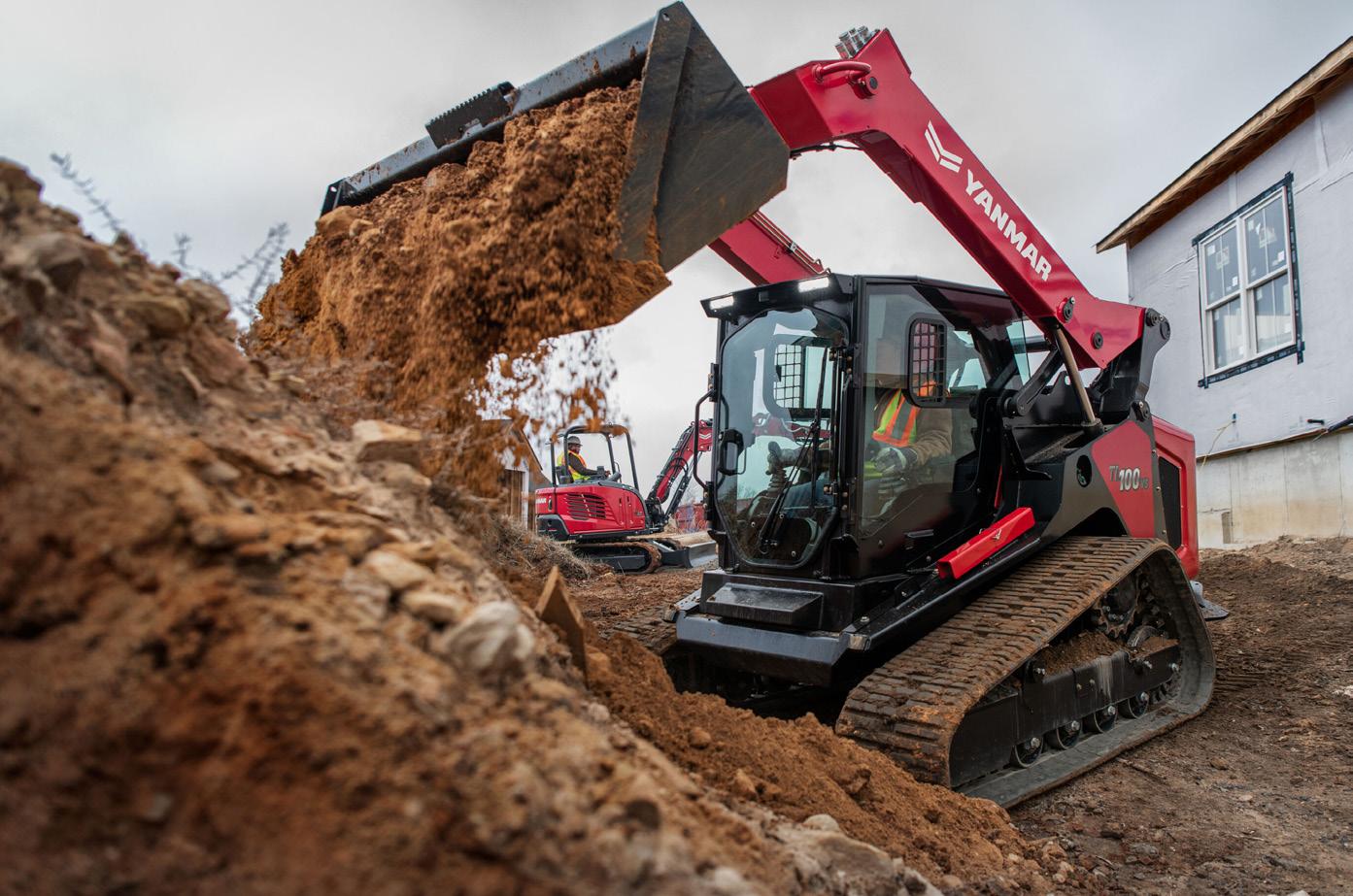
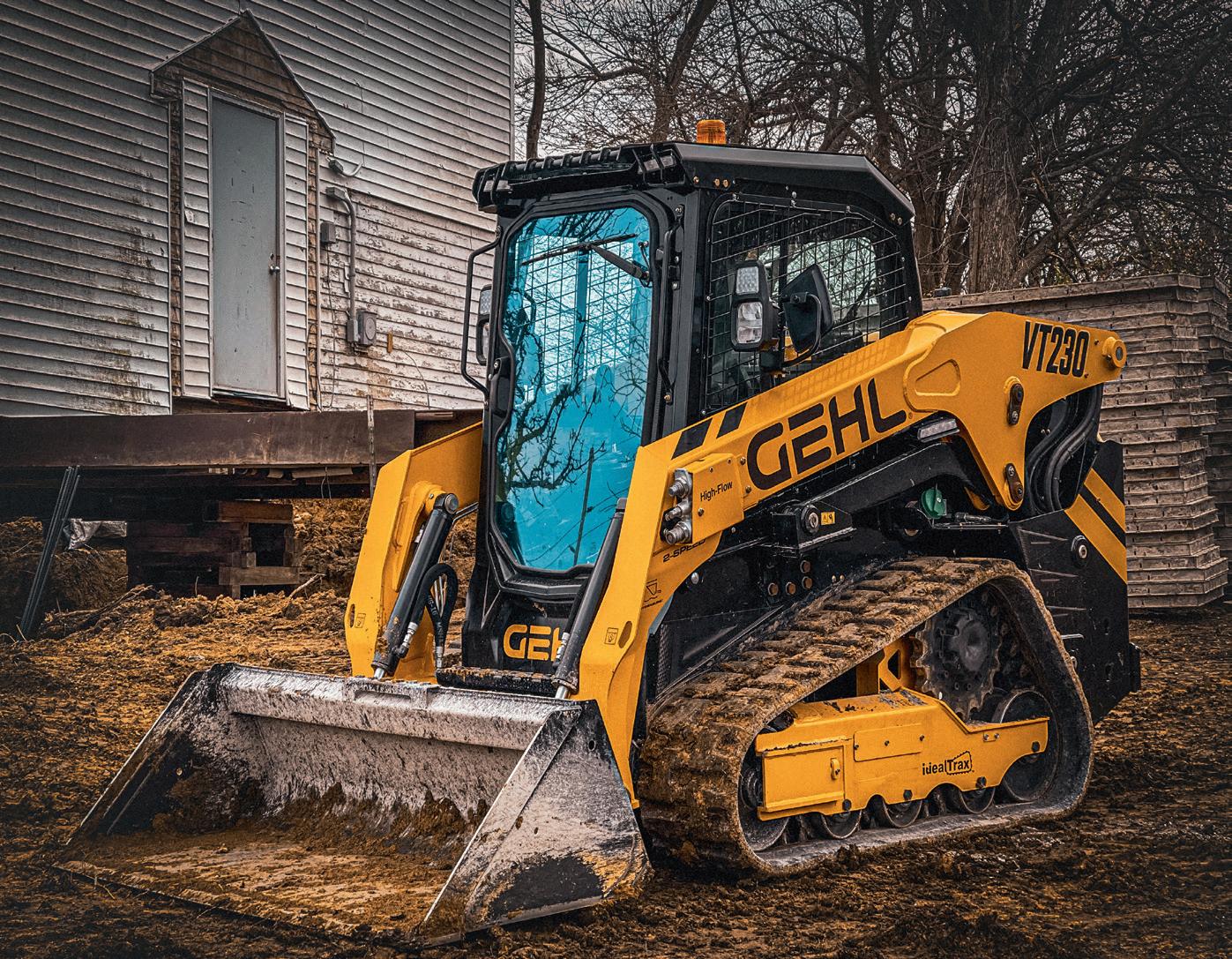
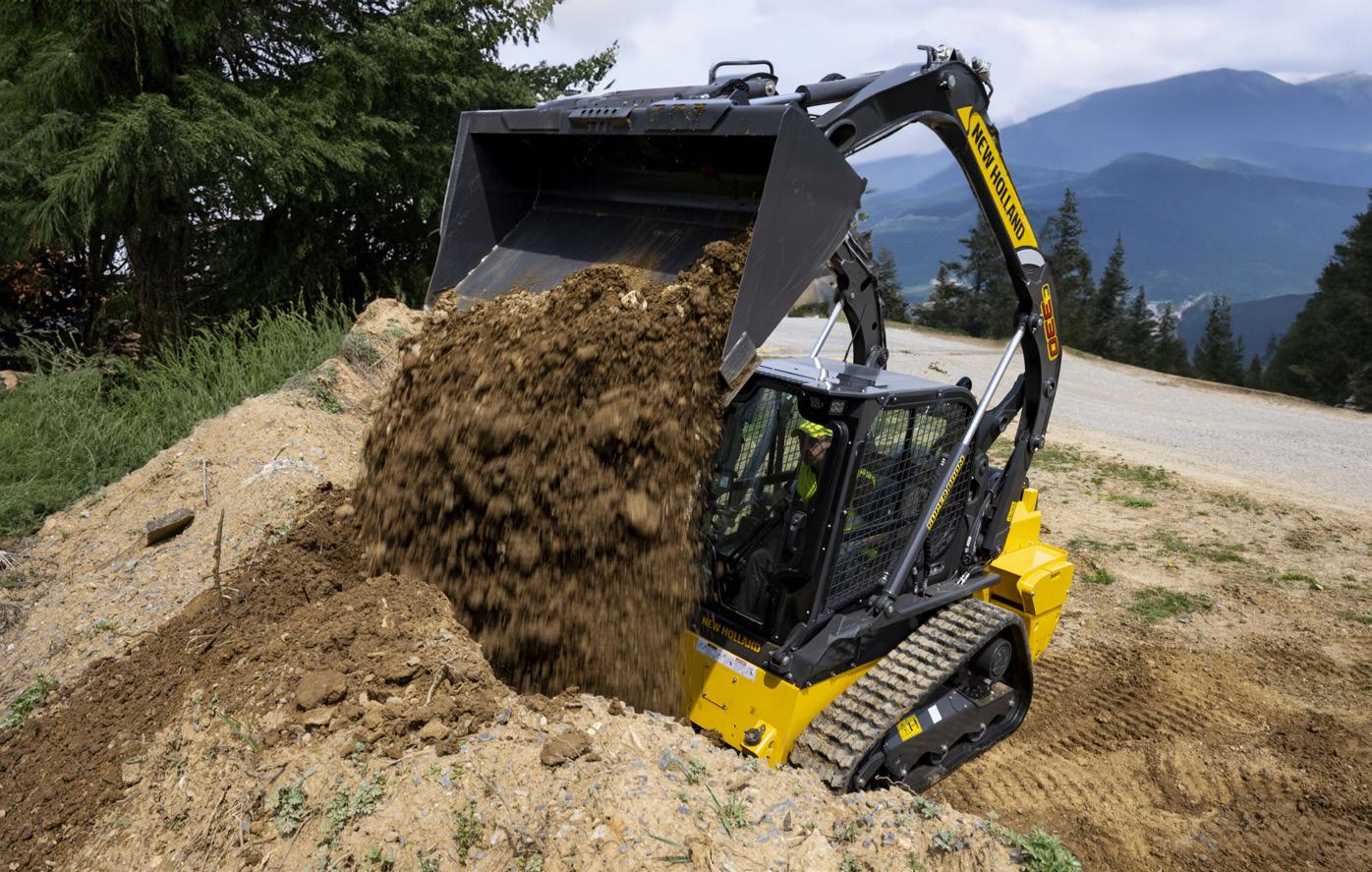
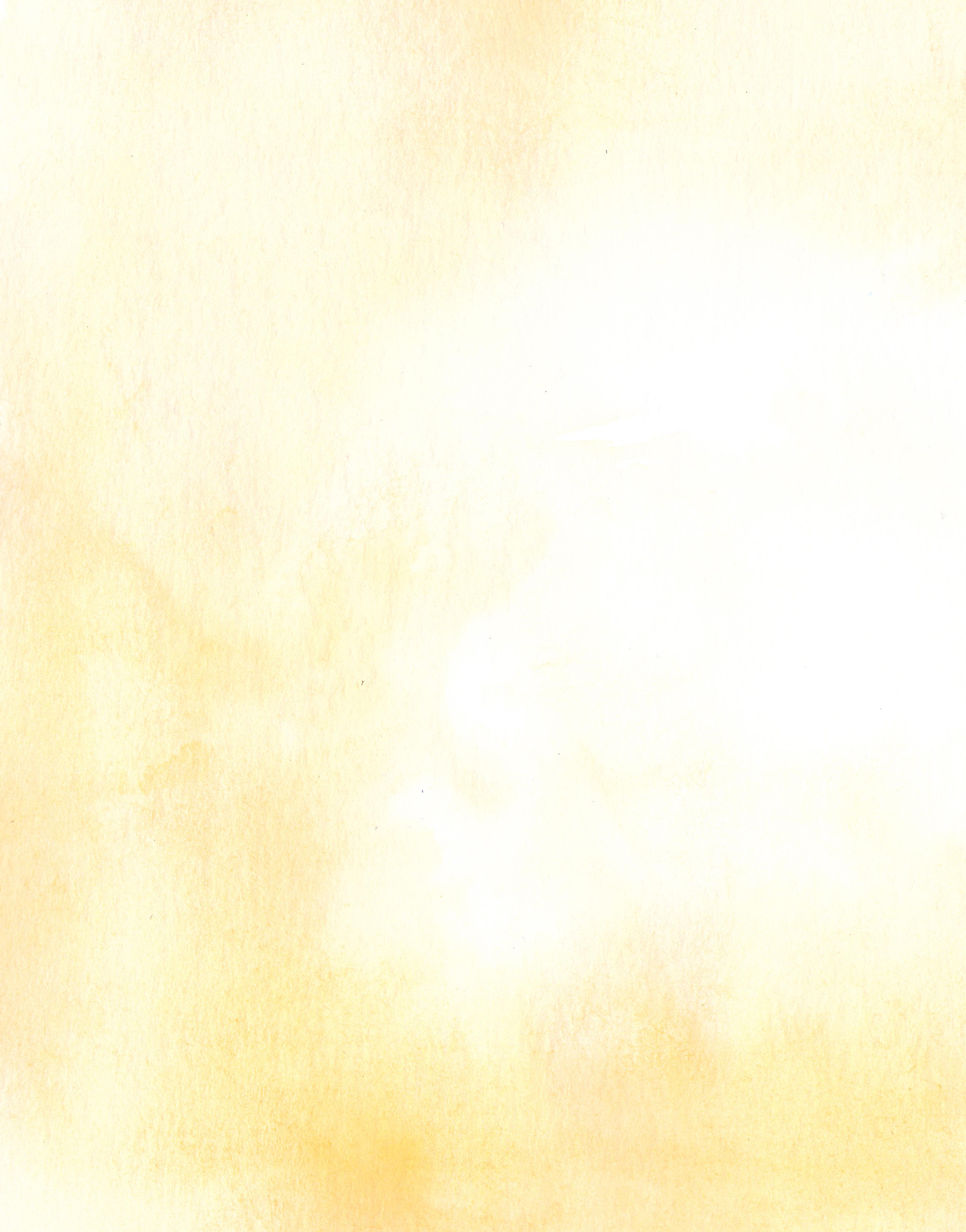
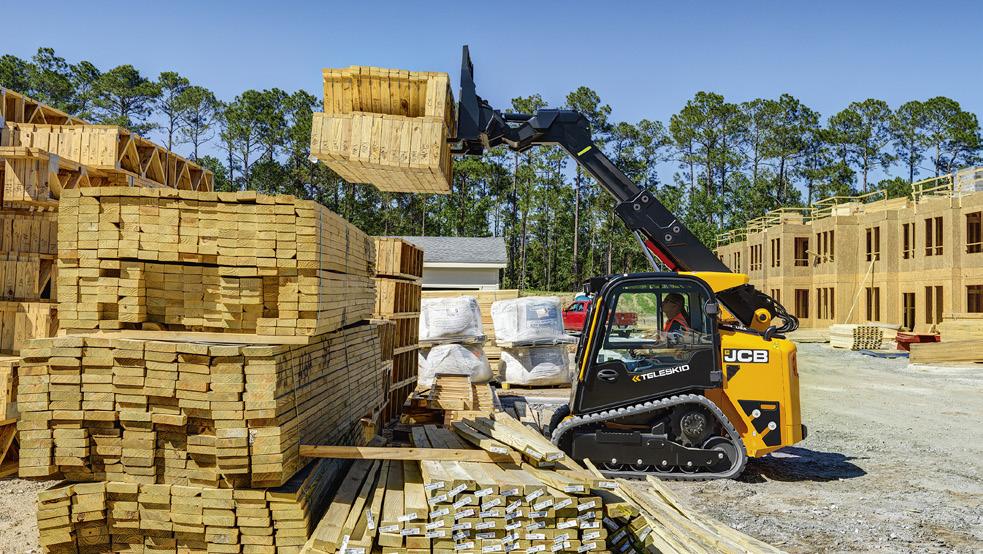
JOHN DEERE
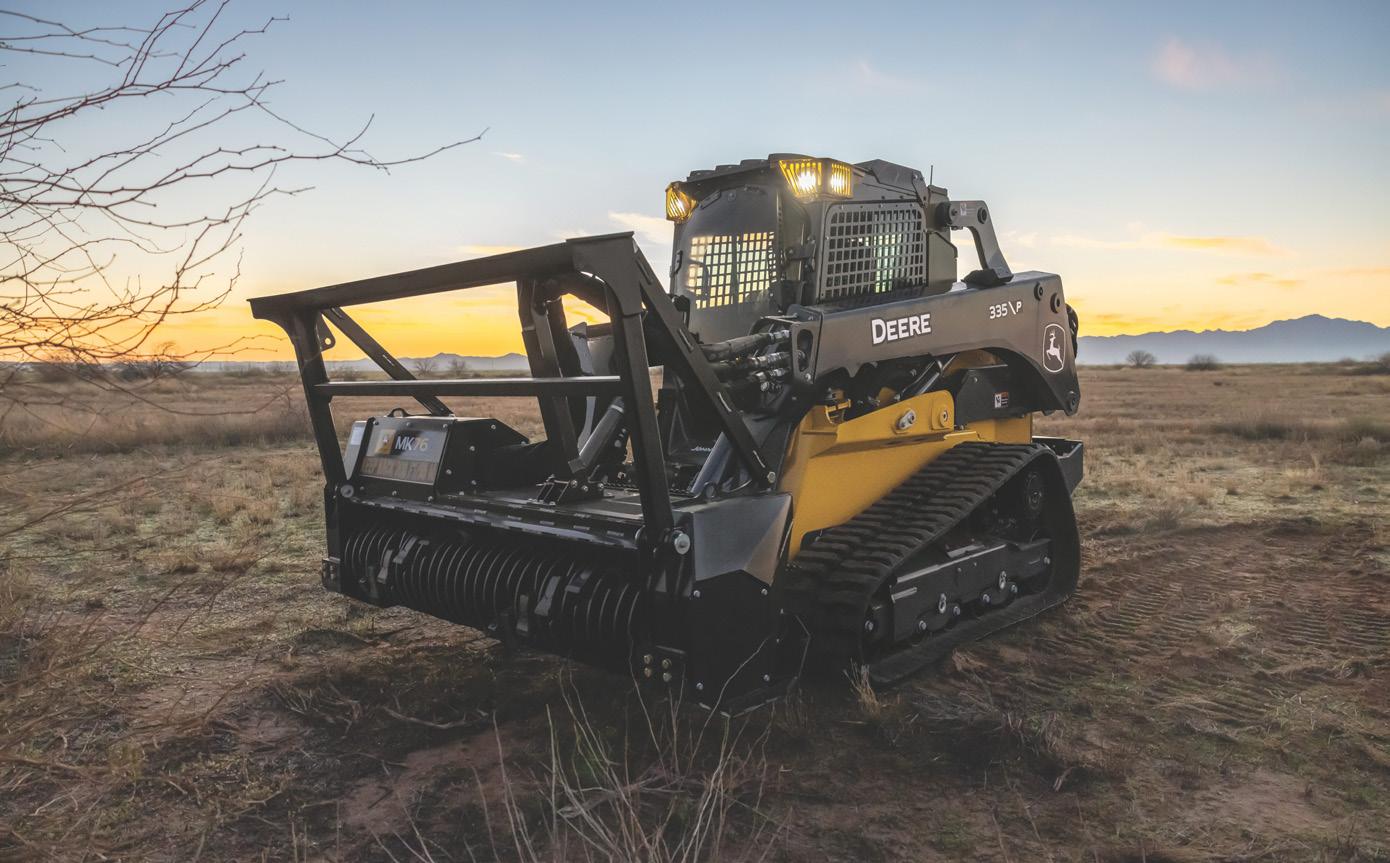
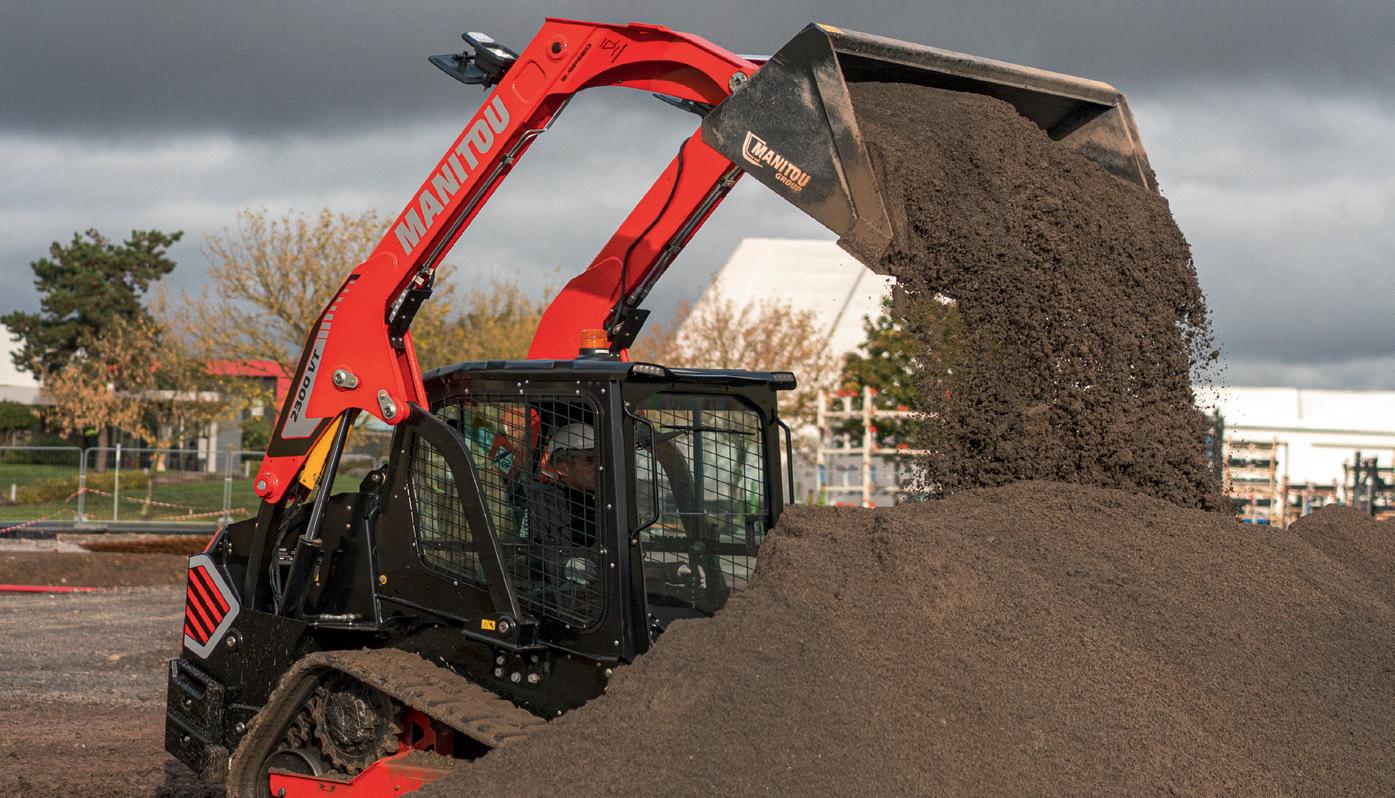
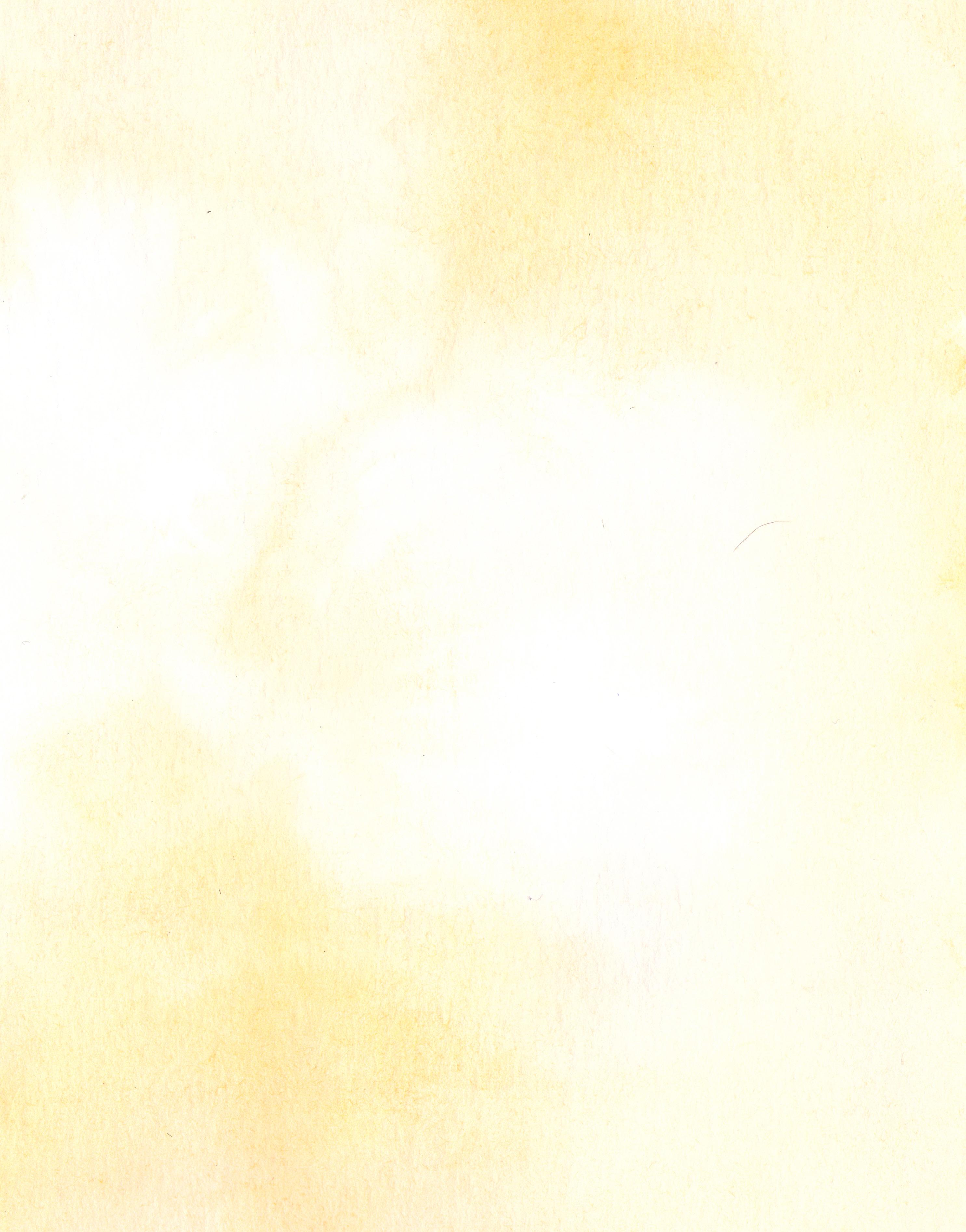


Cutting the Jobsite DOWN TO SIZE
Innovations in mulchers, stump grinders and tiltrotators offer construction contractors more options for site preparation. Here’s how you can optimize your attachment arsenal.
Land and brush clearing has long been a necessary stage of most construction jobs.
For many decades, contractors had few options for site preparation. Contractors could send a crew with chainsaws, bucket trucks and chippers to manually cut down and process brush, or firms could buy or lease dedicated mulching units.
Today, contractors need a more efficient approach to land and brush clearing. The demand for site preparation work continues to increase as more land is being developed while many contractors are finding themselves short of labor.
“Labor is definitely harder to come by since the pandemic, which has led to an increased need in versatility of equipment,” said Ryan Bricker, senior product manager for Fecon.
That’s where land and brush clearing attachments can change the game for contractors. With an attachment like a drum mulcher, “you could put one operator inside the safety of a cab, whether that’s an excavator or skid steer or purposebuilt forestry machine,” Bricker said, “and they can cut, grind and leave the vegetation in place once they’re done.”
The right attachment can reduce contractors’ need for hard-to-find labor. They also replace the need for chainsaws, which pose safety risks, and additional purpose-built land clearing machines like chippers.
Attachment versatility can also make it easier for construction contractors to take on more site preparation work or pursue other business opportunities, such as rightof-way work or fuel reduction.
“A lot of guys want better utilization out of their equipment,” said Michael Noward, regional account manager for Werk-Brau. “They’re going to use their equipment for another type of work, and they might get one of these attachments to make that possible. It’s another way for them to generate more labor dollars on the power unit.”
To meet the growing demand for land and brush clearing attachments, manufacturers have been offering a wider variety of equipment and leveraging innovations in carrier
technology to ensure that the attachments are strong enough to meet contractors’ needs.
“New technologies in the hydraulic motor space really help our attachments,” said Matt Nelson, director of development for Diamond Mowers. “We’re also seeing [that] the carriers—the skid steers and excavators—are able to deliver more power. Now we, the attachment manufacturers, can put that power to the ground and make good use from it.”
CHOOSING THE RIGHT ATTACHMENTS
A high-performing attachment can be a valuable business asset for the contractor who isn’t clearing brush every day. With numerous options, contractors will want to do their homework when determining the appropriate attachments to add to their arsenal. Several key considerations can help you make your purchase decision:
˜ Customer Expectations: What is your customer’s end goal for the project? How the land must look when the job is complete will determine if and how the brush needs to be processed. “If the land [will] be turned into parking lot, it doesn’t really matter what the finish looks like,” said Nelson. “We don’t need super fine mulch. We don’t care about skid steer tracks because it’s going to get dozed anyhow.” However, real estate developers will need contractors to clear the land to match their vision for the property, which could mean preparing for a clean lawn or keeping certain trees.
˜ Jobsite Environment: What the operator may encounter on the jobsite will influence the attachment selection. For starters, the size of the brush or trees that need to be removed will inform whether a brush cutter or mulcher will be most effective. However, the type of trees matters less than you would like. “Everybody thinks they have the biggest, hardest trees. Yes, it takes a little longer to grind a hickory than it does a pine tree.
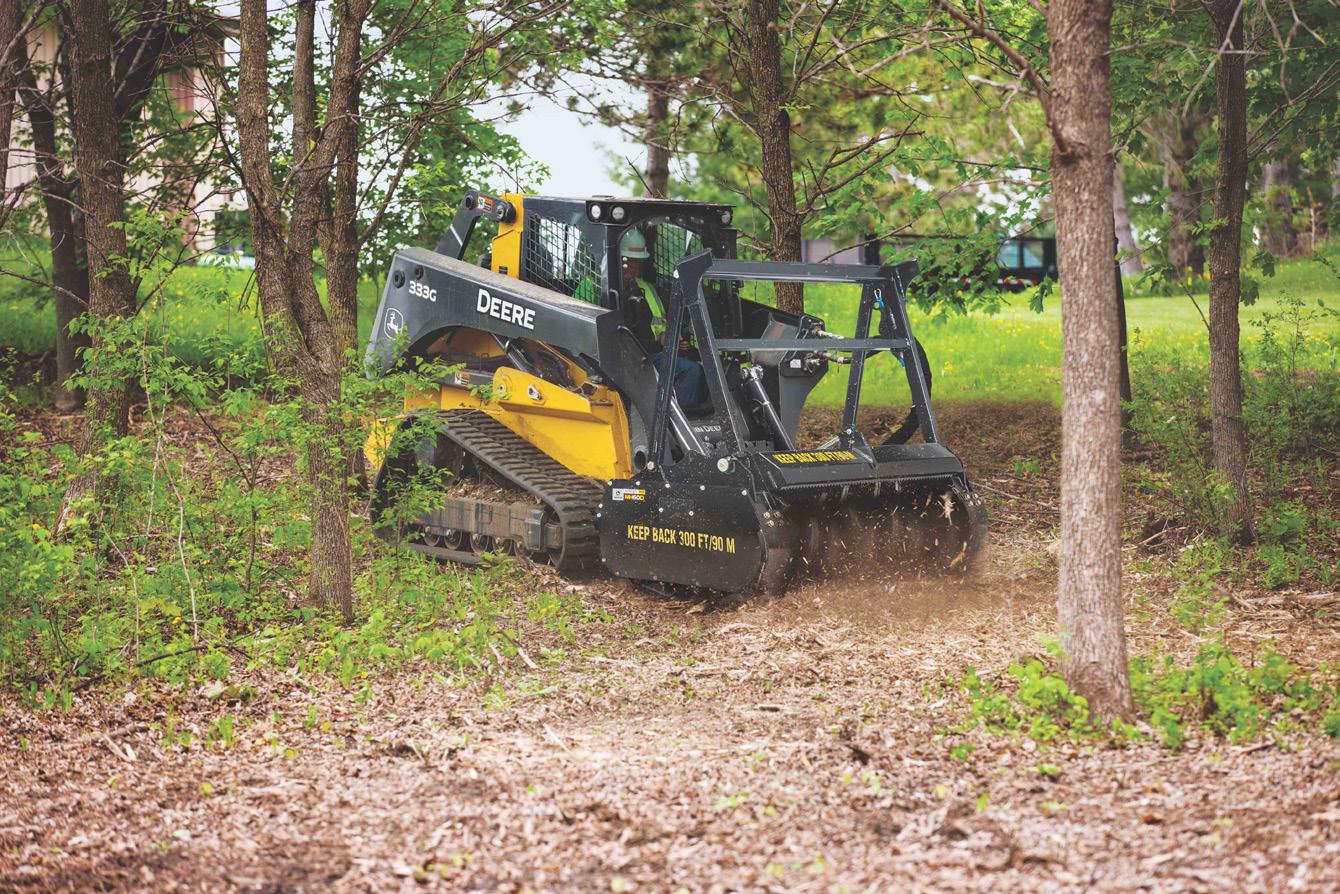
The MH60D Mulching Head for skid steers and compact track loaders features a redesigned mulching chamber and efficiently shreds underbrush and woody materials into beneficial mulch in minutes.
What matters far more is what the terrain under the trees looks like,” said Nelson. “How much ground engagement do you need to expect? By far, the amount of rocks you’re going to contend with is a bigger contributor to the overall business proposition.”
˜ Carrier Compatibility: Once you have the type of attachment narrowed down, your next question is whether the attachment is compatible with the compact track loader (CTL), skid steer or excavator you already own. This includes confirming factors such as lift capacity, sizing and whether hydraulic flows will match.
˜ Cost and Efficiency: Contractors will need to justify the expense of the purchase, as well as the total cost of ownership. For example, when considering a mulcher, contractors will need to budget for teeth and consider the additional wear that mulching can have on undercarriages. Contractors will also want to project the attachment’s impact on operational efficiency. Will it take a while to get replacement parts? How easy is it to switch out the attachment? How quickly will the productivity that the attachment contributes pay off the investment?
CUT & SHREDDED: ROTARY CUTTERS, MULCHERS & GRINDERS
Clearing brush is often the first step in preparing a site for construction. Contractors who need to remove and process brush have several tried-andtrue options.
Rotary Cutters
Rotary cutters, also called rotary mowers or brush cutters, will cut through grass, weeds and smaller
brush material. While effective at tackling undergrowth and stockier, woody plants, these deck-style mowers don’t break down or process the material well.
“They are going to be your lowest cost, both to buy and ... to maintain and operate, so pretty low barrier of entry,” said Nelson. “For contractors who don’t clear brush [daily], they can be really interesting, and they’ll ... quickly cover a lot of ground.”
For intermittent users, Diamond Mowers offers the Brush Cutter Pro, which features two steel blades at a 72-inch cutting width and can handle trees up to 5 inches in diameter. The Brush Cutter Pro X, which comes in 60-inch, 72-inch and 84-inch cutting widths, offers the durability to match the demands of constant, daily use. It features Diamond Mowers’ proprietary Tri-Hex Disc, which can cut brush up to 10 inches in diameter.
Both models are compatible with skid steers and CTLs and feature hydraulic motors sized for enhanced blade performance and safe handling at every flow level.
Disc Mulchers
Disc mulchers feature a flat, spinning disk and are ideal for large land clearing operations where thicker brush and vegetation need to be removed quickly, such as right-of-way clearing for roads or pipeline work.
“Disc mulchers are ... fast and efficient at cutting trees down and doing invasive species eradication,” said Bricker. Fecon recently expanded its lineup of disc mulchers with the release of Disc Hawk. The disc mulcher is built for 75-hp to 132-hp skid steers and CTLs that operate with 30 gallons per minute (gpm) to 50 gpm of auxiliary hydraulic flow.
With a working width of 60 inches, the machine can cut down trees up to
When considering a mulcher, contractors will need to budget for teeth and consider the additional wear mulching can have on undercarriages.
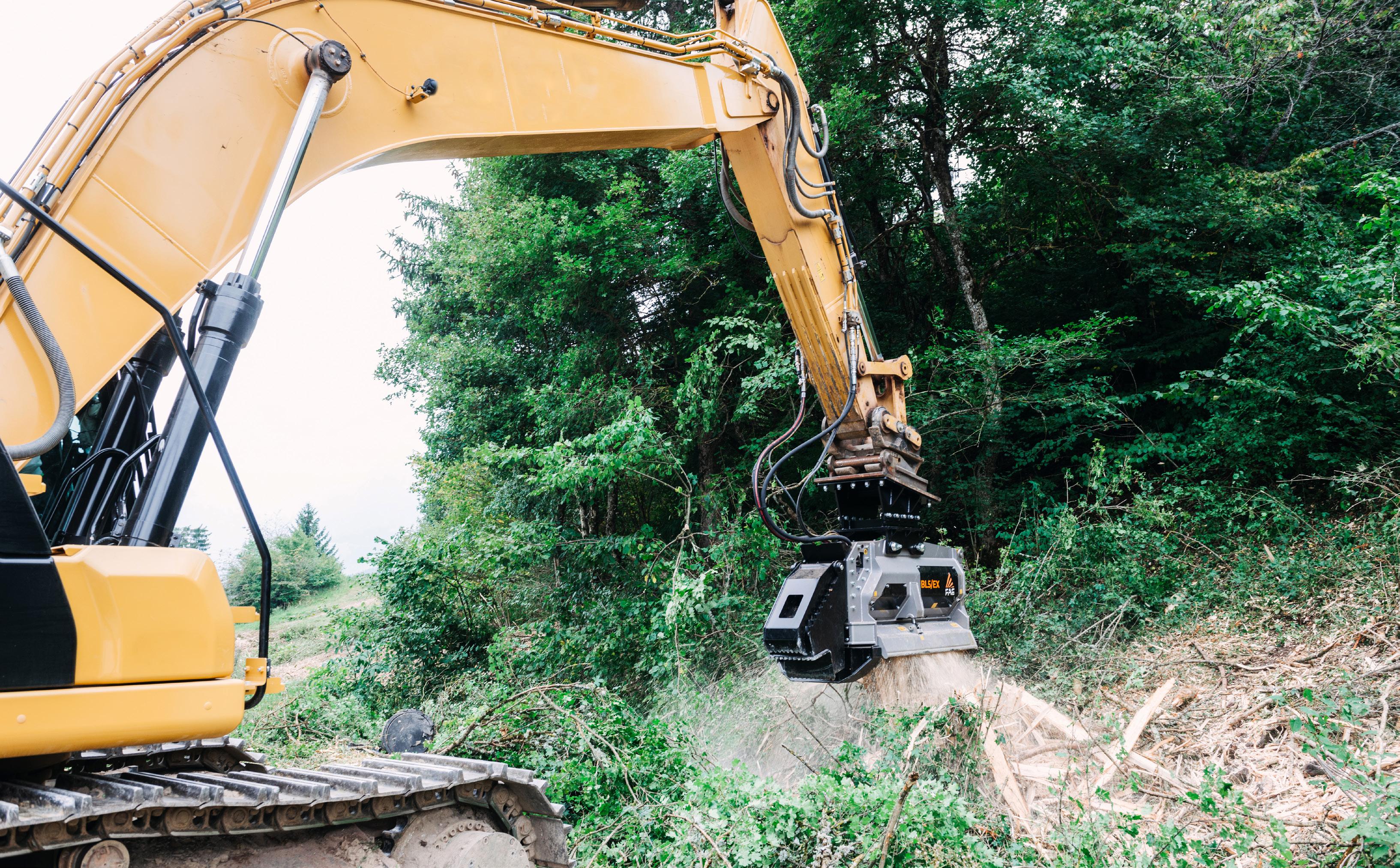
14 inches wide and process trees up to 6 inches wide.
Disc Hawk offers four varied mulching methods, giving operators the flexibility to cut, fell or mulch as needed, including a back-dragging option to clean up already-processed materials on the ground.
For contractors looking for power, Diamond Mowers’ Disc Mulcher Belt Drive Pro X features a 60-inch cutting width, cuts through trees and brush up to 14 inches in diameter and shreds material up to 6 inches in diameter.
According to Nelson, the Disc Mulcher BD Pro X is “the biggest, baddest monster of a disc mulcher.” It provides high torque by using a variable displacement piston motor.
The disc mulcher, which attaches to most skid steers and CTLs, maximizes productivity with a 13-second spool up time.
Drum Mulchers
Contractors looking to cut down and process large trees into a fine mulch will want to look at drum mulchers.
“These mulchers can work ... close to the ground, or they can go up and attack tall trees at 8 feet or 9 feet in the air, push it, cut it and chase it down to the bottom and then clean up the brush,” said Ryan Ruhl, product consultant, compact construction
equipment, John Deere Construction & Forestry.
Deere recently announced the addition of two new drum mulchers designed to work with its 334 and 335 P-Tier models.
The MH72D features a 72-inch, high-capacity smooth drum rotor with carbide teeth, which expands upon its MH60D mulching head.
Deere’s new MK76 offers a 76-inch wide cut and features an optimized knife style head ideal for fibrous vegetation. Featuring a drum narrower in diameter, the MK76 will allow more space to reduce impact of hard rocks on the ground that could chip knives or slow the head’s production, according to Ruhl.
“A smaller diameter rotor will also allow the head to recover much faster,” Ruhl added. “If the operator leaned too hard on a log or stump, it’s going to come back up to speed and be much more productive, much faster.”
These mulching head attachments produce the finest chip of all John Deere mulchers, broadcasting discharge to mitigate piles.
FAE now offers an option to maximize drum mulcher productivity with its new bite limiter technology. The technology, which is available on several FAE mulchers, features special wear-resistant steel profiles that
limit the teeth’s reach and delivers a consistent working speed.
“The bite limiter family allows the operator to operate the unit without as much skill,” said Lee Smith, product manager, FAE.
“Because of the limiters in front of the teeth, the operator can’t take as big of a bite out of the material. It’s an easier, more user-friendly option.”
Stump Grinders
Stump removal can often be an expensive and time-consuming task, according to Bricker. This was a common complaint Fecon heard when talking to contractors. In response, the Ohio-based attachment manufacturer recently acquired Stumper Industries.
“We now offer and manufacturer Stumper, which is a stump grinding attachment that can go on everything from a mini skid steer to a UTV, up to a skid steer and excavator,” said Bricker.
The Stumper series attachments range from 22-inch to 36-inch cutting diameters with up to 12-inch cut depths per pass, according to the company. This gives contractors the ability to tackle everything from small stumps to large stumps and roots. The grinder also offers the ability to maneuver the machine right next to objects, providing optimal visibility and overall safer cuts.
OUT BY FORCE: GRAPPLES
When it comes to land clearing, sometimes the best approach is the most straightforward. Grapples offer contractors the ability to grab and rip out trees, as well as remove stumps and rocks. This versatile tool is extremely handy, especially if the contractor does not need to process brush or wishes to sell the timber they remove.
Steelwrist provides contractors with three types of grapples: a multi grapple, sorting grapple and finger grapple. Each grapple is optimized for use with a tiltrotator, which allows the operator to tilt and rotate the tools for maximum precision.
“For wood and land clearing applications, many people are going to use the multi grapple, which is a bypass grapple that goes through each other to grab,” said Peter Gaj, vice president of sales for Steelwrist.
However, Gaj said the most versatile tool for land or brush clearing is the finger grapple.
“If somebody is going to buy one grapple to do every job, it’s going to be the finger grapple. As those fingers interlock, you can grab trees and tear them down. You can move and carry brush piles,” he said.
“You can grab and rip stumps out and move rocks easily. It’s a grapple that’s used for everything.”
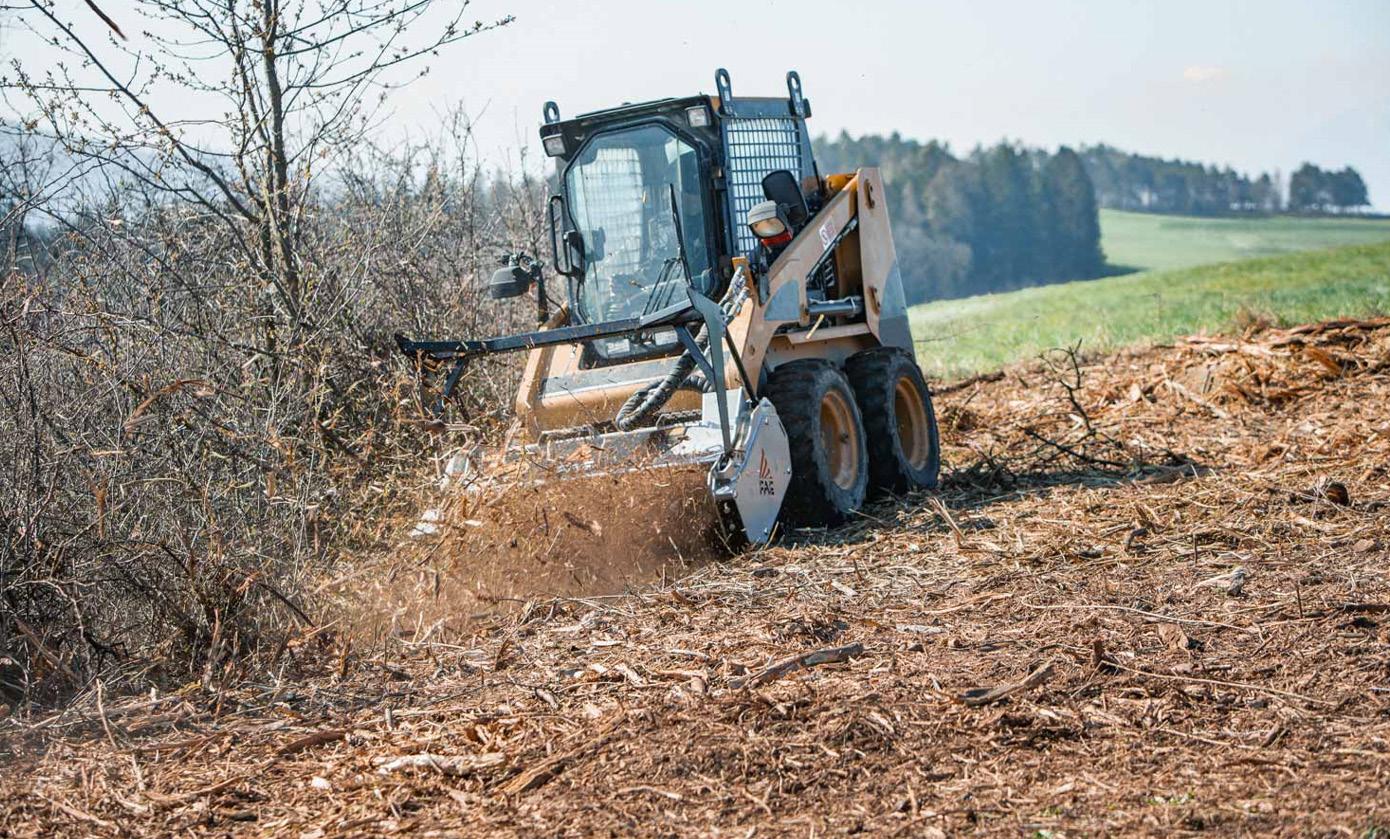
The size of the tree or stump is not an issue for Steelwrist’s finger grapples, which open to up to 6 feet, depending on the size of the attachment and machine. The tool is available in five- and seven-finger versions and is made of Hardox 500 steel with hard facing 600 HB jaws built for longevity.
FOR MAXIMUM EFFICIENCY:
TILTROTATORS & ROTOR COUPLERS
How do you become more efficient with less labor? Gaj of Steelwrist suggests tools like tiltrotators and rotor couples that offer greater maneuverability and productivity.
Tiltrotators
The tiltrotator, which connects to the end of an excavator and can be used with different attachments, provides the ability to rotate and tilt for added flexibility. Steelwrist tiltrotators offer 360-degree rotation and 45-degree tilt in both directions.
“The benefit of that is it makes your excavator three-dimensional,” said Gaj. “You will have to move the excavator a lot less because of the angles and the twists that you can do. It makes your excavator 20% to 30% more efficient.”
Steelwrist, which started in Sweden in 2005 and came to the U.S. in 2017, recently announced the first model of the third generation of Steelwrist tiltrotators, the XTR20. The tiltrotator, which is targeted towards 16-ton to 20-ton excavators, features patented LockSense technology, a sensor system for secure work tool locking. The model will be available in North America as early as December 2024.
Steelwrist currently offers tiltrotators designed for 2-ton to 33-ton excavators in the U.S. All Steelwrist tiltrotators feature steel-cast housing, which is lighter than typical steel iron tiltrotators.
“Not only is that lighter weight on the end of the stick,” said Gaj, “but it gives you more breakout force, more ripping force if you’re de-stumping with a ripper or you’re digging.”
The ability to more precisely maneuver your brush clearing attachments offers an important asset to contractors.
“It can be a huge advantage to be able to tilt and rotate to put your mulcher into that perfect position when you’re working on a slope, uphill or downhill,” said Noward, adding that operators need to be cautious to avoid turning shredded debris towards the windshield.
The tiltrotator’s ability to turn and rotate into tight spaces also allows you to move a shredder around a tree to cut off low branches without moving the machine. This can be an asset for fuel reduction work, which requires that branches be removed up to a certain height on trees.
Werk-Brau, which offers Nox tiltrotators, announced an additional line of tiltrotators through a partnership with Steelwrist. Available for 2-ton to 33-ton excavators, Werk-Brau Powered by Steelwrist Tiltrotators are ideal for use with general purpose and specialty buckets and attachments like rippers, grapples and pallet forks.
Rotor Couplers
Because tiltrotators will require a significant upfront investment, contractors can find a more affordable alternative with rotor couplers. While rotor couplers do not tilt, they allow operators to rotate 360 degrees.
Steelwrist is entering the rotor coupler market with the XR7 and XR20 rotor couplers, which will be available in North America in fall 2024. The XR7 is designed for 4-ton to 7-ton excavators. The XR20 are designed for 14-ton to 20-ton excavators.
The rotor couplers will be available in the standard S-type coupler as well as the Steelwrist SQ wet coupler, which uses automatic oil connection technology to easily change and connect hydraulic attachments.
“If you’re changing attachments a lot, the SQ coupler is the way to go,” said Gaj. “Within 30 seconds, you could change an attachment and hook into another hydraulic one without leaving the cab, and off you go.”
Grace Rybak is a freelance writer for Equipment Today
WORK SMARTER, NOT HARDER WITH ADVANCED TECHNOLOGY
Every contractor needs equipment to make their work easier. In response, several equipment manufacturers have gone one step further by leveraging technology to make attachments and equipment work for them.
John Deere Construction & Forestry offers a way to eliminate the manual attachment setup process. Deere’s new P-tier skid steers and CTLs come equipped with a pressure compensated load sense system for their hydraulic systems.
“Not only does it offer better fuel economy, but from an attachment side of things, the operator can assign names to different attachments within the carrier itself,” said Ruhl. “When they [connect] to the stump shredder, all they need to do is tell the machine what it has connected, and it will automatically adjust the hydraulics on the machine to the preset value for that tool.”
With Fusion, Fecon’s skid steer drum mulchers use artificial intelligence to automatically calibrate to the carrier for maximum productivity.
“Fusion allows the mulcher to actually learn what machine it is hooked up to. It will optimize itself for that specific carrier in real time to maximize the machine’s performance,” said Bricker. “This will end up saving you money and lowering your operating costs over time.”
In addition to optimizing the attachment’s productivity, Fusion eliminates the manual process of calibrating attachments to carriers with different hydraulic flows.
The technology pairs with the Fusion mobile app, which contractors can use to connect to their mulcher and view live performance data—including mulcher hours, rotor speed and hydraulic pressure, flow, and oil temperature.
FAE’s intelligent solution Sonic offers contractors the ability to automatically tune FAE mulcher attachments to carriers. Contractors can monitor performance data and receive alerts through the FAE app to aid troubleshooting.
“Not only does that allow the mulchers to be more productive and easier to install, but [they are] easier to maintain,” said Smith.
FAE also offers a unique solution for contractors who need to clear brush on areas that may be dangerous or difficult for operators to access, such as hilly terrains or areas near power lines or gas or oil pipelines.
The company’s two remote-controlled tracked carriers can handle slopes up to 55 degrees, with the operator controlling the machines from up to 500 feet away.
The RCU75 from FAE is equipped with 74-hp Kohler engine and is compatible with the BL2/RCU mulcher and the SCL/RCU75 stump cutter.
The RCU55 runs on a 56-hp Kohler engine and is compatible with the BL1/RCU55 mulcher, SCL/RCU55 stump cutter and PMM/RCU55 flail mulcher.
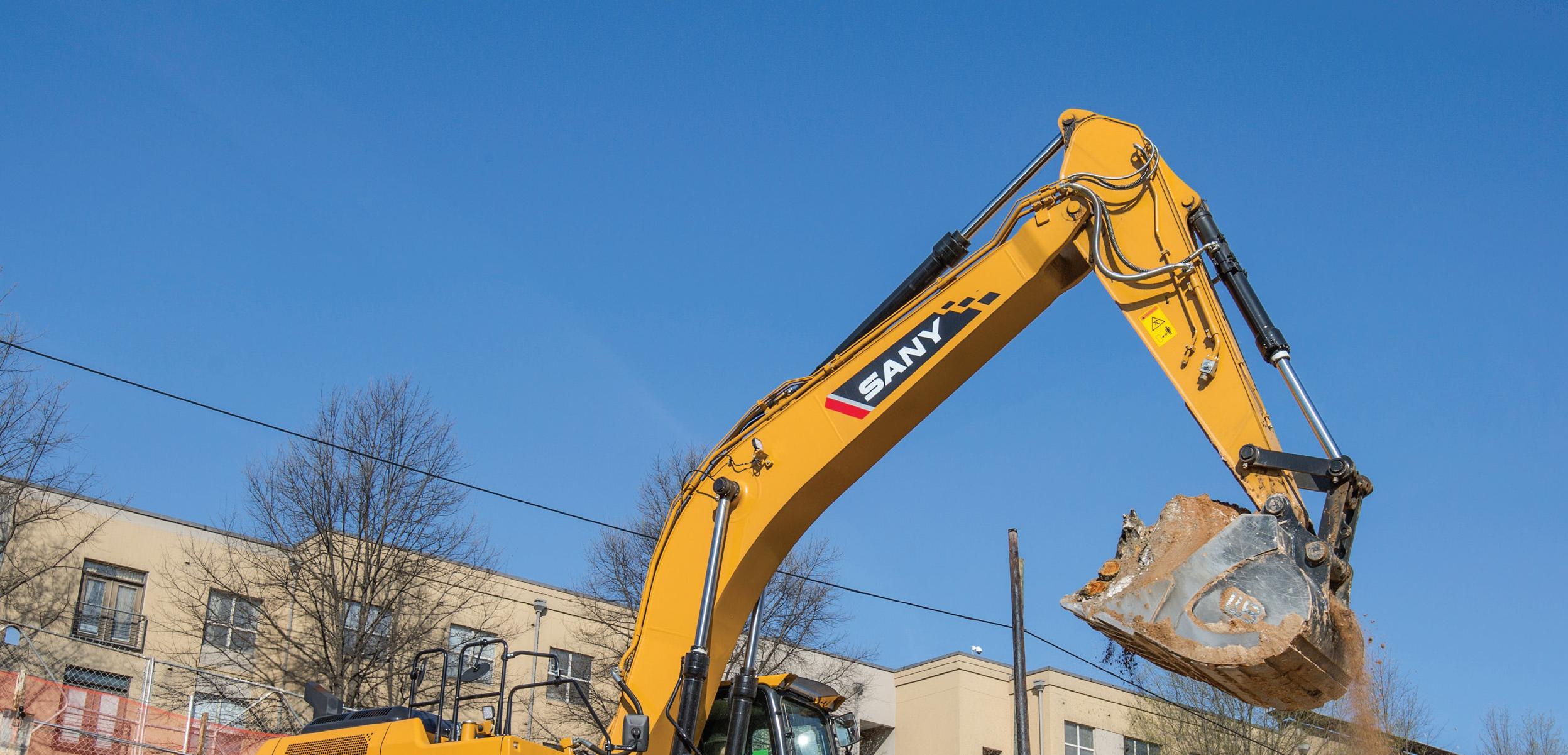
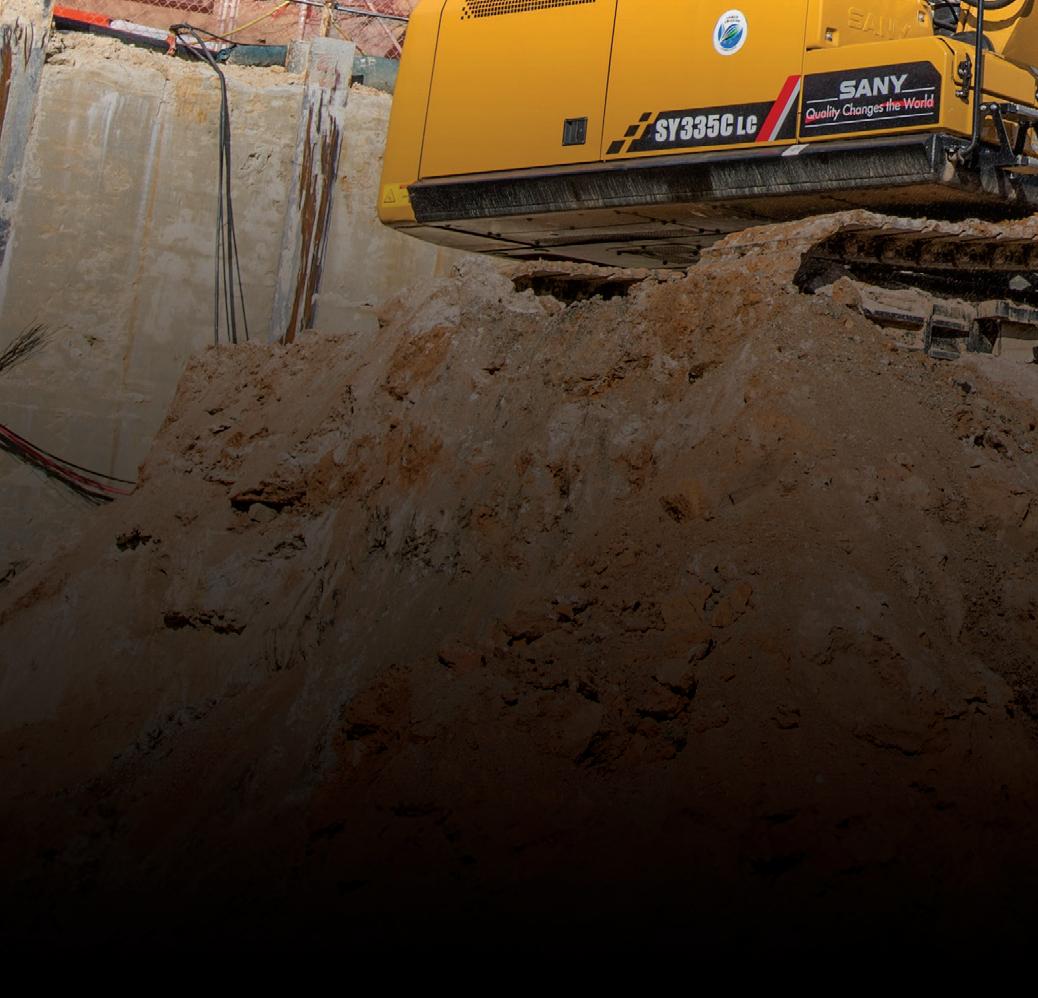
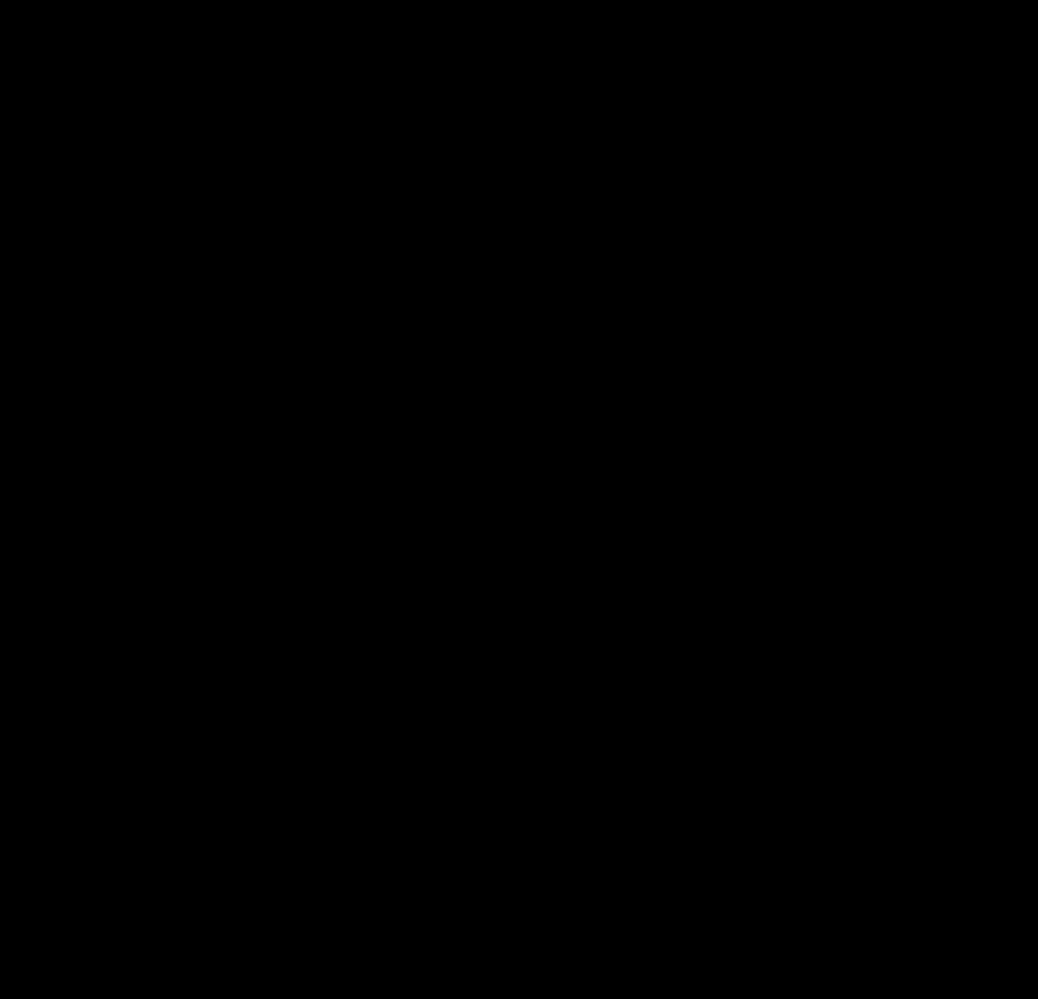
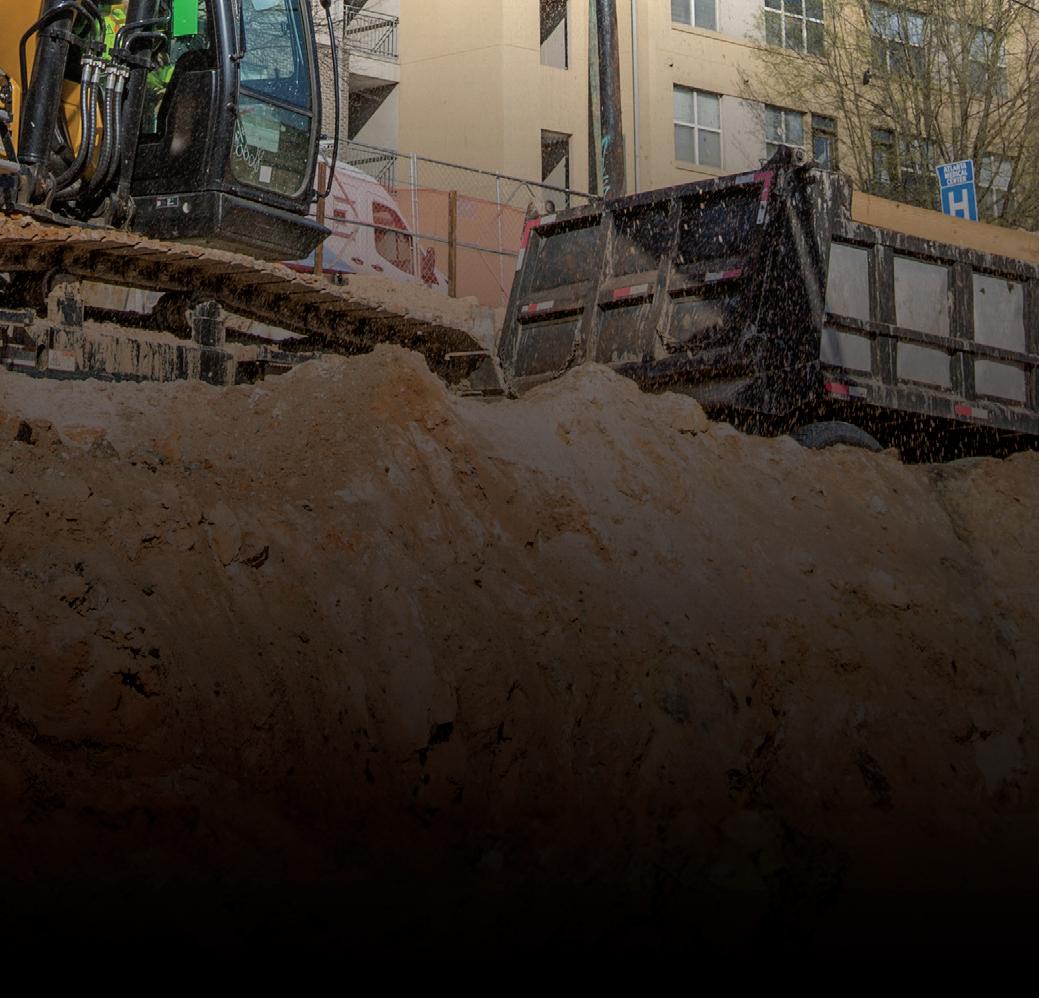
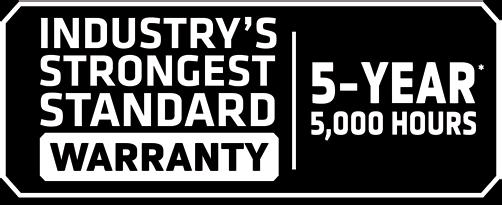
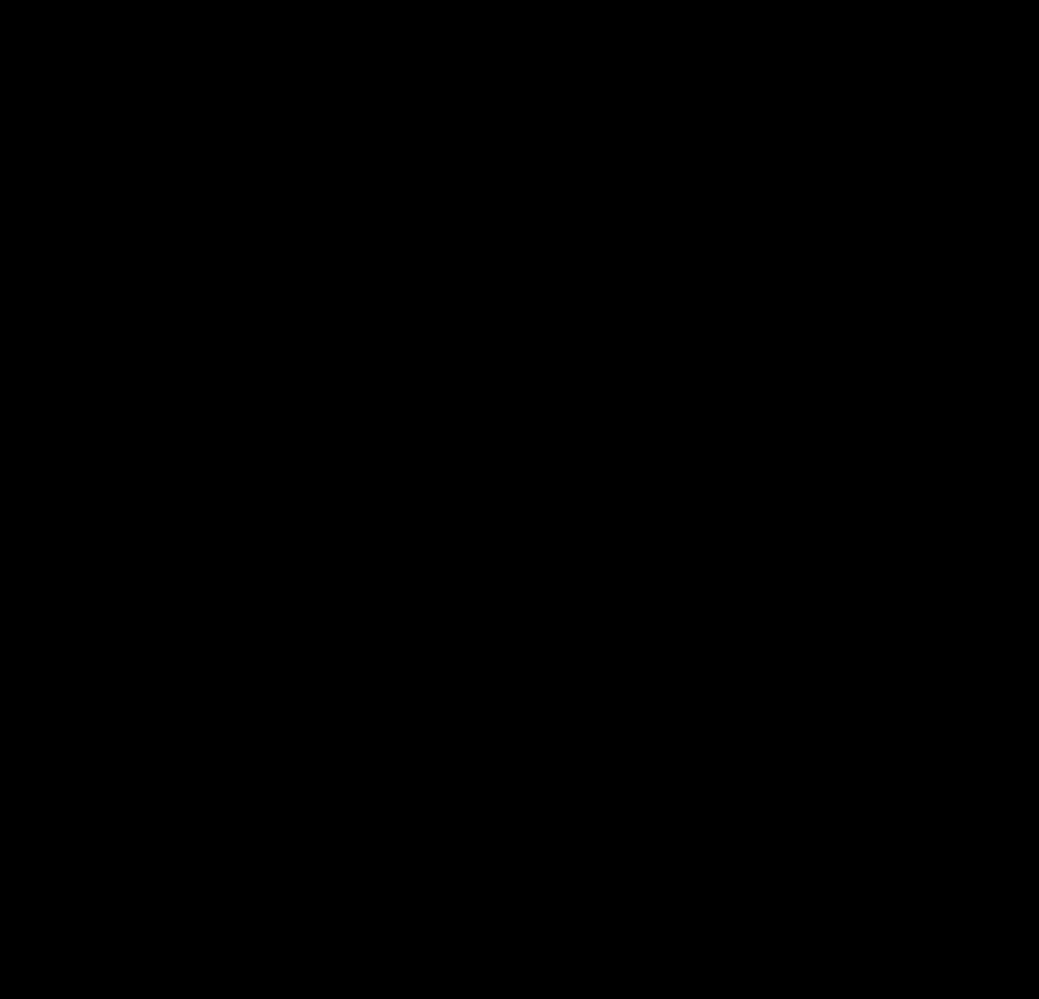
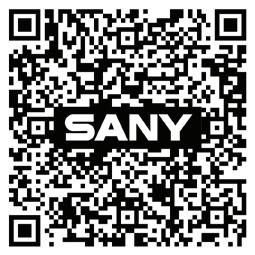

Become a MASTER Mulcher
When operating this equipment for the first time, it’s important to understand the power unit’s hydraulic capabilities and to stay within that range.

Mulching heads, also known as forestry mulchers or horizontal drum mulchers, have grown in popularity recently.
However, achieving success with one of these attachments relies not only on the one you choose but also on how you use it.
The performance may be disappointing if the attachment isn’t properly suited for the skid steer or excavator on which it will be used.
Likewise, production will suffer if the mulcher is operated improperly. Here are some tips on equipment selection and operation to help ensure a good experience.
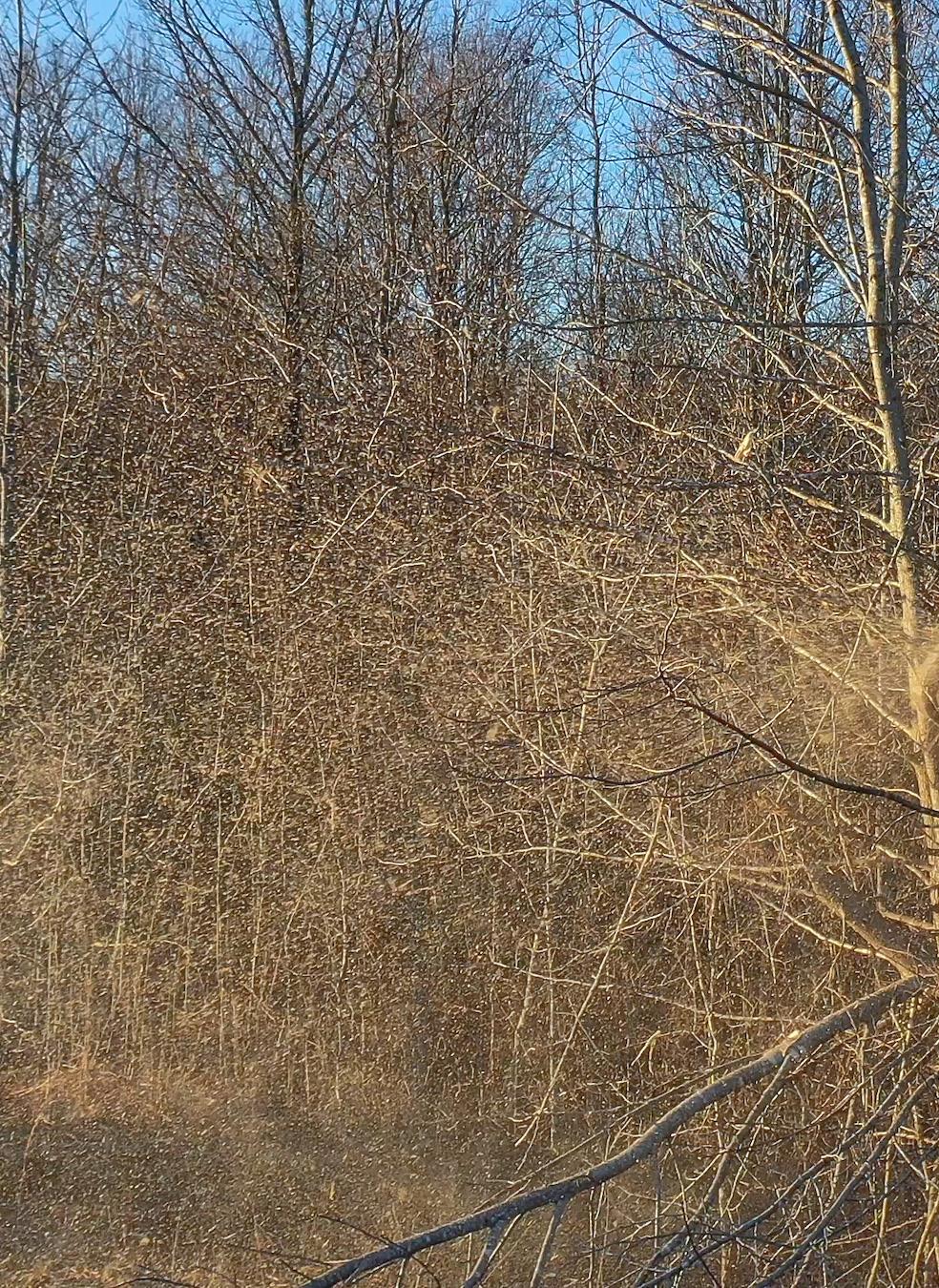
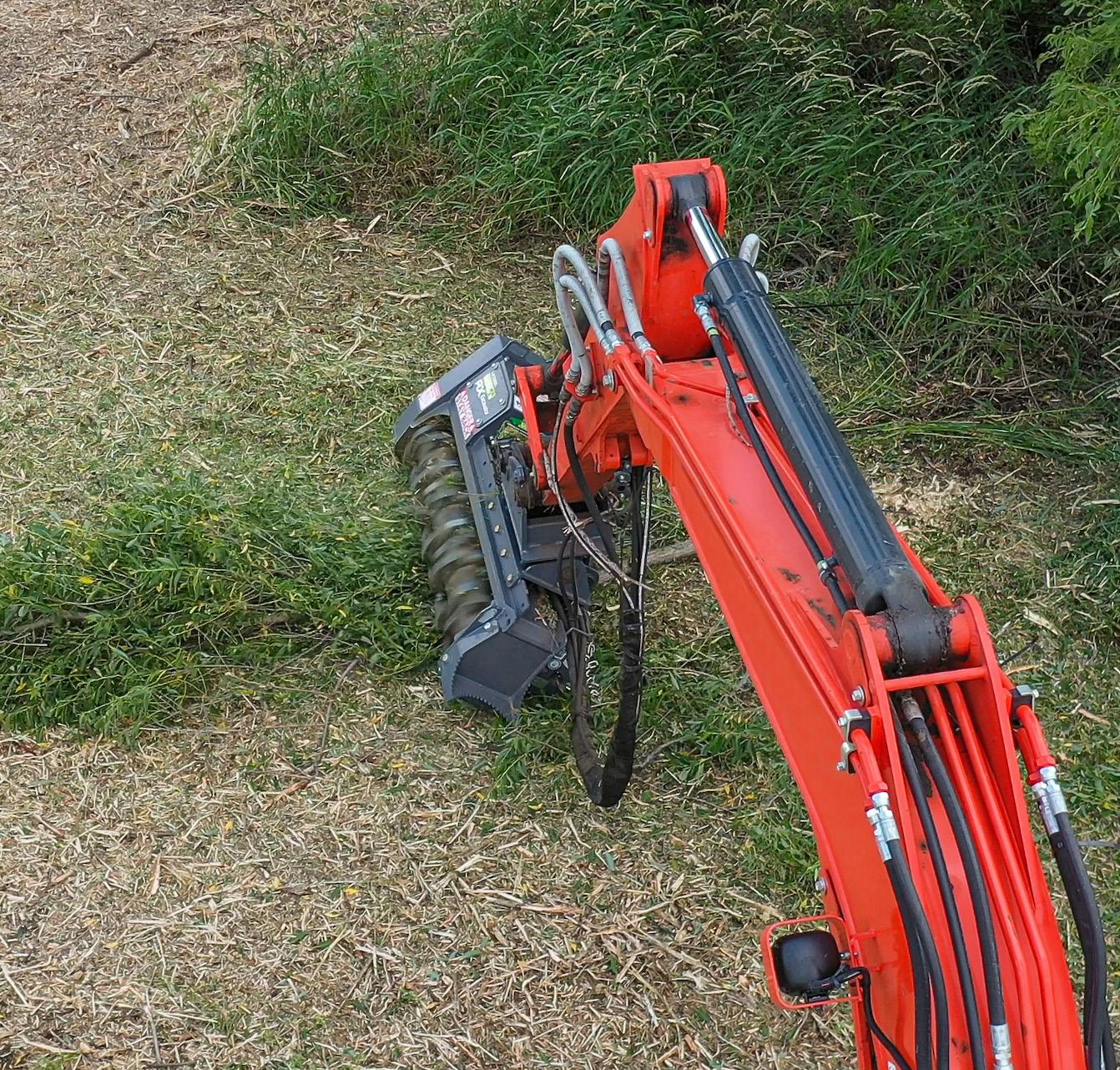
After identifying the appropriate excavator weight class, the mulching head needs to be configured correctly for the hydraulic output of the power unit.
SELECTING FOR SKID STEERS & CTLS
To find the right mulching head for a skid steer or compact track loader (CTL), hydraulic horsepower is much more important than engine power.
To determine the hydraulic horsepower, multiply the gallons per minute (gpm) and psi of the hydraulic system and then divide that number by 1,714.
For instance, a CTL with a hydraulic rating of 36 gpm at 3,450 psi would have a hydraulic horsepower of: 36 x 3450/1,714 = 72.5. Use that number to ensure that the power unit has the needed hydraulics to run the attachment. Mulching heads are available for a wide range of skid
steers, CTLs, and even lower flow models. Keep in mind, however, that performance is directly related to hydraulic power. A skid steer with a higher flow can simply outwork one with a lower flow.
Next, ensuring that the skid steer or track loader has the weight capacity to carry it is important. Also, consider the working conditions. Flotation can be an issue with some power units when a heavy mulching head is used on soft ground.
The weight and balance of the unit make stability another consideration when operating in rough terrain, steep hills, and valleys.
EQUIPPING AN EXCAVATOR
When it comes to excavators, mulching heads are categorized according to weight class. One series may be designed for excavators weighing from 10,000 pounds to 20,000 pounds, while the next series will work for excavators ranging from 18,000 pounds to 36,000 pounds. It continues to scale up to accommodate the largest excavators on the market.
After identifying the appropriate excavator weight class, the mulching head needs to be configured correctly for the hydraulic output of the power unit. Some mulcher manufacturers offer different hydraulic motor options to handle the flow ratings, while
manufacturers offer different hydraulic motor options to handle various flow ratings, while others have different belt drive configurations.
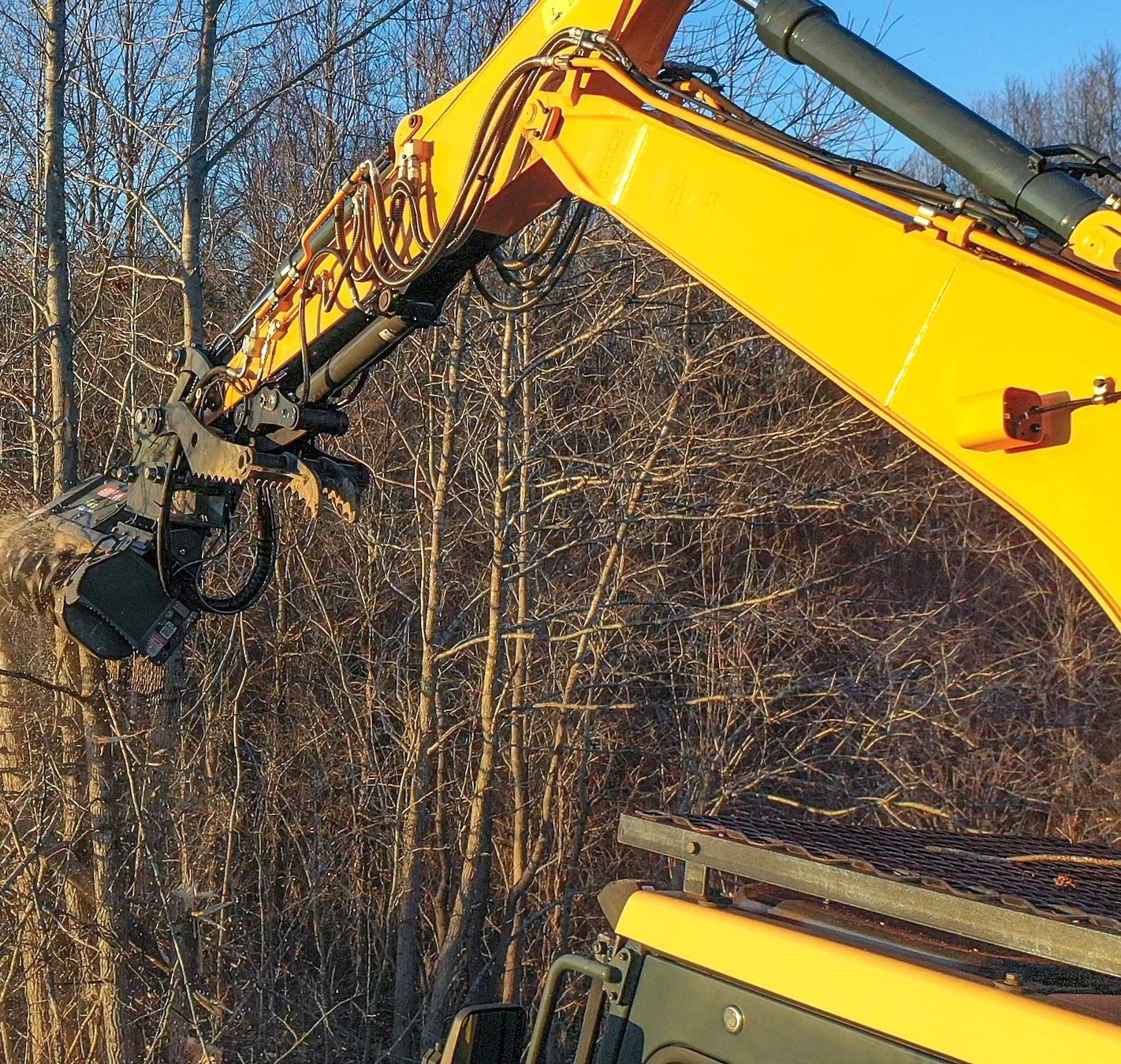
others have different belt drive configurations. For example, the pulley combinations recommended for use on excavators with 15-gpm to 20-gpm hydraulic systems are different than those recommended for 20-gpm to 24-gpm systems. Furthermore, some larger mulching heads may have a piston motor that is adjustable to match the hydraulic output of the power unit.
Another factor that makes excavator attachment selection different than skid steers is the lack of a universal mounting system. That means the end user needs to work with the equipment dealer to ensure that the appropriate mounting style is installed for the type of excavator being used.
Along with the mounting system, a tilting hitch is a strongly recommended accessory when purchasing a mulching head for an excavator because it will significantly improve the operating experience. As the name suggests, a tilt hitch allows the operator to tilt the mulching head from left to right. Keep in mind, however, that not all tilt hitches are the same. Some allow the attachment to be pivoted
up to 45 degrees either way, while others may have a more restricted range of motion.
Finally, most mulching head manufacturers offer a few options unique to excavators. The first is a spade hook, which is helpful for positioning the material to be mulched. A hydraulic thumb can also be added for even better use of the spade hook.
UNIVERSAL FEATURES
Other important considerations apply to skid steer, CTL and excavator mulchers, including the cutting teeth and rotor options. Many mulching heads can be used with either sharpened knives, beaver teeth or carbide teeth.
Knives are popular on mulching heads since they are capable of cutting finer and faster than other styles. The downside is that knives require regular sharpening, which is a deterrent for some.
Like knives, beaver teeth are made of heat-treated steel, but they do not slice as well. The distinctive, pointed shape of beaver teeth helps them pick up material from the
ground, despite being less aggressive than knives. Carbide teeth are a durable, low-maintenance option for less experienced operators. They are often recommended when mulching at ground level in rocky conditions because they are less prone to damage than knives.
The cutting teeth decision leads to a discussion about the rotor. As sharpened knives have become more popular, so have limiting rotors. Because knives have a natural tendency to bite into material more aggressively than what is ideal, a limiting rotor helps control the material in the feed for more efficient performance.
The two main types of limiting rotors available today are ringstyle and depth gauges. Ring-style rotors are generally have the most restriction. Depth gauges aren’t quite as restrictive, which allows operators to pick up material from the ground more easily, especially when using less aggressive carbide teeth.
USING YOUR HEAD
When operating this equipment for the first time, one of the most
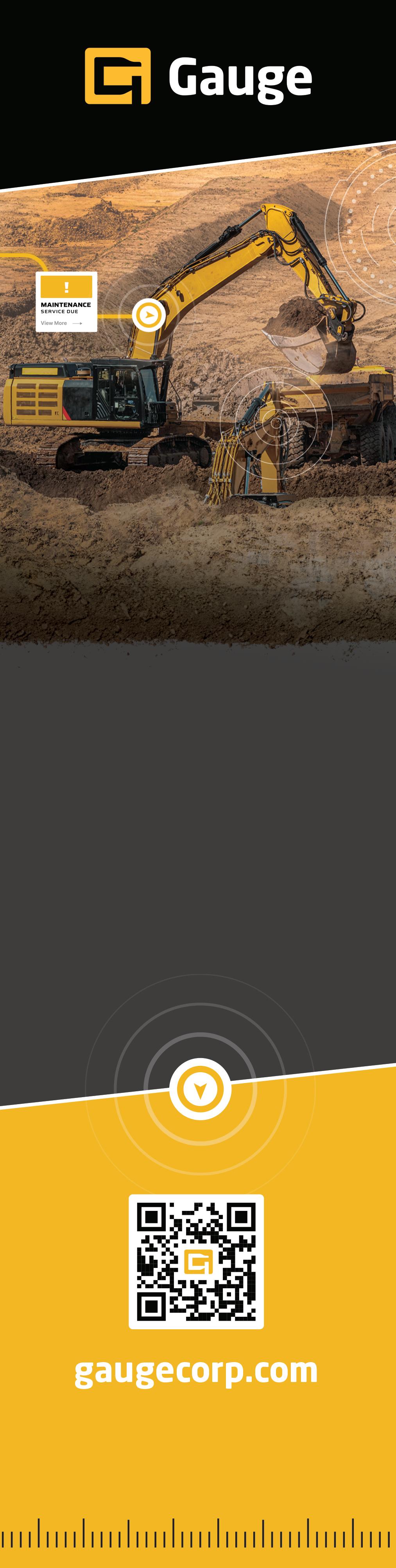
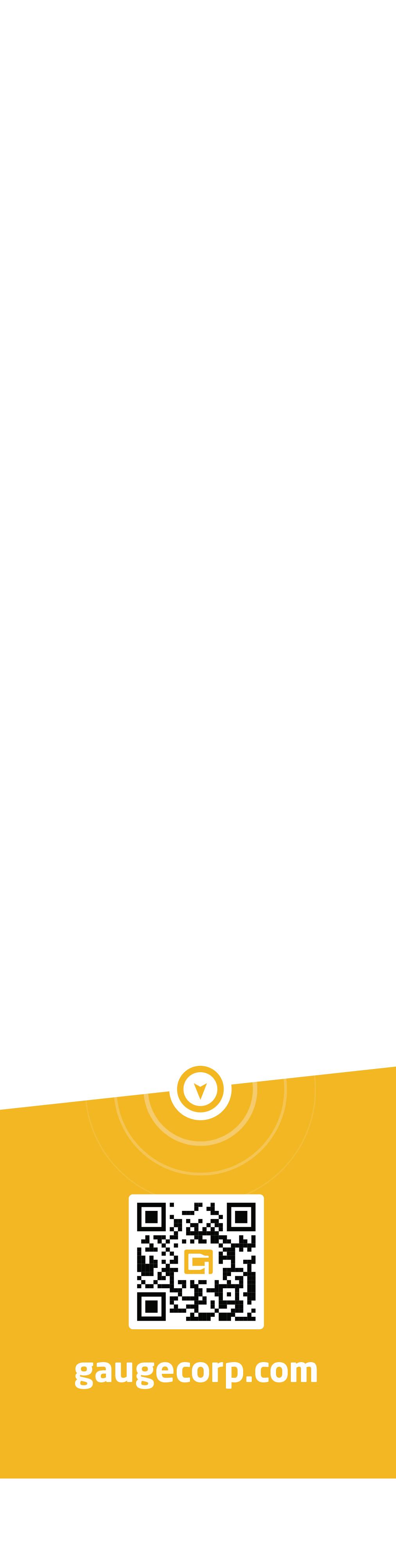

Mulching heads are available for a wide range of skid steers, compact track loaders, and even lower flow models.
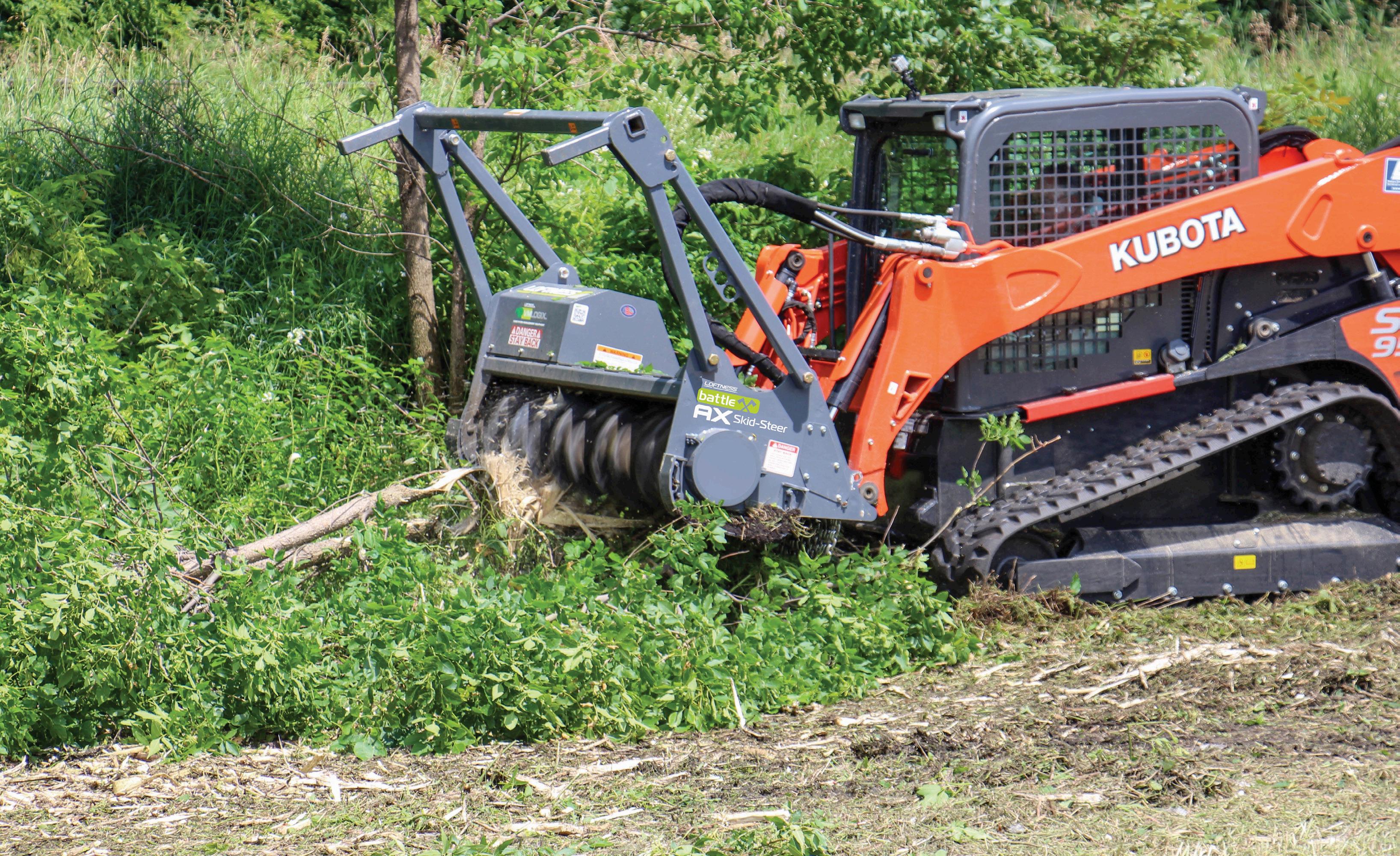
ATTACHES TO ANY WHEEL LOADER
PLACES 300 CUBIC YARDS OF CONCRETE PER HOUR
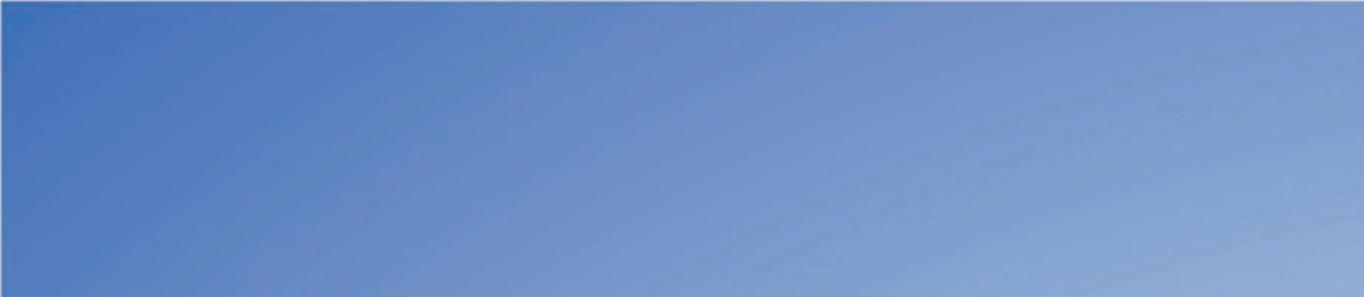
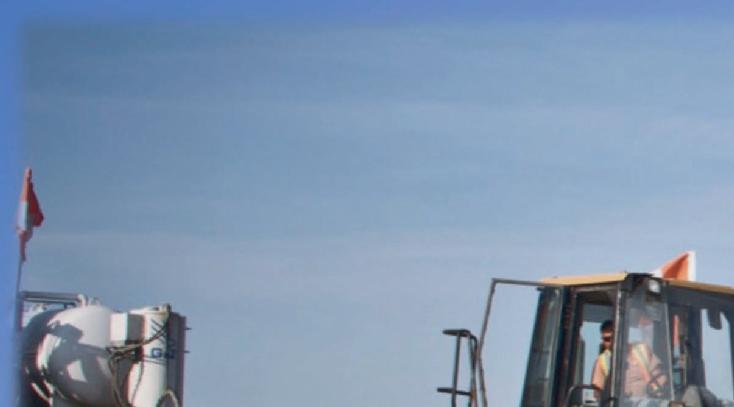
PLACE CONCRETE, ASPHALT, AGGREGATE, SAND, TOPSOIL
PRODUCTION PROVEN
BEING USED ACROSS
AROUND THE

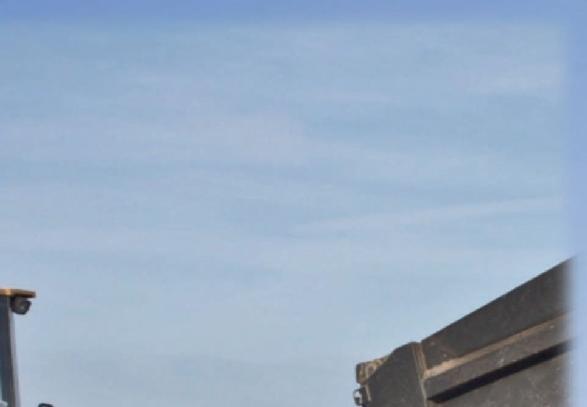
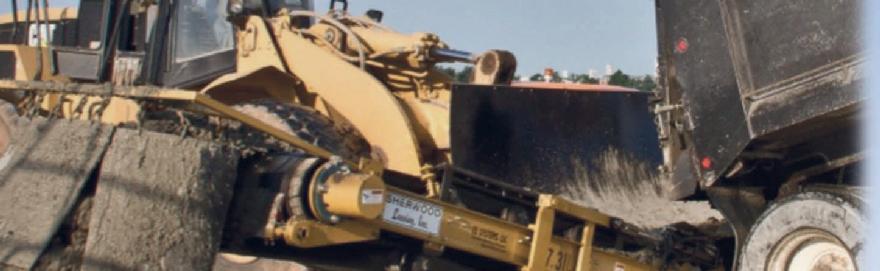
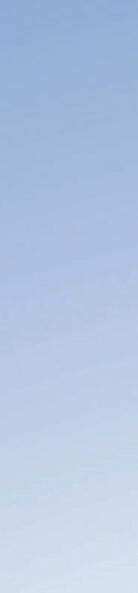
important pieces of advice is to understand the power unit’s hydraulic capabilities and then stay within that range. Operating 500 psi below the maximum hydraulic relief pressure is generally recommended.

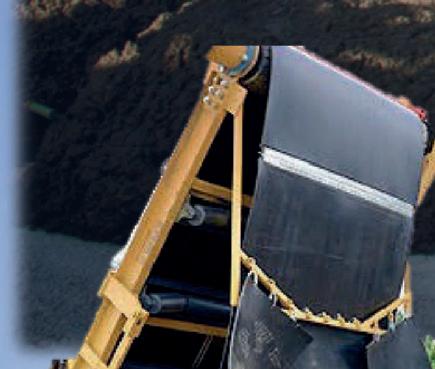

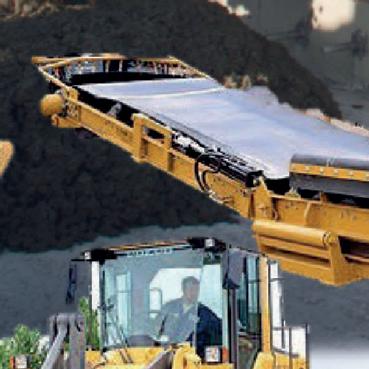
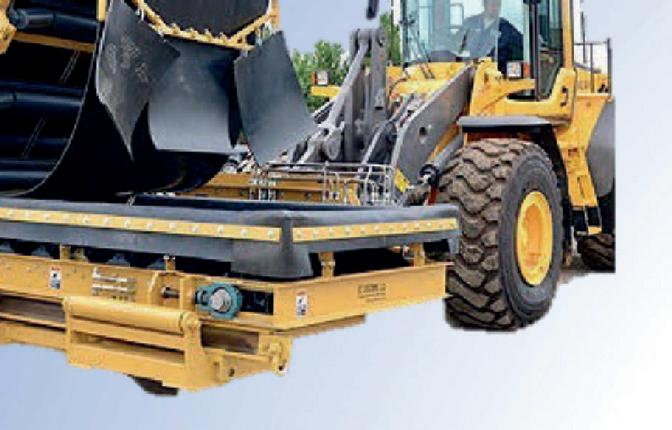
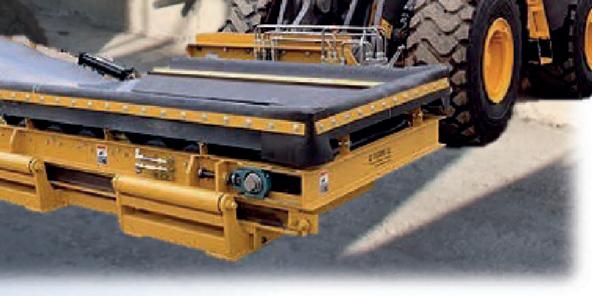
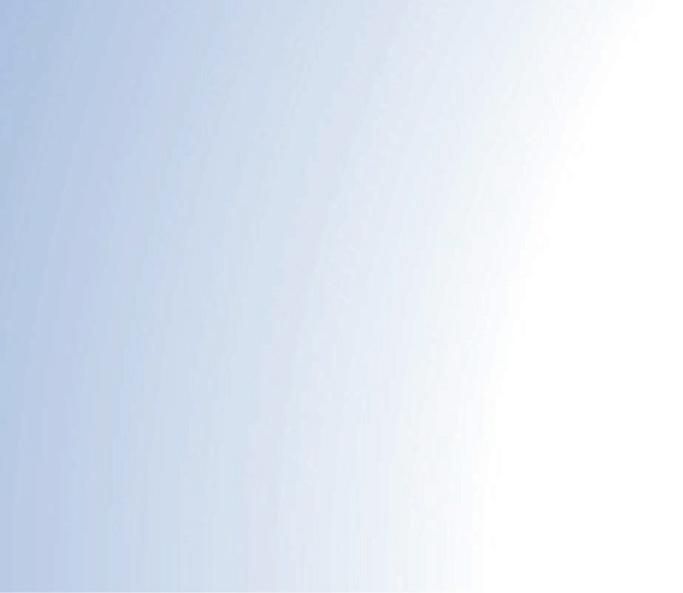
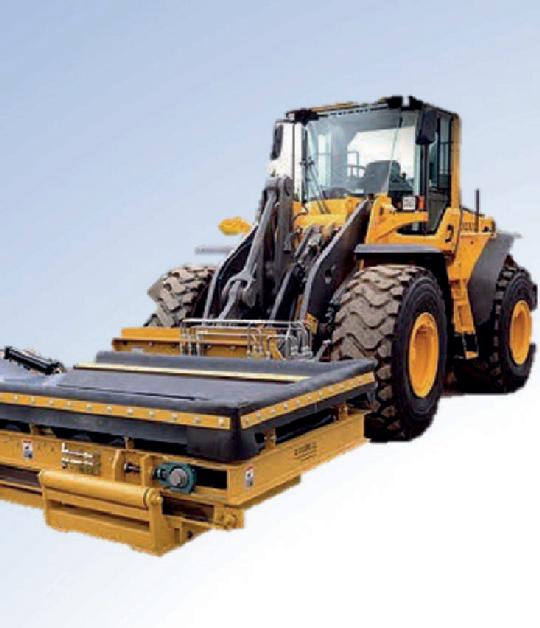

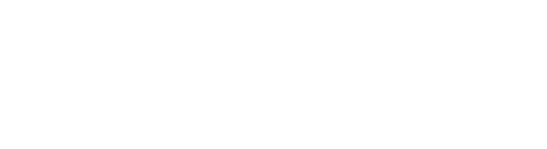
As the load increases, the pressure goes up, and the rotor will slow or stall when the maximum relief pressure is reached. When this happens, performance is decreased, and heat is generated, which could potentially cause damage to the hydraulic system. To reduce the amount of pressure, operators can simply engage material more slowly. Mulching heads can be positioned in different ways to accomplish disparate tasks. This is why operators should consider tilt hitches for excavator models.
For instance, the head can be tilted back to expose the knives to fell standing trees more efficiently.
When mulching material on the ground, lowering the rear of the cutter can be helpful. This technique can pin material to the ground, so it doesn’t eject out the back of the unit. It can also trap material in the cutting chamber for more thorough processing if desired.
Skid steer operators often use a reverse mulching or the back dragging,
technique. Here, the head is tilted forward while the skid steer backs up. Back dragging is effective for sizing material since this action pulls the downed material against the cutter bar and into the chamber. Some units have an adjustable cutter bar to help control particle size and production rate. Some units also have a second cutter bar behind the front bumper, allowing material to be cut twice for more thorough processing. This feature is often referred to as a twostage cutting chamber. Like most other things, experience is the best teacher. Fortunately, there is a lot of demand in:
• Right-of-way vegetation management
• Forestry
• Land clearing
• Other industries
This demand helps newcomers gain meaningful experience with mulching heads. This advice, combined with support from your equipment dealer, will help give you a good head start.
Read more at: eqtoday.co/mulch
Tryg Waterhouse is director of sales at Loftness.
John Deere MH60D Mulching Head Attachment
The MH60D mulching head is designed to remove 8-in. trees and 12-in. stumps as well as shred underbrush and woody materials into mulch.
• Two-speed hydraulic system
• 60-in. high-capacity, smooth rotor design reduces material drag and horsepower requirements
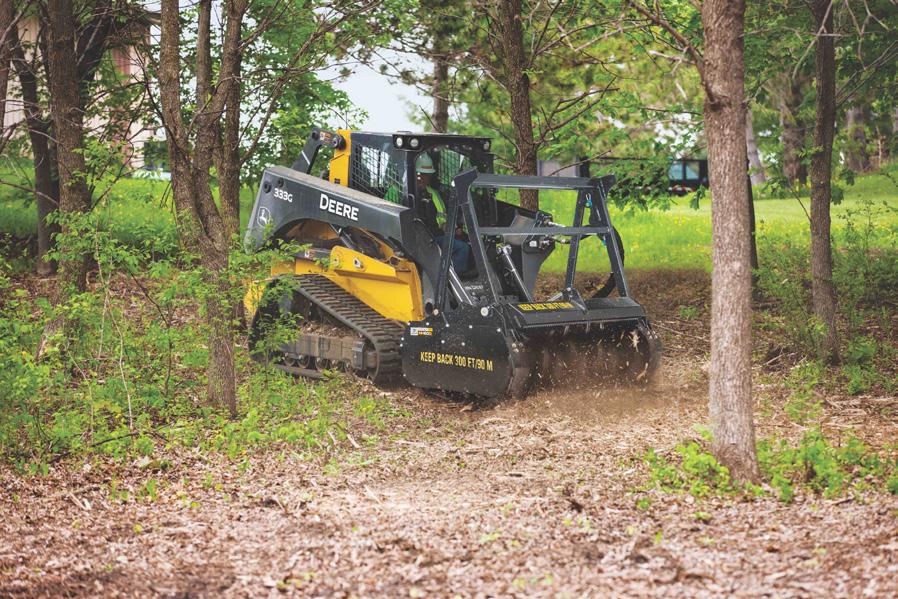
• Redesigned mulching chamber for more efficient material flow
Includes 30 double-carbide-tipped teeth; three-position, heavy-duty push bar; internal counter-combs to create finer mulch; and oversized 2.5-in. sealed rotor bearings
• Optimized for John Deere skid-steer and compact track loaders as well as most competitive models
IronCraft X-treme Tree Reaper Brush Cutter
IronCraft introduced the X-Treme Tree Reaper, a brush cutter attachment for on-farm or commercial land clearing. Engineered for demanding applications, the X-Treme Tree Reaper is available with two direct drive motor options: a 16 gpm to 26 gpm gear motor (case drain not required) or a 17 gpm to 30 gpm bent axis piston motor (case drain required).
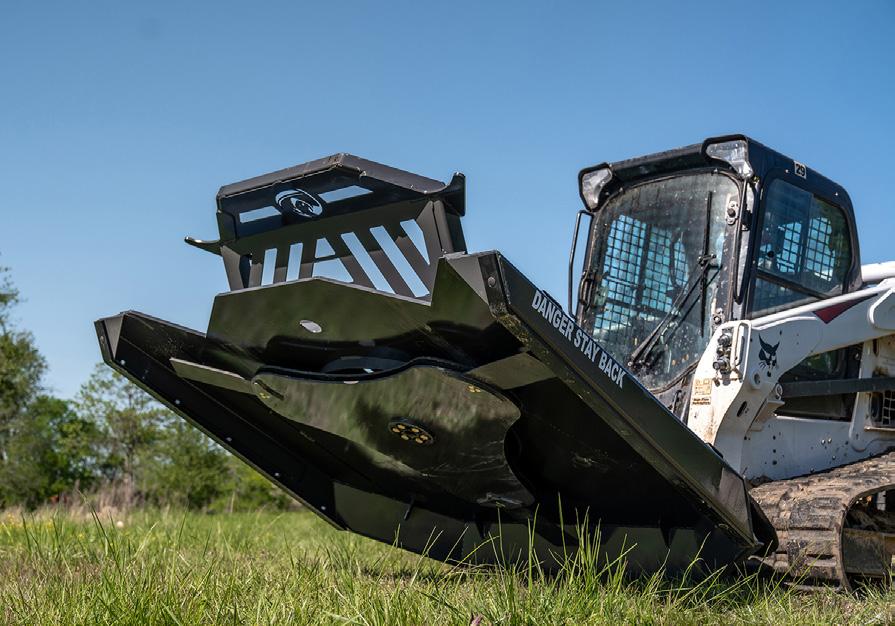
The design includes bolt-on replaceable skid shoes and a tapered deck for lower ground cutting. Three 5/8-in. AR400 blades cut dense brush, limbs and trees to 7 in. in diameter. The non-welded blades can be changed out in the field. Optional grill and mulching teeth are available.
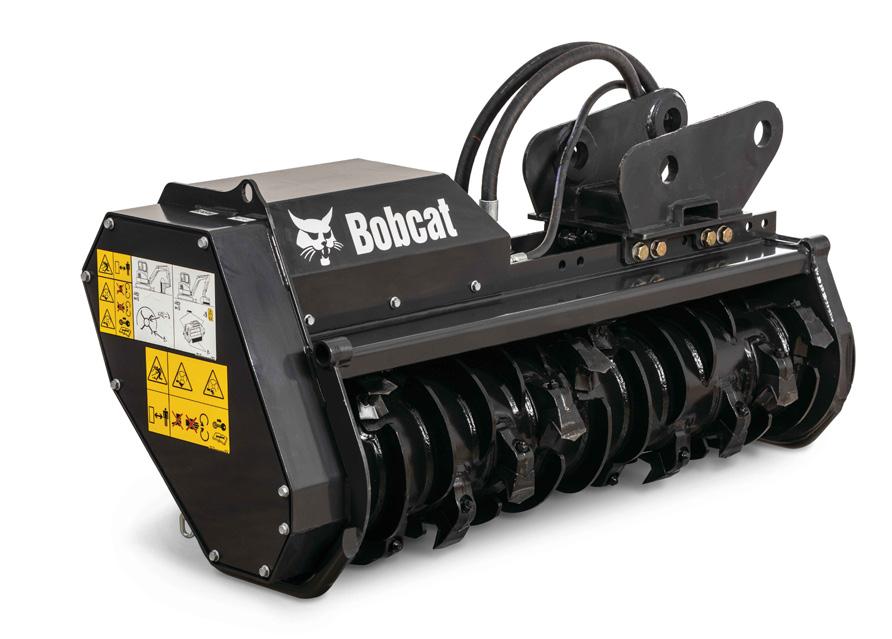
Yanmar C08e Electric Tracked Carrier
Yanmar’s C08e Tracked Carrier is designed for transporting materials and loads around jobsites. With 730-kg to 880-kg operating weight, the machine can take on tough terrains.
It combines a high-performance electric motor that provides 5.5-kW rated and 6.5-kW peak power, with a hydrostatic transmission for handling and operation on inclinations up to 20 degrees. Its haul body can carry between 0.34 cu. m to 0.42 cu. m. The vehicle operates on a 10.4-kWh battery, featuring three selectable working modes—eco, performance and high performance—to extend battery life up to 3 hours in demanding modes.
Operators can access a touchscreen for status monitoring (battery level) and settings.
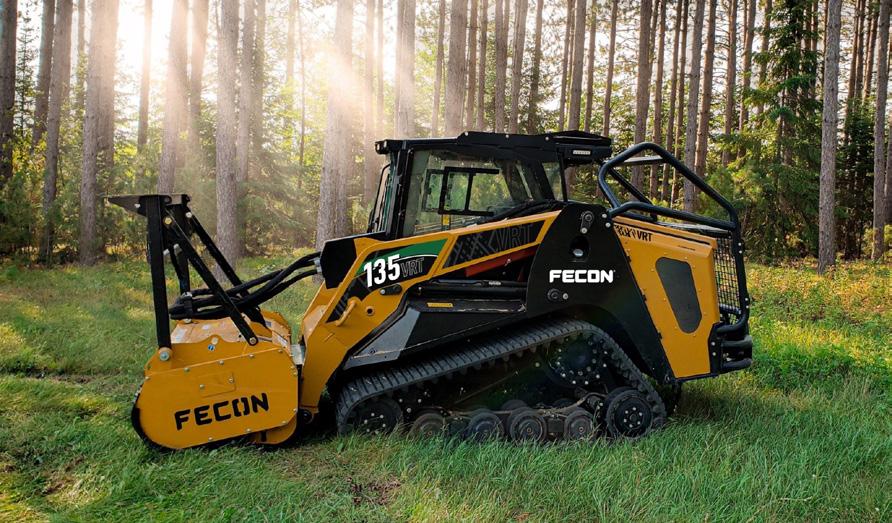
Fecon 135VRT Mulcher
The 135VRT has a 4,150-lb. rated operating capacity with integrated counterweight or hydraulic winch kit and is powered by a 132-hp Cummins 3.8L Tier 4 Final engine. A 50-gpm auxiliary attachment flow provides 119 hp to the VM602SS Bull Hog Forestry Mulcher or other attachments. A 16-gpm reserve allows full machine control without loss of attachment performance. A bite-limiting rotor is fitted with 30 carbide or double-sided tools and maintains rotor rpms to easily mulch material up to 8 inches in diameter.
An improved loader arm design enhances attachment visibility. The full forestry spec cab includes 1/2-in. polycarbonate side windows, a Level 2 FOPS and a complete guarding package. The spacious, comfortable operator station includes an 8-in. color display.
Indeco IMH Series Mulching Heads
The IMH Series of hydraulically-driven, boom-mounted mulching heads can perform a range of land clearing, site prep, invasive vegetation species management, storm damage removal and cleanup applications. Features include:
• Unique tooth design for optimal cutting
• Eight direct-drive and belt-driven highperformance models for carriers from 5 t to 45 t
• Feature HARDOX components and bodies, a single-piece shaft and severeduty bearings for optimal service life and reliability
• Interchangeable mounting brackets allow for any excavator application
Bobcat Drum Mulcher
Bobcat introduced a drum mulcher attachment for select excavators. Previously offered for select compact track loaders and skid steer loaders, drum mulchers can take on heavy brush and trees up to 5 in. thick. This attachment allows excavator operators to clear trees and overgrowth along steep roadsides, riverbanks and other hard-to-reach areas.
Bobcat offers three models, the 28DMX, 36DMX and 50DMX, with cutting widths of 28 in., 36 in. and 50 in. respectively. The mulcher lineup can be operated with excavators ranging from 4 t to 10 t. Featuring axial piston hydraulic motors, these drum mulchers optimize rotor speed and torque for land-clearing applications.
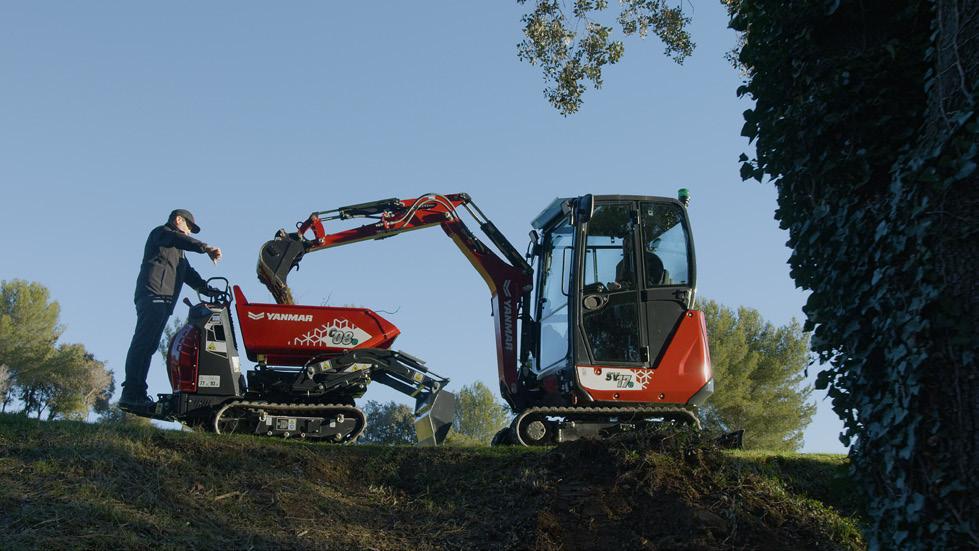
Optional features include external hydraulic connection, paint and turning vessel. For charging, the C08e uses a standard 3.3-kW off-board charger, compatible with a P17 blue plug for grid connection and a REMA socket for direct machine linkage, which fully recharges the battery from 20% to 80% in just 3.5 hours. Additional features include automatic electric motor shutdown and optional vessel configurations.
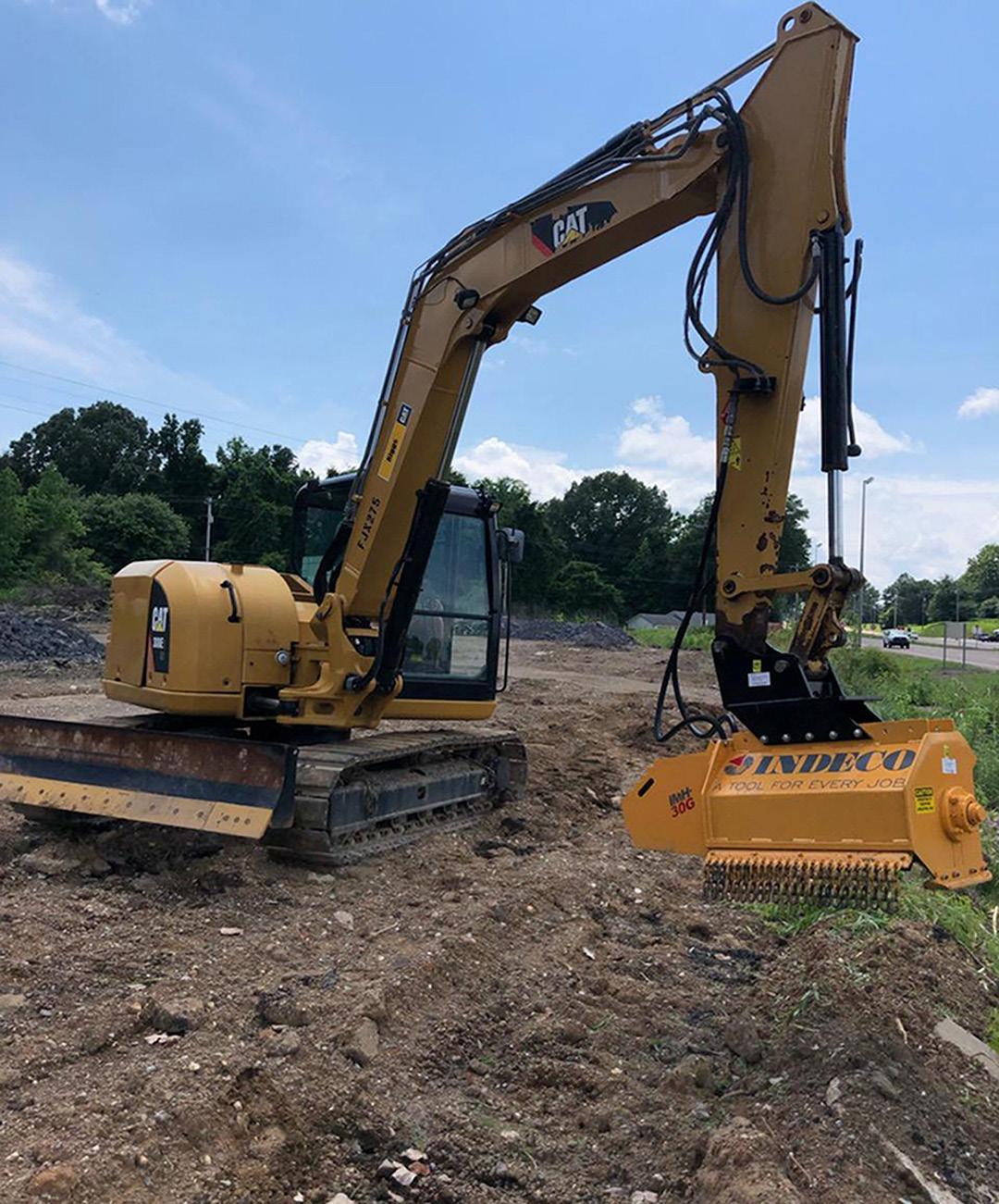
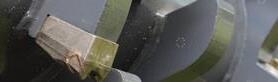
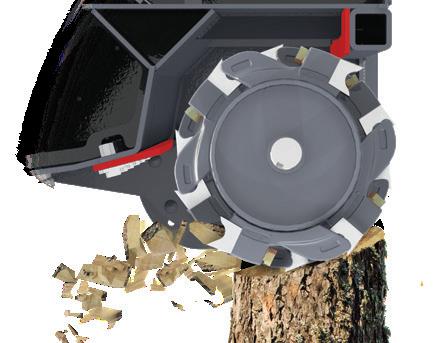
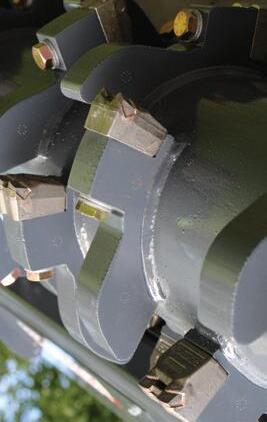


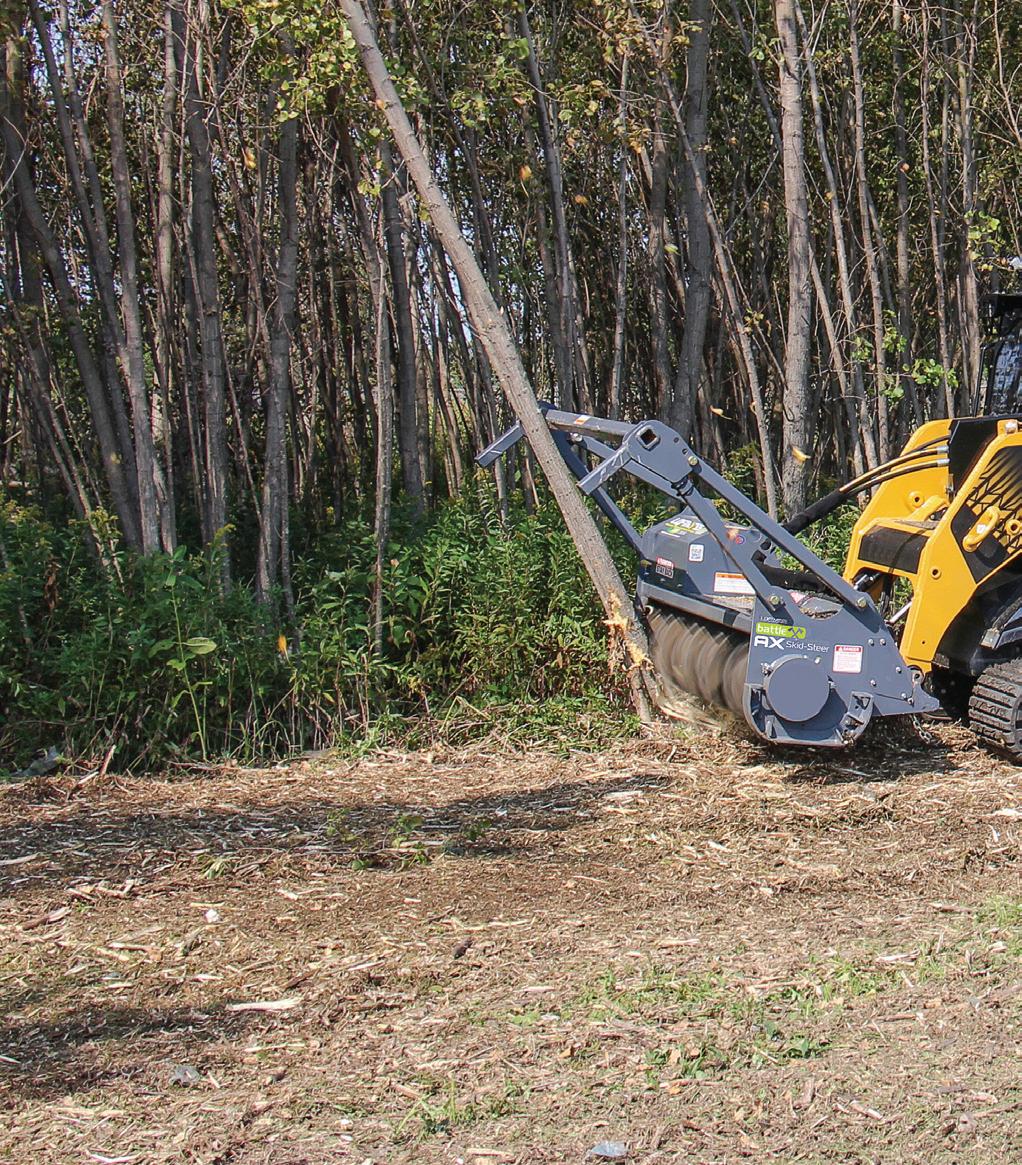
CUT THE CORD: Electrify Tools, Equipment
The construction industry’s shift toward battery-powered tools and equipment is being driven by the increased productivity and versatility they bring to the jobsite.

The lithium-ion batteries of today run longer, charge faster, and are much more powerful and reliable than their ancestors from 10 years ago.
Like many industries, construction is in the middle of a transition away from gas and toward electrical power. Overall demand for lithiumion batteries is expected to increase by more than 30% annually between now and 2030, according to McKinsey.
While the power tool space has long since transitioned to cordless technology with the lithiumion battery, light equipment is experiencing its own mass electrification as lithium-ion battery technology has evolved. Delivering greater power, longer run times, and more reliable performance, a growing slate of battery-powered equipment systems is now able to compete in an arena that’s been dominated by gas engines for decades.
THE BENEFITS OF ELECTRIFICATION
The shift toward electrification is driven by many safety and productivity benefits that make cordless solutions increasingly attractive to construction companies, general contractors, and skilled trade workers.
A major advantage to batterypowered systems is that they eliminate gas headaches by removing noxious emissions and lowering noise levels. Some cordless equipment systems also provide a unified platform of solutions, all powered by the same interchangeable batteries.
Furthermore, battery-powered alternatives are more reliable than gas, with push-button starts that perform consistently under any conditions.
Meanwhile, substantial government incentives are making the long-term investment in cordless electric systems more palatable Finally, a growing number of cities and states are passing laws restricting the use of gas-powered equipment.
No Gas Headaches
As the Centers for Disease Control and Prevention (CDC) noted, skilled trades professionals who regularly work with fume-emitting gas engines are at a higher risk of life-threatening carbon monoxide poisoning.
Gas emissions are especially damaging to personnel working on indoor jobsites and confined spaces with poor ventilation.
Compared to gas alternatives, cordless power tools and equipment can be safely operated for longer periods without installing specialty ventilation to remove emissions.
Less Noise
Another benefit of battery power is its potential to dramatically reduce noise pollution on the jobsite. Roughly 22 million workers are exposed to dangerous levels of noise in the workplace every year, according to
the CDC. Battery-powered tools and equipment are quieter, making for a safer and more productive jobsite.
The lowered noise level reduces the risk of hearing loss and makes it easier for operators to communicate with one another, improving safety on the professional jobsite.
More Reliable
Cordless tools are more reliable than gas engines, with push-button starts
to receive up to $40,000 in federal tax credits for purchases of electric commercial vehicles.
Long-Term Investment
Electrifying their inventory can save contractors time and money longterm by eliminating fuel and engine maintenance expenses. With a single system of compatible batteries, contractors can simply recharge their battery-powered tools and equipment
position cordless tools and equipment to surpass gas-driven alternatives in the years to come.
BOTTOM LINE
The construction industry’s shift toward battery-powered tools and equipment is being driven by the increased productivity and versatility that these solutions can introduce to the jobsite. With power tools having
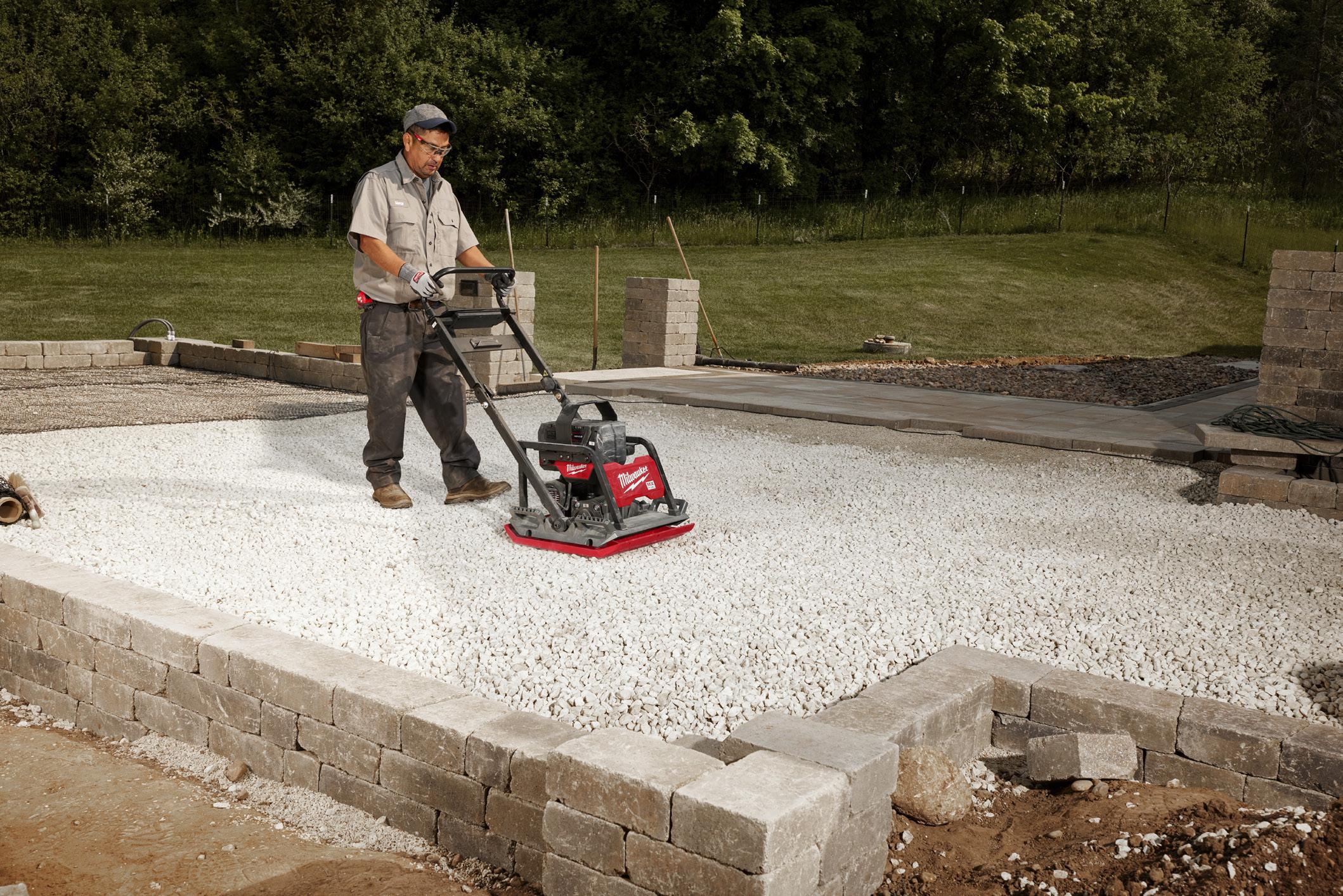
that work every time. Comparatively, starting gas-powered equipment can be difficult, time-consuming and inconsistent.
With battery-powered equipment, you no longer need to worry about priming and choking the engine, ensuring that the on/off switch and throttle are in the correct position, or tricky pull-starts that jam up or simply refuse to turn the engine over.
With lithium-ion battery power, starting even the most heavy-duty piece of power equipment is as simple as pressing a button.
Government Incentives
State and federal tax credits are a popular mechanism that governments use to encourage the adoption of more sustainable electrical alternatives to gas engines. Contractors are wellpositioned to take advantage of these tax credits, provided they’re willing to take the leap to electrification.
Under the Inflation Reduction Act, for example, construction companies and other businesses may be eligible
Battery-powered tools and equipment are much quieter than their diesel counterparts, making for a safer and more productive jobsite.
using onsite electrical utilities instead of paying for gas. Meanwhile, battery power doesn’t have the same upkeep needs as gas engines, which routinely require parts like air filters and pullstart cords to be replaced.
Changing Legislation
Depending on where you live, it may no longer be legal to use certain types of gas-driven tools and equipment.
Concerned about their negative environmental impacts, a growing number of cities and states have laws restricting the use of gas-powered outdoor power equipment.
Battery Technology Innovation
Cordless tools and equipment are in a constant state of evolution. The lithium-ion batteries of today run longer, charge faster and are much more powerful and reliable than their ancestors from 10 years ago.
Meanwhile, the efficiency and power of gas engines has remained largely unchanged over the last several decades. Advancements like these
already cut the cord, construction equipment is now poised for an electric revolution of its own as the overall demand for lithium-ion power rises over the next decade.
Global factors aside, it is difficult to deny the many advantages of converting to an all-electric inventory. From their elimination of gas headaches to their constant evolution, battery-powered tools and equipment deliver a range of benefits that increase efficiency and improve safety on the jobsite.
Read more at: eqtoday.co/electrictool
Alicia Rothenberg is senior manager of product marketing for Milwaukee Tool.
The development of mobile lighting solutions that leverage LED technology and innovative power sources has transformed illuminating jobsites.
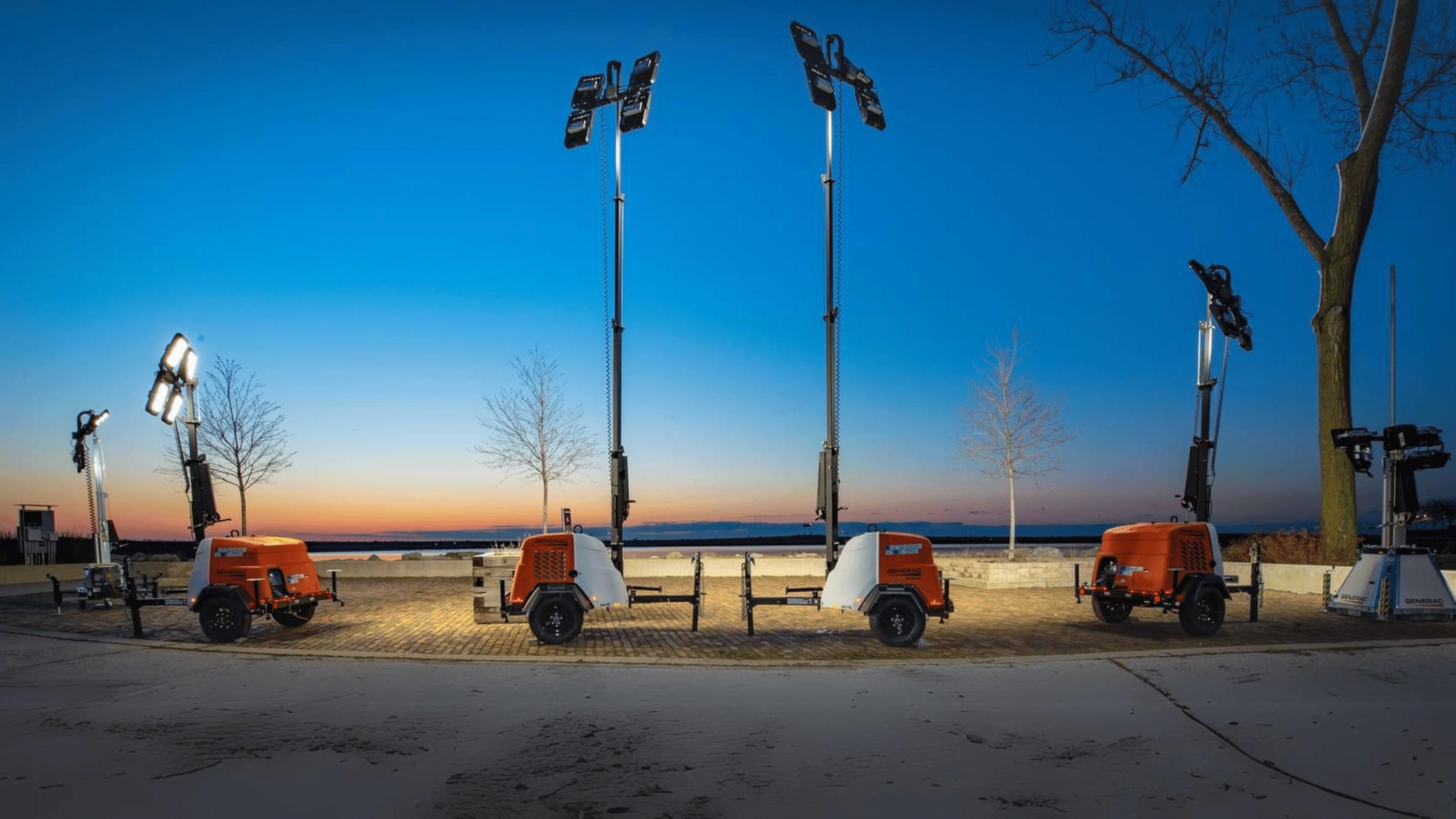
Illuminating Flexibility
The flexibility and efficiency of jobsite lighting are critical to the success of modern construction projects.
In the rapidly evolving construction industry, flexibility and efficiency are paramount. As projects become more complex and timelines tighten, the demand for versatile, reliable lighting solutions has never been greater.
EVOLUTION OF JOBSITE LIGHTING
Traditionally, jobsite lighting relied heavily on diesel-powered light towers equipped with metal halide or highpressure sodium lamps. While these systems provided the necessary illumination, they have been complemented by the advent of LED technology. LED technology offers:
˜ Higher energy efficiency
˜ Longer lifespan
˜ Instant on/off capabilities without the need for warm-up or cool-down periods
This advancement has paved the way for new, more flexible lighting solutions that cater to the dynamic needs of construction jobsites.
ADVANCED MOBILE LIGHTING SOLUTIONS
This transformation has required the development of mobile lighting solutions that use LED technology and innovative power sources. These offer flexibility, efficiency and sustainability.
Battery Power
Battery-powered light towers use advanced battery technology to deliver low-noise, zero-emission lighting solutions. Models offering extended runtime without recharging are ideal for indoor jobsites and events where noise and emissions are a concern. Look for a product that is designed to seamlessly connect with other units to extend lighting areas as needed.
Solar Power
Solar-powered light towers harness solar energy to provide eco-friendly lighting solutions. Ideally, you’ll find models equipped with multiple solar panels and a maintenance-free battery
pack that can operate autonomously with a dusk-to-dawn scheduler.
This design type eliminates the need for fuel, reduces emissions and operates silently, good for environmentally conscious projects.
Efficient Diesel
Combining robust diesel power with advanced LED lighting, diesel-powered light towers offer extended runtime on a single tank.
Those that feature multiple LED fixtures and a compact, durable design are ideal for long-term projects where reliable, high-performance lighting is essential.
Plug-In Light Towers
Designed for sites with access to the grid power, plug-in light towers provide continuous, reliable lighting without the need for fuel. These towers are beneficial for projects in urban or industrial areas where minimizing emissions and noise is critical.
They offer high performance and efficiency with the added convenience of a constant power source.
THE FUTURE OF JOBSITE LIGHTING
As the construction industry continues to push towards sustainability, the role of alternative power sources in jobsite lighting will become increasingly
important. However, diesel-powered light towers will remain a crucial part of the product offering, meeting the high demands for reliable, long-term illumination in different applications.
The commitment to providing the right solution for every situation, from traditional diesel systems to the latest in battery and solar technology, remains steadfast.
The flexibility and efficiency of jobsite lighting are critical to the success of modern construction projects. The range of light towers available exemplifies the dedication to providing versatile, sustainable and reliable lighting solutions.
Whether using traditional diesel power, the latest in battery and solar technology, or plug-in options, innovative lighting solutions are available for a variety of needs— from budget and sustainability to runtime and efficiency—ensuring optimal lighting performance for any application. Read more at: eqtoday.co/joblite
Vince Hunt is senior product manager for Generac.
Generac SLT-D CUBE Stationary Hypercube Light Tower
Generac offers the SLT-D CUBE Stationary Hypercube Light Tower for jobsite illumination in remote areas, construction sites, public locations and more. This portable light tower is powered by a Kubota Z482 two-cylinder diesel engine and equipped with four 320-W LED lights. The solid-state LED lights generate up to 184,000 lumens of output during use (46,000 lumens per LED light).
An included dusk-to-dawn sensor and timer controller automates light operation. The lights are elevated by a galvanized mast with six sections. Operators can manually rotate the mast up to 340 degrees when fully extended. An optional diffuser kit is available for expanding light distribution. A center lifting point and forklift pockets enable transportation around work areas.
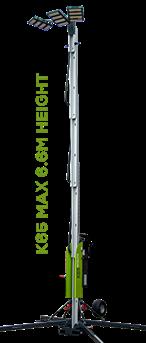
Ritelite Systems K65
Ritelite Systems’ quad pod K65 mobile lighting towers gathers the maximum light emitted from the LEDs (measured in lumens) and enables the user to optimize the light projected onto the work site (measured in lux) to suit the application.
Specially designed optics enable the LED modules to be aligned almost parallel to the ground instead of pointing directly in the worker’s line of sight. This helps prevent accidents on the construction site caused by distraction from light glare. The beam controlled LED light heads are driven by remote and dimmable LED drivers mounted at the base of the mast.
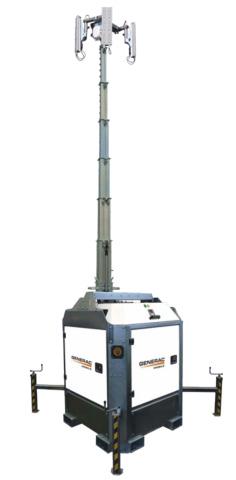
PLS Quasar 360 Balloon Light
The Quasar 360 patented unique latch and slide assembly weighs only 16 lbs. It’s one push to rapidly deploy and another to de-latch the balloon has made it the simplest to set up.
Robotically welded, nickelplated latch and slide are built with rust protection for many years of service. The top and bottom assemblies are anodized billet aluminum to ensure strength.
This design was made to withstand the rigors of heavy construction and outdoor elements. Easy to fabricate mounts for different applications with no set screws to fail.
Portable Lighting Solutions is one of the only balloon light manufacturers to offer a screw in, consumer replaceable LED bulb.

Multiquip GloBug Lights
Multiquip offers battery-powered GloBug light carts for construction site illumination. The following two models are available: Spotlight (GBBAT3S4M) and Balloon Light (GBBAT8BM). The GABBAT3S4M offers four 300-W LED lamps that emit 212,000 lumens of focused directional lighting.
The GBBAT8BM balloon light emits 110,000 lumens of 360 degrees of diffused, non-glare LED light that reduces shadows and promotes safety. Both models have a threestep dimming switch. The telescopic four-stage, 20-ft. mast allows users to control how wide an area to illuminate. The lithium-ion battery features a full 8 hours of run time on GBBAT3S4M and 12 hours of run time on GBBAT8BM at full load.
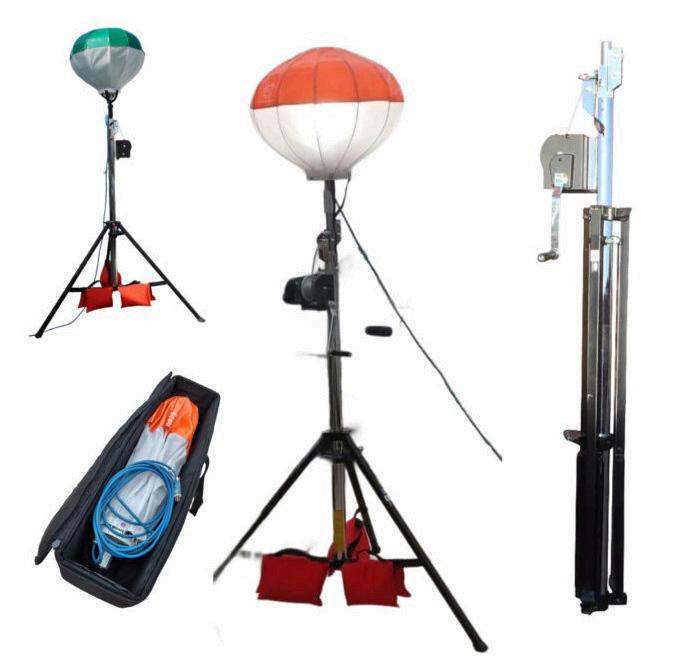
Allmand Bros Hybrid LT-Series Portable Light Tower
Allmand Bros’ Hybrid LT-Series, a concept hybrid light tower for construction projects, is equipped with a Vanguard lithium-ion battery, allowing for all-night operation without noise pollution.
Powered by smart technology, an electronic controller gives users immediate runtime feedback, allowing them to reduce their carbon footprint through light-level settings. Allmand also offers MaxiPower generators, making power accessible in remote work areas.
The entire generator line, which includes the MP8XR, MP15XR, MP25 and MP45, is manufactured in Nebraska. The generators are used in oil fields, drilling rigs, special events and music festivals because they provide reliable, quiet and clean power.
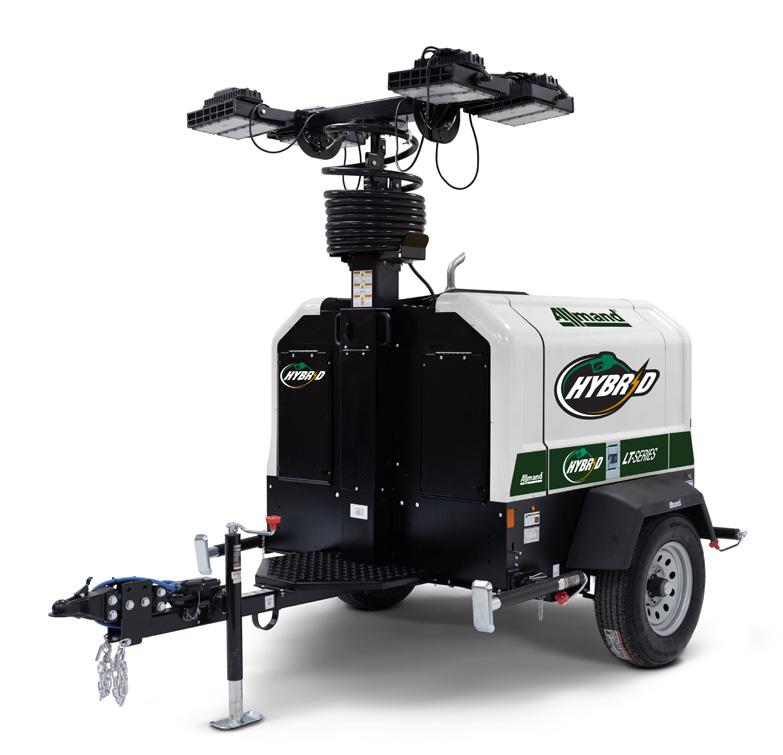
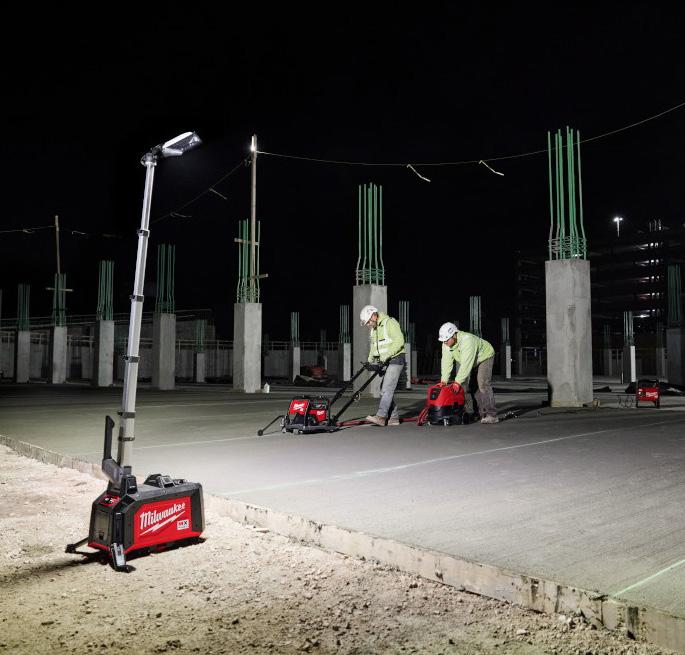
The MX FUEL ROCKET Dual Power Compact Tower Light requires 75% less space to store and transport compared to the MX FUEL ROCKET Tower Light/ Charger. Delivering up to 15,000 lumens of task and area lighting, it provides coverage of more than 2,300 sq. ft., five times the usable light of an M18 ROCKET Dual Power Tower Light. The tower light provides up to 3 hours of runtime on high when powered with the MX FUEL REDLITHIUM XC406 Battery and features dual-power capabilities.
Progress Solar Solutions SLT Series
The SLT Series from Progress Solar Solutions consists of updated mobile solar light towers that are 100% emissions free and use zero diesel fuel. They offer 42 hours of runtime on each charge and qualify for federal and state renewable energy incentives.
The towers feature automatic timers and dawn-to-dusk operation for automated functionality. Solid-state LED technology enables durability in outdoor areas and a lifespan of 50,000+ hours. During use, the light towers offer 52,000 lumens of output. Elevated illumination helps position the lights above busy work areas. Jobsite transportation is facilitated by a singleaxle trailer. Configurations are available for applications in all solar insolation zones.
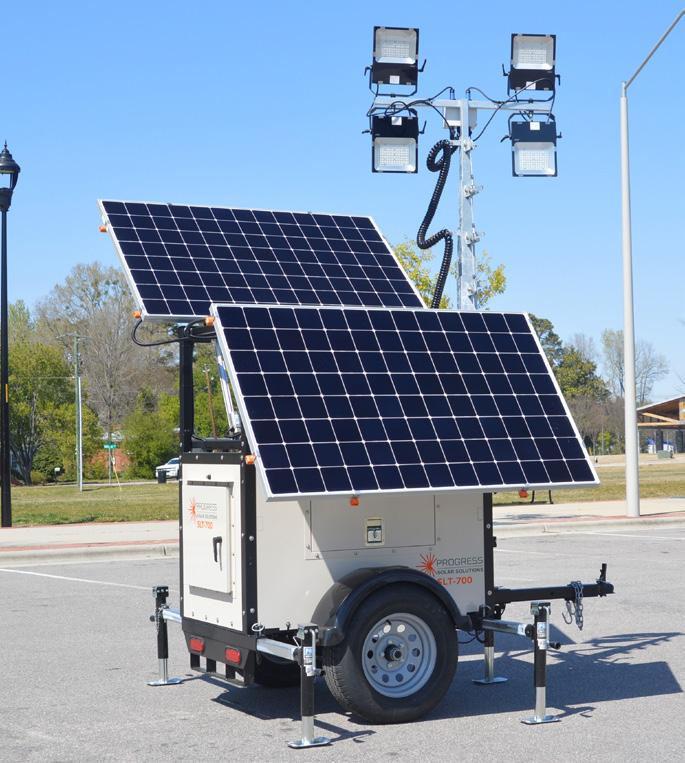
Machine Control in Concrete Applications
With conventional stringliners, the process is vulnerable to human error.
Automated and robotic stringlines help remove that human variable and increase accuracy.
Machine control technologies range from 2D and 3D grade control to automation, robotic control and augmented reality.
GPS/3D control—eliminating the need for placing stringline by hand—is becoming an industry norm, Stephen Bullock, Power Curbers president, pointed out.
These technologies address challenges such as:
• A shortage of qualified labor
• An increased productivity demand to address the backlog in building or repairing infrastructure
• A need to increase profitability
“Contractor’s Guide to Machine Control” on forconstructionpros.com noted how GPS improves labor and resource allocation, how the strategic use of 3D-printed components improves site efficiency, and how its sensors yield more visibility into geography and structures.
These technologies offer the needed boosts in productivity and ROI as well as increased machine efficiency and safety.
The GOMACO company noted that true 3D eliminates human error involved with setting a physical stringline because 3D works from a digital model with a virtual stringline, a constant that cannot be physically changed.
Conventional stringlines are prone to displacement since equipment or people can accidentally hit the lines causing stringline movement and paving errors. Errors may come from the surveyor’s grade control stakeouts, the company pointed out.
AN ABUNDANCE OF MACHINE CONTROL IN CONCRETE WORK OPTIONS
“The development process for curb and gutter machines started in the early 2000s, paused during the Great Recession, and over the past five years has really gained momentum,” Bullock said. “Even contractors who are not yet ready to invest in stringless control systems are ordering machines [that are] GPS-/3D-ready.”
In 1999, GOMACO began paving with 3D on its equipment, and the technology is now used in grade trimming, curb and gutter tight radii, tunnel floors and walkways, airport runways and aprons, highways, interstates, concrete overlays, municipal projects, safety barriers, and golf cart paths, among other applications.
GOMACO works with Leica Geosystems, TOPCON Positioning Systems and Trimble. GOMACO’s controls and programming software are designed to seamlessly interact with 3D.
The 3D computer assesses input from the total stations and prisms, compares that information to the project design model and then outputs the elevation and steer commands to the GOMACO controller.
Sonic sensors are used on GOMACO texture/cure machines to eliminate the need for stringlines on slipform paving projects.
More features continue to be integrated into the system. 3D can now be used to control the firing of an accessory like sidebar inserters and IDBI. Different stringless systems are
Sonic sensors are used on GOMACO texture/cure machines to eliminate the need for stringline on slipform paving projects.
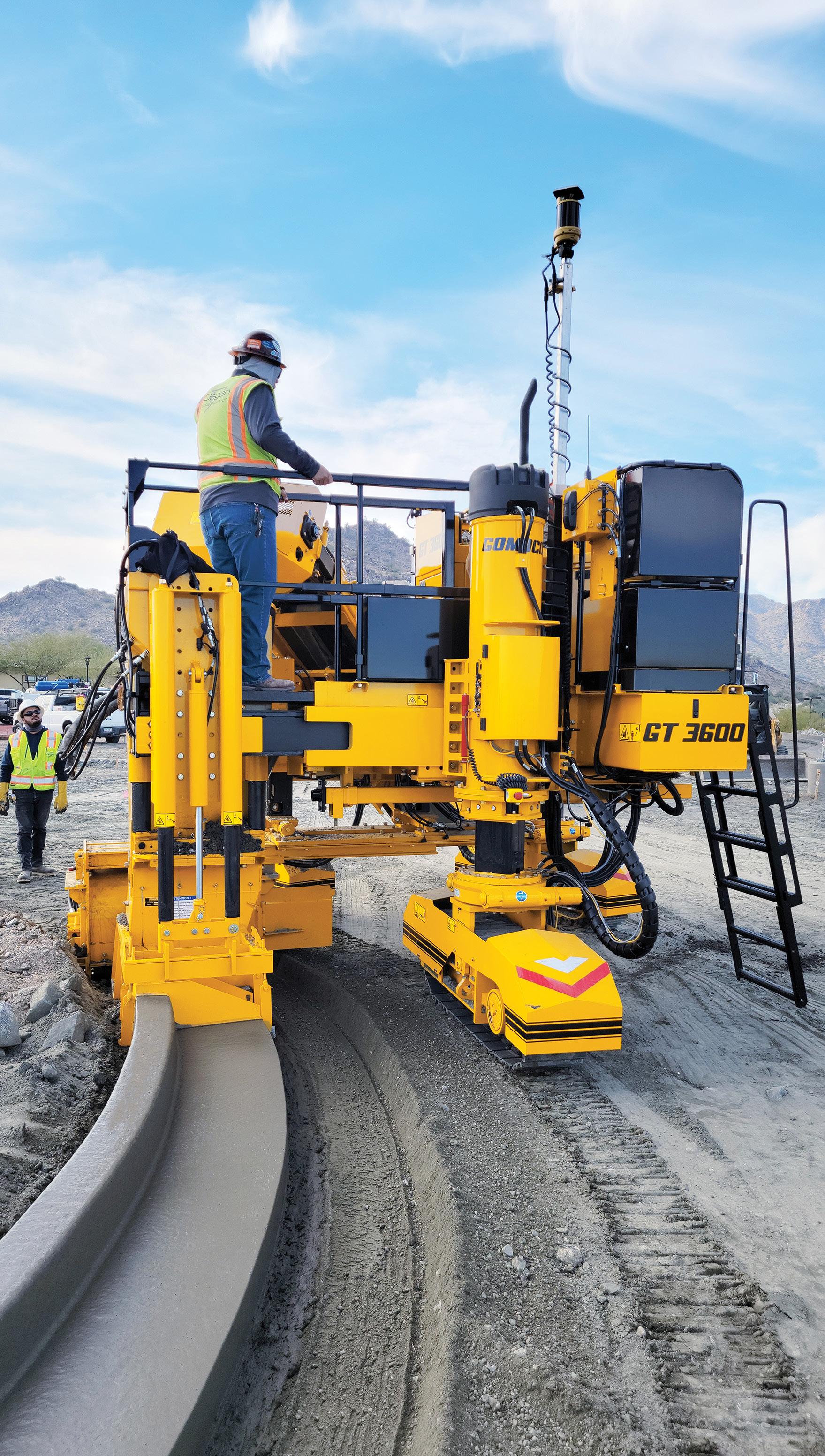
also available for placer/spreaders and texture/cure machines.
“The use of total station GPS and [an] augmented laser system in coordination with GPS gives you the accuracies of different levels,” noted Matthew Morrison, GOMACO’s 3D machine controls manager.
The type of sensor that will be used is dictated by the job. A plethora of different sensors may be used to obtain the right level of accuracy and cost association for a job such as city streets. In contrast, local governing specifications for accuracy in jobs such as highways and airports dictate what sensor will be used in conjunction with 3D machine control

specifically for concrete paving, Morrison said.
“We use a combination of total stations, GPS and laser augmentations to give them the benefits that would be pertinent to the job like a Walmart parking lot where there are 120 islands,” Morrison added.
“For that, we would use a different system than we would use [for] an airport or a highway specification.”
At Miller Formless, slipform pavers from small curb machines to the largest mainline pavers all utilize machine control.
“For decades, the standard has been either analog-based or digital stringline control with proportional hydraulic systems,” noted Tod
Smith, vice president of product and customer experience for Miller Formless.
“These systems automate grade and steering control to achieve a highquality product within acceptable tolerance. In more recent years, there [has been] a shift to integrate 3D control into the machine’s main control system.”
In these cases, the machines are all still capable of using stringline but can also run without string using robotic total stations and/or GPS, said Smith, adding that using 3D systems keeps jobs cleaner, helps decrease set-up time and increases production.
GNSS technology, such as Topcon’s Millimeter GPS, is designed to provide a complete system for concrete work. It uses satellite signals to determine precise positioning, enabling the accurate placement of concrete for different applications like curbing, paving, and general concrete.
Laser technology offers vertical accuracy crucial for concrete work. Topcon’s system employs a rotating laser to ensure precise elevation control, complementing GNSS for comprehensive accuracy in horizontal and vertical dimensions. The same laser can simultaneously control multiple machines, providing realtime elevation feedback to grade checkers.
Topcon integrates robotics systems into concrete paving processes, ensuring uninterrupted and precise data delivery to control systems. These systems can communicate with multiple robotic total stations, providing sub-centimeter accuracy crucial for complex paving projects.
“Contractors can benefit from a combination of GNSS, laser-based, and robotics systems tailored to their specific project requirements and environmental conditions,” said Brian Lingobardo, senior director of intelligent paving business development at Topcon Positioning Systems. “This versatility ensures adaptability across ... concrete construction applications.”
MACHINE CONTROL IN CONCRETE WORK YIELDS SIGNIFICANT BENEFITS
Mobility
“Previously, the way we would do a job is we would have to set stringline that would become a physical barricade to other applications trying to do work within that zone,” Morrison said.
Mobility is the biggest benefit from using machine control, he noted.
It is easier to pave in tight clearance conditions because extra room for stringline is not needed and the contractor has the ability to pave anywhere on the project at any time.
Not only does 3D increase flexibility but it also is designed to improve jobsite logistics, such as not
Miller Formless slipform pavers, from small curb machines to the largest mainline pavers, all use machine control.

having to work around or be limited by stringlines.
“If something is not ready, you can hop to another area and do not have to wait to do any stringline installation. You have a free open site where you can wander out and accomplish any task at hand,” said Morrison, adding that level of mobility makes the ROI “almost incalculable.”
Machine control removes the numerous human errors that come into play by setting up, measuring, setting a pin and keeping the stringline “picture perfect” until the day it is time to pour, Morrison said.
“Between Mother Nature and all the other things indicative of a jobsite, from other machines to wildlife and children, it becomes very difficult to maintain,” he added.
“The ability to take something that somebody has drawn in a CADWorx file and implement it directly onto the ground within the specification given is definitely a huge benefit. There is no interpolation,” said Morrison.
Time Savings
“For us to come off of a truck and take 5 minutes to set up our 3D to go to work versus a couple of days to string a machine jobsite to be ready to go ahead and drop the machine is time savings in a large abundance,” said Morrison.
The reduction in labor needs is the biggest driver for most contractors moving to machine control, Bullock said.
“Setting stringline is laborious and requires expensive [personnel] hours,” he added. “Contractors are excited to reduce crew sizes and eliminate physically demanding stringline setting.”
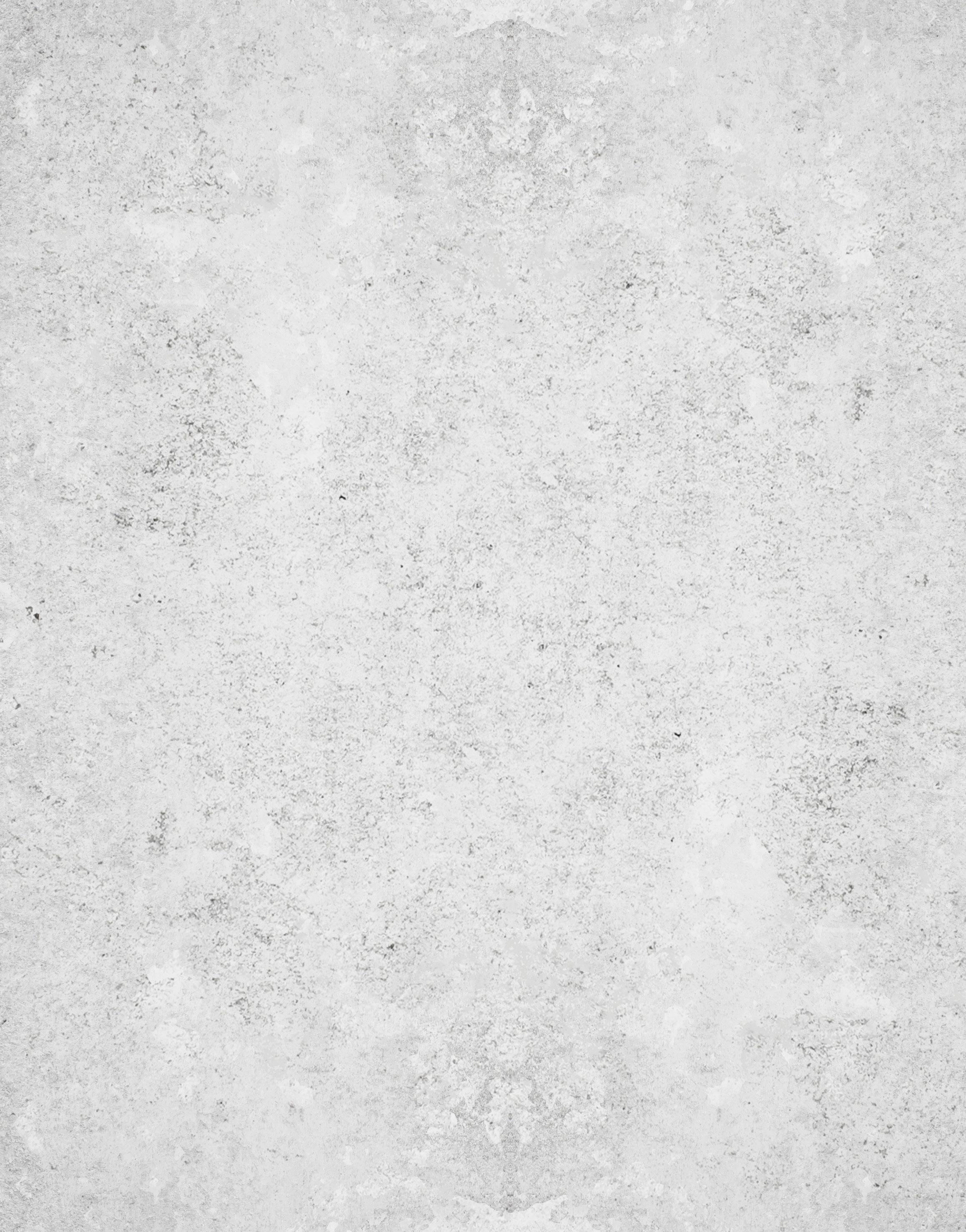
MORE MILES. MORE DEADLINES MET. MORE JOBS.

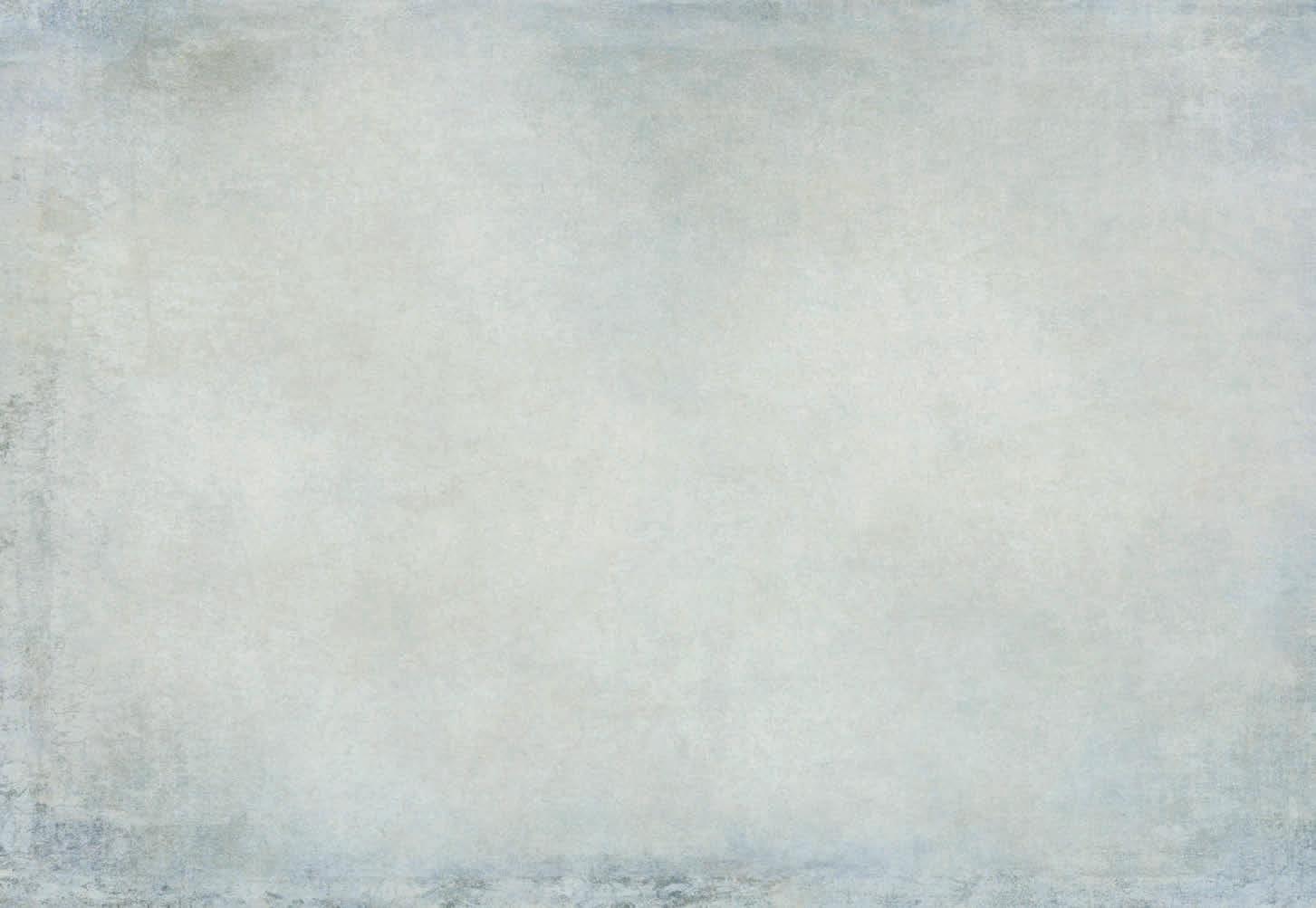
Every job comes with a unique set of circumstances. But the two things all jobs have in common are concrete and deadlines. Which is why we’ve designed our drills to be the fastest, most accurate, operator-friendly machines on the market, keeping your crew safe and on pace for more jobs. No matter the deadline.
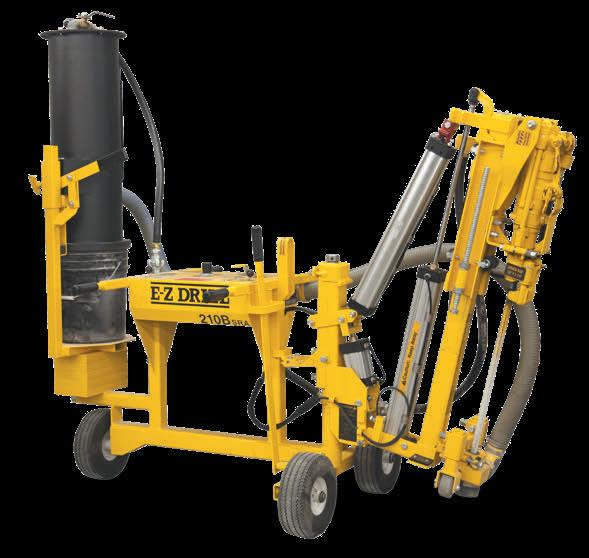
Bullock noted that one of his company’s end users told him “I couldn’t care less about stringless controls, but I can’t find anyone to pound pins anymore.”
“A secondary benefit and one that surprised us was how much machine control opens up the jobsite, especially in tight parking lots,” said Bullock. “Elimination of stringline gives flexibility to concrete trucks, improving flow on the site, and allows for other construction machinery to move more freely.”
Concrete Placement Accuracy
Setting up stringline by hand creates imperfection because of human hands adjusting the line and judging what’s acceptable.
“The accuracy with which GPS/3D systems can control the machine is remarkable,” said Bullock.
Machine control is a necessity to keep the product in proper tolerance, Smith noted.
By eliminating the need for traditional stringline and staking, machine control streamlines the construction process, said Lingobardo.
“Contractors can work more efficiently, saving time and resources while maintaining accuracy,” he said. “Machine control technologies also offer unmatched precision, enhancing the accuracy of concrete placement. This precision is essential for achieving desired grades and smoothness in concrete surfaces.”
This optimization reduces material wastage, contributing to cost savings for contractors, Lingobardo said, adding that machine control minimizes the likelihood of errors during concrete placement, preventing the need for rework.
“Contractors can achieve desired specifications on the first attempt, saving both time and resources,” he said.
Machine control technologies offer flexibility and adaptability in navigating tight paving corridors or overcoming obstacles on construction sites. Lingobardo added that contractors can adjust and
adapt to challenging environments without compromising accuracy or efficiency.
MACHINE CONTROL AUTOMATES CURB & GUTTER WORK WITH ACCURACY
Power Curbers has worked with machine control suppliers to make the interface easy.
“Machine operators use an easy-to-read screen with a virtual map to track the machine throughout the job,” Bullock said. “Between numerical data and the map display, the operator knows exactly where the concrete is going relative to the model. A crew member also can recheck the concrete’s location using a rover as concrete slips out of the mold.”
“Without string, you would need to use a separate 3D system such as Leica, Topcon or Trimble,” said Smith.
“It can also provide contractors with better, more efficient results when working with complex designs and radius work,” Lingobardo said. “Topcon’s LPS paver system facilitates uninterrupted data communication to control systems, ensuring [the] accurate placement of curbs and gutters without the constraints of traditional methods.”
Contractors can navigate tight paving corridors or work around obstacles with ease using Topcon’s machine control technologies, ensuring accuracy and efficiency in curbing applications, Lingobardo said.
According to Morrison, GOMACO has methods of teaching and mentoring contractors on how to automate curbs and gutters without strings to ensure accuracy.
MACHINE CONTROL PREVENTS REWORK
Machine control technologies provide precise grade and steering control, minimizing errors during concrete placement. Contractors can
A LONG WAY TOGETHER
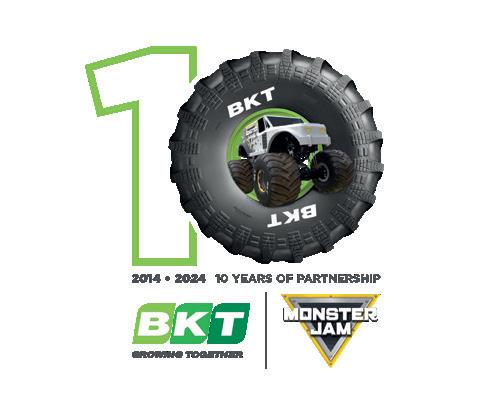
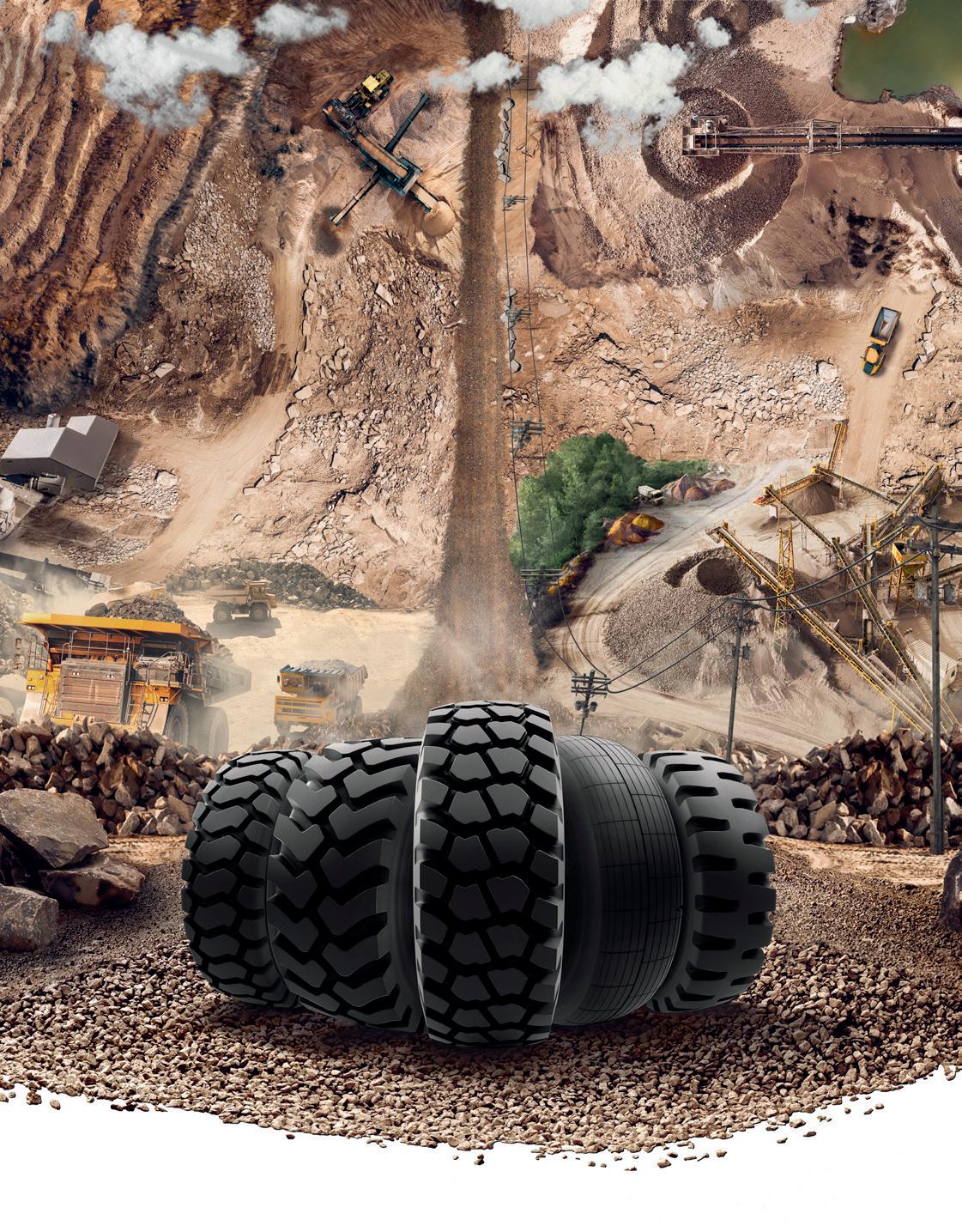

WHEREVER YOU ARE, BKT IS WITH YOU
No matter how challenging your needs, BKT is with you offering a wide range of OTR tires specifically designed for the toughest operating conditions: from mining to construction sites.
Sturdy and resistant, reliable and safe, able to combine comfort and high performance.
BKT is with you, even when work gets tough.


achieve desired specifications with high accuracy, reducing rework.
A CAD design file received before a contractor steps onto the jobsite ensures checks and balances before the paving job is initiated.
“We know that our control is tight,” Morrison said. “We also verify [that] the model ties into all existing structures. We know what our sub-grade looks like because we’ve as-built it, and we know that our grade is within a tolerance.”
“For us to keep our yield—our controlled elevation height versus how much concrete we put on the ground—… as tight as we want to is indicative that we do all those little steps to make sure we control it to the best of our ability.”
Morrison noted that the data is the most important thing with any machine, whether concrete or earthmoving.
“The tighter the specification, the more robust you need to be on your data preparation, your modeling characteristics and completely understanding what you are up against before you take that system and put it in the field. The fieldwork is going through the motions of using these things and
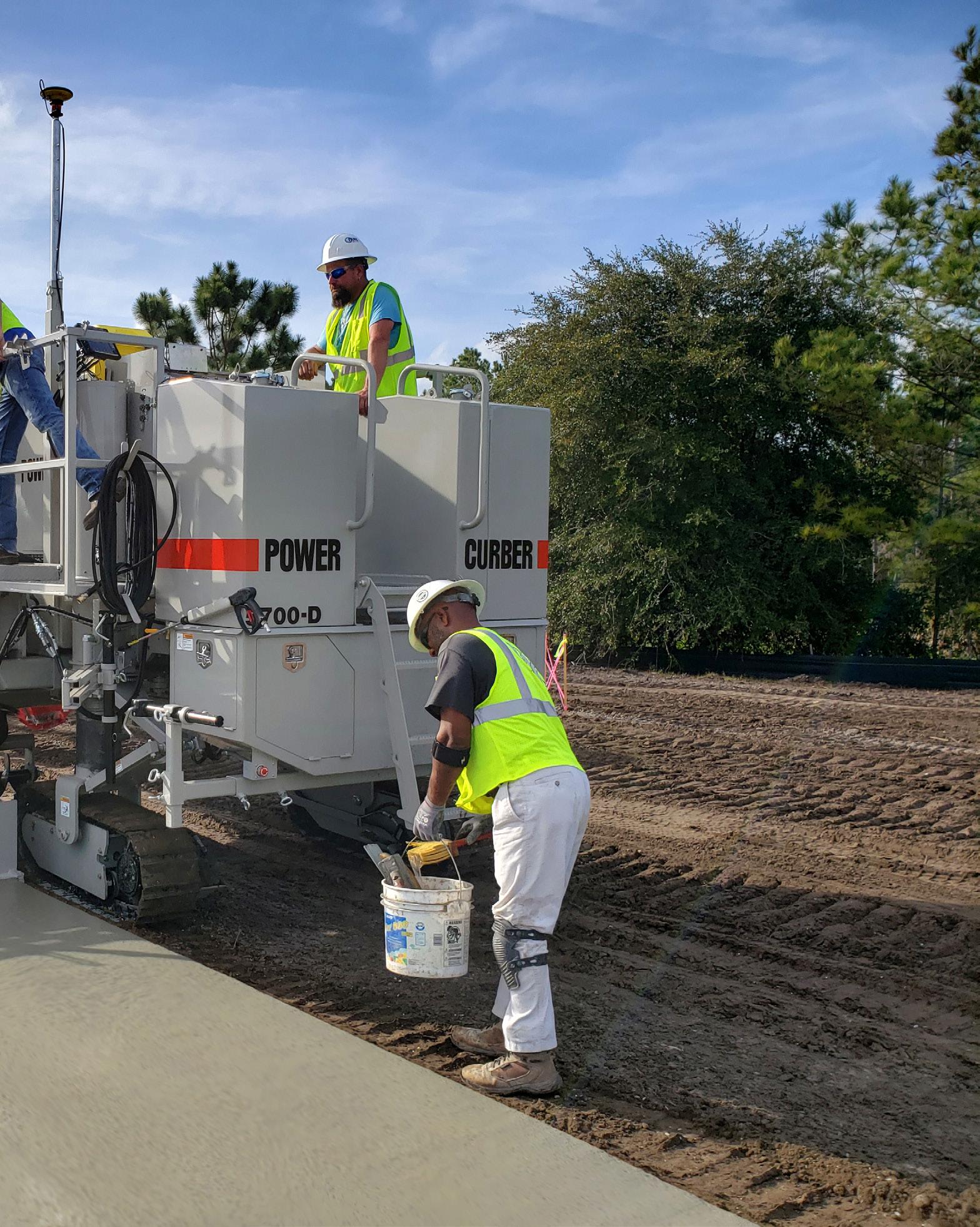
going through the production on the daily data.”
Topcon’s systems offer real-time feedback to operators and grade checkers, allowing for immediate adjustments to ensure proper concrete placement, Lingobardo noted, adding that this proactive approach helps prevent errors before they escalate, avoiding rework scenarios.
“By eliminating the reliance on stringline and staking, machine control streamlines the construction process,” he said. “Contractors can work more efficiently and effectively, reducing the likelihood of mistakes that lead to rework.”
Smith concurred, saying that having that exact location with machine control also enables the contractor to check behind the machine to ensure correct placement.
The technology also levels the playing field for workers regardless of experience, Morrison noted.
“A lot of our machines are smart machines. A smart machine knows where all its appendages are and where all of its accessories are so then it can control them properly in
coordination with the model it is given,” said Morrison.
Using 3D machine control in the field is “quite easy to do on a daily process,” he added. “The things to focus on are the quality of the models, the data we get from the engineers, and the quality assurance and checks we do in the office [before] mobilizing to the machine in the field.”
It is critical to use technology in such a way that it performs as intended. GOMACO noted that signal loss can be caused by obstacles between the line of sight of the total station and the prism on the paver, such as trucks or workers as well as fog or areas with poor quality. Strategically placing total stations can lessen or eliminate fog or sun glare effects.
It is also important that total stations are not set up on windy days where wind may hit them broadside, to anchor the tripods well and position them at closer intervals.
Leica has the auto-target recognition (ATR) lock threshold that monitors the quality of the ATR’s prism following, making sure that the prism is reliably locked onto and tracked to help prevent inaccuracy caused by high winds, fog, dust or heavy rain.
The dual-axis compensator acts as a level to ensure that total stations have not been shaken out of level or knocked over by wind or something else.
If a total station is up to 0.1 degrees off vertical, it will compensate automatically in the measurements for that inaccuracy.
USER FRIENDLY
A key machine control benefit: it is user-friendly. It helps level the playing field in the workforce where workers may have different experience.
“In today’s environment, most machines have ... automation on them from the factory ... All of the things they use in the survey field plays into how easy it is for them to move into stringless on the concrete side,” Morrison pointed out.
Morrison noted that technology integration has produced amazing benefits.
“When I first started doing this a long time ago, it was just focused on 3D making the machine go up, down, left and right,” he said.
Machine control has expanded to automate a significant number of processes in concrete work.
“It is less hassle for you to think about, so in all of the applications that come along with concrete paving, the big benefit is the integration into all these accessories that you’re able to run,” Morrison said.
Read more at: eqtoday.co/mcontrol
TRANSFORMING ENERGY. EVERYWHERE.

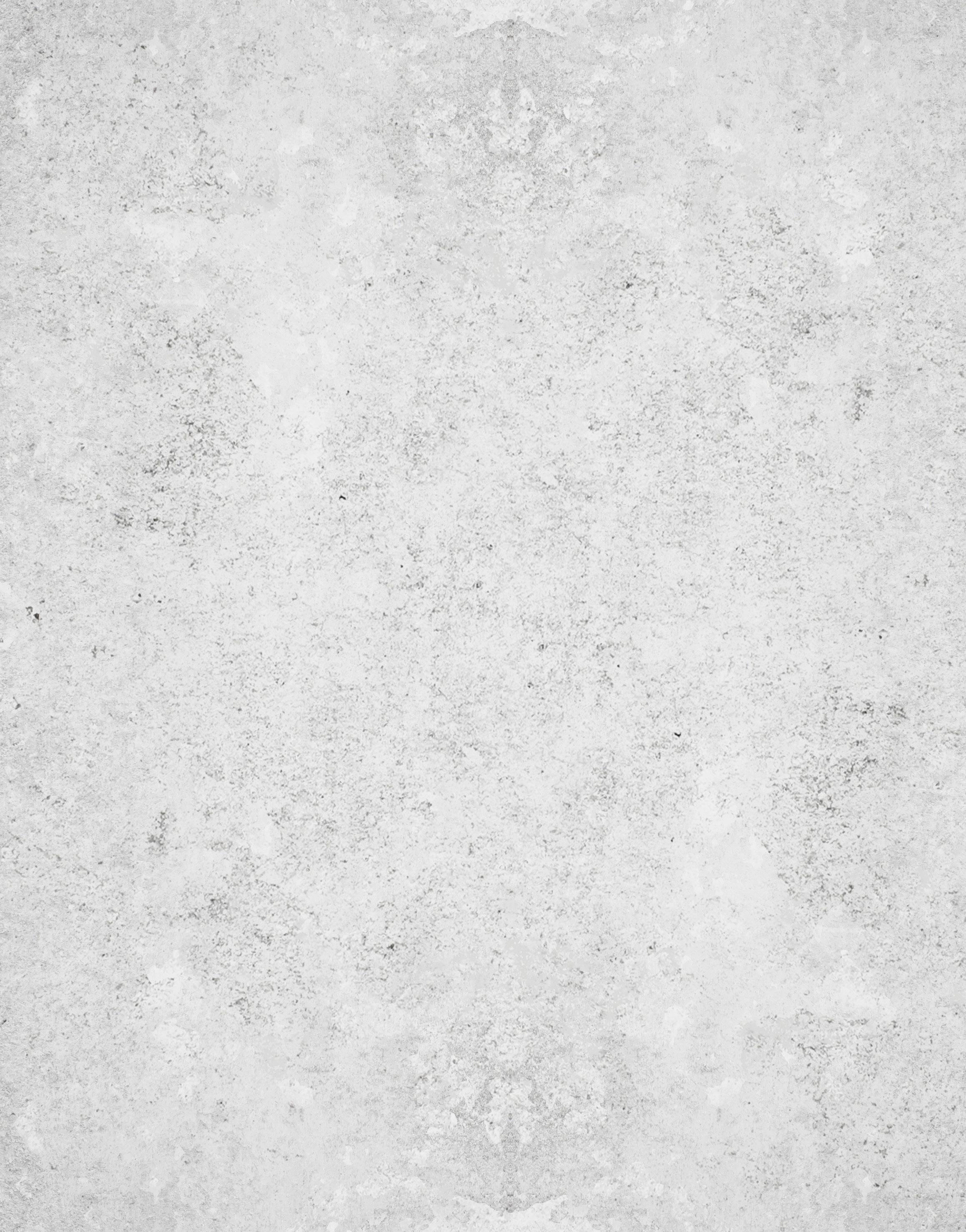
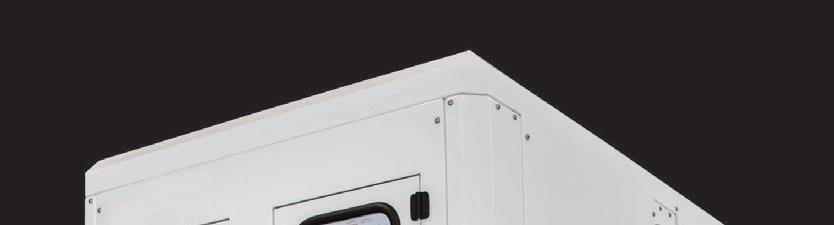
Introducing the MBE, Generac Mobile’s Battery Energy Storage Solution. Featuring built-in telematics and a clever battery that knows when and where to pull energy from to provide a continuous power supply. Built for versatility and durability with two ways to cleaner energy: as a stand-alone solution or hybrid power system when paired with a diesel generator. In a hybrid system, the MBE is designed to work with a generator that results in significant cost savings, reduction of fuel consumption and noise, all while drastically cutting CO2 emissions without sacrificing performance. This state-of-the-art technology provides power system flexibility to construction, events, utilities, urban and remote job site applications.
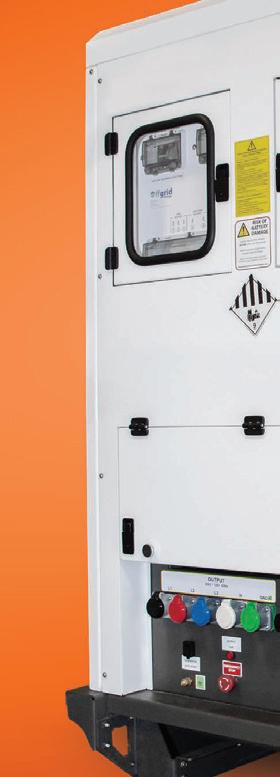
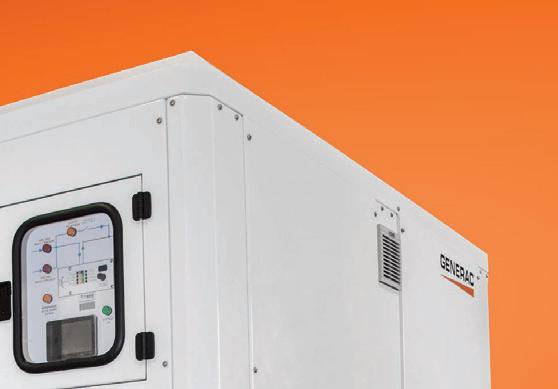
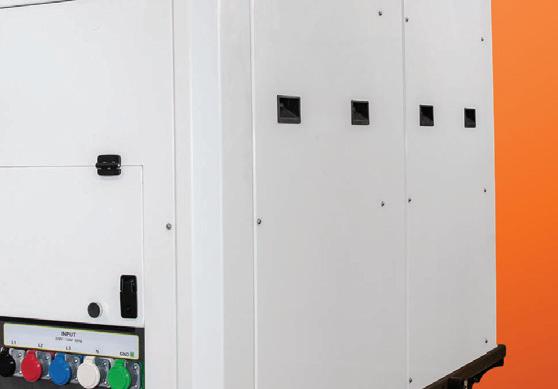
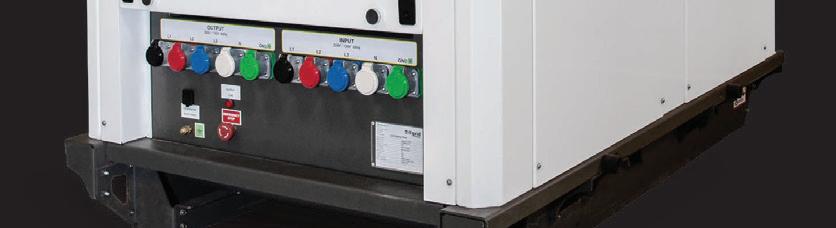
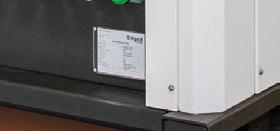
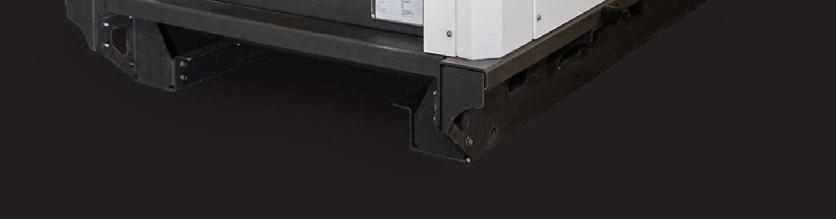

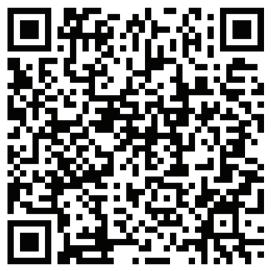
CONCRETE EQUIPMENT
Curb Roller Hydra-Screed HS3000
The Hydra-Screed HS3000 has the weight and strength to move more than 6 in. of concrete along the pour while allowing operators to remain in a standing position.
• Screeds up to 30 ft. in length
• Rubber inserts can easily be removed to accommodate any desired length of pipe, custom V-flume, crowned roller screed and other desired profiles
• Two-way variable speed control
Single pin allows for direction change
• Handles pivot into the desired position
• Requires 3 to 5 gpm at 2,250 psi
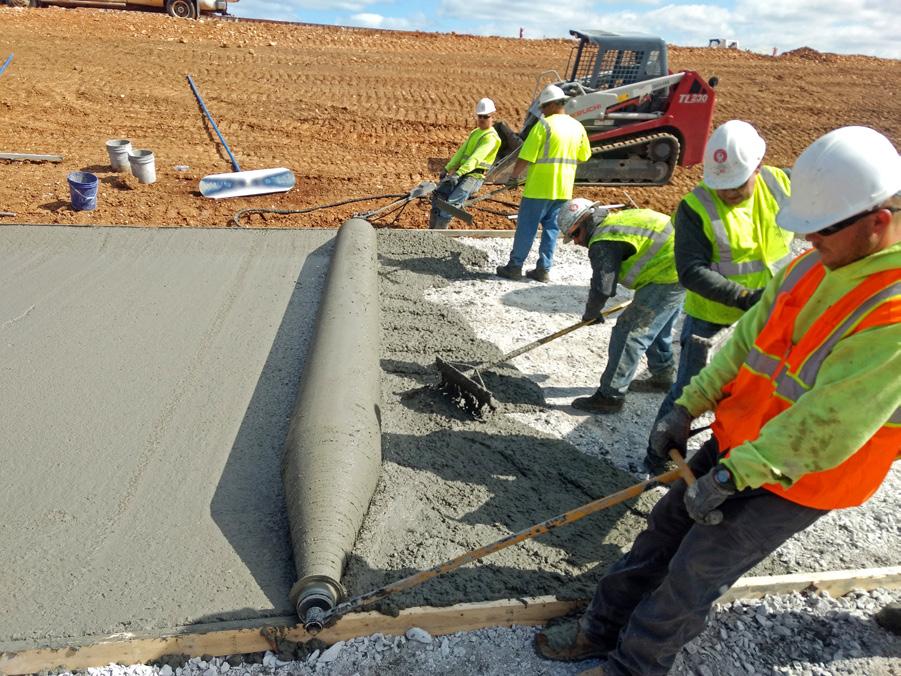
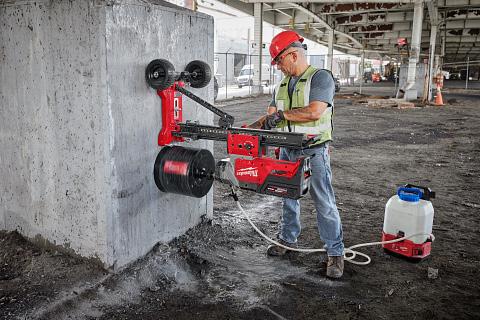
Milwaukee Tool MX FUEL Core Rig With
Stand
Milwaukee Tool launched the MX FUEL Core Rig with Stand, a battery-powered core rig that enables users to core 14-in. holes in reinforced concrete. As part of the MX FUEL Equipment System, the rig delivers four 10-in. holes per charge.
This tool is compatible with all MX FUEL REDLITHIUM batteries. The battery-powered concrete core drill eliminates the need for corded units or extension cords, reducing trip hazards and preventing breakers from tripping or the need for a gaspowered generator. The core rig can be transported and set up without a nearby power source, providing a coring experience without extension cords.
GOMACO CC-1200e Batterypowered Curb Machine
The CC-1200e is equipped with a 48-VDC lithium-ion battery pack that provides enough power for a full day of paving.
Charging options include the standard 8-hr. to 10-hr. normal charge rate or optional 2-hour fast charge system
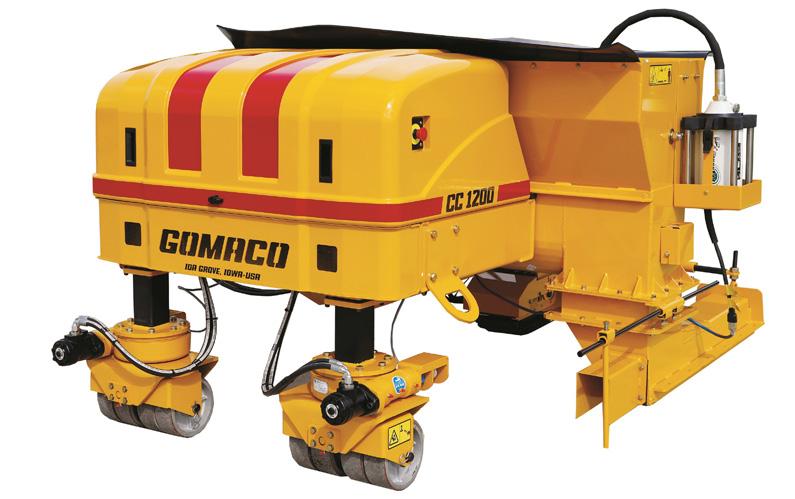
• G+ control system with full-function radio remote control puts all machine operations in the operator’s hands
• Able to slipform a 24-in. radius, depending on mold profile
• Features a 19-cu.-ft. hopper capacity with up to 15 in. of horizontal sliding capabilities for easy alignment with ready-mix trucks
• Curb molds can be interchanged easily and can be positioned on either side for rightside or left-side paving
Makinex MS-150 Mixing Station & Mixer
The MS-150 Mixing Station and Mixer from Makinex for selfleveling cements, compounds, and epoxies is capable of blending up to six bags in seven minutes, all while ensuring precise pouring and reduced waste.
The tool saves time and labor on flooring projects, and curbs operator fatigue and injury thanks to its ergonomic lightweight design. Meticulous mixing and pouring within the single unit is practically guaranteed. It features a removable vacuum attachment for spills and dust suppression, helping to reduce “construction dust”—airborne particles—from construction activities.
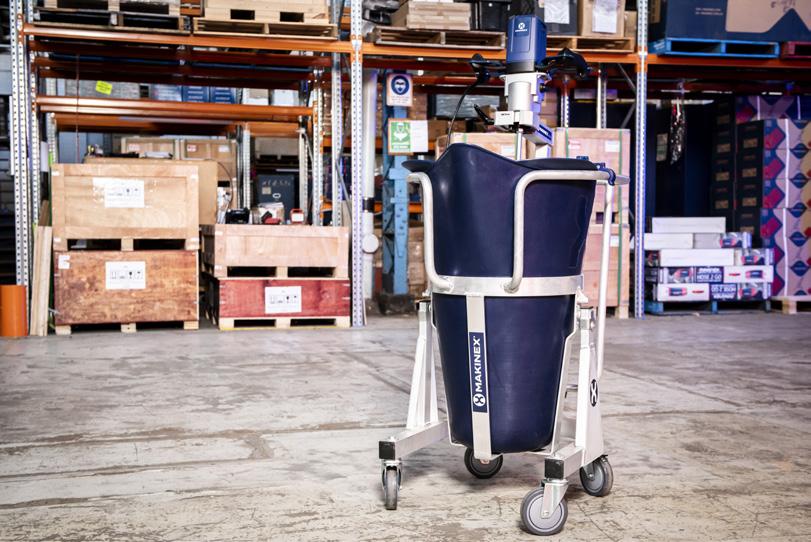
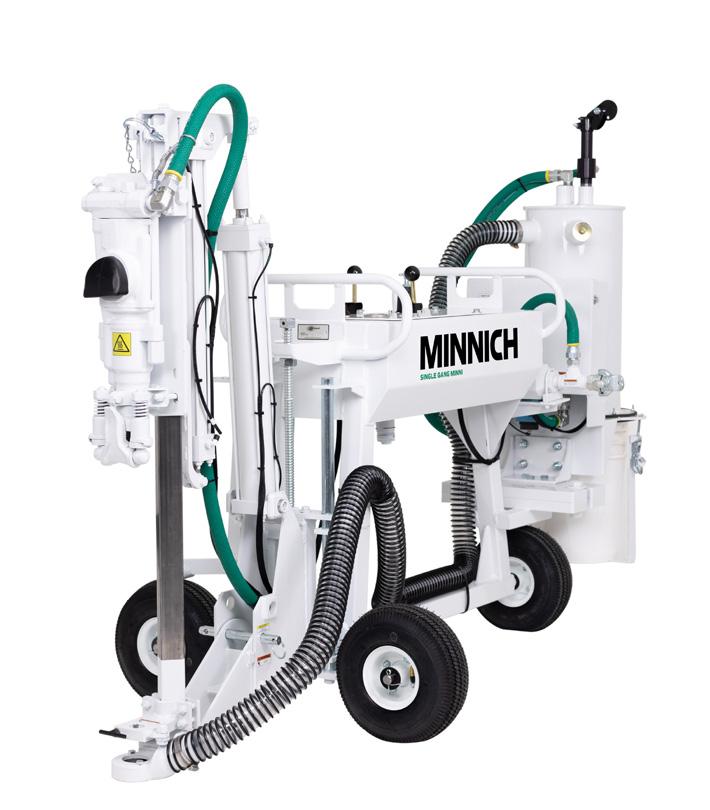
Minnich A-1CL Dowel Pin Drill
The A-1CL dowel pin drill is an on-slab drill that offers horizontal, vertical and 35-degree stitch and skewed drilling positions. The drill is maneuverable but does not include a formal steering system. The A-1CL nomenclature refers to its lightweight design, weighing in at 350 lbs.
The A-1CL reaches a maximum drill depth of 18 in. with an under-collar drill steel length of 24 in. The A-1CL requires 92.2 scfm and 120 psig of pneumatic power. All specs included correspond with the 48-in. model.
The A-1CL will come in four drill widths 48 in., 36 in., 30 in. and 24 in. The optional Minnich dust collection system can be mounted to all Minnich dowel drill units, including the A-1CL for reduced debris on the jobsite and in compliance with OSHA regulations. Concrete dowel pin drilling is an integral part of road construction projects. For these jobs, the dowel pin drilling component must move along safely and in a timely manner.
Ligchine’s SCREEDSAVER ULTRA PLUS
Born with a long reach and a wide pass, the Ligchine SCREEDSAVER ULTRA PLUS was built to screed more and screed faster. Complete with an ultra heavy-duty boom reaching 20 ft. with the new Ultra Performance 14 ft. 6 in. screed head.
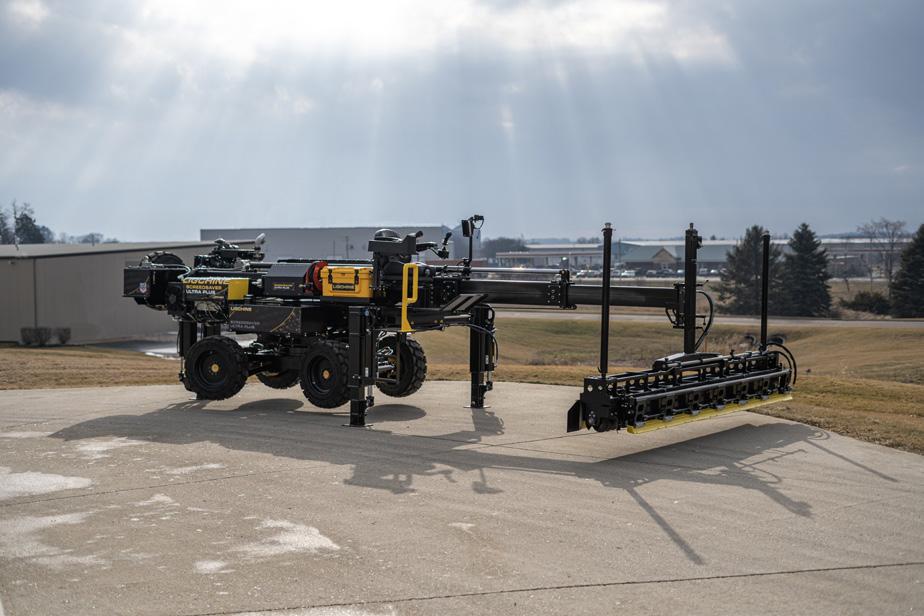
Powering the ULTRA PLUS is a 45-hp Kubota turbocharged diesel engine. For increased maneuverability and traction, the ULTRA PLUS includes selectable four-wheel drive with a two-speed drive range and fourwheel independent steering.
The ULTRA PLUS features an elevated operator’s platform, including a captain’s seat, twin joystick controls, and a 7-in. touchscreen control panel—which also serves as a display for the industry-first SCREEDVIEW camera system. On board, contractors will find a built-in pressure washer for clean-up, two locking toolboxes and two high-capacity water tanks.
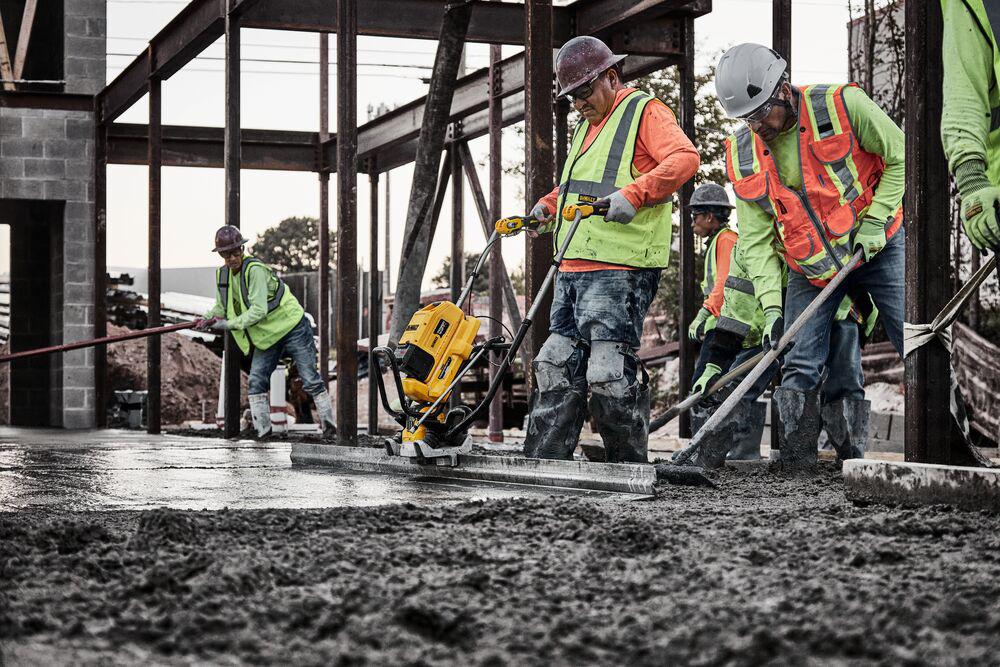
DEWALT POWERSHIFT Screed
DEWALT announced the launch of DEWALT POWERSHIFT, an electrified equipment system for concrete jobsites. Designed to meet the needs of concrete professionals, the electrified line will allow users to transition away from gaspowered equipment.
The system, made up of six concrete tools, uses the same DEWALT POWERSHIFT
554 WH battery and high-speed charger across all tools. The DEWALT POWERSHIFT Screed has the power to break a cold joint and adapts to the three most common bar/board styles.
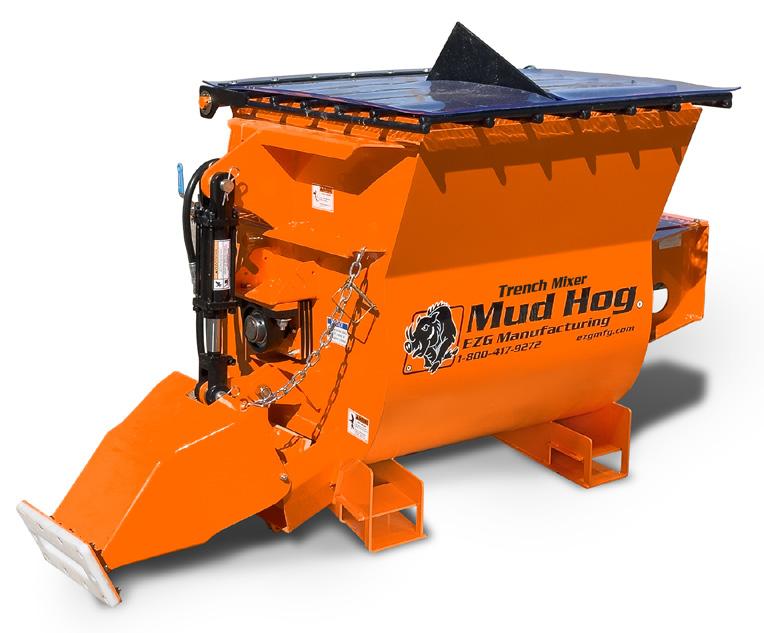
EZG Manufacturing Mobile Mug Hog Trench Mixer
EZG Manufacturing introduced the Mobile Mud Hog Trench Mixer, a hydraulic-controlled solution designed for pour applications in tight spaces and utility work. Designed for microtrenching and utility work, the Mobile Mud Hog Trench Mixer features controlled material flow.
The hydraulic-controlled mixer can be used with walk-behind and standard- or full-sized skid steers. The Mobile Mud Hog Trench Mixer has a range of features that contribute to its performance. It is equipped with sturdy integrated lifting pockets for transport and comes with a standard skid steer attachment plate. The mixing bin accommodates 9 cu. ft. or 1/3 yd. of material, equivalent to eight to nine 80-lb. premix bags.

PEAK PERFORMANCE Starts With the Right Oil & a Strong Maintenance Plan
Using a strategy involving oil analysis and a lubrication team improves uptime and efficiency.
Imagine two different construction fleets, working identical projects in the same region. In one, each piece of equipment uses its own lubricant, specifically chosen to maximize that machine’s performance. In the other, one product has been selected that functionally lubricates the entire fleet. This fleet trades total optimization for a simple and efficient maintenance process with minimal risk of human error and easy substitutions in the case of a sudden shortage or contamination. Which approach is better?
If you’re experienced in the construction sector, you know the answer is “it depends”—on the scale of the project, on the number of machines being used, and even on the climate your fleet operates in. Once you factor in all these variables and complications, it becomes clear that choosing the right single lubricant or library of lubricants and the right team of professionals to support that choice with routine changes or analysis is vital to achieving your goals and providing stand-out service.
WHY YOUR ENTIRE FLEET RELIES ON YOUR LUBRICANT DECISIONS
Everything that happens on your work site is affected by the decisions you make about lubrication, making it almost impossible to overstate its significance. The biggest reason to devote resources to a comprehensive and tactically sound lubrication strategy is simple risk mitigation. Using a suboptimal oil impacts a
machine’s performance and, in many cases, can shorten its lifespan or even cause permanent damage. Whether it’s burning oil or the wrong grade was selected, that decision will result in unplanned downtime, negatively impacting efficiency and causing delays.
A poorly planned maintenance program can also have a negative impact on your bottom line by eating up more time than it needs to, wasting resources, failing to prevent downtime due to equipment failure. It’s a delicate needle to thread: changing oil too frequently is a waste of money and negatively impacts your uptime, while more widely spaced intervals risks loss of efficiency or even, in some cases, permanent damage to equipment.
A further complication is that adjusting a maintenance plan in the middle of a project is difficult. For example, if you change the type of oil a machine uses after three months on the job, that will create inconsistent performance and confusing data that can hamper your ability to assess drain intervals or read the results of an oil analysis.
These changes in performance could have a trickle-down effect on the rest of your fleet, and spikes in wear metals or additives could create misleading analysis results. Experts will agree that consistency is key to a successful lubrication plan, but maintaining consistency when you don’t have a clear vision for what products you want to use and how you want to support them can be challenging.
Finally, factor in the risk of human error, which occurs with even the most professional teams. Every time you add a new product to your supply and every decision that further complicates your lubrication strategy, increases the risk that the wrong oil will be used in the wrong machine or that the lubricant will become contaminated. These simple errors can result in a loss of efficiency, unplanned downtime or even total equipment failure.
DEVOTING TIME TO YOUR LUBRICANT PLAN PAYS OFF DOWN THE ROAD—BIG
The solution is a comprehensive lubrication plan developed and supported by experienced experts who can factor the following into the choice of lubricant and grease supply:
˜ The length and scale of the project
˜ The type of machinery being used
˜ Regional climate
Once the project is underway, that team can support those choices with a regular oil analysis program.
Regular oil analysis can be more effective than routine oil changes. Instead of regularly changing out lubricant and replacing it with fresh product at preset intervals based on past machine performance and original equipment manufacturer (OEM) recommendations, oil analysis involves regularly sampling oil and delivering the samples to a laboratory for analysis. The results are comparable to a blood test performed by a physician. Experts examine the lubricant sample for:
˜ Wear metals, indicating excess wear on the machine
˜ Contaminants, indicating a leak or issues with lubricant storage
˜ Signs of early degradation, indicating that the machines are working harder than anticipated and the lubricant is having trouble maintaining the necessary viscosity
This data can then be used to adjust worksite strategies like switching lubricants, moderating how the machinery is used or any other number of tweaks.
The lubrication engineers who perform the analysis work closely with OEMs, maintaining up-to-date information so they can correctly interpret the results and determine what (if any) problems a piece of equipment might have. They can also determine if the machine will need its next oil change earlier than expected or, in many cases, later than expected. Armed with this data, fleet managers can appropriately plan for downtime with more foresight or take advantage of the extra efficiency to reduce cost and waste and even get ahead of schedule.
LUBRICANT DATA CAN BE ONE OF YOUR
MOST USEFUL TOOLS
A meticulous lubrication plan supported by routine oil analysis has even greater benefits at scale. As the construction industry expands into more diverse fleets powered by a mixture of power sources like battery electric and hydrogen the benefits of these strategies will become even more pronounced. Access to detailed data about your fleet can result in greater efficiency, allowing you to meet or exceed sustainability goals while decreasing costs without delaying or compromising results. Experts can also recommend specific greases and other supporting products that will work ideally with the best lubricants. They can also help fleet managers decide how many specific lubricants to use for their fleet, balancing the advantages of optimizing machine performance and efficiency with the possibility of contamination or human error resulting in the wrong lubricant being administered to the wrong machine. When performed correctly, this proactive, rather than reactive, approach will provide:
˜ Longer machine life
˜ More efficient production
˜ Earlier prediction of incoming challenges
˜ Smoother, faster, better performance for your entire team Once establish a plan, lubricant data becomes one of the most important tools in your fleet. It provides unparalleled insight into the performance of your equipment and arms you with the knowledge necessary to provide exceptional results.
Read more at: eqtoday.co/peakoil
Stephanie Phillips is the NA CV product line manager for Mobil.
Some machine control systems help operators automate and fine-tune tasks like leveling, digging and grading all the way up to creating complex, multidimensional site profiles.
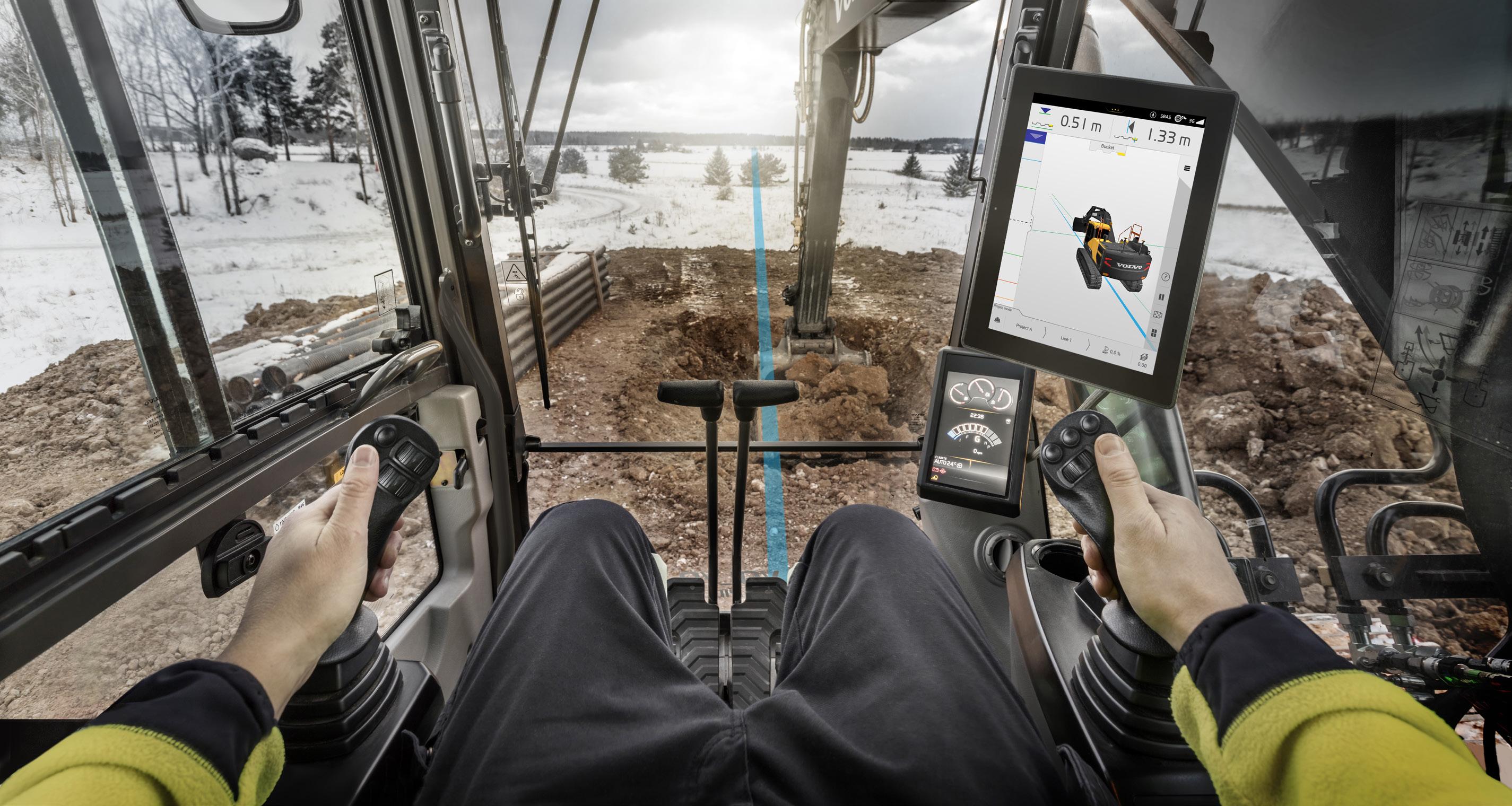
Can MACHINE CONTROL Systems Really Improve Profits?
This technology dramatically improves accuracy, from load weight to trench depths, angles and directions, to the compaction density of a newly laid asphalt mat.
Over the years, we’ve seen operators with lots of experience do some amazing things with their machines. Maybe they have an eye for adjustments that improve precision, or perhaps they know which features to use and when to boost productivity or efficiency.
But with today’s advancements in heavy equipment technology, even skilled operators can benefit from a real-time assistance to enhance their daily performance.
Automated machine movements and incredibly small refinements in technique can be the key to meeting project specs, cutting down on or eliminating costly rework, and maximizing profitability. This is where machine control systems factor in.

On-board weighing provides real-time insight into the bucket’s load to make overloading, underloading, reweighing and waiting times a thing of the past.
MAXIMIZING EXCAVATOR ACCURACY & SAFETY
Let’s look at excavators first. Some excavators come with machine control systems that guide the operator through functions to automate the digging process. Once the parameters of the job are entered and it’s launched, the excavator automatically adjusts the boom and bucket movements to make precise cuts, following the desired shape and delivering the right angle of grade. With this added precision, rework is virtually eliminated, allowing the operator to complete the project on time and move to the next task. For those working on dangerous or difficult jobsites, remote-controlled solutions open new opportunities. This impressive add-on allows you to operate an excavator from a distance in areas with hazardous substances (like in a potash mine) or poor ground conditions (like mud). Simply put, remote control provides a safer view in situations where the visibility from inside the cab is deficient or unsafe.
ON-THE-GO PRECISION FOR LOADERS
Machine control systems provide valuable benefits to more than just excavator operators. On-board weighing apps for wheel loaders, for example, are popular because many are so easy to use.
On-board weighing makes quick work of accurate loading. If you have a truck with a target of 23 tons, your operator can fill their bucket and dynamically weigh it—often without even being stationary. As they drive up to tip the load into a haul truck, it’ll lock in the weight. This means the
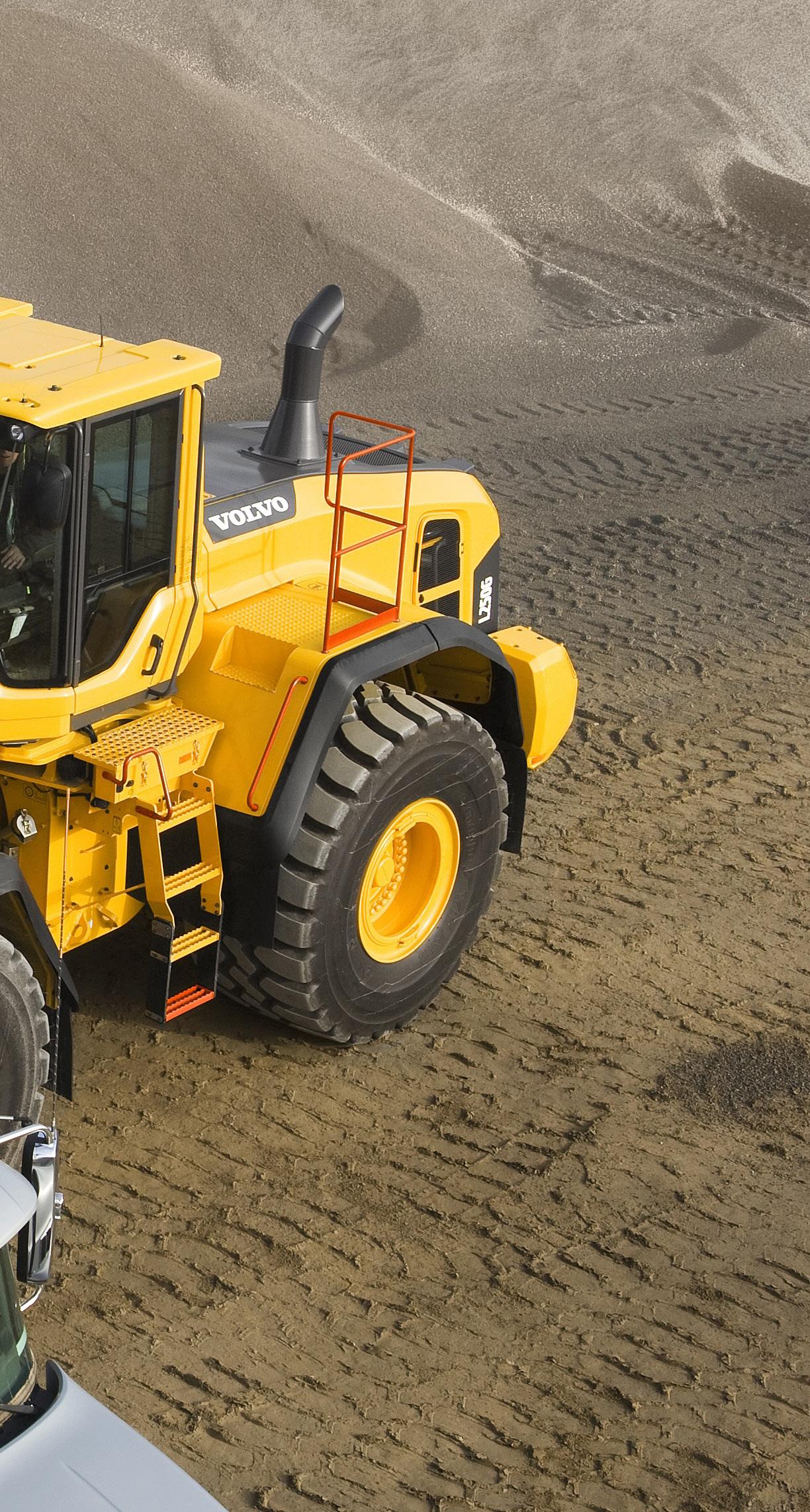
operator can see the exact weight of the load they’re about to dump. If they unload 12 tons on the first pass, the next bucket needs to weigh 11 tons. They can grab the second load, tip off any excess weight at the pile and reweigh it at exactly 11 tons and then dump it before the truck heads off for the scale. Most operations use an on-board weighing
app to ensure that the load is accurate before they send their trucks to the scales, which is important because the scale weight is what’s used for billing and invoicing purposes.
Several manufacturers include some type of weighing program on their loaders. Some also allow companies to monitor and control the total loads of multiple trucks.
How does that work? Suppose a highway contractor needs 60,000 tons of sand and 40,000 tons of gravel delivered to a concrete batching plant. If nine trucks are delivering to this customer, you can use this advanced feature to set up a work order:
˜ Set the target at 60,000 tons of sand and 40,000 tons of gravel.
˜ Add the names of each of your nine

of
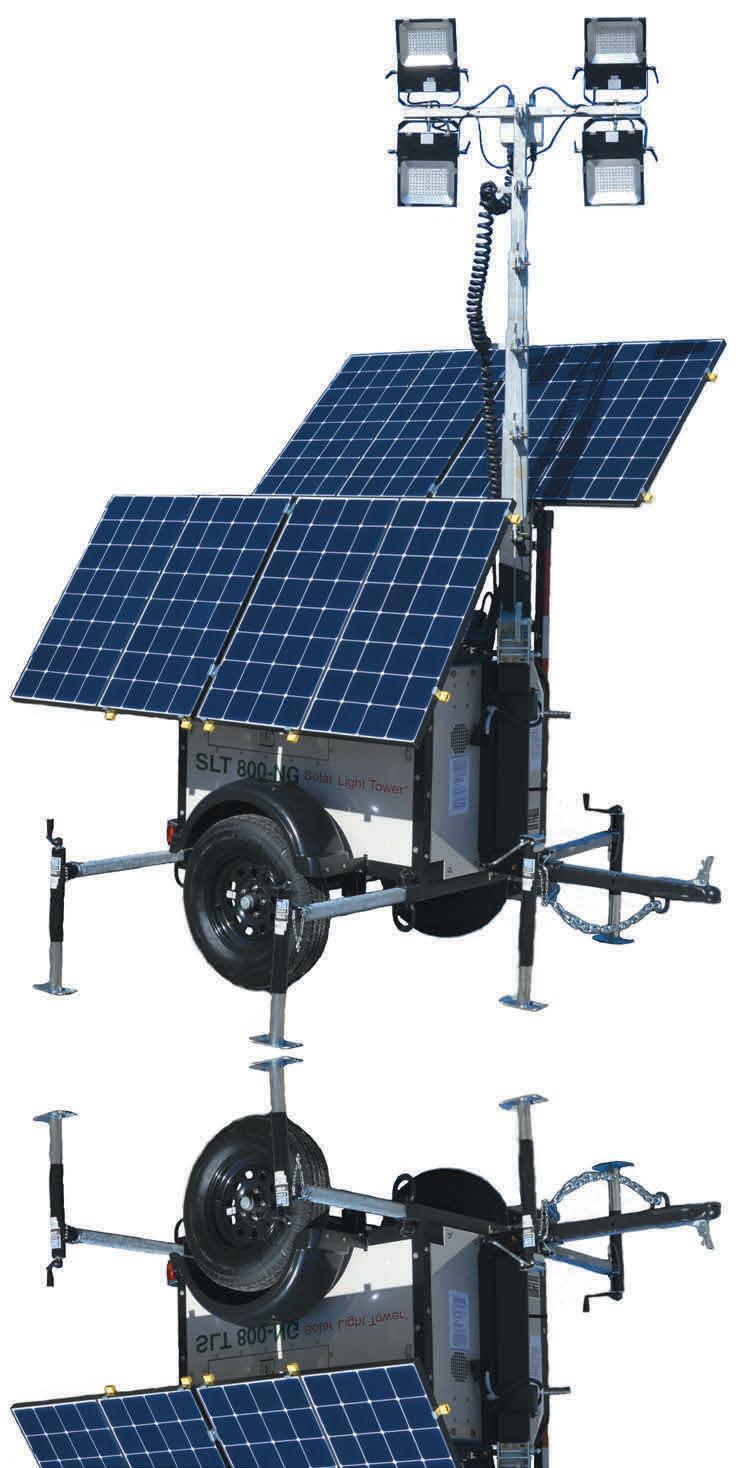
Use Mobile Solar Light Towers!
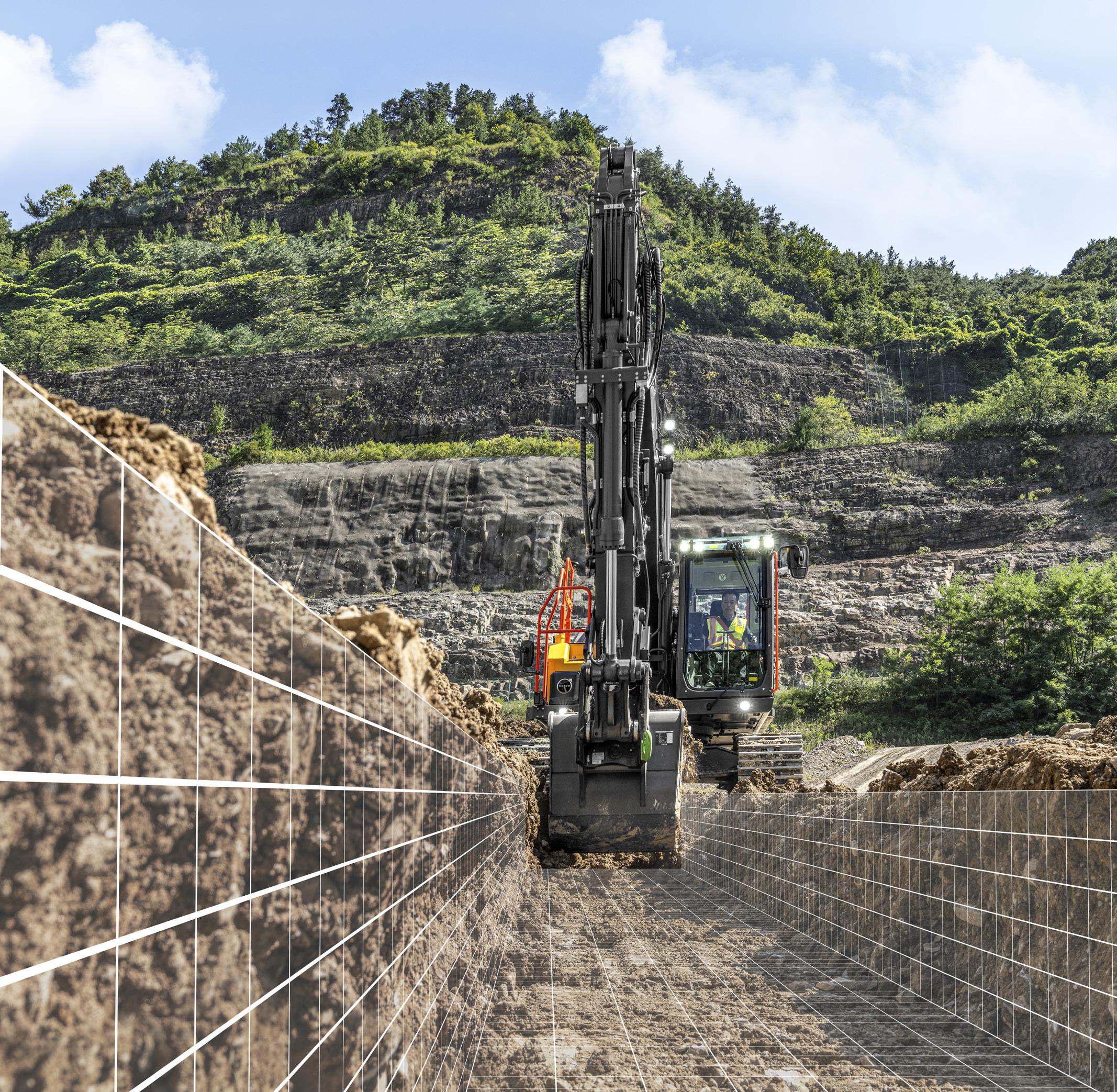
trucks. This makes it especially easy if your trucks have different weight restrictions.
˜ Set up the material you’re delivering (sand and gravel). This gives you the ability to monitor and track the material that’s being delivered by each truck. The operator in the cab can also monitor what they are loading throughout the day.
A feature like this allows site managers to go in at the end of the day and export data from a flash drive: the different projects, trucks and material that was delivered or sold. They see every truck load and when a particular operator started loading a truck, when they finished, what material they took and what the truck name was. Using these types of machine control features, they know exactly when they’re ready for the next stage based on the data—and it doesn’t matter if they’re 6 miles away or 600.
LEVELING UP PRODUCTIVITY & PROFITS
Machine control features improve accuracy, from load weight to trench depths, angles and directions, to the compaction density of a newly laid asphalt mat. In nearly every instance, this accuracy equates to reduced mistakes and/or earned bonuses—and when increased productivity and efficiency are factored in, most who use these features experience higher profits.
In an industry where precision and efficiency earn more bids and drive profitability, machine control
A system with an in-cab tablet that incorporates sensors and GPS technology can support accuracy and efficiency.
systems represent a bit of a paradigm shift. For owners and operators, these tools aren’t just about automating processes but are about enhancing the capabilities of the machines in beneficial ways.
It’s not that operators aren’t good at what they do— in fact, most operators learn quickly and adapt their skills to show management and the other operators on site exactly what they can do. Machine control systems simply help make good operators great and great operators exceptional.
When a company has all its operators at the top of their game, profits rise. When researching new machines, it’s worth the time and effort to ask which machine control systems are available and how they work for the brand(s) you’re considering. Undergoing a cost/benefit analysis may help you select one brand over another if their machine control system has a more favorable return on investment.
Our advice is simply: Ask and learn. What do you have to lose?
Read more at: eqtoday.co/angles
Matthew McLean is product manager, Dig Assist, for Volvo Construction Equipment (CE). Eric Yeomans is product manager, Load Assist, Volvo CE.
4 BENEFITS of Construction Technology Subscriptions
These options are now available for a range of products, from on-machine grade control systems to off-machine base stations, data collectors, rovers and total stations.
So close and yet so far. That’s the perception of many small and midsize construction contractors when it comes to technology investments. Tech like machine control and laser scanners hold the promise to drive efficiency and productivity, often for a hefty cost.
While the benefits may be clear, the time and cost to deploy these solutions are a barrier many don’t believe they can breach. That’s where subscriptions for construction technology can help. They are now available for products, from on-machine grade control systems to off-machine base stations, data collectors, rovers and total stations.
Subscriptions are fast becoming a preferred way to implement technology with confidence and affordability. This article covers four key advantages to today’s construction-focused subscription programs.
1. LOWER UPFRONT CAPITAL INVESTMENT & FASTER APPROVALS
For contractors, one of the most noted advantages of subscriptions is the lower upfront capital investment when compared to traditional purchase models. With monthly or annual payments, new technology is simply more financially feasible.
Subscriptions can also enable faster approvals, since the monthly costs are lower than large upfront investments. For example, someone may be able to approve $1,200 per month but not a $65,000 purchase. These lower thresholds mean new purchases can receive a green light more quickly.
The lower upfront capital investment is an advantage that Redman Construction Inc., a familyowned contractor based in Brockport, New York, is fully realizing. To this company, a subscription is a way to build toward a digital ecosystem while keeping the company’s long-term debt ratios down.
JP McKinley, vice president for Redman, said subscriptions offer a solution for the various requests that come from bankers, accountants and bonding agents.
Subscriptions have helped that company produce financial reports, maintain good credit and save money.
2. FLEXIBILITY TO SCALE & TEST
A subscription program can provide flexibility to scale a technology suite depending on the workload, without the full risk of ownership. It allows businesses to start with a basic offering and gradually adopt new technologies. Need a new technology for a specific project? It’s available. They can build their capabilities through incremental upgrades.
This approach also allows organizations to more easily try new technologies rather than waiting until their next major purchase cycle. For instance, ready access to new technology is one way contractors are driving productivity and safety. National design build contractor Power Design, headquartered in St. Petersburg, Fla., operates in 23 states across the U.S. on more than 300 active projects. Through a subscription program, the group looked to pair building information modeling with robotic total station technology to support field installations using point layout technology—a 3D-modeling, virtual solution. Superintendents have reported a 300% to 500% increase in layout speed.
3. ALWAYS CURRENT SOLUTIONS
The equipment with subscription technology likely has a longer and more useful lifespan, largely because of regular updates compared to traditional purchase models.
Also, in most cases, upgrades are automatically included as part of the subscription, allowing customers to continually adopt improvements instead of using outdated solutions for extended periods.
4. FULL TECHNICAL SUPPORT
With subscriptions, software updates are typically loaded automatically and configured while hardware is inspected and, if needed, repaired/replaced at no additional cost.
Technical support is a significant differentiator from more traditional purchase plans. A subscription fundamentally changes the relationship between the vendor and the customer.
With traditional purchases, the relationship is more transactional, only occurring when a new purchase is made every few years.
Subscriptions also encourage vendors to continually deliver value and meet customer needs, since customers have the option to easily switch to a competitor if not happy. This raises the
options, make sure to consider the total cost of ownership of a piece of technology across projects large and small. Also, think about the storage, logistics and upgrades when new advances become available when weighing alternatives.
No two subscriptions are created equal. This is an evolving model, make
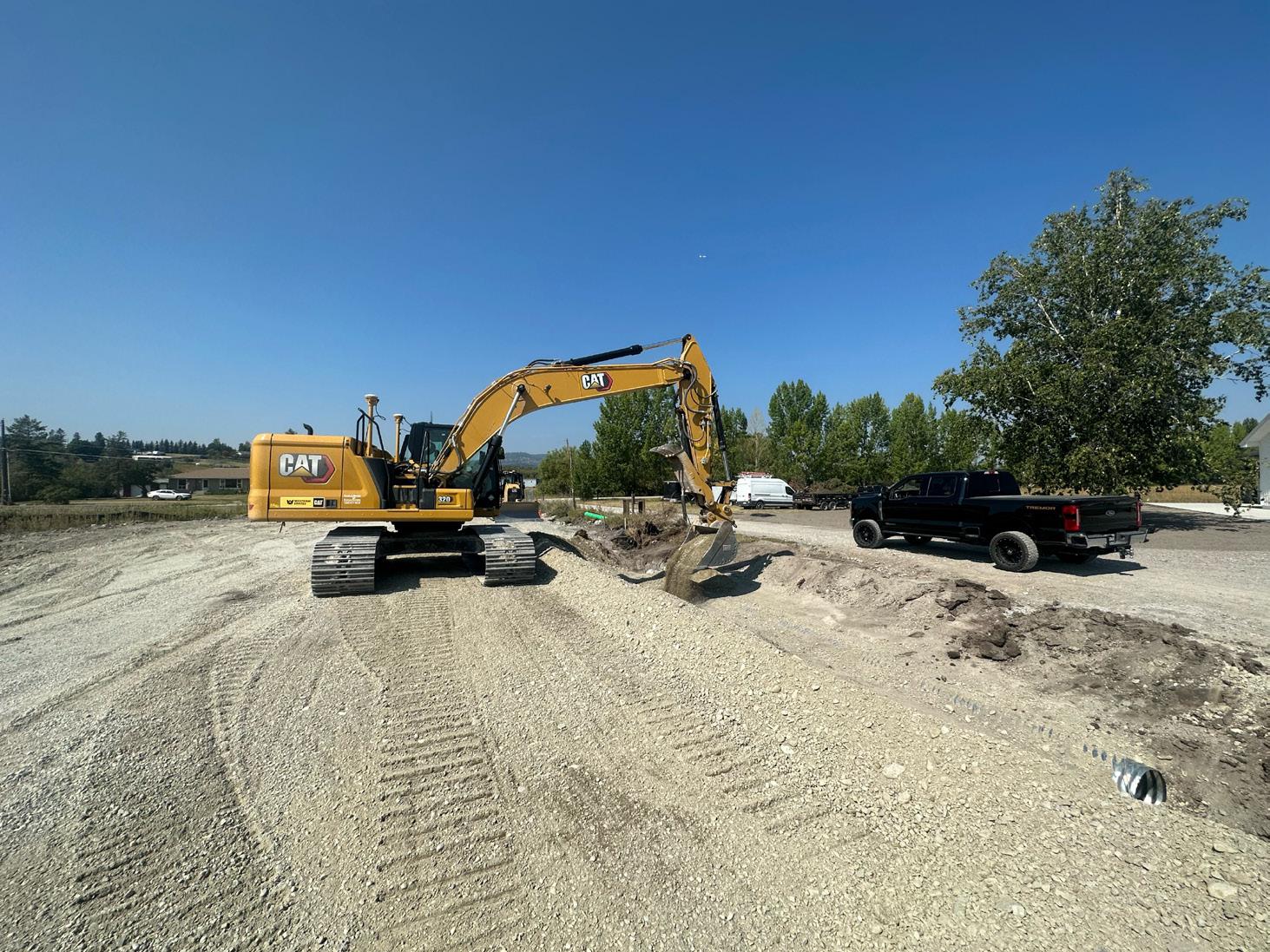
Subscriptions make investing in GNSS across a fleet simpler.
bar for vendors to stay on top of their service delivery.
ADVICE MOVING FORWARD
An increasing number of subscription programs are available for construction. If your organization is considering this model, look beyond the lower upfront cost. A subscription can do much more than simply make it easier to invest in technology, by:
˜ Providing more flexibility
˜ Giving faster access to new technologies
˜ Encouraging vendors to continuously improve
These models can be ideal for maintaining the latest hardware and software and ensuring a full factory warranty and repair or replacement of accidentally damaged hardware. When evaluating subscription versus more conventional purchasing
sure you understand what equipment and technologies are included and if associated maintenance and upgrades are included. Ask questions about what happens when the subscription ends.
Finally, know what support and training is included in the subscription plan. When it comes to sophisticated solutions such as robotic total stations, machine control and more, day-to-day support and training is essential.
Subscriptions are here to stay and will continue to evolve to best meet industry needs. When done right, they’re a terrific way for contractors to invest in technology with less risk and more return-on-investment.
Digital Tools Transform ACCESS MANAGEMENT
RFID technology unlocks more efficient control of jobsite and equipment access.`
Digital technology is poised to revolutionize construction jobsites, making them smarter, safer and more efficient. One aspect of daily operations ripe for improvement is access management.
On large, busy jobsites, managing site access is essential to the safety and protection of people and property. A secure jobsite perimeter is the first line of defense against accidents and other incidents involving trespassers, vandalism theft. Restricting access to potentially hazardous areas and zones is equally important to minimizing risk, as safety managers well know.
While most large contractors use some method of site access control, fewer companies currently invest in a method of equipment access management, despite the benefits of keeping unauthorized personnel off aerial lifts, forklifts, excavators and other heavy equipment.
Digital tools that facilitate both jobsite management and equipment access management also streamline access control and provide increased visibility and accountability. RFID badges are “key” to a scalable, streamlined solution.
MANAGING JOBSITE ENTRY & EXIT
For decades, jobsite access management consisted of paper signin sheets at guard stations. Lining up to sign in created congestion and delays, and people who were determined to sneak past these checkpoints often found a way. Modern methods that use software and
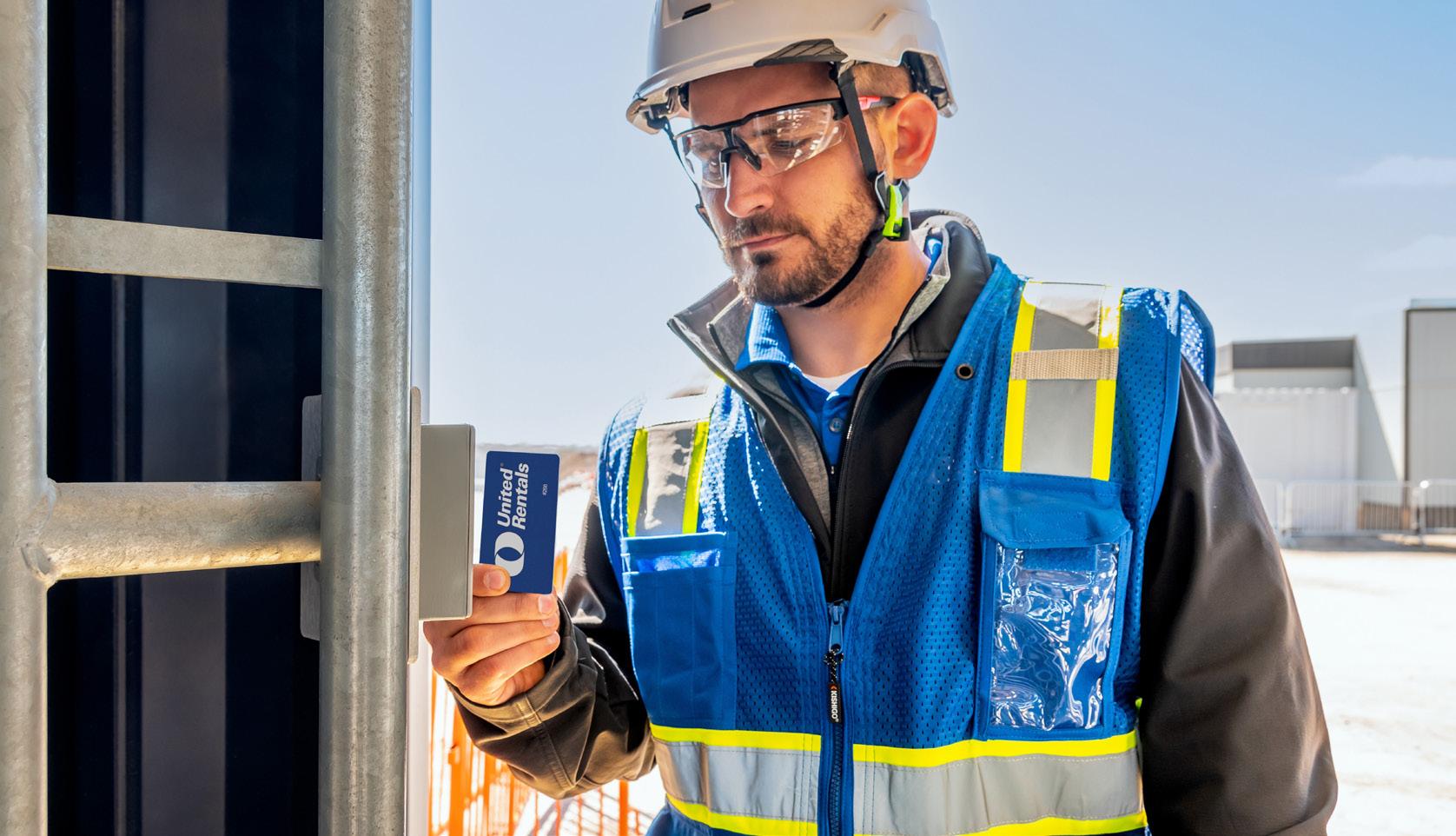
hardware to automate access control represent a leap forward.
Many of these systems use company-issued ID badges, fobs or other credentials to authenticate entrants based on worker profiles stored in a software platform. The profile may contain only basic information—such as name, badge number, company, and trade or craft— or additional information such as operator certification and training. Companies can assign roles and rights based on this data during onboarding.
Badges may be enabled with a magnetic stripe, barcode or RFID tag, but RFID technology has distinct advantages. RFID tags can store more data than magnetic stripes. RFID readers can read multiple tags at once, unlike barcode readers, and they can read badges from a greater distance than previous technologies.
At jobsite entrances, including gates and vehicle access points, authorized workers tap their badges on RFID readers for access. Additional readers may be placed in strategic places on the jobsite to control access to specific buildings or areas.
Smart turnstiles equipped with RFID readers take site access control to the next level.
Modular units integrate easily with perimeter fencing. Security cameras and facial recognition software can be added as part of a comprehensive site security program.
CONTROLLING ACCESS TO EQUIPMENT
Inappropriate use of equipment is a leading cause of construction equipment accidents. Workers who lack the proper training and certification are more likely to misuse equipment and cause an accident that results in injury to themselves, injury to workers on foot or damage to the equipment and nearby structures.
Keeping unauthorized operators, including untrained workers and unauthorized subcontractors, off equipment not only reduces accident
Digital tools that facilitate jobsite management and equipment access management streamline access control and provide increased visibility and accountability.
risks but also helps protect companies against liability.
Keypad ignition locks that require a PIN are one effective solution. Ideally, managers assign a unique PIN to each individual operator to prevent PIN sharing and track machine usage by operator. A next-generation approach that saves time and effort uses RFID readers added to the equipment locks. Rather than entering a code, workers tap their badges to access equipment that they are authorized to operate.
Companies can assign equipment access privileges by trade, group or individual for specific pieces of equipment or equipment category classes. If a person’s privileges need to be revoked for any reason, changing the rights assigned in the worker profile restricts access immediately.
A badge approach to equipment access control provides accurate real-time and historical insights into equipment use.
Worker-specific usage data increases accountability in the event of an accident or equipment damage.
It can also help companies identify authorized operators who may need additional safety training.
AUTOMATION DRIVES PRODUCTIVITY & EFFICIENCY
Digital tools automate processes, potentially resulting in significant labor efficiencies and productivity gains. For example, badge-based jobsite access reduces the need for security personnel at entry points and frees up guards to focus on other tasks, such as inspecting bags.
Badge-based equipment access relieves administrators from the timeconsuming task of assigning PINs for each piece of equipment and each authorized operator.
Attendance data is automatically generated and instantly accessible, so supervisors and project managers can monitor workforce presence and verify worker hours for payroll purposes. Historical data on hours spent on the jobsite by different trades and crafts
can help managers optimize workforce usage and scheduling. Accurate records of worker hours, breaks and overtime can aid in compliance with contracts and labor regulations.
Should an accident or a jobsite emergency such as a fire or hurricane occur, clear visibility into who is on site and who is in a specific building or area can facilitate a faster, more effective emergency response. Managers can easily access worker profiles to obtain emergency contact information if needed.
LOOKING TO THE FUTURE OF ACCESS MANAGEMENT
As projects become larger and more complex, access management is an even more critical component of jobsite safety, security and productivity.
A jobsite that’s connected from end to end gives large construction companies unprecedented visibility into and control over who passes through jobsite barriers, enters sensitive or restricted areas and operates equipment, all while driving tangible improvements in efficiency and productivity.
In the foreseeable future, a truly seamless solution will leverage one cloud-based software platform to connect jobsite access management and equipment access management and allow the same worker profile and ID badge to serve both purposes. In the meantime, onestop-shop rental companies can help general contractors evaluate access management approaches and choose tools that work best for the project, the jobsite and the budget.
Read more at: eqtoday.co/rfid
Kevin Noonan is product development manager at United Rentals.
FLEET MANAGEMENT Products
Continental
ContiConnect Lite App
Continental launched ContiConnect Lite, an app for digital tire management.
ContiConnect Lite creates a bridge between tire sensors and tire management and offers a free-of-charge gateway to selected ContiConnect features.
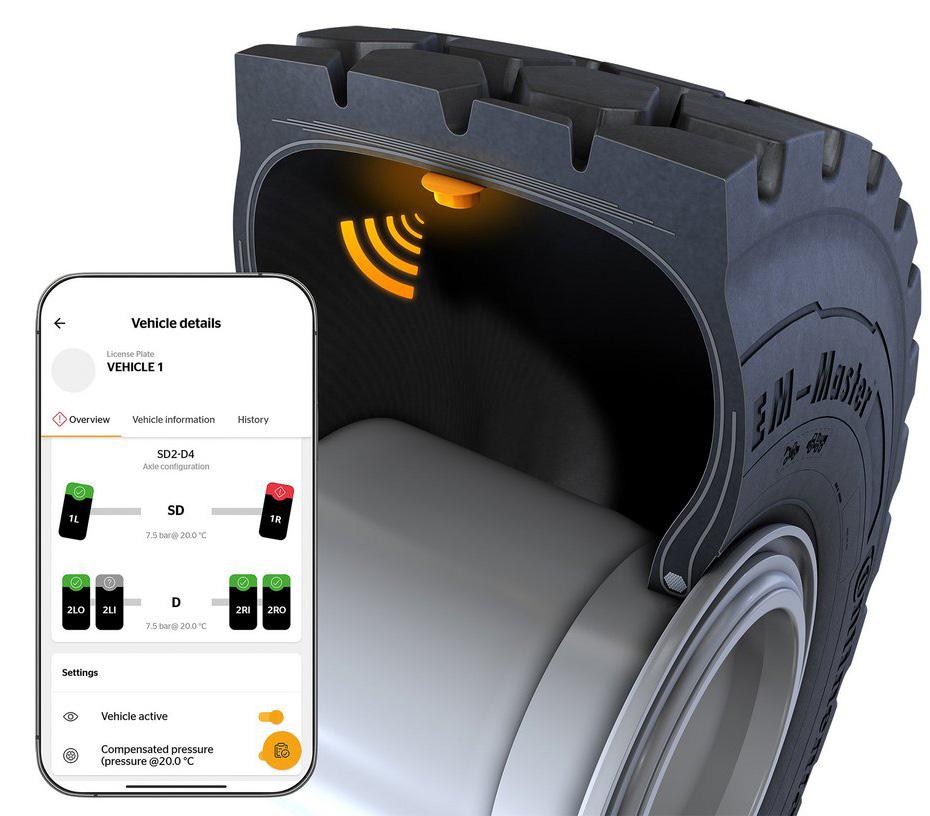
It can now be used on tires with an integrated Gen2 sensor. During 2024, Continental has been delivering its off-the-road radial (OTR) tires with a Bluetooth-enabled sensor. Thanks to the Bluetooth-enabled sensor, the tire data can be read using a smartphone. In addition to OTR tires, Continental also offers digital tire management for its truck tire customers.
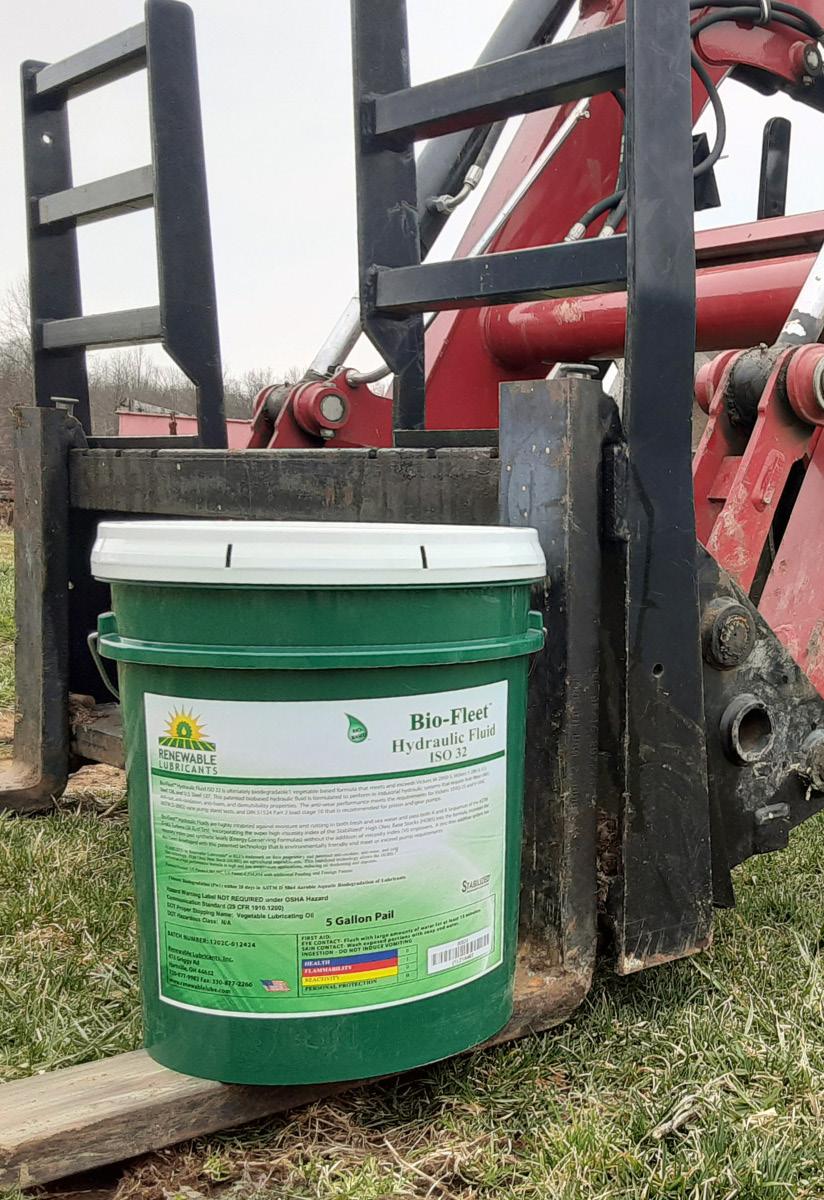
Renewable Lubricants
Bio-Fleet Hydraulic Fluid
Renewable Lubricants introduced biodegradable BioFleet Hydraulic Fluids, which perform like synthetics and can be used in frequent oil change environments. These patented formulations meet or exceed common performance protocols including Vickers M-2950-S, Vickers 1-286-5, U.S. Steel 126, and U.S. Steel 127. Anti-wear performance meets requirements for Vickers 35VQ-25 and V-104C (ASTM D-2882) vane pump stand tests and exceeds DIN 51524 Part 2 and 3 (HLP/HVLP) load stage 10 that is recommended for vane, piston and gear pumps.
Capable of withstanding moisture and rusting in both fresh and sea water, the fluids are for hydraulic equipment operating outside where high moisture and dusty environments are present.
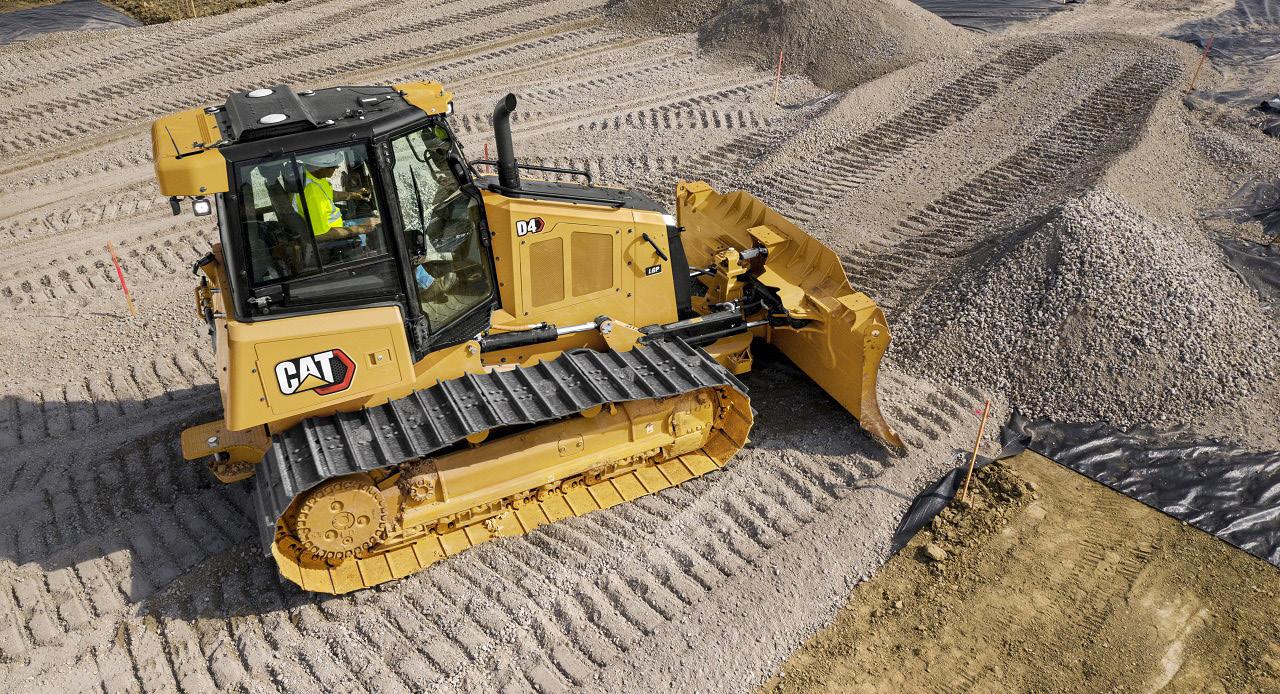
Caterpillar Technology Package Upgrades for Medium Dozers
Caterpillar’s two technology package upgrades for its medium dozer line are standard on several models. Formerly attachment ready option (ARO) with Assist, the Cat Assist with ARO suite of features will be included as a standard feature on Cat D4, D5, D6, D6 XE and D7 models.
Additionally, Cat Grade with 3D Ready option provides flexibility for customers upgrading to Cat Grade with 3D on D4, D5 and D6 dozer models. Features include: stable blade, traction control, auto carry, blade load monitor, slope assist and steer assist.

Double Coin All-Steel ST Radial Tires
CMA and Double Coin introduced two new allsteel ST radials to the Double Coin lineup. The additions are 16-in. sizes for construction projects and trailer applications Available sizes include ST235/80R16 and ST235/85R16. Features include steel casing allows for heavy carrying capacity, optimized tread depth for reduced heat build-up, wide shoulders for stability.
Trelleborg XP1000 Tire
Trelleborg offers the XP1000 tire for rugged and intense applications on construction sites. The XP1000 tire delivers performance, with extra traction and minimal tire vibration during use. This tire is available in different rubber compounds, including ProTEX: a non-marking electrically conducting compound engineered for material handling applications operating in potentially explosive environments.
Equipped with Pit Stop Line technology, Trelleborg XP1000 supports safety and tire change planning. Once 100 hours of operating time remains, an orange band appears on the tread, helping forklift drivers and fleet managers schedule tire changes.
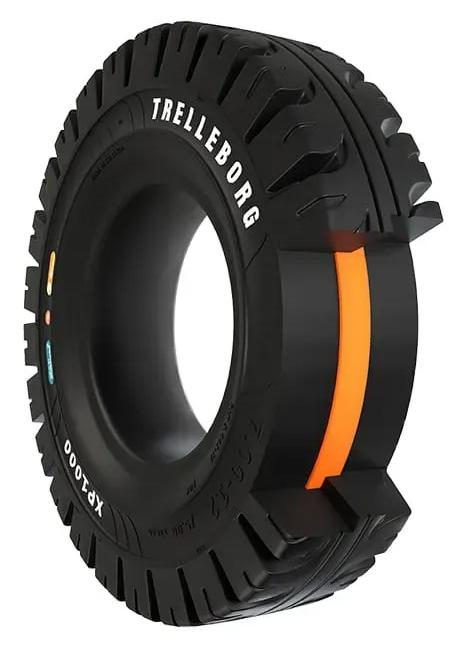
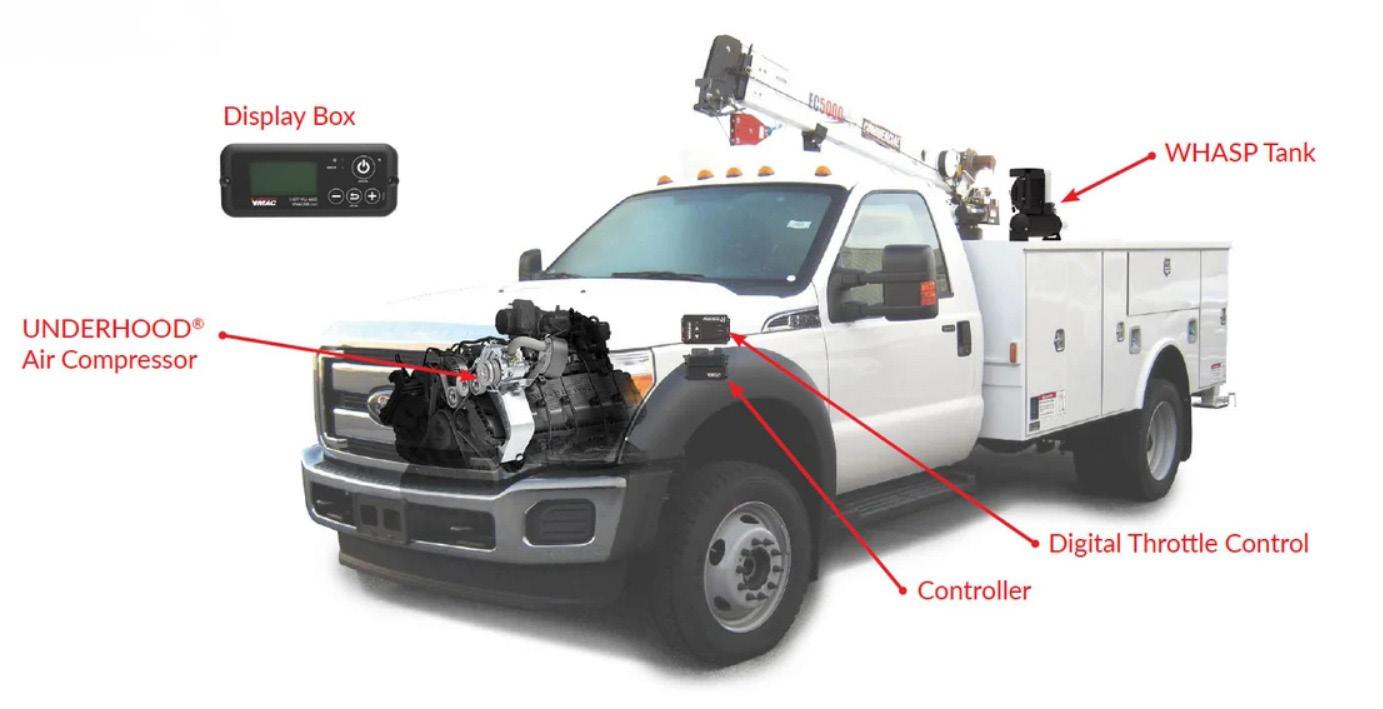
VMAC Digital Controls & Telematics for UNDERHOOD 40 Air Compressors
VMAC introduced the new UNDERHOOD 40 with advanced digital controls and telematics. VMAC’s advanced digital controls integrate with the vehicle, providing insights to operators and fleet managers about the performance and maintenance of their UNDERHOOD40 systems. The UNDERHOOD40’s digital controls include telematics, built-in soft start, safety controls and diagnostics.
Engineered for trucks and commercial vans, the UNDERHOOD40 delivers up to 40 cfm at 100% duty cycle while freeing up truck deck and cargo space and decreasing GVW by up to 290 lbs. Available now for most popular 2023+ commercial work trucks and vans, the UNDERHOOD40 with digital controls and telematics supports operations on jobsites.
Discovering the Latest in Excavator Technology
From designing modern electrohydraulic control systems to adding advanced object detection technologies, excavator manufacturers are pushing the boundaries of what these machines can accomplish.
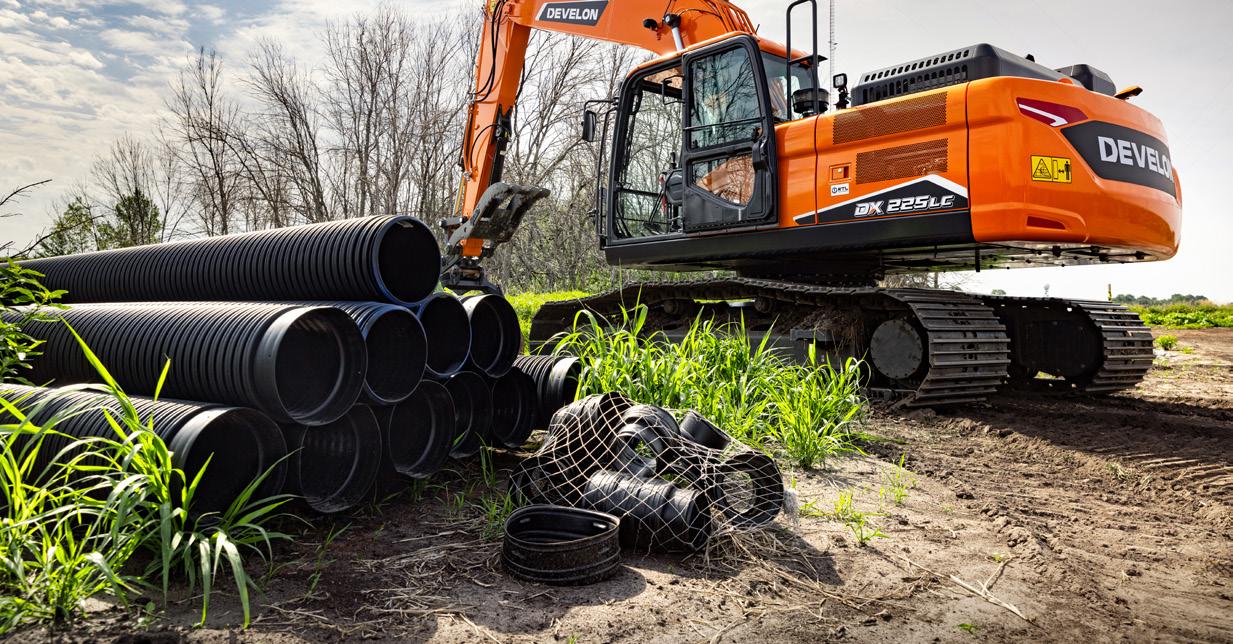
Technological advancements have revolutionized excavators, elevating them from basic digging machines to versatile tools that redefine efficiency and safety at jobsites.
From designing modern electrohydraulic control systems to adding advanced object detection technologies, excavator manufacturers are pushing the boundaries of what these machines can accomplish. As a result, these machines have become indispensable. Here are some excavator innovations.
ELECTROHYDRAULIC CONTROL SYSTEM
An electrohydraulic control system has increased safety and efficiency. The system uses electrical and hydraulic components to manage the excavator’s movements and functions. It integrates electronic sensors, controllers and actuators with traditional hydraulic components, providing more
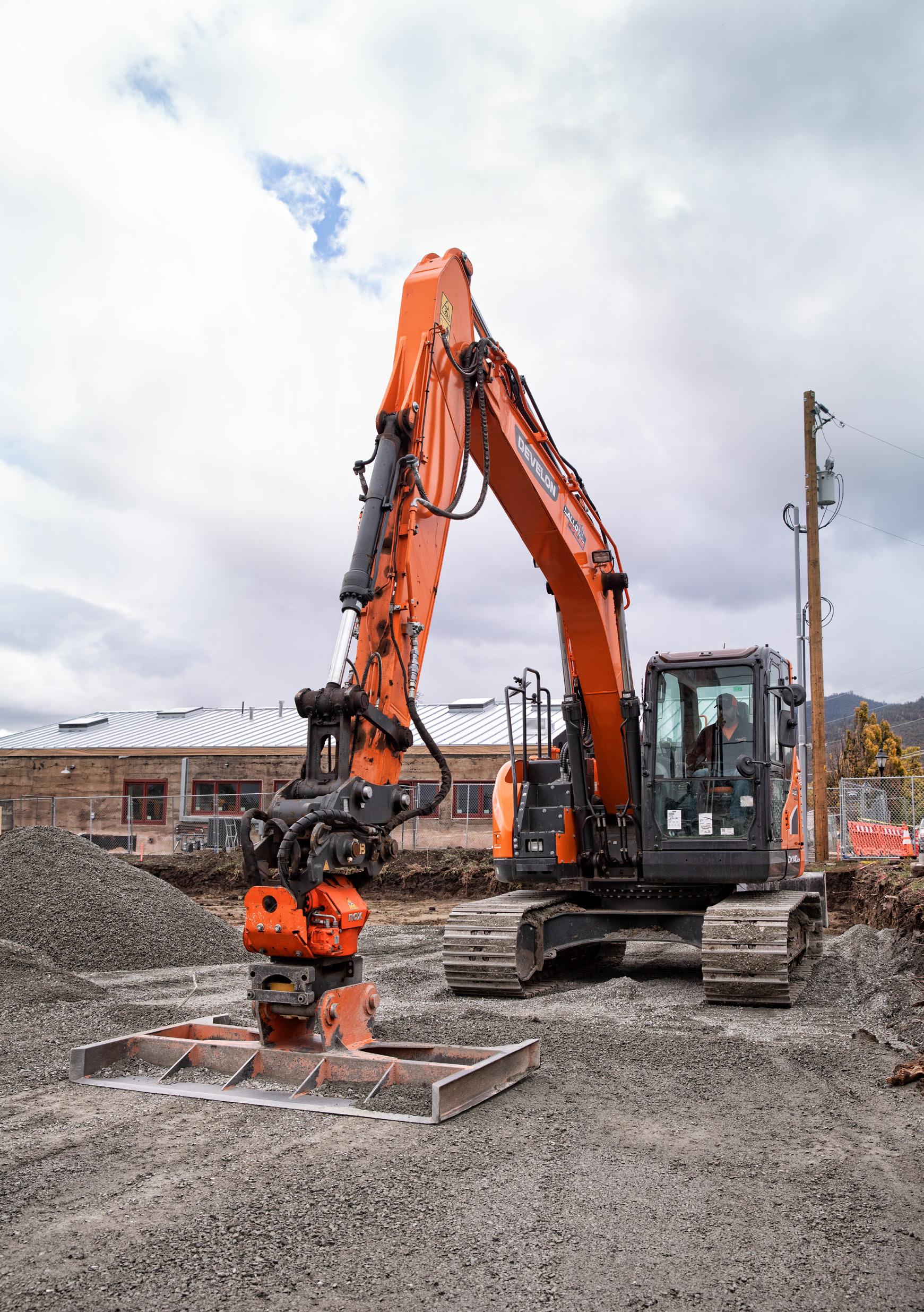
An electrohydraulic control system has increased precision, safety and efficiency in construction and earthmoving operations. The system uses both electrical and hydraulic components to manage the excavator’s movements and functions.
precise and efficient control over the excavator’s operations.
An electrohydraulic control system in an excavator can include the following features:
˜ Programmable joystick switches that provide ease of operation
˜ A fully electronic joystick
˜ Swinging sensor to measure and monitor swinging motion
˜ Equipment sensors on the boom, arm, bucket and upper body, including a laser catcher to assist with the 2D grading system
GRADE ASSIST
Grade assist systems for excavators are used to achieve precise and accurate surface grading or leveling. They ensure that the desired slope, elevation and contour of the terrain are achieved. When excavator operators activate the grading system, a touchscreen setting allows them to set the assist mode—allowing the computer to
assist the operator through audio and visual displays. The operator controls the arm function and the machine automatically manages the bucket and boom to maintain the desired grade or slope. The touchscreen monitor can give operators better control over the direction of travel, as well as more precision when setting the bucket-tooth depth, height and slope.
2D GRADING SYSTEM
Along with other advanced machine guidance and machine control systems, the 2D grading system is a valuable technology. The 2D system allows operators to work off a single plane, such as a straight-line trench, from Point A to Point B. By using sensors and controllers, the 2D grading system can achieve the precise slope and elevation required for the job. This eliminates the manual labor involved in traditional grading methods and improves productivity by
The excavator is equipped with GPS receivers or proximity sensors that monitor the machine’s position relative to predefined coordinates or objects on the jobsite.
streamlining the grading process and reducing the time and effort required.
FINE SWING FUNCTION
The fine swing function controls the rotational movement of the excavator’s upper structure, known as the swing motion. Activating the fine swing function gives operators improved control when lifting an object and enhances accuracy when placing it. Additionally, it increases operator safety in certain lifting applications, like pipe laying, and can prevent damage caused by the object falling from the excavator. This function can be manually turned on or off by the operators, giving them control over whether the feature is active. When the function is activated, the “overrun” disappears, allowing the excavator to reach maximum swing speed while removing any sudden jerks or shocks from the turn.
VIRTUAL WALL SETTING
Precision technology features, such as a virtual wall setting, help operators improve safety when working in confined spaces. The excavator is equipped with GPS receivers or proximity sensors that monitor the machine’s position relative to predefined coordinates or objects on the jobsite. For instance, if there are obstacles near the machine, the operator can set limits to prevent the machine from swinging past them.
They can also adjust the settings for arm extension and set upper and lower limits. If the excavator gets too close to the obstacles, the system alerts the operator and restricts the machine’s movement. The function can be overridden at any time.
LIFT ASSIST MODE
Excavators regularly lift or crane objects on jobsites. With lift assist, operators can remove the guesswork from the process. This function measures and displays the current weight of the bucket as materials are being loaded and the tipping load. It also alerts the operator when the total loading weight is exceeded.
The sensors are accurate to within 3%. This function can alleviate concerns about tipping the machine if the object is too heavy (for example, large rocks, concrete blocks and heavy machinery components).
ONBOARD WEIGHING SYSTEM
An onboard weighing system uses load cells and sensors to measure the weight of the material and provide real-time feedback to the operator. It can accurately measure the amount of material loaded into the machine and reduce the trips required to move the necessary material.
In addition, an onboard weighing system can help minimize fuel use and equipment wear. It helps companies comply with weight restrictions and prevents overloading, which can result in fines and damage to the machine. It also contributes to a safer work environment for operators and other personnel.
AROUND VIEW MONITOR CAMERA SYSTEMS
Around view monitor (AVM) camera systems display a full view of the machine’s surroundings. Depending on the machine, AVM systems can offer up to 360 degrees of visibility through the monitor.
This enables operators to identify obstacles that may not be visible from their seats, reducing the risk of injuries. AVM systems also enhance productivity by minimizing the time required for operators to check their surroundings manually.
Another feature becoming standard on many excavators is a
rearview camera. With a rearview camera, operators can more safely maneuver around any object or person within the camera’s line of sight. The camera view can be seen on the LCD monitor by pressing a button to activate the feature. Some manufacturers have increased the camera’s field of view or have included sensors to alert the operator if they are about to hit something—also known
as object detection. Object detection improves safety by enhancing awareness and compensating for blind spots. The sensors emit a sound to alert machine operators when they are about to bump an object. The sound may get louder or more frequent the closer the machine gets to the object.
Excavator technologies have become smarter, more efficient and more productive than ever, pushing
the boundaries of the way construction projects are executed and shaping the future of the industry.
Read more at: eqtoday.co/excavatortech
Jacob Sherman is a dealer and product marketing manager for DEVELON.
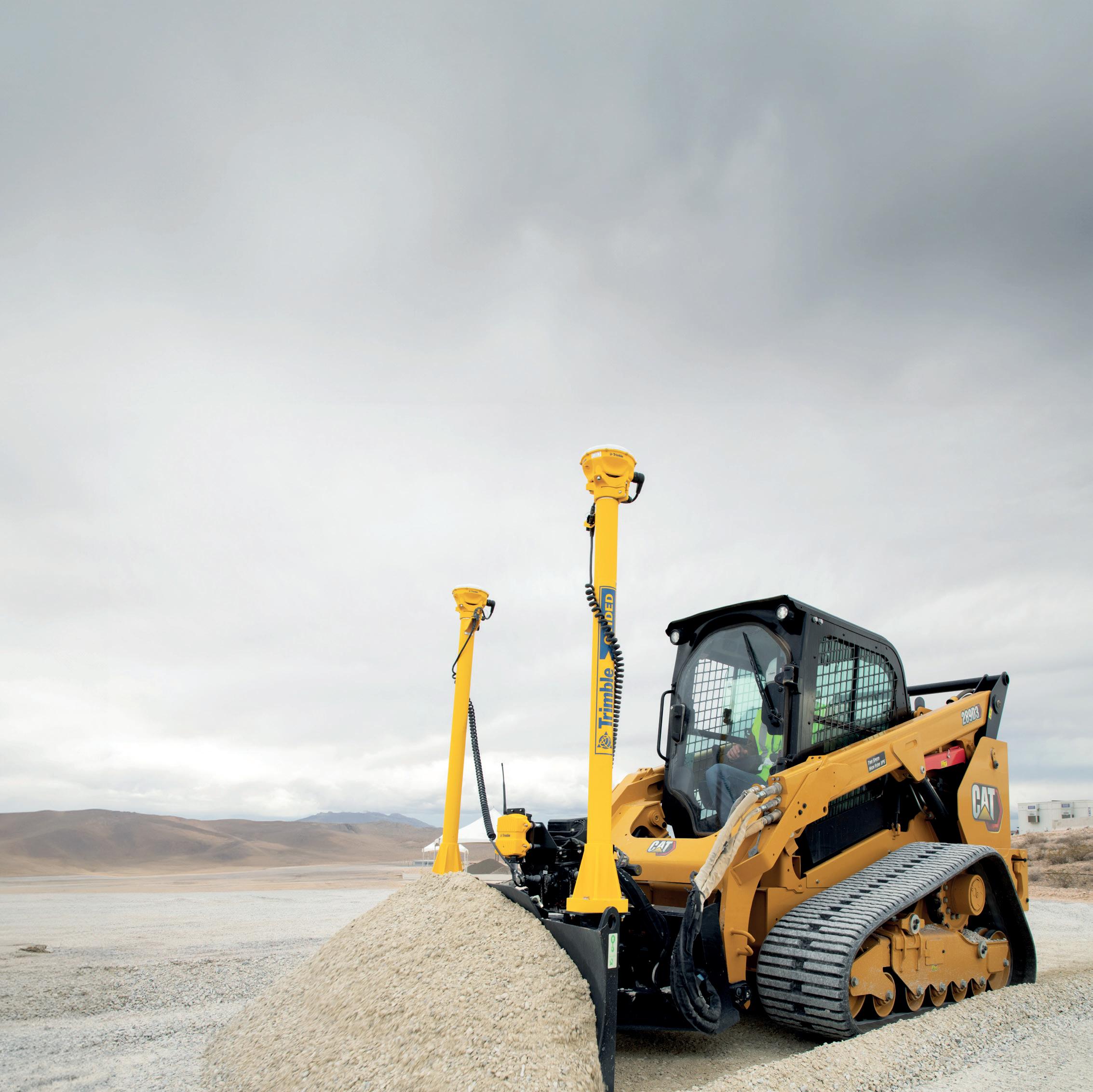
4 Construction Tech Pros Share Insights on the Connected Jobsite
An insider’s guide: What it takes to equip and run a connected jobsite for operational improvement and efficiency.
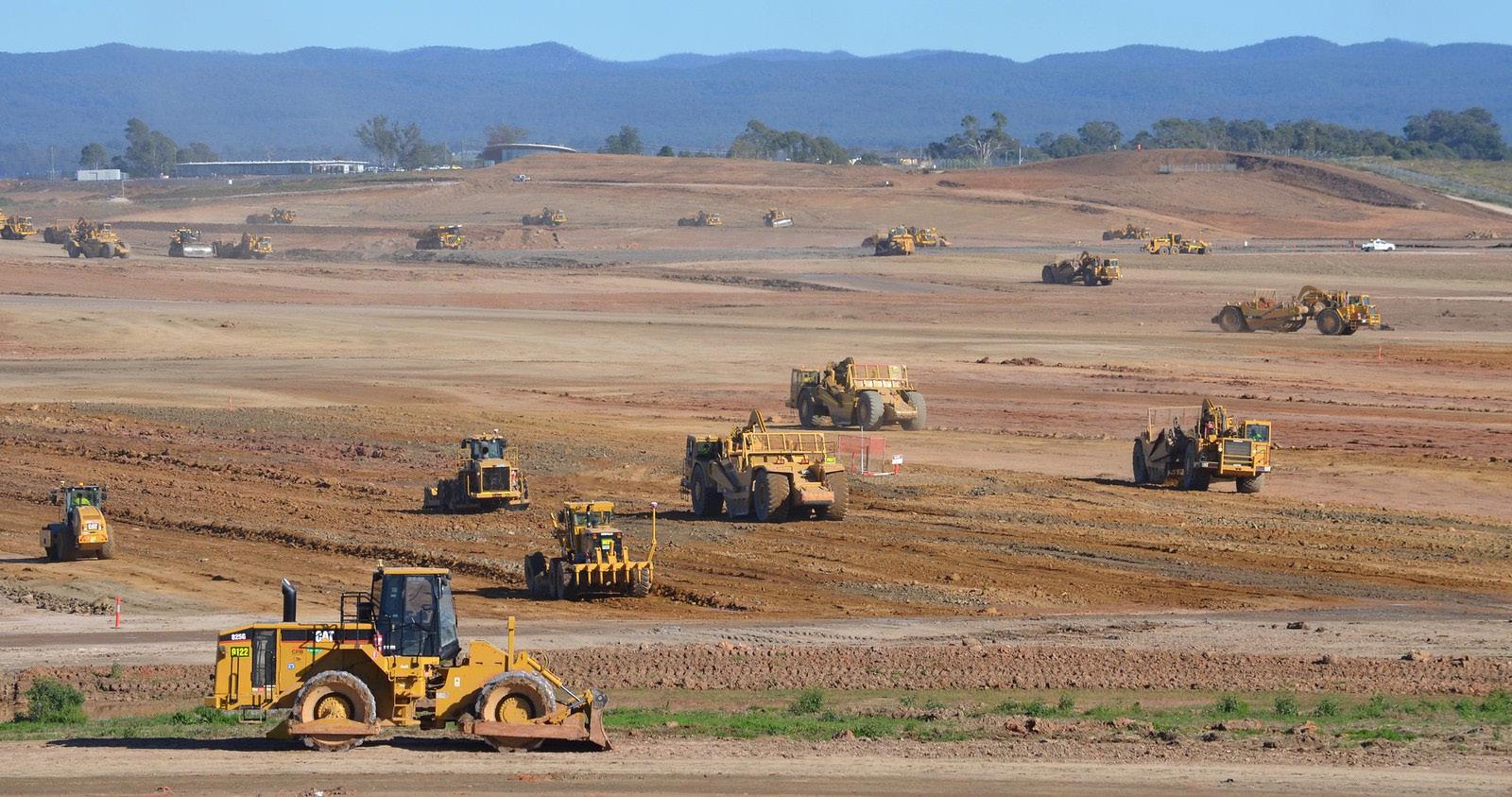
It has been said that great dozer operators are never hired based on their ability to fill out paperwork, timecards, maintenance reports, progress updates or budget forecasts. This represents the information chain contractors require to compile accurate bids; maintain construction schedules; and ultimately, satisfy customers. With data flowing from all directions inside and outside the jobsite, having a more connected, reliable way to manage and communicate data is critical for a successful and profitable project.
As Michael Tilson Thomas, artistic director Laureate of the New World Symphony, puts it, “A major part of what a conductor does is get a large group of people to agree on where ‘now’ actually is.”
Do you know where “now” is on your jobsite? If not, you may be prime for a more connected jobsite. Four
construction industry technology pros to discuss what requirements must be met to achieve a fully connected, wellfunctioning jobsite.
WHAT IS A CONNECTED JOBSITE ?
A connected jobsite tracks all the materials, equipment, tools and talent on a jobsite, sharing the data in realtime with personnel and systems in the field and office to measure a project’s progress against the master plan. This usually involves equipment hardware, such as sensors, cameras, and telematics, communicating with construction-specific software and systems via Wi-Fi, cellular networks, or GPS capabilities.
The idea is to streamline the acquisition, communication, and processing of jobsite data—with minimal paperwork or delay—so that timely decisions can be made that
positively affect the profitability and quality of work in progress.
A connected jobsite can be large or small, from 20,000-acre airport sites to compact office parking lots. Contractors outfitted with full capabilities can track multiple projects across a region, gaining a single source of truth across the enterprise from one central control hub.
“There may be hundreds of pieces equipment, idle or in play, ranging from loaders and trench diggers to smaller tools, like buckets and jackhammers, spread over miles of territory at one time,” said Larry Baker, CEO of FleetWatcher. “There’s no way to keep track of it all without some sort of digitally connected system,” he said. “If you can’t see it, you can’t track it. And if you can’t track it, you can’t improve your operation. It’s that simple.”
WHAT ARE THE TELLTALE SIGNS OF A NON-CONNECTED JOBSITE?
Non-connected jobsites are generally managed manually, by walking the site, carrying hard copies of plans and updates, and discussing progress with machine operators directly or over cell phones. Data is gathered after the fact and usually involves “guesstimates” of data such as hours worked, materials moved and fuel burned. These records usually lead to miscalculations, errors, and time and materials wasted, along with expensive re-work to correct mistakes after the fact.
According to Chris Richardson, senior director of industry workflow for Trimble Civil Construction, the difference between jobsite connectivity and non-connectivity comes down to “sneaker-net.” That is, “someone wearing boots (sneakers) running all over the place to distribute updates and check progress—not a very good way to run a business.”
Gage Witt, senior product consultant for Caterpillar, echoes the sentiment. “You may be seeing good, steady or even growing productivity, but the profit doesn’t match. That’s a sign that your jobsite is out of sync.”
Other signs include:
˜ Excessive fuel consumption when machines run idle
˜ Persistent cost and schedule overruns
˜ Design changes that take days to filter into the field
˜ Unexpected equipment maintenance
˜ “Stale” jobsite information
˜ Time sheets based on the “honor” system
˜ Lost equipment
According to Baker, problems, such as excessive idle time, need to be corrected as they happen if you want behaviors to change. If you don’t know what’s happening and don’t do something about any issues right away,
A connected jobsite can be large or small, from 20,000-acre airport sites to compact office parking lots.
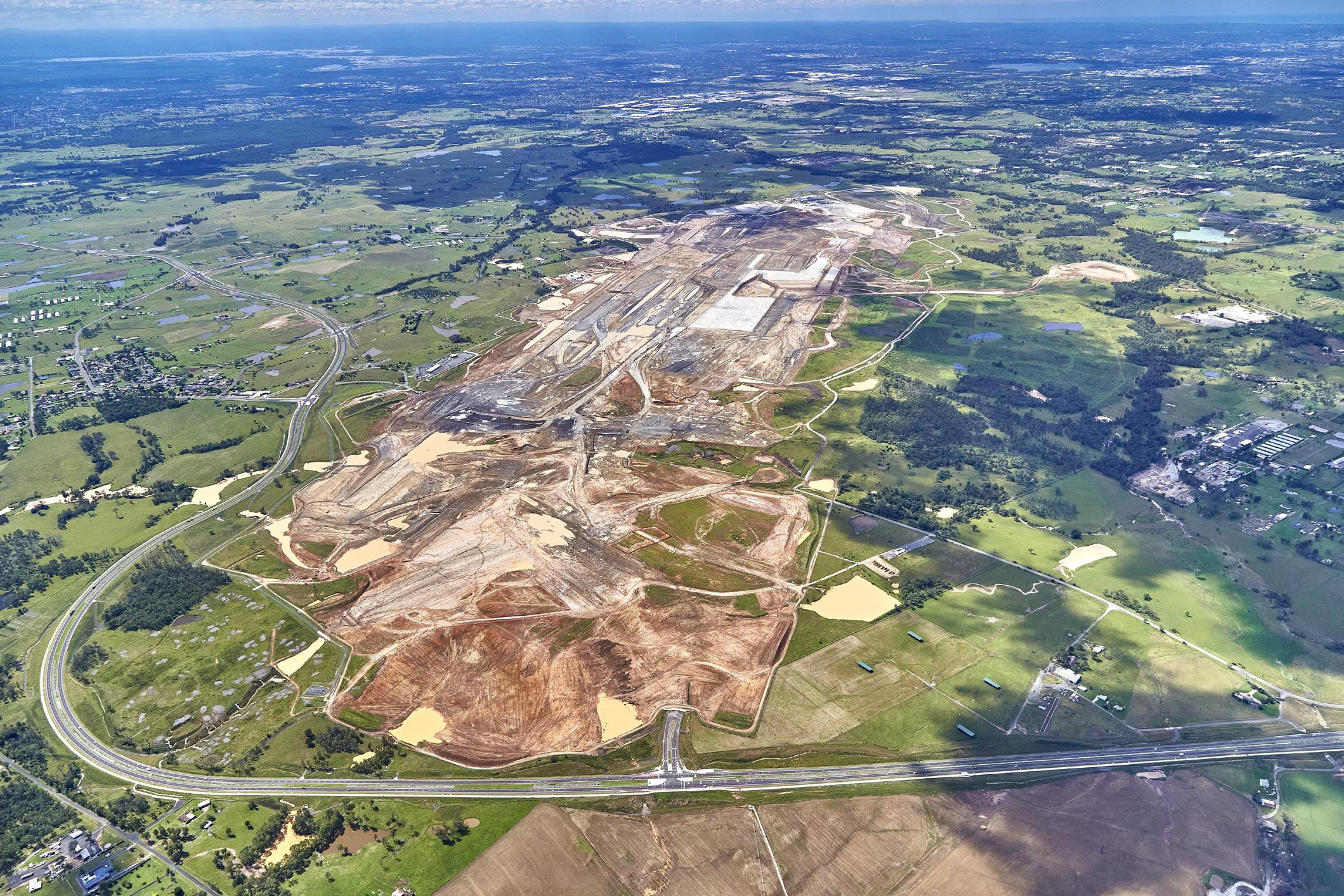
the opportunity to make changes is never coming back.
WHAT TECHNOLOGIES ARE REQUIRED FOR FULL CONNECTIVITY?
The experts agreed that data is the most important driver of a connected jobsite. For this reason, equipping a jobsite to manage data effectively is critical. Data collection hardware, supported by back-end software that makes sense of that data, forms a sound technology foundation. However, nothing of value can be achieved without linking the data collectors with the data receivers, and that points to the Internet. With this in mind, let’s survey the basics.
Hardware generally refers to the devices that collect data on the jobsite. Hardware includes Internet of Things (sensors) and telematics devices that automatically report the use, whereabouts and operating condition of the tools and equipment in the field. They may display information on your machines’ screens, on a laptop positioned in a jobsite trailer or in the corporate office. They provide the feeds your team needs to monitor the site, share plans and communicate effectively as work progresses.
Software enables the jobsite. It reads the inputs that your hardware collects and helps your team members make sense of the information collected. Construction-specific software may allow you to modify design models on the fly, survey equipment conditions, monitor costs in real-time, update schedules, even assemble bids based on past field calculations.
A good software package will help you analyze trends, build forecasts
and manage tasks. When integrated with back-end systems, managing inventory, procurement, and finance operations becomes easier, payroll becomes simplified, and compliance with safety and operational standards can be assured.
None of this is possible unless the hardware and software work together. Cloud systems are ideal for this kind of collaboration. They provide:
˜ Browser-based access to information over any device
˜ Support massive computing power to crunch numbers in near real-time
˜ Facilitate application integration, either through open-source technology or common application programming interfaces
“The internet is the pipeline that makes the connection possible,” said Richardson. “That’s always the first piece to consider in a digitally connected world.”
From there, connectivity options expand. Mike Kucharski, vice president of sales and marketing for Gauge Telematics, lists several options for a GPS-connected jobsite, including wide-area cellular networks; local area Wi-Fi connectivity; satellite communications for remote area access and near-field communications; or Bluetooth connectivity, for low-cost, short-range connections.
“GPS technology simplifies the integration of such core jobsite elements as [manufacturer] data, onand off-road GPS devices, ERP systems and other fundamental equipment management technologies,” Kucharski said.
WHERE IS THE BEST PLACE TO START?
“If you’re not already operating connected jobsites, a good place to start would be to try a simple locater to track where an asset is,” said Caterpillar’s Witt. “Connecting your fleet is easier than you may think. The first time you recover [a] lost asset, avoid downtime due to some major maintenance project or realize a fuel savings at the end of a quarter, you’ll see you’ve more than paid for the initial investment. It’s all about [the] return on investment.”
Some hardware and software components are offered on a subscription basis. This is one way to test a system short-term. Pick a manageable jobsite and outfit it for connectivity. At the end of the test, determine how you came out and where you can improve. Expand your base from there.
His company represents an enterprise asset and fleet management platform that tracks and manages equipment-intensive operations with telematics and other tools.
“The goal is to create a single source of truth, from the corporate office to field supervisors, machine operators, maintenance techs, suppliers and other stakeholders, including customers,” Kucharski said.
Full connectivity relies on assembling the correct hardware, software and virtual connections necessary to collect, store, assess and analyze the data contractors need to run a successful operation.
“It doesn’t take much to equip a few big machines, like loaders, trenchers, or dozers, with sensors and start tracking their location and condition,” said Baker. “The information you get in real-time will tell you what equipment is producing and what’s not. That should be enough to convince you of the value of connecting everything.”
Many contractors manage jobsites across a wide region, where as many as 300 to 400 machines may be out in the field. It’s not unusual for one to be stolen.
“Once a machine is tagged, the data is available 24/7,” said Witt. “We helped a customer recover a stolen machine within a day of its [going] missing. Had it not been tagged, that could have been a $50,000 loss.”
Kucharski developed an equipment management maturity curve delineating tactical/traditional activities, such as tracking equipment hour and location information on the low end, up to advanced fleet monitoring of large equipment in remote areas, such as mining and
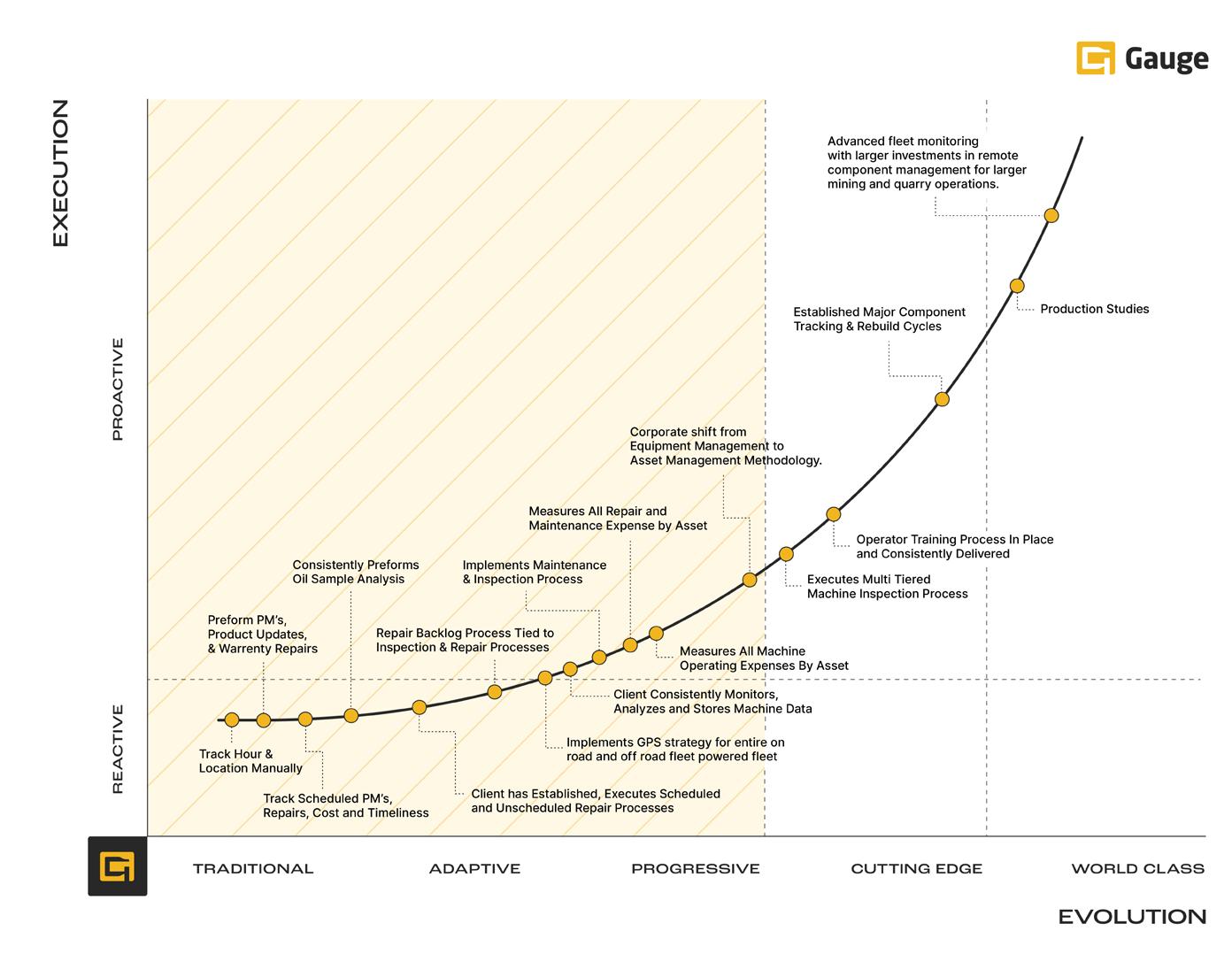
quarry operations, at the strategic/ world-class end of the spectrum.
“The key is to start the journey where you are and get better … as you progress along the curve,”
Kucharski said. “Your goal should be to understand cost, manage fleet age, ensure reliability and maximize utilization.”
WHAT ARE THE BENEFITS OF A CONNECTED JOBSITE?
“I’d say [the benefits begin] the moment you start working with a digital design model,” Richardson said. “Having your design information in a digital format immediately sets you up for instant sharing of updates, which immediately reduces errors and rework and improves the accuracy and quality of the finished product.”
Kucharski stated that “connectivity is the backbone for moving up the maturity chart, where significant operational efficiencies start to unfold.”
Detailed information becomes the norm, aiding in productivity planning, operator consistency and workforce improvement. Costs come down and profitability goes up, matching any gains in productivity. All equipment can be accounted for, including maintenance status and fuel us, adding to efficiency and equipment lifetime value.
Back-office functions also run smoother, eliminating information blind spots and delays associated with traditional paperwork and factgathering. Bids, budgets and schedules become more accurate, supporting sales efforts while building the brand. And above all, customer satisfaction increases, enhancing loyalty and expanding word-of-mouth advertising.
WHAT ADVICE WOULD YOU GIVE SOMEONE REGARDING CONNECTED JOBSITES?
Take some time to assemble your brain trust and evaluate your processes. Where are the bottlenecks? Where are the leaks? What is it you want to improve?
“If you are honest, you will find an opportunity to improve performance on every jobsite,” said Witt. “By identifying what you value most, you will be able to determine the hardware, software, subscriptions that will benefit your operation most and compress the time it takes to get there.”
Talk to several suppliers and schedule a few demonstrations. Read their contracts and make an informed decision. If you need to hire a consultant to guide you in the process, find one but own the decision.
And don’t forget, people will always be involved. “Within the grand scheme of things, you can monitor equipment, but what you really need to do is to get all your people on board,” said Baker.
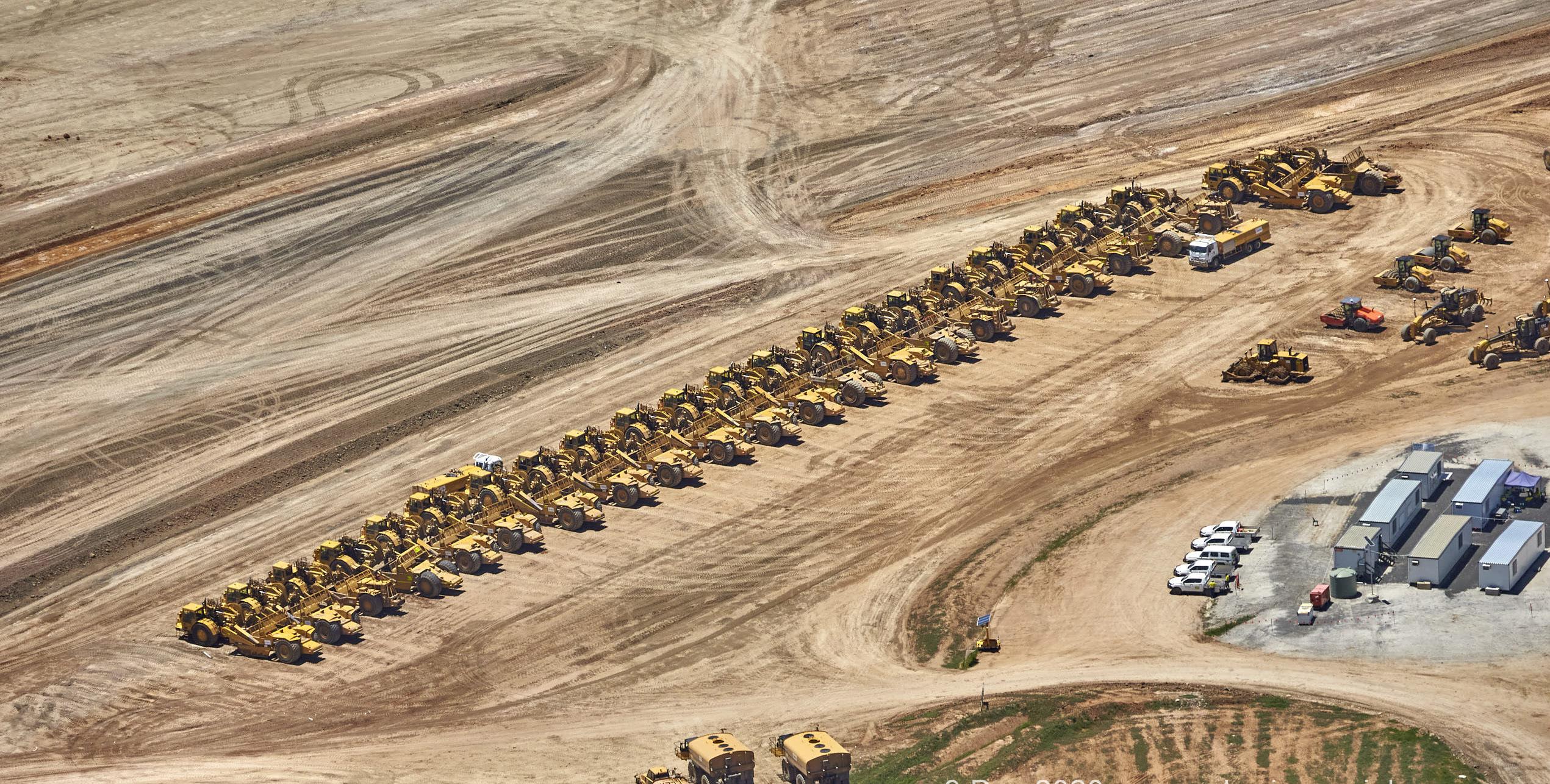
Many contractors manage jobsites across a wide region, where as many as 300 to 400 machines may be out in the field. It’s not unusual for one to be stolen.
“You can only improve what you measure, and if they understand what matters most, they will be more likely to get on board and drive the train into the station.”
OVER TIME, MILLIONS CAN BE MADE
The benefits of a connected jobsite far outweigh the risk or expense. Understanding what is happening “now” on your jobsite can compress project turnaround times, improve productivity and create a huge competitive advantage for your company.
“In an information war, the one who knows first is the one who performs best,” said Richardson.
In a short period of time, connecting your machines to your people and your people to what’s happening in the field can lead to decisions that contribute millions to your bottom line. So, why wait? Connect your jobsite for enhanced operational efficiency and improve your project throughput—“now.”
Read more at: eqtoday.co/connected
Joe Zagorski is a freelance writer for Equipment Today
SUCCESS STORY: AUTOMATED PROJECT REPORTING ON THE CLOUD
CLIENT: EARTHWORKS AND LANDSCAPE CONTRACTOR SPECIALIZING IN SITE DEVELOPMENT, GOLF COURSES, AND LANDSCAPES ( Source: Trimble)
OBJECTIVE: CREATE A CONTINUALLY UPDATED RESOURCE FOR ALL SITE DATA (LABOR, EQUIPMENT AND MATERIALS)
SOLUTION: IMPLEMENTED A REAL-TIME, CONNECTED DATA WORKFLOW FOR AS-BUILT REPORTING ON THE CLOUD. THIS INCLUDED:
• Enabled analysis of data gathered from machine control systems, to track progress and improve productivity
• Leveraged a connected data environment for the enterprise-wide storing and sharing of data
• Deployed a single, integrated platform for managing projects in real-time
• Integrated hardware from multiple vendors
RESULTS
• Reduced costly rework
• Injected more data into daily planning
• Enabled push notifications, exception-based reporting
• Automated smart reports for dirt moved, grade verifications, daily task tracking, etc.
• Gained ability to instantly project whether projects are making money
• Met or exceeded margins
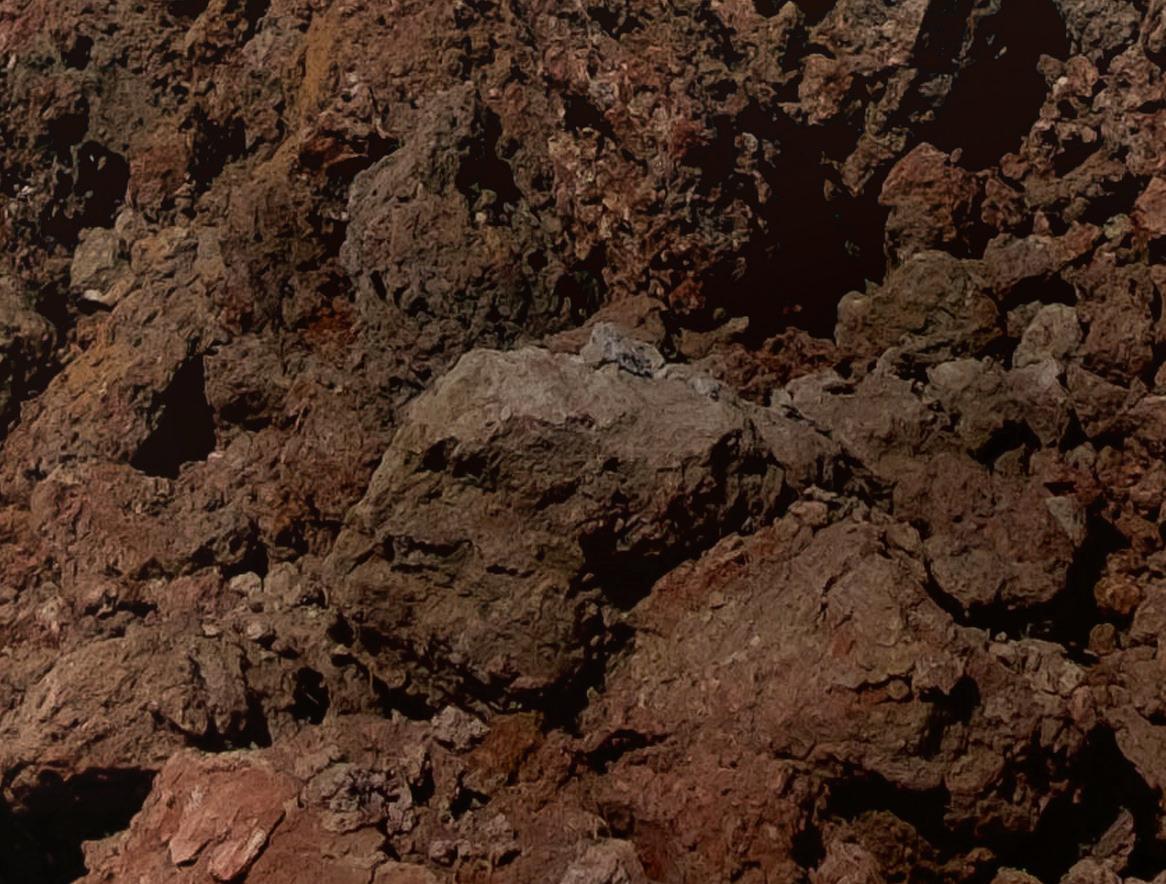
THE DOER’S DREAM

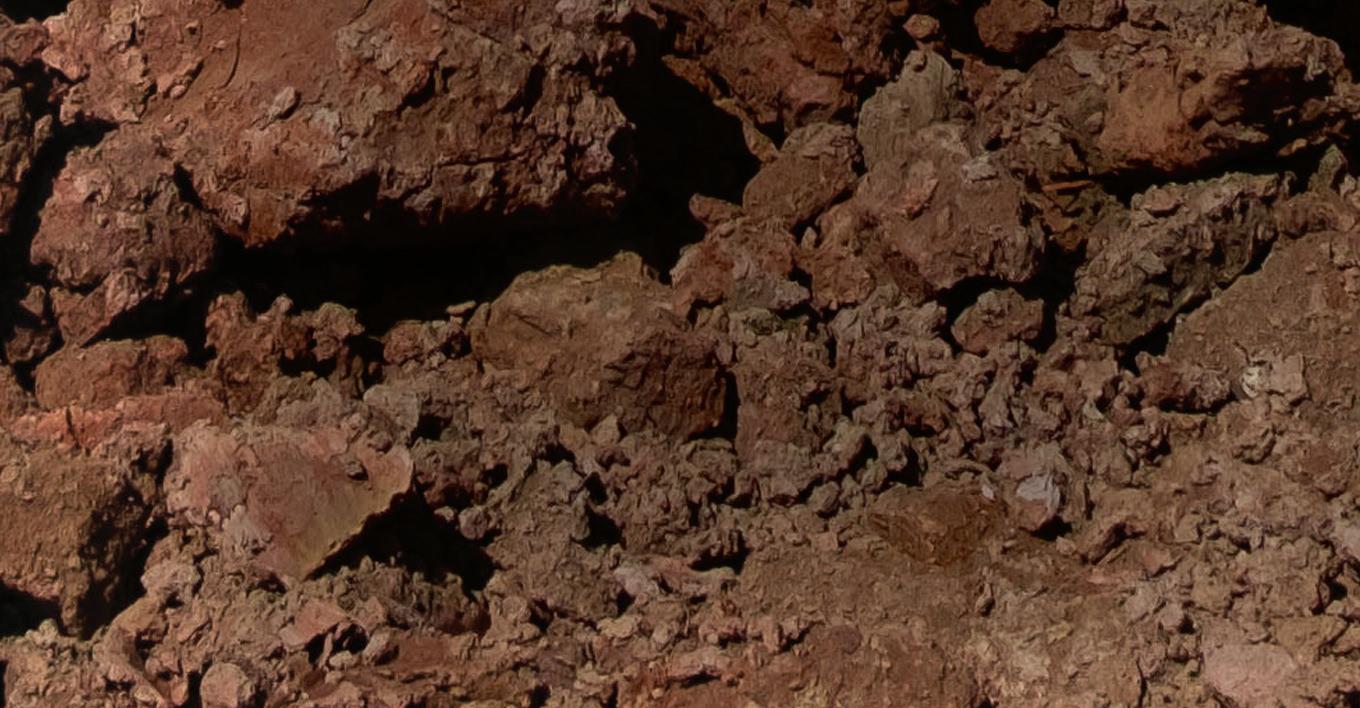
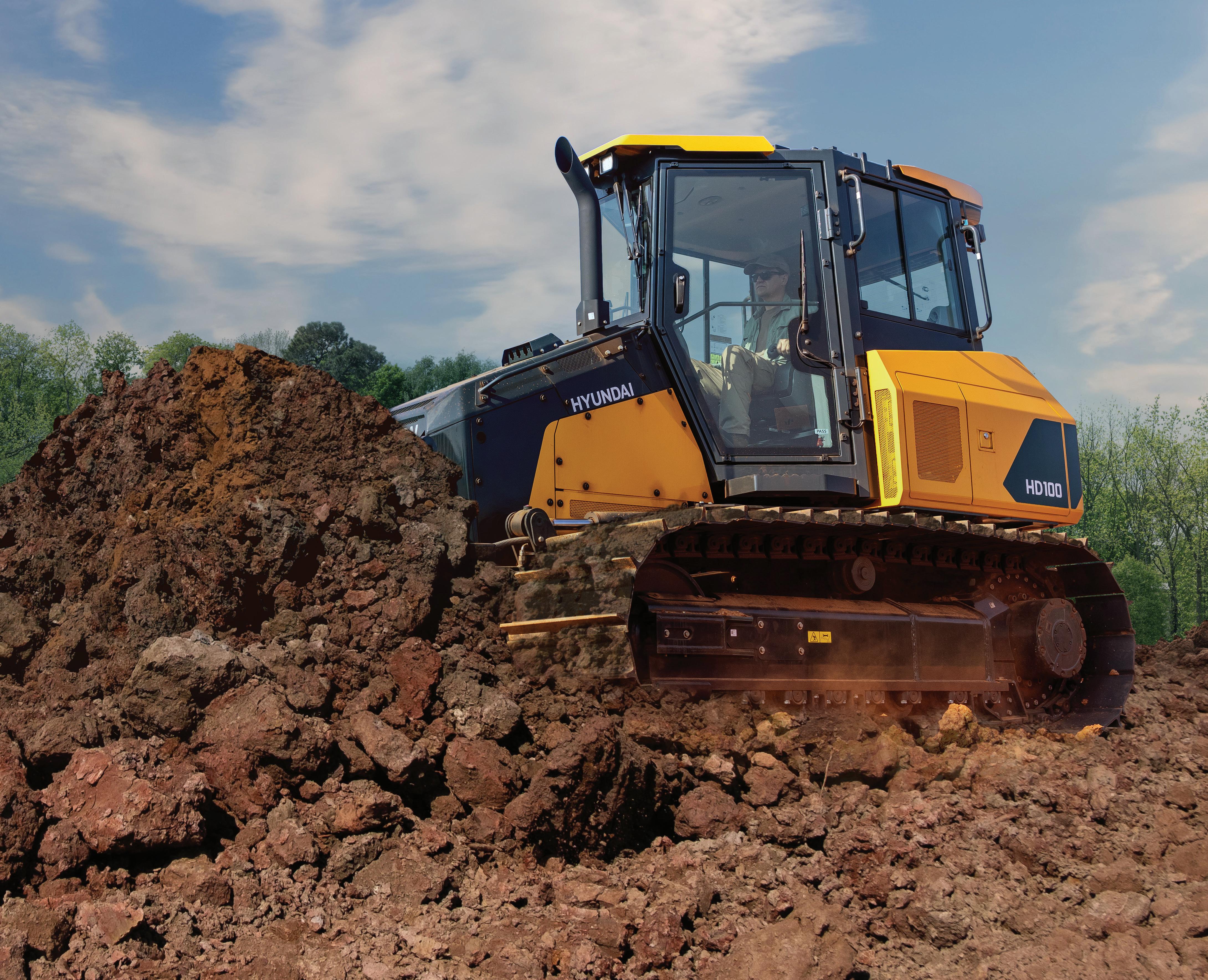
MAKE YOUR MOVE

No wonder so many first-time Hyundai users become longtime fans. See the Hyundai difference yourself at your local dealer, or na.hd-hyundaice.com.
Push
... more material with the new Hyundai HD100 crawler dozer's best-in-class power-to-weight ratio.
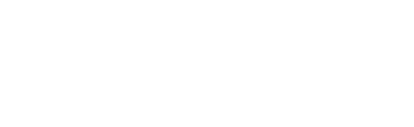
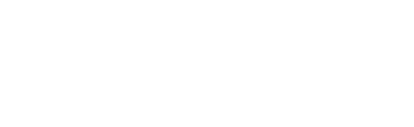
See ...more than ever with the unobstructed view to the blade.
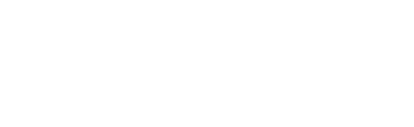
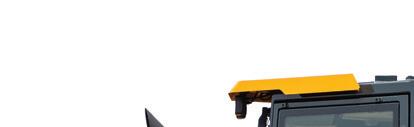
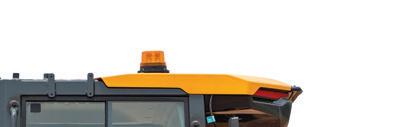
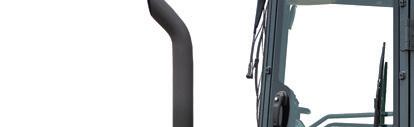
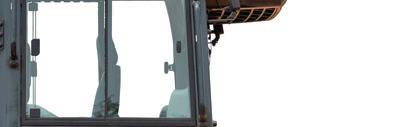
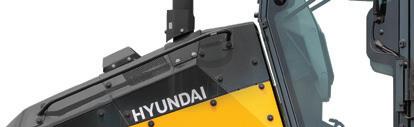
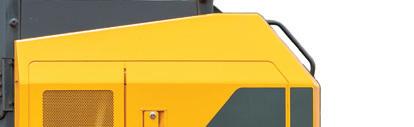
Engage
...more accurately and more productively with standard 2D or optional 3D machine guidance.
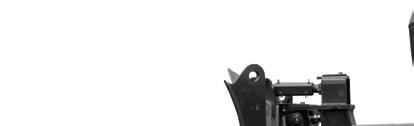
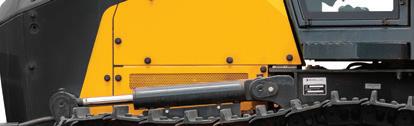
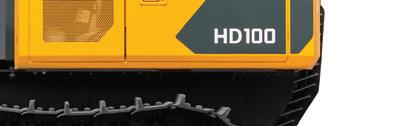
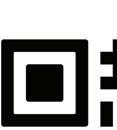

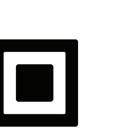

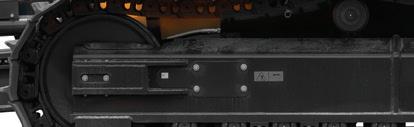
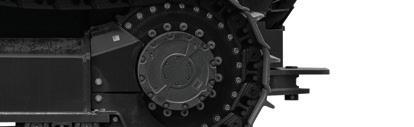
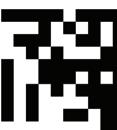
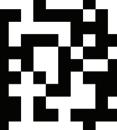
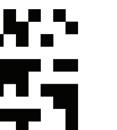
Doze
...with confidence, knowing your new 115 hp Hyundai crawler dozer delivers the quality and value you expect from Hyundai, with the peace of mind that comes with our industry-leading warranty.
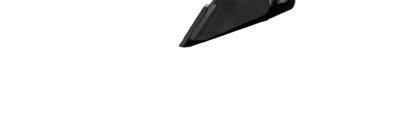
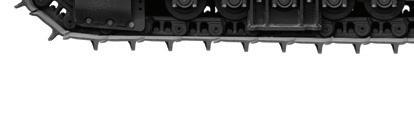
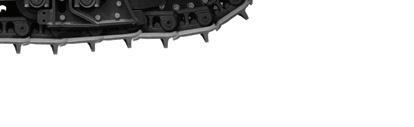
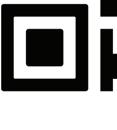
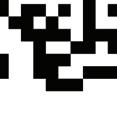
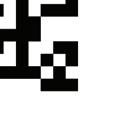
Take a Closer Look at Your Rising Costs
With prices on the upswing, be sure to double check your own costs to see how they compare with this time last year. Talk to vendors, and let them know you’re paying attention.
How is the economy treating you this year? Are you having fun yet? Probably, if you had a nice construction backlog coming into 2024, or work in a warm climate where more people are migrating to, or if you are lucky enough to get a piece of the government programs building, or refurbing manufacturing or chip sites. But no matter where you stand, there are plenty of issues you need to keep an eye on to protect profits and cash flow. We might as well start out by dealing with the elephant in the room, known as inflation and/or shrinkflation. Either the price goes up for the same volume you are used to buying, or the price stays the same, but you receive a smaller amount of product. Now, I know you fall under the former, but not so sure you incur the latter. Could it be you purchased a box of nails that looked to be a little smaller or was a little lighter than you are used to? Hey, why should you be immune to what those bad manufacturers and distributors are doing to the folks buying groceries?
We hear that inflation is under control. Then we hear about a 3.5% increase year-over-year in a recent government report. And that 3.5% is on top of the pandemic inflation that seems likely to stay around. You also hear bankruptcies are up 30% this
year compared to last year, and those bankruptcies are a result of not being able to manage cash flow related to the higher prices and higher interest rates now tied to business bank loans. I hope you are not incurring any similar problems, and if you are or think you will be, I encourage you to take steps to reduce costs and improve productivity.
I know. That is easy to say, but a lot tougher to do.
I am staring at a chart titled, “Where Inflation Is and Isn’t.” It covers a 12-month period, from March 2023 to March 2024. It includes 29 cost categories and reflects both increases and decreases in prices during the Marchto-March time period. Insurance, rent, housing, restaurants, payroll and transportation are 4% or higher, with insurance increasing 22%. And I know if you are in the construction business that your insurance rates have increased dramatically. If they have not, there is something wrong.
Moving on, energy, alcohol, medical treatment and recreation have increases in the 2.5% range. Gasoline and groceries are in the 1.2% range. (I do not believe the grocery percentage is accurate). If I told my wife that grocery prices only increased 1% during the
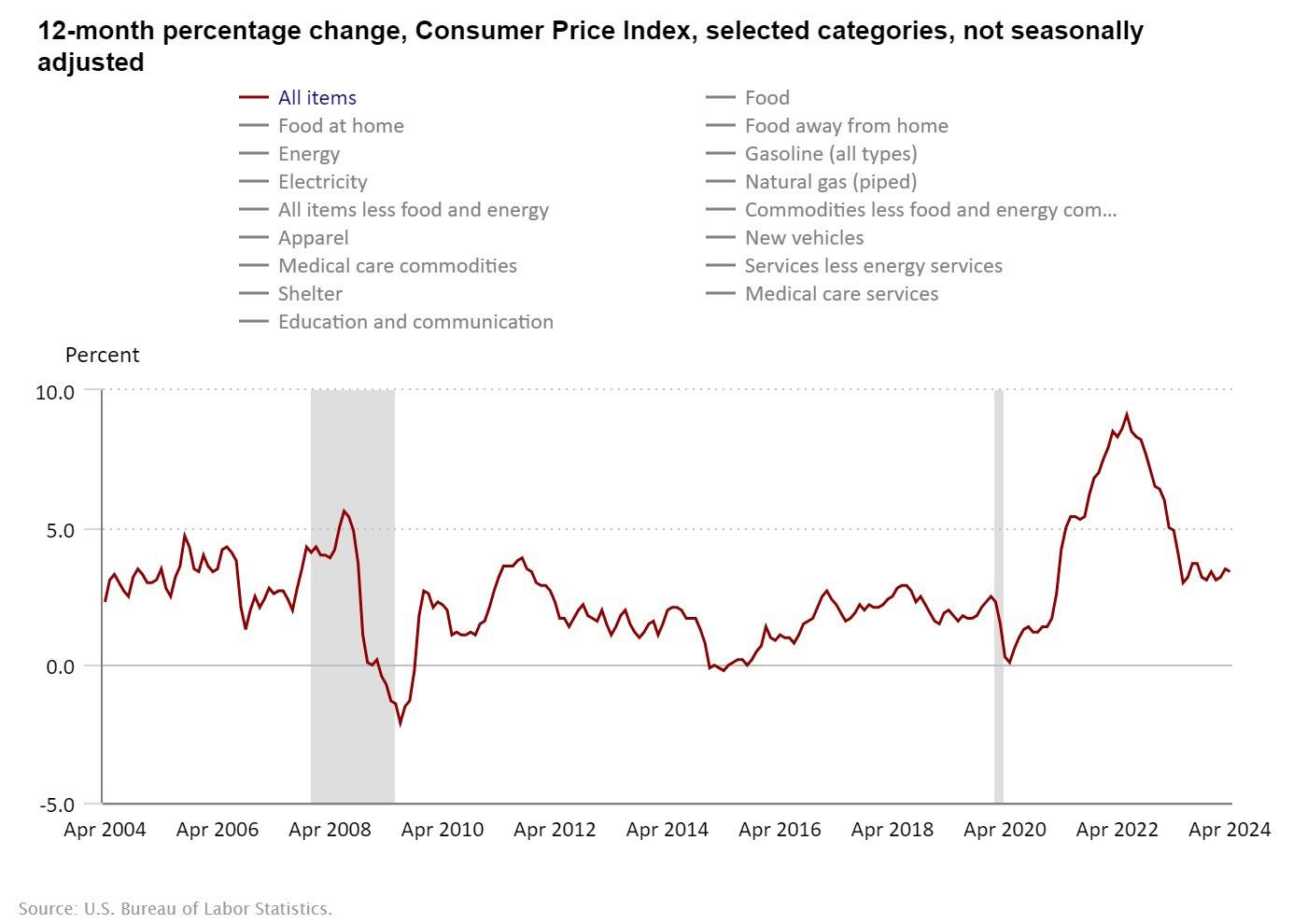
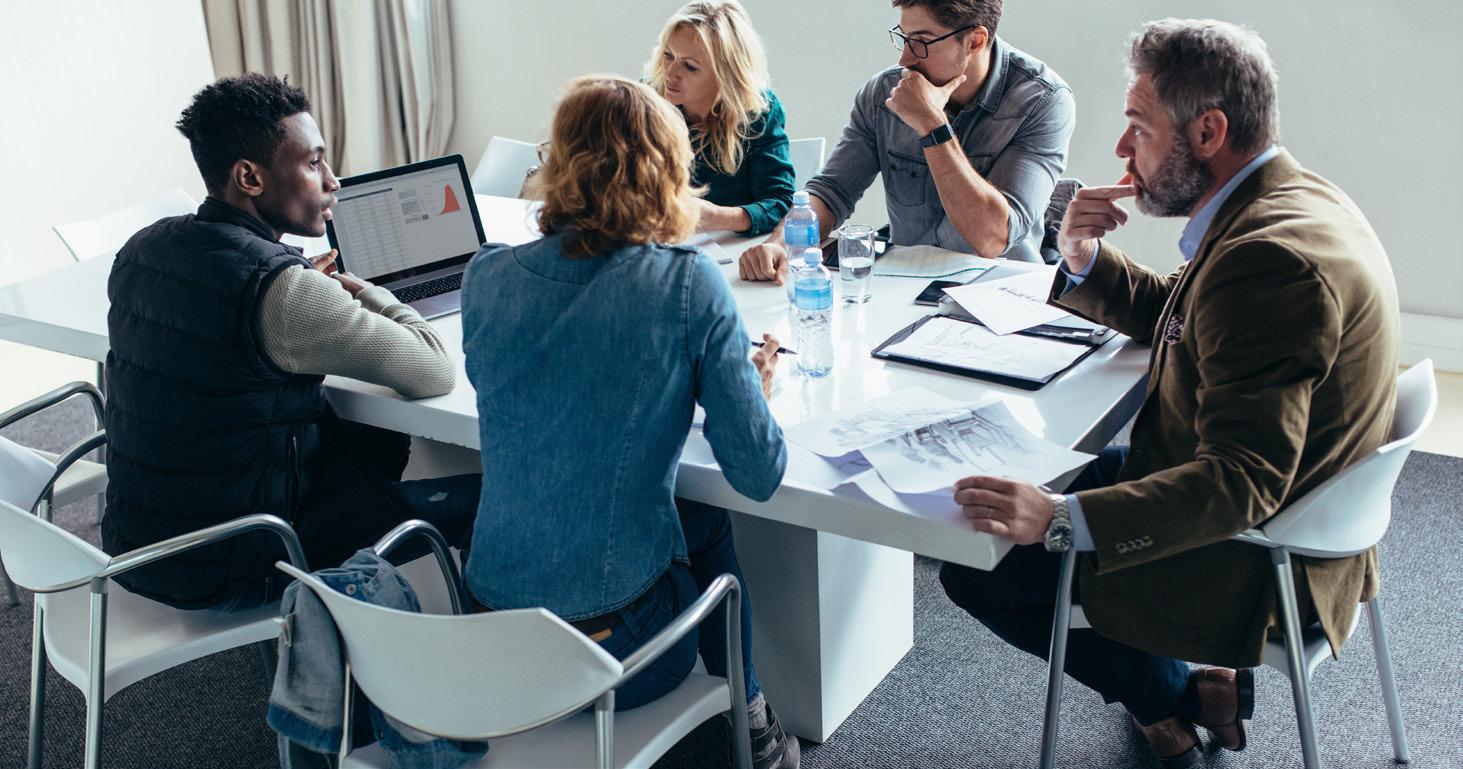
past 12 months, she would pull out a Walmart receipt from March 23 and tell me to duplicate the purchases and we would eat what I bring home. I think we might starve.
Believe it or not, there are 10 items where the prices decreased. New vehicles -0.01%; electronics -0.08%; hotel rooms -1.9%; used vehicles -2.2%; school supplies – 3%, furniture -3.8%; appliances -6.3%; airfare -7.1%; toys -8.2% and rental cars -8.8%. I guess some of these categories are related to the housing market, and the auto markets, but not much else tied directly to construction.
Add all these expense categories up, and you wind up with a net 3.5% increase for the year in question. That is 75% above the 2% goal. I bet your budgets are not off that much.
My daily reading program tells me the housing markets are still tight, with new starts falling 8% in February, with the higher insurance and interest rates not helping matters along with a need for experienced personnel.
Do yourself a favor and take a dive into your accounts payables and the checks you write to pay vendors. I would assign someone or have your system produce today’s line-item charges against what you were paying in prior years to get an indication of which way prices are headed. With the industry in a slump, you would expect prices to be on the negative side, if I added them to that chart I was looking at. In addition, check the invoices coming in and make some phone calls to let your
vendors know you are looking at their invoices. And in terms of insurance, I find that by using a real pro who knows the construction business can help you manage your insurance costs if you abide by the terms of the policy. You would be surprised by what you can do to lower rates if someone goes through the policy and helps you understand how you are being charged.
Follow the same process for payroll. Check the reports so you can see who is getting paid and for what they are getting paid. I would also ask for an analysis of hours worked monthly for the last 12 months. Is what you are seeing make sense? Or should you take up a program to review the entire payroll operation to ensure cost is what you expect it to be? If they know you are looking, there will be fewer problem areas popping up.
You now have some homework to do to reduce costs and get the payroll under control. Why don’t you prepare a chart like the one I was looking at and compare your direct expenses in terms of materials and payroll and see how it compares to 12 months ago. And then continue to upgrade that chat every month going forward; just delete the oldest month and add the new one -just like on the stock market reports you see, a 12-month running total of costs and payroll.
Garry Bartecki is managing member of GB Financial Services LLP and a consultant to the Independent Equipment Dealers Association.
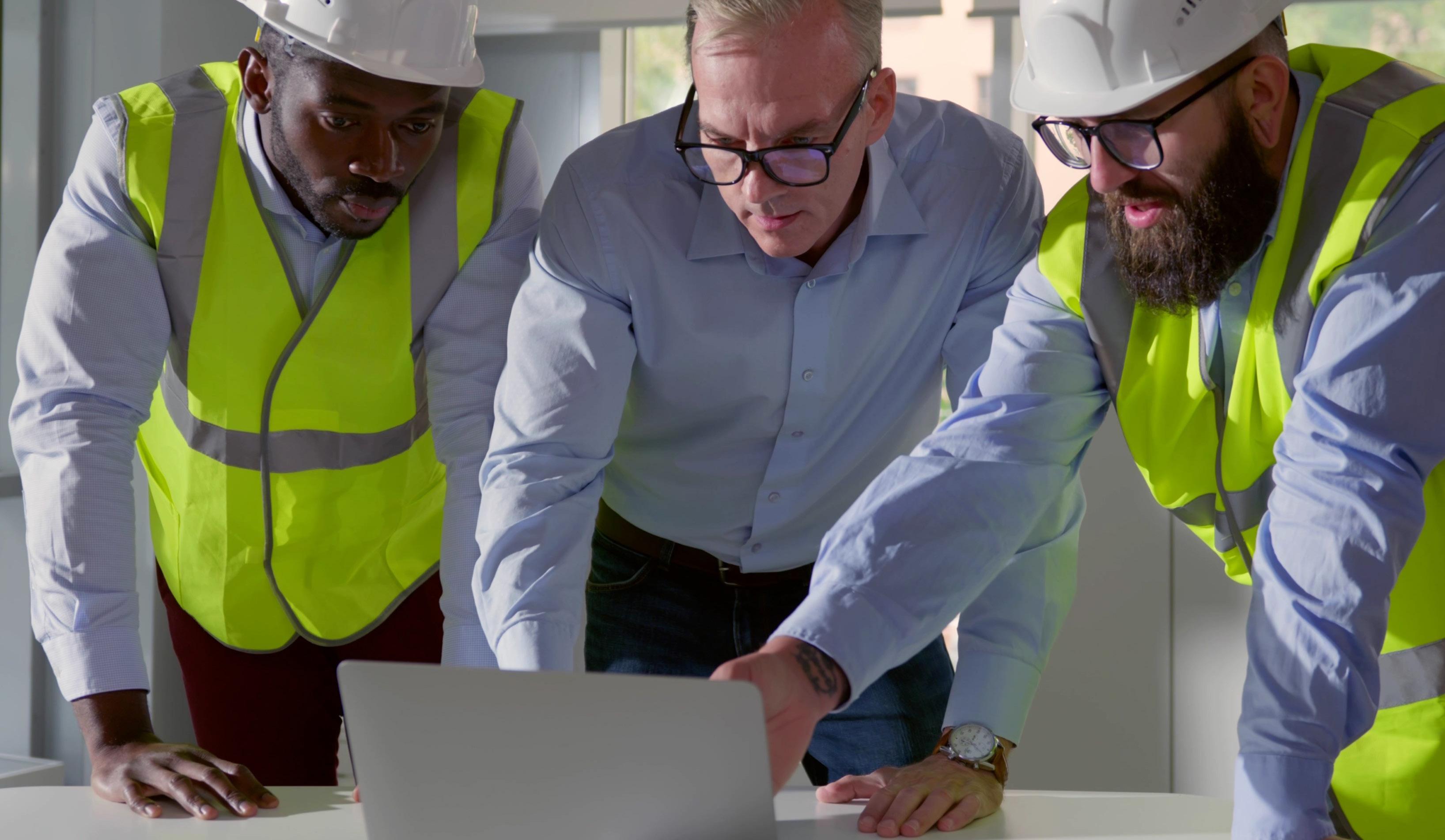
How to Build a Construction Execution Team
Construction is not like any other business. The multiple fragments of a construction process are industries in themselves. And the most complex of all is executing the construction itself. Onboarding a workforce and establishing a system for your construction execution is not as simple as doing it for others.
Therefore, one has to be thoughtful when assembling their construction workforce. Generally, the construction industry operates on the concept of intradependency. One construction organization depends on another construction organization for services that the former cannot provide. However, this practice does come with the possibility of risking your brand.
Your revenue and branding depending on others is not suitable for you or your organization’s growth.
That is why it makes sense to form your own in-house construction execution team. But the procedure is quite challenging, too. This article shares a guide for forming an in-house construction execution workforce for your construction business.
LIST OUT YOUR ORGANIZATION’S STRUCTURE
It should start with listing your requirements. What are all the work functions your execution workforce will address? A construction workforce could address all the possibilities of construction work, but it should have
its limitations, too. As an initiator, you should be conscious of the revenue sources for your organization. Then detail each job and its requirements for your revenue sources.
The process should be in reverse: listing out the description of the most ideal candidate and then finding the most relevant human resource close to your description. However, the challenge is finding a suitable set of people for your construction jobs. It is usually not so organized, like hiring for a white-collar workforce. Even with solutions for the construction workforce, the challenges are multiplied by problems like the construction industry’s skill shortage, and high attrition rates. You should:
Check out this article for guidelines that will help you set up a successful program.
˜ Have a proper plan for your organization
˜ Detail your human resource requirements and standard operating procedures
˜ Divide the document into chunks for job requisitions and onboarding
˜ Periodically update your work documents as your needs change
˜ Complete upskilling in between work as the document changes
BUILD A TEAM FROM SCRATCH RATHER THAN OUTSOURCING TALENT
Outsourcing a skill set and hiring a talent for a period of time may look better but definitely not in the long run, especially in construction work. The ownership of construction work is

Onboarding a workforce and establishing a system for your construction execution is not as simple as doing it for others.
much more than responsibilities. The demands of the majority of your clients would be all-in-all work ownership, which is also about probing and checks post-execution, too.
You can deploy most of the advanced tools on the market, but ultimately, the responsibility of work and communication between stakeholders in construction are still very humane.
It is you or a particular human face who should be responsible in front of the client for his or her requirements. This problem cannot be solved by outsourcing or hiring as needed. This temporary approach to onboarding construction talent gives your workforce a chance to have a casual outlook at work. They will only be answerable to you not to your client.
Therefore, it is sensible to assemble your construction execution workforce and make them fully liable to your organization’s needs.
But the road to building your own team has multiple hurdles. There is actually no quantified science behind selecting the very early employees for your organization. Appropriate finds could be people near your organization, profiles on portals or referrals. Once your team is established, the challenge becomes retaining them. To do this:
˜ Be very flexible in hiring the first slot in your organization
˜ Tools and online resources help, but it’s your organization’s value that attracts
˜ Build a separate, dedicated team for personnel management.
˜ Your earliest hires would automatically form a chain of hiring events.
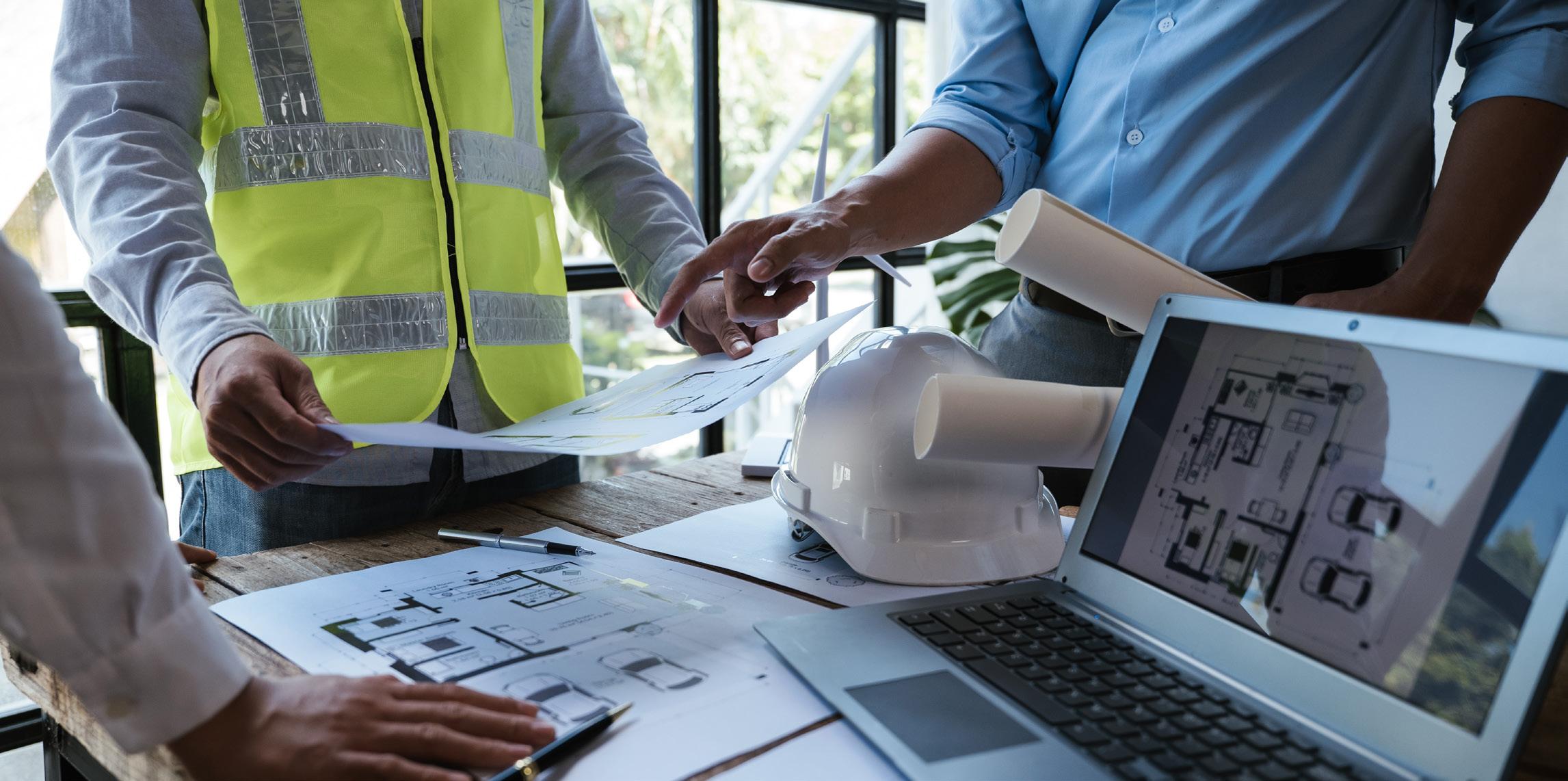
GAMIFY THE WORK EXPERIENCE SO THE WORKFORCE STAYS
Human resource management, in parallel with your work operations may not understand all that they need to do, particularly in sectors like architecture, engineering and construction industry.
Your human resource management is quite sorted when you are right with branding your organization. You need to convey your branding to the workforce you intend to connect with.
Working conditions in the construction industry are relatively worse compared to many industries.
With 170,000 recorded injuries and 20% of suicides being attributed to construction work plus economies post-COVID 19, employee retention is the all-time worst in the sector.
This signifies that employee and employer branding is more important in the construction industry than in any other.
The construction workforce is mostly made up of blue-collar workers who may not be as knowledgeable about the complex technologies around them.
Also, the knowledge gap between the white-collar workforce and the blue-collar workforce in the construction sector is huge.
Management struggles to convey the process for execution, and the workforce is hitting an all-time low on productivity.
The best approach to go forward would be to gamify the work experience for
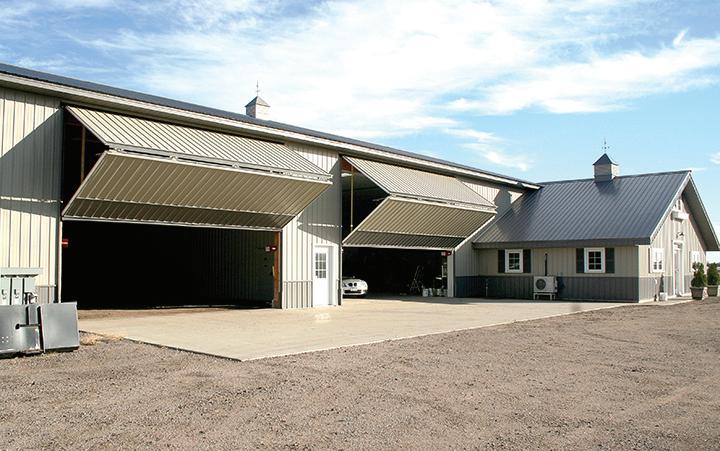
Provide incentives, which are obviously more than the basics.
Some incentives and ideas are:
˜ Training and upskilling
˜ Economic perks such as life insurance and employee stock ownership plans
˜ An environment where they are heard
˜ A diverse workforce that can act as a human library for learning from experiences
PRIORITIZE DIVERSITY
& INCLUSION
In today’s time, you may be tired of the hearing that you must have diversity in your workforce. But have you ever wondered why it is an inevitable requirement for organizations these days?
Consider this as one good marketing, branding and sales effort in combination. The simple meaning of growth for your business is to accommodate more clients, and that includes those from diverse backgrounds. So, you will have a diverse set of revenues for your operations.
Now consider two scenarios: one organization with less diversity and one organization with a diverse workforce. Which one do you think has a better probability of acquiring clients from diverse cultures and geographies?
Diversity in the workforce will allow your organization to connect better with clients from diverse backgrounds. And this could be more true when you are in the construction sector. A person from a certain location would be well-versed in construction practices, material usage and industry standards because of his or her geography.
On the very same concept, multiple people from different geographies could bring a scope of expertise to projects from different locations.
And no one should ignore the fact that diverse minds bring diverse perspectives to the organization. Who knows, a woman taking up the tool job or a male in the people management role might bring some great results. Currently, women make up only 2% of the industry, and it is surely not benefiting the industry. Do the following to expand your diversity:
˜ Allow your organization a chance to experiment with talent
˜ Training sessions should allow innovation, discussion and growth in hierarchy to flourish
˜ Nothing is fixed; keep documenting your diverse learnings
ESTABLISH BUSINESS PRINCIPLES
If you cannot differentiate yourself from the existing players in the construction market, then you shouldn’t start. You have to differentiate first. The what, how and why of your organization should be very clear to you and your workforce. ˜ What your organization stands for ˜ Why clients should opt for you ˜ How you are different from others Even if it is about the productivity of your organization, the diferentiator is not a set of tools that you are deploying to track your workforce’s productivity. It is your organization’s principles. Principles will make your construction work efficient and lucrative for businesses. You can prioritize the fundamentals of: ˜ Selection and training of the labor force ˜ Effective communication for streamlined management ˜ Economic incentivization
Keeping the fundamentals right, you should also bring about a change in the system that can gravitate the market towards your organization. Your company will bring a unique value proposition to clients, either for saving their investment or providing them with an additional gain from the rest of the value providers.
One last thing to note is that your unqualified set of principles should aim for productivity, but they should be based on empathy. A system that is not just about tracking your workforce’s hours but a corporate responsibility where each of the stakeholders has an incentive to perform well and do well for themselves and your organization.
• Trailer Weight: 8,380 lbs.
• Overall Width: 102", Length: 31'4"
• Deck Length: 21’ Flat (model shown)
• 6’ Beavertail
• Deck Height: 34"
• Tires: Eight 215/75R17.5 (H)
• Brakes: Air (Full ABS System)
• Ramps: 72" Long x 22” Wide
Range: 102" Max. 29" Min.
• Lighting: 100% Sealed Wiring harness
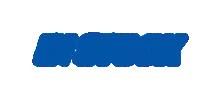
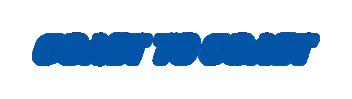
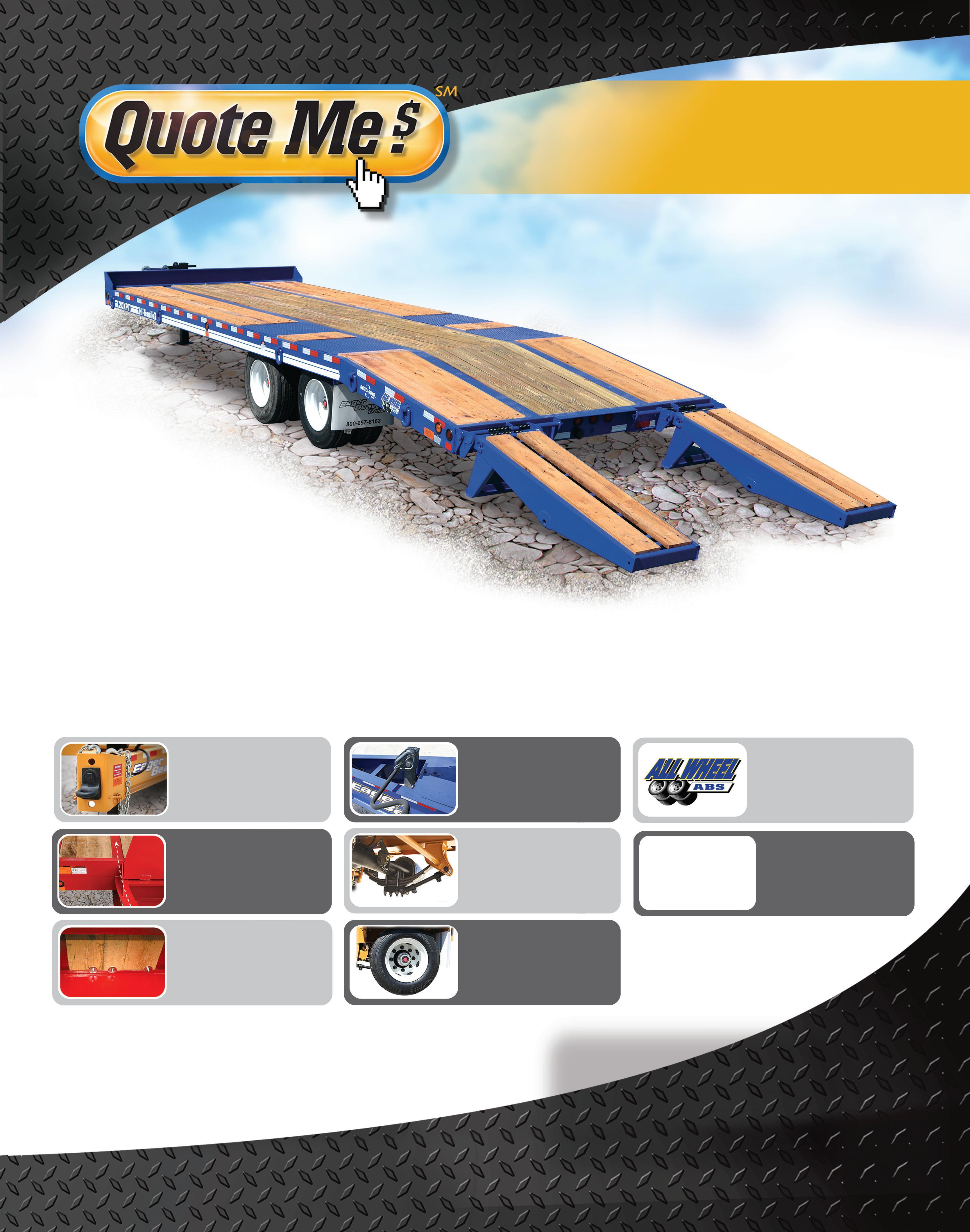
TECHNOLOGY FOR CAT® EXCAVATORS
CAT® GRADE WITH ASSIST
Cat Grade with Assist for Cat Excavators can help make jobs MORE EFFICIENT by getting to GRADE FASTER, with MORE ACCURACY.
Available as part of Cat Grade, it automates bucket and boom movements for more precise cuts with less effort.

BENEFITS INCLUDE:
✔ SIMPLIFIES OPERATION ✔ HELPS IMPROVE EFFICIENCY ✔ HELPS IMPROVE ACCURACY
✔ HELPS REDUCE REWORK
ADDITIONAL CAT ASSIST TECHNOLOGY OPTIONS
BUCKET ASSIST
Maintains bucket angle and keeps the cut accurate in sloping, leveling, fine grading and trenching applications.
01 03 02 04
BOOM ASSIST
Automatically raises the boom to keep the excavator from lifting off the ground when digging, lifting or rotating under load.
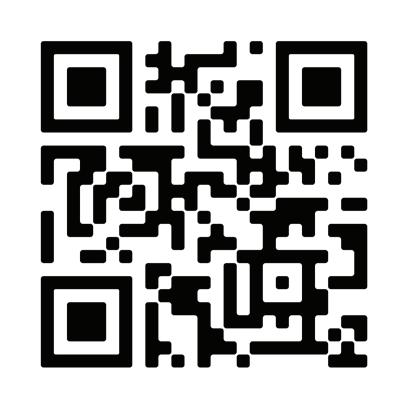
SWING ASSIST
Automatically stops excavator swing at defined points when truck loading and trenching, helping to reduce fuel usage and improve cycle times.
TILT ASSIST
Takes over bucket angle movements to automatically maintain the desired slope.